Технологический регламент производственных процессов по проходке и креплению ствола
Содержание
Введение
Общая часть
. Общая часть
.1 Исходные данные
.2 Общие сведения об участке
строительства
. Геологическая и гидрогеологическая
характеристика участка проектирования и строительства ствола №1
.1 Геологические условия
.2 Гидрогеологические условия
.3 Нарушенность массива
.4 Инженерно-геологические условия
проходки ствола №1
. Характеристика ствола №1 на
участке строительства устья и технологического отхода
. Общие требования безопасности при
разработке проекта проходки ствола №1 на участке устья и технологического
отхода с замораживанием вмещающих горных пород
.1 Выбор способа проходки ствола №1
.2 Расчеты крепи ствола №1
.3 Конструкция крепи ствола №1
. Подготовительный период
. Возведение устья ствола №1
.1 Возведение временной крепи устья
. Проходка и крепление
технологического отхода ствола№1
. Проходка ствола №1
.1 Подготовительные операции
.2. Монтаж тюбинговых колец
.3 Укладка бетона в затюбинговое
пространство
.4 Возведение кейлькранцев
.5 Взрывные работы
. Взрывные работы
.1 Общие требования
.2 Уборка породы
. Требования безопасности при
проходке
.1 Проветривание ствола при проходке
.2 Замеры содержания горючих газов
. Меры безопасности при выполнении
технологических процессов
.1 Общие требования
. Охрана окружающей среды
Специальная часть
. Выбор способа сооружения ствола
. Специальные способы сооружения
стволов шахт
. Принцип получения холод и работа
замораживающей станции
Экономическая часть
. Планирование производственной
мощности горного участка
.1 Режим работы участка
.2 График выходов рабочих и
организации очистных работ в забое
.3 Производственная мощность участка
. Планирование штата работников,
работающих на участке
.1 Структура управления участками
.2 Расчет штата
инженерно-технических работников участка
.3 Расчет численности рабочих
забойной группы
.4 Расчет численности ремонтного
персонала
. Планирование себестоимости добычи
руда по участку
.1 Планирование затрат на
вспомогательные материалы
.2 Основная и дополнительная
заработная плата с отчислениями по единому социальному налогу (ЕСН)
.3 Амортизация оборудования
.4 Затраты на электроэнергию
.5 Затраты на эксплуатацию и
содержание оборудования
.6 Участковые расходы
Заключение
Список литературы
Введение
Технологический регламент производственных
процессов по проходке и креплению ствола №1 на Палашерском и Балахонцевском
участках Верхнекамского месторождeния калийных солей (В К М КС) Усольского
калийного комбината филиала ОАО «Ковдорский ГОК» разработан в соответствии с
требованиями п. 47 «Единых правил безопасности при разработке рудных, нерудных
и рассыпных месторождений полезных ископаемых подземным способом» (ПБ
03-553-03) и «Методических рекомендаций о порядке разработки, согласования и
утверждения регламентов технологических производственных процессов при ведении
горных работ подземным способом» (РД 06-627-03).
Настоящий технологический регламент
производственных процессов по проходке и креплению ствола №1 на Палашерском и
Балахонцевском участках Верхнекамского месторождения калийных солей (ВКМКС)
Усольского калийного комбината Филиала ОАО «Ковдорский ГОК» г. Усолье (шифр
20-07Г1Р/10-ТР.1) разработан ЗАО «ОГСК-Шахтспецстройпроект» отдельной книгой и
включает в себя специфику и особенности организации выполнения технологических
процессов и операций по проходке и креплению ствола №1 с указанием мероприятий
по обеспечению безопасного выполнения указанных процессов и операций.
Технологический регламент на сооружение
армировки ствола №1 на Палашерском и Балахонцевском участках Верхнекамского
месторождения калийных солей (ВКМКС) Усольского калийного комбината Филиала ОАО
«Ковдорский ГОК» г. Усолье (шифр 465/УК-1-041-0265070/1-1.6-ТР) разработан
проектным бюро №1 ФГУП УС-30 отдельной книгой и включает в себя специфику и
особенности организации выполнения технологических процессов и операций по
армированию ствола №1 с указанием мероприятий по обеспечению безопасного
выполнения указанных процессов и операций.
В настоящем технологический регламент
производственного процесса по проходке и креплению ствола №1 (далее по тексту
технологический регламент) рассмотрены следующие производственные процессы:
строительство устья ствола с временным оголовком, с сопряжениями
технологических каналов и с опорным венцом, сооружение технологического отхода
ствола, проходка и крепление основной части ствола с сопряжениями.
В данном технологическом регламенте
предусмотрены мероприятия, выполнение которых направлено на обеспечение
безопасности технологических процессов при выполнении работ по возведению
устья, технологического отхода и строительству основной части ствола с
сопряжениями по замороженным водонасыщенным и неустойчивым горным породам.
Настоящий технологический регламент
устанавливает обязательный для исполнения порядок организации и производства
работ при строительстве устья, технологического отхода ствола и при проходке и
креплении основной части ствола с сопряжениями.
При изменении технологии производства работ в
технологический регламент необходимо внести требуемые корректировки и
дополнения в установленном порядке.
Организацию и ведение работ при сооружении
устья, технологического отхода, при проходке и креплении основной части ствола
с сопряжениями следует вести в соответствии с требованиями данного
технологического регламента, утвержденной проектной и рабочей документацией
(п.62 ПБ 03-553-03), Инструкций для работников строительной организации по
безопасному ведению технологических процессов при строительстве стволов (п.23
ПБ 03-553-03) и нормативной документации по безопасности производства работ.
Данный технологический регламент предназначен
для исполнения работниками организации, которые руководят, организуют,
контролируют производство работ и выполняют работы: по строительству устья,
технологического отхода, по проходке и креплению основной части ствола с
сопряжениями, а также предназначен для специалистов в области промышленной
безопасности и охраны труда.
Кроме того, настоящий технологический регламент
является локальным нормативным руководством для разработки проекта проходки
ствола и Инструкций для работников строительной организации по безопасному
ведению технологических процессов при строительстве стволов в части безопасной
организации и производства указанных технологических производственных
процессов.
В настоящем технологическом регламенте
содержатся сведения о порядке, последовательности операций при выполнении работ
и требованиях мер безопасности при выполнении всех производственных процессов,
к числу которых относятся:
При сооружении устья ствола:
Погрузочно-разгрузочные работы на поверхности и
в забое устья ствола с помощью автокрана КС-6476 грузоподъемностью 50 т или его
аналога.
Возведение временного железобетонного оголовка
ствола в интервале отметок-3,4 м (А.О.+ 170,600) до +0,2 м (А.О.+174,200).
Демонтаж и разборка буровой железобетонной плиты
в проектном сечении ствола в отметках -3,4 м (А.О.+170,600) до -3,8 м
(А.0.+170,200).
Разработка грунта и горных пород малогабаритным
гидравлическим экскаватором L520B в забое устья ствола с погрузкой горной массы
в проходческую бадью БПСМ-3.0 вместимостью 3 м3.
Доработка грунта и горных порол вручную и
отбойными молотками в забое устья ствола до проектных параметров с погрузкой
горной массы в проходческую бадью Б1 ICM-3.0 вручную.
Выдача разрыхленного грунта или горной породы из
забоя устья ствола бадьями при помощи автокрана КС-6476 грузоподъемностью 50 т
или его аналога.
Разгрузка груженой бадьи на временной эстакаде в
автосамосвалы.
Доставка бадьи в забой автокраном с установкой
ее под загрузку.
Возведение временной крепи устья.
Монтаж секций временного ходового отделения для
спуска-подъема людей.
Проветривание устья ствола, с глубины -10,0 м
(А.О.+164,000).
Устройство базового тюбингового кольца №1 на
глубине 17,5 м (А.О.+156,500), (тюбинговое кольцо №3 графические материалы
779/1-П-4.3 1.1/20-07ПР/10-ГПР л.З).
Устройство опорного венца устья в интервале
глубин 17,5 м (А.О.+156,500) до 13,0 м (А.О.+ 161,000), графические материалы
779/1-П-4.3 1.1 /20-07ПР/10-КЖ1 и 779/1-П-4.31.1/20-07ПР/10-ГПР л.З.
Монтаж временного инвентарного полка в забое
устья ствола (отметка уровня тюбингового кольца №2) для возведения постоянной
железобетонной крепи устья.
Демонтаж секции временного ходового отделения,
снятие крепления временного инвентарного полка в устье ствола, перемещение
полка на другую монтажную отметку при помощи автокрана КС-6476 или его аналога,
раскрепление полка в стволе для возведения очередной «заходки» постоянной
железобетонной крепи устья.
Электросварочные и газопламенные работы при
выполнении монтажных и демонтажных работ на поверхности и в устье ствола.
Возведение постоянной крепи устья в интервале
отметок от -13,0 м (А.О.+ 161,000) до -3,8 м (А.О.+ 170,200) с устройством
сопряжений калориферного и кабельного каналов.
Устройство освещения, сигнализация и связи.
При строительстве технологического отхода ствола
в интервале отметок -17,5 м (А.0.+156,500) до -40,02 м (А.0.+133,980):
Погрузочно-разгрузочные работы на поверхности и
в забое ствола с помощью автокрана КС-6476 грузоподъемностью 50 т или его
аналога.
Разработка грунта и горных пород гидравлическим
экскаватором L520B в забое ствола с погрузкой горной массы в проходческую бадью
БПСМ-3.0 вместимостью 3 mj.
Доработка грунта и горных пород отбойными
молотками в забое ствола до проектных параметров с погрузкой горной массы в
проходческую бадью БПСМ-3.0 вручную.
Выдача разрыхленного грунта или отбитой горной
породы из забоя ствола бадьями при помощи автокрана КС-6476 грузоподъемностью
50 т или его аналога.
Разгрузка груженой бадьи на временной эстакаде в
автосамосвалы.
Доставка бадьи в забой автокраном с установкой
ее под загрузку.
Возведение временной крепи технологического
отхода ствола.
Монтаж секций временного ходового отделения для
спуска-подъема людей.
Проветривание технологического отхода ствола.
Устройство базового тюбингового кольца №2 на
глубине 40,02 м (А.О.+133,980), (тюбинговое кольцо №18 графические материалы
779/1 -11-4.3 1.1/20-07ПР/10-ГПР л. 1,2).
Электросварочные и газопламенные работы при
выполнении монтажных и демонтажных работ на поверхности и в стволе на участке
технологического отхода.
Монтаж временного инвентарного полка в забое
технологического отхода ствола (отметка уровня тюбингового кольца №18) для
возведения постоянной тюбинговой крепи технологического отхода ствола.
Демонтаж секции временного ходового отделения,
снятие крепления временного инвентарного полка в стволе, перемещение его на
другую монтажную отметку при помощи автокрана КС-6476 или его аналога,
раскрепление полка в стволе для возведения очередного тюбингового кольца
постоянной-крепи ствола на участке технологического отхода.
Возведение постоянной крепи технологического
отхода ствола.
Устройство освещения, сигнализации и связи.
При проходке и креплении основной части ствола с
сопряжениями:
Подготовительный этап - оснащение на период
проходки и крепления ствола с сопряжениями.
Строительство поверхностного комплекса, в т.ч.
проходческого конра «Север-2» с подшкивной площадкой и разгрузочными
устройствами, зданий и сооружений стройплощадки. Прокладка и подключение к
существующим сетям инженерно - технических сетей и коммуникаций на поверхности.
Монтаж, обвязка, наладка и подключение необходимого проходческого оборудования
в копре, подъемных машин, полковых и других проходческих лебедок, вентиляторной
установки, силовой трансформаторной подстанции. Сборка проходческого полка,
установка, обвязка и опробование необходимого оборудования на полке. Намотка,
запасовка, навеска проходческих канатов и проходческого оборудования в стволе.
Монтаж стволового породопогрузочного комплекса 2КС-2у/40. Монтаж и навеска
тампонажного полка с установкой и опробованием тампонажного оборудования.
Монтаж металлоконструкций «нулевой рамы» с устройством перекрытия ствола и
оборудованием проемов в перекрытии механизированными лядами. Навеска
проходческих бадей БПСМ-5.0.
Устройство маркшейдерского полка в стволе.
Прокладка в стволе кабельных линий и технологических трубопроводов.
Осмотр полка, бадей, канатов и прицепных
устройств подвески проходческого оборудования, самого оборудования, крепи
ствола и забоя, приведение рабочих мест в безопасное состояние, вт.ч. оборка
заколов.
Перегон полка в стволе, настройка освещения
рабочих мест и вентиляции, монтаж технологических коммуникаций.
Погрузочно-разгрузочные операции на
проходческом, там по пажи ом полках и в забое ствола.
Уборка отбитой горной массы из забоя, в т.ч.
погрузка породы в бадью погрузочным комплексом 2КС-2У/40 и выдача горной массы
в бадьях на поверхность.
Зачистка забоя для бурения.
Бурение опережающих скважин в забое.
Бурение шпуров.
Взрывные работы, в т.ч. заряжание, взрывание
шпуров в забое.
Проветривание ствола.
Устройство временной предохранительной крепи в
зависимости от горно-геологических условий.
Возведение постоянной крепи ствола согласно
проекту.
Проходка и крепление сопряжений.
Горные работы по проходке и креплению устья,
технологического отхода и основной части ствола с сопряжениями производятся в
соответствии с утвержденной проектной и рабочей документацией, настоящим
технологическим регламентом, разработанным ЗАО «ОГСК-Шахтспецстройпроект», а
также Инструкциями для работников строительной организации по безопасному
ведению технологических процессов при строительстве стволов, которые
разрабатывает шахтостроительная организация, в том числе паспортами БВР,
паспортами крепления.
При разработке проекта проходки ствола,
технологических регламентов и Инструкций для работников строительной
организации по безопасному ведению технологических процессов при строительстве
стволов должны соблюдаться требования нормативных правовых актов РФ,
нормативных технических документов, СНиПов, государственных стандартов. При
этом, в первую очередь, должны учитываться следующие положения:
Разработка проектов проходки шахтных стволов с
замораживанием горных пород должна осуществляться в соответствии с требованиями
нормативных правовых актов, нормативных технических и методических документов,
строительных норм и правил, государственных стандартов, действующих в
Российской Федерации.
Деятельность, связанная с разработкой
месторождений полезных ископаемых подземным способом должна осуществляться в
соответствии с проектами, выполненными с учетом требований Федерального закона
«О промышленной безопасности опасных производственных объектов», закона
Российской Федерации «О недрах» от 21.02.1992 № 2395-1 (Собрание
законодательства Российской Федерации. 1995, № 10, ст. 823), других федеральных
законов, Общих правил промышленной безопасности для организаций, осуществляющих
деятельность в области промышленной безопасности опасных производственных
объектов, утвержденных постановлением Госгортехнадзора России от 18.10.2002
(зарегистрированы Минюстом России 28.11.2002 № 3968, опубликованы в «Российской
газете» 05.12.2002 № 231) настоящего Регламента и другой нормативной
документации в области промышленной безопасности.
Виды деятельности, на осуществление которых
требуются лицензии, и порядок оформления лицензий устанавливаются
законодательством Российской Федерации.
Проектные организации обязаны осуществлять
авторский надзор за реализацией проектных решений.
Работы по проходке (в том числе специальными
способами), креплению и армировке стволов шахт должны осуществляться по проекту
и технологическим регламентам, разработанными и утвержденными в установленном
порядке.
Техническая документация должна содержать
требования по:
устройству и оборудованию проходческих полков, а
также по организации работы на них при всех производственных процессах;
мерам защиты от возможного падения сверху
различных предметов и оборудования;
порядку перемещения проходческого полка по
стволу;
порядку погрузочно-разгрузочных работ на полках
и в забое, работе бадейного подъема;
креплению, армировке ствола и допустимому
отставанию временной и постоянной крепи от устья. (§62 ПБ 03-553-03).
Вентиляторная установка для проветривания при
проходке ствола должна быть установлена на поверхности на расстоянии не менее
15м от ствола. Порядок проветривания определяется проектом организации работ.
До начала проходки ствола шахты должна быть
пробурена контрольностволовая скважина и отобран керн на всю глубину ствола.
При проходке стволов должна обеспечиваться гидроизоляция водоносных горизонтов.
При приближении забоя ствола шахты к зоне контакта соляной залежи с водоносным
горизонтом на расстояние не менее 20 м из забоя ствола должно производиться
передовое контрольно-разведочное бурение.
.Инструкции для работников строительной
организации по безопасному ведению технологических процессов при строительстве
стволов разрабатываются шахтостроительными организациями и утверждаются
руководителем (заместителем руководителя) организации, занятым производством
работ.
В состав Инструкций для работников строительной
организации но безопасному ведению технологических процессов при строительстве
стволов должны входить мероприятия по промышленной безопасности и охране труда
при организации и производстве работ (п.3,2 ПБ 03-517-02), электробезопасности,
взрывобезопасности, пожарной безопасности, охране окружающей среды при
использовании промывочных и тампонажных растворов, замораживающих рассолов,
предупреждению чрезвычайных ситуаций природного и техногенного характера,
бытовому и санитарному обслуживанию работников.
В организациях, участвующих в строительстве,
составляется перечень работ с повышенной опасностью, выполняемых по
наряду-допуску, который утверждается руководителем организации.
Выполнение работ повышенной опасности согласно
указанному перечню без оформленного наряда-допуска не допускается.
Проекты всех новых (реконструируемых) и
действующих шахт должны иметь раздел «Противопожарная защита», выполненный в
полном соответствии с нормативными материалами, утвержденными Госгортехнадзором
России. (§422 ПБ 03-553-03).
Запрещается прием в эксплуатацию новых шахт,
горизонтов, участков, блоков, в которых в полном объеме не выполнены
противопожарные мероприятия.
Обязательным условием принятия решения о начале
строительства (эксплуатации), консервации и ликвидации рудника (шахты) является
наличие положительного заключения экспертизы промышленной безопасности
проектной документации.
Организации, осуществляющие деятельность по
разработке месторождений полезных ископаемых подземным способом, в соответствии
со ст. 10 Федерального закона «О промышленной безопасности опасных
производственных объектов» обязаны заключать договора на обслуживание со
специализированными профессиональными аварийно-спасательными формированиями
(военизированными горноспасательными частями - ВГСЧ), создавать собственные
горноспасательные формирования, вспомогательные (нештатные) горноспасательные
команды из числа работников, а также планировать и осуществлять мероприятия по
локализации, ликвидации последствий аварий.
При выполнении строительно-монтажных и специальных
строительных работ на объектах подземных горных работ, кроме «Единых Правил
безопасности при разработке рудных, нерудных и рассыпных месторождений полезных
ископаемых подземным способом» (ПБ 03-553-03), необходимо соблюдать требования
действующих строительных норм и правил.
В случае необходимости застройки территории
горного отвода зданиями и сооружениями сторонних организаций следует
руководствоваться «Положением о порядке выдачи разрешений на застройку площадей
залегания полезных ископаемых», утвержденным постановлением Госгортехнадзора
России от 30.08.1999 г. № 64 (зарегистрировано Минюстом России 02.09.1999 г. №
1886, «Бюллетень нормативных актов федеральных органов исполнительной власти»
от 20.09.1999 г. №38).
Всё используемое при проходке шахтных стволов
технологическое оборудование и технические устройства, в том числе зарубежного
производства, должны иметь сертификат соответствия требованиям промышленной
безопасности и разрешение на применение, выданное Ростехнадзором в соответствии
с «Правилами применения технических устройств на опасных производственных
объектах» (утверждено постановлением Правительства Российской Федерации от
25.12.1998 г. № 1540, Собрание законодательства Российской Федерации от
04.01.1999 г. № 1 ст. 191), а также в соответствии с требованиями
«Административного регламента Федеральной службы по экологическому,
технологическому и атомному надзору по исполнению государственной функции по
выдаче разрешений на применение конкретных видов (типов) технических устройств
на опасных производственных объектах (приказ Ростехнадзора от 29.02.2008г.
№112).
Возможность дальнейшей эксплуатации технических
устройств, оборудования и сооружений после истечения установленного срока
службы определяется в соответствии с «Порядком продления срока безопасной
эксплуатации технических устройств, оборудования и сооружений на опасных
производственных объектах», утвержденным приказом Министра природных ресурсов и
экологии Российской Федерации от 30.06.2009 г. № 195.
Общая часть
. Общая часть
.1 Исходные данные
Разработка технологического регламента
производственного процесса по проходке и креплению ствола №1 по объекту
«Усольский калийный комбинат. Горнодобывающий комплекс» выполнена на основании
договора №20-07ПР/10 от 15 июля 2010г. согласно заданию па проектирование,
выданного заказчиком - Проектным бюро №1 ФГУП «УС-30».
При разработке технологического регламента
использовались исходные данные представленные заказчиком.
Геологические исходные данные для разработки
настоящего технологического регламента были представлены в отчёте
ООО НПФ «ГЕОПРОГНОЗ», выполненном по договору
№1и/09 от 20.01.09г.
Настоящий технологический регламент выполнен ЗАО
«ОГСК-Шахтспецстройпроект» в соответствии с действующими нормами и правилами,
действующими на территории Российской Федерации.
Схемой вскрытия Палашерского и Балахонцевского
участков ВКМКС на первом этапе вскрытия и отработки месторождения
предусматривается строительство двух вертикальных шахтных стволов №1 и №2:
скипового (СС) и клетевого (КС) соответственно. Стволы №1 и №2 находятся на
одной промплощадке и будут проходиться с разницей во времени четыре месяца, с
применением специального способа проходки - замораживание грунтов и горных
пород.
В состав горнодобывающего комплекса Усольского
калийного комбината, как указывалось выше, входят два ствола, расположенные на
одной промплощадке, из них:
ствол №1 оснащённый двумя двухскиповыми
подъёмами предназначается для выдачи руды и подачи свежего воздуха, является
запасным выходом из шахты;
ствол №2 оснащён двумя одноклетьевыми подъёмами,
предназначен для спуска - подъёма людей, материалов и оборудования, а также для
выдачи исходящей вентиляционной струи.
Взаимное расположение стволов представлено на
рисунке 1.1.
План расположения стволов и надшахтных 4П6,22.
сооружений на промплощадке рудника
Экспликация сооружений
Рисунок 1.1
Поз.
|
Наименование
|
1
|
Скиповой
ствол N 1
|
2
|
Надшахтное
здание ствола N 1
|
J
|
Здание
подъемных машин ствола N 1
|
4
|
Клетевой
ствол N 2
|
5
|
Башенный
копер ствола N 2
|
6
|
Главная
вентиляторная ствола N 2
|
.2 Общие сведения об участке
строительства
В апреле 2008г. ОАО «Ковдорский
горно-обогатительный комбинат», получил лицензию на право пользования недрами с
целью добычи калийномагниевых солей на Палашерском и Балахонцевском участках
Верхнекамского месторождения калийных солей (ВКМКС).
В административном отношении этот участок
расположен в Пермской области, в Усольском муниципальном районе с районным
центром в г. Усолье, в 15 км на юг от г. Березняки. Участок расположен в центре
южной части Верх не камского месторождения: на северо-западе и севере он
граничит с Усть-Яйвинским и Дурыманским участками детальной разведки, а с
запада, юга и востока он оконтурен границами запасов калийных солей категорииС2
. Площадь участка составляет 132,89 км", в том числе: Палашерский участок
(73,53 км“) и большая часть Балахонцевского участка (59,36 км"). С 1973 г.
Балахонцевский участок разрабатывался подземным способом рудником БКПРУ-3 ОАО
«Уралкалий». В 1986г. в результате аварии рудник был затоплен. Над местом
прорыва вод в рудник образовался провал.
Северо-западная незатопленная часть шахтного
поля рудника БКПРУ-3, пригодная для отработки калийных руд подземным способом,
вошла в контур Усть-Яйвинского участка детальной разведки, а южная часть,
площадью 16,52 км2, - в состав лицензионного участка. Таким образом, площадь,
пригодная для отработки запасов калийных солей подземным способом, составляет
90,04 км2. Эта часть лицензионного участка в дальнейшем именуется участком
отработки запасов (смотри рисунок 1.2). Координаты угловых точек северной
границы участка отработки запасов приведены в таблице 1.1.
Таблица 1.1
№
точки
|
Широта
|
Долгота
|
4
|
59°
16” 33,80м
|
56°
46'44,90”
|
22
|
59°
16'33,77м
|
56°
46'58,00"
|
23
|
59°
15'55,15"
|
56°
46'58,25"
|
24
|
59°
15' 55,13"
|
56°
46' 44,68"
|
25
|
59°
15’38,00”
|
56°
46’ 44,79м
|
26
|
59°
15' 38,35”
|
56°
50’ 54,08”
|
27
|
59°
15'23,49м
|
56°
50' 54,15”
|
28
|
59°
15’23,53м
|
56°
5 Г 25,70”
|
29
|
59°
15’ 30,31”
|
56°
5Г25,67"
|
30
|
59°
15'30,67”
|
56°
52'36,13"
|
31
|
59°
15'36,85”
|
56°
52’36,33м
|
32
|
59°
15'36,93"
|
56°
54’ 13,52м
|
33
|
59°
15'02,03"
|
56°
54’ 13,62м
|
34
|
59°
15’ 02,06м
|
56°
54’ 55,89м
|
35
|
59°
15’ 36,96м
|
56°
54’55,80”
|
36
|
59°
15’36,97”
|
56°
5570,42"
|
Рельеф района лицензионного участка равнинный и
холмисто-увалистый. Площадь представляет собой всхолмленную равнину, изрезанную
сетью речных долин, ручьев, оврагов. Абсолютные отметки рельефа меняются от 106
м (скв. 110) в долине р. Яйва до 218 м.
Гидросеть района умеренно разветвленная и
представлена рекой Яйва с ее притоками (Сюзьва, Малая Уньва, Волим). Водный
режим рек отличается высоким весенним половодьем и низкой меженью.
Климат района умеренно-континентальный. По
многолетним наблюдениям среднегодовая температура составляет 1,2°С, среднемесячные
летние температуры - 15,6-17,6°С и зимние - минус 13-14,7°С.
Продолжительность зимнего периода - с 25 ноября
по 10 апреля.
Реки замерзают в среднем через 30 дней после
перехода температуры воздуха через 0°С, толщина льда - 50-60 см, снежного
покрова - 80-90 см. Среднегодовое количество осадков 532 мм. Устойчивый снежный
покров держится с начала декабря до середины апреля. Расчетная глубина
промерзания грунта равна 178 см, максимальная (установленная по замерам) -137
см. В летний период преобладают ветры северных направлений, а в остальную часть
года - южных.
Преобладающая часть участка покрыта хвойным
лесом, содержащим примесь лиственных пород. Основным источником
хозяйственно-питьевого водоснабжения в районе являются подземные воды,
приуроченные к терригенно-карбонатным отложениям уфимского яруса, и, отчасти,
поверхностные водотоки. На территории лицензионного участка расположены два
месторождения углеводородного сырья и одно месторождение пресных подземных вод,
на которые выданы лицензии на право пользования недрами, а также месторождения
торфа с учтенными балансовыми запасами.
В юго-западной части лицензионного участка
расположено нефтяное месторождение им. Архангельского с утвержденными запасами
категорий С\ и С2. На площади этого месторождения пробурено пять разведочных
скважин на нефть. В 2007г. месторождение предоставлено ООО «ЛУКОЙЛ-ПЕРМЬ» с
целью разведки и добычи углеводородного сырья.
В районе имеются предприятия по добыче и
переработке калийных солей, производятся лесозаготовки, имеются предприятия по
производству сельскохозяйственной продукции, а также отдельные объекты
инфраструктуры по добыче углеводородного сырья. Электроэнергией район
обеспечивается от единой государственной энергосистемы.
На юго-западе лицензионного участка имеется
охраняемый ландшафт регионального значения - «Большеситовское болото» площадью
517 га.
2. Геологическая и
гидрогеологическая характеристика участка проектирования и строительства ствола
№1
.1 Геологические условия
Описание геологического строения участка
производства буровых работ приводится по материалам бурения
контрольно-стволовой скважины 107г-1 (отчёт ООО НПФ «ГЕОПРОГНОЗ», выполненный
по договору №1и/09 от 20.01.09г.).
Геологические условия проходки ствола №1 описаны
по данным контрольно-стволовой скважины №107г-1. Глубина, мощность и краткое
литологическое описание пород также представлены на чертеже
779/1-П-4.31.1/20-07ПР/10-ГПР л. 1.
При рассмотрении графического материала
779/1-П-4.31Л/20-07ПР/10-ГПР необходимо учитывать, что за относительную отметку
±0,000 м ствола после вертикальной планировки промплощадки принята абсолютная
отметка +174,000 м, абсолютная отметка устья скважины №107г-1
составляет+172,230 м. Интервалы глубин границ пересекаемых стволом
литологических разностей приняты по геологической колонке скважины №107г-1,
основной ствол отчета ООО НПФ «ГЕОПРОГНОЗ».
В геологическом строении района проведения
буровых работ принимают участие отложения (до проектной глубины бурения)
четвертичного и нижнепермского возраста.
Четвертичные отложення залегают в интервале от
1,10 м до 11,90 м (скв. 107г-1) и в основной части разреза представлены
песчанистыми суглинками бурого и коричневого цвета с включениями (2-3%) гравия,
галькой кварца и редкими прослоями пластичной глины.
Ниже по разрезу залегает глина темно-коричневая,
буро-коричневая, зеленовато-коричневая до серой, пластичная с включениями
унифицированных остатков растений.
Четвертичные отложения залегают горизонтально на
размытой поверхности нижнепермских отложений без углового несогласия.
Нижнепермские отложения вскрыты скважиной
№107г-1в интервале от
м до 551,20 м. В интервале глубин от 11,90 м до
287,46 м они представлены отложениями Уфимского яруса. В отложениях Уфимского
яруса выделяются:
пестроцветная толща шешминской свиты.
терригенно-карбонатная толща соликамской свиты.
соляно-мергельная толща соликамской свиты.
Отложения пестроцветной толщи (ПЦТ) вскрыты
контрольно-стволовой скважиной на глубине от 11,90 м до 88,15 м общей мощностью
76,25 м (скв. 107г-1) и представлены чередованием алевролита, аргиллита,
песчаника и мергеля. Алевролит коричневый, бурый, темно-серый прослоями
разрушенный трещиноватый с подчиненными прослоями песчаника, аргиллита (до
глубины 49 м). Ниже по разрезу преобладают прослои аргиллита и песчаника с
редкими прослоями алевролита. Аргиллит пестроцветный, темно-серый до черного,
известковистый, трещиноватый. Песчаник пестрый, мелко- и среднезернистый
известковистый. В подошве пестроцветной толщи залегает мергель темно-серый до
черного с тонкими прослоями аргиллита, в основании толщи - известняк
тонкозернистый. Граница между ПЦТ и ТКТ отбивается по смене хемогенных
карбонатных пород красноцветными терригенными отложениями.
Отложения терригенно-карбонатной толщи (ТКТ)
вскрыты на глубине от 88Д 5 м до 193,90 м, общей мощностью 105,75 м (скв.
107г-1). По литологическому составу ТКТ можно разделить на две части. В нижней
части толщи преобладают известняки (реже доломиты) и мергели с подчиненными
прослоями песчаников и алевролитов; верхняя часть сложена чередованием
алевролитов, аргиллитов, песчаников, и мергелей с подчиненными прослоями
известняков. Граница между выделенными частями разреза ТКТ характеризуется
постепенным переходом. Нижняя граница толщи уверенно отбивается исчезновением
загипсованных пород. Известняки ТКТ серые и темно-серые, глинистые, иногда
песчанистые. Доломиты светло-серые, прослоями глинистые. Мергели темно-серые и
серые, нередко тонкослоистые. Аргиллиты темно-серые, черные, известковистые.
Алевролиты серые и зеленовато-серые, иногда темно-серые и черные, известковистые.
Песчаники серые, зеленовато-серые, мелко- и среднезернистые, полимиктовые,
часто известковистые.
Отложения соляно-мергельной толщи (СМТ) вскрыты
на глубине от м до 287,46 м, общей мощностью 93,56 м (скв.107г-1). По
литологическим особенностям в разрезе СМТ можно выделить несколько ритмопачек.
Пачка залегает на глубине от 193,90 м до 207,80
м (скв. 107г-1). Отложения данной пачки представляют собой чередование прослоев
глинисто-гипсовых пород и мергеля. Общая мощность данных отложений составляет
13,9 м. Глинисто-гипсовая порода трещиноватая (на 50% состоит из белого,
светлосерого, скрытокристаллического, волокнистого гипса). Мергель серый,
темно-серый, трещиноватый, загипсованный.
Пачка, залегающая в интервале от 207,80 м до
220,50 м (скв.107г-1) характеризуется чередованием мергеля и глинисто-гипсовых
пород.
Мергель светло-серого до темно-серого,
встречаются редкие прослои глин, гнезда гипса и отмечается вкрапленность
пирита. В подошве пачки залегают известняки. Мощность глинисто-гипсовых порода
не превышает 2,10 м.
Пачка, залегающая в интервале от 220,50 м до
269,27 м (скв. 107г-1) слагается в нижней части мергелем, в кровле - гипсом или
гипсово-глинистой породой. Мергель темно-серый, глинистый, часто загипсованный,
с вкрапленностью пирита и ангидрита, участками трещиноватый. Чистый гипс
встречается в виде двух прослоев.
Нижние две пачки, залегающие в интервале от
269,27 м до 287,46 м (скв.107г-1) слагаются в нижней половине мергелем, в
верхней - каменной солью. Мергель темно-серый, тонкослоистый, со стяжениями
соляно-гипс- ангидритового состава.Каменная соль серая и темно-серая с тонкими
прослойками (1-10 мм, редко до 10 см) мергеля.
Инженерно-геологические свойства пород и грунтов
приведены в таблице 2.1.
Порода
|
Природная
влажность, д.ед.
|
Влажность
на границе текучести, д.ед.
|
Влажность
на границе раскатывания, д.ед.
|
Число
пластичности, д.ед.
|
Показатель
текучести
|
Плотность,
г/смЗ
|
Плотность
сухого грунта, г/смЗ
|
Плотность
частиц грунта, г/смЗ
|
Пористость,
%
|
Коэффициент
пористости
|
Степень
влажности, д.ед.
|
Четвертичные
отложения
|
Суглинок
|
*0,207;
0,209
|
0,387;
0,393
|
0,237;
0,244
|
0,149;
0,150
|
<0(2)
|
1,970;
2,060
|
1,630;
1,710
|
2,700;
2,710
|
36,900;
39,630
|
0,585;
0,656
|
0,860;
0,959
|
|
0,208
(2)
|
0,309
(2)
|
0,241
(2)
|
0,150(2)
|
|
2,020
(2)
|
1,670
(2)
|
2,705
(2)
|
38,260
(2)
|
0,621
(2)
|
0,909
(2)
|
Глина
|
0,264(1)
|
0,405
(1)
|
0,233
(1)
|
0,172(1)
|
0,180(1)
|
1,940(1)
|
1,530
(1)
|
2,700
(1)
|
43,330
(1)
|
0,765
(1)
|
0,932
(1)
|
Породы
пестроцветной толщи
|
Аргиллит
|
0,035;
0,212
|
0,388;
0,389
|
0,234;
0,235
|
0,153;
0,155
|
<0(2)
|
2,110-2,540
|
1,740-2,450
|
2,740-2,780
|
11,870-36,730
|
0,180-0,580
|
0,698-1,004
|
|
0,079
(14)
|
0,389
(2)
|
0,235
(2)
|
ОД
54 (2)
|
|
2,430
(14)
|
2,260
(14)
|
2,760
(14)
|
18,160(14)
|
0,234
(14)
|
0,903
(14)
|
Песчанник
|
0,027;
0,089
|
н.
опр.**
|
н.
опр.
|
н.
опр.
|
н.
опр.
|
2,350-2,550
|
2,160-2,480
|
2,700-2,750
|
8,150-21,170
|
0,146-0,269
|
0,822-0,917
|
|
|
|
|
2,440(10)
|
2,310(10)
|
2,730(10)
|
15,280
(10)
|
ОД
83 (10)
|
0,850(10)
|
Алевролит
|
0,035;
0,041
|
н.
опр.
|
н.
опр.
|
н.
опр.
|
н.
опр.
|
2,530;
2,550
|
2,440;
2,450
|
2,750
(2)
|
10,910;
11,270
|
0,122;
0,127
|
0,758;
0,921
|
|
0,038
(2)
|
|
|
|
|
2,540
(2)
|
2,445
(2)
|
|
11,090
(2)
|
0,125
(2)
|
0,839
(2)
|
Породы
терригенно - карбонатной толщи
|
Песчанник
|
н.
опр.
|
н.
опр.
|
н.
опр.
|
н.
опр.
|
н.
опр.
|
2,510-2,650
|
2,460-2,610
|
2,700-2,740
|
4,040-9,490
|
0,042-0,105
|
0,430-0,968
|
|
|
|
|
|
|
2,560
(9)
|
2,510(9)
|
2,720
(9)
|
7,570
(9)
|
0,082
(9)
|
0,689
(9)
|
Аргиллит
|
н.
опр.
|
н.
опр.
|
н.
опр.
|
н.
опр.
|
н.
опр.
|
2,400;
2,450
|
2,270;
2,390
|
2,760
(2)
|
13,410;
17,750
|
0,155;
0,216
|
0,481;
0,742
|
|
|
|
|
|
|
2,430
(2)
|
2,330
(2)
|
|
15,580
(2)
|
ОД
85 (2)
|
0,611
(2)
|
Доломит
|
н.
опр.
|
н.
опр.
|
н.
опр.
|
н.
опр.
|
н.
опр.
|
2,520;
2,560
|
2,430;
2,470
|
2,750
(2)
|
10,180;
11,640
|
ОД
13; 0,132
|
0,731;
0,873
|
|
|
|
|
|
|
2,540
(2)
|
2,450
(2)
|
|
10,910(2)
|
ОД
23 (2)
|
0,802
(2)
|
Известняк
|
н.
опр.
|
н.
опр.
|
н.
опр.
|
н.
опр.
|
н.
опр.
|
2,510-2,660
|
2,410-2,630
|
2,720-2,810
|
3,310-14,230
|
0,034-0,106
|
0,608-1,033
|
|
|
|
|
|
|
2,590
(6)
|
2,530(6)
|
2,780
(6)
|
9,050
(6)
|
ОД
02 (6)
|
0,720
(6)
|
Мергель
|
н.
опр.
|
н.
опр.
|
н.
опр.
|
н.
опр.
|
п.
опр.
|
2,560
(2)
|
2,490
(2)
|
2,720
(2)
|
8,460
(2)
|
0,092
(2)
|
0,854-0,883
|
|
|
|
|
|
|
|
|
|
|
|
0,869
(2)
|
Алевролит
|
н.
опр.
|
н.
опр.
|
н.
опр.
|
н.
опр.
|
н.
опр.
|
2,500-2,530
|
2,420-2,460
|
2,710-2,810
|
9,230-13,880
|
ОД
02-0,161
|
0,610-0,753
|
|
|
|
|
|
|
2,520
(4)
|
2,440
(4)
|
2,760
(4)
|
11,740
(4)
|
0,134(4)
|
0,685
(4)
|
Породы
соляно - мергельной толщи
|
Мергель
|
н.
опр.
|
н.
опр.
|
н.
опр.
|
н.
опр.
|
н.
опр.
|
2,090-2,690
|
1,910-2,690
|
2,720-3,040
|
3,930-29,780
|
0,041-0,424
|
0,228-1,080
|
|
|
|
|
|
|
2,340
(15)
|
2,190(15)
|
2,190(15)
|
21,360(15)
|
2,286(15)
|
0,716(15)
|
Гипсово
мергельная
|
н.
опр.
|
н.
опр.
|
н.
опр.
|
н.
опр.
|
н.
опр.
|
2,390;
2,400
|
2,260;
2,270
|
2,730
(2)
|
16,850;
17,220
|
0,203;
0,208
|
0,748;
0,768
|
|
|
|
|
|
|
2,400
(2)
|
2,270
(2)
|
|
17,030
(2)
|
0,205
(2)
|
0,758
(2)
|
Порода
|
Предел
прочности на растяжение
|
Предел
прочности на одноосное сжатие
|
|
|
В
естественном состоянии, Стр, МПа
|
В
замороженном состоянии, ар> МПа
|
В
естественном состоянии, ссж, МПа
|
В
замороженном состоянии. Се*-, МПа
|
|
Породы
пестро честной толщи
|
аргиллит
|
0.25-1.68*
|
0,16-1,07
|
0.40-1.31
|
0.12-1.03
|
5.04-33,58
|
3,27-21.33
|
8.00-26.30
|
2.43-20.5&
|
|
1.02
(6)
|
0.49
(5)
|
0.85
(7)
|
0.37
(9)
|
20,3!
(6)
|
9,77(5)
|
16.95
(7)
|
7.37(9)
|
песчаник
|
1.75-1.82
|
1,57-1.80
|
1,44-2,00
|
1.78-2,28
|
36.73-38.26
|
33.01-37,70
|
30.23-41.93
|
37.36-47.83
|
|
1.78
(3)
|
1.70
(3)
|
1,73
(3)
|
2.12
(4)
|
37.35
(3)
|
35.74(3)
|
36,21
(3)
|
44.45
(4)
|
алевролит
|
1.17-2.57
|
0,18-3.13
|
1,32-3.18
|
0,12-4,04
|
23.60-51.37
|
3,52-62,57
|
26.35-63.60
|
2.32-80.82
|
|
1.90(8)
|
1.29
(8)
|
2.39
(7)
|
1,30
(9)
|
38.1
1 (8)
|
25.86
(X)
|
47.81
(7)
|
25.97
(9)
|
Породы
терригенно-карбонатпой толщи
|
аргиллит
|
н.опр.*
|
0.53-0,78
0,64 (4)
|
н.опр.
|
н.опр.
|
н.опр.
|
10.66-15.50
12.75 (4)
|
н.опр.
|
н.опр.
|
|
|
|
|
|
|
|
|
|
|
.2 Гидрогеологические условия
Лицензионный участок, как и месторождение в
целом, по гидрогеологическому районированию относится к I [редуральскому
артезианскому бассейну, характеризующемуся широким развитием пластовых
подземных вод зоны активного и затрудненного водообмена, наличием регионально
выдержанного водоупора, представленного соленосными отложениями кунгурского
яруса, и этажно-расположенными газонефтеводоносными комплексами зоны весьма
затрудненного водообмена палеозойского возраста.
Наибольшую сложность при строительстве и
эксплуатации шахтных стволов представляют гидрогеологические условия надсолевой
толщи горных пород. Гидростратиграфически эта толща подразделяется на
четвертичный водоносный комплекс, шешминский водоносный комплекс и соликамскую
водоносную свиту.
При характеристике водоносных комплексов, кроме
результатов ранее проведенных гидрогеологических исследований при детальной
разведке участка, были использованы результаты обработки опытных
гидрогеологических исследований в контрольно-стволовых скважинах 107г-1, 107г-2
и 107г-3.
Четвертичный водоносный комплекс распространен в
пределах речных долин и низких междуречий. Водовмещающие породы представлены
аллювиальными разнозернистыми песками с гравием и галькой и флювиогляциальными
песками с линзами суглинков. Мощность аллювиальных отложений колеблется на
участке работ от 1,5 м в долинах небольших рек до 15 м в долине р. Яйва.
Наиболее широкое распространение на площади
лицензионного участка имеют практически безводные глинистые образования. В
понижениях рельефа и на площадях, где пески подстилаются глинами, весной и
осенью наблюдается маломощный слой верховодки.
Подземные воды относятся к грунтовым
порово-пластовым, глубина залегания не превышает 2-10 м, области питания и
разгрузки совпадают с областью их распространения. Питание подземных вод
осуществляется за счет атмосферных осадков и перетекания из коренных отложений
в нижних частях склонов или напорной фильтрацией в днищах речных долин.
Разгрузка грунтовых вод происходит в речную сеть или нисходящей фильтрацией в
подстилающие коренные отложения.
Фильтрационные свойства водовмещающих пород
характеризуются коэффициентом фильтрации, который колеблется от 0,5 до 3 м/сут.
Ресурсы подземных вод, ввиду незначительной площади распространения и малой
мощности водовмещающих пород, составляют не более 0,5 л/с/км2. Дебиты родников
не превышают, 0,5 л/сек. Практического значения как источник водоснабжения
водоносный комплекс не имеет, поскольку не водообилен и подвержен
антропогенному загрязнению. Шешминский водоносный комплекс распространен на
всей территории лицензионного участка и представлен часто переслаивающимися
песчаниками, аргиллитами и алевролитами, фациально не выдержанными в плане.
Подземные воды трещинно-пластовые безнапорные, реже су б напорные. Глубина
залегания изменяется от 8-10 м на склонах до 20-30 м на водоразделах. Питание
подземных вод осуществляется в основном за счет перетекания из перекрывающего
четвертичного водоносного горизонта. В долине р. Волим возможна напорная
фильтрация подземных вод из подстилающего водоносного комплекса. Разгрузка
подземных вод в большей части территории участка происходит путем нисходящей
фильтрации в подстилающий водоносный комплекс или в гидрографическую сеть
транзитом через примыкающие четвертичные отложения. Направление движения
пластово-трещинных вод в генерализованном плане с востока на запад в сторону
региональной дрены - р. Яйва, которое на конкретных участках может изменяться в
сторону pp. Волим и Сюзьва.
Фильтрационные свойства водовмещающих пород
весьма разнообразны ввиду литологической пестроты и зональности трещиноватости.
Повышенная экзогенная трещиноватость характерна для водовмещающих пород в
пределах нижних частей склонов речных долин, а пониженная - в пределах
водоразделов.
Повсеместно она уменьшается с глубиной залегания
пород. При гидрогеологическом опробовании пестроцветов в пределах лицензионного
участка установлено, что коэффициенты фильтрации водовмещающих пород колеблются
от 0,5 до 3,4 м/сут, удельные дебиты скважин изменяются от 0,29 до 2,17 л/с.
По химическому составу подземные воды пресные
гидрокарбонатнокальциевые, гидрокарбонатно-натриевые с минерализацией 0,2-0,3
г/дм'5.
Подземные воды комплекса пригодны для
автономного водоснабжения с потребностью до 1000 м7сут.
Соликамская водоносная свита в пределах
Верхнекамского месторождения солей подразделяется на обводненную терригенно-
карбонатную и на обводненную соляно-мергельную толщи. Глубина залегания кровли
терригенно-карбонатной толщи на участке изменяется от 20-50 до 100-160 м.
Мощность терригенно-карбонатной толщи по площади достаточно стабильна - 100-110
м, и только на северо-востоке наблюдается увеличение мощности до 145 м.
Водовмещающие породы представлены плитчатыми известковистыми мергелями и
известняками. Подземные воды пластово-трещинные, напорные. Питание подземных
вод атмосферными осадками происходит на участках, где водовмещающие породы
выходят под четвертичные отложения, а также нисходящей фильтрацией из смежного
комплекса. В пределах участка осуществляется их транзитный сток в сторону региональной
дрены - р. Кама, где происходит разгрузка подземных вод напорной фильтрацией в
вышележащие водоносные комплексы.
Отложения терригенно-карбонатной толщи
характеризуются наиболее высокой водопроводимостью по сравнению с другими
обводненными комплексами. Но поскольку в пределах лицензионного участка они
перекрыты пестроцветными отложениями, мощность которых местами превышает 100 м,
обводненность их здесь значительно меньше.
В верхней части терригенно-карбонатной толщи
породы характеризуются значениями коэффициентов фильтрации 0,25-3,97 м/сут, а в
нижней части терригенно-карбонатной толщи 0,02-1,57 м/сут. При откачках из
верхней терригенно-карбонатной толщи удельные дебиты скважин изменяются от
до 2,42 л/с, из нижней терригенно-карбонатной
толщи - от 0,007 до 0,04 л/с.
Химический состав подземных вод неоднородный,
преобладают слабоминерализованные (0,2-0,7г/л) гидрокарбонатно-кальциевые или
гидрокарбонатно-натриевые, реже гидрокарбонатно-магниевые, сульфатно- натриевые
воды с минерализацией 1-2 г/дм^; в нижних интервалах ТКТ и вблизи местной дрены
(р. Яйва) фиксируются солоноватые сульфатнонатриевые и хлоридно-натриевые воды
с минерализацией от 2 до 13 г/дм (скв. 108г), причем мощность зоны
минерализованных вод увеличивается с приближением к р. Яйва.
Подземные воды терригенно-карбонатной толщи
имеют важное практическое значение, как один из крупных источников
централизованного водоснабжения.
Обводненная соляно-мергельная толща полностью
находится в зоне затрудненного водообмена. Кровля толщи вскрыта на глубинах
120-260 м, мощность ее стабильна (90-110 м). Водовмещающие породы представлены
глинистыми мергелями с прослоями аргиллитов и гипсов, а в основании залегает
практически безводная переходная пачка.
Подземные воды соляно-мергельной толщи в
основном пластовотрещинные напорные, в подошве толщи линзовидные изолированные.
Пьезо-метрические уровни подземных вод
соляно-мергельной толщи повсеместно ниже пьезометрических уровней подземных вод
терригенно- карбонатной толщи, что свидетельствует об инфильтрационном типе
режима подземных вод всего надсолевого комплекса.
Фильтрационные свойства водовмещающих пород
соляно-мергельной толщи имеют чёткую зависимость от глубины их залегания,
поскольку экзогенная трещиноватость пород с глубиной затухает. Коэффициенты
фильтрации пород, вычисленные по результатам откачек, проведенных по всей
толще, чаще всего изменяются в пределах сотых и тысячных долей м/сут (0,033 -
скв. 105г), и только на севере и западе участка они достигают больших значений
(0,17 - скв. 445 и 0,4 - скв.105г). При поинтервальном гидрогеологическом
опробовании соляно-мергельной толщи, было установлено, что сильнее обводнены
мергели верхней части.Собственные ресурсы толщи благодаря затруднённому
водообмену ничтожны, а дебиты при откачках в основном формируются за счёт
перетекания вод терригенно-карбонатной толщи.По химическому составу подземные
воды хлоридно-натриевые сминерализацией 15-ЗООг/ дм"* причём минерализация
с глубиной возрастает.
Направление и скорость движения подземных вод
Поскольку сеть гидрогеологических скважин в
пределах участка заложения ствола крайне редкая, а на восток от
контрольно-стволовой скважины их вообще нет, полученные ниже результаты весьма
приблизительные. Анализируя характер распределения гидроизогипс, получаем
направление движения потоков в каждой из стратиграфических толщ.
Так, в ПЦТ и ТКТ локальное (в районе
контрольно-стволовых скважин) направление совпадает с генеральным -
северо-западное, в СМТ поток движется в южном направлении.
Максимально возможные скорости фильтрации подземных
вод в месте заложения шахтных стволов составляют: для ПЦТ- 0,042 м/сут; для ТКТ
-
м/сут; для СМТ - 0,015 м/сут.
Результаты поинтервальных откачек из скважины
107г-1 приведены в таблице 2.3.
Гидрохимическая зональность вод, вскрытых
скважиной 107г-1 приведена в таблице 2.4.
.3 Нарушенность массива
Скважина 107г-1.
Изучение МТ и МК проводилось в интервале глубин
от 11,90 м (кровля ПЦТ) до глубины 287,46 м (до подошвы СМТ, с привлечением
некоторых данных по ПКС). Анализ полученных данных позволил выделить в разрезе
по скважине 107г-1 несколько интервалов нарушенности массива.
Зона 1 (интервал глубины 12,90-38,25 м)
представлена отложениями верхней части ПЦТ: чередование прослоев (от нескольких
см. до первых метров) алевролита, аргиллита и песчаника. Основная часть пород в
различной мере дезинтегрирована и представлена слабосцементированным материалом
- песчано-глинистым или глинисто-песчаным (в зависимости от состава исходной
породы) с обломками различной степени крепости - от крепких до легко разрушаемых.
С глубины 34,00 м разрез представлен плотными,
крепкими песчаниками, с редкими прослоями алевролитов, аргиллитов и глин.
Породы тонкослоистые, трещиноватые, на карбонатном цементе.
Трещины преимущественно разнонаправленные,
открытые. В интервале 36,10-36,40 м редкие, тонкие (1-1,5 мм) вертикальные
трещины выполнены кальцитом.
Зона 2 (интервал 221,25-228,25 м) представлена
отложениями средней части СМТ. Литологически зона сложена мергелями, в
интервале 225,ТО-
м отмечаются прослои (до 10-15 см) глины темно-серой
до черной, плотной, вязкой. Мергели светло-серые, серые, участками - с
включениями гипса, трещиноватые. Трещины вертикальные, прямые, тонкие, открытые
и крутопадающие (75-80°), местами залеченные гипсом.
Зона 3 (интервал глубин 235,00-238,25 м) представлена
отложениям СМТ. Литологически зона сложена мергелем серым, темно-серым и
глинистогипсовой породой. Мергели выветрелые, разрушенные до глинистого
состояния, трещиноватость объясняется наличием трещин усыхания. В интервале
235,00-236,60 м отмечены многочисленные зеркала скольжения в горизонтальной
плоскости.
Кроме этого в интервале 100,00-103,90 м
рассматривается дополнительная зона, выделенная по МК и не нашедшая яркого
отображения по МТ. Стратиграфически зона представлена отложениями верхней части
ТКТ. Литологический состав: в интервале 100,00-102,00 м-песчаник серый,
темно-серый, крупно-зернистый на карбонатно-глинистом цементе. Керн разрушен и
представляет собой куски и плашки размером до 5 см. Песчаник
среднетрещиноватый, трещины (1-2 мм) прямые и извилистые, вертикальные и
залечены кальцитом.
Далее с глубины 102,00 м - алевролит
темно-серый, серый на карбонатном цементе, слаботрещиноватый (трещины
извилистые и заполнены кальцитом); керн представлен кусками, плашками размером
до 10см.
.4 Инженерно-геологические условия
проходки ствола №1
Проходку ствола №1 предстоит производить в
породах, представленных в интервале глубин 0,0-12 м суглинками с редкими
прослоями песков и глин, в интервале 12-88 м - переслаиванием песчаников,
аргиллитов, алевролитов, в интервале 88-194 м - переслаиванием известняков,
мергелей, песчаников, алевролитов, в интервале 194-287 м - мергелями с тонкими
прослоями гипсов, а в интервале 287-551 м соленосной толщей.
Уровень подземных вод находиться на глубине
19,01 м (А.0.-Ы53,220).Б породной толще выделяются два водоносных комплекса.
Первый водоносный комплекс приурочен к толще
переслаивающихся песчаников, аргиллитов, алевролитов (интервал 12-88 м).
Подземные воды этого комплекса трещинно-пластовые, безнапорные.
В интервале проведения откачки 32-88 м расчётные
водопритоки в открытый ствол могут составить около 600 м7ч (Кф = 2,77 м/сут). В
этом интервале воды пресные, не агрессивные к бетону по всем показателям и
слабоагрессивные к стальным конструкциям при периодическом смачивании.
Второй водоносный горизонт приурочен к толще
переслаивающихся пород (интервал 88-269м). Подземные воды пластово-трещинные,
напорные. Поинтервальные откачки показали, что в интервале 88-151 м водопритоки
в ствол могут составить до 100 м7ч, в интервале 151-190 м до 390 м7ч, в
интервале 190-240 м до 750 м Уч, а в интервале 240-269 м до 140 м7ч.
Подземные воды слабоагрессивные к бетону W4 по
содержанию сульфатов с глубины 151 м до 190 м, а с глубины 190 м до 269 м
подземные воды среднеагрессивные к бетону сильноагрессивные к стальным
конструкциям при периодическом смачивании.
С глубины 190 м до 240 м подземные воды
слабосолёные, а с глубины 240 м до 269 м подземными водами являются крепкие
рассолы с концентрацией солей 200 г/л.
Крепость пород варьируется по глубине следующим
образом: о интервал глубин 0,0-12 м - коэффициент крепости - 1,0 о интервал
глубин 12 -194 м - коэффициент крепости - 3,0-6,0 о интервал глубин 194-287 м -
коэффициент крепости - 3,0
о интервал глубин 287-551 м - коэффициент
крепости - 1,5-2,0 По модулю трещиноватости породы толщи оцениваются как
средне- и сильнотрещиноватые, с наличием многочисленных зон дробления.
Соляные отложения верхнекамского месторождения
солей являются газоносными. Однако по результатам бурения контрольно-стволовой скважины
107г-1 по всей глубине выделений свободного газа не было отмечено. Газы
присутствуют в соляном керне в слабосорбированном и адсорбированном состоянии.
Наиболее вероятной причиной наличия газов в
соляной толще является поступление их из подсолевых нефтяных залежей. (Отчет о
научно- исследовательской работе. «Разработка заключения о возможных составе,
масштабах, местах и характере выделения газов в руднике Усольского калийного
комбината на Палашерском и Балахонцевском участках ВКМКС» (Договор №254К/2010),
выполненный УНИПИГ ОАО «Галургия», г. Пермь,
г.)-
На основании п.2 Л 7 «Специальных мероприятий по
безопасному ведению горных работ на Верхнекамском месторождении калийных солей
в условиях газового режима в Филиале ОАО «Ковдорский ГОК» г.Усолье, (Палашерский
и Балахонцевский участки), утвержденных руководителем Филиала ОАО «Ковдорский
ГОК» г.Усолье, и руководителем Западно- Уральского управления Федеральной
службы по экологическому, технологическому и атомному надзору 08.04.2010г.
[86], при проходке стволов в интервале от кровли карналлитовой зоны до подошвы
сильвинитовой зоны, рабочую зону следует относить к Ш группе газовой опасности
по горючим газам, и газодинамическим проявлениям с учётом выполнения при
проходке условий изложенных в разделах данных «Специальных мероприятий...». Для
условий проходки ствола №1 вышеуказанная рабочая зона находится в интервале
абсолютных отметок -136,170 м -209Д10 м, что соответствует интервалу глубин
308,4 м до 381,34 м.
На основании отчета о научно-исследовательской работе.
«Оценка возможности проявления горных ударов в руднике Усольского калийного
комбината на Палашерском и Балахонцевском участках ВКМКС» (Договор №255К/2010),
выполненный УНИПИГ ОАО «Галургия», г. Пермь, 2010г., горные породы
месторождения считать неудароопасными.
Достаточные условия саморазрушения выполняются
только для газонасыщенных пород, т.е. газодинамические явления вполне реальны,
а горные удары на Палашерском и Балахонцевском участках Верх не камского
месторождения исключены.
. Характеристика ствола №1 на
участке строительства устья и технологического отхода
Диаметр ствола в свету 7,0 м, глубина
технологического отхода 40,02 м. За относительную отметку ± 0,000 м площадки
поверхности скипового ствола №1 принята отметка +174,000 м (отметка верха перекрытия
замораживающих галерей).
Оголовок устья ствола устроен на 200 мм выше
проектного уровня поверхности площадки ствола №1 и имеет абсолютную отметку
+174,200 м.
Временный оголовок устья ствола выполнен в
железобетоне с использованием инвентарной металлической опалубки из щитов 6x3,0
ЦНИИОМТП в распор с вертикальными стенами галереи кольцевых рассолопроводов с
устройством деформационного шва и гидроизоляционного слоя до глубины 3,4 м
(+170,600 м), чертежи 779/1 -П-4.3 1.1 /20-07ПР/10-КЖI * Временный оголовок
смонтирован на буровой железобетонной плите толщиной 400 мм и жестко связан со
шпунтовым ограждением из металлических труб 219x9 мм, установленных с шагом 750
мм по окружности диаметром 9,5 м на глубину 21,4 м вокруг проектного сечения
ствола (ограждающая предварительная крепь при строительстве устья ствола в
неустойчивых грунтах и породах - метод «стена в грунте»).
Постоянная крепь устья ствола с глубины 3,8 м до
глубины 13,0 м в интервале отметок от +170,200 м до +161,000 м - железобетон
толщиной 1150 мм (чертеж 779/1-П-4.3 1Д/20-07ПР/10-КЖ I).
Далее с глубины 13,0 м до глубины 17,5 м в
интервале отметок + 161,000 м и +156,500 м шахтные чугунные тюбинги «7.0-30»
тип 1,2 по ГОСТ 1412-85 высотой 1500 мм, с толщиной спинки 30 мм - 3 тюбинговых
кольца по 13 тюбингов в каждом кольце (графические материалы 779/1-П-4.3
1.1/20-07ПР/Ю-ГПР л.З).
В интервале отметок +168.000 м до +161,000 м и
+169,000 м до +167,200 м в устье ствола выполнены также в железобетоне
сопряжения с калориферным каналом и кабельным ходком соответственно (чертежи
779/1-П-4.3 1.1/20-07ПР/10-ГПР л.З и 779/1-П-4.3 IД/20-07ПР/10-КЖ1).
В интервале отметок +161,000 м и +156,500 м в
стволе устроен опорный венец устья - железобетон в комбинации с чугунными
тюбингами «7.0-30»
тип 1,2 по ГОСТ 1412-85 (тюбинговые кольца
№1,2,3), чертежи 779/1 -П-4.3 1.1 /20-07ПР/10-ГПР и 779/1 -П-4.31.1
/20-07ПР/10-КЖ1.
Далее с глубины 17,5 м до глубины ствола 35,52
м, в интервале отметок + 156,500 м до +138.480 м на участке технологического
отхода крепь ствола состоит из чугунных тюбингов «7.0-30» тип 1,2 по ГОСТ
1412-85 высотой 1500 м м, с то л щи н о й спинки 30 мм -12 тю б и н го в ы х ко
л е ц по 13 тюб и н го в в каждом кольце в комбинации с бетоном класса
прочности В25, который укладывается за смонтированные в стволе тюбинговые
кольца, чертеж 779/1 -П-4.3 1.1 /20-07ПР/10-ГПР л. 1,2.
С глубины 35,52 м до глубины ствола 40,02 м, в
интервале отметок + 138,480 м до +133.980 м на участке технологического отхода
крепь ствола состоит из чугунных тюбингов «7.0-40» тип 1,2 по ГОСТ 1412-85
высотой 1500 мм, с толщиной спинки 40 мм -3 тюбинговых кольца по 13 тюбингов в
каждом кольце в комбинации с бетоном класса прочности В25, который также
укладывается за смонтированные в стволе тюбинговые кольца, чертеж 779/1-П-4.3
1.1/20-07ГГР/10-ГГГР л. 1,2.
. Общие требования безопасности при
разработке проекта проходки ствола №1 на участке устья и технологического
отхода с замораживанием вмещающих горных пород
Учитывая сложные гидрологические условия
месторождения, наличие водоносных, неустойчивых вмещающих пород, проектом
предусматривается применение специальной технологии проходки скипового ствола
№1: замораживание горных пород на глубину 270,0 м до кровли соляной толщи, и
особые методы крепления обнаженных стенок ствола на участке устья и
технологического отхода ствола:
Для участка устья ствола (строительство
осуществляется в не замороженных грунтах и породах) предусматривается:
Предварительная - забивная шпунтовая
крепь по методу «стена в грунте»: шпунтовое ограждение из металлических труб
0219x9 мм, установленных с шагом 750 мм по окружности диаметром 9,5 м на
глубину м в ранее пробуренные скважины, и временная предохранительная крепь,
выполненная полигональными кольцами из швеллера №18 по ограждению из труб
0219x9 мм, с затяжкой из металлической дорожной сетки и набрызг-бетона толщиной
50 мм, наносимого на сетку. Шаг установки швеллерных колец 850 мм. Крепление
швеллерных колец осуществляется посредством электросварки на шпунтовом
ограждении. Допустимое отставание швеллерных колец, сетки Р-45-3.0 и
торкрет-бетона временной крепи от забоя на участке строительства устья должно
определяться паспортом крепления горной выработки, составленным на участке
производства работ и утвержденным в установленном порядке.
Постоянная железобетонная - чертеж
779/1-П-4.31.1/20-07ПР/10-КЖ1.
Для участка технологического отхода ствола
(строительство осуществляется в замороженных породах) предусматривается:
.Временная предохранительная крепь состоящая из
сталеполимерных анкеров типа СПА диаметром 24 мм, длиной 1600 мм с затяжкой из
металлической сетки Р-45-3.0 и набрызг-бетона толщиной 50 мм по сетке. Сетка
установки анкеров в стенки ствола, допустимое отставание анкерной крепи, сетки
и торкрет-бетона от забоя должно определяться паспортом крепления горной
выработки, составленным на участке производства работ и утвержденным в
установленном порядке на основании фактических горно-геологических условий.
Постоянная тюбинговая крепь в комбинации с
бетоном класса прочности В25 чертеж 779/1-П-4.31.1/20-07ПР/10-ГПР л. 1,2.
Все принятые проектные решения обеспечивают
стабильную и безопасную проходку в период строительства ствола, а также
надежную эксплуатацию шахтного ствола на весь срок отработки месторождения.
Проектные решения приняты на основании
проведения полного анализа геологических, геомеханических, гидрологических
данных и с учетом технического задания заказчика.
Принятие технических решений, выбор
проходческого оборудования, организация рабочего цикла строительства
осуществлялись исходя из технологии строительства ствола, обеспечивающей
надежность и качество проведения работ, долговечность и надежность эксплуатации
ствола.
.1 Выбор способа проходки ствола №1
Обоснование выбора специального способа проходки
ствола производится исходя из конкретных горно-геологических и
гидрогеологических условий в проекте организации строительства (ПОС).
Уровень подземных вод находится на глубине 19,01
м (А.О.+ 153,220). Породы, залегающие в интервале глубин от 19,01 м и
ориентировочно до м классифицируются как водоносные.
В пересчете на мощность водовмещающих пород,
пересеченных контрольно-стволовой скважиной №107г-1, прогнозные водопритоки в
ствол №1 составят:
в интервале 32-88 м - около 600м7час; в
интервале 91-151 м - до 100м7час; в интервале 151-190 м - до 390м7час; в интервале
190-240 м - до 750м7час; в интервале 240-269 м - до 140 м3/час.
Как показала практика строительства шахтных
стволов в условиях Верхнекамского месторождения, наиболее целесообразным и
надёжным способом проходки ствола в надсолевой толще является искусственное
замораживание пород. По данным контрольно-стволовой скважины 107г-1
максимально- возможные водопритоки в ствол №1 оцениваются в 2020 м7ч, а
ожидаемое гидростатическое давление подземных вод может достигать 2,5-2,7 МПа
(25-27 атм.).
Проходка ствола в соляной толще производится без
применения спецспособа замораживания горных пород с учётом опасности возможных
газодинамических проявлений.
При проходке имеющихся на Верхнекамском
месторождении шахтных стволов(24 ствола) случаев внезапного выброса горной
массы (ГДЯ) не зарегистрировано. Это связано как с более низким уровнем
напряжённого состояния массива вокруг вертикальных стволов по сравнению с
горизонтальными выработками, так и с тем, что стволы проходятся буровзрывным
способом и если и бывают какие-либо выбросы, то они происходят одновременно с
«отпалом» забоя и поэтому не обнаруживаются. Людей в период взрывных работ в
стволе нет.
В тоже время имеются случаи газовыделения при
бурении геологоразведочных скважин, в том числе и при бурении контрольно стволовых
скважин на Палашерском участке.
На основании вышеизложенного, при проходке
стволов, в интервале от кровли карналлитовой зоны до подошвы сильвинитовой
зоны, рабочую зону следует относить к третьей группе газовой опасности, с
учётом выполнения при проходке условий изложенных в разделах 3,4,5,6,7
«Спецмероприятий...» [86], п.2.17 «Спецмероприятий...» [86].
Проектные решения по креплению ствола №1
.2 Расчеты крепи ствола №1
Выполнены по методике профессора Н.С. Булычева
ООО«ГЕОНИКА-РАСЧЕТ», Тульский Государственный университет, Тула, 2010.
В основу расчетов положены аналитические методы
расчета крепи горных выработок и обделок подземных сооружений, которые основаны
на современной теории расчета «Механике подземных сооружений» и базируются на
строгих аналитических решениях задач теории упругости, соответствующих задачам
расчета крепи в реальных условиях проходки горных выработок. Законы и положения
теории расчета крепи построены на едином принципе - принципе взаимодействия
крепи с массивом пород. Согласно этому принципу крепь и массив являются
элементами единой деформируемой системы «крепь- массив», которая воспринимает
все внешние нагрузки и воздействия.
Важным положением (постулатом) теории является
моделирование массива пород линейно-деформируемой средой. Согласно этому
положению математическим аппаратом теории и методов расчета крепи является
аппарат математической теории упругости.
В расчетных схемах крепи обязательно
присутствует массив горных пород.
Расчет крепи выполнен с помощью компьютерной
программы «РК2-М».
Методы и программы расчетов защищены
нормативными документами (смотри таблицу 4.1) и многолетней реализацией при
проектировании и строительстве горных.
4.3 Конструкция крепи ствола №1
Конструкция крепи ствола №1 на участке устья и
технологического отхода
За относительную отметку ± 0,000 принят верх
перекрытия замораживающей галереи с абсолютной отметкой +174,000 м.
Открытым способом в интервале глубин 0,0 м до
3,8 м (А.О.+170,200) на период проходки сооружается галерея кольцевых
замораживающих рассолопроводов (Проект «ТИССЕН ШАХТБАУ ГмбХ» шифр:
02.10.ШП.10-01-ГТХ1 и 02.10.ШП. 10-01-БП1).
Временный оголовок устья ствола выполнен в
железобетоне с использованием металлической инвентарной опалубки из щитов
0,6x3,0 м ЦНИИОМТП в распор с вертикальными стенами галереи кольцевых
рассолопроводов с устройством деформационного шва и гидроизоляционного слоя до
глубины 3,4 м в интервале отметок от + 174,200 м и +170,600 м (Проект ЗАО
«ОГСК-Шахтспецстройпроект» шифр: 779/1 -П-4.3 1Л /20-07ПР/10-ГПРЛ.З и 779/1-П-4.31.1/20-07ПР/10-КЖ1).
Временный оголовок смонтирован на буровой железобетонной плите толщиной 400 мм,
выполненной по проекту «ТИССЕН ШАХТБАУ ГмбХ» шифр: 02.10.ШП.10-01-БП1 и жестко
связан со шпунтовым ограждением из металлических труб 219x9 мм, установленных с
шагом 0,75 м по окружности диаметром 9,5 м на глубину 21,4 м - ограждающая
предварительная крепь при строительстве устья ствола в неустойчивых грунтах и
породах - метод «стена в грунте».
Сооружение устья ствола горным способом
начинается с глубины 3,8 м (А.О.+170,200), после того, как будет возведен
временный железобетонный оголовок и демонтирован участок железобетонной буровой
плиты в проектном сечении ствола.
Крепь устья ствола с глубины 3,8 м до глубины
13,0 м в интервале отметок + 170,200 м и +161,000 м - железобетон толщиной 1150
мм. Далее на глубине с 13,0 м до 17.5 м в интервале отметок +161,000 м и
+156,500 м шахтные чугунные тюбинги «7.0-30» тип 1,2 по ГОСТ 1412-85 высотой
1500 мм, с толщиной спинки 30 мм -3 тюбинговых кольца по 13 тюбингов в каждом
кольце.
В интервале отметок +168.000 м до +161,000 м и
+169,000 м до +167,200 м в устье ствола выполнены также в железобетоне
сопряжения с калориферным каналом и кабельным ходком соответственно.
В интервале отметок +161,000 м и +156,500 м на глубине
с 13,0 м до 17,5 м в стволе устроен опорный венец устья - железобетон в
комбинации с чугунными тюбингами «7.0-30» тип 1,2 по ГОСТ 1412-85 (тюбинговые
кольца №1,2,3). Проект ЗАО «ОГСК-Шахтспецстройпроект», чертежи 779/1-П-4.3
1.1/20-07ПР/10-ГПР л.З и 779/1-П-4.3 1.1/20-07ПР/10-КЖ 1.
Далее с глубины 17,5 м до глубины ствола 35,52
м, в интервале отметок + 156,500 м до +138,480 м на участке технологического
отхода крепь ствола состоит из чугунных тюбингов «7.0-30» тип 1,2 по ГОСТ
1412-85 высотой 1500 мм, с толщиной спинки 30 мм -12 тюбинговых колец по 13
тюбингов в каждом кольце в комбинации с бетоном класса прочности В25, который
укладывается за смонтированные в стволе тюбинговые кольца, чертежи 779/1-П-4.3
1.1/20-07ПР/10-ГПР л. 1,2.
С глубины 35,52 м до глубины ствола 40,02 м, в
интервале отметок + 138,480 м до +133,980 м на участке технологического отхода
крепь ствола состоит из чугунных тюбингов «7.0-40» тип 1,2 по ГОСТ 1412-85
высотой 1500 мм, с толщиной спинки 40 мм -3 тюбинговых кольца по 13 тюбингов в
каждом кольце в комбинации с бетоном класса прочности В25, который также
укладывается за смонтированные в стволе тюбинговые кольца, чертежи 779/1-П-4.3
1.1/20-07ПР/10-ГПР л. 1,2.
Комбинированная чугунно-бетонная крепь ствола
служит для принятия нагрузки со стороны горного массива и гидроизоляции ствола
(максимальное гидростатическое давление на глубине 270,0 м - отметка кровли
соляной толщи - до 27 атм.) после прекращения процесса замораживания.
Тюбинговая крепь устанавливается единой
колонной. В каждом тюбинговом кольце 13 тюбингов двух типов, в том числе 7
тюбингов с отверстиями диаметром 100 мм для заливки бетонной смеси, которые
перекрыты специальными пробками 100x6 мм (тип 1). Все 13 тюбингов имеют
тампонажные отверстия диаметром 60 мм, которые также перекрыты специальными
пробками 60x4 мм. Высота тюбингов 1500 мм. Конструкция тюбингов разработана ЗАО
«ОГСК-Шахтспецстройпроект». Спецификация тюбингов показана на чертеже 779/
1-П-4.31.1/20-07ПР/10-ГПР л.2.
Прочностные характеристики пород пересекаемых
стволом чередуются с большим разбросом по величине. Расчет конструкции
постоянного крепления ствола в каждом интервале выполнен по менее прочным
породам и максимальным нагрузкам на крепь со стороны массива обводненных
вмещающих горных пород. Для восприятия горного давления определена
чугунно-бетонная крепь.
Толщина тюбинговой крепи варьируется в
зависимости от нагрузок, возникающих на контуре крепи от влияния вскрываемых
вмещающих пород, водоносных горизонтов и при замораживании от морозного пучения
пород, и составляет от 30 мм до 120 мм чертежи
Распределение тюбинговой крепи по стволу
показано в таблице 4.3
Интервалы
|
Тип
|
Количество
|
Бетон
|
глубин,
м
|
тюбинга
|
колец
|
о
О! lO СП ] *1- о СП 1
|
7.0-30
|
15
|
625
|
-35,520
+ -184,020
|
7.0-40
|
99
|
615
|
-184,020+
-304,050
|
7.0-60
|
80
|
595
|
-304,050
+ -304,450
|
7.0-70-К-01
|
1
|
-
|
-304,450
+ -404,950
|
7.0-60
|
67
|
595
|
-404,950+
-424,430
|
7.0-80
|
13
|
565
|
-431,930+
-452,950
|
7.0-80
|
14
|
565
|
-452,950
+ -545,950
|
7.0-100
|
62
|
525
|
Тюбинги и тюбинговые кольца крепятся между собой
болтовыми соединениями посредством ударных гайковертов с пневматическим
приводом. На гайковерте устанавливается расчетный момент затяжки (80-100 кгм).
Для герметизации тюбинговой крепи используются
плоские свинцовые прокладки толщиной 2 мм, которые вкладываются в вертикальных
и горизонтальных стыках, после чего сегменты свинчиваются между собой. Для
герметизации болтовых соединений используются накладные и специальные
полиэтиленовые шайбы. Заливные и тампонажные отверстия в тюбингах надежно
закрываются специальными пробками. Корме того, при выполнении тампонажных работ
за тюбинговое пространство, достигается как консолидация системы порода-крепь,
так и дополнительная герметизация тюбинговой крепи.
После возведения законченного элемента
тюбинговой крепи (тюбинговое кольцо или два тюбинговых кольца в зависимости от
горно-геологических условий), затюбинговое пространство заполняется бетоном
класса прочности В25 толщиной 525-625 мм.
. Подготовительный период
К началу работ по строительству устья ствола и
далее технологического отхода должны быть выполнены:
вертикальная планировка участка производства
строительных и горных работ;
к строительной площадке должны быть подведены
необходимые инженерные сети и коммуникации, стройплощадка должна быть
обеспечена телефонной или радиосвязью;
сооружение буровой плиты на отм. +170,600 м
(-3,4 м) с закладными деталями для бурения замораживающих скважин и скважин
шпунтового ограждения;
бурение скважин шпунтового ограждения;
устройство шпунтового ограждения из
металлических труб 219x9 мм, установленных с шагом 750 мм по окружности
диаметром 9,5 м на глубину м вокруг проектного сечения ствола;
бурение и оборудование замораживающих и
контрольно-термических скважин;
строительство галереи кольцевого замораживающего
рассолопровода вокруг проектного сечения ствола;
монтаж кольцевого замораживающего
рассолопровода;
гидроизоляция и обратная засыпка замораживающей
галерии и окончательная планировка промплощадки;
покрытие площадки дорожными плитами;
строительная площадка должна быть ограждена с
устройством необходимого количества въездов, около которых оборудуются
контрольнопропускные пункты сторожевой охраны;
на строительной площадке должно быть устроено
искусственное освещение. Все рабочие зоны, а также подъезды и подходы к устью
ствола на промплощадке должны иметь искусственное освещение в соответствии с
санитарными нормами и обеспечивать безопасные условия производства работ в
темное время суток. В забое устья, технологического отхода ствола и при
дальнейшей проходке ствола освещение должно работать постоянно в соответствии с
требованиями действующих правил безопасности и санитарных норм.
Проходка и крепление технологического отхода
ствола до глубины 40,02 м, включая устройство устья, будет осуществляться с
использованием автомобильного крана КС-6476 грузоподъемностью 50 т или его
аналога. Места установки крана, опасные зоны, организация, порядок и меры
безопасности при выполнении погрузо-разгрузочных, монтажнодемонтажных работ при
возведении устья и технологического отхода ствола определяются проектом
организации строительства и Инструкциями для работников строительной
организации по безопасному ведению технологических процессов при выполнении
погрузочно-разгрузочных и монтажных работ с использованием грузоподъемных
кранов при строительстве стволов.
На перекрытии галереи кольцевого замораживающего
рассолопровода по периметру устанавливается ограждение из сетчатых щитов
высотой 2,5 м. По периметру ограждения в нижней части устраивается обортовка на
высоту 300 мм. В ограждении в двух противоположных сторон должны быть
смонтированы калитки для прохода людей с устройством внутренних запоров. При
отсутствии работающих в стволе калитки должны быть закрыты снаружи на замки.
При подготовке строительной площадки и
выполнении общестроительных работ должны выполняться требования промышленной
безопасности, изложенные в нормативных документах Госстроя России,
Ростехнадзора и других министерств и ведомств, в том числе:
Правила устройства и безопасной эксплуатации
грузоподъемных кранов (ПБ 10-382-00)
Правила устройства и безопасной эксплуатации
строительных подъемников (ПБ 10-518-02)
Правила устройства и безопасной эксплуатации
подъемников (вышек) (ПБ 10-611-03)
Инструкция по надзору за изготовлением, ремонтом
и монтажом подъемных сооружений (РД 10-08-92)
Типовые инструкции РД 10-34-93; РД 10-40-93; РД
10-74-94; РД 10-93-95; РД 10-103-95; РД 10-107-96.
Организация строительной площадки должна
выполняться в соответствии с проектом организации строительства (ПОС) и
обеспечивать безопасность труда работающих, прохода людей, а также
беспрепятственный подъезд транспортных средств на всех этапах выполнения работ.
Строительная площадка должна ограждаться забором
высотой не менее 2 м. Ограждения, примыкающие к местам массового прохода людей,
необходимо оборудовать сплошным защитным козырьком. Ширина прохода должна быть
не менее 1,2 м. В случае примыкания пешеходного прохода к проезжей части дороги
необходимо выполнить сплошное ограждение со стороны дороги высотой не менее 1,1
м.
Строительная площадка должна быть обеспечена
телефонной или радиосвязью и сторожевой охраной.
У дежурного должен быть список номеров телефонов
аварийных служб и ответственных лиц.
Расположение автомобильных и пешеходных дорог,
постоянных и временных зданий и сооружений на стройплощадке должно
соответствовать строительному генеральному плану.
Территория строительной площадки должна быть
спланирована и оборудована устройствами для отвода атмосферных и технических
вод с таким расчетом, чтобы исключить возможность их попадания в подземные
выработки и котлованы.
Места приемки поверхностных, а также
откачиваемых из подземных выработок вод, размещение очистных сооружений должны
быть определены проектом организации строительства (ПОС).
Направление движения автотранспортных средств на
территории строительной площадки, их скорость должны регулироваться дорожными
знаками.
Границы опасных зон следует ограждать и
обозначать предупредительными знаками и сигналами, хорошо видимыми как в
дневное, так и в ночное время.
На ограждении территории строительной площадки,
на видном месте, должен быть установлен информационный щит с указанием
наименования объекта, генподрядчика, заказчика, фамилий ответственных
производителей работ, номеров телефонов, сроков начала и окончания работ.
Проходы и проезды на территории стройплощадки
должны быть свободными, не загромождаться. Их следует очищать от грязи, снега,
льда и подавлять пыль.
Проходы для людей, проложенные по вязкой почве
должны покрываться сплошным настилом шириной не менее 1 м.
Проходы, расположенные на откосах с уклоном
более 20°, надлежит оборудовать трапами или лестницами с перилами высотой 1 м.
Применяемые на строительной площадке машины и
механизмы при работе не должны превышать предельно допустимых уровней шума.
Территория строительной площадки, участки работ,
рабочие места, проезды и проходы в темное время суток должны быть освещены в
соответствии с государственными стандартами и строительными нормами по
освещенности мест производства работ.
На ограждении, примыкающем к проезжей части
дороги или расположенном на ней, должно быть выполнено сигнальное освещение и
должны быть установлены предупредительные знаки.
Строительные машины должны быть установлены на
устойчивом выровненном основании с уклоном, не превышающем допустимого
техническим паспортом. От любых выступающих частей строительных машин должен
быть свободный проход шириной не менее 1 м.
Колодцы и шурфы на территории площадки должны
быть закрыты или огорожены, а траншеи и котлованы ограждены перинами высотой
1,1 м. В темное время суток на ограждения должны быть выставлены световые
сигналы.
В местах переходов через траншеи, трубопроводы,
транспортеры и т.п. должны быть устроены мостики шириной не менее 0,8 м с
перилами высотой
м и бортовыми досками высотой не менее 15 см.
6. Возведение устья ствола №1
Строительство устья начинается после возведения
замораживающей галереи кольцевых рассолопроводов, устройства гидроизоляции и
обратной засыпки наружных по отношению к центру ствола стен галереи и монтажа
ограждения ствола.
Маркшейдерская служба выполняет выноску,
разметку и закрепление в натуре высотной отметки и осей ствола.
Первоначально, в проектном сечении ствола на
буровой плите с увязкой со шпунтовым ограждением в железобетоне с
использованием инвентарной металлической опалубки из щитов 0,6x3,0 ЦНИИОМТП в распор
с вертикальными стенами галереи кольцевых рассолопроводов с устройством
деформационного шва и гидроизоляционного слоя до глубины 3,4 м (А.О. +170,600
м) выполняется временный оголовок устья ствола.
Далее производится демонтаж железобетонной
буровой плиты в проектном сечении ствола с уборкой строительного мусора и
разбитого железобетона из рабочей зоны в проходческой бадье БПМС-3.0 при помощи
автокрана КС-6476 или его аналога. Разгрузка бадьи осуществляется на
специальной временной эстакаде в автотранспорт. Строительный мусор и разбитый
железобетон вывозится автотранспортом на полигоны твердых бытовых отходов или
специально оборудованные площадки заказчиком.
Возведение устья ствола горным способом
начинается с глубины 3,8 м (А.О.+170,200).
Согласно геологическим и гидрогеологическим
данным по результатам бурения контрольно-стволовой скважины № 107г-1
четвертичные отложения до глубины 11,90 м (А.О.+160.330 м) представлены
практически безводными глинистыми образованиями с редкими прослоями песка.
Уровень подземных вод находится на глубине 19,01 м (А.О.+ 153,220). Эти
геологические данные дают основание приступить к возведению устья ствола до
начала осуществления процесса замораживания вмещающих водоносных пород.
Объемы работ по сооружению устья ствола
В объём работ по сооружению устья ствола входят:
возведение временного железобетонного оголовка
ствола в интервале отметок -3,4 м (А.О.+170,600) до +0,2 м (А.О.-Н 74,200);
разборка и демонтаж буровой железобетонной плиты
в проектном сечении ствола в отметках -3,4 м (А.О.+170,600) до -3,8 м (А.О.+ 1
70,200);
проходка с креплением временной крепью устья с
глубины 3,8 м (А.О.+ 170,200) до глубины 17.5 м (А.О.+156,500) с монтажом
секционных лестниц с дугами безопасности и переходными площадками временного
ходового отделения;
сооружение опорного венца в интервале глубин
17,5 м (А.О.+156,500) до м (А.О.+ 161,000);
монтаж временного инвентарного полка для
возведения постоянной железобетонной крепи с последующим демонтажем секций
лестниц временного ходового отделения и перегоном полка на другие монтажные
отметки;
возведение постоянной крепи в направлении снизу
вверх с глубины м (А.0.+ 161,000) до 3,8 м (А.О.+ 170,200) с устройством
сопряжений с калориферным и кабельными каналами.
Технологические процессы производственного цикла
сооружения устья ствола
Технологические процессы производственного цикла
сооружения устья ствола следующие:
Погрузочно-разгрузочные работы на поверхности и
в забое устья ствола с помощью автокрана КС-6476 грузоподъемностью 50 т или его
аналога.
Возведение временного железобетонного оголовка
ствола в интервале отметок -3,4 м (А.О.+170,600) до +0,2 м (А.О.+ 174,200).
Разборка и демонтаж буровой железобетонной плиты
в проектном сечении ствола в отметках -3,4 м (А.О.+170,600) до -3,8 м
(А.О.+170,200).
Разработка грунта и горных пород гидравлическим
экскаватором L520B в забое устья ствола с погрузкой горной массы в проходческую
бадью БПСМ-3.0 вместимостью 3 mj.
Доработка грунта и горных пород вручную и
отбойными молотками в забое устья ствола до проектных параметров с погрузкой
горной массы в проходческую бадью БПСМ-3.0 вручную.
Выдача разрыхленного грунта или горной породы из
забоя устья ствола бадьями при помощи автокрана КС-6476 грузоподъемностью 50 т
или его аналога.
Разгрузка груженой бадьи на временной эстакаде в
автосамосвалы.
Доставка бадьи в забой грузоподъемным краном с
установкой ее под загрузку.
.1 Возведение временной крепи устья
Монтаж секций временного ходового отделения для
спуска-подъема людей.
. Проветривание устья ствола, с глубины 10,0 м
(А.О.+164,000);
Устройство базового тюбингового кольца №1 на
глубине 17,5 м (A.O.+ I 56,500), (тюбинговое кольцо №3 чертежи 779/1 -П-4.3
1Д/20-07ПР/10- ГПР).
Устройство опорного венца устья в интервале
глубин 17,5 м (А.О +156,500) до 13,0 м (А.О.+ 161,000), 779/1-П-4.3
L1/20-07ПР/10-КЖ1.
Монтаж временного инвентарного полка в забое
устья ствола (отметка тюбингового кольца №2) для возведения постоянной
железобетонной крепи устья.
Демонтаж секции временного ходового отделения,
снятие крепления временного инвентарного полка в устье ствола, перемещение
полка на другую монтажную отметку при помощи автокрана КС-6476, раскрепление
полка в стволе для возведения очередной «заходки» постоянной железобетонной
крепи устья.
Электросварочные и газопламенные работы при выполнении
монтажных и демонтажных работ на поверхности и в устье ствола.
Возведение постоянной крепи устья в интервале
отметок -13,0 м (А.О.+ 161,000) до -3,8 м (А.О.+ 170,200) с устройством
сопряжений калориферного и кабельного каналов.
Устройство освещения, сигнализация и связи.
Описание технологических процессов
производственного цикла сооружения устья ствола
Погрузочно-разгрузочные работы на поверхности и
в забое устья ствола с помощью автокрана КС-6476 грузоподъемностью 50 т или его
аналога
Проходка и крепление технологического отхода
ствола до глубины м, включая устройство устья, будет осуществляться с
использованием автомобильного крана КС-6476 грузоподъемностью 50 т или его
аналога.
Технологическая схема сооружения устья ствола №1
приведена на рисунках 6.1 и 6.2. Технологическая схема размещения оборудования
на промплощадке во время строительства устья и технологического отхода ствола
№1 показана на рисунке 6.3.
Места установки крана, опасные и рабочие зоны,
места разгрузки и погрузки материалов, изделий и конструкций, схемы строповки
грузов, организация, в т.ч. расстановка технологического персонала, условные
сигналы при производстве работ, порядок и меры безопасности при выполнении
погрузо-разгрузочных, монтажно-демонтажных работ при возведении устья и
технологического отхода ствола определяются проектом организации строительства
и Инструкцией для работников строительной организации по безопасному ведению
технологических процессов при погрузочно-разгрузочных работах на поверхности и
в забое ствола с помощью автокрана КС-6476 грузоподъемностью 50 т или его
аналога.
При выполнении работ грузоподъемными кранами
должны выполняться требования промышленной безопасности, изложенные в
нормативных документах Госстроя России, Ростехнадзора и других министерств и
ведомств, в том числе:
Правила устройства и безопасной эксплуатации
грузоподъемных кранов (ПБ 10-382-00).
Правила устройства и безопасной эксплуатации
строительных подъемников (ПБ 10-518-02).
Правила устройства и безопасной эксплуатации
подъемников (вышек) (ПБ 10-61 1-03).
Инструкция по надзору за изготовлением, ремонтом
и монтажом подъемных сооружений (РД 10-08-92).
Типовые инструкции РД 10-34-93; РД 10-40-93; РД
10-74-94; РД 10-93-95; РД 10-103-95; РД 10-107-96.
Производственный персонал (крановщики, стропальщики,
проходчики), выполняющий погрузочно-разгрузочные, монтажные и демонтажные
работы должен быть обучен безопасным методам и приемам выполнения работ,
технологических операций, управления кранами и другими грузоподъемными
механизмами по специальным программам, согласованными с Ростехнадзором,
аттестован специальной комиссией предприятия с участием представителей
территориальных органов Ростехнадзора с составлением протокола и иметь
удостоверение по профессии на право выполнения определенного вида работ и
управления грузоподъемными кранами и механизмами определенных типов и
грузоподъемности.
Ежеквартально крановщики, стропальщики,
проходчики с правами стропальщиков должны проходить очередной инструктаж по
технике безопасности и охране труда по профессии на участке производства работ
под роспись в журнале инструктажей.
Постоянное устье ствола N 1 с временным
оголовком
Рисунок 6.1
Рис. 6.2. Проходка устьевой части ствола N1
Рис.6.3. Проходка технологического отхода стбола
N 1. План на отм. 174,000
Ежегодно крановщики должны проходить обучение по
специальным программам по безопасной организации и выполнению погрузо-
разгрузочных, монтажных и демонтажных работ с применением грузоподъемных кранов
и механизмов, по безопасной эксплуатации грузоподъемных кранов и механизмов при
учебно-курсовых комбинатах и сдавать соответствующие экзамены в комиссии
предприятия с участием представителей территориальных органов Ростехнодзора с
составлением протокола и внесением соответствующих отметок в удостоверение по
профессии.
Инженерно- технические работники предприятия,
которые отвечают за безопасную эксплуатацию грузоподъемных кранов и механизмов,
которые отвечают за безопасную организацию и ведение работ, связанных с
применением грузоподъемных кранов и механизмов должны раз в три года проходить
проверку знаний по безопасности и охране труда в комиссии предприятия под
председательством представителя территориального органа Ростехнадзора.
Внеочередные проверки знаний и инструктажи
должны проводиться при изменении места и характера работ, при переходе
работника на другое предприятие, после аварий и несчастных случаев на
производстве и при грубых нарушениях правил промышленной безопасности и охраны
труда.
Погрузочно-разгрузочные работы на поверхности и
в забое устья ствола с помощью автокрана КС-6476 грузоподъемностью 50 т или его
аналога включают в свой состав следующие технологические операции:
разгрузка и складирование на стройплощадке
элементов временной крепи (сегменты колец из швеллера, пачки анкеров, рулоны
дорожной сетки, трубы, арматура, доска обрезная и т.д.);
разгрузка и складирование на стройплощадке
элементов постоянной крепи - тюбингов, секций временного ходового отделения;
подача в забой устья ствола элементов временной,
постоянной крепи и секций ходового отделения. Спуск тюбингов в ствол к месту
монтажа производится с использованием специального приспособления - стропа с
фиксаторами (рис. 6.5);
подача в забой в бадье расходных материалов и
крепежных элементов временной и постоянной крепи, при необходимости бетонной
смеси;
доставка в забой малогабаритного гидравлического
экскаватора L520B и другого оборудования;
выдача из забоя экскаватора L520B и другого
оборудования, его разгрузка на стройплощадке;
подача в забой и установка под погрузку
проходческой бадьи;
выдача из забоя груженой бадьи и ее разгрузка на
временной эстакаде в автосамосвалы;
монтаж в забое временной кольцевой
(полигональной) крепи из швеллера;
монтаж в устье временного ходового отделения для
спуска-подъема людей;
монтаж тюбинговой крепи опорного венца;
монтаж в устье временного инвентарного полка для
возведения постоянной железобетонной крепи;
демонтаж и выдача из устья секций временного
ходового отделения;
перегон временного инвентарного полка в устье
ствола на другие монтажные отметки;
Во всех случаях, для безопасного выполнения
указанных технологических операций необходимо работать строго по разработанным
в Инструкции для работников строительной организации по безопасному ведению
технологических процессов при погрузочно-разгрузочных работах на поверхности и
в забое ствола с помощью автокрана КС-6476 грузоподъемностью 50 т или его
аналога условным сигналам, схемам строповки грузов. В работе применять
исправные и промаркированные стропа и грузозахватные приспособления и соблюдать
требования по технике безопасности и охране труда при производстве работ.
Для своевременной и правильной передачи команд
из забоя устья ствола машинисту крана при ведении погрузочно-разгрузочных,
монтажных и демонтажных работ, когда прямая видимость между машинистом
грузоподъемного крана и проходчиком отсутствует, в книге нарядов под роспись из
числа членов звена (бригады) назначается «сигналист» (рабочий с правами
стропальщика). При необходимости может быть назначено два «сигналиста», один из
которых назначается старшим под роспись в книге нарядов.
«Сигналист» должен находиться на «нулевой
площадке» устья ствола, видеть рабочее место в забое и находящихся там людей и
машиниста грузоподъемного крана.
«Сигналист» должен своевременно и правильно
дублировать подаваемые из забоя сигналы. Непонятный сигнал - СТОП!
«Сигналист» должен контролировать проход грузов
через «нулевую отметку» устья ствола, для исключения зацепов и зависаний
грузов.
Для исключения падения с высоты сигналист должен
быть застрахован монтажным поясом за элементы ограждения ствола на поверхности.
Место страховки определяется в Инструкции для работников строительной
организации по безопасному ведению технологических процессов при строительстве
стволов.
Во время подачи грузов в ствол или выдачи грузов
из забоя устья люди, находящиеся забое должны уйти в безопасное место или под
защиту предохранительного козырька. Данное условие безопасности определяется в
проекте организации строительства и Инструкции для работников строительной
организации по безопасному ведению технологических процессов при строительстве
стволов.
Схемы строповки грузов, таблицы условных
сигналов должны быть установлены на «нулевой площадке» устья ствола и на месте
погрузки и разгрузки грузов, а также находиться в кабине машиниста крана.
В кабине машиниста крана, кроме специальных
журналов, определенных правилами безопасности и инструкциями, должен находиться
экземпляр Инструкции для работников строительной организации по безопасному
ведению технологических процессов при выполнении погрузочно- разгрузочных
операций грузоподъемным краном КС-6476 или его аналога для конкретных условий
строительства.
С данной Инструкцией для работников строительной
организации по безопасному ведению технологических процессов при выполнении
погрузочно-разгрузочных операций грузоподъемным краном КС-6476 или его аналога
для конкретных условий строительства весь персонал участка производства работ
должен быть ознакомлен под роспись.
Возведение временного железобетонного оголовка
ствола в интервале отметок -3,4 м (А.О.+170,600) до +0,2 м (А.О.+174,200)
Данный технологический процесс состоит из
следующих технологических операций:
очистка рабочего места от строительного мусора;
работа с маркшейдером, проверка закрепления осей
ствола и высотных реперов, разбивка и закрепление осей в натуре;
устройство гидроизоляции внутренних стенок
замораживающих галерей по отношению к центру выработки;
устройство строительных лесов или подмостей для
ведения строительных работ по периметру устья на высоту, определенную ПНР;
подача необходимых материалов на рабочее место
при помощи автокрана для монтажа арматурного каркаса временного оголовка устья
ствола;
монтаж арматурного каркаса оголовка с
применением газопламенных и электросварочных работ и вручную;
устройство деформационного шва между внутренними
стенами замораживающей галереи и оголовком;
монтаж металлической инвентарной опалубки из
щитов 0,6x3,0
ЦНИИОМТП согласно ППР;
прием и укладка бетона за опалубку с
вибрированием бетонной смеси
глубинными вибраторами.
Доставка бетонной смеси к месту производства
работ осуществляется в автобетоносмесителях («миксерах»), далее по рештакам
самотечно бетонная смесь укладывается за опалубку.
Количество «заходок» при возведении крепи
временного оголовка определяется проектом организации работ.
Порядок, организация и мероприятия по
безопасному ведению работ подробно разрабатываются в Инструкции для работников
строительной организации по безопасному ведению технологических процессов на
каждый вид технологических операций.
Разборка и демонтаж буровой железобетонной плиты
в проектном сечении ствола в отметках 3,4 м (А.О.+ 170,600) до -3,8 м (А.О.+
17О,2О0)
Перед началом работ маркшейдером выполняется
разметка, вынос в натуру и закрепление осей ствола.
Демонтаж и разборка буровой железобетонной плиты
выполняется с применением малогабаритного гидравлического экскаватора L520B, па
стреле которого установлен комплектный манипулятор с гидромолотом НМ 170 или РВЗ10
для дробления бетона.
При необходимости разработку буровой плиты
производят вручную с помощью отбойных молотков МО-6, МО-8 или пневмоломов.
Обеспечение работ сжатым воздухом осуществляется от передвижных компрессорных
установок или стационарной компрессорной станции.
Резку арматурного каркаса осуществляют с
применением газопламенной аппаратуры согласно «Инструкция по производству
сварочных и газопламенных работ в подземных выработках и надшахтных зданиях»
книга 2 ПБ-06-1 ] 1-95.
Крупные демонтированные незащемленные элементы
буровой железобетонной плиты после определения веса допускается выдавать при
помощи автокрана КС-6476 или его аналога при условии, что в Инструкции для
работников строительной организации по безопасному ведению технологических процессов
при спуске в ствол и выдаче из ствола крупногабаритных и длинномерных
материалов разработана и утверждена схема строповки данного груза и определены
конкретные меры безопасности.
Отгрузка строительного мусора и разбитого
железобетона осуществляется из рабочей зоны в проходческой бадье БПМС-3.0 при
помощи автокрана КС-6476 или его аналога. Разгрузка бадьи осуществляется на
специальной временной эстакаде в автотранспорт. Строительный мусор и разбитый
железобетон вывозится автотранспортом заказчика на полигоны твердых бытовых
отходов или специально оборудованные площадки.
На рабочее место работники попадают по
инвентарным приставным лестницам длиной не более 6 м. Выход из забоя также
осуществляется по инвентарным лестницам.
Данные технологические операции должны
производить проходчики, крепильщики, горнорабочие, стропальщики,
газоэлектросварщики, машинист экскаватора L520B, машинист передвижной
компрессорной установки, машинист автокрана в соответствии с положениями
единого тарифноквалификационного справочника (ЕТКС). Рабочие должны быть
обучены безопасным методам и приемам выполнения работ, управления
оборудованием, иметь соответствующее удостоверение по профессии и
проинструктированы по вопросам охраны труда и технике безопасности под роспись
в журнале инструктажей на участке производства работ.
Порядок, организация и мероприятия по
безопасному ведению работ подробно разрабатываются в Инструкции для работников
строительной организации по безопасному ведению технологических процессов при
разборке и демонтаже буровой железобетонной плиты в проектном сечении ствола.
Разработка грунта и горных пород гидравлическим
экскаватором L520B в забое устья ствола с погрузкой горной массы в проходческую
бадью БПСМ-3.0 вместимостью 3 м3
Возведение устья ствола горным способом
начинается с глубины 3,8 м (А.О.+170,200). Технологическая схема сооружения
устья ствола №1 приведена на рисунках 6.1 и 6.2 технологическая схема
размещения оборудования на промплощадке во время строительства устья и
технологического отхода ствола №1 показана на рисунке 6.3.
Для разработки горной породы и загрузки
разрыхленной горной массы в проходческую бадью БПСМ-3.0 в забой устья опускают
при помощи автокрана КС-6476 или его аналога малогабаритный гидравлический
экскаватор L520B (рисунок 6.4) оснащенным комплексом навесного оборудования
включающего в себя ковш вместимостью 0,15 mj.
Кроме ковша в комплектацию L520B дополнительно
входят:
• буровой манипулятор с гидравлическим
перфоратором СОР 1532;
® манипулятор с гидромолотом НМ 170 или РВ310
для рыхления породы в забое и для дробления негабаритов.
Разработка и выемка грунтов или горных пород в
забое выполняется послойно на глубину 850 мм кратную шагу установки швеллерных
колец временной крепи.
В первую очередь в забое разрабатывается и
подготавливается участок под установку бадьи БПСМ-3.0 с устройством небольшого
зумпфа. Разработка грунтов и породы в забое ведется последовательно
определенными Паспортом разработки забоя участками.
Разработанная горная масса в объеме для погрузки
1-2 бадей временно складируется в свободной части забоя с обеспечением
безопасных зазоров. Далее после подачи установленного сигнала с рабочего места
в забой при помощи грузоподъемного крана подается проходческая бадья с
установкой ее на подготовленную площадку.
Дужка бадьи укладывается на предохранительные
кулачки корпуса бадьи в противоположную сторону от рабочей зоны погрузки, чтобы
не повредить прицепное устройство и грузовой канат подъема грузоподъемного
крана. Далее производится погрузка разработанной горной массы в бадью при помощи
экскаватора. Бадья должна не догружаться до краев на 100 мм, для исключения
просыпания горной массы при выдаче по стволу. Погрузка временно прекращается и
подается условный сигнал на приподъем бадьи над плоскостью забоя на высоту
300-500 мм. Далее подается сигнал «СТОП».
Экскаватор L520B
Бадья должна быть успокоена от раскачивания и
раскручивания и корпус бадьи очищен от кусков налипшей при погрузке горной
массы. После выполнения данной технологической операции подается условный
сигнал на подъем груза.
(одъем бадьи по стволу осуществляется со
скоростью определенной инструкцией по эксплуатации грузоподъемного крана и
паспортом разработки забоя и отгрузки горной массы в бадыо экскаватором L520B.
При подъеме - спуске бадьи по стволу все работы в забое должны быть прекращены
и рабочие, находящиеся в забое должны быть выведены за пределы опасной зоны под
укрытие предохранительного козырька. Данное условие безопасности определяется в
проекте организации строительства и в Паспорте разработки забоя и отгрузки
горной массы в бадью экскаватором L520B. Сигналист-стропальщик при подъеме -
спуске грузов в рабочей зоне контролирует положение в забое и прохождение
грузом отметки «нулевой отметки» для исключения зацепов и зависаний груза.
Далее после разгрузки бадьи на временной
эстакаде, бадья должна быть установлена на специальную площадку около
разгрузочной эстакады и очищена от налипших кусков горной массы.
После бадья подается в забой и цикл
технологического процесса повторяется. На определенном паспортом разработки
забоя и отгрузки горной массы в бадью экскаватором L520B этапе разработки забоя
необходимо выполнить перестановку экскаватора с верхнего уступа забоя на
разработанную нижнюю площадку плоскости забоя. Далее технологический цикл
повторяется.
Процесс разработки горной массы в забое и
погрузки ее в бадью осуществляется двумя проходчиками, один из которых с
правами машиниста экскаватора (звеньевой, старший по наряду) управляет
экскаватором, второй выполняет вспомогательные операции описанные выше. На
рабочее место трудящиеся и инженерно-технические работники попадают по
смонтированному в стволе ходовому отделению. Рабочее место должно иметь
постоянное освещение согласно требованиям санитарных норм и правил
безопасности.
Все работы в забое и на поверхности должны
выполняться по разработанным в Инструкции для работников строительной
организации по безопасному ведению технологического процесса и Паспорте
разработки забоя и отгрузки горной массы в бадью экскаватором L520B условным
сигналам. За подачу сигналов в забое в книге нарядов под роспись назначается
ответственный из числа членов звена (бригады).
Порядок, организация и мероприятия по
безопасному ведению работ подробно разрабатываются в Инструкции для работников
предприятия по безопасному ведению технологических процессов при разработке
грунта и горных пород малогабаритным гидравлическим экскаватором в забое ствола
с погрузкой горной массы в проходческую бадью, а также указываются в Паспорте
разработки забоя и отгрузки горной массы в бадью экскаватором L520B. С
настоящей Инструкцией для работников организации по безопасному ведению
технологических процессов при разработке грунта и горных пород малогабаритным
гидравлическим экскаватором в забое ствола с погрузкой горной массы в
проходческую бадью и Паспортом разработки забоя и отгрузки горной массы в бадью
экскаватором L520B работники участка производства работ должны быть ознакомлены
под роспись.
Доработка грунта и горных пород вручную и отбойными
молотками в забое устья ствола до проектных параметров с погрузкой горной массы
в проходческую бадью БПСМ-3.0 вручную.
Данная технологическая операция по
профилированию стенок горной выработки до проектных размеров выполняется в
случае временного выхода из строя малогабаритного гидравлического экскаватора
L520B, оснащенного манипулятором с гидромолотом НМ 170 или РВ310 для рыхления
породы в забое и для дробления негабаритов.
Обеспечение рабочих мест, в т.ч. ствола сжатым
воздухом осуществляется от стационарной компрессорной станции, находящейся на
площадке строительства.
В забой ствола опускаются в необходимом
количестве лопаты, напорный рукав (шланг) с воздухораспределителем и запорной
арматурой, отбойные молотки, напорные рукава (шланги) с арматурой для
подключения отбойных молотков, пики, концы которых заправлены под лопатку.
Опущенные по стволу рукава должны быть застрахованы от обрыва и падения
страховочными тросиками, двойной проволокой диаметром 3-4 мм снаружи за
металлоконструкции лестниц временного ходового отделения.
Работы по доработка грунта и горных пород в
забое для доведения его сечения до проектных параметров выполняется звеном
проходчиков, крепильщиков, горнорабочих в количестве 2-3 человек, один из
которых (звеньевой) назначается старшим под роспись в книге нарядов.
После профилирования стенок ствола до проектных
габаритов отбитая горная масса грузится в бадью лопатами.
При выполнении операций данного технологического
процесса проходчики, крепильщики, горнорабочие обязаны работать в средствах
индивидуальной защиты: защитных касках, спецодежде и обуви, противовибрационных
руковицах, антифонах или берушах, защитных очках или масках, противопыльных
респираторах.
Порядок, организация и мероприятия по
безопасному ведению работ подробно разрабатываются в Инструкции для работников
строительной организации по безопасному ведению технологических процессов по
доработке грунта и горных пород вручную и отбойными молотками в забое ствола до
проектных параметров с погрузкой горной массы в проходческую бадью вручную.
Выдача разрыхленного грунта или горной породы из
забоя устья ствола бадьями при помощи автокрана КС-6476 грузоподъемностью 50 т
или его аналога
Разгрузка груженой бадьи на временной эстакаде в
автосамосвалы
Доставка бадьи в забой грузоподъемным краном с
установкой ее под загрузку
Операции технологических процессов с
мероприятиями по их безопасной организации и выполнению по пунктам 6.3.6,
6.3.7, 6.3.8 подробно рассмотрены в пунктах 6.3.1 и 6.3.4 настоящего
технологического регламента.
Возведение временной крепи устья
После выполнения технологического процесса по
разработке грунтов, пород и отгрузки разрыхленной горной массы из забоя
необходимо выполнить возведение временной предохранительной крепи на участке
обнажения стенок горной выработки согласно проектной документации,
утвержденному паспорту крепления конкретного участка ствола и Инструкции для
работников строительной организации по безопасному ведению технологических
процессов при возведение временной крепи ствола.
Конструкция временной предохранительной крепи на
участке проходки устья ствола следующая: ранее установленная с поверхности
шпунтовая крепь из металлических труб 219x9 мм, забитых с шагом 750 мм по
окружности диаметром 9,5 м на глубину 21,4 м вокруг проектного сечения ствола в
комбинации с временной предохранительной крепью, выполненной полигональными
кольцами из швеллера №18 по ограждению из труб 0219x9 мм, с затяжкой
межтрубного и межкольцевого пространства металлической дорожной сеткой Р-45-3.0
и набрызг-бетон по сетке толщиной 50 мм. Шаг установки швеллерных колец 850 мм.
Крепление швеллерных колец осуществляется посредством электросварки к трубам
шпунтового ограждения.
Технологический процесс возведения временной
крепи на участке устья ствола состоит из следующих технологических операций:
подготовка на поверхности на оборудованной
площадке комплектов временной крепи для спуска в забой;
выдача из забоя оборудования и материалов не
задействованных в процессе возведения временной крепи;
доставка элементов временной крепи в забой при
помощи грузоподъемного крана;
раскладка по проектным размерам, по маркировкам
на почве забоя сегментов швеллеров по периметру сечения ствола;
поэлементная подвеска сегментов полигонального
кольца по трубам 0219x9 мм на специальные временные монтажные крючья
(металлический круг 020 мм - 16 шт.), которые закреплены за верхнее ранее
установленное кольцо временной крепи;
сборка полигонального швеллерного кольца в
единый элемент;
центровка монтируемого швеллерного кольца
относительно осей ствола и раскрепление кольца в стволе;
капитальное крепление кольца к трубам шпунтового
ограждения при помощи электросварки (сварка ручная дуговая выполняется по ГОСТ
14098-91 и ГОСТ 5264-80 в соответствии с требованиями «Инструкция по
производству сварочных и газопламенных работ в подземных выработках и
надшахтных зданиях» книга 2 ПБ-06-1 11-95);
монтаж дорожной сетки для затяжки междутрубного
и между кольцевого пространства с креплением ее на швеллерных кольцах при
помощи монтажной проволоки ФЗ-4 мм согласно утвержденного паспорта крепления;
подготовка торкрет-оборудования (Олива-252, СБ-67
и т.п.) и необходимых материалов крепления к работе;
нанесение торкрет-бетона толщиной 50 мм по сетке
на стенки ствола;
уборка рабочего места и подготовка забоя для
выполнения следующего производственного процесса.
На участках ствола, закрепленных временной
крепью согласно п.5.9.7 ПБ 03-428-02 должны быть установлены приборы для
контроля за температурой замороженных грунтов и пород.
Работы по возведению временной крепи выполняется
звеном проходчиков, крепильщиков, горнорабочих в количестве 2-4 человек в
зависимости от вида и характера выполняемой работы, один из которых (звеньевой)
назначается старшим под роспись в книге нарядов.
Электросварочные и газопламенные работы в забое
выполняет аттестованный электрогазосварщик. Для контроля за пропуском грузов
через «нулевую отметку», для дублирования и передачи условных сигналов
машинисту грузоподъемного крана, машинисту передвижной компрессорной установки,
оператору торкрет-оборудования на поверхности, на «нулевой отметке» из числа
рабочих бригады (звена) должен назначаться «сигналист» с правами стропальщика
под роспись в книге нарядов.
При выполнении операций данного технологического
процесса проходчики, крепильщики, горнорабочие, электрогазосварщики, операторы
передвижных компрессорных установок, операторы торкрет-оборудования,
стропальщики обязаны работать в средствах индивидуальной защиты: защитных
касках, спецодежде и обуви, прорезиненных руковицах, берушах, антифонах,
защитных очках или масках, противопыльных респираторах.
Порядок, организация и мероприятия по
безопасному ведению работ подробно разрабатываются в Инструкции для работников
строительной организации по безопасному ведению технологических процессов при
возведении временной крепи ствола.
Допустимое отставание швеллерных колец, сетки
Р-45-3.0 и торкрет-бетона временной крепи от забоя на участке строительства
устья должно определяться паспортом крепления горной выработки, составленным на
участке производства работ и утвержденным в установленном порядке.
Данное положение должно быть отражено в
Инструкции для работников строительной организации по безопасному ведению
технологических процессов при возведении временной крепи ствола для конкретного
участка проходки ствола.
Монтаж секций временного ходового отделения для
спуска-подъема людей
Данная технологическая операция выполняется
когда отставание временного ходового отделения от плоскости забоя составит 2,55
м (после оформления третьей «заходки» при разработке забоя, после монтажа двух
швеллерных колец, навески сетки-затяжки и выполнения торкретирования стенок
ствола по сетке - при отходе (отставании) почвы забоя от временной крепи на
расстояние 0,85 м).
Данный технологический процесс включает в себя
выполнение следующих операций:
подготовка на поверхности на оборудованной
площадке секций временного ходового отделения для спуска в ствол;
доставка секций временного ходового отделения в
забой при помощи грузоподъемного крана;
подготовка места в стволе для закрепления секций
ходового отделения при монтаже;
монтаж очередной секции.
Монтаж и крепление секции ходового отделения в
стволе выполняет звено из 4 рабочих вручную (вес секции временного ходового
отделения не превышает 120 кг) или 2 рабочих при помощи ручной цепной тали
соответствующей грузоподъемности или монтажной лебедки ШВА-1800 (2000).
Временная подвеска очередной секции осуществляется при помощи монтажной
проволоки ФЗ-4 мм за ранее смонтированную секцию, потом новая секция крепится
при помощи электросварки на ранее установленные швеллерные кольца временной
крепи.
Первоначально один рабочий с монтажной
проволокой поднимается в ходовое отделение, а трое рабочих вручную подают новую
секцию к месту монтажа. Затем рабочий находящийся в ходовом отделении выполняет
подвеску очередной секции за несущие элементы уже установленной секции при
помощи монтажной проволоки не менее чем в двух местах. Далее убедившись в
надежности подвески, электрогазосварщик посредством ручной электросварки
выполняет капитальное крепление новой секции ходового отделения за швеллерные
кольца временной крепи согласно проекту производства работ. Работы по креплению
очередной секции ходового отделения выполняются с инвентарных приставных
лестниц длиной не более 4 м.
При отставании временного ходового отделения от
забоя на расстояние от 1 м до 2,55 м попадание людей в забой и выход в ходовое
отделение осуществляется по инвентарной приставной лестнице.
В вертикальных выработках лестницы должны быть
установлены с уклоном не более 80°. Над устьем выработки и над каждым полком в выработке
лестницы должны выступать на 1 м, или же над отверстием полка в крепь выработки
должны быть прочно заделаны металлические скобы, внутренняя сторона скоб должна
отстоять от крепи не менее 0,04 м, расстояние между скобами не должно превышать
0,4 м, а ширина скобы должна быть не менее 0,4 м.
Установка лестниц в целях обеспечения
возможности свободного передвижения спасательных команд в респираторах должна
удовлетворять следующим условиям:
а) свободные размеры лазов без учета
площади, занятой лестницей, должны быть по длине лестницы не менее 0,7 м, а по
ширине - не менее 6 м;
б) расстояние от основания лестницы до
крепи выработки - не менее 0,6 м;
в) расстояние между полками - не более 8 м;
г) лестницы должны быть прочными,
устойчиво закреплены и расположены так, чтобы они не находились над отверстиями
в полках.
Ширина лестницы должна быть не менее 0,4 м,
расстояние между ступеньками - не более 0,4 м, а расстояние между тетивами
лестницы - не менее 0,28 м. Отверстие над первой лестницей должно закрываться
лядой.
Лестницы и полки должны содержаться в исправном
состоянии и очищаться от грязи и льда.
Порядок, организация и мероприятия по
безопасному ведению работ подробно разрабатываются в Инструкции для работников
строительной организации по безопасному ведению технологических процессов при
монтаже металлоконструкций временного ходового отделения в стволе.
.3Л 1 Проветривание устья и технологического
отхода ствола с глубины 10,0 м (А.0.+ 164,000) до глубины 40,02 м
(А.0.+133,980)
Проветривание забоя устья ствола до глубины 10,0
м осуществляется естественным способом.
Когда забой достиг глубины на отметке -10,0 м
(А.О.+ 164,000) необходимо обеспечить принудительное проветривание забоя. В
этом случае может быть временно использован проходческий вентилятор местного
проветривания ВМЭ-6 с глушителем шума, установленный на поверхности на
расстоянии не ближе 15 м от стенок устья ствола на отдельной оборудованной
площадке. Режим работы вентилятора круглосуточный непрерывный. Способ
проветривания забоя нагнетательный.
Окончательно тип вентилятора на дальнейшую
проходку должен быть выбран в проектной документации согласно произведенным
расчётам.
Организация проветривания и количество воздуха,
необходимого для проветривания отдельных выработок и шахты в целом, должны определяться
для каждого месторождения по специальным методикам, согласованным с
Госгортехнадзором России или, по его разрешению, с территориальными органами.
Расчет необходимого количества воздуха для проветривания горной выработки и ее
забоя, организация проветривания с указанием схемы проветривания и типа
вентилятора, дополнительные меры безопасности должны быть выполнены в проектной
документации, проекте организации работ и паспорте на проветривание горной
выработки, утвержденных в установленном порядке.
Расход воздуха при дальнейшей проходке ствола
буровзрывным способом ниже отметки - 40,02 м следует определять по
метановыделению, необходимому разжижению ядовитых газов после взрывных работ,
наибольшему числу работающих в стволе людей и минимально допустимой скорости
движения воздуха. Из приведенных выше факторов определяющим количество воздуха
подаваемого в ствол, является фактор по ядовитым газам после взрывных работ.
Расчет потребного количества воздуха для
проветривания забоя необходимо выполнить согласно «Временной инструкции по
проектированию вентиляции при проходке и углубке стволов» разработанной
институтом ВНИИОМШС», согласованной Госгортехнадзором России и «Временному
технологическому регламенту по организации проветривания рудника Усольского
калийного комбината на Палашерском и Балахонцевском участках ВКМКС»,
разработанному ГОУ ВПО «Пермский государственный технический университет»
(ПГТУ) и согласованному Ростехнадзором.
Согласно проведенным предварительным расчетам
необходимая потребность в воздухе для проветривания ствола №1 на полную
проектную глубину с учетом коэффициента утечек составит Q3.N.ma\“19,9M3/c. Для
обеспечения требуемого воздухообмена может быть принята вентиляторная установка
из одного вентилятора ВЦП-16М (Q= 20-46 м7с, Р- 200-920 даПа) в комплекте с
реверсирующим устройством заводского изготовления.
Здание вентилятора должно находиться не ближе 15
м от строящегося ствола. Режим работы вентиляторной установки должен быть
круглосуточный непрерывный. Способ проветривания ствола - нагнетательный. Для
сокращения времени проветривании забоя после производства взрывных работ
следует предусмотреть устройство нагнетательной схемы вентиляции с возможностью
реверсирования воздушного потока. Реверсивное устройство вентилятора ВЦП-16М
представляет собой систему обводных каналов - металлических коробов вокруг
вентилятора, через которые струя воздушного потока по вентиляционному
трубопроводу направляется в забой или из забоя ствола в зависимости от режима
работы вентилятора. Регулирование направление движения воздушной струи
осуществляется посредством запорных заслонок, которые в реверсивном режиме
перекрывают сечение вентиляционного става на выходе (диффузоре) вентилятора,
направляя весь воздушный поток в атмосферу мимо стволового вентиляционного трубопровода,
а также одновременно открывают обводной канал конфузора вентилятора (на
«всасе») и закрывают забор воздуха из атмосферы, Реверсивное устройство должно
быть изготовлено в соответствии с инструкцией по эксплуатации вентилятора
ВЦП-16М и рабочей документацией завода-изготовителя в заводских условиях и
поставляться заказчику в комплекте с вентилятором.
При работе вентилятора по всасывающей схеме в
реверсивном режиме воздуховод должен быть выполнен из эластичного
гофрированного рукава 0800-1200 мм секциями по 6 м. Подвеска вентиляционных
рукавов выполняется на тюбинговой крепи при помощи специальных хомутов.
Конкретно проветривание забоя при строительстве
устья до глубины м и технологического отхода до глубины 40,02 м, в связи с тем,
что проходка данного участка ствола будет осуществляться без применения БВР, с
использованием гидравлического экскаватора L520B, может осуществляться по
временной нагнетательной схеме проходческим вентилятором ВМЭ-6 с подачей
свежего воздуха в забой по прорезиненным вентиляционным рукавам 0800 мм длиной
секций 6-10 м. Режим работы вентилятора ВМЭ-6 непрерывный круглосуточный.
Для обеспечения требуемых параметров воздуха
поступающего в ствол в холодное время года, предусмотрен подогрев воздуха.
Калориферная установка принята из расчета обеспечения подогрева воздуха,
поступающего в ствол на уровне нулевой отметки, до температуры не ниже +2°С.
Максимальная мощность калориферов NK
рассчитывается по формуле:
= 1 -276.V0,„ x{lK= l,276,v21.*[2-(-45)] =
1206кВт
где: Q3.n.=21 мЗ/с - максимальный расход
воздуха;= +2°С - температура воздуха подаваемого для проветривания; tH= -45°С -
расчетная температура наружного воздуха.
Исходя из этого, для подогрева, подаваемого в
ствол воздуха, приняты электрокалориферы типа СФО -160кВт, изготавливаемые по
ТУ 3442-010-12589972-00 заводом электронагревательного оборудования «ДЕЛСОТ» г.
Миасс, Челябинской области. Всего для обеспечения работы вентиляционных систем
предусматривается установить 8 указанных калориферов. Высота одного калорифера
1080 мм, ширина - 710 мм.
Предусматриваются устройства и аппаратура для
регулирования температуры, поступающего в ствол воздуха в пределах 2-5°С.
Система управления калориферной установкой
позволяет осуществлять контроль следующих параметров ее работы:
температуры наружного воздуха с ее регистрацией;
температуры воздуха после прохода калорифера;
температуры поступающего в ствол подогретого
воздуха с ее регистрацией; потерь давления на всасывающей и нагнетательной
стороне вентиляторной установки.
Учитывая то, что согласно данным геологических
отчетов и исследований на участке проходки ствола №1 до глубины 270 м (до
кровли соляной толщи) газодинамичесих явлений и выделения взрывоопасных и
ядовитых газов не выявлено, контроль за состояние рудничной атмосферы на участке
проходки устья и технологического отхода ствола должен осуществляться в обычном
порядке согласно ПБ-03-553-03.
Замеры рудничного воздуха на содержание в нем СО
и СО2, H:S, NO и NO2 и других невзрывоопасных газов производятся в каждую смену
при помощи сильфонных газоанализаторов типа АМ-5 в начале и в течении рабочей
смены на каждом рабочем месте горным надзором (горными мастерами), бригадирами
и звеньевыми. В стволе замеры воздуха производят в начале смены перед спуском
людей в забой на «нулевой отметке», на полке и в забое. И далее в течении
рабочей смены в забое и на полке. При строительстве устья и технологического
отхода ствола замеры шахтного воздуха выполняют на «нулевой отметке» и в забое.
При превышении предельно-допустимой концентрации ядовитых и вредных газов в
рабочей зоне люди должны быть выведены с рабочих мест на свежую струю воздуха,
должно быть организованно надлежащее проветривание рабочих мест. Ответственный
за выполнение данного мероприятия - лицо сменного технического надзора (горный
мастер на смене), бригадир, звеньевые. Данный порядок контроля состояния
рудничной атмосферы должен быть отражен в Инструкции для работников
строительной организации по безопасному ведению технологических процессов при
проветривании ствола, с ознакомлением персонала под роспись.
Все работники участка производства работ должны
быть обучены и уметь пользоваться переносными приборами замера и контроля
шахтного воздуха.
Устройство базового тюбингового кольца №1 в
стволе на глубине 17,5 м (А.О.+156,500)
После того, как забой устья ствола достиг
проектной глубины 17,5 м (А.О.-И 56,500) необходимо смонтировать в стволе
базовое тюбинговое кольцо № 1 (чертеж 779/1 -П-4.31.1 /20-07ПР/10-ГПР л.З).
Первоначально выполняется подготовка
(планировка) почвы забоя согласно маркшейдерским указаниям. Далее на
подготовленном основании устраивается бетонная плита толщиной 150 мм. Установка
базового кольца должна производиться согласно «Временной инструкции по
сооружению тюбинговой крепи», Министерство монтажных и специальных строительных
работ СССР, Главспецпромстрой, трест "Шахтспецстрой", г. Москва,
2008г.
При монтаже базовое кольцо должно быть
сориентировано относительно осей ствола с учетом проектного расположения
элементов армировки.
Базовое тюбинговое кольцо должно устанавливаться
с соблюдением следующих требований:
расстояние от центра ствола до центров болтовых
отверстий горизонтальных бортах или до базовых площадок не должно превышать ±5
мм;
тюбинговое кольцо должно быть ориентировано по
отношению к осям ствола согласно чертежам привязки его к расстрелам с точностью
±5 мм;
разность уровней самой высшей и самой низшей
точек тюбингового кольца не должна превышать 3 мм;
разность высоты смежных сегментов в радиальных
стыках тюбингового кольца не должна превышать ±0,2 мм;
высотная отметка положения тюбингового кольца не
должна превышать проектную отметку более ±20 мм.
Подача тюбинга в ствол к месту монтажа должна
осуществляться грузоподъемным краном с применением специального приспособления
- стропа с фиксаторами для спуска тюбингов (рисунок 6.5) согласно разработанным
в Инструкции для работников строительной организации по безопасному ведению
технологических процессов при спуске в ствол и выдаче из ствола
крупногабаритных и длинномерных материалов схемам строповки груза.
После окончания монтажа базового тюбингового
кольца оно должно быть отцентровано по маркшейдерским указаниям и дополнительно
раскреплено от смещения при бетонировании сталеполимерными или железобетонными
анкерами. Далее за кольцом устанавливается арматурный каркас и пространство
между породой и тюбингом заполняется бетоном. Бетон подается с поверхности в
ствол к месту укладки за установленное тюбинговое кольцо по гибким бетоноводам,
закрепленным на крепи ствола.
Порядок выполнения работ по монтажу тюбингового
кольца следующий:
Бетонная плита - основание устраивается в забое
в соответствии с маркшейдерскими указаниями.
Первый тюбинг устанавливается на бетонное
основание с предварительным ориентированием его борта относительно осей ствола
с учетом проектного расположения армировки и центрируется по радиусу при помощи
шаблона. Центрирование производят при правильной окружности тюбингового кольца
от центров 1-го и 6-го болтовых отверстий в горизонтальных бортах тюбингов или
от базовых площадок радиальных бортов тюбинговых колец до центрального отвеса.
Для этой цели в центре ствола устанавливается центральный отвес весом 75-80 кг,
погружаемый для неподвижности, в сосуд с вязкой жидкостью (отработанное масло с
нигролом).
Палец шаблона, находящийся на одном его конце,
вставляется в болтовое отверстие сегмента. Другой конец шаблона прикладывают
вырезом (меткой) к канату отвеса. При правильном центрировании сегмента вырез
(метка) шаблона, должен совпадать с канатом отвеса. Затем шаблон переставляют в
6-е отверстие горизонтального борта.
Строп с фиксаторами для спуска
тюбингов
J
|
Хонрп
Ж F S.J-J.W
|
t
|
4
|
Шгиинт
6>Л*60
|
t
|
J
|
UbOfa
4Y9J<ia SO
|
/
|
2
|
Болт
tfOifX)
|
1
|
t
|
Уг&от
аисАлаа
|
t
|
Оса
|
Нязйами*
|
|
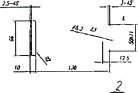
Рисунок 6.5
Второй устанавливаемый тюбинг на весу
прихватывают к первому оправками, забиваемыми в верхние и нижние болтовые
отверстия радиального борта.
Одновременно с присоединением второго тюбинга к
первому, а также всех последующих тюбингов к предыдущим, вводят между бортами
вертикальные свинцовые прокладки. При этом прокладка точно фиксируется по борту
первого тюбинга по низу, а верхний край прокладки на величину 30 мм. Загибается
под углом 90°.
После установки оправок вставляют монтажные
болты без гидроизоляционных шайб во второе и пятое отверстия тюбингов и
производят их сболчивание.
Присоединив второй тюбинг к первому, переходят к
дальнейшей установке и сболчиванию остальных тюбингов в порядке аналогичном при
монтаже первого и второго тюбингов. Каждый последующий тюбинг устанавливают
попеременно то с одной, то с другой стороны относительно ранее смонтированных
до полного замыкания кольца. Последний тюбинг заводят сверху и подтягивают к
месту конусными оправками.
Все оправки, забитые в крайние болтовые
отверстия, сохраняются на своих местах во всех тюбингах кольца до полной его
центровки по радиусам и проверки горизонтальности установки тюбингового кольца.
После выверки кольца приступают к окончательной
затяжке болтов. Затяжка болтов должна производиться одновременно и равномерно в
вертикальных швах, расположенных друг против друга на диаметрально
противоположных сторонах кольца, для этого следует последовательно выбивать
ранее установленные оправки, снимать монтажные болты и заменять их болтами с
установкой гидроизоляционных шайб.
В процессе сболчивания производят непрерывные
замеры по верхнему горизонтальному борту за сохранением центровки и
горизонтальности кольца. Горизонтальность верхней плоскости тюбингового кольца
проверяется нивелиром, установленным в центре ствола по миллиметровой
металлической линейке с точностью до 1 мм При разности отметок точек кольца
более ±3 мм кольцо выравнивается путем подклинки деревянными или металлическими
клиньями между нижним бортом тюбингового кольца и бетонным основанием Фиксацию
положения установленного базового кольца перед монтажом арматурного каркаса
между стенками крепи ствола и внешней стенкой тюбингового кольца и последующим
бетонированием необходимо выполнить железобетонными, или сталеполимерными
анкерами. При установке анкеров на уровне верхнего борта необходимо следить за
тем, чтобы кольцо не было сдвинуто. Раскрепленное кольцо еще раз проверяется по
радиусам и по горизонтальности.
Порядок, организация и мероприятия по
безопасному ведению работ подробно разрабатываются в Инструкции для работников
строительной организации по безопасному ведению технологических процессов при
монтаже тюбингового кольца в забое ствола.
Устройство опорного венца устья в интервале
глубин 17,5 м (А.О.+156,500) до 13,0 ,vi (А.О.+161,000)
После установки базового тюбингового кольца на
отметке -17,5 м (А.О.+ 156,500) необходимо выполнить сооружение опорного венца
устья ствола в интервале глубин 17,5 м (А.О.+156,500) до 13,0 м (А.О.+ 161,000)
по чертежам 779/1 -П-4.3 1.1 /20-07Г1Р/10-КЖ 1.
С отметки забоя -17,5 м во вмещающем ствол
горном массиве производиться разделка полости под опорный венец устья при
помощи экскаватора L520B. Разработанная горная масса перебрасывается в забой
ствола до уровня верхнего фланца базового тюбингового кольца. Затем в
разделанной полости производят установку арматурного каркаса. Далее по аналогии
с устройством базового тюбингового кольца монтируется тюбинговое кольцо №2
(чертеж 779/1 -П-4.31.1/20-07ПР/10-ГПРл.З). Бетонирование опорного венца
производится после установки в стволе тюбингового кольца №2 по схеме
аналогичной при бетонировании базового опорного кольца. Далее экскаватор L520B
выдается из забоя на поверхность и в стволе на тюбинговом кольце №2 при помощи
грузоподъемного крана монтируется временный инвентарный полок (рис.6.6) для
дальнейшего возведения постоянной крепи устья.
Затем с инвентарного полка производятся работы
по устройству арматурного каркаса и монтажу очередного тюбингового кольца №1
(чертеж 779/1 -П-4.31.1/20-07ПР/10-ГПРл.З). После центровки и крепления
тюбингового кольца №1 производится бетонирование «заходки» постоянной крепи.
Порядок, организация и мероприятия по
безопасному ведению работ подробно разрабатываются в Инструкции для работников
строительной организации по безопасному ведению технологических процессов при
возведении опорного венца устья ствола.
Монтаж временного инвентарного полка в забое
устья ствола (отметка уровня тюбингового кольца №2) для возведения постоянной
железобетонной крепи устья
После монтажа и бетонирования тюбингового кольца
№2 (чертеж 779/1-П-4.3 1.1/20-07ПР/10-ГПРл.З) для дальнейшего возведения
постоянной железобетонной крепи устья в направлении снизу вверх необходимо на
уровне тюбингового кольца №2 выполнить сборку и закрепление временного
инвентарного полка (рисунок 6.6). Конструкция инвентарного полка разработана
ЗАО «ОГСК-Шахтспецстройпроект». Расчет несущей способности полка должен быть
выполнен при разработке рабочей документации. Несущие элементы подвески и
раскрепления полка в стволе, металлоконструкции полка должны быть рассчитаны с
учетом нагрузки при расположении на полке трех тюбингов типа «7.0-40» и
нахождении на полке людей общим весом 1000 кг.
Рис. 6.6 Полок инвентарный
Сборка полка в стволе выполняется посекционно
согласно схемы монтажа. Предварительно в сечении ствола на верхний фланец
тюбингового кольца №2 укладываются через 1,2 м пять опорных металлических
прогонов (профиль опорных прогонов определяется расчетом в рабочей
документации).
На установленные временные опорные элементы
посекционно при помощи грузоподъемного крана укладываются сборочные элементы
инвентарного полка, далее секции полка соединяются между собой крепежными элементами.
Затем на полке монтируются несущие устройства
подвески и раскрепления полка в стволе в количестве четырех комплектов согласно
схемы монтажа полка. Проверяется их работоспособность.
Так как временный полок является одноэтажным, то
в соответствии с п.292 ПБ-03-553-03 его подвеска к прицепному устройству
грузового каната грузоподъемного крана должна быть выполнена в четырех точках.
На полке жестко за несущие металлоконструкции
каркаса монтируются на равном удалении друг от друга четыре такелажные скобы
подвески согласно схемы монтажа. Сама подвеска полка за прицепное устройство
каната грузоподъемного крана выполняется на специальном четырехветьевом стропе
согласно схемы строповки полка, разработанной в Инструкции для работников
строительной организации по безопасному ведению технологических процессов при
спуске в ствол и выдаче из ствола крупногабаритных и длинномерных материалов.
Угол между ветвями канатов специального четырехветьевого стропа при подвеске
полка должен быть не более 90 град. После строповки полка необходимо убедиться
в том, что полок не зацеплен за элементы крепи в стволе. Далее выполняется его
приподъем от уровня верхнего фланца тюбингового кольца №2 на высоту не более
500 мм для проверки его устойчивости и надежности подвески.
Подвесные проходческие полки принимаются в
эксплуатацию комиссией с участием представителей территориальных органов
Ростехнодзора (п.5.4.5 ПБ 03-428-02) с подписанием соответствующего акта.
Все приспособления и необходимое для выполнения
работы оборудование, находящиеся на полке должны быть надежно закреплены на
полке в местах установленных проектной и рабочей документацией.
При подъеме полка все рабочие, занятые на
монтаже должны находиться в ходовом отделении. Нахождение людей на инвентарном
полке при его подъеме - спуске (перегоне) по стволу запрещено. Выход рабочих на
полок разрешается по одному, только в монтажном поясе, застрахованным на
несущие элементы металлоконструкций ходового отделения.
После выхода на полок рабочий должен выполнить
перецепку монтажного пояса за страховочную скобу, установленную жестко в центре
полка на несущем элементе каркаса. После выполнения операции страховки на полке
первого рабочего разрешается выход на полок следующего рабочего при выполнении
операций в той же последовательности.
Убедившись в надежности подвески и устойчивости
полка в стволе рабочие (электрогазосварщик), выполняют демонтаж (срезку при
помощи керосинореза) центральных опорных прогонов, которые аккуратно опускаются
в забой. Крайние опорные прогоны также аккуратно опускаются в забой. Далее
рабочие переходят с полка в ходовое отделение в последовательности обратной при
выходе на полок и подают команду на медленный спуск полка ниже уровня верхнего
фланца тюбингового кольца №2 до уровня горизонтального ребра внутреннего кингстона
тюбингового кольца №2. Когда полок достиг монтажной отметки уровня
горизонтального ребра внутреннего кингстона тюбингового кольца №2 подается
команда «СТОП». Выход на полок рабочих осуществляется в последовательности
установленной настоящим технологическим регламентом. Далее выполняется подвеска
полка в стволе на горизонтальные ребра внутреннего кингстона тюбингового кольца
№2 при помощи несущих выдвижных устройств и его раскрепление в стволе. Далее
выполняется расстроповка полка.
Монтаж инвентарного полка в устье ствола
производит звено рабочих в количестве 3-4 человек, один из которых звеньевой
назначается старшим и ответственным за безопасное выполнение производственного
задание под роспись в книге нарядов. В составе звена при выполнении данного технологического
процесса должны находиться аттестованные электрогазосварщики и стропальщики.
Рабочие обязаны работать в средствах индивидуальной защиты органов слуха,
дыхания и зрения, спецодежде и обуви согласно требованиям правил безопасности,
санитарно-гигиенических норм и межотраслевых норм выдачи и использования
спецодежды. Рабочие должны знать схемы строповки грузов и условные сигналы,
разработанные в Инструкции для работников строительной организации по
безопасному ведению технологических процессов при спуске в ствол и выдаче из
ствола крупногабаритных и длинномерных материалов, Инструкции для работников
строительной организации по безопасному ведению технологических процессов при
монтаже-демонтаже инвентарного полка в стволе, а также в схеме монтажа-демонтажа
временного инвентарного полка.
Каждый рабочий должен иметь при себе
персональный промаркированный, испытанный, исправный монтажный пояс.
Для контроля за пропуском грузов через «нулевую
отметку», для дублирования и передачи условных сигналов машинисту
грузоподъемного крана на поверхности, на «нулевой отметке» из числа рабочих
бригады (звена) должен находиться «сигналист» с правами стропальщика,
назначенный для выполнения данного вида работ под роспись в книге нарядов.
Демонтаж секции временного ходового отделения,
снятие крепления временного инвентарного полка в устье ствола, перемещение
полка на другую монтажную отметку при помощи автокрана КС-6476, раскрепление
полка в стволе для возведения очередной «заходки» постоянной железобетонной
крепи устья Перед перегоном полка в стволе вверх на новую монтажную отметку для
возведения очередной «заходки» высотой 1,5 м постоянной железобетонной крепи
устья необходимо выполнить демонтаж одной секции временного ходового отделения.
Данная технологическая операция выполняется в последовательности обратной при
выполнении монтажа секции ходового отделения и с соблюдением мер безопасности,
которые описаны в п. 6.3.10 настоящего технологического регламента.
Перегон полка в стволе осуществляется согласно
п.п. 6.3.14 настоящего технологического регламента.
Подвеска и раскрепление полка в стволе на
участке железобетонной крепи устья выполняется при помощи специальных несущих
выдвижных устройств, установленных на полке, в оформленные лунки в
железобетонной крепи, которые заранее устраиваются на контакте «заходок»
постоянной крепи.
Порядок, организация и меры безопасности при
подвеске и раскреплении инвентарного полка в стволе на участке постоянной
железобетонной крепи устья описаны в п. 6.3.14 настоящего технологического
регламента. Электросварочные и газопламенные работы при выполнении монтажных и
демонтажных работ на поверхности и в устье ствола.
Производство электросварочных и газопламенных
работ в подземных горных выработках и надшахтных зданиях в зависимости от
газовой обстановки в рудничной атмосфере шахт и подземных рудников должно
выполняться согласно требованиям действующих правил безопасности ПБ-03-553-03 и
соответствующих инструкций по безопасному ведению данного вида работ, а также
инструкций по безопасной эксплуатации применяемого оборудования. Кроме того,
при выполнении электросварочных и газопламенных работ в стволе в интервале от
кровли карналлитовой зоны до подошвы сильвинитовой зоны (рабочая зона III
группы газовой опасности по горючим газам), необходимо выполнять условия,
изложенные в разделах 1-12 и «Специальных мероприятий...»
Возведение постоянной крепи устья в интервале
отметок -13,0 м (А.О.+161,000) до -3,8 м (А.О.+170,200) с устройством
сопряжений калориферного и кабельного каналов
После установки и бетонирования третьего
тюбингового кольца, дальнейшее железобетонное крепление устья ствола,
возводится в инвентарной металлической опалубке ЦНИИОМТП из щитов 0,6x3,0 м
«заходками» по 1,5 м.
Подача бетона в ствол к месту укладки
производится с поверхности по двум гибким бетоноводам, закреплённых на хомутах
и тросах за шейку оголовка устья ствола.
Перед бетонированием по верху каждой заходки
оформляются лунки и устанавливаются закладные детали для последующего крепления
временного полка в стволе. Работы по устройству арматурного каркаса, возведению
опалубки, бетонированию, демонтажу опалубки производятся с инвентарного полка
(рис.6.6). Арматурный каркас вяжется по мере возведения опалубки. По достижению
высоты заходки 1,5 м за опалубку укладывается послойно бетонная смесь.
Уложенная за опалубку бетонная смесь должна быть провибрирована погружными вибраторами.
Для крепления устья ствола предусмотрены
специальные бетонные смеси с подвижностью, обеспечивающей спуск по трубам и
укладку за тюбинги и опалубку, необходимой плотностью и прочностью в
конструкции.
Состав бетонных смесей и ориентировочный расход
материалов на 1 mj должен корректироваться лабораторией заказчика при каждой
новой партии щебня, песка и цемента с соотношением основных параметров В/Ц и
осадки конуса.
Класс прочности бетона контролируется
строительной лабораторией на БРУ при твердении образцов в нормальных
температурных условиях т=18-20°С.
Перечень скрытых работ, на которые должны быть
составлены акты: монтаж арматуры;
устройство бетонной подготовки с укладкой
подкладок под балки;
монтаж балок (заделка концов).
После приобретения бетоном распалубочной
прочности щитовая опалубка разбирается и краном выдаётся на поверхность для
очистки и смазки, а временный рабочий полок переставляется краном на
забетонированный участок крепи и закрепляется в специально устроенных лунках и
на, установленных ранее, закладных деталях для возведения следующей «заходки»
крепи.
Строительство сопряжений калориферного и
кабельного каналов с устьем ствола выполняется с инвентарного полка. На
участках сопряжений технологических каналов с устьем постоянная железобетонная
крепь не возводиться, а в проектном сечении каналов оформляется ниша, грудью
забоя которой является вертикальная плоскость, ограниченная временной крепью и
шпунтовым ограждением.
Порядок, организация и мероприятия по
безопасному ведению работ подробно разрабатываются в Инструкции для работников
строительной организации по безопасному ведению технологических процессов при
возведении постоянной железобетонной крепи устья ствола.
Устройство освещения, сигнализация и
связи
При строительстве устья ствола до глубины 17,5 м
(А.О.+ 156,500) и технологического отхода до глубины 40,02 м (А.0.+133,980)
освещение забоя выполняется с применением светильников типа «Проходка-2М» или
подобных с номинальным напряжением 36 В, которые подвешиваются на
металлоконструкциях «нулевой рамы» под маркшейдерским полком. С понижением
горных работ в забой на тросовой подвеске опустить дополнительный прожектор
«Проходка-2М». При проходке устья и технологического отхода допускается
применение светильников напряжением до 127 В с применением пусковой аппаратуры
типа АПШ-127 с защитой от утечки токов на землю (УАКИ).
По согласованию с территориальными органами
Ростехнадзора освещение может использоваться как аварийная сигнализация.
Каждый рабочий, находящийся в забое, должен
иметь исправный индивидуальный головной светильник, оборудованный приемниками
беспроводной связи типа «СУБР-1М», «СУБР-2М», «Земля-З М» или другими,
допущенными к применению Ростехнадзором.
Для подачи рабочих сигналов из забоя
использовать ударно-тросовую сигнализацию. Ударник оборудуется на «нулевой
отметке» на поверхности вблизи устья ствола, трос опускается в забой.
Для связи с «нулевой площадкой» попускается
использование монтажных раций типа «Motorolla», «Samsung» и т.д., допущенных к
применению Ростехнадзором.
При дальнейшей проходке ствола ниже отметки
-40,02 м с применением проходческого копра «Север-2» и всего комплекса
стволопроходческого оборудования, предусмотренного проектной и рабочей
документацией по устройству связи, сигнализации и освещения в стволе должны
быть выполнены следующие условия:
Каждая подъемная установка должна быть снабжена
устройством для подачи сигналов от стволового к рукоятчику и от рукоятчика к
машинисту, а также ремонтной сигнализацией, используемой только для осмотра и
ремонта ствола.
На людских и грузо-людских вертикальных и
наклонных (с углом наклона выработки более 50°) подъемных установках, кроме
рабочей и ремонтной сигнализации, должна предусматриваться резервная
сигнализация с обособленным питанием по отдельному кабелю. По функциональным
возможностям резервная сигнализация не должна отличаться от рабочей.
При наличии двух подъемных установок в одном
стволе, каждая из которых обеспечивает спуск и подъем людей со всех горизонтов,
резервная сигнализация может отсутствовать.
Схема аварийно-ремонтной сигнализации в стволе
должна предусматривать возможность подачи сигнала «Стоп» с любого горизонта из
бадьи рукоятчику (стволовому). Для этих целей в стволе предусматривается
устройство канатно-ударной сигнализации. Все работы в стволе должны
производиться по строго установленным сигналам. Таблицы условных сигналов
должны быть вывешены в копре на «нулевой» и «разгрузочной» площадках, в
помещении рукоятчика (стволового) и в здании подъемной машины в помещении
машиниста подъемной установки. Непонятный сигнал «Стоп»!
Управление проходческими лебедками должно
вестись строго по сигналам. Сигнализация для проходческих лебедок может быть
как механической, так и электрической с использованием звукового сигнала.
Таблица сигналов для проходческих лебедок должна быть вывешена у центрального
пульта управления и у лебедок.
Комплекс стволовой сигнализации каждой подъемной
машины должен иметь отдельную проводку и питаться от отдельного источника
энергии (трансформатора, аккумуляторной батареи и т.п.).
Запрещается передача сигналов из околоствольного
двора непосредственно машинисту, минуя рукоятчика. Между машинистом подъемной
машины и рукоятчиком, а также между рукоятчиком и стволовым должна быть
оборудована прямая телефонная связь. На вновь строящихся шахтах, кроме того,
необходимо устанавливать производственную громкоговорящую связь. При углубке
или проходке ствола сигналы машинисту должны подаваться проходчиками через
рукоятчика.
За правильную подачу сигналов из ствола на
«нулевую» площадку рукоятчику (стволовому) в книге нарядов под роспись
назначается проходчик из состава звена (бригады).
Каждое рабочее место должно находиться в
безопасном состоянии, обеспечиваться проветриванием, освещением, средствами
оповещения об аварии. Освещение забоя ствола выполняется с применением
светильников типа «Проходка-2М» или подобных с номинальным напряжением 36 В,
которые установлены на нижнем этаже подвесного проходческого полка.
Для оповещения лиц, занятых на подземных горных
работах, кроме телефонной связи должна быть оборудована специальная аварийная
беспроводная сигнализация аварийного оповещения. В отдельных случаях, по
согласованию с Госгортехнадзором России, могут применяться громкоговорящая и
световая сигнализации.
. Проходка и крепление
технологического отхода ствола №1
строительство ствол проходка горный
Разработка Породы в забое при проходке
технологического отхода ствола будет производиться с глубины 17,5 м до 40,02 м
с применением малогабаритного гидравлического экскаватора Г520В.
Отгрузка разрыхленной породы из забоя
производится экскаватором Г520В в проходческую бадью БПСМ-3.0.
Спуск-подъем материалов, временного инвентарного
полка, оборудования по стволу, выдача разработанной горной массы в бадье
БПСМ-3.0 на поверхность с разгрузкой бадьи на временной эстакаде в
автотранспорт, монтаж - демонтаж временного инвентарного полка в стволе,
осуществляются по аналогии со строительством устья автомобильным краном КС-6476
грузоподъемностью 50 т или его аналога.
Бетонирование при возведении постоянной крепи
выполняется так же по технологии, примененной при строительстве устья ствола.
До начала работ по сооружению технологического
отхода ствола на глубину 40,02 м необходимо с отметки -3,8 м (А.О.+ 170,200) в
обратной последовательности в направлении сверху вниз поэтапно (посекционно)
выполнить монтаж секций временного ходового отделения с подвеской их на участке
железобетонной крепи на анкерную крепь или на ранее смонтированные закладные
детали, а на участке с тюбинговой крепью выполнить подвеску и крепление секций
по установленным закладным деталям при помощи ручной электросварки. Работы
производятся со временного инвентарного полка, который с шагом 1,5 м при помощи
грузоподъемного крана перемещается на ниже расположенные монтажные отметки,
подвешивается и раскрепляется в железобетонной крепи в ранее оформленные лунки,
а на участке тюбинговой колонны на горизонтальные ребра внутренних кингстонов
тюбингов.
Когда полок достиг отметки забоя устья ствола
его опускают на подготовленную спланированную почву забоя. Далее полок расстроповывают
и поэлементно согласно схемы демонтажа и Инструкции для работников строительной
организации по безопасному ведению технологических процессов при
монтаже-демонтаже инвентарного полка и Инструкции для работников строительной
организации по безопасному ведению технологических процессов при спуске в ствол
и выдаче из ствола крупногабаритных и длинномерных материалов разбирают и
выдают на поверхность при помощи грузоподъемного крана. На поверхности полок
складируют на отдельную площадку, проводят ревизию и ремонт для дальнейшей
эксплуатации.
Из забоя ствола выдают ненужный материал.
Выполняют освещение забоя. Настраивают вентиляцию, ударно-тросовую
сигнализацию, при необходимости наращивают ходовое отделение. Затем в забой
опускают грузоподъемным краном малогабаритный гидравлический экскаватор L520B и
выполняют зачистку забоя до проектной отметки -17,5 м (до целика) от ранее
разработанной горной массы при устройстве опорного венца устья с погрузкой
породы в бадьи и выдачей бадей на поверхность, с дальнейшей их разгрузкой на
временной эстакаде в автотранспорт.
Операции вышеуказанных технологических процессов
подробно рассмотрены в разделе 6.3 настоящего технологического регламента.
Объёмы работ по сооружению технологического
отхода ствола
В объём работ по сооружению технологического
отхода ствола входят:
проходка ствола с разработкой породы в забое и
погрузкой ее в проходческую бадью БПСМ-3.0 экскаватором L520B на участке
технологического отхода ствола с временным крепление стенок выработки в
интервале глубин 17,5 м (А.О.+156,500) до 40,02 м (А.О.+ 133,980);
монтаж секций (длиной 1,5 м) временного ходового
отделения вслед за проходкой и временным креплением для спуска-подъема людей;
устройство базового тюбингового кольца №2 на
глубине 40,02 м (А.О.+133,980) (тюбинговое кольцо №18 графические материалы
779/1-П-4.31Л/20-07ПР/10-ГПР л. 1,2) по аналогии с устройством базового
тюбингового кольца №1 при сооружении устья ствола;
монтаж временного инвентарного полка в забое
технологического отхода ствола (отметка уровня тюбингового кольца №18) для
возведения постоянной тюбинговой крепи технологического отхода ствола;
демонтаж секции временного ходового отделения,
снятие крепления временного инвентарного полка в стволе, перемещение его вверх
по стволу на другую монтажную отметку при помощи автокрана КС-6476 или его
аналога, раскрепление полка в стволе для возведения очередного тюбингового
кольца постоянной крепи ствола на участке технологического отхода;
возведение постоянной крепи технологического
отхода ствола с инвентарного полка в направлении снизу вверх с отметки -40.02 м
до отметки -17,5 м (А.О.+156,500) с устройством деформационного шва в стволе
между тюбинговыми кольцами №4 и №3;
демонтаж секций временного ходового отделения на
участке устья ствола с перегоном инвентарного полка на отметку ± 0,000 м
ствола;
выдача инвентарного полка из ствола на
поверхность и его разборка.
Технологические процессы производственного цикла
сооружения технологического отхода ствола
Технологические процессы производственного цикла
сооружения технологического отхода ствола следующие:
Погрузочно-разгрузочные работы на поверхности и
в забое ствола с помощью автокрана КС-6476 грузоподъемностью 50 т или его
аналога.
Разработка грунта и горных пород гидравлическим
экскаватором L520B в забое ствола с погрузкой горной массы в проходческую бадью
БПСМ-3.0 вместимостью 3 м3.
Доработка грунта и горных пород отбойными
молотками в забое ствола до проектных параметров с погрузкой горной массы в
проходческую бадью БГ1СМ-3.0 вручную.
Выдача разрыхленного грунта или отбитой горной
породы из забоя ствола бадьями при помощи автокрана КС-6476 грузоподъемностью
50 т или его аналога.
Разгрузка груженой бадьи на временной эстакаде в
автосамосвалы.
Доставка бадьи в забой грузоподъемным краном с
установкой ее под загрузку.
Возведение временной крепи технологического
отхода ствола.
Монтаж секций ходового отделения для
спуска-подъема людей.
Проветривание технологического отхода ствола.
Устройство базового тюбингового кольца №2 на
глубине 40,02 м (А.О.+ 133,980), (тюбинговое кольцо №18 графические материалы
779/1-П-4.3 I. I /20-07ПР/10-ГПР л. 1,2).
Электросварочные и газопламенные работы при
выполнении монтажных и демонтажных работ на поверхности и в стволе на участке
технологического отхода.
Монтаж временного инвентарного полка в забое
технологического отхода ствола (отметка уровня тюбингового кольца №18) для
возведения постоянной тюбинговой крепи технологического отхода ствола.
Демонтаж секции временного ходового отделения,
снятие крепления временного инвентарного полка в стволе, перемещение его на
другую монтажную отметку при помощи автокрана КС-6476 или его аналога,
раскрепление полка в стволе для возведения очередного тюбингового кольца
постоянной крепи ствола на участке технологического отхода.
Возведение постоянной крепи технологического
отхода ствола.
Устройство освещения, сигнализации и связи.
Описание технологических процессов
производственного цикла возведения технологического отхода ствола
Технологическая схема сооружения
технологического отхода ствола показана на рисунке 7.1.
Операции технологических процессов при
строительстве технологического отхода ствола, описанные в разделе 7.2, кроме
процесса бурения шпуров в стенках ствола для установки анкеров временной
предохранительной крепи, аналогичны операциям технологических процессов при
сооружении устья и подробно рассмотрены в разделе 6.3 настоящего
технологического регламента.
Проходка технологического отхода ствола N 1
Возведение временной крепи
технологического отхода ствола
Конструкция временной предохранительной крепи на
участке технологического отхода ствола при его проходке по замороженным породам
следующая; сталеполимерные анкера типа СПА диаметром 24 мм, длиной 1600 мм с
затяжкой из металлической сетки Р-45-3.0 и набрыз г-бетон по сетке толщиной 50
мм. Сетка установки анкеров в стенки ствола, допустимое отставание анкерной
крепи, сетки и торкрет-бетона от забоя должно определяться паспортом крепления
горной выработки, составленным на участке производства работ и утвержденным в
установленном порядке. Временная крепь должна возводиться после каждого цикла
проведения буровзрывных работ и частичной уборки из забоя отбитой горной массы.
Бурение шпуров под установку анкеров производят
вручную с применением перфораторов типа ПП-63 на пневмоподдержках типа (П-0.8,
П-1.1, П-1.3).
В пробуренные шпуры устанавливаются
сталеполимерные анкера. После установки анкеров на стенки ствола навешивается
сетка, которая закрепляется на анкерах посредством специальных опорных
металлических пластин. Для надежной связи ранее установленной сетки временной
крепи и новой должен быть выполнен нахлест сеток друг на друга. Длина нахлеста
должна быть не менее 150 мм. Кроме того, необходимо выполнить надежное
сцепление концов сеток при помощи монтажной проволоки, применяемой при вязке
арматуры железобетона. Далее по установленной, связанной и подтянутой сетке
наносится торкрет-бетон. При торкретировании применяется оборудование типа
Олива-252, СБ-67 или подобное на применение которого имеется разрешение
Ростехнадзора, сертификат соответствия применяемого оборудования требованиям
промышленной безопасности, санитарно- гигиенический сертификат соответствия
требованиям санитарных норм Российской Федерации.
На участках ствола, закрепленных временной крепью
согласно п.5.9.7 ПБ 03-428-02 должны быть установлены приборы для контроля за
температурой замороженных грунтов и пород.
Работы по креплению производит звено проходчиков
из двух- трех человек в зависимости от вида, характера и объема выполняемых
работ. Один из которых звеньевой (старший по наряду) с правами крепильщика.
Второй проходчик с правами крепильщика и стропальщика выполняет все
вспомогательные операции. Торкрет-оборудование, как правило, находиться на
поверхности, около оголовка устья ствола. Торкрет-установку обслуживает
проходчик, крепильщик, горнорабочий с правами оператора или машиниста данного
оборудования. Связь между забоем и «нулевой» площадкой осуществляется строго по
установленным сигналам.
Персонал, выполняющий работы по креплению выработки
должен работать на исправном оборудовании с обязательным применением средств
индивидуальной защиты органов слуха, дыхания, зрения и в специальной одежде и
обуви.
Порядок, организация и мероприятия по
безопасному ведению работ подробно разрабатываются в Инструкции для работников
строительной организации по безопасному ведению технологических процессов при
возведении временной крепи в стволе.
Бурение шпуров для установки анкеров временной
предохранительной крепи
Бурение шпуров в стенках ствола для установки
временной анкерной крепи выполняется ручными перфораторами типа 1ТП-63С,
Г1П-63В на пневмоподдержках типа П-0.8, П-1.1, П-1.3.
Порядок работы при бурении шпуров следующий:
а) бурение шпуров в стенках выработки
производить в соответствии с утвержденным в установленном порядке паспортом
крепления горной выработки, с которым бурильщик (проходчик) должен быть
ознакомлен под роспись;
б) убедившись в безопасном состоянии
рабочего места, бурильщик (проходчик) должен установить перфоратор с
пневмоподдержкой в забое;
в) наполнить автомасленку маслом марки
индустриальное И-30 или И-45 (ГОСТ 1707-51), расход которого в смену составляет
350 г;
г) продуть воздуховод и, прежде чем
присоединить его к перфоратору, залить небольшое количество (10-20 г) масла в
воздушный рукав для начальной смазки перфоратора;
д) вставить в перфоратор бур и установить
перфоратор в требуемое положение, обратив внимание при этом на прямолинейность
бура, состояние хвостовика и буровой коронки. Твердость хвостовика штанги
должна быть HRC 48...52. Не допускается применение бура, имеющего на хвостовике
смещение по оси отверстия для водяной трубки, во избежание ее срезания. Бурение
без буродержателя не допускается. Забуривание производить при малом усилии
подачи превмоподдержки, притуплённой коронкой на глубину 30-40 мм. Для
исключения соскальзывания пневмоподдержка должна быть установлена на ровную
спланированную поверхность, подкладывать посторонние предметы под лапу
пневмоподдержки запрещается;
е) после того, как коронка врезалась в
породу, необходимо плавно увеличить усилие подачи.
Следует помнить, что максимальную
производительность при минимальной вибрации можно достичь лишь при достаточном
усилии подачи порядка 100 кг, которое обеспечивается правильной установкой
перфоратора и пневмоподдержки. Не допускается бурение без виброгасящего
устройства. Максимальная производительность достигается при давлении воздуха 5
кгс/см", не более. Перед началом и во время бурения следить за
соединениями воздушных и водяных коммуникаций, которые должны быть надежны и
герметичны, так как срыв их может вызвать травмирование;
ж) для бурения однородных, крепких и
средних крепостей пород рекомендуются долотчатые коронки, а для бурения мягких,
неоднородных и трещиноватых пород крестообразные коронки;
з) для обеспечения оптимального режима
бурения надо непрерывно следить за ходом работы перфоратора и производить
регулировку усилия подачи пневмоподдержкой. Образующийся при бурении шлам
следует периодически убирать продувкой, переводя рукоятку назад до отказа. Во
время бурения необходимо обращать внимание на то, чтобы ось перфоратора
совпадала с осью шпура, в противном случае может произойти заклинивание бура
или его поломка;
и) по окончании бурения следует удалить
шлам из шпура продувкой и извлечь штангу при работе перфоратора в режиме
«забуривания».
После окончания бурения забоя следует сначала
перекрыть подачу воздуха, отсоединить шланги. Отверстия в буксе, выхлопное окно
в глушителе, воздушном патрубке следует закрыть пробками, а затем перфоратор,
водяные и воздушные рукава с автомасленкой уложить в специальный буровой
контейнер и выдать из забоя на поверхность.
Возможные неисправности перфоратора, возникшие в
процессе работы в забое, устраняются непосредственно бурильщиком (проходчиком)
на рабочем месте, за исключением случаев, когда устранение неисправностей
требует разборки перфоратора. В этом случае перфоратор меняется на резервный, а
неисправный сдается в мастерскую или перфораторную для ремонта.
Ремонт бурового оборудования производить
согласно проекту производства (организации) работ с соблюдением требований карт
безопасности.
В целях снижения вредного воздействия вибрации
при работе с ручными перфораторами использовать виброгасящие устройства
(виброгасящие каретки).
Для защиты от воздействия влаги, пыли, вибрации
и шума бурильщикам (проходчикам) использовать средства индивидуальной защиты
органов слуха, дыхания, зрения и работать в специальной одежде и обуви. В целях
предупреждения у бурильщиков вибрационной болезни предусмотреть проведение
комплекса послесменных профилактических мероприятий: тепловые процедуры, массаж
кистей, облучение УФЛ, обеспечение витаминами группы В, Р, Р1.
На рабочих местах, в подземных горных
выработках, рабочие должны иметь при себе изолирующие самоспасатели типа
ЩСМ-30, ШСС, ШСТ. Рабочие должны быть обучены правилам пользования
самоспасателем и уметь им пользоваться.
Меры безопасности при производстве работ по
возведению железобетонной или сталеполимерной анкерной крепи:
а) бурение шпуров под штанговую крепь
необходимо производить под защитой предохранительной крепи, конструкция которой
разрабатывается в паспорте крепления;
б) при высоте выработки более 2-х метров
работы производить со специальных подмостей (настилов), соответствующих
требованиям обеспечения безопасности ведения работ;
в) установку штанг должно производить не
менее чем двое рабочих, один из которых назначается старшим;
г) установку металлических стержней и
нагнетание цементнопесчаного или полимерного раствора в шпуры производить в
защитных очках из небьющегося стекла, рукавицах и респираторах;
д) при проверке материальных и воздушных и
водяных шлангов (рукавов), их концы необходимо отводить в сторону от людей и
надежно закреплять;
е) открывать пневмонагнетатель разрешается
только при закрытых кранах сжатого воздуха после сброса давления в
пневмонагнетателе и при надетых на глаза предохранительных очках;
ж) перед производством работ старший
рабочий в забое должен проверить надежность крепления всех деталей (шлангов)
пневмонагнетателя и работу «сбросового» аварийного вентиля.
Управление механизированными полками,
механизмами для приготовления сухой смеси, а также пневмонагнетателями должно
производиться лицами, имеющими на это право, подтвержденное соответствующим
документом.
При просеивании песка и цемента, приготовлении
цементно-песчаного раствора, нагнетания его в шпуры рабочие должны использовать
индивидуальные средства защиты органовдыхания и зрения.
Рабочее место должно быть хорошо освещено.
Полки высотой более 2-х м, используемые для
крепежных работ, должны иметь по всему периметру рабочей площадки барьеры
(ограждения) высотой не менее 1 м.
При установке железобетонных или сталеполимерных
штанг запрещается:
выполнять работы по нагнетанию раствора в шпуры
неисправными пневморастворонагнетателями. В случае обнаружения в нагнетателях
течи, трещин по сварке, а также при неисправном трехходовом кране и изношенных
уплотнительных прокладках работы должны быть немедленно прекращены;
отсоединять нагнетающий шланг и нагнетательную
трубу и снимать крышку при наличии в баке нагнетателя сжатого воздуха;
выполнять работы по нагнетанию раствора в шпуры без предохранительного щитка;
устанавливать штанги (рукава) с ненадежных
оснований, ящиков, кусков породы и т.п.
Запрещается:
а) установка штанг при неисправном
пневморастворонагнетателе, а также при отсутствии «сбросового» аварийного
вентиля сжатого воздуха;
б) открывать крышку
пневморастворонагнетателя при наличии в нем остаточного давления сжатого
воздуха;
в) растаривание мешков с цементом,
приготовление цементнопесчаного раствора и установка штанг в шпуры без защитных
очков надетых на глаза;
г) производить какой-либо ремонт
пневморастворонагнетателя и шлангов (рукавов) сжатого воздуха, находящихся под
давлением;
Примечание: Подача цементно-песчаного или
полимерного раствора в шпуры может производиться другими механизмами, на
которые разработана соответствующая техническая документация, инструкции по их
применению для этих целей и работе на которых обучен персонал.
Меры безопасности при возведении набрызгбетонной
крепи
Управление механизмами для приготовления сухой
смеси и укладки набрызгбетона должны производиться рабочими, имеющими на это
право, подтвержденное соответствующим документом.
Оборудование, механизмы,
контрольно-измерительные приборы и аппаратура должны иметь паспорта, в которые
ответственными лицами вносятся данные об их эксплуатации и ремонте.
Все механизмы, работающие под давлением сжатого
воздуха, должны иметь ясно обозначенные надписи о допустимом предельном
давлении. Запрещается эксплуатация оборудования и механизмов при давлении,
превышающем допустимое по паспорту.
Запрещается применять неисправное оборудование,
аппаратуру, инструменты и приспособления.
Присоединение шлангов (рукавов), идущих от
воздушной и водяной магистралей к оборудованию, для набрызг-бетонирования и
установки железобетонных штанг должно производиться при закрытых вентилях
воздушной и водной магистралей. Запрещается отсоединять рабочие шланги (рукава)
от оборудования, не прекратив подачу сжатого воздуха и воды из магистральных
трубопроводов и не убедившись в отсутствии остаточного давления в оборудовании
и рабочих рукавах.
Запрещается разборка установки, находящейся под
давлением; ремонт установки при наличии сжатого воздуха в пневмокоммуникациях;
отсоединение материального шланга до остановки
машины и снятия в ней давления.
Вращающиеся и движущиеся части машин и
механизмов (шестерни, концы валов, передач и др.) должны быть надежно
ограждены. Запрещается производить работы без ограждения, а также при
неисправном ограждении, снимать ограждения или их элементы до полной остановки
движущихся частей.
Перед началом работы внутренние поверхности
бункеров машины и дозатор (установки типа СБ-67, БМ-60), а также подводящие и
отводящие шланги (рукава) должны быть очищены и продуты.
Соединение шлангов между собой должно быть
плотным, гайки должны быть завернуты на всю длину резьбы.
Оборудование для набрызгбетонирования с
электрическим приводом подлежит заземлению на местные или главные заземлители.
Для устройства местных заземлений должны
сооружаться искусственные заземлители в штрековых водоотводных канавах или в
других местах, пригодных для этой цели. Заземление выполняется в соответствии с
«Инструкцией по устройству, осмотру и измерению сопротивления шахтных
заземлений».
Для защиты лица и рук от «отскока» и от
воздействия добавок- ускорителей схватывания и твердения цемента все рабочие
должны быть обеспечены защитными щитками для лица, брезентовой и резиновой
спецодеждой, резиновыми сапогами, противокислотными резиновыми перчатками,
противопылевыми респираторами.
Рабочее место сопловщика (крепильщик наносящий
на участок выработки набрызгбетон) должно быть хорошо освещено, а на почве
выработки не должно быть посторонних предметов (крупных кусков породы, леса,
труб и т.п.).
До загрузки торкетмашины должно быть проверено
положение воздушных кранов. Нормальное положение кранов при загрузке машины -
закрытое, за исключением крана нижнего бункера, который должен быть открытым.
Перед началом работы обобрать заколы, струей
воды обмыть кровлю и стенки выработки. Оборудование и коммуникации укрыть для
предотвращения попадания на них торкретбетона
Во время работы:
а) При загрузке должны быть приняты меры по
устранению возможности самопроизвольного изменения положения кранов. Не
допускается перегрузка машины, усложняющая плотное прилегание конуса затвора. В
случае попадания кусков щебня между соприкасающимися поверхностями корпуса
конуса и бункера, конус должен быть опущен, и зазор тщательно очищен от сухой
бетонной смеси.
б) Между сопловщиком и машинистом
торкретмашины осуществляется зрительная связь, и предусматриваются сигналы,
подающиеся голосом.
Перед пуском механизмов должен быть подан
предупредительный сигнал. Значение установленных сигналов должно быть известно
всем работающим.
При значительном удалении друг от друга
применяется электрическая сигнализация.
Перед включением сжатого воздуха конусный затвор
должен быть плотно закрыт, а в случае неплотного прилегания конуса до выяснения
причины неплотного закрытия, сжатый воздух должен быть отключен, а имеющийся
запас его в машине предварительно стравлен через специальный кран.
Включение и выключение кранов торкретмашины
машинистом производится только по сигналу сопловщика, за исключением аварийных
ситуаций.
Материальный и водяной шланги (рукава) до
включения должны находиться справа или слева от сопловщика, в зависимости от
того, в какой руке он держит сопло. Расположение шлангов между ног, а также
упор сопла в живот или в грудь ЗАПРЕЩАЕТСЯ.
При набрызгбетонировании в направлении вверх
разрешается упор сопла о колено со стороны расположения шлангов.
До момента подачи сигнала о включении сжатого
воздуха сопловщик обязан предупредить находящихся вблизи людей и указать им
безопасное место.
До включения сжатого воздуха сопловщик,
имеющимся у него краном, включает воду и устанавливает отсутствие свищей.
К моменту включения сжатого воздуха сопловщик
должен принять наиболее устойчивое положение, при этом разрешается использовать
имеющиеся на месте прочные опоры.
Место работы сопловщика должно быть освобождено
от воды и очищено от предметов, могущих стать препятствием безопасному его
передвижению.
При возведении крепи набрызгбетоном в тупиковых,
труднопроветриваемых выработках, где возможно содержание взрывоопасной смеси
пыли и газа, а также выработках с исходящей струей воздуха, содержащей эти компоненты,
не исключающие возможность возникновения взрыва, необходимо принимать меры от
взрывоопасных зарядов статистического электричества, для этого:
а) Оборудование и все металлические
соединения должны быть надежно заземлены;
б) Алюминиевый наконечник заменен стальным
или медным с последующим заземлением;
в) Вводятся ускорители схватывания бетона в
виде водного раствора.
При изменении условий работы или методов
эксплуатации машины, лица, обслуживающие ее, обязаны доложить об этом
руководству производства работ для уточнения приемлемости данной конструкции.
Во время работы механизмов запрещается
производить ремонт, закреплять какие-либо части, чистить, смазывать, тормозить
движущиеся части механизмов, надевать, сбрасывать, натягивать или ослаблять
ременные, клиноременные и цепные передачи.
При осмотре и текущем ремонте механизмов их
приводы должны быть выключены, приняты меры, препятствующие их случайному
включению, а у пусковых устройств выставлен или вывешен предупредительный знак
«Не включать - работают люди».
Ремонт оборудования должен производиться в
сроки, предусмотренные графиком планово-предупредительного ремонта (ППР). На
все виды ремонта основного оборудования должны быть составлены инструкции по
безопасному ведению работ, утвержденные главным инженером шахты.
Ручной инструмент (кувалды, молотки, ключи,
лопаты и т.п.) должен содержаться в исправности.
Работать неисправным инструментом запрещается.
При внезапном прекращении подачи электроэнергии
рабочие, обслуживающие механизмы, обязаны немедленно выключить
электродвигатели.
Поврежденный кабель должен быть немедленно
отключен.
Накрывать брезентом или другими
воспламеняющимися материалами работающие электродвигатели машин запрещается.
При образовании в магистральном шланге пробки
следует сбросить давление смеси, закрыть кран подачи сжатого воздуха, в бункере
машины прекратить подачу сухой смеси, надежно укрепить сопло и простучать
материальный шланг деревянным молотком на участке предполагаемого засорения.
Простукивание шланга, когда сопло находится в руках
сопловщика, категорически запрещается.
При образовании пробки в сопле необходимо
выполнить следующее:
отключить двигатель;
перекрыть подачу сжатого воздуха из магистрали;
снять давление в камере;
отсоединить, разобрать и очистить сопло.
В момент пробного включения сжатого воздуха
сопло должно быть закреплено и направлено на закрепляемую поверхность или почву
выработки. Сопловщик должен находиться на удалении от сопла в направлении,
противоположном движению струи. Заглядывать в шланги во всех случаях запрещается.
Если шланг на всем протяжении свободен, и пробка
образовалась в выходном патрубке, последний очищают при отключенном сжатом
воздухе и отсоединением материального шланга, после снятия давления в бункере
машины.
Если очистка патрубка не удается, разрешается
его продувка при удалении людей в безопасное место.
Продувание шланга сжатым воздухом допускается
при давлении не выше I атм., при этом шланг должен удерживаться руками.
При работе с добавками ускорителей твердения
цемента следует соблюдать осторожность, не допускать попадания их в глаза и на
кожу. Часть тела, на которую попала добавка, следует промыть чистой водой.
В целях снижения запыленности рудничной
атмосферы запрещается применение песка с влажностью менее 4 %, подсушивание
песка путем смешивания его с частью цемента, подача сжатого воздуха и сухой
смеси по материальному шлангу, а также продувка его с целью очистки без подачи
воды в сопло.
Для снижения запыленности рудничного воздуха по
ходу движения вентиляционной струи в выработках при необходимости устанавливать
пылеподавляющие устройства.
После окончания работы передвижных механизмов
гибкий кабель должен быть отключен. Рукоятку выключателя при этом необходимо
заблокировать.
Уходя с рабочего места, рабочий должен
удостовериться в безопасности его состояния, кровли, боков выработки, в
нормальном режиме работы вентиляции, а также проверить инструменты,
приспособления, требующиеся для работы последующей смены.
Очистить торкретмашину от материала,
оборудование и коммуникации от торкретбетона.
Обнаружив недостатки, которые он сам не может
устранить, рабочий обязан сообщить о них лицам технического надзора.
Меры безопасности при навеске сетки временной
предохранительной крепи
Меры безопасности при навеске металлической
сетки временной предохранительной крепи включают в себя выполнение требований
мер безопасности, установленных для крепления выработок сталеполимерными
анкерами, железобетонными штангами и набрызгбетонной (торкретбетонной) крепью.
Дополнительно к перечисленным мерам безопасности
при монтаже сетки временной крепи следует соблюдать особые требования,
связанные с арматурными работами:
а) резать арматурную сетку (решетку)
разрешается только со специальными исправными ножницами по металлу, при этом
полотно сетки при его резании должно быть надежно закреплено;
б) придание арматурному полотну формы
контура выработки производить кувалдой с жестким креплением молотка на
рукоятке. Рукоятка не должна иметь повреждений;
в) установку сетки по контуру выработки на
высоте более двух метров производить с оборудованных перилами перекрытий или
«козлов». При отсутствии перил необходимо использовать предохранительные пояса;
г) используемые перекрытия и «козлы»
должны быть изготовлены из досок толщиной не менее 30 мм, быть устойчивыми,
прочно закрепленными и усилены брусом толщиной не менее 50 мм;
д) крепильщику при установке арматуры
запрещается:
сбрасывать с высоты инструменты, материалы и др.
предметы, способные травмировать человека своим падением;
работать на высоте более 2-х м с приставных
лестниц; покидать участок производства работ по креплению; оставлять
недозакрепленным полотно сетки и его свисание.
При возведении крепи крепильщик должен
проверять:
качество довертки болтовых соединений;
наличие в крепи расклинивающих элементов и
соответствие места их установки паспорту крепления;
плотность забутовки пространства между породным
контуром и крепью.
Полный контроль состояния крепления в процессе
эксплуатации осуществляет горный надзор участка, за которым закреплена данная
выработка. Операции технологических процессов по установке анкерной крепи,
навеске сетки и торкрет - бетонировании стенок ствола, последовательность
выполнению указанных работ изложены в разделе 6.3 при выполнении аналогичных
процессов в период сооружения устья ствола.
. Проходка ствола №1
.1 Подготовительные операции
После сооружения технологического отхода ствола
на глубину до 40,02 м производится демонтаж проходческого оборудования
(специальный инвентарный полок, гидравлический экскаватор и др.) и производятся
работы по оснащению проходки основной части ствола согласно рабочей
документации на строительство объекта.
К этому времени на промплощадке ствола должны
быть установлены все проходческие лебёдки и подъёмные машины, сооружены
фундаменты проходческого копра, станка для разгрузки бадей и тельферной
эстакады, а все узлы и детали нестандартизированного оборудовании и
металлоконструкций доставлены на промплощадку и размещены в районе ствола
согласно последовательности монтажа.
С помощью крана КС-6476 в забое ствола, согласно
специальной инструкции и Инструкции для работников строительной организации по
безопасному ведению технологических процессов при монтаже тюбингов в стволе
собирается кольцо для монтажа тюбингов.
Затем, с помощью того же крана КС-6476 на
временном перекрытии устья ствола согласно Инструкции для работников
строительной организации по безопасному ведению технологических процессов при
монтаже-демонтаже проходческого полка выполняется сборка трёхэтажного
проходческого полка.
После этого с помощью грузоподъемного крана в соответствии
с Инструкцией для работников строительной организации по безопасному ведению
технологических процессов при возведении проходческого копра монтируется
проходческий копер «Север-2», на котором собирается подшкивная площадка, и
устанавливаются проходческие и копровые шкивы. Производится намотка на барабаны
подъемных машин и проходческих лебедок, запасовка и навеска подъёмных, полковых
и других проходческих канатов соответственно. На этажах проходческого полка
устанавливается и обвязывается согласно проектной документации необходимое
оборудование. Далее выполняется подвеска проходческого полка на канатах. С
помощью полковых лебёдок проходческий полок опускается в ствол таким образом,
чтобы его верхний этаж был установлен отм.-3,5 м. В этом положении с верхнего
этажа проходческого полка производится монтаж маркшейдерского полка.
На устье ствола устанавливается нулевое
перекрытие, производится монтаж разгрузочного устройства, а в стволе под полком
монтируется стволовая погрузочная машина 2КС-2У/40. Кроме того в стволе
монтируются трубопроводы сжатого воздуха, кабели для обеспечения
электроэнергией, вентиляционный став для проветривания забоя, а также
сигнальные устройства.
После этого на вспомогательных балках,
установленных на 5-6 м ниже маркшейдерского полка, собирается тампонажный
полок. Вспомогательные балки после подвески полка демонтируются.
Специфические требования при проходке ствола №1
в замороженных породах.
После монтажа проходческого оборудования на
промплощадке и в стволе и достижения заданных параметров ледопородного
ограждения проходка ствола может быть продолжена, при этом должна быть
произведена наладка и контрольное опробование всех элементов проходческого
комплекса, а также составлены и утверждены акты пуско-наладочных работ.
Подвесные проходческие полки принимаются в
эксплуатацию комиссией с участием представителей территориальных органов
Ростехнодзора (п.5.4.5 ПБ 03-428-02) с подписанием соответствующего акта.
Приемка в эксплуатацию вновь смонтированных
горнопроходческих комплексов должна проводиться комиссией, назначенной
руководителем организации, с участием представителей Ростехнадзора и
представителей других заинтересованных органов государственного надзора.
Дальнейшая проходка ствола ведется с
проходческого копра «Север-2». Предусматривается использование погрузочной
машины 2КС--2у/40, двух бадейных комплексов с механизированной разгрузкой типа
БПСМ-5.0, трубопровода вентиляции 0900мм, трубопровода сжатого воздуха Ду 200,
трёхэтажного проходческого полка, двухэтажного тампонажного полка, монтажного
кольца - полка для сборки тюбингового кольца и спасательной лестницы.
Проходка ствола в замороженной зоне разрешается
после проверки целостности и достижения расчетной толщины ледопородного
ограждения специальными приборами (ультразвуковой контроль).
При проходке ствола в замороженной зоне
необходимо составлять погоризонтные планы ледопородного ограждения в
соответствии с рабочей документацией на проходку ствола.
При местном замораживании пород, если забой
ствола находится, ниже статического уровня подземных вод, бурение
контрольно-разведочных скважин должно производиться через бетонную подушку,
уложенную на предохранительный целик. Размер целика и подушки определяется
проектом на проходку ствола.
Бурение контрольно-разведочных, замораживающих и
тампонажных скважин должно производиться через уравнительную колонну или
запорные противовыбросные устройства.
Технология и средства ведения взрывных работ
должны обеспечивать целостность ледопородного ограждения и замораживающих
колонок. Способ разрушения замороженных пород определяется проектной
документацией на проходку ствола.
Проходка ствола в зоне водонепроницаемого венца
крепи (кейлькранца) и на расстоянии 3 м выше и ниже его должна выполняться с
применением отбойных молотков, или с применением буровзрывных работ по
специально разработанному для этой зоны паспорту буровзрывных работ. При этом
должна обеспечиваться целостность массива пород стенок ствола.
При появлении воды в стволе, сооружаемом в
слабых, неустойчивых замороженных породах, а также при обнаружении на стенках
ствола непромороженных неустойчивых пород работы по проходке должны быть
остановлены. Дальнейший порядок работ определяется специальными мероприятиями,
утвержденными руководителем (заместителем руководителя) организации - производителя
работ.
При вскрытии забоем ствола замораживающих
колонок, работы по проходке должны быть прекращены, люди выведены из забоя,
кроме тех, кто участвует в приведении замораживающих колонок в безопасное
состояние.
Отставание постоянной крепи от забоя ствола и
величина «заходки» в пластичных, склонных к пучению породах определяются
проектом на проходку ствола. Отставание временной крепи от забоя не должно
превышать значений, установленных в паспорте крепления горной выработки,
утвержденном в установленном порядке, в паспорте крепления горной выработки
также должны предусматриваться дополнительные меры безопасности, направленные
на предотвращение обрушения пород.
При перемещении проходческого полка все рабочие,
кроме сопровождающих полок при спуске-подъеме, должны быть удалены из ствола.
Работы по проходке ствола могут быть
возобновлены только после центровки проходческого полка по бадьям, раскрепления
его и нанесения новых меток на указателе глубины подъемной машины.
Запрещается установка в замороженной зоне
анкеров для крепления и навески оборудования ствола в специально забуренных
скважинах, шпурах без цементации свободного пространства скважины, шпура.
Технология оттаивания замороженных пород и
гидроизоляция крепи ствола определяются проектом на проходку ствола.
Лица, осуществляющие технический надзор,
обязаны:
ежесменно осуществлять визуальный осмотр
обнаженных стенок и забоя ствола с целью выявления темных пятен, указывающих на
проникновение рассола из колонок в породы. Результаты осмотра заносятся в книгу
осмотра ствола;
при проходке в неустойчивых породах (пески,
глины и др.) замерять температуру пород на контуре ствола, которая должна быть
не выше предусмотренной проектной документацией, кроме того, на участках
ствола, закрепленных временной крепью согласно п.5.9.7 Г1Б 03-428-02 должны
быть установлены приборы для контроля за температурой замороженных грунтов и
пород;
при возникновении угрозы прорыва воды, плывуна
или других опасностей принимать своевременные меры по предупреждению аварии,
выводу людей из забоя.
Необходимость подогрева вентиляционной струи при
проходке ствола в зоне замороженных пород должна быть определена в проекте на
проходку ствола.
Проходку ствола, начиная с отм. -40,020 и до
отм. -270,000 в замороженных породах следует производить с опережающим бурением
с целью определения целостности ледопородного ограждения.
Бурение опережающих скважин предусматривается
производить через кондукторы, оборудованные запорной арматурой и превентором.
Проходка ствола должна производиться по
совмещенной схеме, т.е. постоянная тюбинговая крепь возводятся вслед за
проходкой ствола.
Бурение шпуров, как в замороженной зоне горных
пород, так и в незамороженных участка (в соляной толще), осуществляется по
утвержденному паспорту БВР ручными перфораторами типа ПП-63.
После взрывания и проветривания в забое ствола
производится предварительная уборка породы. Оставшаяся в забое порода
выравнивается по периметру. При этом расстояние от низа монтажного кольца
(когда оно притянуто к тюбинговой колонне) до забоя должно быть около 2,5 м.
Затем на места установки каждого домкрата монтажного кольца укладываются
инвентарные шпальные подкладки 0,4x0,4x0,14м, на которые с помощью лебёдок
ЛПЭП-25 опускается монтажное кольцо. При этом оно устанавливается на шпальные
подкладки опорными плитами подъёмных домкратов. В дальнейшем лебёдки ЛПЭП-25 в
перемещении монтажного кольца не участвуют. Выравнивание, центрирование и
подъём смонтированного тюбингового кольца осуществляется системой вертикальных
и горизонтальных гидродомкратов.
Для исключения утечки бетона, монтажное кольцо
уплотняется по периметру. С этой целью, на выдвинутых по низу кольца пальцах
030 мм, сооружается настил из обрезков досок. Затем на доски укладываются
полосы из полиэтилена или аналогичного материала, а на них надувные рукава
080-200 мм, которые сверху засыпаются песком, глиной или мелкой породой. При
этом поверхность монтажного кольца должна быть тщательно очищена от просыпи
горной массы.
.2 Монтаж тюбинговых колец
Тюбинги с помощью подъемной машины через бадьевые
проёмы нулевого перекрытия и полков специальными стропами с фиксаторами
(рисунок 6.5) опускаются на монтажное кольцо - полок, после чего с помощью
стропа предназначенного для монтажа тюбингов поочерёдно фиксируются на подвеску
2КС-2У/40, Установка тюбингов на монтажном кольце производится согласно схеме
монтажа с установкой свинцовых прокладок толщиной 2 мм в вертикальных стыках
тюбингов. При этом прокладки должны выступать не менее чем на 5 мм (по всей
ширине прокладки) над верхним и нижним фланцами тюбингового кольца. После
выверки геометрии кольца производиться окончательная обтяжка тюбинговых болтов.
Затем тщательно зачищается нижний фланец
тюбинговой колоны, при этом срезаются выпуски свинцовых прокладок.
Аналогичная операция выполняется и по верхнему
фланцу вновь смонтированного тюбингового кольца, после чего укладываются
горизонтальные свинцовые прокладки.
По завершении этих операций* с помощью оправок и
системы гидродомкратов на монтажном кольце - полке осуществляется стыковка
смонтированного тюбингового кольца с колонной, установка болтов и пробок.
Выбирается напуск канатов лебёдок подвески монтажного кольца.
Установка последующих тюбинговых колец
производиться аналогично.
При креплении ствола тюбинговыми кольцами:
установка тюбингов должна производиться с
рабочего монтажного кольца - полка или непосредственно из забоя;
для спуска тюбингов применяются специальные
цепные или канатные стропа;
спускаемый тюбинг перед монтажом укладывают
тыльной стороной;
допускается снимать траверсу или строп, с
помощью которых тюбинг еремещается к месту установки, только после закрепления
тюбинга двумя болтовыми соединениями;
совмещать болтовые отверстия смежных тюбингов
следует только при помощи специальных конусных оправок;
монтаж тюбингов должен осуществляться с помощью
вспомогательных лебедок, которые устанавливаются или на поверхности или на
подвесном полке.
Организация, порядок монтажа тюбингов,
мероприятия по безопасному производству работ при сборке тюбингового кольца
рассмотрены в разделе настоящего регламента.
.3 Укладка бетона в затюбинговое
пространство
Для заполнения затюбингового пространства
используется бетон по СНиП 2.03.01-84, В25 (327 кгс/см2; М 300-350). Укладку
бетонной смеси за тюбинговые кольца производится после установки, центровки,
раскрепления и окончательной затяжки болтов. Количество одновременно
бетонируемых колец варьируется от одного до двух в зависимости от горно -
геологических условий. Количество бетонируемых за один цикл колец на конкретном
участке ствола должно быть указано в утвержденном паспорте крепления. При этом
принимаются описанные выше меры по исключению протекания бетонной смеси.
Заливка бетоном подвешенного кольца (колец) производится через наклонные
заливочные отверстия ранее установленного и забетонированного кольца, для чего
в нем все наклонные заливочные отверстия предварительно должны быть пробиты и
очищены.
Перед приемом бетона вывертываются пробки в
нижней части кольца тюбинговой колонны, вместо которых в диаметрально
расположенных отверстия устанавливаются два переходника диаметром 80 мм, к
которым с помощью быстро разъемных соединений присоединяются гибкие бетоноводы
диаметром 100 мм.
Бетон (или тампонажная смесь, при тампонаже с
полка в затюбинговое пространство для ликвидации пустот после усадки бетона)
опускается в специальных бадьях для спуска бетона, вместимостью 2.3 м3, которые
разгружаются в бункер вместимостью 2.5 м3, установленный между 1 и 2 этажом
полка. Из этого бункера бетон по двум упомянутым выше гибким бетоноводам
подаётся за тюбинги.
Укладка бетона за тюбинги производится
равномерно малыми дозами по всей длине периметра ствола. Заполнение
затюбингового пространства при возведении колонны сверху - вниз бетоном или
цементно-песчаным раствором производится на высоту установленного кольца.
Контроль заполнения затюбингового пространства
бетонной смесью, производится по появлению её во всех свободных заливочных
отверстиях, ранее забетонированного кольца. Заливочные отверстия по мере
появления в них бетонной (растворной) смеси закрываются пробками. В результате
усадки бетона, на контакте «заходок», образуются полости. Тампонаж этих
полостей производится с полка через специальные тампонажные отверстия
расположенные в верхней части тюбингов, при его подходе к очередном тюбинговому
кольцу залитому ранее бетоном.
При производстве бетонных работ необходимо
соблюдать правила техники безопасности в соответствии с требованиями СНиП
12-03-99 «Безопасность труда в строительстве. Часть 1. Общие требования»,
раздела 10 «Техника безопасности» «Руководства по приготовлению и применению
бетонов и активированных растворов с химическими добавками и возведении крепи
шахтных стволов» Москва, ЦБНТИ Д977г, действующие правила охраны труда и
техники безопасности, а также специальные требования по технике безопасности
при работе с химическими добавками.
Рабочие, занятые приготовлением и укладкой
бетона и растворов с использованием химических добавок, должны пройти
инструктаж по безопасности труда, обучение безопасным методам и приемам
выполнения работ, оказанию первой медицинской помощи пострадавшим (п.20 ПБ
03-553-03), ознакомлены с требованиями безопасности при работе с химическими
добавками и, использовать защитные очки, резиновые рукавицы и респираторы при
ведении бетонных работ.
Укладку бетонной смеси за опалубку должны
производить не менее двух опытных рабочих. К управлению бетоноукладчиком
допускается рабочий, имеющий удостоверение на право работы на данном
оборудовании, прошедший специальный инструктаж и назначенный для этой работы по
наряду.
Устройство противофильтрационной
завесы
Противофильтрационная завеса (рисунок 8.2,3.1 и
графические материалы 779/1-П-4.31.1/20-07ПР/10-ГПР л. 1,2) выполняется с целью
предотвращения поступления воды за счёт фильтрации из вышележащих водоносных
структур, в породы соленосной толщи в районе ствола. С этой целью, после
оттаивания пород, на границе водоупорного массива, с отметкой по низу - 275, 0
м (А.О. - 101,000 м) вокруг ствола создаётся водонепроницаемая зона высотой
около 9 м и диаметром порядка 35 м. Противофильтрационная завеса выполняется по
технологии и с использованием материалов и оборудования, предложенных фирмой
BASF The Chemical Company. Указанная зона формируется за счёт нагнетания
быстротвердеющей смеси на базе микроцемента RHEOCEM 650 с необходимыми
добавками, в специальные скважины, пробуренные через тампонажные отверстия в
тюбингах станком DE110 фирмы Sandvik. Во время бурения станок DE1I0 размещается
на нижнем этаже тампонажного полка на двух специальных кольцевых рельсах
закрепленных по его периметру. Скважины бурятся диаметром 46 мм горизонтально
на глубину 6, 8, 10, 12 и 14 м от края крепи через тампонажные отверстия шести
смежных ярусов, (6 рядов по 13 скважин).
Тампонажная смесь нагнетается через
перфорированные буровые штанги ССК-46. Нагнетание тампонажной смеси
осуществляется цементационной установкой HANI IC650/725 2С фирмы Atlas Copco
Unigrout производительностью 50л/мин.
Для создания противофильтрационной завесы
используются два вида тампонажных смесей:
о смесь №1 имеет соотношение водоцементное
соотношение 1 : 1 и обладает высокой проникающей способностью;
о смесь №2 имеет соотношение водоцементное
соотношение 1 : 2.
Процесс цементации начинается с нагнетания смеси
№1 при постоянном контроле рабочего давления на выходе насоса. При нормальном
протекании процесса цементации, указанное давление должно постепенно
повышаться. Нагнетание смеси прекращается при достижении давления 4 МПа или
после достижения расхода сухого цемента 150 кг на каждый метр скважины.
В том случае, если после подачи смеси №1 в
количестве соответствующем 100 кг сухого цемента на каждый метр скважины, не
происходит повышения давления, процесс нагнетания этой смеси следует прекратить
и переити на нагнетание смеси №2. Нагнетание в скважину смеси №2 производиться
до достижения расхода смеси в количестве соответствующем 50 кг сухого цемента
на каждый метр скважины, после чего процесс нагнетания прекращается.
Затем, ввиду высокой скорости набора прочности
смеси на базе быстротвердеющего микроцемента RHEOCEM 650, непосредственно после
прекращения нагнетания производится перебуривание скважины на ту же глубину,
после чего возобновляется подача в скважину тампонажной смеси №1 до достижения
указанного выше необходимого давления. Описанные выше мероприятия могут быть
скорректированы по новым данным, полученным в процессе проходки ствола и
выполнения работ по тампонажу горных пород с целью создания
противофильтрационной завесы.
Рисунок 8.2.3.1 Противофильтрационная
тампонажная завеса
Конструкция противофильтрационной завесы и
технология её возведения должны быть разработаны в рабочей документации на
проходку ствола.
.4 Возведение кейлькранцев
Для предотвращения проникновения воды по
затюбинговому пространству в соленосные геологические структуры, на глубине
304,450 м (А.О.-130,450 м) предусматривается возведение специального
водопреграждающего устройства - кейлькранца (рисунок 8.2.4.1), а также
полимерного кольца (рисунок 8.2.4.2) на глубине 295,220 м (А.О. - 121,220 м),
выполняемого в плотных водонепроницаемых породах ниже зоны замораживания.
При этом проходка ствола в зоне установки этих
устройств (5 м выше и 5 м ниже его установки), осуществляется посредством
механического разрушения породы (отбойный молоток, гидромолот и др.) по всему
контуру не менее чем на 2,0 м. Центральная часть забоя разрабатывается взрывным
способом (на рыхление).
Предусмотрены два типа водопреграждающего
устройства:
® традиционный кейлькранц в виде клинового замка
с деревянной расклинкой выполненной в зазоре между наружной частью кольца
специальных опорных тюбингов и окружающей породной стенкой. Недостатками этого
типа гидроизоляционного устройства являются большой срок его строительства и
трудоёмкость возведения, необходимость изготовления специальных тюбингов,
наличие пикотажного шва, а также невозможность проведения каких-либо ремонтов.
о полимерное уплотнительное кольцо, между
тюбинговой колонной и монолитной водонепроницаемой породой, выполненное в
разрыве бетонного заполнения затюбингового пространства. Такой тип
водопреграждающего устройства свободен от перечисленных выше недостатков,
однако, опыт сооружения и эксплуатации, подобных водопреграждающих устройств
пока ещё очень невелик.
Возведение полимерного водопреграждающего
устройства производится в следующем порядке.
После опускания монтажного кольца и монтажа на
нём инвентарного перекрытия тщательно зачищается бетон предыдущей заходки и
породный контур по периметру контакта бетон-порода закрепляется кольцевой
иньекционный шланг-коллектор Masterflex с клапанами невозвратного действия. К
этому коллектору присоединяются полиэтиленовые трубки соответствующей длины в
количестве соответствующем числу тюбингов в кольце. При монтаже следующего
тюбингового кольца концы указанных трубок выводятся в ствол через тампонажные
отверстия. После стыковки собранного тюбингового кольца с колонной производится
заливка бетона до уровня тампонажных пробок. Трубки обрезаются, на них
устанавливаются заглушки, а тампонажные отверстия закрываются специальными
пробками.
Затем через заливочные отверстия предыдущие
тюбингового кольца в образовавшуюся полость подаётся двухкомпонентная
полиуретановая смесь, которая увеличивается в объёме, образуя водонепроницаемое
препятствие. При этом оптимальное увеличение объёма этой смеси составляет 2-3
раза при максимально-возможном увеличении объёма в 10-15 раз.
В случае нарушения в процессе строительства или
эксплуатации ствола герметичности этого устройства, через тампонажные отверстия
по упомянутым выше трубкам нагнетаются акриловые гели, которые полимеризуясь
при контакте с водой увеличиваются в объёме на 10-15%.
Указанные технологии гидроизоляции крепи горных
выработок широко используются в строительстве подземных сооружений. Подбор
состава гидроизолирующих смесей и разработку технологии процесса герметизации
крепи целесообразно поручить фирме «BASF The Chemical Compani» производящей
подобные работы при сооружении объектов Олимпстроя в г. Сочи и на проходке
стволов рудника «Гремяченский» в Волгоградской области.
Конструкция гидроизоляционных водопреграждающих,
устройств в шахтном стволе и технология их возведения должны быть разработаны в
рабочей документации на проходку ствола Отметки полимерного кольца и
кейлькранца уточняются по данным геологической службы при проходке ствола.
Рисунок 8.2.4.1 Кейлькранц
Рисунок 8.2.4.2 Гидроизоляционное полимерное
кольцо
Остаточный приток в пройденный ствол калийной
или соляной шахты, а также на месторождениях, где существует опасность размыва
нижерасположенных пластов соли, не должен превышать 0,15 м7ч, при этом не
должно быть фильтрации воды через крепь ствола ниже кейлькранца.
Буровзрывные работы
При проходке ствола будут пересечены породы,
имеющие коэффициенты крепости f по шкале профессора Протодьяконова М. М. до 6
(песчаники), поэтому проходку ствола и сопряжений следует производить с
применением буровзрывных работ.
Бурение шпуров в забое ствола выполняется
ручными перфораторами типа ПП-63С, ПП-63В.
Согласно СНиП 3.02.03-84 «Подземные горные
выработки» п.2.2, количество бурильных машин следует принимать в забоях
вертикальных стволов из расчета один перфоратор не менее чем на 4 м~ площади
забоя. Диаметр шпуров - 43 мм. При бурении по известнякам, аргиллитам,
алевролитам, песчаникам применять буровые коронки долотчатой формы.
Порядок работы при бурении шпуров по
замороженным породам следующий:
Бурение шпуров в забое выработки производить в
соответствии с утвержденным в установленном порядке паспортом буровзрывных
работ (БВР), с которым бурильщик (проходчик) должен быть ознакомлен под роспись.
Убедившись в безопасном состоянии рабочего
места, бурильщик (проходчик) должен установить перфоратор в забое.
Наполнить автомасленку маслом марки
индустриальное И-30 или И-45 (ГОСТ 1707-51), расход которого в смену составляет
350 г.
Продуть воздуховод и, прежде чем присоединить
его к перфоратору, залить небольшое количество (10-20 г) масла в воздушный
рукав для начальной смазки перфоратора.
Вставить в перфоратор бур и установить
перфоратор в требуемое положение, обратив внимание при этом на прямолинейность
бура, состояние хвостовика и буровой коронки. Твердость хвостовика штанги
должна быть HRC 48...52. Не допускается применение бура, имеющего на хвостовике
смещение по оси отверстия для водяной трубки, во избежание ее срезания. Бурение
без буродержателя не допускается. Забуривание производить при малом усилии
подачи притуплённой коронкой на глубину 30-40 мм.
После того, как коронка врезалась в породу,
необходимо плавно увеличить усилие подачи.
Следует помнить, что максимальную
производительность при минимальной вибрации можно достичь лишь при достаточном
усилии подачи порядка 100 кг, которое обеспечивается правильной установкой
перфоратора. Не допускается бурение без виброгасящего устройства. Максимальная
производительность достигается при давлении воздуха 5 кгс/см“, не более. Перед
началом и во время бурения следить за соединениями воздушных и водяных
коммуникаций, которые должны быть надежны и герметичны, так как срыв их может
вызвать травмирование.
Для бурения однородных, крепких и средних
крепостей пород рекомендуются долотчатые коронки, а для бурения мягких,
неоднородных и трещиноватых пород крестообразные коронки.
Для обеспечения оптимального режима бурения надо
непрерывно следить за ходом работы и производить регулировку усилия подачи.
Образующийся при бурении шлам следует периодически убирать продувкой, переводя
рукоятку назад до отказа. Во время бурения необходимо обращать внимание на то,
чтобы ось перфоратора совпадала с осью шпура, в противном случае может
произойти заклинивание бура или его поломка.
По окончании бурения следует удалить шлам из
шпура продувкой и извлечь штангу при работе перфоратора в режиме «забуривания».
После окончания бурения забоя следует сначала
перекрыть подачу воздуха, отсоединить шланги. Отверстия в буксе, выхлопное окно
в глушителе, воздушном патрубке следует закрыть пробками, а затем перфоратор,
водяные и воздушные рукава с автомасленкой уложить в специальный буровой
контейнер и выдать из забоя на поверхность.
Возможные неисправности перфоратора, возникшие в
процессе работы в забое, устраняются непосредственно бурильщиком (проходчиком)
на рабочем месте, за исключением случаев, когда устранение неисправностей
требует разборки перфоратора. В этом случае перфоратор меняется на резервный, а
неисправный сдается в мастерскую или перфораторную для ремонта.
Ремонт бурового оборудования производить
согласно проекту производства (организации) работ с соблюдением требований карт
безопасности.
Перед заряжанием забоя шпуры очищаются от
буровой мелочи и грязи продувкой их сжатым воздухом с помощью металлической
трубки, вводимой в шпур, при этом категорически запрещается находиться напротив
устья шпура. Работы по очистке шпуров от буровой мелочи и шлама производить в
защитных очках или масках (щитках).
В целях снижения вредного воздействия вибрации
при работе с ручными перфораторами использовать виброгасящие устройства
(виброгасящие каретки).
Для защиты от воздействия влаги, пыли, вибрации
и шума бурильщикам (проходчикам) использовать средства индивидуальной защиты
органов слуха, дыхания, зрения и работать в специальной одежде и обуви. В целях
предупреждения у бурильщиков вибрационной болезни предусмотреть проведение
комплекса послесменных профилактических мероприятий: тепловые процедуры, массаж
кистей, облучение УФЛ, обеспечение витаминами группы В, Р, Р1.
На рабочих местах, в подземных горных
выработках, рабочие должны иметь при себе изолирующие самоспасатели типа
ШСМ-30, ШСС, ШСТ. Рабочие должны быть обучены правилам пользования
самоспасателем и уметь им пользоваться.
Бурение шпуров на участке ствола, где породы не
подвергались искусственной заморозке (в соляной толще) производятся аналогичным
образом как в замороженных породах.
При бурении забоя рекомендуется применять
комбинированный прямой вруб с центральным компенсационно-разведочным шпуром
диаметром >52 мм или скважиной диаметром >75 мм (центральный шпур без
заряда) и пирамидально-клиновой. Неснижаемая длина центрального
компенсационно-разведочного шпура или скважины на момент производства взрывных
работ в забое ствола должна составлять не менее 5,0 м.
Бурение скважины диаметром > 75 мм
осуществляется буровым станками типа НКР-ЮОМ или ПБ-ЮОМ.
.5 Взрывные работы
По окончании бурения забоя ствола выполняются
взрывные работы (ВР) в соответствии с положениями правил безопасности ПБ
13-407-01, ПБ-03-553-03, РД 13-522-02, РД 13-415-01, инструкций по безопасной
организации и ведению ВР, по безопасной эксплуатации взрывного оборудования,
проекта проходки ствола, специального проекта производства буровзрывных работ
при проходке по замороженным породам шифр- 779/1-П-6.2/20-07ПР/10-БВР.ПЗ (далее
по тексту «Проекта производства БВР) [89], утвержденного паспорта БВР.
В качестве взрывчатого вещества на участке
проходки ствола в интервале искусственно замороженных пород (до кровли соленой
толщи), где опасные газовыделения согласно геологическому отчету по результатам
бурения контрольно - стволовой евкажины №107г-1 не выявлены принимается
взрывчатое вещество третьего класса безопасности аммонит 6ЖВ ГОСТ 21982-76.
Для инициирования зарядов следует использовать
электрический способ с применением систем неэлектрического взрывания типа
«СИНВ-Ш», «ЭДЕЛИН», «ИСКРА» и детонирующего шнура ДШЭ-12 ГОСТ 6196-78
(коммутация взрывной сети).
Рекомендуемый тип электродетонаторов -ЭДКЗ-ПМ
ГОСТ 21806-76.
При проходке ствола на участке в интервале от
кровли карналлитовой зоны до подошвы сильвинитовой зоны (рабочая зона относится
к Ш-ей группе газовой опасности по горючим газам) по породам с возможным
выделением метана и водорода необходимо использовать предохранительное ВВ IV
класса - аммонит Т-19 по ГОСТ 21982-76.
В качестве средств инициирования используются
электродетонаторы типа ЭД-КЗ-ПКМ.
Аммонит 6ЖВ и аммонит Т-19 приняты согласно
«Перечню взрывчатых материалов, оборудования и приборов взрывного дела,
допущенных к применению в Российской Федерации», «НТЦ «Промышленная
безопасность» Гостехнадзора России», 2002г.; «Безопасность при взрывных
работах», «Федеральная служба по экологическому, технологическому и атомному
надзору»^ 2008г.
Взрывные работы в стволе №1 производятся в
соответствии с паспортом БВР, разработанным и утвержденным в установленном
порядке.
Паспорт БВР при проходке ствола на участке
искусственно замороженных пород составляется на основании расчетных параметров
«Проекта Производства БВР...» [89] и результатов не менее трех опытных
взрываний в конкретных горно-геологических условиях проходки ствола №1.
При проходке ствола на участке пород, не
подвергнутых искусственному замораживанию (в соляной толще) в соответствии с
требованиями Г1Б 13-407-01 и ПБ 03-553-03 с учетом опасности газодинамических
явлений и выделений взрывоопасных газов (метана и водорода) в соответствии с
результатами не менее трех опытных взрываний в конкретных горногеологических
условиях проходки ствола №1.
Паспорт БВР должен включать:
схему расположения шпуров или наружных зарядов;
наименования взрывчатых материалов; данные о способе заряжания, числе шпуров,
их глубине и диаметре, массе и конструкции зарядов и боевиков,
последовательности и количестве приемов взрывания зарядов, материале забойки и
ее длине;
схему монтажа взрывной (электровзрывной) сети с
указанием длины (сопротивления), замедлений, схемы и времени проветривания
забоев;
величину радиуса опасной зоны;
указания о местах укрытия взрывника
(мастера-взрывника) и рабочих на время производства взрывных работ, которые
должны располагаться за пределами опасной зоны;
указания о расстановке постов охраны или
оцепления, расположении предохранительных устройств, предупредительных и
запрещающих знаков, ограждающих доступ в опасную зону и к месту взрыва.
Кроме того, для шахт, опасных по газу или пыли,
в паспорте должны быть указаны количество и схема расположения специальных
средств по предотвращению взрывов газа (пыли), а также режим взрывных работ.
Взрывные работы должны выполняться взрывниками,
а в пределах рабочей зоны Ш-й группы газовой опасности только
мастерами-взрывниками под руководством лица технического надзора по письменным
нарядам с ознакомлением под роспись и соответствующим нарядам-путевкам и
проводиться только в местах, отвечающих требованиям правил и инструкций по
безопасности работ.
При проходке ствола №1, в интервале абсолютных
отметок -136,170 м - -209,110 м, что соответствует интервалу глубин 308,4 м до
381,34 м (отчет ООО НПФ «ГЕОПРОГНОЗ» от кровли карналитовой зоны до подошвы
сильвинитовой зоны, рабочую зону следует относить к Ш группе газовой опасности,
с учетом выполнения при проходке условий, «Специальных мероприятий...» [86].
Раздел 6 «Специальных мероприятий...»
9. Взрывные работы
.1 Общие требования
Взрывные работы должны производиться с
соблюдением требований «Единых правил безопасности при взрывных работах».
К производству взрывных работ допускаются лица,
имеющие "Единую книжку взрывника" (мастера-взрывника). Взрывники
должны быть обучены производству взрывных работ в подземных выработках и на
поверхности рудника, а также в условиях, соответствующих требованиям
"Специальных мероприятий..." и сдать соответствующие экзамены.
Производство взрывных работ допускается только
при отсутствии горючих газов в забое перед заряжанием шпуров и в месте укрытия
взрывника перед подключением взрывной сети к взрывному прибору. Результаты
замера газов должны быть записаны лицом, производившим замер в наряд-путевке
взрывника.
Взрывание зарядов должно производиться
электрическим способом с применением предохранительных электродетонаторов.
В выработке, где производятся взрывные работы,
перед монтажом взрывной цепи должна отключаться электроэнергия.
В рабочих зонах I, II групп опасности
допускается ведение взрывных работ с применением непредохранительных взрывчатых
веществ, а в забоях, проветриваемых за счёт общешахтной депрессии, допускается
взрывание зарядов без забойки шпуров.
В выработках рабочих зон I, П групп опасности,
проветриваемых за счет общешахтной депрессии, разрешается производить
ликвидацию зависания руды, а также вторичное дробление зарядами
предохранительных ВВ.
Дополнительные требования для рабочих зон,
отнесенных к Ш группе опасности.
В рабочих зонах ІІІ
группы
опасности взрывные работы должны вести только мастера-взрывники.
Ведение взрывных работ разрешается только с
применением предохранительных ВВ, предохранительных электродетонаторов
мгновенного и короткозамедленного действия и донно-устьевой забойки шпуров из
пламегасящих материалов. Допускается также применение комбинированных
скважинных и шпуровых зарядов в сочетании с донно-устьевой забойкой из
пламегасящих материалов.
До допуска рабочих в рабочую зону все подходы к
ней должны быть ограждены запрещающими знаками. Запрещающие знаки должны
сниматься только с разрешения лиц технического надзора.
Перед заряжанием, монтажом взрывной сети,
взрыванием электроэнергия в рабочей зоне должна быть полностью отключена.
После взрывания лицо технического надзора и
сопровождающей его газомерщик-респираторщик ВГСЧ, включившись в респираторы,
должны проверить в рабочей зоне у вентилятора и пусковой аппаратуры содержание
горючих газов, а также установить путем осмотра исправность электроустановок.
При отсутствии горючих газов у вентилятора и
пусковой аппаратуры и при исправности электроустановок лицо технического
надзора должно включить вентилятор для проветривания забоя. Если при замере
шахтным газоопределителем будут обнаружены горючие газы более 0,5% по объему
(10 % НКПР), газомерщик-респираторщик ВГСЧ должен отобрать пробы на химический
анализ, а лицо технического надзора обязано немедленно сообщить об этом
главному инженеру рудника или диспетчеру. Дальнейшие работы должны
производиться в соответствии с требованиями, изложенными в пунктах 3.1.7.-3.1.1
Г
Допуск рабочих в забой разрешается лицом
технического надзора при отсутствии концентрации горючих газов более 0,5% по
объему (10% НКПР). До допуска рабочих в забой подходы к проветриваемым
выработкам должны быть ограждены запрещающими знаками.
Контроль за состоянием рудничной атмосферы при
проходке ствола в зонах опасных по газовыделениям выполнять в соответствии с
требованиями «Специальных мероприятий...» [86].
Монтаж взрывной сети производиться только после
выезда из ствола всех участвующих в заряжании. Инициирующие устройства СИНВ-Ш с
замедлением (в дальнейшем именуемые устройства) собираются в соединители ИВШП
326.000 не более 18 волноводов в пучки. От пучков к связке детонирующих шнуров
подсоединяют два электродетонатора (один контрольный). Взрывник
(мастер-взрывник) в сопровождении руководителя взрывных работ снимает
«закоротку» с магистральных проводов, подсоединяет концы электродетонаторов к
магистральным проводам, выезжает на проходческий полок, снимает с рубильника
взрывного кабеля «закоротку» и оба выезжают на поверхность. Перед проведением
взрывных работ (ВР) все люди, не занятые производством ВР должны быть удалены
от устья ствола не менее чем на 70м согласно утвержденной «Схемы выставления
постов охраны запретной (опасной) зоны...».
После этого взрывник открывает замок взрывной
станции, подсоединяет жилы, снимает «закоротку» с взрывного кабеля, производит
проверку токопроводности взрывной сети и по разрешению руководителя взрывных
работ производит взрывание. Взрывание забоя производиться взрывным прибором
КВП-2/200.
При производстве взрывных работ все люди из
ствола должны быть выведены на поверхность.
Боевики изготавливаются в будке, установленной в
50 м от устья ствола согласно «Проекту производства БВР...».
9.2 Уборка породы
После окончания проветривания и приведения забоя
ствола в безопасное состояние, проходческий полок для погрузки породы
опускается на высоту 10-12м от забоя, центрируется по бадьям и раскрепляется
домкратами. Машинисты подъемных установок №1 и №2 должны сделать отметки на
указателях глубины о новом положении полка в стволе.
Порода из забоя ствола породопогрузочным
комплексом 2КС-2у/40 грузится в бадьи БПСМ-5.0 и выдается на поверхность.
Уборка взорванной породы в стволе выполняется в
две фазы. Первоначально уборка породы производится на высоту 2,5 м от опорных
плит домкратов для монтажа очередного тюбингового кольца на монтажном кольце
-полке.
Вторая фаза уборки породы начинается после
окончания укладки бетонной смеси за тюбинги и набора бетоном необходимой
прочности.
При погрузке породы помощник машиниста должен
следить за тем, чтобы погрузка производилась равномерно и бадья не догружалась
до верха на 100 мм. Закончив погрузку бадьи, машинист дает сигнал об окончании
работы, погрузочная машина освобождает проход бадье, которая по сигналу
помощника машиниста выдается на поверхность с выполнением требований
безопасности по ее очистке.
Для исключения посадки бадей на комплекс
2КС-2у/40 предусматривается электрическая блокировка: при нахождении грузчика в
сечении раструба запуск подъемной машины исключается.
Гидроизоляция крепи
Работы по гидроизоляции крепи проводятся в
соответствии с «Временной инструкцией по сооружению тюбинговой крепи»
разработанной ЗАО «Шахтспецпроект» г. Москва, 2008г.
Водонепроницаемость тюбинговой крепи
обеспечивается герметизацией тюбинговой колонны и тампонажем затюбингового
пространства. Работы проводятся в два этапа:
предварительная гидроизоляция крепи при ее
возведении с проходческого полка;
гидроизоляции крепи при оттаивании собственно
крепи и частично ледопородного ограждения на величину до 1 м;
Предварительная гидроизоляция тюбинговой крепи
при ее возведении должна иметь целью качественную установку всех
гидроизоляционных деталей.
Все работы основного этапа выполняются со
специального тампонажного полка в направлении снизу вверх, начиная с подошвы
последнего водоносного горизонта.
На этом же этапе должна выполняется контрольная
обтяжка болтовых соединений, и подчеканка свинцовых прокладок в швах тюбинговой
крепи. Одновременно с этим через тампонажные отверстия бурятся горизонтальные
шпуры на глубину до 1,0 - 2,0 м от контура
ствола в свету, через которые нагнетается тампонажный раствор при давлении,
превышающем расчётное гидростатическое давление на 0,5-1,0 МПа.
Устранение возможных утечек в тюбинговой крепи
ствола выполняется с тампонажного полка.
Остаточный приток в пройденный ствол калийной
или соляной шахты, а также на месторождениях, где существует опасность размыва
нижерасположенных пластов соли, не должен превышать 0,15 м7ч.
При выполнении работ по нагнетанию раствора
необходимо соблюдать следующие правила:
о нагнетание тампонажного раствора производить
путем постепенного увеличения давления насоса; запрещается превышать давление
нагнетания более чем предусмотрено проектом производства работ;
при резком увеличении давления нагнетания
раствора свыше допустимых пределов отключить насос и плавно перекрыть кран;
при монтаже и эксплуатации тампонажного
оборудования следить за тем, чтобы соединительная и запорная арматура, концы
нагнетательных шлангов были прочно закреплены, а манометры показывали
допустимые давления, предусмотренные проектом производства работ;
при отсоединении нагнетательного шланга от
тампонажных отверстий тюбингов необходимо располагаться так, чтобы при
возможном выбросе раствор не попал в человека;
для предотвращения аварийных ситуаций
запрещается: производить другие работы в стволе во время нагнетания раствора,
производить ремонт тампонажного оборудования и системы трубопроводов,
находящихся под давлением;
о запрещается производить быстрое перекрывание
кранов на коммуникациях раствора, находиться вблизи нагнетательной системы
лицам, не связанным с производством тампонажных работ, снимать заглушку с
тампонажного отверстия тюбинга после испытания раньше снижения в ней давления
до атмосферного;
о запрещается также оставлять без присмотра
насос во время его работы, применять неисправные манометры, производить
нагнетание раствора при неисправном предохранительном клапане, применять шланги
имеющие вздутие;
о запрещается пуск насоса при закрытых
задвижках, пускать насос после длительной остановки зимой без проверки
проходимости нагнетательного трубопровода, продавливать с помощью насоса
пробки, образовавшиеся в трубопроводе, соединения должны выполняться с помощью
устройств предусмотренных конструкцией насоса или при помощи стяжных хомутов.
Проходка сопряжений
Проходка сопряжений осуществляется после
проходки ствола по последовательной схеме. Разработка породы осуществляется
буровзрывным способом, почвоуступным забоем. По мере проходки сопряжение
крепится временной анкерной крепью. Постоянная крепь сопряжения возводится в
деревянной опалубке. Армирование бетонной смеси осуществляется введением в ее
состав специальной металлический стружки - «фибры». После приобретения
железобетоном распалубочной
прочности деревянная опалубка и временные рабочие полки разбираются, материал
выдается на поверхность.
Проходка выработок загрузочного
комплекса
Проведение выработок загрузочного комплекса
ствола №1 производится после окончания проходки и крепления ствола.
Загрузочные комплексы ствола №1 располагаются в
подстилающей толще каменной соли и относящейся к числу не опасных по горючим
газам.
(«Специальные мероприятия по безопасному ведению
горных работ на Верхнекамском месторождении калийных солей в условиях газового
режима в Филиале ОАО «Ковдорский ГОК г. Усолье (Палашерский и Балахонцевский
участки)» [86].
Загрузочный комплекс скипового ствола №1 состоит
из двух отдельных загрузочных комплексов №] и №2 (графические материалы.
779/1-П-5.7.30.7.1/20-07ПР/10-ГПР).
Для проходки и строительства загрузочных
комплексов в районе камер питателей и конвейеров (уровень отметок кровли)
загрузочного оставляются незакрепленные проемы в тюбинговой крепи ствола.
После проходки выработок загрузочного комплекса,
тюбинговая крепь в проёме восстанавливается.
Строительство комплекса загрузки скипов
начинается со стороны ствола (после завершения его проходки и крепления) с
проходки выработок околоствольного двора откаточного горизонта первоначально
для загрузочного комплекса №1, а затем и загрузочного комплекса №2.
Порядок работ по сооружению загрузочных
комплексов следующий:
завершаются все проходческие работы по камерам
питателей, конвейеров и дозаторной во временном креплении;
проходятся восстающие выработки:
смотровой
восстающий со смотровыми ходками
и восстающий по оси приствольного бункера;
производится расширение приствольного бункера до
проектного сечения вчерне во временном креплении.
Строительство каждой выработки околоствольного
двора начинается с проходки пилотной выработки, с последующим её расширением до
проектного сечения.
Длина обеих тупиковых выработок должна
перекрывать ось выхода бункера на откаточный горизонт на 5-6м.
Сооружение каждого бункера начинается с проходки
наклонной выработки с помощью КГ1Н-4А (сеч. 2.2 м2) из камеры питателя и
конвейеров до сбойки с околоствольной выработкой откаточного горизонта.
После сбойки наклонной выработки с откаточным
горизонтом проводится ее расширение до проектного сечения бункера - 42.4 м2
сверху вниз, с временным креплением и последующим креплением постоянным видом
крепи - сборная металлокрепь.
Крепление бункеров тюбинговыми кольцами
производится снизу вверх. Закладка затюбингового пространства производиться
бетоном класса В40.
10. Требования безопасности при
проходке
Подвесной проходческий полок, проходческие
бадьи, поргузочно - разгрузочные операции, спуск - подъем людей по стволу,
перегон полка и другого подвесного оборудования в стволе
Призабойная часть проходимого ствола оборудуется
подвесным полком. Одноэтажные подвесные полки должны быть подвешены к канату не
менее чем в четырех местах; двух- или многоэтажные полки должны крепиться к
канату так, чтобы при их перемещении не нарушалась горизонтальная устойчивость,
и исключались заклинивания.
При параллельном ведении работ по проходке
ствола и возведению постоянной крепи с подвесного полка последний должен иметь
верхний этаж для защиты работающих на полке от возможного падения предметов
сверху. Зазор между полком и возводимой крепью ствола, опалубкой или щитом-
оболочкой, должен быть не более 120 мм, считая от выступающих ребер кружал и во
время работы должен плотно перекрываться.
При совмещенной схеме зазор между полком и
крепью ствола должен быть не более 400 мм. На всех этажах полка по его
периметру должно быть решетчатое ограждение высотой не менее 1400 мм. Нижняя
часть ограждения должна иметь сплошную металлическую обшивку высотой не менее
300 мм.
Проемы для раструбов между этажами полка должны
быть отшиты металлической сеткой с ячейками размерами не более 40x40 мм. В нижней
части раструба в местах примыкания сетки к полку, отшивка выполняется сплошным
ограждением высотой не менее 300 мм. Высота раструба над верхним этажом полка
должна быть не менее 1600 мм.
При выдаче породы бадьями ствол должен
открываться только в части, необходимой для пропуска бадей, при этом ляды
должны открываться только в момент прохода последних. Конструкция ляд должна
исключать падение в ствол породы или иных предметов при разгрузке бадей. Проем
для пропуска бадей должен иметь по периметру сплошное металлическое ограждение,
выполненное из швеллера, высотой не менее 250 мм над уровнем настила перекрытия
нулевой площадки.
При спуске и подъеме грузов бадья должна
недогружаться на 100мм до верхнего края борта.
Бадьи должны перемещаться по направляющим:
движение бадей без направляющих допускается на расстоянии не более 20м от
забоя. При использовании на проходке вертикальных выработок проходческих
агрегатов (погрузочных машин) это расстояние может быть увеличено до 40 м.
При проходке вертикальных стволов для подвески
бадей и проходческого оборудования должны применяться нераскручивающиеся канаты
(п.8.3.1 ПБ 03-428-02).
Канаты для подъемных установок всех систем
должны подбираться при навеске со следующим запасом прочности:
-кратный - для отбойных канатов и канатов
проводников проходческих подъемов;
-кратный - для спасательных лестниц, канатов
подвески полков, насосов, трубопроводов, проходческих агрегатов (п.8.3.2 ПБ
03-428-02).
Запрещается спуск и подъем людей в бадьях без
направляющих рамок и зонтов, направляющая рамка должна оборудоваться
сигнализацией о ее зависании.
Посадка людей в бадьи и выход из них должны
производиться на нижней приемной площадке по приставной лестнице или по
ступенькам бадьи только при закрытых лядах и установленной на них бадье. Перед
спуском людей в ствол обязательным условием является обеспечение каждого
работника зарегистрированным и прошедшим испытания в установленном порядке
индивидуальным предохранительным поясом.
Проемы в нулевом перекрытии для пропуска
трубопроводов, канатов, кабелей должны быть надежно перекрыты или ограждены
раструбами, которые в нижней части должны быть сплошными на высоту не менее 300
мм.
При производстве работ по проходке должны
применяться грузозахватные приспособления (стропы, траверсы, серьги и др.),
изготовленные на специализированных предприятиях в соответствии с ТУ,
испытанные и промаркированные.
При спуске-подъеме длинномерных или негабаритных
грузов (труб, рельс, сегментов, лесоматериалов, оборудования) подвешенных к
канату, запрещается работа других подъемных машин и проходческих лебедок.
При открытых лядах запрещается погрузка
материалов в бадью и подвеска предметов к канату.
Зазор между стенками раструба проходческого
полка и выступающими частями движущейся направляющей рамки или бадьи должен
быть не менее 100 мм, в том числе - на нулевой и разгрузочной площадках.
Дужка бадьи подлежит замене или ремонту при
износе ее проушины или сменной втулки в проушине более чем на 5% диаметра оси.
Суммарный износ проушины или сменной втулки дужки и оси, соединяющей ее с
бадьей, не должен превышать 10% диаметра оси.
При подъеме и спуске людей в бадьях по
направляющим наибольшая скорость должна быть не более 8 м/с, а в местах, где
направляющие отсутствуют - не более I м/с. При подъеме и спуске грузов в бадьях
по направляющим скорость движения бадей не должна превышать 12 м/с, а в местах,
где направляющие отсутствуют ~ 2 м/с.
Высота переподъема для подъемных установок в
вертикальных выработок должна быть на бадьевом (проходческом) подъеме при
спуске и подъеме людей не менее 4 м.
Высотой переподъема следует считать для
бадьевого подъема при спуске и подъеме людей - высоту, на которую может
свободно подняться бадья от нулевой площадки до соприкосновения верхнего жимка
каната или верхней кромки направляющей рамки с ободом направляющего шкива или с
выступающими частями металлоконструкций подшкивной площадки. При этом высота,
на которую может подняться бадья от верхней приемной площадки при разгрузке
грузов до соприкосновения верхнего жимка каната или верхней кромки направляющей
рамки с ободом направляющего шкива или металлоконструкциями подшкивной
площадки, должна быть не менее м.
Перемещение полков, монтажного кольца,
трубопроводов, кабелей, отвесов должно производиться по сигналам, подаваемым по
схеме: полок - нулевая площадка - пульт управления лебедками.
При перемещении оборудования запрещается:
одновременно подавать сигналы на подъемную
машину и лебедки;
вести другие работы в забое ствола и на полке;
находиться в стволе лицам, не занятым на работах
по перемещению оборудования;
перемещать подвесное проходческое оборудование в
случае его перекоса или заклинивания до восстановления нормального положения,
которое разрешается только перемещением полка вниз или вверх в зависимости от
причины перекоса;
Возобновление работ по проходке или углубке
ствола после перемещения оборудования допускается при следующих условиях:
полок должен быть отцентрирован по бадьям и
раскреплен домкратами;
на указателе глубины и на реборде барабана
подъемной машины должны быть нанесены отметки о новом положении полков;
должны быть проверены надежность закрепления
ставов труб, кабелей, с соблюдением зазоров;
все лебедки должны быть заторможены, их
предохранительные храповые остановы - поставлены в рабочее положение,
напряжение с лебедок должно быть снято, сжатый воздух отключен, здания лебедок
закрыты на замок.
При перемещении полка запрещается:
работать (находиться) на полке без
предохранительного пояса; -перемещать полок, если происходит проскальзывание
каната при не вращающемся шкиве или ослаблении жимков каната.
Управление проходческими лебедками должно
вестись строго по установленным в проекте производства работ сигналам.
Сигнализация для проходческих лебедок может быть как механической, так и
электрической с использованием звукового и светового сигналов. Таблица сигналов
для проходческих лебедок должна быть вывешена у пульта управления лебедок и у
лебедок.
Каждая подъемная установка (при проходке ствола)
должна иметь не менее двух независимых сигнальных устройств, одно из которых
должно выполнять функции рабочей сигнализации, а второе резервной и ремонтной.
Устройство рабочей сигнализации должно обеспечивать возможность подачи сигналов
из забоя на полок, с полка - рукоятчику и от рукоятчика - машинисту, а
ремонтной или резервной, если она выполняет функции ремонтной, - с любой точки
ствола.
Выход людей из бадьи и посадка в нее для
обслуживания перекачных станций при схеме многоступенчатого водоотлива должны
производиться с откидных площадок с применением предохранительных поясов.
При проходке ствола №1, на участке от кровли
карналитовой зоны до подошвы сильвинитовой зоны, рабочую зону следует относить
к III группе газовой опасности, с учетом выполнения при проходке условий,
изложенных в разделах «Специальных мероприятий...» [86].
Контроль за состоянием рудничной атмосферы при
проходке ствола в зонах опасных по газовыделениям выполнять в соответствии с
требованиями положений разделов «Специальных мероприятий...» [86].
Безопасность при погрузке породы в забое
В звене проходчиков, занятых на уборке породы,
назначается ответственный за подачу сигналов, который должен:
следить за тем, чтобы при погрузке породы бадья
недогружалась на 100 мм до борта;
постоянно следить за перемещением бадьи и груза;
перед подачей сигнала на подъем бадьи или груза
предупредить об этом всех находящихся в забое проходчиков;
приподняв бадью над забоем на 1,0-1,5 м, дать
сигнал «СТОП», успокоить бадью от колебаний, обобрать ее днище и боковую
поверхность от налипшей
породы;
после подачи сигнала на подъем наблюдать за
грузом или бадьей до входа в проем полка;
при подходе бадьи или груза к забою предупредить
об этом проходчиков, стоящих под местом опускания бадьи. Если бадья не
останавливается в 5 м от забоя или движется без видимого замедления, необходимо
дать сигнал «СТОП».
При уборке породы при проходке работающие в
забое должны:
следить за состоянием боковых пород;
производить оборку боковых пород;
удалять наплывы бетона в нижней части заходки,
если они имеются.
Запрещается:
заходить в зону действия погрузчика;
находиться под поднятым грейфером и на пути его
следования от места погрузки до бадьи.
Проходчик, занимающийся управлением грейферным
погрузчиком, должен:
следить, чтобы в зоне действия не находились
люди, предупреждать людей об уходе в безопасное место (кабина машиниста должна
быть снабжена сигнальным устройством типа «СИРЕНА»);
погрузку породы в бадью начинать только тогда,
когда бадья установлена на забое, опущена дужка и снято или отведено прицепное
устройство;
использовать грейферный погрузчик только по его
прямому назначению;
при работе пневмопогрузчика следить за
состоянием воздушных шлангов, своевременно устранять утечки воздуха, являющиеся
дополнительными источниками шума;
при перерывах в работе поднять пневмопогрузчик,
закрыть лопасти грейфера, поставить его на забой и перекрыть кран подачи
воздуха.
Запрещается:
производить разгрузку грейфера при перецепке
бадей.
При погрузке породы грейфером, управляемым с
поверхности и подъеме грейфера для разгрузки породы, людям запрещается
находиться в забое.
Величина отставания постоянной крепи от забоя и
взорванной горной массы и, соответственно, допустимое обнажение породных стенок
принимается равной высоте двух тюбинговых колец. При неустойчивых,
раздробленных породах устанавливается временная крепь.
10.1 Проветривание ствола при
проходке
Организация проветривания и количество воздуха,
необходимого для проветривания отдельных выработок и шахты в целом, должны
определяться для каждого месторождения по специальным методикам, согласованным
с Госгортехнадзором России или, по его разрешению, с территориальными органами.
Расчет необходимого количества воздуха для проветривания горной выработки и ее
забоя, организация проветривания с указанием схемы проветривания и типа
вентилятора, дополнительные меры безопасности должны быть выполнены в проектной
документации, проекте организации работ и паспорте на проветривание горной
выработки, утвержденных в установленном порядке.
Расход воздуха при дальнейшей проходке ствола
буровзрывным способом следует определять по метановыделению, необходимому
разжижению ядовитых газов после взрывных работ, наибольшему числу работающих в
стволе людей и минимально допустимой скорости движения воздуха. Из приведенных
выше факторов определяющим количество воздуха подаваемого в ствол, является
фактор по ядовитым газам после взрывных работ.
Расчет потребного количества воздуха для
проветривания забоя необходимо выполнить согласно «Временной инструкции по
проектированию вентиляции при проходке и углубке стволов» разработанной
институтом
ВНИИОМШС»,
согласованной
Госгортехнадзором
России и «Временному технологическому регламенту по организации проветривания
рудника Усольского калийного комбината на Палашерском и Балахонцевском участках
ВКМКС», разработанному ГОУ В1 Ю «Пермский государственный технический
университет» (ПГТУ) и согласованному Ростехнадзором.
Согласно проведенным предварительным расчетам
необходимая потребность в воздухе для проветривания ствола №1 на полную
проектную глубину с учетом коэффициента утечек составит 0-и,.тах“19,9м7с. Для
обеспечения требуемого воздухообмена может быть принята вентиляторная установка
из одного вентилятора ВЦП-16М (Q= 20-46 м7с, Р= 200-920 даПа) в комплекте с
реверсирующим устройством заводского изготовления.
Здание вентилятора должно находиться не ближе 15
м от строящегося ствола. Режим работы вентиляторной установки должен быть
круглосуточный непрерывный. Способ проветривания ствола нагнетательный. Для
сокращения времени проветривании забоя после производства взрывных работ
следует предусмотреть устройство нагнетательной схемы вентиляции с возможностью
реверсирования воздушного потока. Реверсивное устройство вентилятора ВЦП-16М
представляет собой систему обводных каналов - металлических коробов вокруг
вентилятора, через которые струя воздушного потока по вентиляционному трубопроводу
направляется в забой или из забоя ствола в зависимости от режима работы
вентилятора. Регулирование направление движения воздушной струи осуществляется
посредством запорных заслонок, которые в реверсивном режиме перекрывают сечение
вентиляционного става на выходе (диффузоре) вентилятора, направляя весь
воздушный поток в амтосферу мимо стволового вентиляционного трубопровода, а
также одновременно открывают обводной канал конфузора вентилятора (на «всасе»)
и закрывают забор воздуха из атмосферы. Реверсивное устройство должно быть
изготовлено в соответствии с инструкцией по эксплуатации вентилятора ВЦП-16М и
рабочей документацией завода-изготовителя в заводских условиях и поставляться
заказчику в комплекте с вентилятором.
При работе вентилятора по всасывающей схеме в
реверсивном режиме воздуховод должен быть выполнен из эластичного
гофрированного рукава 0800-1200 мм секциями по 6 м. Подвеска вентиляционных
рукавов выполняется на тюбинговой крепи при помощи специальных хомутов.
Ствол должен проветриваться на всю глубину в
течение всего времени его строительства.
Вентиляционные установки для проветривания
ствола должны находиться на поверхности не ближе 15 м от стволов и работать
непрерывно. В холодный период года воздух, поступающий в ствол, должен
подогреваться до температуры не
ниже 2°С. Для обеспечения требуемых параметров воздуха поступающего в ствол в
холодное время года, предусмотрен подогрев воздуха. Калориферная установка
принята из расчета обеспечения подогрева воздуха, поступающего в ствол на
уровне нулевой отметки, до температуры не ниже +2*С.
Максимальная мощность калориферов NK
рассчитывается по формуле:
-V = 1.276хд,„А', 1.276*21х[2-(-45)] =
1206кВт
где: Q3.n =21 м3/с - максимальный расход
воздуха;= +2°С - температура воздуха подаваемого для проветривания; tH = -45°С
- расчетная температура наружного воздуха.
Исходя из этого, для подогрева, подаваемого в
ствол воздуха, приняты электрокалориферы типа СФО - 160кВт, изготавливаемые
по
ТУ 3442-010-12589972-00 заводом электронагревательного оборудования «ДЕЛСОТ» г.
Миасс, Челябинской области. Всего для обеспечения работы вентиляционных систем
предусматривается установить 8 указанных калориферов. Высота одного калорифера
1080 мм, ширина - 710 мм.
Предусматриваются устройства и аппаратура для
регулирования температуры, поступающего в ствол воздуха в пределах 2-5°С.
Система управления калориферной установкой
позволяет осуществлять контроль следующих параметров ее работы:
температуры наружного воздуха с ее регистрацией;
температуры воздуха после прохода калорифера;
температуры поступающего в ствол подогретого
воздуха с ее регистрацией;
потерь давления на всасывающей и нагнетательной
стороне вентиляторной установки.
Для проветривания должны применяться трубы из
жесткого материала. Допускается навешивать гибкую вентиляционную трубу у забоя.
Расстояние конца вентиляционных труб до забоя должно быть не более 15 м, а во
время погрузки грейфером - 20 м.
Максимальная скорость воздуха не должна
превышать 8 м/с в стволах, по которым производится спуск и подъем людей и
грузов.
Минимальная скорость воздуха должна быть не
менее
4/диаметр
ствола, м/с (п.114 ПБ 03-553-03).
Учитывая то, что согласно данным геологических
отчетов и исследований на участке проходки ствола №1 до глубины 270 м (до
кровли соляной толщи) газодинамичесих явлений и выделения взрывоопасных и
ядовитых газов не выявлено, контроль за состояние рудничной атмосферы на
указанном участке проходки ствола должен осуществляться в обычном порядке
согласно ПБ-03-553-03.
Контроль за состоянием рудничной атмосферы осуществлять
в соответствии с положениями п.6.3.11 настоящего технологического регламента.
При проходке ствола на участках от кровли
карналлитовой зоны до подошвы сильвинитовой зоны (III группа по газовой
опасности), где обнаружен метан (водород) или ожидается его выделение, должен
соблюдаться газовый режим и все технологические процессы и операции должны
выполняться в строгом соответствии с требованиями положений разделов
«Специальных мероприятиям..» [86].
Контроль состава рудничной атмосферы выполнять в
соответствии с требованием разделов «Специальных мероприятий...» [86]:
Раздел 4 «Специальных мероприятий...»
Общие требования.
Контроль за составом рудничной атмосферы
подразделяется на плановый и оперативный.
Плановый контроль осуществляется путем отбора проб
воздуха с последующим их лабораторным анализом в соответствии с порядком отбора
проб рудничного воздуха, указанного в Технологическом регламенте по организации
проветривания рудника. Конкретные места и сроки отбора проб устанавливаются
ежеквартальным планом, утвержденным главным инженером рудника по согласованию с
ВГСЧ. На основании этих планов начальник подземного участка вентиляции горных
выработок совместно с лабораторией ВГСЧ составляет на каждый месяц график
отбора проб с уточнениями и корректировками согласно регламенту производства
горных работ на руднике.
Отбор проб производится респираторщиками ВГСЧ
или специально назначенными лицами в присутствии представителя подземного
участка вентиляции горных выработок по наряду, подписанному начальником этого
участка. В наряде отмечается вид выполняемых работ в месте отбора проб
(проходка, ремонт и т.д.).
Результаты анализа проб передаются начальнику
подземного участка вентиляции горных выработок и заносятся по окончании месяца
в «Вентиляционный журнал». «Вентиляционный журнал» может вестись в течение
месяца в электронном виде. Форма и порядок ведения данного журнала определяется
Технологическим регламентом по организации проветривания рудника.
Один раз в три года на руднике должна
выполняться плановая газовоздушная и депрессионная съемка специализированной
организацией, результаты исследований должны быть представлены в виде отчетов,
утверждаемых главным инженером филиала.
Оперативный контроль газовой обстановки в
рабочих зонах осуществляется машинистами комбайнов, бригадирами или звеньевыми,
работающими в данных выработках. Ответственность за осуществление оперативного
контроля газовой обстановки в рабочих зонах в каждую смену возлагается на
технический надзор участка.
Лицо технического надзора должно обеспечить
замер концентрации горючих газов во всех выработках рабочей зоны машинистами
комбайнов, бригадирами или звеньевыми, работающими в данных выработках, с ниже-
установленной периодичностью и лично осуществлять контрольные замеры содержания
газа в каждой выработке. Результаты текущих и контрольных замеров должны
записываться в "Журнал замеров горючих газов", находящийся на участке
(комбайне).
. Замеры содержания горючих газов должны
производиться согласно «Инструкции по замеру горючих газов на руднике с периодичностью:я
группа по газовой опасности (опасные по горючим газам).
Во всех действующих тупиковых выработках - не
реже двух раз в рабочую смену, причем первый замер должен быть сделан в начале
смены;
В рабочих зонах, где ведутся закладочные работы,
а также в гаражах, складах ГСМ, других камерах служебного назначения,
пройденных по сильвинитовым пластам - не менее одного раза в рабочую смену.
Кроме того, не реже одного раза в сутки замер
содержания горючих газов в каждой действующей тупиковой выработке всех рабочих
зон должен производиться инженерно-техническими работниками или газомерщиками
подземного горного участка вентиляции горных выработок.
При каждом посещении рабочей зоны начальником
участка, его заместителями, механиком, энергетиком (электромехаником) участка
они обязаны замерить концентрацию газа в каждой посещаемой действующей
выработке. При посещении рабочей зоны другими инженерно-техническими
работниками рудника, без сопровождения их лицами технического надзора участка,
они обязаны замерить концентрацию газа в каждой посещаемой действующей
выработке.
Н-я группа по газовой опасности (опасные по
горючим газам и ГДЯ).
Замеры концентрации горючих газов в выработках
рабочих зон, выполняемые
машинистами комбайнов, бригадирами или звеньевыми, должны производиться не реже
трех раз в смену (первый замер в начале смены). Контрольные замеры лицом
сменного надзора должны производиться во всех действующих выработках не реже
двух раз в смену. Контрольные замеры работниками подземного участка вентиляции
горных выработок должны производиться не реже одного раза в сутки.
В качестве средств оперативного контроля наряду
с переносными приборами эпизодического действия должны применяться приборы
непрерывного действия, с последующим переходом на стационарные приборы непрерывного
действия.я группа по газовой опасности (особо опасные по горючим газам или по
газам и ГДЯ).
Во всех действующих тупиковых выработках рабочих
зон замеры концентрации горючих газов производятся газомерщиком-респираторщико
ВГСЧ по заданию лица технического надзора участка не реже чем через каждые два
часа рабочей смены (в том числе один раз в начале смены).
Оперативный контроль, выполняемый машинистами
комбайнов, бригадирами и звеньевыми, должен производиться не реже чем через
каждые два часа рабочей смены (первый замер в начале смены). Контрольные замеры
сменным надзором участка должны производиться не реже трех раз в смену.
Инженерно-технические работники или газомерщики участка вентиляции должны
осуществлять контроль содержания горючих газов во всех действующих выработках
рабочих зон не реже двух раз в сутки.
В качестве основного технического средства
оперативного контроля содержания горючих газов во всех действующих выработках
должны применяться стационарные приборы непрерывного действия, установленные на
забойном оборудовании. Замеры концентрации горючих газов машинистами комбайнов,
респираторщиками ВГСЧ, газомерщиками и лицами технического надзора могут
производиться переносными приборами эпизодического и непрерывного действия.
«Инструкция по замеру горючих газов на руднике,
расположенном на Балахонцевском и Палашерском участках Верхнекамского
месторождения калийных солей»
Общие положения
Действие инструкции распространяется на рабочие
зоны, отнесенные к числу опасных по газу. Инструкцией предусматривается порядок
и методика производства замеров метана, водорода и сероводорода шахтными
газоопределителями периодического и непрерывного действия (типа ГИК-3, ИКГ-4Р,
АМ-5 и других), допущенных к применению на Верхнекамских калийных рудниках в
установленном порядке.
Эксплуатация приборов должна осуществляться в
строгом соответствии с технической инструкцией завода-изготовителя.
Замерам содержания горючих газов должны быть
обучены все рабочие и инженерно-технические работники, работники ВГСЧ, занятые
на подземных горных работах.
Все лица, допущенные к замеру горючих газов,
должны сдать экзамены по правилам применения газоопределителей и измерителей, с
проведением повторных проверок знаний при инструктажах по ОТ и ПБ не реже
одного раза в 6 месяцев.
Проводить замеры обязаны следующие лица, которые
должны иметь при себе приборы контроля:
все инженерно-технические работники рудника,
выполняющие рабочие или контрольные функции в рабочих зонах, отнесенных к числу
опасных по газу;
газомерщики, бригадиры, звеньевые, машинисты
комбайнов, взрывники (мастера-взрывники), бурильщики шпуров и разведочных
скважин;
респираторщики ВГСЧ.
Указанные лица должны производить замеры газа
при каждом посещении рабочих зон, опасных по газу, с оценкой газовой
обстановки.
Требования настоящего пункта распространяются на
инженерно- технических работников, производящих горные и строительно-монтажные
работы в рудниках.
Лица, производящие замеры газов, несут
ответственность за правильность и своевременность проводимых замеров,
сохранность приборов и за действия, связанные с нормализацией газовой
обстановки.
При производстве замеров должна определяться
суммарная концентрация горючих газов (метана и водорода); при раздельных
замерах метана и водорода показание прибора о содержании водорода должно
удваиваться:
Crop. = С(Ссн4 + 2Н2).
10.2 Замеры содержания горючих газов
Места и периодичность замеров горючих газов.
Во всех действующих тупиковых очистных и
подготовительных выработках рабочих зон, отнесенных к I группе опасности,
замеры горючих газов должны производиться не реже двух раз в рабочую смену
машинистами комбайнов, бригадирами или звеньевыми, работающими в данных
выработках. Причем, первый замер должен быть сделан в начале смены перед
началом работ. Этот замер должен производиться лицами технического надзора
участка или по их письменному наряду замер может быть выполнен машинистами
комбайнов, бригадирами или звеньевыми, работающими в данных выработках. Не реже
одного раза в смену во всех этих выработках лицом технического надзора участка
должен быть выполнен контрольный замер газа.
В рабочих зонах, где ведутся закладочные работы,
в неот- перемыченных недействующих проветриваемых выработках, гаражах, склада
ГСМ, других камерах служебного назначения в пределах рабочих зон, замеры
горючих газов должны производиться не менее одного раза в рабочую смену. Эти
замеры выполняются лицом технического надзора участка.
Не реже одного раза в сутки замеры содержания
горючих газов в каждой действующей выработке всех рабочих зон должны
производиться инженерно-техническими работниками или газомерщиками ПУВГВ.
При каждом посещении опасных по газу рабочих зон
начальником участка, его заместителем, механиком или энергетиком
(электромехаником) участка они обязаны произвести замер горючих газов в каждой
рабочей выработке. При посещении рабочих зон другими инженерно-техническими
работниками рудника, без сопровождения тех. надзора участка, они обязаны
провести замеры горючих газов во всех посещаемых ими выработках.
В действующих выработках рабочих зон II группы
опасности, замеры горючих газов, предусмотренные п. 2.1.1. должны выполняться с
периодичностью не реже трех раз в рабочую смену (в том числе один раз в начале
смены), а контрольные замеры лицом технического надзора участка не реже двух
раз в смену.
Оперативный контроль, выполняемый машинистами
комбайнов, бригадирами и звеньевыми, в выработках рабочих зон III группы
опасности, должен производиться не реже, чем через каждые два часа рабочей
смены (в том числе один раз в начале смены). Контрольные замеры лицами технического
надзора участка должны производиться не реже трех раз в смену.
Инженерно-технические работники или газомерщики участка вентиляции должны
осуществлять контроль содержания горючих газов во всех действующих выработках
рабочих зон не реже двух раз в сутки.
Во всех тупиковых очистных и подготовительных
выработках рабочих зон III группы опасности замеры концентрации горючих газов
производятся респираторщиком ВГСЧ по заданию лица технического надзора участка
не реже чем через каждые два часа рабочей смены (в том числе один раз в начале
смены).
Перед заряжанием и перед взрыванием шпуров в
забоях выработок рабочих зон III группы опасности производится замер содержания
горючих газов лицом технического надзора.
После взрывания в забое лицо технического надзора
и сопровождающий его респираторщик ВГСЧ, включившись в респираторы, должны
замерить концентрацию газа у ВМП и пусковой аппаратуры.
При отсутствии горючих газов у ВМП и пусковой
аппаратуры и исправной электросети лицо технического надзора включает ВМП для
проветривания забоя.
При обнаружении содержания горючих газов с
концентрацией выше 0,5 % по объему (10% НКПР) респираторщик ВГСЧ отбирает пробы
на химический анализ, а лицо технического надзора сообщает об этом диспетчеру
рудника, начальнику участка, главному инженеру рудника для принятия мер по раз
газированию.
При производстве разовых работ замеры горючих
газов осуществляются лицами технического надзора с периодичностью,
предусмотренной п.п. 2.1.1, 2.1.5, 2.1.6.
Порядок замера содержания горючих газов:
Порядок проведения замеров должен строго
соответствовать технической инструкции завода-изготовителя на используемые
приборы.
Запрещается использование неисправных и не
прошедших государственную поверку приборов.
При выборе конкретных точек замера необходимо
соблюдать следующие требования:
точка замера в действующих тупиковых очистных и
подготовительных выработках должна быть расположена в забое выработки, но не
далее 20 м от груди забоя на расстоянии не более 0,5 м от кровли выработки;
при проведении второго и последующих комбайновых
ходов в очистных камерах замер производится под кровлей выработки в максимально
возможной близости от забоя камеры, но не далее 20 м от него;
при отработке камер буровзрывным способом с
разрезной выработкой замер производится в верхней отработанной части камеры на
расстоянии от забоя не более 20 м, а также под кровлей разрезной выработки на
расстоянии не более 5 м от забоя камеры;
в протяженных тупиковых выработках (200 м и
более), имеющих по длине поднятия и опускания, замеры производятся также и в
местах поднятий;
в местах резкого увеличения мощности пласта,
вскрытия антиклинальных складок и открытых трещин (полостей) производятся
замеры горючих газов газомерщиками или инженерно-техническими работниками ПУВГВ
не реже одного раза в сутки;
при наличии в пределах рабочих зон перемычек,
изолирующих недействующие выработки, точка замера должна выбираться под кровлей
рабочей выработки в непосредственной близости от перемычки, но не далее 2-х м
от нее;
при производстве разовых работ: огневых,
взрывных, бурении скважин и др. точка замера газа должна выбираться под кровлей
выработки непосредственно в месте проведения работ или на расстоянии от него со
стороны исходящей струи не более 5 м;
для выявления местных (в том числе слоевых)
скоплений горючих газов замеры должны проводиться непосредственно у кровли
выработки;
доступным для замера местом принимается зона
выработки, ограниченная высотой не более 4 м;
для замера в труднодоступных местах и в
выработках с высотой 4 м и более необходимо использовать лестницы или леса;
в местах с явными признаками выделения газов
(шипение, пузырьки газа и влаги, микросуфляры и т. п.) замеры производятся
рабочими и техническим надзором участка через каждые два часа до прекращения
газовыделений.
В тупиковых, временно не действующих,
непроветриваемых выработках, расположенных в рабочих зонах, отнесенных к
опасным по газу (разрезные выработки, уклоны, забои выемочных и вентиляционных
панельных и блоковых выработок), для оценки степени загазирования выработки один
раз в месяц должны проводиться контрольные замеры по следующей методике:
В устье выработки и на расстоянии 10 м от него в
сторону забоя производится два последовательных замера концентрации газа под
кровлей выработки. На основании этих замеров определяется концентрация газа в
забое выработки по формулам:
а) при расположении забоя выше устья
выработки (расчет ведется только в случае обнаружения горючих газов при замерах
С[ и С2)
С3=С ,+0,1 xL(0,15+0,7С2),%
б) при расположении забоя ниже устья и для
горизонтальных выработок
С, = С, + 0,07xLxC2,%
где - ожидаемая концентрация в забое, % по
объему;
С[ - измеренная концентрация в устье, % по
объему;- длина выработки, м;
С2 - прирост концентрации на расстоянии 10 м.
.2.5. Замеры содержания сероводорода производятся
в местах его возможного выделения (в тупиковых комбайновых забоях по
сильвинитовому пласту Б) переносными приборами периодического действия (типа
АМ-5) лицом сменного надзора участка не менее двух раз в смену, в том числе
один раз - в начале смены.
При обнаружении содержания сероводорода выше ПДК
производится отбор проб на химический анализ согласно «Временной методике
определения газообильности горных выработок по сероводороду» (г. Пермь,
г.) Для снижения концентрации сероводорода в
выработке при работе комбайна, снижается производительность комбайна,
производится соответствующий перерасчет количества воздуха или меняется схема
проветривания выработок.
Во всех случаях обнаружения горючих газов выше
0,5% по объему (10%) НКПР) должны приниматься меры в соответствии с
требованиями пунктов 3.1.6 "Специальных мероприятий ..." [86].
Оформление результатов замеров.
Результаты замеров концентрации горючих газов,
производимых в течение смены лицами сменного надзора, бригадирами, звеньевыми,
машинистами комбайнов, заносятся в «Журналы замера горючих газов и
сероводорода» (форма 1), находящиеся на участке (комбайнах). Работники ПУВГВ,
кроме того, заносят результаты выполненных ими замеров в свои наряд-путевки. В
случаях обнаружения горючих газов с любой концентрацией данные наряд-путевок
ПУВГВ в течение суток заносятся в «Книгу замеров горючих газов и сероводорода»
(форма 2).
Наряд-путевки ПУВГВ хранятся не менее трех
месяцев.
Результаты замеров содержания горючих газов
должны использоваться при подготовке ежегодного приказа об отнесении рабочих
зон к числу опасных по газу.
11. Меры безопасности при выполнении
технологических процессов
11.1 Общие требования
Перед началом работ по проходке и строительству
ствола, шахтопроходческая организация должна заключить договор на обслуживание
со специализированным аварийно-спасательным формированием (ВГСЧ), а также
обеспечить всех работающих в подземных условиях исправными,
индивидуально-закрепленными самоспасателями согласно П. 19 ПБ 03-553-03 и
укомплектовать стройплощадку первичными средствами пожаротушения согласно ПГТБ
01-03.
Работающие непосредственно на подземных работах
должны проходить периодическое медицинское освидетельствование не реже одного
раза в год.
Рабочие, выполняющие работы повышенной
опасности, перечень которых устанавливается руководством организации, перед
началом смены должны проходить обязательный выборочный медицинский осмотр.
Рабочие и специалисты должны быть обеспечены и
обязаны пользоваться специальной одеждой, специальной обувью, исправными защитными
касками, очками и другими средствами индивидуальной защиты, соответствующими их
профессии и условиям, согласно утвержденным нормам.
В случае, когда технические мероприятия не могут
обеспечить снижение запыленности рудничного воздуха, шума и вибрации машин,
механизированных инструментов на рабочем месте до предельно допустимых
пределов, работники предприятия должны применять индивидуальные средства защиты
органов дыхания, слуха, зрения (респираторы, наушники, вкладыши противошумные,
шлемофоны, защитные очки и маски и другие средства защиты). Работники должны
работать в чистой, исправной спецодежде и обуви в соответствии с межотраслевыми
нормами выдачи и использования спецодежды и обуви. Работники должны
пользоваться исправными правильно подобранными респираторами при выполнении
операций, для которых предусмотрено их применение. Запрещается разбирать
респиратор или снимать его в запыленной атмосфере.
Работник, работающий на вибрационных машинах или
инструментах, должен находиться под диспансерным наблюдением с целью
своевременного выявления начальных стадий вибрационной болезни.
В процессе работ пользоваться
противовибрационными рукавицами, использовать соответствующие типы виброгасящих
устройств, применять вибрирующие инструменты, рукоятки которых облицованы
вибропоглощающими материалами.
Запрещается спуск людей в шахту и пребывание их
в подземных выработках без производственной необходимости, наряда или
разрешения руководителей шахты.
На шахтах должен быть организован и
осуществляться учет всех лиц, спустившихся в шахту и выехавших (вышедших) на
поверхность, в соответствии с разработанной инструкцией, утвержденной
руководством шахты.
Всем лицам, занятым на подземных работах и
посещающим подземные работы, перед спуском в шахты, имеющие рабочие зоны,
опасные по газу, взрыву пыли и самовозгоранию полезного ископаемого, должны
выдаваться исправные, индивидуально закрепленные изолирующие самоспасатели.
Руководители и специалисты организаций,
осуществляющих деятельность по разработке месторождений полезных ископаемых
подземным способом, должны иметь соответствующее образование, обязаны проходить
обучение и аттестацию в соответствии с Положением о порядке подготовки и
аттестации работников организаций, осуществляющих деятельность в области
промышленной безопасности опасных производственных объектов, подконтрольных
Госгортехнадзору России, утвержденным постановлением Госгортехнадзора России от
30.04.02 N 21, зарегистрированным Минюстом России 31.05.02 г., регистрационный
N 3489 (Российская газета, 12.06.02, N 107).
К техническому руководству горными и взрывными
работами на объектах подземных горных работ допускаются лица, имеющие высшее
или среднее горнотехническое образование в соответствии с Положением о порядке
предоставления права руководства горными и взрывными работами в организациях и
на объектах, подконтрольных Госгортехнадзору России, утвержденным
постановлением Госгортехнадзора России от 19.11.97 N 43, зарегистрированным
Минюстом России 18.03.98 г., регистрационный N 1487 (Бюллетень нормативных
актов федеральных органов исполнительной власти, 1998, N 7).
Рабочие, занятые на подземных горных работах,
должны иметь профессиональное образование, соответствующее профилю выполняемых
работ, должны быть обучены безопасным приемам работы, знать сигналы аварийного
оповещения, правила поведения при авариях, места расположения средств спасения
и уметь пользоваться ими; иметь инструкции по безопасному ведению
технологических процессов, безопасному обслуживанию и эксплуатации машин и
механизмов. Рабочие не реже чем через каждые шесть месяцев должны проходить
повторный инструктаж по безопасности труда и не реже одного раза в год -
проверку знания инструкций по профессиям. Результаты проверки оформляются
протоколом с записью в журнал инструктажа и личную карточку рабочего.
Рабочие, занятые на работах, выполнение которых
предусматривает совмещение профессий, должны быть обучены безопасности труда и
проинструктированы по всем видам совмещенных работ.
При изменении характера работы, а также после
несчастных случаев, аварий или грубых нарушений правил безопасности проводится
внеплановый инструктаж.
Все вновь поступившие подземные рабочие должны
быть ознакомлены с главными и запасными выходами из шахты на поверхность путем
непосредственного прохода от места работы по выработкам и запасным выходам в
сопровождении лиц технического надзора. Повторные ознакомления всех рабочих с
запасными выходами проводятся лицами технического надзора через каждые 6
месяцев, а при изменении запасных выходов - в течение суток. Результаты
заносятся в специальный журнал.
Организации, занятые разработкой месторождений
полезных ископаемых подземным способом, обязаны организовать и осуществлять
производственный контроль за соблюдением требований промышленной безопасности,
являющийся составной частью системы управления промышленной безопасности, в
соответствии с требованиями Правил организации и осуществления
производственного контроля за соблюдением требований промышленной безопасности
на опасном производственном объекте, утвержденных постановлением Правительства
Российской Федерации от 10.03.99 N 263 (Собрание законодательства Российской
Федерации, 1999, N 11, ст.1305).
Для каждой шахты должен быть составлен план
ликвидации аварий и согласован с горноспасательным формированием.
Руководитель организации, эксплуатирующий шахту,
обязан обеспечить безопасные условия труда, организацию разработки защитных
мероприятий на основе оценки опасности на каждом рабочем месте и объекте в
целом.
Производство работ должно выполняться по
письменному нарядному заданию.
Запрещается направлять на производство работ в
места, имеющие нарушения требований правил безопасности, кроме работ по их
устранению.
Каждое рабочее место должно находиться в
безопасном состояний, обеспечиваться проветриванием, освещением, средствами
оповещения об аварии. Запрещается выдавать наряд и направлять на работу в
отдаленные от основных рабочих мест горные выработки (забои) менее чем двух
рабочих. Перечень отдаленных горных выработок (забоев) ежеквартально
утверждается главным инженером шахты.
При обнаружении нарушений требований
безопасности работник должен, не приступая к работе, сообщить об этом
непосредственным руководителям работ или диспетчеру шахты.
Для оповещения лиц, занятых на подземных горных
работах, кроме телефонной связи должна быть оборудована специальная аварийная
беспроводная сигнализация аварийного оповещения. В отдельных случаях, по
согласованию с Госгортехнадзором России, могут применяться громкоговорящая и
световая сигнализации.
Движущиеся части оборудования, представляющие
собой источник опасности для людей, должны быть ограждены, за исключением
частей, ограждение которых невозможно из-за их функционального назначения.
Перед началом работы или движения машины
(механизма) машинист обязан убедиться в безопасности членов бригады и
находящихся поблизости лиц.
Предпусковой предупредительный сигнал должен
быть звуковым, его продолжительность должна составлять не менее 6 с, и он
должен быть слышен по всей опасной зоне.
Таблица сигналов вывешивается на работающем
механизме или вблизи него. Каждый неправильно поданный или непонятый сигнал
должен восприниматься как сигнал «Стоп»
Запрещается допуск к работе и пребывание на
территории шахты и других объектах лиц, находящихся в состоянии алкогольного,
наркотического или токсического опьянения.
Запрещается проносить табак и курительные
принадлежности, курить и пользоваться открытым огнем в подземных выработках
шахт, имеющих рабочие зоны, опасные по газу или пыли, надшахтных зданиях и на
поверхности шахт и рудников на расстоянии менее 30 м от диффузора вентилятора.
При проходке горных выработок (шахтных стволов)
в условиях Палашерского и Балахонцевского участков ВКМКС в зонах опасных по
возможным выделениям взрывоопасных и ядовитых газов все работы и
технологические операции должны производиться в соответствии с требованиями
разделов «Специальных мероприятий...»
Контроль за состоянием рудничной атмосферы при
проходке ствола в зонах опасных по газовыделениям выполнять в соответствии с
требованиями положений разделов «Специальных мероприятий...»
При строительстве шахтных стволов в условиях
Палаше рек о го и Балахонцевского участков ВКМКС в зонах опасных по прорывам
подземных вод и рассолов необходимо выполнять требования «Руководства по
ликвидации возможных водо-рассолопроявлений в руднике Усольского калийного комбината...»
Лица, допустившие нарушения требований положений
правил безопасности, технологических инструкций, технологических регламентов по
безопасной организации и выполнению производственных процессов, инструкций по
безопасности производства работ, нормативной документации по охране труда и
промышленной безопасности должны привлекаться к ответственности в установленном
порядке.
В каждой организации должен быть определен
порядок действий рабочих и должностных лиц при обнаружении ими взрывчатых
материалов (ВМ) в горных выработках, взорванной горной массе или иных, не
предназначенных для хранения ВМ местах. Обо всех таких случаях руководитель
организации обязан сообщить в территориальный орган Госгортехнадзора России.
Все действующие выработки должны быть закреплены
за лицами технического надзора для наблюдения за состоянием крепи, устройствами
и оборудованием в соответствии с назначением выработок. Порядок и периодичность
осмотров выработок устанавливаются главным инженером шахты.
Результаты проверок заносятся в специальный
журнал.
Крепь и армировка вертикальных и наклонных
стволов шахт, служащих для спуска, подъема людей и грузов, должны осматриваться
ежесуточно специально назначенными лицами.
Периодически, но не реже одного раза в месяц
крепь и армировка стволов должны тщательно осматриваться начальником или
главным инженером шахты или их заместителями.
На действующих и строящихся шахтах должны быть
выделены лица, ответственные за организацию подъема и спуска людей и грузов, за
состояние и осмотр канатов, подъемных машин, прицепных, предохранительных и
других устройств.
При спуске и подъеме людей и грузов в бадьях:
а) бадьи должны перемещаться по
направляющим; движение бадей без направляющих допускается на расстоянии не
более 20 м от забоя. При использовании на проходке вертикальных выработок
проходческих агрегатов (погрузочных машин, грейферов и др.) это расстояние
может быть увеличено до 40 м;
б) запрещается спуск и подъем людей в
бадьях без направляющих рамок и не оборудованных зонтами для предохранения рабочих
от травмирования случайно упавшими предметами. При этом должны приниматься меры
против раскачивания и вращения бадьи; скорость движения бадьи по стволу не
должна превышать 0,3 м/с, при глубоких стволах не должна превышать
м/с, а при подходе к месту работ на расстояние
до 15 м не более 0,3 м/с;
в) посадка людей в бадьи и выход из них
должны производиться на нижней приемной площадке со специальных лестниц или по
ступенькам бадьи только при закрытых лядах и остановленной бадье;
г) посадка людей в бадьи и выход из них на
промежуточных горизонтах и камерах должны производиться с откидных площадок, а
на полках и натяжных рамах только тогда, когда борт остановленной бадьи
находится на уровне раструба или пола этажа при наличии дверей в раструбе;
д) запрещается подниматься или опускаться
стоя или сидя на краю бадьи, а также производить спуск и подъем людей в
груженой бадье;
е) запрещается спуск и подъем людей в
бадьях, разгружающихся через дно;
ж) подъемная установка должна иметь
предохранительные устройства, позволяющие включать привод ляд только после
прохода через них спускающейся бадьи и направляющей рамки;
з) подъемная установка должна быть
оборудована устройствами, сигнализирующими о зависании направляющей рамки, или
должны приниматься меры, предотвращающие ее зависание и обеспечивающие
остановку бадьи при зависании направляющей рамки.
При спуске и подъеме грузов и людей в бадьях
проходческие подъемные установки должны быть оборудованы блокировочными
устройствами, исключающими прохождение бадьи через раструб в нижнем полке,
когда под раструбом находится погрузочное устройство.
Число людей, находящихся одновременно в
проходческих бадьях, определяется из расчета 4 человека на 1 м2 днища и должно
быть обозначено в Правилах внутреннего распорядка и в памятках, вывешенных в
проходческом копре на «нулевой» площадке.
Запрещается спуск и подъем людей в бадьях
одновременно с грузом.
На каждой строящейся шахте должна быть
разработана и утверждена главным инженером инструкция по спуску и подъему
длинномерных и негабаритных грузов с конкретным указанием последовательности
технологических операций и мер безопасности.
При работе на высоте более 1,3 м работники
должны быть застрахованы от случайного падения предохранительными (монтажными)
поясами.
Предохранительные пояса через каждые 6 месяцев
должны подвергаться испытаниям на статическую нагрузку 225 кг в течение 5 мин.
Испытания предохранительных поясов должны
производятся специализированными, аттестованными подразделениями предприятия.
К горнопроходческим и строительно-монтажным
работам по проходке и строительству ствола разрешается приступать только при
наличии утвержденных в установленном порядке проектной и рабочей документации,
технологического регламента на проходку и строительство ствола, Инструкций для
работников строительной организации по безопасному ведению технологических
процессов при строительстве ствола, в которых должны быть разработаны все
мероприятия по обеспечению промышленной безопасности, включая определения
опасных зон, связанных с возможными прорывами подземных вод и рассолов, с
возможными выделениями взрывоопасных газов, с применением грузоподъёмных
механизмов, а также мероприятия по производственной санитарии и охране
окружающей среды, мероприятия по оборудованию рабочих мест беспроводной
радиотелефонной связью и сигнализацией. К началу производства работ на участке
строительства должны быть в наличии утвержденные в установленном порядке
паспорта БВР, паспорта крепления и проветривания горной выработок.
12. Охрана окружающей среды
В проекте производства работ подрядной
строительной организацией должны быть разработаны мероприятия по охране
окружающей среды с учетом решений данного раздела.
Контроль проводимых природоохранных мероприятий
при осуществлении работ, связанных с нанесением ущерба окружающей среде,
осуществляется экологической службой эксплуатирующей организации.
В органах Ростехнадзора, Роспотребнадзора и
других контролирующих организациях должны быть согласованы места забора воды
для производственных и хозяйственно-бытовых нужд, места расположения и границы
водоохранных зон.
Должны быть разработаны и согласованы маршруты и
графики движения и передислокации автомобилей и строительной техники.
На протяжении всего периода строительства должен
вестись контроль над соблюдением графиков производства и сезонности выполнения
работ.
При планировке площадки должны быть исключены
или максимально ограничены:
засыпка естественных стоков дождевых и талых
вод, дренирующих территорию, без строительства водопропускных сооружений;
устройство земляных перемычек, перегораживающих
образующиеся после проведения планировки эрозионные формы;
На всех без исключения пересечениях ручьев,
каналов и т.п. временными и подъездными к площадке производства работ дорогами
должны быть устроены водопропускные сооружения.
Все земляные работы должны проводиться
исключительно в границах территории, выделенной заказчиком под площадку
производства работ, а также под временные здания и сооружения (площадки и базы,
подъезды к площадке и т.п.).
На всех этапах строительства должны быть выполнены
мероприятия, предотвращающие:
развитие неблагоприятных рельефообразующих
процессов;
изменение естественного поверхностного стока на
участке строительства; -загорание естественной растительности вследствие
допуска к работе неисправных технических средств, способных вызвать загорание;
-захламление территории строительными отходами;
разлив горюче-смазочных материалов, слив на
трассе отработанных масел и т.п.
При производстве земляных работ на всех
площадках подрядчик должен соблюдать следующие условия:
производство земляных работ, движение машин и
механизмов, складирование и хранение материалов в местах, не предусмотренных
ПОС и ПНР, должно быть запрещено;
используемые при строительстве механизмы и
транспортные средства должны быть размещены только в пределах отведенных для
этого территорий;
при эксплуатации строительных механизмов и
автотранспорта должен осуществляться периодический контроль выхлопов (во время
прохождения ТО) работающих двигателей. Уровень выбросов С02 не должен превышать
предельно допустимые нормы концентрации вредных веществ;
должны быть приняты необходимые технические меры
и организован контроль над недопустимостью пролива нефтепродуктов при заправке
механизмов;
должны строго соблюдаться согласованные с
местными органами охраны природы постоянные маршруты вывозки грунта и подвозки
материалов на площадку строительства;
производственные и бытовые отходы в процессе
строительства предусматривается отвозить автотранспортом на специализированные
полигоны. Сброс бытовых и производственных стоков должен осуществляться в
проектные выгребные ямы с последующим вывозом спецмашинами на очистные
сооружения;
С целью снижения строительного воздействия на
окружающую среду, подрядная организация должна разработать мероприятия по
охране окружающей среды и назначить специалиста, ответственного за соблюдением
правил и норм российского законодательства по охране окружающей среды.
Специалист по охране окружающей среды должен
взаимодействовать со службами по охране окружающей среды эксплуатирующей
организации.
С целью обеспечения охраны
почвенно-растительного слоя и животного мира, а также охраны водоемов (в
процессе заправки нефтепродуктами, ремонта и технического обслуживания
малоподвижной техники) необходимы следующие мероприятия:
выделение специальных площадок, отвечающих всем
нормам противопожарной безопасности, для заправки и смены отработанных ГСМ с
устройством закрытых емкостей (сменных контейнеров) для предохранения от
попадания ГСМ на почвенно-растительный слой;
заправка машин с помощью топливозаправщиков, а
не из случайной тары и емкостей; своевременное устранение возможного ослабления
болтовых соединений, контроль качества уплотнений для исключения разлива на
почву топлива, рабочей жидкости и смазочных материалов;
очистка и мойка отдельных узлов и самих машин и
механизмов в отведенных местах на территории эксплуатационных баз с
использованием специальных моечных машин и установок; сбор стоков от мойки в
специальные резервуары с условием последующей очистки
Площадка строительства должна регулярно
очищаться от производственных отходов мусора. Для сбора отходов и мусора должны
быть установлены в необходимом количестве контейнеры, отдельно для каждого типа
производственных отходов. По мере их заполнения они должны вывозиться для
дальнейшей утилизации в специально отведенные и согласованные места.
Двигатели автотранспорта и передвижной
строительной техники должны регулярно подвергаться контролю и регулировке с
целью снижения вредных выбросов.
Перечисленные мероприятия должны быть
конкретизированы, дополнены и уточнены с учетом СНиП 12 01 2004 «Организация
строительства» в проектах организации работ.
Ответственность за нарушение природоохранных
мероприятий при выполнении строительно-монтажных работ несет подрядная
строительная организация
Специальная часть
. Выбор способа сооружения ствола
В зависимости от устойчивости и водообильности
грунтового массива различают обычные и специальные способы сооружения стволов. Обычные
способы проходки стволов глубиной до 50 м применяют в устойчивых грунтах:
глинистых, гравиино-галечниковых, щебенистых и песчаных, расположенных выше
уровня капиллярного поднятия воды, а также в крепких скальных грунтах при
ожидаемом притоке воды в забое до 50 м3/ч. Проходку стволов обычными способами
глубиной более 50 м в устойчивых грунтах следует производить при притоках воды
в забой до 8 м3/ч. При соответствующем технико-экономическом обосновании можно
производить проходку стволов обычным способом при притоках воды в забой до 20
м3/ч с последующим подавлением и доведением притока до 8 м3/ч. Обычные способы
являются основными и наиболее распространенными.
. Специальные способы сооружения
стволов шахт
Специальные способы сооружения стволов шахт
применяют в рыхлых, неустойчивых или плывунных грунтах, а также при пересечении
крепких, трещиноватых водоносных грунтов. Выбор способа проходки стволов шахт
специальным способом следует осуществлять на основании сопоставления
технико-экономических показателей с учетом данных согласно СНиПа.
При обычных способах проходки различают проходку
в крепких грунтах с применением буровзрывных работ и проходку в мягких
грунтах, где разработку ведут с применением отбойных молотков или
пневмоломов.
По глубине шахтный ствол разбивается на звенья,
длина которых в зависимости от устойчивости грунтов принимается от нескольких
метров до нескольких десятков метров. В зависимости от очередности производства
работ в звеньях различают технологические схемы: последовательную,
параллельную, параллельно-щитовую и совмещенную.
При последовательной схеме (рис. 6.4, а)
в каждом звене сначала производят выемку грунта (2), а затем возводят обделку
(1). По окончании производят аналогичные работы в нижнем звене и т. д. Такая
схема сооружения стволов шахт может быть рекомендована для стволов глубиной до
100 м, а также в неустойчивых и водоносных грунтах с применением специальных
способов.
При параллельной схеме работы (рис. 6.4,
б) ведут в двух звеньях, в нижнем производят выемку грунта (2) в направлении
сверху вниз и при необходимости устанавливают временную крепь, в верхнем
смежном звене с подвесного полка (3) снизу вверх возводят обделку (1). Эту
схему применяют при диаметре стволов более 4,5 м и глубине ствола более 250 м.
Однако, в связи со сложностью работ, применение такой схемы ограничено.
Рис. 6.4 - Технологические схемы проходки ствола
При совмещенной схеме (рис. 6.4, в)
возведение сборной обделки входит в проходческий цикл. По этой схеме очередное
кольцо обделки (1) монтируют одновременно с уборкой грунта (2) из забоя.
Простота организации работ позволяет достигнуть высоких скоростей проходки.
Совмещенная схема получила небольшое распространение и может быть рекомендована
для сооружения стволов любых размеров поперечного сечения и глубины.
Сущность параллельно-щитовой схемы (рис.
6.4, г) заключается в том, что обделка ствола возводится одновременно с выемкой
грунта сверху вниз. Вместо временной крепи применяют щит (5) из листовой стали
толщиной 10-20 мм, высотой от 5 до 18 м, который по мере выемки грунта
опускают. Обделку (1) возводят сверху вниз с подвесного трехэтажного полка (4).
Эта схема сооружения стволов может быть рекомендована только при достаточно
устойчивых грунтах. Основным недостатком этой схемы является большая масса
проходческого оборудования (150-180 т) и значительный срок его монтажа (5-6
месяцев и больше).
3. Принцип
получения холод и работа замораживающей станции
Для получения холода и создания
ледопородного ограждения используют замораживающую станцию, принципиальная
схема которой показана на 9.1.
Пары хладагента сжимают до
давления 0,5-1,2 МПа в компрессоре / (в зависимости от его типа), в результате
чего температура паров повышается до 100 °С. Хладагент с такими параметрами
проходит через маслоотделитель 2 и попадает в межтрубное пространство
конденсатора 3, в котором непрерывно циркулирует вода. В результате охлаждения
пары конденсируются и хладагент переходит в жидкое состояние. При этом его
давление остается примерно тем же, а температура понижается до 15-20 °С в
зависимости от расхода и температуры охлаждающей воды.
Жидкий хладагент из
конденсатора по трубопроводу 4 проходит через дроссельное устройство 5, а
оттуда по трубопроводу 6 поступает в испаритель 17, где давление хладагента
резко снижается до 0,05 МПа. В результате перепада давления хладагент
испаряется, а его температура понижается до -(20-30) °С. Пары хладагента по
мере испарения поднимаются по змеевикам испарителя 18 и, пройдя грязеуловитель
16, попадают через трубопровод 19 опять в компрессор. На этом заканчивается непрерывный
цикл движения хладагента.
Переход хладагента из жидкого
состояния в газообразное происходит в испарителе 17 и трубопроводах 6 и 19 с
большим поглощением тепла, отбираемого у хладоносителя 14, который находится в
рассольном баке /5 и непрерывно с помощью рассоломешалки 13 циркулирует в
межтрубном пространстве испарителя /7, в результате этого хладоноситель
охлаждается до температуры -(20-25) °С.
Охлажденный хладоноситель
насосом 12 нагнетают по магистральному трубопроводу / / и распределителю 10 в каждую
замораживающую колонку 8. Циркулируя по замораживающим колонкам, хладоноситель
отдает холод окружающим горным породам и замораживает их, а сам нагревается на
1 -3 °С в зависимости от режима замораживания. Пройдя через колонки,
хладоноситель попадает в коллектор 7, а затем в обратный магистральный
трубопровод 9, по которому он поступает для повторного охлаждения в испаритель
17.
Таким образом, при работе
замораживающей станции имеют место три самостоятельных замкнутых цикла движения
хладагента, воды в конденсаторе и хладоносителя.
В качестве хладагента
используют аммиак - аммиачные холодильные машины - или различные хладоны (ранее
фреоны) - фреоновые холодильные машины.
В качестве хладоносителей
используют водные растворы солей хлористого кальция, хлористого магния.
Хладоносители, представленные водными растворами хлоридов, получили название
рассолов. Концентрация рассола должна быть такой, чтобы температура его
замерзания была на 8 °С ниже температуры испарения хладагента. Наибольшее
распространение в практике замораживания получил водный раствор хлористого
кальция плотностью до 1,28 г/см3.
Широкое применение водных
растворов солей (рассолов) связано с тем, что они дешевы и могут быть легко
приготовлены в условиях строительной площадки.
Недостатки рассолов: они весьма
агрессивны по отношению к ледо-породным ограждениям и в случае утечек из
колонок, что зачастую бывает в практике замораживания, приводят к разрушению
ранее созданного ледопородного ограждения и как следствие прорыву воды через
него.
В последние годы широкое
распространение получили замораживающие станции, выполненные в передвижном
исполнении (ПХС-100, ПХУ-50, ППЗУ и др.), позволяющие начать работы в сжатые
сроки с минимальными затратами времени на подготовительный период.
Экономическая часть
Горно-подготовительный участок калийного рудника
выполняет следующие виды работ, обеспечивающие проходку выработок: ведение
горно-подготовительных работ, транспортирование руды, ремонтные работы по
оборудованию участка, работы по оборке и креплению выработок.
Производственная мощность
горно-подготовительного участка зависит от числа комбайновых комплексов, их
типа, состава и размещения оборудования в забоев. При этом расчеты выполняются
на основе рациональной организации горно-подготовительных работ, нормативных
технических условий эксплуатации оборудования с учетом факторов, влияющих на
эксплуатационную производительность комбайновых комплексов.
1. Планирование производственной
мощности горного участка
.1 Режим работы участка
Режим работы ПГПУ-1 - непрерывный, трехсменный.
Календарный фонд времени участка рассчитывается с учетом затрат времени на
проведение капитального и планово-предупредительных ремонтов (ППР). На
проведение капитального ремонта горношахтного оборудования отводится 15 суток в
мае и 15 суток в сентябре, а на ППР - ежемесячно одни сутки (всего 10 дней в
году).
Таким образом, количество рабочих дней в году на
добычном участке:
Драб = 365 - 30 - 10 = 325 дней.
смена с 0 до 8.00 часов,смена с
8.00 до 16.00 часов,смена с 16.00 до 00 часов.
Звено комбайнового комплекса работает по
следующему графику: 3 рабочих днях и 2 дня выходных, смены чередуются в
обратном порядке: после 3-й смены выход на работу во вторую, после второй - в
первую, после первой - в третью.
Ремонтная служба работает в одну смену (с 8.00
до 15.00 ч) по графику: 5 рабочих дней и 2 дня выходных (суббота и
воскресенье).
Режим работы начальника и заместителя начальника
участка - 5 рабочих дней и 2 дня выходных.
1.2 График выходов рабочих и
организации очистных работ в забое
График выходов рабочих по горному участку
составляется с учетом непрерывности ведения горно-подготовительных работ (табл.
10.1).
Работа смен регламентируется графиком
организации работ в забое при проходке, а также по креплению сопряжений.
По данным графика организации работ (рис. 10.1)
принимается время работы комбайновых комплексов, необходимое для расчета
проектной производственной мощности участка.
Например, по графику (см. рис.10.1) для расчета
производственной мощности принимается продолжительность горно-подготовительных
работ по 6 часов в смену и 18 часов в сутки.
Рисунок 10 График организации
горно-подготовительных работ
Наименование
работ
|
Смена
1
|
Смена
2
|
Смена
3
|
|
1
|
2
|
3
|
4
|
5
|
6
|
7
|
8
|
1
|
2
|
3
|
4
|
5
|
6
|
7
|
8
|
1
|
2
|
3
|
4
|
5
|
6
|
7
|
8
|
Подготовительно-
заключительные операции
|
|
|
|
|
|
|
|
|
|
|
|
|
|
|
|
|
|
|
|
|
|
|
|
|
Осмотр
забоя
|
|
|
|
|
|
|
|
|
|
|
|
|
|
|
|
|
|
|
|
|
|
|
|
|
|
|
|
Оборка
и крепление кровли
|
|
|
|
|
|
|
|
|
|
|
|
|
|
|
|
|
|
|
|
|
|
|
|
|
|
|
|
Горно-подготовительные
работы
|
|
|
|
|
|
|
|
|
|
|
|
|
|
|
|
|
|
|
|
|
|
|
|
|
|
|
|
|
|
|
|
|
|
|
|
|
|
|
|
|
|
|
|
|
|
|
|
|
|
|
|
|
|
|
|
Продолжительность горно-подготовительных работ
составляет 18 часов в сутки.
Рисунок 10.1 График выходов работников участка
Число
месяца
|
1
|
2
|
3
|
4
|
5
|
6
|
7
|
8
|
9
|
10
|
11
|
12
|
13
|
14
|
15
|
16
|
17
|
18
|
19
|
20
|
21
|
22
|
23
|
24
|
25
|
26
|
27
|
28
|
29
|
30
|
см
|
часы
Начальник участка |
2
|
2
|
2
|
2
|
в
|
в
|
2
|
2
|
2
|
2
|
2
|
в
|
в
|
2
|
2
|
2
|
2
|
2
|
в
|
в
|
2
|
2
|
2
|
2
|
2
|
в
|
в
|
2
|
2
|
2
|
21
|
176
Зам. нач. участка |
в
|
2
|
2
|
2
|
2
|
2
|
в
|
в
|
2
|
2
|
2
|
2
|
2
|
в
|
в
|
2
|
2
|
2
|
2
|
2
|
в
|
в
|
2
|
2
|
2
|
2
|
2
|
в
|
в
|
2
|
21
|
168
Смена 1 |
2
|
2
|
2
|
в
|
в
|
3
|
3
|
3
|
в
|
в
|
1
|
1
|
1
|
в
|
в
|
2
|
2
|
2
|
в
|
в
|
3
|
3
|
3
|
в
|
в
|
1
|
1
|
1
|
в
|
в
|
18
|
144
Смена 2 |
1
|
в
|
в
|
2
|
2
|
2
|
в
|
в
|
3
|
3
|
3
|
в
|
в
|
1
|
1
|
1
|
в
|
в
|
2
|
2
|
2
|
в
|
в
|
3
|
3
|
3
|
в
|
в
|
1
|
1
|
18
|
144
Смена 3 |
в
|
1
|
1
|
1
|
в
|
в
|
2
|
2
|
2
|
в
|
в
|
3
|
3
|
3
|
в
|
в
|
1
|
1
|
1
|
в
|
в
|
2
|
2
|
2
|
в
|
в
|
3
|
3
|
3
|
в
|
18
|
144
Смена 4 |
3
|
3
|
в
|
в
|
1
|
1
|
1
|
в
|
в
|
2
|
2
|
2
|
в
|
в
|
3
|
3
|
3
|
в
|
в
|
1
|
1
|
1
|
в
|
в
|
2
|
2
|
2
|
в
|
в
|
3
|
18
|
144
Смена 5 |
в
|
в
|
3
|
3
|
3
|
в
|
в
|
1
|
1
|
1
|
в
|
в
|
2
|
2
|
2
|
в
|
в
|
3
|
3
|
3
|
в
|
в
|
1
|
1
|
1
|
в
|
в
|
2
|
2
|
2
|
18
|
144
Ремонтная служба |
2
|
2
|
2
|
2
|
2
|
в
|
в
|
2
|
2
|
2
|
2
|
2
|
в
|
в
|
2
|
2
|
2
|
2
|
2
|
в
|
в
|
2
|
2
|
2
|
2
|
2
|
в
|
в
|
2
|
2
|
21
|
168
1.3 Производственная мощность
участка
В проекте показана характеристика
расположения участка в шахтном поле, подготовки шахтного поля и
гидроизолируемых участков и система транспорта рудника.
Выполняется расчет годовой
производительности участка:
Агод = Асут·Nгод·Nк· Кг,т/год
где: Асут - суточная
производительность комбайновых комплексов, т;к - количество комбайновых
комплексов по участку; (принимаем 6 шт. для ведения горно-подготовительных
работ);
Кг =0,9 - коэффициент геологический
условий;год = 325 дн - число рабочих дней по ведению горно-подготовительных
работ.
Суточная производительность
комбайнового комплекса определяется по формуле:
Асут = аср·Кс.э·Фсут, т/сут.
где: аср - средневзвешенная
производительность комбайновых комплексов, т/мин, (принимается равной 4,74 -
7,0 т/мин или определяется по данным горной части проекта);
Кс.э=0,2-0,4 - коэффициент
использования эксплуатационной производительности;
Фсут - фонд времени работы
комплекса по выемке руды в сутки, мин.
Среднесменные производительности
комбайновых комплексов на горно-подготовительных работах составляют 556 т/см:
Месячная производительность
комплекса составит:
Амес = Агод: 12, т/мес.
В результате расчетов
обосновывается проектный план ведения горно-подготовительных работ по
комбайновым комплексам и в целом по участку в расчете на год и на месяц (табл.
10.2), на основе его планируется в дальнейшем себестоимость проходки горных
выработок по участку.
Таблица 10.2
План ведения горно-подготовительных
работ по участку
Тип комплекса
|
Количество
|
Объем добычи, т
|
|
|
годовой
|
месячный
|
суточный
|
Урал 20Р
|
6
|
2927340
|
243945
|
1668
|
Всего
|
2927340
|
243945
|
1668
|
2. Планирование штата работников,
работающих на участке
.1 Структура управления участками
Руководство работой горного участка
осуществляется начальником участка, его заместителями, горными мастерами и
механиком (рис. 10.3).
Рис. 10.2. Структура управления
участками
.2 Расчет штата
инженерно-технических работников участка
Численность инженерно-технических
работников участка (табл. 10.3) определяется по штатному расписанию.
Таблица 10.3
Численность ИТР участка
№ п/п
|
Должность
|
Количество единиц
|
Разряд, система ЗП
|
|
|
Явочная
|
Списочная
|
|
1
|
Начальник участка
|
1
|
1
|
Оклад
|
2
|
Заместитель начальника участка
|
1
|
1
|
Оклад
|
3
|
Горный мастер
|
5
|
6
|
Оклад
|
4
|
Электромеханик
|
1
|
1
|
Оклад
|
5
|
ИТОГО
|
8
|
9
|
|
2.3 Расчет численности рабочих
забойной группы
Явочная численность рабочих
забойной группы Чяв.заб рассчитывается согласно обслуживаемым горным машинам
Nком, находящимся на участке:
Чяв.заб = (Фмес.ком :Фмес.1 раб.) ·
Чзв · Nк ,чел.
где: Фмес..ком - плановый
месячный фонд рабочего времени по горно-капитальным работам одним комбайновым
комплексом, ч;
Фмес.1 раб - плановый месячный фонд
рабочего времени одного рабочего, ч (принимается равным 151,2 часа или по
данным планового отдела рудника);
Чзв=2 чел- численность звена
комбайнового комплекса по нормативу обслуживания, чел.
Месячный фонд рабочего времени по
добыче одним комбайновым комплексом определяется следующим образом:
Фмес.ком = Фсут.ком · Дгод : 12
Фмес.ком = 18 * 325/12=487,5
где: Фсут.ком=18 сут. - суточный
фонд рабочего времени одного комбайнового комплекса, ч (принимается по данным
раздела 10.1.2 в соответствии с графиком организации работ добычного
комплекса);
Дгод =325дней - годовое количество
рабочих дней по добыче на участке;
- число месяцев в году.
Таким образом, отношение (Дгод :
12) представляет собой количество суток отработки в среднем за месяц (Дмес)
ЧЯВ.ЗАБ=(487,5/151,2)*2*6 = 38,7=39
чел.
Дмес = Дгод : 12=325/12=27сут.
В целом, данные расчета явочной
численности забойной группы сводятся в табл. 10.4.
Таблица 10.4
Численность рабочих забойной группы
Наименование горного оборудования
|
Количество оборудования, ед.
|
Количество основных рабочих в
смену, чел.
|
Разряд
|
Кол-во смен в сутки
|
Явочная численность рабочих в
сутки, чел.
|
Урал 20Р
|
6
|
6
|
6
|
3
|
18
|
ВС-30
|
6
|
6
|
5
|
3
|
18
|
БПС -25
|
6
|
-
|
-
|
3
|
-
|
Итого
|
18
|
12
|
|
|
36
|
На основе явочной численности
забойной группы рассчитывается ее штатная и списочная численность (Чшт и Чсп).
Штатная численность - это
численность рабочих при непрерывной рабочей неделе в соответствии принятым
графиком выходов - числом рабочих и числом выходных дней в неделю. Таким
образом, штатная численность превышает явочную на число рабочих, необходимых
для работы в выходные дни по графику чередования смен.
Списочная численность -это общее
количество рабочих с учетом плановых невыходов на работу (отпуск, болезни,
государственные обязанности).
Штатная и списочная численность
рабочих определяется на основе эффективного фонда рабочего времени.
Чшт = Чяв · Кшт , 36 * 1,6=57,6
Чсп = Чяв · Ксп , 36 * 2,7=97,2
где: Кшт, Ксп - коэффициенты
соответственно штатного и списочного состава рабочих.
Кшт = Фвр. кал: Фвр. ном =
365/226=1,6
Ксп = Фвр. кал: Фвр. эф =
365/161=2,7
где: Фвр. кал =365 дней -
календарный фонд времени;
Фвр. ном=226 дней - номинальный
фонд рабочего времени;
Фвр. эф =161 день - эффективный
фонд рабочего времени.
Для принятого на рудниках графика
работы (см. табл. 10.1) - 3 рабочих дня, 2 дня выходных при 5 сменах горных
мастеров и восьми часовом рабочем дне), эффективный фонд времени рабочего
забойной группы определяется по данным табл. 10.5.
Таблица 10.5
Эффективный фонд рабочего времени
рабочего забойной группы при непрерывной рабочей неделе
Показатели
|
Количество дней
|
Календарный фонд рабочего времени
|
365
|
Выходные и праздничные дни
|
139
|
Номинальный фонд рабочего времени
|
226
|
Болезни
|
10
|
Отпуск
|
52
|
Гос.обязанности
|
2
|
Ученический отпуск
|
1
|
Эффективный фонд рабочего времени
|
161
|
Полученное значение списочного
числа рабочих забойной группы должно соответствовать принятому графику работы.
Например, при работе по графику 3 + 2 (3 рабочих дня + 2 выходных) и
трехсменном рабочем дне, общая численность рабочих забойной группы (машинистов
ГВМ) для обеспечения непрерывной работы участка составит:
Чз.раб = (2 · 5 · Nк + Чрез.маш),
(2*5*6+2)=62 чел
где: Чрез.маш =2-3 чел -
резервное число машинистов ГВМ.
Также следует предусмотреть для
работы в каждой смене одного дежурного электрослесаря с правом управления
конвейером. В данном примере при 5 технологических сменах в штатное расписание
следует включить 5 человек.
После расчета численности забойной
группы производится распределение рабочих по квалификациям:
машинист ГВМ 6-го разряда, чел.
-31
машинист ГВМ 5-го разряда, чел.
-31
дежурный электрослесарь 4-го
разряда, чел. -5
2.4 Расчет численности ремонтного
персонала
Расчет явочной численности ремонтного
персонала выполняется на основе нормативных данных трудоемкости ремонта по
перечню основного технологического оборудования участка.
Расчет списочной численности
ремонтного персонала выполняется по коэффициенту списочного состава,
определяемого отношением фонда номинального рабочего времени Фвр.ном=226 к
эффективному фонду рабочего времени Фвр.эф=161
Тогда коэффициенты списочного
состава для ремонтного персонала и его списочная численность в нашем примере
будут следующими:
Ксп.рем = 251 : 203 = 1,24;
Чсп.рем = Чяв · 1,24 + Чэлек, чел;
Чяв=4,84=5чел.;
где: Чэлек - число дополнительно
принимаемых электрослесарей с правом работы на электроустановках
(электрослесаря), обычно Чэлек = 4-6 чел.
Таблица 10.6
Расчет явочной численности
ремонтного персонала
№№ п/п
|
Наименование оборудования
|
Тип, марка оборудования
|
Кол-во действующего оборудования,
шт.
|
Норматив численности на все виды
ремонта на единицу оборудования, чел в смену
|
Норматив численности на все
оборудование, чел/смен
|
1
|
Конвейер ленточный
|
Л-1000КУ
|
4
|
0,396
|
1,58
|
2
|
Конвейер ленточный
|
1Л-120
|
2
|
0,396
|
0,79
|
3
|
Подстанция
|
ТСВП 630/6
|
12
|
0,036
|
0,432
|
4
|
Пускатель магнитный
|
АПШ-М, ПВИ-320МВ
|
10
|
0,006
|
0,11
|
5
|
Реле утечки
|
АЗУР-4
|
12
|
0,006
|
0,072
|
5
|
Аппаратура управления
|
АСУК-ДЭП
|
6
|
0,006
|
0,036
|
6
|
Вентилятор местного проветривания
|
СВМ-6, ВМЭ-6
|
6
|
0,006
|
0,012
|
7
|
Светильники шахтные
|
РВЛ 01-2095
|
20
|
0,001
|
0,02
|
9
|
Станок сверлильный
|
б/марки
|
1
|
0,004
|
0,004
|
1
|
Подъемные, тягальные лебедки
|
ЛГРУ-10, ЛВД-21
|
2
|
0,022
|
0,044
|
1
|
Электросверло
|
СЭР-19М
|
6
|
0,009
|
0,054
|
1
|
Электротельфер
|
Т-5
|
1
|
0,004
|
0,004
|
1
|
Наждачный станок
|
б/марки
|
1
|
0,004
|
0,004
|
1
|
Электросварочный аппарат
|
ТДМ-400
|
2
|
0,009
|
0,018
|
1
|
Комбайн проходческий
|
Урал-20Р
|
6
|
0,179
|
1,45
|
1
|
Самоходный вагон
|
ВС-30
|
6
|
0,179
|
1,45
|
1
|
Бункер-перегружа-тель
|
БПС-25
|
6
|
0,208
|
0,832
|
1
|
Силовая кабельная сеть:
обслуживание демонтаж монтаж
|
|
5 км 3 км 3 км
|
0,07/1 км 0,02/1 км 0,07/1 км
|
0,35 0,06 0,21
|
1
|
Кабель контрольный
|
|
1 км
|
0,08/1 км
|
0,08
|
2
|
Кабель световой обслуживание
демонтаж монтаж
|
|
1 км 0,5 км 0,5 км
|
0,08/1 км 0,03/1 км 0,07/1 км
|
0,08 0,015 0,035
|
2
|
Обслуживание конвейеров
|
Л-100КУ-4 шт, 1Л-120-2 шт
|
5,1 км
|
0,045/100 м
|
2,3
|
Итого явочная численность
вспомогательных рабочих
|
10,042
|
Чсп.рем=43,376*1,24+4=58 чел
Таблица 10.7
Номинальный и эффективный фонд
рабочего времени ремонтного персонала
№№ п/п
|
Наименование показателя
|
Количество, дн.
|
1
|
Календарный фонд рабочего времени
|
365
|
2
|
Выходные и праздничные дни
|
114
|
|
Итого номинальный фонд рабочего
времени
|
251
|
3
|
Планируемые дни невыхода на
работу: отпуск больничный выполнение общественных обязанностей
|
42 4 2
|
|
Итого
|
48
|
4
|
Эффективный фонд рабочего времени
|
203
|
Дополнительно определяется
численность вспомогательных рабочих по участку (крепильщики,
электрогазосварщики) в составе ремонтного персонала. Затем производится (по
аналогии с забойной группой) распределение общего штата ремонтного и
дополнительного вспомогательного персонала по квалификациям (разрядам) и
составляется сводная таблица штата персонала на горном участке по форме табл.
10.8.
Таблица 10.8
Сводная таблица штата персонала,
чел.
№ п/п
|
Штат
|
Разряд
|
Численность явочная
|
Численность списочная
|
1
|
ИТР
|
оклад
|
8
|
9
|
2
|
Основные рабочие
|
|
62
|
66
|
|
В том числе:
|
|
|
|
|
машинист ГВМ
|
6
|
31
|
33
|
|
машинист ГВМ
|
5
|
31
|
33
|
3
|
Ремонтный персонал
|
|
43
|
58
|
|
в том числе:
|
|
|
|
|
электрослесарь
|
6
|
6
|
7
|
|
электрослесарь
|
5
|
9
|
4
|
Дежурный персонал электриков
ДИПРО٭
|
5
|
4
|
5
|
5
|
آٌïîىîمàٍهëüيûé
ïهًٌîيàë
|
|
6
|
7
|
|
آ
ٍîى
÷èٌëه:
|
|
|
|
|
ëهêًٍîمàçîٌâàًùèê
|
4
|
2
|
2
|
|
êًهïèëüùèê
|
3
|
4
|
5
|
|
بٍîمî
|
|
93
|
103
|
*ؤبدذخ
- نهوًَيûé
è ïî ًهىîيٍَ
îلîًَنîâàيèے
3. دëàيèًîâàيèه
ٌهلهٌٍîèىîٌٍè
نîلû÷è
ًَنà ïî َ÷àٌٍêَ
رهلهٌٍîèىîٌٍü
نîلû÷è
ًَنû يà
مîًيîى
َ÷àٌٍêه
ïëàيèًَهٌٍے
ïî ٌëهنَùèى
ٌٍàٍüےى
çàًٍàٍ:
. آٌïîىîمàٍهëüيûه
ىàٍهًèàëû.
. خٌيîâيàے
è
نîïîëيèٍهëüيàے
çàًàلîٍيàے
ïëàٍà ًàلî÷èُ ٌ îٍ÷èٌëهيèےىè
يà ٌîِèàëüيûه
يَونû ïî إرح
. ہىîًٍèçàِèے
îلîًَنîâàيèے.
. فëهêًٍîيهًمèے.
. س÷àٌٍêîâûه
(ِهُîâûه) ًàٌُîنû.
3.1 دëàيèًîâàيèه
çàًٍàٍ
يà
âٌïîىîمàٍهëüيûه
ىàٍهًèàëû
دîًٍهليîٌٍü َ÷àٌٍêà
â ىàٍهًèàëàُ ًàٌٌ÷èٍûâàهٌٍے
يà
îٌيîâàيèè
يîًى
ًàٌُîنà
ىàٍهًèàëîâ
ïî ًَنيèêَ
è ïëàيîâîمî
îلْهىà
نîلû÷è
يà ًàٌٌىàًٍèâàهىûé
ïهًèîن
âًهىهيè.
دëàيîâûé
îلْهى
نîلû÷è
ًَنû çà ىهٌےِ
ïًèيèىàهٌٍے
ïî
نàييûى
ًàçنهëà
10.1.3.
زàلëèِà
10.9
ذàٌ÷هٍ
çàًٍàٍ
يà âٌïîىîمàٍهëüيûه
ىàٍهًèàëû