Разработка технологического процесса для изготовления детали 'Чашка левая' в условиях серийного производства на станках с ЧПУ
Введение
Данный дипломный проект выполнен по
специальности «Металлорежущие станки и
инструменты» учреждения образования «Минский государственный
автомеханический колледж». Он представляет собой заключительную работу по
обобщению знаний полученных на всех предметах цикла обучения.
Основной целью этого проекта является разработка
технологического процесса для изготовления детали «Чашка левая» в условиях
серийного производства на станках с ЧПУ, а также внедрение
высокопроизводительного быстропереналаживаемого оборудования (станков с ЧПУ,
промышленных роботов, систем автоматизированного проектирования). В процессе
работы спроектировать деталь, методы ее получения и обработки. Составить
маршрутный и операционный процесс. Выбрать обрабатывающий инструмент и его марка.
В процессе выполнения необходимо рассчитать стоимость получения данной детали,
рассчитать режимы резанья и припуски на механическую обработку, выбрать и
привести характеристику оборудования, на котором производится обработка данной
детали.
. Технологический раздел
1.1 Анализ и конструкция узла
Чашка левая входит в состав дифференциала
редуктора ведущего моста автомобиля МАЗ.
Дифференциал предназначен для передачи,
изменения и распределения крутящего момента между двумя потребителями и
обеспечения, при необходимости, их вращения с разными угловыми скоростями.
Дифференциал является одним из
основных конструктивных элементов трансмиссии
<#"864206.files/image001.jpg">
Рисунок 1 - Дифференциал редуктора моста
автомобиля МАЗ
.2 Конструкционно-технологический анализ детали
Рисунок 2 - Чашка левая 103-2403019
Конструкция детали «Чашка левая» представляет
собой тело вращения. Метод получения заготовки - штамповка, поэтому
конфигурация наружного контура и внутренних поверхностей не вызывает значительных
трудностей при изготовлении.
Нетехнологичными элементами в данной детали
являются отверстия диаметром 12 миллиметров находящиеся под углом к оси
заготовки. Так же чашка имеет множество точных по исполнению, а также взаимному
расположению размеров и поверхностей, что снижает технологичность изделия,
большое количество отверстий расположенных на равном расстоянии друг от друга.
Так же к не технологичным элементам следует отнести шлицевой венец, поскольку
используются малопроизводительный метод обработки
В остальном деталь достаточно технологична,
допускает применение высокопроизводительных режимов обработки, имеет хорошие
базовые поверхности для первоначальной обработки и довольно проста по
конструкции. Расположение отверстий допускает многоинструментальную обработку.
Конструкторскими базами детали являются шлицы,
центральное отверстие диаметром 65 миллиметров и наружный диаметр 159,5
миллиметров, технологическими и измерительными - торцы, наружные цилиндрические
поверхности.
Материалом заготовки «Чашка левая» является
сталь 40 ГОСТ 1050-88. Данный материал подобран исходя из воспринимаемых
нагрузок и условий работы.
В качестве количественных показателей
рассмотрим: массу детали, коэффициент точности обработки, коэффициент
шероховатости поверхностей.
Масса детали m
= 9 кг.
Масса заготовки mз
=
10 кг.
Коэффициент использования материала:
(1)
где m
- масса детали;
mЗ
- масса заготовки.
Коэффициент точности обработки и коэффициент
шероховатости поверхностей определяем в соответствии с ГОСТ 18831-73. Для этого
рассчитываем среднюю шероховатость обработанных поверхностей и среднюю точность
обработки. Смотрите таблицы 1 и 2.
Таблица 1 - Определение коэффициента
шероховатости
Шi
класс
|
n i
|
Шi
∙
n
i
|
9
|
3
|
27
|
4
|
4
|
16
|
3
|
3
|
9
|
2
|
2
|
4
|
Сумма
|
12
|
56
|
Коэффициент шероховатости:
(2)
где Шср - средний квалитет
шероховатости поверхностей;
где Шi
- шероховатость i-ой
поверхности, класс;
ni
-
количество поверхностей данной шероховатости;
Условие Кш >0,18 выполняется, т.е.
по шероховатости деталь технологична.
Таблица 2 - Определение коэффициента точности
Ti квалитет точности
|
n i
|
Тi
∙
n
i
|
6
|
1
|
6
|
8
|
2
|
16
|
9
|
4
|
36
|
11
|
5
|
55
|
14
|
1
|
14
|
13
|
127
|
Коэффициент точности:
где Тср - средний квалитет точности
поверхностей;
где Ti
- квалитет точности i-ой
поверхности;
ni
-
количество поверхностей данного квалитета;
Условие Kт
> 0,8 выполняется, т.е. по точности деталь технологична.
По результатам качественной и количественной
оценки можно сказать, что деталь технологична. В целом будем считать деталь
«Чашка левая» технологичной для использования ее в узле «Дифференциал».
Деталь изготавливается из сталь 40 ГОСТ 1050-88
- сталь углеродистая конструкционная. Данный материал обладает относительно не
высокой стоимостью, но обеспечивает необходимые эксплуатационные свойства
готового изделия. Механические свойства и химический состав стали представлены
в таблицах 3 и 4 соответственно.
Таблица 3 - Механические свойства сталь 40 ГОСТ
1050-88
sв, МПа
(относительно
удлинение)
|
d5, %
|
НВ
|
510
|
6
|
190
|
Таблица 4 - Химический состав Сталь 40 ГОСТ
1050-88 в процентах
Si
|
Mn
|
Cu
|
As
|
Ni
|
S
|
C
|
P
|
Cr
|
0.17-0.37
|
0,5-0,8
|
0,25
|
0,08
|
0,25
|
0,04
|
0,37-0,45
|
0,035
|
0,25
|
.3 Обоснование метода получения заготовки
На выбор метода получения заготовки оказывают
влияние: материал детали, её назначение и технические требования на
изготовление, объём и серийность выпуска.
Деталь «Чашка левая» изготовляют из стали 40
ГОСТ 1050-88. Данный материал является относительно не дорогостоящим, но
подобран исходя из воспринимаемых нагрузок и условий работы.
Для данной детали заготовку целесообразно
получать методом пластической деформации (ковка, штамповка, периодический
прокат, обжатие на ротационно - ковочных машинах, электровысадка), т.к. они
позволяют получать заготовки по форме и размерам наиболее близкие к готовой
детали, что значительно повышает производительность механической обработки.
Метод получения заготовки, поковки, это метод
горячей штамповки в закрытых штампах.
Горячая штамповка в закрытых штампах
характеризуется тем, что полость штампа в процессе деформирования остается
закрытой. Зазор между подвижной и неподвижной частями штампа постоянный и
небольшой, образование в нем облоя не предусмотрено. Устройство таких штампов
зависит от типа машины, на которой штампуют. Например, нижняя половина штампа
может иметь полость, а верхняя - выступ (на прессах), или верхняя - полость, а
нижняя - выступ (на молотах). Закрытый штамп может иметь две взаимно
перпендикулярные плоскости разъема. При штамповке в закрытых штампах необходимо
строго соблюдать равенство объемов заготовки и поковки, иначе при недостатке
металла не заполняются углы полости штампа, а при избытке размер поковки по
высоте будет больше требуемого. Отрезка заготовок должна обеспечивать высокую
точность.
Сравним два метода получения заготовки: поковка
и круглый прокат.
Произведем расчет экономии материала. Расчет
выполнен по методике рассмотренной в учебнике «Проектирование технологических
процессов механической обработки в машиностроении».
Исходные данные:
Масса детали q
= 9 килограмм.
Масса заготовки Q
= 10 килограмм.
Si
- стоимость 1 тонны заготовок, 10959930 белорусских рублей.
Sотх
- стоимость 1 тонны отходов, 2367380 белорусских рублей.
Формула расчета стоимости заготовки:
(6)
где КТ = 1,05 - коэффициент,
зависящий от класса точности;
Кс = 0,9 - коэффициент, зависящий от
группы сложности;
Кв = 0,9 - коэффициент, зависящий от
материала и массы;
Км = 1,93 - коэффициент, зависящий от
марки заготовки;
Кп = 1 - коэффициент, зависящий от
объема производства;
Произведем расчет экономии материала при
использовании проката диаметром 235 миллиметров.
Исходные данные:
Масса детали q
= 9 килограмм.
Масса заготовки Q
= 47,3 килограмм.
Si
- стоимость 1 тонны заготовок, 10959930 белорусских рублей.
Sотх
- стоимость 1 тонны отходов, 2367380 белорусских рублей.
Формула расчета стоимости заготовки:
Из расчета видно, что поковка более экономически
выгодно, чем прокат, за счет приближенности формы заготовки к форме готовой
детали, следовательно меньших припусков на обработку, а соответственно более
меньшим использованием материала.
.4 Назначение припусков на механическую
обработку детали
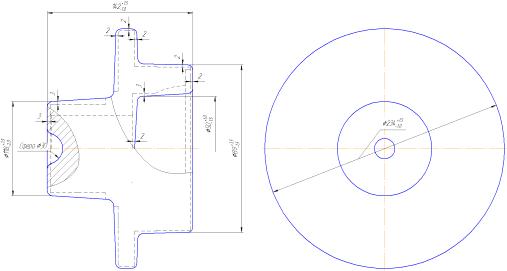
На все указанные поверхности назначают припуски
и допуски по ГОСТ 7505-89, табличные значения припусков занесены в таблицу 5.
Таблица 5 - Припуски и допуски на обрабатываемые
поверхности вала коронной шестерни.
Поверхность
|
Размер,
мм
|
Припуск,
мм
|
Допуск,
мм
|
1
|
Ø160,6-0,25
|
2*2
|
+3,5
-1,5
|
2
|
Ø108+0,35
|
2*3
|
+1,0
-1,5
|
3
|
Ø85,6-0,14
|
2*3
|
+3,5
-2,0
|
4
|
137
|
2,
3
|
+1,5
-1,0
|
.5 Разработка маршрутного процесса обработки
детали
Технологический маршрут обработки детали
представлен в таблице 6.
Таблица 6 - Технологический маршрут обработки
ступицы
Название
операции
|
Содержание
операции
|
Оборудование
|
1
|
2
|
3
|
005
Токарно-револьверная
|
Сверлить
отверстие
|
Ст.
мод. 1425
|
010
Токарная с ЧПУ
|
1.
Точить наружный контур 2. Точить передний торец 3. Расточить отверстие
|
1П756ДФ3
|
015
Токарная с ЧПУ
|
1.Точить
наружный контур 2.Точить задний торец 3. Расточить отверстие
|
1П756ДФ3
|
020
Термическая обработка
|
|
|
025
Токарная с ЧПУ
|
1.Точить
наружный контур 2.Точить задний торец 3. Расточить отверстие
|
1А734Ф3
|
030
Токарная с ЧПУ
|
1.
Точить наружный контур 2. Точить передний торец 3. Расточить отверстие
|
1А734Ф3
|
035
Вертикально-сверлильная
|
1.
Сверлить отверстия диаметром 13,0 мм. 2. Сверлить отверстия диаметром 15,0
мм.
|
Вертикально-сверлильный
станок 2Н135БС
|
040
Вертикально-сверлильная
|
Сверлить
отверстия диаметром 12,0 мм.
|
Вертикально-сверлильный
станок 2Н125
|
045
Слесарная
|
|
Верстак
|
050
Шлицефрезерная
|
Фрезеровать
шлицы
|
Зубофрезерный
5В312
|
055
Зубозакругляющая
|
Закруглить
шлицы
|
Зубозакругляющий
5Е580
|
060
Горизонтально-фрезерная
|
Фрезеровать
2-е лыски
|
Горизонтально-фрезерный
FU4008
|
065
Слесарная
|
|
Верстак
|
070
Контроль приемочный
|
|
Стол
ОТК
|
.6 Разработка операционного процесса обработки
детали
.6.1 Выбор и обоснование технологического
оборудования операции с ЧПУ
Данный станок подходит для обработки исходя из
точности выполняемых размеров, направления ведения обработки, количества
используемых на операции инструментов, серийности выпуска детали, соответствия
габаритов рабочего пространства и других факторов. Заготовка крепится в
трехкулачковом патроне по наружной поверхности с упором в торец. Для обработки
всех поверхностей детали на операции требуется 5 инструментов.
Анализируя технические характеристики и габариты
рабочего пространства, наиболее целесообразно выбрать станок фирмы МЗАЛ модели
1А734Ф3.
Станок модели 1А734Ф3 является типичным для
современных станков с ЧПУ и предназначен для токарной обработки наружных и
внутренних поверхностей деталей типа тел вращения различной сложности, а также
для нарезания резьбы. Он применяется в серийном в массовом производстве.
Рисунок 4 - Cтанок
производства МЗАЛ модели 1А734Ф3
Техническая характеристика станка 1А734Ф3
представлена в таблице 7.
Таблица 7 - Техническая характеристика станка
1А734Ф3
Наименование
параметра
|
Значение
параметра
|
Класс
точности по ГОСТ 8 - 82
|
2
|
Наибольший
диаметр обрабатываемого изделия, мм: Над станиной Над суппортом
|
560
320
|
Наибольшая
высота обрабатываемого изделия, мм
|
200
|
Наибольший
диаметр сверления за один проход, мм
|
32
|
Конец
шпинделя (условный размер) по ГОСТ 12595 - 85
|
2
|
Отверстие
в шпинделе изделия, мм
|
100H7
|
Расстояние
от низа основания полуавтомата до торца шпинделя, мм
|
1180
|
Наибольшая
высота сечения устанавливаемых резцов,
|
32
|
Пределы
частоты вращения шпинделя, об/мм
|
14
- 1000
|
Количество
автоматически переключаемых скоростей шпинделя
|
бесступенчатое
регулирование
|
Количество
суппортов
|
2
|
Наибольшее
перемещение суппортом, мм: В вертикальном направлении В горизонтальном
направлении
|
600
300
|
Скорость
быстрых перемещений суппортов, м/мин: В вертикальном направлении В
горизонтальном направлении
|
10
10
|
Скорость
рабочих подач суппортов, мм/мин
|
1
- 1250
|
Дискретность
задания перемещения суппортов, мм: В вертикальном направлении В
горизонтальном направлении
|
0,001
0,001
|
Количество
позиций револьверных головок
|
4+4
|
Наибольший
крутящий момент на шпинделе, Н•м
|
4000
|
Мощность
привода главного движения, кВт
|
11
|
Наибольшее
усилие подачи резца, Н: В вертикальном направлении В горизонтальном
направлении
|
20000
20000
|
Показатели
надежности: Срок службы до первого капитального ремонта, год Ресурс по
точности, тыс часов
|
14
9
|
Габаритные
размеры полуавтомата, мм Длина Ширина Высота
|
4100
4050 3500
|
Занимаемая
площадь, м
|
16,6
|
Масса
полуавтомата, кг: Полная Без гидро - электрооборудования и оснастки
|
13470
9000
|
Рисунок 5 - Стойка ЧПУ фирмы Siemens
модели Sinumerik
840 D
Станок оснащен УЧПУ фирмы Siemens
модели Sinumerik
840 D
Техническая характеристика системы ЧПУ:
- модуль управления PCU50.3-C.
ЧПУ центральное управление NCU 571.5 - для
станка до 6-ти координат572.5 - для станка с 7-ми и выше координатами.
пульт управления системы с плоским цветным
дисплеем OP10C - 10,4“
механическая панель MCP483C.
переносной пульт управления B-MPI оснащен
электрическим маховичком.
дополнительный пульт управления для AVN (в
станках с использованием автоматической замены инструментов).
система позволяет проводить одновременное
движение:
4 линейных координатах (X,Y,Z,W) в линейной
интерполяции.
2 из 4-х линейных координат в круговой интерполяции.
винтовая интерполяция, то есть одновременное
движение 2-х координат? в круговой интерполяции и 3-я координата в линейной
интерполяции ( из 4-х линейных координат) в случае необходимости следующая 4-я
координата в линейной интерполяции.
инкремент программирования.
в ротационной координате B ( поворотный стол )
0,001o.
цифровое управление числом оборотов шпинделя.
ориентированный стоп шпинделя ( угловая
ориентировка положения шпинделя с инкрементом 0,1o).
нарезание резьбы с постоянным шагом.
нарезание резьбы метчиком без или с
использованием выравнивающей втулки.
система изображает сигнализацию ошибок в
текстовом вид.
возможность подсоединения двух измерительных
зондов.
поворот системы координат - Цикл 800.
Look Ahead - разработка блоков NC программы
наперед.
.6.2 Инструментальная оснастка операционного
процесса
На станке фирмы МЗАЛ модели 1А734Ф3 в качестве
режущего инструмента применяются резцы. Практически весь инструмент закупается
у ведущего производителя Sandvik,
благодаря чему обеспечивается высокая точность и сохраняется необходимая
производительность. Резцы закрепляются на 12-ти позиционной револьверной
головке с помощью вспомогательного инструмента. Режущий инструмент должен
отвечать следующим требованиям: отличаться высокой режущей способностью,
обеспечивать долговечность и надежность работы, обеспечивать благоприятные
условия стружкоотвода, характеризоваться стабильностью качества и высокой
стойкостью, обладать возможностью настройки на размер вне станка, быть
технологичным в изготовлении и относительно простым по конструкции.
Рисунок 6 - Эскиз обработанной детали после
токарной операции
Таблица 8 - Содержание токарной операции с ЧПУ
Наименование
перехода
|
Комплекс
оснастки
|
1
|
2
|
01.Точить
наружный контур
|
РИ:
Резец 2190-4207, пластина режущая WNUM100608-CT25M ВИ:
Державка 9410-275 СИ: Штангенциркуль ШЦ 1-125-0,1 ГОСТ 166
|
02.Расточить
отверстие
|
РИ:
Резец 2109-4411, пластина режущая СNMM 120408
СТ25М ВИ: Державка 9410-358 СИ: Штангенциркуль ШЦ 3-250-0,05 ГОСТ 166
|
03.
Точить внутреннюю поверхность
|
РИ:
Резец 2109-4410, пластина режущая СNMM 120408
СТ25М ВИ: Державка 9410-358 СИ: Штангенциркуль ШЦ 3-250-0,05 ГОСТ 166
|
05.Точить
отверстие
|
РИ:
Резцовая вставка 2109-4289, пластина режущая CNMM 120408 CK25M ВИ:
Державка 9416-305 СИ: Профилометр мод. 296
|
.6.3 Расчет координат опорных точек
Координаты опорных точек движения, рассчитываем
по карте наладки на токарную операцию. Координаты опорных точек заносим в
таблицу 9.
Таблица 9 - Координаты опорных точек на токарную
операцию
Этапы
обработки
|
Номер
опорных точек
|
Координаты
опорных точек,мм Х Z
|
1
|
2
|
3
|
4
|
01.Точить
поверхности
|
1 2 3 4 5 6 7 8 9 10 11
|
160,5 160,5 235
231,4 223,4 230 230 160 160 160 150
|
-31
-53 -52 -56,6 -53,6 -53,6 -54 -54 -53,6 0,2 0,2
|
02.Расточить
отверстие
|
1 2 3 4 5 6 7 8 9 10 11
12 13 14 15 16 17
|
122,4
122,4 106,2 108 108 69,03 63,03 63,03 108 100 10 151 151 154 154 150 250
|
2
-5 -36 -34 -55,7 -55,7 -59,1 -56,4 -56,4 -48 -48 -48 0,5 0,5 -4,8 200 200
|
03.
Точить поверхность
|
1 2 3 4 5 6 7 8 9 10
|
63,5
63,5 63 63 64,8 64,8 64 64 65,03 250
|
1
-55 -96,66 -56 -56 -96,6 -96,6 -56 -56 200
|
04.
Расточить отверстие
|
1 2 3 4 5
|
154,8
154,8 152 159 153
|
6
-5 1 1 -2
|
.7 Расчет режимов резания и норм времени
Исходные данные:
Наименование детали - чашка левая.
Материал - сталь 40.
Точность обработки - Ø155+0,025
мм.
Шероховатость поверхности - Ra
= 2,5 мкм.
Метод получения заготовки - поковка.
Состояние поверхности - без корки.
Масса - 9 кг.
Припуск на обработку - Ø155-2*1,5
мм.
Модель станка - 1А734Ф3
Расчет режимов резания представлен в приложении
А.
Благодаря техническим характеристикам станка
режущего и вспомогательного инструмента назначить следующие режимы резания,
приведенные в таблице 10.
Таблица 10 - Cводная
таблица режимов резания
Выполняемый
переход
|
Режимы
резания
|
|
D или B,мм
|
L, мм
|
i
|
S, мм/об
|
n, об/мин
|
V, м/мин
|
1
|
2
|
3
|
4
|
5
|
6
|
7
|
8
|
01.Точить
поверхности
|
160,49
|
22
|
1
|
1
|
0,3
|
160
|
80
|
|
230
|
65
|
|
|
0,35
|
|
115
|
02.Расточить
отверстие
|
123
|
36
|
0,2
|
2
|
0,1
|
280
|
105
|
|
108
|
17
|
0,5
|
1
|
0,25
|
|
95
|
|
151
|
15
|
|
|
|
190
|
90
|
|
154
|
5
|
|
|
0,2
|
|
92
|
03.Точить
поверхности
|
65,03
|
40
|
0,3
|
3
|
0,1
|
300
|
61
|
04.
Точить поверхности
|
155,012
|
5
|
0,2
|
1
|
0,1
|
250
|
121
|
|
120
|
17
|
|
|
|
|
94
|
.8 Разработка управляющей программы
Разработка управляющей программы является одним
из важнейших этапов подготовки к работе на станках с ЧПУ.
Настройка станка и ввод программы осуществляются
следующим образом. Выполняется размерная привязка каждого инструмента в системе
координат станка, производимая методом проверочных рабочих ходов обработкой
цилиндрических поверхности и торцов и последующим измерением фактически
полученных размеров, учитываемых затем при вводе в память УЧПУ координат
исходных точек движения инструменте. Далее на пульте оператора набирают
программу, предварительно составленную технологом-программистом. Затем набирают
кадры программы. После набора каждого кадра нажимают клавишу, в результате чего
кадры последовательно вводятся в память УЧПУ.
При обработке ряда деталей припуск бывает
настолько велик, что его приходится снимать за несколько рабочих ходов. Это
приводит к существенному увеличению объема программы. Для упрощения
программирования применяются вспомогательные функции задания цикла обработки.
Система автоматически определяет число рабочих ходов.
. Наладка станка с ЧПУ на обработку детали
Монтаж станка является одним из факторов
влияющих на точность и качество производства.