Название
оборудования
|
Номер
расположения в плане
|
Компрессорная
станция КТ-6 КТ-7
|
1
|
Станок
заточной 2А-64
|
2
|
Станок
заточной для поршневых колец
|
3
|
Ножницы
для резки металла
|
4
|
Заточной
станок
|
5
|
Инструментальный
стол
|
6
|
Фрезерный
станок КУСОН-3 1989 № 55
|
7
|
Токарный
станок
|
8
|
Фрезерный
станок ФС-250 1989 № 8707
|
9
|
Фрезерный
станок 6М-83 1965 № 731
|
10
|
Токарный
станок 1К62 1986 № 67924
|
11
|
Станок
токарно-винторезный 1М-63 1972 № 9358
|
12
|
Поперечно-строгательный
станок тип-736
|
13
|
Станок
сверлильный В1-32ГА 1988 № 463
|
14
|
Станок
токарно винторезный ДИП-400
|
15
|
Станок
для резки листовой стали
|
16
|
Стенд
обкатки компрессоров
|
17
|
Трубогибной
станок
|
18
|
Стенд
магнитопорошковой дефектоскопии деталей локомотивов СМПД-МД 2007 № 45
|
19
|
Станок
балансировки роторов
|
20
|
21
|
Станок
притирки клапанов
|
22
|
Кантователь
гидропривода
|
23
|
Пресс
|
24
|
Склад
газа для сварки
|
25
|
Мойка
ручная
|
26
|
Стенд
проверки на плотность секций охлаждения
|
27
|
Приспособление
для проверки производительности масляных насосов редукторов
|
28
|
Автоматическая
мойка агрегатов
|
29
|
Рабочий
стол слесаря
|
30
|
Место
для ремонта агрегатов
|
31
|
Место
для неисправных агрегатов
|
32
|
Кран
мостовой
|
33
|
Шкаф
для персонала
|
34
|
Газовая
сварка
|
35
|
Кузнечная
печь
|
36
|
Наковальня
|
37
|
Кузнечный
молот
|
38
|
Умывальник
|
39
|
Электрический
щит
|
40
|
Огнетушитель
|
41
|
Место
для курения и приема пищи
|
42
|
Ящик
с песком
|
43
|
Пожарный
кран
|
44
|
Мусорный
бак
|
45
|
Телефон
|
46
|
Источник
уличного освещения, направление освещения
|
47
|
Место
для исправных агрегатов
|
48
|
. Описание прав и обязанностей мастера и
бригадира
Мастер участка производства:
Осуществляет руководство возглавляемым участком.
Обеспечивает производство участком продукции (работ, услуг) в установленные
сроки, высокого качества, определенной номенклатуры (ассортимента), повышение
производительности труда, снижение трудоемкости продукции на основе полной
загрузки оборудования и использования его технических возможностей, повышение
коэффициента сменности оборудования, рациональное расходование сырья, материалов,
топлива, энергии. Своевременно подготавливает производство, обеспечивает
расстановку рабочих и бригад, контролирует соблюдение технологических
процессов, оперативно выявляет и устраняет причины их нарушения. Участвует в
разработке новых и совершенствовании действующих технологических процессов и
режимов производства, а также производственных графиков. Проверяет качество
выпускаемой продукции или выполняемых работ, осуществляет мероприятия по
предупреждению брака и повышению качества продукции (работ, услуг). Принимает
участие в приемке законченных работ по реконструкции участка, ремонту
технологического оборудования, механизации и автоматизации производственных
процессов и ручных работ. Организует внедрение передовых методов и приемов
труда, аттестации и рационализации рабочих мест и совмещения профессий.
Обеспечивает выполнение рабочими норм выработки, рациональное использование
производственных площадей, оборудования, оргтехоснастки (оснастки и
инструмента), равномерную работу. Осуществляет формирование бригад (их
количественного, профессионального и квалифицированного состава), разрабатывает
и внедряет мероприятия по рациональному обслуживанию бригад, координирует их
деятельность. Устанавливает и своевременно доводит производственные задания
бригадам и отдельным рабочим (не входящим в состав бригад) в соответствии с
утвержденными планами и графиками производства, плановые показатели по
использованию оборудования, сырья, материалов, инструмента, топлива, энергии,
фонда заработной платы. Осуществляет производственный инструктаж рабочих,
проводит мероприятия по выполнению правил охраны труда, техники безопасности,
производственной санитарии и пожарной безопасности, технической эксплуатации
оборудования и инструмента, а также контроль за их соблюдением. Содействует
развитию совмещения профессий, расширению зон обслуживания и применения других
прогрессивных форм организации труда, вносит предложения о пересмотре норм
выработки и расценок, а также о присвоении в соответствии с Единым
тарифно-квалификационным справочником работ и профессий рабочих разрядов
рабочим, принимает участие в тарификации работ и присвоении квалификационных
разрядов рабочим участка. Анализирует результаты производственной деятельности,
контролирует расходование фонда заработной платы, установленного участку,
обеспечивает правильность и своевременность оформления первичных документов по
учету рабочего времени, выработки, заработной платы. Содействует
распространению передового опыта, починов, развитию творческих инициатив,
внедрению рационализаторских предложений и изобретений. Обеспечивает
своевременный пересмотр в установленном порядке норм трудовых затрат, внедрение
технически обоснованных норм и нормированных заданий, правильное и эффективное
применение систем заработной платы и премирования. Принимает участие в
осуществлении работ по выявлению резервов производства, в разработке
мероприятий по созданию благоприятных условий труда, повышению культуры
производства, рациональному использованию рабочего времени. Контролирует
соблюдение рабочими производственной и трудовой дисциплины, правил внутреннего
трудового распорядка. Представляет предложения о поощрении отличившихся рабочих
участка или привлечении к дисциплинарной ответственности за нарушение
производственной и трудовой дисциплины. Организует работу по повышению
квалификации и профессионального мастерства рабочих и бригадиров, обучению их
вторым профессиям.
Мастер участка производства имеет право:
Представлять на рассмотрение руководителя
предприятия предложения по вопросам своей деятельности. Получать от
руководителей структурных подразделений предприятия информацию, связанную с
вопросами своей деятельности. Подписывать и визировать документы в пределах
своей компетенции. Требовать от руководства предприятия оказания содействия в
исполнении своих должностных обязанностей.
Должностные обязанности бригадира:
Организация работ на рабочих местах по
установленному технологическому процессу. Руководство бригадой рабочих
различных производственных подразделений. Обеспечение своевременного выполнения
бригадой утвержденного плана работ. Расстановка рабочих бригады по объектам.
Обеспечение рабочих мест материалами и деталями. Обеспечение выполнения
требований техники безопасности, охраны труда и противопожарных правил.
Инструктаж рабочих бригады по применению рациональных приемов работ,
приспособлений и устройств. Наблюдение и контроль за качеством выполняемых
работ. Приемка работ и сдача объектов мастеру. Контроль за расходованием
материалов. Учет объема выполняемых работ и оценка их качества. Содержание
оборудования и инвентаря исправным. Права бригадира:
Бригадир предприятий железнодорожного транспорта
и метрополитенов имеет право давать подчиненным ему сотрудникам поручения,
задания по кругу вопросов, входящих в его функциональные обязанности. Бригадир
предприятий железнодорожного транспорта и метрополитенов имеет право
контролировать выполнение производственных заданий, своевременное выполнение
отдельных поручений подчиненными ему сотрудниками. Бригадир предприятий
железнодорожного транспорта и метрополитенов имеет право запрашивать и получать
необходимые материалы и документы, относящиеся к вопросам своей деятельности и
деятельности подчиненных ему сотрудников. Бригадир предприятий железнодорожного
транспорта и метрополитенов имеет право взаимодействовать с другими службами
предприятия по производственным и другим вопросам, входящим в его
функциональные обязанности. Бригадир предприятий железнодорожного транспорта и
метрополитенов имеет право знакомиться с проектами решений руководства предприятия,
касающимися деятельности подразделения. Бригадир предприятий железнодорожного
транспорта и метрополитенов имеет право предлагать на рассмотрение руководителя
предложения по совершенствованию работы, связанной с предусмотренными настоящей
Должностной инструкцией обязанностями. Бригадир предприятий железнодорожного
транспорта и метрополитенов имеет право выносить на рассмотрения руководителя
предложения о поощрении отличившихся работников, наложении взысканий на
нарушителей производственной и трудовой дисциплины. Бригадир предприятий
железнодорожного транспорта и метрополитенов имеет право докладывать
руководителю обо всех выявленных нарушениях и недостатках в связи с выполняемой
работой.
. Описание системы оплаты труда мастера,
бригадира и рабочего
Система оплаты труда мастера -
повременная. Это наиболее распространенная система оплаты труда. Она
применяется практически в любой отрасли. При повременной оплате труда зарплата
начисляется пропорционально отработанному времени независимо от результатов работы.
Для работников устанавливаются специальные тарифы (оклады, дневные и часовые
тарифные ставки). Начислять заработную плату при повременной системе оплаты
труда довольно просто. Для этого достаточно табеля учета рабочего времени. Он
ведется по унифицированной форме № Т-13, утвержденной постановлением
Госкомстата России от 05.01.2004 № 1.
Чтобы рассчитать зарплату
работника, нужно умножить отработанное им время в днях или часах на
соответствующую тарифную ставку.
Пример оплаты труда мастера ООО
"ТМХ Сервис" Уссурийск за июль 2015 года:
Заработная плата мастера
рассчитывается по формуле:
Z=(C∙T∙K)-N-P,
(6.1)
где С - стоимость работы
мастера за час (102 рубля); T
- количество рабочих часов за июль 2015(184); K
- региональный коэффициент(1,6 - Приморский край); N
- подоходный налог (13% от заработной платы); P
- профсоюзный взнос (1% от заработной платы).
Заработная плата мастера за
июль 2015 года составляет 19369 рублей, кроме того к данной зарплате могут
прибавляться премиальные за определенные достижения цеха.
Система оплаты труда бригадира
- сдельная. Сдельная система оплаты труда применяется для тех сотрудников,
результаты труда которых могут быть реально посчитаны. В основном это
работники, занятые в производстве. Причем речь идет не только о рабочих у
станка, но и о работниках интеллектуального труда, например редакторах в
издательстве. В последнем случае конечными продуктами будут подготовленные к
публикации литературные произведения (книги, статьи и т. п.), объем которых
легко просчитать. А за единицу продукции может быть принято определенное
количество отредактированных авторских знаков или авторских листов.
Организация, которая решила
установить сдельную систему оплаты труда, должна разработать сдельные расценки
на каждый вид производимой продукции для всех этапов производства. Далее расчет
заработной платы происходит следующим образом. В конце месяца в бухгалтерию
передаются сведения о продукции, выработанной каждым сотрудником, труд которого
оплачивается сдельно. Количество продукции умножается на соответствующие
сдельные расценки.
Пример сдельной расценки
производства ремонтов ООО "ТМХ Сервис" Уссурийск:
Рисунок 6.1 - Сдельная расценка
производства ремонтов
Пример расчета сдельной
заработной платы бригадира:
Бригадир слесарной бригады за
месяц отремонтировал 15 воздухопроводов тепловоза ТЭМ 2, 40 клапанов
трубопровода, 50 воздухопроводов ТЭП 70, к тому же бригадир получил доплаты за
управление бригадой в размере 5000 рублей, тогда зарплата бригадира будет
считаться за сумму произведений выполненных работ (с учетом расценок тарифного
плана) и вычитанных из нее подоходного налога и профсоюзного взноса, с учетом
регионального коэффициента:
((15∙202,64+40∙42,22+50∙219,52+5000)∙1,2)-3230-249=21366
Зарплата бригадира за месяц
составит 21366 рублей.
Система оплаты труда рабочего -
сдельная, расчет заработной платы рабочего не отличается от расчета заработной
платы бригадира, за исключением того что у рабочего нет управленческих доплат.
7. Порядок составления нарядов
на работу и требований на запасные части и материалы
Наряд-допуск выдается на срок, необходимый для
выполнения заданного объема работ. В случае невыполнения работы в указанное в
наряде-допуске время или изменения условий производства работ работы
прекращаются, наряд-допуск закрывается, возобновление работ разрешается только
после выдачи нового наряда-допуска. На каждую бригаду (звено), участвующую в
производстве работ повышенной опасности, наряд-допуск должен оформляться в двух
экземплярах (один находится у лица, выдавшего наряд-допуск, другой выдается
ответственному руководителю работ). Бланк наряда-допуска должен быть заполнен
ясно, конкретно и четко, в соответствии с Порядком заполнения. Исправления
текста не допускаются. При выполнении работ на территории действующего
предприятия лицо, выдающее наряд-допуск от организации, учитывая имеющиеся или
могущие возникнуть опасности (постоянно и потенциально опасные производственные
факторы), а также в соответствии с определенными актом-допуском мероприятиями
выписывает наряд-допуск в трех экземплярах (третий экземпляр выдается
ответственному лицу действующего предприятия), согласовав меры безопасности и
порядок производства работ с ответственным лицом действующего предприятия (цеха,
участка). Для выполнения работ в охранной зоне линии электропередачи, связи,
других инженерных коммуникаций организация обязана подать заявку предприятию,
эксплуатирующему эти сооружения, с указанием вида, характера, места, времени
начала и окончания работ, а также список ответственных руководителей,
ответственных исполнителей работ и лиц, имеющих право выдачи нарядов-допусков,
с указанием фамилий, инициалов, должностей и групп по электробезопасности и
получить письменное разрешение на право производства работ. Наряд-допуск на
производство работ в охранной зоне воздушной линии электропередачи, связи,
других инженерных коммуникаций должен быть утвержден руководителем (главным
инженером, техническим директором) организации и подписан лицом, ответственным
за эксплуатацию линии со стороны владельца. В подразделениях, выполняющих
указанные работы и расположенных на расстоянии более 50 км от своих
организаций, наряд-допуск утверждает руководитель подразделения или другой
ответственный руководитель (специалист), прошедший соответствующее обучение и
уполномоченный на это приказом по организации. Количество нарядов-допусков,
выдаваемых одновременно одному ответственному руководителю работ, определяется
лицом, выдающим наряд-допуск, исходя из физической возможности выполнения
ответственным руководителем своих обязанностей. При этом у ответственного
руководителя работ не должно быть более трех незакрытых нарядов-допусков
одновременно. Ответственному исполнителю работ может быть выдан только один
наряд-допуск. По окончании смены, а также при перерывах в работе на праздничные
дни и дни отдыха ответственный исполнитель работ обязан передать наряд-допуск
ответственному руководителю работ на хранение. При возобновлении работ
ответственный руководитель обязан лично убедиться в том, что условия их
производства не изменились, и только после этого возвратить наряд-допуск
ответственному исполнителю работ. Возобновление работ без наряда-допуска
запрещается. Срок хранения закрытого наряда-допуска - 30 дней. Выдача и возврат
нарядов-допусков регистрируются в Журнале учета выдачи нарядов-допусков на
производство работ повышенной опасности или совмещенных работ. Журнал должен
быть пронумеровал, прошнурован и скреплен печатью организации. Журналы, чистые
бланки и закрытые наряды-допуски должны храниться у лица, выдающего их. Срок
хранения журнала 6 месяцев с момента последней записи. Ответственный
руководитель работ не имеет права принимать наряд-допуск, осуществлять допуск
бригады (звена) к работе, если характер и условия работ, меры безопасности не
отражены в наряде-допуске в требуемом объеме или не соответствуют правилам
безопасности. За отказ принять наряд-допуск и осуществить допуск персонала в
указанных случаях он ответственности не несет. Ответственный исполнитель работ
не имеет право получать наряд-допуск и начинать работу бригады (звена), если
характер и условия работ, меры безопасности не соответствуют действующим
правилам и инструкциям по безопасности труда или не отражены в наряде-допуске в
требуемом объеме.
Требования на запасные части и материалы
составляет мастер цеха и отправляет на склад, запасные части или материалы
списываются со склада и отправляются в цех.
. Индивидуальные задания
.1 Замена шариковых подшипников вентиляторного
колеса воздухопровода
Единственной изнашиваемой деталью вентиляторного
колеса является подшипник. При замене подшипника нужно использовать следующий
ряд операций:
) Сначала нужно снять внутреннюю крышку колеса,
закрепленную шестью шестигранными болтами ГОСТ 7805-70, болты в свою очередь
соединены проволокой общего назначения ГОСТ 3282-74 через отверстие в шляпках.
Перекусываем проволоку используя кусачки по металлу ГОСТ 28037-89 в промежутках
между болтами и изымаем проволоку пассатижами ГОСТ 17438-72 либо плоскогубцами
ГОСТ 5547-93.
) Откручиваем болты торцевым гаечным ключом с
внутренним шестигранником изогнутый соответствующего размера ГОСТ 25788-83. Для
беспрепятственного откручивания нужно смочить место крепления болтов
смазывающими компонентами (дизельное топливо, керосин, в специализированных
цехах различные спреи от заклинивания) и использовать торцовый гаечный ключ с
внутренним шестигранником изогнутый ГОСТ 25788-83, откручиваем болты по
диагонали, преждевременно ослабив каждый.
) Открутив болты и сняв внутреннюю крышку, таким
же образом снимаем наружную крышку. Теперь нужно снять корпус подшипников, он
крепится внутри колеса наглухо. Выбиваем корпус подшипников, далее снимаем
стопорное кольцо поддевая его плоской отверткой ГОСТ 17199-88, далее снимаем
центрирующее кольцо и выбиваем первый подшипник ГОСТ 8338-75, после снятия
промежуточного кольца - второй подшипник ГОСТ 8338-75.
) Далее замачиваем все детали и само
вентиляторное колесо в керосиновой ванне, чистим и обтираем начисто.
) Напрессовываем первый новый подшипник ГОСТ
8338-75, ставим промежуточное кольцо, напрессовываем второй подшипник ГОСТ
8338-75, ставим центрирующее кольцо и напрессовываем на него стопорное кольцо.
) Обильно и тщательно смазываем корпус с
подшипниками набивая смазочным материалом ГОСТ 9490-75.
) Запрессовываем корпус подшипников обратно в
колесо. Закручиваем внутреннюю крышку на болты по диагонали, смазав отверстия
для закручивания - керосином или топливом, также смазав болты. Закручиваем
внешнюю крышку по диагонали, смазав отверстия для закручивания - керосином или
дизельным топливом, также смазав болты. Операции по замене подшипников
вентиляторного колеса закончены.
.2 Организация ремонта в электромашинном
отделении - ремонт и сборка тяговых двигателей и их диагностирование -
разработка организации рабочего места слесаря
.2.1 Организация ремонта в электромашинном
отделении
В электромашинном отделении ремонтируют тяговые
электрические машины в объеме ТР-3 и СР с полной их разборкой. Отделение
располагается рядом с участком ремонта тележек и включает в себя также
пропиточно-сушильное отделение и испытательную станцию.
При ТР-3 (СР) тяговых двигателей производят
пропитку и сушку обмоток якорей и полюсных катушек, при необходимости замену
бандажей и клиньев, делают осадку обмоток якорей, наплавку подшипниковых щитов
и их крышек, наплавку конусов валов, ремонт или замену полюсных катушек,
обточку и продорожку коллекторов, ремонт щеткодержателей и замену щеток, ремонт
моторно-осевых подшипников.
В депо на участках ремонта электрических машин
организуют поточные линии ремонта якорей тяговых двигателей, подшипниковых
щитов, остовов, разборки и сборки тяговых двигателей. Создают также линии
ремонта главных генераторов, возбудителей и вспомогательных генераторов,
вспомогательных электрических машин.
После разборки колесно-моторных блоков тяговые
электродвигатели поступают в моечную машину для наружной обмывки, после чего
определяется объем ремонта электродвигателя и он подается на линию разборки.
Затем якорь, подшипниковые щиты и остов передают на соответствующие линии ремонта.
Отремонтированные якоря и полюсные катушки транспортируются в
пропиточно-сушильное отделение. После пропитки и сушки изоляцию катушек полюсов
и якорей испытывают на электрическую прочность.
.2.2 Ремонт и сборка тяговых двигателей
При малом периодическом ремонте тепловоза
производятся следующие работы по тяговым электродвигателям: продувка внутри и
обдувка снаружи сжатым воздухом, осмотр, очистка, протирка коллекторов, замена
негодных пружин щёткодержателей и щёток с подбором последних по обоймам и притиркой
по коллектору; регулировка нажатия щёток на коллектор и зазоров между
коллектором и щёткодержателями. В доступных местах проверяют укладку и
крепление проводов и межкатушечных соединений; мегомметром проверяют состояние
изоляции обмоток полюсов и якоря; проверяют зазор у моторно-осевых подшипников,
добавляют в них смазку; измеряют продольный разбег остова относительно колёсной
пары и через каждые 30000 км пробега тепловоза добавляют смазку в
роликоподшипники якоря; проверяют состояние остова и устраняют неисправности в
его подвешивании, кроме того, осматривают изоляцию подводящих проводов и
соединительные рукава для подачи охлаждающего воздуха; снимают нижние половины
кожухов для осмотра зубчатой передачи.
При большом периодическом ремонте, помимо работ,
предусмотренных малым периодическим ремонтом, делают ревизию подбивке
моторно-осевых подшипников.
При подъемочном ремонте все тяговые
электродвигатели вместе с колёсными парами выкатывают из-под тепловоза,
разбирают и ремонтируют с пропиткой якоря. Щётки заменяют новыми, коллекторы
протачивают, продороживают и шлифуют. Методом падения напряжения проверяют
обмотку якоря на отсутствие межвитковых замыканий, осматривают пайку петушков.
Проверяют межкатушечные соединения и выводные провода. Производится освидетельствование
крепления полюсных сердечников и насадка катушек. Осуществляется ремонт
механической части остова. Через один ремонт, связанный с пропиткой, делают
ревизию полюсных катушек со сменой негодной покровной изоляции, заменой
негодных выводных проводов, с пропиткой и покрытием лаком всех катушек.
Вкладыши моторно-осевых подшипников в случае замены или заливки пришабривают к
шейкам оси, а негодные якорные роликовые подшипники заменяют.
При заводском ремонте производят:
) разборку и сборку тяговых электродвигателей со
снятием катушек;
) ремонт катушек с заменой корпусной или
покровной изоляции, проверкой межвитковой и межслойной изоляции, перепайкой или
заменой неисправных выводных проводов;
) ремонт остова с наплавкой или металлизацией и
расточкой горловин под подшипниковые щиты и моторно-осевые подшипники;
наплавкой и строжкой плоскостей соединения остова с шапками и восстановлением
резьбовых и проходных отверстий;
) ремонт или замену сердечников полюсов,
моторно-осевых шапок, подшипниковых щитов, крышек подшипниковых щитов,
коллекторных люков и других деталей остова;
) ремонт якорных подшипников с расклепкой
сепараторов;
) замену или перезаливку моторно-осевых
подшипников;
) ремонт щёткодержателей с разборкой и заменой
деталей.
После окончания подъемочного и заводского
ремонта тяговые электродвигатели испытывают на стенде под нагрузкой.
Осмотр тяговых электродвигателей. На рисунке
8.2.2.1 представлены продольный и поперечный разрезы тягового электродвигателя
ДК-304Б, установленного на тепловозах ТЭ1 и ТЭ2.
Рисунок 8.2.2.1 - Общий вид тягового
электродвигателя ДК-304Б
Где 1 - коллектор; 2 - крышка подшипника; 3 -
внутреннее кольцо роликового подшипника; 4 - упорное кольцо подшипника; 5 -
наружное кольцо роликоподшипника; 6 - коллекторные болты; 7 - подшипниковый
щит; 8 - коллекторный люк; 9 - шайба коллектора передняя; 10 - коллекторные
пластины; 11 - шайба коллектора; 12 - уравнительные соединения; 13 - катушка
главного полюса; 14 - передняя нажимная шайба якоря; 15 - сердечник главного
полюса; 16 - болты крепления сердечников полюсов; 17 - стержень сердечника
главного полюса; 18 - железо якоря; 19 - обмотка якоря; 20 - стальные накладки;
21 - фланец; 22 - рамка; 23 - стальной бандаж; 24 - задняя нажимная шайба якоря;
25 - задний подшипниковый щит; 26 - внутреннее кольцо подшипника; 27 -
лабиринтное кольцо; 28 - накладка; 29 - прилив верхний (носик); 30 -
щёткодержатель; 31 - крышка коллекторного люка; 32 - кронштейн щёткодержателя;
33 - ушки; 34 - верхняя половина моторно-осевого подшипника; 35 - выступ
остова; 36 - крышка; 37 - пружина; 38 - маслёнка; 39 - нижняя половина
моторно-осевого подшипника; 40 - шапка; 41 - соединительные болты; 42 - фланец;
43. 49 - приливы; - немагнитная прокладка; 45 - стальная рамка; 46 - площадка;
47 - остов; 48 - бортики; 50 - заклёпки; 51 - прилив нижний; 52 -
вентиляционные отверстия; 53 - вал; 54 - крышка заднего подшипникового щита; 55
- наружное кольцо заднего роликоподшипника; 56 - якорь; 57 - углубления под
болты; 58 - шайбы пружинящие; 59 - сердечник дополнительного полюса; 60 -
катушка дополнительных полюсов.
Во время осмотра электродвигателей необходимо
следить затем, чтобы при открытии крышек люков 31 внутрь остова не попали
посторонние предметы, а также вода, грязь, пыль или масло. Для этого перед
открытием люков прилегающие части и сами люки надо очистить скребками и
протереть салфетками. После открытия люков в случае необходимости остов внутри
продувают сухим воздухом давлением до 3 атмосфер. Продувка воздухом, имеющим большее
давление, может привести к повреждению изоляции. Стенки остова внутри в
доступных местах протирают чистой безворсовой салфеткой, которую рекомендуется
смочить бензином или углеродистым нитрохлоридом. Эти вещества удаляют вместе с
пылью масло, попавшее внутрь остова. Применение для протирки хлопчатобумажных
концов запрещается.
Затем производится осмотр якоря и в первую
очередь коллектора, по внешнему виду которого почти всегда можно судить о том,
нормально или ненормально работал тяговый электродвигатель. Признаком его
нормальной работы и хорошей коммутации является тёмно-бронзовый или фиолетовый
цвет коллекторных пластин под щётками. Если потемнение (обычно синего цвета)
распространено по всему коллектору, то это свидетельствует о перегреве
электродвигателя. При чрезмерном нагреве может произойти выплавление петушков.
Шероховатость, заусеницы и прочие незначительные неровности коллектора
устраняют шлифовкой при помощи колодки, прикрепляемой на кронштейне к остову
тягового электродвигателя. На колодке закрепляется фетр. Фетр покрывают
стеклянной бумагой, при помощи которой и шлифуют коллектор. При пользовании
этим приспособлением тепловоз перемещают маневровым локомотивом или собственным
ходом на одной тележке. При таком способе другие тяговые электродвигатели
тележки, на которой находится зачищаемый якорь, должны быть выключены.
Случайные забоины могут быть зачищены стеклянной бумагой без вращения якоря.
При этом следует помнить, что местная зачистка коллектора искажает его
цилиндрическую поверхность, поэтому к такому способу устранения местных
неровностей на коллекторе следует прибегать в исключительных случаях. Очищенный
коллектор протирают салфеткой, смоченной бензином. После осмотра коллектора
проверяют, нет ли ослабления бандажей якоря и нарушения пайки петушков. Бандажи
у миканитовых конусов должны быть чистыми, иметь гладкую стекловидную
поверхность. Если это условие не выдержано, бандаж надо покрыть глифталевой
эмалью № 1201 (красная эмаль). Запрещается закрашивать петушки с торца.
Тщательному осмотру подвергается щёточный аппарат, т. е. щётки, щеткодержатели,
их кронштейны, пружины, а также изоляторы. Проверяется нажатие пружин на щетки,
состояние щеточных шунтов и крепление щёткодержателей на кронштейнах. Особо
важное значение имеет состояние поверхности щёток, соприкасающейся с
коллектором, и величина нажатия щёток. Поверхность щёток должна быть гладкой,
без выщербин, отколов и трещин. Щётки должны свободно перемещаться в обоймах
щёткодержателей. Изношенные и с отколотыми краями щетки заменяют; новые щетки
притирают по коллектору стеклянной бумагой, как это показано на рисунке 8.2.2.2
Щёткодержатели с трещинами, неисправным нажимным механизмом, наплывами и
поджогами в щёточных обоймах заменяют.
Рисунок 8.2.2.2 - Притирка щеток по коллектору
Где 1 - щетка; 2 - стеклянная бумага; 3 -
коллектор. Чтобы удалить металлическую пыль, образовавшуюся при зачистке
коллектора, и угольную пыль после постановки новых щёток, притёртых по
коллектору, остов, изоляторы и доступные части якоря с коллектором очищают
волосяной щеткой. Для протирки изоляторов рекомендуется применять
приспособление, представленное на рисунке 8.2.2.3. Приспособление делают из
стального полуцилиндра прикрепляемого шарнирно к деревянной рукоятке 2. На внутреннюю
поверхность полуцилиндра приклеивают или приклёпывают медными заклёпками 3
войлок 4. Диаметр наклеенной цилиндрической поверхности войлока соответствует
диаметру изолятора. Изоляторы, ослабшие в месте постановки, а также имеющие
трещины и повреждённую глазурь на поверхности более 20%, заменяют. Поверхность,
повреждённую менее чем на 20 %, разрешается закрашивать эмалью № 1201.
Рисунок 8.2.2.3 - Приспособление для протирки
изоляторов
Где 1 - стальной полуцилиндр; 2 - рукоятка; 3 -
заклёпки; 4 - войлок. Изоляцию обмоток катушек и якоря при малом периодическом
ремонте осматривают и измеряют её сопротивление. Осмотром устанавливают чистоту
поверхности, а также отсутствие повреждённых и потемневших или обуглившихся мест.
Потемневшая или обуглившаяся изоляция межкатушечных соединений и выводов
полюсов должна быть вскрыта, а болтовое крепление этих соединений проверено и
при необходимости закреплено. Для измерения сопротивления изоляции служит
мегомметр типа М-1101, получивший наибольшее распространение в тепловозном
хозяйстве. Зажим Л (линия) присоединяют к проверяемой цепи, а зажим 3 (земля) -
к зачищенной металлической поверхности, не изолированной от земли.
Сопротивление холодной изоляции тяговых электродвигателей должно быть при малом
периодическом ремонте не менее 1,5 МОм. Если наблюдалось грение какого-либо
подшипника, необходимо отнять шапку и, осмотрев подшипник набивку и шейку,
устранить причину, вызывавшую грение. При удовлетворительном состоянии трущихся
поверхностей набивку всё же необходимо сменить. Если в период эксплуатации,
предшествовавший осмотру моторно-осевых подшипников, не наблюдалось грения, то
только добавляют смазку. При этом её уровень в масляной камере (рисунок
8.2.2.1) не должен превышать 90 мм при измерении наклонно вставленным в
отверстие масленки 38 стержнем. В установленные сроки производится ревизия
подбивки. Смазку в роликовые подшипники якоря добавляют через каждые 30000 км
пробега тепловоза. Со стороны шестерни добавляют 150-230 г смазки и со стороны
коллектора - 50-75 г. Смазка должна быть одной марки. Следует помнить, что при
недостаточной смазке подшипник перегревается, а излишняя смазка будет
выдавливаться через лабиринтное уплотнение и попадать внутрь остова, на
коллектор, намиканитовый конус и т. д., что может повести к порче изоляции и
даже к аварии тягового электродвигателя. При осмотре подвешивания тяговых
электродвигателей проверяют целость пружин, сменных накладок 28 и носиков
(приливов) 29 и 51. Механизм подвешивания смазывают солидолом. У ведомых и
ведущих шестерён проверяют состояние зубьев. Кожухи зубчатой передачи
осматривают для того, чтобы установить, нет ли в них трещин. Трещины устраняют
сваркой. Нижние половины кожухов очищают от старой смазки, а затем закладывают
осернённую смазку в количестве, достаточном для покрытия нижних зубьев ведомой
шестерни (0,9-1,3 кг в каждый кожух). Лишняя смазка вредна, так как она будет
вытекать через неплотности в кожухе и загрязнять тяговые электродвигатели,
колёсные пары и детали экипажа.
Разборка тяговых электродвигателей. Тяговые
электродвигатели выкатывают из-под тепловоза вместе с колёсными парами. Для
перемещения тягового электродвигателя в электроцех в депо пользуются малой
колёсной парой, подкатываемой под остов двигателя (рисунок 8.2.2.4).
Рисунок 8.2.2.4 - Перемещение тягового
электродвигателя вместе с колесной парой по рельсам
В цехах, производящих подъемочный ремонт,
мастерских и на заводах после выкатки из-под тепловоза тележек вместе с колёсными
парами и тяговыми электродвигателями производится подъёмка тележечных рам, а
тяговые электродвигатели вместе с колёсными парами остаются на рельсах. Далее
их разбирают, для чего остов устанавливают носиком книзу. В первую очередь
вывёртывают болты 41 (рисунок 8.2.2.1), прикрепляющие шапку 40 к остову, затем
отнимают шапки вместе с подбивкой и нижним вкладышем моторно-осевого подшипника
39. После этого отвёртывают болты, прикрепляющие кожух зубчатой передачи, обе
половинки кожуха снимают и укладывают на разборной площадке. Освобождённую
колесную пару снимают с остова, а затем удаляют верхнюю половинку
моторно-осевого подшипника 34. Электродвигатель устанавливают на низкий
стеллаж, очищают скребками и салфетками, смоченными керосином, и обдувают воздухом.
Только хорошо очищенный электродвигатель может быть подвергнут дальнейшей
разборке. При разборке сначала спрессовывают ведущую шестерню. Для этого
отгибают лепестки предохранительной шайбы и отвёртывают гайку, закрепляющую
шестерню на валу якоря. Шестерню снимают при помощи гидравлического пресса.
Существует несколько конструкций прессов, применяемых для этой цели. Наиболее
простой пресс показан на рисунке 8.2.2.5 Он состоит из стального ступенчатого
цилиндра 15, в котором перемещаются главный поршень 7, снабжённый уплотняющей
кожаной манжетой 14, и малый поршень 4 с манжетой 6. В главный поршень
вставляется упор 10, упирающийся в торец вала электродвигателя. Малый поршень
соединяется при помощи болта 3 с рабочим винтом 2, на конце которого укреплена
трещотка 1. Для удержания цилиндра от вращения предусмотрен рычаг 5. На цилиндр
навинчивается муфта 13 с заточками, в которые вставляются выступы захватав.
Захват, состоящий из четырёх частей, усилен рёбрами жёсткости А,
располагающимися между зубьями ведущей шестерни 11. Кольцевой выступ захвата
упирается в торец шестерни со стороны подшипникового щита.
Рисунок 8.2.2.5 - Пресс для съёмки ведущей
шестерни
Где 1 - трещотка; 2 - рабочий винт; 3 - болт; 4
- малый поршень; 5 - рычаг; 6 и 14 - манжеты; 7 - главный поршень; 8 - захват;
9 - кольцо; 10 - упор; 11 - ведущая шестерня; 12 - винт; 13 - муфта; 15 -
цилиндр; 16 - винт.
Цилиндр приспособления заправляют смазкой через
центральное отверстие, закрываемое винтом 12, при вывернутом рабочем винте 2.
Для выпуска воздуха при заправке смазкой используют два малых отверстия. Оба
отверстия после заправки закрывают винтами 16, под которые подкладывают медные
прокладки. Съёмка шестерни производится путём ввинчивания рабочего винта 2 в
тело цилиндра. Чтобы при этом не разошлись захваты, предусмотрены
предохранительные, обхватывающие съёмник, кольца 9. Для облегчения съёмки
шестерни последнюю нагревают горячим маслом. На рисунке 8.2.2.6 показана съёмка
шестерни гидравлическим прессом, работа которого основана на том же принципе,
но жидкое масло нагнетается в полость цилиндра плунжерным топливным насосом.
Контроль давления осуществляется манометром. Захват сделан из двух половин,
соединяемых болтами.
Рисунок 8.2.2.6 - Съёмка ведущей шестерни
тягового электродвигателя
После снятия шестерни выжимают лабиринтное
кольцо 27 (рисунок 8.2.2.1), используя для этого приспособление в виде стакана
1 с нарезанным концом (рисунок 8.2.2.7). Для выжимки служит упорный болт 2.
Рисунок 8.2.2.7 - Приспособление для выпрессовки
лабиринтного кольца со стороны шестерни
Где 1 - стакан; 2 - упорный болт. Далее снимают
коллекторные люки и вынимают щётки, предварительно отсоединив шунты.
Вывертывают болты, крепящие крышку 2 подшипника (рисунок 8.2.2.1) и, используя
отжимные болты, крышку выпрессовывают из подшипникового щита. Затем отгибают
стопорную шайбу, отвёртывают торцовые болты, снимают торцовую шайбу и упорное
кольцо подшипника 4. Чтобы не загрязнялась подшипниковая камера, рекомендуется
поставить обратно крышку подшипника и закрепить её двумя болтами. После
указанных операций электродвигатель устанавливают коллектором вниз таким
образом, чтобы можно было свободно вынуть якорь. Отвёртывают болты, укрепляющие
задний подшипниковый щит (со стороны шестерни), и при помощи отжимных болтов
щит выжимают из горловины остова вместе с наружным кольцом 55, сепаратором и
роликами подшипника. Далее на конец вала навинчивают гайку в виде стакана с
ушком и якорь вынимают из остова при помощи крана. Вынутый якорь укладывают на
козлы. Коллектор для предохранения от возможных повреждений обвёртывают плотной
бумагой и обматывают шпагатом. Чтобы вынуть якорь, не снимая шестерни и
лабиринтного кольца, надо удалить болты, прикрепляющие задний подшипниковый
щит, затем шестерню захватить стропами и отжимными болтами выпрессовать из
остова подшипниковый щит. Когда подшипниковый щит выйдет из горловины остова,
его также зацепляют стропами за ушки отжимных болтов и якорь вместе с шестернёй
и подшипниковым щитом свободно извлекают из остова. После выемки якоря остов
поворачивают щёткодержателями кверху, отвёртывают два ранее поставленных болта
у крышки подшипника 2 и выжимают из горловины передний подшипниковый щит (со
стороны коллектора). Затем остов изнутри очищают от пыли и грязи и осматривают
сердечники, полюсные катушки, межкатушечные соединения и щёткодержатели. Полная
разборка остова, производящаяся при соответствующих видах ремонта,
осуществляется в следующем порядке. Разъединяют выводные провода, межкатушечные
соединения главных и дополнительных полюсов, а также шины щёткодержателей.
Затем вывёртывают болты из пальцев кронштейнов щёткодержателей и щёткодержатели
вместе с кронштейнами вынимают из остова. Освобождают от компаундной массы
головки болтов полюсов, все болты вывёртывают и полюсы снимают вместе с
катушками, рамками и пружинными фланцами. Для удобства разборки в первую
очередь удаляют дополнительные полюсы. Снятые катушки, пружинные фланцы и сердечники
маркируют и затем укладывают на стеллаж для дальнейшего осмотра. При заводском
ремонте детали полюсов обезличиваются и поэтому не маркируются. Роликовые
подшипники. Каждый подшипник составляет комплект, состоящий из наружного и
внутреннего колец, сепаратора и роликов. Вследствие незначительных зазоров
между роликами и кольцами, а также Разборку подшипниковых щитов и выемку
наружных колец подшипников с сепараторами производят по следующему
технологическому процессу. Подшипниковый щит (со стороны шестерни) укладывают в
горизонтальное положение (рисунок 8.2.2.8), а на наружное кольцо подшипника
через сегменты 1 передают усилие винтового пресса 2, который упирается в
траверсу 3. Концы траверсы прикреплены болтами 4 к фланцу подшипникового щита
5. Сегменты являются промежуточными деталями для передачи усилий от винтового
пресса к подшипнику. При выпрессовке над сегментами укладывают фиксирующий диск
6, снабжённый выступом, фиксирующим сегменты. Описанное приспособление для
выпрессовки является простейшим; оно применяется в депо с небольшим объёмом
ремонта.
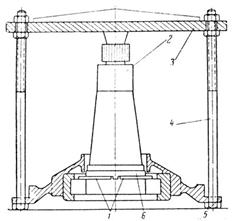
Где 1 - сегменты; 2 - винтовой пресс; 3 -
траверса; 4 - болт; 5 - подшипниковый щит; 6 - фиксирующий диск.
В крупных депо и мастерских подшипники
выпрессовывают при помощи гидравлических прессов. В гидравлических прессах
развиваемое усилие измеряется манометром. Один из таких прессов показан на
рисунке 8.2.2.9.
Рисунок 8.2.2.9 - Гидравлический пресс для
выпрессовки подшипников
Выпрессовка подшипника из подшипникового щита
(со стороны коллектора) после снятия крышки производится в том же порядке, как
и при выпрессовке подшипника со стороны шестерни. В данном случае стакан 1
(рисунке 8.2.2.10) свободно входит в горловину подшипникового щита 2, нажимая
на ролики подшипника 3 при помощи винтового или гидравлического пресса.
Рисунок 8.2.2.10 - Приспособление для
выпрессовки роликового подшипника со стороны коллектора
Где 1 - стакан; 2 - подшипниковый щит; 3 -
роликовый подшипник.
Разобранные подшипниковые щиты и подшипники
подлежат осмотру. Роликовые подшипники. Каждый подшипник составляет комплект,
состоящий из наружного и внутреннего колец, сепаратора и роликов. Вследствие
значительных зазоров между роликами и кольцами, а также наличия приработки в
процессе эксплуатации, заменять отдельные детали в комплекте при текущем
ремонте нельзя. Поэтому каждый подшипник должен быть укомплектован своими
кольцами. Для съёмки внутренних колец с вала якоря необходимо ослабить натяг,
для этого надо нагреть кольца до 90-100°. При этой температуре не может
произойти отпуск закалённых колец. Нагревание колец очень удобно производить
при помощи электромагнитного нагревателя. Электромагнитный нагреватель состоит
из катушки обхватываемой десятью сердечниками 2. Сердечники набраны из листовой
магнитной стали, скреплённой заклёпками. Они укрепляются на корпусе 3 болтами
4. Для удобства пользования к корпусу прикреплены две ручки 5. Если питать
катушку переменным током, то создаваемый магнитный поток будет индуктировать в
кольце подшипника переменный ток, как во вторичной обмотке трансформатора.
Индуктированный ток быстро нагревает кольцо. Удобно снимать кольцо самим
нагревателем, для этого корпус делают разрезным, место разреза соединяется
болтами.
Рисунок 8.2.2.11 - Электромагнитный нагреватель
для внутренних колец подшипников
Где 1 - катушка; 2 - сердечник; 3 - корпус; 4 -
болт; 5 - ручка; 6 - кольцо; 7 - заклепка.
Если наружный диаметр кольца подшипника много
меньше внутреннего диаметра нагревателя, то воздушная прослойка будет создавать
большое сопротивление магнитному потоку, вследствие чего кольцо подшипника
нагревается плохо. Для устранения этого недостатка применяют переходные кольца,
состоящие из двух стальных магнитопроводящих колец 6, скреплённых между собой
заклёпками 7. Кольца 6 имеют один диаметральный разрез, необходимый для того,
чтобы они не могли служить в качестве вторичной обмотки трансформатора. В
условиях мастерских и заводов для каждого подшипника необходимо иметь съёмники
с внутренним диаметром, соответствующим наружному диаметру кольца, что
значительно ускоряет процесс разборки тяговых электродвигателей. Подшипники,
снятые с тягового электродвигателя, промывают в двух керосиновых ваннах. Во
второй ванне при промывке используется жидкая волосяная щётка. Промытые
подшипники обдувают воздухом. Наиболее целесообразно производить промывку
подшипников в моечной машине. Далее производится осмотр подшипников. У
подшипников встречаются следующие дефекты: шелушение, трещины, сколы, вмятины,
задиры, язвины, волнистость и коррозия дорожек качения; сколы, трещины и
коррозия роликов; ослабление заклёпок сепараторов или полное разрушение
сепараторов. Эти дефекты являются следствием неправильной сборки или
некачественного изготовления подшипников, а также недостатка или плохого
качества смазки. Подшипники, имеющие указанные дефекты, заменяют. У признанных
годными по внешнему осмотру подшипников проверяют величину диаметрального
зазора в приспособлении, показанном на рисунке 8.2.2.12. Приспособление состоит
из болта 1, укреплённого на плите 5. Сверху на внутреннее кольцо подшипника
устанавливают конус 3, закрепляемый гайкой 2.
Рисунок 8.2.2.12 - Схема приспособления для
проверки радиального зазора подшипника
Где 1 - болт; 2 - гайка; 3 - конус; 4 -
индикатор; 5 - плита.
Усилием руки нажимают на одну из сторон
подшипника, выбирая таким образом имеющийся у него диаметральный зазор. К
стороне, на которую производили нажатие, подводят индикатор 4 до
соприкосновения его ножки с наружным кольцом подшипника. Затем нажимают на
наружное кольцо подшипника со стороны, противоположной индикатору, и по шкале
индикатора определяют величину зазора. Можно определить зазор при помощи щупа,
который для этого закладывают под ролик. Измерение делают по двум взаимно
перпендикулярным диаметрам у подвешенного подшипника. Накатывать ролик на щуп
запрещается. Диаметральный зазор у новых подшипников и устанавливаемых при
заводском ремонте со стороны шестерни должен быть в пределах 0,07-0,2 мм и у
подшипника со стороны коллектора - 0,05-0,15 мм. При выпуске из текущего ремонта
разрешается оставлять для дальнейшей работы подшипники, имеющие соответственно
диаметральный зазор в пределах 0,07-0,28 и 0,05-0,25 мм. Подшипники,
удовлетворяющие по наружному осмотру и зазорам установленным нормам, проверяют
от руки на шум и лёгкость вращения, сравнивая с эталонным подшипником,
хранящимся в депо (у инспектора- приёмщика МПС). Подшипники, признанные годными
к дальнейшей работе, но не устанавливаемые на электродвигатель, покрывают
техническим вазелином УН-2 или смазкой ПП95-5 (пушечное сало), завёртывают в
парафинированную бумагу и сдают на хранение в кладовую. Ремонт подшипников с
заменой колец и роликов производится в специальных мастерских.
Ремонт катушек, сердечников полюсов и остова
Ремонт катушек и сердечников. При подъёмочном ремонте
катушки и сердечники, как правило, не снимают. В данном случае плотность
посадки катушек проверяют по видимому смещению, натертости и зашлифованным
местам на пружинных фланцах. Катушки с поврежденной изоляцией. Ревизия их со
съёмкой производится через один ремонт, связанный с пропиткой. При заводском
ремонте остов разбирают полностью с компаундировкой или пропиткой катушек.
Катушки, ослабшие на сердечниках, при подъёмочном ремонте уплотняют. При этом
производятся следующие операции:
) снимают изоляцию с межкатушечных соединений, а
сами соединения разъединяют;
) отвёртывают болты крепления сердечников; их
снимают вместе с катушками и маркируют;
) измеряют высоту "окна" катушки и
сердечник;
) чтобы устранить перемещение катушки 1 (рисунок
8.2.2.13) относительно сердечника 6, между фланцем и катушкой по всему
периметру "окна" катушки при последующей сборке укладывают прокладки
4 из электрокартона. Количество и толщину этих прокладок определяют,
сообразуясь с величиной зазора между "окном" катушки, сердечником
полюса и пружинным фланцем;
Рисунок 8.2.2.13- Уплотнение катушек главных
полюсов тяговых электродвигателей ДК-304Б
Где а - при наличии фланца; б - с пружинной
рамкой; 1 - катушка; 2, 4 и 9 - прокладки; 3 - прокладка; 5 - пружинный фланец,
6 - сердечник; 7 - стальные воротники; 8 - пружинная рамка.
) при высоте катушек главных полюсов менее 60 мм
между катушкой и стальной прокладкой 2 дополнительно устанавливают прокладки 3
толщиной 0,5 мм из кровельной листовой стали. Количество прокладок определяют
величиной усадки катушки по высоте. Металлические прокладки перед постановкой
покрывают электроизоляционным лаком № 460.
Рациональнее уменьшать перемещение катушки во
время работы, а следовательно, предупреждать обрыв соединений постановкой
пружинной рамки и изъятием пружинного фланца. В этом случае на место,
освободившееся от отбортованных частей фланцев, помещают уплотнительные
стальные воротники 7 и пружинную рамку 8. Рамку ставят выпуклостью в сторону
сердечника. Такая замена фланца рамкой возможна, если высота катушки не
превышает 60 мм. Пружинные рамки устанавливают комплектно под все главные
полюсы электродвигателя. У дополнительных полюсов закладывают стальные
уплотнительные прокладки 9. Повреждённую покровную изоляцию катушек
восстанавливают или заменяют. Выводные кабели с протёртой и потрескавшейся
резиновой изоляцией также заменяют. Места впайки кабелей в катушках при смене
кабеля или перепайке вскрывают до обнажения патронов, при этом корпусную
изоляцию боковых сторон катушки не снимают, края корпусной изоляции срезают с
постоянным уклоном к вскрытой от изоляции части катушки на длине не менее 25
мм. После пропайки кабеля и патрона, если в этом есть необходимость, катушку
заделывают электроизоляционной замазкой и корпусной миканитовой изоляцией с
постепенным покрытием старой изоляции в прямых частях катушки. Наращивание
выводных кабелей запрещается. Катушки после компаундировки или пропитки при
заводском ремонте опрессовывают по внутренним и торцовым поверхностям с
соблюдением чертёжных размеров. На рисунке 8.2.2.14 показано приспособление для
формовки катушки главных полюсов тягового электродвигателя ДК-304Б. Катушку при
формовке зажимают между плитами 1 приспособления и фигурным клином 2,
разжимаемым клиновидным сердечником 3.
Рисунок 8.2.2.14 - Приспособление для формовки
катушки главного полюса тягового электродвигателя ДК-304Б
Где 1 - плита; 2 - фигурный клин; 3 -
клиновидный сердечник.
Вынутые сердечники полюсов осматривают. Листы
сердечников главных полюсов должны быть прочно соединены заклёпками, головки
которых не должны выступать из плоскости боковин. Стержни главных полюсов,
имеющие резьбу с двумя (и более) сорванными нитками в одном отверстии,
необходимо заменить или отремонтировать. Сорванную резьбу в сердечнике полюса
при отсутствии других неисправностей, требующих переклёпки сердечника,
восстанавливают постановкой втулок с новой резьбой. Аналогичным способом
восстанавливают резьбу у сердечников дополнительных полюсов. Металлические
фланцы главных и дополнительных полюсов, имеющие трещины, отломанные части или
неправильную форму, заменяют. Катушки насаживают на сердечник в подогретом до
70-80° состоянии, после чего сердечники в сборе с катушками устанавливают в остов.
Катушки соединяют между собой и через них в течение 3-4 мин для проверки
плотности контактов пропускают ток, соответствующий часовому режиму. Затем
через катушки пропускают ток 800 А температуру их доводят до 80-85°, после чего
затягивают полюсные болты. При заводском ремонте предусматривается переделка
межкатушечных соединений - с жестких шин на гибкие кабельные. При сборке полюсы
устанавливают в вертикально поставленный остов стороной щёткодержателей вниз.
Категорически запрещается производить подъём катушек за выводные концы. Полюсы
поднимают краном за выступающую часть наружной стороны сердечника или при
помощи приспособления, изображённого на рисунке 8.2.2.15. Приспособление
состоит из опорной скобы, к которой приварен стержень 2. По стержню перемещается
снабжённая втулкой передвижная скоба 3. Захват полюса производится за сердечник
4 с надетым пружинным фланцем 5.
Рисунок 8.2.2.15 - Приспособление для подвески
главного полюса
Где 1 - опорная скоба; 2 - стержень; 3 -
передвижная скоба; 4 - сердечник полюса; 5 - фланец полюса.
Дополнительные полюсы поднимают приспособлением,
показанным на рисунке 8.2.2.16, непосредственно за катушку 1. Катушку зажимают
скобами, неподвижной 2 и подвижной 3, снабжёнными резиновыми прокладками 4 и 5.
Зажим делается гайкой 6. Чтобы резиновые прокладки не выпадали, их приклёпывают
к скобам.
Рисунок 8.2.2.16 - Приспособление для подвески
Где 1 - катушка; 2-неподвижная скоба; 3 -
подвижная скоба; 4 и 5 - резиновые прокладки; 6 - гайка.
Крепление сердечников полюсов производится
болтами, под головки которых закладывают пружинные шайбы. Болты окончательно
затягивают после прогрева катушек. Болты верхнего полюса заливают компаундной
массой. Далее производится окончательный монтаж межкатушечных соединений. Все
места подключений межкатушечных соединений предварительно должны быть хорошо
зачищены, а детали соединений - оцинкованы. У собранного остова до изоляции
межкатушечных соединений проверяют: полярность катушек, величину сопротивления
изоляции относительно корпуса, омическое сопротивление обмотки, электрическую
прочность изоляции, а также состояние кабелей (проводов) наконечников,
контактов межкатушечных соединений, межполюсное расстояние и прочность крепления
полюсов. Полярность полюсов проверяют при помощи прибора (рисунок 8.2.2.17),
который состоит из катушки с железным сердечником и амперметра с двусторонней
шкалой. При пропускании тока по установленным в остове полюсным катушкам в
направлении, предусмотренном схемой тягового электродвигателя, прибор
поочерёдно подносят к каждой катушке. В момент резкого отрыва катушки прибора
полюса стрелка отклоняется в ту или иную сторону и указывает полярность.
Проверку полярности производят также при помощи компаса.
Рисунок 8.2.2.17 - Прибор для проверки
полярности полюсов
Сопротивление изоляции катушек относительно
остова проверяют мегомметром. Сопротивление должно быть не ниже 1,5 мегаома.
Если в процессе проверки будет выявлено, что сопротивление изоляции ниже нормы,
то катушки подвергают сушке. Для этого через них пропускают ток до тех пор,
пока сопротивление не повысится до нормы. Межполюсное расстояние измеряют
штихмасом по концам полюсов, при этом выявляют перекосы полюсов в их посадке на
остове электродвигателя. Изоляцию межкатушечных соединений делают после
предварительной обмазки соединения специальной замазкой, изготовленной из 13%
молотого асбеста, 65% молотого мела, 11% олифы и 11% цапон-лака, взятых по
весу. Асбест и мел высушивают отдельно при температуре 160-200°, размалывают и
просеивают через сито, после чего смешивают. Цапон-лак смешивают с олифой,
вливают в смесь асбеста с мелом и всё это тщательно перемешивают. Замазку
всегда хранят в герметичной таре. Изоляция межкатушечных соединений
осуществляется следующим способом. Накладывают три слоя лакоткани толщиной 0,2
мм вполуперекрышу. Чтобы не было стыков, накладывать слой ленты следует с
предыдущего конца. Каждый слой прокрашивают лаком. По лакоткани накладывают вполуперекрышу
один слой киперной ленты, пропитанной лаком. Концы киперной ленты прошивают
oсуровыми нитками. Поверхность киперной ленты и узла соединения закрашивают
лаком № 1154. Ремонт остова и подшипниковых щитов. Для нормальной работы щеток
существенное значение имеет расположение подшипниковых щитов относительно
остова. Для работы зубчатой передачи не менее существенную роль играет
расположение оси колёсной пары относительно якоря, а следовательно,
относительно подшипниковых щитов, поэтому в заводских условиях при ремонте
остова делают обмер его и подшипниковых щитов. По механической части остова
тягового электродвигателя производят следующие измерения и работы.
Микрометрическим штихмасом замеряют диаметры горловин под подшипниковые щиты.
При измерении определяют их овальность. Если овальность превышает 0,6 мм,
необходимо произвести ремонт горловин. Горловины исправляют расточкой до
следующего ремонтного размера или наплавкой с последующей расточкой, при этом
натяг должен быть +0,08-0,02 мм. Микрометрическим штихмасом измеряют диаметры
моторно-осевых горловин и шапок. Измерение производится в трёх местах каждой
горловины: на расстоянии 10-15 мм от рабочих торцов горловин и в середине. При
овальности и конусности более 0,2 мм производится расточка до ремонтного
размера или наплавка с последующей расточкой и доведением овальности и
конусности не более 0,07 мм. Перед расточкой между привалочными плоскостями
шапки и остова помещают прокладку толщиной 0,5 мм. Микрометрическим, специально
для этого изготовленным штангелем производят измерения между посадочными
плоскостями обеих горловин и их шапок. На основании измерения определяют, какой
натяг или зазор имеют шапки по посадочным плоскостям. При текущем ремонте
допускается постановка шапок с зазором по посадочным плоскостям до 0,05 мм. При
заводском ремонте производится наплавка посадочных поверхностей и их обработка
с таким расчётом, чтобы была обеспечена посадка в интервале между зазором 0,03
и натягом 0,045 мм. Линейкой или штангелем измеряют длину остова по торцам
моторно-осевых горловин и горловин под подшипниковые щиты. При износе торцов,
превышающем нормы, торцы восстанавливают наплавкой с последующей обработкой на
станке. Ввертыванием резьбовых калибров проверяют резьбу под болты
подшипниковых щитов и моторно-осевые болты. Если проходной калибр не проходит,
резьбу исправляют соответствующим метчиком. Отверстия с изношенной и сорванной
резьбой восстанавливают, для чего отверстия заваривают, а затем рассверливают
по кондуктору и снова нарезают. Перед заваркой старую резьбу удаляют
сверлением. Допускается постановка специальных вварных втулок. Остов
внимательно осматривают для выявления трещин. Особенно тщательно осматривают
торцы моторно-осевых горловин, сами горловины и подвешивающие носики. Трещины
заваривают электросваркой с разделкой швов и последующей зачисткой. Трещины
разделываются V-образно или Х-образно. По концам сквозных трещин сверлят
сквозные отверстия диаметром 8-10 мм. При заварке замкнутых трещин концы их
должны быть подогреты. Для заварки применяют электроды типа Э42 или Э42А. Ток
при диаметре электродов 5 мм - 220-250 А. Производить заварку при температуре
ниже 0° и на сквозняке не разрешается. Трещины, идущие от кромки горловины,
следует заваривать от конца трещины к кромке. Масляные камеры шапок
моторно-осевых подшипников проверяют на плотность керосином. Дефектные места
вырубают и заваривают с последующей проверкой на плотность; внутреннюю
поверхность покрывают маслостойкой эмалью. Расточка моторно-осевых горловин и
горловин под подшипниковые щиты производится с одной постановки; при этом
обязательно проверяют:
) расстояние между осями горловины под
подшипниковые щиты и моторно-осевые подшипники; непараллельность допускается не
более 0,25 мм,
) диаметры обеих горловин под моторно-осевые
подшипники и подшипниковые щиты.
У подшипниковых щитов производятся измерения
посадочных мест в горловину остова и посадочных мест под роликовые подшипники.
Измерения делают по двум перпендикулярным диаметрам. На основании измерений
определяют величину натяга или зазора. При ремонте проверяют плотность
постановки крышек коллекторных люков. Внутреннюю их поверхность, так же как
остова и подшипниковых щитов, окрашивают светлой маслостойкой и дугостойкой
эмалью. Изношенные накладки носиков заменяют новыми с цементированной
поверхностью. Ослабшие по заклёпкам накладки при текущем ремонте можно
приваривать по контуру. Подтяжка заклёпок не разрешается.
Ремонт якоря.
Деффектовка якоря. После тщательной продувки и
очистки как снаружи, так и вентиляционных каналов якорь подвергают осмотру и
проверке. Проверяют омическое сопротивление обмоток и сопротивление изоляции
относительно корпуса, отсутствие межвиткового замыкания и качество пайки
петушков. При деффектовке проверяют состояние внутренних подшипниковых колец. В
случае обнаружения на кольцах выработки, задиров, трещин и слабины в посадке
кольца снимают с вала. Вал в местах постановки внутренних колец подшипников и
шестерни, (коническая часть вала) проверяют магнитным дефектоскопом. Коническую
часть вала проверяют калибром покраске. Поверхность прилегания вала к калибру
должна быть не менее 65%; если площадь прилегания меньше, производится
притирка. Резьбовым калибром третьего класса проверяют резьбу вала. При наличии
ослабленной или повреждённой резьбы разрешается перерезать её на меньший
диаметр или восстанавливать наплавкой. Перед наплавкой хвостовик вала нагревают
до 200°. После указанных работ якорь устанавливают в центры токарного станка и
индикатором определяют биение конической части вала, посадочных мест под подшипники
(если они снимались) и лабиринтные кольца. Проверка конуса вала производится на
расстоянии 15 мм от конца и посередине конуса. Посадочные места под подшипники
проверяют по их середине. Биение вала может происходить вследствие: погнутости
вала, овальности посадочных мест под подшипники и шестерни, а также если сбиты
центры вала и неисправен станок. При выпуске из текущего ремонта биение по
беговой дорожке колец подшипников со стороны шестерни не должно быть более 0,05
мм, а со стороны коллектора - более 0,04 мм. Производить сварочные работы у
вала, кроме восстановления нарезанного конца под гайку и центров, запрещается.
Валы, погнутые и имеющие трещины, подлежат замене. При проверке биения следует
помнить, что, согласно правилам ремонта, в случае выработки посадочных мест под
подшипники, разрешается ставить втулки толщиной 3 мм. При помощи микрометра и
линейки определяют диаметр рабочей части коллектора, его ширину, выработку и
диаметр по петушкам. Проверяют биение коллектора по неизношенной поверхности. При
выпуске из подъёмочного ремонта биение коллектора относительно внутреннего
кольца подшипника допускается до 0,06 мм и при выпуске из заводского ремонта -
не более 0,04мм. Коллекторы, изношенные по диаметру выше нормы, подлежат
замене. Мегомметром измеряют сопротивление изоляции якоря. При нулевом
показании мегомметра обмотка якоря должна быть перемотана, а при сопротивлении
менее 1,5 мегаом якорь должен быть подвергнут сушке в печи. Обточка,
продороживание и шлифовка коллектора. Если при осмотре и измерении якоря были
определены выработка коллектора или биение, превышающее норму, коллектор при
текущем ремонте подлежит обточке. При заводском ремонте обточка обязательна.
Хорошие результаты даёт обточка коллектора при окружной скорости 120 м/мин, что
соответствует числу оборотов якоря 110 об/мин. Глубина резания при этом 0,2 мм
и подача резца 0,12 мм. Чтобы медная стружка при обточке коллектора не попадала
на ближайшие части якоря, их закрывают картоном. Запрещается устранять
выработку коллектора при помощи напильников. Если выработка коллектора доходит
до миканитовых прокладок, то перед обточкой рекомендуется коллектор
предварительно продорожить, чтобы предохранить слюду миканита от выкрашивания.
Обточенный на станке коллектор продороживается. Существует несколько
приспособлений для продороживания коллекторов. На рисунке 8.2.2.18 представлено
одно из приспособлений, применяемое в депо и мастерских.
Рисунок 8.2.2.18 - Приспособление для
продороживания коллектора
Где 1 - суппорт; 2 - вал; 3 - рукоятка; 4, 7 и 8
- ремни; 5 - винт; 6 - шкив; 9 - кронштейн; 10 - фреза; 11 - резец.
Приспособление устанавливают на бабке токарного
или другого подобного станка, имеющего центры, в которые устанавливается якорь.
Приспособление прикрепляют к бабке своим суппортом 1. На суппорте устанавливают
электродвигатель (мощностью 0,65 кВт, шкив которого через ремень 4 приводит во
вращение шкив 6. Шкив 6 насажен на вал, другой конец которого также снабжён
шкивом. Последний шкив в свою очередь через ремни 7 и 8 вращает рабочий
шпиндель с фрезой 10. Вся система передаточных шкивов монтируется на
кронштейне, который может быть укреплён в нужном положении винтом 5.
Горизонтальное перемещение приспособления осуществляется салазками суппорта при
помощи рейки, перемещаемой зубчаткой, насаженной на вал 2. Для поворачивания
зубчатки служит рукоятка 3. У приспособления имеется кронштейн 9 для держателя
резца 11, предназначенного для снятия заусениц у коллекторных пластин.
Расстояние между резцом и фрезой соответствует толщине нескольких пластин, это
сделано с таким расчётом, чтобы снятие заусениц производилось у ранее
продороженных пластин. Якорь для продороживания поворачивают вручную, так как
расстояние между коллекторными пластинами имеет значительные допуски и поэтому,
если использовать делительную головку для описанного приспособления, можно
повредить коллекторные пластины по целому месту. У продороженного на станке
коллектора дополнительно снимают заусеницы при помощи шабера, так как не все
заусеницы могут быть удалены на станке. Продороженный коллектор шлифуют при
помощи деревянной колодки, на которую наклеивают стеклянную бумагу. Колодку
закрепляют в суппорте станка. Поверхность колодки, обращенная к коллектору,
должна соответствовать его диаметру. Во время шлифовки рекомендуется давать
станку прямой и обратный ход для удаления оставшихся заусениц. Необходимо
помнить, что заусеницы, перекрывающие межламельное пространство, нарушают
нормальную коммутацию. После шлифовки рабочей поверхности коллектора зачищают
поверхности петушков и коллектор обдувают сжатым воздухом с таким расчётом,
чтобы стеклянная пыль, остатки миканита и медная пыль не попали в обмотку
якоря. Смена отдельных секций якоря. В случае незначительных повреждений
верхнего слоя обмотки якоря (повреждение в лобовой части от замыкания на
корпус) ремонт может быть произведён без полной перемотки якоря. В данном
случае якорь прогревают в печи до 90° для размягчения изоляции, что даст
возможность поднять секцию без повреждения её изоляции, и снимают бандажи.
Нагретый якорь устанавливают наклонно под углом 45° и повреждённую секцию
отпаивают от коллектора электрическим паяльником. После отпайки секцию вынимают
плоскогубцами из шлиц пластин, выбивают клин, удерживающий секцию в пазу, и
вынимают её из паза; повреждённые места проводников освобождают от изоляции.
Если проводник не имеет повреждений, то секцию вновь изолируют и помещают в
печь на несколько часов, где выдерживают при температуре 90°. Залуженные концы
секции вставляют в шлицы коллекторных пластин при помощи плоскогубцев и
стальной подбойки. В пазовую часть секцию заправляют при помощи фибровой
подбойки и закрепляют текстолитовыми клиньями. Длина фибровой подбойки должна
быть примерно равна половине длины пазовой части секций. Для укладки лобовых
частей секции применяют деревянную подбойку, изготовляемую из твёрдых пород
дерева. Все типы подбоек должны иметь закругления по краям радиусом 4-5 мм.
Если нет никаких неисправностей, то якорь подвергают пропитке и сушке. Изоляцию
отремонтированного якоря подвергают испытанию на электрическую прочность
переменным током напряжением 1900 В. В случае повреждения нижнего слоя секций
вынимают верхний ряд на протяжении целого шага и ремонт осуществляют способом,
описанным выше. При больших повреждениях секций производится полная перемотка
якоря.
Смена бандажей.
У якорей тяговых электродвигателей применяют два
типа бандажей: проволочные и шпагатные. Проволочные бандажи 23 (рисунок
8.2.2.1) накладывают поверх секций якоря и уравнительных соединений (для двигателей
ДК-304Б, строившихся до 1951 г.), шпагатные - на миканитовый конус снаружи, а в
лобовой части секции и уравнительных соединениях - внутри. Ослабшие бандажи
подлежат обязательной замене с последующей проверкой на разрыв при повышенной
скорости вращения якоря. При заводском ремонте бандажи заменяют независимо от
их состояния. Для проволочных бандажей применяют бандажную проволоку. Натяжение
проволоки создаёт в ней напряжение, равное 0,5-0,7 предела текучести. Расчётные
напряжения от центробежной силы обмотки должны быть меньше, чем напряжения от
натяжения проволоки, что надо иметь в виду в случаях применения проволоки
различного диаметра для одних и тех же типов электрических машин. При замене
бандажной проволоки во время ремонта проволокой другого диаметра число витков
бандажа меняется обратно пропорционально квадрату отношения диаметров (а не
отношению диаметров, как это иногда делается). Бандажирование производится на
специальных бандажировочных и токарных станках, снабжённых приспособлением для
натяжения проволоки. В процессе бандажирования натяжение должно быть
постоянным. Натяжение на станках создаётся пропусканием проволоки через канавки
блоков и дополнительным усилием, полученным за счёт тормоза или груза. Для
контроля за величиной натяжения используют динамометр. На рисунке 8.2.2.19
представлен бандажировочный станок типа ПКБ ЦТЭ. Станок состоит из станины 7,
передней 2 и задней 7 бабок, каретки 4 и системы блоков предварительного
натяжения бандажной проволоки 13. Станину коробчатого сечения изготовляют из
чугуна. Для перемещения по направляющим каретки и задней бабки служит рейка 11,
укреплённая посередине станины. Передняя бабка приводится в движение
электродвигателем 10 через клиноремённую и червячную передачу. Она состоит из
чугунного корпуса, червячного колеса, шпинделя и червяка, муфты включения и
планшайбы. На передней стенке корпуса крепится кнопочный пост управления 3 и
переключатель числа оборотов. На конце вала червяка между кронштейном и задней
стенкой корпуса смонтирован конический фрикцион 9. Включение фрикциона
осуществляется нажатием на педаль 15, а выключение - пружиной 16. Регулирование
усилия нажатия и усилия отключения фрикциона производится затяжкой или
ослаблением пружины.
Рисунок 8.2.2.19 - Станок для бандажирования
якорей
Где 1 - станина; 2 - передняя бабка; 3 - пост
управления; 4 - каретка; 5 - динамометр; 6 - приспособление для продороживания
коллектора; 7 - задняя бабка; 8 - храповой механизм; 9 - конический фрикцион;
10 и 12 - электродвигатели; 11 - рейка; 13 - блоки; 14 - механизм передвижения;
15 - педаль; 16 - пружина.
Задняя бабка 7 состоит из корпуса, плиты,
пиноли, механизма закрепления пиноли и механизма передвижения. Задняя бабка
перемещается по направляющим посредством механизма передвижения 14, состоящего
из вала и шестерни. Храповой предохранительный механизм 8 препятствует
перемещению задней бабки, после того как установлен якорь. Кроме
предохранительного механизма, на плите предусмотрены также зажимные болты. Пиноль
служит для окончательного зажима вала якоря в центрах. Закрепление пиноли
делают зажимным устройством токарного типа. Каретка 4 служит для рядовой
укладки проволоки на бандажируемом якоре и для регулирования величины натяжения
проволоки, которое осуществляется системой подвижных и неподвижных блоков. На
каретке расположен динамометр 5, показывающий величину натяжения проволоки.
Станок может быть приспособлен для продороживания коллекторов. Для этого на
заднюю бабку устанавливают приспособление 6 съёмного типа. Приспособление
состоит из кронштейна, коробки, плиты и подвижных салазок. На подвижных
салазках установлен электродвигатель 12 и укреплён рычаг несущий шпиндель с
фрезой. Связь между электродвигателем и шпинделем осуществляется клиноремённой
передачей. Посредством конических шестерён и упорного винта, расположенных
внутри кронштейна, осуществляется перемещение всего приспособления вверх и вниз
по вертикальным направляющим. Для закрепления концов бандажей и предохранения
витков от раздвигания применяют замковые и промежуточные скобочки из белой
жести толщиной 0,25 мм для бандажной проволоки диаметром 0,6-1,2 мм и 0,36 мм
для проволоки диаметром 1,5-2 мм. Скобочки укладывают при намотке первого витка
бандажа. Начало и конец проволоки перекрывают таким образом, чтобы между
замковыми скобочками бандаж имел на одну проволоку больше, чем в остальных
сечениях. На рисунке 8.2.2.20 показаны узел соединения концов бандажей тягового
электродвигателя ДК-304Б при помощи замковых скоб (а) и наложение бандажей у тягового
электродвигателя ЭДТ-200А. Под проволочным бандажом в данном случае укладывают
подбандажную изоляцию, состоящую из гибкого миканита, электрокартона,
асбестовых лент и бумаги. Промежуточные скобы, располагающиеся на равных
расстояниях по окружности, отгибают на 4-5 витков. У бандажа, находящегося со
стороны коллектора, под четыре витка проволоки дополнительно укладывают гибкий
миканит и чехол из сурового полотна.
Рисунок 8.2.2.20-Бандажная укладка на якорях тяговых
электродвигателей
Где а - крепление концов бандажа тягового
электродвигателя ДК-304Б; б - двойной бандаж тягового электродвигателя.
Намотка бандажа должна производиться таким
образом, чтобы между витками не было промежутков. Поэтому витки проволоки подбивают
один к другому тупым бородком, по которому слегка ударяют молотком. Натяжение
бандажной проволоки должно быть при диаметре 2 мм 200 кг и диаметре 2,5 мм -
310 кг. Для более равномерного распределения центробежной силы и предохранения
бандажной проволоки от мгновенной размотки при обрыве проволоку и скобочки
подвергают пайке (сплавом ПОС-60 или чистым оловом). При пайке незакрытую часть
обмотки временно изолируют киперной лентой. Пайка производится сначала только у
скобочек, а затем и по всей поверхности проволоки. Бандаж между скобочками
пропаивают частями с таким расчётом, чтобы не произошло его ослабления при
нагревании. Рекомендуется пропаивать диаметрально расположенные части. Для
пайки бандажей служит электрический паяльник, дающий температуру поверхности до
400°; в качестве флюса применяется раствор канифоли в бензине. Применение для
пайки бандажей кислоты, вредно действующей на изоляцию, запрещается. На
бандажах не должно быть наплывов сплава, поэтому в процессе пайки бандажи
очищают металлической щёткой от канифоли и оставшихся наплывов сплава. При
пайке необходимо следить за тем, чтобы не произошло подгорания изоляции, сплав
не попал в обмотку и не было контакта между бандажом и железом якоря. При
ремонте запрещается: остукивать проволочные бандажи над пазом, производить
зачистку бандажей инструментом, наносящим поперечные риски на проволоке,
оставлять на бандажах и других местах якоря капли и сплески припоя и флюса, а
также выступающие над поверхностью бандажа концы витков проволоки в замке. Во
время намотки и пайки следует также обращать внимание на то, чтобы у бандажной
пропаянной проволоки и скобочек не было трещин. Пайка петушков коллектора. В
случаях подплавления припоя петушков коллектора производится их пайка при
помощи электрического паяльника или в заводских условиях в специальных ваннах с
электрическим обогревом. В качестве припоя применяется сплав ПОС-61, а в
качестве флюса-канифоль в сухом виде или раствор ее в бензине. Перед пайкой
проверяют, нет ли межвиткового замыкания. Чтобы припой не попадал на обмотку
при ручной пайке, якорь устанавливают в наклонное положение коллектором вниз.
На рисунке 8.2.2.21 показана ванна для пайки коллектора. Ванна состоит из
каркаса 9, в котором имеется цилиндрический 6 и кольцевой 3 резервуары, обогреваемые
электрическим током. В кольцевой резервуар на тросах 2 при помощи блоков 5 и
привода 1 опускается цилиндрической формы поплавок 4у вытесняющий расплавленный
припой к петушкам коллектора. Чтобы припой не попадал на пластины коллектора,
якорь 7 уплотняют при помощи асбестового шнура 8. По окончании пайки поплавок
поднимают электродвигателем 10 к верху и припой стекает обратно в кольцевой
резервуар. При таком способе пайки получается значительная экономия
дорогостоящего припоя и во много раз сокращается время пайки.
Рисунок 8.2.2.21 - Ванна для пайки коллектора
Где 1 - привод; 2 - трос; 3 - кольцевой
резервуар; 4 -поплавок; 5 - блоки; 6 - цилиндрический резервуар; 7 - якорь; 8 -
уплотнение (асбестовый шнур); 9 - каркас; 10 - электродвигатель.
Ремонт вала. В случаях ослабления внутреннего
кольца подшипника на валу якоря или задира вала применяют два способа
восстановления поверхности. Один способ - металлизация и второй - насадка
промежуточной втулки между валом и внутренним кольцом. Восстановление
поверхности металлизацией включает три операции: подготовку поверхности под
металлизацию, металлизацию и окончательную обработку. Место посадки подшипников
якоря перед металлизацией должно быть очищено от грязи, масла и обточено с
образованием рваной поверхности (шаг 0,75 мм, глубина 0,5 мм). Рваную
поверхность нарезают за один проход без смазки и охлаждения. Разрыв времени
между окончанием нарезания поверхности и началом металлизации не должен
превышать 2 ч во избежание окисления поверхности. Металлизация осуществляется
на токарном или специальном станке. Число оборотов вала соответствует окружной
скорости металлизируемой поверхности 10-15 м/мин. Пистолет-распылитель для
металлизации устанавливают в суппорте, перпендикулярно к металлизируемой
поверхности, или выше центровой линии вала на 3-5 мм. Скорость перемещения
суппорта с пистолетом за один оборот вала 1,5 мм. Для увеличения силы сцепления
распылённых частиц рекомендуется несколько подогреть металлизируемую поверхность.
В качестве металлизационного материала применяют стальную проволоку с
содержанием углерода 0,3-0,4%. Металлизированную поверхность доводят до
требуемых размеров при помощи обточки и шлифовки обычным способом. Посадка
втулок на вал состоит из следующих операций:
) проточки вала на станке с соблюдением
переходных радиусов;
) изготовления втулки со стенкой толщиной 3 мм с
радиусом под галтель и натягом под запрессовку в пределах 0,05-0,06 мм;
) посадки втулки, нагретой до 110-120°, на вал;
) обработки наружной поверхности втулки по 8-му
классу чистоты с таким расчётом, чтобы натяг под запрессовку кольца роликового
подшипника был в пределах 0,00-0,03 мм. Степень плотности посадки втулки
проверяют остукиванием.
Рисунок 8.2.2.22 - Общий вид станка для
балансировки типа 15ВЛ
Где 1 - электродвигатель; 2 - клиноремённая
передача; 3 - рычаг; 4 - шкив; 5 -пластины; 6 - тормоз; 7 - труба маятниковой
рамы; 8 - роликовая опора; 9 - поперечина; 10 - вертикальная стойка; 11 -
фундамент; 12 - чертилка; 13 - индикатор; 14 - пружина; 15 - винт.
Для установки балансируемых деталей на
поперечинах укрепляют роликовые опоры 8. При балансировке деталей с
подшипниками качения ролики иногда заменяют подушками, в которые входят
наружные кольца подшипников. Одним концом маятниковая рама опирается на
спиральные пружины 14, а другим при помощи накрест расположенных стальных
пластин 5 подвешена к вертикальным стойкам 10. Пластины позволяют маятниковой
раме поворачиваться вокруг своей оси и удерживаться от продольных и
вертикальных перемещений. Каждая пружина закреплена верхним концом к подушке,
связанной с маятниковой рамой, а нижним - к шайбе, соединённой с винтом,
который служит для установки маятниковой рамы в горизонтальное положение.
Положение пружин относительно маятниковой рамы может меняться, чем достигается
изменение периода собственных колебаний рамы. Балансируемый якорь приводится во
вращение от электродвигателя 1, смонтированного на стойке. Шкив электродвигателя
через клиноремённую передачу 2 связан со шкивом 4, смонтированным на рычаге 3.
Приблизив рычагом ремень к валу балансируемого якоря, приводят его во вращение.
Вал якоря служит в данном случае натяжным устройством. Во время разгонки якоря
маятниковую раму затормаживают штурвалом тормоза 6, зажимающего сухарями концы
пружинящих пластин, которые связаны с маятниковой рамой. Угол отклонения
маятниковой рамы от её среднего положения ограничивается упором, выполненным из
угловой стали, в котором сделан соответствующий вырез для пластины. Амплитуды
колебаний рамы записывает откидная чертилка 12 на закопчённом стекле; для
фиксации малых амплитуд предназначен токарный индикатор 13, закреплённый на
специальной стойке. Рама станка устанавливается на фундаменте по уровню. Для
получения более точных результатов балансировки якорей тяговых
электродвигателей на станках 15ВЛ Главное управление локомотивного хозяйства
рекомендует устанавливать двойные пружины под маятниковую раму. Технологический
процесс балансировки якорей тяговых электродвигателей в депо и мастерских
состоит из трёх этапов: подготовки и установки якоря на станке, определения
места расположения и величины противовеса и определения величины остаточного
дисбаланса. Для правильной установки якоря тягового электродвигателя на станке
необходимо произвести следующие операции: снять кольца ролико-подшипников и
тщательно очистить якорь; концы вала обтереть сухой салфеткой; маятниковую раму
затормозить тормозом; приподнять якорь и установить его на ролики поперечин
маятниковой рамы так, чтобы вертикальная плоскость, проходящая через середину
заднего бандажа, совпала с осью вращения маятниковой рамы; убедиться в
отсутствии зазора между валом и установочными роликами; отпустить тормоз;
поворачивая маховички у спиральных пружин, установить якорь с маятниковой рамой
в горизонтальное положение. Далее следует произвести разгон якоря
электродвигателем 1 (рисунок 8.2.2.22) до 200-300 об/мин. Для устранения
посторонних колебаний, появляющихся при разгоне якоря, тормоз следует слегка
прижать пока колебания не прекратятся и затем отпустить до упора. После 5-10
сек свободного вращения якоря чертилку надо прижать к закопчённому стеклу;
затем остановить якорь, откинуть чертилку, вынуть стекло из гнезда и измерить
линейкой наибольшую амплитуду колебания маятниковой рамы; нанести мелом на
торце коллекторной коробки четыре метки через 90° одна от другой; прикрепить к
торцу коллекторной коробки против одной из меток уравновешивающий груз
произвольного веса (в качестве уравновешивающего груза обычно применяется
мастика); после этого снова привести во вращение якорь и записать максимальную
амплитуду колебаний. Эти же операции необходимо произвести последовательно для
четырёх положений противовесов, каждый раз устанавливая уравновешивающий груз
против одной из меток на торце коллекторной коробки. Величину амплитуды
записывают против соответствующего положения противовеса, например: Истинное
положение противовеса всегда будет находиться между двумя наименьшими
значениями амплитуды колебаний. В приведённом примере оно находится где-то
между третьей и четвёртой метками. Для нахождения истинного положения
противовеса уравновешивающий груз нужно перемещать между этими метками до тех
пор, пока амплитуда колебания маятниковой рамы станет наименьшей. Дальнейшее
уменьшение амплитуды колебания производится за счёт изменения веса
уравновешивающего груза. Изменять вес груза надо до тех пор, пока его
уменьшение или увеличение не будет больше уменьшать амплитуду колебания
маятниковой рамы. Затем следует точно взвесить уравновешивающий груз (мастику),
при котором амплитуда колебания маятниковой рамы была наименьшей, и отметить
место уравновешивающего груза. На основании этих определений устанавливают
величину остаточного дисбаланса. После этого необходимо затормозить маятниковую
раму, поднять якорь, повернуть его на 180° и установить на станке так, чтобы
вертикальная плоскость, проходящая через приваренный противовес, совпала с осью
вращения маятниковой рамы. Затем снова произвести последовательно все операции
для определения места противовеса. Определив вес уравновешивающих грузов,
изготовляют стальные пластины того же веса и приваривают их в отмеченных
местах.
Ремонт и установка щеткодержателей. Притирка
щеток и проверка нажатия их на коллектор.
У тяговых электродвигателей разных серий
тепловозов осуществлена различная конструкция щёткодержателей. На рисунке
8.2.2.23 изображён щёткодержатель электродвигателя ДК-304Б. Корпус 1
щёткодержателя, отлитый из бронзы ОЦС-3-12-5, прикрепляется к кронштейну щёткодержателя
4 двумя болтами 2, снабжёнными пружинными шайбами 3. Для фиксации положения
щёткодержателей относительно коллектора корпус щёткодержателя и кронштейн имеют
гребёнчатую поверхность.
Рисунок 8.2.2.23 - Щёткодержатель тягового
электродвигателя ДК-304Б
Где 1 - корпус щёткодержателя; 2 - болт; 3 -
пружинная шайба; 4 - кронштейн щёткодержателя; 5 - болт; 6 - палец; 7 -
миканитовый цилиндр; 8 - изолятор; 9 - ленточная пружина; 10 - ось; 11 -
шплинт; 12 - щётка; 13 - втулка; 14 - шайба; 15 - пружинная шайба; 16 - винт.
Кронштейн прикрепляется к остову двумя болтами
5, которые ввёрнуты в стальные пальцы 6, изолированные от кронштейна
миканитовыми цилиндрами 7. На концы миканитовых цилиндров надеваются фарфоровые
изоляторы 8. В собранном виде пальцы щёткодержателя испытывают на электрическую
прочность по отношению к корпусу переменным током напряжением 4000 В в течение
1 минуты. Миканитовый цилиндр не должен иметь ослабления посадки на пальце,
сопротивление изоляции должно быть не менее 50 мегаом. Наличие гребёнчатой
поверхности позволяет достаточно точно устанавливать корпус щёткодержателя
относительно коллектора с зазором 2-4 мм. Для этого под обойму щёткодержателя
на поверхность коллектора накладывают деревянную дощечку толщиной 3 мм, шириной
30 мм и длиной 150 мм. Перемещая корпус щёткодержателя до совпадения зубьев
гребёнки, укрепляют болты 2, которые свободно входят в овальные отверстия
корпуса 1. Затем проверяют фактически полученный зазор между корпусом и коллектором,
причём для обоих краёв обойм расстояния до коллектора должны быть одинаковы.
Проверку правильности установки щёткодержателей относительно остова делают при
помощи шаблона, имеющего форму скобы с упорами. У тяговых электродвигателей
плоскость симметрии щёток должна проходить через центр якоря. При
незначительных и несквозных повреждениях глазури изоляторы при текущем ремонте
не заменяют. Разработанные отверстия под болты у корпуса щёткодержателя
восстанавливают наплавкой. При текущем ремонте трещины корпусов разделывают и
заваривают газовым пламенем с предварительным подогревом. Заваривать трещины у
основания прилива не разрешается. Для уменьшения размеров обойм под щетку
разрешается производить их осадку в горячем состоянии или отжиг при температуре
600-650°. После термической обработки размеры обойм доводятся до нормы путём
протяжки или опиловки. Щёткодержатели тяговых электродвигателей ДК-304Б, а
также двигателей ЭДТ-200А (тепловозов ТЭ3) имеют другую конструкцию (рисунок
8.2.2.24); их щёткодержатели имеют меньший вес и изменённое крепление к остову.
Регулирование щёткодержателя относительно остова производится перемещением
пальцев 1 в зажимах.
Рисунок 8.2.2.24 - Щёткодержатель тягового
электродвигателя ДК-304Б и ЭДТ-200А
Где 1 - палец.
Для правильной работы щёток необходимо
установить нормальное нажатие на них (для тепловозов ТЭ1, ДЭ2 и ДА
3-4 кг). Уменьшенное против нормы нажатие вызывает искрение, а увеличенное -
повышенный износ коллектора и щёток. Нажатие на щётки измеряется пружинными
весами (динамометром), захватывающими конец ленточной пружины 9 в месте
прилегания её к щётке (рисунок 8.2.2.23). В корпусе щёткодержателя 1 закреплена
ось 10 с насаженными на неё втулками 13; втулки имеют прорезы, в которые заведены
концы ленточных пружин. Другие концы пружин упираются в щётки 12. За эти концы
и зацепляют пружинные весы. У втулок 13 предусмотрены отверстия, при помощи
которых втулка может быть установлена в различные положения, чем и
обеспечивается регулирование нажатия пружин на щётки. После регулирования
втулки закрепляются разводными шплинтами 11. Следует отметить, что
регулирование нажатия пружин на щётки затруднено особенно у тепловозов с
трёхосными тележками. Поэтому величину нажатия нужно тщательно регулировать при
ремонте тяговых электродвигателей, когда тележки выкачены из-под тепловоза. При
постановке новых щёток величину нажатия принимают ближе к верхнему допускаемому
пределу; это даёт возможность при износе щётки по высоте до 30 мм сохранить
необходимое давление. В случае замены щёток последние должны быть притёрты по
коллектору. Притирку можно производить непосредственно на тяговом
электродвигателе или в специальном приспособлении. Приспособление (рисунок
8.2.2.25) представляет собой барабан 7, укрепляемый на вертикальном валу 6,
нижний конец которого вращается в подшипнике 8. Верхний конец вала вращается в
подшипнике 5, смонтированном в стойке 2. Для вращения барабана служит маховик
3, снабжённый рукояткой 4.
Рисунок 8.2.2.25 - Приспособление для притирки
щёток
Где 1 - стеклянная бумага; 2 - стойка; 3 -
маховик; 4 - рукоятка; 5 - верхний подшипник; 6 - вертикальный вал; 7 -
барабан; 8 - нижний подшипник; 9 - плита; 10 - щётка; 11 - щёткодержатель; 12 -
кронштейн; 13 - валик для стеклянной бумаги.
Притираемые щётки 10 вместе со щёткодержателем
11 укрепляются на кронштейнах 12, которые в свою очередь прикрепляются к плите
9. Для навивки на барабан стеклянной бумаги 1 служит валик 13. Ввиду того что
диаметр барабана обычно не совсем точно соответствует диаметру коллектора,
окончательную притирку делают на самом тяговом электродвигателе. Для этого
между коллектором и щётками прокладывают стеклянную бумагу или абразивной
поверхностью к щёткам. После притирки щётка всей своей поверхностью должна
прилегать к коллектору, а после нескольких часов работы эта поверхность должна
стать блестящей. Шунты окончательно притёртых щёток закрепляют винтами 16
(рисунок 8.2.2.23) с постановкой шайб 14 и 15.
Сборка тягового электродвигателя.
Сборка остова электродвигателя производится в
порядке, изложенном в разделе "Ремонт катушек полюсов сердечников и
остова". Подшипниковые щиты после ремонтных операций (очистки, заварки,
наплавки) проверяют по их комплектности с остовом. Далее делают подбор
подшипников, если их надо заменить, а в случае установки старых проверяют
соответствие номеров на внутренних и наружных кольцах. Подшипник со стороны
коллектора устанавливают в щит так, чтобы его посадка была в интервале между
натягом 0,016 и зазором 0,061, а со стороны шестерни - соответственно натягом
0,018 и зазором 0,068 мм. Овальность посадочных мест допускается при текущем
ремонте до 0,08 мм и заводском - до 0,05 мм. Запрессовка подшипника
производится прессом в холодном состоянии. Категорически запрещается вставлять
подшипники при помощи ударов. После запрессовки ролики и сепаратор смазывают
смазкой 1-13. Внутренние кольца подшипников, снятые с вала якоря или
устанавливаемые вновь, подогревают в масляной ванне до 100-110° в течение 40
мин. Одна из конструкций масляных ванн показана на рисунке 8.2.2.26. В этой
ванне подогревают кольца подшипников с большими габаритными размерами, чем
подшипники тяговых электродвигателей, и, в частности, буксовые подшипники.
Рисунок 8.2.2.26 - Ванна для подогрева
подшипниковых колец в масле
Где 1 - сосуд; 2 - крышка; 3 - ручка; 4 -
асбестовая изоляция; 5 - полочка; 6 - балочка; 7 - кольцо подшипника; 8 -
крючок; 9 - спускной кран; 10 - штуцер; 11 - электрическая печь.
Ванна для подогрева подшипников в масле
представляет собой железный сосуд 1 ёмкостью 260 л с двойными стенками,
закрываемый сверху двустворчатой крышкой 2. Боковые стенки и крышка оборудованы
ручками 3 для подъёма ванны и открывания крышки. Между двойными стенками и у
ручек крышки предусмотрена асбестовая изоляция 4. К внутренним стенкам ванны
приварены полочки 5, на которые укладываются балочки 6; к балочкам
подвешиваются кольца подшипников 7 на крючках 8. Для слива масла в нижней части
ванны имеется спускной кран 9; в штуцер 10 вставляется термометр для контроля
температуры. Ванна подогревается электрической печью 11. Печь может быть
выдвинута для ремонта и осмотра. Масло в ванне необходимо периодически
фильтровать и менять. Перед нагревом подшипникового кольца измеряют диаметры
вала и кольца. Натяг должен быть в пределах 0,00-0,03 мм. Нагретое кольцо
должно свободно входить на вал и прижиматься к упорному бурту. Подготовленные к
сборке остов вместе со щёткодержателями (если они не разбирались),
подшипниковые щиты с подшипниками и якорь с внутренними кольцами размещают на
сборочной площадке. Затем в остов запрессовывают подшипниковый щит со стороны
коллектора. Запрессовка ведётся; равномерным завёртыванием диаметрально
расположенных болтов. Щит можно запрессовывать как в горизонтальном, так и в
вертикальном положении остова. У запрессованного щита проверяют щупом, нет ли
зазора между торцом горловины остова и прилегающей к нему плоскостью
подшипникового щита. Зазоры допускаются не более 0,15 мм на восьмую часть
окружности. Остов с подшипниковым щитом устанавливают краном на деревянную
рамку коллекторной стороной вниз. Якорь обдувают воздухом и опускают в остов.
При повороте якоря из горизонтального положения в вертикальное под вал со
стороны коллектора помещают подкладку с тем, чтобы упор во время подъёма
приходился на вал, а не на коллектор. Перед опусканием якоря внутреннее кольцо
подшипника смазывают консистентной смазкой с предварительной обтиркой чистой
салфеткой. Крышку подшипникового щита со стороны шестерни временно закрепляют
несколькими болтами. Подшипниковый щит в таком виде опускают на остов и
закрепляют болтами в таком же порядке, как и щит со стороны коллектора.
Плотность постановки щита в остов проверяют щупом. Далее остов устанавливают в
горизонтальное положение и отвёртывают болты, временно укрепляющие крышку со
стороны шестерни. Щупом проверяют диаметральные зазоры у подшипников. Якорь в
подшипниках должен свободно поворачиваться от руки. При затруднительном вращении
якоря следует проверить, нет ли перекосов в креплении подшипниковых щитов,
касания между якорем и сердечниками полюсов, а также обоймами щёткодержателей и
коллекторами. Кроме проверки вращения якоря, проверяют при помощи индикатора
торцовое биение наружных колец подшипников. На рисунке 8.2.2.27 а, изображено
приспособление, используемое для проверки биения кольца со стороны коллектора.
Приспособление состоит из корпуса в котором просверлены три отверстия для
болтов 2, прикрепляющих корпус к валу якоря. Для укрепления индикатора
используют стойку 3 и кронштейн, снабжённые зажимами. Принцип устройства
приспособления для проверки биения кольца со стороны шестерни (рисунок 8.2.2.27
б) аналогичен описанному выше приспособлению. Коническая втулка 5, имеющая тот
же конус, что и конец вала, укрепляется гайками 6 и 7.
Рисунок 8.2.2.27 - Приспособления для проверки
торцового биения колец подшипников
Где а - со стороны коллектора; б - со стороны
шестерни; 1 - корпус; 2 - болт; 3 - стойка; 4 - кронштейн; 5 - втулка; 6 и 7 -
гайки.
Чтобы получить устойчивые показания при
измерении биения, остов с якорем устанавливают в наклонное положение. Величина
торцового биения у подшипника со стороны коллектора допускается не более 0,14
мм, а со стороны шестерни - не более 0,20 мм. Если биение оказалось выше нормы,
необходимо проверить, все ли болты подшипниковых щитов туго затянуты и нет ли
других дефектов (заусеницы, грязь на посадочных поверхностях и т. п.). После
проверки биения определяют величину осевого разбега якоря, который должен
находиться в пределах 0,15-0,4 мм. Проверка осевого разбега производится при
установленном упорном кольце подшипника (со стороны коллектора), поставленных
на место и закреплённых болтами упорной и стопорной шайбах. Если осевой разбег
якоря мал, следует прошлифовать на необходимую величину торцовую часть упорного
кольца со стороны коллектора. Если осевой разбег якоря велик, надо заменить
упорное кольцо или прошлифовать торцовую часть кольца, прилегающего к внутреннему
кольцу подшипника, и соответственно этому конусную часть, сохраняя при этом
чертёжный угол скоса. Подобрав кольцо, вновь проверяют осевой разбег якоря.
После произведённых проверок закладывают консистентную смазку, и крышки
подшипниковых щитов устанавливают на место. Всего должно быть заложено в
подшипниковую камеру со стороны коллектора 600 г смазки и со стороны шестерни
1200 г. Как уже отмечалось выше, избыточное количество смазки может вредно
отразиться на работе тягового электродвигателя. При окончательной постановке
крышек подшипников для заполнения зазора между крышками и подшипниковыми щитами
их торцовые поверхности покрывают свинцовыми белилами. На вал якоря
напрессовывают в горячем состоянии лабиринтное кольцо (со стороны шестерни),
затем устанавливают на место коллекторные люки. У собранного электродвигателя
проверяют зазоры между щёткодержателями и петушками, щёткодержателями и рабочей
поверхностью коллектора; они должны быть отрегулированы в соответствии с
нормами. Затем устанавливают на место притёртые заранее щётки. При заводском
ремонте щёткодержатели устанавливают после постановки крышек подшипников. При
помощи длинного щупа измеряют зазор между полюсами и якорем. Для проверки
правильности монтажа подшипников электродвигатель включают под напряжение
75-100 В. После сборки тягового электродвигателя торцовую поверхность
лабиринтного кольца, остов, подшипниковые щиты и коллекторные люки покрывают
лаком. Насадку ведущей шестерни на вал якоря делают в нагретом состоянии.
Недостаточно плотная насадка шестерни может привести к провертыванию её на валу
во время работы, так как никаких стопорящих устройств у посадочного конуса не
предусмотрено. Слишком плотная насадка может вызвать появление трещин в теле
шестерни, а кроме того, делает затруднительной и даже невозможной съемку
шестерни с вала при последующем ремонте. Поэтому шестерни насаживают в
определённом порядке. Посадочные поверхности вала якоря и отверстия шестерни
тщательно протирают салфеткой, смоченной в бензине. На этих поверхностях не должно
быть заусениц и ржавчины. По краске проверяют прилегание конических
поверхностей; оно должно быть не менее 65%. Если поверхность прилегания менее
65%, делают притирку. Перед посадкой шестерни приспособлением, изображённым на
рисунке 8.2.2.28, устанавливают зазор 1,3-1,5 мм между штифтом 5
микрометрического винта и торцом вала 6 (у холодной шестерни). Затем шестерню
нагревают до 100° в электрической печи или Кипящей воде с раствором соды (10 г
на 1 л воды) и вместе с приспособлением насаживают до упора- штифта
микрометрического винта 4 в торец вала. В таком состоянии шестерня остаётся на
валу до полного её охлаждения. Приспособление своим стержнем 2 как до нагрева
шестерни, так и после нагрева устанавливают в одну и ту же впадину между
зубьями, чтобы не исказить замеров.
Рисунок 8.2.2.28 - Приспособление для проверки
посадки ведущей шестерни на вал якоря
Где 1 - шестерня; 2 - стержень; 3 - кронштейн; 4
- микрометрический винт; 5 - штифт; 6 - вал якоря.
После насадки шестерни на конец вала ставят
замочную пластину и гайку, которую затягивают усилием в 50 кг при помощи ключа
с рычагом длиной 1 м.
8.2.3 Диагностика тяговых электродвигателей
Для диагностирования тяговых электродвигателей
используются основные методы диагностирования: неразрушающий контроль и
разрушающий контроль.
Неразрушающий контроль.
Неразрушающий контроль включает в себя:
электрический, вихретоковый, тепловой, радиоволновой, ультразвуковой методы,
виброакустический. Неразрушающий контроль - последняя и в ряде случаев
единственно возможная технологическая операция, позволяющая выявлять
недопустимые дефекты в технических объектах и тем самым предотвращать
возникновение чрезвычайных ситуаций на железнодорожном транспорте.
Техническая диагностика - область знаний,
охватывающая теорию, методы и средства определения технического состояния
объектов. Техническое диагностирование - процесс установления технического
состояния объекта с указанием места, вида и причин возникновения дефектов и
повреждений.
Надёжностью является наиболее полной оценкой
качества объектов (изделий). Под надёжностью понимают свойство объекта
(изделия) сохранять во времени в установленных пределах значения всех
параметров, Характеризующих способность его выполнять требуемые функции в заданных
режимах и условиях применения, технического обслуживания, ремонтов, хранения и
транспортирования. Надёжность - сложное свойство, состоящее из сочетания таких
свойств, как безотказность, долговечность, ремонтопригодность и сохраняемость.
Безотказность - это свойство объекта (изделия) непрерывно сохранять
работоспособное состояние в течение некоторого времени или наработки.
Долговечность - свойство объекта (изделия) сохранять работоспособное состояние
до наступления предельного состояния при - установленной системе технического
обслуживания и ремонта. Ремонтопригодность - свойство объекта (изделия),
заключающееся в приспособленности к предупреждению и обнаружению причин
возникновения отказов и повреждений, а также поддержанию и восстановлению
работоспособного состояния путём проведения технического обслуживания и
ремонтов.
Ультразвуковая дефектоскопия
Ультразвуковой контроль основан на способности
ультразвуковых волн проникать в металл на большую глубину и отражаться от
находящихся в нем дефектных участков. В процессе контроля пучок ультразвуковых
колебаний от вибрирующей пластины вводится в контролируемый шов. При встрече с
дефектным участком ультразвуковая волна отражается от него и улавливается
другой пластиной, которая преобразует ультразвуковые колебания в электрические.
Эти колебания после усиления подаются на экран электронно-лучевой трубки
дефектоскопа, свидетельствуя в виде импульса о наличии дефектов. При контроле
щуп перемещают вдоль шва, прозвучивая таким образом различные по глубине зоны
шва. По характеру импульсов судят о протяженности дефектов и глубине их
залегания. К преимуществам ультразвуковой дефектоскопии относятся: возможность
обнаружения внутренних дефектов, большая проникающая способность, высокая
чувствительность, возможность определения места и размера дефекта. Вместе с
тем, метод имеет ряд отрицательных особенностей. К ним относится необходимость
специальных методик контроля отдельных типов изделий, высокой чистоты
поверхности детали в месте контроля, что особенно затрудняет дефектоскопию
наплавленных поверхностей. Поэтому указанным методом контролируются детали, для
которых разработаны необходимые технологии, регламентирующие зоны и
чувствительность контроля; места ввода ультразвуковых волн в изделие; тип
дефектоскопа; тип искательной головки.
Вихретоковая дефектоскопия.
Метод вихретоковой дефектоскопии дает
возможность обнаружения поверхностных и подповерхностных дефектов. Он основан
на использовании действия вихревых токов, возникающих в поверхностном слое
контролируемой детали от пронизывания его магнитным потоком, на первичную или
особую измерительную катушку. Сущность метода состоит в следующем. Если к
контролируемой поверхности приблизить катушку, по которой протекает переменный
ток, то в металле возникнут замкнутые вихревые токи. Величина этих токов
зависит от частоты возбуждающего тока, электропроводности и магнитной
проницаемости материала изделия, относительного расположения катушки и детали,
от наличия на поверхности дефектов типа нарушения сплошности. Магнитное поле
вихревых токов направлено против основного магнитного потока и несколько гасит
его, что может быть измерено величиной полного сопротивления генерирующей
катушки. В случае изменения вихревых токов, изменяется и полное сопротивление.
Изменение величины вихревых токов может быть обнаружено с помощью другой
(измерительной) катушки.
Виброакустический метод.
Виброакустический метод - это наиболее
эффективный из известных методов технической диагностики двигателей. Метод
позволяет на работающем двигателе вести обнаружение ключевых дефектов,
определяющих его надежность и ресурс, проводить локацию местоположения
дефектов, контролировать и управлять их развитием.
.2.4 Организация рабочего места слесаря
Рабочим местом называется часть производственной
площади цеха или мастерской с оборудованием, приспособлениями, инструментом и
материалами, необходимыми для выполнения определенного производственного
задания. Обеспечение высокой производительности труда в значительной мере
зависит от правильной организации рабочего места. Организация рабочего места
является важнейшим звеном организации труда. Правильный выбор и размещение
оборудования, инструментов и материалов создают наиболее благоприятные условия
работы. Правильно организованным считается такое рабочее место, на котором при наименьшей
затрате сил и средств благодаря рациональной и культурной организации труда
достигаются наивысшая производительность и высокое качество продукции.
Правильной организации рабочего места можно достигнуть рационализацией трудовых
приемов, механизацией процессов работы, устранением непроизводительных затрат
рабочего времени, применением передовых методов труда.
К организации рабочего места предъявляются
следующие требования:
) рабочее место должно быть чистым, на нем
должны находиться только те предметы, которые необходимы для выполнения данного
задания;
) инструмент, заготовки и документация должны
располагаться на рабочем месте на расстоянии вытянутой руки; при этом те
предметы, которыми рабочий пользуется более часто, следует класть ближе, на
площади, ограниченной дугами небольшого радиуса, и наоборот (Рисунок 8.2.4.1);
Рисунок 8.2.4.1- Расположение инструмента на
слесарном верстаке
) режущий или ударный инструмент, который берут
правой рукой, кладут с правой стороны; тот, который берут левой рукой,- с левой
стороны;
) инструмент, который работающий берет обеими
руками, следует располагать, возможно ближе к его корпусу, чтобы удобнее было
его брать;
) приспособления, материалы и готовые изделия
нужно располагать в различных ящиках на отведенных для них местах, причем более
мелкие и часто употребляемые нужно помещать в верхних, а более тяжелые или же
редко применяемые - в нижних ящиках;
) точные и измерительные инструменты должны
храниться в специальных футлярах или же деревянных коробках;
) режущие инструменты (напильники, метчики,
сверла, развертки и др.) следует предохранять от ударов и загрязнения, не
разбрасывать и не накладывать друг на друга, а укладывать на деревянные
подставки (планшеты);
) после окончания работы весь инструмент и
приспособления, применяемые при работе, необходимо очистить от грязи и масла,
протереть. Верстак очистить щеткой от стружки и мусора.
Рабочее место слесаря может быть организовано
по-разному, в зависимости от характера производственного задания. Однако
большинство рабочих мест слесаря должно быть оборудовано слесарными верстаками,
на которых устанавливают тиски и раскладывают необходимые инструменты,
приспособления, материалы, документацию (технологические карты, чертежи,
наряды) и пр. Хорошее помещение, отведенное для слесарных мастерских, в
значительной мере способствует правильной организации рабочего места слесаря, а
также повышению производительности труда и качества выполнения работ.
Расстояние между отдельными рабочими местами, а также проходы (1,5-1,6 погонный
метр) между слесарными верстаками устанавливаются в зависимости от технических
и технологических требований и условий техники безопасности. Рабочие места
должны иметь хорошее освещение и вентиляцию; полы возле верстаков должны быть
ровными и исправными.
8.3 Конструкция и технологический процесс
ремонта дизеля ПД1М
.3.1 Описание конструкции поршня ПД1М и
технологический процесс восстановления ручьев поршня дизеля ПД1М
Конструкция поршня показана на рисунке 8.3.1.1.
Рисунок 8.3.1.1 - Конструкция поршня ПД1М
Где
1-выемка; 2-отверстия с резьбой для крепления скобы; 3-уплотнительные
трапецеидальные кольца; 4- уплотнительные прямоугольные кольца;
5-маслосрезывающие кольца; 6-поршневой палец; 7-заглушка; 8-отверстие с резьбой
для выемки заглушки; 9-маслоотводящие отверстия; 10-шатун.
Поршень дизеля ПД1М (рисунок 8.3.1.1) отлит из
алюминиевого сплава (силумина) ПС-12, твердость которого HB
= 80 - 100. Коэффициент теплопроводности силумина в 4,25 раза больше, а
удельный вес в 2,75 раза меньше, чем у чугуна. Использование сплава ПС-12
позволило не применять охлаждения поршня, несмотря на сравнительно большую
мощность (167 л.с.), развиваемую в каждом цилиндре. Сверху поршни хорошо
охлаждаются воздухом, поступающим через впускные каналы, а снизу - брызгами
масла, образующимися в картере во время работы дизеля.
К достоинствам поршня относятся:
1. Значительное уменьшение его веса;
2. Уменьшение удельного давления на
подшипники и шейки коленчатого вала;
. Увеличение срока службы их из-за
уменьшения сил инерции.
Головка поршня выполнена тонкостенной с плавным
переходом от верхней части к стенкам. Вверху торец головки (днище) имеет
вогнутую поверхность. Такая форма днища способствует лучшему смешиванию
распыленного топлива с воздухом, а следовательно лучшему его сгоранию. На днище
выфрезерованы четыре выемки 1 для открывания впускных и выпускных клапанов при
верхнем положении поршня. Два отверстия 2 имеющие резьбу, служат для крепления
скобы при выемке и постановке поршня в цилиндр. На головке поршня расположены
четыре уплотнительных кольца 3 и 4. Головка поршня на длине 170 мм проточена на
конус, вершина которого направлена в сторону камеры сгорания. Такая форма
головки исключает возможность заклинивания поршня при нагревании во время
работы, так как верхняя часть головки нагревается сильнее, а следовательно и
расширяется больше. На юбке поршня расположены три маслосрезывающих кольца 5,
причем одно из колец находится выше, а два других ниже отверстия под поршневой
палец. У пятого и седьмого ручьев сняты фаски. В ручьях для масло срезывающих
колец в поршне просверлены радиальные отверстия, а на фасках - наклонные
отверстия, через них стекает масло, снятое маслосрезывающими кольцами со стенок
цилиндровой гильзы. Внутри поршень имеет приливы (бобышки), в которых расточены
отверстия для поршневого кольца. Снаружи с двух сторон поршня в отверстиях
сделаны выточки, в которые вставляются с натягом заглушки 7, удерживающие палец
от осевого перемещения во время работы поршня. Заглушки изготовлены из сплава
ПС-12, их наружная поверхность имеет такую же форму, как поверхность юбки, что
не дает им возможности поворачиваться вокруг своей оси. В центре заглушки
имеется отверстие 8 с резьбой для винта приспособления, при помощи которого
выпрессовывается заглушка. По упорному пояску заглушек снизу сделаны прорези,
соединенные с отверстиями в выточках. Масло после смазки пальца через прорези в
заглушках и отверстия в бобышках сливается в картер. Юбка поршня снаружи вокруг
отверстий под палец имеет с обеих сторон прямоугольные углубления.
Необходимость в этих углублениях вызывается тем, что при сильном нагревании
юбка принимает овальную форму, причем большая ось вала располагается по оси
пальца, так как в этих местах сосредоточена основная масса метала. Если не
делать холодильников, то неизбежно произойдет защемление поршня в местах
наибольшего расширения юбки, то есть по оси пальца. По нижнему краю юбки с
внутренней стороны имеется поясок, служащий базой при обработке и проверке
поршня по диаметру. Торцовая плоскость юбки является базой при обработке и
проверке поршня на станке. Юбка поршня по длине обработана на конус. На головке
поршня расположены четыре уплотнительных кольца, из которых два верхних имеют
трапецеидальное сечение (рисунок 8.3.1.2 б) и хромированы по образующей, а два
последующих кольца - прямоугольное сечение (рисунок 8.3.1.2 а). Применение двух
первых колец трапецеидального сечения позволило устранить пригорание колец на
поршнях, что достигается особенностью работы трапецеидальных колец. При
конусных торцовых поверхностях кольцо работает как клин. Во время боковых и
радиальных перемещений трапецеидального кольца в канавке зазор между канавкой и
кольцом изменяется и образующиеся там отложения выжимаются прежде, чем они
успевают затвердеть и сделать кольцо неподвижным.
Рисунок 8.3.1.2 - Уплотнительные кольца поршня
дизеля ПД1М
Где а - прямоугольное сечение; б -
трапецеидальное сечение.
Наружная цилиндрическая поверхность прямоугольного
кольца выполнена с конусом в один градус тридцать минут на высоте 3,5 мм.
Конусность делается для быстрейшей приработки кольца к цилиндровой гильзе. С
этой же целью уплотнительные кольца покрывают тонким слоем полуды толщиной не
более 0,01 мм. Боковые (торцовые) поверхности тщательно шлифуют. Замок кольца
имеет косой срез под углом 45. Твердость кольца должна быть HB
= 97 - 102. На верхней плоскости колец электрографом делается надпись
"верх". Кольцо устанавливают вершиной конуса вверх к камере сгорания.
Для повышения срока службы уплотнительных колец наружную образующую часть двух
трапецеидальных колец покрывают пористым хромом. В этом случае скос не
делается, а замок хромированных колец выполняется прямым. Срок службы
хромированных колец повышается в три-четыре раза, при этом увеличивается так же
и срок службы обычных цилиндровых гильз. По наружной поверхности
маслосрезывающего кольца (рисунок 8.3.1.3) посередине проточена кольцевая
канавка, в которой профрезерованы двадцать радиальных сквозных пазов. Таким
образом, кольцо состоит как бы из двух частей - верхней и нижней, соединенных
узкими перегородками, которые остаются после фрезеровки сквозных отверстий. Как
верхняя, так и нижняя часть кольца имеет конусный срез в одну сторону. Такая
конструкция дает возможность маслосрезывающему кольцу при движении поршня вверх
скользить по маслу, а при движении вниз острыми кромками соскабливать масло со
стенок цилиндровой гильзы по направлению к картеру.
Рисунок 8.3.1.3 - Маслосрезывающее кольцо поршня
дизеля ПД1М
При постановке кольца необходимо следить, чтобы
вершина конуса была направлена вверх к камере сгорания. Маслосрезывающие кольца
имеют прямой замок. Уплотненные и маслосрезывающие кольца покрывают слоем полуды
толщиной не более 0,01 мм.
Технологический процесс восстановления ручьев
включает в себя последовательность следующих операций:
) Надеть и привести в порядок спецодежду:
застегнуть пуговицы на куртке, обшлагах рукавов, головной убор.
) Подготовить средства индивидуальной защиты,
проверить их исправность.
) Подготовить слесарный инструмент,
приспособления, проверить их исправность.
) Быть внимательным, не отвлекаться на
посторонние дела и разговоры, не отвлекать других.
) Не допускать на свое рабочее место лиц не
имеющих отношения к порученной работе.
) Работать в предусмотренной нормами спецодежде,
спецобуви.
) Перед включением оборудования убедиться, что
его пуск не угрожает безопасности рядом работающих людей.
) Наружную поверхность поршня осмотреть.
) Радиальные риски, царапины и местные
углубления на поверхности ручьев устранить: При наличии указанных дефектов
ручьи проточить на токарном станке до одного из ремонтных размеров. Для первых
двух трапецеидальных колец 0-градация-4,3+0,03; 1-градация-4,9+0,03;
2-градация-5,5+0,03. Для прямоугольных компрессионных колец
0-градация-5,0+0,02; 1-градация-5,6; 2-градация-6,2; 3-градация-6,8. Для
маслосрезывающих колец 0-градация-8,0+0,02; 1-градация-8,4; 2-градация-8,8;
3-градация-9,2.
) Излом перемычек между ручьями, подплавление и
задир на головке более 3 мм, трещины длиной до 25 мм в местах перехода выступов
к днищу поршня, несквозные трещины в днищ, разработанные ручьи устранить.
Указанные дефекты разрешается восстанавливать газовой наплавкой, которая производится
в следующей последовательности:
А) Поршень отчистить от нагара. Взависимости от
дефекта производить соответствующую разделку поршня. Если поврежденная
поверхность не захватывает область ручьев - наплавку производить без разделки
поверхности поршня. При повреждении ручьев производить разделку поршней под
наплавку на станке. Перед наплавкой поршень равномерно нагреть в электропечи до
температуры 300-350 °С. При отсутствии электропечи разрешается подогрев поршня
производить кислородно-ацетиленовой горелкой, при этом пламя должно быть
направлено внутрь поршня со стороны юбки для удержания тепла после подогрева
пустотелую часть поршня (со стороны юбки) и часть наружной поверхности закрыть
асбестовым кожухом, что позволит наплавить поршень с одного нагрева.
Б) В качестве присадочного материала применять
круглые прутки диаметром не более 10-12 мм, длиной 300-350 мм, изготовленные из
материала поршня.
В) Наплавку поршней производить ванным способом
(пятачком), для чего свариваемое место подогреть автогенной горелкой до
образования ванны (картера) при этом поршень должен быть установлен наклонно
20-45° к горизонту. Наплавку производить за один проход. Превышение
наплавляемого слоя над образующей поверхностью поршня допускается не более 5
мм. При ремонте верхней части головки поршня наплавку производить с
направлением от торца головки в сторону ручьев. После наплавки поршень
немедленно охладить в закрытой печи. В местах наплавки непровары, черновины,
поры, шлаковключения и другие дефекты не допускаются. После механической
обработки наплавленного поршня допускается на дне ручьев и на головке наличие
единичных мелких пор размером не более 10 мм
при расстоянии между ними не менее 50 мм.
Используемое оборудование и материалы: Горелка ГС-3
№6; Прут силуминовый; Ацетилен; Струбцина; Токарный станок; Печь индукционная.
.3.2 Технологический процесс ремонта поршня
дизеля ПД1М
Технологический процесс ремонта поршня дизеля
ПД1М включает в себя последовательность следующих операций:
) Надеть и привести в порядок спецодежду:
застегнуть пуговицы на куртке, обшлагах рукавов, головной убор.
) Подготовить средства индивидуальной защиты,
проверить их исправность.
) Подготовить слесарный инструмент,
приспособления, проверить их исправность.
) Быть внимательным, не отвлекаться на
посторонние дела и разговоры, не отвлекать других.
) Не допускать на свое рабочее место лиц не
имеющих отношения к порученной работе.
) Работать в предусмотренной нормами спецодежде,
спецобуви.
) Перед включением оборудования убедиться, что
его пуск не угрожает безопасности рядом работающих людей.
) Наружную поверхность поршня осмотреть.
) При наличии сквозных трещин и сколов, рисок
глубиной более 1 мм или задиров на направляющей части (юбки) площадью более 50
см
,
а также более 5 надрывов длиной до 25 мм - поршень заменить.
) При наличии овальности более 0,3 мм поршень
заменить. Овальность поршня определяется как разность диаметров поршня
измеренных в плоскостях перпендикулярных и параллельных оси поршневого пальца.
(Контрольное приспособление для измерения диаметра поршня - МК 400-1 Микрометр
ГОСТ 6507-90)
) Увеличение диаметрального зазора между поршнем
и втулкой проверить. Диаметральный зазор определяется как разность диаметров
втулки и поршня. Чертежный размер внутреннего диаметра цилиндровой втулки 318
+0,05 мм. Зазор определяется от двух положений поршня - для ВМТ и НМТ в двух
поясах. При наличии зазора в ВМТ для поршня с тепловой канавкой более 3,6 мм и
для НМТ более 0,75 мм поршень разрешается восстанавливать наплавкой верхней
головки или механической раздачей нижней части. Раздачу производить при помощи
струбцины, установленной в центрирующую заточку юбки. Сначала раздачу юбки
поршня производить на 0,05-0,1 мм в плоскости оси поршневого пальца, а затем
выждав 15-20 минут переставить струбцину перпендикулярно оси пальца. При
механической раздаче увеличение диаметра более 0,2 мм не допускается. После
раздачи юбки и запрессовки заглушек поршневого пальца, овальность поршня не
должна превышать 0,25 мм. Перед наплавкой произвести предварительный подогрев
поршня до температуры 300-325 °С. Наплавку производить нейтральным пламенем за
один проход. Диаметр прутка из силумина 10-12 мм. Наплавленный метал должен
возвышаться над основным металлом поверхности поршня на 3-5 мм. Наплавленный
поршень охлаждать в печи. Произвести механическую обработку наплавленного
поршня до чертежного размера. ( Оборудование и материалы: Горелка ГС-3 №6; НИ
250 - 450 - 2 Нутромер ГОСТ 868-82; МК 400-1 Микрометр ГОСТ 6507-90; Прут
силуминовый; Ацетилен; Кислород; Струбцина; Токарный станок; Печь индукционная)
) Отверстия под поршневой палец на предмет
увеличения овальности и конусности более 0,05 мм на диаметре 128 мм проверить.
Указанный дефект разрешается устранить шабровкой. (Примечание: наплавлять
отверстия бобышек поршней запрещается) Используемое оборудование: Шабер ТУ
2-035-365-74; НИ 100-60-2 Нутромер ГОСТ 868-82.
) Радиальные риски, царапины и местные
углубления на поверхности ручьев устранить: При наличии указанных дефектов
ручьи проточить на токарном станке до одного из ремонтных размеров. Для первых
двух трапецеидальных колец 0-градация-4,3+0,03; 1-градация-4,9+0,03;
2-градация-5,5+0,03. Для прямоугольных компрессионных колец
0-градация-5,0+0,02; 1-градация-5,6; 2-градация-6,2; 3-градация-6,8. Для
маслосрезывающих колец 0-градация-8,0+0,02; 1-градация-8,4; 2-градация-8,8;
3-градация-9,2.
) Излом перемычек между ручьями, подплавление и
задир на головке более 3 мм, трещины длиной до 25 мм в местах перехода выступов
к днищу поршня, несквозные трещины в днищ, разработанные ручьи устранить.
Указанные дефекты разрешается восстанавливать газовой наплавкой, которая
производится в следующей последовательности:
А) Поршень отчистить от нагара. Взависимости от
дефекта производить соответствующую разделку поршня. Если поврежденная
поверхность не захватывает область ручьев - наплавку производить без разделки
поверхности поршня. При повреждении ручьев производить разделку поршней под
наплавку на станке. Перед наплавкой поршень равномерно нагреть в электропечи до
температуры 300-350 °С. При отсутствии электропечи разрешается подогрев поршня
производить кислородно-ацетиленовой горелкой, при этом пламя должно быть
направлено внутрь поршня со стороны юбки для удержания тепла после подогрева
пустотелую часть поршня (со стороны юбки) и часть наружной поверхности закрыть
асбестовым кожухом, что позволит наплавить поршень с одного нагрева.
Б) В качестве присадочного материала применять
круглые прутки диаметром не более 10-12 мм, длиной 300-350 мм, изготовленные из
материала поршня.
В) Наплавку поршней производить ванным способом
(пятачком), для чего свариваемое место подогреть автогенной горелкой до
образования ванны (картера) при этом поршень должен быть установлен наклонно
20-45° к горизонту. Наплавку производить за один проход. Превышение
наплавляемого слоя над образующей поверхностью поршня допускается не более 5
мм. При ремонте верхней части головки поршня наплавку производить с
направлением от торца головки в сторону ручьев. После наплавки поршень
немедленно охладить в закрытой печи. В местах наплавки непровары, черновины,
поры, шлаковключения и другие дефекты не допускаются. После механической
обработки наплавленного поршня допускается на дне ручьев и на головке наличие
единичных мелких пор размером не более 10 мм
при расстоянии между ними не менее 50 мм. Используемое оборудование и
материалы: Горелка ГС-3 №6; Прут силуминовый; Ацетилен; Струбцина; Токарный
станок; Печь индукционная.
) Зазор между пальцем и отверстиями в поршне
измерить. Для измерения зазора необходимо поставить поршень в вертикальное
положение и пропустить щуп между пальцем и отверстием поршня с обеих сторон.
При увеличении натяга более 0,01 мм или зазора более 0,14 мм разрешается восстанавливать
посадку путем хромирования пальца. Хромирование пальца производить компонентами
CrO
-150
г/л и H
CO
-
1,25 - 1,50 г/л, при этом сила тока должна быть 350-400 А из расчета 35 А/дм
площади хромирования. Толщина хромировочного слоя не более 0,1 мм. Чертежный
размер наружного диаметра поршня 128 +/- 0,1 мм. После хромирования палец
отполировать. На отполированной поверхности неметаллические включения и
волосовины, видимые невооруженным взглядом, а также трещины, риски, забоины не
допускаются. Используемое оборудование и материалы: Набор щупов №5; CrO
;
H
CO
.
) Кожух поршневого пальца осмотреть и обстучать.
Вмятины кожуха выправить, трещины заварить, концы кожуха при необходимости
завальцевать. Указанные дефекты устранять, не вынимая кожуха из пальца.
Отремонтированный палец опрессовать дизельным маслом при температуре 70-80 °С
под давлением 2,0-2,5 атм в течение трех минут. При этом допускается в местах
развальцовки выступание масла в виде капель. Допускается опрессовка дизельным
топливом ГОСТ 305-42 при температуре 20-30 °С.
) Палец осмотреть. При наличии трещин палец
заменить. Допускается к работе пальцы, имеющие волосовины на рабочей
поверхности.
) Поверхность заглушки поршневого кольца в
отверстии поршня на предмет ослабления проверить. При наличии указанного дефеката
разрешается наваривать заглушки. Поршневое кольцо проверить на предмет
превышения его овальности и конусности более 0,05 мм на диаметре 318 мм.
Используемое оборудование: МК 400-1 Микрометр ГОСТ 6507-90. Поршневые кольца,
имеющие предельную овальность и конусность восстановить хромированием до
чертежного размера 318 мм. Увеличение диаметра поршневого кольца против
чертежного размера допускается не более 0,2 мм.
Заключение
За время прохождения практики я ознакомился с
слесарной работой, структурой работы ТМХ-сервиса Уссурийск, освоил методики
ремонта некоторых деталей и агрегатов узлов подвижного состава.
Список используемой литературы
1) Данковцев В.Т. Техническое
обслуживание и ремонт локомотивов: Учебник для вузов ждт / В.Т. Данковцев, В.И.
Киселев, В.А. Четвергов / Под редакцией В.А. Четвергова, В.И. Киселева, М.: ГОУ
"Учебно-методический центр по образованию на железнодорожном
транспорте" 2007 год.
) Кудряшова Е.А. Методическая
разработка урока производственного обучения "Демонтаж, ремонт и монтаж
шатунно-поршневой группы дизеля ПД1М"
) Лугинин Н.Г. Ремонт тепловозов /
Государственное транспортное железнодорожное издательство / Москва 1956 год