Разработка структурной схемы производства безнапорных железобетонных труб
МИНИСТЕРСТВО ОБРАЗОВАНИЯ И НАУКИ
РЕСПУБЛИКИ КАЗАХСТАН
Рудненский индустриальный институт
Кафедра строительства и строительного
материаловедения
ПОЯСНИТЕЛЬНАЯ ЗАПИСКА
к курсовой работе
Тема: "Разработка структурной
схемы производства безнапорных железобетонных труб "
Дисциплина: Процессы и аппараты
Рудный 2011г.
Содержание
Введение
1. Характеристика изделия
2. Характеристика сырьевых материалов
2.1 Вяжущие вещества
2.2 Заполнители
3. Основы теории элементарных процессов и закономерности
отдельных стадий технологического процесса
3.1 Кинематика смешения
3.2 Формование центрифугированием
3.3 Тепловлажностная обработка
4. Расчет состава
4.1 Расчет потребностей сырьевых материалов
5. Выбор структурнойсхемы производства
6. Технологическая схема производства безнапорных труб
методом центрифугирования
7. Выбор оборудования технологической линий
8. Расчет процесса центрифугирования труб
9. Техника безопасности
Заключение
Список использованой литературы
Введение
Рост производства сборного железобетона вызывается
непрерывным расширением объемов капитального строительства.
В связи с этим, перед строителями и работниками
промышленности строительных материалов поставлена задача совершенствования
технологии производства железобетонных изделий и конструкций.
Промышленность сборного железобетона в настоящее время
изготовляет почти целиком перекрытия для промышленных, гражданских и жилых
зданий, более 30% фундаментов зданий, более 30% стен зданий и сооружений, более
60% каркасов промышленных зданий.
Расход сборного железобетона за последние годы в жилищном,
гражданском и промышленном строительстве быстро растет за счет увеличения
удельного веса полносборных домов.
В нашей стране разработана система унификации
объемно-планировочных решений промышленных зданий, сооружений и объектов
жилищно-гражданского строительства. Изданы единые каталоги бетонных и
железобетонных изделий для промышленного и жилищно-гражданского строительства.
Унифицированные изделия составляют около 80% общего объема железобетона.
Основным направлением развития сборных железобетонных
конструкций являются снижение материалоемкости и металлоемкости изделий и
конструкций, повышение степени заводской готовности, снижение энергетических
затрат.
Однотипные изделия различают по типоразмерам, если конструкции
и размеры различны, а также по маркам, если изделия одного типоразмера имеют
различные армирование, закладные детали или технологические отверстия.
Выбор технологии изготовления определяется формой изделий, их
габаритами, массой, видом бетона и принятым армированием.
В промышленности сборного ж/б в зависимости от номенклатуры и
вида изготовляемой продукции различают следующие типы предприятий:
специализированные - домостроительные комбинаты (ДСК); заводы и цехи
крупнопанельного домостроения (КПД); заводы объемно-блочного домостроения
(ОБД); заводостроительные комбинаты (ЗСК); сельские строительные комбинаты
(ССК); узкоспециализированные заводы и цехи по строительству труб, шпал, опор
ЛЭП и других изделий специального назначения; универсальные заводы ж/б изделий;
комбинаты промышленных предприятий; полигоны ж/б изделий.
Домостроительные комбинаты выпускают комплекты изделий и
конструкций для различных типов жилых домов - панели наружных и внутренних
стен, плиты перекрытий и покрытий, санитарно-технические кабины, лестничные
марши и доборные элементы, а также производят их монтаж.
В промышленном и гражданском строительстве нашей страны около
90% сборного ж/б составляют типовые унифицированные конструкции, при разработке
которых определяющим является требование заводской технологичности изделий. Это
требование обуславливает предельную массу изделий, их форму и размеры, вид
армирование и т.п.
Сборные железобетонные изделия производят, в основном,
линейными, плоскостными, блочными и объемными. К линейным относят колонны,
фермы, ригели, балки, прогоны; к плоскостным - плиты покрытий и перекрытий,
панели стен и перегородок, стенки бункеров и резервуаров; к блочным - массивные
фундаменты, стены подвалов и прочее; к объемным - санитарно-технические кабины,
блок-комнаты, коробчатые элементы силосов, кольца колодцев.
По условиям транспортного оборудования длина элементов, как
правило, не превышает 25 м, ширина 3 м и масса 25 т. Армируют изделия в
большинстве случаев сварными сетками, каркасами и укрупненными арматурными
блоками.
Для сборным ж/б конструкций применяют бетоны в широком
диапазоне плотности, прочности, морозостойкости и водонепроницаемости. Для
несущих ж/б конструкций широко используют тяжелый бетон марок М 150 - М 800,
плотностью 2200-2500 кг/м3, конструкционные бетоны на пористых заполнителях
марок М 150 - М 500, плотностью 1200-2200 кг/м3; для ограждающих конструкций
используют легкие бетоны марок М 50 - М 100 плотностью 700-1000 кг/м3.
Основными направлениями в совершенствовании железобетонных
конструкций (снижение стоимости при одновременном повышении качества) являются:
) удовлетворение требований непрерывно развивающихся
"Технических правил но экономному расходованию строительных
материалов" (ТП-101-81);
) применение конструктивных решений, снижающих массу
конструкций и позволяющих наиболее полно использовать: физико-механические
свойства исходных материалов, местные строительные материалы, бетоны высоких
классов (40 и выше), лёгкие бетоны, холодную пропитку бетонов мономерами и
высокопрочную арматуру (1000 МПа и выше), механизированное и автоматизированное
изготовление конструкций;
) повышение долговечности, надежности и технологичности
конструкций, снижение их приведённых затрат, материалоёмкости, энергоёмкости,
трудоемкости изготовления и монтажа;
) разработка новых, уточнение и упрощение существующих
методов расчета конструкций, особенно пространственных, тонкостенных и с
предварительным напряжением арматуры;
) развитие методов расчета с использованием ЭВМ и
высокопроизводительных методов конструирования (САПР), технологии изготовления
и возведения конструкций сборных, сборно-монолитных и монолитных;
) повышение качества, упрочнение и удешевление стыков сборных
и сборно-монолитных конструкций;
) изучение физико-химических и механических процессов
взаимодействия стальной арматуры с бетоном в целях наиболее эффективной борьбы
с появлением и раскрытием трещин в конструкциях;
) совершенствование методов подбора и изготовления бетона
(особенно легкого и ячеистого), с тем чтобы получать железобетон с заранее
заданными свойствами;
) повышение сейсмической и динамической стойкости
конструкций;
) увеличение долговечности конструкций в зданиях с
агрессивными средами, а также при эксплуатации в низких и высоких температурах.
Основным направлением технической политики в области
строительства являются снижение его стоимости, энергоемкости и трудоемкости при
высокой долговечности и надежности зданий, повышение технологичности как
отдельных элементов, так и конструкций в целом. К настоящему времени наибольшее
распространение в жилищно-гражданском строительстве получили полносборные
каркасные и бескаркасные многоэтажные здания и здания из объемных элементов.
Целью курсовой работы является разработка структурной схемы
производства безнапорных железобетонных труб.
Основные задачи курсовой работы:
привести технологические характеристики безнапорных
железобетонных труб и сырьевого материала;
изучить технологию получения труб;
описать теории элементарных процессов и общие закономерности
отдельных стадий технологического процесса;
выполнить технологические расчеты;
произвести расчет основного оборудования.
1.
Характеристика изделия
В основу классификации сборных ж/б изделий и конструкций
положены следующие признаки: вид бетона, его плотность, вид армирования,
внутреннее строение и назначение.
По виду бетонов и применяемых вяжущих различают изделия из
цементных бетонов - тяжелых на обычных плотных заполнителях, особо тяжелых
бетонов и легких бетонов на пористых заполнителях, ячеистых бетонов и
специальных бетонов - жаростойких, химически стойких, декоративных. По
плотности применяемых бетонов изделия могут быть из особо тяжелых бетонов
плотностью более 2500 кг/м3, тяжелых бетонов плотностью 1800-2500 кг/м3, легких
бетонов плотностью 500-1800 кг/м3, особо легких (теплоизоляционных) бетонов
плотностью менее 500 кг/м3.
По виду армирования ж/б изделия делят на предварительно
напряженные и с обычным армированием.
По внутреннему строению изделия могут быть сплошными и
пустотелыми, изготовленными из бетона одного вида, - однослойные, двухслойные,
многослойные, изготовленными из разных видов бетона или с применением различных
материалов (например, теплоизоляционных).
Ж/б изделия одного вида могут также отличаться типоразмерами,
например, блок стеновой, угловой, подоконный. Изделия одного типоразмера могут
разделяться по маркам.
Выбор метода изготовления различных изделий и конструкций
зависит от номенклатуры, технологических особенностей каждого метода и объема
производства. При этом решающее значение имеют технико-экономические показатели
производства конкретных изделий тем или иным методом.
Ж/б конструкции, как указано выше, классифицируют: по области
применения - для промышленного, жилищно-гражданского и других видов
строительства; по назначению в зданиях и сооружениях - на элементы фундаментов,
перекрытий, стен и т.п.; по геометрической форме - на линейные, плитные,
блочные, решетчатые и др.; по форме и структуре поперечного сечения - на
сплошные, пустотные, ребристые, слоистые, массивные и др.; по характеру
армирования - на бетонные (неармированные) и железобетонные (с обычной или
предварительно напряженной арматурой); по виду бетона - из тяжелого, легкого,
ячеистого.
Изделия должны иметь максимальную степень заводской
готовности. Составные или комплексные изделия поставляют потребителю, как
правило, в законченном виде, не требующем (если это не предусмотрено проектом)
дополнительной отделки.
Железобетонные трубы безнапорные предназначены для прокладки
подземных трубопроводов, транспортирующих самотеком бытовые жидкости и
атмосферные сточные воды, а также подземные воды и производственные жидкости,
не агрессивные к железобетону.
Производство железобетонных труб осуществляют из тяжелого
бетона. Их изготавливают по технологии виброгидропрессования. Такие
железобетонные трубы имеют более высокие технические характеристики по
сравнению с известными аналогами. Более высокие показатели по прочности и
трещиностойкости, морозостойкости (не менее F200) и
водонепроницаемости (не менее W6).
Качество поверхностей внутренней части раструба позволяет
обеспечивать быстроту и технологичность монтажа, а также достигать практически
абсолютной герметичности трубопровода, т.к. поверхность обработана методом
шлифования.
Трубы предназначены для прокладки подземных трубопроводов,
транспортирующих самотеком бытовые жидкости и атмосферные сточные воды, а также
подземные воды и производственные жидкости, не агрессивные к железобетону и
уплотняющим резиновым кольцам.
Трубы имеют диаметр условного прохода 400, 500, 800, 1000,
1200 и 1500 мм. и полезную длину - 5 м.
Трубы подразделяются на три группы несущей способности:
первую - при расчетной высоте засыпки грунтом 2м;
вторую - при расчетной высоте засыпки грунтом 4м;
третью - при расчетной высоте засыпки грунтом 6м;
Рис.1 Объемный эскиз трубы
Прочностные характеристики труб должны обеспечивать их
эксплуатацию при расчетной высоте засыпки грунтом в следующих усредненных
условиях укладки:
основание под трубой - грунтовое плоское для труб диаметром
условного прохода 400-500 мм. или грунтовое профилированное с углом охвата 90
градусов для труб, диаметром условного прохода 800-1500 мм;
засыпка грунтом, плотностью 16,7 кН/куб. м. (1,7 тс/куб. м.)
с углом внутреннего трения - 30 градусов и нормальной (неконтролируемой)
степенью уплотнения для труб диаметром условного прохода 400-800 мм. и
повышенным уплотнением для труб, диаметром условного прохода 1000-1500 мм.;
временная нагрузка на поверхности земли класса НК-80 по
СНи12.05.03-84.
Трубы обозначаются марками в соответствии с ГОСТ 23009 и ГОСТ
6482-88. Марка труб состоит из буквенно-цифровых групп, разделенных дефисом.
Первая группа содержит обозначение трубы, ее диаметр
условного прохода в сантиметрах и полезную длину в дециметрах. Во второй группе
указывается несущая способность, обозначаемую арабской цифрой.
Пример:
диаметр условного прохода 1000 мм., полезной длиной 5 м. с
подошвой 3-й группы по несущей способности: ТСП-150.50-3.
Трубы - водонепроницаемые и выдерживают испытательное гидравлическое
давление, равное 0,05 МПа (0,5 кгс/кв. см.).
Трубы удовлетворяют ГОСТ 13015-200:
по показателям фактической прочности;
по морозостойкости бетона;
по отклонению защитного слоя бетона до арматуры;
по маркам стали для арматурных изделий.
Трубы изготовлены из тяжелого бетона по ГОСТ 26633-91* класса
по прочности при сжатии не ниже В30.
Качество материалов, применяемых при изготовлении бетона,
обеспечивает выполнение технических требований, установленных ТУ, и
удовлетворяют требованиям следующих стандартов:
цемент - ГОСТ 10178-85*;
заполнители - ГОСТ 8267-93 и ГОСТ 8736-93* (наибольшая
крупность зерен
крупного заполнителя - 10 мм.);
вода - ГОСТ 23732-79.
Качество применяемых при изготовлении бетона добавок
соответствует требованиям ГОСТ и ТУ на эти добавки.
Таблица 1. Характеристика выбранной железобетонной трубы
Марка бетона
|
Размер, мм
|
Масса, кг
|
Расход
|
|
D
|
d
|
L
|
|
Бетон, Арматура, кг
|
|
300
|
1000
|
800
|
5000
|
1105
|
0,46
|
47
|
2.
Характеристика сырьевых материалов
Качество бетона в большей степени зависит от используемых
материалов. Правильный выбор материалов для бетона, учитывающий как требования
к бетону, так и свойства самих материалов, имеет важное значение в технологии
бетона. При этом должна достигаться максимальная экономия цемента и трудовых
затрат на производство бетона.
2.1 Вяжущие
вещества
Для приготовления бетона строительных конструкций наиболее
широко используют неорганические вяжущие вещества. Различают вяжущие
неорганические вещества водного (цементы) и воздушного (известь, гипс и др.)
твердения.
Наиболее широкое применение в производстве бетона получил
портландцемент (ПЦ). ПЦ - гидравлическое вяжущее вещество, твердеющее в воде
(лучше всего) или на воздухе. Это порошок серого цвета, получаемый тонким
помолом клинкера с добавкой гипса. Для получения цемента высокого качества
необходимо, чтобы его химический состав, а следовательно, и состав сырьевой
смеси были устойчивы. При помоле к цементному клинкеру можно добавлять 10-20%
гранулированных доменных шлаков или активных минеральных добавок. ПЦ называют
цемент, не содержащий в своем составе минеральных добавок, кроме гипса. Чисто
клинкерный ПЦ без добавок применяют для высокопрочных бетонов, в производстве
сборного ж/б, особенно предварительно напряженных конструкций, при
строительстве в особых условиях (на Севере и в районах с сухим и жарким климатом).
Наиболее распространенными цементами являются ПЦ с добавками (составляют около
60% всех выпускаемых цементов). Они могут применяться для большинства
монолитных и сборных ж/б конструкций, если к последним не предъявляются особые
требования.
Основное влияние на качество цемента оказывает содержание
трехкальциевого силиката (С3S), т.е. алита, который обладает свойствами быстротвердеющего
гидравлического вещества высокой прочности. Двухкальциевый силикат (С2S), белит, - медленно
твердеющее гидравлическое вяжущее средней прочности. Трехкальциевый алюминат
(С3А) твердеет быстро, но имеет низкую прочность. Изменяя минералогический
состав цемента, можно варьировать его качество.
Цементы высоких марок и быстро твердеющие изготовляют с
повышенным содержанием С3S (алитовые цементы). Цементы с высоким содержанием белита
(белитовые) - медленно твердеющие, однако прочность их нарастает в течение
длительного времени и в возрасте нескольких лет может оказаться достаточно
высокой.
Основное свойство, характеризующее качество любого цемента -
это его прочность (марка). Прочность цемента при сжатии составляет 30-60 МПа,
соответственно прочность балочек на изгиб - 4,5-6,5 МПа. Растворная смесь
должна иметь расплыв конуса на встряхивающем столике 106-115 мм. У большинства цементов
это достигается при В/Ц=0,4.
Действительную прочность цемента называют его активностью.
Так, при проектировании состава бетона лучше использовать активность цемента,
т.к. это обеспечивает более точные результаты и экономию цемента.
Цементная промышленность выпускает в основном цементы марок
400-550, а по особому заказу - марки 600. прочность цемента высоких марок
нарастает быстрее, чем у цементов низких марок.
Помимо требований к прочности к цементам предъявляются и
другие требования, причем наиболее важными из них являются нормальная густота и
сроки схватывания.
Нормальная густота ПЦ составляет 22-27%. Нормальная густота
увеличивается при введении в цемент при помоле тонкомолотых добавок. Наименьшую
густоту имеют чисто клинкерные цементы.
безнапорная труба железобетонная сырьевой
Сроки схватывания определяют начало и конец процесса
превращения материала в твердое тело. По стандарту требуется, чтобы начало
схватывания при температуре 200С наступало не ранее 45 минут, а конец
схватывания - не позднее 10 часов с момента затворения цемента водой. Сроки
схватывания можно регулировать путем добавления в бетонную смесь при ее
приготовлении различных химических добавок. Сроки схватывания уменьшаются с
повышением температуры бетона и уменьшением В/Ц.
ПЦ имеет, как правило, тонкий помол: через сито № 008 должно
проходить не менее 85% общей массы цемента. Средний размер частиц цемента
составляет 15-20 мкм. Тонкость помола цемента характеризуют также удельной
поверхностью зерен, содержащихся в 1 г цемента. Цемент среднего качества имеет
удельную поверхность 2000-2500 см2/г, высокого качества - 3500 см2/г и более.
Истинная плотность ПЦ без добавки составляет 3,05-3,15 г/см3.
Плотность ПЦ при расчете состава бетона условно принимают в уплотненном
состоянии - 1100 кг/м3, а истинная 3,1 г/см3.
2.2
Заполнители
Заполнители занимают в бетоне до 80% объема и оказывают
определенное влияние на свойства бетона, его долговечность и стоимость.
Введение в бетон заполнителей позволяет резко сократить расход цемента,
являющегося наиболее дорогим и дефицитным компонентом бетона. Кроме того,
заполнители улучшают технические свойства бетона. Жесткий скелет из
высокопрочного заполнителя несколько увеличивает прочность и модуль деформации
бетона - уменьшает деформации конструкций под нагрузкой, а также уменьшает
ползучесть бетона - необратимые деформации, возникающие в бетоне при длительном
действии на него нагрузки. Заполнитель уменьшает осадку бетона, способствуя
получению более долговечного материала. Усадка цементного камня при его твердении
достигает 1-2 мм/м.
Пористые естественные и искусственные заполнители, обладая
малой плотностью, уменьшают плотность легкого бетона, улучшают его
теплотехнические свойства.
Стоимость заполнителя составляет 30-50% (а иногда и более)
стоимости бетонных и ж/б конструкций, поэтому применение более дешевых и
доступных заполнителей в ряде случаев позволяет снизить стоимость
строительства, уменьшает объем транспортных перевозок, обеспечивает сокращение
сроков строительства.
Правильный выбор заполнителей для бетона, их разумное
использование - одна из важнейших задач технологии бетона. К заполнителям для
бетона предъявляются требования, учитывающие особенности их влияния на свойства
бетона. наиболее существенное влияние на свойства бетона оказывают зерновой
состав, прочность и чистота заполнителя.
В бетоне применяют крупный и мелкий заполнители. Крупный
заполнитель, зерна которого крупнее 5 мм, подразделяют на гравий и щебень.
Мелким заполнителем в бетоне является естественный или искусственный песок.
Щебень из горных пород - неорганический зернистый сыпучий
материал с зернами крупностью св. 5 мм, получаемый дроблением годных пород,
гравия и валунов, попутно добываемых вскрышных и вмещающих пород или
некондиционных отходов горных предприятий по переработке руд (черных, цветных и
редких металлов металлургической промышленности) и неметаллических ископаемых
других отраслей промышленности и последующим рассевом продуктов дробления.
Щебень из гравия должен содержать дробленые зерна в количестве не менее 80 % по
массе. Допускается по согласованию изготовителя с потребителем выпуск щебня из
гравия с содержанием дробленых зерен не менее 60 %. Гравий и щебень должны быть
морозостойкими и обеспечивать требуемую марку легкого бетона по
морозостойкости. Потеря массы после 15 циклов попеременного замораживания и
оттаивания не должна превышать 8%.
Искусственные гравий, щебень и песок (далее гравий, щебень и
песок) следует изготовлять в соответствии с требованиями настоящего стандарта
по технологическим регламентам, утвержденным в установленном порядке.
При расчете состава бетона условно принимают в уплотненном
состоянии - 1500 кг/м3, а истинная 2,7 г/см3.
По согласованию изготовителя с потребителем допускается
изготовление гравия и щебня от 2,5 до 10 мм и смеси фракций от 5 до 20 мм и для
теплоизоляционных засыпок - от 5 до 40 мм.
Песок представляет собой рыхлую смесь мелких зерен,
образовавшуюся в результате выветривания изверженных (реже осадочных) горных
пород. Иногда песок получают дроблением горных пород, но такой песок гораздо
дороже естественного и применяется только для специальных целей.
Песок, в зависимости от зернового состава, подразделяют на
три группы:
- для конструкционно-теплоизоляционного бетона;
- для конструкционного бетона;
- для теплоизоляционного бетона.
.3 Вода для приготовления бетона
Для приготовления бетонной смеси используют водопроводную
питьевую воду, а также любую воду, имеющую водородный показатель pH не менее 4 (т.е.
некислую, не окрашивающую лакмусовую бумагу в красный цвет). Вода не должна
содержать сульфатов более 2700 мг/л (в пересчете на SO4) и всех солей более
5000 мг/л. В сомнительных случаях пригодность воды для приготовления бетонной
смеси необходимо проверять путем сравнительных испытаний образцов,
приготовленных на данной воде и на обычной водопроводной.
Для приготовления бетонной смеси можно применять морскую и
другие соленые воды, удовлетворяющие приведенным выше условиям. Исключением
является лишь бетонирование внутренних конструкций жилых и общественных зданий
и надводных ж/б сооружений в жарком и сухом климате, т.к. морские соли могут
выступить на поверхности бетона и вызвать коррозию стальной арматуры.
Для поливки бетона следует использовать воду такого же
качества, как и для приготовления бетонной смеси.
Таблица 2. Характеристика сырьевых материалов
щебень
|
портландцемент
|
песок
|
вода
|

кг/м3
г/см3
Кг/шт
кг/м3
г/см3
Кг/шт
кг/м3
г/см3
Кг/шт
В/Ц
Кг/шт
|
|
|
|
|
|
|
|
|
|
|
1500
|
2,7
|
657,1
|
1100
|
3,1
|
153,3
|
1300
|
2,5
|
207,4
|
0,57
|
87,4
|
3.
Основы теории элементарных процессов и закономерности отдельных стадий
технологического процесса
3.1
Кинематика смешения
Смешение (перемешивание) - это процесс образования однородных
систем путем приведения в тесное соприкосновение сыпучих тел, жидкостей или
газов. Смешение сыпучих тел, жидких, вязко-пластичных и других сред
осуществляется механическим, гидравлическим (поточным), пневматическим и
другими способами. Наиболее распространен из них механический способ. Машины,
применяемые для перемешивания, называются смесителями.
Механизм действия процесса перемешивания является весьма
сложным, зависит от большого количества факторов и главным образом от
конструкции смесителя и режима его работы. Смешение (рисунок 2) складывается из
следующих механических операций: перемешивание групп частиц из одного места в
другое, так называемое конвективное смешивание (I); перераспределение
частиц при их перемешивании, так называемое диффузионное смешивание (II); сосредоточение частиц
в отдельных местах (III) смесителя, так называемое сегрегация частиц.
Рисунок 2 - Зависимость коэффициента неоднородности от
времени смешения
Идеально в результате смешения должна получиться такая смесь
материала, что в любой её точке (пробе) к каждой частичке одного из компонентов
примыкают частицы другого компонента в количествах, определяемых заданным
соотношением. Например, если материал состоит из трех компонентов, массы
которых относится как числа А: В: С, то в любом достаточно малом объёме, взятом
в случайной точке смесителя, после смешения массы компонентов тоже должны
относится как числа А
: В
: С
. Однако такое идеальное расположение
частиц в смеси в реальных условиях не наблюдается. Чтобы оценивать качество
смешения одной случайной величиной, смесь (материал) условно считают
двухкомпонентной. Для этого из смеси выделяют какой-либо один компонент,
называемый основным, остальные компоненты объединяют во второй условный
компонент. По степени распределения ключевого компонента в смеси, то есть
втором условном компоненте, судят о качестве смешения. Разработано довольно
много формул для расчёта критерия качества смешения. Например, при непрерывном
увеличении поверхности раздела между компонентами за сёт внедрения (диффузии)
процесс смешения представляется в следующем виде:
S=S
(1-e
)
где
S - текущая величина поверхности раздела; S
- максимальная возможная поверхность раздела; е - основание
натурального логарифма; к - коэффициент пропорциональности; t - время смешения.
Иногда процесс смешения связывают с влиянием размера и плотности
частиц отдельных компонентов, то есть с влиянием сегрегации (расслоения).
Степень перемешивания без учета расслоения (содержание данного компонента в
контрольных пробах в долях от теоретического):
M=1-e
где А - постоянный коэффициент, учитывающий свойства материала,
тип и режим работы смесительной машины; t - время перемешивания.
Современное производство строительных материалов, потребляющее
многокомпонентные сырьевые смеси, предъявляет повышение требования к процессу
смешения, поскольку качество готовых изделий во многом зависит от однородности
и качества сырья.
Наибольшее распространение для оценки качества смешения получил
коэффициент неоднородности (вариации), %:
где
- среднее квадратичное отклонение
концентрации ключевого компонента в пробах, %; С - среднеарифметическое
значение концентрации ключевого компонента в пробах, %; С
- значение концентрации ключевого
компонента в i-й пробе; n - число анализируемых (отработанных для анализа) проб. При
приготовлении бетонов и растворов качество смешения обычно оценивают по
коэффициенту вариации прочности случайных образцов (кубиков). При модернизации
или создании нового бетоносмесителя эффективность смешения оценивается
сопоставлением кубиков прочности бетона и коэффициента вариации прочности,
получаемых после испытания машин до и после модернизации.
Под кинетикой смешения понимается закономерность протекания
процесса во времени. Закономерность изменения концентрации вещества в потоке
при смешении описывается уравнением:
Где,
Q - расход компонентов, м
/с; С
, С - концентрация индикатора
соответственно на входе в смеситель и на выходе из него, кг/м
; d
- время; V
- объём рабочего органа смесителя, м
Среднее время пребывания частиц в ячейках (зонах) смесителя:
где g
(n) - вероятность нахождение ключевого компонента в m-й ячейке при идеальном его расположении по объёму
смесителя; n - количество переходов;
- интервал времени (времени скачка).
Среднее время пребывание частиц в условных ячейках (зонах)
смесителя, определяет качество смешения, зависит от конструкции и режима работы
смесителя и технологических свойств перемешиваемых компонентов смеси и
определяется экспериментально.
В большинстве промышленных смесителей получают смеси с качеством
смешением ниже 20%.
3.2
Формование центрифугированием
Рисунок 3 - Расчетная I и принципиальная II схемы центрифуг
а - роликовой; б - ременной; в - осевой.
Под центрифугированием (труб, опор для линий электропередач и
т.д.) в промышленности строительных материалов понимают процесс уплотнения
неоднородных смесей в поле центробежных сил.
Центробежная сила инерции, действующая на частицу смеси:
где m - ее масса; 
- угловая скорость вращения; r - радиус вращения центра тяжести частицы; G - вес частицы; g -
ускорение силы тяжести; n - число
оборотов.
Существует понятие о критической окружной скорости, начиная с
которой частицы под действием силы тяжести не будут отрываться от внутренней
поверхности формы в верхнем положении (рис.3, I). Для этого должно быть соблюдено условие Fц≥G, тогда:
nкр≥
Уплотнение смеси следует проводить при такой скорости вращения,
которая обеспечивает необходимую начальную прочность изделия, достаточную для
распалубки его и дальнейшей транспортировки.
Обычно начальная прочность свежеотформованной трубы
характеризуется величиной уплотняющей силы на наружной поверхности:
Fнар=
= 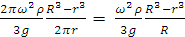
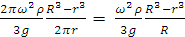
Зная необходимую прочность наружной поверхности трубы R', можно рассчитать
требуемое число оборотов центрифуги:
nтр = 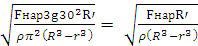
Внутреннее давление, развивающееся в формуемой массе в результате
действия центробежных сил, непосредственно воспринимается жидкой фазой. В
результате этого возникает избыточное гидростатическое давление, под влиянием
которого жидкость фильтруется. Фильтрация будет проходить до тех пор, пока
сопротивление движению жидкости в поровых каналах формуемой смеси за счет ее
уплотнения не сравняется с избыточным гидростатическим давлением.
Гидростатическое давление изменяется по толщине изделия неравномерно. Оно
минимально на внутренней поверхности и максимально на внешней. Поэтому вначале
жид - кость наиболее полно отжимается из наружных слоев массы и все в меньших
количествах по мере приближения к внутренней поверхности. Отсюда и
водосодержание массы неравномерно - оно больше во внутренних слоях и меньше во
внешних. Так, для бетонных изделий из-за неравнопрочности внутренних и внешних
слоев (в результате разного В/Ц) это имеет первостепенное значение.
Неравноплотность центрифугированной массы выражается не только
структурной неоднородностью гидратированного связующего за счет отжатия из него
воды к уменьшения толщины гидрат - ных оболочек, но и в характере распределения
зерен заполнителя по толщине изделия. Более крупные зерна за счет большей
центробежной силы прижимаются к наружной поверхности, а мелкие зерна
концентрируются ближе к внутренним слоям. Поэтому центрифугированные массы в
отличие от вибрированных имеют меньшую однородность распределения зерен
заполнителя по толщине изделия. Этот органический недостаток центрифугированных
масс может быть устранен при послойном уплотнении.
При малых толщинах последовательно загружаемых и уплотняемых слоев
отдельные фракции заполнителя распределяются в них более равномерно. В процессе
уплотнения последующего слоя крупные зерна заполнителя внедряются во внутреннюю
часть предыдущего слоя и вытесняют более дисперсную часть связующего во внешнюю
часть второго слоя. Аналогичные явления происходят и при уплотнении последующих
слоев. В результате достигается более равномерная структура смеси по толщине
изделия. Число слоев при раздельном их уплотнении при прочих равных условиях
зависит от толщины стенки: чем она больше, тем больше должно быть уплотняемых
слоев. Послойный способ формования целесообразно применять к смесям, имеющим
большую разницу в массах отдельных частиц (например, бетонные смеси) и
нежелательно для смесей, масса отдельных частиц которых близка по величине.
Уплотнение смеси методом центрифугирования производят в
специальных машинах, называемых центрифугами. По способу закрепления форм различают
центрифуги роликовые со свободным вращением форм, ременные с подвеской формы на
бесконечных ремнях, огибающих холостые и приводные шкивы, и осевые или
шпиндельные (рис.6, II).
Осевые центрифуги имеют высокие скорости вращения и позволяют
уплотнять более жесткие смеси. Недостаток их - сложность конструкции и
трудность загрузки смеси в форму. Применяются они для производства относительно
коротких изделий.
Роликовые центрифуги проще в изготовлении, однако их недостаток -
значительный шум при работе. Кроме того, они требуют высокой степени
сбалансированности формы, в противном случае возможно сбрасывание формы со
станка. Ременные центрифуги менее чувствительны к балансировке форм, менее
шумны при работе, но требуют повышенного ухода из-за износа ремней.
3.3
Тепловлажностная обработка
Тепловлажностной (или гидротермальной) обработкой называют
процесс одновременного воздействия на материал теплоты и влаги. В производстве
строительных материалов тепловлажностной обработке как основной технологической
операции подвергают бетонные изделия, силикатный кирпич, некоторые виды
безобжиговых огнеупоров, композиции на основе полистирола и поливинилхлорида.
Тепловая обработка минеральных строительных материалов ускоряет силикатное
твердение составляющих, а полимерных материалов - вспенивание соответствующих
композиций.
В качестве теплоносителей для тепловлажностной обработки
применяют водяной пар, горячую воду и нагретый воздух с повышенной
относительной влажностью. В последнем случае за счет выделения влаги из материала
теплоноситель представляет паровоздушную смесь с большим или меньшим
содержанием влаги. Тепловлажностная обработка может осуществляться при
атмосферном давлении в камерах, формах, шнеках и при повышенном давлении в
автоклавах и герметических формах.
Процесс обработки, как правило, делят на три периода: нагрев
материала до температуры греющей среды, выдержка при максимальной температуре,
охлаждение. Окончанием периода нагрева считают время, при котором поверхность
материала нагреется до температуры теплоносителя. Второй период часто условно
называют периодом изотермической выдержки. Условность названия связана с тем,
что центральные слои материала в начале периода продолжают нагреваться, так как
их температура отстает от температуры поверхности. Период охлаждения протекает
без подачи теплоносителя в установку.
При тепловлажностной обработке полимерных материалов в
горячей воде окончанием процесса является прекращение вспучивания материала.
Механизм тепло - и массопереноса при тепловлажностной
обработке. Если при тепловлажностной обработке изделий греющей средой является
пар или паровоздушная смесь с высокой относительной влажностью, а температура
поверхности материала ниже температуры точки росы, то на поверхности изделия
образуется пленка влаги. Для выяснения процессов, проходящих в материале,
рассмотрим бесконечную пластину и проанализируем направление составляющих
потока массы qm. Величина и направление составляющей потока qmuпри прочих равных
условиях будет определяться временем, прошедшим с момента формования изделия до
помещения его в тепловую установку. Если оно значительно, то в толще пластины
за счет испарения влаги с поверхности успеет установиться пораболический
характер распределения влаги. При внесении пластины в паровую среду на ее
поверхности образуется пленка конденсата и влагосодержание поверхности Unстанет больше
влагосодержания центра £/ц. Через некоторый
промежуток времени за счет диффузии влаги от поверхностных слоев к центру
влагосодержание в пластине будет характеризоваться кривой, сплошной линией.
Таким образом, в начале процесса пропарки влага движется от
центра и от поверхности изделия к плоскости х, причем сама эта плоскость
постепенно перемещается от поверхности к центру.
Механизм тепло - и массообмена при тепловлажностной обработке
в случае отсутствия пленки конденсата на поверхности материала принципиально не
отличается от механизма, разобранного при сушке изделий. Знание этого механизма
позволяет регулировать технологические параметры тепловой обработки таким
образом, чтобы исключить возможность "пересушки" бетона, особенно его
поверхностных слоев, и в то же время снизить общую влажность изделий. Так, при
пропарке керамзитобетона в щелевых камерах, оборудованных ТЭНами, в течение
всего периода тепловой обработки из бетона уделяется 50.70 кг влаги, что вполне
безопасно, так как оставшейся воды с избытком хватает на гидратацию цемента.
Конечная влажность бетона при этом составляет 10.13% против 18.20% при обогреве
паром. А это значит, что такие панели в течение нескольких лет в процессе
эксплуатации будут иметь большее термическое сопротивление, чем панели,
прошедшие термическую обработку в камерах обогрева паром. Поэтому пониженная
влажность стеновых панелей приводит к значительной экономии теплоты на
отопление и улучшает санитарно-гигиенические условия жилья.
Рассмотрим теперь механизм тепло - и массообмена при обогреве
материала горячей водой. Пусть неограниченная пластина помещена в емкость с
циркулируемой водой. Известно, что на поверхности твердого тела имеется
неподвижный пограничный слой. Тогда температура воды в емкости /в будет выше
температуры пограничного слоя, который отдает часть своей теплоты материалу, а
температура материала tMниже температуры этого слоя, т.е. будет
выполняться неравенство
K>ta>tM.
В этом случае направление частных потоков влаги qmu, qmtи qmpдля всех трех периодов
аналогично разобранному выше при обогреве материала паром.
В заключение необходимо отметить, что приведенные механизмы
тепло - и массообмена (в том числе и при сушке материала) справедливы только
для тепло - и влагоизолированной бесконечной пластины с двумя противоположными
открытиями поверхностями.
Характер описанных процессов будет изменяться в зависимости
от конфигурации обрабатываемого изделия (куб, тело вращения и т.д.), методов
нагрева (всесторонний, двусторонний, односторонний), расположения открытой
поверхности (горизонтальное, вертикальное), конструкции формы и ряда других
факторов, которые могут существенно изменить величину и направление
соответствующих градиентов. Эти процессы специфичны не только для отдельных
производств - керамики, бетона, пластмасс, но и технологических особенностей
тепловой обработки одного и того же материала. Например, механизм тепло - и
массообмена при тепловой обработке бетона в кассетах будет отличаться от механизма
при обогреве бетона в термоформах.
Под режимами тепловлажностной обработки обычно подразумевают
длительность отдельных периодов обработки, максимальную температуру обработки,
а также параметры греющего теплоносителя - его температуру, относительную
влажность и скорость перемещения относительно обрабатываемого материала. Для
минеральных вяжущих материалов длительность периода изотермической выдержки и
максимальная температура этого периода определяется требуемой степенью
завершенности силикатного твердения вяжущего и допустимой температурой нагрева
данного конкретного вяжущего.
Известно, например, что тепловая обработка, как правило, в
той или иной степени снижает показатели физико-механических свойств бетона по
сравнению с его твердением во влажных условиях при обычной температуре. Причем
это снижение тем больше чем интенсивнее и жестче режимы тепловой обработки.
Жесткость режимов прежде всего определяется интенсивностью роста и снижения
температуры на первом и последнем этапе тепловлажностной обработки, которые
вызывают возникновение в материале напряженного состояния. Определяющим
условием возникновения в материале напряжений является тепло - и массоперенос.
Как показано ранее, возникновение градиентов температуры,
влагосодержания и давления вызывает движение влаги в материале и,
следовательно, различные по величине деформации усадки и набухания коллоидного
капиллярно-пористого тела. Ни усадка, ни набухание сами по себе не вызывают
напряженного состояния материала. Напряжения появляются за счет недопущенных
деформаций.
Принципиальным отличием рассматриваемого процесса является
смена знаков возникающих напряжений. В отличие от сушки при обогреве паром
поверхностные слои испытывают напряжение сжатия, а центральные слои -
растяжения.
Поскольку сам процесс тепло - и массопереноса в каждом
конкретном случае зависит от величины и характера пористости, тепло - и
массопроводности материала, формы и размеров изделия и множества других
факторов, попытки ряда исследователей рассчитать режим пропаривания исходя из допустимой
скорости нагрева (в первооснове - из величины возникающих напряжений) пока не
увенчались успехом. Поэтому основным остается принцип экспериментального
подбора режимов обработки по оценке физико-механических свойств полученных
изделий. Однако ряд серьезных практических выводов качественного характера
все-таки можно сделать, если хорошо представлять себе механизм процессов тепло
- и массообмена. Например, ранее было показано, как формируется перепад
давлений внутри материала и было отмечено, что он образуется за счет нахождения
в материале газовой фазы. Поэтому если массу во время формования подвергнуть
вакуумированию, то количество воздуха в ней резко понизится. Совмещая этот
процесс с одновременным предварительным разогревом смеси, можно значительно
снизить возникающие на первой стадии тепловой обработки внутренние напряжения в
материале. Следовательно, можно увеличить допустимую скорость нагрева изделия,
сократив, тем самым, длительность общего цикла пропаривания.
Период изотермической выдержки с точки зрения нарушений в
структуре материала является наиболее спокойным, поскольку Vi° и VP сначала уменьшаются, а
затем практически исчезают.
Период охлаждения для материалов, набирающих прочность за
счет гидратационного твердения, является самым ответственным. Если в первый
период частичные нарушения структуры могут залечиваться вследствие углубления
реакций гидратации, то в третий период этих залечиваний в большом объеме
происходить не может.
4. Расчет
состава
Исходные данные:
марка бетона - 300;
удобоукладываемость - 2см,Rсж = 30МПа;
Физические свойства материалов:
цемента ρн=1100кг/м³,ρист = 3,1г/см³, ПЦ400;
щебня ρн=1500кг/м³,ρист = 2,7г/см³.
Решение:
) Водоцементное отношение:
В/Ц=А1Rц/ (Rб-0,5А1Rц)
В/Ц=0,60*400/ (300-0,5*0,60*400) =0,57
) Расход воды
Расход воды определяют в зависимости от заданной подвижности
бетонной смеси и наибольшей крупности зерен крупного заполнителя.
В=190 м³
) Расход цемента
Ц=
,
Ц=
=333,3
) Расход заполнителей

+ В +
+
= 1000
) Расход щебня
Щ =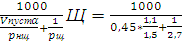
= 1428,5
6) Расход песка
П = 
= 450,9
) Расчетная плотность бетонной смеси составит:
pбс=Ц+В+П+Щ
pбс=333,3+190+450,9+1428,5=2402,7
Таблица 2 - Расход компонентов бетонной смеси
Наименование
компонентов
|
Расход
компонентов
|
|
на 1 м3
бетонной смеси, кг
|
Цемент
|
333,3
|
Песок
|
450,9
|
Щебень
|
1428,5
|
Вода
|
190
|
4.1
Расчет потребностей сырьевых материалов
Таблица 3 - количество рабочего времени
Наименование
цеха
|
Количество
|
Годовой фонд
времени (ч)
|
|
Рабочих дней в
году
|
Часов в смене
|
|
Бетоносмесительный
|
253
|
1
|
8
|
4048
|
. В год необходимо:
1) Бетонной смеси=2402,7∙10000=24027000
кг=24027 т
) Портландцемента=333,3∙10000=3333000
кг=3333 т
) Воды=190∙10000=1900000 кг=1900 т
) Щебня=1428,5∙10000=14285000 кг=14285 т
) Песка=450,9∙10000=4509000 кг=4509 т
2. Расчет на сутки:
1) Бет. см=24027: 253=94,97 т
) ПЦ=3333: 253=13,17 т
) В=1900: 253=7,5 т
) Щ=14285: 253=56,46 т
) П=4509: 253=17,8 т
3. Расчет на час:
1) Бет. см=94,97: 8=11,87 т, 2) ПЦ=13,17: 8=1,65 т
) В=7,5: 8=0,94 т, 4) Щ=56,46: 8=7,06 т
) П=17,8: 8=2,23 т
Таблица 4 Потребности в сырьевых материалах
Сырье и
полуфабрикаты
|
Единица
измерения
|
Потребность
|
|
|
час
|
смена
|
сутки
|
год
|
Бетонная смесь
|
т
|
11,87
|
94,97
|
94,97
|
24027
|
Цемент
|
т
|
1,65
|
13,17
|
13,17
|
3333
|
Вода
|
т
|
0,94
|
7,5
|
7,5
|
1900
|
Щебень
|
т
|
7,06
|
56,46
|
56,46
|
14285
|
Песок
|
т
|
2,23
|
17,8
|
17,8
|
4509
|
5.
Выбор структурнойсхемы производства
При заводском изготовлении железобетонных изделий широкое
распространение нашли три основных способа производства:
- агрегатно-поточный;
- конвейерный;
- стендовый
(кассетный).
Агрегатно-поточныйспособ изготовления конструкций характеризуется
расчленением технологического процесса на: отдельные операции или их группы;
выполнением нескольких разнотипных операций на универсальных агрегатах;
наличием свободного ритма в потоке; перемещением изделия от поста к посту;
формы и изделия переходят от поста к посту с произвольным интервалом, зависящим
от длительности операции на данном рабочем месте, которая может колебаться от
нескольких минут (например, смазка форм) до нескольких часов (пост твердения
отформованных изделий). Агрегатно-поточный способ отличается также тем, что
формы и изделия останавливаются не на всех постах поточной линии, а лишь на
тех, которые необходимы для данного случая. Агрегатно-поточный способ
организации производства характеризуется возможностью закрепления за одной
поточной линией изделий, различных не только по типоразмерам, но и по
конструкции. Эта возможность создается наличием на поточной линии
универсального оборудования. Межоперационная передача изделий на таких линиях
осуществляется подъемно-транспортными и транспортными средствами. Для
ускоренного твердения бетона при агрегатно-поточном способе обычно применяются
камеры периодического или непрерывного действия. Небольшой объем каждой секции
камеры позволяет затрачивать минимум времени на загрузку и выгрузку изделий, а
большое число таких секций создает условия для непрерывной подачи
отформованного изделия в камеру твердения.
Рис. 3 Схема производства, труб по поточно-агрегатной
технологии
- форма для труб диаметром 1000 мм; 2 - рама; 3 - форма для
труб диаметром 1200 мм; 4, 5 - мостовые краны; 6 - автоматический захват
грузоподъемностью 8 т для труб длиной 4120 мм; 7 - стенд для гидроиспытания
железобетонных труб диаметром до 1000 мм; 8 - стенд для гидроиспытаний
железобетонных труб диаметром 1200 и 1500 мм; 9 - бетонораздатчик; 10 - стенд
для бетонирования; 11 - поддон; 12 - промежуточный склад труб; 13 - участок
хранения форм; 14 - формы для труб диаметром 1500 мм.
Агрегатно-поточная технология отличается большой гибкостью и
маневренностью в использовании технологического и транспортного оборудования, в
режиме тепловой обработки, что важно при выпуске изделий большой номенклатуры.
Конвейерный способ характеризуется следующими признаками:
максимальное расчленение технологического процесса на операции, выполняемые на
отдельных рабочих постах; перемещение форм и изделий от поста к посту с регламентированным
ритмом. Изделия в процессе обработки передаются конвейерным устройством
пульсирующего действия, автоматически при этом создаются условия более полной
синхронизации. Конвейерный метод организации производства характеризуется
принудительным ритмом, т.е. перемещение формуемых изделий осуществляется в
строгой последовательности через одни и те же формовочные посты, с определенной
заданной скоростью передвижения. Это требует в качестве важнейшего условия
комплексную механизацию операции с применением автоматического технологического
оборудования. Обычно для межоперационного транспорта применяют механизированные
транспортные средства линейного типа - тележечные конвейеры, состоящие из
определенного числа поддонов-тележек, которые перемещаются тяговой цепью по
рельсовым путям. Параллельно линии формования, но обычно в обратном
направлении, осуществляется термовлажностная обработка изделий. [8]. В
зависимости от вида устройства для тепловой обработки изделий конвейерные линии
выполняют с камерами многоярусного, щелевого и ямного типов, а также с
пакетирующими устройствами для бескамерной тепловой обработки изделий в
термоформах. Линии также могут различаться в зависимости от формовочного
оборудования. Как правило, каждая конвейерная линия специализируется на выпуске
одного вида изделия. Конвейерный метод производства железобетонных изделий
позволяет добиться комплексной механизации и автоматизации технологических
процессов изготовления изделий, значительного повышения производительности
труда и увеличения выпуска готовой продукции при наиболее полном и эффективном
использовании технологического оборудования. Применение этого метода
рационально при массовом выпуске изделий по ограниченной номенклатуре с
минимальным числом типоразмеров.
В данной курсовой работе будет целесообразно применить
агрегатно-поточный способ производства, так как этот способ позволяет
использовать различное технологическое оборудование, различные по размерам
формы. Агрегатно-поточный способ для мелкосерийного производства является
наиболее выгодным. При несложном технологическом оборудовании, небольших
производственных площадях и затратах на строительство этот способ дает высокий
съем продукции с 1 м2 производственной площади цеха. Здесь сочетаются небольшие
затраты труда со сравнительно низкими удельными капитальными вложениями. Этот
способ позволяет разделить технологические операции по специализированным
постам, создать условия для организации четкого пооперационного контроля
качества изделий, обеспечивает высокий коэффициент использования оборудования и
оборачиваемость форм.
Агрегатно-поточный способ характеризуется:
- возможностью закрепления за одной поточной
линией изделий, различных не только по типоразмерам, но и по конструкции.
- небольшой объем каждой секции камеры
позволяет затрачивать минимум времени на загрузку и выгрузку изделий (что
создает условия для непрерывной подачи отформованного изделия в камеру
твердения).
- технология отличается большой гибкостью и
маневренностью в использовании технологического и транспортного оборудования, в
режиме тепловой обработки.
6.
Технологическая схема производства безнапорных труб методом центрифугирования
Приготовление бетонной смеси ведут путем перемешивания в
определенных пропорциях цемента, воды, песка и щебня крупностью не более 10 мм.
Арматурные каркасы изготовляют на специальных станках.
Станок, предназначенный для изготовления каркасов труб диаметром 400-900 мм,
оборудован специальным шаблоном для образования раструба; для труб 1000 -
1500мм каркас раструба вяжется отдельно вручную.
Арматурные каркасы раструбных труб диаметром 500.1300 мм при
формовании изготовляют на станке СМЖ - 117 А. Станок имеет планшайбу с приводом
вращения, сменные цилиндрические и конусные оправки, тележку, на которой
размещается конусная оправка; механизм перемещения, используемый для
протягивания продольных стержней; сварочный агрегат, установленный на тележке;
механизм подачи спиральной арматуры; диск для укладки продольных стержней. Для
изготовления арматурных каркасов труб с диаметром свыше 1400 мм применяют станок
СМЖ-420.
Трубы изготовляют в разъемных металлических формах. Для
сборки и разборки форм в пролете предусмотрены специальные посты, которые
оборудованы консольными кранами, устройствами для снятия раструбообразователей,
электрической талью, пневмоинструментом, оборудованием для очистки полуформ.
После укладки арматурного каркаса в нижнюю полуформу, мостовой кран
устанавливает верхнюю полуформу, пневматический гайковерт сболчивает полуформы,
после чего в форму вставляют раструбообразователь н втулочное кольцо. Собранную
форму мостовым краном транспортируют к стенду, где на форму надевают бандажи,
после чего она устанавливается на центрифугу. Вверху форма поджимается
роликами, предохраняющими ее от выброса в процессе центрифугирования.
Продолжительность загрузки ложкового питателя смесью - 1мин.
Формы диаметром до 800 мм загружают в один прием, а остальные - в два.
Продолжительность цикла формования 25-38мин.
Шлам, образовавшийся в процессе центрифугирования, сливается
через торец формы с помощью гидроподъемника, установленного на каждой
центрифуге.
После центрифугирования мостовой кран подает форму с изделием
на стенд для снятия бандажей и кантования в вертикальное положение. Затем форма
переносится на пост тепловой обработки, где она закрепляется в вертикальном
положении. Тепловую обработку осуществляют путем пуска пара по внутреннюю
полость трубы. Выдержка изделий перед тепловой обработкой составляет для труб
диаметром 400-800мм - 1,8ч. для труб 1000-1200мм - 2,7ч. После тепловой
обработки форму с изделием транспортируют на пост распалубки, где с помощью
мостового крана и тали поворачивают из вертикального в горизонтальное
положение. Здесь форма разболчивается, снимается верхняя полуформа, затем
извлекается готовое изделие.
Трубы после маркировки и приемки ОТК устанавливают на
самоходную тележку для вывода на склад готовой продукции.
В зимнее время изделия выдерживают в помещении на площадке
промежуточного складирования в течении 4 часов.
Из партии в 200 шт. по две трубы испытывают на прочность,
трещиностойкость, водонепроницаемость соответственно на прессе для механических
испытаний и установке для гидравлических испытаний труб.
Безнапорные трубы можно изготовлять на центрифугах, используя
при этом ненапрягаемую арматуру. Для производства этих труб не требуется
навиваемой арматуры и укладки защитного слоя. Стальные формы для 6езнапорных
труб применяют двух типов: для труб диаметром 500… 1500 мм - длиной 5000 мм, а
для труб диаметром 300… 400 мм - длиной 3200 мм.
Роликовая центрифуга (рисунок4) состоит из фундаментной рамы
1, ведущих роликов 7, приводимых в движение от электродвигателя 2, цепной
передачи 12 и дифференциала 11, ведомых роликов 9, удерживающих роликов 5,
смонтированных на кронштейнах стойки 6 и гидроподъемника 8. Тахометр 3 с
приводом от зубчатой передачи 13 предназначен для контроля за числом оборотов
роликов и формы. Тормоза 10, управляемые ручным насосом 14, применяются для
замедления вращения роликов и формы после окончания процесса центрифугирования.
Рис.4 Роликовая центрифуга
а - общий вид: б - кинематическая схема
Для предотвращения разбрызгивания массы предусмотрены щитки
4. Процесс изготовления железобетонных труб происходит следующим образом. Форму
с вставленной в нее арматурой и раструбообразователем укладывают бандажами на
лотки гидроподъемника 8. При опускании гидроподъемника бандажи формы ложатся на
ведущие и ведомые ролики, поворачивается кронштейн 6 и фиксируются по бандажу
удерживающие ролики 5. После разгона формы, вращающейся за счет трения между ее
бандажами и ведущими роликами, внутрь вводится ложковым питателем бетонная
смесь. В результате быстрого вращения смесь распределяется равномерным слоем по
стенкам формы и за счет центробежных сил уплотняется. По окончании процесса
формаостанавливается, кронштейн с роликами отводится в сторону и краном
формавместе с изделием снимается и переносится в отделение термической
обработки.
Изготовление безнапорных труб начинают с подготовки форм:
очистки, смазки и сборки. Внутрь форм вставляют арматурные каркасы, а затем
надевают днища форм. После этого форму с каркасом устанавливают на центрифугу.
При вращении центрифуги внутрь формы с помощью ленточного питателя или
ложечного бетоноукладчика подают бетонную смесь, которая ложится ровным слоем
по всей поверхности формы. После укладки бетона в формы с изделием с помощью
крана или кантователя устанавливают раструбом вниз в вертикальном положении на
пост пропаривания. После приобретения бетоном 70% проектной прочности форму
приводят в горизонтальное положение, разбирают, извлекают из нее изделие и
направляют на склад готовой продукции.
Производство железобетонных безнапорных труб можно вести и в
вертикальных установках. Установка для изготовления труб диаметром 400 и 500 мм
состоит из формовочной рамы с полуформой, находящейся в вертикальном положении,
и горизонтальной рамы с поддоном. Пустотообразователи с виброголовкой
заглублены в колодце. На очищенный и смазанный поддон укладывают два арматурных
каркаса. Затем формовочную раму переводят в горизонтальное положение и
соединяют с поддоном замковым механизмом. Далее формовочную и горизонтальную
рамы возвращают в первоначальное положение; После подачи пустотообразователя в
формы через направляющие и раструбообразователи начинают укладывать бетон.
Процесс формования длится 15 мин, затем извлекают пустотообразователи и
формовочную раму устанавливают в горизонтальное положение. Верхнюю полуформу
возвращают в вертикальное положение, а поддон с отформованным изделием
перемещают в камеру пропаривания. На одной установке одновременно формуют две
раструбные трубы.
Безнапорные трубы диаметром 800 мм и длиной 5000 мм можно
изготовлять на поточно-агрегатной линии с помощью центрифугирования.
Изготовление труб начинают с процесса навивки на сердечники напряжения
продольной арматуры. Затем на специальном стенде собирают спиральную
напряженную арматуру и скрепляют ее с продольной. После этого сердечник с
арматурным каркасом укладывают в полуформу, установленную на тележке
формовочного конвейера. Бетонную смесь укладывают бетоноукладчиком, затем
устанавливают верхнюю полуформу, и собранная форма поступает на центрифугу. При
скорости центрифугирования 94 об/мин бетон распределяется по внутренней
поверхности формы. При повышении скорости до 463 об/мин бетон уплотняется и
химически связанная вода удаляется через фильтрующее полотно, которым
выкладывается форма изнутри. Далее форму устанавливают на конвейер, а затем на
кантователь и распалубливают. Тележка и подвешенный к ней сердечник с трубкой
перемещаются к тоннельной пропарочной камере непрерывного действия, состоящей
из двух параллельно расположенных секций.
Каждая секция камеры по длине разбита на три зоны: 1 -
разогрев изделия до 700С, 2 - выдержка при температуре 700С и 3 - остывание
изделия до 200С. У выходного конца камеры передаточная тележка передает трубу
на кантователь, который поднимает трубу для расцепки с транспортной тележкой и
поворачивает ее в горизонтальное положение. Трубу укладывают на катки
самоходной тележки и перемещают к съемнику стержня, где стержни арматурного
каркаса обрезают и тем самым передают напряжение на бетон. Продолжительность
технологического процесса 22 ч.
При поточно-агрегатной схеме производства каждая труба и
форма последовательно проходят соответствующие посты технологической линии.
Такая схема наиболее приемлема при центробежном способе производства труб.
Загрузку центрифуг бетонной смесью осуществляют ложковыми
питателями, бетононасосами или бетонораздатчиками, а пропаривание труб
производят в горизонтальном или вертикальном положении. С технико-экономической
стороны, себя оправдывает двухступенчатое пропаривание труб с предварительным
пропариванием труб в течение 2…3 ч. Последнее обеспечивает получение бетона с
прочностью 6…8МПа и позволяет производить распалубку форм.
Трубы по конструкции стыкового соединения бывают: а)
раструбные со стыковым соединением, уплотняемым герметиками; б) раструбные со
стыковым соединением, уплотняемым резиновым кольцом; в) фальцевые со стыковым
соединением, уплотняемым герметиками.
К трубам предъявляются требования по коррозионной стойкости,
морозостойкости, водонепроницаемости, бетон должен иметь отпускную прочность,
равную 70.90% марочной.
Испытания на водопоглощение и водонепроницаемость проводят
один раз в три месяца, на морозостойкость - один раз в шесть месяцев.
Морозостойкость бетона определяется по ГОСТ 10060.
7. Выбор
оборудования технологической линий
Технологический процесс производства центрифугированных труб
включает в себя изготовление арматурных каркасов, укладку каркасов в формы,
сборку форм на постах распалубки, чистки и смазки форм, транспортирование форм
с каркасом и установку на центрифуги, формование труб на формовочных постах с
подачей бетонной смеси, съем форм с центрифуг и их перемещение на посты
тепловлажностной обработки с кантованием в вертикальное положение,
тепловлажностную обработку труб в формах с подачей пара внутрь трубы,
транспортирование форм с трубой, кантование в горизонтальное положение и
распалубку, испытание труб, установку на самоходную тележку и вывоз на склад
готовой продукции.
Таблица 5 Оборудование технологической линии
№
|
Оборудование
|
Характеристика
|
1
|
Центрифуга для
труб диаметром 1000 мм
|
Роликовая
|
2
|
Лотковый
питатель для труб диаметром 1000 мм
|
Емкость лотка
V=1,15; 1,81 м3
|
3
|
Стенд для
снятия бандажей и поворачивания форм в вертикальное положение
|
Грузоподъемность
2 т
|
4
|
Станок для
изготовления арматурных каркасов
|
Для труб
диаметром 1000 мм
|
5
|
Пресс для
механического испытания труб
|
Для труб
диаметром 1000 мм
|
6
|
Установка для
гидроиспытания труб
|
Для труб
диаметром 1000 мм
|
7
|
Бункер
раздаточный
|
Емкость 1,8 м3
|
8
|
Формы для труб
диаметром 1000-1500 мм
|
-
|
8.
Расчет процесса центрифугирования труб
Рисунок 5 - Схема сил, действующих на частицу
Метод центрифугирования основан на том, что при вращении формы
относительно собственной оси на частицы бетонной смеси начинают действовать
центробежные силы, которые и приводят к уплотнению бетонной смеси путем ее
прессования. Центрифугирование труб осуществляется в горизонтальном положении.
При этом результирующая сила, действующая на некоторую частицу бетонной смеси
массой т.:
P 
(1)
где R - радиус расположения частицы от оси
вращения; 
- угловая скорость формы.
Когда рассматриваемая частица находится в точкеA (рис.5), угол 
= 0, acos
=1. Следовательно:
PA = mR
- mg (2)
Когда рассматриваемая частица находится в точке В, угол 
= 
, acos
= - 1. Следовательно:
PB = mR
- mg (3)
Из этого вытекает, что давление в точке А ниже, чем в точке В. Это
обстоятельство заставляет бетонную смесь равномерно распределяться по
внутренней поверхности формы. Результирующая центробежная сила, действующая на
кольцо бетонной смеси радиусом гх, толщиной стенкиdr1 и длиной L:
dPn= 2
dr1 (4)
Интегрируя последнее выражение от R1 доR, получим
Pn= 2
2
(R3-
(5)
где Rl,R -
соответственно внутренний и наружный радиусы трубы.
Для того чтобы определить прессующее. давление на наружной
поверхности трубы, достаточно правую и левую части последнего выражения отнести
к наружной поверхности трубы.
P0= 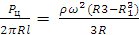
(6)
Это выражение характеризует связь давления на поверхности трубы с
ее параметрами и угловой скоростью центрифуги. Экспериментально установлено,
что при распределении бетонной смеси угловая скорость формы
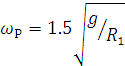
= 94 (7)
При уплотнении бетонной смеси прессующее давление согласно экспериментальным
данным должно быть Р0 = Py = 0.1 - 0.15
МПа. Последнее на основании (6) дает возможность определить угловую скорость,
необходимую для уплотнения бетонной смеси
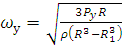
=463 (8)
В зависимости от установки и закрепления форм центрифуги Разделяют
на осевые или шпиндельные, в которых торцы формы закрепляют на передний
приводной и задней опорной бабках; свободнороликовые, в которых форма свободно
опирается на опорные ролики, и ременные, в которых форма подвешивается на
бесконечных перекрещивающихся ремнях, огибающих приводные и холостые шкивы.
Из-за сложности крепления форм и невозможности формования длинномерных изделий
осевые центрифуги применяют редко.
Форма одной из свободнороликовых центрифуг опирается на приводные
ролики, которые связаны между собой валами с зубчатыми муфтами. Эти ролики а
следовательно, и лежащая на них форма получают вращение от электродвигателя
через клиноременную передачу. Поддерживающие ролики установлены на гидроцилиндрах.
Такое расположение поддерживающих роликов позволяет менять диаметр формуемых
труб. Для снижения уровня шумов при работе центрифуги в качестве опорных и
поддерживающих роликов используют иногда автомобильные баллоны. В ременных
центрифугах вместо роликов используют бесконечные ремни, на которых
вывешивается форма. Такие центрифуги различных конструктивных исполнений
применяют для формования железобетонных труб длиной 5 - 20 м и диаметром до 4-5
м. При формовании изделий с диаметром до 800 мм формы заполняют бетонной смесью
до их установки на центрифугу. При формовании труб большего диаметра формы
заполняют непосредственно на центрифуге посредством специальных питателей,
например ложковых.
Центрифугированные трубы изготовляют из пластичных бетонных
смесей. Однако в процессе их изготовления благодаря действию центробежных сил
происходит отжим из бетонной смеси избыточной воды, которая вытекает из формы в
виде шлама. Это обеспечивает свежеотформованному изделию достаточную прочность
для его транспортирования в форме к камерам тепловлажностной обработки. Как
следует из выражений (7) и (8), угловая скорость центрифуги зависит от диаметра
формуемой трубы. Кроме того, привод должен обеспечивать работу центрифуг с
угловой скоростью 
р, необходимой для распределения бетонной смеси, и угловой
скоростью 
у, необходимой для ее уплотнения. Таким образом, приводы центрифуг
должны обеспечивать в широком диапазоне регулирование угловой скорости форм.
Это достигается установкой в системе привода коробок передач, вариаторов,
многоскоростных асинхронных электродвигателей. В последние годы для этого
широко применяют электродвигатели постоянного тока с тиристорными регуляторами
скорости.
Центрифуги рассчитывают по заданным размерам формуемых трубR, R1 иL в такой последовательности.
По выражению (7) определяют необходимую угловую скорость 
р распределения бетонной смеси, а по выражению (8) - угловую
скорость 
у уплотнения.
Находят мощность (Вт) приводного электродвигателя, необходимую для
работы центрифуги в режиме уплотнения:

=75 (9)
где 
- момент трения в опорах;

- момент трения формы о воздух;

- КПД привода.
Для роликовых центрифуг:
где Dб - диаметр бандажа, м; Dp - диаметр опорных роликов, м; a - угол между осями опорных роликов; µ - приведенный к валу
коэффициент трения скольжения подшипника качения, µ= 7*10-3; dB - диаметр вала под подшипниками качения,
м; 
- коэффициент трения качения опорных роликов по бандажам, 
= 5*10-4 м;
В центрифугах с предварительной загрузкой форм бетонной смесью
проверяют пусковой момент (Н*м) приводного электродвигателя:
Мпуск = Мтр + Мст
где Мст - статический момент массы бетонной смеси (Н*м) при ее
подъеме на угол 45°;
Мст = 0,47L
R3sin3
(b - центральный угол сегмента, в котором располагается
после загрузки в форму бетонная смесь).
Полученное значение Мпуск должно удовлетворять неравенству
Мпуск< Мд, где Мд - пусковой момент электродвигателя. При приводе от
асинхронных электродвигателей с короткозамкнутыми роторами Мд = 1,8Мн, где Мя -
номинальный момент электродвигателя.
Для производства берем частоту вращения барабана 463 об/мин.
9. Техника
безопасности
Многие цехи в результате выполнения технологических процессов
создают значительное выделение пыли, конвекционного или лучистого тепла, паров
и вредных газов; в формовочных цехах используются вибрационные механизмы,
которые оказывают отрицательное влияние на состояние здоровья рабочего, они же
являются источником шума и т.д.
В целях предотвращения загрязнения воздуха помещений с вредными
выделениями: оборудование, приборы, трубопроводы и другие источники, выделяющие
теплоту, должны быть теплоизолированы; агрегаты и оборудование, при
эксплуатации которых происходит влаговыделение, должны быть укрыты и
изолированы; технологические процессы, связанные с выделением пыли, следует
изолировать так, чтобы их работа осуществлялась без участия людей, а
выделяющиеся технологические выбросы в виде пыли, паров и вредных газов перед
выпуском в атмосферу должны быть подвергнуты очистке.
При работе вибрационных механизмов шум характеризуется
уровнем звукового давления в децибелах, а вибрация - виброскоростью.
Звуковое давление измеряют шумометром на расстоянии 1 м от
источника шума и 1.5 м от пола, Состав частот производственного шума определяют
с помощью анализатора спектра шума АШ-2Ми др., а амплитуду колебаний в пределах
0,05-1,5 мм в диапазоне частот 15-200 Гц - виброметром ВИП-4.
Виброскорость определят по формуле:
V = 2πAf,
где А - амплитуда; f - частота колебаний.
Уровень шума и вибрации на рабочих местах не должен превышать
допустимые пределы. В противном случае необходимо устраивать звуковую и
вибрационную изоляцию помещений, рабочих мест и машин, например установку
виброплощадок на массивные фундаменты; установку машин с вибраторами на пружинные
или резиновые виброизоляторы, обязательное крепление форм на виброплощадках и
ударных столах, приямков звукопоглощающими материалами.
В качестве индивидуальной защиты в помещениях с большой
концентрацией пыли необходимо пользоваться респираторами Ф-45 или ПРБ-1,·
герметичными защитными очками и спецодеждой.
В арматурном цехе при ведении сварочных работ необходимо:
заземлять сварочные аппараты, Применять очки и щитки со светофильтрами, на
рабочие места укладывать резиновые коврики, ограждать сварочные посты защитными
экранами, а при работе правильно-отрезных станков их кожух подключать к местной
системе аспирации. Формование изделий осуществлять при включенной звуковой
сигнализации, управление формовочными машинами должно быть дистанционным. При
тепловой обработке изделий следует не допускать утечки пара из камер, загружать
и выгружать камеры с помощью автоматических траверс.
Заключение
В данной курсовой работе был рассмотрен способ производства
железобетонных изделий, а именно безнапорных железобетонных труб
агрегатно-поточным способом. Агрегатно-поточная технология отличается большой
гибкостью и маневренностью в использовании технологического и транспортного
оборудования, в режиме тепловой обработки, что важно при выпуске изделий
большой номенклатуры.
Агрегатно-поточный способ для мелкосерийного производства
является наиболее выгодным. При несложном технологическом оборудовании,
небольших производственных площадях и затратах на строительство этот способ
дает высокий съем продукции с 1 м2 производственной площади цеха. Здесь
сочетаются небольшие затраты труда со сравнительно низкими удельными
капитальными вложениями. Этот способ позволяет разделить технологические
операции по специализированным постам, создать условия для организации четкого
пооперационного контроля качества изделий, обеспечивает высокий коэффициент
использования оборудования и оборачиваемость форм.
Агрегатно-поточный способ характеризуется:
- возможностью закрепления за одной поточной
линией изделий, различных не только по типоразмерам, но и по конструкции.
- небольшой объем каждой секции камеры
позволяет затрачивать минимум времени на загрузку и выгрузку изделий (что
создает условия для непрерывной подачи отформованного изделия в камеру
твердения).
- технология отличается большой гибкостью и
маневренностью в использовании технологического и транспортного оборудования, в
режиме тепловой обработки.
В качестве вяжущего используется портландцемент М400, в
качестве крупного заполнителя используется щебень с предельной фракцией 10 мм,
в качестве мелкого заполнителя используется песок фракции 0,14 - 5 мм.
В курсовой работе произведен расчет потребности в сырьевых
материалах на 1 м³ бетонной смеси. Кроме
того представлены основы теории элементарных процессов и общие закономерности
проведения отдельных стадий технологического процесса. К теории элементарных
процессов относится кинематика смешения, тепловая обработка, формование
центрифугированием и другие.
Так же в курсовой работе представлено описание основного
оборудования, приведены его основные технологические характеристики и
произведен его расчёт и его конструирование.
Список
использованой литературы
1.
Еремин Н.Ф. Процессы и аппараты в технологии строительных материалов. - М.:
Высш. шк. 1986. - 280 с.
.
Справочник по оборудованию заводов строительных материалов / под ред. М.Л.
Сапожникова, Н.Е. Дроздова. - М.: изд-во литературы по строительству, 1970. -
487 с.
.
Кузьмин А.В., Марон Ф.А. Справочник по расчетам механизмов
подъемно-транспортных машин. Минск: Высшая школа. 1983. - 345 с.
.
Комар А.Г. Строительные материалы и изделия: Учеб. для инж. - экон. спец.
строит. вузов. - 5-е изд., перераб. и доп. - М.: Высш. шк., 1988. - 527 с.: ил.
.
Передельский Л.В., Приходченко О.Е. Строительная экология: Учеб. пособие. -
Ростов н/Д: Феникс, 2003. - 320 с (Серия "Строительство".)
.
Баженов Ю.М. Технология бетона. - М.: Высш. шк. 1987. - 415 с.
.
Рыбьев И.А. Общий курс строительных материалов. М.: Высш. шк., 1987
.
Иванов И.А. Технология легких бетонов на искусственных пористых заполнителях. -
М.: Строй-издат. 1974. - 287 с.
.
Монфред Ю.Б., Прыкин Б.В. Организация, планирование и управление предприятиями
стройиндустрии. М.: Строй-издат, 1989. - 510 с.
.
Исидоров В.В. Справочник по производству искусственных пористых заполнителей. -
М.: Изд. Литер. по стр. 1966. - 320 с.
.
Нациевский Ю.Д. Хоменко В.П., Заиончковский Б.Ф. эффективные строительные
материалы. Справочное пособие. Киев: Буд., 1980. - 261 с.
Бауман
В.А., Быховский И.И. Вибрационные машины и процессы в строительстве. - М.:
Высш. шк., 1977. - 255 с.
.
Григорьев В.Н., Дьяков В.А., Пухов Ю.С. Транспортные машины и комплексы
подземных разработок. - М.: Недра., 1976. - 380 с.
.
Нагибин Г.В. Основы технологии строительных материалов. М.: Росвузиздат., 1963.
- 360 с.
.
Рыбьев И.А. Материаловедение в строительстве. - М.: Академия., 2007.
.
Основин В.Н., Шуляков Л.В., Дубяго Д.С. Справочник по строительным материалам. Ростов-на-Дону.:
Феникс., 2008. - 445 с.