Розробка технологічного процесу складання лонжеронного крила
ВСТУП
Створення такого складного виробу,
як літак, представляло б собою надзвичайно складну задачу, якщо б в процесі
ескізного та технічного проектування його не поділяли на закінчені в
конструктивному й технологічному сенсі частини.
В літакобудуванні прийнято членувати
вироби на агрегати, відсіки, вузли, деталі часто звані збірними одиницями.
В процесі розробки конструкції
спочатку виконують членування планера на агрегати, вузли та з'єднувальні
деталі, які входять в планер, потім агрегати поділяють на відсіки, вузли та
з'єднувальні деталі, які входять до відсіків, та нарешті, вузли відсіків,
агрегатів і планера - на їх складові деталі.
Вочевидь, метод членування літака на
частини буде визначати і членування загального технологічного процесу
виготовлення літака на відповідні складові. Після членування для виготовлення
кожного окремого агрегату, відсіку, вузла розробляють самостійний технологічний
процес.
З метою ув'язки
технологічних процесів виготовлення частин літака проектування загального
технологічного процесу його виготовлення виконується в два етапи. На першому
етапі проектування розробляють директивні технологічні матеріали, які включають
основні вимоги до частин, що виготовляються. На другому етапі розроблюють
докладні технологічні процеси виготовлення частин літака в цілому.
Технологічний процес виготовлення
літака завершується складанням-монтажем його з агрегатів, вузлів і з'єднувальних
деталей з подальшим регулюванням та випробуванням.
Темою даної роботи є розробка
технологічного процесу складання одного з агрегатів літака, а саме,
лонжеронного крила.
Дана робота включає наступні
розділи: призначення, будова та принцип дії лонжеронного крила; основні
матеріали які використовують для виготовлення вузла; технічна вимога щодо
складання лонжеронного крила; технологічний процес складання лонжеронного
крила; інструменти та обладнання що використовують при складанні; передові
методи складання; організація робочого місця слюсаря-складальника літальних
апаратів; правила техніки безпеки при складанні лонжеронного крила та список
використаної літератури.
РОЗДІЛ 1.
Призначення, будова та принцип дії лонжеронного крила
складання лонжеронний крило літальний
Крило в авіаційній техніці -
поверхня для створення підйомної сили.
Крило - основне призначення якого
створення підйомної сили (сила, яка перпендикулярна напрямку вектора
швидкості). Наявність крила - відмінна частина літака. У гелікоптера підйомну
силу створює гвинт. У гвинтокрила - обидва (гвинт і крило) створюють підйомну
силу.
Підйомна сила крила створюється за
рахунок різниці тисків повітря на нижній та верхній поверхнях. Тиск повітря
залежить від розподілу швидкостей повітряних потоків поблизу цих поверхонь.
Завдяки поступальному руху, крило
здійснює роботу по розгону частини потоку. Досягнувши точки відриву біля
задньої кромки, повітря продовжує свій рух вниз по інерції разом з масою,
відхиленої нижньої поверхні крила, що в сумі викликає скіс потоку і виникнення
реактивного імпульсу. Вертикальна частина цього імпульсу і викликає підйомну
силу, яка врівноважує силу тяжіння, горизонтальна частина врівноважується
лобовим опором.
Обтікання крила є дуже складним
тривимірним нелінійним, і часто нестаціонарним, процесом. Підйомна сила крила
залежить від його площі, профілю, форми в плані, а також від кута атаки, швидкості
та щільності потоку і від цілого ряду інших факторів.
Додатково крило використовується для
забезпечення поперечної стійкості та керованості літака, а також як ємність для
пального та база кріплення стійок шасі та двигунів літаків.
Для сприйняття згинального та
крутного моментів і поперечної сили, яка діє в перерізах крила, в його
конструкції є спеціальні силові елементи. Вони повинні розташовуватися вздовж
усього крила для того, щоб передати навантаження, що діють на крило, на вузли
кріплення його до фюзеляжу.
Сукупність цих елементів є силовою
конструкцією або схемою крила.
В залежності від того, якими
елементами сприймаються згинальні моменти, силові конструкції поділяються на:
лонжеронні, кесонні та моноблочні.
Лонжеронним крилом є крило, в якому
згинальний момент в основному сприймається лонжеронами, які мають потужні
пояси. Таке крило включає один або кілька поздовжніх силових елементів -
лонжеронів, які сприймають згинальний момент і поперечну силу. Згинальний
момент сприймають пояси лонжеронів, в яких виникають великі осеві навантаження.
Стінки лонжеронів, сприймаючи практично всю поперечну силу, працюють на зсув.
Крім того, стінки спільно з обшивкою утворюють замкнуті контури, що сприймають
крутний момент.
Лонжерони являють собою поздовжні
балки (мал. 1.1), що складаються
з поясів і стінок. Їх частка в масі крила може доходити до 30-40%. Більша ж
частина маси самого лонжерона припадає на його пояси, в яких при згині
виникають найбільші нормальні напруги, так як їх матеріал найбільш віддалений від
нейтральної осі.
Мал. 1.1
Конструкція лонжеронів балочного і ферменного типів: а, б - балочні: 1 -
стінки, 2 - пояси, 3 - стійки; в - ферменні
Лонжерони балочного типу виконуються
у вигляді складових або монолітних конструкцій ( мал.1.2).
Мал.1.2
Конструкція складового (а,б) та монолітного (в) лонжеронів
При такій простій конструкції
лонжерона досягається найбільш ефективне використання матеріалу, а отже, і
мінімальна маса. Пояси лонжеронів являють собою катані або пресовані профілі
різного перерізу, зручні для з'єднання з обшивкою і стіною (мал.1.3).
З умови однакової міцності площин перерізу поясів до кінця крила повинні
зменшуватися.
Мал. 1.3
Перерізи лонжеронів
Завдяки лапкам на поясах лонжеронів
(мал. 1.2,
а та мал. 1.3, з,и)
спрощується кріплення обшивки і стінки до поясу, стають менше витрати перерізу
під отвори. Кореневі частини лонжеронів закінчуються потужними стикувальними
вузлами, які передають сили і моменти з консолей крила на центроплан або
безпосередньо на фюзеляж. Крім лонжеронів в такому крилі можуть бути поздовжні
стінки. Вони відрізняються від лонжеронів. Панелі обшивки зі стрингерним
набором, кріпляться до лонжеронів. Лонжерони передають навантаження на
шпангоути фюзеляжу літака за допомогою моментних вузлів. Лонжеронні крила мають
порівняно тонку обшивку, підкріплену стрингерами та нервюрами. Товщина обшивки
та підкріплюючого його набору, визначаються з умов роботи на зрушення та
кручення. При зміні крила обшивка в стислій зоні має низьке значення критичної
напруги. У підсумку участь обшивки в сприйманні згинаючого моменту обмежується
роботою її в розтягнутій зоні, де вона лише розвантажує нижні пояси лонжеронів.
В крилі, де застосовується один
лонжерон, зазвичай його розташовують у місці максимальної будівної висоти
профілю (у літаках з малою швидкістю польоту на 30 - 40 % хорди, у швидкісних
на 45 - 60 % хорди). Для отримання контуру здатного сприймати кручення, а також
бази для кріплення елеронів й засобів механізації на крилі з одним лонжероном
на 65 - 70 % його хорди від носка розташовується поздовжня стінка.
В дволонжеронних крилах передній
лонжерон зазвичай розташовується на 15 - 25 % хорди, задній на 60 - 70 %,
максимальна будівельна висота профілю у такого крила не використовується для
раціонального розподілу матеріалу в конструкції, тому вага дволожеронного крила
при різних параметрах завжди більша за однолонжеронне. На кручення працює
контур, який створений обшивкою та стінками переднього та заднього лонжеронів.
Крило однолонжеронне з працюючою
обшивкою, має в плані форму двох трапецій і складається з трьох частин:
· центроплану;
· двох відокремлених
консолей.
Стиковка консолі крила з
центропланом здійснюється вузлами підвіски на основному і допоміжному
лонжеронах.
Центроплан (мал. 1.5)
складається з двох половин, з'єднаних загальним основним лонжероном. Каркас
кожної половини центроплана утворений основним лонжероном 1, переднім 2 і
заднім 3 допоміжними лонжеронами, стрингерами 4 і 5, вісьмома нервюрами і
працюючою обшивкою (мал.1.5).
Основний лонжерон центроплана 1
встановлений в місці максимальної товщини профілю крила, він сприймає
згинальний момент і поперечну силу. Поперечна сила сприймається стінкою
лонжерона, а згинальний момент - його полками. Основний лонжерон проходить
через середню частину фюзеляжу, і його стінка приклепується до 15-го і 16-го
шпангоутам. У стінці основного лонжерона є два окантованих вирізи для проходу
каналів повітрозбірника. Вхідні канали повітрозбірника кріпляться гвинтами до
передньої кореневій частини центроплану.
На передній стінці основного
лонжерона кріпляться сталеві вузли навішування основних стійок шасі. На торцях
основного лонжерона розташовані по два вузла кріплення консолей крила. За
допомогою болта він кріпиться до шпангоуту № 11 фюзеляжу (мал.1.4).
Коренева частина лонжерона з'єднується зі шпангоутом № 19 фюзеляжу за допомогою
заклепок і болтів. Задній допоміжний лонжерон сприймає частину згинального
моменту і поперечної сили крила. Стрингер 4 розташований між основним
лонжероном і заднім допоміжним лонжероном, служить опорою для обшивки. Крім
того, він виконує силову задачу: працює на розтягування і стиснення, сприймаючи
частина згинального моменту крила.
Мал. 1.4 Центроплан: 1 - основний
лонжерон; 2 - передній допоміжний лонжерон; 3 - задній допоміжний лонжерон; 4,
5 - стрингери; 6, 7 - вузли кріплення консолі до центроплану; 8 - підшипник
управління щитками-закрилками: 9, 10 - напрямні на нервюрах 1«а» і 8«б» кареток
щитків-закрилків; 11 - стінка; 12 - вузол кріплення циліндра щитків-закрилків;
13 - балка вузла кріплення циліндра щитків шасі; 14 - повітрозбірник; 15 -
обтічник; 16 - вузол кріплення переднього допоміжного лонжерона; 17 - стикова
(щілинна) стрічка
Нервюри призначені для утворення і
збереження в польоті форми профілю крила у всіх його перетинах. Середні частини
нервюр кріпляться заклепками до основного і допоміжного лонжеронів за допомогою
вертикальних жорсткостей, виготовлених з пресованих профілів. Посилені нервюри
кріпляться до основного лонжерону крім заклепок додатковими лапками. Хвостовики
нервюр своїми відбортівками кріпляться до заднього допоміжного лонжерону. Форма
їх нижньої частини відповідає контуру закрилка. Обшивка призначена для
утворення поверхні, необхідної для обтікання крила потоком повітря з метою
створення підйомної сили. Будучи складовою частиною силової схеми крила,
обшивка сприймає крутний момент, а також частково і згинальний момент, працюючи
при цьому на розтяг-стиск.
У задній частині центроплана
встановлено внутрішній закрилок (мал. 2.6).
У хвостовиках нервюр № 1 і 8 вирізаними фрезеруванням напрямні рейки. При
відхиленні закрилок переміщується назад, при цьому ролики, закріплені на
закрилку, рухаються по напрямних рейках. На нервюрах № 8 встановлений циліндр
управління закрилками. Внизу центроплана є ніші для розміщення в прибраному
положенні основних стійок шасі. Внизу правої половини центроплана встановлена
антена радіовисотомір.
Основний лонжерон консолі (мал. 1.5)
є основною несучою частиною крила, складається з полиць і приклепаних до нього
стінок, виготовлених з дюралюмінієвого листа. До основного лонжерону кріпиться
стикового вузол, який передає з консолі на центроплан згинальний момент і
значну частину поперечної сили. Передній допоміжний лонжерон розташований в
носовій частині крила. Задній допоміжний лонжерон проходить від нервюри № 9 до
нервюри № 14 і несе на собі задній стикувальний вузол консолі.
Мал. 1.5 Закрилок внутрішній: 1 -
лонжерон; 2, 3 - торцеві нервюри; 4 - носок нервюри; 5, 11 - обшивка; 6 - болти
кріплення каретки; 7 - каретка; 8 - направляючі ролики; 9 - хвостовики нервюр;
10 - обтічник; 12 - стрингер; 13 - направляючий штир
При такій простій конструкції
лонжерона досягається найбільш ефективне використання матеріалу, а отже, і
мінімальна маса. Консолі крила (мал. 1.7)
складаються з каркаса і працюючої обшивки. Поздовжній набір каркаса крила
складають:
·
основний лонжерон,
·
передній і задній допоміжні
лонжерони,
·
стрингери.
У поперечний набір каркаса входить
12 нервюр.
Стиковка консолей крила з
центропланом здійснюється за допомогою вузлів підвіски на основному і задньому
допоміжному лонжеронах. Стик консолі крила з центропланом закривається щілинної
стрічкою, яка встановлюється на гвинтах.
Кріплення нервюр консолей крила до
лонжеронів і обшивці аналогічно кріпленню нервюр центроплана. Верхні і нижні
полки нервюр в місці з'єднання з полицею лонжеронів посилені дюралюмінієвим
куточком. Хвостові частини нервюр крила в зоні посадкового щитка мають форму
його профілю.
Нервюри № 15 і 19 посилені куточками
під вузли підвіски елерона. Між нервюрами № 9 і 10 встановлено бомботримачів;
між нервюрами № 17 і 18 знаходиться кронштейн кріплення трубки ПВД.
Мал. 1.6 Консоль крила: 1 - передній
лонжерон; 2 - основний лонжерон; 3 - задній допоміжний лонжерон; 4, 5, 6 -
нервюри; 7 - оглядовий лючок; 8 - стрингер; 9 - турбулізатор потоку; 10 -
хвостові частини нервюр; 11, 12 - вузли підвіски елерона; 13 - закінцівки
крила; 14 - вузол підвіски
У задній частині консолі між
нервюрами № 9 і 14 мається зовнішній закрилок, а в хвостовиках нервюр № 9 і 14
вирізаними фрезеруванням напрямні рейки закрилка. Між нервюрами № 14 і 20 встановлено
елерон.
До нервюри № 20 гвинтами кріпиться
закінцівка крила, на якій розташовані аеронавігаційний вогонь АНО і розрядник
статичної електрики.
На консолях знаходяться антени
відповідача. На лівій консолі встановлена посадкова фара і антена радіовисотомір,
в правій консолі - датчик ГИК-1. На носках лівої і правої консолей крила в
районі елеронів маються пластинки-турбулнзатори, що викликають місцевий
передчасний зрив потоку, які застережуть льотчиків про наближення до швидкості
звалювання (по трясці ручки керування).
Елерон підвішений до крила на двох
вузлах, служить для поперечного керування літаком. Каркас елерона складається
з:
·
з лонжерона,
·
11 нервюр;
·
задньої рейки.
Обшивка товщиною 1 мм пов'язує
каркас в жорстку конструкцію. На задній кромці лівого елерона встановлений
некерований компенсатор. Елерон має аеродинамічну компенсацію.
Мал. 1.7 Елерон: 1 - лонжерон; 2 -
вузли підвіски; 3 - нервюри; 4 - задня рейка; 5 - балансувальний «ніж»; 6 -
балансувальний вантаж
Закрилки (мал.1.8). На літаку
встановлені два внутрішніх (на центроплані) і два зовнішніх (на консолях)
висувних закрилки, що мають три фіксованих положення: прибрано, злітне
(випущені на 15°) і посадочне (випущені на 30 °). Кожне положення закрилків має
світлову і механічну сигналізацію: прибрано - горить червона лампочка,
механічний покажчик прибраний; злітне - горить помаранчева лампочка, механічний
покажчик в першому проміжному положенні; посадочне - горить зелена лампочка,
механічний покажчик в другому, повністю випущеному положенні.
Система прибирання закрилків має
пристосування для автоматичної їх прибирання при швидкості 290 ± 10 км / год.
по приладу.
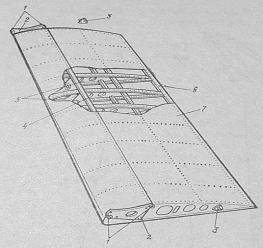
Закрилки виконують два завдання: при
випуску на 15° зменшують довжину розбігу літака при зльоті, під час випуску на
30° зменшують довжину пробігу і посадкової дистанції.
По конструкції всі закрилки
аналогічні. Каркас закрилка складається з:
· лонжерона,
· нервюр;
· задньої рейки.
На торцях кожного закрилка
закріплені чотири пластини. На передніх пластинах встановлені ролики для
переміщення закрилків в напрямних рейках і штирі для кріплення тяг управління
закрилками. На задніх пластинах встановлені штирі, які при прибраних закрилках
входять в спеціальні гнізда, вирізаними фрезеруванням в хвостовиках нервюрах
крила, в результаті чого зменшується вібрація закрилків.
Мал.1.9 Конструкція дволожеронного
крила: 1 - передній лонжерон; 2 - кришка люка заправної горловини паливного
бака; 3 - кришка люка підходу до датчика ІД-3; 4 - контурна нервюра; 5-
швартувальний вузол; 6 - закінцівка; 7- аеронавігаційний вогонь; 8 - распорна
нервюра; 9 - кінцевий вузол навіски елерона; 10 - стрічкова розчалка; 11 -
середній вузол навіски елерона; 12 - люк підходу до середнього вузла навіски
елерона; 13 - обшивка;14-задній стикувальний вузол; 15- задній лонжерон;
16-кришка люка паливоміра; 17 - передній стикувальний вузол; 18 - верхній
косинець переднього лонжерона; 19 - бокова нервюра; 20 - верхній пояс
переднього лонжерона
РОЗДІЛ 2.
Основні матеріали що використовуються для виготовлення деталей лонжеронного
крил
Прагнення збільшити корисне
навантаження літака за рахунок зменшення його ваги обумовлює необхідність
використання витривалих та легких матеріалів.
Можливість використання в
літакобудуванні того або іншого металу або сплаву визначається його фізичними,
хімічними, механічними та технологічними властивостями.
Найбільш широке використання в
літакобудуванні мають такі метали та сплави:
. прості вуглецеві сталі
2. спеціальні леговані, сталі з
добавкою хрому, нікелю, вольфраму,
молібдену, титану та ін.
3. мідь та її сплави (латунь,
бронза)
4. алюміній та його сплав
(дюралю мін, силумін та ін.)
. сплави на основі магнію
. сплави олова, міді та сурми
(баббіти)
Широке розповсюдження в
літакобудуванні знайшли такі матеріали як:
· алюмінієво-літієві
сплави, які використовують в якості легіруючого елементу літій (вагова
щільність 534 кг/м3) та забезпечує зниження ваги конструкції при підвищенні
питомої міцності та жорсткості за рахунок підвищення на 5-8% модуля пружності.
Ці сплави підтримують частку алюмінієвих сплавів в якості основних авіаційних
матеріалів;
· полімерні
композиційні матеріали (ПКМ) майже вдвічі дозволять поряд з підвищенням вагової
ефективності вирішити проблеми ресурсу при статичних і динамічних
навантаженнях;
· нові композиційні
матеріали (КМ) на підставі алюмінієвих і титанових сплавів з використанням
наповнювачей: SiC,
Al2O3,
інтерметаліди та ін. дозволять підвищити ресурсні та теплофізичні
характеристики, модуль пружності та ін. властивості.
З позицій забезпечення безпеки
польотів пасажирських і транспортних літаків необхідні матеріали з підвищеною
довговічністю. До таких матеріалів відносяться металоорганопласти - алори. В
конструкціях з алору тріщина досягне свого критичного значення при кількості
польотів ЛА в п`ять разів більшому порівняно з традиційними матеріалами.
Як вже було відмічено в розділі 3
крила літаків в багатьох випадках визначають статичну витривалість, жорсткість,
ресурс і живучість літаків.
Ресурс крила літака, його жорсткість
і живучість визначають лонжерони, які є одними з відповідальних силових
елементів.
Матеріал, який застосовується для
виготовлення елементів лонжерона, повинен забезпечувати мінімальну вагу
конструкції при достатній міцності, ресурсі та можливо більшої жорсткості,
допускати застосування високопродуктивної технології, бути зручним при ремонті
та недорогим. При виборі матеріалу з високою ваговою ефективністю
використовують питомі показники, які визначаються для кожного виду
навантаження.
За статистикою для виготовлення
поясів лонжерона пасажирських і транспортних літаків найчастіше застосовують
алюмінієво-мідні сплави. Ці сплави мають хороші характеристики витривалості та
живучості, малочуттєвості до концентраторів напружень, що виникають при
складанні.
Лонжерони крила, як вже відзначалось
раніше, є одним з найбільш відповідальних силових елементів крила, які багато в
чому визначають статичну міцність, жорсткість, ресурс і живучість не тільки
крила але й взагалі літака.
Лонжерони крила являють собою збірні
тонкостінні балки регулярна частина яких складається з поясів і стінок,
підкріплених стійками. До зон нерегулярностей належать зони з`єднань,
вирізів й отворів, монолітних потовщень і підсилюючих накладок гампельних
переходів та ін.
Будівельна висота лонжеронів
сучасних літаків знаходиться в діапазоні від 150 до 1200 мм. По вазі лонжерони
складають від 25 до 50 % ваги крила, або 4-5% злітної ваги літака. Кількості у
лонжеронів залежить від конструктивно-силової схеми і ступеня навантаженості
крила. Розташовуються лонжерони на відстані: 15...25% від довжини хорди крила -
передній і 60...70% - задній. Це розташування дозволяє більш рівномірно
розподілити навантаження між лонжеронами.
Крім переднього і заднього
лонжеронів в конструкції кесона крила деяких літаків застосовуються додаткові
проміжні лонжерони, розташовані між лонжеронами, які обмежують кесон.
Розташування лонжеронів і, відповідно, ширина кесона зазвичай визначаються на
етапі загального проектування при аеродинамічному компонуванні крила з
урахуванням геометричних параметрів механізації передньої і задньої крайок
крила, забезпечення потрібного об'єму паливних баків.
Аналіз особливостей конструкції
лонжеронів літаків показав, що основні силові елементи регулярної частини
лонжеронів - пояси, стінки, підкріплюючі стійки - виконуються переважно з
алюмінієвих сплавів, таких, як 1161Т, 1973Т2, 1163Т, 1933Т3. Нижні пояси
(розтягнута зона) виготовляються зі сплавів 1161Т, 1163Т. Ці сплави мають меншу
межу міцності при розтягнутості, але в той же самий час вони мають кращими
усталостними характеристиками порівняно з матеріалами верхніх поясів 1973Т3
(стиснута зона).
Пояси лонжеронів є геометрично
складними елементами конструкції лонжерона зі змінними товщинами за розмахом.
Їх виготовляють з пресованих профілів таврового або кутового перерізу
механічним фрезеруванням. З’єднуються
вони між собою в місцях перестиковки та стикування вузлів за допомогою
заклепочних і болтових з`єднань.
Стінки збірних лонжеронів
виконуються з листового матеріалу (алюмінієвого сплаву 1163Т) механічним або
хімічним фрезеруванням по контуру та товщині. Вони мають монолітні потовщення в
зонах поздовжніх і поперечних стиків, вирізів і отворів, зонах приєднання
підкріплюючих стійок, силових нервюр, приєднань вузлів навішування агрегатів і
систем.
Товщина стінки змінюється, як
правило, в межах від 0,8 до 8 мм. В регулярній зоні товщина стінки змінюється
від 1,2 до 3,5 мм. В зоні установки підкріплюючих стійок або кронштейнів
залежно від їх призначення товщина стінки збільшена в 1,25...1,75 рази. Радіуси
переходів знаходяться в межах від 3 до 5 мм, висота стінок - в проміжку від 0,9
до 0,95 висоти лонжеронів. Для забезпечення мінімуму ваги в стінці виконують
утонення. Підкріплюючі стійки стінок лонжерона виготовлюються з пресованих
профілів таврового або кутового перерізу, і допрацьовуються механічних
фрезеруванням.
В якості кріпильних елементів у
сполуках збірних лонжеронів використовуються заклепки, болти та болт-заклепки.
Вибір типу, нормалі та діаметру кріпильних елементів проводять з умов
забезпечення заданої статичної міцності, втомної довговічності, живучості,
герметичності. Для забезпечення довговічності і герметичності з'єднань
застосовують високоресурсні заклепки з компенсатором. Для забезпечення більш
рівномірного радіального натягу по висоті пакету, використовують клепку
підвищеним тиском і клепку стержнями, а також постановку болтів з радіальним
натягом до 1,2% діаметра болта. У разі застосування болтів крім рівномірного
радіального натягу реалізується велика осьова стяжка пакета.
Болтові з'єднання мають більш високі
ресурсні характеристики, чим заклепувальні, проте вважаються менш
технологічними. Застосовують анодирувані заклепки з алюмінієвих сплавів В65.
Для виготовлення болтів використовуються сталь 30ХГСА, титановий сплав ВТ16, а
також сплави 16ХСН, 14Х17Н2 і ін.
Всі деталі конструкції лонжеронів,
виконані з алюмінієвих сплавів, анодирують, поза зони паливних баків додатково
покривають ґрунтом (грунт ФЛ-086-204 ТУ 16302-79, грунт ЄП-0214 ТУ
6-10-2141-88, грунт ХП-0206 ТУ 6-10-1934-89).
Герметизацію з`єднань виконують
поверхневої і внутрішньої при допомозі герметиків, гумових стрічок і прокладок
спеціального профілю.
Герметизацію сполук в лонжеронах, що
входять в баки-кесони, виконують при допомозі герметиків У-30МЭС-5M, УТ-32НТ,
ВИТЭФ-1НТ, ВГФ-2.
Для внутрішньої герметизації
болтових і заклепочних з`єднань
в лонжеронах застосовуються герметики У-2-28НТ, УТ-32НТ, ущільнювальна стрічка
У-20А. При виконанні складальних операцій клепку заклепок виконують на пресі, а
у важкодоступних місцях - ручним багатовдарним інструментом у відповідності з
інструкцією заводу-виробника. Постановку та затяжку болтів і гайок суворо
регламентують.
Полиці лонжерона виготовлені з
профільованого дюралюмінію. Верхня і нижня полиці пов'язані між собою стінкою з
дюралюмінію товщиною 2,5 мм. У стінці основного лонжерона є два окантованих
вирізи для проходу каналів повітрозбірника. Вхідні канали повітрозбірника
кріпляться гвинтами до передньої кореневої частини центроплану.
На передній стінці основного
лонжерона кріпляться сталеві вузли навішування основних стійок шасі.
На торцях основного лонжерона
розташовані по два вузли кріплення консолей крила. Передній допоміжний лонжерон
виготовлений з листового дюралюмінію товщиною 1,6 мм. За допомогою болта він
кріпиться до шпангоуту фюзеляжу.
Задній допоміжний лонжерон виготовлений
з листового дюралюмінію товщиною 2 мм. На торцях лонжерона розташовані
дюралюмінієві фрезеровані вузли для з'єднання з допоміжним лонжероном консолі
крила. Коренева частина лонжерона з'єднується зі шпангоутом фюзеляжу за
допомогою заклепок і болтів.
Стрингер виготовлений з пресованого
дюралюмінієвого профілю, приклепаний по всій довжині до обшивки.
Нервюри виготовлені з листового
дюралюмінію. Середні частини нервюр кріпляться заклепками до основного і
допоміжного лонжеронів за допомогою вертикальних жорсткостей, виготовлених з
пресованих профілів.
Посилені нервюри кріпляться до
основного лонжерону крім заклепок додатковими сталевими лапками.
Хвостовики нервюр, штамповані з
листового матеріалу, своїми відбортівками кріпляться до заднього допоміжному лонжерону.
Форма їх нижньої частини відповідає контуру закрилка. Обшивка виготовлена з
дюралюмінію. Товщина верхньої і нижньої обшивки між лонжеронами - 2 мм, верхній
обшивки за заднім допоміжним лонжероном - 1 мм.
Дюралюмінієва обшивка товщиною 1 мм
пов'язує каркас в жорстку конструкцію.
Розділ 3.
Технічна вимога щодо складання вузла
Слюсар-складальник при виконані
робіт користується кресленнями, технічними умовами, виробничими інструкціями,
технологічними картами.
На деталі каркаса планера літака
(обшивка, стрингери, нервюри або їхні частини) креслення не виготовляються, і
їх конструктивні параметри вказуються безпосередньо на складальних кресленнях.
Ці деталі виготовляються за робочими шаблонами, знятими з плаза, та за
оснащенням.
На складальних кресленнях наводяться
технічні вимоги до вузла що складається, вказуються його габаритні розміри,
визначається взаємне розташування деталей, містяться вимоги щодо якості
поверхні, допустимі зазори, вимоги до процесу складання, умови і методи
випробувань, вказівки про маркування, посилання на інші документи.
До складальних креслень додається
специфікація, в якій наводиться перелік усіх деталей що входять до даного
складання. Специфікація доповнює складальне креслення и дозволяє виготовити
деталь каркасу планера за шаблонами та оснастці без креслення деталі.
В технічних умовах містяться вимоги
до виробу або його частинам. Вони включають в себе міцнісні, експлуатаційні,
технологічні, тобто міцнісні характеристики (рівень розрахункових навантажень,
запас міцності та жорсткості виробу або вузла); експлуатаційні вимоги
спрямовані на забезпечення простоти і зручності експлуатації майбутнього літака
та його складових; технологічні вимоги забезпечують простоту та оптимальну
вартість виготовлення, ремонту, технічного обслуговування (виготовлення літака
та його вузлів - за простою технологією та з оптимальною вартістю виготовлення,
ремонту, технічного обслуговування та оптимізування вартості - виготовлення
деталей, вузлів літака на основі сучасної технології виготовлення по математичному
та електронному моделюванню).
Виробничі інструкції регламентують
послідовність виконання певного виду робіт (герметизація, клепка, випробування
та ін.). В них наводяться дані про застосовуване обладнання, оснащення та
інструмент, контроль, випробування та ін.
Складання планера організовується за
схемою паралельно-послідовних операцій, починаючи зі складання підвузлів,
вузлів, панелей, агрегатів і закінчуючи загальним складанням літака в цілому.
На підставі розробленої
послідовності складальних операцій створюється схема складання, яка є одним з
основних технологічних документів для складальних цехів.
В схему складання вносять вказівки
про послідовність комплектування виробу, що складається, деталями і вузлами, а
також технічні вимоги на деталі й вузли, що визначають, в якому вигляді вони
подаються на складання.
Крім цього, технологічна схема
складання, визначаючи послідовність збірки (складання), є в той же самий час і
основним вихідним документом для розробки технічних вимог на складальні одиниці
- деталі, вузли, панелі та агрегати.
Зміст технологічних процесів і об'єм
робіт, які виконуються при складанні відсіків та агрегатів, визначається:
· конструкторсько-технологічними
параметрами виробів, які збираються;
· масштабом
виробництва, від якого залежить глибина опрацювання технологічних процесів,
оснащення виробництва спеціальним устаткуванням і форма організації
виробництва;
· прийнятим методом
забезпечення взаємозамінності й точності геометричних розмірів деталей,
панелей, вузлів і відсіків.
До конструкторсько-технологічних
параметрів відсіків відносяться:
· поперечний переріз
(профіль) відсіку;
· форма обводу в
плані;
· наявність
панелювання;
· вид стиків і
роз'ємів при з'єднанні відсіку з іншими відсіками;
· підхід в зону
стикових клепаних, зварних швів (двосторонній і односторонній).
Питома вага того або іншого виду
робіт в загальній трудомісткості процесу складання залежить від конструкції
агрегату і прийнятого методу з'єднання.
РОЗДІЛ 4.
Описання технологічного процесу складання лонжеронного крила
Технологічний процес (ТПВ) - основа
будь-якого виробництва.
ТПВ це комплекс підготовчих робіт
конструкторсько-технологічного характеру, які забезпечують здійснення технологічного
процесу на всіх етапах виробництва.
Державними стандартами встановлена
єдина система організації та управління процесом ТПВ, які передбачають широке
використання прогресивних типових технологічних процесів, стандартного
технологічного обладнання та оснащення засобів механізації та автоматизації
технологічних процесів.
Технологічний процес виготовлення
літака завершується складанням - монтажем його з агрегатів, вузлів і
з`єднувальних деталей з подальшим регулюванням і випробовуванням. Він являє
собою складний комплекс взаємодій обладнання та виконавців з перетворення
вихідних матеріалів у літак. Із-за особливостей конструкції літальних апаратів
і вимог, що до них пред'являються, авіаційне складальне виробництво значно
відрізняється від складання інших виробів машинобудування.
Головна відмінність - велика
трудомісткість і специфічне складальне обладнання. Якщо в інших галузях
машинобудування основну питому вагу в трудомісткості складає виготовлення
деталей, а процеси складання вносять у загальну трудомісткість 10-20%, то у
виробництві літальних апаратів вартість складальних процесів перевищує 50%.
Основними факторами, що визначають
специфіку складальних робіт, є:
·
багатодетальність літального
апарату;
·
мала жорсткість елементів
конструкції. Більшість деталей мають малу жорсткість і при складанні мимовільно
можуть змінювати свою форму під дією ваги або технологічних зусиль, що
виникають при виконанні з'єднань. У зв'язку з цим, для додання заданої форми
об'єкту, який складається з нежорстких деталей потрібні пристосування, які
задають форму;
·
складність просторових форм.
Практично відсутні прості поверхні (які властиві виробам більшості видів
машинобудування) плоскість, циліндр, конус. Складання таких агрегатів пов`язане
з великими проблемами точної ув`язки всіх деталей;
·
великі розміри деяких летальних
апаратів;
·
наявність великої кількості рухливих
частин, які змінюють форму летальних апаратів у польоті, на злеті та при
посадці. В першу чергу це: органи управління і механізації, шасі та ін.;
·
високі вимоги до точності
виготовлення ЛА;
·
різноманітність матеріалів, які
використовуються: металеві сплави великої номенклатури, композиційні матеріали,
неметали та ін.;
·
різноманітність видів з`єднань:
клепаних, болтових, зварних, паяних, клеєних і таке ін. Складні умови для
виконання з`єднувальних швів - замкнутість об`єму агрегатів і відсутність
двостороннього доступу. Високі вимоги до надійності швів, що з`єднують;
·
мала серійність виробництва. Ця
обставина обмежує використання дуже дорогих спеціальних засобів для складання
(наприклад, складальних роботів, які використовуються в автомобілебудуванні).
Доля ручної праці в виробництві ЛА порівняно з іншими машинобудівними галузями
залишається високою;
Процес складання є кінцевим етапом
виготовлення ЛА має визначальне значення для всього виробництва. Складання
організовується за схемою паралельно-послідовних операцій. В схему складання
вносять вказівки про порядок комплектування зібраного виробу деталями і
вузлами, а також технічні вимоги на деталі та вузли, що визначають, в якому
вигляді вони подаються на складання. Середньостатистичний літальний апарат
складається на 70% з алюмінієвих та інших легких сплавів, на 20% з неметалів.
При складальних роботах широко
використовуються наступні операції:
· обробка спряжених поверхонь;
· обробка отворів під
болти і заклепки;
· зварювання;
· правка при
складанні (пружні деформації);
· штампування гнізд
під потаємні головки болтів і заклепок.
Таким чином, для складання літальних
апаратів потрібні оптимальні технологічні процеси складання складних виробів,
необхідні трудомісткі обчислення, пов'язані з вибором схеми складання, з
розрахунком точності складання, нормування трудомісткості і розрахунку
технологічної собівартості збірки і т. п. Ефективність вирішення багатьох конструктивних
і виробничих проблем багато в чому залежить від рівня технічного,
технологічного та організаційного розвитку складальних виробництв. Цей рівень
визначається, насамперед, тими методами складання, які закладаються при
підготовці виробництва і використовуються в серійному виробництві нових
виробів, зокрема авіаційної техніки. У літаків і інших летальних апаратів можна
в якості основних агрегатів виділити:
· планер;
· органи приземлення
(шасі);
· двигуни;
· системи керування,
які обслуговують планер, двигуни та шасі;
· механізми та
агрегати, які забезпечують виконання спеціальних функцій;
· спеціальне
обладнання та засоби зв`язку.
За конструкцією та в технологічному
відношенні вказані агрегати значно відрізняються один від одного, тому
виготовлення їх потребує спеціалізації виробництва.
Планер літака складається з деталей,
вузлів, панелей, відсіків і агрегатів (мал. 4.1).
Мал. 4.1 Членування літака: 1 -
обтічник антени; 2 - передня та задня частини фюзеляжу; 3 - крило; 4 - силова
установка; 5 - кіль; 6, 16 - носок кіля та стабілізатора; 7,14,33,35 - кесони
кіля, стабілізатора, ОЧК та центроплану; 8 - обтічник стабілізатора; 9 -
стабілізатор; 10,18 - кок стабілізатора й фюзеляжу; 11, 17, 30 - тримери; 12 -
руль висоти; 13, 32 - закінцівка стабілізатора й ОЧК; 15 - руль напряму; 19-
хвостова частина фюзеляжу; 20 - гідропідйомник трапу; 21 - гондола двигуна; 22
- стулка гондоли; 23 - повітрозбірник двигуна; 24, 43 - трапи; 25, 26, 42 -
двері; 27 - інтерцептор; 28 - закрилки; 29 - хвостова частина центроплану; 31 -
елерон; 34,36 - носок і підкрилок ОЧК і центроплану; 37, 39, 45 - щитки шасі; 38,
40, 44 - шасі; 41 - підкесонна панель
Деталлю називається елементарна
частина виробу, виготовленого з цільного шматка матеріалу. Деталь є первинним
елементом складання.
Вузол - декілька з`єднаних між собою
деталей каркаса: збірні лонжерони, шпангоути, нервюри і таке інше.
Панель це з`єднання декількох
деталей каркасу з обшивкою.
Агрегат - закінчена в
конструктивному та технологічному відношеннях частина планера, яка складається
з панелей, вузлів і деталей. Агрегати це крила, фюзеляж, елерон, стабілізатор
та ін.
Відсік це частина агрегату.
В складальних цехах літакобудівних
заводів виконуються складальні та монтажні роботи.
Об`єм складальних і монтажних робіт
залежить від кількості деталей, які входять до конструкції планера та кількості
механізмів, приладів та спеціальної апаратури, які встановлюється на планері.
Необхідність членування планера
літака на деталі, вузли, панелі, відсіки, агрегати обумовлено вимогами
виробництва та необхідністю мати конструктивні, експлуатаційні роз’єми
та стики. Технологічні стики створюються з урахуванням можливостей виробництва
на даному етапі його розвитку і визначаються,
зокрема, габаритними розмірами устаткування. На мал. 4.1. показано технологічні
стики крила, які поділяють його на носок 34, кесон 35, хвостову частину центроплана
29 та закінцівку 32. З`єднання деталей, вузлів, панелей і відсіків під час
складання виконуються нероз`ємними, тобто у вигляді технологічних стиків.
Експлуатаційні роз'єми і стики
створюються з метою заміни, огляду або регулювання різноманітних механізмів і
систем під час експлуатації літака.
Складання планера організовується за
схемою паралельно-послідовних операцій, починаючи зі складання підвузлів,
вузлів, панелей, агрегатів і закінчуючи загальним складанням літака в цілому.
На підставі розробленої
послідовності складальних операцій створюється схема складання, яка є одним з
основних технологічних документів для складальних цехів.
В схему складання вносять вказівки
про послідовність комплектування виробу, що складається, деталями і вузлами, а
також технічні вимоги на деталі й вузли, що визначають, в якому вигляді вони
подаються на складання. Крім цього, технологічна схема складання,
визначаючи послідовність збірки (складання), є в той же самий час і основним
вихідним документом для розробки технічних вимог на складальні одиниці -
деталі, вузли, панелі та агрегати.
При розробці технологічних процесів
складання, пристосувань й інструментів при виборі обладнання для складальних
робіт необхідно керуватися вимогами, які ставляться до точності вузла або
агрегату, що збираються.
При складанні планера розрізняють
такі основні види робіт: вузлове складання, яке включає складання окремих
панелей, нервюр, лонжеронів, шпангоутів і ін.; агрегатне складання - складання
окремих відсіків і агрегатів; загальне складання, тобто складання планера з
агрегатів із наступним монтажем на ньому різноманітного обладнання, приладів,
механізмів.
Об'єм складальних робіт визначається
конструкцією планера, фізико-механічними властивостями матеріалів, з яких він
виготовлений, та видами заготовок, з яких виготовлені окремі деталі та вузли.
Трудомісткість складальних робіт для
металевих літаків клепаної конструкції складає приблизно 45...50 % загальної
трудомісткості при виготовленні літака. При виготовленні літака вузлова збірка
складає 12...25%, агрегатна - 18...20% і загальна - 12...15%.
Складання являє собою сукупність
технологічних операцій по встановленню деталей в положення збирання й з'єднання
їх в панелі, вузли, агрегати і літак в цілому.
Послідовність виконання складальних
робіт багато в чому залежить від конструкції, габаритних розмірів і жорсткості
зібраних деталей.
Існує декілька методів складання,
які відрізняються виглядом інструменту, який застосовується при складанні, а
також складальних пристосувань і обладнання.
Найбільш розповсюдженими є:
складання за базовою деталлю, за розміткою, за складальними отворами і
складання з використанням спеціальних складальних пристосувань.
Застосування складання за
складальними отворами (СО) - процес, при якому взаємоположення деталей, які
складаються, визначається положенням існуючих на них складальних отворів. При
базуванні по СО складальні деталі поєднують одне з одним і на період з'єднання
в складальні отвори вставляють фіксатори. Базування по СО можливо при
встановлені в складальне положення елементів поздовжнього та поперечного
наборів.
Місця розположення СО зазначаються в
кресленнях і схемах, складених у конструкторському бюро літакобудівного
(серійного) заводу.
Відповідно з технологічним процесом
складання-клепки на схематичних кресленнях крім СО вказують місця розташування
направляючих отворів (НО) і настановних базових отворів (НБО).
Складальні пристосування
забезпечують потрібне взаємоположення деталей, що з'єднуються, визначене
положення обробляючого інструменту відносно деталі, надання форми недостатньо
жорстким деталям і вузлам під час складання. При цьому створюється наступні
переваги в зрівнянні зі складанням за розміткою: виключається розмітка й
підгонка деталей; прискорюється і становиться простішим процес складання; досягається
взаємозамінність зібраних вузлів, панелей і агрегатів; можлива механізація
процесу складання. Цим і пояснюється широке використання складальних
пристосувань на серійних заводах при виготовленні літаків. При складанні в
пристосуванні з базою «внутрішня поверхня обшивки» панель встановлюється в
складальне положення,спираючись внутрішньою поверхнею на базові поверхні
складального пристосування або на поверхні спеціальних макетних нервюр (мал.
4.2).
Мал. 4.2 Схема
базування по внутрішній поверхні обшивки
Зібрані лонжерони 1 і 5 встановлюють
на НБО на фіксатори в кронштейнах 6 та закріплюють їх в складальному
пристосуванні.
Потім встановлюють між лонжеронами
макетні нервюри 7 на технологічні болти, базуючи їх відносно лонжеронів по СО в
приклепаних до лонжеронів профілів 9 и нервюрах 7.
Між макетними нервюрами встановлюють
нервюри літака 4 з базою по СО, єднаючи їх з лонжеронами заклепками. На
складений таким чином каркас встановлюють панелі 2 з укріпленими компенсаторами
3.
Для встановлення панелей існують два
етапи - попередній і остаточний. Попередньо одну з панелей (ліву) накладають на
базову поверхню макетних нервюр 7 і притискають стрічкою 8 до макетних нервюр.
В такому положенні панелі по НО в компенсаторах 3 просвірлюють отвори під
заклепки в літакових нервюрах 4. Після цього в усіх встановлених нервюрах
літака панель виймають з пристосування, встановлюють другу панель (праву) і
свердлять за НО в компенсаторах отвори під заклепки в нервюрах літака. Після
цієї операції єднають заклепками компенсатори 3 з нервюрами літака 4. Потім
знімають макетні нервюри і встановлюють на їх місце нервюри літака, базуючи їх
на лонжеронах по СО. Знову встановлені літакові нервюри єднають з лонжеронами
заклепками. Потім в стрингерах за НО свердлять отвори під заклепки в усіх
встановлених літакових нервюрах і єднають їх заклепками з компенсаторами.
Виконав усі з’єднання
по правій панелі з каркасом, остаточно встановлюють ліву панель і заклепками
єднають встановлені на ній компенсатори з нервюрами літака.
Після виконання всього об’єму
складальних робіт кесон виймають з пристосування.
Єднання деталей, вузлів, панелей і
агрегатів літаків при складанні виконується різноманітними способами.
Застосовувані в літакобудуванні з’єднання розподіляють на: нерухомі нероз’ємні
(клепка, зварка, пайка, склеювання), нерухомі роз’ємні (болтові, гвинтові) та
рухомі роз’ємні (шарнірні єднання, болтові, вали та підшипники).
За конструктивно-технологічними
ознаками з’єднання
розподіляють на:
· з’єднання,
які виконують силовими точками (заклепками, болтами, зварними точками).
Характерними ознаками таких з'єднань є: ослаблення з'єднувальних деталей із-за
отворів під заклепки та болти і сугріву деталей в зоні постановці зварних
точок; концентрація напружень в деталі в зоні постановці силової точки при
напруженні конструкції; невисока продуктивність труда при постановці силових
точок внаслідок уривчастості виконання з'єднань;
· з'єднання
безперервним швом (зварка роликова та плавленням, склеювання, пайка).
Характерні ознаки таких з'єднань: послаблення з'єднувальних деталей при їхньому
сугріві в процесі зварки, склеювання, пайки; значна концентрація напружень в
деталі в зоні шва; безперервність процесу з'єднання, полегшує механізацію й
автоматизацію;
· комбіновані з'єднання (точечне
зварювання + склеювання, клепка + склеювання, клепано-болтове з'єднання). Такі
з'єднання
мають усі ознаки з'єднань
силовими точками і безперервним швом.
Вибір того чи іншого з'єднання
залежить від конструкції літака і матеріалів, з яких виготовленні його відсіки,
вузли та деталі.
В конструкціях літаків з легких
сплавів переважаючим видом з'єднання
є клепка. При виготовленні літаків із сталі та титану (мається на увазі
обшивка) з'єднання виконуються електроконтактною та дуговою зваркою.
При використанні в конструкції
літака монолітних панелей і вузлів кількість клепаних і зварних з'єднань
зменшується, але збільшується кількість болтових з'єднань. Монолітні вузли і
панелі в цих випадках з'єднують між собою та з обшивкою болтами.
Для конструкцій з композиційних
матеріалів (КМ) найбільше використання знаходять клепані, клеєно-клепані та
штифто-болтові з'єднання.
При складанні вузлів, панелей і
агрегатів літаків з легких сплавів клепка до теперішнього часу залишається
найбільш розповсюдженим видом нероз'ємного з'єднання, так як вона забезпечує необхідну
надійність і ресурс роботи агрегатів планера.
В літакобудуванні застосовується
велика кількість різноманітних типів заклепок. Для відкритих місць конструкції,
де можливий двосторонній підхід в зону клепки, застосовують звичайні стержневі
заклепки. При клепці закритих місць, коли підхід до однієї з головок заклепок
неможливий, застосовують спеціальні заклепки для односторонньої клепки.
Звичайні - стрижневі заклепки
виготовляють з легких сплавів і сталей з потаємними або виступаючими закладними
голівками.
Найбільш розповсюджені типи заклепок
приведені на мал. 4.3.
Мал. 4.3 Види заклепок: 1 - з
плоскою закладною голівкою - ЗП; 2 з потайною закладною голівкою ЗУ-900 або
ЗУ-1200; 3 - з компенсатором ЗУК; 4 - стрижнева; 5- компенсатор; 6 - маркування
матеріалу Д18 на голівці заклепки; 7 - маркування матеріалу Д19П на голівці
заклепки
Усі застосовувані в літакобудуванні
заклепки стандартизовані, мають шифр, який вказує форму закладної голівки,
марку матеріалу, діаметр і довжину.
Заклепки з алюмінієвих сплавів мають
межі міцності на зріз τ
= 180..280 МПа, сталеві заклепки - τ
= 350...500 МПа.
Заклепки зі сплавів В65 і Д18П
термічно оброблюються один раз при виготовленні та ставляться в конструкцію
після природного старіння.
Заклепки з термічно стійкого сплаву
Д19П ставляться в конструкцію у свіже
загартованому стані не пізніше 2 годин після гарту і їх застосовують лише в тих
конструкціях, які нагріваються в процесі польоту.
В з'єднаннях обтічних повітряним
потоком, зазвичай застосовуються заклепки з потаємними головками.
На сучасних літаках такі заклепки
складають приблизно 65...70% від загальної кількості заклепок в літаку.
Технологічній процес клепки, склад
операцій і їхня послідовність багато в чому визначаються вимогами забезпечення
ресурсу та герметичності, типом заклепок, методом складання.
Отвори для заклепок в з'єднувальних
деталях свердлять або пробивають. Найбільш розповсюдженим засобом є свердлення
отворів, бо при цьому вони виходять більш якісними.
Міцність заклепочних з'єднань з
пробитими для заклепок отворами менша, чим таких самих з'єднань з отворами, які
свердлять.
Сучасні тенденції в удосконаленні
процесів клепки пов'язаних,
в першу чергу, зі створенням процесів клепки. Які забезпечують щільне
заповнення гнізда та отвору тілом заклепки, забезпеченням гарантованого натягу
заклепок протягом усього строку експлуатації.
При передачі зусиль повз клепаний
шов в матеріалі листа виникають напруження, які розподіляються нерівномірно по
ширині листа. В зоні отвору ці напруження мають найбільшу величину і є джерелом
виникнення тріщин і руйнування з’єднання при роботі в умовах змінних
навантажень. Існує декілька технологічних методів зниження найбільшого
напруження - концентрації напруження: зміцнення стінок отворів в деталях,
підвищення чистоти поверхні при утворенні отвору, зняття та зміцнення фасок на
кромках отворів. Найбільш ефективним методом є зміцнення матеріалу - стінок
отвору.
При виконанні клепаних з’єднань
зміцнення отворів виконують за рахунок деформації листа - збільшення діаметру
отвору стрижнем заклепки.
В процесі утворення замикаючої
головки заклепки стрижень збільшується в діаметрі та збільшує діаметр отвору,
тобто зміцнює матеріал деталі в зоні отвору під заклепку.
В практиці літакобудування
застосовується декілька засобів клепки, які мають різну ступінь зміцнення і
відповідну до неї витривалість з’єднань.
На мал. 4.4 наведено графік, який
відображає характер зміцнення при різних засобах клепки.
Мал. 4.4 Витривалість потаємних
клепаних з’єднань, виконаних
різними засобами
Засіб Д - постановка звичайних
потаємних заклепок (зміцнюється в основному лист зі сторони замикаючої
головки), витривалість умовно прийнята за 100%.
Засіб ПЗГ (потаємна замикаюча
головка) призводить до зміцнення зенкованого листа и дає деяке підвищення
витривалості при руйнуванні з’єднання
під час вібраційних навантажень по зенкованому листу.
Заклепки з компенсатором (ЗУК) і
стрижневі (ЗУС) забезпечують більш рівномірне зміцнення деталей, які з’єднують,
і призводить до значного підвищення витривалості.
Найбільше і практично рівномірне
зміцнення по товщині деталей можливо отримати при клепці КЗО-ЗУС. При цьому
засобі клепки утворення головок заклепок відбувається в замкнутому об’ємі.
Окрім описаних вище типів заклепок в
літакобудуванні застосовуються і спеціальні - заклепки з високим опором зрізу
та заклепки для односторонньої клепки.
Технологія клепки такими заклепками
і застосовуваний на деяких операціях і переходах інструмент трохи
відрізняються.
Такі заклепки використовуються в
заклепочних з’єднаннях, які сприймають великі зрізні навантаження. В таких з’єднаннях
міцність на зріз заклепок з легких сплавів недостатня, а при використанні
звичайних сталевих заклепок їх необхідно перед постановкою в отвір нагріти, що
значно ускладнює виконання робіт. Технологічний процес утворення з’єднання
заклепками з високим опором зрізу включає такі основні операції: свердлення,
зенкування, розгортання або протягування отворів, постановка заклепок в отвори,
установка кілець і утворення замикаючих головок заклепок. Усі ці операції
виконуються на звичайному клепувальному обладнанні, окрім обтискача 3 (мал.
4.5). Цей обтискач має отвір для виходу зайвого матеріалу після осадки кільця
на стрижень заклепки.
Мал. 4.5 Схема технологічного
процесу постановки заклепок з високим опором зрізу: а) установка заклепки в
отвір; б) надівання кільця; в) обтиснення кільця; г) заклепка після обтиснення
кільця; 1 - стрижень заклепки; 2- кільце; 3- обтискач; 4 - відхід (зайвий
матеріал)
Мал.4.6 Схема технологічного процесу
постановки заклепок із сердечником: 1-свердління отвору; 2-вставка заклепки в
отвір;
3- утворення замикаючої головки; 4 - обрив сердечника; 5 - видалення
виступаючої частини сердечника;6 - готовий виріб
Заклепки з високим опором зрізу
клепають на пресах одинарної клепки або пневмомолотком. Заклепки для
односторонньої клепки застосовують в місцях, де немає доступу до замикаючої
головки заклепки.
В таких випадках використовують
заклепки з сердечником (мал. 4.6.) або гайкопістони. Отвори та гнізда для
головок таких заклепок виконуються звичайним інструментом.
В літаках герметизують кабіни,
приладові та вантажні відсіки. Призначення герметизації - підтримання
надлишкового тиску в кабінах, запобігання витоку палива з кесон-баків, захист
різних відсіків і агрегатів від проникнення в них агресивних рідин і газів і
попадання води під час дощу. Витоки повітря, газів або рідини в швах в
основному відбувається через зазори між контактними поверхнями листів, між
елементами заклепок (стрижень, головки) та стінками отворів в деталях.
Зменшити або повністю усунути витоки
можливо шляхом нанесення герметизуючих матеріалів в зони витоку і використанням
щільної посадки заклепок в отвори.
Замість звичайних заклепок
постановка заклепок з компенсатором і стрижневих призводить к значному
підвищенню герметичності шва.
Найбільший ефект в частині
герметизації швів досягається поєднанням щільної посадки заклепок з наступним
нанесенням герметизуючих матеріалів спеціальних герметиків.
Герметизуючи матеріали мають адгезію
до з’єднувальних деталей и можуть застосовуватися у вигляді плівок, паст та
рідини, допускають взаємне переміщення з’єднувальних деталей без порушення
герметизації. До герметиків пред’являють наступні вимоги:
·
Вони повинні володіти пластичністю,
тобто зберігати герметизуючи властивості при перепадах тиску робочого тіла,
деформаціях шва, впливу високої і низької температур;
·
Повинні мати зчеплення не менш 0,98
МПа з поверхнями деталей, яке не повинно порушуватися при впливі статистичних
та змінних навантажень, різних температур, атмосферних явищ і повітря, газів і
палива;
·
Не повинні надавати шкідливого
впливу на людей і викликати корозійні процеси в зоні герметизації.
В літакобудуванні використовується
велика кількість різноманітних марок герметиків.
Герметики ВГФ-1 і У-2-28 працюють
при температурі від -60 (70) до +250 (300)0 С на літаках зі швидкістю М = 2…3,
а герметики У-30М, УТ-32, У-30мєс-5, ВТУР - від -50 до +1300 С на літаках зі
швидкістю польоту до 277,8 м/с.
Герметик може бути у вигляді пасто
образної маси, розчину, пасти, рідини, стрічки або тканини, яка просочена
герметиком.
Стан герметика залежить
від кількості компонентів,
які до нього входять, і визначають засіб його нанесення та вид застосовуваного
при цьому інструменту й обладнання. Стрічки в зону шва укладають вручну,
умовний індекс засобу нанесення позначається літерою (Л). На кресленні
герметичного шву вказують марку герметика, товщину стрічки та засіб нанесення,
наприклад, якщо було взято герметик У-20А у вигляді стрічки, то зображено
У-20А(Л) (див. Мал. 4.7).
Мал. 4.7 Зона герметизації швів і
засоби нанесення герметика: а - укладання стрічки; б - нанесення пасти шпателем;
в - нанесення герметика пензлем; г - нанесення герметика поливом; 1 - звичайний
джгут; ІІ - джгут з напливом; ІІІ- форма шпателів для нанесення джгутів; IV
- місцева герметизація стику; V
- місцева герметизація заклепки (болта)
Герметики у вигляді пасти наносять
шпателем або шприцом, яким присвоєно індекс (Ш). Герметики, які наносяться
пензлем, розчиняють до в'язкотекучої
рідини, їм надано індекс (К).
Для нанесення герметика поливом,
пульверизатором або окупанням його розчиняють до стану рухомої рідини, яка має
в'язкість,
цьому процесу надано індекс (П) (мал. 5.7, г). Важливою властивістю герметика є
його життєздатність, тобто час, протягом якого герметик наноситься на поверхню
деталей, зберігаючи свої адгезійні властивості - здатність прилипати до
поверхні деталей.
Враховуючи життєспроможність
герметиків, виготовляють його безпосередньо в цеху герметизації перед видачею
на робочі місця
4.1 Типові
приклади складання вузлів і панелей клепаної конструкції (складання лонжерона)
Клепані з'єднання мають широке
використання при складанні вузлів і панелей, які виготовляються з листів і
профілів алюмінієвих, магнієвих і титанових сплавів. Складання вузлів і панелей
клепаної конструкції виконується зазвичай в пристосуваннях з базуванням деталей
по їх поверхням або по складальним отворам.
На мал. 4.8 (а,б,в) показаний процес
складання лонжерона: схема базування (мал. 4.8,а), схема складання (мал.5.8,б),
пристосування та його оснащення (мал. 4.8, в).
Мал. 4.8,а. Схема базування
Мал. 4.8,б. Схема складання
лонжерона
Мал. 4.8, в. Пристосування та його
обладнання
В якості баз прийняті: поверхня
каркасу ПК при створенні обводів; УБО і поверхня ложементів 14 (ЛЖ) для
встановлення і закріплення стінки в пристосуванні; ОСБ і торцева поверхня плити
стику 6 (ПС-Н) при установці стикового вузла 2; поверхня каркасу ПК -
обводообразуючі поверхні поясів 3 і 4 при установці їх на базові поверхні
ложементів (ЛЖ); СО в стінці 1 и стійках 5 при встановленні останніх по
дистанціям нервюр.
Умови постачання деталей на
складання. Стінка 1 подається з обрізаними кромками і торцями. В ній
просвердлені два отвори УБО по хорді та СО по стійках 5.
Стикувальний вузол 2 подається на
складання повністю зібраним із отворами під ОСБ, виконаними на 2*10-3 м менш
діаметру болта для подальшого опрацювання отворів під стикувальні болти крила
на оброблювальному стенді.
В стикувальному вузлі також
просвердлені НО під заклепки, які з'єднують
вузол зі стійкою та поясами.
Пояси 3 і 4 подаються на складання з
обрізаними торцями по НО. Стійки 5 мають СО і НО.
Складання починають з установки
стінки лонжерону 1 по УБО на штифти 25. Потім встановлюють стикувальний вузол
2, спираючи його на поверхню плиті 6 пристосування, і закріплюють на ній
технологічними болтами 18, встановленими в отворах ОСБ. Далі встановлюють пояси
3 і 4, спираючи їх на робочі поверхні ложементів 14. В подовжньому напрямку
пояси фіксують по плиті 6, підтискаючи їх до неї плито-фіксатором 9. В такому
положенні поясу і стінка закріплюються в ложементах пневматичними притисками
15. Стійки 5 закріплюють на стіні 1 по СО за допомогою технологічних болтів ТБ.
Свердління усіх отворів по НО
виконується за допомогою свердлильної установки типа СЗВУ, а клепку заклепок за
допомогою підвісного пневморичажного пресу ПКП. Після закінчення складання
лонжерон знімають з пристосування та передають до наступного етапу складання.
.2 Види та
конструктивно-технологічні характеристики роз'ємних
з'єднань
Роз'ємні з'єднання це з'єднання, які
можна розібрати без порушення елементів конструкції. До них відносяться
різьбові, клинові, шліцьові, шомпольні, штифтові з'єднання.
В конструкціях літаків найбільш
широке використання мають різьбові роз'ємні з'єднання. Розрізняють їх на
болтові, гвинтові, шпилькові з'єднання, які мають різьбу на елементах
кріплення.
З усіх видів різьбових з’єднань саме
широке використання в конструкціях планерів літаків мають болтові з’єднання
(БС). До цього виду з’єднань
відносяться також з’єднання
за допомогою болтів-заклепок.
Болтові з’єднання використовуються
для передачі великих навантажень і для з’єднання пакетів великих товщин (мал.
4.9).
Мал. 4.9 Типові конструкції болтових
з’єднань: а - фланцевий стик із закладним болтом; б - стик «вухо-вилка»
кріплення ОЧК із центропланом; в - кріплення панелі обшивки з каркасом потаємними
болтами; г - кріплення стінки профілю з поясом лонжерону; д - кріплення обшивки
з каркасом потаємними болтами з анкерними гайками
В конструкціях сучасних літаків
кількість болтів досягає 55 тис. штук на легких машинах і 400 тис. штук на
важких.
Частіше за все болти і гайки
виготовляються зі сталі 30ХГСА, 30ХГСНА, з титанового сплаву ВТ16. Застосування
титанових болтів дає суттєвий виграш у масі порівняно зі сталевим кріпленням.
Біля 80 % з'єднань виконуються
болтами з потаємною голівкою, а решта - з виступаючою, головним чином
шестигранною голівкою.
Технологічний процес виконання
болтового з’єднання складається з: утворення та обробки отворів під болти,
встановлення болта в отвір, надягання шайби, нагвинчування і контрування гайки.
Близько 70% всієї трудомісткості
виконання з'єднань витрачається
на утворення та обробку отворів під болти. Ці операції виконуються ручним
механізованим інструментом або в спеціалізованих пристосуваннях з програмним
управлінням за допомогою свердел, набора зенкерів (для отворів великих
розмірів), розгорток, протяжок.
Постановка болтів по легкопресовій
та іншим напруженим посадкам є особливо трудомісткою операцією. Для зменшення
зусиль запресовування болтів використовують змащення ЦИАТИМ-201, петролатум та
ін.
Нагвинчування гайок (затягування БС)
є досить відповідальною операцією.
Величина затягування цілком визначає
працездатність БС працюючих на розтягнення та, в значній мірі, якість з’єднань,
які працюють на зріз.
Тому в особливо відповідальних з’єднаннях
зусилля стягування пакета лімітуються величиною крутного моменту затягування та
виконуються тарованими гайковими ключами.
Трудомісткість виконання БС в 10…15
разів вища трудомісткості виконання заклепочних з’єднань. Тому їх використання
може бути виправдано тільки в тих випадках, коли БС не має можливість змінити
менш трудомісткими видами з’єднань.
Суттєвими факторами, які впливають
на ресурс БС є: матеріал елементів конструкції та кріплення; геометричні
параметри швів БС (відстань від краю листів і між болтами, число болтів в ряду
та ін..); режими і засоби утворення та оброблювання отворів під болти
(швидкість, величина подачі і глибина різання при свердлуванні, розгортанні та
протягуванні отворів); характер посадки болтів в отвори (із зазором, середнім
за величиною або великим радіальним натягом); величина затягування болтів;
інтенсивність і умови експлуатації, погодні та кліматичні умови.
Вірне урахування всіх факторів,
вибір їх оптимального співвідношення дають змогу отримати високоресурсні
болтові з’єднання. Важливим засобом підвищення ресурсу болтових з’єднань є
обробка отворів під болти шляхом пластичного деформування поверхні шарів:
дорнуванням або розкочуванням.
Основними параметрами процесів
дорнування та розкочування, визначаючими точність, чистоту стінок отворів, а також
ступінь підвищення ресурсу БС, є величина натягу при дорнуванні або
розкочуванні (мал.4.10).
При розкочуванні отвори втрачають
циліндричну форму. Його внутрішні стінки набувають форму, яка має назву
корсетність (мал.. 4.10,в).
Зміцнення отворів під болти
дорнуванням і розкочуванням підвищує ресурс БС в 2…5 раз. оптимальним є натяг в
межах (0,6…1,2)%.
Мал.4.10 Основні параметри процесів
зміцнення отворів під болти при: а - дорнуванні: 1 - виріб, 2 - дорн; б -
розкочуванні: 1 - виріб, 2 - розкочувальник; в - корсетність отворів після
розкочування
Дорнування використовують при
наявності двостороннього (а розкочування - при односторонньому) підході до
отвору.
Болти в отворі встановлюються по
одній з посадок із зазором або легкопресовій посадці.
Останнім часом все ширше
використовується встановлення болтів з великою величиною натягу.
При встановленні болтів з великим
натягом на поверхневому шарі отвору створюються значні напруження стиснення.
Крім того, відбувається наклеп поверхневого шару. При достатньо великих натягах
високі напруження стиснення перешкоджають утворенню змінних за знаком напруги в
зоні отвору, які різко знижують втомну міцність конструкції. З цих причин
встановлення болтів в отвори з високим натягом сприяє суттєвому збільшенню
ресурсу БС.
Найбільше збільшення ресурсу
відбувається при натягах (1,2…1,5)% від діаметру болтів. Для зменшення зусиль
запресування заходній частині болта надається конічна або тороідальна форма.
Використання змащування також
зменшує потрібні зусилля запресування. Найбільш ефективними змащуваннями для
вставлення болтів з великим натягом є ЦИАТИМ-201+20% дисульфіду молібдену,
фторопласт, петролатум.
Запресування болтів виконується на
стаціонарних пресах або за допомогою ручних скоб одно ударних молотків
достатньо потужності. В цих випадках болт переміщується в отворі безперервно до
кінцевого встановлення. Цим попереджається схоплення («залипання») болта до
стінок отворів і утворення задирів в процесі запресування. Розподіл прийнятої
величини натягу між операціями зміцнення отворів і встановлення болта також
забезпечує зниження потрібних зусиль запресування.
Найбільш напруженою зоною при
потаємних БС є зона переходу конічної частини отвору в циліндрову (мал. 4.11).
Мал.4.11 Засоби зміцнення зенкованих
отворів під болти з потаємною головкою: а - схема розподілу напружень по
товщині листа з зенкованих отвором: 1 - схема напруження; 2 - епюра кружних
напружень; б - обтискання перехідної кромки: виріб, 2 - конічний обтискач; в -
обтискання конічної частини отвору: 1- виріб, 2 - обтискач; г - підпресовування
болтом: 1- виріб, 2 - пуансон, 3 - болт, 4 - підпір
Особливо відповідальною операцією є
затягування болтів. В з'єднаннях, що працюють на розтягування болта, зусилля
від затягування повинно бути більше (з наданим запасом) зовнішніх зусиль, які
сприймаються даним елементом конструкції.
В противному випадку відбудеться
розкриття стику і руйнування конструкції.
Збільшення затягування до 0,6...0,7
від межі плинності матеріалу болта зменшую концентрацію напружень, затримує
виникнення та розвиток фреттинг-корозії по контактних поверхням і в наслідок
цього суттєвозбільшує втомну міцність БС.
Разом с тим, збільшення затягування
різко підвищується жорсткість БС і конструкції в цілому. Для збереження
первісної величини затягування у часі застосовуються кернування торців стрижня
болта та гайки, спеціальні шайбі, шплінти та інші методи контровки. В
з'єднаннях з КМ з цією ж метою використовуються головки болтів, гайок, шайб із
збільшеною опорною поверхнею. БС з анкерними гайками складають до 50% потаємних
болтових з'єднань.
При наявності підходів для
використання спеціального інструменту замість болтів з гайкою рекомендується
застосовувати болти-заклепки (мал. 4.12).
Вони складаються з двох деталей:
стрижня та обтискаючого кільця 1. Стрижень має гладку циліндричну дільницю 2,
який дорівнює за довжиною товщині пакету, середня дільниця 5 з торованими на
ній кільцевими ребрами, проточку 6, по якій відкривається стрижень при
закінченні обтискання кільця, і хвостовик 7 з кільцевими ребрами. За хвостовик проходить
захоплення
стрижня пресом при затягуванні до моменту обриву.
Стрижні виготовлюються з
алюмінієвого сплаву або сталі.
Мал. 4.12 Болт-заклепочне з'єднання:
а - пристрій болт-заклепка: 1 - обтискувальне кільце, 2 - гладкий стрижень, 3 -
напівкругла головка, 4 - потаємна головка, 5- середня дільниця стрижня, 6 -
калібрована проточка, 7 хвостовик; б - схема встановлення болт-заклепки: 1 -
захватно-обстискувальний пристрій, 2 - обтискні губки, 3 - з'єднувальний пакет,
4 стрижень болта-заклепки, 5 - обтискувальне кільце, 6 - губки відривного
пристрою; в - загальний вигляд болт-заклепочного з'єднання: 1 - обтискувальне
кільце, 2 - з'єднуємий пакет, 3 - стрижень
Обтискаючи кільця виготовлюються з
алюмінієвих сплавів або м'яких сортів сталі. Для конструкції з КМ
болти-заклепки виготовлюють із збільшеною опорною поверхнею головки, а під
обтискаюче кільце встановлюють опорну шайбу.
Витрати праці на виготовлення
болт-заклепочних з’єднань
в 1,3…2 рази менші порівняно зі звичайними БС.
Як вже було зазначено раніше,
ступінь членування літака і його агрегатів на деталі та складальні одиниці
залежить від особливостей конструкції літака в цілому ( наявність монолітних
панелей і вузлів); габаритних розмірів агрегатів і відсіків; матеріалів;
засобів з'єднання; програми випуску та ін.
Раціональне членування конструкції
літака на окремі вузли, панелі, відсіки та агрегати дозволяє значно спростити
складання та зменшити трудомісткість складальних робіт за рахунок механізації і
автоматизації складальних процесів.
На підставі схеми членування літака
та розробленої послідовності складальних операцій складають схему складання ЛА (Мал.4.13).
Мал. 4.13 Варіанти членування та
схема складання літака
За конструктивно-технологічними
ознаками відсіки та агрегати можна поєднати в три
групи:
· відсіки та агрегати
непанельованої конструкції - вони зазвичай складаються з окремих деталей і
невеликих вузлів. Їх складання потребує складних складальних пристосувань,
скорочує можливості розширення фронту робіт, потребує громіздкого обладнання;
- відсіки та агрегати
панельованої конструкції, які складаються з панелей,вузлів збірної і монолітної
конструкцій. В цьому випадку використовують простіші пристосування, створюються
умови для розширення фронту робіт і механізації процесів складання;
- агрегати, які членовані на
відсіки. В більшості випадків такі агрегати складаються з відсіків, які на
складання поступають коли в них виконаний весь комплекс складальних, монтажних
і регулювальних робіт. Цей процес по суті являє стиковку відсіків і з'єднання
комунікацій за стиками та роз'ємами.
Мал. 4.14 Членування агрегату крила
на відсіки
Міцність, аеродинамічні властивості
та герметичність зібраних відсіків і агрегатів повинні задовольняти технічним
вимогам.
Ці вимоги включають:
· точність
розположення елементів відсіків і агрегатів відносно один одного та базових
вісій виробу;
· точність лінійних і
кутових параметрів літака у відповідності з нівелювальними даними;
· точність положення
шасі, лінії тяги і т.ін.
Всі перераховані вимоги виконуються
за методом залежного виготовлення виробів, при якому широко використовують
тверді носії форм і розмірів виробів і їх елементів.
1. конструкторсько-технологічними
параметрами виробів, які збираються;
2. масштабом виробництва, від
якого залежить глибина опрацювання технологічних процесів, оснащення
виробництва спеціальним устаткуванням і форма організації виробництва;
. прийнятим методом
забезпечення взаємозамінності й точності геометричних розмірів деталей,
панелей, вузлів і відсіків.
До конструкторсько-технологічних
параметрів відсіків відносяться:
· поперечний переріз
(профіль) відсіку;
· форма обводу в
плані;
· наявність
панелювання;
· технологія
складальних робіт, яка залежить від герметизації швів у відсіку;
· вид стиків і
роз'ємів при з'єднанні відсіку з іншими відсіками;
· підхід в зону
стикових клепаних, зварних швів (двосторонній і односторонній).
Питома вага того або іншого виду
робіт в загальній трудомісткості процесу складання залежить від конструкції
агрегату і прийнятого матоду з'єднання.
Мал.4.15 Схема конвеєрів, які
застосовуються при складанні агрегатів (крил): а - возовий; б - підвісний; в -
естакадний; г- ланцюговий; 1 - ланцюг конвеєра, 2 - монорейка, 3 -- козелок, 4
- естакада, 5 - возок, 6 поворотна траверса, 7 - м'які опори для крил, 8 -
ланцюгові зірочки, 9 - ланцюги
Трудомісткість і цикл робіт по
складанню та монтажу відсіків і агрегатів багато в чому залежить від
конструкції пристосувань і конвеєрів, які застосовуються на стапельному або
поза стапельному складанні. Конвеєри, які застосовані при поточному поза
стапельному складанні крил, розподіляють на дві групи: підлогові та підвісні
(мал.5.15).
Підлогові конвеєри - возового та
ланцюгового типів (мал. 5.15, а,г) - менш зручні в роботі, тому що займають
велику площу виробничого приміщення та ускладнюють підходи до місць виконання
робіт.
Підвісні конвеєри - монорейкові та
естакадні (мал. 5.15, б,в) - більш зручні роботі. При підвісних конвеєрах краще
використовуються виробничі площі, є можливість повертати виріб в зручне для
складальника положення, монтувати деталі можуть кілька складальників одночасно
на різних рівнях від підлоги. Цим скорочується кількість стендів складальної
лінії і скорочується цикл складання.
При розробці технології поточного
складання відсіків або агрегатів необхідно на підставі техніко-економічних
розрахунків встановити, який тип конвеєру найбільш вигідно застосувати для
конструкції, яка роздивляється.
В той же час треба мати на увазі, що
для складання відсіків, агрегатів або виробів в цілому незалежно від програми
випуску в серійному виробництві поточна форма організації робіт вигідніша, ніж
операційне складання, при якому технологічне оснащення та пристосування не
встановлюються за ходом технологічного процесу і цикли робіт, які в ньому
виконуються, не узгоджені.
Після складання відсіку або агрегату
фактичні розміри, які визначають положення стикувальних вузлів і отворів під
СБ, виходять за межі допусків. Це відбувається внаслідок виникнення різного
виду виробничих похибок й деформації складальних пристосувань і виробів, що
складаються.
Для забезпечення взаємозамінності
відсіків і агрегатів після їх складання виконують опрацювання роз'ємів і стиків
на спеціальних розділювальних (обробних) стендах.
Розділ 5.
Інструменти та обладнання які використовують при складанні вузла
При складанні вузлів, панелей і
агрегатів літаків і вертольотів з легких сплавів клепка до цього часу
залишається найбільш поширеним видом нероз'ємного з'єднання, так як вона
забезпечує необхідну надійність і ресурс роботи агрегатів планера. Процесу
клепки передує утворення отворів під заклепки. Залежно від вимог до точності та
іншим характеристикам для утворення та обробки отворів застосовують комбінації
свердління, зенкерування, розгортання, протягування, пробивання, розкачування,
дорнування. Якість підготовки отворів є вирішальним фактором ресурсу з'єднання.
Трудомісткість підготовки отворів становить до 30 % від загальної
трудомісткості виконання з'єднання.
Свердління.
Свердління застосовується для
утворення попереднього розміру отвору. З допомогою свердління в остаточний
розмір можна отримати отвори 12...14 квалітетів. Часто свердління поєднують з
зенкуванням гнізда під потаємні головки заклепок і болтів. Свердління може
проводитися: на свердлильних верстатах; на спеціалізованих напівавтоматичних
установках на базі свердлильно-зенкувальних агрегатів (СЗА); на
свердлильно-зенкувальних установках (СЗУ); на свердлильно-зенкувальних
вбудовуються в складальну оснастку пристроях (СЗВУ); ручним механізованим
інструментом (свердлильні машини, дрилі, обробні пристрої). Тип обладнання
вибирається в залежності від форми габаритів вузлів, агрегатів, діаметру
отворів, вимог точності і зручності підходу до місця обробки. Орієнтування
інструменту при підготовці отворів діаметром до 16 мм провадиться: з допомогою
підтримуючих пристроїв СЗУ; по кондуктору; без кондуктора з боку каркасу: по
напрямних отворів; з боку обводів; з допомогою триноги, призм, косинців, що
забезпечують перпендикулярність свердління опорної площини пакета.
Свердлильно-зенкувальні установки,
як правило, комплектуються з двох уніфікованих агрегатів:
свердлильно-зенкувального агрегату (СЗА); підтримує агрегату (АП). При
необхідності підтримує агрегат в СЗУ може бути і спеціальним. Агрегати
шифруються наступним чином: СЗА-02М - свердлильно-зенкувальний агрегат, другої
моделі, модифікований; АП-02-155-СЗУ - агрегат що підтримує, другої моделі, з
повним ходом пінолі 155 мм, для свердлильно-зенкувальних установок. СЗА можуть
працювати в ручному і автоматичному режимі, забезпечуючи свердління і
зенкування отворів діаметром до 8 мм і продуктивність до 24...26 отворів в
хвилину. У стаціонарних свердлильних установках, а також в установках,
вбудованих в складальну оснащення, що використовуються машини свердлильні або
свердлильно-зенкувальні з автоматичною подачею. Вони призначені для утворення
отворів діаметром 5...40 мм в алюмінієвих, титанових сплавах, високоміцних
сталях, композиційних матеріалах. Шифровка машин: МСП-8 - машина свердлильна
(МС) з автоматичною подачею (П), найбільший діаметр оброблюваного отвору 8 мм
(8); МСП-12Т - для свердління отворів в титанових (Т) сплавах; МСП-12К-ДЛЯ
свердління отворів в композиційних (До) матеріалах; МСЗП-35У - машина свердлильно-зенкувальна
(МСЗ) з автоматичною подачею (П), найбільший діаметр оброблюваного отвору 35 мм
(35), кутова (У). Буква "А" в шифрі вказує на паралельність осей
робочого органа і приводу. В умовах стапельного складання на відсіках і агрегатах
переважно використовуються ручні свердлильні машини. По конструктивному
виконанню типажем передбачено два типи свердлильних машин: машини свердлильні з
рукояткою пістолетного типу; машини свердлильні кутові.
Зенкування отворів.
Зенкування застосовується для
наступних операцій: остаточної обробки отворів з полем допуску 11... 12
квалітетів; підвищення точності попередньо просвердлених отворів, під подальше
розгортання або протягування; обробки в один або кілька переходів з метою
збільшення діаметру попередньо просвердлених отворів, в тому числі і отворів зі
сходинкою, що утворюється в пакеті в процесі установки деталей в складальне
положення.
При зенкуванні використовуються
зенкери. Зенкери мають три-чотири ріжучі кромки, тому процес різання проходить
більш стійко, ніж свердління.
Зенкування застосовують для
збільшення діаметру попередньо просвердленого отвору, тому зусилля осьової
подачі менше, а шорсткість приблизно вдвічі менше, ніж при свердлінні.
Зенкування може бути прямим і зворотним. При прямому зенкуванні з метою
підвищення точності або збільшення діаметру попередньо просвердлених отворів
застосовуються зенкери з направляючою. Спільну обробку отворів після установки
деталей в складальне положення при розбіжності осей роздільно підготовлених
попередніх отворів виконуються спеціальним зенкером, використовуючи отвір
діаметром D в якості направляючого. Зворотне зенкування отворів виконується
спеціальними насадними зенкерами. Базування зенкера здійснюється за
оброблюваного отвору допомогою змінних направляючих втулок, встановлюваних на
шпиндель машини. В якості мастильно-охолодної рідини при зенкуванні отворів
застосовують мастило МР-4 або масло індустріальне І-40А. Для зенкування з
автоматичною подачею застосовуються свердлильно-зенкувальні машини типу МСЗП.
Розгортання отворів.
Коли потрібно отримати отвори
точніше 10-го квалітету, застосовується остаточна обробка розгортанням. Ручне
розгортання здійснюється, як правило, з малим припуском (0,02...0,2 мм) з
невеликими подачами (0,1...0,5 мм/об) для забезпечення спокійних умов різання,
хоча подачі за рекомендаціями, які передбачають максимальну стійкість
розгорток, повинні бути великими. Стружка при розгортанні утворюється в умовах,
дуже схожих на пряме різання, так як ріжучі кромки складають невеликий кут з
утворюють отвори. Шорсткість поверхні 0,04...5 мкм, точність отворів може бути
отримана в межах 7...8-го квалітетів. Ручне розгортання допускається
застосовувати у випадках, коли підходи в конструкції не дозволяють
використовувати механізоване розгортання.
Операція механізованого розгортання
застосовується для остаточної обробки отворів з полем допуску 7...9 квалітетів
у пакетах, які включають алюмінієві, титанові сплави та сталі. Механізованим
розгортанням забезпечується обробка отворів діаметром 4...45 мм у пакетах товщиною
8...225 мм, в тому числі отворів, розташованих у важкодоступних місцях
конструкції виробу. Механізоване розгортання отворів здійснюється розгортаючими
машинами типу МР. Модель розгортаючої машини вибирають в залежності від
діаметру оброблюваного отвору, матеріалу пакету і підходів до отвору.
Механізованим розгортанням обробляють попередні отвори, підготовлені з
допусками по 12-му квалітету з наступним припуском під остаточну обробку: 0,5
мм для отворів діаметром 4...27 мм; 0,7 мм для отворів діаметром 30...45 мм.
Механізоване розгортання отворів здійснюють комплектом розгорток, які базуються
на оброблюваного отвору без використання додаткової направляючої оснастки. При
розгортанні в умовах агрегатного складання слід керуватися наступними основними
рекомендаціями: малі отвори діаметром 4 мм обробляють спеціальними розгортками;
отвори діаметром 6... 12 мм глибиною до 5d у пакетах з алюмінієвих і титанових
сплавів обробляють розгортками по ОСТ 1 52 485-86; великі отвори діаметром
5...45 мм у пакетах, які включають титанові сплави та сталі середньої міцності
(σв≤ 1100 МПа),
обробляти розгортками з швидкорізальної сталі; отвори в пакетах, які включають
титанові сплави підвищеної міцності і сталі типу 14Х17Н2, рекомендується
обробляти розгортками з маловольфрамової швидкорізальної сталі Р12Ф2К5МЗ,
Р12Ф2К8МЗ, Р12ФЗК10МВ та ін.
В авіаційній промисловості найбільш
поширені наступні види свердлильно-зенкувальне обладнання: універсальні
свердлильні верстати; спеціальні свердлильно-зенкувальні верстати (автомати) і
установки; свердлильно-зенкувальні й агрегатні головки. Область застосування
того або іншого виду обладнання залежить від ступеня членування літака, умов
підходу в зону свердління, конструкції і габаритних розмірів вузла, панелей,
відсіків, програми випуску виробів. В даний час 40 ... 50 % отворів свердлять і
баньки ручними пневматичними дрилями, а решта обробляють на універсальних
свердлильних, агрегатних верстатах і спеціальних свердлильно-зенкувальних
установках. У промисловості систематично ведуться роботи по збільшенню обсягу
механізації і автоматизації свердлильно-зенкувальних операцій, удосконалюються
конструкції літаків і вертольотів, розробляються і впроваджуються нові
свердлильно-зенкувальні верстати, автомати та установки. Пневматичні дрилі застосовують
головним чином на агрегатній та загальній збірці, де використання верстатів та
автоматів неможливо. Універсальні свердлильні верстати використовують для
свердління отворів в полицях лонжеронів і нервюр, стикових профілях і вузлах.
Клепка суцільних заклепок загального
призначення.
З'єднання суцільними заклепками
полягає в пластичній деформації стрижня заклепки з формуванням замикаючих (або
обох головок, включаючи заставну) виступаючої частини. Цей процес здійснюється
за допомогою удару пневмомолотки і підтримки, тиском преса або розкочуванням за
допомогою спеціальних машин. Удар молотка може
наноситися з боку замикаючої головки заклепки, і тоді метод клепки називають
прямим, або з боку застави - зворотний метод клепки. Клепка тиском преса
отримала, відповідно, назву пресової клепки.
Пресова клепка має наступні переваги
в порівнянні з ударною: значно поліпшуються психофізіологічні умови роботи
клепальників внаслідок зниження впливу шуму і вібрації; підвищуються втомні
характеристики з'єднання внаслідок більш щільного і рівномірного заповнення
отворів осаджувальним стрижнем заклепки по товщині пакету; по вказаній вище
причині в ряді випадків можна відмовитися від герметизації з'єднання, що
забезпечує зниження маси конструкції; підвищується продуктивність праці в
півтора-два рази при скороченні числа робітників на 50...75 %.
При пресовій клепці замикаюча
головка утворюється в результаті тиску преса на стрижень заклепки, чому
обов'язково передує стиснення пакету. Обидві дії: стиснення пакету і деформація
стрижня заклепки - виконуються безперервно за один хід плунжера преса.
Клепальні преси поділяються на такі: стаціонарні групової клепки; стаціонарні
одиночної клепки; переносні ручні. Можливість застосування того чи іншого преса
залежить від підходів до місця клепки, діаметра расклепуємих заклепок, розмірів
вузлів і панелей та інших конструктивних і технологічних факторів. У
промисловості застосовують різні преси для групової і одиночної клепки: КП-403,
КП-405, КП-501А, КП-503, КП-602. Порівняно з клепальними автоматами число
обмежень застосування клепальних пресів істотно менше. На клепальних пресах
можна клепати вузли і панелі з алюмінієвих, титанових сплавів і сталей
будь-якими суцільними стрижневими заклепками. Це дозволяє розширити обсяг
безударної клепки, включаючи автоматичну і заклепками з одностороннім підходом,
до 60...70% від всього обсягу заклепочних сполук.
Якість клепки контролюють зовнішнім
оглядом з'єднань і простукуванням заклепок. Зовнішнім оглядом виявляють дефекти
замикаючих головок або підсічку листів. Простукуванням визначають слабо
затягнуті заклепки. Маломірні, погано оформлені і збиті на сторону головки
виявляють шаблонами. Погане прилягання головок перевіряють щупами. Дефективні
заклепки висвердлюють, а замість них ставлять нові. Герметичність з'єднання
перевіряють повітряної або гідравлічної пробій. Вузли, які не мають замкнутого
простору, перевіряють методом вакууму. Нещільність сполуки виявляють по
повітряних бульбашок після змочування поверхні мильною водою. При гідропробі
нещільності виявляють падінням тиску по манометру або з виступу крапельок
вологи на зовнішній поверхні. Величину пробного тиску вказують в технічних
умовах.
РОЗДІЛ 6.
Передові методи складання
Виробництво складних наукоємних
виробів машинобудування сьогодні неможливо без забезпечення їх інформаційною
підтримкою на всіх стадіях життєвого циклу. Переходу до САLS-технологій
в великому ступені сприяли досягнення в області інформаційних технологій,
програмування, розробки обчислювальної техніки.
В сучасних економічних умовах все
більше виробництв звертаються до так званої «віртуальної» форми організації
виробництва.
Особливе значення при складанні
агрегатів ЛА має значення - об'ємна ув'язка деталей і вузлів, які забезпечують
отримання аеродинамічних обводів заданої точності. Сучасний рівень проектування
передбачає створення тривимірної комп'ютерної моделі створюваного виробу.
Паралельно створюється модель технологічної оснастки, що забезпечує правильну
взаємну орієнтацію деталей при зборці.
Тривимірні моделі виробів у сучасному
промисловому виробництві є основою проектування виробів і технологічних
процесів. При цьому в переважній більшості випадків спочатку створюється
модель, а лише потім виріб. Однак існує чимало випадків, коли необхідно
отримати модель в САПР по вже наявному виробу (тілу). До таких випадків можна
віднести:
автоматизоване рішення задачі
контролю форми виготовленого вироба;
створення моделі заготовки з метою
отримання ефективних керуючих програм для устаткування з ЧПУ;
уточнення положення об'єкта перед виконанням
технологічних операцій.
У загальному випадку задача
отримання тривимірної моделі тіла по натурному зразку може бути задана як
задача визначення координат безлічі точок тіла. Однак безліч точок тіла
нескінченно, тому виникає необхідність визначення координат кінцевої безлічі
опорних точок з побудовою на їх основі апроксимуючих граней.
Підвищення продуктивності
складальних робіт забезпечується механізацією і автоматизацією проведення
основних типових технологічних операцій - розмітки, крою, свердління і клепки.
Силові вузли конструкції планера ЛА
типу лонжеронів, нервюр і шпангоутів. Їх відносять до плоскокаркасних вузлів
(ПКУ). Основний спосіб з'єднання ПКУ - заклепувальні з'єднання. На частку
свердлильно-клепальних робіт (СКР) припадає 30 ... 45% трудомісткості
складальних робіт. Трудомісткість свердління становить 30%, зенкування 13%,
вставка заклепок 4%, расклепування заклепок 53%. В даний час при виконанні СКР
широко використовуються пластикові автомати. Однак, специфіка виробництва,
складність конструкції ЛА, різноманіття умов підходу до зони клепки, різниця
заклепок по діаметру, мала протяжність швів, обумовлюють застосування ручних
дрилів та клепальних молотків, використання яких не дозволяє досягти високої
продуктивності праці, не гарантує стабільності якості з'єднань і шкідливо
впливає на організм людини.
У вітчизняному та зарубіжному
літакобудуванні намітилася тенденція до використання замість пресованих
профілів у конструкціях літальних апаратів профілів з листового плаковного
матеріалу, що пов'язано
з рядом переваг як конструктивного, так і технологічного характеру останніх.
Так, наприклад, за рахунок застосування листових профілів можливе отримання
виграшу у масі конструкції із-за мінусового допуску на листі. Для авіаційної
промисловості характерні підвищені вимоги до точності, які пред'являються
до виробів.
Крім використання всіх перелічених
новітніх методів складання поширюється застосування роботів-змій. Роботи-змії
стають одним із популярних напрямів робототехніки. Цей вид роботів відрізняється
модульністю, гнучкістю і специфічними можливостями переміщення в просторі.
Досі монтаж повітряного судна
включає високу частку ручних процесів, що обмежує обсяги виробництва. Особливо
серйозною проблемою з точки зору автоматизації залишається крило літака.
Основна причина полягає в складній внутрішній структурі крил, які складаються з
серії порожніх камер. Доступ до цього простору можливий тільки через вузькі
люки розміром 45 на 25 см. Це трудомістка робота, яка вимагає інтенсивного
фізичного навантаження, не кажучи вже про ризики для здоров'я через летких
органічних сполук.
Звичайні промислові роботи дуже
негнучкі щоб проходити через вузькі отвори. Їх жорсткі руки не здатні досягти
віддалених ділянок робочої області, яка в крилах літаків досягає п'яти метрів у
довжину. У цьому випадку може допомогти тонкий робот з шарнірними важелями.
Робот оснащений шарнірними важелями,
складається з восьми послідовно з'єднаних модулів, які можуть повертатися в
дуже вузькому просторі і здатні досягати найвіддаленіших порожнин крила. Така
конструкція якраз властива роботам-зміям.
Рука робота має 2,5 метра в довжину
і може переміщати інструменти вагою до 15 кг на додаток до власним вагою. В
кожну секцію робота інтегрований двигун невеликого розміру. Кожна секція маніпулятора
може переміщатися незалежно і повертається на кут до 90 градусів.
Робот також включає мобільну
платформу для переміщення по крилу літака.
РОЗДІЛ 7.
Організація робочого місця слюсаря-складальника літальних апаратів
Робочим місцем називається певний
ділянку виробничої площі цеху, відділення, групи, закріплений за даним
робітником (або бригадою робітників), призначений для виконання заданої роботи.
Робоче місце обладнують складальним
оснащенням і організаційно-технічними пристроями (верстатом, підставками,
відкотними або стаціонарними настилами і т.ін.), які повинні забезпечити
зручність виконання робіт і безпечні умови праці. Раціональна організація
робочого місця сприяє підвищенню продуктивності праці і якості роботи.
Всі деталі і складальні одиниці
повинні зберігатися на підставках або стелажах. При роботі в складальних
пристосуваннях повинні бути забезпечені вільні підходи до робочим зонам,
можливість швидкої фіксації зібраного вироби, швидкої і легкої виїмки готового
сайту відсіку, агрегату з пристосування, повинно бути передбачено хороше
освітлення, застосування засобів механізації при виконанні трудомістких
операцій.
Для установки важких деталей і
вузлів в пристосування, а також для виїмки з пристосувань готових вузлів,
відсіків, агрегатів робочі ділянки повинні бути обладнані
підйомно-транспортними засобами.
Поза робочого сильно впливає на його
продуктивність праці (рис.7.1). Зручна робоча поза забезпечується збереження
тривалої працездатності.
Мал.7.1 Вплив пози
робітника на виробничий процес
Раціональне освітлення створює
сприятливі умови для роботи, попереджає зорове і загальне стомлення, сприяє
підвищенню продуктивності праці і якості роботи.
Освітленість робочого місця в
механоскладальних цехах повинна дорівнювати 500 лк.
Робоче місце бригади
робітників-складальників оснащене високопродуктивним свердлувальним і
клепальним обладнанням з підтримуючими або підтримувально-вирівнювальними
пристроями, наждачними точилами, верстаками з паралельними лещатами.
Слюсарі-збирачі мають переносні
ящики для інструментів.
При виконанні слюсарно-складальних
робіт користуються різноманітним ручним і механізованим інструментом. До
ручного інструменту відносяться: ріжучий інструмент (свердла, зенкери,
розгортки, протяжки, напилки, абразивний інструмент та ін.); допоміжний
інструмент (молоток, підтримки, обтискачі, керн, вороток та ін.);
слюсарно-складальний інструмент (викрутки, гайкові ключі, струбцини та ін.) ;
вимірювальний та перевірочний інструмент (масштабна лінійка, нутромір,
штангенциркуль, шаблони для перевірки форми і розмірів замикаючих головок
кріпильних елементів і т. п.).
До механізованого
слюсарно-складального інструменту належить інструмент, у якого головний робочий
рух здійснюється двигуном, а допоміжний рух і керування інструментом
виконується вручну.
Для виконання слюсарно-складальних
робіт використовується наступний механізований пневматичний інструмент:
інструмент обертальної дії (свердлильні, розгортаючи, шліфувальні машини,
гвинтоверти, гайковерти, зачисні і фрезерні машини та ін.); інструмент ударної
дії (клепані молотки, пневмокернери та ін.);, інструмент давильної дії (ручні
преси, протяжні).
РОЗДІЛ 8.
Правила техніки безпеки при складанні лонжеронного крила
До роботи слюсарем-складальником
допускаються особи у віці не молодше 18 років, що пройшли медичний огляд та не
мають медичних протипоказань, які у навчальному закладі отримали професію
слюсаря-складальника ( п.1.2 ПІ 1.4.72-298-2004).
До самостійної роботи допускаються
слюсарі-складальники після отримання вступного та первинного інструктажів,
стажування безпосередньо на робочому місці протягом 2-15 змін (залежно від
стажу, досвіду та характеру робіт) під керівництвом досвідченого
кваліфікованого слюсаря складальника (п.1.3 ПІ 1.4.72-298-2004).
При агрегатній збірці широко
застосовують пневматичний інструмент, що генерує шум та вібрацію. Тривалий
вплив шуму і вібрації негативно позначається на здоров'ї людини, викликає
вібраційну хворобу, глухоту і розлад нервової системи.
Значну частину складальний робіт
виконують з драбин, трапів, настилів, підставок; це вимагає прийняття
спеціальних заходів безпеки. Драбини повинні бути обладнані міцними, щільними
настилами з бортами, висота яких з зовнішньої сторони повинна бути не менше 180
мм, а з боку агрегату - не менше 50 мм. Зазор між виробом та настилом має бути
не більше 15 мм. На драбинах висотою 1 м повинні бути перила висотою не менше 1
м. При роботі на підмостках, настилах драбин необхідно укладати інструмент і
деталі так, щоб виключити їх падіння. При роботі на драбинах, настилах
забороняється спиратися на виріб або облокочуваться на перила (бар'єр),
перегинатися через бар'єри і т. п. На багатоповерхових дробинах не можна
водночас працювати один над одним із-за можливості падіння
деталей, інструментів.
При роботі на площинах крила,
фюзеляжі та інших неогороджених поверхнях висотою більше 1,5 м необхідно
застосовувати запобіжні пояси та страхувальні канати, закріплені за спеціальні
нерухомі вузли на виробі й натягнуті вздовж фюзеляжу та площин, взуття не
повинно ковзати.
Перед початком роботи слюсарі-складальники
проходять атестацію, де перевіряють їх знання та практичні навички безпечної
праці. При виконанні робіт на висоті більшою за 1,5 м робітників навчають за
спеціальною програмою, атестують та видають дозвіл на виконання цих робіт.
Жінкам не дозволяється розклепувати заклепки великих розмірів (більш за 5 мм з
алюмінієвих сплавів і 4 мм зі сталі). Слюсар-складальник повинен працювати
тільки в спеціальній одежі: бавовняному комбінезоні, віброзахисних рукавичках і
навушниках (антифони "Беруші"). При транспортуванні агрегатів за допомогою
кранів необхідно надягати захисну каску. При виконанні клепальних робіт повинні
використовуватися демпфуючі килимки, підлокітники, наконечники, які
виготовляються з вібропоглинаючих і віброізолюючих матеріалів. Свердлильні
роботи, що виконуються з допомогою ручного механізованого інструменту,
необхідно проводити в захисних окулярах. Рукоятки пневмоінструменту повинні
мати ізоляційні покриття або захисне обклеювання. На шліфувальні та ручні
шліфувальні машинки встановлюють захисний кожух. Необхідно періодично перевіряти
справність обмежувальної пружинки для фіксації обтискачів в пневмомолотці.
Перед включенням інструменту необхідно перевіряти надійність затяжки різьбових
з'єднань і закріплення свердла, шарошки, фрези, обтискача і т. п. При
свердлінні перегородок (підлоги, обшивки фюзеляжу тощо) працюють не повинні
знаходитися в зоні з боку ріжучого інструменту. При виконанні свердлильних,
клепальних робіт деталі повинні бути надійно затиснуті рубильниками,
фіксаторами пристосування або в лещатах. Зміну ріжучого інструменту можна
проводити тільки після повної зупинки шпинделя (патрона) верстата або ручного
механізованого інструменту. Ріжучий інструмент слід затискати в патроні
(шпинделі) тільки за допомогою спеціального фіксуючого ключа. При зміні
пневматичного інструмента необхідно від'єднувати шланг від повітряної мережі,
перекривати доступ повітря до інструменту, перегинаючи шланг, забороняється.
При свердлінні, зенкуванні, цековці деталей з титанових сплавів необхідно
користуватися тихохідними дрилями, не допускати застосування інструменту з
тупою ріжучою кромкою або малим кутом заточування із-за можливості займання
стружки.
Біля робочих місць, на яких
обробляються деталі з магнієвих і титанових сплавів, повинен знаходиться ящик з
сухим піском. Титанову і магнієву стружку негайно прибирають з робочого місця в
спеціальні залізні ящики з кришкою.
При виконанні клепальних робіт
встановлюються додаткові перерви, під час яких робітники зобов'язані виконувати
фізіопрофілактичні заходи. В цілях підвищення опірності організму робочих дії
вібрації 2 рази на рік повинні проводитися оздоровчі заходи під наглядом
медичних працівників.
При виконанні клепально-складальних
робіт у замкнутих відсіках при температурі більше + 30С ведучий і
підручний повинні мінятися місцями через кожні 30 хвилин. При тривалих перервах
у роботі необхідно вимикати пневмоінструмент, не можна переходити з одного
робочого місця на інше з працюючим ручним механізованим інструментом.
Забороняється залишати включеним технологічне обладнання, неприбраним робоче
місце на стапелі або в агрегаті.
Категорично забороняється
застосовувати стиснене повітря для обдування одягу та очищення робочого місця.
При проведенні робіт в агрегатах,
пристосуваннях їх необхідно заземлювати, заземлюється також все електрообладнання
та електроінструмент. На робочих місцях повинно бути передбачено місцеве
освітлення: при агрегатній збірці на великих складальних пристосуваннях -
лампами денного світла зовні і зсередини, при остаточній збірці - зсередини
виробу, а також переносними лампами розжарювання, які працюють від електричної
мережі напругою 12 або 36 В. Проходи, виходи, підступи до первинних засобів
пожежогасіння, електрообладнання повинні бути завжди вільними. Обтиральний
матеріал збирають у спеціальні металеві ящики з кришками і в міру накопичення
виносять в пожежобезпечне місце.
СПИСОК ВИКОРИСТАНОЇ ЛІТЕРАТУРИ
1. Довідник
молодого слюсаря-складальника літальних апаратів/ А.П.Худайберганов та ін., М.:
Машинобудування, 1987.
2. Горячев
А.С., Білоглазов І.М., Лисенко Д.М. Збірка клепаних вузлів і агрегатів
літальних апаратів: Навчальний посібник. - Куйбишев: КуАІ, 1986.
3. Житомирський
Г. І., Конструкція літаків: Підручник для студентів авіаційних спеціальностей
вузів - М.: Машинобудування, 1995.
. Конструкція
літаків: Підручник для вузів / Під ред. проф. О. А. Гребе-нькова. - К.: Вид-во
Казанського державного університету, 1999.
5. Колганов
І.М. Складальні роботи при виробництві широкофюзеляжних літаків. Технологічні
процеси, вибір варіанта: Навчальний посібник для студентів вузів, що навчаються
за спец. «Літако- і вертольотобудування». - Ульяновськ: УлГТУ, 1998.
6. Тараканов
Л.М. Літак Ту-154А. - М., Машинобудування, 1976.
7. Волошин
Ф.А., Кузнєцов А.Н., Покровський В.Я., Соловйов А.Я. Літак Ту-154. - М.,
Машинобудування, 1975. Ч. 1, 2.
. Технологія
літакобудування: Підручник для авіаційних вузів/А.Л. Абібов та ін., 2-ге вид. -
М.:Машинобудування, 1982
. Авіаційне
матеріалознавство/С.С.Бакастов, П.П.Маркеллов - 2-ге вид., виправ. - М.:
Воєнвидат, 1941
. Марочник
сталей і сплавів. 2-ге вид., допов. і виправ./ А.С.Зубченко та ін. -
М.:Машинобудування, 2003
. ЄСКД.
Міждержавний стандарт. Основні вимоги до креслень. - ГОСТ 2.109-73, М.:
Держкомстандарт, 2002
. Комаров
Ю.Ю. Основи технології виробництва літальних апаратів: Навчальний посібник -
М., 2009
. Технологія
складання металевих та композитних конструкцій/ В.І.Халіулін та ін. - Казань:
вид. КазНІТУ ім. А.Н.Туполева - КАІ, 2014
. Проектування
лонжеронів крила літака: навч. посібник / Л.В.Капітанова та ін. - Х.: Нац.
аерокосмічний ун-т «ХАІ», 2006
. Примірна
інструкція з охорони праці під час виконання слюсарно-складальних робіт з
виготовлення ЛА, ПІ-1.4.72-298-2004, К.: Мінпромполітики України, 2004
. Вашуков
Ю.А., Ломовський О.В., Шаров А.А. Технологія та обладнання складальних
процесів. - Самара: СГАУ ім.. С.П.Корольова, 2001
. Федоров
В.Б. Технологія складання виробів авіаційної техніки -Челябінськ: вид.
ЮУрГУ,2003
. Технологія
складання літаків / І.М.Колганов, П.Б.Томов - Ульяновськ: УлГТУ, 1999
. Шишков
М.М. Марочник сталей і сплавів: Довідник. Вид. 3-є, допов. - Донецьк:
Юго-восток, 2002
. Фридляндер
І.Н. Алюмінієві деформуючі конструкційні сплави - М.: Металургія, 1984
. Квасов
Ф.І., Фридляндер І.Н. Алюмінієві сплави типу дюралюмін. - М.: Металургія, 1984
. Машинобудування:
Енциклопедія. Том 11-3. Цвітні метали і сплави. Композиційні металеві матеріали
/ під ред.. І.Н.Фридляндера. - М.: Машинобудування, 2001.