Разработка мероприятий по организации ремонта техники в СХПК 'Дубрава'
Введение
Машина в правовой литературе определяется как
источник повышенно опасности. Обладая большой кинетической энергией, он при
высокой скорости и столкновении с препятствием превращается в разрушительную
силу. Свидетельство тому ничем не оправданная гибель людей в
дорожно-транспортных происшествиях. По числу жертв наземный транспорт и с/х
машины являются самым опасным среди других видов транспорта. Данные
исследований показывают, что наземный транспорт в 3 раза опасен воздушного и в
10 раз железнодорожного транспорта.
Большинство аварий происходит из-за нарушений
правил дорожного движения. Однако из общего их числа 10-15 % - из-за
неудовлетворительного технического состояния машины. Особенно опасны
неисправности тормозных систем, которые чаще всего сводятся к неодновременному
торможению колес, течи тормозной жидкости, заклиниванию тормозных механизмов и
т.д. Совершенно недопустима неисправность рулевого управления, увеличение люфта
на рулевом колесе, заедание или тугое его вращение, ослабление креплений рулевого
привода. Не менее важным является крепления колес и состояния шин. Ослабленная
гайка, «лысая» покрышка - потенциальные причины дорожно-транспортного
происшествия.
Один из гарантов безаварийной эксплуатации машин
- своевременное диагностирование и устранение неисправностей. Поддержание
автомобиля в технически исправном состоянии в значительной мере зависит от
уровня развития и условий функционирования ремонтно-технологической базы
предприятия, представляющих собой совокупность зданий, сооружений, оборудование,
оснастки и инструмента, предназначенных для технического обслуживания и ремонта
машин.
На основании вышеизложенного, задачи дипломного
проектирования сформулирована следующим образом:
выполнить анализ хозяйственной деятельности
предприятия;
разработать проект совершенствования технологии
ремонта машин;
разработать мероприятия по охране труда для
данной ремонтной мастерской;
рассчитать технико-экономические показатели
разработанных мероприятий.
1. Краткая характеристика природных и
экономических условий СХПК «Дубрава» Комсомольского района ЧР
.1 Месторасположение, почвенно-климатические
условия, землепользование
Землепользование СХПК «Дубрава» Комсомольского
района расположена в южной части Чувашии. СХПК «Дубрава» объединяет селения:
Полевые Шептахово, Починок-Быбыть, Кайнлык, Старый Сундырь.
Административно-хозяйственным центром является д. Починок-Быбыть, расположенный
в 15 км от районного центра села Комсомольское и в 122 км от столицы республики
- г. Чебоксары.
Транспортная сеть с пунктами сдачи с/х продукции
осуществляется по асфальтированным дорогам.
Территория землепользования имеет вытянутую
форму с юга на север.
По данным Чебоксарской метеорологической станции
среднегодовая температура воздуха составляет + 2,7 °С. Средняя дата последнего
весеннего заморозка приходиться на 14 мая. Продолжительность безморозного
периода составляет в среднем 117 дней. Сумма положительных температур выше + 10
°С, среднегодовая количество осадков 632 мм. Средняя глубина промерзание почвы
- 102 см. Устойчивый снежный покров ложиться в третей декаде ноября или в
первой декаде декабря. Высота снежного покрова составляет 33 см.
Гидротермический коэффициент - 1,2.
Уровень залегания грунтовых вод зависит от
характера рельефа и геологических пород. На водораздельном пласте уровень их
колеблется в пределах от 5 до 12 метров. На территории хозяйства имеются озера,
которые имеют противоэрозионное и хозяйственное значение.
Землепользование хозяйства расположено в
пределах Приволжской лесостепи и характеризуется распространением
растительности, лесостепного типа. Древесная растительность представлена дубом,
березой, кленом, липой и т.д.
Травянистая растительность под пологом леса
представлена разнотравьем: клевером красным и белым, мятликом луговым, костром
безостым и т.д.
В травяном покрове лугов преобладают злаковое
разнотравие - мятлик луговой, постер, клевер белый и розовый, икотник,
тысячелистник.
В условиях хорошей увлажненности почвы и
отсутствия стравливания травостоя скатом, в этих местах можно получить хороший
урожай сена.
После засорения сорной растительностью,
преимущественно по посевам яровых зерновых культур. Преобладающим видом сорной
растительности является хвощ полевой, осот розовый и желтый, вьюнок полевой,
сурепка обыкновенная, дикая редька, ромашка и др.
По механическому составу в хозяйстве преобладают
супесчаные и суглинистые почвы.
1.2 Современное состояние сельскохозяйственного
производства и перспектива его развития
Существующее производственное направление
хозяйства зерново-животноводческое.
Основной отраслью в растениеводстве является
производства зерна, кормов и картофеля, а в животноводстве - производство
молока и мяса КРС.
Согласно плану экономического и социального
развития на перспективу производственного направления хозяйства сохраняется и
получает свое дальнейшее развитие.
Намеченный на перспективу рост урожайности с/х
культур будет, достигнут за счет осуществления комплекса мероприятий,
направленных на повышение плодородия почв и эффективного использования земель и
материальных ресурсов, основными из которых является:
освоение научно-обоснованных
севооборотов;
внедрения прогрессивных (интенсивных и
индустриальных) технологий возделывания с/х культур;
- возделывание высокоурожайных сортов с/х
культур с хорошим качественными показателями;
рациональное использование органических и
минеральных удобрений в сочетании с существованием лесных почв на основе
разработанной системы применение удобрений по каждому севообороту;
осуществление долговременной программы
мелиорации, повышения эффективности использования мелиорированных земель;
применения интегрированной системы защиты
растений от вредителей, болезней и сорняков;
целесообразное проведение противоэрозионных,
агротехнических мер по защите почв от эрозии;
своевременное и качественное выполнение всех
технологических приемов по возделыванию с/х культур.
Комплекс мероприятий для повышения урожайности
с/х культур, продуктивности животных требует немалых финансовых вложений. В
условиях рынка, когда не приходиться ждать материальной помощи от государства
или от кого-либо, нужно рассчитывать только на свои силы, возможности, исходя
из имеющихся ресурсов. Только в условиях материальной заинтересованности,
материальной ответственности, эффективного использования имеющихся основных и
оборотных средств можно достичь положительных результатов.
1.3 Размеры производства и специализация
хозяйства
Таблица 1.1 - Земельные угодия и их
использование.
Показатели.
|
2008
г.
|
2009г.
|
2010
г.
|
|
га.
|
%
|
га.
|
%
|
га.
|
%
|
Общая
земельная
|
1145
|
100
|
1125
|
100
|
1125
|
100
|
площадь.
|
|
|
|
|
|
|
Всего
с/х угодий.
|
839
|
73,3
|
832
|
74
|
832
|
74
|
из
них: пашни
|
729
|
63,7
|
723
|
64,2
|
723
|
64,2
|
сенокосы
|
25
|
2,2
|
25
|
2,2
|
25
|
2,2
|
пастбища
|
85
|
7,4
|
84
|
7,5
|
84
|
7,5
|
Леса
|
101
|
8,8
|
101
|
9
|
101
|
9
|
Пруды
и водоемы
|
20
|
1,7
|
20
|
1,8
|
19
|
1,8
|
Приусадебные
|
60
|
5,2
|
46
|
4,1
|
46
|
4,1
|
участки
|
|
|
|
|
|
|
Прочие
угодия
|
-
|
-
|
-
|
-
|
-
|
-
|
Орошаемые
|
-
|
-
|
-
|
-
|
-
|
-
|
Как видно из таблицы общая площадь земельных
угодий уменьшалось на 20 га. Также уменьшились площади с/х угодий и пашни
соответственно на 7 и 6 га. На 1 га уменьшалась общая площадь пастбищ, прудов и
водоемов. На 14 га уменьшалась площадь приусадебных участков. Прочих и
орошаемых угодий в хозяйстве в настоящее время.
Таблица 1.2 - Основные показатели размеров
предприятия и производства в хозяйстве.
Показатели
|
2008
г.
|
2009
г.
|
2010
г.
|
Общая
площадь с/х угодий, га
|
839
|
832
|
832
|
Всего
пашни, %
|
86,9
|
86,9
|
86,9
|
Всего
посевов, га
|
729
|
713
|
715
|
Среднегодовое
количество работников, чел
|
101
|
85
|
71
|
Производственные
основные фонды, тыс. руб
|
7335,0
|
10210
|
8556,8
|
Валовая
продукция, тыс. руб.
|
563,3
|
354,0
|
314,4
|
в
т.ч. растениеводства
|
185
|
157
|
240
|
животноводства
|
448
|
283
|
204
|
Поголовье
КРС, гол
|
538
|
460
|
467
|
Как видно из таблицы удельный вес пашни в
структуре общей площади с/х угодий остался без изменений. За последние 3 года
площадь посевов уменьшилась на 14 га. Количество работников уменьшилось на 30
человека по сравнению с 2008 годом и уменьшилось на 16 человек по сравнению с
2009 годом. Производственные основные фонды, валовая продукция также
уменьшилась. Поголовье КРС на 2009 год превысило на 7 голов по сравнению с 2008
годом.
Таблица 1.3 - Размер и структура товарной
продукции
Продукция
|
2008
г.
|
2009
г.
|
2010
г.
|
Всего
за Згода
|
%
|
Растениеводство,
руб.
|
201425
|
194473
|
220750
|
616648
|
42
|
Животноводство,
руб.
|
348450
|
281174
|
261980
|
891604
|
58
|
Всего,
руб.
|
549875
|
475647
|
482730
|
1508252
|
100
|
Из таблицы видно, что в структуре товарной
продукции основную часть составляет продукция животноводств.
1.4 Размер и структура посевных площадей,
урожайность с/х культур
Таблица 1.4 - Размер и структура посевных
площадей.
Культура
|
2008
г.
|
2009
г.
|
2010
г.
|
|
га.
|
%
|
га.
|
%
|
га.
|
%
|
Озимые
зерновые
|
80
|
10,97
|
123
|
17,25
|
83
|
11,61
|
Яровые
зерновые
|
140
|
19,2
|
97
|
13,6
|
137
|
19,16
|
Зернобобовые
|
30
|
4,12
|
30
|
4,21
|
45
|
6,29
|
Итого
|
250
|
34,29
|
250
|
35,06
|
265
|
7,06
|
Картофель
|
5
|
0,69
|
5
|
0,7
|
5
|
0,7
|
Кормовые
корнеплоды
|
20
|
2,74
|
25
|
,5
|
25
|
3,5
|
Многолетние
травы
|
155
|
21,26
|
170
|
23,84
|
167
|
23,36
|
Однолетние
травы
|
299
|
41,02
|
263
|
6,89
|
253
|
35,38
|
Всего
посевов
|
729
|
100
|
713
|
100
|
715
|
100
|
Из таблицы видно, что площадь посевов зерновых
получили за последние годы небольшой прирост. Также немного увеличились площади
под кормовые культуры и многолетние травы. Но площадь однолетних трав и всего
посевов уменьшилось.
Таблица 1.5 - Урожайность сельскохозяйственных
культур.
Культура
|
2008
г
|
2009
г
|
2010
г
|
В
среднем по району
|
Озимые
зерновые, ц/га.
|
24,5
|
25
|
21,5
|
20,8
|
Яровые
зерновые, ц/га.
|
23,2
|
19,8
|
21
|
20,3
|
Зернобобовые,
ц/га.
|
21,3
|
22,6
|
23
|
21,4
|
Всего
зерновых и
|
17,4
|
29
|
23,1
|
22,4
|
зернобобовых,
ц/га.
|
|
|
|
|
Картофель,
ц/га.
|
153,1
|
132
|
164
|
93,1
|
Кормовые
корнеплоды, ц/га.
|
666
|
326
|
387
|
381
|
Многолетние
травы, ц/га.
|
51,9
|
49,7
|
46,3
|
51,2
|
на
сено
|
|
|
|
|
на
зеленую массу
|
240,7
|
254,6
|
260,2
|
254,2
|
Однолетние
травы, ц/га.
|
4,5
|
29,8
|
38,1
|
37,2
|
на
сено
|
|
|
|
|
на
зеленую массу
|
-
|
-
|
-
|
-
|
Из таблицы видно, что урожайность зерновых и
зернобобовых, картофеля по сравнению с предыдущими годами осталось на одном
уровне. При этом урожайность выращиваемых культур в хозяйстве мало отличается
от средне районного значение урожайности по этим культурам.
1.5 Обеспеченность хозяйства основными
средствами производства, рабочей силой и их использование
Таблица 1.6 - Обеспеченность хозяйства основными
средствами производства.
Показатели,
их наименование
|
2008
г.
|
2009
г.
|
2010
г.
|
Стоимость
производственных основных средств с/х назначения в расчете: на 100 га
сельхозугодий, тыс. руб.
|
5594,0
|
15557,8
|
10536,9
|
на
100 га пашни, тыс. руб.
|
6438,1
|
18154,4
|
12261,1
|
Мощность
всех двигателей в л.с. в расчете:
|
|
|
|
на
1 га пашни
|
13,3
|
13,6
|
14,2
|
на
среднегодового работника
|
20,7
|
24,1
|
29,3
|
Наличие
тракторов: физических
|
21
|
21
|
Наличие
зерновых комбайнов, шт.
|
4
|
3
|
3
|
Приходиться
на 1 зерновой комбайн посевов зерн, га.
|
62,5
|
83,3
|
88,4
|
Наличие
автомобилей, шт.
|
19
|
19
|
21
|
Имеющиеся в наличие в хозяйстве основные
средства производства позволяют проводить основные с/х работы в оптимальные
агротехнические сроки. Из вышеприведенной таблицы видно, что за 3 года
количество тракторов уменьшалось на две единицы. В следствии этого увеличился
объем работ на единицу техники, что говорит о необходимости наиболее
эффективного использования имеющейся в наличии техники.
Таблица 1.7- Уровень использования средств
производства в хозяйстве.
Показатели
|
2008
г.
|
2009
г.
|
2010
г.
|
Стоимость
валовой продукции в расчете на
|
12,0
|
2,7
|
3,6
|
100
руб. производственных основных
|
|
|
|
фондов
с/х назначения, руб.
|
|
|
|
Отработано
работниками хозяйства всего,
|
|
|
|
тыс.
чел. - дней.
|
124
|
102
|
95
|
тыс.
чел. - час.
|
991
|
824
|
709
|
Обработано
на 1 усл. эт. га:
|
|
|
|
машино-дней.
|
135,6
|
140,4
|
139,8
|
машино-смен.
|
147,8
|
153,0
|
153,8
|
Коэффициент
сменности работы тракторов
|
1,09
|
1,09
|
1,1
|
Убрано
в расчете на 1 зерновой комбайн, га.
|
62,5
|
83,3
|
88,4
|
Выполнено
транспортных работ в расчете на
|
7441
|
6933
|
7104
|
1
тонну грузоподъемности автомобиля, т.км.
|
|
|
|
Из таблицы видно, что стоимость валовой
продукции в расчете на 100 руб. производственных основных фондов с/х назначения
уменьшалось за последние годы примерно в 3,3 раза из-за малого прироста
стоимости валовой продукции (т.е. в натуре произведено меньше продукции по
сравнению с 2008 годом). Объем работ на единицу техники увеличился за 3 года.
Таблица 1.8 - Обеспеченность хозяйства рабочей
силой и ее использование.
Показатели
|
2008
г.
|
2009
г.
|
2010
г.
|
Всего
трудоспособных, чел.
|
101
|
85
|
71
|
в
т.ч. механизаторы.
|
21
|
17
|
15
|
Приходиться
на 1 среднегодового работника: пашни, га.
|
2,53
|
2,8
|
3,1
|
сельхозугодий,
га.
|
1,76
|
2,07
|
2,41
|
Отработана
одним трудоспособным: тыс. чел. - час.
|
2,07
|
2,05
|
2,06
|
тыс.
чел. - дней.
|
0,26
|
0,25
|
0,28
|
Производственно
валовой продукт на 1 среднегодового работника, тыс. руб.
|
11,8
|
8,8
|
9,1
|
За последние годы числа работников в хозяйстве
уменьшилось по сравнению с 2008 годом (в 2009 г. на 16 человек, а в 2010 году
на 30 человек). Соответственно пашня и сельхозугодия на 1 среднегодового
работника увеличились по сравнению с 2008 г.
1.6 Уровень механизации работ в растениеводстве
Таблица 1.9 - Механизация работ в
растениеводстве
Наименование
работ
|
Выполнено
работ
|
|
всего
|
в
т.ч механику
|
%
|
Посев
корневой свеклы, га
|
25
|
25
|
100
|
Кошения
всех видов растений
|
420
|
420
|
100
|
Стогование
сена
|
-
|
-
|
-
|
Уборка
сена пресс-подборщиком, га
|
203
|
203
|
100
|
Копнения
сена
|
-
|
-
|
-
|
Скирдование
соломы, га
|
265
|
265
|
100
|
Копка
картофеля, га
|
5
|
5
|
100
|
Скирдования
соломы, га
|
265
|
-
|
-
|
Погрузка
картофеля, га
|
5
|
-
|
-
|
Внесения
минеральных удобрений, га
|
110
|
110
|
100
|
Уборка
зерновых культур, га
|
220
|
220
|
100
|
Из таблицы видно, что в хозяйстве основные виды
с/х работ механизированы. Но на таких работах, как погрузка соломы и картофеля
все еще используется ручной труд.
1.7 Основные технико-экономические показатели
К основным технико-экономическим показателем
относиться: размер ОПФ, объем валовой и реализованной продукции, прибыль,
годовой фонд заработной платы, производственная площадь.
К удельным показателям относиться: фондоотдача,
фондовооруженность, рентабельность, производительность труда, выпуск продукции
на квадратный метр производственной площади.
Таблица 1.10 - Основные технико-экономические
показатели.
Наименование
показателей
|
Годы
|
|
2008
г.
|
2009
г.
|
2010
г.
|
Стоимость
ОПФ, тыс. руб.
|
7335,0
|
10210
|
8556,6
|
Производственная
площадь, м2
|
328
|
328
|
328
|
Фондовооруженность,
руб./чел.
|
72,6
|
120,1
|
120,5
|
Фондоотдача,
тыс. руб./тыс. руб.
|
0,12
|
0,027
|
0,035
|
Производительность
труда, тыс. руб./чел.
|
7,8
|
8,82
|
9,11
|
Выпуск
продукции, руб/м
|
17,1
|
10,7
|
9,58
|
Оплата
труда, руб.
|
734
|
906
|
9
53
|
Среднегодовая
численность работников, чел
|
101
|
85
|
71
|
Уровень
рентабельности, %
|
8,6
|
7,3
|
6,8
|
Темп
роста производительности труда, %
|
8,6
|
11,5
|
3,2
|
Темп
роста зарплаты, %
|
4,6
|
18,9
|
4,9
|
Товарная
продукция, руб.
|
54975
|
475647
|
482730
|
Валовая
продукция, тыс.руб.
|
563,3
|
354,0
|
314,4
|
Реализация
продукции, руб.
|
548965
|
474518
|
481823
|
Себестоимость
единицы продукции, руб.
|
0,7
|
0,8
|
0,81
|
.8 Состав МТП
Таблица 1.11- Состав и годовая наработка
машинно-тракторного парка хозяйства
№
|
Марка
машины
|
Число
|
Годовая
|
п/п
|
|
машин
в парке
|
наработка
одной машины, у.э.га
|
|
1.
Тракторы
|
|
|
1.1
|
Т-150
|
1
|
800
|
1.2
|
ДТ-75
|
4
|
1024
|
1.3
|
МТЗ-80/82
|
12
|
1670,4
|
1.4
|
Т-40А
|
3
|
186
|
|
2.
Автомобили
|
|
|
2.1
|
ГАЗ-53Б.
|
10
|
22900
|
2.2
|
ЗИЛ-130
|
2
|
13700
|
2.3
|
Камаз-5320
|
1
|
35500
|
2.4
|
УАЗ-469
|
4
|
30400
|
|
3.
Комбайны
|
|
|
3.1
|
СК-5М
«Нива»
|
3
|
140
физ. га
|
|
4.
Сельскохозяйственные машины
|
|
|
4.1
|
ПЛН-5-35
|
1
|
|
4.2
|
ПЛН-4-35
|
2
|
|
4.3
|
БДСТ-2,5
|
2
|
|
4.4
|
БЗТС-1,0
|
70
|
|
4.5
|
ЗККШ-6
|
3
|
|
4.6
|
С-11У
|
1
|
|
4.7
|
СП-16
|
1
|
|
4.8
|
СГ-21
|
1
|
|
4.9
|
КПС-4
|
3
|
|
4.10
|
КОН-2,8
|
1
|
|
4.11
|
СЗУ-3,6
|
3
|
|
4.12
|
СЗТ-3,6
|
1
|
|
4.13
|
СУПН-8
|
1
|
|
4.14
|
КСМ-6
|
1
|
|
4.15
|
ОП-1600
|
1
|
|
4.16
|
2ПТС-4М
|
14
|
|
4.17
|
ПС-10
|
1
|
|
4.18
|
КС-21
|
3
|
|
4.19
|
ГВК-6
|
1
|
|
4.20
|
СКУ-0,5
|
1
|
|
4.21
|
ППЛ-Ф-1,6
|
1
|
|
4.22
|
ЖВН
|
5
|
|
4.23
|
К-541
|
1
|
|
4.24
|
ПРТ-10
|
1
|
|
2. Разработка мероприятий по организации ремонта
техники в СХПК «Дубрава»
.1 Определение общего объема транспортных и
механизированных работ
Общий объем тракторных и механизированных работ
в условиях эталонных гектарах, взятый на планируемый год:
Мт = 
Бд • Кд , у. эт. га.,
где Кд - переводной коэффициент для
данной культуры
Бд- площадь пашни под данной
культурой,
п - число возделываемых культур.
Мт1 = 100 • 7
= 700 у.
эт.
га.;
Мт2
= 200 • 4,5 = 900 у.
эт.
га.;
Мт3
= 138 • 2,2 = 30,6 у.
эт.
га.;
Мт4
= 244 • 3,0 = 732 у.
эт.
га.;
Мт5
= 15 • 5,7 = 85,5 у.
эт.
га.;
Мт6
= 25 • 1,2 = 30 у.
эт.
га.;
Мт7 = 24 • 8,5 = 204 у. эт. га.; MTi
= Мт = 2955,1 у. эт. га.;
Таблица 2.1 - Общий объем тракторных и
механизированных работ.
№
|
Культура
|
Объем
Мт по культурам,
|
п/п
|
|
у.
эт. га.
|
Озимые
зерновые
|
700
|
2
|
Яровые
зерновые
|
900
|
3
|
Сеяные
травы однолетние
|
303,6
|
4
|
Сеяные
травы многолетние
|
732
|
5
|
Вика
|
85,5
|
6
|
Сенокосы
естественные
|
30
|
7
|
Корнеплоды
корневые
|
204
|
|
ИТОГО
|
2995,1
|
Полученный расчетом объем тракторных и
механизированных работ увеличиваем на 25% с учетом энергоемких системных и
индустриальных технологий и мелиоративных работ.
Мтк = 1,25 • Мт = 1,25 • 2995,1 = 3698,8 у. эт.
га.;
В дальнейших расчетах используют величину Мтк.
2.2 Распределение объема Мтк по маркам
тракторов.
Распределения объема работ необходимо для
определения годовой загрузки тракторов по маркам и определение трудоемкости их
ремонта.
Рт = Кп • В, у. эт. га.,
где Кп- переводной коэффициент для данной марки
тракторов (табл. П2);
В - заданная годовая наработка тракторов данной
марки, мото-ч.
Таблица 2.2 - Распределения объема тракторных и
механизированных работ.
№
п/п
|
Марка
трактора
|
Число
тракторов
|
Заданная
наработка Вд, м-ч.
|
Годовой
объем Рх на 1 трактор, у.эт.га.
|
Суммарный
годовой объем Ртс, у.эт.га.
|
1
|
Т-150К
|
1
|
400
|
800
|
800
|
2
|
ДТ-75М
|
4
|
200
|
256
|
1024
|
3
|
МТЗ-80/82
|
12
|
160
|
139,2
|
1670,4
|
4
|
Т-40А
|
3
|
100
|
62
|
186
|
|
|
|
|
ИТОГО
|
3680,4
|
Полученные числа суммируем по маркам.
Ртс = 
Кп • В • пm = 3680,4 у. эт. га.,
где пт - число тракторов данной
марки в парке,
m - число марок тракторов в парке.
Проверка: Мтк - 0,05 • Мтк = 3509,1
у. эт. га.
Мтк + 0,05 • Мтк = 3878,4 у. эт.
га.; Условие Ртс = Мтк± 0,0 Мтк выполняется.
.3 Расчет трудоемкости капитального
и текущего ремонта тракторов
Для расчета трудоемкости
капитального и текущего ремонтов используем данные таблицы 2.2., исходя из
нормативов трудоемкости ремонта для каждой тысячи мотто-ч объема тракторных и
механизированных работ (Ртс).
2.3.1 Трудоемкость капитального ремонта
тракторов данной марки
Ткр = Нк * 
*β, чел.*ч.
где Нк - нормативы удельной
трудоемкости на капитальный ремонт тракторов: [8, стр. 31.]
Т-150К: Ткр = 52 * 
*1,15 = 46 чел.*ч.
ДТ-75: Ткр = 80 * 
*1,15 = 94,2 чел.*ч.
МТЗ 80/82: Ткр = 70 * 
*1,15 = 134,4 чел.*ч.
Т-40А: Ткр = 70 * 
*1,15 = 14,9 чел.*ч.
β = 1,15 -
коэффициент, учитывающий зональные особенности эксплуатации машин (для
Волго-Вятского района β = 1,15 ).
[8, стр. 31.]
2.3.2 Трудоемкость текущего ремонта тракторов
данной марки
Ттр = Нт * 
*β, чел.*ч.
где Нт - нормативы удельной
трудоемкости на текущий ремонт тракторов. [8, стр. 31.]
Т-150К: Ттр = 76 * 
*1,15 = 69,9 чел.*ч.
ДТ-75: Ттр = 110 * 
*1,15 = 129,5 чел.*ч.
МТЗ 80/82: Ттр = 97 * 
*1,15 = 186,3 чел.*ч.
Т-40А: Ттр = 106 * 
*1,15 = 22,6 чел.*ч.
Таблица 2.3 - Трудоемкость капитального и текущего
ремонтов тракторов.
№
|
Марка
трактора
|
Трудоемкость
ремонта, чел.-ч.
|
п/п
|
|
капитального
|
текущего
|
всего,
чел.-ч.
|
1
|
Т-150К
|
46
|
69,9
|
115,9
|
2
|
ДТ-75М
|
94,2
|
129,5
|
223,7
|
3
|
МТЗ-80/82
|
134,4
|
186,3
|
320,7
|
4
|
Т-40А
|
14,9
|
22,6
|
37,5
|
|
ИТОГО
|
289,5
|
408,3
|
697,8
|
.4 Расчет трудоемкости капитального и текущего
ремонта автомобилей
Трудоемкость ремонтов автомобилей определяют в
зависимости от годового пробега автомобилей и нормативов трудоемкости на 1000
км пробега.
2.4.1 Трудоемкость капитального ремонта
автомобилей данной марки
Ттр = Нт * 
*na * β * γ, чел.*ч.
где Нк - нормативы трудоемкости на
капитальный ремонты автомобилей; [8, стр. 32.]
Пг - годовой пробег автомобиля
данной марки, км.
па - число автомобилей данной марки.
ГАЗ-53Б: Ткр = 1,5 * 
*10 * 1,15 * 1,1 = 434,5 чел.*ч.
ЗИЛ-130: Ткр = 1,6 * 
*2 * 1,15 * 1,1 = 55,4 чел.*ч.
КамАЗ-5320: Ткр = 2,6 * 
*1 * 1,15 * 1,1 = 116,7 чел.*ч.
УАЗ-469: Ткр = 2,5 * 
*4 * 1,15 * 1,1 = 384,5 чел.*ч.
.4.2Трудоемкость текущего ремонта
автомобилей данной марки
Ттр = Нт * 
*na * β * γ, чел.*ч.
где Нх - нормативы трудоемкости на
текущий ремонты автомобилей. [8, стр. 32.]
ГАЗ-53Б: Ттр = 5,9 * 
*10 * 1,15 * 1,1 = 1709,1 чел.*ч.
ЗИЛ-130: Ттр = 6,2 * 
*2 * 1,15 * 1,1 = 214,8 чел.*ч.
КамАЗ-5320: Ттр = 10,5 * 
*1 * 1,15 * 1,1 = 471,5 чел.*ч.
УАЗ-469: Ттр = 10,3 * 
*4 * 1,15 * 1,1 = 1584,3 чел.*ч.
Результаты заносим в таблицу 2.4.
Таблица 2.4 - Трудоемкость капитального и
текущего ремонтов автомобилей.
№
п/п
|
Марка
автомобиля
|
Трудоемкость
ремонта, чел.-ч.
|
|
|
капитального
|
текущего
|
всего,
чел.-ч.
|
1
|
ГАЗ-53Б
|
434,5
|
1709,1
|
2143,6
|
2
|
ЗИЛ-130
|
55,4
|
214,8
|
270,2
|
3
|
Камаз-5320
|
116,7
|
471,5
|
588,2
|
4
|
УАЗ-469
|
384,5
|
1584,3
|
1968,8
|
|
ИТОГО:
|
991,1
|
3979,7
|
4970,8
|
.5 Расчет трудоемкости капитального и текущего
ремонтов самоходных комбайнов
Трудоемкость капитального и текущего ремонтов
комбайнов определяют по средне союзным нормативам трудоемкости ремонта с учетом
коэффициента охвата ремонтом, до ремонтной и фактической наработки.
.5.1 Трудоемкость капитального ремонта комбайнов
данной марки
Ткр = Нк * 
*nк, чел.*ч.
где Нк- норматив трудоемкости одного
капитального ремонта комбайна;
пк - число комбайнов данной марки,
Вф - фактическая годовая наработка
одного комбайна,
Ви - до ремонтная наработка
комбайнов,
,8 - коэффициент перевода до
ремонтной наработки в послеремонтную.
СК-5М «Нива»: Ткр = 330 * 
*3 = 173,25 чел.*ч.
.5.2 Трудоемкость текущего ремонта
комбайнов данной марки
Ттр = Нт * nк, чел.*ч.
где Нт - норматив трудоемкости на
один текущий ремонт комбайна.
СК-5М «Нива»: Ткр = 150 • 3 = 450
чел.- ч.,
Результаты сводим в таблицу 2.5.
Таблица 2.5 Трудоемкость капитального и текущего
ремонтов самоходных комбайнов
№
п/п
|
Марка
комбайна
|
Трудоемкость
ремонт, чел.-ч.
|
|
|
капитального
|
текущего
|
Всего,
чел.-ч.
|
1
|
СК-5М
«Нива»
|
173,25
|
450
|
623,25
|
|
ИТОГО:
|
173,25
|
450
|
623,25
|
2.6 Расчет трудоемкости текущего ремонта
прицепных и навесных сельскохозяйственных машин
.6.1 Трудоемкость текущего ремонта
сельскохозяйственных машин данной марки
Трудоемкость определяется по формуле:
Тсх = К0 • nм • Нсх, чел.- ч.,
где Kо - коэффициент охвата ремонтом
сельскохозяйственных машин (в расчетах принимают Ко=0,8);м - число
сельскохозяйственных машин данной марки в парке;
Нсх - норматив годовой трудоемкости текущего
ремонта
сельскохозяйственных машин данной марки. [8,
стр. 32.] (К0 • nм) - число ремонтов.
Плуги:
ПЛН-5-35: Тсх = 0,8 • 1 • 21 = 16,8 чел.- ч,
ПЛН-4-35: Тсх = 0,8 • 2 • 17 = 27,2 чел.- ч.,
Бороны дисковые:
БДСТ-2,5: Тсх = 0,8 • 2 • 34 = 54,4 чел.- ч.,
Бороны зубовые:
БЗТС-1,0: Тсх = 0,8 • 70 • 4 = 54,4 чел.- ч.,
Катки:
ЗККШ-6: Тсх = 0,8 • 3 • 20 = 48 чел.- ч.,
Сушки:
С-11У: Тсх = 0,8 • 1 • 11 = 8,8 чел.- ч., СП-16:
Тсх = 0,8 • 1 • 28 = 22,4 чел.- ч., СГ-21: Тсх = 0,8 • 1 • 34 = 27,2чел.- ч.,
Культиваторы:
КПС-4: Тсх = 0,8 • 3 • 22 = 52,8 чел.- ч.,
КОН-2,8: Тсх = 0,8 • 1 • 27 = 21,6 чел.- ч.,
Сеялки зерновые:
СЗУ-3,6: Тсх = 0,8 • 3 • 63 = 151,2 чел.- ч.,
СЗТ-3,6: Тсх = 0,8 • 1 • 83 = 66,4 чел.- ч.,
Сеялки кукурузные:
СУПН-8: Тсх = 0,8 • 1 • 57 = 45,6 чел.- ч.,
Картофелесажалки:
КСМ-6: Тсх = 0,8 • 1 • 98 = 78,4 чел.- ч.,
Опрыскиватели:
ОП-1600: Тсх = 0,8 • 1 • 38 = 30,4 чел.- ч.,
Прицепы:
ПТС-4М: Тсх = 0,8 • 14 • 48,3 = 540,96 чел.- ч.,
Протравливатели:
ПС-10: Тсх = 0,8 • 1 • 50 = 40 чел.- ч.,
Косилки:
КС-21: Тсх = 0,8 • 3 • 10 = 24 чел.- ч.,
Грабли тракторные:
ГВК-6: Тсх = 0,8 • 1 • 30 = 24 чел.- ч.,
Стогометатели:
СКУ-0,5: Тсх = 0,8 • 1 • 30 = 24 чел.- ч.,
Пресс-подборщик:
ППЛ-Ф-1,6: Тсх = 0,8 • 1 • 45 = 36 чел.- ч.
Жатки:
ЖВН-6: Тсх = 0,8 • 5 • 60 = 240 чел.- ч.,
Зерноочистительные машины:
К-541: Тсх = 0,8 • 1 • 62 = 49,6 чел.- ч.,
Машина для внесения удобрений:
ПРТ-10: Тсх = 0,8 • 1 • 39 = 31,2 чел.- ч.,
Результаты расчетов сводим в таблицу 2.6.
Таблица 2.6 - Трудоемкость текущего ремонта СХМ.
№
|
Наименование
и марка машин
|
Число
|
Трудоемкость,
|
п/п
|
|
ремонтов
|
чел.-ч.
|
1
|
Плуги:
ПЛН-5-35
|
0,8
|
16,8
|
|
ПЛН-4-35
|
1,6
|
27,2
|
2
|
Бороны
дисковые: БДСТ-2,5
|
1,6
|
54,4
|
3
|
Бороны
зубовые: БЗТС-1,0
|
56
|
224
|
4
|
Катки:
ЗККШ-6
|
2,4
|
48
|
5
|
Сушки:
С-11У
|
0,8
|
8,8
|
|
СП-16
|
0,8
|
22,4
|
|
СГ-21
|
0,8
|
27,2
|
6
|
Культиваторы:
КПС-4
|
2,4
|
52,8
|
|
КОН-2,8
|
0,8
|
21,6
|
7
|
Сеялки
зерновые: СЗУ-3,6
|
2,4
|
151,2
|
|
СЗТ-3,6
|
0,8
|
66,4
|
00
|
Сеялки
кукурузные: СУПН-8
|
2,4
|
45,6
|
9
|
Картофелесажалки:
КСМ-6
|
0,8
|
78,4
|
10
|
Опрыскиватели:
ОП-1600
|
0,8
|
30,4
|
11
|
Протравливатели:
ПС-10
|
0,8
|
40
|
12
|
Косилки:
КС-21
|
2,4
|
24
|
13
|
Грабли
тракторные: ГВК-6
|
0,8
|
24
|
14
|
Стогометатели:
СКУ-0,5
|
0,8
|
24
|
15
|
Пресс-подборщик:
ППЛ-Ф-1,6
|
0,8
|
36
|
16
|
Жатки:
ЖВН-6
|
4
|
240
|
17
|
Зерноочистительные
машины: К-541
|
0,8
|
49,6
|
18
|
Машина
для внесения удобрений: ПРТ-10
|
0,8
|
31,2
|
19
|
Прицепы:
2ПТС-4М
|
38,64
|
540,96
|
|
ИТОГО
|
123,44
|
1884,9
|
Общую трудоемкость текущего ремонта всех
сельскохозяйственных машин увеличивают на 25% для учета энергоемкости
интенсивных и индустриальных технологий:
Тсхм = 1,25 • Тсх = 1,25 • 1884,9 = 2356,1 чел.-
ч.,
В дальнейших расчетах используют величину Тсхм.
2.7 Расчет трудоемкости ремонта оборудования
животноводческих ферм
Трудоемкость ремонта оборудования
животноводческих ферм определяют учитывая имеющееся в хозяйстве поголовье скота
и птицы и нормативы трудоемкости ремонта в расчете на одну голову:
где Нж - норматив трудоемкости ремонта,
Дойное стадо КРС: Тж = 1,32 • 144 = 199 чел.-
ч.;
КРС на откорм и выращивание: Тж = Нж • Пж = 1,11
• 224 = 248,6 чел.- ч.; Результаты расчетов по каждой ферме сводят в таблицу
2.7 и подсчитывают суммарную трудоемкость.
Таблица 2.7 - Трудоемкость ремонта оборудования
по животноводческим фермам.
№
п/п
|
Наименование
фермы
|
Трудоемкость
ремонта по ферме, чел.-ч
|
1
|
Ферма
КРС молочного
|
190
|
2
|
Ферма
КРС мясного
|
248,6
|
|
ИТОГО:
|
438,6
|
2.8 Расчет трудоемкости дополнительных ремонтных
работ
.8.1 Неплановый ремонт тракторов, автомобилей,
комбайнов, сельскохозяйственных машин и оборудования животноводческих ферм
Тнп = 0,03 • Тм = 0,03 • [(Ткр + Ттр)т + (Ткр +
Ттр)а + (Ткр + Ттр)к +
+Тсхм]чел.- ч.,
где: Тм - общая трудоемкость ремонта машин;
(Ткр + Тхр)т - общая трудоемкость капитального и
текущего ремонта тракторов;
(Ткр + Ттр)а - общая трудоемкость капитального и
текущего ремонта автомобилей;
(Ткр+Ттр)к - общая трудоемкость капитального и
текущего ремонта комбайнов;
Тсхм - общая трудоемкость текущего ремонта
сельскохозяйственных машин.
Тнп = 0,03 • [(289,5 + 408,3) + (991,1 + 3979,7)
+ (173,25 + 450) +
+2356,1] = 259,4 чел.-ч.,
Тм= 8646,6 чел.- ч.,
2.8.2 Расчет трудоемкости восстановления деталей
при ремонте машин
Тв = 0,08 • (Тм + Тж + Тнп) = 0,08 • (8646,6 +
438,6 + 259,4) = 747,5 чел.- ч.,
2.8.3 Расчет трудоемкости ремонта и изготовления
ремонтных приспособлений и инструмента
Ти - 0,05 • (Тм + Тж + Тнп + Тв) =
= 0,05 • (8646,6 + 438,6 + 259,4 + 747,5) =
504,5 чел.- ч.,
.8.4 Расчет трудоемкости ремонта
ремонтно-технологического и другого оборудования мастерской
Тро = 0,05 • (Тм + Тж + Тнп + Тв + Ти)= 0,05 •
(8646,6 + 438,6 + 259,4 + 747,5 + 504,5) = 529,8 чел.- ч.,
2.9 Определение общего годового объема работ по
ремонту сельскохозяйственной техники в хозяйстве
Тсхт = Тм + Тж + Тнп + Тв + Ти + Тро = 8646,6 +
438,6 + 259,4 + 747,5 + 504,5 + 529,8 = 11126,4 чел.ч.,
По результатам расчета составляют сводную
таблицу объема ремонта сельскохозяйственной техники хозяйства таблица 2.8:
Таблица 2.8 - Годовой объем работ по ремонту
сельскохозяйственной техники в хозяйстве
№
п/п
|
Наименование
ремонтных работ
|
Трудоемкость
ремонта, чел.-ч.
|
|
|
капитального
|
текущего
|
всего
чел.-ч.
|
1
|
Ремонт
тракторов
|
289,5
|
408,3
|
697,8
|
2
|
Ремонт
автомобилей
|
991,1
|
3979,7
|
4970,8
|
3
|
Ремонт
комбайнов
|
173,25
|
450
|
623,25
|
4
|
Ремонт
с/х машин
|
X
|
2356
|
2356,1
|
5
|
Ремонт
оборудования животноводческих ферм.
|
X
|
438,6
|
438,6
|
6
|
Неплановый
технический ремонт с/х техники.
|
X
|
259,4
|
259,4
|
7
|
Восстановление
деталей.
|
X
|
747,5
|
747,5
|
8
|
Ремонт
приспособлений.
|
X
|
504,5
|
504,5
|
9
|
Ремонт
ремонтно-технологического оборудования
|
X
|
529,8
|
529,8
|
10
|
Оказание
услуг арендаторам и населению
|
X
|
X
|
X
|
|
ИТОГО
|
1453,8
|
9673,8
|
11127,6
|
2.10 Расчет годовых фондов рабочего времени
рабочих и оборудование
Расчет годовых фондов рабочего времени и
оборудования рассчитывается из производительности смены.
Различают номинальный и действительные годовые
фонды времени рабочих и оборудования.
Номинальный годовой фонд времени работы - это количество
рабочих часов в соответствии с режимом работы без учета возможных потерь
времени. Его определяют по формуле:
Фн.о. = (Кр • tсм - Кп • tc) • n,
где Кр - число рабочих дней в году;-
продолжительность смены, ч;
Кп - число предвыходных и предпраздничных дней,
в которых
сокращается рабочая смена; - время на которое
сокращается смена, ч; - число смен.
Действительный годовой фонд времени выражают
фактически отрабатываемое время рабочих или оборудованием с учетом потерь. У
рабочих эти потери связаны с отпуском, болезнями, декретными, с сокращением
рабочих дней подростков. Потери рабочего времени оборудования связаны с его
простоем в техническом обслуживании и ремонте, а так же со сменностью работы.
Действительный годовой фонд времени работы
рабочего Фдр определяют вычислением из его номинального фонда времени всех
потерь времени.
Фд.р. = (Фн.о. - Ко * tсм) * ηр
где К0 - общее число рабочих дней отпуска в
году; см - продолжительность смены, ч;
ηр - коэффициент
потери рабочего времени;
Действительный годовой фонд времени работы
оборудования:
Фд.о = Фн.о* nc * ηo,
где nс - число рабочих смен в сутки;
ηо - коэффициент
использования оборудования.
Таблица 2.9 - Годовые номинальные (Фн0) и
действительные (Фд0) фонды
Тип
оборудования
|
Фн.о,
ч.
|
η
|
Фд.о,
ч.
|
Металлорежущие,
деревообрабатывающие, гальванические, стенды для разборочно-сборочных работ.
|
1995
|
0,98
|
1955
|
Кузнечнопрессовое,
термическое, контрольно измерительные стенды.
|
1995
|
0,970
|
1935
|
Сварочное,
моечные установки.
|
1995
|
0,97
|
1935
|
Коэффициент использования оборудования учитывает
потери времени на проведение его технического обслуживания и ремонта, зависят
от числа рабочих смен. Простои оборудования, вызванные простоями в организации
производства, при проектировании не учитывают.
Таблица 2.10 - Годовые номинальные (Фн.р) и
действительные (Фд.р) фонды времени рабочих
Категория
специалиста
|
Специальность
рабочего
|
Фн.р.,
ч.
|
ηГ
|
Фд.р,
Ч.
|
1
|
Кузнец,
медник, электрогазосварщик, аккумуляторщик.
|
1995
|
0,88
|
1756
|
2
|
Мойщик,
вулканизаторщик, гальвонилщик, испытатель.
|
1995
|
0,89
|
1736
|
3
|
Слесарь,
плотник, токарь.
|
1995
|
0,90
|
1796
|
3. Выбор типового проекта ремонтной мастерской
Существующая мастерская имеет в плане
прямоугольную форму. Прилагается пристрой до получения в плане прямоугольника,
более близкого к квадрату.
Полученную форму прямоугольника оценивают
коэффициентом целесообразности плана здания мастерской по формуле:
ηц = 
ηц = 0,88
где Р - площадь здания мастерской,
м2;
Р - периметр здания мастерской, м;
,282 - отношение квадратного корня
из площади круга к длине окружности.
Сравнив полученный коэффициент с
табличными значениями, коэффициент квадрата 0,86 заключаем, что принятая форма
плана мастерской достаточно близка специальной. Приступим к компоновке корпуса
мастерской, сначала выбираем схему основной линии. Анализ показывает, что в
данном случае наиболее целесообразной является поточная схема.
В состав ремонтной мастерской
хозяйства входят следующие производственные участки: участок испытания и
обкатки двигателей, участок текущего ремонта, участок ремонта и обкатки с/х
машин, участок мойки и разборки машин, склад запасных частей, участок ремонта
электрооборудования, кузнечный участок, слесарно-механический участок, участок
ремонта и регулировки топливной аппаратуры, сварочный участок.
Кроме этого, предусматриваются
служебно-бытовые помещения.
3.1 Распределение годового объема работ по
ремонту сельскохозяйственной техники
Капитальный ремонт тракторов, автомобилей и
комбайнов выполняют на специализированных ремонтных предприятиях, поэтому
трудоемкость капитальных ремонтов исключает из объема работ, порученных
ремонтной мастерской хозяйства.
Разборочно-сборочные работы при текущем ремонте
автомобилей выполняют водители в автогараже, поэтому ремонтной мастерской
передают 50% работ по текущему ремонту автомобилей (восстановительные,
контрольно регулировочные и др. специализированные работы).
Специализированным предприятиям передают 20%
объема работ по ремонту оборудования животноводческих ферм, оставшиеся 15%
выполняют на месте слесари животноводческих ферм, а 65% объема передают
центральной ремонтной мастерской.
В ремонтной мастерской хозяйства выполняют 80%
объема работ по ремонту технологического оборудования, 20% передают на
специализированные предприятия.
Оставшийся ремонтной мастерской объем работ
увеличивают на 10% по каждому наименованию перечня табл. 3.1. Увеличение
трудоемкости обусловлено низкой механизацией работ в мастерских хозяйств.
Таблица 3.1 - Годовой объем работ по ремонту
сельскохозяйственной техники выполняемой в ремонтной мастерской.
|
|
|
В
т. ч. по видам работ
|
№
п.п
|
Перечень
работ
|
Всего,
чел.-ч
|
диагностика
|
разборка,
сборка
|
мойка,
очистка
|
слесарно-механическая
|
сварочная
|
кузнечно-термическая
|
другие
работы
|
|
|
|
5%
|
57%
|
6%
|
8%
|
7%
|
15%
|
2%
|
1
|
Ремонт
тракторов
|
449,13
|
22,4
|
256
|
26,9
|
35,9
|
31,4
|
67,3
|
8,9
|
2
|
Ремонт
автомобилей
|
2188,7
|
109,
4
|
1247,5
|
131,3
|
175
|
153,2
|
328,
3
|
43,
7
|
3
|
Ремонт
комбайнов
|
247,5
|
12,3
|
141,0
|
14,8
|
19,8
|
17,3
|
37,1
|
4,9
|
4
|
Ремонт
СХМ
|
2591,7
|
129,
5
|
1477.2
|
155,5
|
207,
3
|
181,4
|
388,
7
|
51,
8
|
5
|
Ремонт
оборудования животноводческих ферм.
|
312,3
|
15,6
1
|
178,01
|
18,73
|
24,9
8
|
21,86
|
46,8
4
|
6,2
4
|
6
|
Неплановый
технический ремонт с/х техники.
|
285,3
|
14,2
6
|
162,6
|
17,1
|
22,8
|
19,9
|
42,7
|
5,7
|
7
|
Восстановление
деталей.
|
878.7
|
-
|
-
|
-
|
544,
4
|
184,5
|
149,
3
|
-
|
8
|
Ремонт
приспособлений.
|
601,5
|
30
|
342,8
|
36,1
|
48,1
|
42,1
|
90,2
|
12
|
9
|
Ремонт
ремонтно-технологического оборудования
|
630,1
|
|
|
|
390,
6
|
132,3
|
107.
1
|
|
|
ИТОГО:
|
8184,9
|
323,
4
|
3805,1
|
400,4
|
1468
,8
|
783,9
|
1257
.5
|
133
,2
|
3.2 Расчет ремонтно-технологического
оборудования ремонтной мастерской
К основному оборудованию ремонтного предприятия
относиться оборудование, на котором выполняется основные, наиболее сложные
операция ремонта машин, агрегатов и восстановления деталей. Это мощные машины,
токарные, расточные и шлифовальные станки, конвейерные установки для сбора
машин, стенды для испытания и обкатки узлов и агрегатов. Потребность в
остальном оборудовании определяют, исходя из принятого технологического
процесса по устанавливаемому нередко оснащение рабочих мест оборудованием.
Количество моечных машин для наружной мойки
определяют по формуле:
Sм = 
= 
= 0,108 шт.
Принимаем одну моечную машину.
где Q - общая масса деталей,
подлежащих мойке за планируемый период в данной машине, кг; - время мойки одной
партии деталей сборочной единицы, ч. (t = 0,5 ч);
Фд.о - действительный фонд времени
оборудования, ч. ( Фд 0=1955 г); - масса деталей одной загрузки, кг.
η0 - коэффициент, учитывающий
одновременную загрузку моечной
машины по массе (ηо=0,6...0,8);
[1, стр. 90]
ηt - коэффициент
использования моечной машины по времени (ηt=0,8...0,9);[1,стр.
90]
Количество металлорежущих станков определяем по
формуле:
Sст = 
= 
= 1,55
где Тст - годовая трудоемкость
станочных работ, чел.-ч;
Кн - коэффициент неравномерности
загрузки предприятия (Кн=1,1...1,3); [1,стр. 92]
ηо- коэффициент использования
станочного оборудования (ηо=0,86...0,9);[1,стр.
92]
Полученное количество станков
распределяют по видам, пользуясь, процентным соотношением и расчеты сведем в
таблицу.
Таблица 3.2 - Перечень металлорежущих станков
мастерской.
№
п/п
|
Ремонтно-технологическое
оборудование
|
Марка
оборудования
|
Расчетноe
число, шт.
|
Принятое
число, шт.
|
1
|
Токарные
станки
|
16К20
|
0,77
|
1
|
2
|
Фрезерные
и строгальные станки
|
6Р80Ш
|
0,48
|
1
|
3
|
Сверлильные
станки
|
2А135
|
0,18
|
1
|
4
|
Шлифовальные
станки
|
ЗУ10В
|
0,10
|
1
|
Количество сварочного оборудования находят по
формуле:
Nсв = 
= 
= 0,9 шт.,
где Тсв - трудоемкость сварочных
работ, чел.-ч.
Фоб - фонд времени сварочного
оборудования, ч;
ηсв - коэффициент
использования сварочного оборудования.
Принимаем 1 сварочный трансформатор марки ТД-300
и 1 сварочный генератор У Г-10.
Количество обкаточных стендов для трансмиссии
определяем по формуле:
Sст = 
= 
= 1,18
где tn - продолжительность обкатки и
испытания данного объекта, ч.(tn = 2,25ч);
ηn - коэффициент, учитывающий
возврат объектов для повторной обкатки,
(ηn
= 1...1,05);об
- общий ремонт, (d0б = 2 ч);
К
- коэффициент, учитывающий использования установки по времени, (К
=0,86...0,95).
Принимаем 1 стенд.
.3 Расчет штата работников ремонтной мастерской
Потребную численность производственных рабочих
рассчитывают по трудоемкости работ с учетом годового номинального фонда рабочего
времени ремонтной мастерской (Фн = 1995 ч при односменной работе в год):
NП = 
= 
= 4,1 чел.,
В том числе находим среднее годовое
число производственных рабочих по видам работ (табл. 3.1):
Потребность в рабочих для
диагностикипg = 
= 
= 0,16 чел.,
Потребность в рабочих на разборке,
сборке и регулировке машинрр = 
= 
= 1,9 чел.,
Потребность в рабочих на мойке и
очисткерм = 
= 
= 0,2 чел.,
Потребность в рабочих для слесарно-механических
работ
Nсм = 
= 
= 0,73 чел.,
Потребность в сварщикахсв = 
= 
= 0,39 чел.,
Потребность в кузнецахрк = 
= 
= 0,63 чел.,
где Т - годовой объем
соответствующих работ (табл. 3.1).
Потребное число вспомогательных
рабочих
Nв = 0,1 * Nп = 0,1 • 4,1 = 0,41 чел.,
Численность инженерно-технических работников
(ИТР):итр = 0,1 • (Nп + Nв) = 0,1 • (4,1 + 0,41) = 0,45чел.,
Численность служащихс = 0,02 • (Nп + Nв) - 0,02
• (4,1 + 0,41) = 0,1 чел.,
Численность младшего обслуживающего персонала
(МОП)моп = 0,02 • (Nп + Nв) = 0,02 • (4,1 + 0,41) = 0,1 чел., Весь штат
ремонтной мастерской= Nп + Nв + Nитр + Nс + Nмоп =
= 4,1 + 0,41 + 0,45 + 0,1 + 0,1 = 5,16 чел.,
Численность персонала мастерской сводят в
таблицу 3.3.
Таблица 3.3 - Сводная ведомость штата
мастерской.
№
|
Персонал
мастерской
|
Расчетная
численность, чел.
|
Принятая
численность, чел.
|
п/п
|
|
|
|
1.
|
Производственные
рабочие в т. ч.:
|
4,1
|
4
|
1.1
|
диагносты
|
0,16
|
1
|
1.2
|
слесари
по разборке и сборке машин
|
1,9
|
2
|
1.3
|
рабочие-мойщики
|
0,2
|
-
|
1.4
|
рабочие
слесарно-механического участка
|
0,73
|
1
|
1.5
|
сварщики
|
0,39
|
1
|
1.6
|
кузнецы
|
0,63
|
1
|
1.7
|
маляры
|
0,06
|
-
|
2.
|
Вспомогательные
рабочие
|
0,41
|
1
|
3.
|
ИТР
|
0,45
|
1
|
4.
|
Служащие
|
0,1
|
1
|
5.
|
МОП
|
0,1
|
1
|
|
ВСЕГО:
|
5,16
|
8
|
3.4 Расчет общей площади и площадей
специализированных отделений и участков ремонтной мастерской
Производственную площадь отделений и площадь
вспомогательных участков рассчитывают по удельной площади, приходящейся на один
условный ремонт (300 чел.-ч.):
Фпл = 
* Фусл. = 
* Фусл. = 54 * Фусл. м2,
где Фусл. - удельная площадь,
значения которой для различных участков мастерской приведены в табл. 16.
При расчетах используют значения
Фусл, соответствующие участку, для которого выполняется расчет. Значение Тг
всегда остается постоянным (таблица 3.1). Результаты расчета сводят в таблице
3.4. Окончательно площадь участков принимают после разработки технологической
планировки мастерской.
В составе вспомогательных участков предусматривают
контору (до 20 м ), красный уголок с кабинетом по охране труда,
санитарно-бытовой узел (до 45 м). Дополнительно предусматривают площадь 9-12 м
для кладовой. Газогенераторную размещают в отдельной пристройке.
Таблица 3.4 - Площади отделений и участков
ремонтной мастерской
№
п/п
|
Производственные
помещения
|
Производственная
площадь, м2.
|
|
|
удельная
площадь, м /усл.р.
|
по
расчету
|
принято
|
1
|
2
|
3
|
4
|
5
|
1
|
Разборочно-моечное
отделение
|
1,230
|
63,96
|
64
|
1.1
|
Участок
наружной очистки машин
|
0,3
|
15,6
|
16
|
1.2
|
Участок
диагностики, мойки, разборки, дефектации и комплектовки
|
0,930
|
48,36
|
48
|
2
|
Отделение
восстановления деталей
|
0,930
|
48,36
|
49
|
2.1
|
Участок
слесарно-механический
|
0,356
|
18,5
|
19
|
2.2
|
Участок
кузнечно-термический
|
0,205
|
10,66
|
11
|
2.3
|
Участок
сварки
|
0,103
|
5,35
|
5
|
2.4
|
Участок
медницко-жестяницких работ
|
0,167
|
8,68
|
9
|
2.5
|
Участок
полимерных материалов
|
0,099
|
5,14
|
5
|
3
|
Сборочное
отделение
|
3,093
|
160,8
|
161
|
3.1
|
Участок
ремонта электрооборудования
|
0,124
|
6,44
|
6
|
3.2
|
Участок
обойно-столярный
|
0,171
|
8,89
|
9
|
3.3
|
Участок
регулировки гидросистем
|
0,091
|
4,73
|
5
|
3.4
|
Участок
регулировки топливной аппаратуры
|
0,081
|
4,21
|
4
|
3.5
|
Участок
текущего ремонта двигателей
|
0,208
|
10,81
|
11
|
3.6
|
Участок
контрольного испытания двигателей
|
0,159
|
8,26
|
8
|
3.7
|
Участок
сборки СХМ и агрегатов
|
1,245
|
64,74
|
65
|
3.8
|
Участок
ремонта оборудования ЖФ
|
0,142
|
7,38
|
7
|
3.9
|
Участок
ремонта и монтажа шин
|
0,129
|
6,7
|
7
|
3.10
|
Участок
окраски, заправки, регулировки и ТО машин
|
0,743
|
38,63
|
39
|
|
Итого
производственной площади
|
5,253
|
273,15
|
274
|
4
|
Вспомогательные
участки
|
1,051
|
54,65
|
54
|
|
ВСЕГО:
|
6,304
|
327,8
|
328
|
4. Санитарно-технические расчеты
.1 Расчет водоснабжения мастерской
В ремонтных предприятиях вода расходуется на
мойку машин, агрегатов, узлов и деталей, на хозяйственные нужды.
Годовой расход воды на мойку машин и деталей
находится из условия: на одну мойку машины расходуется от 500 до 1000 литров, а
двигателя от 200 до 400 литров QМ = 95 м3.
Для приготовления эмульсии воды берут из расчета
4 литра смену на один металлорежущий станок. Тогда годовой расход на станок
механического охлаждения составит:
Qсм = 
, м3
где
S0 - количество станков, работающих с охлаждением; - расход воды на один
станок, g = 4 л; - число смен работы станка, n = 1; - число рабочих дней в
году, d = 258.
см
= 
= 4,12 м3
Расход
воды на бытовые нужды устанавливается из расчета 25 литров за смену на каждого
работающего в мастерской.
см
= 
, м3
где
n - количество рабочих, работающих в данной мастерской; - число рабочих дней в
году; - расход воды на одного рабочего.
см
= 
= 45,4 м3
Расход
воды для душевых - 40 литров на каждого пользующего душем. Укрупнено считается,
что душ принимают 70 % от общего числа работающих.
д
= 
= 115,5 м3
На
неучтенные нужды полученное количество воды увеличивается на 20 %.
=
0,2 * (Qр + Qд + Qсм + Qм )= 0,2 * (45,4+115,5+4,12+95) = 52 м3,
Годовой
расход:
г
= Q + Qр + Qд + Qсм + Qм = 52 + 45,4 + 115,5 + 4,12 + 95 = 312,12 м3,
4.2 Расчет освещения
Проектирование освещения ведется в соответствии
со строительными нормами и правилами СН-245-63.
Требования, предъявляемые к освещению:
Достаточная освещенность рабочего места;
Постоянность освещения;
Отсутствие разницы в освещении различных
участков;
Отсутствие разницы теней.
Количество ламп, необходимых для освещения,
подсчитываем по формуле:
n = 
,
где Еср - средняя освещенность,
лк.;- площадь помещения, м ;
К - коэффициент запаса освещения;-
световой поток ламп, лм.;
η - коэффициент использования
светового потока.
Коэффициент использования светового
потока определяется в зависимости от показателя:
φ = 
,
где S - площадь пола, м3;
Нп - высота подвеса, м;
а и b - ширина и длина помещения
соответственно.
Выбираем лампы типа ЛБ - 40.
Таблица 4.1 - Количество ламп по
отделением мастерской.
№
п/п
|
Наименование
участка
|
Еср,
лк.
|
Fo,
лм.
|
S,
м2
|
η
|
n
|
1
|
Разборочно-сборочное
|
35
|
4100
|
64
|
0,42
|
12
|
2
|
Механический
|
95
|
4100
|
19
|
0,37
|
2
|
3
|
Сварочный
|
60
|
4100
|
5
|
0,37
|
2
|
4
|
Вулканизационный
|
60
|
4100
|
11
|
0,37
|
2
|
5
|
Кузнечный
|
55
|
4100
|
11
|
0,37
|
3
|
6
|
Инструментальный
|
70
|
1710
|
11
|
0,37
|
2
|
7
|
Аккумуляторный
|
60
|
4100
|
11
|
0,37
|
2
|
8
|
Медницко-жестяницкий
|
60
|
4100
|
19
|
0,37
|
2
|
9
|
Ремонта
СХМ
|
60
|
4100
|
65
|
0,37
|
5
|
10
|
Ремонта
двигателей
|
100
|
4100
|
11
|
0,37
|
2
|
11
|
Ремонта
электрооборудования
|
120
|
1710
|
6
|
0,37
|
3
|
12
|
Ремонта
ТА
|
120
|
1710
|
6
|
0,37
|
3
|
13
|
Бытовые
помещения
|
40
|
1710
|
50
|
0,37
|
4
|
4.3 Расчет отопления
Температура воздуха в производственном помещении
ремонтного предприятия устанавливается в соответствии с характером выполняемых
работ.
Расчет отопления сводиться к определению годовой
потребности топлива и количества нагревательных элементов.
Максимальный годовой расход тепла, необходимый
для отопления и вентиляции помещения:
м = Vм * (go + gв) * (tв - tн), ккал/час,
где Qм - объем помещения по наружному объему,
м3;о, gв- удельный расход тепла на отопление и вентиляцию. = 0,45...0,55
ккал/час. м . град. в = 0,15...0,25 ккал/час. м . град. в= 15 °С, tн = - 30 °С,
Vм = 4320 м3.м = 4320 * 0,6 * (30 - 15) = 38880 ккал/час,
Годовой расход условного топлива:
Py = 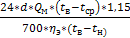
,
где
Ру - годовой расход условного топлива, кг;ср - средняя за отапливаемый сезон
температура; tср = 5,3. - число дней отапливаемого сезона, d =184 дня;
ηэ - КПД котельной
установки, ηэ = 0,7.
Py = 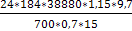
= 26,05т,
Годовой расход натурального топлива
Рн = Ру * ηн * 
где ηн -
коэффициент перевода.
При отоплении углем ηн = 1,17.
Рн = 26,05 * 1,17 = 30,4 т.,
Количество дров для растопки
принимаемые в размере 5 % от расхода угля:
Р’д = 
,
где Рд = 0,05 * Рн = 1,52 т.
Р’д = 
= 2,33 м3
Площадь нагревательных элементов
определяется из выражения:
= 
,
где Ки - коэффициент теплоотдачи, равной
для ребристых труб 7,4 ккал/час. м3 . град.’ср - средняя расчетная температура
теплоносителя в нагревательном приборе, t’ср = 100 °С.
= 
= 61,8 м2
Количество нагревательных приборов
рассчитывается по формуле:
= 
,
где F - поверхность нагрева одного
нагревательного прибора. Чугунная стена типа «Москва» имеет поверхность F =
0,25 м2.
= 
= 247 шт.,
.4 Расчет вентиляции
Во всех производственных помещениях
ремонтного предприятия принимается естественная, а в ряде отделений и
искусственная вентиляция, которая в зависимости от способа организации
воздухообмена подразделяется на местную и общую.
Общеобменную механическую вентиляцию
проектируют в помещениях без выделения пыли, газа и т.д.
Местную механическую вентиляцию
используют для удаления вредных выделений непосредственно с места их образования.
Величина воздухообмена
подсчитывается по формуле:
в = Vn * n
где Vn - объем помещения;- кратность
воздухообмена. Затем по рассчитанному воздухообмену выбирают тип, номер,
паспорт и КПД вентилятора по формуле:
= 
,
где Uв - напор воздушного потока,
кг/м ;
ηв - КПД вентилятора;
ηn - КПД передачи;
1,2... 1,5 - коэффициент, учитывающий потери
напора воздушного потока.
Данные расчетов неустановленной вентиляции
производственных помещений вводим в таблицу 4.2.
Таблица 4.2 - Перечень отделений с искусственной
вентиляцией и ее характеристика.
№
п/п
|
Наименование
участка
|
Произв.
Вентиляция м3/час
|
Марка
|
Мощность
эл. дв. кВт
|
Кратность
|
1
|
Участок
ТА
|
500
|
ЭВР-2
|
1,2
|
3
|
2
|
Участок
по ремонту электрооборудования
|
500
|
ЭВР-2
|
1,2
|
3
|
3
|
Сварочный
|
700
|
ЭВР-2
|
1,5
|
5
|
4
|
Аккумуляторный
|
700
|
ЭВР-2
|
1,5
|
5
|
5
|
Вулканизационный
|
500
|
ЭВР-2
|
1,2
|
3
|
6
|
Кузнечный
|
1000
|
ЭВР-2
|
1,5
|
5
|
5. Анализ существующих конструкций
.1 Анализ существующих устройств
На данный момент существует несколько устройств,
предназначенных для снятия фрикционных накладок. Все они относятся к гаражному
оборудованию, а именно к устройствам для снятия фрикционных накладок с колодок
колесного тормоза транспортных средств и с дисков сцепления.
. Устройства для фрикционных накладок, авторское
свидетельство В 60 8 5/00 № 1574498 состоит из кронштейна 3 (рис. 1.) с
установленным на нем поворотном диском 11, смонтированный в наклонных
направляющих основания, суппорт 8 с резцом 9, приводимый пневмоцилиндром 14,
шарнирно закрепленную на кронштейне 3 рычажную систему с установленными
роликами 12. Для снятия накладки с тормозных колодок, колодка устанавливается
на диск 11 и маховиком 6 подводится к резцу 9.
Рисунок 5.1 - Устройство для снятия накладок с
пневмоприводном.
Для снятия накладок с диска сцепления его
устанавливают на установочные ролики 12 и с помощью маховика подводят к резцу,
при вертикальном перемещении кронштейна срабатывает рычажная система, ролики 12
раздвигаются, ход кронштейна 3 уменьшается, вследствие чего диск сцепления
приобретает более устойчивое положение.
. Устройства для снятия фрикционных накладок с
колодок тормоза, авторское свидетельство В 60 8 5/00 № 1174301.
Рисунок 5.2 - Устройство для снятия накладок с
гидроцилиндром
Станок содержит станину 1 и привод,
вспомогательный гидроцилиндр 2 с регулируемым ходом, насос 3 и электродвигатель
4. К станине 1 шарнирно присоединяется коромысло 5 со сменными вогнутыми и
выпуклыми установочными элементами для колодок, выполненными в виде призмы 6 и
пальца 7.
При обработке колодок с выпуклой базой
используется призма, а при обработке колодок с выгнутой базой в призму
устанавливают палец.
При помощи общей оси коромыслом 5 к станине
присоединяется обойма 8, в которой смонтированы передние 9 и задние 10 ролики
представленными ребордами 11. Для регулировки положения обоймы служит винтовой
механизм 16.
Лезвие ножа 12 расположено под углом к образующей
обода колодки для облегчения неодновременного срезания заклепок.
Держатель 13 ножа установлен в цилиндрической
направляющей 15,соединенной с обойной 8,что обеспечивает ножу три степени
свободы: возможность вращения вдоль направляющей и вращение вокруг двух осей.
На направляющей установлена пружина 14,для
сжатия которой служит педаль 18.
В средней части станины смонтирован спуск 19 для
перемещения обработанных колодок, а верхний - стол для размещения колодок,
подлежащих обработке.
Для управления работой гидроцилиндра служит
распределитель. Рукоятка распределителя с помощью рычага может
взаимодействовать с упором, размещенным на коромысле 5. Фиксация положений
рукоятки и перемещение ее за пределами мертвого положения производится при
помощи пружины.
. Устройство для снятия фрикционных накладок с
колодок колесного тормоза транспортного средства, авторское свидетельство В 60
8 5/00 № 906752.
Рисунок 5.3 - Устройство для снятия фрикционных
накладок.
Устройство содержит основание 1, двигатель 2,
редуктор 3 с валом 4 и две параллельные щеки 5 с перекладиной 6. Щеки 5
выполнены с отверстиями 7 под вал 4 редуктора 3.
На валу 4 между щеками 5 вертикально и жестко
установлены диски 8, которые выполнены с пазами 9 и упорами 10 под тормозные
колодки 11 с фрикционными накладками 12. В отверстия 13 тормозных колодок 11
вставляется палец 14. Расстояние между дисками 8 выбирается равное ширине
тормозных колодок 11 (наибольших), умноженное на количество их одновременно
надеваемых на палец 14.
На перекладине 6, расположенной в верхней части
щек 5, установлен нож 15 с возможностью поворота вокруг перекладины 6.
Положение ножа 15 регулируется по углу наклона в
зависимости от радиуса закругления тормозной колодки и фиксируется в
определенном положении регулировочным винтом 16. Основание снабжено защитным
экраном 17 и бункером 18.
Устройство работает следующим образом.
Тормозные колодки 11 одинакового радиуса
закрепления в количестве, например, 2 штук, своими отверстиями 13 надеваются на
палец 14. Палец 14 с тормозными колодками 11 укладывается в пазы 9, обращенные
своими открытыми концами вверх. Нож 15 устанавливается под необходимым углом
наклона, обеспечивающим, плотное соприкосновение его с поверхностью тормозной
колодки 11 и закрепляется в этом положении винтом 16.
Включается двигатель 2. Вал 4 редуктора 3
начинает вращаться вместе с жестко установленными на нем дисками 8. Диски 8 в
свою очередь увлекают консольно закрепленные тормозные колодки 11. При вращении
дисков 8 тормозные колодки 11 подходят к ножу 1 5, который попадает в выступ
между поверхностью тормозных колодок 1 1 и торцом изношенных фрикционных
накладок 12 поддевает последние. По мере вращения дисков 8 пазы 9 занимают
положение, когда открытые концы их обращены вниз, палец 14 с тормозными
колодками 11 (с которых сняты фрикционные накладки) выпадает из дисков 8 в
бункер 18. В этот момент в пазы 9, выполненные на другом участке дисков 8,
вкладывается другой палец 14 с новой партией тормозных колодок 11.
. Устройство для снятия фрикционных накладок с
колодок колесного тормоза, авторское свидетельство В 60 8 5/00 № 1291466.
Рисунок 5.4 - Устройство для срезания
фрикционных накладок с многоступенчатым барабаном.
Устройство содержит основание 1, на котором
смонтированы многоступенчатый барабан 2 с приводом, состоящим из редуктора 3 и
электродвигателя 4. На барабане 2 в радиальных пазах установлен подвижно
механизм фиксирования тормозных колодок 5, состоящий из подпружиненного стержня
6 и втулки 7, кинематически связанных с неподвижным копиром 8 и подвижной
планкой 9. На основании 1 установлен в вертикальной плоскости механизм
перемещения ножа 10 и планки 9 с упором 11 и состоящий из пары винт - гайка с
рукояткой 12 лоток. 13 для очищенных колодок, а также кожух 14 для отвода
обломков фрикционных накладок и бункер 15 с ориентирующим пазом 16.
Устройство работает следующим образом.
Включают, электродвигатель 4 и через редуктор 3
приводится, в движение многоступенчатый барабан 2. Установленные в пазу загрузочного
бункера колодки перемещаются вниз и попадают на барабан таким образом, что один
конец колодки находится в бункере, а другой - в прорези барабана 2.
Контакт колодки с барабаном при этом находится
на линии, и при вращении гладкого барабана колодка остается на месте, так как
силы трения в месте контакта недостаточно, чтобы увлечь колодку. Механизм
фиксации, находящийся в радиальном пазу барабана 2, при движении своим стержнем
6 обкатывает поверхность копира 8 и при подходе к отверстию ушка колодки заходит
в него и увлекает ее за собой, а вторая колодка автоматически занимает ее
место, причем колодка устанавливается на свой радиус таким образом, что
заклепки ее не касаются выступов барабана.
При дальнейшем движении тормозная колодка
подходит к ножу 10, который попадает в выступ между поверхностью тормозных
колодок 5 и торцом изношенных фрикционных накладок, снимая последние, которые
отводятся через проем держателя ножа и кожух 14. После того как нож 10 снимет
полностью накладку, происходит вывод стержня 6 из ушка колодки за счет пружины
и профиля копира, и колодка по лотку 13 устремляется в тару. В это время
подходит следующий механизм фиксации колодки и цикл повторяется.
Для перевода устройства на другой типоразмер
колодки необходимо загрузить в бункер соответствующие колодки и повернуть
рукоятку 12, пока упор 11 не займет другое крайнее положение. При этом нож 10
переместится на касательную другого радиуса, а планка 9 займет нижнее
положение.
При вращении барабана 2 стержень 6 сначала,
попадая под планку 9, начнет перемещаться вместе с втулкой 7 вниз по
радиальному пазу до того момента, пока ось стержня 6 совпадает с осью отверстия
ушка колодки и при дальнейшем движении барабана 2 стержень 6, взаимодействуя с
копиром, зайдет в ушко колодки. В дальнейшем процесс происходит аналогично
описанному.
Изобретение позволяет повысить
производительность, культуру производства и расширить типоразмеры
обрабатываемых деталей.
. Устройство для снятия фрикционных накладок с
колодок колесного тормоза, авторское свидетельство В 60 8 5/00 № 1100166.
Рисунок 5.5 - Устройство для снятия накладок.
Устройство содержит основание 1, на котором
смонтирована поворотная плита 2, кинематически соединенная с приводом,
состоящим из редуктора 3 и электродвигателя 4. На поворотной плите расположены
быстросъемные пальцы 5, на которые устанавливаются тормозные колодки 6 и
съемный шлицевой вал 7, на котором устанавливается диск сцепления. На основании
1 горизонтальной плоскости установлен держатель 8 в виде двуплечего рычага, на
одном плече 5 которого установлен основной нож 9, подпружиненный пружинами 10,
а на другом - жестко установлен дополнительный нож 11. Держатель 8 установлен
на валу 12 с возможностью ограниченного вертикального перемещения вдоль
него при помощи рукоятки 13. Пружина 14 служит
для выборки осевого зазора резьбового соединения вала 12 и рукоятки 13. Вал 12
нижним концом соединен с червячным колесом самотормозящейся пары 15, а червяк -
с рукояткой 16. При помощи рукоятки 16 осуществляются поворотные перемещения
держателя. Устройство работает следующим образом.
Для снятия фрикционной накладки с тормозной
колодки 6 ее устанавливают на быстросъемные пальцы 5 поворотной плиты 2. Затем
вращением рукоятки 16 червячной пары 15 осуществляют подачу держателя 8 с ножом
9 к основанию срезаемой фрикционной накладки, при этом усилие на червячную пару
15 передается от ножа 9 через пружину 10. Включают электродвигатель 4, вращение
поворотной плиты 2 должно быть по часовой стрелке. При вращении поворотной
плиты нож снимает фрикционные накладки. Благодаря пружинам 10 обеспечивается
самоустановка ножа в случае изменения радиуса закругления тормозной колодки и
предотвращается его поломка.
Для снятия фрикционной накладки с диска
сцепления быстросъемные пальцы 5 снимаются, и диск своей центральной втулкой со
шлицевыми пазами устанавливается на съемный шлицевой вал 7 поворотной плиты 2.
Затем вращением рукоятки 16 червячной пары 15 подводят держатель 8 с
дополнительным ножом 11 к диску сцепления, при этом направление вращения
рукоятки 16 противоположное, чем в предыдущем случае. 45 Вращением рукоятки 13
устанавливают дополнительный нож 11 по вертикали таким образом, чтобы лезвие
ножа установилось напротив стыка между фрикционной накладкой и металлической основой
диска сцепления. Включают электродвигатель 4, при этом вращение поворотной
плиты 2 должно быть против часовой стрелки, и вводят нож 11 встык между
фрикционной накладкой и металлической основой диска сцепления. При вращении
поворотной плиты нож снимает фрикционную накладку.
. Устройство для снятие фрикционных накладок с
колодок колесного тормоза транспортных средств, авторское свидетельство В 60
85/00 № 673496.
Устройство содержит основание 1, поворотную
плиту 2, установленную на диске 3, кинематически соединенном, через редуктор 4
с приводным двигателем 5. На поворотной плите расположены пальцы 6, на которые
устанавливаются тормозные колодки 7 с фрикционными накладками 8. Диск 3
является шестерней, сцепленной с шестерней 9 редуктора.
Рисунок 5.6 - Устройство для снятия фрикционных
накладок.
Основание снабжено защитным экраном 10 и
бункером 11 на колесах для сбора срезанных фрикционных накладок. К основанию
крепится нажимное приспособление 12, содержащее направляющую 13 с Т-образным
пазом а, в котором подвижно установлен держатель 14 с укрепленным на нем ножом
15. Ходовой винт 16 снабжен упорным кольцом 17 и выполнен с шейкой 18,
заканчивающейся буртиком 19, расположенным в отверстии «а» держателя, сам
держатель снабжен ограничительными стержнями 20, контактирующими с торцовой
поверхностью буртика 19 со стороны шейки 18. Между кольцом 17 и держателем 14
установлена пружина 21. Направляющая выполнена с резьбовой наделкой 22, а
ходовой винт выполнен с маховичком 23 и рукояткой 24. К направляющей 13
прикреплен указатель 25 хода ножа 15.
Устройство работает следующим образом.
Тормозную колодку 7 с фрикционной накладкой 8
устанавливают на пальцы б поворотной плиты 2, затем вращением рукоятки 24
ходового винта 16 осуществляется подача ножа 15 к основанию срезаемой
фрикционной накладки. При этом усилие на держатель 14 ножа 15 передается через
упорное кольцо 17 и пружину 21. Пружина отвращается поломка ножа и ходового
винта 21, воздействуя на держатель 14 ножа 15, перемещает его по Т-образному
пазу "а". Включением двигателя 5 приводят во вращательное движение
диск 3 поворотной плиты 2. При вращении поворотной плиты нож снимает
фрикционные накладки, которые попадая в защитный экран 10,направляются в бункер
11.Нагрузки, воспринимаемые ножом 15, передаются на ходовой винт 16 через
пружину 21, при этом обеспечивается самоустановка ножа в случае изменения
радиуса закругления тормозной колодки и предотвращается поломка ножа и ходового
винта.
5.2 Основание выбора конструкции
Выбираем конструкции основанные на авторских
свидетельствах В 60 8 5/00 № 673496 и В 60 8 5/00 № 1100166. При совмещении
отдельных частей данных устройств получаем более простой стенд, который можно
использовать как для снятия фрикционных накладок с колодок колесного тормоза
так и с дисков сцепления. Увеличивается размер обрабатываемых деталей. Так же
стенд отличается тем, что повышается долговечность работы ножей. Они
установлены на соответствующем плече ножодержателя. Цель выбора такого типа
конструкции - повышение надежности и производительности устройства. Он
получается простой в эксплуатации и в обслуживании.
5.3 Описание стенда и его работы
Стенд относится к горизонтальному оборудованию,
а именно к устройствам для обрезки фрикционных накладок с тормозных и с дисков
сцепления транспортных средств.
Стенд содержит основание 1, на котором
смонтирована поворотная плита 4, редуктор червячный 3, электродвигатель 2. На
поворотной плите расположена быстросъемная планшайба 5 которая установлена на
шлицевом валу. К поворотному столу 4 планшайба 5 соединяется через штырь,
который служит фиксатором. На основании 1 установлена направляющая 14 с
Т-образным выступом в котором перемещается ножодержатель 15. На конце
ножодержателя 15 установлен нож 11 и дополнительный нож 12. для фиксации
ножодержателя выполнен фиксатор 19 в виде клина, для фиксации ножодержателя в
крайних рабочих положениях сделан стопор 17. При помощи рукоятки 13
осуществляется перемещение патрона с ножами по вертикали, а при помощи рукоятки
16 осуществляется движение пиноли 18 с патроном в горизонтальном направлении.
Рисунок 5.7 - Стенд для срезания фрикционных
накладок с колодок колесного тормоза и дисков сцепления.
Для снятия фрикционных накладок с тормозной
колодки ее устанавливают на быстросъемную планшайбу. При помощи кольца 9
колодка фиксируется на вилке и преодолевая усилие пружины ось планшайбы,
прижимает колодку к планшайбе. При этом ножодержатель должен сходится в крайнем
осевом положении на основании 1 и зафиксирован фиксатором 19. При помощи
рукоятки 13 пиноли 18 с патроном и ножом 11 должен быть установлен в крайнем
нижнем положении. Рукояткой 16 через ходовой винт патрон с ножом 11
перемещается к планшайбе на основании срезаемой фрикционной накладки. Срезанные
накладки по направляющей сбрасываются в бункер.
Для снятия фрикционной накладки с диска
сцепления быстросъемная планшайба 5 снимается и диск своей центральной втулкой
со шлицевыми пазами устанавливается шлицевой вал поворотной плиты. Вращение
рукоятки 13 устанавливается дополнительный нож 12 по вертикали, таким образом,
чтобы лезвие ножа установилось напротив стыка между фрикционной накладкой и
металлической основой диска сцепления.
Включают электродвигатель 2, при этом вращение
поворотной плиты должна быть против часовой стрелки и рукояткой 16 вводят нож
12 встык между фрикционной накладкой и металлической основой диска сцепления.
При вращении поворотной плиты нож снимает фрикционную накладку.
6. Расчет конструкторской разработки
.1. Определение мощности, необходимой на срез
заклепок и подбор электродвигателя
τв = 0,6 • GB,
где GB = 340МПа - латунная проволока марка Л80
полутвердая.
τв = 0,6 • 340 = 204
МПа,
Напряжение среза определяют по формуле:
τср = 
= τв * k ,
где
Ft - сила, необходимая на срез заклепок, Н.- диаметр заклепки, мм. - число
заклепок.
к
- коэффициент запаса прочности, k = 1,1... 1,2.
Отсюда
сила, необходимая на срез определяется:
=

* z * τв * k = 
* 2 * 204 * 1,1 = 5636 Н;
Определение
момента на приводном валу:= Ft*r,
где
г - радиус план шайбы, м. г = 0,25 м.
Т
= 5636-0,25 = 1409 Н • м;
Определяем
мощность, необходимую на срез заклепок:
P
= T * ω ,
где ω
- угловая скорость, рад/сек.
ω = 
= 
= 0,62 рад/с.;
P = 1409 *0,62 = 873,5 кВт;
Определяем требуемую мощность электродвигателя:
Рпотр = 
,
ηобщ = η1 *
η2 * η3 ,
где η1 - КПД пары
подшипников качения,η1
=
0,99. [19. стр. 5].
η2 - КПД ременной
передачи, η2 = 0,95. [19. стр. 5].
η3 - КПД червячной
передачи, η3 = 0,85. [19. стр.
5].
ηобщ = 0,99 * 0,95 *
0,85 = 0,75;
Потребная мощность электродвигателя:
Рпотр = 
= 1,16 кВт;
По полученным данным выбираем
электродвигатель 100L8/700 мощностью 1,5 кВт и п = 750 об/мин. [19. табл.
18.36].
После выбора электродвигателя
выбираем общее передаточное число:общ = 
,
Полученное Uобщ распределяют между
типами и ступенями передач. Принимаем:рем.перед. = 2,85черв.перед. = 2,85
.2 Расчет ременной передачи
Исходные данные для расчета ременной
передачи N = 1,5 кВт; n = 750 об/мин; ω = 78,5 рад/с.
Момент на валу двигателя
= 
= 
= 19,1 Н*м
2. При данном моменте рекомендуемое сечение О.
Выбираем сечение О с целью получения минимального количества решений= 8,5 мм; b
= 10 мм; h = 6 мм; у0 = 2,1 мм. Площадь сечения А = 0,47 см2.
Рисунок 6.1 - Основные размеры приводного
планового ремня типа О.
Диаметр малого шкива в соответствии с
рекомендациями принимаем d1 =63 мм. [25. стр. 216].
Диаметр
большого шкива= d1 - u-(l -ξ),
где
u - передаточное отношение ременной передачи;
ξ -
коэффициент скольжения; ξ =
0,01...0,02; [25. стр. 219].= 63 * (1 - 0,015) = 186,16 мм;
Стандартный
диаметр по ГОСТ 17383-73:=180 мм;
Скорость
ремня
υ = 
= 
= 2,47 м/с;
Частота вращения ведомого вала
= 
= 
= 258,5 об/мин;
Коэффициент скольжения принят ξ = 0,015.
. Принимаем межосевое
расстояние в соответствии с конструкцией
а0 = 500 мм;
. Длина ремня
= 
=
= 
= 1388 мм;
По ГОСТ 1284-68 принимаем L = 1320
мм.
. Окончательное межосевое расстояние
a = 0,25[ L -Δ1 + 
],
где Δ1 = 0,5
*π*(d1 + d2) = 0,5 * 3,14*(63 +180) = 381,5 мм;
Δ2 = 0,25 * (d2 - d1)2 = 0,25 * (180-63)2 =
3422,2 мм;
a = 0,25 * [1320-381,5+
] = 465,5;
10. Угол охвата на шкиве (малом)
α1 = 
= 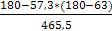
= 65,50;
. Коэффициент режима на
указанной нагрузке
Ср=1; [25. стр. 225].
. Коэффициент угла охвата
Сα = 0,95; [25. стр. 225].
. Исходная длина ремня= 1320
мм; [25. стр. 227]. Относительная длина L/L0 - 1320/1320 = 1;
. Коэффициент длины ремня=l;
[25. стр. 226].
. Исходная мощность при d1 =
63 мм и υ = 2,47 м/с=
0,4 кВт; [25. стр. 227].
. Поправка к моменту на
передаточное отношение
ΔТu = 5 * 102 Н * м; [25. стр.
228].
. Поправка к мощности
ΔNU = 10-7 * ΔТu * n1 =
10-7 * 500 * 750 = 0,37 кВт;
. Допускаемая мощность на
один ремень
[N] = (N0 * Сα * CL + ΔNU) - Ср =
(0,4 * 0,95 * 1 + 0,37) * 1 = 0,75 кВт;
. Число ремней
’ = 
= 
= 2;
. сила предварительного
натяжения ремня= 780 * N/(υ * Сα * Ср * z) +
qm * υ2,
где qm - масса 1 м длины ремня, кг.
qm = 0,18 кг/м.= 780 * 1,5/(2,47 * 0,95 * 1 * 2) + 0,18 * 2,472 = 250,55 Н;
. Усилие на вал= 2 * F0 * z *
sin(α/2) = 2 *
250,55 * 2 * sin(163,5/2) = 994,18 Н;
.3 Проверка прочности шпоночных
соединений
Расчет шпоночного соединения на
ведущем валу (электродвигателя).
Принимаем шпонку, предназначенную
для нормальной высоты. Основные размеры шпонок по ГОСТ 23360-78. [ст. сэв
75-189].
Материал шпонки - сталь 45.
Термообработка - нормализация.
Момент передается с вала на шкив
боковыми узкими гранями шпонки. При этом возникает напряжение смятия GCM , а в
предельном сечении шпонки направления среза τ.
Рисунок 6.2 - Параметры соединения
призматической шпонкой.
Для упрощения расчетов допускают,
что шпонка врезана в вал на половину своей высоты, напряжение Gсм
распределяется равномерно по высоте и длине шпонки, а равнодействующие этих
напряжений равна ~d/2. Рассматривая равновесие вала ступицы при этих допущениях,
получаем условия прочности в виде:
см = 
≤ [Gсм];
τ = 
≤ [τ];
Gсм = 
= 13,1 МПа ≤ [Gсм] = 110 МПа;
[24. стр.78]
τ = 
= 5,6 МПа ≤ [τ];
Прочность шпоночного соединения
обеспечена.
На входном валу червячного
редуктора.
см =
= 
= 3,08 МПа ≤ [Gсм];
Принимаем на входном валу червячного
редуктора шпонку предназначенную нормальной высоты 14x9x52.
6.4 Расчет шлицевого соединения
Основным критерием работоспособности
шлицевых соединений является сопротивление рабочих поверхностей смятия и
изнашиванию в результате относительных перемещений, обусловленных деформациями
и задирами. Для обеспечения необходимой работоспособности выполняют проверочный
расчет на смятие и изнашивание по условным напряжениям G:
на
смятие:
Gсм = 
≤ [Gсм],
на изнашивание:≤ [Gизн]*Кр,
где Т - крутящий момент,
передаваемый соединениям, Н*м;- высота поверхности контакта зубьев, мм;, dm -
длина и средний диаметр зубчатого соединения, мм;
[Gизн] - условные допускаемые
напряжения при расчете соединения на изнашивание, МПа. [25. стр. 188];
Кр - коэффициент, учитывающий число
циклов нагружения зубьев.
= 
= (
= 4,54;
где N - суммарное число оборотов
соединения.
= 
= 0,26 МПа ≤ [Gсм] = 20 МПа;
[26. стр.187].= 32 *4?5 =144 МПа; [26. стр.188].
Принимаем шлицевое соединение при
работе с планшайбой.x 42 x 48
x 8
;
7. Охрана труда на СХПК «Дубрава»
Комсомольского района Чувашской Республики
Научно-технический прогресс
неизбежно рождает новые проблемы, связанные с охранной труда, решение которых
возможно лишь на основе глубоких знаний, базирующихся на результатах научных
исследований. Охрана труда как система законодательных, социально-гигиенических
и организационных мероприятий, направлено на обеспечение безопасности,
сохранение здоровья и работоспособности человека в процессе труда.
Эти положения заключены в
конституции Российской Федерации. Обеспечение здоровых и безопасных условий
закон возлагает на администрацию предприятий, учреждений, организаций. Добиться
этого администрация должна путем применения современных средств безопасности и
обеспечение санитарно гигиенических условий предотвращающих профессиональные
заболевания. Правила по охране труда единые, для всех отраслей народного и
межотраслевого хозяйства, которые утверждаются правительством Российской
Федерации, либо по его поручению другими государственными органами. Конкретные
требования безопасности к каждому производству, машине, станку или рабочему
месту излагаются в специальных правилах.
.1 Анализ состояние охраны труда в
хозяйстве
На СХПК «Дубрава» Комсомольского
района Чувашской Республики нарушение законов не наблюдается. Соблюдаются все
правила, юридические нормы приема на работу, а также увольнения с работы.
Рабочее время и время отдыха соблюдаются. В хозяйстве установлена шестидневная
рабочая неделя с одним выходным днем.
В более напряженные периоды
сельскохозяйственные работы ведутся и в выходные дни, при этом работа ведется
обычно в 1,5 или 2 смены.
Большое внимание уделяется труду
женщин и подростков со стороны должностных лиц.
В условиях не очень твердого
финансового положения, все же, средства, направляемые на улучшение охраны труда
в хозяйстве используются постоянно и по назначению. Действует кабинет по охране
труда и техники безопасности, по ряду материалов и наглядной агитации. Наряду с
успехами по обеспечению техники безопасности существуют отдельные недостатки:
не уделяется должного внимания вопросам санитарии, плохое обеспечении
спецодеждой, средствами индивидуальной защиты, в мастерской не хватает
грузоподъемных механизмов.
Таблица 7.1 - Анализ травматизма в хозяйстве
№
п/п.
|
Наименование
показателей
|
Число
пострадавших при несчастных случаях
|
|
|
2008
|
2009
|
2010
|
|
Причины:
|
|
|
|
1
|
Неисправности
машин, механизмов
|
1
|
-
|
-
|
2
|
Неисправности
индивидуальных средств защиты
|
-
|
-
|
-
|
3
|
Нарушение
правил по охране труда
|
-
|
2
|
1
|
4
|
Падение
человека
|
-
|
-
|
-
|
5
|
Прочие
|
3
|
4
|
5
|
|
Итого:
|
4
|
6
|
6
|
|
Основные
источники
|
|
|
|
1
|
Машины,
механизмы, оборудование в т.ч.: трактора
|
-
|
1
|
-
|
|
комбайны
|
2
|
1
|
2
|
|
автомашины
|
1
|
-
|
1
|
|
станки
|
-
|
-
|
-
|
2
|
Электрооборудование
|
1
|
-
|
1
|
3
|
Ядохимикаты
|
-
|
-
|
-
|
4
|
Животные
|
-
|
1
|
-
|
5
|
Прочие
|
-
|
3
|
2
|
|
Итого
|
4
|
6
|
6
|
|
По
отраслям производства
|
|
|
|
1
|
Растениеводство
|
1
|
2
|
2
|
2
|
Животноводство
|
-
|
1
|
2
|
3
|
Ремонтные
работы
|
2
|
-
|
-
|
4
|
Строительство
|
-
|
1
|
1
|
5
|
Транспортные
работы
|
1
|
2
|
1
|
6
|
-
|
-
|
-
|
|
По
основаниям профессиям
|
|
|
|
1
|
Доярки
|
-
|
1
|
2
|
2
|
Скотники,
конюхи
|
-
|
-
|
-
|
3
|
Транспортные
работники
|
1
|
2
|
1
|
4
|
Станочники,
слесари
|
2
|
-
|
-
|
5
|
Шофера
|
-
|
-
|
-
|
6
|
Разнорабочие
|
1
|
3
|
3
|
|
Итого
|
4
|
6
|
6
|
|
Общие
показатели
|
|
|
|
1
|
Среднесписочная
численность рабочих
|
101
|
85
|
71
|
2
|
Количество
несчастных случаев
|
4
|
6
|
6
|
3
|
Среднее
продолжительность нетрудоспособности одного пострадавшего, дней
|
15
|
21
|
23
|
4
|
Количество
дней нетрудоспособности, дней
|
60
|
126
|
138
|
5
|
Показатель
частоты травматизма
|
84
|
15
|
17,4
|
6
|
Показатель
тяжести травматизма
|
15
|
21
|
23
|
7
|
Показатель
потерь рабочего времени
|
125,5
|
314,2
|
400
|
8
|
Материальные
последствия негативных случаев
|
-
|
-
|
-
|
Примечание: несчастных случаев со смертельными
исходами нет. Показатели частоты травматизма.
Кч = 
*1000, [26. стр.51].
где n1 - число пострадавших с
утратой трудоспособности и со смертельным исходом, чел.р - среднесписочное
число рабочих и служащих, чел.
Имеет тенденцию к росту. Также
растет и показатели тяжести травматизма, определяемый по формуле:
Кт = 
, [26. стр.51].
где Дн - число человеко-дней
нетрудоспособности у всех пострадавших за учетный период.
n2 - число пострадавших с утратой
трудоспособности без учета погибших.
Показатель потерь рабочего времени Кп по 1000
работающих.
Кn = 
, [26. стр.51].
Анализируя показатели таблицы 7.1
можно сделать вывод, что основными причинами производственного травматизма в
хозяйстве является несоблюдения элементарных правил по охране труда. По
основным профессиям наибольшее число пострадавших от несчастных случаев падает
на разнорабочих, затем на транспортных работников.
Прогнозирование травматизма начинаем
с выбора исходного года. Исходный год Г4 = 2007 и Г, = 2008, Г2 = 2009, Г3 =
2010. Имеем τi = Гi - Г4
[26. стр. 52], а математическое ожидание величина τi:
mτ = 
= 
* (1+2+3) = 2
где n - общее число лет, включенных
в анализ.
Математическое ожидание mк
показатель частоты травматизма Кu
mτ = 
= 
* (8,4+15+17,4) = 13,6
где Kui - показатель травматизма за
i анализируемый год.
Коэффициент
= 
=
= 
*
[(1-2)+(8,4-13,6)+(2-2)*(15-13,6)+(3-2)*(17,4-13,6)] = 3
Среднее квадратичное отклонение
(дисперсия) Дτ анализируемого
времени
Дτ = 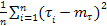
= 
* [(1-2)2+(2-2)2+(3-2)2 ]= 
;
Дисперсия Дк показатель частоты
травматизма
= 
2 = 
*
[(8,4-13,6)2+(15-13,6)2+(17,4-13,6)2] = 14,48;
Тогда линейная зависимость изменение травматизма
по годам
Ku = a * τi
+ b + ΔKu
= 4,5 * τi
+ 4,6 + ΔKu
,
где a и b коэффициенты, определяемые по
формулам:
a = 
= 
= 4,5;= mк
- a * mτ
= 13,6 - 4,5 *2 = 4,6;
ΔKu = (Ku - mк);
Случаи производственного травматизма
- причина неудовлетворительной организации обучение рабочих, ИТР и других
специалистов безопасным приемом работы. Производство не полностью обеспечены
правилами, инструкциями, плакатами по ТБ, охране труда и производственной
санитарии. Следует помнить, что все правила и инструкции по ТБ, а также
выделенные на улучшение условий труда материальные и денежные средства не могут
быть эффективными, если не действует служба по ТБ и производственной санитарии.
В хозяйстве имеются средства тушение
пожаров: одна пожарная машина, один водоем для забора воды, огнетушители и
другие противопожарные приспособление, в административных и производственных
зданиях имеются планы эвакуации.
7.2 Мероприятие по улучшению охраны труда в
хозяйстве
Для устранения указанных выше недостатков
составляется план мероприятий, способствующих устранению причин, приводящих к
производственному травматизму.
Таблица 7.2 - Мероприятия по охране труда.
№
|
Наименование
мероприятий
|
Ответственность
за исполнение
|
Срок
исполнения
|
Отметка
о выполнении
|
и/и
|
|
|
|
|
|
|
|
|
|
1
|
Оформить
кабинет по технике безопасности и охране труда
|
инженер
по ТБ
|
III
кв.
|
-
|
2
|
Проводить
обучение по правилам
|
инженер
по
|
Посто
|
|
|
ТБ
и ОТ.
|
ТБ
|
янно
|
|
3
|
Обеспечить
все участки производства правилами, инструкциями по ТБ и ОТ, наглядной
агитацией
|
Начальник
производственн ого подразделения
|
II
кв.
|
-
|
4
|
Установить
дополнительные грузоподъемные механизмы
|
Главный
инженер
|
II
кв.
|
-
|
5
|
Установить
дополнительную вентиляцию на МТР
|
Главный
инженер
|
I
кв.
|
+
|
6
|
4-5
числа каждого месяца проводить «День охраны труда»
|
инженер
по ТБ
|
Ежем
есячн о
|
+
|
7
|
Доукомплектовать
противопожарные щиты на всех участках.
|
Начальник
производственн ого подразделения
|
III
кв.
|
-
|
Эти мероприятия должны определенным образом
снизить производственный травматизм, так как они все в основном направлены на
предупреждение производственных травм.
.3 Меры безопасности при эксплуатации
проектируемой машины
Опасные и вредные факторы, являющиеся причинами
возникновение различных травм, а также отказов конструктивных узлов машины,
могут быть объективные субъективные. Опасные ситуации могут возникать при
монтаже, а также при работе машины. Субъективные факторы могут выступить в лице
неопытного оператора, безответственного отношение к требованиям мер
безопасности со стороны рабочего персонала. Перечень мер безопасности,
приводимых ниже, призваны предупреждать возникновение травм ликвидировать их,
возникающие последствие воздействия опасных и вредных факторов:
К обслуживанию стенда допускаются лица,
изучившие правила эксплуатации и ухода, а также прошедшие специальный
инструктаж.
Работа на стенде в неосвещенных помещениях не
допускается.
Перед началом работы необходимо осмотреть и
проверить надежность соединения узлов устройства, а также заземление.
Категорически запрещаются:
Проводить технический уход, очистку, смазку,
регулировку и любой ремонт во время работы стенда (очистку производить только
щеткой).
Работа на устройстве при ослабленном креплении узлов
и агрегатов.
Работа на устройстве при неисправном заземлении.
Во время работы просовывать руки в движущее
части стенда.
8.Технико-экономическая оценка проекта
.1 Абсолютные технико-экономические показатели
предприятия
К основным абсолютным технико-экономическим
показателям ремонтной мастерской следует отнести: стоимость основных
производственных фондов, удельный вес активной части фондов, размер оборотных
средств, производственную площадь, количество основного оборудования, программу
предприятию в условных ремонтах и в денежном выражении, численность
производственного персонала, себестоимость ремонта изделия, объем валовой
(товарной) продукции, прибыль и годовую экономию предприятия.
Стоимость основных производственных фондов
предприятия рассчитывается по формуле:
Соп= С01 + С02; (8.1)
где Соп - стоимость ОПФ проектируемого
предприятия, руб.
С01 - стоимость ОПФ исходного предприятия, руб.
С02 - стоимость ОПФ вновь водимого, руб.
Со1 = Сзд2 + Соб2 + Сnu2; (8..2)
где Сзд2 и Соб2 - стоимость произведенного
здания и установленного оборудования соответственно, руб.
Сnu2 - стоимость приборов, приспособлений
инструмента.
Стоимость производственного оборудования.
Сзд2 = С’зд * Fn (8.3)
где С’зд - средняя стоимость
строительно-монтажных работ, отнесенная к 1 м2 производственной площади
ремонтной мастерской, руб./м- дополнительная вводимая производственная площадь,
м2 .
Сзд2 = 10500 *135 = 1417500 руб.
Стоимость установленного оборудования, приборов,
приспособлений, инструмента, инвентаря.
Соб2 = С’об * Fn ; (8.4)
Сnu2 = C’nu * Fn ; (8.5)
где Соб и С'nu - удельные стоимости оборудования
и приборов, инструмента, приспособлений на 1 м2 .
Соб2 = 2250 * 135 = 303750 руб.= 750 * 135 =
101250 руб.
Со2 = 1417500 + 303750 + 101250 = 1822500 руб.
Соп = 5467500 + 1822500 = 7290000 руб.
Стоимость ОПФ составляет Соп = 7290000 руб.
Численность промышленного - производственного
персонала: рабочих - 4; работающих - 8.
Производственная площадь Fn = 540 м2.
Дополнительные капитальные вложения определяем
по формуле:
ΔК = Соп-Соu; (8.6)
где Соп, Соu - стоимость ОПФ проектируемого и
исходного предприятия, руб.
8.2 Расчет плановой калькуляции себестоимости
ремонта изделия
Себестоимость ремонтной продукции - это
выражение в денежной форме текущих затрат ремонтного предприятия на ее
производство и сбыт. Себестоимость ремонта изделия рассчитываем по формуле:
Сц = Спр.н + Сз.п + Ср.м + Соп , (8.7)
где Спр н - полная заработная плата
производственных рабочих;
Сз.п - нормативные затраты на запасные части;
Ср.м - нормативные затраты на ремонтные
материалы;
Соп - стоимость общепроизводственных расходов.
Полная заработная плата производственных
рабочих:
Спр.н = Спр + Сдоп + Ссоц , (8.8)
где Спр - основная заработная плата
производственных рабочих;
Сдоп - дополнительная заработная плата рабочих;
Ссоц - отчисление на социальное страхование.
Спр = 0,01 * tизд * Сч * Kt (8.9)
где tизд - нормативная трудоемкость ремонта
изделия;
Сч - часовая ставка рабочих, начисляемая по
среднему разряду за 1 час. - коэффициент, учитывающий доплату за сверхурочные
работы; (Kt =1,025 ...1,030). [2. стр. 181].
Спр = 11650,9 * 27,98 * 1,025 = 74638,5 руб;
Сдоп = 
, (8.10)
где Rдоп = 7…10% - начисления на
дополнительную зароботную плату рабочих.
Сдоп = 
= 7463,8 руб;
Отчисление на социальное
страхование.
Ссоц = 
= 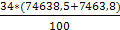
= 25944,3 руб; (8.11)
Спр.н = 74638,5 + 7463,8 + 25944,3 =
108046,64 руб;
Затраты на запасные части берется 75
% от основной оплаты производственных рабочих.
Сзч = 0,75 * 10804,64 = 81034,9 руб;
Затраты на ремонтные материалы
берутся в размере 6 % от стоимости запасных частей.
Срм = 0,06 * 8034,9 = 4862,09 руб;
Стоимость общепроизводственных
накладных расходов вычисляется по формуле:
Соп = 
, (8.12)
где Ron - процент
общепроизводственных накладных расходов;
оп = 
, (8,13)
статей годовых общепроизводственных расходов.
Ноп - годовые затраты по отдельным статьям
общепроизводственных расходов, руб.
С гпр - основная годовая заработная плата
производственных рабочих, руб.
С гпр = Тоб * С2 * Kt = 15615,8 * 62,5 * 1,025 =
1000387,1 руб; (8.14)
где Тоб - общая трудоемкость на выполнение всего
годового объема работ.
Сумму годовых затрат по отдельным статьям
общепроизводственных расходов рассчитывают с помощью формул [2 табл. 91] и
заполним в таблицу 8.1.
Таблица 8.1 - Плановая смета годовых
общепроизводственных расходов.
№
п/п
|
Наименование
статьи расходов
|
ИИсходные
значения, нормативов
|
Расчетная
формула
|
Годовые
затраты нор,руб
|
1
|
Основная
заработная плата общепроизводственного персонала (ИТР, вспомогательных
рабочих, служащих и МОП).
|
Ситр,
Свс, Ссл, Смоп
|
12(Ситр
+ Свс + Ссл + Смоп)
|
60000
|
2
|
Дополнительная
заработная плата персонала
|
15%
Ситр 11%(Свс+Ссл) 9%Смоп
|
12[0,15Сытр+
+0,11(Свс+Ссл)+ +0,09 Смоп].
|
9000
|
3
|
Отчисления
с заработной платы на социальное страхование.
|
4,4
% основной и допол. зарпл. персонала
|
4,4(
+ )/100
|
3036
|
4
|
Амортизация
здания Амортизация оборудования Амортизация приборов, инструментов.
|
Азд
в % от Сзд Аоб в % ОТ Соб Апи в % ОТ Спи
|
(2,5...3,0)Сзд/100
(10...13) Соб/100 (13...14) Спи/100
|
136687
121500 52650
|
5
|
Текущий
ремонт: здания оборудования
|
1,5%
от Сзд 3,5...4%от Соб
|
1,5
Сзд/100 (3,5...4)Соб/100
|
82012
42525
|
6
|
Содержания
оборудования малоценного инвентаря.
|
0,4...0,5%
от Соб 300 руб ис. 1 произ. работ.
|
(0,4...0,5)
Соб/100 300 Рпр
|
4860
2400
|
7
|
Электроэнергия
осветительная.
|
Wг.oc,
Сос=700 руб. на 1000 кВт-ч, ηс = 0,8
|
560
Wг.oc/1000
|
11509
|
8
|
Пар,
потребляемый для производственных целей, отопления и вентиляции.
|
Qo.b+Qn;
Сп=1 руб. за 1 кг.
|
1000(
Qo.b+Qn)
|
153,7
|
9
|
Вода
для производственных целей и бытовых нужд.
|
QrB;
Св=10руб. на 1 м3
|
10000
Qг.в /1000
|
3120
|
10
|
Сжатый
воздух.
|
Qвоз;
Своз=0,3 руб. за 1 м3
|
300
(Qвоз)/1000
|
4506
|
11
|
Вспомогательные
материалы.
|
1,5...2%
от (Ср.м+Сзч)
|
(0,015...0,020)*
(Ср.м+Сзч)
|
1288,4
|
12
|
Охрана
труда.
|
50...70руб.
на 1 работающего.
|
(50...70)Рср
|
660
|
13
|
Изобретательная
и рационализаторская работа.
|
50...
100 руб. на 1 работающего.
|
(50...100)Рср
|
660
|
14
|
Командировки,
литература.
|
300
руб на 1 ИТР
|
300
Ритр
|
300
|
15
|
Прочие
расходы. Общая сумма общепроизводственных расходов.
|
3%от
n= 15
|
0,03*
|
16106
552973
|
Rоп =
= 55,2 %
Таким образом:
Соп =
= 41257 %
Полная себестоимость ремонта
(цеховая).
Сц = 108046,6 + 81034,9 + 4862,09 +
41257 = 235199,9 руб;
.3 Расчет оборотных средств
Совокупность оборотных фондов и
фондов обращения в стоимостной форме, образует оборотные средства ремонтной
мастерской.
Оборотные средства мастерской по
принципам организации делят на нормируемые (Соб.н) и ненормируемые (Соб.нен),
т.е:
Соб = Соб.н + Соб.нен (8.15)
где Собн - строго регламентированные
вышестоящими органами оборотные средства и размещенные в сфере производства.
Соб.нен - все оборотные средства,
находящиеся в среде обращения.
Обычно Соб.нен = 0,2 * Соб.н; (8.16)
Тогда Соб.н = 1,25 * Соб.н; (8.17)
Нормируемые оборотные средства
определяются по формуле:
Соб.н = (Nпр/dк) * 
* ДЗi + Сн.п ,
где Nnp - годовая программа ремонта
машин в приведенных единицах; - число календарных суток в году;
i - нормативные удельные затраты,
руб.;
Д3; - нормативные календарные сутки
запаса по статьям затрат, сутки;
Сн.п - стоимость незавершенного
производства, руб.
Значения 3t и Д3; по каждой статье
затрат определяют по [2. стр. 93]. Результаты расчетов сводим в таблицу 8.2.
Таблица 8.2 - Расчет нормативных
годовых затрат.
Элемент
оборотных средств.
|
Рекомендуемые
удельные затраты на ремонтируемое изделие. з„ руб.
|
Нормативные
календарные сутки запаса.
|
3i
* ДЗi
|
Агрегаты
и сборочные единицы обменного фонда.
|
1,2%
годового выпуска продукции по полной себестоимости ремонта изделий.
|
-
|
28223,3
|
Запасные
части
|
С’з.ч
- стоимость запасных частей на единицу ремонта.
|
90
|
7293141
|
Сырье,
основные материалы покупные полуфабрикаты, ремонтные материалы.
|
С'р.м
- стоимость ремонтных материалов на единицу ремонта.
|
60
|
291725,4
|
Прочие
материалы.
|
60
|
29172,5
|
Малоценные
и быстроизнашивающие ся предметы.
|
400...
500 руб. на одного производственного рабочего.
|
-
|
3200
|
Годовая
продукция.
|
Отпускная
цена ремонта изделия.
|
2...3
|
587999,7
|
Итого:
|
|
|
8208060,5
|
Nпр = 
= 
= 52 усл.рем; (8.18)
Таким образом, нормируемые оборотные
средства будут равны:
Соб.н = (
) * 8208060,5 = 1169367,5 руб;
Тогда Sоб = 1,25 * 116967,5 =
1461709,4 руб;
Соб.нен = 0,2 * 116967,5 = 233873,5
руб;
Валовая продукция на планируемый год
устанавливается по выражению:
Вп = Nnp * Сц = 52 * 235199,9 =
12230394,8 руб; (8.19)
где Nnp - годовая производственная
программа проектируемой ремонтной мастерской в предельных единицах;
Сц - цеховая себестоимость ремонта
изделия.
Годовая экономия (прибыль) от
снижения себестоимости ремонта изделия.
Эг - (зуд.т * Wг.н - Сц) * Nnp,
(8.20)
где зуд.т - удельные затраты на
текущий ремонт соответствующей марки машины;г.н - норматив годовой наработки.
Эг = (250818 - 235199,9) * 52 =
812141,2 руб;
8.4 Ожидаемые удельные (относительные) техника-экономические
показатели мастерской
Показатели, характеризующие эффективность
использования оборотных средств (коэффициент оборачиваемости Коб и период
оборачиваемости
оборотных средств Дп) определяют по формулам:
Коб = 
= 
= 8,3; (8.21)
Период оборачиваемости оборотных
средств.
Дп = 
= 
= 43,9 ; (8.22)
где dK - число календарных дней в
году.
Срок окупаемости капитальных
вложений определяется по формуле:
Ог = 
= 
= 3,4 ; (8.23)
Основные технико-экономические
показатели проектируемой и исходной ремонтной мастерской сводим в таблицу 8.3.
Таблица 8.3 - Основные
технико-экономические показатели проектируемой и исходной ремонтной мастерской.
№
п/п
|
Наименование
показателей.
|
Значение
показателей.
|
|
|
проектируемого
|
исходного
|
1
|
Стоимость
ОПФ, руб.
|
7290000
|
5467500
|
2
|
Стоимость
оборотных средств, руб.
|
1461709,4
|
1096281,7
|
3
|
Годовая
программа в приведенных ремонтах, шт.
|
52
|
29
|
4
|
Общая
трудоемкость, чел.
|
15615,8
|
8734
|
5
|
Полная
себестоимость ремонта изделия, руб.
|
235199,9
|
282239,8
|
6
|
Численность
промышленно-производственного персонала, чел.
|
4
|
8
|
7
|
Валовая
ремонтная продукция, руб.
|
12230394,
8
|
5823997,1
|
8
|
Производственная
площадь, м .
|
540
|
405
|
9
|
Балансовая
прибыль, руб.
|
536652
|
147654
|
10
|
Фондоотдача,
руб. на 1 руб.
|
1,6
|
1,06
|
11
|
Фондовооруженность,
руб./чел.
|
662727,2
|
341718,7
|
12
|
Напряженность
использования производственных площадей, руб./м .
|
13500
|
7340
|
13
|
Напряженность
использование производственного оборудования, руб./ед.об.
|
1822500
|
1366875
|
14
|
Рентабельность
ремонта, %
|
34,5
|
25,3
|
15
|
Затраты
на 1 руб. товарной продукции, руб.
|
0,85
|
0,95
|
16
|
Коэффициент
оборачиваемости.
|
8,3
|
5,31
|
17
|
Период
оборачиваемости, дней
|
43,9
|
68,7
|
18
|
Производительность
труда на одного работающего, руб./чел.
|
1111854
|
363999
|
19
|
Производительность
труда 1 работающего без затраты на запасные части, руб./чел.
|
1104487,2
|
354637,1
|
Структура затрат на ремонт:
Полная заработная плата - 108046,6 руб. - 46%.
Затраты на запасные части - 81034,9 руб. - 35 %.
Затраты на ремонтные материалы - 4862,09 руб. -
3 %. Общепроизводственные расходы - 41257 руб. - 17,6 %.
.5 Технико-экономические показатели
конструкторской разработки
Затраты на изготовление конструкция. Работы по
изготовлению конструкции выполняются на том же предприятии, для которого она
предназначена.
Затраты на изготовление конструкции можно
подсчитать по формуле:
Сц.кон = Ск.д + Со.д + Сп.д + Соб.н + Соп ,
(8.24)
где Ск.д - стоимость изготовления корпусных
деталей, руб.
Со.д - затраты на изготовление оригинальных
деталей, руб.
Сп.д - цена покупных деталей, изделий,
агрегатов, руб.
Соб.н - полная заработная плата (с начислениями)
производственных рабочих, занятых на сборе конструкции, руб.
Соп - общепроизводственные расходы, руб.
Стоимость изготовления корпусных деталей
определяют:
Ск.д = Q * Сг.д, (8.25)
где Q - масса материала (по чертежам)
израсходованного на изготовление корпусных деталей, руб;
Сг д - средняя стоимость 1 кг готовых деталей,
руб.
Рама - С’к.д = [(8 * 1,46 + 4 * 0,78) * 3] * 50
= 2200 руб;
Стол - С”к.д = (0,89 * 50) * 50 = 2226 руб;
Ск.д = С’к.д + С”к.д = 2226 + 2200 = 4426 руб;
Затраты на изготовление оригинальных деталей.
Со.д = Спр.м + См , (8.26)
где Спр.м - заработная плата производственных
рабочих, занятых на изготовление оригинальных деталей, руб;
См - стоимость материала заготовок, руб.
Полная заработная плата.
Спр.н = Спр + Сд + Ссоц, (8.27)
где Спр и Сд - основная и дополнительная
заработные платы производственных рабочих, руб;
Ссоц - начисления на социальное страхование,
руб.
Основная заработная плата производственных
рабочих.
Спр = tср * Сr * Кд ,(8.28)
где tср - средняя трудоемкость изготовления
отдельных оригинальных деталей, чел.-час.- годовая ставка рабочих, начисляется
по среднему разряду, руб.
Кд - коэффициент, учитывающий доплаты к основной
зарплате, равный 1,025…1,030; [2. стр. 181].
Сп р = (2,0 + 2,0 + 4 + 2,0 + 10 + 40 + 5 + 2) *
6,25 * 1,025 = 429,2 руб;
Дополнительная заработная плата.
Сд =
= 
= 34,3 руб; (8.29)
Начисления на социальное
страхование.
Ссоц =
= 
= 20,3 руб; (8.30)
Общая заработная плата составит.
Спр н = 429,2 + 34,3 + 20,3 = 483,8
руб;
Стоимость материала заготовок для
изготовления оригинальных деталей.
Смз = Сз * Qз , (8.31)
где С3 - цена килограмма материала
заготовки, руб;
Q3 - масса заготовки, кг.
Смз = (10,3 * 0,6) + (11,3 * 0,5) + (10,3 *
0,09) + (1 * 0,3) + (10,3 * 50) + (300) =
= 6,18 + 5,65 + 1 + 0,3 + 515 + 300 = 828,13
руб;
Со.д= 483,8 + 828,13 = 1311,9 руб;
Цена корпусных деталей, изделий, агрегатов. Сп.д
берется по прейскуранту. Редуктор - 10300 руб.
Электродвигатель - 3500 руб.
Ремень - 200 руб.
Болты, гайки, шайбы - 50 руб.
Сп.д = 10300 + 3500 + 200 + 50 = 14050 руб;
Полная заработная плата производственных
рабочих, занятых на сборке конструкции.
Сс.бк = Ссб + Сд.сб + Ссоц , (8.32)
где Ссб и Сд.сб - основная и дополнительная
заработная плата производственных рабочих, руб.
Ссоц - начисления на социальное страхование,
руб.
Основную заработную плату производственных
рабочих занятых на сборке конструкции, рассчитываем по формуле:
Ссб = Тсб + Сг + Кд , (8.33)
где Тсб - нормативная трудоемкость сборки
конструкции, чел.-час.
Тсб = Кс * ∑tc6, (8.34)
где Кс - коэффициент учитывающий соотношение
между полным и оперативным временем сборки и равный - 1,08.
∑tсб - суммарная трудоемкость сборки
составных частей конструкции, чел.-час.
Тсб = 1,08 * (5 * 0,5 + 1 * 16 + 0,45 * 33 + 0,7
* 1 + 3,6 * 2 + 4,78 * 1 + 26,7 * 2 + 0,6 * 9) + (1,0 * 30) = 2,25 чел.- час;
Ссб = 2,25 * 62,5 * 1,03 = 145,4 руб.;
Дополнительная заработная плата.
Сд.сб = 
= 11,6 руб;
Начисления на социальное
страхование.
Ссоц =
= 
= 6,9 руб;
Общая заработная плата рабочих занятых на сборе
конструкции:
Ссб.к = 145,4 + 11,6 + 6,9 = 163,9 руб.
Общепроизводственные (цеховые) накладные расходы
на изготовление конструкции.
Соп = 
, (8.35)
где С’пр - основная заработная плата
производственных рабочих, участвующих в изготовлении конструкции.п - процессы
общепроизводственных расходов.
С’пр = Спр + Ссб = 483,8 + 163,9 =
647,7 руб; (8.36)
Соп = 
= 312,1 руб;
Сцк = 483,8 + 163,9 + 4426 + 1311,9
+ 10300 + 3500 + 200 + 50 =
=20435,6 руб.;
Общая стоимость изготовления
конструкции.
Сцк = 20435,6 руб.;
8.6 Технико-экономические показатели конструкции
Эксплуатационные затраты.
Э3 = От + Ам + Рф + Эн + Спроч, (8.37)
где От - оплата труда, руб.
Ам - амортизационные отчисления, руб.
Рф - затраты на ремфонд, руб.
Эн - энергетические затраты, руб.
Спроч - прочие затраты, руб.
Оплата труда.
От = Тр * Сг = 310 * 50 = 15500 руб.; (8.38)
Амортизационные отчисления.
Ам = 
= 
= 2288,7 руб.;
Ремфонд.
Рф = 
= 
= 1736,9
Затраты на электроэнергию.
Эн = Nэд * Тр.ч * 0,7 = 1,5 * 1995 *
0,7 = 2094,7 руб.;
Прочие затраты, берутся 2.. .3 % от
оплаты труда:
Спроч = 0,025 * 15500 = 387,5 руб.;
Э3 = 15500 + 2288,7 + 1736,9 + 2094,7 + 387,5 =
22007,8 руб.;
Годовая экономия эксплуатационных затрат.
Эг = Эз.о - Эз.р , (8.39)
где Эз.о - эксплуатационные затраты существующей
конструкции;
Эз.р - эксплуатационные затраты разрабатываемой
конструкции.
Эг = 28609,1 - 22007,8 = 6601,3 руб.;
Срок окупаемости конструкции.
Ток =
= 
= 3,09 год; (8.40)
Коэффициент эффективности.
Кэ =
= 
= 0,32; (8.41)
Годовой экономический эффект от
внедрения конструкции.
Эф = Эг - Е * (CK1 - СК0), (8.42)
где СК1 и СК0 - стоимость новой и
старой конструкции, руб.
Е - нормативный коэффициент
эффективности.
Эф = 6601,3 - 0,2 * (26566,2 -
20435,6) = 5375,2 руб.;
Заключение
Предполагаемый проект организации
совершенствования ремонта машин в СХПК «Дубрава» Комсомольского района ЧР дает
целый ряд высоких технико-экономических показателей по сравнению с исходными.
Увеличение программы предприятия и снижения себестоимости ремонтной продукции
существенно увеличивается прибыль предприятия, существенно повышается процент
рентабельности продукции. Улучшение этих факторов непосредственно скажется на
материальном положении рабочих.
Предполагаемый проект позволит
улучшить мощность ремонтной мастерской в связи введением новых производственных
площадей.
Проект предусматривает:
Участок диагностики двигателей;
Отделение диагностики;
Помещения для оборудования;
Отделение ТО.
Внедрение этого проекта позволит
улучшить организацию технического обслуживания и ремонта. Позволит обеспечить
проведение технического обслуживания и ремонта на том уровне, который
гарантирует увеличение надежности техники, срока службы техники,
эксплуатационных показателей техники, безопасность, производительность,
экономичность, рентабельность.
Наличие выше перечисленных
положительных факторов перед исходными показателями ремонтной мастерской делает
целесообразным внедрение предлагаемого проекта.
Список использованной литературы
ремонт мастерская
техника экономический
Курсовое
и дипломное проектирование по ремонту машин / И.С. Серый А.П. Смелов, В.Е.
Черкун. - 4-е изд., перераб. и доп.- М: Агропромиздат, 1991.- 184 с, ил.
Булей
И.А., Иванщенко Н.И., Меньшиков В.Д. Проектирование ремонтных предприятий с.-х.
- Киев: Высшая школа, 1981.
Курсовое
проектирование деталей машин. / В.Н. Кудрявцев, Ю.А.
Державин,
И.И Арефьев; Под. общ. ред. В.Н. Кудрявцева. Учебное
пособие
для студентов вузов. - Л.: Машиностроение, 1984 - 400 с, ил.
Допуски
и посадки: Справочник В 2-х г / В.Д. Мягков, М.А. Палей. - 6-е
изд.,
перераб. и доп. - Л.: Машиностроение, 1982. - 543 с, ил.
Куклин
Н.Г., Куклина Г.Е. Детали машин: Учебник для машиностроительных специальностей
техникумов: - 4-е изд., перераб. и доп., - М.: Высшая шк., 1987. - 383 с, ил.
Детали
машин. Учебник для машиностроительных техникумов/ Ю.Н.Березовский, Д.В.
Чернилевский, М.С. Петров; Под. ред. Н.А. Бородина. - М.: Машиностроение, 1983.
- 384 с, ил.
Курсовое
проектирование деталей машин. Учебное пособие для машиностроительных
специальностей техникумов / С.А.Чернавский, К.Н. Боков, И.Н. Чернин и др. - 2-е
ид., перераб. и доп. - М.: Машиностроение, 1988.-416 с, ил.
Кулаков
М.М. Методические указания и справочно-информационные материалы для студентов
факультета механизации с.-х., - Чебоксары, -1989.
П.Н.
Калинев, В.Н. Богословский и др. Отопления и вентиляция. Учебник для вузов. В
2-х том. - М.: Стройиздат., 1975. - 483 с.
Левицкий
B.C. Машиностроительное черчение. Учебник для студентов высших технических
учебных заведений. - М.: Выс. шк., 1988 - 351 с, ил.
Бабусенко
СМ. Проектирование ремонтных предприятий. - М.: Колос, 1981.-235 с, ил
Черепанов
С.С. Организация специализированного ремонтного
производства.
М.: Колос, 1970. - 223 с, ил.
Борисов
В.И. Общая методология конструирования машин. - М.:
Машиностроение,
1978. - 120 с, ил.
Дунаев
П.Ф., Леминов О.П. Расчет допусков размеров. 3-е изд., перераб. и доп. - М.:
Машиностроение, 2001. - 304 с, ил.
Анурьев
В.И. Справочник конструктора-машиностроителя: в 3-х т. т.1. -5-е изд., перераб.
и доп. - М.: Машиностроение, 1980. - 728 с, ил.
Анурьев
В.И. Справочник конструктора-машиностроителя: в 3-х т. т.2. -5-е изд., перераб.
и доп. - М.: Машиностроение, 1980. -743 с, ил.
Анурьев
В.И. Справочник конструктора-машиностроителя: в 3-х т. т.1. -5-е изд., перераб.
и доп. - М.: Машиностроение, 1980. -557 с, ил.
Методическое
указание по экономическому обоснованию дипломных проектов (для студентов
факультета механизации с.-х.), Чебоксары, - 1980.
Дунаев
П.Ф., Леликов О.П. Детали машин. Курсовое проектирование.: Учеб. пособие для
машиностроительных специальностей техникумов. -М.: Высш. шк., 1984. - 336 с,
ил.
Ульман
И.Е., Г.А. Тонн, И.М. Терштейн и др. Ремонт машин. Изд. 2-е., перераб. и доп.
-М.: Колос, 1976. - 448 с, ил.
Надежность
и ремонт машин. / В.В. Курчаткин, Н.Ф. Тельков, К.А. Агнасов и др. - Под ред.
В.В. Курчаткина. - М.: Колос, 2000. - 776 с, ил.
Иванщиков
Ю.В., Лебедев В.Г. Курсовое проектирование по монтажу, эксплуатации и ремонту
технологического оборудования. Учебное пособие. Чебоксары, 2002. - 77 с, ил.
Петров
Н.А., Осипов К.А. Сборник задач и примеров по резанию металлов и режущему
инструменту: Учеб. пособие для техникумов по предмету «Основы учения о резании
металлов и режущий инструмент». 4-изд., перераб. и доп. - М.: Машиностроение,
1984. - 400 с, ил.
Иванов
М.Н. Детали машин. Учеб. для машиностроительных спец. вузов. - 4-е изд.,
перераб. - М.: Высш. шк., 1984. - 336 с, ил
Кудрявцев
В.Н. Детали машин. Учеб. для машиностроительных спец. вузов. - Л.:
Машиностроение. Ленингр. отд-ие, 1980. - 464 с, ил.
Охрана
труда / Ф.М. Канарев, В.В. Бугалевский, М.А. Пережогин и др. -М.:
Агропромиздат., 1988.
Ремонт
машин / Под. ред. Тельнова Н. Ф. - М.: Агропромиздат., 1992. -560 с, ил.
(Учебники и учеб. пособия для высш. учеб. заведений).
Иванщиков
Ю.В. Методика разработки технической документации на восстановление деталей.
Методическое указание по проектированию технологических процессов. - Чебоксары,
2002. - 93 с.