Влияние реологических характеристик бетонной смеси на выбор оптимальных режимов уплотнения при статическом прессовании
Федеральное
агентство по образованию Российской Федерации
Государственное
образовательное учреждение высшего профессионального образования
Самарский
государственный архитектурно-строительный университет
Кафедра
Производства строительных материалов, изделий и конструкций
Курсовая
работа
по
дисциплине: Процессы и аппараты в технологии строительных материалов
на
тему: Влияние реологических характеристик бетонной смеси на выбор оптимальных
режимов уплотнения при статическом прессовании
Самара,
2011
Введение
Современное строительство немыслимо без бетона.
Это один из самых массовых строительных материалов, также самый сложный
искусственный композиционный материал, который может обладать совершенно
уникальными свойствами. Он применяется в самых разных эксплуатационных
условиях, гармонично сочетается с окружающей средой, имеет неограниченную
сырьевую базу и сравнительно низкую стоимость. Также можно добавит возможность
широкого использования местного сырья, малую энергоемкость, экологическую безопасность
и эксплуатационную надежность.
Бетон - один из древнейших строительных
материалов. Из него построены галереи египетского лабиринта, часть Великой
Китайской стены, ряд сооружений на территории Индии, Древнего Рима и др.
Однако, использование бетона для массового строительства началось только во
второй половине XIX
века. В то время его использовали для возведения монолитных конструкций и
сооружений.
Широкое развитие получила технология бетона в
России (тогда еще Советском Союзе) со времени первых крупных гидротехнических
строительств (Волховстроя и Днепростроя). Профессора Н.М.Беляев и
И.П.Александрин возглавили ленинградскую научную школу по бетону и внедрили в
практику строительства первые научные методы подбора состава бетона,
значительно повысившие его качество. В 30-е годы ученые московской школы бетона
разработали методы зимнего бетонирования, тем самым обеспечили круглогодичное
возведение бетонных конструкций, создали ряд ннных видов бетона, что позволило
более широко использовать бетон при возведении жилых и производственных зданий,
разработали способы повышения долговечности бетона, основы технологии сборного
железобетона.
Применение бетонных конструкций сыграло решающую
роль в строительстве первых пятилеток и в перебазировании промышленности в
восточные районы страны в годы Великой Отечественной войны.
.
Общие сведения о бетоне
Бетон -
искусственный каменный материал, получаемый в результате затвердевания
рационально подобранной, тщательно перемешенной и уплотненной смеси вяжущего
вещества, заполнителей и воды. В ряде случаев может содержать специальные
добавки. До затвердевания эту смесь называют бетонной.
Состав бетонной смеси должен
обеспечить бетону к определенному сроку заданные свойства (прочность,
морозостойкость, водонепроницаемость)
В строительстве широко используют
бетоны, приготовленные на цементах или других неорганических вяжущих веществах.
Эти бетоны обычно затворяют водой. Цемент и вода являются активными
составляющими бетона. В результате реакции между ними образуется цементный
камень, скрепляющий зерна заполнителей в единый монолит.
Между цементом и заполнителями
обычно не происходит химического взаимодействия, поэтому заполнители часто
называют инертными материалами. Эти материалы существенно влияют на структуру и
свойства бетона, изменяя его пористость, сроки схватывания, поведение при
воздействии нагрузки и внешней среды. Они значительно уменьшают деформации
бетона при твердении и тем самым обеспечивают получение большеразмерных изделий
и конструкций.
В качестве заполнителей используют
преимущественно местный горные породы и отходы производства. Применение этих
дешевых заполнителей снижает стоимость бетона, так как заполнители и вода
составляют 85-90%, а цемент всего 10-15% от всей массы бетона. Для снижения
плотности бетона и улучшения его теплотехнических свойств используют
искусственные и природные пористые заполнители.
Для регулирования свойств бетона и
бетонной смеси в их состав вводят различные химические добавки и активные
минеральные компоненты, которые ускоряют или замедляют схватывание бетонной
смеси, делают ее более пластичной и удобоукладываемой, ускоряют твердение
бетона, повышают его прочность и морозостойкость, регулируют собственные
деформации бетона, возникающие при его твердение, а также при необходимости изменяют
и другие свойства бетона.
1.1 Классификация
бетонов
В настоящее время в строительстве используют
различные виды бетона. Разобраться в их многообразии помогает классификация
бетонов.
Согласно п.1 ГОСТ 25192-82 «Бетоны.
Классификация и общие технические требования», классификация бетонов
производится по: основному назначению, виду вяжущего, виду заполнителей,
структуре и условиям твердения.
· По назначению различают бетоны
· обычные (для промышленных и
гражданских зданий)
· специальные - гидротехнические,
дорожные, теплоизоляционные, декоративные, а также бетоны специального
назначения (химически стойкие, жаростойкие, звукопоглощающие, для защиты от
ядерных излучений и др.).
· По виду вяжущего вещества
подразделяют на цементные, силикатные, гипсовые, шлакощелочные, асфальтобетон,
пластобетон (полимербетон) и др.
· По виду заполнителей бетоны могут
быть на плотных, пористых или специальных заполнителях.
· По структуре бетоны могут быть
плотной, поризованной, ячеистой или крупнопористой структуры.
· По условиям твердения бетоны
подразделяют на твердевшие:
· в естественных условиях;
· в условиях тепловлажностной
обработки при атмосферном давлении;
· в условиях тепловлажностной
обработки при давлении выше атмосферного (автоклавного твердения).
Дополнительно к классификации ГОСТ 25192-82
используется классификация:
· По объёмной массе бетоны
подразделяют на
· особо тяжёлый (плотность свыше 2500
кг/мі) - баритовый, магнетитовый, лимонитовый
· тяжёлый (плотность от 1800 до 2500
кг/мі) - гравийный, щебёночный (базальтовый, известняковый, гранитный)
· легкий (плотность от 500 до 1800
кг/мі) - керамзитобетон, пенобетон, газобетон, арболит, вермикулитовый,
перлитовый
· особо лёгкий (плотность менее 500
кг/мі)
· По содержанию вяжущего вещества и
заполнителей различают бетоны
· тощие (с пониженным содержанием
вяжущего вещества и повышенным содержанием крупного заполнителя),
· жирные (с повышенным содержанием
вяжущего вещества и пониженным содержанием крупного заполнителя),
· товарные (c соотношением
заполнителей и вяжущего вещества по стандартной рецептуре).
1.2 Компоненты для
приготовления бетонной смеси
Готовая бетонная смесь, она же товарный бетон -
подвижный состав из четырёх основных компонентов, замешиваемых в определенной
пропорции: цемент, щебень, песок, вода.
Цемент (вяжущее вещество) и вода - главные
компоненты бетона. Собственно на них возложена основная функция - связать все
компоненты в единую монолитную структуру. Соблюдение правильной пропорции этих
двух компонентов (водоцементное отношение) - главнейшая задача в производстве
бетона. Цемент, взаимодействуя с водой (гидратация цемента), способен
схватываться и твердеть, образуя так называемый цементный камень. Цементный
камень при затвердевании деформируется. Объемная усадка достигает 2 мм/м. Вроде
и не много, но из-за неравномерности этих усадочных процессов, возникают
внутренние напряжения, появляются микротрещины. Эти микротрещины практически не
видны, но прочность и долговечность цементного камня снижается. Для того, чтобы
уменьшить эти деформации, в состав вводят заполнители:
а) крупные заполнители- щебень;
б) мелкие заполнители - песок.
Роль этих заполнителей - создать структурный
каркас, который воспринимает усадочные напряжения, и в результате - готовый
бетон даёт меньшую усадку. Также увеличивается прочность и модуль упругости
бетона (снижение деформаций конструкции под нагрузкой), уменьшает ползучесть
(когда бетон необратимо деформируется при длительных нагрузках). Заполнители
существенно удешевляют бетон. Ведь цемент стоит значительно дороже чем щебень и
песок.
Для регулирования свойств бетона, бетонной смеси
и экономии цемента применяют различные добавки. Их подразделяют на:
а) Химические, вводимые в бетон в количестве от
0,1 до 2,0%. Эти добавки улучшают свойства бетонных смесей, регулируют сроки
схватывания и твердения, регулируют пористость и плотность, регулируют
деформации бетона, повышают защитные свойства, повышают стойкость бетона к
расслоение, снижают растворо- и водоотделение, придают бетону особые свойства:
гидрофобность, антикоррозийность и др.;
б) Минеральные, вводимые в количестве от 5 до
20%. Используются для экономии цемента, получения плотного каркаса при малых
расходах цемента и повышения стойкости бетона.. Эти материалы представляют
собой порошки различной минеральной природы, получаемые из природного или
техногенного сырья (золы, молотые шлаки и горные породы, микрокремнезем и др.).
Минеральные добавки отличаются от заполнителей мелкими размерами зерен (менее
0,16 мм и меньше), а от химических добавок тем, что они не растворяются в воде,
являясь по существу тонкой составляющей твердой фазы бетона;
в) Органоминеральные добавки. Их получают путем
объединения органических и минеральных компонентов, обладающих модифицирующими
свойствами. Эти добавки снижают водопотребность, повышают морозостойкость и
прочность бетона, снижают усадочные деформации и др. Как правило
органоминеральные добавки выпускаются в порошкообразном виде, что облегчает их
введение в бетонную смесь при ее приготовление.
.
Методика определения состава, приготовления и уплотнения бетона
.1 Подбор состава
бетона
В результате проектирования состава бетона
должно быть определено такое соотношение между материалами, при котором будет
гарантирована прочность бетона в конструкции с учетом технологии ее
изготовления, необходимая подвижность бетонной смеси и экономичность бетона,
т.е. минимальный расход цемента.
Подбор состава включает в себя определение
номинального состава, расчет и передачу в производство рабочего состава.
Номинальный состав бетона определяют в следующей
последовательности:
· устанавливают характеристики
исходных материалов, производят расчет начального и дополнительных составов
бетона, делают пробные замесы всех составов с корректировкой
удобоукладываемости бетонной смеси;
· изготавливают и испытывают образцы
бетона по всем требуемым показателям качества;
· обрабатывают полученные результаты и
выбирают номинальный состав с требуемыми показателями качествами при
минимальном расходе вяжущего.
Приведенная методика подбора состава бетона
распространяется на все его виды. Учитывая большой объем вычислений, все
расчеты и анализы полученных данных выполняются на компьютере по специальной
программе, разработанной для этих целей.
. Расчет начального и дополнительных
составов бетона начинают с определения цементно-водного отношения по формулам
(1) или (2), исходя из заданного класса (марки) бетона. Выбор марки цемента
производят по таблицы 1.
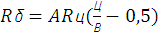
- для бетонов с 
(1)

- для высокопрочных бетонов с 
(2)
где Rц -
активность цемента; А и А1- характеризуют качество используемых заполнителей и
цемента:
Материалы:
заполнители и цемент
|
А
|
А1
|
Высококачественные
|
0,43
|
Рядовые
|
0,60
|
0,40
|
Пониженного
качества
|
0,55
|
0,37
|
Таблица 1
Марка
бетона
|
М150
|
М200
|
М250
|
М300
|
М350
|
М400
|
М450
|
М500
|
М600
|
Марка
цемента
|
300
|
300
400
|
300
400
|
400
500
|
400
500
|
500
600
|
550
600
|
550
600
|
600
|
. Количество воды затворения находят в
зависимости от заданной подвижности или жесткости бетонной смеси по графикам
или таблицам с учетом водопотребности мелкого заполнителя.
. Расход цемента находят, зная количества
воды затворения и водоцементное отношение:

.
Если расход цемента на 1м3 бетона
окажется меньше допускаемого по нормам, то количество его следует увеличивать
до требуемой нормы, сохранив прежнее 
. Расход воды при этом
пересчитывают, исходя из увеличенного расхода цемента. Минимальный расход
вяжущего: для бетонных конструкций - 200 кг/м3 ; для железобетонных - 220 кг/м3
; для конструкций, работающих в агрессивных средах - 250 кг/м3.
4. Расход крупного и мелкого заполнителей
определяют исходя из следующих положений:
а) объем плотно уложенного бетона (принимают в
расчете равным 1 м3 или 1000 дм3 без учета воздушных пустот) слагается из
объема зерен мелкого и крупного заполнителей и объема цементного теста,
заполняющего это положение и называемое уравнением абсолютных объемов, может
быть представлена в следующем виде:

(3)
б) пустоты между зернами крупного заполнителя
должны быть заполнены растворной частью с учетом некоторой раздвижки зерен,
величина которой определяется коэффициентом раздвижки Kразд

(4)
где Ц, В, П и К - расходы соответственно
цемента, воды, песка и крупного заполнителя, кг/м3; pЦ, pВ, pП, pК - плотности
этих материалов; pН.К. - насыпная плотность крупного заполнителя; VПУСТ.К
- относительный объем пустот крупного заполнителя, определяемый по формуле:
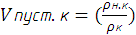
;
КРАЗД -коэффициент раздвижки (
1,05…1,15 - для жестких бетонных смесей, в среднем 1,1; для подвижных смесей -
по графику в зависимости от объема цементного теста Vц.т.
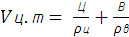
,
с учетом водопотребности песка (Вп)

).
K’разд
Vц.т., дм3
Рис. 1. Значение K’разд для
пластичных бетонных смесей, изготовляемых с применением песка средней крупности
(Bп = 7%)
Решая совместно приведенные выше два
уравнения, получаем формулы для определения расходов:
крупного заполнителя (кг/м3)
песка (кг/м3)
Таким образом определен начальный
состав бетона в виде расхода (кг/м3) компонентов: Ц, В, П, К. Он может быть
выражен в относительных единицах (по отношению к массе цемента): 1:
:
:
Состав бетона проверяют и уточняют
путем пробного замеса бетонной смеси, приготовляемой из производственных материалов.
Лабораторный состав бетона,
полученный для сухих заполнителей, пересчитывают на рабочий состав с учетом
влажности заполнителей, которая может меняться в процессе производства работ.
2.2 Технология
приготовления бетонной смеси
Технология приготовления бетонной смеси включает
подготовку материалов, их дозирование и перемешивание составляющих.
ü Большинство операций по подготовке
материалов (дробление заполнителей, удаление загрязняющих примесей и др.)
осуществляют на предприятиях, производящих материалы. Непосредственно на
заводах ЖБИ или стройплощадках проводят, если имеется необходимость, активацию
цемента, приготовление раствора химдобавок, оттаивание и подогрев заполнителя
(в зимнее время);
ü Дозирование материалов - самая
важная ступень в технологии приготовления бетонной смеси. На современных ЖБИ
используют в основном весовые дозаторы, т.е. дозирование материалов по массе:
цемент, воду и добавки - с точностью до ±1%; заполнители - с точностью до ±2%.
Точное отмеривание составных частей бетона необходимо для того, чтобы его
свойства совпадали с заданными и гарантировалась необходимая однородность
смеси. Кроме того, неточность в дозировании ведет к перерасходу цемента -
наиболее дорогой составной части бетона. Если же работы ведутся в полевых условиях
(непосредственно на стройплощадках), то заполнители иногда дозируют по объему.
В этом случае необходимо учитывать их влажность, особенно песка, так как
увлажнение резко меняет объем, кроме того изменяется подвижность смеси,
соотношение между крупным заполнителем и песком. В результате нарушения состава
могут заметно ухудшиться его свойства.
ü Перемешивание составляющих
компонентов является завершающей ступеней в приготовление и не менее важной,
чем процесс дозирование. В процессе перемешивания материалы равномерно
распределяются по всему объему, зерна цемента и заполнителя смачиваются водой,
в результате получается однородная масса, свойства которой в любом месте объема
одинаковы. Вид и состав бетона оказывают непосредственное влияние на требования
к перемешиванию. Так, например подвижные смеси перемешиваются легче жестких,
крупнозернистые лучше, чем мелко- или тонкозернистые и т.д. Так же в
зависимости от вида и характеристик смеси применяют различные способы
перемешивания: это могут быть смесители свободного падения, в которых
перемешивание проходит при вращение барабана-смесителя в результате
многократного подъема и сбрасывания материалов (крупнозернистые подвижные смеси
с заполнителем из плотных пород) и в смесителях принудительного действия, в
которых происходит более энергичное перемешивание с помощью вращающихся лопаток
(жесткие мелкозернистые и легкобетонные смеси на пористых заполнителях).
Большое влияние на качество перемешивания оказывает его продолжительность. При
недостаточной продолжительности перемешивания ухудшается однородность и
понижается прочность бетона. Увеличение продолжительности перемешивания сверх
оптимальной мало сказывается на свойствах бетона и бетонной смеси (прочность
бетона повышается, но крайне незначительно).
2.3 Уплотнение
бетонной смеси
На свойства бетона еще большее влияние, чем
перемешивание, оказывает уплотнение бетонной смеси. Недоуплотнение приводит к
резкому уменьшению прочности бетона, ухудшает его долговечность и др. Из
различных способов уплотнения наибольшее распространение получило вибрирование.
На заводах ЖБИ изделия обычно формуют на специальных виброплощадках, монолитный
бетон в конструкциях уплотняют глубинными (подвижные бетонные смеси) и
поверхностными вибраторами. При таком способе уплотнения смеси сообщаются
механические колебания, в результате чего связи между частицами постоянно
нарушаются, силы трения и сцепление уменьшаются. Бетонная смесь приобретает
свойства тяжелой жидкости и под влиянием сил тяжести расплывается, заполняя
форму, и уплотняется.
Определенный интерес представляют
безвибрационные методы уплотнения. Из них наибольшее распространение получили:
литьевой, набивной и центрифугирование.
) При литьевом способе применяют очень
подвижные или литые смеси. Такие смеси не требуют вибрации, хорошо заполняют
форму и уплотняются под действием собственной массы. Однако, в этом случае
применяют специальные мероприятия, препятствующие расслоению смеси (вводят
химические добавки или тонкомолотые водоудерживающие добавки). Такой метод
широко применяется в монолитном строительстве.
) Набивной способ позволяет эффективно
уплотнять бетонные смеси с низким водосодержанием и водоцементными отношениями.
При этом составляющим смеси сообщаются определенное количество кинетической
энергии, под действием которой бетонная смесь забрасывается в форму и
уплотняется. Обеспечивая достаточно высокое уплотнение, этот способ не
позволяет получить гладкой открытой поверхности, и требуют дополнительных
мероприятий по ее отделки.
) При центрифугировании бетонная смесь
помещается в цилиндрическую форму, при вращении которой она уплотняется за счет
действия центробежных сил, а излишняя вода отжимается на внутреннюю поверхность
формуемого слоя бетона и удаляется самотеком из формы. Таким способом формуются
трубы, опоры линий передач и др. цилиндрические изделия.
Также для удаления излишней воды из бетонной
смеси после ее укладки в форму применяют вакуумирование, гидропрессование и
электоосмос
Для формования изделий небольших размеров из
жестких бетонных смесей используют прессование и штампование, чаще всего
совместно с вибрированием, которое улучшает удобоукладываемость смеси за счет
снижения ее структурной вязкости - вибропрессование.
2.4 Контроль
качества бетонной смеси и бетона
Для проверки качества бетона следует
своевременно и правильно отбирать пробу и изготавливать из нее контрольные
образцы. Обычно это делает лаборант. Он же наблюдает за правильностью хранения
образцов, а также производит их испытание.
Число подлежащих испытанию серий образцов бетона
каждой марки назначают из расчета одной серии (три образца) на следующие объемы
работ: для массивных сооружений - на каждые 100 м3 уложенного бетона, для
массивных фундаментов под оборудование - на каждые 50 м3 уложенного бетона, но
не менее одной серии на каждый фундамент, для каркасных конструкций - на каждые
20 м3 уложенного бетона. Число серий следует увеличивать до 2-3 при ранних
сроках ввода в эксплуатацию конструкций менее, чем через 28 дней после укладки
бетона, и при особых условиях работы. Изготовление и хранение контрольных
образцов производят по ГОСТ 10180. Для определения прочности бетона на сжатие
изготавливают образцы-кубы, размеры которых зависят от наибольшей крупности
зерен заполнителя.
Перед укладкой бетонной смеси формы очищают от
остатков бетона, а внутреннюю поверхность смазывают отработанными минеральными
маслами или смазкой, препятствующими сцеплению затвердевшего бетона с
поверхностью форм.
Укладка бетонной смеси в формы и ее уплотнение
должны быть закончены не позднее чем через 20 мин после отбора пробы. Методы
укладки и уплотнения бетонной смеси в формах зависят от ее подвижности. Особо
подвижную бетонную смесь с ОК ≥ 120 мм укладывают в формы высотой до 150
мм включительно в один слой, а формы высотой 200 мм и более - в 2 слоя равной
толщины, и каждый слой уплотняют штыкованием металлическим стержнем диаметром
16 мм по спирали от краев к центру образцов. При штыковании нижнего слоя
стержень должен достигать дна формы, при штыковании второго слоя стержень
должен проникать на глубину 2-3 см в лежащий ниже слой. Число штыкований
каждого слоя бетонной смеси принимают из расчета 10 погружений стержня на
каждые 100 см2 поверхности. По окончании штыкования верхнего слоя избыток
бетона срезают металлической линейкой вровень с краями формы, а поверхность
образца заглаживают.
Для пластичных и жестких бетонных смесей, уплотняемых
при формовании изделий вибрированием, образцы изготовляют также с применением
вибрирования. Бетонную смесь укладывают в форму с некоторым избытком, после
чего форму устанавливают на стандартную лабораторную виброплощадку и закрепляют
зажимами. Затем включают виброплощадку и секундомером фиксируют время
вибрирования. Вибрирование должно продолжаться до полного уплотнения,
характеризуемого прекращением оседания бетонной смеси, выравниванием ее
поверхности и появлением на ней цементного раствора. Обычно это время
соответствует показателю жесткости, увеличенному на 30 с.
После уплотнения образцы в формах, покрытых
влажной тканью, хранят в помещении при температуре 10-20°С в течение 1 суток,
затем их вынимают из форм, маркируют и до момента испытания помещают в камеру
нормального твердения при температуре (20±2)°С и относительной влажностью не
менее 95%. Образцы в камере укладывают на стеллажи в один ряд по высоте с
промежутками между ними, обеспечивающими обдувание каждого образца воздухом.
Качество бетона и его работа в конструкциях и
сооружениях определяется его свойствами. Важнейшим свойством бетона является
его прочность - способность сопротивляться разрушающим нагрузкам или другим
факторам. Бетон относится к таким строительным материалам, которые хорошо
сопротивляются сжатию, значительно хуже - срезу и еще хуже - растяжению. Потому
бетонные конструкции обычно проектируют таким образом, чтобы бетон в них
воспринимал сжимающие нагрузки. Поэтому одной из важнейших характеристик бетона
является прочность на сжатие. смесь
бетон уплотнение прессование
Прочность на сжатие образцов-кубов определяют
следующим образом. Образцы извлекают из камеры влажности хранения, осматривают
и обнаруженные на опорных гранях дефекты в виде наплывов удаляют напильником
или шлифовальным кругом, а мелкие раковины заполняют густым цементным тестом.
Затем определяют рабочее положение образца при испытании и отмечают краской или
мелом грани, которые будут прилегать к опорам. Опорные грани выбирают так,
чтобы сжимающая сила при испытании образца была направлена параллельно слоям
укладки бетонной смеси в форму. Образцы обмеряют металлической линейной с
точностью до 1 мм, а затем взвешивают на технических весах. Рабочую площадь
сечения образца (в см2) определяют как среднее арифметическое площадей обеих
опорных граней. Образцы перед испытанием должны в течение 2-4 ч (от момента
извлечения из камеры) находиться в помещении лаборатории. Во время испытания
образец ставят в центр нижней опорной плиты пресса по оси. Затем включают
электродвигатель гидравлического привода пресса. Нагрузку на образец при
испытании увеличивают непрерывно и равномерно со скоростью 0,4-0,8 МПа/с до
разрушения образца.
Прочность на сжатие бетона R6 (в
МПа) определяют как отношение разрушающей силы Р (в Н) к первоначальной площади
поперечного сечения образца S (в м2): 
; Прочность на сжатие бетона
вычисляют как среднее арифметическое результатов испытания трех
образцов-близнецов при условии, что наименьший результат испытания одного из
трех образцов отличается от следующего показателя не более чем на 15%. В случае
если наименьший результат испытания отличается больше чем на 15% от следующего
большего показателя, то предел прочности вычисляют как среднее арифметическое
из двух наибольших результатов. Марку бетона определяют как предел прочности на
сжатие бетонного образца-куба с ребром 150 мм. При длине ребра куба 70, 100,
200, 300 мм предел прочности пересчитывают, пользуясь соответственно следующими
коэффициентами: 0,85; 0,91; 1,05 и 1,10.
В случае, когда прочность бетона (в
контрольных образцах), уложенного в конструкцию, окажется ниже требуемой по
проекту, загружение конструкций эксплуатационной нагрузкой запрещается. При
этом немедленно должны быть приняты меры по созданию необходимых
температурно-влажностных условий для прогрессивного нарастания прочности бетона
в более поздние сроки (2-3 месяца): обогрев паром и поливка бетона водой. После
испытания в эти поздние сроки дополнительной серии контрольных бетонных
образцов необходимо решить вопрос о прочности конструкции. Если полученные
результаты оказались ниже предусмотренных проектом, следует совместно с
проектной организацией разработать мероприятия по усилению конструкций и
обеспечению надежности сооружения в соответствии с его назначением.
Кроме испытания прочности бетона на
сжатие, также контролируются такие показатели как: морозостойкость, плотность,
влажность, удобоукладываемость, пористость, водопоглащение, определяют
водонепроницаемость, истираемость,
3. Влияние реологических
характеристик цементно - песчаных композиций на выбор оптимальных режимов
уплотнения при статческом прессовании
Формирование свойств бетона
начинается с приготовления, укладки и затвердевания бетонной смеси. Эти операции
во многом определяют будущее качество бетона и изделия. Поэтому очень важно
хорошо знать свойства бетонной смеси, зависимость их от различных факторов,
умело управлять процессами приготовления, укладки и затвердевания бетонной
смеси.
Наиболее важным свойством бетонной
смеси является удобоукладываемость или формуемость, т. е. способность смеси
растекаться и принимать заданную форму, сохраняя при этом монолитность и
однородность. Удобоукладываемость определяется подвижностью (текучестью)
бетонной смеси в момент заполнения формы и пластичностью, т. е. способностью
деформироваться без разрыва сплошности.
Для описания поведения бетонной
смеси в различных условиях используют ее реологические характеристики:
предельное напряжение сдвига, вязкость и период релаксации. Для определения
этих свойств, применяют специальные вискозиметры. Подобные испытания выполняют
главным образом в научно-исследовательских лабораториях.
В производственных же условиях
контролируют чаще всего подвижность (текучесть) смеси, для чего применяют
приборы, позволяющие быстро и сравнительно просто получать необходимую
характеристику бетонной смеси.
Основное влияние на эти свойства
оказывают количество и качество цементного тести, так как именно цементное
тесто, являясь дисперсной системой, имеет высокоразвитую поверхность раздела
твердой и жидкой фаз, что способствует развитию сил молекулярного сцепления и
повышению связанности системы. Решающее влияние на свойства бетонной смеси
оказывает расход воды, так как он определяет объем и строение жидкой фазы и
развитие сил сцепления, характеризующих связанность и подвижность всей системы.
3.1 Физико -
механические основы формования и уплотнения
Формовочные смеси в производстве строительных
материалов обладают рыхлой нестабильной структурой, высокой пористостью и
большим объемом вовлеченного воздуха. Необходимым условием получения
однородного по плотности и прочности изделия является уплотнение подготовленных
смесей на стадии их формования.
Поведение структурных систем, которыми являются
практически все формовочные смеси в производстве строительных материалов,
определяется в основном природой и физико-химическими составом твердения фазы.
В процессе уплотнения твердая фаза формовочных
смесей находится под воздействием силового поля, слагаемого из сил тяжести
частиц и внешнего силового поля (давления, удара, встряхивания, колебательных
движений и т.д.). Вместе с тем частицы находятся под воздействием внутренних
сил в системе (сил вязкого и сухого трения, межмолекулярного сцепления,
капиллярного давления и т.д.), которые определяют физико-механичские и
реологические характеристики формуемой смеси.
3.2 Статическое
прессование
Формование прессованием заключается в наложении
на смесь, заполняющую форму, давления, под действием которого материал
перераспределяется в объеме формы и частицы смеси размещаются более компактно.
Статическое прессование производится в жестких пресс-формах, прессующее усилие
направлено по одной оси.
Эффективность уплотнения при прессовании
оценивается величиной коэффициента уплотнения:

,
где pм - средняя плотность готового
образца; p - средняя плотность прессуемого материала.
Различают 3 стадии прессования,
различающихся по характеру перемещений и пластической деформации уплотняемого
материала.
стадия: наблюдается в основном
«автономное» поведение частиц, происходит их интенсивное взаимное перемещение,
повороты, при этом характер напряжений на контактах различный и непрерывно
меняется.
стадия: характеризуется значительным
уменьшением «автономности», преобладанием местной пластической деформации на
контактах и незначительной ролью местных упругих разгрузок.
стадия: протекает при фиксированных
контактах и преобладания пластической деформации во всем объеме частиц. Этому
соответствует значения коэффициента уплотнения 0,85-0,90.
Степень уплотнения готовых образцов
имеет важнейшее значения. Это связано с дальнейшим поведением образцов в
процессе тепловой обработки, а также эксплуатационными характеристиками
изделий. Плотность готового образца, прежде всего зависит от продолжительности
и величины давления прессования, а также от вещественного состава, свойств
компонентов и условий подготовки прессуемой массы. Время выдержки различных
образцов при заданном давлении в процессе прессования существенно влияет на
качество получаемых образцов. С увеличением выдержки изделий при прессовании
увеличивается деформация структурных элементов системы и релаксация напряжений.
В производстве строительных
материалов статическое прессования, как способ формования изделий, получил
широкое распространение при изготовлении различного вида керамических изделий и
небольших по величине бетонных изделий.
3.3 Влияние состава смеси и
продолжительности прессования при заданном давлении на плотность и прочность
получаемого материала
Цель работы: определить оптимальную
продолжительность прессования смеси для получения образцов максимальной
плотности и прочности.
Подбор состава цементно-песчаных композиций и
исследование влияния продолжительности выдержки при заданном давлении
прессования на плотность и прочность получаемых изделий
Группа ЗТ-91
№
бригады
|
Состав
бетонной смеси
|
pТ,
г/см3 ср.плотность образца
|
Р,(МПа)
давление прессования
|
p,
г/см3 ср.плотность прессуемого материала
|
kУПЛ
|
R,(МПа) прочность образца
|
Бригада
№1
|
В/Ц=0,16
Ц/П 1:1,5
|
2,49
|
5
|
2,20
|
0,88
|
101,6
|
|
|
|
10
|
2,26
|
0,91
|
181,2
|
|
|
|
20
|
2,32
|
0,93
|
228,4
|
|
|
|
30
|
2,36
|
0,95
|
211,8
|
|
|
|
40
|
2,37
|
0,96
|
245,9
|
|
|
|
60
|
2,39
|
0,96
|
284,0
|
|
|
|
100
|
2,47
|
169,4
|
Бригада
№2
|
В/Ц=0,18
Ц/П 1:1,5
|
2,46
|
5
|
2,06
|
0,84
|
88,8
|
|
|
|
10
|
2,12
|
0,86
|
168,4
|
|
|
|
20
|
2,18
|
0,89
|
204,1
|
|
|
|
30
|
2,22
|
0,90
|
229,6
|
|
|
|
40
|
2,25
|
0,91
|
234,7
|
|
|
|
50
|
2,28
|
0,93
|
257,1
|
|
|
|
75
|
2,30
|
0,93
|
338,3
|
|
|
|
100
|
2,32
|
0,94
|
229,6
|
|
|
|
125
|
2,32
|
0,94
|
169,4
|
Бригада
№3
|
В/Ц=0,20
Ц/П 1:1,5
|
2,44
|
5
|
2,11
|
0,86
|
203,6
|
|
|
|
10
|
2,16
|
0,88
|
222,4
|
|
|
|
20
|
2,22
|
0,91
|
172,0
|
|
|
|
30
|
2,27
|
0,93
|
248,4
|
|
|
|
40
|
2,31
|
0,95
|
252,0
|
|
|
|
50
|
2,31
|
0,95
|
244,9
|
|
|
|
75
|
2,33
|
0,95
|
|
|
|
100
|
2,35
|
0,96
|
231,6
|
|
|
|
125
|
2,37
|
0,97
|
153,6
|
На основе полученных данных в ходе эксперимента
выявляем закономерности влияния состава прессуемых смесей, продолжительности
прессования при заданном давлении и величины давления на плотность и прочность
получаемых образцов. Строим графики зависимости.
Группа ЗТ-92
№
бригады
|
Состав
бетонной смеси
|
pТ,
г/см3 ср.плотность образца
|
Р,(МПа)
давление прессования
|
p,
г/см3 ср.плотность прессуемого материала
|
kУПЛ
|
R,(МПа) прочность образца
|
Бригада
№1
|
В/Ц=0,16
Ц/П 1:2,5
|
2,44
|
5
|
1,98
|
0,81
|
109,1
|
|
|
|
10
|
2,04
|
0,84
|
131,4
|
|
|
|
20
|
2,10
|
0,86
|
165,8
|
|
|
|
30
|
2,12
|
0,87
|
172,5
|
|
|
|
40
|
2,15
|
0,88
|
239,8
|
|
|
|
50
|
2,17
|
0,89
|
121,2
|
|
|
|
75
|
2,21
|
0,91
|
114,8
|
|
|
|
100
|
2,22
|
0,91
|
193,9
|
|
|
|
125
|
2,23
|
0,91
|
183,0
|
Бригада
№2
|
В/Ц=0,18
Ц/П 1:2,5
|
2,49
|
5
|
1,96
|
0,79
|
89,6
|
|
|
|
10
|
2,00
|
0,81
|
123,5
|
|
|
|
20
|
2,04
|
0,82
|
|
|
|
30
|
2,09
|
0,84
|
125,5
|
|
|
|
50
|
2,14
|
0,86
|
122,0
|
|
|
|
75
|
2,18
|
0,88
|
159,0
|
Бригада
№3
|
В/Ц=0,20
Ц/П 1:2,5
|
2,45
|
5
|
1,96
|
0,80
|
52,0
|
|
|
|
10
|
2,01
|
0,82
|
29,1
|
|
|
|
20
|
2,07
|
0,85
|
66,7
|
|
|
|
30
|
2,11
|
0,86
|
125,5
|
|
|
|
40
|
2,14
|
0,87
|
108,2
|
|
|
|
50
|
2,16
|
0,88
|
100,0
|
|
|
|
60
|
2,17
|
0,89
|
108,2
|
|
|
|
75
|
2,17
|
0,89
|
107,4
|
|
|
|
100
|
2,22
|
0,90
|
98,0
|
На основе полученных данных в ходе эксперимента
выявляем закономерности влияния состава прессуемых смесей, продолжительности
прессования при заданном давлении и величины давления на плотность и прочность
получаемых образцов. Строим графики зависимости.
4. Анализ
результатов
Для выявления закономерностей влияния состава
смеси, величины давления и продолжительности прессования на плотность и
прочность получаемого материала, следует целенаправленно менять состав
исследуемой смеси, путем изменения водоцементного отношения (0,16; 0,18 и 0,20),
величины давления (от 5 до 125 МПа) и продолжительности прессования.
С увеличением прессующего давления уплотнение
смеси происходит не равномерно. Вначале усадка массы сравнительно большая, а с
ростом давления - уменьшается. Одновременно с этим изменяется плотность,
прочность и коэффициент уплотнения образцов.
Группа ЗТ-91
Бригада №1:
при В/Ц=0,16, Ц/П 1:1,5 и изменении нагрузки с 5
до 100 МПа, средняя плотность изменяется с 2,20 до 2,47 г/см3, коэффициент
уплотнения от 0,88 до 0,99;
Бригада №2:
при В/Ц=0,18, Ц/П 1:1,5 и нагрузки от 5 до 125
МПа, средняя плотность изменяется в пределах от 2,06 до 2,32 г/см3, а
коэффициент уплотнения - от 0,84 до 0,94;
Бригада №3:
при В/Ц=0,20, Ц/П 1:1,5 и нагрузки от 5 до 125
МПа, средняя плотность изменяется от 2,11 до 2,37 г/см3, коэффициент уплотнения
- от 0,86 до 0,97.
Группа ЗТ-92
Бригада №1:
при В/Ц=0,16, Ц/П 1:2,5 и изменении нагрузки с 5
до 125 МПа, средняя плотность изменяется с 1,98 до 2,23 г/см3, коэффициент
уплотнения от 0,81 до 0,91;
Бригада №2:
при В/Ц=0,18, Ц/П 1:2,5 и изменении нагрузки с 5
до 75 МПа, средняя плотность изменяется с 1,96 до 2,18 г/см3, коэффициент
уплотнения от 0,79 до 0,88;
Бригада №3:
при В/Ц=0,20, Ц/П 1:2,5 и изменении нагрузки с 5
до 100 МПа, средняя плотность изменяется с 1,96 до 2,22 г/см3, коэффициент
уплотнения от 0,80 до 0,90;
Проанализировав данные результаты можно сделать
вывод, что, чем ниже В/Ц и П/Ц, тем лучше уплотняется смесь, следовательно
коэффициент уплотнения возрастает.
§ Ю.М.Баженов, Технология бетона. -
Издательство Ассоциации строительных ВУЗов. - М. 2003
§ В.Г.Микульский, Строительные
материалы. - Издательство Ассоциации строительных ВУЗов. - М. 2000