Материалы
В качестве материала для основных связей корпуса принимается
низколегированная судостроительная сталь категорий Ф32, Д32, Е32, с пределом
текучести 315 МПа (32 кгс/мм2), для полособульба 30810 - категории
А40 с пределом текучести 395 МПа (40 кгс/мм2).
Для рубок, выгородок в прочном корпусе, мелких фундаментов и
креплений принимается углеродистая сталь категорий А и В, имеющая предел
текучести 235 МПа (24 кгс/мм2).
Рубки, мостики
Рубки и мостики выполняют по комбинированной системе набора.
Шпация набора рубки 600 мм.
Открытые места на крыльях ходового мостика защищены ветроотбойными
конструкциями. Конструкции в районе магнитного компаса выполняются из
маломагнитной стали.
Защита корпуса от коррозии и окраска
Защита корпуса от коррозии и обрастания осуществляется
применением современных, стойких к морской воде и нефтепродуктам красок.
Цистерны пресной воды выполняются из стали с последующей
окраской.
2. Мероприятия по
обеспечению непотопляемости судна
Сигналы: общесудовая тревога, сигналы
звонком громкого боя, сирены, в машинном отделении световой сигнализацией,
(команда) тревога дублируется голосом по радиотрансляции, экипаж действует
согласно своих расписаний по тревогам.
Общесудовая: сбор в столовой команды,
полная герметизация всех помещений надстройки (дверей, люков, шахт М.О.).
Действуют по распоряжению командира АСП.
По борьбе с пожаром:
Личный состав аварийной партии прибывает к
месту пожара, выявляет очаг, т.е. место, величину пожара, возможность его
изоляции, если имеется возможность произвести полную локализацию и принять
срочные меры по спасению людей «отрезанных» огнем если таковые имеются. О всех
наблюдениях докладывать командиру АСП по рации.
По борьбе с водой - члены экипажа
действуют согласно расписанию своих обязанностей по борьбе с водой. Подносят и
работают с аварийным инструментом. Ставят опоры. Готовят цементный ящик,
готовят и при необходимости заводят пластырь. В машинном отделении по
распоряжению командира АП (2-ой механик) готовят и при необходимости вводят в
работу балластно-осушительную систему. По приказу капитана открывают клапана
аварийного осушения машинного отделения.
Спасательные средства
Шлюпки
Моторные:
количество, вместимость, мест 1X37
С ручным механическим приводом:
количество, вместимость, мест 1X37
Шлюпбалки
тип Гравитационные
Шлюпочные лебедки - тип Электрические
Плоты:
тип «Викинг»
количество, вместимость, мест 4х10
. Противопожарные
средства
Насосы: количество - тип Два -
центробежные 100/80А
Один - центробежный 63/80 аварийный
подача, м3/ч 2X100
X63
напор, м 3 - 80
привод Электрический
Паротушение УК, глушители ДГ, дымо труба В
К
Углекислотное тушение глушители ДГ, дымо
труба В К, МО
Помещение АДГ, ресивер малярная МО
и трюмы
Основные технические характеристики двигателя B&W 6L60MCE
Диаметр цилиндра 0,60 м
Ход поршня 2,05 м
Цилиндровая мощность 1480 кВт
Среднее эффективное давление 1,7 Мпа
Удельный эффективный расход топлива 0,169
кг/кВт
Давление в продувочном ресивере 0,36МПа
Давление в конце сжатия 10,9МПа
Максимальное давление сгорания 12,5Мпа
Механический к. п. д 0,91
Детали остова
Фундаментная рама является основанием для
деталей остова, предназначена для укладки коленчатого вала и служит емкостью
для сбора масла, вытекающего из узлов смазывания двигателя. Рама нагружена
массой двигателя, силами давления газов, силами инерции поступательно движущихся
и вращающихся масс.
Рама образована продольными и поперечными балками, которые
должны иметь требуемую жесткость.
Продольные балки оснащены верхними обработанными полками для
установки на них картера и нижними опорными полками (лапами) для крепления
двигателя к судовому фундаменту.
Поперечные балки расположены между цилиндрами и по торцам
рамы. В верхней части поперечных балок выполнены гнезда (постели) для рамовых
подшипников коленчатого вала, а в стенках балок вертикальные каналы (колодцы)
для анкерных связей и отверстия для перетекания масла вдоль рамы.
Фундаментная рама сварная стальная увеличенной жёсткости со
вставными литыми гнёздами рамовых подшипников
Рамовые подшипники состоят из нижнего и
верхнего вкладышей, которые укладывают в гнёзда фундаментной рамы и прижимают
крышкой. Для образования стабильной масляной плёнки необходим определённый
зазор между шейкой вала и вкладышем подшипника. У стыков вкладышей фрезеруют
масляные холодильники, которые служат для лучшего распределения масла по длине
подшипника в клиновом зазоре, улавливают механические частицы и обеспечивают
смазывание вала в начале вращения. Масло подводится к холодильникам по
внутренним каналам, а из масляной системы сверху через крышку по трубе.
Крышка подшипника крепится шпильками. От проворачивания
вкладыши фиксируют штифтом, а от осевого смещения-торцевыми буртами.
Вкладыши рамовых и мотылевых подшипников
выполнены толстостенными с заливкой баббитом марки R4. Крейцкопфные вкладыши
у двигателей серии RTA могут быть выполнены из баббита или из сплава алюминия с оловом с
тонким гальваническим покрытием для приработки.
Станина состоит из литых
А-образных стоек, соединённых продольными сварными балками.
Цилиндровая втулка имеет высокий бурт со
сверлёнными каналами для охлаждения. Характерно крепление втулки в блоке.
Посадочный пояс расположен примерно на середине высоты втулки, нижняя часть
втулки обдувается воздухом.
Блок цилиндров также составной, собран
из отдельных блоков с рубашкой охлаждения. Цилиндры «сухие», охлаждающая вода
циркулирует между втулкой и напрессованной на нее обечайкой.
Крышка цилиндра стальная кованая со
сверлёнными каналами обычной (не колпачковой) конструкции. Охлаждающая вода из
цилиндра в крышку поступает через два переходных патрубка из основной крышки во
вставку-по двум патрубкам.
Использование прямоточно-клапанной
продувки предопределило схожесть многих конструктивных решений, принятых фирмой
в двигателях серии RTA, с аналогичными узлами двигателей фирмы «Бурмейстер и Вайн»:
также в центре крышки помещается единственный выпускной клапан с гидравлическим
толкателем, по периферии камеры сгорания расположены от двух до четырех
форсунок.
Решая проблему надежности выпускного
клапана, фирма использовала опыт создания и эксплуатации выпускных клапанов СОД
серии Z40.
Для уменьшения динамических нагрузок на клапан применен
гидравлический привод, хорошо зарекомендовавший себя в эксплуатации двигателей
фирмы «Бурмейстр и Вайн», но вместе возвратных механических пружин применен
воздушный демпфер с постоянной подпиткой воздухом нужного давления. Это
исключило вибрацию и колебания, сопровождавшие работу пружин и вызывавшие
фреттинг-коррозию торца штока клапана и поломки пружин. Кроме того, применено
механическое устройство, проворачивающее клапан в момент его посадки на седло.
За счет этого обеспечивается постоянная притирка клапана к седлу, удаление
нагара с посадочного пояска и выравнивание температурного поля тарелки клапана.
Клапан и седло изготовлены из теплостойкого сплава Nimonic. Интенсивное охлаждение
седла клапана по каналам из полости охлаждения его корпуса позволило
предотвратить ванадиевонатриеву коррозию.
Детали движения
Поршень состоит из кованой
стальной головки и юбки, отлитой из чугуна. Головка изготовлена из жаропрочной
молибденовой стали. Стенки цилиндрической части головки утолщены для более
эффективного охлаждения. В головке установлены шесть уплотнительных колец.
Днище поршня выпуклое; благодаря этому достигается значительное снижение
температуры головки поршня по сравнению с вогнутым днищем, кроме того, предотвращается
опасность скопления топлива на днище и создаются более благоприятные условия
для работы уплотнительных поршневых колец. Все кольца имеют косые замки,
которые при установке колец на поршень чередуются попеременно с наклоном влево
и вправо. Юбку поршня верхним торцом крепят к головке, ее нижний конец крепят к
пальцу крейцкопфа четырьмя прочными шпильками.
Шток изготовляется из
углеродистой стали и соединяется с кованой стальной поперечиной кольцевой
торцевой поверхности при помощи полого направляющего хвостовика с гайкой.
Сальник штока имеет четыре уплотнительных
и три маслосъемных кольца, размещенных в чугунных проставках. Все кольца
чугунные, разрезные, состоящие из трех частей. Кольца прижимаются к штоку
спиральными обжимными пружинами. Крышка уплотняется по рубашке цилиндра
маслостойкими резиновыми кольцами. Уплотнительные кольца получают смазку от
циркуляционной системы.
Крейцкопф - двусторонний с
четырьмя ползунами из литой стали. Поперечина, выполненная из легированной
стали, - с полыми шейками для головных подшипников и ползунов, по торцам имеет
крышки. Рабочие поверхности ползунов и их втулок залиты баббитом.
Скользящее соединение ползунов с цапфами
поперечины создает более равномерное прилегание их к параллелям на стойках
станины при работе двигателя. Кроме того, такое исполнение крейцкопфа по
сравнению с конструкцией, где ползуны прикрепляются к поперечинам болтами,
упрощает монтаж механизма движения двигателя.
Добившись высокого качества обработки
постелей и вкладышей подшипников, фирма перешла к применению вкладышей в
крейцкопфных и мотылевых подшипниках. Нижние вкладыши крейцкопфных подшипников
заливаются антифрикционным алюминиево-оловянистым сплавом, содержание олова в
котором составляет около 40%. Усталостная прочность такого сплава значительно
выше прочности баббита, однако главным преимуществом баббита как
антифрикционного материала является его способность поглощать твердые частицы
загрязнений, попадающие между трущимися поверхностями. Алюминиево-оловя-нистые
покрытия в этом отношении значительно уступают баббитам, поэтому во избежание
задиров при попадании посторонних частиц в период приработки на рабочую
поверхность вкладышей наносится свинцово-оловянистое покрытие. Для повышения
надежности работы крейцкопфного узла поверхности цапф крейцкопфов
обрабатываются по более высокому классу чистоты, чем у двигателей серии RND, а сами поперечины
полностью симметричны, что позволяет использовать обе поверхности скольжения
(верхнюю или нижнюю) в качестве рабочих.
Для улучшения условий работы этого узла
фирма перешла на смазку шеек крейцкопфа под давлением 1,6 МПа при давлении в
циркуляционной системе смазки около 0,4 МПа. Примерно за 90° п. к. в. до ВМТ
силы инерции и давление масла приподнимают поперечину, а за 50° п. к. в. до ВМТ
она снова ложится на подшипник. Благодаря повышению давления смазки радиальные
перемещения поперечины увеличились вдвое. За счет этого масла через зазоры в
подшипнике стало проходить больше, улучшились его смазка и теплоотвод от
поверхностей трения. Мотылевые подшипники смазываются от отдельного контура.
Шатун - с отъемными головными
и мотылевым подшипниками. Стержень шатуна изготовлен из углеродистой стали и
выполнен с жесткой безвильчатой головкой и отверстиями для подвода смазки от
головных подшипников к мотылевому. Мотылевый подшипник имеет четыре шатунных
болта, а головные - по два шатунных болта из легированной стали с центрирующими
поясками. Подшипники, изготовленные из литой стали с заливкой баббитом рабочих
поверхностей, имеют прокладки для регулирования масляных зазоров, а между
шатуном и мотылевым подшипником - прокладку для изменения степени сжатия при
износе втулки цилиндра.
Коленчатый вал полусоставной. Мотылевые
шейки и щеки мотылей откованы за одно целое. Щеки в горячем состоянии соединяют
с рамовыми шейками. Упорный подшипник с одним упорным кольцом имеет подушки
переднего и заднего хода. Его корпус крепится к корпусу судна и, кроме того, к
фундаментной раме, чем надежно обеспечивается соосность упорного вала с
коленчатым валом. На кормовом конце упорного вала закреплен маховик с зубчатым
венцом, с которым соединяется шестерня валоповоротного устройства, имеющего
электропривод. Шатун и его отдельная мотылевая головка стальные кованые.
Верхняя головка, также отдельная, отливается из стали. Мотылевый и верхний
головной подшипники заливают белым металлом того же химического состава, что и
вкладыши рамовых подшипников. Своей нижней шлифованной и полированной
поверхностью он по всей длине опирается на верхний головной подшипник шатуна. К
каждому концу пальца крепятся два ползуна, залитые белым металлом.
Системы дизеля
Система циркуляционной
смазки -
система с сухим картером. Запас масла хранится в сточной цистерне, которая
располагается непосредственно под дизелем. Наличие цистерны большого объёма
позволяет уменьшить кратность циркуляции, повысить эффективность очистки и
продлить срок службы масла. Циркуляционная система смазывания автоматизирована.
Масло из сточной цистерны через приёмный фильтр забирается циркуляционными
насосами и через маслоохладитель и фильтры тонкой очистки подаётся к
коллекторам охлаждения поршней и смазывания подшипников. Для пополнения системы
маслом предусмотрена запасная цистерна. Сепарация масла осуществляется
автономной системой. Режимы управления задаются с пульта и предусматривают автоматическое
выполнение следующих операций: контроль за уровнем масла в сточной и запасной
цистернах, корректировкой сигналов в штормовую погоду, включающих в действие
сепарационную установку при ухудшении качества масла, поддержание резервного
насоса.
Масло по трубопроводу через редукционный
клапан поступает к рамовым подшипникам и по трубопроводу на головные подшипники
и ползуны, а также на охлаждение поршней.
Система охлаждения
цилиндров
- замкнутая, с температурой воды на выходе 65-70° С и на входе - 55-60° С.
Центробежные насосы пресной и забортной воды имеют привод от электромотора.
Пресная вода с антикоррозийной присадкой подводится к цилиндрам под давлением
1,2 атм по трубопроводу и отводится через вставки крышек по трубопроводу через
магистраль. От этой системы осуществляется охлаждение корпусов турбин
нагнетателей, а от трубопровода - охлаждение корпусов заслонок.
На выходе из дизеля по отливной трубе вода
направляется в деаэратор центробежного типа, где от воды отделяется
паровоздушная смесь, сбрасываемая в расширительную цистерну. Из деаэратора вода
возвращается к циркуляционным насосам.
Элементы автоматики обеспечивают
выполнение следующих операций: автоматическое регулирование и контроль уровня в
расширительной цистерне; регулирование заданной температуры воды на входе в
дизель при помощи терморегулятора; пуск резервного насоса; прогревание дизеля
перед пуском; контроль температуры воды на выходе по цилиндрам.
От независимых систем производится
охлаждение пресной водой форсунок и поршней. Подвижная труба телескопического
устройства закреплена во фланце штока поршня, а неподвижная - к крышке, которая
является корпусом сальника.
Для предотвращения обводнения
циркуляционного масла уплотнение телескопии прикреплено к съемной крышке со
стороны подпоршневой полости.
В стальном стакане размещены втулка из
двух частей с направляющим кольцом, четыре уплотнительных кольца из кожи и
проставочные кольца. Обжатие уплотнения производится направляющей втулкой.
На охлаждение поршней вода подводится и
отводится по телескопическим трубкам.
Забортной водой под давлением 0,6 ати
осуществляется охлаждение пресной воды, воздухоохладителей и циркуляционного
масла.
Форсунка охлаждается благодаря постоянной
циркуляции топлива.
В данном дизеле применены ТНВД
золотникового типа с регулированием по концу подачи. При этом предусмотрен не
только отсечной клапан, момент открытия которого определяется положением
топливной рукоятки или указателч нагрузки при работе на всережимном регуляторе,
но и клапан на всасывании, не связанный с органами регулирования цикловой
подачи.
Топливные насосы высокого давления
объединены с гидравлическими толкателями выпускных клапанов в сдвоенные блоки -
один блок на два цилиндра С учетом увеличения нагрузки от привода клапанов
диаметр распределительного вала увеличен, а его установка на двигателе
обеспечивает повышенную жесткость и прочность.
В связи с тем, что кулачная шайба привода
выпускного клапана имеет симметричный профиль и нулевую заклинку по οтношению к кривошипу своего цилиндра, отпадает необходимость в ее
реверсировании. Для реверса кулачных шайб ТНВД в каждом блоке предусмотрен
небольшой гидравлической сервомотор, разворачивающий обе топливные шайбы на
заданный угол реверса.
Форсунка - закрытого типа с
конической иглой, нагруженной утопленной пружиной через толкатель. Затяжка
пружины на давление начала подачи 270 кГ1см2 регулируется изменением
толщины шайбы под нажимным болтом.
Игла имеет направляющую, выполненную
вместе с соплом, которое имеет десять отверстий диаметром 0,9 мм. Втулка
толкателя ограничивает подъем иглы в 1 мм.
Направляющая иглы прижимается к торцу
корпуса вместе с колпачком из жаростойкой стали гайкой и уплотняется
маслостойким резиновым кольцом. Штифт обеспечивает совпадение отверстий в
корпусе и направляющей.
Распылители имеют два ряда отверстий, расположенных под
разными углами по отношению к оси цилиндра. Это позволило уменьшить диаметр
сопловых отверстий и обеспечить лучшее распределение топлива по объему камеры
сгорания.
На новой серии двигателей RTA, производство которых начато
в 1983 г., была применена прямоточно-клапанная продувка.
Система наддува - с постоянным давлением.
Выпускные газы направляются в коллектор, а затем в газовую турбину,
расположенную над коллектором. Воздух от компрессора через охладитель поступает
в двухкамерный продувочный ресивер. Система обеспечивает устойчивую работу
дизеля в диапазоне нагрузок 25-100%. Лишь при более низких нагрузках включаются
две расположенные по торцам ресивера и включенные последовательно с ГТК
электровоздуходувки.
В целом система наддува в двигателях RTA аналогична системам
предшествующих серий, но в ней используются неохлаждаемые турбокомпрессоры
нового поколения VTR4 с к.п.д., равным 0,65; система утилизации теплоты наддувочного
воздуха предусматривает автоматическую регулировку его температуры; конструкция
ресивера продувочного воздуха упрощена; все элементы турбокомпрессора
скомпонованы в виде модуля, единого для всех модификаций дизелей серии RTA
судно дизель непотопляемость
4. Обслуживание дизеля
Пуск дизеля
Пуск дизеля разрешается только на
сжатом воздухе, применение других газов запрещено Подготовка пополнить пусковые
баллоны до рабочего давления (норма 3МПа), продуть баллоны, плавно открыть
стопорные клапаны на воздушной магистрали, спустить влагу из продувочного ресивера,
воздухоохладителя.
Проворачивание и пробные пуски - открыть
индикаторные краны и провернуть дизель ВПУ на 2-3 оборота, при проворачивании
убедиться в отсутствии влаги в цилиндрах и свободном вращении вала по
показаниям амперметра ВПУ, дизель прослушать, провернуть на воздухе при
открытых индикаторных кранах, произвести пробные пуски на топливе на передний и
задний ход. При обнаружении неисправностей подготавливать дизель к работе
запрещается (протечки воды, топлива, масла в трубопроводах, при включении циркуляционных
насосов может произойти порыв). При запуске циркуляционных насосов всех систем
проверить автоматический запуск резервных насосов (пуск со стенбайт).
Перед вводом в зацепление ВПУ необходимо
получить разрешение с мостика на проворачивание дизеля. Открыть индикаторные
краны, закрыть стопорные клапана на воздушных баллонах и магистрали, все
управление на «стоп», (при введении ВПУ органы управления должны отключаться
автоматически, что должна показать запись на светящемся табло) Пробные пуски на
воздухе и топливе производятся только по разрешению с мостика.
Возможные неисправности.
.загрязнение воздухоохладителя на
воздушной стороне (окислились пластинки, замаслились).
.загрязнение воздухоохладителя по водяной
стороне (шли по мелководью (реке) не перешли на бортовой кингстон).
.загрязнение фильтра компрессора (подлежит
периодической замывке, или полной смене фильтров (кошмы, синтепона)).
.забиты дренажные трубки.
Сорта применяемых масел и топлива.
Циркуляционные масла марки НД - содержащие
моющие и антикисло гные присадки. Из наиболее употребляемых так же Мобилгард
324 и 424, Шел - Арджина - 30. Для редуктора и упорного - Редукторное - 380. Турбинное - 412,
для систем автоматики марки Мобил №12,14. Для системы гидравлики рулевых машин,
швартовых лебедок, открытия трюмов, Мобил - 340, 420.
Высокое качество топлива гарантирует
надежную эффективную работу дизеля на всех режимах работы.
Плотность дизельных то плив 830-890 кг/мЗ Марки Л, 3,
ЗС, А Вязкость 3-6 сст
Вязкость до 600-700 сст.
Обязанности моториста по подготовке дизеля
к пуску.
К операциям по подготовке относятся
подготовка топливной системы, масляной системы, подготовка системы водяного
охлаждения, подготовка системы пуска, надува, подготовка валопровода,
проворачивание валоповоротного устройства при подаче цилиндровой смазки,
пробный пуск Операции по пуску дизеля должны выполняться в последовательности
предусмотренной заводом изготовителем, возможны дополнительные меры которые
возникли в ходе эксплуатации СЭУ, они должны быть внесены в машинный журнал ТЭС
и выполняться только по распоряжению старшего механика Наружный осмотр -
проверить отсутствие посторонних предметов (в особенности на рабочих узлах),
исправность КМП и штатных светильников, исправность кожухов, ограждений,
креплений плит настила (масляные пятна стереть).
Подготовка топливной системы
Спустить отстой из всех топливных цистерн,
проверить уровень заполнения (норма 7-80%) наполнение расходных цистерн производить
только через сепаратор (подогрев до 80°С), установить все клапана в рабочее
положение, проверить все элементы системы, пустить топливоподкачивающие насосы,
прокачать магистраль, удалить воздух, прокачать магистраль высокого давления
ТНВД - форсунки при пуске дизеля на тяжелом топливе включить подогрев (норма
вязкости 9-15 сст, при скорости подогрева не более 2°С/мин) Подготовка систем
смазывания
проверить уровень масла во всех цистернах
(норма 75-80%) пополнить все масленки, установить все клапана в рабочее
положение, включить подогрев (на среднеоборотных двигателях, тронковых ввиду
сильного загрязнения масла, сепаратор постоянно в работе) запустить
циркуляционные насосы (проверить резервные), двигатель проворачивать только при
включенном насосе. Проверить уровень масла и удалить воду в цистерне смазки
коромысел (рокеров). Уровень масла в опорных подшипниках, емкость смазки
симплекса, турбины I ступени.
Подготовка системы охлаждения
Проверить уровень во всех цистернах
(расширительной) при необходимости пополнить до верхнего уровня на шкале,
установить все клапаны в рабочее положение, пустить циркуляционный насос
(проверить резервный) включить подогрев (как правило если на ГД не
производились работы по ремонту (замене) ЦПГ, двигатель постоянно стоит на «подогреве»
45-55°С) при скорости нарастания температуры не более 10° за час, пустить и
проверить циркуляционные насосы забортной воды, насосы-охлаждения форсунок
(проверить уровень в расширительной и дождать начала слива воды с системы в цистерну,
убедившись что каждая форсунка охлаждается).
Подготовка систем пуска, продувки наддува:
пополнить пусковые баллоны до рабочего значения (норма 3 МПа) продуть баллоны,
плавно открыть стопорные клапаны на воздушной магистрали, продуть магистраль и
влагоотделители, спустить влагу из продувочного, воздухоохладителя. Открыть
индикаторные клапаны. Открыть индикаторные клапаны (т.е. проверить открытие).
Подготовка валопровода: произвести
наружный осмотр всю линию валопровода, проверить уровень масла в опорных,
расширительной редуктора и упорного подшипника, проверить клапана системы
охлаждения забортной воды, уровень в цистерне симплекса
Проворачивание и пробные пуски: открыть
индикаторные краны и провернуть дизель ВПУ на 2-3 оборота, при проворачивании
убедиться в отстутствии влаги или топлива в цилиндре, вал должен свободно
вращаться (следить за показанием амперметра) провернуть дизель на воздухе,
закрыть индикаторные и провернуть на топливе на передний и задний ход.
Двигатель готов.
Обслуживание дизеля во время работы
За 5-20 минут до пуска с мостика поступает
команда, с получением которой завершают все операции по подготовке к пуску и
докладывают на мостик о готовности установки к работе. Пуск дизеля производят
только по команде с мостика, после пуска проверяют показания всех КИП и
прослушивают дизель на предмет отсутствия посторонних стуков, шумов и вибрации.
Пуск дизеля ни с жатым воздухе, применение других газов запрещено. После ввода
дизеля в режим (после окончания маневров) пусковой воздух перекрывается Во
время работы дизеля необходимо контролировать:
. Давление масла, идущего на смазку дизеля
(6 кг), редуктора (4,0) и упорного подшипника (4,0).
. Температура масла (52°С).
. Уровень масла, в сточных и напорных
цистернах, турбокомпрессорах
. Давление воды для охлаждения ЦПГ
турбокомпрессоров, масло, воды и воздухоохладитель.
. Температурой входящей и выходящей воды,
охлаждающей ЦПГ масло, водо и воздухоохладитель
. Температуру охлаждающей воды (топлива)
на входе в форсунки и выходе с них
. Уровень воды в расширительной и сточных
цистернах.
. Уровень топлива и его температуру в
расходных цистернах.
. Давление топлива после
топливоподкачивающего насоса, температуру или вязкость топлива перед топливными
насосами высокого давления.
. Давление воздуха в пусковых баллонах
. Давление и температуру продувочного
воздуха до и после воздухоохладителей.
. Параметры в системе управления дизелем
. Температуру выпускных газов по
цилиндрам, в выпускных коллекторах, перед и после турбокомпрессоров.
. Температуру узлов трения (подшипников
дизеля, редуктора, упорного подшипника и др.)
. Наличие масляного потока в
контрольно-смотровых стеклах.
. Плотность посадки пусковых клапанов
цилиндров производить ощупыванием воздушных труб (на практике видно визуально
по задымившейся краске на проводной трубе). В случае обнаружения неисправности
при возможности устранить после тщательного анализа ее возникновения
Если по условиям плавания остановить
дизель нельзя (узкость, канал, река) принять все меры для обеспечения
работоспособности дизеля.
Остановка дизеля, вывод из работы
обслуживание на стоянке
При выводе дизеля из работы выполняют
следующие операции
Вывести из работы топливную систему,
предварительно пополнив расходные цистерны (75-80%) При недлительных стоянках и
низкой t°
в машинном отделении тяжелое топливо подогревают, t° держат 45°-60°
Вывести из действия систему воздушного
пуска Давление постоянно поддерживается воздушными компрессорами авотомат
Включения при понижении давления (повышен откл) в пределах 20-26 кг/м2 Закрыть
клапана воздушной магистрали воздухохранитель двигателя.
Систему охлаждения (пресной воды) и
смазывания оставить в работе до остывания дизеля, при достижении температуры
равной температуре пресной воды (охлаждения) ДГ, циркуляционный насос ГД
останавливается и система соединяется с системой охлаждения пресной водой ДГ,
температура воды поступающей от ДГ равна 49°-55°, что дает избежать больших
перепадов температур на ГД, он ставится на «подогрев», что дает в дальнейшем
при необходимости ввести в работу ГД в течении 10-15 минут Масляный насос
выключается через 60-90 минут после остановки ГД.
Открыть индикаторные краны и провернуть
ВПУ на 2-3 оборота, впоследствии это производить 1 раз в 4 часа, дабы избежать
залегания поршневых колец, открыть продувочные краны на ресиверах
При длительной стоянке зачехлить приемные
фильтры трубокомпрессоров
Остановить насос охлаждения форсунок
Смазать детали не имеющих централизованной
смазки (топливную рейку)
Обслуживание дизеля на стоянке
Во время стоянки необходимо периодически
проворачивать коленчатый вал на несколько оборотов валоповоротным устройством
при включенном насосе масляной системы ВП\ проворачивается 1 раз за вахту (4
ч), насос работает в течении 1 ч (может и более) двигатель тронковый, сильное
загрязнение масла, насосом мы не даем «осесть» грязи на дне сливного танка, что
облегчает постоянно работающему сепаратору «отбить» грязь от масла.
Следить за работой масляного сепаратора,
постоянно 1-2 раза производя «отстрел» за вахту, как можно лучше очистить масло
от неорганических (воды) примесей. Следить чтобы «подогрева» главного двигателя
была постоянной (50°С), смотреть за уровнем воды в расширительной главного
двигателя и расширительной охл. форсунок.
Основные неисправности в работе дизеля.
Дизель не пускается на воздухе закрыты
стопорные клапаны
заедание элементов системы пуска ДАУ
нарушена регулировка газораспределения
не отключено ВПУ
зажат тормоз валопровода или сальник
дейдвуда
гребной винт (задевает, обмоток) -
замерзла вода в дейдвуде
коленвал не установлен в пусковое
положение (только для вспомогательных двигателей)
Дизель не пускается на топливе
нет топлива, закрыты клапана
низкое давление топлива
высокая вязкость (низкая t° подогрева)
воздух в системе
вода в системе
дизель плохо прогрет
мал угол опережения подачи (поздняя подача)
открыты краны прокачки форсунок
низкая компрессия в цилиндрах нарушение в
регулировке ТНВР
заедание топливных реек или элементов
регулятора, нарушено соединение тяги топл. реек.
Неисправность по частоте вращения.
Дизель не развивает заданную частоту вращения.
повышено сопротивление движению судна
неисправность регулятора частоты вращения
нарушена связь между топливной рукояткой и
регулятором или между регулятором и ТНВД ухудшение качества рабочего процесса
(плохой распыл топлива, низкое давление или высокая температура продувного
воздуха)
задир поршня в одном из цилиндровой.
Дизель внезапно останавливается:
срабатывание системы аварийной защиты
закрылся быстрозапорный клапан на топлив.
магистрали
в топливную систему попал воздух
Дизель идет в разнос
резкий сброс нагрузки при одновременной
неисправности регулятора
большой запрос масла в цилиндры
При разносе следует немедленно принять
меры по прекращению топливоподачи, но надежнее прекратить подачу продувочного
воздуха.
Повышена температура выпускных газов
одного цилиндра
. перегрузка цилиндра (большая подача
топлива)
. плохое распыление топлива (дефекты ГД)
. плохая компрессия
. поздняя подача топлива (мал угол
опережения)
. загрязнение окон
Всех цилиндров
. перегрузка дизеля (ухудшение внешних
условий)
. низкое давление продувочного воздуха
. высокая температура продувочного воздуха
. воспламенение маслянистых отложений в
подпоршневых или продувоч ресивере.
Ненормальные стуки и шум.
Стуки в цилиндре:
перегрузка цилиндра (большая подача
топлива)
. большой угол опережения подачи топлива
. большие зазоры между поршнем и втулкой
(на тропковых дизелях)
. обрыв и выпадение клапана в цилиндр
. задир поршня (снижается частота
вращения, повышается температура охлаждающей воды на выходе из цилиндра)
Стуки в клапанах
. большие теплые зазоры
. заедание клапана в направляющей (поршень
ударяет по клапану)
. поломка пружины
Стуки, шум в передаче
. слабое натяжение цепи Плохая смазка
. сильный износ или поломка зубьев
шестерни
. работа привода в зоне резонансных
колебаний
Оборудование поста регулировки топливной
аппаратуры.
Пост регулировки топливной аппаратуры как
правило оборудован в помещении, отвечающем требованиям пожарной безопасности и
имеющий надежную вентиляцию.
Пост должен быть оборудован специальным
счьидом для испытания топливной аппаратуры, в который входит ручной пресс и
монометр со шкалой до 100 Мпа.
Для разборки (полной) в помещении должен
находиться слесарный стол, со стендом для ключей, и тиски, а так же емкости для
чистки и замывки топливной аппаратуры. Проверку и регулирование топливной
аппаратуры производят с периодичностью предусмотренной инструкцией
завода-изготовителя.
5. Рулевое устройство
Рулевое устройство состоит из:
·
полубалансирного
обтекаемого руля площадью около 41 м2;
·
прямого
баллера, соединение с пером руля - конусное на шпонке;
·
штыря;
·
2
опорных и 1 опорно-упорного подшипников.
Прокладка руля осуществляется электрогидравлической,
четырехцилиндровой плунжерной рулевой машиной с номинальным крутящим моментом
1000 кНм. Рулевая машина обеспечит прокладку руля при полном переднем ходе и
при работе одного насосного агрегата с 35° одного борта на 30° другого борта в течение
28 секунд.
6. Швартовное и буксирное устройство
Швартовное и буксирное устройства снабжаются следующими
канатами:
·
швартовные
канаты: 16 шт.; D=225…250 мм (окружность), L каждого 200 м; материал
синтетический; разрывное усилие 540 кН (55 тс);
·
буксирный
трос: 1 шт.; D=65
мм; L=280
м; материал - сталь; разрывное усилие 1660 кН (169 тс).
Швартовные канаты хранятся:
·
2 шт.
на барабанах якорно-швартовных лебёдок;
·
6 шт.
на барабанах швартовных лебёдок;
·
7 шт.
на вьюшках приводных с тормозами;
·
1 шт.
на деревянных решетках.
Буксирный трос хранится в носовой тросовой кладовой на вьюшке
с ручным приводом.
7. Краткое описание судовых систем
Система бытового водоснабжения
На судне предусматривается единая система бытовой пресной
воды, обеспечивающая все бытовые потребители пресной воды питьевого качества.
Обеззараживание воды производится в установках
ультрафиолетового облучения, в состав которых входят лампы и фильтры -
освежители. Общая пропускная способность установок около 30 м3/час.
Система сточная и шпигатная
Сточные воды от унитазов санузлов надстройки и оборудования
медблока отводится за борт через установку для очистки и обеззараживания
сточных вод или цистерну сбора сточных вод емкостью 14,5 м3.
Хозяйственно-бытовые воды отводятся за борт или через
установку для очистки сточных вод. Предусмотрена возможность сбора этих вод в
специальную цистерну емкостью 29м3.
Удаление воды с открытых частей предусматривается через
систему шпигатов за борт.
Системы отопления и хозяйственного пароснабжения
Паровое отопление предусматривается в хозяйственных,
санитарно - бытовых и других помещениях, требующих отопления и не обслуживаемых
системой кондиционирования воздуха или электроотоплением. Система выполняется
однопроводной.
Хозяйственный паропровод предусматривается для снабжения
паром водонагревателей, потребителей камбузного и прачечного блоков,
воздухонагревателей общесудовой и машинной вентиляции. Система выполняется
двухпроводной.
Системы водораспыления.
Для тушения остатков нефтепродуктов
третьего разряда (дизельное топливо, мазут, смазочные масла) в машинных и
котельных отделениях на судне применяется система водораспыления. Она выполнена
в виде систем нижнего и верхнего водораспыления, используемых для тушения
пожара тяжелых нефтепродуктов, находящихся в нижней части отсека или вверху при
затоплении отделения или аварии. Расстояние между ярусами выбрано не более 5 м.
Каждый ярус включен независимо от других. Кольцевой трубопровод яруса имеет
водораспылители (рис. 3.), отстоящие друг от друга на расстоянии 1,2-1,5 м.
распылителя.
Водораспылитель
Распылители размещены под палубой
защищаемого помещения, над топливными и масляными цистернами, под плитами
отделений, над сточными колодцами и льялами, под платформами, цистернами и
другим оборудованием так, чтобы обеспечить орошение мест, в которые может попасть
растекающееся топливо. Снабжение водой системы водораспыления производиться от
автоматически включаемого насоса. Для надежности система имеет два независимых
источника получения воды. При снабжении ее водой от системы водотушения питание
должно поступать по двум независимым участкам магистрали водотушения.
Принципиальная схема систем верхнего и нижнего водораспыления показана на рис.
4.
Каждый ярус с водораспылителями имеет
самостоятельный быстродействующий клапан, до места установки которого система
постоянно заполнена водой. При открытии этого клапана вода заполняет
трубопровод с распылителями. В дежурном положении быстродействующий клапан
закрыт, а импульсный трубопровод заполнен водой. Как только из импульсного
трубопровода будет выходить вода и давление в нем упадет, быстродействующий
клапан откроется - система водораспыления начнет работать. Для спуска воды из
импульсного трубопровода имеются краны, которые могут управляться вручную из
охраняемого и смежного с ним помещения.
Трубопроводы системы водораспыления изготовлены, из медных
труб диаметром 30 мм с бронзовой арматурой.
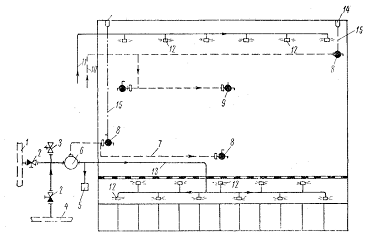
/ - магистраль системы водотушения; 2 -
клапан невозвратно-запорный; 3 - клапан предохранительный; 4 - труба от системы
водотушения; 5 - звуковой сигнал; 6 - клапан быстродействующий; 7 - импульсный
трубопровод системы нижнего водораспыления; 8 и 9 - краны спускные; 10 -
импульсный трубопровод системы верхнего водораспыления; 11 - разгрузочный
трубопровод системы верхнего водораспыления; 12 - водораспылитель; 13 -
разгрузочный трубопровод системы нижнего водораспыления; 14 - втулка палубная
валикового привода; 15 - валик привода
Система пожаротушения СО2
Ликвидация пожаров в судовых помещениях
углекислотой осуществляется методом объемного тушения. Для повышения
эффективности тушения произведена герметизация помещений, в которых применяется
углекислота.
На судне углекислота хранится в стальных
баллонах вместимостью 30-40 л, в которых она находится в жидком состоянии. Для
судовых систем углекислотного пожаротушения, работающих при давлении порядка
12,5 МПа (-125 кгс/см2), используют стандартные 40-литровые баллоны,
содержащие по 25 кг углекислоты. Баллоны размещены группами по 8-16 штук в
вертикальном положении головками вверх. Они надежно закреплены в местах,
расположенных вдали от жилых и служебных помещений, так как углекислота
относится к удушающим газам и при высокой концентрации в воздухе (22% и выше)
опасна для жизни.
При выходе из баллонов и внезапном
расширении углекислота испаряется, превращаясь в газ. При этом объем ее
увеличивается более чем в 500 раз. Часть углекислоты в результате переохлаж -
дения переходит в твердое состояние - снежные хлопья, которые, попадая в очаг горения,
мгновенно превращаются в газ. Углекислый газ, опускаясь к очагу пожара и
обволакивая горящие вещества и предметы, вытесняет воздух и снижает таким
образом содержание кислорода в зоне горения. В связи с этим горение
прекращается. Эффективность пожаротушения достигается при достаточно высокой
концентрации углекислоты в атмосфере помещения (22-23%).
Углекислотная система, предназначенная для
тушения пожара в больших судовых помещениях (рис. 4), состоит из баллонов для
хранения углекислоты 3, сборного 7 и распределительного // коллекторов с
невозвратными клапанами 9, трубопроводов, связывающих систему с охраняемыми
помещениями, предупредительной сигнализацией.
Для безопасности людей станция размещена в
надстройке, имеющей непосредственный выход на открытую палубу, вдали от жилых и
служебных помещений. Станция пожаротушения ограничена отдельными
газонепроницаемыми переборками и палубами с тепловой изоляцией, а также
оборудована отопительными приборами и вентиляцией. Температура в помещении
станции умеренная и не превышает + 40°С, так как при дальнейшем ее увеличении
возможно
усиленное испарение углекислоты и опасное
повышение давления в баллонах.
Для предотвращения утечки углекислоты
предусматривается установка на каждом баллоне быстродействующего запорного
клапана 4 с предохранительной мембраной, которая при определенном давлении
разрушается, а углекислота через предохранительный трубопровод 2 стравливается
в атмосферу. Для контроля за плотностью закрытия баллонных клапанов на сборных
коллекторах установлены манометры, реагирующие на утечку газа из каждого
баллона. В охраняемых помещениях выпускные трубопроводы системы оканчиваются
соплами или перфорированными трубами (в глушителях, котлах, дымовых трубах),
направляющими выходную струю углекислого газа к возможным очагам пожара. В
невысоких помещениях сопла расположены у подволока в один ряд. В помещениях,
имеющих высоту более 5 м, сопла установлены в два яруса. Система включается
вручную с помощью рычажного механизма 20 и дистанционно с помощью устройства / как
из помещения самой станции, так и с постов управления, расположенных на
мостике, в центральном пункте управления энергетической установкой и в других
местах. Дистанционное управление осуществляется с помощью электропередач.
Ручное управление является резервным.
В соответствии с Правилами Регистра
судовые помещения и емкости в случае возникновения в них пожара должны быть
заполнены углекислотой на 30% их объема в течение 15 мин.
На выпускных трубопроводах проходные краны
сблокированы с датчиками предупредительной звуковой и световой сигнализации 12,
подающей сигналы опасности при открывании крана и поступлении углекислоты в
охраняемое помещение. По сигналу опасности люди должны покинуть помещение и
принять меры по его герметизации. После ликвидации пожара трубопроводы
углекислотной системы продуваются сжатым воздухом через клапаны 10, затем
закрываются быстродействующие клапаны на баллонах и проходные краны на
распределительном коллекторе. В быстродействующих клапанах заменяют
деформированные мембраны и отмечают использованные баллоны специальным ярлыком
или надписью «пустой». Трубопроводы углекислотной системы окрашены под цвет
помещения и имеют маркировку в виде красного и синего колец, расположенных на
расстоянии 25 мм друг от друга.
Схема углекислотной системы пожаротушения:
1 - устройство для дистанционного пуска; 2 -
предохранительный трубопровод; 3 - баллон, 4 - быстродействующий клапан,
5-тросовая тяга; 6 - рычаг; 7 - сборные коллекторы, 8 - свисток, 9 - невозвратные
клапаны; 10 - клапан для подвода сжатого воздуха, 11 - распределительный
коллектор, 12 - датчик сигнализации; 13 - 18 - охраняемые судовые помещения; 19
- труба для отвода газа в предохранительный трубопровод; 20 - рычажный механизм
для ручного включения группы баллонов
Общесудовые системы
Система балластная
На судне балластная система выполняется
самостоятельной и в качестве резерва соединяется с осушительной. Она имеет
трубопроводную сеть, позволяющую наполнять и осушать как группы, так и
отдельные цистерны. Двухстороннее движение воды обосновывает установку в
трубопроводах системы запорных клапанов, управлять которыми можно вручную или
дистанционно, что зависит от размещения оборудования и необходимой степени
автоматизации его работы. Вся регулирующая арматура, клапанные коробки и
манипуляторы располагается в районе машинного отделения, где и установлены
балластные насосы. Каждая цистерна обслуживается независимым трубопроводом,
прокладываемым в пределах междудонного пространства в виде отдельных линий или
все трубопроводы размещаются в специальном коридоре. Прокладка труб упрощается
и устраняется необходимость прохода их через топливные или масляные цистерны.
Следовательно, устраняется возможность порчи водой жидкостей другого назначения
или откачки их за борт при неисправности балластного трубопровода, но
конструкция днищевого перекрытия при этом усложняется.
Минимальные внутренние диаметры труб в
зависимости от объема цистерны регламентируются Правилами Регистра. Требуемый
диаметр труб устанавливается на основе гидравлического расчета трубопровода с
проверкой обеспечения возможности всасывания воды из наиболее удаленной
цистерны при данной высоте всасывания насоса, обычно не превышающей 5-6 м. Для
работы балластной системы полный напор насоса в большинстве случаев не
превосходит 15-20 м вод. ст. Производительность насосов (100-400 мя1час)
на сухогрузных и пассажирских судах должна обеспечить прием (удаление) всего
балласта за 8-10 час. не более, а наибольшей цистерны - за 2 часа. На танкерах
для перекачки балласта используются грузовые насосы.
В балластной системе используются
бесшовные стальные оцинкованные или футерованные полиэтиленом трубы, а арматура
- чугунная, бронзовая или стальная. Путевые разъемные соединения - фланцевые.
Для контроля за количеством воды в
цистернах устанавливаются уровнемеры, показания которых передаются на пост
управления, где осуществляются требуемые маневры по управлению системой. Для
дистанционного управления используется электрический, гидравлический или
пневматический приводы, а в качестве резерва - ручной валиковый.
Забортная вода в отсеки принимается через
днищевой или бортовой кингстоны, приемные отверстия которых должны
располагаться в слоях свободной от ила или песка воды (рис. 18). Для защиты
системы от проникновения ила или песка на приемном трубопроводе устанавливается
фильтр-грязевая коробка (см. рис. 9, б), а для очистки от остатков
нефтепродуктов, если таковые окажутся в балластируемой цистерне, имеется
сепаратор балластных вод.
Заполнение цистерн, размещенных ниже ватерлинии, может быть
произведено самотеком через кингстон, а также насосом с последующим
распределением по отсекам. На рис. 2 показана принципиальная схема балластной
системы вместе с осушительной, где для сокращения количества арматуры
использована распределительная коробка.
Принципиальные схемы балластной,
осушительной и системы аварийного осушения машинного отделения на сухогрузном
судне.
/ - решетка сборного колодца; 2 - грязевая
коробка; 3 - коробка с невозвратно-запорными клапанами; 4 - коробка с запорными
клапанами; 5 - трубы осушительной системы грузовых трюмов; в-трубы балластной
системы; 7 - кингстон; 8 - клинкет; 9 - фильтр - грязевая коробка; 10 - коробка
с запорными клапанами - манипулятор; // - насос балластный; 12 - насос
осушительный; 13 - коробка с запорными клапанами; 14 - сепаратор
трюмно-балластных вод; 15 - ручной насос; 16 - сетка защитная на приемном
отростке аварийного осушения машинного отделения; 17 - трубы осушения машинного
отделения.
Система кондиционирования воздуха
Системы комплексной обработки воздуха -
систем кондиционирования воздуха - процессы нагревания, охлаждения, увлажнения
или осушения воздуха, а также фильтрации. Удовлетворение условий обитаемости в
жилых помещениях требует обеспечения в помещениях не только определенных
тепло-влажностных параметров воздуха, но и его определенной подвижности,
чистоты, газового состава, ионного спектра, шумового уровня и др. Комплексная
обработка воздуха совершается в аппаратах, получивших название кондиционеров,
представляющих собой агрегаты, состоящие из фильтров, вентиляторов,
воздухонагревателей, охладителей, увлажнительных камер, средств глушения шумов,
приборов автоматического регулирования процессами обработки воздуха. Кроме
того, имеются средства защиты, автоматически отключающие те или иные элементы в
случаях возникновения аварийных режимов работы. Средства автоматического
управления дублируются ручными приводами.
Принципиальная схема высокоскоростной
двухпроводной системы судна показана на рис. 3. Трубопровод, подающий воздух от
первой ступени обработки, рассчитывается на 30% всего подаваемого системой
воздуха. Вторая ступень и трубопровод, подающий от нее воздух в помещение,
рассчитывается на возможность обработки и подачи 100% расчетного количества
воздуха.
Как видно из рис. 3, приведенная схема
системы допускает использование как наружного, так и рециркуляционного воздуха
или их смеси. Для нагрева и охлаждения воздуха система использует воду,
предварительно нагреваемую или охлаждаемую (на рисунке показана работа системы
на цикл нагревания). Контроль температуры наружного и обрабатываемого воздуха
производится датчиками температуры, импульсы которых используются для привода в
действие регулировочных клапанов, установленных на трубопроводах с
теплоносителем. Датчик влажности, размещенный в канале рециркуляционного
воздуха, через систему реле обеспечивает регулирование расхода пара,
подаваемого в камеру увлажнения. На случай выхода из строя автоматических
регуляторов расхода греющей (охлаждающей) воды и увлажняющего пара
предусмотрено ручное управление, для чего на трубопроводах имеются клапаны с
ручным приводом.
Схема построения системы не изменяется, если для нагрева
воздуха использовать пар, для охлаждения - рассол или хладагент непосредственно
от холодильной машины.
Принципиальная схема двухпроводной
высокоскоростной системы кондиционирования воздуха.
/ - вентилятор высоконапорный; 2 - фильтр;
3 - воздухонагреватель (охладитель) первой ступени; 4 - элиминатор
(каплеотдели-тель) первой ступени; 5 - камера увлажнения; 6 -
воздухонагреватель (охладитель) второй ступени; 7 - элиминатор второй ступени;
8 - воздухосборник второй ступени; 9 - трубы подачи воздуха из первой ступени
обработки; 10 - трубы подачи воздуха из второй ступени обработки; 11 - отвод
влаги; 12 - отвод теплоносителя (холодоносителя) из воздухонагревателя
(охладителя); 13, 14 - электроприводное устройство регулировочного клапана; 15
- датчик влажности; 16 - датчик температуры
судно дизель непотопляемость
8. Безопасность труда при
эксплуатации судовых дизелей
Двигатели внутреннего сгорания (дизели)
должны обслуживаться с соблюдением техники безопасности. и регулярно проходить
проверку на изнашивание деталей, повреждение подшипников и ослабление
креплений.
При эксплуатации дизелей должны
выполняться требования, изложенные в РД 31.21.30-83 «Правила технической
эксплуатации судовых технических средств», а также в инструкциях
заводов-изготовителей.
Подготавливая дизельную установку к пуску,
необходимо тщательно осмотреть главный дизель, вспомогательные механизмы, КИП,
автоматические и сигнальные устройства. Перед включением валоповоротного
устройства следует убедиться, нет ли людей в картере и на подвижных частях
дизеля. В любом случае на органах управления дизеля должен быть вывешен плакат
с предупредительной надписью о том, что валоповоротное устройство включено или
выключено. Для обеспечения безопасной работы энергетической установки
необходимо провернуть вал дизеля валоповоротным устройством на 2-3 оборота,
затем проверить его действие сжатым воздухом и произвести пробные пуски дизеля
на передний и задний ход, убедившись при этом в отсутствии воды или топлива в
цилиндрах.
Перед пробными пусками необходимо
отключить валоповоротный привод и закрыть индикаторные краны, а также убедиться
в исправности форсунок, пус-ковых, всасывающих и форсуночных клапанов. Заедание
игл форсунок, пропуски воздуха в воздушной магистрали, неплотные посадки
клапанов в свои гнезда могут явиться причиной опасных взрывов в цилиндрах
дизеля и в воздухопроводе. Для обеспечения безопасности труда при обслуживании
дизеля указанные неисправности следует немедленно устранить.
Опасность взрыва может возникнуть в случае
попадания топлива в цилиндры при прокачивании топливных насосов с закрытыми
контрольными клапанами у форсунок. Поэтому заполнять топливные трубопроводы и
прокачивать топливные насосы разрешается только при открытых контрольных
клапанах.
При наличии механизмов дистанционного
управления дизелем пробные пуски следует производить со всех постов управления.
Пробные пуски дизеля можно производить только после получения разрешения от
вахтенного помощника капитана, убедившись в отсутствии людей под кормовым
подзором, а также шлюпок и других плавсредств.
Перед пуском дизеля необходимо проверить
исправность аппаратуры автоматики, сигнализации и защиты дизеля, а также всех
его систем. Обнаруженные течи и пропуски в топливной арматуре и топливопроводах
необходимо немедленно устранить.
При заполнении пусковых баллонов воздухом
необходимо, следить за тем, чтобы давление в баллонах не превышало
установленного. Воздушные баллоны и арматуру необходимо оберегать от ударов и
повреждений. Во избежание скопления в воздуховодах паров топлива опасной
концентрации их очищают с помощью пара или моющих химических средств и затем
продувают сжатым воздухом. При получении баллонов со сжатым воздухом -
необходимо убедиться в том, что в них находится воздух, а не кислород или
какой-либо другой горючий газ. При пуске дизеля во избежание ожогов не рекомендуется
находиться вблизи предохранительных клапанов ресивера, а также на верхних
решетках возле цилиндровых крышек на пути возможного потока прорвавшегося газа.
Для осуществления контроля работы дизеля на уровне верхних решеток следует
определить безопасное место, удобное для обзора.
По еле пуска дизеля на топливе необходимо
убедиться в том, что пусковые клапаны закрыты. При открытых пусковых клапанах
(зависание их и т.д.)' прорыв горячих газов в воздухопровод может привести к
взрыву и тяжелой аварии. Признаками этого является уменьшение давления
пускового воздуха и нагревание подводящего к пусковому клапану трубопровода.
Если при пуске дизеля появятся резкие
стуки, пропуски газов и другие отклонения в работе, его необходимо немедленно
остановить. После обнаружения и устранения неисправности дизель может быть
вновь пущен в работу. Присутствие посторонних лиц в машинном отделении судна
запрещено.
Неправильное обслуживание дизеля, особенно
в начальный период его работы, может привести к аварии дизеля. Так, сокращение
времени прогрева и форсирование нагрузки дизеля может привести к задирам или
заклиниванию поршней. Форсирование нагрузки непрогретого дизеля допускается
только в исключительных случаях, связанных с обеспечением безопасности судна
или угрозой человеческой жизни.
При выведении дизеля на номинальный режим
работы необходимо как можно быстрее переходить зону критической частоты
вращения вала дизеля, указанную в инструкции по обслуживанию. Работа дизеля на
критической частоте вращения, отмеченной на тахометре красным сектором,
категорически запрещается. В процессе работы дизеля необходимо следить за
исправностью предохранительных и редукционных клапанов, регуляторов
безопасности, за безотказным действием вспомогательных механизмов, не допуская
утечек воды, масел, топлива и газов через соединения трубопроводов. При прорыве
выпускных газов в машинное отделение необходимо усилить работу вытяжной
вентиляции и устранить пропуск газов.
При внезапном снижении давления масла в
смазочной системе дизеля необходимо его немедленно остановить и устранить
неисправность. В случае обнаружения подтекания в трубопроводах, подводящих
топливо к форсункам, запрещается во избежание травмы ощупывать трубки и
закрывать рукой место разрыва трубок.
Опасно резкое самопроизвольное увеличение
частоты вращения вала дизеля в результате потери или поломки лопастей винта, а
также внезапного оголения винта при сильном волнении моря. Если при этом не
срабатывает предельный регулятор, необходимо уменьшить подачу топлива. При
увеличении частоты вращения сверх максимальной, отмеченной на тахометре красной
чертой и оговоренной инструкцией по эксплуатации, необходимо уменьшить частоту
вращения или остановить дизель.
Большую опасность представляет масло,
скопившееся в продувочном устройстве двухтактного дизеля. Если продувочный
воздух будет заносить масло в цилиндры, то может произойти серия взрывов и
дизель пойдет вразнос даже при выключении подачи топлива. В этом случае для
быстрой остановки дизеля надо закрыть доступ воздуха в продувочный насос или
любой орган за- : бора воздуха к дизелю. Для предотвращения такой опасности
необходимо регулярно контролировать наличие масла в ресивере и вовремя удалять
его.
Во избежание травм нельзя протирать
ветошью движущиеся детали работающего дизеля и других механизмов. В процессе
работы дизеля запрещается открывать люки картера, чистить и обтирать детали. Не
разрешается также подкачивать вручную топливо в цилиндры работающего дизеля. Во
время продувания индикаторных кранов цилиндров дизеля следует находиться в
стороне от струи газа. Регулирование и ремонт форсунок, а также впускных и
выпускных клапанов рабочих цилиндров в процессе работы дизеля не допускается.
После остановки дизеля, прежде чем
приступить к осмотру и работам в картере, необходимо принять все меры,
исключающие возможность пуска или проворачивания вала дизеля до полного
окончания работ. Для этого необходимо закрыть запорный клапан на пусковой
воздушной магистрали, перекрыть доступ топлива к дизелю, ввести в зацепление
валоповоротное устройство, вывесить предупредительный плакат у пульта
управления дизеля о пребывании людей в картере.
При осмотре дизеля люки горячего картера в
целях безопасности могут быть открыты не ранее чем через 15-20 мин после
остановки дизеля. Картерные крышки массой свыше 20 кг при отсутствии
механизированного привода должны открывать и закрывать не менее 2 чел.
Для обеспечения безопасности труда
вскрытый картер дизеля необходимо тщательно провентилировать. Вблизи картера
запрещается проводить работы с открытым огнем (газорезка, электросварка и др.).
При пуске на судне одного из дизелей
двухвальной установки необходимо надежно застопорить валопровод остановленного
дизеля и предупредить об этом работающих на нем людей.
Такие же меры надо принять для обеспечения
безопасности в случае остановки для осмотра или ремонта •одного из дизелей
двухвальной установки.
Если необходимо остановить один из двух
дизелей, работающих на общий гребной вал через гидромуфту, то вначале дизель
отключают от гидромуфты, затемвключают в зацепление его валоповоротное
устройство и на пульте управления вывешивают плакат с надписью «Не включать!
Работают люди».
Неправильная эксплуатация дизелей часто
приводит к опасным перегревам их деталей, что может вызвать взрыв в картерах.
Предотвратить взрывы в картерах дизелей
можно путем рациональной их вентиляции, систематического контроля технического
состояния нагревающихся деталей, ввода в картер инертных газов и проведения
ряда конструктивных мер по обеспечению безопасности: установки
предохранительных клапанов, разделительных сеток в кривошипных камерах,
ослабляющих силу взрыва и т.д.
В случае появления сигнала детектора
«масляного тумана» или «густого белого тумана» из сигнальной (вентиляционной)
трубы картера необходимо повторно проверить срабатывание детектора в
соответствии с указанием инструкции по эксплуатации. При повторном появлении
сигнала детектора «масляного тумана» следует остановить дизель, не отключая
насосы смазки и охлаждения. Лицам, находящимся в машинном отделении, нужно
принять меры, обеспечивающие безопасность в случае взрыва в картере дизеля,
подготовить средства пожаротушения.
После исчезновения признаков опасной
концентрации масляного тумана, но не раньше чем через 20 мин после остановки
дизеля, необходимо выключить масляный насос и открыть щиты картера для
определения причин образования масляного тумана.
При остановке дизеля на продолжительный
период необходимо провернуть его вал валоповоротным устройством и закрыть
индикаторные краны.
При спуске людей в цилиндры дизеля для выполнения осмотров,
замеров и других работ необходимо использовать предназначенные для этого трапы.
Производить работы по опрессовке форсунок дизелей нужно только на оборудованных
для этого стендах с соблюдением рекомендованных инструкцией мер по обеспечению
безопасности.