Проектирование механизированного фрезерного приспособления
Курсовая работа
Проектирование
механизированного фрезерного приспособления
1. Краткое описание приспособлений
фрезерный
силовой привод резание
Данное фрезерное приспособление предназначено для обработки
корпуса.
В приспособление устанавливаются заготовка, закрепляемая
винтом.
Принцип работы:
Немеханизированное приспособление:
Рабочий устанавливает заготовку, затем ключом вращает винт и
зажимает её. Происходит фрезерование плоскости. Далее рабочий снимает
заготовку. Цикл повторяется.
Механизированное приспособление:
Рабочий устанавливает заготовку, включает гидроцилиндр на её
зажим, далее происходит фрезерование плоскости, затем включает гидроцилиндр на
отжим заготовки, снимает ее, и устанавливает следующую. Цикл повторяется.
2. Силовой расчёт
2.1
Расчёт режимов и сил резания
Торцевая фреза Р6М5: D=50; z=12; B=36 мм
. Глубина фрезерования: t=3 мм
. Подача: Sz=0,06 мм/зуб.
. Скорость резания
u=0,15
m=0,2
КМV - коэффициент на обрабатываемый материал.
КПV=1,0 - коэффициент, учитывающий состояние
поверхности.
КИV=1,0 - коэффициент, учитывающий материал
инструмента.
По полученной скорости рассчитаем число оборотов фрезы n:
Полученное значение n округляем по
паспорту станка n=200 об/мин
Фактическая скорость резания равна
. Определение силы резания
Сила резания - окружная сила
Значение всех коэффициентов и степеней определяем по таблицам.
5. Определение крутящего момента
. Мощность резания:
Для последующих расчетов нам потребуется знать составляющие силы
резания.
При фрезеровании торцевой фрезой относительные значения
составляющих сил имеют вид:
PH/Pz=0.3 PH=0.3* Pz=0.3*1939,77=581,93H
Pv/Pz=0.9 Pv =0.9 *Pz=0.9*1939,77=1745,79H
2.2
Определение потребной силы закрепления
Проверка на сдвиг под действием горизонтальной и вертикальной
нагрузки PH и PV.
Уравнения равновесия:
K·PH·l+k·PV·x-W·f1·l1-N·f2·l2=0-N=0
Решая совместно два уравнения, найдем потребную силу
закрепления:
W=
К - коэффициент запаса который находится по формуле:
4,32
Где: К0 =1,5 - гарантированный коэффициент запаса;
К1 =1,6 - коэффициент, учитывающий возрастание сил
обработки при затуплении инструмента;
К2 - 1,2 коэффициент, учитывающий непостоянство сил
резания из-за непостоянства снимаемого при обработке припуска;
К3 =1 - коэффициент, учитывающий изменение сил
обработки при прерывистом резании;
К4 =1 - коэффициент, учитывающий непостоянство
развиваемых приводами сил зажима;
К5 =1 - коэффициент, учитывающий непостоянство развиваемых
сил зажимных устройств с ручным приводом;
К6 =1 - коэффициент отражающий неопределенность
положения мест контакта заготовки с установочными элементами и изменение связи
с этим элементом трения, противодействующих повороту заготовки на базовой
плоскости.
Потребная сила закрепления W=15,6кН
2.3 Выбор и расчет силового привода
Для обеспечения усилия выбираем гидропривод, а в качестве
двигателя берем гидроцилиндр для уменьшения габаритов и легкого монтажа
фрезерного приспособления.
Вбираем гидроцилиндр по потребной силе закрепления W.
Для нашего случая походит гидроцилиндр 7021-0121 ГОСТ19899-74
с параметрами:
. Давление в гидросистеме р=10МПа
. Усилие на штоке цилиндра Wц=12,3кН
. Dпорш= 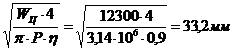
Выбираем ближайший стандартный диаметр.
Dпорш=40
мм; dшток=20 мм
2.4 Расчет на прочность наиболее нагруженной детали
Наиболее нагруженной деталью приспособления являются винты
крепления гидроцилиндра к плите.
Рассчитаем вал на сжатие по формуле:
,
где: i=4-количество винтов; Р=12300Н-сила на штоке цилиндра; d=0,00414 мм-внутренний
диаметр резьбы М5
[σ]=610МПа-допускаемое
напряжение на растяжение (материал сталь45)
Условие выполняется, значит, исполнительные размеры
приспособления выбраны правильно.
3. Расчёт точности приспособления
При обработке заготовки необходимо выдержать следующий размер
высоту детали 118±0,04
Расчет на точность приспособления будем вести на высоту
118±0,04 по формуле:
где:
- допуск выполняемого при обработке
размера заготовки
=1,2 - коэффициент, учитывающий, что не все параметры, входящую в
формулу, подчиняются нормальному распределению
=0,8 - коэффициент, учитывающий уменьшение предельного значения
погрешности базирования при работе на настроенных станках
=0,7 коэффициент, учитывающий долю погрешности обработки в
случайной погрешности, вызываемой от приспособления
=0,08 мм - погрешность закрепления выбирается по таблице П4 [3]
=0 - погрешность базирования
=0 - погрешность установки приспособления на станке
- погрешность положения заготовки, возникающая в результате
изнашивания элементов приспособления
где β2=0,25 - коэффициент ля установочного
элемента: вкладыш из стали У8А;
N=88600 шт./год-количество контактов заготовки с опорой (см.
пункт 4); n=0,4
- коэффициент по износу.
- перекос инструмента
- погрешность настройки станка
= 0,01 мм-допуск на координату установки
=0,006 мм-допуск на щуп;
=0,035 погрешность настройки, вносимая рабочим
=0,12 экономическая точность данного метода обработки
По этой формуле мы определили погрешность изготовления
приспособления
=0,71 мм для выдерживания размера заготовки 118±0,04
4. Технико-экономическое сравнение двух вариантов приспособления
Сравнение будем вести по технологической себестоимости при
использовании немеханизированного и механизированного приспособления.
Себестоимость изготовления деталей для немеханизированного
приспособления определяется по формуле:
;
Для механизированного приспособления:
.
где:
- заработная плата рабочего, отнесённая к
одной детали
где:
- штучное время изготовление партии
деталей
- тарифная ставка рабочего первого разряда (300 рублей/час)
- тарифный коэффициент (третьего разряда - 1.3)
Р - годовые затраты на эксплуатацию приспособления
;
n - коэффициент использования источника давления.
;
n=1 - число обрабатываемых заготовок в приспособлении
-основное время; Sz-подача
на зуб; z-число зубьев фрезы; n-число оборотов фрезы; l-длина обрабатываемой поверхности; l1, l2-длина врезания перебега соответственно
tус=0,18 -
время на установку и снятие заготовки;
tзо - время
на закрепление и открепление заготовки(tзо=0,25
мин для ручного и tзо=0,12 мин для механизированного приспособления);
tос=0,08
мин - время на очистку станка от стружки;
tп=0,09 мин - время на управление станком по переходу;
Для немеханизированного приспособления:
tв1=0,18+0,25+0,08+0,09=0,6
мин
Для механизированного приспособления:
tв2=0,18+0,12+0,08+0,09=0,47
мин
tО.О,;Т,О,;ОТ=8%
tопер=0,08*(t0+ tв) - время на организационное
технологическое обслуживание и отдых.
Для немеханизированного приспособления:
tО.О,;Т,О,;ОТ1=8% tопер=0,08*(1,92+0,6)=0,2 мин
Для механизированного приспособления:
tО.О,;Т,О,;ОТ2=8% tопер=0,08*(1,92+0,47)=0,17 мин
Для немеханизированного приспособления:
Для механизированного приспособления:
Заработная плата рабочего, отнесенная к одной детали:
Для немеханизированного приспособления:
Для механизированного приспособления:
=250% - цеховые накладные расходы
- себестоимость изготовления приспособления
;
где С0-стоимость одной условной детали приспособления;
Zn-число деталей приспособления;
Zс-количество
десятков крепёжных деталей в приспособлении;
k0 -
коэффициент сложности приспособления.
Для немеханизированного приспособления:
Количество деталей в приспособлении Zn= 19, следовательно,
группа сложности 3
Коэффициент сложности приспособления k0=1,7
Количество десятков крепёжных деталей в приспособлении Zc = 2,4
Для механизированного приспособления:
Количество деталей в приспособлении Zn= 25, следовательно,
группа сложности 3
Коэффициент сложности приспособления k0=1,7
Количество десятков крепёжных деталей в приспособлении Zc = 2,8
Для привода:
Количество деталей в приспособлении Zn= 6, следовательно,
группа сложности 2
Коэффициент сложности приспособления k0=1,5
Количество десятков крепёжных деталей в приспособлении Zc = 0,4
Для немеханизированного приспособления:
А1 = (19+2,4)·100·1,7 = 3638 руб.
Для механизированного приспособления:
А2 = (25+2,8)·100·1,7 = 4726 руб.
Стоимость изготовления привода:
960 руб.
- годовая программа выпуска деталей изготовленных данным
приспособлением.
Для немеханизированного приспособления:

Для механизированного приспособления:

=0,5 - коэффициент проектирования
=3 года - срок эксплуатации приспособления
=0,3 - коэффициент эксплуатации
Себестоимость изготовления деталей.
Для немеханизированного приспособления:
Для механизированного приспособления:
;
2291,3 руб.
Определение годового экономического эффекта:
(61,9-57,4)·95688=440164 руб.
Определение срока окупаемости приспособления в годах:
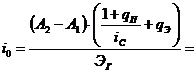
Вывод: механизированное приспособление использовать выгодно, так
как оно быстро окупается (с экономической точки зрения) и позволяет повысить
годовую программу выпуска с 87948 шт. /год до 95688 шт./год.
Список литературы
1.
Ваганов В.М., Гринёв Д.В. «Технологическая оснастка. Технико-экономические
расчёты». Псков «Издательство ППИ» 2010 г.
.
Горохов В.А. Проектирование и расчёт приспособлений. Минск «Высшая школа» 1986
г. 233 с.
.
Справочник технолога машиностроения. В 2-х т. Т2 под редакцией
А.Г.
Косиловой и Р.К. Мещерикова 4-е изд. Переработанное и дополненное. М.;
Машиностроение 1985 г.