№ участка
|
1
|
2
|
3
|
4
|
5
|
1,441,441,441,441,44
|
|
|
|
|
|
1,921,921,921,921,92
|
|
|
|
|
|
1,921,921,921,921,92
|
|
|
|
|
|
Выполним проверку стенки балки на устойчивость.
Определим критический поток потери устойчивости стенки
(Рис.1.3) по формуле

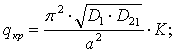
(1.9)
где
; (1.10)
; (1.11)
; (1.12)
; (1.13)
-линейный размер стенки на участке от начала балки (0) до
координаты стойки балки (х1) (
=3000 мм),
-коэффициент опирания (
) [3], зависящий от упругих характеристик
КМ и отношения сторон стенки.
Если неравенство
выполняется и критические напряжения в стенке, рассчитанные по
формуле (1.9), не превышают предел прочности материала то проектирование
толщины стенки заканчивают.
В случае не соблюдения условий устойчивости, используют два
основных способа их обеспечения: увеличением толщины стенки за счет введения
дополнительных слоев из основного материала или применением стенки с сотовым заполнителем.
Выбор конструктивного решения определяется минимумом массы конструкции.
В данном случае условие устойчивости выполняется.
1.3
Проектирование стойки-балки
Для крепления подкоса к балке и обеспечения передачи усилий
используем стойку-балку. На рис.1.5 представлен эскиз выбранного
конструктивно-технологического решения стойки-балки с указанием параметрических
размеров.
Для изготовления стойки-балки выберем 30ХГСА с пределом прочности
.
Рис.1.5 Эскиз стойки-балки.
1.3.1
Расчет параметров пластины
Определим толщину δ металлической пластины,
используемой для передачи потока касательных усилий со стенки на стержень, по
третей гипотезе прочности
; (1.14)
где
Реакции в опоре - 
Отсюда:
;
;
где B=40 мм - ширина пластины.
Конструктивно принимаем
.
1.3.2
Расчет вилки
Расчетное усилие для вилки составит (рис.1.6):
.
Рис.1.6 Схема нагружения стойки-балки
По заданной нагрузке подбираем подшипник ШМ-15 с параметрами:

;

.
По значению внутреннего диаметра подшипника (
) подбираем значение диаметра крепежного элемента.
Материал крепежного элемента - 30ХГСА.
Определим толщину вилки из условия прочности крепежного элемента
на смятие
; (1.15)
где
=15 мм.
Отсюда:
мм.
Проверим крепежный элемент на срез
Условие работы крепежного элемента на срез выполняется.
В соответствии с рядом нормальных линейных размеров (ГОСТ 6636-69)
принимаем
мм.
Определим наружный диаметр вилки из условия прочности на разрыв в
ослабленном сечении
; (1.16). Отсюда
мм.
В соответствии с рядом нормальных линейных размеров (ГОСТ 6636-69)
принимаем
мм.
Из условия прочности вилки на срез до края, определим а -
расстояние до края
; (1.17)
;
.
Конструктивно принимаем а=7,5 мм.
Проверим выполнение условия прочности вилки на смятие
; (1.18)
условие прочности вилки на смятие выполняется.
1.3.3
Расчет клеевого соединения
Для соединения стойки-балки со стенкой используем клеевое
соединение. Для склейки деталей используем клей ВК-9.
Конструктивно выбираем длину соединения l=100 мм, ширина
пластины В=40 мм. Разбиваем поверхность пластины на 10 квадратов 20х20 (мм).
Усилия в каждом квадрате возникают разные. Наиболее нагруженный квадрат будет
под номером 1 (рис.1.7). В центре каждого квадрата условно ставиться болт
эквивалентной площади.
Рис.1.7 Схема нагружения клеевого соединения
Крутящий момент возникающий в пластине

(1.19)
Сила возникающая от крутящего момента в 1 квадрате

(1.20)
где 
м - расстояние от центра пластины до центра 1 квадрата.
Усилие приходящееся, на каждый квадрат от центральной силы

(1.21)
где n=10 - количество квадратов.
Полное усилие определяется как геометрическая сумма 

(1.22)
Проверим выполнение условия прочности клеевого соединения на
отрыв:

(1.23)
где 
- площадь квадрата.
Клеевое соединение выдерживает приложенные нагрузки.
1.4
Проектирование узла крепления балки
Для крепления балки к фюзеляжу и передачи усилий используется
стыковой узел. На рис.1.8 представлен эскиз выбранного
конструктивно-технологического решения стыкового узла с указанием
геометрических размеров.
Рис.1.8 - Эскиз узла крепления балки
Для изготовления узла крепления выберем 30ХГСА с пределом
прочности
.
1.4.1
Расчет параметров пластин
Выбираем максимальные результирующие усилия, действующие в
стыковом узле (при первом расчетном случае)

; (1.24)
Отсюда
.
Так как полки одинаковые, суммарное усилие
действует на половине расстояния
.
Определим толщину δп пластины для верхней и нижней полок, используемой для
передачи осевых усилий, возникающих в полках, на стыковой узел. При определении
толщины учитываем распределение осевого усилия между верхней и нижней полкой
; (1.25)
Отсюда
;
где ширина пластины связана с шириной полки - b=18 мм.
Конструктивно принимаем толщину стойки и пластин
.
1.4.2
Расчет клеевого соединения на стенке
Для соединения стойки-балки со стенкой используем клеевое
соединение. Для склейки деталей используем клей ВК-9.
Конструктивно принимаем 
Ширина соединения - В=100 мм (рис.1.9).
Рис.1.9 - Эскиз клеевого соединения узла крепления балки
Разбиваем поверхность пластины на 16 прямоугольников 54х25 (мм).
Усилия в каждом прямоугольнике возникают разные.
Наиболее нагруженный прямоугольник будет под номером 1 (рис.1.9).
В центре каждого прямоугольника условно ставиться болт эквивалентной площади.
Крутящий момент возникающий в пластине

(1.19)
Сила возникающая от крутящего момента в 1 прямоугольнике

(1.20)
где 
м - расстояние от центра пластины до центра 1 прямоугольника.
Усилие приходящееся, на каждый квадрат от центральной силы

(1.21)
где n=16 - количество прямоугольников.
Полное усилие определяется как геометрическая сумма 

(1.22)
Проверим выполнение условия прочности клеевого соединения на
отрыв:

(1.23)
где 
- площадь квадрата.
Клеевое соединение выдерживает приложенные нагрузки.
1.4.3
Расчет проушины
При проектировании проушины расчетное усилие составит:
.
Конструктивно примем диаметр крепежного элемента
.
Определим толщину проушины из условия прочности крепежного
элемента на смятие.
Откуда
мм.
В соответствии с рядом нормальных линейных размеров (ГОСТ 6636-69)
принимаем
мм.
Определим наружный радиус проушины из условия прочности на разрыв.
Откуда
мм;
где К=4 - коэффициент концентрации.
Из условия прочности проушины на срез до края найдем а -
расстояние до края
;
.
Конструктивно принимаем а=4 мм.
В соответствии с рядом нормальных линейных размеров (ГОСТ 6636-69)
принимаем
мм. Проверим выполнение условия
прочности проушины на срез
- условие прочности проушины на срез выполняется.
2.
Проектирование стержня
2.1
Проектирование поперечного сечения
Конструкция стержня состоит из двух частей: самого стержня и
соединительных фитингов. Наиболее часто задачу проектирования стержня разбивают
на два этапа: определение параметров основной части и законцовок, с последующим
согласованием общих размеров.
В качестве критерия проектирования стержня будем использовать
критерий минимума массы. Целевая функция имеет вид
. (2.1)
В ходе проектирования стержня необходимо определить следующие
параметры:
- R - средний радиус стержня;
- δ - толщина стенки
стержня.
Проектируемый стержень изготавливается пултрузией с
дополнительными наружными слоями, выполненными намоткой под углом 90°.
Включение в структуру пултрузионного стержня 2-х слоев материала с армированием
90° не оказывает существенного влияния на упругие и прочностные характеристики
материала. Такое допущение дает возможность описать физико-механические
свойства КМ такими зависимостями
Значения физико-механических характеристик материала стержня
приведены в таблице 1.3.
Вследствие эксплуатации балки при нагружении двумя системами
внешних сил, в подкосе может возникнуть как растягивающее, так и сжимающее
усилие, что необходимо учитывать при проектировании. Расчетные значения
нагрузок составляют
Определение геометрических параметров стержня проведем по
следующему алгоритму:
1. Используя условие местной осесимметричной потери
устойчивости определим минимальную потребную толщину стенки по формуле
. (2.2)
2. Используя условия прочности при работе стержня на
растяжение-сжатие определим минимальный радиус стержня по формуле
(2.3)
3. Проверим выполнение условий общей потери
устойчивости (2.4) и местной неосесимметричной потери устойчивости
; (2.4)
(2.5)
где
и
- параметры волнообразования;
- длина стержня,
мм.
В случае не выполнения условий общей и местной неосесимметричной
потери устойчивости увеличиваем радиус до тех пор, пока условия не выполняться.
При достижении существующих конструктивных ограничений на радиус стержня
находим необходимую толщину стенки стержня при его максимальном радиусе.
В результате расчетов для проектируемого стержня получены
следующие значения искомых параметров:
мм;
мм.
В связи с технологическими ограничениями принимаем значения
искомых параметров:
мм;
мм.
2.2
Проектирование законцовок стержня
Для изготовления законцовок стержня, переходной втулки и оси,
соединяющей пару ухо-вилка выберем 30ХГСА с пределом прочности
. На рис.2.1 представлен эскиз законцовки
стержня с указанием геометрических размеров.
Рис.2.1 - Эскиз законцовки стержня
2.2.1
Расчет параметров резьбовой части
Определим минимальный внутренний диаметр резьбы из условия
прочности резьбы на срез
, (2.6)
где: N - усилие в стержне:
Н;
k - коэффициент
запаса: k=3;
Р - шаг
резьбы: P=3мм;
z - число
витков резьбы: z=8;
- предел прочности материала:
МПа;
Отсюда
мм.
Конструктивно принимаем резьбу М26Ч3 ГОСТ 9150-59 [1].
Проверим выполнение условия смятия резьбы
; (2.7)
гдеd1 - внутренний диаметр резьбы: d1=23мм;
- предел прочности материала на смятие:
МПа;
МПа.
Условие прочности на смятие резьбы выполняется.
Конструктивно принимаем длину резьбовой части законцовки lp=48
мм. Определим диаметр облегчающего отверстия d0 из условия
прочности
; (2.8)
Отсюда
мм.
В соответствии с рядом нормальных линейных размеров (ГОСТ 6636-69)
принимаем
(мм).
2.2.2
Расчет уха
Для устранения несоосности и перекоса отверстий уха и вилки
предусматриваем установку шарнирного подшипника в отверстии уха.
В соответствии с усилием в стержне был выбран подшипник ШМ15
ГОСТ 3635-78 со следующими характеристиками (рис.2.1):
С=9200 Н;
dп=15 мм;
Dп=28 мм;
b1=12 мм;
b=8 мм.
Выполним Крепление подшипника в проушине, как показано на
рис.2.1 Конструктивно определяем толщину проушины Н=13 мм.
Определим наружный диаметр проушины из условия прочности на
разрыв
; (2.9)
Отсюда
мм.
В соответствии с рядом нормальных линейных размеров (ГОСТ 6636-69)
принимаем
мм.
Проверим выполнение условия прочности проушины на смятие
; (2.10)
- условие прочности проушины на смятия выполняется.
Из условия прочности на срез проушины до края определим а -
расстояние до края
; (2.11)
;
.
Принимаем а=3мм.
2.2.3
Расчет крепежного элемента
Выполним проверку условия прочности на срез крепежного
элемента, соединяющего вилку и проушину. Материал крепежного элемента 30ХГСА.
; (2.12)
где d - внутренний диаметр подшипника, d=15мм;
- условие прочности крепежного элемента на срез выполняется.
Выполним проверку условия прочности на смятие крепежного элемента
; (2.13)
- условие прочности крепежного элемента на смятие выполняется.
3.
Расчет нервюр
3.1
Проектировочный расчет усиленных нервюр
Усиленные нервюры помимо сохранения аэродинамического контура
и восприятия воздушной нагрузки, предназначены для восприятия больших
сосредоточенных нагрузок от прикрепленных к ним агрегатам (от шасси,
двигательных установок, баков, узлов подвески элеронов и закрылков и т.д.).
Кроме того, усиленные нервюры применяются для восприятия касательных сил с
контура обшивки и передачи их или на другой контур, или являются элементами
местного усиления конструкции в местах, где происходит резкое перераспределение
нагрузки (нервюры, окантовывающие вырез по люк шасси, бортовая нервюра и т.д.).
Так как воздушная нагрузка значительно меньше действующих на нервюру
сосредоточенных сил, то при проектировочном расчете ею обычно пренебрегают.
Сечения поясов нервюр постоянные и при проектировочном расчете их можно
определить по наибольшему изгибающему моменту, действующему в плоскости нервюры
[4].
Проведем расчет усиленной нервюры расположенной в районе узла
навески элерона.
Схема нагружения нервюры показана на рис.3.2.
Т.к. реакции распределяются пропорционально изгибным
жесткостям полок, которые, в свою очередь, пропорциональны квадрату высот,
можем записать:
. (3.1)
Второе уравнение для определения неизвестных:
; (3.2)
где
=8688 Н.
Отсюда можем найти R1 = 7155Н, а R2 = 1533H.
Крутящий момент определяется по формуле
, (3.3)
где
- расстояние от
до центра жесткости сечения;
Определим центр жесткости (рис.3.1):
,
м
Рис.3.1 Положение центра жесткости
Рис.3.2 Схема нагружения силовой нервюры
Формой поперечного сечения для нервюры был выбран швеллер. Полки
будут иметь угол укладки
, а стенка -
. Стенка и полка изготавливается из
стеклопластика. Свойства материала приведены в таблице 1.3.
Проектирование нервюры производится на основе разделения функций
ее элементов (изгибающих момент и осевая сила воспринимаются полками, а
поперечная сила - стенкой). Условием оптимальности нервюры является минимум
погонной массы, определяемой выражением:
, (3.4)
где
,
- плотности материалов полки и стенки соответственно;
- ширина полок;
- толщина заплечиков.
Ограничениями на проектные параметры нервюры являются условия
прочности полок и стенки, а также их соединения:
; (3.5)
; (3.6)
; (3.7)
, (3.8)
где
,
,
,
- пределы прочности КМ верхней и нижней полок, стенки, а также
соединяющего их материала соответственно;
- эффективная высота стенки:
, (3.9)
где
- строительная высота стенки.
Из условия (3.8) с учетом (3.9) запишем выражение для определения
минимального потребного значения ширины полок [3]:
, (3.10)
где
- максимальное поперечное усилие,
действующее в лонжероне;
- предел прочности соединения (т.е. клея), FC= 29,4
МПа;
- текущая строительная высота стенки.
Определяем минимальную потребную ширину
.
. (3.11)
Однако при такой ширине полок условие их прочности не будет
выполняться, следовательно, ширина полок по длине балки принимается
.
Определим толщину полок
, (3.12)
где
- максимальный изгибающий момент,
= 1387,2·103 Н·мм;П
- предел прочности материала полки, FП = 280 МПа.
Толщину полок округляем в большую сторону до целого количества
слоев, причем так, чтобы полки не теряли устойчивость, поэтому принимаем
толщину полки равную 1,25 мм.
Толщину стенки определим по формуле
(3.13)
где,
- максимальное поперечное усилие,
действующее в лонжероне;
- предел прочности материала стенки, FC= 280 МПа;
- минимальная строительная высота стенки
Толщину стенки округляем в большую сторону до целого количества
слоев и кратных 4. Принимаем
.
3.2
Расчет устойчивости стенки нервюры
Принимаем, что стенка воспринимает только поперечную силу
, от действия которой в плоскости стенки
возникает поток касательных усилий
. Формула Эйлера для определения критических усилий, при которых
происходит потеря устойчивости стенки, имеет вид:
, (3.14)
где
- изгибные жесткости КМ стенки, которые
вычисляются по формулам:
где Еx, Еy - модули
упругости стеклопластика;
δct - толщина стенки, мм;
μxy, μyx - коэффициенты Пуассона пакета стенки;
Gxy - модуль
сдвига пакета стенки;
- коэффициент опирания, который зависит от упругих характеристик
КМ стенки и отношения сторон стенки;
а - длина
рассматриваемого участка между передним лонжероном и задней стенкой,
;
Критические напряжения, вычисленные по формуле (3.14), не должны превышают
предела прочности материала стенки
(3.15)
Данные для расчета приведены в табл.3.1.
Таблица 3.1 - Данные для расчета стенки на устойчивость
δct, мм х, мм D1∙103Н∙мм D2∙103
Н∙мм D3∙103 Н∙мм D1/D2 D1/D3 
Н/ммqd
Н/мм
|
|
|
|
1
|
1522
|
2,145
|
1,43
|
1,224
|
1,5
|
1,752
|
168,1
|
39,9
|
14,47
|
Действующие напряжения (qd) не должны превышать
критические (qкр). Как видим, условие устойчивости стенки выполняется
(qd<qкр).
В проектируемом крыле 10 силовых нервюр
(КП.407.458м.08В.13.00.00.09СБ). Проектировочный расчет всех нервюр аналогичен
выше указанному алгоритму.
4.
Расчет обшивки крыла
Обшивка крыла образует внешнюю поверхность крыла. От качества
поверхности крыла в определенной степени зависят его аэродинамические
характеристики.
Обшивка может быть гладкой или трехслойной. Соединение
обшивок в местах стыка может быть встык или внахлест. Наиболее простым является
соединение внахлестку, но оно вызывает наибольшее аэродинамическое
сопротивление. Наилучшим в аэродинамическом отношении и получившим, поэтому
наибольшее распространение на современных самолетах является соединение встык.
При соединении обшивок встык необходимо предусматривать обязательный температурный
зазор равный 1мм. Стык обшивок осуществляется по элементам силового каркаса:
лонжеронам, стрингерам, нервюрам [2].
На современных самолетах применяется трехслойная обшивка.
Несущие слои чаще всего выполняются из стеклоткани или углеткани, а в качестве
заполнителя - пенопласт или сотовый заполнитель. Несущие слои приклеиваются к
заполнителю.
Трехслойная обшивка имеет ряд преимуществ по сравнению с
гладкой. Трехслойная обшивка имеет большую поперечную жесткость, а
следовательно и высокие критические напряжения. Также она обладает хорошими
теплоизоляционными свойствами. Но трехслойная обшивка имеет и недостатки.
Технология изготовления сложна, сложен контроль качества склейки несущих слоев
к заполнителю, затруднен ремонт обшивки. Большие трудности встречаются при
осуществлении стыков частей обшивки. Необходимо обеспечивать соединение не
только несущих слоев, но и заполнителя, который обеспечивает их совместную
работу.
В данном проекте обшивка крыла изготовляется из
стеклопластика (табл.1.3).
4.1
Проектирование обшивки
Расчет обшивки будем вести на участках между нервюрами, так
как в этих местах необходимо обеспечить выполнение условий устойчивости и
прогиба. Для этого разделим обшивку на 3 участка. Геометрические размеры и
нагрузки на участках (рис.4.1) приведены в табл.4.1.1 участок - между бортовой
и первой нервюрой, 2 участок - между первой и второй нервюрой, 3 участок -
между второй нервюрой и третьей нервюрой (КП.407.458м.08В.13.00.00.00 СБ).
Нагрузки действующие на крыло на этих участках были рассчитаны в прочностном
расчете.
Рис.4.1 Участки обшивки
Таблица 4.1 - Геометрические размеры участков и нагрузки на
них
Номер участка
|
Размер участка (а<b)
|
Mz, Н мм
|
1
|
а = 400 b = 1880
|
6037000
|
2
|
а = 400 b = 1880
|
6753000
|
3
|
а = 400 b = 1880
|
2481400
|
Определим моменты, действующие в контурах:
(4.1)
(4.2)
, (4.3)
где
- площадь контуров:
мм2;
мм2;
мм2;
Полученные значения моментов для каждого участка сведем в табл.4.2
Рассчитаем потоки касательных усилий к контурах:
(4.4),
(4.5),
(4.6)
Полученные значения в табл.4.2
Таблица 4.2 - моменты, и потоки касательных усилий,
действующие в контурах
Номер участка
|
М, Н мм
|
q, Н/мм
|
|
М1 105М2 106М3 105q1q2q3
|
|
|
|
|
|
1
|
0,181
|
5,822
|
0,034
|
1,777
|
10,08
|
0,773
|
2
|
0, 202
|
6,512
|
0,038
|
1,988
|
11,27
|
0,865
|
3
|
0,074
|
2,393
|
0,014
|
0,730
|
4,14
|
0,317
|
Следовательно, нагрузка, действующая на обшивку qd
составляет: 1 участок - 10,08 Н/мм, 2 участок - 11,27 Н/мм, 3 участок - 4,14
Н/мм.
Расчет гладкой обшивки
Толщину обшивки рассчитываем из условия прочности по формуле
, (4.7)
где
- толщина монослоя;
- предел прочности материала на сдвиг.
Полученные значения толщин обшивок для каждого участка равны
0,5мм.
В связи с технологическими оганичениями увеличим значение велчины
обшивки до 4 мм.
Проверим полученные значения толщин обшивок на соблюдения условий
устойчивости и прогиба.
Проверка на устойчивость:
Рассчитаем изгибные и крутильные жесткости для каждого участка:
Определим коэффициент операния k для каждого участка, данные
сведем в табл.4.3:
Таблица 4.3 - Данные для расчета стенки на устойчивость.
Номер участка
|
b/a
|
D1/D2
|
D3/D1
|
k
|
1
|
2,686
|
1
|
0,571
|
5,14
|
2
|
2,686
|
1
|
0,571
|
5,14
|
3
|
2,686
|
1
|
0,571
|
5,14
|
Определим критические касательные усилия для каждого участка:
(4.8)
Должно выполняться условия
, сравнивая данные занесенные в табл.4.4, можно сделать вывод, что
условие по устойчивости обшивки выполняется
Таблица 4.4 - Значения критических и действующих усилий
Номера участков
|
qкр, Н/мм
|
qd, Н/мм
|
1
|
264,599
|
10,08
|
2
|
264,599
|
11,27
|
3
|
264,599
|
4,14
|
Проверим по допускаемым прогибам
(2.9)
где k1 - ограничение на относительный прогиб, 0,01;
р - распределение давления по хорде.
Полученные значения для каждого участка занесем в табл.4.5
Таблица 4.5 - Данные для расчета обшивки на прогибы.
Номера участков
|
Р
|
|
1
|
0,0086
|
0,0088
|
2
|
0,008
|
0,0088
|
3
|
0,0076
|
0,0088
|
Условия выполняется.
Обшивка приклеивается к полкам нервюр и лонжеронов клеем ВК -
9. Проводиться поэтапная склейка: вначале внутренняя, а затем наружная.
5.
Расчет элерона
Элероны служат для обеспечения поперечной управляемости
самолета. Они представляют собой рулевые поверхности, расположенные на концах
крыла у задней кромки и отклоняемые вверх или вниз. Отклонение одного элерона
вверх, а другого вниз приводит к созданию поперечного момента, вызывающего крен
самолета.
К элеронам предъявляются следующие основные требования:
) эффективность на всех режимах полета самолета;
) минимальное сопротивление в неотклоненном положении;
) минимальный момент рыскания при крене, при этом разворот
самолета должен происходить в сторону крена;
) малые шарнирные моменты;
) полная весовая балансировка при наименьшей массе
балансировочных грузов;
) исключение возможности заклинивания при деформациях крыла в
полете;
) простота монтажа и демонтажа элерона на крыле при
обеспечении взаимозаменяемости.
5.1
Параметры элерона, его навеска на крыле
Длина элерона составляет 3 м, хорда элерона - 0,358 м
(КП.407.458м.08В.13.00.00.02. СБ).
До конца крыла элерон обычно не доводят, чтобы предотвратить
ранний срыв потока при его отклонении в концевых сечениях крыла, приводящий к
увеличению лобового сопротивления и уменьшению эффективности поперечного
управления.
В сечениях крыла, где расположен элерон, при отклонении
последнего изменяются кривизна профиля и угол атаки. Это приводит к появлению
дополнительных аэродинамических сил. На полукрыле с отклоненным вниз элероном
коэффициент подъемной силы увеличивается, а на полукрыле, где элерон отклонен
вверх, уменьшается. Эта разность в подъемных силах вызывает крен самолета в
сторону полукрыла с отклоненным вверх элероном. Отклонение элеронов приводит и
к изменению лобового сопротивления обеих половин крыла. При отклонении элеронов
на одинаковые углы вверх и вниз лобовое сопротивление поднятого полукрыла
(элерон на ней отклонен вниз) может оказаться больше сопротивления опущенного
полукрыла (элерон на нем отклонен вверх). Это создаст момент рыскания в сторону
поднятого полукрыла, что противоречит условиям нормального пилотирования,
требующим разворота самолета в сторону крена.
Для обеспечения разворота в сторону крена при нейтральном
положении руля направления необходимо, чтобы коэффициент лобового сопротивления
опущенного полукрыла, на котором элерон отклонен вверх, был больше коэффициента
лобового сопротивления, поднятого полукрыла, на котором элерон отклонен вниз.
Достичь этого можно тремя способами:
) смещением оси вращения элерона к его нижней поверхности.
Здесь при отклонении элерона вниз носок его не выводит за габаритные размеры
крыла, чем обеспечивается плавность обтекания. При отклонении же элерона вверх
носок его выходит в поток, плавность обтекания нарушается, что приводит к
значительному увеличению сопротивления;
) комбинацией первых двух способов.
При полете на больших, близких к критическим, углах атаки на
полукрыле, на котором элерон отклонится вниз, может наступить срыв потока, что
вызовет падение коэффициента подъемной силы. При этом коэффициент подъемной
силы на полукрыле с отклоненным вниз элероном, может оказаться меньше
коэффициента подъемной силы полукрыла с отклоненным вверх элероном, что вызовет
крен самолета в сторону, противоположную требуемой. Такое нарушение поперечной
управляемости при полете на больших углах атаки особенно опасно при посадке и
взлете.
В данной работе используется дифференциальный элерон, углы
поворота которого вверх и вниз составляют 25є и 15є соответственно.
Элерон навешивается на крыле на двух или более узлах. Осуществить
навеску элерона на двух узлах технологически проще, в этом случае легче
обеспечиваются требования взаимозаменяемости, и уменьшается возможность
заклинивания элерона при деформации крыла в полете. При увеличении числа опор
уменьшаются величины перерезывающих сил и изгибающих моментов, что ведет к
снижению, массы элерона, уменьшаются его прогибы, что выгодно в
аэродинамическом отношении, повышается живучесть. Но одновременно увеличивается
возможность заклинивания элерона при деформации крыла, усложняется
технологический процесс навески элерона и обеспечение требований
взаимозаменяемости. С целью более простого обеспечения требований
взаимозаменяемости элерон иногда навешивается на ориентирующихся по размаху
кронштейнах. При этом один из кронштейнов крепится жестко, чтобы элерон не мог
перемещаться вдоль оси вращения. Выбор числа опор в большой степени зависит от
размеров элерона.
В данной работе элерон навешивается на крыле на двух узлах.
Схема крепления элерона к крылу показана на сборочном чертеже.
Рычаг управления элероном с целью уменьшения максимального
крутящего момента, а, следовательно, и массы элерона, желательно размещать в
сечении, в котором крутящей момент справа и слева будет одинаковым. Однако по
ряду соображений общей компоновки крыла это не всегда может быть осуществлено.
Часто рычаг управления элероном находится в его корневых сечениях. В этом
случае упрощается проводка управления, масса ее получается меньшей, рычаг
управления элероном из-за большей строительной высоты в этих сечениях может
либо совсем не выходить за обводы крыла, либо выходить незначительно, что
улучшает аэродинамику. Но в любом случае рычаг управления желательно размещать
в сечении узла навески. Если этого не сделать, то от усилия в тяге управления
элерон будет нагружаться изгибающим моментом, причем величина его будет тем
больше, чем дальше от узла будет располагаться рычаг управления.
5.2
Аэродинамическая компенсация элеронов
При отклонении элерона действующая на него аэродинамическая
сила создает относительно оси вращения момент, который называется шарнирным.
При больших размерах элерона или значительных скоростях
полета действующая на элерон сила может быть очень большой, а следовательно, и
большим будет шарнирный момент.
Для уменьшения величины шарнирного момента, а значит, и для
облегчения усилия при отклонении элерона применяются различные типы
аэродинамической компенсации. Основным требованием к аэродинамической
компенсации является обеспечение ее эффективности при возможно меньшем
ухудшении аэродинамики крыла. Применяются следующие виды аэродинамической
компенсации: роговая, осевая, внутренняя и сервоком-компенсация. В данном
проекте для элерона применяем осевую аэродинамическую компенсацию.
Осевая аэродинамическая компенсация осуществляется смещением
оси вращения элерона назад, что приводит к уменьшению величины шарнирного
момента из-за уменьшения плеча силы. Таким образом, осевой компенсатор
представляет собой площадь элерона, расположенную впереди его оси вращения.
Размеры осевых компенсаторов колеблются в широких пределах и доходят до 25 %
площади элерона. Дальнейшее увеличение площади осевого компенсатора может
повести к перекомпенсации. В данном проекте осевая компенсация принята 20%. К
недостаткам осевой компенсации следует отнести возникновение дополнительного
сопротивления при выходе за габаритные размеры крыла носка элерона при больших
углах отклонения, Этот недостаток особенно сильно проявляется при больших
относительных размерах осевой компенсации.
Из всех видов аэродинамической компенсации осевая компенсация
получила наибольшее распространение.
5.3
Нагрузки, действующие на элерон
На элерон в полете действуют аэродинамические силы.
Величина и распределение нагрузки определяются по результатам
продувок в аэродинамической трубе при неотклоненном и отклоненном положении
элерона. Силами тяжести конструкции элерона ввиду их малости пренебрегают.
При отсутствии результатов продувки используют распределение
нагрузки по размаху и по хорде элерона показанное на рис 5.1
Распределение нагрузки по хорде берется по трапеции, причем высота
ординаты нагрузки у передней кромки равна
, а у задней кромки равна
[7].
Распределение нагрузки по размаху - пропорционально хордам, но на
концевом участке элерона, равном 0,1 полуразмаха крыла, ординаты нагрузки
удваиваются. Если концевая кромка элерона отстоит от конца крыла более чем на
0,1 полуразмаха крыла, то увеличение удельной нагрузки на конце элерона не
делается.
Рис.5.1 Распределение нагрузки
Определим величину скоростного напора для элерона:
, (5.1)
где
- плотность воздуха,
кг/м3;
- максимальная скорость самолета,
м/с;
а величину
по формуле:
(5.2)
Па;
Па.
Определим распределение нагрузки на элерон по размаху:
Н/м (5.3)
где
- хорда элерона.
Величина нагрузки по размаху будет иметь постоянное значение
Н/м.
Опоры элерона, строго говоря, упругие, но в расчетах их обычно
считают жесткими ввиду относительно большой изгибной жесткости крыла.
Опоры расположим так, чтобы максимальный изгибающий момент был
наименьшим. Методом перебора (меняя расположение опор) определили, что
наименьший изгибающий момент возникает при таком расположении опор, как
показано на рис.5.2 Эпюры поперечных сил и изгибающих моментов приведены на
рис.5.2.
Рис.5.2 Эпюры поперечных сил и изгибающих моментов
5.4
Проектирование лонжерона элерона
Лонжерон обычно представляет собой балку швеллерного или
двутаврового сечения. В данном проекте лонжерон представляет собой швеллер. К
лонжерону крепятся узлы навески элерона и тяга управления им.
Полки и стенка лонжерона элерона будут изготавливаться из
углеткани, характеристики материала приведены в табл.1.3
Обобщенные нагрузки на элерон
приведены в табл.5.1.
Таблица 5.1 - Величины поперечных сил и изгибающих моментов
Проектирование балок производится на основе разделения
функций ее элементов (изгибающих момент и осевая сила воспринимаются полками, а
поперечная сила - стенкой). Условием оптимальности балки является минимум
погонной массы, определяемой выражением:
, (5.4)
где
,
- плотности материалов полки и стенки соответственно;
- ширина полок;
- толщина заплечиков.
Ограничениями на проектные параметры балки являются условия
прочности полок и стенки, а также их соединения:
; (5.5),
; (5.6)
; (5.7),
, (5.8)
где
,
,
,
- пределы прочности КМ верхней и нижней полок, стенки, а также
соединяющего их материала соответственно;
- эффективная высота стенки:
,
Н=100 мм - строительная высота стенки.
На основании допущения
, выражение принимает вид:
. (5.9)
Из условия (3.8) с учетом (3.9) запишем выражение для определения
минимального потребного значения ширины полок:
, (5.10)
где
- максимальное поперечное усилие, действующее
в лонжероне;
- предел прочности соединения (т.е. клея),
МПа.
Конструктивно ширина полок по длине балки для лонжерона элерона
принимается
.
Для определения значений толщины полок следует воспользоваться
алгоритмом, приведенным в работе [3], выведенным из условия прочности.
. Для произвольно заданных значений
вычисляются толщины
, при которых условия прочности для верхней полки будут
выполняться.
. Подставляем найденные пары величин в условие прочности для
нижней полки.
. Фиксируем найденные значения
и
проверяем, чтобы условие удовлетворяли все
сочетания толщин полок (значения толщин полок пересчитаны на целое число
монослоев).
Используя для расчета программу MathCAD, получили значения верхней
и нижней полок 0,96 мм (8 слоев).
. Для определения параметров стенки достаточно взять наибольшую
поперечную силу.
Толщина стенки определяется по следующей зависимости [3]:
, (5.11)
где:
- максимальное значение поперечной силы;
- предел прочности материала стенки,
МПа;
Толщину полок округляем в большую сторону до целого количества
слоев, причем так, чтобы полки не теряли устойчивость, а толщину стенки - до количества
слоев кратных 4.
Толщина стенки лонжерона 0,96 мм (8 слоев).
Расчет устойчивости стенки лонжерона
Принимаем, что стенка воспринимает только поперечную силу
, от действия которой в плоскости стенки
возникает поток касательных усилий
.
Формула Эйлера для определения критических усилий, при которых
происходит потеря устойчивости стенки, имеет вид:
, (5.12)
где:
- изгибные жесткости КМ стенки, которые
вычисляются по формулам:
(5.13)
где: Еx, Еy - модули
упругости углепластика с армированием ±45;
δct - толщина стенки, мм;
μxy, μyx - коэффициенты Пуассона пакета стенки;
Gxy - модуль
сдвига пакета стенки;
- коэффициент опирания, который зависит от упругих характеристик
КМ стенки и отношения сторон стенки [6];
) а - длина рассматриваемого участка,
.
Критические напряжения, вычисленные по формуле (5.12), не должны
превышают предела прочности материала стенки
(5.13)
Данные для расчета приведены в таблице 5.2.
Найдем действующие касательные усилия в стенке по формуле:
(5.14)
Действующие напряжения, вычисленные по формуле (5.14), не должны
превышают предела прочности материала стенки, а главное критических напряжений:
(5.15)
(5.16)
Таблица 5.2 - Данные для расчета стенки на устойчивость
δct, мм D1∙104Н∙мм D2∙104
Н∙мм D3∙104 Н∙мм D1/D2 D1/D3 
Н/мм
Н/мм
|
|
|
|
0,96
|
0,972
|
0,972
|
0,414
|
1
|
2,438
|
168.1
|
2.282
|
1.635
|
Условие устойчивости стенки выполняется (qd<qкр).
5.5
Расчет обшивки элерона
КТР лонжерона представлено на рис.5.3
Рис.5.3 КТР лонжерона
Элерон заполняется пенопластом по шаблонному методу, после
соединения лонжерона с проушинами. Толщину обшивки элерона рассчитываем по алгоритму,
описанному выше (см. п.4), толщину обшивки принимаем равную 1мм.
5.6
Расчет узлов навески
Управляющие поверхности самолета: рули,
элероны, триммеры, гасители подъемной силы и другие элементы соединяются с
неподвижными частями конструкции самолета при помощи узлов навески (соединение
"ухо-вилка"), основными элементами которых являются кронштейны.
Форма кронштейнов зависит от того, к каким
силовым элементам конструкции они крепятся. Так, кронштейн, который
устанавливается на плоской стенке, как правило, выполняется плоским. Часто
кронштейны устанавливаются на двухпоясных плоских балках типа лонжеронов или
нервюры. В этом случае кронштейн может быть выполнен или в виде трехзвенной
фермы, или в виде плоской, зашитой стенкой рамы.
Представим кронштейн в виде рамы,
закрепленной на двух опорах, которыми являются болты крепления подошвы
кронштейна. При проектировании кронштейна чаще всего его рассматривают как
двухпоясную плоскую балку. При этом принимают, что изгибающий момент полностью
воспринимается поясами, а перерезывающая сила - стенкой. В нашем проекте мы
приняли, что кронштейн является силовым элементом, продолжением силовой нервюры
(частью стойки балки КП.407.458м.07В.13.00.00.01СБ). На основании проведенных
расчетов запишем порядок проектирования кронштейна (алгоритм проектирования).
КТР кронштейна представлен на рис.5.4
Заданы: R - нагрузка на кронштейн,
приложенная на оси вращения управляемой поверхности, R=1008 Н (см. п.5.3); l -
расстояние от точки приложения нагрузки до плоскости крепления кронштейна на
двухпоясной балке, l = 0,2 м; Вmax - возможная максимальная ширина
основания кронштейна из условия подхода при установке его между поясами
лонжерона, В=0,13 м.
Рис.5.4 КРТ кронштейна
Ширину В выбирает с целью уменьшения массы, следовательно,
разносить пояса кронштейна возможно дальше, т.е. до значения Вmax.
Кронштейн выполняется из материалов Д16 (
=450МПа).
. По заданной силе подбирают подшипник, устанавливаемый в проушину.
По данным проушины определим геометрические параметры вилки на кронштейне.
Подшипник запрессовывается в проушине по соответствующей посадке и кернится.
Толщина проушины должна быть равна
,
где ап - ширина внешней обоймы подшипника;
с - расстояние от края проушины до внешней обоймы подшипника.
Для допускаемой нагрузки Р=1008 Н по ГОСТ 8338-75 выбираем
подшипник ШМ5 с такими геометрическими параметрами:
наружный диаметр D=14 мм;
внутренний диаметр d=5 мм;
ширина внутреннего кольца В=6 мм;
2. Определяют размеры проушины и вилки.
Расчет проушины ведется не на смятие, а на разрыв, так как соединение
подшипника с проушиной неподвижное и σсм= 315МПа. Диаметр
оси, соединяющего кронштейн навески узлов, определяют по внутреннему диаметру
подшипника. Применяем стандартные оси диаметром 5мм по ГОСТ 9650-80.
Из условия разрыва в ослабленном сечении определяем ширину, т.е.
:
, (5.17)
где
- коэффициент концентрации,
.
,
мм.
В соответствии с рядом нормальных линейных размеров по ГОСТ
6636 - 69 и по конструктивно - технологическим соображениям принимается D = 16
мм.
Толщина стенок вилки равна 6 мм (1 стенка - 3мм), зазоры для
возможности поворота подшипника 0,5 мм и паза под проушину 6мм - составляют
общую ширину вилки равную 13 мм;
3. Определяют конфигурацию кронштейна. Из основания,
ограниченного размером Вmах, проводим линии по обшивке, а затем
касательные к вилке. Они будут являться границей поясов кронштейна;
. Определяют площадь сечения поясов
кронштейна. Ширину кронштейна принимают постоянной, равной толщине проушины. В
зоне перехода с вилки кронштейн переходит в двутавр.
Толщина пояса кронштейна остается
постоянной по его длине - δкр= 5 мм, ширина - bmax=
30 мм, bmin= 26 мм.
Стенку выполняют постоянной толщины - δст= 5 мм. Материал стенки убирают с помощью вырезов;
. Рассчитывают болты крепления кронштейна.
Болты подбирают из условия работы на разрыв и срез. Для уменьшения нагрузки на
болты их следует размещать как можно дальше от оси кронштейна, располагая на
уровне поясов. Ширину основания, на которой располагаются болты (рис.5.4),
желательно брать как можно меньшей для уменьшения влияния местного изгиба
основания под каждым болтом. При этом минимальное расстояние от стенки
кронштейна до оси болта определяется из условия возможности подхода гаечным
ключом. Если для передачи осевой и перерезывающей сил достаточно крайних
болтов, то целесообразно убрать среднюю часть основания. Этим облегчают сборку
и уменьшают поверхность основания, которую надо обрабатывать для точного
прилегания ее к стенке.
Растягивающие усилия, приходящиеся на все
болты,
, (5.18)
где n - число болтов сверху или снизу;б - расстояние
между верхними болтами;
. (5.19)
Усилие среза, воспринимаемое болтом:
, (5.20)
где2n - полное число болтов;
. (5.21)
По каждому усилию по ГОСТ 7805-70 подбирают диаметр болта. Из двух
диаметров выбирают наибольший - d=5 мм. Следовательно, на кронштейне ставим 4
болта.
. Рассчитывают толщину основания кронштейна. Основание кронштейна
надо рассчитать на смятие под болтами и на местный изгиб под отдельным болтом.
Из условия смятия толщина основания
,
где Рб. ср.
max - наибольшее срезывающее усилие, действующие на болт;б -
диаметр болта;
σсм - напряжение смятие основания.
Так как толщина
основания постоянна, то расчет ее проводим по наиболее нагруженному болту.
Принимает толщину
основания δосн=5 мм.
Проушина на
лонжероне элерона имеет толщину основания равную 2мм, а крепление проушины к
лонжерону так же при помощи 4 болтов, но меньшей длинны.
6.
Расчет качалки
6.1
Расчет геометрических параметров качалки
Отклонение элерона вниз увеличивает угол
атаки крыла, и если полет происходит уже на достаточно больших углах, то
большое отклонение элерона вниз может вывести данную половину крыла на
закритические углы атаки и вызвать срыв с этой части крыла - самолет вместо
того, чтобы выправить крен, начнет его увеличивать. С целью предупреждения
такого явления применяют дифференциальное отклонение элеронов: вверх 25є и вниз
15є.
Для того, чтобы при отклонении ручки
управления на одинаковые углы вправо и влево элерон отклонялся на разные углы
можно применить дифференциальную качалку. Управление, при котором отклонение
командного рычага на один и то же угол в разные стороны вызывает отклонение
рулевой поверхности на неодинаковые углы, носит название дифференциального.
Простейшим элементом дифференциального управления является двуплечий рычаг, к
которому тяги подходят под разными углами. Как КТР был применен вид качалки
изображенный на рис.6.1
Рис.6.1 КТР качалки элерона
Отклонение рычага вправо или влево на угол
приводит к перемещениям тяги 1 на
одинаковые расстояния в разные стороны (
) и тяги 2 на неодинаковые расстояния (
). Величины
и
связаны с углами
и
и радиусом рычага
следующими зависимостями:
(6.1)
(6.2)
Величина степени дифференциальности зависит лишь от углов
и
:
(6.3)
Зная геометрические параметры элерона и углы его отклонения, можем
найти перемещения
и
, соответствующие последним:
; (6.4)
, (6.5)
где
- максимальная строительная высота
элерона,
.
Подставляя данные значения в формулы (6.4) - (6.5), получаем:
;
.
Находим величину дифференциальности качалки:
.
Задав угол отклонения качалки
, находим угол
по формуле (6.3), а из уравнения (6.1) находим радиус качалки
. Материал качалки алюминиевый сплав Д16.
Соединение качалки с тягами управления представляет собой ухо-вилку.
В тягах устанавливается шарнирный подшипник ШМ-5, с такими
геометрическими параметрами: наружный диаметр D = 14 мм; внутренний диаметр d =
4 мм; ширина кольца В =6 мм (ГОСТ 8338-75). Геометрические параметры тяги были выбраны
с учетом усилия на рычаг управления 200Н. Учитывая частотные характеристики и
ссылаясь на РДК-43, были выбраны дюральалюминиевые тяги диаметром
.
6.2
Расчет проушины в тягах управления
Проушина работает на разрыв в ослабленном сечении, смятие,
срез. Соответствующие условия прочности имеют вид:
; (6.6)
; (6.7)
, (6.8)
где:
- геометрический параметр проушины.
σв, σсм, τср - пределы прочности материала на разрыв, смятие, срез.
Материал проушины алюминиевый сплав Д16 (
МПа).
Из условия на срез крепежного элемента подбираем наружный диаметр
d:
, (6.9)
где:
МПа.
Выразим d:
мм
Конструктивно принимаем d=14 мм (по большему диаметру подшипника).
Из условия на смятие проушины определим
:
мм. (6.10)
Принимаем
= 4 мм, по подшипнику. Из условия на срез
проушины рассчитываем расстояние а для обеспечения соосности.
(6.11)
Выразим из формулы 6.11 а:
мм
Из условия разрыва в ослабленном сечении найдем наружный диаметр
проушины:
, (6.12)
где: n - коэффициент концентрации n=3.
Выразим D:
мм. (6.13)
В соответствии с рядом нормальных линейных размеров по ГОСТ 6636 -
69 и по конструктивно - технологическим соображениям принимается D = 16 мм.
Условие соосности R > а выполняется.
Для полученных значений
и D проверим выполнение условия разрыва в ослабленням сечении:
,
Так как условие разрыва в ослабленном сечении выполняется, то
проушина с выбранными геометрическими параметрами выдержит необходимое усилие.
Определим диаметр оси d из условия прочности на срез по формуле
Принимаем диаметр оси равным 5 мм (ГОСТ 9650-80).
Так как соединение тяги с качалкой представляет собой ухо-вилка
(вилка расположена в качалке, а - ухо в тяге).
6.3
Расчет вилки качалки
При проектировании вилки будем считать, что усилие равно
200Н.
На рис.6.2 представлен эскиз вилки.
Рис.6.2 - Эскиз вилки
Определим толщину вилки из условия прочности крепежного элемента
на смятие:
; (6.14)
откуда
.
В соответствии с рядом нормальных линейных размеров по ГОСТ 6636 -
69 принимаем
. Принимаем
для проушины. Определим наружный диаметр
вилки из условия прочности на разрыв:
; (6.15)
отсюда
В соответствии с рядом нормальных линейных размеров по ГОСТ
6636-69 и по конструктивным соображениям принимаем
.
Так как все условия выполняются, то вилка с выбранными
геометрическими параметрами выдержит необходимое усилие.
Параметры вилок в качалке одинаковые, но в месте соединения тяги 2
(рис.6.1) с качалкой паз в вилке под проушину делается больше для обеспечения
поворота качалки на заданные углы.
6.4
Расчет ступицы
Особенно ответственным узлом качалки является ступица,
которая должна обеспечить свободное вращение качалки без заедания, а также
отсутствие люфта вдоль оси вращения качалки. Для обеспечения базы при возможных
боковых непредвиденных нагрузках в ступице устанавливаются два разнесенных
подшипника [4]. По заданной нагрузке выбираем шариковые подшипники с такими
геометрическими характеристиками: наружный диаметр D = 13 мм; внутренний
диаметр d = 5 мм; ширина кольца В = 4 мм (ГОСТ 3385-75).
Используя приведенные выше формулы, аналогично рассчитываем
ухо качалки в месте присоединения к кронштейну узла навески.
Получаем следующие геометрические параметры:
внутренний диаметр уха:
;
наружный диаметр уха:
;
толщина уха с учетом двух подшипников и втулки составляет
.
Толщину вилки в месте соединения качалки с узлом навески определим
из условия смятия d = 5 мм, R = 283Н.
Определим толщину вилки из условия прочности крепежного элемента
на смятие:
; (6.16)
откуда
.
В соответствии с рядом нормальных линейных размеров по ГОСТ 6636 -
69 принимаем
.
Принимаем
для проушины.
Определим наружный диаметр вилки из условия прочности на разрыв:
; (6.17)
отсюда
В соответствии с рядом нормальных линейных размеров по ГОСТ
6636-69 и по конструктивным соображениям принимаем
.
Так как все условия выполняются, то вилка с выбранными
геометрическими параметрами выдержит необходимое усилие.
Определим диаметр оси d из условия прочности на срез по формуле:
Принимаем диаметр оси равным 5 мм (ГОСТ 9650-80).
Геометрические параметры вилки в месте присоединения тяги к
элерону те же, что и в месте соединения тяги с качалкой.
7.
Расчет закрылка
Закрылок представляет собой отклоняемую
вниз хвостовую часть крыла.