Статистические методы контроля на 'КрЭВРЗ'
Реферат
В данном дипломном проекте приведены результаты
использования простейших статистических методов обеспечения качества колёсных
пар, позволяющие анализировать и своевременно стабилизировать технологический
процесс и улучшить качество колёсных пар на Красноярском электровагоноремонтном
заводе. Статистические методы обеспечения качества основаны на распределении
признаков, выборки значений показателей качества, контроле производства с
применением различных карт.
Внедрение разработанного стандарта предприятия
«Статистические методы контроля» на «КрЭВРЗ» позволит улучшить качество
выпускаемых колёсных пар за счет за счет своевременного проведения анализа
качества с помощью статистических методов контроля и своевременного выявления
несоответствий и устранения причин их появления.
Дипломный проект содержит пояснительную записку из 124
страниц машинописного текста, 13 таблиц, 12 рисунков, 70 литературных
источников, 5 приложений и графическую часть из 8 листов формата А1.
Содержание
Введение
. Анализ методов статистического контроля
.1 Общие технологические схемы производства
.2 Обработка металлов резанием
.2.1 Фрезерование
.2.2 Точение
.2.3 Сверление
.2.4 Шлифование
.2.5 Строгание
.3 Контроль готовой продукции
.4 Понятие о статистических методах качества
.5 История развития статистических методов качества
.6 Простые инструменты контроля качества
.6.1 Контрольный листок
.6.2 Гистограмма
.6.3 Диаграмма разброса
.6.4 Стратификация (расслоение) данных
.6.5 Диаграмма Парето
.6.6 Причинно-следственная диаграмма Исикавы (схема Исикавы)
.6.7 Контрольные карты
.7 «Семь новых инструментов контроля качества»
2. Анализ
технологии производства и оценка качества колёсных пар
2.1 Производственная
деятельность ОАО «КрЭВРЗ»
2.2 Основные
сведения о колёсных парах
2.3 Нормативные
требования к осям и колёсным парам
2.4 Описание
технологического процесса формирования колёсных пар
3. Анализ
качества колёсных пар
3.1 Исследование
проблем, возникающих при ремонте колёсной пары с помощью Диаграммы Парето
3.2 Исследование
причин возникновения несоответствий с помощью причинно-следственной диаграммы
Исикавы
3.3 Анализ стабильности технологического процесса с
помощью 
-R -
контрольных карт
3.4 Оценка настроенности и стабильности технологического
процесса
3.4.1 Оценка настроенности и стабильности технологического процесса по
показателю межбандажное расстояние
.4.2 Оценка настроенности и стабильности технологического процесса по
показателю диаметр колёс по кругу катания
.4.3 Оценка настроенности и стабильности технологического процесса по
показателю ширина обода колёс
4. Мероприятия
по улучшению качества
5. Безопасность
и экологичность проекта
.1 Безопасность проекта
.1.1 Анализ опасных и вредных производственных факторов производства
.2 Общая характеристика опасности производства
.3 Производственная безопасность
.4 Производственная санитария
.5 Пожарная безопасность
.6 Экологичность проекта
.6.1 Охрана атмосферного воздуха
.6.2 Охрана естественных водоёмов и рациональное использование водных
ресурсов
.6.3 Утилизация отходов, защита почвы от загрязнения
.7 Безопасность в чрезвычайных ситуациях
. Экономическая часть
.1 Расчёт затрат на замену микрометра
.1.1 Расчет единовременных затрат на замену микрометра
.1.2 Расчет текущих годовых издержек на эксплуатацию микрометра
.2 Расчет затрат на разработку стандарта организации «Статистические
методы контроля» на ОАО «КрЭВРЗ»
Заключение
Библиографический список
Приложения
Введение
В современном мире чрезвычайно важное значение приобретает
проблема качества продукции. От её успешного решения в значительной степени
зависит благополучие любой организации, любого поставщика. Продукция более
высокого качества существенно повышает шансы поставщика в конкурентной борьбе
за рынки сбыта и, самое важное, лучше удовлетворяет потребности потребителей.
Качество продукции - это важнейший показатель конкурентоспособности
предприятия.
Качество продукции закладывается в процессе научных
исследований, конструкторских и технологических разработок, обеспечивается
хорошей организацией производства и, наконец, оно поддерживается в процессе
эксплуатации или потребления. На всех этих этапах необходимо осуществлять
своевременный контроль и получать достоверную оценку качества продукции.
Для уменьшения затрат и достижения уровня качества,
удовлетворяющего потребителя необходимы методы, направленные не на устранение
дефектов (несоответствий) готовой продукции, а на предупреждение причин их
появления в процессе производства.
Для обеспечения качества при изготовлении изделий из
металла на вагоноремонтных предприятиях - осей колёсных пар, рельс, колёсных
пар, деталей локомотива и других изделий на железнодорожном транспорте и при их
эксплуатации применяются различные методы контроля. Наиболее ответственные
элементы вагонов - оси колёсных пар и колёсные пары. Большие нагрузки, тяжелые
условия и сверхнормативные условия эксплуатации - это факторы, которые приводят
к возникновению усталостных повреждений и дефектов. Также в изделиях
встречаются дефекты заводского происхождения, которые могут явиться источниками
возникновения развивающихся в процессе эксплуатации усталостных повреждений.
Выполнение контроля с помощью различных методов
статистического контроля при ремонте и техническом освидетельствовании изделий
позволит выявить причины возникновения тех или иных дефектов, что существенно
увеличит эксплуатационный ресурс вагонов и, что самое главное, предотвратит
возникновение опасных аварийных ситуаций, обеспечивая при этом безопасность и
бесперебойность пассажирских перевозок.
1. Анализ методов статистического контроля
.1 Общие технологические схемы производства
Объективной основой формирования структуры и способа
действия любого предприятия является жизненный цикл продукции и технологическая
цепь производства. Жизненный цикл продукции включает следующие стадии:
исследование и проектирование продукции и технологии, изготовление, обращение
(складирование, транспортирование, сбыт), эксплуатация (потребление) и
утилизация [45].
Основной завершающей стадией в технологических схемах
производства деталей является обработка металлов механическими методами.
Механическая обработка представляет собой сложный производственный процесс, при
котором осуществляется изменение формы металлических заготовок и изготовление
деталей.
Процессы механической обработки металлов делятся на
две группы:
) обработка со снятием металла;
) обработка без снятия металла.
К методам механической обработки без снятия материала
относятся: прокатка, прессование, волочение, ковка и штамповка. Как правило, это
черновые операции, предполагающие дальнейшую обработку заготовок
резанием с целью получения детали требуемых размеров и
класса шероховатости. Эта группа методов обработки представляет собой различные
виды обработки металлов давлением в пластическом состоянии.
Прокатка металлов является таким видом пластической
обработки, когда исходная заготовка обжимается вращающимися валками прокатного
стана в целях уменьшения поперечного сечения заготовки и придания ей заданной
формы. Существуют следующие способы прокатки:
) продольная;
) поперечная;
) поперечно-винтовая (косая).
При продольной прокатке деформирование заготовки
осуществляется между вращающимися в разные стороны валками. Оси прокатных
валков и обрабатываемой заготовки параллельны (или пересекаются под небольшим
углом). Оба валка вращаются в одном направлении, а заготовка круглого сечения -
в противоположном. В процессе поперечной прокатки обрабатываемая заготовка
удерживается в валках с помощью специального приспособления. Обжатие заготовки
по диаметру и придание ей требуемой формы сечения обеспечиваются
соответствующей профилировкой валков и изменением расстояния между ними. Данным
способом производят изделия, представляющие собой тела вращения (шары, оси,
шестерни и др.).
Поперечно-винтовая или косая прокатка выполняется во
вращающихся в одном направлении валках, установленных в прокатной клети под
некоторым углом друг к другу. Станы косой прокатки используют при производстве
труб, главным образом для прошивки слитка или заготовки в гильзу. В момент соприкосновения
металла с вращающимися валками, имеющими наклон к оси обрабатываемой заготовки,
возникают силы, направленные вдоль оси заготовки, и силы, направленные по
касательной к ее поперечному сечению. Совместное действие этих сил обеспечивает
вращение, втягивание обрабатываемой заготовки в суживающуюся щель и
деформирование.
Хотя сортамент прокатных изделий весьма обширен, все
же представляется возможным весь прокат разбить на следующие основные четыре
группы: сортовой, листовой, трубы, специальные виды проката (бандажи, колеса,
периодические профили и пр.). Наиболее разнообразной является группа сортового
проката, который подразделяется на простые и фасонные профили. Прокат в виде
круга, квадрата, полос плоского сечения относится к простым профилям. Прокат
сложного поперечного сечения относится к фасонным профилям. В зависимости от
назначения фасонные профили подразделяются на профили общего или массового
потребления (угловой профиль, швеллеры, двутавровые балки, шестигранные профили
и др.) и профили специального назначения (рельсы железнодорожные широкой и
узкой колеи, рельсы трамвайные, профили сельскохозяйственного машиностроения,
электропромышленности, нефтяной промышленности и др.).
Весь сортовой прокат подразделяется на четыре группы:
сталь крупносортная, среднесортная, мелкосортная и катанка диаметром от 5,5 до
9 мм.
В зависимости от способа производства и толщины
листовой прокат подразделяется на три основных группы: горячекатаные толстые
листы толщиной 4 мм и более, горячекатаные тонкие листы толщиной менее 4 мм и
холоднокатаные листы всех размеров.
К основным операциям любой технологической схемы
производства проката следует отнести: подготовку исходных материалов; нагрев
перед прокаткой (кроме холодной прокатки, когда, однако, часто требуется другая
операция - соответствующая термическая обработка); горячую и холодную прокатку;
калибровку и производство гнутых профилей; отделку с операциями резки, правки,
термической обработки, удаления поверхностных дефектов, травления и пр.
Волочение металла - это протягивание изделия круглого
или фасонного профиля через отверстие волочильного очка (волоку), площадь
выходного сечения которого меньше площади сечения исходного изделия. Волочение
выполняется тяговым усилием, приложенным к переднему концу обрабатываемой
заготовки. Данным способом получают проволоку всех видов, прутки с высокой
точностью поперечных размеров и трубы разнообразных сечений.
Изделия, полученные волочением, обладают высоким
качеством поверхности и высокой точностью размеров поперечного сечения. Если
изделию требуется придать в основном эти характеристики, то такой вид обработки
называют калибровкой.
Волочение чаще всего выполняют при комнатной
температуре, когда пластическую деформацию большинства металлов сопровождает
наклеп. Это свойство в совокупности с термической обработкой, используют для
повышения некоторых механических характеристик металла.
Волочение выгодно отличается от механической обработки
металла резанием (строганием), фрезерованием, обточкой, так как при этом
отсутствуют отходы металла в виде стружки, а сам процесс заметно
производительнее и менее трудоемок.
Термическая обработка металла перед волочением снимает
наклеп, придает металлу необходимые пластические свойства, обеспечивает
получение наиболее оптимальной структуры. Поэтому термическую обработку
выбирают такой, чтобы в сочетании с пластической деформацией она обеспечивала
максимальные механические и другие характеристики обрабатываемого изделия.
При производстве проволоки и прутков волочением
большое внимание уделяют подготовке поверхности продукта обработки перед
волочением. Удаление окалины в калибровочных и волочильных цехах производят
механическим, химическим и электрохимическим способами, а также комбинациями
этих способов.
Для регламентации технологических операций составляются
технологические карты, в которых расписан весь технологический процесс по
подготовке металла к волочению, маршрут волочения, способы начальной,
промежуточной и окончательной термических обработок, операций отделки и пр. Так
как маршрут волочения представляет собой последовательность изменения размеров
поперечного сечения исходного материала на волочильном стане, а на одной
установке обычно получают изделия с различными размерами поперечного сечения,
то для каждого из них должен быть свой маршрут волочения.
Прессование металла - это вытеснение с помощью
пуансона металла исходной заготовки (чаще всего цилиндрической формы),
помещенной в контейнер, через отверстие матрицы.
Этот способ пластической обработки находит широкое
применение при деформировании как в горячем, так и в холодном состоянии
металлов, имеющих не только высокую податливость, но и обладающих значительной
природной жесткостью, а также в одинаковой мере применим для обработки
металлических порошков и неметаллических материалов.
Процесс прессования выполняется в условиях
неравномерного всестороннего сжатия металла, что положительно сказывается на
увеличении его пластичности. Поэтому прессованием можно обрабатывать металлы и
сплавы с низкой природной пластичностью. Однако трехосное сжатие вызывает
необходимость значительных усилий при обработке. Поэтому прессование требует
повышенного расхода энергии на единицу объема деформируемого тела.
Ковка и штамповка металла включает такие процессы
получения изделий, как ковка, объемная горячая штамповка и штамповка листового
и пруткового материала в холодном состоянии.
При ковке деформирование заготовки осуществляется с
помощью универсального подкладного инструмента или бойков. Бойки чаще всего
бывают плоскими, однако применяют вырезные и закругленные бойки. Нижний боек
обычно неподвижен, верхний совершает возвратно-поступательное движение. В
результате многократного и непрерывного воздействия инструмента заготовка
постепенно приобретает необходимую форму и размеры.
При объемной штамповке придание заготовке заданной
формы и размеров осуществляется путем заполнения металлом рабочей плоскости
штампа.
Листовая штамповка является таким видом пластической
обработки металла, когда для получения деталей типа колпачков, втулок и других
в качестве исходного материала используют лист или ленту. При этом обработка
выполняется без значительного изменения толщины заготовки.
Данными способами получают весьма разнообразные по
форме и размерам изделия из металла, пластмасс и других материалов с различными
степенью точности размеров, механическими и другими характеристиками и
качеством поверхности. Поэтому ковочно-штамповочное производство находит
широкое применение в машиностроении и приборостроении, в производстве предметов
народного потребления и других отраслях народного хозяйства. Получение изделий
ковкой и штамповкой позволяет максимально приблизить исходную форму заготовки к
форме и размерам готовой детали и тем самым уменьшить или полностью исключить
дорогостоящие операции с потерей металла в стружку [45].
.2 Обработка металлов резанием
Обработка резанием является универсальным методом
размерной обработки. Этот метод позволяет обрабатывать поверхности деталей
различной формы и размеров с высокой точностью из наиболее используемых
конструкционных материалов. Он обладает малой энергоемкостью и высокой
производительностью. Вследствие этого обработка резанием является основным,
наиболее используемым в промышленности процессом размерной обработки деталей.
К основным методам механической обработки металла
резанием относятся: фрезерная, токарная, сверление, шлифование, строгание [45].
Существует большое разнообразие типов и моделей
металлорежущих станков. Они различаются по виду технологических процессов,
осуществляемых на данном станке, типу применяемых инструментов, степени чистоты
обрабатываемой поверхности, конструктивным особенностям, степени автоматизации,
числу важнейших рабочих органов станка.
По виду обработки и виду режущего инструмента станки
называются токарными, сверлильными, фрезерными, шлифовальными и т. д.
В зависимости от чистоты обработанной поверхности
станки делят на обдирочные, чистовые, отделочные, доводочные, а по
конструктивным особенностям - на горизонтальные и вертикальные. По степени
автоматизации станки делят на автоматы, полуавтоматы, станки с программным
управлением.
По числу рабочих органов станка (шпинделей, суппортов)
различают сверлильные одношпиндельные, сверлильные многошпиндельные, токарные
односуппортные, многосуппортные и т. п.
Все металлорежущие станки в зависимости от
специализации делят на следующие группы:
) Универсальные, применяемые для обработки
различных по форме и размерам поверхностей на деталях многих наименований.
Универсальные станки используются в штучном и отчасти в мелкосерийном
производствах и в ремонтных цехах.
) Специализированные, применяемые для обработки
различных поверхностей на деталях одного наименования или немногих
наименований, сходных по конфигурации, но различных размеров, например
ступенчатых валиков, колес подшипников качения, шкивов и т. п. Специализированные
станки используются, главным образом, в серийном производстве.
) Специальные, применяемые для обработки одних
деталей, как, например, обточки шеек коленчатых валов, для обточки фасонного
профиля реборд вагонных колес и т. п.
Кроме этого, в зависимости от веса и размеров станки
классифицируют на:
- легкие станки, применяемые для
обработки деталей приборов, часов, швейных машин;
- средние станки весом до 10 т,
применяющиеся, главным образом, в среднем машиностроении;
- крупные станки весом от 10 до 30 т (за
исключением внутри-шлифовальных, шлифовально-притирочных и зубообрабатывающих,
для которых предельный вес составлят 20 т);
- тяжелые станки весом от 30 до 100 т и
особо тяжелые или уникальные (свыше 100 т).
.2.1 Фрезерование
Фрезерование - это метод обработки металла фрезами.
Фрезерованием в большинстве случаев обрабатываются плоские или фасонные
линейчатые поверхности. Фрезерование ведется многолезвийными инструментами -
фрезами [45].
Фреза представляет собой тело вращения, у которого
режущие зубья расположены на цилиндрической или на торцовой поверхности. В
зависимости от этого фрезы соответственно называются цилиндрическими или
торцовыми, а само выполняемые ими фрезерование - цилиндрическим или торцовым.
Главное движение придается фрезе, движение подачи обычно придается
обрабатываемой детали, но может придаваться и инструменту - фрезе. Чаще всего
оно является поступательным, но может быть вращательным или сложным.
Процесс фрезерования отличается от других процессов
резания тем, что каждый зуб фрезы за один ее оборот находится в работе
относительно малый промежуток времени. Большую часть оборота зуб фрезы
проходит, не производя резания. Это благоприятно сказывается на стойкости фрез.
Другой отличительной особенностью процесса фрезерования является то, что каждый
зуб фрезы срезает стружку переменной толщины.
Фрезерование может производиться двумя способами:
против подачи и по подаче. Встречное фрезерование является основным. Попутное
фрезерование целесообразно вести лишь при обработке заготовок без корки и при
обработке материалов, склонных к сильному обработочному упрочнению, так как при
фрезеровании против подачи зуб фрезы, врезаясь в материал, довольно
значительный путь проходит по сильно наклепанному слою. Износ фрез в этом
случае протекает излишне интенсивно.
При работе торцовыми или концевыми фрезами различают
симметричное и несимметричное резание. При симметричном резании ось фрезы
совпадает с плоскостью симметрии обрабатываемой поверхности, а при
несимметричном - не совпадает.
.2.2 Точение
Точение - это обработка резанием наружных и внутренних
поверхностей вращения. Основными видами работ, выполняемых при точении,
являются: обработка цилиндрических, конических, фасонных, торцовых
поверхностей, уступов; вытачивание канавок; отрезание частей заготовки;
обработка отверстий сверлением, растачиванием, зенкерованием, развертыванием;
нарезание резьбы; накатывание. Вращательное движение заготовки называют главным
движением резания, а поступательное движение режущего инструмента - движением
подачи. Различают также вспомогательные движения, которые не имеют
непосредственного отношения к процессу резания, но обеспечивают
транспортирование и закрепление заготовки на станке, его включение и изменение
частоты вращения заготовки или скорости поступательного движения инструмента и
другие [45].
Разновидности точения: обтачивание - обработка
наружных поверхностей; растачивание - обработка внутренних поверхностей;
подрезание - обработка плоских торцевых поверхностей; резка - разделение
заготовки на части или отделение готовой детали от заготовки.
На токарных станках обрабатываются детали типа тел
вращения: валы, зубчатые колеса, шкивы, втулки, кольца, муфты, гайки и др.
Инструменты, применяемые для выполнения токарных работ, называются режущими.
При точении используются различные режущие инструменты: резцы, сверла, зенкеры,
развертки, метчики, плашки, резьбонарезные головки и другие.
Обрабатываемость металлов точением зависит от их
химического состава, структуры, механических и физических свойств. При черновом
точении обрабатываемость оценивают скоростью инструмента при соответствующей
скорости и силе резания, а при чистовой - шероховатостью поверхности, точностью
обработки и стойкостью инструмента.
Обрабатываемость металлов определяют методами,
основанными на оценке изменений стойкости режущего инструмента при различных
скоростях резания. Допустимую скорость резания как критерий оценки
обрабатываемости применяют наиболее часто, так как скорость резания оказывает
весьма существенное влияние на производительность, а следовательно, и на
себестоимость обработки. Считается, что лучшую обрабатываемость имеет тот
металл, который при прочих равных условиях, допускает более высокую скорость
резания. На токарных станках обрабатывают такие конструкционные материалы, как
чугун, сталь, цветные металлы и их сплавы, пластмассы [45].
Токарная обработка металлов, основанная на удалении
припуска и превращении его в стружку, определяется понятием резание металла.
Для успешной токарной работы необходимо, чтобы процесс резания протекал
непрерывно и быстро. Форма обрабатываемой детали обеспечивается, с одной
стороны, относительным движением заготовки и инструмента, с другой - геометрией
инструмента.
Резец является основным инструментом, применяемым при
токарных работах. Он представляет собой стержень прямоугольного (иногда
круглого) сечения и состоит из рабочей части и корпуса. Рабочая часть резца
является режущей частью, на которой находится лезвие инструмента. Корпус резца
служит для установки и крепления инструмента на станке. Рабочая часть резца
имеет переднюю поверхность, главную и вспомогательную задние поверхности,
главную и вспомогательную режущие кромки, вершину лезвия и радиус скругления
режущей кромки. Передней поверхностью называется поверхность лезвия,
контактирующая при резании со стружкой. Задними поверхностями называются
поверхности лезвия, контактирующие при резании с поверхностями заготовки. Одна
из них называется главной поверхностью и расположена в направлении подачи
резца, а другая - вспомогательной задней поверхностью. Режущая кромка лезвия
образуется пересечением передней и задней поверхностей лезвия. Одна из них
называется главной режущей кромкой, так как формирует большую сторону сечения
срезаемого слоя, а другая - вспомогательной режущей кромкой, так как формирует
меньшую сторону сечения срезаемого слоя. Вспомогательных режущих кромок может
быть одна или две.
Токарные станки бывают следующих видов:
) Токарно-винторезный станок - служит для
токарной обработки методом точения наружных поверхностей и торцов деталей с
помощью резцов, а также сверление отверстий в деталях с центральной осью
вращения, зенкерование, развёртывание, тонкого растачивания отверстий нарезания
всех вдов наружных и внутренних резьб с помощью резцов - мётчиков и плашек.
Станок используется в единичном и мелкосерийном производствах, т.к. он
широкоуниверсальный.
) Токарно-карусельный станок. Он относится к
классу средних и тяжёлых станков, которые служат для обработки деталей
диаметром от 500 мм и выше, массой от 50 до 100 кг. Карусельные станки делятся
на одностоечные и двухстоечные.
.2.3 Сверление
Сверление - весьма распространенный способ получения в
обрабатываемой заготовке сквозных или глухих отверстий, а также рассверливания
уже имеющихся отверстий. Режущим инструментом при сверлении являются сверла
[45].
К сверлильным станкам относят собственно сверлильные и
расточные станки.
Станки сверлильной группы разделяют на
вертикально-сверлильные, радиально-сверлильные, одно- и многошпиндельные
полуавтоматы, координатно-расточные, алмазно-расточные, горизонтально-сверлильные
для глубокого сверления, расточные и специальные.
Различают обычное и глубокое сверление. При обычном
сверлении и для получения сквозных или глухих отверстий применяют спиральные
сверла с коническими или цилиндрическими хвостовиками. Первые закрепляют в
шпинделе станка непосредственно или при помощи переходных конусных втулок,
вторые - при помощи двух- и трехкулачковых патронов.
В зависимости от величины партии обрабатываемых
деталей сверление производят по разметке или в кондукторах.
Сверление по разметке применяют при небольших партиях
обрабатываемых деталей и при выполнении ремонтных работ, когда затраты на
изготовление кондуктора не окупаются. В этом случае точность обработки
получается меньшей (не выше 5-го класса). При сверлении по разметке в
зависимости от формы и размеров деталей их устанавливают и зажимают либо
непосредственно на столе станка, либо в приспособлениях. Чаще всего применяют
машинные тиски, призмы и угольники, укрепляемые на столе станка.
При обработке больших партий деталей производит
сверление и кондукторах - специальных приспособлениях, изготовляемых по форме
обрабатываемой детали. Кондукторы позволяют вести сверление без предварительной
разметки детали и получать более высокую точность обработки (до 4-гo класса).
Перед сверлением производится наладка станка
(установка и проверка инструмента, укрепление обрабатываемых деталей и т. д.) и
его настройка (выбор числа оборотов шпинделя и подачи).
1.2.4 Шлифование
Шлифование - процесс резания при помощи абразивного
инструмента - круга, обеспечивающего высокую точность и чистоту обработанной
поверхности. В ряде случаев шлифование применяют как метод предварительной
обработки поверхностей при обдирке литья, поковок, проката, а также при
разрезке заготовок из прутка [45].
Шлифовальный круг представляет собой пористое тело,
состоящее из большого количества мелких зерен. Эти зерна соединены между собой
особым веществом, которое называется связкой. Твердые материалы, из которых
образованы зерна шлифовального круга, называются абразивными материалами.
Процесс шлифования состоит в том, что шлифовальный круг снимает с детали тонкий
слой металла (стружку) острыми гранями своих абразивных зерен.
К особенностям процесса шлифования следует отнести:
) высокую скорость резания;
) сильное размельчение и своеобразный характер
снимаемой стружки;
) невыгодную геометрию режущих зерен шлифовального
круга;
) высокое нагревание обрабатываемой поверхности и
стружки.
Поверхности, обрабатываемые шлифованием, могут быть
простыми и сложными. К простым относятся наружная и внутренняя цилиндрическая
поверхность и плоскость, к сложным - винтовая, эвольвентная и некоторые другие
поверхности.
Для осуществления процесса шлифования необходимо,
чтобы деталь и абразивный инструмент имели соответствующие относительные движения.
В машиностроении наиболее часто применяются следующие виды шлифования: круглое
наружное, круглое внутреннее и плоское.
К круглому наружному шлифованию относятся:
а) шлифование с продольной подачей;
б) шлифование врезанием;
в) бесцентровое шлифование с продольной подачей;
г) бесцентровое шлифование врезанием.
Для осуществления круглого наружного шлифования с
продольной подачей необходимы следующие движения: вращение шлифовального круга,
или главное движение резания; вращение детали вокруг своей оси - круговая
подача детали; прямолинейное возвратно-поступательное движение детали (или
шлифовального круга) вдоль оси детали - продольная подача; поперечное
перемещение шлифовального круга на деталь или, наоборот, детали на круг -
поперечная подача, или подача на глубину шлифования. При шлифовании с
продольной подачей этот вид подачи используется периодически, в конце каждого
двойного хода детали.
Круглое наружное шлифование врезанием отличается от
первого способа шлифования тем, что высота применяемого при этом шлифовального
круга берется равной длине шлифования детали или несколько больше ее. Поэтому
здесь отпадает необходимость в продольной подаче. Поперечная подача применяется
непрерывно в течение всего процесса шлифования. Таким образом, для выполнения наружного
шлифования врезанием необходимы следующие движения: вращение шлифовального
круга, вращение детали вокруг своей оси, или ее круговая подача, и непрерывная
поперечная подача шлифовального круга.
Бесцентровое шлифование представляет собой
разновидность наружного круглого шлифования. Шлифуемая деталь помещается на
опорном ноже между кругами - рабочим и подающим, или ведущим. Для осуществления
процесса бесцентрового шлифования необходимы следующие движения: вращение
шлифовального и подающего кругов, круговая и продольная подачи. Вращением
подающего круга шлифуемой заготовке сообщается вращение и продольная подача,
для получения которой ведущий круг устанавливают под небольшим углом к оси
шлифующего круга.
Круглое внутреннее шлифование - шлифование с продольной
подачей шлифовального круга или заготовки и шлифование врезанием. Для этого
способа шлифования необходимы те же движения, что и при круглом наружном
шлифовании с продольной подачей: вращение шлифовального круга, круговая подача
заготовки, продольная подача заготовки или круга, поперечная подача
шлифовального круга. Круглое бесцентровое внутреннее шлифование осуществляют
без закрепления заготовки.
Плоское шлифование делят на две группы: шлифование
периферией круга и шлифование торцом круга. Для осуществления плоского
шлифования необходимы следующие движения: а) главное движение резание -
вращение шлифовального круга; б) движение подачи шлифуемой заготовки; в)
движение поперечной подачи детали или шлифовального круга в направлении,
перпендикулярном движению подачи; г) движение шлифовального круга на заготовку
или заготовки на шлифовальный круг - подача на глубину шлифования. В том
случае, когда высота шлифовального круга больше ширины шлифуемой заготовки,
поперечная подача отсутствует.
.2.5 Строгание
Строгание - процесс обработки материалов резанием со
снятием стружки, который осуществляется с помощью относительных
возвратно-поступательных движений инструмента или же изделия. Основное движение
выполняет изогнутый строгальный резец, а вот движение подачи - заготовка [45].
Заготовки на строгальных станках поддают обработке при
помощи строгальных резцов, которые делятся по нескольким критериям: по
назначению (фасонные, проходные, отрезные и подрезные), по форме стержня
(прямые, изогнутые), а также по расположению элементов головки (правые и
левые).
Строгальные резцы бывают прямыми и изогнутыми. Прямые
достаточно просты в изготовлении, однако, они менее виброустойчивы в сравнении
с изогнутыми резцами. Именно поэтому их применяют при сравнительно малых
вылетах. В случае работы с большими вылетами рекомендуется использовать
изогнутые резцы, которые получили достаточно широкое применение в
промышленности. В процессе строгания резец изгибается под действием усилий
резания. При изгибе прямого резца его режущая часть углубляется в материал
заготовки, после чего резец работает с заеданием, что понижает качество
обработки, а также дополнительно нагружает инструмент. При изгибе изогнутого
инструмента (резца) его часть, которая режет, отходит от заготовки, после чего
срезает наименьший слой металла. Это все обеспечивает более спокойное
протекания самого процесса резания, особенно при резких колебаниях усилий
резания, которые вызываются изменениями сечения слоя, который срезается, а
также изменениями свойств обрабатываемого материала.
Чтобы обработать металлы строганием применяют
разнообразные станки: кромкострогальные, поперечно- и продольно-строгальные,
строгально-долбежные и прочие. Немаловажный параметр таких станков - скорость
резания, которая равняется скорости движения резца или же изделия. При этом
виде обработки на продольно-строгальных станках основополагающее движение
задается заготовке, а движение подачи - инструменту, то есть, резцу. В процессе
строгания на поперечно-строгальных станках, а также обработке заготовок на
долбежных станках основное движение отведено резцу, а подача - заготовке или же
резцу. Чтобы более полно использовать мощность станка применяют многорезцовое
строгание. Высокопроизводительно чистовое строгание производится при помощи
широких строгальных резцов, которые оснащены пластинами из твердых сплавов:
данный процесс ведется большими подачами - до 20 мм (двойной ход) и больше.
Недостатки строгания: удар резца в начале всякого
рабочего хода, а также холостой ход, что понижает стойкость инструмента и
результативность самой обработки.
Строгание - это прерывистый процесс, удаление
материала происходит только лишь при прямом ходе рабочего инструмента.
Прерывистое резание в процессе строгания вызывает ударное врезание инструмента
в материал самой заготовки, что приводит к динамическим нагрузкам высокого
уровня. Именно поэтому при строгании применяются массивные быстрорежущие
инструменты, а также низкие скорости резания. Холостые ходы определяют
достаточно низкую производительность процесса обработки.
На строгальных станках отделывают плоские поверхности,
пазы, уступы, фасонные линейные поверхности и рифления. Поперечно-строгальные
станки используются в серийном, а также в единичном производстве. Строгание
широко применяется при изготовлении плит и рам, для обрабатывания направляющих
станин станков, кромок листов и направляющих штанг.
.3 Контроль готовой продукции
Контроль качества продукции является составной частью
производственного процесса и направлен на проверку её соответствия
установленным требования в процессе изготовления, потребления или эксплуатации.
Суть контроля качества продукции на предприятии
заключается в получении информации о состоянии объекта и сопоставлении
полученных результатов с установленными требованиями, зафиксированными в
чертежах, стандартах, договорах поставки, технических заданиях, технических
условиях и других документах [28].
Контроль предусматривает проверку продукции в самом
начале производственного процесса и в период эксплуатационного обслуживания,
обеспечивая в случае отклонения от регламентированных требований качества,
принятие корректирующих мер, направленных на производство продукции надлежащего
качества, надлежащее техническое обслуживание во время эксплуатации и полное
удовлетворение требований потребителя. Таким образом, контроль продукции
включает в себя такие меры на месте ее изготовления или на месте ее
эксплуатации, в результате которых допущенные отклонения от нормы требуемого
уровня качества могут быть исправлены еще до того, как будет выпущена дефектная
продукция или продукция, не соответствующая техническим требованиям.
Недостаточный контроль на этапе изготовления серийной продукции ведет к
возникновению финансовых проблем и влечет за собой дополнительные издержки
[47].
Производственный контроль качества включает в себя:
- входной контроль сырья, основных и
вспомогательных материалов, полуфабрикатов, комплектующих изделий,
инструментов;
- пооперационный (межоперационный)
контроль продукции и соблюдения установленного технологического режима;
- систематический контроль состояния
оборудования, машин, режущего и измерительного инструмента,
контрольно-измерительных приборов и др.;
- контроль моделей и опытных образцов;
- приёмочный контроль готовой продукции
(деталей, сборочных единиц, узлов, блоков, изделий).
Входной, межоперационный и приёмочный контроль
подвергаются выборочным и сплошным методам контроля [47].
Сплошной контроль применяется в тех случаях, когда
технологический процесс не обеспечивает достаточной стабильности заданных
размеров и других параметров качества продукции; при неоднородности качества
материалов или комплектующих изделий; после технологических операций, от
которых в значительной мере зависят точность или другие качественные показатели
изделия (например, после чистового шлифования направляющих станины
прецизионного станка, после растачивания отверстий под подшипники в корпусе
редуктора и т. п.) а также при проверке сложной или точной готовой продукции.
При сплошном контроле проверяется каждая единица
продукции в партии. Такой контроль возможен только при использовании
неразрушающих методов испытаний. Результаты сплошного контроля отличаются
достаточной достоверностью. Однако такой контроль длителен, требует большого
штата контролеров и значительных затрат.
При выборочном контроле особое значение имеет
определение оптимальной выборки - количества проверяемых деталей из каждой
партии.
При обычном выборочном контроле ее размер определяется
на основании анализа ряда выборок из различных партий данного наименования
детали без расчетного обоснования. Для более точного и обоснованного
определения размера выборки (при котором учитывается точность проверяемого
параметра, состояние оборудования и оснастки, квалификация рабочего и другие
факторы, определяющие качество работы) применяется статистический метод
контроля, при котором количество деталей из партии, подлежащих проверке,
определяется расчетным путем. Статистический контроль применяется главным
образом при проверке крупных партий деталей.
Выборочный метод контроля обработанных деталей может
обеспечить достаточную информацию об их качестве лишь при хорошо налаженном и
стабильном технологическом процессе.
.4 Понятие о статистических методах качества
Статистические методы контроля - это основа внедрения
всеобщего руководства качеством. Всеобщее руководство качеством (TQM) - это
подход к руководству организацией, нацеленный на качество, основанный на
участии всех ее членов и направленный на достижение долгосрочного успеха путем
удовлетворения требований потребителя и выгоды для членов организации и общества
[32].
Одним из важнейших положений TQM является принятие
решений на основе фактов. Совершенствование качества продукции и процессов
требует внимательной и усердной работы персонала предприятия по выявлению
причин дефектов (отклонений от документации) и их устранению. Для этого
необходимо организовать поиск фактов, характеризующих несоответствия, в
подавляющем большинстве которыми являются статистические данные, разработать
методы анализа и обработки данных, выявить коренные причины дефектов и разработать
мероприятия по их устранению с наименьшими затратами [39].
Проблемами сбора, обработки и анализа информации
занимается математическая статистика, которая включает в себя большое
количество не только известных методов, но и современных инструментов анализа и
выявления дефектов. К таким методам можно отнести корреляционный и
регрессионный анализы, проверку статистических гипотез, факторный анализ,
анализ временных рядов, анализ безотказности и т.д.
Большое распространение в управлении качеством (под
влиянием японских специалистов) получили семь простых методов, применение
которых не требует высокой квалификации персонала и позволяет охватить анализ
причины большинства возникающих на производстве дефектов [32].
Понятие «управление качеством» как наука возникло в
конце 19-го столетия, с переходом промышленного производства на принципы
разделения труда. Принцип разделения труда потребовал решения проблемы
взаимозаменяемости и точности производства. Для этого при ремесленном способе
производстве продукции обеспечение точности готового продукта производилось по
образцам или методами подгонки сопрягаемых деталей и узлов. Учитывая
значительные вариации параметров процесса, становилось ясно, что нужен критерий
качества производства продукции, позволяющий ограничить отклонения размеров при
массовом изготовлении деталей.
В качестве такого критерия Фредериком Тейлором были
предложены интервалы, устанавливающие пределы отклонений параметров в виде
нижних и верхних границ. Поле значений такого интервала стали называть допуском.
Установление допуска привело к противостоянию
интересов конструкторов и производственников: одним ужесточение допуска
обеспечивало повышение качества соединения элементов конструкции, другим -
создавало сложности с созданием технологической схемы, обеспечивающей требуемые
значения вариаций процесса. Очевидно также, что при наличии разрешённых границ
допуска у изготовителей не было мотивации «держать» показатели (параметры)
изделия как можно ближе к номинальному значению параметра, это приводило к выходу
значений параметра за пределы допуска.
В то же время (начало 20-х годов прошлого столетия)
некоторых специалистов в промышленности заинтересовало, можно ли предсказать
выход параметра за пределы допуска. И они стали уделять основное внимание не
самому факту брака продукции, а поведению технологического процесса, в
результате которого возникает этот брак или отклонение параметра от
установленного допуска. В результате исследования вариабельности
технологических процессов появились статистические методы управления
процессами. Родоначальником этих методов был Уолтер Эндрю Шухарт.
Одновременно с этим большое внимание уделялось
разработке теории выборочного контроля продукции. Первые работы в этой области
появились в конце 20-х годов в США, автором их был Г. Додж, ставший в
последствие известным американским учёным [32].
С момента зарождения статистических методов контроля
качества специалисты понимали, что качество продукции формируется в результате
сложных процессов, на результативность которых оказывает влияние множество
материальных факторов и ошибки работников. Поэтому для обеспечения требуемого
уровня качества нужно уметь управлять всеми влияющими факторами, определять
возможные варианты реализации качества, научиться его прогнозировать и
оценивать потребность объектов того или иного качества.
В послевоенное время и в США, и в Европе появились
национальные стандарты по качеству. Центральная роль в разработке нормативных
документов в области качества принадлежит Международной организации по
стандартизации (ISO). Начиная с 90-х годов, идеи теории вариаций,
статистического управления процессами овладели не только
специалистами-математиками, но и стали неотъемлемыми инструментами менеджеров и
работников служб качества.
Большой толчок дальнейшему развитию принципов
управления качеством дал японский учёный Г. Тагути. Он предложил учитывать
вариации свойств продукции на разных этапах её разработки, что для менеджмента
качества явилось революционной идеей. По Тагути нужно было установить те
сочетания параметров изделий и процессов, которые приводили к минимуму вариаций
процессов. Эти процессы, которые стали называть робастными, были устойчивы к
вариациям входных параметров процессов [32].
Используемые в сегодняшней практике предприятий
статистические методы можно подразделить на следующие категории:
методы высокого уровня сложности, которые используются
разработчиками систем управления предприятием или процессами. К ним относятся
методы кластерного анализа, адаптивные робастные статистики и др.;
методы специальные, которые используются при
разработке операций технического контроля, планировании промышленных
экспериментов, расчётах на точность и надёжность и т.д.;
методы общего назначения, в разработку которых большой
вклад внесли японские специалисты. К ним относятся «Семь простых методов» (или
«Семь инструментов качества»), включающие в себя контрольные листки, метод
расслоения, графики, диаграммы Парето, диаграммы Исикавы, гистограммы,
контрольные карты [35].
.5 История развития статистических методов качества
Первое восприятие статистических методов качества в
виде выборки имеет многовековую историю. Выборка - одна или несколько
выборочных единиц, взятых из генеральной совокупности и предназначенных для
получения информации о ней [28]. Ещё несколько столетий тому назад покупатели
зерна и хлопка проверяли свойства товара, прокалывая мешки с зерном или
хлопком, чтобы взять пробу. Можно допустить, что в те времена не было научного
расчёта взятия проб, и следует предположить, что это было делом опыта, как
продавцов, так и покупателей товара.
До тех пор пока ремесленник совмещал в себе функции и
производителя, и контролёра (до середины 19-го века), не было проблем с оценкой
качества изготовленной продукции. Всё изменилось с появлением разделения труда.
Рабочие первых фабричных мануфактур, способные выполнять простые операции
процесса, способные выполнять простые операции процесса, не могли отвечать за
качество своего труда, и тем более за качество готовой продукции. Введение
должности контролёра привело к необходимости нормирования функций контроля и со
временем потребовало разработки научного подхода к оценке качества продукции.
Стремление к производству высококачественной продукции привело к развитию на
промышленных предприятиях контрольного аппарата.
Применение статистических методов контроля качества
труда произошло ещё позже - в первой четверти 20-го века. Именно внедрение
статистических методов позволило значительно сократить трудоёмкость операций
контроля и значительно снизить численность инспекторов (контролёров). Первое
применение научных методов статистического контроля было зафиксировано в 1924
году, когда У. Шухарт использовал для определения доли брака продукции
контрольные карты [35].
Уолтер Эндрю Шухарт с 1918 года работал инженером
фирмы «Western Electric» (США). В 1925 году она была преобразована в фирму
«Bell Telephone Laboratories». Шухарт проработал в ней до 1956 года. Основные
его разработки в области статистического контроля внедрялись в первую очередь
на этой фирме. Шухарт переключил внимание с допускового подхода к управлению
качеством на подход, направленный на обеспечение стабильности процессов и
уменьшение их вариаций. Его идеи до настоящего момента сохраняют актуальность.
Кроме того, Шухарт высказал идею непрерывного улучшения качества, предложив цикл
непрерывного улучшения процессов, носящий сегодня название «Цикл Шухарта -
Деминга». В последние годы этот цикл получил дальнейшее развитие под
воздействием Деминга и стал использоваться как инструмент командной работы по
улучшению качества [35].
Одновременно с Шухартом, в той же фирме в середине
20-х годов инженером Г.Ф. Доджем была предложена теория приёмочного контроля,
получившая вскоре мировую известность.
Большой вклад в систему обеспечения качества контроля
в середине 20-го века внесли американские учёные Д. Нойман, Э. Пирсон, Е.
Фишер. Среди их разработок наибольшую известность получила теория проверки
статистических гипотез. Без знания теории ошибок первого и второго рода
невозможна рациональная оценка выбранного метода статистического контроля [39].
Во время второй мировой войны нехватка ресурсов
заставила искать новые методы контроля с возможно малым числом проверяемых
изделий, особенно при разрушающем контроле. В 40-х годах 20-го столетия
американский математик Абрахам Вальд разработал теорию последовательного
анализа и статистическую теорию принятия решений. Применение теории
последовательного анализа было настолько эффективно (расходы на контроль при
прежней вероятности ошибок снижались до 60 % по сравнению с традиционными
методами), что в США она была объявлена секретным документом и опубликована
только после окончания войны.
Большое влияние на становление статистических методов
контроля, как философии качества, оказал американский учёный Эдвард Деминг. В
начале 50-х годов Деминг проводил широкомасштабное обучение японских
специалистов новым методам обеспечения качества, особое внимание при этом
обращая на статистические методы управления качеством. Его деятельность была
настолько успешной, что уже в 60-х годах американцам пришлось уступить японским
фирмам значительную часть рынков сбыта, в том числе и в самих США.
Американское научное влияние на совершенствование
систем обеспечения качества привело к созданию японской научной школы в области
качества, среди представителей которых следует, прежде всего, отметить К.
Исикаву и Г. Тагути, внёсших большой вклад в развитие статистических методов в
управлении качеством. Каору Исикава впервые в мировой практике предложил
оригинальный графический метод анализа причинно-следственных связей, который
получил название «диаграмма Исикавы» [35]. Сегодня практически невозможно найти
такую область деятельности по решению проблемы качества, где бы не применялась
диаграмма Исикавы.
Генити Тагути - известный во второй половине 20-го
века японский специалист в области статистики. Он развивал идеи математической
статистики, относящиеся, в частности, к статистическим методам планирования
эксперимента и контроля качества. Тагути впервые соединил математической
зависимостью экономические затраты и качество, введя понятие функции потерь
качества. Он первым показал, что потери качества имеют место и в поле допуска -
они появляются с момента несовпадения номинального, заданного технической
документацией, значения параметра и значения исследуемой случайной величины.
Заслуга Тагути также в том, что он сумел найти сравнительно простые аргументы и
приёмы, которые сделали робастное планирование эксперимента в области
обеспечения качества реальностью. Невнимание к методам Тагути - одна из причин
серьёзного отставания российских предприятий в области совершенствования
качества процессов и услуг [32].
Внесли свой научный вклад в развитие статистических
методов и советские учёные: В.И. Романовский, Е.Е. Слуцкий, Н.В. Смирнов, Ю.В.
Линник и др. Так, например, Смирнов заложил основы теории непараметрических
рядов, а Слуцкий опубликовал несколько важных работ по статистике связанных
стационарных рядов. Особенно интенсивно в СССР разрабатывались статистические
методы исследования и контроля качества в массовом производстве, методы
планирования эксперимента Юрием Адлером [35].
В 50-70-х годах прошлого столетия на ряде предприятий
оборонного комплекса СССР активно проводились (под влиянием японского опыта по
повышению качества) работы по внедрению систем управления качеством, в которых
статистические методы в области приёмочного контроля и регулирования
технологических процессов занимали важное место в предупреждении дефектов
продукции.
Российский учёный в области качества В.А. Лапидус
опубликовал ряд трудов по теории и практике управления качеством с учётом
вариаций и неопределённости, в которых изложен «принцип распределения
приоритетов», позволяющий оптимально выстроить отношения поставщика и
потребителя с позиции обеспечения качества. Ему же принадлежит новый подход к
управлению качеством, названный «гибким методом статистического управления»,
который математически опирается на теорию нечётных множеств [35].
1.6 Простые инструменты контроля качества
В середине 1960-х годов в Японии получили широкое
распространение кружки качества. Чтобы вооружить их эффективным инструментом
анализа и управления качеством, японские учёные отобрали из всего множества
известных инструментов 7 методов [35].
Эти методы в научно-технической литературе получили
название «Семь инструментов контроля качества» и «Семь основных инструментов
контроля». В дальнейшем их число увеличилось и, поскольку, общим для них
является доступность для всего персонала организации, их стали называть
«простые инструменты контроля качества». Достоинствами этих методов является
простота, наглядность, визуализация, а также эффективность использования без
специальной математической подготовки.
При всей своей простоте эти методы позволяют сохранить
связь со статистикой и дают возможность профессионалам пользоваться
результатами этих методов и при необходимости совершенствовать их. К простым
инструментам контроля качества относятся следующие статистические методы:
контрольный листок, гистограмма, диаграмма разброса, диаграмма Парето,
стратификация (расслоение), диаграмма Исикавы (причинно-следственная
диаграмма), контрольная карта. Эти методы можно рассматривать и как отдельные
инструменты, и как систему методов (различную в различных обстоятельствах).
Применение этих инструментов в производственных
условиях позволяет реализовать важнейший принцип функционирования системы
менеджмента качества (СМК) в соответствии с МС ISO серии 9000 - «принятие
решений, основанное на фактах». Инструменты контроля качества дают возможность
получить эти факты, достоверную информацию о состоянии изучаемых процессов. Перечисленные
инструменты контроля качества используют в основном исполнители (менеджеры)
первой линии для контроля и улучшения конкретных процессов. Причём это могут
быть как производственные, так и бизнес-процессы (делопроизводство, финансовые
процессы, управление производством, снабжением, сбытом и т.п.). Комплексный
характер управления качеством на всех этапах жизненного цикла продукции и
производства является непременным условием Всеобщего управления качеством [32].
Контроль качества состоит в том, чтобы, проверяя
нужным образом подобранные данные, обнаружить отклонение параметров от
запланированных значений при его возникновении, найти причину его появления, а
после устранения причины проверить соответствие данных запланированным
(стандарту или норме). Так реализуется цикл PDCA, или цикл Деминга.
Источником данных при осуществлении контроля качества
служат следующие мероприятия.
. Инспекционный контроль: регистрация данных
входного контроля исходного сырья и материалов; регистрация данных контроля
готовых изделий; регистрация данных инспекционного контроля процесса
(промежуточного контроля) и т.д.
. Производство и технологии: регистрация данных
процесса; повседневная информация о применяемых операциях, регистрация данных
контроля оборудования (неполадки, ремонт, техническое обслуживание); патенты и
статьи из периодической печати и т.д.
. Поставки материалов и сбыт продукции:
регистрация движения через склады (входная и выходная нагрузка); регистрация
сбыта продукции (данные о получении и выплате денежных сумм, контроль срока
поставок) и т.д.
. Управление и делопроизводство: регистрация
прибыли; регистрация возвращенной продукции; регистрация обслуживания
постоянных клиентов; журнал регистрации продажи; регистрация обработки
рекламаций; материалы анализа рынка и т.д.
. Финансовые операции: таблица сопоставления
дебета и кредита; регистрация подсчёта потерь; экономические расчёты и т.д.
Очень редко для заключения о качестве данные
используются в том виде, в каком они были получены. Это бывает только в
случаях, когда возможно прямое сравнение измеренных данных со стандартом. Чаще
при анализе данных проводятся различные операции: находят среднее значение и
стандартное отклонение, оценивают разброс данных и т.д.
Решение той или иной проблемы с помощью простых инструментов
контроля качества обычно производится по следующей схеме.
. Оценка отклонений параметров от установленной
нормы. Выполняется часто с помощью контрольных карт и гистограмм.
. Оценка факторов, явившихся причиной
возникновения проблемы. Проводят расслоение (стратификацию) по зависимостям
между видами брака (дефектами) и влияющими факторами и с помощью диаграммы
разброса исследуют тесноту взаимосвязей, применяют также причинно-следственную
диаграмму.
. Определение важнейших факторов, явившихся
причиной отклонений параметров. Используют диаграмму Парето.
. Разработка мероприятий по устранению
проблемы.
. После внедрения мероприятий - оценка их
эффективности с помощью контрольных карт, гистограмм, диаграмм Парето.
В случае необходимости цикл повторяют до тех пор, пока
проблема не будет решена.
Регистрацию результатов наблюдений выполняют часто с
помощью графиков, контрольных листков и контрольных карт.
Рассмотрим суть и методику применения указанных
простых методов контроля качества.
1.6.1 Контрольный листок
Контрольный листок - это инструмент для сбора данных и
их автоматического упорядочения для облегчения дальнейшего использования
собранной информации [47].
Контрольный листок используется как для регистрации
опытных данных, так и для предварительной их систематизации. Имеются сотни
различных видов контрольных листков. Чаще всего они оформляются в виде таблицы
или графика.
Контрольный листок может фиксировать как
количественные, так и качественные характеристики процесса (место выявленных
дефектов на изделии, виды отказов и др.). Необходимо тщательно спланировать
сбор данных, чтобы избежать ошибок, которые могут исказить представление об
изучаемом процессе. Могут возникать следующие ошибки: недостаточная точность
измерений из-за несовершенства средств или методов измерений, из-за плохой
информированности сборщиков данных, их низкой квалификации или их
заинтересованности в искажении результатов; совмещение измерений, относящихся к
разным условиям протекания процесса; влияние процесса измерений на изучаемый процесс.
Чтобы избежать этих ошибок, нужно соблюдать следующие правила.
) Необходимо установить суть изучаемой проблемы
и поставить вопросы, нуждающиеся в разрешении.
) Следует разработать форму контрольного
листка, позволяющую с минимальными затратами времени и средств получить
достоверную информацию о процессе.
) Необходимо разработать методику измерений,
исключающую получение данных, не учитывающих важные условия протекания
процесса. Например, измерения следует производить на одном виде оборудования
при использовании определённой оснастки, с указанием режимов процесса,
исполнителя, времени и места протекания процесса. Это позволит в дальнейшем
учесть влияние этих факторов на процесс.
) Необходимо выбрать сборщика данных,
непосредственно имеющего информацию о процессе в качестве оператора, наладчика
или контролёра, не заинтересованного в её искажении, обладающего квалификацией
для получения достоверных данных.
) Со сборщиками данных следует провести
инструктаж о методике измерений или обучить их.
) Средства и методы измерений должны
обеспечивать требуемую точность измерений.
) Следует выполнить аудит процесса сбора
данных, оценить его результаты, при необходимости откорректировать методику
сбора данных [35].
.6.2 Гистограмма
Гистограмма - инструмент, позволяющий зрительно
оценить закон распределения величины разброса данных, а также принять решение о
том, на чём следует сфокусировать внимание с целью улучшения процесса [47].
Этот распространённый инструмент контроля качества
используется для предварительной оценки дифференциального закона распределения
изучаемой случайной величины, однородности экспериментальных данных, сравнения
разброса данных с допустимым, природы и точности изучаемого процесса. Также для
этой цели используют полигон - ломаную линию, соединяющую середины столбцов
гистограммы.
Гистограмма как метод представления статистических
данных была предложена французским математиком А. Гэри в 1833 году. Он
предложил использовать столбцовый график для анализа данных о преступности.
Работа А. Гэри принесла ему медаль Французской академии, а его гистограммы
стали стандартным инструментом для анализа и представления данных.
Основным достоинством гистограммы является то, что
анализ её формы и расположения относительно границ поля допуска даёт много
информации об изучаемом процессе без выполнения расчётов. Для получения такой
информации из исходных данных необходимо выполнить достаточно сложные расчёты.
Гистограмма позволяет оперативно выполнить предварительный анализ процесса
(выборки) исполнителю первой линии (оператору, контролёру и др.) без
математической обработки результатов измерений [35].
.6.3 Диаграмма разброса
Диаграмма разброса - инструмент, позволяющий
определить вид и тесноту связи между парами соответствующих переменных [47].
Это даёт возможность линейному персоналу контролировать ход процесса, а
технологам и менеджерам - управлять им.
Этими двумя переменными могут быть:
· характеристика качества процесса и
фактор, влияющий на ход процесса;
· две различные характеристики
качества;
· два фактора, влияющие на одну
характеристику качества.
Рассмотрим примеры использования диаграмм разброса в
указанных случаях.
К примерам применения диаграммы разброса для анализа
зависимости между причинным фактором и характеристикой (следствием) относятся
диаграммы для анализа зависимости суммы, на которую заключены контракты, от
числа поездок бизнесмена с целью заключения контрактов (планирование
эффективных поездок); процента брака от процента невыходу на работу операторов
(контроль персонала); числа поданных предложений от числа циклов (от времени)
обучения персонала (планирование обучения); расхода сырья на единицу готовой
продукции от степени чистоты сырья (стандарты на сырьё); выхода реакции от
температуры реакции; степени деформации от скорости формовки (контроль процессов);
размера принятого заказа от числа дней, за которое производится обработка
рекламаций (инструкции по ведению торговых операций, инструкции по обработке
рекламаций) и т.д.
При наличии корреляционной зависимости причинный
фактор оказывает очень большое влияние на характеристику, поэтому, удерживая
этот фактор под контролем, можно достичь стабильности характеристики. Можно
также определить уровень контроля, необходимый для требуемого показателя
качества.
Примерами применения диаграммы разброса для анализа
зависимости между двумя причинными факторами могут служить диаграммы для
анализа зависимости между содержанием рекламаций и руководством по эксплуатации
изделия (движение за отсутствие рекламаций); между циклами закалки отожжённой
стали и газовым составом атмосферы (контроль процесса); между числом курсов
обучения оператора и степенью его мастерства (планирование обучения и
подготовки кадров) и т.д.
При наличии корреляционной зависимости между
отдельными факторами значительно облегчается контроль процесса с
технологической, временной и экономической точек зрения.
Применение диаграммы разброса для анализа зависимости
между двумя характеристиками (результатами) можно видеть на таких примерах, как
анализ зависимости между объёмом производства и себестоимостью изделия; между
прочностью на растяжение стальной пластины и её прочностью на изгиб; между
размерами комплектующих деталей и размерами изделий, смонтированных из этих
деталей; между прямыми и косвенными затратами, составляющими себестоимость
изделия; между толщиной стального листа и устойчивостью к изгибам и т.д.
При наличии корреляционной зависимости можно
осуществлять контроль только одной (любой) из характеристик [35].
1.6.4 Стратификация (расслоение) данных
Стратификация - метод разделения полученных данных на
отдельные группы в зависимости от выбранного стратифицирующего фактора. Если
удачно осуществить стратификацию, можно выявить главную причину появления
разброса параметров, уменьшить его и в конечном итоге добиться повышения
качества продукции [47].
Это один из наиболее простых, эффективных и
распространённых методов выявления причин несоответствий, влияния различных
факторов на показатели качества процесса. Японские кружки качества выполняют
стратификацию данных в среднем до 100 раз при решении одной проблемы.
Расслоение данных заключается в разделении результатов
процесса на группы, внутри которых эти результаты получены в определённых
условиях протекания процесса.
Данные, разделённые на группы по признаку условий их
формирования, называют слоями (стратами), а сам процесс разделения на слои
(страты) - расслоением (стратификацией) данных.
Расслоение данных производится часто по следующим
признакам:
· оборудование (тип и форма;
конструкция; срок службы; расположение, фирма-производитель; состояние и др.);
· человеческий фактор (заказчик;
оператор; рабочий, поставленный в замену; мастер; стаж работы; мужчина или
женщина; квалификация и др.);
· исходные материалы (изготовитель; тип
и торговая марка;партия, качество, производитель и др.);
· методы (методы операции; условия
операций - температура, давление и т.д.; система сдачи продукции, метод
контроля, средство измерения и др.);
· время (дата; первая или вторая
половина дня; день или ночь; день недели, смена работы, время года и др.);
· изделие (тип; сорт; качество; партия,
производитель и др.).
Метод расслоения используется практически во всех
областях человеческой деятельности для решения проблем материального характера.
В частности, он применяется на всех этапах жизненного цикла машин. В процессе изготовления
машин его применяют для анализа причин несоответствий при разработке
предупреждающих и корректирующих мероприятий: при расчёте стоимости изделия,
когда требуется оценка прямых и косвенных расходов отдельно по изделиям и по
партиям; при оценке прибыли от продажи изделий отдельно по клиентам и по
изделиям; при оценке качества хранения отдельно по изделиям и по партиям и т.п.
Кроме того, расслоение используется в случае применения других статистических
методов: при построении причинно-следственных диаграмм, диаграмм Парето,
гистограмм и контрольных карт.
Наиболее часто используются три способа реализации
расслоения данных.
. Табличный. Результаты процесса, полученные в
различных условиях, заносятся в отдельные части таблицы и сравниваются между
собой.
. Графический. Результаты процесса наносятся на
график, в котором выделяются зоны, полученные в различных условиях. Результаты
для различных условий процесса сравниваются между собой.
. Дисперсионный анализ. Оценивается доля
дисперсии результатов процесса, полученных в данных условиях, в общей дисперсии
результатов для различных условий. Если эта доля является существенной, значит,
данный фактор влияет на процесс. Метод позволяет количественно оценить степень
влияния фактора на процесс [35].
.6.5 Диаграмма Парето
Диаграмма Парето - инструмент, позволяющий выявить
основные причины проблемы. Он представляет собой разновидность столбиковой
диаграммы, применяемой для наглядного отображения рассматриваемых факторов в
порядке уменьшения (возрастания) их значимости [47].
В 1897 году итальянский экономист В. Парето
сформулировал принцип «неправильного распределения благосостояния в обществе».
Он показал, что 80 % благ контролируется 20 % людей. В 1907 году эта идея была
проиллюстрирована американским экономистом М. Лоренцом с помощью кумулятивной
кривой, совмещённой со столбчатым графиком. Это сочетание и называют диаграммой
Парето [47].
К числу наиболее характерных проблем в работе
предприятия, для решения которых привлекают диаграмму Парето, относятся брак на
различных операциях и в готовой продукции, простои оборудования из-за поломок
или плохой организации производства, большие запасы готовой продукции на складе
предприятия, поступление рекламаций, отказ постоянных партнёров (покупателей)
от сотрудничества, задержки поставок сырья и полуфабрикатов, их низкое
качество.
Различают два вида диаграмм Парето [32]:
) Диаграмма Парето по результатам деятельности.
Она предназначена для выявления главной проблемы и отражает нежелательные
результаты деятельности, связанные: с качеством (дефекты, поломки, ошибки,
отказы, рекламации, ремонты, возвраты продукции); с себестоимостью (объем
потерь; затраты); сроками поставок (нехватка запасов, ошибки в составлении
счетов, срыв сроков поставок); безопасностью (несчастные случаи, трагические
ошибки, аварии).
) Диаграмма Парето по причинам. Отражает
причины проблем, возникающих в ходе производства, и используется для выявления
главной из них: исполнитель работы: смена, бригада, возраст, опыт работы,
квалификация, индивидуальные характеристики; оборудование: станки, агрегаты,
инструменты, оснастка, организация использования, модели, штампы; сырье:
изготовитель, вид сырья, завод-поставщик, партия; метод работы: условия
производства, заказы-наряды, приемы работы, последовательность операций;
измерения: точность (указаний, чтения, приборная), верность и повторяемость
(умение дать одинаковое указание в последующих измерениях одного и того же
значения), стабильность (повторяемость в течение длительного периода),
совместная точность, тип измерительного прибора (аналоговый или цифровой).
С помощью диаграммы Парето анализируют также успехи в
работе отдельных исполнителей, подразделений или фирм и пропагандируют их
достижения. Для оценки эффективности мероприятий по решению какой-либо проблемы
строят повторные диаграммы Парето через некоторое время после внедрения
мероприятий. Для анализа причин, породивших какую-либо проблему, рекомендуется
строить несколько диаграмм Парето для различных групп факторов, влияющих на
данный процесс, и различных показателей его протекания. Часто диаграмма Парето
используется в сочетании с причинно-следственной диаграммой. Причём
причинно-следственная диаграмма может использоваться для выбора причин
какой-либо проблемы, которые затем исследуются в диаграмме Парето. Либо
диаграмма Парето может применяться для ранжирования важности причин по
результатам голосования экспертов.
В основе диаграммы Парето лежит принцип 80/20,
согласно которому 20 % причин приводят к 80 % проблем, поэтому целью построения
диаграммы является выявление этих причин для концентрации усилий по их
устранению.
.6.6 Причинно-следственная диаграмма Исикавы (схема
Исикавы)
Схема Исикавы - инструмент, позволяющий выявить
отношение между показателями качества и воздействующими на него факторами.
Можно сказать, что это инструмент, обеспечивающий системный подход к
определению фактических причин возникновения отказов [47].
Причинно-следственную диаграмму (ПСД) используют для
выявления и систематизации факторов (причин), влияющих на определённый
результат процесса, вызывающих какую-либо проблему при его реализации.
Построение ПСД обычно выполняют на первой стадии анализа процесса. Это
качественный анализ, задачей которого является определение причин проблем.
Затем определяют степень влияния этих причин (диаграмма Парето, корреляционный
и дисперсионный анализ), характер влияния (контрольный листок, диаграмма
разброса, гистограмма, регрессионный анализ, графики и др.), намечают
мероприятия по устранению или уменьшению влияния причин несоответствий.
ПСД из-за её формы иногда называют ещё «рыбьей костью»
или «рыбьим скелетом». Объектом исследования с помощью ПДС может быть проблема
(например, «потребители не удовлетворены») или искомый результат (например,
«полное удовлетворение потребителей»). Причём последний вариант бывает
предпочтительней, так как часто позволяет найти более короткие пути к цели.
ПСД может быть построена индивидуально, но лучше это
делать с помощью команды в режиме «мозгового штурма». К основным рекомендациям
по организации «мозгового штурма» относятся: состав команды (в неё включают как
узких специалистов разного профиля, так и людей, далёких от данной проблемы, но
с высоким творческим потенциалом), порядок работы, роль ведущего и др.
.6.7 Контрольные карты
Контрольная карта (КК) - это инструмент, позволяющий
контролировать протекание процесса и воздействовать на него, предупреждая его
отклонения от предъявленных требований [47].
В отличие от шести других инструментов, дающих
возможность зафиксировать состояние процесса в определённый момент времени,
контрольная карта позволяет следить за его состоянием и при необходимости
воздействовать на него, предупреждая выход из-под контроля [1].
КК предназначены для мониторинга процессов с целью их
анализа, регулирования и контроля. Для решения этих задач используют различные
виды контрольных карт.
КК подразделяют на 3 основных вида: контрольные карты
Шухарта, приёмочные и адаптивные. Все эти контрольные карты работают с
выборочными данными по количественному или альтернативному признаку [29].
Существуют два основных типа КК Шухарта. В КК первого
типа нанесены контрольные границы, рассчитанные на основе выборочных данных, но
не указаны стандартные значения. Контрольные карты этого типа используют для
определения, есть ли в серии наблюдений отклонения, превышающие ожидаемые и
чисто случайные отклонения. Они полностью базируются на оценке выборочных
данных. Эти КК применяют для обнаружения непостоянства системы причин, влияющих
на изменение процесса и определение воспроизводимости показателей качества
продукции или услуг и повторяемости (воспроизводимости) получаемых величин на
стадиях изучения, разработки, постановки продукции на производство или в
начальной стадии процесса обслуживания [1].
Ко второму типу относят КК, контрольные границы
которых определяют на основе установленных стандартных значений для
статистических характеристик, наносимых на карту. КК этого типа служат для
определения, будут ли выборочные значения отличаться от установленных
стандартных значений (т.е. превышают ли эти отклонения ожидаемые случайные
отклонения). Стандартные значения могут быть установлены с учетом следующих
факторов:
а) представительных предварительных данных (например,
полученных на практике с помощью КК при отсутствии указанных стандартных
величин);
б) экономических соображений, потребностей в услуге и
затрат на производстве;
в) желательного или требуемого (установленного)
значения, указанного в технической документации.
Необходимо отметить, что КК этого типа оценивают не
только постоянство системы причин, влияющих на процесс, но ее соответствие
указанным в технической документации стандартным значениям.
По типу используемых выборочных данных КК Шухарта
могут быть двух классов: по альтернативному или по качественному признаку.
Данные по альтернативному признаку менее информативны,
чем по качественному признаку. Для оценки фактического уровня несоответствий
(дефектности) технологического процесса в текущее время по альтернативному
признаку необходимо проконтролировать значительно больше изделий, чем по
количественному.
КК для данных по альтернативному признаку
подразделяются на [29]:
) р-карта - для контроля доли несоответствующих
(дефектных) изделий в выборке;
) np-карта - для контроля числа
несоответствующих (дефектных) изделий в выборке заданного объёма n;
3) c-карта - для контроля числа несоответствий
(дефектов) в единице продукции;
4) u-карта - для контроля среднего числа
несоответствий (дефектов) в расчёте на одно изделие в выборке или на единицу
объёма для нештучной продукции.
Карты для количественных данных отражают состояние
процесса через разброс (изменчивость от единицы к единице) и через расположение
центра (среднее процесса). Поэтому контрольные карты для количественных данных
применяют и анализируют парами - одна карта для расположения и одна - для
разброса.
КК для данных по количественному признаку
подразделяются на:
1) карта
среднего (
) и
размахов (R) или выборочных стандартных отклонений (s);
2) карта
индивидуальных значений (Х) и скользящих размахов;
) карта
медиан (Ме) и размахов (R);
.7 «Семь новых инструментов контроля качества»
Рассмотренные в п.1.3 простые инструменты контроля
качества предназначены для анализа количественных данных о качестве. Они
позволяют достаточно простыми, но в то же время научно обоснованными методами
решать 95 % проблем анализа и управления качеством в разных областях. Они
используют приёмы в основном математической статистики, доступны всем
участникам процесса производства и применяются практически на всех этапах
жизненного цикла продукции.
Однако при создании нового продукта не все факты имеют
численную природу. Существуют факторы, которые поддаются лишь словесному
описанию. Учёт этих факторов составляет примерно 5 % проблем в области
качества. Эти проблемы возникают в основном в области управления процессами,
системами, коллективами, и при их решении наряду со статическими методами
необходимо использовать результаты операционного анализа, теории оптимизации,
психологии и др.
Поэтому JUSE (Union of Japanese Scientists and
Engineers - Союз японских учёных и инженеров) на базе этих наук разработал
очень мощный и полезный набор инструментов, позволяющих облегчить задачу
управления качеством при анализе указанных факторов.
Эти инструменты получили название «Семь инструментов
управления» или «Семь новых инструментов контроля качества» и были собраны
вместе JUSE только в 1979 году.
К «Семи инструментам управления» относятся:
) диаграмма сродства;
) диаграмма (график) взаимосвязей
(зависимостей);
) древовидная (системная) диаграмма (дерево
решений);
) матричная диаграмма или таблица качества;
) стрелочная диаграмма;
) диаграмма процесса осуществления программы;
) матрица приоритетов (анализ матричных
данных).
Сбор исходных данных для инструментов управления
обычно осуществляют в период «мозговых штурмов» с участием как лиц, имеющих
отношение к рассматриваемой проблеме (специалистов в данной и смежных
областях), так и неспециалистов в этих областях, но способных генерировать
продуктивные идеи в новых для себя вопросах.
Сфера применения «Семи новых инструментов контроля
качества» быстро расширяется. Эти методы применяются в области обеспечения
качества, в области контроля, курса, в области делопроизводства и управления, в
области обучения и подготовки кадров, в области контроля производительности и
др.
В области обеспечения качества применение «Семи новых
инструментов» наиболее эффективно на этапе разработки новой продукции и
подготовки проекта; для выработки мер, направленных на снижение брака и
уменьшение рекламаций; для повышения надёжности и безопасности; для обеспечения
выпуска изделий без загрязнения окружающей среды и т. д.
Обучение «Семи новым инструментам контроля качества» в
Японии осуществляет Научное общество «Семи новых инструментов контроля
качества». Каждый цикл подготовки специалистов продолжается 5 месяцев, на
протяжении которых 11 полных дней слушатели изучают и практикуются в применении
«Семи инструментов» [35].
2.
Анализ технологии производства и оценка качества колёсных пар
.1 Производственная деятельность ОАО «КрЭВРЗ»
С 2007 г. ОАО «Красноярский электровагоноремонтный
завод» является самостоятельным юридическим лицом.
Основные виды производственной деятельности завода
состоят в следующем:
ремонт и модернизация электроподвижного состава, его
узлов и агрегатов;
ремонт пассажирских цельнометаллических вагонов в
объеме КР1 и КР2, плацкартных вагонов с водяным и комбинированным отоплением,
купейных вагонов с кондиционированием воздуха и без кондиционирования, вагонов
СВ, вагонов-ресторанов, почтовых, специальных вагонов;
ремонт электропоездов в объеме КР1 и КР2: постоянного
тока серий ЭР-2, ЭР-2Р, ЭР-2Т, ЭД-2Т, ЭД-4, ЭД-4М, ЭД-4МК, ЭТ-2, ЭТ-2М,
переменного тока серий ЭР-9П, ЭР9М, ЭР-9Е, ЭР-9Т, ЭД-9М, ЭД-9МК, ЭД-9Т, ЭД-1;
ремонт тяговых электродвигателей электровозов;
колесных пар, трансформаторов;
ремонт средств измерения;
производство запасных частей подвижного состава;
модернизация электропоездов;
выполнение широкого спектра услуг организациям и
населению.
Завод изготавливает следующие изделия: изделия
механообработки; штампы и инструмент; резинотехнические изделия; системы
вентиляции; гальванические покрытия (хром, никель, цинк); колесные пары нового
формирования электропоездов и вагонов; запасные части подвижного состава
ОАО «КрЭВРЗ» выполняет заказы: железных дорог России,
Белоруссии, Казахстана, Узбекистана; ФГУП «ГХК» г. Железногорск; ФГУП
«Радиосвязь»; ФГУП «Почта России»; транспортных и строительных компаний города.
.2 Основные сведения о колёсных парах
Колесные пары относятся к ходовым частям и являются
одним из ответственных элементов вагона. Они предназначены для направления
движения вагона по рельсовому пути и восприятия всех нагрузок, передающихся от
вагона на рельсы при их вращении. Работая в сложных условиях загружения,
колесные пары должны обеспечивать высокую надежность, так как от них во многом
зависит безопасность движения поездов. Поэтому к колесным парам предъявляются
особые, повышенные требования государственными стандартами, правилами
технической эксплуатации железных дорог, инструкциями по осмотру,
освидетельствованию, ремонту и формированию вагонных колесных пар, а также
другими нормативными документами при проектировании, изготовлении и содержании
в эксплуатации. Конструкция и техническое состояние колесных пар оказывают
влияние на плавность хода, величину сил, возникающих при взаимодействии вагона
и пути, и сопротивление движению.
Работая в современных режимах эксплуатации железных
дорог и экстремальных условиях окружающей среды, колесная пара вагона должна
удовлетворять следующим основным требованиям: обладать достаточной прочностью,
имея при этом минимальную необрессоренную массу (с целью снижения тары
подвижного состава и уменьшения непосредственного воздействия на рельсовый путь
и элементы вагона при прохождении неровностей рельсовой колеи); обладать
некоторой упругостью, обеспечивающей снижение уровня шума и смягчение толчков,
возникающих при движении вагона по рельсовому пути; совместно с буксовыми
узлами обеспечивать возможно меньшее сопротивление при движении вагона и
возможно большее сопротивление износу элементов, подвергающихся изнашиванию в
эксплуатации.
Колесная пара (рисунок 2.1) состоит из оси (1) и двух
укрепленных на ней колес (2). Тип колесной пары определяется типом оси и
диаметром колес, а также конструкцией подшипника и способом крепления его на
оси. Типы вагонных осей различают по размерам и форме шейки - для роликовых
подшипников качения и подшипников скольжения. Размеры оси устанавливают в зависимости
от величины расчетной нагрузки, воспринимаемой ею при эксплуатации.
Рисунок 2.1 - Колёсная пара и форма
Колесные пары Ш-950 предназначены для эксплуатации с
подшипниками скольжения, а колесные пары РУ1-950, РУ1Ш-950, РУ-950 и РУ-1050 -
с роликовыми подшипниками (РУ - роликовая унифицированная, Ш - торцевое
крепление внутренних колец подшипников приставной шайбой). Исходя из расчетной
нагрузки, определяются диаметры шеек (3, 4, 5), подступичной (7) и средней (8)
частей оси. Предподступичная часть (6) является ступенью перехода от шейки к
подступичной части оси и служит для установки уплотняющих устройств буксы. На
подступичных частях (6) прочно закрепляются колеса (2). В настоящее время в
эксплуатации находятся еще небольшое количество колесных пар с осями III типа с
подшипниками скольжения, которые заменяются на роликовые. На торцах их шеек (5)
имеются буртики (6), ограничивающие продольные перемещения подшипников
скольжения, располагающихся в верхних частях.
Рисунок 2.2 - Основные размеры колёсной пары
Для безопасного движения вагона по рельсовому пути на
ось (1) прочно закрепляются колеса (2) (рисунок 2.2) с соблюдением строго
определенных размеров. Расстояние между внутренними гранями колес L составляет:
для новых колесных пар, предназначенных для вагонов, обращающихся со скоростями
до 120 км/ч - (1440 ± 3), свыше 120, но не более 160 км/ч (1440-1;+3). Во
избежание неравномерной передачи нагрузки на колеса и рельсы разность размеров
от торца оси до внутренней грани обода допускается для колесной пары не более 3
мм. Колеса, укрепленные на одной оси, не должны иметь разность по диаметру D
более 1 мм, что предотвращает односторонний износ гребней и не допускает
повышения сопротивления движению [22].
Вагонные оси (рисунок 2.3) являются составной частью
колесной пары и представляют собой стальной брус круглого переменного по длине
поперечного сечения.
Рисунок 2.3 - Типы вагонных осей
На подступичных частях (3) оси располагаются колеса,
укрепленные жестко или подвижно, а на шейках (1) размещаются подшипники.
Вагонные оси различают между собой: размерами, определяемыми в зависимости от
заданной нагрузки; формой шейки оси в соответствии с применяемым типом
подшипника - для подшипников качения и подшипников скольжения; формой круглого
поперечного сечения - сплошные или полые; способом торцового крепления
подшипников качения на шейке оси - корончатой гайкой или шайбой. Кроме того,
оси классифицируются по материалу и технологии изготовления. Между шейками (1)
и подступичными частями (3) находятся предподступичные части (2), служащие для
размещения деталей задних уплотняющих устройств букс, а также снижения
концентрации напряжений в переходных сечениях от подступичных частей к шейкам
оси. В местах изменения диаметров для снижения концентрации напряжений имеются
плавные сопряжения - галтели, выполненные определенными радиусами: от шейки (1)
к предподступичной (2), от предподступичной к подступичной (3) и от средней (4)
к подступичной частям. Снижение концентрации напряжений, вызванных посадкой
внутреннего кольца роликового подшипника, обеспечивается разгружающей канавкой,
расположенной у начала задней галтели шейки оси (рисунок 2.3-г). Оси для
подшипников качения на концах шеек имеют нарезную часть (рисунок 2.3-а) для
навинчивания корончатой гайки, а на торце имеется паз с двумя нарезными
отверстиями для постановки и крепления двумя болтами стопорной планки. В
вагонных осях с креплением подшипников качения при помощи приставной шайбы в
торцах шеек делаются нарезные отверстия для болтов (рисунок 2.3-б) в двух
вариантах: при помощи трех или четырех болтов. Оси для подшипников скольжения
по торцам шеек имеют буртики М (рисунок 2.3-в), служащие для ограничения смещения
подшипников вдоль оси наружу при движении вагона. На торцах всех типов осей
предусмотрены центровые отверстия (рисунки 2.3-д, 2.3-е), служащие для
установки и закрепления оси или колесной пары в центрах при обработке на
токарном станке. Форма и размеры центровых отверстий стандартизированы. Оси
колесных пар, оборудуемых дисковым тормозом, а также оси, на которых
предусмотрена установка привода подвагонного генератора, имеют посадочные
поверхности для установки тормозных дисков или деталей редуктора.
По конструкции вагонные колеса можно разделить на:
безбандажные (цельные); бандажные (составные, состоящие из колесного центра,
бандажа и предохранительного кольца); упругие, имеющие между бандажом и
колесным центром упругий элемент; раздвижные на оси, вращающиеся на оси колеса.
По способу изготовления колеса бывают: катаные и литые. В зависимости от
размеров диаметра, измеренного в плоскости круга катания - 950 и 1050 мм [22].
Учитывая сложные условия работы и повышение надежности
в эксплуатации, поверхность катания колеса должна обладать высокой прочностью,
ударной вязкостью и износостойкостью, а металл диска и ступицы, удерживающихся
на оси силами упругости, необходимой вязкостью. Этим требованиям удовлетворяют
составные колеса, в которых бандаж можно изготовлять из стали повышенной
прочности и твердости, а колесный центр - из более вязкой и дешевой стали.
Кроме того, при достижении предельного износа или появлении другого повреждения
в эксплуатации бандаж можно заменить без смены колесного центра.
Однако в современных условиях эксплуатации железных
дорог из-за существенных недостатков по прочности и надежности, значительной
трудоемкости формирования колесной пары и повышенной массы бандажные колеса в
нашей стране были заменены безбандажными. Причем наиболее совершенными и
надежными в эксплуатации признаны стальные цельнокатаные.
.3 Нормативные требования к осям и колёсным парам
Устанавливаются пять типов колёсных пар с осями типа
РУ1Ш и РВ2Ш и колёсами диаметром 957 мм в зависимости от типа вагона и максимальной
расчётной статической нагрузки от колёсной пары на рельсы (таблица 2.1).
Основные размеры колёсных пар должны соответствовать указанным в таблице 2.2.
Таблица 2.1 - Типы колёсных пар [22]
Тип колёсной пары
|
Тип вагона
|
Конструкционная скорость
вагона, км/ч
|
Максимальная расчётная
статистическая нагрузка от колёсной пары на рельсы, кН (тс)
|
РУ1Ш-957-Г
|
Грузовой
|
120
|
230,5 (23,5)
|
РУ1Ш-957-П
|
Пассажирский
|
160
|
176,6 (18,0)
|
РУ1Ш-957-Э
|
Немоторный электропоезда
|
130
|
186,4 (19,0)
|
РУ1Ш-957-Д
|
Немоторный дизель-поезда
|
120
|
|
РВ2Ш-957-Г
|
Грузовой
|
|
245,2 (25,0)
|
Таблица 2.2 - Основные размеры колёсных пар [22]
Основные размеры
|
Значение
|
Расстояние между
внутренними боковыми поверхностями ободьев колёс в одной колёсной паре, мм
|

|
Разность расстояний между
внутренними боковыми поверхностями ободьев колёс, мм, не более
|
1,5
|
Разность диаметров колёс по
кругу катания в одной колёсной паре, мм, не более
|
1,0
|
Разность расстояний от
торцов предподступичных частей оси до внутренних боковых поверхностей ободьев
колёс с одной и другой сторон колёсной пары, мм, не более
|
3,0
|
Отклонение от соосности
кругов катания колёс относительно оси базовой поверхности, мм, не более
|
1,0
|
Посадка колёс на оси должна быть прессовой.
Поверхности отверстий ступиц колёс должны быть расточены с параметрами
шероховатости Rz ≤ 20 мкм [21]. Допуски формы поверхности отверстий
ступиц колёс не должны превышать: допуск круглости (овальность) - 0,025 мм и
допуск профиля продольного сечения (конусообразность) - 0,05 мм при условии
расположения большего диаметра отверстия ступицы с внутренней стороны колеса.
Перед запрессовкой поверхности отверстий ступиц колёс
и подступичных частей осей должны быть тщательно очищены, насухо протёрты и
покрыты ровным слоем натуральной олифы или термообработанного растительного
масла [24].
При термообработке масло следует нагреть до
температуры от 140 ºС до 150 ºС, выдержать при этой температуре 2-3
ч, а затем после охлаждения дать отстояться не менее 48 ч. Осадок масла не
следует испрльзовать при запрессовке.
Колёса и оси перед запрессовкой должны иметь
одинаковую температуру. Допускается разница температуры не более 10 ºС при условии превышения температуры
колеса над температурой оси.
Колёса на оси должны быть запрессованы на
гидравлических прессах с записью на ленте диаграммы «давление-путь» самопишущим
прибором. Скорость движения плунжера пресса при запрессовке должна быть не
более 3 мм/с.
Длина сопряжения колеса с осью, форма диаграммы
запрессовки, а также условия перепрессовки должны соответствовать требованиям
нормативных технических документов.
Колёсные пары должны быть оборудованы буксовыми узлами
по нормативным техническим документам с подшипниками качения с цилиндрическими
роликами или двухрядными коническими кассетного типа [20].
Буксовые узлы следует монтировать в соответствии с
нормативными техническими документами.
Колёсные пары, предназначенные для пассажирских
вагонов, эксплуатируемых в поездах со скоростями движения свыше 140 км/ч,
должны быть подвергнуты динамической балансировке.
Колёсные пары должны быть окрашены [24, 23].
Конструкция колёсных пар должна допускать их
переформирование для использования на железных дорогах колеи 1435 мм [22].
.4 Описание технологического процесса формирования
колёсных пар
Перед началом технологического процесса колёсная пара
проходит входной контроль, при котором проверяется наличие сертификата на ось и
наличие сопроводительного перечня документов.
После проверки документов ось транспортируется
мостовым краном, производительностью в 10 тонн, для дефектоскопии на расстоянии
10 м. Ось захватывается двухветвевым стропом 2СК2-0,63/1800 грузоподъёмностью
0,63 т и длиной стропа 1800 мм. Строп - это простейшее грузозахватное приспособление
в виде каната или цепи с захватными крюками (скобами).
Колесные пары железнодорожного транспорта
эксплуатируются при неблагоприятных условиях (значительные осевые и радиальные
нагрузки, переменные динамические и ударные воздействия, вибрационные нагрузки,
воздействия электромагнитных полей, высокая скорость вращения, изменяющиеся
климатические условия). Дефектоскопия колёсных пар необходима для контроля их
надежности и работоспособности, которые должны оставаться в указанных условиях
на уровне, оговоренном в нормативно-технической документации, даже при
критических режимах.
После дефектоскопии цельнокатанное колесо
транспортируется на одностоечный токарно-карусельный станок на расстоянии 20 м.
Токарно-карусельные станки предназначены для обработки цилиндрических и
конических (наружных и внутренних) поверхностей, протачивания канавок, отрезки,
обработки торцовых поверхностей, а при использовании приспособлений - для
фасонного точения, нарезания резьбы и др., включая фрезерную и шлифовальную
обработки.
На токарно-карусельном станке на данной операции
производится расточка отверстия в ступице колеса согласно техническому процессу
031.02141.01720.
После расточки отверстия ось стропом передаётся на
прессовый участок на расстоянии 20 м, и отдельно захватом на этот же участок
предаётся цельнокатанное колесо. Колесо на ось напрессовывается гидравлическим
насадочным прессом П6738Б с записью процесса запрессовки самопишущим манометром
(индикатором) на ленте. Прессы предназначены для запрессовки и распрессовки рельсовых
колесных пар железнодорожного транспорта, метро, трамваев, горнорудного и
металлургического транспорта; для запрессовки валов в роторы электромашин,
запрессовки втулок, подшипников, шестерен и других работ. Пресс представляет
собой горизонтальную машину, состоящую из неподвижной левой и подвижной правой
стоек, соединенных между собой двумя тягами и подвижной (упорной) траверсой.
Масса пресса составляет 32000 кг, а номинальное усилие - 6300 кН. Габариты
станка: длина - 11000 м, ширина - 3000 м, высота - 3280 м.
Скорость движения плунжера гидравлического пресса при
запрессовке должна быть не выше 2 мм/с. Масштаб записи диаграммы запрессовки по
длине должен быть не менее 1:2, а 1 мм диаграммы по высоте должен
соответствовать усилию не более 2,5 тс. Прессуемые элементы колесных пар
(цельнокатаные колеса и оси) должны иметь одинаковую температуру; допускается
разница не более 10 ºС при условии превышения температуры колеса над
температурой оси.
Перед запрессовкой элементы колесных пар проверяют и
подбирают по размерам. Посадочные поверхности ступиц колес и подступичные части
осей должны быть тщательно очищены, насухо протерты и покрыты ровным слоем
натуральной олифы или другого вареного растительного масла (льняное, конопляное
или подсолнечное). Качество запрессовки контролируется по индикаторной
диаграмме.
К основным контролируемым параметрам диаграммы
запрессовки относятся:
а) величина конечных усилий;
б) длина сопряжения;
в) форма кривой.
Величина конечных усилий запрессовки должна быть в
пределах 37-55 тс на каждые 100 мм диаметра подступичной части оси.
На основании нормы на каждом предприятии (завод,
вагоноколесные мастерские, депо) необходимо составить таблицу усилий
запрессовки в килограмм-силах на квадратный сантиметр (кгс/см2) и
тонно-силах (тс) для различных диаметров подступичных частей осей (через 1 мм)
с учетом переводного коэффициента пресса из кгс/см2 в тс. Таблица
должна быть утверждена главным инженером службы вагонного хозяйства или главным
инженером завода.
Размеры натягов для достижения требуемых
запрессовочных усилий устанавливаются предприятиями в пределах 0,10-0,25 мм.
Величина конечных усилий Рзк на диаграмме
запрессовки определяется уровнем точки кривой, соответствующей концу процесса
запрессовки (рисунок 2.4-а, 2.4-б). При расположении диаграммы выше (рисунок
2.4-в) или ниже (рисунок 2.4-г) нулевой линии 0-0, а также при перекосе
(рисунок 2.4-д) запрессовка не бракуется, а, конечные усилия должны
определяться также уровнем точки диаграммы, соответствующей концу запрессовки с
учетом величины смещения от нулевой линии. При обнаружении смещенных диаграмм
запрессовки мастер прессового отделения обязан принять необходимые меры для
ликвидации.
Не подлежат бракованию диаграммы, имеющие вначале
запись холостого хода плунжера пресса (рисунок 2.4-е). Величину конечных
запрессовочных усилий в этом случае нужно определять уровнем точки кривой,
соответствующей концу процесса запрессовки, с уменьшением на величину давления
холостого хода.
Рисунок 2.4 - Диаграмма запрессовки
На бланке диаграммы, кроме кривой изменения давления,
должны быть записаны следующие данные: дата запрессовки, тип колесной пары,
номер оси, диаметры подступичной части оси и отверстия ступицы колеса (с
точностью до 0,01 мм), величина натяга, длина ступицы, конечное усилие
запрессовки в тонно-силах, маркировка цельнокатаного колеса, сторона колесной
пары (правая или левая).
Диаграмма запрессовки должна быть подписана: мастером
и начальником вагоноколесных мастерских (ВКМ), а при отсутствии начальника ВКМ
старшим мастером или заместителем начальника вагонного депо (ВЧД) в линейных
предприятиях; мастером и инспектором ОТК на заводе, а на заводах
промышленности, кроме того, заводским инспектором-приемщиком ЦБ МПС. На каждой
забракованной диаграмме делается отметка «Брак» с указанием причины браковки.
По форме нормальная диаграмма запрессовки должна иметь
плавно нарастающую несколько выпуклую вверх кривую по всей длине с начала до
конца.
После прохождения операции напрессовки производится
осмотр колёсных пар. Для этого на участке имеется измерительная стойка
СИРК-Ш-410-530, предназначенная для проверки разности расстояний от
предподступичных частей оси до внутренней боковой поверхности ободьев колёс с
одной и другой стороны колёсной пары. Разность не должна быть более 3 мм.
В колёсной паре проверяется расстояние между
внутренними боковыми поверхностями ободьев колёс, оно может составлять
(1440+2;-1) мм. Также производят измерение разности расстояний между
внутренними боковыми поверхностями ободьев колёс в двух взаимно противоположных
плоскостях колёсной пары. Разность допускается не более 1,5 мм. Для проведения
этих измерений используются: штангенциркуль ШЦ-III-1600-0.1 (ГОСТ 166-89);
межбандажный штангенциркуль ИМ-01-04-60.
После осмотра колёсных пар она транспортируется
траверсой на колесотокарный станок на расстоянии 20 м. Траверса - это
горизонтальная балка металлорежущих станков (главным образом
токарно-карусельных, продольно-строгальных и продольно-фрезерных), вертикально
перемещающаяся по направляющим двух стоек. На этом участке используется
токарно-копировальный станок 1836Б с бесступенчатым регулированием частот
вращения шпинделя и подач. Его основные характеристики: длина - 7260 мм, ширина
- 4720 мм, высота - 2340 мм, мощность двигателя главного движка - 55 кВт, масса
станка - 43500 кг. На этом станке необходимо обточить колёса по кругу катания.
Мостовой кран с траверсой направляют колёсную пару на
следующую операцию - дефектоскопию. На стенде дефектоскопии колёсных пар
производится ультразвуковой контроль оси и колёс. Для этого используются
дефектоскопы УДС-2, УД2-70 и УДС1-22.
Проверку элементов колесных пар дефектоскопами должен
производить дефектоскопист, выдержавший испытание и получивший удостоверение на
право контроля дефектоскопами деталей вагонов. Дефектоскописты ежегодно сдают
испытания комиссиям, в которые входят: в депо и ВКМ - НОДВ (председатель) и
помощник участкового ревизора по безопасности (УРБ), на заводах - главный
инженер завода (председатель), начальник ОТК, начальник цеха и представитель
лаборатории ультразвуковой дефектоскопии (УЗД).
Дефектоскопист является ответственным лицом за
качество проверки дефектоскопом элементов колесных пар. Контроль за работой
дефектоскописта осуществляется мастером, инспектором ОТК или контрольным мастером
отдела технического контроля на заводах промышленности.
Ультразвуковые дефектоскопы предназначены для
ультразвукового контроля узлов и деталей средств железнодорожного транспорта, в
том числе осей (например типов РУ, РУ1, РУ1Ш) и колес, а также сварных
соединении, с целью выявления внутренних дефектов и измерения их координат.
Принцип действия дефектоскопа основан на свойствах ультразвуковых колебаний
отражаться от поверхностей и неоднородностей в контролируемых деталях.
Ультразвуковые колебания в деталях возбуждаются, и отраженные эхо-сигналы
принимаются ультразвуковыми пьезоэлектрическими преобразователями (ПЭП).
Также на этом участке производится вихретоковый
контроль цельнокатанного колеса дефектоскопом ВД-213.5 и магнитопорошковый
контроль оси колёсной пары дефектоскопами МД-12ПШ и МД-12ПС.
Метод вихретоковой дефектоскопии дает возможность
обнаружения поверхностных и подповерхностных дефектов. Он основан на
использовании действия вихревых токов, возникающих в поверхностном слое
контролируемой детали от пронизывания его магнитным потоком, на первичную или
особую измерительную катушку.
Магнитная дефектоскопия отличается высокой
чувствительностью, простотой технологии, наглядностью результатов,
незначительными затратами. Метод основан на обнаружении магнитных потоков
рассеяния, возникающих при наличии дефектов в намагниченных деталях.
При контроле сварных швов на предприятиях по ремонту
подвижного состава широко используется магнитопорошковый метод, сущность
которого заключается в следующем. На контролируемую поверхность намагниченной
детали наносится ферромагнитный порошок в виде суспензии с керосином, маслом
или же магнитный аэрозоль. Под действием магнитных сил рассеяния, выходящих на
поверхность детали в месте дефекта, частицы порошка скапливаются в этом месте в
виде валиков. Форма таких скоплений соответствует форме дефекта.
Чувствительность магнитопорошкового метода зависит от размеров частиц порошка и
методов его нанесения; напряжённости магнитного поля; рода приложенного тока;
формы, размера и глубины залегания дефекта; способа намагничивания; состояния
поверхности. Намагничивание постоянным током даёт возможность обнаружения
подповерхностных дефектов. При контроле магнитопорошковым методом наилучшим
образом выявляются трещины, непровары, несплавления, подрезы.
Порядок магнитопорошкового контроля включает следующие
операции:
подготовку поверхности - очистку от загрязнений,
остатков шлака, окалины;
намагничивание контролируемой детали;
нанесение магнитной суспензии или магнитного порошка
на поверхность контролируемой детали;
осмотр контролируемой поверхности и выявление
дефектов;
размагничивание.
После проведения дефектоскопии колёсную пару
маркируют. Маркировку осуществляют при помощи молотка и клейма. Элементы
колесных пар должны иметь четко обозначенные знаки маркировки и клеймения,
предусмотренные стандартами и техническими условиями:
а) необработанные оси - на подступичной или средней
части оси;
б) грубо или окончательно обработанные оси - на торце
шейки.
Затем повторяется операция по осмотру колёсной пары.
Замеряются следующие параметры:
) разность расстояний между внутренними
боковыми поверхностями ободьев колёс - для измерения требуется штангенциркуль
ШП-III-1600-0.1 и межбандажный штангенциркуль ИМ-01-04-06 (разность должна быть
(1440+2, -1) мм);
) разность расстояний между внутренними
боковыми поверхностями ободьев колёс в двух взаимно противоположных плоскостях
колёсной пары - для измерения требуется штангенциркуль ШП-III-1600-0.1 и
межбандажный штангенциркуль ИМ-01-04-06 (разность допускается не более 1,5 мм);
) разность расстояний от предподступичных
частей оси до внутренней боковой поверхности ободьев колёс с одной и с другой
стороны колёсной пары - для измерения используется измерительная стойка
СИРК-Ш-410-530 (разность должна быть не более 3 мм);
) отклонение от соосности кругов катания колёс
относительно базовой поверхности - для измерения используется измерительная
стойка СИРК-Ш-410-530 (отклонение допускается не более 1 мм);
) разность диаметров по кругу катания колёс
цельнокатанных в колёсной паре - для измерения используется штангебандажемер
Ииз-63-00-00-82 (допускается разность 1,0 мм);
) диаметр шейки оси - для измерения
используются скоба рычажная СР 150 и скоба мод 4150-130 (диаметр должен быть
130+0,052+0,025);
) диаметр предподступичных частей оси - для
измерения используется микрометр МК-175 или скоба мод 4150-165 (диаметр должен
быть 165+0,20+0,12);
) средняя часть оси - для измерения
используется микрометр МК-175, линейка 300, кронциркуль, штангециркуль
Ииз-77-00-82 (диаметр должен быть (172+3) мм);
) толщина обода колеса - для измерения
используется толщиномер цельнокатанных колёс Т447.07.000 (разность толщин
ободов допускается не более 5,0 мм);
) диаметр по кругу катания колеса - для
измерения используется штангебандажемер Ииз-63-00-00-82 (диаметр должен быть
(950+14) мм).
После осмотра колёсной пары следует операция окраски.
Колёса и средняя часть оси обезжириваются моющим средством для последующего
нанесения грунтовки чёрного цвета. Грунтовкой окрашиваются колёса по всей поверхности,
кроме поверхности катания (у колёсных пар грузовых вагонов боковые поверхности
ободьев не окрашиваются), средняя часть оси, места соединения лабиринтного
кольца с предподступичной частью, а также предподступичные части между
лабиринтным кольцом и цельнокатанным колесом.
После окраски необходимо провести естественную сушку
колёсной пары. Затем колёсная пара отправляется на консервацию. Здесь шейка и
предподступичные части оси покрываются консервационным маслом К-17 [25]. Затем
они обворачиваются влагонепроницаемой бумагой и предохраняются деревянными
планками.
Затем на наружную торцевую поверхность обода
цельнокатанного колеса на линейные колёсные пары приклеивается знак
соответствия.
3.
Анализ качества колёсных пар
В ходе преддипломной практики на ОАО «КрЭВРЗ» в
колёсном цехе на участке сборки буксового узла были определены следующие
параметры колёсной пары: межбандажное расстояние, ширина обода колёс и диаметр
колёс по кругу катания. Эти параметры являются основными в колёсной паре. К ним
применяется жёсткий контроль.
Проведём
анализ качества колёсных пар с помощью простых инструментов контроля качества:
диаграммы Парето, причинно-следственной диаграммы Исикавы, а также с помощью 
-R -
контрольных карт Шухарта. Достоинствами этих методов является простота
применения, наглядность и эффективность.
3.1 Исследование проблем, возникающих при ремонте
колёсной пары с помощью Диаграммы Парето
Для анализа данных была построена диаграмма Парето по
причинам. Для построения диаграммы Парето, нами были выявлены и
проклассифицированы главные проблемы, возникающие при ремонте колёсной пары.
Затем мы разработали и заполнили бланк по учёту дефектов с графами для итогов
по каждому проверяемому параметру в отдельности, накопленной суммы числа
дефектов, процентов к общему итогу и накопленных процентов (таблица 3.1). Затем
по данным таблицы построили столбчатую диаграмму и кумулятивную кривую. На
уровне 80 % провели горизонтальную линию до пересечения с кумулятивной кривой и
из точки пересечения опустили перпендикуляр на горизонтальную ось (рисунок
3.1).
Таблица 3.1 - Бланк учёта дефектов
Тип дефекта
|
Количество дефектов
|
Накопленная сумма дефектов
|
Число дефектов по каждому
признаку, % к общей сумме
|
Накопленный процент, %
|
1
|
2
|
3
|
4
|
5
|
Несоответствие
межбандажного расстояния
|
41
|
41
|
34,2
|
34,2
|
Несоответствие диаметра
колес по кругу катания
|
39
|
80
|
32,5
|
66,7
|
Несоответствие ширины обода
колёс
|
18
|
100
|
15,0
|
81,7
|
Трещины (в ободе, диске,
ступице)
|
8
|
108
|
6,7
|
88,3
|
Навары
|
6
|
114
|
5,0
|
93,3
|
Вобоины
|
5
|
119
|
4,2
|
97,5
|
Прочие
|
3
|
122
|
2,5
|
100,0
|
ИТОГО
|
120
|
|
100,0
|
|
Рисунок 3.1 - Диаграмма Парето по показателям качества
Левее перпендикуляра располагаются следующие виды
дефектов: несоответствие межбандажного расстояния, несоответствие диаметра
колёс по кругу катания, несоответствие ширины обода колеса. Перечисленные виды
дефектов составляют более 80 % несоответствий и требуют принятия первоочередных
мер по их устранению.
статистический колесный качество
электровагоноремонтный
3.2 Исследование причин возникновения несоответствий с
помощью причинно-следственной диаграммы Исикавы
Для определения причин, влияющих на появление
несоответствий, мы используем причинно-следственную диаграмму Исикавы.
Для построения диаграммы Исикавы мы выбрали
исследуемый дефект и записали его в середине правого края листа бумаги. Через
центр листа мы провели прямую горизонтальную линию («хребет» диаграммы).
Затем мы определили главные факторы (факторы первого
порядка), влияющие на показатель качества. Главные факторы разделяются по
своему влиянию на 4 основные причины: персонал, средства измерений, технология,
оборудование. От названий главных факторов мы провели стрелки («большие кости»)
к «хребту» диаграммы. Показатели качества и главные факторы мы для наглядности
заключили в рамки. Затем мы определили и записали факторы второго порядка рядом
с «большими костями» факторов первого порядка, на которые они влияют. Дальше мы
определили факторы третьего порядка рядом со «средними костями» факторов
второго порядка, на которые они оказывают влияние. Таким образом, мы построили
диаграмму Исикавы для каждого из выявленных по диаграмме Парето дефектов
(рисунки 3.2, 3.3, 3.4).
По построенной диаграмме Исикавы, можно сделать вывод,
что главными причинами появления дефекта несоответствие ширины обода колеса
являются ошибки персонала, обусловленные некачественным обучением, усталостью и
невнимательностью; использование средств измерений, не заложенных в техническом
процессе; несоблюдение технологических режимов; нарушение технологии и
несоблюдение режимов обработки. Главными причинами появления несоответствия
межбандажного расстояния являются: ошибки персонала, связанные с личными
проблемами, халатностью и невнимательностью персонала; ошибки средств
измерения, связанные с несвоевременной их поверкой; несоблюдение контроля за технологическим
процессом и контролем за безопасностью; несоблюдение регламента и режимов
обточки. Главными причинами появления несоответствия диаметра колёс по кругу
катания являются ошибки персонала, связанные с незнанием технологии ремонта и
некачественным обучением; механические повреждения и несвоевременная поверка
средств измерения; плохая проработка технологии и несоблюдение режимов
обработки; поломка колесотокарного станка, несвоевременное проведение
планово-предупредительных работ и нарушение режима обточки.
.3
Анализ стабильности технологического процесса с помощью 
-R -
контрольных карт
В
колёсном цехе на участке сборки буксового узла из «Журнала учёта замечаний» за
2012 год нами были взяты 150 значений по показателю межбандажное расстояние,
оно должно быть 1440(+1;-1) мм; 150 значений по показателю диаметр колёс по
кругу катания, он должен быть 1050 (+10) мм; 150 значений по показателю ширина
обода колеса, она должна быть 130 (+3;-1) мм.
Для
анализа стабильности технологического процесса ремонта колёсной пары мы
использовали 
-R
контрольные карты для количественных данных. Карты для количественных данных
отражают состояние процесса через разброс и расположение центра.
Сначала
мы построили таблицу для показателя межбандажное расстояние (таблица 3.2).
Таблица
3.2 - Данные для построения 
-R карты
для показателя межбандажное расстояние
№
|
Межбандажное расстояние
|
|
R
|
|
Х1
|
Х2
|
Х3
|
Х4
|
Х5
|
|
|
1
|
2
|
3
|
4
|
5
|
6
|
7
|
8
|
1
|
1439,3
|
1440,0
|
1439,4
|
1439,7
|
1439,0
|
1439,48
|
0,3
|
2
|
1439,6
|
1440,7
|
1439,4
|
1440,3
|
1440,6
|
1440,12
|
1,3
|
3
|
1440,1
|
1439,7
|
1440,3
|
1439,6
|
1439,3
|
1439,8
|
0,7
|
4
|
1439,4
|
1439,9
|
1439,6
|
1439,6
|
1439,0
|
1439,5
|
0,9
|
5
|
1441,0
|
1440,8
|
1439,1
|
1440,2
|
1439,6
|
1440,14
|
1,9
|
6
|
1439,6
|
1440,3
|
1440,9
|
1440,6
|
1440,2
|
1440,32
|
1,3
|
7
|
1440,7
|
1440,5
|
1440,7
|
1440,7
|
1440,7
|
1440,66
|
0,2
|
8
|
1439,6
|
1439,7
|
1439,2
|
1440,0
|
1439,6
|
1439,62
|
0,8
|
9
|
1439,5
|
1440,2
|
1439,6
|
1441,0
|
1440,2
|
1440,1
|
1,5
|
10
|
1440,2
|
1439,3
|
1439,5
|
1440,5
|
1440,2
|
1439,94
|
1,2
|
11
|
1439,7
|
1439,3
|
1440,8
|
1440,2
|
1439,4
|
1439,88
|
1,5
|
12
|
1439,3
|
1441,0
|
1440,6
|
1440,5
|
1440,0
|
1440,28
|
1,7
|
13
|
1440,3
|
1440,0
|
1439,7
|
1440,1
|
1439,9
|
1440,0
|
0,6
|
14
|
1440,7
|
1440,5
|
1440,1
|
1439,2
|
1440,3
|
1440,16
|
1,7
|
15
|
1439,2
|
1440,6
|
1439,7
|
1439,3
|
1441,0
|
1439,96
|
1,8
|
16
|
1439,2
|
1439,2
|
1440,9
|
1440,3
|
1440,5
|
1440,02
|
1,7
|
17
|
1439,8
|
1439,2
|
1440,2
|
1440,2
|
1439,2
|
1439,72
|
1,0
|
1440,5
|
1440,4
|
1439,1
|
1440,2
|
1439,4
|
1439,92
|
1,4
|
19
|
1440,1
|
1440,8
|
1439,7
|
1439,1
|
1439,3
|
1439,8
|
1,7
|
20
|
1440,6
|
1439,2
|
1440,0
|
1439,7
|
1439,8
|
1439,86
|
1,4
|
21
|
1440,1
|
1440,0
|
1440,8
|
1439,3
|
1440,3
|
1440,1
|
1,5
|
22
|
1440,3
|
1439,4
|
1440,1
|
1440,9
|
1439,4
|
1440,02
|
1,5
|
23
|
1439,2
|
1440,9
|
1439,5
|
1440,2
|
1441,0
|
1440,16
|
1,8
|
24
|
1439,0
|
1440,4
|
1440,2
|
1440,5
|
1439,3
|
1439,88
|
1,5
|
25
|
1439,7
|
1440,4
|
1440,6
|
1440,3
|
1440,9
|
1440,38
|
1,2
|
26
|
1439,5
|
1440,6
|
1439,7
|
1440,3
|
1439,2
|
1439,86
|
1,4
|
27
|
1439,8
|
1440,2
|
1439,1
|
1439,5
|
1440,5
|
1439,82
|
1,4
|
28
|
1440,1
|
1439,5
|
1440,7
|
1439,3
|
1440,4
|
1440,0
|
1,4
|
29
|
1439,1
|
1439,3
|
1439,5
|
1440,9
|
1439,8
|
1439,72
|
1,8
|
30
|
1440,1
|
1440,0
|
1439,0
|
1440,9
|
1439,8
|
1439,96
|
1,9
|
Итого:
|
|
|
|
|
|
1439,97
|
1,33
|
Затем мы вычислили среднеарифметическое значений в
каждой подгруппе, размах показателя качества в каждой подгруппе, нашли
среднеарифметические средних и размахов подгрупп. Формулы для нахождения
перечисленных выше параметров представлены в Приложении А.
Затем мы вычислили контрольные границы. Значения
коэффициентов А2, D3, D4 определяются по ГОСТ
Р 50779.42-99 [32].

-карта.
Центральная линия:
CL=
=1439,97.
Верхний
контрольный предел:
UCL=
+A2·R=1439,97+0,577·1,33=1440,74.
Нижний
контрольный предел:
=
-A2·R=1439,97-0,577·1,33=1439,20
карта.
Центральная линия:
СL=R=1,33.
Верхний
контрольный предел:
=D4·R=2,114·1,33=2,81.
Нижний
контрольный предел:
=D3·R=0.
По
полученным значениям таблицы 3.2 мы построили 
-R -
контрольную карту и нанесли на карту центральную линию, нижний и верхний
контрольные пределы, а также нормируемые значения для межбандажного расстояния
1440(+1;-1) мм (рисунок 3.5).
Контрольная
карта средних значений (
-карта)
Контрольная
карта размахов (R - карта)
Рисунок
3.5 - 
-R-карта
для параметра межбандажное расстояние
Вывод:
По построенной 
-R-карте
нельзя точно определить находится ли процесс в статистически управляемом
состоянии. Точки не выходят за границы поля допуска, но на карте средних и на
карте размахов присутствует одна точка, которая максимально приближена к
контрольным границам. Это говорит о наличии особых причины изменчивости -
неслучайных причин, действующих на процесс непостоянно, часто непредсказуемых.
Затем
мы построили таблицу для показателя диаметр колёс по кругу катания (таблица
3.3).
Таблица
3.3 - Данные для построения 
-R-карты
для показателя диаметр колёс по кругу катания
№
|
Диаметр колёс по кругу
катания
|
|
R
|
|
Х1
|
Х2
|
Х3
|
Х4
|
Х5
|
|
|
1
|
2
|
3
|
4
|
5
|
6
|
7
|
8
|
1
|
1058,50
|
1056,01
|
1059,78
|
1052,17
|
1057,23
|
1056,74
|
7,61
|
2
|
1051,92
|
1053,80
|
1052,20
|
1054,79
|
1054,98
|
1053,54
|
3,06
|
3
|
1055,99
|
1059,44
|
1050,30
|
1050,89
|
1058,95
|
1055,11
|
9,14
|
4
|
1053,85
|
1055,33
|
1054,97
|
1055,97
|
1059,87
|
1056,0
|
6,02
|
5
|
1059,77
|
1059,77
|
1052,17
|
1055,36
|
1055,65
|
1056,54
|
7,6
|
6
|
1054,94
|
1054,20
|
1050,44
|
1056,18
|
1057,04
|
1054,56
|
6,6
|
7
|
1058,80
|
1052,46
|
1056,61
|
1054,12
|
1058,83
|
1056,16
|
6,37
|
8
|
1054,58
|
1055,18
|
1058,82
|
1059,16
|
1055,65
|
1056,68
|
4,58
|
9
|
1053,73
|
1056,32
|
1056,88
|
1054,71
|
1055,48
|
1055,42
|
3,15
|
10
|
1056,15
|
1051,77
|
1059,59
|
1058,15
|
1050,83
|
1055,3
|
8,76
|
11
|
1052,02
|
1055,20
|
1058,01
|
1054,67
|
1057,52
|
1055,48
|
5,99
|
12
|
1056,46
|
1059,67
|
1054,02
|
1054,22
|
1054,78
|
1055,83
|
5,65
|
13
|
1055,62
|
1056,33
|
1055,21
|
1054,62
|
1052,47
|
1054,85
|
3,86
|
14
|
1055,99
|
1052,24
|
1053,75
|
1050,95
|
1050,88
|
1052,76
|
5,11
|
15
|
1051,47
|
1056,53
|
1052,47
|
1059,72
|
1050,48
|
1054,13
|
9,24
|
16
|
1053,20
|
1059,25
|
1059,29
|
1050,23
|
1057,03
|
1055,8
|
9,06
|
17
|
1053,60
|
1056,73
|
1051,70
|
1050,57
|
1055,31
|
1053,58
|
6,16
|
18
|
1059,61
|
1059,87
|
1057,41
|
1058,65
|
1056,93
|
1058,49
|
2,94
|
19
|
1058,72
|
1053,50
|
1055,73
|
1054,20
|
1052,81
|
1054,99
|
5,91
|
20
|
1056,18
|
1052,32
|
1053,02
|
1055,80
|
1051,38
|
1053,74
|
4,8
|
21
|
1058,37
|
1056,42
|
1058,59
|
1054,19
|
1059,55
|
1057,42
|
5,36
|
22
|
1052,18
|
1057,71
|
1057,52
|
1057,71
|
1050,94
|
1055,21
|
6,77
|
23
|
1051,53
|
1056,89
|
1052,30
|
1054,52
|
1054,68
|
1053,98
|
5,36
|
24
|
1053,87
|
1052,89
|
1052,43
|
1055,81
|
1055,90
|
1054,18
|
3,47
|
25
|
1057,40
|
1056,37
|
1056,68
|
1058,68
|
1050,55
|
1055,94
|
8,13
|
26
|
1050,79
|
1054,49
|
1050,81
|
1053,32
|
1053,34
|
6,52
|
27
|
1055,48
|
1054,45
|
1057,12
|
1056,75
|
1053,28
|
1055,42
|
3,84
|
28
|
1057,07
|
1054,15
|
1054,70
|
1054,44
|
1051,98
|
1054,47
|
5,09
|
29
|
1054,95
|
1058,51
|
1059,72
|
1052,04
|
1055,97
|
1056,24
|
7,68
|
30
|
1058,33
|
1052,68
|
1059,82
|
1051,31
|
1053,31
|
1055,09
|
8,51
|
Итого:
|
|
|
|
|
|
1055,23
|
6,08
|
Затем мы вычислили среднеарифметическое значений в
каждой подгруппе, размах показателя качества в каждой подгруппе, нашли
среднеарифметические средних и размахов подгрупп. Формулы для нахождения
перечисленных выше параметров представлены в Приложении А.
Затем мы вычислили контрольные границы. Значения
коэффициентов А2, D3, D4 определяются по ГОСТ
Р 50779.42-99.

-карта.
Центральная линия:
=
=1055,23.
Верхний
контрольный предел:
=
+A2·R=1055,23+0,577·6,08=1058,74.
Нижний
контрольный предел:
=
-A2·R=1055,23-0,577·6,08=1051,72.
карта.
Центральная линия:
СL=R=6,08.
Верхний
контрольный предел:
=D4·R=2,114·6,08=12,85.
Нижний
контрольный предел:
LCL=D3·R=0.
По
полученным значениям таблицы 3.3 мы построили 
-R -
контрольную карту и нанесли на карту центральную линию, нижний и верхний
контрольные пределы, а также нормируемые значения для диаметра колёс по кругу
катания 1050 (+10) мм (рисунок 3.6).
Контрольная
карта средних значений (
-карта)
Контрольная карта размахов (R-карта)
Рисунок
3.6 - 
-R-карта
для параметра диаметр колёс по кругу катания
Вывод:
По построенной 
-R-карте
нельзя точно определить находится ли процесс в статистически управляемом
состоянии. Точки не выходят за границы поля допуска, но на карте средних
присутствует одна точка, которая максимально приближена к контрольным границам.
Это говорит о наличии особых причины изменчивости - неслучайных причин,
действующих на процесс непостоянно.
Далее
мы построили таблицу для последнего показателя ширина обода колеса (таблица
3.4).
Таблица
3.4 - Данные для построения 
-R-карты
для показателя ширина обода колеса
№
|
Ширина обода колеса
|
|
R
|
|
Х1
|
Х2
|
Х3
|
Х4
|
Х5
|
|
|
1
|
130,23
|
132,14
|
132,72
|
130,71
|
131,97
|
131,554
|
2,49
|
2
|
129,48
|
131,06
|
129,34
|
131,94
|
131,30
|
130,624
|
2,60
|
3
|
131,08
|
130,54
|
131,40
|
131,43
|
131,63
|
131,216
|
1,09
|
4
|
130,59
|
132,22
|
132,94
|
131,56
|
129,66
|
131,394
|
3,28
|
5
|
129,47
|
129,12
|
130,16
|
131,04
|
130,05
|
129,968
|
1,92
|
6
|
131,92
|
132,14
|
129,34
|
131,71
|
130,47
|
131,116
|
2,80
|
7
|
130,01
|
131,06
|
130,08
|
131,45
|
129,46
|
130,412
|
1,60
|
8
|
132,08
|
130,69
|
132,54
|
132,95
|
131,50
|
131,952
|
2,26
|
9
|
131,35
|
131,85
|
131,12
|
132,70
|
130,63
|
131,530
|
2,07
|
10
|
130,08
|
131,16
|
131,37
|
131,46
|
132,44
|
131,302
|
2,36
|
11
|
132,64
|
131,49
|
131,15
|
130,93
|
130,58
|
131,358
|
2,06
|
12
|
129,62
|
129,58
|
131,35
|
131,96
|
132,67
|
131,036
|
3,09
|
13
|
132,57
|
130,56
|
132,36
|
132,15
|
129,25
|
131,378
|
3,32
|
14
|
132,03
|
129,11
|
131,57
|
129,35
|
129,78
|
130,368
|
2,92
|
15
|
130,39
|
130,75
|
132,76
|
131,80
|
131,90
|
131,520
|
2,37
|
16
|
130,25
|
131,24
|
132,51
|
131,27
|
130,89
|
131,232
|
2,26
|
17
|
132,39
|
129,21
|
132,72
|
130,41
|
132,73
|
131,492
|
3,52
|
18
|
129,70
|
132,12
|
131,38
|
129,03
|
132,43
|
130,932
|
3,40
|
19
|
131,25
|
130,27
|
131,72
|
131,81
|
129,26
|
130,862
|
2,55
|
20
|
129,76
|
130,48
|
131,13
|
130,46
|
132,45
|
130,856
|
2,69
|
21
|
130,02
|
130,45
|
129,45
|
129,36
|
132,46
|
130,348
|
3,07
|
22
|
132,85
|
132,20
|
129,71
|
132,40
|
132,18
|
131,868
|
3,14
|
23
|
131,78
|
132,28
|
130,21
|
130,73
|
132,45
|
131,490
|
2,24
|
24
|
129,41
|
131,76
|
129,61
|
131,81
|
129,32
|
130,382
|
2,49
|
25
|
132,47
|
131,66
|
130,26
|
129,97
|
132,35
|
131,342
|
2,50
|
26
|
130,96
|
129,92
|
130,85
|
130,46
|
132,23
|
130,884
|
2,31
|
27
|
130,37
|
131,40
|
129,71
|
130,66
|
132,97
|
131,022
|
3,26
|
28
|
131,77
|
129,24
|
132,89
|
129,80
|
131,98
|
131,136
|
3,65
|
29
|
132,40
|
132,14
|
132,26
|
129,44
|
130,20
|
131,288
|
2,96
|
30
|
130,90
|
130,37
|
130,44
|
129,48
|
132,50
|
130,738
|
3,02
|
Итого:
|
|
|
|
|
|
131,086
|
2,643
|
Затем мы вычислили среднеарифметическое значений в
каждой подгруппе, размах показателя качества в каждой подгруппе, нашли
среднеарифметические средних и размахов подгрупп. Формулы для нахождения
перечисленных выше параметров представлены в Приложении А.
Затем мы вычислили контрольные границы [30].

-карта.
Центральная линия:
=
=131,086.
Верхний
контрольный предел:
=
+A2·R=131,086+0,577·2,643=132,61.
Нижний
контрольный предел:
=
-A2·R=129,56.
карта.
Центральная линия:
СL=R=2,643.
Верхний
контрольный предел:
=D4·R=2,114·2,643=5,59.
Нижний
контрольный предел:
=D3·R=0.
По
полученным значениям таблицы 3.4 мы построили 
-R -
контрольную карту и нанесли на карту центральную линию, нижний и верхний
контрольные пределы, а также нормируемые значения для ширины обода колеса 130
(+3;-1) (рисунок 3.7).
Контрольная
карта средних значений (
-карта)
Контрольная
карта размахов (R-карта)
Рисунок
3.7 - 
-R-карта
для параметра ширина обода колеса
Вывод:
На построенной 
-R-карте
можно увидеть повторяющиеся циклы, что является отсутствием стабильности
процесса. Также на карте средних присутствует одна точка, которая приближается
к нижней контрольной границе.
По
результатам проведения анализа технологического процесса мы не смогли дать
однозначного ответа о его стабильности. Поэтому мы воспользовались
математическими методами для более точного определения стабильности и
настроенности технологического процесса ремонта.
3.4 Оценка настроенности и стабильности технологического
процесса
.4.1 Оценка настроенности и стабильности
технологического процесса по показателю межбандажное расстояние
Для
каждой выборки рассчитывается значение среднего арифметического
и стандартного отклонения S с помощью формул (3.1) и
(3.2):
=
, (3.1)=
, (3.2)
=
=1439,973,=
0,58.
Технологический
процесс (операция) является настроенным по контролируемому параметру х (при
неизвестной дисперсии σ20), если выполняется условие (3.3):
, (3.3)
где
Т0 - центр поля допуска контролируемого параметра;
-
квантиль распределения Стьюдента уровня (
) с ν=n-1;
α - выбранный уровень значимости.
,
,027≤0,061.
В
результате расчёта определено, что условие (3.3) выполняется, что
свидетельствует о соответствии фактического центра группирования
контролируемого параметра в изготавливаемой партии колёсной пары центру поля
допуска. Соответственно, повышение уровня брака на последующих операциях не
будет.
Технологический
процесс является стабильным по настроенности параметра х в течение
контролируемого интервала времени, если выполняется условие (3.4):
, (3.4)
,
- среднее арифметическое двух выборок,
-
квантиль распределения Стьюдента уровня (
) с ν=2.
По
результатам расчетов для определения стабильности технологического процесса по
настроенности параметра межбандажное расстояние
определено:
среднее
арифметическое первой выборки
1 =1439,88;
среднее
арифметическое второй выборки
2 =1440,034;
значение
Sd = 0,116;
квантиль
распределения Стьюдента
= 1,292 при уровне доверительной вероятности α = 0,9 и числе степеней свободы ν = 98.
В
результате расчетов определено:
=0,15,
=0,15,
,15≤0,15.
Технологический
процесс является стабильным по настроенности параметра, т.к. условие (3.4)
выполняется.
3.4.2
Оценка настроенности и стабильности технологического процесса по показателю
диаметр колёс по кругу катания
Для
каждой выборки рассчитывается значение среднего арифметического
и стандартного отклонения S с помощью формул (3.1) и
(3.2).
=
=1055,23,=
2,73.
Технологический
процесс (операция) является настроенным по контролируемому параметру х (при
неизвестной дисперсии σ20), если выполняется условие (3.3):
,
,23≤0,29.
В
результате расчёта определено, что условие (3.3) не выполняется, что
свидетельствует о несоответствии фактического центра группирования
контролируемого параметра в изготавливаемой партии колёсных пар центру поля
допуска, что может привести к повышению уровня брака на последующих
технологических операциях.
Технологический
процесс является стабильным по настроенности параметра х в течение
контролируемого интервала времени, если выполняется условие (3.4).
По
результатам расчетов для определения стабильности технологического процесса по
настроенности параметра диаметр колёс по кругу катания
определено:
среднее
арифметическое первой выборки
1 =1055,547;
среднее
арифметическое второй выборки
2 =1054,817;
значение
Sd =0,545;
квантиль
распределения Стьюдента
= 1,292 при уровне доверительной вероятности α=0,9 и числе степеней свободы ν=98.
В
результате расчетов определено:
=0,73,
=0,70,
0,73≤0,70.
Технологический
процесс является нестабильным по настроенности параметра, т.к. условие не
выполняется.
В
результате расчетов установлено существенное отличие характеристик
распределения значений контролируемого параметра (среднего значения и
дисперсии) в партиях изделий, что может привести к нестабильности выхода годных
деталей и уровня качества колёсных пар в целом.
.4.3
Оценка настроенности и стабильности технологического процесса по показателю
ширина обода колёс
Для
каждой выборки рассчитывается значение среднего арифметического
и стандартного отклонения S с помощью формул (3.1) и
(3.2).
=
=131,09,=
.
Технологический
процесс (операция) является настроенным по контролируемому параметру х (при
неизвестной дисперсии σ20), если выполняется условие (3.3):
,
,09≤0,13.
В
результате расчёта определено, что условие (3.3) не выполняется, что
свидетельствует о несоответствии фактического центра группирования
контролируемого параметра в изготавливаемой партии колёсных пар центру поля
допуска, что может привести к повышению уровня брака на последующих
технологических операциях.
Технологический
процесс является стабильным по настроенности параметра х в течение
контролируемого интервала времени, если выполняется условие (3.4).
По
результатам расчетов для определения стабильности технологического процесса по
настроенности параметра ширина обода колеса
определено:
среднее
арифметическое первой выборки
1 =130,92;
среднее
арифметическое второй выборки
2 =131,07;
значение
Sd =0,228;
квантиль
распределения Стьюдента
= 1,292 при уровне доверительной вероятности α=0,9 и числе степеней свободы ν=98.
В
результате расчетов определено:
=0,15,
=0,30,
,15≤0,30.
Технологический
процесс является нестабильным по настроенности параметра, т.к. условие не
выполняется.
В
результате расчетов установлено существенное отличие характеристик
распределения значений контролируемого параметра (среднего значения и
дисперсии) в партиях изделий, что может привести к нестабильности выхода годных
деталей и уровня качества колёсных пар в целом.
По
результатам оценки настроенности и стабильности технологического процесса
получилось, что по двум показателям диаметр колёс по кругу катания и ширина
обода колеса условия настроенности и стабильности технологического процесса не
соблюдаются. Следовательно, по этим двум показателям необходимо принять
мероприятия по их улучшению.
4.
Мероприятия по улучшению качества
В третьем разделе дипломного проекта мы проверили
анализ стабильности и настроенности технологического процесса ремонта колёсной
пары и выяснили, что по показателям диаметр колёс по кругу катания и ширина
обода колеса условия настроенности и стабильности не соблюдаются в связи с
этим, мы предлагаем рекомендации по улучшению качества.
Показатель ширина обода колеса на ОАО «КрЭВРЗ»
контролируется с помощью микрометра МК-175. Микрометр является измерительным
прибором, предназначенным для измерений с высокой точностью (до 2 мкм).
Микрометр применяют для измерения линейных размеров контактным методом.
Микрометр МК-175 - механический, он относится к гладким микрометрам. Гладким
микрометром называется средство для измерения наружных линейных размеров.
Мы предлагаем заменить гладкий механический микрометр
МК-175 на гладкий электронный МКЦ-25 (рисунок 4.1). Электронный микрометр
МКЦ-25 обладает меньшей погрешностью измерения (±0,002 мм) в сравнении с
механическим микрометром МК-175. В основе конструкции гладких электронных
микрометров лежит микрометрическая пара винт-гайка. Отличие от механических
гладких микрометров состоит в отсутствии шкал на стебле и барабане, результат
измерений снимается с ЖК-дисплея. Цифровое отсчётное устройство определяет не
только точность прибора, но и наличие множества функций, которых нет у
механических аналогов. Электронные цифровые микрометры способны производить
измерения в миллиметрах и дюймах, а так же обладают функцией установки нуля.
Эта функция позволяет электронным микрометрам осуществлять измерения не только
в абсолютной, но и в относительной системах отсчёта. Такая возможность является
значительным преимуществом электронных цифровых микрометров в сравнении с
механическими.
<#"794369.files/image044.gif">
, (6.1)
где
Kcut - затраты на приобретение и доставку СИ, руб.;
Клt
- остаточная стоимость основных фондов, выбывающих в 2012 г, руб.
Кcut
включает стоимость электронного микрометра МКЦ-25 Челябинской компании
«Калиброн» - 2240 руб. за 1 шт.; стоимость доставки микрометра автотранспортом
из г. Челябинска в г. Красноярск транспортно-экспедиторской фирмой «Деловые
линии» составляет 438 руб.
По
выше приведенным данным находим Ксut
Кcut
= 2240+438 = 2678 руб.
Клt
рассчитываем по формуле (6.2)
, (6.2)
где
ПС - первоначальная стоимость микрометра, выбывающего в 2013 г, руб.;
На
- норма амортизации, %;
Тэкспл
- период эксплуатации, лет.
Норма
амортизации На, %, рассчитывается по формуле (6.3)
, (6.3)
где
n - срок полезного использования микрометра, мес.
Срок
полезного использования микрометра устанавливается организацией самостоятельно
и по решению ОАО «КрЭВРЗ» составляет 36 месяцев.
Тогда
по формуле (6.3) норма амортизации микрометра составит

= 2,78
%.
Период
эксплуатации микрометра составляет 3 года.
Первоначальная
стоимость микрометра МК-175, выбывающего в 2013 году составляет 1475 руб.
Подставив
все найденные значения в формулу (6.2), получаем
Клt
=
=1352 руб.
Подставив
полученные значения в формулу (6.1), получаем
Кt
= 2678+1352= 4030 руб.
Сводим
все полученные данные в таблицу 6.2.
Таблица
6.2 - Единовременные затраты на замену микрометра МК-175
Наименование затрат
|
Стоимость затрат, руб.
|
Соотношение затрат, %
|
Затраты на приобретение и
доставку микрометра (Кcut)
|
2678,0
|
66,5
|
Остаточная стоимость
основных фондов (Клt)
|
1352,0
|
33,5
|
Итого
|
4030,0
|
100,0
|
Из таблицы 6.2 можно сделать вывод, что наибольшие
затраты пойдут на приобретение и доставку СИ и составят 2678 руб., а общие
затраты в сумме составят 4030 руб.
.1.2 Расчет текущих годовых издержек на эксплуатацию
микрометра
Текущие годовые издержки эксплуатации Иt в
2013 году содержат следующие составляющие [37]
, (6.4)
где
Иповt - затраты на поверку СИ, руб.;
Ирt
- затраты на текущий ремонт и техническое обслуживание, руб.;
Иаt
- амортизационные отчисления, руб.
Затраты
на поверку СИ, осуществляемую в ФГУ «Красноярский центр стандартизации и
сертификации», составляют 130 руб.
По
сведениям полученным от ОАО «КрЭВРЗ», затраты на текущий ремонт принимаем 1,8 %
от стоимости микрометра, что составит 40,32 руб.
Амортизационные
отчисления рассчитываем по формуле (6.5)
Иat
= 
, руб.
(6.5)
Первоначальная
стоимость электронного микрометра МКЦ-25 составляет 2240 руб. (таблица 6.1).
Норма
амортизации находится по формуле (6.3). Срок полезного использования микрометра
электронного МКЦ-175 составляет три года, т.е. 36 месяцев. Следовательно, норма
амортизации нового средства измерения составит 2,78 %.
Подставляя
все значения в формулу (6.5), получаем
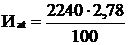
= 62,3
руб.
Подставляем
все полученные значения в формулу (6.4)
Иt
= 130+40,32+62,3 = 232,62 руб.
Сводим
все полученные данные по текущим годовым издержкам на эксплуатацию микрометра в
таблицу 6.3.
Таблица
6.3 - Текущие годовые издержки на эксплуатацию микрометра
Наименование затрат
|
Стоимость затрат, руб.
|
Соотношение затрат, %
|
Затраты на поверку СИ (Иповt)
|
130,0
|
56,0
|
Затраты на текущий ремонт и
техническое обслуживание (Ирt)
|
40,3
|
17,3
|
Амортизационные отчисления
(Иat)
|
62,3
|
26,7
|
Итого
|
232,6
|
100,0
|
Из таблицы 6.3 можно сделать вывод, что самая большая
доля затрат при эксплуатации нового микрометра - это затраты на поверку,
которые составляют 130 рублей.
Общие затраты на замену микрометра находим, как
О=Иt+Кt, (6.6)
Подставляя значения в формулу (6.6), получаем
О=232,6+4030,0=4262,6 руб.
.2 Расчет затрат на разработку стандарта организации
«Статистические методы контроля» на ОАО «КрЭВРЗ»
В 4 части дипломного проекта нами было предложено
разработать стандарт организации (СТО) «Статистические методы контроля»,
поэтому в настоящей части мы рассчитали затраты на его разработку.
Затраты на разработку СТО включают в себя [31], [37]:
- материальные затраты (МЗ);
- затраты на заработную плату (ЗП);
- страховые взносы во внебюджетные
фонды (С);
- амортизационные отчисления (А);
- прочие денежные расходы (Пр).
Таким образом, затраты на разработку стандарта
организации, З, руб., рассчитаем по формуле (6.7)
З = МЗ + ЗП + С + А + Пр, (6.7)
Исходные данные для расчёта затрат на разработку СТО
«Статистические методы контроля» на ОАО «КрЭВРЗ» представлены в таблице 6.4
[31][52], [54], [55], [57].
Таблица 6.4 - Исходные данные для расчёта затрат на
разработку СТО
Обозначение
|
Показатель
|
Значение
|
Единица измерения
|
1
|
2
|
3
|
4
|
РМ
|
Расходные материалы: -
бумага для ксерокса (250 листов) - бумага для записей (500 листов) - ручки (3
шт.)
|
160 100 15
|
руб. руб. руб.
|
Эпк Эп
Эл
|
Энергопотребление: -
компьютера - принтера - лампочек (6 штук)
|
0,55 0,28 0,10
|
кВт кВт кВт
|
Сэ
|
Стоимость 1 кВт
электроэнергии (по сведениям предприятия)
|
3,44
|
руб.
|
Одр
|
Оклад дипломного
руководителя (11 разряд)
|
2400
|
руб., на 0,5 ставки
|
Оик
|
Оклад инженера по качеству
(по сведениям предприятия, 7 разряд)
|
18000
|
руб.
|
Кр
|
Районный коэффициент: - для
бюджетных учреждений - для внебюджетных учреждений
|
20 30
|
% %
|
Снад
|
Надбавка за работу в южных
районах Красноярского края
|
30
|
%
|
С
|
Страховые взносы во
внебюджетные фонды
|
30,2
|
%
|
На
|
Норма амортизации
оргтехники (компьютер, принтер)
|
20
|
%
|
Ск Спр
|
Средняя стоимость
используемого оборудования: - компьютера - принтера
|
15 000 5 500
|
руб. руб.
|
Сначала рассчитаем каждый из перечисленных элементов
затрат [37].
Для того, чтобы посчитать ЗП, необходимо определить
трудоёмкость разработки СТО «Статистические методы контроля». Для этого процесс
разработки стандарта разобьём на 5 этапов и для каждого этапа определим
трудоёмкость [70].
) Подготовительные работы, в том числе определение
структуры СТО, требований к его содержанию.
Т1др= 1 ч, Т1ст = 3 ч, Т1ик=
2 ч.
) Изучение литературы, требующейся для написания
стандарта, написание чернового варианта стандарта.
Т2др = 2 ч, Т2ст = 8 ч.
) Согласование проекта стандарта с дипломным
руководителем и инженером по качеству, его корректировка.
Т3др = 2 ч, Т3ст = 10 ч, Т3ик
= 3 ч.
) Набор стандарта на компьютере, его форматирование.
Т4ст = 9 ч.
) Утверждение СТО с дипломным руководителем и
инженером по качеству.
Т5др = 1 ч, Т5ст = 1 ч, Т1ик
= 1 ч.
Таким образом, трудоёмкость разработки СТО дипломного
руководителя, студента и инженера по качеству можно рассчитать по формуле (6.8)
Т = Т1 + Т2 +Т3 +Т4 + Т5, (6.8)
Тдр= 2+2+2+1=7 ч,
Тст = 3+8+10+9+1=34 ч,
Тик = 2+3+1 = 6 ч.
Материальные затраты на разработку СТО «Статистические
методы контроля» включают в себя затраты на расходные материалы (РМ) и затраты
на электроэнергию (Э) [37], и рассчитываются по формуле (6.9)
МЗ = РМ + Э, (6.9)
где РМ - расходные материалы, руб.;
Э - затраты на электроэнергию, руб.
Исходя из данных таблицы 4, РМ составляют
РМ=160+100+15=275 руб.
Расчёт затрат на Э производим по формуле (6.10)
Э = (Эпк·tпк + Эп·tп
+ Эл·tл)·Сэ, (6.10)
где Эпк, Эп, Эл -
электропотребление, соответственно, компьютера, принтера, лампочек, кВт;пк,
tп, tл - продолжительность работы компьютера, принтера,
лампочек за время написания документа, ч;
Сэ - стоимость 1 кВт электроэнергии, руб.
Продолжительность работы оргтехники принимаем tпк
= 10 ч, tп = 0,3 ч, tл = 40 ч, получим
Э = (0,55·10 + 0,28·0,3 + 0,1·40)·3,44 = 33 руб.
Рассчитываем материальные затраты по формуле (6.9)
МЗ = 275,0 + 33,0 = 308 руб.
Рассчитаем заработную плату дипломного руководителя и
инженера по качеству, разрабатывающих СТО по формуле (6.11)
ЗП
=
, (6.11)
где
Т - трудоёмкость разработки стандарта, ч;
-
число рабочих дней в месяц;
-
количество рабочих часов в день.
Рассчитываем
заработную плату по формуле (6.11)
ЗП
= 
= 1186
руб.
Страховые
взносы во внебюджетные фонды, С, руб., рассчитываем по формуле (6.12) [37]
С
=
, (6.12)
Подставляя
значения в формулу (6.12), получаем
С
=
= 358,2 руб.
Амортизационные
отчисления, А, руб., рассчитаем по формуле (6.13)
=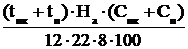
, (6.13)
Норму
амортизации, используемой при написании СТО «Статистические методы контроля»
оргтехники, согласно Постановления Правительства о классификации основных
средств, включаемых в амортизационные, принимаем 20 % [34].
Подставляя
значения в формулу (6.13), получаем
А=
= 29,7 руб.
Прочие
затраты принимаются от 2 до 6 % от остальных категорий затрат (принимаем 4 %)
[37] и рассчитываются по формуле (6.14)
Пр
= (МЗ + ЗП + С + А)·0,04 (6.14)
Пр
= (308,0+1186,0+358,2+29,7)·0,04=75,3 руб.
Таким
образом, стоимость затрат на разработку СТО «Статистические методы контроля»
составят
З=308,0+1186,0+358,2+29,7+75,3=1957,2
руб.
Полученные
результаты расчёта затрат на разработку СТО «Статистические методы контроля»
заносим в сводную таблицу 6.5.
Таблица
6.5 - Затраты на разработку СТО «Статистические методы контроля» для ОАО
«КрЭВРЗ»
Статьи затрат
|
Стоимость затрат, руб.
|
Соотношение затрат, %
|
Материальные затраты
|
308,0
|
15,7
|
Заработная плата
|
1186,0
|
60,7
|
Страховые взносы во
внебюджетные фонды
|
358,2
|
18,3
|
Амортизационные отчисления
|
29,7
|
1,5
|
Прочие затраты
|
75,3
|
3,8
|
Общие затраты
|
1957,2
|
100,0
|
По сводной таблице затрат на разработку СТО
«Статистические методы контроля» можно сделать вывод, что затраты на заработную
плату являются основной частью затрат и составляют 1186 руб.
Заключение
В
настоящем дипломном проекте был проведён анализ качества колёсных пар с помощью
простых инструментов контроля качества: диаграммы Парето, причинно-следственной
диаграммы Исикавы, 
-R -
контрольных карт Шухарта.
По
диаграмме Парето мы определили, что такие дефекты, как несоответствие
межбандажного расстояния, несоответствие диаметра колёс по кругу катания,
несоответствие ширины обода колеса, составляют более 80 % несоответствий и
требуют принятия первоочередных мер по их устранению.
Проведён
анализ построенных диаграмм Исикава, в результате которого мы определили, что
главными причинами появления дефекта несоответствие ширины обода колеса
являются ошибки персонала, обусловленные некачественным обучением, усталостью и
невнимательностью; использование средств измерений, не заложенных в техническом
процессе; несоблюдение технологических режимов; нарушение технологии и
несоблюдение режимов обработки. Главными причинами появления несоответствия
межбандажного расстояния являются: ошибки персонала, связанные с личными
проблемами, халатностью и невнимательностью персонала; ошибки средств
измерения, связанные с несвоевременной их поверкой; несоблюдение контроля за
технологическим процессом и контролем за безопасностью; несоблюдение регламента
и режимов обточки. Главными причинами появления несоответствия диаметра колёс
по кругу катания являются ошибки персонала, связанные с незнанием технологии
ремонта и некачественным обучением; механические повреждения и несвоевременная
поверка средств измерения; плохая проработка технологии и несоблюдение режимов
обработки; поломка колесотокарного станка, несвоевременное проведение
планово-предупредительных работ и нарушение режима обточки.
По
построенным контрольным картам Шухарта и расчёту настроенности и стабильности
технологического процесса ремонта колёсной пары мы определили, что по двум
показателям диаметр колёс по кругу катания и ширина обода колеса условия
настроенности и стабильности технологического процесса не соблюдаются.
Были
разработаны мероприятия по улучшению качества, в которых предложено разработать
стандарт организации «Статистические методы контроля» для ОАО «КрЭВРЗ»,
представленный в приложении А, а также заменить заменить гладкий механический
микрометр МК-175 для измерения ширины обода колеса на гладкий электронный
микрометр МКЦ-25.
В
экономической части настоящего дипломного проекта был произведён расчёт затрат
на разработку стандарта организации «Статистические методы контроля» для ОАО
«КрЭВРЗ», а также на замену микрометра. Расчёт показал, что данный проект будет
экономически выгодным.
Библиографический
список
1. Адлер Ю.П., Шпер В.Л. Контрольные карты Шухарта в действии
[Текст] // Методы менеджмента качества. - 2004. - № 2. - С.34-37
. Баратов, А.Н. Взрывопожарность веществ и материалов и средств их
тушения. Справочное издание в 2-х книгах [Текст] / А.Н. Баратов, А.Я.
Корольченко и др. - М.: Химия,1990. - 201с.
. ГН 2.2.5.686 - 98 Предельно-допустимые концентрации вредных
веществ в воздухе рабочей зоны.- М.: из-во «НЦ ЭНАС»,1998.-58с
. ГОСТ 12.0.003 - 74* Опасные и вредные производственные факторы.
Классификация. - Введ. 01.01.76.- М.: Изд-во стандартов, 1974.-16с.
. ГОСТ 12.0.004-90 ССБТ. Организация обучения безопасности труда.
Общие положения.
. ГОСТ 12.1.003 - 83* Шум. Общие требования безопасности. - Взамен
ГОСТ 12.1.003-76; введ. 01.07.84.- М.: Изд-во стандартов, 1983.-18с.
. ГОСТ 12.1.005 - 88* Общие санитарно-гигиенические требования к
воздуху рабочей зоны. - Взамен ГОСТ 12.1.005-76; введ. 01.01.89.- М.: Изд-во
стандартов, 1988.-16с.
. ГОСТ 12.1.007-90 Вредные вещества. Классификация и общие
требования безопасности. - Взамен ГОСТ 12.1.007-78; введ. 01.01.91.- М.: Изд-во
стандартов, 1990.-20с.
. ГОСТ 12.1.010 - 81 - ССБТ. Электробезопасность. Защитное
заземление. Зануление. - с изм. №1 от 07.1987 г.
. ГОСТ 12.1.012 - 01 Вибрационная безопасность. Общие требования.
- Введ. 01.01.02.- М.: Изд-во стандартов, 2001.-18с.
. ГОСТ 12.1.029 - 80 - ССБТ. Средства и методы защиты от шума, с
изм. от 01.07.81
. ГОСТ 12.2.003 - 91 Оборудование производственное. Общие
требования безопасности. - Введ. 01.07.92.- М.: Изд-во стандартов, 1991. - 18
с.
. ГОСТ 12.2.062 - 81 Оборудование производственное. Ограждения
защитные. - Введ. 01.07.82.- М.: Изд-во стандартов, 1981.-16 с.
. ГОСТ 12.4.021 - 75* ССБТ. Системы вентиляционные. Общие
требования. - М.: Изд-во стандартов, 2001. - 91-94 с.
. ГОСТ 12.4.026 - 01 Цвета сигнальные, знаки безопасности и
разметка сигнальная. Назначения и правила применения. Общие технические требования
и характеристики. Методы испытаний. - Введ. 01.01.02.- М.: Изд-во стандартов,
2001.-22с.
. ГОСТ 12.4.121 - 83 Системы вентиляционные. Общие требования
безопасности. - Введ. 01.01.84.- М.: Изд-во стандартов, 1983.-16с.
. ГОСТ 12.4.124 - 83 Средства защиты от статического
электричества. Общие технические требования. - Введ. 01.01.84.- М.: Изд-во
стандартов, 1983.-24с.
. ГОСТ 17.2.3.02 - 78 Охрана природы. Атмосфера. Правила
установления допустимых концентраций вредных веществ. - Введ. 01.07.79.- М.:
Изд-во стандартов, 1978.-16 с.
. ГОСТ 166-89 Штангециркули. Технические условия. - Введ. 1.01.91.
- М.: Изд-во стандартов, 1980. - 10 с.
. ГОСТ 520-2002 Подшипники качения. Общие технические условия. -
Взамен ГОСТ 520-89. - М.: Изд-во стандартов, 2003. - 40 с.
. ГОСТ 2789-73 Шероховатость поверхности. Параметры и
характеристики. - Введ. 1.01.75. - М.: Стандартинформ, 2006. - 6 с.
. ГОСТ 4835-2006 Колёсные пары вагонов магистральных жедезных
дорог колеи 1520 мм. Технические условия. - Введ. 1.01.2008. - М.:
Стандартинформ, 2007. - 9 с.
. ГОСТ 7409-2009 Вагоны грузовые. Требования к лакокрасочным
покрытиям. - Введ. 1.07.2010. - М.: Стандартинформ, 2010. - 44 с.
. ГОСТ 7931 Олифа натуральная. Технические условия. - М.: Изд-во
стандартов, 1989. - 8 с.
. ГОСТ 10877-76 Масло консервационное К-17. Технические условия. -
Введ. 1.01.77. - М.:Изд-во стандартов, 2002. - 3 с.
. ГОСТ 12549 Вагоны пассажирские магистральных дорог колеи 1520
мм. Окраска. Технические условия. - Введ. 1.07.2004, с изм. от 19.07.2010. - М.:
Изд-во стандартов, 2004. - 15 с.
. ГОСТ Р 1.5-2004 Стандартизация в РФ. Стандарты национальные РФ.
Правила построения стандартов и общие требования к их содержанию. - Введ.
1.07.2005. - М.: Стандартинформ, 2007. - 23 с.
. ГОСТ Р 50779.11-2000 (ИСО 3534.2-93) Статистические методы.
Статистическое управление качеством. Термины и определения. - Введ. 1.07.2001.
- М.: Изд-во стандартов, 2003. - 37 с.
. ГОСТ Р 50779.40-96 (ИСО 7870-93) Статистические методы.
Контрольные карты. Общее руководство и введение. - Введ. 1.06.2006. - М.:
Стандартинформ, 2006. - 13 с.
. ГОСТ Р 50779.42-99 (ИСО 8258-91) Статистические методы.
Контрольные карты Шухарта. - Введ. 1.01.2000. - М.: Изд-во стандартов, 2004. -
31 с.
. Единый тарифно-квалификационный справочник работ и профессий
рабочих, должностей руководителей, специалистов и служащих ЕТКС (утв.
постановлением Минтруда РФ от 21 августа 1998 г. № 37, с изм. от 21.01.00 г.,
4.08.00 г., 20.04.01 г., 31.02.02 г., 20.06.02 г., 28.07.03 г., 12.11.03 г.,
25.08.05 г., 7.11.06 г., 17.09.07 г., 29.04.08 г., 17.11.13 г.).
. Ефимов, В.В. Статистические методы в управлении качеством:
Учебное пособие. - Ульяновск: УлГТУ, 2003. - 134 с.
. И-72 Инструкция по устройству молниезащиты зданий, сооружений и
промышленных коммуникаций. - М.: «НЦ ЭНАС». 2004. - 46с.
. Иванов, И. Н. Экономика промышленного предприятия: учебник / И.
Н. Иванов. - Москва: Инфра-М, 2011. - 393 с.
. Кане, М.М. Системы, методы и инструменты менеджмента качества
[Текст]: Учебное пособие / М.М. Кане [и др.]. - М.: Инфра, 2009. - 560 с.
. Конституция РФ. - М.: Издательство «Приор», 2005. - 32с.
. Курс лекций «Экономика качества, стандартизации и сертификации».
- Красноярск: СибГТУ, 2011. - 106 с.Российская Федерация. Законы. О страховых
взносах в пенсионный фонд Российской Федерации №212 (федеральный закон: принят
Государственной думой 17 июля 2009 г.: одобрен Советом Федерации 18 июля 2009
г.: с ред. от 25.12.12 №269-ФЗ).
. Лазарев, Н.В. Вредные вещества в промышленности. Справочник
[Текст] / Под ред. Лазарева Н.В., Левиной Э.И. - Л.: Химия, 1977. Том 3 - 608с.
. Лапидус В.А. Всеобщее качество (TQM) в российских компаниях /
Гос.ун-т управления Нац. Фонд подготовки кадров. - М.: ОАО «Типография.
Новости», 2000. - 432 с.
. Москаленко, В.Н. Охрана труда. Учебное пособие. Законодательные
и нормативно-правовые акты по охране труда [Текст] / под ред. В.Н. Москаленко,
2-е изд., испр. и дополн. - Красноярск: СибГТУ, 2006. - 686 с.
. НПБ 88 - 2001 Установки пожаротушения и сигнализации. Нормы и
правила проектирования. - М.: ГПС МВД РФ, 2001. - 44с.
. НПБ 105 - 03 Определение категорий помещений, зданий и наружных
установок по взрывопожарной и пожарной опасности.- СПб.: из-во «НЦ ЭНАС», 2003.
-170с.
. НПБ 166 - 97 Пожарная техника. Огнетушители. Требования к
эксплуатации. Основные показатели и методы испытаний. М.: ГПС МВД РФ,1997.-54с.
. Охрана труда. Законодательные и нормативные правовые акты по
охране труда: [учеб. пособие] - [2-е изд.,испр. и доп.] - 615 с.:табл. -
Красноярск, 2006.
. Панов А.А., Аникин В.В, Бойм Н.Г. Обработка металлов резанием.
Справочник технолога/Под общей редакцией канд.тех.наук А.А. Панова. - М.:
«Машиностроение», 1988. - 736 с.
. Пожарная безопасность. Взрывобезопасность [Текст]: справочник /
А.Н. Баратов [и др.].- М.: Химия,1987.-272с.
. Пономарёв, С.В. Управление качеством продукции. Инструменты и
методы менеджмента качества [Текст] / С.В. Пономарёв, С.В. Мищенко, В.Я.
Белобрагин. - М.: РИА «Стандарты и качество», 2005. - 248 с.
. Правила противопожарного режима в РФ (утв. постановлением
Правительства РФ от 25 апреля 2012 г. № 390).
. Правила устройства электроустановок. - М.: изд-во «НЦ ЭНАС»,
2002. - 170 с.
. Российская Федерация. Законы. О защите населения и территорий от
чрезвычайных ситуаций природного и техногенного характера: федер. закон :
[принят Гос. Думой 11 ноября 1994 г.: с изм. от 11.02.2013 г. № 9-ФЗ]
. Российская Федерация. Законы. О гражданской обороне: федер.
закон :[принят Гос. Думой 12 февраля 1998 г.: с изм. от 22.08.2004 г. № 122-ФЗ]
. Российская Федерация. Законы. О страховых взносах в фонд социального
страхования Российской Федерации №212 (федеральный закон: принят
Государственной думой 17 июля 2009 г.: одобрен Советом Федерации 18 июля 2009
г.: с ред. от 25.12.12 №269-ФЗ).
. Российская Федерация. Законы. О противодействии терроризму:
федер. закон : [принят Гос. Думой 26 февраля 2006 г.: с изм. от 8.11.11 г.
35-ФЗ]
. Российская Федерация. Законы. О страховых взносах в Федеральный
фонд обязательного медицинского страхования №212 (федеральный закон: принят
Государственной думой 17 июля 2009 г.: одобрен Советом Федерации 18 июля 2009
г.: с ред. от 25.12.12 №269-ФЗ).
. Российская Федерация. Законы. Трудовой кодекс Российской
Федерации №197 (федеральный закон: принят Государственной Думой 21 декабря 2001
г.: одобрен Советом Федерации 26 декабря 2001 г.: с изм. от 15 февраля 2011 г.
№ 197-ФЗ).
. Российская Федерация. Постановления Правительства. О Единой
государственной системе предупреждения и ликвидации ЧС. - 288 с.: ил.
. Российская Федерация. Постановления Правительства. О районных
коэффициентах, применяемых при установлении трудовых пенсий и пенсий по
государственному пенсионному обеспечению лицам, проживающим в районах Крайнего
Севера и приравненных к ним местностям, а также в районах с тяжёлыми
климатическими условиями №216 от 17.04.2006
. Российская Федерация. Постановления Правительства. О
классификации основных средств, включаемых в амортизационные группы от 01
января 2002 г. №165 [Текст] // Собрание законодательства РФ.-2002.-№1. - Ст.52.
. Саулова, Т.А. Оценка сейсмической безопасности производственных
объектов: учебное пособие по выполнению расчётно-графических работ, курсовых и
дипломных проектов для студентов специальности 280101 / Т.А. Саулова, В.И. Бас.
- Кр-к: СибГТУ, 2006. - 53 с.
. СанПиН 2.1.4.1074 - 01. Питьевая вода. Гигиенические требования
к качеству питьевой воды централизованных систем питьевого водоснабжения.
Контроль качества. - М.: Изд-во Госкомсанэпиднадзор России, 2001. - 25 с.
. СанПиН 2.2.1/2.1.1.1200-03 Санитарно-защитные зоны и санитарная
классификация предприятий, сооружений и иных объектов. - СПб.: типография
«Авангард», 2003. -38с.
. СанПиН 2.2.548 - 96 Гигиенические требования к микроклимату
производственных помещений. - М.: Госкомсанэпиднадзор России, 1996. - 20с.
. СНиП 2.04.02 - 02 Водоснабжение. Наружные сети и сооружения.-
М.:Госстрой России, 2002.-159 с.
. СНиП 2.09.04 - 01 Административные и бытовые здания.- М.:
Минстрой России, 2001.-19с.
. СНиП 21-01-02 Пожарная безопасность зданий и сооружений.- М.:
Госстрой России, 2002.-23с.
. СНиП 23-05 - 03. Естественное и искусственное освещение. - М. :
Изд-во ГУП ЦПП, 2003. - 50 с.
. СНиП 41.01.03 Отопление, вентиляция и кондиционирование.- М.:
Госстрой России, 2003.-54с.
. Степановских, А.С. Охрана окружающей среды [Текст] / А.С.
Степановских. - Курган.: «Звуралье», 1998. - 512с.
. Титов, В. И. Экономика предприятия: учебник / В. И. Титов. -
Москва: Эксмо, 2008. - 411 с.
. Экономика предприятия [Текст]: учебное пособие / Л.Н. Нехорошева
[и др.]. - Минск: Белорусский государственный экономический университет, 2010.
- 718 с.
Приложения
Приложение А
СТАНДАРТ ОРГАНИЗАЦИИ
СТАТИСТИЧЕСКИЕ МЕТОДЫ КОНТРОЛЯ ДЛЯ ОАО «КрЭВРЗ»
ОАО «КрЭВРЗ»
Директор ОАО «ЭВРЗ»
___________ А.Р.Гирш
.06.2013 г.
СТО 015 - 2013
Введен впервые
.06.2013 г.
СТАНДАРТ ОРГАНИЗАЦИИ
_____________________________________________________________
СТАТИСТИЧЕСКИЕ МЕТОДЫ КОНТРОЛЯ ДЛЯ ОАО «КрЭВРЗ»
__________________________________________________________
Дата введения 2013-06-15
1 Область применения
Настоящий стандарт организации устанавливает
графический метод статистического управления процесса ремонта колёсной пары с
помощью простых инструментов контроля качества. В настоящем стандарте описана
методика построения следующих простых инструментов контроля качества: диаграммы
Парето, причинно-следственной диаграммы Исикавы, контрольной карты Шухарта.
Настоящий стандарт организации является обязательным для ОУК, ОТК.
2 Нормативные ссылки
В настоящем стандарте организации использованы ссылки
на следующие стандарты:
ГОСТ Р 1.5-2004 Стандартизация в РФ. Стандарты
национальные РФ. Правила построения стандартов и общие требования к их
содержанию
ГОСТ Р 50779.11-2000 (ИСО 3534.2-93) Статистические
методы. Статистическое управление качеством. Термины и определения
ГОСТ Р 50779.40-96 (ИСО 7870-93) Статистические
методы. Контрольные карты. Общее руководство и введение
ГОСТ Р 50779.42-99 (ИСО 8258-91) Статистические
методы. Контрольные карты Шухарта
3 Определения
В настоящем стандарте предприятия применяются термины
с соответствующими определениями:
.1 стандарт организации: Стандарт, утвержденный
и применяемый организацией для целей стандартизации, установленных статьей 11
Федерального закона «О техническом регулировании», для совершенствования
производства и обеспечения качества продукции, выполнения работ, оказания
услуг, а также для распространения и использования полученных в различных
областях знаний результатов исследований или испытаний, измерений и разработок.
.2 диаграмма Парето: Разновидность столбиковой
диаграммы, применяемой для наглядного отображения рассматриваемых факторов в
порядке уменьшения (возрастания) их значимости.
.3 причинно-следственная диаграмма Исикавы:
Инструмент, позволяющий выявить отношение между показателями качества и
воздействующими на него факторами.
.4 контрольный листок: Инструмент для сбора
данных и их автоматического упорядочения для облегчения дальнейшего
использования собранной информации.
.5 контрольная карта: Инструмент, позволяющий
контролировать протекание процесса и воздействовать на него, предупреждая его
отклонение от предъявленных требований.
.6 контрольная карта Шухарта: Основной
статистический инструмент для анализа стабильности ТП, выявления
производственных факторов, дестабилизирующих ТП, а также для своевременной под
наладки ТП без его остановки (если это возможно) или своевременной остановки
ТП, когда он выходит из удовлетворительного состояния.
4 Обозначения и сокращения
4.1 СТО: Стандарт организации.
.2 ТП: Технологический процесс.
.4 ОУК: Отдел управления качеством.
.5 ОТК: Отдел технического контроля.
5 Статистические методы контроля
.1 Общие положения
5.1.1 Статистические методы контроля применяются для
анализа стабильности ТП ремонта колёсных пар.
.1.2 Порядок применения простых инструментов
контроля качества для анализа стабильности ТП ремонта колёсных пар
осуществляется в соответствии с настоящим СТО.
.1.3 Отчёты по проведению статистических методов
контроля хранятся в ОУК, который в свою очередь, может передавать отчёты ОТК.
.1.4 Начальник ОУК назначает ответственного за
проведение статистических методов контроля и осуществляет непосредственное
руководство за его деятельностью.
.1.5 Ответственного за проведение статистических
методов контроля назначает начальник ОУК
.1.6 На должность ответственного за проведение
статистических методов контроля начальником ОУК назначается инженер по
качеству, прошедший инструктаж по проведению статистических методов контроля,
имеющий высшее образование и стаж работы не менее 5 лет.
.1.7 Должностные обязанности, права и ответственность
назначенного инженера по качеству устанавливаются должностной инструкцией,
которая согласовывается с начальником отдела и утверждается руководителем
организации.
.1.8 Назначенный инженер по качеству в своей
деятельности руководствуется:
нормативными правовыми актами, другими руководящими и
методическими материалами по статистическим методам контроля;
Уставом организации;
приказами, распоряжениями руководителя организации
(непосредственного руководителя);
настоящим стандартом организации.
.1.9 Статистические методы контроля должны проводиться
назначенным инженером по качеству каждые 3 месяца, а также по мере
необходимости.
.1.10 Для проведения метода «мозгового штурма»
назначенным ответственным инженером по качеству самостоятельно набирается
группа из 6 человек, которые будут принимать в нём участие.
.1.11 Участники «мозгового штурма» утверждаются
начальником ОУК.
.1.12 Участниками «мозгового штурма» могут быть
служащие ОУК и ОТК.
6 Диаграмма Парето
6.1 Диаграмма Парето используется для выявления
главных причин несоответствий, возникающих в ходе ремонта колёсной пары.
.2 Порядок построения Диаграммы Парето.
.2.1 Выявление проблем, связанных с несоответствием
параметров колёсной пары.
.2.2 Классификация выявленных проблем по отдельным
факторам.
.2.3 Разработка контрольного листка для регистрации данных
и подсчёт итогов.
.2.4 Сбор и анализ статистического материала по
каждому фактору.
.2.5 Заполнение контрольного листка.
.2.6 Разработка таблицы для данных с графами для
итогов по каждому проверяемому признаку в отдельности, накопленной суммы числа
дефектов, процентов к общему итогу и накопленных процентов (пример таблицы
представлен в Приложении Б).
.2.7 Расположение данных, полученных по каждому
проверяемому признаку, в порядке значимости и заполнение таблицы.
.2.8 Подготовка оси (одна горизонтальная и две
вертикальных) для построения диаграммы Парето.
.2.9 Нанесение на левую ось ординат шкалу с
интервалами от 0 до общей суммы числа выявленных факторов, а на правую ось
ординат шкалу с интервалами от 0 до 100, отражающую процентную меру фактора.
.2.10 Разделение оси абсцисс на интервалы в
соответствии с числом исследуемых факторов или относительной частотой.
.2.11 Построение столбиковой диаграммы, у которой
высота столбца (откладывается по левой шкале) равна числу появлений
соответствующего фактора. Столбцы диаграммы располагают в порядке уменьшения
значимости фактора. Последний столбец характеризует "прочие", т. е.
малозначимые факторы (пример диаграммы Парето представлен в Приложении В).
.2.12 Построение на диаграмме кумулятивной кривой.
Каждая точка кривой ставится над соответствующим столбцом столбиковой
диаграммы.
.2.13 Нанесение на диаграмму обозначений и надписей.
.2.14 Проведение анализа Диаграммы Парето.
7 Причинно-следственная диаграмма
Исикавы
7.1 Диаграмма Исикавы используется для первоначального
ранжирования факторов, воздействующих на несоответствия, возникающие в ходе
ремонта колёсной пары, и выбора приоритетов для устранения проблемы или
улучшения показателя.
.2 Порядок построения диаграммы Исикавы (пример
диаграммы Исикавы представлен в Приложении Г).
.2.1 Выбор показателя качества для улучшения.
Выбранный показатель записывается в середине правого края чистого листа бумаги.
Показатель необходимо сформулировать как можно точнее причинно-следственную
диаграмму будет затруднительно использовать для решения конкретной проблемы.
Через центр листа проводится прямая горизонтальная линия («хребет» диаграммы),
слева упирающаяся в край листа, а справа в показатель для анализа.
.2.2 Определение главных факторов (факторов первого
порядка), влияющих на показатель качества. От названий главных факторов к
«хребту» диаграммы проводятся стрелки («большие кости»). Показатель качества и
главные факторы на диаграмме заключаются в рамку.
.2.3 Определение и запись факторов второго порядка
рядом с «большими костями» факторов первого порядка, на которые они влияют.
Названия факторов второго порядка с «большими костями» соединяются стрелками
(«средние кости»).
.2.4 Определение и запись факторов третьего порядка
рядом со «средними костями» факторов второго порядка, на которые они оказывают
влияние. Названия факторов третьего порядка со «средними костями» соединяют
стрелками («малые кости»).
.2.5 Для определения факторов второго, третьего и т.д.
порядков рекомендуется использовать метод «мозгового штурма».
.3 Правила проведения «мозгового штурма».
.3.1 Необходимо установить определенную цель.
.3.2 Участвовать в обсуждении должны все участники
команды.
.3.3 Сотрудники должны ощущать безопасность участия и
высказывания своего мнения.
.3.4 Не допускается никакой критики, все идеи
записываются, ни одна идея сразу не отвергается.
.3.5 Предложения не ограничиваются только факторами,
относящимися к деятельности говорящего.
.3.6 Рекомендуется исключить бесплодные разговоры,
ценя идеи и сознательное оперирование фактами.
.3.7 Членов команды следует поощрять для раскрытия
творческого потенциала.
.3.8 Лицам руководящего состава не рекомендуется
высказываться первыми.
.3.9 Членам команды следует подхватывать и развивать
идеи других.
8 Контрольные карты Шухарта
8.1 Цель контрольных карт - обнаружить неестественные
изменения в данных из повторяющихся процессов и дать критерии для обнаружения
отсутствия статистической управляемости. Процесс находится в статистически
управляемом состоянии, если изменчивость вызвана только случайными причинами.
8.2
Для анализа стабильности технологического процесса ремонта колёсной пары
применяются 
-R
контрольные карты для количественных данных. Карты для количественных данных
отражают состояние процесса через разброс и расположение центра.
.3
Порядок построения 
-R -
контрольной карты.
.3.1
Сбор данных по показателям, которые были выявлены в результате анализа
диаграммы Парето. Данные берутся из «Журнала учёта замечаний» в колёсном цехе
на участке сборки буксового узла. По каждому из показателей берутся 150
значений. Значения показателей разбиваются на несколько подгрупп.
.3.2
Разработка таблиц для занесения данных по каждому показателю.
.3.3
Заполнение таблиц для каждого показателя.
.3.4
Вычисление среднеарифметического значения в подгруппе по формуле 8.1.

, (8.1)
где
n - количество значений в подгруппе;- индекс подгруппы;- индекс измеренного
показателя качества в подгруппе.
.3.5
Вычисление размаха показателя качества в подгруппе по формуле 8.2.

, (8.2)
где
Хmax - максимальное значение в подгруппе;
Хmin
- минимальное значение в подгруппе.
.3.6
Вычисление среднеарифметических средних и размахов подгрупп по формулам,
соответственно, (8.3) и (8.4).
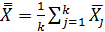
, (8.3)
где
k - количество подгрупп.
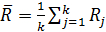
(8.4)
.3.7
Вычисление контрольных границ для каждого показателя. В таблице 1 приведены
формулы расчёта контрольных границ.
Таблица
1 - Формулы контрольных границ для 
-R -
контрольной карты
Статистика
|
Центральная линия
|
UCL и LCL
|
Индивидуальное значение X
|
|
 ± А2·
|
Скользящий размах
|
|
D3·R, D4·R
|
Примечание: значение
коэффициентов А2, D3, D4 определяются по
ГОСТ Р 50779.42-99
|
8.3.8
Нанесение 2 вертикальных осей. Оси наносятся в левой стороне листа. Оси
рекомендуется располагать одну под другой и использовать верхнюю для построения
графика значений 
, а
нижнюю для построения графика значений R.
.3.9
Нанесение горизонтальных осей. Горизонтальные оси разбиваются на интервалы,
представляющие собой подгруппы.
.3.10
Нанесение на карту вычисленных в п.8.3.7 центральных линий, нижних и верхних
контрольных пределов.
.3.11
Нанесение точек контролируемых параметров показателя качества в соответствии с
получаемыми данными (пример 
-R
представлен в приложении Д).
.3.12
Проведение анализа контрольной карты.
Приложение
Б
Пример
результатов регистрации данных по типам дефектов для построения диаграммы
Парето.
Таблица
Б1 - Результаты регистрации данных
Типы дефектов
|
Число дефектов
|
Накопленная сумма числа
дефектов
|
Процент числа дефектов по
каждому признаку к общей сумме
|
Накопленный процент
|
Деформация
|
104
|
104
|
52
|
52
|
Царапины
|
41
|
146
|
21
|
73
|
Раковины
|
20
|
166
|
10
|
83
|
Трещины
|
10
|
176
|
5
|
88
|
Пятна
|
6
|
182
|
3
|
91
|
Разрыв
|
4
|
186
|
2
|
93
|
Прочие
|
14
|
200
|
7
|
100
|
Итого
|
200
|
|
|
|
Приложение В
Пример построения диаграммы Парето.
Рисунок В1 - Диаграмма Парето
Приложение Г
Пример построения причинно-следственной диаграммы
Исикавы.
Рисунок Г1 - Причинно-следственная диаграмма Исикавы
Приложение Д
Пример
построения 
-R -
карты.
Рисунок
Д1 - 
-R-контрольная
карта