Проект цеха точного литья производительностью 500 тонн в год
СОДЕРЖАНИЕ
РЕФЕРАТ
ПЕРЕЧЕНЬ
ЛИСТОВ ГРАФИЧЕСКИХ ДОКУМЕНТОВ
ВВЕДЕНИЕ
. ПРОЕКТНАЯ
ЧАСТЬ
.1
Обоснование места строительства проектируемого цеха
.2
Производственная программа
.3 Выбор
режима работы цеха и расчёт фондов времени
1.4
Выбор сплавов и их характеристика
.5 Модельный
участок
1.5.1 Выбор и
расчет оборудования для модельного отделения
.6 Участок
изготовления литейных форм
.6.1 Выбор и
расчет оборудования для нанесения огнеупорного
покрытия
.6.2
Оборудование для сушки огнеупорного покрытия
.6.3 Выбор и расчет
оборудования для выплавления модельного состава
.7
Прокалочно-заливочное отделение
.7.1 Выбор и
расчет оборудования для прокалки форм
.7.2 Расчет
шихты
.7.3 Выбор и
расчет количества плавильных печей
.7.4 Выбор и
расчет парка ковшей
.8 Отделение
обрубки, очистки и термообработки отливок
.8.1
Предварительная очистка блоков отливок от оболочки формы
.8.2
Отделение отливок от литниковой системы
.8.3
Окончательная очистка отливок
.8.4
Исправление дефектов
.8.5 Расчет
оборудования для термообработки
.9 Балансы
материалов
.9.1 Баланс
металла
.9.2 Баланс
смесей
.10 Расчет
складов
.11
Внутрицеховой транспорт
.
ТЕХНОЛОГИЧЕСКАЯ ЧАСТЬ
.1 Анализ
конструкции детали и условий ее эксплуатации. Конструирование отливки
.2
Обоснование выбора способа изготовления отливки
.3 Выбор и
обоснование места и уровня подвода металла
.4 Выбор и
обоснование конструкции литниково-питающей системы
.5 Расчет
элементов литниково-питающей системы
.6
Проектирование и изготовление пресс-формы
.7
Технологический выход годного
.8 Изготовление
моделей
.8.1Требования
к модельным составам
.9
Изготовление литейной формы
.9.1.Приготовление
гидролизованного раствора этилсиликата
2.10
Плавка металла и заливка форм
2.10.1
Устройство индукционного плавильного комплекса
.10.2
Футеровка тигля индукционной печи
.10.3
Футеровка ковша
2.10.4
Выплавка стали в индукционном плавильном комплексе УИП-250-2,4-0,25 с кислой
футеровкой
2.11 Контроль
качества металла
.12
Разработка технологического процесса изготовления отливки
.13 Анализ
возможных видов брака и меры их предотвращения
.
ЭКОНОМИЧЕСКАЯ ЧАСТЬ
.1
Организация труда и планирование численности персонала
.2
Организация и расчёт заработной платы персонала
.3 Расчёт
капитальных вложений
.4
Планирование себестоимости продукции
.4.1
Калькуляция себестоимости годных отливок из стали
.5
Технико-экономические показатели проекта
.
БЕЗОПАСНОСТЬ ЖИЗНИДЕЯТЕЛЬНОСТИ
.1
Безопасность труда
.1.1 Общие
положения
.1.2
Микроклимат и тепловое излучение
.1.3 Защита
от теплового излучения
.1.4
Производственное освещение
.1.5 Безопасность
труда на складах шихтовых материалов
.1.6
Безопасность труда в плавильном отделении
.1.7
Безопасность труда в обрубном отделении
.1.8
Электробезопасность
.1.9 Защита
от повреждения механическим оборудованием
.1.10 Защита
от вибрации
.1.11 Защита
от шума
.1.12
Запыленность, загазованность
.1.13
Вентиляция
.2
Чрезвычайные ситуации
.2.1 Защита
персонала от ЧС
.
ПРИРОДОПОЛЬЗОВАНИЕ И ОХРАНА ОКРУЖАЮЩЕЙ СРЕДЫ
.1 Оценка
экологичности проекта
БИБЛИОГРАФИЧЕСКИЙ
СПИСОК
РЕФЕРАТ
Ключевые слова: ЛИТЬЕ ПО ВЫПЛАВЛЯЕМЫМ МОДЕЛЯМ, ИНДУКЦИОННАЯ ПЕЧЬ,
ОТЛИВКА, ПРЕСС-ФОРМА, ЭТИЛСИЛИКАТ, ПРОЕКТИРОВАНИЕ ЦЕХА, СЕБЕСТОИМОСТЬ, ОХРАНА
ТРУДА, ОХРАНА ПРИРОДЫ.
Цель работы - разработка проекта нового литейного цеха. Настоящий проект
разработан согласно заданию на дипломное проектирование.
В данном дипломном проекте рассматривается проект цеха точного литья с
установкой следующего оборудования:
индукционных печей УИП-250-2,4-0,25,
шприц-машины для изготовления восковых моделей производства компании Cleveland
Tool and Machine CTM-WI 15, бака с мешалкой для обмазки блоков модели 9190 и
пескосыпа «кипящий слой» модели 9191 для нанесения огнеупорного покрытия
Тираспольского завода ОАО «ЛитМаш», установки для сушки огнеупорного покрытия
683, бойлерклава производства компании LBBC
Technologies для вытопки модельного состава, абразивоструйной
машины модели PB1500PMB, а также дробемет модели SB1015A1.
Выбранное оборудование обеспечит экономически эффективное производство
отливок.
В проектной части дипломного проекта приведена производственная программа
литейного цеха и режим работы цеха. Произведен подбор и краткое описание
необходимого оборудования. В технологической части предложен технологический
процесс изготовления отливок способом литья по выплавляемым моделям. В
экономической части дипломного проекта приведено экономическое обоснование
проекта, приведены расчеты инвестиционных затрат, а также срока окупаемости
цеха при внедренной технологии. В главе, посвященной охране труда,
рассматриваются вопросы безопасности жизнедеятельности. Описываются условия
труда работников, указаны классы условий труда, меры предупреждения и снижения
вредных и опасных факторов производства. В пятой главе рассмотрена степень
влияния производства на окружающую среду. Рассчитан класс опасности
производства.
ВВЕДЕНИЕ
Литье по выплавляемым моделям (ЛВМ) способ получения отливок в
многослойных оболочковых неразъемных разовых формах, изготовляемых с
использованьем выплавляемых, а также выжигаемых и растворяемых моделей
однократного использования. Промышленное применение этого метода обеспечивает
получение из любых литейных сплавов фасонных отливок массой от нескольких
граммов до десятков килограммов со стенками, толщина которых в ряде случаев
менее одного миллиметра, с высокой точностью размеров и чистотой поверхности.
Указанные возможности метода позволяют максимально приблизить отливки к готовой
детали, а в ряде случаев получить детали, не требующие дополнительной
обработки. В результате значительно снижается трудоемкость и стоимость
изготовления изделий, сокращается расход металла и инструментов, уменьшается
энергоемкость производства, сокращается потребность в рабочих станочниках
высокой квалификации, в станочном оборудовании и приспособлениях,
производственных площадях.
Применение ЛВМ позволяет проектировать сложные тонкостенные детали,
объединять отдельные детали в компактные цельнолитые узлы, уменьшая массу и
габаритные размеры изделий, создавать конструкции, невыполнимые какими либо
другими методами обработки.
В связи с большой номенклатурой производимых отливок высокая степень
автоматизации этого производства нецелесообразна, поэтому снижение
себестоимости продукции возможно с введением удешевленной комбинированной
технологии. Данная технология позволяет получать высокое качество поверхности,
со снижением затрат приходящихся на материалы используемые в производстве.
Экономичность и целесообразность применения способа ЛВМ определяется
правильно подобранной номенклатурой отливок. Более рационально изготавливать
мелкие, а также сложные и ответственные отливки, к которым предъявляются
высокие требования по точности и чистоте поверхности.
1. ПРОЕКТНАЯ ЧАСТЬ
.1 Обоснование места строительства проектируемого цеха
Для проектирования литейного цеха необходимо наличие развитой
производственной и непроизводственной инфраструктуры. Сырьё и готовая продукция
доставляются железнодорожным и автомобильным транспортом. Для доставки рабочих
используют преимущественно автомобильный транспорт. Литейное оборудование
потребляет большое количество электроэнергии. Таким образом, в производственную
инфраструктуру литейного цеха входят автомобильные дороги, электрические сети,
водопровод.
Непроизводственная инфраструктура включает жилые дома, учреждения и
организации здравоохранения, образования, связи, социального обеспечения, сферы
услуг и т.д. Создание непроизводственной инфраструктуры вместе с проектируемым
предприятием ведёт к огромным затратам. Экономически в долгосрочной перспективе
создание инфраструктуры может быть оправдано за счёт снижения затрат на
транспортировку сырья или готовой продукции при неизменном спросе на неё.
Прогнозировать спрос на длительный срок в современных условиях чрезвычайно
опасно. Поэтому, исходя из всего вышесказанного, предлагается расположить цех
на территории города Екатеринбурга в промышленном районе.
.2 Производственная программа
Производственная программа - это краткосрочный план работы литейного цеха
на определенный период времени (обычно на год). Она содержит данные для
планирования деятельности всех подразделений литейного цеха. Производственная
программа составляется на основе технологической документации на каждый вид
отливок. Планирование производственной программы литейного участка производится
на основании заказов цехов предприятия.
Проектом цеха литья по выплавляемым моделям предусмотрено:
• годовой выпуск годного литья 500 тонн в год:
Сталь 45Л;
Сталь 35Л;
• номенклатура до 35 наименований.
Производственная программа предполагается стабильной по месяцам.
Приведённая производственная программа составлена по отливкам -
представителям и представлена в таблице 1.1.
Таблица 1.1
Производственная программа
№ п. п
|
наименование отливки
(артикул)
|
марка сплава
|
масса отливки, кг
|
количество отливок в блоке,
шт
|
масса отливки с литниковой
системой, кг
|
выход годного, %
|
масса модельного состава на
блок, кг
|
масса огнеупорного покрытия
на блок, кг
|
количество отливок в год,
шт
|
масса отливок в год, кг
|
масса отливок с литниковой
системой в год, кг
|
количество блоков в год, шт
|
масса модельного состава в
год, без учета возврата 50%, кг
|
масса модельного состава в
год, с учетом возврата 50%, кг
|
масса огнеупорного покрытия
в год, кг
|
1
|
2
|
3
|
4
|
5
|
6
|
7
|
8
|
9
|
10
|
11
|
12
|
13
|
14
|
15
|
16
|
1
|
вилка (№66-02.01.020Б)
|
35Л
|
0,32
|
10
|
0,52
|
62
|
0,06
|
0,21
|
15000
|
4800
|
7800
|
1500
|
93,6
|
46,8
|
312
|
2
|
вилка лебедки
(66-02.02.063Б)
|
35Л
|
0,4
|
8
|
0,65
|
62
|
0,08
|
0,26
|
23000
|
9200
|
14950
|
2875
|
224,25
|
112,13
|
747,5
|
3
|
вилка кардана (БКГМ
142.01.01Б)
|
35Л
|
2,5
|
4
|
3
|
83
|
0,36
|
1,2
|
5390
|
13475
|
16170
|
1348
|
485,1
|
242,55
|
1617
|
4
|
втулка кронштейна
(БКМ-317.10.10.0115)
|
35Л
|
0,48
|
6
|
0,81
|
59
|
0,1
|
0,33
|
15000
|
7200
|
12200
|
2500
|
244
|
122
|
813,33
|
5
|
втулка поворотная
|
35Л
|
0,7
|
4
|
1,2
|
58
|
0,14
|
0,48
|
14090
|
9863
|
16908
|
3523
|
507,24
|
253,62
|
1690,8
|
6
|
вал коленчатый левый
(СП-6500.00.00.00.004Л)
|
35Л
|
4,4
|
1
|
6,4
|
69
|
0,77
|
2,56
|
4900
|
21560
|
31360
|
4900
|
3763,2
|
1881,6
|
12544
|
7
|
вал коленчатый правый (СП-6500.00.00.00.005Л)
|
35Л
|
4,2
|
1
|
6,2
|
68
|
0,74
|
2,48
|
5040
|
21168
|
31248
|
5040
|
3749,76
|
1874,88
|
12499,2
|
|
8
|
вал коленчатый левый
(СП-6000.03.00.00.000)
|
35Л
|
3
|
1
|
5
|
60
|
0,6
|
2
|
5300
|
15900
|
26500
|
5300
|
3180
|
1590
|
10600
|
|
9
|
вал коленчатый правый (СП-6000.04.00.00.005)
|
35Л
|
3
|
1
|
5
|
60
|
0,6
|
2
|
1200
|
3600
|
6000
|
1200
|
720
|
360
|
2400
|
|
10
|
забурник (БК-01202.36.001)
|
45Л
|
7,2
|
1
|
9,2
|
78
|
1,1
|
3,68
|
1600
|
11520
|
14720
|
1600
|
1766,4
|
883,2
|
5888
|
|
11
|
забурник (БК-02801.36.001)
|
45Л
|
8,3
|
1
|
10,3
|
81
|
1,24
|
4,12
|
1730
|
14359
|
17819
|
1730
|
2138,28
|
1069,14
|
7127,6
|
|
12
|
корпус редуктора
(К-4500.08.02.02000-01)
|
35Л
|
4
|
1
|
6
|
67
|
0,72
|
2,4
|
3000
|
12000
|
18000
|
3000
|
2160
|
1080
|
7200
|
|
13
|
корпус (БМ-302Б.02.02.801)
|
35Л
|
3,2
|
1
|
5,2
|
62
|
0,62
|
2,08
|
2400
|
7680
|
12480
|
2400
|
1497,6
|
748,8
|
4992,
|
|
14
|
ключ поддерживающий (ШК-1000.00.00.00.005-01)
|
35Л
|
2,7
|
4,7
|
57
|
0,56
|
1,88
|
2400
|
6480
|
11280
|
2400
|
1353,6
|
676,8
|
4512
|
|
15
|
ключ поддерживающий
1(ШК1000.00.00.00.005-02)
|
35Л
|
2,7
|
1
|
4,7
|
57
|
0,56
|
1,88
|
4360
|
11772
|
20492
|
4360
|
2459,04
|
1229,52
|
8196,8
|
|
16
|
крышка тормоза (ШК-1000.00.00.00.007)
|
45Л
|
1,15
|
4
|
1,65
|
70
|
0,2
|
0,66
|
5230
|
6014,5
|
8630
|
1308
|
258,89
|
129,44
|
862,95
|
|
17
|
кронштейн
(ШК-1000.19.00.00.001)
|
35Л
|
2,3
|
2
|
3,3
|
70
|
0,4
|
1,32
|
2800
|
6440
|
9240
|
1400
|
554,4
|
277,2
|
1848
|
|
18
|
муфта угловая
(К-5600.11.00.00.003)
|
35Л
|
1,1
|
2
|
2,1
|
52
|
0,25
|
0,84
|
9500
|
10450
|
19950
|
4750
|
1197
|
598,5
|
3990
|
|
19
|
накладка (БЛ.30.01.101)
|
35Л
|
1,6
|
4
|
2,1
|
76
|
0,25
|
0,84
|
5840
|
9344
|
12264
|
1460
|
367,92
|
183,96
|
1226,4
|
|
20
|
накладка (БЛ.80.01.102)
|
35Л
|
4
|
1
|
6
|
67
|
0,72
|
2,4
|
12400
|
49600
|
74400
|
12400
|
8928
|
4464
|
29760
|
|
21
|
опора (1200.01)
|
35Л
|
3,9
|
1
|
5,9
|
66
|
0,71
|
2,36
|
12000
|
46800
|
70800
|
12000
|
8496
|
4248
|
28320
|
|
22
|
ручка (К-1200.00.00.00.004)
|
45Л
|
0,5
|
10
|
0,7
|
71
|
0,08
|
0,28
|
16350
|
8175
|
11445
|
1635
|
137,34
|
68,67
|
457,8
|
|
23
|
рычаг (РСУ-45.00.00.00.003)
|
35Л
|
1,4
|
2
|
2,4
|
58
|
0,29
|
0,96
|
12000
|
16800
|
28800
|
6000
|
1728
|
864
|
5760
|
|
24
|
рычаг переключения
(66-02.02.404)
|
35Л
|
0,5
|
8
|
0,75
|
67
|
0,09
|
0,3
|
36000
|
18000
|
27000
|
4500
|
405
|
202,5
|
1350
|
|
25
|
рычаг (66-05.01501А)
|
35Л
|
0,25
|
10
|
0,45
|
56
|
0,05
|
0,18
|
20400
|
5100
|
9180
|
2040
|
110,16
|
55,08
|
367,2
|
|
26
|
рычаг (К-1500.02.00.00.002)
|
35Л
|
2,1
|
1
|
4,1
|
51
|
0,49
|
1,64
|
7750
|
16275
|
31775
|
7750
|
3813
|
1906,5
|
12710
|
|
27
|
сменная челюсть
(РСУ-45.03.00.000)
|
35Л
|
2,4
|
1
|
4,4
|
55
|
0,53
|
1,76
|
11100
|
26640
|
48840
|
11100
|
5860,8
|
2930,4
|
19536
|
|
28
|
тройник
(К-4500.21.00.00.004)
|
35Л
|
0,57
|
10
|
0,77
|
74
|
0,09
|
0,31
|
20400
|
11628
|
15708
|
2040
|
188,5
|
94,25
|
628,32
|
|
29
|
угольник концевой
(К-4500.11.00.00.006Л)
|
45Л
|
0,92
|
8
|
1,17
|
79
|
0,14
|
0,47
|
15360
|
14131,2
|
17971
|
1920
|
269,57
|
134,78
|
898,56
|
|
30
|
угольник
(К-4500.21.0000.002)
|
45Л
|
0,54
|
10
|
0,74
|
73
|
0,09
|
0,3
|
27300
|
14742
|
20202
|
2730
|
242,42
|
121,21
|
808,08
|
|
31
|
угольник
(К-4500.21.0000.003)
|
45Л
|
0,66
|
8
|
0,91
|
73
|
0,11
|
0,36
|
18300
|
12078
|
16653
|
2288
|
249,8
|
124,9
|
832,65
|
|
32
|
угольник
(К-1200.01.01.00.001)
|
45Л
|
0,8
|
6
|
1,13
|
71
|
0,14
|
0,45
|
24000
|
19200
|
27200
|
4000
|
544
|
272
|
1813,33
|
|
33
|
фланец (БКГМ 142-00-1А)
|
45Л
|
2,5
|
1
|
4,5
|
56
|
0,54
|
1,8
|
10300
|
25750
|
46350
|
10300
|
5562
|
2781
|
18540
|
|
34
|
фланец (66-04.04.100А)
|
45Л
|
0,42
|
8
|
0,67
|
63
|
0,08
|
0,27
|
30000
|
12600
|
20100
|
3750
|
301,5
|
150,75
|
1005
|
|
Итого
|
401440
|
500345
|
774435
|
137047
|
81435
|
162870
|
390855
|
Итого с учетом брака
отливок (4 %)
|
417498
|
|
805412
|
142529
|
84692
|
169385
|
406489
|
Итого с учетом брака
оболочек (1%)
|
|
|
|
143954
|
|
|
410554
|
|
|
|
|
|
|
|
|
|
|
|
|
|
|
|
|
|
|
|
|
|
|
|
|
|
|
|
|
|
|
.3 Выбор режима работы цеха и расчёт фондов времени
ступенчатый (последовательный) - с разделением операций во времени в
неизолированном общем помещении. Этот режим преимущественно применяется в
условиях индивидуального и мелкосерийного производства;
параллельный - при котором все технологические операции выполняются
одновременно на различных производственных участках.
Для данного цеха выбираем двухсменный параллельный режим работы с
выходными и праздничными днями, дающий сокращение времени производственного
цикла изготовления отливок, а также позволяющий рационально использовать
оборудование и производственные площади цеха. Двухсменный режим выгоден также
тем, что позволяет проводить профилактический осмотр и ремонт оборудования в
течение третьей смены. Третья смена при этом используется для подготовки
производства, наладки, ремонта оборудования и является резервом на случай
необходимости увеличения выпуска продукции.
В соответствии с принятым режимом работы рассчитываем фонды времени
работы оборудования, рабочих мест.
Номинальный фонд времени Тн - полное время работы цеха, в
течение которого должен работать цех без каких-либо потерь за исключением
праздников и выходных дней (фонд времени рабочих мест):
Тн=(К-В-П)∙С∙Ч (1)
где К - количество дней в году;
В - количество выходных дней в году;
П - количество праздников в году;
С - количество рабочих смен в сутки
Ч - длительность рабочей смены.
Таблица 1.2
Баланс рабочего времени оборудования
№ п/п
|
Показатель
|
Количество дней
|
1
|
календарный фонд времени
|
365
|
2
|
выходные дни
|
104
|
3
|
праздничные дни
|
11
|
Тн=(К-В-П)∙С∙Ч=(365-104-11)∙2∙8 =4000
ч
Действительный фонд времени - годовое время, в течение которого
фактически работают рабочие, и производится работа на оборудовании или на
рабочем месте при установленном в цехе режиме работ. Действительный фонд
рабочего времени оборудования равен номинальному за вычетом времени на
планово-предупредительные и капитальные ремонты. Точное время на
планово-предупредительные ремонты неизвестно, оно планируется.
Действительный фонд времени работы оборудования рассчитывается с учетом
коэффициента потерь рабочего времени Кп по формуле:
Тд = Тн(1-Кп), (2)
где Кп - коэффициент потерь времени работы оборудования.
Этот коэффициент в основном обусловлен простоями оборудования из-за
поломок и, следовательно, зависит от интенсивности эксплуатации.
Таблица 1.3
Коэффициент потерь времени работы оборудования
Оборудование
|
Коэффициент потерь времени
работы оборудования, % (при 2-х сменном режиме)
|
индукционные печи
|
5
|
термические печи
|
3
|
технологическое
оборудование (механизированное) для мелкого литья
|
4
|
технологическое
оборудование (автоматизированное) для мелкого литья
|
5
|
Тд = Тн(1-Кп) = 4000(1-0,05) = 3800 ч -
для индукционных печей;
Тд = Тн(1-Кп) = 4000(1-0,03) = 3880 ч -
для термических печей;
Тд = Тн(1-Кп) = 4000(1-0,05) = 3800 ч -
для автоматизированного оборудования;
Тд = Тн(1-Кп) = 4000(1-0,04) = 3840 ч -
для механизированного оборудования.
1.4 Выбор сплавов и их характеристика
Отливки по выплавляемым моделям изготавливают практически из всех
литейных сплавов: углеродистых и легированных сталей, коррозионно-стойких и
жаростойких сталей и сплавов, чугуна и цветных сплавов.
При литье по выплавляемым моделям наиболее часто применяют среднеуглеродистую
сталь 35Л, из которой можно получать сложные тонкостенные отливки, в том числе
крупногабаритные.
Сталь 35Л - относится к среднеуглеродистым сталям, которые в литейном
производстве применяют для большинства стальных отливок, т.к. литейные свойства
их несколько выше, чем низкоуглеродистых сталей: ниже температура плавления;
выше жидкотекучесть; меньше образуется газов и не металлических включений в
отливке; меньше опасности образования горячих трещин; меньше пригар на
отливках. Однако пониженная теплопроводность стали, приводит к образованию
повышенных напряжений.
Отливки по выплавляемым моделям изготавливают практически из всех
литейных сплавов: углеродистых и легированных сталей, коррозионно-стойких и
жаростойких сталей и сплавов, чугуна и цветных сплавов.
При литье по выплавляемым моделям наиболее часто применяют
среднеуглеродистую сталь 35Л, из которой можно получать сложные тонкостенные
отливки, в том числе крупногабаритные.
Сталь 35Л - относится к среднеуглеродистым сталям, которые в литейном производстве
применяют для большинства стальных отливок, т.к. литейные свойства их несколько
выше, чем низкоуглеродистых сталей: ниже температура плавления; выше
жидкотекучесть; меньше образуется газов и не металлических включений в отливке;
меньше опасности образования горячих трещин; меньше пригар на отливках. Однако
пониженная теплопроводность стали, приводит к образованию повышенных
напряжений. Химические и механические свойства сталей указаны в таблицах 1.4 и
1.5 соответственно.
Таблица 1.4
Химические свойства сталей
Марка стали
|
Массовая доля элемента, %
|
|
С
|
Si
|
Mn
|
Cr
|
Ni
|
Cu
|
S
|
P
|
35Л
|
0,32-0,40
|
0,20-0,52
|
0,35-0,90
|
≤0,30
|
≤0,30
|
≤0,30
|
≤0,045
|
≤0,040
|
45Л
|
0,42-0,5
|
0,20-0,52
|
0,40-0,90
|
≤0,30
|
≤0,30
|
≤0,30
|
≤0,040
|
≤0,040
|
Таблица 1.5
Механические свойства сталей
Марка стали
|
Предел текучести σ0,2, МПа
|
Временное сопротивление σв, МПа
|
Относительное удлинение δ, %
|
Относительное сужение ψ, %
|
Ударная вязкость, кДж/м2
|
35Л
|
280
|
500
|
15
|
25
|
350
|
45Л
|
320
|
550
|
12
|
20
|
290
|
1.5 Модельный участок
Выплавляемые модели изготовляют запрессовкой модельного состава в
пресс-формы. Модельные составы, запрессовываемые в пресс-формы, образуют модели
с гладкой поверхностью, которые затем вручную припаиваются на стояк, с помощью
питателей. К свойствам модельных составов предъявляют комплекс требований,
которые могут иметь существенные различия в зависимости от конфигурации,
размеров и назначения отливок, необходимой размерной точности их и качества
поверхности, масштабов и характера производства, принятого технологического
варианта процесса изготовления оболочек форм, требований к уровню механизации и
экономическим показателям производства. Требования во многом определяются также
природой и свойствами самого модельного состава. Необходимо, чтобы свойства
составов обеспечивали получение высококачественных моделей при одновременной
технологичности составов. Большинство используемых модельных составов
обеспечивает получение качественной поверхности модели и точного
воспроизведения внутренней полости пресс-форм. При правильном выборе
коэффициента усадки размеры модели также удается получить с достаточной
точностью. Наиболее трудно гарантировать точную геометрическую форму, так как
модельный состав при затвердевании изменяет размер. Всем вышеперечисленным
условиям удовлетворяет модельный состав ПС 50-50 - он и будет использоваться в
проектируемом цехе.
.5.1 Выбор и расчет оборудования для модельного отделения
Для приготовления модельного состава из материалов с температурой
плавления не выше 90˚С будет использована шприц-машина для изготовления
восковых моделей производства американской компании Cleveland Tool and Machine с инжекционной запрессовкой CTM-WI 15,
производительностью 0,59 м3/ч. Необходимое количество оборудования
для приготовления модельной массы можно рассчитать по формуле:
(3)
где
Q - годовая потребность в модельном составе с учетом
брака, т;
q -
производительность установки, м³/ч;
Тд
- действительный годовой фонд рабочего времени оборудования, ч;
ρм -
плотность модельного состава, кг/м³ (ρм =0,9)
Принимаем
количество установок CTM-WI 15 - 1.
Технические
характеристики шприц-машины CTM-WI 15 для прессования восковых моделей:
усилие
смыкания пресса, т: 0-13,6
скорость
закрытия/открытия пресса, мм/сек: 38
ёмкость
бака для модельного состава, л: 28
объем
разового впрыска, см3: 1639
давление
на материал при впрыске, бар: 6
максимальная
скорость впрыска, см3/сек: 163
время
цикла впрыска, сек: 0-999
давление
в гидросистеме, бар: 138
ёмкость
бака гидросистемы, л: 38
масса
(в стандартной комплектации), кг: 1600
габаритные
размеры, мм: 1980х1750
1.6
Участок изготовления литейных форм
Стенки
оболочковой формы, изготовленной по методу ЛВМ, представляют собой прочную
керамическую корочку, полученную в результате нанесения на модель нескольких
слоев суспензии и обсыпки. Суспензия представляет собой смесь жидкого
связующего и огнеупорного наполнителя. Обсыпкой является огнеупорный сыпучий
материал. В качестве суспензии будет использоваться этилсиликатное покрытие, в
состав которого в качестве связующего входит гидролизованный этилсиликат ГС-40
(массовая доля: 30-40%), а в качестве огнеупорного материала - пылевидный кварц
(массовая доля: 60-70%).
Формовочные
смеси для литья по выплавляемым моделям стали представляют собой суспензию, состоящую
из жидкой фазы - связующего, и твердой фазы - огнеупорного материала с
определенной величиной зерна.
.6.1
Выбор и расчет оборудования для нанесения огнеупорного покрытия
Для
нанесения огнеупорной суспезнии на блоки будет использоваться агрегат 9190 -
бак с мешалкой для обмазки блоков, Тираспольского завода ОАО «ЛитМаш».
Для
расчета количества агрегатов используется формула:
(4)
где
Q - годовая потребность суспензии с учетом брака, т;
q -
производительность установки, м³/ч;
Тд-
действительный годовой фонд рабочего времени оборудования, ч.
Выбираем
2 установки для нанесения огнеупорного покрытия.
Технические
характеристики установки 9190:
габаритные
размеры, мм: 1035х950х1540
производительность,
кг/ч: 90
вместимость,
м3: 0,063
установленная
мощность, кВт: 1,5
масса,
кг: 450
Для
нанесения огнеупорного покрытия на модельные блоки будет использоваться два
агрегата модели 9191 - пескосып «кипящий слой» Тираспольского завода ОАО «ЛитМаш».
Технические
характеристики установки 9191:
габаритные
размеры, мм: 920х745х1170
вместимость,
м3: 0,132
расход
сжатого воздуха, м3/ч: 2
масса,
кг: 170
.6.2
Оборудование для сушки огнеупорного покрытия
Выбираем
установку сушки блоков для послойного отверждения и сушки огнеупорного покрытия
на основе этилсиликата модели 683 (4 штуки - для увеличения скорости процесса). Способ сушки - вакуумно-аммиачный.
Техническая
характеристика установки 683:
производительность
- 12 блоков/час;
габаритные
размеры, мм: длина - 1000;
ширина
- 1300;
высота
- 2000.
.6.3
Выбор и расчет оборудования для выплавления модельного состава
Для вытопки восковых моделей будет использоваться Бойлерклав
производства компании LBBC Technologies. Вследствие быстрого (за 3-4 секунды до
6 бар) набора давления пара и температуры в рабочей камере расплавление воска
по границе раздела «воск-керамика» происходит прежде, чем начнется объемное
расширение модельной массы в форме, благодаря чему сводится к минимуму
растрескивание керамических форм. Вторым фактором, снижающим вероятность
растрескивания керамических оболочковых форм в результате объемного расширения
модельной массы, является то, что высокое рабочее давление пара в камере
(порядка 9,0 - 9,5 бар) сжимает керамическую форму снаружи, противодействуя ее
растяжению из-за объемного расширения модельной массы.
Расчет
количества оборудования производится по формуле:
(4)
где
Q - годовая потребность в блоках с учетом брака, шт;
q -
производительность установки, блок/ч;
Тд-
действительный годовой фонд рабочего времени оборудования, ч
Выбираем
1 установку для выплавки модельного состава.
Технические
характеристики установки:
габаритные
размеры, мм: 3160х3770х2470
производительность,
блок/ч: 105
установленная
мощность, кВт: 4
масса,
кг: 3500
1.7
Прокалочно-заливочное отделение
.7.1
Выбор и расчет оборудования для прокалки форм
Для
прокалки форм будут использоваться электропечи сопротивления камерные типа ПВО.
Данные печи предназначены для обжига керамики, огнеупоров и других материалов.
Печи оборудованы распашной дверью и выкатным подом. Перемещение пода
осуществляется вручную по рельсовым направляющим на двух колесных парах, с
помощью специальной рукоятки. Для улучшения теплоизоляции под печи оснащен
песчаным затвором. Рассчитываем требуемую производительность оборудования,
принимая n=3:
(5)
где
Q - годовая потребность огнеупорного покрытия с учетом
брака, т;
Тд-
действительный годовой фонд рабочего времени оборудования, ч;
n - количество
печей.
В
цехе будут установлены электропечи с выкатным подом для обжига ПВО-1,2-500.
Технические
характеристики ПВО-1,2-500:
Тмакс,°С:
1200
рабочее
пространство (шир/дл/выс), мм: 600/1000/800
габаритные
размеры (шир/дл/выс),, мм: 1290/2580/1835
мощность
/ напряжение, кВт/В: 30/380
масса
печи, кг: 1200
1.7.2
Расчет шихты
Шихту
рассчитывают, пользуясь следующими исходными данными: требуемый химический
состав, химический состав шихтовых материалов, угар элементов.
Расчет
шихты будет производиться на примере марки стали 35Л. Для выплавки стали в
проектируемом цехе будут использоваться индукционные тигельные печи, емкостью
0,25т. Расчёт шихты для приготовления сплава 35Л производится на 100 кг сплава.
Процесс плавки протекает быстро. Химический состав сплава 35Л и его угар
указаны в таблицах 1.6 и 1.7 соответственно.
Таблица
1.6
Химический
состав сплава 35Л (ГОСТ 977-88)
Основной компонент
|
Легирующие компоненты, %
|
|
C
|
Mn
|
Si
|
Cr
|
P
|
S
|
Ni
|
Cu
|
Fe
|
0,32-0,4
|
0,5-0,8
|
0,17-0,37
|
<0,25
|
<0,035
|
<0,04
|
<0,25
|
<0,25
|
Расчёт шихты производим на средний химический состав сплава, % масс:
углерод - 0,36; марганец - 0,65; кремний - 0,27.
Таблица 1.7
Угар элементов
Элемент
|
Fe
|
C
|
Si
|
Mn
|
Cr
|
Fe
|
C
|
Si
|
Угар, %
|
1-3
|
5-15
|
10-20
|
30-50
|
5-10
|
1-3
|
5-15
|
10-20
|
Расчет шихты ведется на основные элементы, и проверяют на допустимую
величину вредных примесей.
При расчёте шихты главным образом учитывается угар элементов, который
отображается по формуле:
(6)
где
Кш -расчетное содержание компонента в шихте, кг;
Кс
- заданное содержание компонента в сплаве, кг;
У
- принимаемый угар, %.
Химический
состав шихтовых материалов указан в таблице 1.8.
Таблица
1.8
Химический
состав шихтовых материалов
Компоненты шахты
|
Химический состав, %
|
|
C
|
Mn
|
Si
|
P
|
S
|
Fe
|
возврат собственного
производства
|
0,36
|
0,68
|
0,36
|
0,02
|
0,02
|
98,68
|
стальной лом
|
0,21
|
0,63
|
0,3
|
0,05
|
0,03
|
98,47
|
ФС 75
|
-
|
0,7
|
77
|
0,05
|
0,04
|
22,21
|
ФМn 88
|
-
|
75,1
|
2
|
0,35
|
0,03
|
22,52
|
Расчет содержания Si:
Требуемое содержание в отливках 0,27 % Si (У=15).
Кш = 0,27*100/(100-15) = 0,32 % или 0,32 кг.
Вносится Si в шихту с
возвратом: 0,27*60/100 = 0,162 кг.
Вносится Si в шихту со
стальным ломом: 0,3*32/100 = 0,09 кг.
Вносится Si в шихту со
стальной стружкой: 0,35*9/100 = 0,0315 кг.
Следует ввести Si в
шихту с ферросилицием:
,32-0,162-0,09-0,0315=0,0365кг.
Требуется ферросилиция 0,0365*100/77 = 0,05 кг.
Расчет содержания Mn:
Требуемое содержание в отливках 0,65 % Mn(У= 40).
Кш = 0,65*100/(100-40) = 1.08 % или 1.08 кг.
Вносится Mn в шихту с
возвратом: 0,65*60/100 = 0,39 кг.
Вносится Mn в шихту со
стальным ломом: 0,8*32/100 = 0,24 кг.
Вносится Mn в шихту со
стальной стружкой: 0,9*9/100 = 0,081 кг.
Следует ввести Mn в
шихту с ферромарганцем:
,08-0,39-0,24-0,081= 0,369 кг.
Требуется ферромарганца 0,369*100/75 = 0,5 кг.
Расчет содержания Fe:
Железо является основным компонентом сплава, содержание, его должно быть
98,72 % или 98,72 кг. (у = 2).
Кш = 98,72*100/(100-2) = 100,7 % или 100,7 кг.
Вносится Fe в шихту с
возвратом: 98.7*60/100 = 59.22 кг.
Вносится Fe в шихту с ФМn 88: 12*0,5/100 = 0,06 кг.
Вносится Fe в шихту со
стальной стружкой: 98.31*9/100 = 8.8 кг.
Следует ввести Fe в
шихту со стальным ломом:
,7-59,22-8,8-0,06 = 32,6 кг.
Требуется стального лома 32,6*100/98,5 = 32 кг.
Расчет содержания С:
Требуемое содержание в отливках 0,36 % С(У=10).
Кш = 0,36*100/(100-10) = 0,4 % или 0,4 кг.
Вносится С в шихту с возвратом: 0,36*60/100 = 0,22 кг.
Вносится Mn в шихту со
стальным ломом: 0,35*32/100 = 0,15 кг.
Следует ввести С в шихту со стальной стружкой:
,4-0,22-0,15 = 0,032 кг.
Требуется стальной стружки 0,032*100/0,44 = 7,44 кг.
В процессе выплавки стали в индукционных печах металл содержит некоторое
количество кислорода, для снижения содержания которого производят раскисление.
Для раскисления нашего сплава вводим в металл гранулированный алюминий, в
расчете 0,01% от веса чистого металла. Алюминий является очень сильным
раскислителем. Присадки алюминия в металл позволяют полностью избежать
возникновения пористости отливок вследствие окисления углерода и выделения
пузырьков окиси углерода.
Значит, при завалке шихты на 100 кг приготовляемого сплава составляющие
необходимы в следующем количестве:
Стальной лом = 39,44 кг.
Ферромарганец = 0,5 кг.
Ферросилиций = 0,05.
Возврат собственного производства = 60 кг.
Гранулированный алюминий - 0,01 кг.
.7.3 Выбор и расчет количества плавильных печей
Для оборудования дискретного действия рассчитываем количество единиц, а
для оборудования непрерывного действия - производительность.
Для индукционной тигельной печи рассчитываем требуемую производительность
оборудования по формуле (5), принимая n=2:
где
Q - годовая потребность в металле, т;
n - количество
печей, шт;
Тд
- действительный фонд времени.
Количество
плавильных агрегатов рассчитывается по формуле (7):
(7)
где
Q - потребное количество жидкого металла для
обеспечения производственной программы, т.;
Тд-
действительный годовой фонд времени работы оборудования, час;
V - ёмкость
оборудования;
Т
- такт работы оборудования.
Необходимое
количество составит:
Выбираем
две печи УИП-250-2,4-0,25 производства ЗАО
«РЭЛТЕК».
Технические
характеристики установки УИП-250-2,4-0,25 указаны в
таблице 1.9.
Таблица
1.9
Технические
характеристики УИП-250-2,4-0,25
Мощность, кВт
|
Частота тока, Гц
|
Номинальная емкость, т
|
Скорость плавки, т/ч
|
Расход охлаждающей воды, м³/ч
|
Расход эл.энергии, кВт/ч
|
250
|
2400
|
0,25
|
0,33
|
10
|
.7.4 Выбор и расчет парка ковшей
Для приема металла из печи УИП-250-2,4-0,25,
транспортировки его к месту расположения форм и заливке стали в формы
используется чайниковый ковш, емкостью 40 кг.
Расчет ковшей, одновременно работающих, проводим по формуле:
(8)
где
q - производительность плавильной печи, т/ч;
Т
-время оборота ковша, мин;n - число одновременно работающих печей,
шт
m - емкость
ковша, т
Принимаем,
что будет использоваться один ковш. Кроме того, один ковш будет находиться в
резерве.
1.8 Отделение обрубки, очистки и термообработки отливок
В данном отделении последовательно осуществляются следующие операции:
первичная очистка отливок;
отделение отливок от литниковой системы;
предварительная проверка отливок;
подготовка под заварку и заварка дефектов;
термическая обработка отливок;
выполняется вторичная дробеметная обработка;
правка отливок и проверка качества.
.8.1 Предварительная очистка блоков отливок от оболочки формы
q = Q/Tд*n =
143954/(3800*1) = 38 блоков/час;
Исходя из расчётов, выбираем одну «Установка для отделения керамики
модели 6А92».
Разрушение остатков керамической формы и удаление их с поверхности блока
в цехе будет производиться на установке для удаление керамики 6А92,
представляющий собой механизм имеющий звукоизолирующую станину, внутри которой
закреплен цилиндр с направляющими траверсами, грязесборник, отбойный механизм,
регулируемый упор и плиту со сменными вставками .
Характеристика установки приведена в таблице 1.10.
Таблица 1.10
Техническая характеристика установки модели 6А92
Наибольший размер
обрабатываемого блока, мм
|
Наибольшая
производительность блоков в час
|
Габаритные размеры, мм
|
Масса, кг
|
диаметр
|
длина
|
|
длина
|
ширина
|
высота
|
|
400
|
500
|
80
|
835
|
950
|
2500
|
1355
|
.8.2 Отделение отливок от литниковой системы
Отделение отливок от стояка осуществляется на отрезных станках с
вулканитовыми кругами заводского изготовления.
Станок состоит из станины, зажимного устройства, суппорта для перемещения
блока отливок относительно вращающегося вулканитового круга. На станине имеется
склиз, примыкающий к лотку, для удаления срезанных отливок. Блок отливок
устанавливается между штоками правого и левого цилиндров. При движении суппорта
в направлении вращающегося вулканитового круга происходит срезание отливок от
стояка.
В случае, когда отливку не возможно отделить от стояка при помощи
отрезного станка, применяем газовую резку либо отрезные вулканитовые круги.
.8.3 Окончательная очистка отливок
Окончательная очистка отливок будет проходить в напорном
кабинете компании PanBlast. Модель PB1500PMB -это автономная законченная
абразивоструйная машина с циклоном и пылеуловителем. Все операции по
абразивоструйной очистке выполняются внутри рабочей камеры. Пыль, извлеченная
из кабинета во время дробеструйной очистки, осаждается в пылеуловителе, затем
отводится.
Установка оснащена загрузочным поворотным столом с
направляющими рельсами.
Технические характеристики установки PB1500PMB:
Габаритные размеры (высота, ширина, глубина мм): 2120х2200х2000
Размеры рабочей зоны (ширина, глубина, высота, мм): 1500х1200х900
Расход воздуха, м3/мин: 1,27-6,9
Давление, атм: 3,5-7
Масса, кг: 700
Грузоподъемность стола, кг: 250
Так же для очистки отливок будет использоваться дробемет модели SB1015A1.
Характеристики модели:
Габаритные размеры (шир/дл/выс, мм): 2458/2078/1861
Диаметр барабана, мм: 1000
Расход дроби кг/мин: 120
Общая мощность, кВт: 9,7
Максимальная масса загрузки, кг: 300
Скорость вращения барабана, об/мин: 3
.8.4 Исправление дефектов
Исправлять дефекты целесообразно если затраты на исправление
забракованной отливки меньше стоимость её изготовления вновь. Наружные раковины
могут быть заварены. Заварку следует производить методом электросварки,
используя электроды из сплава отливки. Место заварки необходимо зачистить
слесарным путём до чистого металла. После заварки следует произвести слесарную
зачистку. Для снятия напряжений отливки рекомендуют произвести термообработку.
Трещины и спаи заваркой исправлять не рекомендуется.
Слесарная доводка может применяться для исправления отклонений отдельных
размеров отливки от чертежа в пределах поля допуска других размеров, связанных
с исправлением, а также для исправления дефектов поверхности отливок (корольков
и др.). Доводка осуществляется слесарными инструментами и абразивными кругами.
Коробление отливок может быть исправлено правкой. После правки необходимо
провести термическую обработку для снятия напряжений
.8.5 Расчет оборудования для термообработки
После отчистки отливок в дробеструе, отливки поступают на термическую
обработку, которую применяют для получения необходимых механических свойств,
для снятия внутренних напряжений в отливках. Грубозернистая структура и
внутренние напряжения снижают механические свойства металла. Для углеродистых
сталей применяют нормализацию, которая заключается в нагреве отливок до
температуры отливок 900ºС, выдержки и охлаждения с заданной скоростью на
воздухе.
Нормализацией называют разновидность термической обработки, близкой к
полному отжигу и отличаются от него тем, что сплав после выдержки охлаждают на
воздухе.
Отливки из углеродистых сталей подвергают нормализации для исправления
структуры, улучшения механических свойств и обрабатываемости резанием. Так как
при нормализации структура получается более мелкой и равномерной по сравнению с
отжигом, то и механические свойства стали 35Л после нормализации улучшаются.
Для термообработки отливок, полученных по выплавляемым моделям, можно
применять любые термические печи. Независимо от способа нагрева (электричеством
или газом) и конструкции печей (камерные, методические, шахтные или
конвейерные) необходимо выдержать условие без окислительного нагрева, так как
отливки имеют небольшие припуски и чистую поверхность.
Для термообработки будет использоваться электропечь с выкатным подом для
термообработки ПВТ -1,2- 1000 компании УРАЛЭЛЕКТРОПЕЧЬ.
Необходимое количество оборудования определяется по формуле (4):
где
Q - масса отливок на годовую программу;
q -
производительность печи;
Тд
- действительный фонд времени работы печи.
Принимаем,
что в цехе будут установлены 2 печи ПВТ -1,2-1000.
Технические
характеристики ПВТ -1,2-1000
Тмакс,°С:
1200
рабочее
пространство (шир/дл/выс), мм: 680/1600/800
габаритные
размеры (шир/дл/выс),, мм: 1430/4660/1875
мощность
/ напряжение, кВт/В: 75/380
масса
печи, кг: 2100
После
термообработки отливки проходят повторную очистку в дробеметной и дробеструйной
установке для удаления окалины и придания внешнего вида.
.9
Балансы материалов
Литейный
цех, как любая производственная система, перерабатывает сырьевые материалы в
готовую продукцию и отходы. Особенность литейного производства состоит в
наличии технологических циклов, благодаря чему большинство материалов в
производственном процессе используются многократно. Основным сырьем литейного
цеха являются металлы, шлакообразующие и формовочные материалы. Шлакообразующие
материалы используются однократно и полностью переходят в шлак. Таким образом,
баланс материалов литейного цеха обыкновенно разделяют на две части: баланс
металла и баланс смеси.
.9.1
Баланс металла
Баланс
металла составляется на основе расчета шихты в абсолютных показателях от
металлозавалки. Выход металла рассчитывается из производственной программы и
особенностей технологического процесса.
Баланс
металла для стали марки 35Л представлен в таблице 1.11.
Таблица
1.11
Баланс
металла для стали марки 35Л
Приход
|
№ п/п
|
Составляющие
|
Расход металла, т/год
|
1
|
2
|
3
|
1
|
Годные отливки 40 %
|
500
|
2
|
Возвраты в т.ч. прибыли,
литники , стояки (60%)
|
804,3
|
3
|
Скрап, сливы, брак (4%)
|
51,3
|
Итого металлозавалка
|
1355,6
|
Расход
|
1
|
2
|
3
|
1
|
стальной лом
|
505,97
|
2
|
ферромарганец
|
7,1
|
3
|
ферросилиций
|
1,9
|
4
|
гранулированный алюминий
|
0,14
|
Итого металлозавалки
|
1355,6
|
.9.2 Баланс смесей
Баланс формовочной смеси составляется на основе рецептов смеси в
абсолютных показателях от годовой потребности. Баланс формовочной смеси
представлен в таблице 1.12.
Таблица 1.12
Баланс формовочной смеси
Расход
|
№ п/п
|
Составляющие
|
Расход смеси, т/год
|
1
|
2
|
3
|
1
|
общий расход огнеупорного
покрытия
|
410,6
|
2
|
общий расход модельного
состава
|
169,4
|
Приход
|
1
|
модельный состав ПС 50-50
|
15,1
|
2
|
кварцевый песок (50%)
|
183,4
|
3
|
суспензия(50%)
|
183,4
|
Суспензия
|
3.1
|
этилсиликат ГС-40 (40%)
|
73,6
|
3.2
|
пылевидный кварц (60%)
|
112,3
|
.10 Расчет складов
Запас материалов на складе складывается из:
расходуемого запаса qрас, рассчитываемого по формуле Уилсона:
(9)
где
Q - годовой объем потребления материала;
Е
- условно-постоянные затраты на поставку;
Ц
- цена материала;
i - годовые
потери оборотных средств при хранении материала на складе (10%).
резервного
запаса на случай перебоев с поставкой материалов qрез , рассчитываемого на две недели работы цеха по
формуле:
(10)
Для
расчета площади склада используется формула
(11)
где
q - запас материала на складе (q = qрез+ qрас);
-
насыпная плотность материала.
Расчет
складов представлен в таблице 1.13.
Таблица
1.13
Расчет
складов
Материал
|
Годовое потребление, т
|
Цена, тыс. руб/т
|
Расходуемый запас, т
|
Скорректированный запас, т
|
Резервный запас, т
|
Итого запас на складе, т
|
Насыпная плотность Т/м³
|
Высота хранения, м
|
Площадь склада, м²
|
Тип склада
|
1
|
2
|
3
|
4
|
5
|
6
|
7
|
8
|
9
|
10
|
11
|
Этилсиликат ГС-40
|
73,6
|
120
|
5,9
|
6,0
|
4,4
|
10,4
|
0,8
|
1
|
13,5
|
площадка
|
Песок кварцевый
|
183,4
|
2
|
128,7
|
130
|
10,7
|
140,7
|
1,6
|
5
|
17,8
|
бункер
|
Пылевидный кварц
|
112,3
|
5
|
34,5
|
35
|
6,5
|
41,5
|
1,7
|
2
|
13,1
|
площадка
|
Лом стальной
|
505,97
|
12,5
|
129,7
|
130
|
28,9
|
158,9
|
2,3
|
3
|
22,6
|
закром
|
Ферромарганец
|
7,1
|
64
|
3,1
|
3
|
0,49
|
3,49
|
2,7
|
2
|
0,81
|
площадка
|
Ферросилиций
|
1,9
|
54
|
2,4
|
3
|
0,1
|
3,1
|
2,7
|
2
|
0,44
|
площадка
|
Гранулированный алюминий
|
0,14
|
65
|
0,1
|
0,1
|
0,02
|
0,12
|
2
|
2
|
0,05
|
площадка
|
Затраты на поставку:
автомобильный транспорт: 120 т.р. в месяц.
1.11 Внутрицеховой транспорт
Подача сырья в цех и вывоз готовой продукции осуществляется автомобильным
транспортом.
Цех оборудован кранами грузоподъемностью 1 т, которые предназначены для
транспортировки, выгрузки и складирования материалов. Также, краны необходимы
для складирования и погрузки готовой продукции, а так же проведения ремонтных
работ.
Рассчитаем минимально необходимое количество кранов для бесперебойной
работы цеха:
(12)
где
Qi - объем (масса) грузопотока i-го компонента
в год;
Vi -
масса (объем) загрузки ТС i-м грузом;
Тi
- время перемещения i-го груза и возврата ТС в исходное положение.
Тi рассчитывается
по формуле :
(13)
где
Li - расстояние транспортировки i-го груза;
υ - скорость крана (30-60 м/мин);
t - время
погрузочно-разгрузочных работ.
Рассчитаем
количество кранов, необходимое для транспортировки материалов:
Из
расчёта следует, что для выполнения производственной программы достаточно и
одного крана. Но в связи с особенностями планировки будут использоваться 2 кран
балки.
2.
ТЕХНОЛОГИЧЕСКАЯ ЧАСТЬ
.1
Анализ конструкции детали и условий ее эксплуатации. Конструирование отливки
Деталь
«Корпус» имеет габаритные размеры:100×70×100, масса 0,6 кг. Отливка является тонкостенной.
Изготавливается из конструкционной среднеуглеродистой стали 35Л.
При
разработке конструкции отливки необходимо учитывать, что ее нужно изготовить с
минимальными затратами, включая механическую обработку. В зависимости от
назначения и требований к качеству по ГОСТ 977-88 отливку «Корпус» относится к
первой группе. Данные отливки не воспринимают большие нагрузки, их конфигурации
и размеры определяются конструктивными и технологическими соображениями.
Осуществляется контроль трех параметров: внешний вид, геометрические размеры,
химический состав.
Припуск
на механическую обработку 1,0-1,5 мм. Предельное отклонение на литейные размеры
по 3 классу точности согласно ГОСТ 2009-55.
Точность
размеров отливки оценивается по отклонению действительного размера от
номинального. Эти отклонения складываются из допусков на размеры полости
пресс-формы, колебания оболочки при прокалке, модели при вытопки. Суммируя все
погрешности согласно ГОСТ 26645-85, допуск соответствует 5-7 классу точности.
Шероховатость
отливки складывается из шероховатости поверхности модельной оснастки; размеров
частиц формообразующих материалов, а именно первого облицовочного слоя;
способности суспензии смачивать поверхность модельного блока; смачиваемости
расплава поверхности литейной формы. Согласно ГОСТ 2789-73 отливка имеет
шероховатость Rz 80.
Для
извлечения модели из полости пресс-формы на поверхности выполняются уклоны до 1° по ГОСТ 3212-80.
.2
Обоснование выбора способа изготовления отливки
Литье
по выплавляемым моделям - метод получения отливок в неразъемных разовых формах,
преимущественно оболочковых, обладающих повышенной точностью.
Изготавливая
данную отливку методом ЛВМ, мы сможем максимально приблизить отливку по форме и
размерам к готовой детали, а в ряде случаев получить литую деталь,
дополнительная обработка которой перед сборкой не требуется. Вследствие этого
резко снижаются трудоемкость и стоимость изготовления изделий, уменьшается
расход металла и инструмента, экономятся энергетические ресурсы, сокращается
потребность в рабочих высокой квалификации, в оборудовании, приспособлениях,
производственных площадях. Метод позволяет изготавливать сложные тонкостенные
отливки (5мм). Так же мы можем изготовить отверстия (10мм) литьем, без
применения стержней. Метод позволяет получать отливки с высокой точностью и
хорошим качеством поверхности.
Применение
литья по выплавляемым моделям открывает перед конструкторами возможности
проектировать сложные тонкостенные конструкции, объединять различные детали в
компактные цельнолитые узлы, уменьшая массу и габариты изделий, создавать
детали, невыполнимые каким-либо другим методом обработки.
Применение
высокоогнеупорных и термостойких материалов для изготовления оболочковых форм,
пригодных для нагрева до температуры выше температуры плавления литейного
сплава и быстрого охлаждения без деформаций и разрушений, позволяет эффективно
использовать методы направленной кристаллизации, получать высоко герметичные
отливки и получать монокристаллические изделия.
2.3 Выбор и обоснование места и уровня подвода металла
Правильный выбор места подвода металла должен обеспечивать хорошее
заполнение формы металлом и качественное питание отливок в процессе
затвердевания. При этом должен реализовываться принцип направленного
затвердевания.
Поэтому металл подводим в массивную часть отливки. Такой подвод металла
обеспечивает заполнение отливки без образования усадочных дефектов.
При выборе места подвода металла руководствуемся следующими
рекомендациями:
следует обеспечить подвод металла в такие места отливки, разогрев которых
будет способствовать усилению направленного затвердевания;
если в отливке могут образовываться внутренние напряжения, то следует
подводить металл таким образом, чтобы уменьшились температурные перепады в ее
частях;
следует стремиться к созданию одностороннего движения металла в форме,
т.е. питатели размещать так, чтобы направление движения металла было в одну
сторону и было исключено встречное движение струй;
подвод металла к отливке следует подводить в массивные части, так как
литниково-питающая система является прибылью;
следует стремиться к осуществлению подвода металла в форму при заполнении
ее наиболее коротким путем.
.4 Выбор и обоснование конструкции литниково-питающей системы
Особенность литниково-питающих систем при литье по выплавляемым моделям
состоит в том, что она выполняет три основные задачи:
. В процессе изготовления блока моделей и оболочки литейной формы
литниковая система является несущей конструкцией, удерживающей на себе модели и
оболочку.
. В процессе заливки она представляет собой систему каналов, через
которые металл подводится к отливке.
. В период затвердевания отливки литниково-питающая система выполняет
роль прибыли.
ЛПС при литье по выплавляемым моделям строят из традиционных элементов:
литниковых воронок, стояков, зумпфов и литниковых ходов, прибылей и
коллекторов. Благодаря, характерной для литья по выплавляемым моделям,
неразъемной форме указанные конструктивные элементы удается расположить
наиболее эффективно, максимально используя объем формы.
При выборе ЛПС необходимо стремиться к соблюдению следующих
принципиальных положений, направленных на получение годных отливок и на
экономичность их производства:
. Обеспечивать принцип направленного затвердевания, т.е.
последовательного затвердевания от наиболее тонких частей отливки через
массивные узлы к прибыли, которая должна затвердевать последней;
. Наиболее протяженные стенки и тонкие кромки ориентировать в форме
вертикально, т.е. наиболее благоприятно для их спокойного и надежного
заполнения;
. Создавать условия для экономичного и механизированного производства
отливок, в том числе: унификацию типоразмеров ЛПС и их элементов с учетом
эффективного использования оснастки, имеющегося технологического оборудования,
печей; возможность применения модельных блоков и форм; удобство выполнения и
минимальный объем механической обработки при отрезке отливок и последующем
изготовлении из них деталей.
Для нашей отливки лучше всего будет применить литниково-питающую систему
1-го типа, где питающий элемент - центральный стояк. ЛПС этого типа
представляет собой стояк компактного сечения, непосредственно к которому с
разных сторон присоединяются небольшие отливки с двумя индивидуальными
питателями. Центральный стояк является одновременно и литниковым ходом, и
коллективной прибылью, а питатели соответственно выполняют и роль шеек
прибылей. Сечение стояка имеет квадратную форму. Это сделано для удобства
наплавки моделей на стояк.
Центральное расположение стояка обуславливает естественное замедление его
охлаждения и способствует направленному затвердеванию периферийно расположенных
отливок. Зумпф в нижней части стояка смягчает отрицательное действие
механического и теплового ударов, имеющих место в начальный момент заливки.
Центральный стояк служит основой для создания
комплексно-механизированного технологического процесса производства небольших
отливок. Применение унифицированного металлического каркаса в качестве несущей
конструкции обеспечивает удобство звеньевой сборки модельного блока и его
высокую прочность при изготовлении оболочковой формы. Уже в отлитом блоке
центральный стояк надежно закрепляется в приспособлениях станков при очистке и
отрезке отливок.
.5 Расчет элементов литниково-питающей системы
Расчет размеров элементов литниково-питающих систем в случае, когда
требуется получить плотные отливки с повышенными механическими свойствами,
рекомендуется производить по методике, разработанной М.Л. Хенкиным на основе
обширных экспериментальных исследований. Данная методика может быть
использована для расчета элементов ЛПС 1 - 3, 7 типов.
Методика предусматривает подвод металла к наиболее массивным узлам отливки.
Исходными данными для определения размеров элементов литниково-питающей
системы является приведенная толщина массива отливки (узла питания) и масса
отливки.
Расчет размеров питателя или стояка производится по формуле (14):
(14)
где
z - приведенная толщина узла питания отливки (отношение
объема массива отливки к его поверхности ); приведенные толщины массивов
отливок могут быть определены по формулам;
Q - масса
отливки в г;
lп - длина
питателя;
dп - приведенная
толщина сечения питателя (отношение площади сечения питателя к его периметру);
dст - приведенная
толщина сечения стояка (отношение площади сечения стояка к его периметру).
В
формуле (14) через приведенные толщины dп, dст и z, а также вес отливки Q отражена зависимость
между размерами литниковой системы и размерами узла питания (термического
узла), а также между размерами самих элементов литниковой системы (стояка и
питателя).
По
формуле (14) рассчитаны размеры литниковых систем для значительного количества
стальных отливок. Полученные данные после производственной проверки сведены в
таблицы, которые позволяет определить размеры элементов литниково-питающих
систем, не прибегая к расчетам.
Нам
необходимо рассчитать размеры элементов литниково-питающей системы для отливки
«Корпус»; материал - сталь 35Л; масса отливки Q = 0,6 кг.
Находим
приведенную толщину массивного узла отливки z:
Z1=
(15)
Z2 = 
Для
Q = 0,6 кг; z = 3,8 мм; lп =
16 мм; по таблице находим Dст = 30 мм; так как сечение стояка имеет квадратную
форму, то принимаем квадратную сторону 30 мм, высота стояка Нст=300 мм.
Находим
приведенные толщины питателя:
d1 = 5,75 мм, размеры - 22 х 22
d2 = 5,00 мм, размеры- 13 х 22
.6
Проектирование и изготовление пресс-формы
Выплавляемые
модели изготавливают в специальных пресс-формах, чаще всего состоящих из двух
частей - матриц с вертикальным или горизонтальным разъемом.
Плоскость
разъема и число разъемов выбирают из условий быстрого и удобного извлечения
моделей.
Пресс-форма
должна отвечать следующим основным требованиям:
обеспечивать
получение моделей с заданной точностью и чистотой поверхности;
иметь
минимальное число разъемов при обеспечении удобного и быстрого извлечения
моделей;
иметь
устройства для удаления воздуха из рабочих полостей;
быть
технологичными в изготовлении, долговечными и удобными в работе.
Выбор типа пресс-формы зависит от точности, предъявляемой к
отливкам, свойств модельного состава и характера производства.
Изготавливаем
пресс-форму из стали 35Л, т.к. этот материал хорошо зарекомендовал себя в этой
области применения, он более долговечен по сравнению с легкими сплавами.
Пресс-форму
проектируют на основании чертежа отливки.
Изготовление
рабочей полости пресс-формы должно производиться с точностью, обеспечивающей
получение отливки по 5-7 классам точности, в зависимости от конструкции,
размеров и требований к отливкам. Однако не следует ужесточать условия
изготовления пресс-форм, назначая более высокие классы точности, так как
неизбежные колебания усадки модельного состава, формы и металла сводят на нет
высокую точность размеров, полученную в пресс-форме. Практически точность
размеров рабочей полости пресс-форм должна быть на 1-2 класса выше требуемой
точности отливок.
Величину
допуска на размер в пресс-форме рекомендуется принимать не более одной пятой
величины допуска на размер отливки.
Для
обеспечения изготовления пресс-форм с минимальной доводкой рекомендуется
уточненный расчет размеров рабочей полости пресс-форм по следующим формулам:
для наружных размеров отливки
lпф = lотл + lотл (К / 100) - 0,5 Δо = lотл (1 +
(К / 100)) - 0,5 ∙ Δо (16)
для внутренних размеров
lпф = lотл + lотл (К / 100) + 0,5 Δо = lотл (1 +
(К / 100)) + 0,5 ∙ Δо (17)
где lпф - номинальный размер рабочей полости пресс-форм, мм;
lотл - номинальный размер отливки, мм;
Δо -допуск на размер отливки, мм;
К- коэффициент
суммарной линейной усадки, %, равная:
К = Умод - Уф ± Умет (18)
где Умод - свободная линейная усадка моделей, %;
Уф - среднее линейное расширение формы при прокалке
перед заливкой, %;
Умет - свободная линейная усадка металла, %.
Уменьшение или увеличение номинального размера пресс-формы на
половину несимметричного допуска (0,5 Δо) в формулах производится для того, чтобы размер пресс-формы, а
следовательно, модели и отливки совпадал со средним, а не номинальным чертежным
размером.
При симметричном допуске на размер (плюс - минус) увеличивать или
уменьшать номинальный размер пресс-форм на 0,5 Δо не следует.
Литниковое
отверстие пресс-формы имеет следующее назначение:
обеспечение
заполнения полости пресс-формы;
снижение
давления в моделях до удаления их из пресс-формы с целью предотвращения
местного вспучивания поверхности.
При
выборе размера литникового отверстия необходимо учитывать давление и
температуру при запрессовке модельного состава, конструкцию и размеры модели, а
также ее положение в пресс-форме. На основании опытных данных размер отверстия
по диаметру рекомендуется делать не менее 5 мм.
Для
обеспечения точного соединения половин пресс-формы друг с другом применяются
центрирующие штыри. Основание и крышка пресс-формы
скрепляются откидными болтами с барашками.
Стержни
предназначены для выполнения в моделях отверстий и полостей, которые не могут
быть выполнены непосредственно пресс-формой, поэтому отверстие в модели
получается с помощью металлического стержня, который извлекается из пресс-формы
сверху. Для удобства его извлечения из пресс-формы нам необходимо
предусматривать ручку. Для фиксации стержня относительно полости пресс-формы
используют фиксирующий штырь.
.7
Технологический выход годного
Рассчитаем
технологического выхода годного без учета брака:
(19)
где
М0 - масса отливки,кг;
n0 - число отливок в блоке (2 отливки);
M0′ - масса литниковой системы,кг;
β - коэффициент объемной усадки (0,06);
a, b -
стороны квадрата, мм;
Hcт
= 275 мм - высота стояка;
γ - плотность сплава, кг/м 3;
Металлоемкость
ЛПС (расход залитого металла в форму, приходящегося на одну отливку)
составляет:
Мзал.отл.=М0/ТВГ
= 0,6/0,45 = 1,3 кг/отл (20)
Рассчитаем ТВГ для нашего случая:
масса отливки Мо − 0,6 кг, no = 2*1 = 2 отливки в блоке; центральный
стояк прямоугольный с размерами а = 3 см, в = 5 см и высотой Н′ст
= 275 мм. Не учитывая брака и пренебрегая массой питателей и некоторым
увеличением массы на участке воронки, получим, что масса блока при плотности
стали γ = 7,8 кг/дм3 будет:
М'о = (π*а*в ) Н′ст∙ γ = (3,14∙ 0,3*0, 5) ∙2,75∙7,8 = 4,6 кг;
Мо n'o = 0,6∙2 = 1,2 кг,
откуда, при коэффициенте объемной усадки β
= 0,06,
ТВГ' = Мо n'o /[( Мо n'o + М'лс) (1
+ β)] = 1,2/[(4,6+ 6,6) 1,06] =0,40=40%
В практике производства отливок по выплавляемым моделям обычно ТВГ
= 0,1 - 0,6, наше значение ТВГ(40%) входит в этот интервал.
.8
Изготовление моделей
Процесс
изготовления моделей включает операции приготовления модельных составов, получения
моделей отливок и ЛПС, отделки и контроля моделей, сборки их в блоки и контроля
последних.
Готовят
состав в баке для расплавления модельного состава. Для приготовления
кондиционной модельной массы в плавильный агрегат загружают 90% возврата
твердого модельного состава и 10% свежих материалов. После расплавления
модельный состав, проходя через смеситель шприц-машины CTM-WI 15
и смешиваясь в определенной пропорции с воздухом, превращается в модельную
пасту, которая поступает в головку шприца.
К
свойствам модельных составов предъявляют комплекс требований, которые могут
иметь существенные различия в зависимости от конфигурации, размеров и
назначения отливок, необходимой размерной точности их и качества поверхности,
масштабов и характера производства, принятого технологического варианта
процесса изготовления оболочек форм, требований к уровню механизации и
экономическим показателям производства. Требования во многом определяются также
природой и свойствами самого модельного состава. Необходимо, чтобы свойства
составов обеспечивали получение высококачественных моделей при одновременной
технологичности составов (простоте их приготовления, удобстве использования,
возможности утилизации).
.8.1
Требования к модельным составам
.
Состав должен точно воспроизводить конфигурацию рабочей полости пресс-формы и
ее поверхности, не прилипать к пресс-форме. Поверхность модели должна быть
чистой, глянцевой.
.
После затвердевания в пресс-форме состав должен иметь твердость и прочность
достаточные для того, чтобы модели не деформировались и не повреждались на всех
технологических операциях.
.
Усадка состава при охлаждении и расширение его при нагреве должны быть
минимальными и стабильными.
.
Состав должен быть несложным в приготовлении, иметь минимальное число
компонентов, желательно недорогих и недефицитных.
.
Температура плавления модельного состава должна быть невысокой, в пределах
60-100 Сº.
В этом случае облегчается изготовление
моделей и удаление их из полости литейных форм. Одновременно температура начала
размягчения состава должна быть не ниже 32-35 С, т.е. на 10-15 С превышать
температуру помещений, в которых изготовляют, хранят модели, собирают в блоки и
наносят на них суспензию.
.
Выплавляемый модельный состав должен обладать хорошей жидкотекучестью в
расплавленном состоянии для облегчения изготовления моделей и выплавления их из
форм.
.
Модельные составы, запрессовываемые в пастообразном состоянии, должны обладать
в этом состоянии хорошей текучестью, позволяющей получать модели с четкой
проработкой контуров полости пресс-формы и ее поверхности при малых давлениях
прессования.
.
Продолжительность затвердевания модельного состава в пресс-форме должна быть
минимальной.
.
Плотность состава должна быть невысокой. Желательно, чтобы она была менее 1000
кг/м3. Это облегчает работу с модельными блоками, уменьшает
опасность поломки их и деформации под действием собственной массы моделей, а
при выплавлении моделей в горячей воде способствует лучшему отделению
модельного состава для повторного использования.
.
Химическое взаимодействие состава с материалом пресс-форм, а также со связующем
раствором и огнеупорной основой суспензии недоступно.
.
Модельный состав должен хорошо смачиваться суспензией.
.
Хорошее спаивание модельного состава весьма желательно, так как это облегчает
сборку блоков припаиванием и соединение сложных моделей, изготовляемых по
частям.
.
Зольность модельного состава должна быть минимальной.
.
Структура состава должна быть механически однородной.
.
Желательно, чтобы модельный состав был пригодным для многократного повторного
использования, потери его в процессе применения были минимальными, а
технологические свойства не ухудшались при работе и хранении.
.
Модельный состав в любом состоянии должен быть безвредным для здоровья
работающих, также как и продукты его деструкции, образующиеся, например, при
прокаливании форм. Отходы модельного состава не должны загрязнять окружающую
среду.
Недостаточное
соответствие свойств модельных составов оптимальным свойствам является одной из
важнейших причин высокой трудоемкости изготовления моделей и сборки блоков в
ряде отраслей промышленности, невысокой размерной точности отливок,
значительного брака моделей и дефектов оболочек форм, связанных с недостатками
модельных составов. Недостатки применяемых модельных составов одна из причин
значительных технологических потерь на основных операциях процесса литья по
выплавляемым моделям.
Воскообразные модельные составы применяются для изготовления
моделей мелких отливок средней сложности по 5-7-му классу точности. Выбираем
модельный состав ПС50. Для изготовления
моделей будет использоваться состав Парафин - 50%, Стеарин - 50%. Это
обусловлено хорошим соотношением цены и качества данного модельного состава и
отработанной технологии изготовления моделей на данном составе. При низкой
стоимости он обладает высокой жидкотекучестью (650 мм по спиральной пробе),
низкой зольностью (0,03-0,1 % по массе) и усадкой равной 1,0 %. Единственным
недостатком является температура размягчения (35-370С).
Модельные
составы ПС50 хорошо смачивается суспензией, имеет невысокую температуру
плавления, достаточную жидкотекучесть, низкую зольность, пригодны для
многократного использования.
Предварительное
приготовление модельного состава состоит в поочередном или одновременном
расплавлении составляющих, фильтровании расплавов и разливке их в
формы-изложницы. В условиях серийного и массового производства расплав можно не
сливать в изложницы, а подавать либо непосредственно на операцию изготовления
модели либо на приготовление пастообразного состава. При подготовке выплавляемых
модельных составов используют до 90 % возврата, собранного при удалении моделей
из оболочек форм. Не следует нагревать состав более чем на 50-60 °С выше температуры плавления. Возврат модельного состава, содержащего
легко омыляемые компоненты необходимо не только освежать, но и периодически
регенерировать. Разработаны методы, обеспечивающие надежное разделение
выплавляющей среды (обычно горячей воды) и модельного состава.
Пресс-форму
очищают, протирают, обдувают, смазывают рабочую поверхность, собирают.
Температура
пресс-формы оказывает решающее влияние на качество моделей, особенно при
изготовлении моделей свободной заливкой. Пресс-формы перед началом работы
обычно подогревают, введением в них модельного состава.
При
этом первые две три модели отправляются в переплав. Оптимальная температура
пресс-формы зависит от свойств состава и формы модели. Для модельного состава
типа ПС50 она находится в пределах 22 - 28˚С. Колебание точности моделей,
и низкая температура увеличивает внутренние напряжение в моделях и приводит к
короблению и образованию трещин в них.
За
время разборки для выема модели и сборки, пресс-формы обычно не успевают
охладиться до оптимальной температуры. Поэтому применяют принудительное
охлаждение, например погружение в воду. В автоматической пресс - форме
предусмотрены ходы, по которым циркулирует вода, которая и является источником
охлаждения.
Наиболее
выгодным и практичным способом запрессовки в нашем случае, является запрессовка
с применением пастообразного состава ПС50, содержащего воздух. Запрессовка
происходит с помощью высокопроизводительных установок для изготовления
выплавляемых моделей.
Использование
пастообразного состава, содержащего воздух, хорошо тем, что воздух
предотвращает образование наружных усадочных дефектов, повышает точность и
стабильность размеров моделей, не требуется дополнительная подпрессовка.
Модели, полученные таким способом менее теплопроводны, что так же существенно
влияет, как на период формирования линейной оболочки (так как может вызвать
растрескивания еще не прочных ее слоев) так и во время процесса вытапливания,
когда модельный состав оказывает значительное давление на оболочку формы.
Процесс
изготовления моделей в пресс-формах включает подготовку пресс-формы, введение в
ее полость модельного состава, выдержку модели до затвердевания, разборку
пресс-формы и извлечение моделей, а также охлаждение моделей до температуры
производственного помещения.
Подготовка
пресс-формы: пресс-форму очищают (протирают, обдувают), смазывают их рабочую
поверхность, собирают, в ряде случаев подогревают или охлаждают. Очистку, т.е.
удаление частиц модельного состава, оставшихся в углублениях и отверстиях
полости пресс-формы, производят обычно обдувкой сжатым воздухом. Состав,
прилипший к пресс-форме, удаляют деревянными счищалками.
Заполняем
пресс-форму модельным составом запрессовкой в пастообразном состоянии.
Готовые
модели после извлечения их из пресс-форм и предварительного визуального
контроля охлаждают в проточной воде или обдувкой на воздухе.
Собираем
модели в блоки припаиванием моделей деталей к модели литниковой системы с
помощью подогретого ножа, шпателя или специального электропаяльника. Нагретое
лезвие ножа или электрического паяльника помещают между посадочной частью
питателя модели и моделью литниковой системы в месте, где модель должна быть
припаяна. Затем одной стороной плоской части лезвия касаются одновременно
питателя модели, а другой - посадочного места модели литниковой системы,
оплавляя их, после чего нож быстро убирают и соединяемые части слегка прижимают
одну к другой.
После
сборки моделей в блоки необходима выдержка для полного охлаждения всех частей
модельного блока до температуры производственного помещения.
Для
естественного охлаждения и хранения блоков перед нанесением оболочки их
устанавливают или подвешивают на стеллажи, этажерки, подвесные
конвейеры-накопители, ставят в шкафы или термостаты. Устройства для хранения
модельных блоков изготовляют и устанавливают так, чтобы исключалась опасность
поломки моделей и загрязнения их поверхности. В помещении, где хранятся, блоки
недопустимы колебания температуры.
Дальше
следует этап сборки. Применяют два способа сборки моделей в блоке: припаиванием
и сборкой модельных звеньев.
Так
как отливка “Корпус” это крупная отливка, то модельный блок собирается
припаиванием. Нагретое лезвие ножа или электропаяльника помещают между
посадочной частью питателя модели и моделью литниковой системы в месте, где
модель должна быть припаяна. После оплавления обоих сторон нож убирают, а
соединяемые части слегка прижимают. На стояк напаивают 8 моделей. Для сборки
применяют, полые стояки, на которые наращивают слои модельного состава толщиной
2 - 5 мм. Состав наносят многократным погружением и охлаждением стояков в
расплав модельного состава.
.9
Изготовление литейной формы
Литейная
форма - инструмент для обработки расплава металла в целях получения отливки с
заданными размерами, шероховатостью поверхности, структурой и свойствами.
Основа способа литья по выплавляемым моделям - оболочка: неразъемная, горячая,
не газотворная, газопроницаемая, жесткая, с гладкой контактной поверхностью,
точная.
Литейную
форму изготовляем в виде многослойной оболочки, которую получаем нанесением
суспензии с последующей обсыпкой и сушкой. Поверхность блока моделей смачивают
суспензией окунанием и тут же обсыпают зернистым материалом. Суспензия
прилипает к его поверхности и точно воспроизводит конфигурацию; зернистый же
материал внедряется в слой суспензии, смачивается ею, фиксирует суспензию на
поверхности блока, создает скелет оболочки и утолщает ее.
Свеженанесенный
слой оболочки практически не обладает прочностью и удерживается на поверхности
блока только благодаря действию сил смачивания; упрочнение его происходит в
процессе сушки - химического твердения. Оболочку формируют последовательно:
смачивают блок суспензией, обсыпают и сушат. Обычно наносят 4-6 слоев, а при
изготовлении крупных отливок до 12 и более. Первый облицовочный слой обсыпают
мелкозернистым (0,1-0,16 мм) материалом, чтобы получать гладкую контактную
поверхность.
Формовочные
материалы включают основу, связующее, растворители, добавки. Основа может быть
пылевидной для суспензий и зернистой для обсыпки слоев суспензий на блоках
моделей.
Материал
основы оболочки - кварц кристаллический (температура плавления 1712°С, плотность 2650 кг/м3, коэффициент линейного расширения
13,7*10-61/ °С). Кварцевый песок применяют для обсыпки
облицовочного (контактного) слоя марки 1К016, 1К020, а для последующих - более
крупные, например 1К0315.
Подготовка
материалов основы включает дробление, помол, промывку, химическую активацию,
прокаливание и промывание.
Связующей
оболочкой формы служит тугоплавкий неорганический окисел или соединение
окислов, образующиеся из связующих растворов при сушке и прокаливании оболочек.
Кислые
связующие широко представлены растворами этилсиликата, из которых образуются в
оболочке аморфная двуокись кремния.
Этилсиликат
- прозрачная или слабоокрашенная жидкость с запахом эфира. Это продукт реакции
этилового спирта с четыреххлористым кремнием при непрерывном их смешивании и
охлаждении в реакторе.
Для
гидролиза этилсиликата вводят подкисленную соляной кислотой воду. Суспензия и
оболочка должны обладать следующими наиболее существенными свойствами: точно
воспроизводить микрорельеф поверхности и конфигурацию моделей, обладать высокой
прочностью, термической и химической стойкостью, газопроницаемостью и спос
Наиболее распространенным в настоящее время исходным материалом для связующего
является этилсиликат различных марок 32,40,50 и готовые связующие. Этилсиликат
(эфир ортокремневой кислоты) представляет собой прозрачную жидкость, слегка
окрашенную в желтый или бурый цвет. Он является продуктом реакции этилового
спирта с четыреххлористым кремнием при непрерывном их смешивании :
SiCl4 + 4C2H5OH = 4HCl + (C2H5O)4Si
Этилсиликат
в том виде, как выпускается промышленностью, не является связующим, а
представляет собой исходный материал для получения связующих растворов. Гель SiO2
из этилсиликата не выпадает. Нужно
получить менее устойчивое вещество, что достигается гидролизом этилсиликата.
Применение этилсиликата как связующего объясняется тем, что он, взаимодействуя
с водой (гидролиз - процесс замещения этоксильных групп (C2H5O)
гидроксильным (ОН), способен выделять кремнезем по реакции:
(C2H5O)4Si +
2H2O = SiO2 + 4C2H5OH
Сначала
образуется золь кремнезема m SiO2*n H2O,
коллоидный раствор, который используется для приготовления покрытия, т.е. для
смешивания с пылевидным кварцем. В дальнейшем при сушке золь переходит в гель
(студенистый нерастворимый осадок), обволакивающий и склеивающий песчинки, затем
- в аморфный кремнезем, а после прокаливания - в кристаллический кремнезем.
Таким образом, после прокаливания огнеупорное покрытие состоит только из
кристаллического кремнезема, что обеспечивает высокую огнеупорность покрытия.
Спирт C2H5OH, образующийся по приведенной выше реакции, удаляется
из огнеупорного покрытия испарением при сушке. Однако вода с этилсиликатом
почти не смешивается, поэтому реакция гидролиза идет очень медленно. Для
ускорения реакции применяют катализатор - соляную кислоту.
2.9.1
Приготовление гидролизованного раствора этилсиликата-40
Перед
приготовлением гидролизованного раствора этисиликата-40 производится расчет
необходимого количества спирта, соляной кислоты (водный раствор хлористого
водорода) и воды на получение в готовом гидролизованном растворе
этилсиликата-40 массовых долей двуокиси кремния и хлористого водорода.
Расчет
необходимого количества спирта, воды и соляной кислоты производится на 1 дм3
(литр) этилсиликата.
Количество
спирта (Х) в литрах вычисляют по формуле:
Х=
(dэ · (c-a)) /
(dр·a) =
1050·(38-20)/790·18 = 1,2л (21)
dэ - плотность этилсиликата - 40,кг/м3
c - массовая
доля двуокиси кремния в исходном этилсиликате, %
a - требуемая
массовая доля двуокиси кремния в гидролизованном растворе этилсиликата - 40,%
dр -- плотность спирта, кг/м3
Количество
воды (У) в литрах вычисляют по формуле:
У=((3·dэ
· c·n)/1000)
- ((х·dр·е)/1000)
=
=
((3·38·0,5·1050)/1000) - ((1,2·790·4)/100) = 0,32л (22)
n - число молей
на 1 моль двуокиси кремния принимается для воздушно-аммиачной сушки 0,4-0,5;
dэ - плотность этилсиликата - 40,кг/м3;
c - массовая
доля двуокиси кремния в исходном этилсиликате,%
е
- содержание воды в спирте, %
dр -- плотность спирта, кг/м3
х
- количество спирта, л
Количество
соляной кислоты (Z) в литрах вычисляют по формуле:
Z =B·(dэ
+ dр + Х + У) - С HL/(k·d HL) =
=
0,3·(1050+790+1,2+0,32) - 1,5/ (36·1180) = 0,02л (23)
В
- требуемое содержание хлористого водорода в гидролизованном растворе
этилсиликата, %
dэ - плотность этилсиликата - 40,кг/м3
dр - плотность спирта, кг/м3
х
- количество спирта, л
У
- количество воды, л
С
HL - массовая
доля хлористого водорода в этилсиликате, %
d HL - плотность соляной
кислоты, кг/м3
k - концентрация
соляной кислоты, %
Расчет
на 1 л. этилсиликата:
X = 1,2л.
(спирт)
Y = 0,32 л.
(вода)
Z = 0,02 л.
(соляная кислота)обностью аккумулировать теплоту отливки.
Формирование
оболочки включает: приготовление связующего и суспензии, смачивание ею блока
моделей, обсыпку блока зернистым огнеупором, сушку оболочки.
Связующие
получают гидролизом ЭТС, для чего вводят воду. Гидролиз сопровождается
поликонденсацией.
ЭТС
и вода, а также продукты гидролиза хорошо растворяются в спиртах и ацетоне.
Поэтому гидролиз ЭТС для получения связующего раствора проводят подкисленным
раствором воды в спирте или ацетоне.
Для
интенсификации гидролиза применяют катализатор - соляную кислоту.
Суспензия
должна обладать комплексом свойств:
•
седиментационной устойчивостью - свойство суспензии не расслаиваться;
•
смачиваемостью поверхности моделей и оболочек - смачивание поверхности блоков
моделей особенно важно при формировании первого облицовочного слоя, так как при
этом образуется контактный слой оболочки;
•
быть живучей - продолжительность жизни суспензии, т.е. сохранение
технологической вязкости до начала ее желатинизации.
При
нанесении первого слоя суспензии удаляется с поверхности моделей
адсорбированный воздух и смачивает поверхность блока. Смачивать суспензией
модели можно только после полного завершения процессов их усадки. При нанесении
последующих слоев оболочка впитывает жидкую составляющую суспензии, вследствие
чего последняя постепенно густеет, повышается ее вязкость. Повышение вязкости
связано также с испарением органических растворителей даже при добавке в
суспензию антииспарителя. Вязкость суспензии поддерживают в определенных
пределах постоянным добавлением в нее разбавленного раствора, степень
разбавления которого устанавливают опытным путем.
Последний
слой оболочки наносят без последующей обсыпки зернистым материалом. Такой прием
несколько повышает общую прочность оболочки и предотвращает осыпание
поверхностных зерен при выплавлении моделей. При извлечении смоченного блока из
суспензии его поворачивают в различные направления с такой скоростью, чтобы
успел стечь излишек суспензии и она равномерным слоем покрывала поверхность
моделей. Далее на слой суспензии немедленно наносят зернистый обсыпочный
материал.
Обсыпка
блоков зернистым огнеупором производится в «кипящем слое».
Сушку
оболочек производим на воздухе и в вытяжном шкафу в парах аммиака.
Готовность
оболочек к формированию на нем очередного слоя оценивают с водноспиртовыми и
водными суспензиями по содержанию в процентах остаточной влаги методом
взвешивания. Предварительно экспериментально устанавливают допустимую
наибольшую влажность, например 1,3-1,5 %.
Модели
удаляют из оболочек после формовки блоков выплавлением горячим паром. Блоки
загружают в камеру бойлерклава и выдерживают до расплавления модельного
состава.
Прокаливаем
оболочки и формуем их. Формовка необходима для фиксации оболочек в опоке,
упрочнения и и разделения с целью исключения взаимного разогрева в процессе
заливки их металлом.
Опоки
для формовки выбирают согласно технологической карте. После чего насыпать на
дно опоки 20-150-миллиметровый слой песка(постель) в зависимости от высоты
оболочки. И на постель из песка устанавливают прокаленные огнеупорные оболочки
с зазором 30-40 мм для исключения взаимного разогрева после заливки металлом.
Но, оболочки, в опоке, должны быть предназначены для выплавки одной
номенклатуры. Литниковые воронки и прибыли закрывают специальной крышкой, после
чего промежутки между формами, а так же между формами и стенками заполняют
наполнителем (лучше - нагретым) - формовочным песком.
Перед
заливкой форм металлом провести их окончательную очистку и продувку сжатым
воздухом.
При
прокаливании решаются три задачи: удаление газотворных составляющих, повышение
прочности, нагрев оболочки для лучшего заполнения полостей металлическим
расплавом.
2.10 Плавка металла и заливка форм
В производстве литья по выплавляемым моделям сталь плавят без
окисления, чаще всего методом переплава в электрических индукционных плавильных
комплексах небольшой емкости, используют чистый металлический скрап, чистый
возврат и ферросплавы.
2.10.1
Устройство индукционного плавильного комплекса
Индукционный
плавильный комплекс УИП-250-2,4-0,25, предназначен для плавки углеродистых и
легированных сталей, а так же цветных металлов.
Печь
индукционная состоит из следующих основных сборочных единиц: индуктора,
каркаса, стойки (постамента) печи, футеровки, водоохлаждаемых кабелей.
Охлаждение
индуктора осуществляется проточной водой поступающей в него по напорным
рукавам.
Футеровка
печи представляет собой набивной тигель.
.10.2
Футеровка тигля индукционной печи
1.
Подготовка индуктора
Перед
началом футеровочных работ индуктор обувают сжатым воздухом и внимательно
осматривают. Особое внимание уделяется состоянию электроизоляционного покрытия
и герметичности индуктора.
Внутреннюю
поверхность индуктора покрывают выравнивающей обмазкой в два слоя толщиной 4-5
мм.
Состав
изоляционной обмазки:
бакелитовый
лак ГОСТ 901-71 30%
кварц
молотый, пылевидный
КП1,
КП2 ГОСТ 9077-82 70%
Тщательно
смешанные компоненты наносятся на внутреннюю поверхность индуктора,
предварительно покрытого свежим слоем бакелитового лака. Затем сушат при 50-60 ˚C в
течении 24 часов.
Покрытый
смазкой индуктор обкладывают изнутри слоем миканита ГОСТ 6121-75,толщиной 0,5
-1,0 мм. Соединение листов миканита выполняется внахлест. Вторым слоем
выкладывается асбестовый картон ГОСТ 2850-75, толщиной 5мм.
2.
Приготовления массы для футеровки тигля
Данная
футеровка рекомендуется для выплавки углеродистых низколегированных и
инструментальных сталей по кислому процессу.
Футеровочную
массу приготавливают из следующих компонентов:
кварцит
молотый, пылевидный КП1 ГОСТ 9077-59
кварцит
молотый ПКМИ-97,5 ТУ 14-8-246-77
кварцит
молотый Первоуральского завода для тиглей индукционных печей. Можно применять
кварцит марки ПКММ ТУ 14-8-99-74 или кварцит молотый Красногорского
огнеупорного завода марки ПКМ ТУ 14-8-141-75. Влажность кварцита перед набивкой
должна быть не более 0,5%.
борная
кислота ГОСТ 18704-75 должна иметь влажность не более 0,2%.Борную кислоту с
повышенной влажностью просушить при температуре 80 -100 ˚С и просеять
через сито с размером ячейки в свету 0,15мм.
В
процентном соотношении футеровочнную массу готовят следующим образом: - кварц
молотый, пылевидный КП1-18,8%;
кварц
молотый ПКМИ-97,5 -80,0;
борная
кислота -1,2;
Все
компоненты перемешиваются в лопастных мешалках в течении 5-10 мин до получения
однородной массы. Малое количество можно перемешивать вручную.
Далее
на подину наносится слой чистого кварцита, равный 1/4 толщины днища и
утрамбовывается ручной трамбовкой. Затем насыпают слой футеровачной массы
толщиной 30-50 мм и утрамбовывается пневмовибратором. На взрыхленную
поверхность утрамбованного слоя (глубиной 5-6 мм) наносится новый слой
футеровочной массы толщиной 20-40 мм и снова виброуплотняется. Затем
устанавливается шаблон для набивки стенок. Его следует отцентрировать и
загрузить грузом или шихтой, равной 1/3 емкости печи для предотвращения
смещения его в процессе набивки. Взрыхленная поверхность подины, не занятая
шаблонам засыпается футеровочной массой и уплотняется. Затем аналогично
набивается тигель до уровня шаблона.
3.
Уход за футеровкой тигля
После
каждой плавки производится осмотр футеровки тигля. При обнаружении обвалов
футеровки или трещин производится обмазка тигля футеровочной смесью. Подмазку
тигля можно производить, как в горячем, так и в холодном состоянии.
.10.3
Футеровка ковша
Для
футеровки ковша применяется набивная масса из следующих компонентов:
кварцевый
песок 1К 016А ГОСТ 2138-85 - 50%
пылевидный
кварц КП-1,КП-2 ГОСТ 9077-85- 50%
натриевое
жидкое стекло, плотностью 1,4 г/cм
Толщина
футеровки должна быть не менее 30 мм. Сушку ковша производят как можно
медленнее, а подогрев перед заливкой в максимально короткий срок. Образующиеся
трещины замазываются набивной смесью с последующей подсушкой.
2.10.4 Выплавка стали в индукционном плавильном комплексе
УИП-250-2,4-0,25 с кислой футеровкой
1. Шихтовые материалы для плавки стали 35Л
- лом стальной ГОСТ 2787-86;
возврат собственного производства;
ферромарганец ФМn 1,0 ГОСТ
4755-80;
ферросилиций ФС 45 ГОСТ 1415-78;
В качестве раскислителя применяется:
Гранулированный аллюминий
Шлаки, при плавке стали в электрических индукционных печах, имеют
низкую температуру и недостаточно активны. Процессы диффузного раскисления в
таком случае очень затруднены, поэтому шихтовые материалы необходимо подбирать
с малым содержанием серы и фосфора.
2. Подготовка шихтовых материалов к плавке
Все шихтовые материалы применяемые для плавки сталей, должны быть
очищены от пыли, грязи, масел, песка, а в зимнее время от льда и снега.
Категорически запрещается загружать в печь влажные шихтовые материалы.
Максимальные размеры отдельных кусков не должны превышать 500х200х100 мм.
Ферросплавы должны быть раздроблены на куски не более 50 мм.
Для обеспечения заданного маркой химического состава металла,
плавильщиком или мастером участка производится расчет шихты и записывается в
плавильный журнал. Основным в расчете шихты является правильная оценка угара
основных элементов выплавляемого металла.
3.
Плавка стали и раскисление
Шихта
загружается в следующей последовательности. На дно тигля укладываются часть
мелкой шихты и чугун, более крупные куски шихты укладываются ближе к стенкам
тигля. Остальную часть шихты укладывают так, чтобы добиться максимальной
плотности ее укладки. В процессе расплавления металла производится осаждение
шихты и загрузка оставшейся ее части, не допуская образования
"мостов".
При
образовании ванны жидкого металла кварцевым песком ГОСТ 2138-91 наводится
кислый шлак, предохраняющий металл от окисления.
Плавка
металла ведется на максимальной мощности печи. При достижении температуры
металла в печи не ниже 1600 ˚С необходимо снять шлак, произвести замер
температуры и после этого начинать раскисление. Измерение температуры
производится термопарой погружения, градуированной по ГОСТ 3044-84. В начале
раскисления вводится ферромарганец и наводится шлак за 2-5 минут до выпуска
металла из печи зеркало металла, очищается от шлака и вводится ферросилиций.
Силикокальций и алюминий вводится в печь непосредственно пред разливкой в
количестве 0,10-0,15% от веса жидкого металла. Допускается часть алюминия для
раскисления металла вводить непосредственно в ковш.
4.
Разливка металла
Температура
металла в печи по окончании плавки должна быть 1700-1720˚С, температура
заливки металла 1600 -1670˚C. Пpи достижении этой температуры
металл из печи выпускается в новый ковш, нагретый до температуры 600 -700˚С.
Для
заливки форм используют стальные футерованные чайниковые ковши.
Ручной
разливочный ковш с расплавом подается на участок заливки от плавильной печи.
Заполнение форм металлом должно производиться ровной непрерывной струёй,
направленной в центр литниковой воронки. Высота струи металла при заливке не
должна быть большой во избежание размыва стенок литниковой системы и засорения
формы.
Высота
струи металла над литниковой чашей в начале заливки должна быть не более 50 мм
с последующим увеличением до 100-150 мм. Во избежании образования усадочных
раковин и недоливов следует сразу заполнить литниковую систему и держать ее
полностью заполненной до конца заливки.
.11
Контроль качества металла
Химический
состав стали определяется по образцам каждой плавки, согласно ГОСТ 977-88.
.12
Разработка технологического процесса изготовления отливки
Процесс
изготовления моделей состоит из подготовки пресс-формы, заполнения рабочей
полости пресс-формы модельным составом, выдержки для затвердевания модели,
разборки пресс-формы и выталкивании модели, выдержки моделей в воде до
окончания усадки.
Подготовка
пресс-формы заключается в очистке, смазке рабочей полости и сборке. Смазку из
эмульсии или чистого трансформаторного масла наносят тонким слоем на рабочую
поверхность пресс-формы. Густая и неравномерная смазка вызывает образование
раковин и шероховатости на поверхности модели.
Заусенцы
на моделях зачищают вручную с помощью специальных ножей. Следы смазки
пресс-формы, влаги и других прилипших посторонних частиц к поверхности моделей
чаще всего удаляют сжатым воздухом. Отделку моделей целесообразно совмещать с
контролем их качества.
Модели
отливки припаиваются к моделям литниковой системы вручную подогретым ножом. На
получаемые блоки в несколько слоев наносится жидкая формовочная смесь или
обмазка, состоящая из пылевидного огнеупорного материала и связующего
(гидрализованного раствора этилсиликата). Модельные блоки погружают в суспензию
(погрузить блоки плавно, без толчков во избежание поломки моделей и для получения
слоя покрытия без воздушных пробок и пузырей; после извлечения блок медленно
поворачивать в различных направлениях для стекания избытка суспензии; при
нанесении первого слоя модельный блок, после извлечения из суспензии, выдержать
на воздухе 5-6 сек. И повторно погрузить в суспензию). Обсыпают обмазанные
блоки песком (обсыпку производить не позднее чем через 10 сек. После нанесения
покрытия). Затем просушить нанесенный слой огнеупорного покрытия (режим сушки -
в соответствии с паспортом на установку; допускается следующий режим сушки: 1
час - на воздухе, 35 мин - в вытяжном шкафу в парах аммиака, 20 мин - на
воздухе при температуре цеха). Нанести и просушить второй и последующий слои
покрытия (количество слоев в соответствии с картой технологического процесса
литья по выплавляемым моделям на деталь).
Затем
модель выплавляется горячим паром в бойлерклаве (время выдержки 5- 10 мин) и
получается тонкая керамическая оболочка. Оболочку устанавливают в неразъемную
опоку, закрыв литниковые чаши керамических форм, и засыпают песком или другим
наполнителем с целью предохранения ее от разрушения при заливке металла. Далее
форма прокаливается при 950 - 1000 ° С. Во время
прокалки оболочки выгорают остатки модельного состава, удаляются продукты
неполного гидролиза, испаряется вода и другие газотворные вещества. Кроме того,
происходит спекание частичек связующего с частичками огнеупорного пылевидного
материала.
Металл
заливается сразу после прокалки, т.е. в горячую форму. Температура заливки форм
в соответствии с картой техпроцесса на деталь. При заливке не допускается
прерывание струи металла. Высота струи над литниковой чашей не более 100 мм. В
процессе заливки литниковая чаша должна быть заполнена металлом. В середине
разливки каждой плавки залить контрольные образцы для химического анализа
Затем
следуют операции охлаждения залитых форм, выбивки отливок из оболочки и их
очистка. Очистка отливок от керамики осуществляется механическими методами.
Механическая очистка выполняется на пневматических установках. Затем отливки
отделяются от литниковой системы и подвергаются окончательной очистке в
дробеструе.
После
очистки отливки подвергаются термической обработке с целью измельчения
структуры и упрочения.
Исправление
дефектов отливок:
.
зачистить отливки от заусенцев, корольков;
.
заварить дефектные участки при необходимости;
.
рихтовать отливки при необходимости.
Технический
контроль:
.
проверить химический состав литья;
.
проверить отливки на соответствие чертежу;
.
проверить отливки на соответствие техническим требованиям;
.
проверить микроструктуру для отливок по перечню (на 1-2-х деталях от партии).
Каждая
партия отливок предъявляется для технического контроля с маршрутным листом, где
указаны дата и номер плавки в соответствии с плавильным журналом. К маршрутному
листу прилагается «Результат хим. анализа» состава (бланк формы № 1), а для
отливок 2 группы - результат испытаний механических свойств.
Образцы
для анализа хим. состава и образцы для определения механических свойств сплава
направлять в лабораторию отдела.
Партии
отливок без результатов анализа хим. состава, а для отливок 2 группы
-результатов механических испытаний - приемке ОТК не подлежат.
.13
Анализ возможных видов брака и меры их предотвращения
Чаще
всего брак отливок вызывается нарушением технологии литья по выплавляемым
моделям. Необходимо строго следить за хорошей подготовкой исходных материалов,
точным соблюдением температурных режимов при запрессовке модельных составов,
сушке и прокаливании форм, плавке и заливке металла. Оборудование и оснастка должны
быть в удовлетворительном состоянии.
1.
Дефекты поверхности
Повышенная
шероховатость появляется в результате недостаточной чистоты и
неравномерной смазки поверхности прессформы, плохого смачивания поверхности
модели обмазкой, образования в полости формы налета кремнезема («пушка»),
«пробой» первого облицовочного слоя суспензии песком при обсыпке блоков, также
вследствие излишней вязкости модельного состава, ведущая к выкрашиванию
непрочного первого слоя оболочки при выплавлении моделей.
Рабочая
поверхность прессформы должна тщательно очищаться от остатков модельного
состава, воды и излишней смазки после выталкивания модели. Необходимо следить
за равномерным распределением смазки по поверхности прессформы.
Обмазка
плохо смачивает модели в случае, если на их поверхности остаются следы смазки
прессформы. Необходимо обезжирить модели мыльным раствором в воде. Другой
причиной является плохая смачиваемость обмазкой модельного состава. В связи с
этим в обмазку следует добавлять поверхностно активные вещества или заменять
модельный состав.
Чтобы
избежать «пробоя» первого слоя необходимо, не применять крупнозернистый песок
для обсыпки первого слоя суспензии. Консистенцию и состав суспензии для первого
слоя подбирать так, чтобы он был равномерным и достаточным по толщине на всех
поверхностях моделей в блоке.
Необходимо
упрочнять первый слой оболочки. Применять модельные составы с малой вязкостью.
Заливы.
Металл проникает в трещины оболочки, образуя «гребешки», или между слоями
оболочки, образуя «наплывы». Трещины появляются при низкой прочности оболочки.
Причины низкой прочности - некачественные исходные материалы или нарушения
режимов изготовления формы. Оболочка растрескивается также от давления
модельного состава при его выплавлении. В этом случае необходимо использовать
другой модельный состав с меньшим коэффициентом теплового расширения.
Образованию
трещин способствуют тепловые расширения материалов оболочки при прокаливании.
Следует соблюдать установленные режимы прокаливания особенно для форм с жидким
наполнителем.
Образование
на поверхности моделей и между слоями оболочки воздушных пузырьков из-за
плохого смачивания поверхности моделей суспензией и плохой подготовки
суспензии. Необходимо суспензию для облицовочных слоев формы после
перемешивания выдерживать для удаления пузырьков воздуха. Для интенсификации
этого процесса производить выдержку под вакуумом и при вибрации. Строго
соблюдать установленные соотношения твердых и жидких компонентов суспензии,
тщательно перемешивать их, обеспечивая соблюдение установленной для данного
слоя вязкости. Избегать выполнения литых резьб, глубоких отверстий малого
диаметра, узких пазов. Выполнять галтели во внутренних углах отливок.
Образование
трещин в оболочке под давлением опорного наполнителя. Нужно для крупных отливок
увеличивать число слоев оболочки формы. Применять крупнозернистый песок для
обсыпки последних слоев оболочки и добавку цемента в песок. Формировать при
изготовлении оболочек высокопористые промежуточные слои, снижающие напряженно
состояние оболочек. Применять для опорного наполнителя материалы с малым
коэффициентом теплового расширения и малой объемной массой. Избегать
горизонтального расположения в опоке отливок с большими плоскими поверхностями.
Механические
повреждения оболочек форм на всех операциях процесса. Предохранять оболочки и
формы от механических повреждений на всех технологических операциях.
Пригар
на отливках образуется в результате химического взаимодействия материалов
оболочки и отливки или перегрева отдельных участков формы.
Необходимо
использовать формовочные материалы, химически инертные к применяемому литейному
сплаву.
Причиной
может служить перегрев металла при заливке форм, необходимо соблюдать
оптимальную температуру заливки сплава с учетом конфигурации отливки.
Сильный
разогрев отдельных участков полости формы металла, через которые подходит
большая часть металла. Необходимо рассредоточить подвод металла к отливкам,
уменьшить массивные узлы, увеличить расстояние между отливками в блоке.
Недолив
- это незаполнение металлом отдельных частей отливки. Одна из причин - это
пониженная жидкотекучесть металла в результате пониженной температуры его при
заливке или газонасыщенности.
Дефекты
литниковой системы (недостаточные сечения питателей или других элементов,
неправильный выбор места подвода металла к отливке). Необходимо исключить
заполнение отливки встречными потоками металла. Изменить расположение, число и
размеры элементов ЛПС. Сократить время заполнения формы. Улучшить конструкцию
блока для создания необходимого статистического давления металла.
2.
Внутренние дефекты
Засоры,
т.е. открытые или закрытые полости в теле отливки, заполненные материалом
оболочки, появляются при смывании струей металла «заусенцев» на оболочке,
которые образуются в щелях между небрежно спаянными моделями и литниковой системой.
Попадание формовочных материалов в полость формы через трещины в оболочке. Для
предупреждения этого необходимо предупреждать образование трещин в оболочке
формы.
Загрязненность
модельного состава - очищать модельный состав, отстаивать и фильтровать.
Попадание
в полость оболочки формовочного песка при формовке в опорный наполнитель,
прокаливании, заливке и транспортировании форм. Необходимо ставить оболочку в
опоку так, чтобы край воронки возвышался над наполнительным песком на 10-15 мм.
Закрывать литниковую воронку перед формовкой металлическим колпачком. Перед
прокаливанием формы смачивать поверхность песка вокруг воронки раствором
жидкого стекла. Отстаивать инжектором сор из полости формы перед заливкой.
Усадочные
раковины и пористость в стенках возникают при недостаточном питании отдельных
частей отливки во время ее затвердевания.
Основной
мерой борьбы с усадочными дефектами является изменение конструкции литниковой
системы, а в некоторых случаях и самой отливки. Литниковая система должна
обеспечивать направленное затвердевание отливки. Для этого необходимо
установить прибыли над массивными частями отливки, изменить размеры питателия,
чтобы через него обеспечить питание отливки от стояка или коллектора, выровнять
толщину стенок отливки.
Раковины
газовые. Открытые или закрытые полости в теле отливки, обычно с чистой и
гладкой поверхностью, иногда окисленные. Раковины могут быть одиночные,
групповые и в виде сыпи.
Повышенная
газотворность литейной формы, неполное удаление из оболочки формы остатков модельного
состава, наличие газотворных примесей в формовочных материалах приводят к
образованию газовых раковин. Соблюдать режимы прокаливания, обеспечивающие
полное удаление из формы газотворных составляющих. Применять наиболее
эффективные методы удаления моделей из оболочки формы. Не допускать в
производство формовочные материалы, содержащие газотворные примеси. Промывать и
прокаливать формовочные огнеупорные материалы, засоренные органическими
примесями.
Газовые
раковины из-за недостаточной газопроницаемости литейной формы. Для обсыпки
необлицованных слоев оболочки применять крупнозернистые материалы с размером
зерен 0,3-2,5 мм. Выполнять в средней части оболочки высокопористые слои,
используя в обсыпочном материале выгорающие, разлагающиеся, а также пористые
материалы. При введении в сухой наполнитель борной кислоты или буры в качестве
упрочнителя поддерживать их содержание на нижнем пределе (1,5%).
Газовые
раковины из-за неправильно сконструированной ЛПС, способствующей инжектированию
воздуха в струю металла при заливке.
Трещины
горячие. Поверхностные или сквозные надрывы стенок отливки. Разрыв имеет
окисленную поверхность.
Нетехнологичность
конструкции отливки и блока, значительная концентрация напряжений в острых
углах, сложных замкнутых контурах, резких переходах от массивных узлов к тонким
сечениям приводят к образованию трещин.
Образование
трещин из-за недостаточной податливости литейной формы. Сократить число слоев
оболочки формы. При излишне высокой прочности оболочки снизить ее до
технологически необходимой. Применять оболочки с пористыми прослойками.
Трещины
холодные. Поверхностные или сквозные надрывы стенок отливки с чистой или слегка
окисленной поверхностью.
Причины
образования холодных трещин могут быть те же, что и горячих. Внутренние
напряжения возникающие в горячих отливках возрастают при охлаждении их до
комнатной температуры. Повышению напряженности способствует продолжающая усадка
отливки при охлаждении, фазовые превращения в металле отливки, происходит с
изменением объема, неравномерном охлаждении.
Напряжения
от внешних воздействий на отливку, например, резких ударов при выбивке и
обрубке.
3.
Несоответствие отливки по геометрии
Отклонение
размеров отливок от требуемых. Неточность размеров моделей вследствие
применения модельных составов с большой и непостоянной усадкой, несоблюдения
оптимальных режимов изготовления моделей, недостатков конструкции пресс-форм.
Изменить
рецептуру модельного состава. Применять модельные составы высокой
термоустойчивости. Отработать и соблюдать оптимальные режимы изготовления и
хранения моделей.
Изменить
конструкцию пресс-формы, обеспечив надежность крепления ее половин и вставок,
съем моделей, исключающий возможность деформации их и искажения размеров при
выемке из пресс-форм. Деформация литейной формы в результате объемных измерений
формовочных материалов при неравномерном нагреве и охлаждении различных частей
формы недостаточной прочности облицовочного слоя формы.
Коробление.
Деформация отливок, вызывающая отклонение ее размеров от чертежных.
Нетехнологичность конструкции отливки, приводящая к значительному короблению
моделей и отливок на различных этапах технологического процесса.
Изменить
конструкцию отливки. Ввести специальные технологические приливы, ребра
жесткости, стяжки, препятствующие изменению формы моделей и отливок под
действием возникающих термических и усадочных напряжений. Коробление моделей
следствие недостаточной формоустойчивости и большой усадки модельного состава,
а также небрежного хранения моделей собранных в модельные блоки.
Заменить
модельный состав более формоустойчивым, прочным с меньшей и стабильной усадкой.
Хранить модели и модельные блоки в шкафах-термостатах, при постоянной
оптимальной температуре в положении, исключающем деформацию моделей под
действием собственного веса. Использовать специальные дрейеры - подставки для
моделей. Тонкостенные модели сборкой проверять на коробление специальным
инструментом (шаблонами) или по прямолинейным образующим (лекальной линейкой).
3.
ЭКОНОМИЧЕСКАЯ ЧАСТЬ
В экономической части данного проекта представлены основные экономические
расчёты, которые позволяют определить технико-экономические показатели, а также
экономическую эффективность представленного проекта.
3.1
Организация труда и планирование численности персонала
Численность рабочих определяется отдельно по следующим категориям:
рабочие основные и вспомогательные;
руководители;
специалисты;
служащие.
Различают списочную и явочную численность рабочих. Списочная численность
- это численность работников списочного состава на определённую дату с учётом
принятых и выбывших в этот день работников. Явочная численность - это
количество работников, явившихся на работу. Разница между явочным и списочным
составом характеризует количество целодневных простоев (плановые невыходы на
работу).
Для литейных цехов наиболее распространенным является расчёт численности
основных рабочих по нормам обслуживания агрегатов:
(24)
, (25)
где
Чяв - явочная численность рабочих, чел.;
Чсп
- списочная численность рабочих, чел.;
А
- количество одноимённых агрегатов;
с
- число смен в сутки;
Ксп
- коэффициент списочного состава.
Таблица
3.1
Баланс
рабочего времени одного рабочего за год, дни
Статья баланса
|
Рабочие
|
|
основные
|
вспомогательные
|
Календарный фонд времени, Тк
|
365
|
365
|
Выходные дни, Тв
|
104
|
104
|
Праздничные дни, Тпр
|
9
|
9
|
Номинальный фонд времени, Тн
|
252
|
252
|
Плановые невыходы на
работу, Тнев
|
39
|
30
|
в том числе: - основной и
дополнительный отпуск -по болезни -выполнение государственных и общественных
обязанностей -прочие причины
|
30 7 1 1
|
24 5 - 1
|
Действительный фонд
времени, Тд
|
213
|
222
|
Коэффициент списочного
состава, Ксп
|
1,18
|
1,13
|
Таблица 3.2
Структура персонала цеха
Категории
|
Количество человек
|
Удельный вес в общей
численности, %
|
Рабочие в том числе
|
30
|
|
основные
|
15
|
34,1
|
вспомогательные
|
15
|
34,1
|
руководители
|
5
|
11,4
|
специалисты
|
5
|
11,4
|
4
|
9,1
|
Итого
|
44
|
100
|
3.2
Организация и расчёт заработной платы персонала
Заработная плата на производственном предприятии представляет собой выраженную
в денежной форме часть совокупного продукта, которая поступает в личное
пользование рабочих и служащих в соответствии с количеством и качеством
затраченного ими труда. Под фондом оплаты труда понимается сумма денежных
средств, установленная в плановом порядке, для оплаты труда работникам, занятым
производством и реализацией продукции. На металлургическом предприятии фонд
оплаты труда планируется раздельно для производственного и непроизводственного
персонала.
Годовой фонд оплаты труда рабочих складывается из фондов основной и
дополнительной заработной платы.
Основная заработная плата включает в себя:
заработок по тарифу;
приработок сдельщика;
премии за выполнение плана;
доплаты за работу в вечернее и ночное время;
доплаты за работу в праздничные дни.
Все составляющие основной заработной платы суммируются и корректируются
на районный коэффициент, который для условий Урала составляет 15 %.
Дополнительная заработная плата включает в себя оплату отпусков
очередных, дополнительных и учебных, оплату времени выполнения государственных
обязанностей. При проектировании дополнительная заработная плата принимается в
размере 10 % от основного заработка с учётом районного коэффициента.
Определение заработка по тарифу выполним, укрупнено, т.е. по средней
тарифной ставке, которая рассчитывается по группе рабочих, работающих в
одинаковом режиме с одинаковым балансом рабочего времени и оплачиваемых по
одной тарифной ставке.
Средняя тарифная ставка (Тср) по формуле средней взвешенной
арифметической:
, (26)
где
Т1, Т2…., Т6 - тарифные ставки соответствующих
разрядов;
Ч1,Ч2….,
Ч6 - явочное число рабочих этих разрядов.
Тср=69,65
руб./час
Количество
отработанных человеко-часов на программу определяется умножение списочного
количества рабочих на действительный фонд времени одного рабочего в году.
Заработная
плата по тарифу для группы рабочих определяется умножением средней тарифной
ставки на количество отработанных человеко-часов.
Приработок
сдельщика рассчитывается умножением заработка по тарифу на планируемый процент
перевыполнения норм выработки. Для проектируемого цеха планируемая норма
перевыполнения плана 5 %.
Премии
за выполнение плана для основных рабочих составит 40 %, а для вспомогательных
30 % от суммы заработка по тарифу и приработка сдельщика (сдельный заработок).
Размер
доплаты за работу в вечернее время определяется с учётом коэффициента доплат (Кд):
, (27)
где
Твеч - продолжительность вечернего рабочего времени;
Квеч
- коэффициент доплат за работу в вечернее время, 20 %;
Тс
- количество рабочих часов в сутки.
Для
расчёта размера доплаты заработок по тарифу умножается на коэффициент доплаты.
Результаты
расчётов годового фонда оплаты труда рабочих приведены в таблице 3.3.
Таблица
3.3
Годовой
фонд оплаты труда рабочих
|
Основные рабочие
|
Вспомогательные рабочие
|
Всего
|
Количество рабочих
|
15
|
15
|
30
|
Средняя тарифная ставка
|
69,65
|
69,65
|
|
Затраты времени на
программу
|
386058
|
112385
|
498443
|
Зарплата по тарифу
|
4201400
|
1235705
|
5437105
|
Приработок сдельщика
|
73273
|
22226
|
95499
|
Премии
|
364694
|
102623
|
467317
|
Доплата за вечернее время
|
-
|
-
|
-
|
Итого основная зарплата
|
4639367
|
1360554
|
5999921
|
С учётом районного
коэффициента
|
5335272
|
1564637
|
6899909
|
Дополнительная заработная
плата
|
591210
|
105478
|
696688
|
Всего
|
5926482
|
1670115
|
7596597
|
Расчёт фонда оплаты труда руководителей, специалистов и служащих
производится в следующем порядке:
определяется годовая сумма основной заработной платы по окладам: для
руководителей и специалистов расчёт ведётся на 11 рабочих месяцев, для служащих
- 11,3 месяца;
премии для руководителей и специалистов составляют 40 %, для служащих -
30 % от суммы окладов;
для сменного персонала рассчитываются доплаты за работу в вечернее время
по нормативам установленным для рабочих;
дополнительная заработная плата - 10 % от основной заработной платы,
скорректированная на районный коэффициент.
Результаты планирования годового фонда оплаты труда руководителей,
специалистов и служащих приведены в таблицах 3.4, 3.5 и 3.6.
Таблица 3.4
Годовой фонд оплаты труда руководителей (руб)
|
Начальник цеха
|
Заместитель начальника
|
Старший мастер
|
Мастер участка
|
Всего
|
Количество
|
1
|
2
|
3
|
4
|
5
|
Оклад за месяц
|
25000
|
20000
|
18000
|
16000
|
79000
|
Сумма окладов
|
275000
|
220000
|
198000
|
352000
|
1045000
|
Премии
|
140800
|
110000
|
88000
|
79200
|
418000
|
Доплата за работу в
вечернее время
|
-
|
-
|
-
|
-
|
-
|
Итого основная заработная
плата
|
385000
|
308000
|
287100
|
510400
|
1490500
|
С учетом районного
коэффициента
|
442750
|
354200
|
330165
|
586960
|
171407
|
Дополнительная заработная
плата
|
44275
|
35420
|
33016
|
58696
|
171407
|
Всего
|
487025
|
389620
|
363181
|
645656
|
1885483
|
Таблица 3.5
Годовой фонда оплаты труда специалистов (руб)
|
Энергетик
|
Механик
|
Технолог
|
Экономист- нормировщик
|
Всего
|
1
|
2
|
3
|
4
|
5
|
6
|
Количество
|
1
|
1
|
2
|
1
|
6
|
Оклад за месяц
|
17000
|
17000
|
18000
|
14000
|
66000
|
Сумма окладов
|
187000
|
187000
|
396000
|
154000
|
924000
|
Премии
|
74800
|
74800
|
158400
|
61600
|
369600
|
Доплата за работу в
вечернее время
|
-
|
-
|
-
|
-
|
0
|
Итого основная заработная
плата
|
261800
|
261800
|
554400
|
215600
|
1293600
|
С учётом районного
коэффициента
|
301070
|
301070
|
637560
|
247940
|
1487640
|
Дополнительная заработная
плата
|
30107
|
30107
|
63756
|
24794
|
148764
|
Всего
|
331177
|
331177
|
701316
|
272734
|
1636404
|
Таблица 3.6
Годовой фонд оплаты труда служащих (руб)
|
ОТК
|
кладовщик
|
лаборант
|
всего
|
Количество
|
1
|
2
|
2
|
4
|
Оклад за месяц
|
16000
|
15000
|
15000
|
48000
|
Сумма окладов
|
244000
|
213000
|
294000
|
751000
|
Премии
|
72000
|
60000
|
97000
|
229000
|
Доплата за работу в
вечернее время
|
-
|
-
|
-
|
0
|
Итого основная заработная
плата
|
316000
|
273000
|
391000
|
980000
|
С учётом районного
коэффициента
|
363400
|
313950
|
449650
|
1127000
|
Дополнительная заработная
плата
|
23252
|
19710
|
31504
|
74466
|
Всего
|
386652
|
333660
|
481154
|
1201466
|
3.3 Расчёт
капитальных вложений
При расчёте капитальных вложений учитываются капитальные вложения в
строительство цеха, а также на приобретение технологического оборудования.
Результаты расчётов приведены в таблице 3.7.
Таблица 3.7
Расчёт капитальных вложений и амортизационных отчислений
Наименование
|
Кол-во
|
Цена единицы
|
Сумма, руб
|
Годовая норма амортизации
|
Сумма амортизационных
отчислений
|
Здания и сооружения, м³
|
3400
|
2000
|
5800000
|
0,02
|
116000
|
УИП-250-2,4-0,25
|
2
|
1800000
|
3600000
|
0,07
|
252000
|
Печь прокалочная
ПВО-1,2-500
|
3
|
900000
|
1800000
|
0,07
|
126000
|
Шприц-
машина CTM-WI 15
|
1
|
1500000
|
1500000
|
0,09
|
135000
|
9190-бак с мешалкой для
обмазки блоков
|
1
|
400000
|
400000
|
0,09
|
36000
|
9191-пескосып "кипящий
слой"
|
1
|
300000
|
300000
|
0,09
|
27000
|
Бойлерклав для вытопки
восковых моделей
|
1
|
2000000
|
2000000
|
0,09
|
180000
|
Термическая печь ПВТ-1,2-
1000
|
2
|
400000
|
800000
|
0,09
|
72000
|
Итого основное оборудование
|
|
|
15200000
|
|
894117
|
Подъемно-транспортное
оборудование
|
|
|
3930000
|
0,1
|
393000
|
Прочее оборудование
|
|
|
2300000
|
0,1
|
230000
|
Всего по оборудованию
|
|
|
21430000
|
|
1648461
|
Предполагается, что транспортные расходы по доставке необходимого
оборудования и затраты на монтаж входят в цену оборудования.
Затраты на приобретение и монтаж подъёмно транспортного оборудования
принимаются в размере 60 % от стоимости технологического оборудования.
Затраты на прочее оборудование составляют 25 % от стоимости основного
оборудования.
Сумма амортизационных отчислений (Аотч) рассчитывается
следующим образом:
, (28)
где
С - стоимость основных фондов, которая включает в себя, кроме цены
оборудования, затраты на доставку и монтаж;
НА
- годовая норма амортизации в долях целого.
3.4 Планирование
себестоимости продукции
Для проведения расчёта себестоимости необходимо составление сметы
расходов на содержание и эксплуатацию оборудования, а также сметы цеховых
расходов, которые приведены соответственно в таблицах 3.8 и 3.9.
Таблица 3.8
Смета расходов на содержание и эксплуатацию оборудования
Статья затрат
|
Оплата труда
вспомогательных рабочих
|
1941264
|
Отчисления на социальные
нужды
|
691090
|
Амортизация оборудования
|
1694750
|
Эксплуатация оборудования
|
456950
|
Ремонты оборудования
|
957375
|
Прочие расходы
|
917089
|
Итого
|
5741429
|
Таблица 3.9
Смета цеховых расходов
Статья затрат
|
Сумма, руб
|
Оплата труда
административно-управленческого персонала
|
2310661
|
Отчисления на социальные
нужды
|
822595
|
Амортизация зданий и
сооружений
|
126400
|
Содержание зданий и
сооружений
|
252800
|
Ремонты зданий и сооружений
|
126400
|
Охрана труда
|
651210
|
Прочие расходы
|
956287
|
Итого
|
4546355
|
.4.1
Калькуляция себестоимости годных отливок из стали
Калькуляция себестоимости годных отливок из стали приведена в таблице
3.10.
Таблица 3.10
Калькуляция себестоимости годных отливок из стали
Статья затрат
|
Кол-во на 1т
|
Цена, руб/т
|
Сумма, руб
|
Количество на программу
|
Сумма, руб
|
|
1
|
2
|
3
|
4
|
5
|
6
|
|
Лом стальной
|
598,8
|
2,5
|
1497
|
1497000
|
3742500
|
|
Возврат собственного
производства
|
394,6
|
2,5
|
986,5
|
986500
|
2466250
|
|
ФМн-70
|
16
|
16,8
|
268,8
|
40000
|
672000
|
|
ФС-75
|
16
|
25
|
400
|
40000
|
1000000
|
|
Итого
|
1073,4
|
|
1329,3
|
2683500
|
3323250
|
|
Угар и безвозвратные потери
|
73,4
|
|
|
183500
|
|
|
Итого металла в готовом
изделии
|
1000
|
|
|
|
|
|
ПС 50-50
|
10.7
|
35
|
374.5
|
374500
|
1123500
|
|
Этилсиликат ГС-40
|
9.4
|
213
|
2002.2
|
2002200
|
3006600
|
Песок наполнитель
|
99
|
23
|
2277
|
2277000
|
3831000
|
Оплата труда
производственных рабочих
|
47.4
|
108
|
5119.2
|
5119200
|
15357600
|
Отчисления на социальные
нужды
|
130
|
3.4
|
442
|
442000
|
1326000
|
Расходы на содержание и
эксплуатацию оборудования
|
|
|
1432,7
|
|
5741429
|
Цеховые расходы
|
|
|
510
|
|
4546355
|
Итого цеховая себестоимость
|
|
|
1406
|
|
5741429
|
Общезаводские расходы
|
|
|
2707,5
|
|
4546355
|
Итого производственная
себестоимость
|
|
|
11350,7
|
|
28376851
|
Внепроизводственные расходы
|
|
|
908,5
|
|
2271165
|
Всего полная себестоимость
|
|
|
12259
|
|
31258016
|
|
|
|
122,6
|
|
306480
|
|
|
|
12381,8
|
|
31354030
|
|
|
|
|
|
|
|
|
Отчисления на социальные нужды составляют 35.6 % от затрат на оплату
труда.
Общезаводские расходы - это расходы по управлению и организации
производством по предприятию в целом, укрупнено, принимаем их 15 % от стоимости
передела. Стоимость передела - это цеховая себестоимость за вычетом
материальных затрат.
Внепроизводственные расходы связаны с реализацией продукции и приближённо
равны 1 % от производственной себестоимости.
3.5
Технико-экономические показатели проекта
Рентабельность каждого вида продукции определяется по следующей формуле:
, (29)
где
С - себестоимость вида продукции;
Ц
- цена вида продукции.
Фондоотдача
рассчитывается следующим образом:
, (30)
где
В - выпуск всех видов продукции в стоимостном выражении;
Сопф
- стоимость основных производственных фондов.
Основные
технико-экономические показатели рассматриваемого проекта приведены в таблице
3.11.
Таблица
3.11
Основные
технико-экономические показатели проекта, год
Показатель
|
Величина
|
Объём производства
продукции: в натуральном выражении, тыс. т в стоимостном выражении, тыс. руб.
|
500 85000
|
Технологический выход
годного, % стальные отливки
|
40
|
Численность работающих,
чел., в том числе рабочих
|
44 30
|
Производительность труда,
тыс. т/чел.: одного работающего одного рабочего
|
18,211 25,322
|
Полная себестоимость всего
выпуска, тыс. руб. в том числе: стальных отливок единицы продукции, тыс. руб.
стальных отливок
|
61124,4 30954,5 12,4
|
Стоимость основных
производственных фондов, тыс. руб.
|
110047,5
|
Прибыль от реализации
продукции цеха, тыс. руб.
|
23547,3
|
Рентабельность продукции, %
стальных отливок
|
45
|
Фондоотдача, руб./руб.
|
0,88
|
Дополнительные затраты на осуществление проекта и график реализации
проекта приведены в таблице 3.12.
Таблица 3.12
Инвестиционные затраты на проект
Статья затрат
|
Года
|
Сумма, тыс.руб
|
|
1
|
2
|
3
|
4 начало выпуска продукции
|
|
Инвестиционные затраты
всего
|
|
|
|
|
|
в том числе
|
|
|
|
|
|
- научно-исследовательские
расходы
|
100000
|
|
|
|
100
|
- проектно-изыскательские
расходы
|
100000
|
|
|
|
100
|
- затраты на сертификацию
|
|
1 554 030
|
|
|
1 554
|
- затраты на здания,
сооружения,
|
|
5800000
|
|
|
5800
|
- затраты на оборудование и
его монтаж
|
|
|
22000000
|
|
22000
|
Итого
|
2000000
|
7 354 030
|
22000000
|
|
313530
|
В таблице 3.13 проведен расчет эффективности инвестиционных вложений и
показателей эффективности проекта. Норма дисконта принята 8,25% годовых.
По расчету видно, что инвестиционные затраты окупаются на шестом году от
начала реализации проекта, т.е. когда начинается выпуск и поступление средств
за продукцию. На рисунке 1 изображен финансовый профиль проекта, на котором
наглядно виден срок окупаемости.
Рисунок 1 Финансовый профиль проекта
Таблица 3.13
Расчет чистого дисконтированного дохода и показателей эффективности
проекта
Показатели
|
Годы
|
1
|
2
|
3
|
4
|
5
|
6
|
7
|
8
|
9
|
Итого
|
Поступление средств
|
0
|
0
|
0
|
75 000 000
|
75 000 000
|
75 000 000
|
75 000 000
|
75 000 000
|
75 000 000
|
|
Текущие выплаты
|
0
|
0
|
0
|
14 519 887
|
14 519 887
|
14 519 887
|
14 519 887
|
14 519 887
|
14 519 887
|
|
Инвестиционные затраты:
|
2 000 000
|
7 354 030
|
22 000 000
|
0
|
0
|
0
|
0
|
0
|
31 354 030
|
Научно-исследовательские
расходы
|
100 000
|
0
|
0
|
0
|
0
|
0
|
0
|
0
|
100 000
|
Проектно-изыскательские работы
|
100 000
|
0
|
0
|
0
|
0
|
0
|
0
|
0
|
100 000
|
Затраты на сертификацию
|
0
|
1 554 030
|
0
|
0
|
0
|
0
|
0
|
0
|
1 554 030
|
Затратты на здания
сооружения
|
|
5 800 000
|
0
|
0
|
0
|
0
|
0
|
0
|
5 800 000
|
Затраты на оборудование и
его монтаж
|
|
0
|
22 000 000
|
0
|
0
|
0
|
0
|
0
|
22 000 000
|
Коэффициент дисконтирования
(Е=8,25%)
|
0,924
|
0,853
|
0,788
|
0,728
|
0,673
|
0,621
|
0,574
|
0,530
|
|
Текущая прибыль
|
0
|
0
|
0
|
17 880 113
|
17 880 113
|
17 880 113
|
17 880 113
|
17 880 113
|
89 400 565
|
Дисконтированная прибыль
|
0
|
0
|
0
|
13 021 429
|
12 029 033
|
11 112 271
|
10 265 377
|
9 483 028
|
55 911 139
|
|
Дисконтированные
инвестиционные затраты
|
184 758
|
7 726 559
|
13 508 291
|
0
|
0
|
0
|
0
|
0
|
21 419 607
|
|
Чистый дисконтированный
доход
|
-184 758
|
-7 726 559
|
-13 508 291
|
13 021 429
|
12 029 033
|
11 112 271
|
10 265 377
|
34 491 532
|
Чистый дисконтированный
доход нарастающим итогом
|
-184 758
|
-7 911 316
|
-21 419 607
|
-8 398 178
|
3 630 855
|
14 743 126
|
25 008 504
|
34 491 532
|
|
Индекс доходности
|
|
|
|
|
|
|
|
|
2,610
|
Срок окупаемости проекта,
лет
|
|
|
|
|
|
|
|
|
4,5
|
Вывод
По итогам основных экономических расчётов, приведённых в данном разделе,
можно с большой степенью вероятности считать реализацию представленного проекта
целесообразной.
Период возврата денежных средств 4,5 года.
4. БЕЗОПАСНОСТЬ ЖИЗНИДЕЯТЕЛЬНОСТИ
Безопасность жизнедеятельности - деятельность, направленная на сохранение
жизни и здоровья человека в среде обитания, призванная выявлять и
идентифицировать опасные и вредные факторы, разработать методы и средства
понижения негативного влияния их на организм до приемлемых значений, выработать
меры по ликвидации последствий чрезвычайных ситуаций мирного и военного
времени. Решение вопросов БЖД необходимо для создания безопасных и безвредных
условий жизнедеятельности, проектирования новых технологий и технологических
процессов в соответствии с современными требованиями по экологии и безопасности
их эксплуатации с учетом устойчивости функционирования объектов промышленности
и технических систем, прогнозирования и принятия грамотных решений в условиях
чрезвычайных ситуаций по защите населения и производственного персонала от
возможных последствий аварий, катастроф, стихийных бедствий, а также в ходе их
ликвидации. Соблюдение правил, норм и требований БЖД обязательно для учреждений
всех организационно-правовых форм, независимо от сферы деятельности и
ведомственной подчиненности при проектировании, строительстве, реконструкции и
эксплуатации цехов и участков, проектировании, монтаже, изготовлении и наладке
нового оборудования, эксплуатации, техническом обслуживании, ремонте и
модернизации действующего оборудования, разработке, внедрении и
совершенствовании технологических процессов. При организации и эксплуатации
агломерационных цехов и участков должны соблюдаться действующие правила
Конституции Российской Федерации (ст. 37, 42) , Трудового кодекса Российской
Федерации, «Системы стандартов безопасности труда» (ССБТ) и других
нормативно-правовых актов по охране труда, утвержденных в установленном
порядке.
Конституция Российской Федерации закрепляет право человека на охрану
здоровья. Это право обеспечивается развитием и совершенствованием техники
безопасности и производственной санитарии, проведением широких профилактических
мероприятий.
В Трудовом кодексе Российской Федерации отражены правила организации
охраны труда на предприятиях, планирование и финансирование мероприятий по охране
труда; правила по технике безопасности и производственной санитарии; правила и
нормы по специальной охране труда женщин, молодежи и лиц с пониженной
трудоспособностью; правила, регулирующие деятельность органов государственного
надзора и общественного контроля в области охраны труда, правовые нормы, в
которых предусматривается ответственность за нарушение Трудового кодекса
Российской Федерации. Проектирование, строительство, эксплуатация,
реконструкция, расширение, техническое перевооружение, консервация, ликвидация
сталеплавильных цехов, изготовление, монтаж, наладка, обслуживание и ремонт
технических устройств, проведение подготовки и аттестации работников
осуществляется в соответствии с требованиями ССБТ, «Общими правилами
промышленной безопасности для организаций, осуществляющих деятельностей в
области промышленной безопасности опасных производственных объектов» (ПБ
11-552-03) , утвержденных постановлением Госгортехнадзора Российской Федерации
от 18.10.02 № 61, «Общих правил безопасности для металлургических и
коксохимических предприятий и производств» (ПБ 11-493-02) , утвержденных
постановлением Госгортехнадзора Российской Федерации от 21.06.02 № 39 и других
юридических документов. Важность и необходимость обеспечения безопасности труда
очевидна, так как жизнь и здоровье человека признаны главной ценностью
общества. Полностью безопасных и безвредных производств не существует. Реальные
условия характеризуются наличием некоторых опасных и вредных производственных
факторов. Задача охраны труда - свести до минимума вероятность поражения или
заболевания работающего с одновременным обеспечением комфорта при максимальной
производительности труда.
Целью данного дипломного проекта является проект цеха точного литья. Цех
проектируется таким образом, чтобы условия труда были максимально безопасными,
и были благоприятны с точки зрения экологии. Создание экологически чистых и
безопасных условий труда обеспечит высокую производительность и культуру
производства.
Цех расположен на территории города Екатеринбурга в его северной части, в
промышленном районе. Это расположение оптимально подходит для экологической
безопасности, т.к. на территории Екатеринбурга преобладают преимущественно
западные и юго-западные ветра, тем самым минует жилые кварталы города,
расположенные южнее.
Екатеринбург находится в зоне умеренно континентального климата с
характерной резкой изменчивостью погодных условий, хорошо выраженными сезонами
года. Уральские горы, несмотря на их незначительную высоту, преграждают путь
массам воздуха, поступающим с запада, из европейской части России. В результате
Средний Урал оказывается открытым для вторжения холодного арктического воздуха;
в то же время с юга сюда могут беспрепятственно проникать теплые воздушные
массы Прикаспия и пустынь Средней Азии. Поэтому для Екатеринбурга и характерны
резкие колебания температур и формирование погодных аномалий: зимой - от
суровых морозов до оттепелей и дождей, летом - от жары выше +30º
С до заморозков.
Средняя температура января - −14 ºC
Средняя температура июля - +19 ºC
Среднегодовая
температура
<#"699387.files/image034.gif">
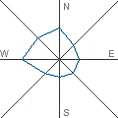
|
|
|
январь
|
апрель
|
июль
|
октябрь
|
.1 Безопасность труда
.1.1 Общие положения
В процессе работы на работников цеха возможно воздействие следующих
опасных и вредных производственных факторов по ГОСТ 12.0.003-74:
движущиеся машины и механизмы; подвижные части производственного
оборудования; передвигающиеся изделия, заготовки, материалы; разрушающиеся
конструкции;
повышенная запыленность и загазованность воздуха рабочей зоны;
повышенная температура поверхностей оборудования, материалов;
повышенная температура воздуха рабочей зоны;
повышенный уровень шума на рабочем месте;
повышенный уровень вибрации.
расположение рабочего места на значительной высоте относительно
поверхности земли (пола).
Идентификация опасных и вредных производственных факторов
Опасным производственным фактором называется такой производственный
фактор, воздействие которого на работающего в определенных условиях приводит к
травме, резкому ухудшению здоровья или летальному исходу.
Для проектируемой технологии характерно выделение вредных веществ и
содержание пыли, кроме того, в литейном производстве имеют место значительные
выделения тепла, газа и пыли.
К факторам, негативно воздействующим на обслуживающий персонал, следует
отнести: выделение пыли и газов на плавильно - заливочном участке при
производстве и разливке стали, а также пары аммиака, выделяющиеся при сушке
модельных блоков в сушильных шкафах ШСП-0,25-1,2; высокую температуру
поверхностей оборудования, излучение, шум и вибрацию.
Источниками повышенной опасности, в части возможного травматического
воздействия, являются оборудование и его узлы, совершающие
возвратно-поступательные, поступательные и вращательные движения, оборудование
и трубопроводы, подверженные воздействию нагретых до высокой температуры материалов,
а также оборудование и световая арматура, использующее опасное для жизни
человека напряжение электрического тока.
Источниками поражения электрическим током в цехе являются прокалочные
печи, термические печи, электроприводы кранов и других механизмов. Причинами
поражения могут быть несоблюдение персоналом правил техники безопасности,
нарушение изоляции токоведущих частей механизмов.
К вредным факторам относят шум, вибрацию, тепловое излучение, пыль, газы,
пары; к опасным - электрический ток, движущиеся части оборудования, отлетающие
частицы металла, возможность пожара.
.1.2 Микроклимат и тепловое излучение
Метеорологические условия (микроклимат) в производственных условиях
определяются следующими параметрами: температурой воздуха t, °С, относительной
влажностью j, %, скоростью
движения воздуха на рабочем месте V, м/с.
Производительность труда и самочувствие рабочего во многом зависят от
состояния окружающей среды и прежде всего от изменения температуры, влажности,
скорости движения воздуха, атмосферного давления, теплового излучения.
Литейное производство относится к категории тяжелых работ с физическим
напряжением. Технологические операции выполняются в неблагоприятных условиях:
высокие температуры, запыленность, загазованность, излучение. Для тяжелых
категорий работ в соответствии с ГОСТ 12.1.005-88 на постоянных рабочих местах
устанавливаются следующие параметры среды.
В результате периодичности проведения различных операций микроклимат в
цехе неустойчивый, с часто изменяющимися параметрами. Индукционные печи и
термические печи, находящиеся в цехе выделяют радиационное тепло. Кроме
агрегатов источниками значительного выделения тепла является металл и шлак.
Для защиты от вредных производственных факторов в цехе предусмотрена
естественная и искусственная вентиляция, ГОСТ 12.4.021-75 средства
индивидуальной защиты.
Для обеспечения всего цеха вентиляцией и отоплением (СНиП 41-01-2003) в
соответствии с действующими нормами предусматриваются:
установка приточных камер в производственной части корпуса;
местные вытяжки от оборудования;
в бытовых помещениях установка приточных камер. Вытяжка от душевых,
санузлов и других помещений;
в качестве теплоносителя для отопления и вентиляции служит вода от
районной ТЭЦ (температура 70 0С).
Оптимальные и допустимые нормы температуры, относительной влажности и
скорости движения воздуха в рабочей зоне производственных помещений по ГОСТ
12.1.005-88 приведены в таблице 6.1.
Таблица 6.1
Оптимальные и допустимые нормы температуры, относительной влажности и
скорости движения воздуха в рабочей зоне производственных помещений
Период года
|
Категория работ
|
Температура, °С
|
Относительная влажность, %
|
Скорость движения, м/с
|
|
|
Опти мальная
|
Допус тимая
|
Опти мальная
|
Допус тимая
|
Оптималь ная
|
Допуст имая
|
Холодный
|
Средней тяжести II
б
|
17¸19
|
15¸21
|
40¸60
|
75
|
0,2
|
0,4
|
Тёплый
|
Средней тяжести II
б
|
20¸22
|
16¸27
|
40¸60
|
70 (при25 °С)
|
0,3
|
0,2¸0,5
|
Категория работ - средней тяжести II б для всех основных профессий.
Проектируются допустимые условия микроклимата.
4.1.3 Защита от теплового излучения
Средства защиты от инфракрасных излучений по своему назначению
подразделяют на устройства: оградительные, герметизирующие, теплоизолирующие,
для вентиляции воздуха, автоматического контроля и сигнализации, дистанционного
управления, знаки безопасности.
оградительные устройства подразделяют:
в зависимости от вида материала на: непрозрачные, полупрозрачные,
прозрачные;
по способу крепления на объекте на: съемные и встроенные;
по принципу действия на: теплоотражающие, теплоотводящие,
теплопоглощающие и комбинированные.
устройства автоматического контроля и сигнализации по назначению
подразделяют на:
Оперативные (для сигнализации отклонений от заданного уровня
контролируемого параметра) и предупреждающие (для предупреждения о наличии ИК -
излучений от заданного уровня).
Устройства автоматического контроля и сигнализации по способу информации
подразделяют на: цветовые и звуковые.
Устройства дистанционного управления и наблюдения по назначению
подразделяют на: управляющие технологическим процессом и наблюдающие
технологический процесс.
Знаки безопасности по назначению подразделяют в соответствии с ГОСТ
12.4.026-76.
Проектируемое помещение характеризуется наличием повышенного теплового
излучения. Его интенсивность 400 Вт/м2 превышает норму 140 Вт/м2.
Условия труда - вредные, класс - 3.1. По ГОСТ 12.1.005-88 необходимо применение
средств защиты.
Способы защиты от воздействия теплового излучения:
коллективные средства защиты по ГОСТ 12.4.123-83 (экранирование тепловых
излучений; сокращение продолжительности смены, рабочего стажа; вентиляция;
организация подсмен; организация рационального отдыха в период работы);
индивидуальные средства защиты;
для личной профилактики перегревания существенное значение имеет
рациональный питьевой режим (5л/см), который обеспечивает нормальный водно -
солевой обмен, создает благоприятные условия жизнедеятельности организма, для
этого:
применяется подсоленная газированная вода (0,5% NaCl) с добавлением солей калия и витаминов, а также
зеленый байховый чай с добавлением витаминов.
Теплоизоляция нагретых поверхностей является эффектным мероприятием не
только по уменьшению интенсивности теплового излучения, но также для
предотвращения ожогов при прикосновении к этим поверхностям. По действующим
санитарным нормам температура нагретых поверхностей оборудования и ограждений
на рабочих местах не должна превышать 40°С. Также применяются для защиты от
теплового излучения экраны отражающие (листовой алюминий) и поглощающие
(асбестовое полотно).
Из средств индивидуальной защиты применяются:
костюм суконный ГОСТ 12.4.045-87 с маркировкой ТИ от повышенных
температур;
рукавицы суконные ГОСТ 12.4.010-96 с маркировкой ТИ для защиты рук от
теплового излучения и от термических ожогов;
очки ГОСТ Р 12.4.013-97
каска ГОСТ 12.4.091-80
войлочная шляпа
ботинки кожаные ГОСТ 12.4.137-84 с маркировкой ТИ для защиты ног от
теплового излучения и контакта с нагретыми поверхностями, с маркировкой МУН200
для защиты ног от ударов в носочной части.
Все производственные помещения оборудованы общей приточно-вытяжной
вентиляцией согласно СНиП 41.01.2003.
.1.4 Производственное освещение
Освещение в цехе имеет большое значение. При недостаточной освещенности и
плохом качестве освещения состояние зрительных функций человека находится на
низком уровне, повышается утомление зрения в процессе выполнения работы,
возрастает риск производственного травматизма.
Рациональное освещение производственных помещений оказывает положительное
психофизиологическое воздействие на работающих, способствует повышению производительности
труда, обеспечивает безопасность труда, сохраняет высокую работоспособность
людей.
Свет оказывает положительное влияние на эмоциональное состояние человека,
воздействует на обмен веществ, сердечно-сосудистую систему, нервно-психическую
сферу. Он является важным стимулятором не только зрительного анализатора, но и
организма в целом.
Благоприятнее всего для работающих естественное освещение, при котором
производительность труда на 10% выше, чем при искусственном. Дневное,
естественное освещение осуществляется через окна и верхние световые проемы,
стекла которых должны постоянно содержаться в чистоте. Чистка стекол должна
проводиться не реже 2 раз в год.
В связи с тем, что возможности естественного освещения весьма ограничены,
необходимо добиваться рационального освещения искусственным путем.
В цехе используются светильники, количество которых применяется из
расчета обеспечения нормированной освещенности не менее 200 лк по СНиП 23-05-95
. Высота подвешенных светильников под рабочей поверхностью 4м. В светильники
выбираем по ГОСТ 16534-77 лампу ДРЛ-700 с световым потоком Fл = 33000 лм.
В местах расположения технологического оборудования в цехе предусмотрено
ремонтное освещение напряжением 12В выполненное в виде переносных ламп
накаливания.
Все рабочие места в цехе имеют освещенность, соответствующую СНиП
23-05-95 . Это достигается за счет применения естественного и искусственного
освещения в цехе.
.1.5 Безопасность труда на складах шихтовых материалов
Осуществляемые на складах шихтовых материалов шихтовщиком -стропальщиком
операции в основном связаны с использованием подъёмно-транспортного
оборудования, а также существует возможность травмирования при неосторожном
обращении со стальным ломом. Основными вредными факторами в закрытом складе
шихтовых материалов является пыль выделяющиеся при их взвешивании и
транспортировке.
Шихтовщик-стропальщик при выполнении погрузочно-разгрузочных работ должен
использовать защитную спецодежду, кожаные рукавицы, каску.
Погрузочно-разгрузочные работы необходимо выполнять в соответствии с
требованиями ГОСТ 12.3.009-76 ССБТ и ПБ 10-382-00.
.1.6 Безопасность труда в плавильном отделении
В плавильном отделении выполняются операции связанные с подготовкой печей
к работе, плавкой в них шихты, выпуском расплавленных литейных сплавов из печей
и их металлургической обработкой.
Процесс плавки металла сопровождается выделением конвекционного и
лучистого тепла. Для защиты персонала отделения от тепловой и световой энергии
применяется спецодежда: костюм суконный ГОСТ 12.4.045-87, очки ГОСТ Р
12.4.013-97, каска ГОСТ 12.4.091-80, ботинки кожаные ГОСТ 12.4.137-84, защитные
щитки (ГОСТ 12.4.011-89 ССБТ),рукавицы суконные ГОСТ 12.4.010-75 СИЗ, валенки
ТВ ГОСТ 12.4.050-78 СИЗ, вачеги ГОСТ 12.4.010-75 СИЗ. Уровень звука составляет
до 60 дБА.
Для борьбы с тепло- и газовыделениями в плавильном отделении
предусмотрены следующие мероприятия:
Плавильные печи, место заливки форм и стенд для сушки ковшей снабжены
вытяжными зонами.
Приямки для слива металла в ковш защищены ограждениями.
Безопасность труда в плавильном отделении обеспечивается правильной
эксплуатацией плавильной печи и подъёмно-транспортного оборудования, точным
соблюдением технологических режимов шихтовки, подготовки печи к работе и плавки
шихты. Нарушение этих условий может привести к серьёзным авариям, взрыву и
выводу из строя оборудования, а также может стать причиной серьёзных травм.
.1.7 Безопасность труда в обрубном отделении
К основным опасным производственным факторам, характерным для обрубного
отделения относятся: движущиеся части механизмов, подъёмно-транспортное
оборудование. Безопасность труда обрубщиков обеспечивается выполнением
требований ГОСТ 12.3.002-75, ГОСТ 12.2.061-81, ГОСТ 12.2.062-81, ГОСТ
12.2.064-81, ГОСТ 12.2.033-78, ГОСТ 12.1.005-88 (1999, с изм. 1 2000), ГОСТ
12.1.003-83 (1999).
.1.8 Электробезопасность
Электробезопасность - это система организационно-технических мероприятий
и средств, обеспечивающих защиту людей от поражения электрическим током,
электрической дугой, статистическим электричеством и электромагнитным полем.
Организационные и технические мероприятия по защите регламентированы ГОСТ
12.1.009-88 и ПУЭ.
Проектируемый цех по опасности поражения электрическим током относится к
цехам с повышенной опасностью, которая обусловлена наличием высокой температурой,
наличием пыли и сырости.
Устройство и эксплуатация электроустановок, отвечают требованиям охраны
труда - выполнены с питанием от сети 36В с изоляцией металлоконструкций. При
напряжении 220В и более ограждены все части находящиеся под напряжением. Все
ограждения выполняются с блокировкой (механической, электрической,
электромагнитной). Корпуса электродвигателей, кожухи электроаппаратуры,
металлические части оборудования, которые могут оказаться под напряжением,
надежно заземляются.
Исключен несанкционированный допуск в электропомещения всех назначений.
Допуск к ним имеют только электрики соответствующей группы.
Предусмотрено защитное заземление и зануление всех нетоковедущих частей,
могущих оказаться под напряжением в случае пробоя изоляции согласно требованиям
“Правил установки и эксплуатации оборудования” ССБТ ГОСТ 12.1.030-81 . Защитное
заземление выполняется как специальными контурами, так и при помощи
металлических строительных конструкций зданий и сооружений. Для проведения
ремонтных работ, в требуемых случаях, предусмотрена разводка розеточной сети,
безопасным напряжением 12 вольт.
Электрическая сеть на заводе до 1000В с изолированной нейтралью, линейное
напряжение 380В,оборудование имеет защитное заземление <4 Ом.
При расчёте защитного заземления определяется сопротивление системы
заземления, которое зависит от удельного сопротивления грунта. Грунт, на
котором располагается проектируемый цех - суглинок с удельным сопротивлением
100 Ом·м.
Заземление выполнено из металлической водогазопроводной трубы диаметром
60 мм с толщиной стенки 3,5 мм, длиной 3 метра.
Сопротивление одиночного вертикального заземлителя определяется по
формуле:
где
rрасч = rуд ´ y, Ом;
rуд - удельное сопротивление грунта
(суглинок = 100 Ом∙м);
d - наружный диаметр трубы;
y - коэффициент сезонности, (принимаем 1,7);
l - длина трубы, м; l=3 м;
t - глубина залегания заземления, м;
t0 - уровень пола, t0=0,5 м.
rрасч = 100´1,7=170 Ом∙м;
t=0,5
l+ t0;
t=0,5
3+0,5=2,0 м;
=61,3 Ом,
что >4 Ом.
Необходимое
количество вертикальных заземлителей определяется по формуле:
где
RB - расчётное сопротивление, Ом;
R3 - допустимое сопротивление
защитного заземления, Ом; R3=4 Ом;
hв - коэффициент использования вертикальных заземлителей, (принимаем 0,76).
шт
Принимаем
20 трубчатых заземлителей . Заземление выполняется в ряд, трубы забиваются в
землю и соединяются между собой горизонтальной соединительной полосой.
Сопротивление
полосового заземлителя определяется по формуле:
где
rрасч = rуд ´ y1 , y1 =100 · 4,5 = 450 Ом×м;
L = 3·l · (n-1)
L =3·3·
(20-1)=171 м;
d1 =0,5 b, b - ширина
соединительной полосы, м; b=0,005 м.
Ом
Результирующее
заземление определяется по формуле:
где
hn - коэффициент
использования горизонтального полосового электрода, (0,45);
hв - коэффициент
использования вертикальных заземлителей, (принимаем 0,76).
= 3,2 Ом
< 4 Ом
Полное
заземление обеспечивает безопасность работы в случае пробоя изоляции и
попадания напряжения на корпус оборудования в цехе.
4.1.9
Защита от повреждения механическим оборудованием
Для
защиты от механического травматизма в соответствии с ПБ 11-551-03
предусматривается:
Закрытие
кожухами всех вращающихся валов электродвигателей, ременных и цепных передач.
Установка
звуковой сигнализации на мостовых кранах.
Устройство
ограждений на всех лестницах и площадка.
Наличие
индивидуальных средств защиты.
Проходы
между оборудованием, оборудованием и строительными конструкциями соответствуют
требованиям действующих нормативных документов по технике безопасности для
строящихся и реконструируемых объектов.
Все
составляющие технологической цепочки сблокированы таким образом, что при
остановке одного из механизмов останавливаются все предшествующие ему по
технологии.
Перед
включением оборудования предусмотрена предпусковая звуковая и световая
сигнализация.
Все
движущиеся и вращающиеся части снабжены защитными ограждениями, оборудованными
устройствами, блокирующими работу защищаемого механизма при снятии защитного
ограждения.
.1.10
Защита от вибрации
Вибрация
- сложный колебательный процесс, возникающий при периодическом смещении центра
тяжести от положения равновесия или при периодическом изменении формы тела.
Виды
вибрации:
общая
(транспортная, транспортно-технологическая и технологическая);
локальная.
Типы
общей технологической вибрации:
а
- на постоянных рабочих местах производственных помещений предприятий;
б
- на рабочих местах на складах, в столовых, бытовых, дежурных и др.
производственных помещений, где нет машин, генерирующих вибрацию;
в
- на рабочих местах в помещениях заводоуправления, конструкторских бюро,
лабораторий, вычислительных центров, конторских помещениях и др.
В
проектируемом мною цехе тип технологической вибрации - 3а.
Действие
на организм человека вследствие вибрации заключается в следующем:
сосудосуживающий эффект, поражаются нервные, костные ткани, поражается
вестибулярный аппарат, слуховой аппарат, нарушается тонус сосудов, спазм
периферических сосудов, профессиональное заболевание - вибрационная болезнь.
Уровень
вибрационной нагрузки на оператора при работе оборудования в проектируемом цехе
не превышает требований ГОСТ 12.1.012 -90 - вибробезопасность (нормирование).
Эквивалентный уровень виброускорения составляет 80 дБ, что не превышает
предельно допустимого уровня (ПДУ) 92 дБ. Это связано с использованием в качестве
основного оборудования машин, имеющих не ударный характер работы. Условия труда
при технологических процессах допустимые, класс 2.
ГОСТ
12.4.046-78 защита от вибрации (КЗ).
К
средствам индивидуальной защиты относят следующее:
ГОСТ
12.4.002-74 СИЗ: рукавицы
ГОСТ
12.4.024-74 СИЗ: обувь
.1.11
Защита от шума
К
последствиям воздействия шума на организм человека можно отнести следующее:
угнетение центральной нервной системы, изменение скорости дыхания и пульса,
нарушение обмена веществ, возникновение сердечно-сосудистых заболеваний,
гипертонической болезни, возможны профессиональные заболевания - выраженный
кохлеорный неврит (тугоухость).
Согласно
ГОСТ 12.1.003 - 83 уровень звука в цехе не должен превышать допустимого уровня
80 дБА. Фактическое значение 60 дБА, условия труда допустимые, класс 2 по ГОСТ
2.2.2006-05.
Для
снижения уровня шума все шумное оборудование изолировано, т.е. находиться в
отдельном помещении или имеет звукоизолирующий кожух.
Так
же предусмотрены средства индивидуальной защиты для рабочих работающих в
отделениях с повышенным шумом (отделение обрубки и зачистки, шихтовое отделение
при разгрузке и взвешивании шихты, плавильное отделение).
К
средствам индивидуальной защиты относят следующее:
ГОСТ
12.4.208-99 СИЗ: наушники
ГОСТ
12.4.209-99 СИЗ: вкладыши (беруши)
Нормативный
документ для КЗ - ГОСТ 12.1.029.80 -Защита от шума.
Для
рабочих, работающих в этих отделениях, предусмотрены организационные
мероприятия: сокращение времени пребывания людей в условиях с повышенным шумом,
лечебно-профилактические мероприятия и т.д.
.1.12
Запыленность, загазованность
На
человека, находящегося на рабочем месте, также воздействуют вредные вещества.
Приведем их ПДК, класс опасности и действие на организм, используя ГОСТ
12.1.005-88 оптимальные и дополнительные ПДК вредных веществ в воздухе рабочей
зоны.
Таблица
4.4
ПДК
и классы опасности вредных веществ
Наименование
|
Величина ПДК, мг/м3
|
Преимущественное агрегатное
состояние в условиях производства
|
Класс опасности
|
Особенности действия на
организм
|
Аммиак
|
20
|
п
|
IV
|
Ф, А
|
СО
|
20
|
п
|
IV
|
О
|
Fe2O3
|
6
|
п
|
III
|
Ф
|
NiO
|
0,05
|
а
|
I
|
К
|
SiO2
|
6
|
п
|
III
|
Ф, К
|
SO2
|
10
|
п
|
III
|
А
|
NO
|
5
|
п
|
III
|
О
|
NO2
|
2
|
п
|
III
|
О
|
Условные обозначения:
п - пары или газы,
а - аэрозоль,
о - вещества с остронаправленным механизмом действия, требующие
автоматического контроля за их содержанием в воздухе,
А- вещества, способные вызывать аллергические заболевания в
производственных условиях,
К-канцерогены,
Ф- аэрозоли преимущественно фиброгенного действия.
В целях создания допустимых условий труда и предупреждения травматизма рабочих
, проектом предусматриваются следующие меры защиты:
средства индивидуальной защиты органов дыхания(СИЗОД) в соответствии с
ГОСТ 12.4.005-85,
средства защиты работающих ГОСТ 12.4.011-89,
респираторы ГОСТ 12.4.028-76,
Общеобменная вентиляция ГОСТ 12.4.021-75 в плавильном отделении
обеспечивается вытяжкой через шахты на крыше. Приток воздуха направляется к
рабочим местам в виде воздушных душей. Количество приточного воздуха
компенсирует вытяжку общеобменной и местной вентиляции.
Для исключения попадания в атмосферу газа и пыли предусматривается отсос
газов во время плавки, а также в момент загрузки шихты в индукционную печь. Для
удаления загрязненного воздуха над местом, где переливается металл из печей в
раздаточные ковши, предусмотрен вытяжной зонт.
Вредные газы удаляются через систему местной вытяжной вентиляции при
помощи зонтов и местных отсосов ГН 2.1.6.1338-03 -предельно допустимые
концентрации загрязняющих веществ в атмосферном воздухе населенных пунктов.
.1.13 Вентиляция
Задачей промышленной вентиляции является создание нормальных санитарно -
гигиенических условий труда, обеспечение чистоты воздуха и заданных
метеорологических условий в производственных помещениях, особенно необходима
качественная вентиляция в модельном отделении, в котором находятся сушильные
шкафы, и а также находится установка для вытопки модельного состава.
В цехе предусматривается приточно-вытяжная вентиляция с искусственным и
естественным побуждением в соответствии с ГОСТ 12.4.021-75. Для удаления пыли,
паров, газов из атмосферы цеха и обеспечения предельно - допустимых норм
содержание вредных веществ в воздухе.
Для более эффективного удаления выделяющихся вредных веществ
предусмотрены местные отсосы непосредственно от мест выделение пыли, газов и
аэрозолей.
При производстве стали и её разливки, возникает технологический отсос
значительных объемов воздуха. Полностью компенсировать отсос организованным
притоком технологически трудно, поэтому израсходованный объем воздуха
необходимо пополнить неорганизованным притоком через неплотности ограждающих
конструкций, аэрационный фонарь. Для создания санитарно-гигиенических условий
труда в разливочном и печном отделении необходимо, по возможности, более полно
разделить воздушные потоки технологического и санитарно-гигиеничекого назначения.
Во всех производственных помещениях, где постоянно находятся люди,
независимо от степени загрязнения воздуха в них, устанавливается искусственная
или образуется естественная вентиляция. Естественная вентиляция осуществляется
через специальные боковые двери, окна (проемы), жалюзи в стенках, через
специальные люки, сделанные в кровле цеха, через вытяжки и т.д.
Все основные приточно-вытяжные вентиляционные и аспирационные установки в
рабочее время должны работать непрерывно. Остановка их допускается лишь на
короткое время с разрешения начальника участка и начальника цеха.
Запрещается включение технологического оборудования до пуска
обслуживающих его вентиляционных систем.
.2 Чрезвычайные ситуации
Чрезвычайная ситуация - это неожиданная, внезапно возникшая обстановка на
определенной территории или объекте экономики в результате аварии, катастрофы,
опасного природного явления или стихийного бедствия, которые могут привести к
человеческим жертвам, ущербу здоровью людей или окружающей среде, материальным
потерями нарушению условий жизнедеятельности людей (ГОСТ 22.0.02-94 ЧС. Термины
и определения).
Урал-зона неопределенной сейсмичности, аномальных температур и аномальных
осадков. Эти причины могут привести к следующим природным ЧС: землетрясения,
наводнения, селевые потоки, оползни, обвалы, массовые лесные и торфяные пожары,
снежные заносы и лавины, а также засухи, длительные проливные дожди, сильные
устойчивые морозы. Близость расположения цеха к Белоярской атомной
электростанции может привести к техногенным ЧС.
В данном цехе возможны следующие ЧС: пожар, массовое поражение током.
Возникновение и развитие чрезвычайных ситуаций может привести к
дезорганизации и остановке производства, нанести материальный ущерб, а также
создать угрозу жизни и здоровью производственного персонала.
Для управления объектом в чрезвычайных ситуациях будет создано
формирование гражданской обороны, которое возглавит начальник цеха. Он
осуществляет руководство через штаб отряда.
.2.1 Защита персонала от ЧС
Защита рабочих и служащих при возникновении чрезвычайных ситуаций
является важнейшим фактором повышения устойчивости работы любого объекта. При
реконструкции предусмотрено рассредоточение размещения сооружений на территории
объекта, так как это важно в противопожарном отношении.
Рассмотрим ЧС пожар:
Каждый работник при обнаружении пожара или признаков горения (задымления,
запах гари) обязан:
Немедленно сообщить об этом по внутризаводскому телефону в пожарную
охрану (при этом необходимо назвать корпус и место пожара, сообщить свою
фамилию), а также сообщить своему руководителю.
Принять по возможности меры по эвакуации людей, тушению пожара и
сохранности МЦ.
При тушении использовать имеющиеся средства пожаротушения (огнетушители,
внутренние пожарные краны, песок)
. Руководитель, прибывший к месту пожара, обязан:
Продублировать сообщение о пожаре в пожарную охрану
Возглавить руководство тушением пожара до прибытия пожарной охраны
Выделить для встречи пожарной охраны работника, хорошо знающего
расположение подъездных путей и гидрантов
Удалить из опасной зоны всех работников не занятых в ликвидации пожара, а
при необходимости организовать их спасение, используя при этом свои силы и
средства
При необходимости отключить электроэнергию (за исключением
противопожарной защиты)
Прекратить все работы в помещении предприятия, кроме работ связанных с
мероприятиями по ликвидации пожара
Обеспечить соблюдение требований безопасности работниками, принимающими
участие в тушении пожара
По прибытии пожарных подразделений проинформировать руководителя тушения
пожара об обстановке, проведенной работе по ликвидации пожара и об особенностях
данного предприятия (его конструктивные и технологические особенности), о числе
людей участвующих в тушении пожара и т.п.
Защита работающего персонала от пожара предусматривает проведение
следующих мероприятий:
организационные - инструктаж работающего персонала;
эксплуатационные - своевременные профилактические осмотры, ремонты и
испытания технологического оборудования;
технические - цех имеет проходы и выходы для экстренной эвакуации людей,
пожарные проезды и проходы к средствам пожаротушения, имеется пожарная
сигнализация.
Одной из возможных чрезвычайных ситуаций в цехе литья по выплавляемым
моделям может быть выброс жидкого металла. Причины - взаимодействие расплава с
водой, которая может быть внесена при загрузке сырой шихты и ферросплавов,
возврата собственного производства, либо при взаимодействии с непросушенной
футеровкой ковша, либо при повреждении охладительной системы печи.
Управлять объектом в данной чрезвычайной ситуации практически невозможно,
т. к. скорость реакции огромна, поэтому надо всячески предупреждать подобные
ситуации путем профилактических осмотров и ремонтов, соблюдения правил хранения
и эксплуатации вспомогательных приспособлений и инвентаря.
Также предусмотрено заглубление в грунт сетей и сооружений
коммунально-энергетического хозяйства объекта.
Избежать возникновения техногенных чрезвычайных ситуаций должно точное и
строгое соблюдение технологии производства, а также правил и инструкций по
технике безопасности. При возникновении таких ситуаций разработана система
эвакуации, схема оповещения инженерно-технических работников цеха. Разработана
инструкция по безаварийной остановке цеха в течение 10 минут по получении
сигнала опасности, которая заключается в:
отключении наружного освещения;
отключении рабочего напряжения машин, механизмов, работающих на
территории всех отделений и корпусов цеха;
тушении производственного огня (остановка технологического процесса).
Мероприятия и защита от последствий землетрясений разделяются на
предварительные и действия непосредственно во время землетрясения.
Предварительные меры защиты включают:
сейсмостойкое строительство;
подготовку служб спасения и ликвидации последствий;
обучение населения правилам поведения во время землетрясения;
наличие в цехе запасов продуктов, воды на 3-5 суток, аптечек первой
медицинской помощи;
закрепление в цехе столов, шкафов и другого оборудования к полу (стенам).
С началом землетрясения люди, находящиеся в зданиях, должны срочно
покинуть помещение и выйти на открытое место (за 25-30 с). При невозможности
покинуть здание, встать в дверной проем, в проемы капитальных внутренних стен.
Выключить свет. После прекращения подземных толчков покинуть помещение. Далее
необходимо включиться в работу по спасению людей.
Пожарная безопасность ГОСТ 12.1.004-91
Пожаром называется неконтролируемое горение вне специального очага,
наносящее материальный ущерб. Горение - это быстропротекающая химическая
реакция, как правило, соединения вещества с кислородом воздуха, сопровождающаяся
интенсивным выделением теплоты и света. Для возникновения горения требуется
наличие трех факторов: горючего вещества, окислителя и источника загорания
(импульса). Окислителями могут быть не только кислород, но и хлор, фтор, бром,
йод, окислы азота и т. д.
При проектировании и строительстве производственных зданий и сооружений
необходимо учитывать категорию их пожарной опасности. Согласно СП 12.13130-2009
в зависимости от характеристики обращающихся в помещении веществ и их
количества помещения подразделяются по пожарной и взрывной опасности на
категории А, Б, В, Г, Д.
Литейный цех относится к категории Г- умеренная пожароопасность. Конечным
продуктом является отливки - негорючий материал в горячем состоянии, при
производстве которого негорючие сырьевые материалы (лом, ферросплавы и др.)
доводятся до расплавленного состояния. Общая степень огнестойкости I с пределом огнестойкости 120 мин
СНиП 21.01-97 . Пожарная безопасность обеспечивается системой пожарных
водоводов, кранов и гидрантов, а также за счет нормативных разрывов между
зданиями, сооружениями, сетями и коммуникациями. Ко всем объектам
обеспечивается подъезд пожарных автомашин по автодорогам и спланированной
территории.
Производственные объекты оборудуются системами пожаротушения и средствами
сигнализации о возникновении пожара, а также защищаются от несанкционированного
доступа.
Наиболее частые причины возникновения пожаров в производстве стали -
неосторожное обращение с огнем, неисправность производственного оборудования,
нарушения технологического процесса, нарушения правил эксплуатации
электрооборудования, несоблюдение мер пожарной безопасности при проведении
электрогазосварочных работ и некоторые другие.
Причины неэлектрического характера:
неправильное устройство и неисправность котельных, вентиляционных и
отопительных систем, отопительных приборов и технологического оборудования;
неисправность систем питания и смазки в работающих двигателях механизмов;
нарушение технологического процесса (герметизации оборудования,
выделяющего пыль, газы, и др.);
нарушение требований пожарной безопасности при газосварочных работах,
резке металлов, пользовании паяльными лампами;
халатное и неосторожное обращение с огнем - курение, оставление без
присмотра нагревательных приборов, разогрев деталей и сушка (в том числе
помещений) открытым огнем и т. п.;
самовозгорание или самовоспламенение веществ.
Причины электрического характера:
короткие замыкания, перегрузки, искрения от нарушения изоляции, что
приводит к нагреванию проводников (проводов линий, обмоток) до температуры
воспламенения изоляции;
электрическая дуга, возникающая между контактами коммутационных аппаратов
(разъединителей, рубильников), не предназначенных для отключения больших токов
нагрузки, а также при дуговой электросварке;
неудовлетворительные контакты в местах соединения проводов (скрутки) и их
сильный нагрев вследствие большого переходного сопротивления при протекании
электрического тока;
аварии с маслонаполненными аппаратами (трансформаторами, выключателями),
когда происходят выброс в атмосферу и воспламенение продуктов разложения
минерального масла и смеси их с воздухом;
искрение в электрических аппаратах и машинах, а также искрение в результате
электростатических разрядов и ударов молнии (разрядов статического и
атмосферного электричества);
неисправность (замыкания) в обмотках электрических машин при отсутствии
надлежащей защиты.
Для ликвидации начинающихся очагов пожара силами рабочих и служащих все
производственные, складские, вспомогательные помещения, наружные установки, а
также пожароопасные участки территории цеха обеспечены по действующим нормам
первичными средствами пожаротушения, пожарным ручным инструментом и пожарным
инвентарем.
Первичные средства пожаротушения: внутренние пожарные краны, ручные
огнетушители, гидропульты, ручные насосы, бочки с водой, ящики с песком, кошмы,
необходимый ручной пожарный инструмент и пожарный инвентарь (ведра, ломы,
топоры, лопаты, кирки, багры, пожарные стенды, щиты и др.).
Средства тушения загораний и пожаров: внутренние пожарные краны,
огнетушители, кошмы, песок.
Места размещения каждого вида пожарной техники обозначены указательными
знаками. Подходы к огнетушителям и другому оборудованию, требующему ручного
обслуживания, удобны и не загромождены. Для лучшей видимости элементы
строительных конструкций (участки колонн и ограждений, пола) у мест
расположения пожарной техники выделены красными полосами шириной 200 мм, а
пожарная техника (огнетушители, пожарный инструмент и инвентарь) окрашена в
красный цвет.
Эвакуация производственного персонала с любого участка цеха
осуществляется через выходы (в т.ч. аварийные) из помещения цеха. При
нахождении работающего на высотных отметках цеха необходимо эвакуироваться на
нулевой уровень по лестницам (СНиП 21.01-97- пожарная безопасность зданий и
сооружений).
При возгорании необходимо действовать следующим образом:
) позвонить в пожарную службу по телефону 01.
) оповестить весь персонал через соответствующую систему, эвакуировать
персонал, согласно плану эвакуации и вызвать пожарную бригаду;
) ограничить распространение огня и потушить пожар надлежащим образом
согласно специально разработанному плану пожаротушения.
Также предусмотрена автоматическая сигнализация (НПБ 110-99
Автоматизированные установки пожаротушения и сигнализация)
Из комплексной оценки всех изложенных материалов можно сделать следующие
выводы:
. По микроклимату: категория работ - средней тяжести II б для всех
основных профессий. Проектируются допустимые условия микроклимата.
. По теплоизлучению: цех характеризуется наличием повышенного теплового
излучения от индукционных печей. Его интенсивность 400 Вт/м2
превышает норму 140 Вт/м2. Условия труда - вредные, класс - 3.1. По
ГОСТ 12.1.005-88 необходимо применение средств защиты.
. Освещенность помещений цеха не менее 200 лк в соответсвии со СНиП
23-05-95 . В соответсвии с ГОСТ 16534-77 установлены лампы ДРЛ-700 со световым
потоком Fл = 33000 лм.
. По электробезопасности:
Цех по степени опасности поражения электрическим током имеет категорию
ПО. Поэтому для обеспечения безопасности работы обслуживающего персонала для
всего электрооборудования, находящегося под напряжением, предусмотрено защитное
заземление с Rз < 4 Ом при рабочем U=380 В согласно ГОСТ 12.1.030 - 81.
. Уровень вибрационной нагрузки на оператора при работе оборудования в
цехе не превышает требований ГОСТ 12.1.012 - 90. Фактическое значение
виброускорения составляет 80 дБ, что не превышает предельно допустимого уровня
(ПДУ) 92 дБ. Это связано с использованием в качестве основного оборудования
машин, имеющих не ударный характер работы.
. По степени пожарной безопасности литейный цех в соответствии с
правилами пожарной безопасности относится к категории "Г-умеренная
пожароопасность" (СП12.13130-2009), то есть имеет место производство, в
котором используются негорючие вещества в раскаленном и расплавленном
состоянии, процесс обработки которых сопровождается выделением лучистой
энергии, искр и пламени. Общая степень огнестойкости I с пределом огнестойкости
120 мин.
. По уровню шума: Фактический уровень звука- 60 дБА, ПДУ - 80 дБА.
Уровень звука в проектируемом цехе не превышает допустимого уровня. Условия
труда допустимые, класс 2 согласно Р 2.2.2006-05.
.Итоговые условия труда - вредные кл.3.1 согласно согласно Р 2.2.2006-05.
5. ПРИРОДОПОЛЬЗОВАНИЕ И ОХРАНА ОКРУЖАЮЩЕЙ СРЕДЫ
Скорость увеличения вредного воздействия средовых факторов и
интенсивность их влияния уже выходит за пределы биологической приспособляемости
экосистем к изменениям среды обитания и создает прямую угрозу жизни и здоровью
населения. Принципиальный недостаток развиваемых до последнего времени
технологий заключается в том, что они приводят к нарушению круговорота веществ
в биосфере, при которой природные ресурсы превращаются в загрязнения окружающей
среды.
Для предотвращения негативных последствий воздействия загрязняющих
веществ на отдельные компоненты природной среды необходимо знать их предельные
уровни, при которых возможна нормальная жизнедеятельность и функционирования
организма.
Основной величиной экологического нормирования содержания вредных
химических соединений в компонентах природной среды является ПДК.
ПДК - это такое содержание вредного вещества в окружающей среде, которое
при постоянном контакте или при воздействии за определенный промежуток времени
практически не влияет на здоровье человека и не вызывает неблагоприятное
воздействие на его потомство.
Загрязнение биосферы.
Основные вещества, загрязняющие атмосферу делят на две группы: газы и
твердые частицы.
Способы борьбы:
. Нужно производить очистку газов от вредных веществ (например,
использовать центробежные фильтры типа «циклон» или скрубберы);
. Рассеивать вредные вещества до концентрации меньше ПДК [17,18].
. Налаживание безотходных технологий (наиболее перспективных) - вредные
вещества утилизируются.
Тепловое загрязнение атмосферы.
Продуктами горения углеводородов, используемых при напылении, является СО2.
При парниковом эффекте повышается концентрация СО2 => увеличение
температуры поверхности слоя земли => отражение тепловых лучей и задержание
их около Земли => еще больший разогрев температуры атмосферы и воды.
Шумовое загрязнение среды.
Шум отрицательно влияет на биологические функции человека: повышает
давление, усиливает стрессовое состояние, повышается утомляемость, раздражение,
уменьшается работоспособность, головные боли, ухудшение самочувствия.
Для снижения уровня шумового загрязнения, на пути его распространения,
необходимо установить звукопоглощающие и звукоизолирующие преграды (экраны,
перегородки, кожухи, кабины и др.) выполненные из плотных твердых материалов
(металла, дерева, пластмасс, бетона и др.). Хорошие звукопоглощающие свойства
имеют легкие и пористые материалы.(минеральный войлок, стекловата, поролон и
др.).
.1 Оценка экологичности проекта
Для того чтобы определить какие параметры производства нужно
контролировать и какие мероприятия для оздоровления окружающей среды необходимо
проводить, рассчитываем категорию опасности производства.
В зависимости от массы и видового состава выбросов в атмосферу, в
соответствии с «Рекомендациями по делению предприятий по категории опасности»
определяют категорию опасности предприятия (КОП):
где
Мi - масса I-го вещества в выбросе;
ПДКi -
среднесуточное ПДК I-го вещества;
n-количество
загрязняющих веществ;
аi
-безмерная величина, позволяющая соотнести степень вредности I-го
вещества с вредностью сернистого газа (Значения аi в
зависимости от класса опасности следующие: класс 2-1,3; класс 3-1; класс
4-0,9).
В
зависимости от величины КОП предприятия подразделяют на следующие классы
опасности: класс 1>106, класс 2-104-106;
класс 3-103-104; класс 4-<103.
Перечень
вредных веществ, выбрасываемых в атмосферу в проектируемом цехе, приведен в
таблице 5.1.
Таблица
5.1
Перечень
вредных веществ, выбрасываемых в атмосферу
Наименование
|
ПДК, мг/м³
|
Класс опасности
|
аi
|
Кол-во выбрасываемого
вещества Mi, т/год
|
CO
|
3
|
4
|
0,9
|
20,77
|
SiO2
|
0,1
|
3
|
1
|
32.57
|
Fe2O3
|
0,04
|
3
|
1
|
26,17
|
Аммиак
|
0,2
|
4
|
2
|
5,98
|
SO2
|
10
|
3
|
1
|
10,42
|
NO
|
5
|
3
|
1
|
8,36
|
NO2
|
2
|
3
|
1
|
9,65
|
Рассчитаем категорию опасности производства:
Данное
производство относится к 3 категории опасности, поэтому должны проводиться
некоторые мероприятия отмеченные в таблице 5.2.
Таблица
5.2
Перечень
мероприятий, подлежащих контролю в зависимости от КОП
Перечень мероприятий,
подлежащих контролю
|
Категория предприятия
|
|
1
|
2
|
3
|
4
|
Сведения о залповых
выбросах
|
+
|
+
|
-
|
-
|
Мероприятия по
регулированию выбросов при неблагоприятных метеорологических условиях (НМУ)
|
+
|
+
|
+
|
-
|
План мероприятий по
снижению выбросов загрязняющих веществ в атмосферу с целью достижения
нормативов предельно допустимых выбросов (ПДВ)
|
+
|
+
|
-
|
-
|
Контроль за соблюдением
нормативов ПДВ: на источниках выброса на контрольных точках
|
+ +
|
+ -
|
+ -
|
- -
|
Примечание: + − мероприятие выполняется; - − мероприятие не
выполняется.
Очистка сточных вод.
Состав производственных сточных вод зависит от характера
производственного процесса и отличается большим разнообразием.
В зависимости от состава примесей и специфичности их действия на водные
объекты сточные воды могут, разделены на следующие группы:
) Воды, содержащие неорганические примеси со специфическими токсичными
свойствами.
) Воды, в которых неорганические примеси не обладают токсичными
действием.
) Воды, содержащие нетоксичные органические вещества.
) Воды, содержащие органические вещества со специфическими токсичными
свойствами.
Методы очистки сточных вод:
Классификация примесей сточных вод по фазово-дисперсной характеристике
позволяет произвести систематизацию примесей для последующего выбора
эффективной схемы очистки.
Сущность этой классификации состоит в том, что все примеси по их
отношению к дисперсионной среде разделены на четыре группы:
I -
взвеси, с размерами частиц более 10-1 мкм, суспензии и эмульсии,
обусловливающие мутность воды.- коллоидно-расстворенные вещества, с размером
частиц 10-1-10-2 мкм, коллоиды и высокомолекулярные
соединения, обусловливающие окисляемость и цветность воды, вирусы.
III -
молекулярно-растворенные вещества, с размером частиц 10-2-10-3
мкм, газы, растворимые в воде, органические вещества, придающие ей запахи и
привкусы;
V -
вещества, диссоциирующие на ионы (электролиты), с размерами частиц менее 10-3мкм,
соли, кислоты, основания, придающие воде жесткость, щелочность и
минерализованность.
Все сточные воды предприятия должны подвергаться очистке от вредных
веществ перед сбросом в водоем. Для выполнения этих требований применяют
механические, химические, биологические, а также комбинированные методы
очистки. Состав очистных сооружений выбирают в зависимости от характеристики и
количества поступающих на очистку сточных вод, требуемой степени их очистки,
метода использования их осадка и от других местных условий.
В составе очистных сооружений должны предусматриваться решетки или
решетки дробилки, песколовки и песковые площадки, усреднители, отстойники,
нефтеловушки, гидроциклоны, флотационные установки, илоуплотнители,
биологические фильтры, аэротенки, сооружения для насыщения очищенных сточных
вод кислородом и другие.
Решетки должны иметь прозоры 16мм. Механизированная очистка решеток от
отбросов предусматривается при количестве отбросов 0,1м3/сутки.
Песколовки тангенциальные применяют для станций очистки
производительностью до 50 000м3/сут. Горизонтальные
производительностью свыше 10 000м3/сут и аэрируемые
производительностью свыше 20 000м3/сут.
Отстойники выбирают с учетом производительности станций очистки сточных
вод: до 20 000м3/сут вертикальные, свыше 15 000м3/сут
горизонтальные, свыше 2 000м3/сут радиальные, до 10 000м3/сут.
двухъярусные.
Осветлители проектируют в виде вертикальных отстойников с внутренней
камерой флокуляции с естественной аэрацией за счет разницы уровней воды в
распределительной чаше и осветлителе.
Нефтеловушки применяют для задержания нефтяных частиц при концентрации их
в сточной воде более 100мг/л. Глубина проточной части 2м, ширина секции 36м,
отношение длины к глубине 1520.
Гидроциклоны (открытые и напорные) применяют для отделения из сточных вод
оседающих и грубодисперсных примесей. Открытые гидроциклоны используют трех
типов: гидроциклоны без внутренних устройств для выделения из сточных вод
крупно и мелкодисперсных примесей гидравлической крупностью 5мм/с и более;
гидроциклоны с диафрагмой и многоярусные (при расходе 200м3/сут на
один аппарат) для выделения из сточных вод примесей крупностью 0,2мм/с и более,
а также нефтепродуктов.
Методы механической очистки (отстаивание, флотация, фильтрование,
осаждение в центробежном поле) позволяют обычно выделить частицы крупнее 10-50
мкм.
Для очистки сточных вод от мелкодисперсных и коллоидных частиц используют
физико-химические методы (коагуляция, флокуляция, электрокоагуляция).
Кроме того, используют термические методы, приводящие к ликвидации
сточных вод, а также методы закачки сточных вод в подземные горизонты и их
захоронению.
Имея данные по расходам сточных вод, их подробную характеристику, а также
требования к очищенной воде, выбирают оптимальный метод очистки с учетом
технико-экономических показателей.
литейный цех отливка
БИБЛИОГРАФИЧЕСКИЙ СПИСОК
1. Иванов В.Н., Казеннов С.А., Курчман Б.С. и др. Литье по
выплавляемым моделям / под общей редакцией Шкленника Я.И., Озерова В.А. Москва:
Машиностроение, 1984.-408с.
. Кнорре Б.В. Основы проектирования литейных цехов / Б.В.
Кнорре. - Машиностроение, 1979.-370 с.
. Кельчевская Н.Р., Романова Л.А., Финкельштейн А.Б.
Организация и планирование литейного производства: Учебное пособие /
Екатеринбург: ГОУ УГТУ-УПИ, 2002.180с.
. ООО «Вилкон» Оборудование для литья по выплавляемым моделям
/ адрес сайта: http://vlikon.com/LitObr/OLBM.html
. Першин П.С. Технология точного литья / П.С. Першин. -
Свердловск: Машгиз, 1955.-135.
. Методическое указание по курсовому и дипломному
проектированию «Проектирование литейных цехов», ГОУ УГТУ-УПИ, Екатеринбург,
2007 г., 35 с.
Сафронов В.Я. Справочник по литейному оборудованию / Москва:
Машиностроение, 1985.-320с.
. Фурман Е.Л., Казанцев С.П. Специальные виды литейного
производства. Часть 2. Литье по выплавляемым моделям: Учебное пособие /
Екатеринбург: ГОУ ВПО УГТУ-УПИ, 2007. 155с.
. Чуркин Б.С. Гофман Э.Б. Технология литейного производства:
учебник/ Екатеринбург: Изд-во УГППУ, 2000. - 662 с.
. Конституция Российской Федерации. - М.: Эксмо, 2008. - 64
с.
. Трудовой кодекс Российской Федерации. М.: Эксмо, 2007. -
245 с.
. ПБ 11-493-02. Общие правила безопасности для
металлургических и коксохимических предприятий и производств.
. ПБ 11-552-03. Общие правила промышленной безопасности для
организаций, осуществляющих деятельностей в области промышленной безопасности
опасных производственных объектов.
. СНиП 23-05-95. Естественное и искусственное освещение.
.ГОСТ 12.1.030-81 ССБТ. Электробезопасность. Защитное
заземление и зануление (И-1-7-87)
. ГОСТ 17.2.3.02-78. Охрана природы. Атмосфера. Правила
установления допустимых выбросов вредных веществ промышленными предприятиями.
Утв. 01.01.80.
. ГОСТ 12.0.003-74. ССБТ. Опасные и вредные производственные
факторы. Классификация.
. СанПиН 2.2.4.548-96. Гигиенические требования к
микроклимату производственных помещений
. ГН 2.1.6.1338-03 Предельно допустимые концентрации (ПДК)
вредных веществ в атмосферном воздухе
. СНиП 41.01.2003. Отопление, вентиляция и кондиционирование
. ГОСТ 12.2.061. ССБТ. Оборудование производственное. Общие
требования безопасности к рабочим местам
. ГОСТ 12.1.005-88 ССБТ. Воздух рабочей зоны. Общие
санитарно-гигиенические требования. М.: Изд-во стандартов, 1989. 23с.
. Правила устройства электроустановок, 2005 г.
. СНиП 21-01-97. Пожарная безопасность зданий и сооружений.
М.: МЧС России, 1997. 14 с.
. СНиП 23-03-2003. защита от шума.
. Безопасность жизнедеятельности. Безопасность
технологических процессов и производств. Охрана труда. Кукин П.П., Лапин В.Л.,
Подгорных Е.А. и др. - М.: Высшая школа, 1999. 316 с.
. ГОСТ 12.1.012-90 ССБТ. Вибробезопасность. М.: Изд-во
стандартов, 1990. 23с.
. ГОСТ 12.1.003-83 ССБТ. Шум. Общие требования безопасности.
М.: Изд-во стандартов, 1984. 10с.
. СП 12.13130-2009. ОПРЕДЕЛЕНИЕ КАТЕГОРИЙ ПОМЕЩЕНИЙ, ЗДАНИЙ И
НАРУЖНЫХ УСТАНОВОК ПО ВЗРЫВОПОЖАРНОЙ И ПОЖАРНОЙ ОПАСНОСТИ