Массообменные процессы
Министерство образования и науки
Российской Федерации
ФГБОУ ВПО «Сибирский государственный
технологический университет»
МАССООБМЕННЫЕ ПРОЦЕССЫ
Рекомендовано
редакционно-издательским советом СибГТУ
В качестве
учебного пособия по курсу «Процессы и аппараты химических производств»
Л.И. Ченцова
М.Н.
Шайхутдинова
В.М. Ушанова
Т.В. Борисова
Е.В. Игнатова
В.М. Воронин
Красноярск 2012
Массообменные процессы: Учебное пособие по курсу «Процессы и аппараты
химических производств» Ч.1/ Л.И.Ченцова, и др. Под общ. ред. Левина Б.Д.,-
Красноярск: СибГТУ, 2012. - 208 с.
Учебное пособие предназначено для курсового проектирования студентов
специальностей 240901, 240403, 240201, 240502, 240406, 280201, 050500, 240801,
260601, 200503, 130603, 080502, выполняющих курсовой проект по дисциплине
«Процессы и аппараты химической технологии». В первой части учебного пособия
приведена методика расчета абсорбционных колонн и примеры расчета аппаратов с
различными контактными устройствами. В приложениях приведены таблицы физико-химических
свойств растворов и газов.
Рецензенты: д.т.н., проф. Сибирского государственного аэрокосмического
университета им. академика М.Ф. Решетнева Е.В. Сугак
©ФГБОУ ВПО Сибирский государственный технологический университет, 2012
Оглавление
Введение
Глава 1. Методика расчета процесса физической абсорбции
.1 Материальный баланс процесса абсорбции
.2 Тепловой баланс процесса абсорбции
.3 Определение основных размеров абсорбера
.4 Методы расчета высоты насадки и числа тарелок в абсорбере
.5 Расчет абсорберов с подвижной шаровой насадкой
.6 Расчет распыливающих абсорберов
.7 Расчет газопромывателей
.7.1 Расчеты параметров полых газопромывателей с определением
степени очистки по вероятностному методу
.7.2 Расчеты характеристик пенных пылеуловителей с
провальными, дырчатыми и щелевыми тарелками с определением степени очистки по
вероятностному методу
.7.3 Расчеты аппаратов
.7.4 Расчеты параметров скрубберов Вентури с определением
степени очистки по вероятностному методу
.7.5 Расчеты мокрых скрубберов по энергетическому методу
.7.6 Пенные аппараты
Глава 2. Примеры расчета абсорбционных аппаратов
.1 Расчет насадочного абсорбера
.2 Расчет тарельчатого абсорбера
.3 Расчет струйного абсорбера Вентури
.4 Расчет абсорбционной установки
.4.1 Насадочная колонна
.4.2 Тарельчатая колонна
Библиографический список
Приложения
Введение
Курсовой проект по дисциплине «Процессы и аппараты химических
производств» является заключительной частью курса. Цель курсового
проектирования - закрепить и расширить знания по теоретическому курсу, привить
студентам навыки самостоятельной работы по расчету аппаратов, графическому
оформлению проекта, познакомить со специальной технической литературой,
справочниками, каталогами.
Настоящее учебное пособие предназначено для студентов химико-технологических
специальностей, выполняющих курсовой проект по одному из видов массообменных
процессов, а именно: абсорбции, ректификации или сушке.
Абсорбция находит широкое применение во многих технологических процессах,
а также для очистки отходящих газов химических производств.
Процессы ректификации также являются необходимой стадией многих
технологических процессов.
Для проведения процессов абсорбции и ректификации применяются колонные
аппараты различного типа, отличающиеся один от другого способом контакта фаз и
видом контактного устройства. Целью расчета установок абсорбции и ректификации
является определение основных размеров колонны, ее гидравлического
сопротивления, материальных потоков и расхода тепла.
Сушка является заключительной стадией многих технологических процессов.
Наиболее широко распространен способ конвективной сушки, заключающейся в
подводе тепла к высушиваемому материалу и уносу испаренной из материала влаги с
помощью горячего теплоносителя.
Основным аппаратом установки является сушилка, которая может быть
барабанной, кипящего слоя, аэрофонтанной или пневматической. В зависимости от
физико-химических свойств материала и степени его измельчения выбирается тип
сушилки. Сушилка должна обеспечить максимальный контакт между высушиваемым материалом
и теплоносителем, обладать максимальной пропускной способностью по материалу и
сушильному агенту, иметь минимальное гидравлическое сопротивление.
В учебном пособии изложены общие принципы и методика расчета
абсорбционных и ректификационных колонн, получивших наиболее широкое применение
в промышленности: тарельчатых - с колпачковыми, ситчатыми и клапанными
тарелками, насадочных, скрубберов Вентури.
Даны общие принципы и методика расчета сушилок с псевдоожиженным слоем,
барабанных, аэрофонтанных и пневматических.
Каждый раздел сопровождается примерами расчета установок, а также
методикой расчета вспомогательного оборудования. Приложения к разделам включают
необходимый справочный материал для расчета.
Учебное пособие составлено сотрудниками кафедры Промышленной экологии,
процессов и аппаратов химических производств СибГТУ. Введение и глава 7
составлены проф. Б.Д. Левиным, первый раздел - Л.И. Ченцовой, В.М. Ушановой,
Е.В. Игнатовой, второй раздел - М.Н. Шайхутдиновой, Т.В. Борисовой, третий
раздел - Л.И. Ченцовой, М.Н. Шайхутдиновой, В.М. Ворониным.
Условные обозначения:
G -
массовый расход, кг/с
V -
объемный расход, м3/с
t -
температура, оС
∆P - перепад давления, Па
Y -
концентрация газовой фазы, кмоль/кмоль
X -
концентрация жидкой фазы, кмоль/кмоль
-
концентрация газовой фазы, масс. %
-
концентрация жидкой фазы, масс. %
c -
удельная теплоемкость вещества, Дж/кгК
л - коэффициент теплопроводности, Вт/мК
л - коэффициент трения
I, i - энтальпия пара и жидкости, Дж/кг
r -
удельная теплота парообразования, кДж/кг
с - плотность жидкости, кг/м3
м - динамический коэффициент вязкости, Па с
d -
диаметр трубопровода, м
l -
длина трубы, м
W -
количество испаряемой влаги, кг/с
Uн, Uк - начальная и конечная влажность
материала, %
H -
высота массообменного аппарата, м
Н - напор насоса, м
D -
диаметр аппарата, м
Глава 1. Методика расчета процесса физической абсорбции
Абсорбцией называют процесс поглощения растворимого компонента газовой
смеси жидким поглотителем. Абсорбцию применяют в промышленности для получения
готового продукта (производство кислот), разделение газовых смесей (получение
бензола из коксового газа), улавливания вредных (H2S, СО, влаги) и ценных
(рекуперация спиртов и др.) компонентов.
При абсорбции происходит контакт жидкости и газа; при этом масса одного
из компонентов газовой фазы переносится в жидкостную фазу или наоборот
(десорбция). При наличии разности концентраций или парциальных давлений между
фазами (движущая сила процесса) происходит процесс массопередачи, который
прекращается при достижении процесса равновесия.
Механизм процесса переноса массы сводится к молекулярной и турбулентной
диффузии. При молекулярной диффузии, происходящей в неподвижной фазе и
ламинарном потоке, перенос массы характеризуется коэффициентом диффузии D. При
турбулентной диффузии перенос вещества осуществляется движущими частицами среды
и определяется гидродинамическим состоянием потока. Механизм переноса веществ
через границу раздела фаз является кардинальным вопросом теории массопередачи и
окончательно не решен. Предполагая что, диффузионные сопротивления в жидкой и
газообразной фазах обладают свойством аддитивности, можно записать основное
уравнение массопередачи:
, (1.1)
где K - коэффициент массопередачи; F - площадь поверхности
контакта фаз; Dср - средняя
движущая сила процесса; М - количество поглощенного вещества.
Среднюю движущую силу процесса можно выразить через разность парциальных
давлений поглощаемого компонента и его равновесного значения на входе и выходе
из абсорбера Dpср (в мм рт. ст., кгс/см2), разность
молярных составов DХср и DYср (в кмоль на 1 кмоль смеси), разность относительных
молярных составов DXср , DYср (в кмоль на 1 кмоль носителя), разность молярных
концентраций DСср (в кмоль/м3). Так, при выражении
движущей силы через парциальные давления на входе и выходе из абсорбера
Dpвх = pн - p*ниDpвых = pк - p*к, (1.2)
где pн и pк -
парциальное давление поглощаемого компонента в газе на входе и выходе из
абсорбера; p*н и p*к -
равновесное давление поглощаемого компонента в жидкости на входе и выходе в
абсорбер.
Среднее значение движущей силы определяется либо как среднее
арифметическое, либо как среднее логарифмическое по аналогии с теплопередачей.
Коэффициент массопередачи (абсорбции) определяют в зависимости от способа
выражения движущей силы процесса. Если движущую силу выражают через
концентрации в газовой фазе, то уравнение для расчета K имеет вид
. (1.3)
Коэффициент массопередачи, отнесенный к концентрации жидкости, определяют
из соотношения
.(1.4)
В этих выражениях by и bx -
коэффициенты массоотдачи, которые характеризуют количество вещества,
переносимого внутри фазы в единицу времени через единицу поверхности при
движущей силе, равной единице; m - константа фазового равновесия,
определяемая как тангенс угла наклона линии равновесия (с учетом масштаба
диаграммы) к оси абсцисс.
Коэффициенты массоотдачи определяют из критериальных уравнений,
приводимых в литературе, для различных случаев абсорбции.
Процесс абсорбции идет до состояния равновесия, характеризуемого
равновесным распределением растворимого газа между инертным газом (носителем) и
жидкостью, и выражается законом Генри. Константу фазового равновесия m
выражают в зависимости от принятых единиц концентрации. Значения константы m
приведены в справочной литературе (константа Генри). Для пересчета размерности
констант используют специальные формулы.
Принципиальная схема абсорбционной установки представлена на рисунке 1.1.
Расчет любого по конструкции абсорбционного аппарата состоит из трех
основных стадий:
1. на основании заданных и равновесных
концентраций для рассчитываемой системы газ-жидкость определяется количество абсорбента,
необходимого для поглощения заданного количества газа;
2. при известных предельных нагрузках по
газу и жидкости находят площадь поперечного сечения колонны;
3. на основании уравнений кинетики
процесса, данных равновесия и материального баланса определяется поверхность
межфазного контакта фаз или эквивалентные ей величины - высота насадки или
число тарелок.
1 - вентилятор (газодувка); 2 - абсорбер; 3 - брызгоотбойник; 4, 6 -
оросители; 5 - холодильник; 7 - десорбер; 8 - куб десорбера; 9, 13 - емкости
для абсорбента; 10, 12 - насосы; 11 - теплообменник - рекуператор
Рисунок 1.1 - Принципиальная схема абсорбционной установки
Данные по растворимости газа некоторых систем газ - жидкость,
использующиеся для построения линии равновесия, приведены в Приложении А 1.
1.1 Материальный
баланс процесса абсорбции
Если принять, что расход инертной части газовой фазы по высоте аппарата
не изменяется, а также в ходе процесса температура газовой и жидкой фаз
остаются постоянными, то минимальный расход абсорбента Lmin может быть определен из уравнения
материального баланса по формуле (1.5), в кмоль / с
G0 (Yн - Yк) = Lmin (Xк* - Xн),(1.5)
где Xк* - равновесное содержание поглощаемого компонента в
жидкой фазе, относительно газа, Yн,
поступающего в аппарат, выраженного в относительных мольных концентрациях; G0 - расход инертного газа (воздуха), кмоль/с.
Таблица перевода концентраций из мольных и массовых в относительные
приведена в Приложении А 2.
.(1.6)
Минимальный удельный расход абсорбента lmin (кмоль жидкости / кмоль газа)
находится из уравнения
. (1.7)
Фактический удельный расход абсорбента l больше минимального и определяется из соотношения
l = e × lmin , (1.8)
где e -
коэффициент избытка поглотителя.
Величина коэффициента избытка поглотителя зависит от требований
технологии и изменяется в пределах от 1,1 до 2,0. Как правило, для тарельчатых
аппаратов e =
1,1 - 1,4; для насадочных аппаратов e = 1,4 - 2,0. Выбор величин e, а, следовательно, l, должен соответствовать оптимальным
технико-экономическим условиям работы абсорбера и находится
технико-экономическим расчетом.
Общий расход абсорбента L,
кмоль/с, находится как произведение удельного расхода на количество инертной
фазы
L = l
× G0. (1.9)
Равновесная концентрация поглощаемого компонента Xк* может быть определена по рисунку 1.2, на пересечении
Yн с линией равновесия, построенного по данным
растворимости его из соотношения
Y* =
× x = m X. (1.10)
Выразим
Y* в
относительных мольных концентрациях
.(1.11)
Равновесную
конечную концентрацию Xк*
можно также рассчитать по уравнению
.(1.12)
Концентрация
поглощаемого компонента в уходящей из абсорбера жидкости Xк
определяется
из уравнения
. (1.13)
Уравнение 1.13 является уравнением рабочей линии процесса и координата Y - X представляет прямую линию АВ, тангенс угла наклона
которой к оси Х равен удельному расходу жидкости l (рисунок 1.2).
Рисунок 1.2 - Рабочая линия абсорбции
Из уравнения материального баланса определяют количество поглощенного
компонента Ма, кмоль/с
Ма = G0 × (Yн - Yк) = L × (Xк - Xн). (1.14)
1.2 Тепловой
баланс процесса абсорбции
При растворении газа (при хемосорбции) в жидкости выделяется большое
количество тепла. При отсутствии отвода тепла температура жидкости повышается,
что ведет к возрастанию равновесного парциального давления компонента,
изменению линии равновесия, уменьшению движущей силы процесса, ухудшению
условий процесса.
Количество тепла Q,
кДж/с, выделившееся при абсорбции, равно
Q = M
× Ф = Ф × L × (Xк - Xн), (1.15)
гдеФ - дифференциальная теплота растворения, кДж/кмоль.
Дифференциальные теплоты растворения некоторых газов приведены в [9].
Если абсорбция ведется без отвода тепла, то вся выделившаяся теплота идет
на согревание жидкости
Q = L
× С × (t2 - t1), (1.16)
где C - теплоемкость жидкости, кДж/кмоль.
Из уравнения теплового баланса абсорбера, работающего без отвода тепла,
определяют температуру жидкости на выходе из абсорбера
Q = Ф × L × (X2 - X1) = L × С × (t2 - t1), (1.17)
тогда
t2 = t1
+
× (X2 - X1). (1.18)
Отвод тепла при абсорбции предусмотрен, если температура жидкости
повышается больше чем на 10oС.
Тогда, в тарельчатых абсорберах на тарелках укладываются змеевики, охлаждаемые
водой. Расход воды на охлаждение определяется решением теплового баланса.
Отвод тепла, выделяющегося при абсорбции в насадочных аппаратах,
производится рециркуляцией жидкости, рисунок 1.3.
Насыщенный раствор, выходящий из абсорбера, частично насосом 2
перекачивается через холодильник 3 и возвращается в процесс, оставшаяся часть -
выводится из системы.
Чтобы компенсировать поток абсорбента, выводимый из системы, на абсорбцию
непрерывно подается свежий поглотитель, в количестве Lо.
Кратность циркуляции n = L1 / L0 представляет собой отношение количества абсорбента,
протекающего через абсорбер L1 к количеству
свежего абсорбента.
1 - абсорбер; 2 - насос; 3 - холодильник
Рисунок 1.3 - Абсорбционная установка с рециркуляцией поглотителя
Кратность циркуляции определяют решением уравнения теплового баланса, при
этом задаются температурой абсорбента (жидкости) на выходе из аппарата t2:
G0 × Ф × (Yн - Yк) = L2 × С2 × t2 - L1 × С1 × t1,(1.19)
гдеФ - дифференциальная теплота растворения, кДж/кмоль;
C1, С2 - теплоемкость поступающей и выходящей
из колонны жидкости, кДж/кмоль.
Уравнение (1.19) решается совместно с уравнением материального баланса L2 = L1 + L.
Концентрацию
жидкости Xн
, поступающей на абсорбцию, определяют по уравнению
Yн - Yк = l × (Xк - X0) = n × l × (Xк - Xн ),(1.20)
.(1.21)
1.3
Определение основных размеров абсорбера
Технологический расчет абсорбционных аппаратов позволяет определить их
основные размеры - диаметр и рабочую высоту. Расчет диаметра и рабочей высоты
зависит от внутреннего устройства аппарата.
Определение диаметра абсорбера
Величина поперечного сечения аппарата, м2, определяется расходом газовой
фазы и допустимой скоростью
, (1.22)
где Vсек - объемный секундный расход газовой фазы, приведенной
к рабочим условиям, м3/с;
w0 - фиктивная
скорость газа, отнесенная к полному сечению аппарата, м/с.
Объемный расход (м3/с), приведенный к рабочим условиям, определяется по
формуле
(1.23)
где Gг - расход газа, кг / с;
T0, T - нормальная и рабочая температура
газа, К;
r0, rг - плотность газа при нормальных и рабочих условиях,
кг/м3.
Значение w0 для насадочных
абсорберов принимается равным
(0,75-0,9), от предельно допустимой скорости wп , и определяемой по формуле
,(1.24)
где wп - предельная скорость газа (пара) в режиме
эмульгирования, отнесенная к полному сечению абсорбера, м / с;
ry и rx
- плотности газа и жидкости, кг/м3;
L
и G - массовые расходы жидкости и газа, кг/с;
а
- удельная поверхность насадки, м2 / м3;
А и В - коэффициенты, зависящие от типа насадки, таблица 1.1;
mх, mв - вязкость, соответственно, поглотителя при
температуре в абсорбере и воды при 20оС, Па×с;
Vсв - свободный
объем насадки, м3/м3;
g
- ускорение свободного падения, м/с2.
Характеристики насадок а и Vсв приведены в Приложении А3.
Таблица 1.1 - Значения коэффициентов А и В
Тип насадки
|
А
|
В
|
Трубчатая
|
0,47 +1,5
lg (dэ / 0,025)
|
1,75
|
Плоскопараллельная хордовая
|
0
|
1,75
|
Пакетная
|
0,062
|
1,55
|
Кольца Рашига внавал
|
- 0,073
|
1,75
|
Кольца Палля
|
- 0,49
|
1,04
|
Седла размером 25 мм
|
- 0,33
|
1,04
|
Седла размером 50 мм
|
- 0,58
|
1,04
|
Кроме того, для определения скорости w0 в насадочных абсорберах может быть использовано
уравнение
Rey =
0,045 Ar0,57
. (1.25)
Через Rey определяют w0
w0 =
, (1.26)
где rу, mу
- плотность и вязкость газа при рабочих условиях.
Критерий Архимеда определяют по уравнению
, (1.27)
где rx
- плотность жидкости при рабочих условиях, кг/м3;
dэ -
эквивалентный диаметр насадки, зависящий от характеристики насадки
dэ =
, (1.28)
где w0, найденная по этому методу, составляет 80 % от
wп.
Диаметр колонны, м, определяется по формуле
. (1.29)
Затем выбирается стандартный диаметр абсорбера и уточняется скорость газа
. (1.30)
Ниже приведены нормальные ряды диаметром колонн (в м), принятые в
химической и нефтеперерабатывающей промышленности
в химической промышленности - 0,4; 0,5; 0,6; 0,8; 1,0; 1,2; 1,4; 1,6;
1,8; 2,2; 2,6; 3,0; в нефтеперерабатывающей промышленности - 1,0; 1,2; 1,4;
1,6; 1,8; 2,0; 2,2; 2,4; 2,6; 2,8; 3,0; 3,2; 3,4; 3,6; 3,8; 4,0; 4,5; 5,0; 5,5;
6,0; 6,4; 7,0; 8,0; 9,0.
Определение плотности орошения
Для обычных насадочных колонн после определения диаметра абсорбера
необходимо рассчитать действительную плотность орошения U, которая должна быть не менее Uопт
U =
³
Uопт = в × а, (1.31)
где в - коэффициент; при абсорбции аммиака водой
в =
4,38×10-5 м3/м2 с, при абсорбции паров органических жидкостей
в
= 2,58×10-5 м3/м2 с; а - удельная поверхность насадки, м2/м3.
Если плотность орошения U меньше
оптимальной плотности орошения Uопт,
меньше единицы - насадка не полностью смочена. Это учитывается коэффициентом
смоченности насадки y, определяемым
по рисунку 1.4 y
не должен быть меньше 0,8 - 0,9.
Для увеличения плотности орошения следует применять насадку с меньшей
удельной поверхностью, чтобы снизить Uопт. Максимальное смачивание насадки достигается при (U / Uопт) > 1, тогда y
= 1. Для равномерного смачивания насадки должно соблюдаться следующее
соотношение диаметра колонны Dк и диаметра
насадки dн.
≥
8. (1.32)
Скорость газа и диаметр тарельчатого абсорбера
В колоннах с колпачковыми тарелками имеет место пузырьковый режим работы,
при этом скорость газа £ 0,5 м/с. В колоннах с ситчатыми тарелками скорость газа £ 1 м/с, при этом возникает пенный
режим работы тарелки.
1 - кольца Рашига; 2 - хордовая насадка
Рисунок 1.4 - Коэффициент смачиваемости y при различном отношении U/Uопт
Режим газовых струй возникает при скорости газа больше 1 м/с, в этом
режиме работают специальным образом сконструированные тарелки - пластинчатые.
Скорость газа должна быть ниже некоторого предельного значения wп, при котором начинается брызгоунос
w=(0,75¸0,9)× wп. (1.33)
Значение wп приближенно можно определить по
рисунку 1.5 для тарелок с круглыми колпачками. Для тарелок других конструкций
значения предельной скорости wп, найденные
по графику, следует умножить на поправочный коэффициент.
Допустимую оптимальную скорость газа (пара) в колонне (м/с) определяют по
формуле
, (1.34)
где С - коэффициент, зависящий от конструкции тарелки и расстояний
между ними, принимается по рисунку 1.7.
При выборе коэффициента С ориентировочное значение расстояния
между тарелками принимают для колпачковых 200-300 мм, для ситчатых 300-400 мм.
Рисунок 1.5 - Определение предельной скорости газа в свободном сечении
абсорбера при различном расстоянии между тарелками
Тарелки
|
Коэффициент
|
С прямоугольными колпачками
|
0,7
|
Ситчатые
|
1,35
|
Провальные
|
1,5
|
Для клапанных тарелок скорость газа определяют из равенства
, (1.35)
где G - масса клапана, кг;
S0 -
площадь отверстия под клапаном, м2;
о - коэффициент сопротивления, равный 3.
По ГОСТ 16452-79 диаметр отверстия под клапаном равен 40 мм, масса
клапана 0,04 кг.
Затем проверяют минимально допустимое расстояние между тарелками,
обеспечивающее работу гидравлического затвора на тарелке. Минимальное
расстояние между тарелками со сливными устройствами определяют по формуле
, (1.36)
где DР - гидравлическое сопротивление
орошаемой тарелки, Па;
rx - плотность жидкости, кг/м3.
Задаваясь расстояниями между тарелками Нт и определив диаметр колонны Dк по
формуле (1.29) в зависимости от rу/rx значения wп
и wотп, проверяют соответствие расстояния
между тарелками Нт диаметру колонны Dк.
Dк, м
|
< 0,6
|
0,6 - 1,2
|
1,2 - 1,8
|
1,8 и более
|
Нт, м
|
0,16
|
0,3
|
0,46
|
0,6 и более
|
Если полученному значению Dк
не соответствует Нт, его принимают согласно рекомендациям и повторяют
расчет.
Предельные нагрузки по пару в тарельчатых колоннах, работающих при
атмосферном давлении или под вакуумом, в зависимости от расстояния между
тарелками, определяют по рисунку 1.6.
Минимальное расстояние между тарелками Hmin должно обеспечить работу
гидравлического затвора на тарелке. Для тарелок со сливными устройствами Нmin определяется как
Нmin >
. (1.37)
Рисунок 1.6 - Определение предельных нагрузок по пару в тарельчатых
колоннах, работающих при атмосферном давлении или под вакуумом
Для колпачковой тарелки
Нmin =
23300
,
(1.38)
где F - поперечное сечение колонны, м2;
w - скорость
газа в колонне, м / с;
dк - диаметр
колпачка, м;
n - число
колпачков на тарелке.
Принятая величина Нт должна быть равна Нmin или больше.
Рисунок 1.7 - Зависимость коэффициента С от расстояния Н между тарелками
Оптимальная скорость газа в тарельчатых аппаратах составляет 80% от
предельно допустимой, которая находится для колпачковых тарелок по формуле
, (1.39)
где dк - диаметр колпачка, м;
Нт - расстояние
между тарелками, м;
hк - высота колпачка, м.
Для колонн с ситчатыми тарелками предельная скорость газа определяется по
формуле
wп = 0,05
. (1.40)
Для колонн с провальными тарелками предельные скорости определяются по
формуле
wп =
. (1.41)
Величины А и С находятся по следующим зависимостям
lg А = lg В - 1,73
; (1.42)
С
=
, (1.43)
где В - коэффициент (для колонн с решетчатыми, трубчатыми и
дырчатыми провальными тарелками В = 3¸16);
wх , wу - массовые скорости жидкости и газа, кг / м2 ∙с;
dэ - эквивалентный диаметр отверстия или
щели в тарелке, м;
Sс - относительное свободное сечение
тарелки;
mх , mв - вязкость поглотителя и воды при 20oС, Па∙с.
Верхний предел скорости газа wmax определяется по формуле 1.35 при В=16, а нижний предел
скорости wmin при В=3.
Скорость газа в интервале устойчивой работы провальных тарелок может быть
определена с помощью уравнения
Y = В е - 4х .(1.44)
Здесь
Y =
, (1.45)
Х
=
, (1.46)
где w - скорость газа в колонне, м / с;
dэ - эквивалентный диаметр отверстия или
щели в тарелке, м;
Fс - доля свободного сечения тарелки, м2 / м2;
mх, mу - вязкость жидкости и газа при температуре абсорбции, Па∙с.
При нормальной работе тарелки коэффициент В=2,93 - для нижнего
предела и В=10 -для верхнего предела. Для оптимальной работы тарелки
принимают В=6¸8. Принимают стандартный диаметр колонны и уточняют скорость газа в
абсорбере.
1.4 Методы
расчета высоты насадки и числа тарелок в абсорбере
В инженерной практике наиболее часто применяются три метода расчета
процессов абсорбции.
По первому методу кинетика процесса выражается через коэффициенты
массопередачи, а движущая сила рассчитывается по разности концентраций или,
косвенно, с помощью числа единиц переноса.
По второму методу кинетика выражается с помощью высоты единиц переноса -
ВЕП (для насадочных колонн) или числа единиц переноса - ЧЕП, соответствующего
одной тарелке (тарельчатых колонн), а движущая сила рассчитывается через число
единиц переноса.
По третьему методу кинетика выражается с помощью высоты, эквивалентной
теоретической ступени изменения концентрации, - ВЭТС (для насадочных колонн)
или КПД тарелки (для тарельчатых колонн); движущая сила рассчитывается косвенно
через число теоретических ступеней изменения концентрации или теоретических
тарелок.
В соответствии с вышеизложенными методами расчета процесса абсорбции
определяется высота насадочных и тарельчатых колонн.
В основе расчета процесса абсорбции лежит основное уравнение
массопередачи (1.1).
В зависимости от способов выражения кинетики процесса, движущей силы и
вида контактных устройств уравнение (1.1) преобразуется в различные
соотношения, используемые в расчете насадочных и тарельчатых абсорберов.
Расчет насадочных абсорберов
По первому методу расчет насадочных абсорберов ведется в следующем порядке.
Если рабочая и равновесная линия прямые (рисунок 1.8), то высота насадки Ннас
определяется по следующим формулам.
1 - равновесная линия; 2 - рабочая линия
Рисунок 1.8 - Определение средней движущей силы процесса абсорбции
Для легко растворимых газов
Ннас =
. (1.47)
Для трудно растворимых газов
Ннас
=
, (1.48)
где МА - количество поглощенного компонента, кмоль/с, кг/с;
КYV, КХV - объемные
коэффициенты массопередачи, отнесенные к газовой и жидкой фазам, (
), (
);
F - поверхность контакта фаз;
DYср, DХср -
средние логарифмические значения движущей силы по газовой и жидкой фазе.
S -
поперечное сечение колонны, м2.
Средняя
движущая сила определяется по формулам:
D
ср =
; (1.49)
D
ср =
, (1.50)
где
- движущие силы массопередачи на концах
аппарата, рисунок 1.9;
- выражены в относительных массовых концентрациях.
Среднюю
движущую силу можно рассчитать аналогично по формулам (1.45) и (1.46), если
известно уравнение линии равновесия или коэффициент распределения m,
рассчитываемый по уравнению (1.10), ХК* - по уравнению (1.12).
Рисунок 1.9 - Схема распределения концентраций в потоке газа и жидкости в
абсорбере
При абсорбции легко растворимых газов, когда сопротивлением жидкой фазы
можно пренебречь, коэффициент массопередачи КYV определяется по уравнению
.(1.51)
При абсорбции трудно растворимых газов можно пренебречь сопротивлением
газовой фазы и рассчитать КХV по уравнению
. (1.52)
В этих формулах:
;
,(1.53)
где dэ - эквивалентный диаметр насадки, м;
dэст - эквивалентный диаметр стандартной
насадки (25´25´3мм),м;
Reу, Reх - режим движения газовой и жидкой фаз;
Рry¢, Рrх¢, - критерий Прандтля для газовой и
жидкой фаз.
;
;(1.54)
;
,(1.55)
где Dу, Dх - коэффициенты диффузии поглощаемого компонента в газе и
жидкости, м2 /с;
mу, mх - вязкость газа и жидкости, Па×с (Приложения А4-А6);
f - фактор гидродинамического состояния
двухфазной системы.
. (1.56)
Коэффициент
А1 определяется по рисунку 1.10, в зависимости от отношения
; wп - предельная скорость газа, определенная ранее по
формуле (1.24), м /с.
Отношение
зависит от гидродинамического состояния системы:
= 1 -
для точки инверсии;
= 0,85 -
для точки подвисания;
= 0,45 -
для точки торможения газа.
Рисунок 1.10 - Зависимость коэффициента А от отношения wy/wп
Для
колонн, работающих в пленочном режиме
= 0,8.
Коэффициенты
диффузии Dу и Dх (м2 /с) определяются по Приложению А7 или по формуле
, (1.57)
где vA и vB - мольные объемы газов А и В, определяемые
как сумма атомных объемов элементов, входящих в состав газов, см3/моль
(Приложение А8);
МА и
МВ - мольные массы газов А и В;
p -
давление (абсолютное) при абсорбции, кгс/см2;
Т
- температура, К.
, (1.58)
где А, В - коэффициенты, зависящие от свойств растворенного
вещества и растворителя. Для газов А=1, для воды В=4,7, для
метанола и этанола В=2, для ацетона В=1,15.
mх - динамический коэффициент вязкости жидкости, мПа·с;
vА
и vВ - мольные объемы растворенного вещества и растворителя;
МА
и МВ - мольные массы растворенного вещества и растворителя.
Для водных растворов Dх (м2 / с)
можно определять по формуле
. (1.59)
В случае, когда на скорости массопередачи оказывает влияние как
сопротивление жидкой так и газовой фазы, для расчета высоты насадки
используются формулы
(1.60)
Или
, (1.61)
где S - поперечное сечение колонны, м2;
a -
удельная поверхность насадки, м2 / м3;
Кy,
Кx -
коэффициенты массопередачи, отнесенные к газовой или жидкой фазе,
;
DYСР, DХСР -
средняя движущая сила по газовой и жидкой фазам.
Коэффициенты
массопередачи определяются по формула(1.3) и (1.4).
Коэффициенты
массоотдачи по газовой фазевy и жидкой фазе вx определяются
по формулам
для
нерегулярных насадок (внавал)
; (1.62)
для регулярных насадок
, (1.63)
где dэ - эквивалентный диаметр насадки, м;
l - высота элемента насадки, м.
Коэффициент массоотдачи в жидкой фазе определяется по уравнению
. (1.64)
В
этих уравнениях
;
;
;
, (1.65)
где U - плотность орошения, м3 / м2· с.
Плотность
орошения U определяется
отношением объемного расхода жидкой фазы V (м3 / с) к
поперечному сечению колонны S (м2);
.
Приведенная
толщина пленки dпр (м) определяется по формуле
. (1.66)
Второй метод расчета заключается в определении числа единиц переноса и
высоты единиц переноса.
При расчете по газовой фазе
Ннас = nOY × hOY .(1.67)
При расчете по жидкой фазе
Ннас = nOХ × hOХ ,(1.68)
где hOY, hOХ - общая высота единиц переноса в газовой и жидкой фазах.
hOY = hY +
; (1.69)
hOХ = hХ
+ (А¢ × hY ),(1.70)
где hY, hХ - высота единиц переноса по газовой и жидкой фазам, м;
А¢ =
- фактор абсорбции.
m
- тангенс угла наклона линии равновесия;
L, G
- массовые расходы жидкости и газа,
кг / с.
Высота
единиц переноса по газовой фазе определяется:
для
неупорядоченно загруженных насадок
hY = 0,615 dэ × (Rey)0,345 × (Pr’y¢)2 / 3; (1.71)
для упорядоченно загруженных насадок
hY = 1,5 dэ × (Rey)0,26 × (Pry¢)2 / 3
, (1.72)
где dэ - эквивалентный диаметр насадки, м;
l - высота элемента насадки, м.
Высота единицы переноса по жидкой фазе определяется по формуле
hХ = 119 dпр × (ReХ)0,25 × (Pr¢Х)0,5. (1.73)
Число единиц переноса nOY, nOХ определяются по формулам
noy =
;nox =
.(1.74)
Эти уравнения решаются методом графического интегрирования. Для этого
строят кривую зависимости подынтегральной функции от аргумента, рисунок 1.11.
Рисунок 1.11 - Определение nOY
методом графического интегрирования
Задаем ряд значений Y в
пределах YН и YК. Число единиц переноса будет равно
площади подынтегральной кривой S, умноженной на масштаб по осям
noy = S· m1 · m2 ,(1.75)
где S- площадь, ограниченная кривой;
m1 - масштаб по оси ординат; m2 - масштаб по оси абсцисс.
Аналогично,
пользуясь графиком зависимости
от X,
определяют nox.
Третий
метод расчета применяется лишь в том
случае, если отсутствуют данные о коэффициентах массопередачи или высоте единиц
переноса, т.е. об истинной кинетике массопередачи в аппаратах данной
конструкции.
Расчетное
уравнение для определения высоты насадки имеет вид
Ннас = hЭКВ × nТ , (1.76)
где hЭКВ - высота, эквивалентная теоретической ступени изменения
концентрации или теоретической тарелке, м;
nТ - число теоретических тарелок.
Высоту насадки hЭ,
эквивалентную одной теоретической тарелке, для точки начала эмульгирования
(точка инверсии) определяют по формуле
, (1.77)
где w0 = (0,75 - 0,9) от wп , определенной по формуле (1.33);
f - фактор гидродинамического состояния двухфазной
системы, определяется по рисунку 1.10, при отношении
или по формуле (1.56);
FС - свободное сечение колонны, FС = 0,785 DК2;
G, L
- массовые расходы жидкости и газа,
кг / с;
m - среднее значение тангенса угла наклона линии
равновесия.
Если
растворимость абсорбируемого газа подчиняется закону Генри и линия равновесия
представляет собой прямую, множитель
принимается
равным единице.
Высота
насадки, эквивалентная одной единице переноса, зависит от характеристики
насадки и фазового состояния
hЭ = hУ
+
hХ,(1.78)
гдеl
- удельный расход поглотителя, l
=
, кг / кг.
Высота
насадки, эквивалентная одной единице переноса для газовой фазы, определяется по
формулам
для
беспорядочных насадок
hY =
0,615 dэ × (Rey)0,345 × (Pry¢)2 / 3; (1.79)
для регулярных насадок
hY
= 1,5 dэ × (Rey)0,26 × (Рry¢)2 / 3
. (1.80)
Величину hY можно также
определить по формуле
, (1.81)
где f - определяется по рисунку 1.10 для точки инверсии;
Y -
коэффициент смоченности насадки, определяемый по рисунку 1.4, в зависимости от
отношения
, определяемых по уравнению 1.31;
a, Vсв - удельная
поверхность и свободный объем насадки.
Высота
насадки, эквивалентная одной единице переноса для жидкой фазы, определяется по
формуле
hХ = 119 dпр × (ReХ)0,25 × (Pr¢Х)0,5 , (1.82)
где
dэ - эквивалентный диаметр насадки, dэ =
, м.
Критерий
Рейнольдса
Reг =
;Reж
=
;(1.83)
Массовые скорости w
(кг / м2)
wг =
;wж
=
.(1.84)
Диффузионный критерий Прандтля
Prг =
; Prж =
, (1.85)
где mг, mж, rг, rж - вязкости и плотности газа и жидкости;
Dг, Dж - коэффициенты диффузии газа и жидкости.
Приведенная толщина пленки определяется по формуле (1.66).
Число теоретических тарелок определяется по графику, рисунок 1.12, путем
вписывания ломаной AFEDCB… между
рабочей и равновесной линиями. Причем величина nт - число ступеней изменения концентрации или число
теоретических тарелок - может не быть целым числом. Рабочая линия и линия
равновесия на диаграмме Y-Х
строятся в относительных концентрациях
Y - (
) или (
);
Х
- (
) или (
).
Рисунок 1.12 - Определение числа ступеней изменения концентрации
графическим методом
Общую высоту насадочной колонны, м, определяют по формуле
Н = Ннас + h1 + h2 + h3 , (1.86)
где Ннас - высота насадочной части колонны, м;
h1 + h2 + h3 - высота, соответственно, сепарационной части колонны
(над насадкой), нижней части колонны, и между слоями насадки.
Отношение
высоты насадки к диаметру колонны должно удовлетворять условию
= от 1,5 до
10.
Расстояние
от верха насадки до конца абсорбера h1 зависит от
распределительного устройства для орошения насадки и от высоты сепарационного
пространства, в котором часто устанавливают каплеотбойники для предотвращения
брызгоуноса (~2 м).
Расстояние
между днищем абсорбера и насадкой h2 определяется
необходимостью равномерного распределения газа по поперечному сечению колонны.
Обычно это расстояние принимается равным (1-1,5)·D.
В
приближенных расчетах высоты h1 и h2 принимают равными 0,6-1,5 м.
Расстояние
между слоями насадки, h3 , зависит
от высоты перераспределительной тарелки и диаметра колонны, принимается
конструктивно.
Высота
слоя насадки между разрывами принимается 3-4 м.
Гидравлическое сопротивление абсорбера
Гидравлическое сопротивление DРа обуславливает энергетические затраты на
транспортировку газового потока через абсорбер.
Величину DРа,
Па, рассчитывают по формуле
DРа = DРс × 10вU, (1.87)
где DРс -
гидравлическое сопротивление сухой, не орошаемой жидкостью, тарелки, Па;
U -
плотность орошения, м3 / (м2·с);
в -
коэффициент, значения которого приведены в таблице 1.2.
Гидравлическое сопротивление сухой насадки DРс, определяют по формуле
DРс = l ×
, (1.88)
где l -
коэффициент сопротивления;
wо =
- скорость газа в свободном сечении насадки, м / с;
Vсв - свободный
объем насадки, м3 / м3.
Таблица 1.2 - Коэффициент В насадок
Насадка
|
В
|
Насадка
|
В
|
Кольца Рашига в укладку
|
|
Кольца Палля (50 мм)
|
126
|
50 мм
|
173
|
Блоки керамические
|
151
|
80 мм
|
144
|
Седла «Инталокс»
|
|
100 мм
|
119
|
25мм
|
33
|
Кольца Рашига внавал
|
|
50 мм
|
28
|
25 мм
|
184
|
Седла Берля (25мм)
|
30
|
50 мм
|
169
|
|
|
Коэффициенты сопротивления беспорядочных седлообразных насадок
рассчитывают по формуле
l =
+ 2,34.(1.89)
Коэффициенты сопротивления беспорядочно насыпанных, внавал, кольцевых
насадок рассчитывают по формулам
при ламинарном движении, Reу < 40
l =
,(1.90)
при турбулентном движении, Reу > 40
l =
.(1.91)
Коэффициент сопротивления регулярных, в укладку, насадок находят по
формуле
l = lтр + о
, (1.92)
где lтр -
коэффициент сопротивления трению;
о
- коэффициент местного сопротивления,
о =
.
Коэффициент
сопротивления для хордовых насадок
.(1.93)
Общее сопротивление абсорбционной установки определяется с учетом
гидравлического сопротивления газопроводов
DР = DРа + DРтр;(1.94)
,(1.95)
где DРтр -
гидравлическое сопротивление газопроводов, Па;
lтр - коэффициент трения в газопроводах;
L, d - длина и
диаметр трубопровода, м;
S о - сумма коэффициентов местного сопротивления;
rу -
плотность газа при средней температуре, кг / м3;
w -
скорость газа в напорных трубопроводах, принимается в пределах от 5 до 20 м /
с.
Расчет тарельчатых абсорберов
Большое разнообразие тарельчатых контактных устройств затрудняет выбор
оптимальной конструкции тарелки. При этом наряду с общими требованиями (высокая
интенсивность единицы объема аппарата, его стоимость) выдвигается ряд
требований, обусловленных спецификой производства: большой интервал устойчивой
работы при изменении нагрузок по фазе, возможность использования тарелок в
среде загрязненной жидкости, возможность защиты от коррозии, отвод тепла и т.д.
Выбор тарелок производится по ГОСТ 21944-76, ГОСТ 9634-81, ГОСТ 12011-76.
Определение числа тарелок и высоты колонны
1. При приближенных расчетах применяют теоретически менее обоснованный,
но более простой метод определения числа тарелок с помощью коэффициента
полезного действия (з) тарелки.
Число действительных тарелок равно
nд =
,(1.96)
где nт - теоретическое число тарелок - ступеней изменения
концентрации, которое находят графическим методом (построением между
равновесной и рабочей линиями на диаграмме Y-Х, как показано на рисунке 1.12). Координаты рабочей линии и
линии равновесия выражены в относительных концентрациях;
з
- коэффициент полезного действия тарелки, зависит от произведения относительной
летучести поглощаемого компонента и вязкости жидкости при температуре
абсорбции. Определяется по рисунку 1.13.
Коэффициент относительной летучести определяется по формуле
,(1.97)
где РА - парциальное давление поглощаемого компонента при
температуре абсорбции;
РВ -
парциальное давление водяных паров при температуре абсорбции;
м - вязкость
поглотителя (воды) при температуре абсорбции.
Рисунок 1.13 - Диаграмма для приближенного определения среднего к.п.д.
тарелок
Рабочая высота абсорбера Нт , м, определяется по формуле
Нт = (nд - 1) hт,(1.98)
где hт - расстояние между тарелками, выбранное ранее при
определении диаметра колонны.
. Действительное число тарелок определяется также графическим методом с
построением кинетической кривой, рисунок 1.14.
1 - линия равновесия; 2 - рабочая линия; 3 - кинетическая линия
Рисунок 1.14 - Определение числа ступеней изменения концентрации
На основании общих положений массопередачи определяют коэффициент
массопередачи по формуле (1.3).
Коэффициенты массоотдачи в газовой и жидкой фазах определяются по
уравнению
а) для колпачковых тарелок
bУ = 4,77 × 10-4 × wг1,32 × DРх;(1.99)
bх = 33,7 × 10-4 × wг0,79 × DРх;(1.100)
б) для ситчатых тарелок
bУ = 3,03 × 10-4 × wг0,76 × DРх;(1.101)
,(1.102)
где
wг - скорость газа, отнесенная к свободному сечению
колонны, м / с;
DРх - гидравлическое сопротивление жидкости на тарелке, Па.
Число единиц переноса одной тарелки
,(1.103)
гдеSт - рабочая площадь тарелки, м2;
Sт = Sкол - 2 Sслива,(1.104)
где Sкол - площадь сечения колонны, м2;
Sслива -
площадь слива, м2;
GИ. Г. - расход
инертного газа (воздуха), кг / с.
Определяем величину Су
.(1.105)
На графике Y-X (рисунок 1.14) наносят кривую
равновесия Y*=f(X) и строят рабочую линию. Затем проводят для
произвольных значений Х ряд прямых, параллельных оси ординат. На линии рабочих
концентраций отмечаем точки А1, А2, А3, А4, на линии равновесия соответственно
точки С1, С2, С3, С4.
Пользуясь
равенствами
находят на отрезках А1С1, А2С2, А3С3, А4С4, точки В1,
В2, В3, В4. Проводя через полученные точки линию, получим вспомогательную
кинетическую кривую.
Из
точки А1 в пределах заданных рабочих концентраций Yн и Yк
между линией рабочих концентраций и вспомогательной кривой строят ломаную
линию. Полученное число ступеней и дает необходимое для заданных условий число
тарелок.
.
Число тарелок можно найти по модифицированному уравнению массопередачи, в
котором коэффициенты массопередачи для газовой КУf
и для жидкой КХf фаз
относят к единице рабочей площади тарелки
М = КУf × F × DУСР = КХf × F × DХСР ,(1.106)
где М - масса передаваемого вещества через поверхность
массопередачи в единицу времени, кг / с;
F - суммарная
рабочая площадь тарелок в абсорбере, м2.
Необходимое число тарелок nд
определяют делением суммарной площади тарелок F на рабочую площадь тарелки Sт;
,(1.107)
где Sт - рабочая площадь тарелки, м2;
Sт = Sкол - 2 Sслива.
Коэффициенты массопередачи определяют по уравнениям аддитивности фазовых
сопротивлений (1.3 ) и (1.4)

,
где
bYf, bXf - коэффициенты массоотдачи,
отнесенные к единице рабочей площади тарелки, соответственно для газовой и
жидкой фаз, кг / (м2·с);
m -
коэффициент распределения (тангенс угла наклона линии равновесия).
В колоннах, работающих в интенсивных гидродинамических режимах,
коэффициенты массопередачи можно рассчитать по нижеприведенным формулам.
Коэффициенты массоотдачи в газовой и жидкой фазах определяются по
уравнениям
bУf =
6,24 × 10-4 × Dу0,5
×
× h0
;(1.108)
bХf =
6,24 × 10-4 × DХ0,5
×
× h0
,(1.109)
где Dу, DХ - коэффициенты молекулярной диффузии поглощаемого
компонента соответственно в газе и жидкости, м2 /с (Приложение А8);
U -
плотность орошения, м3 / м2·с;
,
- средние
скорости жидкости и газа в барботажном слое, м /с;
e -
газосодержание барботажного слоя, м3 / м3.
Высоту
светлого слоя жидкости на тарелке h0, м, находят по уравнениям
для
колпачковых тарелок
h0 = 0,0419 +
0,19 hпер - 0,0135w
+ 2,46 q ,(1.110)
где hпер - высота переливной перегородки, м;
q - линейная плотность орошения, м3 / (м·с), равная
;
V - объемный
расход жидкости,
, м3 /с;
П
- периметр слива (ширина переливной перегородки), м.
Для
ситчатых и клапанных тарелок в практических расчетах можно пользоваться
уравнением
h0 = 0,787 × q0,2 × hпер 0,56 × wm × [1 -
0,31 exp (-0,11mХ)] ×
, (1.111)
где m - показатель степени, равный 0,05 - 4,6 × hпер ;
mХ -
вязкость жидкости, Па·с;
sХ, sВ - поверхность натяжения жидкости и воды, м Н / м,
(Приложение А9).
Для барботажных тарелок газосодержание можно определить по уравнению
,(1.112)
где
Fr =
.
Определение
высоты тарельчатого абсорбера проводится по уравнению:
Н = Нт + h1 + h2 , (1.113)
где Нт = (nд - 1) × hт - высота тарельчатой части колонны, м;
h1 - высота сепарационной части колонны,
м;
h2 - расстояние от нижней тарелки до
днища, м.
Расстояние h1 от верхней тарелки до крышки
абсорбера зависит от размеров устройства для предотвращения брызгоуноса (~2 м).
Расстояние от нижней тарелки до днища колонны принимается равным (1¸1,5) DК.
В приближенных расчетах, когда диаметр колонны не превышает 1 м, h1 и h2
принимается равным 0,6 - 1,5 м.
Гидравлическое сопротивление тарельчатых колонн
Для тарельчатых колонн гидравлическое сопротивление тарелок и DР равно сумме сопротивления сухой тарелки DР1, сопротивлению, обусловленному силами поверхностного
натяжения, DР2 и сопротивлению газожидкостного слоя
на тарелке DР3:
DР = DР1 + DР2 + DР3.(1.114)
Сопротивление сухой тарелки
DР = о × rr ×
,(1.115)
где о - коэффициент сопротивления;
w0 - скорость газа в отверстиях тарелки,
прорезях колпачка, щелях и других элементах тарелки, через которые проходит
газ, м / с.
Здесь
w0 =
,
где
V -
объемный расход при температуре абсорбции, м3 / с;
j - живое сечение тарелки: j =
- отношение суммарной площади отверстий на тарелке S0 к площади поперечного сечения колонны.
Коэффициент
сопротивления о зависит от типа тарелки (таблица 1.3).
Таблица 1.3 - Коэффициенты сопротивления тарелок
Тарелки
|
о
|
Тарелки
|
Колпачковые
|
4,5 - 5,0
|
Провальные:
|
|
Ситчатые:
|
|
дырчатые
|
2,1
|
j = 0,07 ¸ 0,1
|
1,85
|
решетчатые
|
1,4 - 1,5
|
j = 0,15 ¸ 0,2
|
1,45
|
трубчатые
|
0,9
|
Скорость газа в прорезях колпачка при их полном открытии или в отверстиях
ситчатой тарелки
,(1.116)
где а - коэффициент, равный 1 для колпачковых тарелок, 0,65
- для ситчатых тарелок;
l -
длина прорези колпачка или высота сливного порога для ситчатых тарелок.
Сопротивление, обусловленное силами поверхностного натяжения, ∆Р2
, (1.117)
где s -
поверхностное натяжение жидкости, Н / м;
П -
периметр отверстия (прорези), м;
S
- площадь отверстия (прорези), м;
dэ -
эквивалентный диаметр отверстия (прорези), м.
Гидравлическое сопротивление газожидкостного слоя
DР3 = g × rж × h0 = rп × g × hп ,(1.118)
где rж, rп - плотность
светлой жидкости и пены, кг / м3;
h0, hп - высота светлого слоя жидкости и
пены на тарелке, м.
g - ускорение
свободного падения, м/с2.
Сопротивление столба жидкости на тарелке рассчитывается по формулам
а) для колпачковой тарелки при полном открытии прорезей
DР3 = 1,3g
× К × rж (l
+
+ Dh);(1.119)
б) для ситчатых тарелок
DР3 = 1,3g × К × rж (hпер + Dh),(1.120)
где К - отношение плотности пены к плотности чистой
жидкости,
К = 0,5;
l -
высота прорези, м;
Dh - высота уровня жидкости над сливным порогом, м;
hпер - высота
сливного порога, м.
Величина Dh
определяется по формуле
,(1.121)
где Vж - объемный расход жидкости, м3 / с;
П -
периметр сливной перегородки, м.
Для ситчатых тарелок DР3 можно также рассчитать по формуле
,(1.122)
где h - высота слоя жидкости на тарелке,
м;
L -
расход жидкости, кг / с;
П
- смоченный периметр сливной трубы, м.
Общее гидравлическое сопротивление колонны DРк , Па, равно гидравлическому сопротивлению тарелки,
умноженному на число тарелок в абсорбере
DРК = DР × nд .(1.123)
1.5 Расчет
абсорберов с подвижной шаровой насадкой
Применяют односекционные и многосекционные абсорберы с насадкой диаметром
от 3 до 100 мм и плотностью от 10 до 1000 кг / м3. Материалом для насадки
служит полиэтилен, полипропилен, фторопласт, стирол, резина, металлы.
Соотношение
между диаметром абсорбера и диаметром шаров принимается
³ 10.
Свободное сечение тарелки FС = 0,4 -
0,5 м2 / м2. Скорость газа 5 - 6 м / с. Удельное орошение насадки 0,5 - 0,7 дм3
/ м3. Минимальная статическая высота слоя насадки НТ составляет (5 - 8) dш, а максимальная статическая высота слоя насадки
определяется из соотношения
£ 1.
Скорость
газа, соответствующая началу режима полного псевдоожижения, равна
= 4,6 ×
103 × FС1,54 × exp
.(1.124)
Предельно допустимая скорость газа
w¢КР = 2,9
× FС0,4 ×
. (1.125)
Динамическую высоту слоя насадки можно определить по формуле
НДИН
=
.(1.126)
Высота светлого слоя жидкости, удерживаемой в аппарате, равна
.(1.127)
Газосодержание слоя вычисляют по формуле
j Г = 1,16 × e0 ×
.(1.128)
Высоты сепарационной зоны НСЕП принимают (0,1 - 0,2) НДИН.
Гидравлическое сопротивление абсорбера определяют по формуле
Р = DРС + DРЖ,(1.129)
Где
DРС =
+ g × rж × НСТ ×
(1 - e0) ;(1.130)
DРЖ = 32,1 × w0,82 × L0,56 × НСТ0,6 × FС - 1,03
,(1.131)
где Vж, Vг - расход жидкости и газа, м3 / с;
С =
0,62 и К = 0,8 - коэффициенты для взвешенного слоя насадки;
Lор - 1× 105 кг / м2Ìч - стандартная величина плотности
орошения;
DРС - гидравлическое сопротивление сухой насадки, Па;
e0 = 0,4 - порозность неподвижного слоя насадки;
wН. П. - скорость газа, соответствующая
началу псевдоожижения, м/с, определяем из формулы
или
ReН. П.= 142 ×
,(1.132)
гдеrш - плотность
шара, кг / м3;
L
- плотность орошения, м3 / м2Ìч.
Плотность контакта фаз в слое равна
,(1.133)
где FБ = 1,6 × L0,44 × w00,92 - поверхность контакта фаз в
барботажном слое при НСТ = 0;
w0 - скорость
газа в отверстиях решетки, м/с.
Поверхность контакта в сепарационной зоне определяется по формуле
FС. З. = а С. З. (НС - НДИН) ,(1.134)
где а С. З. = 7,4 × L0,35 × w00,31 - удельная поверхность контакта фаз
в сепарационной зоне, м2 / м3;
НС
- высота секции аппарата, м.
НС = (1,1 ¸ 1,2) × НДИН.(1.135)
Для вычисления числа единиц переноса рекомендуются следующие уравнения
nг = 0,0785×w0,285
×L0,218× FС- 0,935×(Рr¢)- 0,5·
; (1.136)
nж = 2,52 × w1,36 × L-0,41 × Нст0,6 × FС- 1,3
.(1.137)
1.6 Расчет
распыливающих абсорберов
К аппаратам этого типа относятся полые, скоростные прямоточные и
механические абсорберы. В полых абсорберах жидкость распыливается форсунками.
Эффективность абсорбера зависит от количества распыливающей жидкости, угла
конусности факела и распределения их в сечении факела.
Производительность форсунки, м3/с, определяют по формуле
V = x × f
, (1.138)
где Р - давление жидкости перед форсункой, Па;
r ж - плотность жидкости, кг/м3;
f
- площадь выходного отверстия форсунки, м2;
x - коэффициент расхода жидкости, равный 0,2-0,3.
Средний размер капель определяется по формуле
.(1.139)
Константа А и показатели степени m и n
имеют следующие значения
Критерий Рейнольдса Re0
|
К
|
А
|
m
|
n
|
500 - 700
|
0,43 × 10-10 - 0,136 × 10-10
|
4,62 × 10-3
|
0,4
|
0,099 × К -0,086
|
500 - 700
|
0,86 × 10-7 - 6,5
|
6,5
|
0,033
|
27 × К -0,025
|
800 - 2000
|
0,43 × 10-10 - 6,5
|
0,4
|
- 0, 056
|
- 0,07 × К -0,046
|
ЗдесьRe0 =
;К =
,(1.140)
где wж - скорость истечения жидкости из форсунки ~ 9,8 м / с;
d0 - диаметр
выходного отверстия форсунки, (0,25-2,2) мм.
Удельная поверхность капли а равна
,(1.141)
где U - плотность орошения, м3 / м2Ìс;
U1 - абсолютная
скорость капель, м / с;
здесь
;(1.142)
w0 - скорость
падения капли, м / с;
w -
скорость газа, м / с.
Скорость газа в абсорбере принимаем 20 - 30 м / с.
Средний размер капель, образующихся при распылении жидкости
пневматической форсункой
,(1.143)
при равенстве скоростей капель удельная поверхность контакта фаз равна
.(1.144)
Коэффициенты массоотдачи в форсуночном абсорбере определяют по формулам
Nu¢г = 0,36 × 10-4 × Reг0,81 × (Рr¢г) 0,67 ;(1.145)
Nu¢ж = (0,145 - 0,0081wг)(Reж - 30)р × (Рr¢ж) 0,5,(1.146)
где
;(1.147)
,(1.148)
где bгv, bжv - объемные коэффициенты массоотдачи в газовой и
жидкой фазах, 1 / с;
-
приведенная толщина пленки, м.
В
выражении Reг и Reж за линейный размер принят
диаметр горловины d0.
К
прямоточным распыливающим абсорберам относятся форсуночные и бесфорсуночные
аппараты. Гидравлическое сопротивление абсорберов Вентури является суммой
гидравлических сопротивлений трубы - распылителя и каплеуловителя.
Гидравлическое
сопротивление трубы - распылителя равно
;(1.149)
xС = 0,165 + 0,034
[0,06 +
0,028
]
,(1.150)
где xС -
коэффициент гидравлического сопротивления сухой трубы;
xЖ -
коэффициент гидравлического сопротивления при вводе жидкости;
wг = 60-100,
скорость газа в горловине, м /с;
r г, r ж - плотность газа и жидкости, кг / м3;
l г - длина горловины, м;
dэ - эквивалентный диаметр горловины, м;
wзв - скорость звука, м / с;
- число Маха.
xЖ = А × xС × m 1+В,(1.151)
где А и В - коэффициенты, определяемые по справочникам.
< 1А = 0,55В =
0,095m = 1,32
|
|
|
|
> 1А = 0,91В =
0,067m = 3
|
|
|
|
Гидравлическое сопротивление и число единиц переноса в бесфорсуночных
абсорберах вычисляют по формуле
DР = DРС + 18 wг1,08
× m 0,8.(1.152)
Для пульсирующего режима число единиц переноса равно
nог =
0,847
.(1.153)
Для равномерного режима используется другая формула
nог =
0,447 w00,35
.(1.154)
Для абсорберов типа АРТ коэффициент сопротивления равен
x = 1,32 (1 + а × m n),(1.155)
число единиц переноса
nог = 0,43+ В × m,(1.156)
гдеа = j (wг) и В = j( wг),
для пульсирующего режима n = 0,68,
для равномерного режима n =
1,9.
Для определения объема распыливающих абсорберов определяется объемный
коэффициент массопередачи Кyv,
1/с
.(1.157)
Высота единиц переноса h0У
h0У =
.(1.158)
Высота абсорбера H, м
Н = h0У × n 0Г .(1.159)
В абсорберах Вентури трубу - распылитель и каплеуловитель можно
монтировать как раздельно, так и вместе в одном корпусе (рисунок 1.15).
Для практических расчетов число единиц переноса можно определить по
формуле
.(1.160)
Отсюда высота абсорбера Н, м, равна
Н = 100 × n 0Г2,86 ×w0,20 × U- 1,29(1.161)
или, вводя отношение объемных расходов газа и жидкости,
,(1.162)
где U - плотность орошения, м3 / м2
Ìс;
-
отношение объемных расходов газа и жидкости.
Таким
образом, определив число единиц переноса по приведенным ранее формулам,
задаваясь скоростью газа в горловине w, в
допустимых пределах, определяют высоту абсорбера.
а - центральный (форсуночный) подвод жидкости; б - периферийное орошение;
в - пленочное орошение; г - бесформенное орошение
Рисунок 1.15 - Конструкция труб - распылителей
1.7 Расчет
газопромывателей («мокрых скрубберов»)
Термин «скруббер» (англ. scrub - тереть, скрести, чистить щеткой; нем.
schrubben - чистить, скоблить, обтесать начерно) подразумевает наличие в
очистном устройстве движущихся приспособлений для извлечения из газового потока
загрязнителя. Однако в технической литературе название «мокрые скрубберы»
закрепилось за широким классом пылегазоочистных устройств, имеющих
приспособления для создания контакта обрабатываемых выбросов с промывочными
жидкостями. Обеспечить контакт газовых выбросов с жидкостями можно многими
способами, и под названием «мокрый скруббер» объединяют различные устройства от
перфорированных водопроводных труб в воздуховодах и газоходах до сложных
аппаратов с электростатической зарядкой управляемых частиц и капель орошающей
жидкости.
В «мокрых скрубберах», предназначенных для пылезолоулавливания, орошающей
жидкостью, как правило, является вода. Ее расход для разных типов аппаратов
может изменяться от 0,1 до 10 м3 на 1000 м3 обрабатываемых газов. Так как
основным недостатком мокрых способов обезвреживания является необходимость
обработки загрязненных стоков, образовавшихся в процессе очистки газов, то
приемлемыми могут быть лишь способы с минимальным водопотреблением. Вообще до
принятия решения о применении мокрого способа очистки необходимо тщательно
проанализировать свойства обрабатываемых выбросов. Во всяком случае, нельзя
упускать из поля зрения растворимость, реакционную способность (возможность
образования взрывоопасных, коррозионно-активных веществ и вторичных
загрязнителей), коррозионную активность компонентов загрязнителя и
газа-носителя. Для твердых загрязнителей важны также смачиваемость,
схватываемость, слипаемость, для жидких - смачиваемость, плотность, параметры
фазовых переходов.
Рассмотрение широкого круга разнообразных конструкций мокрых скрубберов,
разработанных к настоящему времени, невозможно и не представляется столь
необходимым. Многие из приводимых в технической литературе аппаратов
малоупотребительны из-за несовершенства разработки.
Полые газопромыватели (рисунок 1.16) реализуют наиболее примитивную схему
мокрой очистки с организацией промывки запыленных потоков газа в газоходах
(воздуховодах) или отдельных камерах (емкостях) различной формы. Орошающая
жидкость в них подается навстречу или поперек газового потока (рисунок 1.16).
Рисунок 1.16 - Полые газопромыватели
Чтобы унос жидкости из зоны контакта был незначительным, размер капель
должен быть не менее 500 мкм, а скорость газового потока не должна превосходить
1-1,2 м/с. С целью уменьшения габаритов установки скорость потока увеличивают
(иногда до 5 м/с и более) и устанавливают на выходе аппарата каплеуловители.
Орошающую жидкость разбрызгивают прежде всего с помощью центробежных форсунок,
поддерживая ее давление в пределах 0,3-0,4 МПа. Такие форсунки позволяют
работать на оборотной воде, из которой удалена грубая взвесь. Полые
газопромыватели могут найти применение для осаждения частиц крупнее 10 мкм.
Насадочные скрубберы представляют собой емкости (колонны), содержащие
насадочные элементы разной формы: простые кольца - кольца Рашига, кольца с
перегородками - кольца Лессинга и Палля, седла Берля и «Инталокс», спиральные
розетки Теллера и др. Оптимальная область применения насадочных колонн -
совместная очистка газовых выбросов от газообразных загрязнителей и дисперсных
жидких или твердых растворимых частиц. Такие колонны малопригодны для обработки
газов, содержащих обычные, даже не слипающиеся пыли и непригодны для
слипающихся и схватывающихся вследствие забивания каналов в насадке.
Как и в полых скрубберах, подвод жидкости может быть организован
навстречу или поперек потока.
Пенные газопромыватели представляют собой колонны с перфорированными
перегородками, называемыми тарелками (рисунок 1.17). Для очистки газов чаше
всего используются провальные, щелевые и дырчатые тарелки (рисунок 1.17, а, б и
в).
Диаметр отверстий дырчатых тарелок принимают в пределах 3-8 мм, а
относительное свободное сечение (отношение площади отверстий к площади тарелки)
ffr = 0,15-0,25.
а - провальные; б - щелевые; в - дырчатые
Рисунок 1.17 - Тарелки пенных газопромывателей
Отверстия разбиты по равностороннему треугольнику. Шаг между отверстиями d, мм, определяют по формуле
(1.163)
где D0 - диаметр отверстия, м.
Размеры тарелок приведены в таблице 1.4.
Таблица 1.4 - Геометрические характеристики дырчатых тарелок
d, мм
|
6
|
8
|
9
|
10
|
10
|
11
|
11
|
12
|
13
|
13
|
13
|
14
|
16
|
18
|
D, мм
|
3
|
4
|
4
|
5
|
5,5
|
5
|
6
|
5
|
5
|
6
|
7
|
6
|
7
|
8
|
ffr
|
0,226
|
0,226
|
0,179
|
0,226
|
0,272
|
0,18
|
,271
|
0,157
|
0,134
|
0,193
|
0,263
|
0,167
|
0,174
|
0,179
|
Щелевые тарелки могут выполняться решетчатыми, трубчатыми или
колосниковыми. Трубчатые и колосниковые конструкции изготавливают сварными из
трубок, прутков или пластин. Ширину щели в тарелке b принимают 4-5 мм, свободное
сечение ffr = 0,2-0,25. Необходимое число N щелей в тарелке можно найти по
таблице 1.5
Таблица 1.5 - Зависимость числа щелей в тарелке N от конструктивного
параметра c
N
|
1
|
2
|
3
|
4
|
5
|
6
|
7
|
8
|
9
|
10
|
c
|
0
|
0.866
|
1.688
|
2.498
|
3.296
|
4.093
|
4.887
|
5.679
|
6.471
|
7.257
|
N
|
11
|
12
|
13
|
14
|
15
|
16
|
17
|
18
|
19
|
20
|
c
|
8.042
|
8.832
|
9.620
|
10.411
|
11.20
|
11.982
|
12.776
|
13.654
|
14.352
|
15.138
|
N
|
21
|
22
|
23
|
24
|
25
|
26
|
27
|
28
|
29
|
30
|
c
|
15.925
|
16.713
|
17.50
|
18.287
|
19.074
|
19.860
|
20.648
|
21.432
|
22.219
|
23.005
|
Конструктивный параметр c рассчитывают по формуле
(1.164)
где D - диаметр аппарата, м; lm - длина щели, расположенной в середине
тарелки; ее принимают на 0,01 м меньше диаметра аппарата D.
Общую длину всех щелей ltot - определяют из выражения
(1.165)
Шаг между щелями d
равен
(1.166)
Расстояние между щелями b1, находят следующим образом.
Оптимальная толщина дырчатых и щелевых тарелок 4-6 мм. Удельное орошение
для очистки газов от пыли принимают в пределах 0,4-0.6 на 1 л газов. При этом
минимальная скорость газов, необходимая для создания устойчивого пенного режима
на тарелке, составляет порядка 1 м/с.
Газопромыватели с подвижной насадкой представляют собой емкости, в
которых на опорно-распределительной решетке располагается слой насадочных
элементов, имеющих возможность перемещаться при работе аппарата. Корпуса таких
аппаратов выполняют цилиндрической (рисунок 1.18, а) или цилиндроконической
(рисунок 1.18, б) формы. Цилиндрические аппараты рассчитываются на работу в
режиме псевдоожижения, а цилиндроконические - в режиме фонтанирования. В
отличие от газопромываетелей с неподвижной насадкой, эти аппараты могут
использоваться для улавливания всех видов пыли, за исключением схватывающей и
длинноволокнистой. Аппараты с фонтанирующей насадкой могут работать в более
широком диапазоне скоростей, чем аппараты с псевдоожижением.
Для цилиндрических аппаратов удельное орошение rjr принимается в пределах
0.5-0.7 л/ м3. Опорные тарелки обычно выполняются щелевыми с шириной щелей в
пределах 4-6 мм. Относительное свободное сечение тарелки ffr для слабо
слипающихся не волокнистых пылей принимают около 0,4 м2/ м2, а для смолистых
веществ и пылей, способных образовывать отложения, ffr увеличивают до 0,6 м2/
м2. С целью уменьшения сопротивления слоя используют насадки шаровой или
овальной формы. Наилучший материал насадок - полиолефины (полиэтилен,
полипропилен), ввиду невысокой насыпной плотности. Кроме того, они достаточно
легко очищаются. Рекомендуемая насыпная плотность насадки составляет 200-300
кг/м3. Возможно также использование стеклянных шариков, вспученных материалов
без поверхностных пор. Оптимальный диаметр шаров около 20 мм. Диаметр аппарата
в десять или более раз должен превышать диаметр элементов насадки.
а - цилиндрический; б - цилиндроконический
Рисунок 1.18 - Корпуса газопромывателей с подвижной насадкой
Минимальная высота слоя насадки в неподвижном состоянии должна быть в
пределах 5-8 диаметров шаров, а максимальная - не более диаметра аппарата.
Для цилиндроконических аппаратов рекомендуются полиэтиленовые элементы
насадки диаметром до 40 мм с насыпной плотностью до 120 кг/ м3, а высота
засыпки в статическом состоянии - 650 мм. Угол раскрытия конической части
аппарата должен быть не более 60°. Удельное орошение для цилиндроконических
аппаратов принимают достаточно высоким - около 4-6 л/ м3; при этом унос
жидкости меньше, чем в аппаратах с псевдоожиженном слое. Цилиндроконические
скрубберы могут применяться для очистки газов при их расходе до 40000 м3/ч.
В скрубберах ударно-инерционного действия (называемых в литературе также
газопромывателями ударного действия, импакторными и брызгальными скрубберами,
скрубберами с самораспылением или с самогенерацией капель, ротоклонами типа N)
смесь обрабатываемых выбросов с промывочной жидкостью создается в результате
удара газового потока о поверхность жидкости. Образующиеся при ударе капли
имеют размеры до 400 мкм. Вся энергия, необходимая для создания смеси, подводится
газовым потоком. Наиболее простая конструкция импакторного скруббера
представлена на рисунке 1.19, а.
а - конструкция импактного скруббера; б - скруббер Дойла; в - схема
движения газового потока
Рисунок 1.19 - Скрубберы
Степень очистки в импакторных скрубберах сопоставима с распылительными
скрубберами при одинаковом перепаде давлений. Такие аппараты ударного действия,
как высокоскоростные скрубберы Дойла, способны улавливать частицы пыли
субмикронных размеров, но требуют значительной энергии для создания
достаточного перепада давлений в потоке очищаемых газов.
Аппараты с самораспылением выгодно отличаются от других типов мокрых
скрубберов низким потреблением воды. Для поддержания ее постоянного уровня в
ванне необходимо лишь компенсировать потери со шламами, унос капель через
сепаратор - каплеуловитель, испарение с поверхности и испарение
диспергированной жидкости. Во избежание возрастания потерь от испарения
жидкости нежелательна обработка в аппаратах с самогенерацией капель
высокотемпературных газовых выбросов. Технические характеристики ударных
промывателей ПВМ приведены в таблице 1.6.
Таблица 1.6 - Технические характеристики газопромывателей ПВМ
Показатели
|
Типоразмер промывателя
|
|
3
|
5
|
10
|
20
|
40
|
1
|
2
|
3
|
4
|
5
|
6
|
Номинальная
производительность по обрабатываемому газу, м3/с
|
0,83
|
1,39
|
2,78
|
5,56
|
11,11
|
Марка вентилятора
|
ЦП 13-50 N 3,2
|
ЦП 7-40 N 5
|
ЦП 7-40 N 6
|
ЦП 7-40 N 8
|
ЦП 4-76 N 10
|
Объем воды в промывателе,
м3
|
0,45
|
0,65
|
1,45
|
2,2
|
5,5
|
Масса пылеуловителя (без
воды и электродвигателя), кг
|
754
|
1208
|
1998
|
3050
|
4737
|
Габариты, мм: длина ширина
высота
|
1250 1300 2848
|
1650 1359 3080
|
2500 1514 3412
|
2510 2314 3680
|
4750 2416 4110
|
Длина одной перегородки, м
|
0,8
|
1,21
|
2,0
|
2,0
|
4,0
|
Число перегородок, шт
|
1
|
1
|
1
|
2
|
2
|
Центробежные скрубберы отечественных конструкций в основном имеют
тангенциальный подвод очищаемого газа и пленочное орошение по внутренней стенке
аппаратов. В циклонах с водяной пленкой (ЦВП), рассчитанных на очистку
низкотемпературных газов с любым видом пыли, кроме схватывающейся и реагирующей
с водой, пленка образуется за счет тангенциального подвода воды через ряд
трубок, расположенных в верхней части промывной емкости.
Основные технические характеристики газопромывателя типа ЦВП приведены в
таблице 1.7, а его схема - на рисунке 1.20.
Газопромыватели типа СИОТ работают при повышенных скоростях газового
потока (14-20 м/с), имеют неплохую степень очистки и рассчитаны на улавливание
смачиваемой не волокнистой не схватывающейся пыли при начальной запыленности до
5 г/м3.
Основные характеристики аппаратов приведены в таблице 1.8.
Рисунок 1.20 - Схема газопромывателя типа ЦВП
Таблица 1.7 - Технические характеристики газопромывателей ЦВП
Марка газопромывателя
|
Размеры, мм
|
Расход воды на орошение
стенок, л/с
|
Масса, кг
|
|
диаметр
|
высота
|
расстояние от оси до
патрубка на
|
газовых патрубков, на входе
и выходе, ахb
|
циклона
|
патрубка на входе*
|
|
|
|
|
входе
|
выходе
|
|
|
|
|
1
|
2
|
3
|
4
|
5
|
6
|
7
|
8
|
9
|
ЦВП-3
|
315
|
2434
|
445
|
283
|
110´195
|
0,14
|
1,1
|
63,9
|
ЦВП-4
|
400
|
3004
|
505
|
360
|
140´250
|
0,17
|
1,2
|
106,7
|
ЦВП-5
|
500
|
3684
|
640
|
450
|
175´310
|
0,21
|
1,4
|
161,0
|
ЦВП-6
|
530
|
4554
|
765
|
656
|
220´390
|
0,27
|
1,6
|
237,0
|
ЦВП-8
|
800
|
5699
|
1025
|
720
|
280´495
|
0,35
|
2,0
|
369,7
|
ЦВП-10
|
1000
|
7044
|
1335
|
900
|
350´620
|
0,43
|
2,4
|
569,5
|
* орошение периодическое
Таблица 1.8 - Технические характеристики газопромывателей СИОТ
Показатели
|
Номер газопромывателя
|
|
5
|
6
|
7
|
8
|
9
|
10
|
11
|
12
|
13
|
Производительность, м3/с,
при скорости 14м/с 20м/с
|
3,5 4,9
|
4,9 6,9
|
6,9 9,7
|
9,7 13,9
|
13,9 20,8
|
20,8 27,8
|
27,8 38,9
|
38,9 55,6
|
55,6 77,8
|
Диаметр входа, мм
|
560
|
665
|
790
|
940
|
1120
|
1330
|
1580
|
1880
|
2240
|
Внутренний диаметр
аппарата, мм
|
1344
|
1596
|
1896
|
2256
|
2688
|
3192
|
3792
|
4512
|
5400
|
Максимальный расход воды,
л/с
|
0,56
|
0,78
|
1,1
|
1,5
|
2,1
|
3,1
|
4,3
|
6,1
|
8,6
|
Центробежные скрубберы ЦС ВТИ (рисунок 1.20, б) были разработаны для
улавливания золы из дымовых газов. Аппарат состоит из стального вертикального
цилиндра, конического днища, входного патрубка, оросительной системы и
гидравлического затвора. Внутренняя поверхность аппарата футерована керамической
кислотоупорной плиткой. В середине века аппараты ЦС ВТИ были широко
распространены в энергетике, но имели невысокий коэффициент очистки и сейчас не
изготавливаются. Однако сохранившиеся на предприятиях аппараты могут быть
полезны для предварительной обработки выбросов с высоким содержанием кислых
газов и туманов кислот. Основные технические характеристики аппаратов ЦС ВТИ
приведены в таблице 1.9.
Таблица 1.9 - Технические характеристики газопромывателей ЦС ВТИ
Наружный диаметр, м
|
Высота, м
|
Максимальная
производительность, м3/с
|
Расход воды на орошение,
л/с
|
Коэффициент гидравлического
сопротивления, z
|
0,6
|
3,83
|
1,1
|
0,20
|
46,5
|
0,7
|
4,31
|
1,6
|
0,25
|
42,8
|
0,8
|
4,79
|
2,15
|
0,30
|
40,3
|
0,9
|
5,27
|
2,85
|
0,36
|
38,6
|
1,0
|
5,75
|
3,55
|
0,42
|
37,3
|
1,1
|
6,23
|
4,4
|
0,47
|
36,6
|
1,2
|
6,71
|
5,3
|
0,53
|
35,8
|
1,3
|
7,16
|
6,3
|
0,58
|
35,2
|
1,4
|
7,67
|
7,4
|
0,65
|
34,7
|
1,5
|
8,15
|
8,6
|
0,74
|
34,1
|
1,6
|
8,63
|
9,85
|
0,82
|
33,8
|
1,7
|
9,11
|
11,2
|
0,90
|
33,5
|
Скрубберы Вентури имеют распыливающие элементы в виде орошаемых труб
Вентури или аналогичных устройств для ускорения газового потока, соединенные с
каплеуловителями. Скорость потока начинает расти в конфузоре и достигает в
горловине трубы 40-150 м/с, куда поступает также промывочная жидкость.
Диспергируясь, жидкость вместе с запыленным потоком поступает в диффузор. Однако
приобретенная каплями скорость жидкости оказывается существенно меньшей
скорости потока и частиц пыли. Поэтому процесс осаждения частиц пыли на каплях
при прохождении потока через горловину и диффузор трубы становится сходным с
процессом осаждения в зернистом фильтре с подвижной насадкой.
Более высокая эффективность пылеулавливания по сравнению с полыми
газопромывателями достигается в скрубберах Вентури созданием развитой
поверхности контакта фаз, что требует и значительно более высоких энергозатрат.
Образование тонкодисперсного аэрозоля происходит при этом как за счет
механической диспергации промывочной жидкости, так и вследствие интенсивного
испарения капель при резком падении давления в горловине. Очевидно, это
приводит также к повышению влажности газа и интенсификации капиллярной
конденсации влаги на поверхности частиц пыли. Последняя причина может служить
объяснением того, что степень очистки пыли в скрубберах Вентури слабо зависит
от ее смачиваемости.
В диффузоре трубы происходит рост давления и снижение скорости потока,
что способствует коагуляции мелких частиц. Из диффузора газовый поток выносит
капли жидкости с осевшими на них частицами пыли в каплеуловитель, где
происходит сепарация взвешенных частиц.По величине гидродинамического сопротивления
труб Вентури различают низконапорные и высоконапорные скрубберы. Низконапорные
скрубберы с сопротивлением распылителя до 5 кПа применяются для улавливания
пыли с размерами частиц более 20 мкм.
Эффективное улавливание мелких частиц требует более высоких энергозатрат.
Скрубберы с высоконапорными трубами Вентури могут осаждать частицы размером 0,5
мкм и выше. Скорость потока в высоконапорных трубах приближается к скорости
звука, а их сопротивление достигает нескольких десятков кПа.
Следует отметить, что в распылительных трубах с оптимальным соотношением
размеров подведенная энергия преимущественно расходуется на обеспечение
контакта между газовой и жидкой фазами, и, в конечном итоге, - на очистку
выбросов. Для труб Вентури оптимальными считаются следующие геометрические
характеристики (рисунок 1.21): угол сужения конфузора a1=15-28°, длина горловины l=15 D, угол раскрытия диффузора, аг
= 6-8°. На практике указанные соотношения не всегда выдерживаются, что приводит
к увеличению и без того высоких затрат.
Скрубберы Вентури могут различаться устройством каплеуловителей,
конструкциями и способами установки труб, способами подвода жидкости.
Каплеуловители могут быть выносными (рисунок 1.21, б) или размешаться в одном
корпусе с трубой (рисунок 1.21, в). Трубы могут иметь круглое, кольцевое или
прямоугольное (щелевое) сечение горловины. Трубы с круглым сечением применяют
для небольших расходов, а трубы со щелевым или регулируемым кольцевым сечением
(рисунок 1.21, в) - для больших. При необходимости трубы компонуются в группы и
батареи.
Вода в горловину трубы может подаваться через форсунки различных
конструкций, установленные центрально или периферийно, или стекать в виде
пленки по стенкам конфузора (рисунок 1.21, г, д, е). Худшие показатели по
дроблению капель и. следовательно, по степени очистки имеют бесфорсуночные
трубы Вентури (рисунок 1.21, ж). В то же время они допускают использование
оборотной неочищенной жидкости, что может быть важным при совместном
улавливании газообразных и дисперсных примесей (например, при нейтрализации
кислых газов известковым молоком).
а - геометрические характеристики; б - выносные каплеуловители; в - в
одном корпусе; г, д, е - форсунки различных конструкций; ж - бесфорсуночные
трубы
Рисунок 1.21 - Трубы Вентури
Для использования в промышленности на базе оптимальной конфигурации трубы
Вентури (рисунок 1.21, а) разработан типоразмерный ряд высоконапорных
скрубберов Вентури ГВПВ. Основные характеристики аппаратов этого ряда приведены
в таблице 1.10. В качестве каплеуловителей для них используются малогабаритные
прямоточные циклоны. Орошение производится через цельнофакельные форсунки,
устанавливаемые над конфузором под углом к оси трубы 60°. Аппараты
предназначены для очистки газов с температурой до 400°С и начальной
запыленностью до 30 г/м3. Содержание взвеси в жидкости, подаваемой на орошение,
не должно превышать 500 мг/л.
Разработан также унифицированный ряд скрубберов Вентури с кольцевой
горловиной. Технические характеристики их приведены в таблице 1.11. Скрубберы
предназначены для работы в таких же условиях, как правило, и аппараты
предыдущей серии.
Коагуляционный мокрый пылеуловитель КМП (рисунок 1.21, б) разработанный
Ленинградским институтом Промстройпроект, представляет собой низко направленную
трубу Вентури, оснащенную циклоном ЦВП с периодическим орошением в качестве
каплеуловителя. Подача воды в трубу. Вентури производится центрально в зоне
конфузора в распылительной форсунке, на выходе из сопла установлен отбойник
(тело-препятствие конической формы), дробящий поток жидкости. Диаметр сопла D,
м, определяется из формулы
Таблица 1.10 - Основные характеристики аппаратов
Типоразмер аппарата ГВПВ
|
Площадь сечения горловины
трубы Вентури, м2
|
Диаметр горловины, мм
|
Производительность, м3/с
|
Расход жидкости на
орошение, л/с
|
Давление жидкости перед
форсункой, кПа
|
Габариты, мм
|
Масса, кг
|
1
|
2
|
3
|
4
|
5
|
6
|
7
|
8
|
0,006
|
0,006
|
85
|
0,47..0,97
|
0,33..1,89 0,6..1,39
|
180..370 80..410
|
445´ ´185064/70
|
|
0,010
|
0,010
|
115
|
0,86..1,81
|
0,6..1,39 1,33..3,5
|
80..410 63..400
|
540´ ´2500117/20
|
|
0,014
|
0,014
|
135
|
1,15..2,33
|
0,8..1,33 1,33..1,94
|
80..410 60..700
|
575´ ´2940148/150
|
|
0,019
|
0,019
|
155
|
1,55..3,15
|
1,08..3,55 3,61..6,31
|
80..980 420..710
|
645´ ´3140174/175
|
|
0,025
|
0,025
|
180
|
2,08..4,20
|
1,44..3,61 3,61..8,33
|
150..980 80..450
|
775´ ´3790244/257
|
|
0,030
|
0,031
|
200
|
2,59..5,25
|
1,81..3,61 3,61..10,50
|
60..250 100..910
|
790´ ´40250305/310
|
|
0,045
|
0,045
|
240
|
3,83..7,78
|
2,71..8,33 8,33..15,56
|
60..570 110..390
|
880´1420´4620
|
400/420
|
0,060
|
0,062
|
280
|
5,18..10,50
|
3,61..8,33 8,33..21,0
|
100..570 110..710
|
535/560
|
0,080
|
0,080
|
320
|
6,52..13,22
|
4,21..12,5 12,5..26,44
|
75..570 110..500
|
1545´1480´5940
|
645/675
|
0,100
|
0,107
|
370
|
9,01..18,28
|
6,28..12,5 12,5..36,56
|
80..320 63..540
|
´7240935/975
|
|
0,140
|
0,138
|
420
|
11,50..23,33
|
8,0..12,5 12,5..46,67
|
130..320 63..880
|
´81401160/1200
|
|
Таблица 1.11 - Технические характеристики скрубберов с кольцевой
горловиной
Типоразмеры
|
Производительность, м3/с
|
Скорость газов в свободном
сечении пылеуловителя, м/с
|
Число каплеуловителей, шт.
|
Диаметр, мм
|
Ход обтекателя, мм
|
Высота скруббера, мм
|
Масса, кг
|
|
|
|
|
каплеуловителя
|
горловины трубы Вентури
|
обтекателя в горловине
|
|
|
|
СВ 150/90-800
|
0,56-1,94
|
1,4-5,0
|
1
|
800
|
150
|
90
|
250
|
4095
|
1140
|
СВ 210/120-1200
|
1,94-4,17
|
2,3-5,0
|
1
|
1200
|
210
|
120
|
250
|
4980
|
1900
|
СВ 300/180-1600
|
4,17-8,33
|
2,5-5,0
|
1
|
1600
|
300
|
180
|
350
|
6205
|
3700
|
СВ 400/250-2200
|
8,33-13,89
|
3,0-5,0
|
1
|
2200
|
400
|
250
|
350
|
7400
|
6630
|
СВ 900/820-1600
|
13,89-22,22
|
6,9-11,0
|
1
|
1600
|
900
|
820
|
150
|
9160
|
8060
|
СВ 1020/920-2000
|
22,22-33,33
|
7,1-10,6
|
1
|
2000
|
1020
|
920
|
185
|
11060
|
10730
|
СВ 1620/1420-2400
|
33,33-50,00
|
7,4-11,0
|
1
|
2400
|
1150
|
1020
|
212
|
13165
|
14170
|
СВ 1380/1220-2000
|
50,00-66,67
|
7,1-10,6
|
2
|
2000
|
1380
|
1220
|
245
|
11060
|
19960
|
СВ 1620/1420-2400
|
66,67-94,44
|
7,4-10,4
|
2
|
2400
|
1620
|
1420
|
350
|
13165
|
27000
|
СВ 1820/1620-2800
|
94,44-138,89
|
7,7-11,3
|
2
|
2800
|
1860
|
1620
|
400
|
14880
|
34470
|
,(1.167)
где WL - расход орошающей жидкости, м3/с;
РL - давление жидкости перед соплом, Па.
Характеристики промывателей КМП приведены в таблице 1.12.
Таблица 1.12 - Характеристики промывателей КМП
Показатели
|
Типоразмеры
|
|
КМП-2,5
|
КМП-3,2
|
КМП-4
|
КМП-5
|
КМП-6,3
|
КМП-7,1
|
КМП-8
|
Производительность, м3/с
|
1,94- 3,89
|
3,3- 5,56
|
5,0- 9,72
|
7,78- 15,28
|
12,5- 23,89
|
16,1- 30,56
|
19,44- 38,89
|
Диаметр горловины, мм
|
250
|
320
|
400
|
500
|
630
|
710
|
800
|
Длина, мм
|
2300
|
2800
|
3540
|
3980
|
4480
|
5240
|
5720
|
Ширина, мм
|
1415
|
1845
|
2240
|
2705
|
3190
|
3695
|
4105
|
Высота, мм
|
3350
|
4990
|
5630
|
7645
|
8360
|
9290
|
10060
|
Масса, кг
|
1060
|
1260
|
1848
|
4010
|
5310
|
7308
|
10477
|
Потери давления в скруббере Вентури складываются из сопротивлений
каплеуловителя и распылительной трубы. Сопротивление трубы является основным
параметром, характеризующим эффективность очистки. Точный теоретический расчет
потерь давления в трубе Вентури невозможен. Расчеты выполняют по эмпирическим
данным, считая сопротивление орошаемой трубы Dр как бы составленным из сопротивления сухой трубы Dpd и добавки Dpw, отражающей влияние орошения. В
соответствии с этим условно вводится коэффициент гидравлического сопротивления
сухой трубы Vd и добавочный
коэффициент zw, учитывающий
способ орошения, скорость движения газов и отношение длины горловины трубы к
диаметру l/D.
Величину zw
для аппаратов с центральным или пленочным орошением (рисунок 1.21, г, е) при
соотношении l/D в пределах 0,15-12 и скорости газового потока в горловине более
80 м/с определяют по формуле
(1.168)
а при скорости менее 80 м/с - по формуле
(1.169)
где WL, WG - расходы орошающей жидкости и обрабатываемого газа (по
параметрам входа в трубу), м3/с;
Р =1-1,27(l/D)-0,045 и q=1-0,98 (l/D) -0,026 - показатели степени.
Для аппаратов с периферийным подводом орошающей жидкости в конфузор перед
горловиной (рисунок 1.21, д) величину zW при соотношении l/D = 0,15 и скорости газов более 80 м/с
определяют по формуле
,(1.170)
а при скорости менее 80 м/с - по формуле
(1.171)
Для одиночных труб Вентури с центральными форсунками, установленными
перед конфузором, или батареей труб, орошаемых с предварительным дроблением
потока жидкости, при соотношении l/D = 0,15 и скорости газов в пределах 40-150
м/с величину VW определяют по
формуле
.(1.172)
Для аппаратов с центральным подводом орошающей жидкости, оптимальным
соотношением конструктивных параметров труб и скоростью газов в пределах 40-150
м/с величину zW определяют по
формуле
.(1.173)
Коэффициент гидравлического сопротивления сухой трубы Вентури zd с соотношением l/D = 0,15
принимается в пределах 0,12-0,15, а при большем соотношении (до 10) - может
быть рассчитан по формуле
(1.174)
где D - диаметр круглой или эквивалентный диаметр прямоугольной горловины
трубы Вентури, м;
М - число Маха, которое подсчитывают как отношение скорости газа в
горловине к скорости звука, принимаемые по температуре и давлению на выходе из
трубы.
Сопротивление сухой трубы Вентури Dpd, Па, рассчитывают по формуле
Dpd=VdWG2rG/2,(1.175)
где WG - скорость газов в горловине трубы,
м/с,
rG - плотность газов, кг/м3.
Скорость газов в горловине трубы и плотность газов принимают по
температуре и давлению на выходе из трубы, а для подсчета сопротивления
скрубберов Вентури - приближенно по параметрам газов на выходе из скруббера.
Добавочное сопротивление DРw определяют по формуле
,(1.176)
где rL- плотность орошающей жидкости,
кг/м3.
Все величины в формуле (1.176) принимаются по температуре и давлению на
выходе из аппарата. Сопротивление орошаемой трубы DР подсчитывают как сумму
сопротивлений D Р d и D Р w.
Степень очистки газовых выбросов в мокрых скрубберах может быть найдена
только на основе эмпирических сведений по конкретным конструкциям аппаратов.
Методы расчетов, нашедшие применение в практике проектирования, основаны на
допущении о возможности линейной аппроксимации зависимости степени очистки от
диаметра частиц в вероятностно-логарифмической системе координат. Расчеты по
вероятностному методу выполняются по той же схеме, что и для аппаратов сухой
очистки газов, но имеют еще меньшую сходимость. Иногда расчеты выполняют по так
называемому «энергетическому» методу, исходящему из предположения, что
количество энергии, необходимое для улавливания частиц загрязнителя,
пропорционально степени очистки выбросов независимо от типа очистного
устройства. Оба метода расчета будут рассмотрены применительно к конкретным
типам аппаратов.
1.7.1
Расчеты параметров полых газопромывателей с определением степени очистки по
вероятностному методу
1. Принимают скорость газов w в скруббере около 1 м/с, перепад давления
порядка 200-250 Па и выбирают величину удельного орошения rir в пределах
(0,5-8) 10-3 м3 на 1 м3 газа.
. Определяют среднюю площадь скруббера f, м2,в сечении, перпендикулярном направлению потока газов
,(1.177)
где: W - расход очищаемых газов, м3/с, подсчитанный по температуре и
давлению на выходе из аппарата.
Температуру газов на выходе из скруббера, имевших начальную температуру
150-200 °С и выше, при отсутствии специальных требований, можно принимать на
100 °С ниже начальной, а температуру не нагретых газов - равной начальной.
Находят диаметр аппарата с противоточным орошением или эквивалентный
диаметр для аппарата с поперечным орошением. Высоту аппарата h , м,с круглым
поперечным сечением принимают порядка 2,5 диаметра, а с прямоугольным сечением
- из конструктивных соображений.
. Определяют расход жидкости WL, м3/с, на орошение
.(1.178)
4. Определяют инерционные параметры Y1 для фракций частиц заданного состава
(1.179)
где Dpi - диаметр частицы i-той фракции, м;
рр - истинная плотность частиц, кг/м3;
С - поправка Каннингхема;- определяющий размер, м;
h - динамический коэффициент вязкости газа, Па с.
Значение поправки Каннингхема зависит от диаметра частицы:
Dp106, м
|
0,003
|
0,01
|
0,03
|
0,1
|
0,3
|
1,0
|
3,0
|
10
|
С1
|
90
|
24,5
|
7,9
|
2,9
|
1,57
|
1,16
|
1,03
|
1
|
За определяющий размер при расчете полых скрубберов принимают диаметр
капли орошающей жидкости в пределах (0,6-1) 10-3 м.
.Определяют коэффициент захвата частиц определенных фракций hdri
.(1.180)
При Y=150 величина hdri превышает 0,995; при значениях Y более 170 величину hdri можно принимать равной 1.
. Определяют значения парциальных коэффициентов очистки для скрубберов с
противоточным орошением по формуле
(1.181)
а для скрубберов с поперечным орошением по формуле
,(1.182)
где Wdr - скорость осаждения капли, м/с;- диаметр капли, м.
В полых газопромывателях устанавливаются форсунки грубого распыла,
создающие капли диаметром (0,6-1,0)10-3 м. Скорость осаждения таких капель
можно найти по диаграмме (рисунок 1.22).
. По найденным парциальным (фракционным) коэффициентам очистки и
заданному фракционному составу дисперсных загрязнителей определяют полный
коэффициент очистки htot
и обосновывают возможность применения полого скруббера или отказ от него.
Рисунок 1.22 - Диаграмма скорости осаждения капель
.7.2
Расчеты характеристик пенных пылеуловителей с провальными, дырчатыми и щелевыми
тарелками с определением степени очистки по вероятностному методу
1.Принимают предварительно линейную скорость газового потока w в пределах
2-2,3 м/с и вычисляют диаметр аппарата по заданному расходу. Задаются в
пределах рекомендуемых значений диаметра отверстий или шириной щелей тарелки.
По формуле (1.163) и таблице (1.4) для дырчатых или по формулам (1.164) и
таблице (1.5) для щелевых тарелок находят их геометрические характеристики.
. Принимают величину удельного орошения rir при очистке не нагретых газов
в пределах (0,4-0,6) 10-3 м3/м3. Если необходимо охлаждение газов, величину rir
определяют по тепловому балансу. Находят плотность орошения rir, кг/м3, по формуле
.(1.183)
. Методом последовательных приближений определяют максимальную газовую
wmax скорость, м/с, при которой еще сохраняется пенный режим
,(1.184)
,(1.185)
где рst = 1 кг/(м2с) - стандартная плотность орошения.
Эквивалентный диаметр отверстий Deq, м, для дырчатых тарелок принимается
равным диаметру отверстий, для щелевых - двойной ширине щели.
Если не выдерживается условие
,(1.186)
то расчеты по формулам (1.183 - 1.185) повторяют, задавшись новым
значением w.
. После увязки скоростей определяют диаметр аппарата D,м, из формулы
,(1.187)
где W - расход очищаемых газов, м3/с.
Аппараты с диаметрами более 2 м проектировать нежелательно из-за
невозможности обеспечить равномерное распределение газового потока по
отверстиям тарелки. При необходимости обработки большого количества газовых
выбросов лучше принять к установке несколько аппаратов.
. Определяют гидравлическое сопротивление аппарата DР, Па, по формуле
,(1.188)
где DР1, DР2 - потери давления на входе и
выходе, Па;
DР3 - гидравлическое сопротивление тарелки со слоем пены, Па;
DР4 - гидравлическое сопротивление встроенного каплеуловителя, Па.
Входные и выходные сопротивления рассчитывают как местные потери в
соответствии с конструкцией аппарата (например, внезапное расширение или
сужение на входе, плавный переход и отвод на выходе и т.д.).
Гидравлическое сопротивление тарелки DР2, Па, определяют по формуле
,(1.189)
где DРs - сопротивление, возникающее из-за
действия сил поверхностного натяжения, Па.
Для щелевых тарелок
,(1.190)
а для дырчатых
.(1.191)
Значения коэффициентов поверхностного натяжения для различных жидкостей sL приведены в приложениях.
.Величину брызгоуноса Lfl при установке тарелок не ближе, чем 0,9 м до
верха аппарата, определяют по формуле
(1.192)
где hb - исходная высота слоя жидкости на тарелке, м. Для пенного режима eе можно найти из выражения
.(1.193)
Коэффициент гидравлического сопротивления Vd сухой дырчатой или щелевой тарелки толщиной 4-6 мм
можно принимать в пределах 1,6-1,7.
. Полный коэффициент очистки газовых выбросов от дисперсных загрязнителей
htot подсчитывают по формуле (1.194),
принимая значение D50= 0,85 мкм и lgsh = 0,769. Приведенные эмпирические данные получены при
скорости газов в аппарате wo= 2 м/с и высоте слоя пены на тарелке hofrt= 0,09
м. При других параметрах w1 и h1 степень очистки пересчитывают по формуле
.(1.194)
Ориентировочную высоту слоя пены hfrt, м, можно определить по формуле
,(1.195)
или более точно (при известной начальной высоте слоя жидкости hb )
.(1.196)
.7.3 Расчеты аппаратов
Расчеты выполняют в следующем порядке.
По заданному расходу газа W=6,9 м3/с и рекомендуемой скорости 5 м/с
определяют диаметр аппарата
По таблице 1.9 принимают аппарат с наружным диаметром Dl=1,4 м и
максимальной производительностью 7,4 м3/с; высота выбранного типоразмера
скруббера 7,67 м, расход воды на орошение 0,65´10-3 м3/с. Коэффициент
гидравлического сопротивления V, отнесенный к динамическому давлению газового потока в сечении аппарата,
составляет 34,7. Приняв внутренний диаметр D=1340 мм, уточняем величину
скорости обрабатываемых газов в свободном сечении аппарата
. Скорости витания частиц с размерами до 100 мкм включительно определяют
по графику, частиц большего размера - по формуле (1.170), учитывающей
температуру газовых выбросов. Затем представляют в табличной форме заданный
фракционный состав дисперсного загрязнителя, записывают туда же соответствующие
фракциям скорости витания и находят для них по таблице 1.12 фракционные
коэффициенты очистки hF,
% для аппарата диаметром 1м. Значения hF интерполируют по уточненной скорости газового потока в
сечении аппарата w=4,9 м/с.
Таблица 1.13 - Фракционные коэффициенты очистки, hF,%
Размеры фракции, D, мкм
|
<16
|
16
|
25
|
40
|
63
|
100
|
160
|
250
|
Доля частиц g,% (масс.)
|
3
|
2
|
3
|
11
|
27
|
36
|
10
|
8
|
Скорость витания, м/с
|
<0,005
|
0,012
|
0,03
|
0,08
|
0,2
|
0,5
|
1,2
|
3
|
Коэффициент очистки, %
|
81,8
|
88,2
|
93,0
|
96,0
|
99,0
|
99,0
|
99,0
|
Скорости витания для фракций частиц с размерами до 160 мкм (0,16´10-3) и до 250 мкм (0,25´10-3) равны
Подсчитывают полный коэффициент очистки для аппарата диаметром 1 м.
Уточняют полный коэффициент очистки по диаметру скруббера
Ввиду невысокого коэффициента очистки скруббер ЦС ВТИ не имеет смысла
использовать для очистки даже от таких крупнодисперсных пылей. Специально
проектировать скрубберы данного типа для предварительной очистки газов также
нецелесообразно, так как имеется достаточный выбор более дешевых и менее
громоздких средств сухой очистки газов. В то же время имеющиеся на производстве
бездействующие или используемые не по назначению скрубберы такого типа ввиду
наличия керамической футеровки могут быть использованы, как было отмечено
ранее, для предварительной промывки запыленных газов, содержащих
коррозионно-агрессивные газы.
.7.4
Расчеты параметров скрубберов Вентури с определением степени очистки по
вероятностному методу
1. Выбирают тип скруббера. По заданному расходу газовых выбросов
подбирают по таблицам 1.10 - 1.12 типоразмер аппарата и выписывают его
технические характеристики. Затем по расходу и диаметру горловины трубы
вычисляют скорость газового потока в горловине.
. Принимают коэффициент гидравлического сопротивления сухой трубы Вентури
zd в пределах 0,12-0,15, а при
необходимости (при l/D>0,15)
рассчитывают его по формуле (1.174).
. Учитывая конструкцию скруббера, способ подвода орошающей жидкости в
трубу, скорость газового потока и соотношение длины горловины к диаметру,
подбирают необходимое уравнение (по формулам
1.168 - 1.173) и определяют величину zw.
. По величине zd
вычисляют гидравлическое сопротивление сухой трубы Вентури DРd, по выражению (1.176) - добавочное
сопротивление DРw, и затем -
полное сопротивление орошаемой трубы Вентури.
. Задаются величиной удельного орошения по опытным данным для
аналогичного состава дисперсных выбросов, а при их отсутствии принимают ее в
пределах 0,5-1,5 л/м3.
. Определяют ориентировочный размер капель Dвк, м, орошающей жидкости по эмпирическому соотношению
Нукиямы и Танасавы
, (1.197)
где WrG - скорость газов относительно
капли, м/с, которую принимают равной скорости газового потока в горловине трубы;
hL -
коэффициент динамической вязкости жидкости, Па с;
s - коэффициент поверхностного натяжения жидкости, Н/м (для воды при 20
°С);
hL = 10-3 Па с, s=72,8
10-3 Н/м).
Результаты определения размера капель по уравнению (1.197) следует
рассматривать как оценочные, однако более точных уравнений на настоящее время
нет.
. По формуле (1.179) определяют инерционный параметр Y для каждой фракции заданного состава
дисперсных загрязнителей.
. По формуле (1.180) находят коэффициенты захвата частиц определенных фракций
каплями орошающей жидкости hdr.
. Приняв найденные значения коэффициентов захвата за парциальные
коэффициенты очистки hр,
подсчитывают по формуле полный коэффициент очистки htot.
Точность полученного таким образом значения степени очистки газов невысока.
Другие способы расчетов коэффициентов очистки в скрубберах Вентури по
вероятностному методу также недостаточно точны.
В энергетических методах расчета предполагается, что зависимость
фракционных коэффициентов захвата от энергозатрат можно выразить логарифмически
нормальным законом и аппроксимировать график зависимости hdr = f(A) в вероятностно-
логарифмической системе координат прямой (или близкой к прямой) линией.
Полному коэффициенту осаждения частиц htot в аппаратах придается вид экспоненциальной функции энергозатрат
(1.198)
где А - удельные энергозатраты, Дж/м3, на осаждение частиц загрязнителя;
В и к - эмпирические величины.
Степень очистки связывают с числом единиц переноса (параметром,
характеризующим процессы в массообменных аппаратах) следующим соотношением
(1.199)
Из соотношения (1.199) следует легко запоминающееся правило, полезное при
оценке затрат энергии на очистку: N=2,3N9, где N - количество цифр 9, идущих подряд слева направо в
числе, выражающем требуемую степень очистки, %. Так, для достижения 90% очистки
необходимо обеспечить 2,3 единицы переноса; 99 % - 2,3 × 2=4,6 единиц; 99,99 % - 2,3 × 4=9,2 единиц и т.д.
В таблице 1.14 приведены числа единиц переноса для некоторых значений
коэффициентов очистки, вычисленные по соотношению (1.199).
Таблица 1.14 - Зависимость числа единиц переноса N от требуемой степени очистки газов, h, %
h, %
|
N
|
h, %
|
N
|
h, %
|
N
|
h, %
|
N
|
90
|
2,303
|
99,0
|
4,605
|
99,90
|
6,908
|
99,990
|
9,210
|
95
|
2,996
|
99,1
|
4,710
|
99,91
|
7,013
|
99,991
|
9,316
|
95,5
|
3,101
|
99,2
|
4,828
|
99,92
|
7,131
|
99,992
|
9,433
|
96
|
3,219
|
99,3
|
4,962
|
99,93
|
7,264
|
99,993
|
9,567
|
96,5
|
3,352
|
99,4
|
5,116
|
99,94
|
7,419
|
99,994
|
9,721
|
97
|
3,507
|
99,5
|
5,298
|
99,95
|
7,601
|
99,995
|
9,903
|
97,5
|
3,689
|
99,6
|
5,521
|
99,96
|
7,824
|
99,996
|
10,127
|
98
|
3,912
|
99,7
|
5,809
|
99,97
|
8,112
|
99,997
|
10,414
|
98,5
|
4,200
|
99,8
|
6,215
|
99,98
|
8,517
|
99,999
|
11,513
|
С учетом соотношения (1.198) зависимость (1.199) в расчетах обычно
используют в виде
.(1.200)
Значения коэффициентов В и k для
некоторых видов дисперсных загрязнителей приведены в таблице 1.15.
Очевидно, что определенный произвол, который трудно устранить при подборе
параметров В и k, может внести существенные погрешности в результаты расчетов.
Для получения достоверных результатов требуется и очень корректный подход
к определению доли энергии, затрачиваемой непосредственно на улавливание
загрязнителя. Точное теоретическое определение этой величины невозможно. В
практике проведения расчетов величину А составляют из нескольких позиций
энергозатрат индивидуально для каждого типа газоочистного устройства. Для
рассмотренных конструкций газопромывателей принимают, что доля энергии,
непосредственно обеспечивающая очистку газового потока, складывается из энергии
газового потока, затрачиваемой на создание газожидкостной смеси и энергии
жидкого потока, затрачиваемой на диспергирование жидкости. Потери энергии на
трение и местные сопротивления, возникающие при движении потоков к области
контакта фаз, должны быть исключены из затрат на очистку.
Степень очистки, определенная по энергетическому методу, оказывается
близкой к реальности для таких типов аппаратов, в которых осаждение
загрязнителей обеспечивается преимущественно за счет одного из энергетических
составляющих, а вкладом остальных составляющих допустимо пренебречь в пределах
точности инженерных расчетов. Так, например, для газопромывателей с трубами
Вентури, центробежных сепараторов ЦВП, ЦС, ВТИ, скрубберов ударно-инерционного
действия можно без значительной погрешности принять, что осаждение частиц в них
происходит за счет энергии газового потока. Поэтому сопротивление этих
аппаратов по газу может быть приравнено к величине удельных энергозатрат А в
формуле (1.200).
Таблица 1.15 - Значения В и k для некоторых видов дисперсных
загрязнителей
Наименование загрязнителя
|
В
|
k
|
Аэрозоль из известных печей
|
5,53´10-5
|
1,2295
|
- сульфата меди
|
2,14´10-4
|
1,068
|
- свинца и цинка из штатных
печей
|
6,74´10-3
|
0,478
|
- фосфорной кислоты
|
1,34´10-2
|
0,631
|
Зола-унос, пылевидное
сжигание углей
|
4,34´10-3
|
0,3
|
Пыль ваграночная
|
1,36´10-2
|
0,621
|
- доменная
|
1,925´10-1
|
0,326
|
- колосниковая
|
6,61´10-3
|
0,891
|
-конвертеров при продувке
кислородом сверху
|
9,88´10-2
|
0,466
|
- томасовских
|
2,68´10-1
|
0,259
|
- печей известковых
|
6,5´10-4
|
1,053
|
- карбидных (в дымовых
газах)
|
0,82´10-3
|
0,914
|
- мартеновских на дутье
воздушном
|
1,74´10-6
|
1,594
|
- на дутье, обогащенном
кислородом
|
1,565´10-6
|
1,619
|
- плавильных (для латуни) с
оксидами цинка
|
2,34´10-2
|
0,532
|
- закрытых (для
ферросилиция)
|
6,49´10-5
|
1,1
|
- электрических (для
ферросилиция)
|
2,42´10-5
|
1,26
|
Тоже ферросплавных (для
силикомарганца)
|
6,9´10-3
|
0,67
|
- производства калийных
удобрений
|
9,05´1011
|
2,92
|
- целлюлозы
|
4´10-4
|
1,05
|
- - производства каолина
|
2,34´10-4
|
1,15
|
- мыла (дурнопахнущие
вещества)
|
1,09´10-5
|
1,415
|
- черного щелока, обработка
сухих газов
|
9,3´10-4
|
0,861
|
Тоже предварительно
увлажненных газов
|
1,32´10-3
|
0,861
|
Фосфорных удобрений (после
циклона)
|
1,2´10-1
|
0,454
|
- тальковая
|
2,06´10-1
|
0,351
|
Сажа процесса
электрокрекинга метана
|
10-5
|
1,36
|
Соли натрия в дымовых газах
печей термообработки сточных вод.
|
0,21´10-5
|
1,515
|
Список перечисленных выше аппаратов может быть дополнен пен-1 абсорбером
при условии, что в качестве удельной энергозатраты на очистку газов принимается
сопротивление не всего аппарата, а только тарелок со слоем пены (и при наличии
каплеуловителей и стабилизирующих решеток). Сопротивление же конструктивных
элементов на входе и выходе пенного аппарата (отводов, тройников, расширения и
сужения потока) учитываться не должно. В насадочных скрубберах и центробежных
аппаратах с форсуночным распылением жидкости следует учитывать потери энергии
газового и жидкого потоков. Для полых газопромывателей основные затраты энергии
на очистку связаны с распылом орошающей жидкости. Удельные затраты энергии на
распыливание жидкости А, Дж/м3, при условии использования совершенных
конструкций распылителей, рассчитывают по формуле
,(1.201)
где DР - давление
жидкости перед форсункой, Па.
.7.5
Расчеты мокрых скрубберов по энергетическому методу
1. По расходу, составу и свойствам выбросов, требуемой степени их очистки
выбирают подходящий тип аппарата.
. Из уравнения (1.199) или из таблицы 1.14 находят необходимое число
единиц переноса.
. Принимают значения В и k, используя данные таблицы 1.15, если заданного
вида пыли нет в таблице, желательно провести поиск сведений по другим
источникам. При полном отсутствии необходимых сведений остается принимать
значения В и k для сходных видов пыли, промышленного оборудования,
технологических процессов и т.д.
. Находят из уравнения (1.200) долю энергозатрат А, необходимую для
обеспечения требуемого числа единиц переноса.
. Распределяют найденную величину энергозатрат А между элементами аппарата,
создающими контакт газов с жидкостью, учитывая их конструктивные особенности и
избегая шаблонности.
. Рассчитывают сопротивления указанных элементов, приводя расходы и
другие характеристики потоков к условиям обработки в аппарате.
. Оценивают приемлемость полученных значений сопротивлений аппарата для
имеющихся в наличии или намеченных к установке тягодутьевых устройств. Решение
об использовании аппарата следует принимать с учётом величины материальных и
энергетических затрат, количества образующихся стоков и т.д.
. Если принято решение об использовании рассматриваемого типа аппарата,
определяют по величине сопротивления скорости газового потока и жидкости в
соответствующих элементах, а по ним - требуемые размеры элементов.
. Уточняют размеры элементов, принимая типовые или стандартные изделия,
выписывают их характеристики и подбирают тягодутьевые устройства, насосы,
другое вспомогательное оборудование; производят расчет коммуникаций.
.7.6
Пенные аппараты
Впервые пенный способ очистки запыленных газов предложен и подробно
исследован M. E. Позиным. Аппарат (рисунок 1.23) может работать со свободным
сливом пены или с подпором пены сливной перегородкой (второй режим
предпочтительнее).
1 - корпус; 2 - тарелка; 3 - приемная коробка; 4 - порог; 5 - сливная
коробка
Рисунок 1.23 - Пенный пылеуловитель с переливной тарелкой
Пенный аппарат с дырчатыми тарелками
В аппарате обычно устанавливаются дырчатые тарелки с диаметром отверстий
3-8 мм и свободным сечением от 0,15 до 0,25 м2/м2. Геометрические размеры
тарелок приведены в таблице 1.16
Для уменьшения вероятности забивания отверстий тарелки пылью разработаны
аппараты с провальными тарелками, в которых подвод газов в зону контакта с
жидкостью и отвод последней из этой зоны осуществляется через одни и те же
дырчатые или щелевые отверстия (рисунок 1.24).
Для очистки газов применяются два основных вида провальных тарелок:
дырчатые и щелевые (рисунок 1.25).
Щелевые тарелки подразделяются на решетчатые, трубчатые и колосниковые. Трубчатые
и колосниковые щелевые тарелки изготовляются сварными из трубок, пластин или
прутков.
Таблица 1.16 - Геометрические размеры тарелок с круглыми отверстиями
Шаг отверстий, мм
|
Диаметр отверстий, мм
|
Своб. сечение, м2/м2
|
Шаг отверстий, мм
|
Диаметр отверстий, мм
|
Своб. сечение, м2/м2
|
6
|
6
|
0,226
|
12
|
5
|
0,157
|
8
|
4
|
0,226
|
13
|
5
|
0,134
|
9
|
4
|
0,179
|
13
|
6
|
0,193
|
10
|
5
|
0,226
|
13
|
7
|
0,263
|
10
|
5,5
|
0,272
|
14
|
6
|
0,167
|
11
|
5
|
0,187
|
16
|
7
|
0,174
|
11
|
6
|
0,271
|
18
|
8
|
0,179
|
1 - корпус; 2 - оросительное устройство; 3 - тарелка
Рисунок 1.24 - Мокрый пылеуловитель с провальной тарелкой
Оптимальная толщина тарелки с точки зрения гидравлического сопротивления
должна составлять 4-6 мм.
а - щелевая; б - дырчатая
Рисунок 1.25 - Конструкции провальных тарелок
Диаметр отверстий d0 в тарелках пылеулавливающего аппарата составляет от
4 до 8 мм, ширина щели b = 4-5 мм, а свободное сечение колеблется от 0,2 до
0,25 м2/м2.
В теплообменных аппаратах ширина щели может быть увеличена от 5 до 8 мм,
а свободное сечение - от 0,4 до 0,5 м2/м2.
Необходимое число щелей на тарелке n может быть определено из приведенных
ниже данных:
n
|
X
|
n
|
X
|
n
|
X
|
1
|
0.000
|
11
|
8.042
|
21
|
15.015
|
2
|
0.866
|
12
|
8.832
|
22
|
16.713
|
3
|
1.668
|
13
|
9.620
|
23
|
17.500
|
4
|
2.498
|
14
|
10.411
|
24
|
18.287
|
5
|
3.296
|
15
|
11.200
|
25
|
19.094
|
6
|
4.093
|
16
|
11.982
|
26
|
19.860
|
7
|
4.887
|
17
|
12.776
|
27
|
20.648
|
8
|
5.679
|
18
|
13.564
|
28
|
21.432
|
9
|
6.471
|
19
|
29
|
22.219
|
10
|
7.257
|
20
|
15.138
|
30
|
23.005
|
Параметр X определяется из выражения
Х=0,785D2S0/(l0b),(1.202)
где D - диаметр аппарата, м;- свободное сечение тарелки, м2/м2;- длина
самой длинной щели, расположенной по диаметру тарелки и равной D - 0,01 м.
Общая длина всех щелей
Уl=0,785 D2S0/b,(1.203)
а шаг между щелями
t = l0 / n = c + b,(1.204)
где с - ширина промежутка между соседними щелями, м;- ширина щели, м.
Исходными данными для расчета аппарата являются расход очищаемых газов
Qr, плотность частиц улавливаемой пыли r, и ее дисперсный состав.
Дырчатые тарелки (таблица 1.16) имеют ромбическую разметку (по
равностороннему треугольнику), при которой шаг, м, определяется из выражения
(1.205)
Удельное орошение при очистке газов (без необходимости охлаждения)
составляет от 0,4 до 0,6 л/м3 газов.
Плотность орошения Wж,
кг/(м3 с), находят из выражения
,(1.206)
где m - удельное орошение, м3/м3 газов;
wГ -
минимальная линейная скорость газов, при которой образуется пенный режим в
указанных пределах плотности орошения, может быть принята равной от 1,0 до 1,2
м/с.
Расчет максимальной скорости газов при пенном режиме w кр, м/с, ведется методом
последовательных приближений по эмпирическому уравнению
,(1.207)
где dэ - эквивалентный диаметр отверстий тарелки, м: для дырчатых тарелок
dэ= d0 , для щелевых dэ=2b;
А - коэффициент, определяемый из выражения
,(1.208)
где Wст - стандартная плотность орошения,
равная 1 кг/(м3с).
При расчете предварительно задаются линейной скоростью газов в аппарате Wг, принимая равной от 2 до 2,3 м/с, и
по уравнению (1.206) определяют Wж.
Рабочая скорость газов Wг в
аппарате (на входе в слой пены) должна составлять от 0,9 до 0,95 Wкр. Если Wкр окажется по расчету меньше принятой Wг или больше, чем 1,1Wг, то расчет повторяют с внесением
соответствующих поправок в принятое значение Wг.
Диаметр аппарата D, м,
определяют по уравнению
.(1.209)
Если диаметр аппарата оказывается большим (D>2,5 м), то следует
устанавливать несколько параллельных аппаратов. Большое внимание в этом случае
следует уделять равномерному распределению газов по всей площади сечения
аппарата. Поэтому в аппаратах большого сечения иногда устанавливают вместо
одной две тарелки, полагая, что первая из них (по ходу газов) обеспечивает
равномерное газораспределение.
Полное гидравлическое сопротивление аппарата ДР, Па, определяют по уравнению
,(1.210)
где DРвх -
гидравлические потери при входе газов в аппарат, Па;
DРвых -гидравлические потери при выходе газов из аппарата, Па;
DРт - полное гидравлическое сопротивление одной или нескольких тарелок (в
случае многополочного аппарата) со слоем пены, Па;
DРкап - гидравлическое сопротивление каплеуловителя, встроенного в
аппарат, Па.
Значения DРвх,
DРвых невелики и составляют 50-100 Па.
Полное гидравлическое сопротивление тарелки, Па, определяют по формуле
,(1.211)
где Дсs -
гидравлическое сопротивление за счет сил поверхностного натяжения, Па.
При пенном режиме взаимодействия газов и жидкости коэффициент А
рассчитывают из выражения (1.208).
Для щелевых тарелок ДРу, рассчитывают по уравнению
,(1.212)
где у - коэффициент поверхностного натяжения на границе раздела фаз газ -
жидкость, Н/м.
Для расчета ДРу дырчатых тарелок рекомендуется формула
.(1.213)
Гидродинамический расчет пенных аппаратов с провальными тарелками может
быть проведен по номограмме, приведенной на рисунке 1.26. С помощью номограммы
может быть определен один из четырех параметров (wг, m, do,
S0) при трех других заданных, гидравлическое сопротивление тарелки ДPт, а также высота слоя пены на
тарелке Hn. Номограмма может быть применена при скоростях газов от 0,8 до 2,0
м/с, т. е. в пределах протекания пенного режима.
Для уменьшения уноса брызг верхняя тарелка пенного пылеуловителя должна
быть удалена от места отвода газов из аппарата на расстояние не менее 1,0 м.
Общая эффективность пылеулавливания пенных аппаратов, как с переливными,
так и с провальными тарелками рассчитывается по формуле (1.54) при d50=0,85 мкм
и lg уh = 0,769. Значения d50 и lg уh получены для условий: скорость газов
в аппарате WГ=2 м/с, высота слоя пены на тарелке Hn=0,09 м. Поэтому в случае необходимости для аппаратов с
другими параметрами значения з могут быть уточнены по формуле
,(1.214)
где зо - эффективность при WГ = 2
м/с и НП = 0,09 м.
При очистке газов с большой начальной запыленностью (Свх>15-20 г/м3)
целесообразно применять двухполочные аппараты.
Если аппарат с провальными тарелками используется для кондиционирования
газов (охлаждения, увлажнения и предварительной очистки) или устанавливается
перед другим мокрым пылеуловителем, он может работать при w>wКР, но ниже точки захлебывания.
Скорость газов в аппарате с провальными тарелками, соответствующая точке
захлебывания wЗ ,м/с, может
быть определена из эмпирического выражения
.(1.215)
Рисунок 1.26 - Номограмма для гидродинамического расчета пенных аппаратов
с провальными тарелками
Ключ: wГ®m®d0®S0 ®wГ ® ДPт ,
wГ®m®d0®S0 ®Hп.
Доля свободного сечения тарелки ц, занятая газом, рассчитывается по
формуле
,(1.219)
где осух - коэффициент гидравлического сопротивления сухой тарелки; для
обычно применяемых в пенных пылеуловителях дырчатых и щелевых тарелок толщиной
4-6 мм осух »1,6-1,7.
Гидравлическое сопротивление провальных тарелок со свободным сечением Sо £ 0,25 м2/м2 при wГ >wКР, а также провальных тарелок с большим свободным
сечением рассчитывают также по формуле (1.211) с использованием соответствующих
коэффициентов А (таблица 1.17).
Таблица 1.17 - Формулы для расчета коэффициента А для провальных тарелок
различного типа
Тип тарелки
|
Свободное сечение тарелки,
м2/м2
|
Скорость газов в свободном
сечении аппарата, м/с
|
Формула для расчета
|
Дырчатые и щелевые
|
0,15-0,25
|
wГ>wКР
|
(1.216)
|
Дырчатые и щелевые
|
0,3-0,4
|
wГ =0,8-5,0
|
(1.217)
|
Трубчатые
|
0,3-0,4
|
wГ =1,0-3,5
|
(1.218)
|
Пенный аппарат со стабилизатором пенного слоя (ПАСС)
Газопромыватель разработан ЛТИ совместно с институтом
Проектпромвентиляция. Отличие аппарата от газопромывателя с провальной тарелкой
заключается в установке непосредственно на тарелке стабилизатора,
представляющего собой сотовую решетку из вертикально расположенных пластин,
разделяющих сечение аппарата и пенный слой на небольшие ячейки (рисунок 1.27).
Рисунок 1.27 - Стабилизатор
Стабилизатор пены предотвращает возникновение волнового режима на тарелке
вплоть до скорости газов 4,0 м/с, т. е. существенно расширяет скоростной
интервал пенного режима. Благодаря стабилизатору происходит значительное
накопление жидкости на тарелке и, следовательно, увеличение высоты пены по
сравнению с провальной тарелкой без стабилизатора. Применение стабилизатора
позволяет существенно сократить расход воды на орошение аппарата.
Рекомендуются следующие размеры стабилизатора: высота пластин 60 мм;
размер ячеек - от 35x35 до 40х40 мм. Оптимальными условиями работы аппарата
являются: wГ = 2,5-3,5 м/с
и m = 0,05-0,1 л/м3. В аппарате
устанавливаются дырчатые провальные тарелки с dо=3-6 мм и S0=0,14-0,22 м2/м2 и
щелевые (трубчатые) провальные тарелки с b=3-6 мм и Sо=0,12-0,18 м2/м2 .
Диаметр труб в трубчатых тарелках dтр=с=20-32 мм.
Высоту слоя пены Hп, образующейся на дырчатых тарелках, определяют по
номограмме на рисунке 1.28, а, образующейся на трубчатой тарелке - по
номограмме на рисунке 1.28, б.
а - на дырчатых тарелках (ключ: wг®Wж®S0®d0®rж®Hn);
б - на трубчатых тарелках (ключ: wг®Wж®S0®d0®rж®Hn)
Рисунок 1.28 - Номограмма для определения высоты пенного слоя
Гидравлическое сопротивление газопромывателя ПАСС рассчитывается по
формуле (1.210), причем ДРт , м, находят из выражения
.(1.220)
Гидравлическое сопротивление пенного слоя ДРп находится по номограмме,
приведенной на рисунке 1.29.
Ключ: Hn®rж®wг®DRu
Рисунок 1.29 - Номограмма для определения гидравлического сопротивления
пенного слоя аппарата типа ПАСС
Эффективность улавливания пыли в газопромывателе ПАСС может быть
определена на основании значений d50 и lgуз для пенных аппаратов с учетом поправки по уравнению
(1.214).
Типоразмерный ряд газопромывателей ПАСС типа ПВПР (рисунок 1.30)
производительностью по газу от 3000 до 90000 м3/ч, состоящий из 12
типоразмеров, разработан институтом Ленгипрогазоочистка. Корпус аппарата
круглого сечения собирается из секций, что позволяет производить компоновку с
одной или двумя тарелками.
Таблица 1.18 - Технические характеристики газопромывателей типа ПВПР
Наименование
|
Марка аппарата
|
|
ПВ ПР-3
|
ПВ ПР-4
|
ПВ ПР-5
|
ПВ ПР-7
|
ПВ ПР-9
|
ПВ ПР-12
|
ПВ ПР-17
|
ПВ ПР-22
|
ПВ ПР-30
|
ПВ ПР-41
|
ПВ ПР-44
|
ПВ ПР-80
|
Производительность по газу,
м3/ч Основные размеры, мм: D D11 D2 Н/Н* Mасса, кг
|
2500-3400 600 500 300
3890 3190 725
|
3400-4500 700 600 350
424503645 915
|
4500-6200 800 700 400
4550 3950 1120
|
6200-7500 900 700 500
5125 4525 1135
|
7500-10000 1000 800 500
5385 5085 1570
|
10000-15000 1200 1000
600 6835 5835 2640
|
16000-18700 1400 1200
600 7380 6380 3200
|
18700-24000 1600 1400
600 7855 6855 3810
|
24000-32500 1800 1600
800 9330 8330 6440
|
32600-45700 2200 1800
1000 10990 9790 8370
|
45700-64000 2600 2200
1200 12100 10900 11340
|
64000-90000 3000 2400
1200 13520 12320 13090
|
Н* - высота аппарата с одной тарелкой (без средней секции)
Предусмотрено применение тарелок двух типов: дырчатой с S0=0,18 м2/м2 или
трубчатой с S0=0,167 м2/м2 . В верхней части скруббера установлен центробежный
каплеуловитель с цилиндрическим завихрителем. Максимальная температура газов на
входе в аппарат 100 0C, максимальное разрежение 5 кПа. Технические
характеристики газопромывателей ПВПР приведены в таблице 1.18.
1 - брызгоуловитель; 2 - центробежный завихритель;
- патрубок для отвода жидкости из брызгоуловнтеля;
- верхняя секция; 5 - средняя секция; 6 - стабилизатор;
- нижняя секция; 8 - тарелка; 9 - ороситель;
- форсунка для периодического орошения завихрителя
Рисунок 1.30 - Газопромыватель типа ПВПР
Гидродинамический пылеуловитель ГДП (рисунок 1.31) разработан НИПИОТСТРОМ
и предназначен для очистки аспирационного воздуха и газов от пыли, не
схватывающейся в воде. Он является аппаратом непрерывного действия с внутренней
циркуляцией жидкости и периодической разгрузкой уловленных продуктов в виде
шлама или растворов. Это позволяет эксплуатировать аппарат с очень низким
удельным орошением.
Запыленный газ сначала поступает в подрешеточное пространство,
захватывает часть жидкости, а затем, пройдя отверстия решетки (тарелки, в
которых скорость газа составляет 10-12 м/с), контактирует со слоем
турбулизированной пены. Для обеспечения равномерного распределения газа в
свободном сечении решетки, ее отверстия выполнены с увеличением диаметра по
мере удаления отверстий от входного патрубка.
Таблица 1.19 - Технические характеристики газопромывателей типа ГДП-М
Наименование
|
Марка аппарата
|
|
ГДП-5М
|
ГДП-7М
|
ГДП-10М
|
Производительность по газу,
м3/ч
|
5000
|
7000
|
10000
|
Максимальная температура
газа на входе, 0О С
|
250
|
Максимальное гидравлическое
сопротивление, Па
|
1800
|
Запыленность газов на входе,
г/м3
|
До 30
|
Удельное орошение, л/м3
|
0,015-0,05
|
Диаметр аппарата, м
|
1,0
|
1,25
|
1,5
|
Высота аппарата, м
|
2,9
|
3,2
|
3,65
|
Масса в рабочем состоянии,
кг
|
1000
|
1560
|
2200
|
|
|
|
|
|
Очищенный от пыли газ проходит через каплеотделитель и через выходной
патрубок отводится в атмосферу. Уловленная пыль в виде шлама осаждается в
бункерной части и через разгрузочное устройство, периодически выводится из
аппарата. Аппарат обеспечивает высокую эффективность при улавливании частиц
пыли крупнее 5 мкм.
Разработан типоразмерный ряд газопромывателей типа ГДП-М, технические
характеристики которого приведены в таблице 1.19.
1 - корпус; 2 - центробежный каплеуловитель; 3 - реле управления
водоподпиткой; 4 - патрубок для входа газов; 5 - тарелка; 6 - разгрузочное
устройство; 7 - электромагнитный клапан; 8 - гидрозатвор; 9 - регулятор уровня
жидкости; 10 - электромагнитный вентиль
Рисунок 1.31 - Газопромыватель типа ГДП-М
тепловой
абсорбер тарельчатый насадочный
Глава
2. Примеры расчета абсорбционных аппаратов
.1 Расчет
насадочного абсорбера
Пример 1. Рассчитать противоточный абсорбер насадочного типа для поглощения SO2
водой из газа состава (% об.): 7% SO2, 97% N2. Суточный расход газа на входе V2
=120000 м3 ; давление смеси Р = 760 мм рт.ст. На орошение подается вода при
температуре 30 0С. Содержание SO2 в уходящем газе не более 0,3%.
Для упрощения приведенных ниже расчетов газовая смесь и поглотитель
рассматриваются как бинарные, состоящие из распределяемого компонента и
инертной части (носителей); физические свойства их приняты осредненными.
Для линеаризации уравнения рабочей линии абсорбции составы фаз выражают в
относительных концентрациях распределяемого компонента, а нагрузки по фазам - в
расходах инертного носителя. В приведенных ниже расчетах концентрации выражены
в относительных массовых долях распределяемого компонента, а нагрузки - в
массовых расходах носителей.
Геометрические размеры колонного массообменного аппарата определяются в
основном поверхностью массопередачи, необходимой для проведения данного
процесса, и скоростями фаз.
Поверхность массопередачи может быть найдена из основного уравнения
массопередачи (1.1)
где Kx, Ky - коэффициенты массопередачи соответственно по жидкой
и газовой фазам, кг/(м2 с).
Масса поглощаемого вещества и расход поглотителя
Массу диоксида серы, перешедшего в процессе абсорбции из газовой смеси в
поглотитель за единицу времени, находят из уравнения материального баланса
(1.5)
,
где
L, G - расходы соответственно
чистого поглотителя и инертной части газа, кг/с;
-
начальная и конечная концентрация диоксида серы в поглотителе (воде), кг SO2
/кг М;
- начальная и конечная концентрация диоксида серы в
газе, кг SO2/кг Г.
Движущая сила массопередачи
Движущая сила, в соответствии с уравнениями (1.49 и 1.50), может быть
выражена в единицах концентраций как жидкой, так и газовой фаз. Для случая
линейной равновесной зависимости между составами фаз, принимая модель
идеального вытеснения в потоках обеих фаз, определим движущую силу в единицах
концентраций газовой фазы
где
- большая и меньшая движущие силы на входе потоков в
абсорбер и на выходе из него,
(рисунок
2.1).
В
данном примере
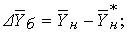


где
и
-
концентрации диоксида серы в газе, равновесные с концентрациями в жидкой фазе
(поглотителе) соответственно на входе в абсорбер и на выходе из него (рисунок
2.1)
Рисунок 2.1 - Схема распределения концентраций в газовом и жидкостном
потоках в абсорбере
В химической промышленности особое значение при выборе насадки имеют следующие
факторы: малое гидравлическое сопротивление абсорбера, возможность устойчивой
работы при сильно изменяющихся нагрузках по газу, возможность быстро и дешево
удалять с поверхности насадки отлагающийся шлам и т. д. Таким требованиям
отвечают широко используемые деревянная хордовая и металлическая спиральная
насадки.
Расчет коэффициентов массоотдачи
Для регулярных насадок (к которым относится и хордовая) коэффициент
массоотдачи в газовой фазе by находят из
уравнения (1.63)
где
- диффузионный критерий Нуссельта для газовой фазы.
Отсюда
by (в м/с)
равен
где Dy-средний коэффициент диффузии диоксида серы в газовой фазе,
м2/с;
-
критерий Рейнольдса для газовой фазы в насадке;
-
диффузионный критерий Прандтля для газовой фазы; my- вязкость
газа, Па×с; l- высота элемента насадки, м.
Для
колонн с неупорядоченной насадкой коэффициент массоотдачи by можно найти из уравнения
(1.62)
Коэффициент массоотдачи в жидкой фазе bх
находят из обобщенного уравнения, пригодного как для регулярных (в том числе и
хордовых), так и для неупорядоченных насадок (1.64)
,
где
- диффузионный критерий Нуссельта для жидкой фазы.
Отсюда
bх (в м/с)
равен
,
где Dх - средний коэффициент диффузии диоксида серы в воде, м2/с;
-
приведенная толщина стекающей пленки жидкости, м;
-
модифицированный критерий Рейнольдса для стекающей по насадке пленки жидкости;
-
диффузионный критерий Прандтля для жидкости.
Составление материального баланса и определение расхода воды
Концентрация SO2 в поступающем газе на 1 кг инертного газа
здесь количество инертного газа, поступающего в абсорбер,
где парциальное давление газа
температура газа TN2 =
273+30 = 303 K; газовая постоянная инертного газа
(азота)
.
Количество SO2, поступающего в абсорбер,
где
Парциальное давление SO2 в поступающем газе
мм
рт. ст.
Концентрация SO2 в уходящем газе на 1 кг инертного газа
где
=31,8 мм рт.
ст. при 30оС, а парциальное давление SO2 в уходящем газе
мм
рт. ст.
Количество поглощенного SO2
где степень извлечения SO2
Определяем
парциальное давление SO2 над поступающей жидкостью. Если на орошение подается
чистая вода
, то
При
парциальном давлении SO2 в поступающем газе pн=53,2 мм рт.ст.
равновесная концентрация SO2 в жидкости, вытекающей из абсорбера,
составит
кг SO2 на 100 кг воды.
Упругость
паров pSO2 над водным раствором при 30оС находим (Приложение А 1) по
концентрации SO2 в растворе (
)
в кг (на 100 кг
H2O)0,020,050,100,150,200,300,500,701,00
|
|
|
|
|
|
|
|
|
|
в мм рт. ст.0,11,74,78,111,819,736,052,079,0
|
|
|
|
|
|
|
|
|
|
Предполагая,
что концентрация воды на выходе достигнет значения
находим минимальный расход воды
Действительный расход поглотителя при 20 %-м запасе
L = 121000 · 1,2 = 145000 кг/ч.
Действительное содержание SO2 в уходящей воде на 100 кг H2O
на
1 кг H2O
= 0,00593
кг.
Парциальное
давление SO2 над уходящей жидкостью при
= 0,593
кг на 100 кг H2O определяем по приведенным выше данным
мм рт. ст.
Расход воды на 1кг инертного газа проверяем по уравнению материального
баланса
.
Определение диаметра абсорбера
В качестве насадки выбираем кокс. Средний размер кусков dср=75 мм;
удельная поверхность насадки а=42 м2/м3; свободный объем Vcв=0,58
м3/м3.
По уравнению определяем скорость газа при захлебывании, учитывая, что при
30оС
;
отсюда wo=0,81 м/с.
Принимаем рабочую скорость газа
.
Площадь сечения абсорбера
откуда диаметр абсорбера Д=1,65 м.
Проверяем выбранную площадь сечения абсорбера по плотности орошения.
Плотность орошения и активная поверхность насадки
Плотность орошения (скорость жидкости) рассчитывают по формуле (1.31)
где S - площадь поперечного сечения абсорбера, м2.
При недостаточной плотности орошения и неправильной организации подачи
жидкости поверхность насадки может быть смочена не полностью. Но даже часть
смоченной поверхности практически не участвует в процессе массопередачи ввиду
наличия застойных зон жидкости (особенно в абсорберах с нерегулярной насадкой)
или неравномерного распределения газа по сечению колонны.
Существует некоторая минимальная эффективная плотность орошения Umin,
выше которой всю поверхность насадки можно считать смоченной. Для пленочных
абсорберов ее находят по формуле
.
Здесь
где
Гmin - минимальная линейная плотность орошения,
;
s - поверхностное
натяжение,
.
В
проектируемом абсорбере плотность орошения U выше Umin, поэтому в
данном случае коэффициент смачиваемости насадки y = 1.
Для
насадочных абсорберов минимальную эффективную плотность орошения Umin
находят по соотношению:
где qэф- эффективная линейная плотность орошения, м2/с.
Для колец Рашига размером 75 мм и хордовых насадок с шагом более 50 мм qэф=
0,033×10-3м2/с; для всех остальных насадок qэф=0,022×10-3м2/с.
Коэффициент смачиваемости насадки y для колец Рашига при заполнении колонны внавал можно
определить из следующего эмпирического уравнения
где
dн - диаметр насадки;
При
абсорбции водой и водными растворами хорошо растворимых газов смоченная
поверхность насадки уменьшается. Поэтому полная смачиваемость достигается при
более высоких значениях Г. Для таких систем значение Гmin может быть рассчитано
по уравнению
где коэффициент A зависит от краевого угла смачивания и изменяется в
пределах 0,12-0,17; Ds - разница между поверхностным натяжением жидкости, подаваемой на
орошение колонны, и жидкости, вытекающей из нее.
Доля активной поверхности насадки yа может быть найдена по формуле
где p и q - коэффициенты, зависящие от типа насадки.
Не вся смоченная поверхность является активной. Наибольшая активная
поверхность насадки достигается при таком способе подачи орошения, который
обеспечивает требуемое число точек орошения n на 1 м2 поперечного
сечения колонны. Это число точек орошения и определяет выбор типа
распределительного устройства.
Плотность орошения насадки
где
1,5
- минимально допустимая плотность орошения.
Оптимальная
плотность орошения
.
Плотность орошения удовлетворяет условию хорошей смачиваемости насадки,
так как
.
Так как плотность орошения значительно больше оптимальной, то
сопротивление колонны может возрасти. Для снижения U следует выбрать
насадку другого типа. Выбираем в качестве насадки кокс: dср=25 мм; а=120
м2/м3; Vcв=0,53 м3/м3. Для этой насадки скорость газа при
захлебывании находим из соотношения
откуда wo=0,422 м/с.
Рабочая скорость газа w
= 0,8∙0,422 = 0,338 м/с. Тогда площадь сечения абсорбера S=4,1 м2 и
диаметр абсорбера Д=2,28 м.
Проверяем снова плотность орошения
Определение высоты насадки
Высоту насадки определяем, исходя из основного уравнения массопередачи.
Рассчитываем среднюю движущую силу процесса.
Движущая сила процесса абсорбции внизу абсорбера
Движущая сила наверху абсорбера
Так как
то среднюю движущую силу процесса определяем по формуле
Рассчитываем коэффициент массопередачи. Полагая, что диффузионное
сопротивление жидкости мало по сравнению с сопротивлением газа, принимаем, что
коэффициент массопередачи K равен коэффициенту массоотдачи bг для газовой фазы.
В первом варианте расчета используем критериальное уравнение
Здесь динамическую вязкость газа находим, как вязкость газовой смеси
где молекулярную массу смеси SO2 и N2 определяем по составу газа
а
динамическую вязкость составляющих газов
и
при 30оС находим по графику (Приложение А 4).
Получаем
mг=0,017 мПа = 0,017×10-3 кг/(м×с).
Диффузионный
критерий Прандтля для газа
.
Здесь коэффициент диффузии SO2 в воздухе при 30оС рассчитываем по
уравнению
где D=0,037 м2/ч - коэффициент диффузии при 00 С и p0=1 кгс/см2.
Рассчитываем диффузионный критерий Нуссельта для газа
Коэффициент массоотдачи
здесь
Необходимая площадь поверхности абсорбции
Высота насадочной части абсорбера
Так как надежных уравнений для однозначного определения коэффициента
массопередачи нет, выполним второй вариант расчета, используя эмпирические
уравнения для объемных коэффициентов массоотдачи (абсорбция SO2 водой в колонне,
заполненной кольцами).
Коэффициент массоотдачи в газовой фазе выражается уравнением

Объемный коэффициент массоотдачи в жидкой фазе (при 30°С)
.
Рассчитаем
объемный коэффициент массопередачи. Так как коэффициенты массоотдачи bгV и bжV выражены
соответственно в 
и 
,
выполним пересчет константы фазового равновесия m. Формулу пересчета можно
записать следующим образом
,
здесь Mж и rж
- молекулярная масса и плотность растворителя.
Принимая для воды Мж= 18 и rж= 1000 кг/м3 , находим
Значение
постоянной mpx для водного раствора SO2 при 30оС находим по таблицам:
Объемный
коэффициент массопередачи
Высота насадочной части абсорбера
где Gа- в кмоль/ч.
Расчет высоты абсорбера по числу единиц переноса (ЧЕП)
Высоту насадки рассчитываем по формуле (1.67). Для определения ЧЕП строим
рабочую линию процесса (рисунок 2.3)
Наносим на график линию равновесия, представляющую собой равновесные
относительные массовые концентрации Y* при различных X. По данным, X=0,0002
кг SO2 на 1 кг H2O и P* = 0,1 мм рт. ст. Пересчитываем
концентрацию Х из относительных массовых долей в молярные по формулам
перевода.
При малых значениях Х для пересчета применяют формулу
Рисунок 2.2 - График к определению числа единиц переноса
Константы фазового равновесия
Равновесная концентрация SO2 в газе на 1 кг N2
или [по формуле(1.11)]
Результаты расчета сведены в таблицу 2.1.
Таблица 2.1 - Результаты расчета
Х
|
0,0002
|
0,0005
|
0,001
|
0,0015
|
0,002
|
0,003
|
0,005
|
0,007
|
р*
|
0,1
|
1,7
|
4,7
|
8,1
|
11,8
|
19,7
|
36
|
52
|
х×104
|
0,563
|
1,41
|
2,81
|
4,22
|
5,63
|
8,45
|
14,1
|
19,7
|
mpx
|
1780
|
12000
|
16750
|
19200
|
21000
|
23400
|
25600
|
26400
|
myx
|
2,34
|
15,9
|
22,1
|
25,3
|
27,7
|
30,8
|
33,8
|
34,8
|
Y*
|
0,0003
|
0,0051
|
0,014
|
0,024
|
0,036
|
0,06
|
0,11
|
0,16
|
Число единиц переноса определяем графически, для чего через середины
отрезков В0 и Аf проводим среднюю линию. Затем через точку В
проводим горизонталь, на которой откладываем отрезок Bb (причем Вa=ab).
В точке b восстанавливаем перпендикуляр bc, продолжая построение
ступенек до точки А. Ступенька Bbc представляет собой единицу переноса.
Число единиц переноса, соответствующее последней неполной ступеньке deA,
находим как отношение отрезка Aе к отрезку ll, проведенному через
середину основания неполной ступеньки de. Отношение Ае/ll = 0,25
и общее число единиц переноса z = 9,25. Рассчитываем высоту насадки,
эквивалентную одной единице переноса (ВЕП).
Для газовой фазы
Проверяем ВЕП по формуле для беспорядочной насадки, уложенной навалом
Среднее значение
.
Для жидкой фазы рассчитываем ВЕП по формуле, в которой приведенная
толщина стекающей пленки жидкости
где mж=0,8 мПа=0,8 × 10-3 кг/(м × с); rж=1000 кг/м3.
Число Рейольдса для жидкости
Диффузионный критерий Прандтля для жидкости
Коэффициент диффузии SO2 в жидкости вычисляем по формуле при 30°С
при 20°С
десь mж=1,005
мПа (вода, 20°С);
Коэффициент b
Для жидкой фазы
hж = 119∙0,402∙10-4∙410-4∙4100,25∙6200,5 =
0,54 м .
Среднее значение константы фазового равновесия
Удельный расход Н2О на 1 кг инертного газа
Высота единицы переноса
Высота насадки
Н = zhzг = 9,25∙0,638 = 5,9 м.
Высоту насадки выбираем как среднее арифметическое результатов расчета по
трем вариантам
Принимая коэффициент запаса 1,5, окончательно находим высоту насадки
Н = 6,67 ∙ 1,5 = 10 м.
Проверяем размерность орошения колонны по сечению. Отношение высоты
насадки к диаметру колонны должно удовлетворять условию H/Д=1,5 - 10,0. Для
нашего случая
Расстояние между днищем абсорбера и насадкой ZН определяется
необходимостью равномерного распределения газа по поперечному сечению колонны.
Расстояние от верха насадки до крышки абсорбера ZВ зависит от размеров
распределительного устройства для орошения насадки и от высоты сепарационного
пространства (в котором часто устанавливают каплеотбойные устройства для
предотвращения брызгоуноса из колонны).
Гидравлическое сопротивление абсорберов
Гидравлическое сопротивление DPa
обуславливает энергетические затраты на транспортировку газового потока через
абсорбер. Величину DPа
рассчитывают по формуле (1.87)
,
где
DPc -
гидравлическое сопротивление сухой (не орошаемой жидкостью) насадки, Па; U-
плотность орошения,
; b- коэффициент, значения которого для
различных насадок приведены в таблице 1.2.
Гидравлическое
сопротивление сухой насадки DPc определяют по уравнению (1.88):
,
где l - коэффициент
сопротивления. Для хордовой насадки (1.93)
-
скорость газа в свободном сечении насадки (в м/с).
Общее сопротивление системы абсорберов определяют с учетом
гидравлического сопротивления газопроводов, соединяющих их.
Анализ результатов расчета насадочного абсорбера показывает, что основное
диффузионное сопротивление массопереносу в этом процессе сосредоточено в жидкой
фазе, поэтому можно интенсифицировать процесс абсорбции, увеличив скорость
жидкости. Для этого нужно либо увеличить расход абсорбента, либо уменьшить
диаметр абсорбера.
Увеличение расхода абсорбента приведет к соответствующему увеличению
нагрузки на систему регенерации абсорбента, что связано с существенным
повышением капитальных и энергетических затрат (возрастают расходы греющего
пара и размеры теплообменной аппаратуры).
Уменьшение диаметра абсорбера приведет к увеличению рабочей скорости
газа, что вызовет соответствующее возрастание гидравлического сопротивления
абсорберов.
Приведенный расчет выполнен без учета влияния на основные размеры
абсорбера некоторых явлений (таких как неравномерность распределения жидкости
при орошении, обратное перемешивание, неизотермичность процесса и др.), которые
в ряде случаев могут привнести в расчет существенные ошибки. Эти явления
по-разному проявляются в аппаратах с насадками разных типов.
2.2 Расчет
тарельчатого абсорбера
В целлюлозно-бумажном производстве для варки целлюлозы используют
варочную кислоту, получаемую путем поглощения диоксида серы из печного газа в
барботажных колонках (абсорберах).
Расчет барботажного абсорбера с провальными тарелками
Пример 2. Рассчитать барботажный абсорбер с провальными тарелками для поглощения
SO2 из крепкого газа серной печи. Количество поступающего газа 10000 м3/ч.
Содержание SO2 в поступающем газе 15% (об.). Требуемая степень поглощения 87%.
На орошение подается свежая вода с температурой 400С. Температура газа на входе
70 0С. Состав поступающего газа (об.): SO2-15 %; N2-80%; О2-5%. Содержание
общего SO2 в получаемом бисульфитном растворе 3% (по объему).
Выбор типа тарелки
С учетом рекомендаций, основанных на практике ЦБП, выбираем тарельчатый
абсорбер с провальными тарелками большого свободного сечения sсв=40% и диаметром отверстий d0=16 мм.
Определение расхода жидкого поглотителя
Находим мольную массу поступающего газа по формуле
где y1, y2, y3-мольные (объемные) доли компонентов газовой смеси,

М1,
М2,М3 - мольные массы компонентов
газовой смеси, кг/кмоль.
.
Мольный расход инертного газа G0, кмоль/с, составит
где Vг-объемный расход печного газа, м3/ч
.
Массовый расход газа G, кг/с, составит
.
Концентрация
SO2 в поступающем газе в относительных мольных величинах Yн,
, составит
.
Содержание
SO2 в уходящем газе в относительных мольных величинах Yк,
, составит
где Сп - степень поглощения SO2.
.
Конечная
концентрация поглощающей жидкости в относительных мольных величинах Xк,
, составит
где
хк-мольная доля SO2 в получаемом бисульфитном растворе,
.
Удельный расход поглотителя (воды) l0 составит
.
Мольный расход поглотителя (воды) L, кмоль/с, составит
.
Тогда массовый расход поглотителя L, кг/с
.
Определение верхнего предела работы абсорбера
Для верхнего предела работы провальных тарелок рекомендовано уравнение
где wmax-скорость газа, соответствующая верхнему пределу
работы абсорбера, м/с;
rw, rж- плотность воды и орошающей жидкости, соответственно,
при 200С, кг/м3;
rг - плотность газа при рабочих условиях, кг/м3;
rвозд. - плотность воздуха при 200С и 0,1 МПа;
L, G, - массовые расходы жидкости и газа соответственно, кг/с.
Плотность газа rг, кг/м3, при
температуре 700С и давлении 1атм находим по уравнению
.
Тогда при rвозд=1,29 кг/м3; rw=rж=1000 кг/м3:
откуда скорость газа в отверстиях, соответствующая верхнему пределу
работы абсорбера равна wmax=9,58
м/с.
Определение рабочей скорости газа
Рабочая (фактическая) скорость газа в отверстиях составляет около 50% от
предельной, тогда имеем wраб=0,5×9,58=4,8 м/с.
Определение диаметра абсорбера
Объемный расход газа VГ, м3/с, при рабочих условиях составит
.
Диаметр абсорбера Д, м, составит
.
Выбираем стандартный абсорбер с диаметром 1000 мм, при этом сечение
абсорбера S, м2, составит
.
Тогда приведенная скорость газа wприв, м/с, составит
.
Скорость газа в отверстиях тарелки, wo, м/с
.
Расчет числа тарелок
Находим число единиц переноса nог для
провальных тарелок в системе SO2-вода по формуле
где
U - плотность орошения,
;
s - живое
сечение тарелки, %.
Плотность
орошения рекомендуется принимать в пределах 10-70
, принимаем U=20
. Тогда
.
Число тарелок n рассчитываем из выражения
.
Устанавливаем абсорбер с 10 провальными тарелками.
Расчет гидравлического сопротивления абсорбера
Многочисленные исследования гидродинамики провальных тарелок живым
сечением до 22% показывают, что гидравлическое сопротивление таких тарелок
складывается из потери давления на трение при прохождении газа через отверстия
тарелки, частично заполненные жидкостью, из гидростатического напора
газожидкостного слоя на тарелке и потери давления на преодоление поверхностного
натяжения жидкости.
Гидравлическое сопротивление DР, Па, для провальных тарелок большого свободного сечения
(25-60%) определяют по зависимости
.
При этом сопротивление 10 провальных тарелок составит DРобщ=322×10=3220 Па.
Расчет расстояния между тарелками
Расстояние между тарелками h, мм, определяем по зависимости
.
Общая высота абсорбционной зоны барботажной колонны Hобщ, м,
составит
.
.3 Расчет
струйного абсорбера Вентури
Пример 3. Рассчитать струйный абсорбер Вентури для поглощения SO2 из
топочных газов. Количество поступающего газа 128000 м3/ч. Температура газа на
входе 240оС. Концентрация SO2 в поступающем газе 1,5 % (об.). Конечная
концентрация SO2 в газовом потоке 0,01 % (об.). Получаемый раствор
бисульфита магния содержит 50 % общего SO2.
Определение расхода жидкого поглотителя
Количество SO2, поступающего с газом V1, м3/ч, составит:
где V - объемный расход поступающего топочного газа, м3/ч;
yн
- начальная концентрация SO2 в поступающем газе, %.
.
Расход поглотителя L, м3/ч, составит:
где Х - содержание общего SO2 в получаемом растворе, %
.
Определение основных размеров абсорбера
Конструкция струйного абсорбера Вентури включает конфузор, горловину,
диффузор.
Расчет горловины
Принимаем скорость газа в горловине абсорбера равной w=30м/с, тогда площадь сечения
горловины Sгорл, м2, будет равна:
.
Диаметр горловины Dгорл, м, составит:
;
.
Расчет конфузора
Площадь сечения конфузора Sконф, м2:
.
Диаметр конфузора Dконф, м:
.
Длина конфузора, lконф, м:
.
Расчет диффузора
Площадь сечения диффузора Sдиф, м2:
.
Диаметр диффузора Dдиф, м:
.
Длина диффузора lдиф, м:
.
Принимаем следующие габаритные размеры абсорбера Вентури: длина конфузора
1,6 м; длина диффузора 7,4 м; общая высота абсорбера 9 м.
Расчет числа ступеней абсорбции
Задаемся удельным расходом жидкости равным m=3,5 л/м3 и
рассчитываем число единиц переноса nог:
.
Число ступеней абсорбции находим из выражения
.
Принимаем к установке три струйных абсорбера Вентури.
Определение гидравлического сопротивления ступеней абсорбции
Сопротивление струйного абсорбера Вентури Dр, Па, определяем по уравнению
.
Сопротивление
трех ступеней абсорбции равно
.
При
этом общий расход жидкости L, м3/ч, на одну ступень с учетом
рециркуляции раствора составит:
.
Затраты электроэнергии на перекачку жидкости
Принимаем, что для продавливания жидкости в количестве 448 м3/ч через
форсунки необходимо давление не менее 7 атм. Тогда мощность насоса N1, кВт,
составит:
где Q- производительность насоса, м3/ч;
Н-
полный напор, м;
r - плотность жидкости, кг/м3 ;
h- коэффициент полезного действия равный 0,5-0,7.
.
Расход электроэнергии на три ступени равен 122×3=366 кВт.
Затраты электроэнергии на перемещение газового потока
Мощность дымососа, необходимая для перемещения газового потока, N2, кВт,
составит:
где Q - производительность дымососа, м3/ч;
Dр - полный напор, Па;
h - коэффициент полезного действия, равный 0,5-0,7.
.
Расход электроэнергии на три ступени равен 13,5×3=40,5 кВт.
Общие затраты электроэнергии
Расход электроэнергии на перекачивание жидкости и перемещение газа
составит N3= 366+40,5=406,5 кВт.
Удельные затраты электроэнергии n, кВт/м3, составят:
.
Определение интенсивности абсорбера
Определяем высоту единицы переноса h, м:
где Н - общая высота аппарата, м;
nог- число
единиц переноса
.
При расчете интенсивности абсорбера исходим из скорости газа, wдиф, м/с, отнесенной к полному сечению выходного
отверстия диффузора, диаметр которого в нашем случае равен 2,13 м. Тогда
.
Интенсивность абсорбера И, с-1, составит:
.
.4 Расчет
абсорбционной установки
Пример 4. Рассчитать
абсорбционную установку для поглощения аммиака из газа водой при температуре 20°С и давлении 855 мм рт.ст. (114,2
кН/м2). Производительность по сухому воздуху - 37775 м3/ч; его состав:
об. %
Сухой воздух 95
Аммиак 1,17
Водяные пары 2,07
Поглощение аммиака в абсорбере - 98%, аммиачная вода на выходе из
абсорбера должна иметь концентрацию аммиака, равную 90% от равновесной.
Абсорбционные колонны необходимо рассчитать в двух вариантах - с насадкой
из керамических колец размером 35´35´4 мм и с колпачковыми тарелками.
Производительность по аммиаку, м3/ч:
Аммиак
.
Сухой
воздух
.
Водяные
пары
.
1 - распылитель поглотительной жидкости; 2 - насадка; 3 - устройство для
перераспределения жидкости; 4 - насос
Рисунок 2.3 - Схема абсорбционной установки
Если учесть, что 1 кмоль идеального газа при температуре 20°С и давлении 855 мм рт. ст. занимает
объем
и допустить, что коксовый газ подчиняется законам идеальных газов, то
производительность по компонентам коксового газа будет следующей, кг/ч:
Аммиак
.
Сухой
воздух
.
Водяные
пары
.
Общая
производительность по сухому воздуху
Плотность газа, поступающего на абсорбцию:
Количество инертного газа, проходящего через колонну за 1 ч:
или
37335 м3.
Количество аммиака, поглощенного за 1 ч:
.
Начальная концентрация аммиака в газе (по закону Авогадро)
.
Уравнение равновесия аммиачно-водного раствора:
,
где H0 - константа фазового равновесия.
Здесь r - коэффициент Генри, для водных растворов аммиака (при 20°С r=2080 мм рт. ст.); p
= 8885 - общее давление, мм рт. ст.
Равновесная концентрация аммиака в жидкости при выходе из абсорбера:
Рабочая
концентрация аммиака в жидкости при выходе ее из абсорбера
.
Количество воды, необходимое для поглощения заданного количества аммиака
за 1 ч:
Рисунок 2.4 - Определение числа ступеней изменения концентраций в
абсорбционной колонне
В воде также растворяются углекислый газ, содержащийся в воздухе.
Коэффициент Генри для водных растворов углекислого газа при 20° С равен 1,08×10-6 мм рт. ст. Аналогичными расчетами находят, что 1 кмоль
воды будет уносить из воздуха 22,9×10-6 кмоль СО2; в пересчете на 4650 кмоль/ч воды это составит
0,104 кмоль (или 2,23 м3) СО2. Практически это почти не отражается на объеме инертного
газа, проходящего через абсорбционную установку. Следовательно, концентрация
аммиака в газе при выходе его из абсорбера
По
найденным начальным концентрациям аммиака в жидкой и газовой фазах строят на
диаграмме y-x (рисунок 2.4) линию рабочих концентраций y=Ax+B, а
по уравнению
- кривую равновесия.
.4.1
Насадочная колонна
Характеристика принятой насадки, согласно заданию, следующая:
Удельная поверхностьs=140 м2/м3.
Свободный объемVсв=0,78 м3/м3.
Масса 1 м3 насадкиGнас=505 кг/м3.
.
Скорость газа w0 в точке
инверсии фаз, соответствующую режиму эмульгирования (считая на полное сечение
колонны), определяют из уравнения
где s - удельная поверхность насадки, м2/м3;
g - ускорение свободного падения, м/сек2; Vсв - свободный объем
насадки, м3/м3; rг и rж - плотность жидкости и газа, кг/м3; mж - вязкость жидкости, мПаÌс; L - расход жидкости, кг/ч; G
- расход газа, кг/ч.
После подстановки соответствующих значений получают

Рабочая скорость газа:
где 0,75 - принятый коэффициент отклонения w от wo.
Необходимый диаметр колонны
.
Высота насадки
(Определяют аналитически или графически)
Аналитическим методом высота слоя насадки может быть рассчитана по
уравнению
,
где Gy - массовый расход инертного газа, кмоль/ч; s - удельная поверхность насадки м2/м3;
S - площадь свободного сечения абсорбера, м2;
К - коэффициент массопередачи,
- число
единиц переноса.
Интеграл
находят графически. Если же равновесная линия прямая (или приближается к
прямой, как в данном примере, рисунок 2.5), то
где
Можно поступить и по-другому. Согласно основному уравнению массопередачи
где
G - количество абсорбируемого газа, кмоль/ч; Kр - коэффициент
массопередачи,
F - поверхность массопередачи, м2;
Dpср - средняя движущая сила процесса абсорбции, кПа.
Так
как

а
то высота насадки
В зависимости от способа выражения движущей силы процесса абсорбции ниже
представлены возможные варианты определения высоты насадки.
I вариант
G=20,3 кмоль/ч
s=140 м2/м3, S=0,785ÌД2=0,785×2,652=5,5 м2 .
Находим движущую силу процесса внизу колонны.
Парциальное давление аммиака на входе в колонну
Парциальное давление аммиака, соответствующее xк
(согласно
заданию).
Движущая сила абсорбции внизу колонны
.
Определяют движущую силу процесса абсорбции наверху колонны
Парциальное давление аммиака в выходящем газе
(согласно
заданию).
, так как
на орошение подается чистая вода.
Движущая
сила процесса абсорбции наверху колонны
средняя движущая сила
.
Коэффициент массопередачи
где
by -
коэффициент массоотдачи со стороны газа (“газовой пленки”),
;
bx - коэффициент массоотдачи со стороны жидкости
(“жидкой пленки”),
, или м/ч; т - константа уравнения,
.
,
где r - константа Генри, кПа; Mж - молекулярная масса
жидкого поглотителя, rж - его
плотность, кг/м3.
При r=2080 мм рт. ст.=2080×0,133=278 кПа, Mж=18 и rж=1000 кг/м3
.
Коэффициент массопередачи для газовой пленки определяют из уравнения
.
.
Здесь
.
.
Из выражения критерия Нуссельта находят значение by:
.
;
-
молекулярная масса газовой смеси.
Таким образом,
.
Коэффициент массоотдачи для жидкой пленки находят из уравнения
.
Критерий Рейнольдса
,
где
;
-
вязкость воды при 20°С.
Критерий
Прандтля
,
где rж - плотность воды, кг/м3; Дж -
коэффициент диффузии аммиака в воде, м2/ч.
Критерий Галилея
,
где dнар - наружный диаметр элемента насадки.
Критерий Нуссельта
.
Из выражения критерия Нуссельта
.
Общий коэффициент массопередачи
.
Когда растворимость газа велика и диффузионное сопротивление жидкости
мало, по сравнению с сопротивлением газа, т. е. когда bx>>by, то bx можно не рассчитывать, так как Ky»by.
Высота насадки
.
вариант
.
Здесь
;
;
.
Согласно рисунку 2.5
;
.
Согласно ранее проведенным расчетам (смотри I вариант)
.
Коэффициент массопередачи Kр пересчитывают в Ky по уравнению
,
откуда
.
Эквивалентная высота насадки
.
Высота насадки
.
Общая высота колонны
,
где Нн - высота слоя насадки; h1 - высота нижней части
колонны;
h2
- высота верхней части колонны; h3 - общее расстояние между десятью
ярусами насадки (при высоте каждого яруса, равном 3,1 м, и расстоянии между
ярусами 0,4 м).
Гидравлическое сопротивление колонны с насадкой
,
где
- сопротивление орошаемой насадки, Па;
-
местные сопротивления, Па.
где Dpсух - сопротивление слоя сухой насадки
по сравнению с неорошаемой, Па.
Сопротивление слоя сухой насадки высотой Нн
где w - скорость, отнесенная к полному
сечению скруббера, м/сек; l=f(Reг) - коэффициент сопротивления.
.
При
.
Сопротивление слоя сухой насадки
.
Параметр орошения
,
где
L - плотность орошения скруббера,
; rж -
плотность жидкости, кг/м3; b - безразмерный коэффициент, являющийся
функцией критерия Рейнольдса, для жидкости равный
.
Значение
критерия Рейнольдса для жидкости определяют из уравнения
,
где
. Значит
.
Параметр
орошения
.
Для
керамических колец с
и
.
Сопротивление орошаемой насадки
.
При движении через насадочную колонну газовый поток несколько раз
расширяется и сужается. В газопроводах средняя скорость газа составляет wг=13 м/с; при заданной производительности по газу Vк.г=37775
м3/ч диаметр газопровода
.
Следовательно, диаметры штуцеров для подвода и отвода будут такие же.
Предварительно определяют площади потока в различных участках колонны.
Площадь поперечного сечения штуцера
.
Площадь поперечного сечения колонны (без насадки)
.
Среднее свободное сечение колонны с насадкой
.
Коэффициенты местных сопротивлений:
а) при выходе газового потока из газопровода в колонну (внезапное
расширение)
;
б) при выходе газового потока из колонны в газопровод (внезапное сужение)
,
;
в) при входе газового потока в насадку (внезапное сужение)
,
;
г) при выходе газового потока из насадки (внезапное расширение)
.
По пунктам «а» и «б» потерю давления на местные сопротивления вычисляют
после определения скорости газового потока в штуцерах (газопроводе).
Скоростное давление
;
;
.
По пунктам «в» и «г» местные сопротивления рассчитывают за фактической
скоростью газового потока в насадке
.
;
;
.
Суммарная потеря давления на местные сопротивления
.
Общее давление, развиваемое газодувкой:
-
атмосферное давление; 1,05 - коэффициент, учитывающий потери давления в
подводящих газопроводах.
Устанавливают
газодувку типа «750-23-2» производительностью Vк.г=600¸700 м3/мин (36000¸42000
м3/ч), с давлением р=0,24¸0,30 amu,
числом оборотов n=4800 об/мин и мощностью на валу Nв=460 квт.
Мощность насосной установки
Насосная установка обеспечивает подачу поглотителя в распылитель,
находящийся наверху скруббера. В соответствии с расчетом и необходимой высотой
абсорбционной (насадочной) колонны принимают следующие исходные данные для
расчета мощности насосной установки:
Производительность G=83700 кг/ч
Высота подъема H=38 м
Избыточное давление перед распылителем Dpизб=0,35 amu
Плотность поглотителя (воды) r=1000 кг/м3
Общий к.п.д. насосной установки h=0,6.
Трубопровод имеет два вентиля, четыре колена под углом 90° и общую длину 38 м.
Мощность, потребляемая насосом, кВт:
,
где V - объем подаваемой жидкости, м3/сек; Dp - давление, развиваемое насосом, Па; h - общий к.п.д. насосной установки.
;
.
Здесь Dpск -
давление, необходимое для создания скоростного напора, Па; Dpтр+м.с - потеря давления на трения и
местные сопротивления, Па; Dpпод - давление, необходимое для подъема жидкости, Па; Dpизб - избыточное давление перед
распылителем, Па.
Скорость жидкостей в трубопроводах допускается в пределах 0,5-2 м/сек;
принимают w=1,5 м/сек.
.
Принимают стальной трубопровод диаметром 159´4,5 мм. Уточняется скорость движения
жидкости:
.
Скоростное давление
.
Потеря напора на трение и местные сопротивления
.
Предварительно подсчитывают значение критерия Рейнольдса
,
где m -
динамический коэффициент вязкости воды, Па·с.
При Re=196000 коэффициент трения l=0,02. Находят, что для колен под углом 90° можно принять xк=0,38 (при Re>2×105 и a/b=3, принятом условно); для вентиля xв=4,4.
Таким образом
;
.
Давление, необходимое для подъема жидкости на высоту H=38 м,
.
Избыточное давление:
.
Давление, развиваемое насосом:
.
Потребляемая мощность:
Устанавливают центробежный насос марки «КМС-100» с характеристикой:
Производительность 100 м3/час
Напор 60 м вод. ст.
Скорость вращения 1450 об/мин
Мощность двигателя 30 квт
.4.2
Тарельчатая колонна
Диаметр колонны
При расстоянии между тарелками hмт=600 мм и плотности газа rг=0,6 кг/м3 допустимая скорость газа w`г=1,52
м/с
.
По каталогу НИИХиммаша выбирают типовую колонну с колпачковыми тарелками
и переливными устройствами; принимают колонну Дкол=3 м с капсульными
колпачками и сегментными переливами.
Уточняют скорость газового потока:
.
Если расчетный диаметр колонны больше стандартного, необходимо подобрать
соответствующее количество колонн меньшего диаметра, равновеликих по общей
площади сечения.
Конструктивный расчет тарелки с капсульными колпачками и
сегментными переливами
Основные размеры колпачковых тарелок нормализированы. При конструировании
колпачков исходят из соблюдения равенства площадей:
,
где S1 - площадь поперечного сечения газового патрубка; S2
- площадь между верхним слоем газового патрубка и колпачком, равная
произведению периметра патрубка на расстояние по вертикали от верхнего края
патрубка до колпачка; S3 - площадь кольцевого пространства между газовым
патрубком и колпачком; Sк - площадь сечения прорезей одного колпачка.
Высоту сливной перегородки принимают в пределах 20-50 мм (рисунок 2.5).
Рисунок 2.5 - Расчет сопротивления столба жидкости на тарелке
Площадь сечения колонны составляет:
.
Принимая живое сечение j=0,12, находят общую площадь сечения патрубков
.
Рисунок 2.6 - Расположение колпачков и переливного устройства на тарелке
При стандартных патрубках размером 70´4 мм площадь сечения одного патрубка:
.
Количество патрубков и колпачков составляет:
.
Колпачки в колонне размещают графически по вершинам треугольников или
концентрически окружностям, в зависимости от диаметра колонны, диаметра
колпачка и размеров сливного устройства. В данном случае по условиям разбивки
колпачков принимают (рисунок 2.6) nк=273.
Площадь
,
где h - расстояние по вертикали от верхнего обреза патрубка до
колпачка.
Из условия S1=S2 находят
.
Площадь S3 составляет:
,
где dвн.к - внутренний диаметр колпачка; dнар - наружный
диаметр патрубка.
Из условия S1=S3 находят при dнар=70 мм:
.
Выбирают колпачки с внутренним диаметром 92 мм и наружным диаметром 100
мм. Прорези - прямоугольные, шириной b=8 мм, высотой l=15 мм.
Площадь сечения одной прорези:
.
Из условия S1=Sк находят количество прорезей в колпачке
.
Общая ширина прорезей в одном колпачке составляет 25×8=200 м, периметр колпачка равен 3,14×100=314 мм. Таким образом, расстояние между
прорезями
.
Ширина сегмента переливного устройства
.
Длина дуги (периметр сливной перегородки)
.
Площадь свободного сечения сливного устройства
,
где
- радиус колонны;
.
Высоту сегмента переливного устройства hп принимают равной 75 мм.
Гидравлическое сопротивление тарелки
Общее сопротивление тарелки
где Dрсух - сопротивление сухой тарелки, Па; Dрx - сопротивление жидкости на тарелке, Па.
,
где x -
коэффициент сопротивления (берется обычно в пределах 4,5¸5); wпр - скорость газа в прорезях при их полном открытии,
м/сек.
,
где a - коэффициент равный 1 для колпачковых тарелок и 0,67 для
ситчатых; l - высота прорези колпачка, м.
При x=5 и a=1.
.
Сопротивление сухой тарелки
.
Сопротивление жидкости на тарелке
,
где Dрст- потеря давления на преодоление
статического сопротивления на тарелке, Па; Dps - потеря давления на преодоление сил
поверхностного натяжения, Па.
При полном открытии прорезей
где g - ускорение силы тяжести, м/сек; r - отношение
плотности пены к плотности чистой жидкости (при расчетах принимают r=0,5);
rж - плотность жидкости, кг/м3; e - расстояние от
верхнего края прорезей до сливного порога, м; l - высота прорези, м; Dh - высота уровня жидкости над сливным порогом, м.
Принимают e=20 мм, а высоту уровня жидкости над сливным порогом,
м, определяют с учетом плотности пены
,
где Vж - объемный расход жидкости, м3/сек; П - периметр
сливной перегородки, м.
.
.
Следовательно,
.
Сопротивление, обусловленное силами поверхностного натяжения, Па
,
где s -
поверхностное натяжение, Па; диаметр отверстия или эквивалентный диаметр
прорези в колпачковой тарелке, м.
Поверхностное натяжение для воды при 20°С
.
Эквивалентный диаметр прорези при полном открытии:
.
Таким образом,
,
сопротивление жидкости на тарелке:
,
общее сопротивление тарелки составляет:
Определение необходимого количества тарелок
По
найденным начальным и конечным концентрациям аммиака в жидкой и газовой фазах
строят на диаграмме y-x линию рабочих концентраций y=Ax+B, а по
уравнению
- кривую равновесия (рисунок 2.8).
Для
определения действительного количества рабочих тарелок в колонне графическим
методом (на основе общих положений массопередачи) необходимо сначала рассчитать
коэффициент массопередачи из уравнения:
,
Где

-
коэффициент массоотдачи в газовой фазе для колпачковых тарелок;
-
коэффициент массоотдачи в жидкой фазе для колпачковых тарелок. В этих формулах:
wy - скорость
газа, отнесенная к свободному сечению колонны, м/сек; Dpx -
гидравлическое сопротивление тарелки, Па; m - средний
тангенс угла наклона равновесной линии на рабочем участке.
В
данном примере: wy=wг=1,5
м/сек;
;
После подстановки соответствующих значений получают:
Рисунок 2.7 - Определение числа тарелок тарельчатого абсорбера
;
;
.
Число единиц переноса одной тарелки
,
где Sт - площадь тарелки, м2; Gин - расход инертного газа,
кмоль/ч.
.
.
Величина отрезков на вертикалях диаграммы Y-X между линией рабочих концентраций и вспомогательной
кинетической кривой
.
На линии рабочих концентраций (рисунок 2.7) наносят ряд точек А1, А2,
А3 и так далее и на линии равновесия соответствующие им точки С1, С2, С3
и т. д.
Пользуясь
полученными равенствами
, находят на отрезках
и так
далее точки
и т. д.
Проводя
через полученные точки
и т.д. линию, получают вспомогательную кинетическую
кривую. Из точки
в пределах заданных рабочих концентраций Yн=0,0119 и Yк=0,000287 между линией рабочих концентраций и
вспомогательной кинетической кривой строят ломаную линию
и т.д. В данном примере такое построение сделать
трудно, так как кинетическая линия почти совпадает с рабочей линией.
В
общем случае указанные линии не совпадают.
Полученное
число ступеней (или отрезков
) и дает
необходимое для заданных условий число тарелок
Гидравлическое сопротивление колонны:
.
Общая высота колонны:
.
Библиографический
список
1. Братчиков Г.Г. Очистка газовых выбросов в
целлюлозно-бумажной промышленности. - М.: Лесная промышленность, 1989. - 256 с.
. Бушмелев В.А., Вольман Н.С. Процессы и аппараты
целлюлозно-бумажного производства.- М.: Лесная пром-сть, 1969.- 408 с.
. Дытнерский Ю.И. Основные процессы и аппараты
химической технологии. Пособие по курсовому проектированию М.: Химия, 1983. -
272 с.
. Касаткин. А.Г. Основные процессы и аппараты
химической технологии, - М., Химия, 1971. - 784 с.
. Непенин Н.Н. Технология целлюлозы. Т.1.
Производство сульфатной целлюлозы. - М.: Лесная промышленность, 1976.- 624 с.
. Оборудование и сооружения для защиты биосферы от
промышленных выбросов. Родионов А.И., Кузнецов Ю.П., Зенков В.В., Соловьев Г.
С. - М.: Химия, 1985. -352 с.
. Основные процессы и аппараты химической технологии:
Пособие по проектированию / Борисов Г.С., Брыков В.П., Дытнерский Ю.И. и др.
2-е изд., перераб. и дополн. М.: Химия, 1991. - 496 с.
. Павлов К.Ф., Романков П.Г., Носков А.А. Примеры и
задачи по курсу процессов и аппаратов. - Л.: Химия, 1976. - 552 с.
. Проектирование процессов и аппаратов химической
технологии, Иоффе И. Л. -Л.: Химия, 1991. -352 с.
. Рамм В.М. Абсорбция газов. - М.: Химия, 1976. - 655
с.
. Ректификационные и абсорбционные аппараты.
Александров И. А. -М.: Химия, 1978.- 280 с.
. ГОСТ 21944-76 Аппараты колонные стальные. Ряд
диаметров. Расстояние между тарелками.
. ГОСТ 9634-81 Колпачки капсульные стальные колонных
аппаратов. Конструкции и размеры. Технические требования.
Приложение А1
Таблицы растворимости газов в воде
Таблица А1.1 - Аммиак NH3
Содержание NH3,
кг на 100 кг H2O Парциальное давление NH3 при 25 0С,
мм рт.ст.
|
0,105 0,791
|
0,244 1,83
|
0,32 2,41
|
0,38 2,89
|
0,576 4,41
|
0,751 5,80
|
1,02 7,96
|
Содержание NH3,
кг на 100 кг H2O Парциальное давление NH3 при 25 0С,
мм рт.ст.
|
1,31 10,31
|
1,51 11,91
|
1,71 13,46
|
1,98 15,75
|
2,11 16,94
|
2,58 20,86
|
2,75 22,38
|
Таблица А1.2 - Двуокись углерода СО2
Общее давление, атм
|
Содержание СО2, кг на 100
кг Н2о
|
|
12 0С
|
180С
|
25 0С
|
31 0С
|
35 0С
|
40 0С
|
50 0С
|
75 0С
|
100 0С
|
25 50 75 100 150 200 300
400 500 700
|
. . . 7,03 7,18 7,27 7,598
. . . 7,86 8,12 . . . . . .
|
3,86 6,33 6,69 6,72 7,07 .
. . 7,35 7,77 . . . . . .
|
. . . 5,38 6,17 6,28 . . .
. . . . . . 7,54 . . . . . .
|
2,80 4,77 5,80 5,97 6,25
6,48 . . . 7,27 7,65 . . .
|
2,56 4,39 5,51 5,76 6,03
6,29 . . . 7,06 7,51 . . .
|
2,30 4,02 5,10 5,50 5,81
6,28 . . . 6,89 7,26 . . .
|
1,92 3,41 4,45 5,07 5,47
5,76 6,20 6,58 . . . 7,58
|
1,35 2,49 3,37 4,07 4,86
5,27 5,83 6,30 . . . 7,43
|
1,06 2,01 2,82 3,49 4,49
5,08 5,84 6,40 . . . 7,61
|
Таблица А1.3 - Окись азота NO
t, 0С H·10-4
|
0 1,69
|
5 1,93
|
10 2,18
|
15 2,42
|
20 2,64
|
25 2,87
|
30 3,10
|
35 3,31
|
t, 0С H·10-4
|
40 3,52
|
45 3,72
|
50 3,90
|
60 4,18
|
70 4,38
|
80 4,48
|
90 4,52
|
100 4,54
|
Таблица А1.4 - Окись углерода СО
t, 0С H·10-4
|
0 3,52
|
5 3,96
|
10 4,42
|
15 4,89
|
20 5,36
|
25 5,80
|
30 6,20
|
35 6,59
|
t, 0С H·10-4
|
40 6,96
|
45 7,29
|
50 7,61
|
60 8,21
|
70 8,45
|
80 8,45
|
90 8,46
|
100 8,46
|
Таблица А1.5 - Двуокись углерода СО2
t, 0С H·10-4
|
0 0,728
|
5 0,876
|
10 1,04
|
15 1,22
|
20 1,42
|
25 1,64
|
t, 0С H·10-4
|
30 1,86
|
35 2,09
|
40 2,33
|
45 2,57
|
50 2,83
|
60 3,41
|
Таблица А1.6 - Окись углерода СО
Парциальное давление СО, мм
рт. ст.
|
H·10-4
|
Парциальное давление СО, мм
рт. ст.
|
H·10-4
|
|
17,7 0С
|
19 0С
|
|
17 0С
|
19 0С
|
900 2000 3000 4000
|
4,77 4,77 4,77 4,78
|
4,88 4,91 4,93 4,95
|
5000 6000 7000 8000
|
4,80 4,82 4,86 4,88
|
4,97 4,98 5,02 5,08
|
Примечание. В таблицах А1.3 - А1.6: Н - константа Генри, размерность Н -
единица давления абсорбируемого газа в газовой фазе, отнесенная к единице
мольной концентрации этого газа в жидкой фазе.
Таблица А1.7 - Двуокись серы SO2
Содержание SO2,
кг на 100 кг Н2О
|
Парциальное давление SO2,
мм рт. ст.
|
|
0 0С
|
7 0С
|
10 0С
|
15 0С
|
20 0С
|
25 0С
|
30 0С
|
40 0С
|
50 0С
|
70 0С
|
90 0С
|
110 0С
|
20 15 10 8 7,5 7,45 6,0
5,0 4,36 4,0 2,5 2,0 1,5 1,04 1,0 0,7 0,51 0,5 0,3 0,2 0,15 0,10 0,05 0,02
|
646 474; 500 308; 310 240
228 . . . 175 148 . . . 110 69 50 38 . . . 23,3; 20 15,2 . . . 9,9 5,1 2,8
1,9 1,2 0,6 0,25
|
657 637 417 . . . 307 . .
. . . . 198 . . . . . . 92 . . . 51 . . . 31 20,6 . . . 13,5 6,9 3,7 2,6 1,5
0,7 0,3
|
. . . 726; 735 474; 470
370 349 . . . 270 226 . . . 170 105 75 59 . . . 37; 35 23,6 . . . 15,6 7,9
4,6 3,1 1,75 0,75 0,3
|
. . . . . . 567 . . . 419
. . . . . . 270 . . . . . . 127 . . . 71 . . . 44 28,0 . . . 19,3 10,0 5,7
3,8 2,2 0,8 0,3
|
. . . . . . 698 580 517 .
. . 430 336 . . . 270 161 110 92 . . . 59; 30 39,0 . . . 26,0 14,1 8,5 5,8
3,2 1,2 0,5
|
. . . . . . 840 670 . . .
. . . 505 . . . . . . 320 . . . 150 . . . . . . 60 . . . . . . . . . . . . .
. . . . . . . . . . . . . .
|
. . . . . . . . . 780 688
750 580 452 420 380 216 170 125 82,5 79; 70 52 . . . 36 19,7 11,8 8,1 4,7 1,7
0,6
|
. . . . . . . . . . . . .
. . . . . 770 665 . . . 510 332 250 186 . . . 121; 110 87 . . . 57 . . . . .
. 12,9 7,5 2,8 0,8
|
. . . . . . . . . . . . .
. . 1243 . . . . . . 778 700 458 340 266 149 172; 160 116 76 82,0 . . . 31,0
20,0 12,0 4,7 1,3
|
. . . . . . . . . . . . .
. . . . . . . . . . . 1272 . . . . . . . . . . . . 301 . . . . . . 146 . . .
. . . . . . . . . . . . . . . . . .
|
. . . . . . . . . . . . .
. . . . . . . . . . . . . . . . . . . . . . . . . . 465 . . . . . . 239 . . .
. . . . . . . . . . . . . . . . . .
|
. . . . . . . . . . . . .
. . . . . . . . . . . . . . . . . . . . . . . . . . . . . . . . . . . 348 . .
. . . . . . . . . . . . . . . . . . .
|
Приложение А2
Таблица А2.1 - Способы выражения концентраций фаз
Выражение концентраций
компонента А
|
x
|
X CX
|
|
|
|
|
x -
или



или

или
MA , MB и МСМ - мольные
массы компонентов и смеси, кг/кмоль; MCM = MAx + MB (1-x) ;r - плотность смеси, кг/м3.
Для
смеси идеальных газов:
Приложение А3
Таблица А3.1 - Характеристика скрубберных насадок из колец и кускового
материала
Вид насадки
|
Размеры элемента насадки,
мм
|
Число элементов в 1 м3
объема, заполненного насадкой
|
Свободный объем,м3/м3
|
Удельная поверхность, м2/м3
|
Масса 1 м3 насадки, кг
|
Кольца фарфоровые . . .
------------ керамические . . ------------ керамические . . ------------
керамические . . ------------ керамические . . ------------ стальные . . . .
. . ------------ стальные . . . . . . Гравий круглый . . . . . . . Андезит
кусковой . . . . . Кокс кусковой . . . . . . . . «- - - - - - - - - » . . . .
. . . . «- - - - - - - - - » . . . . . . . . «- - - - - - - - - » . . . . . .
. . Катализатор синтеза аммиака в кусочках . . . . Катализатор конверсии СО в
таблетках . . . . . . . Катализатор сернокислотный (ванадиевый) в таблетках .
. . . . .
|
8 х 8 х 1,5 15 х 15 х 2 25
х 25 х 3 35 х 35 х 4 50 х 50 х 5 35 х 35 х 2,5 50 х 50 х 1 42 43,2 42,6 40,8
28,6 24,4 6,1 d=11,5; h=6 d=11; h=6,5
|
1 465 000 250 000 53 200 20
200 6 000 19 000 6 000 14 400 12 600 14 000 15 250 27 700 64 800 5 200 000
1 085 000 1 000 000
|
0,64 0,70 0,74 0,78 0,785
0,83 0,95 0,388 0,565 0,56 0,545 0,535 0,532 0,465 0,38 0,43
|
570 330 204 140 87,5 147
110 80,5 68 77 86 110 120 960 460 415
|
600 690 532 505 530 - 430 -
1200 455 585 660 600 2420 1100 614
|
Приложение А3.2 - Характеристики насадок (размеры даны в мм)
Насадки
|
а, м2/м3
|
Vсв, м3/м3
|
dэ, м
|
r, кг/м3
|
Число штук в м3
|
Регулярные насадки
|
Деревянная хордовая
(10х100), шаг в свету: 10 20 30
|
100 65 48
|
0,55 0,68 0,77
|
0,022 0,042 0,064
|
210 145 110
|
- - -
|
Керамические кольца Рашига:
50х50х5 80х80х8 100х100х10
|
110 80 60
|
0,735 0,72 0,72
|
0,027 0,036 0,048
|
650 670 670
|
8500 2200 1050
|
Неупорядоченные насадки
|
Керамические кольца Рашига:
10х10х1,5 15х15х2 25х25х3 35х35х4 50х50х5
|
440 330 200 140 90
|
0,7 0,7 0,74 0,78 0,785
|
0,006 0,009 0,015 0,022
0,035
|
700 690 530 530 530
|
700000 220000 50000 18000
6000
|
Стальные кольца Рашига:
10х10х0,5 15х15х0,5 25х25х0,8 50х50х1
|
500 350 220 110
|
0,88 0,92 0,92 0,95
|
0,007 0,012 0,017 0,035
|
960 660 640 430
|
770000 240000 55000 7000
|
Керамические кольца Палля:
25х25х3 35х35х4 50х50х5 60х60х6
|
220 165 120 96
|
0,74 0,76 0,78 0,79
|
0,014 0,018 0,026 0,033
|
610 540 520 520
|
46000 18500 5800 3350
|
Стальные кольца Палля:
15х15х0,4 25х25х0,6 35х35х0,8 50х50х1,0
|
380 235 170 108
|
0,9 0,9 0,9 0,9
|
0,010 0,015 0,021 0,033
|
525 490 455 415
|
230000 52000 18200 6400
|
Керамические седла Берля:
12,5 25 38
|
460 260 165
|
0,68 0,69 0,7
|
0,006 0,011 0,017
|
720 670 670
|
570000 78000 30500
|
Керамические седла
«Инталокс»: 12,5 19 25 38 50
|
625 335 255 195 118
|
0,78 0,77 0,775 0,81 0,79
|
0,005 0,009 0,012 0,017
0,027
|
545 560 545 480 530
|
730000 229000 84000 25000 9350
|
Примечание. а-удельная поверхность; Vсв-свободный объем; dэ-эквивалентный диаметр; r-насыпная плотность.
Приложение А4
Таблица А4.1 - Динамические коэффициенты вязкости жидких веществ и водных
растворов в зависимости от температуры
Вещество
|
Динамический коэффициент
вязкости, мПа·с (сП)
|
|
-20 0С
|
-10 0С
|
0 0С
|
10 0С
|
20 0С
|
30 0С
|
40 0С
|
50 0С
|
60 0С
|
80 0С
|
100 0С
|
120 0С
|
Азотная кислота, 100 %
Азотная кислота, 50 % Аммиак жидкий Аммиачная вода, 25 % Анилин Ацетон Бензол
Бутиловый спирт Вода Гексан Глицерин, 50 % Диоксид серы (жидк.) Дихлорэтан
Диэтиловый эфир Изопропиловый спирт Кальций хлористый, 25 % раствор Метиловый
спирт, 100 % Метиловый спирт, 40 % Муравьиная кислота Натр едкий, 50 %
раствор
|
1,49 - 0,258 - - 0,5 - 10,3
- 0,479 - 0,455 1,54 0,364 10,1 10,6 1,16 - - -
|
1,24 4 0,251 - - 0,442 -
7,4 - 0,426 - 0,41 1,24 0,328 6,8 7 0,97 - - -
|
1,05 3,05 0,244 - 10,2
0,395 0,91 5,19 1,79 0,397 12 0,368 1,08 0,296 4,6 4,47 0,817 3,65 - -
|
0,92 2,4 0,235 1,72 6,5
0,356 0,76 3,87 1,31 0,355 8,5 0,334 0,95 0,268 3,26 3,36 0,68 2,54 2,25 -
|
0,8 1,88 0,226 1,3 4,4
0,322 0,65 2,95 1,0 0,32 6,05 0,304 0,84 0,243 2,39 2,74 0,584 1,84 1,78 -
|
0,72 1,55 0,217 1,05 3,12
0,293 0,56 2,28 0,801 0,29 4,25 0,279 0,74 0,22 1,76 2,25 0,51 1,37 1,46 46
|
0,64 1,28 0,208 0,855 2,3
0,268 0,492 1,78 0,656 0,264 3,5 - 0,65 0,199 1,33 1,85 0,45 - 1,22 25
|
0,57 1,07 0,199 0,71 1,8
0,246 0,436 1,41 0,549 0,241 2,6 - 0,565 0,182 1,03 1,55 0,396 - 1,03 16
|
0,5 0,9 0,19 0,6 1,5 0,23
0,39 1,14 0,469 0,221 2 - 0,51 0,166 0,8 -0,351 - 0,89 8,03
|
0,39 0,68 - 0,42 1,1 0,2
0,316 0,76 0,357 0,19 1,2 - 0,42 0,14 0,52 - 0,68 5,54 3,62 2,16
|
0,35 0,53 - 0,32 0,8 0,17
0,261 0,54 0,284 0,158 0,73 - 0,36 0,118 0,38 - 0,24 - 0,54 3,97
|
0,31 0,44 - 0,23 0,59 0,15
0,219 0,38 0,232 0,132 0,45 - 0,31 0,1 0,29 - 0,21 - 0,4 3,42
|
Натр едкий, 40 % раствор
«-----------« 30 % раствор «-----------« 20 % раствор «----------« 10 %
раствор Натрий хлористый, 20 % раствор Нитробензол Октан Олеум, 20 % Серная
кислота, 98 % «-----------------« 92 % «-----------------« 75 %
«-----------------« 60 % Сероуглерод Соляная кислота, 30 % Толуол Уксусная
кислота, 100 % «-----------------« 50 % Фенол расплавленный Хлорбензол
|
- - - - - - 0,968 - - 130
95 20 0,556 - 1,06 - - - 1,48
|
- - - - 4,08 - 0,829 - - 90
50 15 0,488 - 0,9 - - - 1,24
|
- - - - 2,67 3,09 0,703 95
55 48 30 10,5 0,433 - 0,768 - 4,35 - 1,06
|
- - - - 1,99 2,46 0,61 60
37 32 20 7,7 0,396 2,1 0,667 - 3,03 - 0,91
|
40 13 4,48 1,86 1,56 2,01
0,54 36,6 25,8 23,1 13,9 5,52 0,366 1,7 0,586 1,22 2,21 11,6 0,8
|
23 9 3,3 1,45 1,24 1,69
0,479 28,8 17,1 15,6 10,6 4,08 0,319 1,48 0,522 1,04 1,7 7 0,71
|
14 6,3 2,48 1,16 1,03 1,44
0,428 20,8 12,9 11,8 8,1 3,42 0,29 1,3 0,466 0,9 1,35 4,77 0,64
|
9,2 4,6 2 0,98 0,87 1,24
0,386 12,8 9,46 8,4 5,9 2,8 0,27 - 0,42 0,79 1,11 3,43 0,57
|
5,44 3,4 1,63 0,91 0,74
1,09 0,35 9 7,5 6,7 4,6 2,4 0,25 - 0,381 0,7 0,92 2,56 0,52
|
3,62 2,16 1,27 0,7 0,57
0,87 0,291 5,3 4,1 3,8 2,8 1,5 0,21 - 0,319 0,56 0,65 1,59 0.435
|
2,72 1,82 1,15 0,65 0,46
0,7 0,245 - 2,7 2,5 1,9 1,07 0,19 - 0,271 0,46 0,5 1,05 0,37
|
2,37 1,71 1,08 0,6 0,38
0,58 0,208 - 2 1,95 1,45 0,9 0,17 - 0,231 0,37 0,4 0,78 0,32
|
Хлороформ Четыреххлористый
углерод Этилацетат Этиловый спирт, 100 % «------------------« 80 %
«------------------« 60 % «------------------« 40 % «------------------« 20 %
|
0,9 1,9 0,79 2,38 - - - -
|
0,79 1,68 0,67 2,23 - - - -
|
0,7 1,35 0,578 1,78 3,69
5,75 7,14 5,32
|
0,67 1,13 0,507 1,46 2,71
3,77 4,39 3,17
|
0,57 0,97 0,449 1,19 2,01
2,67 2,91 2,18
|
0,51 0,84 0,4 1,0 1,53 1,93
2,02 1,55
|
0,466 0,74 0,36 0,825 1,2
1,45 1,48 1,16
|
0,426 0,65 0,326 0,701 0,97
1,13 1,13 0,91
|
0,39 0,59 0,297 0,591 0,79
0,9 0,89 0,74
|
0,33 0,472 0,248 0,435 0,57
0,6 0,6 0,51
|
0,29 0,387 0,21 0,326 0,52
0,45 0,44 0,38
|
0,26 0,323 0,178 0,248 0,43
0,34 0,34 0,3
|
Приложение А5
Рисунок А5 - Номограмма для определения динамического коэффициента
вязкости жидкостей при различных температурах
Жидкость
|
№точки
|
Жидкость
|
№точки
|
Амиловый спирт
|
17
|
Пентан
|
38
|
Аммиак
|
39
|
Ртуть
|
15
|
Анилин
|
8
|
Серная кислота, 111%
|
2
|
Ацетон
|
34
|
Серная кислота, 98%
|
3
|
Бензол
|
25
|
Серная кислота, 60%
|
6
|
Бутиловый спирт
|
11
|
Сернистый ангидрид
|
35
|
Вода
|
20
|
Сероуглерод
|
33
|
Гексан
|
36
|
Терпентин
|
16
|
Гептан
|
31
|
Толуол
|
27
|
Глицерин, 100%
|
1
|
Уксусная кислота, 100%
|
18
|
Глицерин, 50%
|
7
|
Уксусная кислота, 70%
|
12
|
Двуокись углерода
|
40
|
Фенол
|
5
|
Диэтиловый эфир
|
37
|
22
|
Метилацетат
|
32
|
Хлороформ
|
29
|
Метиловый спирт, 100%
|
26
|
Четыреххлористый углерод
|
21
|
Метиловый спирт, 90%
|
24
|
Этилацетат
|
30
|
Метиловый спирт, 30%
|
13
|
Этиленгликоль
|
4
|
Нафталин
|
9
|
Этиленхлорид
|
23
|
Нитробензол
|
14
|
Этиловый спирт, 100%
|
19
|
Октан
|
28
|
Этиловый спирт, 49%
|
10
|
Приложение А6
1 - O2; 2 - NO; 3 - CO2; 4 - HCl; 5 - воздух; 6 - N2; 7 - SO2; 8 - CH4; 9 - H2O;
10 - NH3; 11 - C2H6; 12 - H2; 13 - C6H6; 14 - 9H2 + N2; 16 - CO; 17 - Cl2
Пересчет в СИ: 1 атм = 760 мм рт. ст. = 101325 Па
Рисунок А6 - Номограмма для определения динамического коэффициента
вязкости газов при p = 1 атм
Приложение А7
Таблица А7.1 - Коэффициенты диффузии газов и паров в воздухе (при
нормальных условиях)
Газ
|
D0· 106, м2/с
|
D0, м2/ч
|
Азот Аммиак Бензол Водород
Водяной пар Диоксид серы Диоксид углерода Диэтиловый эфир Кислород Метиловый
спирт Серный ангидрид Серолуглерод Хлористый водород Этиловый спирт
|
13,2 17,0 7,7 61,1 21,9
10,3 13,8 7,8 17,8 13,3 9,4 8,9 13,0 10,2
|
0,0175 0,0612 0,0277 0,22
0,079 0,037 0,0497 0,028 0,064 0,0478 0,034 0,0321 0,0467 0,0367
|
Примечание:
При других температурах и давлениях
Таблица А7.2 - Коэффициенты диффузии газов в воде при 20 0С
Газ
|
D 109, м2/с
|
D·106, м2/ч
|
Азот Аммиак Водород Диоксид
углерода, оксид азота Кислород Хлор, сероводород Хлористый водород (при 120С)
|
1,9 1,8 5,3 1,8 2,1 1,6 2,3
|
6,9 6,6 19,1 6,4 7,5 5,8
8,3
|
Примечание:
При других температурах
Приложение А8
Таблица А8.1 - Атомные и мольные объемы некоторых элементов
Атомный объем, см3/атом
|
Мольный объем, см3/моль
|
В C Cl H N в первичных
аминах N во вторичных аминах N с двумя
насыщенными связями О с двумя насыщенными связями О в альдегидах и кетонах О
в сложных эфирах О в простых эфирах О в высших простых и сложных эфирах О в
кислотах О в соединениях с S, P, N S
|
27,0 14,8 24,6
3,7 10,5 12,0 15,6 7,4 7,4 9,1 9,9 11,0 12,0 8,3 25,6
|
I H2 O2 N2 Воздух
CO CO2 SO2 NO N2O NH3 H2O H2S CS2 Cl2 Br2
I2
|
37,0 14,3 25,6 31,2 29,9
30,7 24,0 44,8 23,6 36,4 25,8 18,9 32,9 51,5 48,4 53,2 71,5
|
|
|
|
|
Структурные постоянные
Бензольное кольцо
|
15
|
Нафталиновое кольцо
|
30
|
Антраценовое кольцо
|
47,5
|
Примечание. При расчете мольного объема химического соединения величину
соответствующей структурной постоянной надо прибавить к сумме атомных объемов
Приложение А9
Таблица А9.1 - Поверхностное натяжение жидких веществ и водных растворов
в зависимости от температуры
Вещество
|
Поверхностное натяжение s × 103 Н/м
|
|
-200С
|
00С
|
200С
|
400С
|
600С
|
800С
|
1000С
|
1200С
|
Азотная кислота, 100% « «
50% Аммиак жидкий Аммиачная вода, 25% Анилин Ацетон Бензол Бутиловый спирт
Вода Гексан Глицерин, 50% Диоксид серы (жидк.) Диэтиловый эфир Дихлорэтан
Изопропиловый спирт Кальций хлористый, 25% раствор Метиловый спирт, 100%
Муравьиная кислота Натр едкий, 50% раствор « « 40% « « « 30% « « « 20% « « «
10% « Натрий хлористый, 20% раствор Нитробензол Октан Серная кислота, 98% « «
92% « « 75% « « 60% Сероуглерод Соляная кислота, 30% Толуол Уксусная кислота,
100% « « 50% Фенол (расплавленный) Хлорбензол Хлороформ Четыреххлористый углерод
Этилацетат Этиловый спирт, 100% « « 80% « « 60% « « 40% « « 20%
|
48,3 - 38 - - 28,7 - 28 -
22,6 - 31 22 37,8 24,7 89,4 26,6 - - - - - - - - 25,8 - 63 74,1 77,3 38,3 -
33 - - - 38,4 32,8 31 29,5 25,7 - - - -
|
44,8 68,2 27 65,7 - 26,2
31,7 26,2 75,6 20,5 72,4 26,8 19,5 35 23,2 86,6 24,5 39,8 - - - - - 82,6 46,4
23,8 55,9 61,9 73,6 76,7 35,3 72,6 30,7 29,7 43 43,1 36 30 29,5 26,9 24 26 28
32 40
|
41,4 65,4 21,2 62,9 42,9
23,7 29 24,6 72,8 18,4 69,6 22,7 17 32,2 21,7 83,8 22,6 37,6 130 108 97 85,8
77,3 79,8 43,9 21,8 55,1 60,9 73,1 76,1 32,3 69,8 28,5 27,8 40 40,9 33,6 27,2
26,9 24,3 22,3 25 27 30 38
|
38,2 62,2 16,8 59,7 40,6
21,2 26,3 22,9 69,6 16,3 66,4 18,8 14,6 29,5 20,1 80,6 20,9 35,5 130 108 96,4
85 76,1 76,6 41,4 19,8 54,3 60,9 72,6 75,4 29,4 66,6 26,2 25,8 37 38,8 31,1
24,4 24,5 21,7 20,6 23 25 28 36
|
35,2 58,8 12,8 56,3 38,3
18,6 23,7 21,2 66,2 14,2 63 14,8 12,4 26,7 18,5 77,2 19,3 33,3 129 107 95,8
84,7 75 73,2 39 17,9 53,7 60,3 72,1 74,5 26,5 63,2 23,8 23,8 33 36,6 28,8
21,7 22 19,2 19 21 23 26 33
|
32,4 55,2 - 52,7 36 16,2
21,3 19,5 62,6 12,1 59,4 - 10,2 24 17 73,6 17,6 31,2 129 107 95,3 83,2 73
69,6 36,7 15,9 53,1 59,7 71,6 73,6 23,6 59,6 21,5 21,8 30 34,4 26,5 19 19,6
16,8 17,3 20 22 24 31
|
29,8 51,5 - 49 33,7 13,8
18,8 17,8 58,9 10 55,7 - 8 21,3 15,5 69,9 15,7 29 128 106 94,4 81,3 70,7 65,9
34,4 13,9 52,5 59,1 71,1 72,7 20,7 55,9 19,4 19,8 27 32,2 24,1 16,3 17,3 14,4
15,5 18 20 22 29
|
27,4 47,5 - 45 31,4 11,4
16,4 16 54,9 79 51,7 - 6,1 18,6 14 65,9 13,6 26,8 128 106 93,6 79,6 69 61,9
32,2 11,9 51,9 58,5 70,6 71,8 17,8 51,9 17,3 18 24 30 21,8 13,6 15,1 12,1
13,4 16 18 19 27
|
Приложение А10
Рисунок А10 - Колонна абсорбирующая Д = 1000 мм. Чертеж общего вида