Химико-технологические процессы и аппараты смежных отраслей
1. Общие сведения о
процессе графитации
У широкого круга углеродных
материалов - от ископаемых углей до природного графита - имеется в основе одно
и то же образовавшие двумерная плоская углеродная сетка Процесс превращения
двумерной структуры углеродных сеток в трехмерную и составляет процесс
графитации.
Рентгенографические исследования
естественных графитов, наиболее близких к структуре идеального кристалла
графит, показали, что атомы углерода расположены в виде параллельных слоев,
расстояние между которыми в предельном случае составляет 0,33526+0,00002 мм. В
каждой плоскости углеродные атомы образуют сетку правильных шестигранников с
расстоянием между атомами 0,142 нм. Различие в способе взаимной укладки плоских
шестиугольных сеток относительно друг друга определяет наличие двух типов
решетки графша - гексагональной и ромбоэдрической.
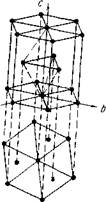
Рис. 1 Структура гексагональной (a) и ромбоэдрической (b) форм углерода
Гексагональная структура наиболее
распространена и представляет собой решетку, где углеродные атомы в каждой
плоскости лежат над и под центрами правильных шестиугольников, находящихся в
ниже- и вышерасположенных плоскостях.
Таким образом, один слой
сдвигается в горизонтальном направлении по отношению к расположенному выше, на
величину
,
которая равна расстоянию между атомами в слое С-С (0,142 нм).
В ромбоэдрической
решетке графита также имеются плоские шестиугольные сетки, которые сдвинуты на
величину
(-0,142
нм) одного и того же знака.
В естественных графитах
содержание кристаллов ромбоэдрической модификации может достигать 30%, в
искусственных графитах она, как правило, не наблюдается.
Свидетельством большей
стабильности гексагональной модификации кристаллов графита является полный
переход в нее ромбоэдрического графита при температурах термообработки 2000 -
3000 С.
Графитация,
представляющая собой увеличение размеров кристаллов вследствие
рекристаллизации, начинается для каждого углеродного сырья при определенной
температуре. Для каждой температуры графитация идет очень быстро и до
определенного предела.
Гомогенная графитация
предполагает протекание процессов графитации в одной твердой фазе и характерна
для графитирующихся углеродных материалов при 2300 - 3000 С. Гетерогенная
графитация через газовую фазу имеет место при температурах выше 3200 °С и
характерна для неграфитирующихся веществ. Возможна гетерогенная графитация и
через жидкую фазу.
При гомогенной графитации
графитирующихся углеродных материалов переходу в состояние трехмерной
упорядоченности предшествует рост диаметра слоев путем слияния в слои соседних
сеток и присоединения неупорядоченного углерода. Количественно этот рост можно
характеризовать величиной диаметра слоя. По данным Франклин, в интервале
1000-2000 °С диаметр слоев нефтяных коксов увеличивается с 1,5 до 20 нм, а
межслоевое расстояние почти не изменяется. На стадии выше 2000 °С рост диаметра
слоя замедляется, а уменьшение
значительно, что
свидетельствует о процессе азимутальной упорядоченности углеродных слоев
относительно друг друга, с приближением кристаллической решетки к идеальной
структуре.
Эти два процесса
сопровождаются третьим - упаковкой гексагональной углеродной сетки в
параллельные слои с образованием пакетов различной толщины. Между хорошо
графитирующимися углеродными веществами и неграфитирующимися по гомогенному
механизму, расположен большой класс материалов, который при одной и той же
температуре графитации может иметь совершенно различные значения степени
графитации (
,
).
Даже хорошо графитирующиеся вещества при нагреве до 3600 °С и под давлением не
достигают межслоевого расстояния, характерного для естественного графита
(0,3354 нм). Такой материал, как термическая сажа, достигает при 2500 °С
определенной степени графитации и далее не меняется.
Предел степени
графитации определяется характером и количеством перекрестных химических связей
между пакетами углеродных слоев. Чем меньше число поперечных связей, тем выше
структурная анизотропия и достигаемая при определенной температуре степень
графитации. Таким образом, графитация характеризуется также постепенным
разрывом поперечных химических связей.
Влияние газовой среды на
формирование свойств кокса в процессе термообработки хорошо известно. в
исходном состоянии коксы имеют структуру пространственного полимера, состоящего
из небольших плоских пачек гексагональных слоев углерода, которые соединены
мостиками из гетероатомов и функциональных групп. Прокаливание такого вещества
в водороде приводит к определенной гидрогенизации его, повышает подвижность
системы и ускоряет происходящие в различных температурных интервалах процессы
упорядочения и разупорядочения. В то же время, окисление углеродисгого вещества
на стадии карбонизации, обуславливающее образование поперечных связей,
препятствует графитированию.
В промышленной практике
используют этот эффект для получения высокопрочных, но плохо графитирующихся
углеродных материалов это механохимическая обработка некоксовых и сажепековых
композиций, обработка кислородом пеков, идущих на коксование.
Наряду с температурой и
газовой средой внутренние напряжения играют значительную роль в процессе
графитации.
Наиболее удобно связь
между напряжением и деформацией с процессом графитации проследить при изучении
пироуглеродов. Увеличение предпочтительной ориентации пироуглерода связано с
большими изменениями размеров, вызванных 10 - 16%-ной усадкой перпендикулярно
подложке и 4 - 5%-ным расширением параллельно подложке. Это можно рассматривать
как самопроизвольную пластическую деформацию, возникающую за счет
самопроизвольно возникающих напряжений. Пластическая деформация при высоких
температурах и направленных внешних нагрузках значительно увеличивает скорость
графитации.
Так
высокоориентированный и хорошо упорядоченный графит можно получать из
пироуглерода, осажденного на нагретую подложку путем отжига осажденного
материала при различных силовых воздействиях, включая непосредственную связь
материала с подложкой.
Влияние добавок
минералов или металлов на процесс графитации известно давно. Особое место среди
элеметов-катализаторов графитации занимает бор и его соединения. При содержании
выше 10% бора большую роль играет механизм растворения и осаждения с участием В4С.
Но так как бор растворяется в значительной степени в графите (до 2,35% при 2350
°С), он может оказывать и непосредственное влияние на параметры решетки
графита.
Наличие предпочтительной
ориентации и отсутствие перекрестных связей, являются основой, объединяющей все
предложенные гипотезы. Использование этих приемов и приводит к понижению
температуры превращения углеродного сырья в совершенный графит. То, что в
отдельных случаях температура графитации снижается до 1000 °С, говорит о
больших технологических возможностях.
Рассмотрение факторов,
влияющих на ускорение процесса графитации показывает, что наиболее
значительными из них являются влияние давления и карбидообразующих добавок. В
технологической практике в последние годы для получения нового класса
материалов, содержащего фазу очень совершенного по кристаллической структуре
графита, влиянием давления и добавок стали пользоваться совместно. Такой
процесс получил название термомеханохимической обработки (ТМХО).
Материалы, полученные
методом ТМХО, значительно превосходят по своим физико-механическим свойствам
материалы, изготовленные методом термомеханической обработки. Особо следует
отметить повышенную плотность, прочность, тепло- и электропроводность этих
графитов. Причем, изменяя соотношение добавок, можно в очень широком интервале
менять такие свойства как тепло- и электропроводность.
2. Технология графитации
Технологическая операция -
графитирование углеродистых материалов - является заключительной стадией
длительного и многопередельного процесса изготовления всех видов
графитированных изделий.
Графитации в основном подвергают
заготовки, прошедшие прессование и обжиг. От них они наследуют большую и
неравномерную пористость и анизометрию. Однако электропроводность и
теплопроводность, а также низкие фрикционные свойства изделия приобретают в
процессе графитации Требования к готовым графитированным изделиям, разумеется,
не ограничиваются только этими свойствами. Они должны обладать рядом других качественных
показателей очень важных при эксплуатации прочностных характеристик,
теплофизических и некоторых химических свойств, которые так же формируются при
графитации.
Требования к готовым графитированным
материалам разнообразны, а возможности процесса графитации ограничены, и
заключаются в воздействии высокой температуры на графитируемые изделия. Поэтому
основные направления в организации свойств графитируемых изделий закладываются
на разных ступенях технологии при выборе сырья и методов его переработки.
В настоящее время производство почти
всех видов графитированных материалов осуществляется по способу Ачесона. В печь
одновременно с изделиями загружается резисторный материал (пересыпка), что
позволяет увеличить электрическое сопротивление рабочей зоны (керна) печи. Но
это мероприятие одновременно изменяет характер нагревания графитируемых
материалов. Если по способу Кастнера электрический ток протекает
непосредственно через изделие и тепло, выделяемое за счет электроэнергии,
равномерно распределено в объеме изделия, то по способу Ачесона основное
количество тепла выделяется в пересыпке, а затем за счет теплопередачи
происходит нагревание изделия. Нагревание протекает с периферии изделия, в
связи с этим в объеме изделия постоянно наблюдаются неодинаковые температуры,
что сопряжено с появлением вредных внутренних напряжений. Уже при создании
этого способа была заложена зависимость тепловых процессов, протекающих в печи
от электрических характеристик как самого керна, так и всей силовой установки.
Процесс графитации следует отнести к категории электротермических. Эти
обстоятельства не только определяют специфику процесса, но и трудности как в
теоретическом плане, так и практическом осуществлении технологии.
Формирование керна является
важнейшим звеном технологии графитации. Но одновременно этот вопрос является
наиболее трудным в его практической реализации, и не все детали его изучены в
достаточной степени. Правильное формирование керна не только обеспечивает
наибольшую производительность и высокие качества изделий, но позволяет
организовать более экономное расходование электроэнергии. Последнее очень важно
не только с позиции более низкой себестоимости продукции, но имеет
народнохозяйственное, значение. Образно говоря, в вопросе формирование керна
сконцентрированы все направления специфической технологии графитации.
Термин «формирование керна»
учитывает технологический регламент, но вместе с тем преследует цель
творческого подхода к процессу, более глубокого рассмотрения некоторых аспектов
теории и, разумеется, критической оценки практики и некоторых результатов
исследований.
Технологу обычно приходится
разрешать вопросы формирования керна в условиях действующего предприятия. При
проектировании и строительстве печей учитывались вопросы формирования керна,
что отражено в конструкции и размерах печи, а также в выборе источников тока.
Эти обстоятельства не облегчают, а наоборот, создают трудности для технолога
при выборе наилучшего варианта, он должен вписываться в реальные параметры
печей и источников тока. При эксплуатации графитировочных цехов продолжительное
время изменяется ассортимент изделий, их размеры. Поэтому при каждом новом
задании приходится искать оптимальные варианты для керна.
Основные вопросы формирования керна,
имеющие решающее значение заключаются в определении оптимальных размеров керна
и расстояния между загружаемыми изделиями. Разумеется, нельзя эффективно
разрешить эти вопросы, оставив без внимания такие материалы, как пересыпка и
теплоизоляционная шихта.
Габариты керна
Под габаритами керна следует
понимать его сечение и длину. Определение этих параметров имеет определяющее
технологическое и экономическое значение. Эта проблема тесно связана с выбором
оптимальных характеристик источников тока, в данном случае печных
трансформаторов. Размеры керна определяются параметрами источника тока,
питающего печную установку. Следовательно, размеры керна должны быть
постоянными, если не меняются параметры силовой установки. Габариты керна
должны оставаться постоянными даже при изменении ассортимента изделий, подвергающихся
графитации. Однако, объективные причины могут создать такие условия, когда
невозможно вписаться в расчетные габариты керна.
Загрузка печи
Способ Ачесона для производства
графитированных изделий характеризуется обязательным введением в керн печи
резисторных материалов (пересыпки). Введение дополнительного сопротивления в
керн печи повышает его омическое сопротивление, но одновременно снижает
полезную вместимость рабочего объема печи. Однако при применении пересыпки
омическое сопротивление керна возрастает во много раз, что позволяет вести
режим графитации при более выгодных электрических параметрах. Это создает
условия для ведения режима при более высоких напряжениях, в большей степени
используется установленная мощность трансформатора, большее количество
электроэнергии потребляется в единицу времени, электрический к.п.д. также
возрастает. Значительное сокращение времени на проведение режима графитации
приводит к увеличению производительности печной установки и повышении конечной
температуры
Шутирование керна
Графитированные электроды, длина
которых достигает 1,7 - 2,0 м должны обладать одинаковым сопротивлением по всей
длине. Такая однородность электродов обеспечивает высокий эксплуатационный
эффект. Практически этого достигнуть трудно, однако стремятся, чтобы разность
свойств между серединой и концами была минимальной.
Качество электродов, в основном,
определяется электропроводностью; чем выше электропроводность, тем выше
допустимая эксплуатационная плотность тока. Следовательно, эксплуатационные
качества электродов определяются этой плотностью.
При тщательной укладке керна перепад
температур по длине печи незначительный и незакономерный, за исключением
участков переходных контактов керн-токоподводы. Измерения показали, что, в этих
местах температура может быть на 200 - 250 °С выше, чем в остальных. Однако на
завершающейся стадии графитации эта разница в температурах почти стирается.
Перепады температур по сечению керна
(перпендикулярно продольной оси) наблюдаются и сохраняются на протяжении всего цикла
графитации. Объясняется это явление значительной теплопроводностью и
теплоемкостью теплоизолирующих материалов, создающих теплообмен с окружающей
средой.
Один из способов для выравнивания
температуры по сечению керна заключается в том, чтобы при формировании керна
создать условия, при которых большая часть тока протекала бы по периферийной
части керна, т.е. в создании шунта.
В электротехнике шунтом называют
ответвление, включенное параллельно основному проводнику, обычно с той целью,
чтобы через основной проводник или прибор шел не весь ток, а только
определенная часть его.
Теплоизоляционная шихта
Боковые поверхности керна печи
нагреваются до температуры выше 2000 °С. Для того, чтобы защитить его от
сгорания и больших тепловых потерь, его со всех сторон закрывают
теплоизоляционной шихтой. К шихте, предъявляют серьезные требования, и
удовлетворить их не просто. Теплоизоляционная шихта должна обладать высокими
теплоизоляционными свойствами, низкой электропроводностью и теплоемкостью,
хорошей газопроницаемостью, она не должна спекаться. Теплоизоляционная шихта
препятствует окислению графитируемых изделий и защищает боковые стенки печи от
воздействия высоких температур. Однако следует учитывать, что при увеличении
теплоизолирующих свойств или слоя теплоизоляционной шихты удлиняется время на
охлаждение и возрастает время, затрачиваемое на цикл работы печи. Для
преодоления этого затруднения в системе одной секции печей строят дополнительно
одну или две печи.
Шихта для заправки пода
Графитировочные печи сооружают из
шамотного огнеупорного кирпича или из жаростойкого бетона. Эти материалы при
температурах 1300-1500 °С резко снижают свои служебные функции, а при более
высоких температурах, которые характерны для графитировочных печей, непригодны
для эксплуатации. Следовательно, при этих температурах подина печи в ее
первозданном виде не пригодна для использования. Другие строительные материалы
также не пригодны при столь высоких температурах. Остается единственный путь,
заключающийся в защите основания пода печи от губительного воздействия высоких
температур. Для этого необходимо на поверхности подины создать защитную
набойку. Для того, чтобы удовлетворить всем требованиям, предъявляемым к
подинной шихте, ее стали приготавливать из смеси углеродистого порошка и песка.
При загрузке графитировочной печи
пространство между рядами загруженных электродов заполняют гранулированным
углеродистым материалом (обычно коксом). Этот материал называют пересыпкой
(иногда ее называют керновой пересыпкой). Основная функция пересыпки заключается
в увеличении активного электрического сопротивления керна и обеспечении
равномерного подвода тока к графитируемым изделиям. Количество пересыпки,
вводимой в керн, составляет около 20% объема керна.
Пересыпка, обладая очень высоким
удельным электросопротивлением (200-300 кОм), значительно увеличивает общее
сопротивление керна.
Если исключить из керна пересыпку,
то сопротивление печи будет столь ничтожно, что даже при огромной силе тока
мощность печи будет незначительна, и процесс графитации затянется на долгое
время. Введение же пересыпки позволит резко увеличить сопротивление керна, что,
в свою очередь, создает условия для большей мощности на керне и значительно
сократит время кампании графитации. В результате сокращения продолжительности
кампании графитации производительность печи возрастет. Введение пересыпки
увеличивает электрический к.п.д. печи.
Есть другой аспект целесообразности
применения пересыпки. Создаются условия работы при более высоких параметрах
трансформатора. При той же силе тока можно применять более высокие напряжения,
что позволяет эффективнее использовать мощность трансформатора.
Для приготовления пересыпки
используют отходы металлургического кокса, вернее, его мелкие фракции, которые
не используются в доменном производстве. Обычно эти материалы называют
«коксовым орешком». Для этих коксов характерно высокие содержание зольных
примесей
Режим графитации заключается в
постепенном нагревании углеродистых заготовок, помещенных в графитировочную
печь, до очень высоких температур, при которых заканчивается процесс
образования искусственного графита. Практически такими температурами могут быть
2500 - 3000 С. При этом должно соблюдаться одно основное требование: не
допустить образования трещин или других каких-либо дефектов в объеме и на поверхности
изделия, что связано со скоростью подъема температуры.
Предельные температуры графитации
определяются требованиями к готовому продукту, а также сырьевыми материалами,
из которых приготовлены полуфабрикаты.
Оптимальные температуры, при которых
должны заканчиваться процессы графитации, устанавливается экспериментально.
Скорость нагревания ограничивается,
с одной стороны, опасностью возникновения трещин на изделиях, а с другой -
стремлением получить более дешевые изделия. Поэтому, температурный режим должен
быть настолько оптимальным, чтобы сохранить изделия от растрескивания и
образования внешних дефектов. Некоторые исследователи называют интервал
температур от 1300 до 2100 °С критическим, в котором протекают наиболее важные
процессы, сопровождаемые усадкой изделий. Рекомендуется этот интервал проходить
медленно, со скоростью ~ 30 °С/ч. Если этот интервал пройти с большей
скоростью, то усадка в изделиях резко снижается, а, следовательно, снижается
плотность и физико-механические свойства.
Организация и выполнение режима
графитации чрезвычайно трудная проблема. Сложность заключается не только в
выполнении, но и в воспроизведении заданных режимов. Если просмотреть записи
режимов графитации для одной и той же печи с одинаковой загрузкой изделиями,
пересыпкой и тепловой изоляцией, одинаковыми заданиями на ведение электрических
режимов, то можно обнаружить, что они отличаются друг от друга как по
длительности процесса, так и по изменениям отдельных характеристик процесса
(мощности, сопротивления и др.) и удельному расходу электроэнергии. Очень
трудно сформировать керн, но еще труднее воспроизвести свойства пересыпки и
теплоизоляционной шихты.
Печная установка графитации
относится к нестандартному типу оборудования, каждый раз при строительстве
нового или модернизации старого цехов графитации обязательно производят расчеты
и проектирование всего комплекса печной установки, учитывая условия, которые
закладываются в плановом задании
Графитации подвергают полуфабрикаты
(заготовки), прошедшие прессование и обжиг. Однако высокие электро- и
теплопроводность изделия приобретают в процессе графитации Высокая температура
является основным фактором для превращения углеродистых заготовок в совершенно
иной материал с характерными свойствами натуральных графитов. Характер теплового
воздействия на графитируемые изделия заключается в достижении очень высоких
температур (выше 2500 °С) при отсутствии окислительной среды, что
обеспечивается в современных графитировочных печах. В задачу
электротехнического обеспечения входит не только количественное обеспечение
электроэнергией Необходимы устройства позволяющие регулировать в широком
диапазоне подводимую мощность к печи
В графитировочных печах можно
производить высокотермическую обработку кусковых (например, получение
термографита) и порошкообразных материалов.
Процесс графитации
относится к числу энергоемких производств Расход электроэнергии в зависимости
от вида и размера изделий составляет 3000-6000
на 1 т изделия.
Организация и выполнение технологических операций должны преследовать цель
максимального сокращения удельных расходов электроэнергии, разумеется не в
ущерб качеству изделий.
Графитировочные печи
относятся к группе электрических однофазных печей сопротивления прямого нагрева
Сопротивлением служат графитируемые материалы, через которые протекает
электрический ток, нагревая их. Поэтому они носят название печей прямого
нагрева Ценность их заключается в том, что в малых объемах печи можно
сконцентрировать большие количества энергии, что позволяет создавать
температуры, достигающие 3000 °С.
Под термином
«электрическая печь» следует понимать весь комплекс печного оборудования,
включая собственно печь, трансформатор и электрическую так называемую короткую
сеть (вторичный токоподвод), т.е. систему проводников, передающих ток рабочего
напряжения от источников питания (трансформатора, генератора и др.) к рабочей
зоне электрической графитировочной печи, где электрическая энергия превращается
в тепловую. Некоторые участки короткой сети могут одновременно служить
элементами конструкции печи (например, токоподводящие электроды).
Графитировочная печь
состоит из корытообразного основания, выложенного из шамотового огнеупора и
двух постоянных торцевых стен с проемами для укладки токоподводящих электродных
пакетов. Боковые стенки обычно делаются не разборными, но существуют
конструкции печей с двумя или одной разборными стенками. Конструкция боковых
стенок определяется технологическими условиями и цеховой обстановкой.
Печи этого типа, широко
применяют в промышленности. Они могут быть с различными конструктивными
решениями токоподводящего пакета электродов, подины, охлаждения печи и др.,
однако принципиальная конструкция печи остается во всех случаях одной и той же.
Размеры печей для
графитации прежде всего зависят от величины загрузки, а следовательно, и от
мощности источников питания. На параметры печей оказывают существенное влияние
геометрические размеры графитируемых изделий. Наибольших размеров печи
применяют при графитации электродов. В промышленной практике используются печи
на загрузку 20-40 т. и даже 130 - 140 т электродов. Ширина печи - очень важный
параметр, потому что определяет не только вместимость печи и сечение керна, но
оказывает решающее влияние на характеристику трансформатора, прежде всего его
силу тока.
При графитации
электродов ширину печи определяет максимальная длина электрода, подлежащего
графитации, поскольку его укладывают перпендикулярно оси печи.
Труднее определить
оптимальную длину печи. В настоящее время создают печи длиной от 3 до 20 м
(длина керна). Более длинные печи при той же мощности трансформатора
экономичнее, так как удлинение керна приводит к повышению теплового и
электрического коэффициентов полезного действия и, как следствие, к увеличению
производительности, уменьшению расхода электроэнергии на 1 т графитированной
продукции.
Подина печи
Основные требования, предъявляемые к
теплоизоляционной шихте заключаются в том, чтобы она обладала высокими тепло- и
электроизоляционными свойствами и чтобы при высоких температурах она и ее
компоненты не плавились
Чтобы обеспечить нормальный режим
графитации, избежать тепловых потерь и утечки тока через подину, перед каждой
кампанией следует производить проверку состояния поданы и устранять замеченные
дефекты. Если обнаружена заграфиченность подины, ее удаляют и набивают новую.
По конструкции подины изготавливают
двух видов охлаждаемые и неохлаждаемые. Последние выкладывают сплошным массивом
на фундаментном основании. В настоящее время они встречаются только на малых по
мощности и производительности печах. Печи с охлаждающимися подинами строят двух
видов с естественным и принудительным охлаждением.
Естественное охлаждение подины
осуществляется воздухом, протекающим через специальные каналы, которые
сооружают под подиной. Каналы располагают поперек печи.
Торцевые и боковые стенки
Торцевая стена - очень важный
элемент графитировочной печи, наиболее уязвимая часть печи, что приводит к ее
ежегодному ремонту. Она должна быть легкой и, вместе с тем, прочной, надежной в
эксплуатации. Основная задача ее заключается в том, чтобы вести в себе
токоподводящий электродный пакет. Поэтому при выборе и расчете токоподводящего
пакета следует стремиться к минимальному объему электродов заделываемых в
торцевую стенку.
3. Токоподводящие
электроды
Электрическая энергия подводится к
рабочему объему графитировочной печи (керну) при помощи электродов.
Электрический ток в современных печах достигает нескольких десятков тысяч
ампер. Для того, чтобы пропустить такой ток, требуются электроды больших
сечений. Изготовить электроды таких больших размеров современная промышленность
не может. Поэтому используют электроды меньших сечений, удовлетворяющим, однако,
в сумме требованиям, предъявляемым к электрическим проводникам по допустимой
плотности тока Токоподводящие электроды, заделанные в торцевую стенку, называют
электродным пакетом.
В качестве токоподводящих электродов
могут использоваться как угольные, так и графитированные электроды. В настоящее
время избегают применения угольных электродов. На них значительно выше потери
электрической энергии, особенно в контактных соединениях Угольные электроды
обладают значительно худшей электропроводностью, чем графитированные, поэтому
плотность тока принимается более низкой, чтобы не вызвать чрезмерного
нагревания электродов и электрических потерь.
Графитированные электроды обладают
лучшей электропроводностью, чем угольные и допускают очень высокую плотность
тока, в результате чего сечение их может быть небольшим. Это очень важное
обстоятельство, так как чем меньше сечение электродов, тем более легка
конструкция торцевой стенки и тем дольше она будет служить. Преимущество
графитированных электродов заключается также в том, что они легче
обрабатываются, при этом достигается высокая точность обработки поверхности.
Это обеспечивает высокое качество контактных соединений с металлическими
проводниками, стойкость против окисления выше, чем у угольных электродов.
Короткой принято называть
электрическую сеть, связывающую источник тока (трансформатор) с собственно
печью. С ростом мощности короткая сеть становится одним из главных факторов,
определяющих электрические и технико-экономические показатели печи. Правильный
выбор схемы сети, сечения, формы проводников и расположение их имеет для
графитировочной печи первостепенное значение.
Короткие сети графитировочных печей
обтекаются большими токами и характеризуются большой массой проводников и
сложностью конфигурации, причем их эксплуатация протекает в тяжелых условиях
Большие токи обусловливают появление вокруг проводников сильных магнитных
полей. Многие явления, с которыми в обычных силовых сетях не считаются
вследствие их незначительности, в графитировочных печах приобретают большое
значение. К ним относятся поверхностный эффект, эффект близости, неравномерная
нагрузка проводников током, нагрев металлических конструкций печи и
токопроводов. Короткая сеть, в противоположность керну, обладает незначительным
активным, но зато большим реактивным сопротивлением, вследствие чего влияет на
к.п.д. и электрические характеристики печи как приемника электрической энергии.
Высокое реактивное сопротивление короткой сети приводит к большому падению
напряжения между трансформатором и печью, а также к загрузке сети большой
реактивной мощностью. Эффект близости наблюдается в случае совместной прокладки
двух или большего количества проводников с током и объясняется влиянием на
проводник переменного магнитного поля соседних проводников Эффект близости
сказывается тем значительнее, чем ближе расположены проводники друг к другу.
Его следствием также является неравномерное распределение плотности тока по
сечению проводника, но смещенное в какую-либо определенную сторону сечения
Направление смещения зависит от знака потока или от направления тока в соседнем
проводнике
Поверхностный эффект вызывается
собственным магнитным потоком проводника, вытесняющим ток ближе к поверхности.
Вследствие этого сечение проводника загружается неравномерно и его сопротивление
как бы повышается. В основном на поверхностный эффект влияет сечение
проводника.
Основными условиями, которым должна
удовлетворять короткая сеть графитировочной печи, являются наименьшая длина,
правильный выбор проводников (с учетом условий их работы) и рациональное
использование их сечения, наиболее рациональная транспозиция проводников,
преследующая цель равномерной загрузки их током. Соблюдение этих условий
позволяет мощность, получаемую из питающей сети, использовать с высоким кпд и
высоким коэффициентом мощности.
4. Характеристика
исходного сырья, поступающего на переработку
Для производства всех видов
углеграфитовых материалов применяют [1] искусственные и естественные материалы,
в которых главной составной частью является углерод.
К естественным материалам, которые
используются в этом производстве, относятся антрациты и натуральные графиты.
Основную же массу углеродистых материалов (преобладающую по своему
количественному применению и фактическому значению) составляют искусственно
приготовленные материалы.
Различные формы углерода получаются
разложением органических веществ. Они могут образовываться из газовой или
жидкой фазы, а также разложением твердых соединений. Из газовой фазы
образуются, например, некоторые сорта сажи, а из жидкой - нефтяные коксы
Исходные материалы и способы переработки их оказывают решающее влияние на
свойства сырьевых материалов.
Все сырьевые материалы [11],
применяемые для производства углеграфитовых материалов, можно разделить на две
основные группы твердые углеродистые материалы и связующие вещества.
Антрацит - основной компонент
угольных электродов и угольных блоков для кладки и футеровки печей, ванн и др.
Применение антрацита для этих изделий улучшает эксплуатационные свойства
главным образом термостойкость. В общем, применение антрацита позволяет
получать более прочные и электропроводные изделия, чем, например кокс.
Антрациты принадлежат т; наиболее
метаморфизированным углям. В соответствии с этим их угольное вещество содержит
много углерода (обычно 92-97%), обладает большой плотностью (1,4-1,7) и
наименьшим выходом летучих веществ (2-8%).
Антрациты разного происхождения
значительно различаются по степени метаморфизма, и по дисперсной структуре. Чем
больше степень метаморфизма, чем меньший выход летучих веществ дает антрацит
при прокаливании, тем больше плотность, твердость и меньше пористость его
углистого вещества. Структурные различия антрацитов состоят в большем или
меньшем развитии у них слоистости. По этому признаку их делят на массивные,
крупнослоистые и тонкослоистые.
Со степенью метаморфизма связаны и
технические свойства антрацитов - поведение их при измельчении и нагревании.
При измельчении распад происходит
прежде всего на элементы отдельности. Затем разрушаются слабые структурные
элементы, а при дальнейшем измельчении начинают разрушаться элементы структуры,
причем степень их измельчений и формы образующихся зерен зависят от природы
этих элементов.
Эти соотношения значительно влияют
на свойства измельченного антрацита. Они определяют форму зерен при каждой
степени измельчения и распределения их по величине. Очевидно, что форма зерен
должна зависеть от степени измельчения. Один и тот же антрацит может давать при
крупном измельчении пластинчатые зерна, а при среднем и мелком измельчении -
изометрические зерна. Если размер зерен антрацита, полученных в результате
измельчения, меньше толщины прослойки или отдельности по трещинам, то он ведет
себя как однородный материал и при измельчении может давать изометрические
зерна.
При нагревании антрациты склонны к
растрескиванию, причем, чем быстрее поднимается температура, тем резче
проявляется растрескивание. При одной и той же скорости нагревания разрушение
антрацита тем больше, чем меньше степень метаморфизма.
Кроме степени метаморфизма, на
термостойкость антрацита влияют структурные особенности. Макроскопически
однородные антрациты литого строения с хорошо или слабо выраженным раковистым
изломом, как правило, оказываются термически нестойкими. Антрациты однородного
сложения, но с хорошо заметными трещинами кливажа, часто с крупнозернистым
изломом отличаются более высокой термической стойкостью.
Несмотря на внешнюю однородность,
антрацит по своей структуре является сложным конгломератом. Только небольшая
часть зольных примесей, распределена равномерно в углистом веществе, значительная
же часть зольных примесей распределена неравномерно. Большая часть их
сосредоточена в тонких прослойках и отдельных включениях.
Для получения изделий высокого
качества необходимо, чтобы антрацит имел максимальное содержание углерода при
минимальном количестве балласта в виде золы, серы и влаги.
Техническими нормами на антрацит
предусматривается содержание не выше 5% золы, 3,5% летучих, 2% серы.
Графиты применяются в производстве
большинства углеграфитовых материалов. Роль, которую они выполняют в технологии
этих материалов, различна, они применяются для различных изделий. При
производстве электродов введение графита в массу улучшает ее пластичность,
снижает внутреннее трение массы, а также трение о стенки контейнера и
мундтштука. что обеспечивает получение более плотных изделий. В этом случае
вводятся небольшие количества графита (4-6%). Но даже такое количество графита
влияет на увеличение электропроводности, теплопроводности и термостойкости
электродов.
В производстве катодных блоков для
электролизных алюминиевых ванн графит служит для повышения стойкости их против
разрешающего воздействия паров натрия.
В электрических щетках графит служит
для регулирования электрического сопротивления, твердости, контактного
сопротивления и фрикционных свойств. В некоторых марках щеток содержание
графита достигает 60-80%.
Графиты или, точнее графитовые
материалы разделяются на два вида: явнокристаллические и скрытокристаллические.
К явнокристаллическим относятся
графиты, состоящие из кристаллов со средней величиной больше 1 мкм, т.е.
видимых невооруженным глазом и под микроскопом. К явнокристаллическим графитам
относятся чешуйчатые и плотнокристаллические натуральные графиты, а также
доменный графит, который выкристаллизовывается из чугуна во время ею
охлаждения.
Чешуйчатые графиты состоят из
отдельных кристаллов или из параллельных сростков, имеющих форму пластинок.
Чешуйки графита в разных месторождениях могут отличаться по величине и
отношению ширины к толщине. Эти различия сказываются на технических свойствах.
Наиболее ценны тонкие чешуйки, так как их порошки наиболее пластичные. Крупные
месторождения плотнокристаллических графитов довольно редки.
Скрытокристаллические графиты иногда
называют аморфными. Они сложены из кристаллов, имеющих величину от 10-4
до 10-6 см, т.е., в плотной массе неразличимы под микроскопом.
К этой же группе относится
искусственный графит, полученный нагреванием углей выше 2000° С. Его структура
определяется характером структуры исходного угля и температурой графитации: чем
плотнее структура угля и выше температура, тем крупнее кристаллы в
искусственном графите. Ориентировка кристаллов та же, какой она была в исходном
угле.
В промышленности натуральные графиты
получают из природных руд. Для превращения графитовой руды в товарные сорта
графитовых материалов ее подвергают обработке. Скрытокристаллические графиты
обогащают рудоразборкой и измельчают, иногда к ним применяют обогащение по
методу избирательного измельчения. Этим путем можно получить концентраты с
зольностью около 3%. Руды явнокристаллических графитов обогащают методом
флотации. Они обогащаются сравнительно хорошо и дают концентраты с зольностью
5-10%.
Натуральные графиты содержат примесь
минералов, не полностью удаленных из них при обогащении руд. Этими минералами
являются главным образом силикаты реже кварц и кальцит. Из силикатов наиболее
постоянной примесью является слюда. Из примесей, вносимых при обогащении
графитовых руд, следует назвать флотационные реагенты - главным образам
металлическое и окисленное железо, попадающее в графит во время размола в
мельницах.
Кокс - один из важнейших видов сырья
для электродного и электроугольного производства, особенно для графитовых
изделий и электроуглей. Наибольшую ценность представляют малозольные коксы
зольность которых не превышает 1%.
В России производят два вида
малозольных коксов нефтяные и пековые. Первые получают коксованием нефтяных
остатков вторые - переработкой на кокс каменноугольного пека.
Каменноугольный кокс
Каменноугольный кокс используется
при производстве угольных электродов, футеровочных и доменных блоков,
электродной массы для дуговых электрических печей (в производстве ферросплавов
и карбида кальция) и набивки подов в некоторых печах.
Каменноугольный кокс получают
коксованием спекающихся каменных углей. В промышленности производят две
разновидности коксов: доменный и литейный. Литейный кокс плотнее и содержит
несколько меньше золы, чем доменный. Поэтому его применяют для производства
электродных материалов.
Доменный (металлургический) кокс
используют в качестве вспомогательных материалов (обычно отходы мелких
фракций).
Пековый кокс
Пековый кокс в основном применяют
для производства анодной массы [15]. В небольших количествах его используют в
производстве электродных материалов, и очень ограниченное применение он находит
н производстве графитированных изделий.
Исходным материалом для производства
пекового кокса служат каменноугольные пеки. В последнее время коксованию
подвергают только высокоплавкие пеки с температурой размягчения около 150 °С.
Коксохимическая промышленность
производит три сорта пекового кокса. Существенно они отличаются только по
зольности. Размеры наибольших кусков не нормируются, обычно они не более 200
мм.
Нефтяные коксы
Нефтяными коксами называют твердые
углеродистые материалы, полученные при коксовании различных нефтяных остатков
[12]. Свойства нефтяных коксов зависят главным образом от вида нефтяных
остатков. Поэтому нефтяные коксы разделяют по роду нефтяных остатков, из
которых они получаются, на две большие группы крекинговые и пиролизные.
Крекинговые коксы получаются из остатков от переработки нефтепродуктов
крекинг-процессом, а пиролизные коксы - из остатков пиролиза.
В пределах каждой из этих групп
приходится различать еще некоторые разновидности, так как пиролиз и крекинг
производятся разными способами с применением различной аппаратуры и при
различном температурном режиме, что в значительной степени влияет на свойства и
состав полученных остатков. Это особенно относится к пиролизным остаткам, так
как условия их получения более разнообразны, чем крекинг-остатков.
Крекинг-процесс ведется при
температурах ниже 500° С. При этих температурах сажа не образуется и
ароматизация крекинг-остатков развивается незначительно. Основным сырьем для
производства нефтяного кокса служат тяжелые остатки, получающиеся в результате
атмосферной и вакуумной перегонки нефти, термического крекинга прямогонных
тяжелых остатков и др.
Плотность и характер пористости
нефтяных коксов зависит главным образом от вида нефтяных остатков, из которых
они получаются.
Различная микроструктура пиролизного
и крекингового коксов существенно влияет на технологические условия
производства изделий из этих коксов Большое количество закрытых микропор в
крекинговом коксе осложняет прессование, ведет к образованию в изделиях трещин
после снятия нагрузки.
Поведение этих коксов при графитации
также различно. Из крекингового кокса получается графит жирный, мягкий на
ощупь, с высокой электропроводностью, изделия легко поддаются механической
обработке и шлифовке. Из пиролизного кокса, наоборот, получается жесткий графит
с меньшей электропроводностью и более низкой плотности.
Чем больше содержание сажистого
углерода в нефтяных остатках, подвергающихся коксованию, тем с худшей
способностью к графитации получаются коксы.
Пиролизный нефтяной кокс
характеризуется наличием двух структур: струйчатой (волокнистой,
ориентированной) и сферолитовой. Струйчатая структура образует межпоровые
стенки и располагается вокруг участков со сферолитовой структурой.
В настоящее время промышленное
производство нефтяных коксов осуществляется в основном двумя способами:
коксование в металлических обогреваемых кубах и замедленное коксование в
необогреваемых камерах. Первый способ постепенно свертывается, как мало
эффективный.
Сажа представляет собой
высокоуглеродистое вещество, получающееся в газовой фазе в процессе неполного
сгорания или термического разложения углеводородного газа или пара [13].
Основная составляющая часть сажи - углерод (более 90%).
Изготовляемые в настоящее время
разнообразные сорта сажи классифицируются по методам производства, гак как они
в первую очередь определяют структуру и свойства сажи, характеризующие ее
поведение при использовании. В производстве электроугольных изделий применяют в
основном три типа сажи: ламповая, термическая и газовая канальная. Наиболее
широкое применение нашла ламповая сажа.
Для всех типов саж
характерна высокая дисперсность Размеры частиц для различных типов саж
колеблются от 90 до 6000
.
Форма сажевых частиц близка к сферической. По данным электронной микроскопии
большинство саж образует более или менее разветвленные цепочки, так называемые
сажевые структуры. Ламповая сажа характеризуется сильно разветвленной
цепочечной структурой. В пределах отдельной цепочки диаметры составляющих
частиц почти одинаковы. Частицы образуют цепочки не простым касанием, они как
бы частично погружены друг в друга.
Термическая сажа не
обладает цепочечной структурой. У термических саж, состоящих из крупных
сферолитов (400-4500
),
в результате слипания последних образуется нежесткая цепочечная структура
второго порядка. У большинства саж частички жестко соединены в цепочки.
Газоканальная сажа
отличается от первых двух значительно большей дисперностью. Частицы
агрегированы в цепочки, которые значительно короче и менее разветвлены, чем у
ламповой сажи.
Сажа обладает низкой
теплопроводностью (0,02-0,03
) и сильно зависит от
уплотнения. Сажа применяется при изготовлении электроугольных изделий (щетки,
осветительные угли и др.). Вследствие высокой дисперсности она обладает
некоторыми особенностями по сравнению с другими углеродистыми материалами. Чем
выше дисперсность сажи, тем большее количество связки требуется вводить в
шихту, что приводит к растрескиванию обожженных изделий. Чтобы исключить это
явление, из сажи и связующего приготавливается «сажевая масса» (первая стадия),
которая служит исходным материалом для изготовления электроугольных изделий.
Добавление в шихту сажевой массы облегчает производственные условия смешивания
и обжига. Сажа очень плохо графитируется, это свойство ее используется при
производстве щеток для машин с тяжелыми условиями коммутации.
Для изделий на основе
сажи характерна изотропность свойств. Появление преимущественной ориентации
агрегатов частиц в этом смысле ничего не меняет, так как основная причина
изотропности заключается в отсутствии преимущественного направления в
ориентации кристаллитов в частицах сажи.
В качестве связующих
могут применяться материалы, которые в процессе обжига коксуются и, оставляя
достаточное количество прочного кокса, придают изделиям необходимую прочность и
однородность [14]. Это - важнейшая функция связующих материалов. Вторая функция
заключается в том, что связующее должно сообщать связность формуемой массе,
пластифицировать ее, т.е. делать возможным прессование из нее изделий.
Прочность же спрессованных изделий должна быть настолько высокой, чтобы они не
деформировались под собственной нагрузкой и при транспортировке. Эти две
функции связующего не зависят одна от другой, но обязательны для любого вида
связующего.
Каменноугольная смола
образуется в процессе высокотемпературного коксования каменных углей. Смола при
обыкновенной температуре представляет собой довольно густую черную жидкость с
характерным запахом и плотностью более единицы. По составу - это смесь большого
количества индивидуальных органических соединений, основные из которых являются
ароматическими.
В смоле всегда имеется
вода. Смола в воде не растворяется, поэтому вода может быть выделена длительным
отстаиванием подогретой смолы.
Качество каменноугольной
смолы определяется следующими показателями: плотностью, вязкостью, выходом
различных фракций масел и пека, коксовым остатком или количеством летучих
веществ, количеством свободного углерода.
Состав и свойства смолы
определяются главным образом условиями коксования и практически не зависят от
разновидности углей, которые подверглись коксованию.
В основном свойства
смолы зависят от температуры подсводового пространства коксовой камеры,
скорости вывода летучих продуктов сухой перегонки угля и способа их охлаждения.
Чем больше скорость коксования, тем выше температура в камере и тем большие изменения
претерпевает смола под ее сводом. В результате этого свойства смолы изменяются
в определенном направлении: утяжеляется ее групповой состав, повышаются
плотность и вязкость, увеличивается содержание «свободного углерода».
Сырую смолу, прежде чем
она поступает в производство, подвергают предварительной обработке, которая
заключается в удалении влаги, легких и средних масел, нафталина. Этот процесс
осуществляется в обычной смолоперегонной реторте. В настоящее время редко можно
встретить производство изделий на одной смоле. Чаще применяют композиции из
смолы и пека.
Каменноуольный пек
представляет собой остаток после разгонки смолы, твердость его может быть
различной, как и температура размягчения. Наибольшее распространение в
электродной и электроугольной промышленности получил пек, имеющий температуру
размягчения 65-70° С и плотность 1.2-1,3. Чем большее количество фракций будет
отогнано из смолы, nем меньше будет получено
пека и тем выше будет температура его размягчения.
На установках
периодической разгонки смолы может быть получен пек с любой заданной
температурой размягчения.
Чтобы повысить
температуру размягчения пека, полученного при обычных условиях разгонки, смолы,
применяют способ продувки горячего воздуха или пара через расплавленную массу
пека. В настоящее время распространен способ продувки горячего воздуха.
Поскольку пеки являются
остатками от перегонки соответствующих смол, им частично присущи свойства этих
смол. Чем сильнее отогнана смола и, значит, тем тверже пек по своей
консистенции, тем больше характерных свойств, обусловленных составными
химическими частями смол, исчезает. Еще больше на изменение индивидуальных
свойств смолы влияет обработка пека воздухом.
В зависимости от
температуры размягчения пеки разделяют на мягкие, средине и твердые. Мягкие
пеки характеризуются температурой размягчения 40-55° С, средние 65-90° С и
твердые пеки имеют температуру размягчения выше 90° С.
Вода, входящая в состав
пека, содержится в нем в двух видах: капельно-жидком и тонко-распыленном.
Капельно-жидкая вода довольно легко отделяется при расплавлении пека.
Распыленная вода выделяется только при нагревании до 130° С. Эта вода вызывает
сильное вспенивание пека при сколько-нибудь быстром нагревании.
Между температурой
размягчения и коксовым остатком (коксовое число) для пеков, полученных из одной
и той же смолы, имеется определенная зависимость - повышение температуры
размягчения приводит к увеличению коксового остатка.
графитация керн кокс
термообработка
Список литературы
1. Чалых Е.Ф. Технология и оборудование электродных и
электроугольных предприятий. М.: «Металлургия», 1972.
2. Крылов В.Н. Производство угольных и графитированных
электродов, ГОНТИ, 1939.
. Красильников А.С. Производство электроугольных изделий.
ОНТИ, 1936.
. Чалых Е.Ф. Технология углеграфитовых материалов.
Металлургиздат, 1963.
. Беляев А.И. и др. Электрометаллургия алюминия.
Металлургиздат, 1953.
. Лейкин В.Л., Сахарук П.А. Электрометаллургия стали и
ферросплавов. Металлургиздат, 1955.
. Плуталова Л.А. Графитовые антифрикционные материалы.
ЦИНТИАМ, 1963.
. Фурсов В.С. Уран-графитовые ядерные реакторы. Изд-во АН
СССР, 1956.
. Крылов В.Н., Вильк Ю.Н. Углеграфитовые материалы и их
применение в химической промышленности. Изд-во «Химия», 1965.
. Соседов В.П., Чалых Е.Ф. Графитация углеродистых материалов.
М.: Металлургия, 1987.
. Веселовский В.С. Требования промышленности к качеству
минерального сырья. Вып.3, Графит, Госгеологиздат, 1952.
. Красюков А.Ф. Нефтяной кокс Изд-во «Химия», 1966.
. Зуев В.П., Михайлов В.В. Производство сажи, Изд-во «Химия»,
1965.
. Чалых Е.Ф., Васильева М.Г. Исследование связующих свойств
каменноугольного пека. Тр МХТИ им. Д.И. Менделеева, 1959.