Разработка конструкции редуктора
Введение
Заданный привод состоит из двух механических
передач:
. Открытая шевронная зубчатая передача
. Закрытая зубчатая передача, называемая
редуктором
. Две муфты
Назначение привода: уменьшение частоты вращения
валов. Главный параметр привода - передаточное число
Целью работы является разработка
конструкции редуктора
Охарактеризуем заданный редуктор:
Закрытая понижающая передача
Редуктор одноступенчатый, так как
имеет место одно зацепление
Редуктор горизонтальный
Редуктор цилиндрический, так как оси
валов параллельны
Достоинства:
Высокая надежность и КПД (до
0,97…0,98)
Большая загрузочная способность
Простота обслуживания
Малая масса
Постоянное передаточное число
Возможность использования
недефицитных материалов
Недостатки:
Требуется высокая точность
изготовления
Появление шума в процессе работы
Высокая жесткость не позволяет
компенсировать нединамические нагрузки
1.
Выбор двигателя, кинематический и силовой расчет привода
.1 Общий КПД привода
.2 Расчётная мощность
1.3 Выбор электродвигателя
Назначаем для привода трёхфазный
асинхронный двигатель серии 4А
Рдв = 22 (кВт)
nдв с = 1000
(об/мин)Табл. П2 Чернилевский
nдв ас =970
(об/мин)
Типоразмер: 200LВ6 dдв= 55 (мм)
1.4 Передаточное число привода и его
разбивка по ступеням.
Пусть Uред = 4,4 ,
тогда
Вывод: передаточное число открытой
передачи принадлежит от 2 до 5. Значит разбивка передаточного числа сделана
верно.
.5 Кинематический и силовой расчет
привода
n1 = nдв
№
вала
|
n, об/мин
|
ω, с-1
|
Р,
Вт
|
Т,
Н·м
|
Вал
дв.
|
nдв = 970
|
ωдв = 101,53
|
Рдв.тр
= 19656
|
Тдв
= 193,6
|
I в
|
n1 = 970
|
ω1 = 101,53
|
Р1
= 19263
|
Т1
= 189,7
|
II в
|
n2= 220
|
ω2
= 23
|
Р2
= 17936
|
Т2
= 779,8
|
III в
|
n3 = 45
|
ω3
= 4,71
|
Р3
= 16000
|
Т3
= 3397
|
2.
Расчет зубчатых колес редуктора
.1 Материал
зубчатых колес
Т2 < 800
Назначаем для колес сталь 45 с термообработкой
улучшение
из Табл. 4.1. Чернилевский
Твердость стали
Для шестерни твердость назначаем
выше, так как износ зубьев ее идет более интенсивно
Твердость стали
Найдем для выбранной стали
допускаемые контактные напряжения.
Sn -
коэффициент безопасности = 1,1…1,2
КHL -
коэффициент долговечности
Принимаем КHL= 1, так как
число циклов нагружения каждого зуба больше базового при долговечности L=17000
часов.
Чернилевский Табл. 4.3.
- предел контактной выносливости
.2 Расчетное контактное допустимое
напряжение
, так как прямозубая передача
.3 Домускаемые напряжения изгиба
Коэффициент безопасности:
2.4 Межосевое расстояние редуктора:
, так как редуктор прямозубый
, так как колеса редуктора
расположены симметрично
коэффициент неравномерности
нагрузки
Принимаем
так как
симметричная
Принимаем по ГОСТ 2185-66 ближайшее
большее:
.5 Нормальный модуль зацепления:
По ГОСТ 9563-60 принимаем: mn =3,5 (мм)
.6 Найдем числа зубьев шестерни и
колеса:
Задаемся предварительно углом β=0°, так как
передача прямозубая.
Принимаем: z1=26; z2=116
Фактическое передаточное число
редуктора:
Найдем процент расхождения с ранее
принятым:
Так как 1,3% < 4% , то такое
расхождение считается допустимым.
.7 Уточним угол
. Передача
прямозубая - уточнение не требуется
.8 Основные размеры зубчатых колес
.8.1 Делительные окружности:
d1=z1·m=26·3.5=91.0
(мм)
d2 =z2 ·m =
116·3.5=406(мм)
.8.2 Диаметры вершин зубьев колес:
.8.3 Диаметры впадин зубьев:
.8.4 Ширина зубчатого венца:
.9 Коэффициент ширины шестерни по
диаметру
.10 Окружная скорость зубчатых колес
=> 8-я степень точности колес
.11 Силы зацепления
Окружная сила:
Радиальная сила:
αω=20˚
Осевая сила:
так как
шевронное зацепление
.12 Проверка прочности зубьев по
контактным напряжениям:
.12.1 Коэффициент нагрузки
Чернилевский §4.3
2.12.2 Контактные напряжения в
зубьях
Вывод: Спроектированная передача
имеет запас прочности по контактным напряжениям.
.13 Проверка прочности зубьев колес
по напряжениям изгиба
.13.1 Коэффициент нагрузки при изгибе:
Табл. 4.6 и 4.7 Чернилевский
.13.2 Коэффициент формы зуба
эквивалентных колес
.13.3 Коэффициент компенсации
погрешности
так как β˚=0
=> прямозубая передача
.13.4 Коэффициент неравномерности
нагрузки
= 1,5 - коэффициент торцевого
перекрытия
n=8 - восьмая
степень точности колес
2.13.5 Найдем отношение
Второе отношение получилось меньше,
значит колесо в зацеплении будет слабым звеном, и проверку по напряжениям
изгиба будем производить только для колеса.
.13.6 Напряжение изгиба в зубьях
колеса
Вывод: запас прочности по
напряжениям изгиба значителен, значит размеры спроектированной передачи верны.
3.
Расчет открытой шевронной зубчатой передачи
Т1 = 189,7 (Н·м)n1
=970 (мин-1)
Т2 = 779,8 (Н·м)n2
=220 (мин-1)
Т3 = 3397(Н·м)n3
=45 (мин-1)
Uотк = 4,89
.1 Межосевое расстояние открытой шевронной
передачи
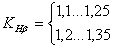
1,2
так как шевронная зубчатая передача
так как колеса расположены
симметрично
346,34(мм)
Принимаем
по ГОСТу
2185-66 ближайшее большее
.2 Нормальный модуль зацепления
По ГОСТ 9563-60 принимаем: mn =4(мм)
.3. Найдем число зубьев шестерни и
колеса.
β=30˚ , так как шевронное
зацепление
Принимаем: z1=26; z2=128
Уточним передаточное число открытой
передачи
Найдем процент расхождения с ранее
принятым:
Так как 0,6% < 4% , то такое
расхождение считается допустимым.
.4 Уточним угол β
β = 29°82
Найденный угол попадает в
рекомендуемый интервал 25˚…40˚ , значит найден верно.
.5 Основные размеры зубчатых колес
.5.1 Делительные окружности
.5.2 Диаметры вершин зубьев колес
3.5.3 Диаметры впадин зубьев
.5.4 Ширина зубчатого венца
.6 Коэффициент ширины шестерни по
диаметру
.7 Окружная скорость зубчатых колес
V=1.378 <
10 м/с => Назначаем 8-ю степень точности колес
.8 Силы зацепления
Окружная сила:
Радиальная сила:
αω=20˚
Осевая сила:
, так как
шевронное зацепление
3.9 Проверка прочности зубьев по
контактным напряжениям
.9.1 Коэффициент нагрузки
Чернилевский §4.3
.9.2 Контактные напряжения в зубьях
Вывод: Спроектированная передача
имеет запас прочности по контактным напряжениям.
.10 Проверка прочности зубьев колес
по напряжениям изгиба
.10.1 Коэффициент нагрузки при
изгибе
Табл. 4.6 и 4.7 Чернилевский
.10.2 Коэффициент формы зуба
эквивалентных колес
.10.3 Коэффициент компенсации
погрешности
3.10.4 Коэффициент неравномерности
нагрузки
= 1,5 - коэффициент торцевого
перекрытия
n=8 - восьмая
степень точности колес
.10.5 Найдем отношение
Второе отношение получилось меньше,
значит колесо в зацеплении будет слабым звеном, и проверку по напряжениям
изгиба будем производить только для колеса.
.10.6 Напряжение изгиба в зубьях
колеса
Вывод: запас прочности по
напряжениям изгиба значителен, значит размеры спроектированной передачи верны.
4.
Расчет первого вала редуктора
4.1 Геометрические
размеры первого вала
Так как передаточное число редуктора больше 2,8,
то технологически выгодно сделать первый вал в виде вала - шестерни.
Диаметр под муфту
для муфты
dдв = 55(мм)
dв1 пр ≈
0,8· dдв≈45(мм)
Назначаем длину муфты равную 82(мм)
для диаметра подшипника равного 45(мм).
Диаметр под подшипник качения.
dn1 = dв1 пр
+(5…10)=50(мм)
Выбор подшипника:
Так как редуктор прямозубый, то на
оба вала устанавливаются радиальные шарикоподшипники, начиная с легкой серии.
ГОСТ 8338-75 легка серия
Таблица 8.10.2 Курмаз
№
|
dn
|
D
|
B
|
C, кН
|
С0
, кН
|
210
|
50
|
90
|
20
|
35,1
|
19,8
|
C - динамическая
грузоподъемность
С0 - статистическая грузоподъемность
L2 = В/2+12+b1/2=10+12+33,75=55,75≈56(мм)
b1 = 67.5(мм)
L2 = B/2+35+Lм
= 10+35+82=127(мм)
.2 Силы действующие на первый вал
Ft=4169.2(H)
Fr=1517.5(H)
Fa=0
Fм1=50√Т1=50√189,7=688,6(Н)
Ма1=Fa·d1/2=0
,так как Fa=0
.3 Построение эпюр. (РИС. 1.)
Первый вал испытывает изгиб с кручением.
Т1 ω1
Вниз
Изгиб
Вертикальный изгиб:
Проверка:
Построение эпюры Mz
R1b Mz1
C1
0 X1
b Fr Mz2
(мм)
c2
Горизонтальный изгиб:
Проверка:
Построение эпюры Mz
R1г My1
C1
0 X1
г Ft My2
(мм)
C2
Fм0
5.
Расчет подшипника первого вала по динамической грузоподъемности
5.1 Суммарные реакции в первой и во второй
опорах
5.2 Расчет будем вести по наиболее нагруженной
опоре один.
Так как осевая сила равна нулю, то этот пункт не
рассчитывается
.3 Эквивалентная нагрузка на второй подшипник.
Кб =1,1 - коэффициент безопасности
КТ=1 - температурный коэффициент
Fa=0 - осева
сила
V=1 - коэффициент,
учитывающий вращение колец(вращение внутреннего колеса)
X=1 - коэффициент
радиальной нагрузки
Y=0 - коэффициент
осевой нагрузки
а1 = 1 - коэффициент надежности
подшипника
а2 = 0,8
α=3 показатель степени
n1=970
(об/мин)
с- динамическая грузоподъемность
Значит радиальный шарикоподшипник
№210 ГОСТ 8338-75 на первый вал подходит.
6.
Расчет второго вала редуктора
.1 Геометрические
размеры первого вала
Так как передаточное число редуктора больше 2,8,
то технологически выгодно сделать первый вал в виде вала - шестерни.
Диаметр под муфту
для муфты
Принимаем dв2 пр 60(мм)
Назначаем длину муфты равную 82(мм)
для диаметра подшипника равного 65(мм).
Диаметр под подшипник качения.
dn2 = dв2 пр
+(5…10)=65(мм)
Выбор подшипника:
Так как редуктор прямозубый, то на
оба вала устанавливаются роликоподшипники конические однорядные, начиная с
легкой серии.
ГОСТ 333-79 легка широка серия
Таблица П7 Чернилевский
№dnDBC,
кНС0
, кН
|
|
|
|
|
|
7513
|
65
|
120
|
31
|
110,0
|
98,0
|
C - динамическая грузоподъемность
С0 - статистическая грузоподъемность
dк= dв2
пр +5=70(мм)
Диаметр под буртик
dб = dк+5=75(мм)
L1 берется с первого
вала. L1=56(мм)
Lм = 8
L3 = B/2+35+Lм
= 31/2+35+82=132,5(мм)
.2 Силы действующие на первый вал
Ft=4169.2(H)
Fr=1517.5(H)
Fa=0
Fм1=125√Т2=3490.61
(Н)
Ма2=Fa·d1/2=0
,так как Fa=0
.3 Построение эпюр. (РИС. 2.)
Первый вал испытывает изгиб с кручением.
Т1 ω1
Вниз
Изгиб
Вертикальный изгиб:
Проверка:
Построение эпюры Mz
R3d Mz3
C3
0 X3
d Fr Mz4
(мм)
c4
0
Горизонтальный изгиб:
Проверка:
Построение эпюры Mz
Fм2 My1
C1
0 X1
м2 R3г
My2
134 (мм)
C2
0
R4г
C30
7.
Расчет подшипника второго вала по динамической грузоподъемности
.1 Суммарные реакции в третьей и четвертой
опорах.
7.2 Расчет будем вести по наиболее нагруженной
опоре один
Так как осевая сила равна нулю, то этот пункт не
рассчитывается
.3 Эквивалентная нагрузка на второй подшипник
Кб =1,1 - коэффициент безопасности
КТ=1 - температурный коэффициент
Fa=0 - осева
сила
V=1 - коэффициент,
учитывающий вращение колец(вращение внутреннего колеса)
X=1 - коэффициент
радиальной нагрузки
Y=0 - коэффициент осевой
нагрузки
а1 = 1 - коэффициент надежности
подшипника
а2 = 0,8
α=3 показатель степени
n1=970
(об/мин)
с- динамическая грузоподъемность
Значит роликоподшипник конический
однорядный ГОСТ 333-79легка широкая серия №7513 на второй вал подходит.
8.
Основные размеры корпуса и крышки редуктора
.1 Толщина стенки корпуса и крышки
редуктор
подшипник зубчатый передача
δ - толщина стенки
корпуса
δ1 - толщина стенки
крышки
δ = 0,025а+1=0,025·250+1=7,25≈8(мм)
δ1 = 0,02а+1=6(мм) Принимаем
- 8(мм)
Диаметры стяжных болтов
d2 ≈ 0.8·d1≈15.5(мм)
Принимаем: М16
.2 Диаметры штифтов
d3 ≈ 0.5·d1 ≈ 9.75≈10(мм)
Назначаем конические штифты ГОСТ 3129-70
9.
Расчет шпоночных соединений
Устанавливаем на валы редуктора призматические
шпонки со скругленными торцами ГОСТ 23360-78
.1 Шпонка первого вала под муфту
dв1=45(мм)
Т1=189,7(Н·м)
b=14(мм)
h=9(мм)
t1=5.5(мм)
Длина шпонки:
L1=lм
- 10=82-10=72(мм)
По ГОСТу 23360-78 принимаем Lпр=70(мм)
Находим σсмятия
дл чугуна
Вывод: шпонка 14х9х70 под муфту на
первый вал подходит
9.2 Шпонка под муфту
dв2=60(мм)
Т1=779,8(Н·м)
b=18(мм)
h=11(мм)
t1=7(мм)
Длина шпонки:
L2=lм
- 10=82-10=72(мм)
По ГОСТу 23360-78 принимаем Lпр2=70(мм)
Находим σсмятия
дл чугуна
Вывод: устанавливаем две шпонки
18х11х70 под муфту второго вала.
9.3 Шпонка под колесо
dк=70(мм)
Т2=779,8(Н·м)
b=20(мм)
h=12(мм)
t1=7,5(мм)
Длина шпонки:
L3=b2
- 10=62.5-10=52.5(мм)
По ГОСТу 23360-78 принимаем Lпр3=56(мм)
Находим σсмятия
дл чугуна
Вывод: устанавливаем две шпонки
20х12х56 под колесо.
10.
Расчет вала в сечении под зубчатым колесом на усталостную прочность (второго
вала)
Считаем, что напряжение σ
изменяются
по симметричному циклу, а напряжение τ по
пульсирующему циклу.
Назначаем для второго вала сталь 45 с
термообработкой нормализация из Табл.3.3 Чернилевского
Твердость
σВ=570(МПа) - предельная
прочность материала
σ-1=0,43σв=245,1(МПа)
τ-1=0,58σ-1=142,2(МПа)
Суммарный изгибающий момент под
колесо
Мz=42.490
My=115.388
Полярный и осевой моменты
сопротивлении.
Амплитуда и среднее напряжение при
симметричном цикле.
- средняя частота
Амплитуда и средняя частота цикла
касательных напряжений.
Коэффициент запаса усталостной
прочности для τ
и
σ.
Табл. 8.8 и 8.5. Чернилевский
Результирующий коэффициент запаса
усталостной прочности
Вывод: условие дл усталостной
прочности выполнено, значит при работе вала от переменных напряжений
микротрещины образовываться не будут.
11.
Смазка зацепления и подшипника
V=4.6(м/с) >
1(м/с) - окружная скорость колес
Колесо и подшипник можно смазывать одной
смазкой.
По Табл. 10.8. Определим вязкость масла для
смазывания передач при 50˚С.
η=28·10-6 (м2/с)
Подбираем марку масла
Индустриальное И-30А ОСТ 20799-75
V-объем масленой
ванны
V=0.25л·Ртреб(кВт)=0,25·19,656=4,9(л)
Способ смазки:
Масло заливается в корпус так, чтобы венцы колес
были в него погружены. При вращении колес масло увлекается зубьями,
разбрызгивается, попадает на внутренние поверхности корпуса, откуда стекает в
его нижнюю часть. Внутри корпуса образуется взвесь частиц масла в воздухе,
масло покрывает поверхность всех расположенных внутри корпуса деталей, при этом
обеспечивается и смазка подшипников качения.
Заключение
В данной пояснительной записке был проведен
расчет привода электрического барабана:
подобран электродвигатель
рассчитаны шевронная передача, цилиндрический
редуктор
подобраны подшипники на валы и муфты на ведомые
валы
проведена проверка шпоночных соединений на
смятие
Спроектированный редуктор прошел:
проверку на контактные напряжении
проверку зубьев на выносливость по напряжениям
изгиба
проверку подшипников на долговечность
В сечении под колесом на ведомом валу была проведена
проверка на выносливость.
Список литературы:
1. Курмаз Л.В., Скойбеда А.Т.
Детали Машин. М.: Высш. Шк.,2005.
2. Чернавский С.А. Курсовое
проектирование деталей машин. М.: Машиностроение, 1988.
. Чернилевский Д.В. Курсовое
проектирование деталей машин и механизмов. М.: Высш. шк., 1980.