Ванная стекловаренная печь
МИНИСТЕРСТВО ОБРАЗОВАНИЯ И НАУКИ
РОССИЙСКОЙ ФЕДЕРАЦИИ
ФЕДЕРАЛЬНОЕ ГОСУДАРСТВЕННОЕ БЮДЖЕТНОЕ
ОБРАЗОВАТЕЛЬНОЕ УЧРЕЖДЕНИЕ ВЫСШЕГО ПРОФЕССИОНАЛЬНОГО ОБРАЗОВАНИЯ
«БЕЛГОРОДСКИЙ ГОСУДАРСТВЕННЫЙ
ТЕХНОЛОГИЧЕСКИЙ
УНИВЕРСИТЕТ ИМ. В.Г. ШУХОВА»
Кафедра Энергетики теплотехнологии
Курсовая работа
по дисциплине: «Высокотемпературные
теплотехнологические процессы и установки»
на тему: «Ванная стекловаренная печь»
Выполнил:
студент гр. ЭТк-42
Бараковский М.С.
Принял: д.т.н, профессор
Кузнецов В.А.
Белгород 2012 г.
Задание
на курсовой проект по ВТПиУ
«Ванная стекловаренная печь»
Исходные
данные
1. Производительность печи: P = 0.5 т/ч
2. Тепловой коэффициент полезного
действия: η=16%
Химический
состав стекла: SiO2= 67%; CaO =17 %; Na
O = 16%
1. Сырьевые материалы: кварцевый песок,
мел, сода.
2. Влажность шихты без стеклобоя: uш=13%
3. Температура варки стекла: tвар =1405 °C
4. Температура отводимой стекломассы: tстк=1125°C
5. Температура горячего воздуха: tв=910°C
6. Коэффициент избытка воздуха aв=1,15
7.
Топливо
месторождение № 12
Индивидуальное
задание
Учесть
присосы холодного воздуха
1. В топливных подводах Δa'хв = 0,08
. На выходе из печи Δa''хв = 0,05
Содержание
Введение
. Конструктивное описание печи
. Виды сырьевых материалов
. Конструктивный расчет печи
. Материальный баланс и объемы технологических газов
. Объемы и состав топливных газов
. Тепловой баланс стекловаренной печи
. Расчет насадки регенератора
. Тепловой расчет регенераторов и рекуператоров
Заключение
Список литературы
Введение
Стекло - твердотельное состояние аморфных веществ. Стеклом называются все
аморфные тела, получаемые путем переохлаждения расплава, независимо от их
химического состава и температурной области затвердевания, и обладающие в
результате постепенного увеличения вязкости механическими свойствами твердых
тел, причем процесс перехода из жидкого состояния в стеклообразное должен быть
обратимым. Целью курсового проектирования является закрепление, углубление и
конкретизация теоретических знаний, полученных студентами при изучении
высокотемпературных процессов и установок. В качестве объекта проектирования
выбрана стекловаренная ванная печь, что в полной мере соответствует
методическим требованиям подготовки энергетиков теплотехнологии.
Стекловаренные печи занимают особое место в производстве строительных
материалов не только по широте их применения, разнообразию типов,
конструктивных схем и режимов тепловой работы, но и по сложности протекающих в
них теплотехнологических процессов, что в итоге приводит к их довольно низкой
тепловой эффективности. Будущим специалистам в области промышленного
энергосбережения предоставляются большие возможности разработки в курсовом
проекте технических решений по совершенствованию высокотемпературной
теплотехнологической установки, учитывая, что тепловой коэффициент полезного
действия стекловаренных печей в настоящее время, как правило, не превышает
20..25 %.
1. Конструктивное описание печи
Электрические печи для варки стекла по сравнению с пламенными печами
имеют следующие преимущества: отсутствие продуктов горения топлива в рабочей
камере печи и потерь тепла с газами, выходящими из камеры; уменьшение потерь
тепла через ограждения рабочей камеры печи, как результат уменьшения площади
ограждений и более эффективной тепловой изоляции кладки; создание оптимального
теплового режима для процесса стекловарения; создание любой газовой среды над
зеркалом стекломассы; уменьшение потерь из шихты и стекломассы летучих
соединений.
Рис.1. Электрическая стекловаренная ванная печь
- порочный бассейн; 2 - рабочие графитовые электроды; 3 - дымовой канал;
4 - нерабочий электрод; 5 - горелки для разогрева печи; 6- карборундовые
нагреватели; 7 - проток; 8 - заземляющий электрод; 9 - выработочный бассейн.
Удельный расход электроэнергии в электрических ванных печах колеблется от
0,8 до 3 кВт*ч/кг сваренной стекломассы, уменьшаясь с увеличением общей и
удельной производительности печи. Удельная производительность в зависимости от
состава стекла и мощности печи 1000 - 5000 кг с 1 м3 зеркала стекла варочной
части печи в сутки. В выработочных частях электрических ванных печей тепловой
режим поддерживается за счет тепла, выделяемого при сжигании газообразного или
жидкого топлива или за счет электроэнергии, превращенной в тепловую. В первом
случае в варочном пространстве выработочного бассейна устанавливают газовые
горелки или форсунки для жидкого топлива, а продукты горения отводят через
дымовые каналы, устроенные в стенах. Во втором случае в стекломассе выработочного
бассейна устанавливают электроды, аналогичные электродам в варочной части печи,
или в газовом пространстве устанавливают электрические нагревателя, передающие
тепло стекломассе лучеиспусканием. Конструктивное решение выработочной части
электрических ванных печей диктуется выработочными приспособлениями.
Электрическая энергия в качестве тепловой используется в пламенных ванных
печах для получения дополнительного количества стекломассы или для повышения
качества стекломассы. С этой целью в стекломассе варочного бассейна пламенных
ванных печей в зоне максимальных температур устанавливают электроды,
обеспечивающие выделение тепла, расходуемого для нагрева стекломассы бассейна и
усиление сыпочного конвекционного потока. При установке вертикальных электродов
через дно печи создается восходящий конвекционный поток стекломассы, образующий
тепловой барьер, препятствующий прохождению непроверенной стекломассы в
выработочный бассейн. Дополнительное тепло, полученное сыпочным конвекционным
потоком, передается нижней поверхности слоя шихты, что совместно с общим
повышением температуры стекломассы в бассейне способствует ускорению процесса
стеклообразования и повышению производительности печи. В некоторых печах для
увеличения теплового потока к нижней поверхности слоя
шихты устанавливают дополнительно горизонтальные электроды. Тепловые
барьеры, создаваемые двухрядной установкой донных молибденовых электродов в
зоне квель пункта, затрудняют прорыв непроверенной стекломассы в выработочный
бассейн, усиливают восходящие конвекционные потоки и улучшают гомогенизацию
стекломассы. Применение дополнительного электронагрева на действующих пламенных
ванных печах обеспечивает увеличение производительности печи на 30-100 % при
высоком коэффициенте использования тепла дополнительного электронагрева.
Введение дополнительного электронагрева незначительно увеличивает потери тепла
через ограждения по сравнению с потерями только при пламенном отоплении печи.
Условно можно считать, что дополнительное тепло расходуется только на получение
стекломассы.
Удельный расход электроэнергии для получения 1 кг дополнительной
стекломассы зависит от удельной и общей производительности печи и от количества
введенного дополнительного тепла и колеблется от 0,6 до 1,2 кВт*ч/кг
дополнительной стекломассы. Конструктивное решение пламенно-электрических
ванных печей соответствует обычным решениям пламенных ванных печей, отличаясь
только установкой электродов для дополнительного электронагрева.
электрическая стекловаренная
ванная печь
2. Виды сырьевых материалов
Сырьевые материалы для производства стекла условно делятся на две группы:
главные и вспомогательные. Главные материалы содержат оксиды, образующие основу
стекла и определяющие его свойства. Вспомогательные материалы содержат
соединения, которые вводятся в стекло для варьирования свойств стекла и
ускорения его варки. Это - красители, глушители, осветлители, обесцвечиватели,
окислители, восстановители и ускорители. I.
Главные материалы: 1) Кремнезем является главной составной частью
промышленных стекол. Около 95% всех производимых промышленностью, стеклоизделий
получают на основе силикатных стекол, концентрация кремнезема в которых
составляет 55-75% и более. Существуют различные природные виды кремнезема:
кристаллический - кварц (горный хрусталь, жильный кварц, кварцевые пески);
скрытокристаллический халцедон, агат, кремень; аморфный опал, трепел, диатомит,
опоки. В последнее время диоксид кремния стали производить искусственно
преимущественно для производства особо чистого кварцевого стекла. 2) Кварцевый
песок. В производстве промышленных стекол применяют кварцевые пески разных
месторождений Кварцевый песок является продуктом разрушения горных пород,
состоит в основном из зерен кварца и обычно содержит различные примеси. Примеси
в песке бывают механическими (зерна других минералов, включения в кварцевое
зерно и др.) и химическими (твердые растворы с кварцем, пленки и др.). Все
примеси могут быть разделены на две группы: вредные - оксиды Fe, Cr, Ti, Мп, V
и др. и невредные - оксиды Al, Ca, Mg, К, Na и др. Первые сообщают стеклу
нежелательную окраску, вторые обычно входят в состав промышленных стекол и
требуют только учета их при расчете состава шихты. 3) Глинозем Al2O3 вводят в состав стекла с помощью технического оксида
алюминия, гидроксида алюминия Al2O3*ЗН2O, полевых шпатов, пегматитов, каолинов и др., а также отходов
горно-обогатительных фабрик - полевошпатового и нефелинового концентратов.
Пегматиты - природная смесь 75% полевого шпата и 25% кварца. На стеклозаводах
применяют обогащенный пегматит (зерно 0,1 - 0,8 мм). Каолины - Al2O3*2Si02*2H2O (Al2O3 39,5 %; Si02 46,5 %; H2O 14 %) применяют для стекловарения после обогащения (Fe2O3 0,4 - 1,0%) .
4) Оксид натрия Na2O в состав стекла вводят через
кальцинированную соду и сульфат натрия. Сода Na2CO3 бывает
кристаллической Na2CO3*10H2O и безводной Na2CO3. В стекловарении применяют главным образом безводную соду,
которая содержит 58,5 % Na20 и
41,5 % С02. Кроме того, соду подразделяют на искусственную, природную, легкую, тяжелую.
Сульфат натрия Na2SO4 применяют преимущественно как
осветляющую добавку в количестве 5 - 15% . 5) Оксид калия К2O вводят в состав стекла при помощи
поташа, содовопоташной смеси и селитры KN03. Поташ К2CO3 состоит из 68,2 % К20 и 31,8 % С02. Поташ должен содержать
не менее 98 %, К2CO3 имеет вид
белого порошка, растворимого в воде, легко поглощающего влагу из воздуха.
) Оксид кальция СаО вводят в состав стекла посредством карбоната кальция
(известняк, мел, мрамор). Известняк - осадочная горная порода белого цвета или
окрашенная соединениями железа в разные оттенки: зеленоватый, желтый, бурый,
красноватый и др. Мел - мягкая осадочная порода белого цвета, иногда слегка
окрашенная примесями. Мрамор - горная порода, отличается высоким содержанием
СаС03-до 99 - 99,5 %, постоянством состава и небольшим количеством оксида
железа до 0,015 %. 7) Оксид магния MgO вводят в состав стекла преимущественно
посредством доломита и может быть введен магнезитом или доломитизированным
известняком. Доломит CaC03*MgC03- природный двойной карбонат кальция и магния,
горная порода, в которой кроме основного вещества содержатся примеси (Si02, A12O3, Fe2O3). II.
Вспомогательные материалы:
) Красители стекла представляют собой соединения различных металлов. С
помощью красителей стеклу можно придать любую окраску. На окрашивание стекла
влияет тип красителя, его концентрация, режим марки и
окислительно-восстановительные условия. Один и тот же краситель в зависимости
от условий варки и концентрации может сообщать стеклу разный цвет. На
интенсивность и оттенок окрашивания стекла влияет также его состав. 2)
Глушители - вещества, при введении которых стекло приобретает способность
рассеивать свет (становится глушеным). В качестве глушителей применяют в
основном соединения фтора и фосфора и гораздо реже олова, сурьмы, циркония.
) Осветлители - материалы, способствующие освобождению стекломассы от
видимых газовых включений. К осветлителям относятся: селитра, оксиды мышьяка (III) и сурьмы (III), диоксид церия, сульфат натрия, фтористые и аммонийные
соли, хлористый натрий. 4) Обесцвечиватели бывают физические, химические и
смешанные. Для физического обесцвечивания - окрашивания стекломассы в цвет,
дополнительный к зеленому, применяют селен, оксиды никеля (II), кобальта (II),
неодима, церия и др. Общая прозрачность при этом снижается. 7) Окислители и
восстановители применяют в ряде случаев при варке стекол специального состава
для создания окислительной или восстановительной сред. В качестве окислителей
применяют нитраты, мышьяк, оксид марганца и др. В качестве восстановителей
применяют углеродсодержащие вещества , соединения олова.
. Конструктивный расчет печи
Определим основные размеры рабочей камеры.
Площадь варочной части:
где Pстк - заданная суточная
производительность, кг/сут;
gв -
допустимый удельный съем стекломассы, кг/(м2 · сут), gв = 910 кг/(м2 · сут)
Варочная часть в плане имеет следующие размеры:
Площадь студочной части при температуре варки 1405 °С принята равной:
Площади
варочной части:
Ширина
студочной части составляет 50 % ширины варочной части:
Ширина
загрузочного кармана:
Длина
загрузочного кармана:
. Материальный баланс и объемы технологических газов
Для расчета состава шихты следует сначала вычислить массовые доли
стеклообразующих окислов в каждом компоненте шихты по его химическому составу
(при условии отсутствия примесей):
CaCO3 = CaO + CO2СO3 = Na2O + CO2
.
По
заданному составу стекла с помощью уравнения материального баланса определяются
теоретические массовые расходы компонентов шихты, необходимые для получения из
них 1 кг., стекла в предположении, что все нелетучие окислы полностью переходят
из шихты в стекло:
Действительный
расход шихтовых материалов может быть несколько выше теоретического вследствие
уноса части шихты дымовыми газами. Особенно велики потери щелочных компонентов
шихты, частично возгоняющихся при высоких температурах. Примем, что потеря на
улетучивание Na2O составляет 5%. Таким образом, пренебрегая стеклобоем,
действительные расходы компонентов шихты на 1 кг стекла определяются по
формулам:
Расход
сухой шихты получим, сложив все расходы ее компонентов:
Расход
влажной шихты при заданной ее влажности uш = 0,13:
Определим
массы веществ, переходящих в газообразную среду при разложении и возгонке
компонентов шихты.
Масса
технологического углекислого газа, выделяющегося из шихты, находится
суммированием по соответствующим компонентам шихты:
,
где
gизв, gсоды - массовые расходы компонентов
шихты, кг/кг стекла ;
XCO2изв , XСO2сода
- массовые доли диоксида углерода в соответствующих
компонентах шихты или приход углерода от добавляемого угля.
Сводная
таблица материального баланса
Таблица
1
Приход веществ
|
кг/кг
|
Расход веществ
|
кг/кг
|
Влажная шихта Gшвл
|
1,453
|
Стекломасса Pстк
|
1
|
|
|
Углекислый газ GCO2тех
|
0,256
|
|
|
Водяной пар GH2Oтех
|
0,2
|
Всего:
|
1,453
|
Всего:
|
1,456
|
(1,456-1,453)×100 / 1,456 = 0,21% < 0,5%
Так как расхождение между приходом и расходом веществ в таблице меньше
0,5% , то материальный баланс составлен правильно.
Объемы технологических газов (при нормальных условиях), определяются,
исходя из их массовых расходов:
объёмный расход технологического углекислого газа:
объемный
расход технологического водяного пара:
,
где
rCO2 и
rH2O - плотность при нормальных условиях соответственно
углекислого газа и водяных паров.
5. Объемы и состав топливных газов
Расчеты объемов воздуха, необходимого для горения, и продуктов сгорания
топлива ведутся на 1 м3 природного газа или на 1 кг мазута. Все объемы
приведены к нормальным условиям (температура О °С и давление 760 мм ртг ст.).
Состав газообразного топлива обычно задается в процентах по объему. В таблице 2
приведены расчетные характеристики природного газа:
Таблица 2
№ п/п
|
Плотность ρт, кг/м3
|
Теплота сгорания Qнр,
кДж/м3
|
Стехиометрические объемы
воздуха и продуктов горения, м3/м3
|
|
|
|
Vв0
|
VCO20
|
VН2О0
|
VN20
|
Vг0
|
12
|
0.741
|
9.32
|
0.98
|
2.10
|
7.39
|
10.47
|
Действительный объем продуктов горения топлива находят как сумму объемов
всех составляющих газообразных компонентов:
Действительный
объем углекислого газа остаются без изменений:
Действительный
объем водяных ларов возрастает за счет влаги избыточного воздуха:
Действительный
объем азота, вносимый избыточным воздухом:
Действительный
объем кислорода, вносимый избыточным воздухом:
По
составу продуктов горения определяют объемные доли составляющих газообразных
компонентов, которые в дальнейшем могут быть использованы для расчета средней
теплоемкости газов. Объемная доля углекислого газа:
Объемная
доля водяных паров:
Объемная
доля азота:
Объемная
доля кислорода:
Проверка:
. Тепловой баланс стекловаренной печи
Для оценки степени энергетического совершенства (или несовершенства)
проектируемой печи, целесообразно составить тепловой баланс термодинамически
идеальной теплотехнологической установки, наделенной некоторыми предельными
свойствами, теоретически обеспечивающими минимальный расход топлива на
проведение теплотехнологического процесса. Так как в идеальной установке
отсутствуют потери тепла, уравнение теплового баланса примет следующий вид:
Qт + Qн.в. + Qш = Qхим +
Qисп + Qстк + Qгтоп
+ Qгтех
Приход тепла
Теплота вносимая топливом (упрощенный подход):
где,
Qтех- теплота технологическая, кВт; Qш-
теплота поступающая с шихтой, кВт.
Теплота
поступающая с шихтой:
,
где
Cш , Cвл - удельные теплоемкости
соответственно шихты и воды; Gшсух, Gвл - массовые расходы
соответственно сухой шихты, и влаги, сопутствующей шихте, кг/кг.
,
где,
Спесок, Cизв, Ссода - удельные теплоемкости соответственно
песка, известняка и соды, которые находим по приложению 5 при tш=200C.
Теплота
вносимая нагретым воздухом, кДж/кг стк:
,
где
aв - коэффициент избытка
воздуха, подаваемого на горение;
Vв° - теоретически необходимый объем воздуха для сжигания 1
м3 природного газа, м3/м3; Cв = 1,426 - удельная объемная
теплоемкость влажного горячего воздуха при температуре tв=9100С ,
кДж/(м3×К); tв = 910 °С - температура горячего воздуха, идущего на горение в идеальной
установке.
Расход
тепла
Расход
тепла на технологические процессы стекловарения:
Теплота
химических реакций стеклообразования:
где
qCaCO3 , qNa2CO3 - удельная теплота
реакций стеклообразования, отнесенная к массе соответствующего
стеклообразующего окисла в составе исходного вещества, кДж/кг; gмел
, gсода - удельные массовые расходы
компонентов шихты, кг/кг стк; XCaOмел, XNa2Oсода - массовые доли стеклообразующих
окислов в соответствующем компоненте шихты.
Теплота стекломассы, отводимой из варочной части печи:
где
Cстк - удельная массовая
теплоемкость стекломассы, отводимой из варочной части печи при температуре tстк
= 1125 °С.
Теплота
испарения влаги из шихты:
,
где
Gвл - расход влаги, испаряющейся из
шихты, кг/кг стк; rисп = 2448 кДж/кг - удельная теплота парообразования
при tш = 20°С.
Расход
топлива:
где
Qт - теплота выделившаяся при сгорании топлива, кВт; Qнр -
теплота сгорания, кДж/м3.
Теплота
отходящих топливных газов:
где
tг = 1480 °С - средняя температура газов на выходе из варочной части печи (принимаем
равной температуре плавления шихты); Vгтоп - объем топливных газов, приходящихся на 1 м3 сгоревшего природного
газа, м3/м3; Cгтоп , - удельная объемная
теплоемкость топливных газов при температуре tг , кДж/(кг×К).
где
CCO2 , CH2O , CN2 , CO2 - удельные объемные
теплоемкости соответственно углекислого газа, водяных паров, азота и кислорода
при температуре tг , кДж/(м3×К); pCO2
, pH2O , pN2 , pO2 - объемные доли соответствующих
топливных газов.
Теплота
отходящих технологических газов:
где
tг = 1480 °С - средняя температура газов на выходе из варочной части печи (принимаем
равной температуре плавления шихты); Vгтех - объемный расход технологических газов, м3/с; Cгтех-удельная объемная теплоемкость технологических газов при температуре tг ,
кДж/(кг×К).
Удельная
теплоемкость технологических газов определяем в зависимости от температуры и
состава газов:
где
CCO2 , CH2O , CN2 , CO2 - удельные объемные
теплоемкости соответственно углекислого газа, водяных паров, азота и кислорода
при температуре tг , кДж/(м3×К); VCO2
, VH2O - объемные расходы
соответствующих технологических газов, м3/с;
Расход
тепла с отходящими дымовыми газами:
Сводная
таблица теплового баланса идеальной стекловаренной печи
Таблица
3
Приход тепла
|
кВт
|
%
|
Расход тепла
|
кВт
|
%
|
С топливом Qт
|
5962
|
71.88
|
На стекловарение Qтех
|
995
|
12
|
С воздухом Qн.в.
|
2295
|
27.66
|
С дымовыми газами Qд.г.
|
4607
|
55.53
|
С шихтой Qш
|
37.86
|
0.46
|
Потери Qп
|
2693
|
32.47
|
Всего:
|
8295
|
100
|
Всего:
|
8295
|
100
|
. Расчет насадки регенератора
Насадку регенератора выкладываем из динасового кирпича прямоугольной
формы с размерами: длина l =
230 мм, высота h = 113 мм,
толщина d = 65 мм.
Ячейка регенератора имеет форму квадрата размером: длина a = 120 мм, ширина b = 120 мм.
Удельная поверхность нагрева, приходящаяся на единицу объема насадки:
Степень
заполнения объема кирпичом:
Удельная
площадь свободного сечения, приходящаяся на единицу площади поперечного сечения
газохода:
Эквивалентная
толщина кирпича:
.
Тепловой расчет регенераторов и рекуператоров
Прежде
всего, необходимо уточнить расход, состав и температуру отходящих газов
стекловаренной печи в воздухонагревательном устройстве с учетом присосов
холодного воздуха.
Объемный
расход дымовых газов:
Объемный
расход газов, поступающих из стекловаренной печи в регенератор:
Объемные
расходы отдельных компонентов в отходящих газах печи и их объемные доли в воздушном
нагревателе:
водяных
паров:
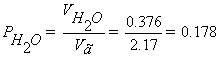
кислорода:
Найдем
температуру газов, поступающих в воздухонагреватель :
где
Cг - средняя удельная теплоемкость газов на выходе из
печи при температуре tг, кДж/м3×К.
Примем
tг'=1380 °С и рассчитаем
теплоемкость газов на выходе из печи:

где
CCO2, CH2O, CN2, CO2 - объемные теплоемкости
соответствующих газов при температуре tг=13800С, кДж/м3×К; pCO2 , pH2O, pN2 , pO2 - объемные доли
отдельных компонентов в отходящих газах печи.
Расчет
теплоты по уравнению баланса.
Объемный
расход воздуха в воздухонагревателе:
Количество
теплоты, воспринятое нагреваемым воздухом, кВт:
где
tв¢, tв¢¢ - соответственно температуры
воздуха на входе и выходе из воздухонагревателя (примем tв¢ =100°С), °С; Cв¢, Cв¢¢ - соответственно средние удельные
теплоемкости влажного воздуха на входе и выходе из воздухоподогревателя, кДж/м3×К.
Обобщенное
уравнение теплового баланса воздухонагревателя:
где
Qг - количество теплоты, отданное
охлаждаемыми газами, кВт; Qп - потери теплоты в окружающую
среду, величина которых составляет 10% от теплоты Qг отданной
газами.
С
помощью уравнения теплового баланса воздухонагревателя находим температуру
газов на выходе из регенератора:
Здесь
tг¢, tг¢¢ - соответственно температуры
газов на входе и на выходе из воздухонагревателя, °С; Cг¢ , Cг¢¢ - соответственно средние удельные
теплоемкость газов на входе и на выходе из воздухоподогревателя, кДж/м3×К.
Примем
tг¢¢ = 700°С и рассчитаем среднюю удельную теплоемкость газов на выходе из
воздухоподогревателя:
где
CCO2¢', CH2O¢', CN2¢', CO2¢' - объемные теплоемкости соответствующих газов при температуре tг¢¢=7000С, кДж/м3×К; pCO2
, pH2O, pN2 , pO2 - объемные доли
отдельных компонентов в отходящих газах печи.
В
расчете воздухонагревательных устройств совместно с уравнением теплового
баланса используется уравнение теплопередачи:
где
Q - тепловой поток через
поверхность теплообмена, Вт; k - коэффициент
теплопередачи, Вт/(м2×К); Dtср - средний
температурный напор, К; F - расчетная
поверхность теплообмена, м2.
Тепловой
поток через поверхность теплообмена:
Средний
температурный напор рассчитываем по формуле логарифмического усреднения:
где Dtб и Dtм - наибольшее и наименьшее значения
разности температур газов и воздуха во входных и выходных сечениях
воздухоподогревателя, К:
Следует учитывать, что в насадке регенератора площадь свободного сечения
для прохода воздуха и газов одна и та же. Поэтому скорости воздуха и газов в
регенераторе взаимосвязаны. Тогда примем скорость воздуха при нормальных
условиях Uв° = 0,5 м/с.
Средняя скорость воздуха в сечении насадки регенератора:
Средняя
температура воздуха:
Найдем
по tв значения коэффициентов теплопроводности и
динамической вязкости: λв = 0.056 Вт/м∙К; νв = 8,017∙10-5 м2/с
Вычислим
число Рейнольдса:
Вычислим
критерий Нуссельта:
Найдем
коэффициент теплоотдачи конвекцией:
Рассчитаем
скорость газов при нормальных условиях:
Средняя
скорость газа в сечении насадки регенератора:
Средняя
температура газа в сечении насадки:
Найдем
по tг значения коэффициентов теплопроводности и динамической
вязкости: λг = 0.113 Вт/м∙К; νг = 1.77∙10-4 м2/с
Вычислим
число Рейнольдса:
Вычислим
критерий Нуссельта:
Найдем
коэффициент теплоотдачи конвекцией:
Эффективная
толщина излучающего слоя:

где
,
Коэффициенты
поглощения лучей газами, рассчитываются соответственно при температурах газов и
стенки:
Температура
стенки обычно принимается средней между значениями температуры воздуха и газов
в расчетном сечении воздухонагревателя:
Степень
черноты eг.в. и поглощательная способность Aг.в.
газов находим по однотипным формулам, полученным на основе закона Бугера:
где
lэф - эффективная толщина излучающего
слоя газов, м; kгв и kгв¢ - коэффициенты поглощения лучей газами, 1/м, рассчитанные соответственно
при температуре газов и при температуре стенки.
Плотность
потока результирующего излучения:
Рассчитаем
коэффициент теплоотдачи излучением для регенераторной насадки:
Коэффициент
теплоотдачи от газов к поверхности нагрева:
В
качестве материала насадки выбираем динас. Рассчитаем коэффициент
теплопроводности насадки lн.в. и ее
теплоемкость Cн.в. при tг¢ = 1045.5 °C:
Рассчитаем
коэффициент теплопередачи от охлажденных газов к нагреваемому воздуху(τ = 1800с):
Определяем
расчетную поверхность нагрева:
Расчетный
объем насадки регенератора:
Основные
размеры регенератора:
площадь
свободного поперечного сечения насадки:
площадь
полного поперечного сечения газохода регенератора:
высота
насадки регенератора:
Заключение
В
качестве объекта проектирования была выбрана стекловаренная ванная печь с
подковообразной схемой движения газов. Производительность печи 0.5 тонны стекла
в час. Из-за сложных теплотехнологических процессов, протекающих
в таких печах, их тепловая эффективность довольно низкая, что и показывает КПД,
который равен η=16%. Это большое поле для работы будущих специалистов в
этой области.
Из
теплового баланса стекловаренной печи видно, что тепловые потери в окружающую
среду очень велики, но часть теряемого тепла можно утилизировать, применив
усовершенствования данной установки.
Совершенствование
данной установки возможно:
·
путем улучшения
герметизации участков стыков печи и регенераторов;
·
путем установки
котла-утилизатора
или сушилки кипящего слоя на выходе из регенератора для подогрева шихты перед
ее загрузкой в печь, то есть использовать теплоту отходящих газов;
·
путем улучшения
теплоизоляции и многое другое.
·
применение
электроподогрева.
Увеличение КПД сможет уменьшить удельные затраты топлива на килограмм
стекломассы, что приведет к снижению себестоимости изделий получаемых из
стекломассы, что повысит их конкурентную способность на рынке.
Список литературы
1. Кузнецов В. А. Высокотемпературные
теплотехнологические установки:
учеб.
пособие. - Белгород:
Изд-во БелГТАСМ, 2001. - 76 с.
2. Левченко П. В. Расчеты печей и сушил
силикатной промышленности: учеб. пособие - М.: Высшая школа, 1968. - 368 с.
3. Роговой М.И., Кондакова М.Н.,
Сагановский М.Н. Расчеты и задачи по теплотехническому оборудованию предприятий
промышленности строительных материалов: учеб. пособие - М.: Стройиздат, 1975.-
320 с.
4. Волгина Ю.М.Теплотехническое оборудование
стекольных заводов.- М.: Стройиздат, 1982.-276 с.