Кут повороту КВ, град.
|
Номер циліндрів
|
Сумарні дотичні зусилля УФ
|
|
1
|
2
|
3
|
4
|
5
|
6
|
|
0
|
0,000
|
1,181
|
-0,584
|
-0,500
|
0,519
|
0,000
|
0,616
|
10
|
-285,000
|
0,983
|
-0,617
|
-0,486
|
0,481
|
2,202
|
2,281
|
20
|
-0,516
|
0,783
|
-0,607
|
-0,409
|
0,509
|
4,340
|
4,000
|
30
|
-0,652
|
0,581
|
-0,557
|
0,316
|
4,368
|
3,792
|
40
|
-0,671
|
0,383
|
-0,482
|
-0,059
|
0,214
|
3,633
|
3,049
|
50
|
-0,575
|
0,190
|
-0,419
|
0,180
|
0,108
|
2,936
|
2,420
|
60
|
-0,389
|
0,000
|
-0,419
|
0,414
|
0,000
|
2,421
|
2,027
|
70
|
-0,153
|
-0,104
|
-0,540
|
0,598
|
-0,108
|
2,078
|
1,771
|
80
|
0,086
|
-0,207
|
-0,821
|
0,691
|
-0,216
|
1,850
|
1,383
|
90
|
0,290
|
-0,306
|
-1,229
|
0,668
|
-0,323
|
1,681
|
0,781
|
100
|
0,433
|
-0,395
|
-1,541
|
0,527
|
-0,426
|
1,526
|
0,124
|
110
|
0,508
|
-0,464
|
-1,234
|
0,290
|
-0,516
|
1,362
|
-0,054
|
120
|
0,519
|
-0,500
|
0,000
|
0,000
|
-0,584
|
1,181
|
0,616
|
Середнє значення сумарної дотичної
сили УФср визначається по
площині під кривою.
Графічним методом
визначено, що УФср = 1,75 мм.
Визначення погрішності
розрахунку динаміки.
Визначення погрішності
розрахунку динаміки зводиться до порівнянні величини індикаторної потужності з
діаграми сумарного дотичного зусилля, з вихідною індикаторною потужністю
двигуна по результатам розрахунку робочого циклу.
Розрахункова величина
індикаторної потужності :
Ni = УФср *µm*

* R 
* 
,кВт
де, УФср = 1,75 - середнє сумарне
дотичне зусилля (зняте безпосередньо з діаграми);
µm= 0,05 мПа /мм - масштаб
по вісі УФ;
Dц = 0,18 м - діаметр циліндра;
R= 0,110 м - радіус кривошипа;
n = 750 об/хв. - кількість
обертів колінчастого вала.
Ni = 1, 75 * 0, 05

* 
= 19 кВт
Індикаторна потужність
двигуна за результатами розрахунку робочого циклу визначається за формулою:
Niц = 13,1* Рі * D
* S* n* I *Z, кВт
де Рі = 1,9097 НМа -
середній індикаторний тиск с урахуванням округлення індикаторної діаграми.
S = 0,22 м - хід поршня
Z - 0,5 - тактність
і = 6 - кількість
циліндрів.
Niц = 13,1* 1,9097 *
* 0,12* 759 * 6*0,5 =
401 кВт
Динамічний
розрахунок вважається виконаним вірно якщо виконується наступна умова: величина
питома ефективна витрата палива яка отримана розрахунком відрізняється не більш
ніж на 5% від спеціолізації.
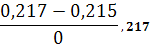
* 100% = 1%
.2.2 Розрахунок
моховика
Визначаємо
величину надмірної роботи в період розгону або уповільнення маховика:
L
над. = 
над *
* Fцил.*R* µт* 
*
,
де 
над - площа, відповідаюча надмірній роботі (визначаємо по діаграмі
сумарних дотичних зусиль), (креслення № 10), 
над = 217 м
Fцил. = 0,0396 
;
R = 0,110 м - радіус кривошипа;
µт
- масштаб діаграми сумарних дотичних сил, НПа/мм;
µт
= 0,05 мПа/мм;
µ2 = 0,75 град/мм
- масштаб кута поворота колінчастого валу.
L
над. = 217 * 
*
0,0396*0,110*0,05*0,75*
= 618 к Дж
Необхідна величина
моменту інерції рухомих части двигуна для необхідної потреби степені обертання
колінчатого вала.
Im
= 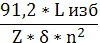
, кг/
де 
- степінь
нерівномірності обертання колінчастого вала

Расчет динамики дизеля
Исходные данные
Тактность (число тактов)
D = 4
Шаг.градусы Н =10.000
Частота вращения коленчатого вала,
об/мин n = 750
Удельная масса поступательных частей
кривошипно-шатунного механизма, кг/м**2 MS =1600.000
Радиус кривошипа, м R= 0.110
Отношения радиуса кривошипа к длине
шатуна L = 0.250
Давление сил тяжести поступательных
масс кривошипно-шатунного механизма, МПа РТ= 0.016\
Давление на поршень с его тыльной
части , МПа РК= 0.207
Давление конца сжатия, МПа РС =
8.392
Максимальное давление в цилиндре,
МПа РZ = 11.750
Cтепень предварительного расширения RO = 1.496
Показатель политропы
сжатия n1 = 1.375
Показатель политропы
расширения n2 =1.219
Степень сжатия ЕР = 12.500
Результаты динамического расчета
AL- Угол поворота кривошипа. Градусы.
PG- Сила давления газов. МПа
PS- Сила инерции поступательных масс. МПа
PD- Движущее усилие. МПа
N- Нормальная сила. МПа
Q- Сила действующая по шатуну. МПа
Z- Радиальная сила. МПа
T- Касательная сила. МПа
Таблиця 2.2.
AL
|
PG
|
PS
|
PD
|
N
|
Q
|
Z
|
T
|
|
Н а п о л н е н и е
|
|
|
|
0.000
|
0.260
|
-1.357
|
1.348
|
0.000
|
-1.348
|
-1.348
|
-0.000
|
10.000
|
0.260
|
-1.325
|
-1.316
|
-0.057
|
-1.317
|
-1.286
|
-0.285
|
20.000
|
0.260
|
-1.231
|
-1.221
|
-0.105
|
-1.226
|
-1.112
|
-0.516
|
30.000
|
0.260
|
-1.080
|
-1.071
|
-0.135
|
-1.079
|
-0.860
|
-0.652
|
40.000
|
0.260
|
-0.884
|
-0.874
|
-0.142
|
-0.886
|
-0.578
|
-0.671
|
50.000
|
0.260
|
-0.654
|
-0.645
|
-0.126
|
-0.657
|
-0.318
|
-0.575
|
60.000
|
0.260
|
-0.407
|
-0.398
|
-0.088
|
-0.408
|
-0.123
|
-0.389
|
70.000
|
0.260
|
-0.159
|
-0.150
|
-0.036
|
-0.154
|
-0.017
|
-0.153
|
80.000
|
0.260
|
0.074
|
0.083
|
0.021
|
0.086
|
-0.006
|
0.086
|
90.000
|
0.260
|
0.280
|
0.290
|
0.075
|
0.299
|
-0.075
|
0.290
|
100.000
|
0.260
|
0.451
|
0.461
|
0.117
|
0.475
|
-0.195
|
0.438
|
110.000
|
0.260
|
0.583
|
0.593
|
0.143
|
0.610
|
-0.337
|
0.508
|
120.000
|
0.260
|
0.678
|
0.688
|
0.153
|
0.705
|
-0.476
|
0.519
|
130.000
|
0.260
|
0.742
|
0.751
|
0.147
|
0.765
|
-0.595
|
0.481
|
140.000
|
0.260
|
0.780
|
0.789
|
0.128
|
0.799
|
-0.687
|
0.409
|
150.000
|
0.260
|
0.800
|
0.810
|
0.102
|
0.816
|
-0.752
|
0.316
|
160.000
|
0.260
|
0.810
|
0.819
|
0.070
|
0.822
|
-0.794
|
0.214
|
170.000
|
0.260
|
0.813
|
0.823
|
0.036
|
0.824
|
-0.816
|
0.108
|
180.000
|
0.260
|
0.814
|
0.824
|
0.000
|
0.824
|
-0.824
|
0.000
|
|
|
С ж а т и е
|
|
|
|
180.000
|
0.260
|
0.814
|
0.824
|
0.000
|
0.824
|
-0.824
|
0.000
|
190.000
|
0.262
|
0.813
|
0.825
|
0.036
|
0.825
|
-0.818
|
-0.108
|
200.000
|
0.268
|
0.810
|
0.827
|
0.071
|
0.830
|
-0.801
|
-0.216
|
210.000
|
0.278
|
0.800
|
0.827
|
0.104
|
0.834
|
-0.769
|
-0.323
|
220.000
|
0.294
|
0.780
|
0.822
|
0.134
|
0.833
|
-0.716
|
-0.426
|
230.000
|
0.315
|
0.742
|
0.157
|
0.821
|
-0.639
|
-0.516
|
240.000
|
0.346
|
0.678
|
0.773
|
0.171
|
0.792
|
-0.535
|
-0.584
|
250.000
|
0.388
|
0.583
|
0.720
|
0.174
|
0.741
|
-0.410
|
-0.617
|
260.000
|
0.446
|
0.451
|
0.646
|
0.164
|
0.666
|
-0.274
|
-0.607
|
270.000
|
0.528
|
0.280
|
0.557
|
0.144
|
0.575
|
-0.144
|
-0.557
|
280.000
|
0.645
|
0.074
|
0.468
|
0.119
|
0.483
|
-0.036
|
-0.482
|
290.000
|
0.820
|
-0.159
|
0.410
|
0.099
|
0.422
|
0.047
|
-0.419
|
300.000
|
1.087
|
-0.407
|
0.429
|
0.095
|
0.493
|
0.132
|
-0.419
|
310.000
|
1.511
|
-0.654
|
0.606
|
0.118
|
0.617
|
0.299
|
-0.540
|
320.000
|
2.204
|
-0.884
|
1.069
|
0.174
|
1.083
|
0.707
|
-0.821
|
330.000
|
3.348
|
-1.080
|
2.017
|
0.254
|
2.033
|
1.620
|
-1.229
|
340.000
|
5.127
|
-1.231
|
3.645
|
0.314
|
3.659
|
3.318
|
-1.541
|
350.000
|
7.279
|
-1.325
|
5.703
|
0.248
|
5.708
|
5.573
|
-1.234
|
360.000
|
8.392
|
-1.357
|
6.784
|
0.000
|
6.784
|
6.784
|
0.000
|
|
Р а б о ч и й х о д
|
|
|
|
360.000
|
11.750
|
-1.357
|
10.141
|
0.000
|
10.142
|
10.142
|
0.000
|
370.000
|
11.750
|
-1.325
|
10.174
|
0.442
|
10.184
|
9.943
|
2.202
|
380.000
|
11.750
|
-1.231
|
10.268
|
0.881
|
10.306
|
9.348
|
4.340
|
390.000
|
8.502
|
-1.080
|
7.171
|
0.903
|
7.228
|
5.758
|
4.388
|
400.000
|
5.868
|
-0.884
|
4.737
|
0.771
|
4.796
|
3.131
|
3.633
|
410.000
|
4.199
|
-0.654
|
3.294
|
0.643
|
3.356
|
1.625
|
2.936
|
420.000
|
3.137
|
-0.407
|
2.478
|
0.550
|
2.538
|
0.763
|
2.421
|
430.000
|
2.443
|
-0.159
|
2.032
|
0.491
|
2.091
|
0.234
|
2.078
|
440.000
|
1.975
|
0.704
|
1.798
|
0.457
|
1.856
|
-0.138
|
1.850
|
450.000
|
1.652
|
0.280
|
1.681
|
0.434
|
1.736
|
-0.434
|
1.681
|
460.000
|
1.422
|
0.451
|
1.623
|
0.412
|
1.674
|
-0.688
|
1.526
|
470.000
|
1.257
|
0.583
|
1.589
|
0.384
|
1.635
|
-0.904
|
1.362
|
480.000
|
1.136
|
0.678
|
1.563
|
0.347
|
1.601
|
-1.082
|
1.181
|
490.000
|
1.047
|
0.742
|
1.538
|
0.300
|
1.567
|
-1.218
|
0.985
|
500.000
|
0.983
|
0.780
|
1.511
|
0.246
|
1.531
|
-1.316
|
0.783
|
510.000
|
0.937
|
0.800
|
1.486
|
0.187
|
1.498
|
-1.381
|
0.581
|
520.000
|
0.907
|
0.810
|
1.465
|
0.126
|
1.471
|
-1.420
|
0.383
|
530.000
|
0.889
|
0.813
|
1.451
|
0.063
|
1.453
|
-1.440
|
0.190
|
540.000
|
0.883
|
0.814
|
1.447
|
0.000
|
1.447
|
-1.447
|
0.000
|
|
В ы п у с к
|
|
|
|
540.000
|
0,234
|
0,814
|
0,798
|
0.000
|
0.798
|
-0.798
|
0.000
|
550.000
|
0,234
|
0,813
|
0,797
|
-0.035
|
0.797
|
-0.791
|
-0.104
|
560.000
|
0,234
|
0,81
|
0,793
|
-0.068
|
0.796
|
-0.769
|
-0.207
|
570.000
|
0,234
|
0,8
|
0,784
|
-0.099
|
0.790
|
-0.728
|
-0.306
|
580.000
|
0,234
|
0,78
|
0,763
|
-0.124
|
0.773
|
-0.664
|
-0.395
|
590.000
|
0,234
|
0,742
|
0,725
|
-0.141
|
0.739
|
-0.574
|
-0.464
|
600.000
|
0,234
|
0,648
|
0.662
|
-0.147
|
0.678
|
-0.458
|
-0.500
|
610.000
|
0,234
|
0,583
|
0.567
|
-0.137
|
0.583
|
-0.323
|
-0.468
|
620.000
|
0,234
|
0,451
|
0.434
|
-0.110
|
0.448
|
-0.184
|
-0.409
|
630.000
|
0,234
|
0,28
|
0,264
|
-0.068
|
0.272
|
-0.068
|
-0.264
|
640.000
|
0,234
|
0,074
|
0.057
|
0.059
|
-0.004
|
-0.059
|
650.000
|
0,234
|
-0,159
|
-0.176
|
0.043
|
-0.181
|
-0.020
|
0.180
|
660.000
|
0,234
|
-0,407
|
-0.424
|
0.094
|
-0,434
|
-0.131
|
0.414
|
670.000
|
0,234
|
-0,654
|
-0.671
|
0.131
|
-0.683
|
-0.331
|
0.598
|
680.000
|
0,234
|
-0,884
|
-0.900
|
0.147
|
-0.912
|
-0.595
|
0.691
|
690.000
|
0,234
|
-1,08
|
-1.097
|
0.138
|
-1.106
|
-0.881
|
0.668
|
700.000
|
0,234
|
-1,231
|
-1.247
|
0.107
|
-1.252
|
-1.135
|
0.527
|
710.000
|
0,234
|
-1,325
|
-1.342
|
0.058
|
-1.243
|
-1.311
|
0.290
|
720.000
|
0,234
|
-1,357
|
-1.374
|
0.000
|
-1.374
|
-1.374
|
0.000
|
.3 Розрахунок систем
двигуна
.3.1 Паливна система
Паливна система
забезпечує уприскування до камери згорання дизеля у певній послідовності у
строгому дозуванні порцій дрібнораспиленого палива.
Паливо з витрачальної
цистерни подається паливопідкачним насосом (1) крізь фільтр (3) у порожнину
всмоктування паливного насосу високого тиску (5) та насосу гідрозапора (12).
Паливний насос високого тиску нагнітає паливо по трубопроводам (6) крізь
форсунки (7)до циліндра дизеля.
Насос гідрозапора
форсунок подає паливо через редукційний клапан (10) по трубопроводу (8)к
форсункам в порожнину над голкою розпилювача, забезпечуючи її запирання.
Редукційний клапан підтримує в запором трубопроводі (8) встановлений тиск
(150кг с /с
), перепускаючи зайве
паливо до порожнини засосування підкачующого насосу по трубопроводам (11).
Трубопровід запорного палива (8)виконує роль накопичувача і має об`єм 750 с
. Тиск в трубопроводі
гідрозапора (8) контролюється манометром (9).
Розрахунок
системи подачі палива
Подача
паливопідкачующого насосу, 
/год.
Wt.n. = 
Ne ge/ 
т
де 
= (1,5…2,0) -
коефіцієнт подачі насоса;
Ne = 324 кВт - ефективна потужність;
ge = 0,215 кг/ кВт * год - питома ефективна витрата палива;

т - щільність легкого
палива кг/

= 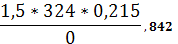
= 124,09 
/год.
Приймається
шестиринчастий насос з подачею.
Площа поверхні
фільтруючого елемента, 
.
Fф
= 
= 124,09 
/год
де 
- припустима швидкість
фільтрації (0,06… 0,12)
Кж*с - коефіцієнт
живого перетину (0,2…0,3)
Fф
= 
= 1,37 
Циклова вагова подача
палива, г/цикл.
gц
= 
г/цикл.
де, і - кількість циліндрів (6)
Z - коефіцієнт тактності (0,5)
n - кількість обертів двигуна за хвилину 750 об/хв
gц
=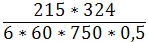
= 0,51 г/цикл.
Циклова об`ємна подача, с
/цикл.
Vц
= 
с
/цикл.
де, 
- щільність палива
0,842 г/ с

= 0,605 
/цикл.
Визначення
конструктивних розмірів плунжерної пори.
Геометрична
тривалість упорскування

= (0,65… 0,75) 
де, 
= 20 - дійсна
тривалість упорскування.

=
0,75 *20 = 15
Хід плунжера
(геометрично корисний)
hr
= 
* 
; мм
де, 
- середня щільність
плунжера ( 0,7…1,5)
hr
= 
* 
= 3,3 мм
Повний хід
плунжера, мм
hn = (3,0…4,2) hr
hn = 3,0*3,3= 9,9 мм
Обираю зі
стандартного ряду хід плунжера рівний hn = 9,0 мм
Діаметр плунжера,
мм
dn = 10
; мм
де ŋn - коефіцієнт подачі, обираю 0,845
dn = 10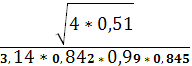
= 0,96*10 = 9,6 мм;
dn = 9,6 мм
Розрахунок
розпилювача форсунки
Час витікання
палива через форсунку, с
∆ t = 
. с
∆ t = 
= 0,0033 c
Середній тиск
газів у період упорскування, МПа
Pr cp =
, МПа
де Pc" = Pc * 1,15 - середній тиск за процес стиску;
Pz = 11,7491 - максимальний
тиск у циліндрі;
Pc" = 8,3922 *1,15 = 9,
651
Pr cp = 
=
10,7 МПа
Середня швидкість
виходу палива через соплові отвори, м\с
Приймаю 50 МПа
V ср = 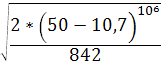
= 305 м/с
Сумарна площа соплових
отворів, м
Fc = 
= 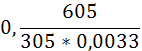
= 0,6 м
Діаметр соплового отвору, мм
Dc = 11,3
= 11,3 
= 2,85 мм
де іс - число
однакових отворів ;
Приймаю іс = 12
Після виконання розрахунку в якості
основних елементів паливної системи прийняти:
а) Паливний насос - шостиплунжерний
, блочний;
б) Паливний фільтр - 2ТФ3,
подвійний, уніфікований;
в) Паливопідкачуючий насос -
шестеренчастий.
.3.2 Масляна система
Система змащування призначена задля
подачі мастила к тертьовим поверхням деталей з цілью змащення тертя та відведення від них тепла.
Система змащування
дизеля циркуляційна, під тиском, та розбризгувачем. До нього входить
приймальний фільтр,масляний насос, масляний насос ручної прокачки, масло
розподільник,реактивний цинтріфуга, масляний фільтр, терморегулятор,
холодильник, трубопроводи та датчики.
А також до схеми системи
змащування входить:
. Місце для
відкачки та наповнення мастилом;
2. Приймальний
фільтр;
3. Редукційний
клапан в кінці масляної магістралі;
4. Фланець для
підключення трубопроводу резервного масляного насоса;
5. Масляний насос;
6. Масляний насос
ручної прокачки;
7. Гніздо для
підключення трубопроводу резервного масляного насоса;
8. Редукційний
клапан масло розподільника;
9. Маслопровід к
муфтє додаткового відбора потужності;
10. Маслопровід від
паливного насоса в картер дизеля;
11. Маслопровід к
посту управління;
12. Датчик тиску
масла до фільтру;
13. Датчик реле
температури масла до філтра;
14. Маслопровід к
паливному насосу;
15. Фільтр масляний;
16. Кран
трьохходовий масляного фільтру;
17. Масляна
магістраль;
18. Терморегулятор;
19. Датчик
температури масла після холодильника;
20. Датчик
тиску масла після холодильника;
21. Маслопровід
к підшипникам розподільного вала.
Розрахунок системи змащення
Кількість теплоти сприйманої маслом
від тертя.
Qтр = 3600 *
Ne ( 1/
м -1); кДж /год.
де 
- (0,35….0,4) - частка теплоти
прийната масла;

м = 0,9;
Ne =
324 кВт.
Qтр = 3600 *
0,35 * 324 ( 
) = 45360 кДж /год.
Розрахунок протоки масла для
відводу Qтр

= 
; 
/год.
де 
- (10…12
) - різниця t вх.
і t
вих.;

2 (кДж\кг) - теплоємкість масла;

920 кг/
;

= 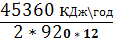
= 2,05 
/год.
Подача центрифуги, що
вмикається в якості частково потокового очищаючого пристрою.
W уср =
(0,1…0,2) 
0,205 
/год.
Подача циркуляційного
масляного насоса ,
/год
Wц.н.
= Kv *
= 1,3*2,05 = 2,665 
/год
де, Kv-
коефіцієнт запасу подачі (1,2…1,5);
Подача насоса ,що відсмоктує,

/год. Приймаємо її на 18% - 20%
більше подачі нагнітального (циркуляційного).
Wотс.
= (1,18…1,25) * Wц.н. = 1,23*5,466 = 6,72 
/год
Площа фільтруючої поверхні
фільтра грубого відчищання масла,
Fфро = 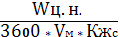
;
де, 
коефіцієнт живого перетину;

= 0,04 м/с - припустима швидкість
масла;
Fфро = 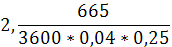
= 0,074 
Площа теплопередающєй
поверхні масло охолоджувача, 
Fм = 
* 
;

= 45 360

коефіцієнт теплопередачі = 1300 кДж
/ 
*год. к d ≥ 10
мм

- коефіцієнт забруднення
холодильника (1,2…1,3)

= 
- 
;

= 
- 
= 34,5 ºС
Fm =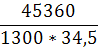
= 1,011 
Площа поверхні фільтра тонкої
очистки, 
Fфто = 
; 

= 1,5 - 2,0 
/год
Fфто = 
= 1,776 
Після виконання розрахунку
головних елементів мастильної системи прийняти:
а) Мастильний насос -
шестеренчастий;
б) Мастильний фільтр:
грубої очистки - сетчатий
подвійний;
тонкої очистки - реактивна
центрифуга; продуктивністю 600 л/год при тиску 6 кгс/с
, 6000 об/хв. та tº- 70ºС
.3.3 Система охолодження
Система охолодження призначена для
зниження температурного рівня деталей, нагрівающіхся від
згорання палива та від тертя, відвід тепла робочих жидкостей та наддувочного
воздуха.
До системи охолодження
входить:
1. Запорні крани муфтові;
. Пароотвід;
. Запорний кран;
. Терморегулятор;
. Підключення системи
підігріва;
. Холодильник наддувочного
воздуха :
І. Насос заборної води;
ІІ. Насос пресної води;
ІІІ. Розширітельний бачок;
ІV.
Водомасло холодильник
V Компрессор
А - кран троьхходовий
а) Заборна вода
Розрахунок системи охолодження
Контур прісної води
Кількість теплоти що відводиться
прісною водою.
Q n.
= 
n.
*ge *Ne*
; кДж /год.
де 
n.
=0,12 - частка теплоти відводиться
прісною водою;
ge
=0,215 кг/кВт - год. - питома витрата палива;
Ne =
324 кВт -ефективна потужність;

= 42700 - низька теплота згорання.
Q n.
= 0,12 *0,215
* 324*42700 = 356937,84 кДж/год.
Подача циркуляційного насоса
прісної води
W n.
=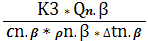
; 
/год
де, 
- коефіцієнт запасу ( 1,2…1,4)

- 4,2 - теплоємність прісної води
кДж/кг

- 1000 кг/
- щільність води;

= t вых.- t вх.
- перепад температур 5-8
W = 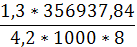
= 13,8 
/год
Площа теплопередающій поверхні
водо водяного холодильника
Fввх = 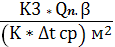
; 
де, 
- коефіцієнт теплопередачі при
трубах із d
10 мм

температурний перепад.

= 0,5 ( 
+ 
) - 0,5 (
+ 
)

- 75 
; 
= 85 
;

= 42 

= 32 

= 05 (85 +75) - 05 (32 + 42) = 45 
;
Fввх = 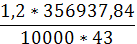
= 0,99 
Після виконання розрахунку в
якості головних елементів системи охолодження прийняти :
а) Насос пресної води -
вихрівой ;
б) Насос проточної води
(забортної) - вихрівой, самовсасиваючий.
в) Водоводяний холодильник
трубчатий.
2.3.4 Система пускового
повітря
Пускове повітря потрібно для
запуску двигуна.
Функція:
Балон пускового повітря
повинний бути заповнений,запірний клапан відкритий.
Клапан блокування пуску
повинний знаходитися в стані, зазначеному на креслені. На двигунах, обладнаних
електронною системою контролю і керування, реле тиску забезпечує проходження
сигналу: (ГОТОВИЙ ДО ПУСКУ).
При спрацюванні пускового
клапана 3 (від ручного чи дистанційного керування) по одному ланцюзі
відбувається подача пускового повітря на розподільник , керуючий пусковими
клапанами у голівках циліндрів; а по іншому ланцюзі пускового повітря проходить
у трубопровід 1, що направляє його до голівок циліндрів.
Розрахунок системи стиснутого
повітря
Розрахунок пускового клапана із
пневматичним керуванням.
Мінімальна тривалість пускового
клапана, що забезпечує беззупиннє послідовне надходження в усі циліндри, у
градусах кута повороту КВ повинна складати у дизелів чотиритактних.

= 
де, і = 6 - число циліндрів

= 
= 120
Кут випередження відкриття пускового
клапана Q
on в середньо обертових
дизелів складає:
Q on
S… 10
до ВМТ
Визначення основних розмірів
пускового клапана:
діаметр прохідного перетину
клапана, мм
D 2
= ( 0,06…0,16) D
де D
- діаметр циліндра
D 2
= 0,1 * 180 - 18,0 мм
діаметр тарілки клапана, мм
D 1 = (1,1…1,15)
D2
D 1 = 1,1
* 18,0 = 19,8 мм
діаметр розвантажувального
поршня, мм
D 3 = (0,9…1,0) D
2
D 3 = 0,95 * 18,0 =
17,1 мм
діаметр стрижня клапана, мм
d = (0,4 …0,7) D
2
d = 0,6 * 18,0 =
10,8 мм
діаметр
пневматичного поршня, мм
D 5 = (1,1…1,4) D
2 ; мм
D 5 = 1,1 *18 = 19,8
мм
хід клапана, мм
h = (0,2…0,3)
D 2
h= 0,25*18 = 4,5 мм
товщина тарілки клапана, мм

= (0,22…0,28) D
2

= 0,25 *18 = 4,5 мм
- кут конуса тарілки клапана,
град

= 30
… 45
вибіраю 45
діаметр корпуса клапана, мм
D 6 = (1,5…1,8) D
2
D 6 = 1,7*1,8 =30,6
мм
діаметр
золотника пускового розподільника, мм
d 3= (0,45…0,5) D
2
d 3= 0,5*18 = 9 мм
хід
золотника, мм
h 3 = (0,8…0,85) d
3
h 3 = 0,8 *9 =7,2 мм
Після виконання розрахунку в якості
головних елементів системи стиснутого повітря прийняти:
Фази газорозподілу всасиваючих клапанов,
град:
відкриття до В.М.Т. -- 55-60 град;
закриття до Н.М.Т. - 25-60 град;
Вихлопні клапана, град:
відкриття до В.М.Т. -- 40-45 град;
закриття до Н.М.Т. - 55-60 град;
.
Розробка конструкції поршня
.1 Опис конструкції поршня
Поршень можна розділити на три
частини, що виконують різні функції: днище, ущільнююча частина і спрямовуюча
частина (спідниця). Днище і ущільнююча частину утворюють головку поршня.
Днище поршня, що утворить з головкою
циліндра камеру згоряння, закінчується біля верхньої кромки канавки під верхнє
поршневе кільце. Цю частину поршня іноді називають жаровим поясом. Форма днища
поршня залежить від форми камери згоряння і розташування клапанів, а в
двотактних двигунах також від системи газорозподілу.
При увігнутому днище форма камери
згоряння наближається до сферичної (при верхньому розташуванні клапанів),
збільшується поверхня, що омивається гарячими газами, і зростає можливість
утворення нагару, при якому різко підвищується тепловий режим. Міцність
увігнутого днища менше, ніж плоского, тому в ряді випадків його підсилюють.
Обробка такого днища також скрутна.
Опукле днище надає камері згоряння
щелевидну форму , що погіршує процес сумішоутворення. Основною перевагою такого
днища є зменшення маси поршня через велику міцності днища і відсутності
підсилюють ребер.
Плоске днище є проміжним за своїми
показниками між двома першими і має найбільше поширення в карбюраторних
двигунах.
У деяких двигунах поршні мають так
звані витискувачі, які сприяють в процесі стиснення досягненню бажаного напрямку
руху заряду, а в процесі згоряння - здійсненню плавного наростання тиску.
У дизелів днище поршня має
різноманітні і в ряді випадків складні форми, що залежать від ступеня
стиснення, способу сумішоутворення, розташування форсунок та інших факторів. Так,
в дизелі з однополостной камерою згоряння днище надає камері згоряння
сприятливу форму. Для збільшення швидкості вихору і поліпшення сумішоутворення
камеру згоряння розташовують у днище поршня. Для підвищення міцності днища
поршня і кращого відведення теплоти з внутрішньої сторони воно має ребра ,
форма яких визначається дослідним шляхом.
Розміри днища поршня вибирають,
виходячи з максимального тиску згоряння , необхідної жорсткості поршня і
максимальної інтенсивності відводу від нього теплоти. Як правило, переходи від
днища поршня до його ущільнюючої частини в площині бобишек роблять масивними у
вигляді суцільних припливів або ребер. З внутрішньої сторони днища теплота від
нього відводиться повітрям і маслом. Наявність ребер не покращує
тепловідведення від днища.
У дизелях, де в днище поршня
розташовується камера згоряння, застосовують примусове охолодження днища шляхом
обприскування його внутрішній поверхні маслом. Для цього масло підводиться
безпосередньо від колінчастого вала по каналу в стержні шатуна до розпилювача з
отвором, що калібрується, розташованому в поршневий головці шатуна, або
розпилюється через нерухомі форсунки , закріпленні у нижній частині гільзи.
Ущільнююча частина поршня
починається від верхньої кромки канавки під верхнє поршневе кільце і кінчається
у нижньої кромки канавки під нижнє поршневі кільця (останнє кільце перед
поршневим пальцем), тобто це та частина поршня , де розташовані канавки для
поршневих кілець.
Ущільнююча частина має діаметр , що
збільшується до низу поршня. Вона передає стінок циліндра до 80 % теплоти , яка
сприймається днищем.
Практично ущільнююча частина поршня
майже не бере участь у передачі бічних сил. Поверхня цій частині поршня має
канавки, внаслідок чого неможливо створити стійку масляну плівку. Величину
зазору між циліндром і ущільнюючої частиною поршня вибирають з умови
запобігання поршневих кілець від впливу гарячих газів і запобігання попаданню
масла в камеру згоряння. Як правило, цей зазор роблять дуже малим (близьким до
нуля). Число компресійних кілець встановлюють залежно від швидкохідності і типу
двигуна.
Для зменшення теплової напруженості
верхнього поршневого кільця канавку під нього слід робити на деякій відстані
від днища поршня , при цьому збільшується висота поршня. У деяких випадках
перед першим поршневим кільцем роблять виточку, яка є повітряним екраном.
Досвід роботи з такими поршнями показав, що ця виточка закоксовується і вплив
її на роботу першого кільця зменшується. Для ущільнення циліндра швидкохідного
двигуна достатньо двох - трьох компресійних і одного або двох маслоз'ємних
поршневих кілець. Більшість двигунів має одне маслоз'ємнє поршневі кільця
(нижнє) для скидання надлишків масла.
У канавках для маслоз'ємних кілець
свердлять один або два ряди отворів для відведення масла всередину поршня. У
випадку двох рядів отворів один ряд свердлять в самій канавці, а інший -
безпосередньо під нею. Діаметр отворів для відведення масла майже збігається з
висотою канавки для масляного кільця. У порушених карбюраторних двигунів
поперечні прорізи, що відокремлюють ущільнюючий пояс, роблять зазвичай в
канавці масло- знімного кільця.
Відведення надлишків олії необхідний
через насосного дії кілець і перепаду тисків при впуску, коли масло поступово
подається до камери згоряння , де воно згоряє і утворює нагар на стінках камери
згоряння і на свічці запалювання. Це відбувається особливо інтенсивно при
зношених поршневих кільцях.
Напрямною частиною називається
частина поршня від нижньої кромки канавки під останнє поршневі кільця перед
поршневим пальцем до кінця поршня. Ця частина поршня служить для рівномірного
розподілення бокового тиску на дзеркало циліндра від сили Vjj, спрямованої по
нормалі до дзеркала циліндра, а також для направлення поршня при русі
співвісний циліндру. У цій частині поршня розміщуються бобишки для поршневого
пальця. Конструкції поршнів нових вітчизняних карбюраторних двигунів
характеризуються такими особливостями : днище - плоске зовні і гладке (без
ребер) всередині; спідниця поршня без розрізів має кільцеву термо регулірующую
вставку; в горизонтальній площині перетин спідниці - овал , по висоті вона має
конічну або бочкоподібну поверхню ; теплові прорізи розташовані в канавці
маслоз'ємного кільця; кожна бобишка поршневого пальця пов'язана з днищем поршня
двома ребрами.
3.2 Розрахунок поршня на міцність
Моменти, згинаючі пластини на
відстані Х від центра.
у тангенціальному напрямку
М1 = 
(
(1+µ)- 
(3+µ));
у радіальному напрямку
Mr = 
(
(1+µ)- 
(1+3µ));
де, r
= 0,085 м - внутрішній радіус днища
µ = 0,3 - коефіцієнт Пуансона для
чавуна.
При х=r
(забитий контур)
М1 = 
= 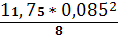
= 0,0106 МН*м
Mr = µ
= 0,3
= 0,00318 МН*м
Для центра днища Х=0,
тому
Мt = Mr = 
(1+M) = 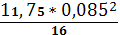
(1+0,3) = 0,007 МН*м
Найбільша напруга на
контурі днища
у тангенціальному напрямку
(
= 
* 
=
* 
Pz
у радіальному напрямку
(
=
µ *
* 
= 
* 
Pz
-у центрі
днища

= 
(1+µ) 
де,
= 0,043М - товщина днища
тоді


* 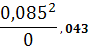
* 11,75 = 34,435 МПа


* 0,3 * 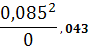
* 11,75 = 10,33 МПа


( 1+ 0,3) * 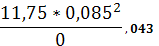
* 11,75 = 11,31 МПа

= 
Pz = 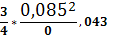
* 11,74 = 34,435
Припустима еквівалентна напруга для
чавуна

= 34,435
Найбільший прогин у центрі
днища х= 0,4, рівномірні навантаження
(Pz = const)


* 
= 
де, D - твердість
круглої пластини (МН *
)
D = 
де, Е = 1,0*
МПа модуль Юнеа для чавуна
тоді

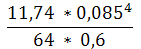
= 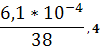
= 1,6 *
(Н)
Теплове навантаження днища
поршня з охолодженням можуть бути визначені по формулі :
q = A*a * 
* 
де, А = 16 * 
- для 4-х такт них дизелів;
а = 15% - відносна
тепловіддача;

- охолоджувана поверхня робочого
циклу, 

n - 
+ 
де,
n
0,8 -
частка активної
поверхні охолодження
поршня;

0,7 - частка активної поверхні
охолодження кришки;
Е - 12,5 - ступінь стиску;
S -
0,22 м - хід поршня;

* 
+3,14*0,8*0,22 * 
= 0,347 
Сm - середня
швидкість поршня;
Сm = 
= 
= 5,5 м/с
Pі =
1,85 МПа - середній індикаторний тиск;
Ŋі = 0,47 - індикаторний
КПД;
q =
16*
* 15 * 
* 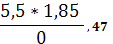
= 0,485 * 
кДж
Осьовий перепад температур
між зовнішньою (нагріва газами) і внутрішньої
(охолоджуваною) масла, поверхнями днища
∆t = 
де 
= 45 (кДж/
град) - коефіцієнт теплопровідості
матеріалу.
∆t =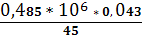
= 46,34
При твердому закладені днища
по контурі радіальні напруги 
rt і тангенцільні
напруги 
tт від
осьового перепаду температур ∆t постійні і
чисельно дорівнює :

= 
) * 
де,
= 1,07 * 
- коефіцієнт лінійного розширення.


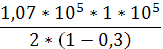
*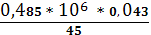
= 354 МПа
Еквівалентні сумарні механічні і
теплові напруги визначають по узагальненій теорії міцності.

= 
(1+µ) * 
+ 

= 
(1+0,3) 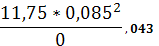
+ 354 = 354, 96 МПа
Припустимі еквівалентні
сумарні напруги для чавуна становлять 
]= 200…400,
тому що 
= 354,96 < 
]
4. Технологічний процес
виготовлення втулки
.1 Технологічний маршрут обробки
втулки
Короткий опис монтируємого
механізму, вузлів його кріплення і фундаменту.
Суднові дизеля призначені для роботи
на суднах всіх класів , типів і призначення. Дізель 6ЧН 18 \ 22 являє собою
встановлені на загальній рамі дизель, генератор, маслопрокачівающій агрегат,
фільтри тонкого очищення масла, охолоджувачі масла і внутрішнього контуру
охолодження дизеля, з'єднані між собою трубопроводами. Агрегати виготовляються
на базі сучасних і оригінальних дизелів як російського, так і зарубіжного
виробництва. Можуть бути застосовані всі системи охолодження , дозволені
класифікаційними спільнотами: двох контурна з теплообмінником для забортної
води; радіаторна, і на вимогу - повітряна. Вхідний до агрегат генератор -
STAMFORD, синхронного типу, з бесщеточной системою збудження, антиконденсатним
підігрівом. На вимогу генератори можуть комплектуватися датчиками температури в
обмотках . Також дизеля можуть бути автоматизовані за будь-якого ступеня
автоматизації та забезпечення синхронізації для роботи в паралель.
Електросистема 2 - полюсна ізолірованнаяс напругою 24 В або 12 В. Паливна
система з подвійними стінками трубопроводів високого тиску з системою
моніторингу витоку або без неї. Перемикані (подвійні) фільтри палива і масла.
Автоматика мікропроцесорного типу. В залежності від проекту або технічних вимог
встановлюються додаткові щити управління і (або) щити контролю для
дистанційного керування. На вимогу встановлюється гидромеханічний або
електронний регулятор швидкості для підтримки необхідної частоти обертання.
Пуск дизеля на вимогу може бути електростартерний або повітряний. Виконання і
комплектація агрегатів залежить від особливостей проекту і строго обмовляється
технічної специфікацією. Документація російською мовою. Сертифікати Російського
Морського Регістру Судноплавства, Російського Річкового Регістру.
Технічні характеристики :
Двигун - 6ЧН 18 / 22
Номінальна потужність - 224кВт ;
Частота обертання - 750 об / хв .
Довжина - 5557 мм
Ширина - 1347 мм
Висота - 2074 мм
Маса - 13100 кг
Дизель встановлюється на фундамент,
що представляє собою жест кую конструкцію з отворами під кріплення механізму,
виконану з пластмаси. Дизель установлюється на 36 опорних арочних амортизаторах
типу А- 500.
Рис. 1. Загальний вигляд
амортизатора типу А-500: 1 - плита; 2 - гумовий масив; 3 - основа
Рис. 2. Загальний вигляд вузла кріплення
1 - прокладка; 2,7 - амортизатори; 3 - прокладка
зі сплаву АМГ; 4 - шайба вирівнюю-щая; 5 - дизель-генератор; 6 - рама; 8 -
втулка; 9,12 - прокладка з тиоколовой стрічки; 10 - шайба оцинкована; 11 -
фундамент пластмасовий; 13 - заземлення.
.2 Аналіз способів монтажу,
застосовуваних для здійснення монтажу заданого механізму
Існує кілька способів монтажу
дизелів. Принципова відмінність між ними в тому , що застосовуючи один з них -
спочатку за шаблоном необхідно поставити амортизатори на фундамент, другий -
спочатку поставити амортизатори на двигун. Далі виробляється центровка,
встановлюються прокладки і виконуються інші необхідні операції.
Для монтажу даного дизеля обраний
перший з перерахованих вище способів .
Технологія монтажу дизеля
відрізняється від інших механізмів тим , що в процесі монтажу необхідно
збенитка якість укладання колінчастого вала двигуна, досягнуте при складанні на
стенді заводу - виготовлювача. Установка механізмів на фундаменти із пластмас
включає, крім загальних монтажних операцій, заформовку в полки фундаменту
металевіських східчастих елементів, які входять у вузол кріплення. До початку
монтажу фундаментні балки повинні бути повністю пріформовани до обшивки і на
бору корпусу судна. Опорні й наполегливо-страхувальні амортизатори кріплять до
шаблону, погодженим з опорною поверхнею рами дизеля. За амортизаторам шаблону
розмічають у фундаментних балках отвори для установки металевих східчастих
елементів. У полках фундаменту по розмітці сверлят отвори. Поверхні фундаменту,
на які будуть склопластик, зачищають шнуровальними машинами до шару
скловолокнистого наповнювача. Склотканина розікраливають і пробивають в ній
отвори для установки металевіських елементів. На зачищені поверхні фундаменту
установлюють металеві елементи, передньорасконсер вировано і знежирені, і на
елементи послідовно наформовивають склопластик. По закінченні періоду
полімеризації смоли опорну поверхність фундаменту обробляють так, щоб
забезпечити щільне прилягання амортизаторів до фундаменту.
Шаблон з амортизаторами знову
встановлюють на фундамент і в заформованими металевих елементах розмічають
отвори під болти кріплення амортизаторів. У металевіських елементах по розмітці
свердлять отвори , через які тимчасово кріплять амортизатори до фундаменту.
Поверхні еле- ментів під головки болтів підрізають таким чином , щоб при
затягнутому болті щуп товщиною 0,05 мм не проходив під головку болта , а шайби
всією поверхнею прилягали до елементів і фундаменту. Якщо елементи виготовлені
з алюмінієво - магнієвого сплава, то між сполучаються поверхнями встановлюють
прокладки з тиоколовой стрічки. Дизель - генератор встановлюють на фундамент на
віджимних болтах і орієнтують по отворах амортизаторів і відносно
горизонтальної площини. У такому положенні провірячи раскепов колінчастого вала
двигуна і співвісність валів двигуна і генератора. Після цього визначають
товщину прокладок і вирівнюючих шайб між амортизаторами і рамою дизеля. Прокладки
з алюмінієво-магнієвого сплаву після обробки для захисту від корозії оксидируют
електрохімічним способом. Прокладки і шайби встановлюють на свої місця і дизель
- генератор остаточно кріплять до амортизаторам . Заземлення рами дизель -
генератора виконують за допомогою мідної шини довжиною 4 м , яку підключають до
металевого чи сту , при формованному із зовнішнього боку корпусу судна.
Співвісність валів відновлюють шляхом перемедомлення на рамі генератора і
підгонкою прокладок між генератором і рамою.
4.3 Правила приймання та методи
контролю
В процесі монтажу контроль
здійснюють майстри і контролери бюро технічного контролю (БТК) цеху. Контроль
ділиться на поопераційний і остаточний. При поопераційній контролі перевіряють
якість обробки фундаменту і щільність пригону компенсуючих ланок, підготовку
від отворів під призонні болти, постановку цих болтів та інші операції , які не
можна перевірити після остаточного кріплення механізму. Працівники БТК
оформляють акт приймання механізма, в якому наводять результати контролю,
номера механізма і пускорегулюючої апаратури. Ці дані за - носять у формуляр
кожного механізму .
Якість остаточного монтажу
визначають:
Правильне положення механізмів на
судні ;
Відповідність кріплення механізму до
фундаменту требованіям креслення;
Відсутність деформацій механізму в
статичному состоянніі ;
Рівень вібрацій механізму в дії.
Перевірку роботи механізмів у
взаємодії з обслуговуючого трубопроводами, арматурою і іншим судновим
оборудованіем виробляють в період швартовних і ходових випробувань судна.
Перевірка правильності положення механізма на судні. Після остаточної установки
координати механізму повинні відповідати вимогам монтажного креслення або
альбому вузлів кріплення, а також вимогам галузевою нормалі на монтаж допоміжних
механізмів. Правильне положення механізму залежить від а) точності суміщення
ориентируючих елементів механізму і фундамента, б) ступеня вертикальності або
горизонтальності расположенні механізмів і в) величини зазорів між механізмом,
судновими конструкціями і сусіднім судновим оборудованням.
Контроль якості кріплення механізму.
Суднові механізми не є абсолютно
жорсткими. У процесі транспортно-навантажувальних і монтажних операцій,
особливо при неправильному кріпленні , виникають деформації механізмів , що
негативно позначається на їх експлуатаційної надійності. Для попередження
деформацій вузли кріплення і підгонка компенсуючих ланок повинні ретельно
контролюватися.
Якість кріплення механізму
характеризується :
Точністю пригону компенсуючих ланок
;
Величиною частини болта, виступаючої
над гайкою;
Надійністю і рівномірністю затяжки
фундаментних болтів;
Відсутністю помітного зминання
граней остаточно закріплених гайок і болтів ; наявністю стопорних засобів і
перемичок заземлення.
Контроль відсутності деформацій
механізмів
Монтаж механізмів повинен
виконуватися з мінімальними деформаціями, в іншому випадку в деталях і вузлах
можуть виникнути неприпустимі напруги. В даний час поки не представляється
можливим виміряти з достатньою точністю монтажні напруги безпосередньо в
цехових і суднових умовах. Замість визначення напружень вдаються до контролю
деформацій, величини яких обмежують визначеними допусками. Завжди прагнуть
контролювати найбільш відповідальні вузли, несправності яких впливають
безпосередньо на експлуатаційну надійність механізмів.
Для контролю деформацій
використовують наступні параметри:
Соосностьвалов сполучених механізмів
;
( Прямолінійність колінчастого вала
двигуна внутрішнього згоряння;
Якість сполучень ' пари шийка валу -
підшипник ;
Якість зубчастих зачеплень .
Контроль наведених параметрів
вимагає часткової розборки механізмів,
що небажано в суднових умовах.
Представляють інтерес методи
контролю деформацій без розбирання механізмів, наприклад шляхом вимірювання
площинності верхньої поверхні загальною фундаментної рами агрегату. Покатування
впровадження цього методу контролю при монтажі турбогенераторів показала, що
зважаючи на наявність зазорів в підшипниках і відсутності контролю
прямолінійності рами в горизонтальної площині практично не досягається
пропорційна залежність між деформаціями рами і співвісністю валів механізмів
агрегату, встановлених на рамі.
Контроль неплощинності відрізняється
трудомісткими измеренями при тривалих регулювальних роботах, які не
забезпечують повторюваність стендової збірки агрегату в случай монтажу на
судні. Контроль тільки неплощинності рами агрегату існуючими засобами
вимірювань недостатній. Цей метод контролю при монтажі може тільки
способствувати зменшенню расцентровок механізмів на судні, але зовсім не виключає
їх. Більш ефективний метод контролю деформацій рами по фактичні навантажень на
опорну поверхню фундаменту від ваги агрегату, який успішно впроваджується при
монтажі крупногабарітних механізмів.
Методи контролю з частковим
розбиранням агрегату
Контроль співвісності валів.
Неспіввісність валів - несовпадання їх геометричних осей характеризується двома
величинами: паралельним зміщенням осей С (в міліметрах) і зламом осей валів ф -
кутовим розкриттям фланців (у міліметрах, віднесених до 1 пог. М діаметра муфти).
При центрування валів один з механізмів беруть за базовий , який неподвдружин,
а другий механізм переміщують віджимними приспособленями до збігу осей валів
обох механізмів .
Неспіввісність валів визначають у
вертикальній і горизонтальних площинах. При визначенні зсувів і ізломів
базовими служать торцеві і циліндричні поверхні фланців, які повинні бути
ретельно оброблені. Оснастка, яку застосовують три центрування валів, залежить
від діаметра фланців, конструкції муфти та допуску на неспіввісність валів. При
діаметрі фланців більше 200 мм застосовують лекальні лінійку 1 і щуп, вимір
якими відрізняється простотою, але менш точно, ніж за стрілами. Центруемий
хутранізм переміщують віджимними пристосуваннями до базового, щоб осьової зазор
між напівмуфтами пружної муфти з = 4мм. При вимірі, наприклад, у вертикальній
площині на одну з напівмуфт накладають лінійку ребром і визначатьь щупом зазор
між ребром лінійки і другий напівмуфтою. Без повороту фланців аналогічно
вимірюють зазор между лінійкою і перший напівмуфтою. Зсув валів в вертикальної
площині дорівнює середній величині зазорів:
Аналогічно зміщення валів у
горизонтальній площині
Рис. 3. Центрування валів механізмів
за допомогою лінійки і щупа
Для визначення злому осей щупом
вимірюють розкриття фланців і по різниці осьових зазорів між торцями напівмуфт,
віднесеної до діаметру муфти, обчислюють величину зламу валів.
Злам осей валів у вертикальній
площині
Діаметр муфт, застосовуваних для
з'єднання валів вспомогательних механізмів, становить від 100 до 180 мм, а
конструкція муфт не завжди дозволяє використовувати лінійку і щуп. При діаметрі
муфт менше 200 мм використовують стріли (рис. 3) з мікрометричними гвинтами,
які бугелями 2 кріплять до ведущій і веденої напівмуфти. Зазвичай встановлюють
дві пари стріл і II , що збільшує кількість вимірювань і підвищує точність
середніх величин , отримуваних під час центрування. При визначенні зміщення
валів вимірюють зазори zi, а при зламі - зазори хi. Кожен із зазорів вимірюють
щупом два рази: у вихідному положенні і (після повороту на 180 ° спільно
базової та центруемого валів).
Для зниження трудомісткості
вимірювань і отримання більш об'єктивних результатів контролю замість
мікрометричних гвинтів і щупа зміна зазорів визначають за індикаторами.
5. Охорона праці
Правовою основою законодавства щодо
охорони праці є Конституція України, Закон України : « Про охорону здоров´я»
, «Про пожежну безпеку», «Про використання ядерної енергії і радіаційний
захист», « Про забезпечення санітарно - епідеміологічного благополуччя
населення», а також Кодекс законів про працю України.
жовтня 1992 року Верховна Рада
України прийняла Закон « Про охорону праці». Цей закон визначає основні
положення по реалізації конституційного права громадян на охорону їхнього життя
і здоров´я
в процесі трудової діяльності, регулює при участі відповідних державних органів
відносини між власником підприємства, установи й організації або уповноваженим
їм органом і працівником з питань безпеки, гігієни праці і виробничого
середовища і встановлює єдиний порядок організації охорони праці в Україні.
Специфічною особливістю українського
закону ,що регламентує правову основу охорони праці, є високий рівень прав і
гарантій працівникам. До позитивних моментів Закону України « Про охорону
праці» безперечно належить закріплення за державою функцій управління і нагляду
за охороною праці. Умови праці на флоті багато багато в чому залежать від
правильної організації роботи плавскладу і від дотримання правил і інструкції з
безпечного ведення робіт. Неухильно підвищує рівень технічної оснащеності
морських судів, що вимагає всебічного удосконалювання організації праці на
флоті.
За стан техніки безпеки на судні
відповідає капітан. Усі заходи щодо охорони праці на судні він проводить
особисто через своїх помічників, що відповідають за безпечне проведення робіт,
відповідно Статуту Служби на судні. Нагляд за безпекою праці на морських судах
здійснюється безупинно протягом усього часу проведення робіт. Він містить у
собі : нагляд за дотриманням робітниками вказівок технічної документації і
виконанням ними правил техніки безпеки, застосуванням безпечних прийомів роботи
і використанням захисних засобів.
5.1 Аналіз потенційно небезпечних і
шкідливих факторів при експлуатації ДВЗ
При роботі дизель - генератора
виникають наступні небезпечні і шкідливі фактори: незахищені механізми і елементи,
які постійно рухаються; шум і вібрація; судина, що працюють під тиском;
виділення шкідливих речовин; теплове випромінювання; пожежна небезпека;
можливість поразки електричним струмом; недостанє освітлення.
.1.1 Механізми, які рухаються і
елементи двигуна
Елементи, що рухаються, формують
навколо себе небезпечну зону, у якій можливе захоплення одягу обслуговуючого
персоналу, у результаті того виникають важкі травми.
До даних механізмів належать
наступні вимоги Правил Регістра [20].
устаткування стаціонарними
огородженнями, обертових і
частин, що рухаються, у виді
кожухів, кришок із суцільного металу або сіток;
постачання блокувальними пристроями
механічного тпу, а у випадку застосування електропривода-пристроями
електричного типу, що припиняють роботу механізму при відкритих огородженнях
або завищених експлуатаційних параметрах;
постачання запобіжними пристроями,
які попереджають вихід на аварійний режим.
Небезпечні зони повинні
забезпечуватися покажчика, табличками, сигнальним розцвіченням, плакатами.
Забороняється робити виправлення дефектів на частинах, які рухаються.
5.1.2 Захист від шуму та вібрації
Рівень шуму - один з найважливіших
показників суднової дизельної установки, що повинний відповідати вимогам
Санітарних правил для морських судів [21].
У суднових дизелів
рівні
шуму перевищують найбільші
значення, що рекомендується
Морським Регістром (не вище 100 дб на відстані 1 м до двигуна), а тим більше
санітарну норму 95 дб. Передача шуму від двигуна відбувається або на корпусі
судна (у виді вібрацій). Тому заходи що до зниження рівня шуму повинні носити
комплексний характер і включати:
зниження основних джерел в цілому
або окремих його вузлах від машинного відділення;
зниження основних джерел шуму самого
двигуна;
звукоізоляцію машинного відділення;
Основні заходи що до зниження
повітряного шуму [4]:
установка ефективних глушителів
на впуску повітря і
випуску газів, що відробили;
у газотурбонагревателів -
застосовування без лопаткових дифузорів, а у лопаткових дифузорів - підбір
оптимальноного числа лопаток.
застосування малошумних камер
згорання;
зниження максимального тиску
згорання.
Основні заходи щодо зниження рівня
шуму механічного походження:
можливе зменшення діаметрального
зазору в поршнях тонкових двигунів;
введення гідравлічних штовхальників
або буферів у клапано-розподільний механізм;
усунення вібрації дизеля, викликаної
неврівноваженими силами і моментами, а також недостатньою твердістю кістяка;
усунення шуму передатних шестірень і
зубчастих коліс, викликаного конструктивними або технологічними причинами;
облицювання вібро поглинаючими
покриттями поверхні катера корпусів нагнітачів, кожухів передач;
капотування дизелів швидкохідного
типу.
Комплексні заходи щодо установки в
цілому:
покриття звукоізолюючими і
звуковбирними матеріалами стін МО;
установка двигуна на віброізолюючих
пристроях;
розміщення двигуна в звукоізолюючому
відсіку з виводом систем управління і контролю до центрального поста;
установка в МО звукоізольованих
кабін.
.1.3 Безпека посудин, що працюють
під тиском
Посудини, які знаходяться під
тиском, можуть викликати серйозні руйнування. Причинами аварій можуть бути:
відсутність або несправність запобіжних клапанів чи редукторів, дефекти при
виготовленні, монтажі і ремонті судів, зносі стінок посудин.
Відповідно до Правил Морського
Регістра, посудини, що працюють під тиском, повинні відповідати наступним
вимогам [20].
- корпуса посудин повинні мати
надійні кріплення до фундаменту;
кожна посудина повинна мати пристрій
продування;
отвори для люків повинні бути тільки
стиковими;
зварені шви посудин повинні бути
тільки стиковими;
міцність фланців, болтів стінок,
зварених швів повинна бути підтверджена розрахунком;
падіння тиску при іспиті на міцність
не повинне перевищувати 0,3…0…0,5% протягом однієї години;
тиск при іспиті на міцність для
сталевих посудин складає :
Р ісn
= 1,5 Р при Р ≤ 0,5 МПа;
Р ісn
= 1,25 Р при Р > 0,5 МПа;
посудини, що працюють під тиском,
встановлюють у місцях, які виключають скупчення людей.
Перед експлуатацією посудини ці
місця повинні бути технічно оглянуті інструктором Морського Регістра.
.1.4 Шкідливі речовини
При роботі дизель-генератора
виділяються шкідливі і токсичні речовини.
Повітряне середовище
Дизель-генераторної повинне контролюватися наступними нормативними актами:
Регістра [16];
Метрологічне забезпечення
в галузі безпеки праці; Методичні
вказівки за контролем повітряного середовища на судах [22],
Санітарними правилами для морських судів [21].
- окис виглецю , 
/
20
окис азоту, 
/
5
бензол, 
/
5
пари свинцю, 
/
0,01
Для підтримання
гранично-припустимих концентрацій шкідливих речовин у дизель-генераторної
використовується система вентиляції.
.1.5 Теплове випромінювання
Нагріті поверхні головного
двигуна є джерелом теплового випромінювання 300…500 Вт/ 
. Для захисту обслуговуючого
персоналу від впливу теплових випромінювань застосовують герметизацію і
теплоізоляцію механізмів, машин, трубопроводів.
.1.6 Пожежна безпека
Пожежі в дизель генераторі
можуть виникнути при порушенні збереження ГЗМ, несправностях газоходу,
скупченнях палива й масла під настилом, вибухах несправностях
електроустаткування. Для запобігання пожеж необхідно дотримувати вимог Регістру
[16],
Посібник із проведення пожежно-профілактичної роботи на судах, а також вимог
Морського Регістра.
Конструктивне рішення захисту
від пожежі-застосування вогнестійких матеріалів і розподіл судна на
протипожежні зони, наявність об`ємно-хімічних і повітряно-пінних систем і
засобів пожежогасіння.
установлення сигналізації
виявлення пожежі;
наявність аварійного виходу з
дизель-генераторної;
автономна система вентиляцій
в дизель-генераторної;
наявність повітряних труб із
запобіжними сітками і поплавками камерами в цистернах палива й масла.
Виходи повітряних труб
розташовані в місцях, які виключають скупчення нафтопродуктів і їхніх пар.
5.2 Розрахунок штучного освітлення
Для розрахунку штучного освітлення в
машинному відділенні використовуємо метод світлового потоку, призначений для
визначення загального рівномірного освітлення горизонтальних поверхонь.
За даним методом визначаються
світловий потік , потужність ламп, а також кількість світильників, необхідних
для забезпечення заданої освітленості.
Світловий потік ламп визначається по
формулі:
Фл = 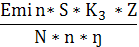
лм,
де, 
min - рівень
мінімальної освітленості по нрмах, ПК;
S -
освітлювана площа приміщення, 
;

- коефіцієнт запасу, що враховує
експлуатаційне зниження освітленості;

- коефіцієнт мінімальної
освітленості;
N -
кількість світильників;
n- кількість
ламп у світильнику;
ŋ -
коефіцієнт використання світлового потоку.
Коефіцієнт використання
світлового потоку ŋ залежить від типу світильників, коефіцієнтів
відображення стелі - qn, cтін
- qc,
розрахункової поверхні або статі - qp- і індексу
приміщення - і.
Індекс приміщення визначають
по формулі:
І =
де, А-
довжина приміщення, м;
В- ширина приміщення, м ;
h - висота
підвісу світильників над освітлюваною поверхнею, м
Розрахуємо освітлювальну установку
машинного відділення судна, що має розміри: довжина А= 7,5 м, ширина В= 9,3м,
висота Н= 3м.
Визначаємо площу МО:
S= A * В =7,5 *
9,3 = 69,75 
Вибираємо
систему загального рівномірного висвітлення з
люмінесцентними лампами.
Вибираємо світильник типу СС-755 з
чотирма лампами ЛБ 15.
Визначаємо індекс приміщення,
прийнявши h-H
= 3м :
І = 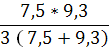
= 1,38
Визначаємо коефіцієнт
використання світлового потоку по наступним параметра: 
= 70 %, 
= 50 %, 
= 30 %, i = 1,38. Він
дорівнює ŋ= 0,42
Вибираємо 
= 1, 3.
Мінімальна освітленість МО
складає Е min =
150 лк.
Визначаємо світловий потік
лампи ЛБ 15, що дорівнює ФЛ= 750 лк.
Коефіцієнт мінімальної
освітленості для люмінесцентних ламп приймається
Z
= 1,1.
Визначаємо необхідну кількість
світильників;
N = 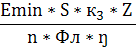
N = 
Приймаємо
для установки 12 світильників
типу СС= 755.
Таким чином можна зробити наступні
висновки: проаналізовані небезпечні і шкідливі фактори при експлуатації ДВЗ,
розроблені заходи що до їх усунення; зроблений розрахунок штучного освітлення,
за результатами якого визначені тип і кількість світильників, що забезпечують
освітленість у МО відповідно до вимог Морського Регістра.
5.3 Охорона навколишнього середовища
Питання охорони навколишнього
середовища останнім часом висунулося в число найважливіших.
Екологічна безпека поряд з
ефективним функціонуванням засобів захисту навколишнього середовища
забезпечується правовим, економічними і соціальними факторами.
Основними законодавчими актами,
спрямованими на забезпечення екологічної безпеки, є :
«Закон України про охорону
навколишнього середовища» від 25.06.19991 р.
- «Водний кодекс України,
прийнятий 18.12.1990 р.
«Кодекс України про надра»,
прийнятий 27.07.1994 р.
«Лісовий кодекс України»,
прийнятий 21.01.1994 р.
При експлуатації судів відбувається
забруднення моря стічними водами, сухим сміттям, харчовими відходами, а також
нафтопродуктами при аварійних розливах, зачищенні танків.
Поряд з цим, велику шкоду
навколишньому середовищу наносять гази дизелів, що відробили, у яких
утримується сажа і компоненти неповного згорання палива.
.3.1 Вимоги міжнародної конвенції
МАРПОЛ 73/78
Успішне рішення питань охорони
навколишнього середовища не може вирішуватися без тісного міжнародного
співробітництва, досягнення діючих строго контрольованих міжнародних угод. В
даний час діє єдиний міжнародний документ, коротко названий Конвенція МАРПОЛ
73/78, що складається з 20 статей Конвенції 1973 р. і 9 статей Протоколу 1978
р., двох протоколів і п`яти
положень у яких обумовлюються вимоги до скидання шкідливих речовин із судів.
Конвенцією МАРПОЛ 73/78 встановлені
особливі райони плавання, у яких заборонені будь-які скидання шкідливих речовин
із судів. У ці особливі зони включені: райони Середземного, Чорного,
Балтійського і Червоного морів, «заток» (між 22º
північної широти і 59º
східної довготи Раса - Ель - Ханд і 25ºпівнічної
широти , 61º
східної Раса - Ель - Фасте)
Положення про скидання нафти в морі
забороняється:
- скидання нафто
утримуючих вод (НВ) із судів місткістю 400 реєстрових тонн і більш, а також з
МКО танкерів, за винятком випадків, коли судно перебуває за межами особливого
району, має хід не менш 4 вузлів, відстань до найближчого берега не ближче 12
миль, зміст нафти в суміші, яка зливається не перевищує 
на судні діє устаткування для
сепарації НВ або система фільтрації;
скидання НВ при
перебуванні судів в особливому районі;
скидання НВ у
територіальних морських водах, за винятком, коли швидкість ходу судна не менш 4
вузлів, зміст нафти в суміші яка зливається , не перевищує 
;
скидання НВ у
внутрішніх морських водах, що мають рибогосподарське значення і знаходяться під
юрисдикцією держави;
Положеннями про
скидання сміття в морі забороняється:
скидання будь-якого
сміття в особливих районах плавання;
скидання
пластику,включаючи синтетичні канати, мережі і вироби з пластика;
поза особливими
районами плавання скидання плаваючого сепараційного матеріалу, кріплення і
пакувального матеріалу на відстані від берега не менш 3 миль;
поза особливими
районами плавання скидання не здрібнених харчових відходів на відстані від берега
не менш 12 миль;
Положеннями про
скидання стічних вод у морі забороняється:
скидання стічних вод
у межах 4 миль від берега, за винятком скидання після обробки їх на відповідних
установках , схвалених Регістром;
скидання стічних вод
у межах від 4 до 12 милями від берега, за винятком скидання після обробки їх на
відповідних установках , схвалених Регістром установках і системах для
дроблення і дезінфекції.
.3.2 Джерела забруднення морського
середовища
Джерела забруднення гідросфери при
експлуатації судів поділяють на три групи:
нафто утримуючі води, що у
залежності від походження поділяють на лояльні води машинного відділення,
баластові води паливних цистерн і вантажних танків, проливні води танкерів і
вантажних танків;
- стічні і
господарського-побутові води;
тверді відходи, що
виникають при обслуговуванні СБУ (дрантя, брухт і т.д.) при забезпеченні
життєдіяльності екіпажа і пасажирів ( харчові, відходи, сміття), при
виробництві вантажних робіт.
Причиною утворення лояльних
вод у МКО є :
протічки нафтопродуктів
через арматуру, фланцеві з`єднання й ущільнення насосів паливних і масляних
систем, а також протічки забортної і прісної води;
відходи нафтопродуктів у
наслідок їхньої фільтрації, переливу,зміни масла, розбиранню механізмів при
ремонті;
промислові води елементів
СЄУ при ремонті й експлуатації.
.3.3 Методи запобігання забруднення
морського середовища
Запобігання забруднення моря
лояльними водами судів здійснюється в такий спосіб:
скорочення експлуатаційних
витоків палива й масла у лояла МКВ в процесі експлуатації суднових двигунів і
механізмів;
- устаткуванням судів
ємкостями для збору чистих і забруднених нафтопродуктів лояльних вод,
пристроями здачі зібраних вод на плавучі збирачі або берег, і автономною
осушувальною системою НКВ для зливу цих вод у моря через сепараторні установки
з контрольованим змістом нафтопродуктів у водах, які зливаються.
удосконалюванням берегових
і плавучих станцій для прийому й очищення вод судів.
Запобігання забруднення
моря судовими стічними водами може бути вирішена:
обробкою стічних вод
безпосередньо на судах за допомогою спеціально встановленого устаткування;
збором і збереженням
стічних вод на судах у спеціальних цистернах з наступною передачею в берегові
очисні споруди або на спеціальні борти.
У залежності від виду відходів вони
можуть віддаватися різним методам знешкодженням - механічному, сорбуційному,
хімічному, біологічному, термічному.
Самим кращим є термічний метод,
тобто спалювання відходів, тому що він дозволяє перетворити небезпечні
речовини, здатні забруднити море у безпечні для морської флори і фауни ( зола,
шлак). Забруднення атмосфери при спалюванні відходів представляється не дуже
небезпечним.
.3.4 Забруднення навколишнього
середовища газами, які відробили.
До складу газів суднових двигунів,
що відробили,внутрішнього згорання входить близько 200 компонентів. По
характеру впливу на організм людини, хімічної структури і властивостями основні
з них можна розділити на шість груп:
- нетоксичні речовини 
,
, 
, водяний пар 
, а також діоксин вуглецю 
;
окис вуглецю С, має
шкідливий вплив приводить до кисневого голодування, а також виникненню порушень
центральної нервової системи людини;
окиси азоту 
по дії на
людський організм більш небезпечні, ніж С;
різні вуглеводні (
з`єднання типу 
), що є представниками всіх
гомологічних рядів, вуглеводні токсичні і беруть участь у фторохімічних
оеакціях з окисами азоту;
альдегіди, в
основному формальдегіди;
сажа, яка є
переносником канцерогенних речовин.
До складу газів дизелів, що
виробили, при використанні сірчастих палив входять також неорганічні гази:
сірчастий ангідрид S
і
сірководень 
Практика показала, що найбільш токсичними
компонентами газів, що відробили, є оксид азоту, концентрація яких залежить від
концентрації камери згорання. Низькооборотні двигуни виробляють більше 
, чим середньооборотні або
високооборотні двигуни. Тому припустима норма 
для мало оборотних дизелів складає
20т/кВт. год.
З 1 січня 2000 р. введений у
дію новий державний стандарт ДСТ 51249-99 «Дизель суднові тепловози і
промислові». Викиди шкідливих речовин з газами, що відробили. Норми і методи
визначення, вимоги які допускається поширювати на дизель в умовах експлуатації,
у тому числі і після капітального ремонту.
Виходячи з цього, а також з
урахуванням положень Закону «Про охорону атмосферного повітря» № 96 -РЗ від
04.05.99р. і прийнятого у вересні 1997 р. Додатка VI
«Правила запобігання забруднення повітряного середовища із судів» до
міжнародної Конвенції МАРПОЛ 73/78 на морському і річному транспорті
продовженні і розширені розлукові роботи по створенню ефективних засобів для
зниження забруднення атмосферного повітря.
.3.5 Методи захисту атмосфери
Відомі наступні методи
фізичної і хімічної обробки газів, що відробили, з метою очищення навколишнього
середовища від шкідливих речовин і теплового забруднення: утилізації теплових
утрат; каталітична, вогньова і рідинна нейтралізація, фільтрація й інше.
Утилізація теплових витрат на
судні здійснюється з метою удосконалювання СЄУ, впливає також і на характер
забруднення навколишнього середовища , зменшуючи величину теплових викидів.
Дія каталітичних
нейтралізаторів заснована на без вогневому окислюванні продуктів неповного
згорання палива С і 
в 
і 
, а також на розкладанні з`єднанань

у вихідні речовини 
і 
.
Вогневе дожигання пальних
елементів газів, що відробили, здійснюється в спеціальній камері при
температурі 700-850 ºС.
Принцип дії рідинних
нейтралізаторів заснований на розчиненні або хімічному зв`язуванні токсичних
компонентів при пропущенні газів, що відробили, через рідину відповідного
складу, такою рідиною може бути і вода. Рідинні нейтралізатори, кріс свого
прямого призначення, гасять розпечені тверді частки газів, що відробили, це
підвищує комфортабельність судна в цілому.
У простих конструкціях
рідинного нейтралізатора, заповненого водою проходячи через шар рідини,гази
нейтралізуються і надходять у вихідну трубу, з якої віддаляються в атмосферу.
Робота рідинного нейтралізатора не залежить від режиму роботи двигуна.
У випускних трубопроводах
двигунів при відсутності утилізаційних парогенераторів встановлюють
іскрогасники, що запобігають викиду розпечених часток палива і сажі в
навколишнє середовище.
Таким чином, у даному
підрозділі розглянуті джерела забруднення морського середовища й атмосфери, та
розроблені заходи щодо запобігання цих забруднень, відповідно до законодавчих
актів, спрямованих на забезпечення екологічної безпеки.
6. Техніко-економічне обґрунтування
прийнятих технічних рішень
Розумне використання вкладень
капіталу можливо тільки за умови проведення ретельних економічних досліджень і
обґрунтування кожного проектного рішення на усіх стадіях його розробки. Звідси
витікає першорядна роль розвитку й удосконалювання методології оцінки
економічної ефективності капіталовкладень стосовно до всього різноманіття задач
у кожній галузі народного господарства. Необхідність економічної оцінки
будь-якого проекту диктується її загальним характером, що дозволяють виразити у
вартісних показниках усі технічні й експлуатаційні , соціологічні переваги і
недоліки можливих варіантів. Проектно-конструкторські розробки служать вихідним
матеріалом для планування, а так само формування довгострокових інвестиційних
програм. Результати економічних обґрунтувань проектів використовуються як база
для планування найважливіших економічних показників, у виконані яких візьмуть
участь побудовані по цих проектах двигуни. Широке впровадження досягнень
науково-технічного прогресу при проектуванні і будівництві двигунів служить
найважливішим джерелом підвищення ефективності проведень, росту продуктивності
праці.
Визначальною техніко-виробничою
формою досягнення фундаментальних наук об`активно виступає розвиток матеріально
- технічної бази виробництва з її стрижнєм - системою машин в широкому
розумінні цього поняття (включаючи технологію). В області створюваних робочих
машин для таких систем науково-технічний прогрес знаходить втілення в різних
конструкційних організаційно технічних формах,збільшення одиночної потужності,
інтеграції машин у системі на основі технологій, підвищення стандартизації.
Економічне обґрунтування виконаної у дипломному проекті припущенної заміни
дизель-генератора великої потужності буде обґрунтовано на підставі порівняння
припущених витрат на початкову вартість закупівлі обладнання, та експлуатаційні
витрати під час експлуатації дизель-генератора на вибраному об`єкті.
Порівняльний аналіз подано нижче у таблиці 10.
Таблиця 6.
Основні параметри
|
Умовне позначення
|
Прототип двигуна
|
Дипломний двигун
|
|
|
|
|
Ефективна потужність; кВт
|
Ne
|
170
|
224
|
Число обертів; хв-1
|
n
|
750
|
750
|
Питома ефективна витрата палива; г/Квт*год
|
qe
|
224,4
|
215
|
Час роботи : одного двигуна протягом року; год. трьох двигунів; год.
чотирьох двигунів; год.
|
tx
|
4380
|
4380
|
|
t`x1
|
|
13140
|
|
t`x2
|
17520
|
-
|
Вартість однієї тони палива; $
|
Cm
|
320
|
320
|
Кількість витраченого палива; т
|
Gm
|
667
|
632
|
Вартість використаного палива; $
|
Gm общ
|
213440
|
204000
|
Вартість двигунів ; $
|
Cm пер.
|
30000
|
31000
|
Витрати ,що пов`язані з установкою додаткового обладненняі
трубопроводів; $
|
-
|
-
|
1000
|
Витрати, що пов`язані з початковими експлуатаційними витратами;
$
|
-
|
243440
|
236000
|
Економічний ефект ; $
|
-
|
7440
|
Висновок: В наслідок
установки двигунів більшої потужності стало можливим встановити замість
чотирьох дизель-генераторів меншої потужності трьох дизель - генераторів
більшої потужності за рахунок двухконтурного охолодження повітря. В такому разі
ми отримаємо економічний ефект який дорівнює 7440 $.
7. Цивільна оборона
.1 Обґрунтування
необхідності дослідження стійкості об’єктів
Громадянська оборона
України є складовою частиною системи державних, соціальних і оборонних заходів,
що проводяться з метою захисту населення і господарства країни від наслідків
аварій, катастроф, стихійних лих, засобів ураження противника, а також для
проведення рятувальних та інших невідкладних робіт в осередках уражень і
стихійних лих .
Під стійкістю роботи
об'єкта народного господарства розуміється здатність об'єкта випускати
встановлені види продукції в обсягах і номенклатурі, передбачених відповідними
планами, в умовах впливу зброї масового ураження та інших засобів нападу
противника, а також пристосованість цьогооб’єкта до відновлення у випадку
ушкодження.
Метою дослідження
стійкості роботи об'єктів і галузей народного господарства є максимальне
зниження впливу вражаючих факторів зброї масового ураження та створення умов
для швидкої ліквідації наслідків нападу .
Для підвищення стійкості
роботи об'єкта народного господарства використовують такі напрямки:
· Забезпечення
надійного захисту робітників і службовців від вражаючих факторів зброї масового
ураження;
· Захист основних
виробничих фондів від вражаючих факторів зброї масового ураження , в тому числі
і від вторинних ;
· Забезпечення
сталого постачання всім необхідним для випуску запланованої на воєнний час
продукції ;
· Підготовка до
відновлення порушеного виробництва;
· Підвищення
надійності і оперативності управління виробництвом і ГО.
7.2 Аналіз видів і наслідків відмов
дизеля 6ЧН 18\22
Аналіз видів і наслідків відмов
(АВНВ) - формалізована, контрольована процедура якісного аналізу проекту,
технології виготовлення, правил експлуатації і зберігання, системи технічного
обслуговування і ремонту виробу, що полягає у виділенні на деякому рівні розукрупнення
його структури можливих (спостережуваних) відмов різного вигляду, в дослідженні
причинно-наслідкових зв’язків, що обумовлюють їх виникнення, і можливих
(спостережуваних) наслідків цих відмов на даному та вищестоячих рівнях, а також
- в якісній оцінці і ранжируванні відмов по тягарю їх наслідків.
АВНВ проводять з метою
обґрунтування, перевірки достатності, оцінки ефективності і контролю за
реалізацією рішень, що управляють, направлених на вдосконалення конструкції,
технології виготовлення, правил експлуатації, системи технічного обслуговування
і ремонту об’єкту і що забезпечують запобігання виникненню і ослабленню тягаря
можливих наслідків його відмов, досягнення необхідних характеристик безпеки,
екологічності, ефективності і надійності.
Завдання що вирішується при
проведенні АВНВ: в процесі АВНВ вирішують наступні завдання:
· Виявляють можливі
види відмов складових частин і виробу в цілому, вивчають їх причини, механізми
і умови виникнення і розвитку;
· Визначають можливі
несприятливі наслідки виникнення виявлених відмов, проводять якісний аналіз
тягаря наслідків відмов і кількісну оцінку їх критичності;
· Складають і
періодично коректують переліки критичних елементів і технологічних процесів;
· Оцінюють
достатність передбачених засобів і методів контролю працездатності і
діагностування виробів для своєчасного виявлення і локалізації його відмов,
обґрунтовують необхідність введення додаткових засобів і методів сигналізації,
контролю і діагностування;
· Виробляють
пропозиції і рекомендації по внесенню змін до конструкції і технології
виготовлення виробу і його складових частин, направлених на зниження
вірогідності і тягарів наслідків відмов, оцінюють ефективність раніше
проведених доопрацювань;
· Аналізують правила
поведінки персоналу в аварійних ситуаціях, обумовлених можливими відмовами
виробів, передбачені експлуатаційною документацією, виробляють пропозиції по їх
вдосконаленню або внесенню відповідних змін в експлуатаційну документацію при
їх відсутності;
· Проводять аналіз
можливих (спостережуваних) помилок персоналу при експлуатації, технічному
обслуговуванні і ремонті виробів, оцінюють їх можливі наслідки, виробляють
пропозиції по вдосконаленню людино-машинних інтерфейсів і введенню додаткових
засобів захисту виробів від помилок персоналу, по вдосконаленню інструкцій з
експлуатації, технічного обслуговування і ремонту виробів.
Проведення АВНВ не відміняє
необхідності виконання розрахунків надійності об’єкту відповідно до загальних
вимог ГОСТ 27,301.
Планування і виконання розрахунків
надійності і АВНВ повинні здійснюватися так, щоб вказані елементи ПОН
доповнювали один одного і взаємно служили джерелами вихідних даних. При цьому
за результатами АВНВ уточнюють критерії відмов об’єкту, моделі, вживані при
розрахунку його надійності, завдання і вміст технічного обслуговування і
ремонту об’єкту, а методи і результати розрахунків надійності використовують
для вірогідності відмов об’єкту, що враховуються при аналізі їх критичності.
АВНВ повинен також забезпечувати отримання вихідних даних для:
· Планування
експериментального відробітку об’єктів; уточнення розподілу вимог надійності
між складовими частинами об’єкту, внесення відповідних змін і доповнень в ПОН
складових частин; встановлення і уточнення вимог по пристосованості об’єкту до
діагностування (придатність) і його ремонтопридатності;
· Відробітки
(вдосконалення) технології виготовлення об’єкту, включаючи планерування
програми, що відбраковує випробування об’єкту і його складових частин в процесі
виробництва; планерування системи технічного обслуговування і ремонту об’єкту,
відробітки експлуатаційної і ремонтної документації;
· Складання
(вдосконалення) програм вчення і тренування експлуатаційного і ремонтного
персоналу, правил його поведінки в аварійних ситуаціях. Використання результатів
АВНВ. Результати АВНВ враховують: при ухваленні рішення про завершеність етапів
видів робіт на стадіях життєвого циклу об’єктів, включаючи приймання ДКР по
розробці об’єктів;
· При сертифікації
об’єктів для перевірки достатності прийнятих при їх розробці і виготовлення
заходів по забезпеченню безпеки.
Критичність відмов при АВНВ оцінюють
з використанням показників, що враховують для кожної аналізованої відмови
об’єкту:
· Вірогідність його
виникнення за час експлуатації;
· Умовна вірогідність
настання всіх можливих несприятливих наслідків відмови, якщо вона може
супроводжуватися декількома різними по характеру і тягарі наслідками;
· Розмір можливого
збитку в результаті настання кожного з очікуваних наслідків відмов.
Значення вірогідності відмов, що
враховуються при оцінці їх критичності, розраховують (прогнозують) прийнятими в
розрахунках надійності методами з врахуванням структури об’єкту, рівнів
нагруженності і режимів роботи його елементів за наявними довідковими або
експериментальними даними про їх надійність. Можливі наслідки кожної відмови
визначають за результатами АВНВ об’єкту, а відповідна умовна вірогідність
настання кожного наслідку розраховують на основі моделей типа «дерева подій»
або прогнозують експертними методами.
Приклад шкали для встановлення
категорії тягаря наслідків відмов
Категорія важкості відказів
|
Характеристика важкості наслідків
відказів
|
4 3 2 1
|
Відмова, яка швидко і з високою
вірогідністю може спричинити значний збиток для самого об’єкту і довкілля,
загибель або важкі травми людей, зірвавши виконання поставленого завдання.
Відмова, яка швидко і з високою вірогідністю може спричинити значний збиток
для самого об’єкту і для довкілля, зрив виконуваного завдання, але створює
малу загрозу життю і здоров’ю людей. Відмова, яка може спричинити затримку
виконання завдання, зниження готовності і ефективності об’єкту, але не
представляє небезпеки для довкілля, самого об’єкту і здоров’я людей. Відмова, яка
може спричинити зниження якості функціонування об’єкту, але не представляє
небезпеки для довкілля, самого об’єкту і здоров’я людей.
|
Висновок
Найбільш критичними
елементами будуть:
· прорив води в
камеру згоряння, що приведе до руйнування шатуна та виходу з ладу двигуна;
· прорив вихлопних
газів, що призведе до спрацювання клапану тиску в картері.
При дотриманні правил експлуатації,
приведених в інструкції з експлуатації двигуна, двигун не є загрозою як для
людини так і для навколишнього середовища, але залишається вірогідність відмови
або виходу з ладу.
Пропозиції для зменшення відмов і їх
наслідків викладено в робочому листі у стовбчику №8.
Формат
|
Зона
|
Позиція
|
Позначення
|
Найменування
|
Кількість
|
Примітка
|
|
|
|
|
|
|
|
А1
|
|
|
ДП.7.090210.6221.06.09.14
|
Документація
|
|
|
А1
|
|
|
ДП.7.090210.6221.06.09.14
|
Зборочне креслення
|
|
|
|
|
|
|
Зборочні одиниці
|
|
|
|
|
|
|
|
|
|
|
|
|
|
Колінчастий вал
|
1
|
|
|
|
|
|
Установка труб холодильника
воздуха ТКР 14
|
|
|
|
|
|
|
Система водяних трубопроводів
|
|
|
|
|
|
|
Фільтр масла
|
|
|
|
|
|
|
Система паливних трубопроводів
|
|
|
|
|
|
|
Стоп - устройство СУЄ -2
|
|
|
|
|
|
|
Паливний насос
|
|
|
|
|
|
|
Кришка циліндра
|
6
|
|
|
|
|
|
Форсунка
|
6
|
|
|
|
|
|
Пост керування
|
1
|
|
|
|
|
|
Картомір в сборі
|
1
|
|
|
|
|
|
Система масляних трубопроводів
|
1
|
|
|
|
|
|
Фундаментна рама
|
1
|
|
|
|
|
|
Блок циліндрів
|
|
|
|
|
|
|
Фільтр масла
|
1
|
|
|
|
|
|
Установка труб холодного воздуха
|
1
|
|
|
|
|
|
Система водяних трубопроводів
|
1
|
|
|
|
|
|
Водомаслоохолоджувач
|
1
|
|
|
|
|
|
Розподільний вал
|
1
|
|
|
|
|
|
Поршень з шатуном
|
6
|
|
|
|
21
|
|
Система масляних трубопроводів
|
1
|
|
|
|
22
|
|
Головний пусковий клапан
|
1
|
|
|
|
23
|
|
Система повітряних трубопроводів
|
1
|
|
|
|
24
|
|
Воздухорозподільник
|
1
|
|
|
|
25
|
|
Ричаги керування
|
1
|
|
|
|
26
|
|
Водяной насос
|
1
|
|
|
|
27
|
|
Паливопідкачуючий насос
|
1
|
|
|
|
28
|
|
Привод паливного насоса
|
1
|
|
|
|
29
|
|
Паливний філтр
|
1
|
|
|
|
30
|
|
Центрифуга
|
1
|
|
|
|
31
|
|
Маслорозподільник
|
1
|
|
А1
|
|
|
ДП. 7090210.6221.06. 01.14
|
Документація
|
|
|
|
|
|
|
Зборочне креслення
|
|
|
|
|
|
|
Зборочні одиниці
|
|
|
|
|
|
|
|
|
|
|
|
1
|
|
ДГ 64Н 18/22
|
4
|
|
|
|
2
|
|
Котел водогрійний
|
2
|
|
|
|
3
|
|
Компресор кондіціонування воздуха
|
2
|
|
|
|
4
|
|
Інсеніратор
|
1
|
|
|
|
5
|
|
Насосу охолоджування води для
кондіціонерів
|
4
|
|
|
|
6
|
|
Баластні насоси
|
2
|
|
|
|
7
|
|
Сепаратор масла
|
1
|
|
|
|
8
|
|
Витратна цистерна масла
|
1
|
|
|
|
9
|
|
Глушник відхідних газів
|
4
|
|
|
|
10
|
|
Дніщевий кінгстоний ящик
|
1
|
|
|
|
11
|
|
Паливоперекачиваючий насос
|
1
|
|
|
|
12
|
|
Бортовий кінгстоний ящик
|
1
|
|
|
|
13
|
|
Компенсатори
|
4
|
|
|
|
14
|
|
Вентиляційна шахта
|
1
|
|
|
|
15
|
|
Отстійна цистерна сточних вод
|
1
|
|
|
|
|
|
|
|
|
|
|
|
|
|
|
|
|
|
|
|
|
Висновок
При виконанні дипломного
проекту були розглянуті і обґрунтовані питання вибору об`єкту де буде встановлено двигун і описана характеристика цього об`єкта. Були зроблені висновки по основним показникам роботи двигуна і
вимоги по його експлуатації. Були проведені основні розрахунки двигуна (робочий
цикл, динаміка системи, міцність поршня). Був розроблений засіб ремонту
циліндро - поршневої групи та порядок його проведення, проаналізовані способи
діагностики паливної апаратури в цілому, та окрема діагностика стану паливної
апаратури, був розглянутий технологічний процес виготовлення втулки.
Наприкінці дипломного
проекту були розроблені заходи з охорони праці, навколишнього середовища та
техніки безпеки.
В заключній частині
дипломного проекту зроблено техніко-економічне обгрунтування прийнятих
технічних рішень.
Список використаної
літератури
1. Судовые среднеоборотные дизели. Хандов З.А., Браславский М.И.- Л:
Судостроения, 1975-320 с.
2. Дизель судовой
6 ЧН 18/22 и 6 Ч 18/22. Техническое описание и инструкция по эксплуатации.
. Спецификация
судна проект 1844 : з-д Коминтерн.
. Ваншейдт В.А.
Конструирование и расчеты прочности судовых дизелей.- Л. Судостроение, 1969 -
640 с.
. ГОСТ- 4393- 82
«Дизели судовые, тепловозные и промышленные. Выбросы вредных веществ с отработанными
газами. Нормы и методы определения».
. Байбаран Д.С.,
Добровольский В.В. Выбор исходных параметров для расчета цикла судовых ДВС и
порядок его проведения. Учебное пособие- Николаев: НКИ, 1976- 42 с.
. Ткаченко С.Г.
Расчеты двигателей внутреннего сгорания при курсовом и дипломном
проектировании. Методические указания. - Николаев: НКИ, 1990- 35 с.
. Ткаченко С.Г.,
Коршиков Ю.С. Расчеты динамики ДВС, имеющих специальные схемы
кривошипно-шатунных механизмов. Учебное пос обие- Николаев: НКИ, 1988.- 36с.
. Эпельман Т.Е.,
Лукин А.И., Ткаченко С.Г. Расчет определяющих параметров основных механизмов и
оборудования СДУ на стадии эскизного проектирования. Учебное пособие- Николаев:
НКИ 1984 - 44с.
. Фомин Ю.Я.,
Никонов Г.В., Ивановский В.Г. Топливная аппаратура дизелей: Справочник.- М:
Машиностроение, 1982 -168 с.
. Вешкельский
С.А., Светличный М.И. Монтаж, эксплуатация и ремонт двигателей внутреннего
сгорания.- М.: Машиностроение, 1978.- 275 с.
. Канне А.Б.
Судовые двигатели внутреннего сгорания: Учебник - 3-е изд.- Л: Судостроение,
1982 -288 с.
. Морденский В.П.
Топливная аппаратура судовых двигателей, изд. 2-е. - Москва : Транспорт, 1973
. Васильев Б.В.,
Кофман Д.И., Эренбург С.Г. Диагностирование технического состояния судовых
дизелей / Под ред. Д-ра тех. наук проф. Б.В. Васильева.- М.: Транспорт1982- 144
с.
. Жидецкий В.Ц.,
Джигерей В.С., Мельников А.В. Основы охраны труда - Львов: Афиша, 2000- 351 с.
. Морской Регистр
судоходства. Правила классификации и постройки морских судов, том 2 . 1999 г.
. Горбань П.Т.
Методические указания по выполнению раздела «Охрана труда и охрана окружающей
среды в дипломных проектах».
. Судовые
средства защиты биосферы. Учебное пособие В.М. Боград, В.В. Лященко, Николаев,
НКИ : 1980- 49с.