Производительность
при резке кубиков, размерами:
|
кг/ч
|
4х4х4 мм
|
250
|
6х6х6 мм
|
500
|
8х8х8 мм
|
750
|
12х12х12 мм
|
1000
|
Число
загрузочных камер Размеры загрузочной камеры, мм, не более Вместимость
загрузочной камеры, дм3 Размеры куска подаваемого шпика, мм
|
2 440х112х112
5,5 110х30х430
|
Установленная
мощность, кВт
|
4
|
Габаритные
размеры, мм, не более длина ширина высота Масса, кг
|
1080 735 1907 810
|
Волчок модели МП-160 имеет номинальный диаметр выходной
решетки 160 мм и производительность 4000 кг/ч. Применяется волчок для
непрерывного измельчения бескостного мяса и мясопродуктов при производстве
фарша для колбасных и других мясных изделий. Конструкция состоит из следующих основных
частей [2]: питающей части: загрузочная чаша, корпус шнеков, шнеки: приемный и
рабочий, горизонтально расположенные в корпусе шнеков; режущей части: ножи.
Рис.2.3.3 Волчок МП-160
Волчок модели МП-160 имеет номинальный диаметр выходной решетки
160 мм и производительность 4000 кг/ч. Применяется волчок для непрерывного
измельчения бескостного мяса и мясопродуктов при производстве фарша для
колбасных и других мясных изделий. Конструкция состоит из следующих основных
частей: питающей части: загрузочная чаша, корпус шнеков, шнеки: приемный и
рабочий, горизонтально расположенные в корпусе шнеков;
режущей части: ножи и набор ножевых решеток, цилиндр с внутренними
спиральными ребрами и гайка, служащая для регулирования зазора между ножами и
решетками в режущем механизме; приводной части: электродвигатель, пост
управления, редуктор специальный цилиндрический и клиноременная передача;
станины: на которой монтируются все сборочные единицы и детали,
электродвигатель и пусковая электроаппаратура.
Технические характеристики:
Производительность, кг/ч 4000
Диаметр выходной решетки, мм 160
Номинальная установленная мощность, кВт 15
Вместимость загрузочного бункера, дм³ 70
Длина, мм 1380
Ширина, мм 600
Высота, мм 1100
Масса не более, кг 815
3.
Расчет освещения
3.1 Характеристика помещений
Первое помещение - цех переработки площадью
71,5 м2. Стены помещения бетонные, штукатуренные, побеленные.
Потолок - бетонные побеленные плиты, высота данного помещения 5 м.
Характеристика: коэффициенты отражения п=30%; Рс=10%; Ррп=10%; класс по среде с
повышенной опасностью, разряд VI, коэффициент запаса - 1,7. Минимальная
нормируемая освещенность - 150 Лк. Размеры помещения 13х5,5х5 м.
Второе помещение - разделочная. Стены
данного помещения кирпичные, штукатуренные, побеленные. Потолок - побеленные
бетонные плиты. Площадь данного помещения 29 м2. высота помещения 5
м. Коэффициенты отражения Рп=30%; Рс=10%; Ррп=10%; класс по среде с повышенной
опасностью, разряд VI, коэффициент запаса - 1,7. минимальная нормируемая
освещенность 150 лк. Размеры помещения 6,5х4,5х5 м.
Третье помещение - комната отдыха. Стены
данного помещения кирпичные, штукатуренные, побеленные,. Потолок - побеленные
бетонные плиты. Площадь данного помещения 19 м2, высота помещения 5
м. Коэффициенты отражения Рп=50%; Рс=30%; Ррп=10%; класс по среде со средней
опасностью, разряд IV, коэффициент запаса - 1,5. минимальная нормируемая
освещенность 80 лк.
Четвертое помещение - склад сырья. Стены
данного помещения кирпичные, покрытые нержавеющей стальной жестью. Потолок -
бетонные плиты. Площадь данного помещения 55 м2 высота помещения 5
м. Коэффициенты отражения Рп=50%; Рс=30%; Ррп=10%; класс по среде с повышенной
опасностью, разряд V, коэффициент запаса - 1,5. минимальная нормируемая
освещенность 80 лк. Размеры площадки 6,5х8,5х5
Площадка перед входом. Стены кирпичные. высота 5
м. Минимальная нормируемая освещенность 2 лк. Размеры площадки 5х2х5м. Коэффициент
запаса равен 1,7.
Пятое помещение - склад готовой продукции. Стены данного
помещения кирпичные, покрытые нержавеющей стальной жестью. Потолок - бетонные
плиты. Площадь данного помещения30 м2 высота помещения 5 м.
Коэффициенты отражения Рп=50%; Рс=30%; Ррп=10%; класс по среде с повышенной
опасностью, разряд V, коэффициент запаса - 1,5. минимальная нормируемая
освещенность 80 лк. Размеры площадки 5х6х5
3.2 Расчет освещения, определение числа ламп их расстановка
Расчет освещения цеха
переработки
Расчет мощности осветительной установки (методом
коэффициента использования светового потока)
Выбор источников света и светильников
Исходные данные: Геометрические размеры 13
х 5.5 х 5 м
Коэффициенты отражения ограждающих конструкций: 30%; 30%; 10%
Нормируемая освещенность Ен = 150 лк (Г-0,0)
Т.к. нормированная освещенность больше 100 лк [5] и высота
подвеса менее 6 м. целесообразно использовать светильник с газоразрядными
лампами. Для этих ламп определяем коэффициент запаса равный 1,5, так как:
) Высота помещения не превышает 6м;
) ГРЛ удобны в эксплуатации, рассчитаны на большие сроки
службы, имеют большой световой поток, высокую световую отдачу и незначительные
размеры, выпускаются на небольшие мощности;
) Работа ГРЛ практически не зависит от температуры окружающей
среды, т.к. в них используется ЭПРА (электронная пускорегулирующая аппаратура)
Система освещения: общее, равномерное - нет необходимости в
местном освещении, работы выполняются с одинаковой точностью по всей площади.
Вид освещения: рабочее, которое необходимо только при работе
персонала в помещении.
Среда: сырая. Согласно исходным данным (КСС-Г; IР54) выбираем из таблицы
варианты светильников.
В качестве светильника выбираем светильник типа ЛСП 3901 -
2х36 со степенью защиты IP54, КСС в нижнюю полусферу глубокий Г1 (0,8…1,2).
Для расчета освещённости данного помещения можем использовать
метод коэффициента использования светового потока, т.к. в этом помещении
высоких затеняющих предметов нет. [5]
Индекс помещения [5]:
, (3.2.1)
где а - длина помещения, м; b - ширина
помещения, м; Нр - расчётная высота помещении, м.
По справочнику с учётом коэффициентов отражения и показателя
помещения находим коэффициент использования светового потока
rпот=0,3; rст=0,3; rп=0,1, h = 75%
Определение числа светильников
, (3.2.2)
где lС, lЭ - относительные светотехнические и
энергетические наивыгоднейшие расстояния между светильниками. Для КСС-Г:
0,8×5 ≤
L ≤ 1,2×5
≤ L ≤ 6
принимаем L = 5 м
Расстояние от края светильника до стен: l = 0,5 ∙ L
l= 0,5 ∙ 5 = 2,5 м.
Число рядов светильников определяется по формуле:
, а число светильников в ряду:
. (3.2.3) Произведём
расчёт:
,
Общее число светильников
(3.2.4)
Определение светового потока одной лампы
Световой поток от одной лампы определяется по формуле:
,
где Ен - нормируемая освещенность в помещении, лк; z-коэффициент неравномерности, z - 1,1.1,2; n-количество
ламп в светильнике; К3 - коэффициент запаса.
Откуда
Отклонение потока лампы от расчетного:
(3.2.5)
Лампа ЛБ-65-7
где Фт - каталожный (номинальный) поток лампы, лм. ФТ=4600
лм.
Отклонение потока лампы от расчетного должно удовлетворять условию
10% ≤ DФ ≤ +20%
Тогда
10% ≤ - 5,5% ≤ +20%
Установленная мощность освещения:
.
Расчет освещения разделочной
Исходные данные: Геометрические размеры 6,5 х 4.5 х 5 м
Индекс помещения
,
где а - длина помещения, м; b - ширина
помещения, м; Нр - расчётная высота помещении, м.
По справочнику с учётом коэффициентов отражения и показателя
помещения находим коэффициент использования светового потока.:
rпот=0,3; rст=0,3; rп=0,1.
h = 70%
Определение числа светильников
,
где lС, lЭ - относительные светотехнические и
энергетические наивыгоднейшие расстояния между светильниками. Для КСС-Г:
0,8×5 ≤
L ≤ 1,2×5
≤ L ≤ 6
принимаем L = 5 м
Расстояние от края светильника до стен: l = 0,5 ∙ L
l= 0,5 ∙ 5 = 2,5 м.
Число рядов светильников определяется по формуле:
, а число светильников в ряду:
.
Произведём расчёт:
,
Общее число светильников
Определение светового потока одной лампы
Световой поток от одной лампы определяется по формуле:
,
где Ен - нормируемая освещенность в помещении, лк; z-коэффициент неравномерности, z - 1,1.1,2; n-количество
ламп в светильнике;
К3 - коэффициент запаса.
Откуда
Лампа ЛБ-40-7. Отклонение
потока лампы от расчетного:
где Фт - каталожный (номинальный) поток лампы, лм. ФТ=2800
лм.
Отклонение потока лампы от расчетного должно удовлетворять условию
10% ≤ DФ ≤ +20%
Тогда
10% ≤ - 5,5% ≤ +20%
Установленная мощность освещения:
.
Аналогично рассчитываем освещение для склада сырья и готовой
продукции. Достаточно нормированной освещенности 100лк. по 2 светильника ЛСП06
с лампами ЛБ40 мощностью 40Вт. Комната отдыха и туалет - душ снабжены
светильником ЛПО 06В с лампами ЛБ40.
Таблица 3.2.1
Светотехническая ведомость
№ Наименование
помещения Площадь Высота подвеса светильников Коэффициенты отражения Вид
освещения Система освещения Норма освещённости Коэффициент запаса Светильник
Лампа Общая мощность установки м2 м
потолка стен пола лк ТИП Кол-во ТИП мощность Вт 1 Цех переработки 71.5 5 30 10 10 Рабочее и дежурное
освещение Общее равномерное освещение 150 1,7 ЛСП3901 3 ЛБ65-7 65 130 2 Склад готовой продукции 30 5 50 30 10 80 1,5 ЛСП06 2 ЛБ40
40 80 3 разделочная 29 5 30 10 10 150
1,7 ЛСП 3901 2 ЛБ40-7 40 80 4 Склад сырья
55.2 5 50 30 10 80 1,5 ЛСП06 2 ЛБ40 40 80 5
Освещение входа 5 125 РКУ 125 1 ДРЛ125 125 125 6 Комната отдыха 19.2 5 50 30 10 100 1,5 ЛПО 06В 2 ЛБ40
40 80 7 компрессорная 14 5 50 30 10 80
1,5 ЛПО06 2 ЛБ40 40 80
|
3.3
Выбор конструктивного выполнения внутренних сетей, формирование групп, определение
сечения проводов и кабелей
Рисунок 3.3.1 "Группы освещения"
Во внутренних осветительных сетях используем провод марки ВВГ.
[11] Способ прокладки выбран непосредственно по строительным основаниям в
пластиковых трубах. К строительным основаниям трубы крепят при помощи
специальных держателей. Допустимые потери напряжения составляют 5%.
Для определения сечения проводов групп осветительной сети
отходящих от магистрального осветительного щитка, произведем расчет.
Определим электрические моменты на каждом участке.
На вводе: 
, (3.3.1)
где 
- мощность i-того
приемника; 
- длина участка.
,
На группе 1:
М1 = Р1∙l1+ Р2∙ (l1+l2)
+ Р3∙ (l1+l2+l3)
кВт∙м,
М1=130∙7+130∙ (7+5) +130∙ (7+5+5)
=4,7кВт∙м;
На группе 2:
М2 = Р4∙l4 + Р5∙ (l4+l5)
+ Р6∙l6 +Р7∙ (l6+l7)
+ Р8∙l8+ Р9∙
(l8+l9)
Вт∙м,
М2 = 80∙4 + 80∙ (4+5) + 80∙6,5+80∙ (6,5+5) +80∙8+80∙ (8+5) =4,16
кВт∙м;
На группе 3:
М3 = Р10∙l10+ Р11∙l11+ Р12∙l12+Р13∙ (l12+l13)
+Р14∙l14+ Р15∙l15+Р16∙ (l15+l16)
кВт∙м,
М3 =5∙80+80∙5+80·7+80∙7,5+10·125+80·5+80·
(5+5) =4,81кВт·м
Рассчитаем сечение провода на каждой группе:
На вводе:

(3.3.2)
где 
- электрический момент i-того
приемника, 
; 
- коэффициент зависящий от напряжения сети, материала жилы, числа
проводов в группе, для медных проводов трехфазной с нулем 380/220 - 72, для
медных проводов напряжением сети 220 В - 12.
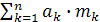
- сумма моментов ответвлений с другим числом проводов, чем у
рассчитываемого участка, кВт м.

- коэффициент приведения моментов, зависящий от числа проводов
расчетного участка в нашем случае равен 1,85, так как ответвление от трехфазной
идет на однофазную.

- предполагаемая потеря напряжения равное 5%.
Принимаем сечение S = 2,5мм2
, Iдоп = 25
А,
Проверяем на нагрев
, 

, следовательно сечение
S=1,5 мм2 удовлетворяет условиям
выбора.
На группе 1:
Принимаем сечение S=1,5 мм2
, Iдоп=18 А
Проверяем на нагрев
, 

, следовательно сечение
S=1,5 мм2 удовлетворяет условиям
выбора.
Определим потери напряжения на первом участке:
% (3.3.3)
Потери напряжения на группе 
DU=4,3-0,26=4,04%
На группе 2:
Принимаем сечение S=1,5 мм2
, Iдоп=18 А
Проверяем на нагрев 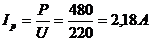

, следовательно сечение
S=1,5 мм2 удовлетворяет
условиям выбора.
Определим потери напряжения на втором участке:
%
Потери напряжения на группе 
DU=4,3-0,23=4,07%
На группе 3:
Принимаем сечение S=1,5 мм2
, Iдоп=18 А
Проверяем на нагрев
, 

, следовательно сечение
S = 1,5 мм2
удовлетворяет условиям выбора.
Определим потери напряжения на третьем участке:
%
Потери напряжения на группе 
DU=4,3-0,26=4,04%
На вводе используется кабель марки ВВГ 5×2,5, остальных помещениях ВВГ 3×1,5
3.4
Проводка и выбор пуско-регулируемой защитной аппаратуры
Выбор вводного распределительного устройства, коммутационной и
защитной аппаратуры
Осветительная сеть питается от щита освещения типа ОЩН с
автоматическими четырехполюсными дифференциальными автоматами АВДТ32 на вводе и
автоматическими выключателями на каждой группе осветительной сети. АВДТ32
представляет собой соединение двух функциональных узлов: электронного модуля
дифференциальной защиты с номинальным отключающим дифференциальным током на 30
мА, согласно ПУЭ, и дифференциальным автоматическим выключателем. Электронный
модуль состоит из дифференциального трансформатора тока, электронного усилителя
с пороговым устройством, исполнительного электромагнита сброса и источника
питания. [10]
Рассчитаем номинальный ток автоматического выключателя для
каждой группы осветительной сети, от щита ОЩН-8, с тепловым расцепителем, по
току расцепителя IТ. расц.
Ток расцепителя IТ. расц определяется по формуле:
, (3.4.1)
где 
- коэффициент надежности, учитывающий разброс по току, Кн
=1,4, 
- расчетный
ток группы А.
Группа 1:
Р = 0,390 кВт, Iрасц = 1,77 А, IТ. расц =
1,4∙1,77 = 2,5 А,
Выбираем автоматический выключатель ВА47-29 с номинальным током
расцепителя 6 А.
Группа 2:
Р = 0,48 кВт, Iрасц = 2,18 А, IТ. расц =
1,4∙2,18 = 3,05 А,
Выбираем автоматический выключатель ВА47-29 с номинальным током
расцепителя 4А.
Группа 3: Р = 0,775 кВт, Iрасц =
3,47 А, IТ. расц = 1,4∙3,47 = 4,86 А,
Выбираем автоматический выключатель ВА47-29 с номинальным током
расцепителя 6 А. [10]
3.5 Составление расчетно-монтажной схемы таблицы сетей освещения
Расчетно-монтажная схема таблица со всему значениями
находится на чертеже "расчетно-монтажная схема таблица осветительной
сети".
Выбор автоматических выключателей системы обеспечивает ее
селективную работу.
На примере щита ОЩН-8 освещения первой группы видно, что при
возникновении короткого замыкания или утечке тока на корпус токоприемника
сработает первым автоматический выключатель (защищает от сверхтоков к. з), в
случае касания человеком корпуса сработает четырехполюсный дифференциальный
автомат АВДТ32. Для остальных групп освещения принцип действия аналогичный,
первым срабатывает ближний находящийся к токоприемнику автоматический
выключатель, а потом четырехполюсный дифференциальный автомат АВДТ32, стоящий
на вводе в щите.
4.
Расчет силовой сети
4.1 Формирование силовой сети
Расчёт силовой сети начинается с выбора схемы
электроснабжения. Для цеховых сетей применяются радиальные и магистральные
схемы электроснабжения. Для крупных объектов возможно использование
комбинированных схем. При радиальной схеме электроснабжения приёмники
электроэнергии (электродвигатели) соединяются независимо друг от друга с
источниками электропитания (силовые распределительные пункты, шкафы
электропитания и др.). При этом электродвигатель соединяется с источником
питания отдельным кабелем. Достоинством такой схемы является высокая
надёжность. [13]
При магистральной схеме электроснабжения потребители одного
типа подключаются к общей линии (шине, шиносборке). Это обеспечивает простоту и
экономичность подключения, но также связано с меньшей надёжностью и
взаимозависимостью работы потребителей.
В данной работе подключение потребителей осуществляется по
магистральной схеме с помощью пятижильных кабелей для асинхронных двигателей.
Прокладка кабелей осуществляется под землёй в пластиковых трубах или подвеской
вдоль стен и опор.
Для электроснабжения пункта первичной обработки молока
установлена комплектная трансформаторная подстанция (КТП). От КТП
электропитание подводится к электрощитовой по подземной кабельной ЛЭП.
В электрощитовой вводно-распределительное устройство ВРУ
установлено со стороны КТП. Основу ВРУ составляет шкаф распределительный
силовой марки СПА77-6, предназначенный для распределения электрической энергии
трехфазного тока частотой 50 Гц. Он имеет рубильник на вводе и автоматические
выключатели для защиты отходящих линий на выводе.
От ВРУ запитаны щит распределительный ЩРН-8 и Бокс 2-2-Н. Щит
ЩРН-8 предназначены для распределения электрической энергии трехфазного тока
частотой 50 Гц. Он имеет четырёхполюсный дифференциальный автоматический
выключатель на вводе и 3 автоматических выключателя ВА 47-29 на выводе. Бокс
2-2-Н служит для респределения, защиты и произведения коммутаций при помощи
магнитных пускателей (шкафы управления). [13]
4.2 Проектирование силовой сети. Определение сечения проводов и
кабелей, выбор пускозащитной аппаратуры, способа прокладки
Рис.4.2.1 Силовая сеть колбасного цеха
Силовую сеть колбасного цеха выполняют кабелем марки ВВГ
прокладывают в пластиковых гофрированных трубах. Определим сечение проводов и
потери напряжения участка 1.2, 2.1, 2.2, 2.3,1.3,1.4 силовой сети.
Исходя из допустимой потери напряжения, рассчитываем сечение на
участке 2.1 (куттер) по формуле:
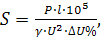
(4.2.1)
где 
- нагрузка линии, кВт; 
- длина линии, м; 
- удельная проводимость материала провода, 
(для меди g = 53, для
алюминия g = 32); U-номинальное напряжение линии, В; 
- допустимая потеря напряжения, %.
Для силовой сети потеря напряжения не больше 5%.
Принимаем стандартное сечение 
,
. Выбранное сечение проверяем по длительно
допустимому току. пределяем ток номинальный для трехфазного
асинхронного двигателя:
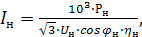
(4.2.2)
где 
- номинальная мощность токоприемника, Рн=2,5
кВт; - номинальное напряжение токоприемника,

В; 
- коэффициент мощности,
; 
- коэффициент полезного действия, 
.
, а условие 
условие выполняется, тогда принимаем сечение S =1,5 мм2
Определим потери напряжения на участке 2.1 по формуле:

(4.2.3)
Исходя из допустимой потери напряжения, рассчитываем сечение на
участке 2.2 (машина шпигорезная) по формуле:
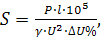
где 
- нагрузка линии, кВт; 
- длина линии, м; 
- удельная проводимость материала провода, 
(для меди g = 53, для
алюминия g = 32); U-номинальное напряжение линии, В; 
- допустимая потеря напряжения, %.
Для силовой сети потеря напряжения не больше 5%.
Принимаем стандартное сечение 
,
. Выбранное сечение проверяем по длительно
допустимому току.
Определяем ток номинальный для трехфазного асинхронного двигателя:
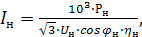
где 
- номинальная мощность токоприемника, Рн=4 кВт;

- номинальное напряжение токоприемника, 
В;

- коэффициент мощности,
; 
- коэффициент полезного действия, 
.

, а условие 
условие выполняется, тогда принимаем сечение S =1,5 мм2
Определим потери напряжения на участке 2.2 по формуле:

Исходя из допустимой потери напряжения, рассчитываем сечение на
участке 2.3 (фаршмешалка) по формуле:
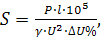
где 
- нагрузка линии, кВт; 
- длина линии, м; 
- удельная проводимость материала провода, 
(для меди g = 53, для
алюминия g = 32); U-номинальное напряжение линии, В; 
- допустимая потеря напряжения, %.
Для силовой сети потеря напряжения не больше 5%.
Принимаем стандартное сечение 
,
. Выбранное сечение проверяем по длительно
допустимому току.
Определяем ток номинальный для трехфазного асинхронного двигателя:
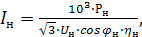
где 
- номинальная мощность токоприемника, Рн=5
кВт;

- номинальное напряжение токоприемника, 
В; 
- коэффициент мощности,
; 
- коэффициент полезного действия, 
.

, а условие 
условие выполняется, тогда принимаем сечение S =1,5 мм2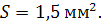

,
Исходя из допустимой потери напряжения, рассчитываем сечение на
участке 2-4 (шприц вакуумный) по формуле:
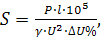
где 
- нагрузка линии, кВт; 
- длина линии, м; 
- удельная проводимость материала провода, 
(для меди g = 53, для
алюминия g = 32); U-номинальное напряжение линии, В; 
- допустимая потеря напряжения, %.
Для силовой сети потеря напряжения не больше 5%.
Принимаем стандартное сечение 
,
. Выбранное сечение проверяем по длительно
допустимому току.
Определяем ток номинальный для трехфазного асинхронного двигателя:
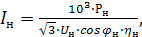
где 
- номинальная мощность токоприемника,
Рн=15
кВт;

- номинальное напряжение токоприемника,

В; 
- коэффициент мощности,

; 
- коэффициент полезного действия, 
.

, а условие 
условие выполняется, тогда принимаем сечение S =1,5 мм2
Определим потери напряжения на участке 2.4 по формуле:

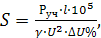
где 
- мощность участка. Исходя из
допустимой потери напряжения, рассчитываем сечение на участке 1.2 (ввод) по формуле:
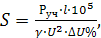
где 
- мощность участка.
Принимаем ближайшее стандартное сечение S=4 мм2 Iдоп=30 А для пяти жильного кабеля.
Выбранное сечение проверяем по длительно
допустимому току.

где 
- количество токоприемников.
Iуч=6,5+10,5+13+6,5=36,5
А.
Iдоп=30 А, Iдоп<Iуч
условие не выполняется, берем сечение
с Iдоп=40 А
Определим потери напряжения на участке 1.2 по формуле:

Исходя из допустимой потери напряжения, рассчитываем сечение на
участке 1.3 (волчок) по формуле:
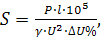
где 
- нагрузка линии, кВт; 
- длина линии, м; 
- удельная проводимость материала провода, 
(для меди g = 53, для
алюминия g = 32);
U-номинальное напряжение линии, В; 
- допустимая потеря напряжения, %.
Для силовой сети потеря напряжения не больше 5%.
Принимаем стандартное сечение 
,
. Выбранное сечение проверяем по длительно
допустимому току.
Определяем ток номинальный:
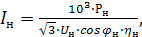
где 
- номинальная мощность токоприемника, Рн=15
кВт;

- номинальное напряжение токоприемника, 
В; 
- коэффициент мощности,
; 
- коэффициент полезного действия, 
.
, а условие Iдоп = Iном
условие выполняется.
Определим потери напряжения на участке 1-3 (установка коптильная)
по формуле:

Исходя из допустимой потери напряжения, рассчитываем сечение на
участке
-4 (установка коптильная) по формуле:
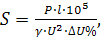
где 
- нагрузка линии, кВт; 
- длина линии, м; 
- удельная проводимость материала провода, 
(для меди g = 53, для
алюминия g = 32);
U-номинальное напряжение линии, В; 
- допустимая потеря напряжения, %.
Для силовой сети потеря напряжения не больше 5%.
Принимаем стандартное сечение 
,
. Выбранное сечение проверяем по длительно
допустимому току.
Определяем ток номинальный:
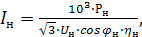
где 
- номинальная мощность токоприемника, Рн=17
кВт;

- номинальное напряжение токоприемника, 
В; 
- коэффициент мощности,
; 
- коэффициент полезного действия, 
.
, а условие Iдоп >Iном
условие выполняется, тогда принимаем
сечение S =8 мм2
Определим потери напряжения на участке 1.4 по формуле:

Выбор
пускорегулирующей и защитной аппаратуры
Силовая сеть колбасного цеха состоит из групповых
распределительного Бокса 2-2-Н и щита ЩРН-8. Которые состоят из вводного и
групповых трехполюсных и однополюсных автоматических выключателей с
термомагнитным расцепителем. Автоматы обеспечивают защиту от перегрузок (имеют
регулируемую уставку 0,8-1
), от короткого замыкания (имеют постоянную и регулируемую уставку
5-10
в зависимости от номинального тока). Выбор автоматических
выключателей проводится согласно формулам.
Для силовых одиночных электроприемников:
Ток уставки теплового расцепителя [11]:
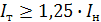
, (4.2.4)
Ток уставки электромагнитного расцепителя:
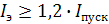
, (4.2.5)
где 
- номинальный ток электроприемника; 
- пусковой ток электродвигателя.
Для групповых силовых (двигательных) электроприемников,
соответственно:

; (4.2.6),

, (4.2.7)
Пускатели и тепловые реле выбираются по табличным данным согласно
номинальному току А.
4.3 Составление расчетно-монтажной схемы - таблицы силовой сети
Результат выбора представим в расчётной схеме - таблице
силовой сети колбасного цеха.
5.
Разработка дымогенератора
5.1 Назначение и анализ конструкции
Дымогенератор - устройство для образования дыма в
коптильных камерах. Дым образуется при тлении древесины (опилок, брусков)
лиственных пород (дуба, ольхи) без воспламенения. В дымогенераторе с
электрическими нагревателями дымообразование регулируют изменением температуры
нагревателя (от 200° до 400°C) и производительностью вентиляторов. Полнота
сгорания опилок обеспечивается подачей воздуха, который охлаждает дым до
температуры, необходимой для копчения. [1]
Классификация дымогенераторов по системе розжига:
Ручной, электронагревателем (тэн), фрикционным диском.
Марки дымогенераторов:
Дымогенератор щеповой ДЩА-З " Генератор дыма
Рис.5.1.1 Дымогенератор щеповой ДЩА-З
Дымогенератор щеповой ДЩА-З предназначен для выработки дыма
из древесной щепы методом тления для копчения мясной, рыбной и других видов
продукции.
Дымогенератор щеповой ДЩА-З используется совместно с
термодымокамерами, климатическими камерами, камерами вяления,
коптильно-варочными камерами отечественного и импортного производства с
единовременной загрузкой до 12 контейнерных еврорам.
Монтаж дымогенератора производится в единой лицевой панели с
пультом управления термодымокамеры и может располагаться как с лицевой стороны
камеры, так и на задней стене камеры. Схема привязки дымогенератора к камере
согласовывается с заказчиком.
Особенности:
исполнение дымогенератора из нержавеющей стали;
герметичная конструкция дымогенератора;
автоматическая подача и дозирование щепы пневматическим
ворошителем;
автоматический розжиг щепы;
полная автоматизация и управление с индивидуального пульта
управления;
регулирование плотности, объема и температуры дыма;
комплектация пневмо-электрической исполнительной системой
"CAMOZZI" (Италия);
эффективная система гашения пламени, предотвращающая
возгорание щепы.
Дымогенератор
щеповой ДЩА-З Технические характеристики:
Установленная мощность, кВт 1
Напряжение питающей сети, В 220 (± 5-10 %)
Давление сжатого воздуха, мПа 0,4-0,6
Давление воды, мПа 0,3-0,4
Расход щепы, кг/час 4-5
Производительность дыма, мЗ/ч до 1000
Габаритные размеры АхВхС, мм 770x1100x1950
Вес, кг 100
Дымогенератор фрикционный ДГФ-50 предназначен для
выработки дыма из бруса лиственных пород дерева сечением 50х50 мм. методом
трения для копчения мясной, рыбной, сырной и других видов продукции.
Фрикционный дым генерируется при температурах 400°С - 450°С и
отличается низким содержанием смоляных компонентов. Отличительной чертой
данного дымогенератора является то, что выработка дыма начинается и
прекращается строго по "команде".
Рис.5.1.2 Дымогенератор фрикционный
Дымогенератор состоит из:
o корпуса;
o электродвигателя;
o направляющего патрубка;
o прижима;
o регулирующихся по высоте
опор;
o заслонки подачи дыма;
o фрикционного диска.
Корпус фрикционного дымогенератора представляет собой каркас,
изготовленный из стали, на который монтируются электродвигатель с фрикционным
диском, дверца для выгрузки золы, направляющий патрубок для бруса и заслонка
для подачи воздуха. Перед запуском дымогенератор должен быть обязательно
заземлен. После запуска электродвигателя в направляющий патрубок с прижимом
устанавливается древесный брус из не смолистых пород древесины (ольха, осина,
бук, дуб и др.).
Эксплуатационные преимущества:
o высокая плотность дыма и
сокращение продолжительности процессов копчения;
o интенсивность генерации и
плотности дыма регулируется через систему управления установки;
o простота и удобство
обслуживания и санитарной обработки;
o компактность и экономия
производственных площадей;
o удобная и простая
загрузка древесного бруса;
o сменные фрикционные диски
обеспечивают мягкость работы агрегата и экономию расходных материалов.
Таблица 5.1.1 Характеристика дымогенератора ДГФ-50
Марка
|
ДГФ - 50
|
Метод получения
дыма
|
трением
|
Габаритный
размер применяемого бруса АхВ, мм
|
50х50
|
Диаметр
патрубка дымохода, мм
|
150
|
Расход бруса,
м/ч
|
0,5 - 1,0
|
Расчетная
производительность дыма, м3/ч
|
до 250
|
Установленная
мощность, кВт
|
3,0
|
Напряжение
питающей сети, В
|
380
|
Габаритный
размер установки AхBхC, мм
|
800х1000х1200
|
Общая масса, кг
|
90
|
Исполнение по
выбору заказчика
|
- нержавеющая
стал
|
Дымогенератор ДГ 104 "
Рис.5.1.3 Дымогенератор ДГ 104
Дымогенератор ДГ 104 Предназначен для выработки дыма, который
подается в термокамеру при копчении колбасных изделий. Дымогенератор -
электрический, имеет отдельный пульт управления, связанный с пультом управления
термокамеры, и работает в автоматическом режиме. [4]
Для очистки дыма вмонтирована система смолоулавливания типа
"водная завеса", что предотвращает закоксование теплообменника и
повышает качество продукции. Предусмотрена автоматическая система
пожаротушения.
Дымогенератор
ДГ 104 Технические характеристики:
Установленная мощность, кВт:
привод ворошителя 0,12
вентилятор 0,18
Электротэн:
напряжение, В 380
мощность, Вт 1500
Максимальная производительность, м/час 100
Габаритные размеры, мм 1400х1000х2100
Масса, кг 300
5.2
Разработка конструкции определение типа и мощности системы поджога
Примем к разработке дымогенератор с фрикционным розжигом так
как
генераторы дыма фрикционного типа имеют ряд преимуществ в
сравнении с дымогенераторами с внутренним или внешнем подводом тепла. При
использовании фрикционных дымогенераторов появляется возможность поддерживания
температуры дымообразования близкой оптимальной, что позволяет получить
коптильный дым наилучшего качества с наименьшим содержанием канцерогенных
веществ. Подбором древесины можно получить дым с заранее заданными качествами
Принцип работы
Работа дымогенератора заключается в трении древесного бруса
различных пород, о фрикционный диск, который находится на вале
электродвигателя, за счет трения образуется определенное количество дыма,
регулируемое задвижкой находящейся в дымопроводе.
На дымогенераторе расположен электродвигатель типа АИР112МА6
Таблица 5.2
Электродвигатель
|
Мощность
|
Частота вращ.,
об/мин
|
Ток, А
|
KПД, %
|
Kоэф. мощн.
|
Iп/ Iн
|
Масса, кг
|
АИР112МА6
|
3 кВт
|
1000
|
7,4
|
81
|
0,76
|
6
|
43
|
5.3
Сечения кабелей, подключение
Исходя из допустимой потери напряжения 5%, рассчитываем
сечение по формуле:
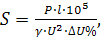
(5.3.1)
где 
- нагрузка линии, кВт; 
- длина линии, м; 
- удельная проводимость материала провода, 
(для меди g = 53, для
алюминия g = 32);
U-номинальное напряжение линии, В;

- допустимая потеря напряжения, %.
Для силовой сети потеря напряжения не больше 5%.
Принимаем стандартное сечение 
,
. Выбранное сечение проверяем по длительно
допустимому току.
Определяем ток номинальный для трехфазного асинхронного двигателя:
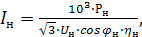
(5.3.2)
где 
- номинальная мощность токоприемника, Рн=3
кВт;

- номинальное напряжение токоприемника, 
В;

- коэффициент мощности,
; 
- коэффициент полезного действия, 
.

, а условие 
условие выполняется, тогда принимаем сечение S =1,5 мм2
Определим потери напряжения по формуле:

(5.3.3)
Подключаем дымогенератор кабелем марки ВВГ 5×1,5 к щиту управления коптильной установки.
[11]
5.4 Автоматическое управление дымогенератора
В конструкции целесообразно использовать реле защиты
электродвигателей с функцией управления типа РЗДУ предназначены для защиты
асинхронных двигателей в аварийных режимах и их управления по схеме
"Работа-Пауза" от счетчика реального времени.
РЗДУ является микропроцессорным устройством с расширенными
функциональными возможностями.
Реле обеспечивают защиту при возникновении
следующих аварийных ситуаций:
от токов короткого замыкания;
от перегрузки двигателя по току или его перегрева при наличии
встроенного терморезистора;
от обрыва фаз питающей сети на стороне высокого 6 (10) кВ или
низкого 380 В напряжения или недопустимой асимметрии фазных напряжений;
реле запрещает пуск двигателя при недопустимом снижении
сопротивления изоляции обмоток двигателя относительно корпуса.
Реле обеспечивает с шагом 1 с программируемую временную
задержку до 1,5 мин на самозапуск электродвигателя при восстановлении
напряжения сети после перерыва.
Реле имеют исполнения со следующими функциями:
автоматическое управление включением и отключением двигателя
по заданной суточной или недельной циклограмме от счетчика реального времени с
установкой до 16 или 32 включений? отключений в сутки;
программирование и просмотр состояния реле от переносного
пульта управления и индикации;
цифровая индикация текущего времени, заданных позиций
программы и состояния реле;
защитное отключение двигателя в функции датчика контроля
технологического параметра;
отключение двигателя по контролируемому току перегрузки
механизма, при работе в стопорящем режиме;
ведение архива данных по количеству отработанного времени и
типам сработавших защит;
наличие информационных выходов для связи с контроллером или
ЭВМ;
наличие исполнений с выносным пультом программирования,
индикации и считывания архива данных и без него.
По согласованию возможна поставка реле с другими
дополнительными функциями.
Исполнения реле по току двигателя:
до 10 А со встроенными трансформаторами тока. Диапазон
задания уставок тока (0,2? 12,6) А - 6 разрядов двоичного кода с дискретой 0,2
А;
от 10 до 100 А со встроенными трансформаторами тока. Диапазон
задания уставок тока (2? 126) А - 6 разрядов двоичного кода с дискретой 2 А;
свыше 100 А со входами по току с внешних трансформаторов
тока. Диапазон задания уставок тока К вн. тт? (0,2? 12,6) А - 6 разрядов
двоичного кода с дискретой К вн. тт? 0,2 А (где К вн. тт - коэффициент
трансформации внешнего трансформатора тока).
Табл.5.4.1 Технические характеристики блока РЗДУ
Величина
|
Параметр
|
Напряжение
питания, В, 50 Гц
|
220
|
Потребляемая
мощность, Вт
|
2
|
Коммутирующая
способность
|
3 А, 380 В
(катушки пускателя 0? 6величины)
|
Максимальный
импульсный ток нагрузки, А
|
5
|
Масса реле, кг
|
0,8
|
Диапазон
рабочих температур, 0С
|
- 40 …55
|
Рис 5.4.1Схема включения блока РЗДУ
6. Подсчет электрических нагрузок колбасного цеха
6.1 Подсчет электрических нагрузок на вводе и выводе щита
Для подсчета электрических нагрузок электроприемников
необходимо знать активную и реактивную мощности. Перечень электроприемников с
активными и реактивными мощностями представлен в таблице:
"Перечень электроприемников с активной и реактивной
мощностями"
-реактивная мощность
Таблица 6.1.1 Перечень электроприемников с активной и
реактивной мощностями
№ п/п
|
Обозначение на
плане
|
Наименование
установки
|
Кол-во, шт.
|
Мощ-ть акт-ная,
Р кВт
|
Коэфф-нт
мощ-ти, cos φ
|
Мощ-ть
реакт-ная, Q квар
|
Мощность полная
1 установки S, кВА
|
tgφ
|
|
1
|
2
|
3
|
4
|
5
|
6
|
7
|
|
1
|
2
|
волчок
|
1
|
15
|
0,88
|
8
|
17
|
0,62
|
2
|
3
|
куттер
|
1
|
2,5
|
0,92
|
1
|
2,7
|
0,54
|
3
|
4
|
Машина
шпигорезная
|
1
|
4
|
0,90
|
2
|
4,4
|
0,43
|
4
|
5
|
Шприц вакуумный
|
1
|
2,5
|
0,88
|
1,3
|
2,8
|
0,43
|
5
|
6
|
фаршмешалка
|
1
|
5
|
0,92
|
2,15
|
5,4
|
0,48
|
6
|
7
|
Коптильная
установка
|
1
|
17
|
0,85
|
10,5
|
20
|
0,54
|
|
|
Освещение лампами
ГРЛ
|
13
|
1,6
|
0,92
|
0,7
|
1,7
|
0,43
|
Для определения полной потребляемой мощности необходимо
подсчитать реактивную мощности. Реактивная мощность установок подсчитываем из
таблицы, согласно работающему оборудованию в пик нагрузок. Мощность активная Р=47,5
кВт и реактивная Q=25,65 квар. Определение полной мощности осуществляется по
формуле:
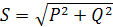
кВА, (6.1.1)
S=

- мощность активная;

- мощность реактивная;
Выбор
источника питания
Источником питания является комплектная трансформаторная
подстанция (КТП). КТП - это электрическая установка, предназначенная для
приема, преобразования и распределения электроэнергии трехфазного тока. Она
состоит из одного трансформатора, распределительного устройства выского
напряжения (РУВН) с коммутационной аппаратурой, комплектного распределительного
устройства (РУ) со стороны низкого напряжения (РУНН), и служит для
распределения электроэнергии между отдельными электроприемниками или группами
электроприемников.
Согласно выполненному подсчету электрических нагрузок в
пункте полная потребляемая мощность равна 54 кВА. Выбираем комплектную
трансформаторную подстанцию мощностью 63 кВА, тип КТП-63/10/0,4.
6.2 Расчет сечения и выбор марки вводного питающего кабеля
Электропитание колбасного цеха осуществляется кабелем марки
ВВГ проложенным под землёй. Для определения сечения кабеля необходимо знать
максимальный длительный ток. Для этого необходимо определить максимальную
потребляемую мощность потребителя. Исходя из таблицы 6.1.1
Полная мощность:
Определим расчетный ток:
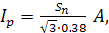
(6.2.2)
Исходя из условия 
, принимаем кабель сечением 35 мм2 с Iдоп=115 А, условие выполняется. Принимаем марку кабеля ВВГ
4х35.
Определяем потери напряжения в кабельных линиях. Допустимые потери
напряжения не должны превышать 4-6%.
Определим потери напряжения по формуле:

(6.2.3)
Потери напряжения на линии:
Проверка
защитных аппаратов на срабатывание при коротких замыканиях
В соответствии с требованиями ПУЭ в электрических сетях
напряжением до 1000 В с глухим заземлением нейтрали при коротком замыкании
защитные аппараты должны надежно обеспечивать отключение. То есть при выбор
автоматических выключателей нужно учитывать что при возникновении короткого
замыкания на линии удаленного токоприемника электромагнитный расцепитель
автоматического выключателя должен обеспечить надежное отключение этой линии.
На примере силовой сети произведем проверку защитных
аппаратов на срабатывание при коротком замыкании.
Для силовой сети самого длинного участка от вводного шкафа
(ВРУ) до токоприемника.
Определим самый отдаленный токоприемник. Это установка
коптильная, общая длина участка составляет 18 м: от вводного щита
электроводонагревателя, сечение жилы 6 мм2 участок1.3 Для участка
определим сопротивление провода, по формуле:
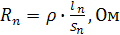
(6.2.4)

- длина проводника n-го участка, м;

- поперечное сечение проводника n-го участка, м2.
Определяем ток короткого замыкания:

(6.2.5)
где 
- однофазное напряжение при коротком замыкании на корпус;
- коэффициент учитывающий сопротивление нулевого рабочего
проводника;
Аналогично производится расчет для других участков.
6.3
Проверка возможности пуска и нормальной работы электродвигателей
При пуске электродвигателя происходит падение напряжения в
сети, а это значит, что если двигатели будут работать под нагрузкой и запустить
еще электродвигатель, то происходит падение напряжения в сети, следовательно
если будет большое падение в электросети, то работающие двигатели могут
остановиться, что не желательно.
Поэтому допустимое падение напряжение не более 15%. По
установки коптильной определим потери в электрической сети, при пуске, по
формуле:

В, (6.3.1)
где R - полное сопротивление линии,
R=0,054
Ом;

- пусковой ток электродвигателя, IП=300
А;
DU = 0,054×300 = 16,2 В.
Так как 16,2 В составляет 4% от напряжения электросети. Значит
пуск установки коптильной не отразится на работающих электроустановках.
При пуске электродвигателя пусковой ток больше номинального тока в
-10 раз, то могут срабатывать автоматические выключатели с
электромагнитными расцепителями.
Для того, чтобы при пуске электромагнитные расцепители
автоматических выключателей не срабатывали, их изготавливают с регулируемым
током расцепления 5-10 Iн.
Исходя из этого, на примере фаршмешалки 5 кВт с номинальным током
11,4 А. пусковой ток фаршмешалки в 7 раз больше Iн, можно
провести проверку. Так как Iп=7 Iн, то
пусковой ток равен 79А, а электромагнитный расцепитель установлен в положение
10Iн. Значит при пуске электродвигателя электромагнитный расцепитель
срабатывать не будет. Такая аналогия приемлема для остальных электродвигателей
7.
Монтаж, наладка и эксплуатация электрического оборудования
.1
Организация монтажа и наладка электрического оборудования
При организации и производстве работ по монтажу и наладке
электротехнических устройств следует соблюдать требования
СНиП 3.01.01-02, СНиП III-4-02, государственных стандартов,
технических условий. Правил устройства электроустановок, ведомственных
нормативных документов, утвержденных в порядке, установленном.
Работы по монтажу и наладке электротехнических устройств
следует производить в соответствии с рабочими чертежами основных комплектов
чертежей электротехнических марок; по рабочей документации электроприводов;
по рабочей документации не стандартизированного оборудования,
выполненной проектной организацией; по рабочей документации
предприятий-изготовителей технологического оборудования, поставляющих вместе с
ним шкафы питания и управления.
Монтаж электротехнических устройств следует осуществлять на
основе применения узлового и комплектно-блочного методов строительства, с
установкой оборудования, поставляемого укрупненными узлами, не требующими при
установке правки, резки, сверления или других подгоночных операций и
регулировки.
При приемке рабочей документации к производству работ надлежит
проверять учет в ней требований индустриализации монтажа электротехнических
устройств, а также механизации работ по прокладке кабелей, такелажу и установке
технологического оборудования.
Электромонтажные работы следует выполнять, как правило, в две
стадии. В первой стадии внутри зданий и сооружений производятся работы по
монтажу опорных конструкций для установки электрооборудования и шинопроводов,
для прокладки кабелей и проводов, монтажу троллеев для электрических мостовых
кранов, монтажу стальных и пластмассовых труб для электропроводок, прокладке
проводов скрытой проводки до штукатурных и отделочных работ, а также работы по
монтажу наружных кабельных сетей и сетей заземления. Работы первой стадии
следует выполнять в зданиях и сооружениях по совмещенному графику одновременно
с производством основных строительных работ, при этом должны быть приняты меры
по защите установленных конструкций и проложенных труб от поломок и
загрязнений. Во второй стадии выполняются работы по монтажу
электрооборудования, прокладке кабелей и проводов, шинопроводов и подключению
кабелей и проводов к выводам электрооборудования.
В электротехнических помещениях объектов работы второй стадии
следует выполнять после завершения комплекса общестроительных и отделочных
работ и по окончании работ по монтажу сантехнических устройств, а в других
помещениях и зонах - после установки технологического оборудования,
электродвигателей и других электроприемников, монтажа технологических,
санитарно-технических трубопроводов и вентиляционных коробов.
На небольших объектах, удаленных от мест расположения
электромонтажных организаций, работы следует производить выездными комплексными
бригадами с совмещением двух стадий их выполнения в одну.
Электрооборудование, изделия и материалы следует поставлять по
согласованному с электромонтажной организацией графику, который должен
предусматривать первоочередную поставку материалов и изделий, включенных в
спецификации на блоки, подлежащие изготовлению на сборочно-комплектовочных
предприятиях электромонтажных организаций.
Окончанием монтажа электротехнических устройств является
завершение индивидуальных испытаний смонтированного электрооборудования и
подписание рабочей комиссией акта о приемке электрооборудования после
индивидуального испытания. Началом индивидуальных испытаний электрооборудования
является момент введения эксплуатационного режима на данной электроустановке,
объявляемого заказчиком на основании извещения пусконаладочной и
электромонтажной организаций.
На каждом объекте строительства в процессе монтажа
электротехнических устройств следует вести специальные журналы производства
электромонтажных работ согласно СНиП 3.01.01-02, а при завершении работ
электромонтажная организация обязана передать генеральному подрядчику
документацию, предъявляемую рабочей комиссии согласно СНиП III-3-02.
Перечень актов и протоколов проверок и испытаний определяется
ВСН, утвержденными в установленном СНиП 1.01.01-02 порядке.
7.2 Планирование работ по ТО и ТР электрического оборудования
Монтажу электротехнических устройств должна предшествовать
подготовка в соответствии со СНиП 3.01.01-02 и настоящими правилами.
До начала производства работ на объекте должны быть выполнены
следующие мероприятия:
а) получена рабочая документация в количестве и в сроки,
определенные Правилами о договорах подряда на капитальное строительство;
б) согласованы графики поставки оборудования, изделий и
материалов с учетом технологической последовательности производства работ,
перечень электрооборудования, монтируемого с привлечением монтажного персонала
предприятий-поставщиков, условия транспортирования к месту монтажа тяжелого и
крупногабаритного электрооборудования;
в) приняты необходимые помещения для размещения бригад
рабочих, инженерно-технических работников, производственной базы, а также для складирования
материалов и инструмента с обеспечением мероприятий по охране труда,
противопожарной безопасности и охране окружающей среды в соответствии со СНиП
3.01.01-02;
г) разработан проект производства работ, проведено
ознакомление инженерно-технических работников и бригадиров с рабочей
документацией и сметами, организационными и техническими решениями проекта
производства работ;
д) осуществлена приемка по акту строительной части объекта
под монтаж электротехнических устройств в соответствии с требованиями настоящих
правил и выполнены предусмотренные нормами и правилами мероприятия по охране
труда, противопожарной безопасности и охране окружающей среды при производстве
работ;
е) выполнены генподрядчиком общестроительные и
вспомогательные работы, предусмотренные Положением о взаимоотношениях
организаций - генеральных подрядчиков с субподрядными организациями.
Оборудование, изделия, материалы и техническая документация
должны передаваться в монтаж в соответствии с Правилами о договорах подряда на
капитальное строительство и Положением о взаимоотношениях организаций -
генеральных подрядчиков с субподрядными организациями.
При приемке оборудования в монтаж производится его осмотр,
проверка комплектности (без разборки), проверка наличия и срока действия гарантий
предприятий-изготовителей.
Состояние кабелей на барабанах должно быть проверено в
присутствии заказчика путем наружного осмотра. Результаты осмотра оформляются
актом.
При приемке сборных железобетонных конструкций воздушных
линий (ВЛ) следует проверять: размеры элементов, положение стальных закладных
деталей, а также качество поверхностей и внешний вид элементов. Указанные
параметры должны соответствовать ГОСТам, а также ПУЭ;
наличие на поверхности железобетонных конструкций,
предназначенных для установки в агрессивную среду, гидроизоляции, выполненной
на предприятии-изготовителе.
Изоляторы и линейная арматура должны отвечать требованиям
соответствующих государственных стандартов и технических условий. При их
приемке следует проверять:
наличие паспорта предприятия-изготовителя на каждую партию
изоляторов и линейной арматуры, удостоверяющего их качество;
отсутствие на поверхности изоляторов трещин, деформаций,
раковин, сколов, повреждений глазури, а также покачивания и поворота стальной
арматуры относительно цементной заделки или фарфора;
отсутствие у линейной арматуры трещин, деформаций, раковин и
повреждений оцинковки и резьбы.
Мелкие повреждения оцинковки допускается закрашивать.
Устранение дефектов и повреждений, обнаруженных при передаче
электрооборудования, осуществляется в соответствии с Правилами о договорах
подряда на капитальное строительство.
Электрооборудование, на которое истек нормативный срок
хранения, указанный в государственных стандартах или технических условиях,
принимается в монтаж только после проведения предмонтажной ревизии, исправления
дефектов и испытаний. Результаты проведенных работ должны быть занесены в
формуляры, паспорта и другую сопроводительную документацию или должен быть
составлен акт о проведении указанных работ.
Электрооборудование, изделия и материалы, принятые в монтаж,
следует хранить в соответствии с требованиями государственных стандартов или
технических условий.
Для крупных и сложных объектов с большим объемом кабельных
линий в тоннелях, каналах и кабельных полуэтажах, а также электрооборудования в
электропомещениях в проекте организации строительства должны быть определены
меры по опережающему монтажу (против монтажа кабельных сетей) систем
внутреннего противопожарного водопровода, автоматического пожаротушения и автоматической
пожарной сигнализации, предусмотренных рабочими чертежами.
В электропомещениях (щитовые, пультовые, подстанции и
распределительные устройства, машинные залы, аккумуляторные, кабельные тоннели
и каналы, кабельные полуэтажи и т.п.) должны быть выполнены чистовые полы с
дренажными каналами, необходимым уклоном и гидроизоляцией и отделочные работы
(штукатурные и окрасочные), установлены закладные детали и оставлены монтажные
проемы.
Cмонтированы предусмотренные проектом грузоподъемные и
грузоподъемные механизмы и устройства, подготовлены в соответствии с
архитектурно-строительными чертежами и проектом производства работ блоки труб,
отверстия и проемы для прохода труб и кабелей, борозды, ниши и гнезда, выполнен
подвод питания для временного электроосвещения во всех помещениях.
В зданиях и сооружениях должны быть введены в действие
системы отопления и вентиляции, смонтированы и испытаны мостики, площадки и
конструкции подвесных потолков, предусмотренные проектом для монтажа и
обслуживания электроосветительных установок, расположенных на высоте, а также
конструкции крепления многоламповых светильников (люстр) массой свыше 100 кг;
проложены снаружи и внутри зданий и сооружений предусмотренные рабочими
строительными чертежами асбестоцементные трубы и патрубки, и трубные блоки для
прохода кабелей.
Фундаменты под электрические машины следует сдавать под
монтаж с полностью законченными строительными и отделочными работами,
установленными воздухоохладителями и вентиляционными коробами, с реперами и
осевыми планками (марками) в соответствии с требованиями СНиП 3.02.01-02 и
настоящих правил.
По окончании отделочных работ в аккумуляторных помещениях
должны быть выполнены кислото- или щелочестойкие покрытия стен, потолков и
пола, смонтированы и опробованы системы отопления, вентиляции, водопровода и
канализации.
До начала электромонтажных работ на открытых
распределительных устройствах напряжением 35 кВ и выше строительной
организацией должно быть закончено сооружение подъездных путей, подходов и
подъездов, установлены шинные и линейные порталы, сооружены фундаменты под
электрооборудование, кабельные каналы с перекрытиями, ограждениями вокруг ОРУ.
резервуары для аварийного сброса масла, подземные коммуникации и закончена
планировка территории. В конструкциях порталов и фундаментов под оборудование
должны быть установлены предусмотренные проектом закладные части и крепежные
детали, необходимые для крепления гирлянд изоляторов и оборудования.
В кабельных каналах и тоннелях должны быть установлены
закладные детали для крепления кабельных конструкций и воздухопроводов. Должно
быть также закончено сооружение водопровода и других предусмотренных проектом
противопожарных устройств.
Трассы для прокладки кабеля в земле должны быть подготовлены
к началу его прокладки в объеме: из траншеи откачена вода и удалены камни,
комья земли, строительный мусор; на дне траншеи устроена подушка из
разрыхленной земли; выполнены проколы грунта в местах пересечения трассы с
дорогами и другими инженерными сооружениями, заложены трубы.
После прокладки кабелей в траншею и представления
электромонтажной организацией акта на скрытые работы по прокладке кабелей
траншею следует засыпать.
В зданиях и сооружениях, сдаваемых под монтаж
электрооборудования, генподрядчиком должны быть выполнены предусмотренные архитектурно-строительными
чертежами отверстия, борозды, ниши и гнезда в фундаментах, стенах,
перегородках, перекрытиях и покрытиях, необходимые для монтажа
электрооборудования и установочных изделий, прокладки труб для электропроводок
и электрических сетей.
Указанные отверстия, борозды, ниши и гнезда, не оставленные в
строительных конструкциях при их возведении, выполняются генподрядчиком в
соответствии с архитектурно-строительными чертежами.
Отверстия диаметром менее 30 мм, не поддающиеся учету при
разработке чертежей и которые не могут быть предусмотрены в строительных
конструкциях по условиям технологии их изготовления (отверстия в стенах
перегородках, перекрытиях только для установки дюбелей, шпилек и штырей
различных опорно-поддерживающих конструкций), должны выполняться
электромонтажной организацией на месте производства работ.
После выполнения электромонтажных работ генподрядчик обязан
осуществить заделку отверстий, борозд, ниш и гнезд.
При приемке фундаментов под трансформаторы должны быт
проверены наличие и правильность установки анкеров для крепления тяговых
устройств при перекатке трансформаторов и фундаментов под домкраты для
разворота катков.
При производстве электромонтажных работ должны быть соблюдены
следующие требования.
При погрузке, разгрузке, перемещении, подъеме и установке
электрооборудования должны быть приняты меры по его защите от повреждений, при
этом тяжеловесное электрооборудование необходимо надежно стропить за
предусмотренные для этой цели детали или в местах, указанных предприятием-изготовителем.
Электрооборудование при монтаже разборке и ревизии не
подлежит, за исключением случаев, когда это предусмотрено государственными и
отраслевыми стандартами или техническими условиями, согласованными в
установленном порядке.
Разборка оборудования, поступившего опломбированным с
предприятия-изготовителя, запрещается.
Электрооборудование и кабельная продукция деформированные или
с повреждением защитных покрытий монтажу не подлежат до устранения повреждений
и дефектов в установленном порядке.
При производстве электромонтажных работ следует применять
нормокомплекты специальных инструментов по видам электромонтажных работ, а
также механизмы и приспособления, предназначенные для этой цели.
В качестве опорных конструкций и крепежных изделий для установки
троллеев, шинопроводов, лотков, коробов, навесных щитков и постов управления,
защитно-пусковой аппаратуры и светильников следует применять изделия заводского
изготовления, имеющие повышенную монтажную готовность.
Крепление опорных конструкций следует выполнять сваркой к
закладным деталям, предусмотренным в строительных элементах, или крепежными
изделиями (дюбелями, штырями, шпильками и т.п.). Способ крепления должен быть
указан в рабочих чертежах.
Цветовое обозначение токоведущих шин распределительных устройств,
троллеев, шин заземления, проводов ВЛ следует выполнять в соответствии с
указаниями, приведенными в проекте.
При производстве работ электромонтажная организация должна
выполнять требования и правила пожарной безопасности при производстве строительно-монтажных
работ. При введении на объекте эксплуатационного режима обеспечение пожарной
безопасности является обязанностью заказчика.
7.3
Определение годового потребления электроэнергии на производственные нужды и
организация учёта электроэнергии
Колбасный цех ежедневно с 8 до 17 часов Общее время работы
составляет 9 ч. Потребление электроэнергии за сутки составляет 345,7 кВт, а за
год 89882 кВт.
Таблица 7.3.1 Суточное потребление электроэнергии
Название
потребителя
|
Мощность кВт
|
Кол-во рабочих
часов, ч
|
Суточное
потребление энергии, кВт ч
|
фаршмешалка
|
5
|
9
|
45
|
Установка
коптильная
|
17
|
9
|
153
|
Шпигорезная
машина
|
4
|
7
|
28
|
куттер
|
2,5
|
5
|
12,5
|
Шприц вакуумный
|
2,5
|
9
|
22,5
|
Освещение
помещения
|
1,6
|
5
|
8
|
Освещение
уличное
|
0,125
|
14
|
1,7
|
Для учета потребляемой электроэнергии используют трехфазный
индукционный счетчик, показания ежемесячно заносят в журнал учета.
8.
Безопасность и экологичность проекта
8.1 Общие положения
Инструкция по охране труда для аппаратчика термической
обработки колбасных изделий [8]:
.1.1 Действие инструкции распространяется на все
подразделения предприятия.
.1.2 Инструкция разработана на основе ДНАОП 0.00-8.03-93
"Порядок разработки и утверждения собственником нормативных актов об
охране труда, действующих на предприятии", ДНАОП 0.00-4.15-98
"Положение о разработке инструкций по охране труда", ДНАОП
0.00-4.12-99 "Типовое положение об обучении по вопросам охраны
труда", ДНАОП 7.1.30-1.02-96 "Правила охраны труда для предприятий
общественного питания"
.1.3 По данной инструкции аппаратчик термической обработки
колбасных изделий и мясопродуктов (далее - аппаратчик) инструктируется перед
началом работы (первичный инструктаж), а потом через каждые 3 месяца (повторный
инструктаж).
Результаты инструктажа заносятся в "Журнал регистрации
инструктажей по вопросам охраны труда". В журнале после прохождения
инструктажа должны быть подписи инструктирующего и аппаратчика.
.1.4 Собственник должен застраховать аппаратчика от
несчастных случаев и профессиональных заболеваний.
В случае повреждения здоровья аппаратчика по вине
собственника он (аппаратчик) имеет право на возмещение причиненного ему вреда.
.1.5 За невыполнение данной инструкции аппаратчик несет
дисциплинарную, материальную, административную и уголовную ответственность.
.1.6. К самостоятельной работе аппаратчиком термической
обработки колбасных изделий и мясопродуктов допускаются лица не моложе 18 лет,
которые прошли медицинский осмотр, обучение по специальности, стажировку у
опытного специалиста и сдали экзамен квалификационной комиссии, сдали санитарный
минимум, имеют профессиональные навыки и удостоверение установленной формы о
присвоении квалификационного разряда, прошли вводный инструктаж, инструктаж на
рабочем месте и инструктаж по пожарной безопасности.
.1.7 При работе аппаратчика на аппаратах с газообразным
топливом и электроподогревом он должен пройти специальное обучение и иметь
соответствующее удостоверение.
.1.8 Аппаратчик должен:
.1.8.1 Выполнять правила внутреннего трудового распорядка.
.1.8.2 Пользоваться спецодеждой и средствами индивидуальной
защиты.
.1.8.3 Проходить периодический медицинский осмотр.
.1.8.4 Выполнять только ту работу, которая поручена
руководителем и по которой он проинструктирован.
.1.8.5 Помнить о личной ответственности за выполнение правил
охраны труда и ответственность за товарищей по работе.
.1.8.6 Не допускать на свое рабочее место посторонних лиц и
не загромождать его.
.1.8.7 Не выполнять указаний, противоречащих правилам охраны
труда.
.1.8.8 Уметь оказывать первую медицинскую помощь пострадавшим
от несчастных случаев.
.1.8.9 Уметь пользоваться первичными средствами
пожаротушения.
.1.9 Основные опасные и вредные производственные факторы,
которые действуют на аппаратчика:
.1.9.1 Движущиеся и вращающиеся части оборудования
(термокамеры, термоагрегаты, приводы, дверь дымогенератора).
.1.9.2 Мясопродукты и колбасные изделия, которые перемещаются
на рамах, в корзинах, трубках, лотках и т.п.
.1.9.3 Повышенные температура и относительная влажность
воздуха рабочей зоны.
.9.4 Повышенная температура поверхностей оборудования,
мясопродуктов и колбасных изделий.
.9.5 Повышенная загазованность воздуха рабочей зоны.
.9.6 Скользкий пол.
.10 Кроме санитарной одежды, аппаратчик обеспечивается
спецодеждой и средствами индивидуальной защиты: ботинки кожаные, рукавицы
комбинированные. При перемещении рам по колеям вручную дополнительно: каска
защитная, козырек защитный.
.11 До начала работы и в течение работы работающие на
предприятии должны проходить медицинское обследование в соответствии с
требованиями, установленными учреждениями санитарно-эпидемиологической службы.
.12 Все работники до начала работы должны пройти подготовку
по программе санминимума и сдать экзамен с отметкой об этом в соответствующем
журнале и в личной медицинской книжке. В дальнейшем все работники, независимо
от сроков их поступления на работу, должны один раз в два года проходить
обучение и проверку санминимума. Лица, которые не сдали санминимум, к работе не
допускаются.
.13. Не допускаются к работе в цехах по производству мясных
продуктов лица, которые страдают заболеваниями, указанными в инструкции о
порядке проведения медицинских обследований лиц, поступающих на работу и
работающих на пищевых предприятиях, на сооружениях водоснабжения, в детских
учреждениях и т.п.
.14. Работники производственных цехов должны при появления
признаков желудочно-кишечных заболеваний, повышенной температуре, нагноении и
симптомах других заболеваний сообщить об этом администрации и обратиться в
медицинский пункт предприятия или другое медицинское учреждение для прохождения
соответствующего лечения.
.15. Работники производственных цехов перед началом работы
должны принять душ, надеть чистую специальную одежду так, чтобы она целиком
закрывала личную одежду, подобрать волосы под косынку или колпак и двукратно
вымыть руки теплой водой с мылом. После окончания работы также принять душ.
.16. Замена спецодежды должна проводиться ежедневно и по мере
загрязнения.
.17. В периоды эпидемиологического неблагополучия по указанию
санитарно-эпидемиологической станции или органов государственного ветеринарного
надзора работники цехов перед мытьем рук должны их дезинфицировать 0,2% -ным
раствором хлорамина или 0,1% -ным осветленным раствором хлорной извести.
.18. В случае недомогания, поражения кожи в виде ранений,
ожогов, гнойников, шелушения следует обратиться в медпункт, при небольших
повреждениях - обрабатывать их антисептическими растворами.
.19. Для предотвращения попадания посторонних тел в сырье и
готовую продукцию запрещается:
.19.1 Заносить и хранить в пищевых цехах мелкие стеклянные и
металлические предметы (кроме металлических инструментов и технологического
инвентаря).
.19.2 Застегивать спецодежду булавками, иголками и хранить в
карманах халатов предметы личного употребления (зеркала, гребешки, обручальные
кольца, значки, папиросы, спички и т.п.).
В каждом пищевом цехе должен быть организован учет бьющихся
предметов.
.20. Не разрешается заходить в производственные цеха без
спецодежды или в спецодежде для работы на улице.
.21. Работники должны следить за чистотой рук. Ногти на руках
необходимо стричь коротко и не покрывать их лаком. Мыть руки необходимо перед
началом работы и после любого перерыва в работе, в случае перехода от одной
операции к другой, после соприкосновения с загрязненными предметами.
После посещения мест общего пользования мыть руки необходимо
двукратно: в шлюзе после посещения уборной до надевания халата и на рабочем
месте, непосредственно перед тем, как приступить к работе.
.22. При выходе из уборной следует продезинфицировать обувь
на дезинфицирующем коврике.
.23. Употреблять пищу необходимо только в столовых, буфетах,
комнатах для употребления пищи или других пунктах питания, расположенных на
территории предприятия или около него.
Не разрешается хранить пищевые продукты в индивидуальных
шкафах гардеробной.
.24. Производственные помещения, в которых установлены камеры
для термической обработки колбасных изделий и мясопродуктов, должны отвечать
требованиям пожарной безопасности по ГОСТ 12.1.004-85 и быть оборудованы
средствами техники пожаротушения согласно ГОСТ 12.4.009-83.
Рядом с входом в камеры должны находиться средства
пожаротушения и противопожарный инвентарь.
.25. Устройство и эксплуатация топок, работающих на
газообразном топливе, должны отвечать Правилам безопасности систем
газоснабжения.
Подача топлива через производственные помещения не
разрешается.
.26. Дымогенераторы должны устанавливаться в отдельном
помещении. Помещение должно быть оборудовано механической общеобменной
вентиляцией.
Конструкция дымогенератора и его двери должна обеспечивать
герметичность.
.27. Содержание оксида углерода (СО) на рабочем месте
оператора от работающего дымогенератора не должно превышать предельно
допустимой концентрации (20 мг/м3).
Должен быть обеспечен непосредственный контроль за содержимым
СО в воздухе рабочей зоны с использованием газоанализатора и сигнализацией о
превышении предельно допустимых концентраций.
.28. Загрузка тирсы в топку должна быть механизирована.
.29. В конструкции кожуха вентилятора и дымопроводов в
наиболее низких их частях должны быть предусмотрены устройства для отвода
конденсата.
.30. Температура дыма должна регулироваться автоматически.
.31. Для предотвращения попадания искр и золы в коптильные
камеры после дымогенераторов должны быть установлены искрогасящие камеры.
.32. Дымогенератор должен быть термоизолирован таким образом,
чтобы температура наружных поверхностей на рабочих местах не превышала 45°С.
.33. Обжаривательные и коптильные неавтоматические камеры
должны быть оборудованы предохранительными решетками.
Поручни должны быть крепкими, исправными и периодически
очищаться. Располагать поручни следует на расстоянии от уровня пола (костра) не
менее, чем 1,5 м.
.34. Камеры должны оборудоваться приборами автоматики и
контрольно-измерительными приборами, позволяющими производить наблюдение и
регулировку процесса, находясь вне камеры.
.35. Обжаривательные и коптильные камеры должны быть
оборудованы зонтами местного отсоса.
.36. Дверь термокамеры должна быть сблокирована с пусковым
устройством. При открытой двери должна прекращаться подача пара и должны
включаться вентиляторы.
.37. Лопасти вентиляторных установок должны быть закрыты
ограждающими решетками.
.38. Воздухопроводы распределения дымовоздушной смеси должны
иметь устройство, обеспечивающее, в случае необходимости, отвод и сброс в
атмосферу подающегося дыма.
Устройство должно быть оборудовано фильтрами.
.39. Усилие при открытии двери секции термокамеры не должно
превышать 80 Н (8,0 кгс).
.40. Загрузочные и разгрузочные дверные проемы автокоптилок
должны иметь сплошные барьеры высотой не менее 1,0 м, предупреждающие падение
работников в шахту.
Двери (загрузочные, разгрузочные, смотровые, ремонтные и
т.п.) должны быть снабжены прокладками, обеспечивающими плотность прилегання их
к дверным рамам и герметичность шахты. Двери должны открываться наружу из
шахты. Подъемные двери автокоптилок щитового типа должны иметь устройства
(засовы, "собачки" и т.п.), препятствующие самопроизвольному их
опусканию при обрыве канатов.
.41. Автокоптилки должны быть оборудованы в местах загрузки и
разгрузки двусторонней звуковой и световой сигнализацией. Приводить
автокоптилки в действие необходимо только с одного места. Кнопки
"Стоп" устанавливаются возле каждого рабочего места, где производится
загрузка или разгрузка продуктов, и на раме привода.
.42. Устройство и обслуживание ротационных печей для
запекания хлебов, буженины, карбоната с газовым подогревом должны отвечать
Правилам безопасности систем газоснабжение, а с электроподогревом - Правилам
безопасной эксплуатации электроустановок и Правилам безопасной эксплуатации
электроустановок потребителей.
Горячие поверхности печи, доступные для обслуживающего
персонала, должны быть изолированы. Ручки на загрузочной дверце должны быть
изготовлены из нетеплопроводного материала.
.43. Над печами, за их торцом, необходимо устанавливать
устройства (зонты вытяжной вентиляции) для удаления газов.
.44. Варочные котлы, работающие под давлением свыше 0,07 МПа
(0,7 кгс/см2), должны отвечать требованиям Правил устройства и
безопасной эксплуатации сосудов, работающих под давлением.
.45. Варочные котлы, работающие под давлением, должны быть
оборудованы манометрами и предохранительными клапанами, отрегулированными на
предельно допустимое давление.
.46. Отвод охлаждающей жидкости должен производиться в
канализацию закрытым способом с разрывом струи.
.47. Варочные котлы и паропроводы должны быть
термоизолированы. Температура наружной поверхности теплоизоляции не должна
превышать 45°С.
Крышка должна плотно закрывать котел, на ней должен быть
установлен клапан, препятствующий превышению давления внутри котла. Крышка
котла оборудуется противовесами, удобными и безопасными приспособлениями для
открывания ее.
.48. Перекидные котлы должны быть оборудованы устройством,
исключающим их самопроизвольное опрокидывание.
Высота верхней кромки котла от площадки обслуживания должна
быть не менее 1,0 м.
Варочные котлы должны быть оборудованы местной вытяжной
вентиляцией, обеспечивающей удаление паров и газов.
.49. Перфорированные корзины для загрузки сырья в котлы
должны иметь надежные фиксаторы створок днища и приспособления для подвешивания
на крюк подъемного механизма.
.50. Паропроводы должны отвечать Правилам устройства и
безопасной эксплуатации трубопроводов пара и горячей воды.
.51. Конструкция ярусов сушилки для колбасных изделий должна
быть надежной. Полезная технологическая нагрузка на 1 м2 яруса может
быть до 390 Н (40 кгс).
.52. Для обслуживания верхних ярусов сушилок должны быть
предусмотрены огражденные площадки и лестницы в соответствии с ГОСТ 26887-86.
2. Требования безопасности перед началом работы
Перед началом работы требуется [8]:
.1 Проверить состояние и пригодность к пользованию санитарной
одежды, спецодежды, спецобуви и других средств индивидуальной защиты.
.2 Надеть санитарную одежду и спецодежду таким образом, чтобы
не было свободно свисающих концов, завязок и прочее. Заправить волосы под
головной убор.
.3 Осмотреть свое рабочее место. Освободить подходы к нему и
не загромождать их во время работы.
.4 Проверить достаточность освещения рабочей зоны, наличие и
исправность деревянной решетки под ногами, убедиться в ее устойчивости.
.5 Повесить на пульт управления плакат "НЕ ВКЛЮЧАТЬ.
РАБОТАЮТ ЛЮДИ!" и при снятом напряжении проверить:
.5.1 Санитарное состояние оборудования, отсутствие в нем
посторонних предметов.
.5.2 Наличие и исправность контрольно-измерительных приборов,
предохранительных устройства и устройств автоматики (манометров, редукционного
и предохранительного клапанов).
.5.3 Состояние уплотняющих прокладок.
.5.4 Наличие и исправное состояние теплоизоляции.
.5.5 Наличие и целостность заземления, ограждения привода.
.6 Проверить в дымогенераторах:
.6.1 Отсутствие золы в дымогенераторе и нагара на колоснике.
.6.2 Наличие и исправность устройств, которые исключают
самопроизвольное опускание подъемных дверей при обрыве канатов.
.6.3 На холостом ходу работу ворошителя, нагнетательного
вентилятора, вентиля подачи воды, работу сигнализации и плавность хода
транспортировочной цепи.
.7 Проверить в камере (обжаривательные, коптильные,
пароварильные):
.7.1 Исправность металлических решеток на полу.
.7.2 Исправность стопоров и скосов подвесных путей,
отсутствие смещения у стрелок, наличие контрреек на поворотах и над местами
прохода людей.
.8 Проверить в ротационных печах с электрообогревом:
.8.1 Исправность ограждения противовеса и надежность
крепления двери.
.8.2 Наличие и исправность люлек и лотков для продукта.
.8.3 На холостом ходу: работу вентилятора и калорифера.
Плавность вращения ротора, люлек с лотками.
.9 В варочных котлах:
.9.1 Осмотреть электротельфер и проверить его работу на
холостом ходу.
.9.2 Осмотреть корзины для загрузки сырья в котел, убедиться,
что приспособления для подвешивания на крюк подъемного механизма в исправном
состоянии.
.9.3 Убедиться в исправности механизма закрывания и
открывания крышки, проверить плотность прилегания крышки к корпусу, не допуская
истечения пара.
.9.4 Проверить, не забились ли продуктами фильтрующая сетка,
барботер и щелевой заборник.
.9.5 Проверить, при необходимости, выпускной кран. Открыть
выпускной кран и продуть его паром.
3. Требования безопасности во время выполнения
работы
Во время выполнения работы требуется:
.1 Пуск оборудования необходимо выполнять сухими руками и
согласно инструкции по эксплуатации завода-изготовителя.
.2 Подачу пара и горячей воды проводить медленно, открывая
вентиль по 1/4 оборота.
.3 Следить за чистотой пола и напольных решеток, не допуская
образования грязи.
.4 Не касаться движущихся частей оборудования, не снимать
защитное ограждение.
.5 Следить за тем, чтобы в оборудование не попали посторонние
предметы.
.6 Следить за герметичностью паропроводов.
.7 Следить за показаниями контрольно-измерительных приборов.
.8 Не оставлять работающее оборудование без присмотра и не
допускать посторонних лиц на свое рабочее место.
.9 Не выполнять на работающем оборудовании чистку,
смазывание, регулирование и устранение неисправностей.
.10. Дымогенераторы:
.10.1. При ручной загрузке необходимо остерегаться ожогов,
стоять сбоку от открытой дверцы.
.10.2. Загрузку тирсы производить специальным приспособлением
(лопатой и прочее).
.10.3. При механической загрузке тирсу следует подавать
постепенно. Во избежание ее спрессовки следует пользоваться ворошителем.
.10.4. Воронку загружать деревянными щепками следует на 1/2
ее высоты.
.10.5. Чтобы щепки попали в камеру, ворушитель включить на
1-2 мин. и произвести поджог.
.10.6. После появления достаточного количества угля и дыма
включить дымогенератор в автоматический режим.
.10.7. По мере накопления в золильном отсеке золы освобождать
его в течение всей смены.
.10.8. Накапливать золу следует в специальной тележке,
заливая ее водой, во избежание возгорания.
.11. В автокоптильне не поднимать упавшую продукцию во время
движения цепи.
.12. Камеры (обжаривающие, коптильные, пароварильные):
.12.1 Загружать колбасные изделия в камеры, а также
перемещать их по подвесным колеям следует по одной раме, толкая от себя. При
этом руки работника должны упираться в верхнюю часть рамы, не ниже ее середины.
Передвигать раму перед собой следует плавно, без рывков.
.12.2 Не следует оставлять перемещаемые по подвесным колеям
рамы на стрелках и скруглениях. Необходимо следить за правильностью положения
стрелок.
.12.3 Рамы и ролики должны быть исправными. Работать следует
в рукавицах. Для защиты глаз от попадания окалины при переводе стрелок
необходимо использовать прозрачный козырек или защитные очки.
.12.4 Разгрузку камер следует производить после
предварительного их проветривания.
Перед разгрузкой следует перекрыть паровой вентиль и вывесить
на нем предупредительную надпись: “НЕ ВКЛЮЧАТЬ. РАБОТАЮТ ЛЮДИ! ”
.12.5 Выгрузку рам из камер необходимо производить при помощи
специальных багров.
.12.6 Не разрешается самостоятельно выжигать сажу.
.13. Печи ротационные:
.13.1 Санитарную обработку печи проводят при температуре
воздуха внутри ее не выше 30°С.
.13.2 Для защиты от ожогов работники, обслуживающие ротационные
печи, должны быть обеспечены рукавицами и нарукавниками.
.13.3 Загрузку печи сырьем следует производить до включения
калорифера.
.13.4 Выгрузку готовой продукции из печи необходимо
производить только после отключения калорифера.
.13.5 При выгрузке лотков из печи и сливе жира необходимо
пользоваться средствами индивидуальной защиты: фартуками, рукавицами, защитными
очками.
.13.6 Растопленный жир необходимо сливать в специальные
емкости, заполняя не более 2/3 их объема.
.13.7 Транспортировку тележек с жиром производить только
после остывания жира.
.14. Котлы варочные:
.14.1 Загружать корзины в котел следует при помощи
электротельфера.
.14.2 Водой котел следует наполнять до уровня сливного
патрубка.
.14.3 При эксплуатации котла для варки субпродуктов
необходимо следить за тем, чтобы уровень воды в нем не понижался и не
повышался.
.14.4 Прежде, чем открыть вентиль подачи пара, следует плотно
закрыть крышку.
.14.5 Перед открыванием крышки следует проверить, закрыт ли
паровой вентиль, открыт ли канализационный вентиль и продувочный кран,
убедиться по манометру в отсутствии давления в котле.
.14.6 При эксплуатации перекидных котлов:
.14.6.1 Загрузка окороков должна проводиться в пустые котлы.
Вода заливается после загрузки. Выгрузка окороков проводится после слива
бульона. Случайно упавшие окорока должны подниматься при помощи крюка.
4. Требования безопасности после окончания работы
4.1 Отключить оборудование от электросети, а на пусковое
устройство вывесить плакат "НЕ ВКЛЮЧАТЬ. РАБОТАЮТ ЛЮДИ!".
.2 Дымогенераторы:
,2.1 Вызвать электромонтера и обесточить дымогенератор.
.2.2 Перекрыть вентиль подачи холодной воды.
.2.3 Очистить бункер ворушителя от остатков тирсы.
.2.4 После остывания оборудовании выгрузить золу.
.3 Камеры:
.3.1 Плотно закрыть все вентили подачи в камеру пара, а также
вентили на магистральном паропроводе.
.3.2 Убедиться, что в камерах не осталась продукция.
.3.3 Входить в камеры можно только при температуре воздуха
внутри нее не выше 30°С.
.4 Привести в порядок рабочее место.
.5 Сложить средства индивидуальной защиты в отведенное для
них место.
.6 Доложить руководителю работ обо всех недостатках, которые
имели место во время работы.
5. Требования безопасности в аварийных ситуациях
5.1 Аварийная ситуация может возникнуть в случае:
возникновения постороннего шума, гудения, повышенной вибрации, ощущения
электротока на металлических частях, повышенной концентрации оксида углерода и
прочее.
.2 При возникновении аварийной ситуации следует немедленно
прекратить работу, отключить оборудование от электросети, оградить опасную
зону, не допускать в нее посторонних лиц, доложить о том, что произошло,
руководителю работ.
.3 Если есть пострадавшие, оказать им первую медицинскую
помощь. При необходимости вызвать "скорую медицинскую помощь".
.4 Оказание первой медицинской помощи:
.4.1 Оказание первой медицинской помощи при отравлении
оксидом углерода.
До приезда врача потерпевшего следует вывести на свежий
воздух, обеспечить ему покой, избегать охлаждения.
В тяжелых случаях давать вдыхать кислород, проводить искусственное
дыхание.
.4.2 Оказание первой помощи при поражении электрическим
током.
При поражении электрическим током необходимо немедленно
освободить потерпевшего от действия электрического тока, отключив
электроустановку от источника питания, а при невозможности отключения -
оттянуть его от токопроводящих частей за одежду или применив подручный
изоляционный материал.
При отсутствии у потерпевшего дыхания и пульса необходимо
сделать ему искусственное дыхание и непрямой (внешний) массаж сердца, обращая
внимание на зрачки. Расширенные зрачки свидетельствуют о резком ухудшении
кровообращения мозга. При таком состоянии оживление начинать необходимо
немедленно, после чего вызвать "скорую медицинскую помощь".
.4.3 Первая помощь при ранении.
Для оказания первой помощи при ранении
необходимо раскрыть индивидуальный пакет, наложить стерильный перевязочный
материал, который помещается в нем, на рану и завязать ее бинтом.
Если индивидуального пакета каким-то образом не оказалось, то
для перевязки необходимо использовать чистый носовой платок, чистую полотняную
тряпку и т.д. На тряпку, которая накладывается непосредственно на рану,
желательно накапать несколько капель настойки йода, чтобы получить пятно
размером больше раны, после чего наложить тряпку на рану. Особенно важно
применять настойку йода указанным образом при загрязненных ранах.
.4.4 Первая помощь при переломах, вывихах, ударах.
При переломах и вывихах конечностей
необходимо поврежденную конечность укрепить шиной, фанерной пластинкой, палкой,
картоном или другим подобным предметом. Поврежденную руку можно также подвесить
с помощью перевязки или платка к шее и прибинтовать к туловищу.
При переломе черепа (бессознательное
состояние после удара по голове, кровотечение из ушей или изо рта) необходимо
приложить к голове холодный предмет (грелку со льдом, снегом или холодной
водой) или сделать холодную примочку.
При подозрении перелома позвоночника
необходимо пострадавшего положить на доску, не поднимая его, повернуть
потерпевшего на живот лицом вниз, наблюдая при этом, чтобы туловище не
перегибалось, с целью избежания повреждения спинного мозга.
При переломе ребер, признаком которого является боль при
дыхании, кашле, чихании, движениях, необходимо туго забинтовать грудь или
стянуть ее полотенцем во время выдоха.
.4.5 Оказание первой помощи при тепловых ожогах.
При ожогах огнем, паром, горячими предметами ни в коем случае
нельзя вскрывать образовавшиеся пузыри и перевязывать ожоги бинтом.
При ожогах первой степени (покраснение) обожженное место
обрабатывают ватой, смоченной этиловым спиртом.
При ожогах второй степени (пузыри) обожженное место
обрабатывают спиртом или 3% -ным марганцевым раствором.
При ожогах третьей степени (разрушение кожной ткани) рану
накрывают стерильной повязкой и вызывают врача.
.4.6 Первая помощь при кровотечении.
Для того, чтобы остановить кровотечение, необходимо:
поднять раненную конечность вверх;
кровоточащую рану закрыть перевязочным материалом (из
пакета), сложенным в клубок, придавить его сверху, не касаясь самой раны,
подержать на протяжении 4-5 минут. Если кровотечение остановилось, не снимая
наложенного материала, сверх него положить еще одну подушечку из другого пакета
или кусок ваты и забинтовать раненное место (с некоторым нажимом);
в случае сильного кровотечения, которое нельзя остановить
повязкой, применяется сдавливание кровеносных сосудов, которые питают раненную
область, при помощи изгибания конечности в суставах, а также пальцами, жгутом
или зажимом. В случае сильного кровотечения необходимо срочно вызвать врача.
.5 Если произошло возгорание, приступить к тушению имеющимися
средствами пожаротушения. При необходимости вызвать пожарную часть.
.6 Выполнять все указания руководителя работ по ликвидации
аварийной ситуации.
Мероприятия
по охране окружающей среды
Современное состояние окружающей среды является глобальной
проблемой во всем мире. Предприятия мясной промышленности являются одним из
источников загрязнения окружающей среды.
Мероприятия по защите окружающей среды на предприятии
осуществляются согласно федеральному закону РФ от 10.01.2002 г № 7-ФЗ ("Об
охране окружающей среды").
Окружающую среду загрязняют сточные воды мясокомбината и
выбросы в атмосферу загрязняющих веществ оборудованием мясокомбината.
Основная особенность сточных вод мясной отрасли - высокое
содержание в них органических загрязнителей, поэтому необходимо направлять
сточные воды перед сбросом их в общую канализацию на локальные очистные
сооружения. С этой целью в составе очистной станции предусматривают сооружения
механической очистки: решетки, песколовки и отстойники.
Решетки служат для извлечения из сточных вод крупных отбросов
- бумаги, тряпок, целлофана, ниток, осколков костей и т.д. Отбросы, снятые с
решеток, сбрасывают в металлические бочки с крышками, которые периодически
вывозят автотранспортом на специальные площадки для компостирования, где их
выгружают, обсыпают грунтом и оставляют в таком виде на 2 года.
Песколовки служат для задержания песка и тяжелых, крупных
загрязнений органического происхождения (кусочки тканей животного и т.п.).
Применяют горизонтальные песколовки с прямолинейным или круговым движением
воды.
Отстойники служат для выделения оседающих и всплывающих
взвешенных веществ из сточных вод предприятий мясной промышленности. Применяют
вертикальные и двухъярусные отстойники, осветлители с естественной аэрацией,
осветители-перегниватели.
Колбасное производство оснащено дымогенераторами, в которых
при сжигании дров или опилок лиственных пород деревьев вырабатывается дым для
термокамер и автокоптилок. При обжарке и копчении колбасных изделий атмосфера
загрязняется оксидом углерода, диоксидом азота, сернистым ангидридом, твердыми
частицами, аммиаком, фенолом и пропионовым альдегидом.
Особенность выбросов в атмосферу загрязняющих веществ от
мясокомбинатов - неприятнопахнущие вещества или одоранты. Многие
технологические процессы, происходящие при тепловой обработке мяса в
присутствии воды, сопровождаются образованием продуктов распада белка. Наиболее
перспективные методы очистки воздуха и отходящих газов следующие: мокрая
очистка и абсорбция, биологическая очистка и адсорбционная очистка с
применением активированного угля, цеолита или ионообменных смол.
Расчет
заземления
На потребительской подстанции для общего заземляющего
устройства с учетом всех повторных заземлений, при количестве отходящих линий
ВЛ не менее 2-х, допустимая величина сопротивления составляет для напряжения
380/220 В:
Rдоп = 4 Ом.
Удельное электрическое сопротивление грунта:
r = 30 Ом×м.
Климатический сезонный коэффициент:
Кс = 1,8
Тогда:
r’ = Кс × r,
r’ = 1,8 × 30 = 54 Ом×м
Определим сопротивление растеканию электрическому току
одиночного заземлителя. Для стержня на глубине h = 0,6 м, длиной 5 м,
диаметром d
= 16×10-3 м:
(8.1)
где: r' - приведенное
удельное сопротивление грунта, Ом×м;
l - длина стержня, м;
d - диаметр стержня, м;
t - глубина центра стержня, м.
t = l/2 + h, t = 5/2 + 0,8 = 3,2
Определим необходимое количество вертикальных заземлителей:
nт = Rв / Rдоп,
где: nт - теоретическое количество стержней.
Принимаем nт = 3 шт.
Действительное количество стержней:
nд = nт / kI
где: kI -
коэффициент взаимного экранирования.
Для a / l = 2 при количестве n = 8: kI = 0,71 при размещении электродов по
контуру.
nд = 3/0,71
= 4,2 шт.
Принимаем nд = 4 шт.
Тогда сопротивление очага электродов Rо равно:
Rо = Rв / nд
Rо = 11,3/4
= 2,8 Ом
Определим длину соединительной полосы, для электродов:
Ln = a × n
где: а - расстояние между электродами, м; n -
действительное количество электродов, шт. Принимаем а =
10 м.
Ln = 10 × 4 = 40 м.
Рассчитаем сопротивление одиночной соеденительной полосы по
формуле:
(8.2)
где: b - ширина полосы, м.
Принимаем b = 0,04 м.
Рис 8.1
Одиночная соединительная полоса
Определим сопротивление заземляющего устройства по формуле:
(8.3)
где: Кz -
коэффициент взаимного влияния вертикальных электродов и соединительной полосы.
Для а / l = 2 при числе
стержней n = 4 при размещении электродов в ряд
принимаем Кz = 0,6.
Условие RЗУ £ Rдоп £ 4 Ом
выполняется, значит, заземляющее устройство рассчитано верно.
Расход материалов для сооружения заземлителя составит: число
стержней - 4 шт., длина стержня - 5 м., диаметр стержней - 16 мм.
Длина всех стержней:
lобщ ст = n × lст,
lобщ ст = 4
× 5 = 50 м.
Расчет
молниезащиты "КФХ Кондратенко Н.И. "
Производственное помещение относится к III категории устройств
молниезащиты, зона Б.
Здания и сооружения, отнесенные по устройству молниезащиты к III категории, защищаются от
прямых ударов молнии и от заноса высоких потенциалов через подземные
металлические коммуникации.
Ожидаемое количество поражений в год здания или сооружения,
не оборудованного молниезащитой, определяется по формуле:
N = [ (S + 6 × h) × (L + 6 × h) - 7,7 × h2] × n × 10-6
Где: L и S соответственно длина и ширина помещения, м; h - наибольшая высота
мельницы, м;
n - среднегодовое число
ударов молний в 1 км2 земной поверхности в районе расположения
мельницы.
N = [ (12 + 6 × 8) × (60 + 6 × 8) - 7,7 × 82] × 5 × 10-6 = 0,3
Проектируемый объект подлежит защите от всех видов
воздействия грозового разряда.
Для объектов III категории, имеющих крышу, молниезащиту
целесообразно выполнять в виде стальной сетки из проволоки d = 6 мм.
Узлы сетки должны быть сварными. Токопроводы прокладываются
по углам стен.
Сопротивление растеканию тока заземлителей не более 10 Ом.
Заземляющие спуски проводятся параллельно фундаменту.
Рисунок 8.2 Заземлитель молниезащиты
Материал заземлителя: уголок 40 х 40 х 4 мм, полоса 4 х 40 мм
9.
Экономика
Технико-экономические расчеты позволяют выбрать наиболее
экономичный вариант электроснабжения в результате сравнения двух или большего
числа технически применяемых и дающих одинаковый энергетический эффект
вариантов по их важнейшим показателям: капиталовложениям и ежегодным издержкам
производства.
Для того, чтобы их определить составляем смету на
оборудование неавтоматизированного и автоматизированного вариантов. (таблица
9.1)
Таблица 9.1
наименование
|
Кол-во, шт
|
Цена, руб.
|
Сумма, р.
|
Дымогенератор
щеповой
|
1
|
36400
|
36400
|
Кабель ВВГ 5×6
|
18
|
92,15
|
1658
|
Кабель ВВГ 5×1,5
|
1,5
|
25,58
|
38,37
|
Регулятор УДГ
35
|
1
|
1700
|
1700
|
Итого
|
|
|
39796
|
Дымогенератор
фрикционный
|
1
|
30200
|
30200
|
Кабель ВВГ 5×6
|
18
|
92,15
|
1658
|
Кабель ВВГ 5×1,5
|
1,5
|
25,58
|
38,37
|
блок РЗДУ
|
1
|
3200
|
3200
|
Итого
|
|
|
35096
|
Рассчитываем капитальные затраты дымогенератора щепового.
Оптовая цена оборудования Ц1 = 39796
Затраты на монтаж М. = 0,2 · Ц1 = 0,2 ·
39796 = 7959,2 руб.
Накладные расходы Нр =0,1 · Ц1 =3979
руб.
Капитальные вложения на разработку и проектирования.
КР =0,015 · Ц1 = 0,015 · 39796 = 600
руб.
Исходя из расчетов, капитальные затраты дымогенератора
щепового.
К1 = Ц1 + М + Нр. + Кр.
= 39796 + 7959,2 + 3979 + 600 = 52334 руб.
Рассчитываем капитальные затраты дымогенератора фрикционного.
Оптовая цена оборудования Ц1 =35096.
Затраты на монтаж М. = 0,2 · Ц1 = 0,2 ·
35096 = 7019 руб.
Накладные расходы Нр =0,1 · Ц1 =3509,6
руб.
Капитальные вложения на разработку и проектирования.
КР =0,015 · Ц1 = 0,015 · 35096 = 526,4
руб.
Исходя из расчетов, капитальные затраты дымогенератора
щепового.
К1 = Ц1 + М + Нр. + Кр.
=35096 + 7019 + 3509,6 + 526,4 = 46151 руб.
данные заносим в таблицу 9.2
Таблица 9.2
Вариант
|
Ц1,
руб.
|
М1,руб.
|
Нр,
руб.
|
Кр, руб.
|
К1,руб.
|
Щеповой
|
39796
|
7959,2
|
3979
|
600
|
52334
|
Фрикционный
|
35096
|
7019
|
3509,6
|
526,4
|
46151
|
Рассчитываем текущие затраты дымогенератора щепового.
Амортизационного отчисления.
Са = 0,142 · К2 = 0,142 · 52334 = 7431
руб
Отчисления на ремонт
Ср = 0,055 · К2 = 0,055 · 52334 =
2878,3 руб.
Стоимость электроэнергии:
Сэ =
Рн - номинальная мощность установки, кВт, Кз - коэффициент загрузки
η - КПД установки, tс - время
работы установки в сутки, час, Дг
- количество рабочих дней в году, дней, Тээ - тариф на
электроэнергию.
Добавление на оплату труда Сот =4000руб.
Прочие расходы.
Спр. = 0,01 (Са + Ср + Сот
+Сэ) = 0,01 (7431 + 2878,3 + 7722+4000) = 220,3
Рассчитываем текущие затраты дымогенератора фрикционного.
Амортизационного отчисления.
Са = 0,142 · К2 = 0,142 · 46151 = 6553 руб
Отчисления на ремонт
Ср = 0,055 · К2 = 0,055 · 46151 = 2538,3
руб.
Стоимость электроэнергии.
Сэ =
Сот =4000руб
Прочие расходы.
Спр. = 0,01 (Са + Ср + Сэ
+ Сот) = 0,01 (6553 + 2538,3 + 4000+5084) = 181,7
Таблица 9.3
Вариант
|
Са,
руб.
|
Ср,
руб.
|
Сэ,
руб.
|
Сот,
руб.
|
Спр,
руб.
|
∑, руб.
|
щеповой
|
7431
|
2878,3
|
7722
|
4000
|
220,3
|
22251,6
|
фрикционный
|
6553
|
2538,3
|
4237
|
3000
|
181,7
|
16510
|
Экономия затрат электроэнергии:
Ээл=Сэщ-Сэф
Ээл=7722-4237=3485
Экономия затрат на обслуживание:
Эо= Срщ - Срф
Эо=2878,3-2538,3=340
Экономия затрат на заработную плату:
Эотр= Сот1 - Сот2
Эотр=0
Экономия затрат по капитальным вложениям:
Эк. вл=К1щ-К1ф
Эк. вл==52334-46151=6183 руб
Суммарная экономия:
∑Э=∑Эщ-∑Эф
∑Э=22251,6-16510=5741,6 руб
Рассчитаем срок окупаемости:
Q=К - Эк. вл/∑Э,
где К - капиталовложения
∑Э - экономия
Q=46151-6183/5741,6=7 лет.
Заключение
В данном дипломном проекте разработана система электрификации
колбасного цеха КФХ "Кондратенко Н. И." произведен расчет системы
освещения, силовой сети, внедрение нового узла дымогенератора фрикционного.
Целью внедрения является снижение затрат на электроэнергию,
обслуживание, более высокое качество производимой продукции.
Библиографический
список
1. Бредихин,
С.А. Технологическое оборудование мясокомбинатов / С.А. Бредихин, О.В.
Бредихина, Ю.В. Космодемьянский, Л.Л. Никифоров. - 2-е изд., испр. - М.: Колос,
2000. - 392 с.: ил.
2. Технологическое
оборудование для переработки продукции животноводства / Под ред.В.М. Баутина. -
М.: Колос, 2001. - 440 с.
. Производство
конечных пищевых продуктов / Под ред.О.Я. Мезенова. - М.: Колос, 2001. - 208 с.
. Рогов,
И.А. Технология и оборудование колбасного производства / И.А. Рогов, А.Г.
Забалина, В.А. Алексахина, Е.И. Титов. - М: Агропромиздат, 1989.
. Козинский,
В.А. Проектирование электрического освещения и облучения в сельском хозяйстве.
Методические указания / В.А. Козинский, И.Н. Светлакова. - Ижевск, 2001.
. Захаров,
А.А. Практикум по применению теплоты и теплоснабжению в сельском хозяйстве /
А.А. Захаров - М.: Колос, 1995.
. Козинский,
В.А. Электрическое освещение и облучение / В.А. Козинский - М.: Агропромиздат,
1991. - 239 с.
. Луковников,
А.В. Охрана труда / А.В. Луковников - М.: Колос, 1984.
. Ильинский,
Н.Ф. Энергосбережение в электроприводе / Н.Ф. Ильинский, Ю.В. Роженновский,
А.С. Горнов. - М.: Высшая школа, 1989.
. Кондратьева,
Н.П. Выбор электродвигателей, аппаратуры управления и защиты электрических
установок. Учебное пособие / Н.П. Кондратьева. - ИжГСХА, 1995.
. Козлов,
В.А. Справочник по расчету проводов и кабелей / В.А. Козлов. - М.: Издательство
"Энергия", 1964.
. Будзко,
И.А. Электроснабжение сельского хозяйства / И.А. Будзко, Н.М. Зуль - М.:
Агропромиздат, 1990.
. Мартыненко,
И.И. Курсовое и дипломное проектирование по комплексной электрификации и
автоматизации / И.И. Мартыненко, Л.П. Тищенко - М.: Колос, 1978.