Дуговая сварка конвейера для грязи
МИНИСТЕРСТВО НАРОДНОГО
ОБРАЗОВАНИЯ
УДМУРТСКОЙ РЕСПУБЛИКИ
ДИПЛОМНАЯ РАБОТА
на тему: «Дуговая сварка
конвейера для грязи»
Выполнил:
учащийся гр. 35
Степанов Павел
Руководитель:
Профессиональное
училище – 4
Ижевск,
2005
Содержание
1.
Введение 3
2. Выбор способа сварки 4
3. Выбор сварочного
оборудования 7
4. Характеристика изделия 11
5. Выбор профиля и материалов 13
6. Техника и технология сборки
конструкции 16
7. Выбор режимов 20
8. Контроль качества 27
9. Охрана труда 35
10. Расчетная часть 40
Список литературы 42
Явление
электрического дугового разряда впервые было открыто русским ученым,
профессором физики Петербургской медико-хирургической академии В.В. Петровым в
1802 году. В своих трудах он не только описал явления электрической дуги, но и
предсказал возможность использования теплоты, выделяемой дугой, для плавления
металлов. Таким образом, В.В. Петров указал на возможность электрической плавки
металлов, однако в то время это открытие не нашло практического применения
из-за низкого уровня развития техники.
Только спустя
80 лет, в 1882 г. талантливый русский изобретатель Н.Н. Бенардос разработал и
предложил практический способ использования электрической дуги для сварки
металлов. По этому способу сварка производилась электрической дугой, возбуждаемой
междуугольным электродом и изделием. Несколько позже, в 1888 г., русский инженер-изобретатель
Н.Г. Славянов разработал способ сварки при помощи металлического электрода.
Н.Н. Бенардос
и Н.Г. Славянов разработали также основные положения и других методов сварки: с
несколькими электродами, в защитных газах, контактной сварки. В царской России
эти изобретения получили ограниченное применение, а затем были почти забыты.
Сварка занимает важное место в различных отраслях промышленности и строительства
благодаря своим преимуществам перед другими способами производства изделий,
например, клепкой, литьем, ковкой и др.
Сваркой называется
процесс получения неразъёмного соединения посредством установления межатомных
связей между свариваемыми частями при их местном или общем нагреве, или
пластическом деформировании, или совместным действием того и другого.
По физическим
признакам, в зависимости от способа используемой энергии, предусматривается три
класса сварки: термический, термомеханический и механический.
Термический
класс включает виды сварки с использованием тепловой энергии (дуговая,
электрошлаковая, газовая, электронно-лучевая, плазменная и др.).
Термомеханический
класс объединяет виды сварки, при котором используется давление и тепловая
энергия (контактная, диффузионная и различные прессовые виды).
Механический
класс включает все виды сварки, осуществляемые механической энергией (холодная,
трением, ультразвуковая, взрывом и др.).
В нашей стране
используются очень много видов сварки: автоматическая сварка под флюсом,
электрошлаковая сварка, газовая сварка, световая сварка, термическая сварка,
контактная сварка, диффузионная сварка, газопрессовая сварка и многие другие
виды.
Способ сварки
в значительной мере определяет не только качество и трудоемкость изготовления
оболочковых конструкций, но и весь технологический процесс в целом. Выбор
способа сварки начинается с определения ряда технически приемлемых вариантов
для соединения. Затем выбирается тип оборудования и составляются
ориентировочные технологические процессы сборки и сварки с укрупненным
процессом нормирования для каждого варианта, подсчитывается суммарная трудоемкость
и экономическая эффективность каждого способа. после сравнения принимается
окончательное решение в пользу того или иного способа сварки.
В настоящее
время в сварочном производстве используются более 130 различных способов
сварки. При этом в ряде отраслей наметились тенденции по применению современной
сварочной технологии для изготовления ответственных конструкций. Среди способов
сварки плавлением все более широкое применение находят концентрированные источники
нагрева, позволяющие осуществлять интенсивное расплавление при повышенных
скоростях сварки: сжатая (плазменная) дуга, элекронный луч, луч лазера. Среди
способов сварки давлением используют сварку токами высокой частоты, сварку
трением, сварку прокаткой и взрывом.
Другим
направлением в совершенствовании сварочных технологий является воздействие на
термодеформационный цикл сварки с целью создания благоприятных условий при
нагреве и охлаждении. Для этого применяют механическое и магнитное колебание
сварочной дуги, импульсные источники питания, регулируемые циклы охлаждения сварных
швов и др.
Таблица 1
Выбор способа сварки по показателям
технологичности
№
|
Показатели технологичности
|
Сварка под флюсом
|
Сварка в среде защитных газов
|
1.
|
Получение
сварных швов с заданным химическим составом и структурой
|
Легирование
через флюс и электродную проволоку
|
Легирование
только через электродную проволоку
|
2.
|
Выгорание легирующих
элементов
|
Минимальное
|
Повышенное
|
3.
|
Потери
электродного металла
|
Отсутствуют
|
Повышенное
|
4.
|
Внешний вид шва
|
Хороший с
плавным переходом от шва к основному металлу
|
Поверхность шва
бугристая, с более резким переходом от шва к основному металлу
|
5.
|
Проплавляющая способность
дуги
|
При одинаковом
режиме глубина проплавления ниже на 5-8%
|
Соответственно
больше на 5-8%
|
6.
|
Производительность
расплавления электродного металла
|
В среднем меньше
на 10%
|
Соответственно
больше на 10%
|
7.
|
Производительность
наплавки
|
Одинаковая
|
Одинаковая
|
8.
|
Зачистка швов
|
Необходимо
полное удаление шлаковой корки перед каждым проходом
|
Не требуется
|
9.
|
Зачистка ЗТВ от
набрызгивания металла
|
Необходима
|
10.
|
Сварка в разных
пространственных положениях
|
Затруднена в
потолочном. В вертикальном и горизонтальном возможна с применением флюсоподдерживающих
устройств
|
В любом
|
11.
|
Наблюдение за сварочной
дугой, ванной и направлением по стыку
|
Затруднено
|
Не затруднено
|
12.
|
Санитарно-гигиенические
требования
|
Выделение
токсических веществ, необходима вентиляция
|
Повышенная
загазованность, излучение, необходима вентиляция и защита от излучения
|
Способ сварки
выбирают из условия обеспечения качества изделия (требуемая точность,
герметичность и другие характеристики). Из равноценных по данному признаку
способов останавливаются на тех, которые характеризуются наименьшими экономическими
затратами и лучшими санитарно-гигиеническими условиями
При небольшом
объеме выпуска два рассматриваемых способа практически равноценны по
экономическим показателям. Однако при серийном и массовом производстве
эффективность способов различна, что необходимо учитывать при сравнительном
анализе.
Выбираем
сварку в среде защитных газов. При сварке в защитном газе электрод, зона дуги
и сварочная ванна защищены струей защитного газа.
В качестве
защитных газов применяют инертные газы ( аргон и гелий) и активные газы
(углекислый газ, азот, водород и др.), а иногда – смеси двух газов и более.
Сварка в среде защитных газов в зависимости от степени механизации процессов
подачи присадочной или сварочной проволоки и перемещения сварочной горелки
может быть ручной, полуавтоматической и автоматической.
По сравнению с
ручной сваркой покрытыми электродами и автоматической под флюсом сварка в
защитных газах имеет следующие преимущества: высокую степень защиты
расплавленного металла от воздействия воздуха; отсутствие на поверхности шва
при применении аргона оксидов и шлаковых включений; возможность ведения
процесса во всех пространственных положениях; возможность визуального
наблюдения за процессом формирования шва и его регулирования; более высокую
производительность процесса, чем при ручной дуговой сварке; относительно низкую
стоимость сварки в углекислом газе.
Области
применения сварки в защитных газах охватывают широкий круг материалов и изделий
(узлы летательных аппаратов, элементы атомных установок, корпуса и трубопроводы
химических аппаратов и т. п.). Аргонодуговую сварку применяют для цветных
(алюминия, магния, меди) и тугоплавких (титана, ниобия, ванадия, циркония) металлов
и их сплавов, а также легированных и высоколегированных сталей.
В последние
годы предприятия России выпускает значительное количество нового сварочного
оборудования. Выбор оборудования для сварочных операций в значительной мере
определяется принятым принятым способом сварки, но при этом необходимо
руководствоваться следующими соображениями.
Номинальная
мощность машины должна быть близкой к мощности, требуемой по установленным
режимам сварки с превышением не более 30%. Это требование диктуется как
экономическими так и технологическими соображениями - как известно большинство
электроустановок имеет оптимальные значения КПД при номинальной загрузке. Некоторый
избыток мощности необходим для запаса при возможных длительных снижениях напряжения
в цеховой сети, как компенсация падения напряжения в контактах и разъемных
соединениях установок и т.д.
Установка
должна обеспечивать необходимую по технологии производительность и позволять
удобно выполнять данную операцию. Следует отдавать предпочтение автоматизированному
оборудованию, т.к. затраты на его ремонт и обслуживание ниже чем расходов,
связанных с большей трудоемкостью работ.
Необходимо
учитывать экономические возможности предприятия в приобретении требуемого
оборудования и имеющуюся номенклатуру выпуска данного оборудования у нас в
стране и за рубежом. При этом тип и технические характеристики можно выбирать
по справочникам, каталогам и Интернет. Например, на сайтах производителей
сварочного оборудования: НПП "Технотрон", ЗАО
"Уралтермосвар".
Автоматы и
полуавтоматы для сварки в среде защитных газов обычно имеют постоянную скорость
подачи электродной проволоки. При этом максимальный диаметр для полуавтомата
составляет 2 мм. При их выборе следует особое внимание уделять механизму торможения
подачи проволоки, который должен обеспечивать ее постоянный выход из мундштука
при прерывании процесса сварки.
Для увеличения
производительности целесообразно выбирать установки с несколькими
автоматическими головками. При этом сварка осуществляется либо в одной сварочной
ванне, либо когда одна дуга несколько опережает другую. Последний способ применяют
для сварки закаливающихся сталей, либо когда требуется снизить остаточные сварочные
напряжения.
Предлагается
использовать компактные и легкие в управление сварочные полуавтоматы серии
Kemppi Pro Evolution разработаны с учетом требований эргономики. Данные
аппараты обеспечивают удобство и надежность работы, с такими стандартными функциями,
как запись применяемого режима в память или автоматический ввод присадочной
проволоки в горелку.
Таблица 2
Технические характеристики сварочного оборудования
Характеристики
|
Pro Evolution 3200
|
Pro Evolution 4200
|
Pro Evolution 5200
|
Напряжение сети, 3-50/60 Гц
|
400В (-15%,...+20%)
|
400В (-15%,...+20%)
|
400В (-15%,...+20%)
|
Сетевой кабель, Предохранитель
|
4 х 6S-5м/25 А
|
4 х 6S-5м/25 А
|
4 х 6S-5м/25 А
|
Диапазон сварочного тока MMA
|
10-320 А
|
10-420 А
|
10-520 А
|
Диапазон сварочного тока TIG
|
5-320 А
|
5-420 А
|
5-520 А
|
Диапазон сварочного тока MIG
|
10-36 В
|
12-41 В
|
10-45 В
|
Макс. сварочный ток
|
46 В/300 А
|
46 В/400 А
|
46 В/500 А
|
Коэффициент мощности на min
|
0.93
|
0.93
|
0.93
|
Габариты Д х Ш х В, мм
|
530 х 230 х 520
|
530 х 230 х 520
|
530 х 230 х 520
|
Масса, кг
|
37
|
41
|
48
|
В комплектах
Pro Evolution применяются надежные проволокоподающие устройства Promig 501,
501L, 511 и 530, снабженные четырьмя подающими роликами. Мягкая и тонкая
алюминиевая присадочная проволока подается также плавно, как и толстая, жесткая
стальная. Благодаря автоматическому вводу проволоки в горелку, замена кассеты с
проволокой производится быстро. Для проволокоподающих устройств выпускаются
различные панели управления, позволяющие ввести дополнительные функции,
ускоряющие работу. К Promig 530 горелка подключается под углом. Эргономическая
поворотная стрела расширяет зону работы Promig 511 и защищает шланги от
повреждений.
Кислородная
резка металла была разработана в начале XIX в. русским ученым Н. Н. Бенардосом
и после создания промышленных методов получения, хранения и транспортировки
кислорода и горючих газов превратилась в ряде производств в основной технологический
метод изготовления деталей.
Наличие в
производстве большого количества устаревшей газорежущей техники потребовало
создания современной унифицированной аппаратуры (резаков), которая подходила бы
ко всем газорежущим машинам, в т. ч. и импортным. Такими являются резаки серии
"Эффект" для машинной термической резки. Резаки "Эффект-М"
выпускают в двух модификациях:
-
диаметр
ствола 28 мм с рейкой;
Все резаки имеют
унифицированные вентильные группы (вентили кислорода подогревающего, режущего и
горючего газа) и отличаются резьбами и наличием трехзаходного шпинделя в
вентиле режущего кислорода.
Стволы
выпускают четырех типоразмеров длиной 210, 246, 342 и 425 мм. Это дает
возможность получить 24 основных исполнений резаков, например, резак
"Эффект 2-28-246" - двухвентильный со стволом диаметром 28 мм, длиной
246 мм, резак "Эффект 3-28-246" - трехвентильный тех же параметров; резак
"Эффект 2-32-425" - двухвентильный со стволом диаметром 32 мм, длиной
425 мм.
Отличительной
особенностью резаков со стволом диаметром 32 мм является наличие воздушного
обдува. В процессе кислородной резки металла выделяется значительное количество
теплоты и продуктов сгорания. Так как на большинстве газорежущих машин
отсутствует надежная система вентиляции, продукты сгорания поднимаются вверх,
что приводит к обугливанию рукавов, кабелей, перегреву суппортов и конструкций
машин со всеми вытекающими из этого последствиями. Особенно это сказывается при
трехрезаковой резке деталей со скосом кромок под сварку. В резаках с воздушным
обдувом вытекающий через кольцевой зазор над мундштуком воздух создает колокол,
локализующий распространение продуктов сгорания и защищающий конструкции от
перегрева.
Некоторые
модели резаков диаметром 32 мм поставляют с дополнительным центральным штуцером
для крепления разметочного устройства либо фотодатчика. При их отсутствии
устанавливается уменьшенная головка с боковым воздушным штуцером.
Все резаки
комплектуют едиными унифицированными щелевыми мундштуками, работающими на
ацетилене, природном газе и пропан-бутане.
Конвейер для грязи состоит из электродвигателя,
одноступенчатого червячного редуктора и приводного барабана. Червячная передача
служит для передачи мощности от первого (I) вала ко второму (II). При передаче мощности
имеют место ее потери на преодоление сил вредного сопротивления. Такие
сопротивления имеют место и в нашем приводе: в зубчатой передаче, в опорах
валов. Ввиду этого мощность на приводном валу будет меньше мощности, развиваемой
двигателем, на величину потерь.
1.1.
Мощность на приводном валу
барабана (мощность полезных сил сопротивления на барабане)



1.3. Общий коэффициент полезного действия
привода.

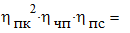
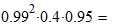
где hпк=0.99 – к.п.д. пары подшипников качения (по таблице 1 [1]),
hчп=0.40 – к.п.д. червячной передачи (по
таблице 1 [1]),
hпс=0.95 – к.п.д. пары подшипников скольжения (по
таблице 1 [1]).
1.4. Потребная
мощность электродвигателя (мощность с учетом вредных сил сопротивления)



1.5. Частоты вращения барабана (третьего
вала)

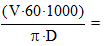
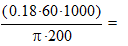
1.6. Ориентировочное передаточное число
привода


где U`1-ориентировочное значение передаточного числа червячной
передачи 1.7. Ориентировочные частоты
вращения вала электродвигателя.



1.8. Передаточное
число привода.




1.9. Передаточные
числа ступеней передач привода


1.10. Частоты вращения валов привода.
Для первого вала


Для второго вала



Частоты
второго и третьего вала одинаковы, следовательно, nIII=nII=17.189
об/мин
1.11. Мощности
на валах.
Мощность на первом валу



Мощность на втором валу



Мощность на третьем валу (для проверки) равна
Рвых



Сварочные
материалы выбирают на основании выбранного способа сварки и исходных данных о
материале сварной конструкции. Эти данные получены в предыдущих разделах при
анализе сварной конструкции и выборе способа сварки.
К сварочным материалам
относятся:
-
cварочная
проволока для механизированной дуговой, электрошлаковой сварки и изготовления
электродов;
-
прутки
для дуговой сварки;
-
проволока
стальная наплавочная;
-
порошковая
проволока для дуговой механизированной сварки и наплавки;
-
покрытые
электроды для ручной дуговой сварки;
-
неплавящиеся
электроды (вольфрамовые, угольные, графитизированные);
-
сварочные
флюсы;
-
газы;
-
порошки
для сварки, наплавки и напыления.
Стальные
электроды изготовляют в соответствии с ГОСТ 9466-75, ГОСТ 9467-75, ГОСТ
100051-75. В ГОСТ 9466-75 электроды подразделяются на группы в зависимости от
свариваемых металлов:
У -
углеродистых и низкоуглеродистых конструкционных сталей;
Л -
легированных конструкционных сталей;
Г -
легированных теплоустойчивых сталей;
В -
высоколегированных сталей с особыми свойствами.
Общее
назначение электродных покрытий – обеспечивание стабильности горения сварочной
дуги и получение металла шва с заранее заданными свойствами (прочность,
пластичность, ударная вязскость, стойкость против коррозии, и др.).
Стабильность горения сварочной дуги достигается снижением потенциала
ионизации воздушного промежутка между электродом и свариваемой деталью.
Покрытия
выполняют защитную функцию, шлаковая защита служит для защиты расплавленного
металла шва от воздействия кислорода и азота воздуха путем образования шлаковых
оболочек на поверхности капель электродного металла, переходящих через дуговой
промежуток, и для образования шлакового покрова на поверхности расплавленного
металла. Шлаковое покрытие уменьшает скорость охлаждения и затвердевания
металла шва, способствуя выходу из него газовых и неметаллических включений.
Шлакообразующими
компонентами являются; титановый концентрат, марганцевая руда, каолин, мрамор,
мел, кварцевый песок, доломит, полевой шпат и др.
Легирование
металла шва производится для придания специальных свойств наплавленному
металлу. Наиболее часто применяются такие легирующие компоненты как хром,
никель, молибден, вольфрам, марганец, титан и др. Легирование металла иногда
производится специальной проволокой, содержащей нужные элементы. Чаще металл
шва легируют введением легирующих компонентов в состав покрытия электрода.
Легирующие компоненты - ферросплавы, иногда чистые металлы.
По видам
покрытия электродов подразделяются:
А - с кислым
покрытием, содержащим окиси железа, марганца, кремния, иногда титана;
Б - с основным
покрытием, имеющим в качестве основы фтористый кальций и карбонад
кальция. (Сварку электродами с основным покрытием осуществляют на постоянном
токе и обратной полярности. Вследствие малой склонности металла к образованию
кристаллизационных и холодных трещин, электроды с этим покрытием используют для
сварки больших сечений );
Ц - с
целлюлозным покрытием, основные компоненты которых - целлюлоза, мука другие
органические составы, создающие газовую защиту дуги и образующие при плавлении
тонкий шлак. (Электроды с целлюлозным покрытием применяют, как правило, для
сварки стали малой толщины);
Р - с
рутиловым покрытием, основной компонент - рутил. Для шлаковой и газовой защиты
покрытия этого типа вводят соответствующие минеральные и органические компоненты.
При сварке на
постоянном и переменном токе разбрызгивание металла незначительно. Устойчивость
горения дуги, формирование швов во всех пространственных положениях хорошее;
П - прочие
виды покрытий.
Для сталей
обычной прочности предназначены электроды: Э38, Э42, Э46, Э50, Э42А, Э46А,
Э50А, Э55 и Э60. Для конструкционных сталей повышенной прочности - электроды:
Э70, Э85, Э100, Э125, Э150. Механические свойства швов и сварных соединений
при применении электродов для сварки конструкционных сталей должны соответствовать
определенным нормам.
Выбираем
электроды УОНИИ-13, которые дают высокое качество металла шва и применяются для
сварки ответственных швов из конструкционных сталей. Такие электроды
выпускаются нескольких марок-УОНИИ-13/45. УОНИИ-ГЗ/55, УОНИИ-13/65 и
УОНИИ-13/85. Цифры после черты означают получаемый предел прочности металла шва
(кгс/мм^). Сварку можно производить при любом положении шва, но только на постоянном
токе обратной полярности. Эти электроды применяют в заводских и монтажных
условиях. Коэффициент наплавки электродов типа УОНИИ-13 достигает 9,5 г/(А-ч).
Наибольший
объём среди других видов сварки занимает ручная дуговая сварка- сварка
плавлением штучными электродами, при которой подача электрода и перемещение
дуги вдоль свариваемых кромок производится вручную. Схема процесса показана на
рис. 3
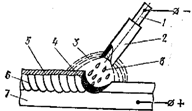
Дуга горит
между стержнем электрода 1 и основным металлом 7. Под действием теплоты дуги
электрод и основной металл плавятся, образуя металлическую сварочную ванну 4.
Капли жидкого металла 8 с расплавляемого электродного стержня переносятся в
ванну через дуговой промежуток. Вместе со стержнем плавится покрытие электрода
2, образуя газовую защиту 3 вокруг дуги и жидкую шлаковую ванну на поверхности
расплавленного металла.
Металлическая
и шлаковая ванны вместе образуют сварочную ванну. По мере движения дуги металл
сварочной ванны затвердевает и образует сварной шов 6. Жидкий шлак по мере
остывания образует на поверхности шва твёрдую шлаковую корку 5, которая
удаляется после остывания шва. Для обеспечения заданного состава и свойств шва
сварку выполняют покрытыми электродами, к которым предъявляют специальные требования
(стальные покрытые электроды для ручной дуговой сварки и наплавки изготовляют в
соответствии с ГОСТ 9467-75).
Сварочный пост
для ручной дуговой сварки оснащается источником питания, токоподводом,
необходимыми инструментами, принадлежностями и приспособлениями.
Сварочные
посты могут быть стационарными и передвижными. К стационарным относят
посты, расположенные в цехе, преимущественно в отдельных сварочных кабинах, в
которых сваривают изделия небольших размеров. Передвижные сварочные
посты, как правило, применяют при монтаже крупногабаритных изделий
(трубопроводов, металлоконструкций, и т.д.) и ремонтных работах. При этом часто
используют переносные источники питания. В зависимости от свариваемых
материалов и применяемых электродов для ручной дуговой сварки применяют
источники переменного или постоянного тока с крутопадающей характеристикой.
Основным
рабочим инструментом сварщика при ручной сварке служит электрододержатель,
который предназначен для зажима электрода и провода сварочного тока. Применяют
электрододержатели пружинного, пластинчатого и винтового типов (рис. 4)
Согласно ГОСТ
14651-78 электрододержатели выпускаю трёх типов в зависимости от силы
сварочного тока: 1 типа - для тока 125 А; 2- 125-315 А; 3-315-500 А.
Для подвода
тока от источника питания к электрододержателю и изделию используют сварочные
провода. Сечения проводов выбирают по установленным нормативам для
электротехнических установок (5-7 А/мм^2).
К
вспомогательным инструментам для ручной сварки относятся: стальные проволочные
щётки для зачистки кромок перед сваркой и для удаления с поверхности швов остатков
шлака, молоток-шлакоотделитель для удаления шлаковой корки, особенно с угловых
и корневых швов в глубокой разделке, зубило, набор шаблонов для проверки размеров
швов, стальное клеймо для клеймения швов, метр, стальная линейка, отвес, угольник,
чертилка, мел, а также ящик для хранения и переноски
инструмента.
Выбор
режима.
Под режимом
сварки понимают совокупность контролируемых параметров, определяющих условия
сварки. Параметры режима сварки подразделяют на основные и дополнительные. К
основным параметрам режима ручной сварки относят диаметр электрода, величину,
род и полярность тока, напряжение на дуге, скорость сварки. К дополнительным
относят величину вылета электрода, состав и толщину покрытий электрода, положение
электрода и положение изделия при сварке.
Диаметр
электрода
выбирают в зависимости от толщины металла, катета шва, положения шва в
пространстве.
Примерное
соотношение между толщиной металла S и диаметром электрода dэ при сварке в нижнем
положении шва составляет:
S,
мм......1-2 3-5 4-10 12-24 30-60
dэ,
мм....2-3 3-4 4-5 5-6 6-8
Сила тока в основном зависит от
диаметра электрода, но также от длины его рабочей части, состава покрытия,
положения сварки. Чем больше ток, тем больше производительность, т. е. большее
количество наплавленного металла:G=aнIсвt, где G- количество
наплавленного металла, г; aн- коэффициент наплавки, г/(А•ч); Iсв-
сварочный ток, А; t-время, ч.
Однако при
чрезмерном токе для данного диаметра электрода электрод быстро перегревается
выше допустимого предела. Что приводит к снижению качества шва и повышенному
разбрызгиванию. При недостаточном токе дуга неустойчива, часто обрывается, в
шве могут быть непровары. Величину тока можно определить по следующим формулам:
при сварке конструкционных сталей для электродов диаметром 3-6 мм Iд=(20+6dэ)dэ;
для электродов диаметром менее 3 мм Iд=30dэ, где dэ диаметр электрода, мм. Сварку швов в вертикальном
и потолочном положениях выполняют, как правило, электродами диаметром не более
4 мм. При этом сила тока должна быть на 10- 20 % ниже, чем для сварки в нижнем
положении. Напряжение дуги изменяется в сравнительно узких пределах-16-30 В.
Дуга может
возбуждаться двумя приёмами: касанием впритык и отводом перпендикулярно вверх
или «чирканьем» электродом как спичкой. Второй способ удобнее. Но неприемлем в
узких и неудобных местах.
Режимом сварки
называют совокупность характеристик сварочного процесса, которые
устанавливаются на основе исходных данных и должны выполняться для получения
сварного соединения требуемого качества. Каждый параметр режима сварки должен
быть обоснован подробными расчетами, анализом и сопоставлением современного производственного
и справочного материала.
В настоящее
время известны и применяются несколько методик расчета режимов. Рекомендуемая
методика для дуговой сварки, как наиболее используемого способа, приведена
ниже.
Для сталей,
чувствительных к термическому циклу сварки параметры режимов рассчитывают из
рекомендуемого диапазона оптимальных погонных энергий, полученных при анализе
свариваемости по условию предотвращения нежелательных структур закалки. При
этом устанавливают вид и режимы термообработки (предварительная, сопутствующая,
последующая и т.д.). В случае, когда по нормам точности изделия появляются
большие деформации, последние подлежат проверки по расчетным методикам и данным
работ. При этом корректируется величина погонной энергии, либо намечаются
другие мероприятия по уменьшению деформаций (обратный прогиб, жесткое крепление
в приспособлении и др.).
Далее
производится определение сварочного тока (по паспортным данным выбранных
электродов или по допускаемой плотности тока для сварочной проволоки), напряжения
дуги, значения эффективного коэффициента полезного действия дуги, а затем по
этим данным и оптимальному диапазону погонных энергий определяют диапазон
скоростей сварки. Затем, исходя из принятого коэффициента наплавки, плотности
наплавляемого металла, сварочного тока и скорости сварки находят площадь
поперечного сечения шва, наплавляемого за один проход.
Для сталей и
металлов, мало чувствительных к термическому циклу сварки и имеющих большой
интервал оптимальных погонных энергий с точки зрения предотвращения трещин,
режимы рассчитываются по условию получения оптимальных размеров и формы ива.
В общем случае
расчетному и иному обоснованию подлежат сила тока, напряжение, диаметр и марка
электрода, марка покрытия, флюса, род и расход защитного газа, количество и
сечение слоев, скорость подачи проволоки, скорость сварки, последовательность
сварки. Полученные данные заносят в таблицу.
Параметрами
режима способа сварки в среде CO2 и смеси газов являются:
-
диаметр
dЭ и марка электродной проволоки,
-
cила
сварочного тока Iсв,
-
скорость
сварки vсв,
-
вылет
электрода lЭ,
-
расход
защитного газа QГ.
Диаметр
электрода устанавливают в зависимости от толщины свариваемых кромок, вида
сварного соединения и размеров шва. Для стыковых соединений приняты практические
рекомендации по выбору диаметра электрода d в зависимости от
толщины свариваемых кромок
I,
|
Мм .
|
. . <2
|
3..
|
.5
|
6.
|
..8
|
9.
|
..12
|
13...15
|
16.
|
..20
|
>20
|
s.
|
Мм . .
|
. . <2
|
3..
|
.4
|
4.
|
..5
|
5.
|
..6
|
6...7
|
7.
|
..8
|
8...10
|
При выполнении
угловых и тавровых соединений принимают во внимание размер катета шва. При
катете шва 3...5 мм сварку производят электродом диаметром 3...4 мм; при
катете 6...8 мм применяют электроды диаметром 4...5 мм. При многопроходной
сварке швов стыковых соединений первый проход выполняют электродом диаметром не
более 4 мм. Это необходимо для хорошего провара корня шва в глубине разделки.
По выбранному
диаметру электрода устанавливают значение сварочного тока. Обычно для каждой
марки электродов значение тока указан на заводской этикетке.
Полученное
значение сварочного тока корректируют, учитывая толщину металла и положение
свариваемого шва. При толщине кромок менее (1,3... 1,6) d3, расчетное значение
сварочного тока уменьшают на 10...15 %, при толщине кромок > d3— увеличивают на 10...15
%. Сварку вертикальных и потолочных швов выполняют сварочным током, на 10...15
% уменьшенным против расчетного.
Сварочную дугу
возбуждают двумя приемами. Можно коснуться свариваемого изделия торцом
электрода и затем отвести электрод от поверхности изделия на 3...4 мм,
поддерживая горение образовавшейся дуги. Можно также быстрым боковым движением
коснуться свариваемого изделия и затем отвести электрод от поверхности изделия
на такое же расстояние (по методу зажигания спички). Прикосновение электрода к
изделию должно быть кратковременным, так как иначе он приваривается к изделию,
т. е. «примерзает». Отрывать «примерзший» электрод следует резким
поворачиванием его вправо и влево.
Длина дуги
значительно влияет на качество сварки. Короткая дуга горит устойчиво и
спокойно. Она обеспечивает получение шва высокого качества, так как
расплавленный металл электрода быстро проходит дуговой промежуток и меньше
подвергается окислению и азотированию. Но слишком короткая дуга вызывает
«примерзание» электрода, дуга прерывается, нарушается процесс сварки. Длинная
дуга горит неустойчиво с характерным шипением. Глубина проплавления недостаточная,
расплавленный металл электрода разбрызгивается и больше окисляется и азотируется.
Шов получается бесформенным, а металл шва содержит большое количество окислов.
Для электродов с толстым покрытием длина дуги указывается в паспортах.
В процессе
сварки необходимо поддерживать определённую длину дуги, которая зависит от
марки и диаметра электрода. Ориентировочно нормальная длина дуги должна быть в
пределах Lд=( 0,5-1,1)dэ, где Lд
- длина дуги, мм; dэ - диаметр электрода, мм.
Длина дуги
оказывает существенное влияние на качество сварного шва и его геометрическую
форму. Длинная дуга способствует более интенсивному окислению и азотированию
расплавляемого металла, увеличивает разбрызгивание, а при сварке электродами
основного типа приводит к пористости металла.
В процессе
сварки электроду сообщается движение в трёх направлениях. Первое движение -
поступательное, по направлению оси электрода. Этим движением поддерживается
постоянная (в известных пределах ) длина дуги в зависимости от скорости плавления
электрода.
Второе
движение-перемещение
электрода вдоль оси валика образования шва. Скорость этого движения
устанавливается в зависимости от тока, диаметра электрода, скорости его
плавления, вида шва и других факторов. При отсутствии поперечных движений
электрода получается так называемый ниточный валик, на 2-3 мм больший диаметра
электрода, или узкий шов шириной е£1,5dэ.
Третье
движение -
перемещение электрода поперёк шва для получения шва шире, чем ниточный валик,
так называемого уширенного валика.
Рис. 5. Траектория
движения конца электрода при ручной дуговой сварке.
Поперечные
колебательные движения конца электрода (рис. 5) определяются формой разделки,
размерами и положением шва, свойствами свариваемого материала, навыком
сварщика. Для широких швов, получаемых с поперечными колебаниями, e=(1,55)dэ.
Под порядком
заполнения швов понимается как порядок заполнения разделки шва по поперечному
сечению, так и последовательность сварки по длине шва.
По
протяжённости все швы условно можно разделить на три группы: короткие - до 300
мм, средние-300-1000, длинные - свыше 1000 мм.
В зависимости
от протяженности шва, материала, требований к точности и качеству сварных
соединений сварка таких швов может выполняться различно рис 6:
Короткие швы
выполняют на проход - от начала шва до его конца. Швы средней длины варят от
середины к концам или обратно ступенчатым методом. Швы большой длины выполняют
двумя способами: от середины к краям (обратноступенчатым способом) и вразброс.
При
обратноступенчатом методе весь шов разбивается на небольшие участки длиной
по150-200 мм, на каждом участке сварку ведут в направлении, обратном общему
направлению сварки. Длина участков обычно равна от 100 до 350 мм. В зависимости
от количества проходов (слоёв), необходимых для выполнения проектного сечения
шва, различают однопроходный (однослойный) и многопроходный (многослойный) швы.
С точки зрения
производительности наиболее целесообразными являются однопроходные швы, которые
обычно применяются при сварке металла небольших толщин (до 8-10 мм.) с
предварительной разделкой кромок.
Сварку
соединений ответственных конструкций большой толщины (свыше 20-25 мм.), когда
появляются объёмные напряжения и возрастает опасность образования трещин,
выполняют с применением специальных приёмов заполнения швов «горкой» или
«каскадным» методом.
При сварке
«горкой» сначала в разделку кромок наплавляют первый слой небольшой длины
200-300 мм, затем второй слой, перекрывающий первый и имеющий в 2 раза большую
длину. Третий слой перекрывает второй и длиннее его на 200-300 мм. Так наплавляют
слои до тех пор, пока на небольшом участке над первым слоем разделка не будет
заполнена. Затем от этой «горки» сварку ведут в разные стороны короткими швами
тем же способом. Таким образом, зона сварки всё время находится в горячем
состоянии, что позволяет предупредить появление трещин. «Каскадный» метод
является разновидностью горки.
Соединения под
сварку собирают в приспособлениях, чаще всего с прихватками. Сечение
прихваточного шва составляет примерно 1/3 от сечения основного шва, длина его
30-50 мм. Угловые швы сваривают «в угол» или «в лодочку» (рис.7).
Рис. 7.
Положение электрода и изделия при выполнении угловых швов:
а – сварка в
симметричную «лодочку», б – в несимметричную «лодочку»,
в – «в угол»
наклонным электродом, г - с оплавлением кромок.
При сварке «в
угол» проще сборка, допускается большой зазор между свариваемыми деталями (до 3
мм), но сложнее техника сварки, возможны дефекты типа подрезов и наплывов,
меньше производительность, так как приходится за один проход сваривать швы
небольшого сечения (катет <8 мм) и применять многослойную сварку. Сварка «в
лодочку более производительна, допускает большие катеты шва за один проход, но
требует более тщательной сборки.
Обеспечение
нормативных требований по технологии и технике сварки - основное условие
получения качественных сварных швов. Отклонения размеров и формы сварного шва
от проектных чаще всего наблюдаются в угловых швах и связаны с нарушением режимов
сварки, неправильной подготовкой кромок под сварку, неравномерной скоростью
сварки, а также с несвоевременным контрольным обмером шва.
Дефекты
сварных швов являются следствием неправильного выбора или нарушения
технологического процесса изготовления сварной конструкции, применения
некачественных сварочных материалов и низкой квалификации сварщика. Дефекты
разделяются на внешние и внутренние. К внешним дефектам относятся: нарушение
установленных размеров и формы шва, непровар, подрез зоны сплавления,
поверхностное окисление, прожог, наплыв, поверхностные поры, незаваренные
кратеры и трещины на поверхности шва.
К внутренним
дефектам относятся: внутренние поры, неметаллические включения, непровар
и внутренние трещины.
Нарушение
установленных размеров и формы шва выражается в неполномерности ширины и
высоты шва, в чрезмерном усилении и резких переходах от основного металла к
наплавленному. Эти дефекты при ручной сварке являются результатом низкой квалификации
сварщика, плохой подготовки свариваемых кромок, неправильного выбора сварочного
тока, низкого качества сборки под сварку. Дефекты формы шва могут быть и
следствием колебания напряжения в сети. При автоматической сварке нарушения
формы и размеров шва являются следствием неправильной разделки шва или
нарушения режима в процессе сварки (скорости сварки, скорости подачи
электродной проволоки, сварочного тока).
Непровар —
местное несплавление свариваемых кромок основного и наплавленного металла —
является следствием низкой квалификации сварщика, некачественной подготовки
свариваемых кромок (малый угол скоса, отсутствие зазора, большое притупление),
смещения электрода к одной из кромок, быстрого перемещения электрода по шву.
Подрез зоны —
узкие углубления в основном металле вдоль края сварного шва — образуются при
сварке большим током или удлиненной дугой, при завышенной мощности горелки,
неправильном положении электрода или горелки и присадочного прутка.
Поверхностное
окисление — окисление металла шва и прилегающего к нему основного металла.
Причины — сильно окисляющая среда, большая длина дуги, чрезмерно большая
мощность сварочной горелки или слишком большой сварочный ток, замедленное
перемещение электрода или горелки вдоль шва.
Прожог —
сквозное отверстие в сварном шве. Основные причины прожога — большой сварочный
ток, завышенная мощность сварочной горелки, малая толщина основного металла,
малое притупление свариваемых кромок и неравномерный зазор между ними по длине.
Наплывы —
результат натекания наплавленного металла на непрогретую поверхность основного
металла или ранее выполненного валика без сплавления с ним. Такие дефекты
могут быть при низкой квалификации сварщика, недоброкачественных электродах и
несоответствии скорости сварки и сварочного тока разделке шва.
Поверхностные
и внутренние поры возникают вследствие попадания в металл шва газов
(водород, азот, углекислый газ и др.), образовавшихся при сварке. Водород
образуется из влаги, масла и компонентов покрытия
электродов. Азот в металл шва попадает из атмосферного воздуха
при недостаточно качественной защите расплавленного металла шва. Оксид углерода
образуется в процессе сварки стали при выгорании углерода, содержащегося в
металле. Если свариваемая сталь и электроды имеют повышенное
содержание углерода, то при недостатке в сварочной ванне
раскислителей и при большой скорости сварки оксид углерода не успевает
выделиться и остается в металле шва. Таким образом, пористость является результатом
плохой подготовки свариваемых кромок (загрязненность, ржавчина, замасленность),
применения электродов с сырым покрытием, влажного флюса, недостатка
раскислителей, больших скоростей сварки.
Неметаллические
включения образуются при сварке малым сварочным током, при применении
недоброкачественных электродов, сварочной проволоки, флюса, загрязненных
кромок и плохой очистке шва от шлака при многослойной сварке. При неправильно
выбранном режиме сварки шлаки и оксиды не успевают всплыть на поверхность и остаются
в металле шва в виде неметаллических включений.
Трещины
наружные и внутренние являются опасными и недопустимыми дефектами сварных
швов. Они образуются вследствие напряжений, возникающих в металле от его
неравномерного нагрева, охлаждения и усадки. Высокоуглеродистые и легированные
стали после сварки при охлаждении закаливаются, в результате чего могут
образоватьсй трещины. Причина возникновения трещин — повышенное
содержание в стали вредных примесей (серы и фосфора).
Методы
устранения дефектов сварных швов. Неполномерность швов устраняется наплавкой
дополнительного слоя металла. При этом наплавляемую поверхность необходимо тщательно
очистить до металлического блеска абразивным инструментом или металлической
щеткой. Чрезмерное усиление шва устраняют с помощью абразивного инструмента или
пневматического зубила.
Непровар,
кратеры, пористость и неметаллические включения устраняют путем вырубки пневматическим
зубилом или расчистки абразивным инструментом всего дефектного участка с
последующей заваркой. Часто применяют выплавку дефектного участка резаком
поверхностной кислородной или воздушно-дуговой резки.
Подрезы
заваривают тонкими валиковыми швами. Наплывы устраняются обработкой абразивным
инструментом или с помощью пневматического зубила.
Наружные
трещины устраняются разделкой и последующей заваркой. Для предупреждения
распространения трещины по концам ее засверливают отверстия. Разделку трещины выполняют
зубилом или резаком. Кромки разделки зачищают от шлака, брызг металла, окалины
и заваривают. Швы с внутренними трещинами вырубают и заваривают заново. При
наличии сетки трещин дефектный участок вырезают и взамен сваркой накладывают
заплату.
Сварка существует в мире
более 100 лет, однако до сих пор имеет место множество проблем, связанных с
контролем качества сварных соединений изделий и обеспечением надежности сварных
конструкций. Среди наиболее важных проблем следует отметить следующие:
-
низкая
эффективность традиционных средств и методов при контроле напряженно-деформированного
состояния сварных соединений и определении зон концентрации напряжений -
источников развития повреждений;
-
отсутствие
в широкой практике научно-обоснованных норм по допустимости размеров дефектов с
позиций механики разрушений;
-
коробление
или изменение формы и размеров конструкции в результате неравномерного нагрева
и охлаждения при сварке;
-
отсутствие
эффективных методов неразрушающего контроля (НК) качества термической и других
технологий обработок сварных соединений с целью снятия остаточных напряжений;
-
отсутствие
эффективных методов НК точечной контактной сварки в изделиях машиностроения; до
сих пор на практике контроль осуществляется на отрыв путем удара по месту
точечной сварки молотком и зубилом;
-
проблемной
задачей является выбор оптимальных технологий сварки, наплавок, напылений;
-
низкая
эффективность традиционных методов НК при контроле контактной сварки труб,
угловых, тавровых сварных соединений.
Одной из
важных и сложных проблем современного неразрушающего контроля (НК) качества
сварных соединений разных типов является поиск и определение в них
"слабого звена" в единой комплексной системе факторов
"структурно-механическая неоднородность - дефекты сварного шва - конструктивный
и технологический концентратор напряжений", т.е. зон с высокой неоднородностью
напряженно-деформированного состояния или зон концентрации напряжений (ЗКН).
Это важно как при изготовлении сварных соединений, т.е. непосредственно после
сварки, для оптимизации технологического процесса, так и при их эксплуатации.
Традиционная
дефектоскопия, ориентированная только на поиск несплошностей в сварных
соединениях, не может обеспечить достоверную оценку их качества. Опираясь
только на результаты дефектоскопии технологу-сварщику трудно выявлять причины дефектности
шва и совершенствовать технологию сварки.
В условиях,
когда на надежность сварных соединений влияет множество факторов, необходим
метод НК, который бы интегрально оценивал состояние металла сварного соединения.
В настоящее
время в России разработан и успешно внедряется в различных отраслях
промышленности принципиально новый метод диагностики металла изделий и сварных
соединений, основанный на использовании магнитной памяти металла (МПМ).
Метод МПМ направлен
на решение указанных выше проблем НК основного металла и сварных соединений
объектов промышленности и транспорта.
МПМ - метод
неразрушающего контроля, основанный на анализе распределения собственного
магнитного поля рассеяния (СМПР) на поверхности изделий с целью определения зон
концентрации напряжений, дефектов и неоднородности структуры металла и сварных
соединений.
Путем
считывания СМПР, отображающего остаточную намагниченность, сформировавшуюся
естественным образом в процессе сварки, нам предоставляется уникальная
возможность выполнять оценку фактического состояния сварного шва. Причем эта
оценка является интегральной, отображающей в каждом шве одновременно
особенности структурного состояния, распределение остаточных напряжений и
дефектов сварки.
Формирование
магнитной (доменной) структуры в сварных соединениях происходит одновременно с
кристаллизацией при остывании металла в магнитном поле Земли и прохождении
через точку Кюри (768ºС) под действием напряжений и деформаций, возникающих
в процессе сварки. На возникающих дефектах сварки образуются узлы закрепления
доменных границ с выходом на поверхность сварного шва в виде СМПР. Таким образом,
путем считывания СМПР, которые формируются в процессе сварки, нам предоставляется
возможность выполнять интегральную оценку фактического состояния сварного шва.
Контроль
методом МПМ осуществляется без зачистки металла и специального намагничивания и
позволяет выполнять экспресс-контроль качества сварных соединений в ручном и
автоматическом режиме и массовом производстве на различных изделиях из
углеродистых, аустенитных и феррито-аустенитных марок сталей.
Контроль
выполняется с помощью специализированных малогабаритных приборов, имеющих
автономное питание, сканирующие и регистрирующие устройства. Приборы типа ИКН (измерители
концентрации напряжений магнитометрические) не имеют аналогов, серийное их
изготовление организовано в России на предприятии "Энергодиагностика"
(г.Москва). Приборы аттестованы в Госстандарте РФ и включены в государственный
реестр средств измерений.
На рис.1
представлена схема контроля стыковых сварных соединений труб. Как видно из
рис.1, феррозондовые преобразователи 1 и 3 располагаются при контроле по зонам
термического влияния (ЗТВ) с обеих сторон шва, преобразователь 2 расположен
между ними посередине, а преобразователь 4 расположен вертикально в
противоположную сторону и предназначен для отстройки от внешнего магнитного
поля.
|
Рис.1. Схема
контроля стыковых сварных соединений труб четырёхканальным датчиком прибора
ИКН-1М-4: 1, 2, 3 - феррозондовые преобразователи сканирующего устройства для
регистрации поля Нр на поверхности сварного шва; 4 - феррозондовый
преобразователь для отстройки от внешнего магнитного поля Нр; 5 - колёса
привода измерителя длины; ΔLб - базовое расстояние между феррозондовыми
преобразователями.
|
На рис.2,а
показано типичное распределение остаточных напряжений на сварном соединении
пластин. На рис.2,б показано распределение тангенциальной составляющей
магнитного поля рассеяния Hpx, которое фиксируется при контроле МПМ при
измерении поля перпендикулярно сварному шву (1, 2, 3 - разные сечения
пластины). Из этих рисунков видна хорошая качественная сходимость распределений
остаточных напряжений и магнитного поля.
Рис.2а.
|
Рис.2б.
|
Известно, что
оперативный контроль качества термической обработки сварных соединений, как
правило, осуществляется только путем измерений твердости металла. Однако, такой
точечный контроль не дает уверенности в отсутствии концентраторов механических
напряжений по всему шву и в прилегающей к нему зоне.
Рассмотрим эффективность
метода МПМ при контроле качества термической обработки сварного шва на отрезке
из низколегированной марки стали типа 12Х1МФ. Термообработка осуществлялась с
нагревом металла шва от индукционной катушки до 700ºС с последующим
охлаждением на воздухе.
На рис.3
представлены магнитограммы, характеризующие напряженно-деформированное
состояние отрезка вдали от сварного шва.
Магнитограммы
получены в результате измерений СМПР вдоль сварного шва по схеме,
представленной на рис.1. Из представленного на рис.3 эксперимента следует вывод
о том, что в качестве стандартного образца сравнения может быть использована
магнитограмма, измеренная рядом со сварным соединением, где влияние сварки
отсутствует.
Известно, что
остаточная деформация металла сварного шва формируется в результате сдвиговой
пластической деформации, происходящей при кристаллизации в процессе остывания
металла. При этом диагностические параметры Нр и его градиент Кин (dHp/dx)
вследствие "магнитодислокационного" гистерезиса, обусловленного
двуединством магнитной плоскости и плоскости скольжения дислокаций, отображают
распределение остаточных деформаций и напряжений вдоль периметра сварного
соединения.
Выполнение
сварочных работ связано с использованием электрических устройств, горючих и
взрывоопасных газов, излучающих электрических дуг и плазмы, с интенсивным расплавлением,
испарением и брызгообразованием металла и т. д. Это требует мер безопасности и
защиты работающих от производственного травматизма.
При
электросварочных работах возможны следующие виды производственного травматизма:
поражение электрическим током; поражение зрения и открытой поверхности кожи
лучами электрической дуги- ожоги от капель металла и шлака; отравление организма
вредными газами, пылью и испарениями, выделяющимися при сварке; ушибы, ранения
и поражения от взрывов баллонов сжатого газа и при сварке сосудов из-под горючих
веществ.
Для
обеспечения условий, предупреждающих указанные виды травматизма, следует выполнять
следующие мероприятия.
Защита от
поражения электрическим током. При исправном состоянии оборудования и
правильном выполнении сварочных работ возможность поражения током исключается.
Однако в практике возможны поражения электрическим током вследствие
неисправности сварочного оборудования или сети заземления; неправильного
подключения сварочного оборудования к сети; неисправности электропроводки и
неправильного ведения сварочных работ. Поражение от электрического тока
происходит при прикосновении к токонесущим частям электропроводки и сварочной
аппаратуры.
Напряжение
холостого хода источников питания дуги достигает 90 В, а при плазменно-дуговой
резке — 200 В. Учитывая, что сопротивление человеческого организма в
зависимости от его состояния (утомленность, состояние здоровья, влажность кожи)
может изменяться в широких пределах (1000...20 000 (Ом), то указанные выше
напряжения являются очень опасными для жизни. Поражение током более 0,05 А
может вызвать тяжелые последствия и даже смерть.
Опасность
поражения сварщика и подсобных рабочих током особенно велика при сварке
крупногабаритных резервуаров, во время работы внутри емкостей лежа или полулежа
на металлических частях свариваемого изделия или при выполнении наружных работ
в сырую погоду, в сырых помещениях, котлованах, колодцах и др.
Во избежание
поражения электрическим током необходимо соблюдать следующие условия. Корпуса
источников питания дуги, сварочного вспомогательного оборудования и свариваемые
изделия должны быть надежно заземлены. Заземление осуществляют медным проводом,
один конец которого закрепляют к корпусу источника питания дуги к специальному
болту с надписью «Земля»; второй конец присоединяют к заземляющей шине или к
металлическому штырю, вбитому в землю.
Для
подключения источников сварочного тока к сети используются настенные ящики с
рубильниками, предохранителями и зажимами. Длина проводов сетевого питания не
должна быть более 10 м. Для того чтобы нарастить провод, применяют
соединительную муфту с прочной изоляционной массой или провод с
электроизоляционной оболочкой. Провод подвешивают на высоте 2,5...3,5 м. Спуски
заключают в заземленные металлические трубы. Вводы и выводы должны иметь
втулки или воронки, предохраняющие провода от перегибов, а изоляцию —
от порчи.
При наружных
работах сварочное оборудование должно находиться под навесом, в палатке или в
будке для предохранения от дождя и снега. При невозможности соблюдения таких
условий сварочные работы не производят, а сварочную аппаратуру укрывают от
воздействия влаги.
Присоединять и
отсоединять от сети электросварочное оборудование, а также наблюдать за их
исправным состоянием в процессе эксплуатации обязан электротехнический
персонал. Сварщикам запрещается выполнять эти работы.
Все сварочные
провода должны иметь исправную изоляцию и соответствовать применяемым токам.
Применение проводов с ветхой и растрепанной изоляцией во избежание несчастного
случая категорически запрещается.
При сварке
швов резервуаров, котлов, труб и других закрытых и сложных конструкций
необходимо пользоваться резиновым ковриком, шлемом и галошами. Для освещения
следует пользоваться переносной лампой напряжением 12 В.
Все сварочные
установки при работе в условиях, требующих особой электробезопасности, должны
иметь устройство для автоматического отключения сварочной цепи или снижения
напряжения холостого хода при обрыве дуги до 12 В с выдержкой не более 5 с.
Большое применение получили устройства типа УСНТ (УСНТ-05, УСНТ-06 и др.). При
холостом ходе первичная обмотка трансформатора питается через ограничительные
резисторы типа УСНТ и напряжение питания снижается до 60...80' В, а вторичное
напряжение холостого хода до 12 В. При возбуждении дуги коротким замыканием
резисторы шунтируются тиристорами и на трансформатор подается полное сетевое
напряжение. После прекращения сварки через 0,5...1 с снова включаются
ограничительные резисторы и напряжение холостого хода снижается до 12 В.
При работах
внутри резервуара или при сварке сложной металлической конструкции, а также при
сварке емкостей из-под горючих и легковоспламеняющихся жидкостей к сварщику
назначается дежурный наблюдатель, который обязан обеспечить безопасность работ
и при необходимости оказать первую помощь.
При поражении
электрическим током необходимо пострадавшему оказать первую помощь: освободить
его от электропроводов; обеспечить доступ свежего воздуха и, если пострадавший
потерял- сознание, немедленно вызвать скорую медицинскую помощь. При
необходимости, до прибытия врача производить искусственное дыхание.
Защита зрения
и открытой поверхности кожи от лучей электрической дуги. Горение сварочной дуги
сопровождается излучением видимых ослепительно ярких световых лучей и невидимых
ультрафиолетовых и инфракрасных лучей.
Яркость
видимых лучей значительно превышает норму, допускаемую для человеческого глаза,
и поэтому, если смотреть на дугу невооруженным глазом, то она производит
ослепляющее действие. Ультрафиолетовые лучи даже при кратковременном действии в
течение нескольких секунд вызывают заболевание глаз, называемое
электрофтальмией. Оно сопровождается острой болью, резью в глазах,
слезотечением, спазмами век. Продолжительное облучение ультрафиолетовыми лучами
вызывает ожоги кожи.
Инфракрасные
лучи при длительном воздействии выбывают помутнение хрусталиков глаза (катаракту),
что может привести к временной и даже полной потере зрения. Тепловое действие
инфракрасных лучей вызывает ожоги кожи лица.
Для защиты
зрения и кожи лица от световых и невидимых лучей дуги электросварщики и их
подручные должны закрывать лицо щитком, маской или шлемом, в смотровые
отверстия которых вставлено специальное стекло — светофильтр. Светофильтр
выбирают в зависимости от сварочного тока ц вида сварочных работ.
Для защиты
окружающих лиц от воздействия излучений в стационарных цехах устанавливают
закрытые сварочные кабины, а при строительных и монтажных работах применяются
переносные щиты или ширмы.
Защита от
брызг металла и шлака. В процессе сварки и при уборке и обивке шлака капли
расплавленного металла и шлака могут попасть в складки одежды, карманы, ботинки,
прожечь одежду и причинить ожоги. Во избежание ожогов сварщик должен работать в
спецодежде из брезента или плотного сукна, в рукавицах и головном уборе. Куртку
не следует заправлять в брюки. Карманы должны быть плотно закрыты клапанами.
Брюки надо носить поверх обуви. При сварке потолочных, горизонтальных и
вертикальных швов необходимо надевать брезентовые нарукавники и плотно
завязывать их поверх рукавов у кистей рук. Зачищать швы от шлака и флюса
следует лишь после их полного остывания и обязательно в очках с простыми
стеклами.
1. Скорость
сварки находится по формуле:
,
где dН – коэффициент наплавки;
УСВ
– сила сварного тока, А;
g
- удельный вес металла, г/см3;
F – площадь поперечного
сечения шва, см2.
Vсв = 1,2 см/сек
2. Вес
наплавленного находится по формуле:
GН = F х g х L,
где g - удельный вес металла,
г/см3;
F – площадь поперечного
сечения шва, см2.
L – длина шва, мм.
GН = 540,0 г
3. Расход
электродов, необходимых для сварки:
GЭЛ = GСТ + CП,
где GСТ – вес стержней;
GСТ = GП : 0,75 х GП = GСТ (0,25 – 0,4);
GП – вес покрытия
GЭЛ = GН х КР,
где КР –
коэффициент,
указывающий расход электродов на 1 кг наплавленного металла.
GЭЛ = 22 шт.
4. Расход
покрытых электродов, шт.
,
где К –
количество покрытых электродов, шт.
G – вес наплавленного
металла;
КВ
– коэффициент выхода наплавленного металла с одного электрода, зависит от
диаметра и марки электрода и выбирается по таблице:
Таблица 4
dЭЛ
|
3
|
4
|
5
|
6
|
ОЗС-3
|
30,9
|
70,7
|
111,1
|
160
|
АНО-6
|
19,4
|
35,2
|
55,3
|
79,6
|
УОНИ
|
18,0
|
|
|
|
МР-3
|
8,8
|
|
|
|
К = 15 шт.
1.
Геворкян
В.Г. Основы сварочного дела - М.: Высш. школа, 1985.-168 с., ил.
2.
Думов
С.И. Технология электрической сварки плавлением - Л.: Машиностроение.1987.-461с.,
ил.
3.
Китаев
А.М., Китаев Я.А. Дуговая сварка-М.: Машиностроение. 1983.-272 с. ил.
4.
Оборудование
и технология сварочного производства: Руководство по дипломному проектированию
/ М. В. Шахматов, В. В. Ерофеев, А. Г. Игнатьев,В. А. Стихин.— Челябинск:
Изд_во ЮУрГУ, 2003.— 78 с.
5.
Павленко
В.В., Кутана И.Д. Автоматизация технологической подготовки в сборочно-сварочном
производстве. – Киев: техника, 1983. – 88 с.
6.
Производство
сварных конструкций: Учебное пособие по курсовому проектированию (Специальность
12.05) / Н.А. Клыков, М.В. Шахматов, В.Н. Голиков, А.В. Пуйко.- Челябинск:
ЧГТУ, 1992.- 124 с.
7.
Рыбаков
В.М. Сварка и резка металлов-М.: Высш. школа, 1979.-214 с., ил.
8.
Стеклов
О. И. Основы сварочного производства - М.: Высш. школа, 1986.-224 с., ил.
9.
Теоретические
основы САПР: учебник для вузов/ В.П. Корячко, В.М. Курейчик, И.П. Норенков. –
М.: Энергоиздат, 1987. – 400 с.
10.
Технология
изготовления и расчет сварных оболочек /М.В.Шахматов, В.В. Ерофеев, В.В. Коваленко.-
Уфа, Полиграфкомбинат, 1999.- 272 с.
12.
Чернов
А.В. Обработка информации в системах контроля и управления сварочным
производством. – Новочеркасск: Государственный технический университет, 1995. –
180 с.
13.
Шебеко
Л.П. Производственное обучение электро-газосварщиков - М.: Высш.
школа,1984.-167 с., ил.