Проектирование цилиндрического редуктора
Назначение привода и его описание
редуктор вал подшипник муфта
Редуктором называется механизм, состоящий из
зубчатых или червячных передач, выполненный в виде отдельного органа и служащий
для передачи вращения от вала двигателя к валу рабочей машины.
Назначение редуктора - понижение угловой
скорости и повышение вращающего момента ведомого вала по сравнению с ведущим.
Применение редукторов обусловлено экономическими
соображениями. Масса и стоимость двигателя при одинаковой мощности понижаются с
увеличением его быстроходности. Оказывается экономически целесообразным
применение быстроходных двигателей с понижающей передачей, вместо тихоходного
двигателя без передачи. Наиболее широко используются асинхронные двигатели с
частотой 750 и 1500 оборотов в минуту.
Редуктор состоит из корпуса, в котором размещают
элементы передачи - зубчатые колеса, валы, подшипники и т.д.
Редукторы классифицируют по следующим основным
признакам: типу передачи (зубчатые, червячные или зубчато-червячные); числу
ступеней (одноступенчатые, двухступенчатые и т.д.); типу зубчатых колес
(цилиндрические, конические и т.д.); относительному расположению валов в
пространстве (горизонтальные, вертикальные); особенностям кинематической схемы
(развернутая, соосная, с раздвоенной ступенью и т.д.). В данном проекте
разрабатывается двухступенчатый коническо-цилиндрический редуктор.
Зубчатые передачи являются основными видом
передач в машиностроении. Их основные преимущества: высокая нагрузочная
способность, и, как следствие, малые габариты; большая долговечность и
надежность работы; высокий КПД; постоянство передаточного отношения;
возможность применения в широком диапазоне мощностей, скоростей, передаточных
отношений. Недостатки: шум при работе, невозможность бесступенчатого изменения
передаточного числа, незащищенность при перегрузках, возможность возникновения
значительных динамических нагрузок из-за вибрации.
Подшипники служат опорами для валов, Они
воспринимают радиальные и осевые нагрузки, приложенные к валу, и сохраняют
заданное положение оси вращения вала. В данном приводе используются роликовые
радиально-упорные и шариковые радиально-упорные подшипники, которые
воспринимают радиальную и осевую нагрузки в конической и цилиндрической
передачах.
Кинематический расчет и выбор
электродвигателя
Рисунок 2.1 - Кинематическая схема привода
Выбор электродвигателя
Исходные данные для проектирования:
Окружная сила на барабане конвейера 
.
Скорость ленты конвейера 
.
Диаметр барабана 
.
Срок службы привода
.
Коэффициенты
Требуемая мощность электродвигателя:
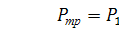
,
где 
- КПД привода.

.
где 
- КПД зубчатой конической передачи,

- КПД зубчатой цилиндрической
передачи,

- КПД пары подшипников качения,

- КПД муфты,

- КПД клиноременной передачи [1,
табл.5.4].
Мощность на ведомом валу привода P4:

.
Тогда

.
Частота вращения ведомого вала
привода n4, и угловая
скорость ведомого вала привода ω4:

,
где D - диаметр
барабана, мм;

- скорость вращения барабана, м/с.

.
Вращающий момент на ведомом валу Т4:

,
где 
- мощность на ведомом валу привода,
Вт.
Определяем частоту вращения
электродвигателя, для этого из табл.1.2[7] выбираем средние значения
передаточных чисел ременной и двух зубчатых передач:
Uр=2,5-передаточное
число клиноременной передачи;
Uт=3-передаточное
число конической косозубой передачи;
Uб=4-передаточное
число цилиндрической косозубой передачи;

.
Принимаем электродвигатель 132М6: 
,

.
Таблица 2.1-Технические данные асинхронного
двигателя из табл 2.4
Двигатель
|
Pном ,кВт
|
nэд ,мин-1
|
nас ,мин-1
|
32М6
|
7,5
|
1000
|
950
|
Общее передаточное число привода:
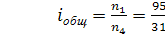
;

.
Произведем разбивку общего передаточного числа
редуктора по ступеням
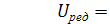
,
где 
- передаточные числа тихоходной и
быстроходной ступеней соответственно.
Из стандартного ряда номинальных
передаточных чисел принимаем 
[2, c.137].
Из стандартного ряда номинальных
передаточных чисел принимаем 
[2, c.137].
Ошибка определения передаточного
числа
Кинематический и силовой расчеты
Частота вращения ведущего вала
привода ω1:

.
Вращающий момент на ведущем валу привода Т1:

.
Частота вращения ведущего вала
редуктора n2 и его
угловая скорость вращения ω2:

,

.
Вращающий момент на ведущем валу
редуктора Т2:

.
Мощность на ведомом валу редуктора P2:

.
Частота вращения промежуточного вала
редуктора n3 и его
угловая скорость вращения ω3:

,

.
Вращающий момент на промежуточном
валу редуктора Т3:
Мощность на ведущем валу редуктора P3:

.
Результаты расчетов заносим в
таблицу 2.2.
Таблица 2.2 - Результаты
кинематического и силового расчета
Вал
|
Частота вращения n, мин-1
|
Мощность P, кВт
|
Вращающий момент Т, Н∙м
|
Угловая скорость ω, c-1
|
I
|
954,0
|
5,88
|
59
|
100
|
II
|
382,0
|
5,53
|
138,7
|
40,0
|
III
|
121,0
|
4,99
|
415,3
|
12,7
|
IV
|
31,8
|
5
|
1501,6
|
3,3
|
Расчет механических передач. Расчет
конической передачи
Выбор материалов, назначение твердости зубьев
Для шестерни и колеса принимаем сталь 40ХН.
Термическая обработка шестерни - улучшение и
закалка ТВЧ. Твердость поверхности зубьев шестерни HRC 45…50.
Термическая обработка колеса - улучшение и
закалка ТВЧ. Твердость поверхности зубьев колеса HRC 42…46.
Расчет допускаемых контактных 𝛔HP
и изгибных σFP напряжений
Допускаемые напряжения при расчете на контактную
усталость активных поверхностей зубьев:

,
где 
- предел контактной выносливости
активных поверхностей зубьев, соответствующий базе испытаний 
;

[3, табл.10.16];

[3, табл.10.16];

- коэффициент безопасности, 
[3, табл.10.16].
Коэффициент долговечности 
:

,
где 
- базовое число циклов перемены
напряжений, принимаем по графику [3, рис.10.41].
Пересчет твердости производится по
графику [3, рис.10.40]:
HRC = 425HB
HRC = 380HB
Тогда

;

- расчетное число циклов перемены
напряжений;
где 
- частота вращения того из колес,
по материалу которого определяется допускаемое напряжение, мин-1;
с - число зацеплений зуба за
один оборот колеса ( с = 1 );

- расчетный срок службы передачи,
час;

;

;

;
Тогда для шестерни:
Так как 
, то принимаем показатель степени m = 20 [3,
с.279].
Для шестерни
Для колеса
Допускаемые напряжения для шестерни
и колеса 
и 
соответственно равны

;

.
Расчетное допускаемое контактное
напряжение

.
Допускаемые напряжения при расчете на
сопротивление усталости зубьев при изгибе определяются по уравнению (отдельно
для шестерни и колеса)
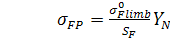
,
где 
[3, табл.10.16] - предел
выносливости зубьев при изгибе;

- коэффициент, учитывающий
шероховатость переходной поверхности, 
[3, c.281];

- коэффициент, учитывающий размеры
зубчатого колеса;

;

;

;
d -
делительный диаметр, мм;

- наименьший коэффициент запаса
прочности, 
[3, табл.10.16];

- коэффициент, учитывающий градиент
напряжений и чувствительность материала к концентрации напряжений;
Коэффициент долговечности 
определяем по формуле
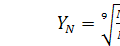
,
где 
- базовое число циклов перемены
напряжений, 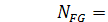
[3, c.281];

- расчетное число циклов перемены
напряжений;
где 
- частота вращения того из колес,
по материалу которого определяется допускаемое напряжение, мин-1;
с - число зацеплений зуба за
один оборот колеса ( с = 1 );

- расчетный срок службы передачи,
час;

;

;

;

.
Тогда для шестерни:
Для колеса:
Для шестерни:
Принимаем 
.
Для колеса:
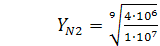
.
Принимаем 
.
Допускаемые напряжения на изгиб для
шестерни и колеса:

;

.
Допускаемые контактные и изгибные
напряжения при кратковременных перегрузках:

, [3, табл.10.16];

.

, [3, табл.10.16].
Производим проектировочный расчет
конической передачи
Средний делительный диаметр шестерни

:

,
где 
- для непрямозубых колес;

- вращающий момент на шестерне;

- коэффициент
ширины шестерни относительно среднего диаметра при 
и 
.
Принимаем 
.

,
где 
- угол делительного конуса
шестерни.

[4, рис.6.19] - коэффициент
распределения нагрузки по ширине венца;

- допускаемые контактные
напряжения.
Т.к. передача быстроходная,
принимаем число зубьев шестерни
Тогда число зубьев колеса

.
Угол делительного конуса колеса
определим по формуле

.
Угол наклона кругового зуба
принимаем
.
Ориентировочное значение среднего
модуля:

,
где 
- для непрямозубых колес;

- вращающий момент на шестерне;

[4, рис.6.19] - коэффициент
неравномерности распределения нагрузки по ширине венца;

- коэффициент, учитывающий влияние
формы зуба и концентрации напряжений, принимается по графику [4, рис.6.14] в
зависимости от эквивалентного числа зубьев zv:

;

.
Для шестерни - 
; для колеса - 
.
Определяем
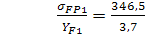
;
Так как 
, то расчет зубьев на прочность при
изгибе будем вести для шестерни.
В качестве допускаемой нагрузки
принимаем 
.
Принимаем 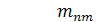
по ГОСТ 9563-60.
Внешний окружной модуль 
:

.
Число зубьев плоского колеса 
:

.
Среднее конусное расстояние 
:

.
Внешнее конусное расстояние 
:

.
Ширина зубчатого венца 
:

.
Принимаем 
.
Расстояние от внешнего торца до
расчетного сечения 
:

.
Средний делительный диаметр 
:

;

.
Внешний делительный диаметр 
:

;

.
Внешняя высота зуба

.
Смещение 
:

.

.
Внешняя высота головки зуба 
:

;

.
Внешнюю высоту ножки зуба 
:

;

.
Угол ножки зуба 
:

;

.
Угол головки зуба 
:

;

.
Внешний диаметр вершин зубьев 
:

;

.
Определим усилия в передаче.
Окружная сила в зацеплении 
:

,
где 
- крутящий момент на валу-шестерне,
Н∙мм.
Принимаем направление зубьев
шестерни - правое, направление зубьев колеса - левое.
Осевая 
и радиальная 
:

.
Проверочные расчеты передачи по
напряжениям 𝛔HP и 𝛔FP
Проверочный расчет на контактную
усталость активных поверхностей зубьев:

,
где 
- коэффициент, учитывающий
механические свойства материала, 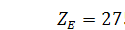
[4, с.127];

- коэффициент, учитывающий форму
сопряженных поверхностей зубьев, 
;

- коэффициент суммарной длины
контактных линий,
где 
- коэффициент торцового перекрытия;
Тогда
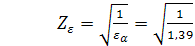
.

[4, рис.6.13] - коэффициент
распределения нагрузки между зубьями;

[4, рис.6.19] - коэффициент
распределения нагрузки по ширине венца;

- коэффициент динамической
нагрузки.
Удельная окружная расчетная сила 
:

,
где 
- вращающий момент на ведущем валу
передачи, Н·мм;

- ширина венца зуба, мм.
Определим значения этих
коэффициентов:
Окружная скорость шестерни:
Принимаем степень точности передачи
- 8 [2, табл.8.2].
Тогда

[2, табл.8.3].
Получим

.
Так как 
, то недогрузка составила

.
Проверочный расчет на сопротивление
усталости при изгибе:

,
где 
- коэффициент, учитывающий влияние
формы зуба и концентрации напряжений, принимается по графику в зависимости от
эквивалентного числа зубьев zv;

- коэффициент, учитывающий наклон
зуба;

.
Принимаем 
.

- коэффициент, учитывающий
перекрытие зубьев;
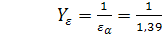
.

- коэффициент распределения нагрузки
между зубьями;

[4, рис.6.19] - коэффициент
распределения нагрузки по ширине венца;

[2, табл.8.3] - коэффициент
динамической нагрузки.

,
где 
- степень точности передачи.
Принимаем 
.
Удельная окружная расчетная сила 
:

,
где 
- вращающий момент на ведущем валу
передачи, Н·мм;

- ширина венца зуба, мм.

.
Прочность зубьев при изгибе
обеспечена.
Так как 
, то недогрузка составила

.
Расчет косозубой цилиндрической
передачи
Выбор материалов, назначение
твердости зубьев.
Для шестерни и колеса принимаем
сталь 40Х.
Термическая обработка шестерни -
улучшение и закалка ТВЧ. Твердость поверхности зубьев шестерни HRC 48…53.
Термическая обработка колеса -
улучшение и закалка ТВЧ. Твердость поверхности зубьев колеса HRC 42…45.
Допускаемые напряжения при расчете
на контактную усталость активных поверхностей зубьев:

,
где 
- предел контактной выносливости
активных поверхностей зубьев, соответствующий базе испытаний 
;

;

- коэффициент безопасности, 
[3, табл.10.16].
Коэффициент долговечности 
:

,
где 
- базовое число циклов перемены
напряжений, принимаем по графику [3, рис.10.41].
Пересчет твердости производится по
графику [3, рис.10.40]:
HRC = 470HB
HRC = 380HB
Тогда

;

- расчетное число циклов перемены
напряжений;
где 
- частота вращения того из колес,
по материалу которого определяется допускаемое напряжение, мин-1;
с - число зацеплений зуба за
один оборот колеса ( с = 1 );

- расчетный срок службы передачи,
час;

;

;

;

.
Тогда для шестерни:
Для колеса
Так как 
, то принимаем показатель степени m = 6 [3,
с.279].
Для шестерни
Для колеса
Принимаем 
.
Допускаемые напряжения для шестерни
и колеса 
и 
:

;

.
Расчетное допускаемое контактное
напряжение

.
Допускаемые напряжения на изгиб для
шестерни и колеса:

;

.
Допускаемые контактные и изгибные
напряжения при кратковременных перегрузках

;

.

, [3, табл.10.16].
Производим проектировочный расчет
цилиндрической передачи
Межосевое расстояние 
:

,
где 
[4, с.109] - вспомогательный
коэффициент для косозубых колес;

- вращающий момент на колесе;

- коэффициент
ширины колеса относительно межосевого расстояния.
Примем 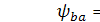
.

[3, рис.10.17] - коэффициент
распределения нагрузки по ширине венца;

- допускаемые контактные
напряжения.
Принимаем 
.
Ширина зубчатого венца колеса 
:

.
Принимаем 
.
Тогда ширина зубчатого венца
шестерни 
:

.
Определяем модуль зубьев 
:

.
Принимаем модуль 
.
Предварительный угол наклона зубьев 
:

.
Суммарное число зубьев 
:

.
Действительное значение угла наклона

:

.
Число зубьев шестерни

;

;

.
Тогда число зубьев колеса

.
Фактическое передаточное число 
:

6;

.
Делительный диаметр
:

;

.
Диаметр вершин 
:

;

.
Диаметр впадин 
:

;

.
Определим усилия в передаче.
Окружная сила в зацеплении 
:

,
где 
- крутящий момент на валу-шестерне,
Н∙мм.
Принимаем направление зубьев
шестерни - правое, направление зубьев колеса - левое.
Осевая 
, Н, и радиальная 
:

;

.
Проверочные расчеты передачи по
напряжениям 𝛔HP и 𝛔FP
Проверочный расчет на контактную
усталость активных поверхностей зубьев:

,
где 
- коэффициент, учитывающий
механические свойства материала, 
[4, с.109];

- коэффициент, учитывающий форму
сопряженных поверхностей зубьев, 
;

- коэффициент суммарной длины
контактных линий,
Расчет клиноременной передачи
По таблице 3.11 [4, ч.1] при моменте

на ведомом
шкиве выбираем ремень сечения Б и его размеры:
Размеры сечения
Площадь сечения
По табл.3.20 [4, ч.1] при угле
профиля канавок
выбираем
диаметры шкивов.
Диаметр ведущего шкива:
Диаметр ведомого шкива:
Фактическое передаточное число:
где
-коэффициент упрогого скольжения.
Расхождение с требуемым передаточным
числом
.
Скорость ремня
Межосевое расстояние а:
Расчетная длина ремня:
Ближайшая стандартная длина ремня:
Уточненное межосевое расстояние:
при надевании ремня:
,
для компенсации вытяжки ремня:
Угол обхвата ремня:
Условие
-выполняется.
Окружное усилие:
Поправочные коэффициенты:
Угла обхвата
-табл.3.7[4,
ч.1]
Скорости
-табл.3.8[4,ч.1]
Режима работы
-табл.3.9[4,ч.1]
Число пробегов ремня:
Условие
выполняется.
Исходное удельное окружное усилие:
при
и при
.
Допускаемое удельное окружное
усилие:
Необходимое число ремней:
где
- площадь сечения одного ремня,
применяется по таблице 3.11 [4, ч.1].
Принимаем z=5.
Сила, действующая на валы:
Расчетная долговечность ремня:
где
-предел усталости для клиновых
кордтканевых ремней;
-показатель степени кривой усталости
для клиновых ремней.
Наибольшее напряжение в ремне

где 
1- напряжение
растяжения в ведущей ветви ремня:
где 
u -напряжение
изгиба на малом шкиве:
где Еu - модуль
упругости при изгибе ремня
где 
ц -напряжение
от центробежных сил:
-где
=1,2, кг/м3-плотность
материала ремня.
Таким образом
Принимаем
Следовательно
Определяем размеры шкивов из
табл.3.20 [4,ч1.] выбираем для заданного сечения следующие параметры:
Диаметры шкивов:
Наружные диаметры шкивов:
Выбор подшипников
Выбор подшипников быстроходного вала
Выбираем роликовый конический
однорядный подшипник 7208А ГОСТ 27365-87.
Запишем параметры подшипника в
таблицу 4.1.
Таблица 4.1 - Параметры подшипника
Подшипник
|
d,
мм
|
D,
мм
|
C,
Н
|
e
|
Y
|
7208
|
40
|
80
|
90000
|
0,37
|
1,7
|
Выбор подшипников промежуточного вала
Выбираем роликовый конический однорядный
подшипник 7208А ГОСТ 27365-87. Запишем параметры подшипника в таблицу 4.2.
Таблица 4.2 - Параметры подшипника
Подшипник
|
d,
мм
|
D,
мм
|
C,
Н
|
e
|
Y
|
7208
|
40
|
80
|
46500
|
0,37
|
1,5
|
Выбор подшипников тихоходного вала
Выбираем роликовый конический однорядный
подшипник 7211А ГОСТ 27365-87. Запишем параметры подшипника в таблицу 4.3.
Таблица 4.3 - Параметры подшипника
Подшипникd,
ммD, ммC, НeY
|
|
|
|
|
|
2007913
|
65
|
100
|
34000
|
0,37
|
1,5
|
Выбор муфт
Зубчатые муфты применяются для
соединения валов нагруженных большими крутящими моментами при различной
комбинации радиальных, угловых и осевых смещений. Определим расчетный момент 
, Н∙м, определяем по формуле.

,
где 
- коэффициент режима работы для
привода для конвейера [5,стр. 195]

- крутящий момент на муфте, Н∙м.
Выбираем
муфту со следующими размерами, записанными в таблицу 4.4
Таблица 4.4 - Геометрические параметры зубчатой
муфты
Сила, нагружающая вал от муфты, 
, Н, определяется по формуле

,
где 
.
Проверку муфты производим по напряжениям смятия
рабочих поверхностей зубьев.

.
где m - модуль
зацепления, мм;
b - длина
зуба, мм.
Окончательно принимаем зубчатую
муфту 1-1000-60-1 ГОСТ 5006-94.
Расчет шпоночных соединений
Методика расчета
Для закрепления на валах зубчатых колес и муфт
применены призматические шпонки, выполненные по ГОСТ 23360-78.
Так как высота и ширина призматических шпонок
выбираются по стандартам, расчет сводится к проверке размеров по допускаемым
напряжениям на смятие при принятой длине.

,
где T
-
крутящий момент на валу, Н∙мм;
d
- диаметр вала, мм;
h
- высота шпонки, мм;
t1
- глубина паза вала, мм;
l
- полная длина шпонки, мм;- ширина шпонки, мм;
Шпонка, удерживающая шкив
Для заданного диаметра вала (
) выбираем сечение призматической
шпонки 
, глубина паза вала 
. Принимаем длину шпонки 
.
Тогда:

.
Принимаем шпонку 8´7´50
ГОСТ 23360-78.
Шпонка, удерживающая коническое колесо
Для заданного диаметра вала (
) выбираем сечение призматической
шпонки 
, глубина паза вала 
. Принимаем длину шпонки 
.
Тогда:

.
Принимаем 2 шпонки 14´9´36
ГОСТ 23360-78.
Шпонка, удерживающая цилиндрическое колесо
Для заданного диаметра вала (
) выбираем сечение призматической
шпонки 
, глубина паза вала 
. Принимаем длину шпонки 
.
Тогда:

.
Принимаем 2 шпонки 20´12´56
ГОСТ 23360-78.
Шпонка, удерживающая зубчатую муфту
Для заданного диаметра вала (
) выбираем сечение призматической
шпонки 
, глубина паза вала 
. Принимаем длину шпонки 
.
Тогда:

.
Принимаем 2 шпонки 18´11´67 ГОСТ
23360-78.
Расчет элементов корпуса редуктора
Толщина стенок корпуса:

;

.
Принимаем 
мм.
Толщина стенок крышки:

.
Принимаем 8мм.
Толщина поясов корпуса и крышки:

;

.
Диаметры болтов:
фундаментных:
Принимаем болты с М16;
крепящих крышку корпуса у подшипников:
Принимаем болты с М12;
соединяющих крышку с корпусом:
Применяем болты с М8.
Проверочный расчет валов.
Проверочный расчет быстроходного вала
Составляем расчетную схему.
Силы в зацеплении:

;

;

.
Радиальная нагрузка на вал со стороны
ременной передачи 
.
Момент при переносе силы 
:

.
Расчетная схема представлена на рисунке 7.1.
Определение реакций опор:
Плоскость XOZ:

;

;

;

.
Проверка:

;

;

.
Проверка: 
.
По полученным данным строим эпюры
Суммарные реакции на опорах:

;

.
Диаметр вала в опасном сечении:
Определяем коэффициент запаса прочности.
Для опасного сечения коэффициент запаса
прочности n
определяется по формуле
где 
- коэффициент запаса прочности по
нормальным напряжениям;

- коэффициент запаса прочности по
касательным напряжениям.
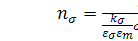
,
где 
[5, табл.10.2] - предел
выносливости при симметричном цикле изгиба, МПа;

[6, табл.8.3] - эффективный
коэффициент концентрации напряжения при изгибе для выточки 
;

[6, табл.8.8] - масштабный фактор,
т.е. коэффициент, учитывающий влияние поперечных размеров;

- фактор качества поверхности; 
[6, с.164] - коэффициент,
учитывающий чувствительность материала к асимметрии цикла нагружения; 
- амплитуда значения нормальных
напряжений, МПа;

,
где 
- изгибающий момент в сечении, Н∙мм;

- момент сопротивления сечения вала,
мм3;

- среднее значение нормальных
напряжений, МПа;

,
где 
- осевая нагрузка на вал, Н.
Тогда

.
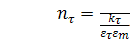
,
где 
[5, табл.10.2] - предел
выносливости при симметричном цикле кручения, МПа;

[6, табл.8.3] - эффективный
коэффициент концентрации напряжения при кручении для выточки 
;

[6, табл.8.8] - масштабный фактор,
т.е. коэффициент, учитывающий влияние поперечных размеров;

- фактор качества поверхности;

[6, с.166] - коэффициент,
учитывающий чувствительность материала к асимметрии цикла нагружения;

- амплитуда и среднее напряжения
циклов касательных напряжений, МПа;

,
где 
- крутящий момент в сечении, Н∙мм;

- полярный момент сопротивления
сечения вала, мм3;
Тогда
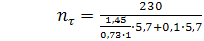
.

.
Проверочный расчет промежуточного
вала
Составляем расчетную схему.
Силы
в зацеплении:
на
коническом колесе:

;

;

.
на
цилиндрической шестерне:

;
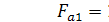
;
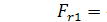
.
Момент
при переносе осевых сил 
:
на
коническом колесе:
на
цилиндрической шестерне:

.
Расчетная
схема представлена на рисунке 6.2.
Определение
реакций опор:
Плоскость
XOZ:

;



;

Проверка:

Плоскость YOZ:

;

;

;

.
Проверка:

По полученным данным строим эпюры.
Суммарные реакции на опорах:

;

.
Диаметр вала в опасном сечении:
Определяем коэффициент запаса прочности.
Для опасного сечения коэффициент запаса
прочности n
определяется по формуле

,
где 
- коэффициент запаса прочности по
нормальным напряжениям;

- коэффициент запаса прочности по
касательным напряжениям.
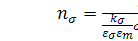
,
где 
[5, табл.10.2] - предел
выносливости при симметричном цикле изгиба, МПа;

[6, табл.8.3] - эффективный
коэффициент концентрации напряжения при изгибе для выточки 
;

[6, табл.8.8] - масштабный фактор,
т.е. коэффициент, учитывающий влияние поперечных размеров;

- фактор качества поверхности;

[6, с.164] - коэффициент,
учитывающий чувствительность материала к асимметрии цикла нагружения;

- амплитуда значения нормальных
напряжений, МПа;

,
где 
- изгибающий момент в сечении, Н∙мм;

- момент сопротивления сечения вала,
мм3;

- среднее значение нормальных
напряжений, МПа;

,
где 
- осевая нагрузка на вал, Н.
Тогда

.
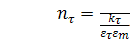
,
где 
[5, табл.10.2] - предел
выносливости при симметричном цикле кручения, МПа;

[6, табл.8.3] - эффективный
коэффициент концентрации напряжения при кручении для выточки 
;

[6, табл.8.8] - масштабный фактор,
т.е. коэффициент, учитывающий влияние поперечных размеров;

- фактор качества поверхности;

[6, с.166] - коэффициент,
учитывающий чувствительность материала к асимметрии цикла нагружения;

- амплитуда и среднее напряжения
циклов касательных напряжений, МПа;

,
где 
- крутящий момент в сечении, Н∙мм;

- полярный момент сопротивления
сечения вала, мм3;
Тогда

.
Получим коэффициент запаса

.
Проверочный расчет тихоходного вала
Составляем расчетную схему.
Силы в зацеплении:
на цилиндрическом колесе:

;
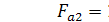
;
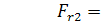
.
Радиальная нагрузка на вал со
стороны зубчатой муфты:

.
Момент при переносе силы 
:

.
Расчетная схема представлена на рисунке
7.3.Определение реакций опор: Плоскость XOZ:

;

;

;

.
Проверка: 
.
Плоскость YOZ:

;

;

;

.
Проверка:

.
Суммарные реакции на опорах:

;

.
Диаметр вала в опасном сечении:
Определяем коэффициент запаса прочности.
Для опасного сечения коэффициент запаса
прочности n
определяется по формуле

,
где 
- коэффициент запаса прочности по
нормальным напряжениям;

- коэффициент запаса прочности по
касательным напряжениям.
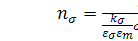
,
где 
[5, табл.10.2] - предел
выносливости при симметричном цикле изгиба, МПа;

[6, табл.8.5] - эффективный
коэффициент концентрации напряжения при изгибе;

[6, табл.8.8] - масштабный фактор,
т.е. коэффициент, учитывающий влияние поперечных размеров;

- фактор качества поверхности;

[6, с.164] - коэффициент,
учитывающий чувствительность материала к асимметрии цикла нагружения;

- амплитуда значения нормальных
напряжений, МПа;

,
где 
- изгибающий момент в сечении, Н∙мм;

- момент сопротивления сечения
вала, мм3;

,

- среднее значение нормальных
напряжений, МПа;

,
где 
- осевая нагрузка на вал, Н;

- ширина шпоночного паза, мм;

- высота шпонки, мм;

- глубина паза вала, мм.
Тогда 
.
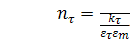
,
где 
[5, табл.10.2] - предел
выносливости при симметричном цикле кручения, МПа;

[6, табл.8.3] - эффективный
коэффициент концентрации напряжения при кручении для выточки 
;

[6, табл.8.8] - масштабный фактор,
т.е. коэффициент, учитывающий влияние поперечных размеров;

[6, с.166] - коэффициент,
учитывающий чувствительность материала к асимметрии цикла нагружения;

- амплитуда и среднее напряжения
циклов касательных напряжений, МПа;

,
где 
- крутящий момент в сечении, Н∙мм;

- полярный момент сопротивления
сечения вала, мм3;

,
Тогда

.
Получим коэффициент запаса

.
Определение долговечности
подшипников. Определение долговечности подшипников быстроходного вала
В таблице 8.1 представлены параметры подшипника 7208А
ГОСТ 27365-87
Таблица 8.1 - Параметры подшипника
Подшипникd, ммD, ммC, НeY
|
|
|
|
|
|
7608
|
40
|
90
|
90000
|
0,35
|
1,7
|
Эквивалентная динамическая нагрузка

,
где X
- коэффициент радиальной нагрузки;
V
- коэффициент вращения кольца (V=1
при вращении относительно нагрузки внутреннего колеса);
Y
- коэффициент осевой нагрузки;
Fr
- радиальная нагрузка на подшипник;
Fa
- осевая нагрузка на подшипник;

[5, табл.7.4] - коэффициент
безопасности;

- коэффициент влияния температуры (
при 
).
Суммарные реакции на опорах

;

.
Осевая сила на валу

.
Осевая составляющая радиальной
нагрузки

;

.
Т.к. 
и 
, то

;

.
Определяем значения X
и Y:

;
Принимаем 
.

;
Принимаем 
.
Тогда эквивалентная динамическая
нагрузка равна

;

.
Т.к.
, то расчет долговечности ведем по
первому подшипнику.
Долговечность подшипника
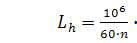
,
где 
- частота вращения вала;
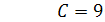
[5, табл. 24.16] - динамическая
грузоподъемность
p -
показатель степени (p=3,33 для
роликовых подшипников).

.
Долговечность подшипника 
, что больше требуемого срока службы

.
Определение долговечности
подшипников промежуточного вала
В таблице 8.2 представлены параметры подшипника 7208А
ГОСТ 27365-87.
Таблица 8.2 - Параметры подшипника
Подшипникd, ммD, ммC, НeY
|
|
|
|
|
|
7208
|
40
|
80
|
46500
|
0,37
|
1,5
|
Эквивалентная динамическая нагрузка

,
где X
- коэффициент радиальной нагрузки;
V
- коэффициент вращения кольца (V=1
при вращении относительно нагрузки внутреннего колеса);
Y
- коэффициент осевой нагрузки;
Fr
- радиальная нагрузка на подшипник;
Fa
- осевая нагрузка на подшипник;

[5, табл.7.4] - коэффициент
безопасности;

- коэффициент влияния температуры (
при 
).
Суммарные реакции на опорах
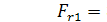
;

.
Осевая сила на валу

.
Осевая составляющая радиальной
нагрузки

;

.
Т.к. 
и 
, то

;

.
Определяем значения X
и Y:

;
Принимаем 
.

;
Принимаем 
.
Тогда эквивалентная динамическая
нагрузка равна

;

.
Т.к.
, то расчет долговечности ведем по
второму подшипнику.
Долговечность подшипника
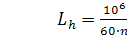
,
где 
- частота вращения вала;
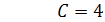
[5, табл. 24.16] - динамическая
грузоподъемность
p -
показатель степени (p=3,33 для
роликовых подшипников).

.
Долговечность подшипника 
, что больше требуемого срока службы

.
Определение долговечности
подшипников тихоходного вала
В таблице 8.3 представлены параметры подшипника 7211А
ГОСТ 27365-87. Таблица 8.3 - Параметры подшипника
Таблица
Подшипникd, ммD, ммC, НeY
|
|
|
|
|
|
2007913
|
65
|
100
|
34000
|
0,37
|
1,5
|
Эквивалентная динамическая нагрузка

,
где X
- коэффициент радиальной нагрузки;
V
- коэффициент вращения кольца (V=1
при вращении относительно нагрузки внутреннего колеса);
Y
- коэффициент осевой нагрузки;
Fr
- радиальная нагрузка на подшипник;
Fa
- осевая нагрузка на подшипник;

[5, табл.7.4] - коэффициент
безопасности;

- коэффициент влияния температуры (
при 
).
Суммарные реакции на опорах

;

.
Осевая сила на валу

.
Осевая составляющая радиальной
нагрузки

;

.
Т.к. 
и 
, то

;

.
Назначение посадок деталей редуктора
Посадки:
цилиндрического зубчатого колеса на вал Н7/p6;
конического зубчатого колеса на вал Н7/p6;
шкива на быстроходном валу редуктора Н7/j6;
зубчатой муфты на тихоходном валу редуктора H7/k6;
крышек с манжетным уплотнением H7/h8;
крышек без уплотнения H7/d11;
колец на валах F8/k6;
стакана в корпус H7/js6;
шпонки в вал N9/h9;
шпонки в ступицу Js9/h9.
Цапфы валов под подшипники выполняем с
отклонением вала k6,
отклонения отверстий в корпусе под наружные кольца подшипников Н7.
Описание сборки и смазки редуктора.
Сборка редуктора
Перед сборкой внутреннюю полость корпуса
редуктора тщательно очищают и покрывают маслостойкой краской. Сборку производят
в соответствии с чертежом общего вида редуктора, начиная с узлов валов:
на быстроходный вал (поз.14) насаживают
подшипники (поз.38), предварительно нагретые в масле до 80-100°С,
затем вал с подшипниками устанавливают в стакан (поз.11);
в промежуточный вал (поз.15) закладывают
шпонку (поз.46) и напрессовывают зубчатое колесо (поз.16), а
затем на вал устанавливают подшипники (поз.38), нагретые предварительно
в масле.
на тихоходный вал (поз.13) устанавливают
зубчатое колесо (поз.17) аналогично рекомендациям, приведенным выше, а
затем устанавливают подшипники (поз.39), нагретые предварительно в
масле.
Собранные валы укладывают в основание корпуса
редуктора (поз.18) и надевают крышку корпуса (поз.19), покрывая
предварительно поверхности стыка крышки и корпуса уплотнительной пастой типа
«Герметик». Для базирования крышки относительно корпуса используют конические
штифты (поз.50). После этого в подшипниковые камеры закладывают смазку,
ставят крышки подшипников (поз.4,5,6,7). Проверяют проворачиванием валов
отсутствие заклинивания подшипников (валы должны проворачиваться от руки) и
закрепляют крышки винтами. Затем ввертывают пробку маслоспускного отверстия (поз.12)
с прокладкой (поз.20) и маслоуказатель (поз.3). Заливают в корпус
масло (2,4 л) и закрывают смотровое отверстие крышкой (поз.2) с
прокладкой из картона; закрепляют крышку болтами. Собранный редуктор обкатывают
и подвергают испытанию на стенде по программе, устанавливаемой техническими
условиями.
Так как окружные скорости редуктора не превышают
12 м/с, то смазывание зубчатых колес может осуществляться картерным способом,
т.е. окунанием зубчатых колес в масло, заливаемое внутрь корпуса.
Из конструктивных соображений принимаем
количество масла, заливаемого в редуктор: 2,4 литра. Это количество масла
удовлетворяет условию 0,5 - 0,8 литра масла на 1 кВт передаваемой мощности.
Контроль уровня масла ведется с помощью маслоуказателя.
Рекомендуемое значение вязкости
масла при
и окружной
скорости до 2 м/с составляет
. Исходя из этого выбираем для
смазки масло И-40А ГОСТ 20799-75.
Для смазки подшипников применяем
пластическую смазку Циатим-201 ГОСТ 6261-74
Литература
.Расчеты
деталей машин: Справ. пособие / А.В. Кузьмин, И.М. Чернин, Б.С. Козинцов. - 3-е
изд., перераб. и доп. - Мн.: Выш. шк., 1986. - 400с.: ил.
.Иванов,
М.Н. Детали машин: Учеб. Для студентов втузов / Под ред. В.А. Финогенова. - 6-е
изд., перераб. - М.: Высш. шк., 2000. - 383 с.: ил.
.Скойбеда,
А.Т. Детали машин и основы конструирования: учебник / А.Т. Скойбеда, А.В.
Кузьмин, Н.Н. Макейчик; под общ.ред. А.Т. Скойбеды. - 2-е изд., перераб. - Мн.:
Выш. Шк., 2006. - 560 с.: ил.
.Курсовое
проектирование деталей машин: Справ. пособие. Часть 1/А.В. Кузьмин, Н.Н.
Макейчик, В. Ф. Калачев и др. - Мн.: Выш. школа, 1982.-208 с., ил.
.Дунаев
П.Ф., Леликов О.П. Конструирование узлов и деталей машин: Учеб. пособие для
техн. спец. вузов.- 5-е изд., перераб. и доп.- М.: Высш.шк., 1998. - 447 с.,
ил.
.Курсовое
проектирование деталей машин: Учеб пособие для учащихся машиностроительных
спе¬циальностей техникумов/С.А. Чернавский, К.Н. Боков, И.М. Чернин и др. - 2-е
изд., перераб. и доп. - М.: Машиностроение, 1987.- 416 с., ил.
.Дунаев
П.Ф. Леликов О.П. Детали машин. Курсовое проектирование: Учеб. пособие для
машиностроит. спец. техникумов. - 2-е изд., перераб. и доп. - Высш. шк., 1990.
- 399 с.