Проект мобильной установки по нанесению покрытий на внутреннюю поверхность резервуаров
Введение
Одной из важных проблем нефтехимии и
нефтепереработки является коррозия емкостного оборудования (сепараторы,
резервуары и т.п.), изготовленного из обычной низкоуглеродистой стали, не
обладающей стойкостью к коррозионно-активным средам.
Известно, что ущерб, причиняемый
коррозией народному хозяйству, не ограничивается невозвратимой потерей металла.
Эффективная защита от коррозии таких больших поверхностей представляет
собой важнейшую научно-техническую проблему, решение которой определяется общим
уровнем развития химической, электротехнической и других отраслей
промышленности. Нормативный срок службы резервуаров составляет 20 лет, но срок
их эксплуатации при антикоррозионной защите может достигать многих десятков
лет. Приведем пример основных способов защиты металлов.
Под неметаллическими покрытиями
подразумеваются покрытия металлов, дерева, штукатурки и других материалов
тонкими слоями неметаллических веществ, обеспечивающих защиту от действия
окружающей среды, а также декоративный эффект. Неметаллические покрытия могут
быть разделены на две основные группы:
органические покрытия;
неорганические покрытия.
Непрерывной средой органических
покрытий является органическое вещество, в лаках и красках - органический
пленкообразователь, в защитных смазках - минеральные масла, а при гумировании -
листы резины или пластические массы.
Неорганические неметаллические
покрытия представляют собою либо полученные на поверхности металлов
неорганические соединения - фосфаты, окислы и т.д., либо покрытия на основе
силикатных эмалей и цемента. Наиболее широкое промышленное значение имеют
органические лакокрасочные покрытия.
Основой лакокрасочного покрытия
являются органическое пленкообразующее вещество и пигмент. В тех случаях, когда
в покрытии присутствуют пигменты, они оказывают существенное влияние на
свойства покрытия.
Пигментированные пленки сильно
отличаются от непигментированных.
Неметаллические покрытия являются
основным практическим средством защиты черных металлов от коррозии. Ежегодно на
производстве разрушаются около 1…2% общего количества черных металлов,
находящихся в эксплуатации.
В последнее время значительно
усилена борьба с коррозией, однако и теперь огромное количество металла
теряется вследствие недостаточно эффективной защиты, в частности из-за
неправильного его окрашивания. Лакокрасочные покрытия имеют существенные
преимущества перед другими видами защитных покрытий. Они в большинстве случаев
наиболее удобны по методу нанесения, выгодны по стоимости работ и часто более
долговечны, чем металлические или другие виды защитных покрытий.
Защитные свойства любого покрытия
обуславливаются двумя важнейшими факторами:
механическими и химическими
свойствами самой пленки;
сцеплением - связью между пленкой и
покрываемой поверхностью.
Первый фактор не зависит от покрываемой
поверхности и всецело определяется свойствами пленкообразователя и других
компонентов пленки.
Второй фактор определяется как
физическими и химическими свойствами покрываемой поверхности, так и силами
взаимодействия этой поверхности с материалом, которым ее покрывают. Этот фактор
в технологии покрытий играет существенную роль.
Применение для металлических
покрытий новых, более эффективных лаков, красок и других материалов, не
содержащих пищевых масел, механизация и автоматизация техники окраски, увеличение
срока службы покрытий - основные средства для решения поставленных задач.
1. Литературный обзор
.1 Способы защиты
резервуаров от коррозии
Поскольку коррозия металлов является
вредным процессом, приносящие большие экономические убытки, то разработке
эффективных способов защиты металлических изделии уделяется много внимания.
Приведем пример основных способов защиты металлов [2].
Изоляция поверхности металла от
агрессивной среды с помощью лаков, красок, эмалей, пластических масс,
пассивирующих и металлических пленок и др. При использовании металлических
покрытии учитывают электрохимические свойства металлов покрытия и основы. По
характеру антикоррозионного действия различают анодные и катодные покрытия.
Анодные обладают в данной среде более отрицательным электродным потенциалом,
чем защищаемый металл. Нарушений целостности покрытия в присутствии электролита
на поверхности изделия образуется локальный гальванический элемент, в котором
анодом растворимым электродом - будет металл покрытия, металл основы - катодом
коррозии подвергаться не будет [2].
Одним из наиболее надежных способов
защиты металла от коррозии является создание на его основе сплава с другими
металлами, обладающего высокой склонностью к образованию пассивных защитных
пленок (легирования) [2].
Обработка коррозионной среды,
снижает её агрессивность. В первую очередь это связано с уменьшением содержания
в агрессивной среде кислорода, который, как показано выше, стимулирует
коррозионный процесс. Например, в паровой энергетике вода подвергается обработке,
направленной на снижение в ней содержания растворённого кислорода. В некоторых
случаях в агрессивную среду вводятся дополнительные вещества - ингибиторы
(замедлители) коррозии. Эти вещества, главным образом высокомолекулярные
органические соединения, адсорбируясь на границе раствор - металл, способствует
росту электродной поляризации на катодных участках локальных гальванических
элементов. Это, согласно основным положениям электрохимической теории коррозии,
уменьшает коррозионный ток и ослабляет коррозию металла. Особенно эффективно
действие ингибиторов при коррозии с выделением водорода [3].
Поддержание такого энергетического
состояния металла, при котором процесс его растворения термодинамически
невозможен или протекает с очень малой скоростью. К этой группе относится
способ защиты металла, находящегося в растворе электролита с достаточно высокой
электрической проводимостью. Защищаемый металл от внешнего источника тока
поляризуется катодно, причём ему сообщается такой потенциал, при котором его растворение
исключается или значительно ослабляется. Анодом в этой системе служит
дополнительный брусок металла, находящийся в данных условиях в пассивном
состоянии [3].
Метод протекторной защиты
заключается в том, что создаётся система, в которой к защищаемой конструкции
присоединён металл (протектор), обладающий более отрицательным потенциалом
(например, цилиндр, при защите стального изделия). Таким образом, создаётся
гальванический элемент, растворимый электродом, анодом которого является
протектор. Защищаемый металл в этой системе работает как катод и коррозии не
подвергается.
Оба последних метода эффективны для
защиты крупных, стационарных металлических сооружений [3].
1.2 Виды покрытий
применяемых при окраске резервуаров
Для окраски большинства резервуаров
применяют эмали типа ХВ-125, ХВ-785, НЦ-132, ХВ-1 120, ЭП-773, лак ПФ-171 с
алюминиевой пудрой, лак каменноугольный, лак ГФ-95 с алюминиевой пудрой,
некоторые другие лакокрасочные материалы специального назначения [1].
В зависимости от состава пигментов и
пленкообразующей основы лакокрасочные покрытия играют роль барьера, пассиватора
и протектора, и их защитные действия обуславливаются двумя основными факторами:
механической изоляцией защищаемой поверхности от внешней среды; химическим или
электрохимическим взаимодействием покрытия с защищаемой поверхностью [1].
Для обеспечения падежной
механической изоляций защищаемой металлической поверхности необходимо получить
сплошное, химически стойкое, хорошо сцепленное с поверхностью лакокрасочное
покрытие требуемой толщины.
В зависимости от способа обработки
поверхности для каждого вида лакокрасочного покрытия установлена минимальная
толщина для шероховатых поверхностей, полученных в результате дробеструйной
обработки, минимально допустимая толщина покрытия должна быть в 2…3 раза
больше, чем по гладкой поверхности, однако адгезия лакокрасочных покрытии,
нанесенных на шероховатую поверхность, значительно лучше [2].
Срок службы лакокрасочных покрытий
по металлу при эксплуатации в агрессивных средах в основном пропорционален
толщине покрытия. Но так как значительное увеличение толщины слоя приводит к
ухудшению адгезии и прочности, необходимо при выполнении лакокрасочных работ
обеспечивать толщину в заданных пределах [1].
Химическое и электрохимическое
взаимодействие покрытия с поверхностью металла обусловлено введением
компонентов, содержащих фосфорную кислоту (фосфатирующие грунтовки), которая
при нанесении на стальную поверхность образует покрытия с высокими адгезионными
и пассивирующими свойствами. Пассивирующими свойствами обладают также
лакокрасочные покрытия, в которых пигментами являются свинцовые сурик, хромат
цинка, бария, стронция, калия и некоторых другие пигменты.
В качестве пленкообразователей
применяют материалы, образующие прочные не набухающие пленки на основе
полиэтилена, полистирола, хлоркаучука, поливиниловых смол, полиакрилов,
алкидных и фенольных смол, а также пластификаторы.
Важным фактором, влияющим на
долговечность лакокрасочного покрытия, является качество подготовки поверхности
под окраску [1].
1.3 Подготовка
поверхности перед нанесением покрытия
Выбор способа подготовки поверхности
Детали или изделия непосредственно
перед нанесением защитных покрытий подвергаются механической, термической,
химической и электрохимической обработке [4].
Механическая обработка
предпринимается для удаления окалины, ржавчины, шлаковых включений, старой
краски, устранения царапин, неровностей и других дефектов.
Термическая обработка применяется
для удаления окалины, ржавчины и старой краски.
К химическим и электрохимическим
видам обработки относятся:
травление и декапирование с целью
удаления окалины и продуктов коррозии;
обработка в щелочных растворах и в
органических растворителях для удаления жировых и масляных загрязнении.
Выбор того или другого способа
подготовки поверхности должен производится в зависимости от характера и
количества загрязнении, природы покрываемого металла, чистоты поступающих на
отделку изделии и, наконец, от назначения наносимого покрытия [4].
Механическая обработка поверхности
Применяются следующие виды
механической обработки:
пескоструйная, дробеструйная или
дробеметная очистка;
крацевание;
шлифовка и очистка ручным
инструментом.
Пескоструйная очистка является одним
из эффективных методов подготовки поверхности. Она особенно пригодна для удаления
окалины, ржавчины и старых покрытий [4].
Сущность процесса пескоструйной
очистки состоит в том, что струя просеянного и просушенного кварцевого песка
направляется сжатым воздухом через специальное сопло на поверхности изделия.
Песок, ударяясь о поверхность изделий, очищает ее; поверхность становится
серой, матовой, приобретая при этом равномерную шероховатость, обеспечивающую
хорошую прилипаемость покрытия.
Крацевание является разновидностью
механической обработки поверхности и заключается в обработке изделий с помощью
быстро вращающихся дисковых проволочных щеток [4].
При крацевании с поверхности изделий
удаляется заусеницы, окалины, окисные пленки, продукты коррозии, травильный
шлак, а также очень тонкий слой металла.
Шлифование производится для придания
изделиям ровной и гладкой поверхности, а также для удаления окисных пленок. Эта
операция широко применяется при подготовке поверхности к окрашиванию и
оксидированию.
Процесс шлифования осуществляется на
станках или ручным способом при помощи абразивных дисков ил кругов,
шлифовочными шкурками, а также порошкообразными абразивными материалами. При
шлифовании острыми режущими гранями мелких зерен абразивных материалов
снимается тонкий поверхностный слой металла [4].
Очистка ручным инструментом является
простым, но трудоемким процессом. Для механического удаления окалины, ржавчины,
различных загрязнений, старой краски применяется металлические скребки,
шпатели, проволочные щетки и т.д.
Термическая обработка поверхности
Удаление окалины, ржавчины, старой
краски, масел и т.д., можно производить при помощи пламени, например
кислородно-ацетиленовой или керосиново-кислородной горелкой. При термической
обработке окалина, имеющая не большой коэффициент теплового расширения, легко
растрескивается и отслаивается. Ржавчина при этой обработке разрыхляется.
Термический способ очистки экономичен и отличается большой производительностью
[4].
Химическая и электрохимическая
обработка
Травлением называется обработка
металлических изделий в растворах кислот, кислых солей или щелочей с целью
удаления окислов с поверхности металла. Технология травления сводится к
погружению изделия в соответствующие растворы, реагирующие с окислами данного
металла.
Декапирование. Для быстрого удаления
легкого налета окислов, образующихся на поверхности очищенных изделий, главным
образом при транспортировке и хранении, применяется обработка в слабых
растворах кислот. Этот процесс носит название и предпринимается непосредственно
перед нанесением защитных покрытий [4].
Обезжиривание
Удаление с поверхности изделия
жировых и масляных загрязнений производят при помощи веществ, которые
растворяют жиры и масла или эмульгируют их.
Для обезжиривания применяются:
органические растворители;
щелочные растворы.
Обезжиривание органическими
растворителями
При обезжиривании органическими
растворителями обычно применяют бензин, лаковый керосин, скипидар, дихлорэтан,
трихлорэтан, тетрохлорэтилен, четыреххлористый углерод. Существенными
недостатками органических растворителей является ядовитость их паров и
сравнительно высокая стоимость.
Обезжиривание щелочными
растворителями
Растворы едких щелочей применяются
для обезжиривания металлов, трудно или совсем не растворяющихся в щелочах, как:
железо, стали чугуна, никеля, меди и др. Нельзя обезжиривать в растворах,
содержащих только едкие щелочи, изделия из олова, свинца, цинка, алюминия, а
также изделии из черных металлов, имеющих оловянную пайку.
В этом случае употребляют растворы
щелочных солей, например углекислый натрий, фосфорнокислый натрий, носит
название и предпринимается непосредственно перед нанесением защитных покрытий
[4].
Обезжиривание
Удаление с поверхности изделия
жировых и масляных загрязнений производят при помощи веществ, которые
растворяют жиры и масла или эмульгируют их.
Для обезжиривания применяются:
органические растворители;
щелочные растворы.
Обезжиривание органическими
растворителями
При обезжиривании органическими
растворителями обычно применяют бензин, лаковый керосин, скипидар, дихлорэтан,
трихлорэтан, тетрохлорэтилен, четыреххлористый углерод. Существенными
недостатками органических растворителей является ядовитость их паров и
сравнительно высокая стоимость.
В этом случае употребляют растворы
щелочных солей, например углекислый натрий, фосфорнокислый натрий, углекислый
калий, растворимое стекло, мыло и др.
Электрохимическое обезжиривание
При электрохимическом обезжиривании
применяются растворы такого же состава, как при химическом обезжиривании.
Производится как анодная, так и катодная обработка; чаще применяют катодное
обезжиривание или комбинированную обработку, - сначала на катоде, а затем на
аноде [4].
Применение ультразвуковых колебаний
для очистки металлических изделий
Ультразвуковые колебания нашли
широкое применение в технике для интенсификации различных технологических
процессов, в частности для ускорения процессов обезжиривания и травления
металлических поверхностей. Наиболее эффективным является применение
ультразвуковых колебаний для очистки мелких деталей, а также сложной
конфигураций, когда обычные способы очистки связаны со значительной
продолжительностью процесса и низким качеством очистки труднодоступных
участков. В настоящее время ультразвуковые колебания применяются также при
очистке средне- и крупногабаритных изделий [4].
1.4 Способы нанесения
покрытий на поверхность резервуаров
Лакокрасочные покрытия наносят на
поверхности резервуаров, пневматическим или безвоздушным распылением, а также
кистью или валиком [1].
В связи с тем, что методы нанесения
покрытия и сушки, а также выбором оборудования, используемого для выполнения
этих операций, зависят от размеров, конструктивных и технологических
особенностей изделий [1].
Преимуществами метода
пневматического распыления является простота и надежность в обслуживании
окрасочных установок, а также возможность применения в различных производственных
условиях при окраске средних, крупных и крупногабаритных резервуаров.
Недостатки метода пневматического распыления - значительные потери
лакокрасочного материала (от 25 до 50%), ухудшение санитарно-гигиенических
условий труда, что обусловлено образованием тумана, и повышенный расход
растворителей. Для снижения потерь лакокрасочных материалов и растворителей, а
также улучшения условий труда разработаны краскораспылители с ограничителем
давления КРП-3 и КРП-4 с усовершенствованным устройством изменения формы
факела. Все большее распространения получает метод безвоздушного распыления под
высоким давлением. Окраску этим методом можно производить как в
производственных помещениях, так и в окрасочных камерах. В этом случай
значительно уменьшается (20%) расход растворителей и улучшаются условия труда,
поскольку применяют более вязкие материалы, и уменьшается туманнообразование.
Однако указанные преимущества могут быть обеспечены только при окраске
поверхностей простой конфигурации [1].
Для выполнения лакокрасочных работ в
производственных помещениях, где производят сборку крупногабаритных изделий
наиболее приемлемы малогабаритные переносные установки типа «Факел-3», «Радуга
0,63П» и «2600Н» производства ВНР и Вильнюсского завода строительно-отделочных
машин по лицензии фирмы «Вагнер» (Швейцария). Установка «Радуга 0,6ЗП’
предназначена для безвоздушного распыления лакокрасочных материалов как одним,
так и двумя краскораспылителями с исходной вязкостью до 50 с (по ВЗ-4) при
давлении до 20 МПа.
В НПО «Лакокраскопокрытие»
разработана установка для безвоздушного распыления КИП-1654 с одним
краскораспылителем в обычном исполнении и другим краскораспылителем КРБ-1,
снабженным поворотной головкой с удлинителем. Краскораспылителем КРБ-1 можно
наносить лакокрасочные материалы на труднодоступные участки изделий. Для
окраски крупногабаритных изделий, имеющих значительные размеры (например,
колонная, емкостная аппаратура), можно использовать краскораспылители КСД-1 со
встроенным в него насосом высокого давления [1].
Преимущество этого краскораспылителя
состоит в том, что он снабжен верхним стаканом для краски, т.е. отпадает
необходимость в применении шлангов большой длины для подачи лакокрасочного
материала в распылительное устройство и исключается их промывка после окончания
работ [1].
Прогрессивным методом окраски
является электростатическое распыление краски. Сущность этого метода
заключается в том, что частицы краски, попадая в зону электрического поля
высокого потенциала, приобретают электрический заряд и осаждаются на подлежащей
окраске заземленной поверхности, имеющий противоположный заряд. Метод позволяет
значительно (от 30 до 50% по сравнению c пневматическими) сократить расход
лакокрасочного материала и создает возможность механизации процесса. Ручные
электростатические распылители можно использовать для окраски изделий сложной
формы и различных размеров.
Для окраски изделий в
электростатическом поле предназначены установки «УЭРЦ-4», «УЭРЦ-5 изготовленные
в нашей стране, а также установки «Хандепрей II» и «Хандепрей III», «Констат
ХГ-2», «Наfe» изготовленные в ВНР.
При окраске изделии в
электростатическом поле применяются разбавители марок РЭ (ГОСТ 18187) которые
представляют собой смеси сложных эфиров, кетонов, спиртов и ароматических
углеводородов.
В условиях единичного и
мелкосерийного производства при коротких перерывах, чтобы исключить высыхание
краски при применении быстросохнущих материалов, необходимо освободить шланг от
краски, а краскораспылитель не разбирая, опустить форсункой вниз в сосуд с
растворителем. Если перерыв в работе более 10 часов, краскораспылитель
необходимо тщательно промыть растворителем [2].
1.5 Виды распыляющих
устройств
Способ распыления зависит от
конструкции распыляющего устройства.
Каждый из распылителей имеет свои
преимущества и недостатки, связанные с особенностями дробления подводимой струи
жидкости, с учётом которых можно выбрать наиболее целесообразную конструкцию
распыления для конкретных условий его работы [5].
По конструктивному выполнению
основных элементов эти устройства можно разделить на следующие классы:
Струйные форсунки являются наиболее
простыми в конструктивном оформлении и представляют собой цилиндрическую
трубку, из которой под давлением вытекает струя жидкости, распадающаяся на
капли и образующая факел с малым углом при вершине [5].
Центробежные форсунки. В таких
форсунках движущаяся под давлением жидкость закручивается в завихрителе с
тангенциально расположенными каналами (ось каналов перпендикулярно размещена
под углом к оси форсунки, но не пересекается с ней). И за счет создаваемого
интенсивного вращательного движения в камере поступает в сопло, на выходе из
которого распадается на мелкие капли, приобретая форму полого конуса. Для
образования такого факела жидкость в форсунку подводятся под большим давлением
от 300 до 1000 кПа. Диапазон изменения давления зависят главным образом от
требуемой дисперсности распыла, физических свойств жидкости и размеров
дозирующих элементов. Вследствии высокого давления жидкости на выходе в
центробежную форсунку размеры ее сопла и тангенциальных каналов обычно
находится в пределах от 0,5 до 3 мм. Форсунки широко применяются для распыления
однородных маловязких жидкостей. Схема центробежной форсунки представлена на
рисунке 1 [5].
Разновидностью центробежных форсунок
являются шнековые форсунки. Отличительный признак этих форсунок состоит в том,
что закручивание жидкости производится с помощью завихрителя, выполненного в
форме шнека, на поверхности которого расположены винтовые каналы [5].
Пневматические форсунки. Эти
форсунки отличаются тем, что жидкость в них дробится под воздействием
подаваемого под давлением воздуха или газа. Схема пневматической форсунки
представлена на рисунке 2.
- сопло с камерой закручивания; 2 -
шайба; 3 - корпус; 4 - гайка;
- завихритель
Рисунок 1 - Конструктивная схема
центробежной форсунки
- диск с тангенциальными каналами; 2
- сопло
Рисунок 2 - Конструктивная схема
пневматической форсунки
Эти форсунки условно можно разделить
на две группы - низкого и высоко го давления. К первой группе относятся
форсунки с избыточным давлением распиливающего агента до 10 кПа, ко второй - от
10 до 1000 кПа и более.
Пневматические форсунки широко
используются для распыления вязких жидкостей и растворов. Их применение
особенно целесообразно, если в растворе твердые частицы. Большие размеры
проходных сечений каналов форсунки значительно снижают возможность их засорения
[5].
Ультразвуковые форсунки. В форсунках
этого типа струя или пленка из щели, дробится под воздействием ультразвуковых
колебании воздуха, создаваемых генератором, или под действием быстрых
вертикальных перемещений пластинки, происходящих с ультразвуковой частотой.
Форсунки имеют хорошую дисперсность
распыления жидкости, достигающую в некоторых конструкциях от 10 до 15 мкм.
Однако эти форсунки, как правило, используются в технологических процессах с
небольшими расходами распыляющей жидкости (от 40 до 80 кг/ч) [5].
Центробежно-распылительные
механизмы. В этих механизмах пленка жидкости, создаваемая при вращении диска,
стекает с его кромок и, становясь неустойчивой, распадается на капли. В
настоящее время определились конструктивные основные схемы механизмов, для
которых четко просматривается тенденция использования больших частот вращения
диска (от 200 до 300 с при окружных скоростях диска от 90 до 150 м/с. Схема
распылительного механизма представлена на рисунке 3 [5].
- распылительный диск; 2 - вал; 3 -
нижний подшипник; 4 - уплотнение;
- верхний подшипник; 6 - опорный
фланец; 7 - корпус; 8 - смотровой глазок; 9 - косозубая передача; 10 -
электродвигатель
Рисунок 3 - Конструктивная схема
распылительного механизма
2. Обоснование темы
дипломного проекта
Металлические вертикальные
цилиндрические резервуары нефтепереработки и нефтехимии работают в тяжелых
эксплуатационных условиях, а именно, при быстроменяющихся температурных
режимах, повышенном избыточном давлении, вакууме, вибрации, неравномерных
осадках, коррозии, быстроразвивающихся дефектах сварных швов.
Резервуарное оборудование,
находящееся в эксплуатации в данный момент на территории Башкортостана, более
чем на 90% выработало свой ресурс. Для реконструкции или ввода в эксплуатацию
нового резервуара требуются значительные капиталовложения.
Статистика отказов показывает, что
основной причиной выхода из эксплуатационного режима резервуаров
нефтепереработки и нефтехимии (порядка 70%) является коррозионный износ
поверхности, вступающей в контакт с агрессивной средой. Для устранения данного
недостатка нашли применение ряд методов, среди которых - применение
коррозионностойких материалов, использование ингибиторов коррозии,
пассивирование поверхности, нанесение коррозионно-стойких покрытий и т.д.
Использование коррозионностойких материалов экономически неэффективно и связано
с трудностями, возникающими при монтаже резервуара. Применение ингибиторов
требует дополнительных затрат на их последующее извлечение. Широко известен
положительный опыт применения лакокрасочных покрытий. Опыт эксплуатации
стальных резервуаров, защищенных покрытиями на основе эпоксидных смол и
эпоксидной шпатлевки ЭП-00-I0 показал, что при нанесении их на металлическую
поверхность, очищенную вручную металлическими щетками, в отдельных случаях
наблюдается целостность покрытия на участках общей площадью до 1 м через 7 лет
эксплуатации, а при подготовке механическим способом - от 10 до 12 лет. Это
свидетельствует в пользу разработки покрытий на основе эпоксидных смол.
Резервуар является крупногабаритным
изделием, и производить его внутреннюю окраску весьма затруднительно.
Проблема заключается в том, что для
покраски внутренней поверхности резервуара необходимо сооружать дополнительные
конструкции (леса и т.п.) которые не всегда можно установить внутри резервуара.
В настоящее время существует
множество установок для нанесения лакокрасочных покрытий, но их устройство
требует постоянного присутствия человека.
В дипломном проекте предлагается
механизировать покрасочные работы внутренней поверхности резервуара.
Для этого предлагается проект
автоматизированной мобильной установки, которая позволит снизить до минимума
участие человека при нанесений лакокрасочных покрытий на поверхность резервуара
и уменьшить влияние токсичных веществ, выделяемых при окраске, на человека.
3. Технологическая часть
.1 Описание технологической
схемы резервуарного парка площадки «Б» ТСЦ
Технологическая схема резервуарного
парка площадки «Б» ТСЦ представлена на чертеже ОПНН-170500-01.00.000.
Компоненты бензинов А-76, Нормаль-80
из цехов №8, 10, 11, 33, 27, 58, до площадки «Б» поступают по трубопроводу 59,
подходящему со стороны площадки «В» в резервуары Р-43ч45, 55ч58, 65ч68.
Бензин из цехов №8, 10, 11, 33, 27,
58 поступает по трубопроводу 157, идущему по восточному ряду в резервуары
Р-43ч45, 55ч58, 65ч68.
Оба потока бензина, перекачиваемых
по 157,59 линиям на площадке «Б», по необходимости, можно соединить в один
поток; с линии 59 в линию 157 переход производится через задвижку №93 и
поступает в резервуары Р-43ч45, 55ч58, 65ч68. С линии 157 в линию 59 переход
производится через задвижку №119 с поступлением в те же резервуары.
Бензин из цеха №10 в резервуары
площадки «Б» может поступать по 13 линии площадки «В» с выходом в коллекторной
насосной 712 площадки «В» в трубопроводы №4, 204, затем с площадки. «В» по
линии 204 поступает на площадку «Б», где через перемычку с задвижкой №89 из
линии 204 в линию 157, а также через коллектор насосной площадки «Б» в линию
157 и в линию 158, а затем в резервуары Р-43ч45, 55ч58, 65ч68.
В резервуарах Р-43ч45, 55ч58, 65ч68
производится циркуляция бензина; для циркуляции установлены смесительные сопла.
Порядок циркуляции бензина в
резервуарах на площадке «Б» следующий: резервуар закачивается компонентами
бензина до замера уровня не выше норм технологической карты, затем производится
циркуляция в течение двух часов для лучшего смешения и получения однородной
смеси.
Циркуляция бензина в резервуарах
может производиться насосом Н-7 или насосами Н-4 (5), причем бензин на насосы
Н-7 и Н-4 (5) может поступать по линии 158, или по линии основного всаса, или
по линии нового всаса и выбрасываться в линию бензин-сопло.
Далее бензин поступает в резервуары
по линии бензин-сопло.
Откачка товарного бензина из
резервуаров парка может производиться насосами Н-4 (5), Н-6 (8) и Н-7 по линиям
201 и 205:
по линии 201 - на ЛПДС, на эстакаду
704 площадки «В» для налива в вагоноцистерны и на установку налива светлых
нефтепродуктов в автоцистерны (АСН) поочерёдно;
по линии 205 - на ЛПДС и на
установку АСН поочерёдно.
Из резервуаров Р-43ч45, 55ч58 бензин
по основному всасу поступает на приём к насосу Н-4, к насосу Н-5 и
выбрасывается на насосы Н-4, 5 и в 201 коллектор.
Из резервуаров Р-65ч68 бензин
поступает по новому всасу на насосы Н-6, 8 и выбрасывается в 205 коллектор.
Коллекторы 201,205 на территории
площадки «Б» разветвляются на ЛПДС, на наливную эстакаду в вагоноцистерны и на
установку АСН.
Бензин из резервуаров Р-43ч45,
55ч58, 65ч68 можно откачивать на ЛПДС, на налив в вагоноцистерны и на установку
АСН по 201, 205 линиям насосом Н-7 по схемам:
Бензин из резервуаров парка площадки
«Б» Р-43ч45, 55ч58, 65ч68 можно откачивать на Яр-Бишкадакское хранилище
насосами Н-4 (5), Н-6 (8) и Н-7 по трём разным трубопроводам: Ш 150 мм, Ш 250
мм и по линии №59 на приём насосов площадки «Д» и далее насосами площадки «Д»
по бензинопроводу Ш 200 мм на Яр-Бишкадакское хранилище:
а) при откачке насосами Н-4, 5 из
резервуаров Р-43ч45, 55ч58 бензин поступает по основному всасу через насосы
Н-4, 5 или по линии 158 из резервуаров Р-43ч45, 55ч58, 65ч68 на приём насоса
Н-5, затем на приём насоса Н-4, а с насосов Н-4, 5 поступает в нагнетательный
коллектор этих насосов, из которого может откачиваться на Яр-Бишкадак по двум
направлениям: в линию Ш 150 мм и в линию 59 на площадку «Д».
б) из резервуаров Р-65ч68 на приём
берётся по всасу и по 158 линии выбрасывается по той же схеме. Задвижка №92
служит разделяющей, когда на Яр-Бишкадакское хранилище закачиваются два разных
нефтепродукта.
Для приёма бензина с
Яр-Бишкадакского хранилища по трубопроводу
Ш 150 мм или Ш 250 мм сделана
обвязка указанного трубопровода в линию 157 в линию 158, а также в 59 линию с
трубопровода Ш 250 мм и с трубопровода Ш 150 мм.
Бензин, перекачиваемый на площадку
«Б» по 157, 59 линиям можно непосредственно с установок направлять на
Яр-Бишкадакское хранилище:
а) по 157 линии в трубопровод Ш 250
мм и в трубопровод Ш 150 мм.
б) по 59 линии в трубопровод Ш 150
мм и в трубопровод Ш 250 мм.
Яр-Бишкадаские трубопроводы Ш 150 мм
и Ш 250 мм между собой закольцованы.
Приём дизельного топлива
непосредственно с установок цехов №9, 10, 14 и из резервуаров производится по
линии 159 в резервуары Р-39ч42. Для товарных операций 159 линия связана с
насосами Н-1, 2, 3.
В резервуары Р-47ч54 дизельное
топливо закачивается по 159 линии с переходом на нагнетание через задвижку №73.
Приём дизельного топлива из цеха №9
может также производиться по дизельному трубопроводу 376 Ш 370 мм и резервному
Ш 200 мм. По трубопроводу 376 в резервуары Р-39ч42 и в резервуары Р-47ч54.
Из №9, 10 цехов приём дизельного
топлива осуществляется с 26 линии в резервную линию в резервуары.
Резервуары Р-39ч42, 47ч54 для
большей оперативности обвязаны дополнительным всасом Ш 300 мм, подходящему к
насосу Н-1, что даёт возможность производить три операции с тремя резервуарами
одновременно: заполнение, циркуляция, откачка на налив в вагоноцистерны или на
ЛПДС.
Для случая раздельной закачки
дизельного топлива в резервуары Р-39ч42, 47ч54 с трубопровода 376 Ш 370 мм на
новый всас существует перемычка с задвижкой 62.
Приём дизельного топлива по
трубопроводу 376 с переходом на новый всас в резервуары Р-39ч42.
Дизельное топливо, перекачиваемое по
резервной линии с установок, по необходимости можно направлять в линию 159 и в
линию нового всаса. Дизельное топливо на приём берётся по линии всаса.
Дизельные насосы Н-1, 2, 3 обвязаны
двумя основными всасами и двумя выкидами, возможен одновременно налив
дизельного топлива в вагоноцистерны с выкидом на наливной коллектор 202, а
откачка на ЛПДС в коллектор 203.
Дизельное топливо из резервуаров
Р-39ч42, 46, 47ч54 можно насосом Н-2 откачивать на Яр-Бишкадакское хранилище:
а) берётся на всас от резервуаров
Р-39ч42;
б) берётся на всас от резервуаров
Р-47ч54.
Имеется возможность откачки
дизельного топлива на Яр-Бишкадакское хранилище непосредственно с установок по
трубопроводу 376 в трубопровод
Ш 150 мм и в трубопровод Ш 250 мм.
Имеется возможность откачки
дизельного топлива на Яр-Бишкадакское хранилище непосредственно с цеха №9 по
резервному трубопроводу в трубопровод Ш 150 мм и в трубопровод Ш 250 мм.
Яр-Бишкадакские трубопроводы Ш 150
мм и Ш 250 мм закольцованы между собой задвижкой №61.
Для освобождения бензиновых
резервуаров до замера «0» есть линия отсоса. Для освобождения резервуаров с
дизельным топливом до замера «0» есть линия отсоса.
Имеются отсекающие задвижки, на
линии всаса - №98, на линии «сопло» - №99, на линии поступления со 157 линии -
№100, на линии всаса - №101.
Через задвижку №93а соединяются две
линии поступления 157 и 59; через задвижку №102 соединяются две линии 158 и 59.
Через задвижку №105 соединяются 158
линия с линией «сопло» к резервуарам Р-65ч68 (не работает - отглушена).
Через задвижку №104 соединяются 157
линия с линией «сопло» к резервуарам Р-65ч68 (не работает - отглушена).
Через задвижку №103 соединяются
линия «сопло» резервуаров Р-43ч45, 55ч58, 65ч68 с линией 157 через задвижку
№106 (данный участок линии не работает - отглушен).
Через задвижку №35 соединяются линия
откачки на ЛПДС с 159 линией (отглушена), №58, 59 задвижки отсекающие задвижки
на трубопроводе Ш 150 мм на Яр-Бишкадак.
Через задвижку №66 соединяются линия
«сопло» Р-65ч68 резервуаров с линией всаса Р-65ч68 резервуаров (отглушена).
Через задвижку №86 (отглушена) есть
возможность направить дизельное топливо на Яр-Бишкадак по трубопроводу Ш 250 мм
через задвижку №61 и задвижки №92, 56, 57.
Через задвижку №67 соединяются линии
Яр-Бишкадакского трубопровода Ш 150 мм с 202 линией через задвижки №71, 77.
Через задвижку №64 соединяется линия
дизельного топлива «новый всас» со всасом бензина (линия отглушена).
Задвижка №16 отсекающая на насосе
Н-4 в 157 линию.
Через задвижку №14 соединяются
дизельное топливо «всас» Р-47ч54 резервуаров с Н-4 на приём (отглушена).
Через задвижку №50 соединяются
дизельное топливо «всас» Р-47ч54 резервуаров со всасом бензиновых резервуаров
Р-65ч68 (отглушена).
Через задвижку №70 соединяются 205
линия с 202 линией через задвижку №71, 77; с Яр-Бишкадакским трубопроводом Ш
150 мм через задвижку №67.
Через задвижку №87 соединяются выкид
насоса Н-4 через задвижку
№18, выкид насоса Н-5 через задвижку
№19 с 205 линией.
Задвижка №76 отсекающая (конечная)
на 205 линии (отглушена).
Через задвижку №9 соединяется всас
дизельного топлива с приёмом Н-3.
Через задвижку №79 на Н-3
соединяется всас с выкидом.
Через задвижку №74 соединяется всас
дизельного топлива Р-47ч54 резервуаров с всасом дизельного топлива Р-39ч42
резервуаров.
Через задвижку №48 соединяется 205
линия с линией дизельного топлива «сопло» резервуаров (отглушена).
Через задвижку №49 соединяется 205
линия с линией дизельного топлива нагнетание Р-47ч54 резервуаров (отглушена).
Имеется возможность откачки Карачаганакского
конденсата с «Оренбурггазпрома» через цех №13 в 202 линию, на Яр-Бишкадак по
трубопроводу
Ш 150 мм через задвижки №77, 71, 67,
56, 57 и обратно с Яр-Бишкадака в цех №13; при этом задвижки №44, 37 закрыты.
Линия 158 является всасом из
бензиновых резервуаров при циркуляции, поэтому задвижки №41, 47 всегда закрыты,
а соединение 158 линии с 201 линией через задвижку №45 (отглушена).
При циркуляции бензинов выкид с
насосов в линию «сопло» задвижка №43 является отсекающей (закрыта).
3.2 Описание технологической
схемы блока перемешивания
Лакокрасочная композиция с емкости
Е-1 подается в перемешивающее устройство М. С емкости Е-2 в перемешивающее
устройство, подается отвердитель (полиэтиленамин). После перемешивающего
устройства лакокрасочная композиция подается на блок нанесения покрытия.
Технологическая схема блока перемешивания представлена на чертеже
ОПНН-170500-02.00.000.
3.3 Описание
технологической схемы мобильной установки
Краска с блока перемешивания
подается в емкость Е-1. Далее с емкости Е-1 через насос Н, краска подается в
смеситель СМ, туда же с компрессора К подается сжатый воздух. После
перемешивания в смесителе газожидкостная смесь подается на форсунку. Затем
происходит распыление лакокрасочного покрытия на окрашиваемую поверхность. Технологическая
схема блока нанесения покрытия представлена на чертеже ОПНН-170500-03.00.000.
4. Экспериментальная
часть
.1 Получение покрытия
Экспериментальная часть включает в
себя приготовление покрытия и определения ее механических свойств. В состав
покрытия входят следующие компоненты: кокс (фракции менее 0,005 мм)
(наполнитель); двуокись титана не модифицированная (пигмент); эпоксидная смола
ЭД-20 (пленкообразователь); ацетон (растворитель); пластификатор; отвердитель
(полиэтиленполиамин); толуол. В таблице 4.1 приведены пропорции компонентов для
получения покрытия.
Таблица 4.1 - Пропорции компонентов
покрытия
Компоненты
|
Единица измерения
|
Количество
|
Эпоксидная смола ЭД-20
|
г
|
100
|
Ацетон
|
мл
|
75
|
Толуол
|
мл
|
75
|
Кокс
|
г
|
130
|
Двуокись титана
|
г
|
17
|
Пластификатор
|
мл
|
48
|
Отвердитель
|
мл
|
7
|
Приготовление покрытия происходит
следующим образом. Эпоксидную смолу растворяем в растворе ацетона и толуола.
Взвешиваем коке и двуокись титана, тщательно перемешиваем и не большими
порциями добавляем в раствор с эпоксидной смолой. Через определенное время
добавляем пластификатор и отвердитель, все перемешивается в течений нескольких
минут, до получения однородной композиции. Подробный ход операций описан в
таблице 4.2.
Таблица 4.2 - Методика приготовления
покрытия
Шаг №
|
Операция
|
Продолжительность, мин
|
1
|
Перемешивание эпоксидной смолы с толуолом и ацетоном
|
50 (до полного растворения смолы)
|
2
|
Перемешивание кокса с двуокисью титана
|
5…10
|
3
|
Перемешивание наполнителя с раствором смолы
|
20
|
4
|
Перемешивание с добавлением пластификатора
|
15
|
5
|
Перемешивание с добавлением отвердителя
|
15
|
4.2 Определение вязкости
лакокрасочной композиций
Определение вязкости осуществляем с
помощью вискозиметра по ГОСТ 8420-57. Готовую лакокрасочную композицию в
количестве 90 мл помещаем в вискозиметр. Открываем заслонку в нижней части
вискозиметра, и засекаем время полного истечения лакокрасочной композиций. Для
обеспечения чистоты эксперимент повторяем три раза и определяем среднее
значение. Результаты исследования зависимости вязкости композиций от концентраций
ацетона, приведены в таблице 4.3. Схема экспериментальной установки показана на
рисунке 4.1.
4.3 Обработка
экспериментальных данных
Производим определение
кинематической вязкости лакокрасочной композиций по формуле
(4.1)
где нв -
кинематическая вязкость воды
=1,005·10-6 м2/с;
tк
- время истечения лакокрасочной композиций из вискозиметра, с;
tв - время истечения воды
из вискозиметра.
Следовательно кинематическая
вязкость композиции для первого случая равна
- вискозиметр по ГОСТ
8420-57; 2 - штатив; 3 - стакан; 4 - заслонка
Рисунок 4.1 - Схема
лабораторной установки
Производим расчет
плотности композиции по формуле
(4.2)
где m - масса композиции, кг;
V - объем композиции, м3/ч.
Тогда плотность композиции для
первого случая равна
Остальные результаты
обработки данных приведены в таблице 4.4.
Таблица 4.4 - Результаты
обработки данных
№ эксперимента
|
Плотность композиций, кг/м3
|
Вязкость композиций, м2/с
|
Вязкость композиций, сСт
|
1
|
1093
|
1,738·10-6
|
1,738
|
2
|
1086,6
|
1,43·10-6
|
1,43
|
3
|
1076,6
|
1,287·10-6
|
1,287
|
4
|
1064,4
|
1,247·10-6
|
1,247
|
5
|
1038,8
|
1,129·10-6
|
1,129
|
6
|
1015,2
|
1,052·10-6
|
1,052
|
По этим данным строим графики
зависимости: плотности лакокрасочной композиций от концентрации растворителя
(рисунок 4.2); вязкости лакокрасочной композиций от концентрации растворителя
(рисунок 4.3); плотности лакокрасочной композиций от вязкости лакокрасочной
композиций (рисунок 4.4).
В ходе проведенных экспериментальных
работ определили вязкость композиций, которая в дальнейшем понадобится для
расчета форсунки и подбора насоса. При проведений экспериментальных работ была
рассмотрена композиция с минимальной концентрацией растворителя 16,5%, это
связано с тем, что композиция с меньшей концентрацией растворителя приводит к
большому расходу лакокрасочной композиций, засорению, к ухудшению механических
свойств покрытия и малому диаметру факела.
Принимаем расчетное значение
вязкости н=1,738 сСт.
Рисунок 4.2 - График зависимости
плотности лакокрасочной композиций от концентрации растворителя
Рисунок 4.3 - График зависимости
вязкости лакокрасочной композиций от концентрации растворителя
Рисунок 4.4 - График зависимости
плотности лакокрасочной композиций от вязкости лакокрасочной композиций
5. Расчетная часть
.1 Расчет форсунки [5]
Цель расчета: Рассчитать форсунку с
периферийной подачей жидкости
Исходные данные:
Абсолютное давление на выходе из
форсунки, Р*вх=4,905 кПа;
Абсолютное давление воздуха на
выходе из форсунки, Р*вых=2,943 кПа;
Температура торможения воздуха на
входе в форсунку, Т*вх=300 К;
Перепад давления жидкости в выходном
сопле форсунки, Рж=7,848 кПа;
Относительный расход жидкости,
б=0,77;
Температура поступающей в форсунку
жидкости, Тж=293 К;
Диаметр сопла форсунки, D=5 мм;
Площадь сопла форсунки, F=0,00196 мм2;
Плотность жидкости, сж=1093
кг/м3;
Угол между осью форсунки у входа в
газовый поток и прямой,
параллельной оси выходного канала
форсунки, и=90о;
Число каналов для подачи жидкости, n=4.
Расчетная схема форсунки
представлена на рисунке 5.1.
Рисунок 5.1 - Расчетная схема
форсунки
Определяем газодинамические
параметры движения воздуха в форсунке по формуле
(5.1.1)
Режим движения воздуха в
сопле форсунки критический, поэтому принимаем: приведенную скорость газа, л=1;
газодинамическую функцию, е1(л)=0,634; газодинамическую функцию
приведенной плотности потока масс, q(л)=1.
Определяем радиальную
составляющую начальной скорости жидкости по формуле
(5.1.2)
где цск - коэффициент
скорости, цск=0,8 [5].
Определяем время
движения жидкости до оси форсунки по формуле
(5.1.3)
Определяем скорость
воздуха в форсунке
(5.1.4)
Определяем плотность
воздуха в форсунку по формуле
(5.1.5)
где Ксж - коэффициент
сжимаемости газа, Ксж=0,99 [5].
Определяем секундный
массовый расход воздуха через форсунку без подачи в нее жидкости по формуле
(5.1.6)
где mг.ж. - расход газа при совместном движений с жидкостью, кг/м;
ез - коэффициент
уменьшения расхода газа, ез=0,5 [5];
мж - коэффициент расхода
жидкости;
mкр - критический расход
газа, кг/с.
Критический расход газа можно
определить по формуле
(5.1.7)
Обозначим
(5.1.8)
Тогда
(5.1.9)
где мг - коэффициент
расхода, мг=0,95 [5];
mг - расход газа, кг/с.
Для принятого
относительного расхода можно ожидать ез=0,5, тогда
mг.ж.=0,5∙2,125∙10-5=1,0625∙10-5
кг/с.
Определяем приближенное
значение расхода жидкости по формуле
(5.1.10)
Определяем коэффициент
сжимаемости по формуле
(5.1.11)
где ш - коэффициент сопротивления
капли, ш=0,43 [5];
dм - медианный диаметр
капли, dм=25∙10-6
м [5].
Определяем соотношение
скорости капли и воздуха с учетом того, что начальная скорость осевой скорости
капли щ0=0 по формуле
(5.1.12)
где щк - скорость,
которую капля жидкости в потоке газа имеет в конце периода t, м/с;
щг.н - начальная скорость
газа, м/с.
Определяем коэффициент b1 по формуле
(5.1.13)
Определяем величину А по
формуле
(5.1.14)
Величина С определяется
из графика на рисунке 42 [5]. Для б=0,77, С=2
По найденной величине А
из графика на рисунке 44 [5] определяем ез=0,571.
Тогда расход воздуха
через форсунку определим по формуле
(5.1.15)
Определим коэффициент
расхода форсунки относительно воздуха и жидкости по формуле
(5.1.16)
Определим расход через
форсунку по формуле
(5.1.17)
Определяем соотношение
напоров жидкости и воздуха в выходном канале форсунки по формуле
(5.1.18)
Из графика на рисунке 46
[5] по найденному значению в определяем коэффициент расхода мж=0,57.
Определяем площадь
поперечного сечения канала для подачи жидкости по формуле
(5.1.19)
Определяем диаметр
канала подачи жидкости
(5.1.20)
Принимаем диаметр канала
для подачи жидкости d=3 мм.
5.2 Расчет насоса
Цель расчета: Рассчитать
и подобрать насос для перекачки лакокрасочной композиций.
Исходные данные:
Давление в емкости, Р1=0,1
МПа;
Температура перекачки, Тп=20
оС;
Длина трубопровода на
линии всасывания, lвс=5
м;
Длина трубопровода на
линии нагнетания, lнаг=25
м;
Число вентилей на
всасывающей линии, n=1;
Расход лакокрасочной
композиций, Q=0,001 м3/с;
Давление в
краскораспылителе, Р2=7,848 кПа.
Определяем диаметр
трубопровода по формуле
(5.2.1)
где
-
скорость течения лакокрасочной композиций, м/с.
Для всасывающего
трубопровода принимаем,
и
определяем диаметр трубопровода
Для нагнетательного трубопровода
принимаем,
и
определяем диаметр трубопровода
Принимаем стандартный
диаметр трубопровода всасывающего трубопровода изготовленного из резины, dвс=0,04 м с толщиной стенки Sвс=0,002
м.
Для нагнетательного
трубопровода принимаем стандартный диаметр трубопровода изготовленного из
резины, dнаг=0,05 с толщиной стенки Sнаг=0,002
м.
Определяем истинную
скорость движения лакокрасочной композиции по трубопроводу по формуле
(5.2.2)
Для всасывающего трубопровода
Для нагнетательного
трубопровода
Определяем число
Рейнольдса по формуле
(5.2.3)
где с - плотность
лакокрасочной композиции, с=1093 кг/м3;
м - вязкость
лакокрасочной композиции, м=1,899∙10-3 Па/с.
Для всасывающего
трубопровода
То есть режим
турбулентный.
Для нагнетательного
трубопровода
То есть режим
турбулентный.
Определяем относительную
шероховатость трубопровода по формуле
(5.2.4)
где Д - абсолютная
шероховатость трубопровода.
Для всасывающего
трубопровода
Принимаем Д=1,5∙10-6
м.
Для нагнетательного
трубопровода
Принимаем Д=1,5∙10-6
м.
Определяем коэффициент
трения
Для всасывающего
трубопровода проверяем следующее условие
(5.2.5)
Условие выполняется,
тогда коэффициент трения определяется по формуле
(5.2.6)
Для нагнетательного
трубопровода проверяем условие
(5.2.7)
Условие выполняется,
тогда коэффициент трения находим по формуле 5.2.6
Определяем сумму
коэффициентов местных сопротивлений
Для всасывающего
трубопровода:
при входе в трубу: о1=0,5
[6];
для вентиля: о2=3,5
[6].
Следовательно сумма
коэффициентов местных сопротивлений определяется по формуле
(5.2.8)
Для нагнетательного
трубопровода:
на выходе из трубы: о1=1
[6];
в форсунку: о2=0,1
[6];
в диафрагме: о3=0,3
[6].
Следовательно, сумма
коэффициентов местных сопротивлений определяется по формуле
(5.2.9)
Определим потери напора
по формуле
(5.2.10)
где g - ускорение свободного падения, g=9,81
м/с2.
Для всасывающего
трубопровода
Для нагнетательного
трубопровода
Общие потери напора определяем
по формуле
(5.2.11)
Определяем напор насоса
по формуле
(5.2.12)
Определяем полезную мощность насоса
по формуле
(5.2.13)
По каталогу насосов
выбираем шестеренчатый насос марки ШФ 5-25. Технические характеристики насоса
представлены в таблице 5.1.
Таблица 5.1 -
Технические характеристики насоса ШФ 5-25
Подача (не менее), м3/ч
|
3,6
|
Давление нагнетания, МПа
|
0,4
|
Частота вращения, об/мин
|
1450
|
Мощность насоса, кВт
|
1,1
|
КПД, %
|
40
|
Перекачиваемая жидкость
|
Наименование
|
Масло, нефть, дизельное топливо
|
|
Температура, К
|
313-343
|
|
Вязкость, сСт
|
6-600
|
Двигатель
|
Тип
|
ПБ-42М
|
|
Мощность
|
1,5
|
Масса, кг
|
18,7
|
5.3 Подбор компрессора
для подачи воздуха в форсунку
По каталогу [11] производим подбор
компрессора марки 24.J1047А.
Технические характеристики
компрессора представлены в таблице 5.2.
Таблица 5.2 - Технические
характеристики компрессора марки 24.J1047А
Модель
|
24.J1047А
|
Подача, м3/ч
|
12
|
Давление, атм
|
8
|
Мощность, кВт
|
1,5
|
Габариты, м
|
Длина
|
0,6
|
|
Ширина
|
0,7
|
|
Высота
|
0,3
|
Масса, кг
|
24
|
5.4 Расчет диаметров
ботов для крепления насосного агрегата к раме
Цель расчета: Проверить болты на
прочность под действием растягивающей силы.
Расчетная схема крепления насосного
агрегата к раме представлена на рисунке 5.4
Определим момент сил:
а) относительно точки А
(5.4.1)
где Q1 - сила действующая на точку А на расстояний L, Q1=183,44 Н;
L - расстояние от точки приложения силы Q1 до точки А, L=361 мм;
l - расстояние между болтами, l=150 мм;
l1 - расстояние от точки А
до места приложения силы Q2, l1=75 мм;
l2 - расстояние от места
приложения силы Q2 до места приложения
силы R2, l2=75 мм;
Q2 - сила действующая на
точку А на расстояний l, Н;
R2 - реакция действующая в
точке А, Н;
преобразовав формулу 5.4.1, получим
(5.4.2)
- электродвигатель; 2 -
муфта; 3 - насос; 4 - рама
Рисунок 5.4 - Расчетная
схема крепления насосного агрегата к раме
б) относительно точки D
(5.4.3)
где l3 - расстояние от места приложения силы Q1
до точки В, l3=286 мм;
R1
- реакция действующая в точке В, Н.
Преобразовав формулу
5.4.3, получим
(5.4.4)
Расчет ведем по наиболее
нагруженным болтам, поэтому из полученных двух значений R1 и R2
выбираем максимальное
(5.4.5)
Определим силу,
действующую на один болт по формуле
(5.4.6)
Рассчитываем болты на
растяжение по следующей формуле
(5.4.7)
где [ур] - допускаемое напряжение для материала болта, [ур]=160 МПа.
По таблице 28 [7]
выбираем болт М6 с внутренним диаметром резьбы dв=4,918
мм и крупным шагом р=1 мм.
Проверяем выполнение
следующего условия
(5.4.8)
Условие 5.4.8
выполняется.
5.5 Расчет диаметра
болтов для крепления компрессора к раме
Цель расчета: Проверить
болты на прочность под воздействием растягивающей силы.
Расчетная схема
крепления компрессора к раме представлена на рисунке 5.5
Определим внешнею силу
действующую на болт по формуле
(5.5.1)
где Q - сила действующая на раму, Q=235,44
Н;
f
- коэффициент трения, f=0,15
[7];
h
- расстояние от точки приложения силы Q
до стойки, h=150 мм;
l
- расстояние между болтами, l=500
мм;- расстояние между болтами, L=600
мм.
Рисунок 5.5 - Расчетная
схема крепления компрессора к раме
По формуле 5.4.7
производим расчет болтов на сжатия
Принимаем материал
болтов Ст3
По таблица 28 [7]
выбираем болт М6 с внутренним диаметром резьбы dр=4,918
мм и крупным шагом p=1 мм.
Проверяем выполнение
условия 5.4.8
Условие 5.4.8 выполняется.
5.6 Расчет мобильной
установки
Расчет крепления форсунки
Определяем изгибающий момент,
действующий на стержень (расчетная схема крепления стержня к цепи представлена
на рисунке 5.6.1) по формуле
Рисунок 5.6.1 - Расчетная схема
крепления стержня к цепи
(5.6.1)
где F - сила, действующая на крепление на
расстояний l, F=30 Н;
l - расстояние от места крепления стержня до форсунки, l=500 мм.
Определим диаметр
стержня по формуле
(5.6.2)
где W - момент сопротивления стержня, мм2.
Момент сопротивления определяется по
формуле
(5.6.3)
где у - допускаемое напряжение стали
Ст 45, у=160 МПа.
Тогда диаметр стержня
равен
Диаметр стержня
округляем до стандартного, принимаем d=8
мм.
Определим площадь
сечения стержня по формуле
(5.6.4)
Определим объем стержня
по формуле
(5.6.5)
Определим массу стержня
по формуле
(5.6.6)
где с - плотность стали Ст 45,
с=7800 кг/м3.
Определяем необходимую
массу противовеса, для этого находим изгибающий момент действующий на стержень
в точке А (расчетная схема представлена на рисунке 5.6.2).
Рисунок 5.6.2 -
Расчетная схема
(5.6.7)
где q1 - нагрузка действующая на стержень, q1=2 Н;
l1 - длина стержня, l1=500 мм;
F1 - сила действующая на
стержень на расстояний l1, F1=30 Н;
q2 - нагрузка действующая
на стержень, q2=0,22 Н;
l2 - длина стержня, l2=100 мм;
F1 - сила действующая на
стержень на расстояний l2, Н;
преобразовав формулу 5.6.7, получим
(5.6.8)
Следовательно, нам
необходим противовес массой m=15,5
кг. Противовес изготавливаем из свинца.
Определяем объем,
который будет занимать противовес по формуле
(5.6.9)
где m - масса противовеса, m=15 кг;
сc - плотность свинца, сс=11300
кг/м3.
Определяем площадь
противовеса по формуле
(5.6.10)
где s - толщина противовеса, с=0,05 м.
Определяем диаметр
противовеса по формуле
(5.6.11)
Общий вид противовеса
показан на чертеже ОПНН-170500-04.00.007.
Расчет цепной передачи
По таблице П33 [7]
выбираем цепь с шагом t=25,4
мм, диаметр валика d=7,95 мм, длина втулки
В=22,61 мм.
Проекция опорной
поверхности шарнира определяем по формуле
(5.6.12)
Диаметры делительных
окружностей звездочек определяем по формуле
(5.6.13)
где z - число зубьев звездочки, z=z1=z2=30.
Диаметры делительных
окружностей звездочек округляем до стандартного, принимаем D01,2=102 мм.
Скорость цепи вычисляем
по формуле
(5.6.14)
где n1 - частота вращения ведущей звездочки, n1=28 об/мин.
Определяем окружное
усилие цепи по формуле
(5.6.15)
где N - мощность, передаваемая цепью, N=0,0495 кВт.
Давление в шарнирах
определяем по формуле
(5.6.16)
где kэ - коэффициент нагрузки (эксплуатаций), kэ=1,43 [7].
Определяем число звеньев
цепи по формуле
(5.6.17)
где аw1 - межосевое расстояние, аw1=40 мм.
Число звеньев цепи
округляем до четного Lt=110;
уточняем аw1=39,9
мм.
Определяем межосевое
расстояние по формуле
(5.6.18)
Определяем монтажное
межосевое расстояние по формуле
(5.6.19)
Определяем число ударов
по формуле
(5.6.20)
Определяем усилие от
провисания цепи при горизонтальном расположений цепи по формуле
(5.6.21)
где kf - для
горизонтальной цепи, kf=6 [7];
q - нагрузка на цепь, q=5,01 кг/м [7];
Fґ - сила действующая на
цепь в месте крепления стержня, Fґ=187,22 Н.
Определяем силу давления
на вал по формуле
Определяем максимальное
давление в шарнирах по формуле
(5.6.23)
Проверяем коэффициент
запаса прочности цепи по формуле
(5.6.24)
где kдин - коэффициент колебания нагрузки (умеренные), kдин=1,3 [7];
Qв - разрушающая нагрузка,
Qв=50 кН [7];
Fц - усилие цепи, Н.
Усилие цепи определяем по формуле
(5.6.25)
Тогда коэффициент запаса
прочности будет равен
Допускаемое значение [n] должно быть не менее 8, то есть условие n ≥ [n]
удовлетворено.
Произведя анализ
вычислений, выбираем мотор-редуктор типа 3МВ-50, технические характеристики
которого представлены в таблице 5.6.1
Расчет звездочки
Определяем диаметр
окружности выступов звездочки по формуле
(5.6.26)
Определим диаметр окружности впадин
звездочки по формуле
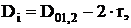
(5.6.27)
где r - радиус впадин, мм.
Таблица 5.6.1 - Технические
характеристики мотор-редуктор типа 3МВ-50
Параметры
|
Значение
|
Внутренний диаметр гибкого колеса, мм
|
52
|
Твых, Н∙м
|
25
|
Передаточное отношение редуктора
|
52
|
nвых,
об/мин
|
28
|
Консольная сила, Н
|
Выходного вала
|
1800
|
|
Входного (редуктора)
|
160
|
КПД, %
|
55
|
Двигатель мотор-редуктора
|
Мощность, кВт
|
0,09
|
|
n,
об/мин
|
1500
|
|
|
|
|
Радиус впадин определяем по формуле
(5.6.28)
Тогда диаметр окружности
впадин звездочки будет равен
Определяем диаметр
проточки звездочки по формуле
(5.6.29)
где h - ширина пластин цепи, h=24,13
мм.
Определяем ширину зуба
цепи по формуле
(5.6.30)
где Ввн -
расстояние между внутренними плоскостями цепи, Ввн=15,88 мм.
Определяем радиус
закругления зуба по формуле
(5.6.31)
где d - диаметр ролика цепи, d=15,88
мм.
Определяем толщину обода
по формуле
(5.6.33)
Определяем толщину диска
по формуле
(5.6.34)
Принимаем, что профиль
зуба в осевом сечений изготавливается со скосом, то угол скоса равен г=20о.
Определяем фаску по
формуле
(5.6.35)
Расчет подшипников
Расчет подшипников
выполнен на ЭВМ по программе «КП ДМ» и представлен в приложений Б.
Расчет стоики на
устойчивость
Расчетная схема стоики
представлена на рисунке 5.6.3.
Определяем площадь
стойки по формуле
(5.6.36)
где D - наружный диаметр стойки, D=50
мм;
d
- внутренний диаметр стойки, d=40
мм.
Определяем момент
инерций стоики по формуле
(5.6.37)
Рисунок 5.6.3 -
Расчетная схема стойки
Определяем радиус
инерций стойки по формуле
(5.6.38)
Определяем приведенную
длину стойки по формуле
(5.6.39)
где µ - коэффициент
приведенной длины, µ=2;
l
- длина стержня, l=12000 мм.
Определяем гибкость
стойки по формуле
(5.6.40)
По таблице 22 [11]
интерполяцией находим коэффициент ц=0,0239
Определяем допускаемое
напряжение на устойчивость по формуле
(5.6.41)
где [у]т -
допускаемое напряжение для стали Ст 3, [у]т=160 МПа.
Определяем
действительное напряжение стойки по формуле
(5.6.42)
где F - сжимающая сила, F=125
Н.
Выполняем проверку
следующего условия
(5.6.43)
Условие 5.6.43 выполняется,
следовательно, устойчивость стержня обеспечена.
Определим теоретическую
массу 1 м стоики по формуле
(5.6.44)
Определим теоретическую
массу 12 м стоики по формуле
(5.6.45)
где l - длина стоики, l=12
м.
.6.6 Расчет болтов для
крепления стойки
Расчетная схема
крепления стоек к плите представлена на рисунке 5.6.4.
Внешнею силу F, действующую на наиболее нагруженный болт стойки определим
определяем по формуле
(5.6.46)
где Q - сила действующая на фланец, Q=500
Н;
z
- число болтов, z=4;
f
- коэффициент трения между фланцевым соединением, f=0,2
[6]
h
- расстояние от точки приложения силы до основания фланца, h=12000 мм;
l
- расстояние между болтами, l=360
мм;
L
- расстояние от стоики до места приложения силы F,
L=600 мм.
Рисунок 5.6.4 -
Расчетная схема крепления стоек к плите
Рассчитываем болт на
растяжение при возможности последующей затяжки по следующей формуле
(5.6.47)
где [ур] - допускаемое напряжение на растяжение, [ур]=160 МПа.
Принимаем болт М10 по
ГОСТ 9150-59 с наружным диаметром резьбы d=10
мм и шагом резьбы p=1,5 мм.
Расчет сварного шва
приварки косынки к фланцу на прочность
Расчет сварного шва на
прочность производим по формуле
(5.6.48)
где М - изгибающим
момент, M=300 Н·м;
s
- толщина косынки, s=0,01 м;
l
- длина сварного шва с учетом не провара, l=0,19
м.
[ур] - допускаемое напряжение для сварных швов из стали Ст3, [ур]=130 МПа.
Условие прочности
выполняется.
Расчет отводного ролика
Определим усилие в
ходовом конце троса по формуле
(5.6.49)
где Q - вес поднимаемого груза, Q=0,5
кН;
з - к.п.д. ролика,
з=0,98;
а - количество рабочих
ветвей троса полиспаста, а=1.
Подставляя числовые
значения, получим
Грузоподъемность
отводного ролика определим по формуле
(5.6.50)
Определим разрывное
усилие для троса по условию прочности по формуле
(5.6.51)
где kз - коэффициент запаса прочности, kз=4,5.
По таблице приложения 1
[6] подбираем стандартный трос ЛК-РО
(1-7-7/7-14) - 1 о.с
ГОСТ 7668-88 имеющий следующие стандартные величины: разрывное усилие троса Rтабл=23,15 кН; расчетная масса 1 м смазанного троса mтр=0,156 кг; диаметр каната d=6,3
мм.
Подбор лебедки производим
по тяговому усилию, диаметру троса и его канатоемкости.
Определим канатоемкость
тяговой лебедки по формуле
(5.6.52)
где h - максимальное расстояние между неподвижным и подвижным
блоком полиспаста, h=12 м;
Rб
- радиус ролика блока, Rб=0,125
м;
m
- число роликов полиспаста, m=1.
Подставляя числовые
значения, получим
Подберем ручную лебедку
ЛР, 0,65 т, Н-45 м, грузоподъемностью 650 кг, канатоемкость 40 м, массой 30 кг.
Расчет общей массы
мобильной установки
Общую массу установки
определим по формуле
(5.6.53)
где mм - масса матор-редуктора, mм=5,5
кг;
mст
- масса стоек, mст=200
кг;
mп.п
- масса подвижной плиты, mп.п=20
кг;
mп.н
- масса не подвижной плиты, mп.п=30
кг;
mп.д
- общая масса остальных деталей установки, mп.д=50 кг.
Расчет центра масс
подвижной плиты
Для определения центра
масс подвижной плиты, производим его вычерчивание в программе «Компас-3D V7». Схема подвижной плиты и результаты расчета представлены в
приложений В.
6. Монтаж основного
оборудования
.1 Монтаж установки для
нанесения лакокрасочного покрытия
Установка для нанесения
лакокрасочного покрытия состоит из двух блоков (смотри чертеж
ОПНН-170500-04.00.000). Блок №1 состоит из плиты (поз. 20), на которой
установлены мотор-редуктор (поз. 27), подшипниковый узел (поз 29), цепная
передача (поз. 30), хомут (поз. 5) и стержень (поз. 18), с закрепленным на нем
краскораспылителем (поз. 6). Блок №2 (смотри чертеж ОПНН-1075-04.03.000)
состоит из подвижной плиты (поз. 2), с приваренными штырями (поз. 3) для
крепления стоек, отводного ролика (поз. 1) и колес, предназначены для
передвижения установки.
Монтаж блоков №1 и №2 осуществляется
за пределами резервуара.
Монтаж блока №1 проводится в
следующей последовательности:
Производим крепление мотор-редуктора
на подвижную плиту, затем крепим кронштейны, на которую в свою очередь
совершаем установку подшипниковых узлов с валами. Далее насаживаем звездочки на
валы и крепим их при помощи стопорных колец. Производим крепление хомута на
цепи. Крепим стержень на хомуте. Производим установку и натяжку цепи.
Монтаж блока №2 проводится в
следующем порядке (смотри чертеж ОПНН-170500-04.03.000):
На неподвижную плиту производим
приварку штырей по ГОСТ 5280-84 для крепления стоек. Также привариваем ушки для
крепления отводного ролика.
Монтаж начинаем с транспортировки
всех узлов установки во внутрь резервуара, через технологическое отверстие,
предварительно вырезанное в стенке резервуара.
Монтаж установки начинаем в
горизонтальном положении.
Производим крепление стоек к блоку
№1 и установку блока №2 на стойки. Далее производим крепление стоек между собой
при помощи швеллеров. Швеллеры между собой крепим уголком, на котором
установлен ролик. Подъем установки в вертикальное положение осуществляем при
помощи лебедки и оттяжек.
После поднятия установки в
вертикальное положение производим крепление краскораспылителя к стержню.
Производим крепление шланга на линии всасывания: крепим шланг к штуцеру насоса
и производим его затяжку при помощи подвесного хомута типа ХК-1 с диаметром 32
мм; производим крепление шланга к штуцеру емкости и производим затяжку хомутом
типа ХК-1 с диаметром хомута 32 мм. На линии всасывания также производим
установку задвижки на выходе из емкости для экстренного перекрытия подачи
лакокрасочной композиции при возникновений неполадок.
Крепление шланга на линии
нагнетания: крепим шланг к штуцеру насоса и производим его затяжку при помощи
подвесного хомута типа ХК-1 с диаметром хомута 42 мм; производим крепление
шланга к штуцеру краскораспылителя и производим затяжку при помощи хомута типа
ХК-1 с диаметром хомута 42 мм. На выходе из насоса устанавливаем манометр для
контроля давления в краскораспылителе.
Осуществляем крепление шланга к
штуцеру компрессора и производим затяжку при помощи хомута типа ХК-1 с
диаметром хомута 42 мм. Также осуществляем крепление шланга к штуцеру
краскораспылителя и производим его затяжку при помощи хомутов типа ХК-1 с
диаметром хомута 42 мм. На выходе из компрессора производим установку манометра
для контроля давления воздуха в краскораспылителе.
6.2 Порядок пуска
установки
Для того чтоб приступить к работе,
необходимо установить блок №2 в верхнее положение. Для этого при помощи лебедки
в ручную осуществляем поднятие блока №2 верхнее положение. Далее совершаем пуск
оборудования в следующем порядке: в первую очередь включаем мотор-редуктора,
затем компрессор и насос. Производим обкатку установки, для этого ее пуск
осуществляем на холостом ходу.
7.
Контрольно-измерительные приборы и автоматика
Современные нефтеперерабатывающие и
нефтехимические производства характеризуется все возрастающей сложностью и
многообразием операций и оборудования. Управление такими производствами возможно
лишь при широком использовании методов и средств автоматизации.
Развитие автоматизации в химической
промышленности связано с возрастающей интенсификацией технологических процессов
и ростом производств, использованием агрегатов большой единичной мощности,
усложнением технологических схем, предъявлением повышенных требований к
получаемым продуктам.
Особое значение придается вопросам
автоматизации процессов нефтехимической технологии в связи с взрыво- и
пожароопасностью перерабатываемых веществ, их агрессивностью и токсичностью, с
необходимостью предотвращения вредных выбросов в окружающую среду. Указанные
особенности, высокая чувствительность к нарушениям заданного режима, наличие
большого числа точек контроля и управления процессом, а также необходимость
своевременного и соответствующего сложившейся в данный момент обстановке
воздействия на процесс в случае отклонения от заданных по регламенту условий
протекания не позволяют даже опытному оператору обеспечить качественное ведение
процесса вручную. Поэтому в настоящее время в нефтеперерабатывающей и в
нефтехимической промышленности максимально используют автоматические
устройства.
Автоматизация приводит к улучшению
основных показателей эффективности производства: повышению производительности
труда, улучшению качества и уменьшению себестоимости выпускаемой продукции.
Внедрение автоматических устройств обеспечивает высокое качество продукции.
уменьшение численности основных рабочих, уменьшение браков и отходов.
Способствует безаварийной работе оборудования, исключает случаи травматизма.
7.1 Выбор и обоснование
параметров контроля и сигнализации
Выбор и обоснование параметров
контроля и сигнализации производим по резервуарам, исходя из процесса,
протекающего в них.
Система управления технологическим
процессом позволяет:
осуществить контроль над ходом
технологического процесса и при необходимости вмешиваться в ход
технологического процесса;
вести учет расхода сырья, готовой
продукции;
обеспечить оперативный персонал
необходимой информацией.
Схемой предусмотрен контроль
следующих параметров:
уровня в резервуарах Р-55, Р-56,
Р-57, Р-58.
Данные параметры контролируется для
того, чтобы не происходило переполнение резервуаров и для составления
материального баланса выпускаемой продукции.
температуры в резервуарах Р-55,
Р-56, Р-57, Р-58.
Данный параметр контролируется
ответственными, и требуют стабильности для получения продукции заданного
качества.
7.2 Выбор и обоснование
схем автоматического контроля
Качество получаемой в
нефтеперерабатывающей промышленности продукции зависит от ряда величин,
определяющих нормальное протекание процесса. Поэтому при построении
автоматических систем регулирования, прежде всего, определяем величины,
подлежащие контролю, а также выявить точки введения управляющих воздействий и
каналы их прохождения по объекту.
Регулирующее воздействие в верхней
части резервуаров Р-55, Р-56, Р-57, Р-58 осуществляется изменением расхода
дизельного топлива.
7.3 Выбор и обоснование
средств автоматизации
автоматизация коррозия
резервуар
В качестве первичного
преобразователя уровня выбраны уровнемеры радиоволновые ВМ 70 А/Р
предназначенные для измерения расстояния до продукта находящегося в резервуаре.
В качестве вторичного прибора выбран ПВ10.1Э для непрерывной записи и показания
величины регулируемого параметра. Сигнализатором служит манометр ЭКМ-1У.
Вследствие того, что работа
резервуаров характеризуется значениями температуры, лежащими в пределах
измерения термопар, в качестве датчиков выбираем термопары типа ТХК. Для
преобразования термо ЭДС в унифицированный электрический сигнал используем
преобразователь Ш-78. Для преобразования унифицированного электрического
сигнала в унифицированный пневматический сигнал служит преобразователь ЭПП-63.
Средства автоматизации, применяемые
на площадке «Б», представлены в таблице 7.1.
7.4 Описание работы схем
автоматического контроля
Уровень в резервуарах Р-55
контролируется следующим образом: сигнал с радиоволнового уровнемера ВМ 70 А/Р
позиция 6а поступает на вторичный прибор ПВ 10.1Э для показания и записи
позиция 6б. Также в этой схеме используется звуковая и световая сигнализация
уровня. Сигнал от датчика ВМ 70 А/Р позиций 6а поступает в электроконтактный
манометр ЭКМ-1У позиций 6в. При повышении уровня выше 70% шкалы вторичного
прибора сигнал от датчика уровня ВМ 70 А/Р позиций 6а замыкает контакты ЭКМ-1У
позиций 6в и в схемы звуковой и световой сигнализации поступает сигнал. Далее
регулирование осуществляет оператор в ручную.
Аналогично регулируется уровень в
следующих резервуарах: Р-56, Р-57, Р-58.
Температура в резервуаре Р-55
измеряется и регистрируется с помощью термопары ТХК-0379-02 позиций 411а и
вторичного прибора КСП4-004 позиций 411б. Аналогично измеряется температура в
резервуарах Р-56, Р-57, Р-58.
Таблица 7.1 - Спецификация на
пpибоpы автоматического контроля и регулирования
№ позиции
|
Наименование измеряемого паpаметpа и характеристика среды
|
Предельные значения паpаметpа
|
Место установки
|
Наименование и характеристика пpибоpа
|
Тип пpибоpа
|
Количество
|
LT 5а
|
Уровень в резервуаре Р-55
|
10,23
|
Вверх резервуара Р-55
|
Уровнемер радиоволновой. Пределы измерения 0,5…35/40 м. Основная
погрешность измерения 1,5%.
|
ВМ 70 А/Р
|
2
|
LT 6а
|
Уровень в резервуаре Р-56
|
13,50 м
|
Вверх резервуара Р-56
|
Уровнемер радиоволновой. Пределы измерения 0,5…35/40 м. Основная
погрешность измерения 1,5%.
|
ВМ 70 А/Р
|
2
|
LT 7а
|
Уровень в резервуаре Р-57
|
10,21 м
|
Вверх резервуара Р-57
|
Уровнемер радиоволновой. Пределы измерения 0,5…35/40 м. Основная
погрешность измерения 1,5%.
|
ВМ 70 А/Р
|
2
|
LT 8а
|
Уровень в резервуаре Р-58
|
10,58 м
|
Вверх резервуара Р-58
|
Уровнемер радиоволновой. Пределы измерения 0,5…35/40 м. Основная
погрешность измерения 1,5%.
|
ВМ 70 А/Р
|
2
|
LTR 5б-8б
|
Регистрация уровня среды в аппаратах
|
|
На щите в операторной
|
Вторичный прибор пневматический для непрерывной записи и
показания величины регулируемого параметра. Основная погрешность 1%.
|
ПВ10.1Э
|
4
|
LIR 5в-8в
|
Сигнализация уровня среды в аппаратах
|
|
За щитом в операторной
|
Манометр пружинный показывающий сигнализи рующий
двухпозиционный. Пределы измерений 0…0,16 МПа. Основная погрешность 1,5%.
|
ЭКМ-1У
|
4
|
8.
Безопасность и экологичность
.1 Основные опасности
производства
В блоке №4 обращается опасное
вещество - бензин, представляющее собой горючую жидкость со слабым запахом.
Общее количество опасного вещества, обращающегося в блоке площадки с течением
времени изменяется. Максимальное значение количества опасного вещества может
быть достигнуто при условии заполнения до уровня максимального взлива всех
резервуаров и может составить 38324 м3.
8.2 Характеристика
опасного вещества, обращающегося в блоке №4 резервуарного парка площадки «Б»
ТСЦ
В блоке №4 резервуарного парка
площадки «Б» ТСЦ ОАО «Салаватнефтеоргсинтез» находится бензин, характеристика
которого приведена в таблице 8.2
Таблица 8.2 - Характеристика
опасного вещества
№ п\п
|
Наименование параметра
|
Параметр
|
1
|
Название вещества
|
Бензин
|
1.1
|
Химическое
|
Бензин
|
1.2
|
Торговое
|
Бензин автомобильный
|
2
|
Формула
|
Сумма углеводородов
|
2.1
|
Эмпирическая
|
|
2.2
|
Структурная
|
|
3
|
Состав, %
|
|
3.1
|
Основной продукт
|
|
3.2
|
Примеси (с идентификацией)
|
Серы не более 0,2%, ароматических углеводородов не более 10%
йодное число не более 2 г йода на 100 гр.
|
4
|
Общие данные
|
|
4.1
|
Молекулярный вес
|
80
|
4.2
|
Температура кипения,°C (при давлении 101 кПа)
|
35
|
4.3
|
Плотность при 20°C, кг/м3 (при давлении 101 кПа)
|
0,720
|
5
|
Данные о взрывопожароопасности
|
Легковоспламеняющаяся жидкость при воздействии кислорода, при
воздействии воды не воспламеняется
|
5.1
|
Температура вспышки
|
-35
|
5.2
|
Температура самовоспламенения
|
415ч530
|
5.3
|
Температурные пределы воспламенения, 0С - нижний -
верхний
|
-27ч-39 -8ч-27
|
5.4
|
Объемные пределы воспламенения, %
|
0,85ч5,01
|
6.
|
Данные о токсической опасности
|
Класс опасности-4
|
6.1
|
ПДК в воздухе рабочей зоны, мг/м3
|
100
|
1
|
2
|
3
|
6.2
|
ПДК в атмосферном воздухе мг/м3
|
5
|
6.3
|
Летальная токсодоза LCt50
мг мин/л
|
216
|
6.4
|
Пороговая токсодоза РCt50
|
-
|
Реакционная способность
|
Не растворяется в воде, при нормальных условиях стабилен,
органический растворитель
|
8
|
Запах
|
Специфический
|
|
|
|
|
|
При работе с лакокрасочными
материалами необходимо строго выполнять правила техники безопасности и
противопожарной техники.
Все работы с лакокрасочными
материалами должны проводиться в резервуарах, оборудованных приточно-вытяжной
вентиляцией и противопожарными средствами. Приточно-вытяжная вентиляция должна
обеспечивать содержание вредных веществ в воздухе рабочей зоны, не превышающее
предельно-допустимые концентрации в соответствии с требованиями ГОСТ
12.1.005-76.
Содержание в воздухе резервуара
вредных паров, газов и пыли, пожароопасность веществ в условиях микроклимата
должны систематически контролироваться.
Порядок и сроки проведения анализов
воздушной среды устанавливаются администрацией предприятия.
8.3 Коллективные и
индивидуальные средства защиты
Индивидуальные средства защиты:
спецодежда, спецобувь, противогазы марки А, БКФ, при высоких концентрациях
противогазы ПШ-1, ПШ-2, ДПА-5, защита кожи рук пастами типа «биологических
перчаток», ожиряющими мазями и кремами.
Средствами коллективной защиты
работающих от воздействия опасных и вредных производственных факторов на
установке являются:
а) приточно-вытяжная общеобменная
вентиляция и аварийная вентиляция, приводимая в действие механическим
побуждением, обеспечивая 8 - кратный воздухообмен. В помещениях насосной и
компрессорной устанавливаем газоанализаторы, позволяющие быстро определить
превышение предельно допустимых концентраций вредных веществ. В операторной
устанавливаем световую и звуковую сигнализацию. При поступлении сигнала от
газоанализатора о превышении ПДК, автоматически включается аварийная
вентиляция;
б) дефлекторы, установленные на крыше
помещений для создания естественной вытяжки воздуха из насосной;
в) для предотвращения обмена
содержимого технологического оборудования с внешней средой, оборудование и
трубопроводы загерметизированны с помощью беспрокладочных уплотнений и
уплотнений с прокладками;
г) во избежание ожогов
обслуживающего персонала все поверхности горячих трубопроводов изолированы;
д) движущиеся детали подвергаем
герметизации при помощи сальниковых уплотнений, торцовых уплотнений;
е) вертикальные лестницы выше 1,5 м
ограждены специальными шатрами из полосового железа;
ж) все лотки укрыты легкосъемными
огнестойкими плитами, в местах перехода через трубопроводы установлены шириной
не менее 1 м.
8.4 Пожарная
безопасность
В резервуарах согласно ГОСТ
12.1.004-76 должна быть обеспечена пожарная безопасность, которая
предусматривает систему пожарной защиты. Система предотвращения пожара
обеспечивает исключение образования горючей среды, источников зажигания, а
также поддержание температуры и давления горючей смеси не ниже максимально
допустимых величин по горючести и уменьшение объема горючей среды ниже
максимально допустимого. К требованиям пожарной безопасности относятся:
ограничения количества горючих
веществ и их размещение;
изоляция горючей среды;
применение средств пожаротушения;
средств пожарной сигнализации;
средств извещения о пожаре.
Для тушения пожара используется
песок, асбестовую ткань (ГОСТ 6102-78), пенные огнетушители марки ОП-5 (ГОСТ
16005-70), углекислотные огнетушители марок ОУ-2 и ОУ-5 (ГОСТ 7276-77 и ГОСТ
9230-77), воздушно-механическую пену (ГОСТ 7183-72) и тонкораспыленную воду.
8.5 Характеристика
взрывоопасности резервуара
Бензин относится к 4 классу
опасности (по ГОСТ 12.1007.76). Объемные пределы взрываемости 0,6-6,5% об.
Температура вспышки 80 єC, а самовоспламенения составляет 300 єC. Предельно
допустимая концентрация в воздухе рабочих зон и производственных помещений
составляет (по ГОСТ 12.1.1005.88)
мг/м3. Наиболее опасный
сценарий аварийной ситуации: сценарий С1 - полное разрушение
резервуара, выброс бензина в пределах обвалования, образование ТВО, взрыв ТВО
от источника зажигания, воздействие ударной волны на соседние объекты,
повреждения соседних объектов, возможно дальнейшее развитие аварий в парке и
поражение обслуживающего персонала, характеризуется наиболее тяжелыми
последствиями и наибольшим ущербом. Вероятность возникновения наиболее опасного
по последствиям сценария составляет 4,95·10 год-1.
Общий энергетический потенциал
взрывоопасности: Е= 1,29·108 кДж;
Относительный энергетический
потенциал: Qв=30,56;
Категория взрывоопасности блока - 2.
Основной поражающий фактор - это
ударная волна взрыва. Количество опасного вещества, участвующего в аварии
составит 2,8040 т и количество опасного вещества, участвующего в создании
поражающего фактора, составит 0,28 т.
Границы зон действия ударной волны
составляет: радиус зон полных разрушений - 28,23 м, радиус зон 50% разрушений -
47,54 м, радиус зон средних разрушений - 71,31 м, радиус зон умеренных
разрушений - 239,18 м, радиус зоны порога повреждения человека - 356,55 м,
радиус зоны расстекления - 397,4 м.
8.6 Возможные аварийные
ситуаций, их ликвидация
Анализ аварийных ситуаций, условий
их возникновения и развития в блоке №4 резервуарного парка площадки «Б» ТСЦ
представлены в таблице 8.6 приложений Г.
8.7
Гражданская оборона и чрезвычайные ситуации
В случае чрезвычайной ситуации
персонал цеха ТСЦ эвакуируется в убежище №66А. Убежище защищает персонал от
воздействия взрывной, световой, радиационной и других видов губительной для
человеческого организма энергии.
План эвакуации персонала цеха ТСЦ в
загородную зону показан на рисунке 8.1 и осуществляется в следующем порядке:
о рассредоточении и эвакуации
сообщает администрация цеха;
с собой брать документы, запас
продуктов на 3 суток, необходимые вещи.
время прибытия на СЭП
а) Колонна пеших 4 ч +10 мин;
отправление с СЭП колонной 1/5 4.
+12
отправление с Зиргана автоколонной
№336 через 4 ч +35 мин.;
б) Едут железнодорожным транспортом
прибытие на СЭП в 24 ч;
отправление от станций Салават в 2 ч
41 мин. поездом №284.
Отправление со станций Мелеуз до
места расселения деревня Узя транспортом сельсовета.
до выезда за город:
выключить газ, электронагревательные
приборы, сдать ключи в домоуправление.
8.8 Расчет молниезащиты
резервуара
Исходные данные:
Высота резервуара, hрез=11950 мм;
Диаметр резервуара, Dрез=22847 мм.
Выбираем многократный стержневой
молниеотвод, предназначенный для защиты объектов с большой площадью, в данном
случай для резервуара.
Определим категорию молниезащиты и
тип зоны защиты в зависимости от среднегодовой продолжительности гроз и
ожидаемого количества поражений резервуара молнией в год.
Ожидаемое количество поражений
молнией в год для сосредоточенных зданий и сооружений (башен, колонн дымовых
труб и др.) N определим по формуле

(8.1)
где hх - наибольшая высота резервуара, hх=11950
мм;
n
- среднегодовое число ударов молнии в 1 км2 земной поверхности
(плотность ударов молнии в землю) в месте расположения резервуара.
Согласно округленным
данным среднегодовая продолжительность гроз в городе РФ Салавате от 40 до 60
часов; для такой среднегодовой продолжительности гроз n=4.
Подставляем числовые
значения в формулу 8.2.1
В зависимости от полученных
значений ожидаемое количество поражений молнией в год для нашего случая
определяем по таблице: II
категория молниезащиты и тип зоны защиты Б.
Схема многократного
стержневого молниеотвода представлена на рисунке 8.2.
Зона защиты
многократного стержневого молниеотвода представляет собой геометрическую
фигуру, вершины которой находятся на высоте h0.
У таких молниеотводов
высотой h≤150 м зона защиты определяется как зона попарно взятых,
соседних стержневых молниеотводов. Зона защиты одиночного стержневого
молниеотвода имеет следующие габариты.
(8.2)
(8.3)
где r0 - размер зоны защиты на уровне земли;
rх - размер зоны защиты на
уровне максимально высокой отметки защищаемого объекта.
Зона защиты двойного
стержневого молниеотвода определяется по формулам (8.2) и (8.3) как зона
одиночных стержневых молниеотводов. Для зоны Б hc
= h0,
=
rx, rc
= r0. Задаемся высотой молниеотвода hм=2
м.
Высота одиночного
стержневого молниеотвода может быть определена по формуле
(8.4)
Определим зону защиты по формуле
(8.2.2)
Определяем размер зоны
защиты на уровне земли по формуле (8.3)
Принимаем 4 молниеприемника высотой
2 м.
Рисунок 8.1 - План эвакуации
персонала цеха ТСЦ в загородную зону (деревню Узя)
Рисунок 8.2 - Зона защиты
многостержневого молниеотвода
9. Экономическая часть
Для проектируемой установки
рассчитаем технико-экономические показатели, себестоимость.
9.1 Расчёт капитальных
затрат и стоимости основных фондов
Создание и внедрение новых
технологических процессов связано со значительными капитальными затратами.
Капитальные затраты - это единовременные вложения в создание основных фондов,
рассчитываются по формуле:
∆К = Коб + Кзд
+ Кс, (9.1)
где Коб - расходы на
оборудования рассчитываем по формуле
Коб = Кот + Кос,
(9.2)
где Коб - затраты на
технологическое и силовое оборудование, руб.;
Кс - расходы на
устройство сооружений приведены в таблице (9.1), руб.
Затраты на оборудование,
приобретаемое со стороны определим по формуле
, (9.3)
где Цот -
оптовая цена оборудования, руб.;
Ктз -
коэффициент транспортно-заготовительных расходов;
Кс -
коэффициент, учитывающий затраты на строительные работы (металлоконструкции -
5%)
Км -
коэффициент, учитывающий затраты на монтаж - 0,05.
Результаты расчета
капитальных затрат сведем в таблицу 9.1
Общая стоимость основных
фондов представлена в таблице 9.2.
Таблица 9.1 - Расчет
стоимости аппаратов и оборудования
Наименование оборудования
|
Ед.изм
|
Колво
|
Стоимость, руб
|
|
|
|
единицы, руб
|
Всего, тыс. руб
|
Насос шестеренчатый ШФ 5-25, N=1,1
кВт Матор-редуктор 3МВ - 50, N=0,09
кВт Лебедка ЛР 0,65 Компрессор С 24J1047А
N=1,5 кВт
|
шт. шт. шт. шт
|
1 1 1 1
|
25000 11714 11000 4785
|
25 11,714 11 4,785
|
Всего на оборудование
|
|
|
|
52,49
|
Неучтенное оборудование
|
%
|
20
|
|
10,49
|
Итого на оборудование
|
|
|
|
62,99
|
Транспортно-заготовительные расходы
|
%
|
10
|
|
6,29
|
Затраты на строительные работы металлоконструкции Затраты на
монтаж
|
% %
|
5 5
|
|
3,15 3,15
|
Всего на расходы
|
|
|
|
12,59
|
Итого на оборудование
|
|
|
|
75,58
|
Таблица 9.2 - Стоимость основных
фондов установки
Виды основных фондов
|
Первоначальная стоимость, тыс. руб
|
Рабочие и силовые машины, оборудование
|
75,58
|
Итого основных фондов
|
75,58
|
Затраты на подготовку территории, временное строительство, 5% от
ОФ
|
3,75
|
Всего основных фондов
|
79,33
|
Стоимость основных фондов составляет
79,33 тыс. руб.
9.2 Расчёт
производственной мощности
Расчет производится для 10
резервуаров общей площадью F=43332 м2.
Расход лакокрасочной композиций
находим по формуле
(9.4)
где m - количество лакокрасочной композиций, потребляемое на 1 м2,
m=0,4 кг.
Производственная
мощность установки - это максимально возможный объём переработки сырья или
выпуска продукции за год при полном использовании оборудования во времени и по
производительности.
Материальный баланс
необходим для расчёта экономической эффективности работы установки. По проекту
установка работает 365 дней в году.
Производственная
мощность установки с учётом рабочих дней в году - 330 и рабочих часов в сутки 8
будет равна 17,3 т/г. Отсюда, следовательно, среднесуточная производительность
будет равна.
(9.5)
где М - мощность
установки по сырью, М=17,3 т/г;
t
- число часов работы, t
=330 сут.
9.3 Расчёт численности
обслуживающего персонала и фонда заработной платы
Расчет потребности количества
рабочих проводится по нормам обслуживания и рабочим местам. Численность
персонала рассчитывается по категориям, профессиям, сменному штату, явочному и
списочному составу. Для определения эффективного фонда рабочего времени
составляют баланс рабочего времени одного рабочего, исходя из принятого режима
работы, действующего положения об отпусках, фактических данных о количестве
невыходов по болезни и другим причинам (таблица 9.3).
Коэффициент подмены рассчитываем по
формуле
(9.6)
где ТНОМ -
номинальный фонд рабочего времени, ч;
ТЭФФ -
эффективный фонд рабочего времени, ч.
Расчёт численности
персонала определим по формуле
(9.7)
где Чя -
явочная численность в одну смену;
Б - число бригад.
Таблица 9.3 - Баланс рабочего
времени одного рабочего на год
Показатели
|
Периодическое производство
|
|
дней
|
часов
|
1. Календарный фонд рабочего времени 2. Выходные 3. Номинальный
фонд рабочего времени 4. Невыходы на работу в том числе: 4.1 Очередные и
дополнительные отпуска 4.2 Дни выполнения государственных обязанностей 4.3
Дни невыхода по болезни 5. Эффективный фонд рабочего времени
|
365 105 260 40 30 5 5 220
|
2920
840 2080 320 240 40 40 1760
|
Результат расчёта численности
персонала на установке для нанесения лакокрасочного покрытия представлен в
таблице 9.4.
Таблица 9.4 - Расчёт численности
персонала
Профессия
|
Разряд
|
Кол-во человек в смену
|
Количество бригад
|
Явочная численность
|
Коэффициент подмены
|
Списочная численность
|
1 начальник установки 2 слесарь
|
4
|
3
|
1
|
13
|
1,14
|
13
|
Итого:
|
|
|
|
4
|
|
4
|
Бригада выполнить работу по окраске
10 резервуаров за 100 рабочих дней, поэтому фонд заработной платы на 10
резервуаров определим по формуле
(9.8)
Подставляя числовые
значения, получим
Результат расчёта фонда заработной
платы на установке для нанесения лакокрасочного покрытия сведён в таблицу 9.5,
9.6.
Таблица 9.5 - Результат расчёта
фонда заработной платы на установке для нанесения лакокрасочного покрытия
Профессия
|
слесарь
|
разряд
|
4
|
Количество рабочих
|
3
|
Тарифная ставка
|
40
|
Эффективный фонд времени
|
220
|
ФЗП тар., руб
|
211200
|
Премия, %
|
50
|
Рублей
|
48000
|
ФЗП час, руб
|
259200
|
ФЗП дневной, руб
|
259200
|
За гособязоности
|
1178,18
|
ФЗП год, руб
|
260378,18
|
Районный коэффициент
|
39056,73
|
ФЗП общ. руб
|
299434,91
|
Зарплата общ., руб
|
136106,78
|
Среднемесячная зарплата
|
3780,74
|
Как видно из таблицы 9.5 заработная
плата составляет 136106,78 рублей, общее количество занятых в производстве 4
чел.
Таблица 9.6 - Расчет фонда
заработной платы ИТР
Профессия
|
Число работников
|
Должностной оклад, руб
|
Надбавка за вредность, руб
|
Районный коэффициент
|
Всего за месяц, руб.
|
Годовой фонд з/п, руб.
|
|
|
|
|
|
|
|
|
|
|
|
|
|
|
|
|
|
|
|
|
|
Начальник установки
|
1
|
10 201
|
1 530
|
1 760
|
13 490
|
40470
|
Итого:
|
1
|
|
|
|
|
40470
|
9.4 Расчёт себестоимости
продукции
Себестоимость продукции - важнейший
экономический показатель проектируемого процесса. Расчет себестоимости единицы
продукции производится путем составления калькуляции себестоимости.
Расход электроэнергии рассчитывается
по формуле
(9.9)
где W - мощность оборудования, рассчитывается по формуле
(9.10)
где Nм - мощность мотор-редуктора, Nм=0,09
кВт;
Nм
- мощность компрессора, Nк=1,5
кВт
Nм
- мощность насоса, Nн=1,1
кВт
Подставляя значения,
получим
кВт;
кВт×ч=1,076
тыс. кВт·ч.
Расчёт себестоимости
продукции представлен в таблице 9.7
Таблица 9.7 - Расчёт
себестоимости продукции
Наименование статей затрат
|
Ед. изм
|
Н расх
|
На весь выпуск
|
|
|
|
Количество
|
Цена, руб
|
Сумма, руб
|
1 Сырьё: краска
|
т
|
|
17,3
|
35683
|
617315,9
|
2 Энергетические затраты электроэнергия
|
тыс. кВт/ч
|
|
1,076
|
746,30
|
803,01
|
3 Зарплата
|
|
|
|
|
136106,78
|
4 Расходы на социальное страхование
|
|
0,365
|
|
|
28955,45
|
5 Расходы на содержание и эксплуатацию оборудования, в т.ч.:
амортизация
|
|
0,1
|
|
|
7933
|
6 Цеховые расходы
|
|
0,03
|
|
|
2379,9
|
Полная себестоимость
|
|
|
|
|
793494,04
|
Себестоимость продукции
|
|
45866,71
|
|
9.5 Расчет основных
технико-экономических показателей
Для установления эффективности
внедрения настоящего проекта рассчитываются его технико-экономические
показатели, производится их комплексный анализ.
Цену единицы продукции рассчитаем следующим
образом
Цк=1,05×С; (9.11)
Цк=1,05×45866,71= 48160,04 руб.
Абсолютные показатели принимаются по
данным предыдущих расчетов. Относительные показатели рассчитываются следующим
образом.
Экономию определим по формуле
Э1=Зд-Зп,
(9.12)
где Зп - затраты после
внедрения установки, руб.;
Зд - затраты до внедрения
установки, руб.
Э1= 1272026-793494,049=
478531,47 руб.
Уровень фондоотдачи определим как
(9.13)
где Ф - среднегодовая стоимость
основных производственных фондов, руб.;
Q - объём производства, руб.
Уровень
производительности труда определим как
(9.14)
где Ч - численность работников, чел.
Подставляя значения, получим
Уровень рентабельности
продукции определи по формуле
, (9.15)
где С - себестоимость
единицы продукции, руб.
Удельные капитальные
затраты определим по формуле
, (9.16)
где Ф - среднегодовая
стоимость основных производственных фондов, руб.;
Q
- объём производства, т.
9.6 Расчет экономической
эффективности
Оценка общей и сравнительной
экономической эффективности позволяет решить вопрос о целесообразности
разработки и внедрения проекта.
Решение о целесообразности
разработки проекта новой установки принимается на основе экономического
эффекта, определяемого на годовой объем производства продукции.
Годовой экономический эффект
определим по формуле
, (6.17)
где Э1 -
экономия от реализации единицы продукции, руб.
- капитальные вложения,
руб.
Коэффициент сравнительной
окупаемости капитальных вложений определим по формуле
, (9.18)
Подставляя значения, получим
Срок окупаемости
определим по формуле
, (9.19)
Подставляя значения, получим
Сравниваем полученные Ес=6
и Т=0,16 год с нормативными Т≤Тн=5 лет и Ес ≥
Ен=0,15. Условие выполняется.
Показатели
|
По проекту
|
1 Абсолютные показатели:
|
|
Суточная производительность, т.
|
0,052424
|
Дни работы
|
220
|
Мощность установки, т.
|
17,3
|
Выход целевой продукции, %
|
100
|
Численность работников, чел
|
4
|
Стоимость основных фондов, руб.
|
79330
|
2 Относительные показатели: производительность труда, руб./чел.
|
208292,2
|
Фондоотдача, руб./ руб.
|
10,05
|
Себестоимость 1 м2. целевой продукции, руб.
|
45866,71
|
Рентабельность продукции, %
|
60
|
Удельные капитальные вложения, руб./т.
|
4585,5
|
3 Показатели экономической эффективности:
|
|
Годовой экономический эффект, руб.
|
466631,97
|
Срок окупаемости капитальных вложений, лет
|
0,16
|
Коэффициент сравнительной эффективности дополнительных
капитальных вложений
|
6
|
Библиографический список
1 Защита химического
оборудования неметаллическими покрытиями /Л.Г. Багатков, А.С. Булатова, В.Б.
Моисеев и др. - М.: Химия, 12989. - 288 с.;
Физическая химия. В 2
кн. Кн. 2. Электрохимия. Химическая кинетика и катализ: Учеб. для вызов /К.С.
Краснова, Н.К. Воробьев, И.Н. Годнев и др.; Под ред. К.С. Краснова - 3-е изд.,
испр. - М.: Высш. шк., 2001. - 319 с.;
Зиневич А.М. Защита
трубопроводов и резервуаров от коррозии. А.М. Зиневич, В.И. Глазков, В.Г.
Котик. - М.: Недра, 1975. - 288 с.;
Пажи Д.Г. Форсунки в
химической промышленности. Д.Г. Пажи, А.М, Прахов, Б.Б. Равикович. - М: Химия,
1982. - 270 с.;
Дытнерский Ю.И. Основные
процессы и аппараты химической технологии /Ю.И. Дытнерский. - М: Химия, 1982. -
270 с.;
Гузенков П.В. Краткий
справочник к расчетам деталей машин /П.В. Гузенков. - М: Высш. шк., 1964. - 270
с.;
Сборник задач и примеров
расчета по курсу детали машин. Учебное пособие для машиностроительных
техникумов. Изд. 4-е, перераб. - М: Машиностроение, 1975. - 286 с.;
Пажи Д.Г., Галустов В.С.
Распылители жидкостей /Д.Г. Пажи, В.С. Галустов. - М: Химия, 1979. - 216 с.;
Дунаев П.В.
Конструирование узлов и деталей машин /П.В. Дунаев, О.П. Леликов. - М: Высш.
шк. 2001. - 447 с.;
Лопастные и роторные
насосы. - М: ЦИНТИхимнефтемаш, 1985. - 76 с.;
Писаренко Г.С.
Сопротивление материалов /Г.С. Писаренко. Под ред. акад. АН УССР - 5-е изд.
перераб. И доп. - К: Вища шк. Головное изд-во, 1986. - 775 с.