Метод сорбционного выщелачивания золота из руд
Реферат
Ключевые слова: золото, цианидное выщелачивание, ионный обмен, пачук.
Данный дипломный проект посвящен проектированию цеха сорбционного
выщелачивания золота из руд месторождения «Покровское» с использованием смолы
АМ-2Б производительностью 1 млн. тонн в год. В ходе выполнения проекта сделан
литературный обзор существующих методов извлечения золота из руд, рассмотрены
их основные достоинства и недостатки. Из всех рассмотренных методов выбран
метод цианидного выщелачивания с пневматическим перемешиванием, как наиболее
эффективный и простой, рассмотрена термодинамика и кинетика данного процесса.
По результатам материального баланса произведены аппаратурный и механический
расчёты основного аппарата, используемого в цехе. Кроме того, предложена
функциональная схема автоматизации производства, рассмотрены основные опасности
и вредности, а также рассчитаны основные технико - экономические показатели.
Содержание
Введение
.Технико-экономическое
обоснование места постройки цеха
. Аналитический обзор методов
извлечения золота
. Теория процесса
. Описание технологической
схемы, пуск и остановка
. Расчётная часть
.1.1 Материальный баланс
стадии цианирования
.1.2 Материальный расчет
процесса сорбции
.2 Аппаратурный расчёт
.3 Гидравлический расчет
.4 Механический расчет
Контроль и автоматизация
.1 Разработка функциональной
схемы автоматизации процесса сорбционного цианирования золота
.2 Перечень технологических
параметров подлежащих контролю, регулированию и сигнализации
.3 Перечень первичных
преобразователей
.4 Использование ЭВМ
.5 Действия
оператора-технолога при пуске, остановке и нормальном режиме ведения
технологического процесса
. План размещения
оборудования
. Охрана труда и охрана
окружающей природной среды
.1 Охрана труда
.2 Охрана окружающей среды
Экономический расчет
.1 Расчет эффективного фонда
времени
.2 Организация труда и
заработной платы
.3 Расчет капитальных затрат
.4 Расчет технологических
затрат
Выводы
Список использованной
литературы
Введение
сорбционный выщелачивание
золото руда
Золото относится к драгоценным металлам, известным также под названием
благородных. В эту группу также входят серебро, платина, осмий, иридий,
палладий, родий и рутений.
Благородные металлы имеет существенные отличия от всех остальных
металлов. Во многом это связано с их уникальными физическими и химическими
свойствами, в том числе каталитической активностью, высокой температурой
плавления и устойчивостью к коррозии. Это является определяющим фактором для
применения благородных металлов в различных областях. Так, золото находит
широкое применение при изготовлении ювелирных изделий, а также в медицине.
Значительное количество золота расходуется на изготовление противоударных и
противовибрационных припоев для пайки различных металлов и сплавов. Также
золото используется в авиационной и космической отрасли, а также в
электротехнике [1].
Такие свойства золота, как химическая стойкость и неизменность в весе,
предопределили использование золота в качестве важнейшего элемента мировой
финансовой системы.
За всю историю, человечество добыло 166,6 тысяч тонн золота. Его
суммарная стоимость составляет около 7 триллионов долларов.
Высокая цена на этот драгоценный металл обусловлена рядом факторов:
малое содержание в земной коре, кларк золота составляет 5×10-7 %;
значительные расходы энергии и материалов, связанные с технологией
извлечения благородных металлов [2].
С целью уменьшения себестоимости золота, активно велись разработки новых,
более совершенных методов извлечения золота из руд. Так, благодаря работам
Багратиона (1843г.), Эльснера (1846г.) и Фарадея (1856г.) о растворении золота
в растворе щелочных цианидов в присутствии кислорода воздуха. В 1890 г. был
построен первый гидрометаллургический завод для извлечения золота цианистым
процессом. Спустя 7 лет в России на Урале в Березовском и Кочкарском
предприятиях были построены цианистые установки. Вскоре этот процесс стали
широко применять для извлечения золота из руд [3].
Целью данного дипломного проекта является рассмотрение метода
сорбционного выщелачивания золота из руд как наиболее изученного и самого
эффективного на сегодняшний день. В дипломном проекте приведены технологические
расчеты, рассмотрены вопросы строительства и организации работы цеха.
1 Технико-экономическое обоснование места постройки цеха
Место строительства цеха сорбционного выщелачивания золота из руд -
Амурская область, поселок Тыгда, месторождение «Покровское».
На выбор места строительства цеха оказывает влияние ряд особенностей:
месторождение «Покровское» по данным анализа проб содержит 8 типов
кварцевых жил золотосеребряной сульфидной формации с содержанием золота от 2,9
до 4,8 г/т.
золото в руде месторождения «Покровское» находится в легко вскрываемой
форме, в основном оно мелковкрапленное. Это говорит о необходимости тонкого
измельчения руды.
использование месторождения «Покровское» позволит осуществлять добычу
золота в размере 75 тонн при годовой добычи до 6,5 тонн.
Производительность карьеров принята равной 2 млн. т/г., что обеспечивает
срок существования предприятия 20 лет.
Месторождение «Покровское» расположено вблизи Транссибирской
железнодорожной магистрали, в 17 км от железнодорожного поселка Тыгда.
Следовательно, основным критерием выбора места постройки предприятия является
удобство транспортировки сырья и готовой продукции.
Электроснабжение региона осуществляется от Зейской ГЭС. Вблизи площадки
рудника проходят ЛЭП 500 и 220 кВ. Этого вполне достаточно, чтобы обеспечить
электроэнергией фабрику по переработке золотосодержащих руд.
Водозабор в поселок Тыгда производится из реки Зея. Происходит полное
обеспечение водой, как самого поселка, так и предприятия.
Технологическое оборудование выбирается исходя из обеспечения надежного
его функционирования при наименьшей его стоимости, гарантированности поставок,
приоритетности российского оборудования.
Климат региона резко континентальный. Глубина промерзания почвы достигает
3 метра, а на низко расположенных участках встречаются зоны вечной мерзлоты.
Средняя температура января -30оС, июня +25оС.
Готовая продуктом предприятия является черновой сплав Доре, содержащий в
сумме 95-96 % золота и серебра. В дальнейшем он будет отправляться на
аффинажный завод [4].
Инженерно-технический состав предприятия ежегодно пополняется как за счет
выпускников сибирских ВУЗов, в частности Томского политехнического
университета, так и за счет других городов, где имеются техникумы и
профессионально-технические училища, которые подготавливают кадры, необходимые
для бесперебойного ведения технологического процесса. К ним относятся Иркутск,
Красноярск, Чита и Зея.
2
Аналитический обзор существующих методов
.1
Гравитационные методы извлечение золота
Благородные
металлы характеризуются высокой плотностью, намного превышающей плотность
минералов вмещающей породы. Поэтому для извлечения самородных благородных
металлов из руд эффективны гравитационные процессы.
В большинстве
золотосодержащих руд содержится некоторое количество крупного свободного золота
(+0,1) мм., которое плохо извлекается флотацией и гидрометаллургическими
методами. Поэтому предварительное выделение его гравитационным обогащением
позволяет снизить потери золота с отвальными хвостами и выделить часть его в
виде быстро реализуемого золотосодержащего концентрата.
В современной
практике извлечения золота из руд применяют следующие основные аппараты для
гравитационного обогащения: шлюзы, гидравлические ловушки, отсадочные машины,
концентрационные столы [5].
2.1.1
Извлечение золота с помощью гидравлических ловушек и отсадочных машин
Обогащение отсадкой основано на разделении минеральных зерен по плотности
в воде, колеблющейся (пульсирующей) относительно разделяемых зерен в
вертикальной плоскости. Пульсация среды создается специальным приводным
механизмом.
Отсадочные машины, как правило, работают в цикле измельчения и успешно
извлекают крупное золото из золотосодержащих руд. В практике
золотоизвлекательных фабрик применяются различные типы отсадочных машин:
пульсаторы, отсадочные машины с резиновыми диафрагмами.
При многократных пульсаций воды, создаваемых диафрагмой, материал
расслаивается по плотности: частицы золота и других тяжелых минералов
проваливаются через постель из металлической дроби или гематитовой руды, и
разгружаются под решето. Легкие зерна пустой породы остаются на поверхности
постели и разгружаются через сливной порог. Вода в отсадочную машину поступает
с перерабатываемым материалом, кроме того, некоторое количество воды вводят
дополнительно под решето. Извлечение золота в концентрат отсадки зависит от
характера включения золота в руде, на отдельных фабриках извлечение золота
доходит до 50%, часто 25 - 30%.
Основными достоинствами отсадочных машин являются возможность переработки
неклассифицированного материала, высокая производительность на единицу
поверхности, возможность работы на пульпах с низким значением отношения Ж:Т
К недостаткам этого метода относят высокие капитальные затраты на
установку и невозможность улавливания мелких частиц золота [5].
Выделение в концентрат свободного золота и минералов, с которыми оно
ассоциировано, может быть успешно осуществлено с помощью, так называемых
гидравлических ловушек. Эти аппараты по сравнению со шлюзами и
амальгамационными аппаратами обладают большей компактностью и расходуют меньше
воды.
Ловушки удобнее всего применять в цикле измельчения - на сливе мельницы.
Гидравлические ловушки представляют собой опрокинутые вниз вершинами конусы или
пирамиды. Снизу в ловушке подается вода с таким расчетом, чтобы скорость
восходящей струи воды не препятствовала осаждению золотых частиц и тяжелых
минералов, и не давало осесть частицам пустой породы. По мере накопления в
ловушке концентрата его выгружают в приемник. По сравнению с ворсистыми шлюзами
гидравлические ловушки улавливают более крупное золото. Наилучшие результаты
ловушки дают при обработке кварцевых руд с крупным золотом.
Выход концентратов из гидравлических ловушек меньше, чем со шлюзов с
мягким покровом. Обычно он составляет - 1% от веса руды, поэтому концентраты из
гидравлических ловушек богаче, но извлечение золота в эти концентраты ниже, чем
в концентраты шлюзов [6].
2.1.2
Извлечение золота на шлюзах
Концентрационные шлюзы являются простейшим обогатительным аппаратом,
применяемом для извлечения свободного золота из руд и россыпей.
Шлюз представляет собой желоб прямоугольного сечения, имеющий небольшой
уклон в горизонтальной плоскости. На дне желоба уложено специальное покрытие
(ворсистая ткань, резиновые коврики), предназначенное для удержания осевших на
дно минеральных зерен.
Обогащение в струе воды, текущей по наклонной плоскости (шлюзу), основано
на различии в характере движения отдельных минеральных частиц под влиянием
динамических воздействий на них струи воды. При таком движении одни частицы под
действием силы тяжести отлагаются на поверхности шлюза, а другие увлекаются и
относятся водным потоком [1].
Важным фактором, влияющим на результаты извлечения золота, является
различие в скоростях жидкости в различных слоях водного потока, текущего по
наклонной плоскости. Непосредственно у самой поверхности шлюза, вследствие
прилипания жидкости, скорость движения жидкости равна нулю, но уже на небольшом
расстоянии от поверхности шлюза эта скорость достигает довольно значительной
величины. При дальнейшем удалении от поверхности увеличение скорости
замедляется. Частица минерала, в зависимости от своего размера, удельного веса,
скорости водной струи (угла наклона шлюза), или упадет на поверхность шлюза или
не успеет достичь зоны нулевых скоростей и будет вынесена потоком со шлюза.
Упавшая на поверхность шлюза частица, в зависимости от своих свойств (размер,
удельный вес), может или остаться на шлюзе или быть смыта.
Преимущество шлюзов состоит в их способности улавливать более мелкое
золото и низких капитальных затратах на установку.
Главный недостаток шлюзов заключается в трудоемкости их эксплуатации и
низкой производительности на единицу площади [6].
2.1.3
Извлечение золота на концентрационных столах
Обогащение (концентрация) на столах - процесс разделения минеральных
частиц по плотности в тонком слое воды, текущей по слабонаклонной плоскости
(деке), совершающей возвратно-поступательное движение в горизонтальной
плоскости в направлении, перпендикулярном направлению движения воды [1].
Минеральные частицы, поступившие на стол, повергаются воздействию сил,
сообщаемых приводом, смывному действию воды, текущей тонким слоем по уклону
поперек прямоугольной или трапецеидальной деки, и силы тяжести. Под действием
силы тяжести частицы оседают на поверхности деки и под влиянием сотрясений деки
в межрифлевом пространстве происходит расслоение материала. Крупные легкие
частицы, находящиеся сверху, легче смываются поперечным потоком воды вследствие
их большого размера и меньшей защищенности нарифлением, чем мелкие тяжелые
частицы, находящиеся внизу. Кроме того, по мере движения материала вдоль стола
высота рифлей становится все меньше, что способствует смыванию более мелких
легких частиц. В результате на столе образуется веер из частиц разной плотности
и крупности, каждая полоса которого собирается в разные приемники.
Основным достоинством концентрационных столов является то, что они
позволяют получать богатые концентраты при высоком извлечении золота.
Поскольку обогащение происходит в тонком слое воды, то основным
недостатком этого метода является низкая производительность. [5,6].
2.2
Извлечение золота амальгамацией
Амальгамацией называют процесс извлечения благородных металлов из руд и
концентратов при помощи жидкой ртути. Измельченный золотосодержащий материал
приводят в контакт с ртутью. Ртуть, соприкасаясь с частицами металла,
избирательно их смачивает на границе раздела с водной фазой. В смачивании
золота ртутью участвует три фазы: золото, ртуть и вода. Чем лучше смачивание,
тем выше показатели амальгамации. На смачивание влияют такие факторы, как
равновесный краевой угол смачивания - ( Ө ) и состояние поверхности
золота. Таким образом, эффективное смачивание достигается при небольшом значении
Ө и свежеобнаженной поверхности золотин. Большая часть неблагородных
металлов не амальгамируется. Введение в сплав с золотом даже 10% серебра уже
значительно понижает смачиваемость этого сплава. После смачивания следует
стадия образования амальгамы вследствие диффузии ртути в частице извлекаемого
металла. После этого амальгама отделяется от рудной пульпы, отжимается от
избытка ртути, подвергается отгонке, в результате которой в реторте остается
губчатое золото, а ртуть конденсируется в холодильнике и возвращается в
процесс. Процесс амальгамации ведут либо в амальгамационных бочках (внутренняя
амальгамация), либо на шлюзах (внешняя) [1,5].
Значительное количество меди и железа, попавшее в ртуть вызывает
затвердевание и хрупкость получаемой амальгамы, что, соответственно, делает
извлечение крайне неэффективным.
Процесс амальгамации имеет большую эффективность, когда частицы
самородного золота вскрыты измельчением и не имеют поверхностных пленок, а
пульпа не содержит твердых эмульгаторов.
В настоящее время амальгамация практически не используется для извлечения
золота из руд и концентратов вследствие трудности обеспечения техники
безопасности при работе с ртутью и возможности загрязнения окружающей среды
[6,8].
2.3
Гидрометаллургические методы извлечения золота из руд
Роль гидрометаллургии в производстве драгоценных благородных металлов
очень велика. Широкое использование гидрометаллургии непосредственно связано с
разработкой и практическим использованием автоклавных процессов, эффективных
ионообменных и экстракционных методов извлечения из водных растворов. Эти
методы позволяют повысить извлечение металлов из рудного сырья, комплексность
его использования с высоким извлечением всех ценных компонентов, и,
соответственно, экономическую эффективность этих методов. Гидрометаллургические
процессы включают в себя извлечение (выщелачивание) металлов из руд и
концентратов при их обработке водными растворами химических реагентов с
последующим выделением из раствора металла или его химического соединения.
Важным фактором для выбора гидрометаллургических методов является избирательное
извлечение металлов из бедных и труднообогатимых руд с минимальными затратами
реагентов в простой аппаратуре при низких температурах. Наглядным примером
служит технология извлечения золота цианистыми растворами. Вследствие истощения
природных ресурсов постепенно в эксплуатацию вводятся месторождения бедных и
упорных руд, для которых высокое извлечение металла из руды в концентрат во
многих случаях может быть достигнуто только сочетанием физических методов
обогащения с гидрометаллургическими операциями, в результате которых получают
«химический концентрат».
Рассмотрим и сравним методы выщелачивания золота из руд [3].
2.3.1
Тиомочевинное (тиокарбамидное) выщелачивание золота
Впервые метод тиокарбамидного выщелачивания для извлечения золота из
сурьмянистых руд был предложен Плаксиным И.И. и Кожуховой М.А. в начале 40-х
годов XX века. Выщелачивание протекает по
реакциям, рассмотренным в таблице 1 [2].
Таблица 1 - Основные полуреакции, протекающие в процессе
Полуреакция
|
Электродный потенциал Eo,
В
|
Auo + 2CS(NH2)2-
2e→Au[CS(NH2)2]2+
|
+0,33
|
Fe3+ +e-
→Fe2+
|
-0,77
|
Суммарная реакция:
Au + Fe2(SO4)3 + 2CS(NH2)2 →{Au[CS(NH2)2]2}2 SO4 +
2FeSO4.
Преимущества метода тиокарбамидного выщелачивания перед цианированием:
скорость процесса растворения золота выше примерно в 10 раз;
меньший удельный расход и коррозионная активность реагента;
небольшое влияние со стороны ионов-примесей;
отсутствие СДЯВ в процессе растворения;
возможность дополнительного вскрытия золота.
К недостаткам этого метода стоит отнести высокую стоимость реагентов
(тиомочевина дороже NaCN на 25%) и
необходимость использования в процессе кислостойкого технологического
оборудования.
Поэтому в промышленном масштабе тиомочевина применяется лишь на
предприятиях с очень богатым концентратом, что оправдывает затраты на реагент
[2,8].
2.3.2
Тиосульфатное и аммиачно-тиосульфатное выщелачивание
В последнее время за рубежом отмечено падение интереса к тиомочевинному
варианту растворения золота из-за высокой токсичности этого реагента. Реальной
альтернативой цианированию является именно тиосульфатное выщелачивание.
Процессы тиосульфатного и аммиачно-тиосульфатного выщелачивания золота
протекают по двум реакциям.
в кислой среде ( тиосульфатное выщелачивание):
4Au + O2 + 8S2O32- + 4H+ → 4Au(S2O3) 23- + H2O,
в щелочной среде (аммиачно-тиосульфатное выщелачивание):
Au + 5S2O32- + Cu(NH3)42+ → Au(S2O3) 23- + 4NH3 +
Cu(S2O3)35-
Извлечение благородных металлов с помощью тиосульфатных растворов
известно от начала XX века. Как
известно, золосодержащие руды подвергали хлорирующему обжигу, а затем
обрабатывали тиосульфатным раствором. Последующие исследования были посвящены
тиосульфатному выщелачиванию золота из различных концентратов при повышенных
температуре и давлении [2].
Аммиачно-тиосульфатное выщелачивание применимо к упорным для цианистого
процесса рудам: марганцевым и медистым. Оптимальные условия сохраняются
поддержанием в растворе рН на уровне 7-8 ед. Это обеспечивает устойчивость
тиосульфат-ионов. Также этим способом можно добывать золото и серебро из
хвостов окислительного выщелачивания в присутствии меди.
Преимущества:
кратковременность процесса выщелачивания;
дешевизна и малая токсичность реагентов;
законченный цикл обработки руды с извлечением Au и Ag на месте;
комплексное использование сырьевой базы.
Несмотря на значительные преимущества метода, имеется и ряд недостатков,
таких как:
высокие (до 50%) потери тиосульфата, которые определяются неоптимальными
значениями концентраций и pH,
наличием некоторых примесей и бактерий, ультрафиолетовым облучением;
сильное разбавление пульпы (отношение Ж:Т = 6:1);
большие затраты на обогрев пульпы до нужной температуры (800С). Поэтому
этот метод не находит широкого промышленного применения [8].
2.3.3
Бактериальное выщелачивание золота
Бактериальное выщелачивание - это избирательное извлечение химических
элементов из многокомпонентных соединений посредством их растворения
микроорганизмами в водной среде. Таким образом, можно извлекать из руд и
отходов производства. ценные компоненты (золото, уран и др.) или вредные
примеси.
Пионерами исследований по бактериальному выщелачиванию золота были
институт Пастера (Франция) и университет г. Дакар (Сенегал), работы которых
появились в печати в 60-х годах XX
века [2].
Существенная интенсификация процесса выщелачивания достигается в
присутствии бактерий. Например, тионовые бактерии Thiobacillus ferrooxidans могут применяться для выщелачивания
меди, никеля, цинка, мышьяка, кадмия, золота и других металлов.
Бактериальные методы извлечения золота из руд базируются на результатах
изучения микрофлоры крупных золоторудных месторождений, позволивших выделить
культуры доминирующих видов бактерий и грибов. Установлено, что повышенной
активностью в процессе растворения золота обладают представители родов Bacillus, Bacterium, Chromobacterium.
Микроскопические грибы, в отличие от бактерий, способны аккумулировать
золото из растворов. Наиболее эффективны представители родов Aspergillus niger и Aspergillus oryzae.
В процессах бактериального выщелачивания золота определяющая роль
принадлежит продуктам микробного синтеза: аминокислотам, пептидам, белкам и
нуклеиновым кислотам. Углеводы в растворении золота участия не принимают [8].
В России и Канаде разрабатываются технологии бактериального выщелачивания
мышьяка и вскрытия тонковкрапленного золота из упорных золотосодержащих
концентратов перед их цианированием. Это позволяет исключить дорогостоящий
процесс обжига, загрязняющий атмосферу ядовитыми соединениями мышьяка.
Преимуществами бактериального выщелачивания являются:
простота аппаратурного оформления процесса;
доступность использования во всех способах выщелачивания, не связанных с
повышенными давлениями и температурой.
возможность быстрого размножения бактерий, особенно при возвращении в процесс
отработанных растворов, содержащих живые организмы.
Основным недостатком этого метода является малая скорость извлечения
золота в биологических процессах по сравнению с другими методами. К тому же при
переработке сульфидных руд происходит усиление дренажа кислых вод, что влечет
за собой закисление окружающего грунта.
Поэтому метод биовыщелачивания применяется в промышленности в меньших
масштабах, чем цианидный метод [9].
.3.4
Извлечение золота с применением органических растворителей
В результате поиска альтернативных процессов появились разработки новых
технологических схем с использованием неводных или смешанных растворителей.
Наибольший интерес представляют системы, где в качестве окислителя применяют
хлорид меди (II), а неводных растворителях − диметилформамид,
диметилсульфоксид и ацетонитрил. Известно, что прибавление смешивающегося с
водой органического растворителя изменяет гидродинамические характеристики
(вязкость, коэффициент диффузии) и диэлектрическую проницаемость среды;
неводный растворитель вступает в реакции ассоциации, сольватации (поверхности,
исходных и промежуточных соединений, продуктов реакции), а также может
выступать в качестве лиганд в реакциях комплексообразования [2].
Было замечено, что золото растворяется в нитрилах: ацетонциангидрине (CH3)2C(OH)CN, лактонитриле CH3CH(OH)CN, гликольнитриле HOCH2CN. Растворение металла происходит только в присутствии щелочи.
Использование органических растворителей, таких как ацетонитрил,
диметилсульфоксид, диметилформамид позволяет повысить скорость растворения
золота и серебра, значительно упрощает процесс извлечения металла из раствора
(путем отгонки растворителя), что открывает перспективу создания эффективных
технологий извлечения и аффинажа.
Основными недостатками этого метода являются высокая стоимость реагентов
и их дефицитность. Ввиду этих обстоятельств метод является неэффективным для
промышленного применения [8].
2.3.5
Бромцианирование
Перед цианированием извлекают свободное золото на амальгамационных или
ворсистых шлюзах. Бромцианирование производят перемешиванием тонкоизмельченной
руды сначала с раствором цианистого натрия при слабой щелочности
продолжительное время. Затем раствор сливают и пульпу нейтрализуют разведенной
серной кислотой, так как щелочь легко разлагает бромистый циан. Далее вновь
перемешивают при щелочности ниже 0,02% CaO и до нейтральной реакции с добавкой бромистого циана
по частям. Перемешивание ведут 4-5 часов в закрытом чане. Слабый водный раствор
бромистого циана не изменяется несколько суток. Бромистый циан получают
смешиванием KBr, KBrO3, KCN, H2SO4 по реакции:
2KBr + KBrO3 + 3KCN + 3H2SO4 = 3BrCN + 3K2SO4 + 3H2O
Стоит отметить, что данный метод не имеет эффективного промышленного
использования ввиду низкой степени извлечения золота [7].
2.3.6
Извлечение золота цианированием
Развитие технологии цианирования было бы невозможным без разработок таких
ученых как Шееле и Багратиона, которые впервые обнаружили способность золота
растворяться в водных растворах цианидов. Так, в России была построена
цианистая фабрика в Березовске (1897), а в 1898г и на Кочкарском руднике [1].
Цианидное выщелачивание на сегодняшний день является основным способом
извлечения золота из руд, как в традиционной технологии, так и при
геотехнологической добыче. В качестве реагента используются соли циановой
кислоты - цианиды натрия или калия концентрацией 0,02-0,3%. Растворение золота
в присутствии окислителя происходит по реакции:
Au + 4NaCN + 1/2O2 + Н2O = 2NaAu(CN)2 + 2NaОН
Золото переходит в раствор в виде золотоцианистого натрия, который
диссоциирует на ионы Na+ и
[Au(CN)2]-.
Комплексный ион [Au(CN)2]- затем направляют на сорбцию
ионообменными смолами, активным углем или осаждают цементацией (Zn мет.)
Преимущества метода цианирования:
высокая степень извлечения - золота до 95%;
низкая стоимость передела;
простота аппаратурного оформления;
температура процесса 20°С;
Самый главный недостаток этого метода - очень высокая токсичность
цианистых солей, ввиду гидролиза NaCN.
Но, несмотря на это обстоятельство, цианидный метод широко используется в
промышленных масштабах [1].
Перколяционное
выщелачивание
Перколяционное выщелачивание - это процесс извлечения золота посредством
естественного фильтрования цианистых растворов через слой золотосодержащей
руды, помещенной в чан с ложным днищем. Метод пригоден лишь для грубозернистых
материалов, частицы которых легкопроницаемы для цианистых растворов, ввиду
малой скорости фильтрации. Золото должно быть достаточно мелкое. Обычно
перколяции подвергают классифицированные пески с частицами крупностью 0,2 - 1мм.
Продолжительность полной обработки песка одной загрузки песка ( обычно 4-8
суток) зависит от скорости просачивания, количества растворов и режима
обработки, определяемых вещественным и гранулометрическим составом песка [1].
Обычно выщелачивание просачиванием осуществляют в чанах круглой или
прямоугольной формы последовательно заливкой порций цианистых растворов
убывающей концентрации. Первые крепкие растворы содержат (0,1- 0,2) % NaCN,
средние 0,05-0,08 и слабые 0,03-0,05 %.
Полученные золотосодержащие растворы идут на осаждение золота.
Выщелоченные и промытые пески выгружают сухим или гидравлическим способом.
Расход реагентов зависит от характера обрабатываемого материала и
составляет (0,25-0,75) кг цианида и 1- 2 кг извести на 1 т сухого песка.
Преимущества перколяционного выщелачивания:
простота аппаратурного оформления;
относительная дешевизна процесса;
небольшой расход электроэнергии.
Недостатком же является невысокое (обычно 60%) извлечение золота. Поэтому
использование этого метода в промышленности малоэффективно[5].
Кучное
выщелачивание
Процесс кучного выщелачивания заключается в том, что руда, уложенная в
виде штабеля (кучи) на специальном водонепроницаемом основании (площадке)
орошается сверху цианистым раствором. При медленном просачивании раствора через
слой руды происходит выщелачивание золота и серебра. Стекающий снизу раствор
идет на извлечение благородных металлов [1].
Метод пригоден для переработки руд, указанных в пункте 2.3.6.1. Обычно
кучному выщелачиванию подвергают руду после дробления до крупности 5-20 мм.
Присутствие глинистых веществ снижает проницаемость кучи, замедляет
выщелачивание и уменьшает извлечение золота.
Кучное выщелачивание проводят на открытом воздухе на специально
подготовленных площадках. Для придания площадке водонепроницаемых свойств ее
покрывают слоем бетона, асфальта или утрамбованной глины. Кучи орошают
цианистым раствором с помощью специальных разбрызгивающих устройств (форсунок),
установленных над ними.
Золотосодержащий раствор, вытекающий из оснований кучи, стекает в
облицованные пластиком дренажные канавки, проложенные рядом с кучей вдоль ее
длинных сторон, и по ним отводится в пруд-сборник.
Преимущества кучного выщелачивания:
возможность переработки бедных руд;
простота технологического процесса;
низкие капитальные затраты.
Недостатки:
длительность процесса (30-90 суток);
низкое извлечение золота (50-70%).
Ввиду этих недостатков метод используется в промышленности, но не так
эффективно как цианирование перемешиванием [2].
Цианирование
перемешиванием
Цианирование перемешиванием - значительно более эффективный процесс по
сравнению с цианированием просачиванием. Это объясняется хорошим вскрытием
выщелачиваемого золота, благоприятными условиями диффузионного подвода ионов CN¯
и молекул растворенного
кислорода к поверхности золотин, и энергичным накислороживанием пульпы в
процессе выщелачивания.
Рудные пульпы, поступающие на цианирование перемешиванием, имеют
повышенную вязкость, что затрудняет диффузию ионов CN - и молекул растворенного
кислорода к поверхности, растворяющихся золотин. Поэтому необходимо энергичное
перемешивание и непрерывное насыщение пульпы кислородом воздуха.
Процесс ведут при концентрации NaCN, составляющей 0,01-0,1 % (чаще всего
0,02-0,05%) и концентрации СаО, равной 0,01-0,03% (рН 9-11). Цианистые растворы
не агрессивны, поэтому для изготовления оборудования применяют такие доступные
материалы, как обычная углеродистая сталь, чугун [1].
Процесс выщелачивания осуществляют в периодическом или непрерывном
режиме.
Непрерывное выщелачивание получило большее распространение благодаря
полной автоматизации, высокой эффективности использования аппаратов. Также нет
необходимости в использовании мощных двигателей и насосов для перекачки пульпы
из емкостей.
При непрерывном выщелачивании пульпа поступает в цепочку (каскад) из
последовательно соединенных аппаратов, где она перемешивается. Число аппаратов
в каскаде обычно выбирают не менее 4 - 6 (лучше 8 - 12). При меньшем числе
аппаратов значительная доля частиц выщелачиваемой руды проскакивает все
аппараты. Это негативно скажется на эффективности процесса вследствие низкого
извлечения золота.
Основным типом аппаратов для непрерывного выщелачивания является пачук. с
центральным аэролифтом. Это высокий цилиндрический чан с коническим днищем.
Высота чана обычно в 3 - 4 раза превышает диаметр. В центре чана расположен
аэролифт (циркулятор). Последний представляет собой широкую, открытую с обоих
концов трубу, в нижней части которой предусмотрена воздушная рубашка. По трубе
в рубашку подают сжатый воздух, который через прорези поступает в виде
отдельных пузырьков в трубу. Находящаяся здесь пульпа смешивается с воздухом,
образуя воздушно-пульповую смесь, плотность которой меньше, чем плотность
пульпы. Поэтому смесь поднимается вверх и выливается через верхний край трубы.
Более плотная, не содержащая пузырьков воздуха пульпа поступает в трубу снизу.
Пачуки широко применяют как в отечественной, так и в зарубежной
золотоизвлекательной промышленности. Преимущества аппаратов этого типа состоят
в возможности перемешивания весьма густых пульп, простоте устройства и
интенсивной аэрации пульпы [2,5].
2.4 Обзор
существующих методов извлечения золота из цианистых растворов
.4.1
Цементация
С начала развития цианистого процесса и до последнего времени основным и
практически единственным методом осаждения благородных металлов из цианистых
растворов была цементация цинком. В настоящее время этот метод сохраняет
ведущее место в практике золотоизвлекательной промышленности.
Цементацией в металлургии цветных металлов называют процесс восстановления
одного металла другим в водных растворах. В основе метода лежит вытеснение
благородных металлов менее благородными в соответствии с рядом окислительных
потенциалов металлов.
Zn + 4CN- = [Zn(CN)4]2- + 2e- E0 = -1,26B;+ 2CN- = [Au(CN)2]-
+ e- E0 = -0,54B.
Потенциал цинка более отрицателен, чем потенциал золота, поэтому цинк
легко вытесняет его из цианистых комплексов:
Au(CN)2 - + Zn = 2 Au + Zn(CN)42- Kр
= 1×1023
Следовательно, в термодинамическом отношении золото и серебро могут быть
осаждены практически полностью.
Преимущества метода цементации:
высокая степень осаждения золота (до 99,5%).
достаточно быстрое и полное осаждение золота.
К основным недостаткам этого метода относят высокий расход цинка (в 30-40
раз больше стехиометрии) и громоздкость аппаратуры. К тому же низкое содержание
золота (не более 40%) в цинковом шламе говорит о поиске более эффективного
метода, коим и является сорбия [3].
2.4.2
Сорбционное извлечение золота
Сорбцию золота из цианистых растворов можно проводить как на активированном
угле, так и на синтезированных ионообменных смолах.
За рубежом ионообменные смолы не получили промышленного применения в
качестве осадителей благородных металлов из цианистых пульп, это связано с
лучшими сорбционными и кинетическими свойствами активных углей и их более
высокой селективностью по отношению к золотоцианистому комплексу, а такие же их
низкой стоимостью (в 7-12 раз ниже цены ионообменных смол).
Сорбция золота активными углями сопровождается
окислительно-восстановительными процессами. Дицианоаурат-ионы, находящиеся в
растворе, на поверхности угля преобразуются в цианокарбонилы и
восстанавливаются до металлического золота.
Преимущества:
высокая удельная поверхность угля;
низкая стоимость угля, по сравнению с ионитом;
процесс регенерации угля занимает мало времени (6-7 часов).
Однако главным недостатком углей является их низкая механическая
прочность. Да и емкость по золоту у них значительно меньше, чем у тех же
анионообменных смол [1,2].
Сорбцию благородных металлов ионообменными смолами можно осуществлять как
из осветленных цианистых растворов, так и непосредственно из пульп в процессе
цианирования.
Анионообменная смола АМ-2Б, обладает наибольшей селективностью по
отношению к золоту, по сравнению с другими ионитами.
Первый способ предполагает извлечение золота из руды обычными приемами
цианирования с тем лишь отличием, что извлечение золота из цианистого раствора
осуществляют сорбцией его ионообменной смолой.
Второй способ состоит в том, что в контакт с ионообменной смолой приводят
не осветленный золотосодержащий раствор, а непосредственно пульпу в процессе
цианирования. Растворяясь в цианистом растворе, благородные металлы переходят в
жидкую фазу пульпы и, одновременно сорбируются ионитом.
После окончания выщелачивания и сорбции смолу отделяют, а обеззолоченную
пульпу направляют после обезвреживания в отвал.
Насыщенный золотом ионит регенерируют десорбцией золота и примесей и
вновь направляют на сорбционное выщелачивание.
Преимущества сорбции из пульп:
исключение стадии фильтрации и промывки пульпы из технологии. Это
позитивно отражается на экономике процесса ввиду громоздкости и высокой
стоимости этой стадии.
более высокое извлечение золота. В отдельных случаях повышение извлечения
золота может достигать 10 - 20 %.
более быстрое протекание процесса растворения в присутствии ионита по
сравнению с обычным цианированием. Таким образом, ионит частично сорбирует
вредные примеси, влияющие на скорость растворения золота.
В промышленности наиболее часто используют совмещение процессов
цианирования и сорбции, так называемого сорбционного выщелачивания [8,10].
Вывод
Рассмотрев все вышеперечисленные методы извлечения золота из руд можно
сделать следующий вывод. На сегодняшний день самой изученной и эффективной
технологией, применяемой на производстве, является цианидное выщелачивание,
совмещенное с процессом сорбции. Выбор этого метода во многом обусловлен
высокой степенью извлечения золота в раствор (не менее 95%) и малыми затратами
на используемые реагенты. К тому же нет необходимости в дополнительном нагреве
пульпы, так как процесс идет при 200С. Важно отметить, что возможно повторное
использование ионообменной смолы после регенерации. Все эти факты говорят об
экономичности и уникальности этого метода, по сравнению со всеми рассмотренными
выше. Поэтому сорбционное выщелачивание с пневматическим перемешиванием находит
широкое применение, как на территории Российской Федерации, так и за рубежом.
3 Теория
процесса
.1
Физико-химические свойства золота
Золото - тягучий, ковкий металл специфического желтого цвета. Это
химический элемент I группы, 2-й подгруппы периодической системы элементов Д.И.
Менделеева с порядковым номером 79. В таблице 2 приведены основные физические
свойства золота.
Таблица 2 - Физические свойства золота
Свойство
|
Золото
|
Атомная масса, а. е. м.
|
196,967
|
Электронная конфигурация
|
[Xe] 4f14 5d10
6s1
|
Плотность при 20ºС, г/см3
|
19,32
|
Температура плавления, ºС
|
1064,18
|
Температура кипения, ºС
|
2856
|
Удельная теплоемкость,
Дж/(кг∙˚С)
|
130
|
Относительное удлинение
|
30-50%
|
Степени окисления
|
−1, 1, 3, 5
|
Твердость по Моосу
|
2,5
|
Как видно из таблицы 2, золото - тяжелый металл, который имеет большое
относительное удлинение при ковке. Большая плотность золота имеет важное
значение для процессов гравитационного обогащения золотосодержащих руд и россыпей
ввиду того, что остальные рудные породы и минералы имеют плотность значительно
меньше [1].
В химическом отношении золото малоактивно. Даже при высоких температурах
оно не взаимодействует с кислородом, водородом и азотом. В химических
соединениях золото может быть в одно- и трехвалентном состояниях. Золото не
растворяется ни в щелочах, ни в кислотах. Хорошо растворяется только в «царской
водке» по реакции:
Au + HNO3 + 4HCl = HAuCl4 + NO + 2H2O.
Золото растворимо в воде, содержащей в растворе галоген, в растворах
серноватистых солей, хлорных и бромных металлов, марганцовокислой соли и в
присутствии кислорода в растворах цианистых металлов. С ртутью золото образует
соединения AuHg, AuHg2, выше 3000 распадающиеся с образованием твердого
раствора ртути в золоте.
Золото образует комплексные цианистые соединения, NaAu(CN)2, KAu(CN)2, , что лежит в основе процессов
гидрометалллургии.
Обычно комплексные цианистые соли золота получаются непосредственным
растворением металлического золота в растворах щелочных металлов в присутствии
кислорода воздуха.
При нагревании комплексные цианистые соединения золота разлагаются, они
довольно хорошо растворимы в воде, разлагаются кислотами с образованием
синильной кислоты HCN и осадка
цианида золота AuCN [2, 5].
3.2 Термодинамика
процесса цианирования
В процессе цианирования происходит окисление золота кислородом воздуха до
Au+ и его переход в раствор в виде
комплексного аниона [Au(CN)2]¯.
Химизм описывается двумя
последовательно протекающими реакциями:
Au + 4CN¯
+ 2H2O + O2 →
2[Au(CN)2]¯ + 2OH¯
+ H2O2 (1)
2Au + 4CN¯ + 2H2O2
→
2[Au(CN)2]¯ + 2OH¯ (2)
Суммарная реакция:
Au + 8NaCN + 2H2O + O2 → 4Na[Au(CN)2] + 4NaOH (3)
Окислительный потенциал золота весьма высок (φ0=+1,88B).
Наиболее известные окислители имеют меньшие потенциалы и не могут
окислить золото.
Цианистые растворы имеют щелочной характер. Поэтому для этой среды самый
доступный и распространенный в гидрометаллургии окислитель - это кислород,
потенциал которого также уступает золоту:
O2 + 2H2O +4e → 4OH¯, φ0 = + 0,40B (4)
Окислительные потенциалы кислорода при его восстановлении до пероксида
водорода:
O2 + 2H2O +2e → 2OH¯+
H2O2, φ0 = - 0,15B (5)
и пероксида водорода при его восстановлении до гидроксильных ионов:
H2O2 + 2e → 2OH¯, φ0 = + 0,95B (6)
недостаточны для окисления металлического золота и перевода его в раствор
в виде катионов Au+.
Используя уравнение Нернста, можно сделать вывод о том, потенциал металла
в растворе его соли зависит от активности ионов этого металла:
, (7)
где φ - потенциал металла в растворе его соли, В;
φ0 - стандартный потенциал металла,
В;газовая постоянная, R ==8,314 Дж/(мольК);
Т-температура, К;
n -
число электронов, принимающих участие в реакции;- число Фарадея, F=96500
Кл/моль;
αМеn+- активность катионов металла в растворе [3].
Потенциал золота можно снизить, уменьшая активность ионов Au+ в растворе, что и взято за основу
при растворении золота в цианистых растворах.
Ионы Au+ образуют с ионами CN¯
очень прочный комплекс [Au(CN)2]¯, равновесие диссоциации которого
[Au(CN)2]¯ = Au+ + 2CN¯ (8)
сильно сдвинуто влево и характеризуется весьма малой величиной константы
нестойкости (диссоциации):
(9)
Поэтому в присутствии ионов CN¯ активность ионов Au+ резко уменьшается.
Активность ионов Au+ из
уравнения (9) подставим ее в уравнение (6):
После упрощения получим:
(10)
Это выражение характеризует потенциал золота в растворе, содержащем
свободные ионы CN¯:
Au+ +
2CN¯
= [Au(CN)2]¯ + e (11)
Потенциал полуреакции (при α[Au(CN)2]¯ = 1 и α CN¯
= 1) φ0 = - 0,54B.
Зная стандартные потенциалы полуреакций окисления и восстановления,
рассчитаем константы равновесия и изменение изобарно-изотермического потенциала
реакций (1) и (2):
,
,
где К-константа равновесия;
φ0ox, φ0red - стандартные потенциалы окислителя
и восстановителя соответственно, В;
∆G0298-
изменение изобарно-изотермического потенциала реакции в стандартных условиях,
кДж/моль.
Для растворения золота по реакции (1) при 25˚С:
;≈ 2∙1013.
∆G0298= -(-0,15-(-0,54))∙2∙96500∙10-3 = -
75,3кДж/моль.
Для растворения золота по реакции (2) при 25˚С
;≈ 3∙1050.
∆G0298= -(+0,95-(-0,54))∙2∙96500∙10-3 = -
288кДж/моль.
Такие высокие значения констант равновесия и уменьшение
изобарно-изотермического потенциала показывают, что реакции (1) и (2) должны
протекать в сторону растворения золота[3,10].
3.3 Кинетика
процесса цианирования
Для гетерогенных реакций, протекающих с участием двух растворенных
реагентов, установлено, что для каждого давления кислорода имеется критическая
концентрация цианида. Ниже этой концентрации скорость растворения золота
находится в линейной зависимости от нее, а выше скорость практически не зависит
от концентрации цианида и является линейной функцией от давления кислорода.
Если концентрация цианида ниже критической, скорость растворения определяется
доставкой CN¯
- ионов к поверхности, а
выше скорость практически не зависит от концентрации цианида и является
линейной функцией от давления кислорода[3].
В области малых концентраций (докритических) кажущаяся энергия активации
равна 15,1 кДж/моль, что типично для диффузионного режима. При концентрациях
цианида выше критических скорость очень мало зависит от температуры, так как
влияние увеличения коэффициента диффузии кислорода в растворе с ростом
температуры погашается понижением растворимости кислорода (при проведении опыта
в открытом аппарате).
Кинетические закономерности растворения золота в цианистых растворах
хорошо объясняются, если принять электрохимический механизм растворения. На
поверхности металла образуются локальные электрохимические ячейки (анодные и
катодные участки). Их образование обусловлено неодинаковыми энергетическими
уровнями электронов в различных точках поверхности вследствие наличия дефектов,
примесей атомов других металлов. Золото в цианистых растворах служит анодом, а другой
компонент пары - катодом.
На анодных участках поверхности золота образуется комплексный ион и
освобождается электрон:
Au + 2CNˉ = Au(CN)2- + e
На катодных участках поверхности золота или минерала, в который вкраплена
частица золота, происходит восстановление растворенного кислорода с
образованием перекиси водорода и гидроксил ионов:
O2 + 2H2O + 2e = H2O2 + 2OH-
Электрохимический механизм растворения золота доказывается остроумным
опытом Томсона (1947г.). Маленькие шарики золота (120мкм) были погружены в
желатинизированный раствор цианистого калия. Кислород вводился так, что он
диффундировал только в одном направлении. При раздельном протекании катодной и
анодной реакций, на поверхности, обращенной потоку кислорода, очевидно, должна
протекать катодная реакция, и эта часть поверхности частиц не должна
подвергаться коррозии. Действительно, оказалось, что шарики золота растворяются
со стороны, противоположной току кислорода.
Скорость электрохимических процессов при растворении золота высокая, и
поэтому скорость растворения лимитируется подводом реагентов - либо ионов CN¯,
либо растворенного
кислорода.
В том случае, если концентрация CN¯ в растворе значительно меньше, чем
концентрация О2 , очевидно концентрация CN¯ на поверхности частиц и будет равна
0, а концентрация кислорода - близкой к концентрации его в растворе. Скорость
процесса будет определяться диффузией ионов CN¯:
где jAu - количество молей золота,
переходящих в раствор в единицу времени с единицы поверхности;CN¯
- количество г-ионов CN¯,
подводимых в единицу
времени к единице поверхности,
DCN - коэффициент
диффузии,
δCN- эффективная толщина диффузионного слоя,
CCN - концентрация
CN¯
в растворе.
По мере увеличения концентрации CCN возрастает и скорость растворения
золота. Концентрация кислорода на поверхности будет уменьшаться.
При соотношении концентрации CN¯ и О2 в растворе, соответствующем
условию:
концентрации CN¯
и О2 на поверхности
реакции равны нулю. Дальнейшее повышение концентрации CN¯ в растворе при Со=const приведет к
росту концентрации CN¯
на поверхности без
увеличения скорости растворения золота.
Таким образом, соотношение концентраций CN¯ и О2, определяемое данной формулой,
является оптимальным.
При атмосферном давлении воздуха над раствором и температуре 200 С
растворимость кислорода в воде равна 0,27∙10-3 моль/л, следовательно,
увеличение концентрации свободных ионов CN¯ выше 0,01% NaCN не приведет к
увеличению скорости процесса.
Но при дефиците свободного цианида улучшение аэрации раствора также не
увеличивает скорость. Поэтому нужно контролировать состав раствора по двум
реагентам таким образом, чтобы отношение концентрации свободных ионов CN¯
к концентрации О2 было
равно 5-6[5, 10].
3.4 Гидролиз
цианистых растворов. Защитная щелочность
Цианиды щелочных и щелочноземельных металлов являются солями слабой
синильной кислоты HCN и сильных
оснований (NaOH, KOH). При растворении в воде они подвергаются гидролизу:
CN- + H2O = OH- + HCN↑ (12)
Это явление крайне нежелательное, и приводит к значительным потерям
цианида и отравлению атмосферы цеха парами ядовитой синильной кислоты.
Константа равновесия гидролиза КГ имеет вид:
.
Если рассматривать достаточно разбавленный раствор, то активности равны
концентрациям, тогда:
(13)
Константа диссоциации KД синильной кислоты равна:
(14)
Найдя из последнего уравнения значение [HCN] и подставив его в уравнение
(13) получим:
.
Учитывая, что числитель последнего выражения представляет собой ионное
произведение воды КW имеем:
КГ = КW/К .(15)
При 25°С значения КW= 1∙10-14 и КД = 7,9∙10-10, откуда КГ =
1,26∙10-5.
Допустим, концентрация NaCN в
растворе равна С0. Если степень гидролиза NaCN равна h, то концентрация негидролизованной соли
составит (С0-С0h), моль/л. Негидролизованная соль полностью диссоциирована на
ионы, и поэтому концентрация ее равна концентрации иона CN¯:
(16)
При гидролизе образуются эквивалентные количества молекул
и ионов OH-, следовательно
. Так как из одного иона
образуется при гидролизе одна
молекула HCN, то концентрация HCN равна концентрации гидролизованной соли:
(17)
Подставив выражения (16) и (17) в уравнение (13), получим:
, откуда
(18)
Уравнение (17) применимо для расчета степени гидролиза цианида в чистой
воде. Как видно, степень гидролиза значительно увеличивается с уменьшением
концентрации цианида. При концентрациях цианида, применяемых на практике,
степень гидролиза может достигать значительных величин (5 - 10%).
Из реакции (12) следует, что для подавления гидролиза в цианистые
растворы необходимо добавлять щелочь. Найдем степень гидролиза цианистого
раствора концентрации С0 в присутствии щелочи концентрации С01. Концентрации
ионов CN и молекул HCN определяются уравнениями (16) и (17). Появление ионов OH- в растворе обусловлено введением
щелочи и частичным протеканием реакции гидролиза. Если использовать оксид
кальция CaO, дающий в водном растворе гидроксид Ca(OH)2, то концентрация ионов OH¯ будет равна:
(19)
Таблица 3 - Степень гидролиза растворов NaCN
Концентрация NaCN
|
Степень гидролиза, %, при
концентрации CaO в растворе, % (моль/л)
|
%
|
102, моль/л
|
0
|
0,01(1,78∙10-3)
|
0,05(8,92∙10-3)
|
0,5
|
10,20
|
1,1
|
0,32
|
0,07
|
0,2
|
4,08
|
1,7
|
0,34
|
0,07
|
0,1
|
2,04
|
2,5
|
0,35
|
0,05
|
1,02
|
3,5
|
0,35
|
0,07
|
0,02
|
0,408
|
5,4
|
0,35
|
0,07
|
0,01
|
0,204
|
7,6
|
0,35
|
0,07
|
0,005
|
0,102
|
10,5
|
0,35
|
0,07
|
0,002
|
0,041
|
16,1
|
0,35
|
0,07
|
Подставив выражения
,
и
в уравнение (13), получим:
,откуда
.................(20)
Рисунок 1 - Степень гидролиза растворов NaCN при концентрации CaO, ℅: 1 - 0; 2 - 0.01; 3 - 0.05.
Результаты расчетов, выполненных по этому уравнению показывают исходя из
данных таблицы 3 , четвертого и пятого столбца, и рисунка 1, кривых 2, 3), что
даже при небольших концентрациях щелочи степень гидролиза резко снижается. На
практике вводят в цианистые растворы небольшое количество щелочи, которая
защищает их от разложения гидролизом и потому называется защитной. Наиболее
часто используют дешевую известь, выполняющую одновременно функцию коагулянта
при сгущении пульпы.
Величина КГ, а следовательно, степень гидролиза и потери цианида
увеличиваются с повышением температуры. Поэтому процесс цианирования ведется
при обычных температурах (10-20°С)[1,2,5,10].
3.5 Теория
процесса ионного обмена
Ионообменными свойствами обладают очень многие природные и искусственные
соединения. Однако по практическому значению первое место занимают иониты на
основе синтетических смол - ионообменные смолы.
Макромолекула ионообменных смол, состоит из гибких переплетающихся нитей
полимерных молекул, углеводородные цепи которых имеют поперечные связи -
мостики, образующие матрицу смолы. Матрица имеет неподвижно закрепленные на ней
заряженные группы - фиксированные ионы. Заряд фиксированных ионов
нейтрализуется распределенными внутри смолы подвижными ионами противоположного
знака, так называемыми противоионами. Фиксированные ионы связаны с
противоионами и образуют с ними ионогенные группы. Подвижность противоионов
способствует вступлению их в реакцию обмена с ионами того же знака,
находящимися в растворе. Если фиксированные ионы несут отрицательный заряд, то
ионит способен к обмену катионов и называется катионитом, если заряд
положительный, то ионит способен к обмену анионов и называется анионитом.
При контактировании с растворами электролитов катиониты обменивают
находящийся в их структуре противоион, например, катиониты
на эквивалентное количество другого
катиона, находящегося в растворе:
Аналогично аниониты при контактировании с растворами электролитов
обменивают находящийся в их структуре противоион, например анион OHˉ, на
эквивалентное количество другого аниона, присутствующего в растворе
В уравнениях через R обозначен каркас ионита, фаза ионита отмечена
чертой.
Наиболее часто в качестве фиксированных ионов служат:
у катионитов - SO3ˉ,
COOˉ, PO32ˉ.
у анионитов - NH3+, =NH2+, ≡NH+,≡N+.
Очевидно, что ионный обмен может протекать только при условиях, когда
ионогенная группа диссоциирована. По степени диссоциации ионогенной группы,
содержащей в качестве противоиона ион
или
, ионообменные смолы делят на сильно
или слабокислотные катиониты и сильно - или слабоосновные аниониты.
Сильноосновные аниониты способны к обмену анионами как в кислой так и в
щелочной среде. Помимо сильно - и слабоосновных анионитов существуют аниониты
смешанной основности (полифункциональные). Такие аниониты содержат одновременно
сильноосновные четвертично - аммониевые группы и слабоосновные
аминогруппы[2,10].
На всех золотоизвлекательных фабриках, где применяют сорбционную
технологию, чаще всего используют анионит марки АМ-2Б, что означает анионит
макропористый, бифункциональный. Матрица анионита состоит из сополимера стирола
и дивинилбензола, обработанных хлорметиловым спиртом. Содержание дивинилбензола
в смоле составляет 10-12 %, что обеспечивает ей необходимую механическую
прочность. С помощью реакций аминирования в матрицу анионита привиты
сильноосновные активные группы четвертичных аммониевых оснований, а также
среднеосновные группы - третичные амины. Если буквой R условно обозначить
матрицу смолы, то ее формула имеет вид:
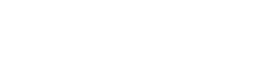
Количество сильноосновных и среднеосновных групп в ионите содержится
примерно поровну. Наличие в анионите двух видов функциональных групп повышает
его селективность по отношению к золоту и увеличивает сорбционную емкость по
сравнению с ранее применявшимся сильноосновным анионитом АМ.
Макропористость анионита значительно улучшает его кинетические
характеристики, так как наличие крупных пор в ионите способствует большей
скорости диффузии ионов внутри смолы, благодаря чему увеличивается общая
скорость ионного обмена.
Основными физико-химическими характеристиками ионообменной смолы являются
обменная емкость, набухаемость, пористость, селективность, механическая
прочность.
В производственных условиях обычно пользуются понятием полезной или
рабочей емкости, которая выражает количество сорбированных ионов, считающихся
полезными в данном технологическом процессе, на единицу массы ионита в
воздушносухом состоянии.
Рабочую емкость смолы определяют путем пропускания с постоянной скоростью
раствора через ионит до появления сорбируемого иона определенной концентрации в
выходящем растворе. Например, при извлечении золота из растворов цианистых
пульп концентрация его в жидкой фазе хвостов должна составлять не более
0,03-0,05 мг/л.
По техническим условиям завода-изготовителя анионит АМ-2Б имеет следующие
количественные характеристики: полная обменная емкость по хлор-иону 3,2
мг-экв/г; размер зерен 0,6-1,2 мм; удельная поверхность ионита 32м2/г; насыпная
масса сухой смолы 0,42 г/см3; влажность товарного анионита 52-58 %; коэффициент
набухания в воде 2,7.
Анионит поставляется в полиэтиленовых мешках массой 33,6 кг.
Транспортировать и хранить его нужно при температуре не ниже 5°С, иначе смола
растрескивается и при загрузке в процесс начинает интенсивно разрушаться. Перед
загрузкой свежую смолу предварительно промывают 3-4 объемами 0,5 %-ного
раствора НС1 или Н2SO4, чтобы удалить содержащиеся в анионите химические
продукты синтеза [8,10].
В процессе сорбционного выщелачивания ионы благородных металлов и
примесей сорбируются анионитом по реакциям:
Помимо комплексных цианистых анионов, смола сорбирует и простые
циан-ионы:
В результате протекания побочных реакций часть активных групп оказывается
занятой анионами металлов примесей, что, естественно, снижает рабочую емкость
анионита по золоту. Количество примесей, содержащихся в насыщенной смоле,
зависит от химического состава руды и режима ее цианирования[5,10].
.6
Термодинамика процесса сорбции
Для правильного выбора режима проведения сорбционного процесса руду
каждого месторождения предварительно исследуют, проводя комплекс лабораторных и
полупромышленных испытаний, после чего рассчитывают производственную аппаратуру
и технологический режим проведения процесса с учетом максимального извлечения
благородных металлов.
Обязательное условие при проведении исследований и испытаний руды -
снятие и изучение изотерм сорбции, которые характеризуют состояние
ионообменного равновесия при постоянной температуре.
Изотермы сорбции позволяют судить о селективности применяемых ионитов,
дают возможность рассчитывать необходимое количество ступеней сорбции,
определять величину средней движущей силы массообмена.
Изотермы сорбции выражают графически и строят в координатах: равновесная
концентрация ионов в смоле - концентрация ионов в растворе. Соответственно на
рисунке 2 показан графический метод расчета ступеней сорбции для ионообменной
смолы АМ-2Б.
Рисунок 2 - Графический метод расчета числа ступеней сорбции
На рисунке 3 рассмотрена группа изотерм сорбции одного и того же иона на
различных ионообменных столах. Анализ иных изотерм позволяет сделать следующие
заключения. Ионит 1 обладает наибольшей селективностью при достаточно высокой
емкости по данному иону. Резкий подъем изотерм 1 при малых равновесных
концентрациях иона в растворе позволяет извлекать данный компонент с
достаточной полнотой. Иониты, имеющие изотерму подобного типа, благоприятны для
извлечения благородных металлов из растворов. Ионит 2 обладает также высокой
емкостью, но менее селективен, чем ионит 1. ионит 3 имеет наиболее
распространенную изотерму сорбции. Ионит 4 характеризует процесс физической
сорбции и практически непригоден для использования в пульповых процессах.[10]
Рисунок 3 - Изотермы сорбции одного и того же иона на различных
ионообменных смолах
3.7 Кинетика
ионного обмена
Процесс ионного обмена состоит из пяти стадий:
) диффузия ионов в растворе к поверхности зерна ионита;
) диффузия ионов внутри зерна;
) протекание реакции обмена ионов;
) диффузия вытесненного противоиона изнутри к поверхности зерна;
) диффузия противоиона в объем раствора.
Стадии первая и пятая, вторая и четвертая, по сути, одинаковы, только
обратны по знаку. Поскольку процесс ионного обмена - многостадийный, общая
скорость обмена определяется скоростью процесса, протекающего наиболее
медленно.
Многочисленными исследованиями установлено, что химическая реакция обмена
(третья стадия) осуществляется очень быстро и, как правило, не определяет общей
скорости ионообменного процесса. Таким образом, в кинетике ионного обмена
решающую роль играют диффузионные процессы. Об этом свидетельствует большое
число экспериментальных данных, полученных в статических и динамических
условиях. Эти данные показывают, что скорость ионного обмена зависит от размера
зерна ионита: при уменьшении крупности зерен скорость ионообменного процесса
возрастает. Отсюда следует, что скорость ионного обмена определяется скоростью
диффузии ионов либо непосредственно в зерне ионита, либо в неподвижном слое
жидкости (называемом пленкой), окружающем зерно ионита. Диффузию ионов в зерне
ионита принято называть гелевой диффузией, диффузию ионов через пленку раствора
- пленочной.
Гелевая диффузия протекает чаще всего медленнее, чем диффузия в растворе.
Происходит это по нескольким причинам. Во-первых, часть пространства в ионите
занята цепями полимерных молекул и поэтому недоступна для диффузии. Во-вторых,
путь диффундирующих ионов в смоле длиннее, так как ионам приходится
перемещаться не по прямой, а по сложной траектории.
В реальных условиях процесс гелевой диффузии зачастую сопровождается
рядом побочных явлений. Для простейших случаев получены некоторые
количественные соотношения. Так, если оба обменивающихся иона обладают
одинаковой подвижностью внутри ионита, справедливо следующее соотношение:
τ = r2/ Dn
где τ - время установления равновесия;
Dn -
коэффициент диффузии ионов в смоле;
r -
радиус зерна смолы.
Из выражения видно, что с увеличением коэффициента диффузии ионов внутри
ионита время перемещения ионов уменьшается, следовательно, скорость обмена
возрастает. Коэффициент диффузии зависит от процента сшивки ионита: чем больше
содержится дивинилбензола в смоле, тем меньше коэффициент диффузии, тем
соответственно больше время ионообмена. Формула показывает также, что скорость
гелевой диффузии прямо пропорциональна квадрату радиуса зерна смолы, т.е. с
увеличением крупности зерен удлиняется путь перемещения ионов внутри ионита, и
скорость диффузии уменьшается.
При пленочной диффузии вокруг каждого зерна ионита в растворе находится
пленка жидкости, которая благодаря силам молекулярного сцепления относительно
прочно связана с поверхностью зерна. В этой пленке перемешивания нет, поэтому
перенос ионов через нее идет только вследствие диффузии. Установлено, что
скорость диффузии в пленке зависит от ее толщины, разницы концентраций раствора
на внешней и внутренней ее границах, а также от коэффициента диффузии в
растворе. Все эти факторы связаны следующим соотношением:
τ = (α / Dp) (СH - СB)
где τ - время;
α - толщина пленки;- коэффициент
диффузии ионов в растворе;
СH и СB - концентрации ионов на поверхности зерен ионита и на внешней
границе пленки.
Из соотношения следует, что скорость диффузии ионов в пленке, окружающей
зерно ионита, можно увеличить путем уменьшения ее толщины в результате более
интенсивного перемешивания раствора со смолой, а также путем увеличения разницы
концентраций ионов на границах пленки благодаря увеличению концентрации ионов в
растворе.
В сорбционном процессе извлечения золота из раствора пульпы скорость
ионного обмена определяется в основном пленочной диффузией ионов.
На стадии регенерации смолы скорость ионообмена лимитируется,
по-видимому, гелевой диффузией, так как процесс идет в неподвижном слое ионита
без перемешивания [1, 2,3,10].
4 Описание
технологической схемы, пуск и остановка
Пульпа поступает в барабанные вращающиеся грохоты (поз. 1-1-1-6), в
которых происходит отделение пульпы от щепы, затем пульпа поступает в пачуки
цианирования (поз. 2-1-2-4), в пачуки поз. 2-1 и поз. 2-3 подается 0,2% раствор
NaCN и 5% раствор NaOH (для
поддержания pH 10-11) из напорных емкостей поз. 7 и 8 соответственно.
Перемешивание осуществляется воздухом.
Цель предварительного цианирования - перевести в раствор 30-40% золота, и
тем самым обеспечить высокую емкость ионообменной смолы по золоту. Затем
частично выщелоченная пульпа поступает в пачуки сорбционного выщелачивания
(поз. 5-1-5-16), где происходит дальнейшее выщелачивание золота и его сорбция
на анионит АМ-2Б, отрегенерированная или свежая смола подается в пачуки поз.
5-7 и поз. 5-15, автоматически передвигаясь противотоком по отношению к пульпе
из последнего аппарата в первый. Насыщенная смола поступает самотеком в
отмывочную колонну (поз. 3), в нижнюю часть которой подается вода для частичной
отмывки смолы от пульпы, далее смола аэрлифтом подается в барабанный
вращающийся грохот (поз. 4), в котором ионит отмывается от илов и песков, после
чего поступает в цех регенереции смолы.
Выщелоченная пульпа из поз. 5-8 и поз. 5-16 поступает на контрольные
грохоты (поз. 6-1,2,3) для улавливания единичных зерен ионита, выносимых с
пульпой при возможном повреждении дренажных сеток. Смолу направляют в поз. 5-7,
выщелоченную пульпу - на обезвреживание. Технологическая схема представлена на
рисунке 4.
В случае аварии или капитального ремонта, остановку процесса производим в
следующем порядке: прекращается подача пульпы, растворов NaCN и NaOH, воздуха.
Затем опустошаем пачуки через патрубки, находящиеся в днищах пачуков.
Рисунок 4 - Технологическая схема
5 Расчетная часть
.1.1
Материальный баланс стадии цианирования
Основной частью расчета является составление материального баланса
процесса. На основании заданной годовой производительности 1 млн. тонн руды и
количества рабочих часов каскада в году (с учетом времени на текущий и
планово-предупредительный ремонт) определяется часовая производительность каскада
по золоту.
Исходные данные:
Элементный состав, % массовый:
Au - 4,5∙10-4- 1,0- 0,02- 0,05- 0,005
Степень цианирования:- 83%
В виде карбонатов:- 53%- 10%
В виде сульфидов:- 11%- 10%- 5% раствор, CaO - 0,1% от массы руды, рН
>10.
Исходя из годовой производительности, рассчитаем часовую
производительность на одну линию:
Qч = 0,5×(Qг /365×24×К) = 0,5×(1000000
/ 365×24×0,85)
= 67,15 т/ч,
где Qч - часовая производительность, т/ч.;
Qг -
годовая производительность по руде, тонн;
- коэффициент использования оборудования с учетом текущих и
планово-предупредительных ремонтов.
Вычислим количество NaCN, необходимые для перевода золота в раствор,
количество воды, кислорода и образовавшихся веществ по реакциям:
,81 х1 х2 х3 y1 y2
Au + 4NaCN
+ ½ O2 + H2O = 2Na[Au(CN)2] + 2NaOH
196 16 18 544 80
Количество:x1 = 250,81×196/394
= 124,768 г/ч
О2 x2 = 250,81×16/394
= 10,185 г/ч
Н2О x3 = 250,81×18/394
= 11,458 г/ч[Au(CN)2] y1 = 250,81×544/394
= 346,296 г/чy2 = 250,81×80/394
= 50,926 г/ч
,118 х4 y3 y4 y5
2CuCO3 + 8NaCN = 2Na2[Cu(CN)3] + 2Na2CO3 + (CN)2↑
,248 0,392 0,376 0,212 0,052
Количество:x4 = 7,118 ×0,392/0,248 = 11,251 кг/ч[Cu(CN)3] y3 = 7,118 ×0,376/0,248 = 10,792 кг/чCO3 y4 = 7,118 ×0,212/0,248 = 6,085 кг/ч
(CN)2 y5 = 7,118 ×0,052/0,248
= 1,492 кг/ч
,336 х5 y6 y7 y8
NiCO3 + 8NaCN = 2Na2[Ni(CN)3] + 2Na2CO3 + (CN)2↑
,238 0,392 0,366 0,212 0,052
Количество:x5 = 0,336×0,392/0,238 = 0,553 кг/ч[Ni(CN)3] y6 = 0,336×0,366/0,238 = 0,517 кг/чCO3 y7 = 0,336×0,212/0,238 = 0,299 кг/ч
(CN)2 y8 = 0,336×0,052/0,238
= 0,073 кг/ч
,384 х6 y9 y10CO3 + H2O = 2NaOH
+ CO2↑
0,106 0,018 0,08 0,044
∑ Na2CO3=6,085+0,299=6,384 кг/ч
Количество:
H2O x6 = 6,384 ×0,018/0,106 = 1,084 кг/ч
NaOH y9 = 6,384 ×0,08/0,106
= 4,818 кг/чy10 = 6,384 ×0,044/0,106 = 2,65 кг/ч
,693 х7 y11 y12+ 4NaCN =
Na2[Zn(CN)4] + Na2S
,097 0,196 0,215 0,078
Количество:x7 = 3,693×0,196/0,097 = 7,462 кг/ч[Zn(CN)4] y11 = 3,693×0,215/0,097 = 8,186 кг/ч2S y12 = 3,693×0,078/0,097
= 2,97 кг/ч
,15 х8 х13 х14
FeS + 6NaCN = Na4[Fe(CN)6] + Na2S
,088 0,294 0,304 0,078
Количество:x8 = 67,15×0,294/0,088 = 224,342 кг/ч[Fe(CN)6] y13 = 67,15×0,304/0,088 = 231,973 кг/ч2S y14 = 67,15×0,078/0,088
= 59,519 кг/ч
,489 х9 х10 х11 y15 y16
Na2S + NaCN + H2O + O2=NaCNS + 2NaOH
0,078 0,049 0,018 0,016 0,081 0,08
∑ Na2S=59,519 +2,97 =62,489 кг/ч
Количество:x9 = 62,489×0,049/0,078
= 39,256 кг/чO x10 = 62,489×0,018/0,078
= 14,421 кг/чx11 = 62,489×0,016/0,078
= 12,818 кг/чy15 = 62,489×0,081/0,078
= 64,892 кг/ч
NaOH y16 = 62,489×0,08/0,078
= 64,091 кг/ч
67,15 x12 y17+ H2O = Ca(OH)2
0,056 0,018 0,074
Количество:O x12 = 67,15×0,018/0,056
= 21,584 кг/ч
Ca(OH)2 y17 = 67,15×0,074/0.056 = 88,734 кг/ч
Итого:
Σ NaCN = 282,989 кг/ч
Σ NaOH = 68,96 кг/ч
Σ (СN)2 = 1,565 кг/ч
Σ H2O = 37,1 кг/ч
Σ O2 = 12,818 кг/ч
Σ СО2 = 2,65 кг/ч
Так как цианид для процесса необходим в избытке, то добавляем 10% от
полученного количества, т. е. 28,299 кг/ч (Σ NaCN = 311,288 кг/ч).
Полученные результаты сведем в таблицу 4.
Таблица 4 - Материальный баланс стадии цианирования
Приход
|
Расход
|
Статьи
|
m, кг/ч
|
Статьи
|
m, кг/ч
|
Твердая фаза
|
Au
|
0,302
|
Au
|
0,044
|
CuCO3
|
13,43
|
CuCO3
|
6,312
|
NiCO3
|
3,358
|
NiCO3
|
3,022
|
ZnS
|
33,575
|
ZnS
|
29,882
|
FeS
|
671,5
|
FeS
|
604,35
|
SiO2
|
772,166
|
SiO2
|
772,166
|
Защитная щелочь
|
CaO
|
67,15
|
Ca(OH)2
|
88,734
|
Жидкая фаза
|
NaCN
|
311,288
|
NaOH
|
68,96
|
H2O
|
37,1
|
NaCNS
|
64,892
|
O2
|
12,818
|
Na[Au(CN)2]
|
0,346
|
|
|
Na2[Cu(CN)3]
|
10,792
|
|
|
Na2[Ni(CN)4]
|
0,517
|
|
|
Na2[Zn(CN)4]
|
8,186
|
|
|
Na4[Fe(CN)6]
|
231,973
|
|
|
NaCN
|
28,299
|
|
|
(CN)2
|
1,565
|
|
|
CО2
|
2,65
|
Итого:
|
1872,687
|
Итого:
|
1872,69
|
5.1.2 Материальный баланс стадии сорбции
Определяем часовой объем пульпы, который необходимо пропустить через
каскад, чтобы обеспечить часовую производительность:
,
где Vчас - часовой объем пульпы: м3/час;час - часовая производительность
каскада по золоту, кг/час;
Снач и Скон - начальная и конечная концентрация Au в пульпе, кг/м3.
Vчас=
0,250/(0,003-0,00003 ) = 87,175 м3/час
Количество ионита, которое нужно при этом использовать, определяется по
исходному уравнению:
где Gсм - часовой расход ионообменной смолы в условных тоннах;раб -
рабочая емкость смолы, кг/усл. тонну;раб - берется в пределах 80 - 90 % от
равновесной емкости;нач - остаточная емкость ионообменной смолы по золоту, получаемая
после регенерации смолы, она составляет 0,3 кг Au на условную тонну[10].
В таблице 5 приведено содержание компонентов в анионите АМ-2Б до и после
регенерации, кг/т.
Gсм =
0,250/(15,2-0,3) = 0,0168 т/час.
Таблица 5 - Содержание компонентов в анионите АМ-2Б
Компонент
|
Аu
|
Zn
|
Сu
|
Fe
|
Ni
|
CN-
|
Насыщенная смола Qраб
|
15,2
|
8,0
|
4,1
|
2,8
|
1,6
|
22
|
Регенерированная смола Qнач
|
0,3
|
0,6
|
1,0
|
0,9
|
0,6
|
0,5
|
Полная емкость АМ-2Б составляет 3,2 кг экв/т.
Поскольку стандартной формой анионита является Сl- - форма, то количество
матрицы в условной тонне АМ-2Б составляет:
- 3,2 · 35,5 = 886,4 кг.
Считаем, что условная тонна анионита АМ-2Б (при полной емкости 3,2 кг
экв/т) в любой ионной форме содержит 886,4 кг матрицы.
При остаточной емкости 0,3 кг золота на тонну анионита АМ-2Б количество
килограмм-эквивалентов золота, в условной тонне будет:
,3/197 = 0,0015 кг экв.
В 1 условной тонне будет содержаться: 3,2 - 0,0015 = 3,198 кг - иона OH-.
Кроме матрицы и ионов в ионообменной смоле находится вода набухания. Удельный
объем набухания анионита АМ-2Б составляет 2,38 м3/т. Из этого объема вычтем
объем матрицы.
Объем матрицы 1 условной тонны АМ-2Б составляет:
Vмат =
886,4 / 910 = 0,974 м3
Следовательно, объем воды набухания в 1 условной тонне АМ-2Б составляет:
2,38 - 0,974 - 0,8 = 0,606 м3, а вес ее составляет - 606 кг.
Ионообменные реакции, проходящие в процессе сорбции.
Таблица 6 - Материальный баланс процесса сорбции
Приход
|
Расход
|
Статьи
|
m, кг/ч
|
Статьи
|
m, кг/ч
|
1.Пульпа, в т.ч.
|
1.Обедненная пульпа
|
[Au(CN2)]-
|
0,317
|
[Au(CN2)]-
|
0,007
|
[Fe(CN6)]4-
|
161,771
|
[Fe(CN6)]4-
|
161,707
|
[Zn(CN4)]2-
|
6,435
|
[Zn(CN4)]2-
|
6,138
|
[Cu(CN3)]2-
|
8,151
|
[Cu(CN3)]2-
|
8,072
|
[Ni(CN3)]2-
|
0,403
|
[Ni(CN4)]2-
|
0,384
|
CNS-
|
46,466
|
CNS-
|
46,466
|
OH-
|
29,308
|
OH-
|
29,308
|
H2O
|
1444,332
|
H2O
|
1444,332
|
CN-
|
15,016
|
CN-
|
14,351
|
SiO2
|
722,166
|
SiO2
|
722,166
|
2.Ионит, в т.ч. матрица
|
14,892
|
2.Насыщенный ионит, в т.ч.
матрица
|
14,892
|
H2Oнабух
|
10,181
|
H2Oнабух
|
10,181
|
[Au(CN2)]-
|
0,0064
|
[Au(CN2)]-
|
0,316
|
[Fe(CN6)]4-
|
0,0572
|
[Fe(CN6)]4-
|
0,121
|
[Zn(CN4)]2-
|
0,0262
|
[Zn(CN4)]2-
|
0,323
|
[Cu(CN3)]2-
|
0,0373
|
[Cu(CN3)]2-
|
0,116
|
[Ni(CN4)]2-
|
0,0278
|
[Ni(CN4)]2-
|
0,0464
|
CN-
|
0,0158
|
CN-
|
Итого
|
2459,609
|
Итого
|
2459,607
|
5.2.1
Аппаратурный расчёт процесса цианирования
Основной задачей при конструировании пачуков является достижение
максимальной интенсивности перемешивания в пачуке при минимальном расходе
энергии.
Определение основных размеров чана
Часовая производительность передела по потоку пульпы поступающей на
выщелачивание:
V=Q×[(1000/ρт)+(R×1000/ρp)]=67,15×[(1000/2700)+(2×1000/1100)]
=146,92м3/ч.
где V - часовая производительность
передела по потоку пульпы,м3/ч;- отношение Ж:Т = 2:1;
ρт - плотность частицы, кг/м3;
ρp - плотность раствора, кг/м3.
Оптимальная продолжительность выщелачивания:
ч,
где
B - величина, зависящая от сложности технологии переработки руды. Принимается
равной 0,2 руб/г;
K1
- часовая себестоимость переработки 1 т руды в пачуках. Принимается равной
0,005 руб/т×час;- константа скорости выщелачивания для данного
рудного материала и условий выщелачивания. Величина постоянная, и равная 0,1
т/г×час;
α1, α2 начальная и конечная концентрация золота в руде,
г/т.[11]
Определение
общего рабочего объема аппаратуры для выщелачивания:общ = V×τ =
146,92×17,33 = 2546,12 м3.
Принимая
общее количество пачуков n=8, рассчитаем объем одного пачука:
Vi= Vобщ/n =
2546,12/8 = 318,27 м3
От
конструкции чана пачука зависит, насколько эффективно используется восходящий
поток перемешивания всего объема пульпы или жидкости в чане. Принимаем пачук с
коническим днищем с углом конуса
α = 600; H:D = 2,5:1
Имея
в виду, что высота конической части пачука: Нкон=0,5∙D∙tgα, а общий объем пачука определяется по формуле [11]:
V = (π/4) ×D3×[(H-Hкон) + 1/3×Нкон]
вычисляем
диаметр чана пачука:
м,
Принимаем
D=6 м. Рабочая высота чана пачука: Н = 2,5×D = 2,5×6= 15 м.
Геометрическая
высота чана: Нг = Н+1 = 16 м.
Определение
скорости восходящего потока в циркуляторе.
Скорость
потока воды, при которой начинается взвешивание частиц размером 0,1-0,25 мм Wвз
≥ 0,6 м/сек.
Скорость
потока во всасывающем патрубке циркулятора должна быть в 2 - 3 раза больше
размывающей скорости. Принимаем скорость восходящего потока в циркуляторе Wц =
2,0 м/сек.
Определение
вязкости пульпы:
,
где:
где
μП - динамическая вязкость пульпы, спз,
μР - динамическая вязкость раствора, спз,- ионная сила раствора, I = 1 г∙ион/литр;
спз
спз;
где
μВ - динамическая вязкость воды. При 200С равна 1,002
спз;
К
- коэффициент, учитывающий содержание в растворе ПАВ и коллоидных частиц,
степень измельчения и минералогический состав выщелачиваемого материала.
Принимаем К = 1,5.
Определим
скорость осаждения крупных частиц руды в растворе. Для этого необходимо
рассчитать критерий Архимеда:
.
где
Ar - критерий Архимеда;
dч - диаметр
частиц, мм;
ρp - плотность раствора, кг/м3;
g - ускорение
свободного падения, м/c2;
μР - динамическая вязкость раствора, спз.
Затем
рассчитаем критерий Рейнольдса:
.
Вычисляем
скорость осаждения крупных частиц пульпы в растворе:
м/с
Определение
скорости нисходящего потока в чане пачука
Скорость
нисходящего потока пульпы в чане пачука должна превышать скорость осаждения
крупных частиц руды в 1,8-2,0 раза.
W = (1,8-2,0) ×Wос = 1,8×1,71×10-2 =3,08×10-2 м/сек.
Определение
диаметра и длины циркулятора:
м.
Принимаем
диаметр циркулятора DЦ = 0,8 м.
Длина
циркулятора принимается конструктивно:ц = 1/3×Н= 1/3×15= 5
м.
Определение
положения циркулятора относительно днища пачука.
Для
того чтобы не происходило заиливание конуса пачука, расстояние от нижнего конца
циркулятора до донного фланца должно быть не более рассчитанного по уравнению
[11]:
м,
где
Dвс - диаметр полусферы всасывания, который рассчитывают по уравнению:
Таким
образом,
,м
Re = (Wц×Dц×ρп) / μп
Re = (Wц×Dц×ρп) / μп = (2×0,8×1370)
/ 2,9×10-3=0,76×106
Следовательно,
расстояние от нижнего конца циркулятора до донного фланца:
Определение
диаметра донного фланца пачука:
ф
= Dвс - 2Hвс ×
ctg 45
Таким
образом, рассчитаем диаметр донного фланца:ф = 2,66 - 2×0,92
× 1 = 0,82 м.
Выбор
конструкции воздухоподающего устройства и глубины его погружения в пульпе
пачука.
В
связи с большим диаметром циркулятора принимаем периферическую подачу воздуха
через отверстия в стенках циркулятора. Для предотвращения забивания отверстий
песками пульпы диаметр отверстия для подачи воздуха принимаем 10 мм (d0=10 мм).
Так
как диаметр циркулятора достаточно велик, а длина его сравнительно мала, то
принимаем подачу воздуха в нижнюю часть циркулятора на расстоянии 1м от нижней
кромки циркулятора.
Расстояние
от уровня пульпы в пачуке до точки подачи воздуха в циркулятор находим по
уравнению:
Н0
= Н - Нвс - 1 = 15 - 0,92 - 1=13,08м.
Принимаем
Н0 = 13,1м. [11].
5.2.2
Аппаратурный расчет процесса сорбции
Для определения точного количества ионообменных пачуков в каскаде следует
определить число теоретических ступеней ионного обмена, необходимого для
достижения заданной степени извлечения золота. Это производится с помощью х-у
диаграмм, где х - концентрация золота в водной фазе (пульпе), у - концентрация
золота в органической фазе (смоле). На у - х - диаграмме строится кривая
равновесных концентраций и прямая линия рабочих концентраций по координатам
двух ее крайних точек (Хнач и Qраб; Хкон и Qнач).
Из рисунка 2 видно, что для уменьшения концентрации золота до Хкон
необходимо 6 теоретических ступеней ионного обмена. Реальное число пачуков
находится путем деления числа теоретических ступеней на коэффициент полезного
действия реальной ступени (в обычных условиях 0,6 - 0,9) [10].
Рассчитаем количество ионообменных пачуков:
При
непрерывном потоке сорбционного выщелачивания необходимо устанавливать на один
аппарат больше, чем по расчету для большей эффективности использования рабочего
объема пачука. Таким образом, в каждую из двух цепочек аппарата добавляем по 1
пачуку и принимаем число ионообменных пачуков в каскаде 12 [11].
5.3
Гидравлический расчет
Определение давления воздуха в воздухоподающем устройстве
Общее давление воздуха в воздухоподающем устройстве перед его истечением
в пульпу должно быть достаточным, чтобы преодолеть статическое давление столба
пульпы Но, а также достаточным для создания скоростного напора и преодоления
сопротивления трения при истечении из отверстия.
Избыточное давление воздуха в воздухоподающем устройстве можно рассчитать
по уравнению [11]:
и = k×H0× ρп× g =
1,2×13,1×1370×9,81 = 211 кПа;
где Pи - избыточное давление воздуха, кПа;
к - коэффициент, учитывающий возможные колебания в пачуке уровня пульпы,
средней плотности ее и избыток давления, необходимый для создания скоростного
напора и преодоления сопротивления трения при истечении из отверстия.
Ho -
расстояние от уровня пульпы в пачуке до точки подачи воздуха,м;
ρп- плотность пульпы, кг/м3;
g -
ускорение свободного падения, м/с2.
Абсолютное давление в системе определяется как сумма избыточного и
атмосферного:
Pаб = Pи + Pа = 211000+101300 = 312,3 кПа. [11].
Определение расхода воздуха
Удельный расход воздуха принимаем 0,03нм3/мин на 1 м3 пульпы
(t = 0°С, Pa = 101,3 кПа), общий расход воздуха при этих условиях:
нм3/мин,
где
Vi - объем пульпы, перерабатываемый в одном аппарате.
Так,
как воздухоподающее устройство расположено на глубине Н0, то фактический расход
через воздухоподающее устройство составит[11]:
Определение
расхода воздуха через одно отверстие

- вязкость воздуха при 0°С,
плотность
воздуха на глубине Н0 при t = 20°С:
кг/м3
Для
создания устойчивого турбулентного потока принимаем= 2∙104.
Таким
образом, расход из одного отверстия d0 = 10 мм при t =20°С:
м3/мин.
[11].
Определение
числа отверстий
Число
отверстий определим по уравнению [11] :
где
N - число отверстий;факт - фактический расход, м3/мин;
Q`возд - расход
из одного отверстия, м3/мин.
Необходимо
расположить отверстия в три ряда. Для этого выбираем ближайшее значение N
=90, т.е по 30 отверстий в каждом. Расстояние между отверстиями 90 мм с
интервалом между соседними рядами 100 мм. Отверстия в рядах располагаем со
смещением на 90 мм. [11].
Расчет
диаметра воздухоподводящего трубопровода
Принимаем
скорость движения воздуха в трубопроводетр = 30 м/с, тогда:
м = 48мм.
[11].
Расчет
потока пульпы и кратности ее обмена
Определение
величины восходящего потока пульпы в пачуке:
,
где
= 95,
∑ξ=ξвых из трубы + ξвходв трубу + ξплавное закругл = 4,0 + 0,3 + 0,1 + 0,1 = 5,4
Определение
кратности обмена пульпы в пачуке в результате перемешивания:
n = 60×Qп/Va = 60×61,85/318,27 = 11,6 объемов в час.
Нормальным
считается n = 8 - 25. [11].
.4
Механический расчет
В соответствии с таблицей 9.1 [12] для расчета выбираем материал
аппарата, стойкий в цианистых растворах, которым является сталь марки 1Х13. По
таблице 2.18 [12] определим механические свойства стали 1Х13:
При t =20оС предел прочности при растяжении σЕ = 580 МН/м2; предел текучести σт = 420 МН/м2; относительное
удлинение при растяжении σу = 20%; ударная вязкость σн = 1,1 МДж/м2.
Расчет обечайки
Расчетное давление в нижней части обечайки:
Р = ρп∙g∙Нп∙10-6,
где P - расчетное давление;
ρп - плотность пульпы, равная
1355т/м3;- ускорение силы тяжести 9,81 м/с2;
Нп - высота столба пульпы, равная 15м.
Р = 1370∙9,81∙15∙10-6 = 0,2 МН/м2.
По таблице 14.5 [12] определяем запас прочности по пределу прочности, nв=2,6.
Тогда номинальное допускаемое напряжение составит:
МН/м2.
Допускаемое
напряжение определяем по формуле [12]:
МН/м2.
Определяем
отношение определяющих параметров σд и Р с учетом коэффициента и паяных соединений
:
[12].
Номинальную
расчетную величину толщины стенки обечайки для денного отношения согласно
таблице 15.6 [12] определяем по формуле:
мм
Величину
суммы прибавки определим по уравнению [12]:
С
= СК+СЭ+СД+С0
где
C - величина суммы прибавки, мм;
СК
- прибавка на коррозию или другой вид химического воздействия рабочей среды на
материал, мм;
СЭ
- прибавка на эрозию или другой вид механического воздействия на материал
рабочей средой;
СД
- дополнительная прибавка по технологическим, монтажным и другим соображениям,
мм;
СО
- прибавка на округление размера.
С
= 2 + 0 + 4 + 0,5 = 6,5 мм= s’ + С = 3 + 7,5 = 9,5 мм.
Проверим
условие 15.5 [12]:
<
0,1, следовательно, условие выполняется.
Допускаемое
давление в обечайке определяем по формуле 15.16 [12]:
МН/м2.
которое
больше расчетного давления, P = 0,2 МН/м2.
Расчет
днища
Материал
днища также изготовлен из стали марки 1Х13. Угол конуса при вершине в днище
60о. Номинальную толщину стенки днища согласно таблице 16.22. определяем по
следующей формуле [12]:
мм.
где
- номинальная толщина стенки днища, мм;- расчетный
диаметр пачука, равный 6000 мм.
P - расчетное
давление, равное 0,2 МН/м2;
-
допускаемое напряжение, МН/м2;
при
коэффициенте днища Х = 30о и
, из
литературных источников [12] следует, что, Y = 1,4.
Номинальную
расчетную толщину стенки днища теперь определим по следующей формуле [12],
принимая φ = 1:
мм,
где
D - расчетный диаметр определяем по уравнению [12], считая
:
За
расчетную величину
принимаем большее значение. Суммарную прибавку к
номинальной расчетной толщине стенки определяем по формуле 14.12 [12]:
С
= Ск + Сэ + Сд + С0 = 2+0+4+1,3 = 7,3.
Толщина
стенки днища
мм.
Принимаем толщину стенки днища s=11 мм.
Допускаемое
давление в днище согласно таблице 16.33 [12]: определяем по формуле 16.28 [12]:
МН/м2,
МН/м2.
Действительное
значение Р является меньше значения определенного выше, т.е. 0,86 МН/м2 >
0,63 МН/м2.
Расчет
строп для укрепления циркулятора
При
пределе прочности при растяжении равном
в = 520
МН/м2, принимаем
кг [12].
Принимаем
4 стропы для укрепления циркулятора, тогда нагрузка на одну стропу равна Р/4 =
100 кг.
мм2.
мм
Диаметр
стропы реальный принимаем d = 8 мм.
Расчет
штуцеров
Штуцера
служат для присоединения к аппарату трубопроводной арматуры и трубопроводов для
подвода и отвода различных жидких или газообразных продуктов, которые могут
быть разъемными и неразъемными. По условиям ремонтоспособности применяются
разъемные соединения (фланцевые штуцера) [13].
Диаметр
патрубков для ввода и вывода реагентов подбирают из расчета, что, чем меньше
диаметр труб, тем эффективнее эксплуатация, но с другой стороны, чем больше
скорость потока, тем больше потери, и, следовательно, энергетические затраты.
Экономически выгодной считается скорость потока для жидкостей перемещающихся
самотеком - 0,5 ÷1,0 м/с.
При
заданной производительности диаметр патрубков может быть определен из уравнения
расхода:
отсюда,
где
d - внутренний диаметр патрубка, м;- объемный расход, м3/с;
-
средняя скорость потока, м/с.
Объемный
расход пульпы равен 0,06 м3/с. Принимаем скорость
ω = 0,5 м/с для ввода исходных веществ; ω = 1 м/с для выхода продуктов реакции.
Рассчитаем
диметры патрубков по формуле[12]:
для
вывода продуктов реакции (пульпа):
мм,
принимаем,
Dy = 300 мм;
для
выхода смолы:
мм,
принимаем
Dy = 150 мм.[13].
6 Контроль и автоматизация
Автоматизация приводит к улучшению основных показателей эффективности
производства: увеличению количества, улучшению качества и снижению
себестоимости выпускаемой продукции, повышению производительности и
эффективности труда, улучшение условий труда обслуживающего персонала.
Внедрение автоматических устройств уменьшает затраты сырья и энергии, сокращает
количество брака и отходов, увеличивает срока работы оборудования. Комплексная
автоматизация процессов химической технологии предусматривает не только
автоматическое обеспечение нормального хода этих процессов с использованием
различных автоматических устройств (контроля, сигнализации, регулирования), но
и автоматическое управление пуском и остановом аппаратов для ремонтных работ и
в критических ситуациях.
Для получения информации о состоянии объекта и условиях работы служат
устройства контроля. Они могут быть выполнены либо в виде отдельных приборов,
предназначенных для визуального контроля параметров процесса, либо являться
составной частью устройств регулирования, сигнализации и защиты.
В данном дипломном проекте разработана схема автоматизации процесса
сорбционного выщелачивания золотосодержащей руды.
Необходимость автоматизации данного процесса обусловлена опасными и
вредными факторами, присутствующими в производстве Au и создающими опасность для людей, контактирующих с
оборудованием. Чтобы избежать этого, применяется комплексная автоматизация с
дистанционным управлением, сводящая к минимуму всё вредное воздействие
производства на работников [15].
6.1 Функциональная схема автоматизации процесса сорбционного цианирования
золота
Объектом автоматизации является цех сорбционного выщелачивания
золотосодержащей руды. Здесь происходят непрерывные процессы цианирования в
четырех пачуках и сорбционного выщелачивания в шестнадцати пачуках. На рисунке
5 представлена только одна из двух одинаковых цепочек аппаратов, соответственно
два пачука цианирования (2-1 и 2-2) и восемь пачуков сорбционного выщелачивания
(5-1-5-8).
Пульпа поступает в барабанные вращающиеся грохоты (1-1-1-3), где происходит
измерение ее расхода, и отделение пульпы от щепы, затем пульпа поступает в
пачуки цианирования (2-1-2-2), в пачук 2-1 подается 0,2% раствор NaCN и 5%
раствор NaOH (для поддержания значения pH в пределах 10-11) из напорных
емкостей 7 и 8 соответственно. Перемешивание осуществляется воздухом. В
процессе сорбционного цианирования золота регулированию подлежат следующие
параметры: рН и концентрация
, уровень пульпы в пачуках 2-1, 2-2; 5-1-5-8. Пульпа
поступает в пачуки цианирования (2-1 и 2-2), затем в пачуки сорбционного
выщелачивания (5-1-5-8), где происходит дальнейшее выщелачивание золота и его
сорбция на анионит, отрегенерированная или свежая смола подается в пачук 5-7
передвигаясь противотоком по отношению к пульпе из последнего аппарата в
первый. Насыщенная смола поступает самотеком в отмывочную колонну (3), в нижнюю
часть которой подается вода для частичной отмывки смолы от пульпы, далее смола
аэролифтом подается в барабанный вращающийся грохот (4), в котором ионит
отмывается от илов и песков, после чего поступает в цех регенерации смолы.
Расход пульпы, поступающей в барабанные грохоты (номинальный расход 200
м3/час), в которых происходит отделение пульпы от щепы, регулируется контуром
1-2. Количество подаваемой воды регулируется контуром 3.
Для контроля давления воздуха предназначен контур 4.
Концентрация
регулируется контуром 9-10.
рН - регулируется контуром 11.
Уровни в пачуках регулируются контурами 13-14, 15-16, 17-18, 22-23,
24-25, 26-27, 28-29, 30-31, 32-33, 34-35, 36-37.
Уровень растворов в напорных емкостях 7, 8 регулируется контурами 5-6,
7-8 соответственно. Выщелоченная пульпа из 5-8 поступает на контрольные грохоты
(6-1,2,3, на схеме автоматизации показан контрольный грохот 6-1) для
улавливания единичных зерен ионита, выносимых с пульпой при возможном
повреждении дренажных сеток. Смолу направляют в поз. 5-7, выщелоченную пульпу -
на обезвреживание.
Значения всех измеряемых параметров выводятся на щитовую. При выходе измеряемых
параметров за допустимые ограничения незамедлительно срабатывает сигнализация
[14,15].
6.2 Перечень
технологических параметров подлежащих контролю, регулированию и сигнализации
Контроль:
уровень пульпы в пачуках;
pH
пульпы в пачуках;
концентрация CN- в пачуках;
расход воздуха в пачуках;
уровень растворов в напорных емкостях;
расход пульпы питающий;
давление воздуха;
Сигнализация:
уровень пульпы в пачуках;
pH
пульпы в пачуках;
концентрация CN- в пачуках;
расход воздуха в пачуках;
уровень растворов в напорных емкостях;
расход пульпы питающий;
Регулирование:
уровень пульпы в пачуках;
pH
пульпы в пачуках;
концентрация CN- в пачуках;
расход воздуха в пачуках;
уровень растворов в напорных емкостях;
расход пульпы питающий.
.3 Перечень первичных преобразователей
1. pH - метр типа «рН - 125»
диапазон рН 0 -12
давление не более 0,5 МПа
температура от +5 до +50, °С
основная погрешность электронного блока:± 0,02
ЭДС, мВ ± 2
Позиции: 5-1, 6-1.
. Индикатор расхода газа ультразвуковой типа «Расход 10.4»
условные диаметры трубопровода 10-500 мм
максимальная допустимая погрешность:
при кратности диапазона расхода 1:10 не более 1,0%
при кратности диапазона расхода 1:2 не более 0,5%.
температура от +5С до +80°С
максимальное давление 2,5 МПа
выходные сигналы: аналоговый 0-5 мА
частотный 0,5-100 Гц
питание от сети ~220 В, 50 Гц
потребляемая мощность не более 50 Вт
Позиция: 2-1.
. Расходомер типа «Метран 310Р»
условные диаметры трубопровода 15-250 мм
максимальная допустимая погрешность не более 1%
температура окружающего воздуха от -50 до + 50 °C
максимальное давление 1,6 МПа
питание от сети ~220 В, 50 Гц
Позиция: 10-1.
. Уровнемер радарный «УЛМ-11А1»
диапазон измерений, 0,6 - 15м,
основная погрешность, ± 3мм
напряжение питания: 220 В
температура окружающего воздуха: -50…..+50 °С
выходной сигнал 4…..20 мА
Позиции: 3-1; 4-1; 7-1; 8-1; 9-1; 12-1; 13-1; 14-1; 15-1; 16-1; 17-1;
-1;19-1.
. Расходомер кориолисовый Метран М-360
условные диаметры трубопровода 10-500 мм
температура окружающего воздуха, С: -50…..+50
питание от сети ~220 В, 50 Гц
диапазоны измерения: массового расхода жидкости 3 ... 31980 кг/ч,
объемного расхода жидкости 3 ... 31980 л/ч, объемного расхода газа 17 ... 1777
м3/ч.
Позиции: 1-1; 20-1.
6.4 Использование ЭВМ
Важной составляющей современной АСУ ТП являются электронные
вычислительные машины. В структурной схеме ЭВМ должны быть специальные
устройства ввода-вывода, которые связывают ее с технологическим процессом.
При этом ЭВМ может быть запрограммирована так, чтобы реагировать на
системы согласно заданному алгоритму управления. Ручное управление
осуществляется обычно лишь в особых случаях, а также при ремонте машин, иногда
при отладке программы. В данном проекте рассматривается схема АСУ ТП с
контроллером, непосредственно связанным с ЭВМ.
Характерная особенность таких систем управления состоит в том, что в них
контроллер и ЭВМ включается в замкнутый контур автоматического управления и
вырабатывается управляющее воздействие, поступающее как сигналы заданий
непосредственно на вход к системам автоматического регулирования.
Поскольку в наших системах контур управления замкнут через контроллер, то
функции оператора сводятся к общему наблюдению за ходом процесса. Остается
необходимость внести коррективы в процесс при изменениях, например, состава
исходных веществ, состава вырабатываемого продукта, рН и т.д.
В щитовой находятся: щит технологического контроля, панель сигнализации,
пульт оператора, дисплей с клавиатурой. На щите технологического контроля
располагаются контрольно-измерительные приборы, панель регулирования. На пульте
оператора находятся показывающие приборы, переключатели режима работа,
задатчики локальных контуров автоматического регулирования, пусковая
аппаратура. Для повышения надежности работы оборудования предусмотрен переход с
автоматического регулирования к ручному управлению. С помощью дисплея по
запросу оператора можно получить информацию о параметрах аварийного участка и
при помощи клавиатуры ввести управляющие воздействия, устраняющие аварийную
ситуацию [16].
6.5 Действия
оператора-технолога при пуске, остановке и нормальном режиме ведения
технологического процесса
Рисунок 5 - Функциональная схема автоматизации
Пуск технологического процесса производится в данном порядке: подача
воздуха, подача пульпы, подача растворов NaCN и NaOH.
При ведении технологического процесса в нормальном режиме
оператор-технолог должен осуществлять наблюдение и контроль параметров.
Также, при необходимости, регулировку параметров процесса.
В случае аварии или капитального ремонта, остановку процесса производим в
следующем порядке: прекращается подача пульпы, растворов NaCN и NaOH, воздуха.
Затем опустошаем пачуки через патрубки, находящиеся в днищах пачуков [4].
7 План
размещения оборудования
Основными габаритными размерами являются длина, ширина и высота
оборудования, расположенного в нем.
При размещении в цехе пачуков, необходимо учитывать создание максимальных
удобств при их обслуживании и ремонте. Ширина прохода между пачуками должна
быть не менее 2м. Зная число аппаратов можно рассчитать площадь, занимаемую под
отделение цеха сорбционного выщелачивания золота.
Длина цеха составит: Lц = 66 м; ширина Вц = 36 м; высота Нц = 25м.
Площадь цеха Sn = 2376м2
В цехе имеются две лестницы с высотой перил не менее 1,2 м со сплошной
обшивкой перил понизу не менее 150 мм.
Площадки и лестницы выполнены из просечно - вытяжного листа или из
сортовой (полосовой) стали с размерами просвета не более 30×30мм.
Лестницы имеют ширину не менее 600 мм, высота ступеньки не более 200 мм,
ширина ступеньки не менее 80 мм.
Трубопроводы не должны примыкать к стенкам, колоннам зданий. Расстояние
между трубопроводом и неподвижной опорой составляет не менее 50 мм. Расстановка
вспомогательного оборудования в цехе должна соответствовать очередности
операций; по точности технологического оборудования и действующими
строительными нормами и правилами[17,18].
Рисунок 6 - План размещения оборудования
8 Охрана
труда и охрана окружающей природной среды
.1 Охрана труда
Охрана труда - система обеспечения безопасности жизни и здоровья
работников в процессе трудовой деятельности, включая правовые,
социально-экономические, организационно-технические, санитарно-гигиенические,
лечебно-профилактические и иные мероприятия. Конституция Российской Федерации,
Трудовой кодекс, Основы законодательства РФ об охране труда, устанавливают
гарантии осуществления права трудящихся на охрану труда, отвечающих требованиям
сохранения жизни и здоровья работников[19].
Статьи из Конституции Российской Федерации[20]:
Статья 7, п. 2.
.«В РФ охраняется труд и здоровье людей, устанавливается гарантированный
минимальный размер оплаты труда, обеспечивается гос. поддержка семьи,
материнства, отцовства и детства, инвалидов и пожилых граждан..».
Статья 37, п. 3.
«Каждый имеет право на труд в условиях, отвечающих требованиям
безопасности и гигиены, на вознаграждение за труд без какой бы то ни было
дискриминации и не ниже установленного федеральным законом минимального размера
оплаты труда».
Статья 39, п.1.
«Каждому гарантируется соц.обеспечение по возрасту, в случае болезни,
инвалидности, потери кормильца, для воспитания детей и в иных случаях,
установленных законом».
Статья 41, п.1.
«Каждый имеет право на охрану здоровья и медицинскую помощь.
Статья 42.
«Каждый имеет право на благоприятную окружающую среду, достоверную
информацию о ее состоянии и на возмещение ущерба, причиненного его здоровью или
имуществу экологическим правонарушением».
Статьи из Трудового кодекса Российской Федерации[21]:
Статья 212. Обязанности работодателя по обеспечению безопасных условий и
охраны труда.
Администрация предприятий, учреждений, обязана обеспечивать надлежащее
техническое оборудование всех рабочих мест и создавать на них условия работы,
соответствующие единым межотраслевым и отраслевым правилам по охране труда,
санитарным правилам и нормам, разрабатываемым и утверждаемым в порядке,
установленном законодательством...
Статья 215. Соответствие производственных объектов и продукции
требованиям охраны труда.
Производственные здания, сооружения, оборудование, технологические
процессы должны отвечать требованиям, обеспечивающим здоровые и безопасные
условия труда...
Статьи из закона РФ «Основы законодательства РФ об охране труда»[22]:
В статьях 3,4,5,9 говорится о том, что государство заботится об улучшении
условий и охране труда на предприятиях. Каждый работник имеет право на условия,
отвечающие требованиям безопасности и гигиены, а администрация обязана внедрять
современные средства безопасности, предупреждающие возникновение
профессиональных заболеваний рабочих и служащих.
8.1.1 Анализ
опасностей и вредностей
В проектируемом цехе сорбционного выщелачивания золота из руд имеют место
следующие опасности и вредности:
. Опасность отравления вредными и химически токсичными веществами. К ним
следует отнести цианид натрия и тиомочевину.
. Опасность получения травм при механическом воздействии. Это
автотранспорт и различные движущиеся механизмы, в том числе барабанные
вращающиеся грохота, кран- балки и др.;
. Опасность поражения электрическим током (электропроводка,
электроприводы механизмов);
. Опасность воздействия вибрации и различных шумов на производстве. К ним
относятся компрессоры, насосы и др.;
. Опасность возникновения пожара.
Помимо этого, на предприятии должны быть соблюдены санитарно-гигиенические
нормы по метеоусловиям. Особое внимание следует уделить освещению, отоплению и
вентиляции цеха[19].
8.1.2 Техника
безопасности при работе с токсичными веществами
Работа с реагентами, а также их хранение производится строго при работе
постоянной искусственной вентиляции. Это крайне необходимо для того, чтобы
содержание вредных веществ в воздухе помещений было не выше ПДК. К вредным
веществам следует отнести пары синильной кислоты, образующихся в результате ее
гидролиза. Значение предельно допустимой концентрации для паров синильной
кислоты составляет 0,3мг/м3.
На предприятии предусматривается обязательный инструктаж по месту
непосредственной работы. Автоматизация технологического процесса внедрена чтобы
не допустить взаимодействия рабочих с потенциально- и особо- опасными объектами
производства. Все рабочие помещения оборудованы общеобменной и аварийной
вентиляцией. Водяное орошение служит устранителем запыленности. По технике
безопасности работа в цехе производится в спецодежде, спецобуви, перчатках и
фартуках (по месту необходимости).Каждый рабочий, имеющий дело с реагентами,
должен уметь оказывать первую помощь пострадавшему при отравлении цианидом или
получении травмы.
Первая помощь при отравлении цианидами. Отравление цианистыми
соединениями характеризуется определенными признаками.
Это ощущение боли в горле, жгучий горький вкус миндаля во рту,
слюнотечение, онемение рта, мышечная слабость, тошнота, затруднение речи,
появление учащенного дыхания. Затем общая слабость увеличивается, появляются
боли и стеснение в области сердца, редкое и глубокое дыхание, сильная одышка,
отдельные короткие вздохи, сопровождающиеся длительными выдохами, тошнота,
рвота, расширение зрачков глаз.
При обнаружении первых симптомов отравления парами синильной кислоты
пострадавшему немедленно дают вдыхать раствор 2-3 капель амилнитрита и выносят
его на свежий воздух. В случае необходимости производят искусственное дыхание.
Вдыхание амилнитрита повторяют через каждые 2-3 минуты, по 15-30 секунд.
Если раствор цианида или сухой цианид попал внутрь организма,
пострадавшему дают на чайной ложке 0,4% - ный раствор перманганата калия или
раствор перекиси водорода. Если яд проник в дыхательные пути, то пострадавшего
немедленно выносят на свежий воздух и дают вдыхать амилнитрит.
Оказав первую помощь при отравлении, нужно немедленно вызвать врача или
быстро доставить пострадавшего в медпункт.
Для оказания первой помощи при отравлении цианистыми соединениями на
каждом рабочем месте должны находиться аптечки с противоядиями и медикаментами.
Первая помощь при попадании щелочей на кожу. Сухой каустик и его растворы
при попадании на кожу вызывают химические ожоги. Если щелочь сразу быстро смыть
большим количеством воды, то на коже может появиться лишь красные пятна.
Попавшую на кожу щелочь необходимо обильно промыть водой и затем 5% - ным
раствором уксусной кислоты.
Смертельная доза Са(СN)2
-40 - 50г.
ПДК веществ: HCN(CH3)2 - 0,5 мг/м3,NaCN-0,3 мг/м3, KCN - 0,3 мг/м3.
Таблица 7 -
Токсические концентрации НСN для
человека, мг/л
[HCN],мг/л
|
Время пребывания и
последствия
|
0,005-0,02
|
У отдельных рабочих
головные боли
|
0,02-0,05
|
При длительном вдыхании
головная боль, тошнота, рвота
|
0,05-0,06
|
Переносится 1 ч без
немедленного действия
|
0,1
|
Опасна для жизни, смерть
наступает в течении первого часа
|
Смерть после 30 мин - 1 ч
|
0,2
|
Смерть после 10 мин
|
0,3
|
В покое человек может
выдержать без головокружения 2 мин
|
0,55
|
Без серьезных последствий
можно выдержать 1 мин
|
3,6
|
При дыхании через
противогаз можно выдержать 30 мин
|
7-12
|
При 5 минутном пребывании
отравление через кожу.
|
Для защиты рабочего персонала от паров синильной кислоты в цехе
применяются СИЗОД, в частности, противогаз ГП-5. Противогаз ГП-5 предназначен
для защиты органов дыхания, глаз и лица человека от отравляющих веществ, радиоактивной
пыли, биологических аэрозолей и других вредных примесей [4,23].
Противогаз ГП-5.
Комплект противогаза ГП-5 включает в себя фильтрующе-поглощающую коробку
малых габаритных размеров; лицевую часть; сумку; незапотевающие пленки;
утеплительные манжеты. Шлем-маска противогаза изготовляется пяти
ростов:0;1;2;3;4. Масса противогаза в комплекте составляет около 1 кг. Для
предупреждения обледенения стекол очков, на них надевают утеплительные манжеты
со вторым стеклом. С целью расширения возможностей противогазов по защите от
СДЯВ для них введены дополнительные патроны (ДПГ-1; ДПГ-3) .
ДПГ-3 в комплекте с противогазом защищает от таких вредных веществ, как
аммиак, хлор, нитробензол, сероводород, сероуглерод, синильная кислота, фенол,
фосген и др. ДПГ-1, кроме того, защищает еще от двуокиси азота, метана
хлористого, окиси углерода и окиси этилена.
В комплект дополнительных патронов входят соединительная трубка и
вставка. С лицевой частью противогаза патрон связан с помощью соединительной
трубки, для чего на один из концов наворачивается горловина. В дне патрона
нарезана внутренняя резьба для присоединения к фильтрующе-поглощающей коробке
ГП-5. Внутри патрона ДПГ-1 два слоя шихты - специальный поглотитель и гопкалит.
В ДПГ-3 - только один слой поглотителя [4,19].
8.1.3
Электробезопасность
В цехе сорбционного выщелачивания все части основного технологического
оборудования в нормальном рабочем состоянии находятся под напряжением. Поэтому
применение защитного заземления и отключения практически исключено. Оборудование,
используемое в цехе, работает от напряжения 220 и 380 В, следовательно оно
относится к классу низковольтного оборудования (до 1000 В). Помещение цеха, в
соответствии с ОСПУЭ - 82, относится к помещениям с повышенной опасностью.
Электрооборудование цеха состоит из приводов барабанных грохотов,
кран-балки, концентрационного стола, приборов автоматического контроля,
вентиляции и освещения.
Основные опасности, обусловленные электрическим током:
. Опасность напряжения прикосновения - при прикосновении человека к
неизолированным токоведущим частям электроустановок, находящихся под
напряжением.
. Опасность напряжения перехода - при прикосновении человека к
нетоковедущим металлическим частям электроустановок, находящихся под
напряжением.
. Опасность токов короткого замыкания.
Для защиты от напряжения прикосновения используются малое напряжение (в
переносных светильниках), изоляция токоведущих частей, предупредительная
сигнализация.
Для защиты от напряжения перехода используется защитное заземление.
Для защиты от токов нагрузки используются автоматическое отключение,
установка плавких предохранителей. При выполнении ремонтных работ производится
отключение установки от источника питания, снятие предохранителей и другие
мероприятия, обеспечивающие невозможность ошибочной подачи напряжения к месту
работы, установку знаков безопасности и ограничений.
Первая помощь при поражении электрическим током. Первая помощь при
поражении электрическим током включает в себя два этапа. Это освобождение
пострадавшего от действия тока и оказание ему первой доврачебной помощи.
Первое действие - быстрое обесточивание установки, вызвавшее поражение
пострадавшего. Для отделения пострадавшего от токоведущих частей следует
воспользоваться сухой палкой, диэлектрическими перчатками для собственной
защиты. Пострадавшего необходимо уложить на спину, на твердую поверхность,
проверить наличие дыхания, пульса (при их отсутствии сделать искусственное
дыхание и наружный массаж сердца). При отсутствии сознания, но сохранении
устойчивого дыхания и пульса нужно дать пострадавшему понюхать нашатырный спирт
и обрызгать его водой.
В зависимости от реакции организма на электрический ток различают
несколько пороговых значений тока через тело человека. Электрический ток,
вызывающий при прохождении через организм человека ощутимые раздражения,
называются ощутимым током. Для постоянного тока эта величина составляет 5 - 7
мА.
Повышение силы тока через организм человека вызывает при определённых
значениях судорожное сокращение мышц, которое невозможно преодолеть. Наименьшее
значение этого тока называется пороговым неотпускающим током. При постоянном
токе среднее значение пороговых неотпускающих токов равно 50 - 80 мА. В
помещении цеха значение тока не превышает 30 мА.
Наименьший электрический ток, вызывающий фибрилляцию сердца, называется
пороговым фибрилляционным током. Для постоянного тока он равен 300мА.
Материал полов должен не пропускать электрический ток, а также должен
быть стойким к воздействию химических веществ, используемых в технологическом
процессе. В данном случае предусмотрен пол из бетона[19].
8.1.4
Метеорологические условия производственной среды
Метеорологические условия производственной среды складываются из
температуры воздуха, его влажности и скорости движения, а также излучений от
нагретых предметов. Метеорологические условия оказывают большое влияние на
здоровье, самочувствие и работоспособность.
Оптимальные нормы температуры, относительной влажности и скорости
движения воздуха в рабочей зоне производственного помещения приведены в таблице
8.
Таблица 8 - Оптимальные метеорологические условия в рабочей зоне
Период года
|
Температура воздуха, °С
|
Относительная влажность, %
|
Скорость движения воздуха,
м/с
|
Теплый, > +10°С
|
22-25
|
60-30
|
0,2-0,5
|
Холодный, <+10°С
|
20-22
|
60-30
|
не более 0,2
|
Помещение цеха относится к помещениям с пониженным тепловыделением,
физические работы относятся к работам средней тяжести.
Большие скорости движения воздушных потоков создают сквозняки,
неблагоприятно действующие на организм человека при высоких, и особенно, при
низких температурах[23].
8.1.5 Шум и
вибрация
Шум и вибрация являются результатом колебания тел, передаваемого
непосредственно или на расстояние другим объектам. Шум и вибрация различаются
частотой колебаний в секунду. Если число колебаний в секунду не превышает 16,
то они воспринимаются человеком как сотрясения и называются вибрацией. Частота
колебаний от 16 до 20000 в секунду воспринимается органами слуха как шум,
колебания с частотой свыше этого предела не ощущаются человеком, и называются
ультразвуками.
Вибрация приводит к преждевременному износу деталей, механизмов, может
вызвать аварию, вредно действует на сердечно-сосудистую и нервную системы
организма, вызывает снижение слуха и даже стойкую глухоту, является причиной
снижения работоспособности, ослабления памяти, внимания, остроты зрения, что
увеличивает возможность травматизма.
Минимальная сила звука, которая воспринимается ухом человека, называется
порогом слышимости. Силу звука, приводящую к болезненным ощущениям, называют
болевым порогом. Между этими порогами лежит область слышимости. В пределах этой
области силу звука измеряют децибелами (дБ). Если порог слышимости оценить в 0
дБ, то болевой порог характеризуется силой звука, равной 70 дБ.
Источниками шума в химической промышленности являются: компрессоры,
насосы, движущиеся детали механизмов, вентиляционные системы и др., сила звука
которых не превышает 70 дБ.
Прежде всего, стремятся устранить или уменьшить шум в источнике его
образования. Агрегаты с повышенным уровнем шума и вибрации стараются размещать
в отдельных изолированных помещениях. Стены покрывают звукопоглощающими
материалами (акустической штукатуркой, перфорированными панелями,
стекловолокном и др.) [23].
8.1.6
Производственное освещение
Естественное освещение создаётся в производственных помещениях через
оконные и другие остеклённые проёмы. Искусственное освещение создаётся
светильниками и может быть: общее, предназначенное для освещения всего рабочего
помещения, местное, освещающее только рабочее место, и комбинированное,
состоящее из общего и местного освещения.
Использовать только местное освещение не разрешается. Это вызвано тем,
что резкая неравномерность освещённости на рабочем месте и в помещении снижает
работоспособность зрения и вызывает его утомление.
Чтобы создать необходимые благоприятные условия для работы, степень
освещённости в производственных помещениях нормируется, норма освещения
составляет 300 лк.
Освещение должно быть равномерным, чтобы глазу не приходилось попадать из
очень светлого места в тёмное и наоборот. Освещение должно быть устроено так,
чтобы глаза рабочих были защищены от «ослеплённости» вследствие прямой или
отражённой блескости. Это достигается правильным устройством осветительной
арматуры, определённой высотой подвеса светильников и их рациональным размещением
в помещении [19,23].
8.1.7
Производственная вентиляция
Вентиляция производственных помещений предназначена для обеспечения
необходимой частоты воздуха путем подачи (приточная) чистого воздуха, а также
для поддержания нормальной температуры воздуха в помещении. Вентиляция в цехе
цианирования и сорбции приточно-вытяжная.
Для расчета вентиляции необходимо знать скорость отсасывания воздуха в
рабочем проеме, диаметр проема, коэффициент отсоса. Скорость воздуха принимаем
равной 1,5 м/с. Объем отсасываемого воздуха определим по формуле [19]:
в = ω∙Fр∙3600∙К,
где Vв - объем отсасываемого воздуха, м3/ч;
ω - скорость воздуха, м/с;р - рабочая
площадь проема, м2;
К - коэффициент подсоса;р = πd2/4 = π∙0,09/4 = 0,07м2в = 1,5∙0,07∙3600∙2
= 763,2 м3/ч
Общеобъемную вентиляцию выбирают согласно СНиП - 3375 для вредных
производств, с кратностью воздухообмена равной 5. Тогда расход воздуха на
вентиляцию будет равен: V = nVв, где n - кратность воздухообмена. V=763,2∙5=3816
м3/ч. [19,23].
8.1.8
Водоснабжение
Промышленные предприятия обеспечиваются водой от собственной системы
водоснабжения. Вода, подаваемая на производственные нужды, должна удовлетворять
требованиям технологического процесса.
При проектировании водопровода производственного здания необходимо
проверять соответствует ли вода, подаваемая наружным водопроводом, требованиям
данного производства или требуется дополнительная обработка воды. При
разработке проекта здания следует предусматривать возможности их применения при
различных системах наружных водопроводов. Внутренние сети водопровода
проектируем по "гибким" схемам с подачей воды на
хозяйственно-питьевые нужды и производственные. Расход воды на внутреннее
пожаротушение следует принимать из расчета действия двух пожарных струй, не
менее 2,5 л/сек каждая, во вспомогательных зданиях, из расчета одной пожарной
струи [23,24].
8.1.9 Система
канализации
В цехе цианирования золотосодержащих руд имеется изолированная
канализация. Все непригодные воды собираются и передаются в цех очистки для
извлечения остатков цианида и их нейтрализации.
Для сбора переливов устанавливается дренажная система каналов, а полы
делают наклонными по направлению к этим каналам. Ширина дренажных каналов в
зависимости от размеров производительности цеха берется от 30 до 40 мм. [24].
8.1.10
Пожарная безопасность
В помещении, где выполняются производственные работы, существует
опасность возникновения пожара из - за:
) наличие деревянной мебели, деревянных оконных рам, дверей, а также книг
и тетрадей;
) присутствие кислорода в воздухе;
) возможность появления импульса воспламенения - короткое замыкание,
наличие горячих поверхностей и т.д.
Помещение должно быть оснащено средствами пожаротушения (огнетушителями
ОХП - 10, ОУ -5 для тушения электрооборудования), имеется пожарный щит, ящик с
песком и система пожарного водоснабжения[23].
8.2 Охрана
окружающей среды
Вопросы охраны окружающей среды отражены в Федеральном Законе об охране
окружающей среды" от 10.01.2002 и в санитарных нормах СанПин
2.2.1/2.1.1.567-96 [24].
В данном производстве образуются жидкие и газообразные производственные
выбросы.
Газообразные - это пары синильной кислоты. Мероприятия по очистке
выбросов: выделение паров синильной кислоты с воздухом в атмосферу недопустимо,
поэтому пары синильной кислоты пропускаются через раствор гидроксида натрия.
ПДК на цианистые соединения в воздухе - 0,03 мг/м3.
Жидкие растворы, хвосты процесса обезвреживания с такими вредными
химическими компонентами, как цианиды и т.д. Эти стоки могут загрязнять
грунтовые и поверхностные воды, а за счет испарения - воздушную среду. Поэтому
растворы не сливаются в окружающие водоёмы, а идут в специальное
хвостохранилище.
По санитарным нормам СанПин 2.2.1/2.1.1.567-96 производственные выбросы
подлежат очистке до допустимых ПДК перед тем, как сбросить в окружающую среду
[24].
В процессе производства химическую опасность представляют растворы,
образующиеся в результате сорбции, которые содержат комплексные соединения
металлов. Крайне недопустимо попадание их в место осуществления забора питьевой
воды. ПДК приведены в таблице 9.
Таблица 9 - Нормативы содержания металлов в питьевой воды согласно СанПин
2.1.4.1074-01 [4].
Соединения
|
ПДК, не более (в мг/л)
|
Алюминий (Аl3+)
|
0,5
|
Железо (Fe, суммарно)
|
0,3
|
Медь (Сu, суммарно)
|
1,0
|
Мышьяк (As, суммарно)
|
0,05
|
Никель (Ni, суммарно)
|
0,1
|
Свинец (Рb, суммарно)
|
0,03
|
Хром (Сr6+)
|
0,05
|
Цинк (Zn2+)
|
5,0
|
Заключение
Все мероприятия по технике безопасности и охране труда разработаны в
соответствии с сантирано-гигиеническими нормативами и ГОСТами. Таким образом,
для обслуживающего персонала созданы благоприятные условия труда.
В разделе охраны окружающей среды мной рассмотрены вопросы образующихся
отходов производства и предусмотрены мероприятия по их обезвреживанию и защите
окружающей среды. Запланированные мероприятия соответствуют санитарным нормам
СанПин 2.2.1/2.1.1.567-96.
Список использованной литературы
1) Чугаев. Л.В. Металлургия благородных металлов - М.:
Металлургия, 1987.- 432 с.
) Меретуков М.А. Золото: химия, минерология, металлургия -
М.: Металлургия, 2008. - 460 с.
) Зеликман А.Н., Вольдман Г. М., Белявская Л. В. Теория
гидрометаллургических процессов - М.: Металлургия, 2003. - 464 с.
) Регламент переработки руды ОАО “Покровский рудник” - 2007.
)Андреев Ю.В. Металлургия благородных металлов (конспект
лекций) - Спб.: Металлургия, 2011. - 79 с.
) Замятин О.В., Лопатин А. Г. Обогащение золотосодержащих
песков и конгломератов - М.: Металлургия, 1975. - 262 с.
)Вязельщиков В.П. Парицкий З.Н. Справочник по обработке
золотосодержащих руд и россыпей - М.: Металлургия, 1963. - 650 с.
)Кетляр Ю А, Меретуков М.А., Стрижко Л.С. Металлургия
благородных металлов - М.: Металлургия, 2005. - 400 с.
)Минеев Г.Г. Биометаллургия золота - М.: Металлургия,1989. -
232с.
)Барченков В.В. Основы сорбционных технологий извлечения
золота и серебра из руд - М.: Металлургия, 1982. - 130 с.
) Шиврин Г.Н., Стрижко В.С. Технологические расчеты процессов
и оборудования золотоизвлекательных заводов. Красноярский ордена Трудового
Красного знамени институт имени М.И. Калинина - Красноярск, 1976. - 92 с.
) Лащинский А.А., Толчинский А.Р. Основы конструирования и
расчета химической аппаратуры - Л.: Химия, 1976. - 304 с.
) Тимонин А.С. Основы конструирования и расчета
технологического и природоохранного оборудования. Справочник. Т. 1, 2, 3. -
Калуга: Издательство Н. Бочкаревой, 2001. - 756 с.
) Лысенюк А.А, Вильнина А.В. Разработка системы управления
технологическим процессом - Томск.: ТПУ,2008. - 34 с.
)Голубятников В.А., Шувалов В.В. Автоматизация
производственных процессов в химической промышленности - М.: Химия, 1985.- 350
с.
) Клюев А. С. Техника чтения схем автоматического управления
и технологического контроля - М.: Энергоатомиздат, 1983. - 376 с.
)Трепененков Р.И. Альбом чертежей конструкций и деталей
промышленных зданий. Изд. 3-е.- М.: Стройиздат, 1980. - 284 с.
) Кузнецов А.Т. Основы строительного дела - М.: Высшая школа,
1968.- 69 с.
) Кушелев В.П. Основы техники безопасности на предприятиях
химической промышленности.- Л.: Химия, 1977 - 279 с.
) Конституция Российской Федерации (по состоянию на 30
декабря 2008 года) - Новосибирск: Сиб. унив. изд-во, 2008.
) Трудовой кодекс Российской Федерации (по состоянию на 30
декабря 2008 года) - Новосибирск: Сиб. унив. изд-во, 2008.
) Закон РФ «Основы законодательства РФ об охране труда» -
Новосибирск: Сиб. унив. изд-во,2008.
) Макаров Г.В, Васин А.Я. Охрана труда в химической
промышленности - М.: Химия, 1989. - 496 с.
) Бобков А.С, Блинов А.А. Охрана труда и экологическая
безопасность в химической промышленности - М.: Химия, 1998. - 400 с.