Зварювальний апарат. Призначення та особливості
Дипломна
робота
Зварювальний
апарат. Призначення та особливості
Зміст
Вступ
Розділ
1. Історія зварювання
.1
Види зварювальних апаратів
.2
Зварювальний трансформатор
.3
Зварювальний випрямляч
.4
Зварювальний генератор
.5
Зварювальний інвертор
1.6
Зварювальний напівавтомат
.7
Зварювальний автомат
Розділ
2
.1
Змащування поверхонь тертя, його значення
.2
Способи і системи змащування вузлів машин
.3
Рідкі змащувальні матеріали. Асортимент рідких змащувальних матеріалів
.4
Консистентні змащувальні матеріали, їх асортимент
.4.1
Асортимент консистентних мастил
.5
Тверді змащувальні матеріали
.6
Види і періодичність технічного обслуговування автомобіля
3.
Інструкція
з охорони праці
Висновок
Список
використаних літературних джерел
Вступ
Серед всього будівельного
устаткування зварювальний апарат займає особливе місце хоча б тому, що жодна
будівництво без нього не обходиться іншого способу надійно з’єднати металеві
конструкції і труби просто не існує. Що могло б замінити зварне з’єднання?
Кріплення анкерами, болтами або заклепками, з’єднання труб хомутами всі ці і
подібні їм способи дають або тимчасове вирішення проблеми, або незастосовні з
безлічі причин. Зварювальні апарати бувають різних конструкцій і типів
трансформатори, випрямлячі, інвертори, генератори, напівавтомати.
Підвищення надійності і збільшення
строків служби є одним з першочергових завдань сучасного машинобудування.
Терміни експлуатації машин при цьому обмежуються в основному недостатньою
зносостійкістю їх складових вузлів і деталей.
Технічне обслуговування це комплекс
операцій, які спрямовані на підтримання автомобіля в справному та працездатному
стані і проводяться в процесі експлуатації автомобіля.
Мета технічного обслуговування і
ремонту підтримування дорожніх транспортних засобів у технічно справному стані
та належному зовнішньому вигляді, забезпечення надійності, економічності,
безпеки руху та екологічної безпеки.
Серед існуючих конструкторських,
технологічних та експлуатаційних методів забезпечення зносостійкості найбільш
ефективними є підходи, пов'язані з раціональним вибором мастильного матеріалу і
системи змащення, зокрема, створення і забезпечення умов для подачі мастила в
зону тертя.
Метою моєї дипломної роботи є
роз'яснення про зварювальні апарати їх призначення та особливості. Також
визначення об'ємів робіт по виконанню ЩТО, ТО1, ТО2, і СТО.
РОЗДІЛ 1. Історія зварювання
В. В. Петров, професор фізики
СанктПетербурзької медикохірургічної академії (1761 1834рр.), у 1802 році
першим у світі відкрив електричну дугу. Він описав явища, що відбуваються в
ній, а також вказав на можливість її практичного застосування. А вже у 1881
році російським винахідником Н. Н. Бенардос (18421905рр.) було застосовано
електричну дугу, яка горіла між вугільним електродом і зварюваним металом, для
з'єднання і роз'єднання сталі. Для утворення шва в ролі присадочного прутка
використовували сталевий дріт. Як джерело електричної енергії використовувалися
акумуляторні батареї. Також М.М. Бенардосом були відкриті й інші види
зварювання: контактна точкова зварка, дугова зварка декількома електродами в
захисному газі, а також механізована подача електрода в дугу. У 1888 році
російський інженер Н. Г. Славянов (18541897рр.) запропонував дугове зварювання
плавким металевим електродом. Він розробив наукові основи дугового зварювання,
застосував флюс для захисту металу зварювальної ванни від дії повітря,
запропонував наплавлення і зварювання чавуну. Н. Г. Славянов виготовив
зварювальний генератор своєю конструкцією. Ним був організований
електрозварювальний цех в Пермських гарматних майстерень, який був перший в
світі. Там він працював з 1883 по 1897р. Н. Н. Бенардос і Н. Г. Славянов
поклали початок автоматизації зварювальних процесів. Їхні винаходи знайшли
практичне застосування тільки після Великої Жовтневої соціалістичної революції
та набули поширення в багатьох країнах світу. Вже на початку 20х рр.. на
Далекому Сході проводили ремонт суден дуговим зварюванням, а також виготовлення
зварних котлів, а дещо пізніше зварювання судів і відповідальних конструкцій. В
1924 році Ленінградським заводом «Електрик» було вперше виготовлено
зварювальний генератор СМ1 і зварювальний трансформатор з нормальним магнітним
розсіюванням СТ2. Адже розвиток і промислове застосування зварювання вимагало
розробки і виготовлення надійних джерел живлення, що забезпечують стійке
горіння дуги. У тому ж році радянський вчений В.П. Нікітін розробив принципово
нову схему зварювального трансформатора типу СТН. Випуск таких трансформаторів
заводом «Електрик» почав з 1927р. У 1928 році вчений Д.А. Дульчевский винайшов
автоматичне зварювання під флюсом. Новий етап у розвитку зварювання відноситься
до кінця 30их років, коли колективом інституту електрозварювання АН УРСР під
керівництвом академіка Є. О. Патона був розроблений промисловий спосіб автоматичного
зварювання під флюсом. Впровадження його у виробництво почалося з 1940р.
Зварювання під флюсом зіграла величезну роль в роки війни при виробництві
танків, самохідних гармат та авіабомб. Пізніше був розроблений спосіб
напівавтоматичного зварювання під флюсом. Наприкінці 40их років отримала
промислове застосування зварювання в захисному газі. Колективами Центрального
науководослідного інституту технологій машинобудування та Інституту
електрозварювання імені Є.О. Патонова розроблена і в 1952 році впроваджена
напівавтоматичне зварювання у вуглекислому газі. Величезним досягненням
зварювальної техніки є розробка колективом ІЕС у 1949 році електрошлакового
зварювання, що дозволяє зварювати метали практично будьякої товщини. Автори
зварювання у вуглекислому газі плавким електродом і електрошлакового зварювання
К.М. Новожилов, Г.З. Волошкевич, К. В. Любавський та ін удостоєні Ленінської
премії. У наступні роки в країні стали застосовуватися: зварювання
ультразвуком, електронно променева, плазмова, дифузійна, холодне зварювання,
зварювання тертям і ін. Великий внесок у розвиток зварювання внесли російські
вчені: В. П. Вологдін, В. П. Нікітін, Д.А. Дульчевскій, Е.О. Патонів, а також
колективи Інституту електрозварювання імені Є.О. Патонова, Центрального науково
дослідного інституту технології машинобудування, Всесоюзного науководослідного
і конструктивного інституту автогенного машинобудування, Інституту металургії
імені А.А. Байкова, ленінградського заводу «Електрик» і ін. Зварювання в
багатьох випадках замінила такі трудомісткі процеси виготовлення конструкцій,
як лиття, з'єднання на різьбленні і кування.
Перевага зварювання перед цими
процесами наступні:
• економія металу 10 ... 30% і
більше в залежності від складності конструкції;
• зменшення трудомісткості робіт,
скорочення термінів робіт і зменшення їх вартості; • здешевлення обладнання;
• можливість механізації і
автоматизації зварювального процесу;
• можливість використання
наплавлення для відновлення зношених деталей;
• герметичність зварних з'єднань
вище, ніж клепаних або різьбових;
• зменшення виробничого шуму і
поліпшення умов праці робітників. Зварювання існує двох видів:
зварювання плавленням, яке
здійснюється при нагріванні сильним концентрованим джерелом тепла (електричної
дугою, плазмою та ін..) кромок зварюваних деталей, в результаті чого кромки в
місці з'єднання розплавляються, мимовільно зливаються, утворюючи загальну
зварювальну ванну, в якій відбуваються деякі фізичні і хімічні процеси;
зварювання тиском, яке здійснюється
пластичним деформуванням металу у місці з'єднання під дією стискаючих зусиль. В
результаті різні забруднення і окиси на зварювальних поверхнях витісняються
назовні, а чисті поверхні зближуються по всьому перетину на відстань атомного
зчеплення.
Виділяють наступні основні види
зварювання:
ручне дугове зварювання до
електроду і металу, що зварюється підводиться змінний або постійний струм, в
результаті чого виникає дуга, постійну довжину якої необхідно підтримувати
протягом усього процесу зварювання;
дугове зварювання під флюсом дуга
горить під шаром зварювального флюсу між кінцем голою електродного дроту.
При горінні дуги і плавленні флюсу
створюється газошлакова оболонка, що перешкоджає негативному впливу
атмосферного повітря на якість зварного з'єднання;
дугове зварювання в захисному газі
проводиться як неплавким (вольфрамовим частіше), так і електродом, який
плавиться; при зварюванні неплавким електродом дуга горить між електродом і
зварюваних металом у захисному інертному газі.
Зварювальний дріт вводиться в зону
зварювання з боку;
зварювання електродом, що плавиться,
виконується на напівавтоматах та автоматах.
Дуга в даному випадку виникає між
голим дротом, який безперервно подається, і зварюваним металом.
В якості захисних газів застосовують
інертні (аргон, гелій, азот) і активні гази (вуглекислий газ, водень, кисень),
а також суміші аргону з гелієм, або вуглекислим газом, або киснем; вуглекислого
газу з киснем та ін..
Газове зварювання нагрівання до
розплавлення зварювальних кромок і зварювального дроту високотемпературним
газокисневим полум'ям від зварювального пальника. Як пальне газу застосовується
ацетилен і його замінники (пропанбутан, природний газ, пари рідких горючих та
ін..).
Електрошлакове зварювання
застосовується для з'єднання виробів будьякої товщини у вертикальному
положенні. Листи встановлюють із зазором між кромками, що зварюються. У зону
зварювання подають дріт і флюс. Дуга горить тільки на початку процесу. В
подальшому після розплавлення певної кількості флюсу дуга гасне, і струм
проходить через розплавлений шлак. контактне зварювання здійснюється при
нагріванні деталей електричним струмом і їх пластичної деформації (здавлюванні)
в місці нагрівання. Місцеве нагрівання досягається за рахунок опору
електричному струму зварюваних деталей в місці їх контакту.
Існує кілька видів контактного
зварювання, що відрізняються формою зварного з'єднання, технологічними
особливостями, способами підведення струму і живлення електроенергією.
Види контактного зварювання:
• стиковим контактним зварюванням
зварювані частини з'єднують по поверхні з'єднуваних торців;
• точковим контактним зварюванням
з'єднання елементів відбувається на ділянках, обмежених площею торців
електродів, що підводять струм і передають зусилля стиснення;
• рельєфне контактне зварювання здійснюється
на окремих ділянках за заздалегідь підготовленим виступам - рельєфів;
• шовним контактним зварюванням
з'єднання елементів виконується внахлестку обертовими дисковими електродами у
вигляді безперервного або переривчастого шва.
Електроннопроменеве зварювання
використання кінетичної енергії електронів, що швидко рухаються в глибокому
вакуумі. При бомбардуванні поверхні металу електронами переважна частина їх
кінетичної енергії перетворюється на теплоту, яка використовується для
розплавлення металу. Для зварювання необхідно: отримати вільні електрони,
сконцентрувати їх і надати їм велику швидкість, щоб збільшити їхню енергію, яка
при гальмуванні електронів при зварюванні перетворюється в теплоту.
Електроннопроменевим зварюванням зварюють тугоплавкі і рідкісні метали,
високоміцні, жароміцні і корозійностійкі сплави та сталі.
Дифузійне зварювання в вакуумі має
такі переваги: метал не доводиться до розплавлення, що дає можливість отримати
більш міцні зварні з'єднання і високу точність розмірів виробів; дозволяє
зварювати різнорідні матеріали: сталь з алюмінієм, вольфрамом, титаном,
металокерамікою, молібденом, мідь з алюмінієм і титаном , титан з платиною і т.
п. плазмовим зварюванням можна зварювати як однорідні, так і різнорідні метали,
а також неметалічні матеріали. Температура плазмової дуги, яка застосовується у
зварювальній техніці, досягає 30 000 С. Для отримання плазмової дуги
застосовуються плазмотрони з дугою прямої або непрямої дії. У плазмотронах
прямої дії плазмова дуга утворюється між вольфрамовим електродом і основним
металом. Сопло в такому випадку електрично нейтрально і служить для стискання
та стабілізації дуги. У плазмотронах побічної дії плазмова дуга створюється між
вольфрамовим електродом і соплом, а струмінь плазми виділяється з стовпа дуги у
вигляді факела. Дугу плазмової дії називають плазмовим струменем. Для утворення
стислої дуги вздовж її стовпа через канал в соплі пропускається нейтральний
одноатомний (аргон, гелій) або двоатомний газ (азот, водень та інші гази та їх
суміші). Газ стискає стовп дуги, підвищуючи тим самим температуру стовпа.
лазерне зварювання.
Лазер оптичний квантовий генератор
(ОПГ).
Випромінювачем активним елементом
в ОРГ можуть бути:
) тверді тіла скло з неодимом,
рубін і ін..,
) рідини розчини окису неодиму,
барвники та ін..,
) гази та газові суміші водень,
азот, вуглекислий газ і ін..,
) напівпровідникові монокристали
арсеніди галію та індію, сплави кадмію з селеном і сіркою та ін.
Обробляти можна метали та неметалеві
матеріали в атмосфері, вакуумі і в різних газах. При цьому промінь лазера
вільно проникає через скло, кварц, повітря. холодне зварювання металів при
додатковому великому тиску до елементів, що з'єднуються, у місці їх контакту
відбувається пластична деформація, що сприяє виникненню міжатомних сил
зчеплення і призводить до утворення металевих зв'язків. Зварювання виробляється
без застосування нагріву. Цим способом зварюють пластичні метали: мідь,
алюміній і його сплави, свинець, олово, титан. зварювання тертям виконується в
твердому стані під впливом теплоти, що виникає при терті поверхонь зварюваних
деталей, з наступним додатком стискаючих зусиль.
Міцне зварне з'єднання утворюється в
результаті виникнення металевих зв'язків між контактуючими поверхнями
зварюваних деталей.
Високочастотне зварювання засноване
на нагріванні металу пропусканням через нього струмів високої частоти з
подальшим здавлюванням обтискними роликами. Таке зварювання може вироблятися з
підведенням струму контактами і з індукційним підведенням струму. зварювання
ультразвуком, при якому нероз'ємне з'єднання металів утворюється при
одночасному впливі на деталі механічних коливань високої частоти і відносно
невеликих стискаючих зусиль. Цей спосіб застосовується при зварюванні металів,
чутливих до нагріву, пластичних металів, неметалевих матеріалів. зварювання
вибухом засноване на впливі спрямованих короткочасних надвисоких тисків енергії
вибуху порядку (100 ... 200) Х 108 Па на деталі, що зварюються.
Зварювання вибухом використовують
при виготовленні заготовок для прокату біметалу, при плакіровці поверхонь
конструкційних сталей металами і сплавами з особливими фізичним і хімічними
властивостями, а також при зварюванні деталей з різнорідних металів і сплавів
Зварювальні апарати поділяються на:
Зварювальний трансформатор
<#"807456.files/image001.gif">
Рис.1 Тип зварювання.
Серед всього будівельного
устаткування зварювальний апарат займає особливе місце хоча б тому, що жодна
будівництво без нього не обходиться - іншого способу надійно з’єднати металеві
конструкції і труби просто не існує. Що могло б замінити зварне з’єднання?
Кріплення анкерами, болтами або заклепками, з’єднання труб хомутами - всі ці і
подібні їм способи дають або тимчасове вирішення проблеми, або незастосовні з
безлічі причин. Зварювальні апарати бувають різних конструкцій і типів -
трансформатори, випрямлячі, інвертори, генератори, напівавтомати - розібратися
в цьому різноманітті допоможе дана дипломна робота.
.2 Зварювальний трансформатор
Його завдання зниження напруги з
електричної мережі до необхідного рівня (нижче 141 V) і регулювання
зварювального струму до бажаних значень.
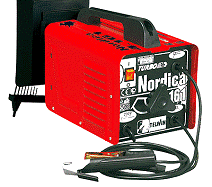
Рис.2 Зварювальний трансформатор.
Конструкція будьякого трансформатора
повинна відповідати ГОСТ 9577, вона включає в себе сталевий магнітопровід
(сердечник) і дві обмотки в ізоляції - первинну (підключається до мережі) та
вторинну (з’єднана з тримачем електродів і об’єктом зварювання). У
трансформаторах популярної серії ТДМ первинна обмотка жорстко з’єднана із
серцевиною, котушки вторинної обмотки віддалені від котушок первинної (їх по
дві на кожну обмотку) на певну дистанцію. Запалювання дуги вимагає напруги на
вторинній обмотці в діапазоні 5560 V, для більшості електродів, застосовуваних
при ручного зварювання, досить 50 V.
Обертанням гвинта з допомогою ручки
сполучені з серцевиною котушки вторинної обмотки переміщаються по вертикалі -
виконується налаштування зварювального струму до необхідних параметрів. При
зближенні обмоток (рукоять обертають за годинниковою стрілкою) зменшуються
індуктивний опір і магнітний потік розсіювання, зварювальний струм при цьому
зростає, зворотним обертанням досягається його зменшення. Діапазон регулювання
зварювального струму: при паралельному з’єднанні котушок в обох обмотках -
65460 А, при послідовному - 40180 А. Рукоятка на кришці трансформатора
призначена для перемикання діапазонів струму.
Що відбувається в зварювальному
трансформаторі при підключенні його до мережі змінного струму? Надходження
змінного струму в первинну обмотку викликає намагнічування сердечника.
Пройшовши через вторинну обмотку, магнітний потік сердечника викликає в неї
змінний струм більш низької напруги, ніж надходить на первинну обмотку. При
більшій кількості витків на вторинній обмотці напруга буде вищим, при меншому -
напруга нижче.
Величина зварювального струму
регулюється за допомогою керованого індуктивного опору, міняючого потік
магнітного розсіювання. Способів зміни зварювального струму два: переміщуються
котушки (як у трансформатори ТДМ), магнітні шунти або витковое (ступеневу)
регулювання; додаток конструкції трансформаторів реактивної котушкою. Вибір
способу регулювання залежить від магнітного розсіювання у даному
трансформаторі: при підвищеному розсіюванні використовується перший спосіб
регулювання; при нормальному - другий.
ККД зварювальних трансформаторів
невисокий - рідко перевищує 80% бар’єр, їх вага значний. Проводячи зварювальні
роботи з цим обладнанням складно добитися високої якості шва, хіба що
використовувати особливі стабілізуючі електроди, здатні поліпшити зварний шов.
Однак мінуси зварювальних трансформаторів компенсуються невисокою ціною і їх
невибагливістю.
1.3 Зварювальний випрямляч
<#"807456.files/image003.gif">
Рис.3 Зварювальний випрямляч.
Регулювання зварювального
струму в випрямлячі виконується трьома способами: збільшенням/зменшенням
дистанції між обмотками; з допомогою дроселя насичення; обмоток трансформатора,
розділених на секції. Схеми, за якими збираються зварювальні випрямлячі -
трифазна мостова і однофазна бруківка з двухполупериодным випрямленням. Зборка
по першій схемі більш поширена, оскільки побудований за нею випрямляч містить у
конструкції менше число вентилів - при цьому зварювальний дуга горить більш
стійко.
Зварювальний випрямляч дуже
нестійкий до перегріву - необхідно постійно стежити за справністю вентиляторів
охолодження, інакше зварювальний апарат згорить.
Зварювальні випрямлячі
призначені для перетворення змінного струму в постійний і живлення ним
зварювальної дуги.
Випрямлячі класифікуються:
за числом обслуговуваних
постів - одно та багатопостові;
за числом фаз живлення -
однофазні й трифазні;
за типом вентилів - діодні,
тиристорні, інверторні;
за способом регулювання
струмом або напругою - із механічним регулюванням рухомими обмотками (типу ВД
для ручного зварювання), які регулюються зміною коефіцієнта трансформації
силового трансформатора (типу ВС для механізованого зварювання у вуглекислому
газі), з регулюванням методом магнітної комутації (типу ВСЖ), які регулюються
за допомогою дроселя насичення (типу ВДГ); із регулюванням тиристорами
(універсальні випрямлячі);
за схемою випрямлення -
однонапівперіодні, трифазні, шестифазні;
за призначенням - для ручного
дугового зварювання (зі спадаючими зовнішніми характеристиками), для
механізованого зварювання під флюсом (зі спадаючими зовнішніми
характеристиками), для механізованого зварювання у вуглекислому газі (з
похилоспадаючими зовнішніми характеристиками), універсальні (для всіх видів
зварювання з круто та похилоспадаючими характеристиками).
Основними елементами
випрямляча є: трансформатор, регулюючий пристрій і напівпровідникові вентилі
(селенові, кремнієві або германієві), які проводять струм тільки в одному
напрямку. Для зменшення розбризкування електродного металу та для згладжування
пульсації струму у коло постійного струму деяких випрямлячів умикають дросель.
Випрямлячі малих струмів (до
315 А) роблять за трифазною мостовою схемою; середніх струмів (до 500 А) - за
шестифазною із зрівняльним реактором; великих струмів (понад 1000 А) - за
шестифазною кільцевою схемою випрямлення.
Для ручного дугового
зварювання використовуються випрямлячі типів ВД102, ВД201, ВД306 Д (БУСПТИГ)
(ТИГДС), ВД506 Д (ММАДС) та інші, де:
БУСП - блок керування
зварювальним процесом;
ДС - постійний струм;
ТИГ - режим аргонодугового
зварювання неплавким електродом;
ММА - режим дугового
зварювання покритим електродом;
МИГ/МАГ - режим
напівавтоматичного зварювання плавким електродом у середовищі захисних газів.
Для механізованого зварювання
використовують випрямлячі типу: ВС300, ВДГИ301,ВСЖ303, ВДГ401 та ін.
До джерел живлення
універсального призначення відносяться випрямлячі типу:ВДУ504, ВДУ506С
(МИГ/МАГ), ВДУ601, ВДУ1250 та ін., а також інверторні - «Пирс160», ВДУ230ІУХЛ4,
Рісо140.
У багатопостових випрямлячах
типу ВДМ1001, ВДМ1601, ВДМ3001 та інших, струм регулюється баластним реостатом
РБ301, РБ501, а напруга дуги при механізованому зварюванні у вуглекислому газі
- баластним реостатом РБГ і дроселем ДГ301, які з'єднані паралельно й
вмикаються послідовно з дугою.
Особливістю інверторних
випрямлячів є те, що трансформація (перетворення) напруги здійснюється на
підвищеній частоті. Це дає можливість знизити у 45 разів масу джерела живлення,
у 78 разів габарити устаткування, на 710% збільшити к.к.д., підвищити
зварювальні властивості порівняно із звичайними джерелами живлення струму.
У тиристорних випрямлячах
регулювання режиму зварювання та створення зовнішніх характеристик здійснюють
за допомогою тиристорного вирівнювального блоку. Тиристор - це керований
кремнієвий вентиль. Він має третій керуючий електрод і призначений для
випрямлення та регулювання сили струму. Керування тиристорами здійснюється
фазозсувним пристроєм, яким можна змінювати за фазою кут відкривання тиристора
щодо початку синусоїди напруги живильної сітки і тим самим регулювати середнє
значення випрямленого струму. Фазозсувний пристрій має малу потужність, а
значить і невеликі розміри та масу. Випускають тиристорні універсальні випрямлячі
ВДУ504, ВДУ505, ВДУ506, ВДУ601, ВДУ1201. Для плазмового різання розроблені
тиристорні випрямлячі типу ВПТМ500 та ін.
Для малоамперної дуги з
неплавким електродом на постійному або імпульсному струмі випускають
транзисторні випрямлячі АП4 та АП5, у яких регулювання струму здійснюється
транзисторами. Транзистор - це керований напівпровідниковий вентиль, в якому
опір змінюється під впливом керуючого сигналу. їх вмикають у зварювальне коло
послідовно з випрямлячем. Зварювальний струм регулюється плавно та безінерційно
зміною струму керування транзисторів. Він не залежить від коливань напруги
живильної сітки й зміни напруги на дузі. Транзисторні випрямлячі безпечні у
роботі, оскільки напруга холостого ходу не перевищує 40 В. Такі джерела
живлення застосовують для аргонодугового зварювання вольфрамовим електродом
будьякого металу малої товщини.
.4 Зварювальний генератор
<#"807456.files/image004.gif">
|
|
Рис.4. Схеми зварювальних
генераторів постійного струму
Під час холостого ходу ЕРС
генератора і напруга на головних щітках a, b і на дузі залежатимуть тільки від
магнітного потоку паралельної обмотки. При горінні дуги зварювальний струм
проходить через послідовну (серійну) обмотку , увімкнену так, що її магнітний
потік Фс спрямований проти магнітного потоку Фп. Тому ЕРС генератора, яка
індукується в обмотці якоря генератора результуючим магнітним потоком, також
знизиться, і це зумовить зниження напруги на дузі. При короткому замиканні
потік Фс майже дорівнюватиме потоку Фп, тому результуючий магнітний потік і
напруга на головних щітках a, b і на дузі також знизяться майже до нуля.
Зварювальний струм у генераторах
цього типу регулюється зміною струму збудження паралельної обмотки за допомогою
реостата 2 або зміною числа витків паралельної і серієсної обмоток.
Багатопостові зварювальні генератори
постійного струму
(рис. 4.3, б) мають послідовну 1 і паралельну З обмотки збудження, які
створюють магнітні потоки відповідно Фс і Фп одного напряму, тому зовнішня
характеристика у цих генераторах не спадна, а жорстка. Щоб мати спадну
характеристику на дузі, на кожному робочому місці послідовно з дугою вмикають
баластні реостати 4. При замиканні зварювального кола частина напруги
генератора втрачається на баластному реостаті за рівнянням
Up =І R,
де Up− втрата напруги на
реостаті, В; R − опір реостата, Ом. Отже, напруга на дузі
UД= UГ+ Uр
де UГ − напруга генератора, В.
При короткому замиканні втрата
напруги на баластному реостаті майже дорівнює напрузі на затискачах генератора
і тому напруга на дузі спадає майже до нуля. Баластним реостатом регулюють
також силу зварювального струму, а реостатом 2 змінюють напругу холостого ходу
генератора.
Зварювальні генератори, встановлені
на одному валу з двигунами, називають зварювальними перетворювачами. Це
однопостові генератори ПСО300, ПСО500, багатопостовий ПСМ1000 та ін.
Зварювальні генератори створюються
за кількома схемами, серед яких найбільш популярні дві. Перша - обмотка
порушення незалежна, розмагнічування відбувається через послідовну обмотку.
Харчування такого генератора виконується через випрямляч з селеновими вентилями
від мережі змінного струму - утворюється магнітний потік, индуктирующий напруга
на щітки генератора, що викликає порушення дуги. Змінюючи (перемикаючи) на
послідовній обмотці число витків, оператор зварювання регулює зварювальний
струм до необхідних характеристик.
Друга за популярністю схема
зварювального генератора - обмотка порушення паралельна, обмотка
розмагнічування послідовна. Для магнітних полюсів таких генераторів потрібно
феромагнітна сталь - вони повинні володіти залишковим магнетизмом. В якості
джерела живлення використовується бензиновий (дизельний) двигун.
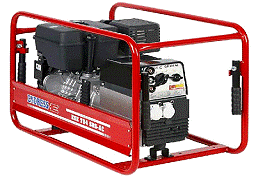
Рис.5. Зварювальний генератор.
За своїми характеристиками
зварювальні генератори далеко не ідеальні - вони дорогі, мають складну
конструкцію, їх ККД низький (0,7), високий витрата електроенергії (5 кВт/год на
кг розплавленого металу). Проте в польових умовах без них не обійтися - тільки
бензинові (дизельні) зварювальні генератори забезпечать запалювання і стійкість
дуги у відсутності електромережі.
1.5 Зварювальний інвертор
<#"807456.files/image006.gif">
Рис.6. Зварювальний інвертор.
Як побудований зварювальний
інвертор. В порівнянні зі звичайним зварювальним пристроєм - набагато
складніше. Інвертор - це пристій силової електроніки, який працює на великих
струмах, високих частотах і різницях потенціалів(напругах). Вхідна напруга
двічі перетвоюється: зпочатку зі змінного 220 вольт в постійний струм, пізніше
у високочастотну напругу зі змінним струмом, частота 200кГц. Як відомо з
електротехніки, чим вище значення частоти, ти меншою буде вага і габарити
трансформатора, який передає однакову електричну потужність. Отже при зменшенні
частоти струму у 1000 разів, маса і габарити трансформатора зменшуються у 10
разів. Виходить, що й сам інвертор буде невеликим та з малою масою.
Перетворення частоти
здійснюється широтноімпульсним модулятором, за основу якого йдуть
високочастотні перетворювачі останнього покоління - модулі IGBT (біполярний
транзистор з ізольованим затвором) або MOSFET (полярний транзистор на основі
переходу металоксиднапівпровідник).
Пройшовши трансформатор,
високочастотна змінна напруга знову випрямляється і подається на зварювальну
дугу. Координування роботи всіх елементів, контроль параметрів і зворотній
зв’язок зі зварною дугою здійснюється цифровими процесорами на програмуємих
мікросхемах.
Технічні можливості
зварювальних інверторів. Вони абсолютно унікальні. Насправді інвертор зі всєю
своєю системою електроніки майже думає за зварювальника, безперервно аналізуючи
процеси на дузі. Ось лише деякі програми, закладені в мікросхеми процесора:
Вимкнення напруги на
зварювальній дузі при короткому замкненні електрода, який вкоротив до деталі
(фя anti sticking). Зпрацьовує за пів секунди після короткого замикання.
Залипання електрода до деталі і перегріву інвертора не відбувається.
А ось при вірному збудженні
дуги - легким торканням(чирканням) електрода в деталь, інвертор виробляє
додатковий імпульс струму (фя hot start). Збудження, тобто запал, дуги суттєво
полегшується.
При неминучих невеликих
коротких замиканнях у процесі зварювання, інвертор виробляє рід коротких, але
потужних імпульсів струму, які руйнують створювані в процесі перетинки з
рідкого металу (фя arc force). Дана функція особливо актуальна при зварюванні
короткою дугою.
Накінець при використанні зварювального
інвертора ми отримуємо:
стабільний постійний струм,
який не залежить від перепадів вхідної напруги;
дуже незначне розбризкування
металу в процесі зварки;
обширні можливості
налаштування режимів для всіх видів зварювання плавленням - штучним електродом,
аргоннодуговим і напівавтоматичним;
виключно низьке
енергоспоживання, що дуже важливо при включенні інвертора в побутову мережу або
його живленні від бензогенератора.
Сфери застосування
зварювальних інверторів. Це усі види електродугового та плазмового зварювання і
різання. Обмежень тут немає. Глобальний перехід усієї зварювальної техніки і
технології на інверторні джерела живлення стримує лише інерція мислення і
повсюдно налагоджене виробництво звичайних трансформаторів. На переналагодження
розгорнутого виробництва звичних трансформаторів та випрямлячів, звичайно ж,
потрібні час та гроші.
На нинішній день, інвертори
широко застосовують в наступних видах зварювання:
Ручне дугове зварювання
штучними електродами, зачасту маркується абревіатурою ММА (metal manual arc).
Тут зварювальні інвертори отримали найширше використання. Це бумовлено, в першу
чергу, невеликою вагою та енергоспоживаням. Зварювальник без проблем рухається
разом з пристроєм, вмикаючи його в любу, в тому числі побутову електропроводку.
Аргонно дугове зварювання
(TIG - tungsten inert gas) на змінному та постійному струмах. Тут переваги
інверторів виражаються не так у малій масі та енергоспоживанні, як у можливості
точного регулювання багаточисленних параметрів режиму. Для аргоннодугового
зварювання це є найважливішим, тому що зварюють відповідальні вироби з високими
вимогами до якості та зовнішнього виглядо зварного шва.
Плазмоводугове різання (PAC -
plasma arc cutting) це найновіша сучасна технологія. Швидкість різання висока,
а крайка рівна і акуратна - відразу під зварювання. Тут інвертори CUT знайшли
своє почесне місце, завдяки їх вмінню забезпечити стабільність основної та
чергової дуги, а головне внаслідок мобільності таких апаратів.
Перспективи розвитку
зварювальних інверторів. По великому рахунку, інверторні схеми відкривають нову
сторінку у світі зварювання. В сьогодення, на їх принципу вже серйозно
виготовляються багатофункційні зварювальні апарати. Найбільше розповсюдження
отримали інвертори, які суміщають зварювання MMA, TIG і CUT або MIG/MAG, TIG і
MMA. Зустрічаються і іннакші поєднання. Справа в тому, що інверторна схема
дозволяє, так би мовити, “на ходу” змінювати тип зовнішніх вольтамперних
характеристик джерела живлення. Саме тип вольтамперних характеристик є основною
властивістю джерела для певного виду зварювання. І якщо звичайний апарат
призначений, наприклад, для зварювання MIG/MAG, то шточним електродом він не
має можливості зварювати. А інверторна схема - інша справа. Тут і тип характеристик(вольтамперних)
та інші параметри без проблем переналаштовуються під потрібний тип зварювання.
1.6 Зварювальний напівавтомат
<#"807456.files/image007.gif">
Рис.7. Зварювальний напівавтомат.
Напівавтомати діляться по
роду захисту зварювального шва:
напівавтомати для зварки під
шаром флюсу.
напівавтомати для зварки в
захисних газах.
напівавтомати для зварки
порошковим дротом.
Найбільше широке застосування
отримали напівавтомати для зварки в захисних газах. Зварюють конструкції з вуглецевих
і легованих сталей, а так само з кольорових металів.
Як захисний газ застосовують
вуглекислий газ, стислий в балонах, який подається через редуктор рівномірним
тиском по шлангах, до пістолета, безпосередньо в зону зварки. Зварка в
захисному газі має ряд переваг в порівнянні із зваркою покритими електродами.
До технологічних переваг
відносяться:
висока продуктивність процесу
і хороша якість швів.
можливість ведення
напівавтоматичної зварки коротких швів у всіх просторових положеннях.
можливість зварки з'єднань на
вазі без додаткових підкладок, що утримують метал від витікання, а також зварки
металів малої товщини.
До виробничих переваг
відносяться:
відсутність шкідливих
виділень і мала токсичність при зварці.
Економічні переваги:
низька вартість зварних
з'єднань, виконаних у вуглекислому газі порівняно з вартістю зварних з'єднань,
виконаних електродами.
висока якість з'єднань і
технологічні переваги.
Можна також додати, що
зварювальний напівавтомат це не замінима річ в господарстві приварити, заварити,
а якщо є своя техніка, то сам бог велів, машина іноді вимагає косметичний
ремонт. Навчитися проводити якісні зварні шви набагато простіше, ніж дуговою
зваркою електродами.
При покупці зварювального
напівавтомата визначіться, яка у вас напруга в домашній мережі, можлива напруга
нижче норми. Тоді необхідно вибрати напівавтомат потужніший, оскільки
потужність апарату залежить безпосередньо від напруги мережі.
Якщо у вас вдома напруга
мережі три фазна 380В, то це самий кращий варіант для покупки напівавтомата,
який працює на трьох фазах 380В, тому що джерело зварювального струму
випрямлене (плюс і мінус), а самий якісний випрямлений струм, виходить тільки
на трьох фазних випрямлячах струму, що дуже впливає на якість зварки.
Подача захисного газу до
об’єкта зварювання дозволяє витіснити кисень, не даючи тому окисляти зварний
шов, тим самим значно покращуючи характеристики зварювання.
Переваги зварювального
напівавтомата: досягнення міцного зварного шва довжиною до кількох метрів,
легка і безпечна зварювання тонкого металу (будьяких марок сталі та сплавів
алюмінію). Блок управління дозволяє зберегти задані режими зварювання, з
подальшою їх активацією.
Недоліки: потреба в
громіздких балони з газом, високий витрата недешевого інертного газу (у
середньому MIGзварювання зажадає витрати аргону 9 л/хв).
.7 Зварювальний автомат
Зварювальний автомат -
механізм який являє собою конструктивне об'єднання зварювальної головки
<#"807456.files/image008.gif">
Рис.8. Зварювальний трактор.
Зварювальний трактор має:
плавне регулювання швидкості
подачі електродного дроту (зварювального струму);
плавне регулювання швидкості
переміщення візка (швидкості зварювання);
дистанційне включення і
плавне регулювання зварювальної напруги;
регулювання зварювальної
головки:
а) навколо вертикальної осі
несучої колонки на кут 90° з фіксацією положення;
б) навколо своєї повздовжньої
осі на кут 45° з фіксацією положення;
в) по вертикалі і горизонталі
на 50 мм від середнього положення за допомогою двох гвинтових суп портів;
переміщення зварювальної
головки в комплекті з блоком керування, бункером і касетою вздовж несучої
колони з фіксацією положення;
конструкцію бункера, яка
дозволяє візуально контролювати в ньому рівень флюсу;
систему відсмоктування
залишків флюсу в бункер після зварювання.
РОЗДІЛ 2
2.1 Змащування поверхонь тертя, його
значення
Як відомо, від 50 до 80% всіх
випадків передчасного виходу з ладу машин в легкій промисловості, а також в
інших галузях промисловості, викликано неякісним або недостатнім змащуванням
поверхонь тертя. Ефект підвищення стійкості до зношення деталей, до яких було
застосоване змащення, порівняно з деталями, яки працювали без змащування, дуже
великий - змащені деталі працюють в сотні разів довше. Змащувальні матеріали
підбирають в залежності від конструктивних параметрів силового та швидкісного
режиму роботи вузла, в якому відбувається процес тертя. Наприклад, для пари вал
- підшипник вибір мастил залежить від навантаження, кількості обертів, проміжку
між поверхнями тертя, товщині шару мастила, діаметру вала і відношенню довжини
підшипника до його діаметру.
Схема 1. Види руйнувань під час
тертя.
Змащувальні матеріали поділяють на
рідкі, консистентні та тверді. Основну масу їх складають рідкі та консистентні мастила,
що виробляються з нафти - вони мають назву мінеральні мастила.
.2 Способи і системи змащування
вузлів машин
Існують два способи змащування
поверхонь, що зазнають тертя - індивідуальний і централізований. При
індивідуальному способі кожна пара тертя має окремий пристрій змащування,
розташований близько до місця змащування. При централізованому способі декілька
окремо розташованих пар тертя (точок змащення) змащуються одним пристроєм.
Як при централізованому, так і при
індивідуальному способах змащування деталей відбувається або безперервно, або
періодично. При цьому змащувальний матеріал може подаватись як без примусового
тиску (за рахунок сил тяжіння або за рахунок капілярних сил) так і під
примусовим тиском (за допомогою насосів). Подача змащувального матеріалу під
тиском дозволяє йому досягати важко досяжних місць, а також проходити в різних
напрямках по змащувальним каналам.
Мастило, що проходить між
поверхнями, які зазнають змащення, в деяких випадках назад не повертається, в
інших випадках - повертається неодноразово. Відповідно з цім системи змащування
бувають проточні і циркуляційні. Циркуляційні системи - це таки, в яких
змащувальний матеріал використовується по замкненому колу неодноразово. В
проточних системах мастило застосовують один раз. Зустрічаються змішані системи
- з використанням як проточного, так і циркуляційного змащування разом.
Крім пристроїв для подавання мастил
в систему, до складу змащувальних систем також можуть входити пристрої для
розподілу і дозування змащувальних матеріалів, пристрої для контролю стану і
наявності мастил, а також для фільтрування мастил від сторонніх домішок.
Спосіб подавання змащувального
матеріалу в механізм залежить від режиму змащування, надійності подавання,
трудомісткості обслуговування вузлів і по нормам витрат мастил.
Вибір системи змащування залежить
від габаритних розмірів машини, кількості точок змащування і розташування їх в
машині, від співвідношення між кількістю рухомих і нерухомих сполучень в
машині, від зручності доступу до місць змащування при індивідуальному
змащуванні, від можливості нагляду за наявністю змащувального матеріалу в
потрібних місцях та від деяких інших факторів.
Важливе значення для вибору способу
і системи змащування має призначення і вартість механізму. Для розповсюджених і
відносно недорогих машин важливими показниками для вибору є нескладність
пристроїв, швидкість обслуговування змащувальної системи, мале витрачання
змащувальних матеріалів і відносно невисока їх вартість. Для складних,
унікальних і дорогих машин (наприклад, для розпушувально - тріпального агрегату
) вартість мастил і пристроїв не має великого значення - головне, щоб було
забезпечено надійне і високоякісне змащення всіх вузлів, в яких відбувається
процес тертя. В цих випадках використовують високоякісні мастила згідно
рекомендації технічного паспорту і заміна їх на недорогі низькоякісні марки
категорично не дозволяється.
.3 Рідкі змащувальні матеріали.
Асортимент рідких змащувальних матеріалів
Рідкі мінеральні мастила
виготовляються з нафтопродуктів. Сировиною для них є мазут. Мазут - це продукт
переробки нафти, після того, як з неї відігнали легкі фракції - бензин, гас та
інші. З мазуту відганяють дистилят, який поділяють на матеріали для отримання
мастил різної в’язкості. Отриманий продукт підлягає очищенню для видалення
речовин, що негативно впливає на матеріал машин, наприклад - сірчані або
азотисті з’єднання. зварювальний апарат змащування
вузол
Рис.9. Рідкі змащувальні матеріали.
Здатність мастил відокремлювати поверхні
тертя, зменшувати їх зношення, залежить від механічних і фізико - хімічних
властивостей змащувальних матеріалів, найважливішим з яких є в’язкість. Чим
більше навантаження на пару тертя, або чим більший проміжок між деталями тертя,
тим більша в’язкість потрібна для мастила. Чим вище оберти вала, більший
діаметр вала - в’язкість мастила повинна бути менша. Разом з тим треба
пам’ятати, що в’язкість мастил в процесі роботи змінюється із зміною
температури і тиску в зоні тертя. При підвищенні температури в’язкість мастила
настільки зменшується, що воно стає не здатне надійно захищати деталі. При
зниженні температури в’язкість підвищується і мастило може не проходити по
трубопроводу до поверхні тертя. Зміни тиску не так суттєво впливають на
в’язкість, тільки при дуже великому збільшенні тиску в’язкість помітно
збільшується.
Розрізняють динамічну, кінематичну і
умовну в’язкість.
Динамічна в’язкість ηд
має назву - абсолютна або справжня. Вона вимірюється в пуазах.
Кінематична в’язкість ηк
це відношення динамічної в’язкості рідини ηд
до її щільності ρ при
даній температурі. Одиниця кінематичної в’язкості - стокс. В сучасних
стандартах на змащувальні матеріали використовують одну соту частину стокса -
сантистокс.
Умовна в’язкість (ВУ) - це
відношення часу витікання з каліброваного отвору певної кількості мастила до
часу витікання з цього отвору дистильованої води при 20°С. Умовна в’язкість
вимірюється в одиницях Енглера. Для виміру ВУ використовують віскозиметр
Енглера.
Крім в’язкості рідкі мастила
характеризуються такими параметрами, як температура спалаху і температура
запалювання.
Температура спалаху - це така
температура, при якій суміш парів повітря і мастила спалахує при піднесенні до
неї відкритого вогню і відразу гасне.
Температура запалювання вища за температуру
спалаху. При температурі запалювання мастило спалахує і горить не менше як 5
секунд.
Найбільш широко в легкій
промисловості для змащування обладнання серед рідких мастил використовують
індустріальні мастила. Індустріальні мастила по ступені в’язкості поділяють на
легкі, середні і важкі.
Серед легких (кінематична в’язкість
- від 4 до 10 сст при 50ْ Ñ)
íàйбільш відомі - індустріальне Л
(велосіт) і індустріальне Г (вазелінове). Їх застосовують для змащення вузлів,
що працюють на великих швидкостях і малих навантаженнях, наприклад -
швидкохідних веретен крутильних і прядильних машин. Також цими маслами змащують
контрольно - вимірювальні прилади.
Середні індустріальні мастила мають
кінематичну в’язкість 10 - 50 сст при 50°С. вони використовуються для змащування
механізмів при середньому навантаженні і невисоких швидкостях. З них найбільш
поширені:
Індустріальне 12. Кінематична
в’язкість - 12 - 14 сст, температура спалаху 165ْ°Ñ,
çàñòèãàº
ïðè
òåìïåðàòóð³
(30°Ñ).
Âèêîðèñòîâóþòü
äëÿ çìащення тонких
веретен в бавовняному виробництві.
Індустріальне 20 та Індустріальне
20В. Мають кінематичну в’язкість - 18 - 23 сантистокс. Температура спалаху
170°С. Температура застигання (16ْ°Ñ).
Âèêîðèñòîâóþòü
äëÿ
çìàùóâàííÿ
òîâñòèõ
âåðåòåí
ïðÿäèëüíèõ ìашин
бавовняного і шерстяного виробництв, для заливання в масляні ванни різних
вузлів машин легкої промисловості, для змащування підшипників ковзання
електродвигунів потужністю до 10 кВт. Також цим мастилом змащують лічильники на
текстильних машинах. В якості заміни цим маслам може використовуватись турбінне
Л.
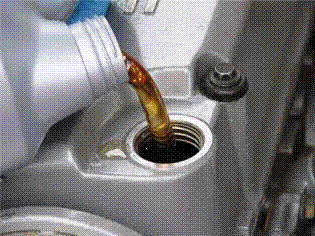
Індустріальне 30. Кінематична
в’язкість 27 - 33 сст. Температура спалаху 180°С. Застигає при температурі (20ْÑ
).
Âèêîðèñòîâóþòü
äëÿ çìàùування
вузлів чесальних, стрічкових, прядильних, стригальних машин текстильного
виробництва, а також для змащення підшипників ковзання електродвигунів
потужністю від 10 до 100 кВт.
Індустріальне 45В. Кінематична
в’язкість ηк
40 - 50 сст. температура спалаху Тспалах ═180ْÑ.
Òåìïåðàòóðà
çàñòèãàííÿ
Òçàñò ═ 8°Ñ.
Âèêîðèñòовують
для змащення вузлів машин обробного виробництва, а також сортувальних і
тріпальних машин бавовняного виробництва. Це масло не рекомендують заливати в
масляні ванни вузлів в зв’язку з його недостатньою стабільністю. Для заливання
в масляні ванни рекомендують масло Індустріальне 45 і Індустріальне 50, або їх
замінник Веретенне АУ. Ці масла також рекомендують заливати в редуктори і
коробки передач верстатів і машин легкої промисловості.
Важкі індустріальні мастила
використовують для змащування важко навантажених деталей, наприклад -
черв’ячних передач або зубчастих коліс, а також деталей, які працюють при
підвищених температурах (наприклад - підшипник ковзання сушильних барабанів
В легкій промисловості, а також при
побутовому обслуговуванні населення також використовують деякі автотракторні,
трансмісійні, дизельні та інші мастила. Мастила, що вказані в технічній
документації обладнання, дозволяється замінювати на інші в випадках
необхідності, але замінник повинний мати показники, близькі до показників
мастила, яке замінюють, особливо це стосується в’язкості.
2.4 Консистентні змащувальні
матеріали, їх асортимент
Консистентні змащувальні матеріали -
це складні колоїдні системи. Вони являють собою пластичні, мазеподібні мастила.
отримані шляхом згущування рідких мінеральних масел солями жирних кислот або
твердими вуглеводнями (парафін, стеарин, церезин).
Найбільш розповсюджені мастила, в
яких в якості згущувача використані кальцієві або натрієві мила. В склад
кальцієвих мастил (солідолів УС) входить вода, без якої ці мастила
розпадаються. Натрієві мастила (консталіни УТ) в своєму складі води не мають. В
зв’язку з цим, солідоли використовують для змащення деталей, яки працюють в
вологому середовищі, а натрієві - для деталей, що працюють в сухому середовищі.
Консистентні мастила відрізняються також температурою плавлення. Мастила на
кальцієвій основі плавляться при температурі нижче 100ْÑ,
à ìàñòèëà
íà îñíîâ³
íàòð³ºâèõ
ìèë - ïðè òåìïåðàòóð³
âèùå 100ْÑ.
Øèðîêî
ðîçïîâñþäæåí³
êîíñèñòåíòí³
ìàñòèëà íà
çì³øàí³é
îñíîâ³, íаприклад
кальцієво - натрієве консистентне мастило типу 1 - 13.Ці мастила дуже стабільні
в умовах підвищеної температури і вологості.
По призначенню консистентні мастила
поділяються на антифрикційні і консерваційні (захисні).
Антифрикційні змащувальні матеріали
призначені для зменшення коефіцієнта тертя і для зниження ступеня зношення
деталей внаслідок тертя. Застосовуються вони, як правило, для змащування частин
машини, до яких важко доставатись, особливо тихохідних та таких, що працюють
при підвищеному навантаженні, а також в умовах частих зупинок і запусків вузла.
Консерваційні мастила призначені
захищати деталі та інші металеві поверхні від корозії під час їх зберігання.
Одним з головних параметрів
консистентних мастил є їх в’язкість. Від ступені в’язкості залежать
експлуатаційні можливості мастила: можливість проходження по трубопроводам,
здатність забезпечення надійного змащення в окремих вузлах, можливість
використання в централізованих системах змащення.
Рис.11. Консистентні мастила.
Крім в’язкості консистентні мастила
характеризує число пенетрацї. По числу пенетрацї визначають можливість
проходження мастил по трубопроводу, що дуже важливо при застосуванні
централізованої системи змащування. Число пенетрацї визначають на пенетрометрі
по величині глибини занурення в мастило сталевого конуса на протязі 5 секунд.
Чим м’якше мастило, тим вище його число пенетрацї.
Дуже важливим показником в
консистентних мастилах є показник температури краплепадіння. Температурою
краплепадіння називають таку температуру, при якій з мастила, яке нагрівають в
особливих умовах, впаде перша крапля. В стандартах на консистентні мастила
температура краплепадіння повинна вказуватись обов’язково, інакше, якщо
застосувати мастило з показником температури краплепадіння нижчим, ніж
температура роботи вузла, то мастило може витікати з цього вузла.
.4.1 Асортимент консистентних мастил
Консистентні змащувальні матеріали
поділяються на низькоплавкі, середньоплавкі і тугоплавкі.
Схема 2. Класифікація консистентних
змазок.
Низькоплавкі мають температуру
краплепадіння до 65ْÑ.
Íàéá³ëüø
ðîçïîâñþäæåíèìè
ñåðåä íèõ º:
êîíñèñòåíòíå
ìàñòèëî ÓÍÇ
(ãàðìàòíå),
ìຠòåìïåðàòуру
краплепадіння 50ْÑ,
óí³âåðñàëüíå,
çàõèñíå.
Âèêîðèñòîâóþòü
äëÿ çàõèñòó
â³ä êîðî糿
ìåòàëåâèõ
ïîâåðõîíü, íå
çàõèùåíèõ
³íøèìè
ïîêðèòòÿìè,
à òàêîæ äëÿ
çìàùóâàííÿ
äåÿêèõ ìàëî
â³äïîâ³äàëüíèõ
ìåõàí³çì³â
â ë³òíþ ïîðó
ðîêó.
êîíñèñòåíòíå
ìàñòèëî ÓÍ
(âàçåë³í
òåõí³÷íèé),
òåìïåðàòура
краплепадіння 54ْÑ,
óí³âåðñàëüíå
çìàùóâàëüíå.
Âèêîðèñòîâóþòü
äëÿ
çìàùåííÿ
ìåõàí³çì³â,
ÿê³ ïðàöþþòü
ïðè ìàëèõ
íàâàíòàæåííÿõ
³ íåâèñîê³é
òåìïåðàòóð³,
íå âèùå 50ْÑ,
à òàêîæ äëÿ
çàõèñòó
ìåòàëåâèõ
ïîâåðõîíü
â³ä êорозії.
консистентне мастило АФ - 70
(приладове), температура краплепадіння 60ْÑ,
âèêîðèñòîâóþòü
äëÿ
çìàùóâàííÿ
ïðèëàä³â, à
òàêîæ
äåÿêèõ
ìåõàí³çì³â
ç ï³äâèùåíîþ
âèìîãîþ äî
ì³öíîñò³
ìàñëÿíî¿
ïë³âêè.
Ñåðåäíüîïëàâê³
ìàç³ ìàþòü
òåìïåðàòóðó
êðàïëåïàä³ííÿ
äî 100ْÑ.
Ñåðåä íèõ
íàéá³ëüø ïîøèðåíèìè
º ìàñòèëà
òðüîõ ìàðîê:
ÓÑ - 1 (ïðåñ - ñîëідол),
УС - 2 (солідол Л) і УС - 3 (солідол Т). Їх виготовляють з мінеральних мастил
високої ступені очищення з додаванням кальцієвого мила. Ці мастила мають вигляд
однорідної мазі від світло - жовтого до коричневого кольору.
УС - 1 використовують в
централізованих системах, які обслуговують вузли тертя при середніх питомих
навантаженнях і в умовах підвищеної вологості.
Солідол Л (УС - 2) використовують
для змащення деталей машин при робочій температурі не вище 60ْÑ
³ ñåðåäí³õ
øâèäêîñò³
òà
íàâàíòàæåíí³.
Ñîë³äîë
Ò (УС - 3) застосовують для змащення
поверхонь тертя, які працюють з підвищеним навантаженням на малих і середніх
швидкостях в умовах підвищеної вологості при температурах не вище 80ْÑ.
Ñèíòåòè÷í³
óí³âåðñàëüí³
ñåðåäíüîïëàâê³
ìàñòèëà âèãîòîâëÿþòü,
ÿê çамінники мінеральних
консистентних середньо плавких мастил УС - 1, УС - 2 і УС - 3. Вони мають
відповідно маркування :УСС 1, УСС - 2 і УСС - 3. Виготовляють синтетичні
солідоли з індустріальних рідких масел, загущених кальцієвими милами
синтетичних жирних кислот.
Крім вище перерахованих солідолів
серед консистентних мастил широко відомо мастило УСА (графітне) - однорідне,
чорного кольору. Виготовлено з суміші кальцієвого мила, мастила - Циліндрове 11
та графіту. Його застосовують для змащування відкритих тяжко навантажених
вузлів тертя.
.Серед тугоплавких консистентних
мастил найбільш відомі:
універсальне тугоплавке водостійке
113, його використовують для змащування підшипників та деяких інших вузлів тертя,
які працюють при середніх і підвищених навантаженнях і при температурі не вище
110ْÑ
ïðè óìîâ³
ï³äâèùåíî¿
âîëîãîñò³ ;
óí³âåðñàëüíå
ÓÒ
(êîíñòàë³í
æèðîâèé) - äëÿ
çìàùóâàííÿ
ï³äøèïíèê³â
³ ³íøèõ
ïîâåðõîíü
òåðòÿ ïðè
òåìïåðàòóðàõ
äî 120ْÑ
(ìàñòèëî ÓÒ1)
òà äî 135ْÑ
(ìàñòèëî ÓÒ2);
óí³âåðñàëüí³
òóãîïëàâê³
ñèíòåòè÷í³
ìàñòèëà ÓÒÑ
1 òà ÓÒÑ2
(êîíñòалін
синтетичний) використовують як замінники жирових консталінів УТ1 і УТ2.
Крім вищевказаних тугоплавких
консистентних мастил використовують мастила спеціального призначення, наприклад
- текстильне мастило І Т, яке використовують для змащування кілець крутильних
машин текстильного виробництва.
.5 Тверді змащувальні матеріали
Із твердих змащувальних матеріалів
найбільш розповсюджені дисульфід молібдену та графітові препарати.
Дисульфід молібдену має структуру,
побудовану окремими шарами речовини. Ці шари легко пересуваються в площині і на
цьому заснована змащувальна дія матеріалу. На основі дисульфіду молібдену
виготовляють порошки і пасти. Порошками натирають поверхні, що зазнають тертя.
Пасти на основі дисульфіду молібдену використовують в парах тертя, які працюють
в умовах, де часте змащування неможливе, а також в умовах дуже високих або
низьких температур.
Графітні матеріали, також дуже
розповсюджені в якості твердих змащувальних засобів. Високі антифрикційні
властивості графіту пояснюються будовою цієї речовини. Вона складається з
окремих шарів. Зв’язки між атомами сусідніх шарів дуже слабкі і вони легко
сковзають один по одному. Змащувальний ефект графітового мастила полягає в тім,
що графіт заповнює собою усі подряпини та западини профілю поверхні. До такої
поверхні змащувальні масла прилипають в 8 - 10 разів краще, ніж до чистої, в
зв’язку з цім коефіцієнт надійності вузла значно покращується.
Графітні мастила використовують
частіше, ніж препарати молібдену, в зв’язку з тим, що графіт порівняно менше
дефіцитний, більш дешевий, більш витривалий при малих навантаженнях і має
більшу стійкість до окислення. Однак, дисульфід молібдену створює на поверхні
металів більш міцну змащувальну плівку.
.6 Види і періодичність технічного
обслуговування автомобіля
Технічне обслуговування це комплекс
операцій, які спрямовані на підтримання автомобіля в справному та працездатному
стані і проводяться в процесі експлуатації автомобіля.
Мета технічного обслуговування і
ремонту підтримування дорожніх транспортних засобів у технічно справному стані
та належному зовнішньому вигляді, забезпечення надійності, економічності,
безпеки руху та екологічної безпеки.
Система технічного обслуговування та
ремонту техніки сукупність взаємопов'язаних засобів, документації технічного
обслуговування і ремонту та виконавців, які потрібні для підтримування і
відновлення якості виробів, що входять у цю систему;
Технічний стан сукупність схильних
до зміни в процесі виробництва чи експлуатації якостей виробу, яка
характеризується в певний момент часу ознаками, встановленими технічною
документацією на цей виріб;
Справний стан (справність) стан виробу, який відповідає усім вимогам
нормативнотехнічної і (або) конструкторської документації;Роботоздатний стан
(роботоздатність) стан виробу, в якому значення усіх параметрів, які
характеризують здатність виконувати задані функції, відповідають вимогам
нормативнотехнічної і (або) конструкторської документації;
Залежно від обсягу робіт, періодичності та працеємкості їх виконання, технічне
обслуговування розподіляється на такі види:
Види технічного обслуговування
контрольний огляд перед виїздом із
парку ( КО);
контрольний огляд в дорозі;
щоденне технічне обслуговування
(ЩТО) ( продоводиться щоденно після заїзду в парк);
технічне обслуговування № 1 (ТО1);
технічне обслуговування № 2 (ТО2);
Сезонне технічне обслуговування (СО)
проводиться навесні і восени при переході на .літній та зимовий періоди
експлуатації.
Щоденне технічне обслуговування (
ЩТО)виконується щодня після повернення автомобіля з лінії в між змінний час і
включає: контрольно оглядової роботи щодо механізмів і систем, що забезпечує
безпеку руху , а також кузову, кабіни , приладів освітлення ; збирально мийні
та сушильно обтиральні операція , а також дозаправку автомобіля паливом ,
маслом , охолоджувальною рідиною . Мийка автомобіля здійснюється за потреби в
залежності від погодних , кліматичних умов і санітарних вимог , а також від
вимог, що пред'являються до зовнішнього вигляду автомобіля.
ПОСЛІДОВНІСТЬ ВИКОНАННЯ ЩТО
. Відкрити капот автомобіля і
зафіксувати його
. Оглянути двигун чи не має
підтікання масла, охолоджувальної рідини, палива.
. Витягнути щуп і перевірити рівень
масла в піддоні двигуна, рівень масла повинен находитися між нижньою і верхньою
позначками, краще щоб ближче був до верхнього рівня. По необхідності долити
масло для цього необхідно зняти кришку сапуна і через неї долити масло і через
23 хвилини перевірити рівень масла.
. Відкрутити кришку радіатора і
перевірити рівень охолоджувальної рідини, вона повинна повністю закривати соті
серцевини радіатора (охолоджувальна рідина повинна добре бути видна в верхньому
бачку радіатора) По необхідності долити
. Закрити кришку радіатора
. Перевірити наявність гальмової
рідини в бачку головного гальмового циліндра.
. Перевірити надійність кріплення
коліс та тиск в шинах. Надійність кріплення коліс перевіряють ударом ноги по
колесу при цьому не повинно бути ні якого люфту в колесі. Тиск в шинах перевіряють
за допомогою манометра по необхідності підкачують
. Запустити двигун подивитися на
прилади контролю тиску масла і зарядку акумуляторної батареї
. Прослухати двигун на стуки. Стуки
можна визначити на слух або за допомогою стетоскопа. При роботі двигуна не
повинно чути не ні яких сторонніх металічних стуків та шумів.
. Перевірити роботу приладів
освітлення, сигналізації якщо не працюють усунути причину
. Перевірити працездатність
зчеплення та коробки передач. Для цього необхідно при працюючому двигуні натиснути
на педаль зчеплення і ввімкнути передачі, передачі повинні вмикатися вільно без
металічного скреготу а після включення передачі автомобіль повинен оставатися
на місці (не повинно бути самовільного руху).
. Перевірити надійність роботи
гальмової системи. Для цього необхідно розігнати автомобіль на рівній площадці
з твердим покриттям і натиснути на гальмову педаль. При цьому педаль не повинна
провалитися до полика а всі колеса загальмувати одночасно
. Перевірити стан рульового
керування. Для цього необхідно заїхати на оглядову яму або естакаду і
перевірити стан шарнірних з’єднань рульових тяг, люфт рульового колеса
. Перевірити стан карданної передачі
(при обертанні не повинно бути люфта), ресор (всі листи повинні бути цілими і
надійно закріпленні до мостів та до рами автомобіля)
. Вимити автомобіль привести кабіну
до порядку.
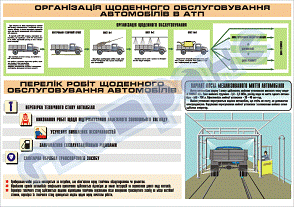
Перше технічне обслуговування (ТО 1)
полягає в зовнішньому технічному огляді всього автомобіля та виконанні у
встановленому обсязі контрольно діагностичних , кріпильних , регулювальних ,
мастильних , електротехнічних і заправних робіт з перевіркою роботи двигуна ,
рульового управління, гальм та інших механізмів .
Друге технічне обслуговування (ТО 2)
включає виконання у встановленому обсязі кріпильних , регулювальних ,
мастильних та інших робіт , а також перевірку дії агрегатів , механізмів і
приладів у процесі роботи
Сезонне технічне обслуговування ( СО) проводиться 2 рази на годи є підготовкою
рухомого складу до експлуатації в холодну і теплу пори року. Окремо СО
рекомендується проводити для рухомого складу, що працює в зоні холодного
клімату. Для інших кліматичних зон СО поєднується з ТО 2 при відповідному
збільшенні трудомісткості основного виду обслуговування
Періодичність технічних
обслуговувань
Технічні обслуговування ТО1 і ТО2
мають періодичність обслуговування, яка визначається пробігом автомобіля.
Технічні обслуговування ТО1 і ТО2
для автомобілів визначаються пробігом автомобіля, що встановлюється залежно від
категорії умов експлуатації.Примірна періодичність технічних обслуговувань
приведена в таблиці
Таблиця №1
№ п\п
|
Автомобілі
|
Періодичність ТО (км. пробігу)
|
|
|
ТО1
|
ТО2
|
1
|
легкові
|
4000
|
16000
|
2
|
вантажні
|
3500
|
14000
|
3
|
автобуси
|
3000
|
12000
|
Методи Технічного обслуговування:
Тупіковий роботи по технічному
обслуговувані виконуються на універсальному посту працівниками різних
спеціальності
Потоковий метод роботи з технічного обслуговування виконуються на декількох
розташованих в технологічній послідовності спеціалізованих постах
Роботи що виконуються при технічном
обслуговувані автомобіля
При ЩТО необхідно:
заправити автомобіль;
перевірити відсутність підтікання
палива, масла і охолоджуальної рідини, а також втрати повітря з пневмосистеми
(при виявленні несправності усунути її);
очистити і вимити автомобіль від
бруду, прибрати всередині кабіну і вантажну платформу,
привести зовнішній вид автомобіля до
належного стану;
усунути всі несправності, які
виявились в дорозі;
оглянути кріплення всіх коліс;
при роботі в умовах великої
запиленості провести обслуговування повітряного фільтра;
злити конденсат із ресиверів
гальмової системи;
в зимовий час злити воду із системи
охолодження;
вимкнути вимикач "маси ».
б) технічне обслуговування № 1
(ТО1).
Перед початком робіт ТО1 проводяться
операції щоденного технічного обслуговування.
перевіряється комплектність
автомобіля, інструментів водія, шанцевого інструмента;
перевіряється кріплення всіх вузлів
і агрегатів, затягування гайок кріплення головок блока циліндрів;
обслуговуються акумуляторні батареї;
перевіряється і регулюється натяг
всіх приводних пасів;
проводять змащувальні роботи згідно
таблиці змащування;
перевіряють і при необхідності
регулюють гальма та рульове керування;
перевіряють тиск у шинах коліс;
перевіряється робота всіх систем і
механізмів автомобіля на ходу.
в) Технічне обслуговування № 2 (
ТО2).
перед виконанням ТО2 виконуються
операції ЩТО та ТО1.
При ТО2:
проводиться поглиблена перевірка
технічного стану автомобіля, оцінюється технічний стан агрегатів, вузлів і
систем автомобіля, уточнюються обсяги робіт при ТО2;
проводяться регулювальні роботи,
згідно з інструкцією по експлуатації автомобіля;
промиваються і замінюються
фільтруючі елементи в системі живлення;
при значному зносі протекторів шин проводиться
їх перестановка згідно схем перестановки;
перевіряється герметичність
гальмових систем;
проводяться змащувальні роботи
згідно карти змащування.
Після закінчення обслуговування перевіряється робота всіх вузлів, агрегатів і
систем автомобіля на ходу.
г) Сезонне технічне обслуговування
(СО).
Проводиться навесні і восени при
переході на літній та зимовий періоди експлуатації. Сезонне технічне
обслуговування машин складається з проведення чергового ТО1 або ТО2 і
додаткових робіт відповідно до наступаючого періоду експлуатації та:
промивання, продування стисненим
повітрям, перевірки і регулювання приладів системи живлення двигуна; заміни
сезонних змащувальних матеріалів та спеціальних рідин в агрегатах і механізмах
машин, всесезонні мастила і рідини замінюються тільки по закінченні терміну їх
роботи;
підфарбування або повного фарбування
автомобіля.
При підготовці машин до експлуатації
в зимовий період додатково до сезонного ТО проводяться:
перевірка і підготовка до роботи
засобів підігріву двигуна, обігріву кабіни і кузова, встановлення засобів
утеплення;
підключення до системи охолодження і
перевірка роботи передпускового підігрівача двигуна та опалювача кабіни;
заправка системи охолодження двигуна
рідиною, що замерзає при низькій температурі;
видалення конденсату із
трубопроводів і каналів системи регулювання тиску повітря в шинах і системи
пневматичних приводів гальм.
зняття з машини засобів утеплення.
3. Охорона праці
1. Загальні положення для
електрогазозварника
.1. До виконання електрозварювальних
робіт допускаються особи, які досягли 18річного віку, визнані придатними для
даної роботи медичною комісією, пройшли спеціальне навчання з безпечних методів
і прийомів ведення робіт та мають кваліфікаційну групу з електробезпеки не
нижче ІІ.
.2. Електрозварник ручного
зварювання, якого приймають на роботу, повинен пройти вступний інструктаж з
охорони праці, виробничої санітарії, пожежної безпеки, прийомів і способів
надання долікарської допомоги потерпілим, бути ознайомлений під розпис з
умовами праці, правами та пільгами за роботу в шкідливих та небезпечних умовах
праці, про правила поведінки при виникненні аварій.
.4. Електрозварник, що приймається
на роботу, після первинного інструктажу повинен протягом 2-15 змін (залежно від
стажу, досвіду і характеру роботи) пройти стажування під керівництвом
досвідченого, кваліфікованого електрозварника ручного зварювання, який
призначається наказом (розпорядженням) по дорожній організації.
.5. Повторний інструктаж з правил і
прийомів безпечного ведення роботи електрозварник повинен проходити:
періодично, не рідше одного разу на
квартал;
при незадовільних знаннях з охорони
праці не пізніше місячного строку;
у зв’язку з допущеним випадком
травматизму або порушенням вимог охорони праці, що не призвело до травми.
.6. Електрозварник ручного
зварювання повинен працювати у спецодязі та спецвзутті, передбачених Типовими
галузевими нормами: костюмі брезентовому або костюмі для зварника, рукавицях
брезентових, черевиках шкіряних. На зовнішніх роботах взимку: куртці та брюках
бавовняних на утеплювальній прокладці, валянках.
.7. Робочі місця повинні бути
забезпечені інвентарними загородженнями, захисними та запобіжними пристроями,
повинні мати достатнє освітлення. В разі потреби, користуватися справним
переносним світильником напругою не вище 42 В, а при роботі в котлах,
цистернах, колодязях - не вище 12 В. Освітленість робочого місця має бути не
менша за 50 лк.
.8. Електрозварник повинен протягом
усього робочого дня тримати в порядку і читоті робоче місце, не захаращувати
проходи до нього матеріалами та конструкціями.
.9. Забороняється проводити зовнішні
електрозварювальні роботи на риштуваннях під час грози, ожеледі, туману, при
вітрі силою 15 м/сек і більше.
.10. Електрозварювальну установку
розміщувати так, щоб були забезпечені вільний доступ до неї, зручність і
безпека при веденні робіт.
При одночасному використанні кількох зварювальних установок їх треба
встановлювати не ближче 350 мм один від одної, а ширина проходів між ними
повинна бути не менше 800 мм.
.11. Електрозварювальну установку
включати в електромережу тільки за допомогою пускового пристрою. Забороняється
живити зварювальну дугу безпосередньо від силової та освітлювальної
електромереж.
Довжина проводів між живильною мережею та пересувною установкою не повинна
перевищувати 10 м. Кабель (електропроводку) слід розміщувати на відстані не
менше 1 м від трубопроводів кисню та ацетилену.
.12. Відстань від місця проведення
електрозварювальних робіт до місця встановлення газогенератора, балонів з газом
та легкозаймистих матеріалів повинна бути не менша за 10 м.
.13. Забороняється зберігати
легкозаймисті матеріали та вибухонебезпечні речовини в приміщеннях для
зварювання.
.14. У закритих приміщеннях і
всередині ємностей електрозварник повинен працювати при наявності
припливновитяжної вентиляції.
Забороняється одночасна робота електрозварника і газозварника (газорізальника)
всередині закритої ємності або резервуара.
.15. Робочі місця при роботі кількох
електрозварників в одному приміщенні слід обгороджувати світлонепроникними
щитами (екранами) з вогнетривкого матеріалу, заввишки не менше 1,8 м.
.16. Виконувати електрозварювальні
роботи на висоті з риштувань та інших засобів підіймання дозволяється тільки
після перевірки майстром їх міцності і стійкості, а також після вживання
заходів, що попереджають спалахування настилів, падіння розплавленого металу і
огарків електродів на працюючих або людей, які проходять поблизу. Забороняється
використовувати випадкові опори.
.17. Електрозварник, при потребі,
повинен спускатися в траншеї (котловани) по приставних драбинах, переходити
через канави і траншеї по перехідних містках.
.18. Електродотримач має бути
заводського виготовлення, легкий, забезпечувати надійне затиснення і швидку
зміну електродів без дотику до струмоведучих частин і бути справний. Держак повинен
бути виконаний з теплоізоляційного діелектричного матеріалу. Забороняється
застосовувати електродо¬тримачі з підвідним проводом у держаку при силі струму
600 А та більше, а також ручний інструмент, що має:
вибої, відколи робочих кінців;
задирки та гострі ребра в місцях
затискання рукою;
тріщини та відколи на затилковій
частині.
.19. Забороняється протирати деталі
перед зварюванням бензином або гасом.
.20. Необхідно стежити, щоб руки,
взуття та одяг були завжди сухі.
. Загальні положення для слюсаря по
ремонту автомобілів.
.1. До самостійної роботи слюсарем
по ремонту автомобілів (далі слюсарем) допускаються особи не молодше 18 років,
які мають професійну підготовку і пройшли:
попередній медичний огляд (при
ухиленні від проходження медичних оглядів працівник не допускається до
виконання трудових обов`язків);
вступний інструктаж;
навчання безпечним методам і
прийомам праці і перевірку знань з безпеки праці;
первинний інструктаж на робочому
місці.
До роботи з електрифікованими
інструментом і обладнанням допускаються слюсарі, які пройшли відповідне
навчання і інструктаж, а також мають першу кваліфікаційну групу з
електробезпеки.
Виконання робіт, не пов`язаних з
обов`язками слюсаря, допускається після проведення цільового інструктажу.
.2. Слюсар зобов`язаний:
.2.1. Дотримуватися норм, правил та
інструкцій з охорони праці, пожежної безпеки і правил внутрішнього трудового
розпорядку.
.2.2. Правильно застосовувати
колективні і індивідуальні засоби захисту, дбайливо відноситися до виданих в
користування спецодягу, спецвзуттю і іншим засобам індивідуального захисту.
.2.3. Негайно повідомляти своєму
безпосередньому керівнику про будьякий нещасний випадок, що відбувся на
виробництві, про ознаки професійного захворювання, а також про ситуацію, яка
створює загрозу життю і здоров`ю людей.
.2.4. Виконувати тільки доручену
роботу. Виконання робіт підвищеної небезпеки проводиться за нарядомдопуском
після проходження цільового інструктажу.
.3. Забороняється вживати спиртні
напої, а також приступати до роботи в стані алкогольного або наркотичного
сп`яніння. Палити дозволяється тільки в спеціально обладнаних місцях.
.4. Небезпечними і шкідливими
виробничими факторами для слюсаря при виконанні робіт з профілактичного
обслуговування і ремонту автомобілів є:
падіння вивішених частин
транспортних засобів при обслуговуванні і ремонті підвіски, коліс, мостів тощо;
падіння кузова автомобілясамоскида
при обслуговуванні та ремонті гідропідйомника;
падіння перекидної кабіни вантажного
автомобіля;
падіння деталей, вузлів, агрегатів,
інструмента;
падіння працюючих на поверхні, з
висоти (буфера, драбини, естакади, площадок), в оглядову яму;
рухомі частини вузлів і агрегатів;
наїзди автомобілів: внаслідок
самовільного руху, при запуску двигуна, в`їзді (виїзді) в зону ремонту, русі на
оглядовій ямі та конвеєрі;
термічні фактори (пожежі при
зливанні паливномастильних матеріалів з автомобілів, митті ними деталей,
вузлів, агрегатів, зберіганні та залишенні їх на робочих місцях);
осколки металу, що відлітають при
випресовуванні та запресовуванні шворнів, пальців, підшипників, валів, висей,
під час рубки металу;
наявність у повітрі робочої зони
шкідливих речовин (акролеїну, вуглецю оксиду, вихлопні гази двигуна тощо);
знижена температура повітря в
холодний період року;
недостатнє освітлення;
ураження електричним струмом;
незручна робоча поза;
гострі кромки деталей, вузлів,
агрегатів, інструмента і пристосування.
.5. Працівник повинен бути
забезпечений засобами індивідуального захисту. Згідно з ДНАОП 0.003.0698
«Типові норми безплатної видачі спеціального одягу, спеціального взуття і інших
засобів індивідуального захисту працівникам автомобільного транспорту»
слюсареві по ремонту автомобілів видаються:
костюм віскознолавсановий (термін
носіння 12 місяців);
черевики шкіряні (термін носіння 12
місяців);
берет (термін носіння 12 місяців);
рукавиці комбіновані (термін
носіння 2 місяці);
окуляри захисні (до зносу).
При виконанні робіт по технічному
обслуговуванню і ремонту на оглядових ямах, підйомниках, естакадах додатково
видається:
каска будівельна (чергова).
При виконанні робіт з розбирання
двигунів, транспортування, перенесення і промивки деталей двигунів та при
роботі з етилованим бензином видаються:
костюм віскознолавсановий (термін
носіння 12 місяців);
фартух прогумований (термін носіння
6 місяців);
чоботи гумові (термін носіння 12
місяців);
рукавиці гумові (термін носіння 6
місяців);
рукавиці комбіновані (термін
носіння 2 місяці);
окуляри захисні (до зносу).
При виконанні зовнішніх робіт
узимку, а також у приміщеннях при температурі в них, нижчій за допустиму,
додатково видаються:
куртка бавовняна на утеплювальній
прокладці (термін носіння 36 місяців);
Роботодавець зобов`язаний замінити
або відремонтувати спецодяг, спецвзуття і інші засоби індивідуального захисту,
що прийшли в непридатність, до закінчення встановленого терміну носіння по
причинах, які не залежать від працівника.
.6. При захворюванні або травмуванні
як на роботі, так і поза нею необхідно повідомити про це керівника і звернутися
в лікувальний заклад.
.7. При нещасному випадку потрібно
надати допомогу потерпілому відповідно до інструкції по наданню долікарської
допомоги, викликати працівника медичної служби. Зберегти до розслідування
обстановку на робочому місці такою, якою вона була в момент випадку, якщо це не
загрожує життю і здоров`ю присутніх і не призведе до аварії.
.8. При виявленні несправності
обладнання, пристосування, інструмента повідомити про це керівника.
Користуватися і застосовувати в роботі несправні обладнання і інструменти
забороняється.
.9. Виконуючи трудові обов`язки,
слюсар зобов`язаний дотримуватися наступних вимог:
ходити тільки по встановлених
проходах, перехідних містках і майданчиках;
не сідати і не спиратися ліктем на
випадкові предмети і огорожі;
не підійматися і не спускатися бігом
по сходових маршах і перехідних містках;
не торкатися до електричних
проводів, кабелів електротехнічних установок;
не усувати несправності в
освітлювальній і силовій мережі, а також пускових пристроях;
не знаходитися в зоні дії
вантажопідйомних машин.
.10. Звертати увагу на знаки
безпеки, сигнали і виконувати їх вимоги. Заборонюючий знак безпеки з пояснюючим
написом "Не включати працюють люди!" має право зняти тільки той
працівник, який його встановив. Забороняється включати в роботу обладнання,
якщо на пульті управління встановлений заборонюючий знак безпеки з пояснюючим
написом "Не включати працюють люди!".
.11. При пересуванні по території
необхідно дотримуватися наступних вимог:
ходити по пішохідних доріжках,
тротуарах;
переходити залізничні шляхи і
автомобільні дороги у встановлених місцях;
при виході з будівлі пересвідчитися
у відсутності транспорту, що рухається.
.12. Для питва потрібно вживати воду
з сатураторів, обладнаних фонтанчиків або питних бачків.
.13. Приймати їжу слід в обладнаних
приміщеннях (столовій, буфеті, кімнаті прийому їжі).
.14. Виконання робіт підвищеної
небезпеки проводиться за нарядомдопуском після проходження цільового інструктаж
Висновок
Зварювання справа складна, і цьому
процесу люди навчаються не один рік. Це якщо говорити про професійний підхід до
справи. Якщо ж мова йде про побутовому використанні зварювання, то навчитися
з'єднувати метали з її допомогою досить просто. До того ж сучасне зварювальне
обладнання коштує не дуже дорого, так що в господарстві воно зайвим не буде.
Зварювальний апарат -
електрообладнання, яке використовується для міцного з’єднання металевих
деталей.
Електрозварювання - спосіб
зварювання, при якому для нагрівання і розплавлення металу застосовується
електрична дуга. Температура такої дуги може доходити до 5000 ° С, що набагато
вище температур плавлення всіх існуючих на сьогодні металів.
В даній дипломній роботі ми
розглянули основнні види зварювальних апаратів, визначили їх недоліки та плюси
в порівнянні один з одним.
Визначили яким із зварювальних
апаратів краще зварювати тей чи інший метал. Дізналися та розглянули їх
характеристики.
Також визначили, що собою являє технічне
обслуговування. Його види та основні роботи які при ньому проводяться.
Дізналися навіщо слугує змащування
вузлів та механізмів вантажних та легкових автомобілів.
Розглянули правила поведінки
газоелектрозварників при ручному дуговому зварювані, правила їх поведінки при
роботі та під час небезпечних і надзвичайних ситуацій, способи допомоги при
нещасних випадках та інше.
Список використаних літературних
джерел
1.
Сварные конструкции. Расчёт и проектирование: Учеб. для вузов/Под ред.
Николаева Г.А М.: Высш. шк., 1990.446 с.
.
Холопов Ю.В. Ультразвуковая сварка пластмасс и металлов. Л.: Машиностроение.
Ленингр. отдние, 1988. 224 с.
.
Сварка полимерных материалов: Справочник/К.И. Зайцев, Л.Н. Мацюк, А.В.
Богдашевский и др.; Под общ.ред. К.И. Зайцев, Л.Н. Мацюк
М.:
Машиностроение, 1988. 312 с.
.
Ф. А. Хромченко: «Сварочное пособие электросварщика.» М. Энергоатамиздат, 1989.
- 114 с.: ил. (Бка тепломонтажника).
.
«Оборудывание для дуговой сварки»: Справочное пособие (Под ред. В.В. Смирнова.
Л.: Энергоатомиздат. Ленинградское. Отделение, 1986. - 656 с.: ил.
.
Гитлевич А.Д., Этингоф Л.А.:«Механизация и автоматизация сваросного
производства», М., Машиностроение, 1979г.
.
Положение о техническом обслуживании и ремонте подвижного состава
автомобильного транспорта. М.: Транспорт, 1986.
.
Суханов, Б.Н. и др. Техническое обслуживание и ремонт автомобилей. Пособие по
дипломному проектированию. М.: Транспорт, 1991.
.
Румянцев С.И. и др. Техническое обслуживание и ремонт автомобилей. Учебник для
ПТУ. М.: Машиностроение, 1989.
.
Крамаренко Г.В., Барашков И.В. Техническое обслуживание автомобилей. М.:
Транспорт, 1982.
.
Кузнецов Ю.М. Охрана труда на авторемонтных предприятиях. М.: Транспорт, 1990.
.
Семенов Н.В. Техническое обслуживание и ремонт автобусов. М.: Транспорт, 1987.
Ðàçìåùåíî
íà Allbest.ru