Привод шаровой мельницы
Тема
проекта: “Привод шаровой мельницы”
ВВЕДЕНИЕ
привод
шаровая мельница
Целью выполнения курсового проекта является
развитие способностей к самостоятельному решению поставленных перед ним
конструкторских задач.
Проектированием называется процесс разработки
технической документации для производства изделия. При этом под
конструированием понимают детальную разработку элементов проектируемого
изделия. Техническую документацию, получаемую в результате проектирования,
называют проектом.
К задачам проектирования следует отнести
следующее:
- формирование умений и навыков в чтении
кинематических схем, сборочных чертежей, выполнения основных расчетов с целью
выбора рациональных стандартных элементов привода;
- приобретение опыта в решении
поставленных конструкторских задач при выполнении компоновочных и сборочных
чертежей привода и его основных узлов, оформлении текстовых документов,
публичной защите принятых технических решений.
В настоящее время широко используются
многоступенчатые приводы, которые могут в себя включать ременную, червячную,
цепную, зубчатую и др. передачи.
Привод - совокупность механизмов, включающая
двигатель, служащий для передачи движения рабочим органом.
Редуктором принято называть, механизм, состоящий
из зубчатых или червячных передач, выполненных в виде отдельного агрегата и
служащих для передачи мощности от двигателя к рабочей машине.
Редуктор состоит из корпуса, в котором
помещаются элементы передачи - зубчатые колеса, валы подшипники и т. д.
Редукторы служат как механизмы понижения угловой скорости и соответственно
повышения момента; однако механизмы для повышения угловой скорости, выполненные
в виде отдельных агрегатов (ускорители или мультипликаторы) так же иногда
называют редукторами.
При конструировании должны быть выбраны оптимальные
параметры изделий (привода), удовлетворяющие следующим требованиям: небольшие
габариты, меньшая стоимость, наибольший КПД.
Ременные передачи обладают следующими
достоинствами:
· простота конструкции;
· плавность и бесшумность работы;
· невысокие требования к точности
расположения деталей передачи;
· предохранение от перегрузки за счет
возможности проскальзывания ремня по шкиву.
Наряду с достоинствами ременные передачи
обладают и некоторыми существенными недостатками:
· большие габариты;
· непостоянство передаточного числа
из-за проскальзывания ремня по шкиву;
· большая нагрузка на валы и опоры;
· низкая долговечность ремней.
Передаваемая мощность - обычно не более 50 кВт,
передаточное число - до 6.
Во всех отраслях машиностроения и приборостроения
наиболее широкое применение нашли зубчатые передачи благодаря ряду их
достоинств: постоянству передаточного числа; отсутствию проскальзывания;
большой несущей способности при сравнительно малых габаритах и массе; большой
долговечности; работе в обширном диапазоне режимов нагружения; сравнительно
малым нагрузкам на валы и опоры, высокому КПД, простоте обслуживания и ухода. К
недостаткам зубчатых передач можно отнести высокие требования к точности
изготовления колес и сборки передач и необходимость повышенной жесткости
корпусов, валов, опор; шум, особенно при высоких частотах вращения и
недостаточной точности; вибрации; низкую демпфирующую способность.
1 КИНЕМАТИЧЕСКИЙ
РАСЧЕТ ПРИВОДА
.1 Кинематическая
схема привода
Рис. 1.1. Привод вибрационного конвейера.
Вал электродвигателя 1 соединен с входным валом
редуктора 2, выходной вал редуктора 3 соединен с валом 4 посредством зубчатой
передачи.
Из задания к курсовому проекту нам известна
мощность на выходном валу Р4 =7,5кВт; угловая скорость рабочего вала ω4=
9мин-1; соответственно частота вращения рабочего вала n4=86
c-1.
.2 Определение расчетной мощности привода
Расчетная мощность электродвигателя определяется
по формуле:

кН - мощность на приводном валу
конвейера, кВт;

общий КПД привода;
где 
КПД муфты;

КПД закрытой конической передачи;

КПД закрытой цилиндрической
передачи;
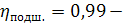
КПД подшипников;
n = 3 - число
пар подшипников в приводе.
.3 Выбор электродвигателя
По табл. 16.7.1/1/ выбираем
двигатель серии 4А с номинальной мощностью 
Таблица 1.1
Nо
|
Тип
двигателя
|
Номинальная
мощность Рном, кВт
|
Частота
вращения, об/мин
|
|
|
|
синхронная
|
при
номинальном режиме nном
|
1
|
4А132М2У3
|
11,0
|
3000
|
2930
|
2
|
4А132М4У3
|
11,0
|
1500
|
1460
|
3
|
4А160S3У3
|
11,0
|
1000
|
960
|
4
|
4А160М8У3
|
11,0
|
750
|
730
|
.4 Определение общего передаточного числа
привода и выбор стандартного редуктора
Находим общее передаточное число для каждого
варианта:
Производим разбивку передаточного
числа, принимая для всех вариантов передаточное число редуктора постоянным 
Результаты расчетов заносим в табл.
2.2.
Таблица 1.2
Расчет передаточных чисел привода
Передаточное
число
|
Варианты
|
|
1
|
2
|
3
|
4
|
Общее
для привода
|
34,07
|
16,977
|
11,163
|
8,488
|
Редуктор
|
4
|
4
|
4
|
4
|
Зубчатая
передача
|
8,517
|
4,244
|
2,791
|
2,122
|
Анализируя полученные значения передаточных
чисел, приходим к выводу, первый и четвертый вариант затрудняют работу привода
посредством одноступенчатого цилиндрического редуктора и зубчатой передачи
из-за соответственно маленького и большого передаточных чисел.
Из рассматриваемых четырех вариантов
предпочтительнее второй, т.к. получается среднее приемлемое значение.
Таким образом выбираем двигатель
А132М4У3 (

; передаточные числа: привода u=16,977;
редуктора 
; 
4,244.
Исходя из полученного передаточного
числа 4 и необходимого варианта сборки 41 по ГОСТ 20373-94 и категории
точности. Имеем редуктор К-4-41-1.
Общие технические условия данного
редуктора регламентированы ГОСТ Р 50968-96. Данный ГОСТ распространяется на
конические одноступенчатые редукторы с номинальным внешним делительным
диаметром de2<1000мм.
/2/
Диаметры входного вала редуктора -
10мм и допускаемый передаваемый момент Т1= 8 Нм, диаметры выходного вала
редуктора - 18мм и допускаемый передаваемый момент Т2= 31,5 Нм,
Ресурс передачи валов - 25000ч,
ресурс передачи подшипников - 12500ч.
Основные размеры редуктора возьмем
из:
1. ГОСТ 27142-86 Редукторы конические и
коническо-цилиндрический. Основные параметры.
ГОСТ 6636-69 Основные нормы взаимозаменяемости.
Нормальные линейные размеры.
.5 Определение силовых и кинематических
параметров привода
Определим мощность на каждом валу привода:
Определим частоту вращения и угловую скорость на
каждом валу:
Вращающий момент:
Результаты вычислений занесем в табл. 1.3.
Таблица 1.1.1
Сводная таблица результатов кинематического
расчета привода.
№
вала
|
Мощность
Р,кВт
|
Угловая
скорость ω,
с-1
|
Частота
вращения п, мин-1
|
Крутящий
момент Т, Нм
|
Двигатель
|
11
|
152,891
|
1460
|
57,754
|
1
|
8,83
|
152,891
|
1460
|
57,754
|
2
|
8,659
|
152,891
|
1460
|
56,605
|
3
|
8,23
|
38,22
|
365
|
53,797
|
4
|
7,5
|
9
|
86
|
49,531
|
2 РАСЧЕТ ОТКРЫТЫХ ПЕРЕДАЧ
Расчет зубчатой передачи
Определение твердости термообработки и
материалов зубчатых колес.
По табл.3.1/4/ определяем марку стали: для
шестерни - сталь 45, твердость поверхности 48…50HRCэ;
для колеса - сталь 45, твердость ≤210НВ2.
По табл.3.2./4/ определяем механические
характеристики стали:
- для шестерни (сталь 45) твердость
48…50HRCэ,
термообработка - улучшение, Dпред=125мм,
Sпред=80мм;
- для колеса (сталь 45) твердость
179…207НВ2, термообработка нормализация, Dпред
и Sпред любые;
Определяем среднюю твердость зубьев шестерни и
колеса:
Определение допускаемых напряжений изгиба.
Рассчитаем коэффициент долговечности

Число циклов перемены напряжений
соответствующее пределу выносливости 
для обоих колес.
Т.к. 
и 
, то коэффициенты долговечности 
и 
.
По табл. 3.1. определяем допускаемое
напряжение изгиба, соответствующее числу циклов перемены напряжений 
.
Определяем допускаемое напряжение
изгиба, т.к. передача реверсивная, то полученное допускаемое напряжение
уменьшаем на 25%.
Определение допускаемых контактных
напряжений.
Рассчитаем коэффициент долговечности

.
Наработка за весь срок службы:
- для колеса
- для шестерни
Число циклов перемены напряжений 
, соответствующее пределу
выносливости, находим по табл. 3.3/1/ интерполированием:
Т.к. 
и 
, то коэффициенты долговечности 
и 
.
По табл.3.1/1/ определяем
допускаемое контактное напряжение
Определяем допускаемое контактное
напряжение
Рассчитаем среднее допускаемое
напряжение:
Проектный расчет.
. Определяем межосевое расстояние.
где 
- вспомогательный коэффициент
(Стр.58/4/);

- коэффициент ширины венца колеса
(Стр.58/4/)

- коэффициент неравномерности
нагрузки по длине зуба.
Полученное значение межосевого
значение из ряда нормальных линейных размеров.
. Определим модуль зацепления
из условия 
, т.е.
от 
. Принимаем m=2мм.
- 
- 
3. Определяем суммарное число зубьев
шестерни и колеса:
Полученное значение округлим до в меньшую
сторону до целого числа.
. Определим число зубьев шестерни:
Полученное значение округлим до
ближайшего целого числа 
. Определим число зубьев
колеса 
. Определим фактическое
передаточное число:
. Определим фактическое межосевое
расстояние:
. Определяем основные геометрические
параметры:
делительный диаметр:
диаметр вершин:
диаметр впадин:
ширина венца:
Проверочный расчет
. Проверяем межосевое расстояние:
. Проверяем пригодность заготовок колес.
Условие пригодности заготовок колес:
Для выбранного материала колесо и шестерня могут
иметь любой размер.
. Проверим контактное напряжение:
где К=376 - вспомогательный коэффициент;

- окружная сила взацеплении;

- коэффициент, учитывающий
распределение нагрузки между звеньями рис.4.2./2/.

коэффициент динамической нагрузки,
зависящий от окружной скорости колес и степени точности передачи.
12. Проверим напряжение изгиба зубьев
шестерни и колеса:
где 
- коэффициент, учитывающий
распределение нагрузки между зубьями;

- коэффициент неравномерности
нагрузки по длине зуба;

коэффициент динамической нагрузки,
зависящий от окружной скорости колес и степени точности передач (табл.4.3/4/);

коэффициенты формы зуба шестерни и
колеса. (табл.4.4. /4/)

коэффициент, учитывающий наклон
зуба.
3 ПРЕДВАРИТЕЛЬНЫЙ РАСЧЕТ ПРИВОДНОГО ВАЛА
Основной расчетной нагрузкой валов является
вращающий Т и изгибающий М моменты.
На данной стадии проектирования нам известен
лишь вращающий момент Т (Нм), передаваемый каждым из валов редуктора.
Изгибающий момент М нам не известен, так как мы не знаем осевых размеров ступиц
зубчатых и червячных колес, шкивов, звездочек, полумуфт, подшипников, крышек и
т. п., что не дает возможности установить местоположение опор вала и
действующих на него нагрузок. В то же время разработка конструкции вала
невозможна без определения хотя бы приближенно диаметра одной из его ступеней.
Поэтому при проектном расчете вала предварительно определяют диаметр одного из
его участков, исходя из условия прочности только на кручение при пониженных
допускаемых напряжениях [т] с той целью, чтобы компенсировать влияние
напряжений изгиба и концентрации напряжений.
Валы предназначены для установки на них
вращающихся деталей (зубчатых колес, шкивов, звездочек и т.п.) и передачи
крутящего момента.
Конструкция валов в основном определяется
деталями, которые на них размещаются, расположением и конструкцией
подшипниковых узлов, видом уплотнений и технологическими требованиями.
Валы воспринимают напряжения, которые меняются
циклично от совместного действия кручения и изгиба. На первоначальном этапе
проектирования вала известен только крутящий момент, а изгибающий момент не
может быть определен, т.к. неизвестно расстояние между, опорами и действующими
силами. Поэтому при проектировочном расчете вала определяется его диаметр по
напряжении кручения, а влияние изгиба учитывается понижением допускаемого
напряжения кручения.
Диаметр вала (мм) определяют по формуле
(см.с.66) /2/:
(3.1)
где Т - крутящий момент на рассматриваемом валу
(Н×мм),
[tкр]
- пониженные допускаемые напряжения кручения (Н×мм2).
Для валов, изготавливаемых из сталей 35, 40. 45,
40Х, 40ХН. допускаемые напряжения принимаются:
выходных концов вала [tкр]
= (15-40) МПа;
промежуточных валов в местах посадки колес [tкр]
= (10-20) МПа.
При этом при выборе материала валов необходимо
учитывать материал зубчатых колес. Для зубчатых колес с более высокой
твердостъю необходимо принимать материал с более высокой прочностью. Меньшие
значения [tкр] рекомендуется выбирать для быстроходных
валов, большие [tкр] - для тихоходных.
Полученное значение диаметра должно быть
округлено по ГОСТ 8639-69 до бли ближайшего из ряда диаметров: 10: 10,5: 11:
11,5: 12; 13; 14; 15; 16; 17; 18; 19; 20; 21; 22; 24; 25; 26; 28; 30; 32; 34;
36; 38; 40; 42; 48; 50; 52; 55; 60; 63; 65; 70; 75; 80; 85; 90; 100; 105; 110;
120 и т. д.
Диаметры остальных участков вала назначают по
конструктивным соображениям с учетом удобства посадки на вал подшипников
качения, зубчатых колес и т.д. и необходимости фиксации этих деталей на валу в
осевом направлении.
Обычно применяется ступенчатая конструкции
валов, которая обеспечивает удобство сборки и разборки, а также простоту
фиксации детали от осевого перемещения.
На рисунке 3.1 представлен пример конструкции
ступенчатого вала. В конкретном случае некоторые участки могут отсутствовать,
однако соотношения диаметров сохраняются.
d1=d
- по расчету;
d2=d1+(5-10)
мм - под уплотнение с учетом стандартов на них;
d3=d2+(2-10)
мм - под внутреннее кольцо подшипников с учетом стандартов на них;
d4=d3+(5-10)
мм - под зубчатое колесо;
d5=d4+(5-10)
мм - диаметр буртика для удержания колеса.
Рис. 3.1
Выбор материалов валов.
Так как предполагается ведущий вал изготавливать
заодно с шестерней, то выбор материала вала определяется выбранным материалом
для шестерни, следовательно, ведущий вал изготавливается из стали 50. Твердость
НВ 255, термообработка - улучшение.
Промежуточный вал по тем же причинам
изготавливаем из стали 35XМ.
Твердость HB 285.
Термообработка - улучшение.
Ведомый вал изготавливаем из стали 50,
термообработка - улучшение. Твердость НВ 255.
Определение геометрических параметров ступеней
валов.
Предварительный расчет валов производим на
кручение по пониженным значения допускаемых напряжений.
Для IV
вала [t]к=10 МПа.
Диаметры валов электродвигателя, входного и
выходного валов редуктора берем стандартные приведенные в атласе для необходимых
моделей.
Таблица 3.1
IV вал
Ступень
|
Диаметр
|
Длина
|
Под
зубчатое колесо
|
d1=30мм
|
l=65 мм
|
Под
буртик
|
d2=d1+10=40мм
|
l2= 20мм
|
Под
узел подшипника
|
d3= d2+10=50мм
|
l3=80мм
|
Под
барабан
|
d4=d3+10 =60мм
|
l4 =75мм
|
Под
узел подшипника
|
d5= d3
|
l5 =70мм
|
Предварительный выбор подшипников
IV вал.
Выбираем шариковые радиальные
однорядные подшипники средней серии, т.к. на подшипник будет действовать
большая частота вращения и незначительная осевая нагрузка.
Подшипник 310 ГОСТ 8338-75.
d=50 мм -
внутренний диаметр;
D=90 мм -
наружный диаметр;
В=23 мм - ширина.
Выбор муфты.
Выбираем муфту упругую - втулочно-пальцевую ГОСТ
21424-93 для соединения электродвигатель и редуктор.
Тдв=57,75Нм; dдв=38мм;
Для соединения выходных концов двигателя и
быстроходного вала редуктора, установленных, как правило, на общей раме,
применены упругие втулочно-пальцевые муфты и муфты со звездочкой. Эти муфты
обладают достаточными упругими свойствами и малым моментом инерции для
уменьшения пусковых нагрузок на соединяемые валы.
Применяемые муфты обеспечивают надежную работу
привода с минимальными дополнительными нагрузками.
Основной характеристикой для выбора муфты
является вращающий момент Т, Н·м, установленный стандартом.
На работу муфты существенно влияют толчки, удары
и колебания, обусловленные характером работы приводимой в движение машины.
Поэтому расчет муфты ведут не по номинальному моменту, а по расчетному:

(2.1)
где 
- коэффициент режима работы.
Муфты, имеющие широкое
распространение, стандартизованы. Основными характеристиками муфты являются
момент, на передачу которого муфта рассчитана, и диаметры соединяемых валов.
Стандарт допускает сочетание муфт с
различными диаметрами посадочных отверстий, если эти муфты предназначены для
передачи одного и того же номинального вращающего момента.
Самая простая из жестких не разъемных муфт -
втулочная муфта, представляющая собой цельную втулку, надеваемую на концы валов
и закрепляемую на концы валов и закрепляемую на них штифтами, шлицами или
шпонками. Втулочные муфты, простые, дешевые по конструкции нашли довольно
широкое применение в легких машинах для соединения валов диаметром до 100мм.
Применение таких муфт ограничено тем, что при сборке и разборке валов требуются
значительные смещения их в осевом направлении, а также тем, что эти муфты
требуют очень точного совмещения осей валов. Материал втулок - сталь 35, 40,
45, а втулок больших размеров - чугун СЧ21, СЧ24 и др.
Муфту выбираем по крутящему моменту и диаметрам
выходных валов редуктора и двигателя.
Диаметр вала электродвигателя d=38мм.
(табл.16.7.2/1/)
Диаметр входного вала редуктора d=32мм
(ГОСТ 27142-86)
По полученным данным выбираем муфту.
На конце выходного вала редуктора устанавливаем
муфту типа 1. Выбор муфты зависит от крутящего момента на конце вала. Поэтому
выбираем муфту 250-1-38-1-32 ГОСТ 20742-93
4 КОНСТРУКТИВНЫЕ РАЗМЕРЫ ДЕТАЛЕЙ ОТКРЫТОЙ ПЕРЕДАЧИ
4.1 Цилиндрические колеса
Зубчатые колеса небольших размеров (da2
< 100 мм) изготовляют точением из круглого проката. При dа2
=100. ..500 мм колеса изготовляют из заготовок, получаемых ковкой или
штамповкой.
Колеса, заготовки которых получают ковкой,
обычно имеют конструкцию. У таких колес все поверхности обрабатывают. Для того,
чтобы уменьшить объем точной механической обработки, которой подвергаются
торцовые поверхности ступиц и зубчатых венцов, на дисках колес выполняют
выточки 1 ...2 мм с более грубой обработкой. При диаметрах da2
= 250...500 мм колеса, с целью уменьшения массы.
Колеса, заготовки которых получают штамповкой,
имеют форму, показанную на рис. 6.1,г. Заготовка колеса после штамповки имеет
достаточно чистую поверхность и не требует механической обработки нерабочих
поверхностей. С целью облегчения выемки заготовки из штампа принимают значения
штамповочных уклонов γ> 7°
и радиусов закруглений R
> 6 мм.
Ступица может быть расположена симметрично или
несимметрично относительно обода.
Следует отметить, что при серийном производстве
наибольшее распространение имеют заготовки, получаемые штамповкой или ковкой.
Рекомендации по определению размеров основных элементов цилиндрических колес
приведены в табл. 6.1./1/
Рис.4.1. Конструкция цилиндрических колес
В результате ранее выполненных расчетов (см. п.
2.1) были получены следующие размеры:
d2 =195 мм; da2
= 201 мм; df2 =187,5 мм;
b2 =52мм; mn
=3мм; β=
14,25°; z2T
=63.
Учитывая мелкосерийный способ производства и
принимая во внимание размер dа2
= 201 мм, изготовление колеса будем производить из заготовки, получаемой
штамповкой.
С целью использования пространства в средней
части редуктора ступицу колеса выполняем несимметричной относительно обода,
смещая её влево.
На основании табл. 6.1/1/ для способа получения
заготовки колеса - штамповка
(рис. 6.1,г) рассчитываем размеры конструктивных элементов колеса.
а) обод: S
= 2,2 mn+0,05 b2
=15,8мм;
б)ступица: d
= ds= 90 мм,
в)диск: с = 0,35; b2
=0,35 63 =22 мм;
Размеры фасок в отверстаи ступицы по табл. 2П.42
/1/ f=2,5 мм. Такой же
размер фасок принимаем по углам наружной поверхности ступицы и обода колеса.
Размер фасок на торцах зубьев f3
= (0,5...0,7) mn
=(0,5...0,7) 4 = 2...2,8мм.
Принимаем стандартное значение f3
= 2,5 мм (см. примечание 2 к табл. 6.1).
Так как средняя твердость поверхности зубьев
колеса Ннвг ~ 285,5 НВ <350 НВ, то принимаем угол фасок на торцах зубьев аф
| 45° (см. примечание 3 к табл. 6.1)./1/
5 ЭСКИЗНАЯ КОМПОНОВКА
Компоновочные схемы изделия составляют для того,
чтобы оценить соразмерность узлов и деталей привода. Ранее выбранные редуктор и
электродвигатель , если их рассматривать отдельно не дают ясного представления
о том что же в конечном итоге получилось. Нужно их упрощенно изобразить вместе
с приводным валом, на одном листе, соединенными друг с другом непосредственно,
с применением муфты. Компоновочные схемы выполняют в масштабе уменьшения 1:2
или 1:4. Они служат прообразом чертежа общего вида.
Соразмерность узлов вызывается требованиями
целесообразности и технической эстетики.
При размещении двух узлов на плите, например,
электродвигателя и редуктора, выясняют, нельзя ли расположить базовые
поверхности плиты в одной плоскости. Известно, что такое расположение упрощает
конструкцию плиты (рамы ) и удешевляет ее изготовление. Иногда путем некоторых
конструктивных мероприятий удается опорные поверхности двигателя и редуктора
вывести в одну плоскость.
Некоторые типы соединительных муфт, например,
муфты упругие втулочно-пальцевые, с резиновой звездочкой и др., характеризует
большая радиальная жесткость. Для уменьшения отклонения от соосности валов
электродвигателя и редуктора под лапы электродвигателя устанавливают
компенсаторные прокладки. Путем подбора или подшлифовки этих прокладок обеспечивают
требуемую соосность валов электродвигателя и редуктора.
Рис.5.1. Пример эскизной компановки
6 ПРОВЕРКА ДОЛГОВЕЧНОСТИ ПОДШИПНИКОВ ПРИВОДНОГО
ВАЛА ПО ДИНАМИЧЕСКОЙ ГРУЗОПОЪЕМНОСТИ
.1 Определим усилия, девствующие на рабочий вал
Определим окружную силу закрытой зубчатой
передачи:
Определим радиальную силу:
Примем силу от барабана равную F=15кН.
Из компоновки линейные размеры: l1
=80мм; l2=77мм; l3=72мм.
Схема нагружения вала представлена в пункте 8.
Момент относительно точки А равен нулю:
Момент относительно точки D
равен нулю:
Поведем проверку:
сумма проекций сил на ось Х

сумма проекций сил на ось У

Условия выполняются, значит, усилия
найдены, верно.
Найдем силы, действующие на подшипник:
Определение динамической грузоподъемности
подшипника.
Характеристики подшипников:
условное обозначение подшипника - 310;
диаметр под вал d=50
мм;
диаметр внешнего кольца D=110мм;
ширина колец подшипников В=25 мм;
динамическая грузоподъёмность С=61,8 кН;
статическая грузоподъёмность С0=36 кН.
Эквивалентная динамическая нагрузка Р для
роликовых подшипников рассчитывается по формуле:
Р=V·Fr·Кб·Кт,
где R
- радиальная нагрузка, действующая на подшипник, Н; V
- коэффициент вращения, при вращении внутреннего кольца по /3/ V=1;
Кб - коэффициент безопасности по /2/ принимаем Кб=1,1; Кт - температурный
коэффициент, по /2/ при температуре подшипника менее 1000С Кт=1;
е=0,19 (лист 362 /12/)
Р=1·111·1.1·1=122,1Н.

- срок службы передачи.
Расчетная динамическая
грузоподъемность:

- подшипник пригоден.
7 ПРОВЕРКА ПРОЧНОСТИ ШПОНОЧНЫХ СОЕДИНЕНИЙ
Зубчатые колеса, шкивы, звездочки и другие
детали крепятся на валах с помощью шпоночных или шлицевых соединений,
предназначенных для передачи крутящих моментов.
В редукторах общего назначения из-за простоты
конструкции, сравнительно низкой стоимости и удобства сборки и разборки широко
применяются соединения призматическими шпонками.
Для соединения валов со ступицами деталей
(зубчатые и червячные колеса, шкивы ременных передач, звёздочки цепных передач,
муфты) применяют шпоночные и шлицевые соединения, а также соединения с натягом,
которые препятствуют относительному повороту вала и установленной на нём детали
и передают вращающий момент Т.
Основным элементом данного соединения является
шпонка. В индивидуальном и мелкосерийном производстве наибольшее
распространение получили призматические шпонки со скруглёнными или плоскими
торцами. Все размеры шпонок и допуски на них стандартизованы. Стандарт
предусматривает для каждого диаметра вала d
определенные размеры поперечного сечения шпонки (ширину b
и высоту h) и глубины пазов
(вала t1 и ступицы t2)
Полную длину шпонки l принимают
на 5... 10 мм меньше длины ступицы детали и затем округляют до стандартного
размера.
Поперечные размеры призматических шпонок ( b x h
) выбираются из таблицы по известному диаметру вала d.
Длину шпонки выбирают из ряда:
; 8; 10; 12; 14; 16; 18; 20; 25; 28; 32; 36; 40
45; 50; 55; 63; 70; 80; 90; 100
Длина шпонки l назначается из стандартного ряда
так, чтобы она была несколько меньше длины ступицы (примерно 5…10 мм.).
Рис. 7.1 Схема шпоночного соединения
Табл. 7.1. Шпонки призматические ( ГОСТ
23360-78) ( Размеры в мм)
Диаметр
вала
|
Сечения
шпонки b x h
|
Глубина
паза t1
|
|
|
|
|
|
|
Св.
10 до 12
|
4
х 4
|
2,5
|
"
12 " 17
|
5
х 5
|
3
|
"
17 " 22
|
6
х 6
|
3,5
|
"
22 " 30
|
8
х 7
|
4
|
"
30 " 38
|
10
х 8
|
5
|
"
38 " 44
|
12
х 8
|
5
|
"
44 " 50
|
14
х 9
|
5,5
|
"
50 " 58
|
16
х 10
|
6
|
"
58 " 60
|
18
х 11
|
7
|
"
65 " 75
|
20
х 12
|
7,5
|
"
75 " 85
|
22
х 14
|
9
|
"
85 " 95
|
25
х 16
|
9
|
Таблица 7.2
Призматические шпонки, устанавливаемые на IV
вал
Диаметр
вала
d
|
Сечение
шпонки
|
Глубина
паза
|
Длина
шпонки
l
|
|
b
|
h
|
t1
|
t2
|
|
40
|
12
|
8
|
5,5
|
3,8
|
40
|
Для изготовления
шпонок применяют сталь чистотянутую ГОСТ 8787.
7.1 Расчет шпонки на смятие
После определения размеров шпонки производим
проверочный расчет соединения по напряжениям смятия:
(5.1)
где
Т - крутящий момент на валу, Нмм;- диаметр вала, мм;
l - рабочая длина шпонки, мм;
(h-t1) -
сминаемая высота шпонки, мм;
[GСМ] -
допускаемые напряжения смятия, при чугунной ступице
[GСМ] = 50-80
МПа. и при стальной ступице [GСМ] = 110-190 МПа
Шпонка,
соединяющая IV вал и
зубчатое колесо:
.2
Расчет шпонки на срез.
где
Т - крутящий момент на валу, Нмм;- диаметр вала, мм;
l - рабочая длина шпонки, мм;
b -ширина шпонки, мм;
k - высота
шпонки
над валом, мм;
[tСР] -
допускаемые напряжения смятия, [tСР] = 70 МПа
Шпонка,
соединяющая IV вал и
зубчатое колесо:
8
УТОЧНЕННЫЙ РАСЧЕТ ПРИВОДНОГО ВАЛА
Для
построения эпюр определяем значения изгибающих моментов в характерных сечениях
вала.
Поскольку
передача прямозубая, то на вал действуют следующие силы - окружная, радиальная
и усилие от барабана.
Вертикальная
плоскость YOZ:
MB: 
Н·м;
MC: 
Н·м;
MC: 
Н·м;
Горизонтальная
плоскость XOZ:
MB: 
;
MB: 
Н·м;
Передача
вращающего момента происходит вдоль оси вала от сечения D к сечению С
(эпюра Мk): Мk=T=49,53 Нм;
.1
Расчет вала на выносливость
При расчете валов сопротивление усталости
учитывают все основные факторы, влияющие на их прочность, а именно: характер
напряжения, статические и усталостные характеристики материалов, изменение
предела выносливости вследствие концентрации напряжений и влияния абсолютных
размеров оси или вала, состояние поверхности и поверхностное упрочнение.
Валы рассчитываются на сопротивление усталости
по следующей формуле:
где 
- коэффициент запаса прочности при
изгибе;

- коэффициент запаса прочности при
кручении;
где 
и 
- пределы выносливости при изгибе и
кручении при симметричном цикле нагружения Табл. 14.2.1. /2/;

и 
- амплитуды циклов при изгибе и
кручении;

и 
- средние напряжения циклов при
изгибе и кручении;

и 
- эффективные коэффициенты
концентрации напряжений при изгибе и кручении Табл.16.2/1/

и 
- коэффициенты чувствительности к
асимметрии.
При отсутствии осевой силы, действующей
на ось или вал, и расчете оси или вала без учета растяжения или сжатия, что в
обоих случаях соответствует симметричному циклу напряжений в сечениях вала,
среднее напряжение цикла при изгибе 
=0, а амплитуда цикла при изгибе 
=
, где 
- расчетное напряжение на изгиб в
рассматриваемом сечении вала. При частом реверсировании вала принимают, что
напряжение на кручение изменяется по симметричному циклу, и в соответствии с
этим напряжение цикла при кручении 
=
, где 
-расчетное напряжение на кручение в
рассматриваемом сечении вала. Табл. 14.2.1./2/.
Напряжение на изгиб в
рассматриваемом сечении вала.
где М - изгибающий момент в заданном
сечении.
W - момент
сопротивления сечения вала по шпоночной канавка
Напряжение кручения
где 
- момент сопротивления сечения вала
по шпоночной канавка
В качестве материала вала примем: сталь 45 с
улучшением, диаметр заготовки не более 125мм, твердость не ниже 250НВ, σВ
=730МПа, σТ =390МПа, σ-1
=280МПа, τ-1=170МПа.
Расчет коэффициентов
Диаметр вала в сечении С d
= 50 мм. Концентраторы напряжений в данном сечении - ступенчатый переход с
галтелью.
Для каждого из концентраторов напряжений
определим отношения Kσ/Kd
и Kτ/Kd.
При σВ
=730МПа - Kσ=1,7
и Кτ
= 1,45;при изгибе Kd=0,85;
при кручении Kd=0,73.
Посадочная поверхность вала под колесом
шлифуется. Тогда по табл. 11.4/4/ коэффициент Kf
= 1.
Поверхность вала дополнительно не упрочняется.
Тогда коэффициент Kv
=1. Суммарные коэффициенты
KσD=(
Kσ/Kd+
Kf-1)
=1,7/0,85+1-1=2,0;
KτD=(
Kτ/Kd+
Kf-1)=1,45/0,73+1-1=1,99;
Осевой момент сопротивления сечения:
Полярный момент сопротивления сечения:
Амплитуда напряжений цикла:
Коэффициенты запаса по нормальным касательным
напряжениям:
Коэффициенты запаса по усталости в сечении С:
Диаметр вала в сечении В d
=35 мм. Концентраторы напряжений в данном сечении - шпоночный паз.
Для каждого из концентраторов напряжений
определим отношения Kσ/Kd
и Kτ/Kd.
По табл. 11.2 /4/ при σВ
=730МПа - Kσ=1,9
и Кτ
= 1,7;при изгибе Kd=0,865;
при кручении Kd=0,755.
Посадочная поверхность вала под колесом
шлифуется. Тогда по табл. 11.4/4/ коэффициент Kf
= 1.
Поверхность вала дополнительно не упрочняется.
Тогда коэффициент Kv
=1. Суммарные коэффициенты
KσD=(
Kσ/Kd+
Kf-1)=1,9/0,865+1-1=2,197;
KτD=(
Kτ/Kd+
Kf-1)=1,7/0,755+1-1=2,252;
Осевой момент сопротивления сечения:
Полярный момент сопротивления сечения:
Амплитуда напряжений цикла:
Коэффициенты запаса по нормальным касательным
напряжениям:
Коэффициенты запаса по усталости в сечении С:
Условие прочности выполняется.
9 СБОРКА ПРИВОДА
.1 Описание порядка сборки привода
В первую очередь необходимо закрепить раму
привода к фундаменту специальными болтами.
Этапы сборки привода:
. По имеющимся чертежам привода на раму
устанавливают электродвигатель и редуктор. Необходимо выставить соосно
электродвигатель и редуктор так, чтобы между торцевыми поверхностями
соединяемых валов был зазор 3 - 5 мм. Затем оценивается расстояние между
заплечниками валов электродвигателя и редуктора. Если длина выбранной муфты
совпадает с длиной между заплечниками валов, то никаких проблем не возникает и
можно приступить к дальнейшей сборке привода. Если длина выбранной муфты больше
длины между заплечниками валов, то зазор между валами электродвигателя и
редуктора следует увеличить. Если длина выбранной муфты меньше длины между
заплечниками валов, то между заплечниками валов и муфты следует установить
дистанционные кольца.
Соединив электродвигатель и редуктор с помощью
муфты, можно присоединять их к раме, согласно чертежу привода.
. На выходной вал редуктора устанавливаем
шестерню и закрепляем ее с помощью шпоночного и винтового соединения.
. Вал вставляем в корпус подшипников,
прикрепленный к раме в соответствии с чертежом, и с обеих сторон устанавливаем
подшипники и закрываем их крышками, как показано на сборочном чертеже.
ЛИТЕРАТУРА
1. «Детали машин и основы
конструирования» Скойбеда А.Т., Кузьмин А.В., Макейчик Н.Н. - Мн.: Высшая
школа, 2000.
2. «Справочник конструктора
-машиностроителя» т.3 Анурьев В.И. - М.: Машиностроение, 2001
. «Детали машин. Курсовое
проектирование» Санюкевич Ф.М. - Брест: БГТУ 2003г
. «Курсовое проектирование
деталей машин» Шейнблит А.Е. -М.: Высшая школа, 1985
. «Детали машин» Гузенков
П.Г. - М.: Высш. шк. 1986
. «Справочник конструктора
-машиностроителя» т.1 Анурьев В.И. - М.: Машиностроение, 2001
. «Справочник конструктора
-машиностроителя» т.2 Анурьев В.И. - М.: Машиностроение, 2001
. «Конструирование узлов и
деталей машин» Дунаев П.Ф., Леликов О.П. - М: Высшая школа, 1985.
. «Курсовое проектирование
деталей машин» Чернавский С.А. - М.: Машиностроение, 1979.
. «Детали машин» Иванов М.Н.,
Иванов В.Н. - М.: Высшая школа, 1975.
. «Курсовое проектирование»
Дулевич А.Ф., Новиков С.А., Сурус А.И., Царук Ф.Ф. - Мн.: БГТУ, 1997.
12. Подшипники качения:
Справочник-каталог/ Под ред. Нарышкина В.Н. и Коросташевского Р.В. - М.:
Машиностроение, 1984 - 280с.