Типовая
кривая
|

|
|
Концентрированная
(К)
|
0,4-0,7
|
0,6-0,9
|
Глубокая
(Г)
|
0,8-1,2
|
1,0-1,4
|
Косинусная
(Д)
|
1,2-1,6
|
1,6-2,1
|
Полуширокая
(Л)
|
1,4-2,0
|
1,8-2,3
|
Равномерная
(М)
|
1,8-2,6
|
2,6-3,4
|
опт =0,9 х 3,2= 2,88
Крайние светильники устанавливают на
расстоянии
=(0,3-0,5)
от стены в соответствии с наличием и отсутствием рабочих поверхностей у стен.
Светильники с люминесцентными лампами располагают обычно рядами параллельно
стенам с окнами или длинной стороне помещения. В зависимости от уровня
нормированной освещенности светильники располагают непрерывными рядами или
рядами с разрывами. Расстояние между рядами определяется так же, как и
расстояние между светильниками в ряду.
По известному значению L, длине А и
ширине В помещения определяют число светильников по длине помещения:
(2.3)
число светильников по ширине
помещения,
(2.4)
и общее число светильников в
помещении:
(2.5)
Если расчет расстояния между
светильниками в ряду и между рядами производится с учетом только
, то
полученные значения NA и NB округляют в сторону наименьшего значения, если по
, то в
сторону большего. После чего размещают светильники на плане помещения и
определяют действительные расстояния между светильниками в ряду и между рядами
(2.6)
По справочным данным определяют
коэффициент использования светового потока. Этот коэффициент учитывает долю
светового потока светильников, доходящую до рабочей поверхности. Коэффициент
использования светового потока
прямо пропорционален КПД
светильника, зависит от формы кривой силы света светильника, возрастает с увеличением
степени концентрации светового потока, с увеличением площади помещения и
уменьшения расчетной высоты, с увеличением коэффициента отражения ограждающих
конструкций, уменьшается по мере удаления формы помещения от квадрата.
Расчетный световой поток лампы в
светильнике вычисляется методом коэффициента использования:
, (2.7)
где S - площадь помещения, м2;=
1,0-1,3 - коэффициент неравномерности;- количество светильников в помещении;
Ен=300 лк нормируемая освещенность;
Индекс помещения
(2.8)
(2.9)
Световой поток лампы
(2.10)
Выбираем лампу ЛХБ-40 световой поток
которой равен
со
светоотдачей 75 лм/Вт. Отклонение каталожного данного от расчетного
(2.11)
С
ветильник выбираем по справочнику
марки ЛПО 28-2х40(потолочный, подвесной с рассеивателем для двух ламп ЛХБ 40)
ОСТ 160.533.44-79. На рабочих местах над двумя столами добавляется местное
освещение светильники марки НКС01-100 ТУ 16.545.013-95. По найденному потоку
(если светильник многоламповый, то по потоку, приходящемуся на одну лампу),
пользуясь каталожными данными, выбирают типоразмер лампы и ее мощность. Если
ближайшие лампы имеют световой поток, отличающийся от расчетного более чем на
10-20%, то выбирают лампу с большим потоком и уточняют число светильников.
Аналогично производим расчет
установки светильников на другие помещения (бухгалтерия, кабинет директора,
склад, бытовое помещение, коридоры).
Схема расположения светильников
представлена на чертеже ЭиАСХ ДП 2110000 Э7.
Определяем электрические моменты на
каждом участке
На вводе:
На группе 1:
На группе 2:
На группе 3:
На группе 4:
На группе 5:
На группе 6:
. Рассчитаем сечение проводов на
каждом участке
(2.12)
На вводе: принимаем сечение S = 1,5
мм2.
Сечение проверяем на нагрев: IН =
P/3U = 1420/3·220 = 2,15 А.
Для выбранного сечения IДОП = 19 А,
т.е. IДОП > IН, следовательно сечение S = 1,5 мм2 удовлетворяет всем
условиям выбора.
Определяем потери напряжения на
первом участке
(2.13)
Допустимые потери напряжения
оставшейся сети
ΔU = 3- 0,06 = 2,94%.
(2.14)
На группе 1: принимаем сечение с
запасом S = 1,5 мм2.
Сечение проверяем на нагрев: IН1 =
P/U = 480/220 = 2,2 А.
Для выбранного сечения IДОП = 19 А,
т.е. IДОП > IН1, следовательно сечение S = 1,5 мм2 удовлетворяет всем
условиям выбора.
Определяем потери напряжения на
группе 1:
(2.1.1)
Аналогично ведем расчет на другие группы.
Выбор щитка освещения выбирается по условиям
среды, количеству модулей и распределения по группам. Выбираем щиток марки ЩРН
1-12.
В щите устанавливаем двухмодульные автоматы.
2.1 Расчёт вентиляции
Так как электромонтажникам приходится часто
работать на сварочном аппарате в рабочее время произведем расчёт вентиляции
сварочного участка и пропиточного участка.
. Расчёт необходимого воздухообмена.
Для приближённого способа определения
необходимого воздухообмена применяется коэффициент кратности воздухообмена -
Kв, который показывает, сколько раз в течение часа должен меняться воздух.
Необходимый воздухообмен определяется из
выражения:
= Kв·V, м3/ч, (2.1.2)
где Kв - коэффициент кратности воздухообмена,
для сварочного участка равен 5.- объём помещения, м3.=5·64=320 м3/ч.
. Расчёт производительности вентиляции для
сварочных установок.
Производительность вентиляции для сварочных
установок определяется по часовому расходу электродов и процентному содержанию
в них токсичных компонентов: марганца, хрома и фтористых соединений.
При ручной дуговой сварке из металлических
электродов выделяется в воздух 3% марганца, 0,4% хрома и 3,4% фтористых
соединений.
Необходимая производительность вентиляции м3/ч
определяется по формуле:
, (2.1.3)
где G - масса израсходованных
электродов, кг/ч- содержание вредных компонентов в электродах г/кг- содержание
выделяющихся токсичных веществ, % д и qн - допустимая концентрация токсичных
веществ соответственно в воздухе помещения и в наружном воздухе, г/м3.
За час расходуется 0,5 кг
электродов. Зная, что в 1 кг электродов содержится 67,2 г. марганца, допустимая
концентрация окиси марганца в воздухе 0,3мг/м3. Подставляя все данные в
формулу, получим
м3/ч (2.1.4)
Выбираем центробежный вентилятор
марки ВЦ 4-70-5.
. Выбор мощности электродвигателя
для вентилятора.
Мощность электродвигателя для
выбранного вентилятора находим по формуле
, (2.1.5)
где L - производительность
вентилятора, м3/ч
Н - давление, создаваемое
вентилятором, Па
hв
- к.п.д. вентилятора
hп
- к.п.д. ременной передачи от двигателя к вентилятору, hп = 0,95.
кВт (2.1.6)
Выбирается электродвигатель
закрытый, обдуваемый серии 4А. Паспортная мощность Р=2,2 кВт. Тип двигателя
80А2/2850.
На проектируемом участке
предлагается вытяжная система вентиляции рабочей зоны электросварочных работ и
рабочей зоны пропиточного участка.
2.2 Выбор сечения проводов и кабелей
Расчет электрических сетей
напряжением 0,4 кВ
Однолинейная схема электроснабжения
цеха представлена на чертеже ЭиАСХДП 2110000ЭЗ. Для включения и отключения
электроприемников и других электрических целей служат рубильники, пакетные
выключатели, контакторы, магнитные пускатели и автоматические выключатели
(автоматы). Аппаратной защитой являются также предохранители.
Выбор электрических аппаратов
производят по роду тока, напряжению, мощности, числу полюсов, а также по исполнению
в зависимости от условий окружающей среды и условиям защиты от ненормальных
режимов работы электроприемников и электрических цепей.
Магнитные пускатели предназначены
для дистанционного или автоматического управления трехфазными асинхронными
электродвигателями и другими электроустановками мощностью 75 кВт напряжением до
500 В. Пускатели осуществляют нулевую блокировку (защиту от произвольного
включения и работы на чрезмерно пониженном напряжении), а при наличии в них
теплового реле защищают электродвигатели от перегрузок недопустимой
длительности.
В сельскохозяйственном производстве
рекомендуется использовать магнитные пускатели серий ПМЕ и ПАЕ.
Встраиваемые в магнитные пускатели
тепловые реле типов ТРН (двухполюсные с температурой компенсацией) и ТРП
(однополюсные без температурной компенсации) предназначены для защиты
трехфазных асинхронных электродвигателей от перегрузок.
Автоматические выключатели
предназначены для защиты электрических установок от перегрузок и токов
короткого замыкания, а также для нечастых оперативных коммутаций электрических
цепей. При проектировании сельскохозяйственных предприятий рекомендуется
применять автоматические выключатели серий АЕ-200, ВА -99 и т.д.
Выбирают автоматические выключатели
по напряжению
,по току
,
номинальному току теплового и электромагнитного расцепителя на номинальный ток
электродвигателя.
Для защиты одиночного
электродвигателя с короткозамкнутым ротором ток вставки электромагнитного
расцепителя выбирают по условию:
(2.2.1)
а для защиты группы двигателей по
условию
. (2.2.2)
Результаты выбора коммутационной и
защитной аппаратуры занесены в расчётную схему-таблицу ЭиАСХ ДП 2110000 Э7.
Для защиты нагревательных устройств,
электрических ламп и других электроприемников или сетей, нагрузка которых
равномерна, а продолжительность пусковых токов не превышает долей секунды, токи
плавких вставок предохранителей и тепловых расцепителей автоматических
выключателей выбирают по расчетному току сети или номинальному току электроприемника
с учетом коэффициента запаса, равного 1,1;1,2 т.е.
BСT ³ (1,1…1,2) Iрасч (2.2.3)
Номинальный ток предохранителей,
предназначенных для защиты линий для защиты линий, от которых питаются
несколько электродвигателей или электродвигатели и другие электроприемники, ток
плавкой вставки определяют по формуле
BCT ³ K0
K3 IH +
(2.2.4)
где K0 - коэффициент одновременности
для группы приемников;
КS - коэффициент загрузки каждого
приемника;- номинальный ток каждого приемника;
K3 IH - ток нагрузки электрической
цепи за исключением двигателя с наибольшим пусковым током A;
- наибольший пусковой ток одного из
двигателей, А;
α - коэффициент, учитывающий
условия пуска двигателя с наибольшим пусковым током.
Номинальный ток патрона
предохранителя не должен быть меньше номинального тока плавкой вставки.
Электромагнитный пускатель в цепи электродвигателя вытяжного вентилятора в
зависимости от условий окружающей среды и схемы управления по номинальному
напряжению
,
номинальному току, по току нагревательного элемента теплового реле
.Выбираем
электромагнитный пускатель серии ПМЕ-212; величина пускателя № 2; наибольший
ток 25А.
Расчёт автоматических выключателя
для электродвигателя вытяжного вентилятора мощностью 2,2кВт
Номинальный ток электродвигателя:
(2.2.5)
где Р - мощность электродвигателя
[Вт], Uн- номинальное напряжение.
(2.2.6)
Максимальный рабочий ток:
, (2.2.7)
где Iн - номинальный ток
электродвигателя.
(2.2.8)
Определяем расчетный ток теплового
расцепителя:
(2.2.9)
Принимаем автоматический выключатель
ВА 47 - 29 3Р с номинальным током автомата Iн= 16А, номинальным током
расцепителя Iн.р.= 12А. Устанавливаем ток вставки расцепителя
. Ток
срабатывания электромагнитного расцепителя выбираем по условию
, Принимаем
.
Выбор сечения проводников в сетях
напряжением до 1000В, прокладываемых в помещениях тесно связан с выбором
плавких вставок и установок расцепителей автоматических выключателей.
К выбору сечения проводника
приступают после того как определён номинальный ток плавкой вставки или ток
вставки расцепителя автомата.
, (2.2.10)
где
, (2.2.11)
где kп - поправочный коэффициент
kп=1 при нормальных условиях прокладки; з - коэффициент кратности допустимого
тока, в нашем случае он равен 1.0;з - ток теплового расцепителя автоматического
выключателя.
Расчет силового кабеля питания
вытяжного вентилятора, который идет от силового щита к электродвигателю
.
(2.2.12)
Номинальный ток расцепителя автомата
рассчитан выше.
Выбираем кабель КГ, проложенный
открыто на скобках по стене сечением
. Производим проверку по допустимому
падению напряжения
, где
-
допустимое падение напряжения;
, где Uн - номинальное напряжение
, (2.2.13)
где
- падение напряжения.
, (2.2.14)
где Р - мощность установки [кВТ];
- длина кабеля [м]; - сечение
кабеля [мм2];
с - коэффициент учитывающий
материалы жил, сеть и т.д. в нашем случае
с = 46
(2.2.15)
Остальные кабели рассчитываются
аналогично.
Расчетная схема силовой
распределительной сети представлена на чертеже ЭиАСХ ДП 211000 Э7. К выбору
сечения проводника приступают, после того как определен номинальный ток плавкой
вставки или ток вставки расцепителя автомата. При этом по условию нагревания
длительным расчетным током по условию соответствия сечения провода выбранному току
срабатывания защитного аппарата
, по условию соответствия сечение
провода выбранному току срабатывания защитного аппарата
, (2.2.16)
где Iпр - длительно допустимый ток
проводника, А; дл - длительный расчетный ток электроприемника или
рассматриваемого участка сети, А;
Кп - поправочный коэффициент,
учитывающий условия прокладки;
КЗ - кратность допустимого
длительного тока проводника по отношению к номинальному току или току
срабатывания защитного аппарата;
При нормальных условиях прокладки,
когда температура среды равна 25°С для проводов и 15°С для кабелей, Кп=1.
Значение К3 определяют из таблицы в
зависимости от значения тока защитного аппарата I3, характера сети, изоляции
проводников и условий их прокладки.
По наибольшему значению Iпр,
выбирают сечение провода или кабеля по таблицам длительно допустимых токовых
нагрузок ПУЭ.
В качестве расчетных токов
ответвлений к отдельным электроприемникам принимают их номинальные токи.
Расчетный (длительный) ток
магистрали (А) определяют по формуле:
, (2.2.16)
где Sp-расчетная полная нагрузка
магистрали, кВ-А;н - номинальное напряжение сети, В.
Расчетная полная нагрузка:
, (2.2.17)
где Рр и Qp - соответственно
расчетные активная и реактивная мощности, передаваемые по участку сети.
Расчетная активная нагрузка (кВт)
магистрали определяется из следующего выражения:
, (2.2.18)
где Ру - установленная (паспортная)
мощность каждого из электроприемников, работающих во время ожидаемого максимума
более 0,5 ч, кВт;
Кз - средний коэффициент загрузки к.
п. д. токоприемника;
Рук - установленная мощность каждого
из электроприемников, работающих менее 0,5 ч, кВт; - длительность непрерывной
работы каждого из электроприемников мощностью Pук (t<0,5), ч.
Расчетная реактивная мощность
участка:
, (2.2.19)
где tg φн -
соответствует номинальному коэффициенту мощности cos φ
электроприемника.
Проводник, выбранный по условию
допустимого нагрева, необходимо проверить по допустимой потере напряжения.
Допустимая потеря напряжения для внутренних электропроводок не должна быть
больше 2,5%.
3. РАСЧЁТ ОДНОФАЗНОЙ СЕТИ
Таблица 3.1 - Параметры
электроприемников
Вид
электроприемника
|
Параметры
электроприемников
|
|
Uн,
В
|
Ру,
кВт
|
Кз
|
Η
|
Компьютер
|
220
|
0,8
|
1
|
1
|
Паяльники
2 шт.
|
220
|
0,2
|
1
|
1
|
Пылесос
|
220
|
1,5
|
1
|
1
|
Электродрель
|
220
|
0,5
|
0,8
|
0,8
|
Трансформатор
|
220
|
1,0
|
0,80
|
0,98
|
Сварочный
аппарат
|
220
|
5
|
0,80
|
0,98
|
Расчетная нагрузка.
Активная мощность:
(3.1)
Реактивная мощность: (3.2)
Полная мощность:
(3.3)
Расчетный (длительный) ток
магистрали:
(3.4)
Выбираем по справочнику провод ПВ 1
4х2,5 и автоматический выключатель С 25.
.1 Расчет трехфазной нагрузки
Таблица 3.2 - Параметры
электроприемников
Вид
электроприемника
|
Параметры
электроприемников
|
|
Uн,
В
|
Ру,
кВт
|
Кз
|
Cosφ
|
Сушилка
(ТЭН)
|
380
|
6,0
|
0,6
|
0,78
|
Вентилятор
сушилки
|
380
|
1,5
|
0,7
|
0,89
|
Заточной
станок
|
380
|
0,72
|
0,2
|
0,89
|
Парилка
|
380
|
4,5
|
0,6
|
0,78
|
Лебедка
|
380
|
0,72
|
0,4
|
0,89
|
Вытяжной
вентилятор
|
380
|
2,2
|
0,7
|
О,89
|
Испытуемыйэлектродвигатель
|
380
|
75
|
0,2
|
0,89
|
Активная мощность:
(3.3.1)
Реактивная мощность: (3.3.2)
Полная мощность: (3.3.3)
(3.3.4)
п расчетная =1,44+4,2+49,86=55,5кВт
(3.3.5)
Схема расположения силового
оборудования и розеток в цехе представлена на чертеже ЭиАСХ ДП 2110000 Э7
4. ТЕХНОЛОГИЯ РЕМОНТА
ЭЛЕКТРОДВИГАТЕЛЕЙ
.1 Разборка электрических машин.
Удаление старой обмотки
Разборка электрических машин на
составные части не представляет затруднений. Необходимо только максимально
механизировать выполнение отдельных операций, применяя электро- или
гидрогайковерты, съемники, тали и т. п., а также соблюдать осторожность при
выемке роторов крупных машин, чтобы не повредить ротором железо пакетов статора
или его обмотку.
Наиболее трудоемкая операция при
разборке удаление старой обмотки. Это делают следующими методами: механическим,
термомеханическим, термохимическим, химическим и электромагнитным.
Сущность механического метода
заключается в том, что корпус электрической машины с пакетами стали статора и
обмоткой устанавливают на токарный или фрезерный станок и резцом или фрезой
обрезают одну из лобовых частей обмотки. Затем при помощи электро- или
гидропривода удаляют (вытягивают) из пазов оставшуюся часть обмотки (крюком за
оставшуюся лобовую часть ее). Однако при таком удалении обмотки в пазах есть
остатки изоляции, и требуются дополнительные затраты на их удаление.
При термомеханическом методе
удаления старой обмотки электрическую машину со срезанной лобовой частью
обмотки помещают в обжиговую печь при температуре 300...350°С и выдерживают там
несколько часов.
После этого оставшаяся часть обмотки
легко удаляется. Часто машину помещают в печь со всей обмоткой (ни одна из
лобовых частей обмотки не срезана), но в этом случае после обжига обмотку из
пазов удаляют только вручную.
Равномерное тепловое поле в
обжиговой печи создать трудно. Нередко в печи происходит возгорание изоляции
обмоток, приводящее к резкому увеличению температуры в печи, особенно в некоторых
ее зонах. При повышении температуры выше допустимой могут покоробиться корпуса
машин, особенно это относится к алюминиевым корпусам. Поэтому машины с
алюминиевыми корпусами обжигать не рекомендуется. Некоторые предприятия
исследуют распределение температур внутри печи при ее работе и определяют зоны,
в которых можно расположить электрические машины с алюминиевыми корпусами.
При обжиге в печи происходит отжиг
листов стали статора, заметно уменьшаются удельные потери в стали и повышается
к. п. д. машины. Но при этом выгорают лаковые пленки между пакетом стали и
корпусом и между отдельными листами стали. Последнее приводит к тому, что после
2...3 обжигов нарушается тугая посадка между пакетом и корпусом, пакет начинает
проворачиваться в корпусе машины, ослабляется прессовка пакета. Поэтому
прогрессивным можно признать обжиг изоляции обмоток машин в расплавах солей
(каустика или щелочи).
Обжиг в расплавах солеи проводят при
температуре 300°С (573К) при алюминиевых корпусах и 480°С (753 К) при чугунных
в течение нескольких минут. Полное отсутствие доступа воздуха к объекту обжига,
а также возможность регулирования температуры в необходимых пределах позволяют
применять этот способ обжига и для машин с алюминиевыми корпусами. Коробление
последних исключается полностью.
При термохимическом методе удаления
обмотки электрическую машину, подготовленную к обжигу (одна из лобовых частей
обмотки срезана), опускают в емкость с раствором каустической соды или щелочи.
Машина находится в растворе при температуре 80...100°С в течение 8... 10 ч,
после чего ее обмотку можно легко удалить из пазов пакетов статора. При таком
методе никакого коробления корпусов произойти не может. Этот способ особенно
оправдывает себя при масляно-битумной изоляции обмоток.
При химическом методе электрическую
машину с обмоткой помещают в емкость с моющей жидкостью типа МЖ-70. Эта
жидкость летучая и токсичная, поэтому, работая с ней, необходимо соблюдать
правила техники безопасности. Технология удаления обмоток такова: загрузка
емкости ремонтируемыми машинами, герметизация емкости, заполнение ее жидкостью,
процесс реакции, на который обычно расходуется ночное нерабочее время,
удаление, жидкости, продувка емкости, освобожденной от жидкости, чистым
воздухом, разгерметизация и открытие емкости, выемка электрических машин и
удаление обмотки из пазов статора.
Электромагнитный метод заключается в
следующем. Изготовляют однофазный трансформатор со съемным якорем и одним
съемным, точнее сказать, заменяемым стержнем. На незаменяемый стержень
наматывают намагничивающую обмотку на напряжение сети. На второй съемный
стержень надевают один или несколько статоров двигателей, изоляцию обмоток
которых необходимо обжечь. Диаметр заменяемого стержня подбирают таким образом,
чтобы получить наименьший (порядка 5 мм) зазор между расточкой статора и
стержнем. Метод удобен тем, что при нем можно регулировать температуру нагрева
статора путем изменения подводимого к намагничивающей обмотке напряжения или
переключения числа ее витков. При этом методе можно обжигать машины как с
чугунными, так и с алюминиевыми корпусами.
4.2 Ремонт обмоток
По конструктивному исполнению
обмотки электрических машин делятся на три вида: концентрические, высыпные и
шаблонные. Последние, в свою очередь, подразделяются на обмотки с непрерывной
компаундированной изоляцией и гильзовой. Их применяют в крупных машинах с
напряжением 3,6 кВ и выше, поэтому в данной книге они не рассматриваются.
Практически ремонт обмоток
заключается в удалении старой и выполнении новой обмотки, имеющей те же или
улучшенные данные пазовой изоляции и обмоточного провода.
Концентрическая обмотка наиболее
устаревшая, трудоемкая и находит применение только в электрических машинах с
закрытыми пазами. Изготовление этой обмотки состоит из следующих основных
операций: изготовление при помощи шаблонов пазовых изоляционных гильз, материал
для которых выбирают в зависимости от напряжения машины и класса ее
нагревостойкости; закладка гильз в пазы; заполнение гильз металлическими или
деревянными шпильками по размерам изолированного обмоточного провода; выбор
схемы намотки, при которой получаются наименьшие напряжения между рядом
лежащими проводниками в пазу машины; подготовка провода к намотке катушек,
заключающаяся в удалении изоляции на концах подготовленного к намотке катушки
провода и парафинирование его для облегчения протаскивания в пазах; намотка
двумя обмотчиками наименьшей по размерам катушки с применением специальных
шаблонов для формирования лобовых частей катушки; намотка остальных катушек, их
соединение и изолирование.
При изготовлении всыпных обмоток
сначала заготавливают и укладывают в пазы изоляционные пазовые коробочки. При
этом следует иметь в виду, что в машинах старых серий пазовые коробочки состоят
из двух слоев электрокартона и одного слоя лакоткани. На смену им пришли
пазовые коробочки, состоящие из пленкоэлектрокартона, а в настоящее время в
малых машинах новых серий используется только один тонкий слой изоляционной
пленки. В этих условиях использование новых материалов, в том числе и
обмоточных проводов, при ремонте электрических машин старых серий значительно
увеличивает их надежность и при необходимости может сопровождаться заметным
увеличением мощности машины. Наоборот, при ремонте машин новых серий необходимо
использовать только соответствующие качественные материалы и обмоточные
провода, иначе ремонт машины приведет к снижению ее надежности, ухудшению
технико-экономических показателей и резкому снижению ее мощности. Кроме того,
необходимо учитывать узкую специализацию и механизацию работ на
электромашиностроительных заводах и более низкий уровень технологии работ на
ремонтных предприятиях, что также сказывается на качестве работ, коэффициенте
заполнения паза машины и ее надежности. Следующей операцией по выполнению
обмотки является намотка на специальные, регулируемые по размерам шаблоны
катушек. Далее следует укладка катушек в пазы, установка клиньев, в качестве
которых в малых по мощности машинах новых серий могут быть также использованы
пленка, соединение и бандажирование обмотки изоляционными шнурами или чулками с
установкой изоляционных межфазовых прокладок на лобовых частях обмотки. Если
необходимо соединить отдельные катушки, их изолируют линоксиновыми,
полихлорвиниловыми или стеклолаковыми трубками.
Соединения между катушками могут
быть выполнены или пайкой (соединяемые концы обслуживают, скручивают и опускают
в ванну с расплавленным припоем), или контактной сваркой при помощи ручных
клещей с графитовым электродом.
Сушку обмоток электрических машин,
предшествующую пропитке и после нее, проводят в сушильных печах (конвективный
способ), потерями в стали статора или ротора (индукционный способ), потерями в
обмотках (токовый способ) и инфракрасным облучением (радиационный способ).
Обычно электроремонтные предприятия
имеют вакуумные или атмосферные сушильные печи, объем которых определяется из
расчета 0,02...0,04 м3/кВт мощности машин, для которых печь предназначена.
Нагреватель может быть электрическим, в том числе и ламповым, паровым или
газовым. Мощность нагревателя определяется из расчета примерно 5 кВт на 1 м3 объема
печи. В печи должна обеспечиваться рациональная циркуляция воздуха. Таким
образом, мощность сушки тем больше, чем больше число и мощность подвергающихся
сушке машин. Продолжительность сушки колеблется от нескольких часов (6...8) для
малых машин и до нескольких десятков часов (70...100) для больших машин.
Сушка машин индукционным способом
требует намагничивающей обмотки. Этот способ удобен для сушки крупных машин,
которые лучше сушить на местах установки или ремонта, а не в сушильной печи.
Этот способ экономичнее предыдущего как по затратам мощности, так и по
продолжительности сушки.
Сушка токовым способом еще более
выгодна. Продолжительность сушки сокращается по сравнению с сушкой в печах в
5...6 раз, а расход электроэнергии в 4 и более раз. Недостатком этого способа
сушки является необходимость иметь регулируемый источник питания нестандартного
напряжения. При этом схемы соединения обмоток могут быть различными.
Температура сушки и ее режим зависят от класса нагревостойкости машины и марки
пропиточного лака. Об окончании сушки можно судить по установившемуся
сопротивлению высушиваемой изоляции (при данной неизменной температуре).
Наиболее распространенный способ
пропитки-погружение подогретой до 60...70°С обмотки в лак примерно той же
температуры. Число пропиток зависит от назначения машины, в
сельскохозяйственном производстве рекомендуется проводить до трех пропиток.
Продолжительность пропиток составляет 15...30 мин первой и 12...15 мин
последней.
После вакуумной сушки для особо
ответственных машин можно применять пропитку под давлением. Но для обеспечения
первого и второго процессов требуется относительно сложное оборудование.
Обмоточно-изоляционные работы.
Оборудование, приспособления,
инструменты: ручные рычажные ножны; штангенциркуль 150 мм; нож; ножницы
портняжные; приспособление для формовки пазовых коробочек.
Заготовка изоляции
Рис. 4.1 - Внешний вид пазовой
коробочки с манжетой для усиления: 1 -пазовая коробочка, 2 - отогнутая манжета
Определить размеры заготовок пазовой
коробочки по размерам паза электродвигателя. Отрезать рычажными ножницами
заготовку для одной пробной пазовой коробочки. Отформовать на приспособлении
пазовую коробочку. Усилить выступающую часть пазовой коробочки, обеспечив
размер вылета пазовой коробочки. Внешний вид пазовой коробочки с манжетой для
усиления показан на рис. 4.1. Ширина манжеты должна быть 8-20 мм (в зависимости
от типоразмера электродвигателя).
Рис. 4.2 - Расположение пазовой
коробочки в пазу и вылет манжеты: а - манжета, образованная внутренним слоем
пазовой коробочки, б - манжета, образованная тремя слоями пазовой коробочки; 1
- пакет железа, 2 - электрокартон, 3 - внутренний слой лакоткани или миканита
Заложить для контроля пазовую
коробочку в паз и уточнить размеры заготовок. Расположение пазовой коробочки в
пазу показано на рис. 4.2, а длина вылета приведена в табл. 4.1.
Таблица 4.1 - Примерная длина вылета
пазовой коробочки из паза для электродвигателей разной мощности
Мощность
Электродвигателя
|
кВт
кВт
|
Длина
вылета пазовой коробочки, мм
|
|
При
двухслойной манжете
|
При
трехслойной манжете
|
До
5'
|
10
|
8
|
От
5 до 40
|
15
|
12
|
От
40 до 100
|
20
|
15
|
Отрезать рычажными ножницами полосы
изоляционного материала шириной, равной длине заготовки. Нарезать из этих полос
рычажными ножницами заготовки по развернутой ширине пазовой коробочки.
Отформовать заготовки и скомплектовать пазовые коробочки. Определить по
электродвигателю размеры междуслойных прокладок в пазу и междуфазовых прокладок
в лобовой части. Заготовить по одной пробной прокладке и уточнить их размеры по
электродвигателю. По уточненным размерам заготовить аналогично междуслойные
прокладки в пазу и комплект междуфазовых - в лобовых частях.
Изготовление выводных проводов.
Оборудование, приспособления, инструменты:
круглогубцы специальные; паяльник; ванна для пайки; линейка масштабная;
штангенциркуль; кусачки для резки провода; щипцы или клещи для снятия изоляции.
Выбрать провод необходимого сечения. Разрезать
по длине на куски необходимой длины. После резки зачистить концы проводов от
изоляции, удалить оксидную пленку, скрутить жилы и облудить. Длина зачистки
провода от изоляции должна обеспечивать надежность закрепления и пайки или
сварки. Обычно длина зачистки не превышает 10-20 мм. Зачищать провод от
изоляции ножом не допускается во избежание подрезания токопроводящей жилы
провода. Для удаления изоляции применяют специальные щипцы и приспособления
(клещи), рис. 6. Провода с волокнистой изоляцией требуют закрепления концов
изоляции, которое производят электроизоляционными трубками. Одновременно с
заделкой концов производят маркировку проводов. Перед заделкой концов
многожильных проводов жилы скрутить специальными круглогубцами свернуть кольцо
для крепления на клеммнике.Зачищенные и скрученные концы выводов подвергнуть
горячему лужению. Для этого концы проводов погрузить на 1-2 с в электрованну с
расплавленным припоем ПОС-40, предварительно покрыв место лужения спиртовым
раствором канифоли.
Инструмент для удаления изоляции с выводных концов
см. на рисунке 4.3.
Рис. 4.3 - Инструмент для удаления изоляции с
выводных концов
Намотка статорных секций намотка секций и
катушек.
Оборудование, приспособления, инструменты:
микрометр, приспособление для шаблонировки катушек; намоточный станок; шаблон
для намотки; штангенциркуль; линейка 500 мм; ножницы портняжные; омметр.
Закрепить шаблон на станке (на рис. 4.4 показан
ручной станок) для намотки катушек. Закрепить провод на первой ступеньке
шаблона и намотать вручную начало катушки.
Рис. 4.4 - Станок для ручной намотки катушек с
раздвижным шаблоном: 1 - колодка шаблона; 2 - диск; 3 - счетчик оборотов; 4 -
рукоятка; 5 - станина
Намотать катушку.
Сделать переход на другую ступень шаблона.
Намотать катушку. Данные операции повторить до
завершения намотки секции.
Перевязать каждую катушку в двух местах по
разъему шаблона отходами провода. В случае обрыва провода допускается одна
пайка на шаблон с выводом ее на лобовую часть с изоляцией хлорвиниловой
трубкой.
Снять шаблон с катушкой со станка, вынуть
катушку, перевязать ее в одном месте и уложить в тару.
Замерить сопротивление и проверить вес катушки.
Укладка обмоток статора асинхронных
электродвигателей.
Оборудование, приспособления, инструменты:
подставка для укладки; инструмент обмотчика (рис. 4.5); плоскогубцы; молоток;
молоток резиновый; ножницы портняжные; пресс гидравлический ПГ-1; паяльник;
игла специальная для бандажировки; индикатор ИДО -0,5; пинцет; сварочный
трансформатор 1,0кВт 1З В и латтар; мегомметр.
Рис. 4.5 - Набор инструмента обмотчика: а -
фибровая пластинка; б - фибровый язык; в - обратный клин; г - угловой нож; д -
выколотка; е - топорик; ж и з - ключи для гибки роторных стержней
Подготовка статора к укладке
Продуть статор сжатым воздухом. Тщательно
проверить состояние пазов; при обнаружении заусениц произвести их опиловку.
Заложить в пазы электродвигателя пазовые коробочки, обеспечив их одинаковые
вылеты. Оправить заложенные пазовые коробочки оправкой и установить статор на
специальную подставку.
Укладка секций
Взять комплект секций на электродвигатель и
положить слева от подставки. Взять одну группу фазы и развязать нитки,
связывающие группу.
Первую секцию согнуть. Секцию сгибать так, чтобы
части секции, вкладываемые в пазы, были параллельны. Вязки сдвинуть на лобовые
части.
В первый паз вставить одну сторону секции,
заправляя проводники руками, оправкой, изготовленным из твердых пород дерева
или текстолита, эбонита и т.д. Первым пазом считается паз (если смотреть
слева), лежащий напротив кармана или места выхода из статора выводных концов.
Укладку производят по часовой стрелке. Закрепить секции пазовой крышкой. Обжать
секцию в пазу гладилкой и заклинить клином.
В зависимости от шага по пазам отсчитать
необходимый паз и вставить в него вторую сторону секции, повторяя операции по
укладке первой стороны. Уложить в том же порядке остальные катушки секции
согласно схеме. Вставить лобовые межфазные прокладки. Статор установить вертикально,
расправить концы секций и надеть на них поливинилхлоридные или линоксиновые
трубки. На концы секций в местах межкатушечных соединений надеть
поливинилхлоридные или линоксиновые трубки по одной на каждое. Зачистить места
сварки от изоляции и соединить катушки. Подсоединить выводные концы. Места
соединений сварить при помощи сварочного трансформатора. Концы обмотки
свариваются на стыковом аппарате. Для этого к зачищенным и скрученным вместе
проводам прикладывают металлический электрод. В данном случае используют
плоскогубцы, к которым присоединен один провод от сварочного трансформатора.
Ручки плоскогубцев изолированы. К концу скрутки
прикладывают угольный электрод. Возникшая дуга оплавляет провода и сваривает
их. Момент сварки изображен на рис. 4.6. Зачистить место сварки, отогнуть
скрутку и надвинуть трубку.
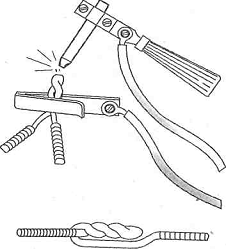
Рис. 4.6
Соединение проводов: скрутка и изолировка.
Надвинуть линоксиновую (поливинилхлоридную) трубку большего диаметра на
отогнутую скрутку с выводным концом так, чтобы каждый ее конец находил на
трубку меньшего диаметра не меньше чем на 10 мм. Уложить выводные концы,
направив их к карману или месту вывода, а затем связать в пучок.
Забандажировать лобовую часть киперной лентой, хлопчатобумажным шнур-чулком или
стеклошнур-чулком, прошивая обмотку возле каждого паза. Шнур завязать узлом у
первого паза. Повернуть статор и забандажировать вторую лобовую часть.
Установить статор в приспособление для прессовки. Выводные концы заправить в
соответствующую прорезь. Отпрессовать лобовую часть. Повернуть статор и
отпрессовать вторую лобовую часть. После опрессовки произвести перетяжку
бандажа. Развязать крепление шнур-чулка, выбрать слабину, образовавшуюся при
опрессовке и завязать узлом заново. При изготовлении приспособления, для
опрессовки лобовых частей статора необходимо учитывать, что после опрессовки
обмотки лобовых частей немного пружинят, увеличивая размер на 2-3 мм. Кроме
того, необходимо также учитывать увеличение размера лобовых частей обмотки на
2-3 мм после пропитки и сушки. Произвести контроль обмотки индикатором ИДО
-0,5. Отправить статор на пропитку и сушку.
4.3 Пропитка и сушка статорных
обмоток
Процесс пропитки включает в себя следующие
этапы: сушка до пропитки; пропитка; сушка после пропитки. Оборудование: печь
сушильная с регулированием обмена воздуха и аппаратурой для регулирования и
контроля температуры, бак для пропитки статоров, вентиляция, тельфер,
мегомметр.
Пропитка статорных обмоток.
Пропитка - это процесс заполнения обмотки и ее
изолировки специальными лаками или составами с последующей запечкой. В процессе
пропитки воздушные включения и пустоты в обмотках и изоляции заполняются
лаками, что приближает ее конструкцию к монолиту. Пропитку выполняют лаками
МЛ-92 на основе растворителей с содержанием пленкообразующих веществ от 30до
70%. Пропитка цементирует витки обмоток, снижает механический износ изоляции,
замедляет процессы теплового старения и увлажнения электроизоляционных
материалов, так как она уменьшает площадь их соприкосновения с окружающей
средой. При этом повышается электрическая прочность изоляции вследствии
заполнения пор и капилляров обмотки лаками, имеющими более высокую
электрическую прочность, чем воздух. Пропитка снижает превышение температуры
обмоток, так как теплопроводность лаков намного выше теплопроводности воздуха.
Необходимо соблюдать следующие условия:
Лак довести до нормальной консистенции и
вязкости, разбавитель должен быть подобран с учетом недопустимости коагуляции
лаков.
Не реже 1 раза в неделю, а также при каждой
загрузке в бак очередного статора проверять вязкость лака и его качество по
лаковой пленке, нанесенной на полоску конденсаторной бумаги или кальки. Для
этого лак в баке тщательно перемешать, погрузить в него полоску чистой бумаги
шириной 40…45 мм и длиной 150…200мм, вынуть и после того, как стекут излишки
лака, осмотреть качество пленки. Лак хорошего качества образует гладкую,
ровную, без просветов пленку.
Очистить от пыли и загрязнений статор до
предварительной сушки.
Сушка до пропитки. Она необходима для удаления
влаги из обмоток, а также для снятия внутренних напряжений в эмалевой изоляции
проводов, которые возникают при эмалировании провода и намотки. Длительность
нагрева режима сушки для пропитки до температуры 70град зависит от массы
статора, степени увлажнения изоляции.
Пропитка. Нагретый статор погружают в бак с
лаком и лак под действием гидравлического давления и капиллярных сил проникает
в обмотку, вытесняя воздух, содержащийся в пространстве между проводниками,
заполняя поры и пустоты. Время нахождения статора в лаке от 20мин. до 1час.
Затем статор поднимают в баке над лаком и после стекания излишнего лака в
течении 15-30мин. Все эти действия производят с закрытой крышкой на баке и
включением вытяжной вентиляции.
Обмотки электрических машин пропитывают один,
два или три раза в зависимости от условий эксплуатации и предъявляемых к ним
требований. В процессе пропитки необходимо постоянно проверять вязкость и
густоту лака, так как растворители испаряются и лак загустевает. При этом
значительно снижается его способность проникать в изоляцию проводов обмотки,
расположенных в пазах сердечника статора или ротора. Поэтому в пропиточную
ванну периодически добавляют растворитель.
Обмотки электрических машин
<#"551098.files/image101.gif">
Рис. 4.7 - Установка капельной
пропитки статоров электрических машин УКПМ-904
Капельная пропитка - это дозированная подача
пропиточного состава на разогретую лобовую часть обмотки статора,
обеспечивающая максимальное заполнение межвиткового пространства за счет
действия капиллярных сил. УКПМ-904 - это установка, реализующая данный метод.
Она предназначена для пропитки и токовой сушки обмоток статоров асинхронных
электрических двигателей мощностью до 100 кВт.
Можно выделить следующие достоинства данного
метода:
Повышение ресурса изделий за счет полного
заполнения межвиткового пространства обмоток
Снижение трудоемкости пропитки за счет
исключения последующих операций промывки и протирки изделия по сравнению с
пропиткой в автоклаве или окунанием
Экономия пропиточного состава за счет его
непосредственного, дозированного попадания в обмотку изделия
Исключение громоздких энергоемких электропечей
Широкая номенклатура пропитываемых изделий
Контроль температуры в ходе процесса
Возможность плавного изменения тока нагрева
Легкоперенастраиваемые зажимы крепления
пропитываемого изделия к платформе установки
Возможность загрузки на установку
крупногабаритных и тяжелых статоров при помощи тельфера
Совмещение процесса пропитки с сушкой обмотки
статора - цикл занимает 1,5-2 часа
Технические характеристики показаны в таблице
4.3.1, пропиточные составы в таблице 4.2.
Таблица 4.2 -Технические характеристики
Габариты
пропитываемых статоров
|
Наружный
диаметр, мм
|
до
500
|
Масса,
кг
|
до
300
|
Емкость
бачка для пропиточного состава, л
|
6
|
Питание
|
380
В, 50 Гц, 7 кВт
|
Площадь,
занимаемая установкой, м²
|
1,5
|
Компаунды
|
Лаки
|
эпоксидные
типа ЭК-1М
|
без
растворителей типа Б-ИД-9127, АС-9115 и др.
|
полиэфирные
типа КП-18, КП-34, КП-50 и др.
|
с
растворителем типа МЛ-92, ГФ-95, КО-933, К-67 и др.
|
4.4 Материал для пропитки
Однокомпонентные пропиточные электроизоляционные
составы для пропитки обмоток электрических машин и аппаратов окунанием или
методом вакуум-нагнетательной пропитки.
Пропиточные составы КП-303БК и КП-303ВК - для
машин с изоляцией класса нагревостойкости F и H - 5 и 180°C. Пропиточный состав
КП-303Б - для машин с изоляцией класса нагревостойкости B и F - 130 и 155°C.
Пропиточный состав КП-307 - для машин с изоляцией класса нагревостойкости F и H
- 155 и 180°C.Компаунды серии КП отличаются сочетанием высокой влагостойкости и
цементирующей способности,рабочих температурах (от 130°C), с высокой скоростью
сушки и большим сроком жизни с инициатором. см. таблицу 4.3.
Таблица 4.3
Наименование
показателей
|
КП-303БК
|
КП-303ВК
|
Условная
вязкость при температуре (20±0,5)°C, с (ВЗ-246)
|
110-160
|
50-100
|
Продолжительность
просыхания в толстом слое до степени 3, мин, не более
|
15
|
15
|
Продолжительность
просыхания в тонком слое до степени 3, мин, не более
|
15
|
15
|
Цементирующая
способность, Н, не менее (R, М (15-35)°C, 45-75%)
|
300
|
300
|
Пропиточный состав Dolphon CC-1144 /LV - для
машин с изоляцией класса нагревостойкости B, F, H, C - 130, 155, 180 и 220°C.
Особенно рекомендуется для тяговых двигателей и других высоконагруженных машин,
в том числе электродвигателей постоянного тока. Пропиточный состав Dolphon
CC-1105 - для машин с изоляцией класса нагревостойкости B, F, H, C - 130, 155,
180 и 220°C. Отличается низкой вязкостью и, как следствие, превосходным
проникновением в обмотку. Рекомендуется в первую очередь для пропитки статора
трёхфазных электродвигателей. Пропиточный состав Dolphon XL 2102 - для машин и
трансформаторов с изоляцией класса нагревостойкости H - 180°C.Образует прочную
и эластичную пленку. Перечисленные компаунды серии Dolphon отверждаются при
140-170°C.Все Компаунды обеспечивают более высокую, чем электроизоляционные лаки,
степень заполнения обмотки. Расход компаундов в 2-2,5 раза меньше, чем у
электроизоляционных лаков. Относительно невысокая вязкость компаундов позволяет
осуществлять пропитку обмоток, нагретых до 50-80°C, холодным компаундом, что
существенно повышает жизнеспособность компаундов в пропиточной ванне и снижает
энергозатраты. Кроме того, уменьшается вытекание компаунда из обмотки сразу
после пропитки. Компаунды полимеризуются без выделения летучих продуктов.
Пропиточные электроизоляционные лаки:
Пропиточный электроизоляционный лак 5328/А.
Прозрачный водорастворимый пропиточный электроизоляционный лак, высыхающий при
комнатной температуре. Особенно хорошо применяется в качестве защитного лака
для обмоток, трансформаторов, лобовых частей обмоток, деталей электронного и
электрического оборудования, механических частей двигателя, оболочки статора.
Успешно используется вместо защитных лаков, содержащих растворители. Образует
пленку с оптимальными показателями по вязкости и защите от влажности,
воздействия пыли с абразивными свойствами, химикатов, минеральных и
трансформаторных масел. Отверждение происходит за 2-3 часа при температуре
60-70°C. См. таблицу 4.4.
Таблица 4.4 - Пропиточный электроизоляционный
лак 5328/А
Вязкость,
воронка №4 DIN при 25°C
|
24-28
с
|
Удельный
вес при 25°C
|
1020±50
г/дм3
|
Уровень
рН
|
7,5-9,0
|
Данные
по обработке
|
|
Время
сушки при 20°C, без отлипа
|
90
мин.
|
Отверждение
|
24
ч
|
(или)
Доотверждение после сушки
|
2-3
ч при 60-70°C
|
Конечные
свойства
|
|
Прочность
на пробой, 50 Гц/25°C
|
100
кВ/мм
|
Качество
пленки
|
глянцевая,
высоковязкая
|
Адгезия
к металлам и стандартным пластмассам
|
очень
хорошая
|
Результат
испытания на а коническом стержне
|
трещины
отсутствуют
|
Пропиточный электроизоляционный лак ВС-346/А
Для пропитки статоров электродвигателей
погружных насосов. Пропиточный электроизоляционный лак ВС-346/А -
высокотемпературный прозрачный отверждаемый лак, отличающийся исключительной
совместимостью с эмаль-проводами различных типов. Электроизоляционный лак
обладает превосходной эластичностью и адгезией. Сохраняет работоспособность до
215°C. Может использоваться также в качестве защитного покрытия изделий,
предварительно пропитанных компаундами типа Dolphon CC-1105 - для повышения их
влагостойкости.
Пропиточная смола Dolphon PDR 1962
Однокомпонентный пропиточный состав на основе
эпоксидной смолы и латентного ускорителя, не содержащий растворителя. Класс
нагревостойкости F-H. Предназначена для пропитки предварительно нагретых
объектов (окунание и вакуум-нагнетательная пропитка: 50-60°C, капельная
пропитка: до 180°C): якорей, статоров и роторов электродвигателей, обмоток
трансформаторов, трансформаторных установок, полюсных катушек и роторов
синхронных генераторов и тяговых двигателей, статорных обмоток высоковольтных и
низковольтных ветровых генераторов. Также идеально подходит для нанесения в
виде покрытия (метод окунания) для защиты от действия соленой воды, фреона и
повышенных температур. Отличается высокой химической и влагостойкостью,
хорошими механическими и электри свойствами, отличной адгезией к металлическим подложкам
и хорошими диэлектрическими свойствами при температурах до 170°C. Пропиточный
состав обладает выдающейся стабильностью в ванне при повышенных температурах и,
как следствие, длинным сроком жизни при условии регулярного пополнения запаса и
охлаждения смолы. А также имеет очень короткое время желирования и потому
Практически не стекает в процессе желирования и отверждения. Срок хранения - 6
месяцев при 20°C, в оригинальном контейнере. Ниже см. таблицу 4.5.
Таблица 4.5 - Пропиточная смола Dolphon PDR 1962
Вязкость
по Брукфилду RTV, мПа: - при 25°C - при 70°C
|
1200-1500
65-80
|
Плотность
при 25°C, г/см3
|
1,15±0,05
|
Температура
стеклования, °C
|
150
|
Время
желирования при 130°C, мин.
|
5-7
|
4.5 Участок пропитки и сушки обмоток
электродвигателей
Участок пропитки и сушки предназначен для
ремонта обмоток электродвигателей. В состав оборудования входят:
) Станция теплообмена и вакуумирования (поз.1);
) Установка пропиточная (поз.2), состоящая из
двух емкостей, соединенные между собой трубопроводами;
) Две печи вакуумные, 1ая печь V =0,8м3; 2ая
печь V =9м3 (поз.3).
Рис. 4.8 - Участок пропитки
Пропитка лаком, ремонтируемого
изделия, осуществляется в одной из емкостей, в которую при откачке насосом
воздуха, перетекает лак из другой емкости. В результате осуществляется
качественная пропитка. После необходимой выдержки по времени, вакуумный насос
выкачивает воздух из пустой емкости и лак перетекает обратно. Пропитанное
изделие, в зависимости от габаритов, помещается в печь вакуумную, где при
температуре до 200°С происходит сушка и запекание лака. Процесс осуществляется
в автоматизированном режиме. Работа всех установок происходит одновременно и
независимо друг от друга. В вакуумных печах так же возможно производит сушку
трансформаторов. Время высыхания лака в вакуумных печах - до 5 часов, после
достижения заданной температуры. (Время сушки зависит от габаритов изделия.)
Возможна замена лака МЛ - 92 на компаунд КП -34 или КП -98, что позволяет уйти
от взрывозащищенного исполнения участка см. таблицу 4.7. Станция теплообмена и
вакуумирования
Таблица 4.6 - Техническая
характеристика станции
Наименование
показателя
|
Значение
|
1.
Питающее напряжение, В
|
220/380
|
2.
Частота тока, Гц
|
50
|
3.
Габариты станции, мм
|
|
-
длина
|
1510
|
-
ширина
|
1425
|
-
высота
|
1490
|
4.
Масса, кг
|
1110
|
5.
Агрегат вакуумный золотниковый АВЗ-180 наибольшее рабочее давление кПа
(мм.рт.ст)
|
20(150)
|
Расход
охлаждающей воды, м3/ч
|
1,3
|
Уровень
звуковой мощности, ДБА
|
90
|
Двигатель
4АМР16084 мощность, кВт
|
15
|
Напряжение,
В
|
380
|
Масса
агрегата, кг, не более
|
870
|
6.
Аппарат теплообменный (маслоохладитель) типа МВ 10
|
|
Расход
воды л/мин
|
|
-
номинальный
|
400
|
-
максимальный
|
800
|
Масса,
кг
|
70
|
Рис. 4.9 - Установка пропиточная
Таблица 4.7 - Техническая
характеристика установки
Наименование
показателя
|
Значение
|
1.
Питающее напряжение, В
|
220/380
|
2.
Частота тока, Гц
|
50
|
3.
Потребляемая мощность, кВа
|
3
|
4.
Максимальный объем заливаемого лака МЛ-92, л
|
1500
|
5.
Внутренний диаметр бака, мм
|
1800
|
6.
Полезный объем бака, л
|
1980
|
7.
Наибольшая высота пропитываемого изделия, мм
|
760
|
8.
Габариты бака, мм
|
|
-
высота
|
1100
|
-
диаметр
|
1800
|
10.
Масса, кг
|
3200
|
|
|
|
Рис.4.10 - Печь вакуумная V=0,8 м3 и
V=9 м3
Таблица 4.8 - Техническая
характеристика
Наименование
показателя
|
Значение
V=0,8м3
|
Значение
V=9м3
|
1.
Число обслуживающего персонала, чел
|
1
|
1
|
2.
Питающее напряжение, В
|
220/380
|
380
|
3.
Частота тока, Гц
|
50
|
50
|
4.
Потребляемая мощность, кВа
|
20
|
60
|
5.
Сила тока на обмотке, А
|
44
|
69
|
6.
Количество витков, шт
|
|
|
-
внутренней обмотки
|
88
|
89
|
-
средняя обмотка
|
-
|
82
|
-
наружной обмотки
|
87
|
89
|
7.
Площадь покрытого сечения медной жилы, мм2
|
16
|
16
|
8.
Диаметр провода обмотки в изоляции, мм
|
9,9
|
9,9
|
9.
Мощность индукционного нагревателя, кВА
|
16,8
|
56,2
|
10.
Расход воды для охлаждения, м3/ч
|
0,04
|
0,04
|
11.Габаритные
размеры, мм
|
|
|
-
высота
|
1020
|
2680
|
-
диаметр внутр.
|
1000
|
2200
|
12.
Масса, кг
|
1200
|
3200
|
|
|
|
|
|
На рисунке 4.11 показана малая печь V=0,8 м3 и
на рисунке 5 показана большая печь V=9 м3.
Рис. 4.11 - Печь вакуумная малая
Рис. 4.12 - Печь вакуумная большая
Достоинство капельного метода -
простота, возможность быстрой реализации токовой сушки, всего 6л пропитки.
Недостаток - испарения, Необходимость принудительной вентиляции.
Вакуумный метод требует более
сложного и дорогостоящего оборудования, значительного объема пропитки, обучение
персонала. Опытная установка пропитки обмоток статоров позволяет решить данные
проблемы см. рис. 4.13.
Рис. 4.13 - Опытная установки
пропитки статоров
Способ пропитки
вакуумно-нагнетательным методом осуществляется по следующей технологии.
Предварительно высушенную, прогретую
до температуры 60-90°С станину обмотанным статором устанавливают на стенд.
Перед началом процесса пропитки внутреннюю полость станины герметизируют с
помощью верхней и нижней крышек, прижимаемых через резиновые прокладки к торцам
станины, закрепляя с помощью домкрата, чем создают естественный автоклав. Затем
проводят вакуумирование обмотки статора до остаточного давления 3,0Ч103 Па,
продолжительность 3 мин, открывают вентиль 8 на трубопроводе 9, подающем
пропиточный состав, например, лак К0-916к с вязкостью 30-45 с по вискозиметру
ВЗ-246 (ГОСТ 9070-75). Через смотровое окно, расположенное на верхней крышке,
контролируют уровень лака (уровень лака должен стать выше лобовой части обмотки).
Затем создают давление внутри установки до 0,3 МПа для дополнительного
нагнетания лака, продолжительность 15 мин. После этого, сняв давление, сливают
лак. Затем создают повторный вакуум до остаточного давления 5,0Ч103 Па в
течение 1-2 мин для интенсивного испарения растворителя. Затем производят
разгерметизацию станины, открывают верхнюю крышку, снимают станину со стенда и
производят сушку в печи.
В таблице представлен режим пропитки
обмотки статора электродвигателя.
Данный способ пропитки обмоток
электродвигателя позволяет упростить технологический процесс пропитки за счет
того, что для его осуществления не требуется специальное оборудование -
автоклав. В процессе пропитки снижается количество расходуемого лака, т.к. в
описываемых выше способах изделие с обмоткой помещают в емкость с лаком, и лак
покрывает всю поверхность изделия, которое помещено в автоклав (и ту
поверхность, которую нужно пропитывать, и ту поверхность, которой не требуется
пропитка по технологическому процессу), что увеличивает расход дорогого
пропиточного лака, а в предложенном способе лак подается непосредственно в
полость станины, которую необходимо пропитать, что повышает качество пропитки,
обмотки.
Данный способ особенно эффективен
для пропитки крупных электрических машин мощностью свыше 15 кВт, когда
осуществление вакуумного способа пропитки требует применения специальных
автоклавов значительных габаритов. По предлагаемому техническому решению на
опытном производстве ОАО НИИВЭМ смонтирована и внедрена в марте 2000 года
установка для пропитки обмоток вакуумно-нагнетательным методом
(Технологическая инструкция БЯИН.
520208.066), которая подтверждает приемлемость и осуществляемость данного
способа пропитки. Отмечено хорошее качество пропитки обмотки электродвигателей
см.таблицу. 4.9.
Таблица 4.9 - Режим пропитки обмотки
статора электродвигателя
№
п/п
|
Наименование
операции
|
Температура,
°С
|
Продолжительность
операции
|
1.
|
Предварительная
сушка в печи
|
130
|
1ч
|
2.
|
Герметизация
станины
|
|
|
3.
|
Вакуумирование
до остаточного давления 2,94Ч103 Па
|
|
3
мин
|
4.
|
Заполнение
станины лаком, создание давления 1,01ё3,04Ч103 Па
|
|
5
мин
|
5.
|
Выдержка
под давлением 1,01ё3,04Ч103 Па
|
|
15
мин
|
6.
|
Снятие
давления и слив лака
|
|
5
мин
|
7.
|
Создание
повторного вакуума12,75Ч103 Па
|
|
1
мин
|
8.
|
Стекание
лака
|
|
15
мин
|
9.
|
Сушка
в печи
|
120
180
|
2
ч 8 ч
|
4.6 Режимы сушки и пропитки
Ориентировочные данные по режимам сушки и
пропитки приведены в табл. 4.10. При выборе режимов необходимо иметь в виду
следующее:
Приведенное в таблице время сушки является
ориентировочным. Более точно время сушки может быть установлено по
сопротивлению изоляции и отсутствию отлипа. Большие значения времени,
приведенные в таблице, относятся к машинам 100 кет и выше, меньшие - к малым
машинам менее 1 кет. Чем толще изоляция обмоток от корпуса, чем больше витков в
катушках-секциях, тем больше время сушки и пропитки.
. Для машин нормального исполнения, работающих в
сухих помещениях, пропитка обмотанных статоров, роторов, якорей, а затем
покрытие проводятся 1-2 раза.Для машин повышенной влагостойкости пропитка
статоров, роторов, якорей проводится 2-3 раза; влагостойкого и химостойкого
исполнения - до 5 раз. Покрытие производится дважды. Каждая последующая
пропитка проводится с сокращением времени пребывания в лаке и удлинением
времени сушки после пропитки. Для якорей (роторов) с открытым пазом и
креплением обмотки бандажами во избежание их ослабления рекомендуется проводить
все пропитки, кроме последней, с временными бандажами. Перед последней
пропиткой накладывают гоостоянные бандажи, проводят сокращенную по времени
сушку и затем последнюю пропитку и наиболее продолжительную сушку. Для
вращающихся обмоток время сушки должно быть выбрано достаточным, чтобы
предупредить разбрызгивание лака при запуске машины м.табл. 4.10.
Таблица 4.10 - Режимы сушки
Деталь
|
Провод
|
Время
сушки до пропитки, ч
|
Лак
|
Время
сушки после пропитки, ч
|
|
Класс
изоляции
|
|
|
|
Катушки
многовитковые (шунтовые и т.д.)
|
пэл,
пэв, пэтв ПЭЛШО, ПЭЛБО пэтсо пэтксо
|
1-4
|
321т,
ПФЛ8в, 458 321т, ПФЛ8в, 458 447, 321, МЛ92 МГМ8 ЭФЗБСУ
|
10-30
|
Катушки,
секции
|
ПБД
ПСД псдк
|
2-6
|
без
корпусной изоляции 2-6 с корпусной изоляцией 4-12
|
Обмотанные:
статоры, роторы (всыпная шаблонная обмотка)
|
А,
Е В F н
|
3-10
|
321
т, ПФЛ8в, 458 447, 460 МГМ8, МЛ92 ЭФЗБСУ, К47
|
5-20
|
Якори
|
А,
Е В F Н
|
3-10
|
321
т, ПФЛ8в 458 447, 460 МЛ92 МГМ8 ЭФЗБСУ
|
8-25
|
Индукторы
|
В
F
|
3-10
|
9-627,
321 ЭФЗБСУ
|
8-25
|
3. Пропитка секций и катушек проводится 2 раза.
Мягкие секции всыпной обмотки пропитывают в жидком лаке (10-12" ВЗ-4).
.Пропитка катушек из эмальпровода ПЭЛ, ПЭВ, ПЭТВ
проводится водоэмульсионными лаками (32IT, ПФЛ8В) или лаком № 458 на скипидаре,
так как другие растворители, в особенности бензол, вредно действуют на эмалевую
изоляцию провода. Температура и время пребывания в лаке выбираются
минимальными. Многовитковые катушки целесообразно пропитывать с применением
вакумм-прощесса. Температуру сушки проводов с винифлексовой изоляцией во
избежание потери гибкости изоляции следует принимать не выше 100° С.
. Режимы сушки для покровных лаков-эмалей
приведены в табл. 4.11.
Таблица 4.11 - Режимы сушки
Класс
изоляции
|
Лак,
эмаль
|
Сушка
|
|
|
Температура,
"С
|
Время,
час
|
А,
Е, В F, Н F, Н А, Е, В
|
СПД,
460 ПКЭ 14 ПКЭ 19 СВД, КВД 462п
|
105-125
120
|
6-12
3-4
|
|
|
180Н-200
120 20° ± 5°С
|
12-18
8-12 18-24
|
.Нанесение покровных лаков воздушной сушки (№
462, СВД) пульверизатором проводится дважды с промежуточной подсушкой 30 мин.
Для ускорения сушки покровных лаков-эмалей воздушной сушки может применяться
нагрев до 70-80° С. Покровные лаки рекомендуется наносить на горячие
(неостывшие) обмотки.
. Пропитка машин химически стойкого исполнения
проводится лаками № 477, 1154, 9-627; покрытие - эмалью СПД.
. Полюсные катушки, намотанные из шинной меди с
проклейкой витков цементирующими лаками, роторы турбогенераторов, изоляционные
гильзы и формованные из миканита детали подвергаются запеканию.
Температура при запекании колеблется для
шеллачных лаков в пределах 125-150° С, бакелитовых 100- 120° С, глифталевых
150-200° С. Подъем температуры должен быть плавным с выдержкой на промежуточных
температурах.
Время запекания зависит от сложности детали и
колеблется от получаса (гильзы, катушки на ребро) до нескольких дней (роторы
турбогенераторов).
. Для защиты лобовых частей обмотки статоров
небольших асинхронных двигателей от разрушающего действия пыли, влаги, кислот,
щелочей применяется обмазка пастой типа ЭЛСИ (бакелитовый или глифталевый лак
35%, тальк 32%, цемент 32%, растворитель - толуол). Пасту наносят рукой или
деревянной лопаточкой дважды. После первого нанесения пасты, заполняющей все
неровности лобовой части, следует сушка на воздухе, а затем в течи при
температуре 80-120° С в течение 4-6 чДалее, наносится второй слой, создающий
гладкую ровную поверхность лобовой части без отдельных выступающих проводников
и т. п. После сушки второго слоя поверхность лобовой части покрывается
покровным лаком или эмалью. Следует иметь в виду, что обмазка лобовой части
ухудшает теплоотдачу и на 10-15% снижает допустимую по нагреву мощность. Перед
нанесением пасты на обмотку, бывшую в эксплуатации, следует тщательно очистить
обмотку от пыли, грязи, масла и т. п. Таким образом, мы в результате анализа
методов пропиток обмоток электрических машин выбрали наиболее подходящий для
ООО «Статор» вакуумнагнетательный метод, а с целью удешевления конструкции
предлагаем использовать вместо бака сам статор электрической машины, выполнив
его герметизацию с помощью подручных средств.
4.7 Разработка установки для
пропитки статоров асинхронных электродвигателей
Установка пропитки обмоток статоров УПС-10
Общие сведения
Установка УПС-10 предназначена для пропитки и
термообработки обмоток однофазных и трехфазных статоров асинхронных
электродвигателей. Конструкция и принцип работы
Основные узлы установки: вращающийся стол с
расположенными на нем приспособлениями для закрепления пропитывающих статоров,
устройство для дозирования и распределения пропиточного состава, электропривод
и устройство для токового нагрева пропитываемых обмоток. Установка роторного
типа имеет 16 позиций. Пропитка осуществляется капельным методом,
термообработка - путем нагрева током промышленной частоты 50 Гц. Оба процесса
выполняются автоматически по заданной программе.
Условия эксплуатации
Температура окружающей среды от + 160 до +350 С;
окружающая среда - невзрывоопасная; климатическое исполнение УХЛ; категория размещения
4 по ГОСТ 15150-69. Технические данные см в таблица 4.12.
Таблица 4.12
Длительность
цикла пропитки и термообработки, мин
|
10…32
|
Метод
пропитки
|
капельный
|
Метод
термообработки
|
токовый
|
Количество
позиций, шт
|
16
|
Количество
позиций пропитки
|
3
|
Температура
нагрева обмотки статора, max, 0С
|
165
|
Частота
вращения статора, об/мин
|
25
|
Потребляемая
мощность, кВт
|
16*,
25**, 27**
|
Габаритные
размеры, мм
|
1800х1500х3075*
1800х1500х2830** 1800х1500х3410**
|
Масса,
кг
|
3860*,
3990**, 4250**
|
Параметры
обрабатываемого изделия
|
|
Наружный
диаметр сердечника статора, мм
|
89…140*
89…106**
|
Внутренний
диаметр статора, min, мм
|
50
|
* - параметры для однофазного электродвигателя
** - параметры для трехфазного электродвигателя
Рис. 4.14 - Установка вакуумная
пропиточная
Предназначена для пропитки обмоток
статоров электродвигателей с предварительным созданием разрежения в пропиточном
баке.
Процесс пропитки состоит из
нескольких циклов:
загрузка изделий; - откачивание
воздуха (создание разряжения); - выдержка изделия в вакууме (-0,75 кг/см2); -
перекачивание лака из резервного бака в пропиточный; - пропитка; -
перекачивание лака из пропиточного бака в резервный; - выдержка изделия до
прекращения каплепадения; - выгрузка изделия.
Длительность циклов программируется
на ПУ. Процесс пропитки полностью автоматизирован.
Таблица 4.13
1.
Диаметр пропиточного бака, мм
|
1600
|
2.
Высота пропиточного бака, мм
|
по
желанию заказчика
|
3.
Создаваемое разряжение, кг/см2
|
-0,75
|
4.
Установленная мощность, кВт
|
8.5
|
5.
Габариты, мм /масса, кг - установка пропиточная вакуумная - шкаф управления -
станция гидрораспределительная
|
5500х2260х3100/
3100 840х340х1500 /150 1170х1120х1500 / 420
|
СТАНДАРТНОЕ ОБОРУДОВАНИЕ КОМПАНИИ ARRAS MAXEI
Компания ARRAS MAXEI предлагает 2 стандартных
типа пропитки: вакуумная (VM), а также сочетание вакуумной пропитки и пропитки
под давлением (VMP).
• модель VM/VMP включает в себя резервуар,
установленный под автоклавом, что позволяет существенно сэкономить место.
Пропиточная установка см. на рисунке 4.15.
Рисунок 4.15
Оборудование VM и VMP
Компания ARRAS MAXEI предлагает полный диапазон
стандартного оборудования диаметром от 500 до 2000 мм
Подача лака осуществляется под действием
пониженного давления в автоклав и обратно в резервуар под действием силы
тяжести.
Конструкция оборудования соответствует
Европейской директиве 97/23/CE по оборудованию, работающему под давлением, в
том числе стандарту CEI на материалы, предназначенные для использования в
условиях высоких температур. Стандартная схема установки для пропитки моточных
изделий см. на рисунке 4.16.
Рис. 4.16 - Стандартная схема установки для
пропитки моточных изделий
Применение высококачественных вакуумных насосов
в установках пропитки.
Вакуумные насосы являются основой в процессах
сушки и пропитки, а также для подачи лака подсасыванием.
Их конструкция позволяет достичь постоянных
значений вакуума в соответствии со значениями кривой давления паров лака и
избежать дистилляции.
Установки включают в себя несколько типов
уловителей и осушителей для лучшей защиты насоса и уменьшения частоты
технического обслуживания (насос без смазки поставляется по дополнительному
запросу). Картриджный вакуумный уловитель
Вакуумный уловитель на основе проволочной
мочалки
Вакуумная установка75 VMP
Вакуумная установка100 VM
Автоклавы оснащены опорными кронштейнами,
благодаря которым открытие и закрытие крышки осуществляется без особых усилий.
После подъема крышка поворачивается вправо или влево (по желанию клиента),
открывая тем самым полный доступ в область загрузки/разгрузки. Смотровое окно с
подсветкой обеспечивает прекрасную видимость внутренней поверхности автоклава в
процессе пропитки.
Для сосудов, работающих под давлением,
используются специальные зажимы крышки, обеспечивающие удобство и быстроту
фиксации.
Опорные кронштейны для открытия и закрытия
крышки.
Закрытие крышки в версии VM.
Окно и подсветка для обзора внутренней
поверхности автоклава.
Схему электрическую принципиальную пропиточной
установки см. на рисунке 4.17.
Рис. 4.17 - Схема электрическая принципиальная
пропиточной установки
Принцип действия: при нажатии кнопки SBQ1 замыкается
КМ1 и включается вакуумный насос. Кнопка SBQ1блокируется контактом КМ1.1 и
включается сигнализация лампочки HL1. При подогреве лака автоклава через
контакт температурного реле замыкается магнитный пускатель КМ2. Кнопка SBQ3
включает нагнетательный насос. С помощью магнитного пускателя КМ3 включается
нагнетательный насос при определения условного давления размыкается цепь.
Переключатель S1включает таймер с световой и звуковой сигнализацией на время
технологического процесса. Установка для пропиток обмоток статоров асинхронных
электродвигателей см. на рисунке 4.18.
Рис. 4.18 - Установка для пропиток обмоток
статоров асинхронных электродвигателей
Установки для пропитки методом «вакуум-давление»
(VPI) предназначены для пропитки в вакууме и под давлением. В основном данная
технология применяется для пропитки роторов и статоров электрических
вращающихся машин и электродвигателей, больше известных как приводные двигатели
(поездов, подъемных механизмов и др.…), а также обмоток (катушек)
трансформаторов среднего и высокого напряжения. В ряде случае метод
«вакуум-давление» применяется для создания монолитности и механической
прочности моточных изделий.
Процессы пропитки под вакуумом с использованием
давления (VPI) имеют следующие преимущества:
• применение смол и лаков без использования
однокомпонентного растворителя
• более качественная пропитка смолой и/или лаком
благодаря использованию пористого изоляционного материала.
• более качественный теплообмен проводников
• устранение локального перегрева
• уменьшение объема изоляционного материала
Установки вакуумно-нагнетательной пропитки,
предлагаемые ООО ТЦ «Виндэк» отличает высокая степень автоматизации с
возможностью контроля оператором и дистанционного контроля.
Для установок характерны простота использования,
безопасность и гибкость.Рабочее давление пропитки может составлять до 8 атм., а
значение вакуума < 0,5 мбар. Установки ТЦ «Виндэк» обеспечивают постоянное
качество пропитки.
В большинстве модификаций установки вакуумно-нагнетательной
пропитки состоят из:
•Резервуар (бак подготовки) для подготовки и
хранения смол,лаков в условиях вакуума
•Миксер для создания максимально однородной
консистенции пропиточного вещества
•Контур нагрева и / или охлаждения резервуара
для хранения
•Теплообменник для нагрева смолы в процессе
подачи в автоклав
•Контур нагрева автоклава
•Горизонтальное или вертикальное исполнение
автоклава
•Автоматическое или ручное открытие
5. ТЕХНИКА БЕЗОПАСНОСТИ И
ПРОТИВОПОЖАРНЫЕ МЕРОПРИЯТИЯ
Ответственность за соблюдение требований правил
техники безопасности возлагается на администрацию предприятия, а также на
инженерно-технический персонал, непосредственно руководящий производством
работ. Вопросами техники безопасности и охраны труда занимается директор предприятия
ООО «Статор». Лицом ответственным за электрохозяйство на предприятии назначен
мастер. В пределах порученных им участков работы он обязан:
организовать обучение, инструктирование,
проверку знаний и допуск к самостоятельной работе электротехнического персонала;
организовать безопасное проведение всех видов
работ в электроустановках;
обеспечить своевременное и качественное
выполнение технического обслуживания, планово - предупредительных ремонтов и
профилактических испытаний электроустановок;
Безопасность работ при эксплуатации и ремонте
электрооборудования регламентирована Межотраслевыми Правилами по охране
труда(Правила безопасности при эксплуатации электроустановок ).
Директор ООО «Статор» и мастер имеют 5 группу по
электробезопасности, электромонтер 4 группу, а обмотчик 3группу по
электробезопасности. Все работники имеют удостоверения установленной формы и
ежегодно проходят обучение и очередную проверку знаний в комиссии Искитимского
отделения Ростехнадзора по СФО. На группу по электробезопасности по правилам
безопасности, правилам технической эксплуатации, пожарной безопасности,
правилам пользования защитными средствами, правилам устройства
электроустановок, правилам освобождения пострадавшего от электрического тока и
оказания первой помощи пострадавшему. Проверка состояния здоровья работников
проводится периодически, в порядке, предусмотренном Минздравом.
.1 Общие правила по техники
безопасности и противопожарной безопасности при проведении работ в
электроустановках до 1000 В
Лицом, ответственным за электрохозяйство
предприятия, назначен приказом мастер. Перечень должностей и профессий
электротехнического персонала, которым необходимо иметь соответствующую группу
по электробезопасности, составлен и утвержден руководителем предприятия.
Перечень должностей и рабочих мест, требующих присвоения 1 группы по
электробезопасности (неэлектротехнического персонала) определен руководителем
предприятия, им является бухгалтер. Инструктаж проводится ежегодно с записью в
журнал. Все работы, которые проводят электротехнические работники предприятия
ООО «Статор» разрешены перечнем работ выполняемых в порядке текущей
эксплуатации, которые утверждены руководителем предприятия. Это небольшие по
объему виды работ, выполняемые в течение рабочей смены в электроустановках до
1000, выполняемые со снятием напряжения. Подготовка рабочего места
осуществляется теми же работниками, которые в дальнейшем проводят необходимую
работу. Работа в порядке текущей эксплуатации, включенная в перечень, является
постоянно разрешенной, на которую не требуется каких либо дополнительных
указаний, распоряжений, целевого инструктажа. В перечне работ указывается
условия обеспечения безопасности и возможности единоличного выполнения
конкретных работ для обмотчика и электромонтера. Регистрация работ производится
записью в оперативном журнале. Перед допуском к новой производственной работе
или при переводе с одной работы на другую руководитель работ (мастер) обязан
подробно ознакомить работника с правилами внутреннего распорядка, с
особенностями данного рабочего места, цеха и с безопасными приемами и способами
выполнения поручаемой работы, а также указать на недопустимые приемы работы,
применение которых может повлечь за собой несчастный случай.
К работе на подъемно-транспортном,
сушильно-пропиточном оборудовании и испытательном стенде допущены обученные
лица, имеющие документ на право допуска к работе и прошедшие специальный
инструктаж по технике безопасности. Работа в цехе связана с повышенной
пожароопасностью. Поэтому все работы, с применением открытого огня, с
образованием искр, а также курение запрещено в цехе и вывешена табличка.
В целях пожарной безопасности в цехе вывешены
два огнетушителя и установлен ящик с песком на пропиточном участке.
.2 Основные правила
электробезопасности
Сопротивляемость человека действию
электрического тока непостоянна и зависит от времени действия, состояния
кожного покрова, влажности среды и т. п., а также от напряжения и силы тока.
При поражении током силой в 0,01 А человек ощущает нервное потрясение, при
поражении током силой более 0,015 А человек часто не может самостоятельно
освободиться от соприкосновения с токоведущими частями, ток силой в 0,1 А -
смертелен. Защиту при косвенном прикосновении следует выполнять если напряжение
в электроустановке превышает 50В переменного и 120В постоянного тока. В
помещениях с повышенной опасностью 25В переменного и 60В постоянного, особо
опасных и в наружных установках 12В переменного, 30В постоянного. Для защиты от
поражения электрическим током в случае повреждения изоляции должны быть
применены по отдельности или в сочетании следующие меры защиты при косвенном
прикосновении: защитное заземление; автоматическое отключение питания;
уравнивание потенциалов; выравнивание потенциалов; двойная или усиленная
изоляция; сверхнизкое напряжение; защитное электрическое разделение цепей;
изолирующие непроводящие зоны, площадки. Для защиты от поражения электрическим
током в нормальном режиме должны быть применены по отдельности или в сочетании
следующие меры защиты от прямого прикосновения: основная изоляция токоведущих
частей; ограждения и оболочки; установка барьеров; размещение вне зоны
досягаемости; применение сверхнизкого (малого) напряжения. Для дополнительной
защиты от прямого прикосновения в электроустановках до 1000В следует применять
УЗО (устройство защитного отключения). В цехе ООО «Статор» выполнены следующие
меры по электробезопасности: в цехе выполнена основная система уравнивания
потенциалов, имеется главная заземляющая шина в ВРУ 0,4кВ, соединяющая между
собой следующие проводящие части а) РЕN -проводник питающей линии, б)
заземляющий проводник, присоединенный к заземлителю повторного заземления цеха,
в) металлические трубы коммуникаций, входящих в цех - горячее и холодное
водоснабжение, отопление, канализация, г) металлические части системы
вентиляции. В цехе выполнена дополнительная система уравнивания потенциалов,
которая соединяет между собой все одновременно доступные прикосновению
металлические открытые проводящие части, включая доступные прикосновению
металлические части строительных конструкций здания цеха, а также нулевые
защитные проводники. Выполнена дополнительная мера защиты от поражения
электрическим током человека и от возникновения пожаров в электропроводке и
электрооборудовании - это в розеточных группах установлены УЗО АД - 12. УЗО
отключается при токах утечки 30ма. Повторный искусственный контур заземления
выполнен в помещении цеха из круглой стали вертикальными заземлителями
диаметром 16мм и длиной по 3м, расстояние между ними 3м. Соединены они между
собой горизонтальными заземлителями с помощью сварки круглым железом диаметром
10мм. Используются также естественные заземлители это металлическая колонна и
рельсы. У испытательного стенда и рабочих столов лежат изолирующие коврики. Для
работы в электроустановках до 1000в применяются основные (штанги, изолирующие
перчатки, инструмент с изолирующими ручками, указатели напряжений), и
дополнительные средства защиты(коврики, галоши, накладки). Все средства защиты
испытываются в соответствии с нормативным требованиями в установленные сроки.
Имеется комплект переносных плакатов (предупреждающие, запрещающие,
предписывающие, указательные).
5.3 Безопасность жизнедеятельности
Правила безопасности.
Факторы, влияющие на исход электротравм:
) Сила тока
) Время протекания
) Путь тока через организм человека
Наиболее часто встречающиеся пути:
. нога-нога - 0,4% энергии проходит через
сердце.
. рука-рука - 0,4 - 3,3% (наиболее опасный путь
прохождения)
. рука-нога - занимает промежуточное положение
между 1и2.
). Место вхождения тока в организм (действие
тока на организм усиливается при замыкании контактов в акупунктурных точках
(зонах).
). Состояние организма человека (прежде всего,
нервной системы).
). Условия окружающей среды (температура,
влажность).
Повышенная температура, влажность повышают
опасность поражения эл. током. Чем ниже атмосферное давление, тем выше
опасность поражения.
Рис. 5.1 - Простейшая схема
электрического сопротивления человека
Кожа действует как конденсатор
(большое сопротивление).
Величина эл. сопротивления меняется
в зависимости от напряжения:
Рис. 5.2 - Схема двухполюсного
прикосновения
= 1000 Ом = 1 кОм =40 кОм -
сопротивление человека
Прикосновение в сетях с заземленной
нейтралью (при однофазном прикосновении).
(иногда используют r0) (5.3.1)
≤ 4 Ом - сопротивление
заземления нейтрали.
, (5.3.2)
где rП - сопротивление пола, об -
сопротивление обуви, од - сопротивление одежды.
Двухполюсное сопротивление считается
наиболее опасным.
Сети с изолированной нейтралью
используются для питания небольших лабораторий.
Приведенные формулы справедливы для
работы установок в нормальном режиме (т.е. при сохранении нормативных значений
сопротивления изоляции).
В аварийных ситуациях человек
попадает под действие линейного напряжения (при неисправности фаз). К аварийным
режимам относятся режимы, для которых характерно следующее: происходит случайно
электрическое соединение частей электроустановки, находящейся под напряжением,
с землей или заземленными конструкциями; появление напряжения на частях
(корпусах) оборудования.
5.4 Опасность поражения
электрическим током и первая помощь при электротравме
Любое поражение электрическим током,
даже на первый взгляд незначительное, может быть опасным, т.к. действие тока на
внутренние органы (сердце, нервную систему) иногда проявляются не тотчас же, а
несколько позже. Поэтому во всех случаях поражения электрическим током или
молнией после оказания первой помощи пострадавшего нужно (в лежачем положении,
осторожно) как можно скорее доставить в лечебное учреждение. Электротравма -
поражение электрическим током, а также патологические изменения в тканях
(внешних покровах, внутренних органах, нервной системе) и психике, которые
вызываются в организме под влиянием электрического тока. Повреждения зависят от
непосредственного прохождения электрического тока через организм и от той
энергии, в которую ток преобразуется (тепло, свет, звук) при разряде в
непосредственной близости от человека. Общие и местные явления, вызываемые
воздействием тока на организм, могут варьироваться от незначительных болевых
ощущений, при отсутствии органических и функциональных изменений со стороны
органов и тканей, до тяжелых ожогов с обугливанием и сгоранием отдельных частей
тела, потерей сознания, остановки дыхания, сердца и наступлением смерти.
Поражение электрическим током может
произойти как от отдельных частей электроустановок, неизолированных, с
повреждением или влажной изоляцией, так и через посторонние предметы, случайно
оказавшиеся в соприкосновении с ними. Токи высокого напряжения могут поражать
разрядом через воздух на расстоянии или через землю, например при падении на
нее провода высоковольтной сети. Поражение молнией (атмосферным электричеством)
может произойти при непосредственном разряде на человека, а также и на
расстоянии - через землю или через провода воздушной электрической сети
(осветительной, телефонной и пр.). Наиболее опасным считается переменный ток
частотой в 50 Гц, силой начиная с 0,1 А или 100 мА и напряжением свыше 250 В.
Примечания:
Данные соответствуют прохождению
тока через тело человека по пути рука - рука или рука - ноги.
Пороговый фибрилляционный ток - это
наименьшее значение фибрилляционного тока, т.е. тока, вызывающего при
прохождении через организм фибрилляцию сердца. Его значение при 50 Гц
составляет 50-350 мА. При этом ток 67 мА вызывает фибрилляцию лишь у 1 человека
из тысячи, 367 мА - у 999 человек из тысячи и ток 157 мА - у 500 человек из
тысячи, т.е. у 50% людей.
Однако опасными и смертельными могут
оказаться и значительно меньшие величины тока. С другой стороны, напряжение,
измеряемое тысячами вольт, и токи силой в несколько ампер могут оказаться
несмертельными. Вопрос об истинных причинах такой парадоксальности остается еще
неразрешенным, равно как и вопрос о первопричине и механизме смерти при
электротравме и зависимости ее от параметров тока. При этом большое значение
имеет реактивность организма и психическое состояние в момент поражения током.
При электротравме развиваются отеки
на почве повышенной проницаемости сосудов, поражается мышца сердца (миокард).
Наиболее характерны разнообразные изменения в различных отделах нервной системы,
свидетельствующие и значительном раздражении и перевозбуждении ее. Из местных
повреждений характерны омертвения кожи не только на местах "входа" и
"выхода" тока, но и по его ходу. Особенность местной электротравмы
заключается в безболезненности при слабых степенях поражений ("знаки
тока") и невозможности при значительных ожогах немедленно определить
границы погибших тканей. Из симптомов электротравмы преобладают
сердечно-сосудистые расстройства (иногда довольно стойкие), головные боли, расстройства
функций органов слуха и равновесия, повышение внутричерепного давления, потеря
памяти о происшествии, вызвавшем электротравму.
Первая помощь, при электротравме
заключается в мерах спасания (освобождения пострадавшего от прикосновения к
проводнику тока), в оживлении, борьбе с угрожающими жизни явлениями, в
предупреждении осложнений. Для освобождения от действия тока необходимо
выключить рубильник, вывернуть предохранительные пробки на щитке. Если это
невозможно, то спасающий должен освободить пострадавшего из-под действия тока,
предварительно обеспечив свою безопасность: надеть резиновые или сухие
шерстяные перчатки или обернуть руки сухой тканью, надеть галоши или встать на
сухую доску, оттянуть провод или пострадавшего сухой веревкой, деревянной
палкой и т.д. Одновременно нужно вызвать врача (скорую помощь). И оценив
правильно состояние пострадавшего принять меры по оказанию первой помощи
пострадавшему.
При потере сознания, но наличии
признаков жизни применяются энергичные меры, возбуждающие деятельность сердца и
дыхание (искусственное дыхание, массаж сердца и т.п.). Однако отсутствие
признаков жизни не дает права считать пострадавшего мертвым, т.к. при
электротравме возможно состояние так называемой "мнимой смерти",
объясняющееся резким нарушением функций центральной нервной системы без наличия
каких-либо необратимых изменений. Поэтому мероприятия по оживлению организма
должны проводиться длительно и непрерывно, до появления признаков жизни или
действительных признаков смерти. Первая помощь и лечение при электрических
ожогах в общем те же, что и при ожогах термических.
На рану и обожженные места в месте
вхождения тока надо наложить сухую стерильную повязку. Если пострадавший
находится в сознании, его надо уложить в постель, напоить сладким крепким
горячим, чаем или кофе и обеспечить ему полный покой. Поражение молнией дает
картину, сходную с поражением электричеством, и требует аналогичных мер первой
помощи и лечения.
5.5 Пожарная опасность
технологических процессов и меры профилактики
статор электродвигатель электрический
сеть
На промышленных предприятиях
пожарную опасность представляют хранение, обработка и транспортировка различных
горючих материалов (топливо, изоляционные и смазочные масла, битумы, лаки,
растворители, органические пленки, пряжа, бумага и др.).Согласно Строительным
нормам и правилам (СНиП П-М.2-72) в зависимости от характеристики обращающихся
в производстве веществ и их количества производства подразделяются по пожарной
и взрывной опасности на категории А, Б, В, Г, Д и Е.
Производства категории А
(взрывоопасные и пожароопасные) характеризуются применением или образованием в
производственном процессе горючих газов с нижним пределом взрываемости 10% и
менее; жидкостей с температурой вспышки паров до 28°С включительно при условии,
что указанные газы и жидкости могут образовывать взрывоопасные смеси в объеме,
превышающем 5% объема помещения; вещества, способные взрываться и гореть при
взаимодействии с водой, кислородом воздуха и друг с другом.
Производства категории Б
(взрывоопасные и пожароопасные) характеризуются наличием горючих газов, нижний
предел взрываемости которых более 10% к объему воздуха; жидкости с температурой
вспышки паров выше 28 до 61 °С включительно; жидкости, нагретые в условиях
производства до температуры вспышки и выше; горючие пыли и волокна, нижний
предел взрываемости, которых 75 г/м3 и менее, при условии что указанные газы,
жидкости и пыли могут образовать взрывоопасные смеси в объеме, превышающем 5%
объема помещения.
Производства категории В
(пожароопасные) характеризуются наличием горючих жидкостей с температурой
вспышки паров выше 61°С; горючей пыли или волокон, нижний предел взрываемости
которых более 65 г/м3 к объему воздуха; веществ, способных только гореть при
взаимодействии с водой, кислородом воздуха или друг с другом; твердых сгораемых
веществ и материалов. Производства категории Г характеризуются наличием веществ
и материалов в горючем, раскаленном или расплавленном состоянии, процесс
обработки которых сопровождается излучением тепла, искр и пламени; твердых
жидких и газообразных веществ, которые сжигаются или утилизируются в качестве
топлива.
Производства категории Д
характеризуются наличием только несгораемых веществ и материалов в холодном
состоянии.
Производства категории Е -
взрывоопасные. Они характеризуются наличием газов (без жидкой фазы) и
взрывоопасной пыли в таком количестве, что они могут образовать взрывоопасные
смеси в объеме, превышающем 5% объема помещения. При этом количество этих
веществ таково, что по условиям технологического процесса возможен только взрыв
без последующего горения. В производствах категории Е могут быть также
вещества, способные взрываться (без последующего горения) при взаимодействии с
водой, кислородом воздуха или друг с другом.
Отнесение производства к одной из
перечисленных категорий принимается по нормам технологического проектирования
или по специальным перечням производств, устанавливающим категории взрывной,
взрывопожарной и пожарной опасности, утвержденным отраслевыми министерствами.
При классификации производств по
пожарной опасности к категориям А, Б и В не следует относить те производства, в
которых твердые, жидкие и газообразные вещества сжигаются в качестве топлива
или в порядке утилизации их, а также те производства, в которых технологический
процесс совершается с применением открытого огня.
В электроустановках причины пожаров
и взрывов могут быть электрического и неэлектрического характера. Причинами
электрического характера являются:
а) искрение в электрических
аппаратах и машинах, а также искрение в результате электростатических разрядов
и ударов молнии;
б) токи коротких замыканий и токовые
перегрузки проводников, вызывающие их перегрев до высоких температур, что может
привести к воспламенению их изоляции;
в) неудовлетворительные контакты в
местах соединения проводов, когда вследствие большого переходного сопротивления
при протекании электрического тока выделяется значительное количество тепла и
резко повышается температура контакт;
г) электрическая дуга, возникающая
между контактами коммутационных аппаратов часто как следствие неправильных
операций с ними (например, отключение нагрузки разъединителем), а также при
дуговой электросварке;
д) аварии с маслонаполненными
аппаратами (выключатели, трансформаторы и др.), когда происходят выброс в
атмосферу и воспламенение продуктов разложения минерального масла и смеси их с
воздухом;
е) перегрузка и неисправность
обмоток электрических машин и трансформаторов при отсутствии надлежащей защиты.
К причинам пожаров и взрывов
неэлектрического характера можно отнести:
а) неосторожное обращение с огнем
при проведении газосварочных работ;
б) неправильное обращение с
газосварочной аппаратурой, с паяльными лампами и нагревателями для плавления
кабельных масс и пропиточных составов;
в) неисправность котельных,
производственных печей, отопительных приборов и нарушение режимов их работы;
г) неисправность производственного
оборудования (перегрев подшипников и т.п.), нарушение производственного
технологического процесса, в результате чего возможно выделение горючих газов,
паров, пыли в воздушную среду;
д) курение в пожароопасных и
взрывоопасных помещениях и установках;
е) самовозгорание некоторых
материалов.
Для устранения причин пожаров и
взрывов на производстве проводятся различные профилактические мероприятия -
технические, эксплуатационные, организационные и режимные.
К техническим мероприятиям относится
соблюдение противопожарных норм при проектировании и сооружении зданий,
устройстве отопления и вентиляции, выборе и монтаже электрооборудования, а
также устройстве защиты от электростатических разрядов, молниезащиты и др.
Эксплуатационные мероприятия
предусматривают правильную техническую эксплуатацию производственных агрегатов,
котельных, компрессорных и других силовых установок и электрооборудования,
правильное содержание зданий и территории предприятия.
К организационным мероприятиям
относятся обучение производственного персонала противопожарным правилам,
создание на предприятии добровольных пожарных дружин, издание необходимых
инструкций и плакатов по противопожарной технике.
Режимными мероприятиями являются
ограничение или запрещение в пожароопасных местах применения открытого огня,
курения, производства электро- и газосварочных работ. Работы с огнеопасными и
взрывчатыми веществами должны быть оформлены специальным нарядом.
5.6 Расчёт заземления
С целью обеспечения
электробезопасности все технологическое оборудование с электроприводом должно
быть надежно заземлено. Сопротивление заземления должно быть не более 10 Ом.
Расчёт заземления сводится к
определению сопротивления одного заземлителя, и если его сопротивление
превышает допустимое Rв >10 Ом, то определяется необходимое количество
заземлителей. А также необходимо рассчитать длину соединительной полосы.
Заземлители выполним из круглой
стали диаметром 0,04 м.
Постоянный контур заземления выполняется
так, чтобы верхние концы забитых вертикально стержней находились на глубине t
< 0,8 м. Для этого делается траншея глубиной t, забиваются стержни
(заземлители) 1 длиной l=3-5м и верхние концы свариваются полосой 2.
Рис. 5.3 - Контур заземления: 1 -
заземлитель; 2 - соединительная полоса
Сопротивление такого одиночного
стержня определяется по формуле:
, Ом, (5.6.1)
где ρ - удельное
сопротивление земли равный для суглинка 100 Ом·м,
Ом. (5.6.2)
Количество стержней вертикального
заземления nв определяется по формуле:
в=
, (5.6.3)
где Rд - требуемое безопасное
сопротивление (не более 10 Ом);
ηс - коэффициент сезонности,
равный 1,6…2;
ηэ - коэффициент
экранирования, равный 0,5…0,85.в=
=6,95≈7. (5.6.4)
Заземлители приварены к
соединительной полосе с поперечным сечением 40х4 (b=4), проложенной в грунте от
поверхности земли до середины ширины полосы на глубине h=0,5 м. Определим длину
соединительной полосы.
. (5.6.5)
Сопротивление полосы будет
равняться:
. (5.6.6)
Общее сопротивление заземление
заземляющего устройства Rо определим по формуле:
. (5.6.7)
Согласно нормам измерение
сопротивления заземляющих проводников измеряется при текущем и капитальных
ремонтах заземлённого оборудования, но не реже, чем раз в год. Осмотр наружных
частей заземляющей проводки и проверки надёжности присоединения оборудования к
ней делается одновременно с осмотром соответствующего оборудования, но не реже
одного раза в шесть месяцем. Измерения сопротивления заземлителей обычно
делается с помощью специального измерителя заземлений типа Ф-4103, М-416, МС-08
или измерителем кажущегося сопротивления ИКС-1.
6. ЭКОНОМИЧЕСКОЕ ОБОСНОВАНИЕ
ДИПЛОМНОГО ПРОЕКТА
Целесообразность автоматизации
технологических процессов определяется расчетом экономической эффективности,
который производится по технико-экономическим показателям предприятия в
расчетном году. Достоверность определения экономического эффекта во многом
зависит от методики его расчета и правильности выявленных внутрипроизводственных
резервов (увеличение производительности оборудования, уменьшение потерь,
энергозатрат и др.), реализация которых возможна с помощью автоматизации.
В соответствии с действующей
методикой расчет экономического эффекта проводят по следующей схеме:
Экономическую эффективность проекта
можно определить путем установления срока окупаемости затрат на данную
конструкцию.
экономическая эффективность
проектируемого оборудования определяется затратами, связанными с его
изготовлением и использованием.
Еср=(С1-С2)/(К2-К1), где
Еср - сравнительная экономическая
эффективность,
С1,С2 - текущие затраты базового и
проектируемого варианта,
К1,К2 - капиталовложения базового и
проектируемого вариантов.
Капиталовложения: К=Цоб+Моб+Нр+Кпр,
где
Цоб - стоимость оборудования [руб.],
Моб - стоимость монтажа [руб.],
Нр - накладные расходы [руб.],
Кпр - затраты на проектирование
[руб.].
Таблица 6.1 - Смета на предлагаемое
оборудование
№
п/п
|
Наименование
|
Марка
|
Сумма
затрат,
|
1
|
Автоклав
|
|
56000
|
2
|
Вакуумный
насос
|
|
14650
|
3
|
Шестерёнчатый
насос
|
|
12859
|
4
|
Вентиль
|
|
450
|
5
|
Промежуточное
реле
|
РПУ
2М 2116620
|
506
|
6
|
Пульт
управления
|
ПКЕ
2223
|
203
|
7
|
Шкаф
|
ШРН
ЩМП1(1Р30 396/310/220)
|
928
|
8
|
Прибор
ЭКМ
|
ТКП
160 ЦПУХЛ
|
690
|
9
|
Пускатель
ПЛМ
|
1160
220В/380В
|
215
|
10
|
Пускатель
ПЛМ
|
2100Б
220В/380В
|
370
|
11
|
Автомат
вводный
|
ВА
47-29-4Р 25А
|
115
|
12
|
Автомат
ТЕН
|
ВА
47-29-3Р 16А
|
115
|
13
|
Автомат
Вакуум.
|
ВА
47-29-3Р 6А
|
115
|
14
|
Автомат
Шест.
|
ВА
47-29-3Р 6А
|
115
|
15
|
Силовой
кабель
|
ВВГ
5х2,5
|
675
|
16
|
Кабель
|
ВВГ
4х1,5
|
144
|
17
|
Ёмкость
для лака
|
|
3560
|
18
19
|
Труба
Уголок
|
|
1062
1460
|
1
|
Бак
пропитки
|
|
6700
|
2
|
Бак
пропарки
|
|
7800
|
3
|
Шкаф
|
ШРН
ЩМП1(1Р30 396/310/220)
|
928
|
4
|
Прибор
ЭКМ
|
ТКП
160 ЦПУХЛ
|
690
|
5
|
Кабель
|
ВВГ
4х1,5
|
144
|
6
|
Автомат
ТЕН
|
ВА
47-29-3Р 16А
|
155
|
|
|
Итого:
|
) Рассчитаем капитальные затраты базового
оборудования:
.1) Стоимость монтажа
Моб=20%Цоб=0.2·16077=3215,4 руб.
.2) Накладные расходы Нр=10%Цоб=0.1· 16077=
1607,7руб.
.3) Затраты на проектирование
Кпр=1.5%Цоб=0.015·16077 =241,155 руб.
.4) Исходя из расчётов, капитальных затрат.
Базового оборудования.
К=16077 +3215,4 +1607,7 +241,155 =21141,3руб.
2) Рассчитаем капитальные затраты предлагаемого
оборудования:
.1) Стоимость монтажа
Моб=20%Цоб=0.2·94232=18846,4 руб.
.2) Накладные расходы Нр=10%Цоб=0.1·94232 =
9423,2 руб.
.3) Затраты на проектирование
Кпр=1.5%Цоб=0.015·94232 =1413,5 руб.
.4) Исходя из расчётов, капитальных затрат.
Предлогаемого оборудования.
К=94232 +18846,4 + 9423,2 + 1413,5 =
123915,1руб.
Данные по расчетам капиталовложения заносим в
таблицу 6.3.
Таблица 6.2 - Капиталовложения
Показатели
|
Ед.
изм.
|
Усл.
обознч.
|
Варианты
|
|
|
|
Предлагаемое
|
Базовое
|
Стоимость
мантожа
|
Руб.
|
Моб
|
18846,4
|
3215,4
|
Наклодные
расходы
|
Руб.
|
Нр
|
9423,2
|
1607,7
|
Затраты
на проектирование
|
Руб.
|
Кпр
|
1413,5
|
241,155
|
Цена
установки
|
Руб.
|
Цоб
|
94232
|
16077
|
Итого:
|
Руб.
|
К
|
123915,1
|
21141,3
|
) Рассчитаем текущие затраты на предлагаемый
вариант:
Текущие расходы складываются из:
С=Сот+Са+Сто+Сэ+Спр, где
Сот - оплата труда [руб.];
Са - амортизационные отчисления [руб.];
Сто - затраты на техобслуживание и текущий
ремонт [руб.];
Сэ - затраты на электроэнергию [руб.];
Спр-прочие затраты [руб.].
.1) Амортизационные отчисления:
Са=0,142·К=0,142·123915,1=17596 руб.
.2) Отчисление на ремонт:
Сто=5.5%К=0,055·123915,1=6815,33 руб.
.3) стоимость электроэнергии:
Сэ=(Рн·kз /η)·tс·Dг·Tэ,
где Р - номинальная мощность потребителя [КВт], η
- КПД
потребителя, tс - время работы оборудования в сутки [час] t=8; Dг - число
рабочих дней в году D=250, Т - тариф на электроэнергию [КВт·час] Т=1,86.
Сэ=2.15·8·250·1,86=7998 руб.
.4) Сот1 - оплата труда в чистом виде
Сот1=tс·Dг·Чс·nо=8·250·50·1=100000 руб, где tс - время работы оборудования в
сутки [час] t=8; Dг - число рабочих дней в году Dг=250, Чс - часовая тарифная
ставка 50; nо - количество обслуживающего персонала nо=1;
.5) Материальные затраты на (лак):
Зм =Р·Ц=60·150=9000 руб.
.6) Сот2 - дополнительная оплата труда:
Сот2=0,4·Сот1=0,4·100000=40000 руб.;
.7) Сот3 - районный коэффициент:
Сот3=0,25·(Сот1+Сот2)=0,25· (100000+40000)=35000
руб
.8) Сот4 - отпускные отчисления:
Сот4=0,0904·(Сот1+Сот2+Сот3)=0,0904·(100000+40000+35000)=15820
руб.;
.9) Сот5 - отчисления на социальные
нужды(ЕНС+отчисл по травмат.):
Сот5=0,278·(Сот1+Сот2+Сот3+Сот4)=0,278·(100000+40000+35000+15820)=
53048= руб.
.10) Сот = Сот1+Сот2+Сот3+Сот4+Сот5
=100000+40000+35000 +15820+53048= 43868руб.
.11) Прочие расходы:
Спр=0,01·(Сот+Са+Сто+Сэ)=0,01·(17596+6815,33+7998+243868)=
2763руб.
) Рассчитаем текущие затраты на базовый вариант:
Текущие расходы складываются из:
С=Сот+Са+Сто+Сэ+Спр, где
Сот - оплата труда [руб.];
Са - амортизационные отчисления [руб.];
Сто - затраты на техобслуживание и текущий
ремонт [руб.];
Сэ - затраты на электроэнергию [руб.];
Спр-прочие затраты [руб.].
.1) Амортизационные отчисления:
Са=0,142·К=0,142·21141,3=3002,1 руб.
.2) Отчисление на ремонт:
Сто=5.5%К=0,055·21141,3=1163 руб.
.3) стоимость электроэнергии:
Сэ=(Рн·kз /η)·tс·Dг·Tэ,
где Р - номинальная мощность потребителя [КВт], η - КПД
потребителя, tс - время работы оборудования в сутки [час] t=24; Dг - число
рабочих дней в году D=250, Т - тариф на электроэнергию [КВт·час] Т=1,86.
Сэ=1,72·24·250·1,86=19195,2 руб.
.4) Сот1 - оплата труда в чистом виде
Сот1=tс·Dг·Чс·nо=8·250·50·1=100000 руб, где tс - время работы оборудования в
сутки [час] t=8; Dг - число рабочих дней в году Dг=250, Чс - часовая тарифная
ставка 50; nо - количество обслуживающего персонала nо=1;
.5) Материальные затраты на (лак):
Зм =Р·Ц=100·150=15000 руб.
.6) Сот2 - дополнительная оплата труда:
Сот2=0,4·Сот1=0,4·100000=40000 руб.;
.7) Сот3 - районный коэффициент:
Сот3=0,25·(Сот1+Сот2)=0,25· (100000+40000)=35000
руб
.8) Сот4 - отпускные отчисления:
Сот4=0,0904·(Сот1+Сот2+Сот3)=0,0904·(100000+40000+35000)=15820
руб.
.9) Сот5 - отчисления на социальные
нужды(ЕНС+отчисл по травмат.):
Сот5=0,278·(Сот1+Сот2+Сот3+Сот4)=0,278·(100000+40000+35000+15820)=
53048= руб.
.10) Сот = Сот1 +Сот2+Сот3+Сот4+Сот5 =
100000+40000+35000+15820+53048 = 243868руб.
.11) Прочие расходы:
Спр=0,01·(Сот+Са+Сто+Сэ)=0,01·(3002,1+1163+19195,3+243868)=
2672,3руб.
Результаты расчетов затрат заносим в таблицу 6.4
Таблица 6.3 - Текущие затраты
Показатели
|
Ед.
изм
|
Усл.
обозн.
|
Вариант
|
|
|
|
Предлагаемый
|
Базовый
|
Амортизационные
отчисления
|
Руб.
|
Са.
|
17596
|
3002,1
|
Отчисление
на ремонт
|
Руб.
|
Ср.
|
6815,33
|
1163
|
Стоимость
электроэнергии
|
Руб.
|
Сэ.
|
7998
|
19195,2
|
Оплата
труда
|
Руб.
|
Сот.
|
243868
|
243868
|
) рассчитаем сравнительную экономическую
эффективность:
Еср=(288040.33-284900,6)/(123915,1-21141,3)= 0,3
) Срок окупаемости
То=1/Еср=1/0,3=3,3 года
Вывод: таким образом, время на окупаемость
данного проекта составляет 3,3 года, то с экономической точки зрения внедрения
проекта целесообразно и обусловлено.
Заключение
В данном дипломном проекте составлено 11 схем на
формате А1:, выполнен электротехнический расчет: нагрузок, освещения,
электросиловой части, вентиляции, а также рассмотрены вопросы технологии
ремонта электрических машин и разработка пропиточной установки для пропитки
статоров асинхронных электродвигателей. Кроме того, представлены главы по
безопасности жизнедеятельности, экологической безопасности, пожарной безопасности.
Литература
1. Справочник
инженера-электрика сельскохозяйственного производства: учеб, пособие. - М.:
Информагротех, 1999.
2. Сибикин
Ю.Д., Сибикин М.Ю. Справочник по эксплуатации электроустановок промышленных
предприятий. - М.: Высш. шк.: Изд. Центр «Академия», 2001.
. Антонов
В.М. и др. Эксплуатация и ремонт электрических машин. - М.: Высш. шк., 1989.
. Правила
устройства электроустановок. - СПб.: Изд-во «ДЕАН», 1999.
. Акимова
Н.А., Котеленец Н.Ф., Сентюрихин Н.И. Монтаж, техническая эксплуатация и ремонт
электрического и электромеханического оборудования: Учебник. - М.: Высш. шк.:
Изд. Центр «Академия», 2000.
. Электрооборудование
и автоматизация сельскохозяйственных агрегатов и установок. Л.С. Герасимович,
Л.А. Калинин, А.В. Корсаков, В.К. Сериков. - М.: Колос, 1980.
. Теплотехника,
отопление, вентиляция и кондиционирование воздуха. В.М. Гесев, Н.И. Ковалев,
В.П. Попов, В.А. Потрошков. - Л.: Стройиздат, 1981.
. Электротехнология
и электрическое освещение. - М.: Агропромиздат, 1990.
. Охрана
труда в электроустановках. Под ред. Проф. Б.А. Князевского. Издание 2-е,
перераб. и доп. М.: Энергия, 1977.
. Справочник
электрообмотчика асинхронных электродвигателей. В.И. Лихачев М., 2005 г.