Технологический процесс обработки детали
СОДЕРЖАНИЕ
Введение
Технологическая
часть
.1
Назначение и условия работы детали
.2
Химический состав, физико-механические характеристики
.3
Формирование группы деталей и конструирование КД
.4
Определение кода комплексной детали по классификатору ЕСКД
.5
Расчет годовой приведенной программы запуска деталей
.6
Оценка технологичности детали
.7
Оценка степени подготовленности детали к производству
.8
Выбор и обоснования метода получения заготовки
.9
Расчет припуска на обработку, операционных размеров и допусков
.10
Расчет режимов резания
.11
Определение норм времени при работе на станках с ЧПУ
.12
Выбор режущего инструмента
Конструкторская
часть
.1
Определение количества оборудования основного производства
.2
Расчёт системы инструментального обеспечения
.3
Расчёт массы стружки
.4
Подбор оборудования
.5
Устройство автоматической смены инструмента
.6
Модульное оборудование системы. Удаления отходов производства.
.7
Структура ГАЛ
.8
Назначение РТК ионно-плазменного нанесения покритий
.9
Специальная часть
.10
Разработка системы стабилизации катодного тока
.11
Архитектура МК 80512
Охрана
труда
.1
Анализ вредных факторов на производстве64
.2
Определение требуемого воздухообмена в помещении
Экономическая
часть
.1
Расчет себестоимости и цены вала-шестерни
.2
Полная себестоимость изготовления вала-шестерни
Вывод
Перечень
ссылок
РЕФЕРАТ
Проведено
опис конструкції деталі, її призначення і умови роботи. Обґрунтування вибору
матеріалу деталі. Вибір обладнання, ріжучого інструмента. Визначення режимів
різання для токарної, свердлильної та фрезерної обробки.
В
конструкторській частині було розроблено токарний РТК, свердлильно-фрезерний,
зубофрезерний, шліфувальний та РТК іонно-плазмової обробки. Визначення
кількості обладнання основного виробництва.
Проаналізовано
нанесення покриттів на поверхню вуглецевої сталі та покриття на основі нітриду
титана.
Спроектовано
систему вимірювання і стабілізації катодного току випаровувача.
ВВЕДЕНИЕ
Современному
машиностроению с серийным характером производства присущи постоянное усложнение
конструкции и увеличение номенклатуры выпускаемых изделий, частая смена
объектов производства, сокращение сроков освоения новой продукции. Эффективным
средством реализации указанного является широкое применение гибких
производственных комплексов (ГПК) - гибких автоматизированных участков (ГАУ) и
гибких автоматизированных линий (ГАЛ), управляемых от ЭВМ и работающих по
принципу гибко перестраиваемой технологии.
Гибкие
производственные системы (ГПС) - это совокупность в различных сочетаниях
оборудования с ЧПУ, роботизированных технологических комплексов (РТК), гибких
производственных модулей (ГПМ), отдельных единиц технологического оборудования
и систем обеспечения их функционирования в автоматическом режиме в течение
заданного промежутка времени, обладающая свойством автоматической переналадки
при производстве изделий различной номенклатуры в установленных пределах
значений их характеристик.
По
организационным признакам выделяют следующие ГПС: гибкая автоматизированная
линия (ГАЛ), гибкий автоматизированный участок (ГАУ), гибкий автоматизированный
цех (ГАЦ).
Разработка
технологических процессов входит основным разделом в технологическую подготовку
производства.
Технологический
процесс разрабатывают на основе имеющегося типового или группового процесса. По
технологическому классификатору формируют технологический код. По коду изделие
относят к определенной классификационной группе и действующем для нее
технологическому процессу. Важным этапом разработок является нормирование
технологического процесса.
Базовой,
исходной информацией для проектирования служат: рабочий чертеж детали,
технологические требования, регламентирующая точность, параметры шероховатости
и другие требования качества, объем готового выпуска изделия. Маршрутную
технологию разрабатывают, выбирая технологические базы и схемы базирования, для
всего технологического процесса. Выбирают две системы баз - основные и
черновые. Всю механическую обработку распределяют по операциям, таким образом,
выявляют последовательность выполнения операций и их число.
Построение
маршрутной технологии во многом зависит от конструктивно-технологических
особенностей детали и требования точности, предъявляемых к ее основным
поверхностям.
Деление
всего объема обработки на операции, выбор оборудования, формирования операций
по содержанию зависят также от условий производства.
В
маршрутной технологии в процессе обработки с учетом места каждой операции в
маршрутной технологии. Операционная технология позволяет выдать задание на
конструировании специального оборудования. Средствами автоматизации, на
разработку средств технологического оснащения и метрологического обеспечения
технологического процесса. Определяющий возможность организации поточного
производства.
Технологичность
конструкции детали определяют с учетом условий её производства. Выявляют
возможные трудности обеспечения параметров шероховатости поверхности, размеров.
Форм и расположения поверхностей детали (ширина канавок и пазов, фасок и т.п.)
должны быть унифицированы.
Заготовку
выбирают исходя из минимальной себестоимости готовой детали для заданного
годового выпуска. Чем больше форма и размеры заготовки, приближаются к форме и
размерам готовой детали, тем дороже она в изготовлении но тем проще и дешевле
её последующая механическая обработка и меньше расход материала. Выбор
заготовки после соответствующих технико-экономических обоснований назначение
точности по соответствующему ГОСТу на заготовку и указанием на чертеже
заготовки наносят общие припуски и обозначают отверстия. Которые образуются в
результате обработки, а в заготовке отсутствуют.
Деление
всего объема обработки на операции, выбор оборудования, формирования операций
по содержанию зависят также от условий производства.
В
современной авиационной технике детали работают в особо сложных
эксплуатационных условиях одновременного действия статических, динамических и
термоциклических нагрузках, температуры, а также агрессивной коррозионной и
эрозионной среды. Это приводит к появлению различных дефектов: развитию
усталостных трещин, коррозии и др. В подавляющем большинстве случаев эти
дефекты, прежде всего, возникают в тонком поверхностном слое деталей.
Практика
проектирования производства, эксплуатации и ремонта деталей авиационной техники
показывает, что радикальным средством повышения их эксплуатационных характеристик
является создание деталей со специальными свойствами поверхностных слоев.
Объединение ряда технологий в одной комбинированной, очевидно, имеет
значительную перспективу, когда сочетание физических процессов и методов
обработки позволяет получать поверхности деталей с целым комплексом уникальных
свойств.
токарный сверлильный фрезерный оборудование
1
ТЕХНОЛОГИЧЕСКАЯ ЧАСТЬ
.1
Назначение и условия работы детали
Обрабатываемая
комплексная деталь - является представителем деталей типа тело-вращения,
применяется в редукторах для изменения скорости вращения.
Зубчатое
зацепление находит широкое применение в современной технике, необходимо для
передачи крутящего момента с изменением частоты вращения валов, а также для
точной передачи движения между валами при относительно небольшом крутящем
моменте. Зубчатые передачи обладают рядом преимуществ, по сравнению с
передачами других типов (ременными, цепными) они обеспечивают передачу больших
мощностей, сохраняют постоянство передаточных отношений, имеют высокий КПД (до
0,99%), отличаются высокой надежностью, долговечностью и относительно малыми
габаритами.
.2
Химический состав, физико-механические характеристики
Материал
обрабатываемой детали сталь 45Х. Сталь 45Х - углеродистая, конструкционная
сталь. Физико-механические характеристики и химический состав Ст 45Х:
наибольшая
нагрузка, предшествующая разрушению σв=1030
МПа;
предел
текучести σт=850
МПа;
твердость
150 HB;
модуль
упругости Е=83000, МПа;
-
плотность γ=7,8
10-3, кг/м3;
термообработка
- термоулутшение;
-
0,45% углерода.
1.3
Формирование группы деталей и конструирование комплексной детали
При
формировании деталей в группу были подобраны детали сходные по конструктивному
назначению и типо-размерному ряду, со схожими технологическими и базовими
поверхностями в количестве 4. Для каждой детали был проведён анализ
поверхностей и их нумерация. На базе деталей группы была выбрана реальная
комплексная деталь, включающая в себя все поверхности деталей группы.
В
дальнейшем разработка технологического процесса будет осуществлятся для
комплексной детали. За счет этого процесс будет называтся групповым, что
позволяет распространить область применения унификации на состав
инструментального оснащения, сократить виды специализаций рабочих мест,
разработать каталоги групповых карт настройки станков. Все это в свою очередь
приводит к снижению денежных затрат на производство.
1.4
Определение кода комплексной детали по классификатору ЕСКД
Базовое
обозначение является общим для всех исполнений, оформленных одним групповым
чертежом, и представляется в графе 2 углового штампа основных надписей чертежа
и в таблице исполнительных размеров для первого исполнения.
Порядковый
номер исполнения присваивается для всех исполнений, кроме первого, с 01 до 99 (рис.1).
Код классификационной характеристики присваивают изделию и конструкционному
изделию по классификатору ЕСКД
Структура
кода классификационной характеристики:
Рисунок
1 - Код детали
Деталь
являет собой тело вращения, типа колец, дисков, шкивов, блоков, стержней,
втулок, стаканов, колонок, валов, осей, штоков, шпинделей с длинной свыше 0,5
до 2 D; с центральным сквозным отверстиям, круглым в поперечном сечении, без
резьбы, ступенчатая; с пазами и/или шлицами на наружной поверхности; с
отверстием вне оси детали.
.5
Расчет годовой приведенной программы запуска деталей
N
=10000 шт. m
=7,1 кг.
N
=12000 шт. m
=7 кг.
N
=11000 шт. m
=7,7 кг.
N
=11000 шт. m
=6,9 кг.
Для
расчета приведенной программы запуска необходимо для каждой детали найти общий
коэффициент привидения
Кпрі=Кмі·Ксі·Кслі
(1.1)
где
Кпр- общий коэффициент приведения, Км- коэффициент приведения по
массе, Ксл- приведенный коэффициент по сложности, Кс - коэффициентприведенной
по серийности
, (1.2)
где
масса i-той
детали,
масса комплексной
детали;
;
;
;
;
, (1.3)
где
объем
выпуска i-той детали,
объем
выпуска комплексной детали;
;
;
;
, (1.4)
где
количество
поверхностей i-той детали,
количество поверхностей комплексной
детали;
;
;
;
;
К
=К
· К
· К
=0,92·0,94·0,95=0,82156;
К
=К
· К
·К
=0,91·0,97·0,92=0,81208;
К
=К
· К
·К
=0,97·0,96·0,97=0,88464;
К
=К
· К
· К
=0,9·0,96·0,95=0,8208.
, (1.5)
где
- годовая
приведенная программа выпуска.
, (1.6)
где
- годовая
программа запуска, a=0..10%, b=0…8%
Такт
выпуска деталей
, (1.7)
где
Фд=4015 - действительный годовой фонд времени
.6
Оценка технологичности детали
Технологичность
детали - это свойство детали, заложенное в ней при проектировании и позволяющая
получить наиболее рациональными способами деталь с требуемым качеством при
минимальных затратах труда, средств и материала.
Анализ
технологичности комплексной детали по точности
Найдём
средний квалитет детали:
, (1.8)
гдеN-
количество поверхностей, Т - значение степени точности
Коэффициент
точности:
(1.9)
Используя
условие: если Кт.ч.≥0,8, значит деталь
технологична.
Анализ
технологичности комплексной детали по шероховатости
Найдем
среднюю шероховатость:
,(1.10)
где
R-значение степени шероховатости
,(1.11)
где
Кш- коэффициент точности по шероховатости
С
учётом условия, что
, то деталь
считается технологичной, в данном случаедеталь также технологична. С учётом
наличия зубьев детали можно считать не технологичной.
Оценка
коэффициента использования материала для базового варианта
КИМ=
, (1.12)
где
- масса
детали,
масса
простой фигуры
Находим
массу простой фигуры
; (1.13)
по чертежу
Конструкция
детали позволяет улучшить её технологичность, так как конструкция детали
позволяет использовать высокопроизводительные методы обработки, деталь имеет удобные
цилиндрические поверхности для установки и закрепления, заданные точности и
шероховатости обоснованы.
1.7
Оценка степени подготовленности детали к роботизированному производству
Перевод
деталей и изделий на автоматическое производство предъявляет к ним выполнение
требований технологии.
Все
свойства взаимосвязанные и в совокупности определяют его качественную оценку.
Для анализа детали характерные свойства разделяют на семь ступеней. Каждая
ступень качественно характеризует определенную совокупность свойств. Получение
кодового номера детали и определение его категории сложности.
Ступень
1: ассиметрия центра тяжести
000
Ступень
2: несцепляемость
000
Ступень
3: стержневые
000
Ступень
4: круглые прямые
Ступень5:
одна ось вращения, одна плоскость
Ступень
6: Центральное отверстие ступенчатое с нессиметричной формой концов
Ступень
7: Отверстие на образующей сквозное
Кодовый
номер детали 2012175
Сума
цифр кодового номера- b=18
Категория
сложности автоматизации-2
Автоматизация
средней сложности. Требуется отработка систем ориентировки и загрузки детали в
рабочие органы. Целесообразна экспериментальная проверка.
.8
Выбор и обоснования метода получения заготовки
Метод
получения заготовки - паковка на горизонтально-ковочной машине. Данный метод
подходит больше чем другие по нескольким причинам:
коэффициент
использования материала получаетсяминимальным;
благоприятное
расположение волокон;
Поковка
- одна из основных разновидностей обработки металлов давлением. Поковкой
изготавливают заготовки для ответственных деталей автомобилей, тракторов,
сельскохозяйственных машин, железнодорожных вагонов, самолетов, станков,
швейных машин, а также слесарного и медицинского инструмента и многих других
деталей.
Степень
сложности поковки вычисли по формуле
, (1.14)
где
-масса
поковки,
-масса
цилиндра;
при
этом: С1=0,63…1; C2=0.32…0.63; C3=0.16…0.32; C4≤0.16.
Находим
массу поковки
определена
раннее по формуле (1.13)
Находим
массу поковки
(1.15)
Соответственно
степень точности выбираем C2. Для поковок группы С2=0,32…0,63.
Класс
точности поковки для ГКМ Т4(ГОСТ 7505-89)
Группа
стали М1 (М1-сталь с массовой долей углерода до 0,45% или суммарной массовой
долей легирующих элементов до 2%).
Исходный
индекс для последующего назначения основных припусков, допусков и допускаемых
отклонений определяется в зависимости от массы, марки стали, степени сложности
и класса точности поковки по ГОСТу 7505-89. Исходный индекс 12.
1.9
Расчёт припуска на обработку, операционных размеров и допусков на наиболее характерны
поверхности детали
Количество
необходимых переходов по требованиям точности
,(1.16)
где
- квалитет
заготовки, Тдет- квалитет детали.
Количество
необходимых переходов по требованиям шероховатости
, (1.17)
где
Rzз- шероховатость поверхностей исходной заготовки, Rдет-
шероховатость поверхности готовой детали.
Расчет
числа переходов для наиболее ответственных поверхностей.
Поверхность
3:
n
Поверхность
5:

Поверхность
7:
n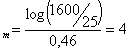
Поверхность
9:
n
Куф=0,03/0,86=0,03
Поверхность
17:
n
Поверхность
15:

Поверхность
12:
n
Куф=0,03/1,14=0,026
Поверхность
21:
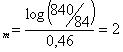
Поверхность
1, 14:

Поверхность
10, 14:
n
Принятое
количество необходимых переходов выбираем максимальным из n
, n
, n
.
Расчеты
представлены в табл. 1.1
Таблица
1.1-Количество ступеней обработки
№
пов- ти
|
Размер
|
Заготовка
Квалитет/допуск
|
Деталь
|
Кол-во
ступеней обработки
|
Т-ть
по ступеням
|
Ш-ть
по ступеням Rz мкм
|
Методы,
Виды обработки
|
|
Д
|
Т
|
Rz
|
Т
|
Rz
|
nT
|
nШ
|
Куф
nф
|
nS
|
1
|
2
|
3
|
4
|
5
|
6
|
1
|
2
|
3
|
4
|
5
|
6
|
|
3
|
Ǿ150
|
15 1600
|
100
|
11/250
|
10
|
2
|
2
|
|
2
|
12/400
|
|
|
|
|
|
32
|
|
|
|
|
|
Фрез-ние
черновое
|
|
|
|
|
|
|
|
|
|
|
|
11/250
|
|
|
|
|
|
10
|
|
|
|
|
Фрез-ние
чистовое
|
5
|
Ǿ160
|
15 1600
|
100
|
8/63
|
5
|
3
|
3
|
|
3
|
12/400
|
|
|
|
|
|
50
|
|
|
|
|
|
Точ-ие
черновое
|
|
|
|
|
|
|
|
|
|
|
|
11/250
|
|
|
|
|
|
25
|
|
|
|
|
Точ-ие
чистовое
|
|
|
|
|
|
|
|
|
|
|
|
|
8/63
|
|
|
|
|
|
5
|
|
|
|
Точ-ие
тонкое
|
7
|
Ǿ
170
|
15 1600
|
100
|
6/25
|
5
|
4
|
3
|
|
4
|
12/400
|
|
|
|
|
|
50
|
|
|
|
|
|
Точ-ие
черновое
|
|
|
|
|
|
|
|
|
|
|
|
11/250
|
|
|
|
|
|
25
|
|
|
|
|
Точ-ие
чистовое
|
|
|
|
|
|
|
|
|
|
|
|
|
8/63
|
|
|
|
|
|
10
|
|
|
|
Шлифование
черновое
|
|
|
|
|
|
|
|
|
|
|
|
|
|
6/25
|
|
|
|
|
|
5
|
|
|
Шли-ие
чистовое
|
9
|
Ǿ
180
|
15 1600
|
100
|
8/63
|
5
|
3
|
3
|
3
|
3
|
12/400
|
|
|
|
|
|
40
|
|
|
|
|
|
Точ-ие
черновое
|
|
|
|
|
|
|
|
|
|
|
|
11/250
|
|
|
|
|
|
25
|
|
|
|
|
Точ-ие
чистовое
|
|
|
|
|
|
|
|
|
|
|
|
|
8/63
|
|
|
|
|
|
5
|
|
|
|
Точ-ие
тонкое
|
20
|
Ǿ
36
|
15 1000
|
100
|
12/250
|
40
|
2
|
1
|
|
2
|
|
|
|
|
|
80
|
|
|
|
|
|
Сверление
черновое
|
|
|
|
|
|
|
|
|
|
|
|
12/250
|
|
|
|
|
|
40
|
|
|
|
|
Сверление
чистовое
|
Таблица
1.1-Количество ступеней обработки
№
пов-ти
|
Размер
|
Заготовка
Квалитет/допуск
|
Деталь
|
Кол-во
ступеней обработки
|
Т-ть
по ступеням
|
Ш-ть
по ступеням Rz мкм
|
Методы,
виды обработки
|
|
Д
|
Т
|
Rz
|
Т
|
Rz
|
nT
|
nШ
|
Куф
nф
|
nS
|
1
|
2
|
3
|
4
|
5
|
6
|
1
|
2
|
3
|
4
|
5
|
6
|
|
15
|
Ǿ
125
|
15 1600
|
100
|
8/63
|
4
|
3
|
3
|
|
3
|
12/400
|
|
|
|
|
|
40
|
|
|
|
|
|
Растачивание
черновое
|
|
|
|
|
|
|
|
|
|
|
|
10/160
|
|
|
|
|
|
20
|
|
|
|
|
Растачивание
чистовое
|
|
|
|
|
|
|
|
|
|
|
|
|
8/63
|
|
|
|
|
|
4
|
|
|
|
Проточивание
|
12
|
Ǿ
300
|
15 2100
|
100
|
8/81
|
5
|
3
|
3
|
3
|
3
|
12/520
|
|
|
|
|
|
50
|
|
|
|
|
|
Точ-ие
черновое
|
|
|
|
|
|
|
|
|
|
|
|
11/320
|
|
|
|
|
|
25
|
|
|
|
|
Точ-ие
чистовое
|
|
|
|
|
|
|
|
|
|
|
|
|
8/81
|
|
|
|
|
|
5
|
|
|
|
Точ-ие
тонкое
|
1,
14
|
380
|
15 2300
|
100
|
11/230
|
10
|
2
|
3
|
|
3
|
12/570
|
|
|
|
|
|
50
|
|
|
|
|
|
Подрезка
торца черновая
|
|
|
|
|
|
|
|
|
|
|
|
11/230
|
|
|
|
|
|
25
|
|
|
|
|
Подрезка
торца чистовая
|
10
|
36
|
15 1000
|
100
|
8/39
|
10
|
2
|
3
|
|
3
|
12/250
|
|
|
|
|
|
50
|
|
|
|
|
|
Подрезка
торца черн
|
|
|
|
|
|
|
|
|
|
|
|
11/
160
|
|
|
|
|
|
25
|
|
|
|
|
Подрезка
торца чист.
|
|
|
|
|
|
|
|
|
|
|
|
|
8/39
|
|
|
|
|
|
10
|
|
|
|
Шлифование
|
Определение
припуска расчетно-аналитическим методом
Определяем
элементы минимального припуска:
Для
каждого перехода, исходя из определенных выше величин, находим минимальное
значение припуска:
, (1.18)
где
Z- припуск, h- дефектный слой для штамповки,
-отклонение заготовки,
-погрешность
установки, Rz - широховатость.
Шероховатость
Rz и значение глубины дефектного слоя h для штамповки
определяем по ГОСТ 7505-89 для каждого из переходов.
Пространственные
отклонения исходной заготовки определяются по формуле (1.21)
Остаточные
коробления и смещения после каждого вида обработки определяется по формуле:
,
где
-допуск на
поверхность при фрезерно - центровальной оеерации
, (1.19)
где
-пространственное
отклонение исходной заготовки, Куф- коэф-фициент уточнения
формы, характеризующий уменьшение пространственных отклонений от исходной
заготовки до рассматриваемого этапа обработки.
-
погрешность установки вызывается биением кулачков токарного патрона и перекосом
детали. Величина погрешности устанавливается. Величина коробления
кор. После
соответствующей термообработки определяется.
Определяем
номинальные значения припуска из 2Zmin и допуска для
предыдущего перехода (величину допуска выбираем из таблицы минимального
потребного числа ступеней обработки поверхности):
, (1.20)
где
Zmin- минимальное значение припуска,T-квалитет поверхности.
Определяем
расчетный размер для каждого перехода.
Для
наружных поверхностей:
, (1.21)
где
- диаметр
поверхности согласно расчетам,
- максимальный диаметр поверхности.
Для
внутренних:
, (1.22)
где
- диаметр
поверхности согласно расчетам,
- минимальный диаметр поверхности.
Для
наружных поверхностей
, (1.23)
где
-
номинальное значение припуска.Для внутренних поверхностей
, (1.24)
, (1.25)
Имея
значения Dmin и Dmax, находим значения 2Zmax и
2Zmin.
Для
внутренних поверхностей
(1.26)
(1.27)
Для
внешних поверхностей
(1.28)
(1.29)
Результаты
расчета заносим в табл. 1.2
Таблица
1.2-Расчетно - аналитический метод
Поверхность
№3 Ø150
h11
№оп
|
Обработка
|
Rz
|
h
|
∆
|
E
|
2Zmin,
мм
|
Тd,
мм
|
2Zном,
мм
|
dp,мм
|
dmax
|
dmin
|
2zmax
|
2zmin
|
Техн.
р-р
|
Rz
|
|
Штамповка
|
100
|
150
|
1,35
|
-
|
|
+1,8
-1,0
|
|
154,96
|
156,7
|
153,9
|
|
|
100
|
|
|
Фрез-иечерновое
|
32
|
50
|
0,081
|
-
|
3,2
|
0,4
|
4,2
|
150,76
|
150,7
|
150,3
|
6,4
|
3,2
|
32
|
|
|
Фрез-иечистовое
|
10
|
25
|
0,067
|
-
|
0,362
|
0,25
|
0,76
|
150
|
150
|
149,7
|
0,95
|
0,3
|
10
|
|
Поверхность
№5 Ø160
h8
|
№оп
|
Обработка
|
Rz
|
h
|
∆
|
E
|
2Zmin,
мм
|
Тd,
мм
|
2Zном,
мм
|
dp,
мм
|
dmax
|
dmin
|
2zmax
|
2zmin
|
Техн.
р-р
|
Rz
|
|
Штамповка
|
100
|
150
|
1,35
|
-
|
|
+1,8
-1,0
|
|
165,45
|
167,2
|
164,4
|
|
|
100
|
|
|
Точ-ие
черновое
|
50
|
60
|
0,081
|
-
|
3,2
|
0,4
|
4,2
|
161,25
|
161,2
|
160,8
|
6,4
|
3,2
|
50
|
|
|
То-ие
чистовое
|
25
|
20
|
0,067
|
-
|
0,382
|
0,25
|
0,78
|
160,47
|
160,4
|
160,2
|
1,03
|
0,3
|
25
|
|
|
То-ие
тонкое
|
5
|
5
|
0,054
|
-
|
0,224
|
0,063
|
0,47
|
160
|
160
|
159,9
|
0,54
|
0,2
|
5
|
|
Поверхность
№7 Ø170
h6
|
№оп
|
Обработка
|
Rz
|
h
|
∆
|
E
|
2Zmin,
мм
|
Тd,
мм
|
2Zном,
мм
|
dp,мм
|
dmax
|
dmin
|
2zmax
|
2zmin
|
Техн.
р-р
|
Rz
|
|
Штамповка
|
100
|
150
|
1.35
|
-
|
|
+1.8
-1.0
|
|
175.6
|
177.4
|
174.6
|
|
|
100
|
|
|
Точ-иечерновое
|
50
|
60
|
0.081
|
-
|
3.2
|
0.4
|
4.2
|
171.4
|
171.4
|
171.0
|
6.4
|
3.2
|
50
|
|
|
Точ-ие
чистовое
|
25
|
20
|
0.067
|
-
|
0.384
|
0.25
|
0.78
|
170.6
|
170.6
|
170.4
|
0.97
|
0.46
|
25
|
|
|
Шлифование
черновое
|
10
|
10
|
0.054
|
-
|
0.224
|
0.063
|
0.47
|
170.2
|
170.2
|
170.1
|
0.46
|
0.23
|
10
|
|
|
Шлифование
чистовое
|
5
|
5
|
0.027
|
-
|
0.148
|
0.025
|
0.21
|
170
|
170
|
169.9
|
0.23
|
0.14
|
5
|
№оп
|
Обработка
|
Rz
|
h
|
∆
|
E
|
2Zmin,
мм
|
Тd,
мм
|
2Zном,
мм
|
dp,мм
|
dmax
|
dmin
|
2zmax
|
2zmin
|
Техн.
р-р
|
Rz
|
|
Штамповка
|
100
|
150
|
1.35
|
-
|
|
+1.8
-1.0
|
|
185.33
|
187,1
|
184,3
|
|
|
,
|
100
|
|
Точ-иечерновое
|
40
|
25
|
0.081
|
-
|
3.2
|
0.4
|
4.2
|
181.13
|
181,1
|
180,7
|
6,4
|
3,2
|
40
|
|
|
Точ-ие
чистовое
|
25
|
10
|
0.067
|
-
|
0,292
|
0.25
|
0.69
|
180,44
|
180,4
|
180,1
|
1
|
0,3
|
25
|
|
|
Тонкое
|
5
|
5
|
0.054
|
-
|
0,197
|
0.1
|
0.44
|
180
|
180
|
179,9
|
0,5
|
0,1
|
5
|
|
Поверхность
№12 Ø300
h8
|
№оп
|
Обработка
|
Rz
|
h
|
∆
|
E
|
2Zmin,
мм
|
Тd,
мм
|
2Zном,
мм
|
dp,мм
|
dmax
|
dmin
|
2zmax
|
2zmin
|
Техн.
р-р
|
Rz
|
|
Штамповка
|
100
|
150
|
1,51
|
-
|
|
+2,0
-1,2
|
|
307,2
|
309,2
|
306
|
|
|
100
|
|
|
Точ-иечерновое
|
50
|
25
|
0,09
|
-
|
3,52
|
0,52
|
4,72
|
302,7
|
302,7
|
302,1
|
7,1
|
3,3
|
50
|
|
|
Точ-ие
чистовое
|
25
|
10
|
0,73
|
-
|
0,33
|
0,32
|
0,85
|
301,85
|
301,8
|
301,5
|
1,2
|
0,3
|
|
25
|
|
Точ-ие
тонкое
|
5
|
5
|
0,06
|
-
|
1,53
|
0,081
|
1,85
|
300
|
300
|
299,9
|
1,9
|
1,5
|
|
5
|
Поверхность
№15 Ø125
Н8
|
№оп
|
Обработка
|
Rz
|
h
|
∆
|
E
|
2Zmin,
мм
|
Тd,
мм
|
2Zном,
мм
|
dp,мм
|
dmax
|
dmin
|
2zmax
|
2zmin
|
Техн.
р-р
|
Rz
|
|
Штамповка
|
100
|
150
|
1,35
|
120
|
|
+1,0
-1,8
|
|
119,4
|
120,4
|
119,4
|
|
|
100
|
|
|
Растач-ие
черновое
|
40
|
50
|
0,081
|
100
|
3,2
|
0,4
|
4,2
|
123,6
|
123,2
|
123,6
|
3,8
|
3,2
|
40
|
|
|
Растач-ие
чистовое
|
20
|
20
|
0,067
|
80
|
0,42
|
0,25
|
0,82
|
124,47
|
124,1
|
124,47
|
0,5
|
1,27
|
20
|
|
|
Протачивание
|
4
|
6
|
0,054
|
25
|
0,28
|
0,063
|
0,53
|
125
|
124,9
|
125
|
0,5
|
0,9
|
4
|
|
|
|
|
|
|
|
|
|
|
|
|
|
|
|
|
|
|
|
|
|
|
|
|
|
|
|
|
|
Определение
припуска нормативным методом
Сущность
нормативного метода состоит в назначении (установлении и оптимизации) общего
припуска на формообразующие операции в зависимости от применяемых методов
обработки, требуемой точности, шероховатости и размеров поверхности на основе
опытно-статистических данных. Метод базируется на опытных данных, которые не
могут учитывать конкретные условия построения технологического процесса.
Поэтому нормативные припуски почти всегда получаются завышенными. Припуски были
назначены из нормативно технической документации.
Результаты
расчета представлены в табл.1.3
Таблица
1.3-Нормативный метод
Поверхность
№ 19 Ø18
H12
Обработка
|
2Zmin,мм
|
Td,мм
|
dр,мм
|
dmax
|
dmin
|
2zmax
|
2zmin
|
Техн.
р-р
|
Rz
|
Штамповка
|
-
|
+0,8
-1,7
|
17,0
|
17,8
|
17,0
|
-
|
-
|
100
|
|
Сверление
|
1,0
|
0,18
|
18,0
|
18,18
|
18
|
1,18
|
0,2
|
18+0,18
|
32
|
Поверхность
№17 Ø130
H12
Обработка
|
2Zmin,мм
|
Td,
мм
|
dр,мм
|
Dmax
|
dmin
|
2zmax
|
2zmin
|
Техн.
р-р
|
Rz
|
Штамповка
|
-
|
+1,0
-1,8
|
128
|
129
|
128
|
-
|
-
|
100
|
|
Однократ
ное растачивание
|
2,0
|
0,4
|
130
|
130,4
|
130
|
2,4
|
1,0
|
130+0,4
|
40
|
Поверхность
№20 Ø36
H12
Обработка
|
2Zmin,мм
|
Td,
мм
|
dр,мм
|
dmax
|
dmin
|
2zmax
|
2zmin
|
Техн.
р-р
|
Rz
|
Штамповка
|
-
|
+0,8
-1,7
|
34,5
|
35,3
|
34,5
|
-
|
|
100
|
|
Сверление
|
1,5
|
0,42
|
36
|
36,42
|
36
|
1,92
|
0,7
|
36+0,42
|
32
|
Расчёт
линейных операционных размеров
Расчет
припусков на торцы возможно проводить двумя методами: аналитическим и
нормативным. Минимальные припуски на обработку торцов определяют по формуле:
, (1.30)
где
Rz- шероховатость поверхности, h- дефектный слой для
штамповки,
-отклонение
заготовки ,
-
погрешность установки.
Погрешность
установки выбираем, точность и качество.
Рассчитанные
припуски на торцы представлены в табл.1.4.
Определение
припуска операционных размеров расчетно-аналитический
Определяем
элементы минимального припуска:
Для
каждого перехода, исходя из определенных выше величин, находим минимальное
значение припуска:
, (1.18)
где
Z- припуск, h- дефектный слой для штамповки,
-отклонение заготовки,
-погрешность
установки, Rz - широховатость.
Шероховатость
Rz и значение глубины дефектного слоя h для штамповки
определяем по ГОСТ 7505-89 для каждого из переходов.
Пространственные
отклонения исходной заготовки определяются по формуле (1.21)
Остаточные
коробления и смещения после каждого вида обработки определяется по формуле:
,
где
-допуск на
поверхность при фрезерно - центровальной оеерации
, (1.19)
Таблица
1.4-Расчет припусков на торцевые поверхности
Поверхность
№ 1, 14 370h
Поверхность
обработки Rz Мкм h мкм
мм
МкмZmin
ммОбоз- начение
|
|
|
|
|
Штамповка
|
100
|
150
|
1.3
|
120
|
-
|
+2.5
-1.5
|
Подрезка
торца черновая
|
50
|
50
|
0.078
|
100
|
1.55
|
0.57
|
Подрезка
торца чистовая
|
25
|
25
|
0.065
|
80
|
0.22
|
0.23
|
Поверхность
№10 36h8
|
|
|
|
|
|
|
|
|
|
Поверхность
обработки Rz мкм h мкм 
МкмZmin
ммОбоз-начение
|
|
|
|
|
Штамповка
|
100
|
200
|
0,86
|
120
|
-
|
+1,5
-0,7
|
Подрезка
торца черновая
|
50
|
100
|
0,51
|
100
|
0,35
|
0,25
|
Подрезка
торца чистовая
|
25
|
40
|
0,043
|
80
|
0,21
|
0,16
|
Шлифование
|
10
|
10
|
0,034
|
25
|
0,14
|
0,039
|
Расчет
операционных размеров на торцы детали требует выявления и решения размерных
цепей. В качестве первого этапа этого процесса является составление размерной
схемы обработки. На размерной схеме указываются технологические размеры в виде
однонаправленных стрелок с точкой, лежащей на поверхности, являющейся
технологической базой обработки данной поверхности.
Другой
конец стрелки присоединен к обрабатываемой в данной операции поверхности. При
составлении размерной цепи выбирается кратчайший путь замыкания через минимальное
количество звеньев. Технологическая размерная цепь содержит три разновидности
звеньев: технологические размеры - S, конструкторские размеры - А,
припуски - Z.
Технологические
базы определены на этапе разработки плана техпроцесса, качества обработок определено
на этапе расчета количества обработок по точности и шероховатости.
Перед
построением схемы необходимо проверить:
на
размерной схеме техпроцесса количество операционных размеров, включая размеры
заготовки. Оно должно равняться количеству операционных размеров плюс припуски.
Методика
расчета размерных цепей зависит от того, является замыкающее звено
конструкторским размером или припуском. Если замыкающим размером является
припуск Z, оставленный для последнего перехода, то сначала вычисляют его
минимальную величину Zmin. Далее получают исходное уравнение
размерной цепи относительно Zmin.
; (1.31)
где
Spmin- наименьший граничный размер увеличивающего звена, Sqmax
- наибольший граничный размер уменьшающего звена.
Если
искомый размер Sxесть уменьшающим звеном, то:
; (1.32)
Если
искомый размер Sx является увеличивающим звеном, то:
; (1.33)
Допуск
этого размера был установлен при формировании плана обработки, что позволяет
определить номинальный размер:
;
; (1.34)
где
ESx и Eix - верхнее и нижнее отклонение.
Для
определения номинального и максимального значений припуска исходное уравнение
составляют относительно Z с указанием предельных отклонений составляющих
звеньев:
; (1.35)
По
разности номинальных размеров находят номинальное значение припуска zн,
а по разности предельных отклонений звеньев - предельные отклонения размера
припуска:
; (1.36)
; (1.41)
; (1.42)
Из
уравнения находят номинальное значение искомого размера.
; (1.37)
Если
же замыкающим звеном размерной цепи является конструкторский размер А,
то решение исходного уравнения дает номинальное значениеискомого размера
составляющего звена Sx.
; (1.38)
. (1.39)
Схема
размерных цепей представлена на рис. 1.1
Рисунок
1.1-Схема размерных цепей
Размерные
цепи представлены табл. 1.5
Таблица
1.5- Размерные цепи
Замык.
Размер
|
Исходное
уравнение
|
Расчетный
размер
|
Допуск
мм.
|
Принятый
размер
|
Предельное
значение припуска
|
  -0,039 _
|
|
|
|
|
|
Z45min=0,14
|
Z45min=S6min-S7max
|
S6min
= Z45min +S7max =0,14+36=36,14
|
-0,039
|
36,14-0,039
|
Z34min=36,14-0,039
-36-0,039=
|
Z56min=
0,21
|
Z56min=S4min-S6max
|
S4min
= Z56min +S6max = =0,21+36,14=36,35
|
-0,16
|
36,35-0,16
|
Z34min=36,35-0,16-36,14-0,039=
|
Z23min=
0,22
|
Z23min=S3min-S4max
|
S3min
= Z23min +S4max = =0,22+36,35=36,57
|
-0,23
|
36,57-0,23
|
Z34min=36,57-0,23-36,35-0,16=
|
Z67min=
0,35
|
Z67min=S1min-S3max
|
S1min
= Z67min +S3max = =0,35+36,57=36,92
|
-0,25
|
36,92-0,25
|
Z67n=36,92-0,25-36,57-0,23=
|
Z12=1,55
|
Aзаг=S1+Z12
|
Aзаг=36.92+1.55=38.47
|
+1,5
-0,7
|
38,47 Z67n =38,47 -36,92-0.25=
|
|
Вдет=380-0,23
|
Вдет=S5
|
S5=380
|
-0,23
|
380-0,23
|
-
|
Z45min=0,22
|
Z89min=S2min
-S5 max -Z89min
|
S2min=S5max+Z12
min + Z89min==380+1,55+0,22=381,77
|
-0,57
|
381,57-0,57
|
Z89=381,77-0,23-380-0,23=1,77
|
Z910min=1,55
|
Z910min=Взаг.max
- S2min-Z12min
|
Взаг.max=
S2min+Z12min + +Z910min =
=381,77+1,55+1,55=384,77
|
+2,5
-1,5
|
384,77 Z910=384,77 -381,77-0,57=
|
|
1.10
Расчет режимов резания
Определение
режимов резания для токарной обработки для диаметральных размеров
Глубина
резания определяется по формуле
, (1.40)
где
D - диаметр поверхности до обработки, d - диаметр заготовки после обработки.
Например,
для поверхности №7 (Æ170 h6):
для
чернового точения t1=3.2мм;
для
чистового точения
мм;
Величина
подачи на станках СЧПУ для технологических операций определяем по эмпирическим
формулам [1]
Для
чернового точения
, (1.41)
где
k = 0,150; x = -0,330; y =
0,190; z = 0,200 - для
углеродистых и легированных сталей; Dmax, - максимальный диаметр
изделия, D0 -диаметр
обрабатываемой в данном переходе поверхности, мм
мм/об;
Для
чистового и тонкого точения
, (1.42)
где
Dmax - наибольший диаметр обрабатываемой поверхности детали,
мм; Rz- параметр шероховатости, мкм; k1, k2,
b - коэффициенты.
Для
углеродистых и легированных сталей: k1 = 0,00012; k2
= 0,013; b = 0,012.
Для
чистового точения
мм/об;
Определение
скорости резания
, (1.43)
где
Т - период стойкости инструмента, Т=60мин.
-
коэффициент;, y, m - показатели степени для определения скорости резания;
для
чернового и чистового точения
=340, x=0,15, y=0,45, m=0,2.
Коэффициент
является
произведением коэффициентов, учитывающих влияние материала заготовки Кмv, состояние
поверхности Кпv, материала инструмента Киv, т.е.
, (1.44)
, (1.45)
Кг=1,
nv=1,
, Кпv=0,8,
Киv=1,
тогда
;
для
чернового точения
м/мин;
для
чистового точения
м/мин;
Частота
оборотов
, (1.46)
где
D - диаметр обработанной заготовки;
для
чернового точения
об/мин;
для
чистового точения
об/мин;
Для
бесступенчатого регулирования скорости вращения шпинделя, вибираем ближайшее к
расчетным меньшее значение оборотов подачи из паспортных данных станка.
об/мин,
190 об/мин
Пересчет
Сила
резания
, (1.47)
где
Ср - постоянная, x, y, n - показатели степени для определения силы
резания, Ср=300, x=1, y=0,75, n=-0,15; поправочный коэффициент kp
представляет собой произведение ряда коэффициентов, учитывающих фактические
условия резания, т.е.
, (1.48)
, (1.49)=0,75;
, Кφр=0,89; Кγр=1,
тогда
К
;
для
чернового точения
Н;
для
чистового точения
Н;
Мощность
, (1.50)
для
чернового точения
кВт;
для
чистового точения
кВт;
Минутная
подача
, (1.51)
где
n - частота оборотов;
для
чернового точения
мм/мин;
для
чистового точения
мм/мин;
Крутящий
момент
(1.52)
для
чернового точения
Нм;
для
чистового точения
Нм;
Определение
режимов резания для токарной обработки для торцевых поверхностей
Глубина
резания
подрезка
торца черновая t1=1,55мм;
подрезка
торца чистовая t2=0,11 мм;
Величина
подачи на станках СЧПУ для технологических операций определяем по эмпирическим
формулам
Для
черновой подрезки торца :
, (1.53)
где
k = 0,150; x = -0,330; y =
0,190; z = 0,200 - для
углеродистых и легированных сталей; Dmax, D0- максимальный диаметр изделия
и диаметр обрабатываемой в данном переходе поверхности, мм
мм/об;
Для
чистовой подрезки торца
, (1.54)
где
Dmax - наибольший диаметр обрабатываемой поверхности детали,
мм; Rz- параметр шероховатости, мкм; k1, k2,
b - коэффициенты.
Для
углеродистых и легированных сталей: k1 = 0,00012; k2
= 0,013; b = 0,012.
мм/об;
Определение
скорости резания
, (1.55)
где
Т - период стойкости инструмента, Т=60мин.
-
коэффициент;, y, m - показатели степени для определения скорости резания;
для
черновой и чистовой подрезки торца
=340, x=0,15, y=0,45, m=0,2;
Коэффициент
является
произведением коэффициентов, учитывающих влияние материала заготовки Кмv,
состояние поверхности Кпv, материала инструмента Киv, т.е.
,
(1.56)
, (1.57)
Кг=1,
nv=1,
, Кпv=0,8,
Киv=1,15,
тогда
К
;
подрезка
торца черновая
м/мин;
подрезка
торца чистовая
м/мин;
Частота
оборотов
, (1.58)
где
D - диаметр обработанной заготовки;
подрезка
торца черновая
об/мин;
подрезка
торца чистовая
об/мин;
об/мин,
260 об/мин.
Для
бесступенчатого регулирования скорости вращения шпинделя, вибираем ближайшее к
расчетным меньшее значение оборотов подачи из паспортных данных станка.
Пересчет
Сила
резания
, (1.59)
Ср
- постоянная, x, y, n - показатели степени для определения силы резания, Ср=300,
x=1, y=0,75, n=-0,15; поправочный коэффициент kp представляет собой
произведение ряда коэффициентов, учитывающих фактические условия резания, т.е.
, (1.60)
, (1.61)
=0,75;
, Кφр=0,89; Кγр=1,
тогда
;
подрезка
торца черновая
;
подрезка
торца чистовая
Н;
Мощность
, (1.62)
подрезка
торца черновая
кВт;
подрезка
торца чистовая
кВт;
Минутная
подача
, (1.63)
где
n - частота оборотов;
подрезка
торца черновая
мм/мин;
подрезка
торца чистовая
мм/мин;
Крутящий
момент
(1.64)
подрезка
торца черновая
Нм;
подрезка
торца чистовая
Нм;
Значения
расчетов режимов резания по остальным диаметральным поверхностям приведены в
табл.6
Определение
режимов резания для сверлильной обработки
Глубина
резания определяется по формуле= 0,5 D, (1.65)
где
D - диаметр отверстия.
Например,
для поверхности №19 D=18 мм, тогда t =
мм.
Подача
при сверлении на станках с ЧПУ [1]
, (1.66)
где
k, x - коэффициент пропорциональности и показатель степени,k=0,025, x=0,77, Dсв
- диаметр отверстия, мм.
мм/об
Скорость
резания
, (1.67)
где
Т - период стойкости инструмента, Т=45мин.
- коэффициент; q, y, m - показатели
степени;
=9,8, q=0,4;
y=0,5; m=0,2;
Коэффициент
является
произведением коэффициентов, учитывающих влияние материала заготовки Кмv,
состояние поверхности Кlv, материала инструмента Киv.
, (1.68)
, (1.69)
Кг=1,
nv=0,9,
, Кпv=0.8,
Кlv=0,7,
тогда
;
м/мин.
Сила
резания
(1.70)
где
Ср - постоянная, q, y - показатели степени для определения силы
резания, Ср=300, q=0.4, y=0,75; поправочный коэффициент
p=
, (1.71)=0,75;
,
тогда
Н.
Крутящий
момент
, (1.72)
где
См - коэффициент, q, y - показатели степени для определения
крутящего момента, См=0,0345, q=2, y=0,8; поправочный коэффициент kp=1,1,
тогда
Нм.
Частота
оборотов
, (1.73)
об/мин.
Мощность
резания
, (1.74)
кВт.
Минутная
подача
, (1.75)
где
n - частота оборотов;
мм/мин;
Определение
режимов резания для фрезерования
Глубина
резания
Фрезерованию
подлежит поверхность №3,=3,2мм.
Подача
при фрезеровании плоскостей, пазов и уступов на станках с ЧПУ определяется по
формуле:
(1.76)
где
k=0,007, x=1,27, y=-0,64, р=-0,44 - соответственно коэффициент
пропорциональности и показатели степени; kSZ=0,6 - поправочный
коэффициент на подачу в зависимости от параметров шероховатости; Dф
- диаметр фрезы, мм; Z=6 - число зубьев фрезы.
мм/об.
Формула
для определения скорости фрезерования
; (1.77)
где
Cv=145, m=0,37, x=0,24, y=0,26, q=0,44, u=0,1, p=0,13 -
соответственно коэффициент пропорциональности, поправочный коэффициент на
скорость резания для измененных условий работы и показатели степени; Т=80мин -
период стойкости режущего инструмента; В=36мм - ширина фрезерования.
Коэффициент
является
произведением коэффициентов, учитывающих влияние материала заготовки Кмv,
состояние поверхности Кnv, материала инструмента Киv,
т.е.
, (1.78)
, (1.79)
Кг=1,
nv=1,
, Кпv=1,
Кuv=1, тогда
;
Тогда
м/мин.
Сила
резания
; (1.80)
где
n - частота вращения фрезы, определяется по формуле:
; (1.81)
об/мин.
Ср=68.2
- постоянная; x =0,86, y=0,72, u=1, q=0,86, w=0, В=36,=6 - показатели степени
для определения силы резания,
Н
Крутящий
момент определяем по формуле
(1.82)
Нм.
Мощность
фрезерования
(1.83)
кВт.
Минутная
подача
(1.84)
мм/мин
Результаты
расчета режимов резания длятокарной обработки, сверлильной обработки,
фрезерования сведены в табл. 1.6
Таблица
1.6-Режимы резания
Номер
и наименование перехода t, мм
,
мм/об
,
об/мин
,
об/мин
,
м/мин
,
м/мин
,
кВт , кВтSМ,
мм/мин
|
|
|
|
|
|
|
|
|
005
подрезка торца черновая
|
1,55
|
0,916
|
64,689
|
60
|
60,937
|
61,1
|
2,94
|
3
|
58,632
|
005
точение черновое Ø
123,6
|
3,2
|
0,793
|
129,199
|
130
|
50,937
|
50,95
|
4,16
|
4,2
|
102,333
|
010
подрезка торца черновая
|
1,55
|
0,916
|
64,689
|
60
|
60,937
|
61,1
|
2,94
|
3
|
58,632
|
010
точение чистовая Ø
124,47
|
0,635
|
0,308
|
230,649
|
230
|
90,53
|
90,54
|
0,665
|
70,84
|
015
подрезка торца чистовая
|
0,11
|
0,355
|
138,341
|
140
|
130,317
|
130,32
|
0,175
|
0,18
|
48,99
|
015
точение чистовое Ø
130
|
1,0
|
0,568
|
167,227
|
170
|
68,262
|
68,27
|
1,303
|
1,31
|
94,856
|
015
точение чистовое Ø
135
|
1,1
|
0,568
|
158,74
|
160
|
67,29
|
67,3
|
1,41
|
1,42
|
94,856
|
020
подрезка торца чистовая
|
0,11
|
0,355
|
259,389
|
260
|
130,317
|
130,32
|
0,175
|
0,18
|
91,945
|
020
точение чистовое Ø
130
|
1,0
|
0,568
|
167,22
|
170
|
68,26
|
68,27
|
1,31
|
1,32
|
94,85
|
020
протяжная Ø
125
|
0,45
|
0,1
|
305,887
|
300
|
120,061
|
120,07
|
0,258
|
0,26
|
30,5
|
030
точение черновое Ø
161,2
|
3,2
|
0,833
|
98,719
|
100
|
49,596
|
49,6
|
7,61
|
7,62
|
81,676
|
030
точение черновое Ø
171,4
|
3,2
|
0,844
|
92,406
|
90
|
49,326
|
49,33
|
0,086
|
0,09
|
77,611
|
030
точение черновое Ø
181,1
|
3,2
|
0,853
|
86,825
|
80
|
49,073
|
49,04
|
0,087
|
0,089
|
73,686
|
030
подрезка торца черновая
|
0,35
|
1,497
|
64,833
|
60
|
61,073
|
61,074
|
0,964
|
0,97
|
95,809
|
030
точение черновое Ø
302
|
3,3
|
0,936
|
49,752
|
50
|
46,866
|
46,87
|
4,541
|
4,52
|
46,841
|
035
точение чистовое Ø
160,4
|
0,15
|
0,373
|
209,373
|
200
|
105,121
|
150,13
|
0,206
|
0,21
|
77,957
|
035
точение чистовое Ø
170,6
|
0,23
|
0,373
|
191,162
|
190
|
102,043
|
102,05
|
0,308
|
0,31
|
108,543
|
035
точение чистовое Ø
180,4
|
0,15
|
0,178
|
223,194
|
220
|
126,149
|
126,15
|
0,138
|
0,14
|
39,694
|
035
подрезка торца чистовая
|
0,105
|
0,355
|
139,31
|
140
|
131,23
|
131,24
|
0,168
|
0,17
|
49,345
|
035
точение чистовое Ø
301,5
|
0,15
|
0,373
|
112,857
|
110
|
106,312
|
106,32
|
0,421
|
0,43
|
41,03
|
040
точение тонкое Ø
160
|
0,1
|
0,113
|
292,225
|
290
|
146,814
|
146,82
|
0,074
|
0,08
|
32,996
|
040
точение тонкое Ø
180
|
0,05
|
0,113
|
288,216
|
280
|
162,9
|
163
|
0,041
|
0,05
|
32,544
|
040
точение тонкое Ø
300
|
0,75
|
0,113
|
116,506
|
110
|
109,749
|
109,75
|
0,439
|
0,44
|
13,108
|
045
фрезерование черновое Ø
150,7
|
3,2
|
0,217
|
29,89
|
30
|
28,157
|
28,16
|
24,157
|
24,16
|
644,498
|
045
сверление Ø
18
|
0,2
|
0,231
|
265,479
|
260
|
15,005
|
15,01
|
0,875
|
0,86
|
61,31
|
045
сверление Ø
36
|
1,7
|
0,395
|
119,924
|
120
|
13,556
|
13,56
|
1,556
|
1,56
|
46,972
|
050
фрезерование чистовое Ø 150
|
0,15
|
0,333
|
87,455
|
80
|
82,383
|
82,39
|
0,411
|
0,42
|
2003
|
1.11
Определение норм времени при работе на станках с ЧПУ
Нормой
времени согласно ГОСТ 3.1109-82 называют регламентированное время выполнения
некоторого объема работ (операций) в определенных производственных условиях
одним или несколькими исполнителями соответствующей квалификации.
Определение
норм времени для токарной обработки на станках с ЧПУ
Норму
штучного времени на операцию при работе на станках с ЧПУ находят по формуле
Тшт
= Та + ТвКtb + Тоб (1.85)
где
Та - время автоматической основной работы по программе;
Время
автоматической работы вычисляют по формуле
Та
= Тоа + Тва, (1.86)
где
Тоа - время основной автоматической работы.
(1.87)
где
Li - длина пути, проходимого инструментом или деталью в направлении
подачи при обработке i-го технологического участка с учетом длины врезания и
перебега; SMi - минутная скорость подачи на данном участке, мм/мин;
i = 1, 2, 3, ..., m - число технологических участков обработки;
Расчетную
длину определяют в виде суммы:
L
= l + l1 + l2 (1.88)
где
l - длина обрабатываемой поверхности; l1 - длина врезания, l2
=5мм -длина перебега инструмента;
(1.89)
где
t - глубина резания, мм; j - угол в
плане лезвия режущего инструмента;
SMi
-
минутная скорость
подачи
на данном участке, мм/мин;
i=1,2,3.....т
- число технологических участков обработки;
для
чернового точения
мм;
для
чистового точения
мм;
для
тонкого точения
мм;
для
чернового точения
мин;
для
чистового точения
мин;
для
тонкого точения
мин;
где
Тва - время вспомогательной автоматической работы
Тва
= Тх + Тост (1.90)
где
Тх - время вспомогательной автоматической работы на подвод детали
или инструментов от исходных точек в зоны обработки и отвод из зоны, установки
инструмента на размер, изменения величины и направления подачи; Тост
- время технологических пауз-остановок подачи и вращения шпинделя для проверки
размеров, осмотра или смены инструмента, перезакрепления детали.
для
чернового точения Тва=0,001+0,0005=0,0015мин;
для
чистового точения Тва=0,0009+0,0001=0,001 мин;
для
тонкого точения Тва=0,001+0,0001=0,0011 мин;
для
чернового точения Та=5,932+0,0015=5,9335 мин;
для
чистового точения Та=6,35+0,001=6,351мин;
для
тонкого точения Та=8,425+0,0011=8,4261 мин;
где
Тв - время выполнения ручной вспомогательной работы, не
перекрываемое временем автоматической работы станка:
Тв
= Тву + Твсп + Тви (1.91)
Время
Тву предусматривает выполнение следующих работ: установку, выверку
(при необходимости) и закрепление детали; открепление и снятие детали; очистку
приспособления от стружки.
Тву
= а×QХ (1.92)
где
Q - масса детали, кг; а=0,18, Х=0,42 - коэффициент пропорциональности и
показатель степени.
мин; Твсп=0,64мин;
Вспомогательное
время на контрольные измерения при работе на токарных, сверлильных и фрезерных
станках
(1.93)
где
Du, Lu - диаметр и длина измеряемых поверхностей; К=0,2,
Х=0,18, Y=0,25 - коэффициент пропорциональности и показатели степени.
мин; Тв=0,197+0,64+1,35=2,187
мин;
где
Кtb=0,76 - поправочный коэффициент на вспомогательное время для
учета характера серийности работ;
где
Тоб - время, затрачиваемое на обслуживание рабочего места
для
чернового точения
мин;
для
чистовогo точения
мин;
для
тонкого точения
мин;
Тоб=0,01(Та+ТвКtb) (1.94)
для
чернового точения
мин;
для
чистовогo точения
мин;
для
тонкого точения

мин;
Норма
времени на обработку партии деталей Тпарт определяется формулой
Тпарт
= ТштNd + Тп.з ; (1.95)
где
Nd - количество деталей в партии, обрабатываемых на одном станке; Тп.з
- время подготовительно-заключительной работы на одном станке.
Тпз
= а + вnи + СРр + dРпп, (1.96)
где
а=11,3, в=0,8, С=0,5, d=0,4 - коэффициенты пропорциональности; Рр -
число режущих инструментов или блоков; nи - число устанавливаемых
размеров, набираемых переключателями на пульте управления станком.
Тпз=15,6
мин;
для
чернового точения Тпарт=156,56 мин;
для
чистовогo точения Тпарт=161,15 мин;
для
тонкого точения Тпарт=64,93 мин;
Норма
штучно-калькуляционного времени
Тшк
= Тшт Тпз / Nd (1.97)
для
чернового точения Тшк=3,16мин;
для
чистовогo точения Тшк=3,245 мин;
для
тонкого точения Тшк=1,468 мин.
Определение
норм времени для сверлильной обработки на станках с ЧПУ
Норму
штучного времени на операцию при работе на станках с ЧПУ находят по формуле
Тшт
= Та + ТвКtb + Тоб, (1.98)
где
Та - время автоматической основной работы по программе;
Время
автоматической работы вычисляют по формуле
Та
= Тоа + Тва, (1.99)
где
Тоа - время основной автоматической работы.
(1.100)
где
Li - длина пути, проходимого инструментом или деталью в направлении
подачи при обработке i-го технологического участка с учетом длины врезания и
перебега; SMi - минутная скорость подачи на данном участке, мм/мин;
i = 1, 2, 3, ..., m - число технологических участков обработки;
Расчетную
длину определяют в виде суммы:
L
= l + l1 + l2 (1.101)
где
l - длина обрабатываемой поверхности; l1 - длина врезания, l2
=3 мм -длина перебега инструмента;
(1.102)
где
j - угол в
плане лезвия режущего инструмента; D - диаметр режущего инструмента или
обрабатываемого отверстия, мм;
мм;
мин;
где
Тва - время вспомогательной автоматической работы
Тва
= Тх + Тост; (1.103)
где
Тх - время вспомогательной автоматической работы на подвод детали
или инструментов от исходных точек в зоны обработки и отвод из зоны, установки
инструмента на размер, изменения величины и направления подачи; Тост
- время технологических пауз-остановок подачи и вращения шпинделя для проверки
размеров, осмотра или смены инструмента, перезакрепления детали.
мин; Тост
не учитываем; Тва=0,0015 мин;
Та=2,2445
мин;
где
Тв - время выполнения ручной вспомогательной работы, не перекрываемое
временем автоматической работы станка;
Тв
= Тву + Твсп + Тви (1.104)
Время
Тву предусматривает выполнение следующих работ: установку, выверку
(при необходимости) и закрепление детали; открепление и снятие детали; очистку
приспособления от стружки.
Тву = [aQXNdY
+ 0,4(nБ - 2)] (1.105)
где
Q - масса детали, кг; а=0,285, Х=0,4, У=0,33 - коэффициент пропорциональности и
показатель степени,nБ.- количество болтов для крепления
детали.
мин; Твсп=0,64мин;
Вспомогательное
время на контрольные измерения при работе на токарных, сверлильных и фрезерных
станках, мин
(1.106)
где
Du, Lu - диаметр и длина измеряемых поверхностей;
К=0,187, Х=0,21, Y=0,3 - коэффициент пропорциональности и показатели степени.
мин;
Кtb=0,76
- поправочный коэффициент на вспомогательное время для учета характера
серийности работ;
Тв
=1,405мин;
Тоб
- время, затрачиваемое на обслуживание рабочего места
Тоб=0,01(Та+ТвКtb) (1.107)
мин;
мин;
Норма
времени на обработку партии деталей Тпарт определяется формулой
Тпарт
= ТштNd + Тп.з; (1.108)
где
Nd - количество деталей в партии, обрабатываемых на одном станке; Тп.з
- время подготовительно-заключительной работы на одном станке.
Тпз
= а + вnи + СРр + dРпп; (1.109)
а=10,
в=1,1, С=0,5, d=0 - коэффициенты пропорциональности; Рр - число
режущих инструментов или блоков; nи - число устанавливаемых
размеров, набираемых переключателями на пульте управления станком.
Тпз=
14,8 мин;
В
серийном производстве определяется норма штучно-калькуляционного времени
Тшк
= Тшт Тпз / Nd; (1.110)
Тшк=
0,15мин.
Определение
норм времени для фрезерной обработки на станках с ЧПУ
Норму
штучного времени на операцию при работе на станках с ЧПУ находят по формуле
Тшт
= Та + ТвКtb + Тоб, (1.111)
где
Та - время автоматической основной работы по программе;
Та
= Тоа + Тва, (1.112)
Время
автоматической работы вычисляют по формуле
(1.113)
где
Тоа - время основной автоматической работы.i - длина
пути, проходимого инструментом или деталью в направлении подачи при обработке
i-го технологического участка с учетом длины врезания и перебега, мм; SMi
- минутная скорость подачи на данном участке, мм/мин; i = 1, 2, 3, ..., m -
число технологических участков обработки;
Расчетную
длину определяют в виде суммы:
=
l + l1 + l2; (1.114)
где
l - длина обрабатываемой поверхности; l1 - длина врезания, l2
=5 мм -длина перебега инструмента;
; (1.115)
мм;
мин;
Тва
- время вспомогательной автоматической работы
Тва
= Тх + Тост (1.116)
где
Тх - время вспомогательной автоматической работы на подвод детали
или инструментов от исходных точек в зоны обработки и отвод из зоны, установки
инструмента на размер, изменения величины и направления подачи; Тост
- время технологических пауз-остановок подачи и вращения шпинделя для проверки
размеров, осмотра или смены инструмента, перезакрепления детали.
мин; Тост
- не учитываем; Тва=0,0029мин;
Та=0,085
мин;
Тв
- время выполнения ручной вспомогательной работы, не перекрываемое временем
автоматической работы станка;
Тв
= Тву + Твсп + Тви (1.117)
Тв=1,575
Время
Тву предусматривает выполнение следующих работ: установку, выверку
(при необходимости) и закрепление детали; открепление и снятие детали; очистку
приспособления от стружки.
Тву = [aQXNdY
+ 0,4(nБ - 2)] (1.118)
где
Q - масса детали, кг; а=0,527, Х=0,236,У=0,86 - коэффициент пропорциональности
и показатель степени.
мин; Твсп=0,64мин;
Вспомогательное
время на контрольные измерения при работе на токарных, сверлильных и фрезерных
станках, мин
(1.119)
где
Du, Lu - диаметр и длина измеряемых поверхностей;
К=0,187, Х=0,21, Y=0,3 - коэффициент пропорциональности и показатели степени.
мин;
Кtb=0,15
- поправочный коэффициент на вспомогательное время для учета характера
серийности работ;
Тоб
- время, затрачиваемое на обслуживание рабочего места
Тоб=0,01(Та+ТвКtb); (1.120)
мин;
мин;
Норма
времени на обработку партии деталей Тпарт определяется формулой
Тпарт
= ТштNd + Тп.з; (1.121)
где
Nd - количество деталей в партии, обрабатываемых на одном станке; Тп.з
- время подготовительно-заключительной работы на одном станке.
Тпз
= а + вnи + СРр + dРпп (1.122)
а=11,5,
в=1,2, С=0,3, d=0,5 - коэффициенты пропорциональности; Рр - число
режущих инструментов или блоков; nи - число устанавливаемых
размеров, набираемых переключателями на пульте управления станком.
Тпз=
16,5 мин;
Тпарт=
13,16 мин;
В
серийном производстве определяется норма штучно-калькуляцион-ного времени
Тшк
= Тш т Тпз / Nd; (1.123)
Тшк=
0,24 мин.
Результаты
расчетов норм времени длятокарной обработки, сверлильной обработки, фрезерной
обработки, приведены в табл.1.7
Таблица
1.7-Нормы времени
Номер
и наименование операции
|
Та
|
Тв,
МИН
|
Ktb
|
Топ,
МИН
|
Тоб
|
Тшт,
МИН
|
Тпз,
МИН
|
Nd
|
Тпар,
МИН
|
Тшк
|
|
Тоа
|
Тва
|
Тву
|
Твсп
|
Тви
|
|
|
|
|
|
|
|
|
точение
черновое
|
5,932
|
0,0015
|
0,655
|
0,64
|
3,12
|
0,76
|
2,49
|
14,95
|
22,82
|
15,6
|
57
|
156,56
|
3,16
|
точение
чистовое
|
6,35
|
0,001
|
0,655
|
0,64
|
3,12
|
0,76
|
2,56
|
15,396
|
23,57
|
15,6
|
57
|
161,15
|
3,245
|
точение
тонкое
|
8,425
|
0,0011
|
0,655
|
0,64
|
1,15
|
0,76
|
1,03
|
6,189
|
14,45
|
15,6
|
57
|
64,93
|
1,468
|
фрезерование
черновое
|
0,082
|
0,0029
|
0,655
|
0,64
|
0,28
|
0,76
|
0,22
|
1,352
|
0,24
|
16,5
|
57
|
13,16
|
0,603
|
фрезерование
чистовое
|
0,022
|
0,0015
|
0,655
|
0,64
|
0,17
|
0,76
|
0,14
|
0,873
|
0,16
|
16,5
|
57
|
8,6
|
0,502
|
растачивание
черновое
|
3,21
|
0,0015
|
0,655
|
0,64
|
0,24
|
0,76
|
0,25
|
1,535
|
0,28
|
15,6
|
57
|
16,3
|
0,57
|
растачивание
чистовое
|
4,77
|
0,0011
|
0,655
|
0,64
|
0,63
|
0,76
|
0,57
|
3,46
|
0,63
|
15,6
|
57
|
23,6
|
0,943
|
протягивание
|
10,50
|
0,0011
|
0,655
|
0,64
|
0,1
|
0,76
|
0,27
|
1,643
|
0,3
|
15,6
|
57
|
17,43
|
0,591
|
растачивание
Ø
130
|
2,243
|
0,0015
|
0,655
|
0,64
|
0,17
|
0,76
|
0,18
|
1,098
|
0,2
|
15,6
|
57
|
11,73
|
0,486
|
сверление
|
0,905
|
0,0033
|
0,655
|
0,64
|
0,11
|
0,76
|
0,13
|
0,797
|
0,15
|
14,8
|
57
|
8,57
|
0,414
|
1.12
Выбор режущего инструмента для каждого перехода
Выбор
режущего инструмента для токарной обработки
Выбираем
марку инструментального материала - твердый сплав Т15К6 (ГОСТ 3882-74).
Выбираем
токарный сборный проходной резец (ГОСТ 20872-80) с механическим креплением
твердосплавных пластин клином. Размеры резца: h=25мм, b=25мм, ho=25мм, L=140мм,
f=32мм, диаметр описанной окружности 22мм. Приведен на рис.1.2
Рисунок1.2-
Токарный сборный проходной резец с механическим креплением
Размеры
пластины приведен в таблице 1.8 согласно ГОСТ19043-80.
Таблица1.8-Размеры
пластины
|
l,
mm
|
d,
mm
|
s,
mm
|
r,
mm
|
m,
mm
|
Черновой
|
25
|
25
|
3.18
|
1,2
|
13.89
|
Чистовой
|
25
|
25
|
3.18
|
0,8
|
13.89
|
Выбор
режущего инструмента для сверлильной обработки
Для
сверлильной обработки выбираем сверло спиральное из быстрорежущей стали (Р18) с
коническим хвостовиком (рис.1.3), для станков с ЧПУ (средняя серия).
Рисунок1.3-
Сверло спиральное
Выбор
режущего инструмента для фрезерной обработки
Для
фрезерной обработки выбираем фрезу концевую с коническим хвостовиком (ГОСТ
17026-71) со следующими геометрическими размерами (рис.1.4):
Материал
- твердый сплав Т15К6.
Рисунок1.4-
Фреза концевая с коническим хвостовиком
2.
КОНСТРУКТОРСКАЯ ЧАСТЬ
.1
Определение количества оборудования основного производства
Программа
запуска определяется по формуле:
=tг/to
,
(2.1)
где
tг- годовая трудоёмкость изготовления детали, to- штучное время
изготовления одной детали.
=
tг/to = 18000∙60/75 = 14400 (шт.)
Расчётное
количество оборудования определяется по формуле:
Срi
= toi ∙Nz/Ф∆∙60; (2.2)
где
toi- оперативное время изготовления детали на данном типе оборудования,
(мин), Ф∆ - действительный фонд времени работы оборудования. Эта
величина связана с режимом работы оборудования. Для автоматизированного
производства и двухсменного режима работы,
Ф∆=
4025 ч.
Поскольку
количество оборудования должно выражаться целым числом, расчётные значения
следует округлить до ближайшего целого значения Спi.
Расчёт
количества токарных станков:
Срт
= toт∙Nz/Ф∆∙60 =
Принимаем
один токарный станок: Спт = 1.
Расчёт
количества фрезерных станков:
Срф
= tоф∙Nz/Ф∆∙60 =
Принимаем
один фрезерный станок: Срф = 1.
Расчёт
количества сверлильных станков:
Срс
= toс∙Nz/Ф∆∙60 =
Принимаем
один сверлильный станок:Срс = 1.
Расчёт
количества зубофрезерных станков:
Срз
= toз∙Nz/Ф∆∙60 =
Принимаем
один зубофрезерный станок: Срз= 1.
Расчёт
количества шлифовальных станков:
Срш
= tош∙Nz/Ф∆∙60 =
Принимаем
один шлифовальный станок: Срш = 1.
Расчёт
количества моечного оборудования:
Срм
= tом∙Nz/Ф∆∙60 =
Принимаем
одну единицу моечного оборудования: Срм= 1.
Расчёт
количества контрольного оборудования:
Срк
= tок∙Nz/Ф∆∙60 =
Принимаем
одну единицу контрольного оборудования: Срк = 1.
Коэффициент
загрузки оборудования.
Средний
коэффициент загрузки оборудования на участке определяется по формуле:
Кz
= ∑Cpi/∑Cпi;(2.3)
Подставляя
полученные ранее значения, определяем
Кz
= ∑Cpi/∑Cпi=
Расчётное
значение коэффициента загрузки соответствует концепции гибкого производства.
Полученные
данные используем для построения диаграммы загрузки рис.2.1:
Рисунок2.1-Коэффициент
загрузки станка.
.2
Расчёт системы инструментального обеспечения
Количество
необходимого инструмента в год определяется по формуле:
=
ttooli∙Nz/Tres∙(1+∆l/∆n),
(2.4)
где
ttooli - штучное время работы инструмента при I - й операции; Tres
- период стойкости инструмента
=
toi /notooli ;(2.5)
Определим
количество инструмента, необходимого для каждого станка в течении года.
Время
работы инструмента на токарных операциях:
ttoolт
= toт /notoolт
=
(мин)
Количество
инструмента:
т
= ttoolт∙Nz/Tres∙(1+∆l/∆n) =
(инструментов)
Для
токарного станка необходимо в год 213 инструментов.
Время
работы инструмента на фрезерных операциях:
ф
= toф /notoolф
=
(мин)
Количество
инструмента:
ф
= ttoolф∙Nz/Tres∙(1+∆l/∆n) =
(инструментов)
Для
фрезерного станка необходимо в год 100 инструментов.
Время
работы инструмента на сверлильных операциях:
с
= toс /notoolс
=
(мин)
Количество
инструмента:
с
= ttoolс∙Nz/Tres∙(1+∆l/∆n) =
(инструментов)
Для
сверлильного станка необходимо в год 17 инструментов.
Время
работы инструмента на зубофрезерных операциях:
з
= to /notoolсз=
(мин)
Количество
инструмента:
ntoolз
= ttoolз∙Nz/Tres∙(1+∆l/∆n) =
(инструментов)
Для
зубофрезерного станка необходимо в год 57 инструментов.
Время
работы инструмента на шлифовальных операциях:
ш
= ttoolш /notoolсш=
(мин)
Количество
инструмента:
ш
= ttoolш∙Nz/Tres∙(1+∆l/∆n)=
(инструментов)
Для
шлифовального станка необходимо в год 80 инструментов.
Число
инструментов на один день для каждого типа станков:
=
ntooli/253
(2.6)
Число
инструментов на один день для токарного станка:
т
= ntoolт/253
= 213/253 = 0.84
Число
инструментов на один день для фрезерного станка:
ф
= ntoolф/253
= 100/253 = 0.39
Число
инструментов на один день для сверлильного станка:
с
= ntoolс/253
= 17/253 = 0.067
Число
инструментов на один день для зубофрезерного станка:
з
= ntoolз/253 =
57/253 = 0.22
Число
инструментов на один день для шлифовального станка:
ш
= ntoolш/253
= 80/253 = 0.31
Для
всех типов станков достаточно оснащения.
Масса
детали определяется по формуле:
m∆
= V∆∙ρ∆ = 8 (кг), (2.7)
где
V∆ - объём детали, ρ∆ - плотность
детали.
.3
Расчёт массы стружки
Определим
количество стружки от одной детали:
=
mz - m∆ = 10-8 = 2 (кг)
Определим
массу стружки за один день:
٭st = Q∆∙
Qst
= 57∙2 = 114(шт.)
Где
Q∆ - количество деталей, обрабатываемых за один день:
∆
= Nz/253 = 14400/253 = 57 (шт.)
Определяем
среднее количество стружки возле одного станка:
٭٭st = Q٭st
/Nm = 114/5 = 22,8 (кг)
Где
Nm - количество станков, обрабатывающих со снятием стружки.
Под
основным технологическим оборудованием (ОТО) понимаем металлообрабатывающие
станки входящие в ГПС, набор станков зависит от технологического назначения
системы.
Основным
критерием определяется возможность включения станка в ГПС его уровень
автоматизации по этому критерию можно определить какие станки, каких доработок
требуют.
Исходя
из этого, при создании ГПМ отбираются станки, которые имеют автоматический цикл
обработки включения переключения скоростей и подач, а также автоматический либо
механический зажим изделия в приспособлении.
Для
возможности стыковки ПР необходимо следующие модернизации станков:
автоматизированного
зажима и освобождения изделий на станке (наличие автоматического зажимного
приспособления);
возможность
диалога между станком и роботом (УЧПУ);
автоматизированной
очистки базовых поверхностей установочного приспособления или стола станка -
для станков с горизонтальным столом и токарных станков вертикальной компоновки.
(Наличие устройства смыва или сдува стружки);
автоматизированное
перемещение ограждения или изменение его конструкции для станков с ограждением;
автоматизированного
поджима заготовки к торцу патрона. (Для токарных станков горизонтальной
компоновки);
автоматический
поджим заготовки к опорной плоскости, устанавливаемого приспособления для
сверлильно-фрезерно-расточных станков;
наличие
устройства дробления стружки для токарных станков;
наличие
торцевых или поводковых патронов для кругло-торце- шлифовальных и
шлицеобрабатываемых станков;
автоматизированной
запрессовки заготовок на оправку или применениедругих методов базовой заготовки
для зубообработки станков;
автоматизированное
перемещение и фиксация положения изделия на позиции загрузки.
Станок
токарный
Исходя
из режимов резания и характеристик детали, для токарных операций подбираем
станок модели 1720ПФ30.
Станок
предназначен для токарной обработки наружных и внутренних поверхностей деталей
типа тел вращения со ступенчатым и криволинейным профилем, а также для
нарезания резьбы в автоматическом режиме по управляющей программе.
Габаритный
план токарного станка представлен на рис.2.2
Рисунок
2.2- Габаритный план токарного станка мод. 1720ПФ30
Станок
вертикальный сверлильно-фрезерный
Исходя
из характеристик детали, для вертикально сверлильно-фрезерных операций
подбираем станок модели 21105Н7Ф4
Станок
предназначен для комплексной обработки деталей с одной установки в позиционном
и контурном режимах программного управления. может быть использован в
мелкосерийном и серийном производстве.
Габаритный
план сверлильно - фрезерного станка представлен на рис.2.2
Рисунок
2.2- Габаритный план сверлильно - фрезерного станка модели 21105Н7Ф4
Станок
круглошлифовальный
Исходя
из характеристик детали, для круглошлифовальной операций подбираем станок
модели 3М153У.
Предназначен
для наружного шлифования цилиндрических, конических и торцевых поверхностей
деталей при установке их в центрах. Изготовляется для нужд народного хозяйства
и на экспорт.
Класс
точности станка по ГОСТ 8-77.
Габаритный
план круглошлифовального станка представлен на рис. 2.3
Рис
2.3- Габаритный план круглошлифовального станка модели 3М153У
Зубофрезерный
станок
Исходя
из характеристик детали, для зубофрезерной операций подбираем станок особо
высокой точности5В317.Габаритный план горизонтального зубофрезерного станка
представлен на рис. 2.4
Рис2.4-Габаритный
план горизонтального зубофрезерного станка
Промышленный
робот М20П
Для
обслуживания станков всех типов подбираем промышленный робот М20П, схема
которого приведена на рис.2.5
Рис2.5-
Промышленный робот М20П
Промышленный
робот с ЧПУ М2ОП предназначен для автоматизации установки - снятия заготовок и
деталей, смены инструментов и других вспомогательных операций при обслуживании
станков с ЧПУ, предназначенный для продолжительной работы без участия
оператора.
.5
Устройство автоматической смены инструмента
В
ГПС смена инструмента происходит автоматически. Основная цель - сократить время
простоя дорогостоящих станков. Смену инструмента осуществляют следущие
устройства:
накопители,
револьверные головки(РГ), магазины инструментальных гильз, инструментальные
магазины;
загрузочно-разгрузочные
устройства для смены и установки инструмента в шпиндель станка;
промежуточные
конвейеры.
РГ
представляют собой несколько инструментальных шпинделей смонтированных в
поворотном корпусе. Смена инструмента происходит за 2-3 сек. Применяем РГ с
перпендикулярным расположением к оси головки, представлены на рис. 2.6.
Рисунок2.6-
Перпендикулярная револьверная головка
Используются
они в основном на токарных операционных станках.
В
много операционных и операционных токарных станках используются револьверные
магазины на 12-16 инструментов, представлено на рис. 2.7.
Рисунок
2.7- Револьверный магазин
Имеется
три типа РМ: поворотные и цепные . Поворотные - дисковые и барабанные.
В
наших станках будут установлены перпендикулярные револьверные головки, так как
они полностью обеспечат количество необходимого инструмента.
2.6
Модульное оборудование системы. Удаления отходов производства. Технологические
проблемы удаления стружки
Дляобслуживания
станков всех типов подбираем пылестружкоотсасывающий агрегат ВЦНИИОТ - 900
В
условиях автоматического режима обработки удаление стружки из зоны резания
является одним из важных условий надежной, качественной и
высокопроизводительной обработки изделий на металлорежущем оборудовании ГПС.
Наличие стружки может привести к появлению дефектов на обрабатываемой
поверхности, вызвать преждевременный износ режущего инструмента, его затупление
и поломку.
Для
удаления стружки используются системы (рис. 2.8).
Рисунок
2.8-Структурная схема системы удаления отходов производства
Для
надежной работы системы удаления и переработки стружки должна быть обеспечена
однородная фракция стружки (обычно длинной 1…2 см).
.7
Структура ГАЛ
В
результате подбора оборудования была розработана структура ГАЛ, представлена на
плакате , ГАЛ состоит из станков: токарного 1720ПФ30, сверлильно-фрезерного
21105Н7Ф4, круглошлифовального 3М153У, зубофрезерного 5В317,промышленного
робота М20П для обслуживания станков,передвижного отсасывающего агрегата
ВЦНИИОТ 900. Для упрочнения зубчатого венца необходимо РТК для нанесения
ионно-плазменного покрития, представленного на плакате.В качестве приема
передачи устройства в данном РТК используется тактовый стол модели СТ 220.
Рисунок
2.9- Передвижной отсасывающий агрегат ВЦНИИОТ 900.
.8
Назначение и принцип работы РТК ионно-плазменного нанесения покрытий
Äàííûé
ÐÒÊ, ïðåäñòàâëåííûé
íà ëèñòå 7, ïðåäíàçíà÷åí
äëÿ íàíåñåíèÿ
èîííî-ïëàçìåííîãî
ïîêðûòèé (TiN, Ti) íà
çóáüÿ âàëà-øåñòåðíè,
ñ öåëüþ ïîâûøåíèÿ
èõ èçíîñîñòîéêîñòè.
À, ñëåäîâàòåëüíî,
óâåëè÷åíèÿ âðåìåíè
èõ ðàáîòû.
Â
äàííîì ÐÒÊ ðåàëèçóþòñÿ
âñå íåîáõîäèìûå
îïåðàöèè äëÿ ïîëó÷åíèÿ
êà÷åñòâåííûõ
ïîêðûòèé, à èìåííî
äîñòèæåíèå íóæíîé
÷èñòîòû ïîâåðõíîñòíîãî
ñëîÿ ïóòåì ïðîìûâêè
è ïîñëåäóþùåé
ñóøêè èñõîäíûõ
äåòàëåé, à äàëåå
íàíåñåíèå ïîêðûòèÿ
â óñòàíîâêå «Áóëàò-6».
Çàãðóçêó óñòàíîâêè
è òðàíñïîðòèðîâêó
äåòàëåé îñóùåñòâëÿåò
ïðîìûøëåííûé
ðîáîò Ì20Ï40.01-02. Äåòàëè
ðàñïîëîæåíû ïî
îäíîé â ñïåöèàëüíîì
äåòàëåäåðæàòåëå.
Ðîáîò ïðèíèìàåò
äåòàëè è ïîñëå
èîííî-ïëàçìåííîé
îáðàáîòêè ñëàæèâàåò
íà òàêòîâûé ñòîë.
Â
ñîñòàâ ÐÒÊ âõîäÿò
äâå óñòàíîâêè
«Áóëàò-6», ðîáîò
Ì20Ï40.01-02, òðè âàííû
ÓÇÓ-025, øêàô äëÿ
ñóøêè äåòàëåé,
òàêòîâûé ñòîë
òèïà ÑÒ220 ñ äåòàëÿìè,
óñòðîéñòâà êîíòðîëÿ,
èçìåðåíèÿ è óïðàâëåíèÿ.
.9
Ñïåöèàëüíàÿ ÷àñòü
Îáîñíîâàíèå
âûáîðà ìàòåðèàëà
ïîêðûòèÿ è ñïîñîáà
åãî íàíåñåíèÿ
Ìåòîä
êîíäåíñàöèè
è èîííîé áîìáàðäèðîâêè
çà ñ÷¸ò åãî âûñîêîé
òåõíîëîãè÷íîñòè
ïîçâîëÿåò íàíîñèòü
êîìïîçèöèîííûå
è ìíîãîñëîéíûå
ïîêðûòèÿ ñîñòàâîâ
è ñâîéñòâ íà
îñíîâå êàðáèäîâ
è íèòðèäîâ ìåòàëëîâ
IV - VI ãðóïï ïåðèîäè÷åñêîé
ñèñòåìû òàáëèöû
Ìåíäåëååâà ïðàêòè÷åñêè
íà ëþáûå ýêñïåðèìåíòàëüíûå
ìàòåðèàëû ïðè
óâåëè÷åíèè ñòîéêîñòè
èíñòðóìåíòà
îò 2 äî 5 ðàç.
Ê
îáùèì òðåáîâàíèÿì
äëÿ ïîêðûòèé, íàíîñèìûõ
íà âåíåö øåñòåðíè,
ìîæíî îòíåñòè:
1) âûñîêóþ ïëîòíîñòü
è ñïëîøíîñòü,
èñêëþ÷àþùèå
äîñòóï àêòèâíûõ
ðåàãåíòîâ ê ïîâåðõíîñòè
ìàòåðèàëà; 2) ïðåäåëüíî
ìàëûå êîëåáàíèÿ
òîëùèíû ïîêðûòèÿ
íà ðàáî÷èõ ïîâåðõíîñòÿõ
; 3) ñòàáèëüíîñòü
ñâîéñòâ ïîêðûòèÿ
íà ðàáî÷èõ ïîâåðõíîñòÿõ
; 4) âîçìîæíîñòü
ïîëó÷åíèÿ ïîêðûòèé
ïðîñòûì è ýêîíîìè÷íûì
ñïîñîáîì; 5) âðåìåííóþ
ñòàáèëüíîñòü
ñâîéñòâ ïîêðûòèé.
Äëÿ
âàëà ñîñòàëè
45Õ ìû âûáèðàåì
ïîêðûòèå TiN.
Ñëåäóåò
îáðàòèòü âíèìàíèå
íà ðàçëè÷èå ñâîéñòâ
íàíîñèìîãî ïîêðûòèÿ
è ïîäëîæêè. ×òîáû
íå ïðîèñõîäèëî
îòñëîåíèå ïîêðûòèÿ
(èç-çà ðàçëè÷èÿ
çíà÷åíèé òåðìè÷åñêîãî
ðàñøèðåíèÿ), è
äëÿ ïîâûøåíèÿ
àäãåçèè ìåæäó
ïîêðûòèåì è ïîäëîæêîé,
íà èíñòðóìåíò
íàíîñÿò ñíà÷àëà
ñëîé ÷èñòîãî
òèòàíà òîëùèíîé
0,5 ìêì. Íàëè÷èå
ïðîìåæóòî÷íîãî
ñëîÿ ñíèæàåò
èíòåíñèâíîñòü
äèôôóçèîííûõ
è àäãåçèîííûõ
âèäîâ èçíàøèâàíèÿ
èíñòðóìåíòà
è ïîâûøàåò äëèòåëüíîñòü
åãî ðàáîòû.
Îäíèì
èç âàæíåéøèõ
ïàðàìåòðîâ ïîêðûòèÿ,
îêàçûâàþùèå
âëèÿíèå íà ðàáîòîñïîñîáíîñòü
ðåæóùåãî èíñòðóìåíòà
ÿâëÿåòñÿ òîëùèíà
ïîêðûòèÿ. Áîëüøîå
âëèÿíèå íà òîëùèíó
îêàçûâàþò óñëîâèÿ
ïðîòåêàíèÿ ïðîöåññà
ðåçàíèÿ. Ñ îäíîé
ñòîðîíû, òîëñòûå
ïîêðûòèÿ çàìåòíî
ïîâûøàþò èçíîñîñòîéêîñòü,
íî ïðè ýòîì âîçíèêàþò
òðåùèíû è óìåíüøàåòñÿ
àäãåçèÿ, îáðàçóÿ
ìíîæåñòâî äåôåêòîâ
íà ïîêðûòèè.Âèçóàëüíî
ïîêðûòèå èìååò
çîëîòèñòî-æ¸ëòûé
öâåò.
Äëÿ
ïîêðûòèé TiN íàíîñèìûõ
íà çóáüÿ øåñòåðíè
îïòèìàëüíàÿ
òîëùèíà êîëåáëåòñÿ
â ïðåäåëàõ 4,0-6,0 ìêì.
Áîëüøèì
äîñòîèíñòâîì
ïîêðûòèé íàíåñåííûõ
â âàêóóìå ÿâëÿåòñÿ
âîçìîæíîñòü
èõ ëåãèðîâàíèÿ
(ïóòåì îäíîâðåìåííîãî
èñïàðåíèÿ äðóãèõ
âåùåñòâ) äëÿ óâåëè÷åíèÿ
ìèêðîòâåðäîñòè
è èçíîñîñòîéêîñòè.
Ïîëó÷åíèå
ìàêñèìàëüíîé
ïðîèçâîäèòåëüíîñòè
Ïîëó÷åíèå
ìàêñèìàëüíîé
ïðîèçâîäèòåëüíîñòè
âîçìîæíî, åñëè
ïàðàìåòðû ïîòîêà
áóäóò â äèàïàçîíå,
îãðàíè÷åííîì
èçîñêîðîñòüþ
Vå
= 10-9 ì/ñ. Âñå ýòî
âûäâèãàåò òðåáîâàíèå
ê ñèñòåìå óïðàâëåíèÿ:
1) íåîáõîäèìî óïðàâëåíèå
ýíåðãèåé ÷àñòèö
ïî âñåé ïëîùàäè
ðàáî÷åãî ñòîëà
óñòàíîâêè (êîãäà
ðàñïðåäåëåíèå
ïëîòíîñòè òîêà
íåðàâíîìåðíî
ïî ïîâåðõíîñòè,
(ðèñ.2.10) íåîáõîäèìî
óïðàâëåíèå ïëîòíîñòüþ
èîííîãî òîêà
(ïðèìåíÿþòñÿ ìàãíèòíàÿ
è ýëåêòðîñòàòè÷åñêàÿ
ôîêóñèðîâêà
è ðàñôîêóñèðîâêà).
Ðèñóíîê
2.10 - Ðàñïðåäåëåíèå
ïëîòíîñòè òîêà
Äëÿ
äàííîé ïàðû «ìàòåðèàë
äåòàëè - ñîðò èîíà»
ïîëó÷èì êàðòèíû
èçîñêîðîñòåé
íà çàâèñèìîñòè
ïëîòíîñòè òîêà
îò ýíåðãèè èîíà
è ââåäåì èõ â ñèñòåìó
óïðàâëåíèÿ, êîòîðàÿ
ìîæåò èçìåíèòü
ïîòåíöèàë äåòàëè
è ñ ïîìîùüþ ôîêóñèðîâàíèÿ
ïîòîêà èîíîâ
îáåñïå÷èòü â
çîíàõ íàõîæäåíèÿ
äåòàëåé íàèáîëåå
ïðèåìëåìîå ïî
ïðîèçâîäèòåëüíîñòè
çíà÷åíèå ïëîòíîñòè
òîêà è ýíåðãèè
èîíà. Óïðàâëåíèå
ìîæåò îñóùåñòâëÿòüñÿ
ñ ïîìîùüþ ÝÂÌ
òèïà IBM, à òàê æå
äðóãèìè ìèêðîïðîöåññîðíûìè
óñòðîéñòâàìè.
Îãðàíè÷åíèÿ
ýíåðãèè èîíîâ
èç-çà ñíèæåíèÿ
àäãåçèè è êîãåçèè
Àäãåçèÿ
è êîãåçèÿ îïðåäåëÿþò
ñöåïëÿåìîñòü
ïîêðûòèÿ ìàòåðèàëà
äåòàëè è, êàê ïîêàçàëè
èññëåäîâàíèÿ
êà÷åñòâà ïîêðûòèé
ïðè ðàçëè÷íûõ
ýíåðãèÿõ èîíîâ
è äàâëåíèÿ àçîòà
â âàêóóìíîé êàìåðå
óñòàíîâîê òèïà
«Áóëàò» è «Ïóñê»,
ñóùåñòâóþò ìèíèìàëüíûå
ýíåðãèè (40…70 ýÂ) è
äèàïàçîí äàâëåíèé
àçîòà â êàìåðå
(5×10-4…10-2
Òîð), ïðè êîòîðîì
àäãåçèÿ áóäåò
íà äîïóñòèìîì
óðîâíå. Âñå ýòî
íàêëàäûâàåò
îãðàíè÷åíèå
íà ìèíèìàëüíóþ
ýíåðãèþ èîíà
è äèàïàçîí äàâëåíèé
â âàêóóìíîé êàìåðå(ðèñ.2.10).
Îãðàíè÷åíèå
ïî ýíåðãèè ìîæåò
áûòü âíåñåíî
â óïðàâëÿþùóþ
ïðîãðàììó ìèêðîïðîöåññîðà.
Îáåñïå÷åíèå
òðåáóåìîãî äèàïàçîíà
äàâëåíèé àçîòà
ìîæíî îñóùåñòâèòü,
ïðèìåíÿÿ áëîê
óïðàâëåíèÿ äàâëåíèåì,
êîòîðûé òàêæå
óïðàâëÿåòñÿ ìèêðîïðîöåññîðîì.
Ðèñóíîê
2.11- Çàâèñèìîñòü
ïëîòíîñòè òîêà
îò ýíåðãèè ÷àñòèö
Ìèêðîòâåðäîñòü
ïîâåðõíîñòíîãî
ñëîÿ äåòàëåé ïðè
ïëàçìåííî-èîííîé
îáðàáîòêå
Ìèêðîòâåðäîñòü
çàâèñèò îò äàâëåíèÿ
ðåàêöèîííîãî
ãàçà (â ñëó÷àå
ïîëó÷åíèÿ ïîêðûòèé
òèïà íèòðèäîâ
è êàðáèäîâ). Òàêàÿ
çàâèñèìîñòü
ïðåäñòàâëåíà
íà ðèñ.2.12.
Ðèñóíîê
2.12-Çàâèñèìîñòü
ìèêðîòâåðäîñòè
îò äàâëåíèÿ ðåàêòèâíîãî
ãàçà
Ñðàâíèâàÿ
âåëè÷èíó ìèêðîòâåðäîñòè
èíñòðóìåíòà
ñ ïîêðûòèåì è
áåç íåãî , ìîæíî
çàìåòèòü, ÷òî
ìèêðîòâåðäîñòü
äåòàëåé ñ ïîêðûòèåì
â 2…3 ðàçà âûøå, ÷åì
áåç íåãî äàæå
ê êîíöó ðåëàêñàöèè
îñòàòî÷íûõ íàïðÿæåíèé.
Àíàëèç
äàííûõ ïî èçìåíåíèþ
ìèêðîòâåðäîñòè
ïîâåðõíîñòíîãî
ñëîÿ äëÿ ðàçëè÷íûõ
óñëîâèé íàíåñåíèÿ
ïîêðûòèé ïîêàçàë,
÷òî ïîâûøåíèå
ìèêðîòâåðäîñòè
äåòàëè ïî îòíîøåíèþ
ê ìàññèâíîìó
îáðàçöó èç ìàòåðèàëà
ïîêðûòèÿ ñîñòàâèò
âåëè÷èíû 0,365…3,33, à
ïî îòíîøåíèþ
ê ìàòåðèàëó äåòàëè
- 1,1…5,8.
Âëèÿíèå
ðàçëè÷íûõ òåõíîëîãè÷åñêèõ
ïàðàìåòðîâ íà
øåðîõîâàòîñòü
ïîâåðõíîñòè
Èññëåäîâàíèÿ
âëèÿíèå ïîòåíöèàëà
íà ïîäëîæêå íà
âåëè÷èíó øåðîõîâàòîñòè
ïîêàçàëè, ÷òî
øåðîõîâàòîñòü
ìèíèìàëüíà ïðè
ïîòåíöèàëå ïîäëîæêè
100 Â (ðèñ. 2.13).
Ðèñóíîê
2.13- Çàâèñèìîñòü
øåðîõîâàòîñòè
îò ïîòåíöèàëà
íà ïîäëîæêå
Â
ñëó÷àå èñïîëüçîâàíèÿ
ðåàêòèâíîãî
ãàçà äëÿ òåõíîëîãè÷åñêèõ
öåëåé âåëè÷èíà
äàâëåíèÿ ðåàêòèâíîãî
ãàçà âëèÿåò íà
øåðîõîâàòîñòü
ïîâåðõíîñòè.
Òàê íà ðèñ. 2.14 ïðåäñòàâëåíà
çàâèñèìîñòü
øåðîõîâàòîñòè
Ra îò äàâëåíèÿ
àçîòà ïðè ïîëó÷åíèè
ïîêðûòèÿ èç íèòðèäà
òèòàíà. Ïðè äàâëåíèè
ïîðÿäêà 2·10-1Ïàøåðîõîâàòîñòü
ñîõðàíÿåò ïîñòîÿííîå
çíà÷åíèå,à çàòåì
ñíèæàåòñÿ.
Ðèñóíîê
2.14- Çàâèñèìîñòü
øåðîõîâàòîñòè
îò äàâëåíèÿ àçîòà
Âåëè÷èíà
øåðîõîâàòîñòè
ïîêðûòèÿ çàâèñèò
è îò åãî òîëùèíû.
Òàê, ïî èññëåäîâàíèÿì,
â êîòîðûõ áûëî
ïðîàíàëèçèðîâàíî
âëèÿíèå òîëùèíû
ïîêðûòèÿ íà âåëè÷èíó
øåðîõîâàòîñòè
äåòàëè (ðèñ.2.15.). Âèäíî,
÷òî ïðè òîëùèíå
ïîêðûòèÿ ïîðÿäêà
äåñÿòè ìèêðîìåòðîâ
øåðîõîâàòîñòü
äîñòèãàåò 2…3 ìêì,
òîãäà êàê ïðè
òîëùèíå ïîðÿäêà
2 ìêì øåðîõîâàòîñòü
ñîñòàâèò 0,08 ìêì.
Ðèñóíîê
2.15- Çàâèñèìîñòü
øåðîõîâàòîñòè
îò òîëùèíû ïîêðûòèÿ
Â
ðåçóëüòàòå àíàëèçà
ïðîâåäåííûõ èññëåäîâàíèé
áûëè ïîäîáðàíû
îïòèìàëüíûå
ðåæèìû íàïûëåíèÿ,
ïðèâåäåíû â òàáë.
2.1
Òàáëèöà
2.1- Îïòèìàëüíûå
ðåæèìû íàïûëåíèÿ
Ñòàäèè
|
Ð(ìì
ðò. ñò.)
|
Iä,
À
|
Iô,
À
|
Iñò,
À
|
Uï
(Â)
|
t ìèí.
|
Ò0
Ñ
|
nîá/ìèí
|
Îòêà÷êà
âàêóóìíîé êàìåðû
|
7
×10-5
|
|
|
|
|
50
|
|
|
Èîííàÿ
î÷èñòêà
|
6
×10-5
|
80
|
0,5
|
3
|
300-700-1000
|
8
|
500
|
2
|
Íàíåñåíèå
ïîêðûòèÿ (Ti)
|
6
×10-5
|
80
|
0,3
|
3
|
120
|
1
|
500
|
2
|
Íàíåñåíèå
ïîêðûòèÿ (TiN)
|
4
×10-3
|
80
|
0,3
|
3
|
120
|
15
|
500
|
2
|
Èçó÷åíû
òåõíîëîãè÷åñêèå
ðåæèìû íàíåñåíèÿ
ïîêðûòèÿ Ti-TiN. Ïîêàçàíî,
÷òî íàèáîëåå
îïòèìàëüíàÿ
òåìïåðàòóðà äëÿ
Ti 500 0Ñ. Ïðè ýòîé
òåìïåðàòóðå ôîðìèðóåìîå
ïîêðûòèå îáëàäàåò
âûñîêèìè ïðî÷íîñòíûìè
õàðàêòåðèñòèêàìè,
à òàêæå íå ïðîèñõîäèò
ðàçðóøåíèå îñíîâû.
Óðîâåíü
ïîäà÷è àçîòà
â êàìåðó íàõîäèòñÿ
â äèàïàçîíå äëÿ
íàíåñåíèÿ ïîêðûòèÿTi-TiN
6×10-5…4×10-3ìì.ðò.ñò.
Ìèêðîòâåðäîñòü
ïðè ýòîì äàâëåíèè
ñîñòàâëÿåò 1900 ÌÏà.
Ïîêàçàíî,
÷òî äëÿ ïîëó÷åíèå
çàäàííîé òîëùèíû
ïîêðûòèÿ âðåìÿ
êîíäåíñàöèè
äëÿ ïîêðûòèÿ
Ti-TiN 15 ìèí. Îïòèìàëüíàÿ
òîëùèíà ïîêðûòèÿ,
ïîëó÷åíà â ðåçóëüòàòå
ýêñïåðèìåíòà
äëÿ çóá÷àòîãî
âåíöà øåñòåðíè
óïðî÷íÿåìûìè
ïîêðûòèåì Ti-TiN ñîñòàâëÿåò
4…5 ìêì.
2.10
Ðàçðàáîòêà ñòàáèëèçàöèè
êàòîäíîãî òîêà
èñïàðèòåëÿ óñòàíîâêè
íàïûëåíèÿ «Áóëàò-6»
Âî
âðåìÿ ïðîöåññà
óïðî÷íåíèÿ çóá÷àòîé
øåñòåðíè âàëà
íåîáõîäèìî ñòàáèëèçèðîâàòü
ðåæèì íàïûëåíèÿ
äëÿ îáåñïå÷åíèÿ
ðàâíîìåðíîãî
íàíåñåíèÿ ïîêðûòèÿ,
ïîòîìó ÷òî òîê
â öåïè êàòîäà
ñîñòàâëÿåò ïîðÿäêà
100À.
Íåïîñðåäñòâåííîå
ïîäêëþ÷åíèå ñõåìû
óïðàâëåíèÿ íåâîçìîæíî,
ïîýòîìó ìû èñïîëüçóåì
ñïåöèàëüíûé äàò÷èê
òîêà, ñîñòîÿùèé
èç ôåððèòîâîãî
êîëüöà ñ íàìîòàíîé
îáìîòêîé äàò÷èêà,
ýòî êîëüöî îäåâàåòñÿ
íåïîñðåäñòâåííî
íà ïðîâîä ïîäâîäÿùèé
ýíåðãèþ ê êàòîäó,
íàïðÿæåíèå ñ
äàò÷èêà òîêà
ïîñòóïàåò íà
ïðåäâîðèòåëüíûé
óñèëèòåëü óñèëèòåëü,
ñîáðàííûé íà
òðàíçècòîðåVT1. Ïðåäâîðèòåëüíûé
óñèëèòåëü ñîãëàñîâûâàåò
âûõîäíîå ñîïðîòèâëåíèå
äàò÷èêà òîêà
ñî âõîäà ìèêðîïðîöåññîðà
DD1, äàëåå ñõåìà
ïîòäåðæûâàåò
ïîñòîÿíñòâî
êàòîäíîãî òîêà
êîòîðîå çàäàåòñÿ
ñ ïîìîùó êëàâèàòóðû
è êîíòðîëèðóåìà
ìîíèòîðîì.
.11
Àðõèòåêòóðà
ÌÊ 8051
Ýòîò
ÌÊ ìîæíî ñ÷èòàòü
êëàññè÷åñêèì
îáðàçöîì, ïî îáðàçó
è ïîäîáèþ êîòîðîãî
ïîçäíåå áûëî ñîçäàíî
ìíîæåñòâî äðóãèõ
èçäåëèé. ÖÏ - ãëàâíûé
óçåë ÌÊ. Ñ íèì
ñâÿçàíî òàêîåâàæíåéøåå
ïîíÿòèå, êàê ñèñòåìà
êîìàíä.
Ñèñòåìà
êîìàíä - ýòî óíèêàëüíûé,
õàðàêòåðíûé
äëÿ äàííîãî ÖÏ
íàáîð äâîè÷íûõ
êîäîâ, îïðåäåëÿþùèõ
ïåðå÷åíü âñåõ
åãî âîçìîæíûõ
îïåðàöèé. Êàæäûé
òàêîé êîä îïðåäåëÿåò
îäíó îïåðàöèþ
è íàçûâàåòñÿ
êîäîì îïåðàöèè
èëè êîìàíäîé.
×åì áîëüøå êîäîâ
èñïîëüçóåòñÿ
â ñèñòåìå êîìàíä,
òåì áîëüøå îïåðàöèé
ñïîñîáåí âûïîëíèòü
ÖÏ. ÌÊ 8051 - âîñüìèðàçðÿäíûé,
ïîýòîìó êîäû
îïåðàöèé ó íåãî
èìåþò ðàçìåð
8 áèò. Òåîðåòè÷åñêè
ìîæåò áûòü âñåãî
256 âîñüìèáèòíûõ
êîäîâ îïåðàöèé.
 8051 èñïîëüçóþòñÿ
255.
Ìíîãîêðàòíî
ïðîãðàììèðóåìûå
ìèêðîñõåìû ïîäðàçäåëÿþòñÿ
íà ÌÊ, îñíàùåííûå
ÏÇÓ ñî ñòèðàíèåì
óëüòðàôèîëåòîâûì
îáëó÷åíèåì (âûïóñêàþòñÿ
â êîðïóñàõ ñ “îêíîì”),
è ÌÊ ñ ýëåêòðè÷åñêè
ïåðåïðîãðàììèðóåìîé
ïàìÿòüþ. Íåäîñòàòîê
ÌÊ ñ ÏÇÓ ñî ñòèðàíèåì
óëüòðàôèîëåòîâûì
îáëó÷åíèåì - î÷åíü
âûñîêàÿ ñòîèìîñòü
è îòíîñèòåëüíî
íåáîëüøîå ÷èñëî
öèêëîâ çàïèñè/ñòèðàíèÿ
(çàâèñèò îò ñóììàðíîé
äîçû îáëó÷åíèÿ
êðèñòàëëà è îáû÷íî
íå ïðåâûøàåò
15...20).
Àðõèòåêòóðà
ÌÊ 8051 ïðåäïîëàãàåò
ðàçäåëüíîå èñïîëüçîâàíèå
ïàìÿòè ïðîãðàìì
è äàííûõ è íîñèò
íàçâàíèå ãàðâàðäñêîé.
Îáû÷íî òàêóþ
àðõèòåêòóðó
èñïîëüçóþò äëÿ
ïîâûøåíèÿ áûñòðîäåéñòâèÿ
ñèñòåìû çà ñ÷åò
ðàçäåëåíèÿ ïóòåé
äîñòóïà ê ïàìÿòè
ïðîãðàìì è äàííûõ,
íî â 8051 îíà áûëà
ïðèìåíåíà ñ öåëüþ
ïîëó÷åíèÿ ïàìÿòè
ïðîãðàìì è äàííûõ,
íå òðåáóþùèõ
îäèíàêîâîãî
ðàçìåðà. Àíòèïîä
ãàðâàðäñêîé -
àðõèòåêòóðà
ôîí Íåéìàíà
- ïðåäïîëàãàåò
õðàíåíèå ïðîãðàìì
è äàííûõ â îáùåé
ïàìÿòè è íàèáîëåå
õàðàêòåðíà äëÿ
ìèêðîïðîöåññîðîâ,
îðèåíòèðîâàííûõ
íà èñïîëüçîâàíèå
â êîìïüþòåðàõ.
Ïðèìåðîì ìîãóò
ñëóæèòü ìèêðîïðîöåññîðû
ñåìåéñòâà x86.
Òàéìåðû
Ò0, Ò1 - øåñòíàäöàòèðàçðÿäíûå
ïðîãðàììèðóåìûå
òàéìåðû/ñ÷åò÷èêè,
êîòîðûå ìîãóò
çàïðîãðàììèðîâàíû
íà âûïîëíåíèå
öåëîãî ðÿäà ôóíêöèé.
Â
8051 ðåàëèçîâàí óíèâåðñàëüíûé
àñèíõðîííûé
ïîñëåäîâàòåëüíûé
ïðèåìîïåðåäàò÷èê
(UART), ïîääåðæèâàþùèé
ïðîòîêîë ñòàíäàðòà
RS-232C, ÷òî îáåñïå÷èâàåò
âîçìîæíîñòü
îðãàíèçàöèè
ñâÿçè ýòîãî ÌÊ
ñ ïåðñîíàëüíûì
êîìïüþòåðîì. Êðîìå
RS-232C, ïîïóëÿðíûìè
ïðîòîêîëàìè â
ìèðå âñòðàèâàåìûõ
ñèñòåì ÿâëÿþòñÿ
RS-485, (äâóõïðîâîäíàÿ
äâóíàïðàâëåííàÿ
øèíà), SPI (ïîñëåäîâàòåëüíûé
ïåðèôåðèéíûé
òðåõïðîâîäíûé
èíòåðôåéñ), Bitbus (ïîñëåäîâàòåëüíàÿ
ìàãèñòðàëü óïðàâëåíèÿ),
CAN (ìåæêîíòðîëëåðíûé
ñåòåâîé èíòåðôåéñ),
USB (óíèâåðñàëüíàÿ
ïîñëåäîâàòåëüíàÿ
øèíà) è íåêîòîðûå
äðóãèå. Ïðàêòè÷åñêè
äëÿ ëþáîãî òèïà
ïîñëåäîâàòåëüíîãî
êàíàëà ñåãîäíÿ
ìîæíî íàéòè ÌÊ,
èìåþùèé â ñâîåì
ñîñòàâå ñîîòâåòñòâóþùèé
ïîñëåäîâàòåëüíûé
ïîðò.Ïàðàëåëüíûå
ïîðòû ââîäà/âûâîäà
- òàêæå îáÿçàòåëüíàÿ
÷àñòü ëþáîãî
ÌÊ. Îáû÷íî èõ
èñïîëüçóþò äëÿ
ñâÿçè äëÿ ñâÿçè
ñ áëèæàéøèì îêðóæåíèåì
- äàò÷èêàìè è
èñïîëíèòåëüíûìè
ìåõàíèçìàìè.
Âçàèìîäåéñòâèå
ëþáîé ÌÊ-ñèñòåìû
ñ îïåðàòîì è îáúåêòîì
óïðàâëåíèÿ ìîæíî
ïðåäñòàâèòü íà
ïîêàçàíîé íà
ðèñ. 2.17  îáùåì ñëó÷àå
îáúåêò óïðàâëåíèÿ
ñíàáæåí èñïîëíèòåëüíûìè
óñòðîéñòâàìè
è äàò÷èêàìè.
×åëîâåê-îïåðàòîð
âîçäåéñòâóåò
íà ÌÊ ñ ïîìîùüþ
çàäàþùèõ óñòðîéñòâ
è ïîëó÷àåò èíôîðìàöèþ
î ñîñòîÿíèè îáúåêòà
èç ïîêàçàíèé
óñòðîéñòâ èíäèêàöèè.
Ïåðâûå
ïðåäñòàâëÿþò
ñîáîé ïåðåêëþ÷àòåëè,
êíîïêè, ïåðåìåííûå
ðåçèñòîðû, âòîðûå
- ñâåòîâûå (â òîì
÷èñëå ãðàôè÷åñêèå
è áóêâåííî-öèôðîâûå)
èíäèêàòîðû,çâóêîèçëó÷àþùèå
è äðóãèå ñèãíàëüíûå
óñòðîéñòâà.
Ðèñóíîê
2.17-Âçàèìîäåéñòâèå
ëþáîé ÌÊ-ñèñòåìû
ñ îïåðàòîì è îáúåêòîì
óïðàâëåíèÿ.
Âñå
ïîêàçàííûå íà
ñõåìå ôóíêöèîíàëüíûå
óçëû è ñâÿçè îáÿçàòåëüíû
ëèøü â êîìïëåêñíûõ
äèàëîãîâûõ ñèñòåìàõ
êîíòðîëÿ è óïðàâëåíèÿ.
 òàê íàçûâàåìûõ
ðàçîìêíóòûõ
ñèñòåìàõ óïðàâëåíèÿ
ÌÊ ðàáîòàåò “âñëåïóþ”,
íå ïîëó÷àÿ íèêàêîé
èíôîðìàöèè î
ñîñòîÿíèè îáúåêòà.
Èíîãäà îí äàæå
íå âûäàåò îïåðàòîðó
íèêàêèõ ñâåäåíèé
î ðàáîòå (êàê ñâîåé,
òàê è îáúåêòà),
îñîáåííî, åñëè
èìååòñÿ âîçìîæíîñòü
îöåíèâàòü ðåçóëüòàòû
óïðàâëåíèÿ, íàáëþäàÿ
çà ñàìèì îáúåêòîì.
 çàìêíóòûõ ñèñòåìàõ
óïðàâëåíèÿ ÌÊ
êîððåêòèðóåò
óïðàâëÿþùèå âîçäåéñòâèÿ
íà îáúåêò â çàâèñèìîñòè
îò ïîêàçàíèé
äàò÷èêîâ, íî óñòðîéñòâà
èíäèêàöèè íå
îáÿçàòåëüíû
è çäåñü. Ñèñòåìû
êîíòðîëÿ íå ñîäåðæàò
èñïîëíèòåëüíûõ
óñòðîéñòâ, à ñ
ïîìîùüþ çàäàþùèõ
îïåðàòîð ëèøü
âûáèðàåò êîíòðîëèðóåìûå
ïàðàìåòðû èëè
ïåðåêëþ÷àåò ðåæèìû
ðàáîòû èíäèêàòîðîâ.
3
ÎÕÐÀÍÀ ÒÐÓÄÀ
.1
Àíàëèç âðåäíûõ
ôàêòîðîâ íà ïðîèçâîäñòâå
Óñëîâèÿ
òðóäà íà ðàáî÷èõ
ìåñòàõ â ïðîèçâîäñòâåííûõ
ïîìåùåíèÿõ ñêëàäûâàþòñÿ
ïîä âîçäåéñòâèåì
áîëüøîãî ÷èñëà
ôàêòîðîâ, ðàçëè÷íûõ
ïî ñâîåé ïðèðîäå,
ôîðìàì ïðîÿâëåíèÿ,
õàðàêòåðó âîçäåéñòâèÿ
íà ÷åëîâåêà.
Âðåäíûé
ïðîèçâîäñòâåííûé
ôàêòîð - ïðîèçâîäñòâåííûé
ôàêòîð, âîçäåéñòâèå
êîòîðîãî íà ðàáîòàþùåãî,
â îïðåäåë¸ííûõ
óñëîâèÿõ, ïðèâîäèò
ê çàáîëåâàíèþ
èëè ñíèæåíèþ
ðàáîòîñïîñîáíîñòè.
Îïàñíûé
ïðîèçâîäñòâåííûé
ôàêòîð - ïðîèçâîäñòâåííûé
ôàêòîð, âîçäåéñòâèå
êîòîðîãî íà ðàáîòàþùåãî,
â îïðåäåë¸ííûõ
óñëîâèÿõ, ïðèâîäèò
ê òðàâìå èëè äðóãîìó
âíåçàïíîìó óõóäøåíèþ
çäîðîâüÿ.
Âðåäíûé
ïðîèçâîäñòâåííûé
ôàêòîð, â çàâèñèìîñòè
îò èíòåíñèâíîñòè
è ïðîäîëæèòåëüíîñòè
âîçäåéñòâèÿ,
ìîæåò ñòàòü îïàñíûì.
Â
öåõå ìåõàíè÷åñêîé
îáðàáîòêè âîçíèêàþò
ñëåäóþùèå ôàêòîðû
îïàñíîñòè è âðåäíîñòè:
ïîâûøåííûé
óðîâåíü âèáðàöèè;
ïîâûøåííûé
óðîâåíü øóìà
íà ðàáî÷åì ìåñòå;
ïîâûøåííàÿ
òåìïåðàòóðà âîçäóõà
ðàáî÷åé çîíû;
ïîâûøåííûå
âûäåëåíèÿ îò ãåðìåòèçèðóþùèõ
âåùåñòâ;
ïîâûøåííîå
íàïðÿæåíèå â ýëåêòðè÷åñêîé
öåïè, çàìûêàíèå
êîòîðîé ìîæåò
ïðîèçîéòè ÷åðåç
òåëî ÷åëîâåêà;
îñòðèå
êðîìêè, çàóñåíöû,
øåðîõîâàòîñòü
íà ïîâåðõíîñòè
çàãîòîâîê èíñòðóìåíòîâ
è îáîðóäîâàíèÿ.
Ðàññìîòðèì
âûøå ïåðå÷èñëåííûå
ôàêòîðû.
Âèáðàöèÿ
Íà
ðàáî÷èõ-êëåïàëüùèêîâ
â öåõå äåéñòâóþò
ëîêàëüíûå âèáðàöèè
îò ïíåâìîìîëîòêà
ïðè ðàñêë¸ïûâàíèè
çàêëåïîê. Ëîêàëüíàÿ
âèáðàöèÿ âûçûâàåò
ñïàçìû ñîñóäîâ,
êîòîðûå íà÷èíàþòñÿ
ñ êîíöåâûõ ôàëàíã
ïàëüöåâ ðóêè è
ðàñïðîñòðàíÿþòñÿ
íà âñþ êèñòü, ïðåäïëå÷üå,
çàõâàòûâàÿ ñîñóäû
ñåðäöà. Âñëåäñòâèå
ýòîãî ïðîèñõîäèò
óõóäøåíèå ñíàáæåíèÿ
êîíå÷íîñòåé
êðîâüþ. Îäíîâðåìåííî
íàáëþäàåòñÿ
âîçäåéñòâèå
âèáðàöèé íà íåðâíûå
îêîí÷àíèÿ, ìûøå÷íûå
è êîñòíûå òêàíè,
âûðàæàþùèåñÿ
â íàðóøåíèè ÷óâñòâèòåëüíîñòè
êîæè, îêîñòåíåíèè
ñóõîæèëèé ìûøö
è îòëîæåíèè ñîëåé
â ñóñòàâàõ ðóê
è ïàëüöåâ, ÷òî
ïðèâîäèò ê áîëÿì,
äåôîðìàöèÿì è
óìåíüøåíèþ ïîäâèæíîñòè
ñóñòàâîâ - à ýòî
âèáðàöèîííàÿ
áîëåçíü. Âñå óêàçàííûå
èçìåíåíèÿ óñèëèâàþòñÿ
â õîëîäíûé è óìåíüøàþòñÿ
â òåïëûé ïåðèîä
ãîäà. Ïðè ëîêàëüíîé
âèáðàöèè íàáëþäàþòñÿ
íàðóøåíèÿ äåÿòåëüíîñòè
öåíòðàëüíîé íåðâíîé
ñèñòåìû, êàê è
ïðè îáùåé âèáðàöèè.
Ñðåäñòâà çàùèòû
îò ëîêàëüíîé
âèáðàöèè: âèáðîçàùèòíûå
ðóêàâèöû, ïåð÷àòêè
è íàêîëåííèêè
êîæàíûå èëè çàìøåâûå,
ñ ïðîêëàäêàìè
èç ãóá÷àòîé
ðåçèíû è áåç íèõ.
Êðîìå òîãî èñïîëüçóþòñÿ
ðàçëè÷íûå ïðîòèâîâèáðàöèîííûå
óñòðîéñòâà ðó÷íîãî
ìåõàíèçèðîâàííîãî
èíñòðóìåíòà.
Íàïðèìåð,
êëåïàëüíûå ìîëîòêè
âûïóñêàþòñÿ
ñ ïíåâìàòè÷åñêèìè
àìîðòèçàòîðàìè
è ýëàñòè÷íûìè
ðóêîÿòêàìè, çíà÷èòåëüíî
óìåíüøàþùèìè
àìïëèòóäû âèáðàöèé.
Çíà÷èòåëüíûé
ýôôåêò ãàøåíèÿ
âèáðàöèè èíñòðóìåíòà
âðàùàþùåãî äåéñòâèÿ
äîñòèãàåòñÿ
áàëàíñèðîâêîé
âðàùàþùåéñÿ
÷àñòè.
Øóì
Ïðîèçâîäñòâåííûé
øóì îòðèöàòåëüíî
äåéñòâóåò íå
òîëüêî íà ëþäåé,
ðàáîòàþùèõ íà
øóìíûõ ïðîèçâîäñòâåííûõ
ó÷àñòêàõ, îí
è íà âåñü êîíòèíåíò
ëèö, îáñëóæèâàþùèõ
äàííîå ïðîèçâîäñòâî,
è íà íàñåëåíèå,
ïðîæèâàþùåå âáëèçè
òåððèòîðèè çàâîäà.
Èñòî÷íèêàìè
øóìà ÿâëÿþòñÿ
êëåïàëüíûå îïåðàöèè,
âûïîëíÿåìûå, êàê
ïðàâèëî, ïíåâìîìîëîòêàìè,
à òàêæå êëåïàëüíûìè
ïðåññàìè. Êðîìå
òîãî, øóì âîçíèêàåò
îò ñâåðëèëüíûõ
è çåíêîâàëüíûõ
îïåðàöèé. Â çàâèñèìîñòè
îò óðîâíÿ è õàðàêòåðà
øóìà, åãî ïðîäîëæèòåëüíîñòè,
à òàêæå îò èíäèâèäóàëüíûõ
îñîáåííîñòåé
÷åëîâåêà, øóì
ìîæåò îêàçûâàòü
íà íåãî ðàçëè÷íîå
äåéñòâèå.
Ïàðàìåòðû
ìèêðîêëèìàòà
â ïðîèçâîäñòâåííîì
ïîìåùåíèè.
Ìèêðîêëèìàò
â ïðîèçâîäñòâåííûõ
óñëîâèÿõ îïðåäåëÿåòñÿ
ñëåäóþùèìè ïàðàìåòðàìè:
à)
òåìïåðàòóðîé
âîçäóõà, t28° (Ñ);
á)
îòíîñèòåëüíîé
âëàæíîñòüþ j=40-60%;
â)
ñêîðîñòüþ äâèæåíèÿ
âîçäóõà íà ðàáî÷åì
ìåñòå v
(çèìîé
- 0.2... 0.5 ì/ñ, ëåòîì - 0.2... 1
ì/ñ).
Îïàñíîñòü
ïîðàæåíèÿ ýëåêòðè÷åñêèì
òîêîì
Â
öåõàõ ìåõàíè÷åñêîé
îáðàáîòêè âåðîÿòíîñòü
ïîðàæåíèÿ ýëåêòðè÷åñêèì
òîêîì î÷åíü íåáîëüøàÿ,
ââèäó îòñóòñòâèÿ
ìàãèñòðàëüíûõ
ýëåêòðîïðèâîäîâ
è çàçåìëåíèÿ.
Ïîæàðíàÿ
áåçîïàñíîñòü
Ïîæàðû
íà ìàøèíîñòðîèòåëüíûõ
ïðåäïðèÿòèÿõ
ïðåäñòàâëÿþò
áîëüøóþ îïàñíîñòü
äëÿ ðàáîòàþùèõ
è ìîãóò ïðè÷èíèòü
ìàòåðèàëüíûé
óùåðá. Ñòàòèñòèêà
ïîêàçûâàåò, ÷òî
â îñíîâíîì ïðè÷èíîé
ïîæàðà ñëóæèò
íàðóøåíèå òåõíîëîãè÷åñêîãî
ðåæèìà (33% îò âñåõ
ñëó÷àåâ). Ýòî îáúÿñíÿåòñÿ
ðàçíîîáðàçèåì
è ñëîæíîñòüþ
òåõíîëîãè÷åñêèõ
ïðîöåññîâ. Ñëîæíîñòü
ïðîòèâîïîæàðíîé
çàùèòû óñóãóáëÿåòñÿ
ðàçìåðàìè ïðåäïðèÿòèé,
áîëüøîé ïëîòíîñòüþ
çàñòðîéêè, óâåëè÷åíèåì
âìåñòèìîñòè
òîâàðíî-ìàòåðèàëüíûõ
ñêëàäîâ. Â öåõå
îñîáóþ ïîæàðîîïàñíîñòü
ïðåäñòàâëÿåò
ïðèñòðîéêà, à
èìåííî, àðõèâû
÷åðòåæåé è òåõ.
Äîêóìåíòàöèè.
Ïðîèçâîäñòâî
öåõà ïî ñòåïåíè
ïîæàðîîïàñíîñòè
è âçðûâîîïàñíîñòè
îòíîñÿòñÿ ê êàòåãîðèÿì
Ä, à çäàíèÿ ïî II ñòåïåíè
îãíåñòîéêîñòè.
Ïðåäîòâðàùåíèå
è ìåòîäû áîðüáû
ñ îïàñíûìè è âðåäíûìè
ïðîèçâîäñòâåííûìè
ôàêòîðàìè
Ìåòîäû
áîðüáû ñ øóìîì
Èíæåíåðíûå
ìåòîäû áîðüáû
ñ øóìîì íà ïðîìûøëåííûõ
ïðåäïðèÿòèÿõ
çàêëþ÷àåòñÿ
â ñëåäóþùåì.
.Óìåíüøåíèå
øóìà â èñòî÷íèêå
âîçíèêíîâåíèÿ
â ïðîöåññå êîíñòðóèðîâàíèÿ
è èçãîòîâëåíèÿ
ìàøèí, à òàêæå
ïóòåì ïðàâèëüíîé
ýêñïëóàòàöèè
îáîðóäîâàíèÿ.
.Ïðèìåíåíèå
çâóêîèçîëèðóþùèõ
êîíñòðóêöèé
è çâóêîïîãëîùàþùèõ
ìàòåðèàëîâ, ëîêàëèçàöèÿ
øóìíîãî îáîðóäîâàíèÿ
â ñïåöèàëüíûõ
âûãîðîäêàõ èëè
ïðè ïîìîùè çâóêîèçîëèðóþùèõ
êîæóõîâ.
.Ïðèìåíåíèå
ãëóøèòåëåé ñòðóéíûõ
øóìîâ.
Âñå
ýòè ìåðîïðèÿòèÿ
îáû÷íî îñóùåñòâëÿþòñÿ
ðàçäåëüíî èëè
(÷àùå) â êîìïëåêñå,
â çàâèñèìîñòè
îò óñëîâèé ïðîèçâîäñòâà.
Îðãàíèçàöèîííî-òåõíè÷åñêèå
ìåðîïðèÿòèÿ òàêæå
çíà÷èòåëüíî
ñíèæàþò øóì
ïðîèçâîäñòâà:
à)
çàìåíà øóìíîãî
îáîðóäîâàíèÿ
ìåíåå øóìíûì;
á)
ðàöèîíàëüíîå
ðàñïîëîæåíèå
ìàøèí è àãðåãàòîâ
â öåõå, âûíîñ íàèáîëåå
øóìíûõ â ñïåöèàëüíîå
ïîìåùåíèå èëè
âûäåëåíèå èõ
â îòäåëüíóþ ÷àñòü
öåõà, ÷òîáû îáåñïå÷èòü
â ïîìåùåíèè äîïóñêàåìûé
óðîâåíü øóìà;
â)
òàêîå ïëàíèðîâàíèå
âðåìåíè ðàáîòû
øóìíîãî îáîðóäîâàíèÿ,
÷òîáû â ýòî âðåìÿ
â öåõå ðàáîòàëî
ìåíüøå ëþäåé;
ã)
îçåëåíåíèå òåððèòîðèè
ïðåäïðèÿòèé è
ïðèëåãàþùåé ê
íåé òåððèòîðèè.
Øóì
ïðåäñòàâëÿåò
ñîáîé íåæåëàòåëüíîå
äëÿ ÷åëîâåêà ñî÷åòàíèå
çâóêîâ ðàçëè÷íîé
èíòåíñèâíîñòè
è ÷àñòîòû â äèàïàçîíû
16...2000 Ãö è íåãàòèâíî
âëèÿþùèõ íà ÷åëîâåêà.
Íîðìèðîâàíèå
øóìà ïðîâîäèòñÿ
â ñîîòâåòñòâèè
ñ ÃÎÑÒ 12.1.003-83
Ïðåäîòâðàùåíèåâèáðàöèé
Ðàçëè÷àþò
ãèãèåíè÷åñêîå
è òåõíè÷åñêîå
íîðìèðîâàíèå
âèáðàöèé. Â ñîîòâåòñòâèè
ñ ÃÎÑÒ 12.1.012-78, ïðè ãèãèåíè÷åñêîì
íîðìèðîâàíèå
âèáðàöèé îãðàíè÷èâàþò
ñðåäíåêâàäðàòè÷íûå
âåëè÷èíû âèáðîñòîéêîñòè
èëè âèáðîóñêîðåíèÿ,
êîòîðûå óñòàíàâëèâàþò
â çàâèñèìîñòè
îò âèäà âèáðàöèè,
ïðèðîäû åå ïðîèñõîæäåíèÿ,
íàïðàâëåíèÿ äåéñòâèÿ
è ñðåäíåãåîìåòðè÷åñêèõ
÷àñòîò îêòàâíûõ
ïîëîñ.
Ìåòîäû
áîðüáû ñ ïðîáëåìàìè
ïîäú¸ìíî-òðàíñïîðòíîãî
îáîðóäîâàíèÿ.
Áåçîïàñíîñòü
òðóäà ïðè ïîäúåìå
è ïåðåìåùåíèè
ãðóçîâ â çíà÷èòåëüíîé
ñòåïåíè çàâèñèò
îò êîíñòðóêòèâíûõ
îñîáåííîñòåé
ïîäú¸ìíî-òðàíñïîðòíûõ
ìàøèí è ñîîòâåòñòâèÿ
èõ ïðàâèëàì è
íîðìàì Ãîñãîðòåõíàäçîðà
Óêðàèíû. Â öåõå
èñïîëüçóåòñÿ
êðàí-áàëêà äëÿ
ïåðåìåùåíèÿ ÷àñòåé
ïàíåëåé ôþçåëÿæà
ê ñòàïåëÿì ñáîðêè.
Ïåðåìåùåíèå
ñîïðîâîæäàåòñÿ
ïðåðûâàþùåéñÿ
çâóêîâîé ñèãíàëèçàöèåé,
ïðåäóïðåæäàþùåé
îá îïàñíîñòè.
Íåîáõîäèìûå
ïàðàìåòðû ìèêðîêëèìàòà
îáåñïå÷èâàþòñÿ
âûïîëíåíèåì
ðÿäà ìåðîïðèÿòèé,
à èìåííî:
1.Ìåõàíèçàöèÿ
è àâòîìàòèçàöèÿ
ïðîèçâîäñòâåííûõ
ïðîöåññîâ, äèñòàíöèîííîå
óïðàâëåíèå èìè;
.Ñîâåðøåíñòâîâàíèå
òåõíîëîãèè ïðîèçâîäñòâà
(óìåíüøåíèå òåïëîâûäåëåíèÿ
îáîðóäîâàíèÿ,
åãî ðàöèîíàëüíîå
ðàçìåùåíèå;óìåíüøåíèå
âûäåëåíèÿ âðåäíûõ
âåùåñòâ â âîçäóõ,
ïûëåïîäàâëåíèå
è ò.ä.);
.Òåïëîâàÿ
çàùèòà (ýêðàíû,
èçìåíåíèå òèïà
íàãðåâà);
.Óñòðîéñòâî
âåíòèëÿöèè è
îòîïëåíèÿ (ïîäîãðåâ
èëè îõëàæäåíèå
ïîñòóïàþùåãî
âîçäóõà, êîíäèöèîíèðîâàíèå);
.Ïðèìåíåíèå
ñðåäñòâ èíäèâèäóàëüíîé
çàùèòû.
Ïðåäîòâðàùåíèå
ïîðàæåíèÿ ýëåêòðè÷åñêèì
òîêîì
Âîçìîæíûå
ïîðàæåíèÿ: îò
ïðèêîñíîâåíèÿ
ê îãîëåííûì ïðîâîäàì,
ïèòàþùèì ïåðåíîñíûå
ëàìïû âñëåäñòâèå
ïîâðåæäåíèÿ èçîëÿöèè.
Îñíîâíûìè ìåðàìè
çàùèòû îò ïîðàæåíèÿ
ýëåêòðè÷åñêèì
òîêîì ÿâëÿþòñÿ
ïî (ÃÎÑÒ 12.1.019-79):
.Îáåñïå÷åíèå
íåäîñòóïíîñòè
òîêîâåäóùèõ
÷àñòåé (èçîëÿöèÿ
òîêîâåäóùèõ
÷àñòåé, ðàçìåùåíèå
èõ íà íåäîñòóïíîé
âûñîòå, îãðàæäåíèå,
ïîìåùåíèå â ñïåöèàëüíûå
êîðîáà è äð.);
.Ýëåêòðè÷åñêîå
ðàçäåëåíèå ñåòè
(ðàçäåëåíèå ýëåêòðè÷åñêîé
ñåòè íà îòäåëüíûå
ýëåêòðè÷åñêè
íå ñâÿçàííûå
ìåæäó ñîáîé ó÷àñòêè
ñ ïîìîùüþ ñïåöèàëüíûõ
ðàçäåëÿþùèõ òðàíñôîðìàòîðîâ);
.Äâîéíàÿ
èçîëÿöèÿ;
.Çàùèòíîå
çàçåìëåíèå (ïðåäíàìåðåííîå
ýëåêòðè÷åñêîå
ñîåäèíåíèå ñ
çåìëåé èëè åå
ýêâèâàëåíòîì
ìåòàëëè÷åñêè
íåòîêîâåäóùèõ
÷àñòåé, êîòîðûå
ìîãóò îêàçàòüñÿ
ïîä íàïðÿæåíèåì,
òåì ñàìûì, óñòðàíÿÿ
îïàñíîñòü ïîðàæåíèÿ
ëþäåé ýëåêòðè÷åñêèì
òîêîì ïðè ïîÿâëåíèè
íàïðÿæåíèÿ íà
êîíñòðóêòèâíûõ
÷àñòÿõ îáîðóäîâàíèÿ,
ò.å. ïðè çàìûêàíèè
íà êîðïóñ);
.Ïðèìåíåíèå
ìàëîãî íàïðÿæåíèÿ
( ïðèìåíÿþòñÿ
ïåðåíîñíûå ëàìïû
36Â).
Ïîæàðíàÿ
áåçîïàñíîñòü
Â
öåõå äëÿ óñòðàíåíèÿ
î÷àãîâ âîçãîðàíèÿ
ýëåêòðîïðîâîäêè
èñïîëüçóþòñÿ
îãíåòóøèòåëè
ÎÓ-2, íàõîäÿùèåñÿ
íåïîñðåäñòâåííî
âîçëå ñòàïåëüíîé
ñáîðêè. Êðîìå
òîãî, èñïîëüçóþòñÿ
ÎÕÏ-10 è èìååòñÿ
ïîæàðíûé ùèò.
Íà ëåñòíè÷íîé
êëåòêå â ïðèñòðîéêå
èìååòñÿ ïîæàðíûé
êðàí. Â öåõå ïðåäóñìîòðåíî
5 âûõîäîâ, ðàñïîëîæåííûõ
ðàññðåäîòî÷åíî
ñóììàðíîé øèðèíîé
19ì, âêëþ÷àÿ âûõîä
èç ïðèñòðîéêè.
Ïðàâèëà ïîæàðíîé
áåçîïàñíîñòè
ïî ÃÎÑÒ 12.4.009-83
3.2
Îïðåäåëåíèå òðåáóåìîãî
âîçäóõîîáìåíà
â ïîìåùåíèè ïî
âðåäíûì âåùåñòâàì
Îïðåäåëèòü
òðåáóåìûé âîçäóõîîáìåí
è åãî êðàòíîñòüäëÿâåíòèëÿöèîííîéñèñòåìû
öåõà ïðè íàëè÷èè
è îòñóòñòâèè
ìåñòíûõ îòñîñîâ.
Öåõ èìååò ðàçìåðû
À õ Â, âûñîòà Í
= 8 ì. Â âîçäóøíóþ
ñðåäó öåõà âûäåëÿåòñÿ
ïûëü â êîëè÷åñòâå
W, ìã/ìèí. (ïðåäåëüíî-äîïóñòèìàÿ
êîíöåíòðàöèÿ
ïûëè ÏÄÊ = 4 ìã/ì3).
Êîíöåíòðàöèÿ
ïûëè â ðàáî÷åé
çîíå Ñ
ïðèíèìàåòñÿ
ðàâíîé ÏÄÊ, îíöåíòðàöèÿ
ïûëè â óäàëÿåìîì
èç öåõà âîçäóõà
ðàâíà 30% åå êîíöåíòðàöèè
â ðàáî÷åé çîíå
. Êîíöåíòðàöèÿ
ïûëè â ïðîòî÷íîì
âîçäóõå Ñ
ìã/ì3.
Êîëè÷åñòâî âîçäóõà,
çàáèðàåìîãî
èç ðàáî÷åé çîíû
ìåñòíûìè îòîñàìè,
ðàâíî
= 4500ì3/÷àñ.
Ðåøåíèå:
Èñõîäíûå
äàííûå : À= 160 ì, Â=115
ì, W= 1,1 ìã/ìèí,
Ñ
= 0,7 ìã/ì
.
.
Îïðåäåëÿåì îáúåì
öåõà:
(3.1)
.
Íàéäåì âûäåëåíèå
ïûëè (â ìèëëèãðàììàõ)
çà 1 ÷àñ:
(3.2)
Ïðè
íàëè÷èè ìåñòíûõ
îòñîñîâ òðåáóåìûé
âîçäóõîîáìåí
îïðåäåëÿåì ïî
ôîðìóëå:
(3.3)
Êðàòíîñòü
âîçäóõîîáìåíà
â öåõå ñîñòàâèò:
(3.4)
Ïðè
îòñóòñòâèè ìåñòíûõ
îòñîñîâ ôîðìóëà
(3) óïðîùàåòñÿ:
(3.5)
Êðàòíîñòü
âîçäóõîîáìåíà
â öåõå ïðè îòñóòñòâèè
ìåñòíûõ îòñîñîâ:
(3.6)
4
ÝÊÎÍÎÌÈ×ÅÑÊÀß
×ÀÑÒÜ
.1Ðàñ÷åò
ñåáåñòîèìîñòè
è öåíû òåëà-âðàùåíèÿ
Â
äàííîì ðàçäåëå
ïðîèçâåä¸ì ðàñ÷¸ò
ñåáåñòîèìîñòè
èçãîòîâëåíèÿ
òåëà- âðàùåíèÿ.
Ïðè
ðàçðàáîòêå ïëàíà
ïî ñåáåñòîèìîñòè
ïðîäóêöèè ïðîèçâîäÿòñÿ
ðàñ÷¸òû ãîäîâîé
ñìåòû çàòðàò
íà ïðîèçâîäñòâî
öåõà ïî êàëüêóëÿöèîííûì
ñòàòüÿì çàòðàò
èçäåëèÿ.
Ñìåòà
çàòðàò íà ïðîèçâîäñòâî
öåõà îòðàæàåò
âñå çàòðàòû öåõà
íà ãîäîâóþ ïðîãðàììó.
Ïðè
ñîñòàâëåíèè
ñìåòû çàòðàò
íà ïðîèçâîäñòâî
öåõà ïî êàëüêóëÿöèîííûì
ñòàòüÿì ðàñõîäîâ
çàòðàòû ãðóïïèðóþòñÿ
ñëåäóþùèì îáðàçîì:
.
Ñûðü¸ è îñíîâíûå
ìàòåðèàëû.
.
Ïîêóïíûå êîìïëåêòóþùèå
èçäåëèÿ è ïîëóôàáðèêàòû.
.
Âîçâðàòíûå îòõîäû.
.
Îñíîâíàÿ çàðàáîòíàÿ
ïëàòà ïðîèçâîäñòâåííûõ
ðàáî÷èõ.
.
Äîïîëíèòåëüíàÿ
çàðàáîòíàÿ ïëàòà
ïðîèçâîäñòâåííûõ
ðàáî÷èõ.
.
Îò÷èñëåíèå íà
ñîöèàëüíîå ñòðàõîâàíèå.
.
Ðàñõîäû íà ñîäåðæàíèå
è ýêñïëóàòàöèþ
îáîðóäîâàíèÿ.
.
Öåõîâûå ðàñõîäû.
.
Âîçìåùåíèå èçíîñà
èíñòðóìåíòîâ
è ïðèñïîñîáëåíèé
öåõîâîãî íàçíà÷åíèÿ.
.
Âíåïðîèçâîäñòâåííûå
ðàñõîäû.
Çàòðàòû
íà ïðîèçâîäñòâî
ïðîäóêöèè êëàññèôèöèðóþòñÿ
íà ïðÿìûå è êîñâåííûå.
Ïðÿìûå
- ñâÿçàííûå ñ èçãîòîâëåíèåì
êîíêðåòíûõ âèäîâ
èçäåëèÿ, îòíîñÿòñÿ
íà ñåáåñòîèìîñòü
åäèíèöû ó÷¸òà
è êîòîðûå ìîæíî
ðàññ÷èòàòü íà
åäèíèöó èçäåëèÿ
(ìàòåðèàëû, çàðàáîòíàÿ
ïëàòà è äð.).
Êîñâåííûå
ðàñõîäû îäíîâðåìåííî
ñâÿçàíû ñ íåñêîëüêèìè
òåõíîëîãè÷åñêèìè
ïðîöåññàìè èëè
ðàáîòîé öåõà
ïðåäïðèÿòèÿ â
öåëîì (öåõîâûå
ðàñõîäû, îáùåçàâîäñêèå
ðàñõîäû).
Ñìåòà
çàòðàò íà ïðîèçâîäñòâî
öåõà (çàâîäà) îòðàæàåò
âñå çàòðàòû öåõà
(çàâîäà) íà ãîäîâóþ
ïðîãðàììó è ñîñòàâëÿåòñÿ
â äâóõ ðàçäåëàõ:
ïî ýêñïëóàòàöèîííûì
ýëåìåíòàì è ïî
êàëüêóëÿöèîííûì
ñòàòüÿì ðàñõîäîâ.
Ñìåòà çàòðàò
ïî ýêñïëóàòàöèîííûì
ýëåìåíòàì ïðèìåíÿåòñÿ
äëÿ âçàèìîñâÿçè
áþäæåòà öåõà
ñ áþäæåòîì çàâîäà,
áþäæåòà çàâîäà
ñ áþäæåòîì âûøåñòîÿùèõ
èíñòàíöèé. Ïåðå÷åíü
îñíîâíûõ ñòàòåé
ðàñõîäîâ, ïî êîòîðûì
ðàññ÷èòûâàåòñÿ
ñìåòà çàòðàò
íà ïðîèçâîäñòâî
ïðîäóêöèè, ïðèâåäåíà
âûøå.
.2
Ïîëíàÿ ñåáåñòîèìîñòü
èçãîòîâëåíèÿ
òåëà-âðàùåíèÿ
Ïðè
ðàñ÷¸òå ñåáåñòîèìîñòè
ïðîäóêöèè ðàçëè÷àþò
öåõîâóþ, çàâîäñêóþ
è ïîëíóþ ñåáåñòîèìîñòü
åäèíèöû èçäåëèÿ.
Ïðè ðàñ÷¸òå öåõîâîé
ñåáåñòîèìîñòè
èçäåëèÿ ó÷èòûâàþò
òîëüêî òå çàòðàòû,
êîòîðûå ïðîèçâîäÿòñÿ
â äàííîì öåõå,
áåç ó÷¸òà çàòðàò
äðóãèõ öåõîâ
äàííîãî çàâîäà
ïî èçãîòîâëåíèþ
ýòîãî èçäåëèÿ.
Öåõîâàÿ
ñåáåñòîèìîñòü
âàëà-øåñòåðíè.
Ðàñ÷¸ò
öåõîâîé ñåáåñòîèìîñòè
âàëà-øåñòåðíè
ñîñòîèò â îïðåäåëåíèè
ñëåäóþùèõ ñòàòåé
çàòðàò:
ÑÖ=ÐÌ-ÂÎ+ÎÇÏÐ+ÄÇÏÐ+ÍÇÏÐ+ÐÑÝÎ+ÎÖÐ+ÈÑÏ+ÐÎÏ
ãäå
ÐÌ - ðàñõîäû íà
ñûðü¸ è ìàòåðèàëû;
ÐÌ=ÍÌ·ÖÌ,
ãäå
ÍÌ - ìàññà çàãîòîâêè
âàëà-øåñòåðíè,10
êã:
ÖÌ
- ñðåäíÿÿ ñòîèìîñòü
ìàòåðèàëîâ, 20 ãðí./êã.
ÐÌ=10·20=200
ãðí
ÂÎ
- âîçâðàòíûå îòõîäû
ÂÎ=(ÍÌ
- ÌÃ)·ÖÌ·0,1
ãäå
ÌÃ - ìàññà ãîòîâûõ
äåòàëåé, 8 êã.
ÂÎ=(10-8)·20·0,1=4
ãðí
ÎÇÏÐ-
îñíîâíàÿ çàðàáîòíàÿ
ïëàòà ïðîèçâîäñòâåííûõ
ðàáî÷èõ
ÎÇÏÐ=(
1+(ÍÓÒ+ÍÈÒ)/100)·Ò·Ñ×Ñ,
ãäå
ÍÓÒ è ÍÈÒ - íîðìàòèâû
äîïëàò çà óñëîâèÿ
è èíòåíñèâíîñòü
òðóäà, ñîîòâåòñòâåííî,
5, 10 %;
Ò-
òðóäî¸ìêîñòü
èçãîòîâëåíèÿ
âàëà-øåñòåðíè,
ìèí
= 1,25 ÷åë.-÷.
Ñ×Ñ-ñðåäíÿÿ
÷àñîâàÿ ñòàâêà,
15 ãðí./÷åë.-÷.
ÎÇÏÐ=(1+(5+10)/100)·1,25·15=21,56ãðí
ÄÇÏÐ-
äîïîëíèòåëüíàÿ
çàðàáîòíàÿ ïëàòà
ïðîèçâîäñòâåííûõ
ðàáî÷èõ
ÄÇÏÐ=0,3·ÎÇÏÐ
ãäå
êîýôôèöèåíò
0,3 îïðåäåëÿåò ñðåäíþþ
âåëè÷èíó äîïîëíèòåëüíîé
çàðàáîòíîé ïëàòû
(êàê íîðìàòèâ)
îòíîñèòåëüíî
îñíîâíîé
ÄÇÏÐ=0,3·21,56=6,46
ãðí
ÍÇÏÐ
- îò÷èñëåíèÿ èç
çàðàáîòíîé ïëàòû
ïðîèçâîäñòâåííûõ
ðàáî÷èõ, â ñîö.
ôîíäû, âêëþ÷àåìûå
â ñåáåñòîèìîñòü
âàëà-øåñòåðíè
ÍÇÏÐ
= (ÎÇÏÐ+ÄÇÏÐ)·ÍÍÇÏ/100,
ãäå
ÍÍÇÏ - íîðìàòèâ
íà÷èñëåíèé,
37,5%
ÍÇÏÐ=(21,56+6,46)·37,5/100=8,08
ãðí
ÐÑÝÎ
- ðàñõîäû íà ñîäåðæàíèå
è ýêñïëóàòàöèþ
îáîðóäîâàíèÿ
ÐÑÝÎ=ÎÇÏзÍÐÑÝÎ/100
ãäå
ÍÐÑÝÎ - íîðìàòèâ
ðàñõîäîâ íà ñîäåðæàíèå
è ýêñïëóàòàöèþ
îáîðóäîâàíèÿ,
40%
ÍÐÑÝÎ=(21,56·40)/100=8,62
ãðí
ÎÖÐ
- îáùåöåõîâûå
ðàñõîäû
ÎÖÐ=ÎÇÏзÍÎÖÐ/100
ÍÎÖÐ
- íîðìàòèâ îáùåöåõîâûõ
ðàñõîäîâ, 70 %
ÎÖÐ=(21,56·70)/100=15,09ãðí
ÈÑÏ
- âîçìåùåíèå èçíîñà
ïðèñïîñîáëåíèé
è èíñòðóìåíòà
öåëåâîãî íàçíà÷åíèÿ
ÈÑÏ=ÎÇÏзÍÑÎ/100,
ãäå
ÍÑÎ - íîðìàòèâ
çàòðàò íà ñïåöèàëüíóþ
îñíàñòêó, 15%
ÈÑÏ=(21,56·15)/100=3,23ãðí
ÐÎÏ-
ðàñõîäû íà îñâîåíèå
ïðîèçâîäñòâà
èçäåëèé
ÐÎÏ=(ÐÌ+ÎÇÏÐ)·ÍÎÏ/100,
ãäå
ÍÎÏ - íîðìàòèâ
çàòðàò íà îñâîåíèå
ïðîèçâîäñòâà,
10%
ÐÎÏ
=(200+21,56)·10/100=22,15ãðí
Òàêèì
îáðàçîì, öåõîâàÿ
ñåáåñòîèìîñòü
âàëà-øåñòåðíè:
ÑÖ=200-4+21,56+6,46+8,08+8,62+15,09+3,23+22,15=283,62ãðí
Ïðîèçâîäñòâåííàÿ
ñåáåñòîèìîñòü
èçäåëèÿ:
Ïðîèçâîäñòâåííóþ
èëè çàâîäñêóþ
ñåáåñòîèìîñòü
ðàññ÷èòûâàþò
ïî ôîðìóëå:
ÑÇ=ÑÖ+ÎÇÐ+ÑÈ+ÌÑ+ÏÏÐ,
ãäå
ÎÇÐ - îáùåçàâîäñêèå
ðàñõîäû ÎÇÐ äëÿ
èçäåëèÿ
ÎÇÐ=
ÎÇÏзÍÎÇÐ/100,
ãäå
ÍÎÇÐ - íîðìàòèâ
îáùåçàâîäñêèõ
ðàñõîäîâ, 80%
ÎÇÐ=(21,56·80)/100=17,24ãðí
ÑÈ-
ðàñõîäû íà îáÿçàòåëüíîå
ñòðàõîâàíèå
èìóùåñòâà
ÑÈ=
ÎÇÏзÍÈÑ/100,
ãäå
ÍÈÑ - íîðìàòèâ
ðàñõîäîâ íà ñòðàõîâàíèå
èìóùåñòâà, 5%
ÑÈ=(21,56·5)/100=1,07ãðí
ÏÏÐ
- ïðî÷èå ïðîèçâîäñòâåííûå
ðàñõîäû
ÏÏÐ=ÎÇÏзÍÏÐ/100;
ãäå
ÍÏÐ- íîðìàòèâ
ïðî÷èõ ðàñõîäîâ,
10%
ÏÏÐ=(21,56·10)/100=2,15ãðí
Ïðîèçâîäñòâåííàÿ
(çàâîäñêàÿ) ñåáåñòîèìîñòü
èçäåëèÿ
ÑÇ=283,62+17,24+1,07+2,15=304,06ãðí
Ïîëíàÿ
ñåáåñòîèìîñòü
ÑÏ
= ÑÇ+ÂÏÐ,
ãäå
ÂÏÐ - âíåïðîèçâîäñòâåííûå
ðàñõîäû, ïðèõîäÿùèåñÿ
íà îäíî èçäåëèå
ÂÏÐ=ÑÇ·ÍÂÏÐ/100;
ãäå
ÍÂÏÐ- íîðìàòèâ
ïðîèçâîäñòâåííûõ
ðàñõîäîâ, 5%
ÂÏÐ=(304,06·5)/100=15,20ãðí
ÑÏ=304,06+15,20=319,26ãðí
Ïðèáûëü
15-30%=84,43ãðí
ÍÄÑ-20%
îò îïòîâîé öåíû=63,8ãðí
Òàáëèöà
4.1 - Ðàñöåíêè çàòðàò
íà ïðîèçâîäñòâî
Âèäû
çàòðàò
|
Ôîðìóëà
|
Ðàñ÷åò
(Ãðí)
|
1.
Îñíîâíàÿ çàðàáîòíàÿ
ïëàòà ðàáî÷èõ
|
Î3ÏÐ
|
21,56
|
2.
Äîïîëíèòåëüíàÿ
çàðàáîòíàÿ ïëàòà
|
0,3·
Î3ÏÐ
|
6,46
|
37,5%·
Î3ÏÐ
|
8,08
|
4.
Ñòîèìîñòü îñíîâíûõ
ìàòåðèàëîâ
|
ÐÌ
|
200
|
5.
Âîçâðàòíûå ðàñõîäû
|
ÂÎ
|
-4
|
6.
Àìîðòèçàöèÿ
|
15%
|
3,23
|
7.
Öåõîâûå ðàñõîäû
|
ÎÖÐ
|
15,09
|
8.
Èòîãî öåõîâàÿ
ñåáåñòîèìîñòü
|
ÑÖ
|
283,62
|
9.
Îáùåçàâîäñêèå
ðàñõîäû
|
ÎÇÐ
|
17,24
|
10.
Ïðîèçâîäñòâåííàÿ
ñåáåñòîèìîñòü
|
ÑÇ
|
304,06
|
11.
Âíåïðîèçâîäñòâåííûå
ðàñõîäû
|
ÂÏÐ
|
13,40
|
12.
Èòîãî ñåáåñòîèìîñòü
|
ÑÏ
|
319,26
|
13.
Ïðèáûëü
|
20%
îò ÑÏ
|
84,43
|
14.
Èòîãî öåíà áåç
ÍÄÑ
|
ÑÏ+Ï
|
379,29
|
15.
ÍÄÑ
|
20%(ÑÏ+Ï)
|
63,8
|
16.
Èòîãî öåíà ñ
ÍÄÑ (îïòîâàÿ öåíà)
|
(ÑÏ+Ï)+(20%(ÑÏ+Ï))
|
443,09
|
Âûâîäû:
 äàííîì ðàçäåëå
áûëà ðàññ÷èòàíà
ïîëíàÿ ñåáåñòîèìîñòü
ÑÏ ðàâíà 319,26ãðí,èòîãîâàÿ
öåíà ñ ÍÄÑ, ðàâíà
443,09. Äàííûé ðàñ÷¸ò
ïîçâîëÿåò îïðåäåëèòü
êîíêóðåíòíî-ñïîñîáíîñòü
èçäåëèÿ íà ðûíêå
è öåëåñîîáðàçíîñòü
å¸ ïðîèçâîäñòâà.
Âûâîä
Ïîäâåäÿ
èòîãè ïðîäåëàííîé
ðàáîòû ìîæíî
ñäåëàòü ñëåäóþùèå
âûâîäû:
â
õîäå áàêàëàâðñêîãî
ïðîåêòà áûë ðàçðàáîòàí
òåõíîëîãè÷åñêèé
ïðîöåññ èçãîòîâëåíèÿ
ãðóïïû äåòàëåé
òèïà "òåëî-âðàùåíèÿ":
ðàçðàáîòàíà
çàãîòîâêà, ìàðøðóò
îáðàáîòêè, îïðåäåëåíû
ïðèïóñêè íà ìåõàíè÷åñêóþ
îáðàáîòêó, ðàññ÷èòàíû
ðåæèìû ðåçàíèÿ
äëÿ ðàçíûõ îïåðàöèé.
Áëàãîäàðÿ èñïîëüçîâàíèþ
òàêîãî ìåòîäà
ïîëó÷åíèÿ çàãîòîâêè;
â
êîíñòðóêòîðñêîé
÷àñòè äèïëîìíîãî
ïðîåêòà ðàçðàáîòàíà
ãèáêàÿ àâòîìàòè÷åñêàÿ
ëèíèÿ íà áàçå
÷åòûðåõ ÐÒÊ. ÐÒÊ
ïîçâîëÿåò îñóùåñòâëÿòü
àâòîìàòè÷åñêóþ
çàãðóçêó, îáðàáîòêó,
ðàçãðóçêó è òðàíñïîðòèðîâêó
äåòàëåé, à òàêæå
àâòîìàòè÷åñêè
ìåíÿòü èçíîøåííûé
èíñòðóìåíò. Ïðè
ïðîåêòèðîâàíèè
äàííîãî êîìïëåêñà
ó÷èòûâàëîñü
òðåáîâàíèå ê
åãî ìàêñèìàëüíîé
óíèâåðñàëüíîñòè
è êîìïàêòíîñòè.
ÃÀË îáëàäàåò
îïðåäåëåííîé
ñòåïåíüþ ãèáêîñòè
- íåçíà÷èòåëüíîå
èçìåíåíèå óïðàâëÿþùèõ
ïðîãðàìì, èíñòðóìåíòà
è îñíàñòêè ïîçâîëÿåò
ïåðåíàñòðîèòü
êîìïëåêñ äëÿ îáðàáîòêè
ëþáûõ äåòàëåé
ãðóïïû;
â
âàðèàíòå ýñêèçíîé
ðàçðàáîòàíà
ïëàíèðîâêà ãèáêîé
àâòîìàòèçèðîâàííîé
ëèíèè äëÿ îáðàáîòêè
äåòàëåé òèïà
«òåëî-âðàùåíèÿ»;
Â
ðåçóëüòàòå èñïîëüçîâàíèÿ
äàíîé ãèáêîé
àâòîìàòè÷åñêîé
ëèíèè:
ïîâûøåí
êîýôôèöèåíò
çàãðóçêè ñòàíêîâ
â 2,7 ðàçà;
ïîâûøåíèå
òðóäîåìêîñòè
íà åäèíèöó ïðîäóêöèè
â 3 ðàçà.
Áèáëèîãðàôè÷åñêèé
ñïèñîê
1. Ñïðàâî÷íèê
òåõíîëîãà-ìàøèíîñòðîèòåëÿ:
 2ò. / Ðåä. Êîë.: À. Ã.
Êîñèëîâà (ãë. ðåä.)
è äð.- Ì.: Ìàøèíîñòðîåíèå,1985.-322
ñ.
2. Â.Ï.Áîæêî
- Ïðîåêòèðîâàíèå
òåõíîëîãè÷åñêèõ
ïðîöåññîâ îáðàáîòêè
äåòàëåé íà ìåòàëëîðåæóùèõ
ñòàíêàõ ñ ×ÏÓ:
Ó÷åá. ïîñîáèå
äëÿ êóðñîâ. è äèïëîìí.
ïðîåêòèðîâ. ïî
òåõíîë. ñàìîëåòîñòð.:
 2-õ ÷./ Õ.: Õàðüê. àâèàö.
èí-ò. - 1989.-106ñ.
. Ôåëüäøòåéí
Å.Ý. Ðåæóùèé èíñòðóìåíò
è îñíàñòêà ñòàíêîâ
ñ ×ÏÓ : ñïðàâî÷íîå
ïîñîáèå / Ìí.:Âûø.øê.,
1988.-336 ñ.:èë.
4. Àíàëèç
òåõíîëîãè÷íîñòè
äåòàëåé /Â. Þ. Ãðàíèí,
À.È. Äîëìàòîâ.- Ó÷.
ïîñîáèå. - Õ.: Ãîñ.
Àýðîêîñì. óí-ò
«ÕÀÈ» 1999.-185 ñ.
5. Ìàðî÷íèê
ñòàëåé è ñïëàâîâ/
ïîä.ðåä Â. Ã. Ñîðîêèíà/
Ì: Ìàøèíîñòðîåíèå,
1989.- 324 ñ.
6. Ã.È.Êîñòþê
- Ýôôåêòèâíûé
ðåæóùèé èíñòðóìåíò
ñ ïîêðûòèåì è
óïðî÷íåííûì
ñëîåì. Ñïðàâî÷íèê
/ Õ.:Àíòèêâà,2003.-412ñ.
7. Êîíñòðóêöèÿ
è íàëàäêà ñòàíêîâ
ñ ïðîãðàììíûì
óïðàâëåíèåì è
ðîáîòèçèðîâàííûõ
êîìïëåêñîâ: Ó÷åá.
ïîñîáèå äëÿ ÏÒÓ/
Ë. Í. Ãðà÷åâ, Â. Ë.
Êîñîâñêèé, À. Í.
Êîâøîâ [è äð.] − 2-å
èçä., ñòåð.− Ì.: Âûñø.
øê., 1989.−271 ñ.
8. Ïðîìûøëåííûå
ðîáîòû â ìàøèíîñòðîåíèè:
Àëüáîì ñõåì è
÷åðòåæåé: Ó÷åáíîå
ïîñîáèå äëÿ âóçîâ
/ Ê. Ï. Æóêîâ, Þ. À. Ïàâëîâ,
Î. Í. Òðèôîíîâ [è
äð.]; Ïîä ðåäàêöèåé
ïðîôåññîðà Þ. Ì.
Ñîëîìåíöåâà:
Ìàøèíîñòðîåíèå,
1987.-140 ñ.
. Ðîáîòèçèðîâàííûå
òåõíîëîãè÷åñêèå
êîìïëåêñû è ãèáêèå
ïðîèçâîäñòâåííûå
ñèñòåìû â ìàøèíîñòðîåíèè:
Àëüáîì ñõåì è
÷åðòåæåé: Ó÷åáíîå
ïîñîáèå äëÿ âóçîâ
/ Þ. Ì. Ñîëîìåíöåâ,
Ê. Ï. Æóêîâ, Þ. À. Ïàâëîâ
è äð.; Ïîä îáùåé
ðåäàêöèåé Þ. Ì.
Ñîëîìåíöåâà.
- Ì.: Ìàøèíîñòðîåíèå,
1989.-192 ñ.
10. Ðîáîòèçèðîâàííûå
òåõíîëîãè÷åñêèå
êîìïëåêñû / Ã. È.
Êîñòþê, Î. Î. Áàðàíîâ,
È. Ã. Ëåâ÷åíêî, Â.
À. Ôàäååâ - Ó÷åáíîå
ïîñîáèå - Õ.: Íàö.
Àýðîêîñì. Óí-ò
“ÕÀÈ”, 2003.-214 c.
11. Ðîáîòèçèðîâàííûå
ïðîèçâîäñòâåííûå
êîìïëåêñû (àâòîìàòè÷åñêèå
ìàíèïóëÿòîðû
è ðîáîòîòåõíè÷åñêèå
ñèñòåìû) / Þ. Ã. Êîçûðåâ,
À. À. Êóäèíîâ, Â.
Ý. Áóëàòîâ è äð.;
Ïîä ðåä. Þ. Ã. Êîçûðåâà,
À. À. Êóäèíîâà.
− Ì.: Ìàøèíîñòðîåíèå,
1987.−272 ñ.
. Îñíîâû
îõðàíû òðóäà:
Êîíòðîëüíûå çàäàíèÿ
ïî êóðñó «Îñíîâû
îõðàíû òðóäà»
/ Êîëîñêîâ Â.Þ., Êðó÷èíà
Â.Â. - Õ.:«ÕÀÈ», 2008.-58 ñòð.
Ïåðå÷åíü
ññûëîê
1. Ñïðàâî÷íèê
òåõíîëîãà-ìàøèíîñòðîèòåëÿ:
 2ò. / Ðåä. Êîë.: À. Ã.
Êîñèëîâà (ãë. ðåä.)
è äð.- Ì.: Ìàøèíîñòðîåíèå,1985.-322
ñ.
2. Â.Ï.Áîæêî
- Ïðîåêòèðîâàíèå
òåõíîëîãè÷åñêèõ
ïðîöåññîâ îáðàáîòêè
äåòàëåé íà ìåòàëëîðåæóùèõ
ñòàíêàõ ñ ×ÏÓ:
Ó÷åá. ïîñîáèå
äëÿ êóðñîâ. è äèïëîìí.
ïðîåêòèðîâ. ïî
òåõíîë. ñàìîëåòîñòð.:
 2-õ ÷./ Õ.: Õàðüê. àâèàö.
èí-ò. - 1989.-106ñ.
3. Ôåëüäøòåéí
Å.Ý. Ðåæóùèé èíñòðóìåíò
è îñíàñòêà ñòàíêîâ
ñ ×ÏÓ : ñïðàâî÷íîå
ïîñîáèå / Ìí.:Âûø.øê.,
1988.-336 ñ.:èë.
. Àíàëèç
òåõíîëîãè÷íîñòè
äåòàëåé /Â. Þ. Ãðàíèí,
À.È. Äîëìàòîâ.- Ó÷.
ïîñîáèå. - Õ.: Ãîñ.
Àýðîêîñì. óí-ò
«ÕÀÈ» 1999.-185 ñ.
. Ìàðî÷íèê
ñòàëåé è ñïëàâîâ/
ïîä.ðåä Â. Ã. Ñîðîêèíà/
Ì: Ìàøèíîñòðîåíèå,
1989.- 324 ñ.
. Ã.È.Êîñòþê
- Ýôôåêòèâíûé
ðåæóùèé èíñòðóìåíò
ñ ïîêðûòèåì è
óïðî÷íåííûì
ñëîåì. Ñïðàâî÷íèê
/ Õ.:Àíòèêâà,2003.-412ñ.
. Êîíñòðóêöèÿ
è íàëàäêà ñòàíêîâ
ñ ïðîãðàììíûì
óïðàâëåíèåì è
ðîáîòèçèðîâàííûõ
êîìïëåêñîâ: Ó÷åá.
ïîñîáèå äëÿ ÏÒÓ/
Ë. Í. Ãðà÷åâ, Â. Ë.
Êîñîâñêèé, À. Í.
Êîâøîâ [è äð.] − 2-å
èçä., ñòåð.− Ì.: Âûñø.
øê., 1989.−271 ñ.
. Ïðîìûøëåííûå
ðîáîòû â ìàøèíîñòðîåíèè:
Àëüáîì ñõåì è
÷åðòåæåé: Ó÷åáíîå
ïîñîáèå äëÿ âóçîâ
/ Ê. Ï. Æóêîâ, Þ. À. Ïàâëîâ,
Î. Í. Òðèôîíîâ [è
äð.]; Ïîä ðåäàêöèåé
ïðîôåññîðà Þ. Ì.
Ñîëîìåíöåâà:
Ìàøèíîñòðîåíèå,
1987.-140 ñ.
. Ðîáîòèçèðîâàííûå
òåõíîëîãè÷åñêèå
êîìïëåêñû è ãèáêèå
ïðîèçâîäñòâåííûå
ñèñòåìû â ìàøèíîñòðîåíèè:
Àëüáîì ñõåì è
÷åðòåæåé: Ó÷åáíîå
ïîñîáèå äëÿ âóçîâ
/ Þ. Ì. Ñîëîìåíöåâ,
Ê. Ï. Æóêîâ, Þ. À. Ïàâëîâ
è äð.; Ïîä îáùåé
ðåäàêöèåé Þ. Ì.
Ñîëîìåíöåâà.
- Ì.: Ìàøèíîñòðîåíèå,
1989.-192 ñ.
. Ðîáîòèçèðîâàííûå
òåõíîëîãè÷åñêèå
êîìïëåêñû / Ã. È.
Êîñòþê, Î. Î. Áàðàíîâ,
È. Ã. Ëåâ÷åíêî, Â.
À. Ôàäååâ - Ó÷åáíîå
ïîñîáèå - Õ.: Íàö.
Àýðîêîñì. Óí-ò
“ÕÀÈ”, 2003.-214 c.
. Ðîáîòèçèðîâàííûå
ïðîèçâîäñòâåííûå
êîìïëåêñû (àâòîìàòè÷åñêèå
ìàíèïóëÿòîðû
è ðîáîòîòåõíè÷åñêèå
ñèñòåìû) / Þ. Ã. Êîçûðåâ,
À. À. Êóäèíîâ, Â.
Ý. Áóëàòîâ è äð.;
Ïîä ðåä. Þ. Ã. Êîçûðåâà,
À. À. Êóäèíîâà.
− Ì.: Ìàøèíîñòðîåíèå,
1987.−272 ñ.
. Îñíîâû
îõðàíû òðóäà:
Êîíòðîëüíûå çàäàíèÿ
ïî êóðñó «Îñíîâû
îõðàíû òðóäà»
/ Êîëîñêîâ Â.Þ., Êðó÷èíà
Â.Â. - Õ.:«ÕÀÈ», 2008.-58 ñòð.
Ðàçìåùåíî
íà Allbest.ru