Дослідження структуроутворення в процесі реакційного спікання та гарячого деформування порошкових сумішей систем Fe-Ti-C і Fe-Ti-B4С та розробка технології одержання порошкових зносостійких матеріалів на основі системи Fe-Ti-C(B)
Реферат
Пояснювальна записка: 1 книга, 119
стор., 27 рис., 11 табл., 70 джерел.
Об’єкт дослідження - порошкові
карбідосталі що виготовлені з сумішей елементарних порошків: Fe, Ti, C (лампова
сажа) та B4C, з яких отримують шихти для виготовлення сплавів систем
Fe-Ti-C та Fe-Ti-B4C методами порошкової металургії, а саме шляхом
реакційного спікання з подальшим гарячим штампуванням отриманих зразків та їх
кінечною термічною обробкою.
Мета роботи - дослідження
структуроутворення в процесі реакційного спікання та гарячого деформування
порошкових сумішах систем FeTiC і FeTiB4С та розробка технології
одержання порошкових зносостійких матеріалів на основі системи FeTiC(B).
Методи дослідження -
мікроструктурний та рентгеноструктурний аналізи, випробування механічні характеристик
(на вигин та вязке руйнування) тощо.
Аналіз термодинамічних умов
сплавоутворення при реакційному спіканні порошкових шихт сплавів систем FeTiC і
FeTiB4С проводили за допомогою програми CHEQC (CHemical EQuilibriums
Calculations) на базі пакету програм Astra. Попередній розрахунок вихідних
даних виконувався з використанням пакету програм Microsoft Office Excel 2007 та
хімічної довідкової системи PL Table.
Апаратура: для приготування сумішей
порошків використовували лабораторний баночний змішувач; пресування шихт
проводилося на гідравлічному пресі ГП-60, реакційне спікання шихт проходило в
печі опору Г-30, розігрів заготовок під гарячу штамповку проходив печі шахтного
типу, моделі ШП-1з подальшим гарячим штампуванням у відкритому штампі, на не нахиляємому
одно кривошипному пресі простої дії, моделі КВ 2132, мікроструктурний аналіз
виконували на мікроскопі МИМ-8М, рентгеноструктурний аналіз - на дифрактометрі
марки ДРОН-3М; вимірювання мікротвердості проводили на пристрої ПМТ-3,
механічні випробування отриманих матеріалів: на вигин проводили на
випробувальній машині 123У-10, на вязке руйнування на машині «Plastics Bending
Tester» тощо.
Розшифровку дифрактограм проводили
за допомогою міжнародної рентгенівської бібліотеки ASTM програми електронної
бази PCPDFWIN 2.1, індикування дифрактограм та розрахунки періодів кристалічної
ґратки фаз проводили, Findepike 2.0.
В роботі показано, що отримані з
використанням технології реакційного спікання та гарячого штампування поростих
загготовок зносостійкі матеріали (карбідосталі), по механічним властивостям
перевищують карбідосталі отримані традиційними технологіями та мало
поступаються твердим сплавам, а іноді й перевищують їх.
Ключові слова: реакційне спікання,
титан, вуглець, карбід бору, залізо, гаряча штаповка пороистих заготовок,
спікання в контейнері по схемі плавкого затвору, термодинамічний аналіз.
Abstract
message: 1 book, 119 page., 27
lines., 11 tables., 70 sources.objekt - powder carbidosteel that made from
mixtures of elementarnikh powders: Fe-Ti-C (lamp soot) and B4C, from
which get charges for making of alloys of the systems of Fe-Ti-C and Fe-Ti-B4C
by the methods of powder metallurgy, namely by reactionary sintering with the
subsequent hot punching of the got standards and them by kinechnoy heat treatmentof
work - development of technology of receipt of powder carbidosteel and research
of structurereception is at combination of process of alloyreception and
sintering in packing powder mixtures of the systems of Fe-Ti-C and Fe-Ti-B4C.methods
- microstructure and rentgenostructure analyses, tests, are mechanical
descriptions (on a bend and viscid destruction) and others like that.of
thermodynamics terms of alloyreception at reactionary sintering of powder
charges of alloys of the systems of Fe-Ti-C and Fe-Ti-B4C conducted
by the program CHEQC (Chemical Equilibriums Calculations) on the base of
package of softwares of Astra. The previous calculation of weekend of
information was executed with the use of package of softwares of Microsoft
Office Excel 2007 and chemical certificate system PL Table.: for preparation of
mixtures of powders used a laboratory jar mixer; pressing of charges was
conducted on the hydraulic press of ГП-60, reactionary sintering of charges
passed in the stove of resistance of Г-30, warmed up purveyances under hot
punching passed the stoves of mine type, model of ШП-1, the subsequent hot
punching in the opened stamp, on not slopes one crank press of simple action,
model of KВ 2132, a microstructure analysis was executed on the microscope of
MИM-8М, rentgenostructures analysis - on difraktometr of brand of ДРОН-3М;
measurings of mikrosolidity conducted on the devices of ПМТ-3, mechanical tests
of the got materials: on a bend conducted on the tester machine of 123У-10, on
viscosity destruction on a machine «Plastics Bending Tester» and others like
that.of difraktogram was conducted by the international x-ray photography
library of ASTM by the programs of electronic base of PCPDFWIN 2.1,
indikuvannya difraktogram and calculations of periods of crystalline phases
conducted, Findepike 2.0.is shown in work, that got with the use of technology
of reactionary sintering and hot punching of poreses procurement wearproof
materials (carbidoseel), for carbidosteel is exceeded mechanical properties got
traditional technologies and do not concede to the hard alloys, and sometimes
and exceed them.sintering, titan, carbon, carbide boron, iron, hot punching
porses procurement, sintering in container of scheme fusible breech-block,
thermodynamics analysis.
Зміст
Вступ
.
Літературний огляд
.1
Сучасні тенденції в області створення порошкових зносостійких композиційних
матеріалів на основі заліза
.1.1
Основні принципи підвищення зносостійкості матеріалів
.1.2
Порошкові зносостійкі матеріали на основі заліза
1.2 Технологічні
проблеми процесів гарячого штампування пористих заготовок
(ГПШЗ)
1.3
Вплив параметрів гарячого ущільнення на структуру і властивості отримуваних
матеріалів
Висновки
та постановка завдання досліджень
.
Експерементальна частина
.1
Теоретичні та технологічні основи отримання композитів на основі системи карбід
титану - сталь
.1.1
Основні структурні та технологічні особливості карбідосталей
.1.2
Аналіз структурних діаграм, контактна взаємодія та змочування в системах
сплавів Fe-Ti-C-В
.2
Теоретичні принципи формування боровмісних композитів на основі
залізовуглецевих сплавів
.3
Матеріали, устаткування і методика досліджень
.
Обговорення результатів
.1
Дослідження можливостей отримання композиту Fe-Ti-C(B4C) в
результаті виділення карбідних фаз при спіканні
.1.1
Вивчення умов сплавоутворення при реакційному спіканні порошків системи Fe-Ti-C
.1.2
Структуроутворення при спіканні композиції на базі сплаву на основі заліза з
карбідом бору
.2
Особливості отримання, механічні і трибологічні властивості карбідосталей після
реакційного спікання і гарячого штампування
.3
Розрахунок термодинамічної рівноваги в сплавах систем Fe - Ti - C(B)
Висновок
Список
використаної літератури
Додатки
Вступ
Розвиток основних галузей сучасного
машинобудування пред’являє до застосовуваних в ньому конструкційних та
інструментальних матеріалів рівень вимог, що постійно зростає, зокрема до
високої статичної та динамічної міцності, опору крихкому руйнуванню,
зносостійкості та корозійностійкості в різних умовах експлуатації. Рівень
перерахованих властивостей матеріалів визначає в значній мірі надійність
деталей, вузлів, робочих органів машин, механізмів, технологічного оснащення та
обладнання.
При цьому слід мати на увазі, що
основною причиною виходу з ладу машин та механізмів є, як показує практика, не
поломка, а зношування та пошкодження робочих поверхонь деталей. Особливо
інтенсивно зношуються деталі, що працюють в умовах одночасного впливу великих
питомих навантажень, високих температур та швидкостей ковзання, в абразивних та
агресивних середовищах. Широко застосовувані матеріали, методи їх отримання та
обробки часто виявляються малопридатними або зовсім не придатними при створенні
та експлуатації нових видів техніки як із конструктивних, так і економічних
міркувань.
В той же час, основними тенденціями
в подальшому удосконаленні цих матеріалів та технології їх отримання та обробки
є необхідність економної та раціональної витрати легуючих елементів,
енергетичних та трудових ресурсів.
Проблеми створення маловідходних та
енергозберігаючих технологічних процесів стає досить актуальною також в зв’язку
з поступовим виснаженням запасів мінеральної сировини та органічного пального.
Аналіз структури виробництва та
споживання конструкційних та інструментальних матеріалів для виготовлення ріжучих
та штампових інструментів або для виготовлення деталей машин, що працюють в
умовах інтенсивного стирання показують, що домінуючу роль займають
високолеговані інструментальні сталі і тверді сталі - композиційні матеріали на
основі карбідів, карбоборидів, нітридів, карбонітридів або боридів тугоплавких
металів з металевою зв’язкою, в якості якої використовується головним чином
кобальт, нікель та молібден. Однак, зростаючий кожен рік дефіцит вольфрам-,
нікель-, та кобальтовмісної сировини, а також відсутність в Україні
розроблюваних родовищ цих стратегічних матеріалів та їх висока вартість на
зовнішньому ринку роблять актуальними задачі створення нових та удосконалення
існуючих складів безвольфрамових та економнолегованих зносостійких матеріалів.
Таким чином, короткий аналіз
проблеми дозволяє зробити висновок про перспективний напрямок пошуку, що
заснований на застосуванні при створенні нових ефективних зносостійких
матеріалів схем економного легування при забезпеченні високих фізико-механічних
та експлуатаційних властивостей матеріалів, максимально використовуючи
вітчизняні сировинні бази, а також розробку та застосування ефективних
технологій і методів виробництва матеріалів, забезпечуючи високий коефіцієнт
використання матеріалів.
Успішне рішення цих задач викликає
необхідність розробки та дослідження нових схем та технологічних процесів
виготовлення виробів високої щільності з композиційних порошкових матеріалів з
застосуванням додаткових високоенергетичних методів ущільнення, одним з
найефективніших з яких є гаряча штамповка. В той же час, розвиток і
удосконалення технології отримання порошкових виробів методом гарячого
штампування пористих заготовок неможливо без глибокого розуміння суті явища, що
відбувається при формуванні, спіканні та деформування заготовок, а також їх
кількісного опису. В зв’язку з цим розробка фундаментальних питань механіки
поведінки пористих порошкових композицій при їх обробці тиском є важливим
напрямком в області створення матеріалів з необхідним комплексом функціональних
властивостей і розробки ефективних технологій отримання виробів з застосуванням
методів пластичної деформації.
Поряд з вказаними вище проблемами,
суттєвий вплив на рівень стійкості ріжучого інструменту, а часто і
конструкційних деталей, що працюють в режимі тертя, мають конструкція та
характеристики матеріалу несучих деталей, на які кріпляться останні. Враховуючи
останній фактор, можна сказати, що це досить перспективний та досить ефективний
напрямок розвитку методів підвищення строку служби зношуючихся деталей.
1.
Літературний огляд
1.1 Сучасні тенденції в області
створення порошкових зносостійких композиційних матеріалів на основі заліза
.1.1 Основні принципи підвищення
зносостійкості матеріалів
Вироби конструкційного та
інструментального призначення, працюючі в умовах інтенсивного зношування,
широко застосовуються в сучасному машинобудуванні, добуваючій та будівельній
сферах виробництва. Можливість тривалої експлуатації деталей машин, ріжучого та
формоутворюючого інструменту та їх довговічність в значній мірі зв’язані з
зносостійкістю матеріалів, з яких вони виготовлені.
Основною вимогою, що пред’являється
до матеріалів зносостійких деталей поряд з високою їх міцністю, є підвищена
твердість в поєднанні з відносно високим рівнем пластичності та порівняно низьким
коефіцієнтом тертя (при їх використанні у високо навантажених вузлах тертя).
Аналіз процесів тертя та зношування
дозволили сформувати ряд основних принципів високої зносостійкості матеріалів
[1, 2]:
Структура матеріалу повинна бути
суттєво гетерогенною та складатися з твердих зерен, рівномірно розташованих в
пружно-пластичній металевій матриці. Пружно-пластична матриця повинна
забезпечувати, з одного боку, достатню релаксацію діючих на матеріал
навантажень та знижувати вірогідність втомних тріщин, з іншого боку мінімальну
деформацію. Тверді включення приймають на себе основну частину діючого на
матеріал навантаження та, крім того, є ефективними бар’єрами для рухаючих
дислокацій, що дозволяє різко знизити швидкість пластичної деформації.
Структура поверхневих шарів
матеріалу не повинна суттєво змінюватися в процесі тертя або повинна
перебудовуватися в структуру, що є вигідна з точки зору тертя та зношування.
Поверхня матеріалів що труться
повинна мати меншу міцність, ніж нижче лежачі шари (правило позитивного
градієнту).
Це положення зумовлено необхідністю
зниження втрат на тертя в процесі експлуатації пари тертя. Найбільш ефективна
його реалізація при утворенні та збереженні в процесі експлуатації пари тертя
на робочій поверхні розділюючи плівок, що мають мінімальну міцність зсуву та, в
той же час міцно пов’язані силами адгезії з матеріалом робочої поверхні [2].
Необхідною умовою надійної роботи
зносостійкого матеріалу є висока міцність адгезійного зв’язку між входячими в
його склад твердими включеннями та матрицею, бо через низьку адгезійну міцність
складових тверді включення в композиті викришуються і відбувається абразивне
зношування матеріалу.
Інтенсивне зношування такого роду
двофазних матеріалів визначається вмістом компонентів, розміром зерен фаз, видом
та величиною діючого навантаження та температурою в зоні контакту.
Слід відмітити, що зношування
деталей машин та інструментів може бути викликано як тертям металевих деталей
один об одного, так і впливом робочого середовища - струменем рідини, газу, абразивними
частинками на поверхні деталей та іншими поверхневими процесами (в тому числі і
в сполученні з дією високих температур). В зв’язку з цим, механізм зношування
різний і залежить від умов прикладення навантаження, але в основному він
зводиться до того, що в процесі роботи з поверхні матеріалу вириваються дрібні
частинки [3].
Так, при роботі зносостійких
матеріалів в вузлах тертя їх навантаження характеризується зусиллям, необхідним
для руйнування фрикційних зв’язків між контактуючими поверхнями виробів при
їхньому зсуві та проковзуванні одна відносно іншої. При торканні двох поверхонь
контакти можна спостерігати по вершинам окремих випуклостей, а фактичний
контакт в залежності від умов навантаження та геометрії випуклостей складає від
10-2 до 10-4 номінальної поверхні [2]. В зв’язку з цим
загальне діюче навантаження розподіляється по плямам фактичного контакту, що
передбачає високий рівень навантажень в цих областях.
У випадку абразивного зношування
тверді частинки абразиву інтенсивно взаємодіють як з твердими включеннями
гетерофазного зносостійкого матеріалу, так і з м’якою матрицею. Стійкість проти
зношування при такому виді навантаження буде визначатися за цілим рядом
факторів, таких як твердість та опір твердої фази крихкому руйнуванню,
твердість та властивостями міцності матриці, міцністю. адгезійного зв’язку між
фазами та іншим.
При наявності агресивного середовища
опір зношування залежить і від корозійної стійкості матеріалу. В зв’язку з цим
можна зробити висновок про те, що зносостійкість сплаву визначається комплексом
його фізико - механічних властивостей та умовами навантаження, причому в
залежності від умов зношування оптимальна структура матеріалу і його
властивості можуть бути різними. Так, при абразивному зношуванні стійкість
зростає зі зростанням твердості зношуваного матеріалу, але для різних
матеріалів в різному ступені: при однаковій поверхневій твердості сталей зі
структурою мартенситу + карбіди мають більшу зносостійкість, ніж сталі сталі з
тою ж твердістю, але не маючі надлишкових карбідів [3]. При однаковій твердості
сталі, що має крупнокристалічну структуру, має меншу зносостійкість, ніж сталь
з дрібнокристалічною структурою, через те що у першої опір крихкому руйнуванню
менший.
Включення графіту, погіршують, як
правило, механічні властивості сталі, знижуючи її твердість та абразивну
зносостійкість, підвищуючи, в той же час, зносостійкість останньої при роботі в
вузлах тертя, бо в процесі зношування графітові включення виходять на поверхню
тертя, руйнуються по площинам спаяності, утворюючи дуже тонкі пластинки, і
заповнюють нерівності поверхонь, що труться, запобігаючи сухому тертю металу об
метал та схоплюванню, тобто графітові включення виконують роль твердого
мастила.
Абразивна зносостійкість металів
також може суттєво змінюватись в залежності від умов навантаження. Так автори
[4] разом з абразивною зносостійкістю розглядають ще й ударно - абразивну
зносостійкість. Досліджуючи вплив легуючих елементів на властивості
високохромистих сталей, вони показали, що наявність навіть відносно слабкої
ударної складової суттєво змінює дію елементів на зносостійкість.
Дослідженню процесів зношування
композиційних матеріалів при найрізноманітніших умовах навантаження присвячено
дуже багато робіт [5 - 9]. Їх аналіз показує, що в самому загальному вигляді їх
можна привести до наступного механізму [10]: при дії контертіла або абразивних
частинок на тверді складові матеріалу відбувається їх незначне зміщення
відносно навколишньої порівняно м’якої матриці. Зміщення твердих зерен викликає
видавлювання матеріалу зв’язки з зони, що розташована між твердими включеннями.
Повторне навантаження призводить до того, що фіксуюча дія матриці та викликане
нею зниження навантаження в твердих частинках зменшується до рівня, при якому в
останніх з’являються тріщини. Під час подальших актів навантаження по мірі
видавлювання зв’язки відбувається поступове подрібнення твердих зерен, та їх
уламки видаляються з зони тертя.
У відповідності до запропонованого в
[10] механізму процес в’язкого видавлювання матеріалу зв’язки є первинним та
контролюється швидкістю, тоді як процес крихкого дроблення твердих частинок є
вторинним.
Це дозволяє зробити висновок, про
переважаючу дія фізико - механічних властивостей металевої зв’язки, а також
адгезійних властивостей на границі розподілу фаз тверда частинка - зв’язка щодо
проблеми забезпечення високих експлуатаційних характеристик зносостійкого
матеріалу.
1.1.2 Порошкові зносостійкі
матеріали на основі заліза
Технологія порошкової металургії
дозволяє найбільш повно реалізувати перераховані вище основні умови створення
зносостійких матеріалів з яскраво вираженою гетерогенною структурою [1,2]. З
урахуванням того, що ці матеріали працюють в самих різноманітних умовах: при
різних навантаженнях та швидкостях, при терті кочення та ковзання, абразивному
зношуванні, статичних та ударних навантаженнях, при різних умовах змащування і
т.д., зносостійкі конструкційні матеріали досить різноманітні за хімічним
складом та технології їх виготовлення. Одним з перших характерних прикладів
використання технології порошкової металургії для отримання зносостійких
матеріалів є виготовлення деталей з залізного порошку методом одно-, або
дворазового пресування та спікання, з послідуючою цементацією спечених деталей
в твердому або газовому карбюризаторі. При цьому, як показали результати
досліджень, підвищення пористості зразків перед цементацією більше 10%
забезпечує значний приріст глибини навугюцювання та зниження градієнту
концентрації вуглецю по глибині деталі [11].
Для виготовлення шестерень, що
відрізняються високою зносостійкістю, використовували технологію двократного
пресування та спікання порошкових матеріалів з суміші 85%Fe + 15% чавуну та
сталі, отриманої із суміші порошків заліза - 50% и ШХ-15 - 50%.
Використання основних принципів
отримання зносостійких матеріалів, що передбачають необхідність створення чітко
вираженої нерівновісної структури з суттєвою різницею в мікротвердості основи
сплаву та твердої фази, призвело до розробки зносостійкої порошкової хромистої
сталі ЖЧ25Х3, що виготовляється двократним пресуванням та спіканням із суміші
порошків заліза - 65%, білого чавуну - 25% та хромистої сталі марки Х30 - 10%
[12].
В якості хромовмісної добавок можуть
бути також використані ферохром, хромований залізний порошок або порошок
карбіду хрому. При цьому, передумовами для створення чітко вираженої
нерівноважної структури в даному випадку слугує використання високолегованих
хромистих добавок та застосування режимів спікання, що не призводять до
гомогенізації структури. Після спікання матеріал характеризується нерівноважною
будовою в межах мікрооб’ємів: окремі зерна сплаву з високим вмістом хрому
оточені полем, що являє собою низьколегований ферито-перліт, що набуває після
гартування з 840°С структуру мартенситу або тросто-мартенситу. Мікротвердість
основи становить 5,0 7,0 ГПа, хромистих включень, багатих карбідами - 10,513,0
ГПа [2]. Зносостійкість деталей масляного насосу з порошкової сталі Ж425Х3, не
дивлячись на залишкову пористість в 1012%, перевищує зносостійкість аналогічних
деталей із литої підшипникової сталі ШХ-15 в 24 рази.
Яскравим прикладом порошкових
зносостійких матеріалів, синтез котрих традиційними методами лиття та обробки
тиском практично не можливий, є металоскляні композити, що являють собою
відносно пластичну металеву матрицю, в якій рівномірно розподілені включення
скла, що володіють високою твердістю. Змінюючи склад металевої матриці та вміст
скляної фази, можна отримувати матеріали з широким діапазоном властивостей. При
цьому, механічні властивості спечених металоскляних матеріалів знижуються зі
збільшенням вмісту скла, а їх фрикційні характеристики (коефіцієнт тертя та
інтенсивність зношування) мінімізуються при вмісті скляної фази в межах 610% по
об’єму [2]. Підвищення кількості скляної фази над вказані значення призводить
до погіршення фрикційних характеристик метало скляних матеріалів в зв’язку з
різким зниженням їх міцності, а відповідно і несучої здатності. Характерною
особливістю гетеро фазної структури таких матеріалів є суттєва різниця в
мікротвердості пластичної матриці та твердих включень, що досягає 5,0 ГПа [13].
Як вказувалось раніше, висока
стійкість проти зношування в значній мірі визначається високою поверхневою
твердістю матеріалу, що забезпечується, як правило, за рахунок наявності певної
долі карбідної складової структури. В той же час, відомими прикладами
зносостійкості в умовах високих питомих навантажень та ударів показують
високомарганцеві сталі аустенітного класу, що володіють відносно низькою
твердістю (200 - 250 НВ). Однак, одним з недоліків литих високомарганцевих сталей
є складність їх механічної обробки, в той час як застосування методів
порошкової металургії для виготовлення деталей із аналогічних матеріалів
дозволяє уникнути операції механічної обробки або значно зменшити її об’єм.
Дослідження абразивної зносостійкості зразків, виготовлених з порошку
1,4-1,6%С, 1,4-1,6%Mn та 0-0,12%Nb пресуванням, спіканням при 1200°С з
послідуючою холодною допре совкою, показало їх підвищену стійкість у порівнянні
з литою сталю Г13Л. При цьому, зі зменшенням пористості з 1718% до 1213%
зменшується і коефіцієнт відносного зношування порівняно з литою сталю з 0,97
до 0,82.
В останній час привертають увагу
дослідників борвмісні сплави на основі заліза завдяки їх високій міцності,
твердості та зносостійкості при їх відносно малій вартості. Це дозволяє
розглядати їх як перспективні матеріали для отримання зносостійких сплавів
[14]. Так, результати досліджень показали, що зносостійкість композиційних
наплавочних матеріалів на основі сплаву системи Fe-B-C порівняна, а окремих
випадках і перевищує по зносостійкості матеріали на основі значно більш
дорожчого карбіду вольфраму. Додаткове легування боридів заліза молібденом та
ніобієм підвищує ресурс стійкості сплавів, призначених для роботи при кімнатній
температурі, а легування хромом та ванадієм дозволяє використовувати їх в
умовах підвищених температур до 400°С [15].
Відносно високою міцністю та
зносостійкістю володіють порошкові матеріали, отримані спіканням пресовок з
шихти складу залізо - 0,51,0% карбіду бору [15]. Карбід бору не тільки зміцнює
матеріал, але й також слугує активатором при спіканні: в системах Fe-B-C має
місце евтектичне перетворення, в порошковій суміші залізо - карбід бору при
температурі вище 1100°С відбувається контактне плавлення, а рідка фаза що
з’являється активує ущільнення [16]. Гетерогенна структура отриманого
матеріалу, являє собою леговану матрицю та тверді включення складних карбідів
та боридів, забезпечує підвищену зносостійкість, наприклад, у порівнянні зі
сталю 45, в 33,5 разів [14].
Спроби використання залізоборидних
порошкових композиційних матеріал для роботи в умовах підвищених
термодинамічних навантажень (наприклад, в якості формоутворюючих деталей
кокілів або форкамер дизельних двигунів) призвели до необхідності розробки
технології отримання без пористого псевдосплаву [17]. В зв’язку з цим певний
інтерес представляє технологія одержання порошкових композицій з використанням
методу просочування пористого тугоплавкого каркасу рідкими більш легкоплавкими
металами чи сплавами [18]. При отриманні залізоборидного сплаву в якості
тугоплавкої складової використовується порошок заліза, спресований в заготовки
з пористістю 22 24%, а матеріал просочення складається з сплаву з 3,84%В,
температура плавлення котрого більш ніж на 300 °С нижче за температуру
плавлення сталевих порошків. Евтектичний сплав заліза з бором добре змочує
твердофазне залізо, активно відновлює оксиди. Після просочування відносна
щільність матеріалу складає 9899% при суттєво гетерогенній структурі, що
складається з феритної та евтектичної фаз, мікротвердість котрих складає 1,5
2,3 і 4,0 5,0 ГПа відповідно. Додаткове легування просочуючого сплаву
молібденом, ніобієм та вольфрамом не тільки суттєво підвищує механічні
характеристики композиційного матеріалу, але й його теплостійкість. Матеріал,
отриманий шляхом просочування пористої залізної матриці сплавом складу Fe +
3,8% B + 1,5% Nb + 4,5% Mo, має міцність на розрив 540560 МПа і може
використовуватися для виготовлення формоутворюючих виробів, що працюють при
650700°С.
Автори [19] вказують також на позитивний
вплив додаткової гарячої обробки тиском просочених залізоборидних композицій, в
результаті якої відбувається не тільки до ущільнення матеріалу, але і суттєве
зближення боридних ділянок між собою за рахунок деформації залізної основи.
Аналіз властивостей розглянутих вище
матеріалів дозволяє зробити висновок, що, не дивлячись на відносно високі
характеристики зносостійкості, область їх застосування обмежена через понижену
несучу здатність, що визначається, при однакових умовах, міцність та відносною щільністю
металічної матриці. В зв’язку з цим очевидно, що для суттєво підвищення фізико
- механічних та експлуатаційних властивостей матеріалів, що працюють в умовах
інтенсивного знощування, необхідно застосування технології, що забезпечує
отримання високо щільних заготовок.
Одним з найбільш широко
застосовуваних методів отримання порошкових матеріалів високої, щільності, що
традиційно використовується, зокрема, в твердосплавному виробництві, є метод
спікання в присутності рідкої металічної фази [20]. На відміну від
твердофазного спікання, рушійними силами якого є дифузійні процеси, в’язка
течія та рекристалізація, при появі рідкої фази значно збільшується швидкість
дифузії компонентів, полегшується рух твердих частинок відносно одна одної, в
зв’язку з чим відбувається швидке заповнення пор та капілярів. Це дозволяє за
короткий час досягти близької до теоретичної щільності матеріалу, що
спікається. Крім того, рідка фаза, в якій частково розчиняється речовина
твердої фази, інтенсифікує його перенос, внаслідок чого може змінюватися
рухливість дефектів на границях частинок, можлива поява нових дефектів кристалу
або збільшення напруженого стану гратки твердих частинок під дією змочуючої
рідини [20].
Використання технології рідкофазного
спікання дозволили розробити способ отримання та склади цілого ряду щільних
порошкових матеріалів на основі заліза, що володіють підвищеною твердістю та
зносостійкістю. Вихідними компонентами для отримання сплавів слугують порошок
заліза, карбіди перехідних металів IV-VI груп періодичної системи елементів
Д.И.Менделеева та графіт. Масова частка карбідів перехідних металів (TiC, WC,
Mo2C, Cr2C2, VC, NbC2, TaC) складає
близько 20%, вуглецю 1,55,0%, залізо - залишок. Отримані матеріали володіють
високою міцністю, в’язкістю, твердістю та зносостійкістю, і рекомендуються
розробниками для виготовлення виробів та деталей гірничого обладнання.
Одним з перспективних порошкових
матеріалів для роботи в умовах тертя, абразивного зношування та високої
температури є карбідохромові сплави зі зв’язкою на залізній основі. Перші
спроби створення твердих сплавів на основі карбіду хрому з залізо - вуглецевою
зв’язкою були представлені в [21]. Матеріал містив 20% зв’язки, що представляла
собою відбілений чавун з 3,8% С і відрізнявся високою твердістю (88 HRA), однак
мав надзвичайно низькі характеристики міцності (изг. = 190 МПа).
Низький рівень механічних властивостей цих матеріалів пояснюється активною
взаємодією чавунної складової з карбідом хрому, що призводить до утворення в
складі цементуючої фази значної кількості складних залізохромових карбідів і
зменшення концентрації металевої складваї. В зв’язку з високою крихкістю та
низькою міцністю ці матеріали не знайшли широкого застосування в промисловості.
Значне підвищення міцності
матеріалів системи карбід хрому - залізо - вуглець було досягнуто при
використанні в якості цементуючої зв’язки замість чавуну порошку заліза.
Спікання зразків, що спресовані з порошкової суміші, проходить з інтенсивною
усадкою в температурному інтервалі 1130-1150°С, що викликано появою рідкої
фази, яка утворюється в результаті плавлення евтектики Fe-Cr-C. Дослідження
впливу кількості залізної зв’язки в сплаві на його механічні характеристики
показало, що збільшення вмісту залізу з 40 до 70% призводить до зниження
твердості та підвищенню міцності і ударної в’язкості матеріалу, що пояснюється
підвищеним вмістом більш пластичної металічної складової, що являє собою
вуглецевий ферохром. При вмісті у вихідній шихті до 60% заліза металічна фаза
представлена у вигляді окремих розрізнених включень, а в сплаві з 70% заліза
вона представляє собою основне поле, в якому розташовані розгалужені колонії
залізохромового карбіду. Така перестройка структури викликає різке підвищення
міцності на згинання та ударну в’язкість. Так, зі збільшенням вмісту заліза від
60 до 70% ударна в’язкість збільшується в 3,5, а межа міцності на згинання в
1,6 разів. Мікротвердість карбідної фази складає 13501400, а вуглецевого
ферохрому - 61506200 МПа.
В роботі [22] в якості хромовмісної
добавки для отримання зносостійкого залізохромового сплаву запропоновано
замість карбіду хрому використовувати порошок промислового пічного ферохрому.
Як показав автор, механізм розчинення вуглецевого ферохрому в залізі
аналогічний до механізму розчинення карбіду хрому Сr3C2,
однак процес розчинення ферохрому починається при більш низьких температурах
(1000°С) і в інтервалі температур 1000 1100°С йде швидше, ніж у Cr3C2.
Великий інтерес представляє
можливість використання в якості твердої фази бориду хрому. Порошкові
псевдосплави з CrB2 володіють високою твердістью, стійкістю проти
абразивного зношування, хімічною стійкістю проти концентрованих кислот,
термостійкістю. Спікання сумішей CrB2 (1030%) Fe, супроводжується
максимальною усадкою, проходить в інтервалі температур 1500-1600°С, хоча у
сплавів бориду хрому з залізом рідка фаза з’являється вже при температурі
1100°С. Твердість зразків сплавів CrB2-Fe при підвищенні температури
спікання з 1100°С до 1600°С зростає і досягає максимального значення (8284 HRA)
при 1500-600°С.
Класичним прикладом зносостійких
матеріалів, що володіють суттєво гетерогенною структурою, є карбідосталі,
містячи металеву зв’язку, як правило, із легованих сталей та карбідів з масовою
часткою останніх від 20 до 70% [23,24]. В якості карбідної складової для
карбідосталей найчастіше використовують карбід титану. Співвідношення в
карбідосталі тугоплавких карбідів та сталевої складової вибирають в залежності
від її призначення та вимог, що пред’являються до отримуваного матеріалу. Чим
більше вміст в карбідосталі тугоплавкої фази, тим вище її твердості та
зносостійкість, однак нижче ударна в’язкість. При цьому, як показано [24], не
залежно від складу зв’язки у всіх випадках спостерігається суттєве зниження
міцності на згинання при збільшенні вмісту сталевої зв’язки вище 4550%.
Попередньо в якості металевої
складової карбідосталей використовували вуглецеві сталі, котрі в подальшому з
ціллю підвищення твердості були замінені на високолеговані сталі марок Х12М,
Х18Р15, Х6В3М, Р18, Р6М5 и ін. [23]. В роботі [25] приводяться дані про
використання в якості металевої зв’язки сталі Гадфільда (аустенітного класу).
Структура твердих сплавів
формується, в основному, в процесі рідкофазного спікання, що відбувається при
температурах плавлення евтектики карбід титану - сталь. В процесі спікання
відбувається насичення поверхонь зерен карбіду титану легуючими елементами в
результаті дифузійної взаємодії з ними сталевої зв’язки з утворенням так званих
“кільцевої структури” [23]. Остання дещо знижує поверхневу твердість карбідних
зерен і підвищує пластичність, що сприяє підвищенню загальної пластичності
карбідосталі.
З метою активування спікання
карбідосталі та зниження мінімальної температури процесу автори [25] вводять в
порошкову суміш складу: швидкоріжуча сталь M3/2 - 0,5% (ваг.) С - 5-10% (обємн.)
TiC (або TiN) активуючу добавку Cu3P в кількості 7% (ваг.).
Композиційний матеріал вказаного складу задовільно спікається до практично без
пористого стану при температурі 1140-1170°С і представляє інтерес як
зносостійкий композит з металевою матрицею для автомобільної промисловості.
Дослідження впливу вмісту керамічних частинок на механічні властивості
спеченого матеріалу проказало, що підвищення вмісту останніх від 0 до 10%
викликає ріст твердості (від HV = 671-699 MПa при 0% до 745-770 MПa при 5-10%),
в той час як подальше підвищення вмісту TiC (TiN) до 20% призводить до зниження
твердості внаслідок підвищеної пористості матеріалу після спікання.
Характеристики міцності матеріалу при вмісті твердих частинок в межах 0-10%
знаходиться на рівні изг. = 1,35-1,40 ГПa, а при збільшенні їх
вмісту вище 10% міцність на згинання не перевищує 1,00ГПa [25].
В якості твердої складової в
матеріалах на основі швидкоріжучої сталі з активуючою добавкою Cu3P
поряд з карбідом та нітридом титану можна використовувати карбід ніобію [44], а
також 10% (об.) Al2O3.
Автори роботи [46] вказують про
використанні в якості зносостійкого композиційного матеріалу порошкової сталі
складу 3%Cr 2%Ni 2%Cu 0,8%C Fe - осн. з добавкою 3%(мас.) WC. В ряді
закордонних публікацій приведені дані про можливість заміни кобальту а
традиційних карбідо-вольфрамових твердих сплавах металевими зв’язками на основі
заліза, зокрема - залізо-марганцевим сплавом. Карбідовольфрамовий композит з
сталевою зв’язкою займає по своїм фізико-механічним та експлуатаційним
властивостям проміжне положення між швидкоріжучою сталлю та традиційними
твердими сплавами, та може з успіхом використовуватись для виготовлення
ріжучого інструменту дозволяючи, при цьому, застосовувати більш жорсткі режими
різання у порівнянні з швидкоріжучою сталлю. Псевдо сплав системи WC-Fe-Mn є
перспективним матеріалом для виготовлення високозносостійких конструкційних
деталей.
Альтернативною рідкофазному спіканню
технологією отримання карбідосталей є застосування методу просочування
карбідного каркасу сталевим розплавом. Матеріали, отримані цим методом, як
правило, мають більш високу щільність та ударну в’язкість, ніж отримані
звичаним методом пресування та рідкофазного спікання [23]. Технологія
виготовлення карбідосталей методом просочування включає формоутворення
карбідного каркасу, його попереднє спікання та послідуюче просочування сталевим
розплавом. Просочені по оптимальним режимам зразки зберігають свою форму і, на
відміну від технології рідкофазного спікання, попередні розміри, не мають здутостей
та напливів.
Карбідосталі, як і традиційні
леговані сталі, піддаються всім видам термічної обробки - відпалу, гартуванню
та відпуску. У відпаленому стані їх можна, як правило, піддавати механічній
обробці, а після гартування та відпуску вони володіють високою твердістю (6572
HRCэ) та зносостійкістю. По своїм фізико-механічним та
експлуатаційним властивостям карбідосталі займають положення між твердими
сплавами та інструментальними сталями.
В останній час в технічно розвинених
країнах широке розповсюдження отримала порошкова металургія швидкоріжучих
сталей - високозносостійкого матеріалу, що використовується для виготовлення як
ріжучого так і штампового інструменту, так і високонавантажених деталей
конструкційного призначення. Попередньо методами порошкової металургії
виготовляли швидкоріжучі сталі, що мало відрізнялися по складу від давно
відомих та широко застосовуваних сталей традиційного металургійного переділу
Р6М5, Р6М5К5, Р6М5Ф3 та їх закордонних аналогів. В подальшому більш повне
використання можливостей порошкової металургії дозволило випуск ряду марок
сталей високої продуктивності, до яких можна віднести Р9М4К8-МП, Р12М3Ф2К5-МП,
Р6М5Ф3К9-МП (аналог шведської АSP-30 або японської КНА-30), Р10М3Ф4К10 (FAX-40,
Японія) та цілого ряду інших марок [26]. При цьому, поряд з намаганням
підвищити ступінь легування сталей, а саме підвищення вмісту в їх складі суми
(W + Mo) до 20 30%, вмісту V до 6,59,0%, Со до 815% та підвищення ступеня їх
"пересиченості вуглецем" до 0,250,3%, проводяться роботи по створенню
економно-легонованих безвольфрамових швидкоріжучих сталей.
Порошки швидкоріжучих сталей
отримують розпиленням розплаву водою або нейтральним газом (в основному -
азотом).
При цьому, якщо при виготовленні
виробів з водорозпилених порошків використовується, як правило, технологічна
схема, що заснована на рідкофазному спіканні спресованих заготовок [27], то
основний об’єм швидкоріжучих сталей із газорозпилених порошків отримують з
використанням технології гарячого ізостатичного пресування [26] або гарячої
екструзії [28] порошку в вакуумній камері з мало вуглецевої сталі з послідуючим
переробкою зкомпактованих заготовок в сортовий метал по традиційним технологіям
великої металургії. Представляє інтерес технологія отримання різноманітних
профілів з порошків швидкоріжучих сталей, що включає вакуумне спікання
заготовок з газорозпилених порошків в формах багаторазового використання, їх
гідростатичне ущільнення і послідуюча гаряча екструзію. Застосування
гідростатичного ущільнення спечених пористих заготовок дозволяє збільшити їх
відносну щільність до 0,880,90 та, за рахунок цього, відмовитися від
використання сталевих капсул.
Порівняння мікроструктури та
властивостей матеріалів, отриманих із водо- та газорозпилених порошків
швидкоріжучих сталей, вказує на більш сприятливу форму та більш високу
дисперсність карбідної фази в металі із газо розпилених порошків, чим
пояснюється суттєво і більш висока міцність, ударна в’язкість та, відповідно,
стійкість інструментів.
В роботі [29] повідомляється про
отримання порошкової швидкоріжучої сталі з достатньо високими
фізико-механічними властивостями шляхом прокатки із газорозпилених порошків на
станах прокатки-ковки та станах з багато валковими калібрами.
Дослідження структурних параметрів
отримання матеріалів показує [20, 23], що застосування технології рідкофазного
спікання або просочування карбідного каркасу розплавом металу поряд з
забезпеченням високої щільності заготовки, викликає суттєве погрубішання
структури, ріст карбідного та аустенітного зерен та, як наслідок, призводить до
погіршення фізико-механічних та експлуатаційних властивостей матеріалів у
порівнянні з матеріалами, отриманими з використанням гарячої обробки тиском. Ця
обставина представляє доцільним застосування для отримання низькопористих
структур технологічних прийомів, що виключає використання температур в області
існування значної кількості рідкої фази, в зокрема - методів, заснованих на
гарячій обробці тиском пористих заготовок.
Найбільш широке застосування для
отримання високощільних порошкових матеріалів знайшов метод гарячої штамповки
пористих заготовок (ГШПЗ) [29, 30].
Так, в роботі [31] приведені
результати дослідження можливості використання гарячої штамповки для отримання
порошкової сталі Г13П. Оптимальні параметри технологічного процесу, що складається
з приготування шихти шляхом змішування порошку заліза, лампової сажі та
феромарганцю, холодного пресування та гарячої штамповки пористих заготовок,
забезпечують досить високі механічні властивості (в = 600650 МПа), =
10%, ан = 300400 кДж/м2) та підвищену зносостійкість у
порівнянні з литою сталлю Г13Л, що пояснюється дрібнозернистістю, ячеїстою
структурою та іншими особливостями структури [29]. Міцність та пластичність
сталі Г13П суттєво зростає у випадку застосування попереднього (перед гарячою
штамповкою) спікання пористих заготовок: відносне видовження зростає більше ніж
у двічі, досягаючи 2025%, ударна в’язкість такого матеріалу становить 500650
кДж/м2, міцність - в = 850900 МПа [32].
В той же час, як показали результати
досліджень, стійкість високомарганцевих сталей виявляється недостатньою при
чисто абразивному зношуванні в процесі експлуатації. Для підвищення абразивної
зносостійкості сталі Г13П її зміцнювали карбідом хрому Cr3C2.
Дослідження фізико-механічних
властивостей отриманих матеріалів показало, що навіть невелике додавання Cr3C2
(2,55,0%) різко знижує ударну в’язкість, що призводить до висновку про
недоцільність їх використання в умовах дії ударних навантажень. В той час,
абразивна зносостійкість зразків з вмістом 20% Cr3C2, що
рекомендується автором як оптимальний, знаходиться на досить високому рівні,
перевищуючи зносостійкість загартованої швидкоріжучої сталі.
Результати досліджень структури
матеріалу показують на те, що карбідні включення частково розчиняються в
металевій матриці, а частина атомів хрому в них заміщується залізом, свідченням
чого є зниження мікротвердості включень до 7,011,5 ГПа у порівнянні з вихідною
12,513,0 ГПа. Мікротвердість металевої матриці складає 3,87,0 ГПа.
Високою зносостійкістю відрізняється
також порошковий матеріал, отриманий методом гарячої штамповки пористих
заготовок, спресованих із шихти, що містить порошок заліза, 1112% ферохрому та
0,6% графіту [33]. Після гарячої штамповки такий матеріал мав наступні
властивості: в = 9001000 МПа; ак = 110130 кДж/м2;
твердість 5357 HRCэ. Висока зносостійкість матеріалу пояснюється
його суттєво нерівновісною структурою, що являє собою залізовуглецеву матрицю з
розподіленими в ній твердими частинками карбідів (CrFe)7C3,
оточеними зонами дифузії хрому [33].
Таким чином, приведені дані
дозволяють зробити висновок про перспективність та доцільність застосування
методів порошкової металургії для виготовлення виробів із зносостійких
матеріалів на основі заліза, так як технологія порошкової металургії в
максимальному ступені дозволяє забезпечити умови отримання суттєво
нерівноважної структури матеріалу, що є одним з основних принципів отримання
зносостійких композитів. Одною з переваг технології порошкової металургії щодо
зносостійких матеріалів є, також, можливість синтезу таких високоефективних
матеріалів як, наприклад, карбідосталі, металоскляні матеріали та ін., які
неможливо отримати, використовуючи традиційну технологію металургійного
переділу. В той же час, аналіз приведених даних показує, що для отримання
високоякісних зносостійких матеріалів, що працюють в умовах підвищених
навантажень, доцільно застосування методів, заснованих на гарячій обробці
тиском спечених пористих заготовок (гаряча штамповка, екструзія і т.п.).
1.2 Технологічні
проблеми процесів гарячого штампування пористих заготовок (ГШПЗ)
Формування порошкових виробів при
гарячому штампуванні заздалегідь спресованих пористих заготовок поєднується з
формуванням структури і властивостей їх матеріалу. При цьому, метод ГШПЗ, маючи
багато загального з іншими способами обробки тиском порошкових матеріалів, має
цілий ряд істотних відмінностей. Так, на думку Ю.Г. Дорофєєва [29], при
реалізації методу гарячого штампування практично повністю відсутнє ущільнення
за рахунок структурної деформації, тобто взаємного переміщення частинок, їх
щільнішого укладання і так далі. Підвищена пластичність матеріалу приводить до
пластичної деформації приконтактних зон матеріалу частинок, починаючи практично
з моменту прикладання зовнішнього тиску.
Ущільнення при гарячому штампуванні
пористих заготовок (ГШПЗ) складається із значно більш різноманітних,
протікаючих послідовно або взаємно накладаючих процесів, і перетворень в
оброблюваному порошковому матеріалі в порівнянні з іншими способами обробки
тиском порошкових матеріалів. Так, якщо наклепування матеріалу має місце і при
холодному пресуванні, то при гарячій обробці відбуваються процеси
рекристалізацій, що примушують повніше враховувати температурний і швидкісний
режими процесу. Великого значення набувають також різні неоднорідності в об'ємі
матеріалу: температури, щільності і так далі
При реалізації методу ГШПЗ прийнято
вважати, що ущільнення матеріалу повинне забезпечувати практично безпористий
його стан. Однак існує думка, що це не завжди доцільно. Так, з точки зору
досягнення найбільш високих механічних характеристик, може бути допущена
пористість в межах 2-3% [29]. Не менш важлива й форма пор. Сферичні пори
виконують роль бар’єрів на шляху розвитку тріщини. Навіть для виробів,
працюючих в умовах абразивного зношення, у відповідності до, мінімальний рівень
пористості потрібен тільки у поверхневому шарі, а внутрішні шари можуть мати
певний рівень пористості. Таким чином, метою ущільнення при ГШПЗ в оптимальному
випадку є досягнення рівномірного розподілу пор в об’ємі заготовки, що повинні
мати задану конфігурацію та розміри.
Формування компактного матеріалу з
відособлених частинок порошку полягає не тільки в зменшенні пористості тіла і
збільшенні його контактного перетину. Не менш важливу роль грає якість
контакту,що визначається наявністю металевого зв'язку між поверхневими атомами
контактуючих частинок або утворенням між ними границь із структурою,
відповідною міжкрісталлічним границям. Активація цих процесів відбувається при
розриві насичених зв'язків між атомами металу частинок або атомами елементів
адсорбованих плівок в результаті виходу на ці поверхні дислокацій і вакансій в
процесі пластичної деформації. Крім того, інтенсивна пластична деформація
металу в зоні контактних поверхонь частинок приводить до руйнування оксидної
плівки, винесення із зони контакту чужорідних включень, адсорбованих атомів і
так далі, і сприяє в цілому утворенню якісного металевого контакту, тобто
зрощенню частинок [29].
Механізм зрощення однозначно описати
складно, оскільки він залежить від безлічі чинників. На підставі результатів
досліджень мікро- і субструктури, а також рентгеноструктурного аналізу зон
зрощення на моделях і порошкових зразках, висунута гіпотеза про механізм
зрощення, суть якої полягає в злитті поверхневих зерен на контактних поверхнях
частинок при достатньо інтенсивній пластичній деформації [28]. При цьому,
кристалографічне орієнтування одного з контактуючих зерен трохи змінюється,
оскільки напрями ковзання не збігаються з напрямами напруги зрушення, а в
іншому випадку коли збігаються з сприятливою орієнтацією, процеси ковзання
протікають інтенсивно.
Результати проведених досліджень
показують, що основну роль в зрощенні грає температура нагріву заготовок, їх
початкова пористість і конфігурація, кристалічна будова металу частинок. Ці
чинники визначають характер напруженого стану, ступінь пластичної деформації,
швидкість деформації і, відповідно, ефект термомеханічної дії. Крім того,
наявність оксидів, сульфідів і неметалічних включення на міжчастковій
контактній поверхні перешкоджає зрощенню. Значно меншу роль, на думку авторів
роботи [28], грає час витримки після нагріву заготівки і режим подальшої
термообробки.
Розробка технології гарячого
штампування пористих матеріалів у кожному конкретному випадку значною мірою
ґрунтується на вирішенні однієї з центральних проблем технології визначенні
оптимальних форми, розмірів і пористості заготовок під штампування, а також
схеми деформації, оскільки вказані параметри не тільки визначають
технологічність і техніко-економічну ефективність процесу, але і, значною мірою
якість поковки.
В рамках вирішення вказаних завдань,
особливо для деталей складної форми, встає вибір між виготовленням заготівки
близької до форми поковки і її подальшого гарячого допресування до кінцевих
розмірів і щільності, або виготовленням заготівки простої геометрії і
реалізації при штампуванні значних поперечних деформацій для отримання кінцевої
форми поковки. У практику ГШПЗ перший метод знайшов значно ширше застосування,
оскільки при використанні схем штампування, які забезпечують швидкий перехід
від схеми одноосного стискування до схеми нерівномірного всестороннього
стискування зменшується вірогідність появи тріщин на бічній поверхні заготовок
[34]. Проте, в цій роботі, так само, як і в інших, вказується, що при
реалізації такої схеми навантаження виробу, отримані допресовкою заготовки за
відсутності відчутних поперечних деформацій, зазвичай мають залишкову
пористість близько 2%. Це пояснюється тим, що найбільш інтенсивне закриття пор
відбувається при деформаціях зсуву, а при звичайному гарячому допресуванні в
закритому штампі деформації зсуву зведені, як правило, до мінімуму [34]. Крім
того, дослідження ряду робіт авторів [35, 36] показують, що в порошкових
штамповках є зони ускладненої деформації, аналогічні спостережуваним при осадці
компактних матеріалів. Цю обставину зумовлює наявність нерівномірної щільності
в об'ємі штампованого виробу. Таким чином, вказані чинники приводять до
висновку про необхідність вибору такої форми заготівки під штампування, щоб в
процесі штампування реалізувалися максимальні деформації зсуву. При
перерозподілі нагрітого порошкового матеріалу за рахунок деформацій зсуву
інтенсивно закриваються пори і розриваються окисні плівки, що забезпечує
отримання високої щільності порошкових поковок при деякому зниженні питомих
зусиль деформації. Проте, відповідно до [34], форма і розміри заготовок мають
бути такими, щоб поверхні заготівки, що деформується, розширюючись, досягали б
бічних стінок штампу до моменту утворення поверхневих тріщин. Таким чином, для
вибору оптимальної форми заготовок необхідна оцінка технологічної пластичності
матеріалів, які піддаються деформації. Як критерій деформаційної здатності
матеріалу при штампуванні осесиметричних заготовок в закритому штампі приймають
максимальне відношення діаметру матриці D до початкового діаметру do
заготівки при якому на її бічній поверхні на кінцевій стадії осадки не
з'являються тріщини. Важливе значення при розробці технологічного процесу ГШПЗ
має знання співвідношень між ущільненням і формозміненням заготівки в процесі
штампування для різних матеріалів, початкових значень пористості і схем
деформації. Ущільнення при гарячій осадці інтенсивніше на початковій стадії
деформації коли пористість осаджуваної заготівки вище і поперечна течія майже
відсутня. Так зменшення пористості заготівки на 50% на початковому етапі осадки
супроводжується лише 5%-м збільшенням її діаметру. Даний ефект представляється
позитивним з погляду технології штампування, оскільки на початковому етапі
деформації в закритій матриці це знижує негативну дію сил тертя об стінки
матриці.
Проте, в даний час як в нашій
країні, так і за кордоном, опубліковано обмежене число робіт, присвячених
дослідженню вказаних питань, причому досліджувалися головним чином, тільки
прості схеми вантаження вільні осадки, доущільнення в жорсткій циліндричній
матриці і ін. Так, автори [37], досліджуючи вільну осадку циліндричних зразків,
встановили, що по міру зменшення відношення hk/do
осаджуваного зразка, де hk висота повністю ущільненої заготівки
діаметром do, радіальна деформація Δd/do
зменшується, що пояснюється впливом тертя контактних поверхонь осаджуваного
зразка об плоскість бойків, а ущільнення зразка при одному і тому ж значенні
ступеня осьової деформації збільшується [34].
Дослідження процесу заповнення
матриці і ущільнення при гарячому штампуванні пористих заготовок осадкою в
закритій циліндричній матриці показало, що розподіл щільності по радіальному
перетину заготівки на різних етапах штампування визначали шляхом виміру
твердості в різних точках перетину на заготовках, що відпалювали після
штампування. При штампуванні заготовок осадкою в закритому штампі на початковій
стадії відбувається радіальний рух матеріалу до стінок матриці, із збільшенням
щільності з 75 до 77%. На другій стадії процесу спостерігається зростання
ступеню нерівномірного розподілу щільності в об’ємі з утворенням "мертвих
зон" в нижніх кутах матриці внаслідок тертя матеріалу об стінки матриці і
охолоджування нижнього торця заготівки від холодного нижнього пуансона. Після
цього відбувається остаточне доущільнення заготовки і вирівнювання щільності по
перетину.
При гарячому штампуванні з
елементами витискування спостерігається складніша картина деформації. На
початковому етапі штампування, коли матеріал ще достатньо пористий,
відбувається, головним чином, його доущільнення без значного витискування в
нижню порожнину штампу. З підвищенням щільності матеріалу збільшується
інтенсивність витискування. При цьому, в об'ємі заготівки під видавлюваним
відростком утворюється зона підвищеної пористості, діаметр якої приблизно
дорівнює діаметру відростка, а її висота залежить від співвідношення діаметру
заготівки і видавлюваного відростка: при великому діаметрі відростка зона
ущільнення проходить через всю висоту заготівки. На пізній стадії процесу
відбувається остаточне доущільнення заготовки з утворенням в центрі поковки
найбільш щільної зони, що пояснюється, на думку авторів [38] ефектом різниці
температур по перетину і адіабатичним розігріванням матеріалу в центрі
унаслідок великих зсувних деформацій.
Аналіз вказаних робіт підтверджує
висновок, зроблений при теоретичному дослідженні процесу екструзії пористого
матеріалу, який полягає в тому, що на початковій стадії процесів деформації
пористих заготовок, відбувається інтенсивне їх ущільнення без значного формозмінення.
Досягши деяких критичних значень щільності ущільнення заготівки різко
сповільнюється і деформація здійснюється головним чином за рахунок зміни форми.
Одному з важливих завдань при
розробці і дослідженні процесів гарячого штампування є визначення їх
енергосилових параметрів. Відомо, що процес гарячої пластичної деформації
металів супроводиться двома паралельно протікаючими процесами: наклепуванням
частинок матеріалу і їх рекристалізацією. Ступінь впливу кожного з цих чинників
на енергосилові умови гарячого штампування пористих заготовок визначається їх
початковою пористістю і температурно-швидкісними умовами процесу. У роботах
[34-37] приведені порівняльні результати дослідження енергосилових параметрів
гарячого штампування при різних початкових значеннях пористості і швидкостей
деформації на кривошипному пресі і молоті. У всіх випадках робота деформації і
зусилля при штампуванні на молоті більше, ніж у разі штампування на пресі при
однакових значеннях пористості заготовок, і, навпаки, збільшення швидкості
деформації приводить до зменшення щільності пресувань при однаковій роботі
ущільнення [37]. Це пояснюється тим, що при високих швидкостях деформації
спостерігається відставання роззміцнюючого процесу (рекристалізації) від
зміцнюючого (наклепування), оскільки рекристалізація протікає не миттєво і не
завжди встигає завершитися під час деформації при великій її швидкості.
При гарячому штампуванні на пресі із
зменшенням початкової пористості заготовок q0 тиск ущільнення,
необхідний для отримання пресовок однакової щільності, знижується [36], що може
бути пояснене зменшенням ступеня деформації матеріалу при зниженні θ0.
Зменшення ж ступеня деформації, у свою чергу, призводить до зниження ступеня
гарячого наклепування.
Аналіз результатів досліджень
штампування пористих заготовок на молоті різних авторів приводить до
суперечливих висновків відносно впливу початкової пористості заготовок на
зусилля деформації. Так, якщо в роботі [34] зусилля деформації (так само як і
при штампуванні на пресі) зростає із збільшенням θ0,
то автори [37] вказують на зворотний характер залежності: із зменшенням θ0
тиск зростає, не дивлячись на зниження ступеня деформації і роботи ущільнення.
Зниження температури гарячого
штампування зменшує вплив швидкості на щільність пресовок при однаковій роботі
ущільнення [36]. Підвищення ж температури, збільшуючи пластичність матеріалу і
зменшуючи його опір деформації, сприяє підвищенню щільності за аналогічних умов
деформації.
.3 Вплив параметрів гарячого
ущільнення на структуру і властивості отримуваних матеріалів
Разом з відомими теоретичними і
експериментальними дослідженнями процесів гарячого ущільнення пористих
порошкових матеріалів, був проведений великий комплекс досліджень, присвячених
вивченню впливу параметрів гарячого ущільнення на структуру і властивості
отримуваних матеріалів.
Найбільш широке застосування методи
ГШПЗ знайшли для отримання виробів з порошків на основі сплавів заліза, при
цьому отримувані матеріали по своїх властивостях часто не поступаються, а у
ряді випадків і перевершують компактні матеріали аналогічного складу, що
отримуються звичайними металургійними методами [39]. У роботах [40, 41]
приведені результати досліджень властивостей пористих неіржавіючих сталей
Х23Н18 і Х25, отриманих методом ГШПЗ із заздалегідь легованих порошків. Аналіз
отриманих результатів показує, що гаряче штампування без попереднього спікання
заготовок або дифузного відпалу поковок найчастіше не дозволяє отримувати
щільні вироби з високими фізико-механічними властивостями. Попереднє ж спікання
або дифузійний відпал дозволяє істотно підвищити міцнісні, пластичні і
корозійні характеристики порошкових сталей.
Автори [40, 41], досліджуючи вплив
швидкості гарячого штампування на структуру і властивості поковок із залізного
порошку, показали, що збільшення швидкості ГШПЗ викликає деяке зростання
міцності поковок при однаковій щільності, проте знижує показники пластичності
[34, 36]. Ці дані також знайшли підтвердження за наслідками роботи [35], в якій
показано, що застосування високошвидкісних молотів для штампування заготовок із
сталевих порошків дозволяє отримувати матеріали з достатньо високим рівнем
міцності навіть в порівнянні із сталевим прокатом високої якості.
Істотний вплив на структуру і
властивості порошкових матеріалів, отриманих ГШПЗ, має початкова пористість
заготовок, а також ступінь деформації частинок матеріалу при штампуванні і
приведена робота деформації. Так, автори роботи [36], вказуючи на погіршення
властивостей гарячо-штампованих матеріалів із зменшенням початкової пористості
заготовок, пов'язують це, головним чином, з гіршими умовами довідновлення
оксидів при нагріванні під штампування в середовищі водню для заготовок з
нижчою пористістю, а також більшою неоднорідністю їх пластичної деформації.
Однією з особливостей мікроструктури
гарячо-штампованих порошкових матеріалів є стовбчатість периферійних зерен і
різнозернистість структур центральної і периферійної зон зразків: по міру
наближення до центральної частини зразків розмір зерен збільшується [35, 36].
Автори [36] пояснюють це тим, що первинна рекристалізація тут йде повніше,
оскільки швидкість охолоджування набагато менше, ніж в периферійній зоні. При
цьому, з підвищенням температури гарячого штампування різнозернистість зон
зменшується.
Достатньо сильний вплив на ступінь
різнозернистості має величина пластичної деформації матеріалу основи частинок:
підвищення значення ε0,
яке досягається збільшенням, зокрема, початковій пористості q0
заготовок, приводить до рівномірної фрагментації зерен. При ущільненні
заготовок з низькою пористістю (при θ0
= 5-9%) структура гарячо-штампованого матеріалу грубозерниста і неоднорідна, що
значно знижує його механічні властивості [37].
Механічні властивості
гарячо-штампованих порошкових сталей істотним чином залежать також від
гранулометричного складу початкових порошків: найбільш високий рівень
механічних властивостей спостерігається в сталях, виготовлених з дрібних
порошків [30]. Причиною зниження властивостей сталей при збільшенні розмірів
початкових порошків є важкість довідновлення внутрішньо-частинкових оксидів,
які зберігаються в сталях після спікання, і мають негативний вплив на механічні
властивості матеріалів.
Дослідження впливу конструктивної
схеми гарячого штампування на структуру і властивості отримуваних матеріалів
[42] показало, що відкрите гаряче штампування неспечених заготовок, наближених
формою до готового виробу, приводить до набуття низьких механічних властивостей
матеріалу унаслідок грубих дефектів структури. Помітне підвищення властивостей
досягається шляхом реалізації схем вантаження, що забезпечують інтенсивні
деформації зсуву, зокрема штампування витискуванням [38, 39]. У зв'язку з цим
досить актуальними стають питання розробки нових, дослідження і вдосконалення
відомих ефективних схем деформації і конструктивних рішень для їх реалізації.
Так, автори роботи [39] запропонували метод штампування заготовок з порошку
титану витискуванням з протитиском (підпором). Запропонований метод дозволяє
отримувати з порошкових матеріалів вироби складної форми з властивостями, які
мало відрізняються від властивостей аналогічних виробів з монолітного титану.
Висновки та постановка завдання
досліджень:
Підсумовуючи вище сказане можна
зробити висновки, що серед зносостійких матеріалів, що виготовляються методами
порошкової металургії набувають широкого поширення карбідосталі композити, що
складаються з карбідів з масовою часткою від 10 до 70% і металевої зв'язки з,
як правило, легованій сталі. Як основний карбід для карбідосталей найчастіше
використовують карбід або диборид титана.
Карбідосталі спочатку розроблялися
як сплави, по своїх властивостях проміжні між інструментальними сталями і
твердими сплавами. Традиційні карбідосталі з 40-60% об'ємних доль TіC є
твердими сплавами, багатими металом. Об'ємний вміст тугоплавкої фази в
карбідосталях значно більше, ніж в інструментальних сталях, але менше, ніж в
традиційних твердих сплавах. Це дозволяє після відпалу піддавати їх всім видам
механічної обробки, а після гарту і відпустки карбідосталі володіють високою
твердістю і зносостійкістю, у ряді випадків не поступаючоюся відповідним
характеристикам традиційних твердих сплавів, проте завдяки великому змісту
металевої фази у них істотно вище пластичність і в'язкість.
В той же час, при використанні
традиційної технології отримання карбідосталей, що включає помел і змішування
шихти, що складається з порошків карбіду титана і сплаву на основі заліза,
пресування заготовок і рідкофазне спікання, не вдається повною мірою
реалізувати їх позитивні властивості через неповну змочуваність карбіду титану
сталевою зв'язкою, що пов'язане з частковим окисленням карбідних частинок, що
відбувається при помелі шихти і веде до появи важкоусувуваних пор, що істотно
знижують механічні властивості матеріалу.
При рідкофазному спіканні сплавів
TіC сталь рідка фаза заповнює зазори між твердими частинками і викликає взаємне
переміщення частинок під впливом сил поверхневого натягу. При цьому, процес
спікання супроводиться розчиненням в рідкій фазі дрібних карбідних частинок і
перенесенням їх речовини на більші. В результаті дрібні частинки зникають, а
великі ще більш збільшуються. У зв'язку з цим, при використанні традиційної
технології отримання карбідосталей із застосуванням рідкофазного спікання,
достатньо складно отримати дрібнозернисту структуру, оскільки необхідність
отримання щільного сплаву зумовлює застосування достатньо високої температури
спікання, що активує, разом з ущільненням композиту, активне зростання зерен.
Проте, з досвіду отримання і обробки
гетерофазних матеріалів відомо, що найкращий зв'язок між фазами забезпечується
в умовах виділення фаз при розпаді твердих розчинів. Це ж явище може
спостерігатися при виділенні карбідних фаз з матриці на основі інтерметаллідів.
У разі реалізації цього ефекту з'являється можливість впливати на швидкість
росту карбідних зерен, що зароджуються, і тим самим формувати дрібнозернисту
структуру, здатну підвищити як фізико-механічні параметри матеріалу, так і його
зносостійкість. У зв'язку з вищевикладеним, був запропонований новий підхід до
отримання високозносостійких дрібнозернистих композитів системи карбід титану -
сплав на основі заліза, що полягає в тому, що карбідна фаза не вводиться в
початкову шихту у вигляді порошку карбіду титану, а формується в процесі
сплавоутворення при спіканні порошкових сумішей, що складаються з порошків титану,
заліза і вуглецю.
Аналіз сучасних тенденцій розвитку
матеріалознавства порошкових зносостійких і конструкційних матеріалів на основі
заліза свідчить про актуальність і доцільність розробки нових економно
легірованих сплавів для роботи в умовах підвищених навантажень і інтенсивної
стираючої дії, а також ефективних маловідходних технологій їх виготовлення з
метою забезпечення заданого комплексу властивостей.
Зносостійкість матеріалу при
фрикційному, абразивному або ударно-абразивному зносі визначається комплексом
його фізико-механічних характеристик і умовами навантаження, тому в залежності
від умов його навантаження оптимальна структура матеріалу та його властивості
можуть бути різними.
Основними чинниками, що визначають
надійну роботу зносостійкого матеріалів, поряд з високою несучою здатністю, є,
як правило, підвищена твердість в сполученні з прийнятним рівнем пластичності.
Основоположні принципи отримання зносостійких матеріалів передбачають, також,
необхідність створення чітко вираженої нерівноважної структури з суттєвою
різницею в мікротвердості пластичної матриці та твердої фази.
При використанні традиційної
технології отримання карбідосталей із застосуванням рідкофазного спікання,
достатньо складно отримати дрібнозернисту структуру, оскільки необхідність
отримання щільного сплаву зумовлює застосування високих температур спікання, що
активує, разом з ущільненням композиту, інтенсивне зростання зерен.
Застосування гарячого штампування, практично не змінюючи середній розмір зерен
TIC, в той же час дозволяє істотно подрібнити структуру матричного сплаву,
розміри зерен якої зменшуються в 2-2,5 рази.
На основі використання ефекту появи
низькотемпературної евтектики в системі FeTi був запропонований новий
технологічний підхід до отримання композитів системи карбід титану - сталь, що
полягає в тому, що карбідна фаза не вводиться в початкову шихту у вигляді
порошку карбіду титану, а формується в процесі сплавоутворення при реакційному
спіканні порошкових сумішей, що складаються з порошків титану, сплаву на основі
заліза і вуглецю. Аналіз результатів спікання порошкових сумішей Ti-FeC з
різним початковим змістом компонентів дозволив зробити виcновок, що
максимальний вміст титану в початковій суміші, що забезпечує отримання міцних і
безрозслойних зразків, складає 22-25% (мас.), що відповідає розрахунковому
вмісту карбіду титану в псевдосплаві близько 30%. Із збільшенням змісту титана
і вуглецю в шихті, не дивлячись на наявність в процесі спікання значної
кількості рідкої фази, не тільки відсутня усадка, але навіть спостерігається
помітне об'ємне зростання і розшарування матеріалу унаслідок швидкоплинного
протікання екзотермічною реакцією при взаємодії між титаном і вуглецем, що
супроводжується виділенням значної кількості тепла і газоподібних продуктів
реакції.
Метою роботи є дослідження
структуроутворення в процесі реакційного спікання та гарячого деформування
порошкових сумішах систем FeTiC і FeTiB4С та розробка технології
одержання порошкових зносостійких матеріалів на основі системи FeTiC(B).
2.
Експериментальна частина
.1 Теоретичні та технологічні основи
отримання композитів на основі системи карбід титану - сталь
2.1.1 Основні
структурні та технологічні особливості карбідосталей
Серед зносостійких матеріалів, що
виготовляються методами порошкової металургії, отримали широке застосування
карбідосталі - композити, що складаються з карбідів масовою часткою від 10 до
70% та металевої зв’язки з як правило, легованої сталі. В якості основного
карбіду для карбідосталі найчастіше використовується карбід або диборид титану.
Карбідосталі спочатку розроблялися
як сплави, за своїми властивостями проміжні між інструментальними сталями та
твердими сплавами. Місце псевдосплавів карбіду титану з сталевою матрицею
наглядно можна представити на рис. 2.1.
Рисунок 2.1 Вплив об’ємного вмісту
твердої фази на зносостійкість та основні механічні властивості матеріалів [43]
Традиційні карбідосталі з 40-60%
об’ємної частки ТіС є твердими сплавами, багатими на метал. Об’ємний вміст
тугоплавкої фази в карбідосталях значно більше, ніж в інструментальних сталях,
але менше, ніж в традиційних твердих сплавах. Це дозволяє після відпалу
піддавати їх всім видам механічної обробки, а після гартування та відпуску
карбідосталі мають відносно високу твердість та зносостійкість, в деяких
випадках не поступаючись відповідним характеристикам традиційних твердих
сплавів, однак завдяки високому вмісту металевої фази у них суттєво вищі
пластичність та в’язкість.
Властивості карбідосталей в значній
мірі залежать від властивостей тугоплавкої та металевої складових, а також від
міцності адгезійного зв’язку між ними. Остання повинна мати той же порядок, що
й міцність cкладових псевдосплаву, причому основну роль при утворенні між ними
міцного адгезійного зв’язку відіграє змочування тугоплавкої фази розплавом та
між фазна поверхнева енергія на границі розподілу тугоплавкої фази та металевої
зв’язки [43].
При виборі складових карбідосталей
необхідно також враховувати термодинамічну сумісність фаз. Це означає, що між
твердою фазою та металевою зв’язкою не повинно спостерігатися значного
взаємного розчинення або відбуватися відчутної хімічної взаємодії з утворенням
нових крихких фаз. Нарешті, при виборі компонентів необхідно враховувати також
їх термохімічну взаємодію, тобто компоненти сплаву повинні, по можливості, мати
близькі коефіцієнти термічного розширення, бо при їх суттєвій різниці виникають
відчутні термічні напруження на міжфазній границях, що зменшує міцність
останніх [43]. В зв’язку з цим, найуживанішою основною твердою фазою для
отримання карбідосталей так як і для отримання твердих сплавів, є переважно,
карбіди перехідних металів. Так, в переважній більшості твердих сплавів
використовується в основному монокарбід вольфраму WC завдяки його унікальним
властивостям серед інших твердих металоподібних сполук. Він має найбільший
модуль пружності Е в сполученні з деякою пластичністю при кімнатній температурі
[44]. Тверді сплави на основі WC відрізняються високою зносостійкістю в
поєднанні з високими властивостями міцності [45]. В той же час, для
використання в якості твердої фази карбідосталі з точки зору економічної та
технічної доцільності найбільше поширення знаходять тугоплавкі сполуки титану
(головним чином - TiC та Ti(C, B)). Такий вибір зумовлений, в першу чергу,
достатньо високими характеристиками твердості та пружності в цих сполуках [43].
Карбід титану по мікротвердості
переважає більшість інших карбідів перехідних металів (див. таб. 2.1). Він має
високу термодинамічну стабільність в металевих розплавах, високу температуру
плавлення, низьку щільність, високу корозійну стійкість [44]. Не менш важливо,
те що вихідна сировина для виробництва TiC не є дефіцитною.
Недоліками карбіду титану в
порівнянні з WC є його висока крихкість, великий коефіцієнт термічного
розширення, низька теплопровідність, відносно гірше змочування металами, більш
низька гаряча міцність у порівнянні з WC. Принциповою різницею TiC від WC є те,
що він має широку область гомогенності та здатен утворювати широкі області
твердих розчинів з іншими карбідами металів IV a … VI a підгруп [43, 44].
2.1.2 Аналіз структурних діаграм,
контактна взаємодія та змочування в системах сплавів Fe-Ti-C-В
Вибір оптимальних по властивостям та
складу композитів на основі системи Fe-Ti-C, режимів їх спікання та термічної
обробки заснований на аналізі відповідних діаграм стану системи.
Перед тим як перейти до розгляду
діаграми стану потрійної системи, коротко зупинимося і розглянемо бінарні
системи Fe-Ti та Ті-С.
В системі Fe-Ti (рис. 2.2) існує дві
інтерметалідні фази: Fe2Ti, що містить близько 30,0% Ti, та FeTi с
46,17% Ti з температурами плавлення відповідно 1427 та 1317°С. Сполука Fe2Ti
має більш широку область гомогенності (близько 10% ат. долей при 1300°С), ніж
FeTi (не більше 4% ат. долей).
Таблиця
2.1
Основні фізико-механічні
характеристики карбідів, боридів та нітридів перехідних металів IV a … VI a
підгрупи [239, 241]
Сполука
|
Е, ГПа
|
Мікротвердість
|
α×106,
К-1
|
λ, Вт/(м×К)
|
Тпл, К
|
γ, кг/м-3
|
σзтиснення,
ГПа
|
TiC ZrC HfC VC NbC TaC Cr3C2
Mo2C WC
|
494 410 480 495 479 550 370 531 737
|
3000 2800 2600 2880 2170 1830 1500 1830 1890
|
7,59 7,01 6,80 7,25 7,21 7,8 11,7 7,8 3,9
|
6,8 11,6 16,3 9,8 15,0 31,8 19,1 31,8 29,3
|
3530 3803 4233 2898 3660 2792 2103 2792 3054
|
4930 6730 12600 5360 7560 9040 6680 9040 15700
|
1,38 1,60 - 0,62 2,42 1,75 1,05 - 2,72
|
TiN ZrN HfN VN NbN TaN
|
390 374 480 390 484 576
|
1950 1500 1670 1300 1830 1440
|
9,35 7,24 6,90 9,20 10,1 3,6
|
41,8 28,2 19,0 2,9 4,2 5,5
|
3220 3260 3580 2300 2323 3360
|
5430 7090 11700 6040 8400 13800
|
1,30 1,00 - - - -
|
TiB2 ZrB2 HfB2
VB2 NbB2 TaB2 CrB2 Mo2B5
W2B5
|
541 496 480 340 638 687 450 672 775
|
3370 2250 2900 2800 2590 2540 2070 2330 2660
|
4,6 5,9 6,3 6,1 8,0 8,2 10,5 8,6 7,8
|
66,4 57,9 51,0 42,2 24,0 16,0 31,8 50,2 25,9
|
3063 3473 3523 2673 3050 3473 2473 2473 2640
|
4380 6170 10500 5100 6970 12380 5220 7010
11000
|
1,35 1,59 - - - - 1,28 - -
|
Температура евтектичного
перетворення Fe + Fe2Ti складає, по даним роботи [46], близько
1289°С, однак в літературі приводяться і інші значення (по даним [47] -
1340°С).
Гранична розчинність титану в -Fe, при
температурі евтектики досить висока і складає, по даним різних дослідників, від
8 до 13,74% ат. [41]. При зниженні температури розчинність різко зменшується,
складаючи при 700°С близько 2,3% ат. Розчинність Ti в -Fe більш низька:
максимально 0,70,9 [46] і навіть 0,2% ат. [43] при 11000С.
В системі Ti-C й досі не існує
єдиної думки про температуру плавлення карбіду титану: різні автори вказують
температури від 2940 до 3250°С [46, 47]. Максимальний вміст вуглецю в TiC
змінюється від 50% ат. (20% мас.) при температурі евтектики TiC + С близько
2900 °С, до 47,8% ат. при температурі евтектики -Ti + TiС при 1645°С (Рис.
2.3).
Карбід титану має широку область
гомогенності: низьковуглецева границя діаграми розміщена при температурі
евтектики -Ti + TiС, по даним різних авторів від 18 до 33% ат., що відповідає
складам від TiС0,22 до TiС0,49 [43]. Високовуглецева
границя точно не встановлена. При температурі евтектики TiС + С (2776°С) склад
карбіду близький до TiС1,0, а область гомогенності зазвичай
приймається в межах TiС0,48 - TiС0,98 [40].
Система залізо - титан - вуглець
відноситься до групи систем Me - C - Me, где Me - перехідний метал IV a
підгрупи, Me - метал групи заліза, типовим для якого є квазібінарна рівновага
евтектичного типу між MeC та Fe, Co або Ni [48]. Однак, квазібінарна рівновага
існує лише в достатньо вузьких межах складу карбіду в області гомогенності,
близькому до стехіометричного складу. При зниженні або підвищенні вмісті
вуглецю за межами квазібінарної рівноваги з’являються надлишкові фази, що зазвичай
призводять до зниження механічних властивостей сплавів.
Дослідження системи Fe-Ti-C,
результати яких приведені в публікаціях [49], дозволили визначити, що в
останній існують наступні тверді фази: та тверді розчини на основі титану,
графіт, інтерметаліди FeTi та Fe2Ti, тверді розчини заліза та і
карбідна фаза TiC. Потрійних сполук, що знайдені, наприклад, в системах MeC -
Me, а також подвійних карбідів титану або заліза не знайдено. Щодо твердо
фазної розчинності Ti, Fe і C, то не перевищує 2% ат. в більшості фаз аж до
температури плавлення. Розчинність Fe в TiC0,9 при 1475°С складає
близько 1 ат.%, а у відповідності до [47] - 0,7 мас.% при 1100°С. Твердофазна
розчинність TiC в -Fe або -Fe при будь-яких аж до температури евтектики (1475
°С) не перевищує 0,6 мас.% і швидко знижується зі зниженням температури: 0,2%
при 1200 0С та 0,04% при 920°С [50]. Розчинність вуглецю в фазах Fe2Ti
та FeTi згідно даним [49] не перевищує 0,2 мас.% (2,4 ат.%) і 0,1 мас.% (0,85
ат.%) відповідно.
Рисунок 2.2 - Діаграма стану системи
Fe-Ti
Рисунок 2.3 Діаграма стану системи
Ti-С
На Рис. 2.4 а, б представлені
ізотермічні перерізи діаграм системи Fe - Ti - С, отримані в різний час в
роботах [49]. Для обох приведених перерізів діаграми характерна наявність
областей фазової рівноваги:
Рисунок 2.4 - Ізотермічні перерізи
діаграми стану системи Ti-C-Fe при 1000 (а) та 1100 0С (б)
TiС + -Fe; + -Fe+
Fe, -Fe +
Ці області головним чином цікаві
тим, що оскільки саме в них знаходяться склади сплавів, маючих практичне
значення. В той же час, дані приведені в [49] відрізняються від даних [48]
існуванням трьохфазної області TiС + Fe3C + -Fe, що вказує на той
факт, що підвищення концентрації вуглецю в сплаві TiС - Fe веде до появи не
вільного вуглецю, як у відомих системах Ti-Ni-C або Ti-Co-C, а цементиту Fe3C.
При цьому, дані отримані з обох робіт схожі тим, що при зміщенні по діаграмі
стану в сторону зменшення в сплаві заліза, ширина областей + -Fe + -Fe і + -Fe
зменшується, а областей -Fe + збільшується. З чого слідує, що зі збільшенням в
сплаві вмісту TiC зменшується можливість отримання сплавів, що можна піддати
гартуванню, через те що зі зменшенням вмісту вуглецю нижче лінії:
С + -Fe + -Fe = + - Fe
сплави стають нетермооброблюваними в
зв’язку з відсутністю переходу.
Неоднозначна думка різних
дослідників відносно температури протікання двох псевдобінарних евтектичних
реакцій:
= TiC + Fe2Ti і L = TiC +
-Fe.
Так, по даним [49] ці значення
складають 1370°С и 1475°С відповідно, в той же час [47] вказують на значення
температури 1350 и 1520°С. Дані отримані В.Н. Єременко щодо реакції L = TiC +
-Fe близькі за температурою перетворення (1460°С) до даних [49], однак
різняться у визначенні складу евтектики: 3,8% мас. TiC (7 мол.%) по даним [50]
при 13 мол.% TiC в роботі [49]. В той же час склади евтектик, отримані в
роботах [46] и [49] досить близькі.
Формування структури карбідосталі, а
отже, її основні властивості в значній мірі залежать від характеристик
змочування застосовуваної сталі - зв’язки по відношенню до тугоплавкої фази,
температурної залежності зміни краєвого кута змочування q карбіду титану
сталлю, вихідного стану компонентів по вмісту домішок, що впливають на термокінетичні
параметри процесу спікання. Змочування забезпечує тісний контакт на міжфазній
поверхні тверде тіло - рідина та, таким чином, міцний зв'язок на контактній
поверхні тугоплавкої та металевої фази отриманого композиту. Крім того,
змочування в значній мірі визначає рівномірність розподілення твердої та
металевої фаз в об’ємі матеріалу [41].
Значний інтерес представляє
можливість оцінити впливу легування заліза різними елементами на змочування
карбіду титану. При цьому, в першому наближенні характеристику змочування можна
оцінити виходячи із значення поверхневого натягу розплаву gжт,
зменшення якого призводить до зменшення краєвого кута змочування. У
відповідності до роботи [51] поверхнево - активні елементи, що знижують gжт
є: Cu, B, Si, Zr, P, O, S, Cr, Sb, As, Mn, Ni. Поверхнево неактивним є:
C, N, V, Co, а підвищують значення gжт Ti, Mo, W.
В літературі приведено багато даних
щодо змочування карбіду титану залізом та сплавами на його основі [51-54 та
ін.]. Головним чином, інтерес представляють, дані про змочування TiC в вакуумі,
оскільки технологічні процеси отримання карбідосталей (спікання, просочування)
проводяться, як правило, в вакуумі. В середовищі аргону та особливо водню
залізо та його сплави змочують карбід титану помітно гірше [52], що можна пояснити
наявністю певної кількості залишкового кисню в застосовуваних захисних газах та
погіршенням очищення оксидних плівок в газах на відміну від вакууму.
Краєвий кут змочування TiC чистим
залізом по даним більшості авторів становить 40°, в той час як змочування
карбіду титану сплавами заліза може, в залежності від складу сплаву, чистоти
карбіду та температури, змінюватися в широких межах від 0 до 82° [52, 53].
Автори роботи [54], досліджуючи
контактну взаємодію карбіду титану зі сплавами на основі заліза в
температурному інтервалі 1480-1500°С, показали, що добавки Ni, Cr і Si, введені
в залізо, поліпшують його адгезію до карбіду титану, тобто є міжфазноактивними
елементами, а також сприяють формування гетерофазної, дрібнозернистої структури
контактної зони взаємодії. При цьому, для кожної з розглянутих добавок існує її
оптимальний вміст в сплаві, що мінімізує краєвий кут змочування. Так, зі
збільшенням вмісту нікелю в сплаві до 12 мас.% контактний кут збільшується до
54°, а потім, при вмісті нікелю 20-30 мас.% - зменшується до 11°. Оптимальне
значення вмісту хрому в Fe-Cr сплаві, що забезпечує кут змочування карбіду
титану в межах 30-34°, складає 11-16 мас.%. Більш високі адгезій ні
характеристики по відношенню до TiC забезпечують Fe-Si сплави, що пояснюється
досить високою міжфазною активністю кремнію. При вмісті кремнію в сплаві 2,9
мас.% краєвий кут складає 18°, та досягає нульового значення при 5,4 мас.%
[54]. Іншим сильним розкислювачем є - алюміній, також проявляє в розплавах
Fe-Ni та Fe-Cr значну між фазну активність, призводячи до значного зменшення та
підвищенню роботи адгезії.
Певний інтерес представляє питання
впливу вмісту вуглецю в сталевій зв’язці на змочування карбідної складової.
Автори роботи [52] показали, що при нагріванні в вакуумі рівновісні та
нерівновісні кути змочування карбідів (TiC та ZrC) розплавами Fe-C збільшуються
при підвищенні вмісту вуглецю в залізі від 1 до 4%. Зростання значення при
збільшенні вмісту вуглецю в сталі від 0,6 до 1,0% відмічено в роботі [54]. Ці
дані відповідають загальним уявленням про змочування, згідно до яких по мірі
наближення системи до стану рівноваги, що відбувається при збільшенні вмісту
вуглецю в сталі, взаємодія між карбідом та рідким металом послаблюється, а
значення , відповідно, збільшується [52].
Ступінь змочування карбідів в деякій
мірі змінюється, також, зі зміною складу карбідної фази. Для системи карбід -
метал з хімічною взаємодією на міжфазній границі величина θ
зменшується
разом зі збільшенням дефектності карбіду по вуглецю [53]. Поліпшення змочування
може бути досягнуто, також, шляхом легування TiC карбідами перехідних металів V
а та VI а підгруп, що краще змочуються металами групи заліза, ніж карбіди
перехідних металів Iv а підгрупи, до яких належить TiC. Одним з прикладів
такого підходу є ефект зниження при змочуванні подвійного карбіду (Ti, Nb)C
нікелем [52].
2.2 Теоретичні принципи формування
боровмісних композитів на основі залізовуглецевих сплавів
зносостійкість
штампування порошковий композит
Застосування бору як основний
легуючий елемент для виготовлення зносостійких порошкових композицій на основі
сплавів заліза зумовлюється цілим рядом його унікальних властивостей. Так,
автори [45] вважають, що використання бору (разом з ванадієм, титаном, ніобієм
і так далі) відкриває принципово нові можливості для отримання економно
легірованих сталей, експлуатаційні характеристики яких у багатьох випадках не
тільки не поступаються, але і перевершують рівень властивостей сталей, що
отримуються із застосуванням традиційної системи легування. Вибір бору, окрім
того, цікавий тим, що його евтектичні сплави із залізом мають, як правило, вищу
температуру плавлення, ніж чавун, добре змочують твердофазне залізо,
відновлюють оксиди і, що особливо цінно, схильні до гетерогенізації при
взаємодії з іншими легуючими елементами.
Аналіз діаграми стану FеB (рис.
2.10) показує, що введення бору значно знижує температуру плавлення заліза; що
знаходиться в лівій частині діаграми стану евтектика, що складається з α-Fe
і
бориду Fe2В, має мінімальну в системі Fe-В температуру плавлення
12000С
Борид заліза, як вказують автори
[53], характеризується високою твердістю, зносостійкістю, жаростійкістю і
корозійною стійкістю. Ці властивості бориду заліза використовують, зокрема, для
поверхневого борування сталей в газовій, рідкій або твердій борвмісній фазі
[55, 56].
Аналіз теоретичних уявлень про
механізм легування металів бором вказує на несприятливі умови впровадження і
заміщення заліза бором при боруванні, оскільки для цього потрібна в 300 разів
більше енергія деформації ніж, наприклад, для впровадження в залізо атомів
вуглецю [55].
Рисунок 2.5. Діаграма стану системи
Fe-B
В той же час, в евтектичних сплавах
металів групи заліза з бором відбувається утворення боридних з'єднань при
вельми низьких енергетичних витратах і температурах (Т = Тпл. - Тэвт.
= 300 4000С) [56]. Відмічені закономірності приводять до висновку
про можливість використання тиких чинників для вибіркового легування заліза,
яке полягає в тому, що при формуванні композиційних матеріалів на його основі в
процесі спікання проводиться переважне насичення бором і боридоутворюючими
елементами лише евтектичною складовою композиту. Така можливість досягається
завдяки низькій розчинності бору в залізі (до 0,08%) [45] при високому
коефіцієнті відношення діаметру їх атомів dВ/dFe = 0,76
[55], внаслідок чого дифузії бору з рідкої фази в залізний каркас аж до його
плавлення ускладнюється і практично весь бор витрачається на утворення боридних
з'єднань в евтектичній фазі з утворенням істотно гетерогенної структури
формуємого матеріалу.
Згідно діаграми стану системи залізо
бор [45] в цікавій для практичного застосування її частини утворюються два
боридних з'єднання Fe2В та FeВ.
Напівборид заліза Fe2В
утворюється при змісті бору 8,84% (мас.). Він має тетрагональну
просторово-центровану кристалічну гратку з параметрами а = 5,109 10-10
м, с = 4,249 10-10 м і відношенням с/а = 0,832. Піктометрична
щільність Fe2В знаходиться в межах 6,93 до 7,30 г/см3,
температура плавлення 1410 0С.
При еквімолярному відношенні
компонентів в даній системі утворюється моноборид заліза FеB з масовим вмістом
бору 16,25%. Він має ромбічну структуру; параметри його грат рівні: а = 4,061
10-10 м, в = 5,506 10-10 м, с = 2,952 10-10 м,
піктометрична щільність від 6,47 до 6,8 г/см3 і температура
плавлення 1650 0С [45]. При цьому, моноборид є стійкішим, ніж
напівборид заліза.
При утворенні бориду заліза атом
металу прагне до захоплення валентних електронів бору і заповнення ними
3d-полосы заліза, у зв'язку з чим щільність станів в d-полосе збільшується із
зростанням вмісту бору в бориді. Це приводить до перерозподілу
валентно-активних електронів між зв'язками різних типів таким чином, що
загальна міцність міжатомного взаїмодествія збільшується в результаті посилення
ковалентного зв'язку ВВ. Одночасно з переходом від Fe2В до FеB
змінюються властивості бориду заліза: збільшується питомий електричний опір і
температура плавлення, зростають мікротвердість і модуль пружності [45].
Структурні особливості будови граток
бориду заліза обох типів, ізольованість атомів бору в гратах бориду FеB обумовлює
їх специфічні властивості, зокрема високу твердість, тугоплавкість і
електропровідність.
Висока мікротвердість бориду
(близько 15000 і 20000 МПа відповідно) зумовлює також їх високу крихкість.
Твердість бориду і її збереження до високих температур 8509000С
обумовлена енергетичною стабільністю. Легуючі елементи молібден, вольфрам,
марганець і хром, підвищують твердість бориду Fe2В, а алюміній і
мідь, навпаки, знижують, тоді як на твердість бориду FеB легуючі елементи
впливають слабо [55]. Найбільш висока твердість бориду досягається тоді, коли
хімічний зв'язок атомів з бором здійснюється електронами, що належать переважно
атомам заліза, а атоми бору переходять в стан позитивно заряджених іонів.
Зменшення енергії відбувається при зростанні концентрації нелокалізованих
електронів за рахунок їх розпушуючої дії [54]. По міру збільшення частки
нелокалізованих електронів різко підвищується крихкість боридних з'єднань. При
цьому крихкість бориду FеB вища, ніж Fe2В.
Легуючі елементи, що ослабляють сили
міжатомного зв'язку (алюміній, мідь, нікель) зменшують крихкість бориду FеB, а
хром, марганець, молібден і вольфрам збільшує її [57].
Очевидно, що істотний вплив на
властивості спеченого композиційного матеріалу надає склад боровмісног
легуючого сплаву, використовуваного для введення в початкову шихту бору. За
даними роботи [56] найбільш поширеними в світовій практиці боровмісними
легуючими сплавами є феробор (12 20% B; 2% Si; 2% Al; 0,10% C) і силікобор (23%
B; 4045% Si; 0,2% Al; 0,05% C). Проте, враховуючи відсутність промислового
виробництва порошків вказаних сплавів, а також наявність в їх складі часто
небажаних сторонніх складових (Si, Al), в якості основного борвмісного
легуючого сплаву прийнято використовувати карбід бору.
2.3 Матеріали, устаткування і методика
досліджень
Для проведення досліджень були
використані наступні порошки: порошок заліза ПЖ1М1, порошок титану ПТХ7,
технічний порошок карбіду бору (ГОСТ 5744 - 74, 50 мкм), лампова сажа П514
(ГОСТ 7885).
Першим етапом роботи є приготування
порошкових сумішей, з елементарних порошків Fe, Ti та C (B4C), для
систем: Fe-Ti-C та Fe-Ti - B4C, вміст компонентів 20% Fe, 64% Ti та
16% C (B4C), виходячи із співвідношення 20% Fe - 80% TiC, вміст
карбіду бору аналогічний до вмісту вуглецю навмисно, хоча вміст вуглецю в
системі Fe-Ti-B4C звичайно менший за Fe-Ti-C, (рис. 2.6).
С, ваг%
Температура, °С С, ат%
Рисунок 2.6 - Діаграма стану системи
В - С (приведена з електронної бібліотеки HRW)
Всі математичні розрахунки тут і в
подальшому проводилися з використанням пакету програм Microsoft Office Excel
2007.
Розрахунок наважки шихти для
пресування проводиться за формулою:
n=Vnγср(1-f)k1k2,
(2.8)
де: Vn-об´ем
пресовки, що визначають по заданому відношенню H/d = 0,5…0,8, d - діаметр пресовки,
H - висота пре совки, H - (0,5…0,8)d; а Vn = π
d2 H/4; k1
k2 - коефіцієнти, що враховують втрати матеріалу (k1 =
1,005…1,01; k2 - визначають по вмісту кисню у вихідному матеріалі,
зв´язуючих речовин,
мастил). γk
- середня густина багатокомпонентної шихти, що визначаеться за законом
адитивності:
γср=(γ1
γ2
γ3…
γn)/(γ2γ3…
γn
а1+γ1γ3…
γn
а2+…γ1γ2
γ3…
γn
а(n-1)), (2.8)
де: γ1
γ2
γ3
- густини окремих компонентів шихти; а1,а2,а3
- масова частка окремих компонентів шихти.
Розрахунок проводили виходячи з
таких вихідних даних, що: d = 30 мм, H = 20 мм, з заданою вихідною пористістю f
= 0,2 (20%); приймаючи: k1 = 1,001, k2 = 1.
Отже для суміші системи Fe-Ti-C: γсрFe-Ti-C
= 3,7527 г/см3, GFe-Ti-C =
47,6153 г, відповідно:Fe = 9,5230 г;Ti = 30,4737 гC
= 7,6184 г.
А для Fe-Ti-B4C: γсрFe-Ti-B4C
= 4,3296 г/см3, Gn Fe-Ti-B4C
= 49,1865 г, відповідно:Fe = 9,8373 г;Ti = 31,4793 г;B4C
= 7,8698 г.
Було приготовано шихти, обох
складів, що відповідали масі необхідної на три зразка для кожного з вказаних
складів.
Змішування проводили в змішувачі
типу лабораторному баночному змішувачі з додаванням уайт-спириту та тіл, що
інтенсифікують процес змішування, запобігаючи розшаровуванню порошкових
компонентів шихти. Тривалість процесу змішування складає 1,5 год., швидкість
обертання 60 об/хв. Після змішування порошкова суміш просушувалась до повного
випаровування залишків уайт-спириту, з неї видалялися єрші. Далі складалися
наважки згідно вказаного вище розрахунку.
Пресування заготовок проводилося на
гідравлічному пресі ГП - 65, в прес-формах з діаметром робочого каналу 30 мм,
при навантаженні 500 МПа. Внутрішні стінки прес-форми підлягали змащування
машинним мастилом, для зменшення сил внутрішнього тертя. При пресуванні
заготовок використовувалася двостороння схема пресування.
Спікання заготовок в печі з
резистивним нагрівом Г-30А, потужністю 30 кВт, без контрольованої атмосфери в
активній зоні печі, при температурі 1200°С, на протязі 1 год. Контроль газового
середовища при спіканні заготовок здійснюється за допомогою використання схеми
плавкого затвору (рис. 2.7 (а,б)). Суть схеми полягає у створення
контрольованої відновлювальної атмосфери в об’ємі контейнеру, в якому
здійснюється спікання зразків.
Зразки поміщаються в циліндричний
контейнер, виготовлений з нержавіючої сталі, та запаковуються відповідно до
вказаних вище схем:
Невелика кількість парафіну, що
поміщується на дно контейнеру необхідна для витіснення кисню повітря з об’єму
контейнера, шляхом його розкладання при нагріванні разом з контейнером, за
реакцією:
С18Н38 + 27,5 О2
18 СО2↑ +19 Н2О↑
TiH2 при нагріванні до
температури 300-400°С розкладається згідно реакції:
2
→ Ti + Hатом. ↑
Витісняючи продукти реації розкладу
(газифікації парафіну) та утворююче відновлювальне середовище всередині
контейнеру, для чого потрібно невелика кількість водню, до того ж атомарній
водень має більш високу відновлювальну здатність, що є сприятливим фактом.
Гідрид титану повинен бути розміщеним в об’ємі контейнера з великою
обережністю, через те що титан, що утворюється при розкладанні TiH2
утворює з залізом легкоплавку евтектику, тому це може призвести до прогорання
контейнера.
Роль засипки виконує відпалений
пісок, що прокалюється при температурі 1200 °С на протязі 2 год., це дозволяє
позбавитись від вологи та по можливості газифікувати небажані домішки, тим
самим видаливши їх з об’єму піску.
Шар порошку заліза, це бажаний, але
не необхідний компонент паковки. Він необхідний для поглинання можливого
залишкового кисню в об’ємі контейнеру, через свою досить високу спорідненість
до кисню; його додавання підвищує вірогідність не окислення зразків.
а) контейнер з плавким затвором
зверху;
б) контейнер з плавким затвором
знизу.
Рисунок 2.7 - Схема спікання зразків
в контейнері з плавким затвором
Прокладка з листового азбесту
закладається для герметизації робочого об’єму контейнера, затримуючи вихід
водню та також перешкоджає затіканню розплаву скла всередину.
Невелика кількість піску, розміщена
шаром над азбестовою прокладкою відіграє роль загущувача розплаву скла, при
його плавленні та стіканні в об’єм робочої зони контейнера під своєю вагою, що
додаткова забезпечує чистоту робочого об’єму.
Верхній шар паковки складається з
суміші порошку скла з додаванням 15% бури (Na2B4O7*10H2O),
або борного ангідриду (B2O3), що дозволяє понизити
температуру плавлення скла на 50 °С та сформувати сам так званий плавкий
затвор; ступінь якості затвору можна визначити візуально по його зовнішньому
вигляду, гарним результатом є наявність рівномірної гладкої (дзеркальної)
поверхні затвору, відсутність свищів, каверн на поверхні дзеркала. При
необхідності порошок скла може додаватися в процесі спікання прямо в активну
зону печі.
Різниці між вказаних різновидів
схеми пакування з плавким затвором є, хоча і не суттєва; другий різновид трохи
більш трудомісткий, але й більш надійний в плані створення контрольованого
газового середовища в об’ємі контейнера, через те що контейнер перевернутий, що
додатково перешкоджає виходу водню з робочої зони контейнеру.
Металографічне дослідження:
Вирізка зразків: Вирізка зразків
металографічного дослідження проводилася з зразків, що піддавалися спіканню в
контейнері з плавким затвором при температурі 1200°С на протязі 1 год. Зразки
попередньо мали розміри 30×(20±2) мм.
Заготовки відбирали холодним
способом на метало оброблювальних верстатах. При відборі заготовок, а також при
приготуванні зразків були забезпечені всі заходи по запобіганню зразків від
нагріву та наклепу (зміцнення металу під дією пластичної деформації), що можуть
привести до викривлення структури та зміні властивостей.
При вирізці заготовок холодним
способом передбачався припуск від лінії зрізу до краю зразку розміром приблизно
4 мм.
Розмір і форма зразків визначаються
задачами дослідження. Зазвичай вирізані зразки циліндричної або прямокутної
форми (як в нашому випадку), висота яких рівна 10 мм, а площа досліджуваної
поверхні (шліфа) 2-3 см. Для запобігання пошкодження рук, із зразку були зняті
задирки та гострі краї обпилені терпугом.
Підготовка зразків до шліфування.
Для зручності приготування шліфів отримані зразки розміщувалися в металевих
оправках - кільцях круглої форми і заливалися заливалися епоксидним клеєм марки
ЭДП (ЭПОК01), представляє собою розчин епоксидної модифікованої смоли з
отверджувачем ПЭПА (поліетиленполіамін). Розчин готується з урахуванням
кількості отверджувача по відношенню до 100 частин епоксидної смоли 10 - 12
частин отверджувача ПЭПА. Процес приготування клею супроводжується
екзотермічною реакцією його тверднення, що обумовлено зшивкою полімерних
ланцюгів епоксидної смоли молекулами отверджувача. Час твердіння залежить від
величини приготованої проби та температури вихідної композиції (температури
зовнішнього середовища). При температурі вище 20 °С, час тверднення
скорочується та відповідно навпаки. Клеєва суміш готується безпосередньо перед
його використанням. Для точного дозування епоксидної смоли та отверджувача
рекомендується. Клейова суміш придатна до використання на протязі 1,5-2 годин
після приготування. Максимальна міцність, при температурі 20°С, досягається
через 24 години після заливки зразків. При приготуванні можлива зміна кольору
клейової суміші, але це не впливає на показники суміші. При змішуванні
епоксидної смоли з отверджувачем суміш зазвичай стає жовтуватого кольору. Для
інтенсифікації процесу приготування клейової суміші рекомендується підігрівати
суміш, використовуючи джерела закритого вогню, до температури не вище 75-80°С,
через миттєве спінювання, що робить її непридатною до використання.
Підігрівання призводить до зменшення в’язкості клейової суміші, полегшуючи
оперування нею. Додавання 15-20% ацетону сприяє зменшенню в’язкості клеєної
суміші. Залиті зразки, для прискорення процесу полімеризації, поміщують у
сушильну шафу на 1 годину, при температурі не вище 80°С.
Недолік цього методу в тому що
епоксидна клейова суміш та інші подібні речовини, що використовуються для
фіксації зразку в оправці, забруднюють поверхню шліфа та обробляючого матеріалу
при подальшій обробці.
Шліфування. На торцевій поверхні
зразку готується плоска поверхня, з чітко вираженою кромкою без закруглень.
Зразок оброблюють на станку з обертаючимся абразивним кругом, моделі 3Г71, при
великій швидкості обертання з охолодженням поверхні зразку водою та малим
натискуванням. В інакшому випадку, перегрів і сильна механічна дія можуть
викликати зміну мікроструктури, що призведе до хибного результату дослідження.
Отримана поверхня повинна бути пласкою і не мати завалів. Шліфування
металографічних зразків здійснювалося ручним способом.
При ручному способі шліфування на
жорстку пласку підкладку (товсте скло або лист металу), що розміщена
горизонтально, кладуть наждачний папір. Потім зразок ставлять на наждачний
папір заторцьованою площиною і шліфують з легким натискуванням. Шліфування
ведуть до повного зникнення рисок, що залишилися після операції торцювання.
Коли на шліфі залишаються риски тільки від паперу, шліфування зупиняють.
Шліфувальний папір видаляють з підкладки, отряхуючи з неї зерна абразиву, що
викришилися і частинки металу. Залишки абразиву видаляють також з підкладки та
шліфа, протираючи їх шматком чистої м’якої тканини або ватним тампоном. Після
цього операцію шліфування повторюють на папері з більш дрібним зерном. При
повторному шліфуванні напрямок руху зразку повинен бути перпендикулярним напрямку
рисок, що залишилися від попереднього шліфування (тобто перпендикулярно
попередньому напрямку руху зразку). Операцію шліфування повторюють,
використовуючи послідовно папір з меншим номером зернистості і кожен раз
змінюють напрямок руху шліфа на 90°. Змінення напрямку руху шліфа дозволяє
повністю усунути риски, що залишилися після попереднього шліфування. Закінчивши
шліфування на папері з найменшою зернистістю, зразок промивають проточною водою
і піддають поліровці. При шліфуванні використовувався наждачний папір, що
характеризується номером зернистості (пов'язаний з розміром зерен основної
фракції абразиву) приведеному в таб. 2.2.
Таблиця
2.2
Крупність основної фракції
використовуваного наждачного паперу при шліфуванні шліфів (ГОСТ 3647-80)
Номер зернистості
|
Крупність основної фракції, мкм
|
Номер зернистості
|
Крупність основної фракції, мкм
|
Номер зернистості
|
Крупність основної фракції, мкм
|
200 160 125 100 80 63 50 40 32 25
|
2500 - 2000 2000 - 1600 1600 - 1250 1250 -
1000 1000 - 800 800 - 630 630 - 500 500 - 400 400 - 315 315 - 250
|
20 16 12 10 8 6 5 4 3
|
250 - 200 200 - 160 160 - 125 125 - 100 100 -
80 80 - 63 63 - 50 50 - 40 40 - 28
|
М63 М50 М40 М28 М20 М14 М10 М7 М5
|
63 - 50 50 - 40 40 - 28 28 - 20 20 - 14 14 -
10 10 - 7 7 - 5 5 - 3
|
Полірування. Після завершення
шліфування на поверхні шліфа залишаються тонкі риски. Щоб остаточно вирівняти
поверхню, шліф полірують до дзеркального блиску. Полірування здійснювалося
механічним способом на полірувальному станку, моделі П - 2А. Поліровку
здійснювали на дерев’яному диску, змоченому масляною суспензією з алмазним
порошком 1-2 мкм, при швидкості обертання диску ~80 рад/с. При поліруванні шліф
періодично повертали для більш рівномірної обробки всієї поверхні.
Хімічне травлення. Для виявлення
мікроструктури отриманого матеріалу застосовувався метод хімічного травлення.
При хімічному травленні поверхня шліфа піддається дії хімічних реактивів на
протязі певного часу при певній температурі. Травлення зразків носило загальний
характер. Травлення проводили при кімнатній температурі поетапно з
використанням двох травників. Зважування хімічних речовин для приготування
реактивів проводилося на аналітичних терезах. Попереднє травлення здійснювалося
травником складу А:
пікринова
кислота (C6H2(NO2)3OH -
тринітрофенол)
|
1 г,
|
HCl
|
4 мг,
|
C2H5OH
(розчинник)
|
100 мг.
|
Даний склад застосовується для
виявлення первинної структури при зварюванні або при наплавці вуглецевих та
мало вуглецевих сталей.
Микрошліфи спочатку декілька разів
травлять складом А по 60 с з проміжними переполіровками до усунення слідів
вторинних структур. Після чого промивають проточною водою та сушать етиловим
спиртом.
Основне травлення проводять
травником складу В:
HCl
|
4 мг,
|
CuCl2
|
5 г,
|
C2H5OH (розчинник)
|
25 мг,
|
Дистильована вода (розчинник)
|
30 мг.
|
Виявлення мікроструктури матеріалу
при хімічному травленні проводилося шляхом змочування поверхні шліфа травниками
вказаного складу. При використанні обох травників декілька крапель травника
наносилося на поверхню шліфа піпеткою, витримувалося і змивалося етиловим
спиртом. Після промивки шліфи ретельно висушували на фільтрувальному папері.
Якість травлення перевіряли під мікроскопом, моделі МИМ-7, при тому ж
збільшенні, що й дослідження шліфа.
Очищення шліфів проводилося на
ультразвуковому диспергаторі, моделі УЗДН - А, в розчині складу 50% етилового
спирту та 50% бензину, на протязі 5 хв (час промивки визначався
експериментально). Після промивки можна візуально спостерігати металічний блиск
поверхні мікрошліфа, що зумовлюється очищенням пор зразка від оксидної плівки,
забруднень обумовлених процесами шліфовки та поліровки, а також часткове
позбавлення від клейову суміш, що відбувається за рахунок високої енергії
кавітаційні пухирців.
Мікроскопічне дослідження проводили
візуальним спостереженням на металографічному мікроскопі ,МИМ-8 при
використанні оптичного збільшення 150 та 600.
Вимірювання мікротвердості.
Вимірювання мікротвердості, що дозволяє визначити твердість окремих фаз та
структурних складових тонкого поверхневого шару, проводили на приладі моделі
ПМТ-3. Випробування проводять згідно ГОСТ 9450 - 76. Мікротвердість визначали
на пласкій полірованій чистій поверхні. При приготуванні зразка особлива увага
приділялася до запобіганню наклепуванню та нагріванню поверхні, що може
призвести до відхилення величини мікротвердості. Дослідження здійснювалось при
навантаженні в 50 г, при виборі навантаження керувалися розміром площі ділянки,
твердість якої змінюється, і товщиною зразка. В якості індентора
використовувалась алмазна піраміда з кутом при вершині 136°. Перед початком
випробувань проводилася перевірка приладу на зразках еталонах для встановлення
автентичності його результатів.
Щоб не проводити розрахунки
мікротвердості за формулою згідно методики, використовували таблицями (додатки
до ГОСТ 9450 - 76), в яких приведені значення мікротвердості в залежності від
прикладеного навантаження та довжини діагоналі відбитку.
Точність вимірювань при використанні
окуляру 10 становить ±0,5 найменшого ділення шкали (при збільшенні об’єктиву
30-40×).
Спечені зразки дробилися під прессом
з мінімально можливим навантаженням, запобігаючи наклепуванню матеріалу.
Отриманий порошок просіювався відділяючи фракцію в 100 мкм; та піддають
рентгено-фазовому аналізу разом з шматочками спеченного матеріалу.
Рентгенівський фазовий аналіз проводився на дифрактометрі ДРОН-3.0 в
кобальтовому Кα-випромінюванні
при напрузі U = 30 кВ, струмі І = 17 мА, без фільтру, з використанням
фокусування трубки по схемі Брегга-Берттано. Сканування з кроком 0,05° при
витримці в точці 4 с. Розрахунок результатів рентгенівського аналізу проводився
з використанням програми FindPike, та електронної рентгенівської бібліотеки
PCPDFWIN 2000.
Готувалися аналогічні за складом до
складу лігатури суміші, але їх спікання проводиться в контейнері з плавким
затвором, де зразки поміщені в графітову трубу. Наявність графітової труби
пояснюється окисленням зразків при попередніх спіканнях; її нагрівання
призводить до взаємодії вуглецю труби з повітрям в об’ємі контейнеру, утворюючи
відновлювальну атмосферу.
Розмел спеченої композиції проводили
у планетарному млині, моделі ВПК2111У2, в середовищі етилового спирту, за
режимом:
2,5 хв розмел,
хв зупинка та
охолодження млина,
,5 хв розмел.
Отримана емульсія вивантажувалася з
барабанів разом з розмеленими тілами в піддони та просушувають на повітрі при
кімнатній температурі до повного висихання, випаровування етилового спирту
(приблизно на протязі доби). Після чого проводилося зважування отриманого
порошку (див. таб. 2.3).
Таблиця
2.3
Втрати маси на операції розмелу
порошкових сумішей
Склад порошкової суміші
|
Маса до розмелу, г
|
Маса після розмелу, г
|
Fe - Ti - C
|
150
|
136,20
|
Fe - Ti - B4C
|
150
|
145,85
|
Отримані порошкові систем Fe-Ti-C (B4C
) суміші є лігатурою для приготування шихт призначених для процесу гарячого
штампування. Вихідні склади шихт для процесу гарячої штампування мелють склад:
Fe - 10% TiC,- 20%
TiC,- 30% TiC.
Розрахунок необхідної кількості
проводився виходячи з складу лігатури (20% Fe - 80% TiC), за формулою:
0,8m / (m + x) = y,
де m - маса наважки, г; x -
кратність мас лігатури та порошку Fe,що необхідно додати, г; y - заданий вміст
TiC,%.
В приведеній нижче таблиці (таб.
2.4) показана маса порошку заліза та маси лігатури, яку необхідно додати.
Таблиця
2.4
Співвідношення мас лігатури та
порошку заліза при приготуванні вихідної шихти під гарячу штамповку
Вміст TiC в шихті,%
|
Маса порошку Fe, г
|
Кратність приведених мас
|
10
|
22,5
|
157,5
|
7
|
20
|
45
|
135
|
3
|
30
|
66,(6) ~ 66,7
|
113,4
|
1,(6) ~ 1,7
|
Враховуючи великий вміст карбідної
фази в об’ємі зразків випливає неможливість їх піддання гарячому штампуванню
через їх високу крихкість, тому в якості підтримуючої конструкції
використовується обойма, виготовлена з сталевої водогазопровідної (газової)
труби, згідно ГОСТ 3262-62. Використовується не оцинкованих (чорний), з
зварними швами різновид цих труб, без різьби та фланців.
За умові розмірів штампового
інструменту, з робочим діаметром d = 43 мм та робочою висотою h = 7 мм,
підберемо розмір (диаметр) обойм під гаряче штампування. Відповідно до
приведеної нижче таблиці (таб. 2.7)та враховуючи розміри штампового інструменту
вибираємо трубу під обойму.
Оптимальним при заданих умовах
виявляється труба з умовним проходом в 25 мм (1 дюйм), 25ГОСТ 3262 - 62.
Таблиця
2.7
Сталеві водогазопровідні труби,
згідно ГОСТ 3262-62
Умовний прохід
|
Труби
|
мм
|
дюйми
|
Зовнішній діаметр, мм
|
Маса на 1 кг (без муфти)
|
Товщина стінки, мм
|
15
|
½
|
21,3
|
1,28
|
2,8
|
20
|
¾
|
26,8
|
1,66
|
2,8
|
25
|
1
|
33,5
|
2,39
|
3,25
|
32
|
1 ¼
|
42,3
|
3,09
|
3,25
|
40
|
1 ½
|
48
|
3,84
|
3,5
|
Проводимо розрахунок висоти труби
(рис. 2.8) відповідно до кількості порошкової суміші необхідної для досягнення
заданої щільності після гарячого штампування отриманих зразків (таб. 2.8).
Рисунок 2.8 - Обойма для заготовок
під гарячу штамповку
Розрахунок вихідної висоти обойми
виходячи з наведених умов: розмірів штампового інструменту, щільність зразків
після гарячого штампування.
V = Vтр + Vпор
= const
;трн
= π
(D02 + d02)
h0 / 4;
де Vтрн
- вихідний діаметр труби; D0, d0, h0 - вихідні
зовнішній, внутрішній діаметр та висота обойми відповідно,
трк = π
(Dк2 + dк2)
hк / 4;
де Vтрк
- кінцевий діаметр труби; Dк, dк, hк - кінцеві
зовнішній, внутрішній діаметр та висота обойми відповідно,
к =
D,
де D = 43 мм - діаметр
штампового інструменту,
трн = Vтрк,пн
= π
d02 h0
/ 4,
де Vпн
- вихідний об’єм порожнини в обоймі,
пк = π dк2 hк
/ 4,
де Vпк
- кінцевий об’єм порожнини, після деформації обойми,
пн = Vпк,
Складаємо систему рівнянь:
Vтрн = Vтрк,
(2.9)
Vпн = Vпк.
(2.10)
Враховуючи щільність вільно
насипаного порошку (γнас
- насипна щільність), а також щільність компактного порошку (γк),
перейдемо в рівнянні (2.9) та (2.10) до щільностей і отримаємо систему рівнянь.
π (D02
- d02) h0
γтрн/
4 = π (Dк2
- dк2) hк γтрк/
4, (2.11)
π d02
h0 γн/
4 = π dк2
hк γк/
4, (2.12)
де γтрн
, γтрк
- щільності труби-обойми до та після деформування при гарячому штампуванні
відповідно, γн
, γк
- щільність порошку до гарячого штампування (насипна щільність порошку) та
компактного порошку відповідно.
Припускаючи, що γтрн
= γтрк
(D02 - d02)
h0 = (Dк2 - dк2) hк,
(2.13)
d02 h0
γн=
dк2 hк γк, (2.14)
З рівняння (6) виразимо:
к2 = d02
h0 γн / hк
γк,
та підставимо у рівняння (5), отримуємо:
(D02 - d02)
h0 = (Dк2 -( d02 h0
γн / hк
γк)) hк,
Виражаємо з отриманого рівняння h0:
h0
= Dк2 hк/(( D02 - d02)
+ (d02 γн/
γк)).
(2.15)
Для розрахунку вихідної висоти
обойми визначимо насипної щільності вихідної порошкової суміші. Визначення
насипної щільності проводилося згідно ГОСТ 19440-74.
Результати вимірювань насипної
щільності порошкових сумішей приведені в таб.2.8.
Таблиця
2.8
Насипна щільність порошкових сумішей
Для системи з лігатурою складу
|
Вміст TiC,%
|
Насипна щільність порошкових сумішей, г/см3
|
Fe - Ti - C
|
10
|
3,9083
|
|
20
|
3,6874
|
|
30
|
3,4886
|
Fe - Ti - B4C
|
10
|
3,9220
|
|
20
|
3,9810
|
|
30
|
3,9970
|
Результати розрахунку висоти обойми,
згідно формули (2.15), приведено в таблиці 2.9.
Таблиця
2.9
Результати розрахунку висоти обойми
для зразків під гаряче штампування
Суміш №
|
Для системи з лігатурою
|
Вміст TiC в суміші,%
|
Вихідна висота обойми, мм
|
1
|
Fe - Ti - C
|
10
|
25,6460
|
2
|
|
20
|
25,7120
|
3
|
|
30
|
25,7460
|
4
|
Fe - Ti - B4C
|
10
|
25,6370
|
5
|
|
20
|
25,2080
|
6
|
|
30
|
25,9080
|
Враховуючи отримані результати
вихідної висоти обойми приймаємо висоту обойми за 26 мм. Розрахунки проводили з
урахуванням 5-10% облою зразків при гарячій штамповці.
Пресування зразків під гаряче
штампування проводиться на пресі приведеної вище моделі, при навантаженні в 50
т (620МПа), в матриці з діаметром робочого каналу 40 мм, при вільній засипці
порошкової суміші. Схема пресування заготовок показана на рис 2.9.
Рисунок 2.9 - Схема пресування
заготовок під гарячу штамповку
Отримані заготовки піддають
розігріву до температури 1200°С в середовищі Ar, на протязі 15 хв, в печі
шахтного типу, моделі ШП-1(рис. 2.11 ). Розігріті заготовки підлягають гарячій
штамповці вільною осадкою у відкритому штампі (рис. 2.12), на не нахиляємому
одно кривошипному пресі простої дії, моделі КВ 2132 (рис. 2.13), з номінальним
зусиллям 1600 кН, з швидкістю деформування 1000 м/с.
Рисунок 2.10 - Вигляд заготовок під
пресування під гарячу штамповку
Рисунок 2.13 - Прес, моделі КВ 2132
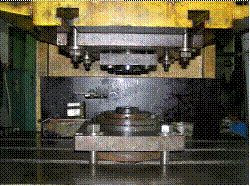
Рисунок 2.12 - Зовнішній вигляд
відкритого штампу
Рисунок 2.11 - Зовнішній вигляд
шахтної печі ШП-1
На рис. 2.14 заготовки після
гарячого штампування, а на рис. 2.11 показаний прес КВ 2132
Рисунок 2.14 - Зовнішній вигляд
заготовок після гарячої штамповки
Після гарячого штампування зразки
піддавали відпалу при 850 0с, після чого проводили їх гарт з
температури 870 0С у воду з подальшим відпустком при 1800С
протягом 3600 с.
Щільності матеріалудо до (після
пресування з металічною обоймою) та після ущільнення методом гарячого
штампування здійснюється за методом гідростатичного зважування, згідно ГОСТ
20018-74. Щільність визначалася з урахуванням щільності води, що змінюється в
залежності від температури навколишнього середовища, таб. 2.10.
Таблиця
2.10
Щільність отриманого зразків
Для сплавів з лігатурою
|
Вміст твердої фази,%
|
Середня щільність зразків, г/см3
|
|
|
Після пресування
|
Після ГШ
|
Fe - Ti - C
|
10
|
7,4225
|
7,7998
|
|
20
|
7,0232
|
7,6781
|
|
30
|
6,9647
|
7,4953
|
Fe - Ti - B4C
|
10
|
7,2113
|
7,6956
|
|
20
|
6,7821
|
7,3987
|
|
30
|
6,6647
|
7,2764
|
Рисунок 2.15 - Схема розкрою на
штапики для визначення механічних властивостей: 1, 2 - зразки на вигин; 3, 4 -
зразки на в’язке руйнування
Отримані зразки спочатку зачищалися
на абразивному крузі, а потім розрізалися на електроіскровому верстаті, моделі
4531, на прямокутні штапики за схемою, рис 2.15. В результаті такого розкрою
циліндричної заготовки були підготовані зразки для механічних випробувань.
Випробування на вигин проводилися по
трьохточковій схемі навантаження. Відстань між опорами становила 20 мм.
Більшість зразків мали розмір 6,25 мм. Випробування проводилися на
випробувальній машині 123У 10, при швидкості навантаження 1 мм/хв. Розрахунок
межі міцності при вигині проводився за формулою:
, (2.15)
де P - зусилля руйнування, Н;-
відстань між опорами, мм;- ширина зразків, мм;- висота зразка, мм.
В’язке руйнування КIс
визначали за схемою трьохточкового вигину при відстані між опорами 16 мм на
машині «Plastics Bending Tester» (Венгрія). Розміри зразків становили мм. По
середині зразка робили надріз глибиною 1,5 мм електроіскровим способом латунним
дротом діаметром 0,2 мм, а потім поглиблювали на 0,2 - 0,5 мм вольфрамовим
дротом діаметром 0,06мм, що при русі з абразивними частинками зношувала
матеріал. Поглиблення проводили на верстаті «Wire Saw type WS-22». Значення
в’язкості руйнування проводили за формулою:
, (2.16)
де а - глибина набрізу,
(2.17)
Твердість зразків визначалася за
допомогою піраміди Віккерса на приладі ТП-2 при навантаженні 30 кг.
Результати механічних випробувань
приведені в таб. 2.11.
Таблиця
2.11
Результати механічних випробувань
Склад матеріалу
|
Вміст твердої фази,%
|
σзг,
МПа
|
KIc
|
HRC (після ГШ)
|
HRC (після відпалу
|
HRC (після гартування та відпуску)
|
Fe - Ti - C
|
10
|
2130 2160
|
23,2 26,8
|
30 - 35
|
25 - 30
|
31 - 37
|
|
20
|
1900 1940
|
24,3 25,0
|
39 - 43
|
29 - 33
|
41 - 45
|
|
30
|
1710 1760
|
51,6 - 52,2
|
66 - 69
|
32 36
|
59 - 64
|
Fe - Ti B4C
|
10
|
2030 2080
|
18,3 20,5
|
33 - 38
|
30 - 34
|
43 - 48
|
|
20
|
1810 1850
|
20,8 23,0
|
43 - 47
|
34 - 39
|
50 - 55
|
|
30
|
1590 1630
|
48,7 - 43,2
|
72 - 75
|
40 - 45
|
68 - 70
|
Випробування зносостійкості
матеріалів з різним вмістом зміцнюючої фази. Умови досліджень.
Швидкість ковзання - V 1,5 м/с. Контактний тиск 2,0 МПа. Тертя без змазки.
Матеріал контр тіла : алмазний круг. Шлях тертя, L-1 км на кожному
навантаженні; S зразка - 5,4-5,6 см2.
Випробування зносостійкості
матеріалів проводилися в парі з алмазним кругом на машині тертя М-22М.
Триботехнічні властивості визначалися по методиці ГОСТ 26614-85. Сутність
методики полягає у визначенні залежності величини зносу і сили тертя від
швидкості ковзання і сили навантаження і в обчисленні їх інтенсивності
зношування і коефіцієнтів тертя.
Вибір швидкості ковзання і
навантаження, при терті без змазки, залежать від складу і міцності
досліджуваних матеріалів (зразок - контртіло) і допустимої температури в вузлі
тертя при фрикційному розігріві.
Композиційні матеріали, які містять
карбіди металів, володіють високою твердістю і тому доцільно їх зносостійкість
визначати в парі з абразивним матеріалом (контртілом). В даному випадку в
якості абразиву використовували алмазний круг АСВ180/125 по ГОСТ16167-80 і
швидкістю ковзання 1м/с з похибкою частоти оберту вала не більше 5%.
Інтенсивність зношування зразка і
контртіла визначалися методом ваги - взвішування зразка і контртіла до і після
випробування через кожний км шляху тертя при ступінчатому навантаженні. Товщина
зразка визначалася з похибкою електронного мікрометра, не більше 0,01.
Результати триботехнічних
випробувань приведені в таб.2.12.
Випробування повторювалися не менше
трьох разів з заміною зразків і за оцінку інтенсивності зношування зразка
приймали середнє арифметичне значення.
Таблиця
2.12
Результати триботехнічних
випробувань
Сплав системи
|
Вміст твердої фази,%
|
Коефіцієнт тертя, f
|
Знос, мкм/км
|
Fe - Ti - C
|
10
|
0,23
|
2,50
|
|
20
|
0,27
|
1,93
|
|
30
|
0,25
|
1,04
|
Fe - Ti B4C
|
10
|
0,24
|
1,97
|
|
20
|
0,25
|
1,45
|
|
30
|
0,26
|
0,98
|
3. Обговорення результатів
3.1 Дослідження можливостей
отримання композиту Fe - Ti - C(B4C) в результаті виділення
карбідних фаз при спіканні
3.1.1 Вивчення умов сплавоутворення
при реакційному спіканні порошків системи Fe - Ti - C
Аналіз отриманих вище результатів,
рівно як і відомі дані інших авторів [59, 61, 61], показують, що при
використанні традиційної технології отримання карбідосталей, що включає помел і
змішування шихти, що складається з порошків карбіду титану і сплаву на основі
заліза, не вдається повною мірою реалізувати їх позитивні властивості із-за
неповної змочуваності карбіду титану сталевою зв'язкою і інтенсивного зростання
карбідних зерен в процесі рідкофазного спікання. Часткове окислення карбідних
частинок, що відбувається при помелі шихти, погіршує їх змочуваність розплавом
стали і веде до появи важкоусувуваних пор, що істотно знижують механічні
властивості матеріалу. Крім того, неможливість надійно забезпечити чистоту
міжфазних меж в спеченому матеріалі знижує міжфазну міцність композиту, що
також негативно позначається на його показниках міцності.
При рідкофазному спіканні сплавів
TiC сплав на основі заліза рідка фаза заповнює проміжки між твердими частинками
і викликає взаємне переміщення частинок під впливом сил поверхневого натягу.
При цьому, процес спікання супроводжується розчиненням в рідкій фазі дрібних
карбідних частинок і перенесенням їх речовини на крупніші. В результаті дрібні
частинки зникають, а крупні ще більш збільшуються. У зв'язку з цим, при
використанні традиційної технології отримання карбідосталей із застосуванням
рідкофазного спікання, достатньо складно одержати дрібнозернисту структуру,
оскільки необхідність отримання щільного сплаву зумовлює застосування досить
високої температури спікання, що активує, разом з ущільненням композиту,
активний ріст зерен.
Проте, з досвіду отримання і обробки
гетерофазних матеріалів відомо, що якнайкращий зв'язок між фазами
забезпечується в умовах виділення фаз при розпаді твердих розчинів. Це ж явище
може спостерігатися при виділенні карбідних фаз з матриці на основі
інтерметаллідов. У разі реалізації цього ефекту з'являється можливість впливати
на швидкість росту карбідних зерен, що зароджуються, і тим самим формувати
дрібнозернисту структуру, здатну підвищити як физико-механічні параметри
матеріалу, так і його зносостійкість.
У зв'язку з вищевикладеним, був
запропонований новий підхід до отримання високозносостійких дрібнозернистих
композитів системи карбід титану сплав на основі заліза, що полягає в тому, що
карбідна фаза не вводиться в початкову шихту у вигляді порошку карбіду титану,
а формується в процесі сплавообразованія при спіканні порошкових сумішей, що
складаються з порошків титану, заліза (стали) і вуглецю [62, 63].
Суть такого підходу заснована на
наступних міркуваннях. Аналіз діаграми стану Fe - Ti (рис.2.2) показує, що у
області концентрацій Ti близько 53 ÷ 77% (ат.)
у системі існує низькотемпературна евтектична зона з температурою плавлення
1085 0С. З діаграми стану видно, що при нагріванні порошкової суміші
вище вказаної температури сплав складатиметься з інтерметалліда FeTi і Ti. При
додаванні до такого сплаву вуглецю, що знаходиться в порошковій суміші, і
враховуючи високу спорідненість вуглецю до титану і хорошу його розчинність в
залізі, створюються сприятливі умови для активної взаємодії між компонентами
шляхом реалізації відомих реакцій:
TiFe
+ C TiC + Fe;(3.1)
Ti
+ C TiC;
частинок карбіду титану, що
супроводжуються виділенням в результаті реакцій.
Реакційне спікання зпресованих
заготовок проведене в по схемі контейнера з плавким затвором показоно на
рисунку 3.2. На рис. 3.1 показаний зовнішній вигляд зразків після пресування.
Рисунок 3.1 - Зразки отримані після
пресування
Рисунок 3.2 - схема спікання зразків
в контейнері з плавким затвором, при наявності графітової труби
Результати експериментального
спікання показують, що при 10000С зразки практично не
спікаются і є рихлою губкою із слабкими міжчастковими зв'язками.
Підвищення температури спікання до
12000С істотно змінює характер одержуваного матеріалу. Зразки після
спікання при таких температурах є достатньо міцними, але розділений на прошарки
конгломерати, зразки, що нагадують на вигляд, одержувані при СВС синтезі. При
цьому після спікання спостерігається помітне об'ємне зростання пресовок.
Зовнішній вигляд зразків після спікання показаний на рис. 3.3.
Рисунок 3.3 - Зовнішній вигляд
зразків після спіканн в контейнері з плавким затвором
Мікроструктури сплавів, одержаних
при реакційному спіканні сумішей, розрахованих на формування різних
стехіометричних значень TiСx, представлені на рисунках 3.3 а, б.
Структури характеризуються рівномірно розподіленими за розміром карбідними
зернами, оточеними прошарками металевої зв'язки. Розмір карбідних зерен складає
0,6-2 мкм, зерна боридів приблизно в 2-3 рази менші.
Фотографії мікроструктури матеріалу зразків
приведені на рис. 3.4 а,б.
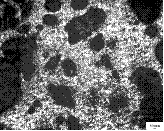
а) б)
Рисунок 3.4
а - Мікроструктура матеріалів системи Fe-Ti-C
а - Fe-Ti-C (×150);
в - Fe-Ti-C (×600);
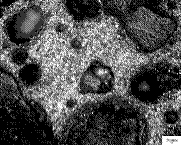
а) б)
Рисунок 3.4 б - Мікроструктура матеріалів
системи Fe-Ti- B4C
а - Fe-Ti-B4C (×150);
б - Fe-Ti-B4C (×600)
Детальне вивчення мікроструктур
показало, що при структутворені має місце акомодація карбідних зерен в місцях
їх зближення, причому металевий прошарок між зернами зберігається і в структурі
практично не спостерігається зрощення карбідних зерен. Карбідні зерна
рівномірно розподілені по обєму і відносно однорідні за розміром.
Таблиця
3.1
Результати вимірювання
мікротвердості фаз
Фаза
|
Н, кг/мм2
|
|
Fe -Ti - C
|
Fe - Ti - B4C
|
TiC
|
2950 - 3000
|
2850 - 2970
|
Fe3C
|
930 - 1050
|
800 - 1000
|
TiB
|
-
|
2700 - 2800
|
TiB2
|
-
|
3300 - 3370
|
Fe
|
75 - 90
|
Ti
|
98 - 105
|
FeB
|
730 - 790
|
Рентгенівський аналіз сплавів
показав наявність в сплаві фаз: у системі Fe Ti C: основа TіC, проте
прісуцтвуєт незначна кількість Fe, що не прореагували, Ti і C, відмічена
наявність цементіта; у системі Fe Ti В4С: також переважна наявність
TіC, Ti, що не прореагував, а також FеB, Ti2В5 (рис. 3.5
а, б).
(а), (б)
Рисунок 3.5 а - Дифрактограми
вихідних порошкових сумішей та спечених зразків сплавів вихідна порошкова суміш
(а), сплав системи Fe - Ti - C (б)
(в), (г)
Рисунок 3.5 б - Дифрактограми
вихідних порошкових сумішей та спечених зразків сплавів вихідна порошкова суміш
(в), сплав системи Fe-Ti-B4C (г)
евтектичної температури (1085 0C).
При цьому, проте, можливий лише дифузійний механізм взаємодії на
контактних поверхнях частинок компонентів.
Після досягнення вказаної
евтектичної температури в областях, близьких до контактних зон, починається
розм'якшення і плавлення компонентів; поверхня контакту між компонентами швидко
збільшується і між ними починається хімічна реакція відповідно до рівняння
(3.1). При цьому, взаємодія між титаном і вуглецем супроводиться екзотермічною
реакцією, проходження якої підтверджується даними ДТА суміші титану, заліза і
вуглецю (рис. 3.6).
а) - при вмісті в суміші 45%Ті;
б) - при місті в суміші 75% ті
Рисунок 3.6 - Крива ДТА системи
залізо - Ti C
При нагріванні суміші порошків
Fe+Ti+С не виявлено поглинання тепла, проте має місце його виділення в
результаті екзотермічної реакції між компонентами, причому початок реакції
відповідає діаграмній температурі плавлення залізо титанової евтектики - 10850С.
Ймовірно, ендотермічний ефект плавлення перекривається значно могутнішим
екзотермічним ефектом.
Одним найбільш з важливих параметрів
екзотермічної реакції є адіабатична температура tад., тобто
температура, до якої мимоволі нагрівається система при протіканні даної
реакції. Наявність рідкої фази максимально сприяє контакту взаємодіючих
компонентів, а тепло, що виділяється в результаті проходження екзотермічної
реакції, додатково стимулює її розвиток.
Отримані результати дозволяють
скласти уявлення про механізм сплавообразованія при спіканні порошкових сумішей
системи. Одним з найбільш важливих параметрів екзотермічної реакції є
адіабатична температура tад., тобто температура, до якої самовільно
нагрівається система при протіканні даної реакції. Наявність рідкої фази
максимально сприяє контакту взаємодіючих компонентів, а тепло, що виділяється в
результаті проходження екзотермічної реакції, додатково стимулює її розвиток.
Унаслідок виділення з рідкої фази
частинок карбіду титану, розплав поступово обідняється титаном; при цьому,
відповідно до діаграми стану Ti Fe, в складі сплаву, що змінюється,
підвищується температура ліквідус, а потім і солідус, і після максимально
повного проходження реакції формування карбідів відбувається кристалізація
розплаву з виділенням частинок TiСх відповідної стехиометрії і
залізної (сталевий) зв'язки. Зерна карбідної фази, що зароджуються, мають
здатність швидко рости, причому інтенсивність їх зростання безпосередньо
залежить від температурних параметрів реакції. Відмічені особливості структури,
пов'язані із збільшенням вмісту вуглецю в суміші, пояснюються, мабуть, тим, що
при цьому створюються умови для інтенсивнішого протікання екзотермічної
реакції, відбувається більше саморозігрівання системи, яка сприяє зростанню
карбідних зерен. З вищевикладеного виходить, що регулюючи температуру
саморозігрівання композиції, можна керувати зростанням карбідних зерен.
Слід зазначити, що схожість
зовнішнього вигляду одержуваних при реакційному спіканні зразків із зразками
карбіду титану, синтезованими із застосуванням методу СВС, і подібність
об'єктів досліджень приводить до необхідності враховувати основні принципи
відомих моделей СВС процесів [63 - 65], вивчених, зокрема, в роботах А.Г.
Мержанова із співробітниками.
Так, в роботі [65] автори
запропонували механізм протікання процесу, який розділили на чотири етапи:
прогрів суміші; плавлення і розтікання титану з одночасною хімічною реакцією;
первинне структуроутворення дрібних карбідних частинок і рекристалізація
карбідних частинок. Авторами відмічено, що при появі розплаву Ti
спостерігається його втягування в дрібнодісперсний вуглець і обволікання
розплавом вуглецевих частинок, а зародки зерен TiC з'являються практично
одночасно з початком розтікання титану. При цьому, спочатку в зоні горіння
утворюється нестехіометричний карбід близький TiC0,5, який в зоні
догорання переходить в TiC. Механізмом перетворення TiC0,5 TiC1,0,
на думку авторів роботи, є одночасне проходження процесу розчинення карбідів з
меншим x в розплаві і кристалізації карбідів з більшою концентрацією вуглецю.
На рис. 3.7 приведені мікроструктура зразків після рідко фазного спікання (а)
та гарячого штампування (б).
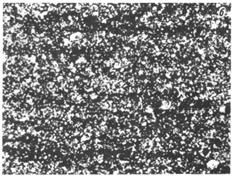
а) б)
а) - після рідкофазного спікання; б)
-після гарячого штапування
Рисунок 3.7 - Мікроструктура зразків
системи Fe - Ti - C
Карбід бору належить до з'єднань,
легко диссоціюючих у контакті з залізом при порівняно невисоких температурах
[67]. В цьому випадку він є джерелом атомарного бору і вуглецю, які при
взаємодії із залізом утворюють тверді з'єднання, що зміцнюють матеріал. У
зв'язку з цим існує можливість конструювання спечених матеріалів на основі
порошкової суміші сплавів заліза і карбіду бору. Використання В4С як
легуючого елементу повинне привести до утворення карбідів і бориду заліза при
спіканні, причому від їх кількості і морфології в значній мірі залежатимуть
властивості спечених матеріалів. Оскільки В4С з'єднання порівняно
бідне вуглецем, можна розраховувати на достатньо однорідний розподіл карбідів
за об'ємом, тоді як з'єднання бору із залізом можуть локалізуватися поблизу
джерела дифузії або зароджуватися на дефектах структури зважаючи на горофільні
властивості бору. Це створює певні передумови для керування структурою
матеріалів.
Аналіз теоретичних уявлень про
принципи взаємодії залізної матриці з бором [67] дозволив припустити наступний
механізм процесів структуроутворення сплавів при спіканні.
На початковому етапі при нагріві до
11000С ще до початку дифузії бору в залізну матрицю частинки B4С
втрачають зв'язок із залізною основою, оскільки коефіцієнти термічного
розширення Fe і B4С сильно розрізняються (Fe = 23,0 ×
10-6
К-1 [162]; B4C = (4,56,3) ×
10-6 K-1
[163]). Об'єм пори, в яку поміщена частинка B4С, зростає за рахунок
релаксації напруги пресування, а також унаслідок збільшення тиску газів в порі.
Не дивлячись на втрату контакту між залізною основою і B4С при 1000
11000С починається утворення нової фази бориду заліза в околиці
частинки карбіду бору. При цьому, слід зазначити, що зважаючи на відсутність
розплаву в системі Fe B C в інтервалі температур до 1100 0С [66]
дифузія бору через рідку фазу виключається. Термодинамічна оцінка швидкості
випаровування бору з B4С і транспорту до поверхні заліза через
газову фазу, проведена в [67], показує, що ці процеси також не можуть пояснити
експериментальну інтенсивність зростання бориду заліза, що спостерігається.
В той же час, слід врахувати, що в
технічному B4С міститься 2-3% (мас.) оксиду бору [67], основна маса
якого в процесі спікання міститься в порі у вигляді розплаву. Така мала
відносна кількість оксиду бору робить маловірогідним механізм дифузії бору до
залізної матриці через розплав B2О3, проте не заперечує
можливість газофазного транспорту з'єднань бору на поверхню заліза з подальшим
їх розкладанням і утворенням атомарного бору [66], оскільки частина оксиду бору
знаходиться в газоподібному стані і в об'ємі пори існують рівновага між
газоподібним і рідким B2О3. При цьому, на поверхні
частинки B4С можливі наступні реакції:
4B2О3+
B4C 6 B2О2 + C (2.1)2О3+
С CО + B2О3 (2.2)
Молекули B2О3
транспортуються через газову фазу до поверхні заліза, адсорбцируются на ній і
диссоціюються по реакції:
3B2О3
2 B2О3 + 2В (2.3)
Атоми бору, що утворюються,
дифундують вглиб заліза, сприяючи прискореному дифузійному зростанню боридного
шару FeВ Fе2В на стінках пори, а молекули B2О3
транспортуються до поверхні частинки B4С, де знов вступають в
реакцію. В той же час, деяка частина вуглецю відповідно до рівняння (2.1) у
вигляді частинок графіту виділяється усередині пори.
Підвищення температури спікання
понад 1100 0С приводить до утворення в системі Fе - C - B рідкої
фази [64], що зумовлює зміну механізму структуроутворення [61]. При цьому,
контактне плавлення відбувається на межі контакту сталевої матриці з карбідом
бору, що викликає формування прошарку рідкої фази. Карбід бору розчиняється в
рідкій фазі:
B4C
4B + C (2.4)
з утворенням на межі Fe-рідка фаза
бориду заліза
+ B Fe B
(2.5)
2Fe + B Fe2
B (2.6)
або цементиту по реакції
Fe + C Fe3C
(2.7)
При цьому, слід зазначити, що
оскільки при розчиненні 1 молю B4С утворюється 1 моль вуглецю і 4
моля бору, початковий склад рідкої фази близький до складу крапки А (рис.3.8)
діаграми Fе-C-B, у зв'язку з чим на поверхні пори вірогідніше утворення шару Fe2В.
По міру розчинення частинки B4С на поверхні Fe2В
формується шар FеB, надлишок вуглецю виділяється у вигляді графіту, а на
поверхні частинках -Fe, що утворилися з рідкої фази, формується бороцементит Fe3(C,В).
Склад рідкої фази, рівноважної з бороцементітом, знаходиться в межах 6-11% B і
13-14% (ат.) С (лінія ВС, рис. 2.6). Термодинамічний аналіз процесу показує
[61], що вміст вуглецю в розплаві при зростанні Fe2В збільшується
достатньо швидко, і на ділянці ВС діаграми Fе-B-C рідка рідка фаза знаходиться
відносно малий час, при якому встигає виділитися невелика кількість Fe3(C,В).
В той же час, зростання Fe3(C,В)
лімітується дифузією заліза через шар бориду Fe2В і FеB.
З підвищенням температури після
завершення розкладання частинки B4С на межі графіту з FеB
відбувається контактне плавлення, внаслідок чого розплав збагачується бором і
його склад швидко приходить в район точки D діаграми Fе-B-C (рис. 3.1), а
незначна кількість карбоборида може виділитися тільки при охолоджуванні
заготівки.
Рисунок 3.8 Ізотермічний розріз
діаграми стану Fe-C-B при 11000С
3.2 Особливості отримання, механічні
і трибологічні властивості карбідосталей після реакційного спікання і гарячого
штампування
Представлені вище результати виявили
ряд проблем, пов'язаних з складнощами в плані отримання відносно міцного і
більш-менш щільного матеріалу після проведення реакційного спікання сумішей
титану, заліза і вуглецю. У одержуваних заготовках, не дивлячись на наявність в
процесі спікання значної кількості рідкої фази, не тільки відсутня усадка, характерна
для традиційних технологій рідкофазного спікання швидкорізальних сталей,
карбідосталей і твердих сплавів, і що забезпечує формування практично
безпористого стану матеріалу, але навіть спостерігається помітне об'ємний ріст
і розшарування матеріалу унаслідок швидкоплинного протікання цілого ряду
фазових і хімічних перетворень, що супроводжуються виділенням значної кількості
тепла і газоподібних продуктів реакції. Унаслідок значного розшарування і
неконтрольованої зміни розмірів і форми, пресовок, що пройшли реакційне
спікання, вони не можуть бути використані як заготовки для подальшої гарячої
обробки тиском. Автор роботи [68] на підставі результатів дослідження
реакційного спікання порошкових сумішей феротитана і сажі однозначно вказує на
неможливість отримання щільного сплаву системи TiC Fe з використанням
традиційної технології спікання. У роботах [69,70] пориста губка, одержана в
результаті реакційного спікання сумішей титану, вуглецю і одного з металів з
групи залізо, ванадій або хром, використовується для отримання порошків для
магнітно-абразивної обробки. У зв'язку з цим, для формування високощільного
композиту вказаної системи в [69] була застосована технологія гарячого
пресування в графітовій прессформе. Проте, не дивлячись на високу якість одержуваних
матеріалів, така технологія унаслідок високої енергоємності, украй низької
стійкості оснащення і низької продуктивності, представляється недостатньо
конкурентоспроможною.
Це вказує на необхідність пошуку
раціональних технологічних схем отримання таких композитів, заснованих на
застосуванні технології гарячої обробки тиском спечених заготовок. У зв'язку з
цим були проаналізовані основні причини інтенсивного розбухання і розшарування
заготовок в процесі реакційного спікання. Останне обумовлено, мабуть,
виникненням в матеріалі пресування внутрішніх напруг, викликаних виділенням
тепла при протіканні реакції між титаном і вуглецем, інтенсивним газовиділенням
при взаємодії вуглецю з киснем, який знаходиться в порошках Ti і Fe, і
напруженнями, що виникають в матеріалі при фазових і хімічних перетвореннях.
При цьому відомо, що збільшення змісту вуглецю в сплаві інтенсифікує процес
газовиділення, утворення пор і розшарувань в сплаві [69]. В той же час, автори
роботи при дослідженні взаємодії між Ti і С в результаті екзотермічної реакції,
виявили істотну залежність адіабатичної температури процесу від змісту так
званого розбавлювача, в якості якого автори використовували карбід титану.
Одним з ефективних інертних
розбавлювачів в екзотермічно реагуючій суміші порошків Ti Fe C є залізо, яке
зменшує температуру синтезу і розмір зерен твердої фази [66]. Таким чином, з
урахуванням приведених даних можна зробити висновок, що збільшення змісту
заліза і зменшення вуглецю в початковій суміші повинно істотно знизити як адіабатичну
температуру процесу, так і інтенсивність його протікання і, відповідно,
інтенсивність газовиділення.
Як випливає з приведених даних, всі
три склади композитів після гарячого штампування і відпалу мають відносно
невисоку твердість, що дозволяє проводити механічну обробку поковок звичайним
твердосплавним інструментом. В той же час, одержані матеріали істотно
відрізняються по здібності сплаву до загартовуваності. Так, карбідосталь з
карбідом титану зниженої стехиометрії практично не піддається гарту, що
характеризується мінімальним підвищенням твердості матеріалу після
термообробки. Дещо вищий за характеристику твердості одержані після гарту
композиту із стехіометричним карбідом титану, і лише сплав з підвищеним вмістом
вуглецю в шихті має здатність піддаватися повноцінному гарту. Украй низька
характеристика загартовуваності перших двох складів обумовлена збідненою
вуглецем металевої зв'язки, що виражається в практично повній відсутності в
сплаві карбідних фаз заліза.
Результати трібологичеськіх випробувань
указують на істотно вищу зносостійкість карбідосталі із зв'язкою з вуглецевої
сталі як в порівнянні з аналогічними карбідосталямі на основі маловуглецевої
залізної зв'язки, так і стандартними легованими сталямі, виготовленими за
традиційною металургійною технологією.
Істотна відмінність зносостійкості
карбідосталей з різним складом металевої зв'язки обумовлена не тільки значною
різницею в значеннях твердості матеріалів, але і неповною відповідністю
структури перших двох складів основним принципам високої зносостійкості
матеріалу. Зокрема, одним з таких принципів є те, що пружнопластична матриця
повинна забезпечувати, з одного боку, достатню релаксацію діючих на матеріал
напружень, а з другого боку - мінімальну деформацію [1,2]. Знижена
мікротвердість ферритної фази металевої зв'язки, мабуть, не забезпечує
достатніх міцносних властивостей, здатних мінімізувати локальну пластичну
деформацію поблизу окремих частинок карбіду титану, що приводить до їх
поступового викришування.
3.3 Розрахунок термодинамічної
рівноваги в сплавах систем Fe-Ti-C(B)
Розрахунок термодинамічної рівноваги
сплавів систем Fe-Ti-C та Fe-Ti-В4C проводився за допомогою програми
CHEQC (CHemical EQuilibriums Calculations) на базі пакету програм Astra.
Попередній розрахунок вихідних даних виконувався з використанням хімічної
довідкової системи PL Table.
Розрахунок проводився для систем
сплавів складу:
Fe - (10 ÷ 80% мас)[Ti
- (10 ÷ 25% мас)C],
Fe - (10 ÷ 80% мас)[Ti
- ( 5 ÷ 95% мас)В4С].
Вихідні умови розрахунку (для обох
систем сплавів) однакові, інтервал температур в якому здійснювався розрахунок
термодинамічної рівноваги систем складає 500-1400оС, а тиск в
системі становить 105 Па.
Виходячи з результатів отриманих при
розрахунку вірогідності зміщення рівноваги при проходженні реакцій у вказаних
системах можна сказати, що для системи Fe - (10÷80%
мас)[Ti - (10÷25%
мас)C] при досягненні відношення масової частки вуглецю до титану,як 20 до 80 в
системі спостерігається утворення стехіометричного карбіду титану. У випадку
меншої кількості вуглецю у суміші сплав складається зкарбіду титану, кількість
якого напряму пов’язана з кількістю вуглецю у вихідні суміші, непрореагувавшого
титану та заліза. Якщо кількість вуглецю перевищує кількість вуглецю необхідну
для утворення стехіометричного карбіду титану, то система складається з карбіду
титану та карбіду заліза (рис. 3.9).
а) - з нестачею С до Ті та Fe;
б) - з оптимальним співвідношенням С
до Ті та Fe;
в) - з надлишком С до Ті та Fe
Рисунок 3.9
- Розподілення твердих фаз в системі Fe - Ti - C
Дослідження термодинамічної
рівноваги в системі Fe-Ti-В4С, в межах варьювання концентрацією
утворюваної твердої фази 10-80% мас по відношенню до Fe, а також змінюючи вміст
В4С по відношення до титану можна зробити висновок, що при вмісті В4С
5-20% мас по відношенню до титану в сисемі рівновага системи ззувається в бік
утворення TiB та TiC з залишишимися, Ti, це повязано з недостатньою кількістю B
та C при розкладанні В4С (рис. 3.10).
а) - з нестачею В та С до Ті
та Fe;
б) - з оптимальним
співвідношенням В та С до Ті та Fe;
в) - з надлишком В та С до Ті та Fe
Рисунок 3.10
- Розподілення твердих фаз в системі Fe-Ti-B4C
При досягненні концентрації В4С
до Ti в системі до 25% мас, всистемі утворюється TiB, TiB2, а також
залишаються TiC та вільне Fe. З чого можна зробити висновок про те, що більш
активний титан у порівнянні з залізом прямує до утворення карбідів та боридів у
першу чергу ніж залізо, а кількість бору та вуглецю не достатня для взаємодії з
залишившимся залізом.
Підвищуючи вміст В4С до
30% мас, ріновага зміщується з утворенням FeВ, TiB2, а також TiC та
Fe, що пояснюється насиченням TiB бором та його переходом в TiB2.
Така ситуація спостерігається аж до концентрації карбіду бору до 50% мас по
відношенню до титану. При концентрації 80% мас твердої фази по відношенню до
заліза, в системі залишається не прореагувавший карбід бору та вуглець, що
залишився в системі внаслідок розкладу певної кількості карбіду бору та не
звязався з Fe або Ti через їх недостатню кількість. Така ситуація
спостерігається при високих вмістах твердої фази до заліза в інтервалі
концентрацій В4С від 45 до 95% мас.
В інтервалі концентрацій карбіду
бору до титану 55-95% мас система ззувається до утворення Fe, C, FeB, Fe3C,
TiC та TiB2. Однак непрореагувавші залізо та вуглець вже при
температурі в 873 К утворюють цементит та невелику кількість залишкового
вуглецю.
Висновки
На основі узагальнення результатів
аналізу сучасних тенденцій розвитку матеріалознавства порошкових зносостійких і
конструкційних матеріалів, експериментальних і аналітичних досліджень процесів
структуроутворення матеріалів і формоутворення деталей розроблені теоретичні
основи і експериментальне обгрунтування комплексного підходу до створення
технологічних процесів отримання ряду нових порошкових композиційних матеріалів
на основі заліза для роботи в умовах підвищених навантажень і інтенсивної
стираючої дії, а також ефективних маловідхідних технологій виготовлення з них
виробів з метою забезпечення заданого комплексу властивостей.
При виборі схеми легування для
отримання економно-легованого порошкового матеріалу була обгрунтована
ефективність застосування бору як основний легуючий елемент для виготовлення
зносостійких порошкових композицій на основі сплавів заліза, що обумовлюється
цілим рядом його унікальних властивостей.
Розроблений новий ефективний
технологічний процес отримання високощільних композитів системи карбід титану -
сплав на основі заліза із застосуванням методу гарячого штампування спечених
заготовок. Досліджені основні закономірності формування структури на всіх
стадіях техпроцесса. Аналіз результатів ДТА суміші швидкорізальна сталь -
карбід титану показав, що поява рідкої фази при спіканні виявляється вже при
температурі 1130-1140 0С унаслідок дифузії вуглецю із
зерен TiС1-x, що контактують з залізом.
Встановлено, що гаряча пластична
деформація порошкового псевдосплаву залізо - карбід титану разом з ущільненням
матеріалу сприяє, також, активації сплавоутворення.
Дослідження основних
физико-механических властивостей карбідосталей, виготовлених по різних
технологічних варіантах (рідкофазне спікання, гаряче пресування в графітових
формах, гаряче штампування пористих заготовок), показали, що застосування
гарячого штампування спечених заготовок приводить до збільшення міцності
матеріалу на вигин і ударної в'язкості в порівнянні з матеріалами, отриманими
рідкофазним спіканням або гарячим статичним пресуванням при збереженні
достатньо високих значень твердості.
На основі використання ефекту
утворення низькоплавкої евтектики в системі Fe - Ti був запропонований новий
технологічний підхід до отримання композитів системи карбід(борид) титану -
сталь, що полягає в забезпеченні формування карбідною складовою псевдосплаву в
результаті екзотермічної реакції при спіканні порошкових сумішей, що
складаються з порошків титану, сплаву на основі заліза і вуглецю. Мікроструктури
сплавів, отриманих при реакційному спіканні сумішей, розрахованих на формування
різних стехіометричних значень TiСx, характеризуються рівномірно
розподіленими за об'ємом карбідними зернами, оточеними прошарками металевої
зв'язки.
Вивчений механізм сплавоутворення в
процесі реакційного спікання порошкових сумішей Fe-Ti- C. Показане, що
регулюючи температуру саморазогрева композиції шляхом зміни складу шихти, можна
керувати зростанням карбідних зерен; із зменшенням змісту вуглецю в початковій
суміші і, відповідно, ступені стехиометрічності отримуваного карбіду титану,
розмір зерен карбідної фази помітно зменшується.
Conclusions
the basis of generalization of
results of analysis of modern progress of materials science of powder wearproof
and construction materials, experimental and analytical researches of processes
of gelation of materials and formreception of details, trends theoretical bases
and experimental ground of the complex going are developed near creation of
technological processes of receipt of row of new powder composition materials
on the basis of iron for work in the conditions of the enhanceable loadings and
intensive wearing away actions, and also effective wasteless technologies of
making from them of wares with the purpose of providing of the set complex of
properties.the choice of alloying chart for the receipt of the economy alloyed
powder material efficiency of application of the coniferous forest was grounded
as basic alloying an element for making of wearproof powder compositions on the
basis of alloys of iron which is stipulated quite a few him unique
properties.new effective technological process of receipt of highlytight compos
of the system is developed a carbide of titan is steel with application of
method of the hot punching of the sintered purveyances. Basic conformities to
the law of forming of structure are investigational at all stages
technological-process. An analysis of results of DTA of mixture is high-speed
steel - the carbide of titan rotined that appearance of liquid phase at
sintering appeared already at the temperature of 1130 - 1140 0C as a
result of diffusion of carbon from grains of TiC1-x, which contact
with steel. It is set that hot flowage of powder pseudoalloy high-speed steel -
the carbide of titan promotes together with the compression of material, also,
activating of alloyreception. The high-quality estimation of distributing of
elements rotined between a matrix and particles of carbide of titan, that in
carbidoseel, got sintering in presence a liquid phase, grains of TіC are
enriched vanadium, tungsten and molybdenum, with the distinctly expressed
circular structure on the limits of grain. In case the use of technology of the
hot punching, the concentration of elements is largely evened, as a result there
is substantially more even distributing of alloying elements on the field of
microsection.of basic physic-mechanical properties of carbidoseels, made on
different technological variants (liquidstate sintering, hot pressing, is in
graphite forms, hot punching of porous purveyances), rotined that application
of the hot punching of the sintered purveyances resulted in the increase of
durability of material on a bend and shock viscidity as compared to materials,
got liquidstate sintering or hot static pressing, at a maintainance enough high
values of hardness.the basis of the use of effect of formation of low-melting
eutecticum in the system Fe - Ti was offered new technological going near the
receipt of compos of the system a carbide (boride) of titan is steel, which
consists in providing of forming the carbidic constituent of pseudoalloy as a
result of exothermic reaction at sintering of powder mixtures, which consist of
powders of titan, alloy, on the basis of iron and carbon. The microstructures
of alloys, mixtures counted on forming of different stoichiometrical values of
TiCx got at reactionary sintering, are characterized the evenly
up-diffused on volume carbidic grains, surrounded layers of metallic
copula.mechanism of alloyreception is studied in the process of reactionary
sintering of powder mixtures of Fe-Ti-C. It is rotined, that regulating the
temperature of autowarm composition by the change of composition of charge, it
is possible to manage growths of carbidic grains; with diminishing of maintenance
of carbon in initial mixture and, accordingly, degree of stoichiometry of the
got carbide of titan, the size of grains of carbidic phase diminishes notedly.
Список використаної літератури
1. Федорченко
И.М., Францевич И.Н., Радомысеоьский И.Д., и др. Порошковая металлургия,
материалы, технология, свойства, области применения: Справочник. - Киев: Наук.
Думка, 1985. - 624 С.
2. Радомысеоьский
И.Д., Сердюк Г.Г., Щербань Н.И. Конструкционные порошковые материалы. - К.:
Техника, 1985. - 152 С.
3. Гуляев
А.П. Металловедение. - М.: Металлургия, 1986 г. - 544 с.
4. Винокур
Б.В., Кондратюк С.Е., луценко Г.Г., Литвиненко Л.Л. Технологические и
эксплуатационные характеристики высокохромистой износостойкости стали // Новые
технологии и материалы в тяжелом машиностроении. - Киев: ИЭС им.Е.О.Патона. -
1987. - С.40-46.
5. Крагельский
И.В. Трение и износ. - М.: Машиностроение, 1968. - 479 с.
6. Трение,
изнашивание и смазка. Справочник / Под ред. И.В.Крагельского, В.В.Алисина. -
М.: Машиностроение, кн.1. - 1978. - 400 с.
7. Демкин
Н.Б. Контактирование шероховатых поверхностей. - М.: Наука, 1970. - 223 с.
8. Костецкий
Б.И. Трение, смазка и износ в машинах. - Киев: Техніка, 1970. - 267 с.
9. Виноградов
В.Н., Сорокин Г.М., Колокольников М.Г. Абразивное изнашивание. - М.: Машиностроение,
1990. - 222 с.
10.Дгебуадзе
Т.Т., Полотай В.В. Исследование механизма изнашивания композиционных материалов
// Порошковые триботехнические материалы. - Киев: ИПМ АН УССР, 1982. - С.15-16.
11.Горбач
В.Г., Москаленко Ю.Н., Мешашті С., Будебан С. Особливості дифузійного насичення
пористого заліза вуглецем // Металознавство та обробка металів. - 1997. - №2. -
С.27-28.
12.Радомысельский
И.Д. Структура и свойства конструкционных спеченных материалов // Порошковая
металлургия. - 1974. - №4. - С.36-45.
13.Радомысельский
И.Д., Щербань Н.И. Порошковые конструкцион-ные материалы. - Киев: О-во “Знание”
УССР, 1983. -16с.
14.Егоров
М.Д., Сапожников Ю.Л., Кацель Р.М., Шохназаров Ю.В. Исследование структуры и
свойств борсодержащих сплавов // Композиционные покрытия: Тез. 3-й н.-т. конф.
- Житомир, 1985. С.36-37.
15.Ткаченко
В.Ф., Коган Ю.И. Особенности структуры и механические свойства спеченных
материалов Fe - B4C // Порошковая металлургия. -1978. - № 5. -
С.69-74.
16.Ткаченко
В.Ф., Коган Ю.И., Ковальчук В.А. Конструкционные спеченные материалы из
порошковой смеси железо - карбид бора // Конструкционные материалы. - Киев,
1978. - С.30-34.
17.Еременко
В.Н.,Найдич Ю.В., Лавренко И.А. Спекание в присутствии жидкой металлической
фазы. - Киев: Наук.думка, 1968. - 123с.
18.Радомысельский
И.Д., Клименко В.Н. Твердые сплавы из порошков карбида хрома и чугуна //
Информ. листок. - Киев. - 1961. - № 12.
19.Гуревич
Ю.Г., Нарва В.К., Фраге Н.Р. Карбидостали. - М.: Металлургия, 1988. - 144 с.
20.Кюбарсепп
Я. Твердые сплавы со стальной связкой. - Таллин: Валгус - ТГУ, 1991. - 164 с.
21.Яблокова
О.В., Кулькеов С.Н., Панин В.Е. Формирование межфазной границы при спекании
карбида титана со сталью Гадфильда // Порошковая металлургия. - 1985. - №7. -
С.37-39.
22.Позняк
Л.А. Инструментальные стали. - Киев: Наук. думка, 1996. - 488 с.
23.Успенский
М.М. Разработка технологического процесса жидкофазного спекания инструмента из
порошков быстрорежущей стали // Порошковые быстрорежущие стали (структура,
свойства, технологии производства инструментов) - Киев: Наук.думка. - 1990. -
С.90-94.
24.Кантин
В.Г., Чмеренко А.Н., Антонишин Ю.Т. и др. Горячее выдавливание капсул с
порошком быстрорежущей стали // Порошковые быстрорежущие стали. - Киев: ИПМ АН
УССР. - 1990. - С.102-107.
25.Дорофеев
Ю.Г. Динамическое горячее прессование пористых порошковых заготовок. - М.:
Металлургия, 1977. - 216с.
26.Дорофеев
Ю.Г., Гасанов Б.Г., Дорофеев В.Ю. и др. Промышленная технология горячего
прессования порошковых изделий. - М.: Металлургия, 1990. - 206с.
27.Дорофеев
Ю.Г., Жердицкий Н.Т., Колесников В.А. Высокомарган-цовистая металлокерамическая
сталь // Порошковая металлургия. - 1970. - № 11. - С.28-31.
28.Жердицкий
Н.Т. Исследование формирования структуры конструк-ционных материалов и изделий,
получаемых динамическим горячим прессованием // автореф. дисс ... д-ра техн.
наук. - М., 1979. - 38с.
29.Клименко
В.Н., Напара-Волгина С.Г., Орлова Л.Н. и др. Механические и триботехнические
свойства износостойких горячештампованных сталей с гетерогенной структурой //
Порошковая металлургия. - 1993. - № 3. - С.42-46.
30.Кун
Х.А. Основные принципы штамповки порошковых заготовок // Порошковая металлургия
материалов специального назначения. - М.: Металлургия. -1977. -С.143-158.
31.Дорофеев
Ю.Г., Синельщиков В.В. Особенности деформации и трещинообразования нагретых
цилиндрических порошковых заготовок // Порошковая металлургия. - 1980. - №1. -
С.25÷30
32.Павлов
В.А., Ляшенко А.П., Богуслаев В.А., Аврунина Г.В. Влияние степени деформации и
температуры штамповки на структуру и свойства изделий из порошкового титана //
Порошковая металлургия. - 1984. - №12.- С.90-93.
33.Грабчак
А.К., Клевцов В.Н., Мартюхин И.Д. и др. Физико-механические свойства деталей из
низколегированных сталей, полученных горячей штамповкой пористых заготовок //
Горячее прессование. - Киев: ИПМ АН УССР, 1977. - С. 19-24.
34.Радомысельский
И.Д., Напара-Волгина С.Г., Орлова Л.Н. и др. Структура, механические и
коррозионные свойства порошковой нержавеющей стали марки Х23Н18 // Порошковая
металлургия. - 1983. - №1. - С.43-49.
35.Нельзина
И.В., Заплатина Ф.В., Радомысельский И.Д. Свойства порошковой нержавеющей стали
Х25, полученной методом горячей штамповки // Порошковая металлургия. - 1984. -
№1. - С.35-39.
36.Живов
Л.И., Сыпко А.В., Долгий Н.И. Опыт штамповки изделий из порошка титана //
Кузнечно-штамповочное производство. - 1975. - №3. - С.47.
37.Кюбарсепп
Я. Твердые сплавы со стальной связкой. - Таллин: Валгус - ТГУ, 1991. - 164 с.
38.Свойства,
получение и применение тугоплавких соединений: Справочник / Под ред.
Косолаповой Т.Я. - М.: Металлургия, 1986. - 928 с.
39.Третьяков
В.И. Основы металловедения и технологии производства спеченных твердых сплавов.
- М.: Металлургия, 1976. - 528 с.
40.Эллиот
Р.П. Структуры двойных сплавов. - М.: Металлургия, 1970. Т.1-2. - 928 с.
41.Хансен
М., Андерко К. Структуры двойных сплавов. - М.: Металлургиздат, 1962. Т.1-2. -
1488 с.
42.Шурин
А.К., Дмитриева Г.П. Фазовые равновесия в сплавах переходных металлов с
тугоплавкими карбидами // Металлофизика. 1974. - Вып.53. - С.91-97.
43.Репина
Э.И., Чапорова И.Н. Фазовые равновесия в системе Ti-Fe-C при 1100 0С
// Диаграммы состояния карбид- и нитридосодержащих систем. Киев: АН УССР, 1981.
- С.146-154
44.Еременко
В.Н. Многокомпонентные сплавы титана. - Киев: Изд. АН УССР. - 1962. - 210 с.
45.Ниженко
В.И., Флока Л.И. Поверхностное натяжение жидких металлов и сплавов. -М.:
Металлургия, 1981. - 208 с.
46.Панасюк
А.Д., Фоменко В.С., Глебова Г.Г. Стойкость неметаллических материалов в
расплавах: Справочник. - Киев: Наукова думка, 1986. - 352 с.
47.Свойства,
получение и применение тугоплавких соединений: Справочник / под ред.
Косолаповой Т.Я. - М.: Металлургия, 1986. - 928 с.
48.Панасюк
А.Д., Кюбарсепп Я.П., Дзыкович И.Я. и др. Контактное взаимодействие карбида
титана со сплавами на основе железа // Порошковая металлургия. - 1981. - №4. -
С.66-72.
49.Похмуровский
В.К. Выносливость сталей и сплавов после их диффузионного насыщения //
Физико-химическая механика материалов. - 1980. - №5. - С.69-74.
50.Гуревич
Ю.Г., Нарва В.К., Фраге Н.Р. Карбидостали. - М.: Металлургия, 1988. - 144 с.
51.Роговой
Ю.И. К разработке износостойких материалов карбид титана - сталь // Порошковая
металлургия. - 1968. - №5. - С.23-27.
52.Соколова
Е.В., Фраге Н.Р., Гуревич Ю.Г., Чумаков В.И. Взаимодействие карбида титана со
сталью Р6М5 // Там же. - 1991. - №1. - С.68-72.
53.Деклараційний
патент 47662 А (Україна). Спосіб виготовлення виробів із порошкових
композиційних матеріалів / Г.А. Баглюк, Л.О. Позняк, С.В. Тихомиров // Бюл.
-№7. - 15.07.2002.
54.Баглюк
Г.А., Позняк Л.А., Гуменюк С.В. Структура и свойства карбидосталей, полученных
за счет выделения карбидной фаз из матричного псевдосплава // 9-й международный
семинар «Новое в разработке, производстве и применении инструментальных
материалов», Запорожье, 4-6 сентября 2002 г. Тез. докл. / УкрНИИСпецсталь, ИПМ
им.И.Н. Францевича НАН Украины. - Киев, 2002. - С.40-41.
55.Потапенко
В.О. Розробка термо-механо-хімічного процесу отримання твердих сплавів TiC-Fe з
феротитану для високозносостійкого інструменту. Автореф. дис…канд. техн. наук.
- Київ: ІПМ НАН України, 1994. - 18 с.
56.Потапенко
В.А. Спекание сплавов TiC-Fe с реакционным формированием карбида титана //
Актуальные вопросы материаловедения. - Киев, ИМП НАН Украины, 1991. - С.98-101.
57.Мержанов
А.Г., Боровинская И.П. Самораспространяющийся высокотемпературный синтез в
химии и технологии тугоплавких соединений // Журн. Всесоюзн. хим. о-ва им.
Менделеева. - 1979. - 24, №3. - С.223-227.
58.Туров
Ю.В., Хусид Б.М., Ворошин Л.Г. и др. Структурообразование при спекании
порошковой композиции железо-карбид бора // Порошковая металлургия. - 1991. -
№6. - С.25-31.
59.Туров
Ю.В., Хусид Б.М., Ворошин Л.Г. и др. Газотранспортные процессы при спекании
порошковой композиции железо-карбид // Порошковая металлургия. - 1989. - №8. -
С.38 -43.
60.Потапенко
В.О. Розробка термо-механо-хімічного процесу отримання твердих сплавів TiC-Fe з
феротитану для високозносостійкого інструменту. Автореф. дис…канд. техн. наук.
- Київ: ІПМ НАН України, 1994. - 18 с.
61.Поліщук
В.С. Інтенсифікація процессів одержання карбідів, нітридів і композиційних
матеріалів на їх основі. Автореф. дис…докт. техн. наук. - Київ, ІПМ НАН
України, 2004. - 43 с.
62.Полищук
В.С., Наливка Г.Д., Кисель Н.Г. Композиционные магнито-абразивные порошки на
основе железа, карбидов титана, ванадия и хрома // Порошковая металлургия. -
1983. - №3. - С.94-100.
Додаток 1
Класична технологічна схема
отримання карбідосталей
Додаток 2
Принципова технологічна схема отримання
карбідосталей з використанням технології реакційного спікання та гарячої
штамповки