Автоматическое управление приводом постоянной частоты вращения
МИНИСТЕРСТВО ОБРАЗОВАНИЯ РОССИЙСКОЙ
ФЕДЕРАЦИИ
БАЛТИЙСКИЙ ГОСУДАРСТВЕННЫЙ
ТЕХНИЧЕСКИЙ УНИВЕРСИТЕТ (ВОЕНМЕХ) им. Д.Ф. Устинова
ВЫПУСКНАЯ КВАЛИФИКАЦИОННАЯ РАБОТА
Тема: Автоматическое управление
приводом постоянной частоты вращения
Непеин Леонид Петрович
Специальность 220401 - «Мехатроника»,
направления 652000 - «Мехатроника и робототехника»
Санкт-Петербург
Содержание
Введение
Исследование приводов постоянной частоты вращения
1.1 Обзор литературных и патентных источников
.1.1 ППЧВ - общее описание и применение
.1.2 Объемная гидропередача (ОГП). Описание и составные части
.1.3 Базовый механизм (БМ). Описание и составные части
.1.4 Механизм управления (МУ). Описание и составные части
.2 Математическое моделирование ОГМП. Основные уравнения
.2.1 Объемный гидропривод
.2.2 Основные уравнения базового механизма
.2.3 Модели объемных потерь в объемной гидромашине
.2.4 Модели гидромеханических потерь в объемной гидромашине
.2.5 Учет потерь в базовом механизме
.3 Выбор программы для реализации математической модели
Математическое моделирование ОГП в среде MATLAB-Simulink
.1 Моделирование основных элементов ОГП
.2 Моделирование базового механизма
.3 Определение входных параметров математической модели
.4 Результаты математического моделирования
.5 Анализ результатов моделирования
Конструирование системы управления привода постоянной частоты
вращения
.1 Нелинейности в системе управления
.2 Методы устранения нелинейностей
.3 Энкодеры. Устройство и принцип работы
.4 Программируемый логический контроллер
.5 Разработка конструкции и технологии печатного узла
контроллера
.5.1 Анализ электрической принципиальной схемы и выбор
элементной базы
.5.2 Выбор и обоснование параметров печатной платы
.6 Конструкторско-технологический расчет платы
.6.1 Расчет параметров проводящего рисунка с учетом
технологических погрешностей его получения
.6.2 Расчет параметров проводящего рисунка с учетом
технологических погрешностей получения защитного рисунка
.7 Анализ ТЗ и выбор конструкции узла с учетом параметров
печатной платы и вида соединителя
.7.1 Расчет теплового режима
.7.2 Расчет защиты от механических воздействий
.8 Технологическое проектирование
.8.1 Обеспечение технологичности конструкции изделия
.8.2 Количественная оценка технологичности конструкции
изделия
.9 Разработка техпроцесса сборки узла
Безопасность жизнедеятельности
.1 Анализ и нормирование ОВПФ
.2 Расчет кондиционирования
.3 Схема пожароэвакуации и оснащение помещения средствами
пожаропредупреждения и пожаротущения
.4 Выводы по организации рабочего места
Технико-экономическая часть
Заключение
Библиографический список
Приложение А
Введение
привод вращение печатный
контроллер
В настоящее время актуальной является проблема преобразования энергии с
наименьшими потерями и наилучшими показателями качества в самых разных отраслях
техники, начиная с авиации и судостроения, и заканчивая ветро- и
гидроэнергетическими установками. Частным случаем преобразования энергии
является получение переменного тока нужного качества с помощью генератора,
который приводится в движение двигателем системы. Качество переменного тока
определяется его частотными характеристиками, которые должны поддерживаться в
нужном диапазоне, независимо от режима работы двигателя. Существуют несколько
способов преобразования частоты переменного тока в подобных системах. В
последнее время все чаще используется метод поддержания постоянной частоты
вращения генератора с помощью привода постоянной частоты вращения (ППЧВ).
Данный привод имеет ряд преимуществ перед электрическими преобразователями
частоты, такие как больший КПД и меньшие массо-габаритные показатели. Его
устанавливают между валами двигателя и генератора, автоматически поддерживая с
определенной точностью частоту вращения генератора постоянной в случае
изменения частоты вращения двигателя или нагрузки. Таким образом, сугубо
электрическая задача стабилизации частоты тока решается чисто механическим
способом - стабилизацией частоты вращения. На кафедре прикладной механики,
автоматики и управления в БГТУ «Военмех» ведутся исследования в целях усовершенствования
ППЧВ.
В наше время наибольшее распространение получили ППЧВ на основе объемной
гидромеханической передачи (ОГМП). При преимуществах в КПД, массе и габаритах,
по сравнению с другими видами передач, подобные приводы имеют некоторые
недостатки. Во-первых, это сложность проектирования ППЧВ, так как от
проектировщика требуется синтез знаний в области сложных планетарных механизмов
с одной стороны, и объемного гидропривода, с другой. Во-вторых, это
нелинейность работы ППЧВ, обусловленная статическими потерями в объемном
гидроприводе при достижении им так называемой «нулевой зоны». Данная
нелинейность серьезно влияет на выходные частотные параметры, ограничивая
применение ППЧВ в системах, где необходимо стабильное качество переменного
тока.
Современное развитие техники предлагает способы избавления от проблемы
«нулевой зоны» с помощью исполнительных органов, влияющих на работу объемного
гидропривода. В данном случае целесообразно использовать мехатронные методы
управления гидроприводом, так как они позволяют объединить исполнительное
устройство с системой управления и слежения за частотой вращения. В качестве
объекта исследования целесообразно использовать математическую модель привода
постоянной частоты вращения, так как на текущем этапе развития компьютерной
техники и программной среды, математическая модель дает точные и наглядные
результаты изменений параметров системы.
Настоящая работа имеет перед собой следующие цели:
· Математическое моделирование работы объемной
гидромеханической передачи в среде Matlab-Simulink.
· Верификация математической модели с экспериментальными
данными.
· Изменение управляющего сигнала для уменьшения нулевой зоны.
· Выбор оптимального управляющего исполнительного органа.
· Проектирование конструкции объемного гидропривода с управляющим
исполнительным органом.
1
Исследование приводов постоянной частоты вращения
.1 Обзор
литературных и патентных источников
.1.1 ППЧВ -
общее описание и применение
В настоящее время актуальным является создание альтернативных источников
энергии, в частности с использованием энергии перемещения воздушных масс. В
связи с этим возникает задача преобразования переменной скорости рабочего
двигателя в постоянную скорость двигателя - потребителя (например,
электрического генератора) с высоким КПД при сохранении малых массогабаритных
показателей. Для решения этой задачи в последнее время все больше используется
привод постоянной частоты вращения (ППЧВ). На кафедре прикладной механики,
автоматики и управления в БГТУ «Военмех» ведутся исследования в целях усовершенствования
ППЧВ.
Также ППЧВ используется в ряде других систем, где необходимо получать
электрический ток стабильной частоты, используя энергию двигателей, скорость
которых является переменной. Это актуально для авиации, судостроения и тяжелого
машиностроения. Например, история развития систем электроснабжения летательных
аппаратов свидетельствует о том, что рост требований к массогабаритным
показателям (материалоемкость) и КПД бортовых источников электроэнергии судовых
и транспортных средств приведет со временем к более широкому использованию ОГМП
в качестве стабилизаторов частоты вращения синхронных генераторов.
Принципиально возможны и целесообразны комбинированные способы стабилизации,
при которых ППЧВ стабилизирует с некоторой точностью частоту вращения, а
электрические способы используются для компенсации погрешностей с точностью,
зависящей от требований потребителей.
Силовая часть ППЧВ состоит из исполнительного двигателя Д, трехзвенного
дифференциала 3 и двигателя-потребителя (в данной работе - электрического
генератора) Г, связанных кинематическими передачами. В процессе работы
переменный момент, развиваемый двигателем Д, преобразуется дифференциалом 3 в
постоянный, который, в свою очередь, через передачу поступает на вал генератора
Г. Дифференциал 3 имеет переменное передаточное отношение, которое должно
изменятся в зависимости от значения входного момента в целях поддержания
постоянного момента на выходе. Для регулирования передаточного отношения
дифференциала 3 предназначен гидравлический привод, состоящий из неуправляемой
объемной гидромашины 2, кинематически связанной с один из звеньев дифференциала
3 и управляемой объемной гидромашины 1, гидравлически связанной с 2. Схема ППЧВ
представлена на рисунке 1.1.
Рисунок 1.1 - Привод постоянной частоты вращения
Привод постоянной частоты вращения устанавливают между валами двигателя и
генератора, автоматически поддерживая с определенной точностью частоту вращения
генератора постоянной в случае изменения частоты вращения двигателя или
нагрузки. Таким образом, сугубо электрическая задача стабилизации частоты тока
решается чисто механическим способом - стабилизацией частоты вращения.
Существуют ППЧВ с внешним и внутренним разветвлениями потока мощности,
двух- и трехпоточные. Однако наибольшее распространение получили передачи типов
А1 и А2. Трехпоточные передачи имеют некоторое преимущество по КПД, однако
сложность базового механизма ограничивает их использование.
Опыт конструирования и результаты исследований показывают, что для
двухпоточных ОГМП наиболее рациональным является привод с одной регулируемой и
одной нерегулируемой гидромашинами. Относительные установочные мощности
определяются выражением
где

;
-
номинальная мощность генератора;

-
диапазон регулирования [9].
На рис. 1.2 представлены структурные схемы ППЧВ на основе передач типов
А1 (рис. 1, а) и А2 (рис. 1, б). Вращение от вала отбора мощности двигателя Д
передается на одно из звеньев дифференциала. Два других звена соединены
соответственно с генератором Г и нерегулируемой гидромашиной 2. Регулируемая
гидромашина 1 через согласующую передачу соединяется либо с генератором (схема
А1), либо с двигателем (схема А2).
На рис. 1.3 приведены обобщенные графики механических и гидравлических
характеристик ППЧВ типов А2 (а) и A1 (б).
Компоновочная особенность передач, представленных на рис. 1.2, состоит в
том, что вал генератора и вал отбора мощности двигателя несоосны. Кроме того,
для уменьшения размеров передачи обычно стремятся соединить генератор и
нерегулируемую гидромашину с соответствующим звеном дифференциала напрямую.
а) б)
Рисунок 1.2 - Компоновочные схемы ППЧВ
Наиболее предпочтительной для применения в приводах постоянной частоты
вращения является компоновочная схема А1. Во-первых, это подтверждается тем,
что данная схема позволяет создавать приводы компонуемые совместно с
генератором. В этом случае имеется возможность создать единый типоразмерный ряд
систем электроснабжения различной мощности и с различным диапазоном
регулирования без привязки к конкретным компоновочным условиям. Во-вторых, их
характеристик ППЧВ, созданного по схеме А1, следует, что зависимость параметра
регулирования гидравлического насоса от передаточного отношения имеет линейный
вид. Можно сказать, что это свойство данной схемы позволит упростить процесс управления
приводом, т.к. параметр регулирования насоса является регулируемой величиной.
.1.2 Объемная
гидропередача (ОГП). Описание и составные части
Объемная гидропередача, являющаяся силовой частью гидропривода, состоит
из объемного насоса (преобразователя механической энергии приводящего двигателя
в энергию потока рабочей жидкости) и объемного гидродвигателя (преобразователя
энергии потока рабочей жидкости в механическую энергию выходного звена).
Объемные передачи устанавливают кинематические связи между ведущей и
ведомой частями. Это значит, что они могут поддерживать на ведомом валу любую
заданную скорость независимо от изменения нагрузки.
Не имея жесткой механической связи между ведущей и ведомой частями,
объемные передачи допускают расположение валов на значительном расстоянии друг
от друга, под углом и в разных плоскостях, допускают изменение вращательного
движения в поступательное и обратно. Все это вместе взятое позволяет при помощи
объемного гидропривода решить многие задачи, которые не могут быть решены
электроприводом и зубчатым редуктором [15].
КПД объемной гидропередачи низок по сравнению с механическими передачами,
так как превращение энергии происходит в 2 этапа: из механической в
гидравлическую на входе, и обратно в механическую на выходе.
Гидравлический привод ОГМП может быть частью единой гидросистемы всей
передачи или иметь автономный круг циркуляции жидкости. В этом наиболее часто
встречающемся случае замкнутый гидропривод состоит из силовой части, систему
управления (регулирования), защиты от перегрузок, подпитки, охлаждения и
отчистки рабочей жидкости.
Типичная гидравлическая схема замкнутого гидропривода приведена на рис.
1.4. Гидрообъемная передача 13 включает насос 5, гидродвигатель 16.
Вспомогательный насос 8 обеспечивает питание механизма управления рабочей
жидкостью и создает минимально допустимое давление в рабочих камерах
гидромашин.
Поток рабочей жидкости от вспомогательного насоса очищается фильтром 7,
снабженным предохранительным клапаном 6. Предохранительный клапан 9 ограничивает
давление вспомогательного насоса.
Редукционный клапан 10 устанавливают в случаях, когда давление подпитки
недостаточно для обеспечения момента поворота регулирующего органа насоса и
требуется большее давление жидкости в системе управления. Это влечет за собой
дополнительную нагрузку на вспомогательный насос и дополнительные потери
энергии.
Поток жидкости от вспомогательного насоса, компенсирующего утечки,
одновременно выполняет функцию охлаждения и очистки ее в силовом контуре. Он
поступает в силовой привод через обратные клапаны 11. Работает тот из клапанов,
который соединяется с гидролинией низкого давления силового привода. В случае
перегрузок срабатывают предохранительные клапаны 12, перепуская жидкость из
высоконапорной гидролинии в низконапорную.
Избыток жидкости вспомогательного насоса, не израсходованный на
управление и компенсацию утечек, через перпендикулярный золотник 14 и
переливной клапан 15 поступает в корпус гидропередачи, откуда, смешиваясь с
рабочей жидкостью из системы управления и утечками, поступает в систему
охлаждения.
Управление регулирующим органом насоса осуществляется через сервозолотник
2 и силовые цилиндры 4. Входной управляющий сигнал поступает через управляющее
звено 3, имеющее обратную связь с регулирующим органом насоса. Механизм
управления может строиться с механической обратной связью, а также с
электрическим входным сигналом и электрической обратной связью.
Жидкость охлаждается в теплообменнике 1, воздушный или водяной радиатор
которого снабжен предохранительным клапаном. Из теплообменника жидкость
поступает в бак 17, откуда забирается вспомогательным насосом [16].
Рисунок 1.4 - Гидравлическая схема замкнутого гидропривода
Единая система ОГМП помимо систем, обслуживающих гидропривод, может
включать систему смазки базового механизма, которую обычно предусматривают в
тех случаях, когда удается подобрать единую рабочую жидкость для гидропривода и
базового механизма. Единая система в основном повторяет автономную. Различие
состоит в том, что дополнительно предусмотрена система откачки жидкости из
картера и система сепарации масла и воздуха.
.1.3 Базовый
механизм (БМ). Описание и составные части
Базовый механизм - механизм, состоящий из зубчатых дифференциалов и
согласующих передач с постоянным передаточным числом.
Основные звенья базового механизма - звенья БМ, соединенные с двигателем,
потребителем, гидромашинами 1 и 2. В дальнейшем рассматриваются передачи,
предназначенные для работы с двухмашинным гидроприводом, и поэтому имеющие три
или четыре основных звена.
Двухпоточная передача имеет базовый механизм с тремя основными звеньями,
одно из которых соединено с двигателем, второе - с потребителем, третье - с
гидромашинной. Вторая гидромашина присоединяется напрямую или через согласующую
передачу с валом двигателя или потребителя. Соединенные трубопроводом
гидромашины замыкают базовый механизм, образую передачу. Базовый механизм
двухпоточных передач может быть и четырехзвенным, однако основными звеньями,
передающими внешние вращающие моменты, являются 3 звена. На рис. 1.5 приведена
структурная схема двухпоточной передачи с четырехзвенным дифференциалом с
последовательным соединением трехзвенных дифференциалов, где Д - двигатель, П -
потребитель, 1, 2 - гидромашины, D1, D2 - дифференциалы.
Рисунок 1.5 - Структурная схема двухпоточный передачи с четырехзвенным
дифференциалом
Следует заметить, что помимо передач с внешним разветвлением потока
мощности в приводах постоянной частоты вращения могут также использоваться
передачи с внутренним разветвлением, в которых роль дифференциала выполняют
машины «двойного вращения». Эти передачи могут быть наиболее компактными,
однако их применение ограничено сравнительно малыми мощностями и передаточными
отношениями, лежащими вблизи единицы, поэтому в данной работе они
рассматриваться не будут.
.1.4 Механизм
управления (МУ). Описание и составные части
Так как целью данной работы является исследование и разработка системы
автоматического управления ППЧВ, необходимо подробно остановиться на механизме
управления объемным гидроприводом.
На рисунке 1.7 изображена условная схема управления объемной
гидромашиной.
Рисунок 1.7 - Система управления объемной гидромашинной. 1-
гидравлический цилиндр, 2- управляющий поршень, 3 - наклонный диск, 4 -
поршень, 5 - блок цилиндров
Систему управления ОГП можно разделить условно на три узла - узел
распределителя, узел управляющего цилиндра, узел наклонного диска [21]. Как
показано на схеме, наклонный диск гидромашины жестко соединен со встроенным
симметричным гидравлическим цилиндром, который перемещает наклонный диск,
создавая угол наклона. Положение цилиндра управляется гидравлическим
пропорциональным распределителем. Для управления объемными гидромашинами могут
использоваться распределители с цилиндрическим или с плоским золотником [20].
Изменение
рабочего объема регулируемой гидромашины и соответсовенное изменение
передаточного отношения ОГМП осуществляются изменением угла наклона
регулирующего органа с помощью механизма управления. Типичным примером МУ с
гидроусилителем является механизм управления, применяемый в гидромашинах типа
Зауэр. Конструктивная схема этого механизма представлена на рис. 1.8, где θ - угол поворота регулирующего органа; z -
управляющее воздействие; a/b - передаточное отношение рычажной передачи; 
-
расстояние от оси силового цилиндра до оси поворота люльки; 
-
приведенный момент инерции регулирующего органа; 
-
площадь силового цилиндра; 
-
коэффициенты расходов через золотник.
Рисунок
1.8 - Конструктивная схема механизма управления гидромашины
В
зависимости от знака рассогласования между положением управляющего звена и
положением регулирующего органа золотник открывается в ту или иную сторону и
жидкость подается из системы подпитки в один из силовых цилиндров механизма
управления. При этом другой силовой цилиндр соединяется с полостью слива.
Для
ОГМП представляет особый интерес МУ с электрогидроусилителем, первый каскад
которого является преобразователем электрического входного сигнала в
управляющее воздействие на сервозолотник. Простейшим примером реализации такого
входного каскада может служить электромагнитный преобразователь (ЭМП).
Однако
чаще всего для удовлетворения требований к управляющему воздействию на
сервозолотник необходимы такие мощности управления, что целесообразным
становится добавление к ЭМП первого каскада гидроусилителя, преобразующего
перемещение электромагнита в перепад давления. Этот перепад управляет
сервозолотником основного каскада. При формировании электрического управляющего
сигнала целесообразно вводить электрическую обратную связь через операционный
усилитель, с помощью которого осуществляется суммирование управляющего сигнала
с сигналом обратной связи и настройка коэффициента управления системы.
Запорно-регулирующим элементом золотниковых гидрораспределителей является
цилиндрический золотник 1, который в зависимости от числа каналов (подводов) 3
в корпусе 2 может иметь один, два и более поясков (рис.1.9, а). На схемах
гидрораспределители обозначают в виде подвижного элемента, на котором
указываются линии связи, проходы и элементы управления. Рабочую позицию
подвижного элемента изображают квадратом (прямоугольником), число позиций
соответствует числу квадратов (рис.1.9, б).
На рис. 1.10 изображен наиболее актульный для нашего гидропривода
гидрораспределитель с электрогидравлическим управлением и его условное
обозначение. Он состоит из основного гидрораспределителя 2 с гидравлическим
управлением и вспомогательного гидрораспределителя 1 с электромагнитным
управлением. Основной гидрораспределитель управляет потоком рабочей жидкости
гидросистемы, а вспомогательный регулирует поток управления. Такие
гидрораспределители применяют в гидроприводах с дистанционным и автоматическим
управлением при больших расходах и высоком давлении в гидросистеме, когда
применение гидрораспределителей с электромагнитным управлением невозможно[16].
а) б)
Рисунок 1.9 - Схема (а) и обозначение (б) гидрораспределителя
Рисунок 1.10 - Гидрораспределитель с электрогидравлическим управлением
.2
Математическое моделирование ОГМП. Основные уравнения
.2.1 Объемный
гидропривод
Математическая модель объемного гидропривода с замкнутой циркуляцией
жидкости основывается на следующих уравнениях[11][25]:
) Уравнение баланса расхода жидкости
Для магистрали нагнетания
где V0 - объем жидкости в трубопроводе; Е
- модуль объемной упругости; Pн - давление в линии нагнетания; Qп - расход
системы подпитки; Qкл - расход через предохранительный клапан; Qм - расход на
входе мотора.
где Dм - рабочий объем, wм - скорость, ηом - механический КПД.
) Расход через клапан
где Рп - давление насоса подпитки; Ркл - давление настройки клапана.
) Подача насоса
где
Dmax - макс рабочий объем, 
- угол
наклона диска.
)
Для сливной магистрали
где
Qм - расход на выходе мотора; Qп - расход подпитки; Qкл - расход через
предохранительный клапан.
)
Уравнение равновесия нагрузок
[11][25]:
где

момент,
генерируемый мотором; J - момент инерции движущихся частей двигателя; F -
коэффициент трения; 
-
внешняя статическая нагрузка.
.2.2 Основные
уравнения базового механизма
Четырехзвенный дифференциал имеет две кинематические и две нагрузочные
степени свободы, т.е. его ранг равен 4. Практически это означает, что для
описания его кинематики и статики необходимы два уравнения, связывающие угловые
скорости основных звеньев, и два уравнения, описывающие связь между вращающими
моментами, подведенными извне к основным звеньям:
где

-
угловые скорости основных звеньев (1, 2, 
, 
); М -
вращающие моменты, подведенные извне к основным звеньям со стороны внешних
валов 
, 
, 1 и 2,
соединяемых напрямую с основными звеньями базового механизма 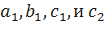
соответственно;

-
силовые передаточные отношения, равные 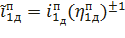
(плюс
или минус определяется в зависимости от направления потока мощности); 
- КПД
при передаче мощности между звеньями 
и 1 в
движении относительно знака 
(аналогично
записываются остальные передаточные кинематические отношения); 
при 
=0 -
кинематическое передаточное отношение.
.2.3 Модели
объемных потерь в объемной гидромашине
В 1940х годах Уилсон опубликовал модель утечек в гидромашинах,
рассматривающую ламинарное течение. Затем модель Уилсона была расширена, с
включением в нее эмпирических коэффициентов утечек и трения. Модель утечек
Уилсона показана в формуле 1.14, где D - рабочий объем гидромашины (на радиан) [24].
Шлоссер
включил в модель Уилсона выражение, учитывающее утечки при турбулентном
течении. Модель Шлоссера показана в формуле 1.15, где Cs - коэффициент
утечек при турбулентном течении, а 
-
плотность жидкости [18].
Тома,
использую простую модель Уилсона и принимая во внимание утечки при турбулентном
течении, определил, что коэффициенты потерь значительно изменяются - до 20%, в
зависимости от условий работы. Исследуя модели шестеренчатых насосов, Тесманн
предложил линейную зависимость утечек от скорости, используя эмпирические
постоянные k1 и k2, как показано в формуле 1.16 [24].
Дзаротти
и Нервенья создали эмпирическую модель, в которой утечки зависели от квадрата
давления, от скорости в степени 1.5 и от параметра регулирования. Они также
ввели эмпирические коэффициенты, чтобы учесть сжимаемость. В их модели,
показанной в формуле 1.17, C1…..5 - эмпирические коэффициенты потерь, а α - угол наклона блока цилиндров в гидромашине. Также, Qу* в
формуле 1.17 показывает общий расход на утечки и сжимаемость [21].
.2.4 Модели гидромеханических потерь в объемной гидромашине
Гидромеханические потери рассматриваются как потери момента. Одной из
основных составляющих гидромеханических потерь являются потери на трение. Можно
выделить два типа потерь на трение: трение, вызванное силами вязкого трения
между движущимися частями, обусловленное присутствием пленки жидкости, известное
также как вязкое трение, и сухое трение, принятое зависимым от давления. Оба
эти типа трения приводят к тому, что результирующий момент становится меньше,
чем идеальный. Идеальный момент, создаваемый гидромотором (Т) может быть
определен по формуле 1.18 [8].
Потери момента, связанные с вязким трением Tв (формула 1.19) зависят от скорости, а связанные с сухим
трением Tc (формула 1.20), зависят от давления.
Сv и Cf - коэффициенты потерь на вязкое и сухое трение, соответственно,
µ - динамическая вязкость жидкости, w - угловая скорость вращения вала, P разница давления на входе и выходе гидромашины. D - рабочий объем гидромашины (на
радиан) [18].
Тв=Сv µwD (1.19)
Tc=Cf PD (1.20)
Потери момента по модели Уилсона определяются по формуле 1.21. Те в
данной формуле - малые потери момента, не зависящие ни от давления, ни от
скорости [24].
Шлоссер представил Те в модели Уилсона как гидродинамические потери
момента, как показано в формуле 1.22 [18].
Тома предположил, что гидродинамическое трение не может быть независимым
от параметра регулирования гидромашины и дополнил модель Шлоссера (1.23) [24].
Хиби
и Ичикава использовали модель Уилсона, изменив коэффициент сухого трения, чтобы
описать потери момента в гидромашинах. Они сформулировали эмпирическую
зависимость коэффициента сухого трения от давления на входе и выходе
гидромашины, P1 и Р2. Формула 1.24 описывает их модель, Cf0, w0, 
и n -
эмпирические константы [21].
Дзаротти
и Нервенья, подобно их модели объемных потерь, создали нелинейную эмпирическую
модель потерь момента с эмпирическими константами С1……С9, как показано в
формуле 1.26. [21].
Дори
предположил, что все эмпирические модели теряют свою общность и гибкость в
применении к различным гидромашинам. Также обширное тестирование обязательно
для всех эмпирических моделей, так как эмпирические константы должны быть
получены из экспериментальных данных.Подобно своей модели утечек, Дори
предложил измененение коэффициентов в модели потерь Уилсона, как показано в
формуле 1.27, где Cv* и Cf* - измененные коэффициенты трения [18].
В
фомуле для Cv*, а и b - коэффициенты, которые определяют Cv
как линейную функцию от α.
Аналогично, коэффициенты c, d, e, f и g
определяют Cf как квадратичную функцию от угловой скорости w
(формула 1.28) [18].
При
моделировании гидрообъемной передачи необходимо также учесть потери на трение в
трубопроводе. Формула 1.26 получается из формулы Дарси-Вейсбаха, преобразуя
потери напора в потери давления [13].
где

-
коэффициент потерь на трение; 
и 
- длина
и диаметр трубопровода. 
-
плотность жидкости, 
- потери
давления.
.2.5 Учет
потерь в базовом механизме
Можно выделить следующие виды потерь в базовом механизме: потери в
зацеплениях, в опорах и гидравлические потери на перемешивание смазки и
выдавливание ее из впадин зубьев в процессе зацепления.
Гидравлические потери трудно поддаются формализованному учету при анализе
кинематических схем, так как зависят от многих конструктивных факторов.
Гидравлические потери при правильно спроектированной системе смазки невелики и
частично могут быть учтены потерями в зацеплениях и опорах в тех случаях, когда
коэффициенты потерь определяются экспериментально. Несмотря на внешнее
различие, все методы расчета имеют общую основу, состоящую в том, что мерой
потерь в зацеплениях и опорах саттелитов является мощность трения, измеренная в
движении относительно водила. Форма учета потерь, принятая при записи выражения
1.2 в дальнейшем в основном сохраняется. Рассмотрим некоторые особенности учета
потерь в базовом механизме применительно к ОГМП.
Предположим,
что силовое передаточное отношение между валом гидромашины 2 и валом
потребителя при остановленном вале двигателя (
)
является функцией передаточных отношений при остановленных водилах двух
планетарных механизмов (
, 
и
передаточного отношения согласующей передачи (
), тогда
В
выражении 1.29 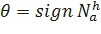
(
-
мощность, передаваемая центральным колесом a в движении
относительно водила). При ведущем колесе a имеем 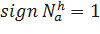
, при
ведомом 
.
Показателем степени = 
зависят
от режима работы гидромашин. Если гидромашина работает в насосном режиме, то 𝜒 = -1, а если в моторном режиме, то = 1. Знаки
показателей степени θ
и 𝜒 изменяются в следующих условиях:
при
i = 1 (режим блокировки) меняются только знаки θ;
при
изменении режима работы звеньев, соединенных с двигателем и потребителем,
например, в процессе торможения, меняются знаки θ и 𝜒;
при
изменении знака скоростей гидромашин, когда i = 
, при
переходе i через координаты скоростных нулевых режимов
гидромашин изменяется зна;
при
реверсе скоростей выходного вала и одновременном изменении знака вращающего
момента потребителя меняются знаки θ и 𝜒, исключение составляют передачи А1.
При
расчете КПД передачи, полученной из планетарного механизма путем остановки
водила, предполагают, что
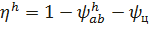
, (1.30)
где

; 
, 
-
коэффициент потерь соответственно в зацеплениях a - g и g - b:

- чисто
зубьев центрального колеса 
; 
-
коэффициент потерь в подшипниках саттелитов.
Коэффициент
трения f , входящий в эти формулы, является сложной функцией
многих факторов: суммарной скорости качения, твердости рабочих поверхностей
зубьев, скорости скольжения профилей на периферийных участках зубьев, вида
смазки, температуры и т. п. При 
его
значение невелико и практически не превышает 
, однако
при 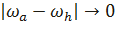
коэффициент
трения увеличивается и может достигать 
.
Увеличение
осредненного коэффициента трения при нулевых или близких к ним суммарных
скоростях качения существенно не отражается на общем КПД рассматриваемых
передач, во-первых, потому, что потери в зацеплениях и подшипниках базового
механизма составляют небольшую долю в общем балансе потреь ОГМП, а во-вторых,
при 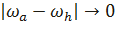
стремится
к нулю и мощность в зацеплении.
.3 Выбор
программы для реализации математической модели
Имитация - это численный метод проведения на вычислительных машинах с
математическими моделями, описывающими поведение сложным систем в течение
продолжительных периодов времени. Принципиальное отличие имитационного
эксперимента от реального заключается в том, что в процессе имитации
эксперимент проводится не с самой системой, а с ее моделью.
Целесообразность применения имитационного моделировании определяется
следующими причинами:
решение задачи аналитическими методами либо невозможно, либо
крайне сложно;
кроме получения средних значений выходных переменных необходимо
наблюдение за их изменением в течении некоторого промежутка времени;
с помощью метода имитационного моделирования могут быть построены
модели, отражающие большую совокупность элементов рассматриваемой системы;
имитационное моделирование свободно от ограничений, присущих
аналитическим методам;
на имитационной модели можно провести эксперименты, которые на
реальном объекте по ряду причин провести невозможно;
имитационное моделирование позволяет проводить долговременные
эксперименты путем сжатия временной шкалы;
результаты имитационного моделирования наглядны и легко
интерпретируемы;
имитация поведения объекта дает представление о том, какие
переменные системы наиболее существенны и как они взаимодействия, практические
еще до создания самого объекта.
В последние годы, благодаря своим функциональным и интерфейсным
возможностям, одним из наиболее широко используемых при проведении различного
рода расчетов и исследований (и в том числе при моделировании и анализе
всевозможных динамических систем) является программный комплекс на базе
математического пакета MATLAB, разработанный фирмой The MathWorcs, Inc. Пакет
MATLAB - это конгломерат высокоуровневого языка программирования, развитого
математического аппарата, основанного на матричном исчислении и реализованного
через набор функций, а также развитых средств отображения, хранения и обмена
информацией.
Кроме основных программ, функций и команд, сосредоточенных в базовом
пакете комплекса, имеется большое количество пакетов расширения MATLAB для
выполнения расчетов специалистами, работающими в самых разных областях науки и
техники.
Одной из наиболее привлекательных особенностей комплекса MATLAB является
наличие в нем эффективного и наглядного средства составления программных
моделей - пакета визуального программирования Simulink. Указанный пакет представляет собой графическую
надстройку, включающую графический редактор и средства связи со средой базового
пакета MATLAB, что позволяет проводить непосредственно в среде Simulink моделирование, анализ,
оптимизацию и другие исследования.
При построении моделей физических систем (гидравлических, механических,
электрических и комбинированных) неизбежно использование блоков, входящих в
состав библиотеки Simulink (по крайней мере, для формирования управляющих
сигналов и визуализации результатов расчетов).
Блоки библиотеки SimHydraulics в общем случае имеют два вида узлов:
энергетические и физических сигналов.
Одним из существенных недостатков библиотеки SimHydraulics является то, что при моделировании
гидромашин необходимо указывать такие параметры, как объемный КПД, механический
КПД в виде констант, взятых из каталога. В настоящей же работе, эти параметры должны
учитываться как переменные величины на протяжении времени работы установки.
Следовательно, имитационная модель должна быть создана с помощью пакета Matlab-Simulink на основе рассмотренных выше
уравнений.
2
Математическое моделирование ОГП в среде MATLAB-Simulink
Современная разработка гидростатических систем включает детальное
изучение явлений, имеющих место в статических и динамических состояниях
системы. Здесь особенное значение приобретают симуляционные тесты, так как они
являются более быстрыми и дешевыми по сравнению с экспериментальными тестами.
Но зачастую симуляционные тесты очень сильно упрощены и не принимают во
внимание точные математические модели. Симуляционные тесты очень полезны, если
создание реальной модели системы очень сложно и требует больших затрат времени.
Определение статических и динамических характеристик системы в последнее время
все чаще производится с помощью симуляционных тестов. Возможность использовать
более мощные компьютеры и программное обеспечение для математического
моделирования и симуляции позволяет строить симуляционные тесты даже для очень
сложных систем [19]. MATLAB-Simulink часто используется для симуляционных
тестом благодаря следующим своим преимуществам:
заметно упрощенная процедура, которая освобождает разработчика от
представления математической модели с помощью языка программирования
возможность использовать базовые математические модели, собранные в
библиотеках и скомбинированные так, как нужно разработчику
возможность исследования моделей систем с широким диапазоном
коэффициентов, в частности, гидравлических систем
возможность сравнения теоретических и экспериментальных результатов
.1 Моделирование основных элементов ОГП
1) Математическая модель регулируемого гидравлического насоса
В симуляционных тестах, будем использовать формулу для идеаальной подачи
насоса (2.1).
где
Qн - идеальная подача насоса (м3/с); e -
параметр регулирования, 
- максимальный
рабочий объем (м3/оборот); n - частота вращения (об/с)
Изображение
математической модели идеальной подачи насоса в MATLAB-Simulink
представлено на рисунке 2.1.
Рисунок
2.1 - Математическая модель идеальной подачи насоса. На входе: 1- параметр
регулирования, 2 - частота вращения, 3 - рабочий объем. На выходе: 1 -
идеальная подача насоса
2) Математическая модель нерегулируемого гидромотора
Нерегулируемый гидромотор обычно описывается двумя формулами. Одна
описывает расход жидкости, а другая - момент, генерируемый двигателем.
Идеальный расход, потребляемый гидромотором, описывается формулой [4](2.2).
где

- расход,
потребляемый идеальным мотором, 
-
частота вращения мотора (об/с), 
-
рабочий объем мотора (м3/об)
Изображение
математической модели идеального расхода гидромотора в MATLAB-Simulink
представлено на рисунке 2.2.
Рисунок
2.2 - Расход идеального мотора. На входе: 1- частота вращения гидромотора, 2 -
рабочий объем. На выходе: 1 - идеальный расход
)
Идеальный момент, развиваемый гидромотором рассчитывается по формуле (2.3)
где
Tидеальн - идеальный момент (Н/м), Vм -
рабочий объем, Р - давление в системе. В MATLAB-Simulink,
данное выражение можно представить следующим образом (рис 2.3)
Рисунок
2.3 - Идеальный момент, развиваемый гидромотором. На входе: 1- рабочий объем, 2
- давление. На выходе: 1 - момент
3) Математическая модель предохранительного клапана
Обычно анализируются статические характеристики клапана, выводящиеся из
его каталожной спецификации. В данном случае мы можем использовать две формулы
для двух различных состояний клапана - когда он открыт (2.4) и когда он закрыт
(2.5).
где

- расход
через предохранительный клапан, 
-
коэффициент наклона статических характеристик клапана, 
-
давление настройки клапана. Графически эта формула представлена на рисунке 2.4.
Рисунок 2.4 - Расход через предохранительный клапан. На входе: 1-
давление в системе, 2 - давление настройки клапана. На выходе: 1 - расход через
клапан
) Математическое моделирование эффекта сжимаемости жидкости.
Эффект сжимаемости жидкости может быть описан следующим выражением (2.6).
где

-
уровень расхода, относящийся к сжимаемости, 
объем
жидкости, находящейся под давлением, 
-
объемный модуль упругости жидкости. Следовательно, с помощью этой формулы можно
связать расход и давление (2.7).
Графически это выражение представлено на рисунке 2.5.
Рисунок 2.5 - Связь расхода и давления. На входе: 1 - расход на
сжимаемость жидкости. На выходе: 1 - давление в системе
) Математическое моделирование нагрузки на гидромотор
Момент Tм, генерируемый мотором находится в
равновесии с результирующим моментом нагрузки двигателя. В общем случае, это
может быть выражено следующим образом (2.8).
где Tи - результирующий момент инерционных
нагрузок, Tтр - результирующий момент трения, Tвн ст - момент внешней статической
нагрузки. Или, раскрывая выражения для моментов
где

момент
инерции движущихся частей двигателя, приведенный к валу гидромотора, F -
коэффициент вязкого трения в двигателе, приведенный к валу двигателя (Н*м*с), Tвн
ст - момент внешней статической нагрузки, wм - угловая
скорость вращения вала гидромотора. Формула (2.9) обычно используется для
вычисления угловой скорости вращения вала гидромотора, с помощью преобразования
в выражение (2.10).
В виде блок-диаграммы это выражение представлено на рисунке 2.6.
Рисунок 2.6 - Вычисление скорости вращения вала гидромотора.
) Математическая модель объемных потерь.
Для выражения объемных потерь (утечек) используется модель Шлоссера,
рассмотренная выше (формула 1.20). Графическое выражение данной формулы,
используемое в модели, изображено на рисунке 2.7.
Рисунок 2.7 - Объемные потери по модели Шлоссера. На входе: 1 -
коэффициент объемных потерь при ламинарном течении, 2 -рабочий объем, 3 -
давление, 4 - вязкость жидкости, 5 - плотность жидкости, 6 - коэффициент
объемных потерь при турбулентном течении. На выходе: 1 - расход на утечки
(объемные потери)
На рисунке 2.7 показан блок вычисления объемных потерь в регулируемом
гидронасосе. Объемные потери в гидромоторе вычисляются аналогично. Вязкость и
плотность жидкости на данном этапе исследования мы полагаем постоянными.
) Математическая модель механических потерь
Для выражения механических потерь) используется модель Шлоссера,
рассмотренная выше (формула 1.21). Графическое выражение данной формулы,
используемое в модели для, изображено на рисунке 2.8.
Рисунок 2.8 - Гидромеханические потери в гидромоторе по модели Шлоссера.
На входе: 1- коэффициент потерь на вязкое трение, 2 - вязкость жидкости, 3 -
рабочий объем, 4 - частота вращения вала, 5 - давление, 6 - коэффициент потерь
на гидродинамическое трение, 7 - плотность жидкости, 8 - коэффициент потерь на
сухое трение. На выходе: 1 - гидромеханические потери
) Математическая модель потерь по длине трубопровода
Для выражения потерь давления по длине трубопровода используется формула
Дарси-Вейсбаха, приведенная к давлению (формула 1.26). Блок в MATLAB, предназначенный для вычисления этих
потерь, представлен на рисунке 2.9.
Рисунок 2.9 - Потери по длине трубопровода. На входе 1 - расход жидкости,
2 - диаметр трубопровода, 3 - вязкость жидкости, 4 - плотность жидкости, 5 -
длина трубопровода. На выходе: 1 - потери давления, 2 - число Рейнольдса
) При модел
ировании ОГП, работающей в замкнутом цикле, необходимо отдельное
моделирование напорной и сливной магистрали. Для этого, рассмотрим два
уравнения баланса расхода жидкости - для напорной и сливной магистрали
соответственно, как было рассмотрено выше в формулах (1.1) и (1.5). Также, при
моделировании двух гидролиний, нужно учесть такое явление, как перетечки
жидкости из полости нагнетания, в полость всасывания. На данном этапе
исследования, будем полагать, что внутренние перетечки пропорциональны давлению
(рис. 2.10).
В этом случае давление в гидросистеме считается как разность давлений в
напорной и сливной линиях.
А общий КПД объемной гидравлической передачи рассчитывается как
произведение коэффициентов полезного действия входящих в нее гидромашин
(формула 2.12).

(2.12)
Рисунок 2.10 - Внутренние перетечки жидкости из полости нагнетания в полость
всасывания. На входе: 1 - давление в гидросистеме 2 - коэффициент перетечек; на
выходе: 1 - внутренние перетечки жидкости
2.2
Моделирование базового механизма
Базовый механизм описывается следующими основными уравнениями (2.13),
(2.14):
где

-
угловые скорости основных звеньев (1, 2, 
, 
); М -
вращающие моменты, подведенные извне к основным звеньям со стороны внешних
валов 
, 
, 1 и 2,
соединяемых напрямую с основными звеньями базового механизма 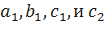
соответственно;

-
силовые передаточные отношения, равные 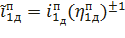
(плюс
или минус определяется в зависимости от направления потока мощности); 
- КПД
при передаче мощности между звеньями 
и 1 в
движении относительно знака 
(аналогично
записываются остальные передаточные кинематические отношения); 
при 
=0 -
кинематическое передаточное отношение.
Для
двухпоточных передач с дифференциалом на входе:
где
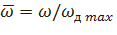
-
относительная угловая скорость; 
, 
-
коэффициенты, зависящие от кинематических (силовых) передаточных отношений
между звеньями базового механизма, 
-
передаточное отношение, 
-
координаты скоростных нулевых режимов гидромашин 1 и 2; 
-
относительный вращающий момент, 
-
коэффициенты, зависящие от потерь в зацеплениях и опорах звеньев базового
механизма.
)
Моделирование коэффициентов потерь 
и 
:
Коэффициенты

и 
могут
быть определены, если известны кинематическая схема и параметры зубчатых колес
и опор базового механизма.
Графическое
изображение данной формулы, используемое в модели, изображено на рис. 2.11:
Рисунок
2.11 - Коэффициент С1
Коэффициент
С2:
Графическое
изображение представлено на рис. 2.12:
Рисунок
2.12 - Коэффициент С2
Следующие
ниже блоки симуляционной программы изображают математические функции, описанные
в системе (2.15).
)
Графическое изображение относительной угловой скорости первого звена базового механизма
в среде Matlab-Simulink представлено на рис. 2.13:
Рисунок
2.13 - Относительная угловая скорость первого звена
)
Для второго звена графическое изображение представлено на рис. 2.14:
Рисунок
2.14 - Относительная угловая скорость второго звена
)
Изображение относительного вращающего момента первого звена:
Рисунок
2.15 - Относительный вращающий момент первого звена
)
Далее представлено изображение относительного вращающего момента второго звена:
Рисунок
2.16 - Относительный вращающий момент второго звена
.3
Определение входных параметров математической модели
В качестве входных параметров основных звеньев ОГМП были выбраны
максимально совпадающие с параметрами исследовательского стенда, разработанного
на кафедре Автоматизации и управления БГТУ «Военмех». Благодаря этому появилась
возможность использовать в работе экспериментальные данные, что существенно
улучшает результаты математического моделирования.
Основной частью стенда является ППЧВ, который состоит из объемного
гидропривода ГПП и дифференциала Д, соединенных по компоновочной схеме А1.
Объемный гидропривод ГПП базируется на двух гидравлических аксиально-поршневых
машинах: регулируемого насоса ГН типа Зауэр и нерегулируемого мотора типа Раух.
В гидропривод ГПП также входит распределительная и регулирующая гидроаппаратура
(на схеме не показана). Подробная схема гидравлического контура привода
показана на рис. 1.5 в главе 1. Гидропривод ГПП получает подпитку жидкости из
накопительного бака Б, которая фильтруется с помощью масляного фильтра МФ. В
этот же бак производится слив объемных утечек из полостей гидромотора ГМ и
гидронасоса ГН. Визуальный контроль давлений в системе осуществляется с помощью
манометров М3 (давление в линии высокого давления), М4 (давление в линии
управления гидронасоса) и М5 (давление на выходе из бака). Аналоговое измерение
давлений осуществляется с помощью датчика давления МД-25Т ДД 1 (измерение
давления в линии управления гидронасоса) и датчика давления МД-250Т ДД2
(измерение давления линии высокого давления). Регулирование угла наклона диска
машины ГН осуществляется с помощью шариковинтовой передачи П2, приводимой в
действие однофазным мотор-редуктором переменного тока РД-9, сигнал управления
котороым формируется вручную или автоматизировано в блоке управления БУ2.
Изменяемы наклон поворота ДУ, который выполнен на базе абсолютного энкодера NACHI. Скорости вращения основных звеньев
ППЧВ измеряются с помощью трех инкрементальных энкодеров - датчиков скорости
вращения: ДС1 (скорость входного звена ППЧВ), ДС2 (скорость вращения вала
гидромотора ГМ) и ДС3 (скорость вращения выходного звена ППЧВ или вала
генератора).
Рисунок 2.17 - Структурная схема стенда с ППЧВ
ППЧВ получает входное воздействие нужной величины от имитатора двигателя
ДВС, который реализован с помощью имитационного гидропривода ИГП и трехфазного
асинхронного двигателя ГД, который зачитывается от щита управления ЩУ.
Гидропривод ИГП получает подпитку жидкости от главной насосной станции НС. Для
контроля давления жидкости линия высокого давления и напорная линия насосной
станции НС снабжены манометрами М1 и М2 соответственно. В процессе работы,
двигатель вращается с постоянной скоростью, однако за счет регулирования
гидронасоса привода ИГП, на вход дифференциала ППЧВ поступает скорость,
изменяющаяся по требуемому закону. Процесс регулирования осуществляется за счет
изменения положения наклонного диска гидронасоса с помощью шариковинтовой
передачи П2, которая приводится в действие однофазным мотор-редуктором переменного
тока ЭД1. Необходимый управляющий сигнал для мотора-редуктора задается вручную
или автоматически с блока БУ1. Структурная схема стенда показана на рисунке
2.17.
В результате эксперимента были получены зависимости основных параметров
объемного гидропривода в зависимости от режима работы. Графики, полученные на
осциллографе, представлены на рисунке 2.18.
Рисунок 2.21 - Сравнение расходов утечек гидромотора «Зауэр № 15» в
зависимости от режима работы
Данные графики были оцифрованы с помощью программы Autodesk AutoCAD 2013. Численные значения зависимостей различных
параметров от времени были представлены в форме матриц и использованы в среде MATLAB-Simulink для получения значений коэффициентов
потерь в объемной гидравлической передаче:
Объемных потерь при ламинарном течении Cs
Объемных потерь при турбулентном течении Сmu
Механических потерь на сухое трение Cd
Механических потерь на вязкое трение Cv
Механических потерь на гидродинамическое трение Сh
Коэффициент трения Bh
В качестве исходных характеристик регулируемого гидронасоса были взяты
характеристики гидромашины Bosch Rexroth
AA4VG с рабочим объемом 40 кубических сантиметров. Ниже приведены
основные входные данные, используемые в математической модели.
· Рабочий объем (см3/оборот): Vg max = 40
· Максимальная частота вращения при максимальном рабочем объеме
Vgmax: nmax=4000 об/мин
· Минимальная частота вращения: nmin=500 об/мин
· Максимальная подача при максимальной скорости и рабочем
объеме:
· qvmax=160 л/мин
· Максимальная мощность при максимальной скорости, максимальном
рабочем объеме и давлении 400 атмосфер: Pmax=107 кВт
· Момент при максимальном рабочем объеме: Tmax=255 Н*м при давлении 400 атмосфер и
Т= 32.4 Н*м при давлении 100 атмосфер
· Момент инерции движущихся частей машины: Iдв=0.0038 кг*м2
· Заполняемый объем: М=1.1 л
· Приблизительная масса: 31 кг
Выбор данной гидромашины обусловлен тем, что по массогабаритным
показателям, а также по частоте, макс объему и развиваемой мощности, она
подходит для установки в объемную гидропередачу ППЧВ и также является
достаточно распространенно применяемой гидромашинной фирмы Bosch.
В качестве входных данных для модели нерегулируемого гидромотора были
использованы данные гидромотора Bosch Rexroth
A4FM с рабочим объемом 40 кубических сантиметров. Эти данные
приведены ниже
· Рабочий объем: Vg=40
см3
· Максимальная частота вращения: nmax=4000 об/мин
· Максимальный расход (при максимальной частоте вращения): qvmax=160 л/мин
· Момент (при давлении 400 атмосфер) Tmax=255 Н*м
· Заполняемый объем: 0.4 л
· Момент инерции движущихся частей двигателя: J=0.0043 кг*м3
· Приблизительная масса: 15 кг.
· Также в качестве входных данных было выбрано:
· Кинематическая вязкость жидкости: υ=18 мм2/с
· Плотность жидкости: ρ=850 кг/м3
· Объемный модуль упругости жидкости E=1.65*1010 Па
· Объем жидкости в трубопроводе VТр=2 л
Используя уравнения баланса расхода и нагрузки, а также применяя
определенные выше модели отдельных элементов ОМГП, мы можем получить
схематичное представление математической модели ОМГП, работающей в разомкнутом
цикле (рис 2.19). Для более компактного представления, некоторые вычисления
собраны в блоки. Более подробная схема с описанием блоков и пояснениями представлена
в приложении 2. КПД ОМГП рассчитывается как произведение объемных и
механических КПД гидромашин и КПД базового механизма.
Рисунок 2.19 - Общий вид схемы MATLAB-Simulink, представляющий математическую
модель ОГМП с гидроприводом, работающим в замкнутом цикле
Листинг рограммы представлен в Приложении А.
Для получения объективных графиков изменения выходных параметров были
смоделированы изменяющиеся параметры регулирования и момента нагрузки на
выходном валу.
Параметр регулирования гидромотора был представлен изменяющимся в полном
диапазоне - от -1 до 1. График изменения параметра регулирования представлен на
рис. 2.20.
Нагрузка на выходном валу ППЧВ была выбрана ступенчатой, чтобы показать
изменение характеристик привода с ростом нагрузки. График изменения нагрузки на
выходном валу представлен на рис. 2.21.
Рисунок 2.20 - График изменения параметра регулирования
Рисунок 2.21 - График изменения нагрузки на выходном валу привода
.4 Результаты
математического моделирования
В результате математического моделирования привода постоянной частоты
вращения в среде MATLAB-Simulink были получены следующие графики
работы системы.
На рис. 2.22 представлен график изменения КПД ППЧВ в зависимости от
значения параметра регулирования и изменения динамической нагрузки на выходном
валу привода:
Рисунок 2.22 - График изменения КПД привода постоянной частоты вращения
Как видно на графике, КПД привода находится в диапазоне от 76% до 81%.
При приближении параметра регулирования гидронасоса к нулю КПД системы
уменьшается, так как большую роль начинают играть потери давления по длине
трубопровода, а так же механические и объемные потери гидромашин. Момент
внешней динамической нагрузки так же влияет на КПД, в положительную сторону при
отрицательном параметре регулирования, и в отрицательную сторону при
положительном. Это объясняется тем, что в режиме ограничения скорости базового
механизма, когда нерегулируемая гидромашина выполняет функции насоса, внешняя
нагрузка также ограничивает скорость на выходном валу базового механизма.
На рис. 2.23 представлен график изменения давления в объемном
гидравлическом приводе:
Рисунок 2.23 - График изменения давления объемной гидропередачи
Давление объемной гидропередачи было рассчитано как сумма давлений в
сливной и напорной линиях, с учетом потерь по длине трубопровода. Как видно на
представленном графике, давление зависит от параметра регулирования, и в точке
перехода параметра через ноль, резко падает до нуля. При повышении внешней
динамической нагрузки давление также повышается. Резкий скачок давления ведет к
открытию предохранительных клапанов. Однако после стабилизации, давление все
равно остается повышенным по сравнению со значением до появления нагрузки.
На рис. 2.24 представлен график изменения скорости выходного вала
привода, полученный в результате симуляционных тестов:
Как видно на данном графике, скорость вращения выходного вала сильно
зависит от изменения внешней динамической нагрузки. Однако следует заметить,
что в реальных условиях внешняя нагрузка почти не изменяется резкими скачками,
и приводу хватает времени, чтобы стабилизировать частоту вращения без резких
перепадов. Также, следует заметить, что, как видно на графике, частота вращения
выходного вала не зависит от параметра регулирования. Так происходит потому,
что в математической модели скорость и направление вращения основных звеньев базового
механизма жестко связана с параметром регулирования гидронасоса. В реальном
механизме данная связь реализована точно наоборот, однако это не влияет на
представленный результат. Из этого можно сделать вывод о важности обратной
связи в приводе постоянной частоты вращения, которая предполагает зависимость
параметра управления от частоты вращения выходного вала базового механизма.
Рисунок 2.24 - График изменения скорости выходного вала привода
постоянной частоты вращения
.5 Анализ
результатов моделирования
Проанализировав результаты работы на данном этапе исследования, можно
сделать следующие выводы.
Была разработана математическая модель привода постоянной частоты
вращения на основе объемной гидромеханической передачи, учитывающая факторы,
необходимые для разработки системы управления. Такими факторами прежде всего
являются - влияние утечек на выходные параметры, влияние внутренних перетечек,
влияние внешней статической нагрузки и динамического момента инерции, влияние
трения, механических потерь и т д. За основу взяты уравнения баланса расхода и
нагрузки, модель утечек Шлоссера, дополненная с учетом утечек в трубопроводе и
внешнего динамического момента, а также результаты экспериментального
исследования изменения утечек гидромашины типа «Зауэр» № 15 в зависимости от
режима работы. Разработанная модель объемной гидравлической передачи,
работающей в замкнутом цикле, представлена в графической среде Matlab-Simulink.
С помощью симуляционных тестов в среде Matlab, получены основные характеристики ОГМП (скорость
выходного вала, КПД объемной гидромеханической передачи, давление в
гидросистеме). Отражено влияние объемных и гидромеханических потерь на эти
характеристики. Полученная схема в среде Matlab позволяет, изменяя различные входные параметры
(скорость вращения насоса, параметр регулирования, нагрузку), получать графики
изменения выходных параметров системы, что позволяет существенно сократить
время расчета и построения выходных характеристик ОГМП.
Полученная модель наглядно показывает положительное влияние обратной
связи между выходным валом базового механизма органом регулирования
гидронасоса. Жесткая обратная связь необходима для того, чтобы избежать влияния
изменения параметра регулирования и нулевых зон гидромашин на частоту вращения
выходного вала. Она является исходным инструментом при разработке системы
управления.
При этом, полученная модель имеет ряд недостатков и нуждается в
доработке. Прежде всего, необходимо произвести точное определение коэффициентов
объемных и механических потерь для рассматриваемых гидромашин. Сделать это
необходимо экспериментально. При создании модели были подобраны коэффициенты,
дающие максимально приближенное значение характеристик гидромашин к
экспериментальным данным. На данный момент можно утверждать, что полученная
модель отражает вид характеристик ОГМП с конкретными гидромашинами и может быть
адаптирована к разным режимам работы и к разным гидромашинам путем изменения
входных данных и корректировки коэффициентов.
3
Конструирование системы управления привода постоянной частоты вращения
Как сказано выше, главная характеристика ППЧВ - стабильность скорости
выходного вала, сильно зависит от обратной связи через изменение параметра
регулирования. Поэтому важно сконструировать систему управления, гибко
изменяющуюся в зависимости от конструкции привода и поддерживающую стабильную
частоту вращения на выходе вне зависимости от режима работы. Частота вращения
выходного вала считывается специальным датчиком - энкодером, после чего
аналоговый сигнал поступает в контроллер. В зависимости от входного сигнала
контроллер выдает управляющий сигнал на распределитель, управляющий цилиндрами,
которые определяют угол наколонного диска гидронасоса.
Пропорциональный распределитель по конструкции похож на дискретный
распределитель и сочетает в себе две функции [17]:
электрически настраиваемого регулятора расхода (как и
пропорциональный регулятор расхода)
распределителя, соединяющего выходные каналы А и В с каналом
питания Р и слива Т (как и дискретный 4/3-распределитель).
На рис. 3.1 представлен пропорциональный распределитель прямого действия
с цилиндрическим золотником.
Если электрический сигнал управления равен нулю, оба электромагнита
выключены. Золотник центрирующими пружинами удерживается в среднем положении,
при котором все каналы перекрыты.
Если управляющий сигнал напряжения имеет отрицательное значение, ток
поступает на правый электромагнит. Золотник смещается влево. Выход В
соединяется с питанием Р, выход А - со сливом Т. Смещение золотника пропорционально
силе тока, поступающего на электромагнит.
Если управляющее напряжение имеет положительное значение, ток поступает
на левый электромагнит. Золотник смещается вправо, соединяя Р с А и В с Т. Ив
этом случае золотника пропорционально силе тока, поступающего на электромагнит.
В случае сбоя питания электроэнергией золотник займет среднее положение,
при котором все каналы перекрыты (аварийно-безопасное).
Рисунок 3.1 - Пропорциональный 4/3 распеределитель прямого действия
.1
Нелинейности в системе управления
Из-за сил трения в золотнике и эффекта намагничивания характеристика
распределителя всегда отличается от идеальной наличием:
порога срабатывания
инверсного диапазона
гистерезиса
. Порог срабатывания (зона нечувствительности). С повышением силы тока,
протекающего по обмотке электромагнита, якорь смещается. Как только ток
перестает изменяться (рис. 3.2а), якорь останавливается. Затем ток должен
вырасти на какую-то минимальную величину, прежде чем якорь снова начнет перемещаться.
Это минимальное изменение входной переменной до начала изменения входной
называется порогом срабатывания или чувствительностью [17]. А величина А (рис
3.2а) называется зоной нечувствительности. Этот же эффект имеет место при
уменьшении тока и смещении якоря в противоположном направлении.
Утечки в уплотнениях цилиндров увеличивают нечувствительность и уменьшают
жесткость системы, которая характеризует поведение системы под нагрузкой.
Утечки в золотнике системы с положительным перекрытием могут, в зависимости от
соотношения утечек и перекрытий, уменьшить зону нечувствительности по сравнению
с системами с нулевым перекрытием; однако наличие их вызовет перелом в
статической характеристике системы.
. Инверсный диапазон. Если входной сигнал сначала изменяется в одном
направлении (возрастает), а затем в другом (падает), то характеристика
распадается на две (рис. 3.2б). Расстояние между ними называется инверсным
диапазоном [17]. Тот же эффект имеет место и в том случае, когда входной сигнал
падает, а затем растет.
. Гистерезис. Если ток изменяется сначала в одном направлении, а затем в
другом во всем диапазоне, характеристика также двоится. Максимальное расстояние
между двумя ветвями характеристики называется гистерезисом (рис. 3.2в).
Значения порога срабатывания, инверсного диапазона и гистерезиса можно
уменьшить с помощью управления положением якоря. Значения этих трех параметров
в обоих случаях обычно такие [17]:
от 3 до 6% от соответствующего диапазона изменения в клапанах без
управления положением
от 0,2 до 1 % от соответствующего диапазона изменения в клапанах с
управлением положением.
а)
б)
в)
Рисунок 3.2 - Зона нечувствительности (а), инверсный диапазон (б) и
гистерезис (в)
.2 Методы
устранения нелинейностей
Методы коррекции характеристик распределителя:
. Дизеринг (осцилляция).
Для преодоления силы статического трения в золотнике распределителя, на
управляющий сигнал накладываются колебания определенной частоты. Это называется
дизерингом или осцилляцией. Синусоидальный или прямоугольный (в виде меандра)
накладываемый сигнал осцилляции обладает эффектом уменьшения гистерезиса
распределителя, вызванного силами трения, действующими в золотнике
распределителя [17]. Частота и амплитуда осцилляции должны быть выбраны так,
чтобы эффективно снижать влияние гистерезиса распределителя без создания
возмущения на выходе. Обычно значение частоты осцилляции задается ниже значения
частоты
Эффект осцилляции возрастает с уменьшением частоты. Выбор частоты зависит
от гистерезиса работающего распределителя и привода и от помех [20].
Аксиальная осцилляция существенно влияет на расходные характеристики
рабочих окон золотниковых распределительных устройств, особенно при
положительных перекрытиях. Если частота осцилляции достаточно велика, а
амплитуда сравнительно мала, то колебания расхода и давления весьма
незначительны [23].
1. Компенсация зоны нечувствительности.
Для того, чтобы улучшить переходные характеристики, когда изменение
расхода обусловлено реверсированием полярности сигнала, может быть введен
управляемый скачок около нулевой области. Такой метод компенсации зоны
нечувствительности называют коррекцией по току [17].
Усиление сигнала - электронный усилитель преобразует напряжение в
электрический ток, сила которого оказывается достаточной для того, чтобы
привести в действие клапан.
Рисунок 3.3 - Обмен сигналами между управляющим устройством и
пропорциональным электромагнитом (блок-схема)
Три основные функции усилителя показаны на рисунке 3.4. Это корректировка
сигнала (для компенсации «мертвой зоны»), широтно-импульсная модуляция сигнала
или ШИМ (для преобразования сигнала), усиление (для получения сигнала нужной
мощности).
Рисунок 3.4 - Блок-схема одноканального усилителя
Одноканальный усилитель применяется для управления клапанами с одним
пропорциональным магнитом. Распределители управляются двумя магнитами, и
поэтому требуют двухканальный усилитель. В зависимости от статуса сигнала
управления, ток поступает или только на левый магнит или только на правый. На
рисунке 3.5 показан принцип широтно-импульсной модуляции (ШИМ). Сигнал в виде
электрического напряжения преобразуется в импульсы. Генерируется примерно 10000
импульсов в секунду [17].
После конечной стадии усиления сигнал в виде импульсов подается на
пропорциональный магнит. Поскольку индуктивность его обмотки высока, сила тока
не может изменяться так же быстро, как напряжение. Величина тока будет только
слегка колебаться около среднего значения. Небольшое напряжение на входе
создает небольшие импульсы. Среднее значение тока, поступающего на обмотку
электромагнита, также небольшое. С ростом напряжения ширина импульсов растет. Среднее
значение тока увеличивается.
Среднее значение тока на выходе усилителя пропорционально поступающему на
вход напряжению.
Некоторая пульсация тока, являющаяся следствием широтно-импульсной
модуляции, заставляет якорь электромагнита и соответственно золотник
распределителя колебаться с малой амплитудой и большой частотой. Это позволяет
избежать сил статического трения. Существенно уменьшаются порог срабатывания,
инверсный диапазон и гистерезис распределителя.
Это уменьшение трения из-за наличия высокочастотного сигнала известно как
эффект дитера. Некоторые модели усилителей позволяют пользователь вводить
дополнительную частоту и амплитуду дитера, независимо от широтно-импульсной
модуляции.
В результате широтно-импульсной модуляции на транзисторах конечного
каскада усилителя имеют место три состояния переключения:
Нижнее значение сигнала. Транзистор заперт. Потеря мощности на нем равна
нулю, тока на выходе нет.
Верхнее значение сигнала. Транзистор открыт. Его сопротивление в этом
состоянии очень мало, потери мощности незначительны.
Фронт сигнала. Транзистор переключается. Поскольку переключение
происходит очень быстро, потери мощности малы.
В целом, потери мощности значительно меньше, чем в усилителе без ШИМ.
Электронные элементы меньше нагреваются, конструкция усилителя становится более
компактной.
Рисунок 3.5 - Широтно-импульсная модуляция
3.3 Энкодеры.
Устройство и принцип работы
Энкодер или преобразователь угловых перемещений - устройство,
предназначенное для преобразования угла поворота вращающегося объекта (вала) в
электрические сигналы, позволяющие определить угол его поворота. Широко
применяются в промышленности.
Энкодеры подразделяются на инкрементальные и абсолютные, которые могут
достигать очень высокого разрешения. Инкрементальный энкодер выдает за один
оборот определенное количество импульсов. А абсолютные энкодеры позволяют в
любой момент времени знать текущий угол поворота оси, в том числе и после
пропадания и восстановления питания. А многооборотные абсолютные энкодеры,
кроме того, также подсчитывают и запоминают количество полных оборотов оси.
Энкодеры могут быть как оптические, резисторные, так и магнитные и могут
работать через шинные интерфейсы или промышленную сеть. Преобразователи
угол-код практически полностью вытеснили применение сельсинов.
Инкрементальные энкодеры предназначены для определения угла поворота
вращающихся объектов. Они генерируют последовательный импульсный цифровой код,
содержащий информацию относительно угла поворота объекта. Если вал
останавливается, то останавливается и передача импульсов. Основным рабочим
параметром датчика является количество импульсов за один оборот. Мгновенную
величину угла поворота объекта определяют посредством подсчёта импульсов от
старта. Для вычисления угловой скорости объекта процессор в тахометре выполняет
дифференцирование количества импульсов во времени, таким образом показывая
сразу величину скорости, то есть число оборотов в минуту. Выходной сигнал имеет
два канала, в которых идентичные последовательности импульсов сдвинуты на 90°
относительно друг друга (парафазные импульсы), что позволяет определять
направление вращения. Имеется также цифровой выход нулевой метки, который
позволяет всегда рассчитать абсолютное положение вала.
Абсолютные энкодеры, как оптические, так и магнитные имеют своей основной
рабочей характеристикой число шагов, то есть уникальных кодов на оборот и
количество таких оборотов, при этом не требуется первичной установки и
инициализации датчика. Поэтому абсолютные энкодеры не теряют свою позицию при
исчезновении напряжения.
Наиболее распространённые типы выходов сигнала - это код Грея,
параллельный код, интерфейсы Profibus-DP, CANopen, DeviceNet, SSI, LWL, через
которые также осуществляется программирование датчиков.
Рисунок 3.6 - Кодовый диск абсолютного энкодера
Абсолютный энкодер не теряет своего значения при потере питания и не
требует возвращения в начальную позицию. Сигнал абсолютного энкодера не
подвержен помехам и для него не требуется точная установка вала. Кроме того,
даже если кодированный сигнал не может быть прочитан энкодером если, например,
вал вращается слишком быстро, правильный угол вращения будет зарегистрирован,
когда скорость вращения уменьшится. Абсолютный энкодер устойчив к вибрациям.
Измерительная система абсолютного энкодера состоит из поворотной оси,
монтированной на двух высокопрецизионных подшипниках, кодового диска,
установленного на ось, а также опто-электронной считывающей матрицы и схемы
обработки сигнала. В качестве источника света служит светодиод, инфракрасные
лучи которого просвечивают кодовый диск и попадают на фототранзисторную
матрицу, расположенную с обратной стороны кодового диска. При каждом шаге
углового положения кодового диска темные участки кода предотвращают попадание
света на те или иные фототранзисторы фототранзисторной матрицы. Таким образом,
темные - светлые участки каждой из дорожек будут отображены на
фототранзисторной матрице и преобразованы в электрические сигналы.
Электрические сигналы, в свою очередь, подготавливаются операционными
усилителями и выходными трайберами для выдачи в виде n -бит бинарного сигнала.
Изменения интенсивности источника светового потока регистрируются с помощью
дополнительного сенсора и компенсируются электронной схемой.
Линейные перемещения предполагают необходимым применение измерительной
системы с n -количеством оборотов. Например, при линейных приводах или при
задачах измерения с помощью зубчатой измерительной штанги, применение
однооборотных датчиков является неприемлемым. В этом случае приходят на помощь
датчики, где дополнительно к измерению угла поворота в пределах одного оборота
также происходит регистрация количества оборотов с помощью дополнительно
встроенного передаточного механизма, т.е. своего рода редуктора из нескольких
кодовых оптических дисков, образуя, таким образом, многооборотный энкодер (
Multi - Turn ).
Крепление
Представленные датчики соединяются с вращающимся объектом посредством
нормального или полого вала, последний может быть как сквозным, так и несквозным
(тупиковым). Вал вращающегося объекта и вал энкодера соединяют механически при
помощи гибкой или жёсткой соединительной муфты. В качестве альтернативы энкодер
монтируют непосредственно на вал объекта, если энкодер имеет полый вал. В
первом случае вероятная несоосность и допустимые биения компенсируются
деформацией гибкой втулки. Во втором возможна фиксация энкодера посредством
штифта.
.4
Программируемый логический контроллер
ПЛК - программируемый логический контроллер, представляют собой
микропроцессорное устройство, предназначенное для сбора, преобразования,
обработки, хранения информации и выработки команд управления, имеющий конечное
количество входов и выходов, подключенных к ним датчиков, ключей,
исполнительных механизмов к объекту управления, и предназначенный для работы в
режимах реального времени.
Рисунок 3.7 - Схема работы ПЛК
Принцип работы ПЛК несколько отличается от «обычных» микропроцессорных
устройств. Программное обеспечение универсальных контроллеров состоит из двух
частей. Первая часть это системное программное обеспечение. Проводя аналогию с
компьютером можно сказать, что это операционная система, т.е. управляет работой
узлов контроллера, взаимосвязи составляющих частей, внутренней диагностикой. Системное
программное обеспечение ПЛК расположено в постоянной памяти центрального
процессора и всегда готово к работе. По включению питания, ПЛК готов взять на
себя управление системой уже через несколько миллисекунд. ПЛК работают
циклически по методу периодического опроса входных данных.
Рабочий цикл ПЛК включает 4 фазы:
. Опрос входов
. Выполнение пользовательской программы
. Установку значений выходов
. Некоторые вспомогательные операции (диагностика, подготовка данных для
отладчика, визуализации и т. д.).
Выполнение 1 фазы обеспечивается системным программным обеспечением.
После чего управление передается прикладной программе, той программе, которую
вы сами записали в память, по этой программе контроллер делает то что вы
пожелаете, а по ее завершению управление опять передается системному уровню. За
счет этого обеспечивается максимальная простота построения прикладной программы
- ее создатель не должен знать, как производится управление аппаратными
ресурсами. Необходимо знать с какого входа приходит сигнал и как на него
реагировать на выходах.
Рассмотрим входа и выхода ПЛК. Существует три вида входов дискретные,
аналоговые и специальные
Один дискретный вход ПЛК способен принимать один бинарный электрический
сигнал, описываемый двумя состояниями - включен или выключен. Все дискретные
входы (общего исполнения) контроллеров обычно рассчитаны на прием стандартных
сигналов с уровнем 24 В постоянного тока. Типовое значение тока одного
дискретного входа (при входном напряжении 24 В) составляет около 10 мА.
Аналоговый электрический сигнал отражает уровень напряжения или тока,
соответствующий некоторой физической величине, в каждый момент времени. Это
может быть температура, давление, вес, положение, скорость, частота и т. д.
Поскольку ПЛК является цифровой вычислительной машиной, аналоговые
входные сигналы обязательно подвергаются аналого-цифровому преобразованию
(АЦП). В результате, образуется дискретная переменная определенной разрядности.
Как правило, в ПЛК применяются 8 - 12 разрядные преобразователи, что в большинстве
случаев, исходя из современных требований по точности управления
технологическими процессами, является достаточным. Кроме этого АЦП более
высокой разрядности не оправдывают себя, в первую очередь из-за высокого уровня
индустриальных помех, характерных для условий работы контроллеров.
Практически все модули аналогового ввода являются многоканальными.
Входной коммутатор подключает вход АЦП к необходимому входу модуля.
Стандартные дискретные и аналоговые входы ПЛК способны удовлетворить
большинство потребностей систем промышленной автоматики. Необходимость
применения специализированных входов возникает в случаях, когда
непосредственная обработка некоторого сигнала программно затруднена, например,
требует много времени.
Наиболее часто ПЛК оснащаются специализированными счетными входами для
измерения длительности, фиксации фронтов и подсчета импульсов.
Например, при измерении положения и скорости вращения вала очень
распространены устройства, формирующие определенное количество импульсов за
один оборот - поворотные шифраторы. Частота следования импульсов может
достигать нескольких мегагерц. Даже если процессор ПЛК обладает достаточным
быстродействием, непосредственный подсчет импульсов в пользовательской
программе будет весьма расточительным по времени. Здесь желательно иметь
специализированный аппаратный входной блок, способный провести первичную
обработку и сформировать, необходимые для прикладной задачи величины.
Вторым распространенным типом специализированных входов являются входы
способные очень быстро запускать заданные пользовательские задачи с прерыванием
выполнения основной программы - входы прерываний.
Конструктивно ПЛК подразделяются на моноблочные, модульные и
распределенные. Моноблочные имеют фиксированный набор входов выходов
В модульных контроллерах модули входов - выходов устанавливаются в разном
составе и количестве в зависимости от предстоящей задачи
В распределенных системах модули или даже отдельные входа-выхода,
образующие единую систему управления, могут быть разнесены на значительные расстояния
.5 Разработка
конструкции и технологии печатного узла контроллера
3.5.1 Анализ
электрической принципиальной схемы и выбор элементной базы
Данное изделие предназначено для эксплуатации в качестве наземной
радиоэлектронной аппаратуры и не подвергается воздействию высоких температур,
давления, не используется в условиях повышенной влажности и цикличности
воздействия температур. Следовательно, по
ОСТ 4.077.000 изделию следует присвоить первую группу жесткости. Группа
жесткости обуславливает требования к конструкции платы, материалу основания и
проводящего рисунка, а также необходимость защиты от климатических,
механических и других воздействий.
Таблица 1 - Факторы, воздействующие на печатную плату контроллера
Наименование
воздействующего фактора
|
Значение фактора
|
Температура окр. среды
|
Повышенная, 0С
|
85±2
|
Повышенная влажность
|
Время выдержки
|
2 сут.
|
Циклическое воздействие
температур
|
Верхнее знач., 0С Нижнее
знач., 0С Число циклов
|
55±2 -40±2 2
|
Поверхностный монтаж выполняется по бессвинцовой технологии, которая
имеет определенные требования:
· Использование бессвинцовых сплавов для пайки;
· Флюс должен соответствовать требованиям защиты окружающей
среды, обладать паяемостью, быть совместимым с материалами, соответствовать
термическим требованиям бессвинцовых сплавов;
· Компоненты должны обладать термической паяемостью,
смачиваемостью, термостойкостью, чувствительностью к влаге, иметь чистую
поверхность без окислов. Не допускается деформация компонентов при пайке.
Термоустойчивость - 2600С в течение 10 секунд; пластмассы не должны содержать
галогенов.
· Плата должна быть ровной, термостойкость должна
соответствовать температурному профилю, иметь оптимизированную конструкцию для
бессвинцовой пайки
Материалы, используемые для изготовления ПП, а также материалы
компонентов должны соответствовать директивам RoHS и WEEE.
Выбор компонентов для поверхностного монтажа.
Так как изготовление печатной планы происходит при помощи селективной
пайки по бессвинцовой технологии, то выбор будет ограничен требованиями к
компанентам именно для этого метода, а именно :
Таблица 2 - Требования к компонентам печатной платы
Толщина печатных плат
(панелей)
|
от 1,0 до 4,2 мм.
|
Форма печатных плат
(панелей)
|
преимущественно
прямоугольная.
|
Минимальный зазор между
паяемыми контактными площадками (рис. 3.2.):
|
0,6 мм
|
Размеры печатных плат
(панелей)
|
от 60x60 до 460x460 мм.
|
Свободное пространство
вокруг паяемых контактных площадок
|
|
(в том числе и расстояния
до соседних площадок SMD-компонентов):
|
|
а) с трех сторон
(рис.3.2.):
|
не менее 1,5 мм;
|
б) с четвертой стороны (в
направлении слива припоя, рис.3.2.)
|
не менее 5 мм.
|
Выбор резисторов:
Номинальные значения резисторов:
R1:
0,25 кОм;
R2*: 3
кОм;
R3: 60
кОм;
R4,R5,R6: 5 кОм;
Были выбраны чип резисторы серии RC0603 (RC -
толстопленочные, 0603 - типоразмер).
Таблица 3 - Электрические параметры резисторов RC0603
Мощность
|
0,063 Вт;
|
Максимальное рабочее
напряжение
|
50В
|
Диапазон номинальных
сопротивлений
|
1 Ом - 22 МОм
|
Точность
|
5%;
|
Диапазон рабочих температур
|
- 55...+ 125 °C
|
Габаритные размеры
|
L = 1,6 мм; W = 0,8 мм; T =
0,5 мм.
|
Рисунок 3.7 - Резистор RC0603
Выбор конденсаторов:
Номинальные значения конденсаторов:
С1: 200 пФ;
C2:
0,1 мкФ;
C3:
1мкФ;
C4:
0,4 мкФ;
Были выбраны керамические чип конденсаторы типа ТКЕ Y5V типоразмер 0603 (конденсаторы этого типа имеют высокую
диэлектрическую постоянную, используются в цепях общего применения).
Таблица 4 - Электрические параметры конденсатора ТКЕ Y5V
Температурный коэффициент
|
+22%
|
Максимальное рабочее
напряжение
|
50В
|
Диапазон номинальных
сопротивлений
|
0,5 пФ - 10 мкФ
|
Точность
|
20%;
|
Диапазон рабочих температур
|
- 25...+ 85 °C
|
Габаритные размеры
|
L = 3,2 мм; W = 1,6 мм;
Tмах = 1,25 мм, у=0,5 мм.
|
Рисунок 3.8 - Схема конденсатора ТКЕ Y5V
Выбор транзисторов:
Все транзисторы (VT1, VT2, VT3, VT4)
являются биполярными структуры n-p-n, поэтому были выбраны транзисторы КТ3249Б9:
Рисунок 3.9 - Транзистор КТ3249Б9.
Таблица 5 - Технические характеристики транзистора КТ3249Б9
Наименование
|
Значение
|
Структура
|
n-p-n
|
Макс. напр. к-б при
заданном обратном токе к и разомкнутой цепи э.(Uкбо макс),В
|
50
|
Макс. напр. к-э при
заданном токе к и заданном сопр. в цепи б-э.(Uкэr макс),В
|
40
|
Максимально допустимый ток
к ( Iк макс,А)
|
0.1
|
Статический коэффициент
передачи тока h21э мин
|
80
|
Граничная частота
коэффициента передачи тока fгр,МГц
|
200.00
|
Максимальная рассеиваемая
мощность к (Рк,Вт)
|
0.075
|
Корпус
|
KT-46
|
Разъем (вилка).
Была выбран разьем - вилка WF-7,
имеющая 7 контактов.
Таблица 6 - Характеристики разъема WF-7
Серия
|
WF
|
Функциональное назначение
|
вилка
|
Способ монтажа
|
пайка на плату
|
Форма контактов
|
прямые
|
Шаг контактов,мм
|
2.54
|
Количество контактов
|
7
|
Материал изолятора
|
нейлон
|
Сопротивление изолятора не
менее,МОм
|
1000
|
Материал контактов
|
фосфористая бронза
|
Покрытие контактов
|
олово
|
Сопртивление контактов не
более,Ом
|
0.2
|
Предельный ток через
контакт,А
|
3
|
Рабочее напряжение ,В
|
250
|
Предельное напряжение не
менее,В
|
1500 В в течение 1 мин..
|
Рабочая температура,°С
|
-30…90
|
Рисунок 3.10 - Эскиз вилки типа WF
.5.2 Выбор и
обоснование параметров печатной платы
В зависимости от условий эксплуатации определяется группа жесткости,
обуславливающая требования к конструкции платы, материалу основания и
проводящего рисунка и необходимости защиты от климатических, механических и
других воздействий. По результатам анализа ТЗ на изделие, в которое входит
разрабатываемый печатный узел, можно определить, что по условиям эксплуатации
печатный узел изготавливается по 1-ой группе жесткости.
Выбор типа печатной платы
Целесообразно использовать двустороннюю печатную плату (ДПП) с
металлизированными монтажными и переходными отверстиями, характеризуемую
повышенной ремонтопригодностью и прочностью вывода навесного элемента с
проводящим рисунком платы.
Для ДПП с металлизацией отверстий используются комбинированный
(позиционный и негативный), полуаддитивный и аддитивный методы получения
проводящего рисунка.
Выбор метода получения зависит от оснащенности производства конкретного
предприятия. В учебных целях выберем комбинированный позитивный метод печатного
монтажа. Метод заключается в получении проводников путем травления
фольгированного диэлектрика и металлизации отверстий химико-гальваническим
способом. Типовой технологический процесс изготовления ДПП позитивным
комбинированным способом приведен в ОСТ 4.ГО.054.233. Защитный рисунок
формируется фотолитографическим способом.
Поверхностный монтаж выполняется по бессвинцовой технологии пайкой
оплавленем. Если говорить о принципиальных моментах, то бессвинцовая пайка
практически ничем, кроме температуры, не отличается от традиционной
Sn/Pb-технологии. Выбранный припой - SnAgCu - сплав олова, серебра и меди
является трехкомпонентным эвтектическим припоем. Преимущество такого типа
заключается в более низкой температуре расплавления (217°С).
Был выбран второй класс точности, т.к. печатные платы этого класса
точности наиболее просты в исполнении, надежны в эксплуатации и имеют низкую
стоимость.
Таблица 7 - Номинальные размеры основных параметров элементов конструкции
печатной платы
Название элемента
|
Класс точности - второй
|
Ширина проводника, t
|
0,45 мм
|
Расстояние между элементами, S
|
0,45 мм
|
Гарантированный поясок, b
|
0,2 мм
|
Отношение диаметра
отверстия к толщине
|
0,4
|
Таблица 8 - Габаритные размеры (по ГОСТ 10317-79) и конфигурация печатной
платы
Название элементаЗначение
|
|
Габаритные размеры
|
60 40 мм
|
Соотношение размеров сторон
|
3:2
|
Толщина печатной платы
|
2 мм
|
Конфигурация печатной платы
|
прямоугольная
|
Шаг координатной сетки
|
0,625 мм.
|
В связи с тем, что разрабатываемый печатный узел принадлежит к 1-ой
группе жесткости, то в качестве материала основания рекомендуется применять
гетинакс, поэтому был выбран гетинакс фольгированный ГФ-2-50 (толщина фольги:
50 мкм; толщина материала с фольгой: 2 мм). Сопрягаемые размеры контура платы
должны иметь предельные отклонения по 12-му квалитету, несопрягаемые - по
14-му.
Основные этапы проектирования ПП.
При проектировании печатных узлов решаются следующие задачи:
1. анализ ТЗ и выбор элементной базы;
2. выбор варианта конструкции узла;
3. выбор типа электрического соединителя
и элементов контроля функционирования;
4. выбор элементов крепления, жесткости
и фиксации;
5. конструирование печатного монтажа;
6. оценка устойчивости к
электромагнитным тепловым и механическим воздействиям.
По результатам анализа условий эксплуатации определена 2 группа
жесткости.
Рисунок 3.11 - Конструкция двусторонней печатной платы, где b -
гарантийный поясок; h - толщина проводящего рисунка; Hф - толщина фольги; hп -
толщина проводящего покрытия; hм - толщина гальванически наращенной меди
.6
Конструкторско-технологический расчет платы
.6.1 Расчет
параметров проводящего рисунка с учетом технологических погрешностей его
получения
Конструкторско-технологический расчет печатных плат проводится с учетом
производственных погрешностей рисунка проводящих элементов, фотошаблонов,
базирования, сверления, экспонирования и т. д. по ОСТ 4.010.019-81 и ГОСТ
23751-79.
) Номинальное значение диаметра монтажного отверстия (для установки
навесного элемента), мм:
, где:
-
максимальное значение диаметра вывода навесного элемента;
-
разность между минимальным значением диаметра отверстия и максимальным
диаметром вывода устанавливаемого элемента (0.1…0.4 мм);
- нижнее
предельное отклонение номинального значения диаметра отверстия.
мм;
Предпочтительные размеры монтажных отверстий выбирают из ряда 0,7; 0,9;
1,3; 1,5 мм, а переходных отверстий из ряда 0,7; 0,9; 1,1.
Следовательно, выбираем размер 0,9.
2) Номинальное значение ширины проводника:
, где:
-
минимально допустимая ширина проводника, мм;
- нижнее
предельное отклонение ширины проводника, мм.
мм;
)
Номинальное значение расстояния между элементами проводящего рисунка:
, где:
-
минимально допустимое расстояние между соседними элементами;
-
верхнее предельное отклонение ширины проводника.
мм;
Центры
монтажных и переходных отверстий располагаются в узлах координатной сетки по
ГОСТ 10317-79.
Диаметральное
значение позиционного допуска расположения центров отверстий относительно
номинального положения узла координатной сетки:
Диаметральное
значение позиционного допуска расположения контактных площадок относительно их
номинального положения:
)
Минимальный диаметр контактной площадки:
, где:
-
номинальное значение диаметра монтажного отверстия;
-
предельное отклонение;
- ширина
гарантированного пояска;
-
глубина подтравливания диэлектрика (для ДПП
).
мм.
)
Минимальное расстояние для прокладки n-го количества проводников между
отверстиями с контактными площадками диаметрами
и
:
, где:
n - количество
проводников;
-
диаметральное значение позиционного допуска расположения проводника
относительно номинального положения (для ДПП 2-го кл. точности
=0.1)
мм
.6.2 Расчет
параметров проводящего рисунка с учетом технологических погрешностей получения
защитного рисунка
Расчет учитывает предельные значения технологических коэффициентов,
полученных в результате экспериментальных исследований точности отдельных
операций.
1) Минимальный диаметр металлизированного отверстия:
, где:
-
толщина платы, мм;
-
отношение диаметра металлизированного отверстия к толщине платы.
мм;
2) Минимальный эффективный диаметр контактной площадки:
;
-
максимальный диаметр просверленного отверстия;
;
св - диаметр сверла;
Δd
- погрешность диаметра отверстия;
;
Мотв - диаметр
металлизированного отверстия;
мм;
мм;
, где
- погрешность расположения отверстия относительно
координатной сетки, обусловленная точностью сверлильного станка;
- погрешность базирования плат на сверлильном станке;
;
) Погрешность расположения
контактной площадки:
;
- погрешность расположения оси контактной площадки
относительно координатной сетки на фотошаблоне;
- погрешность расположения элементов при
экспонировании на слое;
- погрешность расположения базовых отверстий на
фотошаблоне;
;
) Минимальный эффективный
диаметр контактной площадки:
мм.
6) Минимальный диаметр контактной площадки:
;
мм.
Нф - толщина фольги, мм;пм - толщина предварительно осаженной меди;-
толщина металлического резиста;
) Минимальный диаметр окна фотошаблона:
;
мм.
) Максимальный диаметр окна фотошаблона:
;
мм.
∆Dш- погрешность изготовления линии
фотошаблона;
) Максимальный диаметр контактной площадки:
;
мм.
)
Минимальная ширина проводника:
;
мм.
tn1min- минимальная эффективная ширина
проводника;
) Минимальная ширина линии на фотошаблоне:
;
мм.
г - толщина наращенной гальванической меди;
) Максимальная ширина линии:
;
мм.
-
погрешность изготовления линии фотошаблона;
13) Максимальная ширина проводников:
;
мм.
∆Э- погрешность диаметра контактной площадки фотокопии при
экспонировании рисунка;
) Минимальное расстояние между проводником и контактной площадкой:
;
мм
L0- расстояние
между центрами рассматриваемых элементов;
) Минимальное расстояние между контактными площадками:
;
мм.
16) Минимальное расстояние между двумя проводниками:
;
мм.
)
Минимальное расстояние между проводником и контактной площадкой на фотошаблоне:
;
мм.
)
Минимальное расстояние между двумя контактными площадками на фотошаблоне:
;
мм.
)
Минимальное расстояние между двумя проводниками на фотошаблоне:
;
мм.
Контактные
площадки могут иметь произвольную форму. Предпочтительной является круглая.
Контактная площадка, предназначенная под установку первого вывода
многовыводного элемента, должна иметь форму отличную от остальных.
В
результате расчета геометрических параметров двумя методами обеспечиваются
расстояния между элементами печатного рисунка, необходимые для нормального
функционирования схемы. Выбранный класс точности (2 класс) может быть применен.
Проводники
располагают равномерно по площади платы с учетом следующих требований:
- параллельно линии координатной сетки или под углом, кратным 15°;
- параллельно направлению движения волны припоя или под углом к
нему не более 30° со стороны пайки, если проводящий рисунок не покрывают
защитной маской;
- по взаимно перпендикулярным направлениям на соседних
проводящих слоях платы;
- перпендикулярно касательной к контуру контактной площадки.
В соответсвии с проведенными расчетами были высполнены чертежи
микросборки печатной платы, а так же сборочный чертеж печатной платы, представленные
в Приложении Б.
.7 Анализ ТЗ
и выбор конструкции узла с учетом параметров печатной платы и вида соединителя
.7.1 Расчет
теплового режима
Расчет теплового режима блока РЭА выполняется в 2 этапа. На первом этапе
рассматривается вариант с естественным воздушным охлаждением. Итогом расчета
является температура нагрева ЭРЭ, наиболее критичных к перегреву. Если эта
температура не превышает допустимую, то тепловой расчет ограничивается первым
этапом, если же температура нагрева ЭРЭ превышает допустимую температуру, то
необходимо перейти ко второму этапу, т. е. к расчету теплового режима блока с
принудительным воздушным охлаждением. Итогом расчета на втором этапе будет
температура нагрева блока при заданном расходе воздуха. Данная методика
тепловых расчетов относительно проста и имеет погрешность не более 10%. При
разработке блоков, входящих в стойку, в которой предусмотрена принудительная
вентиляция, тепловой расчет необходимо начинать со второго этапа.
Методика расчета теплового режима блока РЭА с естественным воздушным
охлаждением справедлива для вариантов как вертикального, так и горизонтального
расположения печатных узлов (ячеек) в блоке. Для прямоугольного блока область
выделения тепла (нагретая зона) представляет собой параллелепипед, включающий ЭРЭ,
выделяющие тепло, и промежутка между ними.
Длина и ширина нагретой зоны (НЗ) соответственно равны длине и ширине
печатной платы (ПП) без учета участков, служащих для установки лицевых панелей
соединителей, полей направляющих. Высота НЗ для единичного ПУ равна толщине ПП
и высоте наиболее высокого компонента.
Исходные данные:
Размеры
блока:
;
;
;
Размеры
нагретой зоны:
;
;
;
Мощность
рассеивания блока:
Вт;
Мощность
рассеивания блока складывается из мощности рассеиваемой:
микросборкой
;
Вт;
чип-резисторами
P=0,063∙8=0,5 Вт;
операционным
усилителем P=0,5 Вт;
Чип-конденсаторы
не участвуют в расчете, т.к. с увеличением частоты мощность, рассеиваемая
конденсатором уменьшается и при частоте 30кГц стремится к нулю .
Мощность
рассеивания компонента, наиболее критичного к нагреву:к = 63 мВт - навесной чип
конденсатор;
- операционный усилитель;
Площадь
поверхности ЭРЭ, наиболее критичных к перегреву:
;
Максимальная
температура окружающей среды:
;
Количество
вентиляционных отверстий:
;
Площадь
одного отверстия (диаметр отверстия 5 мм):
;
Допустимая
температура компонента:
;
)
Поверхность кожуха блока:
Рисунок 3.12 - Тепловая модель блока
) Поверхность нагретой зоны:
, где:
, где:
= 11000
мм3 - объем печатных плат;
= 2100
мм3 - объем компонентов в узлах;
= 78564
мм3- объем блока.
3) Удельная мощность, рассеиваемая кожухом:
4) Перегрев кожуха блока:
) Удельная мощность, рассеиваемая НЗ:
6) Перегрев нагретой зоны:
7) Суммарная площадь вентиляционных отверстий:
8) Коэффициент перфорации:
)
Коэффициент, учитывающий перегрев при наличии вентиляционных отверстий:
10) Перегрев кожуха блока:
11) Перегрев нагретой зоны:
) Средний перегрев воздуха в блоке:
где:
0.6 - эмпирический коэффициент;
)
Критичная величина перегрева нагретой зоны:
)
Компонент не участвует в дальнейшем расчете, если выполняется:
Вывод: Оба рассматриваемых компонента удовлетворяют условию, значит
необходимый тепловой режим обеспечен при естественном варианте охлаждения.
.7.2 Расчет
защиты от механических воздействий
РЭА подвергается воздействию ударов и вибраций в процессе
транспортировки, погрузки и эксплуатации, что вызывает механические нагрузки и
приводит к деформации и разрушению конструктивных элементов. Поскольку при
ударах возникают вибрации элементов, основные проверочные расчеты сводятся к
оценке вибропрочности.
Исходные данные:
LД=0,046м
- длина блока;
LШ=0,046м
- ширина блока;
HT=0.013м
- высота блока;
Вариант закрепления: по периметру винтами;
Материал РЭА: АМГ6.
1)
Собственная частота ПУ:
, где
Тогда:
)
Напряжение в пластине:
, где
Тогда
)
Запас прочности:
)
Коэффициент передачи при ударе (прямоугольный импульс):
, где
-
коэффициент расстройки.
Получаем:
)
Ударное ускорение:
)
Максимальное относительное перемещение:
Условие
ударопрочности: zmax<0.003*0.071=0.000213
Следовательно,
условие ударопрочности для данного блока РЭА, в состав которого входит ПУ,
выполняется.
.8
Технологическое проектирование
.8.1
Обеспечение технологичности конструкции изделия
Обеспечение технологичности конструкции изделий (ТКИ) предусматривает
взаимосвязанное решение конструкторских и технологических задач, направленных
на повышение производительности труда, достижение оптимальных трудовых и
материальных затрат и сокращение времени на производство, техническое
обслуживание и ремонт изделия.
Уровень ТКИ - совокупность показателей, учитывающих взаимосвязь и
взаимозависимость конструктивно-технологических, технико-экономических
характеристик изделий, требований производства в заданных условиях и
характеризует уровень применяемых методов и принципов проектирования,
организационно-технических мероприятий по технологической подготовке
производства.
ТКИ оценивают количественно с помощью системы показателей, которые,
согласно ГОСТ 14.201-83, делятся на три вида:
- базовые (исходные) значения показателей ТКИ, являющиеся
предельными нормативами технологичности, которые регламентированы для отдельных
видов изделий отраслевыми стандартами и техническим заданием на разработку
изделия;
- показатели ТКИ, достигнутые при разработке;
- показатели уровня ТКИ.
.8.2
Количественная оценка технологичности конструкции изделия
Количественная оценка ТК выражается показателем, численное значение
которого характеризует степень удовлетворения требованиям к технологичности
конструкции. Методика расчета базируется на расчете относительных частных
показателей и комплексного показателя ТК. Состав относительных частных
показателей и значение коэффициентов значимости определяются классом к котором
относится разрабатываемый блок, в нашем случае это класс «электронные блоки».
) Коэффициент использования микросхем:
, где:
- общее
количество микросхем и микросборок в изделии;
- общее
количество ЭРЭ;
-
коэффициент значимости.
)
Коэффициент автоматизации и механизации монтажа изделия:
, где:
-
количество монтажных соединений, которые могут осуществляться механизированным
или автоматизированным способом;
- общее
количество монтажных соединений.
)
Коэффициент автоматизации и механизации подготовки электрорадиоэлементов к
монтажу:
, где:
-
количество ЭРЭ, подготовка которых к монтажу может осуществляться
механизированным или автоматизированным способом.
)
Коэффициент автоматизации и механизации операций контроля и настройки:
, где:
-
количество операций контроля и настройки, которые можно осуществить
механизированным или автоматизированным способом.
- общее
количество операций контроля и настройки.
)
Коэффициент повторяемости ЭРЭ:
, где:
- общее
количество типоразмеров ЭРЭ в изделии.
)
Коэффициент применяемости:
, где:
-
количество типоразмеров оригинальных ЭРЭ в изделии.
)
Коэффициент прогрессивности формообразования деталей:
, где:
-
количество деталей, заготовки которых или сами детали получены прогрессивными
методами формообразования (штамповкой, прессованием, порошковой металлургией,
литьем и т.д.);
- общее
количество деталей.
)
Комплексный показатель технологичности:
)
Уровень технологичности конструкции:
=0,5,
где:
-
нормативный комплексный показатель, который либо определяется расчетным путем,
либо берется из нормативных документов.
.9 Разработка
техпроцесса сборки узла
В электронной промышленности существует шесть общих типов SMT
(Surface-Mount Technology - технология поверхностного монтажа) сборки, каждому
из которых соответствует свой порядок производства.
В данной работе ввиду малого количества элементов и отсутствия
необходимости выбора платы большого размера целесообразно выбрать вид
расположения элементов таким образом, чтобы все элементы располагались на одной
стороне (тип 1C - смешанная сборка: одностороннее расположение компонентов).
Рисунок 3.13 - Расположение элементов печатной платы
При этом элементы поверхностного монтажа устанавливаются на контактные
площадки, а навесные в металлизированные отверстия.
Порядок проведения процесса:
- нанесение припойной пасты;
- установка компонентов поверхностного монтажа;
- пайка оплавлением;
- промывка верхней части платы;
- установка навесных компонентов, монтируемых в отверстия;
- пайка методом селективного окунания;
- промывка.
Для крепления компонентов на плату используется метод нанесения припойной
пасты - непосредственно на контактные площадки печатной платы (выбранный припой
- SnAgCu).
Для установки компонентов поверхностного монтажа используется
автоматическая система CSM7000 производства швейцарской фирмы ESSEMTEC.
Пайка оплавлением:
) Этап предварительного нагрева
В течение данного этапа паяльная паста высушивается, испаряются ее
наиболее летучие компоненты (органические наполнители), удаляется влага из ЭК и
ПП. Скорость подъема температуры обычно составляет 1 - 3°С/сек (по данным [2] 2
- 4°С/сек), максимальная температура составляет от 100 до 150°С. Более быстрый
рост температуры приводит к разбрызгиванию паяльной пасты, образованию шариков
и перемычек припоя, а также может вызвать повреждения термочувствительных ЭК
(появление трещин в керамических чип - резисторах и т.д.). Бессвинцовые сплавы
требую более высоких температур предварительного нагрева - до 150 - 200°С.
) Выдержка
При выдержке происходит минимизация градиентов температур компонентов и
всех областей ПП, активация флюса, очистка паяемых поверхностей. Скорость
подъема температуры выбирается предельно низкой. Температура в конце этапа
приближается к точке плавления (130 - 170°С для эвтектических припоев, 180 -
200°С для бессвинцовых). Следствием слишком быстрого подъема температуры
является недостаточное флюсование и образование шариков припоя; с другой
стороны, низкая скорость обуславливает избыточное окисление пасты и, в
результате, ее разбрызгивание, а также увеличивает без необходимости время операционного
цикла. Время выдержки составляет 60 - 90 сек, иногда до 120 - 150 сек.
Рекомендуется, чтобы разница температур между фазами предварительного нагрева и
оплавления была меньше 100°С.
) Оплавление
В процессе оплавления температура повышается на 1 - 3°С/сек. Чтобы
избежать перемычек припоя, недостаточной смачиваемости, эффектов «холодной»
пайки и коробления, необходимо выдерживать паяемые ЭК при температуре выше
точки плавления (183°C для Sn63, 179°C для Sn62, 217°C для бессвинцовых) по
меньшей мере в течение 30 - 90 сек (предпочтительно 60 сек.). Меньшие значения
(30 - 60 сек) рекомендуются в случае использования покрытий HASL и OSP, большие
(60 - 90 сек) - для покрытий на основе никеля. Температура должна быть
достаточной для обеспечения хорошего смачивания и флюсования (обычно - 215 -
220°C) и на 30 - 40°С превышать температуру эвтектики. ЭК должен находиться при
температуре, отличающейся от пиковой не более чем на 5°С, в течение 10 - 30
сек. Более длительная, чем необходимо, выдержка ведет к избыточному росту
интерметаллических соединений, что придает паяному соединению хрупкость и
уменьшает его усталостную прочность. Также повышенная температура может
активизировать окисление пасты, что ухудшает смачивание. Температура корпуса
ЭК, которая может отличаться от температуры выводов на 15°С, не должна
превосходить 220°С. Небольшие ЭК (объем корпуса V<350 мм3) подвергаются
большему нагреву, чем крупные. Максимальное значение температуры корпуса для
небольших ЭК составляет 240°С. В процессе оплавления не должно происходить
изменения цвета или обугливания ПП.
Пиковая температура в процессе оплавления имеет нижний и верхний пределы.
Нижний предел - температура, минимально необходимая для получения надежных
паяных соединений (определяется, прежде всего, характеристиками припойной
пасты). Верхний предел - максимальная температура оплавления, которая должна
быть ниже, чем:
· тестовая температура, используемая для оценки уровня
чувствительности корпуса ЭК к влажности (MSL);
· температура, при которой происходит повреждение ПП.
Диапазон между нижним и верхним пределами пиковой температуры определяет
т.н. «окно» процесса. Шириной этого окна для традиционной технологии составляет
около 35°С. Для бессвинцовых сплавов окно процесса существенно уже (10 - 20°С),
и существенно возрастают требования к контролю параметров процесса.
Рекомендуемая пиковая температура лежит в границах 230-240 °C
) Охлаждение
Процесс пайки считается завершенным, когда сборка охлаждается с
образованием прочных паяных соединений. Скорость охлаждения непосредственно
влияет на получаемую микроструктуру соединения, а она, в свою очередь, на его
механические свойства. Высокая скорость охлаждения уменьшает размер зерна
интерметаллических соединений и упрочняет паяные соединения, увеличивает
усталостную прочность, соединение получается более блестящим. С другой стороны,
быстрое охлаждение вызывает остаточные напряжения в материалах с различными ТКР
и коробление ПП. Вследствие этого, следует контролировать процесс охлаждения -
как правило, снижением скорости в зависимости от возможностей печи (скорости
воздушного потока, расположения нагревательных элементов, ширины конвейера и
т.д.). Рекомендуемые значения скорости составляют 3 - 4°С/сек до 130 °С (не
более 4°С/сек).
Время нахождения платы под воздействием температуры выше температуры
стеклования Tg (125° - 175°C) должно быть менее 4 минут. Продолжительность
процесса оплавления при подъеме температуры от 45°C до пиковой (215 ± 5°C)
составляет, как правило, от 3,5 до 4 минут; общее время пребывания платы в печи
- от 4 до 6 минут.
Рисунок 3.14 - Типичный профиль оплавления и его деление на этапы
Для пайки оплавлением используется печь BTU PYRAMAX, представленная на
рис. 3.15.
Рисунок 3.15 - Печь BTU PYRAMAX
Установка выводных (DIP) компонентов осуществляется ручным способом с
помощью пинцета.
Селективная пайка - выборочная пайка навесных компонентов на платах с
SMD-компонентами, которая имеет ряд преимуществ. Применение данной технологии
позволяет производить установку SMD-компонентов на паяльную пасту с ее
дальнейшим оплавлением в конвекционной печи, а затем паять навесные компоненты
в системе селективной пайки.
Системы пайки SPA 250 и SPA 400 предназначены для одно- и многоточечной селективной
пайки в азотной среде монтируемых в отверстия компонентов, таких как разъемы,
PGA, крупные компоненты, компоненты пленочной технологии и другие специальные
компоненты на печатных платах размером до 400/400 мм, обеспечивая низкие
затраты азота и качественное смачивание соединений припоем. Установки SPA 250 и
SPA 400 оснащены микропроцессором с сенсорным дисплеем для управления
температурой припоя, высотой волны, продолжительностью пайки, предварительным
нагревом, перемещением по осям X, Y, Z, и спрей-флюсователем. Установки SPA
250/SPA 400 могут быть оснащены набором паяльных насадок для выполнения
операций пайки всех типов компонентов.
4.
Безопасность жизнедеятельности
Производственное
помещение имеет размеры
м. Работает
человек.
Потребляемая мощность электрооборудования
кВт.
Расстояние до подстанции
м. Сеть трехфазная четырехпроводная с
глухозаземленной нейтралью. Виды работ - изготовление печатной платы.
Выполнить
расчеты:
1. Анализ и нормирование опасных и вредных производственных
факторов.
2. Выполнить расчет кондиционирования.
3. Привести схему пожароэвакуации и оснастить помещение средствами
пожаропредупреждения и пожаротушения.
.1 Анализ и
нормирование ОВПФ
Производственные факторы подразделяются на опасные и вредные.
Производственный фактор, воздействие которого на работающего в
определенных условиях приводит к травме или другому резкому ухудшению здоровья,
называется опасным производственным фактором. Производственный фактор,
воздействие которого на работающего в определенных условиях приводит к
заболеванию или снижению работоспособности, называется вредным производственным
фактором.
Согласно ГОСТ 12.0.003-74 ССБТ специалисты по изготовления печатных плат
сталкиваются с воздействием производственных вредных и опасных факторов.
Специфические для производственного помещения, где изготавливаются печатные
платы, вредные и опасные факторы:
· Физические:
. Возможность механических травм.
К физическим факторам относится фактор электробезопасности.
Предельно допустимые значения напряжений прикосновения и токов:
1) Предельно допустимое значение
напряжений прикосновений и токов установлены для путей тока от одной руки к
другой и от руки к ногам.
2) Напряжение прикосновения и токи, протекающие через тело человека при
нормальном (не аварийном) режиме электроустановки, не должно превышать
значений, указанных в таблице 6.5 при аварийном режиме значений указанных в
таблице 9:
Таблица 9 - Напряжение прикосновения и токи
Род тока
|
U, не более
|
I, мА не более
|
Переменный, 50 Гц
|
2,0
|
0,3
|
Переменный, 400 Гц
|
3,0
|
0,4
|
Постоянный
|
8,0
|
1,0
|
Примечание:
а) напряжение прикосновения и токи приведены при продолжительности
воздействия не более 10 минут в сутки и установлены, исходя из реакции
ощущения;
б) напряжение прикосновения и токи для лиц, выполняющих работы в условиях
высоких температур (выше 25°С) и влажности (относительная влажность более 75%), должны быть уменьшены
в три раза.
. Повышенная или пониженная температура воздуха рабочей зоны.
В таблице 10 приведены микроклиматические воздействия на рабочем месте.
. Отсутствие или недостаток естественного света.
Коэффициент естественного освещения для производственных помещений со
зрительно напряженными работами должен составлять в соответствии со СНиП 11-4:
· 0,035 (3,5%) - при одном боковом освещении для наивысшей точности;
· 0,025 (2,5%) - при одном боковом освещении для работ высокой
точности;
· 0,020 (2%) - при боковом освещении для работ высокой
точности.
Таблица 10 - Оптимальные и допустимые нормы микроклимата
Период года
|
Температура,°С
|
Относительная влажность, %
|
Скорость движения воздуха,
м/с
|
|
Оптимальная
|
Допустимая на рабочих
местах
|
Оптимальная
|
Допустимая
|
Оптимальная, не более
|
Допустимая, не более
|
|
|
Верхняя
|
Нижняя
|
|
|
|
|
|
|
Пост.
|
Не пост.
|
Пост.
|
Не пост.
|
|
|
|
|
Холодный
|
22 - 24
|
25
|
26
|
21
|
18
|
40 - 60
|
75
|
0,1
|
0,1
|
Теплый
|
23 - 25
|
28
|
30
|
22
|
20
|
40 - 60
|
70
|
0,1
|
0,1
|
. Недостаточная освещённость рабочей зоны.
Освещенность рабочих мест в производственных помещениях без естественного
освещения должна соответствовать СНиП 11-4:
не менее 300 лк - для работы I и II разряда;
не менее 200 лк - для работы III и IV разряда.
) Повышенный уровень шума и вибрации.
По ГОСТ 12.1.003-83 ССБТ норма дБ по октавам составляет:
Таблица 11 - Допустимый уровень шума
Рабочее место
|
Среднегеометрические
частоты октавных полос, Гц
|
|
63
|
125
|
250
|
500
|
1000
|
2000
|
4000
|
8000
|
дБа
|
^ Допускаемые в
лаборатории
|
94
|
87
|
72
|
78
|
75
|
73
|
71
|
70
|
80
|
Допустимые значения вибрации при интегральной оценке по частоте
нормируемого параметра для длительности воздействия 480 мин :
по виброускорению - Z,X,Y = 4 м/c2;
- по виброскорости - 4 м/с×10-2;
для частот 16 - 1000 Гц - дБ 118 (ГОСТ 12.1.012-91)
Во время работы на лабораторном оборудовании надо использовать для:
электро-индукционной печи ботинки на толстой подошве; смешивающих бегунов,
сверлильного станка и шаровой мельницы звукоизолирующие наушники.
· Химические:
. Воздействие вредных химических веществ на организм человека
(хронические поражения кожи). При очистке плат используются растворы :
фосфатов, натриевая сода, натриевые щелочи и др.;
. Использование пожароопасных и вредных для здоровья веществ
(изопропиловый спирт, ацетон для промывки плат).
Таблица 12 - Предельно допустимые концентрации вредных веществ
№
|
Наименование вещества
|
Предельно-допустимая
концентрация, мг/м3
|
Класс опасности
|
1
|
Хлор
|
1,0
|
2
|
Хлора двуокись
|
0,1
|
1
|
3
|
Сурьма
|
0,3
|
2
|
4
|
Медь
|
1,0
|
2
|
5
|
Ацетон
|
200
|
4
|
6
|
Свинец
|
0,01
|
1
|
7
|
Ртуть
|
0,01
|
1
|
· Психофизиологические:
. Монотонность труда;
. Эмоциональные и нервно - психические перегрузки;
. Перенапряжение анализаторов.
Рабочее место, при выполнения действий в положении сидя должно
соответствовать нормам ГОСТ 12.2.032-78.
Таблица 13 - Параметры рабочего места конструктора
Параметры
|
Рекомендуемые мм.
|
Фактические, мм
|
1
|
2
|
3
|
Высота рабочей поверхности
стола над полом
|
720
|
720
|
Размер рабочей поверхности
|
1600х900
|
1500х800
|
Высота пространства для ног
|
600
|
710
|
Высота сидения
|
450
|
450
|
Ширина сидения
|
500
|
500
|
Высота спинки сидения
|
800
|
800
|
Высота пульта с клавиатурой
|
620-880
|
720
|
Расстояние от экрана до
края стола
|
750
|
800
|
.2 Расчет кондиционирования
) Выбор конструкции местного отсоса.
Т.к. индукционная печь BTU PYRAMAX, используемая для пайки оплавлением
является интенсивным источником тепла, то над ней присутствует устойчивое
струйное течение, а значит, основываясь на [7], мы выбираем зонт с
неравномерным всасыванием по площади.
Радиус источника вредных веществ r = 0.15 м.
Для отсоса улавливающего приточную струю в пределах разгонного участка
высота зонта выбирается из соотношения (h ³ 4r), также необходимо удалять вредные
выбросы в виде окисла сурьмы.
h = 4×0.15 = 1.1 м.
Основные параметры зонта:зонта = r+0.24×h =
0.414 м,=
0.8×R = 0.8×0.414 = 0.3312 м,= 0.6×Rзонта =
0.6×0.414 = 0.248 м,=
0.7×R3 =
0.7×0.15 = 0.105 м.
Рисунок 4.1 - Схема зонта
) Исходные данные для расчета.= 0.15 (м),
Q = 50000×0.55 = 27500 (Вт); по [12] тепловыделение в воздух
рабочей зоны для печи мощностью 50 кВт составляет 55%,
Рисунок 4.2 - Схема местной вентиляции
= 0.05 (м/с),= 1.1 (м),= 0.414 (м),= 31.25 (мг/с) (время плавки /
суммарный угар Sb).= 10 см; h4 = 20 см; h6 = 7 м; h8 = 50 см; = 20 см; 1 -
местный отсос; 2 - шиберная задвижка;
- скруббер Вентури; 9 - вентилятор; 11 - факельный выброс.
) Вычисляем осевую скорость UM и расход воздуха в струе на уровне
всасывания LСТР:
(4.1)
(4.2)
) Находим максимальную и избыточную предельные концентрации вредных
веществ в удаляемом воздухе, соответствующие режиму предельного улавливания:
(4.3)
где G - производительность источника по газовым выбросам, мг/с;пр -
концентрация вредных примесей в приточном воздухе общеобменной вентиляции,
мг/м3;
Спред = 0, т.к. других источников выделения вредных веществ нет.
(4.4)
1. ПДК рабочей зоны по содержанию сурьмы не должно превышать 5
мг/м3.
5) Вычисляем значение безразмерного комплекса М:
(4.5)
где Gр - приходящееся на 1 отсос количество газовой примеси, выделяющейся
в единицу времени от рассредоточенных источников не снабженных местными
отсосами, мг/с;- производительность источника по газовым выбросам, мг/с;
) Находим коэффициент эффективности улавливания вредных веществ h = GУ^
/G и коэффициент эффективности отсасывания вредных веществ Kh = LОТ/LПР.ОТ.:
(4.6)
Методом подбора решаем систему уравнений, откуда находим k h.= 1.12.
) Определяем требуемую производительность отсоса, обеспечивающую
минимальную эффективность улавливания вредных веществ:
(4.7)
8) Выбираем электродвигатель системы вентиляции по имеющимся параметрам:
Расход воздуха Q = 1290,24 м³/ч = 0,36 м³/с;
Давление на выходе p = 1050 Па;
КПД = 0.78;
Частота вращения n = 1000 об/мин
Необходимая мощность двигателя
Ближайший по мощности двигатель 4А132М6, Р = 0,5 кВт, n = 970 об/мин.
.3 Схема
пожароэвакуации и оснащение помещения средствами пожаропредупреждения и пожаротущения
Требуемые степени огнестойкости производственных, общественных и жилых
зданий приведены в таблице СНиП 31-03-2001 «Производственные здания»:
Таблица 14 - Степень огнестойкости зданий
Объем помещения, тыс. м3
|
Категория помещения
|
Степень огнестойкости
зданий
|
Класс конструктивной
пожарной опасности зданий
|
Расстояние, м, при
плотности людского потока в общем проходе, чел/м
|
|
|
|
|
до 1
|
св.1 до 3
|
св. 3 до 5
|
До 15
|
А, Б
|
I, II, III, IV
|
С0
|
40
|
25
|
15
|
|
В1 - В3
|
I, II, III, IV
|
С0
|
100
|
60
|
40
|
|
|
III, IV
|
С1
|
70
|
40
|
30
|
|
|
V
|
С2, С3
|
50
|
30
|
20
|
В соответствии с таблицей можно выбрать категорию помещения - В1, степень
огнестойкости - III, класс
пожарной опасности - С1, расстояние при плотности людского потока в общем
проходе - 40 м.
При изготовлении печатных плат производится промывка печатных плат
изопропиловым спиртом и ацетоном. Поэтому данные работы являются
пожароопасными.
Схема пожароэвакуации представлена на рисунке 4.2.
Помещение оснащено:
1. Автоматический комбинированный извещатель типа КИ-1, реагирует
как на возникновение дыма, так и на повышение температуры. Располагается в
помещении и коридоре.
2. Ручной углекислотный огнетушитель типа ОУ-5 емкостью 5 л,
предназначен для тушения радиоэлектронного оборудования. Время действия
огнетушителя до 60 с, дальность струи 2 м.
. Пожарный кран, предназначен для тушения пожара водой,
устанавливается на высоте 1,35 м от пола, оборудован пожарным рукавом 10 - 20 м
и пожарным стволом.
. Ящик с песком объемом 1% от общего объема помещения
Рисунок 4.2 - схема пожароэвакуации и оснастка помещения средствами
пожаропредупреждения и пожаротушения
4.4
Выводы по организации рабочего места
В данном расчетном задании были проанализированы опасные и
вредные производственные факторы. Специалисты по изготовлению печатных плат
сталкиваются с воздействием производственных вредных и опасных факторов,
которые негативно влияют на здоровье людей, в данной ситуации их много
В
помещении, где изготавливаются печатные платы воздух загрязнен пылью и
токсическими веществами, для очистки воздуха в помещении устанавливается один
кондиционер, который будет подавать и удалять воздух в таком количестве
м3/ч, был выбран электродвигатель 4А132М6, Р = 0,5
кВт, n = 970 об/мин.
Далее
приведена схема пожароэвакуации и оснащена средствами пожаропредупреждения и
прожаротушения.
5
Технико-экономическая часть
В качестве объекта для экономических расчетов были выбраны расходы на
написание программы высокого уровня, так как при конструировании системы
управления ППЧВ на основе математической модели большая ответственность лежит
работе программистов. К тому же данный объект исследования представляет собой
обособленную часть работы по проектированию управляющего устройства, потому
расчет его себестоимости можно выполнить достаточно точно.
Разные источники советуют считать за число операторов в программе
следующие величины:
· число команд на языке ассемблера;
· число логических операторов в программе, операторов перехода,
арифметических операторов и других операторов в исходном коде программы;
· число строк в программе (для языков высокого уровня).
Программа "Моделирование привода постоянной частоты вращения"
разрабатывалась на языке высокого уровня C++. При его разработке были учтены
такие современные рекомендации к структурному программированию как отсутствие
условных и безусловных переходов, запись операторов в одну строку (за
несущественными исключениями), линейный подход к программированию.
Следовательно, за число операторов в программе можно взять число строк в
программе. Следует отметить, что в это число не входят комментарии, указания и
заголовки, так как эти конструкции не используются при нормальном
функционировании программы.
) Расчет трудоемкости разработки программного обеспечения.
Базовый показатель для определения составляющих затрат труда вычисляется
по формуле:
(5.1)
где q - число операторов (исходных команд) в программном продукте, равно
1086; с - коэффициент сложности программы; p - коэффициент коррекции программы
в ходе ее разработки, зависит от точности и корректности поставленной задачи -
принимаем равным 0.06.
Коэффициент сложности программы определяется из таблицы 3.1 на
пересечении "группы сложности" и "степени новизны". При
этом новизна определяется по принципу: А - разработка принципиально новых
задач, Б - разработка оригинальных программ, B - разработка программ с
использованием типовых решений, Г - разовая типовая задача. А сложность
определяется исходя из типа решаемых задач: 1 - алгоритмы оптимизации и
моделирования систем, 2 - задачи учета, отчетности и статистики, 3 -
стандартные алгоритмы. Кроме того, в таблице указан коэффициент недостаточности
описания программы, который потребуется чуть позже.
Таблица 15 - Коэффициенты расчета трудоемкости
Язык программирования
|
Группа сложности
|
Степень новизны
|
КоэффициентB
|
|
|
А
|
Б
|
В
|
Г
|
|
Высокого уровня
|
1
|
1,38
|
1,26
|
1,15
|
0,69
|
1,2
|
|
2
|
1,30
|
1,19
|
1,08
|
0,65
|
1,35
|
|
3
|
1,20
|
1,10
|
1,00
|
0,60
|
1,5
|
Низкого уровня
|
1
|
1,58
|
1,45
|
1,32
|
0,79
|
1,2
|
|
2
|
1,49
|
1,37
|
1,24
|
0,74
|
1,35
|
|
3
|
1,38
|
1,26
|
1,15
|
0,69
|
1,5
|
Программа "Моделирование привода постоянной частоты вращения"
написана на языке высокого уровня, относится к моделированию систем и является
принципиально новой разработкой; то есть коэффициент сложности программы в
данном случае: с = 1,38. Таким образом, находим базовый показатель: Q = 1589.
Далее, рассчитаем составляющие затраты труда, среди которых выделяют:
затраты труда на подготовку и описание алгоритма, затраты труда на исследование
алгоритма, затраты труда на разработку алгоритма, затраты труда на
программирование и отладку и затраты труда на подготовку документации. Почти все
эти параметры будут зависеть от базового показателя, рассчитываемого по формуле
(5.1).
Затраты труда на подготовку и описание задачи может определяться
эмпирически или по формуле (5.2):
, (5.2)
где Tmax - трудоемкость операции в наиболее неблагоприятных условиях
(пессимистическая оценка); Tmin - трудоемкость операции при благоприятных
условиях (оптимистическая оценка); Tнв - трудоемкость операции при нормальных
условиях (наиболее вероятная оценка). Ориентировочные величины оценки
трудоемкости операции подготовки описания задачи в зависимости от числа
операторов q приводятся в таблице 16.
Таблица 16 - Оценка времени подготовки описания задачи
q
|
Tmin
|
Tнв
|
Tmax
|
100 500 1000 1500 2000
2500 5000 10000
|
10 20 25 30 40 50 70 100
|
15 35 50 60 70 80 110 150
|
20 50 75 90 100 110 150
200
|
Затраты труда на исследование алгоритма решения задачи определяются
формулой (5.3):
(5.3)
где Q - базовый коэффициент, рассчитываемый по формуле (5.1), В -
коэффициент недостаточности описания задачи, который берется из таблицы 3 и
равен 1,2; k - коэффициент квалификации программиста, зависит от стажа
работника и определяется из таблицы 3.3.
Таблица 17 - Коэффициенты квалификации программиста
Опыт работы
|
Коэффициент квалификации
|
До двух лет
|
0.8
|
2-3 года
|
1
|
3-5 лет
|
1.1 - 1.2
|
5-7 лет
|
1.3 - 1.4
|
более 7 лет
|
1.5 - 1.6
|
По таблице определяем коэффициент k = 0.8.
Таким образом, находим затраты труда на исследование алгоритма решения
задачи: tис = 30 [чел.час].
Затраты труда на разработку блок-схем алгоритмов (представленных на
рисунках 2.7 и 2.8) вычисляются по формуле (5.4):
(5.4)
Затраты труда на программирование алгоритма по блок-схеме и отладку программы
вычисляются по формулам (5.5, 5.6):
(5.5)
(5.6)
Затраты труда на подготовку документов по задаче состоят из затрат труда
на подготовку рукописей и времени на оформление документов и вычисляются по
формуле (5.7):
(5.7)
Суммарные затраты труда рассчитываются как сумма составных затрат труда
по формуле (5.8):
(5.8)
) Расчет затрат на разработку программного обеспечения.
Заработная плата складывается из двух составляющих: основной заработной
платы и дополнительной.
Основная заработная плата рассчитывается по формуле (5.9):
(5.9)
где t? - суммарные затраты труда, вычисляемые по формуле (3.2); tср -
среднее число дней в месяце, равно 21 дню, умножается на количество часов в
рабочем дне - 8; ТС - тарифная ставка.
Тарифная ставка представляет собой МРОТ (минимальный размер оплаты труда,
по состоянию на май 2009 года равен 4330 рублей [Федеральный закон от
19.06.2000 № 82-ФЗ "О минимальном размере оплаты труда"]),
увеличенный в зависимости от тарифного коэффициента, соответствующего данному
виду работ. Для 12-го разряда работ [Постановления Правительства РФ от 06.01.93
N 14, от 27.02.95 N 189], который соответствует работе программиста, тарифный
коэффициент равен 2.44.
Таким образом, основная заработная плата будет составлять:
Дополнительная заработная плата составляет 20% от основной заработной
платы, рассчитывается по формуле (5.10):
(5.10)
Суммарная заработная плата (или фонд заработной платы, ФЗП) вычисляется
как сумма основной и дополнительной заработных плат по формуле (5.11):
(5.11)
) Результирующая таблица себестоимости.
Суммарные расходы на разработку программного обеспечения считаются как
сумма фонда заработной платы, эксплуатационных затрат, затрат на социальное
страхование, накладных расходов и расходов на материалы и комплектующие.
Итоговая стоимость разработки программного обеспечения представлена в
таблице 18.
Таблица 18 - Результирующая таблица себестоимости
Статья расходов
|
Сумма, руб.
|
В процентахот общей суммы
|
ФЗП
|
Зосн
|
53 643
|
43.78
|
|
Здоп
|
10 728
|
8.76
|
Накладные расходы, Снакл
|
32 158
|
26.26
|
Социальное страхование, СС
|
22 916
|
18.71
|
Эксплуатационныезатраты
|
Сээ
|
568
|
0.46
|
|
СТО
|
660
|
0.54
|
|
Агод
|
1 411
|
1.15
|
Материалы и комплектующие,
СМиК
|
396
|
0.34
|
Итого:
|
122 480
|
|
Заключение
Несмотря на то, что разработанная математическая модель не может в полной
мере описать все аспекты работы привода постоянной частоты вращения, она
является выполненной целью работы. Она описывает два важнейших при
конструировании режима работы ОГМП - режим изменения параметра регулирования, и
режим нагружения внешним динамическим моментом нагрузки. Применение этой модели
уже на этапе конструирования может дать ряд преимуществ.
С помощью симуляционных тестов в среде Matlab, данная модель позволяет получать характеристики ОГМП
(скорость выходного вала, КПД объемной гидромеханической передачи, давление в
гидросистеме). Также в ней отражено влияние объемных и гидромеханических потерь
на эти характеристики. Полученная схема в среде Matlab позволяет, изменяя различные входные параметры
(скорость вращения насоса, параметр регулирования, нагрузку), получать графики
изменения выходных параметров системы, что позволяет существенно сократить
время расчета и построения выходных характеристик ОГМП. В дальнейшем,
планируется обогатить систему математическим выражением различных режимов
работы ОГМП, как то: режим разгона, режим торможения, режим прохода через
нулевые зоны базового механизма и объемного гидропривода. По итогам анализа
этих данных, необходимо произвести корректировку модели и затем переходить к
дальнейшим этапам исследования.
На основе данных математической модели было проведено конструирование
системы управления привода постоянной частоты вращения, а так же
технологическая разработка печатной платы программируемого логического
контроллера. Контроллер является основополагающей частью системы управления,
так как позволяет гибко изменять параметр управления в зависимости от
характеристик конкретного привода, используя зависимости входных и выходных
параметров, полученных из математической модели. Проведена конструкторская
разработка печатного узла с учетом требований помехоустойчивости. Рассчитан
необходимый тепловой режим работы. Произведено топологическое конструирование
платы и расчет геометрических параметров рисунка.
Таким образом, разработанная математическая модель объемной
гидравлической передачи, а также конструкторская и технологическая разработка
печатной платы контроллера, являются одними из исходных инструментов для
разработки системы управления привода постоянной частоты вращения.
Библиографический
список
1. Ануфриев,
И. Е. Matlab 7 / Ануфриев И. Е., Смирнов А. Б.,
Смирнова Е. Н., СПб.: БХВ-Петербург, 2005. 1104 с.
2. Башта,
Т.М. Гидравлика, гидромашины и гидроприводы / T. М. Башта, М., 1982.
424 с.
. Башта,
Т. М. Машиностроительная гидравлика / Т.М. Башиа , М.: Машиностроение, 1971.
672 с.
4. Гейер,
В.Г. Гидравлика и гидропривод: Учеб для вузов. - 3-е изд., перераб. и доп /
В.Г. Гейер, В.С. Дулин, А.Н. Заря, М.: Недра, 1991.
5. Данилов,
Ю. А. Аппаратура объемных гидроприводов: Рабочие процессы и характеристики / Ю.
А. Данилов, М.: Машиностроение, 1990. 272 с.
6. Дьяконов,
В. П. Matlab 6.5 SP1/7 + Simulink 5/6 в математике и моделировании. Серия «Библиотека профессионала» /
В.П. Дьяконов , М.: СОЛОН-Пресс, 2005.576 с.
. Лурье
З. Я., Андренко П. Н. Влияние параметров осцилляции запорно-регулирующего
элемента гидрораспределителя на величину гидродинамической силы// Працi ТДАТУ
Вип. 10. Т. 9
8. Медведев
А. М. Печатные платы. Конструкция и материалы. М.: Техносфера, 2005. - 302 с.
9. Мурашев
Ю.Г. Конструкторско-технологическое проектирование печатных узлов. СПб.:, 1995.
- 92 с.
10. Объемные
гидромеханические передачи: Расчет и конструирование / О. М, Бабаев О. М. [и
др], Л.: Машиностроение, 1987. 256 с.
11. Попов, Д.
Н. Динамика и регулирование гидро- и пневмосистем / Д.Н. Попов, М.:
Машиностроение, 1987. 464 с.
12. Прокофьев,
В.Н. Машиностроительный гидропривод / В.Н. Прокофьев, М. , 1971. 495 с.
. Терехин,
В. В. Основы моделирования в MATLAB.
Ч 2. Simulink. Учебное пособие / В.В. Терехин,
Новокузнецк, 2004.
14. Френкель
,Н.З. Гидравлика. / Н. З. Френкель, "Госэнергиздат" 1956.
. Черных,
И. В. Simulink - среда создания инженерных
приложений / И.В. Черных, М.: «Диалог-МИФИ», 2004.
16. Шарипов,
В. М. Проектирование механических, гидромеханических и гидрообъемных передач
тракторов / В.М. Шарипов, МГТУ «МАМИ», М.: 2002
17. Шейпак,
А.А. Гидравлика и гидропневмопривод. / А.А. Шейпак, А.В. Лепешкин, А.А.
Михайлин. М.: МГИУ 2003.
18. Шольц,
Д. Пропорциональная гидравлика. Основной курс. Пер. с нем. / Д. Шольц. Киев: ДП
"ФЕСТО", 2002.
19. Dorey,
R. Modelling of Losses in Pumps and Motors // First Bath International Fluid
Power Workshop, 8th September, 1988. University of Bath, UK, 1988.
20. Kontz,
M. E. Haptic control of hydraulic machinery using proportional valves // M. E.
Kontz Georgia Institute of Tehnology, December 2007
. Kruse,
E.E. Nonlinear Modeling and Simulation of a Hydrostatic Drive System // E.E.
Kruse Michigan tehnological university 2001.
. Shoukat
Choundhury, M. A. A., Thornhill, N. F. and Shah S.L.. Modeling valve stiction /
preprint (Accepted for Publication in Control Engineering practice, 2004)
. Thoma,
J. Hydrostatic Power Transmission / J. Thoma, Trade and Technical Press
Limited, Morden, Surrey, England, 1964.
. Triet
Hung Ho and Kyong Kwan Ahn. Modeling and simulation of hydrostatic transmission
system with energy regeneration using hydraulic accumulator// Springer. Journal of Mechanical Science and
Tehnology 24, 2010
25. http://mathworks.com
Приложение А
Листинг программы.
#include <stdio.h>
//#include <c8051F040.h>
#include <variable.h>init_dac1(void);
//void set_dac1(void);OSCILLATOR_Init(void);init_timer3 (int
counts);isr_timer3 (void);set_dac1(unsigned char);
//void init_dac0(void);i=0;char v=0x00;main (void)
{ //while(1){
//init_dac1();
//set_dac1();
//EA=1; }=0;=0xDE;=0xAD;_Init ();_dac1();
//init_dac0();_timer3(SYSCLK/SAMPLE_RATE_DAC);=1;(1)
{
}
}OSCILLATOR_Init (void)
{SFRPAGE_SAVE = SFRPAGE; // Save Current SFR page=
CONFIG_PAGE; // set SFR page|= 0x03; // Set internal oscillator to run
// at its maximum frequency= SFRPAGE_SAVE; // Restore SFR
page
}init_dac1(void)
{ char SFRPAGE_SAVE = SFRPAGE;= LEGACY_PAGE;CN |=0x03;=
DAC1_PAGE;CN=0x8C;L=0x00;= DAC0_PAGE;CN=0x84;L=0x00;
//DAC0H=0x00;=SFRPAGE_SAVE;
}set_dac1(unsigned char H)
{ char SFRPAGE_SAVE=SFRPAGE;=DAC1_PAGE;L=0x00;H= H;=
SFRPAGE_SAVE;
}init_timer3 (int counts)
{ char SFRPAGE_SAVE = SFRPAGE;
//SFRPAGE = TMR3_PAGE ;= TMR3_PAGE;CF = 0x00 ; // SYSCLK/12H
= (-counts>>4) ; // reload value for XX HzL = (-counts<<4) ; //
reload value for XX HzH = 0xff;L = 0xff;
//SFRPAGE = LEGACY_PAGE ;|= 0x01 ; // T3 interrupt enableCN =
0x04 ; // T3 run=SFRPAGE_SAVE;
}isr_timer3 (void) interrupt 14
{++;_dac1(v);
}
/*else if (i<=125)
{set_dac1(v);}*/
{(i <=150)
{-;_dac1(v);
}
/*else if (i<=225)
{set_dac1(v);}*/{i=0;}
}