Совершенствование процесса замедленного коксования на установке № 60 ООО 'Лукойл-Волгограднефтепереработка'
ВВЕДЕНИЕ
Процессы коксования решают важнейшую задачу по углублению переработки
нефти, увеличивая ресурсы сырья для производства моторных топлив, а также
обеспечивая безотходность производства.
Согласно федеральной программе “Энергоэффективная экономика ТЭК” глубина
переработки нефти к 2010 году должна увеличиться до 75%, а к 2020 году - до 85%
“при значительном улучшении качества нефтепродуктов, обеспечивающем их
конкурентоспособность”. Однако таких показателей нельзя достичь без включения в
схемы заводов установок коксования [1].
Таким образом, в связи с дальнейшим углублением переработки нефти поиск
путей совершенствования процесса замедленного коксования тяжелых нефтяных
остатков является актуальным, так как именно этот процесс позволяет получать в
больших количествах светлые дистилляты из остаточного сырья, а также не менее
ценный продукт - кокс.
Целью данной работы является улучшение технико-технологических
показателей установки замедленного коксования тяжелых нефтяных остатков.
Объектом исследования является установка замедленного коксования № 60 ООО
«Лукойл-Волгограднефтепереработка».
Предметом исследования является изучение процесса замедленного коксования
тяжелых нефтяных остатков.
Для поставленной цели необходимо решить следующие задачи:
1) провести научно-технический и патентный анализ путей улучшение
технико-технологических показателей;
2) проанализировать теоретические и инженерные основы процесса;
) разработать новую технологическую схему производства;
) произвести инженерно-технологические расчёты основной и
вспомогательной стадий процесса;
) проанализировать безопасность и экологичность производства;
) экономически обосновать принятое решение.
Новизна работы состоит в предложении нового варианта реакторного узла
коксования, в котором установлен циклон для очистки газов коксования от
коксовой мелочи.
Практическая значимость состоит в увеличении производительности установки
по дистиллятам и газам коксования на 5,26% и по коксу на 5,7 %.
Основные
результаты работы докладывались и обсуждались на 47-ой межвузовской
научно-практической конференции (г. Волгоград, 2010 г.), II
Всероссийской научной конференции с международным участием «Научное творчество XXI
века» (г. Красноярск, 2010 г.) и на VI-ой межрегиональная научно-практическая
конференции «Взаимодействие научно-исследовательских подразделений промышленных
предприятий и вузов по повышению эффективности управления и производства
<#"554337.files/image001.gif">
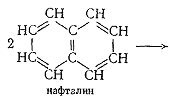
Конденсированные ароматические соединения, находясь в зоне высоких
температур, продолжают уплотняться, и таким образом появляются ещё более
высокомолекулярные соединения, составляющие смолы, асфальтены и наконец,
карбоиды (кокс).
Основными реакциями, влияющими на скорость процесса считаются реакции
разложения и конденсации нативных и вторичных асфальтенов [32]:
асфальтены кокс + легкие продукты
Таким образом, процесс образования кокса является цепью последовательно
протекающих реакций. Конечный продукт - кокс (карбоиды) - получается не сразу,
а через ряд промежуточных соединений. Такими промежуточными соединениями и
являются продукты конденсации и полимеризации, смолы и асфальтены [33].
Схематически это можно изобразить следующим образом:
углеводороды смолы асфальтены кокс
Наиболее полно отражает образование кокса схема на рисунке 2.1, из
которой видно, что лимитирующей реакцией является реакция коксования
асфальтенов вторичного происхождения.
Рисунок 2.1 Схема образования кокса
2.2 Термодинамический анализ процесса
В качестве
рассматриваемой реакции выбираем реакцию конденсации бензола:
Исходные
данные для термодинамических расчетов берем по справочной литературе [28] и
определим стандартные термодинамические данные: теплоемкость, энтальпия,
энтропия и поправочные коэффициенты к теплоемкости для всех реагентов и
продуктов реакции. Эти данные представлены в таблице 2.2.
Таблица
2.2 - Исходные данные для термодинамических расчетов [34]
Вещество
,
кДж/моль
,
Дж/моль·К
,
Дж/моль
|
|
|
|
|
|
|
|
|
а
|
b·103
|
c·106
|
c’·10-5
|
49,03173,26135,1459,50255,01--
|
|
|
|
|
|
|
|
100,5205,85197,07197,07---
|
|
|
|
|
|
|
|
0130,5228,8327,283,26-0,50
|
|
|
|
|
|
|
|
Проведем расчет термодинамических функций:
Определим тепловой эффект реакции при стандартных условиях по формуле
вытекающей из закона Гесса:
,
где
- теплота образования химического вещества из
элементов его составляющих;
,
- стехиометрические коэффициенты в уравнении реакции.
кДж/моль
Определим
тепловой эффект реакции для интервала температур от 573 К до 873 К по формуле,
полученной из уравнения Кирхгофа
и
изменения зависимости теплоемкости от температуры:
,
где
- разность сумм соответствующих коэффициентов в
продуктов реакции и исходных реагентов с учетом их
стехиометрических коэффициентов:
Энтальпию
реакции определяем по формуле:
Изменение
энтропии реакции при стандартных условиях определяем по формуле:
где
- энтропия химических веществ - участников реакции
при температуре 298К
Определим
изменение энтропии реакции в интервале температур от 523К до 773К
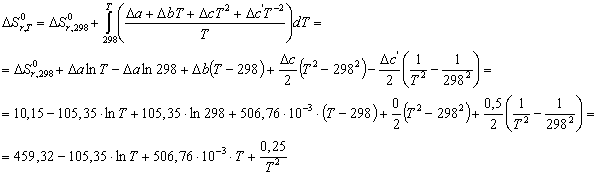
Изменение
энергии Гиббса определяется по формуле:
Из
уравнения изотермы Вант-Гоффа определяем константу равновесия:
Полученные
значения функций представлены в таблице 2.3. Графики функций представлены на
рисунке 2.2.
Таблица
2.3 - Термодинамические функции реакции конденсации
Т,К
,
кДж/моль
,
Дж/моль·К
кДж/моль
|
|
|
|
|
573
|
29,199
|
80,63
|
-17,002
|
35,54
|
623
|
39,076
|
97,15
|
-21,448
|
62,98
|
673
|
50,222
|
114,36
|
-26,742
|
119,3
|
723
|
62,635
|
132,15
|
-32,909
|
239,2
|
773
|
76,316
|
150,4
|
-39,943
|
501,77
|
823
|
91,264
|
169,17
|
-47,963
|
1111
|
873
|
107,480
|
188,3
|
-56,906
|
3856,9
|
Рисунок 2.2. Графики зависимостей изменения энтальпии, энтропии, энергии
Гиббса от температуры и график зависимости константы равновесия от температуры.
Так
как тепловой эффект реакции величина положительная, то есть
, то данная реакция является эндотермической и идет с
поглощением тепла. В интервале температур от 573К до 873К
, следовательно возможно самопроизвольное протекание
реакции в сторону продуктов реакции, с увеличением температуры эта вероятность
увеличивается. Для данной реакции характерно, что с увеличением температуры
происходит увеличение энтропии реакции. Так как реакция эндотермическая, то из
уравнения изобары Вант-Гоффа (p=const):
следует,
что при
и
с
увеличением температуры величина константы равновесия увеличивается, и
положение равновесия сдвигается в сторону продуктов реакции.
2.3 Механизм и кинетика исследуемого процесса
Механизм процесса коксование в настоящее время в полной мере не известен.
Существует несколько теорий механизма образования кокса. Большее
распространение получили [35]:
теория Ф.О. Райса о свободных радикалах;
теория о последовательно-параллельных реакциях [36];
теория З.И. Сюняева о сложных струкурных единицах (ССЕ).
Наиболее полно из них процесс коксования отражает теория З.И. Сюняева
[37].
Теория о ССЕ предложенная З.И. Сюнясвым является одной из первых моделей,
которую можно было использовать для моделирования студнеобразной фазы.
Представления типа «ядро-оболочка» о структурировании в жидкой фазе, позволили
разработать модель для описания студнеобразного состояния системы фактически
определив ступенчатость фазового перехода при термообработке нефтяных остатков.
Эта идея была весьма плодотворной и позволила объяснить ряд экспериментальных
фактов. Вместе с тем возникли очевидные трудности, связанные с механизмом и
закономерностями образования ССЕ. Наиболее уязвимым местом физико-химической
механики нефтяных дисперсных систем явилось то, что в ее рамках не было
обоснованного ответа на вопрос, какова природа сил, ответственных за
структурирование столь разнородных по химическому строению веществ.
Попытки найти причины агрегирования, так или иначе, связывались со
структурами, объединенными под названием асфальтены. Этот факт объясняется тем,
что коксообразование начинается только при достижении определенной концентрации
асфальтенов. Высокотемпературные процессы нефтепереработки, а именно процесс
карбонизации нефтяных систем непременно характеризуется необратимым ростом
твердой фазы, который в общепринятой трактовке, объясняется ростом содержания в
системе фракции асфальтенов.
Экспериментальные данные позволили весь процесс коксования условно
разделить на три этапа [38].
На первом этапе процесса коксования превалируют реакции распада, в
результате чего образуется большое количество дистиллятных фракций, часть
которых испаряется, а часть наиболее тяжёлых фракций остаётся в остатке.
Параллельно с идущими реакциями распада незначительно протекают реакции с
образованием промежуточных соединений, конденсации и реакции глубокого
уплотнения до кокса.
Второй этап реакций коксования характеризуется некоторыми качественными
отличиями от первого. Интенсивность реакций распада и газообразования здесь
примерно такая же, как и в первом этапе, но отмечается резкое снижение
содержания в газах непредельных углеводородов, а молекулярные массы всех
компонентов остатка непрерывно возрастают. На этом этапе возрастает роль
реакций циклизации. Реакции уплотнения на данном этапе также протекают
незначительно.
Третий этап реакций коксования характеризуется непрерывным ростом
содержания асфальтенов в остатке до предельного их количества (24 - 26 %) с
одновременным возрастанием содержания соединений нерастворимых в бензоле
(кокса). Содержание смол масел в остатке, а также молекулярные массы масел,
смол и асфальтенов непрерывно уменьшаются. Эти изменения завершаются
превращением жидкого остатка в твёрдый углеродистый остаток - кокс.
Разложение асфальтенов происходит гомогенно - величина поверхности
реакционной зоны не влияет на скорость реакции и выходы продуктов.
Коксование как первичных, так и вторичного происхождения асфальтенов,
идет по цепному механизму, который может быть описан следующей схемой [35]:
3
(A'.)xA. - неактивный радикал, свободная валентность которого
делокализована или экранирована алкильными и другими группами, или:
(А'.)х (А')2х (5)
где А - молекула асфальтенов; М - молекула относительно легких продуктов
разложения, выделяющихся в газовую фазу.
Схема описывает процесс цепной поликонденсации. Так как образующиеся
высокомолекулярные продукты поликонденсации могут вступать в реакции с
радикалами совершенно так же, как и асфальтены, продуктами реакции в основном
являются сшитые трехмерные полимеры - карбоиды. Несшитые макромолекулы
представляют собой экстрагируемые из кокса сероуглеродом вещества - карбены.
Выход
кокса зависит от ароматизованности асфальтенов - для нативных нефтяных он
составляет 50-60 %, а для более ароматизованных, выделенных из продуктов
деструктивного происхождения - 75-80%. Разложение одного из образцов нативных
асфальтенов проходило по реакции первого порядка с константой скорости:
с-1
Разложение
образца асфальтенов, выделенных из крекинг-остатка термического крекинга,
происходило по реакции полуторного порядка с константой скорости:
см3/2×моль-1/2.с-1
Различие
в кинетике разложения нефтяных нативных асфальтенов и асфальтенов вторичного
происхождения вызвано тем, что в первом случае цепи обрываются по реакции (2а),
а во втором - по реакции (4). При обрыве цепей по реакции (4) скорость
суммарной реакции описывается уравнением:
Считая,
что реакции (2а) и (4) идут с одинаковой энергией активации (так как они в
принципе одинаковы), получаем:
где
b2а и b4 - стерические коэффициенты; Е - энергия разрыва слабейшей связи в
молекуле асфальтенов (типа С6Н5СН2-R), ED ≈ 250 кДж .моль-1; Е - энергия
активации диффузии радикала из клетки, Е ≈ 20-40 кДж .моль-1.
Отношение
b2а/b4 можно рассматривать и как соотношение вероятностей образования при
присоединении радикала к молекуле асфальтенов активного радикала и неактивного.
При
разложении асфальтенов вторичного происхождения кинетическое уравнение имеет
следующий вид:

Полученное
выражение соответствует экспериментальному при Е2а ≈ 25 кДж•моль-1. Этот
порядок обычно соответствует обычному порядку реакции присоединения. B5≈1
- из-за клеточного эффекта, b2а≈10-6 - это подтверждает то, что
происходит присоединение сложного молекулярного радикала по П-связям
алкилированных аренов.
Значения
молекулярной массы карбенов показывают, что длина цепи при разложении
асфальтенов не менее 120-150 звеньев.
Исследование
кинетики образования кокса при разложении асфальтенов в растворах различных
растворителей показало, что кокс образуется только тогда, когда асфальтены
выделяются в отдельную фазу. При выделении асфальтенов из раствора происходит
их конденсация до кокса. Если же асфальтены молекулярно (или в виде малых
ассоциатов) диспергированы в растворителе, то кокс не образуется, что можно
объяснить гибелью радикала ведущего цепь на молекулах растворителя [31].
В
коксообразовании различают понятия «хорошие» либо «плохой» растворитель.
Найдено, что в плохом растворителе кинетика коксообразования при изменении
температуры сильно меняется. При низких температурах равно 350 0С выделение
асфальтенов в осадок идет быстрее чем разложение асфальтенов до кокса. Скорость
лимитируется скоростью реакции конденсации. Энергия активации высока
соответствует значениям энергии активации обычных реакций в поле конденсации.
Порядок реакции находится в интервале от 1 до 1,5.
При
повышении температуры растворяющая способность растворителя сильно понижается и
асфальтены выделяются в виде микрокапель второй фазы. В микрокаплях происходит
образование кокса, границы температурного перехода из одной области в другую
выражается свойствами растворителя и свойствами асфальтенов и различными для разных
случаев.
В
хороших растворителях асфальтены выделяются из раствора при его загустевании,
при этом образуется студень, где каждая молекула асфальтена соприкасается с
другой молекулой. Это способствует развитию цепной реакции без обрыва цепи на
молекулах растворителя, однако, при этом получается пористый кокс, повторяющий
структуру студня. В хороших растворителях имеется пороговая концентрация
асфальтенов, ниже которой коксообразование не идет. Она соответствует
концентрации образования студня, чем более ароматизован растворитель, тем выше
пороговая концентрация, обычно около 55-70%.
Важно
отметить, что скорость образования кокса соответствует скорости образования
асфальтенов. Легкие продукты уходят в газовую фазу и асфальтенов не образуют,
то есть не влияют на процесс косообразования. Поэтому при низком давлении
отгонка легких фракций не снижает выход кокса из сырья. Выход кокса в этом
процессе тем выше, чем больше в сырье содержится асфальтенов или продуктов,
способных образовывать асфальтены [36].
В
настоящее время ученые, руководствуясь теорией Ф.Г. Унгера [37] о парамагнитных
структурах, пришли к пониманию того, что нефтяная ассоциативная комбинация (или
ССЕ) сферически-симметричной формы, представляющая собой студнеобразную
асфальтеновую фазу, состоит из ядра парамагнитных молекул (радикалов) с
большими потенциальными энергиями взаимодействия и оболочек различных
диамагнитных молекул, располагающихся от ядра к периферии в соответствии с
уменьшением их взаимных потенциалов. Вокруг парамагнитного ядра послойно
группируются ароматические, нафтеновые и парафиновые углеводороды.
Гетероатомные соединения как ароматического, так и неароматического рядов,
могут располагаться в различных слоях, начиная с первого. Структурный фазовый
переход происходит при достижении критической концентрации асфальтенов [38].
Затруднения ученых возникли с определением управляющего параметра в подобной
самоорганизующейся системе.
Группа
уфимских ученых попыталось решить эту проблему, разработав теорию фрактального
роста. Суть теории может быть представлена следующим образом. Модель
фрактального роста предполагает наличие некоторого образующего систему элемента
- частицы и наличия взаимодействия ее с аналогичными. Причем не имеет значения
природа частиц, в результате чего она образуется, каков ее размер, а
учитывается лишь дальнейшее поведение частицы в процессе - диффузия, агрегация,
то есть детали процесса.
Применительно
к образованию асфальтенов такими образующими элементами явились ароматические
молекулы с нечетным числом колец и некомпенсированным спином одного из внешних
электронов атома, например, нафтантриловый радикал [38]. Такой выбор
согласуется с выводом Ф.Г. Унгера о решающей роли спин-спиновых взаимодействий
при образовании надмолекулярной структуры. Согласно анализу применимости
агрегационных моделей неупорядоченных систем к нефти и процессам в ней
проведенным В.В. Фарафоновым нижний предел применимости модели фрактального
роста может быть порядка размера атомных ядер, верхний же предел определяется
условиями конкретно поставленной задачи [35].
Было
показано, что фрактальные структуры, возникают как устойчивые образования,
когда требуется осуществить захват пространства малым числом элементов, в роли
которых выступают парамагнитные соединения.
Пока
нельзя быть уверенным в том, что кокс образуется таким образом, так как до сих
пор нет классификации парамагнитной органики.
2.4 Влияние параметров технологического режима на выход продукта
В предыдущем разделе было доказано, что качество сырья влияет на выходы
продуктов, их качество и ход технологического процесса. В зависимости от
свойств исходного сырья подбираются все технологические параметры процесса
коксования - температура, давление, коэффициент рециркуляции.
Выход кокса тем выше, чем больше в сырье асфальтенов и
выше его ароматизованность. Для сырья данной химической природы выход кокса
увеличивается с увеличением глубины отбора дистиллятов. Одновременно растет
выход газа и бензина. Определяется это тем, что доля сырья, подвергающегося
глубокому распаду в жидкой фазе, с утяжелением фракционного состава растет; при
этом снижается доля сырья, переходящего в газовую фазу и подвергающегося
крекингу в очень малой степени.
Повышение ароматизованности сырья существенно влияет
на качество образующегося кокса. Чем выше ароматизованность жидкого продукта в
коксовой камере, тем выше пороговая концентрация асфальтенов, при которой
раствор застудневает и начинается коксообразование, и меньше газовыделение при
поликонденсации асфальтенов (благодаря большей ароматизованности последних); в
результате пористость кокса уменьшается. При меньшем газовыделении высота
вспененного слоя в коксовой камере снижается, и предельная высота, до которой
может быть заполнена коксом камера без опасности переброса в колонну,
повышается. Содержание в сырье асфальтенов и асфальтенообразующих компонентов
определяет время начала коксообразования. Чем меньше асфальтенов в сырье и ниже
скорость их накопления при крекинге, тем больше период до начала
коксообразования.
Для производства электродного кокса наиболее предпочтительны в качестве
сырья дистиллятные крекинг-остатки, а также тяжелые ароматизированные жидкие
продукты различных деструктивных процессов - каталитического и термического
крекинга, пиролиза
Дополнительными источниками сырья могут быть экстракты
масляного производства особенно при переработке малосернистых нефтей. В коксе,
полученном из остаточного сырья, содержится много гетероатомных элементов,
особенно серы, так как в асфальтенах и смолах нефти концентрируются сера-,
азот- и кислород- и металлорганические соединения.
Большие затруднения возникают при коксовании
высокопарафинистых остатков нефти. Алканы очень плохо растворяют асфальтены,
поэтому при нагреве сырья в печи с повышением температуры змеевик быстро
закоксовывается. Кроме того, в условиях коксования алканы подвергаются только
эндотермичным реакциям крекинга, и эндотермичность суммарного процесса с
увеличением концентрации в сырье алканов возрастает. Асфальтены
высокопарафинистых остатков также относительно малоароматизованы, при их
разложении выделяется много газообразных продуктов, что увеличивает высоту
вспененного слоя в камере; образуется высокопористый кокс.
Поэтому при работе на высокопарафинистом сырье
необходимы специальные меры, обеспечивающие достаточно длительную работу
змеевика печи: повышенная кратность циркуляции тяжелых газойлевых фракций
коксования; повышенный расход турбулизатора в печном змеевике. Рециркуляция
тяжелых ароматизованных фракций коксования повышает ароматизованность сырья,
поступающего в печь. Турбулизатор (водяной пар) препятствует осаждению
асфальтенов, выделяющихся из раствора, на стенки печных труб.
Для уменьшения вспенивания в коксовой камере применяют введение в сырье
специальных добавок. Кремнийорганические жидкости, добавляемые в небольших
(менее 0,001 %) количествах, эффективно снижают высоту вспененного слоя в
коксовой камере.
Одним из важнейших условий получения высококачественного электродного
кокса является правильный подбор технологического режима коксования по
температурному интервалу в зависимости от состава сырья. От правильного подбора
и регулирования технологического режима во многом зависит продолжительность
межремонтного пробега установки.
При прочих равных условиях, чем выше температура нагрева сырья, тем выше
качество кокса, ниже содержание летучих веществ в коксе, выше его механическая
прочность и, как правило, выше выход электродных фракций кокса. Однако,
повышение температуры нагрева сырья в реакционном змеевике печи приводит к
более интенсивному закоксовыванию труб печи. Таким образом, возможные пределы
изменения температуры коксования ограничиваются, с одной стороны, условиями
получения качественного кокса, а с другой - длительностью работы реакционного
змеевика печи.
Поэтому, каждому виду сырья подбирается оптимальная температура коксования,
которой следует считать ту область температур, при которой достигается
получение качественного кокса, с одной стороны, и минимальная степень
коксования печных труб и обеспечение длительности межремонтного пробега
установки, с другой стороны.
Из других технологических показателей, влияющих на выход кокса и его
качество, следует считать величину давления, при котором протекает
технологический процесс. Повышение давления в системе приводит к увеличению
выходов кокса, газа, бензина, легкого газойля и к уменьшению выхода тяжелого
газойля.
При повышении давления увеличение выхода кокса обуславливается
вовлечением в процессы коксования тяжелых газойлевых фракций, т.к. при этих
условиях переход их в газовую фазу и удаление из зоны реакции затрудняются. С
другой стороны, данный фактор препятствует удалению из зоны реакций легких
углеводородов, снижает испарение тяжелых промежуточных продуктов (смол
вторичного происхождения), находящихся в порах коксовых частиц, которые и
являются теми летучими веществами, которые ухудшают качество кокса, снижают его
прочность.
Кроме того, высокое давление в системе, а значит и в трубах реакционного
змеевика, способствует более быстрому коксованию труб печи и с этой точки
зрения повышение давления в реакционной зоне нежелательно.
На степень термического разложения сырья в реакторе кроме температуры,
природы сырья большое влияние оказывает время пребывания его в зоне высоких
температур. Жидкая часть сырья претерпевает сложные изменения, прежде чем
окончательно превратится в кокс. Недостаточное время пребывания сырья в зоне
реакции приводит к образованию продуктов с консистенцией, промежуточной между
битумообразной массой и коксом.
Учитывая специфику и природу преобразования сырья в кокс, установлено,
что время коксования должно составлять не менее 24-х часов, в исключительных
случаях время коксования может составлять не менее 12-ти часов, или более 24-х
часов в зависимости от сырья.
Коэффициент рециркуляции Кр характеризует собой количество рециркулята
(тяжелых газойлевых фракций) во вторичном сырье и регулируется изменением
температуры низа колонны. Также на коэффициент рециркуляции оказывает влияние
количество подаваемого в шлема реакторов кулинга. Коэффициент рециркуляции
колеблется в пределах от 1,1 до 2,0 и зависит от давления процесса,
температуры, времени контакта паров с жидкостью.
При выборе «Кр» руководствуются несколькими соображениями:
производительность установки;
улучшение условий работы реакционных змеевиков печи при переработке очень
тяжелых или нетехнологических (высокопарафинистых) остатков нефти;
подбор тепловых эффектов коксования и оптимальной температуры нагрева в
реакционном змеевике печи;
время заполнения коксовых камер.
В ряде случаев в выборе «Кр» исходят и из потребностей в продуктах
коксования.
Вовлечение в сырье коксования более высокоароматизированных, термически
устойчивых углеводородов позволяет несколько снизить температуру нагрева сырья
на выходе из печи без ухудшения качества кокса. С повышением Кр несколько
увеличивается выход кокса от исходного сырья. Одновременно возрастает выход
легкого газойля, а количество тяжелого газойля уменьшается. Однако, увеличение
«Кр» приводит к снижению производительности установки по исходному сырью,
увеличению времени заполнения реактора коксом. Правильный подбор «Кр» и температуры
нагрева вторичного сырья позволяют увеличить межремонтный пробег установки.
Периодичность процесса по заполнению реакционных камер коксом
сопровождается изменением давления и температуры в камерах. При снижении
давления в реакторе возрастает линейная скорость паров, что вызывает
вспенивание жидкой части загрузки в реакторе, повышает вероятность переброса
пены в низ ректификационной колонны. Чтобы избежать резкого колебания давления
в моменты переключения реакторов в период прогрева, данные операции необходимо
выполнять плавно и с большой осторожностью.
Повышение давления в начале подключения объясняется тем, что первые
порции сырья с поступлением в реактор конденсируется, а с увеличением расхода
горячего потока скопившийся конденсат начинает бурно испаряться. Последующее
снижение давления обуславливается снижением температуры в реакторе ниже
оптимальной. После полного испарения и удаления конденсата объем паров резко
уменьшается. Оптимальное (рабочее) давление в реакторе достигается лишь через
30 - 35 минут после подключения его на поток.
Медленное переключение реакторов способствует постепенному испарению
конденсата и более плавному колебанию давления в системе.
Вспенивание сырья и перебросы пены довольно часто наблюдаются в случаях
низкой температуры на выходе из печи, так как в этом случае возрастают
устойчивость пены и высота вспученной массы над коксом.
Возможны случаи переброса пены и после отключения реактора. Это
объясняется тем, что после вынужденного снижения скорости паров вспененная
масса оседает и соприкасается с поверхностью более горячего кокса (разница
температур в слое кокса и пены 40 - 50оС).
В результате повторного испарения жидкости и возможен переброс пены. Для
предотвращения оседания пены и переброса в реактор сразу же подается водяной
пар.
3.
ТЕХНОЛОГИЧЕСКАЯ ЧАСТЬ
3.1 Требования способа к сырью, вспомогательным
веществам и материалам, продуктам процесса замедленного коксования
Таблица 3.1 -
Характеристика сырья, вспомогательных веществ и материалов, изготовляемой
продукции
№ п/п
|
Наименование сырья, материалов, реагентов, катализаторов,
полуфабрикатов, изготовляемой продукции
|
Номер государственного или отраслевого стандарта,
технических условий, стандарта предприятия
|
Показатели качества, обязательные для проверки
|
Норма по ГОСТ, ОСТ, СТП, ТУ (заполняется при необходимости)
|
Область применения изготовляемой продукции
|
1
|
2
|
3
|
4
|
5
|
6
|
1
|
Сырье коксования, в качестве которого может использоваться
смесь из 2х и более нижеперечисленных компонентов: - крекинг-остаток -
экстракт «Дуосол» - асфальт деасфальтизации - гудрон уст. АВТ
|
СТП 019902-401065-94
|
1. Плотность при 20 оС, г/см3 2. Коксуемость, %, не менее
3. Содержание серы, % масс. 4. Концентрация хлористых солей, мг/дм3, не
более 5. Содержание воды, % об.
|
не нормируется, определение обязательно 9,0 не
нормируется 20 следы
|
Сырье установки
|
2
|
Компоненты сырья:
|
|
|
|
|
2.1
|
Экстракты селективной очистки масел
|
СТП 019902-401031-93
|
1. Массовая доля растворителей, %, не более - селекто 2.
Содержание воды
|
Экстракт «Дуосол» 0,08 следы
|
|
|
|
|
3. Температура вспышки, определяемая в закрытом тигле, оС,
не ниже
|
230
|
|
2.2
|
Гудроны с установок ЭЛОУ-АВТ
|
СТП ПР 006-00148599-2004
|
1. Вязкость условная при 100 оС, градусы ВУ, не менее 2.
Температура вспышки, определяемая в открытом тигле, оС, не ниже
|
I вид - 250
|
II вид 11,5 250
|
III вид 11,5 250
|
IV вид 11,5 250
|
|
2.3
|
Крекинг-остаток установок ТК-8, 9
|
СТП 019902-401016-94
|
1. Концентрация хлористых солей, мг/дм3, не более 2.
Коксуемость, %, не менее 3. Содержание воды, %масс, не более Примечание: 1).
При вовлечении в переработку вакуумных погонов АВТ норма по коксуемости - не
ниже 7,0 %
|
10,0 9,0 следы
|
|
2.4
|
Асфальт
|
СТП 019902-401027-93
|
1. Температура вспышки, определяемая в закрытом тигле, оС
|
240
|
|
|
|
|
2. Температура размягчения по кольцу и шару, оС, не ниже
|
25
|
|
3
|
Продукты
|
|
|
|
|
3.1
|
Газ коксования
|
СТП 019902-401083-2001
|
1.Углеводородный состав, в т.ч. С5 и выше, %вес, не более
2. Массовая доля сероводорода, %
|
10 не нормируется, определение обязательно
|
Является сырьем блока 150 уст. № 2, а также используется в
качестве топлива для технологических печей
|
3.2
|
Бензин коксования
|
СТП ПР 010-00148599-2004
|
1. Фракционный состав, оС:
|
комп-т бензинов
|
сырье уст. 2
|
товарный продукт
|
Используется в качестве компонента при ком-
|
|
|
|
- температура начала перегонки, не ниже - 10 %
перегоняется при температуре, не выше - конец кипения, не выше 2. Давление
насыщенных паров, кПа
|
35 (с 01.10. до 01.04. -не норм.) 105 200 66,7 (500)
|
не норм, опр-ние обязательно - « - 200 -
|
35 - 215 79,9 (600)
|
паундировании товарных автомобильных бензинов, сырья блока
стабилизации вторичных бензинов уст. № 2 или товарного продукта
|
|
|
|
3. Испытание на медной пластинке 4. Массовая доля серы, %
(ррm), не более
|
выдерживает не норм, опр-ние обязательно
|
- не норм, опр-ние обязательно
|
выдерживает или 1 класс 0,7 (7000)
|
|
3.3
|
Керосин вторичных процессов (легкий газойль)
|
СТП 019902-401068-2002
|
1. Фракционный состав, оС: - 10 % перегоняется при
температуре, не ниже - 90 % перегоняется при температуре, не выше
|
160 360
|
Используется как компонент печного топлива, судового,
нефтяного топлива (топочных мазутов)
|
|
|
|
2. Температура вспышки, определяемая в закрытом тигле, оС,
не ниже для печного топлива для судового топлива 3. Коксуемость 10 %-ного
остатка, %, не более
|
45 62 0,35
|
|
3.4
|
Газойль замедленного коксования
|
СТП 019902-401069-94
|
1. Плотность при 20 оС, г/см3 2. Коксуемость, %
|
не нормируется не нормируется
|
Используется в качестве мазута, котельного
|
|
|
|
3. Температура вспышки, оС, не ниже - в закрытом тигле - в
открытом тигле Примечание: Температура вспышки определяется при использовании
газойля в качестве компонента нефтяного топлива
|
I, IV кв. II, III кв. (зимой) (летом)
50 - 65 90
|
топлива, сырья установки термического крекинга ТК-8, 9
|
3.5
|
Кокс электродный для алюминиевой промышленности
|
ТУ 38. 301-29-88-97
|
1. Массовая доля общей влаги, %, не более 2. Массовая доля
летучих веществ, %, не более 3. Зольность, %, не более 4. Массовая доля серы,
%, не более 5. Массовая доля кокса с размерами кусков, %, - менее 8 мм, не
более - более 8 мм, не менее
|
КЗ суммарный 3,0* 11,0 0,6 1,8 - 45
|
КЗ (0-25) 3,0* 12,0 0,6 1,8 - 15
|
Крупнокусковой 3,0* 9,5 0,6 1,8 10 -
|
Используется в алюминиевой промышленности и других
отраслях народного хозяйства
|
|
|
|
6. Содержание кусков размером более 250 мм Спекаемость Рога
|
отсутствие не нормируется, определение обязательно
|
- -
|
|
|
|
|
Примечание: * Массовая доля общей влаги свыше 3 % не
является браковочным признаком и учитывается при расчете с потребителем. 1.
При поставке кокса электродного для алюминиевой промышленности марка КЗ (0 -
25) АО «Завод Сланцы» расчет массы кокса производится на сухое вещество.
|
|
3.6
|
Кокс нефтяной малосернистый КЗА, первый сорт
|
ГОСТ 22898-78
|
1. Массовая доля общей влаги, %, не более 2. Массовая доля
летучих веществ, %, не более 3. Зольность, %, не более 4. Массовая доля серы,
%, не более 5. Массовая доля мелочи, %, не более: - куски размером меньше 8
мм 6. Действительная плотность после прокаливания при 1300 °С в течение 5 ч,
г/см3
|
3,0 9,0 0,6 1,5 10,0 2,08 - 2,13
|
|
|
|
|
7. Массовая доля, % не более: - кремния - железа - ванадия
Примечание: 1. Допускается массовая доля общей влаги до 10,0 %
|
0,08 0,08 0,015
|
|
3.7
|
Кокс нефтяной непрокаленный мелкий (с размером
|
ТУ 0258-093-0151806-94
|
1. Массовая доля общей влаги, %, не более
|
3,0
|
Используется в абразивной промышленности и
|
|
кусков 0 - 8 мм)
|
|
2. Массовая доля летучих веществ, %, не более 3. Зольность,
%, не более 4. Массовая доля серы, %, не более
|
11,5 0,8 1,8
|
других отраслях народного хозяйства
|
3.8
|
Мелочь коксовая из отстойников
|
СТП 019902-401075-97
|
1. Массовая доля общей влаги, % 2. Массовая доля летучих
веществ, %, не более 3. Зольность, %, не менее
|
не нормируется, определение обязательно 15,0 0,8
|
Получается при очистке отстойников, используется для
коммунальных нужд.
|
|
|
|
4. Массовая доля серы, %, не более
|
1,8
|
|
|
|
|
|
|
|
|
|
|
|
|
|
|
|
3.2 Выбор конструкции реактора коксования
Реакторы являются основными аппаратами установок замедленного коксования.
В них происходит формирование и накопление нефтяного кокса - целевого продукта
процесса, и, следовательно, правильно сконструированный аппарат определяет
технико-экономические показатели работы установки в целом.
Основной аппарат для процесса замедленного коксования установки № 60 типа
21-10/7 коксо-битумного производства ООО «ЛУКОЙЛ-ВНП» представляет собой
вертикальный пустотелый адиабатический аппарат, который состоит из
цилиндрического корпуса, верхнего полушарового и нижнего конического днищ и
опоры. Аппарат имеет люки: верхний - для ввода гидрорезака и нижний - для
удаления кокса, а также несколько видов штуцеров, представленных в таблице 3.2.
Таблица 3.2 - Данные о штуцерах.
Обозн.
|
Наименование
|
Ду,мм
|
Ру, кгс/см2
|
А
|
Ввод сырья на коксование
|
200
|
40
|
Б
|
Вывод паров нефтепродуктов
|
350
|
40
|
В
|
Вывод паров при пропарке
|
400
|
40
|
Г
|
Люк для ввода гидрорезака
|
700
|
40
|
Д
|
Люк выгрузки кокса
|
1400
|
40
|
Е1-3
|
Ввод антипенной присадки
|
26/65
|
40
|
Ж
|
150
|
40
|
З1-47
|
Для поверхностных термопар
|
М33×2
|
-
|
И
|
Штуцер монтажный
|
-
|
-
|
При этом тяжелое жидкое сырье коксования подается через нижний аксиальный
штуцер, а пары нефтепродуктов после проведения реакции выводятся через один из
верхних штуцеров.
Цикл работы реактора замедленного коксования включает ряд
последовательных стадий: опрессовку водяным паром, разогрев горячими парами
коксования, подключение реактора на поток, коксование, томление, охлаждение
водяным паром и водой, гидровыгрузку кокса.
Корпус реактора выполнен из двухслойной стали 16ГС+08Х13 с толщиной
плакирующего слоя 6 мм, при этом 3 мм этого слоя принято на коррозию. Снаружи
камера покрыта слоем изоляции толщиной 250 мм. Диаметр аппарата составляет 5500
мм, высота - 27900 мм. Максимальные рабочие условия коксовой камеры
представлены в таблице 3.3.
Таблица 3.3 - Рабочие условия (максимальные).
№ п/п
|
Наименования
|
Реакция
|
1
|
Давление кгс/см2
|
вверху камеры
|
Технологическое
|
4
|
|
|
|
Расчетное
|
6
|
|
|
|
Пробное
|
12,5
|
|
|
внизу камеры
|
Технологическое
|
6
|
|
|
|
Расчетное
|
8
|
|
|
|
Пробное
|
15,3
|
2
|
Температура среды
|
t° = 450°С
|
3
|
Температура расчетная
|
стенки корпуса - 475оС
|
|
|
стенки вблизи места ввода сырья - 510оС
|
4
|
Среда
|
Гидравлическая смола - тяжелый газойль Sн20=1156 с содержанием S=0,34%, пары нефтепродукта, кокс,
вода, водяной пар. (Среда взрывоопасная, токсичная)
|
5
|
Объем
|
V = 510000 л
|
В реакторе для проведения замедленного коксования выделяют следующие
основные узлы: верхнее полушаровое днище, корпус, нижнее коническое днище,
опора, а также - штуцеры, представленные в таблице 3.2.
Таким образом, назначение реактора замедленного коксования состоит в
обеспечении оптимальных условий для протекания реакции и получении наибольшего
выхода светлых дистиллятов и кокса высокого качества. В результате анализа,
представленного в таблице 3.3, было выявлено, что конструкция реактора
замедленного коксования полностью удовлетворяет требованиям нового способа, а
именно очистки с помощью циклона парогазовых продуктов коксования от коксовой
мелочи.
Таблица 3.3 - Анализ функций элементов основного аппарата.
Элемент
|
Функция
|
Результаты функционирования
|
|
|
положительные
|
отрицательные
|
1
|
2
|
3
|
4
|
1. Корпус
|
Несет нагрузку от элементов аппарата
|
Несет нагрузку от элементов аппарата
|
_
|
|
Создает основное пространство для проведения реакций с
получением кокса
|
Создает основное пространство для проведения реакций с
получением кокса
|
Металлоемкость конструкции
|
|
Изоляция сырьевой смеси от окружающей среды
|
Изоляция сырьевой смеси от окружающей среды
|
Возможны потери тепла в окружающую среду
|
2. Верхнее полушаровое днище
|
Обеспечивает равномерный вынос коксовых газов из реактора
|
Конструкция проста в изготовлении
|
Возможна разгерметизация
|
3. Нижнее коническое днище
|
Благодаря форме расходящегося конуса увеличивается
поверхность пропариваемого коксового пирога и лучше удаляются жидкие и
газообразные продукты
|
Конструкция проста в изготовлении
|
Возможна разгерметизация
|
4. Опора
|
Закрепляет реактор в вертикальном положении
|
Способствует гашению колебаний реактора.
|
Возможны трещины из-за многократных перепадов температур
|
5. Нижний штуцер
|
Соединение трубопровода с реактором, ввод вязкой жидкой
сырьевой смеси в реактор и изоляция от окружающей среды
|
Ввод сырьевой смеси в реактор и изоляция от окружающей
среды
|
Возможны потери тепла в окружающую среду и разгерметизация
|
|
Подводит острый и перегретый пар
|
Позволяет подогреть реактор перед пуском и охладить и
пропарить перед выгрузкой кокса
|
Возможна разгерметизация
|
|
Подводит охлаждающую воду
|
|
|
|
Вывод паров коксования при пропарке реактора
|
Позволяет вывести пары коксования после пропарки
|
|
|
Вывод водяного конденсата
|
Позволяет опрессовать реактор
|
_
|
6.Верхний штуцер для вывода паров нефтепродуктов
|
Соединение трубопровода с реактором и вывод паров нефтепродуктов
|
Обеспечивает вывод паров нефтепродуктов из реактора
|
Возможна разгерметизация
|
|
Изоляция паров нефтепродуктов от внешней среды
|
Изоляция паров нефтепродуктов от внешней среды
|
|
7. Штуцеры для поверхностных термопар
|
Измерение температуры по всему объему реактора
|
Возможность регулирования процесса по показаниям
температуры процесса
|
Один штуцер позволяет контролировать температуру только по
высоте одной линии
|
8. Штуцер для ввода антипенной присадки
|
Вводит антипенную присадку
|
Снижение пенного слоя в реакторе, т.е. позволяет
увеличивать полезный объем аппарата
|
_
|
9. Штуцер монтажный
|
Предотвращает колебания реактора
|
Способствует гашению колебаний реактора.
|
Возможны трещины из-за многократных перепадов температур
|
10. Люк для выгрузки кокса
|
Необходим для выгрузки кокса из коксовой камеры
|
Вывод целевого продукта из реактора
|
Возможна разгерметизация из-за периодического прикручивания
и откручивания люка, использование ручного труда
|
11. Штуцер для вывода паров при пропарке
|
Соединение трубопровода с реактором и вывод паров пропарки
в емкости утилизации
|
Обеспечивает вывод паров нефтепродуктов из реактора
|
Возможна разгерметизация
|
|
Изоляция паров пропарки от внешней среды
|
Улучшение экологических показателей установки
|
|
12. Люк для ввода гидрорезака
|
Обеспечивает ввод гидрорезака
|
Возможность быстрого гидроудаления кокса
|
Возможна разгерметизация из-за периодического прикручивания
и откручивания люка, использование ручного труда
|
3.3 Построение функциональной схемы процесса
В структуре установки замедленного коксования можно выделить 3 подсистемы
(стадии):
- стадия подготовки сырья.
- стадия химического превращения,
- стадия выделения и охлаждения дистиллятов и газа коксования.
- стадия транспортировки и выделения кокса.
Таким образом, функциональная схема состоит из 4 подсистем, соединенных
последовательными связями. Эти стадии связаны между собой и внешней средой
посредством трубопроводов, управляющих воздействий, теплообмена через
поверхности аппаратов и трубопроводов.
Потоки: - материальные потоки
энергетические потоки
информационные потоки
Потоки на уровне «цех»:
I -
исх. сырье
II -
смесь газа, бензина, вод. пара
III -
керосин
IV -
газойль коксования
V -
бензин
VI -
керосин
VII -
газойль коксования
VIII -
оборотная вода
IX -
газ коксования
X -
дымовые газы
XI -
острый пар
XII -
перегретый пар
XIII -
кулинг (тяж. газойль)
XIV -
вторичное сырье
XV -
газ на сжигание из реакторов
XVI -
вода в систему гидрорезки
XVII -
кокс
Функциональная схема представлена на рисунке 3.1. Тип функционирования
системы: непрерывно работающая технологическая схема. В данной схеме
реализуются основные принципы функционирования ХТС.
Для того чтобы процесс шел быстрее используется:
. непрерывная организация процесса.
. постоянство входящих и выходящих потоков, постоянство связей между подсистемами.
Для того чтобы сырье расходовалось по целевому назначению, используется:
. непрерывность процесса, постоянство параметров.
. отсутствуют механические потери
Для минимального расходования энергии используется:
. Регенерация тепла (тепло потока тяжелого газойля используется для
нагревания исходной сырьевой смеси).
. Получаемый газ коксования используется как топливо в печах.
. Автоматизация процесса.
Рисунок 3.1 Функциональная схема установки замедленного коксования
Все связи данной схемы можно разделить на внешние и внутренние, а внешние
на постоянные и периодические. К внешним можно отнести сырьевой поток смеси
тяжелых остатков из резервуарного парка № 47, а также потоки теплоносителей,
воздуха, топливный газ из топливной сети предприятия.
Кроме того, это потоки, выходящие после проведения процесса: кокс, газ
коксования, бензин, керосин, газойль коксования, дымовые газы печей установки.
К внутренним можно отнести все потоки, перемещаемые между стадиями. Это,
прежде всего, сырьевой поток, потоки дистиллятов, поток коксовых газов,
информационные связи.
Основные функции, выполняемые каждой подсистемой (стадией) и их
результаты функционирования представлены в таблице 3.4.
Таблица 3.4 - Анализ функций подсистем на уровне “установка”.
Подсистема
|
Функция
|
Результаты функционирования
|
|
|
положительные
|
отрицательные
|
1
|
2
|
3
|
4
|
Подготовка сырья
|
Нагрев первичной сырьевой смеси до температуры 380 оС,
получение вторичного сырья и его нагрев до до температуры не выше 510 оС
|
Достигается необходимая температура для протекания процесса
улучшается свойства сырья для получения кокса
|
Большие капитальные затраты, большие энергетические
затраты, сложность оборудования
|
Химическое превращение
|
Проведение химического превращения
|
Превращение вторичного сырья в кокс
|
Сложность регулирования свойств получаемого кокса,
загрязнение воды
|
Выделение и охлаждение дистиллятов и газа коксования
|
Разделение и выделение газа коксования, бензина, керосина,
газойля коксования
|
Получение ценных продуктов - дистиллятов и газа,
использование газа коксования как топлива для стадии подготовки сырья
|
-
|
Транспортировка и выделение кокса
|
Разделение кокса и воды, разделение кокса по размерам
|
Получение товарного продукта
|
Большие капитальные затраты, большие энергетические
затраты, загрязнение атмосферы коксовой пылью
|
По функциональной схеме на уровне цеха и установки можно сделать вывод,
что характер связей и качество функционирования подсистем соответствует новому
способу. Подсистема, которая обеспечивает главную функцию - стадия химического
превращения.
3.4 Разработка базовой технологической схемы
производства кокса и ее описание
С учетом предложенного способа модернизации реакторного узла новая
технологическая схема установки замедленного коксования.
Сырье коксования - смесь тяжелых нефтяных остатков, подается на установку
с температурой не выше 90 - 95оС, из резервуарного парка установки № 56 насосом
Н-1 (Н-1р, Н-1/1) и прокачивается последовательно через три строенных
теплообменника Т-1/1¸3, где нагревается за счет тепла основного циркуляционного орошения
колонны К-1 до температуры 140-200ºС, затем проходит через конвекционный
змеевик печи П-1 и с температурой до 330оС, позиция (поз.) 4 поступает в нижнюю
часть ректификационной колонны К-1 на первую и четвертую каскадные тарелки.
В колонне К-1 предварительно нагретое первичное сырье контактирует с
горячими парами коксования, поступающими в нижнюю часть колонны, под нижнюю
каскадную тарелку из циклона Ц-1 с температурой 410 - 430оС. Стекая вниз,
навстречу газообразным и парообразным продуктам коксования, сырье нагревается
до температуры 350 - 400оС.
В результате контакта первичного сырья с горячими парами коксования в
нижней части колонны К-1 происходит процесс массо- и теплообмена, в результате
которого легкие нефтяные фракции, содержащиеся в первичном сырье, испаряются и
через аккумулятор поступают в виде паров в верхнюю ректификационную часть
колонны, а тяжелые фракции, содержащиеся в парах коксования, наоборот,
конденсируются и поступают в виде жидкости (рисайкла) в нижнюю часть колонны,
образуя с тяжелыми фракциями первичного сырья смесь, называющуюся вторичным
сырьем.
Коэффициент рециркуляции регулируется подачей сырья на первую каскадную
тарелку, а также температурой низа колонны К-1.
Регулирование расхода сырья через первичный змеевик печи П-1 производится
регулятором с коррекцией по уровню в колонне К - 1 поз.3.
Вторичное сырье с низа колонны К-1 поступает на прием печного насоса Н-2
(Н-2а, 2р, 7р), который прокачивает его через реакционный змеевик печи П-1.
Температура вторичного сырья на выходе из реакционных змеевиков печи П-1
поддерживается в заданных пределах регуляторами поз. 8, клапаны которых
расположены на линиях подачи газа к горелкам печи.
Постоянство расходов продукта через реакционные змеевики печи П-1
поддерживается регуляторами расходов поз.40, клапаны которых установлены на
выкиде насосов Н-2 (Н-2р), Н-7р, Н-2а, c сигнализацией нижнего предела.
В случае уменьшения расходов через змеевики печи на мнемосхеме загораются
лампочки, и срабатывает звуковая сигнализация.
Топливом для печей служит топливный газ собственной выработки, топливный
газ из заводской сети или природный газ.
Для предотвращения коксообразования в реакционных змеевиках печи П-1 в
них, в течение всего цикла работы установки, подается турбулизатор.
В качестве турбулизатора используется водяной конденсат, циркулирующей в
системе через емкость Е-1.
Вторичное сырье, нагретое в печи П-1 до температуры 495 - 510 оС поз.8,
подается в коксовую камеру Р-1 (Р-2, Р-3).
В коксовой камере Р-1(Р-2, Р-3) в момент включения на поток и в течение
всего цикла коксования происходят процессы дополнительного испарения нефтяных
фракций из вторичного сырья и отложения твердых частиц кокса на стенках камеры.
При этом внутри коксового "пирога", образующегося внутри камеры во
время коксования, имеется отверстие неопределенной формы и конфигурации, через
которое в камеру продолжает поступать сырье, и отводятся пары коксования.
Образовавшийся в процессе коксообразования кокс аккумулируется в камере,
а пары нефтепродуктов по шлемовому трубопроводу направляются в циклон Ц-1, где
очищаются от коксовой мелочи, и далее идут в колонну К-1 под нижнюю тарелку.
Перед «постановкой» камеры на поток последняя прогревается до 100 - 110оС
и опрессовывается водяным паром в течение одного часа. Образующийся водяной
конденсат дренируется в яму-накопитель (систему вод гидрорезки), или в
канализацию.
Дальнейший разогрев камеры до 330-360оС производится продуктами
коксования, перепускаемыми частично из работающей коксовой камеры.
При достижении температуры низа прогреваемого реактора 330-360оС
дальнейший разогрев производится половиной потока сырья по технологической
схеме работы реактора в течение 2 часов.
После нагрева подготавливаемой камеры и заполнения коксом рабочей камеры
производится переключение камер. Поток сырья направляется в нагретую коксовую
камеру. Сконденсировавшиеся продукты прогрева из Е-30 откачиваются насосом
Н-1/1 в линию на смешение с сырьем коксования.
Заполнение коксовой камеры коксом ведется в течение 28 - 60 часов в
зависимости от коксуемости исходного сырья, качества получаемого кокса и
подключения реакторов.
В соответствии с графиком работы коксовой камеры продолжительность съема
крышек камеры при готовности ее к выгрузке составляет 2 часа, продолжительность
выгрузки кокса из камеры 4 - 12 часов, продолжительность установки крышек
камеры, опрессовка водяным паром ведется 2 - 4 часа.
Температура в камерах Р-1, Р-2, Р-3 измеряется и регистрируется приборами
поз. 7,26,28.
Переключение потока горячего вторичного сырья из одной камеры в другую
производится посредством задвижек.
Для контроля уровня в коксовых камерах и предотвращения переброса пены в
ректификационную колонну на коксовых камерах смонтированы релейные
радиоизотопные приборы взрывозащищенного исполнения РРПВЗ-1 на отметках 22 и 27
метров. По истечении 10-12 часов после загорания лампочки на отметке 27 метров
производят перевод потока сырья на другой, предварительно прогретый реактор.
В колонне К-1 пары коксования, отделившиеся от тяжелой рециркулирующей
фракции, через полуглухой аккумулятор проходят в верхнюю, ректификационную
часть колонны, где происходит их разделение на бензин, керосин (легкий газойль)
и газойль коксования (тяжелый газойль).
Уровень в аккумуляторе К-1 регулируется регулятором поз.12.
Температура в аккумуляторе колонны К-1 регулируется циркуляционным
орошением. Расход циркуляционного орошения, подаваемого в колонну К - 1 на 8-ю
тарелку, поддерживается регулятором поз. 20.
Из аккумулятора колонны К-1 газойль коксования перетекает в колонну К-3.
На перетоке смонтирован регулирующий клапан, который связан с уровнем в
аккумуляторе К-1 поз. 13
Уровень в колонне К-3 поддерживается регулятором поз. LRC - 29, клапан которого установлен
после ХВ-3/2 на трубопроводе откачки газойля коксования с установки.
газойль коксования из колонны К-3, по мере накопления, откачивается
насосом Н-7 (Н-7р) через холодильники ХВ-3/1, 5 секций ХВ-3/2, после которого с
температурой не выше 90 оС, поз. 37 выводится с установки.
С 17-й тарелки ректификационный колонны К-1 в отпарную колонну К-2
отводится фракция керосина (легкого газойля). Количество керосина, поступающего
в колонну К-2, регулируется регулятором поз. 20.
Температура вывода керосина в колонну К-2 контролируется прибором поз.22.
В колонны К-1, К-2 для отпарки легколетучих компонентов подается
перегретый водяной пар с температурой до 500оС.
Расход водяного пара поддерживается регулятором поз.5, клапан которого
установлен на выходе из пароперегревателя печи П-1.
Отпаренный керосин с низа К-2 откачивается с установки насосом Н-5 (Н-5р)
через три секции ХВ-3/2, ХВ-2 и две секции погружного холодильника ХВ-6.
Температура откачиваемого керосина не должна превышать 80 \оС поз.38.
Уровень в колонне К-2 регулируется регулятором поз. 17, клапан которого
установлен на линии между ХВ-2 и ХВ-6.
С верхней части колонны К-1 отводятся пары бензина, водяной пар, газ
коксования с температурой до 170 оС.
Охлаждение потока предусматривается в холодильнике-конденсаторе ХВ-1 и
кожухотрубчатых холодильниках Х-1, Х-1а с водяным охлаждением. Температура
верха К-1 регулируется регулятором поз. 14, клапан которого установлен на линии
подачи острого орошения в колонну К-1.
Газожидкостная смесь из холодильников Х-1, 1а, с температурой не более
45оС, поступает в газосепаратор Е-1, где происходит разделение на газ, бензин и
водяной конденсат.
Бензин из Е-1 насосом Н-3 (Н-3р) частично подается в виде острого
орошения в колонну К-1, а избыточное количество его откачивается с установки.
Защелачивание и ингибирование бензина осуществляется на установке № 57.
Уровень в Е-1 поддерживается регулятором поз. 32, клапан которого
установлен на линии откачки бензина с установки.
Водяной конденсат (технологический конденсат) из нижней части
газосепаратора Е-1 выводится в канализацию.
Уровень раздела фаз в Е-1 регулируется клапаном поз.34.
В соответствии с графиком работы коксовой камеры после заполнения ее
коксом производится пропарка кокса водяным паром 5 - 7 кгс/см2 в течение 8 - 9
часов с целью удаления из кокса легколетучих компонентов и охлаждения кокса.
В схеме установки предусмотрена утилизация продуктов отдува при пропарке
и охлаждении кокса в емкостях Е-4, Е-5 и откачки уровня их насосом Н-1/1 в
линию на смешение с сырьем коксования. После окончания пропарки кокса водяным
паром в коксовую камеру подают охлаждающую воду в течение 6 - 8 часов. Вода на
охлаждение кокса подаётся насосом который подключен к сети оборотного
водоснабжения. Образовавшиеся во время охлаждения пары конденсируются в
холодильниках Х-5 (1, 2), поступают в отстойник Е-5, и далее - в
промканализацию.
Водяные пары образуются до снижения температуры в камере до 100 оС. По
мере охлаждения кокса вода заполняет весь объем камеры. При наполнении реактора
подача воды уменьшается. Охлаждение производится до достижения температуры
верха реактора 90 оС, поз. 26,7,28 , после чего производится вскрытие верхнего
люка реактора, а затем дренирование в систему вод гидрорезки.
Освобождение камер от кокса производится с помощью гидрорезки. Вода на
гидрорезак подается по системе трубопроводов с электрозадвижками к бурильной
штанге. С помощью ротора и лебедки осуществляются вращение и опускание
устройства в камеру для образования центральной скважины в коксовом пироге
диаметром до 0,6 м.
При гидрорезке кокс из камер Р-1, Р-2, Р-3 вместе с буровой водой через
нижнюю горловину выгружается на рампу и поступает на заглубленную площадку
(яму-накопитель), внизу которой имеется фильтрующий слой и коллектор для сбора
воды после фильтрации. Объем ямы-накопителя - 2000 м3.
В яме-накопителе кокс вылеживается не менее 10 часов, где обезвоживается,
после чего загружается в бункер с колосниковой решеткой с размерами ячеек
250х250 мм.
Далее качающимся питателем суммарная масса подается на ленточный конвейер
и далее ленточными конвейерами транспортируется на склад бункерного типа.
Конвейер подает кокс на наклонный инерционный грохот установленный на верху
склада. Последним кокс разделяется на две фракции: 0 - 25 мм и 25 - 250 мм.
Раздельные фракции ленточными конвейерами загружаются в соответствующие бункеры
склада. Уровень заполнения контролируется визуально. После чего производится
отгрузка кокса в железнодорожные вагоны.
.5 Нормы технологического режима и метрологическое обеспечение
Таблица 3.5 -
Нормы технологического режима и метрологического обеспечения подготовки сырья и
стадии синтеза
№ п/п
|
Наименование стадий процесса, аппараты, показатели режима
|
Номер позиции прибора на схеме
|
Единица измерения
|
Допускаемые пределы технологических параметров
|
Требуемый класс точности измерительных приборов ГОСТ
8.401-80
|
Примечание
|
1
|
2
|
3
|
4
|
5
|
6
|
7
|
1
|
Печь П-1
|
|
|
|
|
|
1.2
|
Температура на выходе вторичного сырья из печи П-1, не выше
|
поз.6
|
оС
|
510
|
0,5
|
Показания, регистрация, регулирование
|
1.3
|
Расход первичного сырья в П-1, не менее
|
поз.1
|
м3/ч
|
20
|
1,0
|
показания, регистрация, регулирование
|
1.4
|
Расход вторичного сырья в П-1
|
поз.6.1
|
м3/ч
|
12 - 50
|
1,0
|
показания, регистрация, регулирование
|
2
|
Коксовые камеры Р-1, Р-2, Р-3
|
|
|
|
|
|
2.2
|
Температура верха коксовой камеры, не более
|
поз.7
|
оС
|
460
|
0,5
|
показания, регистрация
|
2.3
|
Температура низа коксовой камеры
|
поз.8
|
оС
|
475 - 510
|
0,5
|
показания, регистрация
|
3
|
Ректификационная колонна К- 1
|
|
|
|
|
|
3.2
|
Температура верха колонны, не выше
|
поз.14
|
оС
|
170
|
0,5
|
показания, регистрация, регулирование
|
3.3
|
Температура низа колонны, не выше
|
поз.36
|
оС
|
400
|
0,5
|
показания, регистрация
|
3.4
|
Температура вывода керосина в колонну К-2, не выше
|
поз.22
|
оС
|
250
|
0,5
|
показания, регистрация, регулирование
|
3.5
|
Температура вывода газойля коксования в колонну К-3, не
выше
|
поз.23
|
оС
|
340
|
0,5
|
показания, регистрация
|
4
|
Температура продуктов на выходе с установки
|
|
|
|
|
|
4.1
|
Температура бензина, не выше
|
поз.37
|
оС
|
45
|
0,5
|
показания, регистрация
|
5.2
|
Температура керосина, не выше
|
поз.37.1
|
оС
|
80
|
0,5
|
показания, регистрация
|
Температура газойля коксования, не выше
|
поз.38
|
оС
|
90
|
0,5
|
показания, регистрация
|
|
|
|
|
|
|
|
|
|
|
|
|
|
3.6 Описание КИП и А
Технологический процесс предусматривает применение дистанционного
управления технологическим процессом и операциями и автоматическую систему
противоаварийной защиты ПАЗ насосов и аппаратов. Система ПАЗ выдает световой и
звуковой сигналы при максимальных и минимальных аварийных параметрах процесса
на узлах. световой сигнал сообщает о состоянии (открыто, закрыто) отсечного
(блокировочного) клапана.
Предусмотрена
возможность дистанционного отключения насосов выключателями со щита в помещении
операторной.
Согласно ПБ 09-540-03, ПБ 09-563-03 печь П-1 оснащена системой
сигнализации и блокировок срабатывающих при следующих условиях: понижении
давления топливного газа и пилотного газа, а также жидкого топлива ниже
допустимого предела, повышении разрежения в топке печи выше допустимого
предела, снижении расхода первичного и вторичного сырья на входе в печь ниже
допустимого предела, снижении давления в змеевике на входе в печь ниже
допустимого предела, превышении температуры продукта на выходе из печи выше
допустимого предела, превышении температуры дымовых газов на «перевале» печи
выше допустимого предела, срабатывании сигнализаторов погасания пламени.
Предусматривается дистанционная подача пара к печи для создания паровой
завесы в случае аварии на установке.
также предусматривается сигнализация на следующие технологические
параметры: уровня в колонне К-1, уровня в емкостях Е-1, Е-5, Е-13, Е-14, Е-17,
Е-30, Е-31, давления жидкого топлива на установку, уровня кокса в реакторах
Р-1,2,3, давления инертного газа;
Существует сигнализации, срабатывающие при понижении давления оборотной
воды на установку, воздуха КИП на установку, давления острого пара на
установку, давления технологического воздуха.
Предусматривается противоаварийная остановка высоконапорного насоса
гидрорезки Н-20, если имеет место одно и более из состояний:
Система противоаварийной автоматической защиты снабжается предаварийной
сигнализацией параметров (световой и звуковой сигнал) и сигнализацией
срабатывания исполнительных органов.
Спецификация КИП и А установки замедленного коксования находится в
приложении 1.
3.7 Аналитический контроль процесса
Таблица 3.6 - Лабораторный контроль технологического процесса
замедленного коксования.
Наименование стадий процесса, анализируемый продукт
|
Место отбора пробы (место установки средства измерения)
|
Контролируемые показатели
|
Методы контроля (методика анализа, государственный или
отраслевой стандарт)
|
Норма
|
Частота контроля
|
1
|
2
|
3
|
4
|
5
|
6
|
1
|
Сырье УЗК
|
Н-1, резервуары
|
1 Коксуемость, %, не менее
|
ГОСТ 19932-99
|
11,0
|
по графику
|
|
|
215¼218 товарного
|
2 Содержание воды, % об.
|
ГОСТ 2477-65
|
следы
|
- « -
|
|
|
парка № 47
|
3 Содержание серы, % масс.
|
ГОСТ 1437-75
|
не нормируется
|
- « -
|
|
|
|
4 Плотность при 20 оС, г/см3
|
ГОСТ 3900-85
|
0,950 … 0,998
|
- « -
|
|
|
|
5 Концентрация хлористых солей, мг/дм3, не более
|
ГОСТ 21534-76
|
16,0
|
- « -
|
2
|
Фракция бензиновая - УЗК
|
Н-3
|
1 Фракционный состав: - температура начала перегонки, не
ниже
|
ГОСТ 2177-99 или ASTM D
86-90
|
Вид 1 не нормир., опр-ние обязательно
|
Вид 2 35
|
по графику
|
|
|
|
- 10 %, 50 %, 90 % перегоняется при температуре, оС, не
выше
|
|
не нормир., опр-ние обязательно
|
не нормир., опр-ние обязательно
|
|
|
|
|
- конец кипения, оС, не выше
|
|
200
|
180
|
|
|
|
|
2 Массовая доля серы, %
|
ГОСТ 19121-73 или ASTM D
4294-03
|
не нормируется, определение обязательно
|
по графику
|
|
|
|
3 Испытание на медной пластинке
|
ГОСТ 6321-92 или ASTM D
130-94
|
выдер-живает
|
не нормируется
|
по требованию
|
3
|
Газ углеводородный УЗК
|
Т-3
|
1 углеводородный состав, в т.ч. С5 и выше, % вес, не более
2 Массовая доля сероводорода, %
|
ГОСТ 14920-79 или ASTM D
2650-88 ASTM D 5623-94 или UOP 212-77
|
10,0 не нормируется, определение обязательно
|
по графику - « -
|
4
|
легкий газойль
|
ХВ-2
|
1 Плотность при 20 оС, г/см3, в пределах
|
ГОСТ 3900-85
|
0,81¼ 0,85
|
по требованию
|
|
|
|
2 Фракционный состав: - температура начала перегонки -10%
перегоняется при Т, н м. оС
|
ГОСТ 2177-99 или ASTM D
86-90
|
не нормируется, определение обязательно 160
|
по графику
|
|
|
|
- 90 % перегоняется при температуре, оС, не выше
|
|
360
|
|
|
|
|
3 Температура вспышки в закрытом тигле, оС, не ниже 4
Коксуемость 10 %-ного остатка, %, не более 5 Температура застывания, оС 6
Содержание воды
|
ГОСТ 6356-75 или ASTM D
93-90 ГОСТ 19932-99 или ASTM D
189-88 ГОСТ 20287-91
|
45 0,35 не нормируется не нормируется, определение
обязательно
|
по графику по требованию - « -
|
5
|
Тяжелый газойль
|
ХВ-3
|
1 Плотность при 20 оС, г/см3 2 Фракционный состав: -
температура начала кипения, оС 3 Коксуемость, %
|
ГОСТ 3900-85 ГОСТ 2177-99 ГОСТ 19932-99
|
не нормируется 250 не нормируется
|
по графику по графику по требованию
|
|
|
|
4 Содержание фенола
|
Методика предприятия
|
не нормируется
|
- « -
|
6
|
Кокс электродный для алюминиевой промышленности
|
С транспортера при погрузке в силосы
|
1 Массовая доля общей влаги, %, не более
|
ГОСТ 27588-91
|
КЗ суммар. 3,0
|
КЗ (0-25) 3,0
|
КЗ крупно- куск. 3,0
|
каждому реактору
|
|
|
|
2 Массовая доля летучих веществ, %, не более 3 Зольность,
%, не более 4 Массовая доля серы, %, не более 5 Массовая доля кокса с
размером кусков, %: - менее 8 мм, не более - более 8 мм, , не менее 6
Содержание кусков размером более 250 мм 7 Спекаемость Рога
|
ГОСТ 22898-78 п.4.9 ГОСТ 22692-77 ГОСТ 1437-75 ГОСТ 8606-93
ГОСТ 22898-78 п.4.3 с доп. по п.5.2 ТУ 38.301-29-88-97 визуально ГОСТ 9318-91
с доп. по п. 5.2. ТУ
|
11,0 0,6 1,8 - 45 отс. не норм.
|
12,0 0,6 1,8 - 15 отс. не норм.
|
9,5 0,6 1,8 10 - - -
|
|
7
|
Кокс нефтяной малосернистый КЗА, первый сорт
|
С трансп. при погрузке в силосы
|
1 Массовая доля общей влаги, %, не более 2 Массовая доля
летучих веществ, %, не более
|
ГОСТ 27588-91 ГОСТ 22898-78 п.4.9
|
3,0 9,0
|
каждому реактору
|
|
|
|
3 Зольность, %, не более 4 Массовая доля серы, %, не более
5 Массовая доля мелочи, %, не более: - куски размером меньше 8 мм 6
Действительная плотность после прокаливания при 1300 °С в течение 5 ч, г/см3
7 Массовая доля, % не более: - кремния - железа - ванадия
|
ГОСТ 22692-77 ГОСТ 1437-75 ГОСТ 22898-78 п.4.3 ГОСТ
22898-78 п.4.4 ГОСТ 22898-78 п.4.6
|
0,6 1,5 10,0 2,08¼2,13 0,08 0,08 0,015
|
|
8
|
Кокс нефтяной непрокаленный мелкий (с размером кусков 0 ¼ 8 мм)
|
С транспортера при погрузке в силосы
|
1 Массовая доля общей влаги, %, не более 2 Массовая доля
летучих веществ, %, не более
|
ГОСТ 27588-91 ГОСТ 22898-78
|
3,0 11,5
|
каждому реактору
|
|
|
|
3 Зольность, %, не более 4 Массовая доля серы, %, не более
|
ГОСТ 22692-77 ГОСТ 1437-75
|
0,8 1,8
|
|
|
|
|
|
|
|
|
|
|
|
3.8 Концепция применения ЭВМ
В работе проведен расчет циклон Ц-1 для очистки отходящих газов
коксования с помощью пакета прикладных программ AspenTech Hysys.
Цель расчётов - показать практическую значимость использования циклона
Ц-1, а также определить количество отделенной коксовой мелочи, степень очистки
газов коксования, гидравлическое сопротивление и необходимое количество
аппаратов.
Рисунок 3.2 Циклон для очистки газов коксования
Исходные данные для расчета:
Производительность по очищенным газам: 3958 кг/ч;
Содержание коксовой мелочи в газах коксования (dч не б. 8 мм) : 0,1 масс. доля;
Температура: 430 0C;
Давление на входе в циклон: 588,4 кПа;
Расчет в данном пакете прикладных программ показал (см. приложение 2),
что использование циклона при заданных условиях позволит отделить 41,89 кг
частиц коксовой мелочи в час, что значительно снизит вероятность закоксовывания
шлемовых труб реактора и реакционного змеевика печи.
Для очистки заданного количества газа необходим один циклон, гидравлическое
сопротивление которого составит 0,1687 кПа.
Также было определено, что при заданном значение эффективности отделения,
которое составит 90% для частиц с диаметром до 8 мм, КПД циклона составит
96,24%.
Таким образом, применение циклона для очистки газов коксования является
актуальным, потери давления в аппарате незначительны, то есть рабочие условия
практически не изменяются.
Геометрические размеры данного аппарата рассчитаны в следующем разделе.
. ИНЖЕНЕРНЫЕ РАСЧЕТЫ
4.1 Расчет реактора коксования
Составим материальный и тепловой балансы коксовых камер, рассчитаем число
и их технологические размеры, определим продолжительность заполнения одной
камеры коксом и проведем прочностной расчет камер.
Составим материальный баланс коксовых камер.
Исходные данные:
Производительность установки по гудрону G = 860 т/сут = 36 т/ч ;
коэффициент рециркуляции Кр = 1,5; давление на входе сырья в камеру Р = 0,4
МПа; температура вторичного сырья на входе в коксовые камеры t=500°С; турбулизатор - водяной пар в
количестве 3% (масс.) от сырья.
Материальный
баланс реакционной камеры коксования.
По данным производственных аналогов, литературного обзора принимаем
следующий выход продуктов (% масс. от сырья):
газ - 11,0, бензин - 8,7, легкий газойль - 27,4, тяжелый газойль - 25,4,
кокс - 26,4; потери - 1,1.
Таблица 4.1 - Качество первичного и вторичного сырья.
Компонент
|
Пределы выкипания, °С
|
t, 0С
|
М
|
ρ, кг/м3
|
хi
|
Первичное сырье
|
Легкий газойль
|
200-350
|
280
|
220
|
890
|
0.02
|
Тяжелый газойль
|
350-480
|
415
|
340
|
950
|
0.04
|
Остаток
|
480
|
560
|
540
|
1045
|
0.94
|
Вторичное сырье
|
бензин
|
35-200
|
115
|
108
|
755
|
0,0006
|
Легкий газойль
|
200-350
|
280
|
220
|
895
|
0,0400
|
Тяжелый газойль
|
350-480
|
415
|
340
|
955
|
0,1174
|
Рециркулят
|
>480
|
500
|
460
|
1000
|
0,2142
|
Остаток
|
>480
|
560
|
540
|
1045
|
0,6278
|
Составляем материальный баланс одной работающей реакционной камеры.
Таблица 4.2 - Материальный баланс реакционной камеры.
Показатели
|
т/ч
|
%(масс.)
|
т/сут
|
Взято
|
Легкий газойль
|
0,72
|
1,33
|
17,28
|
Тяжелый газойль
|
1,44
|
2,67
|
34,56
|
Рециркулят
|
18
|
33,33
|
432
|
Остаток
|
33,84
|
62,67
|
812,16
|
Водяной пар
|
1,08
|
3
|
25,92
|
Σ
|
55,08
|
103
|
1321,92
|
Получено
|
Газ
|
3,96
|
7,34
|
95,04
|
Бензин
|
3,132
|
5,8
|
75,168
|
Легкий газойль
|
9,864
|
18,27
|
236,736
|
Тяжелый газойль
|
9,144
|
16,93
|
219,456
|
Рециркулят
|
18
|
33,33
|
432
|
Кокс
|
9,504
|
17,6
|
228,096
|
Водяной пар
|
1,08
|
3
|
25,92
|
потери
|
0,396
|
0,73
|
9,504
|
Σ
|
55,08
|
103
|
1321,92
|
Пример расчета:
т/ч
т/ч
втор.сырья
= G*Кр = 36 * 1, 5 = 54 т/ч
Gрециркулят = Gвтор.сырья - Gсырья= 54 - 36 = 18 т/ч
Принимаем долю отгона сырья на входе в реакционную камеру е’=0,55 и
проверяем правильность принятого значения по формуле [39]:
Для
этого рассчитываем мольную долю каждого компонента в исходной смеси:
где
- молекулярная масса компонента i.
Затем
определяем давление насыщенных паров компонентов по формуле Ашворта:
где
- давление насыщенных паров
-
температура однократного испарения
-
температура кипения углеводорода или средняя температура кипения углеводородной
фракции.
Функцию
определяем из уравнения
По
этому же уравнению подставляя t' вместо t рассчитывают и функцию
.
Для
легкого газойля t=350°С и t'=280°С, тогда
Давление
насыщенных паров легкого газойля составит
МПа
Константа
фазового равновесия для нефтяных углеводородов при давлении 0,4 МПа
,
где
- давление насыщенных паров компонента i при
температуре однократного испарения.
-
давление, при котором производится однократное испарение, давление в системе.
Аналогичный
расчет проводится по всем компонентам, его результаты сводятся в таблицу.
Исходя
из данных таблицы принятая доля отгона е'=0,55считается верной, т.к.
Результаты
расчета сводим в таблицу 4.3.
Таблица 4.3 - Расчет доли отгона сырья на входе в реакционную камеру при
температуре 5000С.
компонент Gi,
кг/ч Мi ti ρ, кг/м3 Gi/ Мi, кг моль/ч 
МiРi
+1
Мi 

,
кг/ч , кг/ч
|
|
|
|
|
|
|
|
|
|
|
Легкий газойль
|
720
|
220
|
280
|
890
|
3,27
|
0,0193
|
4,24
|
3,3
|
7,5
|
4,57
|
0,0042
|
0,924
|
0,001792
|
70,4
|
649,6
|
Тяжелый газойль
|
1440
|
340
|
400
|
950
|
0,0250
|
8,51
|
5,7
|
1,425
|
1,23
|
0,0203
|
6,902
|
0,013386
|
525,7
|
914,3
|
Рециркулят
|
18000
|
460
|
500
|
1000
|
39,13
|
0,2311
|
106,31
|
1,0
|
0,25
|
0,58
|
0,2434
|
111,964
|
0,217149
|
8527,9
|
9472,1
|
Остаток
|
33840
|
540
|
550
|
1045
|
62,67
|
0,3701
|
199,88
|
0,4
|
0,10
|
0,50
|
0,733
|
395,82
|
0,767673
|
30148
|
3692
|
Водяной пар
|
1080
|
18
|
-
|
-
|
60
|
0,3543
|
6,37
|
-
|
-
|
|
|
0
|
-
|
-
|
|
Σ
|
55080
|
|
|
|
169,31
|
|
325,33
|
|
|
|
1,0009
|
515,61
|
1
|
39272
|
15808
|
Проводим пересчет мольной доли в массовую:
е
=
=1-515,61×(1-0,55 )/ 325,34=0,287.
Количество
жидкой фазы
Gx=55080(1-0,287)=39272
кг/ч
Количество
паровой фазы
Gx=55080×0,287=15808 кг/ч
Плотность
жидкой фазы равна: ρх=39272/(70,4/890+525,7/950+8527,88/1000+30148/1045)=1033
кг/м3
Тепловой
баланс реакционной камеры коксования.
Составим тепловой баланс камеры, чтобы найти температуру паров на выходе
из нее [39].
Количество тепла, вносимое в камеру турбулизатором:
кДж/ч
Количество
тепла, вносимое углеводородными парами:
кДж/ч
Количество
тепла, вносимое жидкой фазой:
кДж/ч
Общее
количество тепла, вводимое в реакционную камеру равно:
кДж/ч
Принимаем
температуру паров на выходе из камеры равной 4400С. Для этой температуры
находим энтальпию продуктов по справочным данным.
Энтальпию
нефтяного кокса рассчитываем на основании средней теплоемкости:
,
где
Ср -средняя теплоемкость кокса, кДж/(кг-К) (по справочным данным Ср=1,4),t -
средняя температура кокса в камере, °С; ее вычисляют по формуле t =
0,5(500+440) =470 °С
тогда
кДж/кг
Тепловой
эффект процесса равен:
кДж/ч
Потери
тепла в окружающую среду вычисляем по формуле:
-
коэффициент теплоотдачи, кДж/(м2
ч
К)
-
наружная поверхность реактора, м2
-
разность температуры между наружной поверхностью реактора и окружающей средой,
0С
Принимаем
коэффициент теплоотдачи от наружной поверхности теплоизоляции в окружающую
среду α
= 33 кДж/(м2
ч
К) и разность температур между изоляцией и окружающей
средой, Δt=500С.
Наружная поверхность изоляции S=600 м2.
кДж/ч
Результаты
определения расхода тепла из коксовой камеры сводим в таблицу. Как видно,
расход тепла при 4400С равен общему количеству тепла, вводимому в реакционную
камеру. Поэтому считаем принятую температуру 4400С правильной.
Таблица
4.4 - Расход тепла из коксовой камеры при 4400С.
Компонент
|
Gi, кг/ч
|
I, кДж/кг
|
Q, кДж/ч
|
Газ
|
3960
|
1450
|
5742000
|
Бензин
|
3132
|
1392
|
4359744
|
Легкий газойль
|
9864
|
1315
|
12971160
|
Тяжелый газойль
|
9144
|
1287
|
11768328
|
Рециркулят
|
18000
|
1261
|
22698000
|
Кокс
|
9504
|
658
|
6253632
|
Водяной пар
|
1080
|
3147
|
3398760
|
потери
|
396
|
1136
|
449856
|
Qпр
|
-
|
-
|
5670000
|
Qпот
|
-
|
-
|
1000000
|
Σ
|
|
|
74311480
|
Проведем
расчет высоты цилиндрической части и диаметра реактора коксования.
Определяем скорость заполнения камеры коксом по формуле:
=Gк / ρ = 9504/850 = 17,18 м3/ч
Где W - скорость заполнения камеры коксом, м3/чк - производительность
установки по готовому коксу, кг/ч
ρ - плотность кокса в камере, кг/м3.
Можно принять ее равной 850кг/м3. На производстве-аналоге используются коксовые
камеры с коническим днищем со следующими размерами:
Рисунок 4.1. Геометрические размеры коксовой камеры.
На рисунке 4.1: Нп - полная высота, Нц - высота цилиндрической части, Нк
- высота конической части, Нс - высота слоя кокса, D - диаметр камеры, d - диаметр днища.
Нп=27800 мм
Нц= 18530 мм
Нк = 4900 мм= 1800 мм
D = 5500 мм
Нс = 16300мм
По этим размерам находим
рабочий объем коксовой камеры по формуле:
=Vц + Vк
ц , Vк - объемы
кокса в цилиндрической и конической частях камеры соответственно, м3
Vц =
м3
Vк =
м3
V=Vц + Vк =
386,6 + 40,6 = 427,2 м3
Определим время заполнения камеры коксом по формуле:
τ = V/ W = 427,2/17,18 = 24,9 ч
В момент окончания цикла коксования слой пены не должен доходить до верха
камеры. Высоту пенного слоя h(м)
при коксовании крекинг-остатков, представляющего собой пену с распределенными в
ней карбоидными частицами, можно определить по формуле:
= κвс*uк
где κвс - коэффициент вспучивания, ч
uк -
скорость роста коксового слоя в камере, м/ч
При температуре сырья t(0С)
на входе в камеру коэффициент κвс рассчитывают по уравнению:
κвс = 4,5+0,11*(486-t) = 4,5+0,11*(486-500) = 2,96.
Вычислим:
uк =
м/ч
=
2,96
0,72 = 2,13 м.
Высота
цилиндрической части камеры составит:
Нц
= 2,13 + 16,28 = 18,41 м.
Тогда
диаметр реактора составит:
м
Принимаем:
Диаметр - 5,5м;
Высота - 27,9 м;
Общий объем - 510 м3.
Общее число камер n = 2, в одной из них протекает процесс, а из другой
выгружается готовый кокс.
Для проектирования установки принимают число камер - 3, для стабильной
работы реакторных камер.
Проведем
прочностной расчет коксовой камеры.
Исходные данные:
Расчетное давления в верхней части камеры Рв = 6 кг/см2 = 0,6 МПа;
Расчетное давление в нижней части камеры Рн = 8 кг/см2 = 0,8 МПа;
Расчетная температура стенки корпуса камеры, изготовленного из стали
16ГС+0,8*13 - 475 0С;
Расчетная температура стенки элементов корпуса, изготовленного из стали
12МХ+0,8*13 - 520 0С;
Материал корпуса камеры:
Верхней части (за исключением верхней горловины) двухслойная сталь
16ГС+0,8*13, нижней части сталь марки 12МХ+0,8*13 по ГОСТ 10885 - 75.
Цилиндрическая часть камеры разбивается по высоте на три участка:
верхний высотой Н1 = 891 см (16ГС+0,8*13);
средний, высотой Н2 = 500см (16ГС+0,8*13);
нижний, высотой Н3 = 500 см (16ГС+0,8*13).
Толщина стенки верхнего участка:
'1 = Р1 * Дв/2*φ*Gдоп - Р1,
где Дв - внутренний диаметр камеры (Дв = 5,5 м);
φ - коэффициент прочности сварного шва (φ
= 0,95);
Gдоп = Gт/nт - допускаемое напряжение для стали марки
16ГС+0,8*13;доп = 52 МПа - при температуре 4750С;
Р1 - рассчитанное давление в верхней части.
Р1 = Рв+(Нi*γ/10),
где γ = 0,0096 г/см3 - удельный вес нефтепродукта;
Рв = 6 кг/см2;
Н1 = высота столба нефтепродукта в верхней части
(Н1 = 6 м).
Р1 = 6 + (600 * 0,096 / 10) = 6,6 кг/см2 = 0,66 МПа;
Тогда S'1 = (0,66 * 5,5) / (2 * 0,95 * 52 - 0,66) = 0,037 м.
Принятая толщина обечайки:
= S'1+ С + С1=0,037+0,003+0,00225=0,04225, где
С - прибавка на коррозию
С1 - величина минусового допуска на лист
Принимаем толщину стенки верхнего участка S1 = 45мм с учетом толщины
коррозионного слоя.
Толщина стенки среднего участка:
'2 = Р2 * Дв / 2*φ*Gдоп - Р2,
где Р2 = Рв+(Н2'*γ/10) - расчетное давление.
Н2' = Н1' + Н2 = 6 + 5 = 11 м - высота столба нефтепродуктов в средней
части.
Расчет давления в средней части:
Р2 = 6 + (1100 * 0,0096)/10 = 7,06 кг/см2 = 0,706 МПа;'2 = (0,706 * 5,5 )
/ (2 * 0,95 * 52 - 0,706) = 0,0396 м.
Принятая толщина S2:=
S'2+ С + С1=0,0396+0,003+0,0024=0,045 мм
С - прибавка на коррозию
С1 - величина минусового допуска на лист
Принимаем толщину стенки верхнего участка S1 = 48 мм с учетом толщины
коррозионного слоя.
Толщина стенки нижнего участка:
S'3 = Р3 * Дв / 2*φ*Gдоп - Р3
где Р3 = Рв+(Н3'*γ/10) - расчетное давление.
Н3' = Н2' + Н3 = 11 + 5 = 16 м - высота столба нефтепродуктов в нижней
части.
Расчет давления в нижней части:
Р3 = 6 + (16000 * 0,0096) / 10 = 7,54 кг/см2 = 0,754 МПа;
S'3 = (0,754 * 5,5 ) / (2 * 0,95 * 52 - 0,754) =0,042 м .
Принятая толщина обечайки
= S'3+ С + С1=0,042+0,003+0,0025=0,0479 мм
С - прибавка на коррозию
С1 - величина минусового допуска на лист
Принимаем толщину стенки верхнего участка S1 = 50 мм с учетом толщины
коррозионного слоя.
Расчитаем толщину верхнего полушарового днища:
= (Рв * R) / (2 * φ * Gдоп - 0,5 * Рв)
где R - радиус днища (R = 2,75);
φ - коэффициент прочности сварного шва (φ
= 0,95);
Gдоп -
допускаемое напряжение (Gдоп =
52 МПа).
S =
(0,6 * 2,75) / (2 * 0,95 * 52 - 0,5 * 0,6) = 0,016 м
Принимаем S = 36 мм с учетом
антикоррозийного слоя и припуска на штамповку.
Расчитаем шароконический переход и конический элемент нижнего днищ:.
. Толщина стенки S1
цилиндрической обечайки на расстоянииу = 0,5√Д*S , и конического элемента на расстоянии lк = 0,5√(Д*S)/cosα; принимается наибольшей, определяем по
формуле:
1 = (Рр * Д * у) / (4 * φ * Gдоп)
S2 =
Рр / (2 * φ * Gдоп - Рр) * Д / cosα
где Рр - давление (Рр = 7,56 кг/см2);
Д - внутренний диаметр (Д = 550 см2);
у - коэффициент формы днища (у = 1,1);
α - угол при вершине корпуса (α
= 30 0);
Gдоп -
допустимое напряжение (Gдоп =
520 кг/см2).
S1 =
(7,56 * 550 * 1,1) / (4 * 0,95 * 520) = 2,31 см
S2 =
7,56 / (2 * 0,95 *520 - 7,56) * 550 / cos 30 0 = 4,9 см
Толщину шароконического перехода принимаем S1 = 55 мм, толщину цилиндрической обечайки на расстоянии lу и
конического элемента на расстоянии lк принимаем S2 = 55мм
lк = 0,5* √(550 * 4,9 / 0,891) = 28 см
Принято lк ≥ 400 мму = 0,5 * √ 550 * 4,9 = 26 см
. Толщина стенки переходного конического элемента из стали 16ГС+0,8*13
к = Рн / (2 * φ * Gдоп - Рн) * Др / cosα
где Др = 310 см - расчетный диаметр (принят из условий
транспортабельности);
r - радиус (r = 275 см).
Sк = 8
/ (2 * 0,95 * 520 - 8) * 310/0,866 = 2,92 см
Принимаем толщину конического перехода нижнего днища 36 мм.
. Толщина стенки конического элемента из стали 12МК+0,8*13 при расчетной
температуре 510 0С.
к = Рн / (2 * φ * Gдоп - Рн) * Др / cosα
где Др = 270 кг/см2 диаметр;
φ - коэффициент прочности сварного шва (φ
= 0,95);
Gдоп -
допускаемое напряжение (Gдоп =
740 кг/см2);
Рн = давление внижней части камеры (Рн = 8 кг/см2).
Sк = 8
/ (2 * 0,95 * 740 - 8) * 270 / 0,866 = 1,79 см
Принимаем Sк = 32 мм с
учетом антикоррозийного слоя.
4.2 Расчет и подбор прочего
технологического оборудования
Рассчитаем геометрические размеры циклона для очистки газов коксования,
отходящих из реактора коксования, и подберем типовой циклон.
В геометрически подобных циклонах влияние сопротивлений всех видов
(местные и обуславливаемые трением) учитывают одним общим коэффициентом ζ,
а вместо действительных
скоростей газового потока на отдельных участках циклона используют условную
скорость Wусл., равную отношению объема газа
проходящего через циклон к его поперечному сечению. Коэффициент сопротивления
для циклонов стандартных конструкций находиться в пределах от 75 до 300 в
зависимости от модификации.
Тогда гидравлическое сопротивление циклона определяется по формуле [40]:
∆р=ζцW2цρ/2
Откуда фиктивная скорость газа в циклоне можно найти по формуле:
ц=(2∆р/ζцρ)1/2=(2*750/180)1/2=2,9 м/с
Диаметр циклона рассчитывается по формуле:
ц=(4Q/π Wц)1/2=(4*0,9/3,14*2,9)1/2=0,629 м,
где расход газа составляет Q=3960/3600*1,212=0,9
м3/с
Найдем секундную производительность циклона: Vц=πD2Wц/4=0,9 м3/с,
таким образом для очистки необходим один циклон.
На основании проведенного расчета выберем стандартный циклон, работающий
при температурах до 4000С, по каталогам производителей. Наиболее подходят
циклоны НИИОгаза (таблица 4.6) и по рассчитанному диаметру и секундной производительности
принимаем циклон ЦН-15-700 с Q=3500-5500
м3/ч, Sсеч.=0,384 м2 .
Таблица 4.6 - Характеристика циклонов ЦН-15.
Типоразмер
|
производительность, м3/час при скорости газового потока в
корпусе циклона;
|
D, мм
|
H1, мм
|
H, мм
|
a x b, мм
|
A x B, мм
|
|
2,5 м/сек
|
4 м/сек
|
|
|
|
|
|
ЦН-15-200х1УП
|
283
|
452
|
200
|
1876
|
912
|
132х52
|
436х436
|
ЦН-15-300х1УП
|
630
|
1 000
|
300
|
2508
|
1368
|
198х78
|
606х606
|
ЦН-15-400х1УП
|
1 100
|
1 800
|
400
|
3080
|
1824
|
264х104
|
706х706
|
ЦН-15-500х1УП
|
1 800
|
2 800
|
500
|
3942
|
2280
|
330х130
|
806х806
|
ЦН-15-600х1УП
|
2 500
|
4 100
|
600
|
4544
|
2736
|
396х156
|
930х930
|
ЦН-15-700х1УП
|
3 500
|
5 500
|
700
|
5206
|
3192
|
462х182
|
1030х1030
|
ЦН-15-800х1УП
|
4 500
|
7 200
|
800
|
6028
|
3648
|
528х208
|
1115х1115
|
ЦН-15-900х1УП
|
5 700
|
9 200
|
900
|
4104
|
594х234
|
1230х1230
|
кокс сера нефтяной гидрообеесеривание
Для него проведем расчет геометрических размеров, зная эмпирические
соотношения геометрических размеров аппарата и диаметра:
Диаметр трубы для вывода очищенного газа- 0,6*700=420 мм
Ширина входного прямоугольного патрубка- 0,26*700=182 мм
Высота входного патрубка - 0,66*700=462 мм
Высота цилиндрической части - 1,74*700=1218 мм
Высота конической части - 2,0*700=1400 мм
Общая высота циклона - 4,56*700=3192 мм
Так как, газы коксования, очищаемые в циклоне, взрывоопасны и температуры
могут превышать 4000С, то выбираем циклон ЦН-15-700 взрывобезопасного
исполнения и модернизированный покрытием из керамических вставок, тем самым
циклон сможет работать при температурах до 6000С, а также увеличиться срок
службы циклона, из-за увеличения устойчивости к абразивному износу.
Рисунок 4.3 Циклон ЦН-15 с бункером и улиткой
Проведем
гидравлический расчет реакционного змеевика печи П-1.
Целью гидравлического расчета является определение давления сырья на
выходе из змеевика печи, так как снижение давление ниже расчетного будет
говорить о процессах коксования, начавших в нем происходить. Так как давление
на входе змеевика печи известно - в нашем случае pвх. = 1,73 МПа, то для отыскания давления на выходе из
змеевика необходимо рассчитать потери напора в нем. В проектируемой печи
происходит частичное испарение вторичного сырья, поэтому гидравлический расчет
змеевика ведем по методу Б. Д. Бакланова [33].
Давление сырья на входе в змеевик печи рассчитываем по формуле:
где DРи - потери
напора на участке испарения; DРн - потери напора на участке нагрева радиантных труб; DРк - потери напора в реакционном
змеевике печи (по одному потоку); DРст. - статический напор, необходимый для подъема сырья в
змеевике от уровня ее ввода в конвекционный змеевик до уровня вывода из
радиантных труб.
Расчет необходимо начинать с определения потерь напора на участке
испарения:
Началом участка испарения называется то сечение змеевика печи, в котором
сырье закипает, то есть достигает температуры начала однократного испарения.
При этой температуре упругость насыщенных паров сырья становится равной
давлению в начале участка испарения.
Каждую
узкую фракцию в соответствии с ее молекулярной массой приравниваем (условно) к
индивидуальному углеводороду (алкану) и находим при нескольких температурах по
диаграмме Кокса для каждой фракции (приравненной к индивидуальному
углеводороду) упругость Pi насыщенных паров. Вычисляем произведения
, выражающие парциальное давление паров каждой
фракции, и по уравнению изотермы жидкой фазы находим для каждой из выбранных
температур упругость паров сырья, то есть давление, при котором сырье закипит
при данной температуре.
Таблица
4.7 - Исходные данные для расчета
Компонент
|
Мi
|
ti
|
РiРi
|
|
|
Легкий газойль
|
220
|
280
|
0,0193
|
3,3
|
0,06369
|
Тяжелый газойль
|
340
|
400
|
0,0250
|
5,7
|
0,1425
|
Рециркулят
|
460
|
500
|
0,2311
|
1,0
|
0,2311
|
Остаток
|
540
|
550
|
0,3701
|
0,4
|
0,14804
|
Водяной пар
|
18
|
-
|
0,3543
|
-
|
-
|
Σ
|
|
|
1
|
|
0,58533
|
Найдем эквивалентную (расчетную) длину радиантных труб для одного потока:
где
= 12,5 м - полная длина трубы; Nр1 =
64 - число радиантных труб в одном потоке; y = 50 - коэффициент,
зависящий от вида соединения труб; dв = 0,l08 м -
внутренний диаметр радиантных труб.
Тогда:
Рассчитаем
эквивалентную длину участка испарения по уравнению:
где
Тогда:
Определим
давление в начале участка испарения по формуле Б. Д. Бакланова:
Потери напора DРн
на участке нагрева радиантных труб найдем по формуле:
где l = 0,031 -
коэффициент гидравлического сопротивления; lн - эквивалентная длина участка нагрева радиантных труб по
одному потоку, м; dв = 0,108 м -
внутренний диаметр радиантных труб; и - массовая скорость сырья в трубах,
кг/(м2×сек); gж - плотность сырья при средней температуре на участке
нагрева радиантных труб.
Массовая скорость сырья в трубах (одного потока):
Подставляя в формулу для DРн числовые значения величин для нефти и мазута, получим:
Потери напора в конвекционном змеевике (по одному потоку) найдем по
формуле:
где l = 0,031; lк - эквивалентная (расчетная) длина
конвекционного змеевика по одному потоку, м; dв = 0,108 м - внутренний диаметр конвекционных труб; uк - массовая скорость сырья в
конвекционных трубах, кг/(м2×сек); gж -
плотность сырья при средней температуре в конвекционных трубах.
Эквивалентная длина конвекционного змеевика по одному потоку:
где
- число труб в одном потоке; lтр. = 12,5 м -
полная длина трубы; y = 50.
Тогда для вторичного сырья:
Массовая скорость:
Подставляя в формулу для DРк числовые значения величин, получаем:
Определяем статистический напор, необходимый для подъема вторичного сырья
в змеевике от уровня ввода в конвекционный змеевик до уровня вывода из
радиантных труб:
где
rж - удельный вес сырья при tср..
Таким образом, давление сырья на выходе из змеевика печи будет:
К
закоксовыванию змеевика (pвых.=0) приводит неправильный температурный режим,
большое содержание коксогенных агентов и частиц коксовой мелочи во вторичном
сырье. Удаление коксовой мелочи из вторичного сырья (мелочь попадает из газов
коксования при контакте с сырьем в ректификационной колонне) позволит снизить
вероятность закоксовывания змеевика на 60%.
5. БЕЗОПАСНОСТЬ И ЭКОЛОГИЧНОСТЬ ПРОЦЕССА ЗАМЕДЛЕННОГО КОКСОВАНИЯ
5.1 Анализ безопасности проектируемого производства
.1.1 Характеристика проектируемого производства
В технологическом процессе замедленного коксования одновременно участвует
большое количество горючих и легковоспламеняющихся жидкостей, поэтому установка
замедленного коксования является пожаровзрывоопасной, а используемые продукты
(гудрон, крекинг-остаток, асфальт), обладают токсичными свойствами.
По классификации взрывоопасных производств установка производства кокса
относится к категории «В-1а», т.е. к производству, где взрывоопасные смеси
могут образоваться при авариях или неисправностях аппаратов и оборудования
[41].
По противопожарной безопасности установка относится к категории А, то
есть к производству, где имеются нефтепродукты с температурой вспышки менее 28°
С (бензин коксования).
Характеристика токсичных свойств сырья и продуктов, получаемых и
применяемых на установке, приведена в таблице 5.1.
Из всех видов опасностей (негативных воздействий),
формируемых в процессе трудовой деятельности на установке замедленного
коксования постоянно действует или потенциально могут действовать следующие
перечисленные опасные и вредные факторы [42].
Физические факторы такие, как повышенная температура
поверхностей оборудования, электрический ток, движущиеся машины и механизмы,
различные транспортно-подъемные устройства и перемещаемые грузы, незащищенные
подвижные элементы производственного оборудования (приводные и передаточные
механизмы). Вредными для здоровья физическими факторами также являются:
повышенная температура воздуха рабочей зоны, высокие влажность и скорость
движения воздуха, повышенные уровни шума, вибрации, запыленность и
загазованность воздуха рабочей зоны, недостаточная освещенность рабочих мест.
Таблица 5.1- Токсические свойства применяемых веществ и материалов.
№ п./п.
|
Наименование сырья, веществ и материалов
|
ПДК Для данного вещества, мг/м3
|
Класс опасности ГОСТ 12.1.007-76
|
Первая помощь при отравлении
|
1
|
2
|
3
|
4
|
5
|
1.
|
Сырьё коксования (смесь тяжёлых нефтяных остатков)
|
300
|
4
|
При легком отравлении газом или парами нефтепродуктов
необходимо доложить старшему оператору и обратиться в медпункт за медицинской
помощью. В случае потери сознания при остром отравлении: пострадавшего необходимо
вынести из загазованной зоны на свежий воздух (при этом спасающий должен
иметь противогаз); обеспечить правильное кровообращение - уложить
пострадавшего на спину, ровно, запрокинуть голову назад (подложить под шею
валик из одежды); устранить в одежде все, что может в какой-то степени
стеснять или затруднять свободное дыхание (расстегнуть ворот, брюки или юбку,
снять ремень, пояс и т. д.); дать понюхать нашатырный спирт, смочив им
кусочек ваты; вызвать скорую помощь и газоспасательный отряд. При покраснении
лица и тяжелом хриплом дыхании пострадавшему необходимо придать полусидячее
положение - прислонить к стене, подложить сверток и т. д. При отсутствии
видимого дыхания приступить к проведению искусственной вентиляции легких до
прибытия скорой помощи или газоспасательного отряда.. При отсутствии пульса
немедленно приступить к непрямому массажу сердца и искусственной вентиляции
легких.
|
2.
|
Компоненты сырья
|
300 300 300 300
|
4 4 4 4
|
|
2.1. 2.2. 2.3. 2.4.
|
Экстракт Дуосол Гудрон с установок АВТ Крекинг- остаток
Асфальт
|
|
|
|
3.
|
Газ коксования
|
300
|
4
|
|
4.
|
Бензин коксования (компонент автомобиль- ного бензина)
|
100
|
4
|
|
5.
|
Лёгкий газойль (керосин коксования)
|
300
|
4
|
|
6.
|
Тяжёлый газойль (керосиногазойлевая фракция) коксования
|
300
|
4
|
|
|
|
|
|
|
|
Химически опасные и вредные производственные факторы
такие, как наличие общетоксических (нефтепродукты, углеводородный газ) веществ.
Наиболее опасными местами на установке являются: горячая насосная,
технологическая насосная, реакторный блок, блок колонн ректификации и трубчатая
печь.
Основными моментами, определяющими опасность на установке, являются:
токсичность продуктов, получаемых на установке (газ, бензин с температурой
вспышки ниже 28°С, наличие коксовых камер, работающих при высоких температурах
(450-500°С), то есть существует возможность получения ожогов и травм при снятии
нижней и верхней крышек реактора, наличие огневой нагревательной печи, наличие
высоких температур и давлений, образование статического электричества при
движении газов и жидкостей по трубопроводам и в аппаратах.
5.1.2 Производственная санитария
Производственная санитария направлена на поддержание нормального
самочувствия и работоспособности человека во время работы на производстве.
Производительность и качество труда на производстве во многом зависят от
метеорологических условий рабочей зоны (температура воздуха, относительная
влажность воздуха, скорость движения воздуха [42].
Состояние воздушной среды в производственных помещениях, по территории
установки контролируется лабораторией ВГСО по графику с записью анализов
воздушной среды в журнал, находящийся на установке.
Таблица 5.2 - Оптимальные значения метеорологических условий в рабочих
зонах производственных помещений
Характеристика помещений и участков
|
Категория работы
|
Период года
|
Температура,°С в пределах
|
Относительная влажность, %
|
Скорость движения воздуха, м/с
|
Операторная
|
Легкая
|
Холодный и теплый
|
17-24 19-30
|
не более 75 в пределах 60-40
|
0,2 0,1-0,3
|
Насосные: -водяная -откачки -горячая -холодная
|
Средней тяжести
|
Холодный и теплый
|
13-23 15-29
|
не более 75 в пределах 60-40
|
0,4 0,2-0,5
|
Освещение в производственных помещениях является одним из важнейших
факторов благоприятных условий труда, улучшения качества выполняемой работы и
безопасности труда. Для этого используется как естественное, так и
искусственное освещение. В производственных помещениях, где в дневное время
пребывают люди, следует предусматривать естественное освещение, как наиболее
гигиеничное и экономичное.
Характеристики искусственного и естественного освещения приведены в
таблицах 5.3 и 5.4.
Таблица 5.3 - Характеристика естественного
освещения.
Наименование помещения
|
Вид освещения
|
Характеристика зрительной работы
|
Наименьший размер объекта различения, мм
|
Норма К.Е.O, %
|
1
|
2
|
3
|
4
|
5
|
Операторная
|
боковое
|
средней точности
|
0,5 1
|
1,35
|
Таблица 5.4 - Характеристика искусственного
освещения
Наименование помещения, блока
|
Характер зрительных работ
|
Вид освещения
|
Наименьший объект различения, мм
|
Количество ламп
|
Значение Ен, лк
|
1
|
2
|
3
|
4
|
5
|
6
|
Операторная Отделение ректификации
|
средней точности грубая
|
общее общее
|
0,5 ÷ 1 -
|
20 11
|
200 30
|
На проектируемом производстве используются средства индивидуальной
защиты.
Каждый рабочий обеспечивается защитной каской, спецодеждой, спецобувью и
рукавицами. Для защиты органов дыхания на установке используются фильтрующие
противогазы марки БКФ и шланговые противогазы ПШ-1. Операторы склада кокса
используют респираторы типа «лепесток».
Газоопасные работы проводить только по оформлению «наряд-допуска» с
проведением инструктажа на рабочем месте с ответственным лицом. Газоопасные
работы проводятся только вдвоем: работающий и наблюдающий с противогазом ПШ-1 в
положении «на готове».
Работы по уборке всех продуктов при аварийных случаях производятся в
фильтрующих противогазах марки "А". Все работающие обеспечиваются
дополнительным двенадцатидневным отпуском, специальным питанием, молоком.
5.1.3 Техника безопасности
Для обеспечения условий безопасной и безаварийной эксплуатации установки
предусмотрен ряд мероприятий в соответствии с существующими правилами и нормами
техники безопасности. Управление технологическим процессом осуществляется
автоматически и дистанционно с помощью пневматических регуляторов,
расположенных на щите управления, установленной в операторной. В помещениях
класса В-1а установлены сигнализаторы довзрывных концентраций с подачей
светового и звукового сигнала в операторную.
Выполнена световая и звуковая сигнализация по опасным нарушениям
технологического режима, которые могут привести к потере качества продуктов,
создать аварийные ситуации и поломки агрегатов и машин и применена схема
безопасной эксплуатации системы гидрорезки, включающая блокировку насосов
высокого давления в соответствии с техническими условиями завода-изготовителя.
При выходе гидрорезака из установленных зон происходит остановка насоса. При
остановке любого агрегата транспортной системы отключаются предыдущие механизмы
для предотвращения завалов;
Также выполнена сигнализация по снижению давления пара, промышленной
воды. Для защиты оборудования, аппаратов, трубопроводов от завышения давления
на ёмкостных и колонных аппаратах, работающих под давлением, установлены
предохранительные клапана в соответствии с рекомендациями по установке
предохранительных клапанов.
На коксовых камерах установлена система предохранительных клапанов
(аварийная) с блокировкой паром. Сброс с предохранительных клапанов аппаратов
предусматривается в факельную линию.
Колонны и ёмкостная аппаратура при подготовке установки к ремонту или при
аварийном положении освобождаются от продукта откачкой по основной схеме до
сброса насоса.
Коксовые камеры выполнены с учётом повышенной опасности продукта,
(самовоспламенение в случае нарушения герметичности фланцевых соединений).
Поэтому, принято повышенное расчётное давление. Уплотнение выполнено по типу
«шип-паз» с металлической прокладкой, жёсткость корпусных фланцев (люков)
обеспечивается увеличенной толщиной и применением быстродействующих механизмов
зажима с гарантированным и равномерным усилием зажима;
Трубопроводы выхода из печей в коксовые камеры по вторичному сырью и
трубопроводы выхода из коксовых камер в колонну К-1 проложены по стационарным
площадкам на катковых опорах. С целью облегчения чистки их от кокса
предусмотрены разъёмы (фланцевые соединения) на коленах трубопроводов и на
прямых участках через 5-8 метров с возможностью разводки участков.
По транспорту и складу кокса предусмотрены следующие мероприятия:
для исключения запыления окружающей среды при рассеве и дроблении
оборудование защищено кожухами, что улучшает санитарные условия окружающей
среды;
включение и выключение дробилки, грохота, ленточных конвейеров и
питателей производится с пульта управления дистанционно и по месту;
основные линии ленточных контейнеров расположены в закрытых галереях, все
вращающие детали закрыты кожухами или имеют ограждения. Уровень механизации,
предусмотренный на установке, исключает ручной труд и создаёт безопасные
условия труда на установке в период выгрузки кокса из камер и транспортировки
его на склад;
Для контроля загазованности в производственных помещениях установлены
приборы автоматического газового анализа - СВК.
Анализаторы довзрывных концентраций установлены в холодной насосной и в
горячей насосной.
При наличии загазованности индикатор прибора показывает величину загазованности,
а при достижении 20 % от нижнего предела взрываемости срабатывает звуковая и
световая сигнализация.
Состояние воздушной среды в производственных помещениях контролируется
лабораторией ВГСО по графику с записью анализов воздушной среды в журнал, хранящийся
на установке.
Таблица 5.5 - Характеристика производственных зданий, помещений и
наружных установок [43].
№п/п
|
Наименование производственных зданий, помещений, наружных
установок.
|
Категория взрывопожарной и пожарной опасности помещений,
зданий, наружных установок.
|
Классификация зон внутри и вне помещений для выбора и
установки электрооборудования.
|
Группа производственных процессов по санитар- ной
характеристике (СНИП 2.09.04-87)
|
|
|
|
Класс взрывоопасной или пожароопасной зоны
|
Категория и группа взрывопожароопасных смесей
|
|
1
|
2
|
3
|
4
|
5
|
6
|
1.
|
Блок печей и дымовая труба
|
Г
|
-
|
-
|
1в
|
2.
|
Реакторный блок
|
Ан
|
В-1Г
|
II А-Т3
|
1в
|
3.
|
Блок ректификации
|
Ан
|
В-1Г
|
II А-Т3
|
1в
|
4.
|
Насосная горячая
|
Ан
|
В-1Г
|
II А-Т3
|
1в
|
5.
|
Насосная холодная
|
Ан
|
В-1Г
|
II А-Т3
|
1в
|
6.
|
Наружная этажерка (пост №1 и №2)
|
Ан
|
В-1Г
|
II А-Т3
|
1в
|
7.
|
Насосная гидрорезки
|
Д
|
Не класс-ся
|
Не класс-ся
|
1б
|
8.
|
Водяная насосная
|
Д
|
Не класс-ся
|
Не класс-ся
|
1б
|
9.
|
Насосная пенотушения
|
Д
|
Не класс-ся
|
Не класс-ся
|
1в
|
10.
|
Операторная
|
Г
|
Не класс-ся
|
Не класс-ся
|
1а
|
11.
|
Отделение дробления
|
В
|
П-II
|
Не класс-ся
|
1в
|
12.
|
Галерея №1
|
Б
|
П-II
|
Не класс-ся
|
1в
|
13.
|
Отделение пересыпки
|
В
|
П-II
|
Не класс-ся
|
1в
|
14.
|
Галерея №2
|
В
|
П-II
|
Не класс-ся
|
1в
|
15.
|
Склад кокса
|
В
|
П-II
|
Не класс-ся
|
1в
|
Для недопущения появления загазованности в промышленных помещениях в
каждой насосной круглосуточно работает вытяжная и приточная вентиляция.
Механизация тяжёлых и трудоёмких работ на установке осуществляется путём
применения передвижного и стационарного подъёмно - транспортного оборудования
(кран-балок различной грузоподъёмности, краны-укосины на колоннах, монорельсов,
поворотных шарнирных устройств, приводных лебёдок, автокранов, грузовых
автомобилей и тягачей).
Компоновка оборудования и расположение зданий, сооружений и эстакад на
установке выполнена с учётом обеспечения свободного подъезда и доступа к
объектам ремонта (теплообменникам, насосам, печам и к другому оборудованию),
позволяющим производить ремонтные работы с применением грузоподъёмных
механизмов, механизированного инструмента и приспособлений.
Всё электрическое оборудование на установке взрывозащищённого исполнения
ГОСТ 12.2.02.-76. Электрооборудование, находящееся на открытой площадке
(кран-укосина, лебёдка) защищены от атмосферных осадков, механических
воздействий. На электроустановках применяются изолирующие и защитные средства,
обеспечивающие электроизоляцию человека от токоведущих частей. Для
предупреждения возникновения опасных искровых разрядов с поверхности
оборудования и тела человека обеспечивается стекание возникающих разрядов
статистического электричества, это достигается тем, что всё оборудование на
установке и трубопроводы заземлено для отвода статического электричества, а на
коксовых площадках имеются увлажняющие устройства так же для снятия
статического электричества (увлажнение кокса).
Для защиты людей от действия электрического тока при прикосновении их к
металлическим корпусам аппаратов, светильников и др., в случае неисправности
изоляции, применяется защитное заземление - преднамеренное электрическое
соединение их с землёй. Сопротивление заземляющего устройства не должно
превышать 4 Ом.
При передвижении нефтепродуктов и легковоспламеняющихся жидкостей, при
истечении пара через свищи трубопроводов и аппаратов, на клиноремённых
передачах и быстровращающихся частях механизмов происходит возникновение
зарядов статистического электричества.
Для предотвращения возникновения и накопления зарядов статистического
электричества все аппараты, ёмкости, трубопроводы, быстровращающиеся части
механизмов заземляются. Присоединение к контуру заземления должно быть не
менее, чем в двух точках.
Одним из импульсов воспламенения горючих веществ, могущих вызвать взрывы,
пожары, вывод из строя оборудования, является молния. Система защиты от молнии
состоит из молниеприёмника, токоотвода и заземления, которое совмещено с
защитным заземлением оборудования.
Проведем расчет заземления для вертикально заглубленных заземлителей
центробежного насоса:
Грунт - суглинок. Заземляющее устройство представляет собой прямоугольник
размером 8*16 м. В качестве вертикальных стержней предполагаются применять
угловую сталь с шириной полки 40 мм, длинной 2,5м, в качестве соединительной
полосы - стальную шину сечением 40*4 мм. Имеются естественные заземлители с
сопротивлением растеканию 4,8 Ом.
Расчетное удельное сопротивление грунта с учетом климатического
коэффициента ψ= 1,4, тогда:
ρрасч = 700 *1,4 = 980 Ом*м
Сопротивление одиночного вертикального заземлителя находим, принимая
эквивалентный диаметр стержней d = 095 * 0,04= 0,038 м, тогда
Длина соединительной полосы равна периметру прямоугольника (8+16)*2=48 м.
Вертикальные стержни размещаются через каждые 2 метра, значит 24 стержня.
Сопротивление соединительной полосы находим по формуле:
а с учетом ηn = 0.44, находим
Окончательно определяем число вертикальных стержней, принимая
предварительно их число - 4, длину 2,5 м и расстояние между ними 2 м, находим
коэффициент использования
ηст = 0,47, откуда
Таким образом, для заземления центробежного насоса потребуется контур
заземления из 24 вертикальных стержней.
5.1.4 Пожарная безопасность производства кокса
Пожарная безопасность представляет собой единый комплекс организационных
и технических мероприятий, направленных на предупреждение пожаров и взрывов. По
пожарной опасности установка типа 21-10/7 относится к группе «А».
На проектируемом производстве для обеспечения пожарной безопасности
выполнены следующие мероприятия:
) сооружения и здания на территории соответствуют I и II степени огнестойкости;
) наиболее подвергающиеся при пожаре действию огня металлоконструкции,
«юбки» колонн и кабельные прокладки оборудованы соответствующей теплоизоляцией
с пределом огнестойкости 0,75…2,0 часа.
На установке имеются следующие средства пожаротушения [44]:
- система пожарного водопровода;
- система пожаротушения пеногенераторными установками,
установленными в горячей насосной;
- паровая завеса вокруг печей П-1, П-2;
- система паротушения;
- пожарный инвентарь: пожарные ящики с песком, лопаты,
огнетушители ОУ-2 и ОХП-10
Таблица 5.6 - Пожароопасные свойства веществ и материалов.
№ п/п
|
Наименование сырья, готовой продукции.
|
Агрегатное состояние
|
Температура, °С
|
Концентрационный предел воспламенения, % объём.
|
|
|
|
вспышки
|
воспламе- нения
|
самовоспла менения
|
Нижний предел
|
Верхний предел
|
1
|
2
|
3
|
4
|
5
|
6
|
7
|
8
|
1.
|
Сырьё коксования
|
горючая жидкость
|
90
|
-
|
350
|
2,0
|
3,0
|
2. 2.1. 2.2
|
Компоненты сырья Экстракт Дуосол Гудрон с установок АВТ
|
горючая жидкость битуминозное состояние
|
270 204 тление
|
270 310
|
370 380-397
|
- -
|
- -
|
2.3. 2.4
|
Крекинг-остаток Асфальт
|
горючая жидкость горючее вещество
|
130 204
|
138 -
|
380 485
|
- -
|
- -
|
3.
|
Газ коксования
|
Горючий газ
|
-
|
-
|
600
|
3,2
|
66,0
|
4.
|
Бензин коксования
|
легковоспламен жидкость
|
30
|
-
|
345
|
0,93
|
5,1
|
5.
|
Лёгкий газойль
|
горючая жидкость
|
>40
|
62-119
|
300-345
|
2,0
|
3,0
|
6.
|
Тяжёлый газойль
|
горючая жидкость
|
70
|
-
|
300-400
|
-
|
-
|
7.
|
Кокс электродный
|
твёрдое горючее вещество
|
|
205-235
|
535-625
|
500 г/м³
|
-
|
У входа в операторную установлен номерной извещатель, включённый в
комплексную слаботочную сеть завода.
На случай пожара конструкций печей П-1, П-2 предусмотрена подача
«острого» пара в камеру сгорания и змеевики печей.
С целью противопожарной защиты имеются два лафетных ствола для блока
колонн и печей. По всей высоте колонн проложены сухотрубы и линии паротушения.
Наружное пожаротушение на установке осуществляется из пожарных гидрантов,
расположенных на сети противопожарного водопровода завода.
По периметру склада кокса предусмотрены пожарные гидранты.
Предусмотрены дренчерные установки в отделении пересыпки, дробильном
отделении и галереях №1 и №2 с ручным включением в работу для тушения пожара в
случае возгорания кокса.
Для тушения пожара в закрытой насосной и на наружной установке
предусматривается автоматическая установка пожаротушения высокократной
воздушно-механической пеной.
При возникновении пожара в насосной воды и присадок при температуре
воздуха в насосной 120-150оС срабатывает датчик пожарной сигнализации и
выдаётся сигнал на автоматическое включение насоса Н-23 подачи воды на
пенотушение, открытие электрозадвижек на линиях подачи раствора в насосную и
пенообразователя в смеситель ПС-2 из ёмкости Е-17/1,2.
5.2 Экологичность исследуемого процесса
На установке замедленного коксования существуют выбросы в атмосферу
вредных веществ и химически загрязненные стоки.
На установке не предусмотрены методы переработки отходов, но существуют
методы их утилизации и снижения их количества. Например, в соответствии с программой
сокращения вредных газовых выбросов в атмосферу и уменьшения потери жидких
нефтепродуктов на установке замедленного коксования применяется схема пропарки
коксовых камер с удлинением времени пропарки в ректификационную колонну.
Пропарка коксовых камер является необходимой технологической операцией и
связана с неизбежными загрязнениями окружающей среды.
Все выбросы в окружающую среду представлены в таблице 5.7.
Объем холодных и горячих выбросов в атмосферу с установки имеет большое
значение, поэтому необходим постоянный контроль за этими процессами. Для
примера приведен метод аналитического контроля за холодными выбросами.
Произведем расчёт рассеивания выбросов из мультициклона М-1, который
очищает коксовую пыль аспирационной системы ЦК-1 галереи транспортировки кокса
в склад.
Расчёт максимальной концентрации коксовой пыли в приземлённом слое
(мг/м3) при его выбросе из одиночного источника с круглым устьем ведется по
формуле:
,
где А1 - коэффициент, зависящий от температурной стратификации атмосферы
(А1=200); М - количество вредного вещества, выбрасываемого в атмосферу, г/с; F - коэффициент, учитывающий скорость
оседания вредных веществ в атмосферном воздухе; n - коэффициент, учитывающий условия выхода газовоздушной
смеси из устья источника выброса; K - коэффициент (в с/м2).
Коэффициент n определяется в
зависимости от скорости воздуха (Vм),
определяемого формулой:
,
где
Н - высота источника выброса от уровня земли, м; ∆Т - разность температур
между выбрасываемой смесью и окружающим воздухом, оС; V1 - объём
газовоздушной смеси, м3/с.
,
где
D - диаметр устья источника выброса, 0,2 м;
Wo - средняя
скорость выхода газа из устья, 4 м/с;
м/с
Таблица 5.7- Характеристика выбросов вредных веществ в атмосферу
Наименование сброса
|
Количество образования выбросов по видам, м3/ч
|
Периодичность выбросов
|
Установленная норма содержания загрязнений в выбросах,
мг/м3
|
1
|
2
|
3
|
4
|
Блок печей - дымовая труба П-1, П-2 - пропарка
|
68731,2 14144,4
|
постоянно
|
оксид углерода - 2,776 сернистый ангидрид - 143,987
углеводороды - 10,999 оксид азота- 127,75 диоксид азота - 6,757 сероводород -
0,3 метилмеркаптан- 0,298
|
Горячая насосная -насосы
|
2120,4
|
постоянно
|
углеводороды -1023,769
|
Холодная насосная - насосы
|
2120,4
|
постоянно
|
пары бензина - 74,703 углеводороды - 28,862
|
Яма накопитель
|
2120,4
|
постоянно
|
пыль кокса - 13,243
|
Галерея транспортировки кокса в склад - приемный бункер
-дефлектор -аспирационная система ЦК-1 -аспирац. система ЦК-2 -аспирац.
система ЦК-3 -аспирац. система ЦК-4 -загрузка в ж/д вагоны
|
2120,4 1058,4 1450,8 1296,0 4690,8 651,6 2120,4
|
постоянно
|
пыль кокса - 12,733 пыль кокса - 102,041 пыль кокса -
44,665 пыль кокса - 25,0 пыль кокса - 46,815 пыль кокса - 17,956 пыль кокса -
101,868
|
Аппаратный двор -аварийный выброс К-1 -воздушка К-1
|
1778,4 1.8
|
постоянно
|
углеводороды - 100000,0
|
Аппаратный двор технологической установки
|
10300806,0
|
|
углеводороды - 5,197 сероводород - 0,012 метилмеркаптан -
0,002
|
-воздушка Е-1 -воздушка Е-13 -воздушка Е-30 -воздушка Е-31
-воздушка К-4
|
1.8 1,8 1,8 1,8 1,8
|
|
углеводороды - 6468000,0 углеводороды - 9999999,99
углеводороды - 9999999,99 углеводороды - 1380000,0 углеводороды - 12000,0
|
Так как Vм < 0,3, то n = 3.
Определим коэффициент K по
формуле:
=
2 для пылей, так как степень очистки мультициклоном выше 90%.
С
учетом очистки мультициклоном до 98-99%, количество вредного вещества составит:
М
= 0,01*1450,8 м3/ч *1,95 г/м3 = 28,2906 г/ч = 0,00786 г/с.
Тогда:
Установленная
норма содержания загрязнений в выбросах 0,009 г/с. ПДК максимально разовое
коксовой пыли составляет 6 мг/м3, а в воздухе рабочих помещений по ГОСТ
12.1.005-88 ПДК составляет 4 мг/ м3.
Таким образом, максимальное содержание вредного вещества в приземном слое
атмосферы не превышает установленную норму, но превышает ПДК.
Также при проведении технологического процесса после пропарки коксовых
камер образуется вода, насыщенная содержанием нефтепродуктов, их предельная
норма содержания в сточных водах.
Для контроля загрязнения сточных вод вредными веществами применяется
периодический метод контроля. Лабораторный периодический контроль загрязнения
сточных вод регламентируется графиком.
На установке предусмотрены следующие виды канализации: водосток,
предназначенный для отвода дождевых и талых вод, а также сточных вод
производства в промышленно - ливневую канализацию и фекальная канализация,
предусмотренная для стоков от душевых и бытовых помещений.
Характеристика образованных сточных вод представлена в таблице 5.8.
Определим экологический тип установки замедленного коксования.
Так как на установке не предусмотрена переработка отходов производства, а
только их частичная утилизация, то установку можно отнести к производству с
возвращением отходов для переработки природе. Следует заметить, что переработка
этих отходов гарантирована внешней и внутренней инфраструктурой
нефтеперерабатывающего завода.
Таблица 5.8 - Характеристика сточных вод
Наименование стока
|
Количество образования сточных вод, м3/ч
|
Периодичность выбросов
|
Место сброса
|
Установленная норма содержания загрязнений в стоках
|
1
|
2
|
3
|
4
|
5
|
Вода с холодильников, сальников насосов, скруббера Е-8
|
16
|
постоянно
|
Сбрасывается в канализацию промстоков
|
нефтепродукты, мг/л, не более 800
|
Вода после охлаждения реакторов с коксом
|
80,0
|
по мере заполнения реактора коксом
|
Сбрасывается в канализацию промстоков
|
сульфиды, мг/дм3, не более 20
|
Определим характеристику вредности технологического процесса:
В = Ва*Вв*Вт,
где Ва, Вв, Вт - частные коэффициенты, характеризующие замкнутость
процесса по использованию соответственно воздуха, воды и твердых материалов.
;
;
;
В этих формулах Vач, Vвч - объем забираемых извне чистого
воздуха и воды, Vав, Vвв - объем возвращаемых во внешнюю
среду воздуха и воды, Gг, Gu - масса готовой продукции и
полезноиспользованных материалов и масса исходных материалов соответственно.Тогда:
В = 0,91*0,92*0,902=0,76. Таким образом, процесс замедленного коксования
относится к частично замкнутым процессам, так как 0,5 < B < 1.
6.
ЭКОНОМИЧЕСКОЕ ОБОСНОВАНИЕ СОВЕРШЕНСТВОВАНИЯ ПРОЦЕССА ЗАМЕДЛЕННОГО КОКСОВАНИЯ
Проектное решение состоит в увеличении продолжительности работы печи
разогрева сырья за счет снижения возможности закоксовывания змеевиков этой
печи. Для этого устанавливается циклон для очистки газов коксования от коксовой
мелочи. Применение циклона позволит интенсифицировать процесс, тем самым
увеличиться выход светлых дистиллятов, газов и кокса.
6.1 Обоснование выбора района размещения
Проектируемое производство размещено на территории ООО
«ЛУКОЙЛ-Волгограднефтепереработка». Выбор района размещения обусловлен
следующими факторами:
производство располагается в относительной близости к сырьевой базе;
проектируемое производство обеспечивается необходимыми
топливно-энергетическими ресурсами, вырабатываемыми на данном предприятии или
находящимися в относительной близости;
географическое расположение завода выбрано с учетом экологических
факторов - в отдалении от населенных пунктов в связи с вредностью и
взрывоопасностью производств.
6.2 Производственная структура и структура управления
Производственная структура включает в себя следующие
элементы:
1.
Цех
2.
Технологические
стадии
3.
Технологические
узлы
4.
Технологические
аппараты
Структура управления проектируемого производства:
1. Руководители:
·
Начальник
установки
·
Механик установки
2. Рабочие:
·
Оператор 4
разряда
·
Оператор 5
разряда
·
Оператор 6
разряда
6.3 Расчет производственной мощности
Производственная мощность установки замедленного коксования представляет
собой максимально возможный выпуск кокса за год при условии полного
использования оборудования по времени и по производительности, рациональной
организации производства, труда и управления. Расчет производственной мощности
произведем по основному аппарату основной стадии процесса замедленного
коксования с учетом непрерывности производства [45]:
Мнх =Пх∙С∙n∙Тэф
,
С=0,274 - выход готовой продукции с единицы сырья;
n - количество установленных параллельно в отделении единиц
однотипного ведущего оборудования, за исключением резервного;
Для оборудования непрерывного действия Тэф
определяется как
где ТКАЛ - годовой календарный фонд времени, равный 365 дней или 8760
часов;
ТВЫХ, ТПР - время, соответственно, выходных и праздничных дней в году.
Данное слагаемое в ТЭФ не учитывается, т.к. установка работает непрерывно;
ТППР - время простоя оборудования в связи с проведением планово -
предупредительных ремонтов в течении года;
ТН.Т.О. - время неизбежных технологических остановок, принимаем с
увеличением времени работы печи разогрева сырья:
ТН.Т.О. = 1 нед.=168 час.
Определим среднегодовой простой оборудования в ремонте:
. Нормативное количество ремонтов всех видов за ремонтный цикл (R)
рассчитывается по формуле:
где
RЦ - нормативная продолжительность ремонтного цикла, ч.
Принимаем продолжительность ремонтного цикла 2 года=17520 час;
ТТЕК
- нормативный межремонтный период для текущих ремонтов, ч. Принимаем равным 4
месяца=2880 час.
Нормативное
количество средних ремонтов за ремонтный цикл (RC):
где
ТС - нормативный межремонтный период для средних ремонтов, 1 год = 8760 ч.-
нормативное число капитальных ремонтов за ремонтный цикл, RK =1.
.
Нормативное время простоя оборудования в ремонте за ремонтный цикл (ТПР):
где
RТЕК, RС, RК - нормативная продолжительность простоя
оборудования, соответственно в текущем, среднем и капитальном ремонтах, ч.
.
Среднегодовой простой оборудования в ремонте (λ =2 - число лет в ремонтном цикле):
Определим
годовой эффективный фонд времени работы оборудования:
Так
как на установке нет параллельно работающего оборудования, то n=1.
Производственная мощность:
6.4 Расчет единовременных затрат
В состав единовременных затрат включаются капитальные
вложения и другие затраты единовременного характера, необходимые для создания и
использования продукции вне зависимости от источников финансирования.
Сумма единовременных затрат на осуществление
мероприятия (в году расчетного периода) определяется по формуле [45]:
пр - затраты научно-исследовательские,
экспериментальные, конструкторские, технологические и проектные работы
(производственные затраты) и прочие затраты, связанные с подготовкой
производства;
Ktос - затраты на формирование оборотных средств;
Ktоб - затраты на приобретение, доставку, монтаж, наладку и
освоение
оборудования; стоимость строительства зданий и
сооружений, затраты на необходимые производственные площади и другие элементы
основных фондов, непосредственно связанные с осуществлением проекта;
Ktсэ - затраты на предотвращение отрицательных социальных,
экологических и других последствий.
Капитальные затраты, связанные со строительством
проектируемого производства определяют в соответствии с выражением:
1
- стоимость зданий и сооружений,
К2
- стоимость основного и вспомогательного оборудования,
К3
- стоимость производственного инвентаря и инструментов,
К4-
прочие затраты.
Таблица 6.1 - Стоимость зданий, сооружений и оборудования проектируемого
производства
№ п./ п.
|
Наименование групп фондов
|
Балансовая стоимость, руб.
|
Норма амортизации, %
|
Сумма годовых амортизационных отчислений, тыс. руб.
|
1
|
2
|
3
|
4
|
5
|
1.
|
Здания
|
|
|
|
1.1
|
Компрессорная
|
1834101
|
1,7
|
31,2
|
1.2
|
Насосная воды
|
4146487
|
1,7
|
70,49
|
1.3
|
Операторная
|
943180
|
1,7
|
16,03
|
1.4
|
Весовая
|
149332
|
1,7
|
25,39
|
1.5
|
Насосная
|
1113454
|
1,7
|
18,93
|
1.6
|
Трансф. подстанция
|
6146433
|
1,7
|
104,5
|
1.7
|
Склад кокса
|
7494642
|
1,7
|
127,4
|
Итого:
|
21827629
|
|
371,07
|
2.
|
Сооружения
|
|
|
|
2.1
|
Постаменты
|
10960690
|
1,7
|
16,43
|
2.2
|
Площадки
|
966712
|
1,7
|
186,33
|
2.3
|
Металлоконструкции
|
5830239
|
1,7
|
99,11
|
Итого:
|
17757641
|
|
301,88
|
3.
|
Передаточные устр-ва
|
|
|
|
3.1
|
Техн.трубопроводы
|
5990391
|
9
|
539,1
|
3.2
|
Эл. освещение
|
2316291
|
9
|
208,5
|
3.3
|
Подъемно - транспортное оборудование
|
396424
|
9
|
35,7
|
Изоляция трубопроводов
|
1315498
|
9
|
118,4
|
3.5
|
Сантехнические сети
|
62639
|
|
5,64
|
Итого:
|
10081243
|
|
907,31
|
4.
|
Рабочие машины и оборудование
|
117018439
|
9
|
10531,7
|
5.
|
Энергетические машины
|
10499841
|
9
|
944,99
|
6.
|
Приборы КИПиА
|
3125410,58
|
9
|
281,29
|
7.
|
Прочие основные фонды
|
41387174,22
|
9
|
3724,85
|
Итого:
|
172030864,8
|
|
15482,83
|
Всего:
|
221697377,8
|
|
17063,09
|
Таблица 6.2 - Сводная стоимость затрат на строительство проектируемого
производства
Наименование групп фондов
|
Стоимость, руб.
|
% к итогу
|
1
|
2
|
3
|
1.Здания
|
21827629
|
9,8
|
2.Сооружения
|
17757641
|
8,0
|
3.Передаточные устройства
|
10081243
|
4,5
|
4.Рабочие машины и оборудование
|
117018439
|
52,8
|
5.Энергетические машины
|
10499841
|
4,7
|
6.Приборы КИПиА
|
3125411
|
1,5
|
7.Прочие основные фонды
|
41387174,22
|
18,7
|
Всего
|
221697377,8
|
100
|
.5 Расчет численности промышленно-производственного персонала
Явочная численность основных рабочих-повременщиков
рассчитывается на основе норм обслуживания [46]:
Чяв
- явочная численность, чел.
Нобс
- норма обслуживания,
m - число
рабочих мест (или число единиц оборудования),
d - количество
смен в сутки.
Списочная
численность включает явочную и подменную численность, необходимую для
обслуживания производства в период предоставления рабочим выходных дней,
отсутствия на работе по причинам законных невыходов и т.д.
Чсп
- списочная численность, чел;
Кнепр
- коэффициент пересчета.
Коэффициент
пересчета для непрерывного производства определяется следующим образом:
кал
- календарный фонд рабочего времени (1560 ч.);
Fэф - эффективный годовой фонд работы рабочего Fэф = 1100 ч.
Расчетные данные по определению численности рабочих сведены в таблице
6.3.
Таблица 6.3 - Расчет численности рабочих
Наименование профессий
|
Тарифный разряд
|
Число рабочих в смену
|
Число смен в сутки
|
Явочное число рабочих
|
Коэффициент пересчета
|
Списочное число рабочих
|
Основные рабочие:
|
|
|
|
|
|
|
Оператор
|
6
|
1
|
2
|
2
|
1,42
|
5
|
Оператор
|
5
|
6
|
2
|
12
|
1,42
|
17
|
Оператор
|
4
|
11
|
2
|
22
|
1,42
|
31
|
Машинист
|
4
|
2
|
2
|
4
|
1,42
|
6
|
Вспомогательные рабочие:
|
|
|
|
|
|
|
Слесарь
|
6
|
1
|
1
|
1
|
1,1
|
1
|
Итого рабочих:
|
|
21
|
|
41
|
|
60
|
Штатная численность руководителей и специалистов
определяется исходя из организационной структуры управления производством и
представлена в виде таблицы 6.4.
Таблица 6.4. Штатная численность руководителей и
специалистов
Наименование должностей
|
Число штатных единиц
|
Руководители:
|
|
Начальник установки
|
1
|
Специалисты:
|
|
Механик установки
|
1
|
6.6 Определение себестоимости продукции
6.6.1 Расчет затрат на оплату
труда
При определении годового фонда оплаты труда
производственных рабочих рассчитывается фонд основной и дополнительной
заработной платы.
Годовой тарифный фонд определяется как [46]:
где
Чспi - списочная численность рабочих i - го разряда;
Тэф
- годовой эффективный фонд рабочего времени, ч;
Ci - часовая
тарифная ставка рабочего данного разряда, руб.
Годовой
тарифный фонд операторов 6 разряда:
Рабочие,
работающие в 2х и 3х сменных режимах, получают доплату за работу в вечернюю
смену в размере 20 %, за работу в ночное время - 40 % часовой тарифной ставки
за каждый час работы в смене.
-
количество смен; к - доля вечернего времени в смене.
Доплаты
операторам 6 разряда:
Доплата
рабочим непрерывного производства за работу в дни государственных праздников:
Ссм
- сменная тарифная ставка рабочего соответствующего разряда, руб.;
п
- число праздничных дней в году, п = 8.
Доплата
операторам 6 разряда за работу в праздничные дни составит:
Процент
дополнительной зарплаты к фонду основной зарплаты:
Фонд
основной заработной платы операторам 6 разряда:
Процент
дополнительной зарплаты операторам 6 разряда:
Следовательно,
общий фонд оплаты труда операторов 6 разряда:
Результаты
расчета оплаты труда рабочих сводим в таблицу 5.
Таблица 6.5. Расчет фонда оплаты труда
производственных рабочих
Должность разряд)
|
Число рабочих
|
Часовая тарифная ставка, руб.
|
Тэф.ч
|
ФЗПтар, тыс. руб.
|
Доплаты, тыс. руб.
|
ФОЗП. тыс. руб.
|
Здоп, тыс. руб
|
ОФЗП, тыс. руб.
|
|
|
|
|
|
В вечернее время
|
В ночное время
|
В праздники
|
|
|
|
Основные рабочие: Оператор 6
|
5
|
63,1
|
1872
|
590,62
|
29,531
|
118,124
|
12,115
|
750,39
|
105,055
|
855,445
|
Оператор 5
|
17
|
54,7
|
1872
|
1740,77
|
87,039
|
348,154
|
36,758
|
2212,721
|
309,78
|
2522,501
|
Оператор 4
|
31
|
47,7
|
1872
|
2768,13
|
138,407
|
553,626
|
54,95
|
3515,113
|
492,116
|
4007,229
|
Машинист 4
|
6
|
47,7
|
1872
|
535,77
|
26,785
|
107,154
|
9,158
|
678,867
|
95,041
|
773,908
|
Вспогательн. рабочие Слесарь 6
|
1
|
63,1
|
2560
|
161,54
|
-
|
-
|
-
|
161,54
|
22,616
|
184,156
|
Итого
|
60
|
|
|
5796,83
|
281,762
|
1127,058
|
112,981
|
7318,631
|
1024,608
|
8343,239
|
Расчет фонда оплаты труда руководителей, специалистов
и служащих
Фонд оплаты труда руководителей, специалистов и
служащих рассчитывается исходя из должностных окладов и количества штатных
единиц. К фонду зарплаты по должностным окладам прибавляются доплаты за работу
в вечерние и ночные часы, за работу в праздничные дни.
Дополнительная заработная плата определяется как:
где
Зосн - основной фонд зарплаты, тыс. руб.;
Тдоп
- среднегодовое количество дней законных невыходов, Тдоп = 30 дней.
Фонд
основной заработной платы механика составляет
Дополнительная
зарплата механика составит:
Результаты
расчета оплаты труда руководителей, специалистов и служащих сводим в таблицу
6.6.
Таблица
6.6. Расчет фонда оплаты труда руководителей, специалистов
Должность
|
Число штатных единиц
|
Месячный оклад, тыс.руб
|
ФЗП. За 11 мес. тыс. руб.
|
Премии, тыс. руб.
|
Здоп, тыс. руб.
|
ОФЗП, тыс. руб.
|
Начальник установки
|
1
|
25,562
|
281,182
|
112,473
|
32,355
|
426,01
|
Механик установки
|
1
|
22,21
|
244,31
|
97,724
|
28,112
|
370,146
|
Итого:
|
2
|
|
525,492
|
210,197
|
60,467
|
796,156
|
6.6.2 Определение расходов на содержание и
эксплуатацию оборудования
Таблица 6.7- Смета расходов на содержание и
эксплуатацию оборудования
Статьи расходов
|
Сумма, тыс. руб.
|
Примечание
|
1. Амортизация производственного оборудования и
транспортных средств
|
10531,7
|
Данные таблицы 10.1.
|
2. Эксплуатация оборудования и транспортных средств: 2.1
Основная и дополнительная зарплата вспомогательных рабочих, обслуживающих
оборудование и транспортные средства 2.2 Отчисление на социальные нужды 2.3
Прочие расходы
|
184,156 48,304 1170,184
|
26,23% от статьи 2.1 1% от стоимости оборудования и
транспортных средств
|
3. Износ малоценных и быстроизнашивающихся инструментов и
приспособлений
|
585,092
|
0,5% от стоимости оборудования
|
4. Прочие расходы
|
62,597
|
0,5% от затрат по статьям 1,2,3.
|
Всего
|
12582,033
|
|
6.6.3 Определение цеховых (общепроизводственных)
расходов
Таблица 6.8 - Смета цеховых расходов
Статьи расходов
|
Сумма, тыс. руб.
|
Примечание
|
1. Содержание аппарата управления 1.1 Зарплата
руководителей. специалистов и служащих 1.2 Отчисления на социальные нужды
|
796,156 208,832
|
Данные таблицы 10.6 26,23 % от статьи 1.1
|
2. Амортизационные отчисления по зданиям, сооружениям, инвентарю
|
672,95
|
Данные таблицы 10.1
|
3. Содержание зданий, сооружений, инвентаря:
|
395,853
|
1 % от стоимости зданий и сооружений
|
4. Охрана труда
|
913,94
|
10 % от зарплаты всего персонала цеха
|
5. Прочие расходы
|
149,387
|
5% от суммы затрат по статьям 1, 2,3,4
|
Всего
|
3137,118
|
|
Для расчета себестоимости продукции составим проектную
калькуляционную таблицу 6.9.
Таблица 6.9 - Проектная калькуляция себестоимости 1 т
керосина
Статьи калькуляции
|
Планово- загот. цена. тыс. руб. /ед
|
Затраты на годовой выпуск
|
Себестоимость единицы продукции
|
|
|
|
количество, нат.ед.
|
сумма, тыс.руб.
|
норма расхода, нат.ед. /т
|
сумма, тыс.руб./т
|
|
1. Сырье и материалы 1.1 Смесь тяжелых нефт. остатков
|
1,2544
|
276000
|
346214,4
|
3,6
|
4,516
|
|
2.Полуфабрикаты 2.1 газ коксования 2.2 бензин 2.3тяж.газойль
2.4 кокс
|
30360 24132 69052 73968
|
4614,7 79635,6 172699,1 65091,8
|
0,4 0,315 0,902 0,966
|
0,0608 1,0395 2,2559 0,85
|
|
Итого за вычетом попутных продуктов
|
|
|
24146,2
|
|
0,3098
|
|
3. Энергоресурсы: 3.1 Вода оборотная
|
0,07
|
51257
|
3587,99
|
0,67
|
0,047
|
|
3.2 Пар
|
0,2538
|
21578,4
|
5476,6
|
0,282
|
0,0716
|
|
3.3 Природный газ
|
0,606
|
22,97
|
13,92
|
0,0003
|
0,0002
|
|
3.4 Газ собственный
|
0,152
|
10732,9
|
1631,4
|
0,14
|
0,0213
|
|
3.5 Электроэнергия
|
0,0018
|
7158050
|
12884,49
|
93,5
|
0,1683
|
|
3.6 Cжатый воздух
|
0,001
|
822020
|
822,02
|
10,74
|
0,0107
|
|
Итого энергетических затрат:
|
|
|
24416,42
|
|
0,3298
|
|
4. Затраты на оплату труда основных производственных
рабочих
|
-
|
-
|
8159,083
|
-
|
0,107
|
|
5. Отчисления на социальные нужды
|
-
|
-
|
48,304
|
-
|
0,0006
|
|
6.Расходы на содержание и эксплуатацию оборудования
|
-
|
-
|
12582,033
|
-
|
0,1643
|
7. Цеховые расходы
|
-
|
-
|
3137,118
|
-
|
0,041
|
Итого: цеховая себестоимость
|
|
|
59919,71
|
|
0,9525
|
8. Общезаводские расходы
|
|
|
1703,56
|
|
0,0223
|
9. Прочие производственные расходы
|
-
|
-
|
374,78
|
-
|
0,0049
|
Итого: производственная себестоимость
|
-
|
-
|
61998,05
|
-
|
0,9797
|
10. Внепроизводст-венные расходы
|
|
|
619,98
|
|
0,0081
|
Итого: полная себестоимость
|
|
|
62618,03
|
|
0,9878
|
|
|
|
|
|
|
|
|
|
6.7 Расчет потребности в оборотных средствах
Величина нормируемых оборотных средств рассчитывается по каждому
отдельному элементу.
Норматив оборотных средств по сырью, материалам и топливу определяется по
формуле [45]:
,
где
Нзап - норма запаса в днях;
Р
- расход сырья, материалов, топлива;
Ц
- цена единицы сырья.
Норматив
по сырью:
тыс.
руб.
по
топливу:
тыс.
руб.
Норматив по прочим затратам определяется как 0,5% от балансовой стоимости
оборудования:
Нмбп
=
= 585,1 тыс. руб.
Норматив
по запасным частям для ремонта определяется как 1,5% от баланса стоимости
оборудования:
Нз.п.ч.
=
= 1755,3 тыс. руб.
Норматив
оборотных средств по готовой продукции определяется:
где ТП
- годовой объем производства в оптовых ценах:
тыс.
руб.
Норматив
в незавершенном производстве не рассчитывается, т.к. процесс является
непрерывным. Нормативы оборотных средств сводятся в таблицу 10.
Таблица 6.10 - Расчет нормативов оборотных средств
№ п/п
|
Элементы оборотных средств
|
Норматив, тыс. руб.
|
1
|
Сырьё
|
5770,24
|
2
|
Топливо и энергия
|
1356,47
|
3
|
Прочие затраты
|
585,1
|
4
|
Запасные части для ремонта
|
1155,3
|
5
|
Готовая продукция
|
25734,7
|
6
|
Итого оборотных нормируемых средств
|
34601,81
|
7
|
Ненормируемых оборотных средств (9% от ст.6)
|
3114,16
|
Всего оборотных средств (ст.6 + ст.7):
|
37751,97
|
6.8 Определение экономической эффективности
Определим экономический эффект проекта по формуле [47]:
,
где
Т - расчетный период осуществляемого проекта;- текущий год расчетного
периода;н, tк - соответственно начальный и конечный год расчетного периода;
αt - коэффециент приведения по факту времени;
∆ПТ
- прибыль от реализации продукции в году t проектируемого;
Зt
- затраты на осуществление проекта в году t.
Расчетный период равен 10 годам, то есть tн = 0 и tк =
9.
Цена единицы продукции с учетом средних рыночных цен и
НДС (18%) составляет 17,288 тыс. руб./т.
Выручка реализации:
Налог
на прибыль начисляется в размере 24% (302611,7тыс.руб.),
таким
образом, ∆П1,…,9= 958270,4 тыс.руб, а ∆П0=0 тыс.руб.
Величину затрат определим как сумму затрат на строительство, стоимости
сырья, топлива, энергии и стоимости нового оборудования и его монтажа.
Тогда величина затрат:
З0 = 221697,38+62618,03+120000 = 404315,41тыс.руб.
Расчетный период равен 10 годам.
Тогда экономический эффект составит:
Для
определения экономической эффективности проектируемого предприятия рассчитаем
его основные технико-экономические показатели и сравним с аналогичными
показателями производства-аналога.
Рассмотрим
материальный баланс установки до и после совершенствования:
Таблица
6.11 - Материальный баланс установки замедленного коксования
Взято:
|
Производство аналог, тыс. т/год
|
Проектируемое производство, тыс т/год
|
Мощность по сырью
|
276
|
276
|
Получено: - газ - бензин - легкий газойль - тяжелый газойль
- кокс - производственные потери
|
28,84 22,92 72,73 65,60 70,27 2,48
|
30,36 24,13 76,56 69,05 74,29 1,56
|
Производительность по сырью
|
262,854
|
275,085
|
Таким образом, увеличивается производительность установки по светлым
дистиллятам и газам на 5,26%, снижаются потери, увеличивается выход кокса на
5,7%.
Определим срок окупаемости принятого технологического решения:
Величина прибыли, получаемой ежегодно, одинакова и срок окупаемости
определим как отношение величины инвестиций к чистой годовой прибыли. Величину
инвестиций определим как сумму затрат на строительство и стоимости сырья,
топлива, энергии.
Тогда величина инвестиций: IC=370630,82+62618,03=433249,12
тыс.руб.
Тогда срок окупаемости:
Срок
окупаемости при округлении составит пять месяцев.
Сравнение
основных показателей эффективности установки замедленного коксования до и после
совершенствования представлены в таблице 6.12.
Таблица
6.12- Показатели эффективности установки замедленного коксования
Наименование показателей
|
Проектируемое производство
|
Производство аналог
|
Отклонение
|
|
|
|
Абсолютное
|
Относительное
|
1
|
2
|
3
|
4
|
5
|
1. Годовой выпуск продукции
|
|
|
|
|
1.1. Натуральных ед. в год (т)
|
76556
|
72728
|
3828
|
5,26
|
1.2. В стоимостном выражении, тыс. руб
|
1323500
|
1257325
|
66175
|
5,26
|
2. Себестоимость
|
|
|
|
|
2.1. единицы продукции, руб.
|
817,94
|
814,31
|
3,63
|
0,45
|
2.2 годового выпуска, тыс. руб.
|
62618,03
|
59223,14
|
3394,89
|
5,7
|
3. Прибыль от реализации продукции, тыс. руб.
|
1260881,97
|
1198101,86
|
62780,11
|
5,23
|
4. Рентабельность
|
|
|
|
|
4.1. продукции, %
|
18,3
|
18,2
|
0,1
|
0,5
|
4.2. производства, %
|
22,3
|
18,9
|
3,4
|
17,99
|
5. Фонд оплаты труда на одного работающего в год, тыс. руб.
|
139,05
|
139,05
|
0
|
0
|
6. Фонд средств потребления на одного работающего в год,
тыс. руб.
|
629,2
|
629,2
|
0
|
0
|
7. Выработка продукции в стоимостном выражении на одного
работающего, тыс. руб.
|
22058,3
|
20995,4
|
1062,9
|
5,06
|
8. Капитальные вложения, тыс. руб.
|
370630,82
|
370460,82
|
170
|
0,046
|
9. Фондоотдача основных фондов, руб/руб
|
6
|
5,75
|
0,25
|
4,352
|
10. Коэффициент оборачиваемости оборотных средств, об/год
|
36
|
34
|
2
|
5,88
|
Технико-экономический расчет подтвердил эффективность работы установки.
Затраты на производство в целом по установке составили 62618,03 тыс. руб.
Керосин (печное топливо) является товарной продукцией, оптовая цена (средняя) с
НДС составляет 17288 руб. за тонну. Тогда ориентировочный размер прибыли
составляет 1260881,97 тыс. руб. в год. Срок окупаемости составит 5 месяцев.
Показатели рентабельности свидетельствуют о высокой эффективности. В оценке
эффективности процесса необходимо также принять во внимание тот факт, что
сырьем в данном производстве является смесь остатков других производств.
7. ВЫВОДЫ
1. Проведен анализ теоретических и инженерных основ процесса замедленного
коксования тяжелых нефтяных остатков и научно-технический и патентный анализ
путей улучшения технико-технологических показателей процесса.
Выяснено, что установка циклона на линии отвода парогазовых продуктов
коксования из реактора позволит увеличить производительность установки по коксу
на 5,7%, светлым дистиллятам и газам коксования на 5,26%.
. Разработана новая технологическая схема установки замедленного
коксования и обеспечена её надёжность контрольно-измерительными приборами и
базовой автоматизацией.
3. Проведены инженерно-технологические расчёты основной и вспомогательной
стадий процесса. Расчет с применением пакета прикладных программ AspenTech Hysys показал, что установка циклона для очистки отходящих
парогазовых продуктов коксования c
содержанием коксовой мелочи до 1% масс. позволит отделить 41,89 кг частиц в час
при КПД циклона 96,24 %.
4. Проанализирована безопасность и экологичность установки замедленного
коксования. Установлено, что по противопожарной безопасности установка
относится к категории «А», по классификации взрывоопасных производств относится
к категории «В-1а».
. Проведены технико-экономические расчеты и показана целесообразность
принятого решения. Определено, что период окупаемости предложенного решения
составит 5 месяцев.
СПИСОК ИСПОЛЬЗОВАННЫХ ИСТОЧНИКОВ ИНФОРМАЦИИ
1. Сухоруков,
В.И. Научные основы совершенствования техники и технологии производства кокса /
В.И. Сухоруков. - Е, 1999. - 394 с.
2. Кауфман,
А.А. Теория и практика современных процессов коксования / А.А. Кауфман, В.Д.
Глянченко, С.А. Косогоров. - Е, 2005. - 61 с.
. Непрерывное
коксование - перспективный процесс переработки остатков сернистых и
высокосернистых нефтей / О.Ф. Глаголева [и др.] // Нефтехимия и
нефтепереработка. - 2004. - №1. - с. 18-22.
. Красюков,
А.Ф. Нефтяной кокс/ А.Ф. Красюков.- М.: Химия, 1966.-144 c.
5. Predel,
H. Petroleum Koks - Entwicklung und Tendenzen / H. Predel, M. Nielsen // Erdol
Erdgas Kohle. -2005. - V.121, №10. - s. 348-352.
. Singh,
H. Verkokung der schweren Erdolreste/ H. Singh// Erdol und Kohle. -1991. -
V.29. - s. 67-70.
7. Ахметов,
С.А. Технология глубокой переработки нефти и газа: учеб. пособ. для вузов /
С.А. Ахметов. - Уфа.: Гилем, 2002. - 560 с.
8. Stell,
J. Worldwide Refining Survey / J. Stell // Oil and Gas Journal. - 2002.
-№100/52. - p. 68.
9. Проблемы
повышения работоспособности реакторов установок замедленного коксования / А.А.
Тихонов [и др.] // Нефтехимия и нефтепереработка. - 2001. - №10. - c. 17-19.
. Пат.
2206594 РФ, МПК С10В 55/00. Устройство ввода сырья в реактор для получения
нефтяного кокса / И.Р. Хайрудинов, А.А. Тихонов, Н.С. Гаскаров.- Опубл.
20.06.2003.
. Переработка
смесевого сырья на установке замедленного коксования типа 21-10/3М Ангарского
НПЗ / И.Е. Кузора [и др.] // Нефтехимия и нефтепереработка. - 2002. - №1. - с.
24-28.
. Использование
тяжелой пиролизной смолы в качестве компонента смесевого сырья на установке
замедленного коксования / Н.Е. Кузора [и др.] // Нефтехимия и нефтепереработка.
- 2002. - №8. - c. 13-15.
13. Malik,
F. Delayed coker design considerations and project execution / F. Malik, G.
Ram, F. Gary // NPRA 2002 Annual Meeting. -2002. -№3. - p.17-19.
14. Пат.
2210585 РФ, МПК С10В 55/00. Состав сырья для переработки на установках
замедленного коксования / И.Е. Кузора, В.М. Моисеев, А.И. Юшинов и др.- Опубл.
20.08.2003.
. Пат.
2179175 РФ, МПК С10В 55/00. Состав сырья для получения электродного кокса
улучшенного качества / И.Е. Кузора, О.И. Дошлов, А.И. Елшин и др.- Опубл.
10.02.2002.
. Опыт
эксплуатации и перспективы развития производства электродного кокса на НПЗ ОАО
“АНХК” / А.И.Елшин [и др.] // Нефтехимия и нефтепереработка. - 2003. - №8. - c. 12-15.
. Что
позволяет Омскому НПЗ делать хороший кокс / М.А. Плеханов [и др.] // Нефтехимия
и нефтепереработка. - 2000. - №8. - с. 5-8.
. Выход
продуктов при коксовании нефтяных остатков различного происхождения / И.Е.
Кузора [и др.] // Нефтехимия и нефтепереработка. - 2005. - №2. - c. 7-10.
. Пат.
2079537 РФ, МПК С10В 55/00. Способ получения нефтяного кокса / Г.Г. Валявин,
В.В. Таушев.- Опубл. 20.05.2007.
. Пат.
2331663 РФ, МПК С10В 55/00. Способ получения нефтяного кокса / И.Р. Хайрудинов,
В.В. Зольников, Б.С. Жирнов и др.- Опубл. 20.08.2008. - Бюл. № 23.
. Выбор
и обоснование технологической схемы переработки крекинг-газойлей с получением
игольчатого кокса и высокоиндексного сырья для техуглерода / Г.Г. Валявин [и
др.] // Нефтехимия и нефтепереработка. - 1998. -№9. - c. 26-28.
. Пат.
2067605 РФ, МПК С10В 55/00. Способ получения нефтяного кокса / В.В. Таушев.-
Опубл. 10.10.1996.
. Пат.
2338771 РФ, МПК С10В 55/00. Способ получения низкосернистого нефтяного кокса /
В.З. Мордкович, А.Р. Караева, Е.Ю. Харитонова и др.- Опубл. 20.11.2008. - Бюл.
№ 32.
. Опыт
модернизации коксового производства в ООО “Лукойл-Волгограднефтепереработка” /
B.C. Андреев [и др.] // Нефтехимия и нефтепереработка. - 2002. - №12. -с.
23-27.
. Получение
электродного кокса улучшенной структуры на Волгоградском НПЗ / B.C. Андреев [и
др.] // Нефтехимия и нефтепереработка. - 2002. - №12. -с. 27-30.
. Нефтяной
кокс. Ресурсы сырья и технология прокаливания / О.Ф. Глаголева [и др.] // Химия
и технология топлив и масел. - 2005. - №3. - с. 22-25.
. Образование
агрегативно устойчивых нефтяных эмульсий в процессе замедленного коксования
тяжелых нефтяных остатков и проблемы их переработки / И. Е. Кузора [и др.] //
Нефтехимия и нефтепереработка. - 2006. - №7. - с. 14-17.
. Совершенствование
систем улавливания продуктов, образующихся при прогреве реакторов, пропарке и
охлаждении кокса на установке замедленного коксования / А.А. Тихонов [и др.] //
Нефтехимия и нефтепереработка. - 2006. - №4. c.10-14.
. Пути
оптимизации схемы охлаждения кокса в коксовых камерах на установке замедленного
коксования / И.Е. Кузора [и др.] // Нефтехимия и нефтепереработка. - 2008. -
№2. -c. 7-9.
. Пат.
2339674 РФ, МПК С10В 55/00. Способ замедленного коксования нефтяных остатков и
реактор коксования / В.В. Таушев, И.Р. Хайрудинов, Е.В. Таушева и др.- Опубл.
27.11.2008. - Бюл. № 33.
31. Магарил,
Р.З. Теоретические основы химических процессов переработки нефти / Р.З.
Магарил. - Л.: Химия, 1985 - 280 с.
32. Burke,
N.E., Hobbs R.E., Kashou S.F. Measurement and modeling of Asphaltene
precipitation / N.E. Burke, R.E. Hobbs, S.F. Kashou // Carbon. - 1990. -№ 11. -
p. 1440-1446.
33. Яценко,
Е.А. Производство битумов и кокса. / Е.А. Яценко, В.Ф. Анисимов, М.А. Иващенко
// Нефтехимия и нефтепереработка. - 2005. - №8. - c. 10-12.
. Краткий
справочник физико-химических величин / сост. Н.М. Барон [и др.]; под ред. А.А.
Равделя, А.М. Пономаревой. - 8-е изд. - Л.: Химия, 1983. - 231с.
35. Этапы
становления представлений о механизмах образования нефтяного кокса/ И.Р.
Кузеев, А.М. Бикбулатова, Э.М. Мовсум-заде // Нефтехимия и нефтепереработка. -
2000. - №10. -с. 27-30.
36. Levis,
I.S. Chemistry of carbonization / I.S. Levis // Carbon. - 1982.- V.20.- p.
519-529.
.
Unger, F.G. Grundlegend Aspekte der Chemie der Erdole. Natur der Harze und
Asphaltene / F.G. Unger, L.N. Andrejeva // Erdol und Kohle Erdgas Petrolchemie.
- 1994. -№1. - s.18-23.
38.
Мухаметзянов, И.З. Структурирование в жидкой фазе и фазовые переходы при
термолизе нефтяных остатков: Дис. канд. техн. наук. - Уфа: УНИ, 1990. -207 с.
.Танатаров
М.А. Технологические расчеты установок переработки нефти / М.А. Танатаров. -
М.: Химия, 1987. - 354 c.
.Дытнерский,
Ю.И. Основные процессы и аппараты химической технологии / Ю.И. Дытнерский. -
М.: Химия, 1991. - 496 с.
41. Кушелев,
В.П. Охрана труда в нефтеперерабатывающей и нефтехимической промышленности /
В.П.Кушелев. - М.: Химия, 1983. - 472с.
. Охрана
труда и экологическая безопасность в химической промышленности / А.С. Бобков [и
др.]. - М.: Химия, 1997. - 400с.
.СНиП
21-01-97. Пожарная безопасность зданий и сооружений. - М.: издательство
стандартов, 2000. - 38 с.
. СНиП II-89-80. Генеральные планы
промышленных предприятий. - М.: издательство стандартов, 1994. - 44 с.
. Экономика
предприятия: учеб. пособ. /Е.В. Арсенова [и др.]. - М.: Высшая школа, 2001. -
371 с.
. Пошерстник,
Н.В. Заработная плата в современных условиях: учеб. пособ. /Н.В. Пошерстник. -
СПб.: Герда, 2002. - 730 с.
47. Коломиец,
И.И. Экономика производственных предприятий: учебник /И.И. Коломиец. - Минск.:
Веды, 2001. - 123 с.
ПРИЛОЖЕНИЕ 1