Механосборочный цех по выпуску гидротурбин с подробной разработкой технологического процесса изготовления детали 'Фланец'
Механосборочный цех по выпуску
гидротурбин с подробной разработкой технологического процесса изготовления
детали "Вал"
РЕФЕРАТ
механосборочный деталь вал конструкция
В ходе дипломной работы разработан технологический процесс изготовления
детали «вал»; определен тип производства; произведен анализ технологичности
конструкции детали; проведен технико-экономический анализ методов получения
заготовки; произведен расчет припусков на механическую обработку; рассчитаны
режимы резания; выбраны режущие инструменты, станок и контрольно-измерительные
средства; произведено техническое нормирование; рассчитана планировка
механосборочного цеха; выполнены технико-экономические расчеты; рассмотрены
вопросы охраны труда и окружающей среды.
При проектировании механического цеха использованы современные методы
строительства с применением унифицированных типовых секций и других элементов.
ВВЕДЕНИЕ
Машиностроение является важнейшей отраслью промышленности. Его продукция
- машины различного назначения - поставляются во все отрасли промышленности.
Машиностроения является основой технического прогресса и в связи с этим его
развитию всегда придавалось большое значение.
Современное мировое машиностроительное производство характеризуется
постоянным наращиванием выпуска продукции, резким повышением требований к его
качеству, позволяющей непрерывно совершенствовать их конструкцию.
Отсюда возникает необходимость организации гибкого переналаживаемого
производства, внедрения гибкого технологического оборудования во всех типах
производства: от мелкосерийного до массового. Главное условие здесь -
обеспечение максимальной экономической эффективности, т.е. производство изделий
с минимальными затратами труда и денежных средств.
Потребности развивающегося машиностроительного производства вызвали в
свое время появление такой технической науки как “Технология машиностроения”.
Технология машиностроения - это наука об изготовлении машин требуемого
качества в установленном производственной программе количестве и в заданные
сроки при наименьшей себестоимости.
Технология машиностроения как научная дисциплина создана советскими
учеными. Начало ее формирования относится к 30-ым годам ХХ столетия. Большой
вклад в развитие технологии машиностроения внесли А.И. Каширин, А.П.
Соколовский, В.М. Кован, Б.С. Балакшин и др. Технология машиностроения
продолжает развиваться и в наши дни.
В настоящее время для решения технологических вопросов в
машиностроительной промышленности разработаны теоретические основы технологии
машиностроения, научно обобщены прогрессивные методы обработки типовых
поверхностей деталей машин, установлены основные принципы проектирования
технологических процессов изготовления деталей машин и сборки. В последнее
время успешно решаются вопросы, связанных с разработкой систем автоматизирования
проектирования технологической подготовки производства и с развитием гибких
производственных систем.
Важная роль в ускорении научно-технического прогресса в машиностроении
отводится подготовке высококвалифицированных инженерных кадров, освоению ими
современных способов изготовления и контроля продукции, методик проектирования
прогрессивных технологических процессов.
В связи с этим выполняемая работа играет значительную роль в подготовке
инженеров-механиков по специальности “Технология машиностроения”.
1. РАЗРАБОТКА ТЕХНОЛОГИЧЕСКОГО ПРОЦЕССА МЕХАНИЧЕСКОЙ
ОБРАБОТКИ БАЗОВОЙ ДЕТАЛИ
механосборочный деталь вал конструкция
1.1 Служебное назначение, техническая характеристика изделия
и базовой детали
Данная деталь представляет собой вал ведущий и предназначена для
осуществления работы зубчатой передачи в редукторе. В детали предусмотрены
фаски для облегчения сборки. Шейки на детали необходимы для установки зубчатого
колеса и подшипников.
Деталь «Вал ведущий» имеет: шейки для посадки
подшипников (Ø30к6Ra1,6 );
шейка для посадки зубчатого колеса (Ø25h8Ra1,6), на которой выполнен шпоночный
паз (b=8h9); резьбовое отверстие
М8 для транспортировки; канавкиØ29,
обеспечивающие выход шлифовального круга.
Принятое поле допуска размеров шеек вала Ø30к6 и сопрягаемого с ним подшипника обеспечивает получение посадки
с натягом. Это гарантирует высокую степень их центрирования.
Поле допуска ширины шпоночного паза вала обеспечивает
соответственно плотный и нормальный вид соединения.
Таким образом, принятая конструкция детали обеспечивает
надежность и долговечность ее работы, т.к. материал детали, ее размеры и
расположение опорных поверхностей обеспечивают высокую жесткость и прочность:
для снижения концентрации напряжения в местах перехода
диаметров предусмотрены галтели;
высокая точность взаимного расположения опорных поверхностей
обеспечивает надежность зацепления.
Изготавливается «Вал
ведущий» из конструкционной легированной стали20ХГОСТ 4543
<#"897768.files/image001.gif"> (1.1)
где
Qу.э. -
количество унифицированных элементов;
Qэ. - количество элеметов.
2 Коэффициент точности обработки:
(1.2)
( 1.3)
где
Ai - квалитет точности для i
- размера;
ni -
число поверхностей детали точностью по Ai
квалитету.
А
=
К
=
>0,8.
Следовательно,
деталь технологична по коэффициенту точности.
.
Коэффициент шероховатости поверхности
, (1.4)
где
Бср- средняя шероховатость поверхности.
, (1.5)
где
Бi- шероховатость i-ой
поверхности;
Ni-
количество поверхностей, имеющих шероховатость Бi.
Б
К
< 0,32.
Деталь
технологична,
Следовательно,
деталь «Вал ведущий» технологична и по коэффициенту шероховатости поверхностей.
1.3 Определение типа производства
Тип производства - классификационная категория производства, выделяемая
по признакам широты номенклатуры, регулярности, стабильности и объёма выпуска
изделий Различают типы производства: единичный, серийный, массовый.
Единичное производство - производство, характеризуемое малым объёмом
выпуска одинаковых изделий, повторное изготовление и ремонт которых, как
правило, не предусматривается.
Серийное производство - производство, характеризуемое изготовлением или
ремонтом изделий периодически повторяющимися партиями. Величина повторяющихся
партий определяет производство как мелкосерийное, или среднесерийное, или
крупносерийное.
Массовое производство - производство, характеризуемое большим объёмом
выпуска изделий, непрерывно изготовляемых или ремонтируемых продолжительное
время, в течение которого на большинстве рабочих мест выполняется одна рабочая операция.
Тип производства по ГОСТ 3.1119-83 характеризуется коэффициентом
закрепления операций:
Кзо= 1 - массовое;
<Кзо<10- крупносерийное;
<Кзо<20- среднесерийное;
<Кзо< 40- мелкосерийное производство;
Кзо>40 - единичный тип производства. В соответствии с
методическими указаниями рд
50-174-80, коэффициент закрепления операций для всех разновидностей (подтипов)
серийного производства
Кзо =ΣПоб
/(ΣРi),
где ΣПоб- суммарное число различных операций за месяц по участку из
расчета на одного сменного мастера; ΣРi- явочное число рабочих участка,
выполняющих различные операции при работе в одну смену.
Программа выпуска продукции - установленный для данного предприятия
перечень изготовляемых или ремонтируемых изделий с указанием объёма выпуска по
каждому наименованию на планируемый период времени. Серийное производство
характеризуется ограниченной номенклатурой изделий, изготовляемых периодически
повторяющимися партиями, и сравнительно большим объемом выпуска, чем в
единичном типе производства. При серийном производстве используются
универсальные станки, оснащенные как специальными, так и универсальными и
универсально-сборными приспособлениями, что позволяет снизить трудоемкость и
себестоимость изготовления изделия. В серийном производстве технологический процесс
изготовления изделия преимущественно дифференцирован, т.е. расчленен на
отдельные самостоятельные операции, выполняемые на определенных станках. При
серийном производстве обычно применяют универсальные, специализированные,
агрегатные и др. металлорежущие станки.
Таблица 1.4 Определение типа производства
Производство
|
Число обрабатываемых
деталей одного типоразмера в год
|
|
тяжелых (массой более
100кг)
|
средних (массой более 10 до
100кг)
|
легких (массой до10кг)
|
Единичное Мелкосерийное
Среднесерийное Крупносерийное Массовое
|
До 5 5-100 100-300 300-1000
Более 1000
|
До 10 10-200 200-500
500-5000 Более 5000
|
До 100 100-500 500-5000
5000-50000 Более 50000
|
Тогда для данной детали массой 6,5 кг при числе обрабатываемых деталей
одного типоразмера 80 штук в год производство мелкосерийное [4,с.42].
1.4 Выбор метода и способа получения заготовки.
Технико-экономическое обоснование
Метод выполнения заготовок для деталей машин определяется назначением и
конструкцией детали, материалом, техническими требованиями, масштабом и
серийностью выпуска, а так же экономичностью изготовления.
Выбрать заготовку - значит установить способ ее получения, наметить
припуски на обработку каждой поверхности, рассчитать размеры и указать допуски
на неточность изготовления.
Так как материал детали сталь 20Х не является литейным, то в качестве
заготовки принимаем обработку металла давлением.
Прокат широко применяется в качестве заготовок и как конструкционный
металл для сварных изделий.
Плюсы: не требует сложного оборудования для получения заготовки. Покупаем
нужный профиль и отрезаем заготовку необходимой длины. Минусы: если деталь
имеет большие перепады ступеней, то заготовка из проката будет иметь небольшой
коэффициент использования материала (много металла уйдет в стружку);
максимальный диаметр 250 мм.
Заготовка может быть получена ковкой на молотах. Данный способ
применяется для деталей типа стержня с утолщением, колец, втулок, деталей с
отверстиями. Применяется для серийного и массового производства.
Преимущества ковки на молотах:
Позволяет получать высокое и стабильное качество металла по всему
сечению;
Возможность изготовления крупных поковок;
Для изготовления крупных поковок требуется сравнительно небольшие усилия;
Применение универсальных машин и в особенности универсального инструмента
позволяет получать широкую номенклатуру поковок и одновременно резко снизить
затраты.
Наряду с этим ковка на молотах имеет существенные недостатки:
низкая точность;
низкая производительность;
большие кузнечные напуски;
большие допуски и припуски.
Кривошипные
горячештамповочные прессы
<#"897768.files/image016.gif">
, (1.6)
где
Q - масса
заготовки, кг
q - масса
готовой детали
Sотх - стоимость 1 т отходов, руб
Стоимость заготовки, полученной штамповкой на КГШП
где kT, kc, kв, kм, kп - коэффициенты, зависящие соответственно от класса точности,
группы сложности, массы, марки материала и объема производства заготовок
Вывод: по минимуму приведенных затрат предпочтение следует отдать
заготовке из проката, что обеспечит наименьшую технологическую себестоимость
детали. Это свидетельствует о правильности выбора заготовки.
1.5 Анализ базового (типового) технологического процесса
механической обработки
Под технологическим маршрутом изготовления детали понимается
последовательность выполнения технологических операций (или уточнение
последовательности операций по типовому или групповому технологическому
процессу) с выбором типа оборудования. На этапе разработки технологического
маршрута припуски и режимы обработки не рассчитывают. Рациональный маршрут
выбирают с использованием справочных данных и руководящих материалов по типовым
и групповым методам обработки. Технологические маршруты весьма разнообразны и
зависят от конфигурации детали, ее размеров, требований точности, от объема
выпуска. Главный принцип - совместить конструкторскую, технологическую и
измерительную базы.
Базовый технологический процесс:
Операция 005: фрезерно-центровальная
Операция 010: токарно - винторезная
Операция 015: вертикально - фрезерная
Операция 020: горизонтално-расточная
Операция 025: круглошлифовальная
При базовом варианте производство детали является мелкосерийным. Для
такого типа производства характерно применение универсального оборудования и
непрогрессивных методов механической обработки. Зачастую в технологических
процессах наряду с универсальным оборудованием применяется и оборудование с
ЧПУ. В процессе изготовления деталь неоднократно перемещается с одной позиции
на другую и на операциях имеет место довольно большое количество переустановов.
Это отражается на операционном времени и увеличивает погрешности установки.
Припуски на обработку достаточно большие, поэтому необходимо значительное время
на их снятие, велики и затраты режущего инструмента.
Базовый ТП имеет следующие недостатки: большое количество
оборудования;большое время, затрачиваемое на перемещение заготовки от станка к
станку; возникновение значительной погрешности базирования из-за частых
переустановок заготовки; понижение точности обработки; большое число
задействованных рабочих мест; большая роль ручного труда; применение
универсального оборудования значительно увеличивает основное технологическое
время обработки заготовки (из-за множества переходов).
Как показал анализ базовый ТП является трудоемким и затраты на
механическую обработку могут быть снижены путем использования современного
оборудования. Предлагаем использовать малооперационную обработку на токарном
центре. При разработке структуры операций механической обработки необходимо
стремиться к достижению наиболее экономичного варианта.
Учитывая все замечания, отмеченные при анализе базового технологического
процесса, как показал анализ базовый ТП является трудоемким и затраты на
механическую обработку могут быть снижены путем использования современного
оборудования. Предлагаем использовать обработку на токарном обрабатывающем
центре. Маршрут обработки:
Операция: Токарная многоцелевая с ЧПУ
Операция: Круглошлифовальная
1.6 Выбор
технологических баз
Выбор технологических баз является основой построения технологического
процесса изготовления детали и имеет большое значение для обеспечения требуемой
точности обработки и экономичности процесса.
Общие рекомендации при выборе баз:
·
технологические
базы должны иметь необходимую протяженность для обеспечения устойчивого
положения заготовки при ее обработке;
·
обрабатываемая
заготовка должна иметь минимальные деформации от действия силы резания,
зажимной силы и от действия собственной массы;
·
в качестве технологической
базы следует принимать поверхности, обеспечивающие наименьшую погрешность
установки.
На первой операции должны быть обработаны те поверхности, которые будут
приняты за технологическую базу для последующей операции.
Так как технологической базой на первой операции будут необработанные
поверхности, следует выбирать те поверхности, которые обеспечивают по
возможности равномерное снятие припусков и достаточно точное взаимное
расположение обрабатываемых и не подлежащих обработке поверхностей.
Если все поверхности детали подвергают механической обработке, то в
качестве базы на первой операции следует выбирать поверхности с наименьшим
припуском, чтобы при последующей обработке не получилось брака из-за недостатка
припуска.
На второй и последующих операциях технологические базы должны быть
возможно точными по геометрической форме и по шероховатости поверхности.
Рекомендуется, если возможно, соблюдать принцип совмещения баз, т.е. в
качестве технологической базы принимать поверхности, которые будут одновременно
измерительной базой, и еще лучше, если они являются также конструкторскими
базами.
Необходимо придерживаться принципа постоянства баз на основных операциях
обработки, т.е. использовать в качестве технологических баз одни и те же
поверхности. Соблюдение этого принципа особенно важно, если измерительные базы
при выполнении различных операций переменны, и в связи с этим затруднительно
осуществить принцип совмещения баз. С целью соблюдения принципа постоянства баз
в ряде случаев на деталях создают искусственные технологические базы, не
имеющие конструктивного назначения (центровые гнезда валов, специально
обработанные отверстия в корпусных деталях при базировании их с помощью
установочных пальцев).
Если по условиям обработки не удается выдержать принцип постоянства базы,
то в качестве новой базы принимают обработанную поверхность, по возможности
наиболее точную и обеспечивающую жесткость установки заготовки.
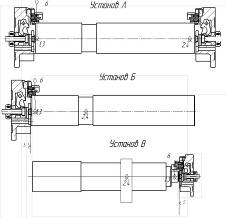
Рисунок 1.1 Схема базирования детали вал
1.7 Выбор оборудования и технологической оснастки
По маршруту обработки и исходя из технологических возможностей производим
выбор станка. При этом учитываем не только точность и шероховатость получаемых
поверхностей, но и стоимость, габариты, производительность, возможность работы
на оптимальных режимах резания, возможность механизации и автоматизации
выполняемой обработки.
1.7.1 Выбор оборудования
Рисунок 1.2 Токарно-обрабатывающий
центр Mori Seiki NL2500/500
Таблица 1.6 Техническая характеристика оборудования
NL1500/500
|
Макс. диаметр обработки, мм
|
366-386
|
Макс. длина обработки, мм
|
700
|
Размер патрона, дюйм
|
10” (12”)
|
Макс. диаметр прутка, мм
|
80
|
Перемещение по оси Х, мм
|
260
|
Перемещение по оси Z,
мм
|
590
|
Перемещение по оси Y,
мм
|
±50
|
Перемещение контршпинделя
(ось В), мм
|
624
|
Макс. скорость шпинделя,
об/мин.
|
4000/6000
|
Макс. скорость приводного
инструмента, об/мин
|
6000[8000]
|
Количество инструментов
|
12
|
Мощность двигателя
шпинделя, кВт
|
26/22
|
Масса станка, кг
|
5900
|
Рисунок 1.3 Круглошлифовальный
станок 3В161
Таблица 1.7 Техническая характеристика оборудования
3В161
|
Макс. диаметр обработки, мм
|
280
|
Макс. длина обработки, мм
|
1000
|
Мощность двигателя
шпинделя, кВт
|
13
|
Масса станка, кг
|
7200
|
.7.2 Выбор режущего инструмента
Одновременно с выбором оборудования и приспособления выбирается
необходимый режущий инструмент.
Режущий инструмент является составной частью комплексной
автоматизированной системы станка с ЧПУ, обеспечивающей его эффективную
эксплуатацию. От выбора и подготовки инструмента зависят производительность и
точность обработки. Для обеспечения автоматического цикла работы требуется
высокая надежность работы инструмента.
Режущий инструмент для станков с ЧПУ должен удовлетворять следующим
требованиям: обеспечение высоких и стабильных режущих свойств;
удовлетворительное формирование и отвод стружки; обеспечение заданных условий
по точности обработки; универсальность применения для типовых обрабатываемых
поверхностей различных деталей на разных моделях станков; быстросменность при
переналадке на другую обрабатываемую деталь или замене затупившегося
инструмента; обеспечение предварительной настройки на размер вне станка
(совместно с применяемым вспомогательным инструментом).
Таблица 1.8 Выбор режущего инструмента
№ операции
|
Наименование операции
|
Режущий инструмент
|
1
|
2
|
3
|
005
|
Токарная многоцелевая с ЧПУ
|
1. Сверло центровочное
2317-0008, ГОСТ 14952-75, Р6М5 2. Резец Sandvik PCLNR 2020K 12HP GC4225 3.
Резец Sandvik SCLCR 1616H 09HP GC4315 4. Резец канавочныйSandvik QS-RF123E11-1616BHP GT 525 5. Фреза концевая Sandvik 2Р340-0800-РА
|
010
|
Круглошлифовальная
|
1. Круг шлифовальный ПП
600х50х305
|
.7.3 Выбор станочных приспособлений
Таблица 1.9Станочное приспособление
№ операции
|
Наименование операции
|
Приспособление
|
005
|
Токарная многоцелевая с ЧПУ
|
1. Патрон трех кулачковый
самоцентрирующийся ГОСТ2675-80 2. Люнет
|
010
|
Круглошлифовальная
|
1. Патрон трех кулачковый
самоцентрирующийся
|
1.7.4 Выбор контрольно измерительных средств
Выбор измерительных средств производится с учетом соответствия точностных
характеристик инструмента точности выполняемого размера, вида измеряемой
поверхности, габаритов и массы детали, а также объема выпуска деталей.
Таблица 1.10 Выбор контрольно-измерительного средства
№ операции
|
Наименование операции
|
Контрольно-измерительные
средства
|
005
|
Токарная многоцелевая с ЧПУ
|
Измерительный щуп "HEIDENHAIN" TS 740 с инфрокрасным
приемопередатчиком: штангенциркуль ШЦ - 320 - 1000 - 0,05 ГОСТ 166 - 89
штангенциркуль ШЦ - II - 500 - 0,05 ГОСТ 166-89 микрометр МК - 50 - 0,01
ГОСТ6507 - 90 глубиномер ГОСТ 761 - 67 Линейка 1000 ГОСТ 427 - 75 Угломер
типа 1 - 2 ГОСТ 5378 - 88
|
010
|
Круглошлифовальная
|
Микрометр
МК40-1 ГОСТ 6507-90; Профилограф-профилометр;
|
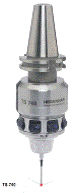
Рисунок 1.4 Измерительный
щуп "HEIDENHAIN" TS
740 с инфракрасным приемопередатчиком
1.8 Разработка операций механической обработки
Операция 005 - Токарная многоцелевая с ЧПУ.
Установить и закрепить заготовку.
Установ А.
Переход 1: проточить под люнет выдерживая размеры 50мм Ø
100мм
Установ Б.
Переход
2: Подрезать торец, выдерживая размеры Æ100
мм.
Переход 3: Просверлить отверстие, выдерживая размеры Æ5мм, 11±0,215 мм.
Переход
4: Точить поверхность, выдерживая размеры Æ100
мм, 300±0,4 мм.
Переход
5: Точить поверхность, выдерживая размеры Æ70-0,74
мм, 105±0,435 мм.
Переход
6: Точить поверхность, выдерживая размеры Æ40-0,62мм
мм, 85±0,37 мм.
Переход
7 : Точить поверхность, выдерживая размеры Æ30
мм, 60±0,37мм
Переход
8:Точить поверхность, выдерживая размеры Æ25
мм, 20±0,26 мм.
Переход
9: Точить поверхность, выдерживая размеры Æ25
мм, 20±0,26 мм.
Переход
10: Точить поверхность, выдерживая размеры Æ30
мм, 60±0,37 мм.
Переход
11: Точить поверхность, выдерживая размеры Æ100
мм,
300±0,65 мм.
Переход
12: Точить поверхность, выдерживая размеры 2х45°
Переход
13: Точить поверхность, выдерживая размеры 2х45°
Переход
14: Точить поверхность, выдерживая размеры 2х45°
Переход
15: Точить поверхность, выдерживая размеры 3х45°
Переход
16: Точить канавку, выдерживая размеры Æ29
мм, 2 мм.
Переход
17: Точить канавку, выдерживая размеры Æ98
мм, 2 мм.
Переход 18: Фрезеровать шпоночный паз, выдерживая размеры
8h9
мм ,18 ±0,2мм.
Переустановить
и закрепить заготовку.
Установ
В
Переход
19: Подрезать торец, выдерживая размеры Æ100
мм.
Переход 20: Просверлить отверстие, выдерживая размеры Æ5мм, 11±0,215 мм.
Переход
21: Точить поверхность, выдерживая размеры Æ100
мм, 170±0,5 мм.
Переход
22: Точить поверхность, выдерживая размеры Æ70
мм, 145±0,5 мм.
Переход
23: Точить поверхность, выдерживая размеры Æ40
мм, 125±0,5мм.
Переход
24: Точить поверхность, выдерживая размеры Æ30
мм, 100±0,435 мм.
Переход
25: Точить поверхность, выдерживая размеры Æ25
мм, 60±0,37 мм.
Переход
26: Точить поверхность, выдерживая размеры Æ25
мм, 60±0,37 мм.
Переход
27: Точить поверхность, выдерживая размеры Æ30
мм, 100±0,435 мм.
Переход
28: Точить поверхность, выдерживая размеры Æ100
мм, 300±0,65 мм.
Переход
29: Точить поверхность, выдерживая размеры 2х45°
Переход
30: Точить поверхность, выдерживая размеры 2х45°
Переход
31: Точить поверхность, выдерживая размеры 2,5х45°
Переход
32: Точить поверхность, выдерживая размеры 3х45°
Переход
33: Точить канавку, выдерживая размеры Æ29
мм, 2 мм.
Переход
34: Точить канавку, выдерживая размеры Æ98
мм, 2 мм.
Переход 35: Фрезеровать шпоночный паз, выдерживая размеры
8h9
мм ,58 ±0,37мм.
Снять
деталь.
Операция
010 - Круглошлифовальная.
Установить
и закрепить заготовку.
Установ
А
Переход
1: Шлифовать поверхность, выдерживая размеры Æ30
мм, 40±0,435 мм.
Переустановить
и закрепить заготовку.
Установ
Б
Переход
2: шлифовать поверхность, выдерживая размеры Æ30
мм, 40±0,435 мм.
Снять
деталь.
1.9 Назначение припусков на механическую обработку
1.9.1 Назначение припусков на механическую обработку и
допусков на размеры по стандарту
Назначение припусков и межоперационных размеров для наружной
цилиндрической поверхности Æ100h8.
Для получения данной поверхности достаточно двух переходов - точения
чернового и точения чистового
Минимальные припуски назначаем из справочника [18, с.193,табл.3.73]:
т. к. диаметр обрабатываемой поверхности находится в интервале св. 80 до
120 мм припуск на обтачивание черновое равен: 2Zmin(обтач.черн) = 2,5 мм,
припуск на обтачивание чистовое равен: 2Zmin(обтач.чист) = 0,3 мм
Назначение допусков.
Допуски назначаем из справочника [18, с.111-119]:
для заготовки из проката обычной точности, диаметр которой находится в
интервале 80÷120 мм, допуск равен:
d = 2,1 мм
после чернового обтачивания получаем поверхность 11 квалитета, диаметр
которой находится в интервале 80÷120 мм.
Допуск равен: d =
0,35 мм
после чистового обтачивания получаем поверхность 8 квалитета, диаметр
которой находится в интервале 80÷120 мм.
Допуск равен: d =
0,54 мм
Расчет минимальных диаметров:
минимальный диаметр для чернового обтачивания получаем вычитанием допуска
из максимального диаметра:
dmin(h8)= dmax(h8) - δ(h8) = 100 - 0,054= 99,946мм
минимальный диаметр для предыдущего перехода получаем сложением
минимального диаметра детали и припуска на механическую обработку:
dmin(11)=
dmin(h8) + 2zmin(h8) =99,946 + 0,3 = 100,246мм.min(14)= dmin(11) + 2zmin(11)
=100,246 + 2,5 = 102,746мм.
Расчет максимальных
диаметров:
максимальный диаметр получаем
прибавлением допуска к минимальному диаметру:
dmax(11)= dmin(1) + δ(11) =
100,246 + 0,35 =100,596 мм
dmax(заг)= dmin(заг) + δ(заг) =
102,746 + 2,1 =104,846 мм
Назначение операционных размеров.
Операционные размеры назначаются следующим образом: в диапазоне
минимального и максимального диаметров выбираем целое число (среднее между dmin и dmax). Затем находим верхнее и нижнее
отклонения. Нижнее отклонение - это разность минимального диаметра и выбранного
целого числа; верхнее отклонение - это разность максимального диаметра и
выбранного целого числа.
Таблица1.11 Расчёт припуска для Æ100-0,054
Наименование перехода
|
2zmin,
мм
|
2zmax,
мм
|
δ,
мм
|
dmin, мм
|
dmax, мм
|
Операционный размер, мм
|
Заготовка
|
-
|
-
|
2,1
|
108,3
|
110,4
|
Æ110
|
Черновое точение (11)
|
7,7
|
10,154
|
0,35
|
100,246
|
100,596
|
Æ100
|
Точение чистовое (8)
|
0,3
|
0,65
|
0,054
|
99,946
|
100
|
Æ100
|
Назначение припусков и межоперационных
размеров для наружной цилиндрической поверхности Æ25h8.
Для получения данной поверхности достаточно двух переходов - точения
чернового и точения чистового
Минимальные припуски назначаем из справочника [18, с.193,табл.3.73]:
т. к. диаметр обрабатываемой поверхности находится в интервале св. 80 до
120 мм припуск на обтачивание черновое равен: 2Zmin(обтач.черн) = 2,5 мм,
для диаметра в интервале до 30 мм припуск на обтачивание чистовое равен:
2Zmin(обтач.чист) = 0,3 мм
Назначение допусков.
Допуски назначаем из справочника [18, с.111-119]:
для заготовки из проката обычной точности, диаметр которой находится в
интервале 80÷120 мм, допуск равен:
d = 2,1 мм
после чернового обтачивания получаем поверхность 11 квалитета, диаметр
которой находится в интервале 18 - 30 мм.
Допуск равен: d =
0,13 мм
после чистового обтачивания получаем поверхность 8 квалитета, диаметр
которой находится в интервале 18÷30 мм.
Допуск равен: d =
0,33 мм
Таблица 1.12 Расчёт припуска для Æ25-0,033
Наименование перехода
|
2zmin,
мм
|
2zmax,
мм
|
δ,
мм
|
dmin, мм
|
dmax, мм
|
Операционный размер, мм
|
Заготовка
|
-
|
-
|
2,1
|
110,4
|
Æ110
|
Черновое точение (11)
|
82,683
|
85,133
|
0,35
|
25,267
|
25,617
|
Æ25
|
Точение чистовое (8)
|
0,3
|
0,65
|
0,054
|
24,967
|
25
|
Æ25
|
Таблица 1.13Расчёт припуска для Æ70-0,74
Наименование перехода
|
2zmin,
мм
|
2zmax,
мм
|
δ,
мм
|
dmin, мм
|
dmax, мм
|
Операционный размер, мм
|
Заготовка
|
-
|
-
|
2,1
|
108,3
|
110,4
|
Æ110
|
Черновое обтачивание h14
|
22,17
|
23,6
|
0,74
|
69,26
|
70
|
Æ70
|
Таблица 1.14Расчёт припуска для Æ40-0,62
Наименование перехода
|
2zmin,
мм
|
2zmax,
мм
|
δ,
мм
|
dmin, мм
|
dmax, мм
|
Операционный размер, мм
|
Заготовка
|
-
|
-
|
2,1
|
108,3
|
110,4
|
Æ110
|
Черновое обтачивание h14
|
68,3
|
71,02
|
0,62
|
39,38
|
40
|
Æ40-0,62
|
Таблица 1.15 Расчёт припуска для L=585±1,15
Технологическая операция
|
2Zmin, мм
|
2Zmax, мм
|
d, мм
|
lmin, мм
|
lmax, мм
|
Операционный размер
|
Заготовка
|
-
|
-
|
1,75
|
594,125
|
595,875
|
595±0,875
|
Подрезка торца
|
2 · 4
|
11,75
|
1,75
|
584,125
|
585,875
|
585±0,875
|
1.9.2 Расчёт припусков на механическую обработку и
межоперационных размеров на одну точную поверхность детали
Выбираем последовательность обработки поверхностей [1 стр.63]:
Квалитет 6 можно получить точением тонким и шлифованием - выбираем
точение тонкое в качестве последней обработки.
Прибавляем к квалитету 6 «3», получаем квалитет 9, который можно получить
точением чистовым, точением тонким и шлифованием. Выбираем точение чистовое;
Прибавляем к квалитету 9 «3», получаем квалитет 12, который можно
получить точением черновым и точением получистовым - выбираем более грубую
обработку - точение черновое; напуск снимаем за два рабочих хода режущего
инструмента, 60-70% за первый проход и 30-40% за второй проход.
Следовательно, для обработки цилиндрической поверхности 30к6 необходимо
точение черновое, точение чистовое и точение тонкое.
Для назначения допусков необходимо также вычислить квалитет заготовки. К
квалитету 12 поверхности, полученной после чернового точения, прибавляем «3» -
получаем квалитет 15заготовки.
Расчет проводим по формуле [1 стр.62]:
2zimin=2(Rzi-1+hi-1+
), где (1.7)
Rzi-1 - высота неровностей профиля на предшествующем
переходе;
hi-1 - толщина дефектного поверхностного слоя на
предшествующем переходе;
ρi-1 - суммарные отклонения
расположения поверхности;
εi-
погрешность установки заготовки на выполняемом переходе
Для
заготовки:
Rzзаг + hзаг=150 +
250=400 мкм [1 стр.63,табл.4.3.],
Суммарная пространственная погрешность заготовки:
,
где
ρко - общая
кривизна заготовки;
ρц -
погрешность зацентровки
где
Δк - удельная кривизна заготовки, по ГОСТ 2590-88 = 0,6мкм/мм
где
δ - допуск на диаметр заготовки, по ГОСТ 2590-88 = 2,1 мм
мкм,
εi- принимаем равной 0
Для точения чернового:
Rzточ.черн.+hточ.черн.=50+50=100мкм [4,с.99,табл.4.27.]
ρ=0,06·465=28 мкм [4,с.118]
εi- принимаем равной 0, т.к. деталь обрабатывается в
центрах.
Для точения чистового:
Rzточ.чист.+hточ.чист.=30+30=60мкм [4,с.99,табл.4.27.]
ρ=0,04·28=1,5 мкм [4,с.118]
εi- принимаем равной 0, т.к. деталь обрабатывается в
центрах.
Для точения тонкого:
Rzточ.
тонк.+hточ.тонк=10+20=30мкм [4,с.99,табл.4.27.]
ρ=0,02·1,5=0,03 мкм [4,с.118]
εi-принимаем равной 0, т.к. деталь обрабатывается в
центрах.
Рассчитаем припуски:
точение черновое:
2zточ.черн. =2(Rzзаг.+hзаг.+
) =2(400+465)=2·865мкм
точение
чистовое:
zточ.чист.=2(Rzточ.черн.+hточ.черн.+
)=2(100+28)=2·128мкм
точение
тонкое:
zточ.тонк=2(Rzточ.чист.+hточ.чист.+
)=2(60+1,5)=2·61,5мкм
Находим
допуски [2 стр.27-28, табл.2.6]:
для
заготовки 15 квалитета, диаметр которой находится в интервале 80÷120мм, допуск равен: d=1400мкм
после
чернового точения получаем поверхность 12 квалитета, диаметр которой находится
в интервале 30÷50мм, допуск равен: d=250мкм
после
чистового точения получаем поверхность 9 квалитета, диаметр которой находится в
интервале 30÷50мм, допуск равен: d=62мкм
после
тонкого точения получаем поверхность квалитета 6, диаметр которой находится в
интервале 30÷50мм, допуск равен: d=13мкм
Находим
расчетный диаметр:
расчетный
диаметр на окончательную обработку находится вычитанием допуска для данного
перехода из максимального диаметра:
dр(m6)= dmax(к6)-d(к6)=30,015
- 0,013=30,002мм
расчетный
диаметр для последующего перехода находится прибавлением к расчетному диаметру
предыдущего перехода двойного расчетного припуска предыдущего перехода:
dр= dр(i-1)+ 2zmin(i-1)/1000
р(9)=30,002+2·61,5/1000=30,125 ммр(12)=30,125+2·128/1000=30,381ммр(заг.)=30,381 +2·865/1000=32,111мм
Для валов расчетный диаметр dр равняется минимальному диаметру dmin. Находим максимальный диаметр dmax прибавлением допуска к минимальному диаметру dmin: dmax= dmin+d,
dmax(9)=30,125+0,062=30,187
мм
dmax(12)=30,381+0,25=30,631
мм
dmax(заг.)=
32,111+1,4=33,511 мм
Таблица
1.16 Результаты расчета припусков для
наружной цилиндрической поверхности Æ30k6(
)
Технолог переход
|
Элементы припуска,
мкм.
|
Расчет. припуск, , мкмРасчет размер, dр, мм
|
Допуск d, мкм
|
Предельные размеры, мм.
|
Предельные значения
припусков, мкм.
|
|
|
RZ +h
|
r
|
ε
|
|
|
|
dmin
|
dmax
|

|
|
Заготовка
|
400
|
465
|
-
|
-
|
80,66
|
1400
|
32,111
|
33,511
|
-
|
-
|
Точение черновое 12
|
100
|
28
|
-
|
2·865
|
80,433
|
250
|
30,381
|
30,631
|
1480
|
3130
|
Точение чистовое 9
|
60
|
1,5
|
-
|
2·128
|
80,135
|
62
|
30,125
|
30,187
|
194
|
506
|
Точение тонкое 6
|
30
|
0,03
|
-
|
2·61,5
|
30,002
|
13
|
30,002
|
30, 0
|
110
|
185
|
Итого:
|
1784
|
3821
|
Рассчитаем предельные значения припусков:
предельное
значение минимального припуска
выполняемого
перехода находится как разность минимальных диаметров предыдущего и
выполняемого перехода:
=dmin(9) - dmin(к6)=30,125
- 30,015= 110мкм
=dmin(12) - dmin(9)=30,381-
30,187= 194мкм
=dmin(заг) - dmin(12)=32,111
- 30,631=1480 мкм
предельное
значение максимального припуска
выполняемого
перехода находится как разность максимальных диаметров предыдущего и
выполняемого перехода:
=dmаx(9) - dmax(к6)=30,187
- 30,002= 185мкм
=dmаx(12) - dmax(9)=30,631
- 30,125= 506 мкм
=dmаx(заг) - dmax(12)=33,511
- 30,381= 3 130 мкм
Сумма
предельных значений припусков записывается в графе «Итого» в соответствующих
столбцах
и
:
∑(
)=
+
+
= 1480 + 194 + 110 = 1784 мкм
∑(
)=
+
+
= 3130 + 506 + 185 = 3821 мкм
1.10 Назначение и расчёт режимов резания
Расчет режимов резания напрямую зависит от выбранного инструмента. В
качестве основного производителя инструмента был выбран Sandvik.
При окончательном выборе любого режущего инструмента производитель дает
рекомендации по выбору режимов резания. На эти данные и будем опираться.
Переход
2, 19: Точить поверхность, выдерживая размеры Æ100
мм, 300±0,5мм. (черновое точение)
Таблица
1.17
1) Определение группы
обрабатываемого материала согласно ISO для стали 20Х ГОСТ 4543-71:
Обрабатываемый материал относится к группе Р (2.02) -низколегированная сталь,
закаленная и отпущенная, твердость по Бринеллю
275НВ.
|
1., стр. 24
|
2) Определение угла
заострения режущего клина: Выбираем обработку негативной пластиной
|
1., стр.3
|
3) Определение условий
обработки: Условия обработки принимаем хорошие, т.к. жесткость станка
высокая, геометрия заготовки достаточно простая, отсутствуют корка и окалина
|
1., стр 4
|
4) Определение геометрии
передней поверхности пластины по глубине резания (ар) и величине подачи (f):
Стружколомы фирмы SandvikCoromant кодируются, как правило, двумя буквами.
Первая буква, как правило, соответствует группе обрабатываемого материала
согласно стандарту ISO. Вторая буква определяет диапазон глубин резания и
подач, при которых обеспечивается удовлетворительное стружколомание. Глубина
резания 5-15, величина подачи 0,5-1,5 принимаем геометрию R (черновой
сружколом). Соответственно стружколомРR
|
1., стр. 6
|
5)
Выбор формы и размера СМП: Для черновой обработки выбираем пластину ромбической
формы (C) с углом при вершине 80° Рассчитываем минимальный
размер пластины по формуле:
где
- глубина резания;
- угол в
плане (
).
Определяем
минимальную длину режущей кромки:
мм
Выбираем
радиус при вершине пластины:
Максимальный
радиус при вершине пластины
;
На
основании каталога и рекомендаций методических указаний, для чернового точения
выбираем пластину CNMG120408PR.1., стр. 7
2., стр. А 49
|
|
6) Выбор инструментального
материала:Инструментальный материал выбираем по рекомендациям производителя
пластин: Для черновой обработки выбираем сплав GC4225.
|
2., стр. А 591-592
|
7) Выбор системы крепления
пластины в державке: Выбираем рычажное крепление пластины к державке:
|
2., стр А109
|
8) Выбор типа и размера
державки: По каталогу SANDVIK выбираем державку C5-PCLNR-35060-12
|
|
9)
Выбор режимов резания: Для определения диапазон глубин подач обратимся к
справочной информации каталога SANDVIK. 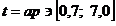
,
принимает
t = ap = 5 мм, S = fn = 0,4 мм/об
Для
выбранного сплава GC4225 и соответствующей группе обрабатываемого
материала (2.02) соответствует интервал скоростей резания Vc'[140; 255]. Выбираем
рекомендованную скорость резания Vc=180м/мин.2., стр. А567
10)
Время контактирования:
;
где
=300мм - длина обработки (чертеж детали);
- подача
на оборот;
- число
оборотов
где
- диаметр резания (чертеж детали)
-
скорость резания
Подставив в формулу
получим:
|
|
Переход
11, 28: Точить поверхность, выдерживая размеры Æ100
мм, 300±0,5мм.
Таблица
1.18
1) Определение группы
обрабатываемого материала согласно ISO для стали 20Х ГОСТ 4543-71:
Обрабатываемый материал относится к группе Р (2.02) -низколегированная сталь,
закаленная и отпущенная, твердость по Бринеллю
275НВ.
|
1., стр. 24
|
2) Определение угла
заострения режущего клина:Выбираем обработку позитивной пластиной
|
1., стр.3
|
3) Определение условий
обработки: Условия обработки принимаем хорошие, т.к. жесткость станка
высокая, геометрия заготовки достаточно простая, отсутствуют корка и окалина
|
1., стр 4
|
4) Определение геометрии
передней поверхности пластины по глубине резания (ар) и величине подачи (f):
Стружколомы фирмы SandvikCoromant кодируются, как правило, двумя буквами.
Первая буква, как правило, соответствует группе обрабатываемого материала
согласно стандарту ISO. Вторая буква определяет диапазон глубин резания и
подач, при которых обеспечивается удовлетворительное стружколомание. Глубина
резания 0,5-2, величина подачи 0,1-1,3 принимаем геометриюF
(чистовой сружколом). Соответственно стружколомРF
|
1., стр. 6
|
5)
Выбор формы и размера СМП: Для черновой обработки выбираем пластину ромбической
формы (C) с углом при вершине 80° Рассчитываем минимальный
размер пластины по формуле:
где
- глубина резания;
- угол в
плане (
).
Определяем
минимальную длину режущей кромки:
мм
Выбираем
радиус при вершине пластины:
Максимальный
радиус при вершине пластины
;
На
основании каталога и рекомендаций методических указаний, для чистового точения
выбираем пластину CCMT 09Т304 PF.1., стр. 7
2., стр. А 291
|
|
6) Выбор инструментального
материала: Инструментальный материал выбираем по рекомендациям производителя
пластин: Для черновой обработки выбираем сплав GC4315. GC4315
(HC) - P15 (P05-P25) Твёрдый сплав с покрытием CVD для чистового и чернового
точения стали и стального литья. Этот сплав рекомендуется для непрерывного
резания и прерывистого резания с лёгкими ударами. Сплав для работы с высокой
скоростью съема металла. Отличные характеристики благодаря новой технологии
покрытия Inveio.
|
2., стр. А 591-592
|
7) Выбор системы крепления
пластины в державке: Выбираем закрепление пластин винтом к державке
|
2., стр , А323
|
8) Выбор типа и размера
державки: По каталогу SANDVIK выбираем державку C5-SCLCR-350060-09
|
|
9)
Выбор режимов резания: Для определения диапазон глубин подач обратимся к
справочной информации каталога SANDVIK. 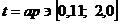
,
принимает
t = ap = 0,3 мм, S = fn = 0,11 мм/об
(рекомендуемые значения)
Для
выбранного сплава GC4225 и соответствующей группе обрабатываемого
материала (2.02) и принятой подачей выбираем рекомендованную скорость резания Vc=500м/мин.2.,
стр.А574
10)
Время контактирования:
;
где
=300мм - длина обработки (чертеж детали);
- подача
на оборот;
- число
оборотов
где
- диаметр резания (чертеж детали)
-
скорость резания
Подставив в формулу
получим:
|
|
Переход
15: Точить канавку 10, выдерживая размеры Æ29
мм, 2мм
Таблица
1.19
1) Определение группы
обрабатываемого материала согласно ISO для стали 20Х ГОСТ 4543-71:
Обрабатываемый материал относится к группе Р (2.02) -низколегированная сталь,
закаленная и отпущенная, твердость по Бринеллю
275НВ.
|
1., стр. 24
|
2) Определение условий
обработки: Условия обработки принимаем хорошие, т.к. жесткость станка
высокая, геометрия заготовки достаточно простая, отсутствуют корка и окалина
|
1., стр 4
|
3) Выбор формы и размера
СМП: Для обработки канавки 2 мм выбираем пластину СТ525
|
1., стр. 7
|
4) Выбор инструментального
материала:Инструментальныйматериал выбираем по рекомендациям
производителя:выбираем сплав СТ525
|
2., стр. В172
|
5) Выбор системы крепления
пластины в державке: Выбираем рычажное крепление пластины к державке:
|
cтр
B38
|
6) Выбор типа и размера
державки: По каталогу SANDVIK выбираем державкуC5-RF123E15C35060E
|
|
7) Выбор режимов резания:
Для определения диапазон глубин подач обратимся к справочной информации
каталога SANDVIK. принимает t = ap
= 0.5 мм, S = fn = 0,1 мм/об Для выбранного сплава GC4225
и соответствующей группе обрабатываемого материала (2.02) соответствует
интервал скоростей резания Vc'[215; 120]. Выбираем рекомендованную скорость резания Vc=150м/мин.
|
2., стр. В172 стр. В174
|
8)
Время контактирования:
;
где
=2мм - длина обработки (чертеж детали);
- подача
на оборот;
- число
оборотов
где
- диаметр резания (чертеж детали)
-
скорость резания
Подставив в формулу
получим:
|
|
Переход 31: Фрезеровать шпоночный паз 29, выдерживая размеры
8h9
мм, L=58 ±0,35мм, 21 мм.
Таблица
1.20
1) Определение группы
обрабатываемого материала согласно ISO для стали 20Х ГОСТ 4543-71:
Обрабатываемый материал относится к группе Р (2.02) -низколегированная сталь,
закаленная и отпущенная, твердость по Бринеллю
275НВ.
|
1., стр. 24
|
2) Определение условий
обработки: Условия обработки - хорошие
|
|
3) Выбор типа и размеров
фрезы: Выбираем тип обрабатываемой поверхности - фрезерование пазов. Если
для обработки необходима фреза диаметром менее 20 мм, цельные концевые фрезы
являются первым выбором для большинства материалов. Диаметр фрезы должен быть
равен ширине паза. Окончательно выбираем цельную концевую фрезу диметром 8
мм. Выбираем 2Р340-0800-РА/GC1630
|
1., стр.16 2., стрJ
283, J 324
|
4) Выбор инструментального
материала Инструментальный материал выбираем по рекомендациям производителя:
выбираем сплав GC1630.
|
2., стр. J324
|
5)
Определение режимов резания: Выбор режимов производится согласно рекомендациям
производителя в зависимости от инструментального сплава. Нашей пластине
соответствуют следующие значения: Подача на зуб
Для
выбранного сплава GC1630 и соответствующей группе обрабатываемого
материала (2.02) и принятой толщиной стружки выбираем рекомендованную скорость
резания Vc=90м/мин.
Число
оборотов:
Скорость
подач:
Время обработки: 2., стр. J490
|
|
.11 Техническое нормирование
В серийном производстве определяется норма штучно-калькуляционного
времени:
tш-к = tш + tп-з/n , [7, стр. 101],
tш - штучное время,
tш = tо + tв + tобсл + tп,
tо - основное время,
tв - вспомогательное время,
tв = tу.с + tз.о + tиз,
tу.с - время на установку и снятие
детали,
tз.о - время на закрепление детали,
tиз - время на измерение детали.
tо + tв = tоп. - оперативное время,
tобсл - время на обслуживание рабочего
места,
tп - время перерывов на отдых и личные
надобности,
tп-з - подготовительно-заключительное
время.
n -
количество деталей в партии:
n = П´А/F = 70´17/254 = 5дет.,
П - годовая программа выпуска,
А - число дней, на которое необходимо иметь запас деталей.
F - число
рабочих дней в году.
Основное время на мех. обработку получаем путем сложения основного
времени каждого перехода.
Операция 005 Токарная многоцелевая с ЧПУ
tо = Σtoi =
tу.с + tз.о =
0,13·2 = 0,26 мин. [7, стр. 199, прил. 5.5].
tиз = 
[7,
стр. 209, прил. 5.16].
tв = 0,26+3,2=3,46 мин.
tоп = 11,521+3,46=14,981 мин.
tп=
tш1 = 
.
Операция 010 Круглошлифовальная
t01 = l/n·S0+ tвыдержки =0,125/0,005·80+1=1,31 мин.
t02 = l/n·S0+ tвыдержки =0,006/0,004·60+1=1,025 мин.
t0= t01+ t02=1,31+1,025=1,335 мин.
tус +tзо=0,8 мин.
tуп=0,11·2 =0,22 мин, tиз=2·0,27=0,54 мин.
tB=tус +tзо +tуп +tиз =0,8+0,22+0,54=1,56 мин.
tоп= t0+tB=1,335+1,56=2,68
мин.
tобсл+ tп=1,5+0,05 tоп=1,63 мин.
tш2=t0+tB+tобсл+tп=1,68+1,63=3,07 мин.
Общее время:
t0ш= tш1+ tш=46,36+3,07=49,43 мин. - время малооперационного
технологического процесса.
t0шб=128,16 мин. - время базового технологического
процесса.
1.12 Сводная таблица режимов резания и норм времени
Таблица 1.21
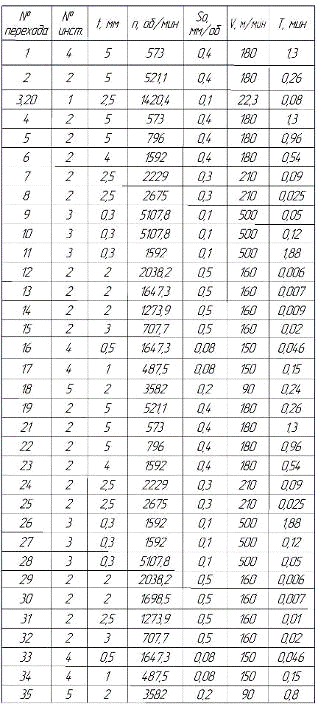
2. СПЕЦИАЛЬНЫЙ ВОПРОС
Для повышения производительности точения наружных поверхностей
разработана конструкция ротационного резца с вращающей чашкой.В качестве чашки
могут быть использованныстандартные режущие пластины с диаметром 35мм.,либо из
инструментальной стали Р6М5.
Применение ротационного резца позволяет повысить скорость резания не
менее чем в два раза по сравнении с резцами той же марки для обычных резцов.
Резец состоит из корпуса,чашки,вилки,отправки.Оптиминальный угол является
20º.
Винт (поз.6) обеспечить
свободное вращение чашки (поз.1) без ощутимого зазора в соединениях с шарами
(поз. 4-2раза).При регулировке зазоров в соединениях с шариками (поз.4-2раза)
гнезда деталей 3,6,9 заполнить консистентной смазкой ШРБ-4. По сравнению с другими резцами он имеет меньшие габариты и
большую жесткость, здесь предусмотрена возможность установки системы охлаждения
подшипников.
Наибольшая эфективность обеспечивается при чистовой,окончательной
обработки поверхностей при глубине резения не превышающую 1..2 мм.При этом
обеспечивается точность по 8-му квалитету и шероховатость поверхности не более Rа 2мкм.
Значительно выше и стойкость ротационных резцов. Резец позволяет производить
высокопроизводительную обработку деталей с припуском до 15 мм за один проход.
Благодаря вращению режущего элемента в процессе обработки стойкость резца от
переточки до переточки более чем в 10 раз выше, чем у невращающегося резца. Ротационный
резец может быть использован также для обработки неметаллических материалов,
например стеклопластиков. Годовой экономический эффект от внедрения резцов на
предприятии составил 3 тыс. руб.
3. РАСЧЕТ И ПЛАНИРОВКА ЦЕХА. ОРГАНИЗАЦИЯ ПРОИЗВОДСТВА
.1 Определение типа производства
Тип производства на начальном этапе проектирования, когда неизвестно
число оборудования и рабочих мест, укрупнено определяют в зависимости от
программы выпуска и массы деталей.Тип непоточного производства - единичный.
3.2 Расчет количества основного
оборудования
Количество металлорежущих станков и прессов в непоточном производстве
определяется по каждому типоразмеру оборудования для каждого участка на основе
данных о станкоёмкости деталей. Число станков каждого типа определяется в
зависимости от трудоемкости и фонда времени работы оборудования по следующей
формуле:
(3.1)
где Фд - действительный годовой фонд времени работы
оборудования, для универсальных станков - ФД=5945ч, для агрегатных
станков - ФД=5990ч., для автоматических линий - ФД=5465ч.
Полученные значения округляем до ближайшего большего целого числа.
,
принимаем Спр 1 = 14шт;
,
принимаем Спр 2 = 39шт;
,
принимаем Спр 3 = 2шт;
;
принимаем Спр 4= 6шт;
,
принимаем Спр 5 = 11шт;
,
принимаем Спр 6 = 3шт;
,
принимаем Спр7 = 8шт;
,
принимаем Спр 8 =7шт;
,
принимаем Спр 9 =19шт;
,
принимаем Спр 10 = 2шт;
,
принимаем Спр 11 = 4шт;
,
принимаем Спр 12 = 1шт;
,
принимаем Спр 13 = 2шт;
,
принимаем Спр 14 = 3шт;
,
принимаем Спр 15 = 8шт;
,
принимаем Спр 16 = 2шт;
,
принимаем Спр 17 = 4шт;
,
принимаем Спр 18 = 5шт;
,
принимаем Спр 19 = 13шт;
,
принимаем Спр 20 = 1шт;
,
принимаем Спр 21 = 2шт;
,
принимаем Спр 22 = 1шт;
,
принимаем Спр 23 = 1шт;
,
принимаем Спр 24 = 3шт;
,
принимаем Спр 25 = 9шт;
,
принимаем Спр 25 = 2шт;
,
принимаем Спр 25 = 4шт;
,
принимаем Спр 25 = 5шт;
,
принимаем Спр 25 = 2шт;
,
принимаем Спр 25 = 1шт;
,
принимаем Спр 25 = 3шт;
,
принимаем Спр 25 = 1шт;
,
принимаем Спр 25 = 1шт;
,
принимаем Спр 25 = 1шт;
,
принимаем Спр 25 = 2шт;
,
принимаем Спр 25 = 2шт;
,
принимаем Спр 25 = 4шт;
,
принимаем Спр 25 = 1шт;
,
принимаем Спр 25 = 2шт;
(3.2)
> 0,9
> 0,95
< 0,9
< 0,95
> 0,9
< 0,95
> 0,9
< 0,95
> 0,9
< 0,95
< 0,9
< 0,95
< 0,9
< 0,95
< 0,9
<0,95
< 0,9
< 0,95
<0,9
< 0,95
< 0,9
< 0,95
< 0,9
< 0,95
< 0,9
< 0,9
< 0,9
< 0,9
< 0,9
< 0,9
< 0,9
< 0,9
< 0,9
<0,9
< 0,9
< 0,9
< 0,9
< 0,9
< 0,9
Необходимо,
чтобы величина коэффициента загрузки не превышала средних по группе
[17.табл.3]. Для тех у которых превышает данный показатель, то производим
пересчет количества оборудования с помощью коэффициента использования
оборудования, по формуле:
(3.3)
,
принимаем С*пр1 = 17 шт.
,
принимаем С*пр2 = 44 шт.
,
принимаем С*пр5 = 13 шт.
,
принимаем С*пр 7 = 9 шт.
,
принимаем С*пр9 = 23 шт.
После
пересчета проверяем значение коэффициента загрузки, по формуле:
(3.4)
< 0,9
< 0,95
< 0,9
< 0,9
< 0,95
Определяем
общее количество станков в цехе:
Со=∑Спрi=17+44+2+6+13+3+9+7+23+2+4+1+2+3+8+2+4+5+13+1+3+1+1+9+3+2+4+4+2+1+3+1+1+1+2+2+4+1+2=216шт.
3.3 Определение количества
оборудования во вспомогательных подразделениях производства
Станочное оборудование применяется в следующих вспомогательных
подразделениях механосборочного цеха: в цеховой ремонтной базе (ЦРБ), в
ремонтной мастерской приспособлений (РМП) и в заточном отделении (ЗО).
, (3.5)
f - норма
количества станков по [17, с.13]:
mцрб= 2%
mрмп= 5%
mзо= 2%
Цеховая
ремонтная база:
С’црб
= mцрб·Сц
= 0,02 · 216 = 4,68 шт.
ПринимаемС’црб
= 5 шт.
Ремонтная
мастерская приспособлений:
С’рмп
= mцзо·Cц=0,05 · 216 = 10,7 шт.
Принимаем
С’рмп = 11шт.
Заточное
отделение:
С’зо
= mзо·Сц+
Спрот/Ки= 0,02·216+3/8+2/6 = 3,027 шт.
ПринимаемС’зо
= 4 шт.
Второе
слагаемое в формуле - количество заточных станков для зубообрабатывающих
инструментов. Третье слагаемое - кол-во станков для протяжных инструментов.
Общее
количество оборудования в цехе по формуле:
Cц общ=Сц+Сцрб+Срмп+Сзо
(3.6)
Сцо
= 216+5+11+4=237 шт.
3.4 Определение состава и численности
в механосборочных цехах непоточного производства
Состав работающих механического цеха в общем случае выглядит следующим
образом: производственные рабочие, главным образом станочники, вспомогательные
рабочие, инженерно-технические работники (ИТР), служащие, младший обслуживающий
персонал (МОП).
Число станочников при укрупненных расчетах определяют для каждого вида
оборудования по формуле:
, (3.7)
где Тс- суммарная станкоемкость изготовления деталей на
станках данного типа на участке или в цехе , ст/ч; Фр - эффективный
годовой фонд времени рабочего , 1820 ч. Км - коэффициент
многостаночного обслуживания - среднее количество станков, обслуживаемых одним
рабочим, Км =1,35.
Pст1=305030,5/1820·1,35=124,148;
принимаем 125человек;
Pст2= 4000,4/1820·1,35=16,282; принимаем
17человека;
Pст3 = 6000,6/1820·1,35=2,442; принимаем
3человек;
Pст4 = 62006,2/1820·1,35=25,23; принимаем26человек;
Pст5 = 148014,8/1820·1,35=60,242;
принимаем61человек;
Pст6 = 25002,5/1820·1,35=10,176;
принимаем11человек;
Pст7 = 10001/1820·1,35=7,418;
принимаем8человек;
Pст8 = 60006/1820·1,35=24,422;
принимаем25человек;
Pст9 = 30003/1820·1,35=12,211;
принимаем13человек;
Pст10 = 96009,6/1820·1,35=39,076;
принимаем 40человек;
Pст11= 19001,9/1820·1,35=7,733;
принимаем8человек;
Pст12 = 6000,6/1820·1,35=2,44; принимаем 3
человек;
Pст13 = 67006,7/1820·1,35=27,271;
принимаем28 человек;
Pст14 = 30003/1820·1,35=12,21; принимаем13
человек;
Pст15 = 30003,6/1820·1,35=13; принимаем13
человек;
Pст16 = 16001,6/1820·1,35=6,52; принимаем7
человек;
Pст17 = 5000,5/1820·1,35=2,035; принимаем3
человек;
Pст18 = 8000,8/1820·1,35=3,25; принимаем4
человек;
Pст19 = 24002,4/1820·1,35=9,78;
принимаем10 человек;
Pст20 = 13001,3/1820·1,35=5,297;
принимаем6 человек;
Число наладчиков определяем по формуле:
, (3.8)
где
Сцi - число станков данной группы; ci - норма обслуживания станков одним наладчиком по [17,
с.17].
Pнал1 = 17/10=1,7 , принимаем 2 человек,
Pнал2= 2/10=0,21, принимаем 1 человек,
Pнал3 = 11/10=1,1 , принимаем 2 человек,
Pнал4 = 3/2=1,5 , принимаем 2 человек,
Pнал5 = 7/3=2,33 , принимаем 3 человек,
Pнал6 = 2/6=0,33, принимаем 1 человек,
Pнал7 = 2/6=0,33, принимаем 1 человек,
Pнал8 = 1/3=0333, принимаем 1 человек,
Pнал9 = 3/16=0,179, принимаем 1 человека,
Pнал10 = 2/16=0,125, принимаем 1 человек,
Pнал11 = 5/16=0,312, принимаем 1 человек,
Pнал12 = 1/6=0,166 принимаем 1 человек,
Pнал13 = 1/6=0,166, принимаем 1 человек,
Pнал14 = 9/16=0,5525, принимаем 1 человека,
Pнал15 = 2/16=0,125 принимаем 1 человека,
Pнал16 = 5/3=1,33, принимаем 2 человека,
Pнал17 = 1/3=0,333, принимаем 1 человека,
Pнал18 = 1/4=0,25 принимаем 1 человека,
Pнал19 = 2/6=0,333, принимаем 1 человека,
Pнал20 = 1/6=0,166, принимаем 1 человека,
Число
сборщиков при непоточной сборке определяют по формуле:
Рсб=0,29Тст/Фр
(3.9)
Общее
число сборщиков:
Pсб общ = 193·1,05=202,65 человек. Принимаем 203 человек.
Pо = 424+26+203=653 человек.
Определим
Определим предварительно распределение производственных рабочих по сменам:
P1о = Pо · 0,5,
(3.10)
P1о = 653· 0,5 = 326,5 , принимаем P1о = 327 человека.
P2о = Pо· 0,3,
(3.11)
P2о = 653· 0,3 = 196,9 , принимаем P2о = 196 человека.
P3о = Pо - (P1о+P2о), (3.12)
где
Ро - общее число производственных рабочих, P1о-число производственных рабочих в первую смену, P2о-число производственных рабочих во вторую смену, P3о -число производственных рабочих в третью смену.
P3о = 653-327-196= 130 ,принимаем P3о = 130 человек.
Число
вспомогательных рабочих (Рв), инженерно-технических работников (Ритр) и
служащих (Рс) определяют по нормам в зависимости от числа производственных
работающих и типа производства
Рв
= Ро * k', (3.13)
Ритр
= Ро* k'' (3.14)
Pc
= Po * k''', (3.15)
где
k',k'',k''' - нормы по [1, с.18-19]
Рв
= Р0· k' = 653·0,25=163,25 чел., принимаем Рв = 164
человек;
принимаем
=22 человек.
человек,
принимаем
человека
Pсл
= Р0·k''' = 653·0,022 = 14,366, принимаем Pсл = 15
человек.
Вспомогательные
рабочие, ИТР и служащие распределяются по сменам следующим образом:
P1В = 164·0,5 = 82, принимаем 82человек,
P2В = 164·0,3 = 49,5, принимаем 50человек,
P3В = 164-82-50 = 32 , принимаем 32 человека
P1ИТР = 90·0,5 = 44,1принимаем 45 человека
P2ИТР = 90·0,3 = 27принимаем 27 человека
P3ИТР = 90-45-27 = 18 человек
P1СЛ = 15·0,7 = 10,5человек, принимаем 11 человек
P2СЛ = 15-11=4 человека.
Число
работников младшего персонала принимаем:
PМОП = =0,015·653=9,795 человек, принимаем PМОП = 10 человек.
Общее
количество работников в цехе:
P =
653+164+114+10+15=956 человек.
Распределение
по сменам работников происходит следующим образом:
P1 = 327+82+57+11+1-=487 человек
P2 = 196+50+35+4=285 человек
P3 = 130+22+32=184 человек
Полученные
данные записываем в таблицу:
Таблица
2.2 Состав и количество работающих
Состав работающих
|
Число работающих
|
|
Всего
|
1 смена
|
2 смена
|
3 смена
|
- Токари
|
145
|
73
|
44
|
28
|
- Расточники
|
61
|
31
|
19
|
11
|
- Карусельщики
|
26
|
13
|
8
|
5
|
- Фрезеровщики
|
78
|
39
|
24
|
15
|
- Сверловщики
|
41
|
21
|
13
|
7
|
- Строгольщики
|
19
|
10
|
6
|
3
|
- Долбежники
|
8
|
4
|
3
|
1
|
- Протяжники
|
3
|
2
|
1
|
|
- Специальные
|
10
|
5
|
3
|
2
|
- Шлифовальщики
|
23
|
12
|
7
|
4
|
- Зуборезчики
|
4
|
2
|
2
|
|
- Центровщики
|
6
|
3
|
2
|
1
|
- Наладчики
|
26
|
13
|
8
|
5
|
- Сборщики
|
203
|
102
|
61
|
40
|
Всего производственных
рабочих:
|
653
|
330
|
201
|
122
|
Вспомогательные рабочие:
|
164
|
82
|
50
|
32
|
Инженерно-технические
работники:
|
114
|
57
|
35
|
22
|
Служащие:
|
15
|
11
|
4
|
|
3.5 Состав и расчет транспортной
системы цеха
Число мостовых кранов в одном пролете: по формуле
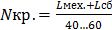
(3.16)
Принимаем
количество мостовых кранов - по 2в каждом пролете. Грузоподъемность кранов Q=75/35
т.
3.6 Определение производственной и
вспомогательной площадей цеха
3.6.1 Производственная площадь цеха
Производственная площадь - площадь, занимаемая производственным
оборудованием, включая места для рабочих, хранение заготовок, деталей, рабочие
места для слесарно-сборочных и слесарных операций, технического контроля,
средств наземного межоперационного транспорта, проходы и технологические
проезды между оборудованием и рабочими местами внутри производственных участков
и отделений.
Площадь участков механической обработки укрупнено определяют по формуле:
мех = Cц · Fуд, (3.17)
где Сц - принятое число станков в цехе; Fуд
- средняя удельная площадь, приходящаяся на один станок или верстак, Fуд
=25м2
Sмех = 216·37,5 = 8100м2;
Площадь участков сборки рассчитывают по двум методикам:
) Либо в долях от площади мехобработки:
Sсб=(0,2…0,5)·Sмех (3.18)
где Sмехплощадь участков механической
обработки
Sсб = 0,35·8100 = 2835 м2;
) Либо по формуле:
Sсб = Pсб1·fуд (3.19)
где Рсб1 - принятое число рабочих-сборщиков в цехе, работающих
в первую смену (таблица 1.2); fуд- средняя удельная производственная
площадь, приходящаяся на одного рабочего, [1, табл.17]).
Для дальнейших расчетов примем Sсб = 3825 м2.
Производственная площадь цеха определяется по следующей формуле:
Sц = Sмех + Sсб (3.20)
где S мех - площадь участков и отделений механообработки, Scб
- площадь участков сборки
Sц = 8100+3825=11925 м2;
3.6.2 Вспомогательная площадь цеха
Вспомогательная площадь - площадь, занятая вспомогательными службами:
ремонтным, инструментальным хозяйством, системой контроля качества, складами и
кладовыми и др.
Размеры вспомогательной площади определяются по нормам. Нормы
определяются по [1, табл.18-21];
. Участок приготовления СОЖ:
Sсож = 10- 35/99 · (300-216) = 70,264 м2;
. Склад ГСМ:
Sгсм = 25 м2;
. Энергетические и санитарно-технические установки:
Sэсту = 75 м2;
. Архив:
Sа = 30 м2;
. Изолятор брака:
Sиб = 30 м2;
. Цеховая ремонтная база:
Sцрб = Сцрб·28,5=5·28,5 =
142,5 м2;
. Ремонтная мастерская приспособлений и инструментов:
Sрмп = С’рмп·22 = 11·22 = 242
м2;
. Заточное отделение:
Sзо = С’зо·12 = 5·12 = 60 м2;
. Помещение для хранения стружки:
Sхс = Cц -(Сц не образ.стржку)·0,375=204·0,375= 76,5 м2,
. Отделение по переработке стружки:
Sпс = Cц -(Сц не образ.стржку)·0,75=204·0,75=153м2
. Мастерская энергетика:
Sмэ = 0,2·Sцрб = 0,2· 142,5 = 28,5 м2;
. Помещение ОТК:
Sотк = 0,05·Sц = 0,04·11925 = 324 м2;
. Помещение КПП:
Sкпп = Сц общ.·0,15=237·0,15=35,55
м2;
. Трансформаторная подстанция:
Sтп = 11925·50/5000 = 119,25 м2;
. Компрессорная установка:
Sку = 0,07·Sц = 0,07·11925 =834,75 м2;
. Вентиляционная камера:
Sвк = 0,075·Sц = 0,075·11925 = 745,3125м2;
. Склад металла и заготовок:
Sмиз = 0,125·Sмех = 0,125·8100 = 1012,5 м2;
. Межоперационный склад:
Sмо = 0,085·Sмех = 0,085·8100 = 688,5м2;
. Склад готовых деталей:
Sгд = 0,1·Sмех = 0,1·8100 = 810 м2;
. Склад покупных и комплектующих изделий:
Sпки = 0,1·Sсб = 0,1·3825 = 382,5 м2;
. Склад готовых узлов:
Sгу = 0,06·Sц = 0,06·11925 = 715,5 м2;
. Склад готовых изделий:
Sги = 0,1·Sц = 0,1·11925 = 1192,5 м2;
.Кладовая абразивов:
Sка = 0,4·Cшлиф = 0,4·12 = 4,8 м2;
. Кладовая ЦРБ:
Sкцрб = 0,15·Sцрб = 0,15·142,5 = 17,8125 м2;
. Инструментально-раздаточная кладовая:
Sирк = 0,475·Сц = 0,475·216 =
102,6 м2;
. Кладовая приспособлений и инструментальной оснастки:
Sкп = 1,6·Сц = 1,6·216 =
345,6 м2;
. Участок хранения, сборки и разборкиУСП и УСПО:
Sусп = 0,45·Сц = 0,45·216 =
86,4 м2;
. Кладовая вспомогательных материалов:
Sвм = 0,1·Сц = 0,1·216 = 21,6
м2;
. Кладовая приспособлений для сборки:
Sкпс = 0,8·Рсб = 0,8·203 =
162,4 м2;
. Кладовая вспомогательных материалов сборки:
Sвмс = 0,1·Рсб = 0,1·203 =
20,3 м2;
. Суммарная площадь вспомогательных подразделений: по формуле 1.44
Sвсп=70,264+25+75+30+30+142,5+168+70+34,75+139+19,2+401,25+30,8+80,25+642+601,875+781,875+521,25+521,25+281,25+561,75+802,5+14,4+97,3+305,8+62,55+13,9+1+12,5=
=8554,639м2
Определяем площадь магистральных проездов:
SМП = (0,4…0,6)·SВСП (3.21)
Где Sвсп - вспомогательная площадь
цеха
SМП = 0,5·8554,639=4277,319 м2
Общая площадь цеха
Sцобщ= Sц + Sвсп + Sмп (3.22)
где Sц - производственная площадь цеха, Sвсп- вспомогательная площадь цеха,Sмп - площади магистральных проездов.
Sцобщ=11925+8554,639+4277,319=24756,9585м2
По полученной площади выбирают унифицированные типовые секции (УТС), из
которых будет состоять цех. Выберем следующие УТС для проектируемого цеха:
Две основных УТС:72х144 м, площадью 10368 м2;
Две вспомогательные УТС 30х72 м, площадью 2160 м2;
Разность площадей: по формуле
SΔ = Sзд - Sцобщ (3.23)
SΔ = 25056 - 24756б9585=299,041 м2.
3.7 Расчет площадей служебно-бытовых
помещений
В механосборочных цехах проектируют следующие помещения:
. Служебные:
а) административно-конторские (кабинет начальника цеха и его
заместителей; планово-диспетчерское бюро; бюро труда и зарплаты; помещение бухгалтерии);
б) инженерно-технические службы (техническое бюро цеха; конструкторское
бюро цеха;
в) залы совещаний.
Площадь служебных помещений при укрупненных расчетах определяется из
следующего расчета:
комнаты административно-конторского персонала и инженерно-технических
служб: по формуле
Sа-к =
sа-к∙(Р1итр + Р1сл) + 18, (3.24)
где sа-к - удельная площадь на одного
работающего, 4 м2;
Р1итр, Р1сл - число ИТР и служащих, работающих в первую смену;
- площадь кабинетов начальника цеха и его заместителя, м2.
Sa-к =
4·(57+11) + 18 = 290 м2;
Площадь отдельных кабинетов не должна быть менее 9 м2.
залы совещаний, определяются по формуле:
Sзс = Sзс∙Ритр, (3.25)
где Sзс - удельная площадь на одного
участника совещаний вместимостью до 100 человек - 1,2 м2 на одно
место, вместимостью более 100 человек - 0,9 м2 на каждое место; Ритр
- число участников совещаний.зс = 0,9·114 = 102,6 м2;
. Бытовые:
а) Гардеробные блоки (гардеробные; душевые; умывальные).
Данные помещения следует объединять в гардеробные блоки. Они должны
располагаться на первом этаже и должны быть отдельными для мужчин и женщин. В
одном гардеробном блоке должно располагаться не более 400 ... 500 человек.
Душевые кабины и умывальники не должны устанавливаться у наружных стен. При
укрупненных расчетах гардеробных блоков площадь определяется из расчета по
формуле:
Sг = sг∙Р, (3.26)
где sг∙ - удельная площадь на
одного работающего, 2,6 ... 2,8 м2;
Р - общее число работающих в цехе.г = 2,7·956 = 2581,2 м2;
Площадь душевых составляет примерно 20 ... 30 % от площади гардеробных
блоков и включается в их состав. Гардеробные и душевые площади помещений
разделяют на мужские (70 … 80 %) и женские (20 … 30%).
Душевые для мужчин Sдуш м= Sгм
·0,25=1935,9·0,25=483,975 м2;
Душевые для женщин Sдуш ж= Sгж ·0,25=645,3·0,25=161,325
м2;
Гардеробные для мужчин Sгм=2581,2·0,75=1935,9 м2;
Гардеробные для женщин Sгж=2581,2-1935,9=645,3 м2;
б) Санитарные узлы (уборные).
Расстояние от санузлов до рабочих мест не должно быть более 75 м. Они не
должны размещаться под и над рабочими помещениями административно-конторских и
инженерно-технических служб, а также под и над столовыми, буфетами,
общественными организациями. Они располагаются на каждом этаже многоэтажных
производственных зданий. Площадь санузлов определяется из расчета, по формуле:
Sсу = Sсу∙Р1, (3.27)
где sсу - удельная площадь на одного
работающего в первую смену, 0,2 м2;
Р1 -число работающих в цехе в первую смену. су = 0,2 ·490 = 98
м2;
Данные помещения также разделяют на мужские (70 … 80 %) и женские (20 …
30%).
Для мужчин Sсу м=0,7·98=73,5 м2;
Для женщин Sсу ж=98-73,5=24,5 м2;
в) Комнаты для личной гигиены женщин.
Данное помещение создается в цехе, если в наиболее многочисленной смене
работает более 50 женщин. При укрупненных расчетах ориентировочная площадь этих
комнат принимается равной:лг = 25...30 м2.
Примем площадь комнаты для личной гигиены женщин:лг = 30 м2.
г) Курительные комнаты для мужчин и женщин.
Площадь курительных комнат определяется из расчета:
Sккм =
Sккм∙Р1м, (3.28)
Sккж =
Sккж∙Р1ж, (3.29)
где Sккм - норма площади на одного
работающего в наиболее многочисленной смене для мужчин 0,03 м2; Sккж - норма площади на одного
работающего в наиболее многочисленной смене для женщин 0,01 м2; Р1м,
Р1ж - число работающих мужчин и женщин в 1 смену.
Sккм =
0,03 ·367 = 11,01м2;
Sккж =
0,01 ·123 = 1,23 м2;
Площадь курительных комнат для мужчин и ля женщин не должна быть менее 9
м2. Поэтому принимаем площади курительных камер:
Sккм =
11,01м2;
Sккж =
9 м2.
д) Комнаты отдыха.
Комнаты отдыха предусматриваются только при тяжелых работах. Площадь этих
помещений следует принимать из расчета, по формуле:
Sко = Sко∙Р1, (3.30)
где Sко - удельная площадь на одного
работающего в первую смену, 0,2 м2;
Р1 -число работающих в цехе в первую смену.ко = 0,2 ·490 = 98 м2.
е) Столовые и буфеты.
В зависимости от числа работающих в наиболее многочисленную смену
предусматривают:
при 250 человек и более - столовые;
менее 250 человек - буфет (с отпуском горячих блюд, поставляемых из
столовой).
Площадь определяется из расчета, по формуле:
Площадь определяется из расчета
Sб = Sс∙Р1, (3.31)
где Sс - удельная площадь на одного
работающего в первую смену, 0,7 м2;
Р1 -число работающих в цехе в первую смену.с = 0,7 ·490 = 343 м2.
ё) Площадь помещения общественных организаций определяется по формуле:
Sоо = Sоо∙Роо, (3.32)
где Sоо - удельная площадь общественных
помещений, приходящаяся на одного работающего, (2…4 м2/чел);
Роо - общее число, находящихся в данном помещении, чел.
Sоо = 3·4=12 м2.
ж) Медпункт рассчитывают по формуле:
Медпункт рассчитывают по формуле:
м = 0,2·88 = 19,6 м2; (3.33)
где Sc - норма площади на одного
посетителя, 0,2 м2;
Полезная площадь служебно-бытовых помещений определяется по формуле:
Sс-б =
Sа-к + Sзс + Sг + Sсу +Sлг + Sккм +
Sккж + Sко + Sс + Sоо + Sм (3.34)
c-б=290+102<6+2581,2+98+30+11,01+9+98+343+12+19,6=3594,41м2.
Выбираем УТС: пристрой длиной 60 м, шириной 12 м высотой - 4 этажа
Вычислим площадь проходов и лестничных клеток по формулам:
Sпрох = 2·60·4 = 480 м2.
Sлк = 6·2,8·2·4 = 134,4 м2
Общая площадь служебно-бытовых помещений, определяется по формуле:
Sос-б
= Sс-б + Sпрох + Sл.к.
(3.37)
Sос-б=
3584,41+480+134,4=4198,81м2.
Превышение площади служебно-бытовых УТС Sc-б над площадью Sос-б не должно быть больше 300 м2:
SΔc-б=4320-4208,81<300 м2.
3.8 Компоновочное решение цеха
Компоновка цеха - взаимное расположение смежных отделений, участков,
складов, пристроек и других структурных элементов цеха.
Вспомогательные службы размещают вдоль наружных стен здания. Оставшаяся
площадь предназначена для размещения оборудования.
При компоновке вспомогательные помещения располагают группами по
технологической однородности выполняемых работ и сразу определяют площади
данных групп помещений:
. ЦРБ, кладовая ЦРБ, мастерская энергетика: по формуле
S1 = Sцрб + Sкцрб + Sмэ (3.38)
1 =142,5+17,8125+28,5=188,8125м2;
2. РМП, кладовая приспособлений и инструмента, участок УСПО, ЗО,
инструментально-раздаточная кладовая, кладовая абразивов: по формуле
2
= Sуспо + Sкпс + Sкп + Sрмп + Sзо
+ Sирк + Sка (3.39)
2
= 86,4+162,4+345,6+242+60+102,6+4,8=1003,8м2;
. ОТК, контрольно-поверочный пункт: по формуле
S3 = Sотк + Sкпп (3.40)
3 = 324+35,55=359,55 м2;
4. Участок СОЖ, ГСМ, энергетические и санитарно-технические установки: по
формуле
S4 = Sсож + Sгсм + Sэсту (3.41)
4=70,264+25+75=170,264м2;
5. Участок хранения стружки, участок по переработке стружки, изолятор
брака: по формуле
S5 = Sхс + Sиб
+ Sпс (3.42)
5 = 76,5+30+153=259,5м2;
6. Компрессорная установка, трансформаторная подстанция, вентиляционная
камера: по формуле
S6 = Sтп + Sку
+ Sвк (3.43)
6 =119,25+834,75+745,3125=1699,3125;
7. Архив, склад вспомогательных материалов: по формуле
S7 = Sа + Sвм
+ Sвмс (3.44)
7 = 30+21,6+20,3=71,9м2;
Затем эти группы разбивают на две макрогруппы, таким образом, чтобы их
площади были примерно равны.
SI = 781,875+129,6+828,65+127,6768+193,75=2634,8765м2
SII=802,5+281,25+432,05+1324,125+46,4=3705,7625
Размеры участков определяем следующим образом: - для составляющих длину
цеха (кроме магистральных проездов): по формуле
Li = Si/ВЦ , (3.45)
LI =SI/ ВЦ =2634,876/144=18,297
м,
Lмех = Sмех/ ВЦ=8100/144=61,031 м,
Lмо = Sмо/ ВЦ=688,5/144=4,781 м,
Lгд = Sгд/ ВЦ=810/144=5,696 м,
Lсб = Sсб/ ВЦ =3825/144=26,5625 м,
Lгу = Sгу/ ВЦ =715,5/144=4,968 м,
LΔ = SΔ/ ВЦ =299,041/144=2,076м,
LII = SII/Вц=3705,7625/144=25,734
м.
Ширина магистрального проезда должна быть в пределах 4,5 … 6 м и
определяется по формуле: по формуле
Lмп = Sмп/(Вц · к) (3.46)
Lмп = 4277,319 / (72 ·5) = 5,940 м
Принимаем k = 5
Проверим общую длину цеха:
L=18,6327+61,39583+7,2396+7,2396+39,0625+7,802083+(5,20001*5)+7,139201+40,0868=173,99993
м ≈174м.
Рассчитаем ширину вспомогательных помещений: по формуле
Группа I:
ВIi= SIi/LI (3.47)
Вмиз = Sмиз /LI=781,875/18,297 =55,336м;
Вцрб = Sцрб/ LI=96/18,297 =7,781 м;
Вкцрб= Sкцрб /LI=14,4/18,297 =0,973 м;
Вмэ = Sмэ /LI=19,2/18,297 =1,556 м;
Вкп = Sкп /LI =305,8/18,297 =18,888м;
Вуспо=Sуспо/LI=62,55/18,297 =4,722м;
Вкпс= Sкпс /LI =125/18,297 =8,875м;
Врмп = Sрмп /LI=168/18,297 =13,226 м;
Взо= Sзо /LI=70/18,297 =3,279 м;
Вирк = Sирк /LI=97,3/18,297 =5,607 м;
Всож = Sсож /LI=57,6768/18,297 =2,01437 м;
Вгсм = Sгсм /LI=20/18,297 =0,6985021 м;
Вэсту = Sэсту /LI=50/18,297 =1,746255м;
Вхс = Sхс /LI=34,75/18,297 =1,21365 м;
Виб = Sиб /LI =20/18,297 =0,6985021м;
Впс = Sпс /LI=139/18,297 =4,8546 м;
Проверим общую ширину помещений группы I:
ВI=27,3071+3,35281+0,5029215+0,6706+2,1846+4,36564+10,6801+5,86742+2,44476+3,398213+2,01437+0,6985021+1,746255+1,21365+0,6985021+4,8546=143,99998м≈144
м.;
Группа II: по формуле
ВIIi= SIIi/LII (3.48)
Вги = Sги /LII= 802,5/40,0868=20,01906 м;
Впки = Sпки /LII= 281,25/40,0868=7,016025 м;
Вотк = Sотк /LII= 401,25/40,0868=10,00953 м;
Вкпп = Sкпп /LII= 30,8/40,0868=0,768333 м;
Втп = Sтп /LII= 80,25/40,0868=2,001905 м;
Вку = Sку /LII= 642/40,0868=16,015247 м;
Ввк = Sвк /LII= 601,875/40,0868=15,0143 м;
Ва = Sа /LII= 20/40,0868=0,49892 м;
Ввм= Sвм /LII= 13,9/40,0868=0,34675 м;
Ввмс= Sвмс /LII= 12,5/40,0868=0,31182 м.
Проверим общую ширину помещений группы II:
ВII=20,01906+7,016025+10,00953+0,768333+2,001905+16,015247+15,0143+0,49892+0,34675+0,31182=143,99993
м≈144 м.
Определим площади каждого участка механической обработки по формуле:

, (3.49)
)
Участок токарной обработки:
Sток = 82·37,5 = 3075 м2;
)
Карусельный участок:
Sкарус =12·37,5 = 450 м2;
)
Сверлильный участок:
Sсверл = 18·37,5 = 675 м2;
)
Расточной участок:
Sраст = 30·37,5 = 1125м2;
)
Фрезерный участок:
Sфрез = 35·37,5 = 1312,5 м2;
)
Специальный участок:
Sспец = 6·37,5 = 225м2;
)
Строгольный участок:
Sстрог = 9·37,5 = 337,5 м2;
)
Протяжной участок:
Sпрот = 2·37,5 = 75м2;
)
Долбежный участок:
Sдолб = 4·37,5 = 150 м2;
)
Зубообрабатывающий участок:
Sзуб = 3·37,5 = 112,5 м2;
)
Шлифовальный участок:
Sшлиф = 12·37,5 = 450 м2;
)
Отрезной участок:
Sотрезн = 3·37,5 = 112,5 м2;
Разделим
полученные участки на 2 примерно равные группы.
.
Токарный, сверлильный, долбежный, зубообрабатывающий:
S1=Sток+Sсвер+Sдолб+Sзуб
(3.50)
S1=3075+675+150+112,5=4012,5м2;
.
Специальный, фрезерый, сстрогальный,протяжной,отрезной, шлифовальный:
S2=Sспец+Sфрез+Sстрог+Sпротяж+Sпрот+ Sотр+Sшлиф
(3.51)
S2=712,5+712,5+900+112,5+112,5=4087,5 м2;
Уточним
длину участка механической обработки:
Lм = Lмех + Lмо + Lмп·(k-m)
(3.52)
где
Lмех длина
участка механической обработки, Lмо ширина
межоперационного склада, Lмп ширина
магистрального проезда
Lм=61,031+2,076=63,107 м2.
Ширина
участков механической обработки:
, (3.53)
где
S1 , S2 - площадь первой и второй групп станков S∆
- дополнительная площадь; Lмп - ширина магистрального проезда; к - число
магистральных проездов; m - число магистральных проездов, уже размещённых в
цехе; х - число вновь назначенных магистральных проездов, размещаемых вдоль
пролётов (1,2,3,4…), выбираемое таким образом, чтобы ширина магистрального
проезда была от 4,5 до 6 м;Lм - уточнённая длина участка механической обработки .
Тогда:
(3.54)
=63,582+64,770+4,73+10,910=143,9992м.
Рассчитаем
длины участков механической обработки по формуле:

(3.55)

(3.56)
где
Si1 , Si2 - площади участков, входящих в состав первой и второй
гупп мехобработки ; B1, B2 - ширина участков механической обработки
Участки
первой группы
Lток = 3075 / 63,582= 46,362 м,
Lкарус = 450/ 63,582= 6,947 м,
Lсвер= 675/ 63,582= 10,616 м,
Lдолб = 150 / 63,582= 2,359 м,
Участки
второй группы
Lспец = 712,5/
=23,67596м,
Lфрез = 712,5/
=23,67596
м,
Lстрог= 900/
=29,90648
м,
Lдолб = 112,5/
=3,73831
м,
Lпрот = 112,5/
=3,73831
м,
Проверим
длину участка механической обработки:
ΣL1 =
13,12796+34,61+26,255925+10,74106=63,106 м.
ΣL2=23,67596+23,67596+29,90648+3,73831+3,73831=63,103м.
3.9 Выбор строительных элементов и
конструкций
Здание цеха
Сетка колонн:
Для основных УТС - 12х36
Для дополнительной УТС - 12х30; 12х30 м.:
Высота цеха - 18 м.
Несущая конструкция:
основные УТС - тип Г [1, рис. 13]
дополнителтные УТС - тип Г [1, рис. 13]
Тип здания - крановое
Высота головки кранового рельса 13,8м
Толщина стен -51см.
Колонны - прямоугольные, размером 600х1900мм.
Сечение подколонника - 1200х2700 мм.
Подошва - 6000х7200 мм.
Перегородки - металлические на каркасе.
Двери:
Вдв=
(3.57)
Вдв=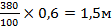
Предусматривается
по 2 двухстворчатой двери ширина - 1,5 м; высота - 2,2 м.
Ворота
(откатные)
Ширина
ворот - 4,5 м;
Высота
ворот - 3 м.
Тамбуры:
Ширина
- 5,1 м;
Глубина-
6,5 м.
Лестничные
клетки:
Ширина
- 2,8 м
Длина
- 3,2 м.
Световые
фонари:
Тип
К [1, рис. 14.] - М-образные с вертикальным остеклением.
Высота
фонарей - 2м.
Ширина
фонарей - 12 м.
Служебно-бытовые
помещения
Тип
задания - пристрой размерами 18х60 м и высотой 4 этажа.
Сетка
колон - 6х6 м.
Высота
этажа - 3,3 м.
Несущие
конструкции - типБ [1, рис. 13]
Ширина
проходов - 2,0 м.
Толщина
пола - 400 мм.
Толщина
покрытия цеха вместе с утиплителем 400мм
4. ТЕХНИКО-ЭКОНОМИЧЕСКИЕ РАСЧЕТЫ
4.1 Расчет себестоимости детали вал
Тема дипломного проекта «Механосборочный цех по выпуску приводов
конвейеров с подробной разработкой технологического процесса изготовления
детали вал ведущий». Экономическое
обоснование проектного решения представляет собой системный анализ
организационных и экономических показателей технического решения. Результаты анализа
должны содержать выводы о целесообразности реализации рассматриваемого решения
с точки зрения его экономической эффективности. Следует отметить, что выбор
проектного решения, перспективного для реализации является многовариантным и
определяется конкретными ситуациями и целями проектирования. Для определения
технико-экономического уровня качества проекта, необходимо провести анализ
технического уровня и показателей качества базовой и проектируемой системы.
Определение стоимости материалов.
Черный вес:
Для изготовления детали вал используется поковка на молотах.
Черный вес = 44,08 кг (ПЗ п. 1.4).
Цена изготовления тонны заготовок [19, с.86] и по данным ОАО «Тяжмаш»:
Цм = 18000 руб/тн (ПЗ п. 1.4).
Чистый вес детали:
Вес детали после механической обработки
Чистый вес =6,5 кг (ПЗ п. 1.4).
Вес отходов:
Определим массу отходов, годящихся к вторичной переработке по формуле
[19, с.134]:
Вес отходов = Черный вес - Чистый вес. = 44,08 - 6,5 = 37,58 кг
Цена отходов [19, с.97]:
Цена отходов = 2500 руб/тн
Определим стоимость заготовки:
Сзаг = Взаг. черн хЦм,
где Взаг. черн - вес заготовки, кг
М - стоимость 1 кг заготовок, руб.
Стоимость заготовки:
-
руб.
Стоимость
отходов (стружки):
руб.
Транспортные
расходы:
На
транспортные расходы приходится 5%.
Транспортные
расходы = 0,05 х Сзаг = 0,05 х 793,44=39,67 руб.
Рассчитаем
стоимость материалов:
Cм = Сзаг
- Сотх + Транспортные расходы
Cм = 793,44 - 93,95+39,67 = 739,16 руб.
Трудоёмкость
изготовления детали:
базовая:
Тб = 2,14 н/ч (по данным ОАО «Тяжмаш»),
по
дипломному проекту:
Тдп = 0,82 н/ч (п 1.10 с. 71).
Часовая
тарифная ставка станочников 4 разряда:
Тставка
= 110 руб/час.
Зарплата
основная производственных рабочих:
базовая
(токарь, фрезеровщик, шлифовщик):
С
зо = Тставка хТб
С
зо = 110х2,14=235,4 руб,
по
дипломному проекту (оператор обрабатывающего центра):
С
зо = Тставка хТдп
С
зо = 110х0,82=90,2 руб.
Зарплата
дополнительная производственных рабочих:
базовая:
где
Кз- коэффициент, характеризующий отношение суммы
дополнительной заработной платы производственных рабочих к основной (0,15 -
0,20).
Сдоп
= 235,4х0,20 = 47,08 руб.
по
дипломному проекту:
Сдоп
= 90,2х0,20 = 18,04 руб.
Общая сумма заработной платы производственных рабочих:
Ссум = Сзо + Сдоп
- базовая:
Ссум = 235,4+47,08 = 282,48 руб.
по дипломному проекту:
Ссум = 90,2+18,04 = 108,24 руб.
Обязательные страховые взносы Снач определяются в соответствии
с установленной нормой отчислений в процентах к расходам на основную и
дополнительную заработную плату производственных рабочих (30%).
Снач = 0,3хСсум
- базовая:
Снач =0,30 х 282,48 = 84,74 руб.
по дипломному проекту:
Снач =0,30 х 108,24 = 32,47 руб.
4.2 Составление смет прямых и цеховых расходов
На статью «Расходы на содержание и эксплуатацию технологического
оборудования» Ср относятся:
¾ содержание, текущий ремонт, амортизация производственного
оборудования транспортных средств и ценных инструментов;
¾ заработная плата основная и дополнительная вместе с
начислениями на социальные нужды вспомогательных рабочих; затраты на воду, пар,
электроэнергию и т.п.;
¾ возмещение износа быстро изнашивающихся инструментов и
расходов по их восстановлению;
¾ затраты на воду, пар, электроэнергию и т.п.;
¾ прочие расходы, связанные с работой оборудования.
На практике чаще используют расходы на содержание и эксплуатацию
технологического оборудования пропорционально основной заработной плате
основных рабочих (200%).
Ср = 2 х Сзо
- базовые:
Ср = 2 х 235,4 = 470,8 руб.
по дипломному проекту:
Ср = 2 х 90,2 = 180,4 руб.
На статью «Цеховые расходы» (Сц) относятся следующие затраты:
¾ основная и дополнительная заработная плата вместе с
начислениями на социальные нужды цехового персонала (инженеров, техников,
экономистов, служащих и др.), а также вспомогательных рабочих, занятых на
хозяйственных работах;
¾ расходы по охране труда и технике безопасности;
¾ содержание, текущий ремонт, амортизация зданий, сооружений и
инвентаря цехового назначения;
¾ расходы по опытам, изобретательству и рационализации;
Цеховые расходы распределяются пропорционально основной заработной плате
основных производственных рабочих (250%).
Сц = 2,5 х Сзо
- базовые:
Сц = 2,5 х 235,4 = 588,5 руб.
по дипломному проекту:
Сц = 2,5 х 90,2 = 225,5 руб.
Итого цеховая себестоимость:
Сцех = См + Ср + Ссум
+ Снач + Сц
- базовая:
Сцех = 739,16+470,8+282,48+84,74+588,5 = 2165,68 руб.
по дипломному проекту:
Сцех = 739,16+180,4+108,24+32,47+225,5 = 1285,77 руб.
На статью «Общепроизводственные расходы» (Соб) относятся
следующие затраты:
¾ заработная плата основная и дополнительная вместе с
отчислениями на социальные нужды заводского административно - управленческого
персонала;
¾ амортизация общезаводских зданий, складов и инвентаря;
¾ расходы по служебным командировкам;
¾ расходы по охране труда;
¾ расходы по подготовке кадров и на организованный набор
рабочей силы;
¾ налоги и сборы, прочие обязательные расходы и отчисления.
Общепроизводственные расходы распределяются пропорционально сумме основной
заработной платы основных производственных рабочих (310%).
Соб = 3,1 х Сзо
- базовые:
Соб = 3,1 х 235,4 = 729,74 руб.
по дипломному проекту:
Соб = 3,1 х 90,2 = 279,62 руб.
Общехозяйственные расходы распределяются пропорционально сумме основной
заработной платы основных производственных рабочих (280%).
Собх = 2,8 х Сзо
- базовые:
Собх = 2,8 х 235,4 = 659,12 руб.
по дипломному проекту:
Собх = 2,8 х 90,2 = 252,56 руб.
Итоговая производственная себестоимость:
Спр = Соб + Собх + Сцех
- базовая:
Спр = 729,74+659,12+2165,68 = 3554,54 руб.
по дипломному проекту:
Спр = 279,62+252,56+1285,77 = 2267,95 руб.
На статью «Внепроизводственные расходы» (Св) относятся
затраты, связанные в основном с реализацией готовой продукции:
¾ расходы по таре и упаковке;
¾ расходы по доставке продукции на станцию отправления;
¾ содержание персонала, обеспечивающего нормальную эксплуатацию
у потребителя в пределах уставленного срока;
¾ расходы на научно - исследовательские работы и др.
Внепроизводственные расходы применяются в размере 3 - 7% производственной
себестоимости.
Св = 0,03 х Спр
- базовые:
Св = 0,03 х 3554,54 = 106,64 руб.
по дипломному проекту:
Св = 0,03 х 2267,95 = 68,04 руб.
Итого полная себестоимость:
Сполн = Спр + Св
- базовая:
Сполн = 3554,54 + 106,64 = 3661,18 руб.
по дипломному проекту:
Сполн = 2267,95 + 68,04 = 2335,99 руб.
Таблица 4.1. Калькуляция затрат на производство детали вал
Наименование показателя
|
Ед. изм
|
Значения показателей
|
Изменение,±
|
|
|
По базовому предприятию
|
По проекту
|
|
|
1
|
2
|
3
|
4
|
5
|
1.
|
Стоимость материалов
|
руб
|
739,16
|
739,16
|
-
|
2.
|
Основная заработная плата
производственных рабочих
|
руб
|
235,4
|
90,2
|
-145,2
|
3.
|
Дополнительная заработная
плата производственных рабочих
|
руб
|
47,08
|
18,04
|
-29,04
|
4.
|
Обязательные страховые
взносы
|
руб
|
84,74
|
32,47
|
-52,27
|
5.
|
Расходы на содержание и
эксплуатацию оборудования
|
руб
|
470,8
|
180,4
|
-290,4
|
6.
|
Общецеховые расходы
|
руб.
|
588,5
|
225,5
|
-363
|
Цеховая себестоимость
|
руб
|
2165,68
|
1285,77
|
-879,91
|
7.
|
Общепроизводственные
расходы
|
руб
|
729,74
|
279,62
|
-450,12
|
8.
|
Общехозяйственные расходы
|
руб
|
659,12
|
252,56
|
-406,56
|
Производственная
себестоимость
|
руб
|
3554,54
|
2267,95
|
-1286,59
|
10.
|
Внепроизводственные расходы
|
руб.
|
106,64
|
68,04
|
-38,6
|
Итого полная себестоимость
|
руб
|
3661,18
|
2335,99
|
-1325,19
|
Относительная экономия затрат: (3661,18-2335,99/3661,18)∙100=36,19%
Снижение трудоемкости в процентах: (0,82/2,14)∙100=38,32%
Годовая экономия затрат при выпуске деталей 80 штук в год (п.1.3, с.10):
Эгод = (С полн БЗ - С полн ДП)
∙ Nвыпуска годовая
Эгод = (3661,18 - 2335,99)·80 = 106015,2 руб.
Годовая экономия с учетом налога на прибыль в размере 20 % составит:
Эгод =106015,2· 0,8 = 84812,16 руб.
Расчёт суммы капитальных затрат по оборудованию.
где
Ц
- цена оборудования в руб.;
С
- количество оборудования;
-
коэффициент, учитывающий затраты на транспортировку (10%).
Для
упрощения производимых расчетов примем следующее допущение - стоимость
строительно-монтажных работ (Ксм) составляет 10% от стоимости основного
оборудования.
Таблица
4.2 Дополнительные капитальные
вложения
Наименование оборудования
|
Модель, тип
|
Кол-во ед.
|
Цена за ед. в руб.
|
Сумма в руб.
|
Источники цены
|
1. Токарно-обрабатывающий
центр
|
MORI SEIKI NL-2500/700
|
1
|
2000000
|
2000000
|
каталог
|
Транспортные расходы
|
200000
|
10% цены станка
|
Монтажные работы
|
200000
|
10% цены станка
|
Всего
|
2400000
|
|
Определяем окупаемость дополнительных капитальных затрат.
Определяем годовую трудоемкость изготовления детали по дипломному проекту:
Тдп = 0,82 н/ч., программа выпуска 80 шт/год (п.1.3, с.10).
Тдп год = 0,82х80 шт = 65,6 ч.
Годовой фонд времени работы станка при трехсменном режиме работы:
Фгод=t x n x k,
где t = 8 ч - время работы в одну смену,
n=3
- количество смен в рабочем дне,
k
= 247 - количество рабочих дней в году.
Фгод= 8х3х247х0,96 = 5690,88 ч.
Расчет эффективного фонда рабочего времени.
Рассчитаем загруженность оборудования:
Определим
дополнительные капитальные вложения на изготовление годовой программы:
Sок
= Sст х η= 2400000∙0,0115= 27600 руб.
где
Sст - стоимость оборудования и его монтажа.
Определим
годовой экономический эффект по формуле:
Ээф
= Эгод - Ен· Sок
Ээф
= 84812,16 - 0,15·27600 = 84812,16
-4140= 80672,16 руб.
Определим
срок окупаемости дополнительных капиталовложений:
Время
окупаемости дополнительных капиталовложений:
,
Ток=
года.
При
нормативном коэффициенте сравнительной экономической эффективности = 0,15
нормативный срок окупаемости равен 1/0,15 = 6,7 года. Поэтому срок окупаемости
по проекту можно считать допустимым.
4.3 Технико-экономические показатели спроектированного цеха
Таблица 4.3 Технико-экономические показатели внедрения нового ТП
механической обработки вала токарно обрабатывающего центра Mori seiki NL2500/700
Наименование показателя
|
Ед. изм
|
Значения показателей
|
Изменение, ±
|
|
|
По базовому предприятию
|
По проекту
|
|
|
1
|
2
|
3
|
4
|
5
|
1.
|
Годовая программа выпуска
|
шт
|
80
|
80
|
-
|
2.
|
Трудоемкость изготовления
|
ч
|
2,14
|
0,82
|
-1,32
|
3
|
Полная себестоимость
|
руб
|
3661,18
|
2335,99
|
-1325,19
|
4.
|
Экономия на единицу
|
руб
|
1325,19
|
5.
|
Экономия на годовую программу
выпуска
|
руб
|
84812,16
|
6.
|
Дополнительные
капиталовложения
|
руб
|
27600
|
7
|
Срок окупаемости
|
лет
|
0,32
|
При одинаковой стоимости материалов трудоемкость изготовления детали вал
по предложенному в дипломном проекте варианту ТП механической обработки снизилась
по сравнению с базовым на 38,32%, что позволило сократить расходы на
изготовление детали и получить экономию на годовую программу в размере 84812,16
руб. Капиталовложения, необходимые для реализации нового ТП в размере 27600
руб., окупятся за 3,84 года, что ниже нормативного срока окупаемости в 20,93
раза.
Анализ показателей свидетельствует о том, что принятые в дипломном
проекте решения технически возможны и экономически целесообразны
5. ОХРАНА ТРУДА И ОКРУЖАЮЩЕЙ СРЕДЫ
5.1 Анализ опасных и вредных факторов производства
В процессе труда человек с помощью имеющихся в его распоряжении орудий
труда воздействует по заданной технологии на предмет труда, инструменты и
оборудование, технологический процесс- основные элементы, формирующие условия
труда. Безопасность труда зависит от уровня организации труда и производства,
от гигиенических параметров окружающей человека производственной среды и ряда
других факторов. Здесь рассмотрим лишь опасные и вредные производственные
факторы, действующие в спроектированном цехе. Условно их можно распределить по
следующим группам:
1. Факторы, возникающие непосредственно при выполнении
технологического процесса. Сюда можно включить такие источники опасности, как
движущиеся и вращающиеся части станков - шпиндели, суппорты, каретки на
протяжных станках. Особую опасность представляют собой шлифовальные станки
из-за исключительно высоких значений скоростей резания (до 35м/с). Высокая доля
ручного труда несколько повышает опасность травматизма на слесарном участке. В
целом цех и технологические процессы, осуществляемые в нём, нельзя отнести к
разряду особо опасных производств, при соблюдении техники безопасности и
технологии, риск получения травм сводится к минимуму, в нормальных условиях
вредные и опасные факторы (такие, как шум, вибрации и т.п.) не способны
привести к профессиональным заболеваниям.
2. Факторы, возникающие при выполнении работ, непосредственно
связанных с осуществлением технологического процесса. К таким факторам в первую
очередь следует относить движущиеся части подъёмно-транспортных устройств,
движение внутрицеховых транспортирующих механизмов и машин. Опасность может
исходить также от межцеховых транспортных средств, перемещающихся внутри здания
цеха.
. Факторы, связанные с выполнением ремонтных, пусконаладочных и
других вспомогательных работ. Здесь опасность заключается, в основном, при
работе с электроустановками и электроприборами высокого напряжения, а также при
ремонте оборудования, расположенного на большой высоте (подъёмно-транспортные
механизмы, приборы освещения и пр.).
Мероприятия по созданию безопасных условий труда, по производственной
санитарии и гигиене изложены в последующих пунктах данного раздела.
5.2 Мероприятия по безопасным условиям труда
При использовании технологическом процессе станков с ЧПУ руководствуются
общими правилами охраны труда. Управление отдельными органами станка
производится с пультов управления, в этом случае пульты управления должны
отвечать правилам охраны труда для постоянных рабочих мест (воздух рабочей
зоны, освещения, шум, вибрация и т.д.). На всех станках с ЧПУ и РТК должны
использоваться системы блокировки, исключающие их перевод на автоматический
цикл в последовательности, не отвечающей требованиям технологического процесса.
Здесь следует применять сигнальные устройства. Они предназначены для извлечения
о ходе технологического процесса, о наличии неисправностей и поломок, как
основного оборудования, так и в системе вентиляции, пневмотранспорта и т.д.
Для периодической смены инструмента, регулировки и подналадки станков с
ЧПУ и автоматов, их смазывания и чистки, а также мелкого ремонта в режиме
автоматической работы должно быть предусмотрено специальное время. Все
предусмотренные работы должны выполняться на обеспеченном оборудовании.
Планировка цеха должна обеспечивать удобный и безопасный доступ
обслуживающего персонала к основному и вспомогательному технологическому
оборудованию, к органам аварийного отключения и управления. При планировке
необходимо исключить пересечения трасс следования оператора и исполнительных устройств
и обеспечить свободу перемещения обслуживающего персонала, сведя до минимума
возможность появления посторонних лиц.
Опасные места в цеху необходимо ограждать и обозначать сигнальными
цветами и знаками безопасности в соответствии с требованиями ГОСТ 12.4.026-76.
При расчете площади ограждаемой зоны следует предусмотреть необходимые
разрывы между стационарным ограждением, для удобного и безопасного выполнения
операций программирования, ремонта и контроля.
Конструкция ограждения не должна затруднять проведения визуального
контроля оператором за работой РТК.
Рекомендуемая высота ограждения 1700 мм от уровня пола при условии, что
расстояние от исполнительного устройства до ограждения составляет 800 мм.
Ограждения рекомендуется выполнять из труб, обшитых металлической сеткой с
ячейкой 60´60 мм.
Ограждения следует окрашивать в соответствии с требованиями ГОСТ 12.4.026-76, в
виде чередующихся наклонных под углом 45°…60°
полос шириной 150-200 мм желтого сигнального и черного цветов при соотношении
ширины полос 1:1.
Перед началом работ наладчик или оператор должен устранить все отмеченные
неполадки, убедится в исправном состоянии основного и вспомогательного
оборудования и средств обеспечения безопасности (ограждений, блокировок,
сигнализации и т.д.) и в отсутствии посторонних лиц и предметов в рабочем
пространстве робота.
Все инструменты должны снабжаться устройствами для ломки и завивки
стружки - это достигается за счет использования специальной формы заточки,
наличие стружко-разделительных канавок, дополнительных поверхностей, наложение
на движение подачи технологических колебаний.
Общие требования безопасности к производственному оборудованию,
установлены ГОСТ 12.2.003-74. Поэтому установленное в цехе оборудование
оснащено защитными комплексными мерами, а именно:
- для предотвращения поражения током все металлические части
оборудования, которые могут оказаться под напряжением, заземлены или занулены;
- вращающиеся и движущиеся элементы станков ограждены или закрыты
кожухами;
для защиты рабочих от попадания стружки на станках установлены
экраны.
Планировка расположения оборудования в цехе с точки зрения ОТ.
Расстояние между станками и элементами здания цеха выдержаны в
соответствии с нормами. Нормы расстояний между средними станками 4000´2000 мм, при их расположении под
углом к проезду, фронтальном расположении друг к другу 1500 мм.
Ширина магистральных проездов в цехе для автопогрузчика до 3т по норме
составляет 3000 мм, расстояние между станками по проезду составляет 35000 мм.
Для движения людей предусмотрены проходы шириной 700 мм. Расстояние от стен и
колонн до тыльной и боковой сторон станков 600 мм.
5.3 Мероприятия по производственной санитарии и гигиене труда
К числу норм по технике безопасности и производственной санитарии
относятся нормы, устанавливающие меры индивидуальной защиты работающих от
профессиональных заболеваний и производственных травм. На работах с вредными
условиями труда, а также на работах, производимых в особых температурных
условиях или связанных с загрязнениями, рабочим и служащим выдаются бесплатно
по установленным нормам специальная одежда, специальная обувь и др. средства
индивидуальной защиты.
В проектируемом цехе обрабатываются детали из стали и чугуна, поэтому в
рабочей зоне от обработки чугуна имеется чугунная пыль. На шлифовальных станках
и на станках для обработки чугуна для снижения пыли применяются местные отсосы.
Шлифование ведется с охлаждающей жидкостью, которая поглощает пыль, выделяемую
при шлифовании.
Местный отсос применяется также в заточном отделении. Естественная вентиляция
осуществляется под воздействием разности температур воздуха внутри и снаружи
здания, а также ветрового побуждения.
Рабочие и служащие обязаны пользоваться в рабочее время выдаваемыми им
средствами индивидуальной защиты. У всех ворот цеха предусмотрены устройства
воздушной тепловой завесы для работы их в холодное время года. Для поддержания
постоянной температуры на рабочем месте, соответствующей установленной норме,
применяется водяное отопление в виде воздушно-подвесных агрегатов. Совмещенный
в агрегате вентилятор позволяет в холодное время года равномерно распределить
тепло по всему объему цеха, а в летнее время он может быть использован как
вентилятор. Агрегат устанавливается на колоннах и стенах здания на высоте 2,5…3
м от уровня пола.
По
действующим санитарным нормам СН 2.2.4./2.1.8.566-96 виброскорость не должна
превышать 92 Дб на рабочем месте (общая вибрация). Установленное в цехе
оборудование, а именно металлорежущие станки, создают вибрацию, не превышающую
санитарные нормы. На воздухоотводах вентиляции, в местах их соединения с
вентиляторами и при прохождении через конструктивные элементы здания применены
гибкие элементы (вставки) из резины, войлока, пробки и др.
Нормированные
параметры шума на рабочем месте определены по СН 2.2.4./2.1.8.562-96, где установлена
допустимая норма звукового давления не более 80 Дб. Установленное в цехе
оборудование считается "шумным". Некоторые типы станков шлифовальной
группы, заточных и станков, оборудованных пневматическими приводами, превышают
допустимые нормы шума.
Для
снижения шума в цехе предусмотрены следующие меры безопасности:
1. Станки объединены по степени их шумности, применено объединение
заточных станков. При этом вокруг таких зон установлено звукопоглощающее
ограждение.
2. Для станков с пневматическими агрегатами предусмотрены глушители
впуска и выпуска воздуха.
. Для снижения шума, образующегося при работе электродвигателей,
насосов, вентиляторов, их устанавливают на отдельные фундаменты.
Основные методы борьбы с вибрациями следующие:
1. Снижение вибрации воздействием на источник возбуждения.
2. Применение прогрессивного оборудования и прогрессивных
конструктивных элементов действующего оборудования.
. Отстройка от режима резонанса достигается либо изменением
характеристик системы (массы или жесткости), либо установлением нового рабочего
режима.
. Вибродемпфирование - процесс уменьшения уровня вибраций путем их
превращения в тепловую энергию. Увеличение потерь энергии в системе возможно
использованием материала с большим внутренним трением.
. Виброизоляция - уменьшение передачи колебаний. В качестве
устройств виброизоляции применяют виброизолирующие устройства типа упругих
прокладок и пружин, виброзащитные рукоятки, плавающие полы и покрытия, упругую
подвеску воздухопроводов и т.п.
Большой ущерб производству наносит шум, он приводит к быстрому утомлению
работающих, увеличению ошибок и повышению количества брака, способствует
возникновению травм. Так как шум и вибрация - понятия близкие, то и методы
борьбы с шумом во многом сходны с методами борьбы с вибрациями, но имеются
некоторые особенности. Необходима рациональная планировка помещений и зданий -
разделение шумных и тихих помещений, применение звукоизоляции, использование
звукопоглощающих покрытий, преград, кожухов, применение глушителей шума,
экранирование источников шума. Естественное освещение нормируется по СНиП
23-05-95. В проектируемом цехе применена комбинированная система освещения:
через окна в стенах и через аэрационные фонари, так как в цехе выполняются
точные зрительные работы. Цех состоит из трех пролетов. Расчет естественного
освещения ведется по среднему (второму) наиболее затененному, пролету
(отсутствует боковое освещение). Естественное освещение нормируется
коэффициентом естественного освещения (КЕО). Для средней полосы при
комбинированном освещении КЕО =3%.
Определим площадь осветительных проемов фонарей:
Sф = (SнeнnфKз) / (Or100), (5.1)
где Sн - площадь пола среднего пролета;
eн - значение КЕО = 3%;
nф - световая характеристика фонарей = 4,7;
Kз
- коэффициент, учитывающий затемнение окон соседними зданиями = 1,3;
Or
- общий коэффициент светопропускания =0,8.
Sф = 1152·0,02∙4,7·1,3/0,8∙10·100 = 17,56 м2.
Высота светового проема фонаря, с учетом того, что остекление
производится с двух сторон:
Рф = Sф /2 L, (5.2)
где L = 72 м - длина пролета;
Рф = 17,56 / 2∙72 = 0,3 м.
Высота оконных проемов = 1,8 м.
Общая площадь Sобщ = 4·72·1,8 = 2600 м2.
Потребный световой поток для освещения производственного помещения
определяется по формуле:
Ф треб = Еn·S·Z·К, (5.3)
где Еn = 200 лк - нормированная минимальная освещенность;
S
= 5184 м2 - площадь освещаемого цеха;
Z
= 1,15 - коэффициент минимальной освещенности (для ламп накаливания);
К
= 1,3 - коэффициент запаса
Ф треб. = 200·10368·1,15·1,3 = 465·104 лм
Расчетное количество осветительных ламп Г215-225-1000 (ГОСТ 2239-79)
имеющих световой поток Фл = 19600лм и световую отдачу 18,6 лм/Вт по
формуле:
= Ф треб. / Фл, (5.4)
где Фл = 19600 лм - световой поток одной лампы.
N = 465·104/19600 = 237,2 штук.
Принимаем N = 238 штук.
Лампы по пролету расположены в два ряда с шагом = 3 м.
Общая мощность ламп в цехе N = 700·238 = 166600 Вт.
5.4 Индивидуальные средства защиты
В производственных условиях не всегда удается устранить все опасные и
вредные производственные факторы, действующие на рабочих местах, путем
проведения общетехнических мероприятий. В этих случаях обеспечение нормальных
условий труда достигается применением средств индивидуальной защиты.
Защита тела человека обеспечивается применением спецодежды, спец обуви,
головных уборов, рукавиц. Костюм х/б, выполненный из прочной х/б ткани
(диагональ) плотностью 250 г/м2, отличает высокое качество. Ровные
швы с применением прочной армированной нити. Универсальность применения
позволяет использовать костюм на самых разных работах. Размеры: с 44 по 62, рост:
170-188.
Крем для защиты кожи рук и для облегчения очистки от масляных и
водонерастворимых рабчих материалов (масло, нефть, краска, лак, клей, смола,
графит, металлическая пыль, сажа, мазут) и органических растворителей (бензин и
другие продукты перегонки нефти, разбавители лаков и политуры, усилители,
очистители). ГОСТ Р 51391-99. Тюбик 100 мл., Бутыль 1000 мл.
Ботинки. Современный метод крепления подошвы - инжектирование (прямой
впрыск). Новый стандарт качества. Союзка и берцы из натуральной кожи. Маслобензостойкая
и антистатичная подошва из полиуретана. Усиленный носок. Размеры: с 40 по 47.
ГОСТ 12.4.137-84.
Рукавицы х/б (двунитка) с ПВХ наладонником. Усиленный наладонник с
полимерными пупырышками на рабочей части для улучшения сцепляемости и увеличения
ресурса. ГОСТ 12.4.010-75.
Перчатки спилковые комбинированные Перчатки высокого качества из
отборного спилка с удобной манжетой в виде краги. Идеальны для работы с грубыми
поверхностями. Надежность, долговечность, прочный захват и высокие показатели
стойкости к механическим нагрузкам. ГОСТ 12.4.010-75.
Органы зрения необходимо защищать очками, щитками и шлемами от
механических повреждений, ультрафиолетового и инфракрасного излучения. Для
защиты от яркого света и излучений применяют очки и щитки со специальными
светофильтрами по ГОСТ 12.4.080-79, так, например, при сварке необходимо
применять маски с темными стеклами ТС-3. Панорамная линза. Защищают от брызг и
летящих частиц. Дополнительная защита от летящих частиц широкими боковыми
щитками. Специальное покрытие против запотевания приносит дополнительный
комфорт при работе ГОСТ 12.4.013-97.
Органы дыхания необходимо защищать распираторами, противогазами. Выбор
средств защиты органов дыхания производится по ГОСТ 12.4.034-85. Универсальное
средство защиты дыхания ЛЕПЕСТОК. Простой, эффективный моноблочный респиратор.
Предназначен для защиты органов дыхания от пылей руд, угля, сухих смол,
удобрений, полимеров, хлопка. Надежное прилегание к лицу любой формы
обеспечивается изгибаемой пластиной на переносице и эластичными лентами
оголовья. В нерабочем состоянии респиратор ЛЕПЕСТОК имеет вид круга,
каркасность полумаски в рабочем состоянии обеспечивается с помощью резинового
шнура, продернутого по периметру круга, и распоркой. Возможность индивидуальной
подгонки под размер лица. ГОСТ 12.4.028-76. Производство Россия.
Для защиты от вибраций, при работе ручным инструментом, следует применять
рукавицы, перчатки, а также виброзащитные прокладки или пластины, которые
снабжены креплениями к руке.
Эти средства должны соответствовать ГОСТ 12.4.002-74. При работе в
условиях общей вибрации применяется обувь (ГОСТ2.4.024-76).
Для защиты от шума применяют вкладыши - вставленные в слуховой канал
мягкие тампоны и жесткие вкладыши в форме конуса (снижение шума 7-40 Дб), шлемы
используют когда вкладыши и наушники не обеспечивают необходимой защиты, так
как шум действует непосредственно на мозг человека. Наушники противошумные.
Простая, но эффективная модель. Рекомендуются для защиты от повторяющегося
воздействия шума с уровнем свыше 85 дБ. Мягкое оголовье.
Беруши. Один из лучших типов берушей. Более мягкие по сравнению с
аналогами. Не создают дискомфортного давления в ушном канале. Вес 5 г. ГОСТ
12.4.209-99.
В качестве средств защиты при работах связанных с электрическим током
применяют диэлектрические резиновые перчатки (до 1000 В), инструмент с
изолирующими рукоятками, диэлектрические галоши, коврики, изолирующие
прокладки, подставки. Исправность средств защиты должна проверяться осмотром
перед каждым их применением, а также периодически через 6-12 месяцев.
5.5 Противопожарная безопасность
Основные виды пожарной техники, предназначенной для защиты от пожаров
предприятий, зданий и сооружений, определены ГОСТ Р 50982-2003 Техника
пожарная. Инструмент для проведения специальных работ на пожаре. Общие
технические требования. Методы испытаний. Постановление Госстандарта России от
12.08.2003 N 257-ст ГОСТ Р от 12.08.2003 N 50982-2003.
Пожары на машиностроительных предприятиях представляют собой
большую опасность для работающих и могут причинить огромный материальный ущерб.
Основной причиной пожаров на машиностроительных предприятиях является
нарушение технического режима. Это связано с разнообразием и сложностью
технологических процессов. Они, как правило, помимо операций механической
обработки включают процессы очистки и обезжиривания, сушки и окраски, связанные
с использованием веществ, обладающих высокой пожарной опасностью.
Также причинами пожара могут быть следующие:
- самовозгорание промасленной ветоши;
- замыкание электропроводки, перегрузка электрооборудования;
выполнение сварочных работ в необорудованных местах;
прямое попадание молнии.
Мероприятия по пожарной безопасности:
1. Хранение ветоши должно производится в несгораемых ящиках, которые
опорожняются в конце смены;
2. Для предотвращения возгорания и замыкания от перегрузок в
электроустановок предусмотрены разные предохранители и автоматы;
. Оборудованы места для проведения сварочных работ;
. Оборудованы места для курения;
. Установлены пожарные щиты;
. Установлены четыре молнии отвода;
. Оборудованы места для промывки и окраски изделий.
Меры по уменьшению последствий от пожара.
o У выходов цеха и в цехе установлены пожарные извещатели.
o Разработаны пути эвакуации людей. При ширине здания и длине,
пожарные выходы предусмотрены с обоих торцов здания и в середине здания.
o В цехе установлены первичные средства тушения пожара -
огнетушители в количестве N=S/600=5184/600=8,64 шт. Принимаем 9 шт.
Огнетушители углекислотные предназначены для тушения горючих веществ,
горение которых не может происходить без доступа воздуха, на промышленных
предприятиях, транспорте, электроустановках под напряжением до 10000 В. Срок до
перезарядки - 5 лет.
В цехе предусмотрен 1 электрощит. Рядом с ним размещаем огнетушитель
углекислотный передвижной ОУ-10. Объём - 10 л, время выхода огнетушащего
вещества не менее 15с. Масса 30 кг. Площадь тушения 1,1 м2. ГОСТ
51057-97.
Остальные огнетушители предусматриваем порошковые.
По торцам здания размещаем 2 огнетушителя ОП-50. Объем - 50 л, время
подачи огнетушащего вещества не менее 20 с. Длина выброса струи - 7м. Масса 100
кг. Площадь тушения 7,5 м2. ГОСТ 51057-97.
По периметру здания на стенах на высоте не более 1,45 м от пола
устанавливаем остальные огнетушители порошковые газогенераторные ОП-8(Г). Масса
заряда до 8 кг, время подачи огнетушащего вещества не менее 13 с. Длина выброса
струи - 3,5 м, масса 16 кг. Площадь тушения 4,5 м2. ГОСТ Р
51057-2001.
o В цехе установлены 4 пожарных гидранта, а с наружной стороны
6 пожарных гидрантов.
o В местах для промывки и покраски деталей предусмотрены
установки пожаротушения пеной.
o В цехе предусматривается создание добровольной пожарной
дружины.
o В каждой смене из числа мастерского состава назначен дежурный
по цеху.
Повысить огнестойкость зданий и сооружений можно облицовкой и
оштукатуриванием металлических конструкций. Предпочтение отдаётся
известково-цементной, асбестоцементной или гипсовой, которые защищают и
деревянные конструкции.
Производится зонирование территории: группирование при генеральной
планировке предприятий в отдельные комплексы объектов, родственных по
функциональному назначению и признаку пожарной опасности; между зданиями
устраивают разрывы для предупреждения распространения пожара.
Устраиваются также противопожарные преграды: стены, перегородки, перекрытия,
двери, ворота, люки, тамбуры, окна.
При проектировании здания необходимо предусмотреть безопасную эвакуацию
людей при пожаре. При возникновении пожара люди должны покинуть здание в
течение минимального времени, которое определяется кратчайшим расстоянием от
места их нахождения до выхода наружу. Эвакуационные выходы должны располагаться
рассредоточено. При этом лифты и другие средства механической транспортировки
людей не учитывают.
На предприятии должна быть совершенная система вентиляции и средства, необходимые
для тушения пожара: огнетушители, ящики с песком, пожарный инвентарь.
5.6 Влияние спроектированного цеха на окружающую среду и
мероприятия по ее защите
Из большого объема промышленных выбросов, попадающих в окружающую среду,
на машиностроение приходится 1-2%. Однако в проектируемом цехе производится
металлообработка деталей с покраской в конце технологического процесса, а это
создает более высокий уровень загрязнения окружающей среды.
Таким образом механосборочный цех является потенциальным загрязнителем
окружающей среды:
- воздушного пространства (выбросы газа, парообразных веществ,
пыли и др.);
- поверхностных водоисточников (сточные воды, утечка жидких
продуктов и т.п.);
почва (накопление твердых отходов, выпадение токсичных веществ
из загрязнённого воздуха, сточных вод).
Основная причина загрязнения водных ресурсов - аварийный или
технологический сброс в водоемы неочищенных или недостаточно очищенных сточных
вод.
Типовой состав сточных вод механосборочного производства следующий:
- отработанные СОЖ, содержащие взвешенные вещества, соду, масла;
- из гидрокамер окрасочного отделения в воду поступают
органические растворители, масла, краска;
из отделения гидравлических испытаний - взвешенные вещества,
масла.
Наиболее экологически опасные загрязнители при металлобработке -
индустриальные масла, металлическая пыль и др.
Твердые отходы механосборочного цеха содержат амортизационный лом
(модернизация оборудования, оснастки, инструмента), стружка и опилки металлов,
древесины, пластмасса, шлаки, золы, осадки и пыль (отходы систем очистки
воздуха).
Количество и характеристики опасных источников загрязнения в
механическом цехе приведены в таблице.
Таблица 5.1 Количество и характеристики опасных
источников загрязнения
Источники
загрязнения
|
Виды загрязнителей
|
Характеристика
|
Металлорежущие
станки
|
Пыль, туманы
масел и эмульсий (СОЖ)
|
До 100г/час
пыли, до 200г/час масла и СОЖ на один станок
|
Системы очистки газовых выбросов по удаляемым веществам
делятся на установки удаления твёрдых частиц (пыли); установки удаления
газообразных загрязнителей (НF, СО, NО и т.д.); установки удаления туманов и брызг.
В механическом цехе для удаления газообразных отходов их
воздуха необходимо применять пылеуловители, циклоны, фильтры, мокрые и сухие
электрофильтры.
Производственные станочные воды образуются при использовании
воды в технологических процессах. На машиностроение проходится до 10% общего
водопользования. Основными видами загрязнения сточных вод механического цеха
являются механические смеси - песок, окалина, пыль и т.п., а также химические
загрязнители - СОЖ, масла, химические соединения.
Количество, состав и характеристика стоков механического цеха
приведены в таблице.
Таблица 5.2 Количество, состав и характеристика стоков
Источники
загрязнения
|
Виды
загрязнителей
|
Концентрация
|
Металлорежущие
станки
|
Отработанные
СОЖ
|
Взвешенные
вещества до 1 мг/м 3; сода до 10 мг/м3; масла до 2 мг/м3
|
В механическом цехе для очистки сточных вод необходимо
применять решетки, отстойники, открытые и напорные гидроциклоны, фильтры, маслоловушки.
Также происходит выделение тепла в окружающую среду:
во-первых, за счет отопления здания в зимний период и дополнительно за счет
работы установленного оборудования. Особенностью тепловыделения от механических
цехов является то, что отсутствует локальный сконцентрированный источник
тепловыделения, а теплопотеря происходит по всей площади цеха, через оконные
проемы, с вентилируемым воздухом. Тем самым создается медленно восходящий поток
воздуха, нарушающий естественное движение воздуха, приводящий к возникновению
разнонаправленных потоков.
Использование отходов производства широко практикуется как в нашей
стране, так и за рубежом. Твёрдые отходы промышленного производства содержат
амортизационный лом. Количество его зависит от изношенности оборудования, а
также от замены деталей во время планово-предупредительного ремонта. На
машиностроительных предприятиях 55 % амортизационного лома образуется от замены
технологической оснастки и инструмента. Отходы незавершённого производства
делятся на:
отходы металла;
отходы дерева;
пыль от систем газоочистки;
промышленный мусор.
При переработке металлолома основными требованиями, при выборе способа
переработки является физическое состояние исходного сырья, вид и размеры
готовой продукции. В настоящее время применяют следующие способы переработки
металлолома и отходов:
пакетирование;
ножничная резка;
брикетирование;
дробление;
переплав;
копровое дробление;
газовая резка;
сортировка.
5.7 Мероприятия по защите окружающей среды
Для уменьшения количества отходов в основном производстве
целесообразно создание и внедрение малоотходных, безотходных и комплексных
технологий. Под безотходной технологией понимают технологию или производство
того или иного продукта. При этом рационально используются все компоненты сырья
и энергии в замкнутом цикле, т.е. не нарушается сложившееся экономическое
равновесие.
Для очистки воздуха, удаляемого вентиляционными системами от твёрдых и
жидких примесей, применяют пылеуловители.
Можно рекомендовать фильтрующие элементы в вытяжных трубах сварочных
кабин.
Предотвращение аварий на складе ГСМ и СОЖ включает в себя ряд мер:
- регулярная проверка и очистка емкостей;
- соблюдение правил эксплуатации оборудования.
Механосборочный цех не представляет опасности для экологии, проведение
каких-либо специальных мероприятий для охраны окружающей среды от вредных
факторов нецелесообразно.
Для уменьшения количества отходов в основном производстве целесообразно
создание и внедрение малоотходных, безотходных и комплексных технологий. Под
безотходной технологией понимают технологию или производство того или иного
продукта с использованием всех компонентов сырья и энергии в замкнутом цикле,
то есть без нарушения сложившегося экологического равновесия.
Малоотходная технология - это промежуточный этап при создании безотходного
производства. При этом вредное воздействие на окружающую среду не превышает
допустимого санитарными нормами уровня.
Малоотходные и безотходные технологии должны обеспечивать:
- комплексную переработку сырья с использованием всех компонентов
на базе создания новых безотходных процессов;
- создание и выпуск новых видов продукции с учетом ее повторного
использования;
переработку отходов производства и потребления с получением
товарной продукции.
Для очистки воздуха, удаляемого вентиляционными системами от
твёрдых и жидких примесей, применяют пылеуловители.
Широкое применение для сухой очистки газов получили циклоны
различных типов (рис. 4.1). Газовый поток вводится в циклон через патрубок 2 по
касательной к внутренней поверхности корпуса 1 и совершает
возвратно-поступательное движение вдоль корпуса к бункеру 4. Под действием
центробежной силы частицы пыли образуют на стенке циклона пылевой слой, который
вместе с частью газа попадает в бункер. Отделение частиц пыли от газа,
попавшего в бункер, происходит при повороте газового потока в бункере на 180°.
Рисунок 5.1 Линия из трех циклонов
Освободившись от пыли, газовый поток образует вихрь и выходит из бункера
через выходную трубу 3.
Все практические задачи по очистке газов от пыли с успехом решаются
цилиндрическими (ЦН-11, ЦН-15, ЦН-24, ЦП-2) циклонами.
Избыточное давление воздуха, поступающего в циклон, не должно превышать
2500 Па. Температура воздуха во избежание конденсации паров воды выбирается на
30-50 ºС выше точки росы, но по условиям
прочности конструкции не выше 400ºС. Производительность циклона зависит
от его диаметра, увеличиваясь с ростом последнего. После очистки воздуха в
первом циклоне он поступает на повторную очистку во второй циклон, а затем в
третий.
ЗАКЛЮЧЕНИЕ
В данном дипломном проекте разработан технологический процесс
на обработку детали вал. При этом учтены требования по внедрению более
прогрессивных методов получения заготовки и методов механической обработки. В
проекте применено оборудование, позволяющее обработать деталь с повышенной
производительностью. Также учтены требования научной организации труда,
эстетики производства, техники безопасности и охраны труда на производстве,
стандартизации и управления качеством продукции.
В результате использования прогрессивных методов и последних научных
разработок, применяемых в проекте, в конечном итоге сокращается себестоимость
детали.
СПИСОК ИСПОЛЬЗУЕМЫХ ИСТОЧНИКОВ
1.Справочник технолога- машиностроителя. В 2-х т. Т.1 /Под
ред. А.Г. Косиловой и Р.К. Мещерякова.- 4-е изд., перераб. и доп.- М.:
Машиностроение: 1985. 458с.
.Справочник технолога- машиностроителя. В 2-х т. Т.2 /Под
ред. А.Г. Косиловой и Р.К. Мещерякова-4-е изд., перераб. и доп.- М.:
Машиностроение:1986. 496с., ил.
3. Анурьев В.И. Справочник конструктора - машиностроителя
В3-х т.- Т.3. 6-е изд. перераб. и доп.-М.: Машиностроение,1982.
. Анурьев В.И. Справочник конструктора - машиностроителя В3-х
т.- Т.3. 6-е изд. перераб. и доп.-М.: Машиностроение,1982.
.Анурьев В.И. Справочник конструктора - машиностроителя В3-х
т.- Т.3. 6-е изд. перераб. и доп.-М.: Машиностроение,1982.
.Горбацевич А.Ф., Шкред В.А. Курсовое проектирование по
технологии машиностроения. Минск: Вышейшая школа, 1983.256с.
7.Горелов В.В., Родионов Л.Ф., Рожнятовский А.В. Курсовое
проектирование по дисциплинам «Технология, машины и оборудование
машиностроительного производства» и «Технология машиностроения» Учебное пособие
для студентов по специальностям 0608.01 и 1201.00/ Сызранский Филиал гос. Тех.
ун-та. Сызрань, 2000.-135с.
.ГОСТ 7829-70 Поковки из углеродистой и легированной
стали,изготовляемые свободной ковкой на молотах.
.Кузнецов Ю.И., Маслов А.Р., Байков А.Н. Оснастка для станков
с ЧПУ.; Справочник. М.; Машиностроение, 1990, 512с.
.Проектирование технологических процессов механической
обработки в машиностроении: Учеб. пособие /В.В. Бабук, А.И. Шкред, Г.П. Кривко,
А.И. Медведев. Под ред. В.В. Бабука.-Мн.: Высш. Шк., 1978. 255с.:ил.
.Общемашиностроительные нормативы режимов резания:
Справочник: В 2-х т. А.Д. Локтев, И.Ф. Гущин, В.А. Батуев и др.: Т.1-М.:
Машиностроение, 1991-640с.: ил.
.Общемашиностроительные нормативы режимов резания:
Справочник: В 2-х т А.Д. Локтев, И.Ф. Гущин, В.А.Батуев и др.: Т.2-М.:
Машиностроение, 1991-304с.:ил.
.Горошкин А.К. Приспособления для металлорежущих станков.;
Справочник.-4-е изд., перераб. и доп.-М.; Машиностроение, 1962, 340 с.:ил.
.Режимы резания металлов.Справочник.Изд.3-е изд.,перераб и
доп. Под ред.Барановского Ю.В.,М.:Машиностроение,1972.-408с
.ДунаевП.Ф.,Леликов О. П.Конструирование узлов и деталей
машин:Учебное пособие для машиностроительных специальностей вузов.-4-е изд.,
перераб. и доп.-М.:Высшая школа,1985-416с.,ил.
.НефёдовН.А.,ОсиповК.А.Сборник задач и примеров по резанию
металлов и режущему инструменту.учеб.пособие для техникумов по предмету «основы
учения о резании металлов и режущий инструмент».-5-е изд.,перераб. и
доп.-М.:Машиностроение,1990-448с
.УютовА.А.Проектирование механосборочных цехов.:Методическое
пособие по курсовому и дипломному проектированию/Самарский государственный
технический университет.:Самара,1998-68с.
.Подъёмно-транспортные машины. Атлас конструкций.Учебное
пособие для вузов .Под ред. Александрова М.П. и РешетоваД.Н.,
М.:Машиностроение, 1973-256с.
. Методические указания к выполнению экономической части
дипломного проекта по специальности 220301. / Сост. В.В. Сухинина, В.Д.
Чичкина. Самара; Самар. Гос. Техн. Ун-т., 2010.
.Иванченко Ф.К. и др.Расчёты грузоподъёмных и
транспортирующих
машин.-Киев.: «Вища школа»,1978.-576с.
.Латышев В.Н.Повышение эффективности СОЖ.-2-е изд.,перераб.и
доп.-М.:Машиностроение,1985.-64с.
.Панкин А.В., Бурдов Д.Н.Изготовление и применение новых
охлаждающе смазывающих жидкостей.-М.:Машиностроение,1964.-176с.
.Юдин Е.Я., Белов С.В., Баланцев С.К.Охрана труда в
машиностроении: Учебник для машиностроительных вузов-2е
изд.-М.:Машиностроение,1983,432с, ил.
.Груздев С.М. Экономика машиностроительного производства в
дипломных проектах.Самар.гос.техн.ун-т.Самара,2004,80с.
.Великанов К.М.Экономика и организация производства в
дипломных проектах:4-е изд.Учебное пособие М.:Машиностроение,1986.-285с