Технические
данные
|
1ПАРС
|
МРГ-700
|
База
агрегата (трактор)
|
Т-ЮОМЗГП
|
К-700,
К-701
|
Тип
механизма для нарезания щелей
|
Баровый
УЗЗ- 20
|
Б2036-210
|
Размеры
прорезаемой щели, мм: - Ширина - Глубина
|
140
|
210,
270
|
|
1700
|
1800-2000
|
Угол
поворота режущего органа, град
|
180
|
180
|
Габаритные
размеры, мм: - Длина - Ширина - Высота
|
5500
|
9000
|
|
3200
|
2880
|
|
3330
|
3750
|
Масса,
кг
|
16100
|
16000
|
Механизм состоит из:
Базовой машины - трактора К-700 или
К-701, снабженного навесным рабочим оборудованием;
Вала отбора мощности, состоящего из
малого карданного вала, фрикционной гидравлической муфты, большого карданного
вала;
Редуктора имеющего предохранительную
кулачковую муфту; -рабочего органа, опускание при врезании и подъем которого
осуществляется гидроцилиндрами трактора;
ходоуменьшителя, представляющего собой
червячно-цилиндрический редуктор с гидромотором и предназначенный для
обеспечения требуемых скоростей передвижения трактора;
Приспособление для удаления грунта от
траншеи шнекового типа.
Рассмотрим устройство и принцип работы агрегата:
Редуктор односкоростной трехступенчатый: первая
ступень цилиндрическая, вторая - коническая, третья - цепная. Общее
передаточное отношение - 17,9. Передача крутящего момента от конической к
цепной передаче происходит через муфту предельного момента.
Ходоуменьшитель имеет привод от гидромотора,
питающегося от гидравлической системы трактора. Дроссель дополнительно
установлен в системе насос - гидромотор для регулирования скорости движения
трактора. При перемещении подвижной шестерни ходоуменьшителя в нейтральное
положение трактор получает возможность работать от собственной коробки передач,
при этом все транспортные скорости машины сохраняются.
Режущий орган состоит из рамы, режущей цепи и
хвостовика. В качестве рабочей цепи используется гусеничная цепь трактора С-100
с некоторой доработкой. К цепи на сварке крепятся башмаки с резцами.
Заглубление и выглубление режущего органа производится домкратами трактора
К-700. Управление домкратами осуществляется через распределитель.
1- трактор К-700; 2 - вал отбора мощности;
3-редуктор; 4 - рабочий орган;
5- ходоуменьшитель; 6 - механизм подъема бара; 7
- узел фиксации рабочего органа; 8 - цепь режущего органа; 9 - механизм
переключения ходоуменьшителя; 10-палец; 11 - муфта шлицевая; 12 - колесо
зубчатое; 13 - тяга; 14 - приспособление для удаления грунта.
Рисунок 8 - Агрегат МРГ-700.
2. Анализ работы агрегата 1ПАРС с точки зрения
надежности
Надежность машин и механизмов зависит от
характера и величины нагрузок, материала и конструкции сопряженных деталей,
качества изготовления, условий эксплуатации и т.д. Воздействие значительной
части этих факторов носит случайный характер (случайные перегрузки, дефекты в
металле), вследствие чего возникающие отказы также оказываются случайными по
своей природе. В результате все величины, используемые при оценке надежности
(время работы до первого отказа или между последовательными отказами, число
отказов за определенное время и т.д.), также являются случайными. Поэтому
основные закономерности, характеризующие надежность оборудования,
устанавливаются на основе статистических данных с применением законов теории
вероятностей и математической статистики.
Выбор тех или иных количественных показателей
надежности зависит от назначения и конструкции изделия, от способа его
использования, а также от того, какие последствия влечет за собой отказ.
Для подавляющего большинства видов оборудования
наиболее важными показателями надежности являются: вероятность безотказной
работы в течение заданного промежутка времени P(t),
интенсивность отказов, средняя наработка между отказами Тср, средняя наработка
до первого отказа Т.
Перечисленные количественные характеристики
использованы в настоящей работе для оценки надежности оборудования на основе
статистических данных об отказах основных узлов и деталей, полученных при
эксплуатации.
Известно, что анализ надежности оборудования
можно проводить двумя методами:
- Рассматривать
характеристики надежности отдельных узлов и деталей оборудования;
- Рассматривать
суммарный поток отказов, не исследуя отказы отдельных элементов.
Так как причины и последствия отказов
оборудования, весьма различны, необходимо использовать первый, более полный и
точный метод.
.1 Результаты оценки надежности агрегата 1ПАРС
на основе статистических данных
Оценку надежности бурового оборудования
производили на основании статистических данных об отказах оборудования,
эксплуатируемого на объектах объединения «Азнефть».
В результате оценки надежности установлены
законы распределения времени безотказной работы и вычислены количественные
показатели безотказности агрегата и его узлов.
Агрегат 1ПАРС.
Количество единиц обследованного
оборудования……….32
Средняя наработка до первого отказа, Т
ср………………..41 сут.
Вследствие различных причин отказов разных узлов
невозможно вывести закон распределения времени безотказной работы.
Режущий орган агрегата 1ПАРС.
Количество единиц обследованного
оборудования………69
Средняя наработка до первого отказа, Т
ср……………….144 ч.
Функция вероятности безотказной
работы......ехр(-0,23tQ,1%)
Функция интенсивности отказов
...0,01810,22
Гидрокран агрегата 1ПАРС
Количество единиц обследованного
оборудования………69
Закон распределения времени безотказной
работы Вейбулла
Средняя наработка до первого отказа, Т
ср…….189 ч.
Функция вероятности безотказной работы
ехр(-0,24t0,44 )
- Функция интенсивности отказов 0,921
0,57
3. Разработка усовершенствованного узла
трактор надежность механизм
Для разработки усовершенствованного узла
рассмотрим динамику гусеничного движителя, в данном случае трактора Т-100МЗГП:
К числу недостатков гусеничных тракторов
относятся большой вес, и различные потери на сопротивление движению гусеничного
трактора.
Рассмотрим сопротивление движению трактора от
деформации грунта. Смятие почвы при движении гусеничного трактора происходит
преимущественно участком передней наклонной ветви гусеницы.
← Направление движения
Рисунок 9 - Распределение сил на гусеницу
трактора
Сопротивление движению трактора, вызываемое
деформацией почвы, можно определить по величине горизонтальной составляющей Х1
общей реакции почвы N на передний
участок гусеничной цепи (рис.9). Напряжение смятия почвы считаем
пропорциональным величине деформации.
Вес трактора уравновешивается реакциями почвы:
G = 2 chbL, (1)
Где b
- ширина опорной части гусеницы,
L - Длина опорной
части гусеницы,
h - Глубина колеи,
c - Коэффициент
сопротивления почвы смятию Таким образом глубина колеи без учета деформации
почвозацепами зависит от коэффициента сопротивления грунта смятию и
определяется следующей зависимости:
h = G
/ 2cbL (2)
Реакции почвы нормальные к поверхностям передних
участков гусеничных цепей, возрастают пропорционально глубине погружения
элементов цепи с изменением величины напряжений. Результирующая этих
элементарных реакций равна:
N = σbl1, (3)
Где l1
- длина лобового участка гусеничной цепи.
Сила лобового сопротивления почвы движению
трактора определяется такой зависимостью:
X1 = σbl1sin
α (4)
Подставляя значение
sin
α = h/l1,
Получим:
X1 = σbh
= ch2b, (6)
Коэффициент сопротивления движению трактора
определенный по деформации грунта может быть представлен отношением силы
лобового сопротивления почвы к весу трактора:
f’= X1/G = h/2L
= G/4cbL2, (7)
Очевидно, что для уменьшения лобового
сопротивления почвы целесообразно длину опорной части гусеницы увеличить с 3000
до 3300.
Тогда
f1’/ f2’= L2/L1 = 10.89/9 = 1.21, (8)
Коэффициент сопротивления почвы движению
трактора уменьшится в 1.21 раза.
.1 Определение основных параметров работы
оборудования
Тяговая сила агрегата на отвале:
Pkp= kb/ηu (9)
Где k-удельное
сопротивление грунта,
b-ширина отвала,
ηu -
коэффициент использования тягового усилия, 0,5
Так для агрегата 1ПАРС ширина отвала равна 3,2
м.
Для определения сил действующих на отвал в
процессе работы определяем максимальное значение удельного сцепления грунта
с=81 кПа при высоте снятия грунта 0,15м удельное сопротивление грунта, будет
определяться следующим образом:
k = 81000*0.15 =
12.2kH, (10)
Следовательно, исходя из выражения (1), тяговая
сила агрегата на бульдозерном отвале будет равна:
Pkp =
12200*3.2/0.5 = 73.2 kH
Определим тяговую мощность агрегата:
Nkp = Pkpν/270 (11)
Где ν
- Скорость движения агрегата, 6 км/ч
Nkp =
73200*6/270 = 1.7 кВт
Объем максимально возможного перемещаемого
грунта на отвале вычисляется по формуле:
Q = 0.75b
= 0.75*3.2 = 2.4 м3, (12)
При максимальной плотности грунта, равной 2.76
т/куб.м, максимальная масса грунта, который способен перемещать бульдозерный
отвал агрегата 1ПАРС:
m = ρ*V
= 2.76* 103 * 2.4 = 6.62m (13)
Часовая производительность бульдозерного отвала
агрегата 1ПАРС определяется по следующему выражению:
W = 1000bv/10000
= 0.1bv;
W = 0.1*3.2*2*6 =
1.8 га/ч (14)
Удельный вес агрегата выражается отношением
конструктивного веса к тяговой мощности на крюке:
gkp = G/Nkp, (15)
Где G
- 16100 кг (по технической характеристике)
gkp =16100/1700
= 9.5 кг/Вт
3.2 Расчет подшипников поворотной опоры
гидрокрана агрегата 1ПАРС
Найдем горизонтальные реакции в опоре поворотной
опоры из суммы моментов всех сил:
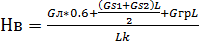
(16)

Наружный диаметр опоры 85 мм,
Толщину стенки 16 мм,
Вес поворотной опоры 2528 Н.
Тогда
Нв=17500+1270+612+3500+2528=25410 Н. (17)
Сопротивление повороту крана. Усилие
при повороте:
Так как ветровой нагрузкой,
действующей на кран, можно пренебречь, то сопротивление будет возникать только
из-за трения в подшипниках:
Мтр=2*0,01*8834*0,065/2+0,015*25410*0,03/2=11,46
Нм (18)
Тогда усилие при повороте:
Fпoв= 11,46/L=11,46/3=3,82
Н (19)
4. Расчет на прочность наиболее
нагруженных деталей
.1 Расчет опоры гидрокрана агрегата
1ПАРС
На рис. 10 представлен расчет
поворотной опоры гидрокрана Проверяем поворотную опору на прочность:

(20)
Рисунок 10 - Расчет поворотной опоры
гидрокрана Проверим далее поворотную опору на совместное действие изгиба и
сжатия.
Для этого подсчитаем:
Площадь сечения S=128 см2,
Главный момент инерции Y=2738 см4,
Радиус инерции г=4,7 см,
Момент инерции сопротивления изгибу W=350 см2,
Вес G=2528 Н.
Рассчитаем гибкость опоры:
(22)
Коэффициент запаса прочности к=1,25
Расчет показал, что поворотная колонна
удовлетворяет условиям прочности.
4.2 Расчет на прочность стального
цилиндрического крепления толкающего бруса к опоре
Толкающий брус крепится к опоре с помощью
цилиндрического стального крепления. Усилие в месте крепления (см рис. 11):
Sкpeп=Smax/efa=10309/e1,5=2300
Н. (23)
Где f-коэффициент
трения, a-угол обхвата
крепления.
Рисунок 11 - Схема крепления толкающих брусьев к
опоре.
Усилие, растягивающее цилиндрическое крепление:
(24)
Суммарное напряжение в болте:
(25)
Где К - запас надежности = 1.5,
l - плечо изгиба =
18мм,
dl - диаметр
болта,
Допустимое напряжение для стали 40 = 180 Мпа,
(26)
Коэффициент запаса прочности равен 1.37
Условие прочности выполняется.
5. Охрана труда и окружающей среды при
эксплуатации оборудования
К работе на агрегате допускаются только лица,
прошедшие специальное обучение по правилам эксплуатации агрегата и техники
безопасности, имеющие удостоверения на право управления и отвечающие за его
техническое состояние.
Перед началом работы, машинист обязан проводить
тщательный осмотр всего агрегата. Проверять состояние режущего органа, его
крепление, натяжение режущей и тяговой цепей. Особое внимание следует обращать
на крепление редуктора и режущего органа.
Безопасность работы и предупреждение аварий в
процессе эксплуатации агрегата обеспечиваются внимательным наблюдением за
работой механизмов и контрольными приборами.
При движении агрегата необходимо внимательно
следить за тем, чтобы рабочие органы не могли задеть людей или посторонние
предметы.
Перед началом работы с навесным оборудованием
звуковым сигналом предупредить находящихся вблизи агрегата людей.
Запрещается:
работа на неисправном агрегате
одновременная работа двух и более
исполнительных органов
производить регулировку, смазку или
очистку механизмов во время работы
движение агрегата с незакрепленными (в
транспортном положении) режущим органом и гидрокраном
движение агрегата с подвешенным на
крюке гидрокрана грузом
работа гидрокраном под проводами линий
электропередач
пребывание посторонних лиц на
работающем агрегате и в зоне его действия
при работе в ночное время рабочее место
должно быть достаточно освещено.
При работе необходимо пользоваться
индивидуальными средствами защиты (брезентовым костюмом, рукавицами,
текстолитовым шлемом и т. д.). При работе верхняя одежда должна быть плотно
застегнута.
Основные мероприятия по предотвращению
опасностей сводятся к следующим:
Всесторонний учет при проектировании
оборудования условий его работы с принятием необходимых запасов прочности;
Осмотр и испытание установок,
оборудования и механизмов;
Использование ослабленных элементов и
устройств для локализации опасности;
Использование контрольно-измерительных
приборов для контроля рабочих параметров и своевременного выявления опасных
нарушений режимов;
Автоматизация производственных
процессов, позволяющая вывести работающих из опасных зон, осуществление
контроля за показаниями приборов и дистанционное управление.
Использование оборудования, относящегося к
комплексу средств для разработки и эксплуатации нефтегазовых месторождений
регламентируется определенными экологическими нормами для данной области
промышленности.
Охрана окружающей среды при эксплуатации
агрегата 1ПАРС заключается в соблюдении мер по экологической безопасности:
При работе агрегата на экологию влияет нарушение
герметичности и прочности уплотнений гидросистемы агрегата. Вследствие
нарушения герметичности возможна утечка смазочных материалов, влекущих за собой
загрязнение окружающей среды. Во избежание этого необходимо регулярно проводить
ряд мероприятий по проверке и, по необходимости, ремонт или замену неисправных
частей агрегата (уплотнений).
Также, согласно экологической политике РФ
существуют определенные нормы по утилизации непригодного для дальнейшей
эксплуатации и ремонта оборудования.
Список используемой литературы
2- Михайловский
Е.В. Теория трактора и автомобиля - М.: «Сельхозгизд», 2000 г.
3- Бухаленко
Е.И. Нефтепромысловое оборудование: Справочник - 2-е изд., перераб. и доп. -
М.: «Недра», 2003. - 559 с.
4- Ишемгужин
Е.И. Теоретические основы надежности буровых и нефтепромысловых машин -
Уфа:-Изд. Уфимск. нефт. ин-та, 2001.-84с.
5- Молчанов
Г.В., Молчанов А.Г. Машины и оборудование для добычи нефти и газа. - М.:
«Недра», 2004. - 464с.