Разработка проекта участка механического цеха для изготовления деталей типа 'Фланец' с применением станков с ЧПУ
Введение
Ведущее место в росте экономики
Республики принадлежит машиностроению, которое обеспечивает материальную основу
технического прогресса всех отраслей народного хозяйства.
В настоящее время машиностроение
располагает мощной производственной базой, выпускающей свыше четверти всей
промышленной продукции республики.
В развитии машиностроения
первостепенной задачей является автоматизация на базе гибких производственных
систем, в том числе применения станков с ЧПУ, роботов, программируемых
манипуляторов, роботехнических комплексов; увеличение применения прогрессивных
конструкционных материалов, снижение металлоемкости машин и оборудования с их
удельной энергоемкости, снижение себестоимости продукции.
Открытое акционерное общество
«Гомельский завод литья и нормалей» входит в состав холдинга «Гомсельмаш»,
обладает правами юридического лица и осуществляет свою деятельность в
соответствии с уставом.
Общество осуществляет следующие
основные виды деятельности:
- Производство сельскохозяйственных
машин;
Производство отливок из чугуна,
стали и цветных сплавов;
Производство машиностроительного
крепежа (болты, гайки, шпильки, заклепки, оси и т.д.);
Производство литейной оснастки,
нестандартного оборудования;
Производство холодновысадочного
инструмента, штампов;
Темой дипломного проекта является:
«Проект участка механического цеха для изготовления деталей типа «Фланец» с
применением станков с ЧПУ».
Целями изменений базового
технологического процесса могут быть:
. повышение степени
механизации путём применения станков с ЧПУ вместо универсального оборудования;
. повышение гибкости
переналадки оборудования путём применения станков с ЧПУ вместо полуавтоматов;
. повышение
производительности путём повышения режимов обработки;
. применения принципа
концентрации операции с целью уменьшения количества операций и сокращения
времени обработки детали.
1. Анализ исходных данных
1.1 Описание конструкции и
служебного назначения детали
Деталь Фланец ЖГР 20215602 входит в
узел ЖГР 20215000 Установка вальцев машины ЖГР-3-02 Жатка для грубостебельных
культур.
По Ø25Н9 деталь устанавливается на торсионЖГР-2-0215604 и
фиксируется в осевом направлении штифтом по отверстию Ø20Н9.
По Ø75h11 деталь устанавливается в рычаг
ЖГР-2-0215050 и закрепляется по отверстиям Ø11 болтами М10.
Деталь изготавливается из Сталь 20
по ГОСТ 1412-2013. Химический состав и механические свойства материала
представлены в таблицах 1.1 и 1.2.
Таблица 1.1 - Механические свойства
материала детали стать 20 ГОСТ 1050-2013
Материал детали
|
Временное сопротивление на разрыв δВ,
кгс/мм2
|
Относительное удлинение, %
|
Предел текучести, кгс/мм2
|
Относительное сужение ψ,
%
|
Ударная вязкость KCU,
кгс/мм2
|
Твёрдость по Бринелю, HB
|
Сталь 20
|
410
|
25
|
245
|
55
|
19
|
125-167
|
Таблица 1.2- Химические состав
материала Сталь 20 ГОСТ 1050-2013
Материал детали
|
C
|
Si
|
Mn
|
Ni
|
S
|
P
|
Cr
|
Cu
|
As
|
Fe
|
Стать 20
|
0,17-0,24
|
0,17-0,37
|
0,35-0,65
|
до 0,25
|
до 0,04
|
до 0,04
|
до 0,25
|
до 0,25
|
до 0,08
|
~98
|
1.2 Определение типа производства и
его характеристика
Тип производства определяется по
коэффициенту закрепления операций (КЗО). Предварительно на основе типового
(базового) технологического процесса его можно определить по формуле:
, (1.1)
где Fд - действительный годовой фонд
времени работы оборудования, час;
N - годовой объём выпуска детали, шт.;
Тшт(шт.-к)ср - среднее штучное (для
массового производства) или штучно-калькуляционное (для серийного производства)
время, мин. При расчете среднего штучного или штучно-калькуляционного времени в
числитель подставляется сумма штучного или штучно-калькуляционного времени, а в
знаменатель - число рабочих мест;
kУ - коэффициент ужесточения заводских норм, kУ=0,7…1,0.
Для выполнения расчетов
проанализируем операции типового (базового) технологического процесса
механической обработки детали, заданной для проектирования, заполняя их в
таблицу 1.3.
Таблица 1.3 - Анализ операций
механической обработки детали
Номер операции
|
Код и наименование операции
|
Модель станка
|
Категория ремонтной сложности
|
Мощность станка
|
Тшт (шт.-к)
|
010
|
4114 Токарно-винторезная
|
16К20
|
-
|
11
|
6,5
|
020
|
4233 Токарная с ЧПУ
|
1П426
|
-
|
39
|
18,53
|
030
|
4114 Токарно-винторезная
|
16К20
|
-
|
11
|
3,45
|
040
|
4234 Фрезерная с ЧПУ
|
ГФ2171
|
-
|
7,5
|
8,32
|
060
|
4262 Горизонтально-фрезерная
|
EW450R
|
-
|
5,5
|
4,3
|
080
|
4214 Вертикально-сверлильная
|
2Н135
|
-
|
4
|
9,43
|
Итого
|
50,53
|
Определяем среднее штучное время по
формуле:
, (1.2)
где Тштi - сумма штучного времени, мин,;
n - число рабочих мест, шт.;
Полученное значение
по таблице 1.4 соответствует среднесерийному типу производства.
Таблица 1.4 - Зависимость между
типом производства и коэффициентом закрепления операций
КЗ.О.
|
Тип производства
|
До 1
|
Массовый
|
Свыше 1 до 10
|
Крупносерийный
|
Свыше 10 до 20
|
Среднесерийный
|
Свыше 20 до 40
|
Мелкосерийный
|
Свыше 40
|
Единичный
|
Величина производственной партии (nд):
, шт
(1.3)
где a - число дней, на которые
необходимо иметь запас деталей.
a=2…5 дней - для крупных деталей;
a=3…15 дней - для средних деталей;
a=10…30 дней - для мелких деталей.
Фр.д. - число рабочих дней в году,
принятое по графику-календарю базового предприятия, или определенное по
методике.
Среднесерийное производство
характеризуется ограниченной номенклатурой изделий, изготовляемых периодически
повторяющимися партиями. При среднесерийном производстве используются
универсальные и специализированные станки, станки с ЧПУ, оснащенные как
специальными, так и универсальными, и универсально сборочными приспособлениями.
Заготовкой служит поковка, что
характерно для данного типа производства. Базовый техпроцесс обеспечивает
требуемую точность изготовления детали, но построен на применении универсальных
станков, что является его основным недостатком.
1.3 Анализ детали на технологичность
Количественный анализ на
технологичность заключается в расчете коэффициента унификации конструктивных
элементов (КУ) и коэффициента использования материала (КИМ).
Для расчета КУ следует провести
отработку элементов детали на унифицированность.
Таблица 1.5 - Отработка элементов
детали на соответствие стандартам
Номер элемента
|
Выдерживаемые размеры
|
Стандарт на элемент
|
1
|
46
|
ГОСТ 6636-69
|
2
|
4
|
-
|
3
|
Ø115
|
ГОСТ 6636-69
|
4
|
Ø25Н9
|
ГОСТ 6636-69
|
5
|
Ø75h11
|
ГОСТ 6636-69
|
(1.4)
где QУ.Э. - число конструктивных
элементов детали, которые выполнены по стандартам: резьбовые, зубчатые,
шлицевые поверхности, шпоночные пазы, фаски, радиусы закругления, отверстия под
крепеж, отверстия центровые, канавки для сбега резьб, резьбовые недорезы,
сбеги, проточки и фаски, канавки для установки уплотнений на деталях пневмо-и
гидроаппаратуры, канавки для выхода резцов при тонком точении и растачивании
или для выхода шлифовальных кругов, поверхности опорные под винты, болты,
гайки, заклепки, шайбы, шурупы и т.д.; или в соответствии с нормальными рядами
размеров и конусов: диаметральные размеры ступеней в отверстиях и на наружных
поверхностях, конические поверхности.
QОбЩ. - число всех конструктивных элементов детали.
Деталь считается технологичной, если
КУ>0,6.
т.е. 0,73>0,6 - следует, что
деталь технологична
Коэффициент использования материала
рассчитывается по формуле:
(1.5)
где тД - масса детали, кг;
Н.расх - норма расхода материала,
кг.
Данные по Н.расх предварительно
можно подобрать по типовому (базовому) технологическому процессу механической
обработки детали.
Деталь считается технологичной, если
КИМ
- для заготовок, полученных поковкой;
При отсутствии типовых данных
Н.расхможно рассчитать по формуле:
Н.расх=тЗ+тОТХ.З., кг (1.6)
где тОТХ..З. - масса отходов при
производстве заготовки.
Для штамповок, полученных на
прессах, и для отливок - от 10% (для крупных (
кг) заготовок) до 20% (для мелких (
кг) заготовок).
Н.расх=4,84+0,48=5,32 кг.
0,23<0,65 - следует деталь не
технологична.
2. Разработка технологии обработки
детали
2.1 Рекомендации по разработке
проектного технологического процесса
Анализ базового технологического
процесса.
Последовательность операций и
переходов механической обработки детали по базовому техпроцессу:
Операция 010 Токарно-винторезная.
1. Подрезать торец и точитьØ115±1,25 как чисто.
2. Сверлить отверстие Ø23+0,5 предварительно.
Операция 020 Токарная с ЧПУ.
1. Точить Ø75h11(-0,19) с подрезкой торца в размер 12±0,5.
2. Точить Ø40+0,6 выдерживая размер
10±0,2.
3. Точить Ø65+0,6 выдерживая размер
6±0,1.
4. Точить <45˚ ±20´, выдерживая размер 6±0,1.
5. Точить <45˚ ±20´, выдерживая размер
10±0,2.
6. Расточить Ø24,4+0,2предварительно.
7. Расточить Ø25Н9(+0,052).
8. Точить фаску 1,6*45.
Операция 030 Токарно-винторезная.
1. Точить деталь, выдерживая
размер 34±0,3.
Операция 040 Фрезерная с ЧПУ.
1. Центровать 3 отверстия.
2. Сверлить 3 отверстия Ø11+0,36.
3. Фрезеровать последовательно
3 понижения выдерживая размеры R11, 7±0,2.
Операция 060
Горизонтально-фрезерная.
1. Фрезеровать деталь
выдерживая размеры 25±0,2 и 50-0,62.
Операция 080
Вертикально-сверлильная.
1. Сверлить отверстие Ø18+0,4 предварительно,
выдерживая размеры 17,5±0,5 и 24±0,2.
2. Зенкеровать отверстие в
размер Ø19,5+0,1.
3. Развернуть отверстие в
размер Ø20Н9(+0,052)с
переустановкой.
4. Цековать отверстие
выдерживая размеры Ø30+0,4, 2±0,5.
Анализ заводского техпроцесса,
показал, что в проектном варианте процесса обработки детали целесообразно
заменить все станки на многоцелевой станок на базе токарного TakisawaTNR-200YS.
Целями изменений базового
технологического процесса могут быть:
- повышение степени
механизации путём применения станков с ЧПУ вместо универсального оборудования;
- повышение гибкости
переналадки оборудования путём применения станков с ЧПУ вместо полуавтоматов;
- повышение
производительности путём повышения режимов обработки.
- применения принципа
концентрации операции с целью уменьшения количества операций и сокращения
времени обработки детали.
Анализ технических требований,
предъявленных к детали.
Рекомендации по их обеспечению и
контролю.
В соответствии с намеченными
изменениями в технологии обработки детали проанализируем технические
требования, предъявляемые к детали, и наметим последовательность обработки
каждой поверхности детали.
Анализ технических требований
представим в табличном виде.
Таблица 2.1 - Анализ технических
требований
Номер конструктивного элемента
|
Размеры и требования к их размерной и геометрической точности
|
Требования к шероховатости поверхности
|
Методы достижения точности: способы базирования и виды обработки
|
Методы контроля и средства измерения
|
1
|
46
|
Ra12,5
|
Базирование в патроне. Подрезка торца
|
Выборочно Штангенциркуль ШЦ -1-125-0,1 ГОСТ 166-89
|
2
|
4
|
Ra6,3
|
Базирование в патроне. Подрезка торца черновое, чистовое
|
Выборочно Штангенциркуль ШЦ -1-125-0,1 ГОСТ 166-89 Контрольное
приспособление
|
3
|
Ø115
|
Ra12,5
|
Базирование в патроне. Точение чистовое
|
Выборочно. ШтангенциркульШЦ -1-125-0,1 ГОСТ 166-89 Контрольное
приспособление
|
4
|
Ø25Н9
|
Ra1,6
|
Базирование в патроне. Растачивание чистовое, получистовое,
чистовое
|
Сплошной. Калибр-пробка Ø25Н9
ГОСТ14810-69
|
5
|
Ø75h11
|
Ra6,3
|
Базирование в патроне. Точение чистовое, черновое
|
Выборочно. Калибр-скоба Ø75h11 ГОСТ18360-93
|
2.2 Выбор вида и обоснование метода
получения заготовки
Описание метода получения заготовки.
Деталь изготавливается в кузнечном
цехе из легированной стали. Заготовку сначала нагревают в нагревательной печи
до температуры 11500, а затем, после нагревания, её отрезают на пресс - ножницах.
Потом происходит повторное нагревание, а затем штампуют при помощи ГКМ - В114.
Затем заготовку отштамповывают в двух ручьях за 2 хода машины.
На горизонтально-ковачных машинах
(ГКМ) производят штамповку поковок без облоя и штампованных уклонов в разъемных
матрицах. При штамповке от прутка отпадает необходимость в предварительной
разделке последнего на мерные заготовки, так как штампы ГКМ имеют отрезной
ручей. Машина имеет жесткую конструкцию, что увеличивает точность поковок.
После всех этих операций заготовку
отправляют на контрольный стол ОТК, где проверяются все необходимые размеры,
также проверяют качество нормализации. Это качество проверяется контролем
температурного интервала по предъявляемой диаграмме нормализации.
Применение штамповки в серийном
производстве достаточно выгодно, так как происходит экономия материала, а
затраты на изготовление штамповки компенсируется экономией электроэнергии при
снятии меньшего припуска при обработке, а также снижением времени на обработку
детали.
Определение допусков на размеры
заготовки, припусков на механическую обработку поверхностей по переходам,
расчет размеров и массы заготовки.
Назначение допусков.
Назначим допуски на все
обрабатываемые поверхности в соответствии с ГОСТ 7505-89 для поковок
(штамповок).
Класс точности -Т4.
Группа стали -М1.
Степень сложности-С1.
Конфигурация поверхности разъёма
штампа -П.
Исходный индекс 10.
Назначим допуски на размеры
заготовки:
Последовательность определения
допусков и предельных отклонений на поковку по ГОСТ 7505-89. Назначение
рекомендуется выполнять в табличной форме, заполняя таблицу по форме таблицы
2.2.
Таблица 2.2 - Назначение допусков на
поковку
Номер поверхности
|
Номинальный размер детали
|
Вид размера
|
Допуск на заготовку с указанием предельных отклонений, мм
|
1
|
46
|
высота
|
|
2
|
4
|
высота
|
|
3
|
Ø115
|
диаметр
|
|
4
|
Ø25h9
|
диаметр
|
|
5
|
Ø75H11
|
диаметр
|
|
6
|
Ø40 <45˚
|
диаметр
|
|
8
|
10
|
высота
|
|
9
|
4
|
высота
|
|
10
|
Ø65 <45˚
|
диаметр
|
|
11
|
34
|
высота
|
|
Назначенные
припусков и расчет размеров заготовки сведём в таблицу 2.3.
механический станок припуск деталь
Таблица 2.3 - Назначение припусков и
расчет размеров заготовки
Номер поверхности
|
Переходы механической обработки поверхности
|
Точность обработки
|
Припуск табличный, Z(2Z), мм
|
Расчет размеров заготовки (d
или D), мм
|
|
|
Квалитет
|
Допуск, мм
|
Шероховатость, Ra,
мкм
|
|
|
1
|
Подрезка торца
|
h14
|
|
Ra12,5
|
1,5
|
46
|
|
Заготовка
|
-
|
|
Rz630
|
1,5
|
46+1,5=47,5
|
|
|
2
|
Подрезка торца начисто
|
h14
|
|
Ra6,3
|
0,5
|
4
|
|
Подрезка торца начерно
|
h14
|
Ra12,5
|
1
|
4-0,5=3,5
|
|
Заготовка
|
-
|
|
Rz630
|
1,5
|
3,5-1=2,5
|
|
|
3
|
Точение чистовое
|
h14
|
|
Ra12,5
|
2,5
|
115
|
|
Заготовка
|
-
|
|
Rz630
|
2,5
|
115+2*2,5=220
|
|
|
4
|
Растачивание чистовое
|
Н9
|
|
Ra1,6
|
0,4
|
25
|
|
Растачивание получистовое
|
Н10
|
|
Ra3,2
|
0,6
|
25-0,4*2=24,2
|
|
Растачивание черновое
|
Н12
|
|
Ra6,3
|
2,1
|
24,2-0,6*2=23
|
|
Заготовка
|
-
|
|
Rz630
|
3,1
|
23-2,1*2=18,8
|
|
|
5
|
Точение чистовое
|
h11
|
|
Ra6,3
|
1,4
|
75
|
|
Точение черновое
|
h14
|
|
Ra12,5
|
2,5
|
75+1,4*2=77,8
|
|
Заготовка
|
-
|
|
Rz630
|
3,9
|
77,8+2,5*2=82,8
|
|
|
6
|
Растачивание чистовое
|
Н14
|
|
Ra12,5
|
1,6
|
40
|
|
|
|
|
|
|
|
|
|
|
|
|
|
Расчет размеров и массы заготовки
Рисунок 2.1 - Эскиз
заготовки
Определим суммарный объём удаляемого
в процессе механической обработки материала, т.е. объем припусков, мм3.
Vотх.мех.обр. = V1 + V2 + … + Vп , мм3 (2.1)
где п - множество удаляемых с поверхности
заготовки припусков.
Формула для расчёта
детали типа диск:
(2.2)
где
- для наружных поверхностях диаметр диска заготовки, а для
внутренних диаметр диска детали;
- для
наружных поверхностях диаметр диска детали, а для внутренних диаметр диска
заготовки;
h - высота припуска
Произведём расчёт
для всех объёмов дисков:
Определим объем припусков:
Vотх.мех.обр. =
+
+
Определим массу отходов механической
обработки, кг;
mотх.мех.обр =Vотх.*ρ, кг (2.3)
где ρ
- плотность материала заготовки, кг/мм3;
mотх.мех.обр =
*7,8*
= 0,55 кг
Произвести расчет массы
спроектированной заготовки по формуле:
mз=mд+mотх.мех.обр, кг (2.4)
где mд - масса детали, кг (принимается по
чертежу детали);
mз=1,2+0,55=1,75 кг
После определения массы спроектированной
заготовки рассчитаем коэффициент использования заготовки (КЗ) и пересчитаем
коэффициент использования материала.
(2.5)
где mЗ - масса рассчитанной заготовки,
кг;
0,69<0,65 следует деталь
технологична.
Пересчитанный коэффициент
использования материала:
, (2.6)
где Нрасх - пересчитанная норма
расхода материала, кг
Для штамповок, полученных на
прессах, и для отливок - от 10% (для крупных (
кг) заготовок) до 20% (для мелких (
кг) заготовок).
Н.расх=1,75+0,18=1,93 кг.
0,654<0,65 следует деталь
технологична
2.3 Разработка
проектного технологического процесса
Составление последовательности
обработки для проектируемого технологического процесса.
010 Многоцелевая с ЧПУ на станке
TakisawaTNR-200YS.
Установ А.
1. Подрезать торец
1 в размер 46-0,6.
2. Точить
поверхность3 в размер Ø115-0,87.
3. Точить
поверхность 5, выдерживая размер Ø77,8-0,74.
4. Расточить
отверстия 10,6 и 4 выдерживая размер Ø19,6+0,2, с подрезкой торцов 9 и 8.
5. Расточить
отверстие 4 выдерживая размер 23+0,084.
6. Расточить
отверстие 4 с образованием фаски 7.
7. Точить
поверхность 5 с подрезкой торца 2.
8. Центровать 3
отверстия 12.
9. Сверлить 3
отверстия 12.
Установ Б.
1. Фрезеровать 3
поверхности 15.
2. Центровать
отверстие 13.
3. Сверлить
отверстие 13 выдерживая размер Ø18+0,18.
4. Зенкеровать
отверстие 13 выдерживая размер Ø17+0,11.
5. Развернуть
отверстие 13.
6. Цековать
отверстие 14.
Выбор и обоснование технологических
баз.
Для установа А в качестве черновой
базы принята поверхность размером 60,5 (двойная направляющая база - лишает
заготовку четырех степеней свободы)
Для установа Б в качестве чистовой
базы принята обработанная поверхность 3(Ø115) (двойная направляющая база - лишает заготовку четырех степеней
свободы). Выбор таких баз обосновано тем что обеспечивается совмещение
технологической и измерительной базы в следствии чего погрешность базирования
будет равна 0.
2.4 Разработка операционного технологического
процесса
Определение режимов резания на
проектируемые операции (переходы). Сводная таблица режимов резания.
Табличный расчёт режимов резания 010
операцию.
Переход 5расточить отверстие 4
выдерживая размер 21,8+0,084.
Рисунок 2.2 - Эскиз обработки детали
I. Выбор режущего инструмента.
Для обработки принят резец расточной
FSTUP1008R/L-08Eс материалом режущей частиSV.
II. Расчёт режимов резания:
Глубина резания рассчитывается по
формуле:
(2.7)
D-диаметр детали перед данным переходом;
d-диаметр детали окончательный.
.
2. Подача.
Рекомендуемая Sо = 0,05 ÷ 0,4 мм/об.
Принимаемая Sо = 0,2 мм/об.
3. Стойкость Т, мин.
Т = 90 мин-1.
4. Скорость резания Vрез, м/мин:
Vрез =Vтабл × Кvс×
Kvo×
Kvj
× Kvm× Kv
× KNt× Kvm× Knm, м/мин (2.8)
где Kvc= 1 - коэффициент
учитывая материал.
Kvo= 1 - коэффициент вида обработки.
Kvj = 0.75 - коэффициент жесткости стали.
Kvm= 1.7 - коэффициент механических свойств обработки материала.
Kv
= 1,15 - коэффициент геометрических параметров резца.
KNt = 0,6 - коэффициент периода стойкости режущей части резца.
Kvm = 1 - коэффициент наличия охлаждения.
Knm = 1 - коэффициент изменение условий работы в зависимости от
механических свойств обработки материала.
Vтабл = 105 м/мин.
V рез = 105× 1× 1 ×
0,75 × 1,7 × 1,15 × 0,6 × 1 × 1 = 92 м/мин.
5. Частота вращения n, мин-1.
n=
, мин-1
(2.9)
n=
= 1274
мин-1
по паспорту станка принимаем n=1250 мин-1.
6. Действительная скорость резания Vд, м/мин.
Vд=
, м/мин
(2.10)
Vд=
=90
м/мин
III. Расчёт машинного времени, То, мин
То =
, мин (2.11)
где Lр.х- длина рабочего хода.
Lр.х.=lрез+y+∆, мм (2.12)
где lрез = 36 мм.
y = 2 мм.
Принимаемое значение ∆=1 мм.
Lр.х.=36+ 2 + 1 =39 мм.
То =
= 0,156 мин.
Расчет режимов резания на 010
операцию.
Переход 9 сверлить 3 отверстия 12.
Рисунок 2.3 - Эскиз обработки детали
I. Выбор режущего инструмента.
Для обработки принято сверло MNS 1850S-DINØ11 мм из материала MNS.
II. Расчёт режимов резания:
. Глубина резания рассчитывается по
формуле:
(2.13)
D-диаметр детали для данного перехода;
2. Подача.
Sо = 0,56 мм/об.
3. Стойкость Т, мин.
Т = 40 мин-1.
4. Скорость резания Vрез,м/мин.
Vрез =Vтабл× Кvт×Kм, м/мин (2.14)
где Кvт= 1,2;
Kм=0,85.
Vтабл=29 м/мин
V рез= 29 × 1,2 × 0,85= 30 м/мин
. Частота вращения n, мин-1
n=
, мин-1
(2.15).
n=
= 869
мин-1.
по паспорту станка принимаем n=850 мин-1.
6. Действительная скорость резания Vд, м/мин.
Vд=
, м/мин
(2.16)
Vд=
=29
м/мин.
III. Расчёт машинного времени, То, мин.
То =
, мин (2.17)
Lр.х.=lрез + y + ∆, мм
где lрез = 7 мм.
y = 3,18 мм.
Принимаемое значение ∆=9,25
мм.
Lр.х.=7 + 3,18 + 9,25 = 19,43 мм.
То =
= 0,12 мин.
Разработка управляющей программы
(УП) обработки детали.
Исходные данные:
Операция 010 Многоцелевая с ЧПУ.
Станок: TakisawaTNR-200YS.
УЧПУ: СNC.
Деталь: Фланец.
Материал: сталь 20 ГОСТ 1050-2013.
Тип производства: Среднесерийный.
Таблица 2.4 - Маршрут обработки
детали
№ перехода
|
Содержание перехода
|
Режущий инструмент
|
Режимы резания
|
3
|
Подрезать торец 1 в размер 46-0,6
|
Резец WNM1616H09 Материал режущей части CNG
|
n=938
мин-1 s=0,8 мм/об
|
4
|
Точить поверхность 3 в размер Ø115-0,87
|
Резец WNM1616H09 Материал режущей части CNG
|
n=1450
мин-1 s=0,8 мм/об
|
5
|
Точить поверхность 5, выдерживая размер Ø
80-0,74
|
Резец WNM1616H09 Материал режущей части CNG
|
n=1397
мин-1 s=0.8 мм/об
|
6
|
Расточить отверстия 10,6 и 4, выдерживая размер Ø
19,6+0,2 с подрезкой торцов 9 и 8
|
Резец FSTUP1008R/L-08L Материал режущей части SV
|
n=1080
мин-1 s=0,5 мм/об
|
Таблица 2.5 - Программа обработки
детали
№ пере хода
|
Эскиз обработки
|
Программа
|
3
|
|
%1 ПС №5 G18
T01 ПС №10 L89
ПС №15 G00 G90 G71 X92,8 Z0 G97 S938E01ПС (и.т.) №20
G01 X50 F0,8 ПС (т.1) №25 G00
Z3 ПС (т.2)
|
4
|
|
№30 X115 Z3 S1450 ПС (т.3) №35 Z-2 ПС (т.4) №40 G01 Z-12 F0,8 ПС (т.5)
№50 G00 X125 ПС (т.6) №55 Z3 ПС (т.7)
|
5
|
|
№60 X800 Z3 S1379 ПС (т.8) №65 G01 Z-4 F0,8 ПС (т.9) №70 G00 X125 ПС (т.10) №75Х150 Z50 ПС (и.п.) №80G40 ПС №85
М05 ПС №90
L90 ПС
|
|
6
|
|
№100 Т02 ПС №105 L89
ПС №110 G00 X73 Z3 S1080 ПС (и.т.)
№115Z0 ПС (т.1) №120 G01
X65 Z-4 F0,5 ПС (т.2) №125 Х52 ПС (т.3) №130 Х40 Z-12
ПС (т.4) №135 Х19,6 ПС (т.5) №140 Z-46
ПС (т.6) №145 Х18,6 ПС (т.7) №150 Z3 ПС (т.8) №155 G40
M05 ПС №160L90
ПС №165 М22 ПС
|
Нормирование проектируемой операции.
Рисунок 2.4 - Эскиз
обработки
Таблица 2.6 -
Описание обработки на проектируемой операции
Наименование переходов технологических и машинных
вспомогательных
|
Величина составляющих ТМВ, мин
|
Установ А
|
подвести инструмент
|
0,1
|
1. Подрезать торец 1 в размер 46-0,6
|
-
|
отвести инструмент
|
0,1
|
изменить скорость резания, S
|
0,2
|
изменить частоту вращения, n
|
0,2
|
подвести инструмент
|
0,1
|
2. Точить поверхность 3 в размер Ø115-0,87
|
-
|
отвести инструмент
|
0,1
|
1
|
2
|
изменить скорость резания, S
|
0,2
|
изменить частоту вращения, n
|
0,2
|
подвести инструмент
|
0,1
|
3. Точить поверхность 5, выдерживая размер Ø77,8-0,74
|
-
|
отвести инструмент
|
0,1
|
изменить скорость резания, S
|
0,2
|
изменить частоту вращения, n
|
0,2
|
сменить инструмент
|
0,3
|
подвести инструмент
|
0,1
|
4. Расточить отверстия 10, 6 и 4 выдерживая размер Ø19,6+0,2,
с подрезкой торцов 9 и 8
|
-
|
отвести инструмент
|
0,1
|
изменить скорость резания, S
|
0,2
|
изменить частоту вращения, n
|
0,2
|
подвести инструмент
|
0,1
|
5. Расточить отверстие 4 выдерживая размер 23+0,084
|
-
|
отвести инструмент
|
0,1
|
изменить скорость резания, S
|
0,2
|
изменить частоту вращения, n
|
0,2
|
сменить инструмент
|
0,3
|
подвести инструмент
|
0,1
|
6. Расточить отверстие 4 с образованием фаски 7
|
-
|
отвести инструмент
|
0,1
|
изменить скорость резания, S
|
0,2
|
изменить частоту вращения, n
|
0,2
|
сменить инструмент
|
0,3
|
подвести инструмент
|
0,1
|
-
|
отвести инструмент
|
0,1
|
изменить скорость резания, S
|
0,2
|
изменить частоту вращения, n
|
0,2
|
сменить инструмент
|
0,3
|
подвести инструмент
|
0,1
|
8. Центровать 3 отверстия 12
|
-
|
отвести инструмент
|
0,1
|
изменить скорость резания, S
|
0,2
|
изменить частоту вращения, n
|
0,2
|
сменить инструмент
|
0,3
|
подвести инструмент
|
0,1
|
9. Сверлить 3 отверстия 12
|
-
|
отвести инструмент
|
0,1
|
изменить скорость резания, S
|
0,2
|
изменить частоту вращения, n
|
0,2
|
сменить инструмент
|
0,3
|
Перехватить деталь
|
0,4
|
Установ Б
|
подвести инструмент
|
0,1
|
1. Фрезеровать 3 поверхности 15
|
-
|
отвести инструмент
|
0,1
|
изменит скорость резания, S
|
0,2
|
изменит частоту вращения, n
|
0,2
|
сменить инструмент
|
0,3
|
подвести инструмент
|
0,1
|
2. Центровать отверстие 13
|
-
|
отвести инструмент
|
0,1
|
изменит скорость резания, S
|
0,2
|
изменит частоту вращения, n
|
0,2
|
сменить инструмент
|
0,3
|
подвести инструмент
|
0,1
|
3. Сверлить отверстие 13 выдерживая размер Ø18+0,18
|
-
|
отвести инструмент
|
0,1
|
изменит скорость резания, S
|
0,2
|
изменит частоту вращения, n
|
0,2
|
сменить инструмент
|
0,3
|
подвести инструмент
|
0,1
|
4. Зенкеровать отверстие 13 выдерживая размер Ø17+0,11
|
-
|
отвести инструмент
|
0,1
|
изменить скорость резания, S
|
0,2
|
изменить частоту вращения, n
|
0,2
|
сменить инструмент
|
0,3
|
подвести инструмент
|
0,1
|
5. Развернуть отверстие 13
|
-
|
отвести инструмент
|
0,1
|
изменит скорость резания, S
|
0,2
|
изменит частоту вращения, n
|
0,2
|
сменить инструмент
|
0,3
|
подвести инструмент
|
0,1
|
6. Цековать отверстие 14
|
-
|
отвести инструмент
|
0,1
|
вернуть в исходное положение S
|
0,2
|
|
вернуть в исходное положение n
|
0,2
|
|
вернуть в исходное положение инструмент
|
0,3
|
|
Итого
|
∑13
|
|
Сумма основного и вспомогательного
машинного времени составляет время цикла автоматическое (ТЦА), т. е. время
работы станка по управляющей программе без вмешательства рабочего:
, мин
(2.16)
где:
- основное машинное время по каждому i - переходу механической обработки;
Оперативное время определяется по
формуле:
ТОП = ТЦА + ТВР, мин (2.17)
где ТВР - вспомогательное ручное время,
мин.
При назначении вспомогательного
ручного времени кроме времени на установку и съем детали, не перекрываемого
времени на измерение назначается время на управление: станком, устройством ЧПУ:
ТВР = tуст + tизм + tуп , мин (2.18)
tуст -0,17 мин
tуп1 - 2,3 мин
tуп2 - 0,12 мин
tуп3 - 0,04 мин
tуп = 2,46 мин
tизм1 - 0,10 мин
tизм2 - 0,045*3=0,135 мин
tизм3 - 0,09 мин
tизм4 - 0,06*2=0,12 мин
tизм5 - 0,07 мин
tизм6 - 0,11 мин
tизм7 - 0,07 мин
tизм8 - 0,13 мин
tизм9 - 0,04 мин
tизм=0,865 мин, т.к tизм< Тц значит оно перекрываемое и в расчётах не учитывается.
ТВР = 0,17+2,46=2,63 мин
ТОП =15,219+
2,63=17,849 мин
Время на обслуживание рабочего места
и отдых назначается в процентах от оперативного по соответствующим таблицам
нормативов и входит в норму штучного времени:
(2.19)
αобс и αотл=14%
Подготовительно - заключительное
время назначается по таблицам и составляется из времени на организационную
подготовку, наладку оснастки и программных устройств, пробную обработку детали
с учетом поправочных коэффициентов:
ТПЗ = ТПЗ орг + ТПЗ нал + ТПЗ
проб.обр., мин. (2.20)
ТПЗ проб.обр-19,8
мин
ТПЗ нал1-4,0 мин
ТПЗ нал2-0,2 мин
ТПЗ нал3-1,0 мин
ТПЗ нал4-1,2 мин
ТПЗ нал5-0,3 мин
ТПЗ нал6-0,8 мин
ТПЗ нал7-1,2 мин
ТПЗ нал8-1,5 мин
ТПЗ нал9-0,4 мин
ТПЗ нал10-2,5 мин
ТПЗ нал = 13,1 мин
ТПЗ орг1-4 мин
ТПЗ орг2-2 мин
ТПЗ орг3-2 мин
ТПЗ орг-8 мин
ТПЗ = 8 + 13,1+
19,8 = 40,9 мин
Расчет
штучно-калькуляционного времени выполняется с учетом величины партии
обрабатываемых деталей, рассчитанной в пункте 1.2 «Определение типа
производства и его характеристика»:
(2.21)
3.
Расчётно-конструкторский анализ контрольного приспособления
3.1 Описание конструкции
приспособления контрольного
На операции 010 для контроля
взаимного расположения трёх отверстий 12
(Ø11), применяется контрольное
приспособление на расположения отверстий. Для контроля параметров калибр
кольцом 1устанавливается на торцевую поверхность детали 5(Ø75h11) при помощи двух ручек 2. Контроль отверстий 8 осуществляют три
штыря 3, которые при соблюдении требования располагаются в отверстиях.
3.2 Расчёт погрешности установки
детали при контроле
Произведём расчёт калибра:
. Предельные отклонения и допуски
диаметров измерительных элементов калибра определяется в зависимости от
позиционного допуска осей изделия
;
.1 для пробок:
F=0,053мм; H=0,012 мм; W=0,016мм
.2 для базовой пробки:
Н0=Н=0,012мм; Wo=W=0,016мм
. Предельные размеры пробок калибра:
.1 для базовой пробки:
Наибольший предельный размер
базового измерительного элемента калибра:
, мм
(3.1)
где dGO-W- размер предельно
изношенного поэлементного проходного калибра, предназначенного для контроля
размера поверхности изделия;
Dко max=75 мм.
Наименьший предельный размер
базового измерительного элемента калибра:
, мм
(3.2)
где Но - допуск на изготовление
базового измерительного элемента калибра; dkomin=75-0,012=74,988 мм
Размер предельно изношенного
базового измерительного элемента калибра:
(3.3)
где Wо - величина износа базового
измерительного элемента калибра;
dko-w=75-0,012-0,016=74,972 мм
.2 для остальных пробок:
Наибольший предельный размер
измерительного элемента калибра:
(3.4)
где Dmin - наименьший предельный
размер отверстия изделия; F - основное отклонение измерительного элемента
калибра; Н - допуск на изготовление измерительного элемента калибра;
dkmax=11-0,4+0,053+0,012=10,665 мм
Наименьший предельный размер
измерительного элемента калибра:
(3.5)=10,665-0,012=10,653 мм
Размер предельно изношенного
измерительного элемента калибра:
(3.6)
где W - величина износа
измерительного элемента калибра;
dk-w=10,665-0,012-0,016=10,637 мм
. Позиционный допуск осей пробок
калибра:
4. Организация производства на
участке
4.1 Определение количества
оборудования на участке
В серийном производстве
пооперационное расчётное количество станков определяется по формуле:
(4.1)
где ΣТШТ-К - суммарное штучно-калькуляционное время по всем операциям,
выполняемым на станке данной модели, мин;
N - годовой объём выпуска детали, шт;
FД - действительный годовой фонд производственного времени работы
оборудования, час (определяется индивидуально для каждой модели оборудования в
зависимости от категории его ремонтной сложности по таблице.
Расчётное количество оборудования
округляют до целого числа всегда в большую сторону.
Коэффициент загрузки оборудования
рассчитывается по формуле:
, %
(4.2)
где Сп - принятое количество станков
данной модели.
Расчётное количество станков для
базового технологического процесса:





Коэффициент загрузки оборудования
для базового технологического процесса:
%
На основании проведённых расчётов
построим график загрузки оборудования для базового варианта технологического
процесса.
Рисунок 4.1 - График загрузки для
базового технологического процесса
Расчётное количество станков для
проектного технологического процесса:

Коэффициент загрузки оборудования
для проектного технологического процесса:
Произведём дозагрузку станка TakisawaTNR-200YS и построим график
загрузки оборудования.
Рисунок 4.2 - График загрузки 85%
для проектного технологического процесса
Перечень однотипных деталей для
догрузки оборудования представлен в виде таблицы 4.1
Таблица 4.1 - Описание
механической обработки однотипных деталей
Наиме-нование и номер деталей
|
Годовой объем выпуска, шт
|
Масса, кг
|
Номер и наименование операции
|
Модель станка
|
Время обработки, мин
|
|
|
Детали
|
Заго-товки
|
|
|
ТМ (ТЦА)
|
ТВР
|
ТШТ-К
|
|
|
|
|
|
|
|
tус(+tп)
|
tизм
|
|
Корпус КВС-0217602
|
15000
|
0,79
|
1,98
|
010 Многоцелевая с ЧПУ
|
Takisawa TNR-200YS
|
3,65
|
0,17
|
0,75
|
4,51
|
Ступица ФРС0105634
|
6000
|
6,54
|
8,04
|
010 Многоцелевая с ЧПУ
|
Takisawa TNR-200YS
|
11,67
|
1,08
|
0,88
|
13,7
|
4.2 Определение
количества производственных рабочих
Численность производственных рабочих
для каждого рабочего места индивидуально определяется по формуле:
(4.3)
где FДР - эффективный годовой фонд
времени станочника, ч.
Произведём расчёт для базового
технологического процесса.


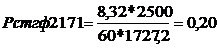

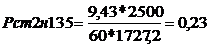
Произведём расчёт для проектного
технологического процесса.

Организация работает в двухсменном
режиме и исходя из этого следует принять количество рабочих для базового ТП -
10 человек, а для проектного - 2 человека.
С целью проведения анализа следует
рассчитать количество станков, которое может обслужить один рабочий на каждой
из анализируемых операций по формуле:
m£
,
станков (4.4)
m=
Принимаем 4 станка.
где: Тзан - время занятости рабочего
обслуживанием станков:
Тзан = tв.н.+ tв.п., мин (4.5)
=4,305
мин
где: tв.н. - время вспомогательное не
перекрываемое:
tв.н.= tус+ tуп, мин. (4.6)
=2,63
мин
где: tус - время на установку и снятие
детали (назначается по нормативам времени вспомогательного);
tуп - время на управление станком и устройством с ЧПУ (назначается
по нормативам времени вспомогательного для станков с ЧПУ в зависимости от типа
системы);
tв.п. - время вспомогательное перекрываемое:
tв.п. = tизм.+ tа.н.+ tпер, мин (4.7)
=1,675
мин
где: tизм. - время на контрольные
измерения (назначается по нормативам времени вспомогательного);
tа.н.. - время активного наблюдения за обработкой (назначается в
процентах от времени основного для станков-полуавтоматов или от времени цикла
автоматического для станков с ЧПУ);
tа.н.= 0,05*To = 0,05*TЦА, мин (4.8)
=0,76
мин
где: tпер. - время переходов от станка к
станку;
tпер. = 0,015*L, мин (4.9)
=0,05
мин
где: L - расстояние, проходимое рабочим
при переходе от одного рабочего места к другому:
L = Lст + Lпром, м (4.10)
L=1,785+1,5=3,285 м
где: Lст - длина станка, м, (по паспорту
станка);
Lпром - расстояниемежду станками, м, (в зависимости от габаритных
размеров станков: от 0,8 до 1,5 м);
TМ.С. - время машинное свободное:
TМ.С.= ТМ - tв.п, мин (4.11)
=16,174
мин
где: ТМ - время машинное; для
станков с ЧПУ время машинное равно времени цикла автоматического (сумме времени
машинного основного и машинного вспомогательного): ТМ=ТЦА
Заключительным этапом расчета
является расчет времени полного цикла многостаночного обслуживания для каждого
станка:
TЦ = Тм.с. + tв.п.= ТЦА+tв.н. = ТОП, мин (4.12)
=15,219+2,63=17,849
мин
и коэффициента
занятости рабочего при обслуживании всех предполагаемых к многостаночному
обслуживанию операций:
Кз = SТзан / TЦ,% (4.13)
где: SТзан - сумма времени занятости рабочего по всем операциям,
предполагаемым к многостаночному обслуживанию;
TЦ - время полного цикла многостаночного обслуживания, которое определяется
по наибольшему значению из анализируемых операций.
Исходя из расчётов можно сделать
вывод что рабочий загружен на 48% рабочего времени что является недостаточным.
Анализ возможности организации
многостаночного обслуживания при обработке однотипных деталей выполнен в форме
таблиц с исходными данными и результатами расчетов.
Таблица 4.2 -
Исходные данные для анализа возможности организации многостаночного
обслуживания
Наименование и номер деталей
|
Номер и наименование операций
|
Модель станка
|
Профессия и разряд работ
|
ТЦА, мин
|
tус,
мин
|
tуп,
мин
|
tизм,
мин
|
Ступица КВС
10109101
|
010 Многоцелевая с ЧПУ
|
Feller FTC350
|
Оператор 5 разряда
|
28,12
|
0,4
|
2,46
|
2,68
|
Ступица КЗК0105603
|
010 Многоцелевая с ЧПУ
|
Mazak HCN6800
|
Оператор 5 разряда
|
13,22
|
0,4
|
0,68
|
0,88
|
Таблица 4.3 -
Результаты расчетов по каждой операции, где оборудование позволяет организовать
многостаночное обслуживание
Модель станка
|
tа.н.,
мин
|
tпер.,
мин
|
tв.н.,
мин
|
Тм.с. мин
|
Тзан, мин
|
m,
станков
|
Тц, мин
|
Кз
|
Takisawa TNR-200YS
|
0,76
|
0,05
|
2,63
|
1,675
|
16,!74
|
4,305
|
4
|
17,849
|
|
FellerFTC-350
|
1,41
|
0,8
|
2,86
|
4,89
|
23,23
|
7,75
|
3
|
30,98
|
|
HCN6800
|
0,661
|
0,129
|
1,08
|
1,67
|
11,55
|
2,75
|
4
|
14,3
|
|
Расчет коэффициента занятости
|
14,745
|
11
|
30,98
|
0,48
|
Для окончательного определения возможности
обслуживания нескольких станков одним высококвалифицированным оператором
станков с ЧПУ построим график многостаночного обслуживания.
Рисунок 4.3 - График многостаночного
обслуживания
Результаты расчёта занесём в таблицу
4.4 с указанием итоговой величины следующих параметров: общая стоимость
станков, штучно-калькуляционное время, принятое число станков, расчетная и
принятая численность производственных рабочих в базовом и проектном вариантах
технологического процесса.
Таблица 4.4 - Расчет количества
оборудования и численности производственных рабочих
Номер операции
|
Модель станка
|
Стоимость станка, млн. руб.
|
Тшт-к, мин.
|
Ср.
|
Сп.
|
Кз,%
|
Профессия рабочего и разряд работ
|
Рст
|
Рп
|
Базовый вариант механообработки
|
010, 030
|
16К20
|
296,235
|
6,5 3,45
|
0,10
|
1
|
10
|
Токарь 3 разряда
|
0,24
|
2
|
020
|
1П426
|
317,394
|
18,53
|
0,19
|
1
|
19
|
Оператор 4 разряда
|
0,45
|
2
|
040
|
ГФ 2171
|
567,904
|
8,32
|
0,09
|
1
|
9
|
Оператор 4 разряда
|
0,20
|
2
|
060
|
EW 450R
|
254,471
|
4,3
|
0,04
|
1
|
4
|
Фрезеровщик 3 разряда
|
0,10
|
2
|
080
|
2Н135
|
104,506
|
9,43
|
0,10
|
1
|
10
|
Сверловщик 3 разряда
|
0,23
|
2
|
Итого
|
1836,745
|
50,53
|
-
|
5
|
-
|
-
|
1,22
|
10
|
Проектный вариант механообработки
|
010
|
Takisawa TNR 200YS
|
1693,545
|
21,758
|
0,23
|
1
|
23
|
Оператор 4 разряда
|
0,52
|
2
|
Итого
|
1693,545
|
21,758
|
-
|
1
|
-
|
-
|
0,52
|
2
|
4.3 Организация труда на участке
В конце каждой смены мастер участка
выдает необходимое количество заготовок для того, чтобы в начале следующей
смены не простаивало оборудование.
Смазывающая и охлаждающая жидкость,
ветошь выдается 1 раз в неделю с запасом. Заготовки транспортируются на участок
из заготовительного цеха, а вспомогательные материалы со складов, которые
находятся непосредственно в цехе или на территории предприятия. Заготовки из
заготовительного цеха на участок и готовые детали с участка в сборочный цех доставляются
электропогрузчиками. После того, как заготовки разгрузят в специально
отведенные места в цехе, их кран-балкой перемещают к рабочим местам в
специальной таре.
Весь внутризаводской транспорт
подчинен заместителю директора по общим вопросам.
Для улучшения работы
внутризаводского транспорта используют сквозной метод и внутрицеховой транспорт
без перегрузок.
Значительная часть запасов
инструмента (70%) хранится на общезаводском центральном складе.
Лучшим способом выдачи инструмента
является его доставка непосредственно на рабочее место. Это освобождает рабочих
от потерь времени при получении инструмента и способствует увеличению их
выработки.
4.4 Разработка плана участка
При разработке плана участка принята
ширина пролета 24 м с шагом колоны 12 м. Кроме того, вдоль стен расположены
колонны через каждые 6 м. На данном участке применяется внутрицеховой
транспорт, служащий для распределения полуфабрикатов между станками и другими
агрегатами, а также для удаления отходов (стружки, облоя и т.п.) за пределы рабочего
места и цеха. Ширина проезда принята, исходя из габаритов деталей, и составляет
3,5 м.
Для обработки детали Фланец ЖГР
20215602 на участке расположен станок TakisawaTNR-200YS.
Кроме детали, заданной для
проектирования на участке обрабатывается и другие детали типа «Опора». Поэтому
на плане участка представлены и другие станки, такие как ИР500ПМФ4, MazakHNC6800 и другие станки.
Оборудование на плане участка
расположено по видам обработки. Кроме того, на участке имеется место мастера,
место контролера, верстак для слесарных работ, моечная машина, тара для
заготовок и готовых деталей.
Площадь участка, занятая
оборудованием для обработки детали Фланец ЖГР 20215602:
S=S
+S
+S
+…+Sn м
(4.14)
где S
-
площадь занимаемая одним станком
S
=[(l×b)×k]×n, м
(4.15)
где l - длина станка, м
b - ширина станка, м
k - коэффициент зависящий от габаритов станка,
k=1,5 ( l×b св.20м
),
k=2 ( l×b св.10-20м
),
k=2,5 ( l×b св.6-10м
),
k=3 ( l×b св.4-6м
),
k=3.5 ( l×b св.2-4м
),
k=4 ( l×b менее 2м
).
n - число станков
В базовом варианте:
Sбаз=(2,505×1,19)
×3,5×2+(4,15×2,6) ×2×1+(3,68×4,17) ×2×1+(2,74×1,58) × ×3×1+(1,03×0,825)
×4×1=89,524 м 2
В проектном варианте:
Sпроект. =(1,785×1,458)×3,5×1=9,11 м2
Общая площадь участка с учётом
станков, обрабатывающих однотипные детали:дозагр.= (3,564×1,580)×3×3+(1,785×1,458)×3,5×4+(3,301×6,795)
×1,5×4=221,7 м2
На плане показан подвод к рабочим
местам энергоносителей, сжатого воздуха, охлаждающей эмульсии.
Участок обеспечен кран-балкой,
грузоподъемностью 3 тоны, уборка стружки осуществляется с помощью подпольного шнекового
конвейера.
Каждое рабочее место оснащается
индивидуальным освещением, обеспечивающим нормальную освещенность рабочей зоны.
Для размещения инструмента и деталей на каждом рабочем месте предусматривается
тумбочка.
На рабочем месте должна быть деревянная
решетка для защиты ног рабочего от стружки и сырости.
4.5 Средства механизации и
автоматизации элементов технологического процесса
Средствами автоматизации
производства являются использование станков с ЧПУ. Для условий серийного
производства нужны такие средства, которые сочетают высокую производительность,
точность обработки и гибкость при частой переналадке. При числовом программном
управлении перемещение рабочих органов станков осуществляется по программе.
Количество стружки (q), образующейся в час, при
выполнении годовой программы по всем типовым деталям, обрабатываемым на
участке, определяют по формуле:
(4.16)
где
- суммарная масса поступающих на участок заготовок типовых
деталей, кг.
-
суммарная масса готовых деталей, кг.
-
суммарный годовой объем выпуска всех деталей обрабатываемом на участке, шт.
Кз - коэффициент загрузки
оборудовании.
Fд - действительный фонд времени оборудования. Час.
При данном количестве стружки должна
быть принята система уборки стружки - М: механизированная с использованием
ручного труда, средств малой механизации и колесного транспорта, доставляющего
стружку в контейнерах в отделение переработки.
5. Мероприятия по энерго- и
ресурсосбережению
При сравнении базового и проектного
вариантов технологического процесса четко видна разница по материальным и
энергическим затратам.
В проектном варианте снизилась масса
заготовки, что позволит сократить затраты металла на каждую заготовку детали и
на годовой объем выпуска деталей.
Снижение металлоемкости заготовки
привело к уменьшению объема стружки при механической обработке. Следовательно,
снижается уровень потребления энергии металлообрабатывающим оборудованием на
каждую деталь и на годовой объем выпуска деталей.
Основными потребителями
энергоресурсов в машиностроительном комплексе являются металлургическое,
термообрабатывающее и гальваническое производство, где мерами энергосбережения
могут быть техническое перевооружение, использование энергии альтернативных
источников, в том числе, отходов собственного производства.
Но и в металлообрабатывающем
производстве используется значительное количество электроэнергии, затрачиваемой
на непосредственную обработку на металлорежущих станках, для работы
вспомогательного оборудования, на освещение, обогрев, на транспортирование
деталей, заготовок и стружки.
К снижению уровня энергопотребления
приводит использование в проектах оборудования с минимальной удельной нормой
потребления электроэнергии и с минимально возможной мощностью
электродвигателей.
, кВт
(5.1)
,кВт
(5.2)
кВт
(5.3)
6. Охрана труда и окружающей среды
6.1 Производственная санитария
Вредный производственный фактор -
это производственный фактор, воздействие которого на работающего в определенных
условиях может привести к заболеванию, снижению работоспособности и (или)
отрицательному влиянию на здоровье потомства.
К производственным вредностям в
механическом цехе (МЦ), где обрабатывается деталь «Фланец» ЖГР 20215602 можно
отнести: шум и вибрации исходящие от механизмов различных машин, недостаток в
освещении, выброс токсичных веществ, запыленность.
Для борьбы с запыленностью в цехе
используют естественную и местную вытяжную вентиляцию.
Для уменьшения шума и вибраций
предусмотрены защитные кожухи с шумо-и вибропоглощающими материалами. Станки
устанавливают на специальные вибропоглощающие опоры.
Максимальный уровень звука для
колеблющегося и прерывистого шума не должен превышать 80 дБА.
В цехе защита от шума
обеспечивается:
а) звукоизоляцией ограждающих
конструкций, уплотнением притворов окон, дверей, ворот и тому подобное.
б) установкой в помещениях и на пути
распространения шума звукопоглощающих конструкций и экранов.
в) применением глушителей
аэродинамического шума двигателя внутреннего сгорания и компрессорах и т.д.
г) созданием шумозащитных зон в
различных местах нахождения людей, использованием экранов и зелёных насаждений.
Вибрация возникает под действием внутренних
или вешних динамических сил вызванных плохой балансировкой вращающихся и
движущихся частей машин, движением техники по неровностям дороги, ударными
процессами технологического характера. Мероприятия по защите от вибрации
подразделяют на технические, организационные и лечебно - профилактические.
Промышленные пыли (аэрозоли) - это
мельчайшие частицы, образующиеся при различных произведенных процессах и
способные длительное время находиться в воздухе во взвешенном состоянии.
Промышленную пыль классифицируют по различным признакам: происхождению,
действию на организм человека, степени дисперсности, фракционному и химическому
составу, электрическим и магнитным свойствам, по взрывоопасности и т. д.Для
защиты дыхательной системы человека от вредных порошкообразных веществ
используют респираторы.
Задачей вентиляции является
обеспечение чистоты воздуха и заданных метеорологических условий в
производственных помещениях. Вентиляция достигается удалением загрязненного или
нагретого воздуха из помещения и подачей в него свежего воздуха.
Кондиционирование воздуха - это создание и автоматическое поддерживание в
помещениях независимо от наружных условий постоянных или изменяющихся по
определенной программе температуры, чистоты и скорости движения воздуха,
наиболее благоприятных для людей или требуемых для нормального протекания
технологического процесса.
В МЦ используется вентиляция с
естественным побуждением и с механическим. При естественной вентиляции
поступление и удаление воздуха происходит через окна, специальные проемы, двери
(неорганизованная вентиляция). Механическая вентиляция осуществляется
вентиляторами и используется приточно-вытяжная система.
Также в цехе предусмотрено
искусственное общее и местное освещение. Для улучшения естественного освещения
производится раз в год чистка стекол окон. Для искусственного освещения
проводятся проверки-рейды для смены перегоревших ламп.
Для проведения большинства видов
работ наиболее рациональным является естественный дневной свет, так как он
обладает в отличие от искусственного биологической активностью, т.е. способен
активизировать биохимические процессы в организме человека, тонизировать его,
убивать патогенные организмы.
Искусственное освещение
предусматривается в помещениях, в которых недостаточно естественного света, или
для освещения помещения в часы суток, когда естественная освещенность
отсутствует. Искусственное освещение подразделяется на рабочее, аварийное,
дежурное и охранное.
По характеру выполняемой работы
требуется усиленное освещение рабочего места, а общего освещения не ограничено,
то в этом случае устраивается дополнительное иное освещение. Одновременное
общее и местное освещение называется комбинированным.
Температурный режим производственных
помещений определяется количеством тепловыделений в цехе или в изолированной
его части от тепловыделяющего оборудования, нагретых и раскаленных изделий,
отопительных приборов, а также от солнечной радиации, проникающей в цех через
открытые и остекленные проемы.
Микроклимат производственных
помещений в цехах должен быть в зависимости от вида выполняемых работ.
Например, рабочие станочной группы имеют категорию работ средней тяжести,
значит, температура воздуха в холодный период года должна составлять 17-19°С,
относительная влажность 40-60%, скорость движения воздуха 0,2 м/с, температура
воздуха в теплый период года -19-22 0С, относительная влажность 40-60%,
скорость движения воздуха не более 0,2 м/с.
Все производственные и
вспомогательные помещения следует оборудовать вентиляцией. Воздух, удаляемый из
оборудования и рабочей зоны в атмосферу, с вредными примесями, должен очищаться
до предельно допустимых концентраций.
Объем производственного помещения на
каждого рабочего должен составлять не менее 15 м3, а площадь не менее 4,5 м2,
высота от пола до потолка - не менее 3,2 м.
Все оборудование, при эксплуатации
которого образуется пыль, должно быть максимально уплотнено, должно исключать
возможность поступления пыли в воздух производственных помещений.
Работы с инструментами, агрегатами и
приборами, создающими вибрацию, надо проводить в отапливаемых помещениях с
температурой воздуха не менее + 16°С, скоростью движения воздуха не более 0,3
м/с и влажностью 40-60%. В производственном цехе установлена естественная и
искусственная вентиляция, которая используется при недостатке естественной
вентиляции.
Производственный цех (участок)
обеспечивается достаточной освещенностью рабочих мест. В светлое время суток
обеспечивается естественное освещение, при его недостатке применяется
искусственное местное. Естественное освещение цеха осуществляется через оконные
проемы. Искусственное освещение бывает двух видов: общее, осуществляемое
светильниками, расположенными в верхней части здания и местное, осуществляемое
за счет светильников, расположенных непосредственно на рабочем месте. Они имеют
светоотражатели, защитный угол которых не менее 30º.
6.2 Безопасность труда
Безопасные условия
труда (безопасность труда) - состояние условий труда, при которых воздействие
на рабочего опасных и вредных производственных факторов исключено или
воздействие вредных производственных факторов не превышает предельно допустимых
значений.
Требование
безопасности при эксплуатации станкаTakisawaTNR-200YS.
Безопасность в
соответствии с ГОСТ12.3.002 обеспечивается выбором:
технологического
процесса, приемов, режимов резания и порядка обслуживания производственного
оборудования;
производственных
помещений и площадок;
исходных
материалов, заготовок и полуфабрикатов, а также способов их хранения и
транспортировки;
производственного
оборудования и его размещения.
Ширина проходов
вокруг станка обеспечивается:
при расположении
оборудования тыльными сторонами друг к другу должно быть не менее 1 метра;
при расположение
передними и тыльными сторонами друг к другу - не менее 1,5 метра;
при расположении
рабочих места друг против друга - не менее 3 метров.
Для обеспечения
защиты от поражения электрическим током при прикосновении к металлическим
нетоковедущим частям, которые могут оказаться под напряжением в результате
повреждения изоляции, используют следующие способы: защитные заземления,
защитные отключения, защитное зануление, применение малых напряжений,
предупредительная сигнализация, знаки безопасности. Помещения в цехе и на
участке, пребывание в которых связано с опасностью для работающих отделены друг
от друга изолирующими перегородками, имеют местную вентиляцию и знаки
безопасности.
Рабочее место
организуется с учетом эргономических требований в соответствии с ГОСТ12.2.061.
При эксплуатации
технического оборудования с электроприводом, человек подвергается не только
опасному воздействию электрического тока, но вредному влиянию магнитных полей.
По степени опасности поражения электротоком механические цеха относятся к особо
опасным.
Конструкция станка
должна сводит к минимуму возникновение для работающих опасных ситуаций при его
наладке, эксплуатации и ремонте.
Органы управления
станком:
доступны и
расположены с учетом эргономических факторов и не находиться в плоскости
режущего инструмента;
сконструированы и
размещены так, чтобы исключалось их непроизвольное перемещение;
размещены
относительно корпуса станка с учетом требуемых усилий для перемещения,
последовательности и частоты использования, а также значимости функций;
- выполнены таким
образом, чтобы исключить возможность скопления в них стружки и других отходов.
Подвижные части
станка (ременные, цепные, зубчатые и др. передачи), расположенные вне корпусов
станка и представляющие опасность для работающего, имеют защитные устройства.
Конструкцией станков предусмотрены предохранительные устройства от перегрузки,
которая может привести к поломке деталей станка или возникновению опасной
ситуации.
В станке для
обработки заготовок со скоростью резания более 50 м/с. рабочая зона выделена в
отдельную камеру.
Для
спроектированного приспособления необходимо выдержать следующие требования:
винты, крепящие
установочные и другие элементы к корпусу приспособления имеют потайную головку.
зажимные механизмы
обеспечивают надежное крепление детали.
применяются
ограничения движущихся частей.
приспособление не
имеет острых кромок и краев.
- зажимные
механизмы размещены с учетом безопасности и удобства при осуществлении зажима.
приспособление
сконструировано таким образом, чтобы исключить возможность скопления в нем
стружки
При закреплении
детали в кулачковом патроне или планшайбе следует захватывать деталь кулачками
на возможно большую величину. Нельзя допускать, чтобы после закрепления детали
кулачки выступали из патрона или планшайбы за пределы их наружного диаметра.
Патроны, планшайбы и другие зажимные устройства, имеющие на наружных поверхностях
выступающие части, ограждаются. В кулачковом патроне без подпора центром задней
бабки разрешается закреплять только короткие, длиной не более 2-х диаметров,
уравновешенные детали. При обработке детали длиной, равной 12 диаметрам и
более, а так же при скоростном и силовом резании деталей длиной, равной 8
диаметрам и более, необходимо применять дополнительные опоры. Нельзя работать
на забитых или сработанных центрах. При обточке длинных деталей следует следить
за центром задней бабки. Во избежание травм режущим инструментом необходимо:
включать сначала
вращение шпинделя, а затем подачу;
соприкасать резец
или другие инструменты с вращающейся обрабатываемой деталью плавно, без ударов,
с лёгким врезанием;
после того как
инструмент плавно врезался в обрабатываемую деталь, включить автоматическую
подачу;
перед остановкой
станка сначала выключить подачу, отвести режущий инструмент от детали, а затем
выключить вращение шпинделя.
резцовую головку
необходимо отводить на безопасное расстояние при следующих операциях: центровании
деталей на станке; зачистке; опиловке, шабровке и измерении деталей.
При смене патрона и
детали необходимо кроме отвода резцовой головки отвести подальше также центр
задней бабки. Следует строго следить за правильностью установки резца и не
подкладывать под него разные куски металла. Резец или другой инструмент должен
зажиматься с минимально возможным вылетом и не менее чем тремя болтами. Каждый
токарь должен иметь набор специально изготовленных подкладок различной толщины,
длиной и шириной не менее опорной части резца. Запрещается затачивать короткие
резцы без соответствующей оправки. При обработке вязких металлов, дающих
сливную ленточную стружку, необходимо применять резцы с выкрутками или
накладными стружко-ломателями или стружко-завивателями.
Категорически
запрещается поддерживать или ловить рукой детали при обработке или их отрезке.
Обрабатываемую
поверхность необходимо располагать как можно ближе к опорному или зажимному
приспособлению. Запрещается класть детали, инструмент и другие предметы на
станину станка и крышку передней бабки. Следует не забывать после закрепления
детали в патроне вынуть торцовый ключ, рукой провернуть патрон и, только
убедившись в свободном вращении, включить станок. Строго запрещается тормозить
вращение шпинделя нажимом руки на вращающуюся часть станка или детали.
Для транспортировки заготовок на
участок, для подъема и установки приспособления на станок применяют
подъемно-транспортные машины, которые при неправильном обслуживании и
эксплуатации могут быть источником опасности. Внутрицеховой транспорт
предназначен для распределения заготовок между станками, удаления отходов. К
нему относятся: тали, транспортеры, кран-балки, тележки.
По окончанию работы необходимо:
выключить станок и
электродвигатель;
привести в порядок рабочее
место, убрать со станка стружку, инструмент, приспособление, очистить станок от
грязи, смазать трущиеся поверхности станка;
ознакомить сменщика и
мастера о всех имеющихся неполадках в работе станка и о принятых мерах.
6.3 Пожарная безопасность
На проектируемом участке
предусмотрены предупреждающие мероприятия, исключающие возможность
возникновения пожара.
В соответствии с НПБ5-2000 все
здания по взрывопожарной и пожарной безопасности делятся на категории: А,
Б,В1-В4, Г1, Г2, Д. Здание ЦМ относится к категории Д.
Категория Д характеризуется наличием
несгораемых веществ и материалов в холодном состоянии.
Для организации пожарной
безопасности предусмотрено противопожарное водоснабжение, которое обеспечивает
подачу воды, необходимую для тушения пожара как внутри, так и снаружи здания.
Внутренний противопожарный
водопровод предназначен для тушения местных очагов возгорания до прибытия
пожарных подразделений. Пожарные краны, рукава и стволы помещают в специальных
шкафчиках на расстояниях 1,5 м от пола.
Первичные средства пожаротушения -
это такие средства, которые используются в начальной стадии загорания. Они
предназначены для ликвидации начинающихся очагов пожара силами персонала,
обнаружившего загорание.
К первичным средствам пожаротушения
в цехе мостов относятся: огнетушители. Пожарные щиты, укомплектованные шанцевым
инструментом (багор, кирка, лопата). Он применяется для тушения разлитой по
полу или земле горящей жидкости, электрооборудования и т.п.
В МЦ используются следующие виды
огнетушителей: жидкостные, углекислотные(ОУ-2А, ОУ-5, ОУ-8, ОУ-25, ОУ-80,
ОУ-400), порошковые и комбинированные(ОК-10). На участке обязательно проводится
противопожарный инструктаж с работающими всех профессий.
Основные противопожарные
мероприятия:
- правильный выбор электрооборудования,
постоянный контроль за
эксплуатацией электрооборудования;
- своевременная смазка трущихся
поверхностей;
- создание определенных условий,
изолирование нагретых деталей от изолированных проводов;
- герметизация трубопровода с
огнеопасными продуктами;
- запрещение хранения на рабочих
местах огнеопасной жидкости в открытых емкостях;
- своевременное удаление
промышленных тряпок и отходов в специально отведенные места.
Для безопасности эвакуации людей,
имеются более двух выходов наружу. Двери, предназначенные для эвакуации, легко
открываются в стороны выхода из здания.
Применение автоматических средств
обнаружения пожаров является одним из основных условий обеспечения пожарной
безопасности, так как позволяет оповестить дежурный персонал о пожаре и месте
его возникновения.
Системы автоматической пожарной
сигнализации состоят из пожарных извещателей, датчиков; линий связи,
применяемой станции.
.4 Охрана окружающей среды
Охране окружающей среды в нашей
стране придается большое значение, что обусловлено в первую очередь резким
возрастанием количества вредных выбросов промышленности, наносящий биосфере
огромный ущерб. В плане мероприятий по охране окружающей среды и рационального
использования природных ресурсов должны быть предусмотрены следующие группы
мероприятий: по охране и рациональному использованию водных ресурсов; по охране
воздушного бассейна.
Мероприятия по охране водных
ресурсов направлены на снижение забора свежей воды из поверхностных и подземных
источников, на уменьшение безвозвратных и непроизводительных условий траты
воды, на прекращение сброса неочищенных сточных вод, сокращение общего объема
стока, извлечения из сточных вод вредных веществ.
Мероприятия по охране воздушного
бассейна направлены на сокращение вредных выбросов в атмосферу, образующихся в
ходе производственного процесса и выбрасываемых транспортными средствами.
Мероприятия обеспечивают снижение не
только «организованных» выбросов, осуществляемых специальными газо - отводами и
вентиляционными системами, но и «неорганизованных», которые попадают в
атмосферу, минуя систему газо - отводов и вентиляции.
К мероприятиям по охране воздушного
бассейна относятся: создание и совершенствование установок по улавливанию и
обезвреживанию вредных выбросов, обеспечение герметичного технологического
оборудования, совершенствование технологических процессов.
Важнейшее значение в охране
окружающей среды имеет также централизованное удаление стружки. На данном
предприятии стружка собирается в бункеры-накопители и отправляется на
дальнейшую переплавку.
Для большинства технологических
процессов машиностроительного производства характерно образование твердых
отходов, а также шума и вибрации. К твердым отходам относится значительное
количество разнообразной пыли, задерживаемой пыле - увлажняющими установками.
Выделенные в процессе очистки
твердые или жидкие примеси утилизируются или вывозятся на свалку. Токсичные
примеси либо подвергаются захоронениям, либо обезвреживаются химическим или
термическим способом. Более высокая степень локализации загрязнений достигнута
путем изоляции и герметизации их источников, которая осуществляется с помощью
специальных камер.
Проблема уменьшения вибрации и
особенно шума имеет большое значение. Для механического цеха характерна
концентрация большого количества металлорежущего оборудования в помещениях,
имеющих плохие акустические характеристики. Работа на металлорежущем станке
требует свободы манипулирования в рабочей зоне станка. Это исключает
возможность применения звукоизолирующих кожухов. Поэтому основным направлением
в борьбе с шумом является его локализация. Для снижения уровня вибрации и шума
применяют высококачественные подшипники, малошумные зубчатые передачи с
электродвигателем.
С точки зрения максимального
предотвращения вредных веществ в производственных условиях наиболее
рациональными и перспективными является механизация и автоматизация
производственных процессов с помощью промышленных роботов, что позволяет
изолировать человека от воздействия пыли и газов.
Заключение
В ходе работы над проектом был
определен тип производства, дана его характеристика, произведён анализ детали
на технологичность, разработана технология обработки детали с применением
станков с ЧПУ; сделано обоснование метода получения заготовки и выбора
технологического оборудования; разработан комплект документов механической
обработки детали и чертежи детали, заготовки.
Анализ заводского техпроцесса,
показал, что в проектном варианте процесса обработки детали целесообразно
заменить все станки на многоцелевой станок TakisawaTNC200YS. За счет этого
пересчитаны режимы резания и нормы времени на обработку детали.
Штучное время на обработку
сократилось на 28,772 масса заготовки и норма расхода материала, которая
сократилась на 3,39 кг, это позволит сэкономить 1424 кг металла за год.
Разработаны мероприятия по энерго- и ресурсосбережению. Годовая экономия
электроэнергии составит 928 кВт.
Сопоставив полученные значения,
приходим к выводу, что предложенный новый технологический процесс экономически
выгоден.
Литература
1. Антонюк В.В. Конструктору станочных приспособлений:
справочное пособие / В.В. Антонюк. - Мн.: Беларусь, 1991.
. Анурьев В.И. Справочник конструктора-машиностроителя; Т.1
/ В.И. Анурьев. - М.: Машиностроение, 2001.
. Гжиров Р.И. Краткий справочник конструктора: справочник -
Л.: Машиностроение, 1983.
. Гжиров Р.И. Программирование обработки на станках с ЧПУ /
Р.И. Гжиров, П.П. Серебреницкий. - Л.: Машиностроение, 1990.
. Горбацевич А.Ф. Курсовое проектирование по технологии
машиностроения / А.Ф. Горбацевич, В.А. Шкред. - Мн.: Высш. шк., 1983.
. Дипломное проектирование по технологии машиностроения:
учебное пособие / под ред. В.В. Бабука. - Мн.: Высш. шк., 1979.
. Допуски и посадки: справочник в 2-х т. / под ред. В.Д.
Мягкова. - Л.: Машиностроение, 1983.
. Жданович В.В. Оформление документов дипломных и курсовых
проектов / В.В. Жданович. - Мн.: УП «Технопринт», 2002.
. Нефедов Н.А. Дипломное проектирование в
машиностроительных техникумах / Н.А. Нефедов. - М.: Высш. шк., 1986.
. Нефедов Н.А. Сборник задач и примеров по резанию и
режущему инструменту / Н.А. Нефедов, К.А. Осипов - М.: Машиностроение, 1990.
. Общемашиностроительные нормативы времени
вспомогательного, на обслуживание рабочего места и
подготовительно-заключительного на работы, выполняемые на металлорежущих
станках: средне-серийное и крупно-серийное производство. - М.: НИИтруда, 1984.
. Общемашиностроительные нормативы времени и режимов
резания для нормирования работ, выполняемых на универсальных и многоцелевых
станках с числовым программным управлением. Часть I и II. - М.: Экономика, 1990.
13. Проектирование технологических процессов в машиностроении:
учебное пособие для вузов / И.П. Филонов [и др.]; под общ. ред. И.П. Филонова.
- Мн.: УП «Технопринт», 2003.
14. Режимы резания металлов: справочник / Ю.В. Барановский [и
др.]. - М.: НИИТавтопром, 1995.
. Справочник технолога-машиностроителя в 2-х т. / под ред.
А.Г. Косиловой. - М.: Машиностроение, 1986.
. Технология машиностроения: методические рекомендации по
выполнению дипломных проектов для средних специальных учебных заведений. Специальность
Т03.01.00 Технология, оборудование и автоматизация машиностроения / М.В.
Крейцер и др. - Мн.: РИПО, 2001.