Передача
|
Элемент
передачи
|
Марка материала
|
Dпред
|
Термообработка
|
HBср
|
σ-1
|
σв
|
σт
|
[σ]Hрас
|
[σ]Fрас
|
|
|
|
Sпред
|
|
|
Н/мм²
|
Коническая
|
Шестерня
|
40Х
|
125 125
|
У
|
285,5
|
410
|
900
|
750
|
514,3
|
220,55
|
|
Колесо
|
40X
|
|
|
248,5
|
375
|
790
|
640
|
|
191,97
|
5.
Расчет прямозубой конической передачи
5.1
Проектный расчет
Исходные данные для расчета:
крутящий момент на выходном колесе Т2 = 34,1 Нм;
частота вращения шестерни n1 = 700 об/мин;
частота вращения колеса n2 = 140 об/мин;
передаточное число передачи uзп = n1 / n2 = 700 / 140 = 5
Основной габаритной характеристикой конической зубчатой
передачи является средний делительный диаметр выходного колеса d¢m², ориентировочную
величину которого определяем по формуле:
где Kзк = 1 - коэффициент для передач с прямыми зубьями;
M = (600 / σHP)2/3 = (600 /
463)2/3 = 1,108 - параметр, уточняющий прочностную характеристику
материала
где σHP = 463 МПа - допускаемое
контактное напряжение на рабочих поверхностях зубьев;
Kk = 47,98 - коэффициент, назначаемый в зависимости
от коэффициента ширины колеса KBe (Принимаем KBe = 0,2.).
Определение характеристик и размеров шестерни и колеса.
Назначаем числа зубьев шестерни и колеса:
z1 = 17;
z2 = 17 ´ uзп = 85.
Находим ориентировочное значение среднего окружного модуля:
m’nm = d’m² / z2 =255/85=3 мм
округляем его до стандартного значения mnm = 3 мм.
Корректируем значение среднего делительного диаметра колеса и
определяем средний делительный диаметр шестерни:
dm² = mnm ´ z2 = 255 мм
dm1 = mnm ´ z1 =51 мм
Углы делительных конусов:
δ’2 = arctg uзп = arctg 5 = 78.40;
δ’1 = 90° - 78.40° = 11.20°;
Внешний окружной модуль:
mte = mnm /(1 - 0,5 ´ KBe) = 3 мм;
Внешние делительные диаметры:
de1 = dm1 /(1 - 0,5 ´ KBe) = 33.56 мм;
de2 = dm² /(1 - 0,5 ´ KBe) =255 мм
Внешнее конусное расстояние:
Re = 0,5 ´ mte ´ (z12 + z22)1/2 = 143,03 мм;
Ширина зубчатого венца:
b2 = Кве Re ≤ 10
de1 / z1= 30 мм
Принимаем b2 = 17 мм
Среднее конусное расстояние:
Rm = Re - 0,5 ´ b2 = 128,03 мм;
Коэффициенты среднего нормального смещения:
xn1 = 2 ´ (1 - uзп -2) (1/ z1)1/2 = 0,36;
xn2 = - xn1 = -0,36;
Высоты ножек зубьев в среднем сечении:
hfm1 = (1,25 - xn1) ´ mnm = (1,25 - 0,36) ´ 1,5 = 1,1 мм;
hfm² = (1,25 - xn2) ´ mnm = (1,25 + 0,36) ´ 1,5 = 2,3 мм;
Внешние диаметры:
dae1 = de1 + 1,64 ´ (1+ xn1) ´ mte ´ cos δ’1° = 51 мм;
dae2 = de2 + 1,64 ´ (1 + xn2)
´ mte cos δ’2° = 255 мм.
Рисунок 5.1.2.1. Зацепление зубчатого конического колеса и
шестерни.
5.2
Проверочный расчет зубчатой передачи
Определение фактического передаточного числа uф и проверка его
отклонения Du от заданного u:
uф = z2 / z1 = 85/17=5
Du = (| uф - u|
/ u) ´ 100% £ 4% = 0 < 4%
Проверка пригодности заготовок колес.
Dзаг £ Dпред = dae1 + 6 = 49,7 + 6 = 54,7
< 125 мм;
Sзаг £ Sпред = 8 ´ me = 8 ´ 1,67 = 13,4 < 125 мм;
Проверочный расчет контактных напряжений.
σH = 13,5´103 (T1 Kp KHβ KHα KHv / b u d2m1 sinδ1)1/2 Zε ZH ≤ [σ]HP
где Kp = 1,3 - коэффициент, учитывающий режим работы
(неравномерный режим);
KHβ = 1,155 - коэффициент,
учитывающий распределение нагрузки по ширине венца конического колеса;
KHα = 1 - коэффициент,
учитывающий распределение нагрузки между зубьями;
KHv - коэффициент, учитывающий динамическую нагрузку
в зацеплении:
где Vm1 - окружная скорость на среднем делительном диаметре шестерни dm1:
м/с
- коэффициент, учитывающий влияние вида передач (
= 0,006);
- коэффициент, учитывающий влияние разности шагов зацепления
шестерни и колеса (
= 82);
Zε - коэффициент, для прямозубых передач Zε = ((4 - eа)/3)1/2
= ((4 - 1,63)/3)1/2 = 0,89; eа -
коэффициент торцового перекрытия eа = 1,38 +
0,01 ´ z1 = 1,38+0,01´25=1,63
ZH - коэффициент, учитывающий форму
сопряженных поверхностей зубьев в полюсе зацепления (ZH = 1,76).
σH = 13,5´103 (7,635´1,3´1,155´1´1,115 / 45,652´17´6,3´sin9,02о)1/20,89´1,76=452,5<463 Н/мм²
Допускаемая недогрузка передачи не более 10%:
DσHP = |[σ]HP - σHP|´100% /
[σ]HP = |463 - 452,5|´100% / 463 = 2,2% < 10%
Проверочный расчет изгибных напряжений шестерни и колеса.
σF2 = YF2 Yβ KFα KFβ KFv Ft / uF b me ≤ [σ]F2
σF =
σF2 (YF1 / YF2) = ≤ [σ]F1
где KFβ =
1 - коэффициент, учитывающий распределение нагрузки по ширине венца;
uF =
0,85 - коэффициент вида конических колес;
KFα = 1 - коэффициент, учитывающий
распределение нагрузки между зубьями;
KHv = 1,172 - коэффициент, учитывающий
динамическую нагрузку в зацеплении;
Ft = 2´T2´103
/ d2 = 2´34,1´103 / 229 = 298 H
YF1 и YF2 - коэффициенты формы зуба шестерни и колеса, которые определяются
в зависимости от эквивалентного числа зубьев шестерни zn1 и колеса zn2:
zn1 = z1 /
cosδ1 = 17 / cos11,20o =
17,3 ® YF1
= 3,4797n2
= z2 / cosδ2 = 85 / cos78,40o = 431,47 ® YF2 = 3,63
Yβ = 1 - коэффициент, учитывающий наклон
зуба.
σF2 = 3,63´1´298´1´1´1,172 / 0,85´17´1,67 = 73,4 < 227 Н/мм²
σF = 69,06´(3,4797 / 3,63) = 69,2 < 268 Н/мм²
6.
Расчет открытой передачи
6.1
Проектный расчет.
Рис. 6.1. Геометрические параметры ремённой передачи
Принимаем ремень нормального сечения в зависимости от
мощности P2 = 0,52 кВт и частоты вращения n2 = 220,63 об/мин.
В зависимости от момента T2 = 22,44 Нм принимаем минимально
допустимый диаметр ведущего шкива d1min = 60 мм.
В целях повышения срока службы ремней принимаем диаметр
ведущего шкива на один порядок выше минимального d1 = 63 мм.
Определяем диаметр ведомого шкива d2:
d2 = d1´uоп´(1 - e) = 224´2,91´(1 - 0,02) = 287,7 мм
где e = 0,02 - коэффициент
скольжения.
Полученное значение округляем до ближайшего стандартного: d2 = 280 мм.
Определение фактического передаточного
числа uф и проверка его отклонения Du от заданного u:
uф = d2 / (d1´(1 - e))
= 4,52
Du = (| uф - u|
/ u) ´ 100% £ 3% = 1,37% < 3%
Определение ориентировочного межосевого
расстояния а, мм:
а ≥ 0,55 (d1 + d2) + h(H) = 194,7 мм
где h(H) = 10,5 мм - высота
сечения клинового ремня.
Определение расчетной длины ремня l, мм:
мм
Значение l округляем до
ближайшего стандартного: l = 1000 мм
Уточняем значение межосевого расстояния по стандартной длине
При монтаже передачи необходимо обеспечить возможность уменьшения
а на 0,01´lдля того, чтобы облегчить надевание ремня на шкив; для
увеличения натяжения ремней необходимо предусмотреть возможность увеличения а
на 0,025´l.
Определение угла обхвата ремнем ведущего шкива α1, град:
Определение скорости ремня V, м/с:
где [V] = 25 м/с - допускаемая скорость.
Определение частоты пробегов ремня U, с-1:
U = V / l £ [U] = 1,7 / 2500 = 0,5 < 30 c-1
где [U] = 30 c-1 допускаемая
частота пробегов.
Соотношение U £ [U] условно выражает долговечность ремня и его соблюдение
гарантирует срок службы - 1000…5000 ч.
Определение допускаемой мощности, передаваемой одним клиновым
ремнем:
[РП] = [P0] СPСαСlСz = 1,55´0,9´0,882´0,9548´1 = 0,85
кВт
где [Ро]=1,55 кВт - допускаемая приведенная мощность,
передаваемая одним клиновым ремнем
С - поправочные коэффициенты:
СP = 0,9 - коэффициент динамической нагрузки
и длительности работы;
Сα =
0,882 - коэффициент угла обхвата α1 на меньшем шкиве;
Сl = 0,9548 - коэффициент влияния отношения
расчетной длины к базовой;
Сz = 1 - коэффициент числа ремней.
Определение количества клиновых ремней z:
z = Рном / [РП] = 0,706 / 1,16 = 0,61 = 2
где Рном = Р2 = 0,706 кВт - номинальная
мощность на тихоходном валу.
Определение силы предварительного натяжения Fo, H:
Н
Определение окружной силы, передаваемой комплектом клиновых ремней
Ft, H:
Н
Определение сил натяжения ведущей F1 и
ведомой F2 ветвей, Н:
Н
Н
Определение силы давления ремней на вал Fоп, H:
Н
.2
Проверочный расчет
Проверка прочности одного клинового ремня
по максимальным напряжениям в сечении ведущей ветви σmax, Н/мм².
σmax = σl + σи + σv £ [σ]p = 7,98 < 10 Н/мм²
где σl - напряжение растяжения:
Н/мм²
где А = 140 мм² - площадь сечения;
σи - напряжение изгиба:
Н/мм²
где EИ = 80 Н/мм² - модуль продольной упругости при изгибе для прорезиненных
ремней;
σv - напряжения от центробежных
сил:
σv = ρv210-6 = 0,0034 Н/мм²
где ρ =
1300 кг/мм³ - плотность материала ремня.
6.2
Параметры клиноременной передачи
Таблица 6.2.1. Сводная таблица
Параметр
|
Значение
|
Параметр
|
Значение
|
Тип ремня
|
клиновой
|
Частота
пробегов ремня U, 1/с
|
0,5
|
Сечение ремня
|
Нормальное Б
(А=140 мм²)
|
Диаметр
ведущего шкива d1
|
63 мм
|
Количество
ремней z
|
2
|
Диаметр
ведомого шкива d2
|
280 мм
|
Межосевое
расстояние а
|
195 мм
|
Максимальное
напряжение σmax, Н/мм²
|
7,98
|
Длина ремня l
|
1000 мм
|
Предварительное
натяжение ремня F0, Н
|
420
|
Угол обхвата
малого шкива α1, град.
|
160
|
Сила давления
ремня на вал Fоп, Н
|
796
|
7.
Вычисление действующих сил в механизмах
.1
Определение сил в зацеплении закрытых передач
Редукторные валы испытывают два вида
деформации - изгиб и кручение. Деформация кручения на валах возникает под
действием вращающих моментов, приложенных со стороны двигателя и рабочей
машины. Деформация изгиба валов вызывается силами в зубчатом зацеплении
закрытой передачи и консольными силами со стороны открытых передач и муфт.
На рисунке 7.1 представлена схема сил в
зацеплении конической передачи. За точку приложения сил принят полюс зацепления
в средней плоскости колеса.
Значения сил определяются по таблице 7.1.
Рис. 7.1.1. Схема сил в зацеплении
конической прямозубой передачи
Таблица 7.1.1. Силы в зацеплении закрытой
передачи
Вид передачи
|
Силы в
зацеплении
|
Значение силы,
Н
|
|
|
на шестерне
|
на колесе
|
Коническая
прямозубая
|
Окружная
|
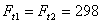
|
|
|
Радиальная
|

|
|
|
Осевая
|

|
|
где
- коэффициент радиальной силы;
- коэффициент осевой силы
7.2
Определение консольных сил
В данной работе конструируется открытая
ременная передача, определяющая консольную нагрузку на выходном конце вала (Fоп = 796 Н - см. п. 6.2).
Кроме того, консольная нагрузка вызывается муфтой, соединяющей двигатель с
редуктором.
Консольная сила от муфты:
Н
F
=125
=1184,27 H

.3
Силовая схема нагружения валов редуктора
Силовая схема нагружения валов имеет целью
определить направление сил в зацеплении редукторной пары, консольных сил со
стороны открытых передач и муфты, реакций в подшипниках, а также направление
вращающих моментов и угловых скоростей валов.
Силы Ft1 и Ft2 направлены так, чтобы
моменты этих сил уравновешивали вращающие моменты Т1 и T2 приложенные к валам
редуктора со стороны двигателя и рабочей машины: Ft1 направлена
противоположно вращению шестерни, а Ft2 - по направлению
вращения колеса.
Консольная сила от ременной передачи Fon перпендикулярна оси вала
и направлена вертикально. Консольная сила от муфты FM перпендикулярна оси вала
и направлена противоположно силе Ft1, что увеличит напряжения и деформацию вала.
Рисунок 7.3.1. Схема нагружения валов конического
одноступенчатого редуктора.
Таблица 7.3.1. Сводная таблица
Параметр
|
Шестерня
|
Колесо
|
Ft, Н
|
298
|
Fr, Н
|
133,625
|
312,791
|
Fa, Н
|
312,791
|
133,625
|
FОП, Н
|
FM, Н
|
196
|
36
|
T, Нм
|
7,1
|
34,1
|
ω, с-1
|
73,3
|
14,66
|
|
|
|
|
Радиальные реакции в подшипниках
быстроходного и тихоходного валов направлены противоположно направлению
окружных (Ftl и Ft2) и радиальных (Frl и Fr2) сил в зацеплении
редукторной передачи. Точка приложения реакции - середина подшипника. Реакции
от действия консольных нагрузок геометрически сложены с реакциями от сил
зацепления. Реакции обозначить буквой R с индексом, указывающим данный подшипник.
8.
Разработка чертежа общего вида редуктора
Основными критериями работоспособности редукторных валов
являются прочность и выносливость. В проектируемом редукторе валы изготовлены
из стали 45.
Проектный расчет валов выполняется по напряжениям кручения
(как при чистом кручении), т.е. при этом не учитывают напряжения изгиба,
концентрации напряжений и переменность напряжений во времени (циклы
напряжений). Поэтому для компенсации приближенности этого метода расчета
допускаемые напряжения на кручение применяют заниженными ([τ] = 10…20 Н/мм²). При этом меньшие
значения [τ]к = 10 Н/мм² - для быстроходного вала, большие [τ]к = 20 Н/мм² - для тихоходного.
.1
Определение геометрических параметров ступеней валов
Редукторный вал представляет собой ступенчатое цилиндрическое
тело, количество и размеры ступеней которого зависят от количества и размеров
установленных на вал деталей.
Проектный расчет ставит целью определить ориентировочно
геометрические размеры каждой ступени вала: ее диаметр d и длину l.
Таблица 8.1.1. Параметры валов
Ступень вала и
её размер d; l
|
Вал
|
|
Тихоходный
|
Быстроходный
|
1-я под элемент открытой передачи или полумуфты d1, мм
Принимаем: d
=25
Принимаем d1= d1дв=15
|
|
|
|
l1, мм
|
l1=
1,5 d1= 37,5 Принимаем L =38l1= 1,4 d1= 21
|
|
2-я под
уплотненные крышки с отверстием и подшипник
|
d2, мм
|
d2=
d1 + 2t = 29 t=2
|
d2=
d1 + 2t = 19 t=2
|
|
l2, мм
|
l2=
1,25 d2 = 36,25 Принимаем L =38l2= 0,6 d4 = 18
|
|
3-я под
шестерню, колесо
|
d3, мм
|
d3= d2 + 3,2r = 35,4 r=2 Принимаем d =36d3= d4 + 3,2r = 36 r=2
|
|
|
l3, мм
|
l3
= 59
|
l3
= 20
|
4-я под
подшипник
|
d4, мм
|
d4=
d2 = 30
|
d4=
d5 + 3 = 30
|
|
l4, мм
|
l4 = T + C = 17,5 + 1,5 = 20
|
l4 = 88,8
|
5-я упорная или
под резьбу
|
d5, мм
|
d5 = d3 + 3f = 40 f = 1,2
|
d5 = 27 M²7 x 1,5
|
|
l5, мм
|
l5 = 103
|
l5= 0,4 d4 = 12
|
8.2
Предварительный выбор подшипников качения
Выбор наиболее рационального типа подшипника для данных
условий работы редуктора весьма сложен и зависит от целого ряда факторов:
передаваемой мощности редуктора, типа передачи, соотношения сил в зацеплении,
частоты вращения внутреннего кольца подшипника требуемого срока службы,
приемлемой стоимости схемы установки.
Предварительный выбор подшипников для каждого из валов
редуктора проводится в следующем порядке:
. В соответствии с таблицей определяем тип, серию и схему
установки подшипников.
. Выбираем из таблицы типоразмер подшипников по величине
диаметра d
внутреннего кольца, равного диаметру второй d2 и четвертой d4 ступеней вала под
подшипники.
. Выписываем основные параметры подшипников: геометрические
размеры - d,
D, В (Т, с); динамическую
Сr и статическую С0r, грузоподъемности. Здесь
D - диаметр наружного
кольца подшипника; Т и с - осевые размеры роликоподшипников.
Таблица 8.2.1. Предварительный выбор подшипников
Передача
|
Вал
|
Тип подшипника
|
Серия
|
Угол контакта
|
Схема установки
|
Коническая
|
Б
|
Роликовые
конические типа 7306
|
Средняя
|
α = 11° -16°
|
врастяжку
|
|
Т
|
Роликовые
конические типа 7208
|
Легкая
|
α = 11° -16°
|
враспор
|
8.3
Разработка чертежа общего вида редуктора
привод двигатель напряжение передача
Чертеж общего вида редуктора устанавливает положение колес
редукторной пары, элемента открытой передачи и муфты относительно опор
(подшипников); определяет расстояние lБ и lт; точками приложения реакций подшипников быстроходного
и тихоходного валов, а также точки приложения силы давления элемента открытой
передачи и муфты на расстоянии lОП и lМ от реакции смежного подшипника.
Параметры ступицы конического колеса:
наружный диаметр:
dст=1,6 ´ d3 = 1,6 ´ 38 = 60,8 мм
длина:
lст=1,3 ´ d3 = 1,3 ´ 38 = 49,4 мм
Зазор х от вращающихся поверхностей колеса до внутренней
поверхности стенок корпуса редуктора:
x = L1/3 + 3 =1181/3 + 3 = 10 мм
В коническом редукторе предусмотрена симметричность корпуса
относительно оси быстроходного вала.
Расстояние у между дном корпуса и поверхностью колеса
принимаем
y = 4x = 40 мм
Вычерчивание ступеней быстроходного вала зависит от положения
подшипников на 4-й ступени: нужно по ширине подшипника Т = 21 мм определить
положение левого подшипника, а
На 2-й и 4-й ступенях валов вычертить основными линиями
(диагонали - тонкими) контуры подшипников в соответствии со схемой их установки
по размерам d,
D, Т, с.
Определить расстояние lБ и lТ между точками приложения
реакций подшипников быстроходного и тихоходного валов. Радиальную реакцию
подшипника R
считать приложенной в точке пересечения нормали к середине поверхности контакта
наружного кольца и тела качения подшипника с осью вала. Для радиально-упорных
подшипников точка приложения реакции смещается от средней плоскости, и ее
положение определяется расстоянием а, измеренным от широкого торца наружного
кольца:
Рисунок 8.3.1. Определение расстояния между точками
приложения реакций в подшипниках
аБ = 0,5 (T + e (d+D)/2)= 0,5 (21 + 0,34
(30+72)/2)=19,17 мм
аT = 0,5 (T + e (d+D)/2)=
0,5 (20 + 0,38 (40+80)/2)=21,4 мм
где d, D, T - геометрические размеры подшипников;
е - коэффициент влияния осевого нагружения.
Тогда при установке подшипников по схеме враспор l=L-2a = 110-2´21,4 = 67,2 мм;
при установке по схеме врастяжку l= L+2a = 118+2´19,17 = 156,34 мм.
Определить точки приложения консольных сил:
а) для открытых, передач. Силу давления ременной передачи FОП принимаем приложенной к
середине выходного конца вала на расстоянии lОП = 55 мм точки приложения
реакции смежного подшипника;
б) сила давления муфты Fм приложена между
полумуфтами, поэтому можно принять, что в полумуфте точка приложения силы Fм находится в торцевой
плоскости выходного конца вала на расстоянии lм = 92 мм от точки
приложения смежного подшипника.
9.
Расчётная схема валов редуктора
9.1
Быстроходный вал
) Вертикальная плоскость
ΣM³ = 0;
Н
ΣM² = 0;
Н
Проверка: ΣY = 0;
Н
б) Горизонтальная плоскость
ΣM² = 0;
Н
ΣM³ = 0;
Н
Проверка: ΣX = 0;
Н
Н
Н
9.2
Тихоходный вал
) Вертикальная плоскость
Н
Проверка: ΣY = 0;
Н
б) Горизонтальная плоскость
Н
Н
Проверка: ΣX = 0;
Н
Н
Н
10.
Проверочный расчет подшипников
Пригодность подшипников определяется сопоставлением расчетной
динамической грузоподъёмности Crp, Н, с базовой Cr = 29,1 кН, или базовой
долговечности L10h, ч, с требуемой Lh = 17000 ч, по условиям:
Crp £ Cr и L10h ≥ Lh
Базовая динамическая грузоподъёмность подшипника представляет
собой постоянную радиальную нагрузку, которую подшипник может воспринять при
базовой долговечности.
10.1
Быстроходный вал
Предварительно выбранные подшипники средний серии 306 Cr =29,1кН,
C0τ =14,6кН
Определение осевой нагрузки Ra
Ra1 = Fa1 = 129,42 Н
Ra2 = Fa2 = 129,42 Н
Определение эквивалентной динамической нагрузки
Так как отношение:
где V = 1 - коэффициент вращения при
вращающемся внутреннем кольце
то:
Н
Н
где
= 1,2 - коэффициент безопасности;
= 1 - температурный коэффициент (t = 100oC);
X = 0,56 - коэффициент радиальной нагрузки для радиального
шарикоподшипника;
Y = 2,3 - коэффициент осевой нагрузки.
Расчет производится по наиболее нагруженному подшипнику, то есть
по подшипнику А:
кН
,44 < 29,1 кН
Так как Crp < Cr более чем в 1,5 раза,
следует взять подшипник более лёгкой серии (лёгкая серия 206 Cr =19,5кН, C0τ =10,0кН)
,44 < 19,5 кН
ч
> 17000 ч
где m = 3 - показатель степени для шариковых
подшипников;
а1 - коэффициент надежности. При безотказной работе
подшипников γ = 90%, а1
= 1;
а23 = 0,75 - коэффициент, учитывающий влияние качества
подшипника и качество его эксплуатации при обычных условиях работы подшипника.
10.2
Тихоходный вал
Предварительно выбранные подшипники лёгкой серии 208 Cr =32кН,
C0τ =17,8кН
Определение осевой нагрузки Ra
Ra1 = Fa1 = 129,42 Н
Ra2 = Fa2 = 129,42 Н
Определение эквивалентной динамической нагрузки
Так как отношение:
где V = 1 - коэффициент вращения при
вращающемся внутреннем кольце
то:
Н
Н
где
= 1,2 - коэффициент безопасности;
= 1 - температурный коэффициент (t = 100oC);
X = 0,56 - коэффициент радиальной нагрузки для радиального
шарикоподшипника;
Y = 2,3 - коэффициент осевой нагрузки.
Расчет динамической грузоподъемности и долговечности
Расчет производится по наиболее нагруженному подшипнику, то есть
по подшипнику А:
кН
,3 < 32 кН
Так как Crp < Cr более чем в 1,5 раза,
следует взять подшипник более лёгкой серии (особо
лёгкая серия 108 Cr =16,8кН, C0τ =9,3кН)
,3 < 16,8 кН
ч
> 17000 ч
где m = 3 - показатель степени для шариковых
подшипников;
а1 - коэффициент надежности. При безотказной работе
подшипников γ = 90%, а1
= 1;
а23 = 0,75 - коэффициент, учитывающий влияние качества
подшипника и качество его эксплуатации при обычных условиях работы подшипника.
Вал
|
Подшипник
|
Размеры d×D×B, мм
|
Динамическая
грузоподъёмность, кН
|
Долговечность,
ч
|
|
Принят
предварительно
|
Выбран
окончательно
|
|
Crp
|
Cr
|
L10h
|
Lh
|
Б
|
306
|
206
|
30×62×16
|
16,44
|
19,5
|
28365
|
17000
|
Т
|
208
|
108
|
40×68×15
|
9,3
|
16,8
|
101520
|
17000
|
Технический
проект
Технический проект выполняется с целью выявления
окончательных технических решений, дающих полное представление о конструкции
деталей и отдельных узлов привода, а также для оценки их соответствия требованиям
технического задания.
В техническом проекте разрабатываются варианты конструкций
зубчатой (червячной) передачи редуктора, элементов открытой передачи, корпуса,
подшипниковых узлов, валов, муфты и выполняется чертеж общего вида привода.
В техническом проекте согласовываются габаритные,
установочные и присоединительные размеры привода, решается ряд эксплуатационных
вопросов, связанных со смазыванием редукторной зубчатой пары и подшипниковых
узлов.
11.
Разработка чертежа общего вида привода
.1
Зубчатые колеса
Основные конструктивные элементы колеса -
обод, ступица и диск.
Обод воспринимает нагрузку от зубьев и
должен быть достаточно прочным и в то же время податливым, чтобы способствовать
равномерному распределению нагрузки по длине зуба.
Зубчатое колесо сделано ковкой, так как
диаметр da=210 мм.
Вал-шестерня выполнен заодно с валом, так
как u>3,15
мм.
Таблица 11.1.1. Параметры зубчатого колеса
Элемент
|
Размер, мм
|
Значение
|
Обод
|
Диаметр
|
dа=100….500 мм(44)
|
|
Толщина
|
S = 2,2´m+ 0,05´ b2
= 3,95
|
|
Ширина
|
b2 = 35
|
Ступица
|
Диаметр
внутренний
|
d =d3 = 60
|
|
Диаметр
наружный
|
dст=1,55´ d=93
|
|
Толщина
|
δст = 0,3 ´ d = 18
|
|
Длина
|
lст = 1,1 ´ d =66
|
Диск
|
Толщина
|
C =
0,5 ´ (S + δст) = 10,975
|
|
Радиусы
закруглений и уклон
|
R≥6; γ≥7°
|
Обод
|
Диаметр
|
dа<100 мм(44)
|
|
Толщина
|
S = 2,2´m+ 0,05´ b1
= 4,1
|
|
Ширина
|
b2 = 38
|
Ступица
|
Диаметр
внутренний
|
d =d3 = 38
|
|
Диаметр
наружный
|
dст=1,55´ d=58,9
|
|
Толщина
|
δст = 0,3 ´ d = 11,4
|
|
Длина
|
lст = 1,25 ´ d =47,5
|
Диск
|
Толщина
|
C =
0,5 ´ (S + δст) = 7,75
|
|
Радиусы
закруглений и уклон
|
R≥1
|
11.2
Шкив открытой передачи
Основные параметры шкива открытой передачи представлены в
таблице 11.2.1.
Таблица 11.2.1. Параметры шкива открытой передачи
Элемент
|
Размер, мм
|
Значение
|
Обод
|
Диаметр
|
dе = 2 ´ t + dр1 = 210
|
|
Ширина
|
B
= (z - 1) ´ e + 2 ´ f = 19
|
|
Толщина
|
δст = 0,8 ´ 1,2 ´ h = 9,7
|
Ступица
|
Наружный
диаметр
|
dст = 1,55 ´ d1 =
29
|
|
Длина
|
lст = 1,2 ´ d1
= 23
|
Диск
|
Толщина
|
C = 1,2 ´ δ = 10
|
11.3 Выбор соединений
Для соединения валов с деталями,
передающими вращающий момент (элементом открытой передачи, муфтой), применяются
шпонки:
§ Под элементом открытой
передачи - Шпонка 6 ´ 6 ´ 14 ГОСТ23360 - 78
§ Под полумуфтой - Шпонка 5
´ 5 ´ 10 ГОСТ23360 - 78
§ Надежное базирование
колеса по валу обеспечивается шлицевым соединением с центрированием по наружному
диаметру: D
- 4 ´ 32 ´ 36H7 / n6 ´ 6F8 / js7 ГОСТ 1139 - 80
11.4
Схемы установки подшипников
Осевое фиксирование тихоходного вала в
двух опорах - враспор.
Обе опоры конструируют одинаково, при этом
каждый подшипник ограничивает осевое перемещение вала в одном направлении.
Внутренние кольца подшипников закрепляют на валу упором в буртики 3-й или 5-й
ступени вала.
Наружные кольца подшипников закреплены от
осевого смещения упором в торцы крышек.
Достоинства: а) возможность регулировки
подшипников; б) простота конструкции опор (отсутствие стаканов и других
дополнительных деталей).
Недостатки: а) вероятность защемления тел
качения в опорах вследствие температурных деформаций; б) более жесткие допуски
на осевые размеры вала и ширину корпуса.
Осевое фиксирование быстроходного вала в
двух опорах - врастяжку.
Обе опоры конструируют одинаково, при этом
каждый подшипник ограничивает осевое перемещение вала в одном направлении.
Внутреннее кольцо одного подшипника упирается в регулировочную гайку;
внутреннее кольцо другого упирается в буртик третьей ступени. Наружные кольца
подшипников упираются широкими торцами в буртики стакана.
Достоинства: а) возможность регулирования
опор; б) малая вероятность защемления тел качения в опорах при температурных
деформациях, так как зазоры в подшипниках будут увеличиваться.
Недостатки: а) высокие требования точности
к резьбе вала и гаек, и к торцам гаек; б) усложнение конструкции опор.
11.5
Конструирование корпуса редуктора
Корпус редуктора служит для размещения и
координации деталей передачи, защиты их от загрязнения, организации системы
смазки, а также восприятия сил, возникающих в зацеплении редукторной пары,
подшипниках, открытой передачи. В проектируемом редукторе принята конструкция
разъемного, литого корпуса, состоящего из крышки (верхняя часть корпуса) и
основания (нижняя часть).
Форма корпуса.
Она определяется в основном
технологическими, эксплуатационными и эстетическими условиями с учетом его
прочности и жесткости. Корпус прямоугольной формы, с гладкими наружными стенками
без выступающих конструктивных элементов; подшипниковые бобышки и ребра внутри;
стяжные болты только по продольной стороне корпуса в нишах; крышки
подшипниковых узлов преимущественно врезные; фундаментные лапы не выступают за
габариты корпуса.
Толщина стенок корпуса и ребер жесткости.
В проектируемом малонагруженном редукторе толщина стенок крышки и основания
корпуса принимается одинаковой:
мм
мм
Принимаем
= 6 мм
Фланцевые соединения.
Для соединения крышки корпуса с основанием по всему контуру
разъема выполнен соединительный фланец. Фланец расположен внутрь корпуса, и его
ширина определяется от наружной стенки.
Рис. 11.5.2.1. Ниша соединительного фланца
Таблица 11.5.2.1. Параметры ниши фланца
Параметр
|
Значение
|
d3, мм
|
10
|
h3 = 2,3´ d3,
мм
|
23
|
h03 = 2, (d3 + δ), мм
|
40
|
K3, мм
|
23
|
С3,
мм
|
11
|
D03, мм
|
18
|
b03, мм
|
14
|
d03, мм
|
12
|
n, шт.
|
8
|
11.6 Выбор муфты
Для соединения выходного конца двигателя и
быстроходного вала применена упругая муфта с торообразной оболочкой. Муфта
проста по конструкции и обладает высокой податливостью, что позволяет применять
её при переменных ударных нагрузках, а также при значительных кратковременных
перегрузках.
Материал полумуфты - сталь СтЗ (ГОСТ
380-88); материал упругой оболочки - резина с пределом прочности при разрыве не
менее 10 Н/мм².
Полумуфта установлена на конусный конец
вала, что позволяет использовать муфту при больших нагрузках, работе с
толчками, ударами и при реверсивной работе.
Для предотвращения осевого перемещения
полумуфты используется круглая шлицевая гайка и многолапчатая шайба.
11.7
Смазывание. Смазочные устройства
Смазывание зубчатого зацепления и
подшипников применяют в целях защиты от коррозии, снижения коэффициента трения,
уменьшения износа, отвода тепла и продуктов износа от трущихся поверхностей,
снижения шума и вибраций.
При смазывании зубчатого зацепления
применяется способ непрерывного смазывания жидким маслом картерным непроточным
способом (окунанием).
Выбор сорта масла зависит от значения
расчетного контактного напряжения в зубьях σн и фактической окружной
скорости колес v (для σн = 514,3 Н/мм² и v = 1,8 м/с применяется сорт масла И - Г - А - 68: где И -
индустриальное; Г - для гидравлических систем; А - масло без присадок; 68 -
класс кинематической вязкости (кинематическая вязкость при 40оС
составляет 61 - 75 мм²/с))
Для одноступенчатых редукторов при
смазывании окунанием объем масляной ванны определяют из расчета 0,4…0,8 л масла
на 1 кВт передаваемой мощности.
Определение уровня масла при окунании в
масляную ванну колеса:
mmn £ hм £ 0,25de2
,5 £ hм £ 65,8 мм
В коническом редукторе должны быть
полностью погружены в масляную ванну зубья конического колеса, поэтому
принимаем hм = 20 мм.
Уровень масла, находящееся в корпусе
редуктора, контролируется круглым маслоуказателем.
При работе передачи масло постепенно
загрязняется продуктами износа деталей передачи. С течением времени оно
стареет, свойства его ухудшаются. Поэтому масло, налитое в корпус редуктора,
периодически меняют. Для этой цели в корпусе предусмотрено сливное отверстие,
закрываемое пробкой с конической резьбой.
При длительной работе в связи с нагревом
масла и воздуха повышается давление внутри корпуса. Это приводит к просачиванию
масла через уплотнения и стыки. Чтобы избежать этого, внутренняя полость
корпуса сообщена с внешней средой путем установки отдушины в смотровом люке.
12.
Проверочные расчеты
После завершения конструктивной компоновки
редуктора проводят ряд проверочных расчетов, которые должны подтвердить
правильность принятых конструкторских решений.
12.1
Проверочный расчет шпонок
Проверка шпонок производится на смятие.
Рисунок 11.1. Шпоночное соединение
Проверка шпонки тихоходного вала - под
элементом открытой передачи.
Параметры шпонки: b = 5 мм; h = 5 мм; l = 10 мм; t1 = 3 мм; t2 = 2,3 мм.
Условие прочности:
Н/мм²
[σ]см
= 110 - 190 Н/мм² -
допускаемое напряжение на смятие, при колебаниях нагрузки уменьшаем [σ]см
на 25%: [σ]см
= 110 ´ 0,75 = 82,5 Н/мм²;
мм² - площадь
смятия:
где lp = l - b = 10 - 5 = 4 мм -
рабочая длина шпонки со скругленными торцами.
Проверка шпонки быстроходного вала - под
полумуфтой.
Параметры шпонки: b = 6 мм; h = 6 мм; l = 14 мм; t1 = 3,5 мм; t2 = 2,8 мм.
Условие прочности:
Н/мм²
[σ]см
= 82,5 Н/мм² -
допускаемое напряжение на смятие;
мм² - площадь
смятия:
где lp = l - b = 6 мм - рабочая длина шпонки со
скругленными торцами.
12.2 Проверочный расчет стяжных винтов
Расчет производится по наибольшей из реакций в вертикальной
плоскости в опорах подшипников.
Определяем силу, приходящуюся на один винт:
FB = 0,5´ RDy = 497,3 Н.
Принимаем K3=3 - коэффициент затяжки при переменной
нагрузке; х = 0,27 - коэффициент основной нагрузки при соединение чугунных
деталей без прокладок.
Определяем механические характеристики материала винтов:
Винты изготовлены из стали 35, класса точности 5.6 (первое число,
умноженное на 100 определяет предел прочности σВ = 500 Н/мм²;
произведение чисел умноженное на 10 определяет предел текучести σт = 300 Н/мм²;
допускаемое напряжение [σ]= 0,2´σт= 0,2´300 = 60 Н/мм².
Определяем расчетную силу затяжки винтов:
Fр = [K3 (l - x) + x] FB =1127,14 Н.
Определяем площадь опасного сечения винта:
мм²
где dp - расчетный диаметр винта;
p = 1,75 мм - шаг резьбы.
Определяем эквивалентные напряжения:
Н/мм²
13.
Расчет технического уровня редуктора
Технический уровень целесообразно
оценивать количественным параметром, отражающим соотношение затраченных средств
и полученного результата.
«Результатом» для редуктора является его
нагрузочная способность, в качестве характеристики которой принимается
вращающий момент Т2, Нм.
Рис. 13.1. График для определения
коэффициента заполнения конического одноступенчатого редуктора
Объективной мерой затраченных средств
является масса редуктора m, кг, в которой практически интегрирован весь процесс его
проектирования. Поэтому за критерий технического уровня можно принять
относительную массу γ = m/T2 т.е. отношение массы
редуктора (кг) к вращающему моменту на его тихоходном валу (Нм). Этот критерий
характеризует расход материалов на передачу момента и легок для сравнения.
.1
Определение массы редуктора
кг
где φ = 0,42 - коэффициент
заполнения, определяемый по графику в зависимости от Re;
ρ = 7,4´103 кг/м³ - плотность чугуна;
13.2
Определение критерия технического уровня редуктора
γ
= m / T2 = 0,65
Рекомендации по уменьшению критериев
технического уровня редуктора: для повышения технического уровня редуктора
необходимо уменьшить толщину стенок редуктора и повысить твёрдость зубчатого
колеса и шестерни.
14.
Разработка рабочих чертежей деталей редуктора
.1
Тихоходный вал
а) Обозначаются базы под изображением
вала: база Е - поверхность пятой ступени вала; база Ж - поверхность второй
ступени.
б) Наносятся комбинированным способом
осевые размеры под изображением вала: сопряженный (14 мм) - длина шпоночного
паза; габаритный (236 мм) - длина вала; посадочные (22, 47, 49 мм); координирующий
положение шпоночного паза (6 мм). Размеры 27, 49, 91 мм отвечают
последовательным этапам токарной обработки вала.
в) Проставляются диаметральные размеры
ступеней вала: 1-я ступень - Ø40 мм; 2-я ступень - Ø28 мм; 3-я ступень - Ø30 мм; 4-я ступень - Ø30 мм; 5-я ступень - Ø25 мм.
г) На сопрягаемые диаметральные и линейные
размеры задаются поля допусков:
Ø
28к6 для
посадочных мест вала (2-я и 5-я ступени) под установку подшипников качения;
Ø
40n6 для посадочного места
вала (1-я ступень) под установку шкива открытой передачи;
Ø 28d9 для посадочного места
вала (2-я ступень) под манжетное уплотнение;
Ø
28a11 для монтажного размера
(2-я ступень) под дистанционную втулку;
Ø
30n6 для посадочного места
вала (3-я ступень) под установку зубчатого колеса;
Р9 для ширины шпоночного паза на 1-й
ступени - на размер 350 мм (d - t1, где t1= 3,5 мм - глубина шпоночного паза на 1-й
ступени) назначается нижнее отклонение - 0,1 мм, так как сечении шпонки 6х6 мм;
на глубину шпоночного паза t1 = 3,5 мм (1-я ступень)
назначается верхнее отклонение + 0,1 мм, так как сечение шпонки 6х6 мм;
H15 на длину шпоночного
паза первой ступени;
h12 и 91h12 для линейных размеров,
определяющих положение опор, фиксирующих осевое положение вала;
д) Наносятся и назначаются условные
обозначения допусков формы и расположения поверхностей:
допуск цилиндричности на Ø 40k6 и Ø 35n6 - 4 мкм; на Ø 36n6 - 5 мкм;
допуск соосности относительно оси
поверхностей Е и Ж на Ø 40k6 - 10 мкм; на диаметре Ø 36n6 - 20 мкм;
допуск перпендикулярности торца вала на Ø 40 мм относительно оси поверхностей Е и Ж - 20 мкм.
е) Проставляются на чертеже вала условные
обозначения шероховатости поверхностей и назначаются параметры шероховатости.
Обозначения параметров шероховатости проставляется на верхних частях изображения
вала, а на торцевых поверхностях - под изображением вала:
на Ø 40k6 и Ø 35n6 под установку подшипников и элемента открытой передачи - 0,8
мкм;
на Ø 36n6 под установку зубчатого
колеса - 0,8 мкм;
на Ø 40d9 под установку резиновой
манжеты - 0,4 мкм;
на торцы вала для базирования подшипников,
зубчатого колеса - 1,6 мкм;
на остальные поверхности вала - 6,3 мкм
(указано в правом верхнем углу чертежа).
ж) Участок второй ступени вала длиной 30
мм подвергнуть термической обработке на глубину h = 0,8…1,0 мм до твердости
40…50 HRC и отполировать. Обозначение термической обработки - утолщенная
штрихпунктирная линия.
14.2
Зубчатое колесо
привод двигатель напряжение передача
а) Обозначается база А - внутренняя
посадочная поверхность ступицы колеса.
б) Наносятся осевые размеры под
изображением колеса координатным способом. Проставляются диаметральные размеры
колес.
в) На сопрягаемые линейные и диаметральные
размеры задать поля допусков (Ø 36H7 для посадочного места
колеса). На размер шлицевого паза d + t2 назначается верхнее отклонение +0,1 мм, так как
сечение шлица <6х6 мм.
г) Наносятся условные обозначения допусков
формы и расположения поверхностей:
допуск цилиндричности на Ø 36H7 - 8 мкм;
допуск перпендикулярности торца колеса на Ø 58 мм относительно оси поверхности А - 30 мкм.
д) Проставляются условные обозначения
шероховатости поверхностей и назначаются параметры шероховатости. Обозначения
параметров шероховатости проставляется на верхних частях изображения колеса, а
на торцевых поверхностях - под изображением колеса:
посадочная поверхность отверстия ступицы Ø 36H7 - 0,8 мкм;
торец ступицы колеса - 1,6 мкм;
поверхность шлицевого паза: рабочая /
нерабочая - 1,6 / 3,2 мкм;
профиль зуба зубчатого венца - 1,6 мкм;
на остальные поверхности назначается
шероховатость - 6,3 мкм (указывается в правом верхнем углу чертежа).
е) Составляются технические требования в
следующем порядке:
требования к материалу зубчатых колес:
269…302 НВ;
радиусы скруглений - 2 мм max;
неуказанные предельные отклонения
размеров: отверстий +t2, валов - t2, остальных ±t2/2.
ж) Составляется таблица параметров
зубчатого венца.
Заключение
В результате разработки сборочного чертежа редуктора были
внесены следующие изменения:
1 Подшипники заменены на более нагруженные;
2 Изменения внесены в корпус редуктора с целью
уменьшения его массы;
Упругая втулочно-пальцевая муфта заменена упругой
муфтой с торообразной оболочкой
Основные параметры привода:
- Рабочий ресурс привода Lh = 70000 ч;
- Серия асинхронного двигателя 4АМ71В4У3 с
номинальной мощностью Pном = 0,55 кВт;
- Передаточное отношение: привода - uобщ = 18,3; закрытой
передачи - uзп = 6,3; открытой передачи - uоп = 2,91;
- Средний окружной модуль mnm = 3 мм;
- Вращающий момент на тихоходном валу T2 = 22,4 Нм;
- Марка материалов зубчатого колеса и шестерни
- сталь 40Х;
- Допускаемое контактное напряжение [σ]Hрас = 514,3 Н/мм².
Список
используемой литературы
1. Курсовое
проектирование деталей машин: Учебное пособие / Шейнблит А.Е. - Калининград
1999 г. - 454 с.
2. Конструирование
узлов и деталей машин: Учебное пособие / Дунаев П.Ф., Леликов О.П. - Москва
2003 г. - 496 с.
. Упрощенные
расчеты на прочность зубчатых передач. Ч. 2. Примеры расчетов конических
передач: Учебное пособие / Р.Д. Сухих, А.П. Цупиков, О.Н. Лущик - СПб: ПГУПС,
2004 г. - 32 с.
. Курсовое
проектирование деталей машин: Методические указания к курсовой работе / доцент
В.А. Шаханов - Кафедра «Теория механизмов и РТС» ПГУПС 2004 г.