Агломерирующий обжиг свинцовых концентратов
Министерство
образования и науки
Государственное
образовательное учреждение высшего профессионального образования
Национальный
Минерально-Сырьевой Университет «Горный»
Курсовая
работа
По
дисциплине: Пирометаллургия
Тема:
Агломерирующий обжиг свинцовых концентратов
Санкт-Петербург
г.
1. Аннотация
В рамках курсовой работы необходимо:
. рассчитать состав шихты, поступающей на
плавку, по заданному содержанию компонентов;
. составить материальный баланс;
. составить тепловой баланс.
. Определить параметры агломашины, в которой
ведется процесс агломерации.
1. Annotation
As part of the course work is
necessary to: 1.calculate the composition of charge entering the melt, for a
given content of the components; 2. Make the material balance; 3. Write the
heat balance. 4. Determine the parameters of sinter, which is the process of
agglomeration. Pages 27, Tables 6, Pictures 4.
2. Краткий
обзор рынка свинца
свинец переработка
обжиг шихта
Мировые запасы свинцово-цинковых руд в основном
сосредоточены в шести странах. В частности запас Китая составляют 15,3% ,
Австралии-29,3%, США-10%,Перу-8% и Мексики - 6% мировых запасов. Запасы России
на январь 2010 года составили около 1,2% мировых.
В течение первого квартала 2010 года на LME
наблюдалось снижение цен на цветные металлы. Причиной этому послужило ухудшение
статистических данных о положении в ключевых экономиках, событиями в Греции,
ослабившими деловой настрой в Европе и курс евро, а также увеличение складских
запасов свинца на LME до 190125 т на 25.05.2010. Начиная с 25 августа
наблюдается рост цен на свинец в связи с тем, что мировой избыток
рафинированного свинца уменьшился до 49 тыс. тонн. Согласно подсчетам объем
производства свинца в мире выросли на 3,7%, а потребление поднялось на 3,8%.
Рис. 1 - Цены LME на свинец в период 9 августа -
2 ноября 2010
Мировой рынок свинца делит между собой
достаточно большое количество относительно мелких компаний. При этом, на долю
рафинированного свинца из добываемых руд приходится всего 45% мирового
производства. Остальной объем составляет, так называемый, вторичный свинец,
полученный благодаря налаженной во многих странах переработке свинцовых
отходов.
Рост спроса на свинец произошел, в основном,
благодаря увеличению его потребления в Китае из-за прогнозируемого увеличения
производства аккумуляторов для автомобилей и мототехники.
Постепенное восстановление
автомобилестроительной отрасли в мире также позволяет производителям строить
оптимистичные прогнозы относительно спроса на аккумуляторный металл. Канадский
производитель свинца Ivernia Inc возобновил добычу руды на ранее закрытой из-за
массового отравления птиц шахте «Magellan» (Западная Австралия) и до конца 2010
года планирует достичь объема в 60 тыс. т свинца.
Китайские компании готовятся в полной мере
обеспечить сырьем рост отечественного автопрома. Jiangxi Copper в 2011 году
запустит первую фазу проекта по производству свинца и цинка, на начальном этапе
выпуск составит 100 тыс. т. Yuguang Lead с австралийской Kimberly Metals
планируют совместно разрабатывать одно из крупнейший неразведанных свинцовых
месторождений в мире - Sorby Hills (Австралия).
В американской компании Doe Run ожидают, что
роста спроса на свинец на мировом рынке в 2011 г. будет происходить с темпом, аналогично
в нынешнем году, - 5-6%.
«Этот год стал большим для потребления свинца,
мы увидели его увеличение на 5-6% по сравнению с 2009 г. и возможно аналогичный
темп роста сохранится в 2011 г.», - отметил Хосе Хансен (Jose Hansen),
вице-президент Doe Run по коммерческой деятельности.
Он также прогнозирует расширение спроса на
свинец в Китае, в основном за счет увеличение производства автомобилей, но и
видит потенциал в ветровой и солнечной энергетике.Run является второй по
величине компанией по добыче свинца на Западе (после BHP Billiton) и третьей -
по выпуску рафинированного металла.
3. Технологическая схема переработки
сульфидных свинцовых концентратов
Основным способом переработки свинецсодержащего
сырья является двухступенчатая технология(см.рис 2), согласно которой
сульфидный свинцовый концентрат сначала подвергают окислительному обжигу для
перевода PbS в форму PbO по реакции
2PbS + 3O2 = 2PbO + 2SO2 + 828,7 кДж;
(1)
PbS + 2O2 = PbSO4 + 820,8 кДж; (2)
оставшийся неокисленным сульфид свинца затем взаимодействует
с оксидом или сульфатом свинца с образованием свободного металла:
PbS + 2PbO 3Pb + SO2 - 238,9 кДж;
(3)+ PbSO4 2Pb + 2SO2 - 427,6кДж.
(4)
и получения спеченного продукта обжига
(агломерата).
Затем шихту, состоящую из смеси агломерата и
кокса, плавят в шахтной печи, где оксид свинца восстанавливается до металла по
реакциям
PbO + C = Pb + CO - 107,7 кДж;
(2.5)+ CO = Pb + CO2 + 65,9 кДж.
(2.6)
Основным жидким продуктом шахтной плавки, в
который извлекается подавляющее количество свинца, является черновой свинец,
содержащий чаще всего 95-99% этого металла, который направляется на
рафинирование. При рафинировании свинца пирометаллургическим способом примеси
удаляют последовательно по одной или группами в несколько операций.
Рафинирование свинца проводят пирометаллургическим методом с использованием
процесса ликвации, за счет различия в сродстве свинца и примесей к тем или иным
реагентам, добавляемым к свинцу, и за счет других различий свинца и примесей.
Рис. 2
4. Описание процесса агломерирующего
обжига
Поступающие на переработку концентраты содержат
в себе,%: 40…78 свинца, 0,6…13 цинка, 0,1…4 меди, 1,8…15 железа, 14…23 серы,
0,8..4 оксида кремния, 0,3…2 оксида кальция и небольшое количество мышьяка и
сурьмы.
Под обжигом концентратов понимают процесс его
нагрева до такой температуры, при которой жидкая фаза или полностью отсутствует
или проявляется в очень небольшом количестве, а обжигаемый материал
претерпевает те или иные физико-химические превращения, полезные для
последующего металлургического передела. При обжиге концентратов сульфиды
металлов превращаются в оксиды. Получение при обжиге сульфатов металла
нежелательно, так как при последующей плавке они будут восстанавливаться до
сульфидов. Сульфидный свинец переходит в штейн, вследствие чего снижается
извлечение свинца в черновой металл. Часто в концентратах присутствуют в
небольших количествах сурьма и мышьяк, связывающие металлы в сурьмянистые и
мышьяковистые соединения. При обжиге эти соединения также переходят в оксиды.
В процессе агломерирующего обжига вводимые в
шихту флюсы ведут себя следующим образом: в первый момент обжига они
механически разъединяют частицы сульфидов, способствуя их индивидуальному
обжигу. Поглощая избыточную теплоту реакции окисления сульфидов на свой нагрев
или диссоциацию(известняк), они снижают температуру шихты, удерживая ее в
течении долгого времени в неспекшемся состоянии, хорошо проницаемом для дутья.
По мере образования оксида свинца протекают следующие реакции:
PbO+Fe2O3=PbO
e2O3+SiO2=PbO
iO2
Это полезные реакции, снижающие
летучесть оксида свинца. Кроме того, силикат свинца, будучи легкоплавким
соединением, является главным цементирующим агентом обожженной шихты и
способствует её хорошему спеканию. Количество жидкой фазы в шихте, за счет
которой идет окускование материала в процессе обжига составляет 20…25%.
При образовании сульфата свинца
присутствующие флюсы способствуют их разложению:
PbSO4+Fe2O3=PbO
e2O3+SO2+1/2O2
+SiO2=PbO
iO2+SO2+1/2O2
PbSO4+CaO=PbO+CaSO4
Таким образом, при агломерирующем
обжиге протекают два процесса: окисление сульфидов металлов и окускование
окисленного материала.
После обжига шихту, состоящую из
смеси агломерата и кокса, плавят в шахтной печи, где оксид свинца
восстанавливается до металла по реакциям
PbO + C = Pb
+ CO - 107,7 кДж;(2)+
CO = Pb + CO2 + 65,9 кДж.(3)
Основной продукт этого процесса -
черновой свинец, который затем направляется на рафинирование.
Эта технология может быть
использована для переработки любых свинецсодержащих материалов, в том числе
вторичного свинецсодержащего сырья.
5. Оборудование, применяемое при
агломерирующем обжиге
Целью агломерирующего обжига
концентрата является удаление из него серы и получение кускового спеченного
материала - агломерата. В современной практике свинцового производства для
агломерирующего обжига практически повсеместно используют прямолинейные
спекательные машины.
Спекательная машина представляет
собой бесконечную движущуюся ленту, состоящую из большого числа чугунных или
стальных тележек (паллет) с решетчатым дном, плотно примкнутых друг к другу. На
паллеты загружают ровный слой шихты высотой 100-400 мм (чаще 200-300 мм).
Перфорированное дно паллет позволяет просасывать или продувать воздух и газы
через слой шихты. По верхним рабочим (горизонтальным) направляющим паллеты
движутся под действием приводного механизма. На разгрузочном конце машины
паллеты по изогнутым направляющим переводятся на наклонные направляющие, по
которым они под действием силы тяжести или дополнительным приводом (на больших
машинах) возвращаются к головной части агломашины. Для облегчения сбрасывания
агломерата с паллет на разгрузочном конце машины, в месте перехода паллет с
горизонтальных направляющих на наклонные, предусмотрен разрыв между паллетами,
вследствие чего паллета, подошедшая к месту разгрузки, скатывается по дуговым
направляющим и ударяется о паллету, находящуюся внизу. Во время удара агломерат
отделяется от решетки и попадает на наклонный грохот, над концом которого
установлена зубчатка для дробления больших кусков агломерата.
Для нагрева шихты до температуры
воспламенения служит зажигательный горн, установленный над слоем шихты в
загрузочном конце машины перпендикулярно движению паллет. Раскаленные газы
зажигательного горна просасываются через слой шихты, нагревая его верхнюю часть
до температуры воспламенения. Топливом в зажигательном горне обычно служат
мазут или природный газ, но можно использовать и твердое топливо.
На заводах работают два вида
спекательных машин: с просасыванием воздуха через слой шихты и с подачей дутья
под давлением под колосники паллет. В машинах с просасыванием воздуха через
слой шихты паллеты с зажженной шихтой далее перемещаются над камерами
разрежения. В машинах с дутьем под колосники сначала насыпается тонкий слой
(25-50 мм) шихты, который проходит под зажигательным горном и воспламеняется.
После этого на него насыпается основной слой шихты (150-250 мм) и паллеты с
шихтой далее движутся над дутьевыми камерами. В машинах с просасыванием газов
разгрузочная часть укрыта колпаком. В машинах с дутьем колпаком укрыта вся
часть машины, расположенная над дутьевыми камерами. Из нее эксгаустером
отсасывают реакционные газы.
Рис. 3
Процесс агломерирующего обжига
начинается сразу после воспламенения нагретого до соответствующей температуры
слоя шихты, развиваясь в остальной части слоя шихты за счет тепла, выделяемого
при окислении сульфидов металлов, содержащихся в шихте (рис. 3).
Процесс окисления имеет место в
сравнительно узкой зоне, которая в машинах с просасыванием газов перемещается
сверху вниз, а в машинах с дутьем воздуха - снизу верх. В зоне обжига и
спекания температура достигает максимальных величин (1000-1100 С) и часть шихты
при этом переходит в расплавленное состояние.
Жидкая фаза смачивает
нерасплавившиеся частицы шихты и цементирует их после затвердевания при
снижении температуры в слое шихты. В результате этих процессов и получается
агломерат.
При высоких температурах в зоне
обжига и спекания окисление сульфида свинца идет главным образом по реакции
(1). Образующийся при этом PbO может взаимодействовать с кремнеземом с
образованием силикатов свинца (mPbO nSiO2), которые могут переходить в жидкое
состояние уже при температурах 700-800 С. Глет может взаимодействовать также и
с другими оксидами шихты, например, с Fe2O3 с образованием ферритов (хPbO
yFe2O3).
В небольших количествах может
образоваться и сульфат свинца PbSO4. в некоторой степени имеют место также
реакции (3) и (4). Таким образом, в агломерате свинец может присутствовать в
виде свободного металла и в виде различных соединений: PbO, mPbO nSiO2, хPbO
уFe2O3, PbSO4, PbS и др.
Другие металлы также будут
находиться в агломерате в виде подобных соединений.
Вертикальная скорость перемещения
зоны нагрева шихты до температуры воспламенения и скорость перемещения зоны
обжига связаны определенной зависимостью.
Нормальное протекание процесса
возможно только в случае, когда первая (v1) равна или несколько больше второй
(v2). На практике часто v1 = 1,5 2 см/мин, а v2 = 1 1,2 см/мин.
Рис. 4
6. Требования, предъявляемые к
агломерату и методы подготовки шихты
Шихта аглообжига состоит из сульфидных свинцовых
концентратов, флюсов и других материалов (полупродукты, оборотные материалы и
пр.). Шихту готовят так, чтобы получить агломерат, удовлетворяющий требованиям
его плавки в шахтной печи. Агломерат должен быть
прочным и пористым;
иметь высокую температуру начала плавления и
небольшой интервал температуры его размягчения;
содержать мало серы (чаще всего 1,1-2,0 %), если
не требуется получать при последующей плавке агломерата в шахтной печи штейн;
по химическому составу соответствовать
требованиям шахтной плавки.
Поскольку флотационные свинцовые концентраты
представляют собой мелкий материал, то флюсы и другие материалы также дробят и
измельчают до крупности 1-6 мм, а оборотный агломерат дробят до крупности менее
6-8 мм.
В современной практике свинцового производства
используют в основном два метода подготовки шихты аглообжига: бункерный и
штабельный. В первом случае в закрытом складе имеется 15-20 (или более)
небольших бункеров емкостью 50-60 м3, в которых содержатся различные материалы.
Материалы из бункеров в нужных пропорциях с помощью питателей подают на сборный
ленточный транспортер.
При штабельном способе на специальных площадках
закрытого склада создается большой запас усредненной проанализированной и
откорректированной шихты. Штабель имеет форму усеченной пирамиды длиной 60-70
м, шириной около 16 м и высотой 5-6 м и содержит 7000-8000 т шихты. При
закладке штабеля отдельные составляющие шихты подаются на площадку штабеля
послойно транспортером. Шихтарник обычно имеет три одинаковых отсека, в одном
из которых идет закладка штабеля шихты, второй заложен и ведется его
опробование, третий вырабатывается специальной шихтопогрузочной машиной.
При любом способе подготовки шихты перед
загрузкой на паллеты агломашины ее хорошо перемешивают и увлажняют. Оптимальная
влажность шихты увеличивается от 4-6 до 10-12 % с уменьшением крупности шихты.
Степень спекания шихты определяется температурой
в зоне обжига и количеством жидкой фазы, образующейся в ней. Температура в зоне
обжига и количество выделяющегося тепла зависит от содержания сульфидов в шихте
и интенсивности протекания окислительных процессов. Если количество сульфидов в
шихте слишком большое и скорость окислительных процессов также весьма велика,
то спекание шихты может произойти задолго до полного окисления сульфидов
металлов и полученный агломерат будет содержать много серы. Следовательно,
необходимо регулировать количество сульфидов (или топлива) в спекаемой шихте, а
также условия их горения.
Смесь свинцовых концентратов и флюсов обычно
содержит 11-13 % серы, иногда больше. Практика показала, что из такой шихты
невозможно сразу получить агломерат с содержанием серы ниже 4 %, что является
недостаточным по условиям плавки продукта обжига в шахтной печи. Существует два
варианта решения этой проблемы: вести обжиг в две стадии или добавить в шихту материалы
с низким содержанием серы.
По двухступенчатой технологии шихту сначала
быстро обжигают на агломашине для предварительного удаления части серы.
полученный агломерат имеет низкое качество и содержит 5-7 % серы. Этого
достаточно, чтобы провести второй обжиг и получить агломерат хорошего качества.
Продукт первого обжига перед подачей на второй обжиг дробят и увлажняют.
При одноступенчатом обжиге для снижения
содержания серы в первичной шихте до 6-7 % к ней добавляют необходимое
количество оборотного агломерата, полученного в этом же процессе. Оборотный
агломерат предварительно дробят. На практике преимущественно используют
одноступенчатую технологию для аглообжига сульфидных свинцовых концентратов.
Для того чтобы агломерат получился не слишком
легкоплавкий, содержание свинца в шихте обычно поддерживают не выше 45-50 %.
В настоящее время на свинцовых заводах
используют агломашины с площадью спекания 20-162 м2 и шириной слоя шихты 1-3 м.
Удельная производительность по шихте на единицу площади спекания составляет
20-30 т/(м2сут). В зависимости от содержания серы в перерабатываемых
свинцовых концентратах производительность агломашин по годному агломерату,
поступающему в шахтную плавку, составляет 5-22 т/(м2сут).
Обжиговые газы, которые получаются в головной
части агломашины, могут содержать до 10-11 % SO2, тогда как газы, получаемые в
разгрузочном конце машины, содержат не более 0,5-1 % SO2. Чтобы использовать
газы аглообжига для производства серной кислоты отбирают часть наиболее богатых
газов, что позволяет извлекать от всех газов аглообжига 60-75 % серы в виде
серной кислоты. Возможна также организация рециркуляции бедных газов путем
подачи их в головную часть агломашины. В этом случае степень извлечения серы из
газов может достигать 85-90 %.
7. Расчет материального баланса
Предположим, что агломерирующему обжигу
подвергается концентрат следующего состава:
Таблица 1 - Состав концентрата
Компонент
|
Содержание,%
|
Pb
|
38,6
|
Zn
|
10,7
|
Fe
|
10,6
|
S
|
23,0
|
SiO2
|
4,9
|
CaO
|
1,6
|
Al2O3
|
4,2
|
Прочее
|
6,4
|
При агломерирующем обжиге свинцовых концентратов
на большинстве заводов получают самоплавкий агломерат, то есть при расчете
шихты предусматривается добавка флюсов в таком количестве, чтобы при
последующей плавке получить шлак выбранного состава.
Расчет ведем на 100 кг концентрата
Предварительно подсчитаем состав шлака при
условии самоплавкого концентрата, то есть при плавке без флюсов. В шлак
перейдут:
(в пересчете на FeO)
,8 Fe - 71,8 FeО
,6 Fe - х
х=13,6 кг;(в пересчете на ZnО)
,4 Zn -81,4 ZnО
,7 Zn-х
х=13,3 кг
и полностью SiO2, CaO и Al2O3.
Принимая сумму FeO,ZnO, SiO2, CaO за 90% как
основных шлакообразующих, составляем таблицу состава при плавке концентрата без
флюсов:
Таблица 2 - Состав шлака при безфлюсовой плавке
концентрата
Компонент
|
Состав
шлака
|
|
кг
|
%
|
SiO2
|
4,9
|
13,5
|
CaO
|
1,6
|
4,3
|
FeO
|
13,6
|
36,6
|
ZnО
|
13,3
|
35,6
|
Итого
|
33,4
|
Самоплавкость концентрата проверим по правилу
Нортона:
Из данных таблицы следует, что
концентрат не самоплавкий и при его переработке для растворения в шлаке всего
образующегося оксида цинка необходимо расходовать все три флюса: кварц,
известняк и железную руду.
Примем в расчете, что шлак будет
получаться с содержанием 22% ZnO. По ошлакованному оксиду цинка подсчитаем
выход шлака:
,3 ZnO - 22%
х -100%; х=60,5 кг
Соотношение между главными
шлакообразующими компонентами при содержании 22% ZnO в шлаке принимаем в
соответствии с условием на самоплавкость: 20% СаО и 40% FeO.
В 60,5 шлака будет содержаться, кг:
-

За вычетом приходящих из концентрата
в шлак требуется добавить с флюсами, кг:
SiO2-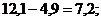

Флюсы имеют следующий состав, %:
кварц 97,0 SiO2;
известняк 1,4 SiO2 и 52,4 СаО;
железная руда 13,0 SiO2; 67,0 FeO и
2,9 СаО
Обозначим количество добавляемых
флюсов так: х - кварца, у -известняка и z-железной руды. Составим таблицу
шлакообразователей, пользуясь которой, можно написать следующие уравнения:
Решая систему этих уравнений, находим
х=5,2кг,у=5,2кг,z=15,8 кг.
Таблица 3 - Шлакообразователи
Материал
|
Масса,
кг
|
SiO2
|
FeO
|
СаО
|
|
|
%
|
кг
|
%
|
кг
|
%
|
кг
|
Кварц
|
х
|
97,0
|
0,97x
|
-
|
-
|
-
|
-
|
Известняк
|
у
|
1,4
|
0,014y
|
-
|
-
|
52,4
|
0,529
|
Железная
руда
|
z
|
13,0
|
0,13z
|
67,0
|
0,67z
|
2,9
|
0,029
|
Таким образом, на 100 кг концентрата необходимо
добавить всего флюсов 26,2 кг. В полученной шихте серы будет
,2 кг - 100%
кг-х, х=18,1%
При одноступенчатом обжиге количество серы в
окончательной шихте будет примерно составлять 7%. Разбавлять серу шихты
необходимо оборотным агломератом, содержащим 1,5% серы.
Обозначив количество оборотного агломерата через
х, находим
7,0 = (100-)
+0,015х
откуда х=66,7 кг, то есть на каждые
33,3 кг шихты потребуется вводить 66,7 кг оборотного агломерата, что от
первоначальной шихты составит:
Количество концентрата в шихте
составит
,2 кг-100 кг
,3 кг-х; х=26,4 кг
Окончательный состав шихты
одноступенчато агломерирующего обжига приведен в таблице
Таблица 4 - Окончательный состав
шихты одноступенчатого агломерирующего обжига
Материал
|
Окончательный
состав шихты
|
%
|
Концентрат
|
100,0
|
26,4
|
Кварц
|
5,2
|
1,4
|
Известняк
|
5,2
|
1,4
|
Железная
руда
|
15,8
|
4,2
|
Оборотный
агломерат
|
252,7
|
66,6
|
Итого
|
378,9
|
100,0
|
8. Тепловой баланс агломерирующего
обжига
Произведем расчет теплового баланса на 100 кг
агломерата.
Высота агломерационного пирога как правило
составляет 200-300 мм. Температура в слое приблизительно равна 1000С.
Приход тепла.
Теплота реакции сгорания части углерода кокса в
CO2 подсчитывается по реакции+ O2 = CO2 + 390500 Дж/моль
выделяется при сгорании 1кг
углерода.
Сгорает 8,32 кг углерода
следовательно выделяется тепла
*8,32 = 270732,8 кДж/кг
Теплота шлакообразования:
При температуре 1000С в шихте
начинается формирование жидкоплавких шлаковых эвтектик:
а) 2CaO +
SiO2 = Ca2SiO4 + 74327Дж/моль
выделяется тепла при образовании
Ca2SiO4 из 2,76 кг CaO
б) 2FeO + SiO2 = Fe2SiO4м + 515,224
кДж/моль
= 515,224кДж/моль
образуется тепла при образовании
Fe2SiO4 из 17,12 кг Fe
в) MgO + SiO2 = MgSiO3 + 196
кДж/моль
=0,987кДж/моль
образуется тепла при образовании
MgSiO3 из 8,0 кг MgO
Всего выделяется тепла при
шлакообразовании 2071кДж.
Вносится воздухом при температуре
t=20 С. Масса воздуха m=287 кг
, средняя теплоемкость воздуха
;
. Физическое тепло, вносимое коксом:
Кокс подается при температуре
tk=20oC. Масса кокса mk=10,62кг
, средняя теплоемкость кокса
;
Физическое тепло руды, вносимой при
20С:
Рассчитываем для 100 кг руды
ш=100 кг
ш=20oCр - средняя теплоемкость руды, рассчитываю по формуле:
CPbO = 46,41
CAl2O3 =
128,84
CSiO2 =
89,97
CCaO =
54,95
O3 = 190,35
CMgO =
52,27
CZnO = 132,04
Тогда средняя теплоемкость руды
будет равна:
Физическое тепло руды:
Приход
тепла
|
Статьи
баланса
|
кДж
|
%
|
Горение
кокса
|
270732,80
|
97,64
|
Шлакообразование
|
2071,00
|
0,74
|
Вносится
воздухом
|
1780,00
|
Физическое
тепло: кокса шихты
|
475,14
2200,00
|
0,17
0,79
|
Всего……………
|
277258,94
|
100
|
Расход тепла.
Тепло агломерата.
Т.к. рассчитанная выше теплоемкость
руды Ср = 1,17
.
Исходя из этого принимаем
теплоемкость агломерата Са =1,9
,
масса полученного агломерата ma =
86,95 кг
температура t =1000C
= 86,95*1,9*1000 = 165300 кДж
Эндотермические реакции.
Разложение известняка:
= CaO + CO2
На образование 1кг CaO расходуется
189400/56,8= 3334,5 кДж, а на 1,38 кг CaO потребуется 1,3*3334,5=4334,85 кДж.
Разложение карбоната магния:
= MgO + CO2
На образование 1 кг MgO расходуется
146105/40,3 = 3625 кДж, а на образование 8 кг MgO потребуется 8*3625 = 29003,5
кДж
. Обезвоживание шихты от физической
и конституционной влаги, которая выходит из гидросиликатов (Ni,Mg)O*nSiO2*mH2O.
Конституционная влага выходит при температуре 700-800С.
MgO*SiO2*H2O
2MgO*SiO2 +
H2O - 56,021 кДж/моль
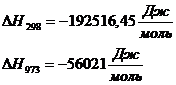
В пересчете на 1 кг MgO
56021/40,3=1390кДж/кг, а на 8кг MgO потребуется
,0*1390 = 11120 кДж.
. Оптимизация вещественного
состояния оксидов Fe: Fe2O3
Будем считать, что 50% Fe2O3
переходит в магнетит, т.е. 11,5 кг Fe2O3.
3Fe2O3 + CO
= 2Fe3O4 + CO2 - 241,384 кДж/моль
В пересчете на Fe2O3 504
Количество тепла, которое пошло на
восстановление 11,5 кг Fe2O3 до магнетита:
*11,5кг = 5797кДж
Найдем количество восстановившегося
магнетита:
3 Fe2O3 -
478,8 2 Fe3O4 - 462,8
,5 X= 11,5*462,8/478,8
= 11,2 кг
Fe3O4
Восстановление магнетита до закиси
железа.
Fe3O4 = 3FeO + 1/2O2 -16910 кДж/моль
В пересчете на Fe3O4 73,05
Количество тепла на восстановление
Fe3O4
,05
*11,2кг = 818,2 кДж
. Тепло, уносимое газами.
Температуру отходящих газов
принимаем в пределах от1000 до1100С.
Тогда унос тепла газами составит
СO2 9,50*0,534*1100 =
5580,30,03*0,540*1100 = 17,82O 32,93*0,418*1100 = 15141,2133,04*0,356*1100 =
12938,46179,5*0,335*1100 = 66145,75
Итого - 99823,54ккал = 23824,2 кДж.
Тепло на испарение влаги.
,52*0,418*1100=7795,8кДж
Расход
тепла
|
Статьи
баланса
|
кДж
|
%
|
Агломерат……...
|
165300,0
|
59,61
|
Эндотермические
реакции………………………
|
4334,8 29003,5
|
1,56 10,46
|
Обезвоживание
шихты………
|
11120,0
|
4,00
|
Оптимизация
вещ. состояния Fe2O3
5797,0 818,2
|
2,09 0,29
|
|
Газы…………………………
|
23824,2
|
8,68
|
Испарение
влаги……………
|
2,81
|
Неучтенные
потери…………
|
29265,4
|
10,50
|
Итого…………..
|
277258,9
|
100
|
Расчет показывает, что на 1 кг агломерата
расходуется 277259 кДж тепла.
9. Расчет печи и газоходной системы
В процессе агломерации шихту с большой скорость
нагревают до температуры размягчения или частичного плавления. Нужное для этого
тепло получают от горения мелкого кокса. Шихта, поступающая на агломашину,
состоит из руды, мелкого кокса и оборотного мелкого агломерата. Работа
спекательной машины оценивается по качеству и количеству получаемого
агломерата.
Производительность спекательной машины (т/сут)
определяется по формуле
= 24*60hbvyk
где Q - производительность машины по шихте,
т/сут- высота слоя шихты, м- ширина паллеты, м- насыпная масса, равная 0,96 -
1,06 т/м3- скорость движения паллет, м/мин
к - коэффициент использования, часы за сутки.
Машина с полезной площадью 50 м2 перерабатывает
в сутки от 1600 до 2000 т шихты.
Скорость движения паллет V определяется в
зависимости от скорости спекания С. Причем время спекания t1 должно
соответствовать нахождения паллет над камерой разряжения t, т.е. t1 = t, где t1
= h: C. Здесь h - высота слоя шихты, равная 250-360 мм; С - скорость спекания
25-35 мм/мин, а t = l: v, где l - длина рабочей части машины - камеры
разрежения, м; v - скорость движения паллеты, м/мин. При t1 = t h: C = l: v
откуда скорость движения паллет v = l* C: h м/мин.
Расчет производительности агломерационной
машины.
Тогда производительность агломерационной машины
в моем примере будет равна
= 2,5 м= 5 м= 1 т/м3= l* C: h , где l = 50 м ; C
= 0,25 м/мин ; h = 2,5 м, значит v = 50*0,25: 2,5 = 5 м/мин
к = 0, 017
Q = 24*60
= 1600 т
шихты за сутки
Оптимальные условия процесса
агломерации зависят от состава шихты и ориентировочно могут быть приняты
следующими:
содержание углерода в шихте 7,5 -
9%, коксика 8 - 10%
влажность шихты 21 - 23 %
содержание возврата в шихте не менее
20%
содержание пыли шахтных печей 15-20%
крупность коксика 3-5 мм, руды 15-20
мм
температура поверхности шихты под
камерой зажигания 1100-1500С
Расход на 1 т агломерата, по данным
комбината «Южуралникель», составляет:
ДАЦ-1 ДАЦ-2
Коксика натурального, кг 155 170,
Коксика условного, кг 121 135,
Природного газа, м3 5,6 5,5,
Электоэнергии, кВт*ч 30 38,
Руды никелевой, т 1,25 1,35.
Выход агломерата от руды и пыли
составляет 75-80%, а только от руды 64-67%.
10. Расчёт газоходной системы
Так как количество отходящих газов
от 100 кг шихты составляет 2550 м3, а производительность печи по шихте 1600
т/сутки, то объёмное количество газов в печи будет
.
Для очистки отходящих газов
предусматриваю установку электрофильтра.
Диаметр поперечного сечения газохода
,
где
- действительная скорость газов в
печи, для рудно - термических электропечей
=2÷3 м/сек, тогда
.
Диаметр устья дымовой трубы
рассчитываю аналогично диаметру газохода, принимая
=6 м/сек,
тогда
.
Высоту дымовой трубы рассчитываю на
основе уравнения Бернулли, исходя из положения, что движение газов в газоходной
системе будет происходить в том случае, если сумма всех потерянных на
преодоление сопротивлений напоров будет компенсирована реальным геометрическим
напором дымовой трубы, тогда высота дымовой трубы рассчитывается по следующему
уравнению:
,
где
- удельный вес наружного воздуха
при температуре 20°С, кг/м3,
=1,2 кг/м3;
- удельный
вес газов в дымовой трубе, кг/м3,при средней температуре;
-
потерянный напор; Н - высота трубы, м;
- скорость движения газов в трубе,
м/с;
- диаметр
устья трубы,
=10,02 м; g
- ускорение свободного падения, g=9,81 м/с2; 0,05 - среднее значение
коэффициента потери напора от трения; 1,3 - коэффициент учитывающий запас тяги
в трубе. Тогда, принимая
=7м/с,
суммарные потери напора как 50% динамического напора отходящих печных газов,
при 300°С =
0,620 кг/м3, получаю следующее уравнение:
Вывод
В данном курсовом проекте был произведен расчет
процесса агломерирующего обжига свинцового концентрата.
. В результате расчета материального баланса мы
определяем состав газов, массу всех газов и массу отдельного компонента. Также
мы видим, что выход полученного агломерата меньше по массе, чем масса
загруженная руда. Это объясняется тем, что в результате процесса агломерации
происходит разложение, например карбонатов, а также выделяется большое
количество газов: СO2, CO, S и др.
. Следует отметить, что приведенные тепловые
балансы являются результирующими и не характеризуют тепловых процессов в
горящем слое. В каждом отдельном слое приход тепла выше вследствие подогрева
воздуха вышележащими слоями, что приводит к повышению температуры в зоне
спекания. Недостаточная регенерация тепла может снизить температуру в горящем
слое и привести к получению агломерата неудовлетворительного качества несмотря
на достаточное количество горючего по тепловому балансу. Поэтому узкая зона
высоких температур, обеспечивающая подогрев дутья и протекание процессов
теплообмена между слоями, является необходимым условием работы при минимальном
расходе горючего.
. Полученные размеры печи и газоходной системы
находятся в пределах размеров соответствующих агрегатов, используемых на
отечественных комбинатах.
Список использованной литературы
3. Орлов
А.К. «Металлургия свинца и цинка» СПб: СПГГИ, 2004.
4. Романтеев
Ю.П., Быстров С.В. «Металлургия свинца и цинка» Лабораторный практикум -
Москва: МИСиС, 2006.
. Орлов
А.К., Коновалов Г.В. «Основы производства и обработки металлов» - СПб:СПГГИ,
2006.
. Уткин
Н.И. «Металлургия цветных металлов» - Москва: Металлургия, 1985.
. Коротич
В.И. «Агломерация рудных материалов» - Екатеринбург: УГТУ, 2003.
. Диомидовский
Д.А. «Металлургические печи», Металлургия, М. 1970 г.
. Н.В.
Гудима «Технологические расчеты в металлургии тяжелых цветных металлов», М.
«Металлургия» 1977г.