Литейный цех литья круглых полых и сплошных слитков из сплавов 7175, АД1, 6082
Введение
Для получения качественной продукции, с оптимальными свойствами, в
металлургической промышленности важно правильное построение производственного
цикла.
Современное литейное производство отличается большой номенклатурой
изделий. Основным полуфабрикатом в металлургии является слиток. В цехах литья
слитков из алюминиевых деформируемых сплавов получают:
· плоские слитки - для прокатного производства;
· круглые сплошные слитки - для прессования профилей и прутков,
ковки и штамповки;
· круглые полые слитки - для производства труб;
Обеспечение необходимого качества слитков достигается правильным
построением технологического процесса, грамотного применения современных
методов обработки расплава (рафинирования, модифицирования), также применением
современного оборудования и оснастки.
Учитывая вышесказанное, применение этого позволяет существенно улучшить
структуру и свойства заготовок. Тем самым, при дальнейшей обработке давлением
повышается стойкость инструмента, стабилизируются и несколько повышаются механические
свойства полуфабрикатов, увеличивается скорость прессования металла, а также
увеличивается степень его деформации.
Улучшение качества поверхности слитка позволяет уменьшить, а в некоторых
случаях и исключить, механическую обработку. Это позволяет значительно
увеличить выход годной продукции на 8 -10%.
1. Характеристика проектируемого цеха
Литейный цех обычно располагается в корпусе, состоящем из трёх пролетов:
шихтового литейного и плавильного.
Для производства сплавов на основе алюминия используют следующие шихтовые
материалы:
первичный алюминий, лома и легирующие компоненты закупаются со стороны и
поступают в цех со склада шихтовых материалов;
внутризаводские отходы, переплав и т.д. поступают из цехов переплава и
обрабатывающих цехов.
Шихтовые материалы в виде отходов собственного производства, лома
алюминиевых сплавов, первичного алюминия и легирующих компонентов поступают
железнодорожным и автомобильным транспортом на шихтовой участок, где проводится
их складирование. Шихтовые материалы в виде отходов и ломов со стороны проходят
входной контроль, стилоскопический анализ и взвешивание. Подобранная и
рассчитанная на плавку шихта подается с помощью мостовых кранов шихтового
пролета на эстакаду плавильного отдела или на участок высококачественного литья
(ВКЛ) к печам, откуда производится загрузка шихтовых материалов с помощью
мульдозавалочных кранов (МЗК) и электромостовых кранов (ЭМК). Плавление
шихтовых материалов и приготовление плавок производится в газовых пламенных
печах с автоматическим регулированием теплового режима.
Для доведения расплава до требуемого химического состава, в плавильных
печах применяются мульдозавалочные краны (МЗК) и электромостовые краны, после
чего производится рафинирование флюсами или смесью газов аргон + хлор, модифицирование
лигатурой Al-Ti-B, съем шлака с помощью мульдозавалочных кранов или напольных
завалочных машин.
Контроль температуры расплава в печи производится при помощи термопара по
показаниям потенциометра. Максимальная температура расплава в печи 7800С.
Перелив плавки из печи в миксер производится с помощью сифона или открытого
лотка.
Литье слитков производится из газовых пламенно-отражательных или
электрических миксеров. Плавильно-литейные агрегаты оснащены поворотными
газовыми миксерами ёмкостью 40 тонн или электрическими миксерами ёмкостью 25
тонн.
В миксере расплав очищают от шлака, вакуумируют, рафинируют флюсами,
аргоном или смесью газов аргон + хлор. Миксеры оборудованы установками
автоматической подачи лигатурного прутка Al-Ti-B для модифицирования расплава
во время литья слитков.
Отливка слитков производится в кристаллизаторы скольжения (круглые
слитки) на литейных машинах с тросовым приводом и гидравлической литейной
машине. Подача металла из миксера осуществляется через лёточное отверстие по
разливочной оснастке к кристаллизаторам. Каждому размеру слитка соответствует
определённая температура и скорость литья. Контроль температуры осуществляется
по показаниям потенциометра. Скорость литья слитков измеряется по прибору
измерения скорости, соединенному с вольтметром.
На участках агрегатов устанавливают процессоры, с помощью которых должны
регулироваться и поддерживаться технологические параметры литья в
автоматическом режиме (скорость и расход воды на охлаждение слитков в
зависимости от длины слитка).
2. Сортамент отливаемых круглых слитков
Диаметры отливаемых круглых слитков определяются мощностью прессов,
применяемых для их деформирования, и качеством самих слитков. В настоящее время
для получения деформированных полуфабрикатов применяют слитки диаметром от 70
до 850 мм. Литьё слитков больших диаметров освоено не для всех сплавов и
применяют только для небольшой номенклатуры полуфабрикатов.
Длину отливаемых слитков стремятся довести до максимума, так как это
повышает выход годного. С другой стороны, увеличение длины слитка усложняет
конструкцию и удорожает изготовление литейной машины. Поэтому длина отливаемых
слитков колеблется в интервале 4-6 м.
По диаметрам сортамент отливаемых сплошных и полых слитков можно
разделить на 4 группы: до 200 мм; от 200 до 400 мм; от 400 до 850 мм; более 850
мм. Отливка слитков первых двух групп не вызывает каких-либо затруднений.
Отливка слитков третьей группы для ряда сплавов требует особых мер по
регулированию состава сплава, режимов литья и конструкции кристаллизаторов, но
может считаться освоенной так же для всех сплавов. Отливка слитков четвёртой
группы освоена только для сплавов, обладающих достаточно хорошими литейными
свойствами.
Круглые сплошные слитки используют для получения профилей, прутков,
поковок и штамповок. А основную массу бесшовных труб из алюминиевых
деформируемых сплавов изготавливают из полых слитков. Из полых слитков методом
прессования получают трубную заготовку под волочение и прокатку, толстостенные
трубы, а так же трубы для изготовления панелей. В серийном производстве
отливают слитки с наружным диаметром от 150 до 850 мм и с внутренним диаметром
от 50 до 600 мм.
Основные размеры слитков и заготовок приведены в таблицах 1 и 2 [1].
Таблица 1 - Основные размеры сплошных слитков и заготовок (длина слитка
4-6 м).
Диаметр слитка, мм
|
Диаметр заготовки, мм
|
Длина заготовки, мм
|
95
|
91
|
250- 400
|
115
|
110
|
250- 400
|
130
|
124
|
250- 400
|
170
|
162
|
250- 400
|
190
|
182
|
300- 500
|
234
|
224
|
400- 600
|
273
|
262
|
400- 1000
|
360
|
347
|
400- 1000
|
430
|
414
|
600- 1000
|
540
|
520
|
600- 1000
|
650
|
630
|
800- 2000
|
840
|
810
|
800- 2000
|
Таблица 2 - Основные размеры полых слитков и заготовок (длина слитка 4- 6
м).
Диаметр слитка, мм
|
Диаметр заготовки, мм
|
Длина заготовки, мм
|
наружный
|
внутренний
|
наружный
|
внутренний
|
|
155
|
52
|
145
|
64
|
250- 350
|
180
|
52
|
170
|
64
|
250- 400
|
220
|
105
|
210
|
114
|
250- 400
|
290
|
90
|
275
|
102
|
300- 600
|
290
|
135
|
275
|
150
|
300- 600
|
365
|
90
|
350
|
102
|
450- 800
|
365
|
138
|
350
|
152
|
450- 800
|
365
|
200
|
350
|
225
|
450- 800
|
420
|
200
|
400
|
225
|
600- 800
|
510
|
290
|
490
|
315
|
600- 800
|
650
|
320
|
630
|
345
|
800- 1500
|
850
|
410
|
830
|
435
|
800- 1500
|
3. Структура, технологические и конструкционные свойства обрабатываемых
материалов
.1 Литейные свойства алюминиевых сплавов
На рисунке 1 показаны схемы зависимости литейных свойств от состава
сплава в двойных системах эвтектического типа [1].
Рисунок 1.- Типовые схемы зависимости литейных свойств алюминиевых
сплавов от их химического состава в системе эвтектического типа: ab -
равновесный солидус; ac - неравновесный солидус; 1 - жидкотекучесть при
постоянном перегреве над ликвидусом; 2- жидкотекучесть при постоянной
температуре заливки в металлическую форму.
Поведение металлов и сплавов в литейных процессах определяется
разнообразными физико-химическими свойствами (температурой ликвидуса, солидуса,
теплоемкостью, теплопроводностью, растворимостью газов) и специфическими
литейными свойствами (жидкотекучестью, усадкой, склонностью к образованию
литейных трещин, склонностью к зональной ликвации и т.д.).
3.1.1 Жидкотекучесть
Жидкотекучесть - это способность металлов и сплавов заполнять литейную
форму. Обычно у алюминиевых сплавов ее оценивают по длине прямого или
спирального прутков, отлитых в строго определенных условиях в земляную или
металлическую форму.
Жидкотекучесть зависит, главным образом, от характера кристаллизации.
Минимальной жидкотекучестью обладают сплавы, которые имеют широкий интервал
кристаллизации. Алюминий затвердевает в виде дендритов, сравнительно быстро
перекрывающих канал. У сплава, затвердевающего в широком интервале температур,
сильно разветвленные первичные дендриты еще быстрее перекрывают все сечение
канала и, несмотря на относительно большое количество жидкой фазы, поток
останавливается на ранней стадии кристаллизации.
3.1.2 Герметичность
Герметичность - это способность отливки выдерживать давление жидкости или
газа без течи. Герметичность - литейное свойство сплава, зависящее от характера
кристаллизации. Она тесно связана с развитием усадочной и газовой пористости.
Герметичность определяется не только суммарным объёмом пор и их распределением
по сечению отливки, но и тем, изолированы ли поры или образуют систему
связанных междендритных каналов. У алюминия и сплавов эвтектического состава
герметичность максимальная, а у сплавов с большим интервалом кристаллизации - минимальная.
3.1.3 Линейная усадка
Линейная усадка - это сокращение линейных размеров отливки, происходящее
в период затвердевания и последующего охлаждения. Механическое торможение
усадки создают форма, металлостатическое давление и трение отливки о форму.
Газовыделение сильно сказывается на той части линейной усадки алюминиевых
сплавов, которая развивается в интервале кристаллизации. Влияние газосодержания
на линейную усадку проявляется только в том случае, когда в отливке имеется
широкая переходная область из жидкости и кристаллов, из которой выделение газов
затруднено.
3.1.4 Склонность к образованию усадочных пустот
В период охлаждения металла или сплава от температуры заливки до начала
кристаллизации, во время кристаллизации и при последующем охлаждении происходит
уменьшение объема, называемое объемной усадкой. На образование усадочных пустот
решающее влияние оказывает объемная усадка металла при кристаллизации. Ее
величину выражают в процентах отношением разности удельного объема жидкого
расплава при температуре ликвидуса и твердого сплава при температуре солидуса к
удельному объему при температуре ликвидуса.
Усадочные дефекты зависят не только от характера кристаллизации, но и от
газовыделения при затвердевании слитка. Усадочные пустоты в промышленных
отливках из алюминиевых сплавов всегда заполнены газом. Под давлением газа
могут образовываться и самостоятельные раковины и поры.
3.1.5 Склонность к образованию литейных трещин
Первопричиной образования литейных трещин в слитках из алюминиевых
сплавов в подавляющем большинстве случаев является затрудненная усадка, которая
может вызвать пластическую деформацию и закончиться разрушением. Значительно
реже литейные трещины возникают под действием внешних сил: силы трения при
вытягивании слитка из кристаллизатора, силы тяжести при зависании слитка, силы
вытягивания слитка из покоробленного кристаллизатора и др.
Литейные трещины обычно подразделяют на «горячие» и «холодные». В
алюминиевых сплавах «горячие» трещины являются кристаллизационными. Они
образуются в эффективном интервале кристаллизации, когда сплав обладает весьма
малой прочностью и очень хрупок из-за наличия жидкой фазы по границам зерен.
Кристаллизационные трещины располагаются в участках слитка, затвердевающих в
последнюю очередь, или вблизи этих участков.
Так называемые «холодные» трещины в слитках из алюминиевых сплавов обычно
образуются при температурах около 200єС и ниже. Холодные трещины, по сравнению
с кристаллизационными менее извилисты и имеют меньше колебаний по ширине в
разных участках. Часто кристаллизационные трещины переходят в «холодные»
трещины.
Если в отливке имеется достаточно широкая переходная область, из которой
затруднено удаление газа при затвердевании, то при увеличении газосодержания
расплава линейная усадка в интервале кристаллизации снижается, и запас
пластичности возрастает, т.е. горячеломкость уменьшается; при вакуумной
дегазации расплава, наоборот, линейная усадка, а вместе с ней и горячеломкость
возрастают. Модифицирование зерна алюминиевых сплавов титаном может значительно
снизить горячеломкость
3.1.6 Ликвация
Ликвацией называют неоднородность химического состава сплава. Ее можно
наблюдать при значительной разнице в плотности составляющих сплава. Ликвация
усиливается при увеличении объема и размеров заготовки, а также при увеличении
скорости и температуры заливки. Различают дендритную (микроликвация) и
зональную (макроликвация) ликвацию.
Зональная ликвация проявляется в изменении состава по сечению слитка.
Если легкоплавкими элементами обогащается центральная часть слитка, то
зональную ликвацию называют прямой, если периферийные - то обратной, а если
промежуточные слои - то внецентренной ликвацией.
Дендритная ликвация проявляется в виде внутрикристаллитной
концентрационной неоднородности и в образовании неравновесных избыточных
составляющих. Она характеризуется разностью концентраций центрального и
периферийного слоев кристаллита.
3.1.7 Склонность к ликвационным наплывам
Ликвационными наплывами называют проявляющиеся изнутри слитка и
затвердевающие на его поверхности участки расплава. Главная причина
возникновения ликвационных наплывов - истечение жидкой фазы под действием
металлостатического давления через каналы кристаллического каркаса в зазор
между слитком и кристаллизатором. Чем больше относительное количество жидкой
фазы в кристаллическом каркасе при температуре линейной усадки, тем ярче
выражены ликвационные наплывы. Игольчатые и пластинчатые интерметаллиды,
образующие кристаллический каркас при высоком содержании жидкой фазы, усиливают
склонность сплава к ликвационным трещинам.
Жидкая фаза выдавливается не через все каналы в кристаллическом каркасе,
а только в тех местах, где нарушена окисная пленка. В связи с этим большую роль
играет состояние окисной пленки и качество внутренней поверхности
кристаллизатора. При затвердевании металла без контакта с кристаллизатором
ликвационные наплывы не образуются.
3.2 Сплав 7175
.2.1 Общее описание сплава 7175
Сплав 7175 относится к высокопрочным деформируемым алюминиевым сплавам
системы Al-Zn-Mg-Cu. Они применяются в авиационном, общем и транспортном
машиностроении. Сплав в основном используется для изготовления крупных поковок
и штамповок и поставляется на экспорт. Сплавы системы Al-Zn-Mg-Cu
характеризуются высокой
прочностью (до 750-800 МПа в долевом направлении для прессованных
полуфабрикатов). Они имеют особенно высокий предел текучести, который на 40-50%
выше, чем у сплавов типа Д16 в естественно состаренном состоянии Т. Сплав
пластичный и обрабатывается в горячем и холодном состоянии. Подвергается
упрочняющей термообработке. Сплав отличается высокой прочностью после
термической обработки, хорошей прокаливаемостью, минимальной анизатропией
свойств готовых штамповок, высокой трещиностойкостью при сохранении статической
прочности и некотором увеличении сопротивления малоцикловой усталости. К
недостаткам сплава относят склонность к быстрому разупрочнению при повышенных
температурах. Неплакированные полуфабрикаты в естественно состаренном состоянии
имеют низкую коррозионную стойкость.
3.2.2 Химический состав сплава 7175
От строгого соблюдения процентного содержания компонентов во многом
зависит качество отливаемых слитков.
Содержание основных компонентов и примесей приведено в таблице 3.
Таблица 3 - Химический состав сплава марки 7175
Вид химического состава
|
Содержание основных элементов и примесей, %
|
Прочие примеси, %
|
|
Si
|
Fe
|
Cu
|
Mn
|
Mg
|
Cr
|
Zn
|
Ti
|
|
У
|
расчётный
|
≤0,04
|
≤0,12
|
≤1,6
|
≤0,02
|
≤2,4
|
≤0,20
|
≤5,5
|
≤0,025
|
-
|
-
|
разливочный
|
≤0,06
|
0,11-0,14
|
1,5-1,7
|
≤0,02
|
2,3-2,6
|
0,19-0,21
|
5,45-5,75
|
0,02-0,03
|
≤0,05
|
≤0,15
|
сдаточный по ГОСТ 4784-97
|
≤0,15
|
≤0,20
|
1,2-2,0
|
≤0,10
|
2,1-2,9
|
0,18-0,28
|
5,1-6,1
|
≤0,10
|
≤0,05
|
≤0,15
|
.2.3 Фазовый состав сплава 7175
Структуру сплава можно описать, руководствуясь соответствующими разрезами
четверной системы Al-Zn-Mg-Cu.
Как показывают разрезы, сплав 7175 имеет сложный фазовый состав, который
изменяется с понижением температуры. При температуре 460°С сплав лежит на
границе б - (б + S). При 200°С и ниже сплав попадает в четырёхфазную область б
+ М(Mg Zn2) +S(Al2CuMg) + T(Al2Mg3Zn3)
, следовательно, основными упрочнителями сплава являются фазы S, T, MgZn2.
В фазе Т растворяется определённое количество меди. По мере увеличения
содержания меди в четверных сплавах Al-Zn-Mg-Cu часть атомов цинка в решетке
фазы Т(Al2Mg3Zn3) замещается атомами меди.
На рисунке 2 показан первичный разрез системы Al-Zn-Mg-Cu [2], а на
рисунках 3 и 4 показана структура сплава в различных состояниях [4].
Рисунок 2 - Первичный разрез системы Al-Zn-Mg-Cu а - при 460°С, б - при
200°С [4].
В литом состоянии в сплавах системы Al-Zn-Mg-Cu по границам дендритных
ячеек бAl-раствора располагаются включения фаз S, M и T. Помимо
перечисленных фаз присутствует нерастворимая (Al, Mn, Fe, Si)-составляющая. В
деформированных и закалённых полуфабрикатах можно встретить не полностью
растворившиеся в процессе нагрева под закалку включения промежуточной фазы S
(Al2CuMg). Сплав 7175 в отожжённом состоянии может иметь следующий
фазовый состав: б , MgZn2, AlMgZnCu (являющийся твёрдым раствором) и
фазы, содержащие хром и марганец. На фазовый состав может оказывать сильное
влияние содержание кремния. Чем больше содержание кремния в сплаве, тем больше
будет образовываться фаза Mg2Si, которая практически не участвует в
упрочнении сплава, поэтому рекомендуется держать содержание кремния на нижнем
допустимом пределе.
Рисунок 3 - Микроструктура сплава 7175 в искусственно состаренном
состоянии.
Рисунок 4 - Микроструктура литого сплава 7175.
На фоне б-твёрдого раствора сложного состава (светлое пятно) видны
выделения S-фазы (серая), MgZn4 и Т-фазы (тёмная). Две последние
фазы трудноотличимы на шлифах вследствие одинаковой их травимости.
3.2.4 Влияние легирующих добавок и примесей на свойства
сплава
Основными легирующими элементами в сплаве являются Cu, Mg, Cr, Zn.
Марганец и хром повышают температуру рекристаллизации и прочностные
характеристики сплава. На рисунке 5 показано влияние марганца на механические
свойства сплавов системы Al-Zn-Mg-Cu.
Рисунок 5 - Влияние марганца на свойства сплавов системы Al-Zn-Mg-Cu в
различных состояниях: а - отожженное (1) и свежезакаленное (2), б - состояние
Т1.
Введение марганца повышает также эффекты закалки и старения. Влияние
хрома на механические свойства сплава в основном аналогично влиянию марганца,
однако хром действует в два раза эффективнее, поэтому для достижения того же
уровня свойств его концентрация в сплаве может быть в два раза меньше, чем
марганца. Марганец и хром ускоряют процессы старения сплава. Максимум прочности
достигается значительно быстрее в сплавах с хромом и марганцем, чем в сплавах
без этих добавок.
Марганец и хром так же положительно влияют и на коррозионную стойкость
сплава 7175 в состоянии Т1. Лучше использовать оба компонента, так как
содержание добавки только одного компонента, появляется склонность к
образованию интерметаллидов, ухудшающих пластичность [10].
Медь, вызывая дополнительное упрочнение, при содержании до 2% даёт
повышение сопротивление коррозионному растрескиванию, пластичности.
Железо и кремний отрицательно влияют на свойства сплава. Кремний снижает
прочностные свойства всех видов полуфабрикатов. Железо в количествах до 0,2%
мало влияет на прочность, а при больших концентрациях вызывает разупрочнение и
снижает эффекты закалки и старения.
3.2.5 Термообработка сплава 7175
Сплав 7175 склонен подвергаться упрочнению при применении закалки и
последующего естественного и искусственного старения. Полуфабрикаты из сплава
7175 подвергают закалке с температуры 465- 475°С. Охлаждение полуфабрикатов в
процессе закалки рекомендуется осуществлять быстро, время переноса их из печи в
закалочную среду не должно превышать 15 сек.
Старение сплавов системы Al-Zn-Mg-Cu протекает в несколько стадий,
характеризующих изменение свойств: на первой стадии (до 80°С) повышение
прочности и электросопротивления, на второй стадии (120…140°С) - дальнейшее
повышение прочности и электросопротивления, на третьей стадии, при более
высоких температурах или длительных выдержках, - снижение прочности,
пластичности и электросопротивления.
Ступенчатый режим старения (выдержка в течение 3 часов при температуре
115- 125°С, затем выдержка в течение 3 часов при температуре 157- 163°С, и
охлаждение на воздухе) обеспечивает более высокую коррозионную стойкость и
улучшает расклепываемость сплава [11].
Отжиг полуфабрикатов из сплава 7175 производится при температуре 430+10
°С. Время выдержки зависит от массивности полуфабрикатов. Так, при
толщинах до 10 мм время выдержки рекомендуется доводить до 60 минут, при
толщине 10..15 мм - до 90 минут, а при толщине 15..20 мм время выдержки
увеличивается до 120 минут. Охлаждение полуфабрикатов следует производить
вместе с печью со скоростью 30..50 °С/час до температуры 150°С. Дальнейшее
охлаждение можно вести на воздухе.
Когда полуфабрикаты подвергаются промежуточному отжигу (для снятия
нагартовки), температура отжига может быть снижена до 390°С. В этом случае
охлаждение ведется на воздухе.
Изделия и полуфабрикаты, деформированные в свежезакаленном состоянии, не
требуют дополнительной перезакалки перед искусственным старением, что является
преимуществом деформирования в свежезакаленном состоянии перед деформированием
в отожженном состоянии.
3.2.6 Механические и физические свойства сплава 7175
Сплав 7175 обладает одной из самых высоких характеристик прочности по
сравнению с основными конструкционными алюминиевыми сплавами.
Сплав удовлетворительно сваривается контактной сваркой, которую ведут при
жестких импульсах тока из-за повышенной чувствительности сплава к
тепломеханическому циклу сварки. При сварке плавлением сплав склонен к
образованию трещин. На рисунке 6 представлено изменение механических свойств
системы Al-Zn-Mg-Cu в зависимости от температуры [5].
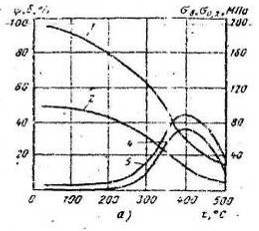
Рисунок 6 - Диаграмма деформирования сплавов системы Al-Zn-Mg-Cu в литом
гомогенизированном (а) и деформированном (б) состояниях: 1- ув, 2- у0,2,
3- д, 4- ш.
Комплекс свойств полуфабрикатов из сплава В95пч при разных видах
термообработки представлен в таблице 4 [6].
Таблица 4 - Типичные механические и коррозионные свойства сплава 7175
после закалки и старения по различным режимам
Режим термообработки
|
ув, МПа
|
у0,2, МПа
|
д, %
|
ат.у., кДж/м2
|
К1с, МПа·м1/2
|
РК*, балл
|
укр**,МПа (по высоте)
|
Т1
|
540
|
470
|
10,0
|
40
|
30,0
|
6..7
|
<60
|
Т2
|
500
|
430
|
11,5
|
60
|
33,5
|
2..3
|
~200
|
Т3
|
470
|
400
|
11,5
|
75
|
36,0
|
1
|
>260
|
* Расслаивающая коррозия ** Критическое напряжение при
стандартных условиях испытания на коррозию под напряжением
|
Основные физические свойства сплава 7175 сведены в таблицу 5 [7].
Таблица 5 - Физические свойства слитков из сплава 7175
Ср. коэфф. линейн. расширения, б·106, 1/град
|
Плотность d·10-3, кг/м3 (при 0єС)
|
Теплопроводность л, Вт/(м·єС) при t, єС
|
Теплоемкость С, кДж/(кг·град) при t, єС
|
Удельное электро сопротивление с·106 Ом·м при
20єС
|
|
|
25
|
100
|
200
|
100
|
200
|
400
|
|
24,0
|
2,85
|
155
|
159
|
163
|
0,922
|
1,00
|
1,09
|
4,2
|
Предельная степень деформации сплава 7175 при горячей обработке
составляет 40..60%.
3.2.7 Литейные свойства сплава 7175
Сплав имеет одни из наиболее низких литейных свойств по сравнению с и
остальными алюминиевыми деформируемыми сплавами. Он обладает низкой
жидкотекучестью, что в совокупности со склонностью сплава к образованию горячих
и холодных трещин существенно усложняет технологию литья этого сплава. На
рисунке 7 показана зависимость литейных свойств сплава от количества легирующих
компонентов (магния и цинка).
Рисунок 7 -
Литейные свойства сплава 7175: 1 - эффективный интервал времени и линейная
усадка кристаллизации; 2 - полная линейная усадка;3 - горячеломкость; 4 - объем
раковин (Vр) и объем пор (Vn); 5 - склонность к зональной ликвации; 6 -
жидкотекучесть.
3.3 Сплав АД1
.3.1 Общее
описание сплава АД1
Сплав АД1 относится к сплавам алюминиевым деформируемым. Высокая
пластичность позволяет производить из сплава АД1 глубокую вытяжку, штамповку,
прокатку до тонкой толщины (фольга). Высокая электропроводность позволяет
применять сплав АД1 для электротехнических целей (проводниковый металл).
Высокая коррозионная стойкость также позволяет расширить применение данного
сплава. Он весьма устойчив в органических кислотах, отсюда его широкое
применение в быту. В неорганических кислотах сплав устойчив лишь при низкой
концентрации. Данный сплав применяется в строительной технике для фасадов
домов, оконных рам и т.д.
.3.2 Химический состав сплава АД1
Содержание основных компонентов и примесей в сплаве АД1 приведено в
таблице 6.
Таблица 6 - Химический состав сплава АД1
Вид химического состава
|
Содержание основных элементов и примесей, %
|
Прочие примеси, %
|
|
Si
|
Fe
|
Cu
|
Mn
|
Mg
|
Cr
|
Zn
|
Ti
|
|
У
|
расчётный
|
≤0,2
|
≤0,25
|
≤0,04
|
≤0,02
|
≤0,04
|
-
|
≤0,04
|
≤0,015
|
-
|
-
|
разливочный
|
≤0,23
|
≤0,29
|
≤0,05
|
≤0,025
|
≤0,05
|
≤0,04
|
≤0,05
|
0,015-0,03
|
≤0,05
|
-
|
сдаточный по ГОСТ 4784-97
|
≤0,15
|
≤0,20
|
1,2-2,0
|
≤0,10
|
2,1-2,9
|
0,18-0,28
|
5,1-6,1
|
≤0,10
|
≤0,05
|
≤0,15
|
Fe/Si≥1,0 Al не менее 99,3%
|
.3.3 Фазовый состав сплава АД1
Чтобы выяснить, какие промежуточные фазы железо и кремний могут
образовывать в сплаве АД1, рассмотрим диаграмму состояния тройной системы
Al-Fe-Si.
Рисунок 8 - Система Al-Fe-Si [2].
Железо незначительно растворяется в алюминии в твердом состоянии, образуя
с ним несколько промежуточных фаз. При ничтожно малых его содержаниях в
структуре алюминия появляется эвтектика Al+Al3Fe. Соединение Al3Fe
выделяется в виде игл, служащих готовыми надрезами в металле, и поэтому железо
снижает пластические свойства алюминия, а также уменьшает коррозионную
стойкость металла.
Кремний не образует с алюминием химических соединений. Сплавы содержат
обычно две фазовые составляющие Al + Si и Al + a (Al - Fe - Si), а фазы Al + b (Al - Fe - Si) и Al - Al3
Fe очень редко присутствуют вместе с первыми фазами. Несмотря на заметную и
переменную растворимость кремний не придаёт алюминию способности к упрочнению
термической обработкой, что связано с неблагоприятным характером распада
твёрдого раствора кремния в алюминии. Растворяясь в алюминии, кремний несколько
упрочняет его, незначительно снижая при этом пластические свойства.
Если в сплаве одновременно присутствуют железо и кремний, то могут
образоваться два тройных химических соединения: б (Al-Fe-Si) и в (Al-Fe-Si).
Соединения б и в практически нерастворимы в алюминии. Они обладают высокой
хрупкостью и снижают коррозионную стойкость сплава. Присутствие этих
соединений, особенно при их размещении по границам зёрен, уменьшает
пластичность сплава. Размер выделений этих фаз уменьшается с увеличением
скорости охлаждения.
3.3.4 Влияние легирующих элементов на свойства сплава АД1
Для получения высококачественных полуфабрикатов из сплава АД1 необходимо,
чтобы содержание примесей в алюминии отвечало следующим требованиям:
1. Содержание железа (при любой сумме железа и кремния) должно в
1,2..1,5 раза превышать содержание кремния. Это будет устранять горячеломкость,
уменьшать склонность к росту зерна при рекристаллизационном отжиге, улучшать
пластичность в холодном состоянии и увеличивать изотропность свойств.
2. Необходима присадка 0,02..0,05% Ti, что также улучшает структуру
в рекристаллизованном состоянии.
. Примесь марганца не должна превышать 0,03%, так как большие
содержания приводят к аномальному росту зерна при рекристаллизационном отжиге.
. Содержание водорода должно быть минимальным: не более 0,20 см3/100
г Al. Это позволит избежать газовых пузырей после отжига.
Примеси железа мало изменяют температуру начала и резко повышают
температуру конца кристаллизации и одновременно сильно измельчают величину
зерна. Примеси меди и кремния в меньшей степени повышают эти показатели.
Хром и марганец значительно повышают температуру рекристаллизации и
незначительно измельчают зерно. Кремний и магний в меньшей степени повышают
температуру рекристаллизации и сильно измельчают размер зерна. Цинк повышает
температуру рекристаллизации алюминия.
.3.5 Термическая обработка сплава АД1
Термообработкой сплав АД1 не упрочняется. Для уменьшения степени
нагартовки или полного её снятия и получения повышенной пластичности
полуфабрикаты подвергают или низкому отжигу (при температурах 150-300°С в
течение 1-3 ч, с последующим охлаждением на воздухе), когда требуется, чтобы
материал ещё сохранял достаточную прочность (полунагартованное состояние), или
высокому отжигу (при температурах 300-500°С в течение 2-10 мин при толщине
полуфабриката до 6 мм и 10-30 мин при толщине полуфабриката более 6 мм с
последующим охлаждением на воздухе. Такой отжиг применяют для получения
пониженной прочности и максимальной пластичности.
При низком отжиге повышение пластичности достигается путем снижения упругих
напряжений в кристаллической решетке. При полном отжиге происходит полное
разупрочнение материала путем рекристаллизации обработки.
.3.6 Физические и механические свойства сплава АД1
Полуфабрикаты и изделия из сплава АД1 поставляются в отожженном, полунагартованном
и нагартованном состояниях.
Модуль нормальной упругости листов из АД1 составляет 71000 МПа, модуль
сдвига 27000 МПа, коэффициент Пуассона 0,31.
Благодаря высокой пластичности полуфабрикаты из АД1 легко можно
подвергать деформации без существенных нагревов. Сплав АД1 отличается высокой
тепло- и электропроводностью, хорошей коррозионной стойкостью и свариваемостью.
Высокая коррозионная стойкость обусловлена наличием на поверхности изделий
очень прочной и плотной окисной пленки. Обрабатываемость резанием вследствие
высокой вязкости у сплава плохая.
На рисунке 9 представлено изменение механических свойств сплава АД1 в
зависимости от температуры [5].
Рисунок 9 - Диаграмма деформирования сплава АД1 в литом гомогенизированном
состоянии: 1- у0,2, 2- ув, 3- д, 4-KCV, 5- ш.
В таблицах 7 и 8 представлены механические свойства сплава АД1 [6].
Таблица 7 -Механические свойства листов из сплава АД1, Т=200С
Состояние листа
|
Толщина листа, мм
|
ув, МПа
|
д , %
|
|
|
Не менее
|
Отожженное Нагартованное Горячекатаное
|
1..10 4..10 5..10,5
|
60 130 70
|
28 5 15
|
Таблица 8 - Механические свойства отожженного сплава АД1 в зависимости от
направления вырезки образцов.
Состояние слитка перед горячей прокаткой
|
Температура горячей прокатки, °С
|
Вдоль прокатки
|
Поперек прокатки
|
Под углом 45° к направлению прокатки
|
|
начало
|
конец
|
ув, МПа
|
д , %
|
ув, МПа
|
д , %
|
ув, МПа
|
д , %
|
После гомогенизации (550..570°С, 20ч) Без гомогенизации
|
520 350 520 350
|
400 270 400 270
|
84 87 82 80
|
42,6 39,2 43,0 41,5
|
81 82 81 80
|
47,0 47,5 43,1 42,0
|
83 80 83 79
|
49,2 49,8 48,5 49,3
|
.4 Сплав 6082
.4.1 Общее описание сплава 6082
Сплав 6082 относится к алюминиевым деформируемым сплавам на основе
системы Al-Mg-Si. Промышленные сплавы системы Al - Mg - Si менее прочны, чем
дуралюмины, но более пластичны и обладают лучшей коррозийной стойкостью.
Сочетание достаточной прочности с высокой технологичностью ип хорошей
коррозионной стойкостью, удовлетворительная свариваемость, хорошее качество
поверхности после анодирования делают сплавы системы Al - Mg - Si
перспективными для использования в различных отраслях народного хозяйства
(строительстве, транспортном машиностроении и т.д.)
Применение сплавов системы Al - Mg - Si в народном хозяйстве
обеспечивает, с одной стороны, хорошие эксплуатационные свойства изделий
(например, длительную службу в атмосферных условиях), с другой стороны,
позволяет сравнительно быстро благодаря их высокой технологичности увеличивать
производство деформированных полуфабрикатов. Вследствие высокой пластичности в
горячем состоянии из них можно изготавливать очень сложные по конфигурации
тонкостенные полые полуфабрикаты. Сплавы системы Al-Mg-Si не имеют склонности к
коррозионному растрескиванию под напряжением. Их коррозионная стойкость
остается такой же высокой после сварки, как и до неё.
.4.2 Химический состав сплава 6082
От строгого соблюдения процентного содержания компонентов сплава во
многом зависит качество изделий.
Содержание основных компонентов и примесей приведено в таблице 9.
Таблица 9 - Химический состав сплава 6082
Вид химического состава
|
Содержание основных элементов и примесей, %
|
Прочие примеси, %
|
|
Si
|
Fe
|
Cu
|
Mn
|
Mg
|
Cr
|
Zn
|
Ti
|
|
У
|
расчётный
|
≤1,0
|
≤0,4
|
≤0,05
|
≤0,6
|
≤0,9
|
≤0,15
|
≤0,12
|
≤0,04
|
-
|
-
|
разливочный
|
0,95-1,1
|
≤0,45
|
≤0,08
|
0,55-0,7
|
0,8-1,0
|
≤0,18
|
≤0,15
|
0,03-0,06
|
≤0,05
|
≤0,15
|
сдаточный по ГОСТ 4784-97
|
0,7-1,3
|
≤0,50
|
≤0,10
|
0,40-1,0
|
0,6-1,2
|
≤0,25
|
≤0,20
|
≤0,10
|
≤0,05
|
≤0,15
|
.4.3 Фазовый состав сплава 6082
Основными легирующими элементами сплава являются магний и кремний. Если
пренебречь небольшими добавками меди, марганца, хрома и железа, то фазовый
состав сплава можно показать с помощью диаграммы состояния тройной системы
Al-Mg-Si (рисунок 10). [2]
Рисунок 10 - Алюминиевый угол системы Al-Mg-Si.
Магний и кремний характеризуются переменной растворимостью в твердом
алюминии. В связи с очень малой растворимостью кремния в алюминии при низких
температурах (200°С) сплав имеет в равновесных условиях гетерогенную структуру.
Фазовый состав сплава 6082 б + Mg2Si + Si.
Промышленный сплав 6082 с содержанием 0,40- 1,0% Mn имеет волокнистую
нерекристаллизованную структуру независимо от технологии изготовления. Этот
сплав благодаря большому количеству марганца является наиболее
коррозионностойким из всех сплавов системы Al-Mg-Si.
Фазой- упрочнителем сплавов на основе системы Al-Mg-Si при термической
обработке служит силицид Mg2Si.
3.4.4 Влияние легирующих элементов на свойства сплава 6082
Марганец и хром в сплавах системы Al-Mg-Si повышают температуру
рекристаллизации, затрудняют рост зерен при вторичной рекристаллизации,
способствуют сохранению нерекристаллизованной структуры изделий после
термообработки.
Титан служит модифицирующей добавкой, улучшающей технологичность сплава
при литье. Модифицирование титаном позволянт снизить склонность сплава к
горячим трещинам при литье. Благодаря интенсивному измельчению структуры литого
слитка титан способствует повышению пластичности и прочности слитка и более
равномерному распределению свойств по сечению. На прочностные свойства готовых
изделий титан практически не влияет, а пластичность несколько повышает.
При таком содержании железа, как в сплаве 6082, заметно уменьшается
склонность сплава к горячим трещинам при литье, измельчается структура готовых
полуфабрикатов благодаря повышению температуры рекристаллизации алюминия.
Медь как примесь в сплаве 6082 не допускается в количествах более 0,10%,
так как она повышает склонность сплава к межкристаллитной коррозии.
Цинк в допустимых количествах (не более 0,20%) не влияет на свойства
сплава 6082.
С повышением содержания кремния в сплаве улучшается способность к
свариваемости. Коррозионная стойкость сплава резко снижается с увеличением фазы
Mg2Si и кремния. Увеличение концентрации магния не снижает
коррозионную стойкость сплава.
3.4.5 Термическая обработка сплава 6082
Сплав 6082 упрочняем термообработкой. Упрочняется этот сплав как при
естественном, так и при искусственном старении.
Температуру нагрева под закалку сплава обычно выбирают в пределах
520..540°С. При естественном старении прирост прочности продолжается в течение
двух недель после закалки. Искусственное старение даёт больший прирост
прочности, по сравнению с естественным. Оптимальные механические свойства
обеспечивает старение по режиму: 160..170°С, 12..15 ч. Коррозионная стойкость авиаля
после искусственного старения уменьшается, в частности, возрастает склонность к
межкристаллитной коррозии.
Механические свойства искусственно состаренных сплавов системы Al-Mg-Si
чувствительны к перерыву между закалкой и старением. Для получения максимальной
прочности сплава необходимо проводить искусственное старение сразу после
закалки. Учитывая выдержку при искусственном старении, можно частично
компенсировать снижение прочности, обусловленное перерывом между закалкой и
старением.
3.4.6 Физические и механические свойства сплава 6082
Для естественно состаренного сплава характерны относительно низкий предел
текучести (100-150 МПа), высокое удлинение (18-25 %), возрастающее
электросопротивление (до 470 Ом∙см), высокая ударная вязкость (0,5-0,6
МДж/м2) и высокая коррозионная стойкость. В искусственно состаренном
состоянии предел текучести достигает больших значений (200-300 МПа), при этом
удлинение снижается до 10%, электросопротивление до 350 Ом∙см, ударная
вязкость до 0,2-0,3 МДж/м2, значительно снижается коррозионная
стойкость. Возникает склонность к межкристаллитной коррозии.
В таблице 10 приведены типичные механические свойства сплава в различных
состояниях.
Таблица 10 - Механические свойства прессованных полуфабрикатов из сплава
системы Al-Mg-Si, Т=200С
Состояние
|
ув, МПа
|
у0,2, МПа
|
д , %
|
у-1, Мпа
|
Т1
|
330
|
280
|
10
|
110
|
Т
|
250
|
150
|
16
|
-
|
М
|
150
|
100
|
20
|
-
|
Сплавы системы Al-Mg-Si склонны к образованию кристаллизационных трещин
при сварке. Пластичность сплава в отожженном состоянии хорошая, в естественно и
искусственно состаренном состояниях удовлетворительная. Обрабатываемость
резанием в отожженном состоянии неудовлетворительная, в естественно и
искусственно состаренном состояниях - удовлетворительная.
3.5 Сплавы для изготовления деталей оснастки
Заготовки для изготовления конусных стержней, кристаллизаторов и поддонов
для отливки круглых слитков вырезаются из гомогенизированных слитков сплава Д1
с химическим составом по ГОСТ 4784.
Гомогенизационный отжиг слитков Д1 проходит в температурном интервале
480-500єС в течение 24-36 часов. Сплав Д1 характеризуется хорошей пластичностью
в горячем состоянии.
Таблица 11 - Состав сплава Д1 по ГОСТ 4784-97.
Содержание основных элементов и примесей, %
|
Прочие примеси, %
|
Cu
|
Mg
|
Mn
|
Fe
|
Si
|
Ni
|
Zn
|
Ti
|
Al
|
У
|
3,5-4,8
|
0,4-0,8
|
0,4-1,0
|
≤0,7
|
0,20-0,8
|
≤0,05
|
≤0,25
|
≤0,15
|
основа
|
≤0,15
|
Таблица 12 - Типичные механические свойства Д1 в закаленном и состаренном
состоянии [8].
Состояние сплава
|
Механические свойства на растяжение
|
Ударная вязкость, МПа
|
|
ув, МПа
|
у0,2, МПа
|
д , %
|
Ш, %
|
|
Свежезакаленный
|
338
|
135
|
20,2
|
40,5
|
370
|
Естественно состаренный
|
425
|
246
|
19,9
|
35,7
|
190
|
Искусственно состаренный при следующих температурах и
времени выдержки: 100єС, 25 ч 120єС, 24 ч 120єС, 12 ч 140єС, 8 ч 140єС, 16 ч
160єС, 4 ч 160єС, 6 ч 200єС, 2 ч 200єС, 4 ч 250єС, 1/2 ч 250єС, 1 ч
|
416 414 417 436 417 418 433 427 433 418 403
|
230 231 223 306 287 259 287 336 369 221 311
|
25,3 27,7 28,8 16,9 17,4 23,9 20,9 10,0 7,6 26,3 12,6
|
39,0 37,5 37,9 35,1 35,0 36,4 37,2 31,3 29,5 38,2 32,8
|
210 210 230 130 110 180 170 90 80 240 190
|
Наиболее распространены корпуса и гильзы, изготовленные из алюминиевых
сплавов типа Д1. Гильзы необходимо закаливать. Внутренняя поверхность гильзы,
соприкасающаяся со слитком, должна быть полированной.
4. Разработка технологического процесса производства слитков
Наиболее распространенным способом производства слитков из алюминиевых
деформируемых сплавов является полунепрерывное литье с непосредственным
охлаждением слитка водой. Этот метод характеризуется высокими скоростями
кристаллизации и обеспечивает получение качественных слитков практически всех
сплавов.
Для реализации этих возможностей необходима разработка эффективного
технологического процесса, начиная от приготовления расплава и заканчивая
выходом годного слитка.
4.1 Шихтовые материалы для производства сплавов
.1.1 Качественный состав шихтовых материалов
Исходными шихтовыми материалами для приготовления алюминиевых
деформируемых сплавов служат первичные металлы, вторичные сплавы и лигатуры,
отходы литейного производства.
Для приготовления шихты, используемой для кондиционных сплавов,
разрешается применять следующие материалы:
1. Алюминий первичный в чушках по ГОСТ 11069-74 и ГОСТ 1070-79;
2. Алюминиевые слитки по ГОСТ 9498-79 и алюминиевые слитки, поставляемые
с других заводов при согласовании с НДТ;
. Реквизиты из алюминия, поставляемые по согласованным техническим
условиям;
. Сплавы алюминиевые марок АК5М2 и АК7М2 в чушках по ГОСТ
1583-73;
. Силумин в чушках марки не ниже СИЛ1 по ГОСТ 1521-76;
. Магний первичный в чушках марки не ниже МГ90 по ГОСТ 804-72;
. Цинк марки не ниже Ц1 по ГОСТ 3640-79;
. Лигатура по СТП 802.03.027-88;
. Отходы производства по СТП 802.03.027-88;
. Слитки промывных плавок;
. Пакетированные и непакетированные отходы со стороны по ГОСТ
1639-78.
Первичный алюминий в виде чушек массой 15 кг, «Т»-образных чушек массой
до 2000 кг, алюминиевые слитки, первичные металлы разрешается использовать в
шихту, не дожидаясь прибытия на них сертификатов.
Запрещается использовать в шихту без протоколов химического анализа или
без сертификатов качества лигатуры, переплав со стороны, лома, поступающие в
вагонах и контейнерах, а также забракованные по химическому составу отходы
плавок своего производства.
В качестве освежения первичным алюминием или отходами используются:
· Первичные металлы: медь, магний, цинк;
· Слитки сплавов марок АМц, АД31;
· Отходы алюминия класса А по СТП 802.14.001-89;
· Алюминиевые слитки, алюминий в чушках и его реквизиты;
· Силумины.
.1.2 Порядок приемки, разгрузки и хранения шихтовых
материалов
Шихтовые материалы поступают в цех автомобильным транспортом в стеллажах,
мульдах, коробках, стопках, рулонах, россыпью и железнодорожным транспортом на
платформах, в крытых вагонах, полувагонах, контейнерах.
Разгрузка шихтовых материалов из крытых вагонов (алюминий в пакетах,
«Т»-образной чушки, катодная медь, цинк, магний, никель в пакетах) производится
электропогрузчиками; из полувагонов (слитки весом 2,5; 8; 10 тонн, «Т»-образная
чушка, пакетированные и нестандартные лома, пакетированный алюминий, трубы,
сыпучие материалы) - согласно «Технологической карте загрузки и разгрузки
полувагонов и платформ мостовыми кранами на складах и в цехах». Разгрузка
непакетированных шихтовых материалов (медь, цинк, магний, чушковый алюминий) производится
вручную. Разгрузка ломов и отходов, поступающих в цех в полувагонах и
автомашинах россыпью, производится с помощью грейфера или вручную, в
зависимости от габаритов отходов; в пакетированном виде - вручную.
Взвешиванию в шихтовом отделе подлежат все шихтовые материалы , кроме
первичного алюминия в виде мелкой и крупногабаритной чушки, вес которых
указывается заводом-изготовителем, железнодорожных вагонов с шихтой (кроме
оборотных отходов), проходящих взвешивание на железнодорожных весах, и автомобильного
транспорта с ломами, отходами и первичными металлами, проходящего взвешивание
на автомобильных весах. Шихта, поступающая в цех в таре, взвешивается вместе с
последней. При этом на таре сваркой должны быть нанесены ее номер и масса.
Шихта, поступающая в цех россыпью, предварительно разгружается вручную в
порожнюю тару, а затем подвергается взвешиванию.
После взвешивания производится распечатка результатов на самоклеящемся
отрывном талоне термоленты в двух экземплярах. Один экземпляр отрывного талона
наклеивается на тару, а второй - в журнал учета. Отрывной талон содержит: номер
накладной; поставщика шихты; массу нетто; массу брутто; массу тары; марку
сплава, переплава, лигатуры или группы и сорта отходов, чистого металла; время
взвешивания; дату взвешивания.
Алюминий в виде мелкой и крупногабаритной чушки, слитки алюминия,
переплав, лигатуры, отходы металлов, чистые металлы разгружаются, складируются
и хранятся на полу шихтового отдела в контейнерах. Складирование бочек с
магнием производится в специально отведенном месте, не выше трех ярусов. Через
каждые пять бочек нижнего яруса устанавливаются деревянные прокладки сечением
не менее 100 х 100 мм по всей длине бочки. Расход бочек производится поярусно,
начиная с верхнего ряда. Запрещается расходовать следующий ярус, не закончив
предыдущий. Бочки с ярусов снимаются при помощи электропогрузчика и
устанавливаются на пол. Вскрытие бочек производится только на полу.
Все лома и отходы алюминиевых сплавов, поступающие в цех от сторонних
организаций, проверяют на радиоактивность. Запрещается использовать в шихту
лома и отходы с уровнем радиации, превышающим допустимый.
.2 Порядок подбора и расчета шихты
Задачей расчета шихты является определение количества её компонентов для
получения 1 тонны жидкого расплава [12].
.2.1 Расчет шихты для сплава 7175
Химический состав сплава 7175 (расчетный) приведен в таблице 13.
Таблица 13 - Расчетный химический состав сплава 7175
Содержание основных элементов и примесей, %
|
Основные компоненты
|
Примеси
|
Zn
|
Mg
|
Cu
|
Cr
|
Fe
|
Si
|
Mn
|
Ti
|
5,4
|
2,3
|
1,5
|
0,19
|
0,15
|
0,04
|
0,03
|
0,025
|
Количество
каждого компонента в расплаве определяется по формуле
Эж = Эк ∙1000/100,
(1)
где Эк - содержание компонента в шихте по химическому составу;
Эж - содержание компонента в расплаве.
ЭAl= 90,365 ∙ 1000/100 = 903,65 кг;
ЭZn= 5,4 ∙ 1000/100 = 54,0 кг; ЭFe= 0,15 ∙
1000/100 = 1,5 кг;
ЭMg= 2,3 ∙ 1000/100 = 23,0 кг; ЭSi= 0,04 ∙
1000/100 = 0,4 кг;
ЭCu= 1,5 ∙ 1000/100 = 15,0 кг; ЭMn= 0,03 ∙
1000/100 = 0,3 кг;
ЭCr= 0,19 ∙ 1000/100 = 1,9 кг; ЭTi= 0,025 ∙
1000/100 = 0,25 кг.
Итого: 1000 кг.
С учетом угара, который в сплаве 7175 составляет 1,2%, количество каждого
компонента определяется по формуле
Эж*= Эж ∙ (100+1,2)/100. (2)
ЭAl= 903,65 ∙ 101,2/100 = 914,49 кг;
ЭZn= 54,0 ∙ 101,2/100 = 54,65 кг; ЭFe= 1,5 ∙
101,2/100 = 1,52 кг;
ЭMg= 23,0 ∙ 101,2/100 = 23,28 кг; ЭSi= 0,4 ∙
101,2/100 = 0,4 кг;
ЭCu= 15,0 ∙ 101,2/100 = 15,18 кг; ЭMn= 0,3 ∙
101,2/100 = 0,3 кг;
ЭCr= 1,9 ∙ 101,2/100 = 1,92 кг; ЭTi= 0,25 ∙
101,2/100 = 0,25 кг.
Итого: 1012 кг.
В сплаве 7175 алюминия первичного (в том числе марки А85 -20%, АВч- 80%)
при приготовлении должно быть не менее 60%. Берем с запасом 80% первичного
алюминия, значит, остальные 20% составляют отходы сплава 7175. Определим
весовое количество компонентов, которое вводится в расплав с отходами:
Qотх = Qш ∙ 20/100, (3)
где Qотх - количество отходов; ш - количество
шихты.отх = 1012 ∙ 0,2 = 202,4 кг
QAlотх = 914,49 ∙ 0,2 = 182,9 кг; Znотх
= 54,65 ∙ 0,2 = 10,93 кг; QFeотх = 1,52 ∙
0,2 = 0,3 кг;Mgотх = 23,28 ∙ 0,2 =4,66 кг; QSiотх
= 0,4 ∙ 0,2 = 0,08 кг;Cuотх = 15,18 ∙
0,2 = 3,04 кг; QMnотх
= 0,3 ∙ 0,2 = 0,06 кг;Crотх = 1,92 ∙
0,2 = 0,38 кг; QTiотх
= 0,25 ∙ 0,2 = 0,05 кг.
Итого: 202,4 кг.
Определим весовое количество основных легирующих компонентов:= 54,65 -
10,93 = 43,72 кг; Cu = 15,18 - 3,04 = 12,14 кг.
Mg = 23,28 - 4,66 = 18,62 кг; Cr = 1,92 - 0,38 = 1,54 кг.
Лигатурой вводим в шихту хром. Химический состав лигатуры представлен в
таблице 14.
Таблица 14 - Химический состав лигатуры Al-Cr.
Наименование
|
Al
|
Легир.
|
Si
|
Fe
|
Cu
|
Mn
|
Mg
|
Zn
|
Ti
|
Al-Cr
|
96,85
|
1,8-3,0
|
0,15
|
0,35
|
0,05
|
0,05
|
0,05
|
0,08
|
0,02
|
Рассчитаем весовое количество лигатуры и её составляющих:
QAl-Cr = 1,54 ∙ 100/2,4 = 64,17 кг; QMnAl-Cr =
0,05∙ 64,17/100 = 0,032 кг;SiAl-Cr
= 0,15∙ 64,17/100 = 0,096 кг; QMgAl-Cr = 0,05∙ 64,17/100 = 0,032 кг;FeAl-Cr = 0,35∙
64,17/100 = 0,225 кг; QZnAl-Cr
= 0,08∙ 64,17/100 = 0,051 кг;CuAl-Cr = 0,05∙ 64,17/100 = 0,032 кг; QTiAl-Cr =
0,02∙ 64,17/100 = 0,013 кг.
Цинк, магний и медь вводят в шихту чистыми компонентами: медь катодная
марок М0, М1 по ГОСТ 859-2001; цинк марок Ц0, Ц1 по ГОСТ 3640-94; магний первичный
марки Мг90 по ГОСТ 804-93.
Рассчитываем количество чистых компонентов:= 43,72 - 0,032 =43,69 кг; Mg
= 18,62 - 0,032 = 18,59 кг;= 12,14 - 0,032 = 12,11 кг.
Рассчитаем количество вводимого чистого алюминия: = 1012- 202,4- 64,17-
43,69- 18,59- 12,11 = 671 кг.
Рассчитаем примеси, вводимые с алюминием:
Первичный алюминий марки А85 -134 кг.= 0,08 ∙ 134/100 = 0,11 кг;
Si = 0,06 ∙ 134/100 = 0,08 кг.
Первичный алюминий марки А95 -537 кг.= 0,025∙ 537/100 = 0,13 кг;
Si = 0,02∙ 537/100 = 0,11 кг.
Проверяем количественный состав примесей: Fe = 0,3 + 0,225 +
0,11 + 0,13 = 0,765 <1,51 кг; Si = 0,08 + 0,096 + 0,08 + 0,11 =
0,366 < 0,4 кг;Mn = 0,06 + 0,032 = 0,092 < 0,3 кг;Ti
= 0,05 + 0,013 = 0,063 < 0,25 кг.
Итоговый состав шихты по расчетам представлен в таблице 15.
Таблица 15 - Состав шихты для сплава 7175
|
Марка
|
Вес, кг
|
Чушковый алюминий
|
А 85 А 95
|
134 537
|
Отходы
|
7175
|
202,4
|
Лигатура
|
Al-Cr
|
64,17
|
Чистые компоненты
|
Zn Mg Cu
|
43,69 18,59 12,11
|
Итого:
|
|
1012
|
В пересчете, учитывая коэффициент выхода годного (п.5.2 «Расчет запуска
на одну тонну годных слитков») в расчете баланса металла, получаем состав
шихты, указанный в таблице 16.
Таблица 16 - Состав шихты для сплава 7175 с учетом коэффициента выхода
годного.
|
Марка
|
Вес, кг
|
Чушковый алюминий
|
А 85 А 95
|
281,74 1129,01
|
Отходы
|
7175
|
425,53
|
Лигатура
|
Al-Cr
|
134,93
|
Чистые компоненты
|
Zn Mg Cu
|
91,87 39,09 25,47
|
Итого:
|
|
2127,66
|
4.2.2 Расчет шихты для сплава АД1
Химический состав сплава АД1 (расчетный) приведен в таблице 17.
Таблица 17 - Расчетный химический состав сплава АД1
Содержание примесей, %
|
Fe
|
Si
|
Cu
|
Mg
|
Zn
|
Mn
|
Ti
|
0,25
|
0,2
|
0,04
|
0,04
|
0,02
|
0,015
|
Количество каждого компонента в расплаве определяется по формуле (1):
ЭAl= 99,395 ∙ 1000/100 = 993,95 кг; ЭZn=
0,04 ∙ 1000/100 = 0,4 кг;
ЭFe= 0,25 ∙ 1000/100 = 2,5 кг; ЭSi=
0,2 ∙ 1000/100 = 2,0 кг;
ЭMn= 0,02 ∙ 1000/100 = 0,2 кг; ЭCu=
0,04 ∙ 1000/100 = 0,4 кг;
ЭTi= 0,015 ∙ 1000/100 = 0,15 кг; ЭMg=
0,04 ∙ 1000/100 = 0,4 кг.
Итого: 1000 кг.
С учетом угара, который в сплаве АД1 составляет 0,75%, количество каждого
компонента определяется по формуле :
Эж*= Эж ∙ (100+0,75)/100.
(4)
ЭAl= 993,95 ∙ 100,75/100 = 1001,4 кг; ЭMn=
0,2 ∙ 100,75/100 = 0,2 кг;
ЭFe= 2,5 ∙ 100,75/100 = 2,52 кг; ЭZn= 0,4 ∙
100,75/100 = 0,4 кг;
ЭSi= 2,0 ∙ 100,75/100 = 2,02 кг; ЭCu= 0,4 ∙
100,75/100 = 0,4 кг;
ЭTi= 0,15 ∙ 100,75/100 = 0,15 кг; ЭMg= 0,4 ∙
100,75/100 = 0,4 кг.
Итого: 1007,5 кг.
В сплаве АД1 первичного алюминия марки А6 при приготовлении должно быть
не менее 40%, значит, остальные 60% составляют отходы сплава АД1.
Весовое количество компонентов, которое вводится в расплав с отходами,
определяется по формуле
Qотх = Qш ∙ 60/100, (5)
где Qотх - количество отходов;ш - количество шихты.отх
= 1007,5 ∙ 0,6 = 604,5 кг
QAlотх = 1001,4 ∙ 0,6 = 600,84 кг; QMgотх
= 0,4 ∙ 0,6 = 0,24 кг;Feотх = 2,52 ∙
0,6 = 1,51 кг; QZnотх
= 0,4 ∙ 0,6 = 0,24 кг;Siотх = 2,02 ∙
0,6 = 1,21 кг; QMnотх
= 0,2 ∙ 0,6 = 0,12 кг;Cuотх = 0,4 ∙ 0,6
= 0,24 кг; QTiотх
= 0,15 ∙ 0,6 = 0,09 кг.
Итого: 604,5 кг.
Рассчитаем количество вводимого чистого алюминия: = 1007,5- 604,5= 403,0
кг.
Рассчитаем примеси, вводимые с алюминием:
Первичный алюминий марки А6. = 0,25 ∙ 403,0/100 = 1,01 кг; Si =
0,18 ∙ 403,0/100 = 0,73 кг.
Проверяем количественный состав примесей: Fe = 1,51+ 1,01 =
2,52 = 2,52 кг; QMg = 0,24 < 0,4 кг;Si = 1,21+ 0,73 =
1,94 < 2,02 кг; QCu = 0,24 < 0,4 кг;Mn = 0,12 <
0,2 кг; QZn = 0,24 < 0,4 кг.Ti = 0,09 < 0,15кг;
Итоговый состав шихты по расчетам представлен в таблице 18.
Таблица 18 - Состав шихты для сплава АД1
|
Марка
|
Вес, кг
|
Чушковый алюминий
|
А6
|
403,0
|
Отходы
|
АД1
|
604,5
|
Итого:
|
|
1007,5
|
В пересчете, учитывая коэффициент выхода годного (п.5.2 «Расчет запуска
на одну тонну годных слитков») в расчете баланса металла, получаем состав
шихты, указанный в таблице 19.
Таблица 19 - Состав шихты для сплава АД1 с учетом коэффициента выхода
годного.
|
Марка
|
Вес, кг
|
Чушковый алюминий
|
А6
|
512,82
|
Отходы
|
АД1
|
769,23
|
Итого:
|
|
1282,05
|
.2.3 Расчет шихты для сплава 6082
Химический состав сплава 6082 (расчетный) приведен в таблице 20.
Таблица 20 - Расчетный химический состав сплава 6082
Содержание основных элементов и примесей, %
|
Основные компоненты
|
Примеси
|
Si
|
Mg
|
Mn
|
Cr
|
Fe
|
Zn
|
Cu
|
Ti
|
1,0
|
0,9
|
0,6
|
0,15
|
0,4
|
0,12
|
0,05
|
0,04
|
Количество каждого компонента в расплаве определяется по формуле (1):
ЭAl= 96,74 ∙ 1000/100 = 967,4 кг;
ЭSi= 1,0 ∙ 1000/100 = 10,0 кг; ЭFe= 0,4 ∙
1000/100 = 4,0 кг;
ЭMg= 0,9 ∙ 1000/100 = 9,0 кг; ЭZn= 0,12 ∙
1000/100 = 1,2 кг;
ЭMn= 0,6 ∙ 1000/100 = 6,0 кг; ЭCu= 0,05 ∙
1000/100 = 0,5 кг;
ЭCr= 0,15 ∙ 1000/100 = 1,5 кг; ЭTi= 0,04 ∙
1000/100 = 0,4 кг.
Итого: 1000 кг.
С учетом угара, который в сплаве 6082 составляет 0,75%, количество
каждого компонента определяется по формуле (4):
ЭAl= 967,4 ∙ 100,75/100 = 974,66 кг;
ЭSi= 10,0 ∙ 100,75/100 = 10,08 кг; ЭFe= 4,0 ∙
100,75/100 = 4,03 кг;
ЭMg= 9,0 ∙ 100,75 /100 = 9,07 кг; ЭZn= 1,2 ∙
100,75/100 = 1,21 кг;
ЭCu= 0,5 ∙ 100,75/100 = 0,5 кг; ЭMn= 6,0 ∙
100,75/100 = 6,05 кг;
ЭCr= 0,15 ∙ 100,75/100 = 0,15 кг; ЭTi= 0,4 ∙
100,75/100 = 0,4 кг.
Итого: 1007,5 кг.
В сплаве 6082 первичного алюминия марки yне ниже А0 при приготовлении
должно быть не менее 10%. Берем с запасом 20% первичного алюминия, значит,
остальные 80% составляют отходы сплава 6082.
Весовое количество компонентов, которое вводится в расплав с отходами,
определяется по формуле
Qотх = Qш ∙ 80/100,
(6)
где Qотх - количество отходов;ш - количество шихты.отх
= 1007,5 ∙ 0,8 =806,0кг
QAlотх = 974,66∙ 0,8 = 779,73 кг; Znотх
= 1,21 ∙ 0,8 = 0,97 кг; QFeотх = 4,03 ∙ 0,8 =
3,22 кг;Mgотх = 9,07 ∙ 0,8 = 7,26 кг; QSiотх
= 10,08 ∙ 0,8 = 8,06 кг;Cuотх = 0,5 ∙
0,8 = 0,40 кг; QMnотх
= 6,05 ∙ 0,8 = 4,84 кг;Crотх = 0,15 ∙
0,8 = 0,12 кг; QTiотх
= 0,4 ∙ 0,8 = 0,32 кг.
Итого: 806,0 кг.
Определим весовое количество основных легирующих компонентов:= 10,08 -
8,06 = 2,02 кг; Mn = 6,05 - 4,84 = 1,21 кг.= 9,07 -7,26 = 1,81 кг;
Лигатурой вводим в шихту марганец. Химический состав лигатуры представлен
в таблице 21.
Таблица 21 - Химический состав лигатуры Al-Mn.
Наименование
|
Al
|
Легир.
|
Si
|
Fe
|
Cu
|
Cr
|
Mg
|
Zn
|
Ti
|
Al-Mn
|
88,42
|
9,0-12,0
|
0,15
|
0,35
|
0,05
|
0,03
|
0,05
|
0,08
|
0,02
|
Рассчитаем весовое количество лигатуры и её составляющих:
QAl-Cr = 1,21∙ 100/10,5 = 11,52 кг; QCrAl-Cr =
0,03∙ 11,52 /100 = 0,003 кг;SiAl-Cr
= 0,15∙ 11,52 /100 = 0,017 кг; QMgAl-Cr = 0,05∙11,52 /100 = 0,006 кг;FeAl-Cr = 0,35∙11,52
/100 = 0,040 кг; QZnAl-Cr
= 0,08∙ 11,52 /100 = 0,009кг;CuAl-Cr = 0,05∙ 11,52 /100 = 0,006 кг; QTiAl-Cr =
0,02∙11,52 /100 = 0,002 кг.
Кремний и магний вводят в шихту чистыми компонентами. Рассчитываем
количество чистых компонентов:=2,02- 0,017 = 2,0 кг; Mg =1,81- 0,006 = 1,8кг.
Рассчитаем количество вводимого чистого алюминия: = 1007,5- 806,0- 11,52-
2,0-1,8 = 186,18 кг.
Рассчитаем примеси, вводимые с алюминием:
Берём первичный алюминий марки А35 кг.= 0,35 ∙186,18 /100 = 0,65
кг; Si = 0,30 ∙186,18 /100 = 0,56 кг.
Проверяем количественный состав примесей: Fe=3,22 + 0,04 +
0,65 = 3,91< 4,03 кг; QTi = 0,32 + 0,002 = 0,322 < 0,4 кг;Cu
= 0,4+ 0,006 = 0,406 < 0,5 кг; QZn = 0,97 + 0,009 = 0,979 <
1,21 кг;Cr = 0,12 + 0,003 = 0,123 < 0,15 кг.
Итоговый состав шихты по расчетам представлен в таблице 22.
Таблица 22 - Состав шихты для сплава 6082
|
Марка
|
Вес, кг
|
Чушковый алюминий
|
А35
|
186,18
|
Отходы
|
6082
|
806,0
|
Лигатура
|
Al-Mn
|
11,52
|
Чистые компоненты
|
Si Mg
|
2,0 1,8
|
Итого:
|
|
1007,5
|
В пересчете, учитывая коэффициент выхода годного (п.5.2 «Расчет запуска
на одну тонну годных слитков») в расчете баланса металла, получаем состав
шихты, указанный в таблице 23.
Таблица 23 - Состав шихты для сплава 6082 с учетом коэффициента выхода
годного.
|
Марка
|
Вес, кг
|
Чушковый алюминий
|
А35
|
308,0
|
Отходы
|
6082
|
1333,35
|
Лигатура
|
Al-Mn
|
19,04
|
Чистые компоненты
|
Si Mg
|
3,3 2,98
|
Итого:
|
|
1666,67
|
4.3 Приготовление сплавов 7175, АД1, 6082
.3.1 Выбор типа печи
Для дальнейшей разработки технологического процесса необходимо выбрать
тип печи [13]. Печи для плавки алюминиевых сплавов должны отвечать ряду
требований:
1. максимальная скорость плавления шихты;
2. оптимальные геометрические характеристики рабочего пространства
печи - увеличение отношения глубины ванны к поверхности расплава для уменьшения
поверхности контакта печной атмосферы с зеркалом расплава;
. равномерный прогрев ванны с целью исключения недопустимого
перегрева;
. полная механизация трудоемких работ;
. печи должны обеспечивать максимальную производительность и
наименьший удельный расход топлива;
. получение высоких технико-экономических показателей: расход
топлива, минимальное использование производственных площадей, удельная
трудоемкость, минимальная себестоимость тонны литья, минимальные безвозвратные
потери металла и ряд других.
Всем вышеперечисленным показателям в наибольшей степени отвечает печь
газовая пламенная отражательная. Печь состоит из следующих основных частей:
рабочего пространства, сжигающих устройств и установки для использования тепла
отходящих продуктов горения - рекуператора [14]. Рабочее пространство и
рекуператор соединены вертикальными дымоотводами - опусками.
При рекуперации тепла на плавильной печи емкостью 40 тонн, обогреваемой
природным газом, при подогреве воздуха до 400-500єС расход газа на тонну
металла снижается примерно на 20-30%.
Особое внимание уделяется футеровке рабочего пространства печи. В
качестве футеровки используют следующие материалы:
1. Кирпич прямой шамотный ША-1 ГОСТ 390-96 №5 230х114х65 ГОСТ 8691-73
в количестве 32,5м3 ( 68250 кг);
2. Кирпич прямой диатомовый Д700 ГОСТ 2694-78 №8 250х125х65 ГОСТ
8691-73 в количестве 7,85м3 (5500 кг);
. Войлок муллитокремнеземистый МКРВ-200 ГОСТ 23619-79 в количестве
5,0м3 (1000 кг);
. Кирпич прямой шамотный легковесный ШЛА-1,3 ГОСТ 5040-96 №5
230х114х65 ГОСТ 8691-73 в количестве 14,5м3 (18850 кг);
. Бетон жаростойкий ЖБФ-2 ТИ 29-002-2000 в количестве 6,3м3
(12600 кг);
. Кирпич прямой высокоглиноземистый МЛС-62 ГОСТ 24704-94 №5
230х114х65 ГОСТ 8691-73 в количестве 12,8м3 (30720 кг);
. Картон муллитокремнеземистый МКРКГ-400 ТУ 14-8-537-93 в
количестве 35м3 (875 кг);
. Кирпич диатомовый ПДК-400 ТУ 5764-002-22531044-99 №5 230х114х65
ГОСТ 8961-73 в количестве 2,7м3 (1080 кг);
. Бетон жаростойкий ЖБФ-7 ТИ 29-002-2000 в количестве 1,8м3
(4860 кг);
. Кирпич пятовый шамотный ША-1 ГОСТ 390-96 №68 ГОСТ 8961-73 в
количестве 22 шт (250 кг);
. Клин торцовый шамотный ША-1 ГОСТ 390-96 №23 230х114х65/45 ГОСТ
8961-73 в количестве 0,4м3 (840 кг);
. Клин ребровый шамотный ША-1 ГОСТ 390-96 №44 230х114х65/55 ГОСТ
8691-73 в количестве 0,3м3 (580 кг).
Стенки ванны футеруют высокоглиноземистым кирпичом с содержанием А10 62%.
Подину печи выкладывают в несколько слоев: сначала кладут шамот, на него
насыпают магнезитовый порошок, а рабочий слой подины укладывают магнезитовым
кирпичом.
Так как на подину печи загружается твердая шихта больших габаритов, то ее
выкладывают из блоков больших размеров, что повышает стойкость подины до 1000 и
более плавок.
Недостатками отражательных печей является повышенный процент угара
металла (5%) и местный перегрев. Трудность тщательного перемешивания расплава
затрудняет получение однородного распределения легирующих компонентов и
качественного рафинирования.
Таблица 24 - Техническая характеристика рекуператорной печи.
Наименование
|
Единица измерения
|
Числовая величина
|
Емкость ванны
|
т
|
40
|
Температура сплава на выдаче
|
єС
|
714-740
|
Время плавки
|
ч
|
4,5
|
Время цикла
|
ч
|
8
|
Производительность печи по расплаву
|
кг/ч
|
8900
|
Технологическая производительность печи
|
кг/ч
|
5000
|
Топливо (природный газ), Q
|
ккал/м3
|
10300
|
Расход газа за период плавки
|
м3/ч
|
650
|
Удельный расход газа
|
м3/т
|
80
|
Расход воздуха для горения
|
м3/ч
|
8125
|
Температура подогретого воздуха
|
єС
|
400
|
Площадь поверхности металла
|
м2
|
25,2
|
Количество горелок
|
шт
|
8
|
Производительность вентилятора
|
м3/ч
|
20000
|
Тепловыделения в цех
|
ккал/ч
|
850000
|
Давление у поверхности металла
|
мм.вод.ст.
|
0,1
|
Давление сжатого воздуха для подъема
|
атм.
|
3-4
|
Объем насадки рекуператора
|
м3
|
36
|
4.3.2 Подготовка печи к плавке
Перед загрузкой печи шихтой для очередной плавки печь очищают от шлака и
других загрязнений с обязательной уборкой шлака из кармана, подины, откоса и
порога печи.
Промывка печи производится при переходе с одного сплава на другой,
отличающийся от предыдущего по химическому составу, а также при возобновлении
работы на агрегате после замены подины или капитального ремонта.
Промывная плавка готовится на чушковом алюминии, отходах алюминия и
отходах сплавов последующей плавки.
.3.3 Порядок загрузки шихты в печь, плавление, обработка
расплава, присадка легирующих элементов
Порядок загрузки шихты впечь следующий:
1. мелкие отходы массой до 50 кг (кроме труб и полых заготовок);
2. чушковый алюминий, переплав, силумин;
. крупный шихтовой материал массой более 50 кг;
. лигатура, медь;
. магний и цинк вводят в жидкий расплав.
Шихта загружается в печь при помощи мульдозавалочного крана в мульдах,
поддонах [12].
Загрузка шихты в печь производится бадьями при температуре под сводом
печи 720-820єС. Если температура под сводом печи перед загрузкой превышает
820єС, следует перевести горелки в режим контрольного факела, т.е. открыть окно
печи. При этом свод печи должен быть закрыт [15]. Далее необходимо остудить
печь до температуры, не превышающей 820єС, после чего отвести свод и произвести
загрузку печи шихтой.
При проведении плавки строго контролируется температура жидкого металла.
Она не должна превышать допустимой для каждого сплава температуры (таблица 25).
Таблица 25 - Температурный режим приготовления плавки для сплавов 7175,
АД1, 6082.
Сплав
|
Температура отбора проб на экспресс анализ, єС
|
Верхний предел температуры металла в печи, єС
|
Температура сплава перед сливом в миксер, єС
|
7175
|
730
|
760
|
730-750
|
АД1
|
720
|
760
|
720-740
|
6082
|
730
|
760
|
720-740
|
В начальный период плавления температура регулируется по температуре
отходящих газов. При появлении в кармане печи расплавленного металла
достаточного уровня устанавливается термопара, и по истечении 3-5 минут
регулирование печи переключается с температуры отходящих газов на температуру
расплава.
После начала оплавления шихты рекомендуется покрывать ее флюсом из расчета
0,5% к массе шихты. После полного расплавления шихты и достижения расплавом
температуры 710єС расплав выдерживается в течение 7-10 минут, а затем с
поверхности расплава, без перемешивания, производится съем шлака. После снятия
шлака производится перемешивание расплава при помощи газодинамического насоса
(ГДИН). Далее, при достижении температуры 730єС производится присадка магния и
введение чушкового цинка при помощи мульдовой коробки в верхние слои ванны печи
с замешиванием в расплав. Затем с помощью титановой ложки отбирается проба
расплавленного металла на экспресс-анализ для определения возможности слива
плавки в миксер.
После получения результатов анализа производится рафинирование расплава
печи, доводка химического состава.
4.3.4 Дегазация и очистка расплавов от неметаллических
включений
Ввиду увеличенной активности алюминия и ряда легирующих элементов
промышленная технология плавки и литья алюминиевых сплавов не обеспечивает
получения чистых заготовок. В заготовках в том или ином количестве вселда присутствуют
неметаллические включения (окислы, карбиды, нитриды, сульфиды, газ, шлаковые и
флюсовые включения, кусочки кладки печи и т.д).
Рафинирование расплавов флюсами
Механизм очистки от взвешенных включений при помощи флюсов основан на
извлечении их из расплава за счет адсорбции, растворения или химического
взаимодействия с расплавленными солями. Эффективность очистки достигается лишь
в том случае, когда флюсы смачивают неметаллические включения лучше, чем
металл. В результате смачивания размер включений увеличивается и они осаждаются
или всплывают. Часть включений удаляется также вследствие флотирующего действия
пузырьков пара, образующегося в процессе диссоциации составляющих флюса [16].
Состав флюсов, применяемых при плавлении из расчета 3 кг на 1 тонну
расплава: 30% NaCl, 47% KCl, 23% криолита .
Практика рафинирования флюсами состоит в следующем. Операцию
рафинирования делят на два этапа. Сначала часть флюса наносят на поверхность
расплава и замешивают в него. Перемешивание ведут до прекращения взаимодействия
между металлом и флюсом. Вторую часть флюса вводят в расплав при помощи
колокольчика погружением его на дно ванны.
Очистка продувкой газами
Очистка продувкой газами основана на двух процессах: диффузии
растворенного газа в пузырьки продуваемого и флотирующего и адсорбирующего
действия их по отношению к неметаллическим включениям и мельчайшим газовым
пузырькам.
Дегазацию алюминиевых сплавов проводят смесью из 20% азота и 80% хлора.
Рафинирование проводят через рабочее окно печи тремя металлическими трубками.
Давление смеси 2-3 кгс/см2. Важным условием такого рафинирования
является 10-15-минутная выдержка после продувки. Она необходима для всплытия
мелких пузырьков. Затем с расплава снимается шлак. После выдержки отбирают
пробы на газонасыщенность. Отбор производится титановой ложкой на глубине не
менее 150 мм от поверхности расплава. При газосодержании выше требуемого сплав
рафинируется повторно. После достижения необходимого уровня газов плавка
переливается в миксер.
Время от конца процесса рафинирования до начала перелива плавки в миксер
должно составлять не более 1,5 часа, время от начала загрузки шихты до начала
слива в миксер - не более 14 часов.
Итак, технологические показатели расхода времени и металла при
приготовлении расплава показаны в таблице 26.
Таблица 26 - Технологические потери металла и времени при плавлении и
очистке расплавов.
Марка сплава
|
Угар металла, %
|
Металл в шлаке, %
|
Сплесы, %
|
Время рафинирования, мин
|
Время отстоя, мин
|
7175
|
1,2
|
0,8
|
0,5
|
45
|
60
|
АД1
|
0,75
|
0,7
|
0,5
|
10
|
30
|
6082
|
0,75
|
0,7
|
0,5
|
30
|
45
|
4.3.5 Перелив плавки в миксер
Перед переливом плавки в миксер с поверхности расплава удаляется шлак.
Перелив плавки в миксер производится по лотку. Перед началом процесса перелива
необходимо удостовериться в соответствии температуры металла в печи с
температурой перелива в миксер.
.4 Литье круглых слитков из сплавов 7175, АД1, 6082
.4.1 Выбор типа миксера
Качество расплава во многом зависит от литейных миксеров. Их атмосфера
должна содержать минимальное количество водяных паров. Глубина ванны должна
быть по возможности большая. Необходимую температуру нужно поддерживать с
большой точностью, а перепад температур по объему расплава должен быть
минимальным [17].
В этой связи целесообразным является применение газовых пламенных или
вакуумных миксеров. Для обогрева газовых миксеров, как правило, применяют
инжекционные горелки. В целях равномерного прогрева ванны и создания избытка
тепловой мощности, необходимой для поднятия температуры металла, вдоль боковых
стенок устанавливают ряд горелок небольшой производительности. Горелки
устанавливают под углом с направлением вверх, под свод, что исключает
воздействие факела на поверхность расплава.
Тепловую нагрузку регулируют по температуре металла. Внедрение
автоматизации позволило получить колебание температур в пределах 10-14єС. При
этом температура поверхности ванны не поднимается выше 725-730єС. Перепад
температур по зеркалу ванны составляет 8єС, а максимальный градиент температур
находится в пределах 15-25єС.
Рисунок 11 - Газовый пламенный миксер.
Корпус газового миксера изготовлен из стальной обшивки, усиленной
стальными прокатными профилями. Изнутри миксер футерован огнеупорными и
теплоизоляционными материалами. Свод миксера плоский, выполнен из огнеупорного
кирпича с заливкой жаростойким бетоном. Для выхода продуктов сгорания в миксере
предусмотрен канал дымоудаления в своде миксера. Также с задней стороны миксера
предусмотрены 4 двери, предусмотренные для обработки и рафинирования расплава,
снятия шлака, осмотра и чистки самого миксера.
.4.2 Подготовка миксера к литью
После каждого слива металла миксер должен быть очищен от шлака с помощью
гребков. При работе агрегата на одной марке сплава разрешается оставлять в
миксере расплав предыдущей плавки количеством не более 8 тонн.
Слив «насухо» проводится в следующих случаях:
· при переходе с одного сплава на другой;
· через каждые 25 плавок при запуске на агрегате одной марки
сплава;
· перед остановкой агрегата.
В начале и конце литья производится отбор проб на экспресс-анализ.
Металл, сливаемый из миксера «насухо», является промывкой. Промывной металл
выдерживается в миксере не менее 3 часов при температуре 700-730єС с
обязательным перемешиванием через каждый час. При сливе металла «насухо»
разрешается отливать последние порции в слитки, увеличив их длину на 1,5 метра.
Капитальная чистка миксеров и доливочных печей от наростов шлака
производится в холодном или горячем состоянии с помощью шлакоуборочной машины
(ШУМ), гребков, пик и пневмоинструмента один раз в месяц во время остановки
агрегата на планово-производственный ремонт (ППР) или по указанию старшего
мастера отдела литья.
В миксере разрешается проводить подшихтовку первичными металлами (Al, Mg,
Zn) и лигатурами в количестве до 200 кг.
После отливки слитков каждой плавки поверхность остатка расплава в
миксере, стены и карманы миксера должны быть очищены от наростов шлака.
Перед переливом плавки миксер должен быть разогрет в автоматическом
режиме нагрева согласно температурному заданию под сводом. Температурное
задание под сводом миксера устанавливается на 100єС выше верхнего предела
температуры литья.
Температура расплава в миксере измеряется на уровне летки термопарой ХА в
защитном чехле по ГОСТ 6616-74.
4.4.3 Рафинирование расплава в миксере
По истечении 10 минут после перелива металла в миксер с поверхности
расплава собирается шлак к порогу, который затем отводится гребком на порог
рабочего окна миксера, выдерживается 5-8 минут и сбрасывается на сухую площадку
или в лайбу перед рабочими окнами миксера.
После снятия шлака сплав рафинируется смесью аргон + 5% хлора по ГОСТ
10157-79 с влажностью не более 0,03 г/м3 в течение 45 минут. Целью
рафинирования является очистка расплава от взвешенных включений и дегазация.
температура начала рафинирования должна быть в пределах температуры литья +
20є. После операции рафинирования с поверхности расплава повторно снимается
шлак и дается отстой.
4.4.4 Подготовка и установка литейной оснастки
К литейным машинам предъявляют следующие требования: простота и
надежность конструкции; высокая производительность; обеспечение получения
качественного литья с высоким выходом годного [18].
Литейные машины состоят из механизма движения (поддона) и
кристаллизатора. Поддон передвигается с помощью тросов и лебедки. Каждая машина
имеет индивидуальный привод, расположенный в приямке. При рабочем ходе машины
обеспечивается регулирование скорости литья слитков, а также быстрый подъем и
опускание поддона. Порядок установки литейной оснастки следующий: поддон
устанавливается на литейной машине и фиксируется. Подкристаллизаторная плита
устанавливается на литейный стол горизонтально по уровню. Кристаллизатор
устанавливается в отверстие подкристаллизаторной плиты на двух поворотных
плитах, которые в момент выгрузки слитков поворачиваются с помощью
гидравлического цилиндра и устанавливаются в вертикальное положение.
Недостатком машины является сравнительно быстрый выход из строя тросов,
также не предусмотрена механизированная выгрузка слитков.
Кристаллизатор - основной элемент литейной оснастки. Для литья слитков из
сплавов 7175, АД1, 6082 будем применять кристаллизаторы скольжения. Эти
кристаллизаторы открыты с обеих торцевых сторон, и слиток в них перемещается
под действием собственной массы. Кристаллизатор состоит из двух основных
частей: корпуса и гильзыСмазку гильз проводят до начала литья маслом вапор - Т.
Вода к кристаллизатору подводится при помощи штуцеров, соединенных
шлангами с системой водооборота. Обычно для подвода воды к кристаллизатору
применяют штуцеры диаметром от1 до 2 дюймов. Число их на один кристаллизатор
может колебаться от 1 до 4 в зависимости от диаметра слитка, диаметра штуцера и
количества и площади отверстий в нижней части кристаллизатора. Шаг между
отверстиями принимают от 4 до 10 мм в зависимости от диаметра слитка.
При отливке полых слитков допускается эксцентриситет осей конуса и нижней
части в пределах 2,0 мм. Пояс охлаждения водой внутренней поверхности слитка
должен быть на уровне пояса охлаждения наружной поверхности или выше, но не
более, чем на 10 мм. Подача металла осуществляется в середину стенки слитка.
Допускается отклонение на 1/5 толщины слитка.
При отливке сплошных слитков литейная оснастка устанавливается так, чтобы
подача металла осуществлялась в центральную зону слитка.
Для обеспечения качественного литья с высокими выходами годного слиток
должен опускаться со строго постоянной скоростью во все время литья. Движение
слитка должно быть плавным, без проскоков и остановок.
Рисунок 12 - Вакуумный миксер, раздача металла в кристаллизатор.
Таблица 27 - Технические характеристики литейной машины
Наименование характеристики
|
Числовая величина
|
Наибольшая масса отливаемых слитков, т
|
40
|
Габариты литейной платформы в плане, мм
|
2800х2800
|
Диаметр отливаемых слитков, мм
|
в пределах габаритов литейной платформы
|
Скорость отливки, мм/мин
|
8 - 210
|
Количество одновременно отливаемых слитков, шт
|
не ограничено
|
При литье нескольких слитков с использованием одной летки металл подают
сначала в распределительную коробку, а затем в кристаллизаторы. Число отверстий
для подачи расплава из коробки в слиток должно быть таким, чтобы расплав
равномерно распределялся по всему сечению слитка. Наиболее распространены
распределительные коробки, футерованные теплоизоляционным картоном. Всю
литейную оснастку перед литьем тщательно просушивают.
Сплав 7175 имеет наиболее низкие литейные свойства по сравнению с
остальными алюминиевыми сплавами. При отливке слитков из сплава 7175 на
начальном этапе производится подлив жидкого алюминия в кристаллизатор для
образования донной части слитка, которая служит «замком» для слитка,
предотвращая растрескивание. Также проводят самоотжиг литниковой части слитка.
До начала литья на поддон в кристаллизаторе, заливают расплав алюминия на
высоту 30-40 мм. Расплаву алюминия дают затвердеть на 30-40%, после чего
начинают литье основного сплава. Самоотжиг литниковой части слитка осуществляют
следующим образом: после прекращения подачи металла слиток опускают на
2/3высоты кристаллизатора. Затем отключают подачу воды и останавливают литейную
машину. При этом кристаллизация последних порций металла происходит без
интенсивного отбора тепла, и верхняя часть слитка разогревается до нужной
температуры. Для сплавов АД1 и 6082 подлив в донную часть осуществляется
металлом собственного сплава.
При литье важными параметрами являются скорость литья и температура
расплава. Увеличение скорости литья должно сопровождаться снижением температуры
расплава в миксере, и наоборот. Температуру расплава в миксере поднимают на
50-100єС выше температуры ликвидуса.
Технологические режимы литья указаны в таблице 28 [1].
Таблица 28 - Технологические режимы литья слитков из сплавов 7175, АД1,
6082
Марка сплава
|
Диаметр слитка, мм
|
Высота кристаллизатора, мм
|
Технологическая скорость литья, мм/мин
|
Количество одновременно отливаемых слитков, шт
|
Температура литья, єС
|
Давление воды, am
|
|
|
|
|
|
|
перед вводом в кристаллизатор
|
перед вводом в стержень
|
7175
|
635
|
180
|
14
|
2
|
720-740
|
0,5-1,2
|
-
|
АД1
|
480
|
180
|
75
|
3
|
710-730
|
0,8-1,0
|
-
|
6082
|
789х350
|
180
|
34
|
1
|
690-710
|
0,6-1,0
|
0,4-0,8
|
Выход на технологическую скорость осуществляется в автоматическом режиме
при помощи регулятора начальной скорости литья и расхода охлаждающей жидкости.
4.4.6 Модифицирование сплавов
Процесс модифицирования представляет собой операцию по добавлению в сплав
специальных компонентов, которые придают ему необходимые свойства. В основном,
целью модифицирования является повышение у сплавов прочностных и пластических
свойств, а также измельчение зерна.
Модификатором служит титан, при добавлении которого в количестве
0,002-0,005% происходит измельчение зерна. Присадка титана осуществляется во
время литья подачей лигатурного прутка Al-Ti-B в промежуточный канал. Подача
прутка осуществляется специальным разматывающим устройством с определенно
заданной скоростью. Такой метод дает ряд преимуществ: равномерное распределение
присаживаемых компонентов по объему расплава и максимальное использование
свойств модификатора.
4.4.7 Фильтрация расплава
Сущность метода состоит в пропускании жидкого расплава через фильтр,
изготовленный из нейтральных или активных по отношению к металлу материалов.
При этом взвешенные включения задерживаются механически или в результате
физического или химического взаимодействия с материалом фильтра.
В нашем случае при литье фильтрацию расплава производят с помощью пенокерамического
фильтра (ПКФ). ПКФ устанавливают перед кристаллизатором, а фильтрацию
производят непосредственно во время слива расплава из миксера в кристаллизатор.
Также для фильтрации при сливе плавки из миксера используют специальную
стеклосетку. Схема фильтрации с помощью ПКФ показана на рисунке 11.
Рисунок 13 - Схема процесса фильтрации через пенокерамический фильтр.
Рисунок 14 - Схема процесса фильтрации через пенокерамический фильтр.
4.5 Гомогенизация слитков
Гомогенизация слитков позволяет устранить или уменьшить дендритную
ликвацию, повысить способность материала к горячему и холодному деформированию,
улучшить механические свойства полуфабрикатов, а также снять внутренние напряжения,
т.е. приводит к большей химической и структурной однородности литого сплава.
Печи для гомогенизации алюминиевых сплавов должны отвечать ряду
требований: иметь высокую производительность; обеспечить удобство загрузки и
выгрузки тяжелых садок, имеющих в период выгрузки высокую температуру;
обеспечивать равномерность скорости нагрева.
Практически все печи гомогенизации строят по одной тепловой схеме - с
принудительной циркуляцией теплоносителя (воздух), подогреваемого в
электрокалориферах. Различают шахтные вертикальные печи (колодцы) и печи с
выкатным подом.
Слитки из сплавов 7175 и 6082 гомогенизируют в электрических колодцах
гомогенизации. Колодцы гомогенизации не требуют промежуточной кантовки слитков
в случае непосредственной перегрузки их из литейных машин и позволяют
сравнительно просто захватывать и выгружать слитки из нагретой печи без ее
охлаждения. Это имеет особое значение для слитков крупных размеров.
Максимальная садка колодцев гомогенизации составляет 60 тонн.
Слитки из сплава АД1, если из них изготавливаются детали ответственного
назначения, обрабатывают в печах гомогенизации с выкатным подом. Максимальная
садка печи 40 тонн. На под этих печей можно укладывать слитки и стеллажи любых
размеров и конфигураций. Загрузка и выгрузка садки имеет то удобство, что
выкатной под находится на уровне пола цеха и свободна для подхода со всех
сторон.
В таблицах 29, 30 и 31 представлены режимы
термообработки, характеристики шахтного колодца и печи гомогенизации слитков из
сплавов 7175, АД1 и 6082 соответственно.
Таблица 29 - Рекомендуемые режимы гомогенизации
слитков [1].
Марка сплава
|
Температурный интервал гомогенизации, єС
|
Длительность выдержки, ч
|
7175
|
450-465
|
36
|
АД1
|
610-630
|
6
|
6082
|
500-520
|
18
|
Таблица 30 - Технические характеристики колодца гомогенизации.
Наименование характеристики
|
Числовая величина
|
Количество колодцев в блоке, шт
|
4
|
Максимальная температура нагрева, єС
|
560
|
Установленная мощность колодца, кВт
|
1080
|
Максимальная садка из круглых слитков, т
|
10
|
Напряжение питания, В
|
500
|
Количество зон в колодце, шт
|
4
|
Номинальный ток фазы нагревателей зоны, А
|
180
|
Мощность фазных нагревателей зоны, кВт
|
270
|
Количество вентиляторов в зоне, шт
|
1
|
Тип вентилятора
|
Ц9-55 №10
|
Производительность вентилятора, м3/ч
|
57000
|
Частота вращения вентилятора, об/мин
|
630
|
Мощность электродвигателя вентилятора, кВт
|
40
|
Скорость воздуха в рабочем пространстве колодца, м/с
|
11-12
|
Таблица 31 - Технические характеристики печи
гомогенизации.
Наименование характеристики
|
Числовая величина
|
Размер рабочего пространства печи, мм: длина ширина
высота
|
10,7 4,2 1,6
|
Максимальная температура нагрева, єС
|
650
|
Исполнение печи
|
левое
|
Максимальная садка из круглых слитков, т
|
40
|
Напряжение питания, В
|
500
|
Термическая мощность печи, кВт
|
1650
|
Номинальный ток фазы нагревателей зоны, А
|
180
|
Мощность фазных нагревателей зоны, кВт
|
270
|
Количество зон
|
6
|
Тип вентилятора
|
Ц9-55 №10
|
Производительность вентилятора, м3/ч
|
56100
|
Частота вращения вентилятора, об/мин
|
630
|
Мощность электродвигателя вентилятора, кВт
|
40
|
Скорость воздуха в рабочем пространстве печи, м/с
|
5
|
Тепловыделение в цех, ккал/час
|
200000
|
Контроль над процессом гомогенизации ведется по
температуре рабочего пространства печи стационарными термопарами,
установленными в каждой нагревательной зоне печи. Отсчет времени выдержки
начинается с момента достижения нижнего предела температуры гомогенизации. Если
во время выдержки произошло отклонение одной или более зон ниже нижнего предела
температуры гомогенизации, то время процесса увеличивается на время, в течение
которого температура была ниже температурного интервала гомогенизации.
4.6 Механическая обработка слитков
Резка заготовок на мерные заготовки производится на
специальных линиях. Для слитков сплавов, склонных к растрескиванию, перед
механической обработкой необходимо произвести гомогенизацию.
Резка слитков идет согласно сменному заданию. Слитки
режутся без раскроя по заданию длин заготовок в карте плавки (см. приложение
Б). Резка слитков на мерные заготовки начинается с литника. Резка идет с
применением смазывающе-охлаждающей жидкости (СОЖ) .
Таблица 32 - Длины отрезаемых концов, ширина резов,
размеры вырезаемых темплетов из сплавов 7175, АД1, 6082.
Марка сплава
|
Размеры слитков, мм
|
Длина отрезаемых концов, мм
|
Ширина реза, мм
|
Толщина темплетов, мм
|
|
|
литник
|
донник
|
|
|
7175
|
635х1450
|
300
|
350
|
20
|
30
|
АД1
|
480х1600
|
120
|
200
|
20
|
30
|
6082
|
789х350х1200
|
300
|
350
|
20
|
40
|
Длины отрезаемых концов, ширина резов, размеры
темплетов в зависимости от марки сплава приведены в таблице 32.
Отбор темплетов идет в следующем порядке:
1. литниковый темплет отбирается после отрезки
литника и клеймится номером первой заготовки;
2. донный темплет отрезается после последней
заготовки и клеймится номером, следующим за последней заготовкой или буквой
«Д».
Заготовки, требующие обточки или расточки направляются
по рольгангам к линии механической обработки.
Для сплава 7175 линия обработки состоит из отрезного
станка модели МП6-716, обточного станка модели КЖ1614ОФI и торцефрезерного
станка модели КЖ 6905.
Линия механической обработки для сплава АД1 состоит из
отрезного станка мод. МП6-716 и торцефрезерного станка мод. КЖ 6905.
Для сплава 6082 линия обработки состоит из отрезного
станка мод. МП6-716, обточного станка мод. КЖ1614ОФI, расточного станка мод.
КЖ-1904 и торцефрезерного станка мод. КЖ 6905.
Рисунок 15 - Слиток после механической обработки.
Характеристики указанных станков приведены в таблицах
33-36 соответственно их перечислению.
Таблица 33 - Станок отрезной модели МП6-716.
Наименование характеристики
|
Числовое значение
|
Габаритные размеры станка, мм длина ширина высота
|
4430 8600 3130
|
Масса станка, кг
|
20000
|
Диаметр разрезаемых слитков, мм
|
500-850
|
Регулирование подачи
|
бесступенчатое
|
Подача бабки пильного диска, мм/мин
|
90-1000
|
Частота вращения шпинделя, об/мин
|
184
|
Скорость резания, м/мин
|
1200
|
Наибольшая длина хода бабки пильного диска, мм
|
900
|
Длина отрезаемой заготовки, мм
|
550-1800
|
Скорость отвода бабки пильного диска, мм/мин
|
2500
|
Производительность, шт/час
|
15
|
Таблица 34 - Станок расточной модели КЖ 1904.
Наименование характеристики
|
Числовая величина
|
Диаметр обрабатываемого изделия, мм наибольший наименьший
|
860 380
|
Диаметр растачивания, мм наибольший наименьший
|
650 300
|
Длина обрабатываемого изделия, мм наибольшая наименьшая
|
1800 550
|
Наибольшая масса обрабатываемого изделия, кг
|
2500
|
Частота вращения шпинделя, об/мин
|
300-1500
|
Рабочая подача, мм/мин
|
200-1000
|
Регулирование
|
бесступенчатое
|
Разностенность,мм
|
до 0,4
|
Шероховатость обработки Rz, мкм
|
20
|
Наибольшая глубина резания, мм
|
до 20
|
Производительность, шт/час
|
8-12
|
Таблица 35 - Станок обточной мод. КЖ 1614ОФI.
Наименование характеристики
|
Числовое значение
|
Диаметр обрабатываемого изделия, мм: наибольший наименьший
|
860 400
|
Наибольшая масса обрабатываемого изделия, кг
|
3500
|
Точность позиционирования, мкм
|
50
|
Частота вращения шпинделя, об/мин
|
120-590
|
Регулирование
|
бесступенчатое
|
Рабочая подача, мм/мин
|
406-312
|
Усилие зажима, тс
|
100
|
Габаоиты станка, мм длина ширина высота
|
11500 7000 5350
|
Длина устанавливаемых заготовок, мм наибольшая наименьшая
|
2000 500
|
Производительность, шт/час
|
15
|
Таблица 36 - Станок торцефрезерный мод. КЖ -6905.
Наименование характеристики
|
Числовое значение
|
Диаметр обрабатываемого изделия, мм: наибольший
наименьший
|
1100 480 480
|
Длина обрабатываемого изделия, мм: наибольшая наименьшая
|
2000 500
|
Длина при двухсторонней обработке, мм
|
1000-2000
|
Частота вращения шпинделя, об/мин
|
585
|
Подача, мм/мин
|
1000
|
Наибольший осевой ход шпинделя, мм
|
525
|
Наибольший ход автоматического калибра, мм
|
70
|
Наибольший ход стола, мм
|
2000
|
Наибольший ход зажимной призмы, мм: правой левой
|
360 470
|
Диаметр фрезы, мм
|
1300
|
Косина реза, мм
|
0,4-0,7
|
Отклонение по длине изделия, мм
|
±(8-10)
|
Шероховатость обработки, Rz, мкм
|
- 20
|
Наибольшая масса обрабатываемого изделия, кг
|
4500
|
Производительность, шт/час
|
12-20
|
.7 Правила приемки слитков
Слитки предъявляются контролеру участка технического
контроля (УТК) на сдаче. Каждый слиток подвергают контролю качества поверхности
и размеров. При арбитражной проверке контролю размеров и качества поверхности
подвергается каждый слиток, проверке кривизны не менее 10% слитков от каждой
партии, контролю химического состава и внутренних дефектов не менее 3%.
Содержание водорода в расплаве при литье слитков определяют периодически, но не
менее одного определения в сутки из каждой разливочной печи. Результаты
указываются в документе о качестве, удостоверяющем качество слитков. При
получении удовлетворительных результатов испытаний хотя бы по одному из
показателей, по нему ведут повторное испытание на удвоенном количестве
образцов, взятой из той же плавки.
В таблице 37 приведены требования, предъявляемые к
готовым слиткам.
Таблица 37 - Нормы допустимых дефектов в слитках из сплавов 7175, АД1,
6082
Сплав
|
Назначение
|
Размер допустимых дефектов в поперечине и их количество, не
более
|
|
|
Шлак, окисные плены
|
Светлые пятна
|
Интерметаллиды
|
|
|
мм2
|
шт
|
мм2
|
шт
|
мм2
|
шт
|
7175
|
Экспорт
|
не допускаются
|
АД1
|
Для прессования профилей и прутков, ковки и штамповки
|
0,5
|
3,0
|
10,0
|
6,0
|
-
|
-
|
6082
|
Экспорт
|
не допускаются
|
К слиткам из алюминиевых сплавов предъявляют следующие требования и
контролируют: химический состав; размер слитка (длина, поперечные размеры ,
кривизна); поверхность на наличие окислов, трещин; контроль макроструктуры на
наличие шлаков, окисных включений, интерметаллидов, крупного зерна; содержание
водорода.
Контроль качества производится: визуально, химическими анализами,
травлением микрошлифа, ультразвуковым исследованием.
4.8 Контроль качества слитков
Контроль качества металла производится
металлографической лабораторией по изломам с помощью измерительной линейки по
ГОСТ 427-75.
Контроль качества слитков проводят следующим образом:
1.
внешний осмотр
поверхности;
2.
контроль
химического состава по ГОСТ 4784 - 97;
3.
контроль размеров
слитка с замером с помощью линейки металлической измерительной по ГОСТ 427 -
75;
4.
контроль косины
реза - линейкой измерительной и угольником проверочным по ГОСТ 3749 - 77;
5.
контроль кривизны
заготовки - линейкой проверочной ГОСТ 8026-75;
6.
контроль излома и
макроструктуры - визуально на наличие дефектов.
5. Экономико-организационные расчеты
5.1 Классификатор производимой продукции
В проектируемом цехе производятся сплошные и полые слитки круглого
сечения из сплавов 7175, АД1, 6082. Их классификация представлена в таблице 38.
Таблица 38 - Размеры слитков в проектируемом цехе.
Сплав
|
Внешний диаметр слитка D, мм
|
Внутренний диаметр слитка d, мм
|
Длина слитка L, мм
|
Программа выпуска, тонн/год
|
7175
|
635
|
-
|
1450
|
20000
|
АД1
|
480
|
-
|
1600
|
30000
|
6082
|
789
|
350
|
1200
|
25000
|
5.2 Определение типа производства
Создание поточного производства при полунепрерывном литье обеспечивается
характером используемого оборудования, механизацией всех транспортных операций,
а также характером самой продукции.
Продукция проектируемого цеха носит характер заготовительной и далее идет
на обработку и получение из неё необходимых полуфабрикатов и изделий в цехах
обработки металлов давлением.
Производство в цехе является крупносерийным, так как оно характеризуется
относительно ограниченной номенклатурой продукции с переналадкой оборудования
при переходе с одной операции на другую.
5.3 Нормирование технологических операций
Технологический процесс изготовления слитков состоит из следующих
операций:
1. Подготовка шихты к плавке;
2. Подача шихты к печи;
. Плавление;
. Литьё слитков;
. Чистка миксера;
. Термообработка слитков;
. Резка слитков на мерные заготовки;
. Сдача заготовок на склад готовой продукции.
Трудоёмкость производства по всем операциям приведена в таблице 39.
Сплав
|
Подготовка шихты
|
Подача шихты
|
Плавление
|
Литьё
|
Чистка миксера
|
Гомоге-низация
|
Резка
|
Сдача
|
У, н/ч
|
7175
|
0,724
|
0,322
|
0,317
|
0,188
|
1,13
|
0,084
|
0,405
|
0,201
|
3,37
|
АД1
|
0,724
|
0,322
|
0,317
|
0,188
|
1,13
|
0,084
|
0,42
|
0,201
|
3,39
|
6082
|
0,724
|
0,322
|
0,317
|
0,188
|
1,13
|
0,084
|
0,405
|
0,201
|
3,37
|
Трудоемкость годовой программы выпуска в нормочасах определяется по
формуле:
Тпр = Q ∙ ТУ, (7)
где Q - годовая программа,
ТУ - суммарная трудоёмкость одной тонны годного в нормочасах.
Для сплава 7175: Тпр = 20000 ∙ 3,37 =67400,0 н/ч;
Для сплава АД1: Тпр = 30000 ∙ 3,39 = 101700,0 н/ч;
Для сплава 6082: Тпр = 25000 ∙ 3,37 = 84250,0 н/ч.
Найдем общую трудоёмкость на всю программу выпуска:
Тпробщ = 67400,0 + 101700,0 + 84250,0 = 253350,0
н/ч.
5.4 Расчет баланса металла
Целью расчета является:
· Определение количества шихтовых материалов, которые необходимо загрузить
в печь, чтобы получить 1 тонну заготовок;
· Определение выхода годного на каждой операции
технологического процесса;
· Определение потерь на каждой операции технологического
процесса изготовления слитков в весовом и процентном отношениях;
· Составление технико-экономической карты.
Исходные данные, размеры слитков и заготовок для расчета баланса металла
приведены в таблице 40.
Таблица 40 - Исходные данные, размеры слитков и заготовок для расчета
баланса металла.
Исходные данные
|
Сплав
|
|
7175
|
АД1
|
6082
|
Диаметр кристаллизатора dкр, мм
|
720
|
495
|
840 х 305
|
Диаметр слитка dсл, мм
|
706
|
480
|
823 х 305
|
Диаметр заготовки dзаг, мм
|
635
|
480
|
789 х 350
|
Длина заготовки Lзаг, мм
|
1450
|
1600
|
1200
|
Количество заготовок nзаг, мм
|
3
|
3
|
4
|
Длина литника Lл, мм
|
300
|
120
|
300
|
Длина донника Lд, мм
|
350
|
200
|
350
|
Ширина темплета Lт, мм
|
30
|
30
|
40
|
Количество темплетов nт, мм
|
3
|
2
|
3
|
Ширина торцовки Lтор, мм
|
30
|
30
|
30
|
Ширина реза Lрез, мм
|
20
|
20
|
20
|
Количество резов nрез, мм
|
7
|
6
|
8
|
Длина слитка Lсл, мм
|
5410
|
5480
|
5970
|
Длина слитка определяется по формуле:
(8)
.4.1 Определение величины потерь на технологических операциях
при производстве слитков
1. Металлургические потери:
· на операции «плавление».
Потери металла на угар определяются по формуле:
(9)
где Мз - металлозавалка на операции «плавление».
Тогда для сплава 6082 Мз = 1007,5 кг;
для сплава АД1 Мз = 1007,5 кг;
для сплава 7175 Мз = 1012 кг.
Тогда потери металла на угар для сплава 6082 g = 0,75%;
для сплава АД1 g =
0,75%;
для сплава 7175 g =
1,2%.
Потери металла в шлаке для сплава 6082 составляют 0,7%;
для сплава АД1 - 0,7%;
для сплава 7175 - 0,8%.
Общие потери составят:
для сплава 6082 - 1,45 %;
для сплава АД1 - 1,45 %;
для сплава 7175 - 2.0 %.
· на операции «литье».
Потери металла на сплесы, съемы шлака для сплава 6082 составляют 0,5%;
для сплава АД1 - 0,5 %;
для сплава 7175 - 0,5 %.
2. Геометрические потери:
2.1 Потери на операции «резка»:
· потери металла при отрезке литниковой и донной частей слитка
определяются по формуле:
(10)
где Lл и Lд - размеры отрезаемых величин;
%мет.пот. - общие металлургические потери сплава.
Для сплава 6082 %мет.пот. = 1,95 %;
для сплава АД1 %мет пот. = 1,95 %;
для сплава 7175 %мет.пот. = 2,5%.
Тогда
для сплава 6082
для
сплава АД1
для
сплава 7175
· потери металла при отборе темплетов составляют:
(11)
Тогда
для сплава 6082
для
спдава АД1
для
сплава 7175
· потери металла на стружку при разрезке слитков на мерные
заготовки определяются по формуле:
(12)
Тогда
для сплава 6082
для
спдава АД1
для
сплава 7175
Общие потери на операции «резка»:
для сплава 6082 составляют 15,26%;
для сплава АД1 - 8,95%;
для сплава 7175 - 15,85%.
.2 Потери металла на операции «обточка»:
(13)
где mп.м.сл. - вес одного погонного метра слитка;п.м.
обт. - вес одного погонного метра обточенной заготовки.
Для сплава 6082 mп.м.сл. = 1486,12 кг;
mп.м. обт. =1346,82 кг;
для сплава 7175 mп.м.сл. = 1537,5 кг;
mп.м. обт. =1243,81 кг.
Тогда для сплава 6082
для
сплава 7175
2.3 Потери металла на операции «расточка»:
(14)
где
mп.м.раст. - вес одного погонного метра расточенной заготовки.
Для сплава 6082 mп.м.раст. = 1271,75 кг.
Тогда
2.4 Потери металла на операции «торцовка»:
(15)
Тогда
для сплава 6082
для
сплава АД1
для
сплава 7175
3. Технологические потери.
Общие потери определяются по формуле:
П = 100 - Употерь - ПВГ, (16)
где ПВГ - плановый выход годного по сплаву.
Для сплава 6082 ПВГ = 60%;
для сплава АД1 ПВГ = 78%;
для сплава 7175 ПВГ = 47%.
Тогда для сплава 6082 П = 100 - 32,93 - 60 = 7,07%.
для сплава АД1 П = 100 - 14,1 - 78 = 7,9%;
для сплава 7175 П = 100 - 36,51 - 47 = 16,49%.
Из общих потерь 75% расходуется при литье слитков, а 25% при мех
обработке.
5.4.2 Расчет запуска на одну тонну годных слитков
Металлургические, геометрические и технологические потери при
производстве слитков указаны в таблице 41.
Таблица 41 - Потери на технологических операциях при производстве слитков
из сплавов 6082, АД1 и 7175.
Вид потерь металла
|
Сплав
|
|
6082
|
АД1
|
7175
|
Металлургические потери, % − при плавлении −
при литье
|
1,45 0,5
|
1,45 0,5
|
2,0 0,5
|
Геометрические потери, % − на операциях резки −
на операции «обточка» − на операции «расточка» − на операции
«торцовка»
|
15,26 7,39 4,39 3,94
|
8,93 - - 3,22
|
15,85 14,92 - 3,24
|
Технологические потери, % − при литье слитков −
при сдаче слитков
|
5,3 1,77
|
5,93 1,97
|
12,37 4,12
|
Итого:
|
40
|
22
|
53
|
Запуск металла на одну тонну годных заготовок определяется по формуле:
(17)
Где Е - сумма всех потерь.
Тогда
для сплава 6082
для
сплава АД1
для
сплава 7175
Состав
шихты с учетом выхода годного перечитывается с помощью коэффициента выхода
годного, который определяется по формуле:
(18)
Где У - угар металла.
Для сплава 7175 У = 25,53 кг; для сплава АД1 У = 9,62 кг; для сплава 6082
У = 12,5 кг.
Тогда
для сплава 7175
для
сплава АД1
для
сплава 7175
Итоговые
технологические параметры для сплавов 7175, АД1 и 6082 приведены соответственно
в таблицах 42, 43,44.
Таблица
42 - Технико-экономическая карта сплава 7175.
Наименование операции
|
Шихта, кг
|
Отходы
|
Выход годного, %
|
|
запуск
|
выпуск
|
наименование
|
вес, кг
|
%
|
|
Подготовка шихты
|
2127,66
|
2127,66
|
|
|
|
100,0
|
Подача шихты
|
2127,66
|
2127,66
|
|
|
|
100,0
|
Плавление, рафинирование
|
2127,66
|
2085,11
|
угар, шлак
|
42,55
|
2,0
|
98,0
|
Литье слитков
|
2085,11
|
1821,92
|
наладка
|
263,19
|
12,37
|
85,63
|
Чистка миксера
|
1821,92
|
1811,28
|
сплесы
|
10,64
|
0,5
|
85,13
|
Гомогенизация
|
1811,28
|
1811,28
|
|
|
|
85,13
|
Резка слитков
|
1811,28
|
1474,05
|
стружка, темплеты, литники, донники
|
337,23
|
15,85
|
69,28
|
Обточка заготовок
|
1474,05
|
1156,6
|
стружка
|
317,45
|
14,92
|
54,36
|
Торцовка заготовок
|
1156,6
|
1087,66
|
стружка
|
68,94
|
3,24
|
51,12
|
Клеймение
|
1087,66
|
1087,66
|
|
|
|
51,12
|
Сдача заготовок на склад
|
1087,66
|
1000,00
|
наладка
|
87,66
|
4,12
|
47,00
|
Транспортировка
|
1000,00
|
1000,00
|
|
|
|
47,00
|
Итого:
|
2127,66
|
1000,00
|
|
1127.66
|
53,00
|
47,00
|
Таблица 43 - Технико-экономическая карта сплава АД1.
Наименование операции
|
Шихта, кг
|
Отходы
|
Выход годного, %
|
|
запуск
|
выпуск
|
наименование
|
вес, кг
|
%
|
|
Подготовка шихты
|
1282,05
|
1282,05
|
|
|
|
100,0
|
Подача шихты
|
1282,05
|
1282,05
|
|
|
|
100,0
|
Плавление, рафинирование
|
1282,05
|
1263,46
|
угар, шлак
|
18,59
|
1,45
|
98,55
|
Литье слитков
|
1263,46
|
1187,43
|
наладка
|
76,03
|
5,93
|
92,62
|
Чистка миксера
|
1187,43
|
сплесы
|
6,41
|
0,5
|
92,12
|
Гомогенизация
|
1181,02
|
1181,02
|
|
|
|
92,12
|
Резка слитков
|
1181,02
|
1066,54
|
стружка, темплеты, литники, донники
|
114,48
|
8,93
|
83,19
|
Торцовка заготовок
|
1066,54
|
1025,26
|
стружка
|
41,28
|
3,22
|
79,97
|
Клеймение
|
1025,26
|
1025,26
|
|
|
|
79,97
|
Сдача заготовок на склад
|
1025,26
|
1000,00
|
наладка
|
25,26
|
1,97
|
78,00
|
Транспортировка
|
1000,00
|
1000,00
|
|
|
|
78,00
|
Итого:
|
1282,05
|
1000,00
|
|
282,05
|
22,00
|
78,00
|
Таблица 44 - Технико-экономическая карта сплава 6082.
Наименование операции
|
Шихта, кг
|
Отходы
|
Выход годного, %
|
|
запуск
|
выпуск
|
наименование
|
вес, кг
|
%
|
|
Подготовка шихты
|
1666,67
|
1666,67
|
|
|
|
100,0
|
Подача шихты
|
1666,67
|
1666,67
|
|
|
|
100,0
|
Плавление, рафинирование
|
1666,67
|
1642,5
|
угар, шлак
|
24,17
|
1,45
|
98,55
|
Литье слитков
|
1642,5
|
1554,17
|
наладка
|
88,33
|
5,3
|
93,25
|
Чистка миксера
|
1554,17
|
1545,84
|
сплесы
|
8,33
|
0,5
|
92,75
|
Гомогенизация
|
1545,84
|
1545,84
|
|
|
|
92,75
|
Резка слитков
|
1545,84
|
1291,51
|
стружка, темплеты, литники, донники
|
254,33
|
15,26
|
77,49
|
Обточка заготовок
|
1291,51
|
1168,34
|
стружка
|
123,17
|
7,39
|
70,1
|
Расточка заготовок
|
1168,34
|
1095,17
|
стружка
|
73,17
|
4,39
|
65,71
|
Торцовка заготовок
|
1095,17
|
1029,5
|
стружка
|
65,67
|
3,94
|
61,77
|
Клеймение
|
1029,5
|
1029,5
|
|
|
|
61,77
|
Сдача заготовок на склад
|
1029,5
|
1000,00
|
наладка
|
29,5
|
1,77
|
60,00
|
Транспортировка
|
1000,00
|
1000,00
|
|
|
|
60,00
|
Итого:
|
1666,67
|
1000,00
|
|
666,67
|
40,00
|
60,00
|
5.5 Расчет оборудования
Целью расчета является определение количества оборудования, необходимого
для выполнения годовой производственной программы проектируемого литейного
цеха.
Годовая программа 75000 тн, в том числе сплава 7175 - 20000 тн, сплава
АД1 - 30000 тн, сплава 6082 - 25000 тн.
.5.1 Расчет технологической трудоемкости
Расчет количества оборудования производится по технологической
трудоемкости каждой операции. Трудоемкость каждой операции определяется на
основании часовой производительности оборудования.
Расчет производят по формулам 19 - 36.
Трудоемкость 1 тонны передела определяется по формуле:
(19)
где Нвыр. - часовая норма выработки агрегата, т/час.
, (20)
где К - вес 1плавки, тн;
Тшт. - норма времени на единицу изделия, час.
На операции «литье» трудоемкость 1 тонны передела определяется по
формуле:
, (21)
где Q - вес слитка, тн;
а норма времени на один слиток определяется по формуле:
, (22)
где Тосн. - основное технологическое время, необходимое для
отливки одного слитка, час.;1 - количество одновременно отливаемых
слитков на одной литейной машине, шт.;
Твсп. - вспомогательное время, необходимое для отливки одного
слитка, час.;
Тдоп. - дополнительное время, Тдоп. = 5%.
Основное технологическое время определяется по формуле:
(23)
где L - длина слитка, мм;- скорость литья, мм/мин.
Вспомогательное время определяется по формуле:
(24)
где Тм = 0,68 мин/т - время на очистку миксера;
Тсн.= 0,48 мин/т - время, необходимое для снятия шлака ;
Траф. - время на рафинирование, мин;
Тотст. - время на отстой расплава, мин;
Ткл. =2 мин - время на клеймение слитков;
Тподг.=10,6 мин - время на подготовку линейной машины;-
количество слитков, отливаемых в одной плавке, шт.
Количество слитков определяется по формуле:
(25)
На операции «гомогенизация» норма выработки определяется по формуле:
, (26)
где К - масса садки колодца, тн.
Масса садки колодца определяется:
, (27)
где n2 - количество слитков, одновременно размещенных в
колодце, шт.
Норма времени на один слиток определяется по формуле:
, (28)
где Тосн. - время выдержки садки в печи, час;
Твсп. - вспомогательное время, час.
Вспомогательное время определяется по формуле:
, (29)
где Тн = 30 мин - время набора температуры;
Тз и Тв - время на загрузку и выгрузку слитков из
колодца гомогенизации. Тз = Тв = 1 час.
На операции «резка» норма времени на один слиток определяется по формуле:
, (30)
где Топ - оперативное время резки.
Оперативное время резки определяется по формуле:
, (31)
где Nр - количество резов в слитке, шт;
П - часовая производительность станка, шт/час;
Твсп. = 1,216 мин - вспомогательное время;
а - дополнительное время; а = 19 %.
Трудоемкость изготовления 1 тонны расплава с учетом выхода годного
определяется по формуле:
, (32)
где Квып. - коэффициент выпуска.
Коэффициент выпуска определяется по формуле:
, (33)
где М - масса материала на данной операции, кг.
Трудоемкость операции в пересчете на годовую программу определяется
формуле:
, (34)
где N - годовая программа.
Необходимое количество оборудования на каждой операции определяется по
формуле:
, (35)
где Fэ - эффективный фонд времени работы оборудования, час;
Кн =1,2 - коэффициент выполнения нормы.
Эффективный фонд времени работы оборудования определяется по формуле:
, (36)
где Fкал = 365 дней - календарный фонд времени;
Д = 6 дней - праздничные дни;
Трем = 30 дней - время плановых ремонтов;
Кисп. = 0,90-0,95 - коэффициент использования оборудования.
По формуле (36) рассчитаем эффективный фонд времени работы оборудования:
5.5.2 Расчет количества оборудования для сплава 7175
· Плавильные печи.
Время на одну плавку Тшт = 10 час, вес одной плавки К =20 тн.
Тогда по формуле (20) получим часовую норму выработки:
Трудоемкость
изготовления одной тонны расплава определим по формуле (19):
Коэффициент
выпуска определим по формуле (33):
Трудоемкость
изготовления 1 тонны расплава с учетом выхода годного определим по формуле
(32):
Трудоемкость
изготовления 1 тонны расплава в пересчете на годовую программу определим по
формуле (34):
Тогда
расчетное количество плавильных печей определим по формуле (35):
Принятое
количество Апр = 3 печи.
· Литейные машины.
Основное технологическое время для производства слитков определяем по
формуле (23):
Количество
слитков, отливаемых в одной плавке, определим по формуле (25): вес слитка 5,74
тн.
Вспомогательное
время определим по формуле (24):
Норму времени на литье одного слитка определим по формуле (28):
Трудоемкость
изготовления 1 тонны слитков определим по формуле (21):
Коэффициент выпуска определим по формуле (33):
Трудоемкость
изготовления 1 тонны слитков с учетом выхода годного определим по формуле (32):
Трудоемкость
изготовления 1 тонны слитков в пересчете на годовую программу определим по формуле
(34):
Тогда
расчетное количество литейных машин определим по формуле (35):
Принятое
количество Апр = 6 машин.
· Гомогенизация слитков.
Максимальная садка колодца гомогенизации К = 60 тонн. Так как вес одного
слитка составляет 5,74 тонну, а в колодец помещают 8 слитков. Тогда садку
колодца определим по формуле (27):
Время
выдержки садки в колодце Тосн = 36 часов.
Вспомогательное
время определим по формуле (29):
Норму времени на гомогенизацию 1 слитка определим по формуле (28):
Норму выработки печи определим по формуле (20):
Трудоемкость
гомогенизации 1 тонны слитков определим по формуле (19):
Коэффициент
выпуска определим по формуле (33):
Трудоемкость
гомогенизации 1 тонны слитков с учетом выхода годного определим по формуле
(32):
Трудоемкость
в пересчете на годовую программу определим по формуле (34):
Тогда
расчетное количество колодцев гомогенизации определим по формуле (35):
Принятое
количество Апр = 2 колодца.
· Линия резки.
Средняя производительность станка линии резки П = 15 шт/час.
Оперативное время резки определяем по формуле (31):
Норму времени на резку 1 слитка определим по формуле (30):
По
формуле (20) получим часовую норму выработки:
Трудоемкость
разрезки слитков определим по формуле (19):
Коэффициент
выпуска определим по формуле (33):
Трудоемкость
разрезки слитков с учетом выхода годного определим по формуле (32):
Трудоемкость
разрезки слитков в пересчете на годовую программу определим по формуле (34):
Тогда
расчетное количество оборудования на линии резки определим по формуле (35):
Принятое
количество Апр = 1 линия.
5.5.3 Расчет количества оборудования для сплава АД1
· Плавильные печи.
Время на одну плавку Тшт = 10 час, вес одной плавки К = 30 тн.
Тогда по формуле (20) получим часовую норму выработки:
Трудоемкость
изготовления одной тонны расплава определим по формуле (19):
Коэффициент
выпуска определим по формуле (33):
Трудоемкость
изготовления 1 тонны расплава с учетом выхода годного определим по формуле
(32):
Трудоемкость
изготовления 1 тонны расплава в пересчете на годовую программу определим по
формуле (34):
Тогда
расчетное количество плавильных печей определим по формуле (35):
Принятое
количество Апр = 2 печи.
· Литейные машины.
Основное технологическое время для производства слитков определяем по
формуле (23):
Количество
слитков, отливаемых в одной плавке, определим по формуле (25): вес слитка 2,69
тн.
Вспомогательное
время определим по формуле (24):
Норму времени на литье одного слитка определим по формуле (28):
Трудоемкость
изготовления 1 тонны слитков определим по формуле (21):
Коэффициент выпуска определим по формуле (33):
Трудоемкость
изготовления 1 тонны слитков с учетом выхода годного определим по формуле (32):
Трудоемкость
изготовления 1 тонны слитков в пересчете на годовую программу определим по
формуле (34):
Тогда
расчетное количество литейных машин определим по формуле (35):
Принятое
количество Апр = 2 машины.
· Линия резки.
Средняя производительность станка линии резки П = 20 шт/час.
Оперативное время резки определяем по формуле (31):
Норму времени на резку 1 слитка определим по формуле (30):
По
формуле (20) получим часовую норму выработки:
Трудоемкость
разрезки слитков определим по формуле (19):
Коэффициент
выпуска определим по формуле (33):
Трудоемкость
разрезки слитков с учетом выхода годного определим по формуле (32):
Трудоемкость
разрезки слитков в пересчете на годовую программу определим по формуле (34):
Тогда
расчетное количество оборудования на линии резки определим по формуле (35):
Принятое
количество Апр = 1 линия.
· Гомогенизация слитков.
Максимальная садка печи гомогенизации К = 40 тонн. Так как вес одного
слитка составляет 2,69 тонну, а в печь помещают 10 слитков. Тогда садку печи
определим по формуле (27):
Время
выдержки садки в печи Тосн =8 часов.
Вспомогательное
время определим по формуле (29):
Норму времени на гомогенизацию 1 слитка определим по формуле (28):
Норму выработки печи определим по формуле (20):
Трудоемкость
гомогенизации 1 тонны слитков определим по формуле (19):
Коэффициент
выпуска определим по формуле (33):
Трудоемкость
гомогенизации 1 тонны слитков с учетом выхода годного определим по формуле
(32):

Тогда
расчетное количество печей гомогенизации определим по формуле (35):
Принятое
количество Апр = 1 печь.
5.5.4 Расчет количества оборудования для сплава 6082
· Плавильные печи.
Время на одну плавку Тшт = 10 час, вес одной плавки К = 30 тн.
Тогда по формуле (20) получим часовую норму выработки:
Трудоемкость
изготовления одной тонны расплава определим по формуле (19):
Коэффициент
выпуска определим по формуле (33):
Трудоемкость
изготовления 1 тонны расплава с учетом выхода годного определим по формуле
(32):
Трудоемкость
изготовления 1 тонны расплава в пересчете на годовую программу определим по
формуле (34):
Тогда
расчетное количество плавильных печей определим по формуле (35):
Принятое
количество Апр = 2 печи.
· Литейные машины.
Основное технологическое время для производства слитков определяем по
формуле (23):
Количество
слитков, отливаемых в одной плавке, определим по формуле (25): вес слитка 7,42
тн.
Вспомогательное
время определим по формуле (24):
Норму времени на литье одного слитка определим по формуле (28):
Трудоемкость
изготовления 1 тонны слитков определим по формуле (21):
Коэффициент выпуска определим по формуле (33):
Трудоемкость
изготовления 1 тонны слитков с учетом выхода годного определим по формуле (32):
Трудоемкость
изготовления 1 тонны слитков в пересчете на годовую программу определим по
формуле (34):
Тогда
расчетное количество литейных машин определим по формуле (35):
Принятое
количество Апр = 4 машины.
· Гомогенизация слитков.
Максимальная садка колодца гомогенизации К = 60 тонн. Так как вес одного
слитка составляет 7,42 тонну, а в колодец помещают 6 слитков. Тогда садку
колодца определим по формуле (27):
Время
выдержки садки в колодце Тосн = 18 часов.
Вспомогательное
время определим по формуле (29):
Норму времени на гомогенизацию 1 слитка определим по формуле (28):
Норму выработки печи определим по формуле (20):
Трудоемкость
гомогенизации 1 тонны слитков определим по формуле (19):
Коэффициент
выпуска определим по формуле (33):
Трудоемкость
гомогенизации 1 тонны слитков с учетом выхода годного определим по формуле
(32):
Трудоемкость
в пересчете на годовую программу определим по формуле (34):
Тогда
расчетное количество колодцев гомогенизации определим по формуле (35):
Принятое
количество Апр = 1 колодец.
· Линия резки.
Средняя производительность станка линии резки П = 15 шт/час.
Оперативное время резки определяем по формуле (31):
Норму времени на резку 1 слитка определим по формуле (30):
По
формуле (20) получим часовую норму выработки:
Трудоемкость
разрезки слитков определим по формуле (19):
Коэффициент
выпуска определим по формуле (33):
Трудоемкость
разрезки слитков с учетом выхода годного определим по формуле (32):
Трудоемкость
разрезки слитков в пересчете на годовую программу определим по формуле (34):
Тогда
расчетное количество оборудования на линии резки определим по формуле (35):
Принятое
количество Апр = 1 линия.
Таблица
45 - Сводная ведомость основного оборудования.
Наименование
|
Количество оборудования
|
Итого
|
|
7175
|
АД1
|
6082
|
|
Печь плавильная
|
3
|
2
|
2
|
7
|
Миксер
|
3
|
2
|
2
|
7
|
Литейная машина
|
6
|
2
|
4
|
12
|
Колодец гомогенизации
|
2
|
-
|
1
|
3
|
Печь гомогенизации
|
-
|
1
|
-
|
1
|
Линия резки
|
1
|
1
|
1
|
3
|
.6 Определение среднесписочного числа производственных
рабочих
Количество производственных рабочих определяется по формуле:
, (37)
Где А - количество оборудования на одну операцию;
Нобс - норма обслуживания оборудования;
Ксм - количество смен;
Кспис - списочный коэффициент.
Определяем количество плавильщиков: Rплав = 7∙1∙3∙1,1=23,1
чел.
Принимаем Rплав = 23 чел.
Определяем количество литейщиков: Rлит = 12∙2∙3∙1,1=79
чел.
Определяем количество термистов: Rтерм = 4∙1/3∙3∙1,1=
4,4 чел.
Принимаем Rтерм = 5 чел.
Определяем количество резчиков: Rрез = 3∙1∙3∙1,1=
9,9 чел.
Принимаем Rрез = 10 чел.
Определяем количество шихтовщиков на МЗК: RМЗК = 1∙1∙3∙1,1=3,3чел.
Принимаем RМЗК = 4 чел.
Определяем количество шихтовщиков по формуле:
, (38)
где Q - годовая программа;
Нвыр - норма выработки;
Фэф - эффективный фонд времени;
Кспис - списочный коэффициент.
Тогда
Принимаем
Rших = 4 чел.
Среднесписочное
количество производственных рабочих по разрядам приведено в таблице 46.
Таблица
46 - Среднесписочное количество производственных рабочих.
Профессия
|
Принятое количество рабочих
|
Шихтовщик МЗК Шихтовщик Плавильщик Литейщик Резчик Термист
|
4 4 23 79 10 5
|
Общее число рабочих
|
125
|
.7 Определение фонда заработной платы производственных
рабочих
Таблица 47 - Фонд заработной платы основных рабочих.
Профессия
|
Количество человек
|
Оклад, руб.
|
Годовой фонд заработной платы, руб
|
Шихтовщик Плавильщик Литейщик Резчик Термист
|
8 23 79 10 5
|
7515 8300 8300 7515 7515
|
721440,0 2290800,0 7868400,0 901800,0 450900,0
|
Суммарный фонд заработной платы, руб.
|
12233340,0
|
Среднемесячная заработная плата основных производственных рабочих
составит 8155,6 рубля.
Таблица 48 - Фонд заработной платы вспомогательных рабочих.
Профессия
|
Кол-во человек
|
Оклад, руб.
|
Годовой фонд заработной платы, руб
|
Контролеры Кладовщицы Лаборанты Распределительный рабочий
Электрик Транспортный рабочий Слесари Техники Подсобные рабочие
|
15 6 12 10 6 7 10 20 6
|
5500 4300 4300 4300 7700 5800 7700 4800 4300
|
990000,0 309600,0 619200,0 516000,0 554400,0 487200,0
924000,0 1152000,0 309600,0
|
Суммарный фонд заработной платы, руб.
|
5862000,0
|
Среднемесячная заработная плата вспомогательных рабочих составит 5309,78
рубля.
Таблица 49 - Штат и фонд заработной платы служащих и ИТР.
Должность
|
Кол-во человек
|
Оклад, руб.
|
Годовой фонд заработной платы, руб.
|
Начальник цеха Заместитель начальника цеха Старший мастер
Сменный мастер Старший механик Старший энергетик Мастер по ремонту Старший
лаборант Технолог цеха ПДБ Нормировочное бюро Конструкторское бюро
|
1 1 2 7 1 1 1 1 5 2 4 3
|
25000 15000 10000 9300 9800 9800 8500 4800 6700 9000 9000
8300
|
300000,0 180000,0 240000,0 781200,0 117600,0 117600,0
102000,0 57600,0 402000,0 216000,0 432000,0 298800,0
|
Среднемесячная заработная плата служащих и ИТР составит 9324,14 рубля.
Таблица 50 - Штат и фонд заработной платы счетно-конторского персонала.
Должность
|
Кол-во человек
|
Оклад, руб.
|
Годовой фонд заработной платы, руб.
|
Табельщик Старший бухгалтер Счетовод Копировщик Заведующий
складом Завхоз Уборщик Гардеробщик
|
1 1 3 2 2 1 4 3
|
5000 6000 5500 4800 4600 4800 4300 4300
|
60000,0 72000,0 198000,0 115200,0 110400,0 57600,0 206400,0
154800,0
|
Среднемесячная заработная счетно-конструкторского персонала составит
4776,5 рубля.
Среднемесячная заработная плата по заводу тогда составит 6891,505 рубля.
.8 Определение стоимости основного оборудования
Стоимость основного оборудования приведена в таблице 52.
Таблица 51 - Стоимость основного оборудования.
Наименование
|
Количество, шт
|
Стоимость, руб.
|
|
|
единица
|
общая
|
Газовая рекуператорная печь Вакуумный миксер Литейная
машина Колодец гомогенизации Печь гомогенизации Линия резки Кран мостовой (G
= 10 тн)
|
8 8 10 3 1 3 6
|
3000000 2500000 600000 1102200 920000 540000 150000
|
24000000 20000000 6000000 3306600 920000 1620000 900000
|
Суммарная стоимость основного оборудования, руб.
|
101196600
|
Суммарная стоимость вспомогательного оборудования в цехе составляет ≈
20% от стоимости основного оборудования, т.е. 20239320 рублей.
Тогда общая стоимость всего оборудования цеха составит 121435920 рублей.
Затраты по монтажу и транспортировке принимаем в размере 10 % от общей
стоимости оборудования: 121435920 ∙ 0,1 = 12143592,0 рубля.
Стоимость затрат на инструмент, приспособления и приборы составляет 15%
от стоимости всего оборудования: 121435920 ∙ 0,15 = 18215388,0 рублей.
Затраты на дорогостоящий инструмент составляют 60% от стоимости всего
инструмента: 18215388,0 ∙ 0,6 = 10929232,8 рубля.
Стоимость производственного и хозяйственного инвентаря составляет 15% от
стоимости всего инструмента: 18215388,0 ∙ 0,15 = 2732308,2 рубля.
Затраты на дорогостоящий инвентарь составляют 60% от стоимости всего
инвентаря: 2732308,2 ∙ 0,6 = 1639384,92 рубля.
.9 Определение стоимости основных фондов цеха
Площадь, объем и стоимость деловых помещений приведена в таблице 53.
Таблица 52 - Площадь объем и стоимость деловых помещений.
Вид помещения
|
Площадь, м2
|
Высота, м2
|
Объем, м3
|
Стоимость 1 м2, руб.
|
Общая стоимость, руб.
|
Производственные Вспомогательные
|
16150 2120
|
12 3
|
193799 6360
|
400 1200
|
6459960 2544000
|
Стоимость основных фондов цеха приведена в таблице 53.
Таблица 53 - Стоимость основных фондов цеха.
Наименование основных фондов
|
Стоимость, руб.
|
Стоимость деловых помещений Стоимость оборудования
Стоимость инструмента Стоимость инвентаря
|
9003960 121435920 18215388 2732308,2
|
Суммарная стоимость, руб.
|
151387576,2
|
.10 Определение цеховой себестоимости
Приведем расчет затрат на 1 тонну годного литья.
Затраты на вспомогательные материалы Звсп=202руб.
Зарплата на 1 тонну годного литья определяется по формуле:
, (39)
где Згод - годовой фонд заработной платы основных и
вспомогательных рабочих;год - годовая программа выпуска.
Тогда
Затраты на оплату труда аппарата обслуживания и управления:
Отчисления
на социальное страхование: 26 % от З1т.
Амортизационные
отчисления - 24,2% от З1т.
Ремонтный
фонд - 150 % от З1т.
Цеховые
расходы - 200% от З1т.
Сумма
всех этих затрат - цехавая себестоимость Сц.
Общезаводские
расходы Сз = 10-12% от Сц.
Общезаводская
себестоимость Собщ = Сц + Сз
Внепроизводственные
расходы Свнепр = 2-5% от Собщ.
Полная
себестоимость Сполн = Сз + Свнепр
Плановые
накопления (прибыль) Сплан = 15-20 % от Сполн.
Сполн
+ Сплан = оптовая цена.
Данные расчета сведены в таблицы 54,55,56.
Таблица 54 - Калькуляция себестоимости 1 тонны годного литья для сплава
7175.
Статья затрат
|
Ед. изм.
|
Кол-во
|
Цена за ед., руб.
|
Сумма, руб.
|
Отходы сплава 7175
|
кг
|
425,53
|
25,8
|
10978,74
|
Чушковый алюминий:
|
|
|
|
|
марки А85
|
кг
|
1129,01
|
49,0
|
55321,5
|
марки А95 Лигатура Al-Cr Чистые компоненты: Zn Mg Cu
Вспомогательные материалы
|
кг кг кг кг кг
|
425,53 134,93 91,87 39,09 25,47
|
50,5 64,3 58,4 61,1 86,0
|
2299,27 8676,0 5365,21 2388,4 2190,42 202,0
|
Итого, руб.
|
37631,54
|
Транспортные расходы Топливо и электроэнергия Безвозвратные
отходы Возвратные отходы
|
% кВт/ч кг кг
|
10 400 100 250
|
1,2 23,6
|
97,15 480,0 2360
|
Сумма выхода годного, руб.
|
40568,69
|
Зарплата Премия Отчисления на социальное страхование
Расходы на содержание оборудования Амортизационные расходы Цеховые расходы
|
руб. % % % % %
|
100 26 150 24,2 200
|
|
70,98 70,98 26,48 106,47 17,18 141,96
|
Цеховая себестоимость, руб.
|
41002,74
|
Общезаводские расходы
|
%
|
10-12
|
|
4100,27
|
Общезаводская себестоимость, руб.
|
45103,0
|
Внепроизводственные расходы
|
%
|
2-5% от Собщ
|
|
1353,1
|
Полная себестоимость, руб.
|
46456,24
|
Плановые накопления (прибыль)
|
%
|
15-20% от Сполн
|
|
6968, 4
|
Оптовая цена, руб.
|
53424,64
|
Таблица 55 - Калькуляция себестоимости 1 тонны годного литья для сплава
АД1.
Статья затрат
|
Ед. изм.
|
Кол-во
|
Цена за ед., руб.
|
Сумма, руб.
|
Отходы сплава АД1 Чушковый алюминий: марки А6
Вспомогательные материалы
|
кг кг
|
769,23 512,82
|
23,0 40,0
|
17692,29 20512,8 202,0
|
Итого, руб.
|
38407,09
|
Транспортные расходы Топливо и электроэнергия Безвозвратные
отходы Возвратные отходы
|
% кВт/ч кг кг
|
10 400 46,0 160,0
|
1,2 21,2
|
97,15 480,0,0 975,2
|
Сумма выхода годного, руб
|
39959,44
|
Зарплата Премия Отчисления на социальное страхование
Расходы на содержание оборудования Амортизационные отчисления Цеховые расходы
|
руб. % % % % %
|
100 26 150 24,2 200
|
|
70,98 70,98 26,48 106,47 17,18 141,96
|
Цеховая себестоимость, руб.
|
40393,49
|
Общезаводские расходы
|
%
|
10-20
|
|
4039,35
|
Общезаводская себестоимость, руб.
|
44432,84
|
Внепроизводственные расходы
|
%
|
2-5% от Собщ
|
|
1333,0
|
Полная себестоимость, руб.
|
45765,84
|
Плановые накопления (прибыль)
|
%
|
15-20% от Сполн
|
|
6864,08
|
52630,72
|
|
|
|
|
|
|
Таблица 56 - Калькуляция себестоимости 1 тонны годного литья для сплава
6082.
Статья затрат
|
Ед. изм.
|
Кол-во
|
Цена за ед., руб.
|
Сумма, руб.
|
Отходы сплава 6082 Чушковый алюминий: марки А35 Лигатура
Al-Mn Чистые компоненты: Si Mg Вспомогательные материалы
|
кг кг кг кг кг
|
1333,35 308,0 19,04 3,3 2,98
|
26,3 34,0 46,0 54,1 61,1
|
35067,05 10472,0 875,84 178,53 182,08 202,0
|
Итого, руб.
|
46977,5
|
Транспортные расходы Топливо и электроэнергия Безвозвратные
отходы Возвратные отходы
|
% кВт/ч % %
|
10 400 217 225
|
1,2 25,9
|
97,15 480,0 5620,3
|
Сумма выхода годного, руб.
|
53174,95
|
Зарплата Премия Отчисления на социальное страхование
Расходы на содержание оборудования Амортизационные отчисления Цеховые расходы
|
руб. % % % % %
|
26 150 24,2 200
|
|
70,98 70,98 26,48 106,47 17,18 141,96
|
Цеховая себестоимость,руб.
|
53609,0
|
Общезаводские расходы
|
%
|
10-20
|
|
5360,9
|
Общезаводская себестоимость, руб
|
58969,9
|
Внепроизводственные расходы
|
%
|
2-5% от Собщ
|
|
1769,1
|
Полная себестоимость, руб.
|
60739,0
|
Плановые накопления (прибыль)
|
%
|
15-20% от Сполн
|
|
9110,85
|
Оптовая цена, руб
|
69849,85
|
6. Безопасность жизнедеятельности
Деятельность - специфическая форма отношения человека
с окружающей средой, содержание которой составляет его целесообразное изменение
и преобразование в интересах людей.
При взаимодействии человека со средой обитания
возникает опасность, т.е. такое воздействие, которое может причинить ущерб
здоровью человека, создать угрозу его жизни, затруднить функционирование
органов человека.
Под безопасностью понимают такое состояние
деятельности (труда), при котором с некоторой вероятностью (риском) исключается
реализация потенциальной опасности. При этом регламентируется определенные
условия. Понятие риска дает возможность нормировать безопасность. В мировой практике
нормированный риск называют приемлемым. Для обычных общих условий деятельности
приемлемый риск гибели человека принимается равным 10-6 (один случай
на миллион). Приемлемый риск и возможность управления им являются объективными
предпосылками развития области знаний, изучающей опасности и защиту от них. Эта
дисциплина получила название «безопасность жизнедеятельности».
Производственная среда - это часть техносферы, обладающая повышенной
концентрацией негативных факторов, поэтому безопасность производственных
процессов определяется, в первую очередь, безопасностью производственного
оборудования, которая обеспечивается на стадии его проектирования .
Все опасные и вредные факторы разделяют на четыре основные группы:
1. физические
2. биологические
3. химические
4. психофизиологические.
Основными травмирующими факторами в металлургии, как и в машиностроении
являются (%): оборудование (41,9) , падающие предметы (27,7), падение персонала
(11,7), заводской транспорт (10), нагретые поверхности (4,6), электрический ток
(1,6), прочие (2).
Современные технические системы повышенной энергетической мощности в
проектируемых цехах имеют вероятность воздействия опасных и вредных факторов на
человека на уровне 10-6 - 10-8 1/год и менее при всех
видах воздействия на систему (отказы техники, ошибки оператора, стихийные
явления).
Это обеспечивается внедрением комплексной механизации и автоматизации,
применением дистанционного управления технологическими процессами и операциями
при наличии опасных и вредных факторов, внедрением системы контроля и
управления технологическими процессами.
6.1 Опасные и вредные производственные факторы
Основным оборудованием для получения круглых слитков в
проектируемом цехе являются: плавильные газовые печи, миксера, литейные машины,
колодцы и печи гомогенизации, а также линия резки.
Перемещение грузов внутри цеха производится мостовыми
кранами и тележками. Так как повседневная деятельность человека связана с
процессом использования техники, то она является потенциально опасной.
Использование техники связано с выработкой, хранением и преобразованием
электрической, химической и других видов энергии в условиях воздействия внешней
среды.
Опасность возникает в результате бесконтрольного
выхода энергии, которая накапливается в материалах и оборудовании или
непосредственно в окружающей среде и человеке и которая сопровождается
возникновением происшествий с ухудшением здоровья людей или их гибелью,
загрязнением природных ресурсов, получением материальных затрат.
Инициаторами и составными звеньями цепи происшествий
служат несанкционированные или ошибочные действия людей, отказы и неисправности
техники и нерасчетные воздействия на них внешних факторов среды обитания.
Устойчивость любой технической системы - это
возможность сохранения ею способности работать при нештатном внешнем
воздействии, а также приспособленность системы к ее восстановлению при
повреждении.
К опасным производственным факторам в проектируемом
цехе относят:
. Электрический ток;
. Движущиеся машины, механизмы;
. Острые кромки;
. Повышенная температура поверхностей оборудования,
материалов.
К вредным производственным факторам в проектируемом
цехе относят:
1.
Запылённость
воздуха рабочей зоны;
2.
Акустические
колебания: шум;
3.
Инфракрасная
радиация;
4.
Загазованность
рабочей зоны;
5.
Смазочно -
охлаждающая жидкость;
6.
Электромагнитное
излучение;
7.
Тепловой поток.
При плавлении в воздух рабочей зоны выделяются
аэрозоли и конденсаты, одни из самых токсичных - аэрозоли оксидов марганца и
цинка.
К газам, загрязняющим окружающую среду, относятся:
окись углерода, углекислый газ, хлор.
Хлор встречается иногда в воздухе вблизи от химических
заводов. Он применяется для хлорирования воды, для получения пластмасс,
растворителей и др., в металлургии применяется для хлорирующего обжига руд цветных
металлов. Это зеленовато - желтый газ с характерным запахом. Раздражает
дыхательные пути, может вызвать отек легких. При хроническом отравлении, у
работающих при невысокой концентрации хлора описано повышение сопротивляемости
к гриппозной инфекции. Но также отмечаются легочные заболевания. У работающих с
хлором отмечены воспаления десен, изъязвление слизистой носовой перегородки,
желудочно-кишечные расстройства, анемия, головные боли, бессонница. При
контакте с кожей вызывает острый дерматит, иногда переходящий в экзему.
Избыточное выделение теплоты в отделениях плавки,
литья и гомогенизации слитков. Температура в этих отделениях существенно
превышает 30°С, при нормальной температуре воздуха 20°С. Интенсивность
теплового потока при открытых створках печи или миксера, например, при чистке
миксера или при переливании расплава, превышает 3,5 кВт/м . Такая интенсивность
уже через две секунды вызывает жжение.
В зависимости от места и условий воздействия
электромагнитного излучения (ЭМИ) различают четыре вида облучения:
профессиональное, непрофессиональное, облучение в быту и облучение,
осуществляемое в лечебных целях, а по характеру облучения - общее и местное.
При длительном воздействии ЭМИ характерно развитие у
человека функциональных расстройств центральной нервной системы [22]. В связи с
этим могут появиться головные боли, повышение или понижение давления, быстрое
развитие утомления. Наблюдаются изменения возбудимости обонятельного,
зрительного и вестибулярного аппарата. При длительном воздействии ЭМИ происходит
стойкое снижение трудоспособности. Для защиты от ЭМИ используют специальные
экраны.
Основными источниками поражения электрическим током
являются: колодцы гомогенизации; электромагнитные трансформаторы; литейные
машины; пролетные краны.
Наличие расплавленного или сильно разогретого металла
вызывает воспламенение или сильный ожог. Также причиной пожара бывает
неисправность в электрооборудовании.
Эти факторы оказывают отрицательное влияние на
человека. Они приводят к ухудшению здоровья человека, получением им различных
заболеваний, увечьям, потери различной степени работоспособности, а также к его
гибели.
6.2 Мероприятия, обеспечивающие безопасность эксплуатации
жизнедеятельности человека и технических систем
Безопасность эксплуатации технических систем
оцениваются по нормативным показателям. Эти показатели регламентируются ГОСТом,
правилами и санитарными нормами. Если разрабатываемое оборудование, условия
труда или технологический процесс не соответствуют нормативным требованиям, то
проводится ряд мер, которые должны улучшить указанные показатели.
Литейный цех относится к горячим с тепловыделением 23,2 Вт/м3
, поэтому защиту от тепловых излучений осуществляют путем теплоизоляции
поверхностей, излучающих тепло. При работе в условиях высокой температуры воздуха
водно-солевой и витаминный обмен значительно изменяется, так как усиленное
потоотделение ведет к потере жидкости, солей и витаминов. Считается допустимым
для человека снижение его массы на 2 - 3% путем испарения влаги (обезвоживание
организма). Отрицательное влияние на центральную нервную систему работы в
условиях высоких температур проявляется в ослаблении внимания, замедления
реакций, ухудшении координации движения.
Спецодежда выполняет роль индивидуальной защиты от вредных воздействий.
Она выбирается воздухо- и влагонепроницаемой и имеет удобный покрой. Обувь и
одежда для различных групп выполнена в разных цветовых и технических
исполнениях (например, у электриков в обувь без металлических гвоздей).
Перед началом работы осуществляется проверка всех движущихся частей
технологического оборудования на холостом ходу, работа распределителей и
другого технологического оборудования.
Повышение электробезопасности в энергоустановках (отрезной,
торцефрезерный станки и т.п.) достигается применением систем защитного
заземления, отключений и других методов и средств защиты, в том числе знаков
безопасности и предупреждающих плакатов и надписей.
Действие электрического тока на живую ткань носит разносторонний и
своеобразный характер. На сопротивление организма воздействию электрического
тока оказывает влияние физическое и психическое состояние человека. Вот почему
уделяется большое внимание эстетическому оформлению производственных помещений
цеха и эргономическим параметрам рабочего места.
В проектируемом цехе для окраски оборудования используются пассивные,
малонасыщенные цвета. Окраска оборудования в сигнальные и отличительные цвета
выполняется в соответствии с требованиями действующих ГОСТ Р 12.4.026-2001
[23].
Правильная организация рабочего места предполагает учет эргономических
требований (экономию движений, исключение неудобных поз при обслуживании
оборудования и пультов управления, правильную компоновку последних).
Для согласования действий работающих в частности крановщиков и
стропальщиков используется информационная сигнализация (звуковые сигналы и
специальные команды).
Все рабочие места и склады освещаются в соответствии с нормами.
Конструктивно освещение внутри производственных помещений реализуется
естественным (через боковые световые проемы в наружных стенах и верхние проемы
через аэрационные и зенитные фонари) и искусственным освещением.
Удаление очищенных выбросов вредных веществ осуществляется применением
систем вытяжной вентиляции.
Для защиты от поражения электрическим током
применяются блокировки и ограждения, заземление и зануление оборудования.
При избыточном выделении теплоты при работе печи и
колодца гомогенизации применяются теплоотражающие плиты для облицовки стен печи
и колодца. Проверяется плотность прилегания дверки к фронту печи, а также плотность
прилегания крышки колодца. Рабочими используется спецодежда для защиты от
избыточной теплоты (это специальные комбинезоны из хлопчато-бумажной ткани,
ботинки, перчатки, очки, каски), при вращении частей отрезных станков и для
защиты от стружки используются защитные очки. Во время работы запрещается
стоять перед диском пилы.
При прорыве расплава в кристаллизаторе соблюдаются
технологические параметры литья: давления воды в кристаллизаторе и скорости
литья. При движении механизмов литейной машины предусмотрено ограждение опасной
зоны, при воздействии паров и газов - эффективный отвод газов через дымоход в
рекуператор и очистка охлажденных газов пылеуловителями, применение эффективных
осевых вентиляторов.
Загрузка "холодной" шихты в печь
производится после предварительной просушки в пламени горелок печи.
Для предотвращения взрыва газа в плавильной газовой
рекуператорной печи предусмотрена автоблокировка подвода газа при падении
давления газа или при прекращении его подвода.
При избыточном выделении теплоты на участке плавления
применяются водоохлаждаемые дверки и крышки, фронтовые теплоотражательные
облицовочные плиты, экранирование источников или рабочих мест, воздушное
душирование; теплоизоляция поверхности плавильной печи. В цехе предусмотрена
система снабжения работающих водой из фонтанчиков.
Санитарно-гигиеническая характеристика проектируемого
цеха приведена в таблице 57 [22].
Таблица 57 - Санитарно-гигиеническая характеристика
проектируемогоцеха.
Наименование показателя
|
Ед. изм.
|
Величина показателя
|
Прим.
|
1. Характеристика производственного помещения: с явными
избытками теплоты (≤23 Вт/м2) с незначительными избытками теплоты (≥
23 Вт/м2)
|
Вт/м2
|
23
|
|
2. Категория работы: легкая Iа, Iб средней тяжести IIа,
IIб тяжелая III
|
Вт
|
IIа, IIб
|
|
3. Оптимальная температура: теплый период года (≥ +100С)
холодный период года (≤ +100С)
|
С
|
17..19 20..23
|
|
4. Относительная влажность: оптимальная допустимая
|
%
|
40..60 15..75
|
|
5. Допустимая скорость движения воздуха: теплый период года
(≥ +100С) холодный период года ((≤ +100С)
|
м/с
|
0,2..1,0 0,2..0,5
|
|
6. Нормируемая освещенность помещения при лампах:
накаливания люминесцентных
|
лк
|
150..200 200..300
|
|
7. Допустимый уровень шума
|
дБ
|
< 80
|
|
8. Предельно допустимые концентрации вредных веществ: паров
(серной кислоты) газов (СО2) нетоксичной пыли
|
мг/м3
|
< 2,0 <20,0 <(0,04..0,4)
|
|
9. Площадь на одного производственного рабочего
|
м2
|
> 4,5
|
Норма 4,5
|
10. Объем на одного производственного рабочего
|
м3
|
> 15
|
Норма 15
|
Средства индивидуальной защиты рабочих
Каждый шихтовщик, резчик, плавильщик и литейщик
обеспечивается следующими средствами индивидуальной защиты:
1 костюм защитный ГОСТ 12.4.045-87
ботинки кожаные ГОСТ 12.4.137-84 (носки ботинок
защищены металлической пластиной во избежание травм при падении тяжестей).
[24].
каска защитная ГОСТ 12.4.207-99 [25].
рукавицы брезентовые ГОСТ 12.4.010-75 [26].
5 очки защитные ГОСТ 12.4.013-97 [27].
щитки защитные ГОСТ 12.4.023-84 [28].
При работе на пилах проверяется наличие и исправность
ограждений всех механизмов. Чтобы диск маятниковой пилы был закрыт кожухам.
Исправность установки и всех механизмов, обслуживающих её работу, проверяются
на холостом ходу. Проверяется местное освещение, исправность вентиляции и
защитного заземления. Устанавливаются мульды или банки для сбора отходов
(концов профилей). Проверяется исправность зубьев (ножей) пильного диска,
надежность его крепления, отсутствие трещин.
На производстве имеются также средства автоматического
контроля и сигнализации. Устройства предупредительной сигнализации предназначены
для предупреждения об опасности. Чаще всего в них используют световые и
звуковые сигналы, поступающие от различных приборов, регистрирующих ход
технологического процесса, в том числе уровень опасных и вредных факторов.
Большое применение находит предупреждающая сигнализация, опережающая включение
оборудования или подачу высокого напряжения.
Подвидом предупредительной сигнализации является
сигнальная окраска. Травмоопасные элементы оборудования выделяют чередующимися
(под углом 45° к горизонтали) полосами желтого и черного цвета. На стенках в
красный цвет окрашивают обратные стороны дверец, ниш для электрооборудования, а
также поверхности схода стружки. Все трубопроводы с горючими газами окрашены в
жёлтый цвет с цветными сигнальными кольцами.
Все вышеперечисленные меры обеспечивают безопасность
эксплуатации технических систем и жизнедеятельности человека.
6.3 Экологическая экспертиза разрабатываемого
технологического процесса
Основными нормативными показателями экологичности
предприятия, производственного оборудования и технологических процессов
являются предельно допустимые выбросы (ПДВ) в атмосферу и предельно допустимые
сбросы (ПДС) в гидросферу. Нормативные показатели являются основой для
проведения экологической экспертизы. Реализация нормативных показателей
достигается путем повышения экологичности проектов промышленных объектов,
оборудования и технологических процессов. К нормативным показателям
экологичности технических систем относятся также допустимые уровни физических
воздействий (шума, вибрации и т.д.).
Сущность ПДВ состоит в том, что идет ограничение
выбросов и обусловлена тем, что при настоящих методах уменьшения отходов
производства почти нельзя полностью избежать выброса в атмосферу вредных
веществ. Нужно уменьшать выбросы до определенных уровней, которые обеспечивали
бы соблюдение предельно допустимых концентраций (ПДК).
Нормы ПДС устанавливаются с учетом ПДК в местах
пользования, оптимального распределения массы сбрасываемых вредных веществ
между пользователями воды и ассимилирующей способности водного объекта.
Основное направление увеличения экологичности
технических систем и технологий - это выработка процессов по переработке и
утилизации отходов, а также разработка малоотходных технологий. Уменьшение
отрицательного воздействия достигается путем увеличения герметичности систем, а
также вводом в конструкцию источника аппаратов нейтрализации или очистки,
применением регенеративных циклов использования рабочих сред.
Основным источником загрязнения атмосферы в
проектируемом цехе пылью, окисью углерода, аэрозолями и избыточной теплотой
являются плавильно-литейные агрегаты (сюда также относятся CH4,O3,N2O).
Отходы литейного производства переплавляются здесь же
(литники, донники, брак), другие переправляются на переработку (сплесы, съемы,
стружка, металл в шлаке).
Основными видами загрязнений сточных вод является
песок, окалина, смазка. Очистка выбросов от пыли происходит устройствами
содержащими в себе фильтры, а также пылеуловителями. Для очистки выбросов от
пыли используются два вида пылеуловителей - сухие и мокрые. Себестоимость
очистки газов в мокрых пылеуловителях выше, чем в сухих, а проблемы, связанные
с потребностью в системах оборотного водоснабжения и хозяйства, ограничивают
возможность применения мокрых пылеуловителей. Из сухих инерционных
пылеуловителей наибольшее распространение получили центробежные аппараты -
циклоны, имеющие ряд преимуществ перед пылеуловителями других типов для
литейного цеха: они просты по изготовлению, монтажу и эксплуатации; обладают
надежной работоспособностью при повышенных температурах -более 500°С (такие
циклоны изготавливают из термостойких сплавов) и почти при любых давлениях
газа; позволяют выделять пыль в сухом виде. Эффективность пылеулавливания в
циклонах не зависит от начальной концентрации пыли, которая в ряде случаях
достигает сотен граммов на кубический метр. В зависимости от характера
протекания газа через циклоны они делятся на прямоточные и противоточные.
Наиболее эффективны противоточные циклоны.
Принцип действия противоточных циклонов следующий
(рис. 16). Газовый поток вводится в циклон через патрубок 2 по касательной к
внутренней поверхности корпуса 1 и совершает вращательно-поступательное
движение вдоль корпуса к бункеру 4. Под действием центробежной силы частицы
пыли образуют на стенке циклона пылевой слой, который вместе с частью газа
попадает в бункер. Отделение частиц пыли от газа, попавшего в бункер,
происходит при повороте газового потока на 180°. Освободившись от пыли, газовый
поток образует вихрь и выходит из бункера, давая начало вихрю газа, покидающему
циклон через выходную трубу 3. Для нормальной работы циклона необходима
герметичность бункера. Если бункер негерметичен, то из-за подсоса наружного
воздуха идет вынос пыли с потоком через выходную трубу.
В качестве пылеуловителей в проектируемом цехе
применяются проти-воточные конические циклоны НИИОГаза марки ЦН-СК-34М.
Подсоединения циклонов к сети газоходов следует осуществлять с помощью
газораспределительных коллекторов запыленного и обеспыленного газа. Выхлопные
патрубки циклонов целесообразно присоединять посредством раскручивающихся
улиток.
Рисунок 16 - Схема циклона.
Для очистки сточных вод от песка используются
песколовки (рис. 17). зависимости от направления движения сточной воды
применяют горизонтальные песколовки с прямолинейным и круговым движением воды,
вертикальные и аэрируемые.
Рисунок 17 - Схема горизонтальной песколовки.
Для очистки сточных вод от окалины, а также от частиц
нефтепродуктов используются отстойники. В зависимости от направления движения
потока сточной воды применяют горизонтальные, радиальные или комбинированные
отстойники.
Для очистки вод от смазки используется флотация - это
интенсификация процесса всплывания маслопродуктов при обволакивания их частиц
пузырьками газа, продуваемого в сточную воду. В основе этого процесса имеет
место молекулярное слипание частиц масла и пузырьков тонкодисперсного в воде
газа. Образование агрегатов "частица - пузырьки газа" зависит от
интенсивности их столкновения друг с другом, химического взаимодействия
содержащихся в воде веществ, избыточного давления в сточной воде и т.п.
В зависимости от способа образования пузырьков газа
различают напорную, пневматическую, пенную, химическую, вибрационную, биологическую,
электрофлотацию и др.
В таблице 58 указаны вредные вещества и их концентрации в соответствии с
их источниками.
Таблица 58 - Вредные вещества.
Наименование
|
Выбросы загрязняющих веществ
|
ПДКмр ПДКсс
|
Класс опасности вещества
|
|
г/с
|
мг/м3
|
т/год
|
|
|
Оксид алюминия
|
0,3114
|
5,5989
|
8,4762
|
-/0,01
|
1
|
Окись азота
|
0,1068
|
1,9197
|
2,9061
|
0,4/0,06
|
3
|
Двуокись азота
|
0,0087
|
0,0308
|
0,4723
|
0,085/0,04
|
2
|
Ангидрид сернистый
|
0,2225
|
3,9997
|
6,0545
|
0,5/0,05
|
3
|
Окись углерода
|
0,5339
|
9,5986
|
14,5307
|
5/3
|
4
|
Масло минеральное нефтяное
|
0,0089
|
17,8
|
0,1773
|
0,05
|
1
|
Объем выполненной работы по контролю состояния воздушной среды
определяется категорией опасности производства (КОП), вычисляем по формуле:
КОП=
,
где М - количество выбрасываемого в атмосферу i-го вредного вещества
т/год;
ПДК - предельнодопустимая концентрация i-го вредного вещества для
селитебной зоны мг/м3;- относительный коэффициент опасности,
применяется в зависимости от класса опасности вещества.
Таблица 59 - Относительный коэффициент опасности
Коэффициент
|
Класс опасности вещества
|
а
|
1,7
|
1,3
|
1,0
|
0,9
|
КОП
|
>108
|
104<КОП<108
|
103<КОП<104
|
< 103
|
Санитарно - защитная зона
|
1000м
|
500м
|
300м
|
100м
|
Сопоставив данные таблиц 58 и 59, получим:
К= (8,48/0,01)1,7 + (2,91/0,4)1 + (0,47/0,085)1,3
+ (6,05/0,1)1 + (14,53/0,2)0,9 + (0,18/0,05)1,7
= (95120,24+7,3+9,24+60,5+47,33+8,83)=95253,44
Полученное значение характеризуется значением 104<КОП<108
, поэтому исследуемый объект относится к II группе опасности санитарной зоны
вокруг предприятия 500м.
Защита почвенного покрова и недр от твердых отходов (образивы, черные и
цветные металлы) реализуется за счет отбора, сортирования и утилизации отходов,
их централизованного захоронения на промышленных свалках и полигонах [20]. При
этом участок захоронения токсичных отходов имеет санитарно - защитную зону
300м. Вторичные отходы (стружка, шлак) после соответствующей переработки
(переплава) поступают в новый технологический цикл.
6.4 Обоснование планировки оборудования и
административно-бытовых помещений
Исходной базой при проектировании цеха служит
производственно-технологическая схема цеха, представляющая собой схему основных
этапов технологического цикла, который включает в себя целый ряд транспортных
операций, связанных с перемещением отливаемых слитков.
В цехе исключается возможность пространственного
пересечения грузовых потоков материалов и обеспечена кратчайшая их
протяженность, что экономически целесообразно и обеспечивает безопасность
технологического процесса.
Производственное здание состоит из трех пролетов шириной 24 м, высотой 12
м.
Основные размеры литейного цеха определены, в первую очередь, числом
установленных процессов и их мощностью. Поэтому оборудование расставлено по
технологическому принципу с соблюдением основных требований поточного производства:
из шихтового отдела металл поступает в печи плавления, после расплавления
переливается в миксер, а слитки отливают на литейных машинах. Изделия поступают
на термообработку и далее на линию, резки и сдаточный участок. В конце цеха
размещаются склады готовой продукции [18].
Основой здания служит каркас, составленный из железобетонных колонн,
закрепленных поверху металлическими фермами, которые расположены поперек
пролета. На металлические фермы уложено перекрытие из железобетонных плит.
Элементы конструкций здания цеха выполняют несущие и ограждающие функции.
Несущие - воспринимают нагрузки, возникающие в здании или вне его, но
воздействующие на здание, это фундаменты, колонны, различные балки и фермы.
Ограждающие защищают здание и его внутренние помещения от внешних
метеорологических факторов, к ним относятся крыша, стены, перегородки [21].
Большую часть стенового ограждения между колоннами занимает оконный
переплет - остекленная рама из металлических профилей. Площадь остекления
относительно большая, поэтому внутри помещения при естественном дневном
освещении обычно светло. Этому способствует также остекление части перекрытия,
которое называется фонарем.
Высота производственного цеха определена возможностью его обслуживания и
проведения ремонтов с помощью мостовых кранов.
Количество мостовых кранов определено из условия /23/, что при длине
пролета до 150м применяются два мостовых крана.
Мостовой кран движется вдоль пролета, а поперек пролета по мосту
передвигается тележка, на которой установлен подъемный механизм с краном. Таким
образом, вся площадь цеха оказывается в зоне действия мостового крана, и с его
помощью можно поднять и переместить груз, расположенный в любой точке цеха.
В цехе поддерживается определенная температурный режим, определенный санитарными
нормами. Для отопления цеха применяют калориферы. При этом учитывается так
называемое «техническое тепло» - выделяемое различными нагревательными
устройствами. Избыток тепла и выбросы после очистки вредных веществ в отдельных
местах цеха удаляются с помощью вентиляции (вытяжная вентиляция) и аэрации -
естественного движения воздуха.
Объем вентилируемого помещения (Vp) составляет
193798,8 куб. метров. Норма вентиляции в час (Nn) составляет 7-12% от объема
цеха.
Соответственно производительность вентиляционной
системы (Уц) должна составлять 13565,9-23255,9 куб. метров воздуха в час. По
полученным цифрам, на стадии проектирования, подберется необходимое
оборудование.
В качестве пылеуловителей в проектируемом цехе
применяются проти-воточные конические циклоны НИИОГаза марки ЦН-34М.
Здесь важно отметить, чтобы исключить создания
сквозняков в помещениях цеха, вентиляционное оборудование необходимо грамотно
расположить по его территории, а для улучшения микроклимата при необходимости
использовать специальное оборудование (тепловые завесы, радиаторы отопления,
«местные» вытяжки).
Организация на предприятии специальной службы по
эксплуатации, наладке и ремонту систем обеспыливания и вентиляции является
обязательным условием при большой чистоте выбросов и для создания нормальных
санитарно-гигиенических условий работы.
Приточно-вытяжная вентиляция - наиболее распространенная система, при
которой воздух подается в помещение приточной системой, а удаляется вытяжной.
Системы работают одновременно. Система применяется в помещениях, в которых
отсутствует выделение вредных веществ (комнаты отдыха, столовая и т.д.).
Количество вторичного и свежего воздуха в помещении регулируется клапанами.
Посредине цеха расположены транспортные проходы и проезды. По ним
передвигается обслуживающий персонал и напольный транспорт (электрокары или
автомашины). Границы проходов, проездов, рабочих мест складских помещений
обозначаются хорошо видимыми знаками.
Участки цехов обработки металлов давлением оснащены средствами
пожаротушения в соответствии с действующими ГОСТами. Количество огнетушителей
различных марок определены из расчета один прибор на 500 - 600 м2
площади цеха. По существующим нормам в цехе устанавливаются пожарные щиты или
шкафы - один на каждые 5000 м2 площади, но не менее двух на
помещение. Количество пожарных кранов определяется из расчета их установки
через каждые 50 м по периметру помещения, а также на каждой лестничной
площадке.
В состав цеха, помимо подразделений, занимающихся выполнением основных
технологических операций, входят некоторые вспомогательные службы. Они занимают
трехэтажный пристрой к основному корпусу. Лестницы во вспомогательных
помещениях делаются двухмаршевыми с числом ступеней не более 18, с шириной от
1,15м до 2,4м. В подвальные помещения кладут одномаршевые лестницы.
Высота конторских и бытовых помещений: комнаты 2,7 и 3,3м , общие залы
3,6 и 4,2м [19].
Наименьшая ширина коридоров 1,4м , наибольшая не ограничивается. Двери в
целях пожарной безопасности должны открываться внутрь коридорного прохода.
.5 Анализ воздействия возможных стихийных действий
В настоящее время существуют два основных направления
минимизации вероятности возникновения и последствий ЧС на промышленных
объектах. Первое направление заключается в разработке технических и организационных
мероприятий, уменьшающих вероятность реализации опасного поражающего потенциала
современных технических систем. В рамках этого направления технические системы
снабжают защитными устройствами - средствами взрыво- и пожарозащиты
технологического оборудования, электро- и молниезащиты, локализации и тушения
пожаров и т.д.
Второе направление заключается в подготовке объекта,
обслуживающего персонала, служб гражданской обороны и населения и действиям в
условиях ЧС.
При существующей вероятности наводнения нужно
учитывать, что здания и сооружения цеха необходимо строить на возвышенностях,
чтобы снизить потери от затопления. В первую очередь это относится к зданиям,
где располагается дорогостоящее оборудование, склады с материалами.
Во избежание послегрозовых последствий
производственные здания снабжаются молниеотводами.
Также к источникам ЧС следует отнести возможность
возникновения пожара в проектируемом цехе, выброс расплавленного металла, а
также взрыв газа в печах. При отсутствии эффективного отвода вредных веществ и
газов, могут оказать губительное действие на здоровье и даже привести к угрозе
жизни.
Причинами разрушения и разгерметизации систем повышенного давления и
пожаров технического характера могут быть:
1. внешние механические воздействия;
2. старение систем (снижение
механической прочности);
3. нарушение технологического режима;
4. изменение состояния герметизирующей
среды;
5. ошибка обслуживающего персонала и
т.д.
В связи с тем, что вероятность возникновения взрыва и, как следствие,
пожара на металлургическом предприятии велика, пожарная безопасность
проектируемого цеха обеспечивается:
1. системой предотвращения пожаров;
2. системой противопожарной защиты;
3. организационно - техническими
мероприятиями;
4. правильной планировкой производственных
помещений.
Взрывозащита систем повышенного давления достигается
организационно-техническими мероприятиями: разработкой инструктивных
материалов, регламентов норм и правил ведения технологических процессов;
организацией обучения и инструктажа обслуживающего персонала; осуществлением
контроля и надзора за соблюдением норм технологического режима, правил и норм
техники безопасности, пожарной безопасности и т. п.
Кроме того, оборудование повышенного давления оснащают системами
взрывозащиты, которые предполагают: применение гидрозатворов или защиту
аппаратов от разрушения при взрыве с помощью устройств аварийного сброса
давления (предохранительные мембраны и клапаны, быстродействующие задвижки,
обратные клапаны и т.д.).
Чтобы внешний вид трубопровода указывал на свойства транспортируемого
вещества, введена их опознавательная окраска (ГОСТ 14202-69): вода - зеленый,
воздух - синий, масло - коричневый
Для выделения вида опасности на трубопроводы наносят предупреждающие
(сигнальные) цветные кольца, количество которых определяет степень опасности.
Так, на трубопроводы взрывоопасных, огнеопасных, легковоспламеняющихся веществ
наносят красные кольца, безопасных или нейтральных веществ -зеленые, для
обозначения глубокого вакуума, высокого давления - желтый цвет.
Все трубопроводы подвергают гидравлическим испытаниям при пробном
давлении на 25% выше рабочего; так для прессов испытания проводят при давлении
400 атмосфер при рабочем в 320 атмосфер.
Для обеспечения безопасной и безаварийной эксплуатации сосуды и аппараты,
работающие под давлением, подвергаются техническому освидетельствованию после
монтажа и пуска в эксплуатацию, периодически в процессе эксплуатации, а в
необходимых случаях и внеочередному освидетельствованию.
При гидравлических испытаниях испытываемую емкость заполняют водой, после
чего давления воды плавно повышают до значений пробного давления (на 25-30%
больше расчетного рабочего). Применяемая вода имеет температуру не ниже 5°С и
не выше 40°С. Разность температур стенки сосуда и окружающего воздуха во время
испытания не должна вызывать конденсации влаги на поверхности стенок сосуда.
Использование сжатого воздуха или другого газа для подъема давления не
допускается [19].
Проход для рабочих составляет два метра, транспортный
проезд при двустороннем движении пять метров. Въезд в производственное
помещение исключает пороги и выступы. Въездной уклон не более 0,05.
Пожарная безопасность проектируемого производства
обеспечивается: организационно - техническими мероприятиями; системами, которые
могут предотвратить пожар, отсечь, отключить, блокировать устройства защиты
производственного оборудования, установкой пожароопасного оборудования в
специально изолированных помещениях; системами противопожарной защиты
(применение средств пожаротушения - огнетушителей, пожарных кранов, установок
сигнализации пожара и пожаротушения, наличием нужного количества и ширины
выходов для эвакуации);
Показатели противопожарной характеристики
производственного помещения приведены в таблице 60.
Таблица 60 - Противопожарная характеристика
проектируемого производственного здания.
Наименование показателей
|
Величина показателя
|
Прим.
|
1. Категория производства по степени пожарной безопасности
|
Г
|
|
2. Степень огнестойкости проектируемого здания
|
II
|
|
3. Наименьшая суммарная ширина проходов для эвакуации
людей, м
|
2,0
|
|
4. Расстояние от наиболее удаленного рабочего до
эвакуационного выхода, м
|
18,0
|
|
5. Число пожарных постов
|
3
|
1 на 5000 м2
|
6. Число пожарных кранов
|
8
|
|
7. Количество огнетушителей: ОХП-10 ОЧ-2
|
22 11
|
|
Выводы
Литейное производство в промышленности считается одним
из самых вредных и опасных, но при правильном проектировании с точки зрения БЖД
и экологии, возможно, влияние вредных факторов на организм человека и
окружающею среду, уменьшить до минимума.
В результате проделанной работы бал спроектирован литейный цех по
производству профилей из алюминиевых сплавов.
Влияние опасных, вредных и травмирующих факторов
сведены к минимуму, все ПДВ и ПДС соответствуют нормам. В результате расчетов
выяснили, что большой опасности для здоровья и жизнедеятельности этот цех не
представляет, как для людей, работающих в нем, так и проживающих поблизости, за
пределами санитарно-защитной зоны.
литье кристаллизатор алюминиевый
7. Специальная часть проекта: «внедрение автоматизированной
установки «ALMEX» для литья круглых слитков»
В настоящее время существенно возросли требования заказчиков к качеству
продукции. В первую очередь требования касаются ультразвукового контроля
изделий на наличие дефектов (категория «А» - контрольный отражатель Ш 1,2 мм,
максимальная величина дефекта - 2,0 мм), содержания водорода (до 0,2 см3/100
гр. металла) и получения регламентированной структуры. Это в свою очередь
повлекло за собой ужесточение требований к качеству литых заготовок. Кроме
того, появляются заказы на крупногабаритные заготовки из высоколегированных
алюминиевых сплавов, производство которых по серийной технологии не
представляется возможным из-за низкой технологичности сплавов и крупных
размеров заготовок.
Используемое на сегодняшний момент в литейных цехах оборудование и
технологическая оснастка, в полной мере не обеспечивает стабильного качества
отливаемых слитков. Для повышения качества отливаемого металла, а также для
расширения номенклатуры отливаемых слитков предлагается внедрить
автоматизированную установку для отливки круглых слитков «Castright II»
производства компании «Almex USA Inc.».
Одним из преимуществ системы Castright является ее автоматизированность.
Это снижает риск возникновения ситуаций, связанных с угрозой здоровью или жизни
рабочих. Более того, если система обнаруживает наличие условий, представляющих
какую-либо опасность, то автоматически включается система преждевременного
(аварийного) прекращения процесса, что также повышает производительность
процесса и снижает расход металла. В систему входит пакет автоматизации и
ультразвуковая проверка качества слитков в процессе литья и после механической
обработки.
При сравнении поверхности слитков, полученных в типовых кристаллизаторах
цеха и кристаллизаторах Almex, визуально очевидно, что последние имеют более
гладкую поверхность.
К преимуществам новой системы литья относятся следующие:
· Достижение механических характеристик металла с чрезвычайно узким
диапазоном разброса.
· Характеристики металла отвечают самым строгим требованиям
процессов обработки давлением для производства изделий авиационно-космической
промышленности.
· Минимальный съем металла при обточке.
· Высокая повторяемость параметров литья от плавки к плавке.
· Равномерные характеристики поверхности слитка по всей его
длине.
· Низкий процент брака.
· Повышенная производительность литейной системы.
· Снижение времени и затрат на профилактический ремонт
кристаллизатора.
Кристаллизаторы применяются для литья круглых слитков диаметром от 82 до
915 мм. Длина отливаемых в кристаллизаторы слитков ~ 6100 мм. Технические
характеристики кристаллизатора представлены в таблице 63.
Таблица 61 - Характеристики отливаемых слитков.
Диаметр готового слитка, мм
|
Число кристаллизаторов
|
Диаметр слитка после отливки, мм
|
480
|
4
|
498
|
635
|
2
|
660
|
785
|
2
|
816
|
Расход воды для охлаждения слитков равен 1,18 - 2,60 л/мин на 1 см
внутреннего периметра кристаллизатора;
Давление воды для охлаждения слитков составляет 0,70 - 0,84 кг/см2
на выходе в литейный стол;
Температура литья в зависимости от диаметра сплава колеблется в пределах
680 - 710°С;
Высота уровня расплава над кристаллизатором 127 мм +/- 10 мм .
Кристаллизаторы спроектированы таким образом, что колебания уровня металла не
оказывают влияния на качество поверхности слитка и процесс образования
микроструктуры.
Рисунок 19 - Схема конструкции кристаллизатора.
Графитовое кольцо и керамический диск установленные в алюминиевом
кристаллизаторе, прошли специальную термообработку для удаления внутренних
напряжений. Керамические диски покрыты суспензией на основе нитрида бора для
предотвращения смачивания их поверхности алюминием.
Минимальный коэффициент теплообмена в кристаллизаторе достигается с
помощью специальной графитовой кольцевой вставки с непрерывной подачей смазки,
направления струи воды охлаждения под определенным углом на поверхность слитка.
Хотя смазка подводится к графитовому кольцу только в двух точках, за счет
пористости графитовой структуры смазка равномерно распределяется по всему
периметру слитка. В результате слиток имеет не только гладкую поверхность, но и
сверхмелкую структуру по всему поперечному сечению. Так как кристаллизатор
короткий, это гарантирует ведение процесса кристаллизации с плоской, неглубокой
лункой. В результате, микроструктура слитков даже больших диаметров имеет
мелкое зерно по всему профилю слитка.
Входной резервуар для подачи расплава выполнен таким образом, что
начальное заполнение кристаллизатора происходит равномерно. Система построена
на «модульном» принципе, позволяющем осуществлять точный контроль параметров
литья, проверку исправности кристаллизаторов, их подготовку и мелкий ремонт.
Применение датчика давления, установленного внутри литейного стола,
позволяет регистрировать малейшие изменения объема подачи охлаждающей жидкости.
Конструкция кристаллизатора предусматривает установку термопары, что
позволяет вести более точный контроль литейного процесса.
Наличие специального устройство (так называемого «протира») для снятия
воды с поверхности затвердевающего слитка делает условия затвердевания и
охлаждения слитка более «мягкими», снижая вероятность образования трещин.
Описание узлов системы
. Кристаллизаторы и приемники металла
Кристаллизатор выполнен из алюминия марки 6061. Остальные металлические
компоненты выполнены из алюминия и нержавеющей стали, обладающей высокой
коррозионной стойкостью. Специальная марка графита используется для графитовой
вставки-кольца. Керамические диски сделаны из композиционного материала на
основе силиката кальция.
Верх кристаллизатора, стенки, кожух канала подвода воды и опорный фланец
сделаны из единого алюминиевого блока. Это обеспечивает структурную прочность
кристаллизатора и упрощает замену одного стола на другой и снижает время
наладки. Перегородки канала подвода воды хромированы; специальные силиконовые
сальники обеспечивают постоянное давление при подаче воды.
Установка кристаллизатора производится с верхней стороны стола, облегчая,
таким образом, замену и профилактический ремонт кристаллизатора.
Вода входит в кристаллизатор радиально, что облегчает соединение с
подводящей жидкость системой. Внутри водоканала в кристаллизаторе установлены
перегородки для более равномерного распределения потока воды и охлаждения
поверхности слитка. Кристаллизатор спроектирован на максимальную эффективность
охлаждения; процесс постоянно контролируется датчиками давления воды.
. Литейный стол
Столы выполнены из толстолистовой конструкционной стали. После окончания
процесса сварки поверхность стола зачищается с помощью дробеструйной обработки
и покрывается специальной краской для защиты от коррозии.
Столы сделаны таким образом, что остаются неподвижными во время процесса
отливки слитка. Для проверки состояния стола и чистки внутренних водоподводящих
каналов в столе расположены специальные окна-люки.
Все поверхности ответственного назначения проходят точную машинную
обработку и строго перпендикулярны друг другу. Это обеспечивает строго
горизонтальную посадку кристаллизатора в литейном столе.
Специальная интегрированная система, включающая набор вертикальных
направляющих, позволяет столу перемещаться вместе с плитой, на которой
установлены приемники металла. Этим обеспечивается точное соединение
распределителя металла, литейного стола и плиты с приемниками металла. Данная
конструкция не требует подгонки всех частей системы при ее установке на литейную
машину. В результате время, необходимое для подготовки к плавке, значительно
сокращается. Этим обеспечивается более высокая производительность литейной
установки.
. Плита приемников металла
Плита изготовлена из толстолистовой конструкционной стали. Она подвергается
дробеструйной обработке и покрывается специальным антикоррозионным составом
согласно стандартам АА (Aluminum Association).
Все поверхности ответственного назначения проходят точную машинную
обработку, поэтому все приемники металла находятся на одном горизонтальном
уровне. Таким образом, обеспечивается синхронность заполнения кристаллизаторов
на начальном этапе литья.
Плита выполнена таким образом, чтобы исключить ее прогиб как во время
плавки (при соприкосновении с горячим металлом), так и в конце процесса, когда
механическая нагрузка на плиту достигает максимума. Профиль плиты выполнен
таким образом, что поток воды после ее отвода не создает брызг.
Модернизация литейной установки
Пакет автоматизации фирмы Almex USA обеспечит следующее:
1. Плавное движение платформы без рывков в начале плавки и при
остановке.
2. Точное перемещение платформы при низких скоростях движения.
. Точность контроля скорости перемещения платформы +/- 1,5% в
пределах скоростей от 10 мм/мин до 200 мм/мин.
. Полностью автоматизированное перемещение платформы в первые 15
минут процесса по методике «STOP & GO», для полного устранения вероятности
образования трещин.
Рисунок 20 - Вид главного экрана управления процессом литья
На экран панели управления выводятся и могут контролироваться следующие
параметры:
1. Литейная инструкция (марка сплава, диаметр слитка, номер плавки,
и т.д.).
2. Величина ускорения и замедления хода платформы.
. Скорость движения платформы.
. Длина слитка в любой момент процесса.
. Данные об расходе охлаждающей воды, ее температуре и давлении.
. Уровень воды в литейной яме, ее температура и число работающих
насосов.
. Перепад давления на входе и выходе из фильтра очистки воды.
8. Состояние контрольных приборов пуска и прекращения подачи воды.
9. Непрерывная индикация температуры металла в миксере и вывод графика
«Температура-Время», а также температуры металла в распределителе.
10. Непрерывное построение любых графиков процесса (максимум 8
параметров). Мгновенный анализ архивных данных процесса литья за последние 90
дней.
. Наличие сигнального устройства оповещающего об отклонении
какого-либо из параметров от допускаемой величины.
. Индикация параметров работы системы автоматической подачи
смазки.
. Индикация параметры работы системы подачи модифицирующего прутка
в желоб.
. Индикация состояния компонентов системы перед началом литья.
15. Индикация уровня металла в распределителе.
Система ультразвукового тестирования
Специальная методика Ultrex, разработанная фирмой Almex USA, позволяет
проводить ультразвуковой контроль качества продукции по двум категориям:
определение трещинообразования в процессе литья плоских и круглых слитков и
ультразвуковая инспекция готовой продукции.
Первая определяет поверхностные трещины и трещины в середине слитка, тем
самым значительно снижая стоимость производства. В зависимости от ситуации,
оператор либо останавливает трещинообразование, либо прекращает литье, а вторая
методика была специально разработана для проверки полуфабрикатов, идущих на изготовление
деталей авиационной промышленности. Проверка проводится после механической
обработки. Дефекты размером от 75 микрон являются достаточно большими, чтобы
повлиять на качество конечной продукции, поскольку размер дефекта увеличивается
в процессе термо-механической переработки.
Технико-экономическое обоснование от внедрения нового агрегата
Экономическая целесообразность нововведения устанавливается при
рассмотрении базового процесса и предлагаемого нового процесса. Определяется по
минимуму приведенных затрат.
где
Зпрi - приведенные затраты на единицу изделия по i - му варианту;i
- себестоимость изготовления единицы продукции по i- му варианту;
Ен
- нормативный коэффициент экономической эффективности капитальных затрат;
Кi
- капиталовложения в расчете на единицу изделия по i - му варианту;
где
КiS - общие затраты на изготовление единицы продукции по
i - му варианту;гi - годовая программа выпуска по i - му варианту
Затем
определяется отношение:
где
DС=(Сбаз - Снов) - разность
себестоимости изготовления единицы продукции по базовому и новому варианту;
DК=|Кнов - Кбаз| - разность
капитальных затрат на единицу изделия по новому и базовому варианту;
Экономический
эффект считается по формуле:
Заключение
В дипломном проекте спроектирован литейный цех литья круглых полых и
сплошных слитков из сплавов 7175, АД1, 6082. Разработан технологический процесс
производства литых заготовок из указанных сплавов. Подобрано необходимое
количество оборудования, приведены его основные характеристики.
В записке представлен расчет стоимости оборудования, рассчитана
себестоимость процесса и определено необходимое количество обслуживающего
персонала. Разработаны необходимые меры по защите от вредных факторов
производства, рассчитан коэффициент опасности производства.
В специальной части дипломной записки спроектирована новая литейная
установка, конструкция кристаллизатора с тепловой насадкой, которая позволяет
отливать слитки лучшего качества, и успешно внедрена в производство на ОАО СМЗ.
Внедрение этой установки позволило модернизировать технологический процесс,
снизить себестоимость продукции, увеличить выход годного и получить
значительный экономический эффект от ее внедрения.
Приведены расчетные данные по требуемым разделам проекта для
специальности 150106. Представлен необходимый графический материал, облегчающий
усвоение материала.
Список используемой литературы
1. Алюминиевые сплавы. Плавка и литье алюминиевых сплавов.
Справочник./ Под общей редакцией Добаткина В.И. - М.: Металлургия, 1983. - 352
с.
2. Захаров А.М. Промышленные сплавы цветных металлов;
фазовый состав и структурные составляющие. М.: Металлургия, 1989. - 256 с.
. ГОСТ 4784-97. Межгосударственный стандарт. Алюминий
и сплавы алюминиевые деформируемые. - М.: Издательство стандартов, 1999. - 12
с.
. Мальцев М.В. Металлография промышленных цветных
металлов и сплавов. М.: Металлургия, 1970. 568 с.
. Мельников А.А., Бунова Г.З. Технология
термообработки алюминиевых полуфабрикатов. Учебное пособие. Самара, СГАУ, 1996.
- 87 с.
. Колачев Б.А., Елагин В.И., Ливанов В.А..
Металловедение и термическая обработка цветных металлов и сплавов. Учебник для
ВУЗов. М.: МИСИС, 1999. - 416 с.
. Авиационные материалы. Справочник в 9 томах. Т.4.
Часть 1./ Под общей редакцией д.т.н. Шалина Р.Е. - М.: ОНТИ, 1982. - 1150 с.
. Колобнев И.Ф. Термическая обработка алюминиевых
сплавов. М.: Металлургиздат, 1961. - 416 с.
. ГОСТ 11069-74. - Государственный стандарт. Алюминий
первичный. - М.: Издательство стандартов, 1998. - 8 с.
. Фридляндер И.Н. Высокопрочные деформируемые
алюминиевые сплавы. М.: ОБОРОНГИЗ, 1960. - 292 с.
. Колачев Б.А., Габидуллин Р.М., Пигузов Ю.В.
Технология термической обработки цветных металлов и сплавов. М.: Металлургия,
1992. - 272 с.
. Сосненко М.Н. Шихтовщик литейного цеха. М.: «Высшая
школа», 1972. - 231 с.
. Юдкин В.С. Производство и литье сплавов цветных
металлов. Ч.2. Технологические основы процессов литья цветных металлов и
сплавов. - М.: Металлургия, 1971. - 424 с.
. Пикунов М.В. Плавка металлов, кристаллизация
сплавов, затвердевание отливок. Учебное пособие для ВУЗов. - М.: МИСИС, 1997. -
376 с.
. Промышленные алюминиевые сплавы. Справочное
издание./ Под редакцией Алиева С.Г., Альтман Н.Б., Амбарцумян С.М. и др. М.:
Металлургия, 1984. - 528 с.
. Горшков И.Е. Литье слитков цветных металлов и
сплавов. М.: Металлургиздат, 1952. - 416 с.
. Липницкий А.М., Морозов И.В., Яценко А.А. Технология
цветного литья. М.: Машиностроение, 1986. - 225 с.
. Городничий Н.И. Литейное производство цветных
металлов и сплавов. М.: металлургия, 1989. - 104 с.
. Охрана труда в машиностроении./ Под редакцией Белова
С.В. М.: Машиностроение, 1983. - 430 с.
. Безопасность жизнедеятельности. Учебник для ВУЗов./
Под редакцией Белова С.В. 2-е издание исправленное и дополненное. М.: «Высшая
школа», 1999. - 448 с.
. Долин П.А. Справочник по технике безопасности. 5-е
издание исправленное и дополненное. М.: Энергоиздат, 1982. - 800 с.
. Справочник по гигиене труда./ Под редакцией Карпова
Б.Д. и Коваленко В.Е. М.: Медицина, 1986. - 536 с.
. ГОСТ Р 12.4.026-2001 «ССБТ. Цвета сигнальные, знаки
безопасности и разметка сигнальная. Назначение и правила применения. Общие
технические требования и характеристики. Методы испытаний».
. ГОСТ 12.4.045-87 «ССБТ. «Костюмы мужские для защиты
от повышенных температур. Технические условия».
. ГОСТ 12.4.207-99 «ССБТ. Каски защитные. Общие
технические требования. Методы испытаний».
. ГОСТ 12.4.010-75 «ССБТ. Средства индивидуальной
защиты. Рукавицы специальные. Технические условия».
. ГОСТ 12.4.013-97 «ССБТ. «Очки защитные. Общие
технические условия».
. ГОСТ 12.4.023-84 «ССБТ. Щитки защитные лицевые.
Общие технические требования и методы контроля.»
Приложение А
Технологические параметры литья слитков из сплава В95 в кристаллизатор с
тепловой насадкой.
Марка сплава
|
В95
|
Параметры
|
Значение
|
Допуск
|
Диаметр, мм
|
660
|
Скорость литья в установившемся режиме, мм/мин
|
19,9
|
|
Номер рецепта
|
0000-0660-0095-1
|
Скорость подачи прутка Al-Ti-B, м/мин
|
0,3
|
|
|
Температура расплава в желобе, град
|
695
|
10
|
Применяется для отливки сплавов
|
Температура воды в кристаллизаторе, град
|
30
|
5
|
7075, 7175, В95, В95пч, В95оч, 1933
|
Уровень металла, мм
|
75
|
25
|
|
Начальная скорость подачи воды, куб.м/час
|
60
|
15
|
Длина дистанционных втулок, мм
|
185
|
Способ распределения воды
|
всего
|
|
|
|
Способ поддержания воды в приямке
|
последный
|
|
Шаг
|
Скорость литья, мм/мин
|
Общий объем воды, куб.м/час
|
Время платформы в остановке, сек
|
Время платформы в движении, сек
|
1
|
20,5
|
60
|
30
|
15
|
2
|
20,5
|
60
|
15
|
15
|
3
|
20,5
|
60
|
5
|
20
|
4
|
20,5
|
60
|
5
|
60
|
5
|
20,5
|
60
|
5
|
120
|
6
|
20,5
|
60
|
5
|
60
|
7
|
20,5
|
60
|
5
|
60
|
8
|
20,5
|
60
|
5
|
60
|
9
|
20,5
|
60
|
5
|
150
|
10
|
20,5
|
60
|
5
|
60
|
11
|
20,5
|
60
|
5
|
30
|
12
|
20,5
|
60
|
5
|
30
|
13
|
20,3
|
60
|
5
|
30
|
14
|
20,1
|
60
|
5
|
60
|
15
|
20,1
|
60
|
0
|
30
|
|
|
|
|
|
|
|
|