Модернізація координатно-розточувального-свердлильно-фрезерного верстата 2А459АФ4
Анотація
Метою дипломного проекту є проект модернізації
координатно-розточувального - свердлильно - фрезерного верстата 2А459АФ4.
У пояснювальній записці зроблений аналіз та огляд верстатів
аналогічного призначення. Вироблено обгрунтування технічних характеристик
проектованого верстата. Виконано кінематичні розрахунки приводу головного руху,
розрахунки на міцність. У записці описана конструкція основних вузлів верстата.
Вироблено економічне обгрунтування проектованого верстата. У записку вкладені
розділи стандартизації контролю якості продукції, охорони праці та безпеки
життєдіяльності, екології.
Вступ
Верстати координатно-розточний групи призначені для обробки
корпусних деталей з високою точністю. Отримання високої точності залежить від
багатьох параметрів. Динамічна точність верстата має істотний вплив на точність
обробки. Сучасний ринок вимагає від виробника верстатів збільшення кількості
номенклатури оброблюваних виробів на верстаті, підвищення швидкості обробки, а
так само підвищення числа одночасно керованих координат від ЧПУ верстата в
процесі обробки виробів.
У даній роботі розроблено свердлильно - фрезерний координатно
розточний верстат з підвищенням частоти обертання приводу головного руху, а
також підвищенням одночасно керованих координат від ЧПУ верстата.
1. Технічне обгрунтування проекту
У сучасному машинобудуванні, для досягнення високого рівня
якості виробництва, перед виробником існує низка питань, за рішенням яких він
стикається з низкою проблем. Вибір номенклатури виробів, способи отримання
заготовок, вибір оптимального технологічного процесу, верстатного обладнання,
вибір засобів контролю готових виробів, рішення з питання реалізації виробів,
ряд питань з визнаних з екологією і багатьох інших. Безумовно, не повинна
опинитися без уваги і економічна сторона на всіх стадіях виробництва.
При виборі верстатного обладнання, в першу чергу, повинна
оцінюватися ступінь завантаженості тієї чи іншої верстата в цеху в цілому. Для
чого проводитиметься аналіз всіх можливих варіантів обробки того чи іншого
виробу.
У даному дипломному проекті проводитися обробка корпусних деталі
підставу люнети з матеріалу Сч 20 ГОСТ1412-85, в якій обробляються два отвори Æ
мм і два отвори Æ
мм,
розташованих під кутом 120ű30'. Обробка
даної деталі має певного роду складність з досягнення точного кута між осями
оброблюваних отворів і точності самої обробки. Обробка на універсальному
обладнанні внесла б не мало клопоту за рішенням даного питання з подальшим
економічним відтінком. Швидше за все, було б потрібно проектування спеціального
пристосування, що чарівно б внесло свою лекту в економічну частину, а так само
наявність необхідного типу верстатів на підприємстві, з достатнім ступенем
точності.
Суттєво полегшило б завдання наявність верстата з ЧПУ і вбудованим
поворотним столом з числовий індикацією, що несказанно б відбилося на часі та
точності позиціонування деталі в процесі обробки. На сьогоднішній момент
промисловість добре оснащена верстатами даного типу, з можливістю чотирьох
координатної обробки і навіть більше, з достатнім ступенем точності починаю від
класу В і аж до С. Без умовно виробництво таких верстатів обходитися не дешево,
набагато легше і дешевше здійснити модернізацію вже наявного устаткування , за
рахунок впровадження нових технологій, сучасних пристроїв, систем, тощо.
У даному дипломному проекті обробка деталі вироблятися на координатній
свердлильно-фрезерному розточувальні верстати з числовим програмним управлінням
моделі 2А459АФ4, який у свою чергу володіє всім поруч можливостей для
досягнення всіх вимог з обробки деталі представника. Верстат володіє наявністю
поворотного столу з ціною поділки 0,001 градусів і достатнім поруч чисел
оборотів шпинделя для обробки деталей даного типу, маси і розміру. Інші
технічні характеристики верстата подані нижче в розділі огляду і аналізу
конструкцій верстатів аналогічного призначення. Заготівля повинна мати
мінімальні деформації від дії сил різання, утиску і власної ваги. При обробці
отвори по сьомому квалітету точності першим технологічним переходом є чорнове
розточування, а за ним слідує чистове розточування. [1].
. (1.1)
При чорновому розточування отворів Æ 45 и Æ 52 мм:

.
При чистовому розточування отворів Æ 45 и Æ 52 мм:
,
де Cv - коефіцієнт; Тm - стійкість різця; t - глибина
різання; S - подача; К - поправочний коефіцієнт.
2. Перегляд і аналіз конструкцій верстатів аналогічного
призначення
Координатно-розточні верстати призначені для обробки отворів
з високою точністю щодо базових поверхонь в корпусних деталях, кондукторних
плитах, штампах в одиничному і дрібносерійного виробництва. На них виробляються
практично всі операції, що виконуються на розточувальних верстатах. Крім того,
на них можна робити розмічальні операції. Для точного вимірювання координатних
переміщень верстати забезпечені різними механічними, оптико-механічними,
індуктивними і електронними пристроями відліку.
За компонуванням верстати виконуються одностієчний і
двохстієчний. Головним рухом є обертання шпинделя, а рухом подачі вертикальне
переміщення шпинделя, поздовжнє й поперечне переміщення столу або стійкі
(поперечне). Настановні руху в одностоєчний верстатах - поздовжнє й поперечне
переміщення столу на задані координати і вертикальне переміщення шпиндельної
бабки у залежності від висоти деталі; у двох стоєчних верстатах - поздовжнє
переміщення столу, поперечне переміщення шпиндельної бабки по траверсі і
вертикальне переміщення траверси з шпиндельної бабою.
Точність лінійних переміщень 2 - 8 мкм, а кутових - до 5 '.
Верстати необхідно встановлювати на спеціальних віброізолюючих фундаментах в
термоконстантних приміщеннях з температурою повітря 20 + 0,2 ° С. Для
досягнення високої точності обробки до основних елементів верстатів висувають
високі вимоги до конструкції верстата, якості виготовлення, монтажу і зборці,
точності систем відліку координат.
Аналіз обробки корпусних деталей, найбільш трудомістких за
характером виконання технологічного процесу, показав, що на свердління отворів
і нарізування різьб витрачається 70% часу обробки, на фрезерування 20% і на
розточування - 10%. Тому одним з найважливіших шляхів підвищення продуктивності
обробки на верстатах свердлильно-розточний групи є скорочення часу установки
заготовки на робочу позицію, зміни і кріплення інструменту, введення комплексної
обробки різними інструментами. Це може бути досягнуте застосуванням пристроїв
попереднього набору координат, систем знаковою індикації, ЧПУ, попередньої
розмірної настройки інструменту поза верстата, автоматичною зміною інструменту,
розширенням можливостей верстатів за рахунок зміни конструкції верстатів з
револьверними інструментальними головками або інструментальними магазинами з
швидкою заміною інструменту. Продуктивність багатоопераційних верстатів в 3 - 8
разів вище в порівнянні з універсальними верстатами.
Нижче представлений огляд верстатів аналогічного призначення,
включаючи модернізуються верстат моделі 2А459АФ4.
.1 Верстати моделі TXK160 Fanuc
Горизонтально-розточний верстат марки TXK160 з ЧПУ Fanuc
(забезпечує контроль за 4-м осях). На верстатах проводиться свердління,
зенкування, розгортання отворів, розточування отворів консольними і
двухопорнимі оправки, фрезерування площин (у тому числі по прямокутному
контуру), нарізування різьб, обточування торців і циліндричних поверхонь за
допомогою радіального супорта планшайби.
Збільшена площа робочого столу і горизонтальне переміщення.
На осях X / Y / Z використовуються прямолінійні напрямні, що
забезпечує високу точність позиціонування.
.1.1 Основні технічні дані
Розмір робочого столу, мм 1300 Х 600
Ширина Т образного паза, мм / кількість пазів 18 / 5
Переміщення по осі X, мм 1050
Переміщення по осі Y, мм 800
Переміщення по осі Z, мм 500
Конус шпинделя Вт 50
Максимальна швидкість обертання шпинделя, об / хв 3000
Потужність електродвигуна основного валу, кВт 5.5 / 7.5
Швидкість подачі X, Y, Z, мм / хв 1-3000
Прискорення вільного переміщення X, Y, Z, мм / хв 18000
Точність позиціонування по осях X, Y, Z, мм ± 0.015
Система управління Е60, М64AS, ANUC
Сумарна потужність кВт 20
Габарити 2550Х3000Х2500
Маса, кг 6000
.2 Верстати моделі TK611C/IV
C/IV є горизонтально-розточувальних верстатів з системою ЧПУ.
Довільний контроль осей X, Y, Z і одночасний контроль всіх трьох осей, з ЧПУ
Fanuc / Siemens. Верстат може бути укомплектований четвертої віссю. Завдяки
обертається столу можна робити обробку складних і великих фігурних деталей і
штампів.
.2.1 Основні технічні дані
Діаметр шпинделя, мм 110
Розмір робочого столу, мм 1320X1010
Кількість Т-образних пазів / ширина, мм 7 / 22
Відстань між двома отворами, мм 125
Максимальна вага завантаження столу, кг 5000
Відстань від центру шпинделя до кришки столу, мм 5-1205
Подовжній і поперечний хід столу, мм 1800X1300
Вертикальний хід шпиндельної бабки, мм 1200
Поздовжній хід шпинделя, мм 550
Максимальний діаметр розточування, мм 240
Максимальний діаметр розсвердлювання, мм 50
Внутрішній конус шпинделя BT50
Максимально допустимий обертаючий момент на шпинделі, Нм 1100
Максимально допустимий обертаючий момент на підрізної
голівці, мм 1100
Радіальний хід державки підрізної головки, мм 160
Максимальний робочий діаметр державки
підрізної головки, мм 630
Максимально допустима сила поздовжньої
подачі на шпинделі, Н 13000
Збільшення швидкості шпинделя Безступінчасте
Збільшення швидкості підрізної головки Безступінчасте
Діапазон швидкостей шпинделя, об / хв 12-1100
Діапазон швидкостей підрізної головки, об / хв 4-130
Потужність основного двигуна, кВТ 11/15
Загальні габарити (ДxШxВ), мм 5347X3420X3190
Вага брутто / нетто верстата, кг 14500/16000
Швидкий хід осей X, Y, W, мм / хв 5000
Швидкий хід шпинделя, мм / хв 3600
Точність позиціонування (x, y, z) X: 0.04, Y: 0.05 Z: 0.06 мм
Точність покрокового позиціонування (x, y, z) X: 0.015 мм
Номінальний діапазон цифрових показань, мм 0.001
Точність індексації обертання робочого столу ± 6''(на 90 °)
.3 Верстати моделі 2А622Ф4
А622Ф4 - горизонтально-розточний з ЧПУ призначений для
обробки великих деталей в умовах індивідуального і серійного виробництва, яким
важко повідомити обертальний головний рух. Оброблювану деталь закріплюють на
столі верстата чи на плиті. Можливо здійснювати чорнове і чистове розточування
отворів, фрезерування площин, свердління, зенкування, розгортання отворів,
нарізування зовнішнього і внутрішнього різьблення та інші технологічні
операції.
Горизонтально - розточний верстат працює таким чином: на
верстаті здійснюється обертання шпинделя при виконанні всіх основних видів
робіт і обертання планшайби при обточування торців радіальним супортом. При
свердлінні, зенкування, розгортання і розточування висувним шпинделем подачі
(або столу) повідомляють рух в поздовжньому напрямку. При розточування отвору
різець встановлюють у Борштанги, один кінець якої закріплений в шпинделі, а
інший обертається в підшипнику люнети стійки. При фрезеруванні площин
здійснюють подачу висувного шпинделя, що несе фрезу, або стіл отримує
переміщення в поперечному напрямку. Верстат дає можливість здійснювати точні
повороти столу на 900 і 1800.
Горизонтально - розточний верстат має нерухому передню
стійку, прикріплену до станини. За вертикальним направляючим стійки
переміщається шпиндельні баба, в яку вмонтований висувний шпиндель, що має крім
обертального руху і переміщення вздовж власної осі. Поворотний стіл верстата з
нерухомою передній стійкої має поздовжнє й поперечне переміщення.
Призначений для токарської обробки по програмі циліндричних,
торцевих, конічних, ступінчастих і криволінійних поверхонь деталей з чорних і
кольорових металів і сплавів, а також для свердління й розточування центральних
отворів, нарізування зовнішніх різьб.
.3.1 Основні технічні дані
Розміри робочої поверхні поворотного столу, мм 250х1250
Найбільша маса виробу, кг 5000
Найбільша поздовжнє переміщення висувного шпинделя, мм 710
Найбільша поздовжнє переміщення поворотного столу, мм 1000
Найбільша верхнє переміщення висувного шпинделя, мм 1000
Номінальна сумарна споживана потужність при повному
навантаженні одночасно працюючих електродвигунів, кВт 40,6
Маса верстата, кг 20500
.4 Верстати моделі ІР500ПМФ4
Горизонтальний свердлильно-фрезерно-розточний верстат моделі
ІР500ПМФ4 з системою програмного керування, автоматичною зміною інструменту і
столів-супутників призначений для високопродуктивної обробки корпусних деталей
з різних матеріалів. Широкі діапазони частоти обертання шпинделя і швидкостей
подач, наявність поворотного столу, високий ступінь автоматизації допоміжних
робіт розширюють технологічні можливості верстатів і дозволяють використовувати
їх у складі гнучких продуктивних систем.
.4.1 Основні технічні дані
Розміри робочої поверхні столу, мм 630х630; 500х500
Кількість кріпильних отворів на поверхні столу 25
Відстань між кріпильними отворами, мм 100
Діаметр отворів для кріплення, мм М20
Найбільші програмовані переміщення
по координатної осі Х, мм 800
Найбільші програмовані переміщення
по координатної осі Y, мм 500
Найбільші програмовані переміщення по координатної осі Z, мм
500
Конус для кріплення інструмента в шпинделі 50
Частота обертання шпинделя, хв-1 20-4500
Межі подач по осях X, Y, Z, мм / хв 1-3600
Потужність головного приводу, кВт 18
Швидкість швидких переміщень настановних по осях X, Y, Z, м /
хв 10000-15000
Кількість інструментів в магазині 30; 60
Найбільший діаметр суміжних інструментів, мм 125
Найбільший діаметр використовуваного інструменту, мм 160
Число позицій пристрою зміни столів-супутників 2
Габарити верстата, мм 4450х4635х3205
Маса верстата, кг 12785
.5 Верстати моделі 2254ВМФ4
Свердлильно-фрезерно-розточувальний верстат з ЧПУ моделі
2254ВМФ4 призначений для виконання свердлильних, фрезерних і розточувальних
операцій при обробці плоских сторін деталей середніх розмірів.
На верстаті можуть бути оброблені вироби з чавуну, сталі,
легких сплавів, кольорових металів, пластмас і ін..
Верстат виробляє чорнове і чистове фрезерування площин та
криволінійних поверхонь, а також свердління, розточування, зенкування і
розгортання точних отворів, нарізування різьб мітчиками і різцями.
.5.1 Основні технічні дані
Розміри робочої поверхні столу, мм 500x630
Конус шпинделя з конусними 7:24 N50AT5
Максимальні координатні переміщення
по осях X, Y, Z, мм 500
Межі частот обертання шпинделя, 1/хв 2-3150
Регулювання швидкостей шпинделя Безступінчасте
Регулювання поздовжніх, поперечних та вертикальних подач
Безступінчасте
Межі поздовжніх, поперечних і вертикальних подач, мм / хв
0,1-10000
Ємність інструментального магазину, шт 30
Потужність двигуна приводу головного руху, кВт 10
Точність позиціонування (лінійного), мм 0,016
Тип системи ЧПУ CNC
Габарити верстата, мм 4610x4510x3235
Вага верстата, кг 7000
.6 Верстати моделі 2А620Ф1-1
Верстат горизонтально-розточний моделі 2А620Ф1-1 призначений
виконання наступних технологічних операцій:
Фрезерування площин, пазів, уступів;
Свердління, розсвердлювання, центрування і зенкування
отворів;
Розточування і розгортання отворів;
Нарізування різьби мітчики;
Верстат оснащений пристроєм цифрової ідентифікації з
преднабором по осях X, Y, Z, і B з застосуванням високоточних датчиків, які
забезпечують точне координатне переміщення рухомих вузлів.
.6.1 Основні технічні дані
Поворотний стіл:
розміри робочої поверхні, мм 1 120х1 250
вантажопідйомність, кг 4000
Розточувальний шпиндель:
діаметр, мм 90
конус шпинделя ISO 45; 40
діаметр планшайби, мм 630
Найбільші переміщення
столу поперечно, X, мм 1250
шпиндельної бабки вертикально, Y, мм 1 000
стійки подовжньо, Z, мм 1 000
шпинделя, W, мм 710
поворот столу, B, град необмежено
Швидкість обертання:
шпинделя, об / хв 10 - 1600
планшайби, об / хв 6.3-160
Межі робочих подач: , Y, Z, мм / хв 1,25 - 1 250 , мм / хв 2
- 200 , мм / хв 0,8-800
Настановні габаритні розміри: довжина, ширина, висота, мм 7
600х3 730х3 220
Потужність головного приводу, кВт 11
Маса, кг 17 000
.7 Верстати моделі 2А459АФ4
Верстат координатний свердлильно-фрезерний з числовим
програмним управлінням моделі 2А459АФ4 призначений для виконання в корпусних
деталях верстатів, машин, штампів і пристосувань різноманітних операцій по
обробці поверхонь і отворів, до розмірів, геометричній формі та становищу яких
пред'являються вимоги високої точності: розточування, свердління, розгортання ,
підрізка торців, фрезерування, нарізування різьблення, точна розмітка і
вимірювання в умовах індивідуального, дрібносерійного і великосерійного
виробництва.
Верстат особливо придатний для обробки отворів, розташованих
на одній осі, паралельних, перпендикулярних або розташованих під довільними
кутами паралельних дзеркала столу осях з високою точністю, як з геометрії, так
і за їх взаємною розташуванню.
Характерною особливістю верстата є наявність вбудованого
поворотного столу, що робить можливою обробку співвісних отворів у
великогабаритних деталях з високою точністю (використовуючи точний поворот
столу на 180°). Крім того. На верстаті можна робити обробку криволінійних контурів.
Контурну обробку круглих отворів фрезою.
Верстат кліматичного виконання УХЛ категорії 4.1 за ГОСТ
15150-69 С.° ± 1 °Але для роботи при температурі 20°±1°С.
Клас точності верстата - А (особливо точні) за ГОСТ 8-82.
.7.1 Основні технічні дані
Основні технічні дані наведені у таблиці
.1 Основні розміри за ОСТ 2Н62-1-80
Таблиця 2.1 Основні технічні дані
Найменування
параметрів
|
Дані
|
Розміри робочої
поверхні столу по ОСТ 2Н62-1-78, мм ширинадовжина
|
1000h14 1000h14
|
Кількість
Т-образних пазів
|
7
|
Відстань між пазами
по ГОСТ 6569-75, мм
|
125±0,4
|
Ширина пазів за
ГОСТ 6569-75, мм направляючогоінших
|
22Н8 22Н12
|
Найбільша маса
заготівлі, встановлюваної на столі, кг
|
2000
|
Найбільша
програмований робоче переміщення по координаті: X, мм Y, мм Z, мм B, градусів
|
1250 1000*¹
800*² 360+1/1000
|
Найменша відстань
від осі шпинделя до робочої поверхні столу, при установці стійки на
координату 330мм, мм
|
30
|
Межі частот
обертання шпинделя, об / хв
|
20…3150±10%
|
Кількість частот
обертання шпінделя: в автоматичному режимі в ручному режимі
|
Безступінчасте з
дискрети 1 об / хв
|
Найбільший крутний
момент на шпинделі, Нм
|
441
|
Діапазон
регулювання частоти обертання шпінделя: з постійною потужністю з постійним
моментом
|
80…3150 20…80
|
Внутрішній конус
шпинделя
|
Конус 40 АТ4
ГОСТ19860-74
|
Найбільший конус в
перехідній втулці
|
Морзе 4
|
Найбільший діаметр
оброблюваного отвору без інтерполяції (різцем), мм
|
500
|
Найбільший діаметр
свердління по сталі, мм
|
50
|
Найбільший діаметр
торцевої фрези, мм
|
200
|
Межі подач по
координаті: X; Y; Z, мм / хв B, град / хв
|
2…2500±10%
0,72…1000±10%
|
Кількість ступенів
подач в автоматичному режимі в режимі ручного введення даних
|
Безступінчасте з
дискрети 1мм/мін
|
Швидкість пошуку в
автомат. режимі / в режимі ручного введення: X; Y; Z, мм / хв B град / хв
|
8000±10%/5000±10% 2000±10%/1000±10%
|
Максимальне зусилля
подачі при різанні по координаті Z, H
|
10000
|
Габаритні розміри
верстата без приставного обладнання не більше, мм Довжина Ширина висота
|
4415 4265 3800
|
Габаритні розміри
верстата з приставним обладнанням не більше, мм Довжина Ширина висота
|
5870 5350 3800
|
Площа займана
верстатом з приставним обладнанням, м ²
|
34,4
|
Маса верстата без
приставного обладнання не більше, кг
|
14600
|
Маса верстата з
приставним обладнанням не більше, кг
|
17900
|
Максимальний
момент, що утримується затискачами від проворота столу, Нм
|
3000
|
Тип системи
числового програмного керування
|
2С42 (Фанук)
|
Число одночасно
керованих координат: при лінійній інтерполяції при кругової інтерполяції
|
4 2+1
|
Вид числового
програмного керування
|
комбіноване
позиційний та контурне)
|
Введення інформації
|
вручну з
перфострічки
|
Код подання
інформації за ГОСТ13052-74
|
7-бітний
|
Спосіб завдання
розмірів
|
абсолютний і по
приросту
|
Межі зміщення нуля
відліку
|
на всій довжині
переміщення
|
Перетворювач
вимірювальний по координаті X, Y, Z, В
|
оптико - електронні
растрові
|
Ціна поділки
відлікових пристроїв переміщень по координаті: X; Y; Z, мм B градусів
|
0,001 0,001
|
Точність
одностороннього позиціонування по координаті: X; Y, мм Z, мм, В кутових сек.в
положеннях 0°, 270 °,
180 °, 90 в решті
|
0,01 0,02 4 8
|
Точність міжосьових
відстаней розточеними отворів, мм
|
0,018
|
Рід струму
живильної мережі
|
Змінний трифазний
|
Частота струму, Гц
|
50
|
Напруга, В
|
380 (+10%/-15%)
|
Рід струму
електроприводів головного руху, переміщення санчат столу, стійки, шпиндельної
бабки, повороту столу
|
Постійна
|
Рід струму
електроприводів гідроагрегату, холодильного агрегату, насоса станції
охолодження
|
Змінний
|
Станцій
гідроприводу з насосними установками продуктивність, л / хв номінальний тиск,
МПа
|
СВ-М3А-40-3Н-1,5-3/6
УЧХЛ 3/6 6,3
|
Ємність бака, л
|
40
|
Найбільше робочий
тиск у гідросистемі, МПа
|
5,5
|
Гідроакумулятор тип
max робочий тиск, МПа ємність, л
|
АГП-Б-10/200 20 10
|
Насос установки
очищення МОР тип продуктивність, л / хв
|
БХ14-44 100
|
Марка масла для
гідросистеми і системи змащення
|
ИГП-18
|
Примітка: Допускається застосування інших комплектуючих
виробів імпортного та вітчизняного виробництва, що не погіршують технічні
характеристики верстата. * ¹ При положеннях координати Z в
інтервалі координат від 0 мм до 545мм і координати В рівній 0°,90°,180°,270°; при положеннях координати Z
в інтервалі координат від 0 мм до 395мм і координати В рівній 45°,135°,225°,315°. *
² При
положеннях координати Y в інтервалі координат від 0 мм до 925мм.
3. Обґрунтування. Технічні характеристики верстатів
.1 Визначення габаритних розмірів оброблюваних заготовок
За заданими в завданні даними:
оброблюваного матеріалу - кол. сплави, чавун, сталі;
матеріалу РІ: швидкорізальні сталі, тверді сплави;
характером виробництва - серійне.
При фрезеруванні:
По заданих B і L визначаються їхні граничні значення [2].-
ширина столу; B = 1000 мм;- довжина столу; L = 1000 мм.
(3.1)
(3.2)
(3.3)
(3.4)
Обчислюються середні значення максимальних і мінімальних діаметрів
фрез.
Для торцевих фрез:
(3.5)
(3.6)
Розраховані діаметри фрез Dmax і Dmin звіряються з низкою бажаних
чисел, після чого вибираються остаточно.
При свердлінні:
По заданому найбільшому діаметру свердління D = 50 мм визначають
найменший діаметр свердління Dmin:
(3.7)
.
При розточування:
По заданому найбільшому діаметру розточування D = 500 мм визначають
найменший діаметр Dmin:
(3.8)
.2 Вибір глибини різання
Для чорнового фрезерування максимальна глибина різання при обробці в
один прохід рівна [2]:
, (3.9)
де Пmax - максимальний припуск на сторону (вибирається за таблицею в
залежності від оброблюваного матеріалу і розмірів оброблюваної заготовки);
Пчіст - чистової припуск. Для всіх розмірів оброблюваних деталей дорівнює Пчіст
= 0,5 мм.
Для стали: Пmax = 6 мм.
Для чавуну Пmax = 5 мм.
Для міді Пmax = 3 мм.
тоді:
Для сталі
Для чугуна
Для меді
Глибина різання при чистової обробки дорівнює чистовому припуск:
Для сталі
Для чугуна
Для меді
.3 Вибір граничних значень подач
Граничні значення подач Smax і Smin вибираються для всіх оброблюваних
матеріалів і для всіх матеріалів інструменту.
Формула для визначення значень подач при фрезеруванні:
(3.10)
де ST - табличне значення подачі на зуб, мм; КSU - коефіцієнт, що
враховує матеріал фрези; КSR - коефіцієнт, що враховує шорсткість оброблюваної
поверхні; КSФ - коефіцієнт, що враховує форму оброблюваної поверхні [2].
Для сталі
Для чугуна
Для меді
Формула для визначення значень подач при свердлінні:
(3.11)
де ST - табличне значення подачі, мм / об; КSl - коефіцієнт, що
враховує глибину свердління; КSЖ - коефіцієнт, що враховує жорсткість
технологічної системи (КSЖ = 0,75); КSU - коефіцієнт, що враховує матеріал
інструменту; КSd - коефіцієнт, що враховує тип оброблюваного отвори; КSМ -
коефіцієнт, що враховує марку оброблюваного матеріалу.
Для сталі
Для чугуна
Для меді
Формула для визначення значень подач при розточування:
(3.12)
де ST - табличне значення подачі, мм / об; КSП - коефіцієнт, що
враховує стан оброблюваної поверхні; КSU - коефіцієнт, що враховує матеріал
інструменту; КSФ - коефіцієнт, що враховує форму оброблюваної поверхні; КSЗ -
коефіцієнт, що враховує вплив загартування; КSЖ - коефіцієнт, що враховує
жорсткість технологічної системи; КSМ - коефіцієнт, що враховує марку
оброблюваного матеріалу.
Для сталі
Для чугуна
Для меді
.4 Вибір граничних швидкостей різання
Граничні значення швидкостей різання вибираються на підставі довідкових
даних [2].
Швидкості різання при фрезеруванні торцевої вибираємо за таблицею:
Для сталі
Для чугуна
Для меді
Швидкості різання при свердлінні, розраховані на обробку одним
інструментом із заданим періодом стійкості при нормальному його затупленія і
роботі з охолодженням, вибираємо за таблицею:
Для сталі
Для чугуна
Для меді
При розточування швидкість різання може бути визначена за формулою:
(3.13)
де VT - табличне значення швидкості різання, м / хв;
КVU - коефіцієнт, що враховує властивості матеріалу інструменту;
КVφ - коефіцієнт, що враховує впливу кута у плані
(КVφ
= 0,9);
КVЖ - коефіцієнт, що враховує жорсткість технологічної системи;
КVП - коефіцієнт, що враховує стан оброблюваної поверхні;
КVО - коефіцієнт, що враховує вплив МОР.
Для сталі 
Для меді
Також необхідно враховувати нарізування різьблення на даному верстаті.
Швидкість різання при нарізуванні різьби мітчиків буде дорівнює: Vmin = 3 - 4 м
/ хв.
.5 Визначення граничних частот обертання шпинделя
Знайдені за таблицями і вказаним вище формулами граничні швидкості
різання дозволяють визначити граничні частоти обертання шпинделя верстата. Вони
визначаються за наступними формулами [4]:
(3.14)
(3.15)
Для фрезерування:
Для свердління:
Для розточування:
З усіх вище розрахованих граничних частот обертання шпинделя верстата
вибираємо максимальну і мінімальну частоти.= 3076 об / хв;= 13,4 об / хв.
Отримані значення звіряємо зі стандартними значеннями за ОСТ Н11-1-72,
після чого вибираються остаточно:= 3150 об / хв;= 20 об / хв.
заготовка верстат налагодження електродвигун
4. Розрахунок і вибір електродвигунів
При виборі нормативної потужності електродвигуна необхідно
враховувати наступне:
режими при чорновій обробці tmax і Smax;
матеріал заготовки;
матеріал різального інструменту - сплав з найменшою
стійкістю.
Потужність електродвигуна приводу головного руху визначається
за формулою [3]:
(4.1)
де η - ККД ланцюга головного руху, який для
даного верстата можна прийняти η = 0,7-0,85; К-коефіцієнт перевантаження
двигуна, який для універсальних верстатів приблизно дорівнює К = 1,25; Nнорм -
нормативна потужність електродвигуна вибирається за таблицею [3]:
при фрезеруванні: Nнорм = 12,1 кВт;
при свердлінні: Nнорм = 8,3 кВт;
при розточування: Nнорм = 6,4 кВт.
З вище перерахованих потужностей вибираємо максимальну
номінальну потужність. Отримані дані підставляємо у формулу (4.1).
Потужність електродвигуна проектованого приводу доцільно порівняти з
потужністю електродвигунів, встановлених на сучасних верстатах даного
типорозміру та дозволяють забезпечити виконання основного обсягу робіт на
верстаті. Відповідно до [4] вибираємо двигун 2ПН160LУХ4:
= 14 (кВт); nн = 800 (об / хв); nmax = 4000 (об / хв).
. Кінематичний розрахунок приводу головного руху
.1 Визначення числа ступенів коробки швидкостей
Вихідні дані:ш. max = 3150 об / хв;ш. min = 20 об / хв.
Двигун 2ПН160LУХ4:дв = 14 кВт;н = 800 об / хв;= 4000 об / хв.
Необхідний діапазон регулювання частоти обертання приводу [4]:
(5.1)
Розрахункова частота обертання шпинделя:
(5.2)
Приймаємо
при
.
Діапазон регулювання (при постійній потужності) на шпинделі:
(5.3)
Діапазон регулювання двигуна:
(5.4)
Так як Rд. N <RN, то необхідна коробка швидкостей.
Число ступенів коробки швидкостей визначаємо за формулою [4]:
(5.5)
Округлюючи отримане значення z в більшу сторону, приймаємо z = 3.
Розглянемо можливість скорочення числа ступенів приводу за рахунок
виникнення розривів у характеристиках:
(5.6)
Таким чином спростити привід не можна, так як в цьому випадку втрати
потужності в розривах характеристики перевищать 20%. Тому слід прийняти z = 3
5.2 Розробка кінематичної схеми коробки швидкостей
Розроблена схема кінематична коробки швидкостей показана на ріс.5.1.
Рис. 5.1 Кінематична схема коробки швидкостей
.3 Побудова графіка частот обертання шпинделя
Побудуємо графік частот обертання шпинделя (ріс.5.2), виходячи з
обгрунтування технічних характеристик верстата наведених раніше
Рис. 5.2 Графік частот обертання шпинделя
Ряд чисел оборотів шпинделя отриманий шляхом безступінчатого
регулювання чисел обертів електродвигуна і редукцією коробки швидкостей.
.4 Розрахунок чисел зубів передач
З побудованого графіка частот обертання відомі величини передавальних
відносин, виробляємо розрахунок чисел зубів [4]:
Між валами I і II:
Між валами II і III:
;
;
;
.
Між валами III і 4:
;
;
;
;
;
;
;
.
Між валами II і 4:
;
;
.
Виробляємо перевірку відхилень дійсних значень частот
обертання шпинделя від табличних, взятих по нормалі H11 - 1. Відхилення не
повинно перевищувати величини допуску на відхилення r=
± 10 (φ-1)%.
При φ = 1,12 маємо:
(5.7)
;
.
;
.
;
.
;
.
;
.
;
.
;
.
;
.
;
.
;
.
;
.
;
.
;
.
;
.
;
.
;
.
;
.
;
.
;
.
;
.
;
.
;
.
;
.
;
.
;
.
;
.
;
.
;
.
;
.
;
.
;
.
;
.
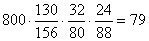
;
.
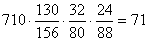
;
.
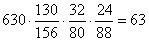
;
.

;
.
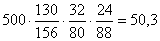
;
.
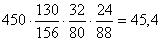
;
.
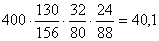
;
.

;
.

;
.
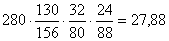
;
.

;
.

;
.

;
.
6. Опис компановки і кінематичної схеми верстата
Основна вимога до базових деталей верстата з ЧПУ, - забезпечити
протягом тривалого часу правильне взаємне розташування і переміщення виконавчих
органів, змонтованих на них.
Основною частиною верстата є станина, на яку монтуються
вузли, механізми та деталі. Для збільшення жорсткості станини, вона має
коробчату форму з ребрами жорсткості. Станина має вібростійкість, забезпечує
зручний відведення стружки і МОР. Аналогічні вимоги пред'являються до
шпиндельної бабі, столу, салазки. Базові деталі зварні (зі сталі). Зварні
конструкції легше литих.
Напрямні базових деталей верстата, забезпечують заданий рух
виконавчих органів; характеризуються високою і малої силою тертя. У даному
верстаті використовуються направляючі ковзання.
Робота приводу головного руху здійснюється від двигуна
постійного струму. З нього через вал I і ремінну клинові передачу рух
передається на вал II. З валу II рух передається через коробку швидкостей на
вал I \ /. Вал I \ / з'єднується зі шпинделем за допомогою муфти.
Безступінчасте регулювання частоти обертання здійснюється
електродвигуном постійного струму, частота обертання електродвигуна змінюється
бесступенчато електронним блоком управління. Двигун полягає в поєднанні з
триступінчатої коробкою швидкостей. Переваги такого приводу: простота
конструкції і легкість управління.
Шпиндель верстата виготовлений точним, твердим, з підвищеною
зносостійкістю посадкових і які базуються поверхонь. Кінець шпинделя
стандартизований. Шпиндель має отвір для встановлення інструмента з конусом
7:24, і конусом Морзе.
Привід подач. Привід подач забезпечує переміщення виконавчих
органів верстата в потрібну позицію, згідно з УП. До приводу пред'являються
високі вимоги. Він повинен мати мінімальні зазори, високу жорсткість;
забезпечити плавність переміщень при малих швидкостях і високу швидкість при
допоміжних переміщеннях; володіти малим часом розгону і гальмування, невеликими
силами тертя, зменшеним нагрівом його елементів, великим діапазоном
регулювання. Зазначені вимоги забезпечуються за допомогою кулько-гвинтовий
передачі, направляючих ковзання.
Загальний вигляд з позначенням складових частин верстата
показаний на ріс.6.1 і ріс.6.2.
Перелік складових частин верстата зазначено у таблиці 6.1.
Кінематична схема верстата (См.ліст
СамГТУ.151002.060.020.006.КЗ).
Рис.6.1 Позначення складових частин верстата
Рис.6.2 Позначення складових частин верстата
Таблиця 6.1 Перелік складових частин верстата
Позиція
|
Найменування
|
Примічання
|
1
|
Станина
|
|
2
|
Телескопічна захист
напрямних станини (стола)
|
|
3
|
Телескопічна захист
напрямних станини (стійки)
|
|
4
|
Телескопічна захист
напрямних станини (стійки)
|
|
5
|
Передача
гвинт-гайка кочення переміщення столу
|
|
6
|
Передача
гвинт-гайка кочення переміщення стійки
|
|
7
|
Стіл
|
|
8
|
Редуктор
|
|
10
|
Стійка
|
|
11
|
Передача
гвинт-гайка кочення переміщення шпиндельної бабки
|
|
12
|
Зажим інструменту
|
|
13
|
Пристрій
попереднього натягу
|
|
14
|
Пристрій шпиндельні
|
|
15
|
Бабка шпиндельна
|
|
16
|
Коробка швидкостей
|
|
17
|
Пристрій
попереднього натягу
|
|
18
|
Опора регульована
|
|
19
|
Опора нерегульована
|
|
20
|
Пристрій
транспортування гідро і електрокомунікацій (до стійки)
|
|
21
|
Пристрій
транспортування гідро і електрокомунікацій (до столу)
|
|
22
|
Охолодження зони
різання і змиття стружки
|
|
23
|
Охолодження зони різання
|
|
25
|
Розведення
гідравліки
|
|
26
|
Гідроагрегат
|
|
27
|
Гідроциліндр
врівноваження шпиндельної бабки
|
|
28
|
Циліндр віджиму
інструменту
|
|
29
|
Гідробак
|
|
30
|
Циліндр
переключення шестерень
|
|
31
|
Циліндр
переключення блока
|
|
32
|
Електрошафи
|
|
33
|
Пульт керування
|
|
34
|
Перетворювач
вимірювальний по координаті X, Y, Z (оптико - електронні растрові
перетворювачі ЛІР 8)
|
можливість
застосування імпортних перетворювачів
|
35
|
Перетворювач
вимірювальний по координаті В (оптико-електронні растрові перетворювач ЛІР
1170 А)
|
можливе
застосування імпортних перетворювачів
|
36
|
Датчик орієнтації
шпинделя (оптико-електронні перетворювач ЛІР 158 Д)
|
|
37
|
Пристрій ЧПУ
|
|
|
|
|
|
7. Міцнісний розрахунок приводів і вузлів верстата
.1 Розрахунок на міцність зубчастих передач
Зубчаста передач 32/80: m = 3 мм; b1 = 30 мм; b2 = 25 мм.
Номінальний обертальний момент, який передається передачею
[4]:
(7.1)
Розрахунковий крутний момент:
Мр = к × Мкр = 1,5 ×
204 = 306Нм. (7.2)
Розрахункове число обертів:
.
Швидкість ковзання:
. (7.3)
Швидкісний коефіцієнт:
.
Коефіцієнт форми зуба:
для
Z = 32;
для Z = 80.
Коефіцієнт тиску: С = 670.
Напруга вигину:
; (7.4)
. (7.5)
Питомий тиск на робочих поверхнях зубів [4]:
(7.6)
Для матеріалу - Сталь 40Х ГОСТ 4543-71 HRc 24 .. 28 зуби HRc
45 .. 50
;
.
Висновок: міцність зубчастої передачі задовільна.
Зубчаста передач 24/88: m = 3 мм; b1 = 34 мм; b2 = 30 мм.
Зубчасті колеса з кутовою корекцією:= 24 - зміщення вихідного
контуру x = 0,4648;= 88 - зміщення вихідного контуру x = 0,6.
Номінальний обертальний момент, який передається передачею:
Розрахунковий крутний момент:
Мр = 1,5 × 450 = 675Нм.
Розрахункове число оборотів:
.
Швидкість ковзання:
Швидкісний коефіцієнт:
.
Коефіцієнт форми зуба:
;
.
Коефіцієнт тиску: С = 670.
Напруга вигину:
;
;
.
Питомий тиск на робочих поверхнях зубів:
.
Для матеріалу - Сталь 40Х ГОСТ 4543-71 HRc 24 .. 28 зуби HRc
45 .. 50
;
.
Висновок: міцність зубчастої передачі задовільна.
Зубчаста передач 50/62: m = 3 мм; b1 = 35 мм; b2 = 30 мм.
Номінальний обертальний момент, який передається передачею:
Розрахунковий крутний момент:
Мр = 1,5 × 450 = 675Нм.
Розрахункове число оборотів:
.
Швидкість ковзання:
Швидкісний коефіцієнт:
.
Коефіцієнт форми зуба:
;
Коефіцієнт тиску: С = 670.
Напруга вигину:
;
;
.
Питомий тиск на робочих поверхнях зубів:
Для матеріалу - Сталь 40Х ГОСТ 4543-71 HRc 24 .. 28 зуби HRc 45 .. 50
;
.
Висновок: міцність зубчастої передачі задовільна.
.2 Розрахунок клиноремінною передачі (Ремінь Б-1120Т ГОСТ1284
- 68)
-
діаметр малого шківа;
-
діаметр більшого шківа;
-
кількість ременів (профіль "Б");
-
площа поперечного перерізу ременя;
-
міжосьова відстань;
-
довжина ременів.
Потрібну кількість ременів [4]:
, (7.6)
N - потужність, яку треба передати; No - потужність, що передається
одним ременем;
- коефіцієнти (при a=175Å).
Визначаємо кількість ременів для різних режимів роботи (таблиця 7.1).
Таблиця 7.1 Потрібну кількість ременів
Режим роботи
|
Передана потужність
і потрібну кількість ременів
|
;
;
;
.N = 6,7 кВт
;
;
;
.N = 8,6 кВт
;
;
;
.N = 13,3 кВт
;
;
;
.N = 5,3 кВт
;
;
;
.N = 2,7 кВт
;
;
;
.N = 8,6 кВт
Висновок: для передачі номінальної потужності електродвигуна
необхідну кількість ременів Z = 4.
Необхідне натягнення однієї гілки ременя:
, (7.7)
де
- потужність, що передається ременем;
= 0,99;
=
0,8;
-
коефіцієнт, що враховує швидкість ременя;
=
84 - чисельний коефіцієнт;
=
0,008 - для профілю "Б".
Для випадку навантаження - 5:
Для випадку навантаження - 6:
Загальна натяг ременя профілю "Б" (ГОСТ1284-68);:
Натяг ременя контролюють, визначаючи зусилля Q, необхідне для
відтягування гілки ременя на величину, рівну 1,55 мм на кожні 100 мм міжцентрова
відстані ріс.7.1
Рис.7.1 Натяг ременя
Для нового ременя "Б", Зі = 6 кгс:
. (7.8)
Для приробиться ременя:
; (7.9)
.
.3 Розрахунок шпинделя на жорсткість
Розрахунок проводиться для шпинделя на жорстких опорах.
Розрахункова схема представляє собою консоль, так як в
передній опорі встановлений дворядний підшипник кочення. При розрахунку не
враховується дія затискаються моменту в підшипнику передньої опори, що має
кілька рядів тіл кочення.
Визначимо силу різання, що виникає при роботі з споживанням
максимальної потужності на різання при фрезеруванні стали фрезою зі сталі Р18
[2]. Значення СР і показників ступенів взяті з [2]. Æ50 мм і числом зубів Z = 6
при глибині різання t = 5 мм маємо Sz = 0,15 мм / зуб. Для фрези зі сталі Р18
діаметром Ширина фрезерування В = 30 мм. Робочі обертів: n = 200об/мін [4].
;(7.10)
; (7.11)
. (7.12)
Для визначення середнього зовнішнього діаметра на консолі
використовується залежність:
, (7.13)
де d - діаметр ділянки валу; l - довжина ділянки валу з одним
діаметром.
Приймемо внутрішній діаметр d = 40мм.
Моменти інерції перерізів підраховуються для кільцевого перерізу.
;
; (7.14)
Прогин на кінці шпинделя і поворот в передній опорі
визначається для варіанту схематизації у вигляді консолі ріс.7.2.
Рис. 7.2 Розрахункова схема
Проведемо розрахунок прогину і кута повороту кінця шпинделя.
Прогин
. (7.15)
Кут повороту переднього кінця шпінделя:
. (7.16)
Найбільший допустимий прогин кінця шпинделя і допустимий
поворот перетину шпинделя в передній опорі:
(7.17)
.
Висновок: даний варіант шпинделя задовольняє вимогам
жорсткості, тому що прогини і кути повороту його кінця не перевищують
допустимих значень.
.4 Розрахунок валів на міцність
Вал 3 (1 варіант навантаження)
Рис. 7.3 Расчетная схема вала 3
Зусилля, що діють на вал
; (7.18)
; (7.19)
; (7.20)
. (7.21)
Опорні реакції і згинальні момент в площині дії окружних сил:
; (7.22)
;
(7.23)
; (7.24)
. (7.25)
Опорні реакції і згинальні момент в площині дії радіальних
сил:
; (7.26)
; (7.27)
; (7.28)
. 7.29)
Сумарні опорні реакції:
; (7.30)
; (7.31)
Сумарний згинальний момент в перерізах:
; (7.32)
.
Наведений момент в перерізах [5]:
; (7.33)
.
Вал3 (2 варіант навантаження)
Рис. 7.4 Розрахункова схема вала 3
Зусилля, що діють на вал [5]:
; (7.34)
; 7.35)
; (7.36)
. (7.37)
Опорні реакції і згинальні момент в площині дії окружних сил:
; (7.38)
; (7.39)
; (7.40)
. (7.41)
Опорні реакції і згинальні момент в площині дії радіальних
сил:
; (7.42)
; (7.43)
; (7.44)
. (7.45)
Сумарні опорні реакції:
; (7.46)
; (7.47)
Сумарний згинальний момент в перерізах:
; (7.48)
Наведений момент в перерізах [5]:
; (7.49)
.
Другий володіє великими наведеними моментами, тому варіант 3 навантаження вала розрахунок
прогинів в перетинах проводиться для другого варіанту навантаження.
Момент інерції перерізу валу знаходимо за формулою:
. (7.50)
Прогин валу в перерізі 1 - 1 і 2 - 2 в площині дії окружних
сил [5]:
(7.51)
(7.52)
Прогин валу в перерізі 1 - 1 і 2 - 2 в площині дії радіальних
сил:
Сумарний прогин в перетинах:
; (7.53)
. (7.54)
.5 Визначення довговічності опор
Підшипник № 207 35 × 72
× 17; С =
20100 Н.
Довговічність підшипника в годинах [4]:
; (7.55)
, (7.56)
де
- розрахункова кількість обертів; р = 3 - степеневий
показник для кулькових підшипників;
-
динамічна еквівалентна навантаження; V = 1 - коефіцієнт обертання щодо вектора
навантаження внутрішнього кільця радіального підшипника; Х = 1 для однорядних
підшипників;
= 1,2 - динамічний коефіцієнт, що враховує вплив
динамічних умов;
= 1 - температурний коефіцієнт;
= 0 - осьова навантаження;
- еквівалентна динамічна радіальна навантаження.
; (7.57)
,
де -
- (середній режим у 2 діапазоні, 30% часу працює привід)
- (середній режим у 1 діапазоні, 60% часу працює привід);
;
,тоді
;
;
.
Висновок: довговічність підшипників задовільна.
Підшипник 116 80×125×22; С=37400 Н.
=
= 1;
=
1,2.
;
;
.
Підшипник №107 35×62×14; С=12500 Н.
=
= 1;
=
1,2.
;
;
;
;
.
Підшипник 1000918 90×125×18; С=25800 Н.
=
= 1;
=
1,2;
;
;
.
.
Висновок: довговічність підшипників задовільна.
.6 Розрахунок на міцність болтового з'єднання шестірні Z = 88
із шестернею Z = 62
Максимальний крутний момент, передається шестернею:
Мкр = 450 Нм. Розрахунковий крутний момент: Мр = 1,5 ×
450 = 675 Нм.
Момент повинен передаватися за рахунок тертя по торцях шестерень. Сила тертя
створюється затягуванням болтів М16, розташованих по колу радіусом R = 65 мм,
поставлених з зазором. Для кільцевого стику з зовнішнім діаметром D1 = 162 мм і
внутрішнім D2 = 90 мм отримуємо:
, (7.58)
де Z = 6 - кількість болтів; F = 0,2 - коефіцієнт тертя в
стику.
Наближене геометричне подобу різьблень дозволяє для орієнтовних
розрахунків користуватися співвідношенням:
; (7.59)
.
Допустимий момент затягування для болтів М16 з Сталі 45:
Висновок: міцність болтів М16 (6 шт.) З Сталі 45 ГОСТ 4543-71
достатня для передачі обертального моменту Мр = 675Нм.
. Опис основних вузлів верстата
.1 Станина
Це базова деталь коробчатої форми з внутрішніми ребрами жорсткості.
У верхній частині станини розташовані дві направляючі ковзання.
На V-подібною і плоскою направляючих розташований стіл, що
забезпечує йому плавність переміщення санчат столу по напрямних станини.
Напрямні станини захищені від попадання бруду, стружки
стрічкової захистом. На передньому торці станини, стрічки захисту закріплені
жорстко гвинтами, інші кінці стрічок натягаються гвинтами. Тим напрямними
станини встановлений привід переміщення санчат столу.
Привод складається з пари гвинт-гайка кочення, з'єднаної
безлюфтовой муфтою з електродвигуном. Завдяки цьому забезпечується весь
діапазон подач рухомих вузлів без застосування редукторів. Ходовий гвинт
встановлений у двох опорах на підшипниках кочення.
Злив відпрацьованого масла (приблизно один раз на тиждень) з
направляючих стійки, опор ходового гвинта, направляючих санчат і столу
відбувається через вікно в станині і збирається в висувний лоток.
Для відліку переміщення санчат столу (координата Х)
застосовується перетворювач лінійних переміщень ЛІР-8. Лінійка перетворювача
закріплена на столі, зчитування голівка на станині. Координата фактичного
положення рухомого органу висвічується на екрані пристрою ЧПУ.
Станина встановлюється на фундаменті на трьох опорах: одна не
регульована і дві регульовані.
Для відключення переміщення санчат на станині встановлені:
Два мікроперемикача, для відключення переміщення в крайніх
положеннях санчат;
Два мікроперемикача - аварійні;
Мікровимикач, для виходу в референтну точку, тобто на нульову
точку відліку руху даного органу.
Відключення переміщення ходу в крайніх положеннях записано в
пам'яті пристрою ЧПУ.
У корпусі станини передбачені два наскрізних отвори для
транспортування верстата. Отвори закриті кришками.
.2 Стойка
Стійка представляє собою коробчату відливку з вертикальними
V-подібною і плоскою направляючими ковзання для переміщення каретки шпиндельної
бабки. Для запобігання попаданню бруду на напрямні ковзання передбачена
телескопічна захист. Щитки захисту ковзають по пазах планок.
У верхній частині стійки встановлено електродвигун,
сполучений безлюфтовой муфтою з ходовим гвинтом, за допомогою якого
переміщується шпиндельні баба. Опори гвинта закріплені на стійці. Гайка
закріплена на шпиндельної бабці.
Електродвигун має вбудований гальмо, що гальмує ходовий гвинт
при відключенні електроживлення.
Є два кронштейна з блоками, до яких підвішується противагу,
призначений для врівноваження ваги шпиндельної бабки.
Противага переміщається всередині стійки.
Для відключення переміщення шпиндельної бабки на стійці
встановлені:
Два мікроперемикача, для відключення переміщення шпиндельної
бабки у крайніх положеннях;
Два мікроперемикача для аварійного відключення переміщення
шпиндельної бабки;
Мікроперемикач - для виходу в референтну точку, тобто на
нульову точку відліку руху даного органу.
Робота мікроперемикачів здійснюється від кулачків,
встановлених на шпиндельної бабці.
В основі станини є напрямні ковзання, V-образна і плоска для
поперечного переміщення стійки по напрямних ковзання станини (координата Z).
Для відліку переміщень стійки застосовується перетворювач лінійних переміщень
ЛІР-8. Лінійка перетворювача розташована полозку, зчитування голівка на
станині.
Привод складається з пари гвинт-гайка кочення, з'єднаної
безлюфтовой муфтою з електродвигуном. Завдяки цьому забезпечується весь
діапазон подач рухомих вузлів без застосування редукторів. Ходовий гвинт
встановлений у двох опорах на підшипниках кочення.
Координати фактичного положення рухомого органу висвічується
на екрані пристрою ЧПУ.
.3 Стіл
Стіл має форму кола, на робочій поверхні столу прорізані
Т-образні пази для закріплення деталей.
Стіл встановлюється на санчатах поздовжнього переміщення.
Привід кругового обертання столу (координата В) складається з
червячно - гвинтовий пари, з'єднаної безлюфтовой муфтою з електродвигуном.
Завдяки цьому забезпечується весь діапазон кругових подач столу.
Для відліку кругових переміщень столу застосовується
перетворювач кругових переміщень ЛІР 1170А.
Координата фактичного положення столу висвічується на екрані
пристрою ЧПУ.
.4 Шпиндельні баба
Шпиндельні баба переміщується у вертикальному напрямі по
напрямних стійки: однією V-образної і однією плоскою. Переміщення здійснюється
за допомогою передачі гвинт-гайка кочення. Гвинт в опорах укріплений на стійці,
гайка на корпусі шпиндельної бабки.
Пара тертя ковзання фторлон - чавун. На шпиндельної бабі
розташоване пристрій освітлення робочої зони.
У шпиндельні бабу входять наступні основні вузли: шпиндельні
пристрій, затиск інструмента, коробка швидкостей. По роликах переміщуються
троси, на яких висить вантаж врівноваження шпиндельної бабки.
Відключення переміщення шпиндельної бабки у крайніх
положеннях здійснюється кулачком, які взаємодіють з мікровимикачів,
встановленими на кронштейні, який закріплений на стійці.
Мікровимикач призначені для подачі сигналу про втиснута або
затиснутому інструменті. На лицьовій стороні шпиндельної бабки розташована
панель, на якій встановлені сигнальні лампи затиску і віджиму інструменту.
Для забезпечення необхідного мінімальних тисків на напрямних
і запобігання відриву шпиндельної бабки від направляючих стійки, на ній
закріплені чотири пристрою попереднього натягу. Силове замикання здійснюється
роликами, які котяться по відповідним планок стоїки при переміщенні бабки.
Необхідне зусилля притиску шпиндельної бабки напрямних стійки забезпечується
підтискаючи пакету тарілчасті пружин.
Для відліку переміщень шпиндельної бабки (координата У)
застосовується перетворювач лінійних переміщень ЛІР-8. Лінійка перетворювача
закріплена на стійці, зчитування голівка на шпиндельної бабці.
.5 Коробка швидкостей
Коробка швидкостей (Див. лист СамГТУ.151003.060.020.008.СБ)
пов'язана муфтою зі шпинделем. Привід коробки швидкостей здійснюється від
електродвигуна постійного струму. Є три діапазони чисел оборотів вихідного валу
коробки швидкостей. Перемикання з діапазону на діапазон здійснюється одним
трьохпозиційним і одним двопозиційні гідроциліндрами.
Нижчий діапазон чисел обертів досягається введенням в
зачеплення зубчастих передач поз.
Середній діапазон чисел обертів досягається введенням в
зачеплення передач поз.
Верхній діапазон чисел обертів досягається введенням в
зачеплення зубчастої муфти поз. і виведенням із зачеплення блоку поз.
У цьому діапазоні обертання від електродвигуна передається
через кліноременную передачу безпосередньо на шпиндель, минаючи зубчасті
передачі.
Усередині кожного діапазону зміна чисел оборотів
безступінчасте, а тиристорного приводу постійного струму. Електродвигун приводу
головного руху закріплений на подмоторной плиті, яка за допомогою гвинта переміщується
вгору для натяжки клинових ременів. Після натяжки ременів подмоторная плита
притягується до коробки швидкостей чотирма гвинтами через віброгасітелі.
Змащення шестерень і підшипників коробки швидкостей
здійснюється централізовано поливом від станції мастила. Злив масла
відбувається через телескопічне пристрій на станину і далі через магістраль
зливу в станцію мастила.
Для орієнтації шпинделя під час автоматичної зміни
інструменту служить датчик ЛІР 158Д, пов'язаний зі шпинделем зубчастою передачею.
Орієнтація шпинделя здійснюється при його повільному повороті до тих пір, поки
неузгодженість між задає сигналом і сигналом з датчика не досягне мінімуму.
Співвісно з вихідним валом з боку клиноремінною передачі
встановлений гідроциліндр віджиму інструменту.
Змащення зубчастих коліс коробки швидкостей - циркуляційна.
Олія - антіскачковое ВНДІ-НП-40.
Змащення підшипників кочення - ЦІАТ-ІМ-201 ГОСТ 6261-59.
.6 Шпиндельні вузол
Шпиндельні вузол (Див. лист СамГТУ.151003.060.020.011.СБ)
встановлюється в корпусі шпиндельної бабки і кріпиться до неї гвинтами. Він
складається з нерухомої гільзи і шпинделя. Як передній і задній опор шпинделя
використані прецизійні дуплексірованние радіально-упорні шарикопідшипники.
Натяг підшипників проводиться за допомогою гайки.
Фіксація гайки від мимовільного відкручування здійснюється
штифтом.
Періодичність заміни мастила в підшипниках шпинделя через 6
... 8 тис. годин роботи верстата.
.7 Пристрій затиску інструменту
Пристрій змонтовано всередині шпинделя (див. лист СамГТУ.151003.060.020.011.СБ).
Затискач інструменту здійснюється тарілчасті пружинами.
При затиску тарілчасті пружини передають осьове зусилля через
штовхач, Цанга, пелюстки якої заходять під втулку стискаються і замикають
грибок, ввернути в інструментальну оправку. Остання притягується до конічної
поверхні шпинделя.
Для запобігання від проворота інструменту в шпинделі, в
процесі обробки деталі, на торці є два виступи. Віджим інструменту виконується
вручну при зупинці всіх можливих переміщень, натиснувши на кнопку на пульті
управління "Віджим інструменту".
При віджиманні інструменту шток гідроциліндра через тягу
переміщує тягу. Пакет тарілчасті пружин починає стискатися. Через 1 мм ходу
тяги, починає переміщатися цанга і при подальшому переміщенні вона виходить з
втулки.
У цей час штовхач, пов'язаний жорстко з тягою, виштовхує
інструмент з конуса шпинделя.
У Цанга, що знаходиться у вільному стані, вставляємо грибок з
інструментом. Натискаємо кнопку «Зажим інструмента», зазначену на пульті
управління. Подається сигнал на скидання тиску у верхній пласт гідроциліндра.
Спрацьовують тарілчасті пружини - інструмент затиснутий.
Контроль за положеннями "інструмент затиснутий" та
"інструмент відтиснуті" здійснюється за допомогою мікровимикачів і
кулачка, жорстко пов'язаного зі штоком гідроциліндра віджимання і затиску
інструменту.
Мікровимикач зблокований з двигуном головного руху. Отже,
якщо інструмент після натиску кнопки «Зажим інструмента» не затиснутий, то
обертання шпинделя не здійснюється.
.8 Стіл поворотний ділильний кантуемий
Стіл поворотний ділильний кантуемий (Див. листи
СамГТУ.151003.060.020.012.СБ, СамГТУ.151003.060.020.013.СБ,
СамГТУ.151003.060.020.014.СБ) з керуванням від пристрою ЧПУ верстата з
діаметром планшайби 360 мм, є прецизійної оснасткою, експлуатується спільно з
координатно - розточувальні або координатно - шліфувальним верстатами,
оснащеними пристроями числового програмного керування (ЧПУ) з резервним каналом
управління і додатковим електроприводом управління.
Стіл призначений для розточування, свердління, розгортання,
нарізання різьб, чистового фрезерування.
Наявність точної вимірювальної системи відліку столу дозволяє
виконувати високоточні контрольно - вимірювальні операції.
Забезпечує обробку корпусних деталей із заданими високими
вимогами до точності розташування оброблюваних поверхонь.
Обробку деталей можна виробляти при горизонтальному та
вертикальному положенні планшайби столу.
Столи придатні для точної обробки деталей без спеціального
оснащення (у тому числі для обробки кондукторів і пристосувань).
Стіл може використовуватися у разі обробки деталей з
охолодженням.
Вид кліматичного виконання УХЛ категорії 4.1 за ГОСТ 15150.
лас точності А.
.8.1 Технічні характеристики
Стіл повинен задовольняти вимогам ГОСТ 16163, ГОСТ 12.2.009,
ГОСТ 12.2.029 і ГОСТ 12.2.049.
Основні технічні дані і характеристики повинні відповідати
вимогам, зазначеним у таблиці 8.1.
Таблиця 8.1 Основні технічні дані
Найменування
показників
|
Розмірність
|
Значення
|
Діаметр робочої
поверхні планшайби
|
мм
|
360
|
Число Т - подібних
пазів
|
шт.
|
8
|
Ширина Т - подібних
пазів за ГОСТ 1574
|
мм
|
12Н12
|
Діаметр
центрального отвору планшайби
|
мм
|
25Н7
|
Відстань від основи
столу до робочої поверхні планшайби
|
мм
|
225
|
Відстань від основи
столу до осі планшайби, при вертикальному положенні столу
|
мм
|
215
|
Найбільша маса
встановлюваної заготовки: - При горизонтальному положенні При вертикальному
положенні
|
кг кг
|
100 80
|
Найбільший кут
повороту планшайби
|
-
|
неграничний
|
Дискретність
завдання переміщення
|
градус(сек)
|
0,001(3.6)
|
Межі частот
обертання планшайби
|
об/мин
|
0…10
|
Найбільше допустиме
зусилля при свердлінні (при горизонтальному положенні планшайби на краю
планшайби)
|
Н
|
1870
|
Найбільший крутний
момент на планшайбі
|
Нм
|
150
|
Споживана
потужність, не більше
|
кВт
|
1,9
|
Вимірювальна
система
|
-
|
оптоелектрична
|
Вид приводу
повороту планшайби
|
-
|
електричний
|
Зажим планшайби
|
-
|
гідравлічний
|
Робочий тиск до
гідроциліндрів затиску столу
|
МПа
|
5,0
|
Габаритні розміри,
не більше: - Довжина - Ширина - Висота - Висота при вертикальному
положенні столу
|
мм мм мм мм
|
647 405 225 405
|
Маса, не більше
|
кг
|
200
|
Встановлений термін
служби до першого капітального ремонту
|
лет
|
10
|
Встановлений ресурс
по точності до першого ремонту, не менше
|
тыс. час
|
10
|
Клас точності столу
|
-
|
А
|
|
|
|
|
Примітка: норми надійності забезпечуються при дотриманні умов
зберігання, монтажу, транспортування, експлуатації і графіків планово -
попереджувальних ремонтів.
9. Опис гідравлічної схеми
.1 Схема гідравлічний принципова
См.ліст СамГТУ.151002.060.020.07.ГЗ.
Перелік апаратури гідросистеми верстата таблиця 9.1.
Таблиця 9.1 Перелік апаратури гідросистеми
Поз.
|
Найменування
|
Кіл.
|
А
|
Гідроагрегат у тому
числі насосного 3БГ12-41А (N = 3 / 6 л / хв, Рном = 10 МПа)
|
1
|
АК
|
Пневмогідроаккумулятор
АПГ - Б - 10/20 ТУ2 - 053 - 1655 - 1986
|
2
|
ДР1
|
Дроселі мастильний
БДІ2
|
1
|
ДР2
|
Дроселі мастильний
БДІ4
|
1
|
ДР3
|
Гідродросель
|
1
|
ДР6
|
ДКМ 6/3
|
1
|
К01
|
Гідроклапан
обратний КОМ 6/3
|
1
|
КП1
|
Гідроклапан
запобіжний КПМ 6/3 - В2
|
1
|
КП2
|
Гідроклапан
запобіжний КПМ 6/3 - В1
|
1
|
КР1
|
Гідроклапан
редукційний КРМ 6/3 В2Р
|
1
|
КР2
|
Гідроклапан
редукційний
|
1
|
КР3
|
КРМ 6/3 В1Р
|
2
|
МН1
|
Манометр ДМ 1001 -
06 МПа - 2,5
|
1
|
МН2
|
Манометр ДМ 1001 -
2,5 МПа - 2,5
|
1
|
МН3
|
Манометр ДМ 1001 -
10 МПа - 2,5
|
1
|
МХ
|
Машина холодильна
ХМСОЖ - 4 ТУ26 - 03 - 332 - 76
|
1
|
|
Система центральна
смазки №725
|
|
П1
|
Живильники М6
(10Д-10Д-35Е-35Е-35ЕВ-35Е)УХЛ4.1
|
1
|
П2
|
Живильники МИ6
(5Д-15Д-15Д-15Д-15Д-15Е) УХЛ4.1
|
1
|
П3
|
Живильники М4
(10Д-15Д-30Д-35Е) УХЛ4.1
|
1
|
П4
|
Живильники МИ3
(15Д-10Е-15Е) УХЛ4.1
|
1
|
Р1, Р2, Р4…Р7
|
Гідроросподільник
ВЕ6574А 31/Г24М
|
Р9, Р10 Р12, Р14
|
Гідроросподільник
ВЕ34 31/Г24М
|
4
|
Р15
|
Гідроросподільник
ВММ644
|
1
|
Р26
|
Гідроросподільник
ВММ6574
|
1
|
РД1РД6
|
Реле тиску 1
ГОСТ26005 - 83
|
6
|
Ф1…Ф2
|
Фільтр 1 Ф1М16 - 25
|
2
|
Ц1
|
Гідроцилиндр
переключення блоків
|
1
|
Ц2
|
Гідроцилиндр
переключення шестерен
|
1
|
Ц3
|
Гідроцилиндр віджима
інструменту
|
1
|
Ц4
|
Гідроциліндр
гідроуравновешіванія шпінд. бабки
|
1
|
Ц5…Ц8
|
Гідроциліндри
затиску поворотного столу
|
4
|
Ц9…Ц10
|
Гідроциліндри
огородження
|
2
|
Ц11…Ц14
|
Гідроциліндри
віджиму палети
|
4
|
Ц15…Ц16
|
Гідроциліндри
фіксації палети
|
2
|
1…31
|
Точки змащування
|
31
|
.1.1 Опис роботи
Гідросистема верстата виконує наступні функції:
) гідроуравновешіваніе шпиндельної бабки;
) віджимання інструменту в шпинделі;
) перемикання коробки швидкостей;
) затискач - віджимання поворотного столу;
) гідроразгрузка направляючих санчат стійки;
) змащення коробки швидкостей і черв'ячної передачі
поворотного столу;
) подача масла в систему централізованої періодичної
змащення;
) відкриття і закриття дверей огородження *;
) віджим стіл - супутника *;
) фіксація й расфіксація стіл - супутника.
Гідросистема верстата складається з:
Гідроагрегату
Машини холодильної
Гідроапаратури, встановленої на верстаті
Виконавчих органів: гідроциліндра перемикання блоку Ц1;
гідроциліндра перемикання шестерень Ц2; гідроциліндра віджиму інструменту Ц3;
гідроциліндра врівноваження шпиндельної бабки Ц4; гідроциліндрів затиску
поворотного столу Ц5, Ц6, Ц7, Ц8; гідроциліндрів огородження Ц9, Ц10 *;
гідроциліндрів віджимання і фіксації столу - супутника Ц11, Ц12, Ц13, Ц14, Ц15,
Ц16 *.
Основні вузли гідроагрегату рис.6; насосна установка А,
гідроблок з апаратурою модульного типу поз.1, блок реле тиску поз.2, фільтри Ф1
та Ф2.
Гідроагрегат здійснює подачу робочої рідини в гідросистему,
систему змащення і розвантаження напрямних, а також в систему централізованої
періодичної змащення.
У гідросистему масло подається від насоса продуктивністю 3 л
/ хв через фільтр Ф1, зворотний клапан К01 і відведення А2. Тиск регулюється
запобіжним клапаном КП1.
Підтримування постійного тиску в гідросистемі здійснюється за
допомогою двох пневмоаккумуляторов АПГ-Б-10/20. При досягненні в гідросистемі
тиску 5 МПа, реле тиску РД2 подає сигнал у пристрій числового програмного
керування (УЧПУ) і через 10 сек. (Час затримки) гідросистема готова до роботи.
У разі підвищення тиску в гідросистемі до 7 МПа, спрацьовує реле тиску РД1,
після чого відбувається аварійний останов верстата.
Контроль тиску:
) у гідросистемі та системі централізованої змащення;
) у системі змащення і розвантаження направляючих -
здійснюється за допомогою манометра МН1 і гідророзподільника Р15, ручку якого в
першому випадку слід повернути від гідророзподільника (положення а), а по-друге
до гідророзподільника (положення б).
Скидання тиску в гідросистемі здійснюється включенням
гідророзподільника Р16. Перемикання діапазону швидкостей приводу головного руху
верстата: перемикання коробки швидкостей здійснюється подачею масла в
трипозиційний гідроциліндр Ц1 перемикання блоку і двопозиційний гідроциліндр Ц2
перемикання шестірні при включенні електромагнітів Y12, Y13, Y14, Y15
гідророзподільників Р2, Р9, Р10. Час перемикання, регульоване за допомогою
дроселів ДР3, ДР4, ДР5 повинно бути в межах 3 ... 5 сек.
При включенні електромагнітів Y12 і Y13 масло надходить в
ліву порожнину двопозиційний гідроциліндра Ц2 - поршень перемішається вправо і
в середню порожнину трипозиційного гідроциліндра Ц1 - поршень переміщується
вліво - 1 ступінь.
При включенні електромагніта Y12 масло надходить в ліву
порожнину гідроциліндра Ц2 - поршень переміщається вправо, і в ліву порожнину гідроциліндра
Ц2 - поршень переміщається вправо - 2 ступінь.
При включенні електромагнітів Y12, Y14, Y15 масло надходить у
праву порожнину гідроциліндра Ц2 - поршень рухається вліво, і в праву і ліву
порожнини гідроциліндра Ц1 - поршень переміщається в середнє положення 3
рівень.
При включенні електромагнітів Y12 і Y14 масло надходить в
ліву порожнину гідроциліндра Ц2 - поршень переміщається вправо, і в праву і
ліву порожнини гідроциліндра Ц1 - поршень переміщається в середнє положення -
нейтраль.
Регулюванням дроселів ДР3, ДР4, ДР5 забезпечити час
перемикання шестірні і блоку шестерень в межах 3 ... 5сек.
Віджим інструменту: віджимання інструменту здійснюється
подачею масла в гідроциліндр Ц3 віджиму інструменту, при включенні
електромагніта Y11 гідророзподільника Р9.
У вихідному положенні гідророзподільника Р9 масло надходить в
штокові порожнину гідроциліндра Ц3, поршнева з'єднана зі зливом - інструмент
затиснутий.
При включенні електромагніта Y11 масло подається в поршневу
порожнину гідроциліндра Ц3, штокові порожнину з'єднана зі зливом, поршень
переміщується вліво - інструмент віджатий.
Зажим і віджиму поворотного столу: затискач і віджиму
поворотного столу здійснюється подачею масла до гідроциліндрів затиску Ц5, Ц6,
Ц7, Ц8 при включенні електромагнітів Y9, Y10 гідророзподільника Р14.
Гідроуравновешіваніе шпиндельної бабки: гідроуравновешіваніе
шпиндельної бабки здійснюється гідроциліндром Ц4. Зі штокові порожниною
гідроциліндра додатково з основним підведенням приєднані рукавами два
пневмогідроаккумулятора, що дозволяють підтримувати постійний тиск до
гідроциліндрів при прискореному переміщенні шпиндельної бабки вгору.
Відкриття та закриття дверей огородження: відкриття та
закриття дверей здійснюється гідроциліндрами Ц9, Ц10, при включенні
електромагнітів Y38, Y39 гідророзподільника Р12. При включенні електромагніта
Y38 масло надходить в гідроциліндр Ц9, з гідроциліндра Ц10 подається на злив,
поршень переміщається вправо - двері огорожі відкриваються.
При включенні електромагніта Y39 масло надходить в гідроциліндр
Ц10, з гідроциліндра Ц9 подається на злив, поршень переміщується вліво - двері
огорожі закриваються. Швидкість руху дверей регулюється дроселем ДР6. Час
відкриття дверей огорожі повинно бути 3 ... 5 сек. Регулювання тиску
проводиться редукційним клапаном КР3.
Віджим і фіксація стіл - супутника: віджим та фіксація стіл -
супутника здійснюється гідроциліндрами Ц11, Ц12, Ц13, Ц14, Ц15, Ц16 при
включенні електромагнітів Y40 і Y41 гідророзподільників Р5 і Р6.
У вихідному положенні електромагніти Y40 і Y41 знеструмлені,
стіл - супутник затиснутий і зафіксовано.
При включенні електромагніта Y40 олія поступає в поршневі
порожнини гідроциліндрів Ц11, Ц12, Ц13, Ц14 і штокові порожнини гідроциліндрів
Ц15 і Ц16. Поршні гідроциліндрів Ц11, Ц12, Ц13, Ц14 переміщаються вгору, а
поршні гідроциліндрів Ц15, Ц16 вниз - відбувається віджимання та расфіксація
стіл - супутника. Контроль віджимання і расфіксаціі здійснюється за допомогою
реле тиску РД6.
При включенні електромагніта Y41 олія поступає в поршневі
порожнини гідроциліндрів Ц15 і Ц16 і за рахунок різниці площ поршня переміщує
його вгору - відбувається фіксація стіл - супутника. Контроль фіксації
здійснюється за допомогою реле тиску РД5.
При відключенні електромагніта Y40 масло з гідроциліндрів
Ц11, Ц12, Ц13, Ц14 надходить на злив, поршні під дією пружин переміщаються вниз
- відбувається затиск стіл - супутника. Контроль затиску здійснюється за
допомогою реле тиску РД6. При відключенні електромагніта Y41 поршні
гідроциліндрів Ц15, Ц16 залишаються у верхньому положенні.
.2 Система централізованої періодичної змащення
См.ліст СамГТУ.151002.060.020.07.ГЗ.
Перелік елементів системи змащення вказаний в таблиця 9.1.
.2.1 Опис роботи системи централізованої періодичної змащення
Подачу масла в систему централізованої періодичної змащення
здійснюється при включенні електромагніта Y16 гідророзподільника Р7.
Система включає в себе центральний живильник П1 (мал.6), в
комплект якого входить вузол зі штоком індикатора, що дозволяє контролювати
його роботу з допомогою мікроперемикача, вторинні живильники, розташовані: П2 -
на полозках стіл, П3 - на стійці, П4 - на шпиндельної бабці.
Система працює наступним чином: включається електромагніт Y16
гідророзподільника Р7, масло від насоса починає надходити до центрального
живильники П1, секції якого подають мастило до вторинних живильника, а від них
до змащуємо точкам. При цьому починає працювати лічильник імпульсів. Після
відліку необхідної кількості ходів штоку - індикатора центрального живильника,
тобто числа імпульсів електромагніт Y16 відключається і подача масла
припиняється. Через необхідний інтервал часу знову включається електромагніт
Y16 і знову походить мастило.
Якщо шток - індикатора робить недостатня або надмірна
кількість ходів, то з'являється попереджувальний сигнал.
Система змащення і розвантаження направляючих стійки: у
систему змащення і розвантаження направляючих стійки масло надходить від насоса
продуктивністю 6 л / хв через фільтр Ф2 (рис.6). Тиск на виході з насоса
регулюється запобіжним клапаном КП2. Контроль тиску в системі змащення
здійснюється манометром МН1 при включенні електромагніта Y21 гідророзподільника
Р15, ручку якого необхідно повернути до гідророзподільника (положення б).
Змащення та охолодження коробки швидкостей: одночасно з
включенням приводу головного руху верстата включається електромагніт Y17
гідророзподільника Р1 і масло під тиском, визначає параметри клапана
запобіжного КП2, подається через блок мастильний ДР2 (рис.6) на змазку коробки
швидкостей. Регулювання кількості мастила здійснюється блоком мастильним ДР2,
поплавці якого повинні знаходитися на ризику зазначеної червоною фарбою
відповідної витраті 0,2 л / хв на кожному відведенні. Контроль наявності
змащення здійснюється за допомогою реле тиску РД4.
Змащення черв'ячної передачі поворотного столу: одночасно з
віджимом поворотного столу включається електромагніт Y18 гідророзподільника Р4
і масло під тиском, визначає параметри КП2 подається через блок мастильний ДР1
(рис.6) на змазку черв'ячної передачі поворотного столу. Регулювання кількості
мастила здійснюється блоком мастильним ДР1, поплавці якого повинні знаходитися
на ризику зазначеної червоною фарбою, відповідної витраті 0,2 л / хв на кожному
відведенні. Контроль наявності змащення здійснюється за допомогою реле тиску
РД3.
Гідроразгрузка направляючих стійки: гідроразгрузка
направляючих стійки відбувається постійно при включеній гідростанції.
Перелік застосовуваних олій та їх аналогів наведено в таблиці
9.2. Карта налаштування електромагнітів таблиця 9.3.
Таблиця 9.2 Перелік застосованих масел
Країна, фірма
|
Марка застосованого
масла
|
РФ
|
Масло ИГП - 18
ТУ38101413 - 78
|
Shell
|
Tellus S32
|
Mobil
|
DTE 24
|
Exxon
|
Nuto HP32
|
BP
|
Energol HLP32
|
Castrol
|
Hyspin AWS32
|
Caltex
|
Rando HD32
|
Gulf
|
Harmony 32AW
|
Elf
|
Olna 32
|
Таблиця 9.3 Карта налагодження електромагнітов
10.
Розрахунок економічного ефекту від модернізації координатно-розточувального -
свердлильно - фрезерного верстата 2А459АФ4
.1 Вихідні дані для розрахунку економічного ефекту від
модернізації
Верстати координатно-розточний групи призначені для обробки
корпусних деталей з високою точністю. Отримання високої точності залежить від
багатьох параметрів. Динамічна точність верстата має істотний вплив на точність
обробки. Сучасний ринок вимагає від виробника верстатів збільшення кількості
номенклатури оброблюваних виробів на верстаті, підвищення швидкості обробки, а
так само підвищення числа одночасно керованих координат від ЧПУ верстата в
процесі обробки виробів.
У даній роботі розроблено свердлильно - фрезерний координатно
розточний верстат з підвищенням частоти обертання приводу головного руху, а
також підвищенням одночасно керованих координат від ЧПУ верстата. Згідно із
завданням пропонується конструкторське рішення верстата в цілях підвищення
швидкості обертання приводу головного руху, а також підвищення функціональності
верстата, а саме підвищення одночасно керованих координат від ЧПУ верстата.
Були проведені наступні заходи:
Установка електродвигуна з підвищеною максимальною частотою
обертання;
Установка більш швидкісних підшипників у шпиндельному вузлі;
Вбудовування поворотного ділильні кантуемого столу з
управлінням від пристрою ЧПУ верстата.
Проведення даних заходів забезпечило фактичне збільшення
максимальної частоти обертання приводу головного руху, а також підвищення
одночасно керованих координат від ЧПУ верстата з 4 на 5.
Вихідні дані представлені в таблицях 1,2,3.
Таблиця 10.1
Вихідні дані для розрахунку витрат на модернізацію верстата
№ п/п
|
Показники
|
Усл. обозн.
|
Ед.изм.
|
Значення
|
1
|
Годинна тарифна
ставка робітників, що беруть участь у проведенні модернізації
|
ЧТСм
|
грн/година
|
8,2
|
2
|
Сумарна
трудомісткість робіт з модернізації
|
Трм
|
година
|
110
|
3
|
Коефіцієнт, що
враховує заробітну плату
|
Кдз
|
-
|
1,2
|
4
|
Районний коефіцієнт
|
Кукр.
|
-
|
1
|
5
|
Коефіцієнт
відрахувань на соціальні потреби
|
Ксн
|
-
|
1,385
|
6
|
Коефіцієнт, що
враховує інші (накладні) витрати на модернізацію встаткування
|
Кпрм
|
-
|
2,5
|
7
|
Вартість базового
встаткування
|
Цобнемод
|
грн
|
37500
|
8
|
Загальна вартість
комплектуючих виробів, замінних у ході проведення модернізації
|
Сзамкомп
|
грн
|
8500
|
Таблиця 10.2 Вихідні дані для розрахунку витрат на
комплектуючі вироби для модернізації верстата
Найменування
комплектуючих виробів
|
Кількість(Qкомпл),
шт
|
Ціна (Цкомпл)
грн/шт
|
Електродвигун
моделі 2ПН160LYX4
|
1
|
3000
|
Підшипники серії
3182111
|
1
|
500
|
Підшипники серії
1788113Л
|
1
|
300
|
Стіл моделі
СК-36-1202
|
1
|
4700
|
Таблиця 10.3 Вихідні дані для розрахунку економічного ефекту
від застосування модернізованого встаткування
Показники
|
Умовне позначення
|
Ед.изм.
|
Базовий варіант
|
Модерн. варіант
|
1. Штучний час
|
tшт
|
хв/шт
|
5
|
4,4
|
2. Річна програма
|
Nвип
|
шт/рік
|
25000
|
25000
|
3. Кількість змін у
день
|
hсмен
|
змін/день
|
1
|
1
|
4. Кількість годин
роботи у зміну
|
Fсмен
|
година/змін
|
8
|
8
|
5. Коефіцієнт часу
роботи встаткування
|
Крн
|
-
|
0,95
|
0,95
|
6. Вартість
устаткування
|
Цоб
|
грн
|
37500
|
-
|
7. Вартість 1 м²
будинку
|
Цзд
|
грн/м²
|
1000
|
1000
|
8. Площа будинку,
занимаетравня еденицей устаткування
|
Sоб
|
м²
|
5
|
5
|
9.Коефіцієнт
враховуючий допольнительную производственну площу
|
Кдоп
|
-
|
1,2
|
1,2
|
10. Годинна тарифна
ставка
|
ЧТС
|
грн/година
|
8,2
|
8,2
|
11. Вартість 1
квт-ч електроенергії
|
Цэл
|
грн/ квт-ч
|
0,70
|
0,70
|
12. Потужність
устаткування
|
Моб
|
кВт
|
5,5
|
5,5
|
13. Норма річних
амортизационных відрахувань дляустаткування
|
Наоб
|
%
|
15
|
15
|
14. Норма річних
амортизационных відрахувань длябудинку
|
Назд
|
%
|
2,5
|
2,5
|
|
15. Норма річних
витрат на поточний ремонт устаткування
|
Нремоб
|
%
|
3
|
3
|
|
16. Норма річних
витрат на поточний ремонт будинку
|
Нремзд
|
%
|
1
|
1
|
|
17. Норма річних
витрат на зміст будинку
|
Нсодзд
|
%
|
3
|
3
|
|
18. Ціна
інструмента
|
Цинстр
|
грн/шт
|
575
|
575
|
|
19. Термін служби
інструмента
|
Тслинстр
|
хв
|
8000
|
8000
|
|
20. Нормативний
коефіцієнт ефективності капітальних вкладень
|
Ен
|
грн/рік/ грн
|
0,15
|
0,15
|
|
|
|
|
|
|
|
|
.2 Розрахунок витрат на проведення модернізації
.2.1 Розрахунок заробітної плати, що беруть участь у
проведенні модернізації, з відрахуваннями
Річна заробітна плата з відрахуваннями, (Сзп , грн)
розраховується по формулі:
(10.1)
де ЧТСм - годинна тарифна ставка, що беруть участь у модернізації
грн/година;
Трм -сумарна трудомісткість робіт з модернізації встаткування, година;
До дз - коефіцієнт, що враховує додаткову заробітну плату;
До урал - районний коефіцієнт;
До сн - коефіцієнт відрахувань на соціальні потреби;

грн
10.2.2 Розрахунок витрат на комплектуючі вироби для
модернізації устаткування
Розрахунок витрат на комплектуючі вироби для модернізації
устаткування (Сзамкомпл , грн) здійснюється по формулі:
, (10.2)
де n-число найменувань комплектуючих виробів,
використовуваних для модернізації встаткування;
Qкомпл - кількість i-х комплектуючих виробів,
використовуваних для модернізації встаткування, шт;
Цкомпл- ціна i-х комплектуючих, грн/шт.
Скомпл=3000·1+500·1+300·1+4700·1=8500 грн
.2.3 Розрахунок інших витрат на модернізацію устаткування
Величина інших витрат (Спрм, грн) визначається пропорційно
витратам на оплату праці:
, (10.3)
де Кпрм- коефіцієнт, що враховує інші (накладні) витрати на
модернізацію встаткування.
грн
.2.4 Розрахунок сумарних витрат на модернізацію устаткування
Розрахунок сумарних витрат на модернізацію встаткування (Смод, грн)
виробляється по формулі:
Смод=Сзпм+Скомпл+Спрм (10.4)
Смод=1499.1+8500+3747.8=13746.9 грн
Таблиця 10.4 Витрати на модернізацію встаткування
Статті витрат
|
Витрати, грн
|
1 Заробітна плата
робітників
|
1499.1
|
2 Витрати на
комплектуючі вироби
|
8500
|
3 Інші витрати
|
3747.8
|
Разом
|
13746.9
|
.2.5 Розрахунок вартості модернізованого встаткування
(Цобмод,грн) здійснюється по формулі:
Цобмод=Цобнемод+Смод-Сзамкомпл (10.5)
де Цобнемод - вартість устаткування до проведення
модернізації, грн;
Сзамкомпл - загальна вартість комплектуючих виробів, замінних
у ході проведення модернізації встаткування, грн
Цобнемод =37500+13746.9-8500=42746.9 грн
.3 Розрахунок економічного ефекту від проведення модернізації
.3.1 Розрахунок зміни трудомісткості
Зниження трудомісткості, ∆Т ,% розраховується по
формулі:
(10.6)
де tштмод - штучний час на обробку деталі з використанням
модернизированого встаткування, хв/шт;штбаз - штучний час при використанні
базової моделі встаткування, хв/шт.
%
.3.2 Розрахунок необхідної кількості устаткування і його завантажень
.3.2.1 Розрахункова кількість устаткування
Розрахункова кількість базового й модернізованого устаткування (З расч)
розраховується по формулі:
(10.7)
(10.8)
Крн - коефіцієнт часу роботи устаткування (приймаємо Крн = 0,95)ном -
номінальний фонд річного часу роботи устаткування, година/рік;
(10.9)
де hсмен - кількість змін у день, змін;смен - кількість годин роботи в
зміну, годину/змін;
- скорочена тривалість змін у передсвяткові дні, годину;ном дн -
номінальний фонд річного часу роботи устаткування, у днях
(10.10)
де Dкален - кількість календарних днів у році, днів;вых - кількість
вихідних днів у році, днів;празд - кількість святкових днів у році, днів;
година/рік
година/рік
.3.2.2 Прийнята кількість устаткування (Із прин )
Сприн баз = 2
Сприн мод = 1
.3.2.3 Завантаження устаткування
Завантаження устаткування (Кзагр , %) розраховується по формулі:
(10.11)
10.3.3 Розрахунок річної продуктивності одиниці встаткування і її змін
.3.3.1 Річна продуктивність одиниці устаткування
Річна продуктивність одиниці устаткування (Пр, шт/рік) розраховується
по формулі:
(10.12)
шт/рік
шт/рік
.3.3.2 Коефіцієнт росту продуктивності устаткування
Коефіцієнт росту продуктивності устаткування (Кпр) розраховується по
формулі:
(10.13)
.3.4 Розрахунок капітальних вкладень
.3.4.1 Розрахунок капітальних вкладень в устаткування
Капітальні вкладення в устаткування (Коб, грн) розраховуються по
формулі
(10.14)
де Цоб - вартість устаткування, грн
грн
.3.4.2 Капітальні вкладення в будинок
Капітальні вкладення в будинок (До зд, грн) визначаються по формулі :
Дозд=Цзд∙Sоб∙Kдоп∙ C ін. (10.15)
де Ц зд - вартість 1м² будинку, грн/м?об - площа будинку, займана одиницею
встаткування, м²
Kдоп - коефіцієнт, що враховує додаткову виробничу площу.
До здбаз = 1000·5·1,2·2=12000 грн
До здмод = 1000∙ 5∙ 1,2∙ 1=6000 грн
.3.4.3 Капітальні вкладення сумарні
Сумарні капітальні вкладення (ДО, грн) визначаються по формулі:
ДО=Коб,+Дозд (10.16)
Кбаз=75000+12000=87000 грн
Кмод=42746,9+6000=48746,9 грн
10.3.5 Розрахунок технологічної собівартості річного випуску виробів
.3.5.1 Розрахунок річної заробітної плати з відрахуваннями
Річна заробітна плата з відрахуваннями (Сзп, грн/рік) розраховується по
формулі:
(10.17)
де ЧТС - годинна тарифна ставка, грн/година;
До дз - коефіцієнт, що враховує додаткову заробітну плату;
До урал - районний коефіцієнт;
До сн - коефіцієнт відрахувань на соціальні потреби;
грн/рік
грн/рік
.3.5.2 Розрахунок річних витрат на електроенергію
Річні витрати на електроенергію (Сэл , грн/рік)
розраховуються по формулі:
(10.18)
де Ц э - вартість 1 кВт година електроенергії, грн/ квт-година;
Моб - потужність електродвигуна, споживана еденицей
Устаткування, кВт:
грн/рік.
грн/рік.
.3.5.3 Розрахунок річних амортизаційних відрахувань для устаткування:
а) Річні амортизаційні відрахування
для устаткування (Самоб, грн/рік) розраховуються по формулі:
(10.19)
де Н а - норма річних амортизаційних відрахувань для даного виду
встаткування, %
грн/рік
грн/рік
б) Амортизаційні відрахування для будинку
Річні амортизаційні відрахування для будинку (Самзд, грн/рік)
визначаються по формулі:
Самзд=Кзд∙Назд/100 (10.20)
де Назд- норма річних амортизаційних відрахувань для будинку, %
Самздбаз=12000∙ 2,5/100=300 грн/рік
Самздмод=6000∙ 2,5/100=150 грн/рік
в) Амортизаційні відрахування сумарні (Сам, грн/рік) розраховуються по
формулі:
Сам=Самоб+Самзд (10.21)
Сам баз=11250+300=11550 грн/рік
Сам мод=6412+150=6562 грн/рік
10.3.5.4 Розрахунок річних витрат на поточний ремонт устаткування
а) Витрати на поточний ремонт устаткування
Річні витрати на поточний ремонт устаткування, (Сремоб, грн/рік)
розраховуються по формулі:
(10.22)
де Н рем - норма річних витрат на поточний ремонт устаткування, %
б) Витрати на поточний ремонт будинку
Річні витрати на поточний ремонт будинку (Сремзд, грн/рік)
розраховуються по формулі:
Сремзд=Кзд∙Нремоб/100 (10.23)
де Нремоб - норма річних витрат на поточний ремонт будинку,
Сремздбаз=12000∙ 1/100=120 грн/рік
Сремздмод=6000∙ 1/100=60 грн/рік
в) Витрати на поточний ремонт сумарні
Річні сумарні витрати на поточний ремонт(Срем, грн/рік) визначаються по
формулі:
Срем= Сремоб +Сремзд (10.24)
Срембаз=2250+120=2370 грн/рік
Среммод=1282,4+60=1342,4 грн/рік
10.3.5.5 Витрати на утримання будинку
Розрахунок річних витрат на утримання будинку (Ссодзд, грн/рік)
ведеться по формулі :
Ссодзд=Кзд∙ Нсодзд /100 (10.25)
де Нсодзд -норма річних витрат на утримання будинку, %
Ссодздбаз=12000∙ 3/100=360 грн/рік
Ссодздмод=6000∙ 3/100=180 грн/рік
.3.5.6 Розрахунок річних витрат на інструмент
Річні витрати на інструмент, (Синстр, грн/рік) розраховуються по
формулі:
(10.26)
де Ц инстр - ціна інструмента, грн/шт;
Р инстр - річна витрата інструмента, шт/рік.
Річна витрата інструмента (Р инстр, шт/рік) визначається по формулі:
(10.27)
де Т сл инстр - термін служби інструмента, хв.
шт/рік
шт/рік
грн/рік
грн/рік
10.3.5.7 Розрахунок технологічної собівартості річного випуску виробів
Технологічна собівартість річного випуску виробів,
(Стехн,грн/рік) розраховується по формулі:
(10.28)
грн/рік
грн/рік
Таблиця 10.5 Витрати на річний випуск деталей з використанням базового
й модернізованого встаткування
Статті витрат
|
Витрати, грн/рік
|
|
Базовий варіант
|
Модерн. варіант
|
1. Заробітна плата
з відрахуваннями
|
28392.4
|
24985.3
|
2. Витрати на
електроенергію
|
8005.9
|
6996.2
|
3. Амортизаційні
відрахування
|
11550
|
6562
|
4. Витрати на
поточний ремонт
|
2370
|
1342.4
|
5. Витрати на
утримання будинку
|
360
|
180
|
6. Витрати на
інструмент
|
8984.3
|
7906.2
|
Разом
|
59662.6
|
47972.1
|
.3.6 Штучна технологічна собівартість
Штучна технологічна собівартість (Сшттехн, грн/шт)
розраховується по формулі:
(5.29)
.3.7 Розрахунок річної економії від зниження собівартості
Економія від зниження собівартості, (З изм, грн/рік) розраховується по
формулі:
(10.30)
.3.8 Розрахунок наведених витрат
.3.8.1 Річні наведені витрати
Річні наведені витрати, (Зприв рік, грн/рік) розраховуються по формулі:
(10.31)
де Е н - нормативний коефіцієнт ефективності капітальних вкладень,
грн/рік/грн;
.3.8.2 Питомі наведені витрати
Питомі наведені витрати, (Зприв уд, грн/рік) розраховуються по формулі
(10.32)
.3.9 Розрахунок річного економічного ефекту
Річний економічний ефект (Эгод, грн/рік) розраховується по формулі:
(10.33)
Результати розрахунків проекту зведені в таблицю 6.
Таблиця 10.6 Техніко-економічні показники проекту
Показники
|
Одиниця виміру
|
Базовий варіант
|
Модерн. варіант
|
1 Річна програма
|
шт/рік
|
25000
|
25000
|
2 Штучний час
|
хв/шт
|
5
|
4,4
|
3 Зниження
трудомісткості
|
%
|
13,63
|
4 Кількість
устаткування
|
одиниць
|
2
|
1
|
5 Річна
продуктивність устаткування
|
шт/рік
|
22480
|
25546
|
6 Коефіцієнт росту
продуктивності встаткування
|
|
1,13
|
7 Капітальні
вкладення в т.ч.: - в устаткування; - у будинок
|
грн
|
87000 75000 12000
|
48746,9 42746,9
6000
|
8 Технологічна
собівартість річного випуску
|
грн/рік
|
59662.6
|
47927.1
|
9 Економія від
зниження собівартості
|
грн/рік
|
11690.5
|
10 Річні наведені
витрати
|
грн/рік
|
72712.6
|
55284.1
|
11 Річний
економічний ефект
|
грн/рік
|
17428.5
|
11. Стандартизація і контроль даної продукції
Стандартизація є засобом підвищення ефективності виробництва,
поліпшення якості продукції, зниження її собівартості. Для оцінки і
гарантування якості виробів, що випускаються потрібні нормативні документи, що
містять необхідні характеристики та показники виробничих матеріалів і виробів.
Якість продукції є найважливішим показником діяльності
підприємства. Якість верстатів залежить від багатьох факторів: технічних, які
визначають рівень конструкції, надійність та інші показники якості конструкції
обладнання, що випускається, технологічні та контрольні процеси його
виготовлення; виробничих, що визначають рівень технологічного обладнання
(насамперед його здатність забезпечувати задані точність і шорсткість
оброблюваної поверхні); кваліфікаційних , що визначаються кваліфікацією
працюючих.
Визначальними показниками якості продукції верстата, оцінюють
його можливу область застосування, є технологічні показники. До них відносяться
технологічні можливості верстата, тобто розміри, форма і матеріал заготовок,
які повинні оброблятися на ньому по 7-му квалітету; точність обробки може бути
досягнута 7-го квалітета завдяки наявності високоточних перетворювачів лінійних
переміщень. У поєднанні з високою жорсткістю несучої системи верстата і
направляючими ковзання, забезпечується можливість автоматичного відпрацювання
малих переміщень, рівних дискретності вимірювальної системи верстата (0,001
мкм), що є вирішальним фактором для отримання високої точності оброблюваних криволінійних
контурів поверхонь, при одночасно керованих від ЧПУ верстата координатах (
лінійна, кругова інтерполяція по осях X, Y, Z, В).
11.1 Карта технічного рівня і якості проектованого верстата
Розробкою методів кількісної оцінки рівня якості займається
наука кваліметрія. Розрізняють диференційований та комплексний методи оцінки.
В основі диференційованого методу лежить порівняння
сукупності одиничних показників якості оцінюваної продукції з відповідною
сукупністю одиничних показників якості базового зразка (аналога), що відображає
найбільш високі вітчизняні або зарубіжні науково - технічні досягнення. Метод
застосовують у випадках, коли необхідно провести аналіз порівняння рівня якості
продукції, що оцінюється і базового зразка за окремими показниками і
встановити, чи сягнуть рівень базового зразка в цілому і які показники найбільш
значно відрізняються від базового. Значення показників якості беруть з даних
технічного завдання, технічних умов або інших конструкторських документів на
даний виріб. До аналогам відносять виріб того ж виду, що й оцінюється, що
володіє спільністю функціонального призначення, масштабів виробництва і умов
застосування. Попередньо виділяють позитивні та негативні показники якості.
Позитивним називають показник якості продукції, збільшення
значення якого відповідає поліпшення якості продукції (для металообробних
верстатів показники продуктивності, потужності приводу головного руху, граничні
розміри оброблюваних поверхонь і т.п.).
Негативним називають показник якості, збільшення значення
якого відповідає погіршення якості продукції (показники габаритів і маси
верстата, часу автоматичної зміни інструменту, рівня звуку на робочому місці
тощо).
За допомогою одиничних показників якості розраховують відносний
показник
якості за формулами:
-
для позитивних одиничних показників; (11.1)
-
для негативних одиничних показників. (11.2)
За результатами застосування диференційованого методу
приймають такі рішення:
- Рівень якості продукції, що оцінюється вище або дорівнює рівню
базового зразка, якщо значення всіх відносних показників
;
Рівень якості продукції, що оцінюється нижче рівня базового зразка,
якщо значення усіх відносних показників
.
У випадках же, коли частина значень відносних показників більше або
дорівнює одиниці, а частина - менше одиниці слід застосовувати комплексний
метод оцінки рівня якості продукції.
С зважений арифметичний показник Q обчислюють за формулою:
, (11.3)
де
- числове значення iго відносного показника якості;
- коефіцієнт вагомості (значимості) iго одиничного
показника; сума коефіцієнтів повинна задовольняти умові
; n - число показників (коефіцієнтів).
Значення коефіцієнтів вагомості
як
правило, визначають експертним шляхом.
Розглянемо як приклад диференційований та комплексний методи оцінки
рівня якості верстата моделі 2А459АФ4 виробництва средневолжского
верстатобудівного заводу.
В якості базового зразка для порівняння прийнятий верстат - аналог
фірми Funuc TXK160.
Таблиця 11.1 Карта технічного рівня
№ п.п.
|
Наименовання
показника
|
Одиниця показника
проектованого верстата Рi
|
Одиниця показника
аналогічний. Верстата Рiδ
|
Відносний показник
qi
|
Коефіцієнт
вагомості mi
|
1 22 33 4 55 66
7 8 8
|
Частота обертання
шпинделя (макс.), об / хв Частота обертання шпинделя (мін.), об / хв Подача
столу (санчат) робоча, мм / хв Подача столу (санчат) прискорена, мм / хв
свердління, мм Переміщення стола, мм Потужність електродвигуна приводу
шпинделя, кВт Розмір робочої поверхні, мм
|
4000 20 2500
8000 50 1250 14 1000
|
3000 63 3000
18000 45 1050 11 1300
|
1,33 3,15 0,83
0,44 1,11 1,19 1,27 0,76
|
0,15 0,15 0,15
0,05 0,15 0,15 0,10 0,10
|
Як випливає з таблиці, 3 відносних показників якості
, а 5
.
За цим для оцінки рівня якості проектованого верстата необхідно скористатися
комплексним показником Q, враховує коефіцієнти вагомості
одиничних показників
.
Комплексний показник розраховується за формулою:
де qi - відносний показник якості;- параметр вагомості.
Оскільки комплексний показник
,
можна зробити висновок, що рівень якості модернізованого верстата вище, або
принаймні не нижче, рівня якості базового верстата.
.2 Аналіз уніфікованих вузлів проектованого верстата
У конструкцію сучасних верстатів застосовують такі уніфіковані вузли,
використання яких знижує вартість виготовлення, експлуатації і ремонту:
автоматичні коробки швидкостей, комплектні електроприводи з асинхронними
електродвигунами постійного струму; механічні варіатори; електромагнітні та
гальмові муфти; беззазорний редуктори; передачі гвинт - гайка кочення
(ковзання) ; гідростатичні передачі.
У даному проектованому верстаті найбільш слабкими ланками слідують
вважати: зубчасті колеса, муфти, датчики зворотного зв'язку.
.3 Засоби активного контролю, використані в проектованому верстаті
У проектованому верстаті застосовані наступні засоби активного
контролю, наприклад, контроль положення робочих органів верстата здійснюється
індуктивними датчиками зворотного зв'язку, які є пристроями, що видають
інформацію про величину фактичного переміщення, положення і швидкості
виконуючих органів верстата. Датчики зворотнього зв'язку входять до системи
подорожнього контролю, включену у вимірювальну схему і схему формування
вихідного сигналу.
По завершенні обробки деталь перевіряється граничними калібрами Ø
и Ø
мм.
.4 Методика випробувань і приймання верстата
Геометрична точність верстата є одним з головних факторів, що
визначають точність обробки деталей машин.
Геометрична точність верстатів нормується ГОСТами, і для кожного типу
верстатів встановлюється певне число інструментальних перевірок в залежності
від технологічного призначення верстатів, їх компонування, рівня автоматизації,
класу точності.
Випробування на точність проводяться в неробочому стані верстата, метою
їх є встановлення відхилень від прямолінійності, площинності; від правильного
відносного положення поверхонь; від правильного руху (обертання без радіального
і осьового биття, прямолінійності руху та ін).
Всі металорізальні верстати, як нові, так і вийшли з капітального
ремонту, піддаються випробуванням на геометричну точність. Під час перевірок
геометричної точності враховується не тільки величина відхилень, але і їх
направлення (знак). Це диктується умовами роботи та необхідністю передбачити
вплив деформацій під навантаженням і поступового зносу тертьових поверхонь на
точність роботи верстата.
При випробуванні верстата на точність застосовуються спеціальні точні
контрольні вимірювальні прилади та інструменти. Більшість перевірок
геометричної точності виробляється з використанням мікрокаторов (типу 05
лабораторна) з технічними характеристиками (ціна поділки 0,0005 мм, межі
вимірювань ± 0,015 мм).
Основні види перевірок на точність наведені нижче.
Площина робочої поверхні
Рис. 11.1
Рис. 11.2
Засіб виміру: за допомогою точної повірочної лінійки і блоку
плоскопа кінцевих мір довжини з точність вимірювання ±0,001 мкм (межі вимірювань 1
... 100мм) (див. рис.11.1). На перевіряється поверхню столу 3 в двох точках
встановлюються дві опори 2 рівний висоти, на які робочою поверхнею кладуть
точну перевірочні лінійку 1. За допомогою блоку плоскопа кінцевих мір довжини 4
вимірюють відстань між лінійкою і перевіряється поверхнею у вибраних точках з
кроком 25-30 мм. У кожному перерізі визначають найбільшу різниця виміряних
відстаней. Відхилення від площинності одно найбільшому з отриманих результатів.
Засіб виміру: точна повірочна лінійка 1, що показує
вимірювальний прилад 4 (мікрокатор типу 05 лабораторна) (див. рис.11.2). На
перевіряється поверхню 1 у двох точках встановлюють дві опори 3 рівний висоти,
на які робочою поверхнею кладуть точну перевірочні лінійку 2. Мікрокатор (типу
05 лабораторна) встановлюють на столі верстата з допомогою штатива ШМ - 3 - 8
так, щоб його вимірювальний наконечник торкався робочої поверхні лінійки і був
перпендикулярний їй. Мікрокатор переміщають по перевіряється поверхні вздовж
лінійки з кроком 25-30 мм. Відхилення від площинності одно найбільшою
алгебраїчної різниці показань показує приладу у всіх перерізах.
Допустимі відхилення:
при довжині вимірювань до 250 мм - допуск 16мкм;
від 250 до 400 мм - допуск 20 мкм;
від 400 до 630 мм - допуск 25 мкм;
від 630 до 1000 мм - допуск 30 мкм;
допускається тільки увігнутість.
Постійність кутового положення столу за його переміщенні: у
поздовжньому і поперечному напрямках.
Рис.11.3
Засіб виміру: рівень (см.ріс.11.3). Стіл встановлюють у
середнє положення в напрямку, перпендикулярному напрямку робочого переміщення.
На стіл встановлюють рівень і стіл переміщають кроками у 50-100 мм на всю
довжину його ходу.
Допустимі відхилення:
при довжині вимірювань до 400 мм - допуск 0,02 (4 ");
від 400 до 1600 мм - допуск 0,03 (6 ").
Торцеве биття опорного торця шпинделя.
Рис.11.4
Засіб виміру: вимірювальний прилад (мікрокатор типу 05
лабораторна) встановлюють на столі верстата з допомогою штатива ШМ - 3 - 8 так,
щоб його вимірювальний наконечник торкався торцевої поверхні кінця шпинделя у
його периферії і був направлений перпендикулярно до неї (см.ріс.11.4). Шпиндель
повертають не менше ніж на два оберти.
Допустиме відхилення: 10 мкм.
Радіальне биття центрує шийки шпинделя.
Рис.11.5
Засіб виміру: вимірювальний прилад (мікрокатор типу 05
лабораторна) встановлюють на столі верстата з допомогою штатива ШМ - 3 - 8 так,
щоб його вимірювальний наконечник торкався зовнішньої поверхні кінця шпинделя
(см.ріс.11.5). Вимірювання проводять в перерізі, в якому коло не переривається
пазами. Шпиндель приводять у повільне обертання.
Допустиме відхилення: 16 мкм.
Радіальне биття конічного отвору шпинделя.
Рис.11.6
Засіб виміру: вимірювальний прилад 3 (мікрокатор типу 05 лабораторна),
контрольна оправлення 2 (см.рис.11.6). У конічне отвір шпинделя 1 закріплюють
контрольну оправку 2 з циліндричною робочою поверхнею. На нерухомої частини
верстата закріплюють вимірювальний прилад так, щоб його вимірювальний
наконечник торкався поверхні оправки і був направлений до її осі
перпендикулярно твірною. Перевірку проводять у двох перерізах а і б на відстані
, у двох взаємно перпендикулярних площинах А і Б, для
чого оправку повертають навколо осі обертання на 90 градусів.
Допустимі відхилення: при ширині столу до 250 мм, L = 150 мм
Допуск в перерізі а) 10 мкм, б) 12 мкм;
при ширині понад 250 мм, L = 300 мм
Допуск в перерізі а) 12 мкм, б) 20 мкм.
Паралельність робочої поверхні столу осі обертання шпинделя.
Рис. 11.7
Засіб виміру: вимірювальний прилад 3 (мікрокатор типу 05
лабораторна), контрольна оправлення 2 (см.рис.11.7). У конічне отвір шпинделя
закріплюють контрольну оправку 2 з циліндричною робочою поверхнею. На столі
перпендикулярно осі оправки встановлюють вимірювальний прилад так, щоб його
вимірювальний наконечник торкався робочої поверхні оправки і переміщають його
на всю довжину оправки.
Вимірювання проводять у двох перерізах оправки, спочатку біля
торця шпинделя, а потім на відстані L від нього. Кожне вимірювання проводять за
двома діаметрально протилежним сторонам оправки (шляхом повороту шпинделя разом
з оправленням на 180 градусів). Для виключення з результатів вимірювання
відхилення від співвісності осі оправки з перевіряється віссю фіксують
показання приладу в А - перерізі 1, Б - перерізі 2. Потім оправку повертають на
180 градусів і повторюючи вимірювання фіксують А2 і Б2. Відхилення від
паралельності прямої, що з'єднує кінці увібрав перетину перевіряється площині і
осі в поперечному перерізі 1 і 2.
.
Допустиме відхилення:
при ширині столу до 160 мм, L = 100 мм - допуск 8 мкм;
при ширині столу від 160 до 250 мм, L = 150 мм - допуск 12
мкм;
при ширині столу понад 250 мм, L = 300 мм - допуск 25 мкм.
Нормативна документація:
. ГОСТ 15945 - 82 «Конуси шпинделів і оправлень з конусними
7:24. Розміри ».
. ГОСТ 6464 - 69 «Верстати координатно-розточувальні. Основні
розміри. - Натомість ГОСТ 6464 - 63 ».
. ГОСТ 18098 - 72 «Верстати координатно - розточувальні і
координатно-шліфувальні. Норми точності ».
. ГОСТ 8 - 82Е «Верстати металорізальні загальні вимоги до
випробувань на точність».
. ГОСТ 2.301 - 68 ... ГОСТ 2.319 - 81 ЕСКД «Загальні правила
виконання креслень».
. ГОСТ 2.116 - 84 ЕСКД «Карта технічного рівня і якості
продукції».
. ГОСТ 3.1404 - 74 ЕСТД «Правило оформлення документів на
механічну обробку».
. ГОСТ 3.1418 - 82 Руські «Правило оформлення документів на
технологічні процеси та операції, що виконуються на верстатах з числовим
програмним керуванням (ЧПК). Обробка різанням ».
. ГОСТ 3.1118 - 82 ЕСТД «Форми та правила оформлення
маршрутних карт».
. ГОСТ 24297 - 80 СПКП «Вхідний контроль якості продукції».
. ГОСТ 27.002 - 83 «Надійність в техніці. Терміни та
визначення ».
. ГОСТ 14.301 - 83 ЕСТПП «Загальні правила розробки
технологічних процесів».
. ГОСТ 12.1.019 - 79 ССБТ «Електробезпека. Загальні вимоги ».
12. Охорона праці і техніки безпеки
.1 Аналіз небезпечних і шкідливих виробничих факторів
Частота появи нещасних випадків при роботі на металообробне
обладнання визначається технологією виготовлення деталей і технічними засобами
оснащення. Як і будь-який металорізальний верстат, модернізований координатний свердлильно-фрезерний
верстат моделі 2А459АФ4, представляє для робочого певного роду небезпека.
Для модернізованого верстата небезпечними факторами є;
Обертові фрези, свердла, розгортки;
Стружка;
Електричний струм.
Шкідливими виробничими факторами є;
Використання МОР при обробці;
Недостатнє освітлення зони різання;
Шум, вібрації.
Для захисту оператора від бризок МОР і стружки застосовують
захисні огородження зони різання. Зона різання закрита металевими щітками.
Щитки виготовлені з алюмінію товщиною 2 мм і мають оглядові вікна зі скла
товщиною 4 мм. Огороджувальні пристрій переміщається по висоті. У конструкції
пристрою передбачена електрична блокування відкривання захисного кожуха.
Безпека праці на верстаті забезпечується його виготовленням
відповідно до вимог ГОСТ 12.2.009 і ГОСТ Р МЕК 60204-1. Вимоги безпеки праці
при експлуатації верстата встановлюються цим розділом, відповідними розділами
керівництв з експлуатації «Електрообладнання», «Гідросистема», «Мастильна
система» і керівництва з експлуатації «Пожежна безпека».
Показники, що забезпечують дотримання загальних вимог безпеки
при експлуатації верстата:
Верстат має зручний відведення МОР із зони обробки і
забезпечений централізованою системою змащення;
Мимовільне опускання шпиндельної бабки виключається
застосуванням противаги;
Інструмент в конусі шпинделя верстатів закріплюється
механізовано.
Утримання інструменту здійснюється пакетом тарілчасті пружин,
що забезпечують його надійне закріплення незалежно від несподіваного припинення
подачі електроенергії або падіння тиску в гідросистемі (при розбиранні
механізованого затиску інструменту необхідно берегтися «вистрілювання»
пружин.);
Час гальмування шпинделя (без інструмента) після його
вимкнення не повинен перевищувати 6 секунд. Гальмування забезпечується
електросхеми приводу головного руху;
Верстат має запобіжні та блокуючі пристрої;
Захист електрообладнання від короткого замикання здійснюється
автоматичними вимикачами;
Передбачений захист приводів подач і головного руху від
перевантажень;
Вступної вимикач верстата забезпечений замком, що охороняє
верстат від випадкового включення;
Для замикання дверцят електрошафи передбачені спеціальні
запори, що закриваються спеціальним ключем;
На електрошаф встановлені знаки напруги;
Станина верстата, корпуси електрошаф оснащені пристроями
заземлення.
Запобіжні пристрої на верстаті моделі 2А459АФ4:
Включення переміщення столу, санчат, шпиндельної бабки
відбувається тільки при досягненні заданої частоти обертання шпинделя;
Аварійний динамічне гальмування приводів за допомогою
вимикачів аварійної зупинки;
Відключення обертання шпинделя одночасно після відключення
приводів подач;
Що виключає можливість подавання команд на віджим інструменту
при обертовому шпинделі;
Включення циклу обробки при незакритих дверцятах огородження
зони різання;
Включення введеного автоматичного вимикача при відкритих
дверцятах електрошафи.
Заходи щодо захисту від небезпечних і шкідливих виробничих
факторів при роботі на верстаті моделі 2А459АФ4:
Обслуговуючому персоналу при роботі необхідно дотримуватися
всі загальні правила техніки безпеки роботи на металорізальних верстатах.
Персонал, допущений в установленому на підприємстві порядку
до роботи на верстаті, а також до його наладці і ремонту зобов'язаний:
Отримати інструктаж з техніки безпеки, відповідно до
інструкцій, розроблених на підставі керівництва по експлуатації та типовими
інструкцій з охорони праці.
Ознайомитися із загальними правилами експлуатації та ремонту
верстата та вказівками з безпеки праці, які містяться в керівництві з
експлуатації «Електрообладнання», «Гідросистема», «Мастильна система», «Пожежна
безпека» і в експлуатаційній документації, що додається до пристроїв і
комплектуючих виробів, що входять до складу верстата.
При транспортуванні і установці верстата:
Для надійного зачалювання і безпечного переміщення верстата і
поставляється до нього обладнання при монтажі, демонтажі і ремонтних роботах,
необхідно перш за все ознайомитися з відповідним розділом «Порядок установки».
В іншому випадку роботи вести забороняється.
При підготовці верстата до роботи необхідно:
Ретельно вивчити призначення органів управління верстатом;
Перевірити заземлення верстата;
Перевірити функціонування системи змащення верстата;
Перевірити роботу всіх механічних і електричних блокувань;
Всі деталі, масою более16 кг, встановлювати на верстат за
допомогою тельфера або крана;
Встановити на стіл верстата огорожу, яка служить засобом
захисту робітника від попадання емульсії, при роботі з охолодженням, і від випадкового
попадання відлетіла стружки.
При роботі верстата:
Під час роботи верстата дверцята огородження відкривати
забороняється;
Включати механізми верстата тільки після перевірки
закріплення оброблюваної заготовки на столі верстата;
Забороняється включати механічне обертання шпинделя при
встановлених в шпиндель центроіскателе з індикатором і мікроскопі -
центроіскателе (у цьому випадку, клавішею «Ручний» на пульті управління,
подається команда на нейтральне положення шпинделя). Після цього, натисканням відповідної
кнопки шпиндель обертається зі швидкістю повільного проворота.
Після закінчення роботи на верстаті необхідно:
Вийняти інструмент з шпинделя;
Відключити верстат від електромережі.
Категорично забороняється знімати або порушувати блокування,
передбачені конструкцією верстата;
Категорично забороняється користуватися стисненим повітрям
при збиранні верстата;
При зніманні поворотного столу обов'язково вимк. пристрій
ЧПУ.
12.2 Електробезпека
Причини поразки електричним струмом при роботі на верстаті
моделі 2А459АФ4: одним з найважливіших питань техніки безпеки є електробезпека.
Дія струму на людину може привести до важкої травми, а в ряді випадків до
летального результату.
Причинами електротравм при роботі на верстаті моделі 2А459АФ4
є: поява напруги на металевих частинах електрообладнання і корпусі верстата в
результаті пошкодження ізоляції струмоведучих проводів при механічному ремонті
або заміні інструменту (коротке замикання струмоведучою лінії (мережі),
відкриті ділянки ліній електропередач, відсутність заземлення), а також не
дотримання загальних вимог безпеки праці з керівництва з експлуатації
«Електрообладнання».
Заходи щодо захисту від електротравм при роботі на верстаті
моделі 2А459АФ4: однією з основних умов, з електробезпеки, є недоступність
струмоведучих ліній спільно з наявністю огороджувальних пристроїв і спец знаків
«Висока напруга».
Мірою захисту від ураження електричним струмом є приміщення
силової частини електроустаткування в окремий відсік верстата, що закривається
дверцятами, спеціального ключа, а частина електропроводів з метою захисту
укладена в броньовані шланги.
На верстаті для живлення електроприводів застосована
трипровідній трифазний мережа з ізольованою нейтраллю.
Метою заземлення є усунення небезпеки ураження електричним струмом
при появі напруги на конструктивних частинах електрообладнання, тобто при
замиканні на корпус. Загальний захист електрообладнання від струмів короткого
замикання здійснюється автоматичним вимикачем. Для виключення перевантаження
передбачений захист приводів подач і головного руху, що здійснюється схемою
захисту від перевантажень і струмовими відсічення відповідних перетворювачів.
.3 Пожежна безпека
Причини спалаху при роботі на верстаті моделі 2А459АФ4: при
роботі верстата можливе виникнення пожежі через недбале зберігання обтирального
матеріалу, тобто промасленим дрантя, яка за певних умов здатна самозайматися:
перевантаження двигунів, викликаної завищеними режимами різання при обробці
деталі, внаслідок короткого замикання струмоведучою лінії, а також з причини
необережного поводження з вогнем.
Заходи щодо попередження та усунення спалаху на верстаті
моделі 2А459АФ4: відповідний інструктаж персоналу, допущеного до роботи на
верстаті, а також дотримання ним вимог безпеки праці при експлуатації верстата
з наступних інструкцій з експлуатації «Електрообладнання», «Мастильна система»,
«Пожежна безпека».
Щоб уникнути виникнення пожежі слід обтиральний матеріал,
просочений робочою рідиною, містити в металевому ящику і в кінці зміни видаляти
з приміщення.
По закінченню роботи або в перервах необхідно обов'язково
вимикати всі електродвигуни верстата.
Захистом верстата від загоряння в результаті перевантажень
служать теплові реле, які реагують на гранично - допустимі значення
електричного струму в електропроводці і розмикають електричний ланцюг до
настання аварійного максимуму струму.
Первинні засоби гасіння: поблизу верстата розташовані два
вуглекислотних вогнегасники типу ОУ - 5 та спеціальні протипожежні покривала з
сортового полотна, а також пісок.
13. Екологія
Охорона навколишнього середовища в даний час - одна з
найбільш нагальних завдань людства. У результаті впливу людини на природу
корінним чином міняється вигляд нашої планети. Тому в епоху сучасної науково -
технічної революції надзвичайно гострою стала проблема порушення екологічної
рівноваги, що виражається в погіршенні якості навколишнього середовища в
результаті забруднення її продовольчими відходами. Промисловість споживає все
більше кисню, зростає виділення вуглекислого газу.
На сучасному рівні розвитку науки і техніки практично
будь-яке виробництво пов'язане з утворенням відходів, стічних вод, шлаків,
викидів в атмосферу.
Модернізований координатний свердлильно-фрезерний верстат
моделі 2А459АФ4 кліматичного виконання УХЛ категорії 4.1 за ГОСТ 15150-69. Клас
точності верстата - А за ГОСТ 8-82.
Верстат повинен експлуатуватися в термоканстантном приміщенні
з температурою 20°±1°С.
Основними чинниками, що впливають на забруднення
навколишнього середовища, при його експлуатації верстата є:
Випаровування МОР;
Шум;
Вібрації, що роблять вплив на робітника - оператора;
Стружка.
Для запобігання впливу цих факторів на оператора і навколишнє
середовище, для верстатів даного типу, повинна бути здійснена кабінетні
компоновка верстата з вбудованою припливно - витяжною вентиляцією. Дані системи
дозволяють підтримувати робочу температуру в необхідних для роботи верстата
діапазонах 20°±1°С, а вібро - акустичні характеристики в межах 68 - 72 децибел. Припливна
вентиляція в даних системах необхідна для очищення повітряного басейну від
випаровування МОР і запобігання попаданню його в навколишнє середовище.
Для запобігання впливу вібрацій на оператора, в основі
верстата знаходиться стенд. Конструкція стенду виглядає наступним чином:
бетонний короб встановлений на бетонних, армованих палях, вкопаний у пісочний
грунт, у днищі короби встановлені демпферних пружини, на яких лежить пресована
гума, на якій у свою чергу встановлений бетонний фундамент у вигляді куба. Щоб
уникнути розповсюдження вібрацій в грунт, і на оборот, впливу зовнішніх
вібрацій на верстат, бетонний фундамент оснащений повітряно - гума ізоляцією,
розташовується між стінками фундаменту і внутрішніми стінками короба. У свою
чергу стенд має розмітку, а виносна панель управління ЧПУ дозволяє оператору
вносити коректування в керуючу програму під час роботи верстата, знаходячись
при цьому поза фундаменту. Дана конструкція стенду дозволяє виконувати роботи
на верстаті з заданою точністю, виключаючи можливість впливу вібрацій на
оператора.
На підприємстві здійснюються різні організаційно - технічні
заходи з охорони повітряного басейну. Виявляються і паспортізіруются джерела
викидів, на них ставляться газоочисні і пиловловлюючі пристрою.
Велике значення на підприємстві мають освітлення, вентиляція,
опалення, захист від шуму, вібрацій, впливу електричного струму, чистота і
порядок на робочому місці.
Для попередження забруднення повітря у виробничих приміщеннях
(цехах) і видалення надлишків вологи, а також для забезпечення повітрообміну
встановлена вентиляція. Передбачаються також пристрої для провітрювання
приміщень. Для періодичної заміни відпрацьованого МОР, в конструкції верстата
передбачені зливні пробки, через які, відпрацьований МОР, переливається в
спеціальні баки для подальшої утилізації. Після закінчення зміни робітник -
оператор проводить прибирання робочого місця. Стружка збирається дрантям і
щітками в спеціалізований бак, звідки пересипається в контейнери для подальшого
транспортування залізницею. В очікуванні транспортування контейнери
зберігаються в складських приміщеннях підприємства. Після закінчення збиральних
робіт оператор здає верстат майстру цеху.
Озеленення території підприємства грає не малу роль в
очищенні повітря. Дерева поглинають вуглекислий газ, виділяють кисень, очищають
повітря oт промислових і вихлопних газів. При цьому зелені насадження
поглинають з повітря не тільки вуглекислий газ, але і очищають атмосферу від
чадного газу, зводять його концентрацію до природної порядку 0,00001%.
В даний час людство має можливість в багатьох галузях
промисловості виробляти продукцію, не надаючи негативного впливу на навколишнє
середовище. До цього відноситься, перш за все, заборона введення в експлуатацію
промислових об'єктів без очисних споруд і суворе виконання умов скидання
стічних вод, а також вдосконалення технології виробництва дозволяє повністю
виключити забруднення середовища.
Заключеня
Згідно із завданням пропонується конструкторське рішення
верстата в цілях підвищення швидкості обертання приводу головного руху, а також
підвищення функціональності верстата, а саме підвищення одночасно керованих
координат від ЧПУ верстата були проведені наступні заходи:
Установка електродвигуна з підвищеною максимальною частотою
обертання;
Установка більш швидкісних підшипників у шпиндельному вузлі;
Вбудовування поворотного ділильні кантуемого столу з
управлінням від пристрою ЧПУ верстата.
Проведення даних заходів забезпечило фактичне збільшення
максимальної частоти обертання приводу головного руху, а також підвищення
одночасно керованих координат від ЧПУ верстата з 4 на 5.
Бібліографічний список
1. А.
Г. Косилової «Довідник технолога - машинобудівника», Т.2, Москва
«Машинобудування», 1986р., 496с., Мул.
.
«Обгрунтування технічних характеристик верстатів: Методичні вказівки до
курсового та дипломного проектування для студентів денного, вечірнього та
заочного відділення спеціальності 0501, 0636. / Укл. Зубенко В. Л., Денисенко
А. Ф., Рабкіна А. Л. / - Куйбишев: КптІ, 1984р., 40с.
.
«Вибір електродвигунів для металорізальних верстатів». Методичні вказівки до
курсового та дипломного проектування. / Житомирський політехнічний інститут;
сост. А. Ф. Денисенко, Житомир, 1992р., 24С.
.
«Проектування і розрахунок приводів металорізальних верстатів: Методичні
вказівки для курсового та дипломного проектування» Державний технічний
університет. Сост. О. М. Садовніков, М. А. Вишняков, Донецьк, 1993р., 40с.
.
«Розрахунок валів металорізальних верстатів з використанням ЕОМ»: Метод. указ.
/ ДОНАСА; Укл. В. І. Степанов. Донецьк, 1994р., 46с.
. В.
Е. Пуш «Конструювання металорізальних верстатів». М., «Машинобудування»,
1977р., 390с.
.
«Верстати й інструменти» № 6, 1968р.
.
«Известия вищих навчальних закладів», «Машинобудування», № 1, № 2, № 3 1978р.